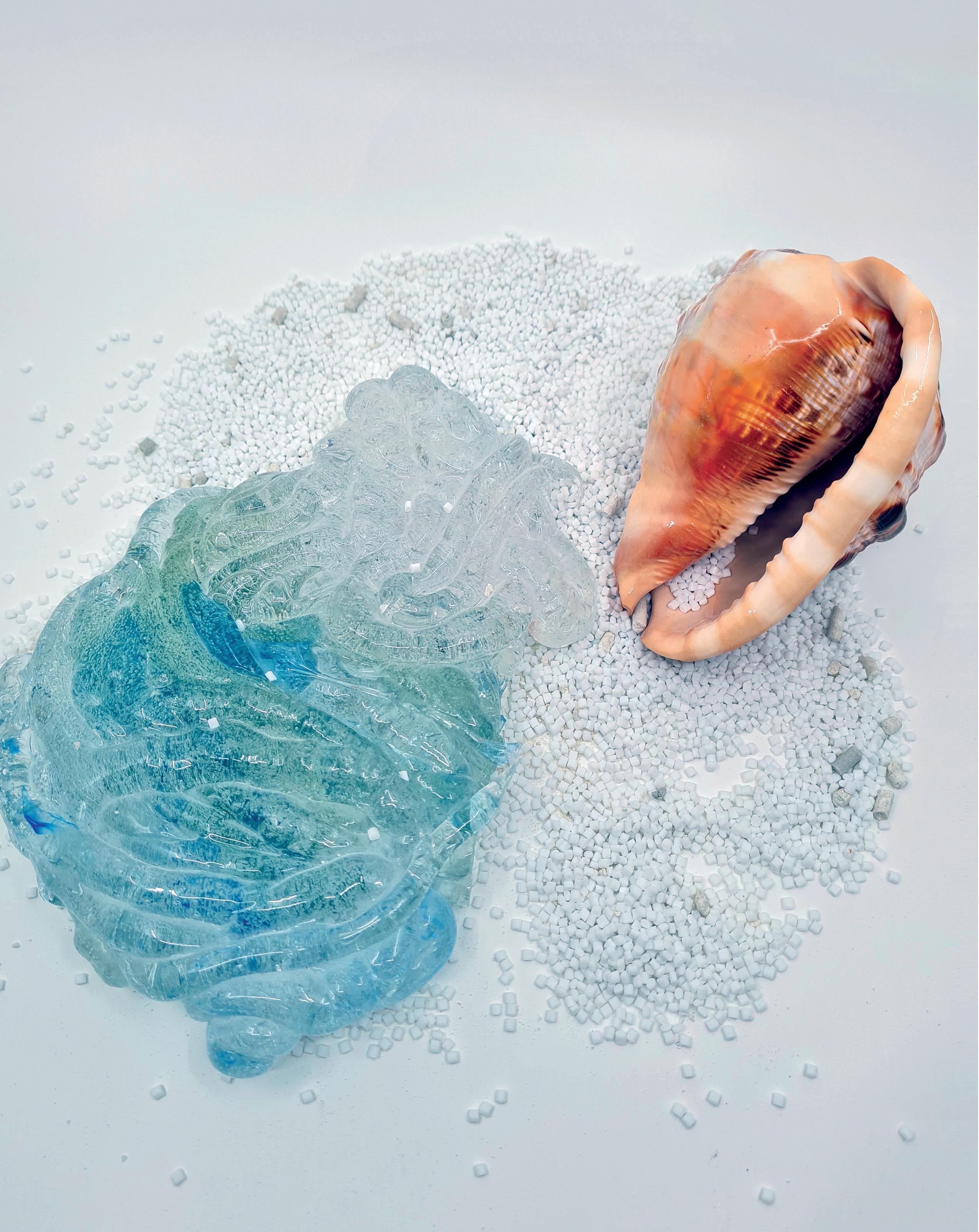



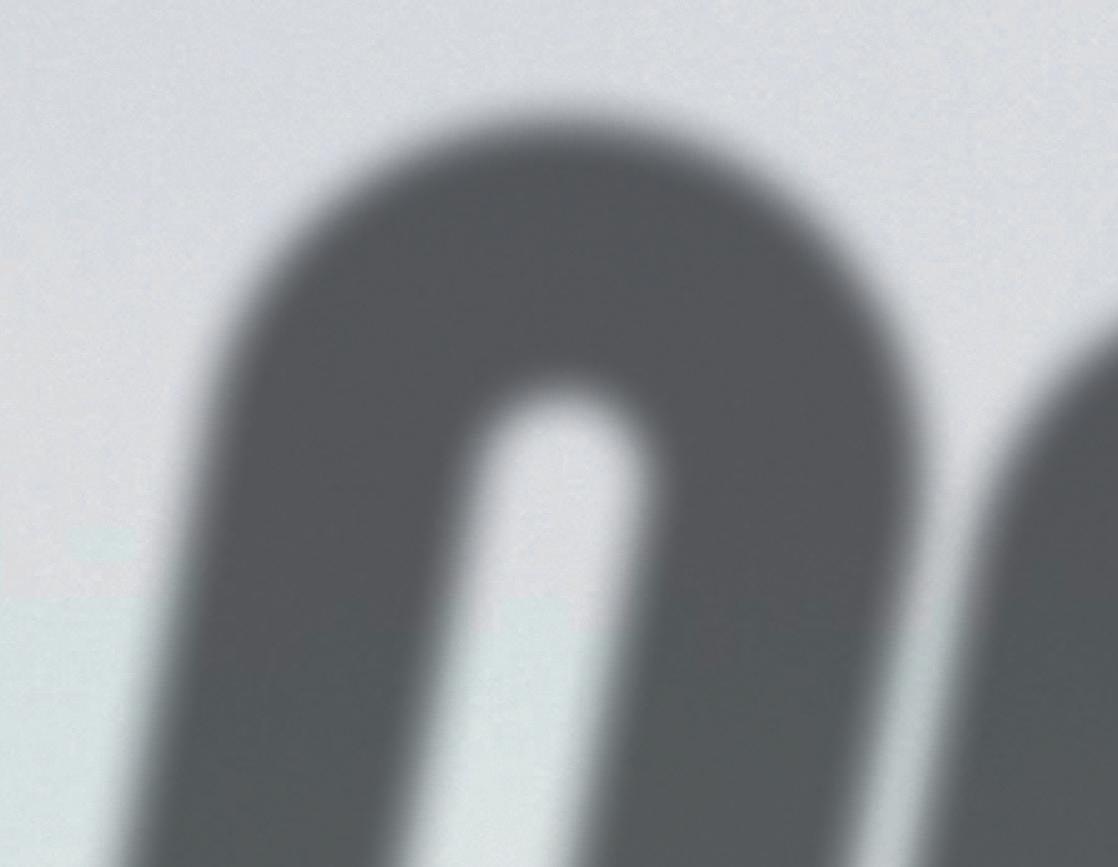
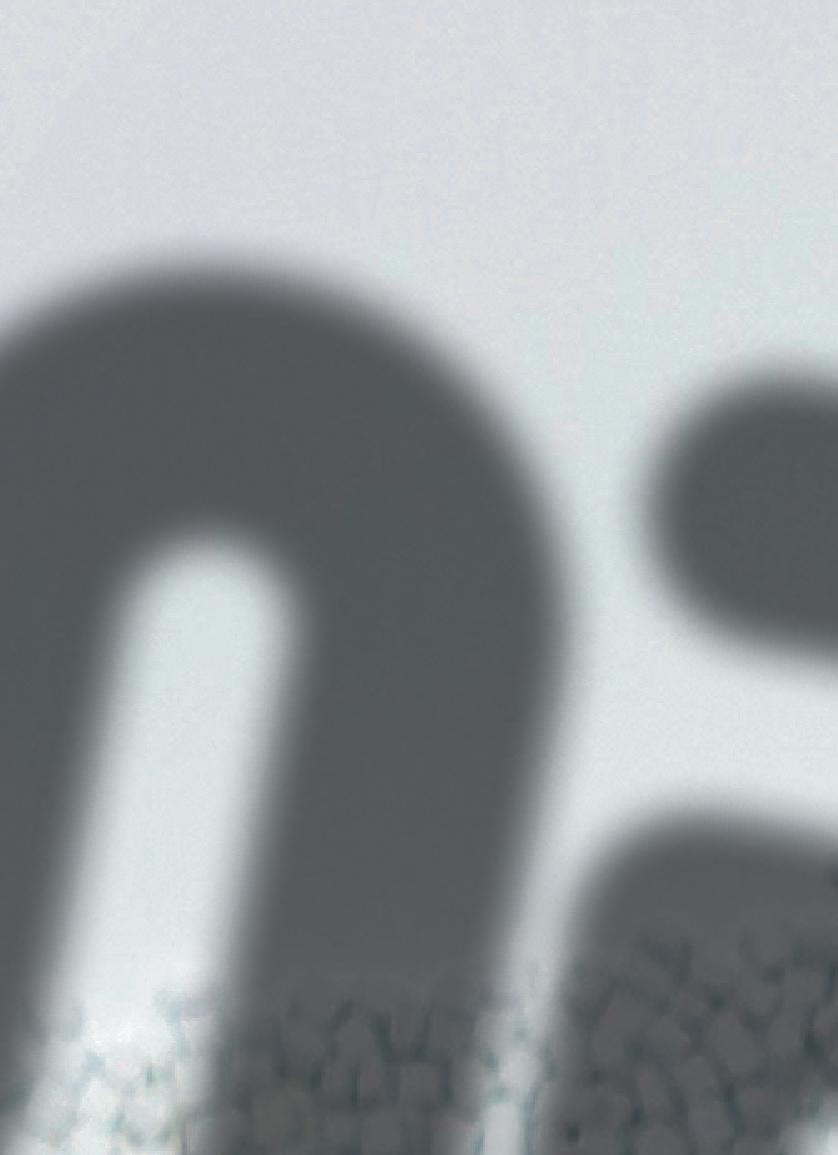

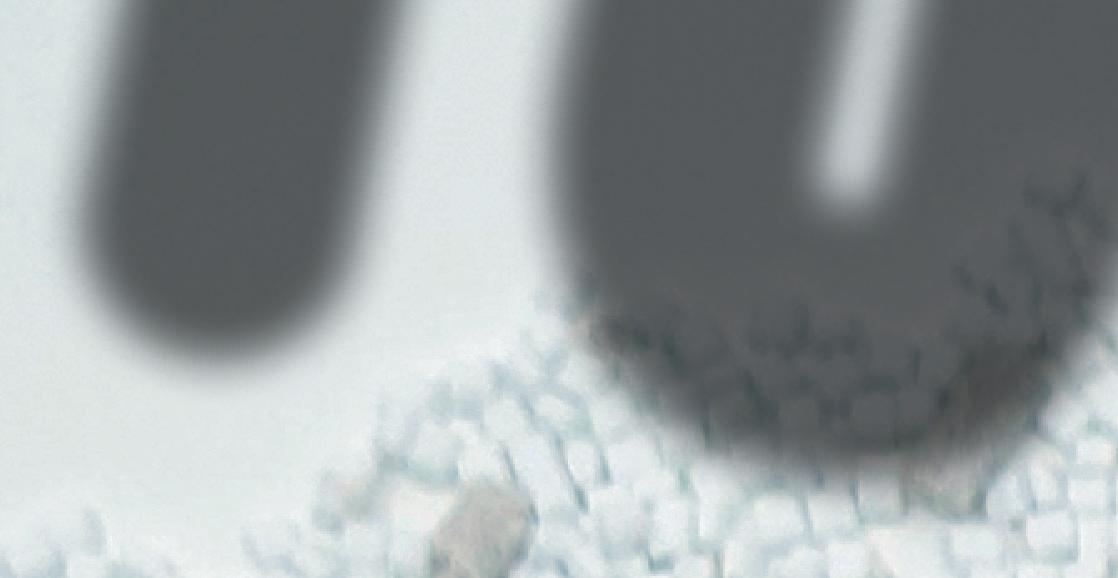

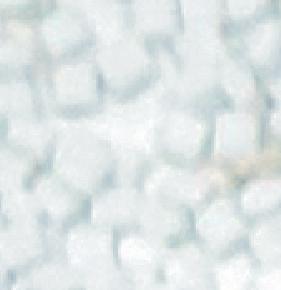
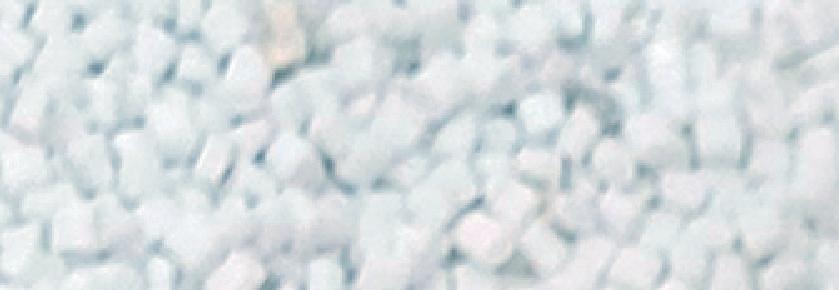
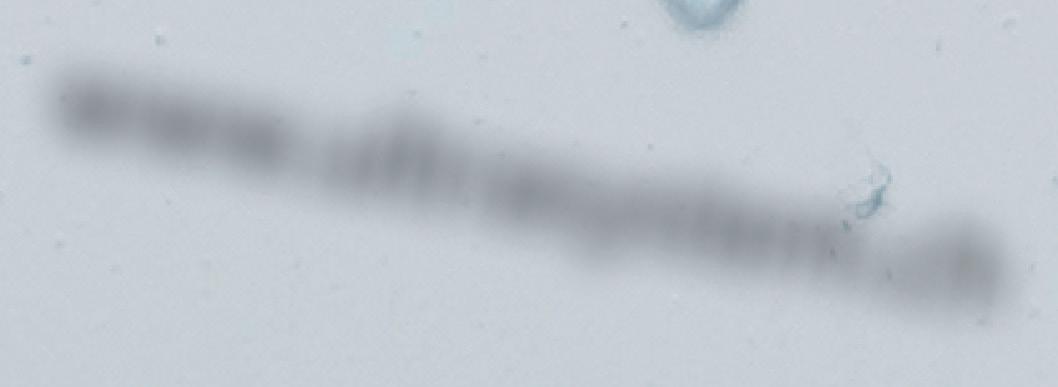




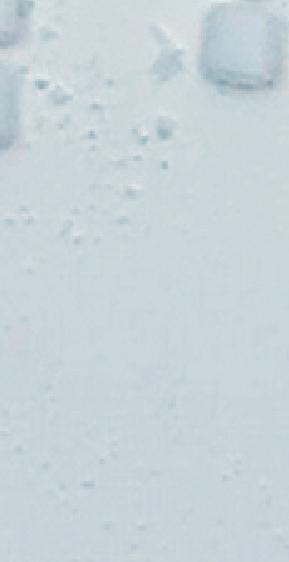






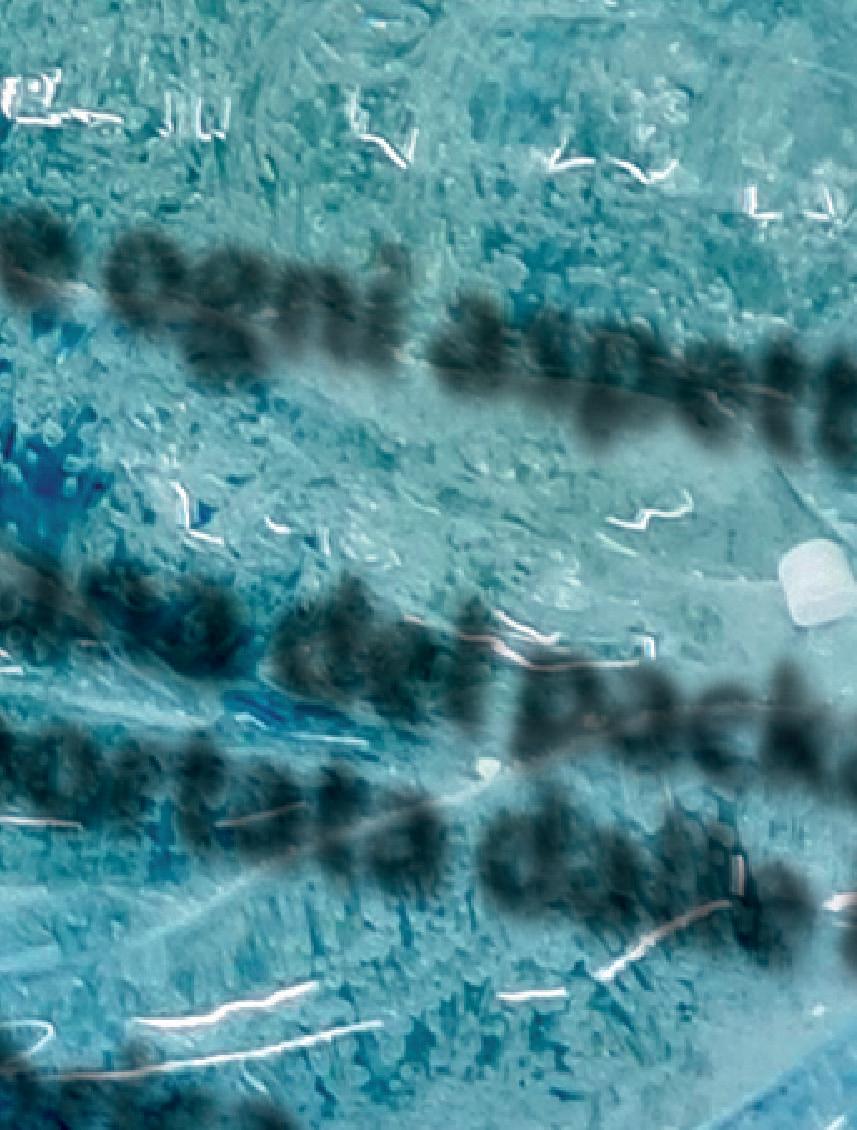
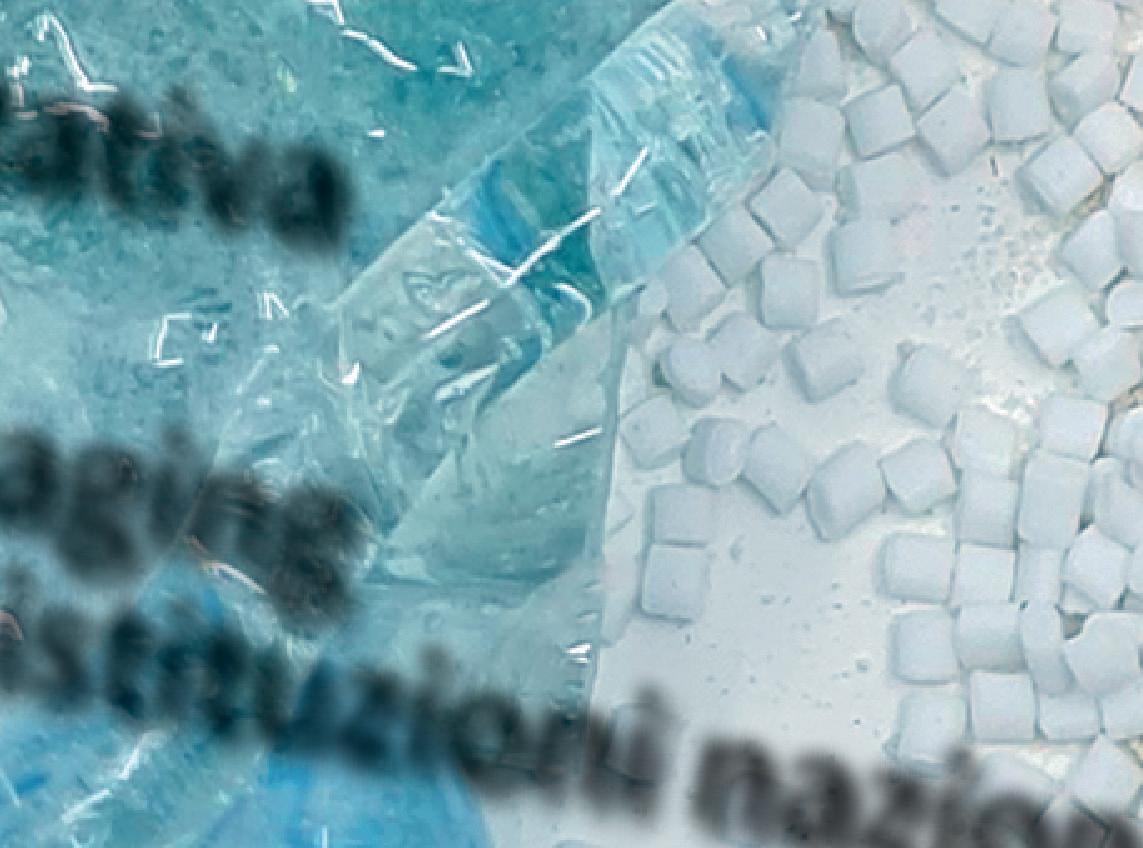


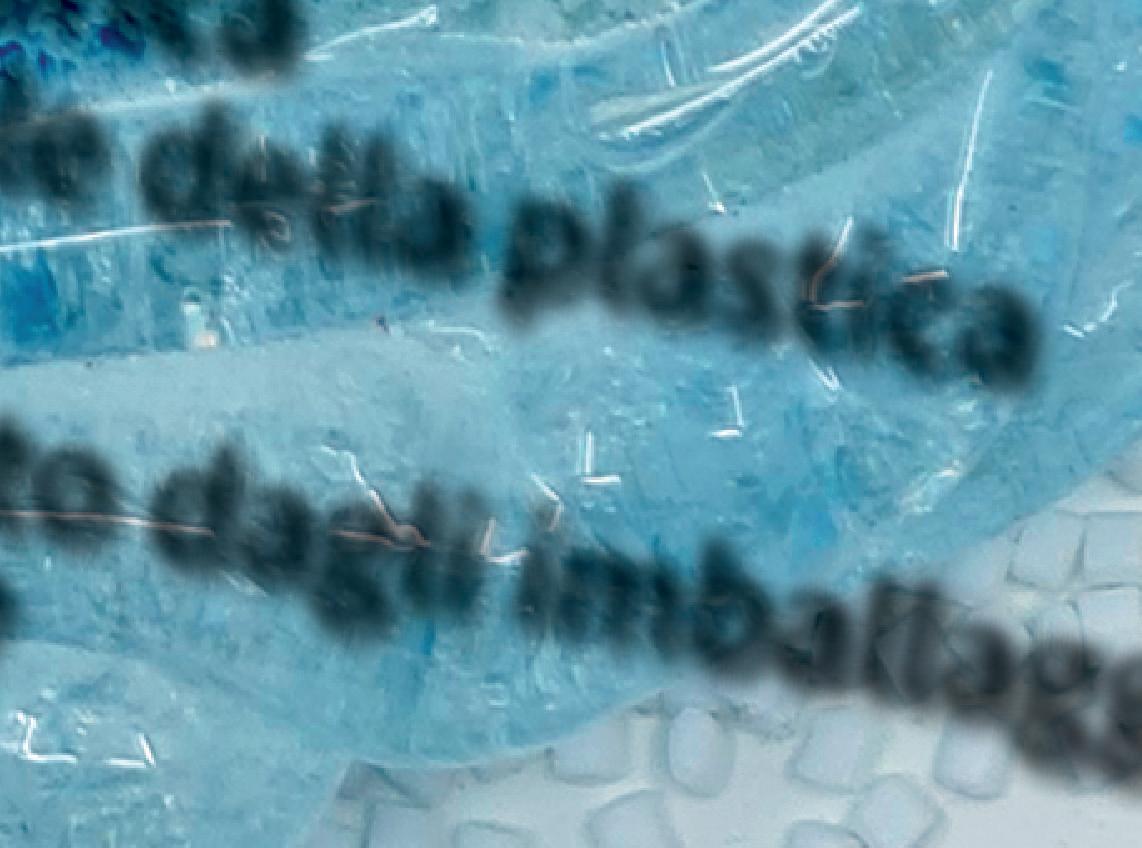


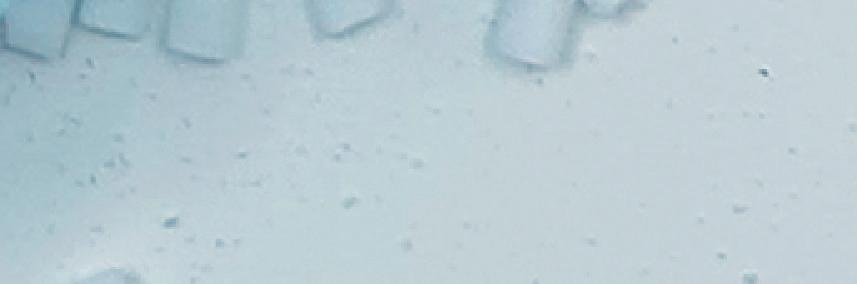
Link International s.r.l. da 15 anni leader in Italia nell’ambito del revamping, manutenzione, reverse engineering e costruzione di riduttori, apre una business unit dedicata ai riduttori di comando estrusori per polimeri.
Realizziamo:
•Progettazione e costruzione di riduttori monovite/bivite (corotanti/controrotanti)
• Revamping di riduttori esistenti, reverse engineering di ingranaggi e cuscini reggispinta
•Condition monitoring con analisi vibrazionali, esami endoscopici, termografie a infrarossi
•Servizi di manutenzione programmata
•Estensioni di garanzia
AZIENDA CERTIFICATA Tüv: ISO9001:ISO45001
international LINK
Via Belvedere 26
20862 Arcore (MB) - Italy
Tel. +39 039 2268758
Fax +39 039 2267494
www.linkinternational.it
info@linkinternational
EDITORIALE
8 Greenwashing, questo... conosciuto
MARKETING
10 Un 2022 oltre ogni aspettativa
13 I beni strumentali in audizione alla Camera dei Deputati
14 Le buone pratiche sono proficue per le aziende
15 Ampio consenso, novità per welfare e relazioni sindacali
15 Lavorare meno e produrre di più
16 Poliuretano flessibile tra alti e bassi
16 Serramenti in PVC ancora in crescita, grazie anche agli incentivi fiscali
17 Un settore attrattivo e promettente
17 Isolamento globale
18 La filiera italiana del packaging è unita e supportata dalle istituzioni nazionali
22 Lavorare insieme per una plastica sempre più riciclabile
24 La produzione di bioplastiche triplicherà nei prossimi cinque anni
26 Nel 2022 recuperate oltre 230.000 tonnellate di PFU
27 Materiali ultraresistenti a base di FDCA
27 Il riciclo chimico di PET arriva in italia
28 Gli investimenti spingono il riciclo UE
30 Il valore aggiunto nella termoformatura: fornire esperienza insieme agli impianti
36 Da piccola fabbrica a multinazionale della plastica
40 Rispondere all’ampliamento del mercato e stimolarne l’ulteriore crescita
42 L’essenziale è invisibile agli occhi…
44 Bilanci e prospettive per il calore di processo
47 Movimenti ottimizzati, tempi di riciclo ridotti
50 Impianto per il riciclo congolese di bottiglie in PET post-consumo
51 Due è meglio che uno
53 Semplificare l’automazione dei processi produttivi
54 Nuova generazione di avvolgitori automatici
55 Quinta generazione di presse elettriche
56 Densificatore a circolo chiuso per scarti post-consumo e post-industriali
57 Industria 4.0 e tracciabilità di processo in un impianto per scaglie di PET
57 Tre piattaforme tecnologiche
58 Si scrive cura dei dettagli si legge personalizzazione
59 Trattamento al plasma ecosostenibile
MATERIALI E APPLICAZIONI
60 Un futuro guidato dagli imballaggi in fibre vegetali?
64 Plastificanti da fonti rinnovabili fino al 50%
65 Nel Belpaese la società tedesca supera i 296 milioni di vendite
66 Ridurre l’impatto ambientale delle applicazioni grafiche
66 Prevedere colore e proprietà dei materiali con l’intelligenza artificiale
67 Spessore maggiore, isolamento termico migliore
67 Additivo senza sostanze a base di PFAS
ELASTICA - LA RIVISTA DI ASSOGOMMA
70 Fluoroelastomeri a rischio di bando
72 La capacità elastica della gomma in base alla prova di trazione
74 Rassegna internazionale di scienza e tecnologia
RUBRICHE E VARIE
79 Progetti, ripartenze e novità per Plast 2023
80 Corsi CESAP
81 Corsi SBS
Il PET è divenuto ormai un materiale diffuso e consolidato per la produzione di imballaggi, in particolare bottiglie di qualsiasi genere. A tal fine, questo materiale deve avere una certa qualità specifica e, ancora oggi, durante la lavorazione presenta diversi problemi. Le principali criticità riguardano i cosiddetti “punti neri”, causati dai residui bruciati di PET all’interno della vite di plastificazione, del cilindro e in alcuni casi anche dei canali caldi, e le striature sulle preforme, dovute ai resti dei masterbatch deteriorati nei cambi di colore.
Questi inconvenienti rallentano molto il ciclo produttivo, che può durare da pochi minuti (nelle migliori condizioni) fino a diverse ore (nei casi peggiori), e aumentano di conseguenza la produzione di scarti, che oggi industrie moderne e competitive non possono permettersi, complice anche il filone della sostenibilità e dell’ecologia, sempre più rivolto a migliorare la produttività diminuendo i rifiuti. I composti di spurgo generici e/o universali aiutano poco a ridurre la produzione di scarti e spesso richiedono molto tempo per la modifica dei parametri di elaborazione e l’impostazione dei valori sulla macchina, come l’aumento della temperatura, lo spostamento della vite e altro ancora.
Il nuovo prodotto Ultra Plast PET-CS2 sviluppato e prodotto da Ultra System specificamente per la pulizia di vite, cilindro e, soprattutto, canali caldi può essere utilizzato durante il normale ciclo produttivo senza alcuna modifica del ciclo stesso e impiegando semplicemente il composto di spurgo come normale PET. In altre parole, non è più necessario arrestare la produzione e vengono eliminati i lunghi tempi di attesa. Ultra Plast PET-CS2 può essere iniettato direttamente nello stampo e può essere stampato: poche iniezioni con il prodotto di spurgo e altrettante poche iniezioni con PET neutro sono sufficienti a eliminare istantaneamente i residui bruciati e resti di masterbatch all’interno del canale caldo così come i punti neri.
Il nuovo prodotto risulta maneggevole, di facile utilizzo e, impiegato opportunamente in base al masterbatch e alle condizioni di canale caldo e macchina, contribuisce a ridurre la produzione di scarti, favorendo una pulizia più semplice, veloce ed efficace, unendo produttività e sostenibilità di processo. L’attenzione per l’ambiente, infatti, è uno degli aspetti principali che guidano lo sviluppo di nuovi prodotti da parte di Ultra System, che, con le sue più recenti innovative formulazioni, ha posto estrema attenzione nel rendere possibile il compromesso tra plastica e pianeta, obiettivo cui punta proprio un uso corretto e regolare di Ultra Plast attraverso la riduzione degli scarti e il miglioramento della qualità di processi e prodotti a favore di un mondo più “green”.
www.ultrasystem.ch
100 anni di azienda a conduzione familiare Hehl. Circa 70 anni di storia per il marchio ARBURG. Il giusto mix per uno dei produttori leader mondiali della tecnica dei materiali plastici presente con successo da anni sul mercato. Cosa ci rende unici? Tradizione, motivazione, innovazione e i giusti collaboratori. Così era, e così è ancora. E via con i prossimi 100 anni!
www.arburg.it
Con fatturato pari a 4,67 miliardi di euro, il 2022 si è chiuso per i costruttori nostrani di macchine e attrezzature per la lavorazione di materie plastiche e gomma oltre ogni aspettativa. La seconda prestazione migliore di sempre da incorniciare e che fa ben sperare e guardare al futuro con fiducia nonostante le difficoltà a livello di politica internazionale ed economiche rimangano tante e non siano ancora del tutto superate.
Dai dati consuntivi ufficiali relativi al 2022 dei costruttori italiani di macchine e attrezzature per la lavorazione di materie plastiche e gomma, pubblicati dal Centro Studi Mecs, emerge un anno, quello da poco terminato, da incorniciare. Infatti, il settore delle tecnologie per la plastica e la gomma rappresentato da Amaplast (l’associazione nazionale dei costruttori di macchine e stampi per materie plastiche e gomma) ha chiuso l’anno con un fatturato pari a 4,67 miliardi di euro, seconda prestazione migliore di sempre. Inoltre, l’incremento rispetto al 2021 è stato del 5% e le previsioni dei preconsuntivi pubblicati a dicembre (pari a 4,5 miliardi di euro) si sono quindi rivelate particolarmente caute. Il bilancio della sola compagine associativa è stato persino migliore (+9% il fatturato rispetto al 2021).
Il risultato è tanto più soddisfacente se rapportato alle numerose difficoltà che il comparto ha dovuto affrontare nel corso
dell’anno - peraltro non ancora del tutto superate - tra i limiti alle esportazioni in Russia, la scarsità di materie prime e componentistica nonché l’incremento dei costi energetici. A permettere all’intero settore di raggiungere questo risultato storico è stato soprattutto l’export, che ha registrato un andamento particolarmente positivo sul finire d’anno, con un valore totale tornato sopra la soglia dei 3 miliardi di euro. Dopo l’ottimo 2021, il mercato interno è rimasto più statico, pur con una variazione positiva dello 0,8% e un fatturato pari a 2,54 miliardi di euro.
Nel dettaglio, l’export dei costruttori italiani - che continua a rappresentare una quota del 70% sulla produzione - risulta in progressione sostenuta verso le tre principali macroaree di destinazione:
• Europa (sia comunitaria, sia extra UE): +8%;
• Americhe: +12%, grazie soprattutto al quadrante meridionale (+33% nel suo complesso, con picchi soprattutto per il Brasile ma anche, pur con valori assoluti più bassi, per Colombia, Cile e Perù); in ambito USMCA, rallentano leggermente gli Stati Uniti (-3%) ma segna un nuovo forte rimbalzo il Messico (+35%);
• Asia: +9%; in Estremo Oriente (+9% in media) spicca il +24% delle vendite in India mentre arretra la Cina (-7%); in Medio Oriente (+11% nel complesso) fanno da traino Arabia Saudita (+36%) ed Emirati Arabi Uniti (+58%).
Dal continente africano giungono segnali piuttosto contraddittori e contrari rispetto a quanto registrato nel corso del 2021: l’export in Nordafrica cala del 24% in media e quello verso i mercati sub-sahariani aumenta nella stessa misura.
Quanto alla merceologia dell’export di settore, tra le macchine per la trasfor-
mazione primaria si osserva una robusta crescita degli estrusori (+23%) e degli impianti per mono e multi-filamenti (+58%), categoria quest’ultima che nell’ultimo triennio in particolare ha registrato una progressione molto sostenuta, partendo dai 74 milioni di euro del 2020 per raggiungere nel 2022 il picco storico di quasi 140 milioni, dopo che nel decennio precedente il ventaglio di valore era stato di 30-50 milioni. Piatto invece l’andamento delle macchine a iniezione e decisamente negativo quello delle macchine per soffiaggio (-19%) e delle termoformatrici (-22%).
Quanto al primo trimestre 2023, l’indagine congiunturale svolta tra gli associati a inizio gennaio ha restituito le seguenti attese:
• +7% gli ordini (rispetto allo stesso periodo 2022); le prospettive sono positive, con intensità sostanzialmente simile, per quanto riguarda il mercato italiano e quelli esteri;
• +6% il fatturato, un dato ancora ampiamente positivo ma leggermente meno brillante di quella indicata nei trimestri precedenti; le vendite all’export, nuovamente, dovrebbero dare maggiori soddisfazioni.
Le prospettive per il 2023 restano incerte, visto il contesto economico e politico ancora in cerca di assestamento. Se da un lato, infatti, è parzialmente migliorata la situazione relativa ai costi energetici e alla disponibilità di materie prime e componentistica, dall’altro continuano a susseguirsi criticità - come la recente crisi degli istituti finanziari - che rendono difficile ogni tentativo di fare previsioni.
Un focus sui concorrenti tedeschi che, in base alle ultime indagini, hanno registrato a consuntivo 2022 un calo di tredici punti degli ordini (particolarmente debole il mercato interno) e, al contrario, un +10% per le vendite (bene soprattutto quelle all’estero). In questo primo scorcio di 2023, inoltre, si accentua la forbice tra gli ordini (-40%, con un crollo di quelli do-
TABELLA 1 - MERCATO ITALIANO DI MACCHINE, ATTREZZATURE E STAMPI PER MATERIE PLASTICHE E GOMMA (MILIONI DI EURO)
TABELLA 2 - AREE DI DESTINAZIONE DELL’EXPORT ITALIANO DI MACCHINE, ATTREZZATURE E STAMPI PER MATERIE PLASTICHE E GOMMA (%)
settore delle tecnologie per plastica e gomma rappresentato da Amaplast ha chiuso l’anno con un fatturato pari a 4,67 miliardi di euro, seconda prestazione migliore di sempre.
L’analisi dei bilanci delle aziende associate ad Amaplast compiuta dal Centro Studi Mecs anche nel 2022 consente di valutare l’andamento dell’industria italiana delle macchine per plastica e gomma, che appare in sostanziale buona salute.
Quanto al primo trimestre 2023, l’indagine svolta tra gli associati Amaplast a inizio gennaio ha restituito le seguenti attese: +7% gli ordini (rispetto allo stesso periodo 2022); prospettive positive per quanto riguarda il mercato italiano e quelli esteri; +6% il fatturato.
mestici) e le vendite (+21% ma in questo caso però la performance migliore è registrata in casa).
Per il settore italiano, il 2023 è soprattutto l’anno di Plast, una delle più importanti
fiere al mondo per l’industria delle materie plastiche e della gomma, organizzata da Promaplast. La fiera tornerà, dopo cinque dall’ultima edizione, dal 5 all’8 settembre 2023 a Fiera Milano Rho (Mila-
no). Le aziende si stanno preparando per mostrare al mondo il meglio del made in Italy sotto il profilo della progettazione, dei materiali, della sostenibilità e delle tecnologie smart.
Anche nel corso del 2022 è stata svolta dal Centro Studi Mecs una approfondita analisi dei bilanci delle aziende associate ad Amaplast, uno strumento utile per supportare le aziende nella valutazione del proprio posizionamento competitivo e delle decisioni strategiche.
Il 93,1% delle aziende è risultato in utile nel 2021, a fronte dell’84,6% nel 2020, e il 58% ha incrementato i propri margini.
Il settore nel suo insieme mostra un’espansione dell’Ebitda di circa un
punto percentuale e della stessa entità è la diminuzione media del costo del lavoro. Infine, il 56% delle imprese, una ventina in più rispetto al 2020, rientra nei “top clusters”.
Pur scontando l’inevitabile “ritardo”, dovuto ai tempi di approvazione e deposito dei documenti contabili relativi all’esercizio finanziario 2021, e alla contemporanea mutevolezza del contesto economico e dello scenario globale, lo studio rappresenta un’interessante sintesi dei principali indicatori economico-finanziari che consentono di valutare l’andamento dell’industria italiana delle macchine per plastica e gomma.
Un settore che appare sostanzialmente in buona salute e in grado di assorbire i contraccolpi delle criticità che negli ultimi anni si sono verificate in rapida
successione: in linea di massima, le imprese raggiungono infatti una buona marginalità e mantengono solidità finanziaria, pur evidenziando un basso livello di patrimonializzazione e una certa dipendenza da fonti finanziarie terze.
L’analisi comprende anche un approfondimento sui bilanci di un campione di concorrenti esteri, allargato quest’anno a una quarantina di aziende europee e asiatiche, eterogenee per merceologia. Rispetto a tali competitor, in particolare quelli europei, i costruttori italiani dimostrano di conseguire Ebitda superiori, a parità di tecnologia e produttività. Al contrario, le imprese estere sembrano in vantaggio per quanto concerne il costo del lavoro, il grado di liquidità e la patrimonializzazione.
Le tre associazioni nazionali di categoria che insieme rappresentano 38,8% del settore dei beni strumentali italiani, Amaplast (che raggruppa i costruttori di macchine e stampi per materie plastiche e gomma), Acimac (che rappresenta i costruttori italiani di macchine e attrezzature per ceramica) e Ucima (che raccoglie i costruttori italiani di macchine automatiche per il confezionamento e l’imballaggio) hanno recentemente partecipato, attraverso la voce di Riccardo Cavanna, presidente di Ucima, all’Audizione “Indagine conoscitiva sul Made in Italy: valorizzazione e sviluppo dell’impresa italiana nei suoi diversi ambiti produttivi” in seno alla X Commissione Attività Produttive, Commercio e Turismo presso la Camera dei Deputati, presentando alcune criticità del settore e le relative possibili soluzioni.
Si è trattato della prima volta che le tre associazioni, che rappresentano altrettanti settori di primissimo piano al mondo con una quota media di esportazioni pari al 75,8% e un saldo commerciale attivo di 9,9 miliardi di euro, hanno avuto la possibilità di presentare direttamente al Governo le criticità che stanno vivendo i tre settori che rispettivamente rappresentano e le possibili soluzioni nel medio-lungo termine.
Tra i focus presentati rientrava
l’Industria 4.0, che dopo la spinta degli ultimi anni, necessiterebbe ora di un programma di medio-lungo periodo per continuare a supportare la transizione digitale delle aziende, anche in un’ottica di sostenibilità ambientale. Gli attuali rinnovi su base annuale dei finanziamenti in materia non consentono, infatti, una programmazione degli investimenti pluriennali necessari per sostenere lo sviluppo in questa direzione. Un altro tema trattato è stato quello dell’innovazione tecnologica e dello sviluppo di competenze,
poiché a riguardo risulta necessario sostenere i piani di investimento delle imprese. Un cambiamento che preveda innovazione e transizione digitale come parte integrante del progresso. Per questo le aziende necessitano di un supporto finanziario, migliorando l’accesso al credito, ma anche di investimenti in programmi di formazione dedicati a formare figure specializzate.
In Italia il numero di diplomati negli istituti tecnici e negli ITS così come quello dei laureati in materie scientifiche (in primis, ingegneri) è del tutto insufficiente a soddisfare le richieste provenienti dal mondo delle imprese. Per colmare il divario fra domanda e offerta occorreranno anni in cui l’obiettivo dev’essere
quello di intraprendere politiche attive (sfruttando anche i fondi del PNRR) volte a potenziare le strutture oggi esistenti e ad avvicinare i giovani agli istituti tecnici. Questa audizione ha rappresentato un’occasione importante poiché i tre settori rappresentati dalle associazioni contano attualmente
1.170 aziende che occupano 57.500 addetti e generano un fatturato di 14,2 miliardi di euro, pari al 38,8% del settore dei beni strumentali italiani (uno dei comparti italiani maggiormente riconosciuto nel mondo per la qualità e l’innovazione tecnologica che è in grado di esprimere) e all’1,4% dell’intero settore manifatturiero italiano, che nel 2021 è valso 1.000 miliardi di euro.
Amaplast, Acimac e Ucima
“Nel comparto dei beni di investimento, Ucimu è la prima associazione, in Italia e in Europa, ad aver realizzato il Bilancio di Sostenibilità di settore. Il prossimo step sarà quello di formalizzare questo processo ed estenderlo a una platea di aziende più ampia”, ha dichiarato la presidente di Ucimu.
L’indice degli ordini di macchine utensili nel quarto trimestre 2022 di Ucimu-Sistemi per Produrre ha registrato un incremento del 3,5% rispetto allo stesso periodo del 2021. In valore assoluto l’indice si è attestato a 133,6 (base 100 nel 2015), nuovo record per il trimestre di riferimento. Il risultato è stato determinato sia dal positivo andamento degli ordinativi raccolti sul mercato estero, sia dagli ottimi riscontri del mercato interno.
In particolare, gli ordinativi raccolti all’estero sono cresciuti del 2,4% rispetto allo stesso periodo del 2021, per un valore assoluto dell’indice si attesta a 103,9. Sul fronte interno, gli ordini raccolti hanno registrato un incremento del 5,4%, per un valore assoluto dell’indice pari a 257, anche questo un nuovo record. “Questa performance, davvero soddisfacente perché si confronta con il risultato del quarto trimestre 2021 già eccezionale, è in gran parte frutto dell’accelerazione delle decisioni di acquisto da parte degli utilizzatori che hanno voluto chiudere gli investimenti entro l’anno 2022 per poter godere del credito di imposta al 40%, consapevoli, visti gli annunci governativi, che, a partire da gennaio 2023, l’aliquota sarebbe stata dimezzata”, ha commentato Barbara Colombo, presidente Ucimu.
Su base annua, l’indice degli ordini ha segnato invece un arretramento del 7,8%, per un valore assoluto di 120,1. Il calo è da attribuirsi alla riduzione della raccolta ordini sul mercato italiano (-20,8%) per un valore assoluto di 144,7. In crescita, invece, gli ordini dall’estero (+2,8%), per un valore assoluto di 115,9.
Tra i fattori che hanno contribuito a spingere gli ordini una menzione spetta anche alla sostenibilità. L’associazione dei costruttori italiani di macchine utensili, robot e automazione
ha recentemente realizzato, in collaborazione con Altis, alta scuola di impresa spin off dell’Università Cattolica del Sacro Cuore, il suo primo Bilancio di Sostenibilità. “La sostenibilità è un campo estremamente proficuo per le aziende perché non solo permette di migliorare i rapporti con i propri stakeholder ma offre anche la possibilità di reinventarsi e allinearsi con lo scenario normativo europeo, il quale sottolinea l’importanza sempre maggiore della diffusione delle buone pratiche ESG. Di fronte a questo Bilancio, si può affermare che già un buon numero di pratiche in linea con i criteri ESG è stato introdotto”, ha affermato Barbara Colombo, presidente dell’associazione.
Il Bilancio di Sostenibilità si riferisce al 2021 ed è stato redatto sulla base delle risposte al questionario di valutazione indirizzato alle 66 imprese associate a Ucimu in possesso del Marchio Ucimu. Tale questionario è stato costruito secondo un’analisi di materialità, ovvero focalizzando l’attenzione sugli ambiti di sostenibilità maggiormente influenzati dall’attività delle aziende del settore. In altre parole, le aree ESG oggetto di valutazione sono state scelte, a partire da 11 obiettivi dell’Agenda ONU 2030, perché più coerenti rispetto al business delle imprese operanti nel settore delle macchine utensili. In generale, dal Bilancio di Sostenibilità 2021 emerge una diffusa mancanza di formalizzazione dei processi: nonostante il 64% delle aziende abbia definito strategie e obiettivi, solo il 24% lo ha fatto in maniera formalizzata. La percentuale relativa alla gestione e monitoraggio dei percorsi sostenibili, seppur più alta (39% in modo formalizzato), rimane al di sotto della metà. D’altra parte, i risultati del bilancio mettono in luce la necessità per le imprese del settore di consolidare la loro attitudine a “comunicare la sostenibilità” attraverso l’implementazione di pratiche aziendali ad hoc.
di Sostenibilità
Le buone pratiche sono proficue per le aziende
Tempi brevi e ampio consenso hanno caratterizzato il recente rinnovo del CCNL per il settore plastica e gomma, accolto con più del 96% di voti favorevoli nelle assemblee dei lavoratori. Importanti novità sono state introdotte in merito al welfare sanitario e sul fronte delle relazioni industriali, che saranno rafforzate anche attraverso il potenziamento dell’Osservatorio nazionale sui due comparti industriali e la prosecuzione dell’attività connessa con il sistema di classificazione degli addetti.
“Le sempre più numerose imprese che rappresentiamo”, ha dichiarato Marco Do, presidente di Federazione Gomma Plastica, “ci consegnano la fotografia di un settore resiliente, che sa innovare
Settimana corta in Tria
e guardare al futuro. Negli ultimi due anni le nostre imprese hanno reagito con determinazione all’emergenza sanitaria e alla crisi energetica, attivando percorsi di cambiamento e sostenibilità. La federazione è impegnata a sostenere e promuovere le buone pratiche aziendali e opera a fianco dei propri iscritti per la realizzazione del green deal italiano ed europeo, non lasciando indietro nessuno. Anche il rinnovo del contratto, avvenuto in tempi rapidi, è segno di responsabilità delle imprese, di solide relazioni sindacali e di attenzione alle esigenze dei lavoratori, oltre il 70% dei quali sono operai e oltre il 90% hanno un contratto a tempo indeterminato”.
A partire da gennaio 2023, Tria ha adottato la settimana corta. Per tutti i dipendenti dell’azienda di Cologno Monzese (Milano) l’orario lavorativo è stato ridotto da 40 a 36 ore settimanali senza che lo stipendio abbia subito variazioni. Si tratta di una decisione che parte da lontano. Quando durante il lockdown della primavera 2020 a causa della pandemia Tria aveva attivato lo smart working e i dipendenti avevano dovuto gestire il proprio lavoro autonomamente senza controllo dell’orario era stato riscontrato un incremento di produttività e fatturato. Nei mesi seguenti a ciò si è aggiunta la progettazione di nuove tecnologie e la loro buona accoglienza al K 2022. Al termine obbligatorio per lo smart working, quindi, il CEO Stefano Venturelli e la direzione hanno avviato uno studio di fattibilità per la settimana lavorativa con orario ridotto, introdotta a partire dall’inizio del 2023 per un periodo sperimentale di sette mesi e accolta con favore dai
dipendenti. Tria è una delle prime aziende in Italia a ridurre l’orario di lavoro settimanale. La sede di Tria a Cologno Monzese (Milano)
Rinnovo CCNL gomma plastica
Migliora la situazione dell’offerta di poliuretano espanso flessibile, ma i prezzi delle materie prime permangono alti. Lo riferisce Europur, l’associazione europea che riunisce i produttori di tali semilavorati, secondo cui il prezzo del gas resta alto e volatile, anche se in Europa è diminuito rispetto alla scorsa estate, mettendo in difficoltà l’intera industria chimica, che utilizza il gas sia come materia prima sia come fonte energetica. Come Cefic, il consiglio europeo dell’industria chimica, aveva segnalato, a ottobre 2022 per la prima volta il Vecchio Continente ha importato più prodotti chimici di quanti ne abbia esportati e l’industria chimica in generale si è trovata a “un punto di rottura”. I principali fornitori tedeschi di materie prime attivi anche nella filiera del poliuretano hanno avvertito che la situazione potrebbe spingerli a breve a dover modificare le proprie strategie europee.
Fortemente dipendente dall’approvvigionamento di materie prime chimiche, l’industria del poliuretano flessibile si è trovata in una posizione precaria lo scorso autunno a causa di tale situazione, resa ancor più difficile dall’interruzione della produzione in tre siti europei produttori di TDI, una delle principali sostanze chimiche utilizzate per produrre blocchi espansi. Tutti i fornitori hanno fatto del loro meglio per stabilizzare l’offerta, utilizzando anche le importazioni di TDI da Asia e Stati Uniti, ma con un allungamento dei tempi di consegna. Parallelamente, la domanda di espansi è diminuita a causa della riduzione della domanda, principalmente dai mercati dell’arredamento e dei prodotti per il riposo. A seguito del calo della domanda, della ripresa della produzione europea e di importazioni stabili di prodotti chimici, la carenza di espansi è in gran parte diminuita in novembre e anche i prezzi delle materie prime chimiche hanno iniziato a stabilizzarsi, sebbene restino alti, con i prezzi del gas ancora elevati.
Secondo Europur, la situazione rimane piuttosto incerta, in quanto la filiera del poliuretano espanso flessibile può essere influenzata positivamente o negativamente da prezzi del gas in Europa e costi operativi dell’industria chimica a causa di fattori quali l’incertezza sulla stabilità dell’approvvigionamento di gas in Europa per gran parte del 2023 o dall’evoluzione della domanda europea di prodotti a base di espansi (materassi e mobili in particolare).
Le finestre in PVC sono sempre più apprezzate per la capacità di unire prestazioni, estetica ed economicità.
Anche nel 2022 il mercato italiano del serramento in PVC ha registrato una crescita importante. È quanto rileva il Gruppo Serramenti e Avvolgibili di PVC Forum Italia, che dal 2013 svolge ogni anno una indagine sul mercato italiano del serramento in PVC grazie ai dati forniti dalla collaborazione di 10 aziende associate (Alphacan, Aluplast, Deceuninck, Finstral, QI Sistemi/Gealan, Profine, Rehau, Salamander, Schüco e QI Sistemi/Veka), che insieme rappresentano gran parte del mercato di riferimento. Dopo il forte incremento del 2021, i serramenti in PVC nel 2022 hanno messo a segno una crescita del 16,8%, con oltre 16,6 milioni di metri lineari di telai per finestre - equivalenti a circa 2,7 milioni di unità finestra campione (1,23 x 1,48) equamente divise tra profili bianchi e pellicolati - immessi nel mercato italiano dalle suddette aziende. Dal calcolo sono esclusi i profili persiana, mentre sono compresi quelli per finestre scorrevoli, quantità equivalenti a circa 49.800 tonnellate sulla base di un peso medio di 18 kg per unità serramento.
Nella spinta alla crescita sono stati determinanti ancora una volta gli incentivi fiscali (dal 50 al 110%) e le scelte d’acquisto degli utenti sempre più rivolte verso il PVC per le sue eccellenti prestazioni tecniche e ambientali così come per l’ottimo rapporto costo/prestazione.
Considerando anche le finestre in PVC importate dall’estero, la cui stima esatta risulta non semplice ma ipotizzabile in circa 1,1 milioni di unità, si arriva a un totale di 3,8 milioni di unità, ossia circa il 52% del mercato totale delle finestre in Italia (quantificabile in 7,3 milioni di unità, compresi tutti i materiali alternativi). Un dato di estremo interesse, considerando che nel 2000 il PVC non copriva neanche il 15% del mercato, a testimonianza di una costante e duratura crescita del materiale negli anni. Il giro d’affari generato nel 2022 dal settore del serramento in PVC risulta essere in totale di circa 2,1 miliardi di euro.
La situazione illustrata da Europur mostra un miglioramento della situazione dellʼofferta di poliuretano espanso flessibile, ma permangono fattori di incertezza, primo fra tutti il prezzo delle materie prime.
La scelta di infissi in PVC premia la loro ormai riconosciuta sostenibilità ambientale, certificata dalla “Product Label” creata da VinylPlus, l’impegno europeo per la sostenibilità del PVC. L’ultimo Bilancio di VinylPlus ha evidenziato nel 2021, nonostante la contrazione delle attività economiche causata dalla pandemia, un riciclo complessivo di 810.775 tonnellate di rifiuti in PVC provenienti dalle diverse applicazioni, 355.329 (quasi il 44%) delle quali provenienti da profili finestra e prodotti correlati. Dal 2000, nell’ambito di Vinyl 2010 prima e ora VinylPlus, sono state riciclate 3,3 milioni di tonnellate di PVC derivanti dai serramenti in PVC.
Il giro d’affari del settore del riciclo di materie plastiche in Polonia si aggira intorno a 613 milioni di euro. È quanto stimato da un recente studio condotto dalla rivista polacca Plastic Review, secondo cui tale valore non molto elevato può essere letto come una buona opportunità di crescita per il settore, ritenuto uno dei più promettenti per l’economia locale nei prossimi anni e in grado di attirare capitali per la rapida implementazione di moderne tecnologie di sviluppo. A sostegno di queste previsioni giocherebbero le vendite di materie plastiche riciclate, cresciute quasi del 50% nel 2021 rispetto all’anno precedente.
Nel Paese operano circa 150 aziende riciclatrici che, in tale anno di riferimento, hanno riciclato circa 440.000 tonnellate e realizzato un fatturato medio intorno a 220.000 euro all’anno. Valori, questi, che,
Nei prossimi anni, il riciclo della plastica potrebbe risultare uno dei settori di investimento più interessanti nellʼeconomia polacca.
secondo lo studio, indicano l’attrattiva esercitata dall’industria del riciclo, con ampi spazi di investimento e margini di crescita. Lo studio è stato realizzato in base all’analisi dei risultati finanziari di
Secondo il recente studio “Global Insulation” di Freedonia Group, gli espansi hanno rappresentato, con il 50%, la quota maggiore della domanda di materiali per isolamento nel 2021. Tali soluzioni sono diffuse in tutte le aree geografiche e nei principali mercati a livello globale. Polistirene, poliuretano e schiume fenoliche sono i materiali isolanti che, tanto in forma di pannelli che in applicazioni a spruzzo, trovano la maggiore diffusione di utilizzo.
In base alle previsioni, la domanda globale di isolamenti in materiali plastici espansi crescerà dell’1,2% all’anno, raggiungendo il valore di 29,1 miliardi di dollari, per un totale di 9,7 milioni di tonnellate nel 2026. Seppure il valore di mercato crescerà a un ritmo relativamente lento, frenato dal calo dei prezzi conseguente all’inflazione elevata e ai livelli relativi alla catena di approvvigionamento, sarà sostenuto da buoni aumenti della domanda.
In termini di materiali, l’EPS dovrebbe continuare a rappresentare la quota
maggiore della domanda, sostenuta dal suo basso prezzo rispetto ad altri materiali espanse, mentre l’aumento dei volumi di XPS sarà supportata dal crescente utilizzo di questo materiale in applicazioni quali tubature e condotte a livello globale, grazie al suo elevato valore R (fattore di isolamento termico).
La crescita dell’impiego di poliuretano
oltre 120 riciclatori di materie plastiche attualmente operanti in Polonia, che hanno permesso anche di stilare una classifica delle principali 77 aziende attive in tale settore.
dovrebbe invece essere la conseguenza di vari fattori, tra cui la crescente diffusione dell’impiego di schiume poliuretaniche a spruzzo, l’espansione nel mercato dell’edilizia non residenziale, dove i materiali plastici espansi trovano ampia diffusione in questo tipo di applicazioni, e la solida crescita nella produzione di frigoriferi e congelatori.
Polistirene, poliuretano e schiume fenoliche sono i materiali isolanti che, tanto in forma di pannelli che in applicazioni a spruzzo, trovano la maggiore diffusione di utilizzo.
Blanchin Metal-PlastPresso la sede della società Galdi si è tenuto il convegno “Regolamento imballaggi e impatto per la filiera del packaging” voluto e organizzato da Amaplast e Ucima per offrire un momento di confronto sulle criticità che il nuovo atto normativo proposto dalla Commissione europea introdurrebbe per le aziende del settore e sulle strategie adottabili per farvi fronte.
La proposta di un nuovo Regolamento del Parlamento europeo e del Consiglio europeo sugli imballaggi e sui rifiuti di imballaggio, presentata dalla Commissione europea il 30 novembre 2022, sta destando grandi preoccupazioni tra gli operatori del settore. L’intera filiera dell’imballaggio si è mobi-
litata da circa un anno per manifestare il proprio dissenso riguardo un atto normativo che, al di là delle criticità che impone al comparto del packaging, se mantenesse la forma giuridica del regolamento risulterebbe “auto-esecutivo” dalla sua entrata in vigore, senza alcuna possibilità di discrezionalità da parte degli Stati membri in quanto a trasposizione delle nuove regole negli ordinamenti nazionali. Questo aspetto di cogenza non supportata da evidenze scientifiche è forse quello che spaventa maggiormente il settore dell’imballaggio e che è emerso chiaramente anche al convegno “Regolamento imballaggi e impatto per la filiera del packaging” voluto e organizzato da Amaplast (l’associazione nazionale dei costruttori di macchine e stampi per materie plastiche e gomma) e Ucima (l’unione dei costruttori italiani di macchi-
ne automatiche per il confezionamento e l’imballaggio), tenutosi presso la sede di Galdi (nella foto di apertura), azienda costruttrice di macchine per l’imballaggi, a Paese (Treviso), il 9 febbraio. Sul palco del convegno si sono ritrovati i rappresentanti a vario titolo della filiera del packaging e delle istituzioni per un confronto sulle diverse criticità delle norme del nuovo Regolamento imballaggi e sulle diverse strategie messe in atto per farvi fronte, tema predominante per il settore e sviluppato nel corso dell’evento, che ha richiamato l’interesse di oltre 150 aziende.
“Noi non siamo contro il cambiamento”, ha dichiarato Riccardo Cavanna, Presidente di Ucima, “Il problema è che que-
Galdisto Regolamento sta creando confusione. Noi abbiamo avuto sempre un ruolo da protagonisti nel portare la filiera a raggiungere importanti risultati in termini di economia circolare, ma abbiamo bisogno di un approccio concreto e che valorizzi il percorso intrapreso finora. L’obiettivo comune è la salvaguardia del nostro pianeta”.
La carenza di indicazioni certe e la mancanza di un’impalcatura normativa ben delineata sono lacune importanti che il confronto non ha mancato di sottolineare. A questo proposito, è bene rilevare che, nel testo della proposta di Regolamento, la Commissione rinvia a una legislazione secondaria, una decina di atti delegati, per dieci anni nei poteri della Commissione Ambiente, tacitamente rinnovabili da Parlamento e Consiglio. Da diverse parti è emerso che l’atto delegato non sia uno strumento idoneo a garantire sufficiente flessibilità e tempestività per rappresentare una realtà così complessa come quella della filiera dell’imballaggio e che si debba piuttosto prevedere una delega di questa materia a organi tecnici competenti, che, con strumenti di “soft law”, quali norme tecniche e linee guida settoriali, possa meglio rispondere alle esigenze del mercato.
Il rimando ad atti delegati della Commissione compare spesso nella proposta di Regolamento con riferimento a punti chiave della nuova disciplina come, per esempio, la riciclabilità degli imballaggi rispetto alla quale la nuova disciplina impone che dal 1° gennaio 2030 tutti gli imballaggi immessi sul mercato dovranno rispettare i criteri di progettazione per il riciclo che saranno identificati con atti delegati adottati dalla Commissione a partire dal 1° gennaio 2027.
“La fattibilità tecnica del nuovo Regolamento non è un aspetto da poco e va valutata attentamente”, ha aggiunto Dario Previero, presidente di Amaplast. “Fare fronte comune tra associazioni ha lo sco-
po di dar voce alle perplessità delle aziende e poter lavorare per individuare la miglior soluzione possibile”.
Per quanto possano essere rivolte alla salvaguardia degli aspetti ambientali del pianeta, messi in pericolo dal proliferare di rifiuti sul territorio, le nuove imposizioni della proposta di Regolamento suscitano spesso perplessità sia per l’ambizione dei risultati, ritenuti in più frangenti di difficile realizzazione, sia per la mancanza di un supporto scientifico a corredo di vere e proprie sfide che rischiano di mettere in ginocchio il settore.
Un esempio è rappresentato dalla preminenza accordata ai processi di riutilizzo/ riempimento degli imballaggi, rafforzata dall’obbligo verticale e orizzontale dato dalla forma giuridica dell’atto normativo, il regolamento, che non è supportato da chiare evidenze scientifiche che dimostrino impatti ambientali complessivi migliori, per esempio nei confronti degli imballaggi monouso/riciclati. Lasciano perplessi gli obiettivi di riutilizzo e i divieti di immissione sul mercato di ampie categorie di imballaggi senza che tali misure siano supportate da valutazioni sul ciclo di vita dei diversi sistemi di utilizzo degli imballaggi e del loro fine vita. Rendendo pubblici metodologia e risultati, la Commissione darebbe tra l’altro a tutti i soggetti interessati dati certi sulla base dei quali riorientare e/o indirizzare ricerca e sviluppo e investimenti.
La partecipazione di Confindustria al convegno ha evidenziato una unità di intenti fra gli operatori del settore e l’organo istituzionale in rappresentanza degli interessi del comparto industriale e produttivo.
È attivo, infatti, un gruppo di lavoro coordinato da Confindustria, composto dalle associazioni della filiera dell’imballaggio, per identificare, valutare e raccogliere le istanze degli operatori industriali alla luce delle nuove disposizioni normative previste dalla proposta di regolamento. Nel corso dell’evento Confindustria ha presentato le strategie attuate in difesa del
settore e di tutta la filiera, affinché la riforma risulti equilibrata e orientata al rafforzamento del sistema-Italia di gestione dei rifiuti di imballaggio, un modello da preservare e difendere.
“Non accettiamo lo spostamento di paradigma del nuovo Regolamento europeo dal riciclo al riuso. È un approccio non suffragato da dati scientifici. Un esempio: il massivo uso di acqua per permettere il riutilizzo”, ha dichiarato Marco Ravazzolo, responsabile per le politiche industriali e per la sostenibilità di Confindustria.
A livello istituzionale era presente anche il Senatore Luca de Carlo, presidente della Commissione industria, commercio, turismo, agricoltura e produzione agroalimentare del Senato, secondo cui “non bisogna farsi intimorire da mode ideologiche che criminalizzano la plastica. L’Italia rappresenta un modello per il riciclo e va difeso”.
Lo sguardo poi si è ampliato grazie al punto di vista portato da Francesca Stevens, segretario generale di Europen (l’organizzazione europea per il packaging e l’ambiente, che ha evidenziato come “in Italia c’è grande attivismo da parte di Confindustria e del Governo per difendere le istanze della filiera italiana del packaging. Da altri Paesi le resistenze sono più morbide, ma serve coesione da parte di tutti
Il palco degli intervenuti, durante un momento del convegno.
Dario Previero (a sinistra), presidente Amaplast, e Riccardo Cavanna (a destra), presidente di Ucima, durante i loro interventi, insieme a Mario Maggiani (al centro), direttore di Amaplast e Ucima.perché la strada che si sta percorrendo è rischiosa per molti aspetti”.
A dimostrazione dell’unità di intenti e di vedute è di novembre la dichiarazione congiunta predisposta proprio da Europen per reagire alla bozza di Regolamento sugli imballaggi. Il documento, condiviso da più di 60 organizzazioni europee, rappresenta un forte segnale di coesione e allineamento dell’industria europea, utilizzato come base per azioni simili in ciascun Paese dell’Unione Europea al fine di sensibilizzare i rispettivi Governi, parlamentari e rappresentanti europei, in linea con quanto fatto da Confindustria e tutto il mondo associativo in Italia.
La parola è stata data anche agli imprenditori, che, insieme a Giflex, l’associazione nazionale che raggruppa i produttori di imballaggi flessibili destinati al confezionamento di prodotti alimentari, far-
maceutici, chimici e altre applicazioni industriali, si sono confrontati sulle criticità innescate dalle normative nei rispettivi settori di attività durante una tavola rotonda.
“Credo che questo regolamento”, ha sostenuto Alberto Palaveri, presidente di Giflex, “non acceleri lo sviluppo, bensì lo freni. Il rischio è quello di ritrovare le nostre aziende più povere e i consumatori meno tutelati sotto il profilo della sicurezza”.
Il tema della sicurezza di prodotto è centrale nella vicenda delle nuove regole sugli imballaggi e i rifiuti di imballaggio. Il riferimento è quasi scontato ma indispensabile e fa riferimento a una funzione basilare dell’imballaggio, quella di proteggere la merce e preservare la salute del consumatore dal danno derivante da un prodotto alterato. La sicurezza e funzionalità degli imballaggi deve essere tenuta in conto per evitare anche altri effetti negativi indesiderati, quali l’aumento dei rifiuti alimentari o di altri prodotti. Le nuove direttive inerenti all’obbligo di riutilizzo o di percentuali crescenti di riciclato contenuto negli imballaggi offrono il fianco a perplessità proprio in tema di sicurezza. Solo a titolo di esempio, risulta difficoltoso garantire la salvaguardia della sicurezza alimentare in presenza di cicli di riutilizzo dell’imballaggio e della necessità di lavaggi a cura del consumatore. Da più parti è stato rilevato che gli imballaggi hanno un ruolo essenziale nella prevenzione dei rifiuti alimentari, proteggendo i prodotti e riducendo al minimo gli sprechi in tutte le fasi della catena del valore. Sarebbe opportuno tenere
in debita considerazione come gli imballaggi possano preservare la sicurezza degli alimenti riducendo al minimo le fonti di contaminazione così come i rifiuti alimentari dovuti al deterioramento. Walter Bertin, presidente e CEO di Labomar, in linea con quanto sostenuto da Palaveri, evidenziando i risultati già ottenuti, ha dichiarato che “ci sono prodotti in commercio che già implicano un basso impatto ambientale, basato sul riciclo. È rischioso rimettere in discussione anni di sviluppo”. La presenza di Walter Bertin ha richiamato l’attenzione sull’industria farmaceutica, una di quelle direttamente interessate dal nuovo Regolamento. In questo ambito, l’imballaggio svolge un ruolo più che mai cruciale e insostituibile nella protezione, nella conservazione e nel mantenimento dell’integrità terapeutica dei prodotti farmaceutici per uso sia umano sia animale, a garanzia della sicurezza e della salute degli uni e degli altri. Il convegno è stato fortemente voluto dalle due associazioni come occasione di incontro con le aziende del territorio, in questo caso quello veneto, per presentare le proprie attività e farsi portavoce di temi caldi per il comparto. In conclusione, a questo proposito risulta appropriato l’intervento di Alessandro Lazzarin, presidente di Latteria del Montello (Nonno Nanni), che ha messo in luce l’importanza di questo genere di eventi, affermando che “con la nostra azienda siamo molto attenti a quel che sta succedendo perché le norme del Regolamento impattano notevolmente sul modo di fare sviluppo. In questa fase serve più chiarezza e ben vengano questi incontri”.
Al convegno gli imprenditori si sono confrontati sulle criticità innescate dalle normative nei rispettivi settori di attività. La proposta di un nuovo Regolamento sugli imballaggi e sui rifiuti di imballaggio presentata dalla Commissione europea sta destando grandi preoccupazioni lungo tutta la filiera dell’imballaggio, che si è mobilitata per manifestare il proprio dissenso. CroccoConsorzi e associazioni di filiera della trasformazione e del riciclo collaborano per coordinare le rispettive attività verso un sempre maggiore riciclo dei prodotti in plastica giunti a fine vita. Da utilizzare come fonti per ottenere nuovi materiali ma anche per produrre combustibili alternativi. Tutto in un’ottica di sostenibilità ed economia circolare per ridurre le emissioni di CO 2
Rispondere al crescente bisogno di sostenibilità degli imballaggi in plastica promuovendo la cultura del riciclo. Sono questi i principi ispiratori del patto siglato da Conai, Corepla, Unionplast e IPPR, i consorzi e le associazioni principali della filiera italiana della trasformazione e del riciclo di materie plastiche, che ha istituito una sinergia finalizzata alla creazione di un nuovo schema di certificazione per attestare la riciclabilità degli imballaggi in plastica e un’azione di maggiore coordinamento e supporto per le attività di divulgazione scientifica, culturale e di ricerca per la diffusione di buone pratiche di sostenibilità ed economia circolare.
Alla base dell’intesa c’è la consapevolezza che solo rafforzando la collaborazione tra tutti i soggetti che si occupano di recupero, riciclo e riciclabilità dei rifiuti di imballaggi in plastica si possa creare maggiore valore per le imprese e le persone promuovendo, contestualmente, una più ampia partecipazione di tutti gli stakeholder. Per realizzare l’economia circolare infatti è fondamentale coinvolgere realtà diverse: consumatori, imprese, scuole, istituzioni e centri di eccellenza, favorendo lo scambio di informazioni sulla riciclabilità degli imballaggi in plastica.
Il patto prevede la stesura da parte degli esperti di Conai, Corepla, Unionplast e IPPR di un disciplinare di certificazione che si affianchi a strumenti nuovi o esistenti per consentire alle aziende di raggiungere livelli sempre più alti di riciclabilità. Il disciplinare
prevederà anche tutti i test di laboratorio necessari per verificare la conformità ai requisiti previsti.
“Un patto che dimostra nuovamente quanto sia importante favorire una seconda vita per gli imballaggi”, ha commentato il presidente di Conai, Luca Ruini. “Mettere insieme esperienze e competenze è essenziale per sviluppare strumenti concreti che aiutino le imprese del nostro Paese, sempre più attente a considerare il riciclo uno strumento chiave del passaggio a un vero modello di economia circolare”.
“L’intesa raggiunta”, ha spiegato il presidente di Corepla, Giorgio Quagliuolo, “amplia ulteriormente lo sforzo di coordinamento che tutti i soggetti impegnati concretamente nell’affermazione di una cultura dell’economia circolare praticano da tempo. Con questo patto mettiamo a fattor comune non solo avanzati sistemi di raccolta e riciclo degli imballaggi in plastica ma anche una visione generale di lungo periodo che supporti le imprese nella ricerca di una progettualità di base improntata a standard di sostenibilità ambientale sempre più elevati ed estesi a tutta la filiera produttiva”.
“Siamo felici che IPPR sia stato scelto come veicolo per traguardare questo importante obiettivo strategico per l’intera filiera delle materie plastiche, impegnata nella realizzazione concreta dell’economia circolare”, ha aggiunto il presidente Libero Cantarella.
Da sinistra: Luca Ruini, presidente Conai; Giorgio Quagliuolo, presidente Corepla; Libero Cantarella, presidente IPPR; Marco Bergaglio, presidente Unionplast.
“Un segnale importante di sostegno alle imprese del nostro settore, che credono fortemente nella sostenibilità della plastica e che lavorano quotidianamente per realizzare imballaggi al contempo riciclabili e altamente performanti”, ha concluso il presidente di Unionplast, Marco Bergaglio.
Combustibili alternativi dai rifiuti plastici
La sigla di un altro protocollo di intesa ha visto protagonista insieme a Corepla anche Federbeton, la federazione che rappresenta i produttori di cemento e calcestruzzo all’interno di Confindustria, per formalizzare una collaborazione sul tema del recupero energetico. Il protocollo prende spunto dalla consapevolezza della necessità di valorizzare gli scarti dell’attività di selezione della raccolta differenziata degli imballaggi in plastica non riciclabili come fonte energetica. L’avvio di questi rifiuti plastici agli impianti di produzione di combustibili alternativi, come il CSS (Combustibile Solido Secondario), consente di sfruttarne l’altissimo potere calorifico e di sottrarli al conferimento in discarica, limitando o azzerando la quota destinata all’esportazione, che, secondo il Rapporto Rifiuti Ispra 2021, è tre volte superiore a quella importata.
Il settore del cemento è fortemente impegnato nella sfida per la decarbonizzazione. La strategia condivisa dalle imprese della filiera prevede diverse azioni che, in tempi diversi, contribuiranno al raggiungimento della neutralità carbonica nel 2050. L’utilizzo di CSS derivato dai rifiuti attualmente non riciclabili, come il plasmix, rappresenta una delle leve immediatamente implementabili. Il tasso di sostituzione calorica con combustibili alternativi nelle cementerie in Italia è fermo al 22%, ben lontano dalla media europea (52%). Da un punto di vista tecnologico, gli impianti italiani sono già attrezzati per raggiungere un livello analogo, ma persistono ostacoli burocratici e culturali che non permettono di esprimere le reali potenzialità del settore. Secondo la stima elaborata dal Laboratorio REF Ricerche, un tasso di sostituzione calorica del 66% in Italia porterebbe al taglio di 6,8 milioni di tonnellate di CO2 emesse in atmosfera con benefici immediati per ambiente e industria.
Firmando il protocollo di intesa, Corepla e Federbeton hanno individuato alcuni campi d’azione e aree di interesse su cui sviluppare la partnership: studi e analisi del contesto di settore a livello nazionale e regionale; politiche per incentivare i processi che possono contribuire a massimizzare il recupero delle plastiche miste, tra i quali rientrano anche i processi di trattamento che portano alla produzione del CSS; iniziative per rendere omogenea sul territorio l’applicazione delle semplificazioni autorizzative che rendono l’utilizzo di CSS equiparabile a quello degli altri combustibili “tradizionali”; informazione e comunicazione per promuovere il dialogo con le comunità locali e l’opinione pubblica nazionale, per una condivisione sempre più consapevole delle scelte.
“Con sempre maggiore determinazione l’Italia persegue l’attuazione di una concreta strategia di transizione energetica puntando ai molteplici obiettivi di tutela dell’ambiente, indipendenza energetica e accessibilità dei costi delle risorse. Il protocollo d’intesa con Federbeton”, ha sottolineato il presidente di Corepla, Giorgio Quagliuolo, “si inserisce in questo solco, consentendo a un importante settore industriale come quello del cemento di elevare il grado di sostenibilità produttiva della filiera e, contestualmente, di valorizzare al massimo i combustibili solidi secondari da rifiuti (CSS) che il nostro sistema può mettere a disposizione. Non è scontato ricordare come, a nostro avviso, i benefici ambientali derivanti dall’impiego di CSS siano legati a fattori importanti come la sostanziale attenuazione delle emissioni di CO2 e il minor consumo di combustibili fossili. Si tratta, di fatto, di applicazioni che si allineano agli obiettivi di sviluppo sostenibile e di decarbonizzazione stabiliti dalle direttive europee e, soprattutto, di una risposta efficace e misurabile alla sfida imprescindibile posta dalla lotta ai cambiamenti climatici”.
“L’uso dei combustibili alternativi rappresenta una soluzione fondamentale per la filiera del cemento e del calcestruzzo. Si tratta di una pratica con grandi potenzialità inespresse, che può portare una riduzione delle emissioni e contribuire a una più efficiente gestione dei rifiuti non riciclabili, a vantaggio della collettività”, ha commentato Roberto Callieri, presidente di Federbeton. “La collaborazione con Corepla conferma, ancora una volta, l’impegno di Federbeton su questo tema e più in generale sui temi dell’economia circolare e della sostenibilità ambientale. L’obiettivo è quello di mettere in campo iniziative comuni per promuovere un contesto normativo e culturale favorevole al raggiungimento degli obiettivi di carbon neutrality”.
La previsione arriva da European Bioplastics, intervenuta all’evento organizzato dal centro tecnologico spagnolo Aimplas, e riguarda in particolare le applicazioni in ambito agricolo. Circa 200 partecipanti hanno assistito alle presentazioni proposte da una ventina di relatori per discutere delle sfide e delle opportunità e conoscere le principali innovazioni del settore. Tra cronaca e resoconto ecco cosa è stato detto.
Èandata in scena nella città spagnola di Valencia l’1 e il 2 marzo l’ottava edizione del seminario internazionale su biopolimeri e compositi sostenibili organizzato da Aimplas, centro tecnologico locale dedicato alle materie plastiche, che ha messo al centro dell’attenzione le sfide e le opportunità che il comparto dovrà affrontare e potrà sfruttare nel prossimo futuro, così come le più recenti applicazioni rese possibili grazie all’impiego di tali materiali.
Oltre 20 relatori hanno offerto il proprio contributo per tracciare il quadro del mercato dei biopolimeri, del loro contributo alla transizione verso l’economia circolare e al raggiungimento degli obiettivi climatici dell’Unione Europea, del loro impatto ambientale e della legislazione che li riguarda. Una dozzina di aziende, invece, ha presentato le proprie innovazioni e storie di successo.
La produzione mondiale annua di bioplastiche è attualmente attesta a circa 2,2 milioni di tonnellate. Tuttavia, come ha illustrato Constance Ißbrücker di European Bioplastics, questo valore dovrebbe all’incirca triplicare e raggiungere i 6,3 milioni di
tonnellate entro il 2027 e le applicazioni che dovrebbero mostrare la crescita più significativa sono quelle legate all’agricoltura, che ora rappresentano il settore verso cui è destinato il 4% della produzione totale, percentuale che, secondo le previsioni, salirà al 5%.
La rappresentante della Commissione europea Theodora Nikolakopoulou ha sottolineato la preoccupazione dell’Unione europea per la protezione dei terreni agricoli e ha riferito che da luglio 2026 sarà obbligatorio che tutti i fertilizzanti ad azione controllata commercializzati nel Vecchio Continente siano biodegradabili. Partendo da una valutazione di impatto ambientale, quindi, in ambito agricolo le bioplastiche giocheranno un ruolo sempre più importante.
Elena Domínguez, ricercatrice che si occupa dello sviluppo delle applicazioni agricole presso Aimplas e coordinatrice tecnica del seminario, ha spiegato come il centro tecnologico spagnolo dedicato alle materie plastiche stia suggerendo alla Commissione europea i criteri che questo tipo di applicazioni dovrebbe soddisfare perché ne sia garantito lo status di manufatti biodegradabili.
Jordi Simón, di Asobiocom, l’associazione spagnola delle plastiche biodegradabili compostabili, ha parlato appunto di applicazioni compostabili e ha sottolineato l’importanza di limitare l’attribuzione di tale qualifica a quelle in cui le bioplastiche apportano valore, mantengono la funzionalità del prodotto e forniscono benefici legati alla fine del ciclo di vita, migliorando la sostenibilità e riducendo l’impatto ambientale. La sessione di interventi su standardizzazioni e certificazioni è stata moderata da Johana Andrade, ricercatrice presso il laboratorio di biodegradabilità e compostaggio di Aimplas e anch’ella coordinatrice tecnica del seminario, che ha evidenziato l’importanza proprio delle standardizzazioni e delle certificazioni quando si comunicano i vantaggi apportati dalle bioplastiche, per garantirne un utilizzo appropriato e gestirne correttamente il fine vita e ottenerne i benefici ambientali previsti. Nel corso di una tavola rotonda sono stati forniti i risultati positivi ottenuti dall’impiego delle plastiche compostabili in casi reali di compostaggio presso impianti industriali, dove è stata verificata l’avvenuta completa biodegradazione e l’ottenimento di compost di qualità.
prietà dei manufatti prodotti con plastiche tradizionali. Aimplas ha inoltre riferito i risultati di alcuni suoi progetti per l’industria del packaging, quali imballaggi biodegradabili con effetto barriera ottenuti da scarti alimentari, film plastici ottenuti dagli scarti del caffè, imballaggi attivi per allungare la vita sugli scaffali dei formaggi ricavati da scarti dell’industria casearia stessa e cartucce per la stampa 3D alimentare. Per completezza di cronaca meritano un accenno anche le soluzioni presentate dal centro spagnolo per l’impiego in ambito agricolo, quali vernici naturali per il controllo delle infestazioni da cocciniglia negli agrumi, schiume per colture idroponiche ricavate dagli scarti delle piume dell’industria avicola e un materiale compostabile simile al cartone ricavato dagli scarti della potatura e della pressatura della vite.
Le sessioni del secondo giorno si sono concentrate infine sulle storie di successo inerenti all’impatto ambientale delle bioplastiche in aree aperte dalla duplice prospettiva dei terreni agricoli da un lato e dell’ambiente marino dall’altro, trattate da organizzazioni come APE, Ercros, Universidade de Vigo e Cajamar.
L’ottava edizione del seminario su biopolimenri e materiali compositi sostenibili organizzato da Aimplas a Valencia ha richiamato un pubblico di circa 200 partecipanti.
Le aziende operanti lungo l’intera catena del valore hanno presentato le proprie innovazioni sul fronte tanto dei materiali quanto dei prodotti, consentendo ai partecipanti di acquisire a riguardo informazioni di prima mano a 360 gradi, dagli additivi che migliorano la lavorabilità e la compatibilità dei biopolimeri alle bottiglie per acqua realizzate in PLA riciclato che hanno le stesse proprietà e qualità di quelle in materiale vergine. Tra le novità realizzate con l’impiego di bioplastiche sono stati proposti anche film ottenuti mediante estrusione in bolla così come una gamma completa di contenitori, chiusure e bottiglie compostabili, tutte soluzioni che possono essere realizzate con le tecnologie convenzionali e offrono le medesime pro -
Nei due giorni di evento è emerso chiaramente che oggi molta attenzione si concentra sull’impatto ambientale dei materiali plastici e che i biopolimeri possono svolgere un ruolo fondamentale nella transizione verso una economia sempre più circolare e gli obiettivi climatici della UE e che uno dei loro campi di applicazione principali e destinato a crescere è quello agricolo.
Nonostante le difficoltà sul fronte economico internazionale e il perdurare della crisi sanitaria, anche nel 2022 l’attività di Ecopneus si è svolta in maniera efficiente e capillare, raccogliendo oltre 230.000 tonnellate di Pneumatici Fuori Uso (PFU) e dando un importante contributo allo sviluppo del mercato della gomma riciclata e della filiera industriale del riciclo dei PFU. Ecopneus gestisce circa il 60% dei PFU generati nel nostro Paese, raccogliendone mediamente 200.000 tonnellate ogni anno, rintracciate in tutta Italia, dai grandi centri ai borghi, dai piccoli comuni montani alle isole minori. Un impegno che non si ferma alla raccolta e al recupero dei PFU ma si spinge oltre, per ampliare le possibilità di impiego della gomma riciclata, stimolando e incentivando il miglioramento continuo dei processi e dei prodotti del trattamento. Nel 2021 Ecopneus ha destinato circa 2 milioni di euro in progetti di ricerca e sviluppo per favorire lo sviluppo del mercato delle applicazioni della gomma riciclata, in termini di qualità dei materiali e di ampliamento dei settori applicativi. Rispetto agli obiettivi di raccolta previsti dalla legge, calcolati sui quantitativi di pneumatici immessi nel mercato dalle aziende associate nel 2021, nel 2022 Ecopneus ha raccolto il 119% del proprio obiettivo di legge, andando incontro al mandato ministeriale del +20% richiesto. Complessivamente nel 2022 Ecopneus ha esaudito oltre 80.000 richieste di prelievo di PFU presso oltre 27.500 gommisti, stazioni di servizio e autofficine in tutte le Province Italiane.
“Anche nel 2022 Ecopneus ha raggiunto importanti risultati garantendo una gestione efficiente ed efficace degli
Pneumatici Fuori Uso di propria responsabilità”, ha dichiarato il direttore generale di Ecopneus, Federico Dossena. “Nel corso dell’anno Ecopneus ha messo in campo tutte le risorse di cui dispone, assicurando una raccolta capillare su tutto il territorio nazionale impegnandosi fortemente per lo sviluppo del mercato della gomma riciclata, come dimostra il sempre maggior impiego in molti settori, dall’edilizia, all’industria, allo sport, alle infrastrutture, dando un importante contributo agli obiettivi globali di sostenibilità e contrasto alla crisi climatica. Risultati possibili grazie ad una filiera fatta di aziende su tutto il territorio nazionale che con Ecopneus sono impegnate e investono in innovazione e ricerca. Anche nel 2023 ci impegneremo ad accompagnare le aziende in questo processo, stimolando lo studio di nuove applicazioni della gomma riciclata e cogliendo tutte le opportunità che la ripresa economica potrà offrire lavorando con etica e trasparenza al servizio del Paese e dell’ambiente”.
Il sistema di riciclo dei PFU gestito da Ecopneus negli anni ha portato un beneficio concreto alla collettività e all’ambiente promuovendo con forza sempre maggiore l’impiego della gomma riciclata in tante applicazioni utili nella vita quotidiana. La gomma che si ottiene dal riciclo PFU è infatti un materiale prezioso e ampiamente utilizzato in tutto il mondo per la realizzazione di superfici sportive, campi da calcio, asfalti silenziosi sicuri e duraturi, isolanti acustici, arredi urbani ecc. A oggi il mercato della gomma riciclata è in costante crescita, ed Ecopneus si sta impegnando in nuovi filoni e settori applicativi attraverso un costante lavoro di ricerca e sviluppo, come il riciclo chimico e le applicazioni in ambito industriale. Nel 2021 l’attività di riciclo di Ecopneus ha consentito di evitare l’emissione di 310 mila tonnellate di CO2 equivalenti, il consumo di quasi 1,23 milioni di m3 di acqua e il prelievo di 282 mila tonnellate di materie prime. Benefici a cui si aggiunge il risparmio per il Paese legato alla riduzione delle importazioni di materiale vergine, che complessivamente si attesta a circa 79 milioni di euro.
Un finanziamento di 4,5 milioni di euro è stato assegnato al progetto Furious, coordinato da Debora Puglia, docente di Scienza e Tecnologia di Materiali, Biopolimeri e Biocompositi del Dipartimento di Ingegneria Civile e Ambientale presso la sede di Terni dell’Università degli Studi di Perugia, risultato vincitore del bando Horizon-JU-CBE-2022-R-01
La tecnologia si caratterizza per semplicità di processo e gestione dei sottoprodotti e non prevede l’utilizzo di sostanze infiammabili o pericolose, risultando una valida soluzione alla crescita di domanda prevista per il riciclo di materiali plastici e di PET in particolare, anche alla luce di normative sempre più stringenti.
Debora Puglia coordina il progetto Furious dell’Università di Perugia per lo sviluppo di materiali innovativi a base di FDCA da impiegare laddove le bioplastiche ancora non soddisfano i requisiti tecnici necessari a sostituire le plastiche tradizionali.
“High performance bio-based polymers for market applications with stringent requirements”, promosso dal CBE JU (Circular Bio-based Europe Joint Undertaking), partenariato da 2 miliardi di euro tra Unione Europea e Bio-based Industries Consortium (BIC) volto a sostenere progetti nell’ambito dell’economia circolare a base biologica e lo sviluppo di nuovi prodotti e soluzioni circolari e sostenibili per il mercato. Obiettivo del progetto Furious è quello di sviluppare nuovi polimeri biologici a base di acido 2,5-furandicarbossilico (FDCA), ampliando così il portafoglio di soluzioni monomateriale innovative in sostituzione delle plastiche tradizionali. “In particolare, grazie a Furious si punta a ottenere nuovi materiali destinati a settori applicativi dove le bioplastiche non riescono a soddisfare i requisiti tecnici necessari o dove le plastiche tradizionali di origine fossile risultano ancora ampiamente utilizzate: gli imballaggi per dispositivi biomedicali ed elettronici, in cui si richiedono resistenza alla sterilizzazione ed elevate proprietà barriera, quello automobilistico, che richiede resistenza all’invecchiamento ultravioletto e proprietà antibatteriche intrinseche, nonché i dispositivi subacquei, dove sono necessarie specifiche proprietà antivegetative e biodegradabilità in acqua di mare. La versatilità dei materiali Furious sarà valutata anche sulla base della loro processabilità, che è un’ulteriore caratteristica obbligatoria da verificare per il reale ingresso sul mercato, rispetto sia alle tecnologie consolidate, come lo stampaggio a iniezione e l’estrusione, sia più innovative, come l’elettro-filatura, la stampa 3D e la stereolitografia; sarà inoltre studiata la riciclabilità meccanica ed enzimatica dei nuovi polimeri a base di furano”, ha spiegato Debora Puglia.
Il progetto, di durata quadriennale, prenderà il via a giugno 2022 e vedrà la partecipazione di 15 partner, fra atenei e aziende, tra cui, per il nostro Paese, Alma Mater Studiorum-Università di Bologna, Consorzio Interuniversitario Nazionale per la Scienza e la Tecnologia dei Materiali di Firenze, Università di Pisa, LCI Italy e Gammatom.
Un accordo per l’industrializzazione, lo sviluppo e la commercializzazione a livello globale della tecnologia ChemPET per il riciclo chimico di materie plastiche, PET in particolare, mediante depolimerizzazione è stato sottoscritto da Saipem e Garbo, azienda chimica italiana. A questo scopo i due partner realizzeranno a Cerano (Novara) il primo impianto su scala industriale per il riciclo chimico in Italia e la tecnologia impiegata, di proprietà di Garbo, consentirà di trasformare i rifiuti plastici in PET in nuovo polimero di qualità utilizzabile nell’industria chimica e alimentare.
ChemPET permette di riciclare tipologie di plastica per cui oggi non esistono soluzioni alternative come il riciclo meccanico (quali, per esempio, le plastiche colorate) e, a differenza di questo, di ottenere nuovo materiale che conserva le proprietà originarie.
“Questo accordo è in linea con la strategia Saipem nei segmenti industriali low carbon e ci consente di arricchire il nostro portafoglio di tecnologie e soluzioni disponibili per l’economia circolare e la chimica sostenibile”, ha commentato Fabrizio Botta, CCO di Saipem. “Questo accordo permette a ChemPET di consolidare la leadership tecnologica in ambito crPET tramite l’immediata industrializzazione delle due unità da 22,5 kTA di Cerano e il licensing della tecnologia su scala globale”, ha aggiunto Guido Fragiacomo, CEO di Garbo.
La capacità di riciclo installata nell’UE27+3 è cresciuta del 17% nel 2021, sostenuta da investimenti stimati in 1,75 miliardi di euro. È quanto rilevato da Plastics Recyclers Europe (PRE), l’associazione europea di settore, nella sua ultima mappatura, sottolineando come, nonostante le recenti sfide che l’industria del riciclo ha dovuto affrontare, l’impegno dei riciclatori per guidare la transizione verso un futuro circolare della plastica rimane forte.
“Negli ultimi anni, i riciclatori europei di materie plastiche hanno affrontato molte sfide. Tuttavia, con i crescenti progressi nella legislazione, derivanti dall’attuazione della strategia sulla plastica e della direttiva sulla plastica monouso, l’industria del riciclo ha superato la crisi mostrando la sua resilienza a fattori esterni”, ha dichiarato Ton Emans, presidente di PRE. “La crescita positiva che possiamo osservare oggi modellerà e rafforzerà ulteriormente il mercato della plastica riciclata verso il raggiungimento degli obiettivi dell’UE”. PRE riferisce che, con oltre 730 siti di riciclo, la capacità
totale nell’UE27+3 ammonta ora a 11,3 milioni di tonnellate. Ciò dimostra che il settore del riciclo della plastica è un importante generatore di occupazione, con oltre 30.000 addetti in tutta Europa, e di fatturato, con 8,7 miliardi di euro, contribuendo in modo sostanziale al benessere socio-economico della regione. Oltre tre quarti della quota totale di polimeri riciclati sono rappresentati da PE e PP flessibili, PET e PE e PP rigidi. Questi flussi hanno mostrato l’aumento più elevato rispetto al 2020. Per quanto riguarda le poliolefine rigide, quasi la metà della capacità di riciclo è destinata ai flussi domestici, mentre nel caso di quelle flessibili, metà della capacità di riciclo è impiegata per i rifiuti commerciali. Germania, Spagna, Italia, Regno Unito e Francia sono i Paesi con le più alte capacità installate e rappresentano i due terzi del mercato totale. Tra i Paesi in forte crescita vengono segnalati Polonia e Paesi Bassi. L’aumento degli investimenti e le nuove capacità hanno creato una solida base per la transizione verso l’economia circolare per la plastica. A questo scopo, PRE ritiene che un quadro legislativo coerente e la sua completa attuazione siano i fattori più importanti per contribuire a una domanda di materiali riciclati senza precedenti. Una accelerazione verso la transizione dovrebbe venire anche dalla nuova proposta di regolamento sugli imballaggi e sui rifiuti di imballaggio, che mette al centro temi cruciali quali la progettazione per il riciclo e il contenuto minimo di riciclato.
EREMA has been the innovation leader for highly efficient plastics recycling systems for 35 years. Our melt filters are at the heart of them. Robust, safe and with high throughput –even with high degrees of contamination. Filters made by EREMA have proven their reliability for decades in the toughest recycling conditions. With our new brand POWERFIL you can now use our high-performance filters for your existing extrusion system. Plug in experience. Plug in performance.
I prodotti e i servizi digitali ENGEL offrono un valido supporto lungo l’intero ciclo di vita del prodotto, dalla progettazione alla campionatura, alla produzione fino alla manutenzione e assistenza. Le soluzioni digitali ENGEL permettono di sfruttare al massimo il potenziale del sistema di stampaggio a iniezione ENGEL e di ridurre in modo sostenibile il CO2 footprint.
Per saperne di più: engelglobal.com/inject-4-0
Un supporto a 360 gradi ai trasformatori, dagli impianti di termoformatura ai fine linea di confezionamento, dalla lavorazione di nuovi materiali all’automazione sempre più spinta che, grazie al know-how dei tecnologi WM Thermoforming Machines, non si applica più solo ai processi massivi, ma pure a quelli finalizzati a lotti più ridotti e spezzettati.
Ivantaggi dell’automazione industriale sono numerosi e, in buona parte, sono già insiti nella definizione di questo paradigma. Un incontro con Ottavio Tonon e Andrea Crespi, rispettivamente sales and product manager e sales area manager di WM Thermoforming Machines, presso la sede della casa svizzera ci ha permesso di apprendere quali sono i benefici che spingono le imprese a investire nell’automazione: in primis la riduzione dei costi operatori e della contaminazione igienica da contatto e la possibilità di sfruttare completamente la capacità produttiva della macchina. Il tutto velocizzando i tempi di consegna delle commesse e riducendo i rallentamenti ai processi produttivi e logistici.
“Non esiste un unico modo di fare automazione industriale”, ha esordito Ottavio Tonon, entrando subito nel merito, “e quella che è possibile fare oggi, in piena epoca digitale, è decisamente differente rispetto a quella di un paio di decenni fa”.
“Le industrie hanno a disposizione più tipologie di automazione a seconda della gamma d’articolo e del volume di produzione”, gli ha fatto prontamente eco Andrea Crespi. “Inoltre, le esigenze delle singole aziende possono essere differenti; soprattutto in termini di flessibilità delle soluzioni d’automazione”.
A integrazione delle parole d’esordio di Tonon e Crespi va sot-
tolineato che quando si parla di automazione la letteratura distingue quattro sistemi: fissi (grandi produzioni industriali e varietà di prodotto molto limitata), programmabili (in base ai lotti di produzione), flessibili (macchinari con alta configurabilità e flessibilità di impiego), integrati (le operazioni sono interamente gestite da computer in modo centralizzato e i processi di controllo sono caratterizzati da un minimo coinvolgimento umano) La casa svizzera ha dimestichezza con i sistemi fissi e flessibili, che gestisce rispettivamente con la gamma FT ed FC di termoformatrici.
“Di base le nostre macchine sono fondamentalmente di due tipologie: le termoformatrici vuoto e pressione, con taglio mediante fustella, della serie FC, per contenitori con cerniere, vassoi, coperchi e blister, e le termoformatrici forma/trancia, con piano mobile inferiore basculante della serie FT, per bicchieri e/o articoli tronco-conici”, ha ripreso Ottavio Tonon. “Per soddisfare le richieste produttive dei trasformatori, entrambe le macchine sono disponibili in versioni di taglia piccola, media e grande. In base poi all’esperienza del trasformatore e/o a ciò che deve pro-
DI ERMANNO PEDROTTI E LUCA MEIdurre, a livello di offerta si valuta la tipologia di prodotto in base alla quale vengono forniti diversi optional e selezionato il tipo di impilatore che possa dare il miglior risultato possibile in funzione della forma da produrre”.
“I sistemi di controllo e comando dispongono di un software base per la gestione di funzioni quali lo scambio dati ad alta velocità per innalzare l’ottimizzazione dei tempi ciclo, come anche l’analisi del consumo d’energia e del funzionamento dei driver”, ci ha spiegato Andrea Crespi, “dopodiché in WM è prassi aggiornare e migliorare time to time i software di base con implementazioni ad ampio raggio che, tramite supporto da remoto, offriamo ai trasformatori che già hanno le nostre macchine”.
Sempre Crespi ha spiegato che, in una sorta di circuito virtuoso, queste migliorie del time-to-time di solito sono frutto di un’analisi da parte dei tecnologi WM Thermoforming Machines sui report operativi che i trasformatori stessi inviano alla casa svizzera.
Certo è che non mancano casi in cui il software, a suo modo, rappresenta un salto generazionale.
Manca davvero poco alla consegna a un importante cliente di WM Thermoforming Machines con sede nel Nord Italia di una macchina che rappresenta un’evoluzione della serie FC - e come tale verrà presentata a Plast 2023 - che, oltre a varie innovazioni meccaniche, sarà dotata di un software di nuova generazione. “Il focus di questo sistema informatico sarà quello di facilitare l’operatore nella risoluzione dei problemi”, ha specificato Tonon, “nel senso che il nuovo software consentirà all’operatore di poter visionare ed esportare tutti gli schemi elettrici e idraulici della sua macchina, inquadrando a monitor la zona dove intervenire in caso di problemi. Il sistema integra anche una funzionalità di manutenzione predittiva, cioè una diagnostica che comunica con il PLC grazie a senso-
ri IO-link; una diagnostica preventiva, che attraverso segnali di allerta a monitor indica all’operatore di effettuare una certa manutenzione; e il troubleshooting, ossia le sequenze che l’operatore deve eseguire per arrivare a risolvere autonomamente il problema. Se poi la difficoltà dovesse persistere, l’operatore ha comunque già sviscerato i punti che poi agevoleranno l’assistenza WM da remoto nell’identificazione globale del problema e nella sua risoluzione”.
Scacco matto al fermo macchina, verrebbe da dire.
Le termoformatrici della serie FC possono lavorare tutti i tipo di materiali termoplastici termoformabili quali PP, PS, APET, CPET, PLA, OPS, XPS e XPET, solitamente utilizzati nella produzione di contenitori con cerniere, vassoi, coperchi e blister. Degna di nota è pure la caratteristica di queste termoformatrici di poter operare con stampi di differenti tecnologie di taglio, con formatura positiva o negativa, che hanno imbutitori elettrici indipendenti e che sono in grado di ospitare differenti soluzioni d’impilaggio.
“Questo software di manutenzione predittiva di nuova generazione entrerà a far parte delle già citate crescite del time-to-time che tanto ci caratterizzano”, ha aggiunto Crespi.
Dopo avere inquadrato sia le famiglie di prodotto sia il modus operandi in simbiosi con il mercato, il “capitolo” clou è quello relativo a come la casa svizzera interpreta oggi l’automazione industriale.
WM e Industria 4.0
“Ripartiamo dal fatto che noi sviluppiamo due tipologie di macchine: le FT e le FC. Le serie FT possono anche essere messe in linea con un estrusore che produce in continuo la foglia, e servono per alte e altissime produzioni”, ha ripreso Tonon. “Poi abbiamo le serie FC che sono più flessibili, che producono di solito articoli per i settori alimentare, tecnico e/o medicale e che non hanno questa continuità nella produzione. Con le FC ci sono quindi cambi stampi frequenti per piccole-medie produzioni. Detto ciò, in WM l’automazione è nata circa 25 anni fa, quando abbiamo iniziato a fare linee complete per piatti e bicchieri con macchine della serie Intec; mi riferisco a produzioni di qualche milione di pezzi al giorno su macchine che andavano 24 ore al giorno 7 giorni alla settimana, dove era impensabile avere un operatore che prendesse il prodotto, lo confezionasse e lo inscatolasse. Possiamo quindi dire che le prime integrazioni di automazione le abbiamo fatte tra la metà e la fine degli anni Novanta, andando a mettere in linea con le nostre termoformatrici delle confezionatrici e delle incartonatrici che, senza soluzione di continuità, confezionavano il prodotto nelle confezioni che troviamo ancora oggi sugli scaffali di un supermercato e quindi lo incartonavano. A quel punto l’operatore doveva semplicemente prendere il cartone e pallettizzarlo”.
Questi gli albori della meccanizzazione integrale in WM Thermoforming Machines dove, di fatto, la casa svizzera si limitava ad acquistare alla bisogna una confezionatrice e una incartonatrice per poi unirle alla sua macchina e far funzionare la linea in sincronia.
“Con il tempo abbiamo sempre più sviluppato il downstream
del fine linea anche nella serie FC, cioè le termoformatrici che fanno medie e basse produzioni”, ha spiegato Tonon. “È facile intuire come le problematiche (nell’automazione) qui siano date proprio dal fatto che sono macchine molto versatili: oggi si fa la vaschetta bassa per prosciutto, domani si fa il coperchio per il bicchiere, poi l’articolo medicale”.
In altre parole, secondo Tonon la sfida nell’automatizzare della serie FC è legata alla varietà degli articoli che, una volta stampati e impilati, va a complicare non poco le ulteriori fasi di raccolta e di convogliamento alle stazioni di confezionamento, incartonamento e pallettizzazione, da dove il bancale esce pronto per il trasporto. La linea FC gestisce una varietà di prodotti, che è solitamente difficile gestire in fase di downstream. WM Thermofroming Machines sta lavorando con diversi partner per rendere sempre più versatili anche i sistemi di automazione.
“Le figure in gioco nello sforzo di meccanizzazione integrale sono molteplici: c’è chi sviluppa l’impilatore e chi la confezionatrice, poi c’è chi sviluppa l’incartonatrice come anche chi sviluppa il pallettizzatore e chi ci fornisce i sistemi di visione e controllo”, ha proseguito Tonon, aggiungendo che qui è a dir poco indispensabile il ruolo del capo-commessa. Non è raro che il cliente di WM sia avvezzo a tali incombenze, che conosca i fornitori e che abbia sue capacità gestionali, per cui è proprio il cliente che fa gli ordini ai fornitori, che convoglia il tutto nella sua azienda e che, prima singolarmente e quindi con la presenza dei tecnici di ogni unità, testi e avvii con cognizione di causa il suo nuovo impianto.
Qualora invece il trasformatore non avesse esperienza e/o sufficiente conoscenza del mercato, è la stessa casa svizzera, essendo il soggetto più rilevante nello sviluppo di queste linee, che si fa carico di convogliare nel Canton Ticino parti quali gli stampi, le confezionatrici e gli altri fine linea per poi testarli e validarli in copresenza del cliente stesso.
“Ciò che chiediamo al cliente è di mandarci il suo materiale per riprodurre quelle che sono le condizioni di lavoro che, poi, si ritroverà in casa”, ha chiosato Tonon. “Perché fin che l’impianto è qui in casa gli eventuali problemi si risolvono in fretta. Se invece lo stesso problema si dovesse manifestare, per esempio, in Vietnam o in Indonesia allora le tempistiche di avvio della linea si dilaterebbero. Eventualità inaccettabile, dato che le tempistiche risultano sovente la discriminate tra una commessa acquisita e una persa”.
L’ultima scossa evolutiva, in ordine di tempo, al concetto di automazione di fabbrica l’ha data Industria 4.0, dove la chiave di volta sono i sistemi ciberfisici (CPS), ossia sistemi fisici strettamente connessi con sistemi informatici che possono interagire e collaborare con altri sistemi CPS.
Il modello FT 700 MSv7 della serie FT.Anche in tal senso WM Thermoforming Machines si è mossa in anticipo. Avendo in tempi non sospetti compreso come la crescita dell’output di dati connessi all’uso di sistemi cibernetici significasse poter contare su una maggiore possibilità di correzione di errori e/o di varianti insiti in un processo produttivo con, aspetto per nulla banale, conseguente possibilità di ottimizzare “in velocità” la produzione stessa, WM ha rafforzato la preesistente sinergia con il suo fornitore strategico di elettronica, l’austriaca B&R, onde sviluppare un supporto ad hoc per il protocollo di dialogo tra dispositivo di termoformatura e ricevitore. Protocollo che, a titolo di cronaca, è OPC-UA, l’architettura di comunicazione nata ad hoc per l’automazione industriale.
“Sarà banale a dirsi, ma gli sforzi descritti da Ottavio e Andrea vanno anche comunicati in modo diretto ed efficace laddove noi lo si ritiene più opportuno”, ha sintetizzato Ivonne Ghislandi, marketing & image manager di WM Thermoforming Machines. “Commercialmente la presenza di WM è già distribuita in tutto il
mondo grazie a venditori e agenti. A livello tecnico e di assistenza, abbiamo fatto in modo di avere nostri dipendenti posizionati strategicamente in Asia e in Sudamerica in modo da coprire le richieste da qualsiasi area del mondo. Questi dipendenti sono stati formati con un training dedicato presso la nostra sede di Stabio, in Svizzera, con i nostri tecnici WM”.
Ivonne Ghislandi ha anche ribadito che per la casa svizzera la comunicazione va ormai ben oltre le fiere. “Se vent’anni fa al di là delle manifestazioni fieristiche c’erano ben pochi strumenti con i quali veicolare la nostra immagine, oggi non è più così”, ha spiegato Ghislandi. “Sarà ancora una volta banale a dirsi, ma si sa che in qualsiasi luogo del mondo si trovi un potenziale cliente, gli basta digitare sul web la parola “termoformatura” per avere in pochi secondi almeno 200 nominativi di costruttori. Per chi deve produrre un prodotto semplice, perciò, ci sono numerose opzioni tra cui scegliere, ma con la nostra offerta di automazione, grazie alle partenrship che abbiamo stretto, possiamo venire incontro anche alle richieste più complesse e specifiche.”
Prima di concludere, Ivonne Ghislandi ha speso altre parole ancora per lodare l’efficacia degli open house e dell’incontro con i clienti. “Giusto per fare un esempio, l’ottobre scorso, in concomitanza con il K 2022 di Düsseldorf dove avevamo in esposizione una FC1000IM2, qui in Canton Ticino avevamo una TWIST700 con un impilatore nuovo, l’MSvS, e, oltre a mostrarla in diretta streaming presso il nostro stand in fiera, abbiamo invitato i clienti a venire a vederla di persona. In generale è sempre possibile e gradito organizzare visite da noi per dare ai clienti l’opportunità di vedere le macchine in funzione e dialogare con i nostri tecnici ed esperti. Ergo: grande soddisfazione per i clienti e per noi”.
Pagina per il settaggio della movimentazione dei piani della stazione di formatura. Vaschetta in PET bicolore prodotta con una macchina FC.La situazione economica della Germania negli anni successivi alla Prima Guerra Mondiale era disastrosa, tanto che nel 1923 il Governo chiese di poter ritardare il pagamento della quota dell’indennità di guerra prevista per quell’anno. A quel tempo, il piccolo villaggio di Freudenstadt, nella Foresta Nera, era un’area tendenzialmente povera che garantiva poche opportunità di lavoro alla popolazione locale costretta a spostarsi in altre zone. In questo scenario inizia l’avventura di Arburg, oggi uno dei maggiori costruttori di presse a iniezione a livello mondiale, che Arthur Hehl, meccanico di precisione fondò in quello stesso 1923 a Lossburg (a pochi chiliometri da Freudenstadt), dove costruì la sua abitazione.
Dura da 100 anni il lungo viaggio intrapreso da Arburg, azienda che nel corso del tempo, ha contribuito a trasformare la Foresta Nera da area depressa a zona di grande interesse economico, garantendo il benessere della piccola comunità di Lossburg dove oggi risiedono poco più di 7.000 abitanti. Ciò che colpisce di questa avventura made in Germany è proprio la contrapposizione tra la grandezza della multinazionale (un fatturato che sfiora i 900 milioni di euro e oltre 3.000 dipendenti) nata praticamente dal nulla, e la piccola località immersa nei suggestivi paesaggi della Foresta Nera formati da conifere rigogliose e pascoli, oggi
sede di un’importante comunità industriale.
Altro aspetto che suscita meraviglia è che nonostante le enormi dimensioni che ha assunto Arburg nel corso degli anni, ancora oggi lo spirito che regna in questa realtà è quello di una grande famiglia. Tanto è vero che i figli del fondatore, Karl ed Eugen Hehl, in tempi di forte crisi, hanno investito fondi privati nella loro azienda per evitare il peggio e salvare il posto di lavoro dei propri dipendenti, poiché garantire il benessere dei lavoratori è uno dei fondamenti della famiglia Hehl. Infatti, come tutte le avventure, anche quella di Arburg è stata segnata da risultati rivoluzionari alternati a battute d’arresto, da tentativi e patimenti, da lungimiranza e talvolta anche da coincidenze fortuite. Ripercorrendo rapidamente le tappe fondamentali della multinazionale tedesca, il 1923 è il primo anno della nuova impresa che vide anche la nascita del figlio maggiore della seconda generazione della famiglia, Karl Hehl, mentre i due fratelli minori, Gerhard ed Eugen, nacquero rispettivamente nel 1925 e nel 1929. È però solo nel 1943-44 che l’azienda assunse il nome attuale di Arburg, che Karl Hehl combinò utilizzando la prima sillaba del nome del padre Arthur (Ar) con l’ultima sillaba del nome della città di Lossburg (Burg).
Dalla sua nascita fino agli anni Quaranta l’azienda produceva beni di largo consumo di uso quotidiano, come cestini per le patate, sottopentole per lo più in metallo, mentre all’inizio de-
La terza generazione alla guida di Arburg: da sinistra, Juliane Hehl, Michael Hehl e Renate Keinath.
gli anni Cinquanta, grazie alla crescita economica della Germania, Arburg ha iniziato a produrre con grande successo anche strumenti medici come i flash con il marchio DuoLux. Tuttavia, questo successo comportava anche un rischio che minacciava l’esistenza stessa dell’azienda. Di fatto, man mano che queste unità flash DuoLux venivano esportate a livello internazionale, crescevano reclami e restituzioni di massa. Il problema era che il clima umido causava la formazione di correnti di dispersione che scaricavano le batterie attraverso i connettori metallici utilizzati per il collegamento alla fotocamera. Era quindi necessario isolare i connettori. La mente tecnica e creativa di Karl Hehl non ci ha messo molto per capire che il materiale ideale per l’isolamento era la plastica. All’epoca, però, non esisteva sul mercato una macchina in grado di sovrastampare i piccoli tappi in plastica, che Karl Hehl riuscì a realizzare in brevissimo tempo. Il risultato fu la prima piccola pressa a iniezione ad azionamento manuale di Arburg e fu anche il punto di partenza per il successo globale di un altro prodotto completamente nuovo: le presse a iniezione “Made by Arburg - Made in Germany”.
Nel 1962 nasce la prima Allrounder 200 il cui gruppo di chiusura orientabile e l’unità di iniezione reversibile consentono di produrre pezzi in diverse posizioni di lavoro. Le Allrounder hanno un grande successo a livello internazionale.
Nel 1978 viene realizzata la Allrounder numero 25.000, nel 1986 vengono aggiunti 25.000 metri quadrati di spazio produttivo, mentre negli anni Novanta vengono aperte le filiali nel Regno Unito e negli Stati Uniti.
A partire dal 2005 la gestione di Arburg passa alla terza generazione della famiglia Hehl: Renate Keinath, figlia di Karl e Julie Hehl, e Michael e Juliane Hehl, figli di Eugen e Gisela Hehl sono i testimoni delle nuove sfide legate alle sostenibilità. Negli ultimi anni, infatti, sono emerse nuove esigenze nell’ambito della lavorazione e del riciclo della plastica che hanno dato
vita al programma “arburgXworld” che racchiude tutte le strategie aziendali volte a contribuire allo sviluppo di un’economia circolare.
Nel 2010, la mente tecnica di Karl Hehl si spegne all’età di 87 anni. Lui e il fratello Eugen, dotato di talento commerciale, hanno plasmato le fortune della famiglia imprenditoriale e dell’azienda di famiglia per decenni, facendo di Arburg un vero leader globale nell’ingegneria delle materie plastiche. Per arrivare a questi risultati sono stati determinanti la volontà di rischiare, l’immaginazione e la lungimiranza.
Nel corso degli anni, Karl ed Eugen Hehl hanno ricevuto numerosi riconoscimenti per il loro lavoro e le loro idee tra cui la cittadinanza onoraria della comunità di Lossburg, il Premio per la Gestione d’Impresa di SPE (Society of Plastics Engineers) e l’inserimento nella Plastics Hall of Fame dalla Plastics Academy, che ha sede a Lowell (Stati Uniti), presso l’università del Massachusetts.
Il 16 febbraio il colosso tedesco ha festeggiato i suoi primi 100 anni di attività presso la propria sede di Lossburg ospitando clienti e inviati stampa provenienti da tutto il mondo al terzo e ultimo evento di gala, dopo che nei giorni precedenti aveva accolto gli ospiti locali prima e quelli di lingua tedesca poi. Celebrazioni che sono continuate anche in occasione degli Anniversary Days, sempre a Lossburg, dall’8 all’11 marzo, dove i visitatori hanno potuto compiere un viaggio multimediale attraverso il secolo di storia dell’azienda. Un’altra particolarità delle Giornate dell’anniversario 2023 è stata il festeggiamento, l’8 marzo, del visitatore numero 100.000 della manifestazione di settore, che dal 1999 attira ogni anno migliaia di clienti da tutto il mondo.
Il portafoglio prodotti di Arburg comprende le presse a iniezione Allrounder con forze di chiusura comprese tra 125 e 6.500 kN, il Freeformer per la produzione
additiva industriale e i sistemi robotici. Nello specifico, l’anniversario dei 100 anni dell’azienda familiare Hehl ha fatto da cornice all’ultima novità tecnologica di Arburg, l’Allrounder 470 H ibrida, una soluzione tecnologica che offre moderne prestazioni quali risparmio energetico e di risorse e una produzione efficiente.
A presentare quelle che sono state battezzate macchine dell’anniversario, le Allrounder 470 H ibride nelle versioni Comfort e Premium, ci hanno pensato i direttori di sviluppo tecnologico e vendite, Guido Frohnhaus e Gerhard Böhm. Si tratta di una nuova generazione di macchine particolarmente performanti in termini di efficienza energetica e tempi di ciclo. Tra i fattori che vi hanno contribuito vi sono il nuovo concetto di gestione dell’olio, la suddivisione della portata per
In occasione del centenario Arburg ha lanciato la Allrounder 470 H ibrida, una soluzione tecnologica che offre moderne prestazioni quali risparmio energetico e produzione efficiente.
i movimenti simultanei degli assi secondari idraulici e l’uso esteso del sistema servo-idraulico Arburg.
Il nuovo concetto di gestione dell’olio con un contenitore ottimizzato, l’alloggiamento del filtro abilitato alla pressione differenziale, la manutenzione predittiva per la sostituzione del filtro e il controllo della pompa dell’olio sono aspetti che garantiscono l’estrema affidabilità delle nuove macchine e il loro funzionamento con un ridotto fabbisogno di energia e risorse. Il messaggio di avvertimento di un filtro sporco compare quando il livello raggiunge il 75%, un tempo sufficiente per consentire l’acquisto di un nuovo filtro ed evitare il fermo macchina.
dei singoli componenti, in alcuni casi in flusso, la qualità di olio
Il nuovo concetto di gestione dell’olio riduce il consumo di energia e di acqua per il raffreddamento, aumentando la durata dei singoli componenti, in alcuni casi in modo considerevole. L’olio idraulico caldo e contaminato viene separato dall’olio idraulico freddo e pulito. Insieme al volume di ritorno costantemente filtrato e raffreddato e a una guida specifica del flusso, la qualità di olio viene migliorata risparmiando un quantitativo del 35%, con un aumento della durata dei componenti.
La suddivisione della portata della pompa idraulica consente di azionare contemporaneamente un asse secondario aggiuntivo. Questa tecnologia ha un effetto particolarmente positivo sulle Allrounder ibride che riescono a consumare meno energia e, allo stesso tempo, a ridurre i tempi di ciclo, due vantaggi che la serie ibrida può offrire.
In particolare, grazie alla facilità d’uso e all’affidabilità, la pressa Allrounder 470 H riduce il consumo energetico del 50% rispetto a una macchina idraulica e, a seconda dell’applicazione, è possibile risparmiare fino a 12.000 kg di CO2 all’anno. Questi aspetti sono fondamentali per poter ridurre tempo e costi legati all’assistenza e alla manutenzione. Proprio per raggiungere questo obiettivo, Arburg ha deciso adottare il servizio di manutenzione predittiva, in grado di segnalare automaticamente il momento in cui risulta necessario sostituire il filtro dell’olio nel
breve termine e riprogrammarlo di conseguenza.
Il sistema servo-idraulico di Arburg (ASH), che ha già dato prova di sé nelle Allrounder idrauliche ed elettriche, è stato integrato nelle Allrounder 470 H Comfort e Premium. L’ASH consente un funzionamento particolarmente efficiente dal punto di vista energetico e delle emissioni di CO2, in quanto il servomotore raffreddato ad acqua e a velocità controllata adatta continuamente il sistema di azionamento all’effettivo fabbisogno di potenza. Ciò significa che quando la macchina si ferma, anche l’azionamento della pompa si blocca senza generare perdite. In questo modo si risparmia fino al 50% dell’energia utilizzata, soprattutto nei processi che hanno lunghi tempi di raffreddamento.
Con la macchina per l’anniversario Allrounder 470 H, Arburg compie un passo importante verso il futuro in cui la famiglia Hehl continuerà a mantenere vivo il proprio interesse per l’innovazione tecnologica con una continua attenzione alla sostenibilità del comparto delle materie plastiche. Il tutto è riassunto nella promessa del marchio “Wir sind da” (Noi ci siamo!). Tutte le generazioni della famiglia Hehl erano e restano consapevoli che non è possibile lavorare senza una responsabilità sociale e la giusta flessibilità per continuare ad affrontare e superare nel miglior modo possibile le sfide del tempo. Tutto questo ha garantito il successo ininterrotto di Arburg che nel corso dei suoi primi 100 anni di vita ha permesso all’industria delle materie plastiche di progredire in modo costante e dinamico.
Il costruttore novarese di linee per riciclo e compounding Binova ha recentemente trasferito la propria sede in una struttura più grande. L’allargamento degli spazi consentirà di pianificare meglio la produzione e rappresenta un ulteriore tassello del programma di crescita dell’azienda. Come confermano anche il buon 2022 e il promettente 2023. Ne abbiamo parlato con il titolare Luigi Borzoni.
Azienda tutto sommato ancora giovane, è nata nel 2006, Binova di fatto può però essere già annoverata tra i costruttori storici di linee per riciclo e compounding di materie plastiche del panorama italiano, e per più di una ragione. Anzitutto perché all’atto della sua costituzione in essa è confluito un insieme di esperienze ultratrentennali maturate dal suo personale tecnico-commerciale nel settore delle materie plastiche.
A ciò si aggiunge il fatto che la sua proposta tecnologica è stata da subito di alto livello. Questo, da un lato perché frutto e naturale sbocco della lunga esperienza appena menzionata su cui sono state gettate le sue fondamenta; dall’altro perché richiesto come condizione necessaria per operare in un settore in continuo divenire e negli ultimi anni esploso sotto la spinta delle istanze di sostenibilità che hanno cambiato il modo di concepire ogni attività umana e quella produttiva in qualsiasi campo, in particolare.
E, ultimo ma non ultimo, l’avere avuto la forza e la capacità di affrontare e di superare praticamente da neonata una serie ininterrotta di crisi: quella economico-finanziaria mondiale del 2008, quella sanitaria della pandemia di covid-19 che, tra i tanti suoi effetti, ha falcidiato molte attività produttive, quella internazionale innescata dalla guerra tra Russia e Ucraina, con tutti i suoi strascichi ancora in atto.
Ecco, dunque, perché Binova a meno di venti anni di vita può essere ritenuta un’azienda storica tra i costruttori italiani di mac-
chine per materie plastiche e gomma: perché da giovane realtà imprenditoriale ha dovuto e saputo subito confrontarsi con la storia, la propria e quella collettiva, e oggi, che le difficoltà sono ancora tante per tutti, investe in una nuova sede, che vuole dire ampliamento della propria attività e del proprio mercato di riferimento. Per farci raccontare un po’ più in dettaglio come è stato compiuto e dove porterà questo ulteriore passo importante abbiamo raggiunto il titolare Luigi Borzoni.
Anzitutto, quali sono i motivi per cui si è resa necessaria una nuova sede e quale sarà il futuro di quella di Oleggio, dove Binova ha operato fino a oggi?
“La vecchia sede era da tempo sottodimensionata per poter pianificare in modo puntuale la produzione delle nostre linee di riciclo e compound, che sono chiaramente piuttosto voluminose. Eravamo da tempo alla ricerca di un possibile ampliamento dei nostri spazi che non si è potuto concretizzare all’interno dello stesso polo industriale di Oleggio. Per poter far fronte al meglio alla crescente richiesta di mercato, abbiamo quindi deciso di investire in una nuova sede operativa di circa 2.000 metri quadri nella zona industriale di Mezzomerico, sempre in provincia di Novara. La nuova struttura si trova a pochi chilometri di distanza dal sito produttivo di Oleggio, in una posizione strategica, facilmente raggiungibile dall’aeroporto di Malpensa, dall’autostrada dei La-
DI LUCA MEIghi e dalla Milano-Torino. Per quanto riguarda la vecchia sede, è stata recentemente venduta a un’azienda che si occupa della costruzione di infissi”.
L’ampliamento degli spazi porterà anche all’introduzione di nuovi macchinari o strumenti necessari per la costruzione delle vostre linee produttive e all’assunzione di nuovo personale?
“Il trasferimento presso la nuova sede rappresenta un ulteriore tassello del programma di crescita dell’azienda, che intende espandere il proprio mercato. Il nuovo stabilimento consentirà di rispondere alla necessità di disporre di maggiori spazi, di mettere in atto la riorganizzazione della gestione del magazzino tramite l’utilizzo di nuovi strumenti informatici, di rafforzare i processi di montaggio e collaudo di più impianti in contemporanea e di incrementare la forza lavoro, grazie anche alla disponibilità di ampi spazi dedicati agli uffici.
Con l’occasione verranno inoltre aggiornate tutte le tecnologie informatiche esistenti allo scopo di snellire i processi di progettazione e approvvigionamento e di pianificare al meglio il flusso dei materiali, le attività di montaggio nonché di migliorare il controllo dei costi. Questo permetterà altresì di migliorare ulteriormente il servizio postvendita e ricambi, se pur già molto efficiente”.
ci nel settore del trattamento degli scarti di ABS e PS contenenti elevate percentuali di inquinanti. In seguito all’installazione di un primo impianto in Francia nel 2020, ne sono stati installati altri quattro presso lo stesso cliente e due presso Stena Recycling (nella foto di apertura), un nuovo cliente italiano. Si denota che sono sempre di più le aziende che, compresa la convenienza derivata dal trasformare gli scarti autonomamente piuttosto che rivenderli a terzi, sono interessate a investire in impianti per il loro trattamento, visti anche gli elevati risultati qualitativi ottenuti dall’impiego del materiale prodotto nelle varie applicazioni di mercato.
“Speriamo in futuro di poter ampliare soprattutto gli spazi esterni, tramite l’acquisizione di un lotto appartenente a una vecchia fonderia che si trova nel retro del capannone. Ma trattandosi di un fallimento al momento non abbiamo informazioni precise in merito alle tempistiche”.
Sulla scia di questo investimento, avete in cantiere anche il lancio di novità tecnologiche o applicative per le vostre linee, magari anche in vista del prossimo Plast 2023?
“Il mondo del riciclo è in costante sviluppo e Binova si è sempre contraddistinta nel saper affrontare nuove sfide per il riciclo e il compounding di nuovi tipi di scarti, ottenendo risultati tecnicamente e qualitativamente sorprendenti. In concomitanza con Plast 2023 abbiamo in programma di allestire una open house per mostrare ai clienti acquisiti e potenziali il nuovo sito produttivo e i macchinari che saranno in montaggio in quel momento”.
Come è andato il 2022 in termini di ordini e di fatturato e quali sono le previsioni per il 2023?
“Binova ha ottenuto eccellenti risultati commerciali e tecnologi-
La nostra linea per riciclo e compound di ABS e PS si basa su componenti di ultima generazione, gestiti da un sofisticato software applicativo, sfruttando una tecnologia 100% made in Italy. L’impianto è composto da un estrusore con tecnologia bivite corotante, capace di garantire un’eccellente miscelazione dei polimeri e un’elevata degassificazione della materia prima. A differenza di un impianto tradizionale con tecnologia monovite, questo tipo di estrusore consente un notevole risparmio energetico, che può arrivare fino al 30%. Inoltre, è in grado di processare materiale contenente anche piccole percentuali di polimeri diversi da quelli dichiarati. I sistemi di degassaggio dell’estrusore estraggono sotto alto vuoto qualsiasi tipo di materiale si formi durante il processo, come vapori, monomeri ecc. In un solo passaggio e con una movimentazione minima dei materiali all’interno dello stabilimento, si ottiene così un doppio risultato, raggiungibile di solito tramite due passaggi: la rigenerazione e il compounding. Il materiale ottenuto risulta essere un prodotto di alto livello qualitativo che, oltre a promuovere un processo ecosostenibile, offre importanti opportunità di applicazione sul mercato.
Tutto ciò ci ha consentito di chiudere il 2022 con degli eccellenti risultati di cui ci riteniamo pienamente soddisfatti. Il 2023, nonostante sia partito in sordina, ci sta dando delle concrete prospettive di successo, grazie all’acquisizione di diversi importanti progetti”.
Un impianto BireC90/48 per riciclo e compounding di scarti plastici in fase di costruzione.
La nuova sede è stata concepita prevedendo già una sua eventuale ulteriore espansione futura?
Un 2022 dinamico e di successo nonostante la complessità degli scenari macroeconomici ha posto le basi per un 2023 interessante e fruttuoso nel segmento del calore di processo.
Fra gli operatori in questo contesto rientra Leister Technologies Italia, filiale italiana della multinazionale svizzera che da oltre settant’anni fornisce soluzioni innovative per macchinari industriali.
Il 2022 è stato caratterizzato da un inizio brillante per la maggior parte dei settori industriali, ma l’entusiasmo in alcuni casi è stato mitigato da un successivo rallentamento e dalle dinamiche inflattive nel corso dell’anno. Anche per Lesiter è stato un anno non banale, con diversi elementi favorevoli che hanno consentito di offrire sempre maggior valore e di affrontare importanti sfide.
Tra gli elementi favorevoli vanno inclusi il contesto macroeconomico, caratterizzato da un generale sostegno alla crescita che ha determinato nei 12 mesi del 2022 una crescita dell’economia italiana vicino ai 4 punti percentuali. Leister fornisce soluzioni in diversi mercati e la fornitura di elementi di tecnologia per il settore dei macchinari industriali ha beneficiato di questo “vento” a favore.
“Il 2022 è stato l’anno in cui siamo tornati a incontrare in presenza i nostri clienti dopo i due anni di pandemia che ci avevano forzato a un lungo “letargo” nella relazione commerciale. Siamo tornati a visitare i nostri clienti in cantiere o presso le loro sedi, ma siamo anche tornati a essere presenti nelle fiere dei numerosi settori dove Leister fornisce tecnologia, da Mecspe a Ipack-IMA, fino a Ecomondo”, ha spiegato Paolo Possa, direttore generale di Leister Technologies Italia.
Nel corso del 2022 la logistica è stata una sfida per molte aziende industriali. Per Leister sono state di supporto le politiche di approvvigionamento della casa madre e gli accorgimenti adottati per assicurare puntualità delle consegne e del servizio per Leister Italia.
Le difficoltà di approvvigionamento di materiali e componenti, in particolare schede elettroniche, hanno costituito il principale elemento di criticità. La casa madre svizzera aveva creato fin dal 2021 una task force per seguire le situazioni più critiche e valutare le misure più opportune a seconda della situazione, ma il picco delle sfide alle catene di fornitura si è verificato nel 2022.
In alcuni casi Leister è intervenuta supportando i fornitori anche nel reperimento sul mercato internazionale di materie prime e componenti. In altri casi è sta-
to necessario ricorrere a nuovi fornitori nell’ottica di ricercare puntualità nei tempi di consegna e qualità adeguati agli standard definiti dall’azienda.
Va segnalato che in diversi casi le difficoltà di approvvigionamento sono state conseguenza di elementi positivi; per diversi prodotti le criticità sono state la conseguenza di volumi cresciuti a livello globale ben al di sopra di quanto immaginabile dopo l’anno particolare del 2020. “Guardando ora al 2023 l’aspettativa è di un graduale ritorno alla normalità passati i primi mesi del nuovo anno. Sia per noi che lavoriamo a diretto contatto col cliente finale, sia per chi opera nella logistica e nella produzione”, ha proseguito Possa.
Prodotti di successo
Numerose soluzioni Leister hanno caratterizzato il 2022: fra queste, Solano AT, pistola ad aria calda fiore all’occhiello dell’azienda, che grazie alla funzione ECO-Mode è in grado di consumare energia elettrica solo quando serve, a vantaggio del comfort nell’ambiente di lavoro nonché della bolletta elettrica.
Dal punto di vista dell’efficienza energetica e di uso intelligente dell’energia vanno ricordati anche i pannelli a Infrarosso Krelus. Questa soluzione offerta per il calore di processo sta trovando sempre più impiego nell’industria, per due motivi principalmente: l’alta efficienza energetica (fino al 90% dell’energia utilizzata si traduce in effetto utile sul materiale da scaldare); la bassa inerzia termica (accensione e spegnimento in tempi estremamente rapidi, a beneficio di sicurezza e riduzione dei tempi per avviare l’impianto).
La forte attenzione a ridurre i consumi da un lato e la ricerca di fonti alternative al gas per il calore di processo dall’altro hanno dato forte impulso a questa soluzione negli ultimi anni, e in modo particolare nel 2022.
Leister produce sistemi per la saldatura
delle materie plastiche con tecnologia laser da oltre vent’anni e in alcuni Paesi e settori, per esempio Germania, e medicale, auto o elettronica ha ricevuto accoglienza estremamente favorevole. Qualità e ripetibilità elevata del processo e assenza pressoché totale di bave o polveri a fine saldatura sono tra le principali ragioni di questo successo.
La filiale italiana è partita più tardi dei colleghi tedeschi e ha cominciato a investire con una certa continuità per sviluppare il mercato locale solo in anni recenti. Dopo una prima presenza con saldatrice laser alla fiera Plast 2015, dal 2019 ha iniziato a promuovere in modo più sistematico questa tecnologia. In generale l’accoglienza è buona, da parte sia di progettisti che di aziende, e cresce di anno in anno il numero di progetti seguiti. “C’è comunque ancora tanto da fare per far conoscere la saldatura laser di materiali plastici in Italia e concretizzare tutto il potenziale che la tecnologia offre”, ha affermato Paolo Possa.
Le novità rispetto al 2022 sembrano essere innanzitutto macroeconomiche. Gli esperti sembrano dirci che il 2023 sarà caratterizzato da un’economia in progressivo “raffreddamento”, a causa della crescita di inflazione e tassi di interesse e al protrarsi del conflitto russo-ucraino. Al momento le previsioni dicono che la crescita dell’economia del nostro Paese rallenterà e le aziende si dovranno accontentare dopo gli ultimi due anni di forte impulso. A prescindere da come andrà in generale l’economia, Leister manterrà il forte impegno a tornare sul mercato con incontri in presenza e con la partecipazione a fiere di settore.
Leister, come da tradizione, proporrà novità di prodotto e prevede di rendere il suo negozio online ancora più ricco e interessante. A poco meno di due anni dalla sua nascita il sito si è affermato come
supporto per l’acquisto di tutti quegli articoli che l’azienda definisce “non problematici”, principalmente accessori, ricambi e piccoli elettroutensili come le pistole ad aria calda, ma nel 2023 l’azienda intende arricchire il negozio online con notizie sempre aggiornate sulle iniziative, racconti dal campo di nuove applicazioni e offerte commerciali. Ultimo ma non meno importante, nel 2023 ricorre il decimo anno da quando Leister Italia è stata fondata. “Stiamo lavorando a una serie di iniziative per raccontare questi 10 anni di lavoro al servizio dei nostri clienti”, ha concluso Possa.
Stà nascendo una nuova gamma di macchine. Scopri di più su
• densificazione in linea
• sviluppato da un progetto nato nel 1997
• 3 modelli per produzioni da 500 a 3.500 kg/h
• densificazione materiali con umidità fino al 20% *
• disegnato anche per retrofit di impianti esistenti
* in abbinamento a sistemi cascata
L’assistente intelligente iQ motion control di Engel coordina i movimenti del robot e della pressa in modo completamente automatico ottimizzando il tempo ciclo.
Sebbene il recente aumento dei costi ne abbia enfatizzato l’importanza, la riduzione del consumo di materie prime e di energia elettrica non è l’unica strategia per migliorare l’efficienza e la marginalità dei processi di stampaggio a iniezione. Un altro fattore importante da considerare è costituito dal tempo ciclo, che gli stampatori tendono a ridurre ottimizzando principalmente le fasi di raffreddamento o di plastificazione. Più raramente si pensa ai movimenti di ingresso e uscita del robot di estrazione, così come a quello di apertura e chiusura dello stampo, soprattutto per componenti con pareti profonde, nonostante il loro impatto sia tutt’altro che trascurabile: si consideri, infatti, il tempo che si potrebbe risparmiare evitando di avviare il robot solo alla completa apertura dello stampo.
Questi aspetti vengono affrontati da Engel concentrandosi sull’interazione tra i movimenti della pressa a iniezione e del robot, ma soprattutto sull’unità di produzione nel suo insieme, facendo in modo che tutti i componenti - pressa, sistema di automazione e accessori - accedano alla medesima piattaforma di controllo e allo stesso database. Questo livello di integrazione è uno dei migliori presupposti per riuscire a ottenere tempi ciclo ridotti, ma la ricerca dei parametri di regolazione adeguati è an-
cora demandata all’operatore, che deve impostare la traiettoria, la velocità e l’accelerazione del movimento di inserimento del robot nell’area stampo. L’assistente intelligente iQ motion control riduce questa complessa operazione a poche impostazioni.
I robot cartesiani si muovono da punto a punto. Durante l’apprendimento, l’operatore ne determina la traiettoria manualmente, specificando un grande numero di punti per ottimizzare il percorso. Grazie alla funzione iQ motion control, implementata di serie sui nuovi robot cartesiani viper di Engel, il robot è in grado di calcolare e ottimizzare il proprio percorso in modo autonomo, delegando all’operatore l’impostazione di pochi parametri e posizioni.
In questo modo, l’assistente intelligente non solo semplifica la procedura di settaggio e rende più rapido l’apprendimento, ma riesce anche a ridurre il tempo ciclo del processo di stampaggio a iniezione. Un altro vantaggio del software iQ è rappresentato dall’interfaccia user-friendly, che permette all’operatore di impostare facilmente la procedura di estrazione direttamente sull’unità di controllo della pressa.
DI DEBORAH LIDAUER , MATTHIAS OBERHERBER E NICOLETTA BONIARDIiQ motion control ottimizza il percorso del robot; la traiettoria viene calcolata nel suo insieme e non generata in base al posizionamento approssimativo dei movimenti sul singolo asse.
Per pianificare il movimento di ingresso del robot nell’area della pressa in modo che raggiunga la posizione di estrazione esattamente nel momento in cui lo stampo termina la corsa di apertura, è necessario tenere conto di alcune condizioni di base: i parametri impostati dall’utente finale (posizione, tolleranze lineari e movimento dello stampo) e i parametri specifici del robot (valori soglia di velocità e accelerazione ecc.).
L’ottimizzazione del movimento di ingresso prevede tre fasi, che iQ motion control elabora automaticamente. Durante la prima fase viene calcolato il tempo di percorso ottimale o tF,opt. In base all’ultimo ciclo, viene misurato il tempo che intercorre tra il raggiungimento della posizione di avvio anticipato impostata e l’apertura dello stampo. Questo intervallo corrisponde al tempo di percorso necessario a far raggiungere al robot e allo stampo le rispettive posizioni finali contemporaneamente.
Durante la seconda fase viene determinato il percorso più breve utilizzando i limiti cinematici specifici del robot (velocità massima, accelerazione massima ecc.), dei singoli assi e della tolleranza lineare definiti dall’operatore. In questo caso, tR,opt è il tempo più breve ottenibile tenendo conto delle particolari condizioni al contorno. Se la funzione di avvio anticipato è disattivata, il robot seguirà questa traiettoria eseguendo il movimento di ingresso tenendo conto dei propri limiti cinematici. La terza fase, infine, prevede l’adattamento del percorso. Quando la funzione di avvio anticipato è attivata, è necessario assicurarsi che il tempo tR,opt sia maggiore o uguale al tempo di percorso ottimale tF,opt. Nel primo caso però, dati i limiti cinematici, il robot non potrà raggiungere la posizione target simultaneamente allo stampo. Al contrario, se tR,opt è inferiore a tF,opt, il robot potrebbe avvicinarsi eccessivamente allo stam-
po; per evitare che questo accada, il percorso viene adattato in modo che il tempo tR,opt sia uguale al tempo tF,opt.
Spesso il tempo ciclo si allunga inutilmente perché i movimenti della pressa e del robot non sono armonizzati. Questo viene evitato nelle isole di stampaggio a iniezione di Engel perché, grazie al sistema di controllo integrato, il robot e la pressa eseguono movimenti coordinati e al momento dell’estrazione si trovano nello stesso istante rispettivamente nella posizione di estrazione e di apertura dello stampo. In questo modo, l’ingresso del robot non provoca alcun allungamento del tempo ciclo.
L’assistente intelligente iQ motion control permette di ridurre ulteriormente il tempo di ciclo. Grazie alla funzione di avvio anticipato integrata nel software, il robot può entrare nell’area della macchina senza attendere che lo stampo termini la propria cosa di apertura. La finestra di dialogo delle impostazioni visualizza un suggerimento per la posizione di avvio anticipato, che si basa sui parametri di impostazione del robot e della macchina, consentendo anche agli operatori meno esperti di sfruttare in modo efficiente e affidabile i vantaggi di questo assistente intelligente di Engel.
Nonostante l’ingresso anticipato del robot nell’area della macchina, è possibile escluderne con certezza una collisione con il semi-stampo mobile, poiché iQ motion control opera con una funzione di sicurezza a due stadi. Il primo corregge il movimento del robot in caso di deviazioni dal movimento dello stampo pianificato, mentre il secondo garantisce che il robot riesca a frena-
movimenti dello stampo corsa dello stampo inferiore alla posizione di avvio anticipato corsa dello stampo maggiore o uguale alla posizione di avvio anticipato movimenti del robot
movimento dell’asse 1
movimento dell’asse 2
re prima del contatto con lo stampo in caso di situazioni eccezionali o di arresto di emergenza.
Inoltre, grazie allo scambio diretto di dati all’interno del sistema di controllo comune a tutte le attrezzature dell’isola di stampaggio, il robot conosce la posizione esatta del piano portastampo mobile ed è quindi in grado di fermarsi in caso di una possibile collisione, evitando così danni allo stampo e alla pinza.
iQ motion control è ideale per ottimizzare anche i processi che prevedono movimenti di estrazione semplici, ma assicura le migliori prestazioni nello stampaggio a iniezione di pezzi con pareti profonde, come componenti di alloggiamenti, cassette o contenitori (foto di apertura), perché la pressa deve eseguire una corsa di apertura dello stampo molto lunga.
Le potenzialità dell’assistente intelligente sono state dimostrate da Engel nel corso di un test condotto con un robot cartesiano viper 12. Durante le prove, condotte mantenendo una corsa di apertura dello stampo di 490 mm e una velocità massima del piano porta-stampo mobile di 1.465 mm/s, è stato ottenuto un tempo ciclo complessivo di 15 secondi. L’avvio anticipato del robot è avvenuto alla quota stampo di 303 mm, valore che ha consentito di ridurre il tempo di attesa (ossia l’intervallo che in-
Lʼottimizzazione del tempo ciclo comporta un aumento significativo della produttività; nellʼesempio considerato, una riduzione del tempo ciclo di 0,59 secondi permette di produrre 236 parti in più per singola impronta al giorno.
tercorre tra il completamento del movimento dello stampo e la fine del movimento di ingresso della pinza nell’area dello stampo) di 0,59 secondi. Il tempo di attesa fa parte a tutti gli effetti del tempo ciclo perché, in quella fase, il movimento dello stampo viene bloccato dal robot. I vantaggi ottenuti sono notevoli. Ipotizzando un processo continuo su tre turni, un tempo ciclo complessivo di 14,41 secondi permette infatti di produrre 236 parti in più per singola impronta al giorno rispetto all’estrazione sequenziale a tre punti.
L’impiego di iQ motion control è indipendente dal tipo di pressa a iniezione e dal sistema di estrazione adottato, poiché si adegua automaticamente sia alla variante di estrazione esistente, che può essere verticale od orizzontale (nel caso delle macchine senza colonne), sia al tipo di deposizione, che può avvenire sul lato dell’operatore, sul lato non operatore oppure all’estremità (quest’ultima nel caso di pezzi a sviluppo longitudinale).
La gamma di robot cartesiani viper è stata ampliata da Engel con l’introduzione di un modello che, con una portata di 3 kg, si pone come entry level della serie, che comprende otto versioni con capacità fino a 120 kg.
Il nuovo viper 4 impiega per la prima volta la tecnologia di azionamento a bassa tensione (48 V, con alimentazione monofase da 230 V CA) che migliora l’efficienza energetica riducendo i consumi e contribuisce a contenere anche l’impronta di carbonio dello stampaggio.
Il modello è indicato per l’installazione su presse a iniezione con forza di chiusura fino a 220 tonnellate. L’ambito di applicazione riguarda principalmente il prelievo dei pezzi dallo stampo e il loro trasferimento su nastro o stazioni di finitura e controllo, con ciclo a vuoto
di 5,5 secondi e tempo di prelievo inferiore al secondo. Dove eccelle, però, è nelle prestazioni energetiche.
In un ciclo standard di 6 secondi con corse complete e la massima dinamica consentita, il consumo energetico è di soli 200 Wh, non dissimile da quello di una postazione di lavoro CAD. Tutti i circuiti del vuoto sono dotati di serie di una funzione di risparmio energetico (che sarà adottata in futuro anche sugli altri modelli sella serie), con una riduzione fino all’80%. La configurazione adottata sul nuovo viper 4 si caratterizza anche per una ridotta contaminazione del filtro dell’aria e funzionamento più silenzioso.
colonne. Operando in una posizione inferiore, può gestire un peso superiore del 30% rispetto alla capacità nominale e operare con una maggiore velocità. Come i modelli procedenti anche viper 4 è dotato del sistema di assistenza intelligente iQ motion control e può essere completamente integrato nell’unità di controllo CC300 delle presse a iniezione
motion control e può essere Engel.
del filtro dell’aria e funzionamento più
Il robot è anche disponibile in una versione con corsa Y ridotta per la rimozione orizzontale dei pezzi su presse Engel victory o e-motion TL, prive di
Una recente fornitura di Sorema
Tra i principali costruttori al mondo di impianti per il lavaggio e il riciclo di materie plastiche, la società italiana Sorema ha installato, in collaborazione con il costruttore austriaco Starlinger, un impianto per il riciclo di bottiglie in PET post-consumo presso il riciclatore congolese OK Plast. In particolare, Sorema ha realizzato le sezioni per la selezione, la macinazione e il lavaggio del materiale, fasi chiave nel processo di riciclo di bottiglie in PET, mentre Starlinger ha fornito la linea per l’estrusione dei granuli di rPET di grado alimentare.
La società Ok Plast ricicla circa 50 tonnellate di rifiuti plastici al giorno provenienti dalla città di Kinshasa. L’impianto fornito rappresenta un ulteriore passo in avanti nella continua espansione del riciclo in Africa e contribuirà a risolvere il problema della gestione e dello smaltimento di rifiuti plastici, offrendo opportunità di lavoro alle comunità locali. Prima di
questa fornitura, in Africa Sorema aveva già realizzato e avviato impianti per il lavaggio e il riciclo in Nigeria, Algeria, Sud Africa, Egitto e Tunisia.
Questo impianto chiavi in mano è stato realizzato con l’obiettivo di produrre scaglie di rPET destinate all’imballaggio alimentare. A tale scopo, raggiunge una produzione utile di 1.100 kg all’ora di scaglie di rPET lavate partendo dalle bottiglie in PET post-consumo, che Ok Plast riceve da vari punti di raccolta situati in diverse zone di Kinshasa. L’unità produttiva fornita dal costruttore italiano contribuirà allo sviluppo in Africa dell’economia circolare attraverso l’upcycling dell’rPET, reintegrato in percentuali crescenti nella produzione di preforme, bottiglie e contenitori per uso alimentare.
La linea di lavaggio per rPET bottle-tobottle comprende diverse sezioni per le fasi di alimentazione automatica, prelavaggio e de-etichettatura, seguite da macinazione a umido, lavaggio a
caldo, flottazione e, infine, risciacquo e asciugatura. La linea incorpora, su due stadi di selezione, rilevatori di colore e di materiale sia per le bottiglie che per le scaglie. Il sistema di monitoraggio digitale Sorema-Scada 4.0 consente, infine, un controllo sia locale che remoto dell’intera linea.
L’ultimo sviluppo negli impianti di Sorema per il lavaggio di bottiglie in PET post-consumo ha riguardato l’aggiornamento del sistema di prelavaggio delle bottiglie. Questo modulo lava le bottiglie dopo la preselezione a secco, rimuovendo le etichette termoretraibili e non, così come tutte le contaminazioni esterne, tra cui possono rientrare materiale organico, sabbia e graniglia. La fase successiva consiste nella macinazione delle bottiglie in scaglie con l’ausilio di mulini ad acqua della serie PRH, costruiti dalla consociata Previero. Il modulo di lavaggio a caldo con ciclo a batch garantisce una qualità altissima delle scaglie per processi bottle-tobottle, con una migliore separazione dei contaminanti organici e delle colle, riducendo al minimo il consumo di acqua, energia e prodotti chimici. Dopo l’asciugatura e la cernita per colore, le scaglie opportunamente trattate vengono convogliate all’estrusore recoStar PET iV+ di Starlinger per ottenere granuli di rPET adatti a produrre nuovi contenitori destinati al contatto diretto con gli alimenti.
L’offerta tecnologica di Sorema è frutto del suo continuo monitoraggio dell’evoluzione del settore dell’imballaggio e dei rifiuti di imballaggio in plastica. Presso il Recycling Research Center dell’azienda ad Alzate Brianza (Como), inoltre, è in funzione un impianto pilota per consentire ai riciclatori di eseguire test completi di riciclo e lavaggio e determinare il bilancio di massa e valutare la qualità dei prodotti ottenuti da tali processi.
Per ottenere polimeri di elevata qualità nei processi di riciclo, la filtrazione è una delle fasi più importanti. A tale scopo Break Machinery ha sviluppato il sistema DUO a doppio filtro, che permette di ottenere un’elevata produttività garantendo al contempo un’alta qualità del prodotto finito. La geometria del disco raschiante e l’innovativo sistema di scarico delle contaminazioni permettono di rimuovere queste ultime in maniera rapida e controllata e di ridurre la quantità di scarto.
DUO è dotato, come spiega il nome, di due dischi forati (“breaker”), aumentando così l’area filtrante e il volume di produzione. Il disco raschiante, posto tra i due filtri, ha lame su entrambi i lati e ruotando rimuove la contaminazione da entrambe le superfici. Inoltre, la sua geometria impedisce ai contaminanti filtrati di rientrare nella massa di plastica fusa. Le superfici filtranti vengono pulite costantemente, così da poter essere utilizzate per periodi più lunghi rispetto ai sistemi tradizionali. Nel funzionamento di DUO, il laser risulta fondamentale. Infatti, i dischi filtranti vengono forati utilizzando le più recenti tecnologie laser e trattati per resistere all’usura, mentre
la geometria conica dei fori conici agevola il passaggio della massa fusa. Il materiale plastico fuso (1) viene convogliato all’interno della camera di filtrazione (2) e passa attraverso due filtri (3) contrapposti l’uno all’altro. Tra i due filtri è posizionato un disco raschiante (4), dotato di lame intercambiabili, che ruotando rimuove la contaminazione depositata sui filtri incanalandola all’interno del disco stesso (5). Il centro del disco raschiante è in comunicazione con una vite di scarico (6) indipendente che espelle il materiale contaminato. Il materiale plastico fuso filtrato (7) dai due filtri si ricongiunge poi nel canale di uscita (8) per passare al processo successivo. L’utilizzo di due filtri consente di contenere le dimensioni della camera di filtrazione e di disporre di ampie superfici filtranti, mentre il principio di funzionamento del sistema permette di lavorare in modalità continua e a pressione costante. Realizzato utilizzando acciai in lega di alta qualità e adottando trattamenti antiusura nei particolari più sollecitati, DUO è progettato per garantire un’elevata resistenza alle pressioni di linea (fino a 350 bar). La particolare geometria del disco raschiante rotante a sei lame assicura un’eccellente pulizia
anche a bassa velocità di rotazione. Lo scarico delle impurità avviene tramite una sola vite in grado di convogliarle da entrambe le superfici filtranti. Il sistema è studiato per filtrare vari tipi di materiali plastici con elevate percentuali di impurità (fino al 15% in peso) e gestire differenti agenti contaminanti quali carta, legno, alluminio, rame ecc. La regolabilità della velocità della vite di scarico permette di gestire anche i materiali più contaminati, mentre le operazioni di manutenzione e di sostituzione di filtri e lame possono essere eseguite senza smontare parti della macchina. Anche le operazioni di manutenzione risultano semplici, veloci ed eseguibili direttamente nel sito produttivo dell’utilizzatore. Il sistema di filtraggio continuo a pressione costante massimizza la produttività della linea. L’efficienza del sistema di pulizia in modalità continua allunga la vita utile del filtro laser, riducendo l’acquisto di materiali consumabili. La rotazione indipendente della vite di scarico rispetto al disco raschiante minimizza lo scarto in funzione della contaminazione e facilita il trattamento di materiali altamente contaminati.
Automatico, autopulente e a pressione costante
Editore Promaplast srl
tel. (+39) 02 8228371
fax (+39) 02 macplas@macplas.it57512490
www.macplas.it
Per la pubblicità: r.pagan@macplas.it
La piattaforma RBTX sviluppata da igus, azienda specializzata nella produzione di soluzioni in tecnopolimeri per la movimentazione industriale, per semplificare l’accessibilità all’automazione si è recentemente arricchita dei cobot di Universal Robots. Da tempo ormai, l’industria non può fare a meno dei robot, ma spesso gli utenti, specialmente quando si tratta di piccole e medie imprese, devono automatizzare un processo senza poter permettersi di sprecare tempo e risorse. La piattaforma RBTX sviluppato da igus a partire dal 2019 riunisce fornitori e utenti di robotica e propone soluzioni semplici a basso costo.
Per proporre soluzioni di automazione flessibili, con integrazione rapida e funzionamento intuitivo, Universal Robots ha iniziato a collaborare con la piattaforma RBTX in Germania, Austria e Svizzera. Tale piattaforma attualmente si avvale della collaborazione di circa 70 aziende che propongono attraverso di essa robot, sistemi di presa e di visione, nastri trasportatori, software e servizi. RBTX fornisce una garanzia di compatibilità per l’intera gamma di software e hardware, in modo che gli utenti possano sempre essere sicuri che tutti i componenti funzionino insieme.
“Con Universal Robots abbiamo acquisito un partner di primo piano, grazie al quale possiamo ampliare la gamma di prodotti disponibili sulla piattaforma RBTX”, ha spiegato Alexander Mühlens, responsabile della divisione Automazione e Robotica presso igus. “Universal Robots non è solo un pioniere dei cobot, ma è anche all’avanguardia per quanto riguarda la programmazione intuitiva dei robot. Tutto ciò combacia perfettamente con il concetto del nostro marketplace che vuole proporre soluzioni di automazione, semplici da implementare anche senza alcuna particolare competenza o conoscenza precedente. Siamo quindi molto soddisfatti di essere riusciti ad assicurarci la partnership di Universal
Robots”. Sulla piattaforma sono già presenti numerosi accessori, compatibili con i cobot Universal Robots, come, per esempio, il settimo asse igus.
“Universal Robots propone soluzioni di automazione facili da integrare che consentono ai clienti di rafforzare la loro competitività e di ottenere un rapido ritorno sull’investimento: questo si sposa molto bene con l’approccio di RBTX”, ha proseguito Andrea Alboni, direttore generale per l’Europa Occidentale di Universal Robots. “Essendo RBTX un marketplace aperto, siamo sempre interessati ad acquisire nuovi partner, perché questo ci permette di offrire agli utenti un numero maggiore di soluzioni individuali. Dopo tutto, stiamo perseguendo l’obiettivo comune di rendere l’automazione il più accessibile possibile”, ha aggiunto Alexander Mühlens. Secondo il principio “build or buy”, su RBTX gli utilizzatori possono trovare un sistema robotico pronto per l’uso a prezzo fisso oppure assemblare i singoli componenti per una soluzione individuale. La piattaforma permette inoltre di sfruttare il RBTXpert, servizio di integrazione da remoto. RBTXpert verifica la fattibilità dell’applicazione attraverso una videochiamata e illustra i vantaggi delle diverse cinematiche. Dopo la consulenza, l’utente riceve un’offerta con l’obiettivo di trovare la soluzione più conveniente. RBTXpert può fornire assistenza anche in fase di messa in servizio. Sulla piattaforma è possibile trovare la soluzione di automazione più adatta alla propria applicazione, corrispondente al proprio budget e senza avere esperienza di automazione o conoscenze di programmazione.
Sulla piattaforma RBTX sviluppata da igus sono approdati recentemente i cobot di Universal Robots, per l’approntamento di soluzioni per l’automazione dei processi produttivi in modo poco oneroso economicamente, aspetto di non poco conto soprattutto per imprese di dimensioni medio-piccole.
I sistemi di nuova generazione della serie CS2 di Coiler System, divisione di CLM dedicata alla progettazione e alla realizzazione di sistemi di avvolgimento automatici, rispondono ai più elevati standard di sicurezza e automazione e sono costruiti secondo il concetto di modularità. Questo consente di configurare ogni avvolgitore secondo le esatte esigenze dell’utilizzatore e di seguirne le evoluzioni nel corso del tempo.
I sistemi di avvolgimento CS2 si contraddistinguono per svariate innovazioni, da quelle “minori”, come il controllo della coda (della bobina) e lo svolgi reggia, alle più importanti, come il guida tubo cartesiano con rotazione del calibro controllata, l’impianto di legatura a camme meccaniche con controllo brushless (progettato per aumentare affidabilità e prestazioni e in grado di offrire determinismo, ripetibilità e controllo) e, soprattutto, il sistema di espulsione in orizzontale della bobina.
Gli avvolgitori della serie CS2, infatti, permettono di produrre una bobina che gode dei benefici sia dell’avvolgimento in verticale (con asse orizzontale), sia della consegna in orizzontale (quindi con asse verticale). Dopo l’avvolgimento e il confezionamento con reggia, l’espulsione della bobina avviene tramite una rotazione di 90° dell’aspo, che consente alla stessa di essere scaricata in piano su di un nastro trasportatore. Questo è l’unico sistema oggi in commercio che permette di avere una posizione esatta della bobina, grazie a un processo controllato e ripetibile. Tale scelta, oltre
a garantire i più elevati standard di sicurezza, consente e favorisce qualsiasi tipo di automazione come, per esempio, l’integrazione di un sistema di pallettizzazione. CLM è un’azienda italiana che opera nel settore della meccanica di precisione e dell’automazione industriale dal 1995. L’esperienza maturata, le attrezzature presenti nei 9.000 metri quadri su cui si estende la sua sede e le numerose tecnologie sviluppate e installate negli anni rendono l’azienda capace di offrire soluzioni ottimali per ogni tipo di esigenza, anche grazie alla progettazione e realizzazione di macchinari personalizzati. L’avanzato livello tecnologico raggiunto ha portato CLM a un elevato livello di fidelizzazione dei clienti, dei quali oltre l’80% si rivolge al costruttore da più di vent’anni, sfruttando il vantaggio di poter interfacciarsi con un interlocutore unico per molteplici tipologie di lavorazioni. E su queste basi che nel 2021 da CLM è nato il progetto Coiler System: una divisione completamente specializzata nella progettazione e nella realizzazione di sistemi di avvolgimento automatici, in grado di offrire la soluzione più adatta per avvolgere e confezionare tubi di ogni tipologia e dimensione. Dalla progettazione all’installazione, fino alla formazione degli operatori: Coiler System affianca il trasformatore in ogni momento, prima e dopo la vendita, assicurandogli supporto e assistenza costanti e tempestivi.
Dettaglio della sezione di espulsione e scarico dell’avvolgitore CS2Specialista nell’avvolgimento e nel confezionamento di tubi Nuova generazione di avvolgitori automatici
Connubio tra la tecnologia nipponica e il design italiano, Negri Bossi ha presentato a Mecspe 2023 (la fiera tenutasi a BolognaFiere dal 29 al 31 marzo) la pressa Nova 5eT nella versione 180-H590, quinta generazione di macchine completamente elettriche, realizzate per garantire efficienza e precisione e al momento disponibili da 50 a 180 tonnellate.
Tra il corredo di caratteristiche della serie Nova 5eT rientrano i nuovi sistemi di chiusura “Flat Clamp”, che esercita un carico ridotto sulla ginocchiera, a beneficio anche della durata dello stampo, e di iniezione “Pre Pack”, che assicura compattezza e costanza della densità della massa fusa, precisione della dose di materiale iniettato e ripetibilità di produzione. La pressa è corredata anche dell’innovativo controllo Tact5 e del sistema di teleassistenza Amico.4.0 per il supporto postvendita tramite connessione WAN
e la gestione della macchina in modalità Industria 4.0 (in linea con lo standard di comunicazione Euromap 77/OPC 40077).
Durante la fiera bolognese, la pressa, che trova nello stampaggio di articoli medicali, di imballaggi e di componenti tecnici i suoi campi di applicazione di elezione, era equipaggiata con uno stampo a 1+1 cavità di ADM e stampava
un occhiale protettivo in policarbonato prodotto da Complastic. La macchina era inoltre munita di ausiliari Piovan e robot Sytrama, società, quest’ultima, parte del gruppo Negri Bossi.
La pressa a iniezione Nova 5eT in versione 180-H590, quinta generazione delle macchine completamente elettriche di Negri Bossi, e, nel tondino, gli occhiali protettivi in policarbonato che venivano stampati a Mecspe 2023.
• Assistenza immediata
• Possibilità di comprendere i problemi in tempo reale
• Rapida risoluzione delle problematiche tramite connessione da remoto e con il semplice utilizzo di smartphone, tablet e smart glasses
• Istruzioni rapide e chiare trasmesse sul campo ai tecnici interni o ai subappaltatori (tramite video, chat, immagini e documenti)
• Traduzione istantanea delle istruzioni fornite
• Modalità di lavoro professionale: si riducono i costi di trasferta, trasporto ed intervento
• Diminuzione del tasso di errore e migliore qualità della risoluzione del malfunzionamento
• Meno visite ripetute e maggior soddisfazione del cliente
• Ottimizzazione del processo ed innovazione nei metodi di gestione aziendale
Liontek è compatibile e abbinabile anche a impianti terzi e quindi è destinato sia a chi già possiede macchine dello stesso costruttore sia a chi utilizza sistemi di altre marche.
Il nuovo densificatore a circolo chiuso Liontek sviluppato recentemente da Tecnova consente di lavorare, in linea e non, a batch, materiale plastico post-consumo, post-industriale o proveniente da impianti di lavaggio. Il densificatore ha un ruolo fondamentale nel ciclo di lavorazione degli scarti in plastica post-consumo e post-industriale, anche considerando che oggi è sempre più difficile trovare materiale con livelli di umidità residua inferiori al 5-10%, quindi perfettamente adatto a un’immissione diretta negli estrusori. La funzione di Liontek risulta fondamentale per ridurre il livello di umidità che spesso va a compromettere la qualità del granulo, la sua lavorazione e di conseguenza le prestazioni del prodotto finale.
La macchina, oltre a completare la gamma con marchio Tecnova oggi disponibile sul mercato, si rivolge a riciclatori e trasformatori nazionali e internazionali sia che già possiedano linee dello stesso costruttore
sia che utilizzino impianti di altre marche, poiché Liontek risulta compatibile e abbinabile anche a sistemi terzi presenti sul mercato. Tra le sue caratteristiche spiccano versatilità di utilizzo, controllo della produttività e del tasso di umidità attraverso uno specifico software, facilità di installazione e funzionamento.
“Oggi si ha una maggiore sensibilità verso il concetto di qualità, anche perché le condizioni iniziali della materia plastica da lavorare sono spesso pessime, soprattutto se derivanti dal post-consumo, e i materiali di scarto risultano essere molto contaminati. Dotare la propria linea con la macchina Liontek è necessario per non perdere in qualità e omogeneità della produzione. Abbiamo già in essere due importanti commesse in Messico e Belgio per le quali sono in corso i primi test”, ha commentato Marco Massaro, CEO di Tecnova.
Liontek nasce da un progetto di Antonio Massaro, attuale presidente di Tecnova, risalente al 1997, di cui in azienda esistono ancora i disegni originali, ma nel tempo abbandonato per altre priorità produttive. Ed è da tale progetto che l’azienda è partita per sviluppare il nuovo impianto. Il densificatore è disponibile in tre modelli per produzioni da 500 a 3.500 kg all’ora ed è in grado di densificare materiali con umidità fino al 20% in combinazione con sistemi di estrusione in cascata ed in funzione del tipo di materiale.
Un componente fondamentale nel riciclo Densificatore a circolo chiuso per scarti post-consumo e post-industriali
Tra le recenti realizzazioni sviluppate da Plastic Systems rientra un impianto chiavi in mano per lo stoccaggio, la precristallizzazione, il dosaggio e l’alimentazione di scaglie di PET a una linea per l’estrusione di lastra destinata alla termoformatura. Il sistema di precristallizzazione permette di aumentare l’efficienza del processo di estrusione, riducendo il rischio di problemi come la formazione di bolle o la deformazione del semilavorato. Inoltre, l’aumento dell’efficienza del processo si traduce anche in migliori proprietà meccaniche e termiche del materiale, che a loro volta accrescono anche la qualità del prodotto finale.
Tra le soluzioni fornite da Plastic Systems vi è anche il sistema per lo scarico del materiale dai silos di stoccaggio esente da ostruzioni e per l’alimentazione continua e uniforme dell’impianto. All’interno di quest’ultimo, inoltre, sono stati inseriti anche i sistemi di recupero del materiale di scarto post-industriale e di dosaggio gravimetrico, che favorisce la stabilità della miscela di prodotto.
Per la supervisione dell’impianto, Plastic Systems ha sviluppato un sistema corrispondente ai requisiti previsti per Industria 4.0 comprensivo di interfacce dedicate allo scambio dati con gli applicativi gestionali del committente. Uno degli aspetti fondamentali di questa realizzazione è rappresentata dalla tracciabilità: il materiale in ingresso viene identificato attraverso dei codici a barre e il sistema di supervisione adatta in automatico le varie fasi del processo in base a quanto rilevato. Plastic Systems oggi è uno dei principali costruttori di impianti per stoccaggio, deumidificazione, trasporto e dosaggio di materie plastiche. Grazie a costanti investimenti in ricerca e sviluppo, la società si distingue per la fornitura di impianti completi di controllo e supervisione, in ottica Industria 4.0. Con oltre 200 impianti realizzati annualmente in tutto il mondo, Plastic Systems copre una vasta gamma di settori, tra cui l’auto, il medicale, il packaging, il riciclo e il compounding mettendo in campo competenze e know-how acquisiti nel corso degli anni per offrire ai trasformatori soluzioni personalizzate e altamente performanti in base alle singole specifiche esigenze.
Veduta di una parte dell’impianto realizzato da Plastic Systems per stoccaggio, precristallizzazione, dosaggi e alimentazione di scagli di PET.
I centri di lavoro verticali di CMS sono sviluppati per massimizzarne la resa in ogni settore di applicazione e per i trasformatori di materie plastiche sono disponibili sulla base di tre piattaforme tecnologiche specifiche con cui configurare di volta in volta la soluzione più idonea per ottenere elevate produzioni e un rapido ritorno dell’investimento: Nesting, HPP e Knife Cutting Technology. Nesting è la piattaforma per la lavorazione in “nesting” appunto di materiali plastici e materiali avanzati mediante soluzioni software e hardware dedicate e consente la gestione di percorsi di taglio, anche quelli più complessi, in modo semplice, rapido e preciso. La stabilità dei pezzi, anche di quelli più piccoli, è sempre garantita grazie a soluzioni quali: piani aspiranti altamente configurabili e caratterizzati da un elevato grado di planarità per la massima precisione di asportazione verticale; fino a 30 zone di vuoto con gestione dinamica, fondamentale quando si ha a che fare proprio con pezzi di piccole dimensioni o pezzi traspiranti; cuffie di aspirazione gestite dal CNC con funzionamento ottimizzato.
HPP (High Performance Plastic)
è invece la soluzione per la lavorazione di componenti in materiale plastico ad alte
prestazioni e consente di configurare il centro di lavoro in modo da esaltare le potenzialità di materiali e componenti nel pieno rispetto delle più severe specifiche di lavorazione. Ciò è possibile grazie a: precisione e ripetibilità ai massimi livelli della categoria; elettro-mandrini in grado di eseguire asportazione e finitura di elevato livello; vasta gamma di soluzioni di staffaggio su piani multifunzionali di ultima generazione; segnali di comando per dispositivi personalizzati sempre disponibili.
Knife Cutting Technology, infine, è la piattaforma con taglio a lama/coltello oscillante, fisso e tangenziale applicato ai centri di lavoro ad alte prestazioni, che rappresentano la base delle soluzioni Hybrid di CMS con una flessibilità di utilizzo estremamente elevata. Si tratta di soluzioni specialistiche che, senza mai rinunciare a prestazioni, rigidità e capacità di asportazione tipiche dei centri di lavoro del costruttore, permettono l’utilizzo della macchina in un’ampia gamma di applicazioni, tra cui: pavimentazioni e coperture flessibili in materiali plastico; taglio di lastre alveolari e a nido d’ape; lavorazione di lastre in elastomeri (guarnizioni); lavorazione di espansi; allestimento di interni auto; illuminotecnica; cartellonistica.
Centri di lavoro CMSLinee integrate per pannelli isolanti
Specializzata nella costruzione di sistemi chiavi in mano per produrre pannelli isolanti a base di PIR (poliisocianurato) e resina fenolica per applicazioni in edilizia, Cannon Ergos amplia la sua offerta con sistemi e macchinari integrati per le lavorazioni a valle delle linee di produzione dei pannelli.
L’azienda mette a frutto così conoscenze ed esperienze nella fornitura di tecnologie impiantistiche per la produzione continua su larga scala e ad alta velocità di pannelli isolanti a base di PIR e resina fenolica con rivestimenti flessibili principalmente per tetti, pareti, pavimenti e soffitti.
La tecnologia che Cannon fornisce con impianti chiavi in mano per la produzione di pannelli isolanti a base di PIR e resina fenolica comprende serbatoi per lo stoccaggio delle materie prime, dispositivi di srotolamento superiore e inferiore per gestire e alimentare le bobine di substrati come carta, fogli di alluminio, rivestimenti in fibra di vetro o minerale, attrezzature per
Linea per il taglio post-lavorazione di pannelli isolanti
preriscaldamento, dosaggio e miscelazione dei componenti di base della resina reattiva, che possono comprendere catalizzatori, agenti espandenti e polimerizzanti e ritardanti di fiamma e sezione di schiumatura e laminazione con trasportatori a doppio nastro, per creare pannelli con i substrati flessibili negli spessori desiderati.
Le attrezzature di post-lavorazione fornite da Cannon Ergos comprendono seghe a taglio trasversale volanti, che dividono il flusso continuo di pannelli laminati in “schede madri” che passano in un’unità di raffreddamento e indurimento utilizzando trasportatori specificamente configurati e vengono successivamente tagliate in diverse sezioni nelle dimensioni finali desiderate. Queste sezioni vengono poi rifilati in senso longitudinale e trasversale, per esempio con profili maschio e femmina o sovrapposti. I pannelli finali vengono gestiti in una stazione di imballaggio completamente automatizzata per produrre pile unite e pallettizzate avvolte in pellicola termoretraibile, pronte per lo stoccaggio e la consegna. Particolare attenzione è stata rivolta all’ottimizzazione di ogni fase della produzione, compresa la post-lavorazione, applicando principi di “lean manufacturing”, sistemi automatizzati e cicli ottimizzati per risparmiare energia, materie prime chimiche e rivestimenti dei substrati.
Il costruttore di sistemi per il trattamento superficiale Ferrarini & Benelli ha presentato alla recente Mecspe 2023 (BolognaFiere, 29-31 marzo) le sue ultime novità per il trattamento al plasma, settore in cui l’azienda negli ultimi si è specializzata con una serie di investimenti e di attività di ricerca e sviluppo mirata. In tale ambito viene proposto In Air Plasma, sistema efficiente ed ecosostenibile che migliora la qualità delle lavorazioni nelle operazioni di incollaggio, evitando l’utilizzo di colle a caldo e i relativi problemi di deformazione delle superfici, e nella stampa, dove, grazie a una maggiore tensione superficiale indotta dal trattamento al plasma, gli inchiostri a base d’acqua possono sostituire quelli a base di solvente, tossici e difficili da smaltire. Questo trattamento non produce ozono - a differenza del trattamento corona - e sfrutta le
caratteristiche del plasma in condizioni di pressione atmosferica, riducendo i consumi energetici. Il trattamento al plasma consente di intervenire sulla superficie di articoli plastici di piccole dimensioni per ottimizzare l’adesione prima delle applicazioni di stampa, verniciatura, fissaggio, rivestimento, isolamento ed etichettatura. Inoltre, è utile anche per effettuare la pulizia di superfici plastiche e metalliche prima di applicare successivi rivestimenti senza utilizzare prodotti chimici. Facilmente integrabile nella linea di produzione dell’utilizzatore, il sistema richiede operazioni di manutenzione ridotte e automatizza le operazioni di trattamento, garantendo lavorazioni qualitativamente ottime e durevoli nel tempo.
Per quanto riguarda le caratteristiche tecniche, In Air Plasma è formato da un generatore digitale ad alta frequenza
collegato a una o più torce in grado di trattare superfici tramite cavo schermato. Il sistema è configurabile con una, due, tre o quattro torce erogatrici per trattare superfici da 10 a 40 mm, mentre per superfici più ampie fino a 70 mm viene equipaggiato con ugelli dalle caratteristiche potenziate. Tra le sue principali applicazioni rientrano la realizzazione di scatole e contenitori resistenti in materiale plastico su linee piega-incolla; il miglioramento del processo di marcatura e codificazione a getto d’inchiostro su tubi in PEX, PE e PVC di diversi diametri, cavi elettrici e componenti che richiedono ottima leggibilità e durata nel tempo; l’incremento dell’adesione di colle, adesivi, sigillanti e guarnizioni.
Il trattamento al plasma consente di intervenire sulle superfici degli articoli plastici per ottimizzare l’adesione di stampe, vernici, fissaggi, rivestimenti, isolamenti ed etichette.
Multinazionale danese con oltre 650 dipendenti, nata come società produttrice di emulsionanti, Palsgaard negli ultimi anni ha deciso di investire anche nell’industria degli imballaggi alimentari in plastica, dando vita a una linea di additivi polimerici a base vegetale che fungono da tensioattivi antiappannanti e antistatici, coadiuvanti di dispersione, modificatori dell’invecchiamento, rivestimenti EPS e agenti distaccanti.
Al fine di aiutare i proprietari di marchi a stare al passo con i tempi rispetto alle norme sempre più stringenti come quelle relative al contatto con gli alimenti, in occasione dell’ultima edizione del K di Düsseldorf, Palsgaard ha presentato la sua nuova linea di additivi denominata Einar. In fiera abbiamo intervistato Ulrik Aunskjaer, direttore della divisione Bio-Speciality Additives, per conoscere qualche dettaglio in più su questi nuovi prodotti e sui progetti in cantiere dell’azienda.
Palsgaard ha studiato una gamma di additivi a base vegetale per polimeri destinati agli imballaggi
alimentari. Quali sono le caratteristiche di queste soluzioni?
“Si tratta di prodotti a base vegetale che possono essere utilizzati sia negli alimenti sia negli imballaggi. Fondamentalmente, siamo produttori di ingredienti alimentari, ma questi stessi prodotti possono essere utilizzati anche nell’industria delle materie plastiche. Tra le caratteristiche che la plastica deve necessariamente avere ci sono le proprietà antistatiche, di conseguenza, gli additivi antistatici sono necessari affinché il prodotto finale in plastica non evidenzi un comportamento elettrostatico nel momento dell’uso o della lavorazione. Questi additivi rappresentano il fiore all’occhiello della nostra linea di prodotti. Un’altra linea è quella
degli additivi anti-appannamento, più orientati al consumatore. Questi prodotti evitano che la confezione alimentare possa appannarsi offrendo diversi vantaggi: innanzitutto, il consumatore può vedere cosa c’è all’interno della confezione; in secondo luogo, si previene la formazione delle goccioline di condensa, un ambiente in cui i batteri possono proliferare. Inoltre, l’assenza di condensa prolunga la durata di conservazione del prodotto all’interno della confezione contribuendo alla riduzione dello spreco alimentare”.
le caratteristiche della vostra linea Einar?
“Einar è il nome che abbiamo dato alla
nostra gamma di additivi antistatici e anti-appannamento. Perché Einar? Einar richiama il nome del fondatore dell’azienda: Einar Viggo Schou. Poiché Palsgaard è il nome della gamma di prodotti per il settore alimentare, cercavamo un nome diverso. Palsgaard è il nome del castello dove è vissuto il fondatore di Palsgaard; è così che siamo arrivati a questo nome. Oggi chiamiamo Einar tutto ciò che produciamo che non fa parte dei prodotti destinati all’industria alimentare. È un modo per presentarsi sul mercato con brand diversi, per lavorare e comunicare con il mondo dei polimeri o del non-food. È possibile presentare sul mercato lo stesso prodotto, ma con due nomi distinti di modo che le attività nel settore alimentare non influenzino le altre e viceversa”.
“Circa 7 o 8 anni fa. Si trattava di qualcosa di nuovo per noi. Nel corso degli anni l’utilizzo dei nostri prodotti è aumentato di pari passo con l’espansione dei polimeri”.
I vostri imballaggi comportano svantaggi rispetto a quelli tradizionali?
“Gli imballaggi tradizionali sono tipicamente a base fossile o derivano da alcune sostanze chimiche oggi messe in discussione. Questo è il motivo per cui il mercato è alla ricerca di alternative più sicure. A volte gli imballaggi prodotti da sostanze chimiche funzionano meglio, mentre i nostri potrebbero non essere efficienti
come dovrebbero, tuttavia, soprattutto negli ultimi anni, anche l’aspetto della sicurezza ha il suo peso nella scelta dei prodotti da parte dei clienti. Ad esempio, quando si parla di masterbatch, i clienti ovviamente hanno molte perplessità. Attualmente, ci stiamo rivolgendo soprattutto ai mercati delle Nazioni Unite nei quali l’industria dei polimeri sta cercando di rendere i processi il più possibile sostenibili e di fare a meno di alcune sostanze chimiche. Einar 981 risponde perfettamente a queste esigenze. Il prodotto, lanciato al K 2022, è destinato all’uso nei reattori che producono polimeri in sostituzione dei prodotti chimici che nel prossimo futuro saranno messi al bando”.
Viste le continue restrizioni
Palsgaard ha studiato una gamma di additivi a base vegetale per polimeri destinati agli imballaggi alimentari.
Un’altra linea è quella degli additivi anti-appannamento, più orientati al consumatore.
plastica tradizionale, forse nei prossimi anni ci saranno diverse aziende che produrranno imballaggi come i vostri. Come crede che si svilupperà il mercato in futuro? Ci saranno più concorrenti?
“Se si guarda al panorama competitivo, vediamo che molte aziende offrono prodotti piuttosto semplici, mentre sono pochissime le realtà che offrono qualcosa di meglio. Penso che Palsgaard si trovi in un’ottima posizione di mercato perché può contare su una gamma completa di prodotti. Inoltre, siamo in grado di offrire supporto o assistenza tecnica, mentre altre aziende non dispongono di uno staff dedicato in grado di assistere i propri clienti. Infatti, diversamente da noi, i nostri concorrenti offrono prodotti che non necessitano di supporto tecnico. Quindi, ritengo che per ottenere buoni risultati non sia sufficiente produrre imballaggi da materie prime vegetali. Il successo in questo settore dipende da diversi fattori: ad esempio, se si opera in Europa occorre
rispettare il regolamento REACH, adottato dall’Unione Europea per migliorare la protezione della salute dell’uomo e dell’ambiente contro i rischi generati dalle sostanze chimiche. In altri paesi, invece, occorre attenersi ad altre normative. Detto questo, non è facile prevedere il futuro perché possono entrare in gioco diversi aspetti collaterali”.
Avete studiato dei progetti specifici per l’espansione delle vostre attività?
“Palsgaard punta molto in alto. Sicuramente continueremo a crescere non solo nel settore dei polimeri ma anche in altri ambiti applicativi. Ad esempio, quando parliamo di additivi sostenibili e sicuri pensiamo anche ai cosmetici, un settore nel quale Palsgaard ha il potenziale per crescere ancora”.
Quali sono i principali oli vegetali che utilizzate?
“Impieghiamo l’olio di palma, realizzato attraverso pratiche di produzione sostenibile, che è il più utilizzato nel nostro settore a livello globale. Inoltre, usiamo l’olio di colza e quello di girasole. Que-
sti sono i tre componenti principali della nostra produzione”.
Questo tipo di applicazioni sono quelle su cui l’azienda oggi punta maggiormente o l’obiettivo principale delle vostre attività resta l’industria alimentare?
Quali sono i vostri progetti futuri, intendete sviluppare ulteriormente queste applicazioni?
“Personalmente sono entrato in Palsgaard quattro anni fa, quando gli imballaggi rappresentavano meno dell’1% della produzione di Palsgaard. Oggi probabilmente gli imballaggi si aggirano tra il 10% e il 15% e per il futuro puntiamo a superare il 25%. Un altro aspetto da considerare è che l’azienda non solo ha grandi ambizioni, ma è anche in grado di portarle avanti. Infatti, in Danimarca Palsgaard sta incrementando la propria capacità produttiva che entro i prossimi due anni dovrebbe raddoppiare rispetto alla quota attuale”.
Avete incontrato difficoltà in alcuni Paesi che forse tendono a usare plastica tradizionale per tutelare gli interessi di grandi colossi del settore petrolchimico?
“Non notiamo particolari resistenze. Penso che dipenda dal singolo Paese e dal suo grado di sviluppo. Ad esempio, da qualche anno non c’è alcuna possibilità di investire in Cina perché gli additivi sono troppo costosi. Abbiamo incontrato difficoltà anche in India perché non è facile trovare potenziali clienti. Ad ogni modo, sono certo che troveremo il modo di vendere i nostri prodotti anche lì. Ci stiamo impegnando nella ricerca di clienti e saremo presto pronti. Inoltre, abbiamo diversi punti di forza che ci permettono di vendere di più e molto più velocemente rispetto ad altri competitor. Siamo fiduciosi”.
La gamma di plastificanti Plaxter di Coim è stata ampliata con il nuovo grado Plaxter E-LB con un contenuto di materie prime da fonti rinnovabili fino al 50%. Il nuovo prodotto è sviluppato per l’impiego in materiali plastici a base di PVC più sostenibili senza bisogno di modificare i processi produttivi o di installare nuovi macchinari.
Tra i settori finali di applicazione dei plastificanti da fonti rinnovabili di Coim per l’impiego in materiali a base di PVC rientrano le finte pelli e i tessuti impermeabili.
stainless steel pipe bends and aluminium couplings suitable for vacuum and pressure conveyors
stainless steel pipe bends in all common pipe dimensions from 38.0 x 1.5 mm till 204.0 x 2.0 mm; radii: 75, 250, 300, 500, 800, 1.000, 1.200 and 1.500 mm (AISI 304)
highly wear-resistant pipe bends: glass pipe bends and HVA NIRO® stainless steel pipe bends
HS Umformtechnik GmbH
D-97947 Grünsfeld Germany
Phone +49 (0) 93 46 / 92 99-0
Fax +49 (0) 93 46 / 92 99-200
www.hs-umformtechnik.de
L’evoluzione della gamma verso soluzioni sostenibili è iniziata già da diversi anni con i prodotti Plaxter P-L, in grado di offrire soluzioni innovative attingendo parzialmente a materie prime di origine rinnovabile. I prodotti della serie Plaxter P-L sono presenti nel mercato con volumi importanti in tutte le applicazioni che coinvolgono prodotti a base di PVC plastificato, come film estensibili trasparenti per la conservazione degli alimenti, finte pelli e tessuti impermeabili per il settore della moda, rivestimenti speciali per cavi elettrici, tubi tecnici per il trasferimento di liquidi o gas, guarnizioni speciali per imballi alimentari e altre applicazioni specifiche.
“Con la nuova serie di prodotti Plaxter E-LB rispondiamo alla domanda crescente di plastificanti più sostenibili da parte del mercato. Continuando lo sviluppo intrapreso con la gamma Plaxter P-L, la serie E-LB offre prodotti con contenuti di materie prime da fonti rinnovabili fino al 50%, rispondendo al contempo alle più elevate esigenze tecniche del mercato. I prodotti Plaxter E-LB sono industrializzabili mediante sostituzioni “drop in” in cui i materiali da fonte fossile vengono sostituiti senza alcuna variazione di processo. Questo approccio importante e vantaggioso per l’utilizzatore è di fatto il marchio di fabbrica dei prodotti da fonte rinnovabile proposti da Coim. Le soluzioni della nuova serie Plaxter E-LB sono state confrontate con i prodotti standard anche dal punto di vista delle potenziali emissioni di CO2 effettuando un calcolo sperimentale comparativo del ciclo di vita (LCA) in modo da poter fornire all’utilizzatore una stima documentale indicativa della riduzione delle emissioni”, ha spiegato Roberto Cattadori, direttore tecnico delle divisioni Polyuretahnes, Polyesters for Coatings, UP Resins, Plasticizers e Peroxides di Coim.
“La nuova gamma Plaxter E-LB rappresenta un ulteriore passo nella transizione dei plastificanti polimerici di Coim verso prodotti sempre più innovativi e rispettosi dell’ambiente, da utilizzare senza cambiamenti applicativi significativi, dimostrando che la chimica di Coim è positiva e sostenibile sotto tutti i profili”, spiega Claudio Birigozzi, business manager Plaxter di Coim.
“Lo sviluppo di questa nuova gamma di prodotti si innesta nella strategia di Coim per la sostenibilità, che integra varie possibilità per realizzazione di nuovi prodotti quali l’impiego di materie prime da fonti biologiche e da riciclo, l’utilizzo di sistemi biodegradabili, compostabili e Low VOC (Volatile Organic Compound), il recupero a valle dei prodotti finiti per il riciclo e il controllo e la riduzione delle emissioni di CO2 sull’intera filiera”, ha concluso Giuseppe Librandi, presidente e CEO di Coim.
Nonostante un contesto internazionale non facile, il produttore tedesco di specialità chimiche Lanxess continua a crescere nel mercato italiano. Le vendite in Italia nel 2022 hanno raggiunto 296,4 milioni di euro, in aumento del 31,4% rispetto a quelle del 2021, pari a 225,6 milioni di euro.
Tre divisioni hanno realizzato la quota maggiore delle vendite: Advanced Industrial Materials, che realizza prodotti chimici di base e fini per successivi impieghi; Lubricant Additives, che offre oli base sintetici, additivi per lubrificanti, pacchetti di additivi e lubrificanti formulati; Polymer Additives, il cui portafoglio di prodotti include una varietà di additivi quali ritardanti di fiamma, plastificanti, coloranti ad alte prestazioni, stabilizzanti all’idrolisi e soluzioni per il trattamento delle acque. Anche la divisione Flavours & Fragrances, creata nel 2021, si è affermata nel mercato italiano, raggruppando le attività nel campo dei prodotti benzilici di Lanxess e dei prodotti chimici speciali per il settore dei beni di consumo della società statunitense Emerald Kalama Chemical, che, acquisita nel 2021, ha già contribuito all’aumento delle vendite nel 2022. Nell’ultimo anno, Lanxess ha continuato a concentrarsi maggiormente sui prodotti chimici speciali, diventando così ancora più stabile e meno dipendente dalle fluttuazioni cicliche. Il gruppo ha completato l’acquisizione della divisione
Microbial Control dalla società statunitense IFF nel luglio 2022. Nel maggio 2022 aveva anche annunciato lo spin-off del ramo d’azienda High Performance Materials, trasferito a una joint venture per tecnopolimeri ad alte prestazioni in fase di costituzione con la società di private equity Advent International. L’operazione frutterà a Lanxess la somma di circa 1,1 miliardi di euro, che il gruppo utilizzerà principalmente per ridurre il proprio debito e quindi rafforzare il proprio bilancio.
L’uso di adesivi privi di solventi consente di ridurre l’impatto ambientale delle applicazioni grafiche, sebbene ciò spesso possa comportare alcuni problemi in termini di prestazioni. Per superare questo inconveniente Avery Dennison ha sviluppato il nuovo adesivo iA Tech, che, come riferisce Natascia Oprandi (product manager Emena di Avery Dannison), offre prestazioni equivalenti ai prodotti a base di solventi: “Questa innovazione si avvale della più recente tecnologia brevettata di adesivi acrilici avanzati (PAAAT) per eliminare completamente i solventi: un obiettivo di lunga data, con grandi vantaggi per i proprietari di marchi e gli utenti nel settore della grafica. È l’ultima aggiunta al nostro portafoglio di soluzioni grafiche sostenibili”.
I prodotti di Avery Dennison 777 Cast Film e Mactac MACal 9300 PRO vengono ora forniti con il nuovo adesivo senza solventi, il cui impiego si traduce una maggiore stabilità dimensionale e in una tra le più basse produzioni di sfrido della categoria. L’adesione è equivalente a quella dei prodotti a base di solvente (20 minuti e 24 ore) e la maggiore stabilità di iA Tech riduce il rischio di fuoriuscita dell’adesivo stesso, consentendo così un
maggior lasso di tempo tra taglio e sfrido.
“Questo adesivo a dispersione acquosa, più affidabile, offre ora agli utenti una maggiore flessibilità, con più tempo per gestire i progetti. Ci sono diversi miglioramenti rispetto agli adesivi in emulsione convenzionali, come la resistenza alla temperatura, la trasparenza e le proprietà sbiancanti che eguagliano le alternative a base di solventi. La coesione, la durata e la resistenza alla migrazione dei plastificanti sono addirittura migliori rispetto ai prodotti con adesivo a solvente”, ha spiegato Mark Gower, direttore ricerca di Avery Dennison, che ha guidato lo sviluppo del nuovo adesivo.
“Siamo particolarmente soddisfatti di aver ottenuto non solo un prodotto a minor impatto ambientale, eliminando l’uso di solventi, ma anche un prodotto con così tanti vantaggi per gli utilizzatori e i proprietari dei marchi. Prevediamo che molti utilizzatori passeranno alla nuova tecnologia per una serie di applicazioni diverse, tra cui il branding aziendale, la marcatura dei veicoli e la grafica delle vetrate. Nel prossimo futuro offriremo il nuovo adesivo anche in una gamma più ampia di prodotti”, ha concluso Oprandi.
Per rendere più rapido lo sviluppo di materiali ad alte prestazioni e ridurne il time-to-market, DSM Engineering Materials ha lanciato Lucidiris, strumento digitale basato sull’intelligenza artificiale. Oltre a prevedere colore e proprietà meccaniche dei materiali, lo strumento è in grado di prescrivere ricette con proprietà cromatiche mirate. Sviluppato per diversi gradi di materiali ad alte prestazioni, sarà ampliato per essere impiegato anche con materiali riciclati. Lucidiris consente, in particolare, la messa a punto di ricette per materiali con proprietà ottiche mirate senza che ne vengano pregiudicate le proprietà meccaniche. Con il suo impiego è possibile prevedere il colore e le proprietà meccaniche dei compound polimerici dopo l’aggiunta di specifici coloranti; valutare lo sviluppo del potenziale spazio colore a determinate proprietà meccaniche critiche; prescrivere i coloranti da impiegare per ottenere specifiche proprietà.
“Lucidiris cambia radicalmente il ciclo di sviluppo “designbuild-test-learn” per le applicazioni dei nostri materiali da parte dei trasformatori. Questo strumento digitale basato sull’intelligenza artificiale rafforza i nostri punti di forza nello sviluppo di materiali colorati e consente di affrontare alcune difficili sfide per il riutilizzo di materiali circolari”, ha affermato Erwin Houben, R&T Manager Digitalization di DSM Engineering Materials.
“E c’è molto altro in arrivo. Lucidiris rappresenta il nostro prossimo passo verso la digitalizzazione dello sviluppo di prodotto. Quello che possiamo fare per lo sviluppo del colore già oggi, sarà possibile per lo sviluppo del prodotto in futuro. La combinazione dell’intelligenza umana con l’apprendimento automatico consentirà di ottenere ricette con molte meno iterazioni e quindi tempi di sviluppo molto più brevi per i nostri clienti”, ha aggiunto Angelika Schmidt, Global R&T Manager Performance Polymers di DSM Engineering Materials.
Lo strumento Lucidiris per la previsione del colore e delle proprietà meccaniche dei materiali si basa sull’intelligenza artificiale. Una possibile applicazione del prodotto Mactac MACal 9300 PRO di Avery Dennison fornito con il nuovo adesivo senza solventi.È stata ampliata l’offerta di lastre alveolari in policarbonato con proprietà di isolamento termico di Exolon. La gamma multi UV Hybrid-X (HX) è adesso disponibile anche con spessore di 50 mm, che completa la famiglia di lastre alveolari HX, già presente sul mercato con spessori di 25, 32 e 40 mm. Il maggiore spessore delle lastre si traduce in migliore isolamento termico, con un eccellente valore di trasmittanza termica pari a 0,85 W/m2 K, ampliando le possibilità applicative delle lastre alveolari grazie a elevate prestazioni meccaniche. Il materiale, inoltre, risulta leggero, resistente agli urti e facile da lavorare. Le lastre multi UV HX/50-32, dotate di uno strato protettivo antiUV coestruso e fuso con il materiale delle lastre stesse in modo omogeneo, sono particolarmente adatte per
rivestimenti in piano, quali verande, vetrate industriali, lucernari, coperture e rivestimenti di facciate.
La struttura HX (in attesa di brevetto) delle lastre Hybrid-X garantisce elevato isolamento, riducendo al contempo il consumo energetico. Contraddistinta
Coadiuvante per l’estrusione in bolla
da una combinazione di pareti e camere d’aria, assicura eccellenti isolamento termico, trasmissione della luce e proprietà meccaniche senza aumentarne il peso e favorendo anche la sostenibilità dei sistemi di illuminazione naturale.
Il nuovo additivo 1001316-N privo di sostanze a base di PFAS (fluoro alchiliche), introdotto da Ampacet come coadiuvante per la lavorazione dei polimeri (PPA) nell’estrusione di film soffiati destinati a svariate applicazioni, offre le stesse prestazioni dei PPA a base di fluoro. A causa dei potenziali rischi per la salute, l’impiego di sostanze a base di PFAS è stato regolamentato in diversi Paesi e ulteriori restrizioni governative potrebbero essere introdotte nel corso di quest’anno.
Sviluppato per essere utilizzato con analogo o simile LDR dei PPA convenzionali di Ampacet, il PPA senza sostanze a base di PFAS risulta conforme agli standard FDA per il contatto con alimenti e paragonabile in termini di costo ai PPA a base di fluoro. Come questi ultimi, elimina la possibile rottura del fuso, diminuisce l’accumulo di materiale nello stampo così da ridurre i tempi di inattività delle attrezzature e incrementare la produttività. Il PPA privo
di PFAS di Ampacet non interferisce con i trattamenti superficiali dei film, come
stampa e laminazione, e non ha alcun effetto sulla sigillatura.
Sezione di una lastra alveolare Exolon multi UV HX50. L’additivo 1001316-N privo di sostanze a base di PFAS è stato introdotto come coadiuvante per la lavorazione dei polimeri nell’estrusione di film soffiati destinati a svariate applicazioni.Lastre alveolari
Spessore maggiore, isolamento termico migliore
Assogomma sta seguendo la vicenda della proposta di restrizione delle PFAS fina dai primi giorni successivi alla sua pubblicazione e presidia da vicino questo importante argomento a difesa di tutto il settore coinvolto.
Nuova restrizione sui PFASLa recente proposta di restrizione delle PFAS ha instaurato uno scenario più severo di quanto fosse ipotizzabile, che, seguendo il principio della “semplificazione”, coinvolge migliaia di sostanze di sintesi, tra cui anche fluoropolimeri e fluoroelastomeri. Con ricadute sul settore che hanno portato le associazioni nazionali ed europee a fare fronte comune per ricondurre la discussione nell’ambito della ragionevolezza basata su una maggiore scientificità.
Lo scorso gennaio le autorità di cinque stati membri (Germania, Olanda, Svezia, Norvegia, Danimarca) hanno presentato all’Agenzia europea Echa una proposta di restrizione riguardante le sostanze per- e poli-fluoro alchiliche, ormai comunemente note come PFAS (per- and polyfluoroalkyl substances). Non si tratta certamente della prima misura restrittiva che colpisce le sostanze organiche fluorurate, ormai da tempo sotto i riflettori delle autorità, né si tratta di una iniziativa inattesa, essendo noto da anni che il dossier fosse in fase di gestazione. Era anche noto che la nuova misura avrebbe avuto una portata molto più generale rispetto a quelle precedenti.
Il testo reso noto concretizza tuttavia lo scenario più severo fra quelli ipotizzati, proponendo un bando generalizzato per tutti i PFAS. Tenendo conto che sotto questa denominazione ricade qualsiasi sostanza contenente almeno un atomo di carbonio metilico o metilenico completamente fluorurato (-CF3 o -CF2-), con pochissime eccezioni, si realizza, non senza sorpresa, che gli estensori del dossier hanno optato per la “semplificazione”, raggruppando in un’unica categoria decine di migliaia di sostanze di sintesi, con proprietà e profili di pericolosità diversis-
simi fra loro, includendo anche i fluoropolimeri e i fluoroelastomeri. Si tratta, come dichiarato da Echa stessa, della più ampia restrizione mai concepita nella UE.
È incontestabile che alcuni PFAS presentino profili di pericolosità critici per l’ambiente o la salute umana. Si tratta infatti di sostanze caratterizzate in generale da una notevole stabilità (il legame carbonio-fluoro è fra i più forti nella chimica organica), che si può tradurre in persistenza nell’ambiente e bio-accumulabilità. Inoltre, se in forma gassosa, possono presentare caratteristiche di gas serra. A livello di salute umana, alcune di queste sostanze possono risultare interferenti endocrini o cancerogene. È altresì noto che alcuni PFAS sono stati in passato protagonisti di gravi episodi di inquinamento, legati al loro uso in alcuni prodotti (per esempio le schiume antincendio negli USA) o in alcuni processi produttivi (si pensi, limitandosi all’Italia, alla vicenda della Rimar in Veneto). Queste criticità hanno riguardato tuttavia solo alcuni PFAS a basso peso molecolare, che ragionevolmente sono stati oggetto nel passato anche recente di misure restrittive più o meno specifiche, come per esempio i PFHxA o il PFOA.
Ben diversa è la situazione dei fluoroelastomeri, o in generale dei fluoropolimeri, che, pur rientrando nella definizione di PFAS, nulla hanno a che vedere con le sostanze coinvolte nelle criticità citate. In virtù del loro elevato peso molecolare, non risultano infatti bio-disponibili e non presentano alcuna delle caratteristiche di pericolosità descritte. Considerare l’intera classe dei PFAS alla stessa stregua - compresi i polimeri/elastomeri - e applicare indiscriminatamente una misura restrittiva come il bando risulta del tutto sproporzionato e ingiustificato sul piano scientifico e introduce oltretutto gravi criticità in diversi settori applicativi. I fluoroelastomeri sono infatti utilizzati in applicazioni dove sono richieste elevate prestazioni in termini, per esempio, di resistenza termica e chimica, che giustificano i costi sensibilmente maggiori che caratterizzano questi materiali.
A titolo di esempio si pensi al settore auto, nel quale l’uso dei fluoroelastomeri nel motore termico è progressivamente cresciuto negli ultimi anni, di pari passo con lo sviluppo tecnologico richiesto dai parametri ambientali sempre più stringenti imposti dalla normativa comunitaria. La necessità di ottenere livelli di efficienza sempre più esasperati ha reso necessario progettare motori termici sempre più compatti, che operano a temperature sempre più elevate. Tali condizioni operative - oltretutto in un ambiente chimico aggressivo - hanno messo fuori gioco i materiali elastomerici utilizzati in passato, richiedendo prestazioni che solo i fluoroelastomeri possono garantire. Che il medesimo legislatore europeo intenda ora bandirli risulta quantomeno paradossale. Si potrebbe obiettare che il destino del motore termico sia ormai segnato in tempi relativamente brevi, ma, posto che su questo cambio di paradigma le incertezze sono ancora rilevanti, sia sul piano tecnologico, che ambientale, oltre che geopolitico, l’elettrificazione, se pur comporterà una relativa riduzione della presenza di questi materiali nei veicoli, non la eliminerà del tutto, considerando che con i fluoropolimeri è realizzata una serie di componenti chiave delle emergenti tecnologie. Tutto questo senza parlare di applicazioni in campo militare. Seppur costituenti una nicchia nel settore della gomma, questi materiali ricoprono pertanto un interesse strategico e sarà fondamentale profondere ogni sforzo per difenderne l’uso, cercando di comunicare efficacemente tutte queste considerazioni.
L’azione di Assogomma e della sua omologa europea Etrma non inizia certamente ora: le due associazioni stanno seguendo il dossier fin dal suo esordio, dando il proprio contributo alle consultazioni pubbliche che nel frattempo sono state promosse. Sul tema sono stati naturalmente attivi anche i produttori di fluoropolimeri, che hanno promosso a livello europeo una RMOA (Risk Management Option Analysis) da contrapporre al
dossier in corso di preparazione da parte delle autorità nazionali coinvolte.
Purtroppo, il dossier recentemente pubblicato costituisce un passo in direzione opposta a quella sperata. Ora, tuttavia, con il passaggio del dossier a Echa, si apre la fase decisiva, nella quale occorrerà cercare di riportare la discussione nell’ambito della scienza e della ragionevolezza. Sarà tuttavia fondamentale il massimo coordinamento fra tutti gli attori della filiera, dai produttori di materie prime a quelli di componenti in fluoroelastomero, fino ai loro utilizzatori, come il settore automobilistico. Proprio in questa direzione si è già mossa Assogomma, che, fin dai primi giorni successivi alla pubblicazione della proposta, ha costituito al proprio interno uno specifico gruppo di lavoro, al quale hanno aderito numerose aziende trasformatrici e più di un fornitore di fluoroelastomeri. In coordinamento con Etrma a livello europeo e Confindustria a livello nazionale, è in fase di definizione una prima raccolta dati, funzionale a predisporre la risposta alla consultazione pubblica. In parallelo, sul fronte istituzionale, il dossier verrà sottoposto all’attenzione dei comitati consultivi di Echa RAC e Seac, responsabili di analizzare la proposta rispettivamente sul piano dell’analisi del rischio e dell’impatto socio-economico. Sulla base di questi pareri Echa formulerà una proposta di restrizione alla Commissione, che coinvolgerà a quel punto nel processo decisionale le rappresentanze degli Stati membri. La parola passerà poi al Parlamento e al Consiglio. Assogomma, pertanto, presidia da vicino questo importante argomento e continuerà a farlo nei mesi a venire a difesa delle imprese associate e di tutto il settore.
O-ring per impieghi in campo pneumatico e idraulico.
Per affrontare la vicenda è apparso fin da subito fondamentale il massimo coordinamento fra tutti gli attori della filiera, dai produttori di materie prime a quelli di componenti in fluoroelastomero, fino ai loro utilizzatori, come il settore automobilistico.
Un corpo puramente elastico ha una deformazione che dipende esclusivamente dalla sollecitazione applicata indipendentemente dalla sua durata. Questo implica che rimuovendo la sollecitazione il corpo riacquista la forma originale. Nella maggior parte dei materiali allo stato solido, come ad esempio metalli o materiali plastici, la deformazione avviene invece tramite stiramento dei legami interatomici e l’energia rimane immagazzinata sotto forma di energia potenziale.
La gomma è in grado di reagire a grandi deformazioni secondo un meccanismo che si basa sulla capacità delle macromolecole di dipanarsi e di muoversi intorno ai punti di legame creati dal processo di vulcanizzazione consentendo al materiale di assumere una forma diversa. In questo ambito, una delle caratteristiche più rilevanti della gomma è l’elasticità, cioè la capacità di ritornare alla propria forma originaria dopo esser stata sottoposta a una o più forze esterne.
internazionali e, per quanto la forma possa essere simile, l’uso di una tipologia di provini rispetto a un’altra porta inevitabilmente a risultati diversi. Il punto della questione è stabilire se e come i risultati di prove di trazione ottenuti con provini di diversa tipologia possano essere correlati in maniera proporzionale.
Esistono numerose norme nazionali e internazionali riguardanti questo tipo di test, la più seguita delle quali è la ISO 37. Nella descrizione della procedura, vengono specificati sette tipi di provini differenti. Tralasciando le tipologie dedicate ai provini ad anello, viene spontaneo domandarsi se vi sia un’effettiva proporzionalità tra i quattro provini dumbbells, di diversa grandezza detti anche “manubri”, o “ossi di cane”.
Si misura lo spessore, si applicano i catarifrangenti, necessari come riferimenti per l’estensimetro laser e, una volta scelta la procedura corretta per il dinamometro, vengono eseguite le prove. Risulta evidente come l’andamento delle quattro curve sia pressoché identico ai bassi allungamenti, per poi discostarsi leggermente all’aumentare della deformazione. Ma i parametri principali che caratterizzano la prova di trazione quali carico e allungamento a rottura, come si comportano?
Una delle prove principali per caratterizzare un materiale, dal punto di vista della capacità elastica, è sicuramente la prova di trazione, che consiste nel sottoporre un provino di dimensioni standard a una forza monoassiale, che viene incrementata fino a provocare la rottura del campione. I provini da utilizzare nelle prove di trazione sono definiti da norme
Già da questi primi dati è possibile osservare una certa proporzionalità tra la grandezza del provino e i principali parametri legati alle proprietà misurate durante il test. Alla riduzione delle dimensioni corrisponde una diminuzione significativa della velocità di prova.
Da una placca a spessore 2 mm vengono ricavati cinque provini per ogni tipologia.
Per quanto riguarda il carico a rottura, i valori sono molto vicini tra di loro (grafico 1). La diminuzione del carico a rottura, al ridursi delle dimensioni del provino, potrebbe essere un andamento tipico del campione testato, mentre l’aumentare dell’errore è sicuramente riconducibile alle minori dimensioni del campione. I risultati ottenuti permettono di valutare il carico a rottura per ogni singolo tipo di provino rispetto alla media e all’intervallo di risultati calcolato usando l’errore. L’allungamento a rottura mostra un andamento analogo a eccezione del provino Tipo 4. In questo caso si riscontra un parziale incremento sia del valore medio per ogni tipo di provino sia dell’errore rispetto alla diminuzione delle dimensioni. Prendendo in considerazione il risultato medio e gli errori per ogni singola
Provino dumbbell per prove di trazione.tipologia di provino e nonostante l’andamento opposto, si può giungere allo stesso tipo di considerazioni fatte per il carico a rottura.
Conclusioni
La norma ISO 37 specifica chiaramente che:
• Il confronto tra due materiali differenti, affinché sia significativo, deve essere fatto su provini dello stesso tipo.
• I provini Tipo 1 e Tipo 2 sono preferibili nello studio dei moduli in confronto a dati di carico ad allungamento di riferimento, mentre i provini di Tipo 3 e Tipo 4 sono l’opzione migliore per prove da eseguire su prodotti finiti o per le verifiche richieste da capitolati specifici.
• La scelta della tipologia di provini da utilizzate nelle prove di trazione può dipendere anche dalla quantità e dalle dimensioni del campione da testare.
A integrazione di quanto dichiarato nella ISO 37, i risultati dello studio riportati dimostrano che c’è una proporzionalità tra le varie tipologie di provini utilizzati nella prova di trazione al netto dell’errore calcolato.
Spessore del campione, temperatura alla quale viene effettuata la trazione e lo strumento di misura sono ulteriori variabili che possono modificare i risultati della prova, soprattutto nel caso in cui il loro controllo non fosse effettuato in maniera accurata.
Il Cerisie, da sempre interessato e coin-
volto in queste problematiche, mette a disposizione le proprie capacità e potenzialità, in termini di strumentazione e personale, per la verifica delle potenziali correlazioni fra parametri apparentemente non dipendenti.
Le principali caratteristiche dei provini da trazione e del loro utilizzo secondo la normativa ISO 37.Venticinquesima puntata della rubrica dedicata agli articoli di stampa estera selezionati dal comitato di redazione di Elastica, composta da Fabio Bacchelli, Rino Gilotta e dal team di Cerisie, coordinati da Maurizio Galimberti.
UNA INDAGINE SULLA DISTRIBUZIONE DEI CROSSLINK NELLA GOMMA NITRILICA MEDIANTE RISONANZA MAGNETICA NUCLEARE “DOUBLE QUANTUM”
Testata: Kautschuk Gummi Kunststoffe, 1, 44 (2023)
Titolo originale: An Examination of the Degree of Crosslink Distribution Heterogeneity in Nitrile Rubber by Double Quantum Nuclear Magnetic Resonance
Autori: Christopher Porter, Badruz Zaman, Richard Pazu
La gomma nitrilica (NBR) è prodotta via polimerizzazione radicalica in emulsione tra acrilonitrile (ACN) e butadiene (B), che si traduce in copolimero a struttura alternata. Il livello di ACN rappresenta il fattore principale nella differenziazione dei gradi in termini di resistenza a olio, grasso e carburanti. Un aumento della concentrazione di ACN determina un incremento della durezza, della resistenza alla trazione e del modulo, con una conseguente riduzione del compression set, della flessibilità a bassa temperatura e della permeabilità ai gas nel vulcanizzato. La sequenziazione dei monomeri lungo la catena polimerica varia a seconda della concentrazione di ACN e della cinetica di polimerizzazione. A causa del rapporto di reattività, l’ACN viene incorporato molto più velocemente del B durante la polimerizzazione ed è noto che una deriva composizionale si verifica ad alti tassi di conversione, causando la formazione di eterogeneità strutturali nel sequenziamento dei monomeri. Ne consegue che la distribuzione diseguale dei livelli di insaturazione lungo la catena polimerica può verosimilmente comportare una distribuzione eterogenea dei crosslink in fase di reticolazione. Tale aspetto influisce negativamente sulle proprietà fisiche finali dei manufatti, con potenziale cedimento delle parti (O-Ring, guarnizioni, tubi flessibili ecc.) durante la vita utile, influendo negativamente sulle proprietà fisiche finali dei manufatti.
Viene esaminato un totale di quattordici compositi NBR (contenuto di acrilonitrile compreso tra 18 e 49% in peso), reticolati a zolfo o perossido e rinforzati con nerofumo. Il ciclo mescola
è stato eseguito su un mescolatore interno da laboratorio, con passaggio finale al mescolatore a rulli. Una piccola quantità di ciascuna mescola è stata sottoposta a estrazione Soxhlet con isopropanolo per 8 ore, al fine di rimuovere gli ingredienti di polimerizzazione e antiossidanti. L’elastomero purificato è stato quindi essiccato a temperatura ambiente e, successivamente, in stufa da vuoto per 24 ore prima dell’analisi NMR. La tecnica H DQ NMR è stata utilizzata per quantificare il grado di reticolazione di un elastomero, così come la distribuzione della densità di reticolazione. Sono state inoltre studiate le differenze nel sequenziamento dei monomeri in funzione del contenuto di ACN. Dal 39 al 49% di ACN si osserva una concentrazione di copolimero alternato vicina all’80%. Alti livelli della triade butadienica B-B-B sono stati invece confermati per i livelli inferiori di ACN. Le densità di reticolazione ottenute via H DQ NMR per entrambi i sistemi di reticolazione (zolfo e
perossido) seguono le tendenze generali del modulo di vulcanizzazione, della durezza e della risposta tensile a bassa deformazione (10%) in funzione del contenuto di ACN. Tuttavia, nonostante le concentrazioni costanti di reticolante, la tecnica H DQ NMR evidenzia una significativa variazione della densità di crosslink a seconda del sistema reticolante. L’NBR vulcanizzato a zolfo possiede una densità di reticolazione più elevata all’aumentare del contenuto di ACN. Al contrario, vengono osservate densità di reticolazione più elevate con gli NBR a minore contenuto di ACN nel caso della reticolazione a perossido. La distribuzione eterogenea della densità di reticolazione varia notevolmente a seconda dei livelli di ACN ed è rappresentata con successo utilizzando analisi statistiche, che mostrano bimodalità e asimmetrie. In conclusione, il reticolo NBR rimane estremamente eterogeneo in natura. Vi sono zone ad alta reticolazione probabilmente causate da effetti di ripartizione dei vulcanizzanti (reticolazione a zolfo) e da alti livelli di reazioni radicaliche nelle zone con triadi B-B-B (reticolazione a perossido). L’indagine ha, infine, rivelato l’utilità della tecnica H DQ NMR per caratterizzare la densità di reticolazione in composti elastomerici contenenti alti livelli di nerofumo e plastificante.
patibile con le mescole in gomma si combinano più ingredienti in un composto granulare ottenendo i seguenti vantaggi:
1. numero ridotto di ingredienti in ricetta
2. granuli pre-dispersi, pre-attivati, privi di polvere, pronti all’uso
3. tempi di mescolazione più brevi
4. eliminazione di sostanze pericolose
5. migliore manipolazione e lavorazione di materiali altamente attivi
6. riduzione del numero di pesate
7. componenti incapsulati con rilascio basso o nullo di VOC (miscele di prodotti organici volatili)
La forma fisica di un tipico prodotto di estrusione reattivo è un granulo non polveroso, non igroscopico e facilmente dosabile. Esistono tre tipi principali di prodotti di estrusione reattivi:
1. la pre-dispersione che consente una migliore distribuzione di un prodotto difficile da incorporare in una mescola
2. la pre-reazione che può includere la miscelazione di due componenti che reagiscono in condizioni specifiche, come temperatura elevata o forza di taglio
3. lo scavenging prevede la “cattura” o la rimozione di un componente nocivo in qualsiasi fase della mescolazione o della vulcanizzazione della gomma.
NUOVI ADDITIVI SOSTENIBILI PER MESCOLE IN GOMMA UTILI A RIMUOVERE RESORCINA, COBALTO E FORMALDEIDE
Testata: Rubber World, dicembre 2022
Titolo originale: “New sustainable rubber compounding additives to remove resorcinol, cobalt and formaldehyde”
Autori: Paul Fithian, Stefan Mark, Ümit Özkütükcü e Markus Piotrowsky, Brüggemann
A C URA DI ROSARIO GILOTTA E CERISIE
Brüggemann, azienda fornitrice di materie prime per l’industria della gomma, ha realizzato un laboratorio di sviluppo mescole nel 2012 creando nuove soluzioni grazie alla sua lunga esperienza nell’impiego di polimeri e additivi; le principali attività consistono nella generazione dei dati, nello sviluppo di nuovi prodotti e nei test per i clienti.
Uno dei primi obiettivi del lavoro di Brüggemann riguarda i prodotti che reagiscono in fase di estrusione. Infatti, con l’utilizzo di un vettore disperdente, a basso punto di fusione e com-
Si nota che, nel caso di un dosaggio significativamente inferiore di un materiale pre-attivato, si hanno prestazioni equivalenti a un attivatore standard. È possibile una miscelazione più uniforme del materiale pre-attivato nella mescola, fornendo una migliore dispersione; si ha infatti una migliore miscelazione con TP 1850, (una pre-dispersione di ZnO attivo in polvere in un vettore) che con una pre-dispersione su supporto, di una polvere di ossido di zinco attivo. Nei paragrafi seguenti vengono illustrati alcuni vantaggi dei prodotti di estrusione reattivi.
TP 1862
La resorcina e il cobalto (Re/Co) hanno una lunga storia di applicazioni mirate a migliorare l’adesione tra gomma e metallo. Sono ampiamente utilizzati nelle mescole degli pneumatici per garantire l’adesione a lungo termine del cord metallico. Tuttavia, le preoccupazioni tossicologiche riguardanti la resorcina indicano che ci si trova di fronte a un potenziale interferente endocrino in presenza di elevati consumi.
La Commissione europea (ECHA, Agenzia europea delle sostanze chimiche) ha recentemente presentato una proposta per inserire il resorcinolo tra le sostanze ad alto rischio (SVHC). Questi recenti sviluppi indicano la necessità di una soluzione sostenibile alternativa per rimuovere la resorcina dalle mescole di gomma.
La catena di approvvigionamento del cobalto e le preoccupazioni sulla tossicità rivelano la necessità di sviluppare soluzioni di adesione gomma-metallo anche senza questo ingrediente.
TP 1862 è un masterbatch pronto all’uso in granuli che ha dimostrato prestazioni equivalenti alle mescole di gomma contenenti Re/Co. Si tratta di un sistema Re/Co senza resina basato su una novolacca, contenente ioni di zinco attivi. Questa combinazione di una resina con zinco altamente attivo conferisce un’elevata resistenza meccanica, mantenendo l’adesione all’acciaio. Inoltre, i processi di invecchiamento possono essere contenuti grazie all’elevata presenza di ossido di zinco attivo. Le fondamentali proprietà di una mescola di adesione per pneumatici si ottengono senza Re/Co. Il TP 1862 dimostra prestazioni equivalenti alle mescole di gomma contenenti Re/Co, mentre lo zinco contenuto nel masterbatch funge da attivatore di vulcanizzazione.
Per gli attuali studi, tutte le mescole sono state prodotte con un mescolatore interno da 1,6 litri e ulteriormente lavorate su un mescolatore a cilindri da 150 mm. Le caratteristiche di vulcanizzazione sono state analizzate tramite un reometro mobile (MDR) a una temperatura di 155°C, e le mescole sono state vulcanizzate a T = 95 °C in una pressa da laboratorio da 400 kN.
Dalle piastre di gomma vulcanizzate, sono stati ricavati i provini per la misurazione dei moduli di trazione, della durezza, resa elastica e compression set. È stato utilizzato cord d’acciaio ottonato (Bekaert 2 + 2 x 0,25 HT, 63,5% Cu) gommato e vulcanizzato per determinare le proprietà di adesione.
Riduzione della formaldeide durante la lavorazione: LP 21-103
La Hexamethoxymethylmelamine (HMMM) è ampiamente utilizzata nell’industria della gomma con risultati eccellenti, in particolare nelle reazioni dell’adesione gomma-rinforzo. Tuttavia, è noto che HMMM rilascia formaldeide durante la lavorazione, classificato come cancerogeno per l’uomo.
L’esposizione di brevi periodi e alti livelli di HMMM può essere in effetti fatale, mentre l’esposizione a lungo termine può causare difficoltà respiratorie, eczema e sensibilizzazione. Pertanto, è prudente ridurre le emissioni di formaldeide dove possibile. Queste esigenze hanno portato allo sviluppo di uno scavenger(trappola) di estrusione reattivo per la formaldeide: LP 21-103. Il test iniziale di LP 21-103 è stato eseguito con il composto di riferimento utilizzando un additivo Re/Co. Lo studio confronta il rilascio di formaldeide quando LP 21-103 viene sostituito con polvere HMMM in una tipica mescola di gomma Re/Co. L’emissione di formaldeide è ridotta di oltre il 96%. Lo studio evidenzia l’esame delle prestazioni dopo la vulcanizzazione di queste mescole mostrando risultati quasi identici per tutti gli elementi testati, come coppia reometrica, tempo di scottatura, durezza, forza di sfilamento e adesione al filo metallico. I test applicativi delle mescole prodotte con LP 21103 non hanno mostrato deficienze prestazionali rispetto alla mescola di riferimento.
Sostituendo LP 21-103 alla HMMM, quasi tutta la formaldeide può essere eliminata durante la lavorazione, senza alcun degrado delle prestazioni della mescola di gomma vulcanizzata.
Prestazioni della mescola a basso contenuto di formaldeide esente da RE/ CO: TP 1862 + LP 21-103
Sulla base dei risultati positivi ottenuti con TP 1862 rispetto a Re/Co e LP 21-103 rispetto a HMMM, sono stati eseguiti ulteriori test sulle mescole di gomma utilizzando entrambi gli additivi. Questi risultati mostrano sostanziali miglioramenti nelle prestazioni suffragati dalle curve reologiche per tre diversi composti, che mostrano prestazioni equivalenti al composto di riferimento standard.
Inoltre, si evidenzia il vantaggio sinergico dell’utilizzo sia di TP 1862 sia di LP 21-103 rispetto a un composto di riferimento con Re/Co e HMMM. Si nota in particolare un aumento del 50% del POF invecchiato quando vengono utilizzati entrambi. Si prevede che l’ottimizzazione degli ingredienti composti rivelerà ulteriori vantaggi, come livelli ridotti di ingredienti per prestazioni simili o leggermente migliori, come richiesto dall’applicazione prevista.
Conclusioni
L’additivo reattivo per estrusione TP 1862 di Brüggemann si può considerare una soluzione sostenibile per eliminare Re/Co dalle mescole di gomma.
In parallelo, LP 21-103 può eliminare quasi tutta la formaldeide generata con HMMM durante la lavorazione della gomma, riducendo l’esposizione umana e la tossicità associata. La combinazione di questi additivi mostra prestazioni significativamente migliori rispetto alle tradizionali ricette di composti. È in corso un›ulteriore ottimizzazione con dosaggio in gomma naturale e in altri tipi di gomme che dovrebbe consentire la realizzazione di mescole migliori con una catena di fornitura più affidabile. Il laboratorio di sviluppo della gomma di Brüggemann è focalizzato su nuovi additivi reattivi per gomma da estrusione per migliorare le prestazioni della mescola, semplificare la lavorazione e migliorare la sicurezza sul posto di lavoro.
DGTS Srl, nell’intento di soddisfare sempre al meglio le esigenze dei suoi clienti, è in grado di offrire un supporto tecnico competente e completo tramite i suoi servizi:
Vendita e Installazione di apparecchiature e strumenti per il Laboratorio Controllo Qualità e Ricerca e Sviluppo per la determinazione delle caratteristiche fisico meccaniche delle materie prime e dei prodotti finiti Corsi di Formazione ed Aggiornamento del personale sull’utilizzo degli strumenti e dei relativi software ed accessori
Presentazione degli strumenti anche presso la sede del cliente, con la possibilità di eseguire prove dimostrative su campioni forniti dal cliente stesso
Assistenza Tecnica post-vendita
Servizio di Taratura e Calibrazione
Servizio di Manutenzione
Servizio di Riparazione
„Montiamo nei nostri impianti di riempimento ed imballaggio solamente componenti di altissima qualità ed affidabilità. Da molti anni utilizziamo per la protezione da sovraccarichi i giunti di sicurezza EAS® della mayr ®.“
Markus Kröger
Franz Tölke GmbH, Sondermaschinenbau.
IT-35020 SAONARA (PD), www.mayr.com
L’industria delle materie plastiche e della gomma ha un appuntamento imperdibile a Fiera Milano dal 5 all’8 settembre: Plast 2023, il salone internazionale dedicato alle tecnologie, ai materiali e alle soluzioni per il settore. Grande attesa, dunque, per una delle fiere di riferimento, che conta già quasi 1.000 iscritti. Diverse decine gli espositori alla loro prima partecipazione o che ritornano dopo un’assenza di qualche edizione, segno dell’attrattività della manifestazione e dell’impegno da parte degli organizzatori a mantenere alta l’attenzione sulla mostra. In parallelo sono confermate la collettiva cinese e iraniana mentre farà il suo debutto quella francese.
Le iscrizioni sono ancora aperte e l’obiettivo è quello di portare a Plast sempre più espositori e visitatori internazionali. Anche per questo l’organizzatore della fiera, Promaplast, ha siglato un accordo sinergico con Ipack-Ima volto a promuovere Plast tra gli operatori del settore imballaggio. Si tratta infatti di un comparto particolarmente affine a quello della plastica, considerato che circa il 40% della domanda di polimeri proviene proprio dal comparto dell’imballaggio. Focus anche sulle delegazioni estere: sono infatti circa 30 i Paesi di tutto il mondo coinvolti nel programma di arrivo di buyer, realizzato con il supporto di ICE-Agenzia.
Il layout espositivo di Plast 2023 si suddividerà in sei padiglioni: il 9 e l’11 saranno occupati dai fornitori di materie prime, macchinari e servizi, il 13 e il 15 saranno dedicati estrusori, impianti per il riciclo e saldatrici, il 22 e 24 saranno rivolti a stampaggio, soffiaggio e ausiliari. Anche all’edizione 2023 verranno riproposti i tre saloni-satellite dedicati ad altrettante filiere d’eccellenza: Rubber (per il mondo della gomma, padiglione 11), 3D Plast (focalizzato sulla produzione additiva e tecnologie affini, padiglione 22) e Plast-Mat (dedicato alle soluzioni in materiali plastici innovativi, padiglione 9). Inoltre, anche grazie alla collaborazione con ICE-Agenzia, è nuovamente prevista l’area StartUp, per dare il giusto risalto alle giovani imprese del settore che propongono soluzioni innovative. The Innovation Alliance, il progetto che vede la partnership di
Plast con Ipack-Ima, Print4All e Intralogistica Italia, propone un nuovo concept. Considerato il riassetto dei calendari fieristici dovuto alla pandemia, le segreterie organizzative stanno lavorando su una reinterpretazione dell’iniziativa articolata in diversi momenti focalizzati su tematiche di attualità trasversali a tutti i settori coinvolti, con l’obiettivo di consolidare il messaggio di filiera alla base del progetto The Innovation Alliance.
Tante, dunque, le novità di Plast 2023, che rappresenta una vetrina strategica soprattutto per i costruttori italiani di tecnologie per l’industria della plastica e della gomma. Un comparto quello italiano che, nonostante l’incerto scenario macroeconomico mondiale, nel 2022 è cresciuto. Infatti, il settore delle tecnologie per la plastica e la gomma rappresentato da Amaplast (l’associazione nazionale dei costruttori di macchine e stampi per materie plastiche e gomma) ha chiuso l’anno con un fatturato pari a 4,67 miliardi di euro, seconda prestazione migliore di sempre. Inoltre, l’incremento rispetto al 2021 è stato del 5% e le previsioni dei preconsuntivi di dicembre (pari a 4,5 miliardi di euro) si sono quindi rivelate particolarmente caute. Il bilancio della sola compagine associativa è stato persino migliore (+9% il fatturato rispetto al 2021).
L’edizione 2018 di Plast aveva registrato la presenza di oltre 1.500 espositori su una superficie di 55.000 metri quadri netti, con oltre 63.000 visitatori e una forte presenza dall’estero, a conferma dell’internazionalità e dell’attrattività della manifestazione. Plast è inoltre affermata come un’ampia vetrina tecnologica, dai materiali ai processi di lavorazione, dai prodotti finiti ai servizi, alle soluzioni più avanzate sviluppate dai costruttori di macchinari, attrezzature, ausiliari e stampi per la lavorazione di plastica e gomma, con oltre 3.500 unità esposte nei sei padiglioni occupati.
Rimandato nel 2021, quando avrebbe dovuto svolgersi secondo la tradizionale cadenza triennale, a causa della pandemia, il 2023 segna finalmente il ritorno di Plast, dal 5 all’8 settembre a Fiera Milano.
Cesap e MIP - Graduate School of Business (la prestigiosa School of Management del Politecnico di Milano) hanno siglato un accordo strategico per l’erogazione, presso il Plastics Smart Hub 4.0 di Monza, di corsi teorici e pratici sulle principali metodologie dell’Operational Excellence, con specifico focus sulle tecnologie e sulle tematiche del mondo di plastica e gomma
World Class Manufacturing
15.05.2023: Design of Experiments (DOE)
23.05.2023: FMEA (Failure Mode and Effect Analysis)
12-13-19-20.06.2023(h 09-13): La programmazione della produzione
29.06.2023: I principali strumenti di problem solving
17-18-24-25.07.2023 (h 09-13): Il product costing e la contabilità industriale
03-04-10-11.07.2023 (h 09-13): Il processo di acquisto e il benchmarking dei fornitori
Lean Six Sigma (Yellow Belt, Green Belt e Black Belt) Cesap ha ottenuto il riconoscimento “Accredited Training Organization” (ATO, ovvero organizzazione accreditata per la formazione), per l’erogazione di corsi di formazione volti alla certificazione Lean Six Sigma, da parte dell’International Association For Six Sigma Certification (IASSC), il più importante organismo mondiale di parte terza (totalmente indipendente) nel campo di formazione e certificazione competenze sulle metodologie Lean Six Sigma.
Lean Six Sigma - Yellow Belt
Lean Six Sigma - Green Belt
Lean Six Sigma - Black Belt
SEGNALIAMO DI SEGUITO GLI APPUNTAMENTI FORMATIVI EROGATI DA CESAP, IN AULA E VIA WEBINAR, CHE SI SVOLGERANNO
NEI PROSSIMI MESI
Materiali
18.05.2023
La colorazione dei polimeri
08.06.2023
Corso base sui polimeri
08-09.06.2023
Corso approfondito sui polimeri
Stampaggio termoplastici
10-17.05.2023 (h 09-13)
Stampaggio a iniezione - Simulazione CAE
16-17-18.05.2023
Stampaggio a iniezione - Corso approfondito
12-13.06.2023
Stampaggio a iniezione - Corso base
Altre tecnologie
09-16-23.06.2023 (h 09-12:30)
Estrusione di materiali polimerici: processo e analisi delle criticità
13-20.06.2023 (h 09-12:30)
Estrusione di materiali polimerici: analisi e simulazione software
07-14.07.2023 (h 09-12:30)
Termoformatura: processo e analisi delle criticità
Attrezzature - Progettazione
06-07.06.2023
Stampi per iniezione - Corso base
Testing e regulatory
10.05.2023
Prove fisico-meccaniche e analisi identificative: elementi indispensabili per la caratterizzazione dei materiali plastici
26-27.06.2023 (h 09-13)
Materiali a contatto con gli alimenti (MOCA)
Sostenibilità e assicurazione qualità
12.05.2023
Riciclo e recupero di rifiuti in plastica e sottoprodotti di materie plastiche
24.05.20 23
Difetti di stampaggio: come evitarli agendo sui parametri macchina
30.06.2023
Materie plastiche riciclate: come impiegarle correttamente
NOTA: Il calendario corsi potrebbe subire variazioni e/o essere ampliato. Vi invitiamo a visitare il sito web Cesap alle sezioni “Materiali e Tecnologie”, “Operational Excellence” ed “Energy Excellence” per tutti gli aggiornamenti sulla programmazione, e per i webinar gratuiti.
CESAP c/o IIP (ISTITUTO ITALIANO DEI PLASTICI)
Via Velleia, 4 - 20900 Monza (MB)
Tel.: +39 039 2045700 - Fax: +39 039 2045784
E-mail: info@cesap.com
www.cesap.com - www.iip.it