LEADERS IN CORROSION PREVENTION & SEALING TECHNOLOGY WWW.DENSO.NET INNOVATIVE, FROMLONGVISCO-ELASTICSELF-HEALINGCOATINGSFORLASTINGPROTECTIONCORROSION ® Volume 22 Number 8 - August 2022
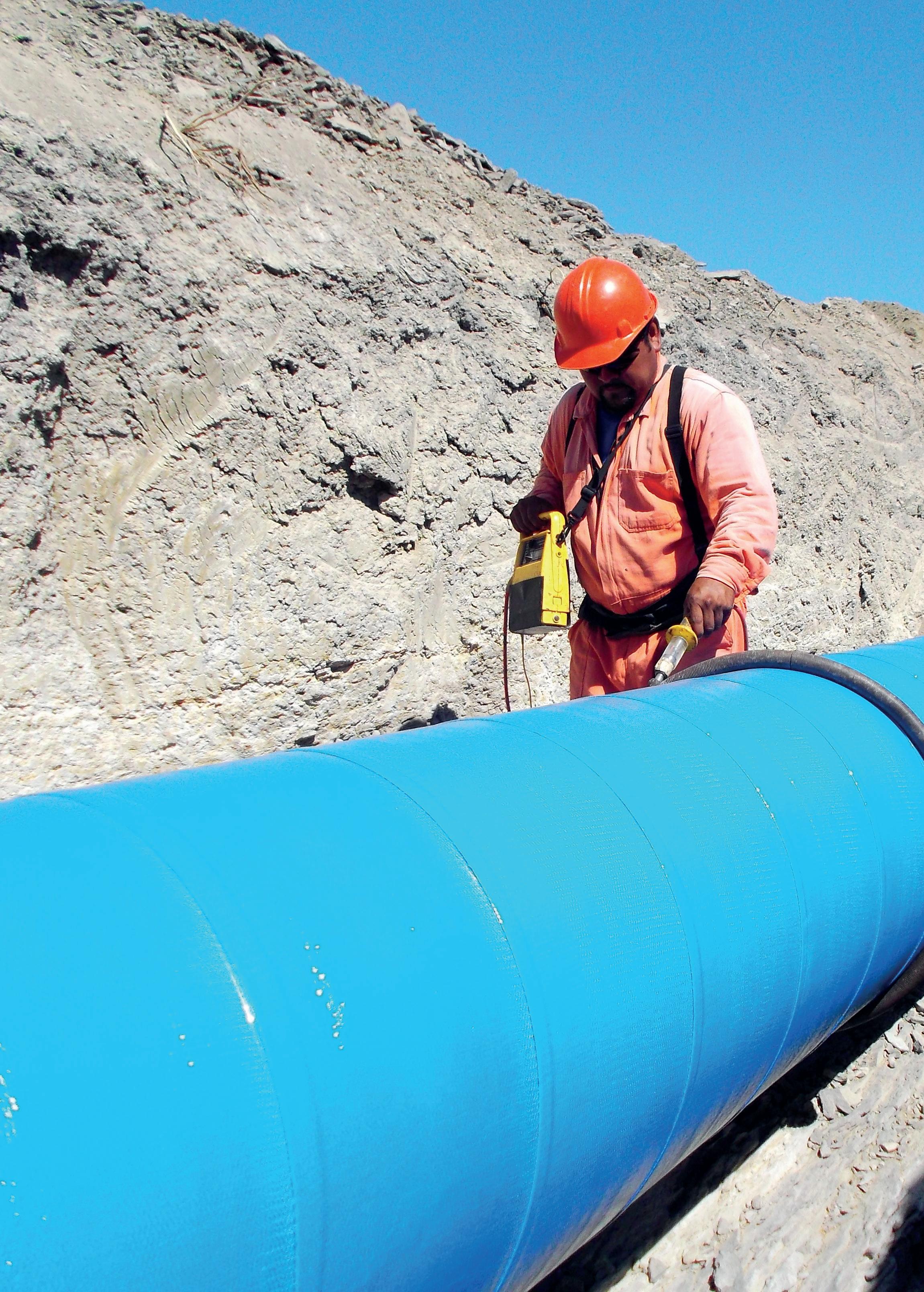
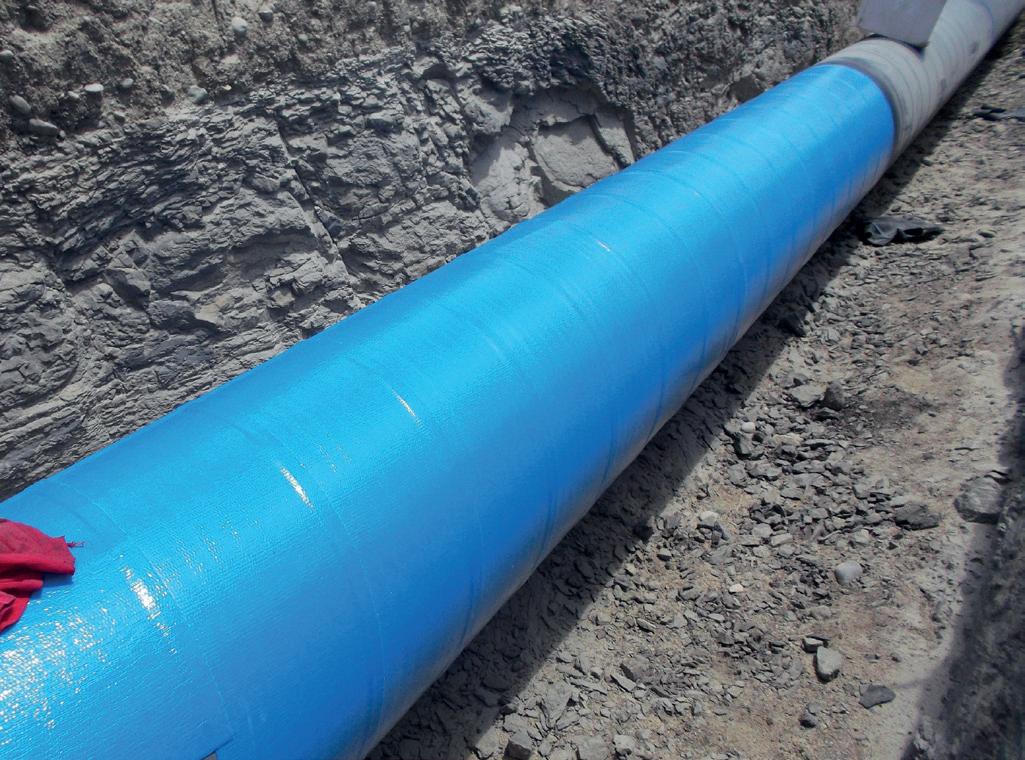
www.rosen-group.com Artificial intelligence solutions are driving life extension, the energy transition, and zero-incidents in the pipeline industry. Combining decades of in-line inspection results, metadata for tens of thousands of pipelines worldwide, and a dedicated team of experts, ROSEN’s Integrity Analytics initiative is the future. As partners we deliver unique insights that enable reliable decision-making for the safety, lifetime, and performance of your assets. AnalyticsIntegrity Visit us at IPC 2022 26-30CalgarySeptember BOOTH #512
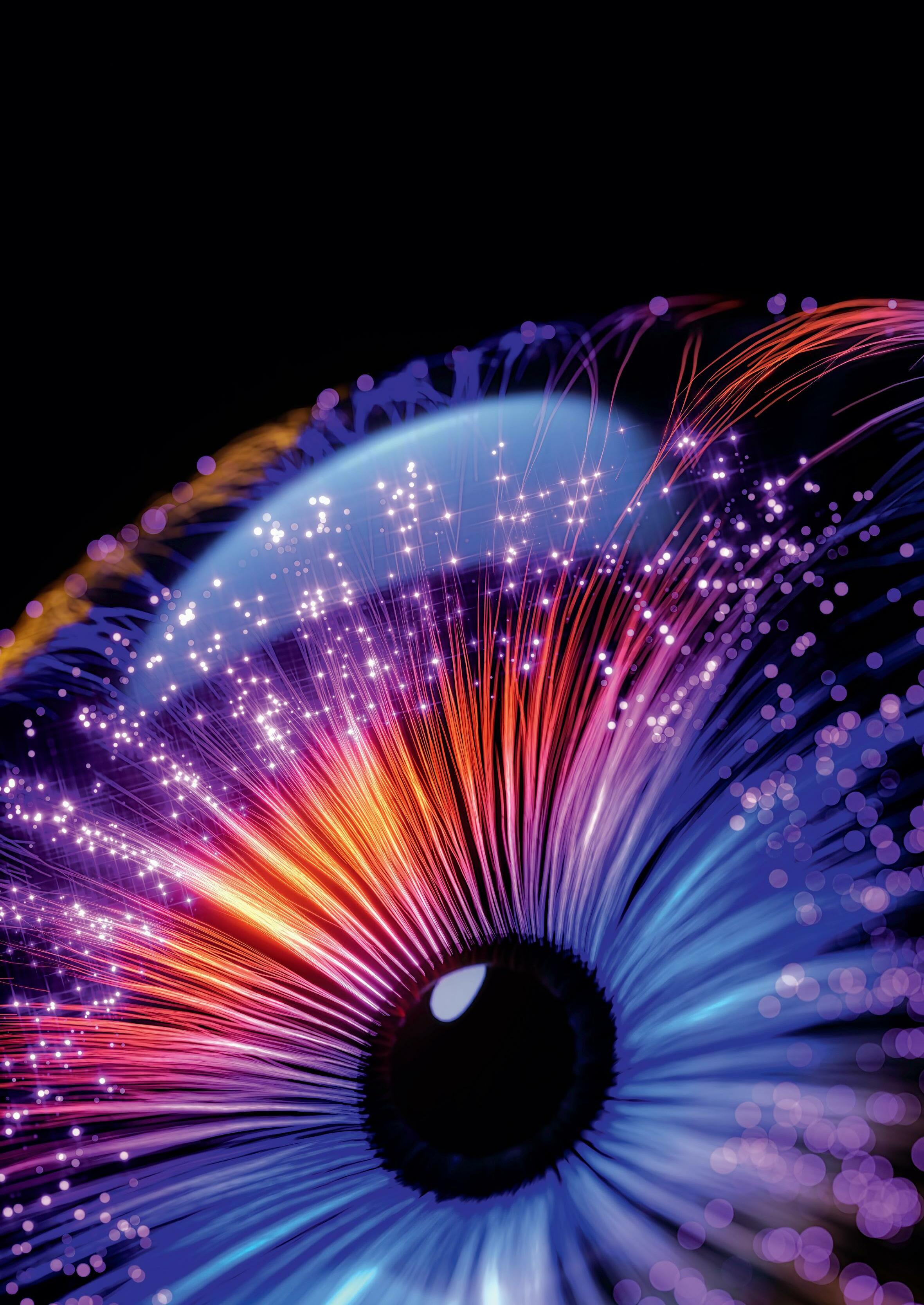
LEADERS IN CORROSION PREVENTION & SEALING TECHNOLOGY WWW.DENSO.NET INNOVATIVE, FROMLONGVISCO-ELASTICSELF-HEALINGCOATINGSFORLASTINGPROTECTIONCORROSION WCD WP Cover_August 2022.indd WORLDPIPELINESAUGUST2022 ® Volume 22 Number 8 August 2022 www.worldpipelines.com OFC_WP_August_2022.indd 1 31
AUTONOMOUS
INLINE
76.
DECOMMISSIONING
69.
Francesco Ciccomascolo, Full Welding Solutions Manager, voestalpine Böhler Welding, Austria, introduces a new solution for orbital pipeline welding with flux cored wires. I the pipeline industry, perfect pipeline girth welds with consistent mechanical properties, paired with high productivity, and low repair rates are key priorities. solutions, which guarantee repeatable high quality welds with reduced downtime, can bring these benefits to costsensitive pipeline contractors. The new solution minimise repair rates, thanks to the wires, the movements and wire feeding precision offered by Böhler Welding’s pipeRunner orbital welding system, and the stable electric arc performance of the TERRA 400 PRM welding power source. ideal for pipeline contractors that want to introduce mechanisation in their welding process within limited budget, avoiding sophisticated operations such as narrow gap preparations and fully automated root pass, for which specific expertise and equipment, such as site bevelling Additionally, each weld seam is executed using single set of parameters from 6:00 o’clock to 12:00 o’clock, thanks to the performance of the system in combination with the Böhler Welding flux cored wires. Hence, key benefits operation. Time comparison with a fully SMAW procedure PRM power source for manually welding the root and hot pass. This can be done with SMAW electrodes, or by In-house welding trials with the new pipeRunner, state-of-the-art programmable mechanised GMAW/FCAW orbital system designed for girth welding of pipelines and process piping. completing manual GTAW root (this latter, e.g. for piping applications or for high alloys and clad pipes). Once these two passes are completed, however, the flux-cored process using Böhler Welding’s pipeRunner orbital bug and the diamondspark range of flux-cored wires for pipeline welding. In order to evaluate the gain in terms of productivity, trial welds on Grade API 5L 70 pipe with diameter performed using the above mentioned method for the fully manual SMAW process on another weld joint. For both, the root consumable used was the FOX CEL (E6010), Böhler Welding’s cellulose electrode designed for verticalrecommended for root run pass welding and offers good deposition efficiency and speed economy, particularly when compared to vertical-up welding. It also offers excellent gap bridging characteristics, and outstanding impact and strength values. FOX CEL 80-P (E8010-P1). This cellulosic electrode meets the strength requirement of the API 5L X70 pipe, and was designed for vertical-down welding of high strength pipeline materials. Both welding consumables are HIC/ For the mechanised fill and capping passes, the diamonspark X70 RC-Pipe (E91T1-K2M-JH4) consumable was used with the weld metal being deposited using pipeRunner moving vertically up from the 6:00 o’clock to alloyed flux-cored wire, the X70 RC-Pipe, the perfect match for this pipe material and ideal for multilayer De Ceukelaire, Head of Hackers, Intigriti, Belgium. Exploring augmented reality Francesca Gregory, GlobalData, UK. MANAGEMENT AND SECURITY Cultivating safety culture Bonney Hodges, Energy Operations Director, ISN, USA. End-to-end AI-powered solutions: the future of pipeline integrity Jason Chadee, SparkCognition, USA. TECHNOLOGY Autonomous shipping: regulations, operations and technology Gareth Burton, VP Technology, ABS, USA. INSPECTON TOOLS Roundtripping the unpiggables Corey Richards, Christopher Holliday (Canada) and Simon Irvine (UK), ROSEN. Inspection tools: a case study Maik Bäcker, EWE Netz GmbH, Hendrik Friemann and Basil Hostage, 3P Services GmbH & Co. KG, Germany. Sweat the small stuff Ken Maxfield (USA) and Mark Briell (Canada), KMAX Inspection LLC. REPAIR A journey into pipeline monitoring Austin Harbison, Smart Technology Manager, CRP Subsea, UK. PIPELINES Routes to recycling Dr Francis Norman, CODA, Australia.
83.
SUBSEA
59.
61.
44 45 PIPELINE OPERATIONS SOFTWARE 49. The application of ethical hacking Inti
RISK
91.
53.
73901472-ISSN Member of ABC Audit Bureau of Circulations ON THIS MONTH'S COVER Reader enquiries [www.worldpipelines.com] C O NTENTS Copyright© Palladian Publications Ltd 2022. All rights reserved. No part of this publication may be reproduced, stored in a retrieval system, or transmitted in any form or by any means, electronic, mechanical, photocopying, recording or otherwise, without the prior permission of the copyright owner. All views expressed in this journal are those of the respective contributors and are not necessarily the opinions of the publisher, neither do the publishers endorse any of the claims made in the articles or the advertisements. Printed in the UK. WORLD PIPELINES | VOLUME 22 | NUMBER 8 | AUGUST 2022 Winn & Coales International Ltd has specialised in the manufacture and supply of corrosion prevention and sealing products for over 90 years. The well-known brands of Denso™ and Premier™ offer a cost-effective and long-term solution to corrosion on buried or exposed steel or concrete, pipes, tanks and structures. Their Viscotaq™ visco-elastic coatings are self-healing, non-toxic, easy to apply and are 100% impermeable to water and oxygen, offering the ultimate level of protection to vital assets. For more information visit www.denso.net 03. Editor's comment 05. Guest comment Gonzalo Montenegro, SEPCON. 07. Pipeline news Updates on Permian Highway Pipeline, NMGP and Trans-Saharan gas project. KEYNOTE FEATURE: SAFETY 11. Raising safety management standards Alexa Burr, Vice President of Segment Standards & Programs, American Petroleum Institute (API), USA, outlines how API standards and programmes foster safety and sustainability in pipeline operations. ENERGY TRANSITION 16. A cleaner energy transition Paul Dickerson, Global Products Lead, Pipeline Management Software, Emerson, USA. 25. Cleaner energy in the pipeline? Nigel Curson, Vice President Technical Excellence, Penspen, UK. CONSTRUCTION BEST PRACTICE 31. Tricks of the trade Aaron Moore, CWI, Product Manager, Miller Electric Mfg. LLC, USA. 33. Protecting your workforce Natalie Henley, Remote Medical International (RMI), Americas. 37. The smartisation of pipe welding Mahyar Asadi, VP Innovations, Novarc Technologies, Canada. STEELS 44. Delivering high productivity Francesco Ciccomascolo, Full Welding Solutions Manager, voestalpine Böhler Welding, Austria. CBP006075 76 PAGE44
87.
65.

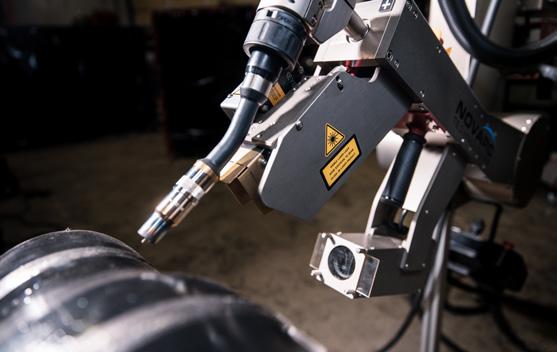
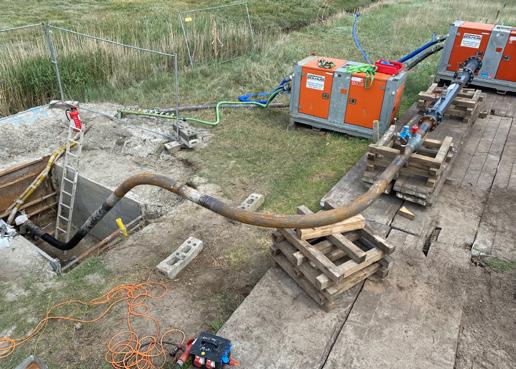
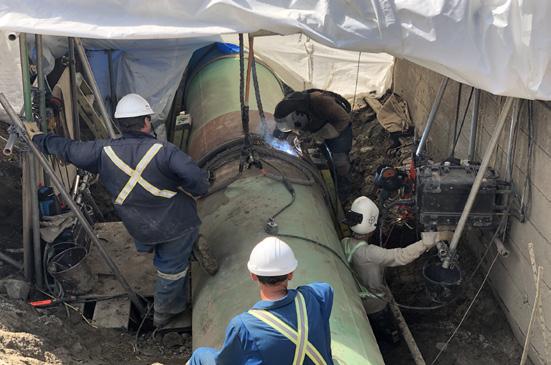
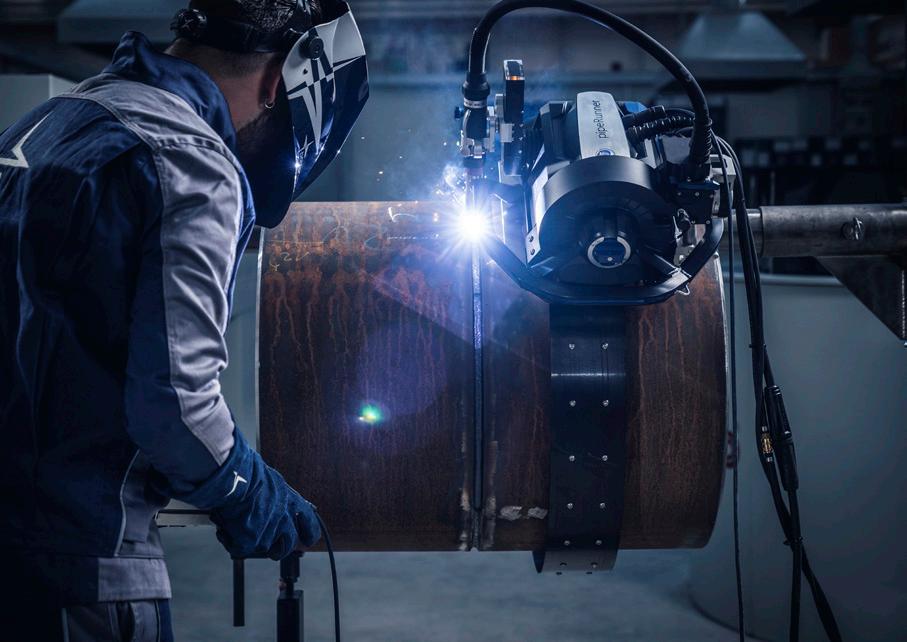
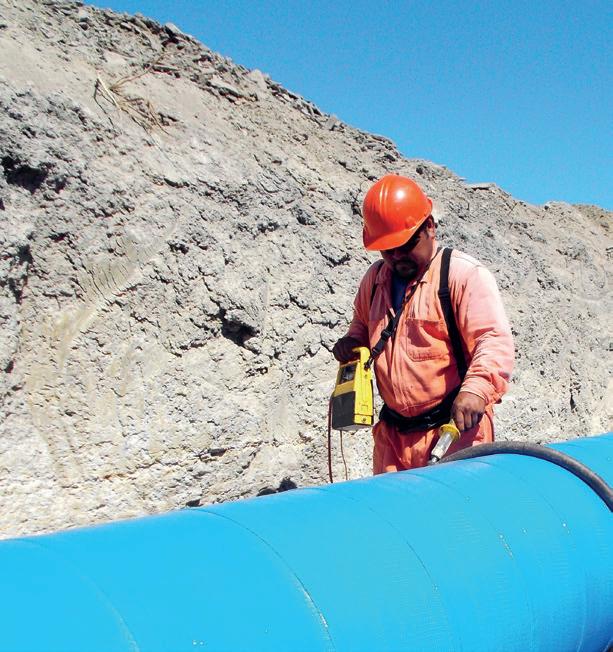
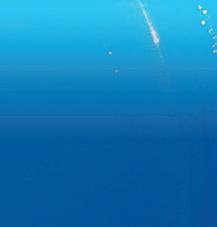
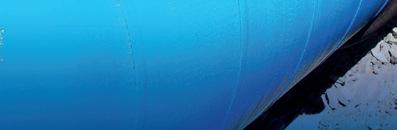

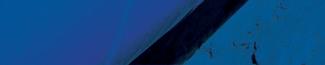
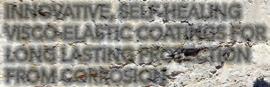
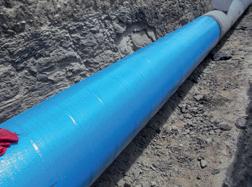
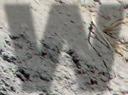











THE CONSTRUCTIONUTILITY Pipeline & Gas Expo 29-31 May 2024THE ONLY DEDICATEDEXHIBITIONEUROPEANFULLYTOTHEMID-STREAMSECTORANDTHEGAS,OIL&WATERDISTRIBUTIONNETWORKS 3rd SOCIALPh.www.pgexpo.euinfo@pgexpo.euBOOKINGS:STANDANDINFOFOREdition+390105704948MEDIA
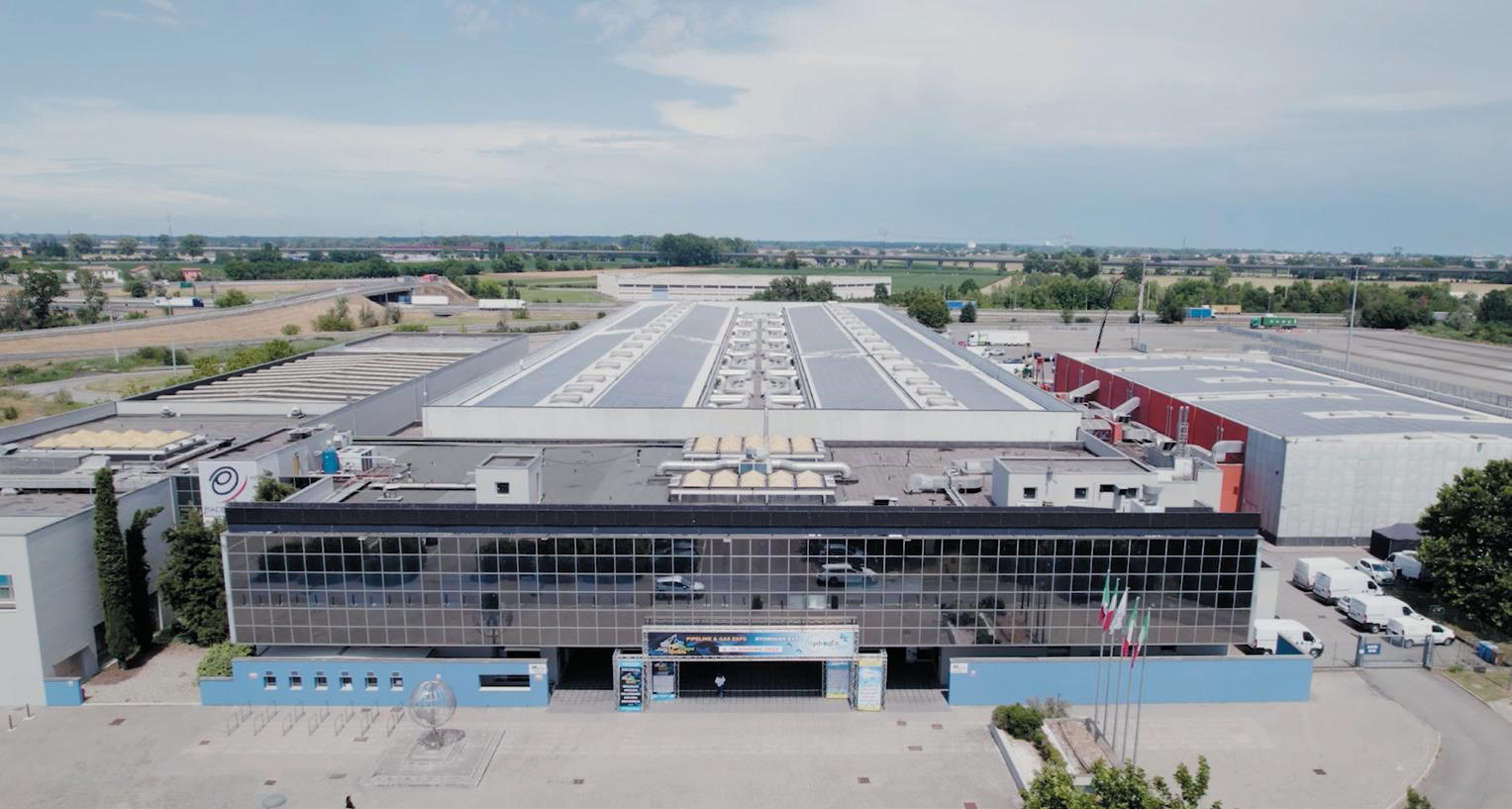
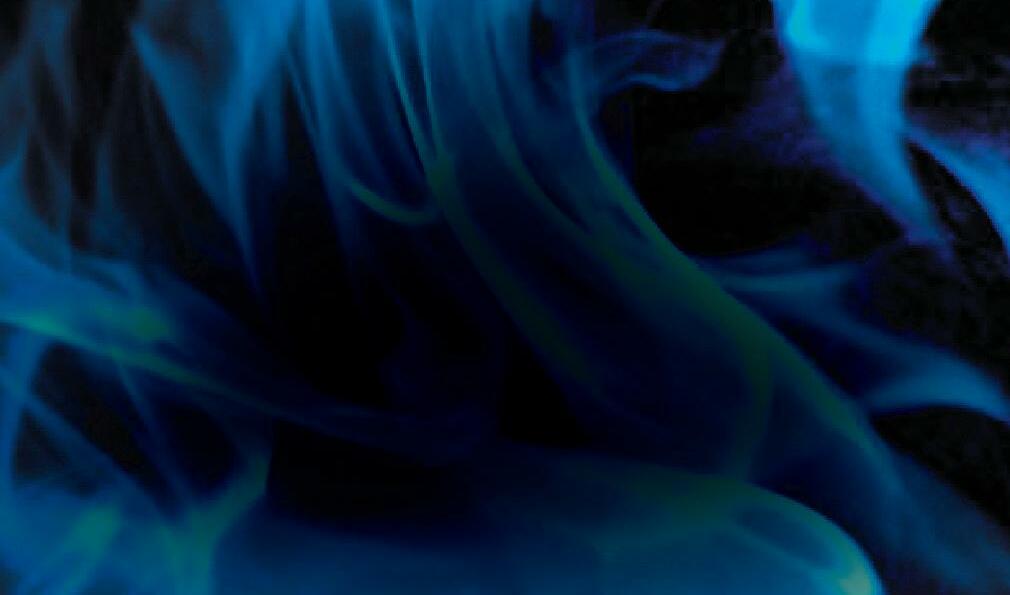
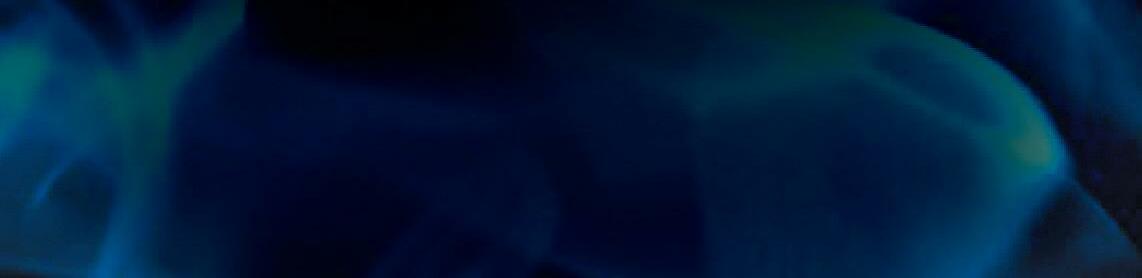







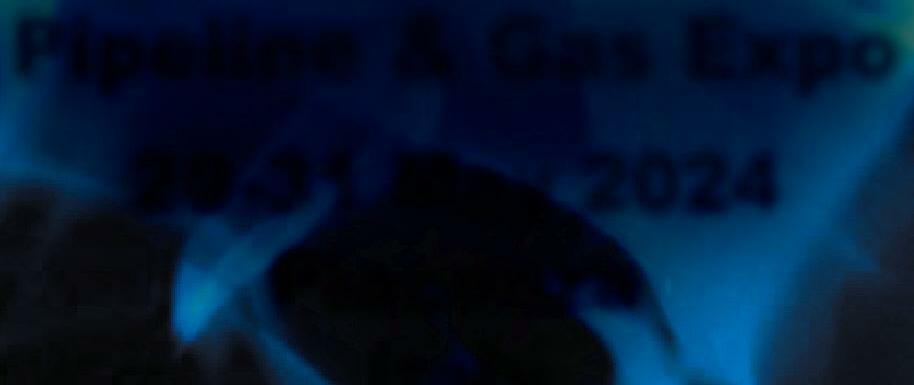
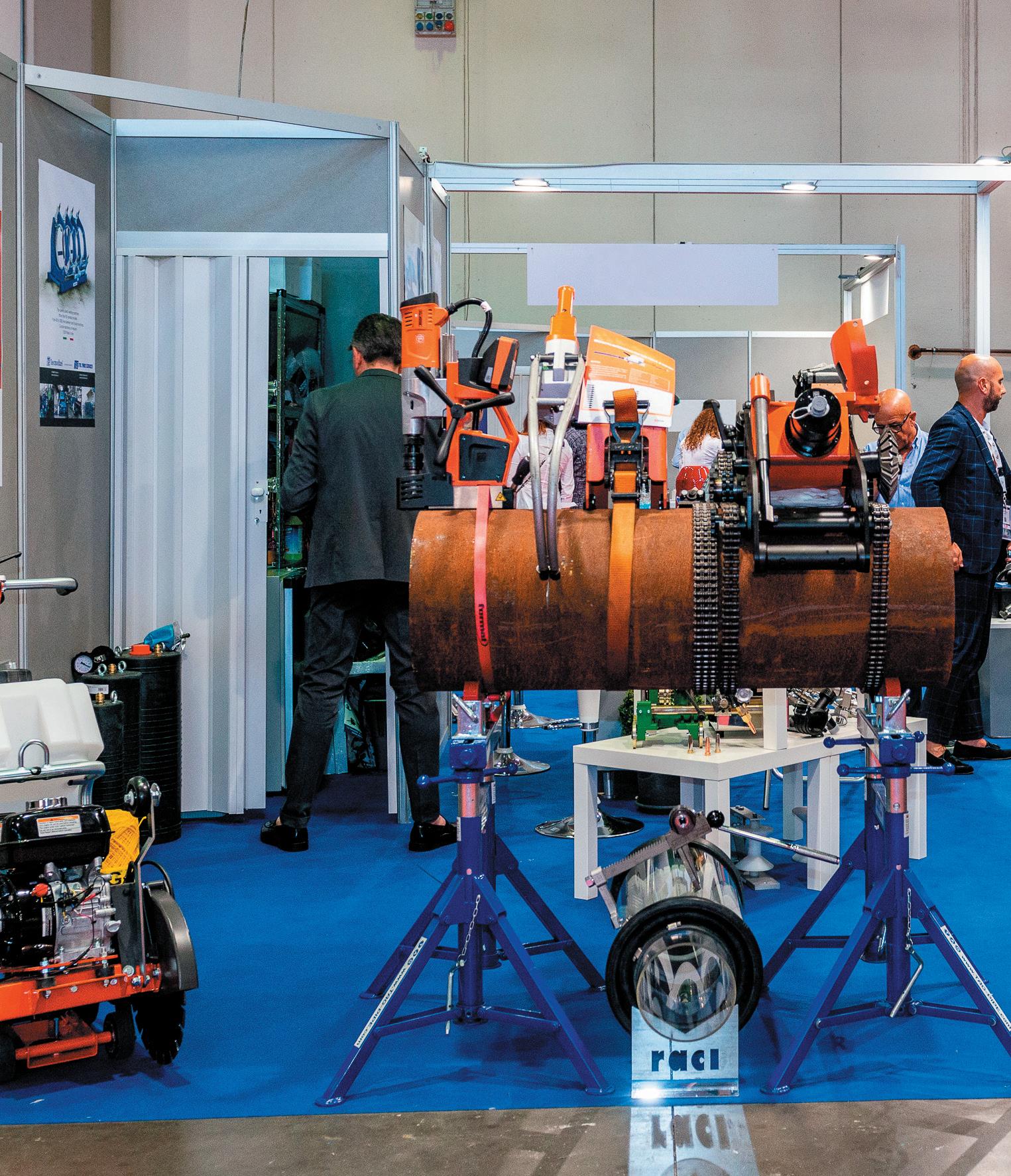
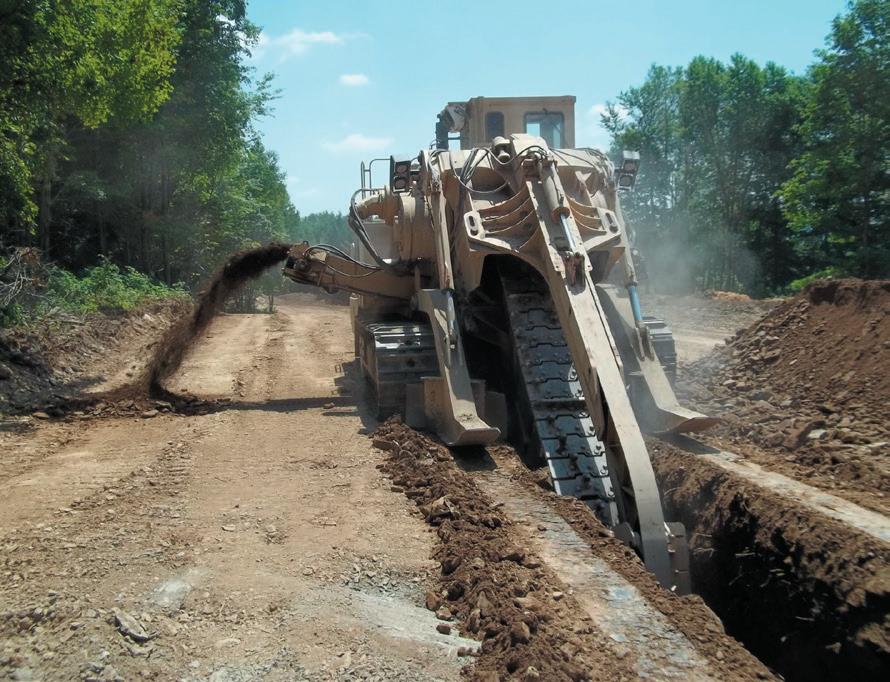
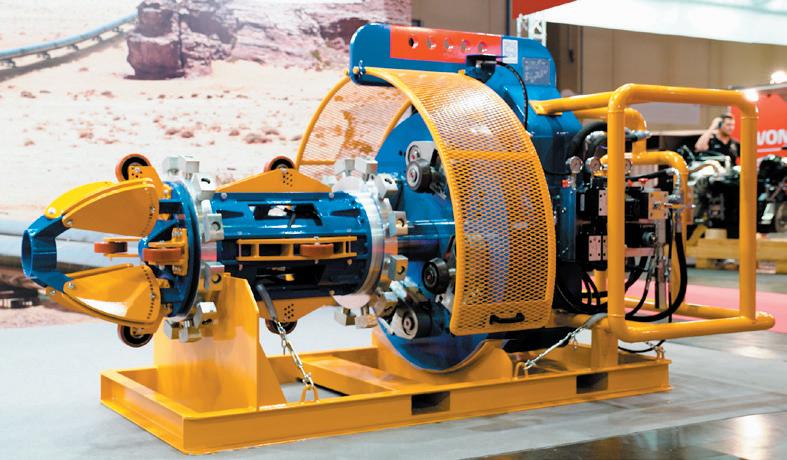
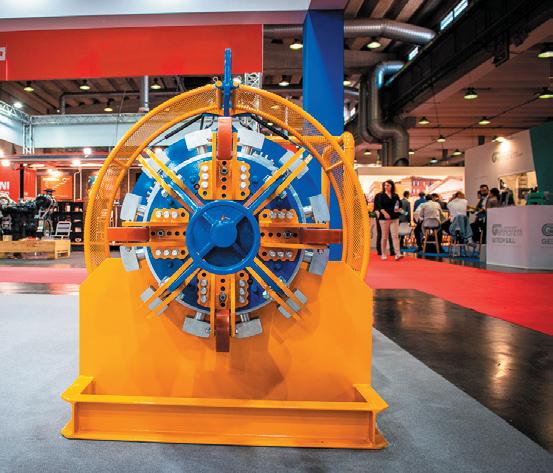
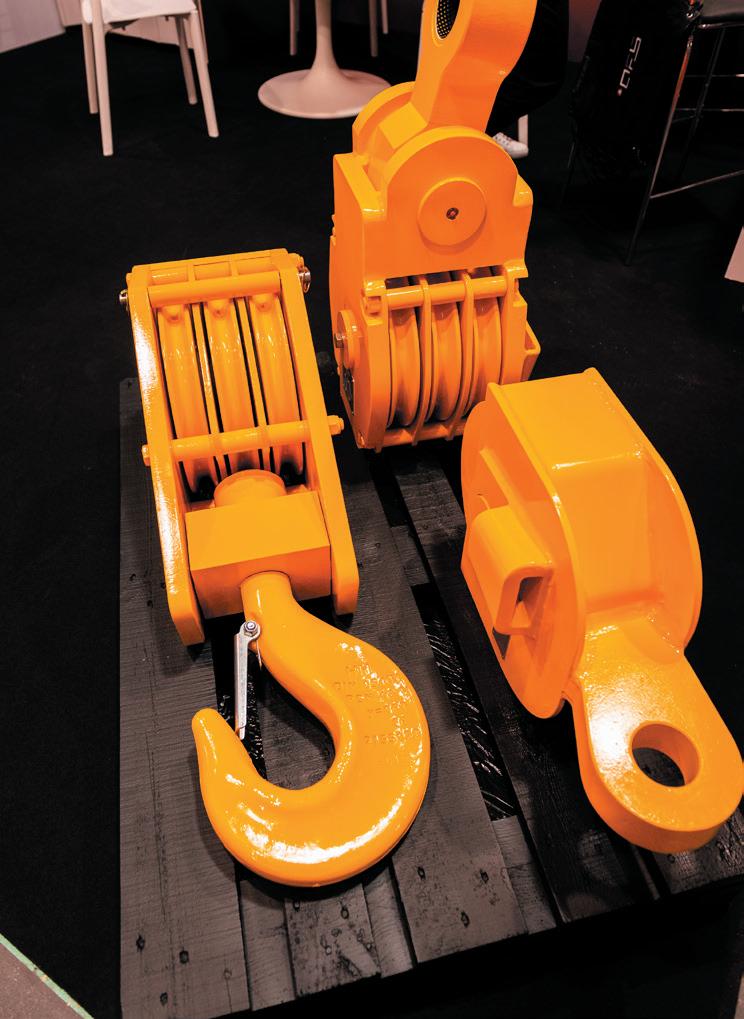
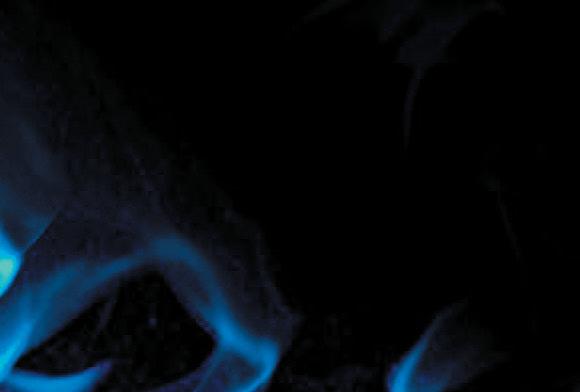
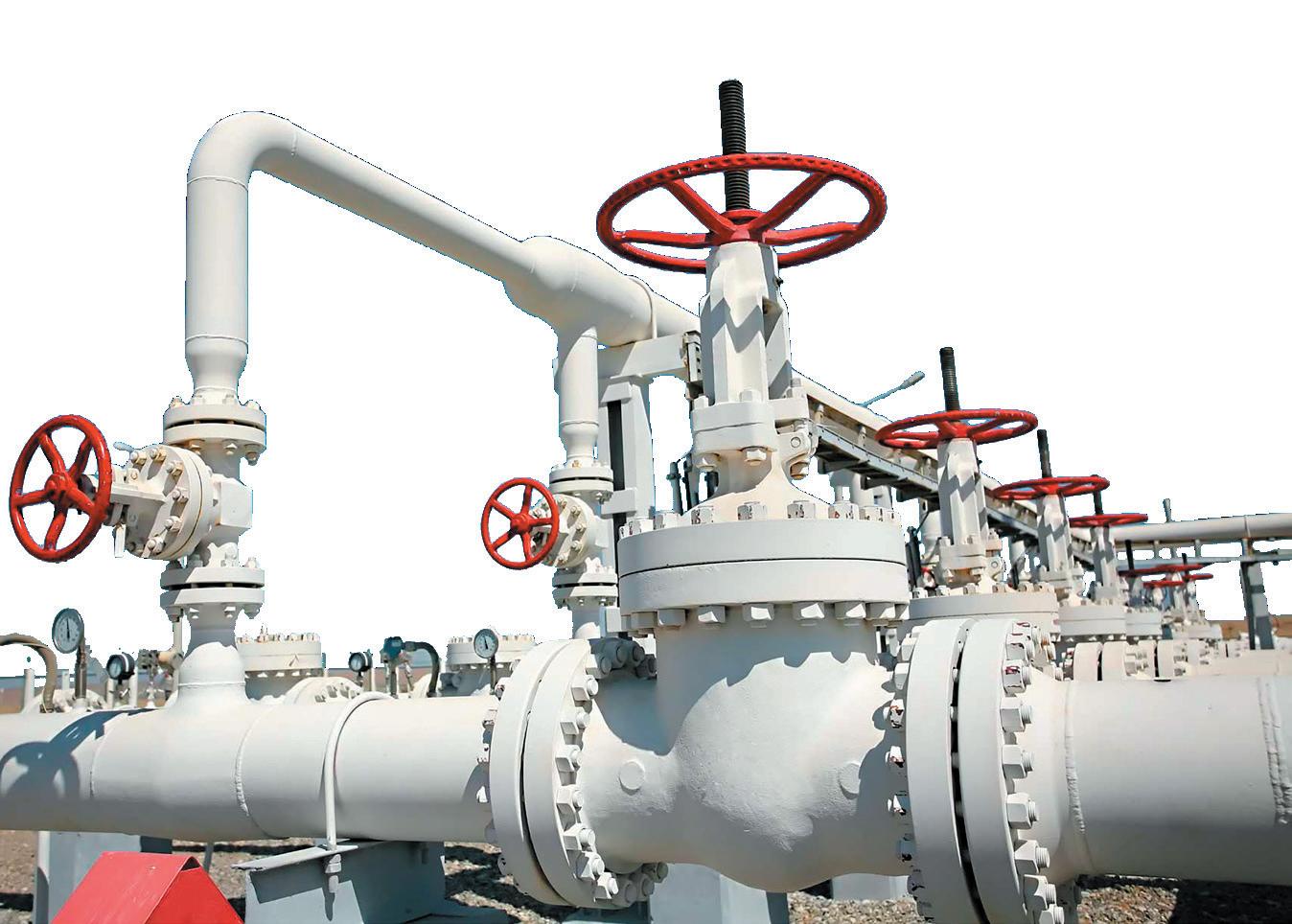
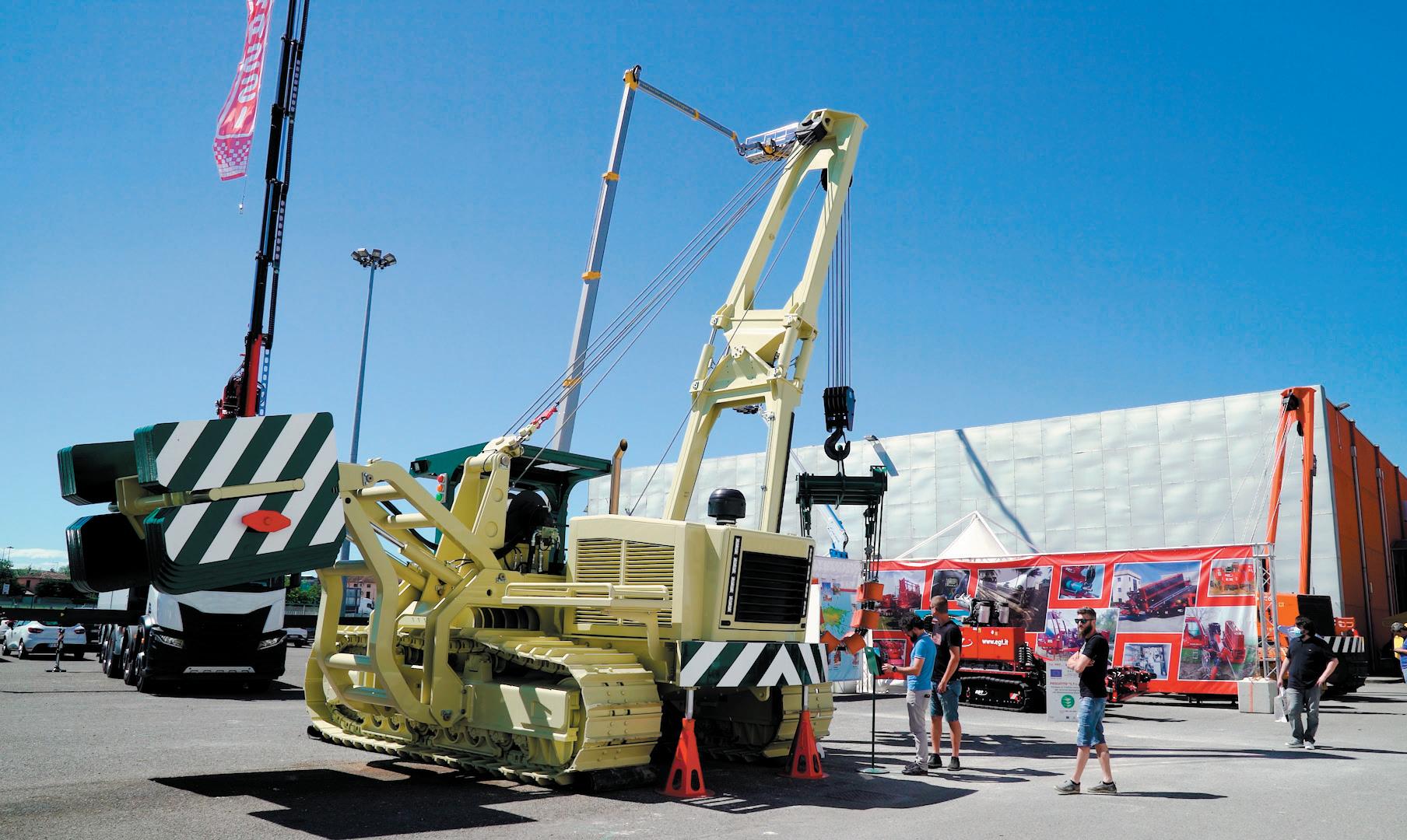
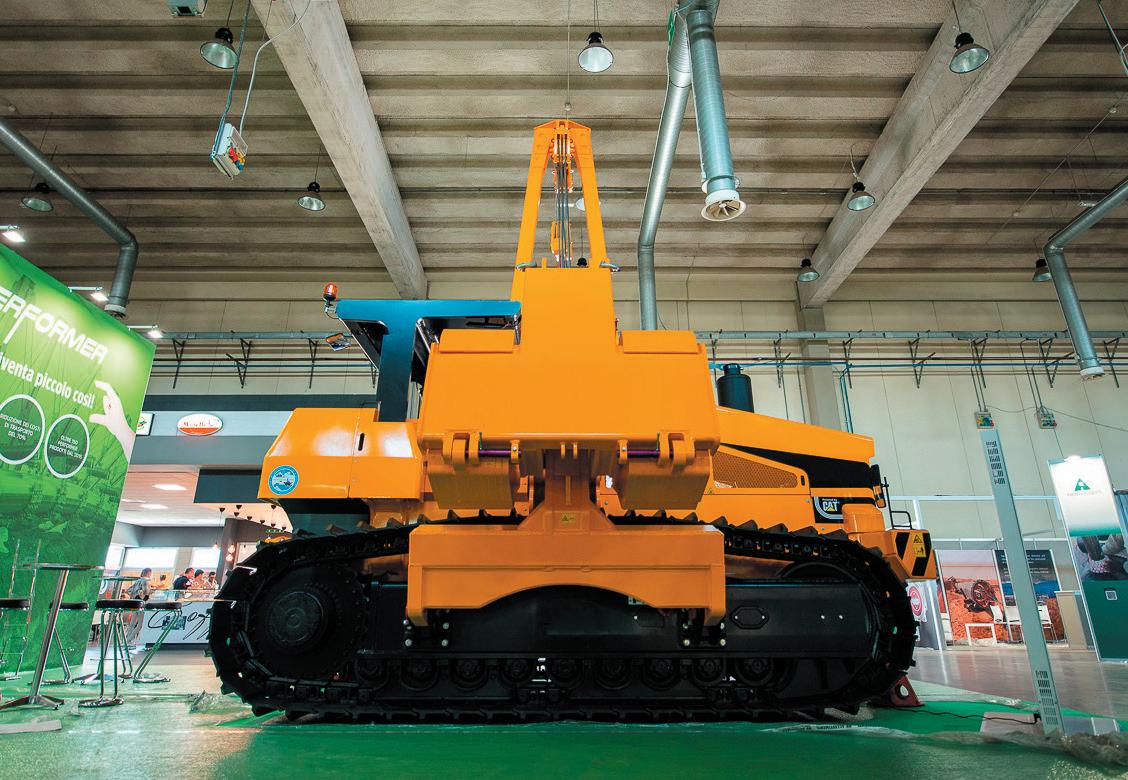



The Siemens Energy-serviced turbine is currently undertaking quite a journey: it was flown from Canada to Germany, and is now being sent from Germany by ferry and then delivered to the Russian Portovaya compressor station by land via Helsinki.
ave you ever had that feeling of unease as you leave the office for a long-awaited vacation, concerned that everything might not go smoothly in your absence? You’ve planned for this, you’ve handed over to the right people and you know you’ll pick things up on your return, but it’s hard to switch off and trust the process.
1. repairs/www.euractiv.com/section/energy/news/putin-warns-of-nord-stream-1-gas-capacity-cuts-over-turbine2. kommersant-2022-07-18/www.reuters.com/business/energy/canada-sent-repaired-turbine-nord-stream-germanySENIOR EDITOR Elizabeth Corner elizabeth.corner@palladianpublications.com MANAGING EDITOR James Little james.little@palladianpublications.com EDITORIAL ASSISTANT Sara Simper sara.simper@palladianpublications.com SALES DIRECTOR Rod Hardy rod.hardy@palladianpublications.com SALES MANAGER Chris Lethbridge chris.lethbridge@palladianpublications.com PRODUCTION MANAGER Calli Fabian calli.fabian@palladianpublications.com EVENTS MANAGER Louise Cameron louise.cameron@palladianpublications.com DIGITAL EVENTS COORDINATOR Stirling Viljoen stirling.viljoen@palladianpublications.com VIDEO CONTENT ASSISTANT Molly Bryant molly.bryant@palladianpublications.com DIGITAL ADMINISTRATOR Leah Jones leah.jones@palladianpublications.com ADMINISTRATION MANAGER Laura White laura.white@palladianpublications.com CONTACT INFORMATION Palladian Publications Ltd, 15 South Street, Farnham, Surrey, GU9 7QU, UK Tel: +44 (0) 1252 718 999 Website: www.worldpipelines.com Email: enquiries@worldpipelines.com Annual subscription £60 UK including postage/£75 overseas (postage airmail). Special two year discounted rate: £96 UK including postage/£120 overseas (postage airmail). Claims for non receipt of issues must be made within three months of publication of the issue or they will not be honoured without charge. Applicable only to USA & Canada: World Pipelines (ISSN No: 1472-7390, USPS No: 020-988) is published monthly by Palladian Publications Ltd, GBR and distributed in the USA by Asendia USA, 17B S Middlesex Ave, Monroe NJ 08831. Periodicals postage paid New Brunswick, NJ and additional mailing offices. POSTMASTER: send address changes to World Pipelines, 701C Ashland Ave, Folcroft PA 19032
H
Germany, the end point of the Nord Stream 1 pipelines, braced itself for the possibility that the halt of gas flow could become permanent. Ahead of the shutdown, Robert Habeck, Germany’s Economy Minister, said: “Everything is possible, everything can happen … It could be that the gas flows again, maybe more than before. It can also be the case that nothing comes. We need to honestly prepare for the worst-case scenario and do our best to try to deal with the situation.”
In early July, Canada declared (after consultation with Germany and the International Energy Agency) that it would issue a temporary exemption to sanctions against Russia in order to allow the return from Montreal of a repaired Russian turbine that is required for the maintenance work to be carried out. In response, the Kremlin said it would increase gas supplies to Europe once the turbine was returned to Russia. Ukraine has objected to this, arguing it helps continue the continent’s dependency on Russian gas.
EDITOR’S COMMENT
Ukraine’s President, Volodymyr Zelenskiy, has told Canada’s Prime Minister, Justin Trudeau, that Ukrainians would “never accept” Canada’s decision to return the turbine, saying the move violated sanctions.2
At the time of going to press, gas had just started flowing again through the 1224 km line and is expected to return to about 40% capacity, similar to levels seen before the shutdown began on 11 July.
The planned shutdown is certainly an opportunity for Moscow to wield its power in the midst of international outrage about its aggressions in Ukraine. Nord Stream 1 gas flows were already running at a reduced rate of 40% before the shutdown, with Russia blaming sanctions (lack of access to spare parts) for this drop. Russian President, Vladimir Putin, had been vocal about potential further reductions in flow, due to the roadblocks in equipment maintenance. Speaking to reporters after a visit to Tehran in July, Putin said there were five gas pumping units operated by Siemens Energy at Nord Stream 1, while one more unit was out of order due to “crumbling of inside lining.” Putin said: “There are two functioning machines there, they pump 60 million cubic metres per day … If one is not returned, there will be one, which is 30 million cubic metres. Has Gazprom something to do with that?”1
It’s a similar situation for the Nord Stream 1 gas pipelines, which were subject to a 10 day shutdown and maintenance period in mid-July. Gas supplies dropped to zero as the twin pipelines underwent what is normally routine, annually-scheduled maintenance. This year is different, though, amid concerns that the pipelines wouldn’t be turned back on.
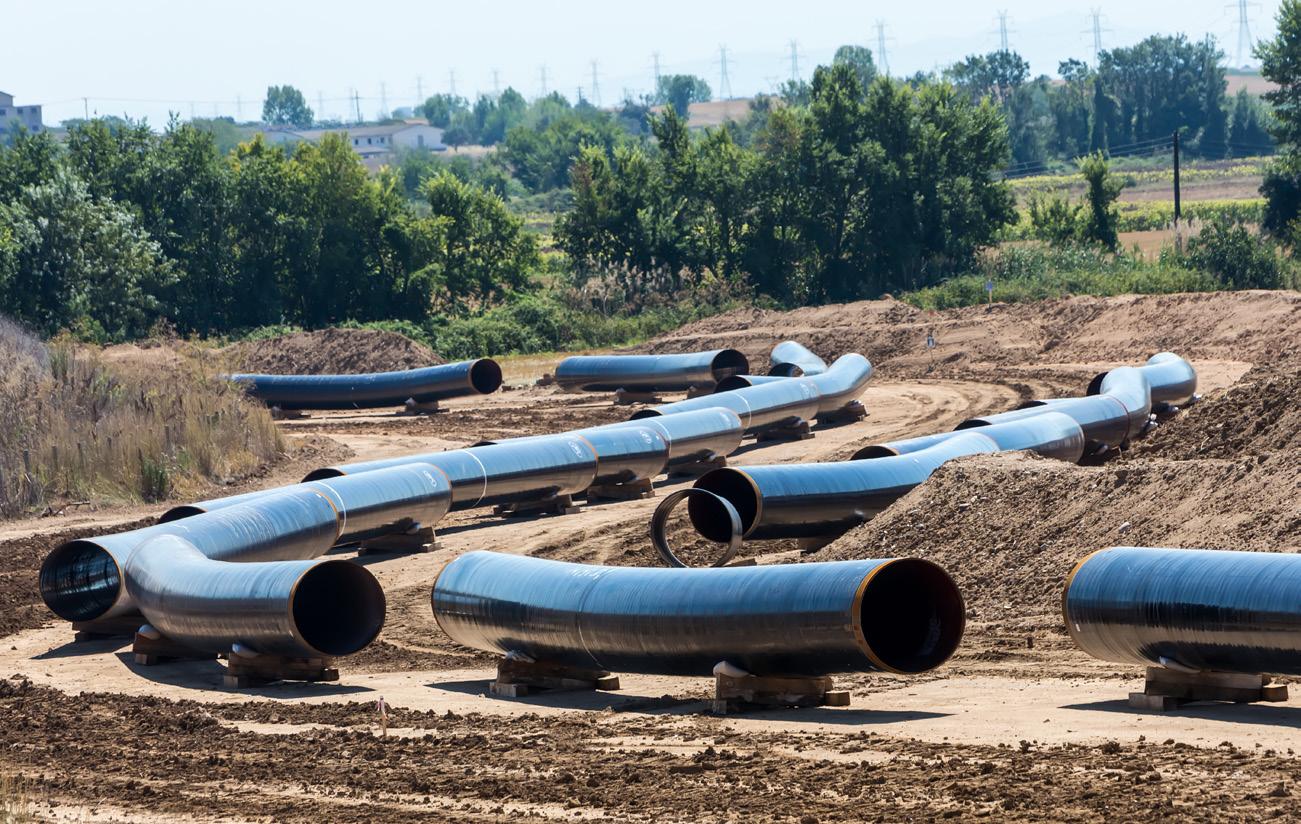
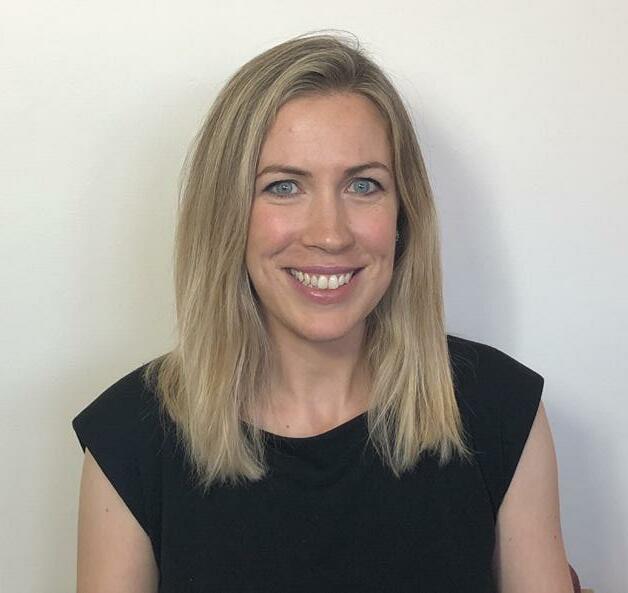
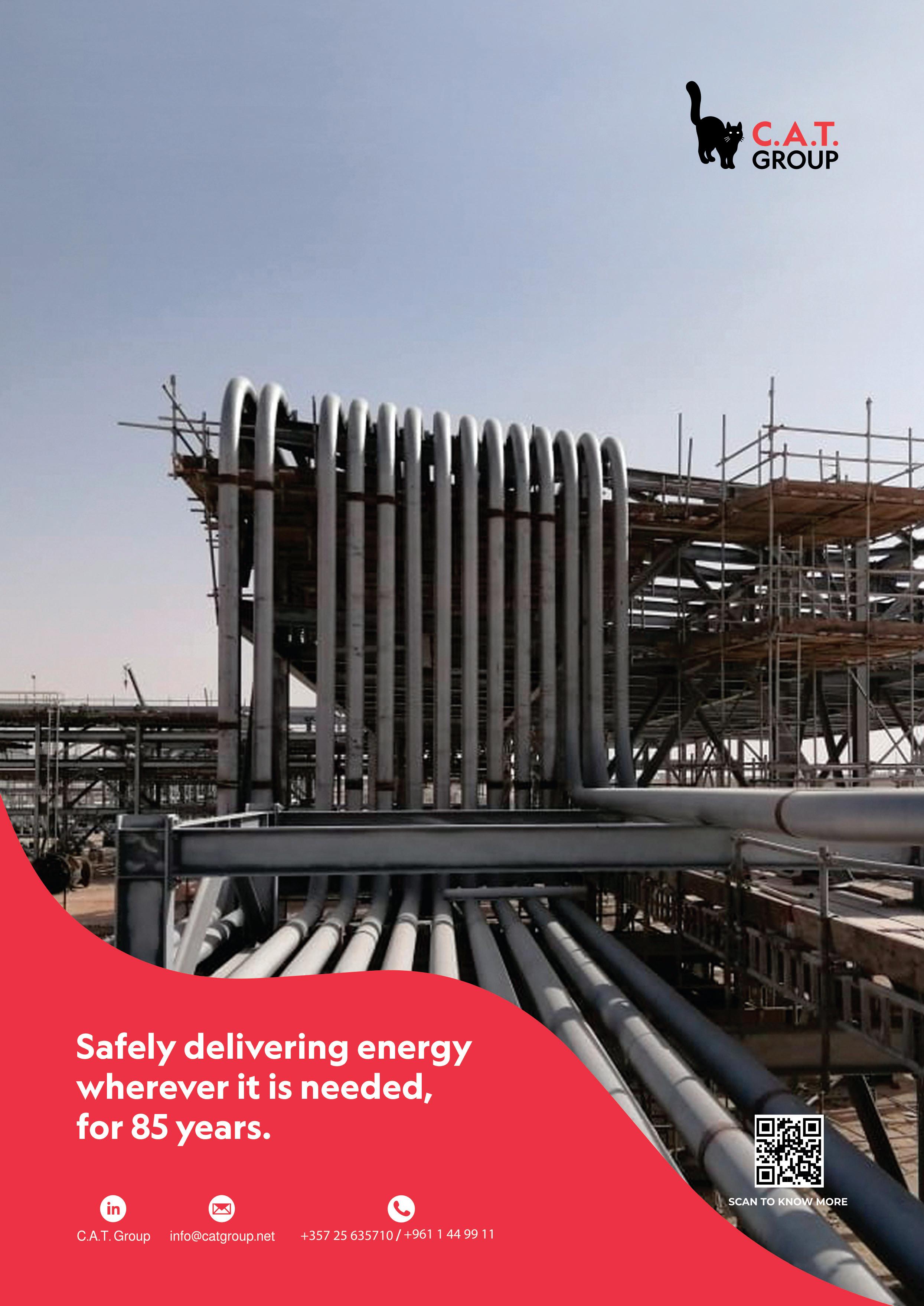
GUEST COMMENT
he Bolivian natural gas reserves (28.6 trillon ft3 2002/10.7 trillon ft3 2017) have always attracted the presence of major industry players. Its strategic location, in the centre of Latin America, and its proximity to the biggest markets in the region (Brazil and Argentina) have enabled the development and construction of large pipeline systems that currently interconnect these three countries.Boththe Brazilian and Argentinian markets have been supplied with important volumes of Bolivian gas in recent decades (between January and October 2021, Bolivia exported 33.63 million m3/d to both markets), despite a decrease in production and exploration projects that put a strain on the capability to meet export contracts.
T
In order to better serve the incremental Argentinian market demand, new natural gas reserves were injected into the system by rapidly developing a connection of wells and enhancing the central processing capabilities of the Incahuasi and MargaritaThe contribution from the private sector was key in this regard. In 2018, Total Energies as the operator worked with SEPCON as the contractor in the Incahuasi conventional gas field. The successful implementation of the pipeline interconnection of the Incahuasi 3 and 5 wells, and the enhancement of the Incahuasi Plant, increased capacity from 7.2 to 11 million m3/d.
In recent months, Repsol’s exploration and drilling activities, as the operator of the Margarita-Huacaya gasfield, and SEPCON as the construction company, have successfully achieved a rapid integration and interconnection of the Margarita 10 well and the Boicobo X1 well to the Margarita Gas Plant. This incorporates an additional volume of 3 million m3/d of natural gas to meet the export CEO of SEPCON, Bolivia, Peru & IPLOCA President 2021 - 2022 Register for free at: www.worldpipelines.com
In the last few months, a strategy to focus on the improvement of exportation and the production of gas was undertaken by the Bolivian government by its Oil and Gas Corporation (YPFB), which has enabled the development of key infrastructure to boost production and supply.
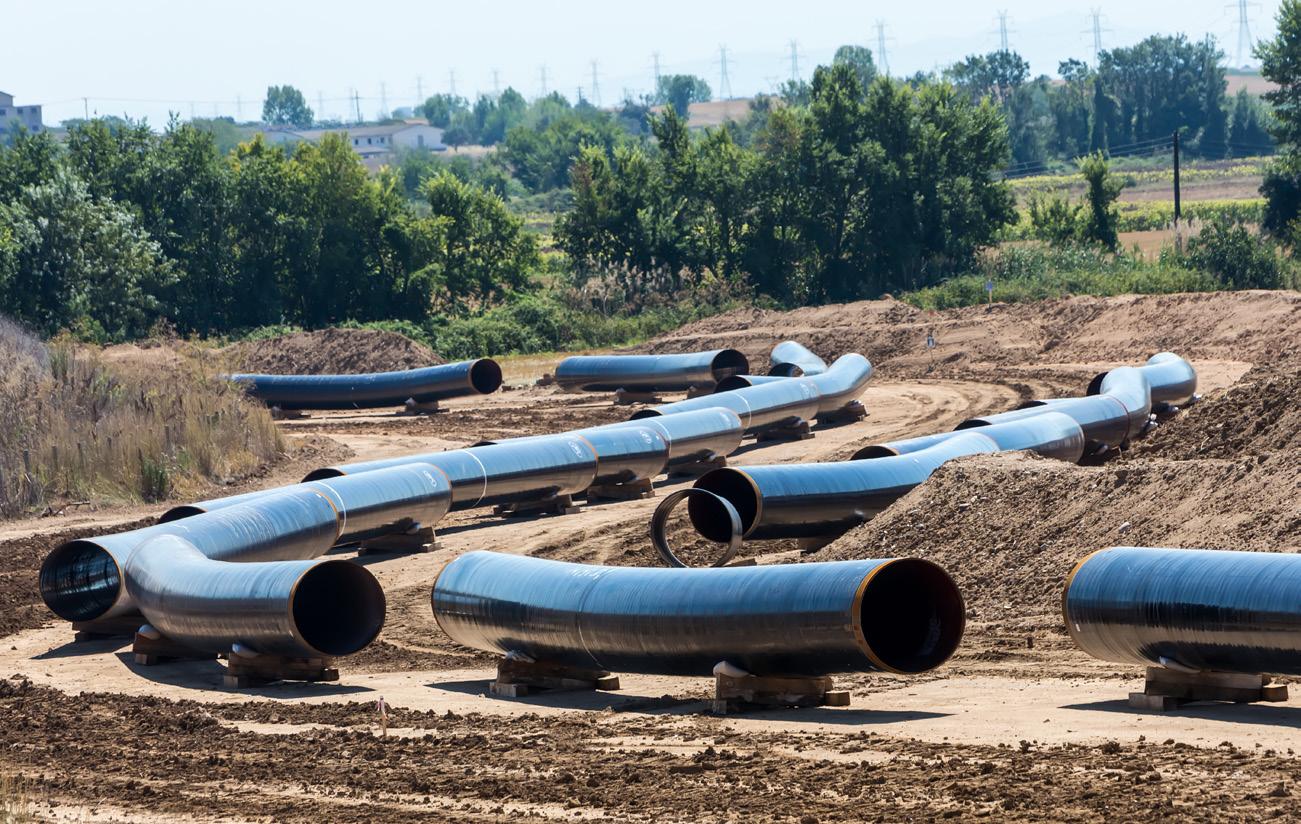
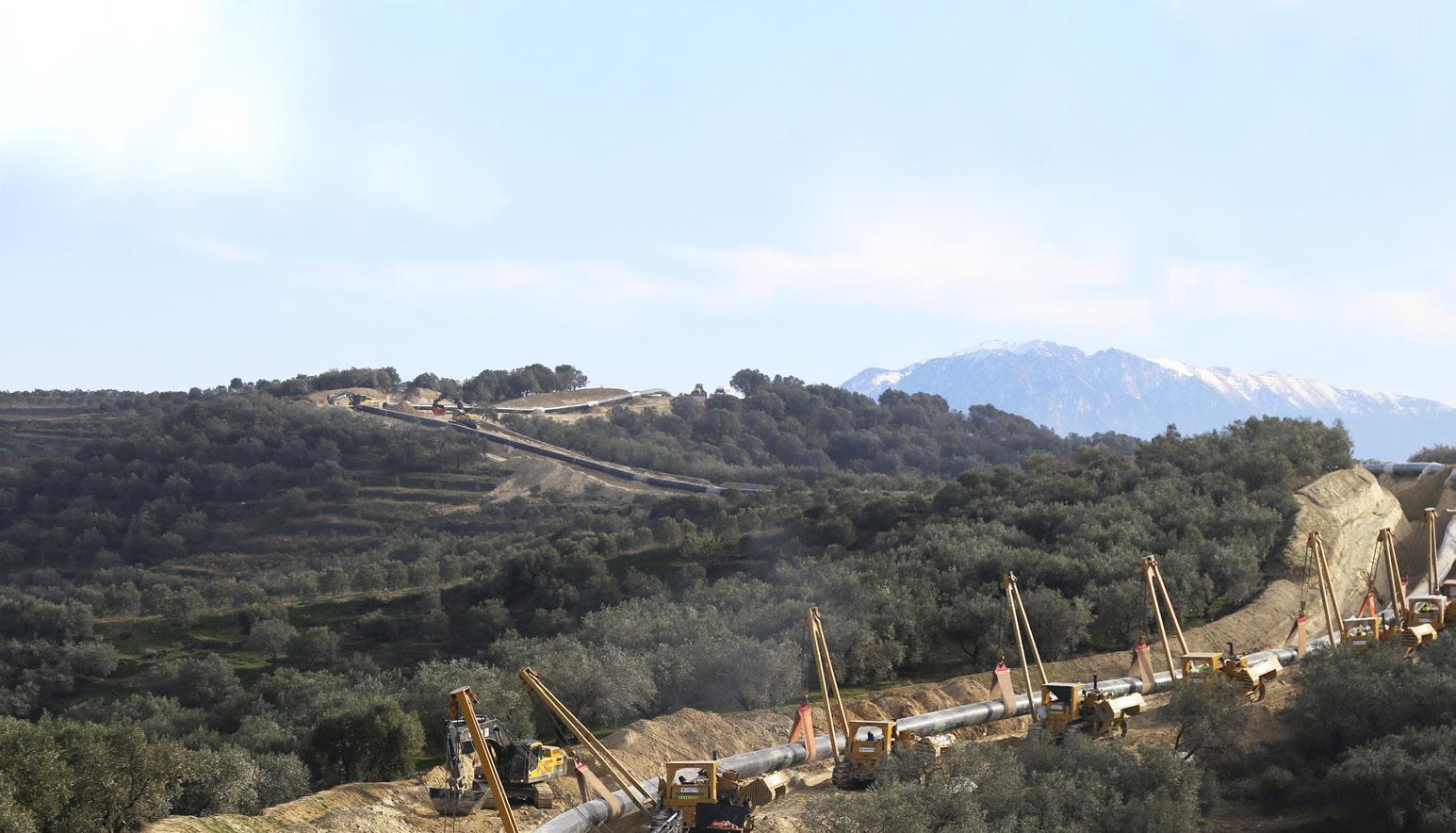
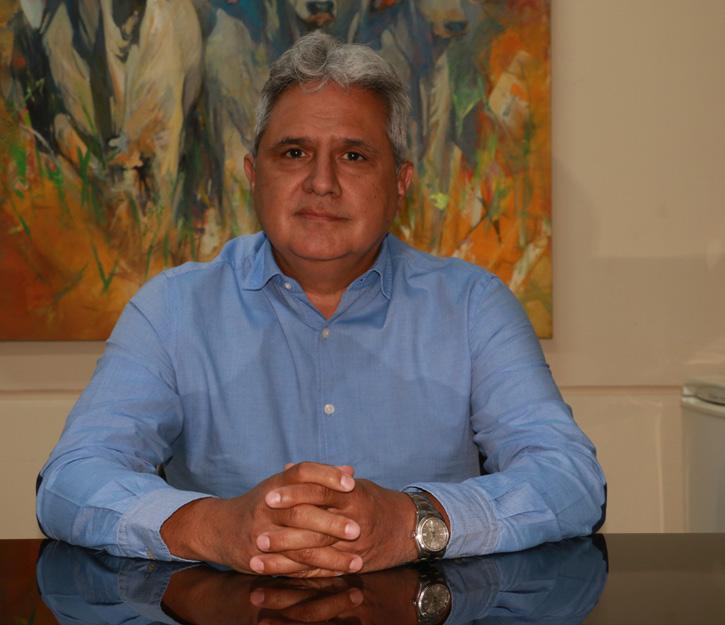
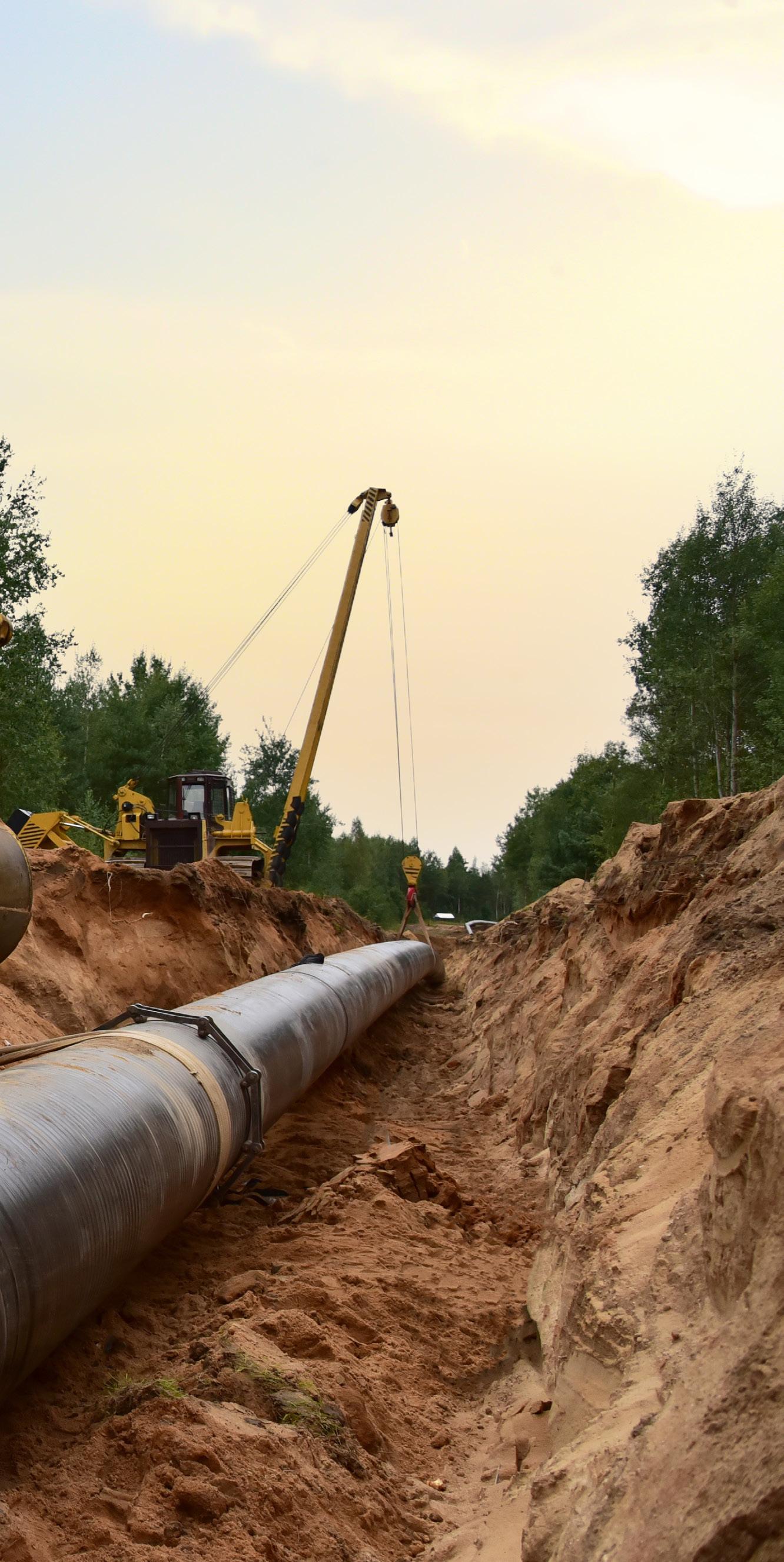
Field CustomCoatingJointandCoatingServices Pipeline Induction Heat (PIH) provide specialist field joint coating services at spool base locations, offshore pipe lay barges and onshore pipeline construction projects around the world, involving the use of stateof-the-art equipment and processes for the application of a wide range of field joint coating materials. PIH also provide Custom Coating services for the application of the latest Thermal Insulation solutions (IMPP and IMPU) to bends and spools. IntegrityInnovationDedicationOffshore Onshore Spoolbase Custom Coating Pipeline Induction Heat Ltd, Burnley, UK Tel: +44 (0) 1282 415 323 Fax: +44 (0) 1282 415 326 E-mail: sales@pih.co.uk Web: www.pipelineinductionheat.com
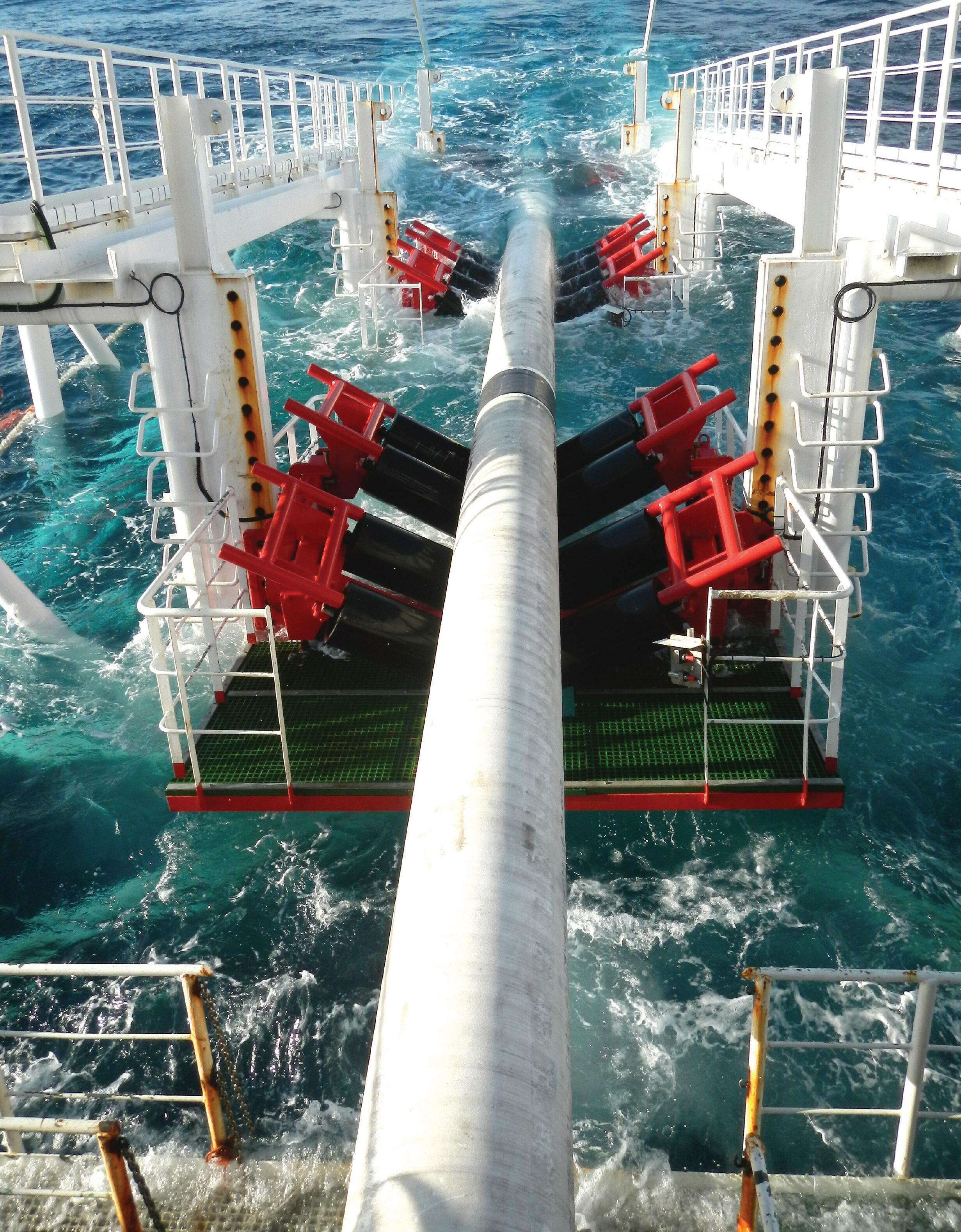
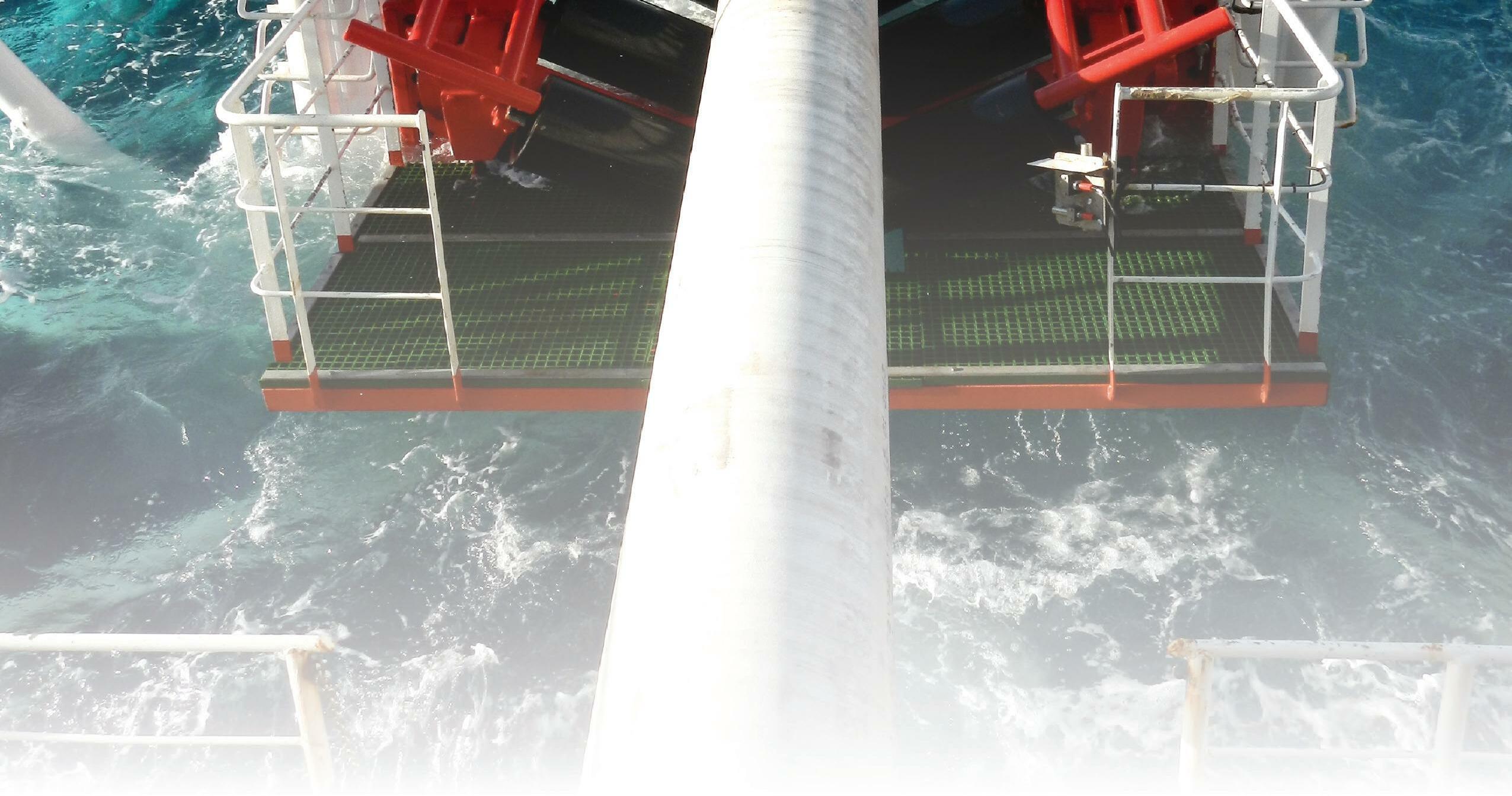
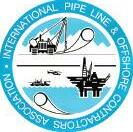
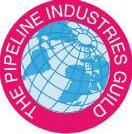
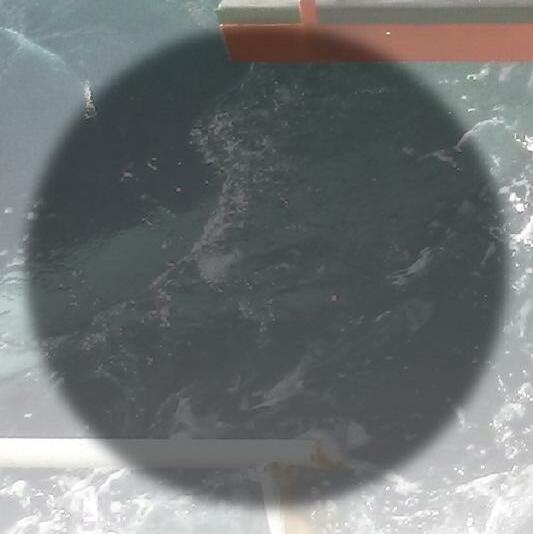
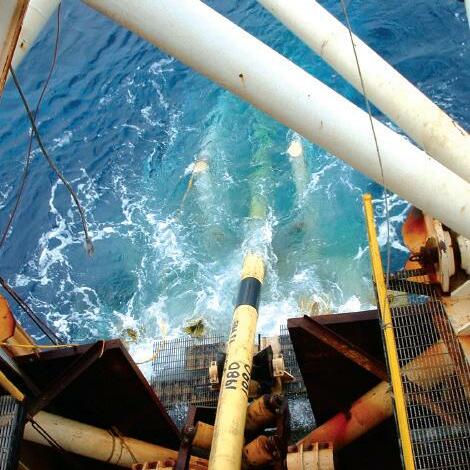
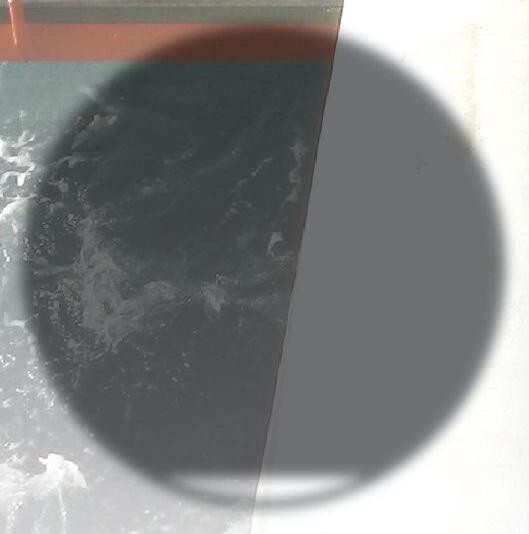
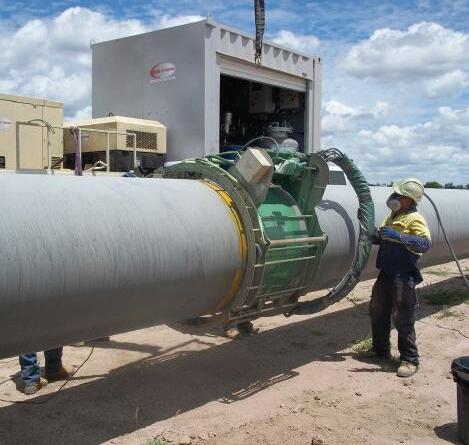
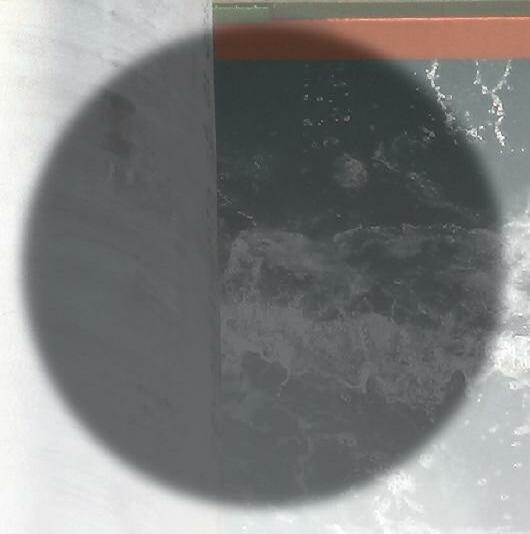
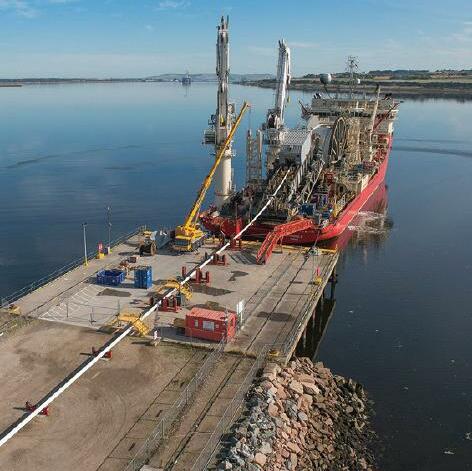
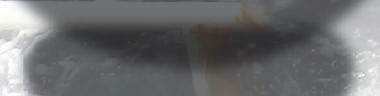


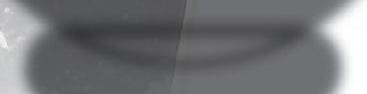

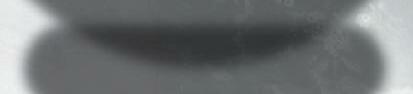


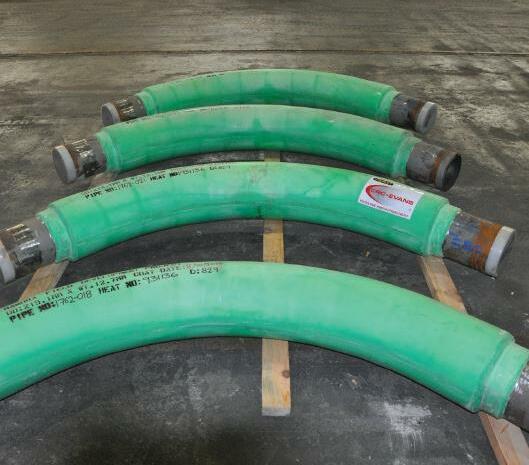
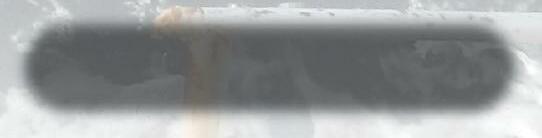



Permian Highway Pipeline, LLC (PHP) has announced a final investment decision (FID) to proceed with its expansion project after securing binding firm transportation agreements for all available capacity. The project will increase PHP’s capacity by approximately 550 million ft3/d. The project will involve primarily additional compression on PHP to increase natural gas deliveries from the Waha area to multiple mainline connections, Katy, Texas, and various US Gulf Coast markets. Pending the timely receipt of required approvals, the target in-service date for the project is anticipated to be 1 November 2023.
Joey Mahmoud, President of Tellurian Pipelines, added, “We anticipate the project will supply upwards of five and one-half billion ft3/d of natural gas, with virtually no emissions. Tellurian is doing its part by making this initial US$240 million pipeline investment as part of the broader Driftwood Pipeline system which will provide enhanced supply reliability to meet the area’s projected industrial growth in a cleaner, more sustainable manner.”
“This expansion couldn’t come at a more critical time, as it will foster future natural gas production growth in West Texas and provide several liquefaction facilities along the Texas Gulf Coast with more affordable, reliable supply,” said Jamie Welch, President and CEO of Kinetik. “In addition, approximately 30 of Kinetik’s customers will gain access to premium priced markets and transportation flow assurance, which is critical to minimising flared volumes.”
ILF and DORIS support strategic gas pipeline from Nigeria to Morocco
The PMC services provided by ILF and DORIS cover the Onshore and Offshore Pipeline and Compressor Station Engineering, the Engineering Surveys, the Environmental and Social Impact Assessment (ESIA) and Land Acquisition (LAS) Studies and the Project Implementation Framework. The project explores the potential to use renewable energy resources to power the pipeline and reduce the project’s carbon footprint.
“With ILF having already been part of the Feasibility Phase and FEED Phase I of this world-scale project, the award of Phase II to us is an evidence of trust by our long term Clients ONHYM and NNPC in our Project Management Excellence and Reliability in delivering world class projects.” said Carles Giro, Area Manager Industrial Plants of ILF.
“DORIS has always demonstrated a great value in complex projects both in terms of safety and cost optimisation. While ONHYM and NNPC are moving one step further in their ambition of bringing alive this mega project, DORIS is delighted to leverage its decades of expertise in offshore developments to support the project in achieving its main objectives: responding to the highest environmental and safety requirements while ensuring the best technico-economic solutions are selected” said Francis Carmigniani, DORIS Engineering Managing Director.
Permian Highway Pipeline announces final investment decision
PHP is jointly owned by subsidiaries of Kinder Morgan, Inc., Kinetik Holdings Inc. and ExxonMobil, with an ownership interest of 26.7%, 53.3% and 20%, respectively.
ILF Consulting Engineers (ILF) with its office in Munich, Germany, together with its Joint Venture Partner DORIS Engineering (DORIS) located in Paris, France, is delighted to have been commissioned to carry out the Project Management Consultancy (PMC) services for the FEED Phase II of this project.
Nigeria, an OPEC member, has the largest gas reserves in Africa and the seventh-largest in the world. The project falls in line with the ‘Decade of Gas Master Plan’ that Nigeria’s President Muhammadu Buhari launched in 2020. On the Moroccan side, this landmark project is part of the South-South cooperation upheld by King Mohammed VI.
When completed, the over 6000 km long gas pipeline will be the longest offshore pipeline in the world and the second longest pipeline at all. It has a planned diameter of 48 in. offshore and 56 in. onshore, with a planned throughput of 30 billion m3/yr. With involving sixteen countries, the pipeline will not only supply the local markets with a sustainable and reliable energy source, it shall also support industrial and economical development, create a competitive regional power market and benefit all West African people, countries, and their economies.
The consortium consisting of NNPC (Nigerian National Petroleum Corporation), Nigeria and ONHYM (Office National Des Hydrocarbures et Des Mines), Morocco, is progressing with the plans for its mega-project Nigeria-Morocco Gas Pipeline (NMGP).TheNMGP, an onshore and offshore gas pipeline crossing the land and/or waters of 16 countries along the Atlantic coast, shall bring Nigerian gas to North Africa and extend to Spain for the European market. The pipeline will also provide a new avenue for the countries along the route to export/import gas to/from their neighbouring countries and Europe.
ILF and DORIS can make use of their combined expertise in the respective fields of competence and provide a fundamental support to ONHYM and NNPC in the delivery of this strategically important project.
WORLD NEWS AUGUST 2022 / World Pipelines 7
“We are excited to have achieved FID on this very important expansion,” said Kinder Morgan Natural Gas Midstream President, Sital Mody. “The project will alleviate transportation constraints out of the Permian Basin so as to further support meeting our domestic and global energy needs.”
Tellurian awards Baker Hughes contract for electric-powered compressor technology Tellurian Inc. and Baker Hughes have announced that Baker Hughes has been awarded a contract by Driftwood Pipeline LLC, a subsidiary of Tellurian Inc., to provide electric-powered Integrated Compressor Line (ICL) technology and turbomachinery equipment for Lines 200 and 300, a natural gas transmission project, proposed to be located in Beauregard and Calcasieu Parishes, in southwest Louisiana.
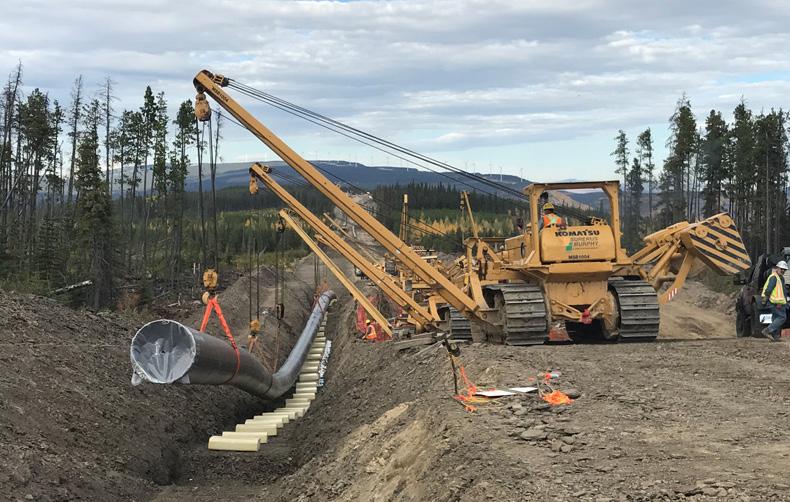
According to DNV’s Energy Transition Outlook 2021, demand for hydrogen in the Indian subcontinent will reach nearly 25 million tpy by 2050, primarily for ammonia production, transportation, and refining.
DNV collaborates on hydrogen with Pipeline Infrastructure Ltd DNV is providing technical advice and support to Pipeline Infrastructure Limited (PIL) on the integration of blended hydrogen into its gas trunkline assets in India – including transmission pipelines, interconnects and spur lines, compressor, valve, and metering stations and equipment.PIL’sinitiative is one of the first hydrogen blended related projects in the transmission space in India, aligned with the government’s launch of India’s National Hydrogen Mission in August 2021, targeting 5 million tpy of hydrogen production by 2030. In conjunction with fiscal support and other incentives, the Mission aims to leverage the nation’s significant renewable energy potential to transform India into a green hydrogen hub, help meet national climate goals and enable India to become a major producer and exporter of hydrogen to Japan, South Korea, and Europe.
Milestones reached for Trans-Saharan gas pipeline project
The Ministry of Petroleum of the Republic of Niger has announced that the country has reached a new milestone in further opening the domestic and regional gas market through a development in the construction of the multi-billion Trans-Saharan gas pipeline (TSGP) alongside Algeria and Nigeria.
WORLD NEWS IN BRIEF 8 World Pipelines / AUGUST 2022
As of 3 June 2022, pipeline companies completed two crude oil pipeline projects in the US, according to the EIA’s recently updated Liquids Pipeline Projects Database. No new hydrocarbon gas liquids or petroleum product pipeline projects were completed in the first five months of 2022. UK TÜV SÜD National Engineering Laboratory is calling upon businesses within the oil and gas industry to take advantage of funding offered by Innovate UK as part of its Analysis for Innovators (A4I) programme. The next competition for grant funding opens in August 2022, with a second opportunity expected in November. USA Accenture is using a proprietary database powered by artificial intelligence (AI) to help Colonial Pipeline, the largest refined products pipeline in the US, reduce regulated and deregulated electric utility rates for its interstate pipeline system.
USA
A Steering Committee will be responsible for updating the feasibility study for TSGP, and will meet at the end of July 2022 in Algiers to discuss how to progress with the TSGP project. With energy poverty increasing across the African continent due to limited investments in energy projects, delays in exploration, production and infrastructure rollout, the COVID-19 pandemic and global energy transition-related policies, the TSGP project will bring in a new era of energy reliability for Africa. With the 4128 km pipeline running from Warri in Nigeria to Hassi R’Mel in Algeria via Niger, the pipeline will not only create a direct connection between Nigeria and Algeria’s gas fields to European markets, but will bring significant benefits for Niger. With over 34 billion m3 of gas, Niger, in its own right, has the potential to become a gas exporter, and with Europe expanding energy ties with Africa, the TSGP project will mark a new era of improved regional cooperation in Africa, enhancing gas monetisation and exports while scaling up Niger-exports to Europe via Algeria.
H.E. Mahamane Sani Mahamadou, Minister of Petroleum for the Republic of Niger, met with H.E. Mohamed Arkab, Minister of Energy and Mines, Algeria, and H.E. Chief Timipre Sylva, Minister of State for Petroleum Resources of Nigeria as well as the Director Generals of NOCs of the three African countries met to discuss the implementation of the TSGP on 20 June 2022, in Abuja. During the meeting – which follows the signing of the ‘Niamey Declaration’ during the 3rd Forum of the Economic Community of West African States in February 2022 – parties established a taskforce and roadmap for the development of the TSGP.
Meanwhile, with the pipeline making headway, opportunities for the country to increase domestic gas utilisation on the back of new reserves from Niger and Nigeria have arisen. With Niger seeking to improve electricity access and ensure energy affordability through increased exploitation of gas, the TSGP initiative will be a game changer. The pipeline will enable up to 30 billion m3 of natural gas to be traded yearly, enhancing regional and international energy trade, enabling Niger to expand the role of natural gas in its energy mix, and address energy poverty.
Sebastian Wagner, Executive Chair of the Germany Africa Business Forum, said, “What we want to see is African financiers rallying towards supporting the rollout of TSGP. Increased oil and gas exploration, production and assets development is what will bring Africa out of energy poverty by 2030.”
FRANCE Schneider Electric has announced it has won the Energy & Sustainability 2022 Microsoft Partner of the Year Award. USA Emerson announced its sustainability strategy to achieve net-zero greenhouse gas Scope 1, Scope 2 and Scope 3 emissions by 2045. The company detailed its goal to reach net-zero and its environmental, social and governance progress in its 2021 ESG report. USA SCF Partners and T.D. Williamson, Inc. have announced an investment partnership.
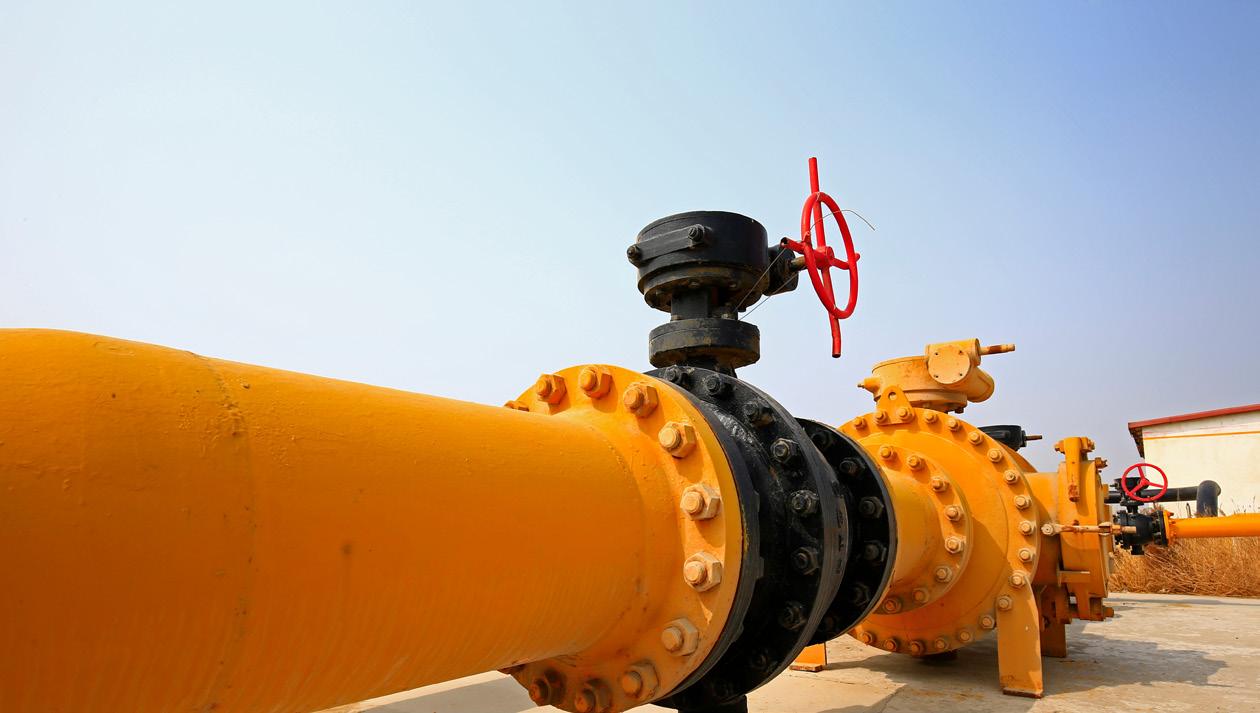
PROTECTIVE OUTERWRAPS SOIL-TO-AIR INTERFACE SYSTEMS BITUMEN & BUTYL TAPES PETROLATUM TAPE SYSTEMS PROTAL 7200™ APPLIEDSPRAY/ROLLER/BRUSHLIQUIDEPOXYCOATING VISCOTAQDENSO™ FOR CORROSION PREVENTION DENSO™ are leaders in corrosion prevention and sealing technology. With over 135 year’s service to industry, our mainline and field joint coating solutions offer reliable and cost effective protection for buried pipelines worldwide. United Kingdom, UAE & India USA & AustraliaCanada&New Zealand Republic of South Africa www.denso.co.zawww.densoaustralia.com.auwww.densona.comwww.denso.net A MEMBER OF WINN & COALES INTERNATIONAL A range of viscoelastic tapes used for corrosion prevention on pipelines, field joints, fittings & Thevalves.unique, self-healing technology of Viscotaq offers asset owners outstanding, long-term protection against corrosion. >>
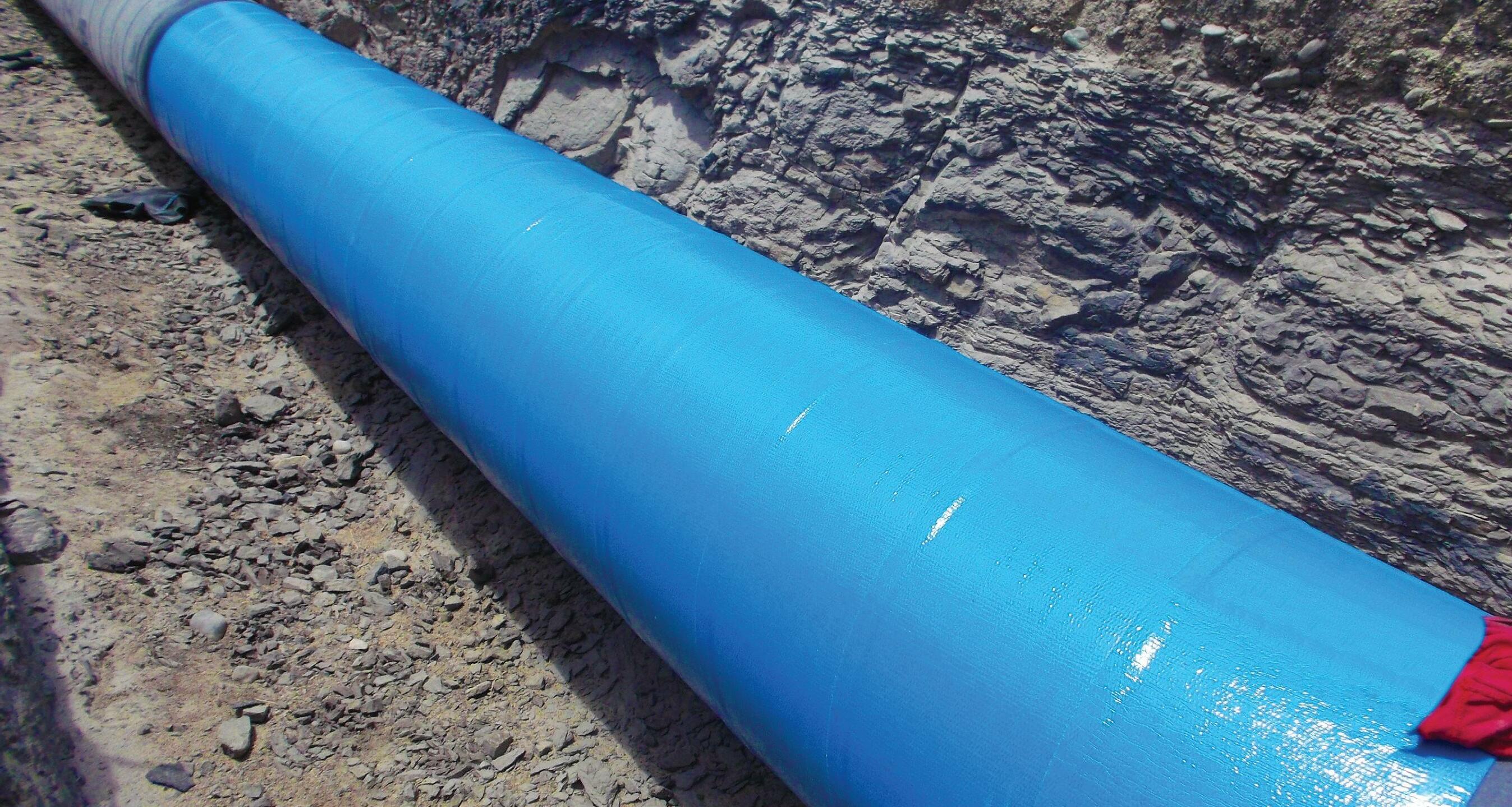
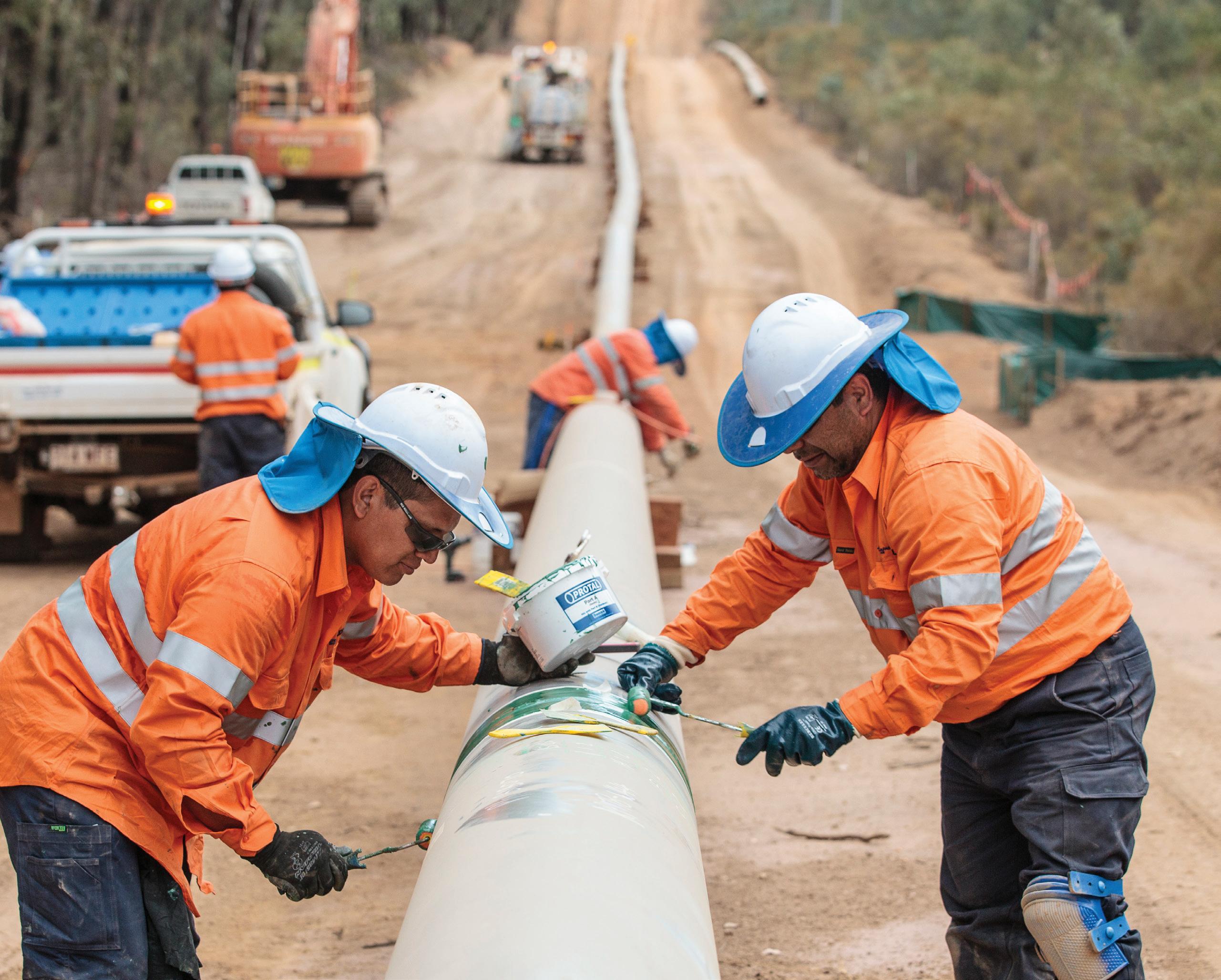
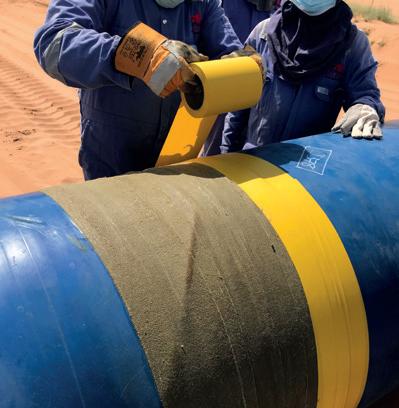
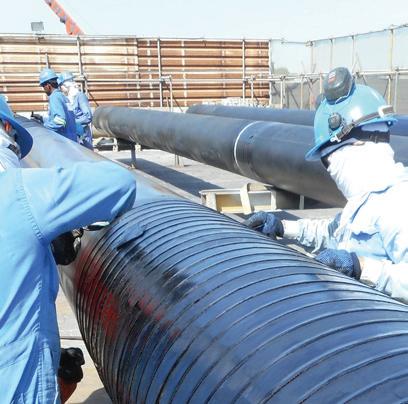
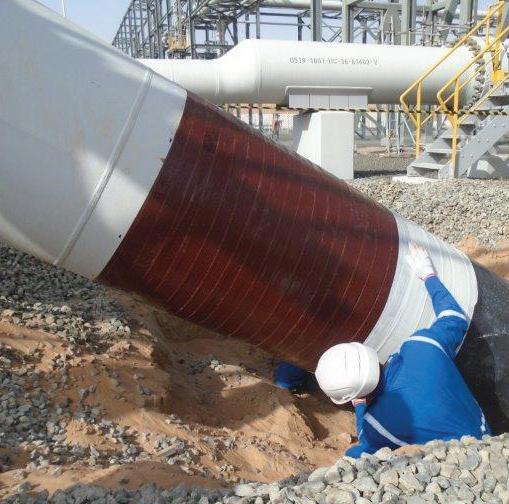
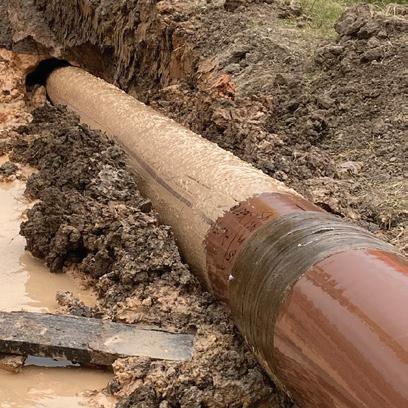
Steve Bray, Commercial Team Manager at CRP Subsea states: “This award continues to strengthen our collaboration with a market-leading installation contractor and build on our unrivalled track-record for both buoyancyEngineeringsolutions.”works are due to commence at CRP Subsea’s World Class buoyancy production facility in the North West of England later this year, with completion and deployment in mid-2023. Rotating Buoyancy Modules are used to mitigate buckling in seabed pipelines, they roll on the seabed reducing lateral friction and berm creation, allowing repeatable and predictable pipeline behaviour. Integral Buoyancy Modules clamp directly to subsea pipelines providing buoyancy at specific locations, they combine the functions of the traditional clamp and buoyancy elements into one unit, so there is no need for a separate internal clamp assembly.
CRP Subsea awarded major deepwater contract
NEWS
Dragos and Emerson announce partnership Dragos Inc., provider of cybersecurity for industrial controls systems (ICS)/operational technology (OT) environments, has announced the expansion of its global agreement with Emerson, one of the world’s largest manufacturers of industrial controls. With this agreement expansion, Emerson has validated the Dragos Platform within its DeltaVTM distributed control system (DCS) providing organisations with greatly enhanced ICS/OT cybersecurity. This extended agreement builds on the initial global agreement between Dragos and Emerson to protect industrial control systems and operational technologies for power producers and water utilities to now include organisations in dozens of industries including oil and gas, chemical, petrochemical, food and beverage, pharmaceutical, pulp and paper, metals and mining, and others.
EVENTS DIARY 10 World Pipelines / AUGUST 2022 Follow us on LinkedIn to read more about the articles linkedin.com/showcase/worldpipelines UPDATEMIDSTREAMTHE • Optimism in North American construction industry remains high • Strohm wins Pipeline Industries Guild award • 3t EnerMech to provide ECITB training in Angola and Guyana • KBRA releases research on Europe’s energy crisis • Vipo wins contract for Jansz-Io Compression project • Double contract wins for Decom Engineering 5 - 8 September 2022 Gastech Milan, Italy www.gastechevent.com 19 - 23 September 2022 IPLOCA 2022 annual convention Prague, Czech Republic convention/2022-conventionwww.iploca.com/events/annual22 - 23 September 2022 Subsea Pipeline Technology Congress (SPT 2022) London, UK sptcongress.com 27 - 29 September 2022 IPE 2022 Calgary, Canada internationalpipelineexposition.com 19 - 20 October 2022 Hydrogen Technology Expo Bremen, Germany www.hydrogen-worldexpo.com 24 - 30 October 2022 bauma Munich, Germany https://bauma.de/en 31 October - 3 November 2022 ADIPEC Abu Dhabi, UAE www.adipec.com 16 November 2022 Global Hydrogen Conference 2022 VIRTUAL www.globalhydrogenreview.com/ghc22
CRP Subsea has recently been awarded a major deepwater contract to provide two of its buoyancy solutions in the Gulf of Mexico. The company’s Rotating Buoyancy Modules will be used to mitigate flowline buckling, combined with innovative Integral Buoyancy Modules, helping to generate a system riser configuration.
CONTRACT
The Dragos OT Security Platform is focused on reducing cyber risk to industrial environments. It provides visibility into assets and vulnerabilities, detects cyber threats to industrial systems, and enables efficient response through forensic investigation and OT-specific playbooks.
In addition, Dragos is incorporating DeltaV DCS platform-specific capabilities into the Dragos platform, including protocol dissectors, asset characterisations, threat behaviour analytics, and investigation playbooks to expand Emerson’s cybersecurity assessment capabilities and enhance threat detection and response for process industries.
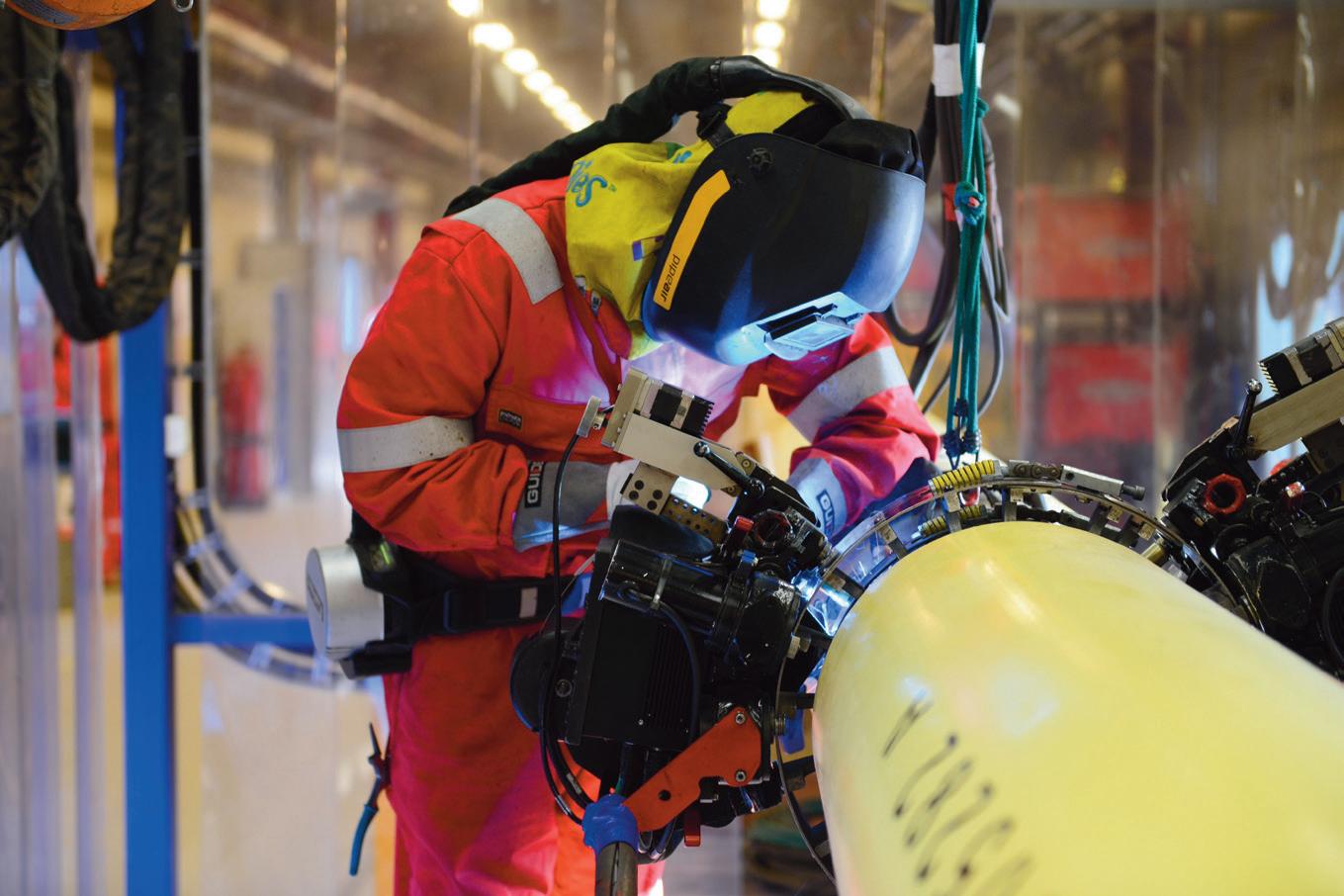
11
As the premier global standards setting organisation for the natural gas and oil industry,
Alexa Burr, Vice President of Segment Standards & Programs, American Petroleum Institute (API), USA, outlines how API standards and programmes foster safety and sustainability in pipeline operations.
T o fuel the world’s growing demand for natural gas and oil, pipelines must function safely and sustainably while maintaining operational integrity. Those principles are behind the American Petroleum Institute’s (API’s) latest pipeline-related standards and established programmes, tailored to the needs of the natural gas, oil, and petrochemical industries worldwide.
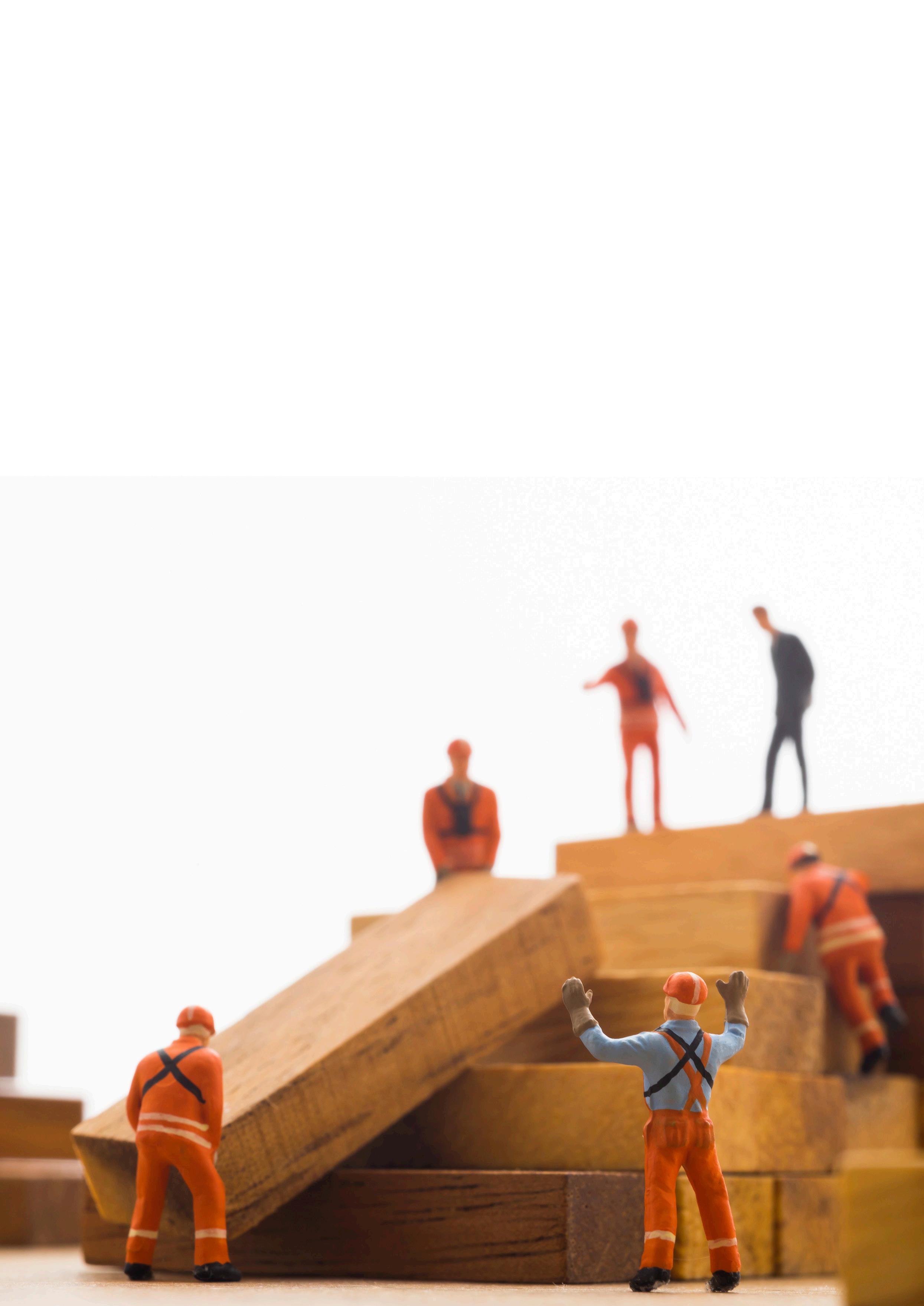
Pipeline Safety Management Systems support operational excellence
API supports the natural gas and oil industry in developing and updating standards that are performancebased and therefore often go above and beyond regulation. For example, in April 2022, API published two revised standards related to leak detection in liquid pipelines to better enable operators to reduce the risk of incidents, and improve operational integrity.
API, in collaboration with key industry stakeholders and often with US federal regulators, develops and maintains more than 800 standards to enhance operational safety, efficiency and sustainability. In all, 35 API standards directly address pipelines and related facilities, with another four 1 st editions in development.
The growth of pipeline infrastructure emphasises the continuing need to prevent leaks, spills, and asset integrity incidents at existing and new facilities. Minimising such events helps to further reduce fugitive emissions, delivery delays, and costly downtime. Against this backdrop, US regulators, including PHMSA, have recently put renewed prominence on pipeline integrity and mitigation of leaks, both inside and outside pipeline facilities to reduce greenhouse gas emissions.
Both in their second editions, RP 1130, Computational Pipeline Monitoring for Liquids, and RP 1175, Pipeline Leak Detection – Programme Management, are designed to enable operators to quickly respond to incidents, mitigating harm to people, the environment and property in the event of an incident.
Enhanced leak detection improves pipeline integrity
In March, PHMSA issued a new rule that requires a pipeline leak to be addressed no more than 30 minutes after identification, bringing even greater emphasis to leak detection practices, such as those detailed in RP 1130 and RP 1175. Among other things, PHMSA’s rule requires operators to install remotely controlled or automatic shutoff valves, or alternative equivalent technologies, on new and replaced onshore natural gas, carbon dioxide and other
12 World Pipelines / AUGUST 2022
“API standards help the industry foster innovation, assure quality and reduce waste,” says Anchal Liddar, Senior Vice President for API’s Global Industry Services (GIS). “Implementing API standards in the pipeline sector can significantly improve safety and performance, bringing benefits to workers, communities, the environment and, operators alike.”
RP 1175 provides guidance for pipeline operators to create effective leak detection programmes (LDP) so they can identify leaks quickly and with certainty, thereby facilitating rapid shutdown and minimising negative consequences.Thesecond edition of RP 1175 was developed to provide a flexible framework for determining which technologies, systems or programmes operators use in establishing LDPs, as leak detection often utilises a multilayered series of technologies and strategies. Additionally, the updated edition incorporates new leak detection technologies, including the role of fibre optic sensing.
While pipelines are the safest way to transport natural gas and oil, implementation of API standards is critical as pipeline and LNG infrastructure is expected to expand in North America and globally over the coming years in response to rising demand. In the US alone, LNG exports are projected to rise to 5.68 trillion ft 3 by 2033, a 65% jump from current levels, according to the US Energy Information Agency.
“Fibre optic sensing-based pipeline leak detection and location software is possibly the most important technological development in pipeline leak detection in recent years. The inclusion of distributed fibre optic sensing in the latest revisions of the API RPs is a testimony to the technology’s contribution to leak detection,” Fibre Optic Sensing Association Executive Director, Mark Uncapher said in a statement. For its part, RP 1130 addresses computational pipeline monitoring (CPM), or algorithmic monitoring tools that are used to enhance the ability of a pipeline controller to recognise hydraulic anomalies that may be indicative of a pipeline leak. CPM systems are intended to provide an alarm and display other related data to the pipeline controllers to aid in an immediate investigation, confirm the reason for the alarm, and initiate an operational response to the hydraulic anomaly when it represents an operational upset or commodity release.
API standards are developed under API’s American National Standards Institute (ANSI) accredited process, ensuring that the standards are recognised for their technical rigor and third-party accreditation. This facilitates acceptance by state, federal, and a growing number of international regulators and national oil companies. In addition, API standards are already widely used voluntarily across industry because of their best-in-class standing.
RP 1173 is the first standard to address SMS requirements for pipeline operators of all sizes, and allows users to gain understanding of how to systematically manage pipeline safety and continuously measure progress to improve overall pipeline safety performance by following a plan-do-checkact (PDCA) cycle for continuous improvement. RP 1173 is specifically applicable to organisations that operate hazardous liquid and gas pipelines, and can be utilised by operators of other pipelines, such as hydrogen.
API Recommended Practice (RP) 1173, Pipeline Safety Management Systems, is a benchmark for the industry that integrates numerous API standards and is incorporated into industry safety programmes. While RP 1173 is specific to pipeline operations, safety management systems (SMS) have helped increase safety in other industries, such as aviation, nuclear power, and chemical manufacturing. Pipeline operators, through API and in partnership with the US Pipeline and Hazardous Materials Safety Administration (PHMSA), state pipeline regulators, and other interested stakeholders developed RP 1173 to enhance the safety of pipeline operations.
STATS GROUP Managing Pressure, Minimising Risk Tethered Tecno Plug® fail-safe double block and bleed isolation of pressurised pipelines while the system remains live and at operating pressure. ZERO-ENERGYPIPELINEZONEPRESSURE DUAL Leak-Tight Seals double block & BLEED isolation isolated pipeline taper lock grips TYPE APPROVED3”-56”
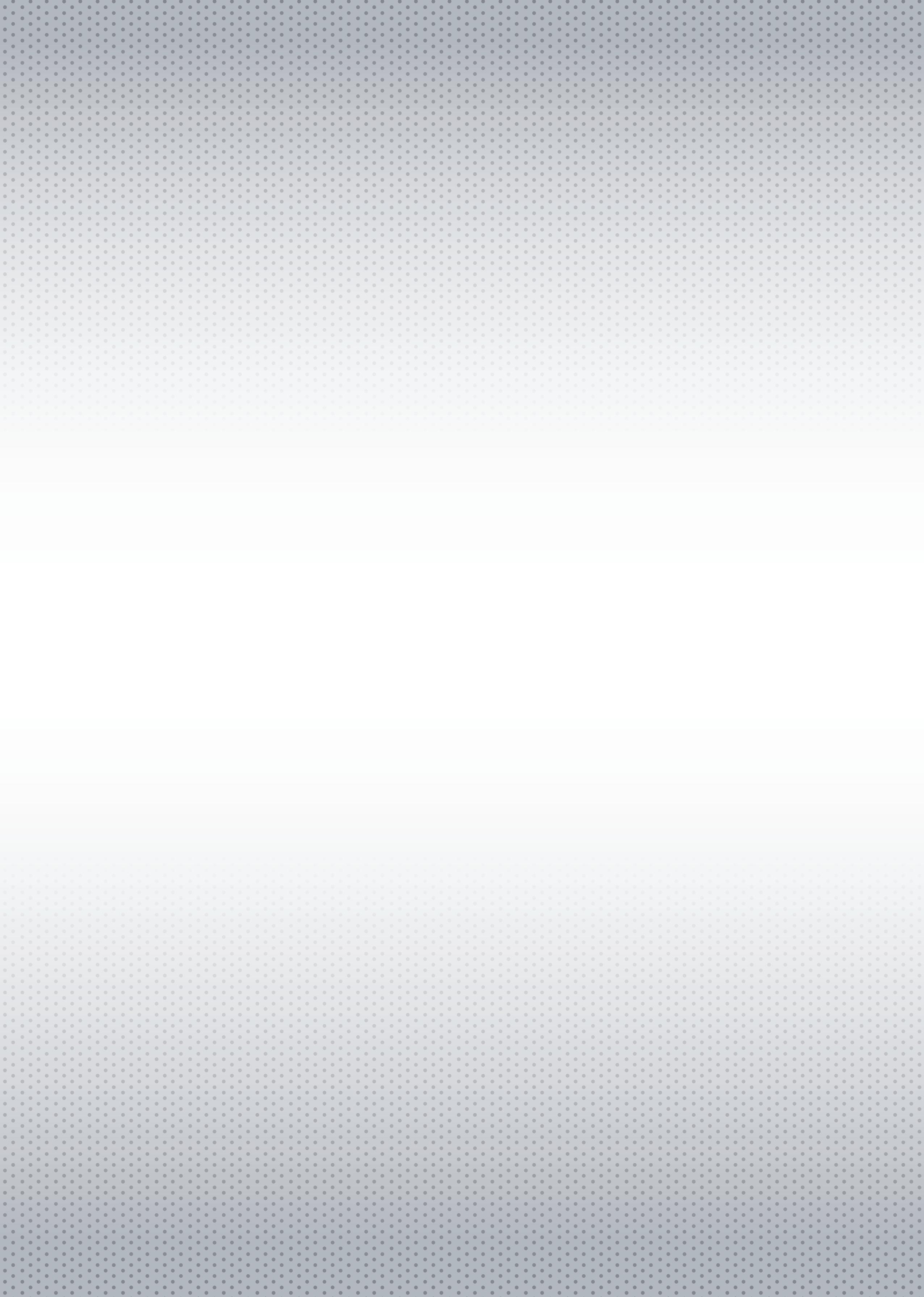
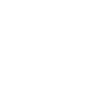
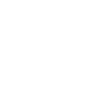
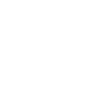
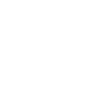
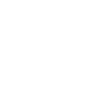
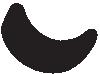
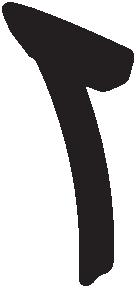

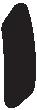
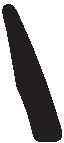


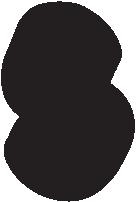
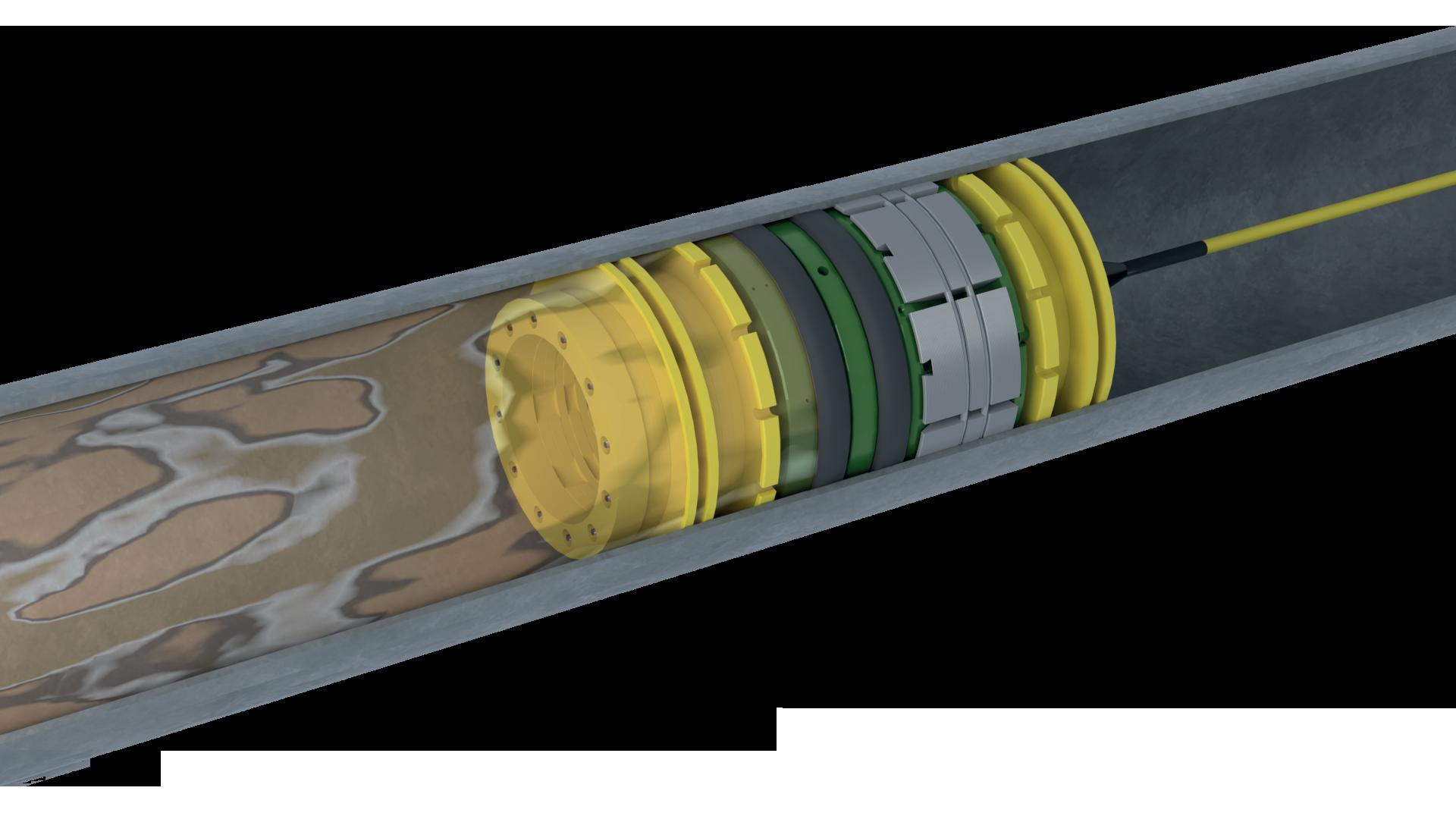
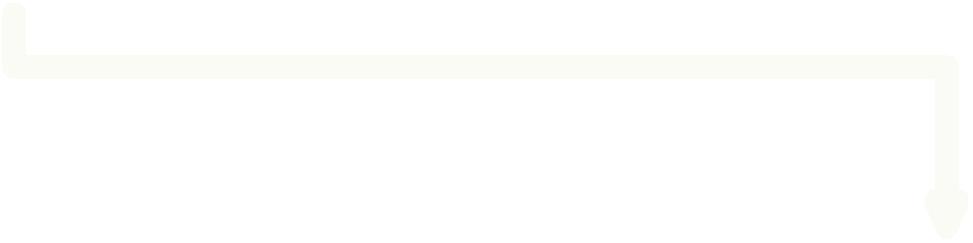
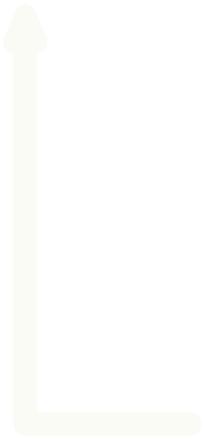
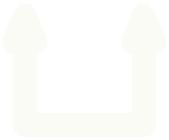

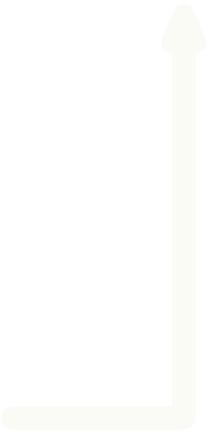
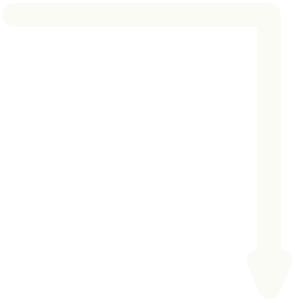
Pipeline operators are proactively implementing integrity management programmes to ensure their facilities are fully operational, maintained, and safe. In addition to Pipeline Safety Management Systems (Pipeline SMS), facility integrity management programmes – a documented set of policies, processes and procedures to manage facility risk – help operators reduce downtime, prevent leaks and curb emissions.InJanuary, API published RP 1188, Hazardous Liquid Pipeline Facilities Integrity Management, 1st edition, to provide guidance to operators to build resilient facility integrity programmes.
hazardous liquid pipelines. RP 1130 and RP 1175 support the US regulator’s priorities by putting additional tools and good practices in the hands of operators to effectively monitor and manage potential liquid pipeline incidents.
Following completion of a rigorous qualification process and exam, future facility inspectors should gain an understanding of phases of pipeline facility construction, including the best safety practices, roles, and responsibilities.Developedwith support from the Canadian Energy Pipeline Association (CEPA) and Interstate Natural Gas Association of America (INGAA) foundations, API’s newest inspection programme is based on RP 1184, Pipeline Facility Construction Inspection, 1st edition, published in October 2021.API has already successfully implemented the first certification programme for pipeline inspectors, API 1169 Pipeline Inspector Programme, a complementary programme to the new Pipeline Facility Construction Inspection certification aimed at helping the industry advance on a path toward a uniform method of identifying and assessing qualifications of facility pipeline inspectors.
14 World Pipelines / AUGUST 2022
Much like RP 1173, RP 1188 utilises a PDCA cycle to promote the continuous assessment and improvement of pipeline facility integrity programmes.
Pipeline SMS assessments help advance industry operations by ensuring that the various components of an operators’ Pipeline SMS are regularly reviewed and continually evolving.“Sharing and learning among the industry enhances the safety and operating performance of pipelines in line with RP 1173 requirements, helping to drive the industry toward the goal of zero-incidents,” said David Murk, API’s Director of Midstream. “Pipeline SMS assessments help the industry implement RP 1173 and we encourage operators of all sizes, whether in North America or internationally, to participate in the programme with their peers.”
The Pipeline Facility Construction Inspection certification, offered through API’s Individual Certification Programmes (ICP), will help to ensure the industry has competent and qualified inspectors for pipeline facility operations, including pump stations, compressor stations, and related facilities.
As part of industry’s commitment to help operators share good practices, API, in collaboration with industry partners, developed the Pipeline SMS Assessment Programme to enhance pipeline safety performance and knowledge sharing among operators.
Recognising that a large portion of reportable leaks and incidents occur at pipeline facilities, rather than along the pipeline right-ofway, this standard covers the integrity management of all pressure containing components directly used in the transport or storage of hazardous liquids within a liquids pipeline facility. It is applicable to pipeline operators and integrity management inspectors.
New pipeline inspection certification fills industry void Additional pipeline construction and infrastructure has led to a growing demand for qualified pipeline facility inspectors. To address this demand, in March 2022 API launched a new certification programme for pipeline facility inspection.
Empowering safe pipeline operations
Third-party assessment aids improvement of pipeline operations
Pipeline facility management is key to safe operations
During a Pipeline SMS assessment, a team of independent, third-party safety management system experts work with operators to fully understand their current pipeline safety processes, programmes, and systems to enhance compliance with RP 1173 in order to drive improvements in safety and pipeline safety performance. The assessment includes an evaluation of how operators incorporate external learnings into their Pipeline SMS. The Pipeline SMS Assessment Programme sets out performance indicators and uses the PDCA cycle to identify safety performance good practices and improvement opportunities for the 10 PSMS elements in RP 1173. The assessment programme helps serve as the ‘Check’ in the PCDA cycle, and allows operators to determine what actions need to be taken, implement them, and regularly review and enact any necessary changes or improvements to their internal programmes.
For nearly a century, API has been the global leader in developing consensus standards for the natural gas and oil industry, enhancing operational safety, environmental protection and sustainability across all segments. To reflect changes in technologies, in-field learning, policy and regulatory requirements, API continuously updates industry standards that foster better industry operations, assure quality, keep costs down, reduce waste, and minimise confusion.
Pipeline safety and integrity are vital to delivering energy to power the global economy. With an anticipated expansion in pipeline infrastructure in the coming years to meet rising demand, the industry must ensure pipelines are safe, sustainable and efficient.
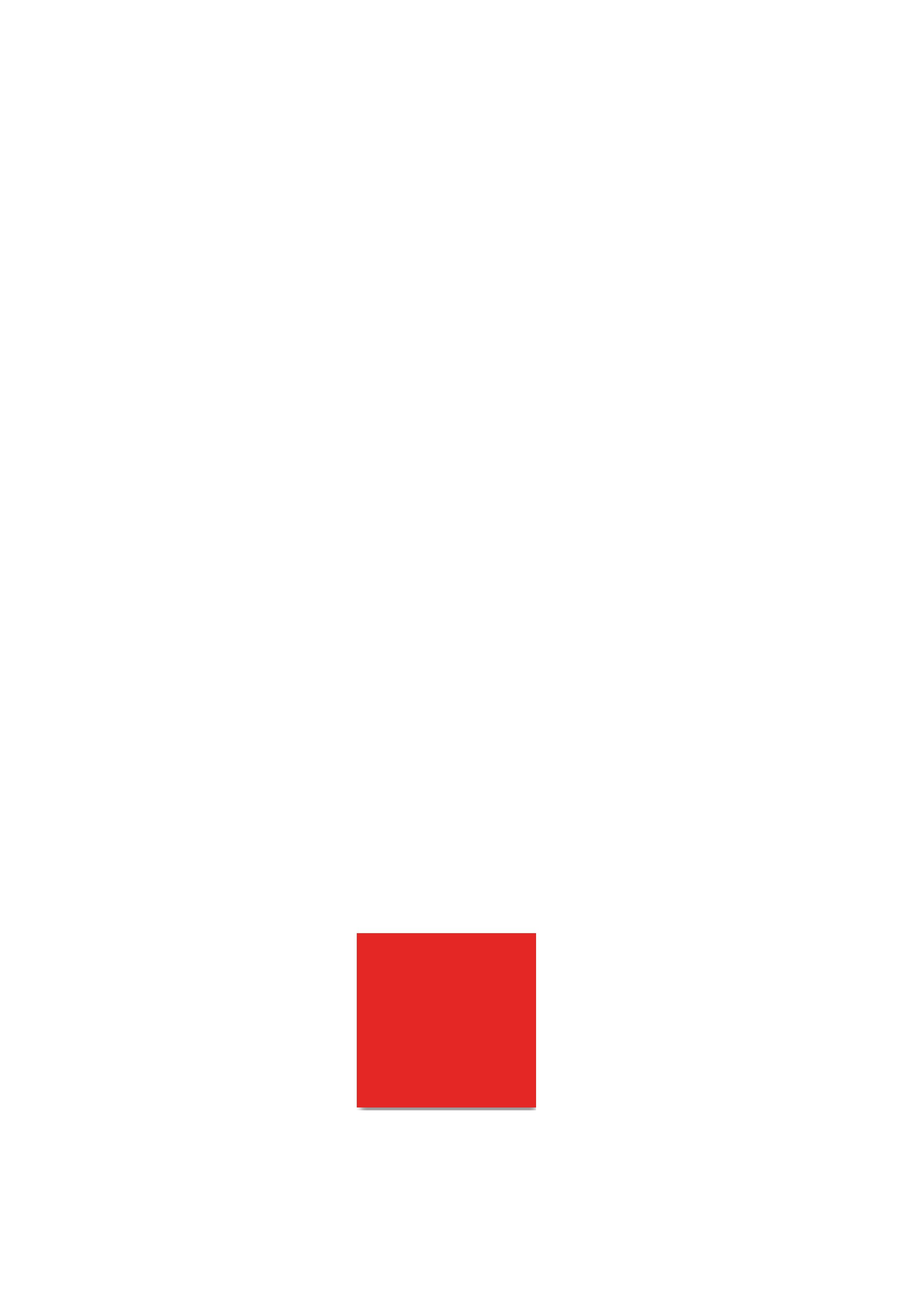
16
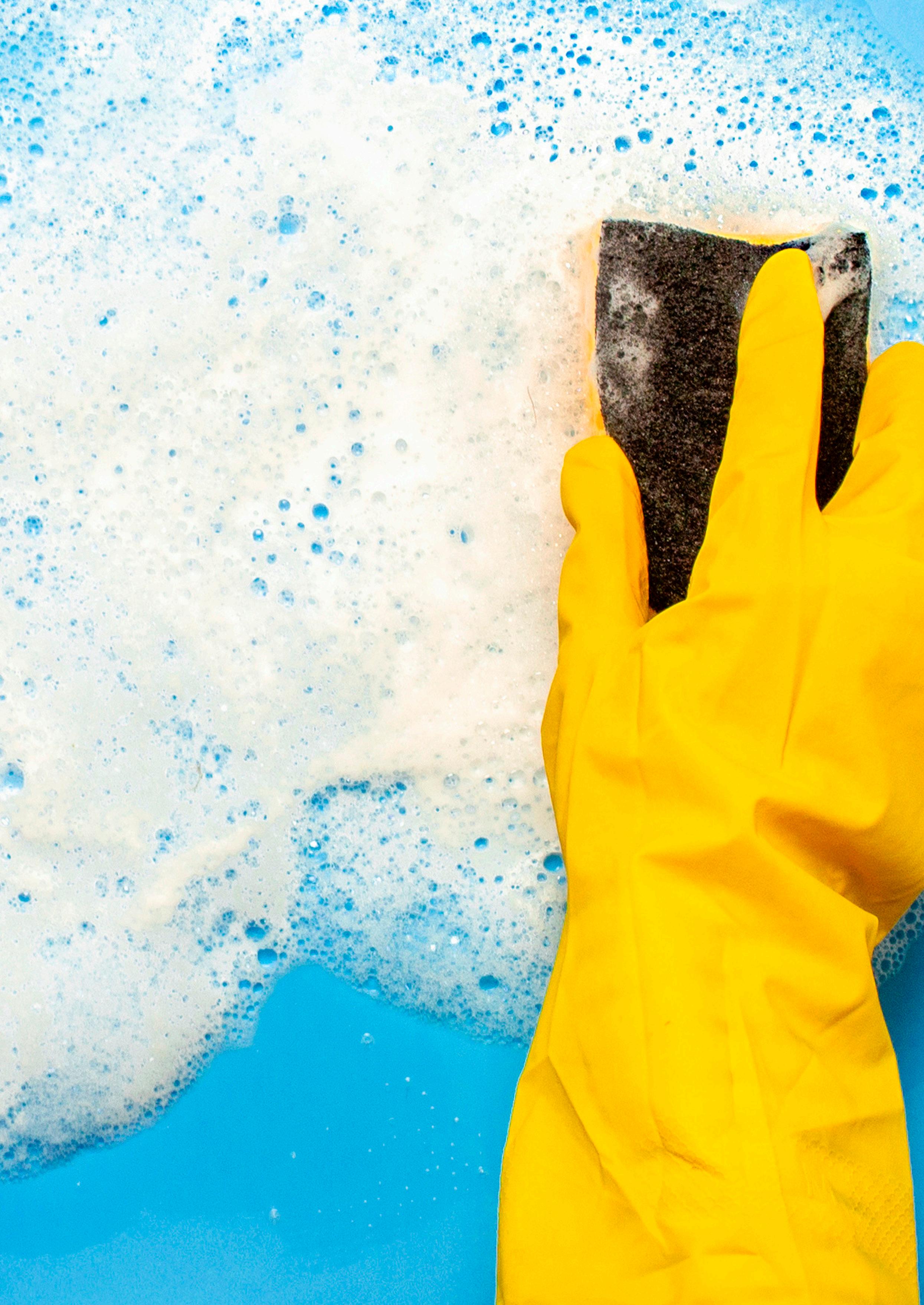
Several other US utilities have proposed or initiated early efforts to test hydrogen blending in natural gas pipeline systems, but they had not announced plans to ship significant hydrogen 17
In the US, approximately 8047 km (5000 miles) of pipelines transport CO2, predominantly to oilfields, where it is used for enhanced oilfield recovery (EOR). A recent report by the Congressional Research Service (CRS), indicating the industry’s stake in the potential to preserve the value of existing pipeline assets while reducing CO2 emissions, was cited as one reason domestic pipeline operators are looking into enriched natural gas and CCS pipeline conversion in the US.
Globally, investment in the lowcarbon energy transition hit a recordsetting US$755 billion in 2021, a yearover-year increase of 27%, according to a new report by research firm BloombergNEF.
Many are opening new forms of dialogue and developing strategic business-to-business partnerships while considering how their pipeline asset management and operations objectives align with currently available technologies, emissions targets, and opportunities for a return.
Storage of hydrogen as a liquid also requires cryogenic temperatures, as its boiling point at one atmosphere pressure is -253°C (-423°F), coupled with insulated storage facilities.
Some operators have already initiated projects to blend hydrogen in natural gas pipelines. In November 2020, as one example cited in the CRS report, Southern California Gas Company and San Diego Gas & Electric Company filed a joint application with state regulators to initiate a hydrogen blending demonstration project in their respective gas distribution systems in California.
The stakes for oil and gas majors steering the ship toward decarbonisation and a cleaner energy transition are high as they consider the most timely, effective capital expenditures.
Paul Dickerson, Global Products Lead, Pipeline Management Software, Emerson, USA, explores preparing pipelines for the new CO2 and hydrogen rush.
Renewable energy in 2021 captured US$366 billion in new investment, a 6.5% increase from the prior year, for new projects and small-scale systems. The energy sector raised the largest amount of capital –US$68.5 billion – a nod to wind, solar power and hydrogen.
Transporting CO2 in pipelines is similar to transporting other pipeline products; it can be transported as a gas or as a dense, liquid or supercritical fluid. Reuters reported in September 2021 there were 15 direct-air capture plants operating worldwide, capturing and sequestering more than 9000 tpy of CO2 from the atmosphere; and direct carbon capture and sequestering from industrial processes are surging.
Future demand Coming demand for carbon capture and storage (CCS), as well as a new hydrogen rush, appears to be well within reach in midstream oil and gas sectors, with aggressive targets being set by energy producers in Europe and around the globe.
A novel blend of new technology and critical infrastructure will be required to sequester CO2 and hydrogen as part of the low-carbon energy transition and changing energy landscape. The transition will dictate a redesign of pipelines, along with greater resource optimisation across pipeline networks that requires risk-modeling software and capabilities such as machinelearning algorithms, self-learning adaptive methods, and simulationbased applications for companies to compete and thrive in the future.The oil and gas industry is taking significant strides developing a more defined and central role in reducing greenhouse gas emissions and capitalising on new forms of production amid a diversified and changing energy landscape.
On hydrogen Gaseous hydrogen can be transported through pipelines much the way natural gas is today, and nearly all hydrogen pipeline shipment in the US and overseas occurs in dedicated hydrogen (or syngas) infrastructure. As of December 2020, there were 2588 km (1608 miles) of active hydrogen pipelines in the US, according to the CRS report. By comparison, there are over 482 803 km (300 000 miles) of US natural gas transmission pipelines, excluding distribution mains, located in the 48 contiguous states and Alaska. More than 90% of these hydrogen pipelines are located along the Gulf Coast in Texas, Louisiana and Alabama, primarily serving refineries and ammonia plants in the region. Comparatively short hydrogen pipelines are located elsewhere in Texas, Louisiana, and in nine other states. California has 16 miles of hydrogen pipeline, Indiana has 14 miles, and the remaining seven states have fewer than 10 miles each. By mass, hydrogen has the highest energy per mass of any fuel. However, its low ambient temperature density results in a low energy per unit volume. Hydrogen is less energy dense by volume – about four times less energy dense – than natural gas, therefore requiring the development of advanced, large-volume transportation and storage methods that have potential for higher energy density.
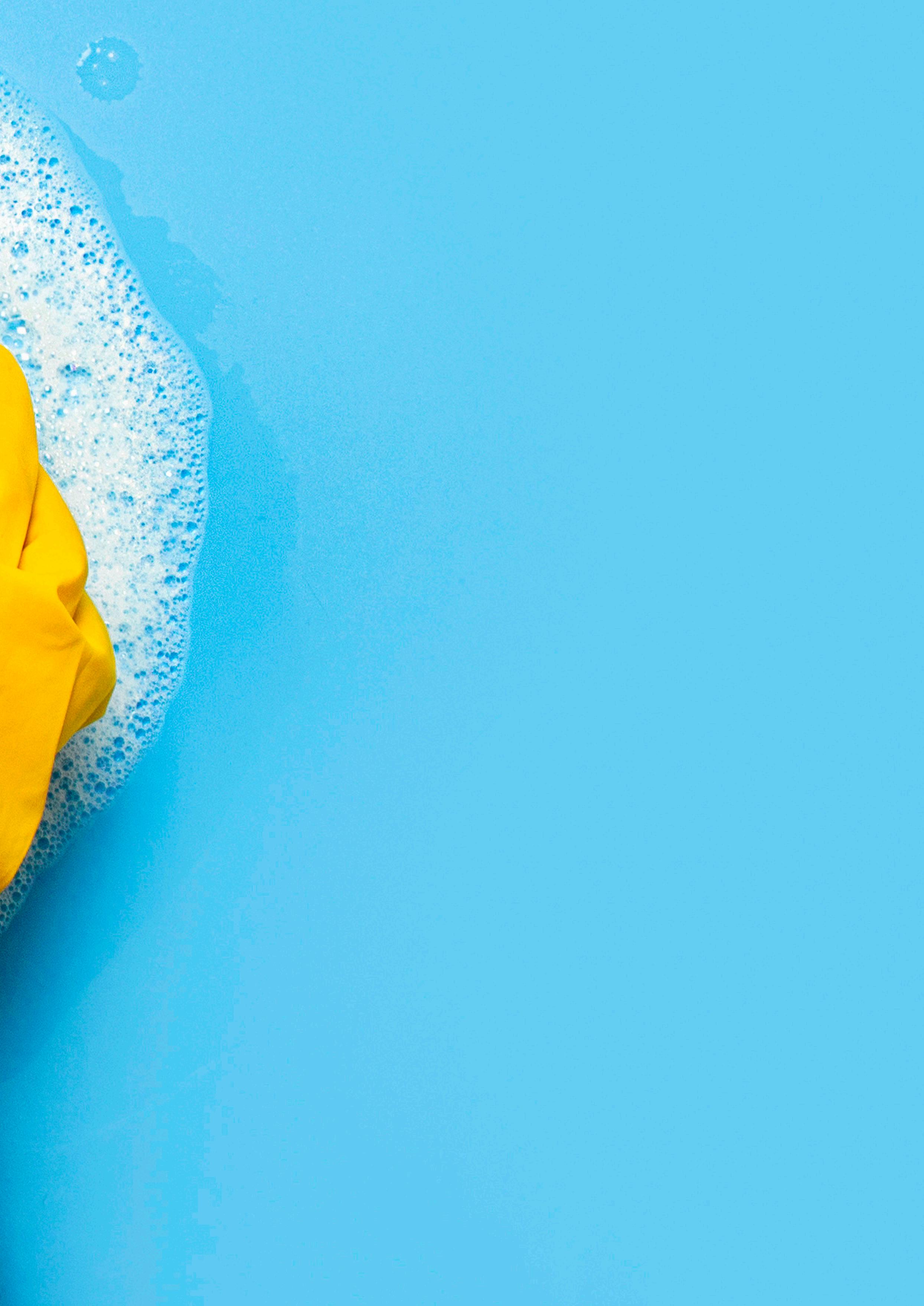
Hydrogen embrittlement (HE), occurring when metals become fragile as a result of the introduction and diffusion of hydrogen into the material, is another leading cause of concern. Hydrogen is a very reactive with a tendency to want to bond with most elements to form hydrides. It disassociates on metal surfaces and dissolves into the meal lattice, weakening pipelines.
A critical area operators must continue to focus on is pipeline asset management that commands a systems-wide thinking approach, encompassing all facets of business operations, risk management and public image.
The analysts assert 20% hydrogen concentrations by volume may be the maximum allowable blend before significant pipeline upgrade costs are required due to potential impacts on pipeline materials. Moving forward, however the blending is qualified or quantified, more dedicated and critical infrastructure will be required to move energy and meet stated emissions reduction targets and needs. This will likely result in a more comprehensive network of pipelines or storage capacity as part of a novel blend – not only in light of the necessary and inevitable continued use of fossil fuels, but as part of the cleaner energy transition and diversification of resources to fuel a cleaner, new energy industrial
The technology and thought leadership exists to help companies run their pipelines more efficiently and more safely, to deliver the products they need. In fact, many companies worldwide are adopting the tools to design systems that are safe and robust – developing partnerships with outside resources to take a collaborative approach that provides the experience necessary to move forward with confidence in the changing energy world.
18 World Pipelines / AUGUST 2022
Addedcomplex.tothislist of physical complexities, pipeline design also needs to be considered. In general, the mathematics
volumes in commercial service. In the UK, several agencies, such as SGN, are testing domestic hydrogen in pilot projects. In Italy, one operator had demonstrated 10% hydrogen blending in a segment of its natural gas transmission network serving several large industrial customers.
Asset management
Equations of state
Commonly known as hydrogen assisted fatigue and fracture, HE affects all major high-strength structural materials.
of flow equations have changed little over the years. Minor adaptions to the flow and energy equations are used in appropriate cases, and of course momentum equations have not changed; however the area of question is how the fluid properties are calculated.
The equations of state used in the industry have been derived from and validated against empirical data in the oil and gas space. Enriching natural gas with hydrogen means the equations of state selection for fluid flow and product blending may require a more careful selection. Suggestions for the best equations have been made, however the computational intensiveness may make some less suited to pipeline design applications.
The setting of CO2 emissions targets for many established oil and gas majors, including those transitioning to become integrated energy players, has included an assessment of Figure 1. As new energy products emerge, Emerson’s advanced GIS solutions will help companies easily identify potential issues in high consequence areas (HCAs) for safer operations.
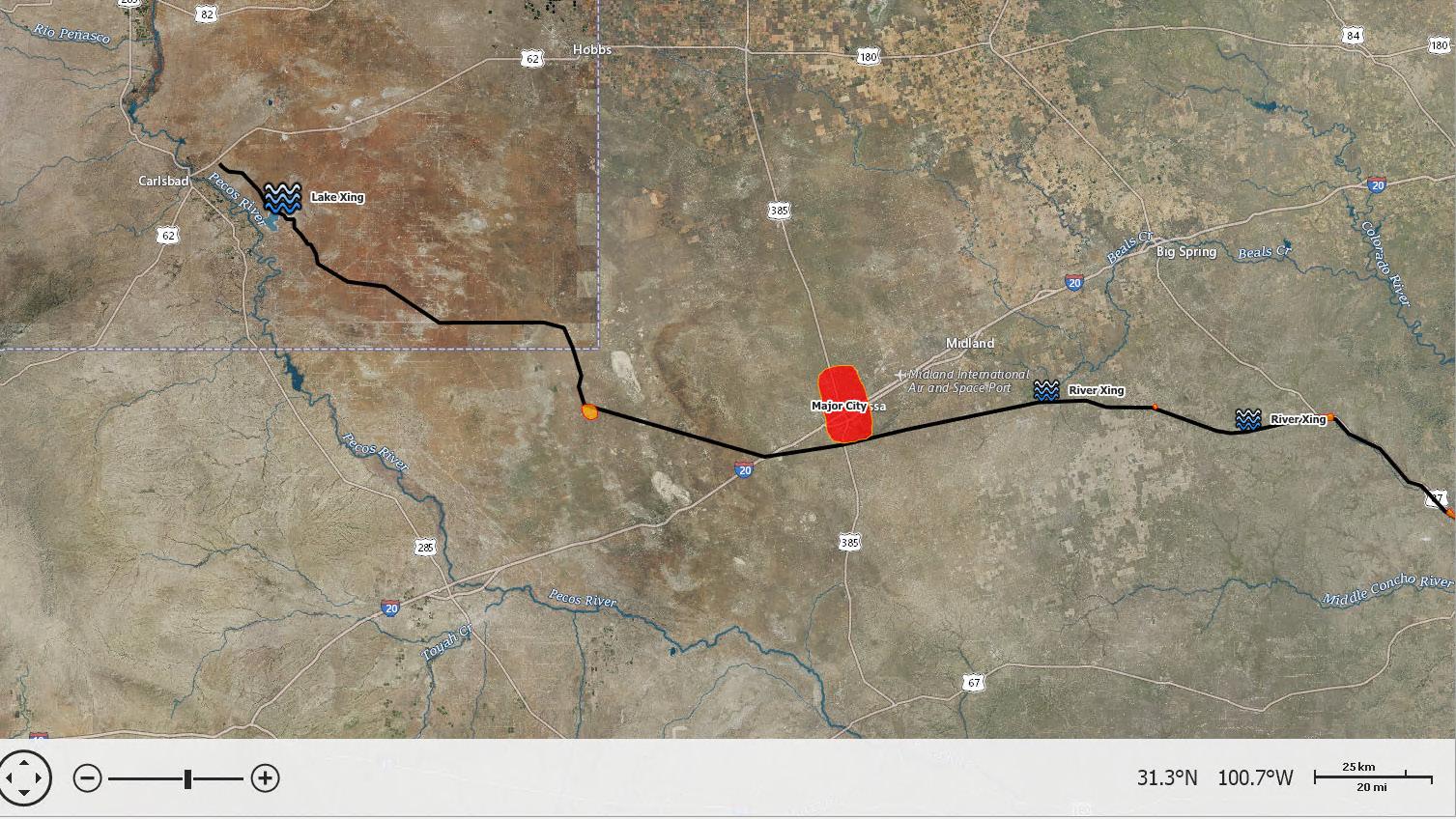
© 2022 Caterpillar. All Rights Reserved. CAT, CATERPILLAR, LET’S DO THE WORK, their respective logos, “Caterpillar Corporate Yellow”, the “Power Edge” and Cat “Modern Hex” trade dress as well as corporate and product identity used herein, are trademarks of Caterpillar and may not be used without permission. HIGH DRIVE A HIGHER LEVEL OF PERFORMANCE ELEVATE YOUR PRODUCTIVITY WITH THE NEW CAT® D7 DOZER Nothing says “Cat® dozer” like high drive undercarriage. It performs better and lasts longer on tough jobs, and it’s just one way the new D7 delivers a higher level of performance. The others? Added power, weight and blade capacity that combine to move more material. Automatic shifting and a standard-setting cab that make operation simple and comfortable. And technology options that can raise your productivity up to 50%. You and your profits will be riding high in this new dozer. Find out more at www.plmcat.com
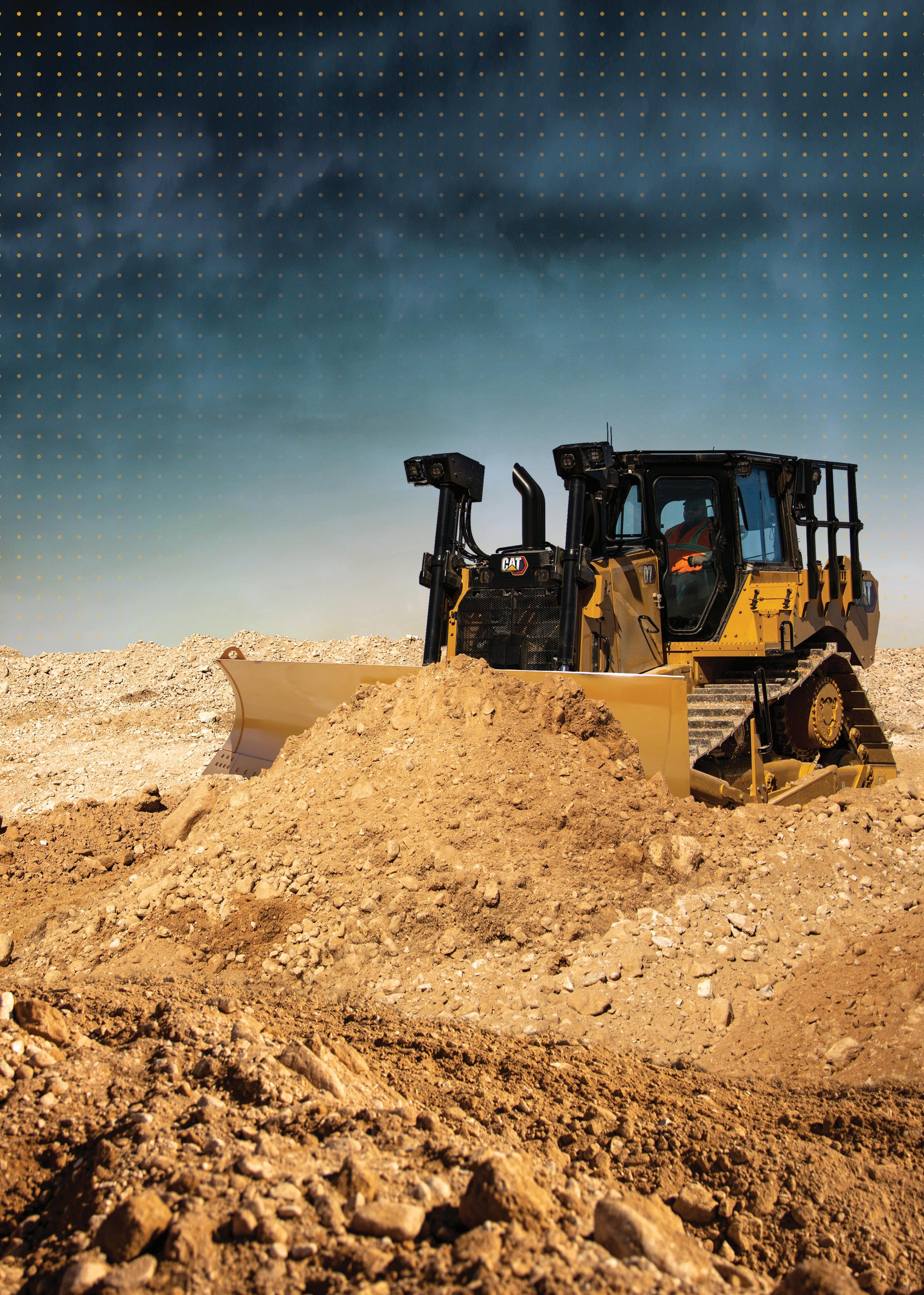
Using powerful simulation-based applications, Emerson’s PipelineManager™ software provides operators with instant insights into daily and routine operations, helping overcome unique challenges often associated with maintaining full compliance with safe operating regulations, and struggling to balance nominations with capacity.
organisational capabilities and operational strategies for efficiency, and to demonstrate where gains are quick and easy to implement.Manynew business relationships are likely to be formed, alongside the development of innovative breakthrough technologies – a combination of the use of data, the acquisition of technology, and access to broad-based experience to improve overallExistingpredictability.software, such as Emerson’s PipelineStudio™ are indicative of offline engineering tools to assist with the natural and liquid gas pipeline planning and design process via advanced simulation techniques. The technology, allowing for steady-state or transient simulations, in high-speed or variable speed interactive modes, offers detailed models of pipes and the common pipeline equipment elements such as valves, compressors, heat exchangers, and other components and other ancillaryEmersoncomponents.isworking to lead the way for pipeline operators and consulting firms worldwide. By empowering engineers and planners with reliable and accurate information, Emerson’s advanced software is leading to better decision making that is resulting in improvements in pipeline design, performance, and throughput. In most cases, the optimisation of pipeline system performance, creation of emergency plans and updates to operational strategy can be achieved without interrupting online production and transmission. Decision points All oil and gas pipelines require attention to design, monitoring for leaks, and protection against overpressure, especially in populated areas. Safety also must always come first when considering hydraulic behaviour of hydrogen enriched gas.
20 World Pipelines / AUGUST 2022
PipelineManager additionally offers advanced, comprehensive leak detection technology ranging from pinhole leaks to ruptures, including those caused by accidents and theft. The software rapidly identifies leaks and efficiently manages operations across the pipeline with real-time access to missioncritical data and the transformation of obscure pipeline data into intuitive charts, graphs and maps. This ensures improved visibility into current operations, enabling quick and accurate response times as the data are consolidated rapidly, from multiple sources and in real-time, helping inform more accurate decision-making processes across the entire pipeline. It paints a detailed picture of current operations and simplifies the tracking of products, fluid composition, ownership, pigs, scrapers and many other activities down the First-levelline.filtering should always be applied to the pipeline design, management or leak detection data, as a way to identify potential data errors, as well as mitigate the potentially negative impact consequences of inaccurate data measurement or poor SCADA system integration. It is essential to incorporate advanced software into the SCADA system to get a complete picture of the pipeline and how it is operating at any given time. With an aging infrastructure adding to the complexity, oil and gas majors are talking more openly, and acting decisively, in terms of their roles – and about setting goals and staying ahead of emissions targets. They are working to develop a Figure 2. Emerson’s PipelineStudio is an offline engineering tool that provides advanced simulation techniques to improve pipeline design, performance and throughput.
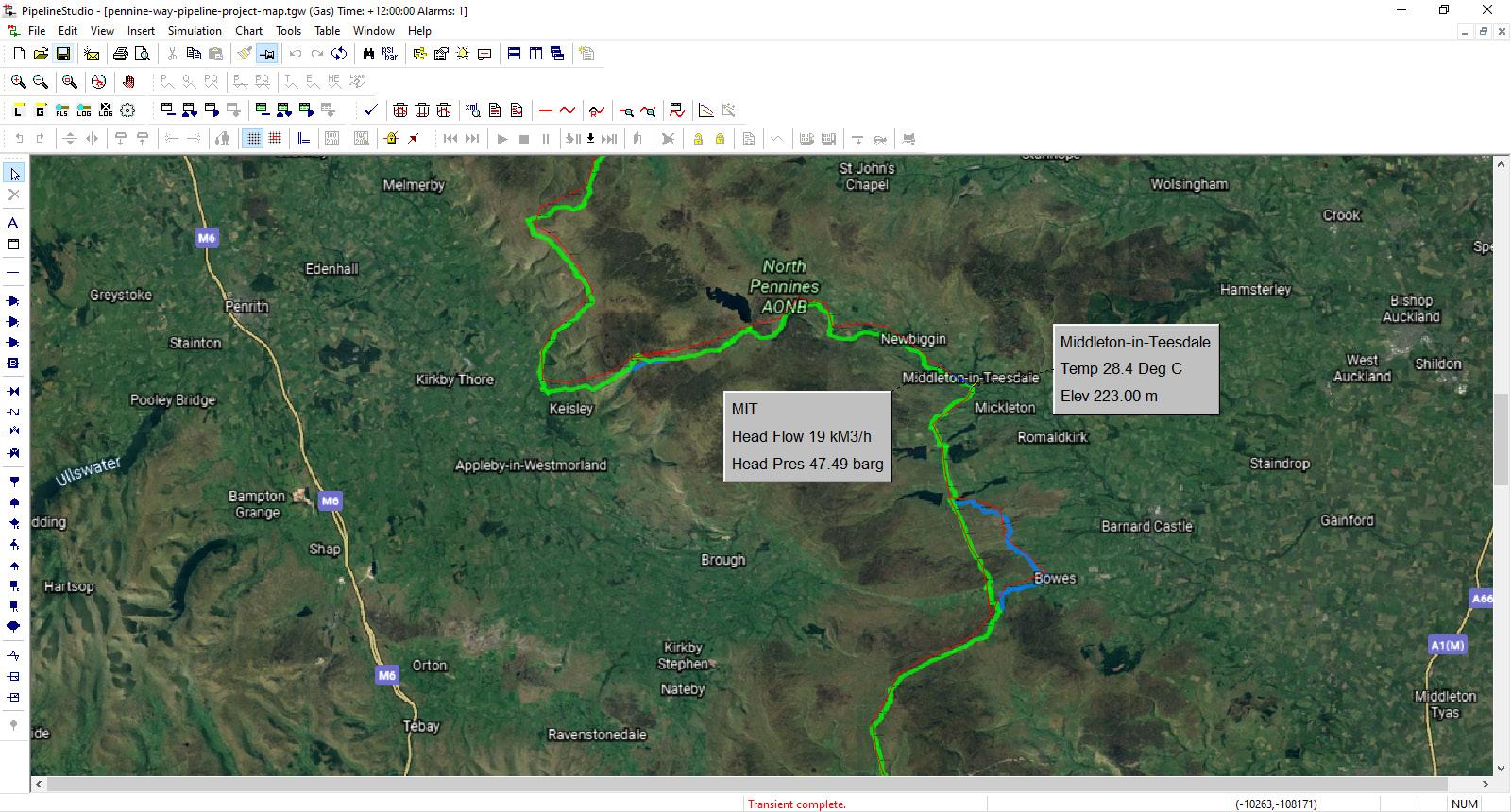
© 2022 – American Petroleum Institute, all rights reserved. API, ICP, the API logo and the ICP logo are trademarks or registered trademarks of API in the United States and/or other countries. API Marketing & Communications: 2022-036 | PDF API CERTIFIED INSPECTORS PROVE THEIR KNOWLEDGE, INCREASE THEIR CAREER POTENTIAL AND HELP DRIVE SAFETY AND OPERATIONAL INTEGRITY IN THEIR FIELD To take the next step in your career visit: www.API.org/ICP CONSTRUCTIONFACILITYINYOURDEMONSTRATEEXPERTISEPIPELINE API’s new pipeline facility inspection certification, ICP 1184, qualifies inspectors for pipeline facility operations including pump stations, compressor stations and related facilities.
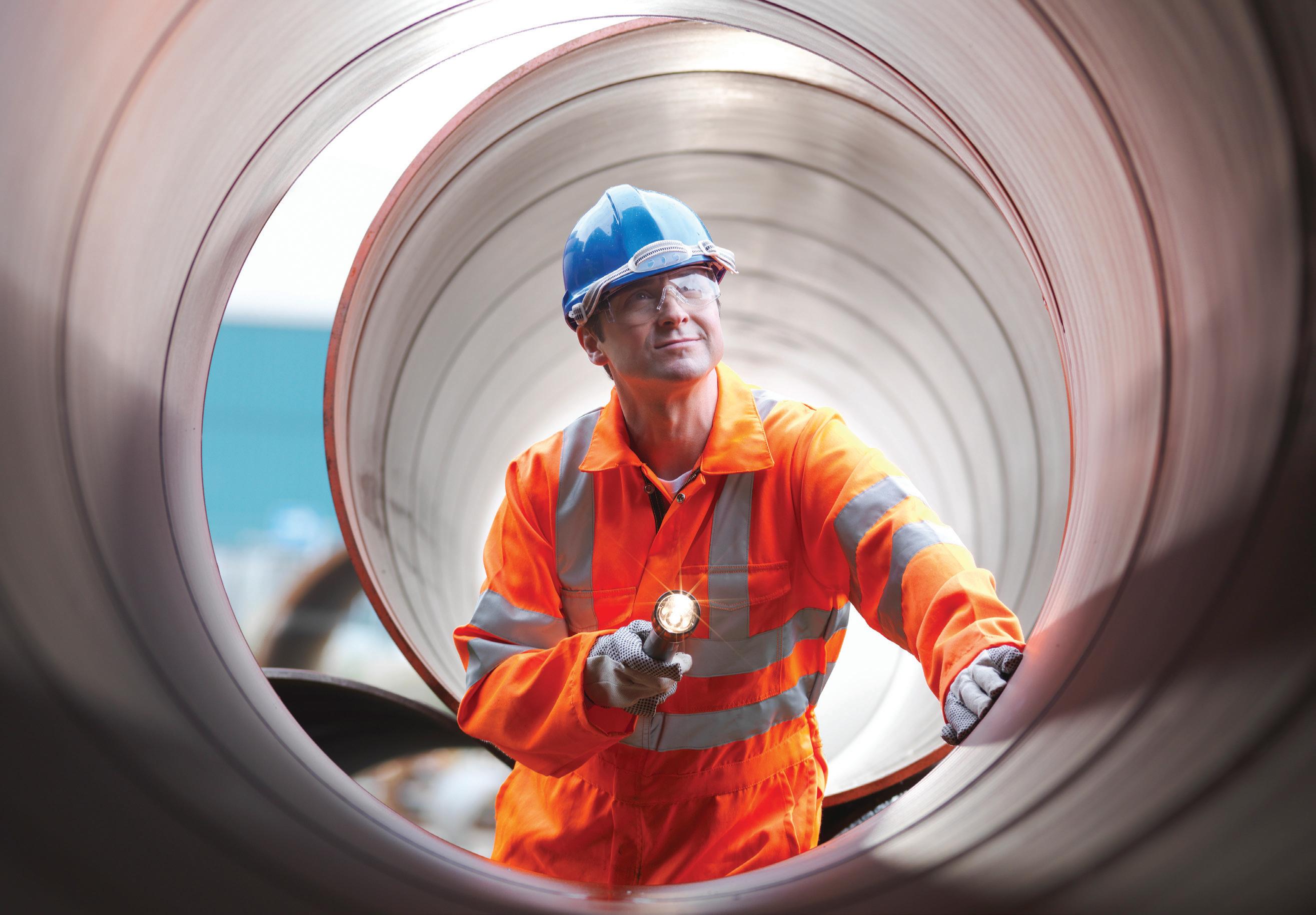
Costs for pipeline construction vary, depending upon length and capacity, right-of-way costs, whether the pipeline is onshore or offshore, whether the route crosses mountains, large rivers, or frozen ground, and other factors. The quantity and distance transported will mostly determine shipping costs.
From the design and development of new and necessary energy infrastructures – to the optimisation of existing assets to meet future demands – inquiries often revolve around subjects associated with where to build extra capacity, the best possible Operators can also more accurately predict compressor pressure by running simulations in PipelineStudio.
22 World Pipelines / AUGUST 2022
Figure 3.
Figure 4. PipelineStudio allows for steady-state or transient simulations with detailed models of pipes, including equipment such as valves, compressors, heat exchangers, and other devices.
clear understanding of the impacts of the energy transition and associated opportunities both in the near and long-term.
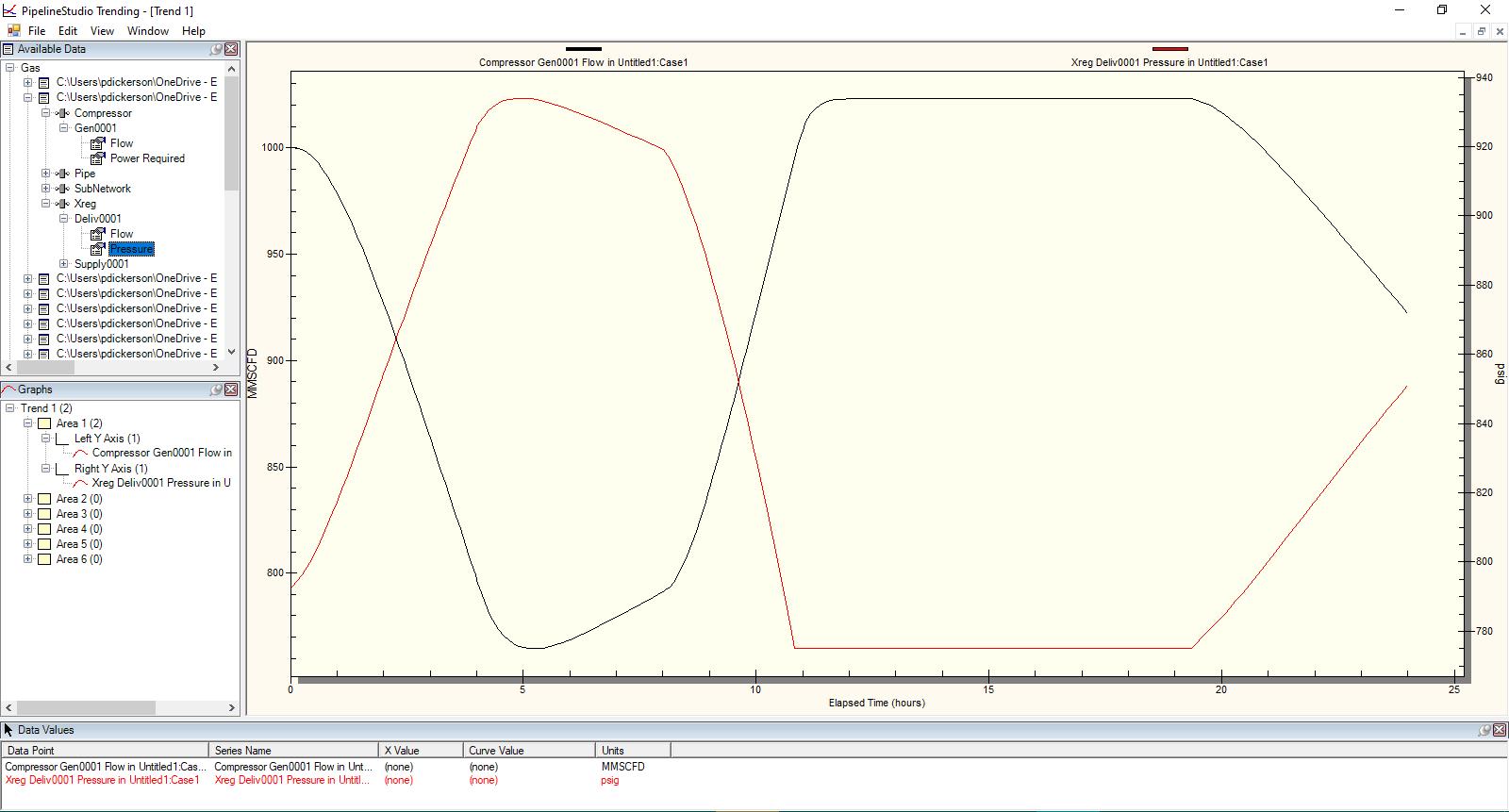
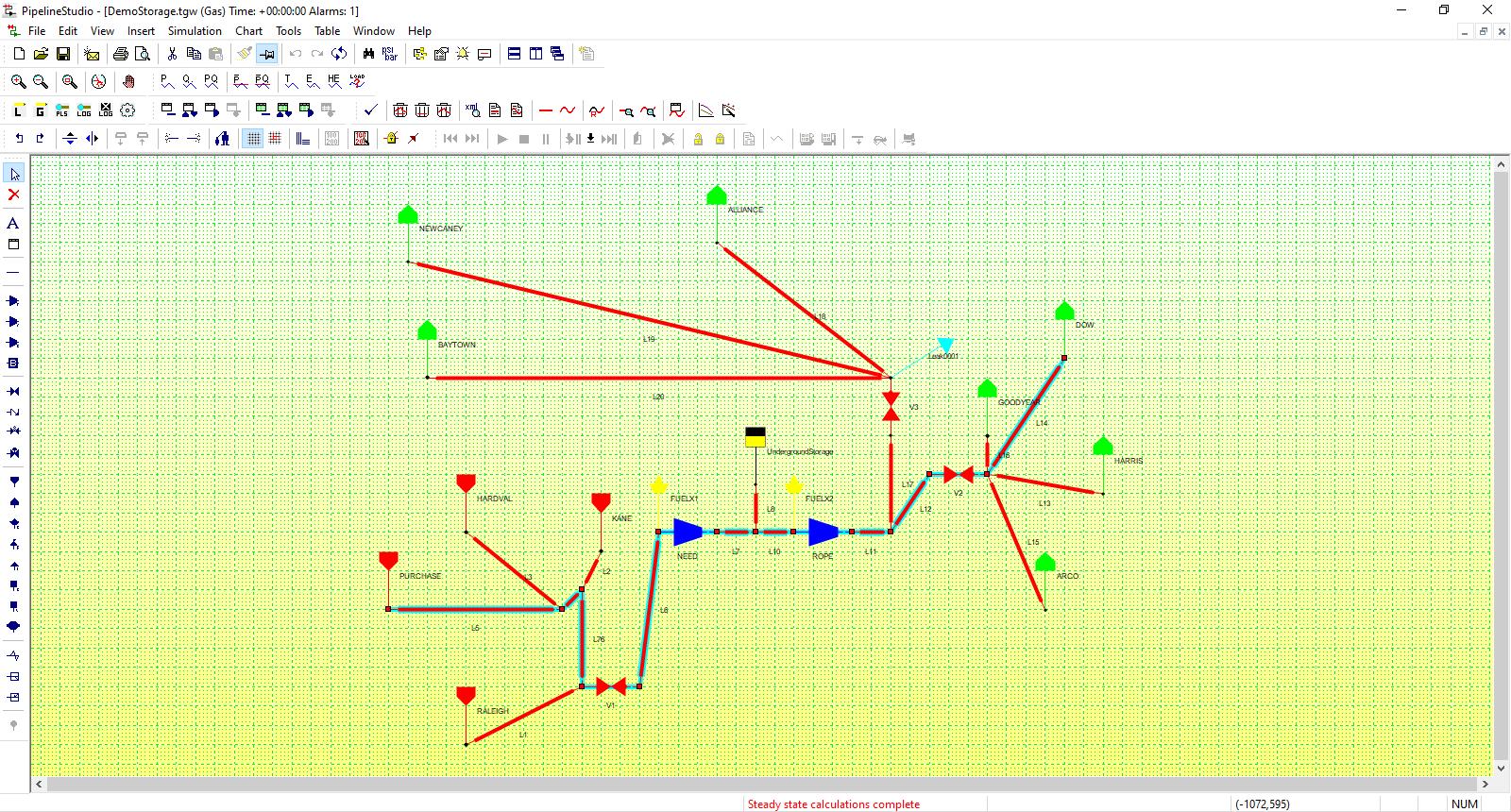
one opportunity is to enrich the natural gas supply we have, a gradual shift away from traditional gas products into hydrogen-based gas products in homes and industries.
Many oil and gas companies are transitioning their operations to handle hydrogen enriched natural gas, pure hydrogen and other potential product variants and blends, and other new forms of energy that are beginning to emerge as viable for transportation, commercial use, homes, and other alternatives.
From our experience at Emerson, staying on top of guidance and advice derived from global markets is key. It is anticipated that the role of simulation, as well as AI, machine-learning algorithms, and self-learning adaptive methods, will play a critical role in the future design of pipelines and resource optimisation across pipeline networks. That includes risk modelling software and capabilities as they relate to pipes that will be used to transport and store CO2 or hydrogen. Of course, there is much analysis and work to be done on the operational side. Reliable simulation-based applications integrated into modern SCADA systems that are readily available today from Emerson will continue to enable pipeline operators to deal effectively with daily concerns, regardless of the products flowing in their pipelines.
Regardless of the intended use of energy pipelines, including which products are being transported and their intended routes, an emphasis on safety and upholding one’s reputation in the industry is paramount for all oil and gas companies proclaiming to be leaders in the move toward cleaner energy. Their sights are set on the mitigation of risks associated with climate change, future proofing their business models and taking leadership positions with environmental sustainability and profitable results among top concerns.
We are in a changing energy landscape with a lot of new momentum running parallel with some uncertainties about which direction everybody is going in from a legislative and geopolitical point-of-view. It is difficult to overstate the role of advanced pipeline solutions from a safety, public image and profitability perspective – both as part of the transition to a ‘net-zero’ emissions mentality and, for growth-oriented oil and gas companies, to retain a competitive edge.
Testing, alongside further pipeline safety design, evaluation of risks, and education and training, will be more important than ever to keep everyone safe and ensure continuity across all operating conditions – in the rush to capitalise on the low carbon energy transition.
points to loop pipelines, ensuing compliance with all regulations, and making room for new plays. New studies and testing will be required. Greater analysis based on feeds of fatigue crack growth data. More deliberate consideration regarding the fact that the current infrastructure is not designed and may not be suited to carry large amounts of hydrogen.Ournumber
Initially this must occur by volume. It will take some time. New momentum
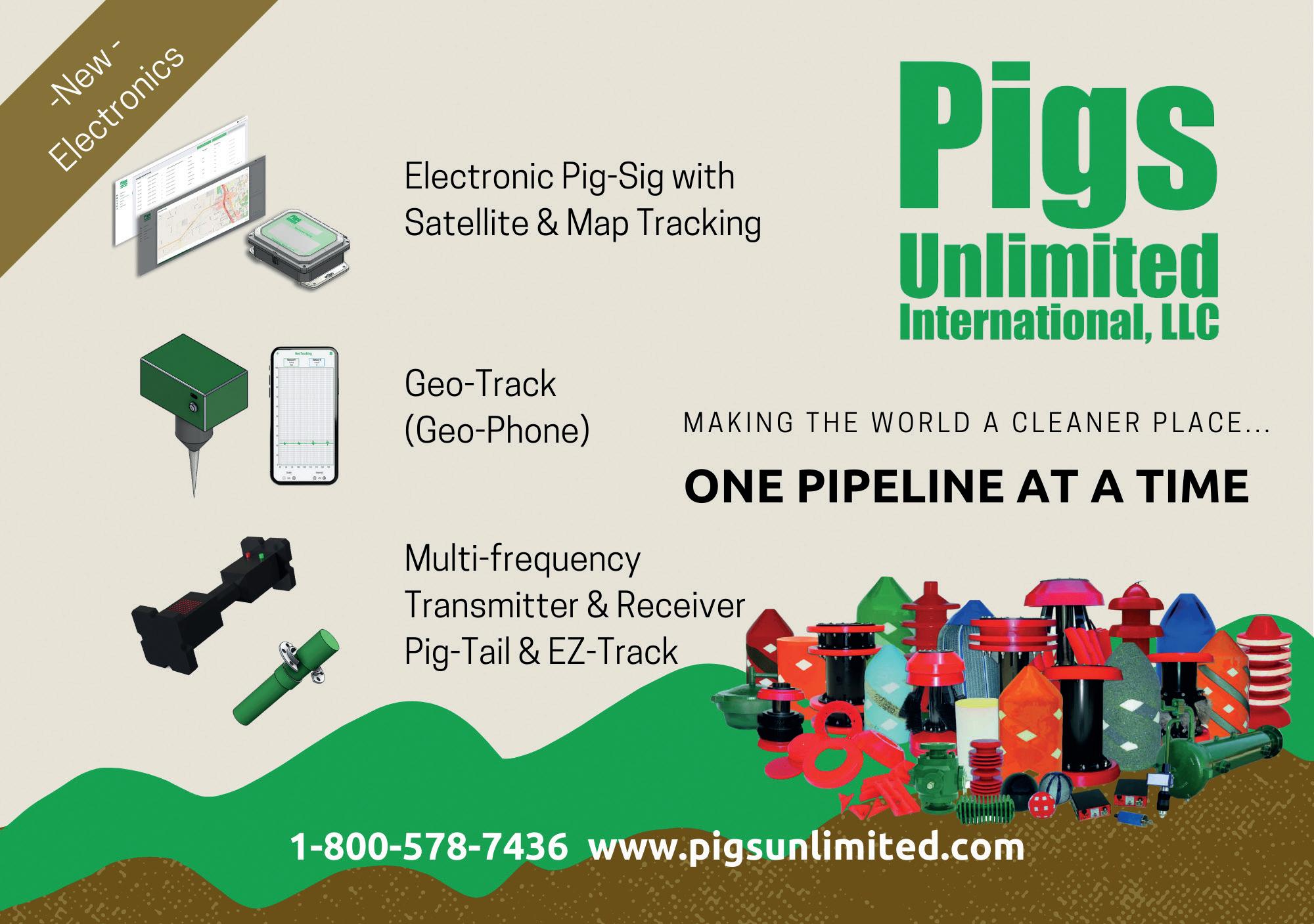
Sicim S.p.A. Via Consolatico Superiore, 96/98 43011 Busseto (PR) - ITALY Tel. +39 0524 930211 - Fax +39 0524 930082 info@sicim.eu - www.sicim.eu
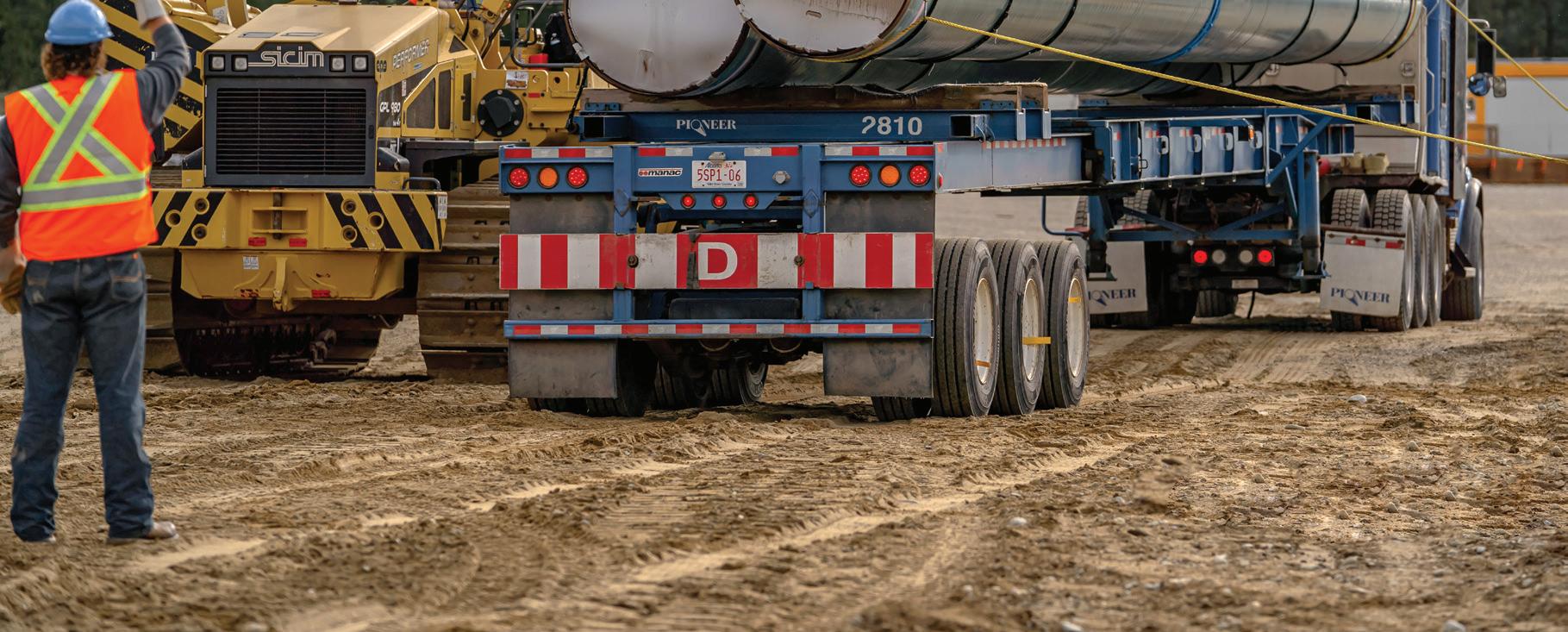

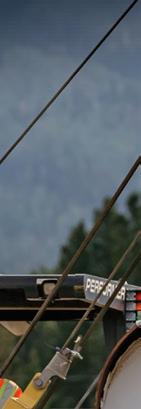
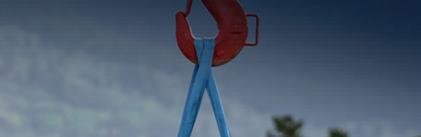

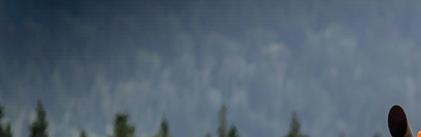
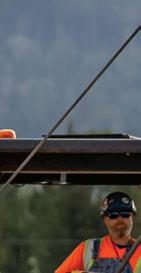
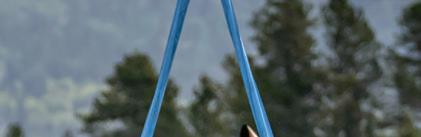
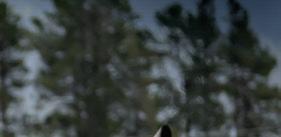
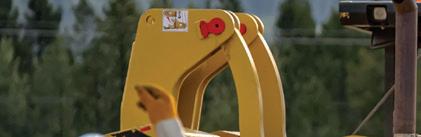
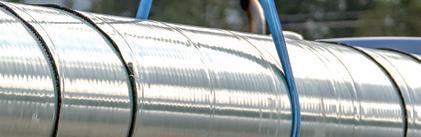
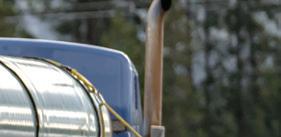
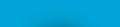

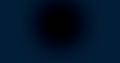
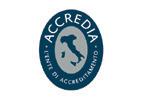
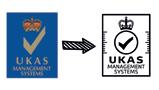
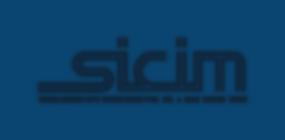



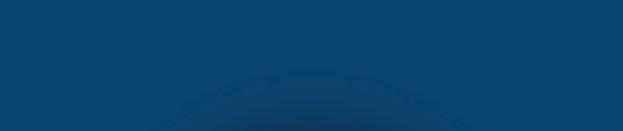

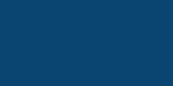

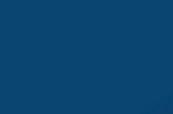

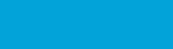





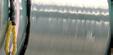
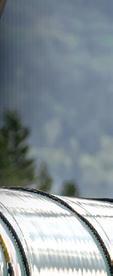

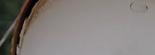

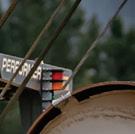
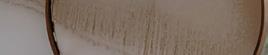
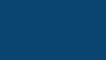
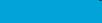
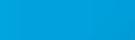
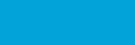
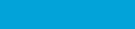


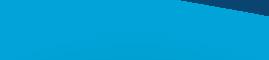

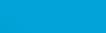
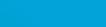











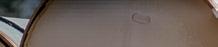










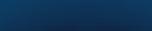





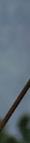


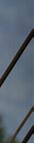


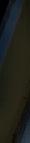


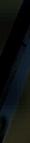
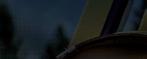
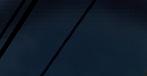
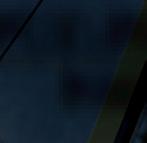
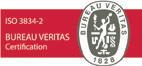
As oil and gas decline, the question of what to do with the infrastructure supporting these industries is important. Some may be reaching the end of their lifetime and will be a target for replacement. However, other parts of the infrastructure remain in good condition with significant potential to repurpose them for new energy sources.
The benefits of hydrogen Hydrogen has emerged as a key player in the energy transition.
Repurposing natural gas transportation systems
The UK’s existing network takes natural gas from five principal import terminals (Bacton, Easington, Milford Haven, Teesside, and St Fergus) and a small number of underground storage facilities.
The UK government’s Ten Point Plan sets out the approach government will take to support green jobs, and accelerate our path to net-zero by 2050 in the UK.1
Nigel Curson, Vice President Technical Excellence, Penspen, UK, talks navigating the pathways towards a national hydrogen network.
R ising oil and gas prices this year have added extra fuel to the calls for a global shift towards alternative and more sustainable sources of energy.
25
The Hydrogen Council estimates the market for hydrogen and hydrogen technologies will reach revenues of more than US$2.5 trillion/yr, and create jobs for more than 30 million people globally by 2050.2
Hydrogen blending with natural gas will be an important step towards net-zero, however, 100% hydrogen must be the end goal to meet the targets. Transitioning to 100% hydrogen with a substantial commitment to green hydrogen produced by renewable power will significantly change the required gas network architecture.
The UK government’s hydrogen strategy suggests up to 35% of the UK’s energy consumption could be hydrogen-based by 2050.3
While immediate pressures – such as the return to economic activity after more than two years of the pandemic, and the war in Ukraine – have diverted short-term attention back towards the security of fossil fuel supplies around the world, the longer-term forecast for oil and gas demand is downwards as the international commitment to the energy transition accelerates.
While the construction of new pipelines, compressor stations and other infrastructure to satisfy different entry and supply points will be essential, much of the existing natural gas pipeline network will be repurposed for hydrogen.
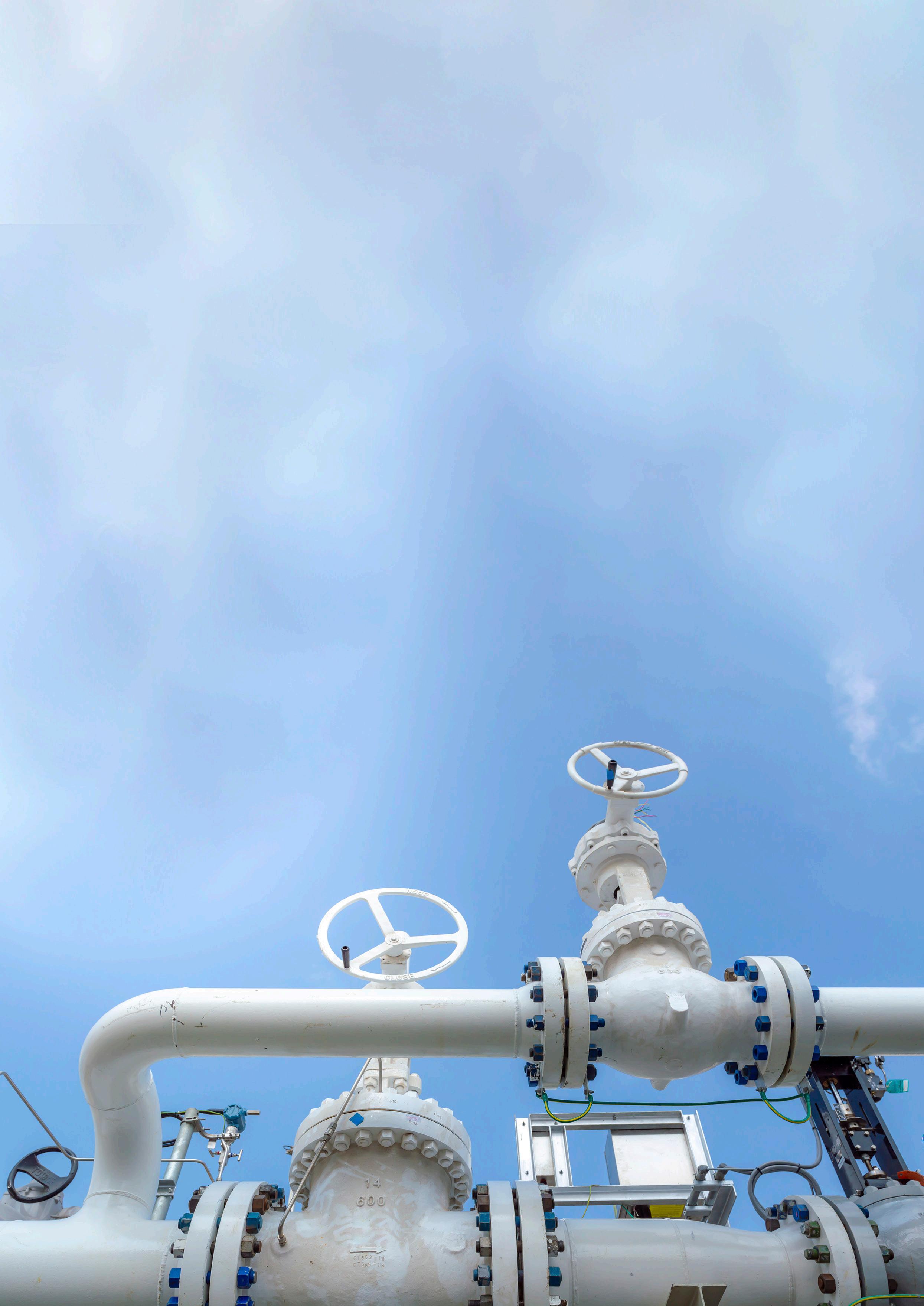
the speed of transition from blue to green hydrogen and the parallel reinforcement of the (renewable) electric grid to support a green hydrogen network are matters for consideration.
embrittlement can lead to a reduction in operational pressure in the pipeline and reduced capacity, a problem when also considering the relatively lower energy value of hydrogen on a volumetric basis (1/3 compared to naturalPossiblegas).
26 World Pipelines / AUGUST 2022
One of the most important issues to consider is the compatibility of the existing network. In systems using steel materials and components, the most important issue relating to hydrogen and pressure-containing equipment compatibility is embrittlement or material degradation.
A likely first step in any strategy is to tackle industrial emissions. Following this, a clear conversion strategy will be essential for the delivery of an effective hydrogen network. Decisions would have to be made on whether to start by linking industrial clusters and then towns and cities. However, the inference is that the process would be incremental with natural gas and hydrogen running alongside each other until a 100% hydrogen network could be developed. This approach would likely require the construction of a few separate hydrogen pipelines with the significant cost exposure that wouldFurthermore,entail.
In a repurposing scenario, for joints and seals, the European Industrial Gas Association (EIGA) and the Compressed Gas Association (CGA) have recommended replacing all flanged joints with welded connections to avoid leaks. Considering some infrastructure has thousands of connections, this could be challenging. However, some experimental results yet to be published indicate leakage might not be such a problem as first anticipated.
High-density polyethylene (HDPE) pipelines make up most of the UK’s gas distribution pipelines, and hydrogen has been found to have little effect on HDPE properties.
Hydrogen embrittlement covers a wide range of degradation phenomena, and is caused by molecular hydrogen diffusing into the metallic matrix. This reduces material toughness, yield strength, and fatigue properties. Hard microstructures are particularly susceptible, including welds or heat-affected zones close to Combattingwelds.
The main sources of fugitive emissions or leaks are venting for operational issues or emissions through cast iron or older infrastructure. Venting and blowdown are critical for normal operations but create emissions. Furthermore, hydrogen’s much lower ignition energy compared to natural gas potentially increases risks. Blowdown normally refers to reducing the pressure of a whole section, not just the content of a vessel. For venting and blowdown, a different approach may be required for hydrogen systems.
Gas is delivered to 22 million homes and industrial users via a transmission and distribution including approximately 7600 km of transmission pipelines, 250 000 km of distribution pipelines, and around 200 000 km of smaller pipelines.
Network compatibility
Technical considerations for the network will include requirements for multiple new and different entry points; the import of hydrogen as a gas, as a super cooled liquid, via ammonia or Liquid Organic Hydrogen Carriers (LOHC) from a global market; the potential requirement for new temporary connections to facilitate the transition; a substantial upgrade of storage requirements to deliver network balancing to accommodate renewables variability; and potentially separate supply networks to accommodate bio-methane and the very pure form of hydrogen required for use in fuel cells.
Critical components are wide-ranging and include hydrogen compressors, electrolysers, valve flanges, and fittings. Before an effective hydrogen network can be established, it is essential to be certain that the products and components used are capable of performing optimally. In some cases, this will require a significant degree of product development and maturity.Compression is necessary for hydrogen to achieve the required energy density. Centrifugal compressors are the compressor of choice for pipeline applications due to their high throughput. However, it may not be possible to repurpose all-natural gas compressors for high percentage hydrogen use. This is because, due to the molecular weight difference of
Reusing as much of the existing onshore and offshore network as possible to deliver domestic supply, security of supply, energy storage, routes to and from storage, carbon capture and storage (CCS), and renewable imports using offshore wind will be important to optimise users’ costs.
There are several factors to be considered in the development of a future-proof, sustainable hydrogen network.
The effect of fugitive and other types of GHG emissions
Critical component/product maturity
Critical network energy balancing of the gas system is delivered by a combination of LNG imports, pressure variation in the network (line pack), and underground storage across severalWithsites.the acceleration of the energy transition, initially, this is likely to continue to be the case, but with hydrogen being blended with natural gas and introduced into the network close to the gas import locations and industry supplied with 100% hydrogen. The hydrogen will be produced by thermal decomposition of methane by steam methane reforming (SMR), auto thermal reforming (ART), or partial oxidation (POX) with carbon capture and storage (blue hydrogen).
Conversion strategy
solutions for steel networks, which are in the very early stages of development, include the use of liners, coatings, or the addition of oxygen to the gas. Much research is still required. Other implications include having to reduce operating cycles because of the reduced fatigue life, and concerns regarding dents since strain hardening could be more susceptible to failure. Non-metallic, fibre-reinforced polymer pipelines produced in half-mile lengths could offer an alternative solution to steel.
With horizontal directional drilling technology from Herrenknecht, pipelines can be installed rapidly, economically and with little to no impact on the environment underneath rivers and other obstacles. Each year Herrenknecht HDD Rigs install over 200 km of new pipelines. herrenknecht.com/hdd/ TRENCHLESS PIPELINE INSTALLATION HDD RIG
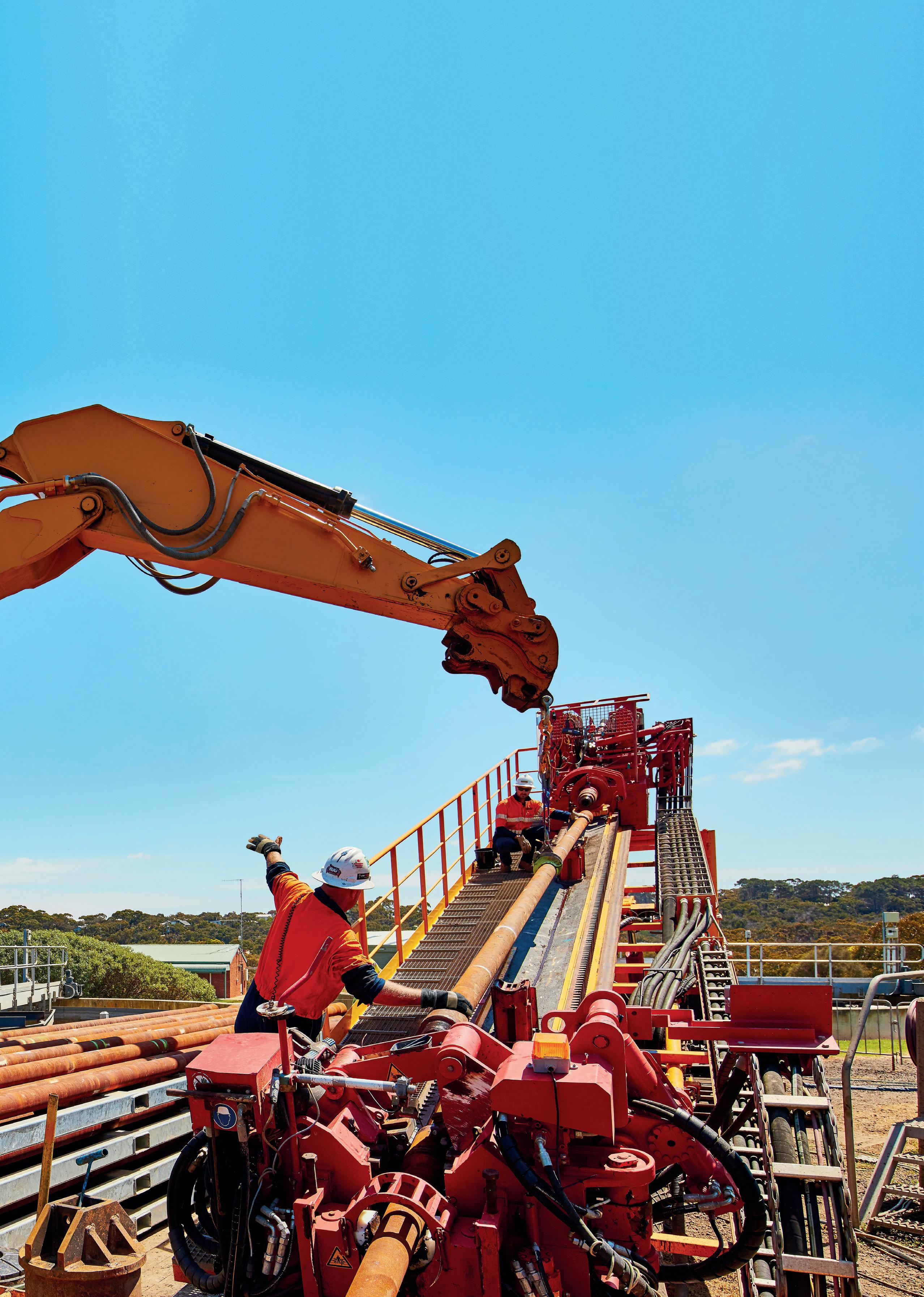
References 1. industrial-revolutionwww.gov.uk/government/publications/the-ten-point-plan-for-a-green2. Hydrogen-Council.pdfhydrogencouncil.com/wp-content/uploads/2017/11/Hydrogen-scaling-upattachment_data/file/1011283/UK-Hydrogen-Strategy_web.pdfassets.publishing.service.gov.uk/government/uploads/system/uploads/
Societal risk and mitigations
28 World Pipelines / AUGUST 2022
hydrogen, centrifugal compressors must operate at top speeds 3.8 times those of natural gas, creating significant stress in the rotor. Also, avoiding hydrogen embrittlement requires more stages and intercooling to a higher degree than natural gas. Alternatives include reciprocal piston compressors, ionic liquid piston compressors, electrochemical hydrogen compressors, and piston-metal diaphragm compressors.
Meeting the challenge
) The design and installation of hydrogen pipelines storage systems, and production systems.
Hydrogen has a much wider range of flammability limits (mixed with air) and significantly lower ignition energy compared to natural gas. This impacts safety around installations and increases hazardous zones that require ATEX-certified electrical equipment. It also increases the ventilation requirements and will require changes in plant layouts, buildings, and equipment.
The study incorporated all pipeline system elements, including the pipeline, inlet and outlet points, block valve stations (BVS), above-ground installations (AGI), pressure reduction stations (PRS), and off-takes.
The hydrogen feasibility technical report contained evaluations of the above-ground equipment and pipelines within the two systems. The company also received an extensive list of recommendations, to ensure the assets are safe and ‘hydrogen ready’ before transitioning, plus an implementation plan of the next steps.
The way ahead? The energy transition is underway, and hydrogen will have a key role in delivering sustainable energy to the UK. To support hydrogen’s growth, the repurposing of existing transportation systems will be critical. However, developing a hydrogen network must be done with caution, bearing in mind the longevity of the likely requirements.
) Assessment of compatibility, capacity, upgrading of equipment, and management of materials testing.
3.
) The support and maintenance of hydrogen and blended hydrogen networks. ) Regulatory support.
Technical specifications and material selection
Uptake of conversion for industrial users
This may include:
)
Industrial users will only convert to hydrogen if they can be reassured that their supply is guaranteed and secure. If, for example, an industrial manufacturer has only a single steam methane reformer to rely on for hydrogen, the concern would be that any breakdown would impact the business. By contrast, the natural gas network has many inputs and is demonstrably extremelyConnectingreliable.the UK’s industrial clusters so they could support each other through a hydrogen network would be one way of creating security of supply, generating manufacturer confidence, and encouraging greater support for the hydrogen industry.
Therecommendations.transitionwork to develop a hydrogen network, and particularly repurposing infrastructure with uncertain provenance, is complex and requires detailed preparation and potentially expensive testing. For asset owners, a critical component of this work is a feasibility assessment and review of existing assets. Uniper UK Ltd recently commissioned Penspen to carry out a fitness for continued service assessment, site audit, hydrogen feasibility technical report, and design and integrity review for the Theddlethorpe to Killingholme (KIPS) and Blyborough to Cottam (BCot) pipeline systems. The systems are designed to provide gas to Uniper’s owned and operated power plants at Killingholme, and the Cottam Development Centre (CDC) respectively.Uniperis investigating blending hydrogen with natural gas at various ratios, up to 100% hydrogen, together with the suitability of the existing BCot and KIPS assets. The company requested a study to determine their feasibility and system compatibility with hydrogen.
The services included a site audit and assessments at various levels. These included a collation and review of documentation; an equipment inventory audit; system flow assurance and thermal input assessment; hydrogen degradation mechanisms; AGI equipment; pipeline design and integrity reviews; safety assessments, including venting and hazardous area zones; maintenance and inspection changes; a pipeline quantitative risk assessment (QRA); personnel competency and training; emergency response; and regulatory requirements.
However, a hydrogen network will require the development of much larger compressors than are available today. In the same way, there are challenges with electrolysers around maintenance, longevity, and potential deterioration of the catalysts. No doubt solvable in time, but much has still to be learned about the manufacture of electrolysers and compressors at scale before we can have confidence in the establishment of a widespread hydrogen network.
In making decisions about the repurposing of natural gas infrastructure for hydrogen, asset owners need to enlist the support of a partner with solid expertise and a full understanding of hydrogen-related projects.
Much research has been done, and much more must still be done, in this rapidly developing area.
The risk is higher for pure hydrogen close to the pipeline, but this reduces faster compared to natural gas as the distance from the source increases. As a result, the ‘zero risk’ distance for pure hydrogen is shorter than it is for natural gas.
srl Loc.Spigarolo,www.laurini.com43011
WELCOME TO THE NEW LAURINI WORLD.
Busseto, Parma, Italia Laurini Officine Meccaniche lauriniofficinemeccaniche
CAN EVEN HAVE A NAME.
TODAY, SUPER-HUMAN MACHINES
At the dawn of times, there were brave men who, armed solely of their force and intelligence, built their instruments, and therefore their world. Then came the time of the machines : with their dark sounds and obscure systems, they served the human race - but at which extent? Today, we embrace the time of the super-human. Today, the true machine is just an extension of your arm. Laurini, from its birth till today, never stopped chasing innovations, dreams, and the future horizon : we work to make possible the impossible. We fight to create your endless possibilities. Meccaniche
Laurini Officine
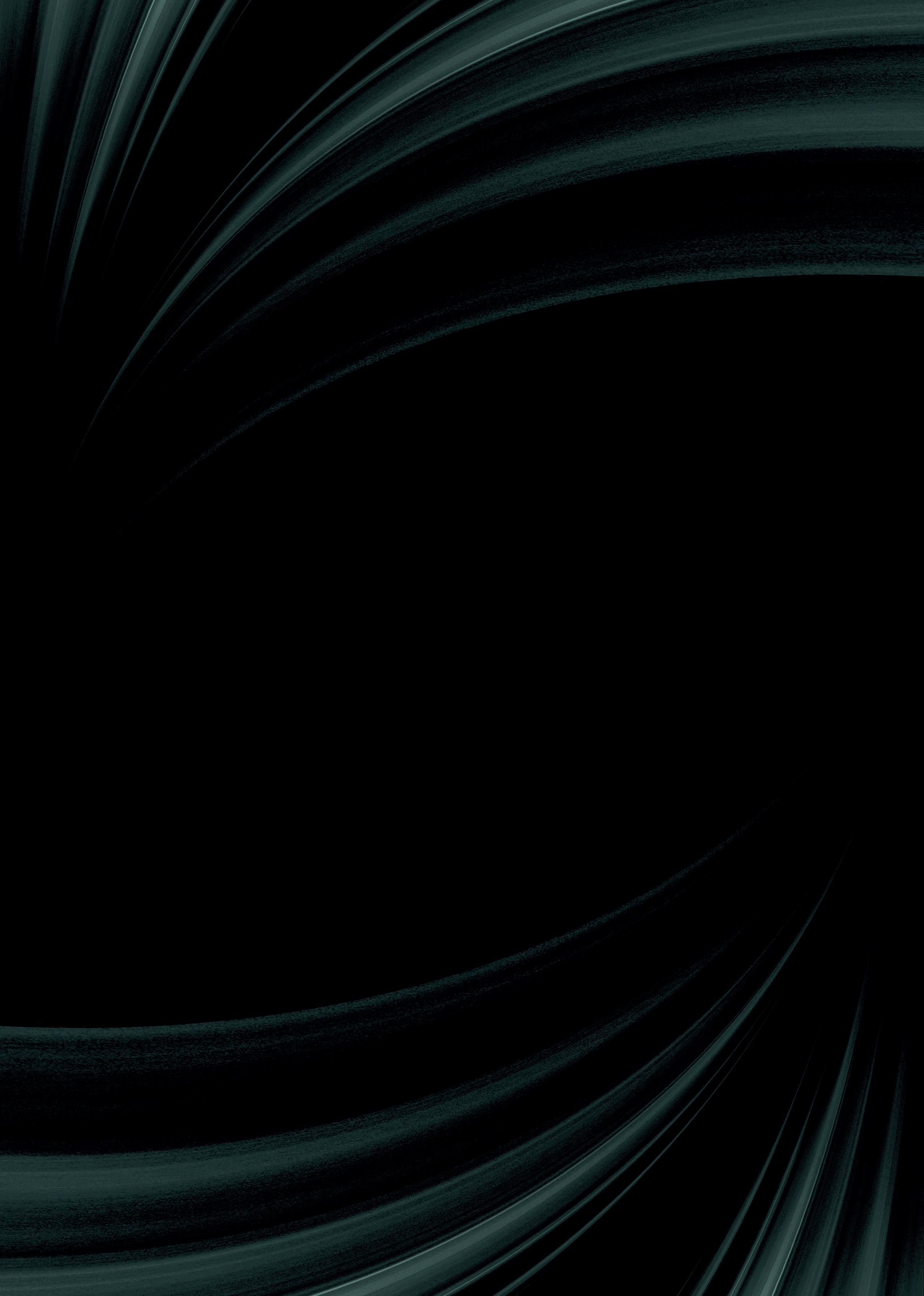
165Spiecapagboulevard de Valmy 92700 Colombes France Ph.: +33 1 57 60 95 15 Follow us on Linkedin Our ambition is to continue being the world’s leading international EPC pipeline and facilities contractor by securing added value to our clients, investing in our people and the communities we work with. WITH SAFETY WITH QUALITY WITH RESPECT TO THE ENVIRONMENT AND WITH SOCIAL RESPONSIBILITY theLayingfuture
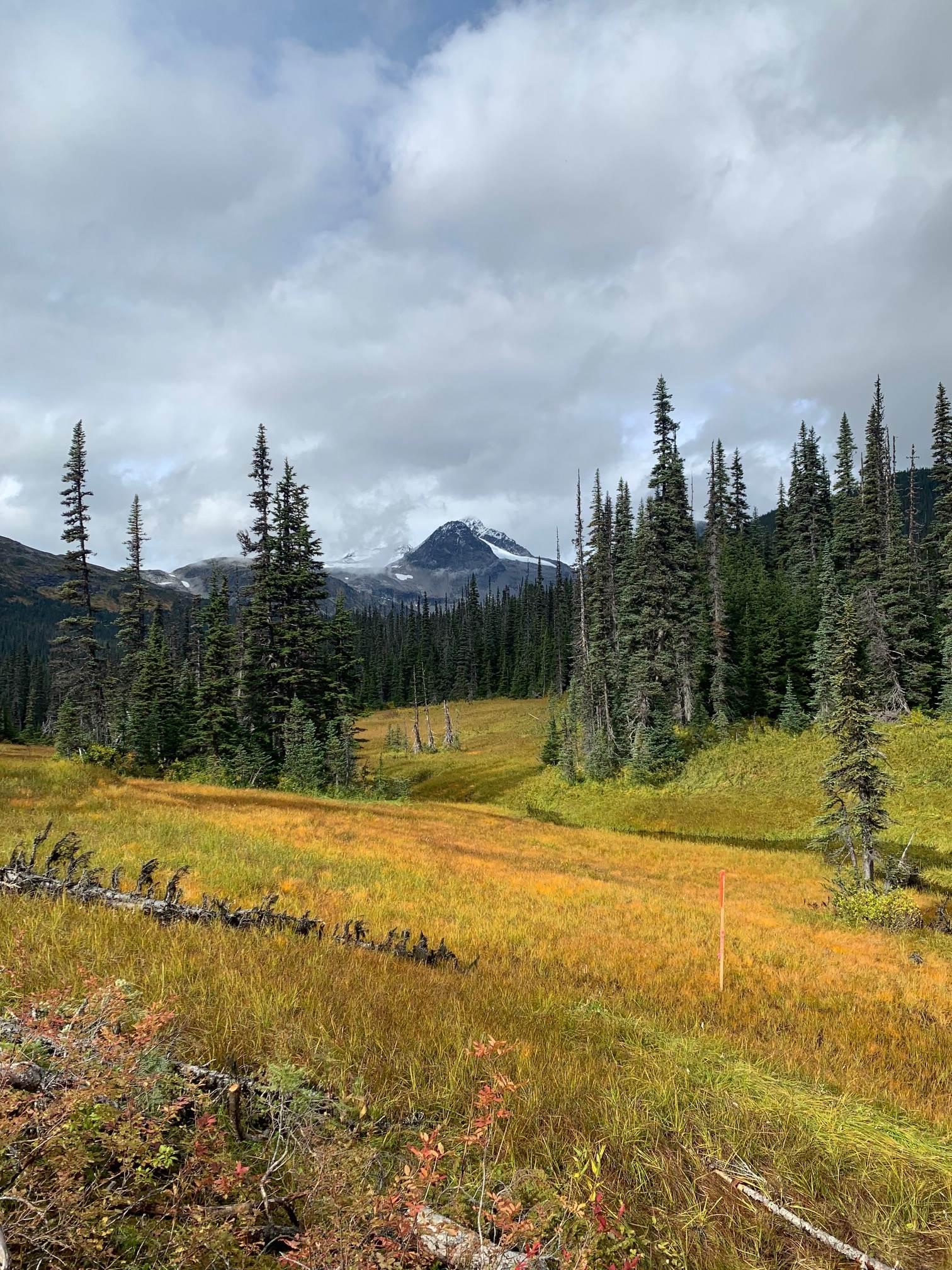
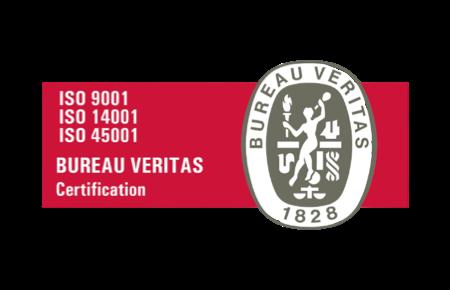

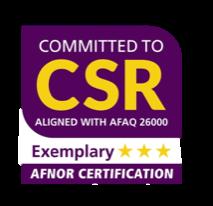

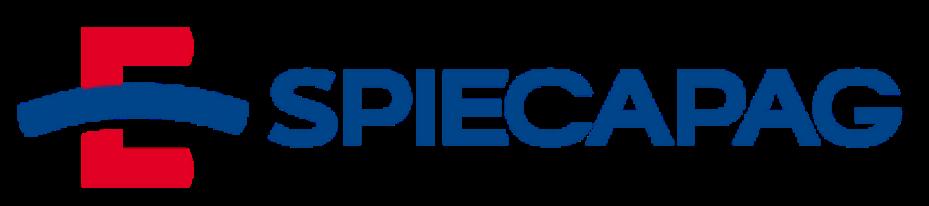
C
Aaron Moore, CWI, Product Manager, Miller Electric Mfg. LLC, USA, outlines the best practices for improving productivity and reducing downtime in pipeline welding.
31
ritical pipeline welds demand highly skilled operators capable of meeting strict quality standards and deadline pressures. Failing to be a consistent performer can be a problem, especially in a next-man-up environment. Maximising productivity in pipeline welding – while prioritising quality and avoiding unnecessary downtime – are the main priorities for pipeline Considerwelders.howsome best practices and choosing the right welding equipment can help save time and maintain quality on the ROW. Pipeline welding priorities
Low-carbon, low-alloy steel pipe has traditionally been welded using the shielded metal arc welding (SMAW) process. Cellulosic filler metal electrodes and downhill welding techniques have remained relatively unchanged over the years, but welding codes, testing procedures, and quality standards have become more stringent. At the same time, contractors face increasing competitive pressures to complete projects more quickly and efficiently. This creates an urgency to ensure projects stay on schedule, meaning high productivity while maintaining weld quality and avoiding repairs is crucial.Forpipeline welders, these changes have meant more pressure to avoid weld defects while keeping up with tight project timelines. Welders often have a quota of the number of weld joints they must complete in a day. They can’t afford to get side-lined by issues with their welding equipment. When that happens, they’re unable to perform their job, or they may need to rely on borrowed equipment.

The use of harder (X70 and above) variations of pipe has become more common in the field, as engineers design pipelines to maximise service life and reduce maintenance costs. However, factors such as heat input, and the diffusible hydrogen value for the filler metal become more critical. As a result, they may require specialised filler metals and welding processes when being constructed.Thedemand for advanced wire welding processes, like pulsed MIG and a modified short-circuit MIG, such as the Regulated Metal Deposition (RMD®) process from Miller, is growing every year. These processes can deliver significant increases in deposition rates and welding speed, while also improving quality and minimising defects. Welders who are proficient with wire welding increase their job opportunities in pipeline welding. Although downhillSMAW welding will be around for the foreseeable future, operators shouldn’t let their welder/generators limit job capabilities, so it’s important to have a welder/generator capable of running different wire processes.
A wireless remote also eliminates the need for the heavy control cable, which reduces setup time as well as cable management and maintenance on the right-of-way.
New features, like industrial USB ports, have been introduced on some welder/generators. Having access to free software updates from the manufacturer gives operators the ability to quickly troubleshoot their machine while also providing the opportunity to stay up to date with arc development. Software for engine-driven welder/generators is continuously being improved and optimised by the manufacturer.
One example is Dynamic DIG™ technology from Miller, which is designed specifically for downhill pipeline welding. It produces a tailorable arc that can be adapted to the welder’s preference and the application. Having an optimised amount of drive in the puddle – combined with a faster adapting arc – means operators can better handle issues like bad fit-up and uneven land thicknesses, ultimately enabling more flexibility to adapt and produce a higher quality of weld. The technology also creates a more manageable, drier puddle, which can maximise drive and penetration and allow the operator to carry a larger puddle at high travel speeds.
Another engine-drive technology to look for is a wireless remote that allows full control of the machine interface in the palm of the operator’s hand. The ability to swap between programmes with the press of a button lets operators adjust settings like amperage, arc control, and dig range for each pass – from the root to the cap pass. This eliminates the time to adjust settings and enables optimal settings for each pass.
3. Choose reliable and consistent equipment Machine reliability and consistent performance are a basic need for pipeline welders. Look for a welder/generator that won’t require different settings in the hottest time of the day vs when the shift started. Also, keep the welder’s helper busy by looking for equipment that can produce auxiliary power while simultaneously welding – without affecting the weld arc.
1. Be flexible to improve versatility
Pipeline welding best practices
For pipeline welders, weld quality and productivity are the two staples that will get them called back for the next job. Following some best practices – and choosing the right welding equipment and technologies – can help operators tackle challenges on the ROW and optimise field welding performance.
Figure 2. The demand for advanced wire welding processes is growing every year. These processes can deliver significant increases in deposition rates and welding speed, while also improving quality and minimising defects in pipeline welding.
32 World Pipelines / AUGUST 2022
Figure 1. Although downhill-SMAW welding will be around for the foreseeable future, operators shouldn’t let their welder/ generators limit job capabilities. It’s important to have a welder/ generator capable of running different wire processes.
2. Take advantage of new engine-drive technologies When looking to maximise weld quality and machine performance, one place to turn is the welding equipment on the rig. Like some filler metals, much of the welding equipment seen in the field has remained unchanged, leaving significant room for improvement in areas of arc quality and adaptability, machine consistency and ease of use. Newer welding technologies can help improve weld quality while also boosting productivity and reducing rework.
Following some best practices can help optimise equipment performance and save time. Consider these three tips for pipeline welding:
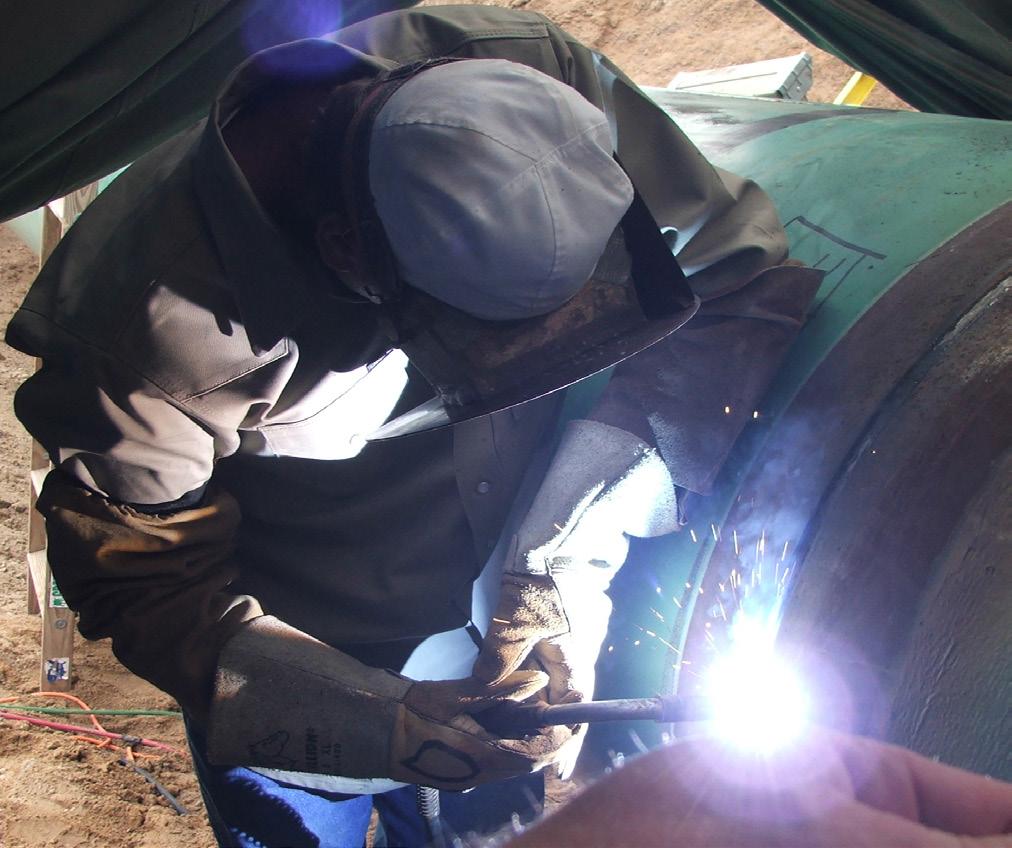
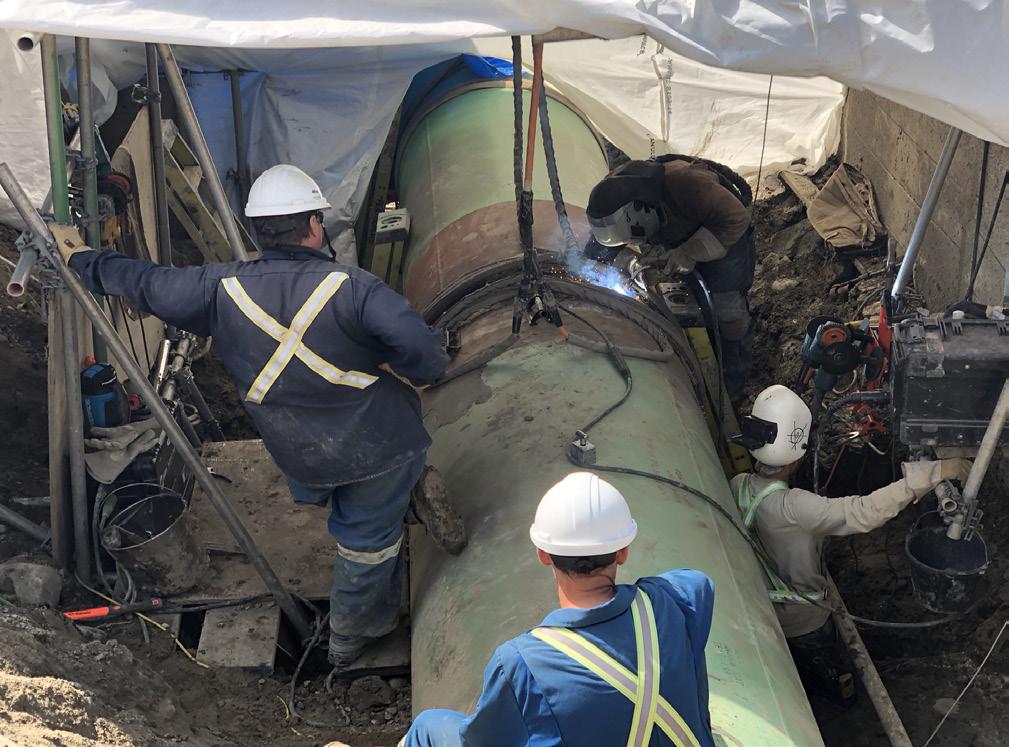
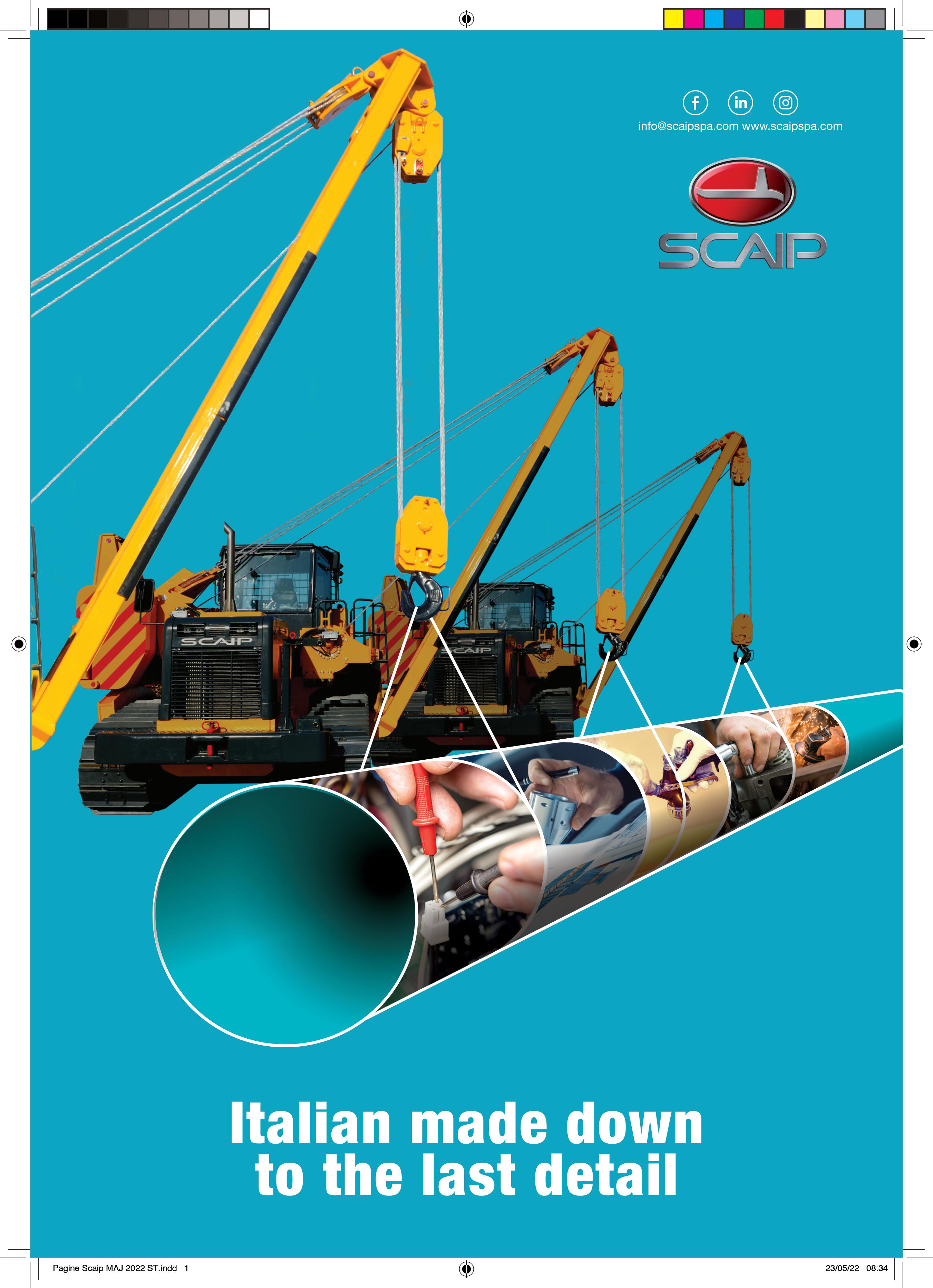
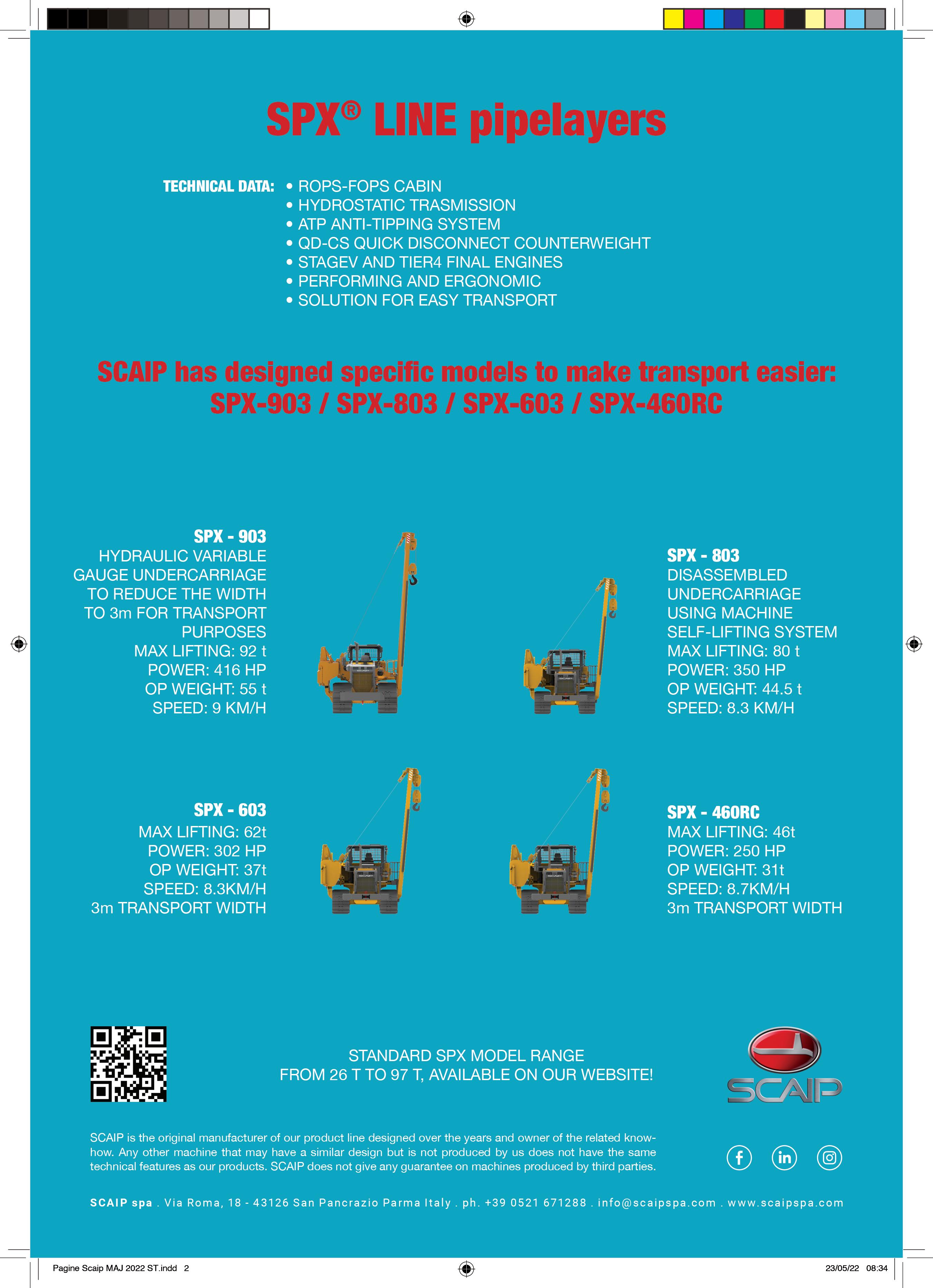
Building trust to protect the workforce
T he impact of labour shortages is being felt in construction industries across the world. Business Insider recently reported that, according to figures from the US government, there are 100 000 fewer workers in the oil and gas industry than pre-pandemic. So, with over 19 000 miles of pipeline construction planned for 2022 in the US alone, it is now more critical than ever to ensure robust health and safety practices are in place to protect the health and wellbeing of the current workforce.
The challenge of labour shortages and rapid staff turnover often leads to a reliance on short-service, temporary or selfemployed workers, which can increase the risk of accidents and injuries on pipeline sites. The risks are increased by a number of factors, including limited experience and a lack of time to deliver consistent health and safety training.
Natalie Henley, Remote Medical International (RMI), Americas, outlines health and safety best practice at pipeline sites.
Additionally, towards the end of construction projects, when timelines are often pressured, workers face the risk of losing focus on essential daily safety measures, as well as neglecting their own health and basic hygiene, which can result in more safetyWithhazards.thisunique set of safety challenges, having specialist medics and Health and Safety Executive (HSE) consultants onsite can help workers manage the challenges of staying healthy and maintaining safety best practice on pipeline projects, improving both their health and job performance, as well as reducing unnecessary recordables. Remote Medical International (RMI) helps organisations to achieve this by providing highly-qualified staff to pipeline construction sites around the world. With over 20 years’ experience in the field, RMI’s safety and medical services champion best practice to ensure the health and safety of the workforce.
The longer the project, the greater the risk that workers will become fatigued, and prone to injury and illness. To tackle this, RMI’s medics take a proactive approach to overall long-term healthcare, creating the safest of working environments. One part of this strategy is achieved with the support of our mobile treatment centres (MTC); four-wheel drive clinics that are equipped to handle rough terrain, allowing medical providers to reach a worker who may need medical assistance.RMIMTCs also allow medics to patrol sites daily and stay in regular communication with the 33

It is essential that all remote medical teams are supported by continuity of care services. When injuries or illnesses on the job require a higher level of care, RMI’s active case management team coordinates and monitors care of the patient throughout the process. By identifying the best local urgent care clinics and emergency departments, this ensures a seamless transition from the job site and back, including care quality screening. As a result, the employer benefits from reduced control costs and the employee receives the expediated medical care that they deserve.
Creating a strong relationship between an onsite medic and the workforce enables delivery of preventative care and training, and ensures that health concerns are addressed quickly, avoiding risk of further injury and illness, and limiting the number of recordable incidents.
RMI medics work alongside the team, protecting workers and preventing as much risk to health as possible. Actions as simple as taking workers out of the rain to dry off, or putting them in the shade and in an air-conditioned truck to cool off when it’s hot, go a long way in preventing accidents and enabling teams to keep working.
Continuity of care
Boosting employee morale
workforce, enabling quick response to incidents and, crucially, preventing delays in treatment from exacerbating health issues and injuries. Having a medic as a constant presence on a site builds trust among workers, and encourages greater transparency, and a safe environment for workers to discuss their health issues. Medics can also provide support to workers struggling with common issues exacerbated by extreme weather, such as fatigue and dehydration which, if left unmanaged, can develop into serious issues which incapacitate workers. By implementing preventative practices, RMI medics have been able to detect undiagnosed diabetes, hypertension and asthma within customer workforces, and provide support in the management of these conditions, creating an open dialogue which leads to workers feeling confident enough to seek out their onsite health provider without mandate or prompting.
On one pipeline construction site, a worker injured his thumb on the job, and the RMI medic was able to quickly treat the injury, give the patient the appropriate medication, and educate them on prevention, all within 20 minutes. Without the MTC, it could have taken three hours to transport the patient to a clinic for treatment, creating a significant disruption to the team for the day, as well as a large and unnecessary bill. This constant support on the ground relieves the pressure on project safety managers to ensure the safety of their teams.
Best practice for leading a healthy lifestyle onsite
Maintaining basic personal hygiene is often a challenge that comes with a transient lifestyle, and is one of the important points our HSE professionals regularly reinforce with staff on pipeline construction sites. 80% of infectious diseases are transmitted through touch; when performing physically demanding task, combined with long hours in the sun, workers should wash their hands frequently to help prevent diseases and illnesses from developing, and stops them from spreading in situations where workers are often living together in basic accommodation. Due to the remote nature of pipeline construction projects, access to nutritious food can be difficult, and in many cases, workers choose unhealthy options from nearby service stations. Workers need reminding that pipeline construction is physically demanding, and that their bodies need quality calories to keep up with the physical demands of their job and keep them safe.
Implementing initiatives that improve the overall wellbeing of workers is an effective way to reduce onsite injuries, maintain morale, protect productivity, and retain talent. When workers are alert, well hydrated, not overworked, and getting enough sleep, they are happier, have more energy and make smarter and safer decisions.RMIassists pipeline construction organisations with quality health benefits and additional wellness programmes, such as fitness classes, nutrition guidance and health check-ups, that help to improve the health and safety of their workforce, reduce risk of injuries and illness, and ensure that workers feel valued.
Figure 1. RMI medic in action. 34 World Pipelines / AUGUST 2022
The presence of an RMI professional on pipeline construction sites is crucial for reinforcing healthy lifestyle best practice among workers, especially as they approach the end of a long project, which is usually the most dangerous phase.
One of the most important habits that our medics work to advocate on hot construction sites is staying hydrated. Pipeline construction is a physically demanding job, where workers are on projects for long hours and frequently in hot weather. Often pipeline workers do not drink enough water to stay hydrated and maintain their health while working outside in the heat all day, and dehydration can lead to low productivity.
Caffeinated energy drinks are very popular among construction workers due to the long hours of work and the energy they need for the job, however, caffeinated drinks
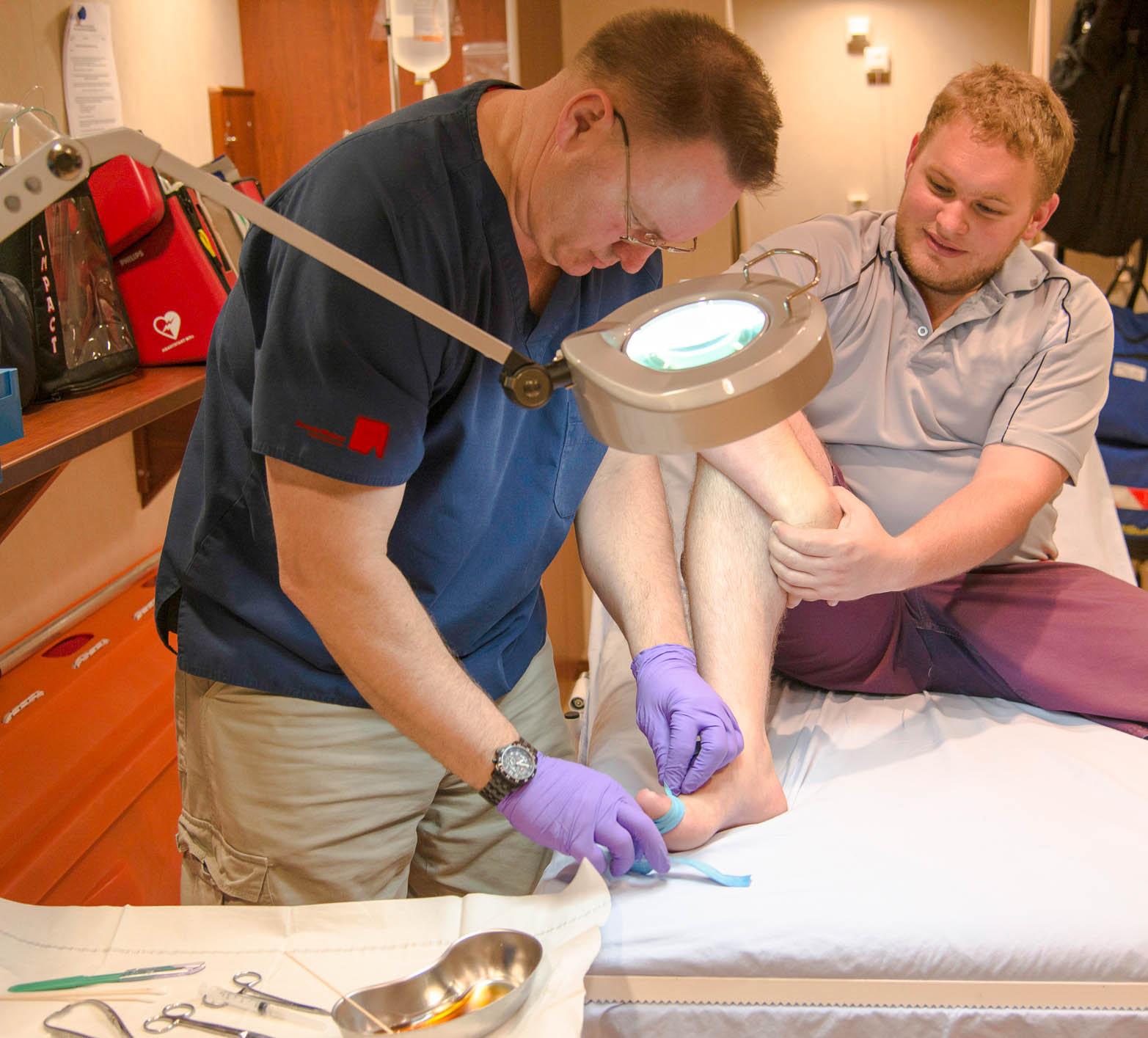
Figure 2. Pipeline being lifted on a construction site.
can lead to dehydration and cause a ‘crash’ in energy. This can be very dangerous when operating vehicles or heavy machinery on worksites, and can potentially put a worker’s life at risk. Instead of relying on caffeinated beverages to cope with the long working days, our medics often recommend that workers should aim for at least eight hours of sleep each night, stay hydrated and take regular breaks to help them stay alert.
Summary Although health and safety best practice procedures can take time to introduce, develop and implement, organisations should prioritise considering all of these to improve and maintain the wellbeing of their most important asset, the workforce. The expertise of RMI health and safety professionals means that they know how best to address this in the most robust way. Intervening and adjusting habits on the worksite will help avoid injuries, increase productivity, and lower costs for any pipeline construction project.
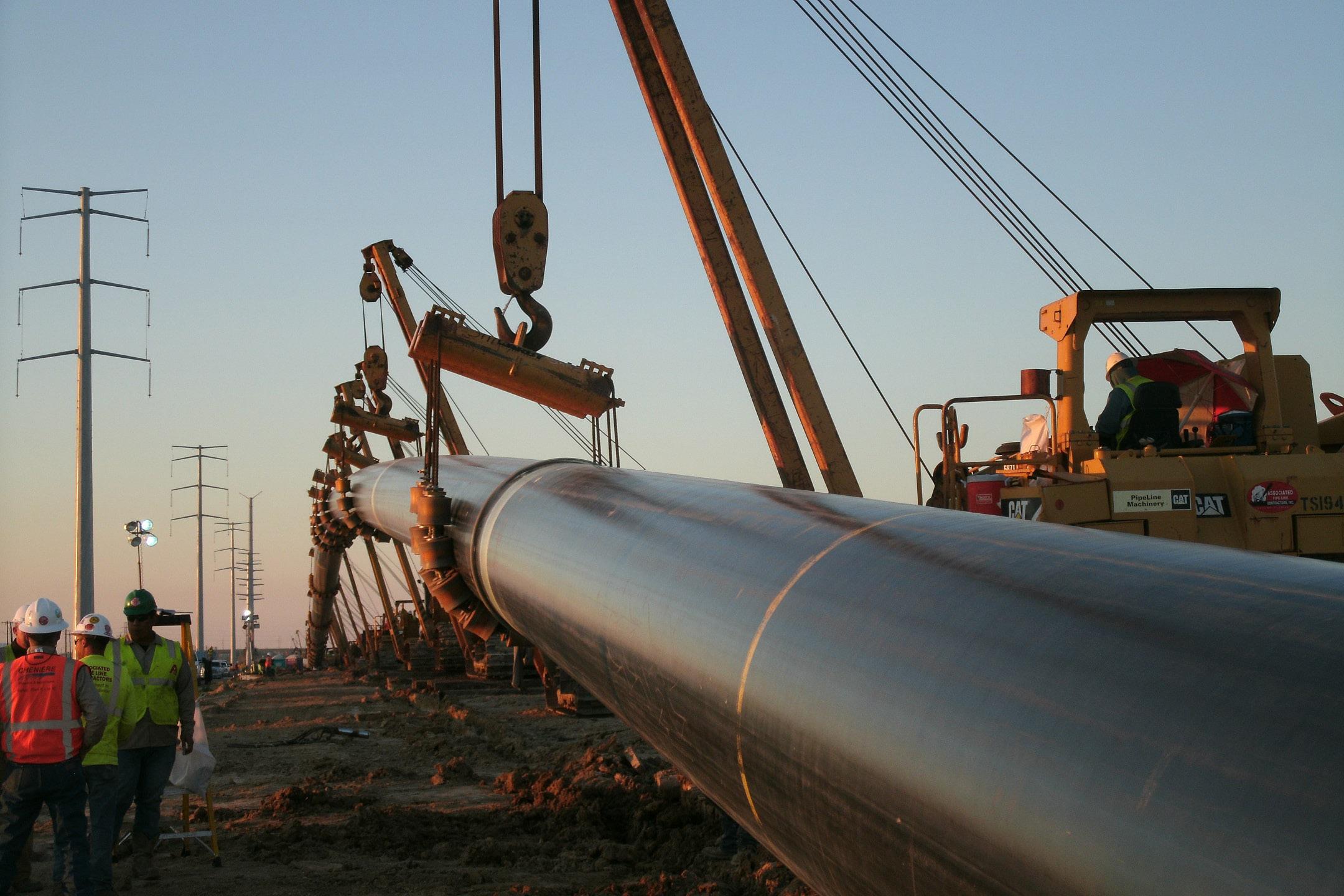
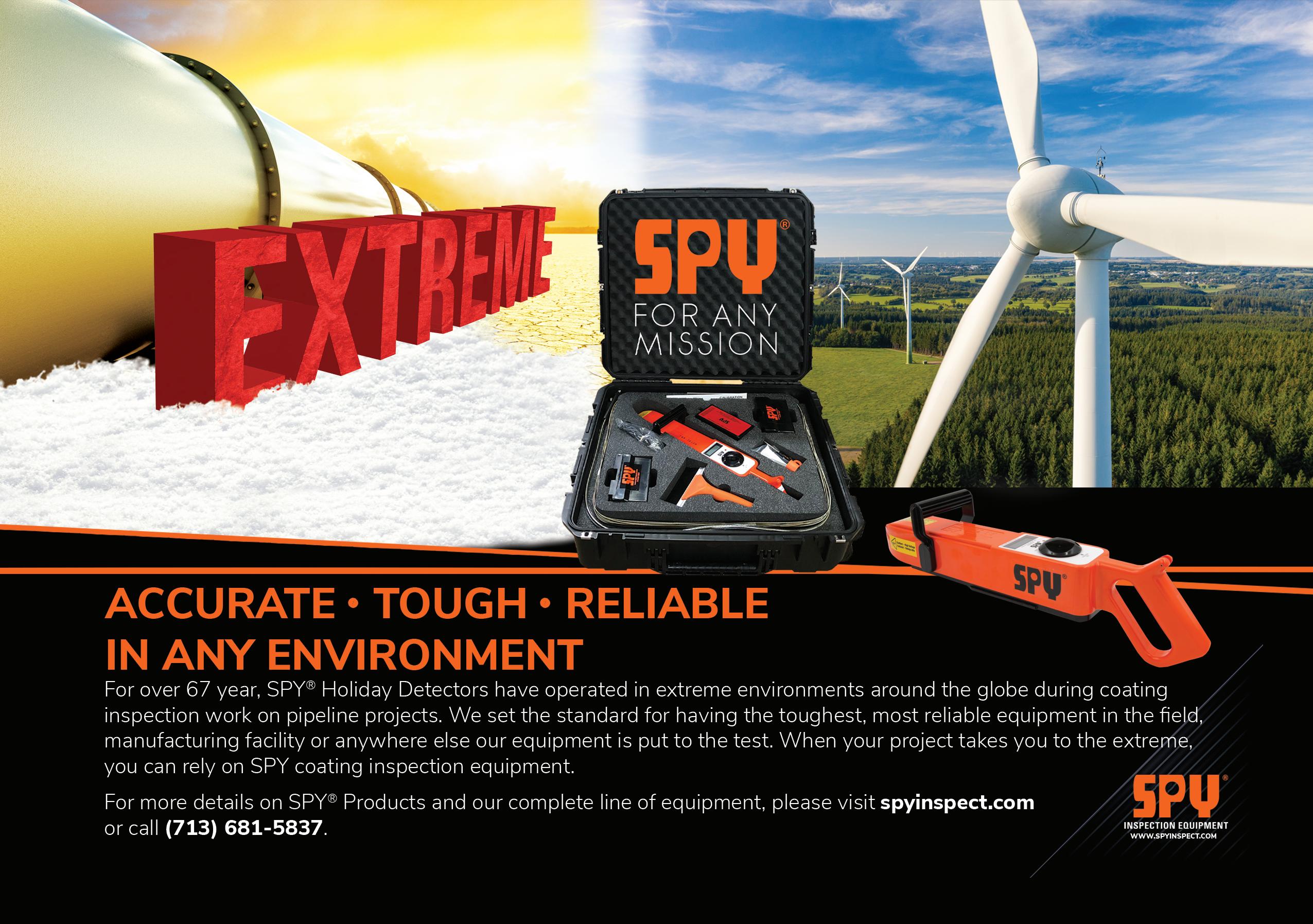
Worldwide Sales-Rental-ServiceDistribution Challenger Services PipelineEquipmentConstruction Challenger Services supplies pipeline equipment to contractors throughout the world. A list of some of the equipment we can supply. Challenger Services designs and produces our own line of pipelayer attachments (pictures above), welder tractors, pipe carriers, stringing trailers, pumps and other specialized equipment. CHALLENGER SERVICES 4530 South Jackson Ave - Tulsa, Oklahoma 74107 USA Tel. +1(918) 447-0055 - Fax +1(918) 447-0067 Email sales@challengerservices.com Web-www.challengerservices.com CONTACT ANDY SOLOMON AT CHALLENGER SERVICES AND LET US PLACE OUR EQUIPMENT ON YOUR NEXT JOB. Pipelayers Welder Tractors (Tack Rigs) Pipe Carriers Pipe Bending Machines Clamps and Mandrels Pipe Facing Machines Beveling Machines Hydraulic Power Units Fill and Test Pumps Charge and Ditch Pumps Pipeline Air Compressors Vacuum Lifters and Pads Boring Machines Holiday Dectors.....and more.
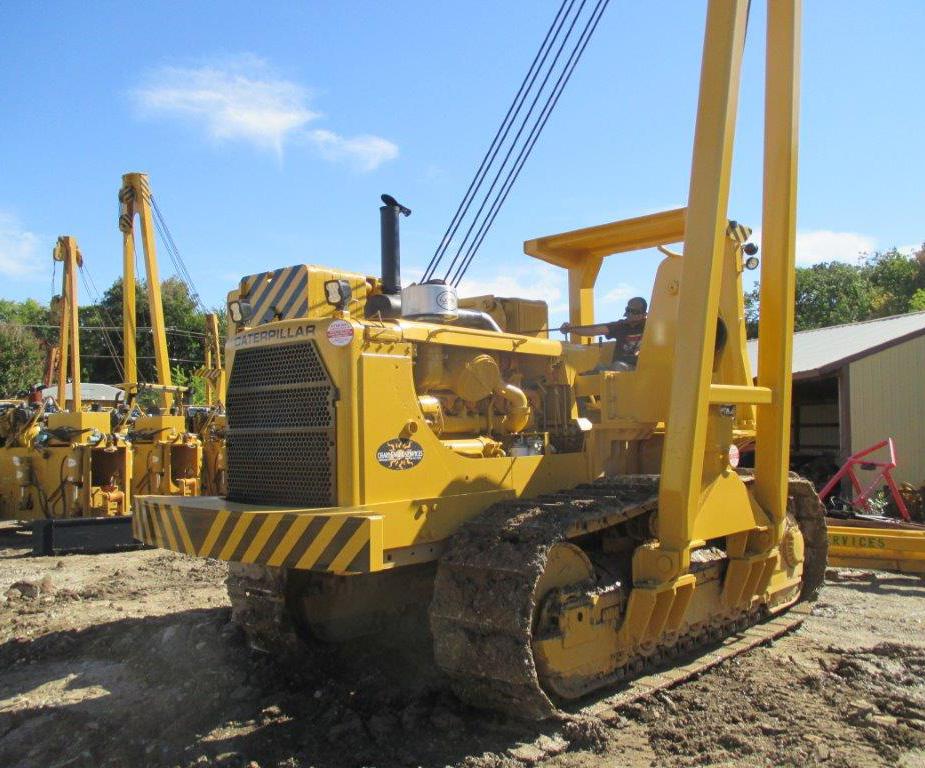
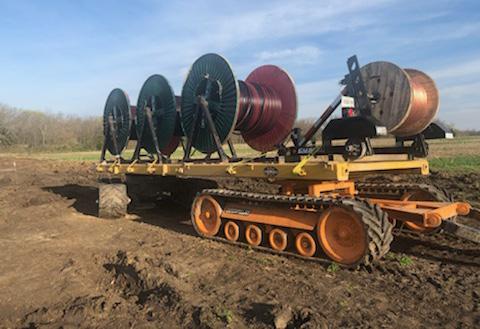
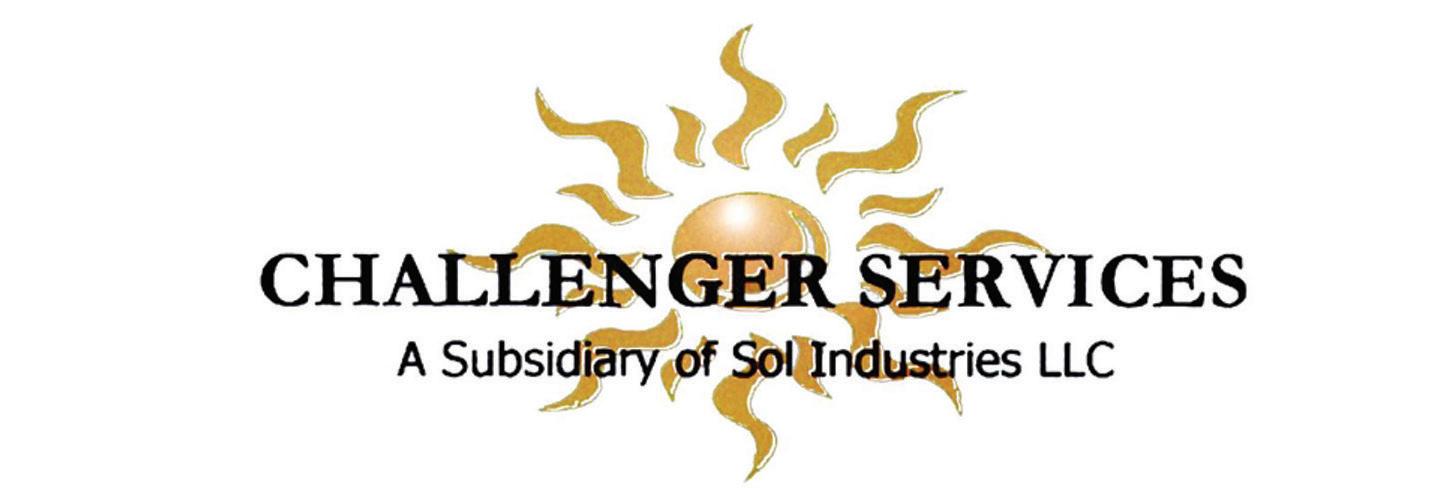
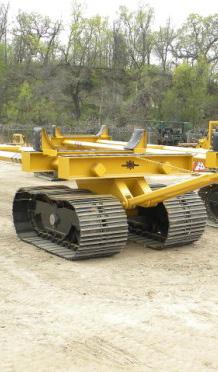
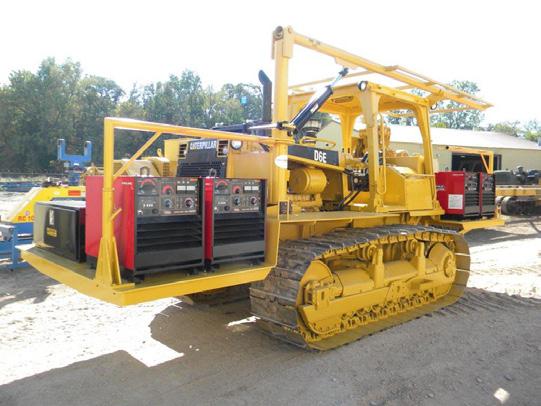
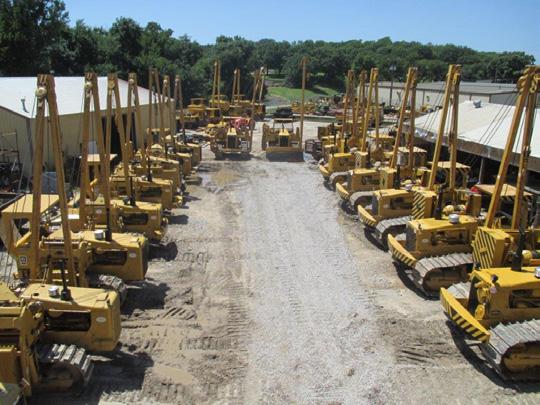
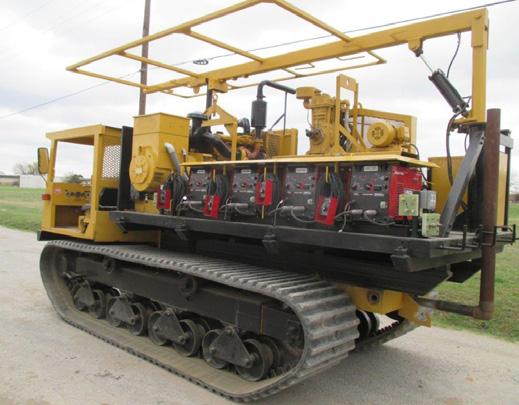
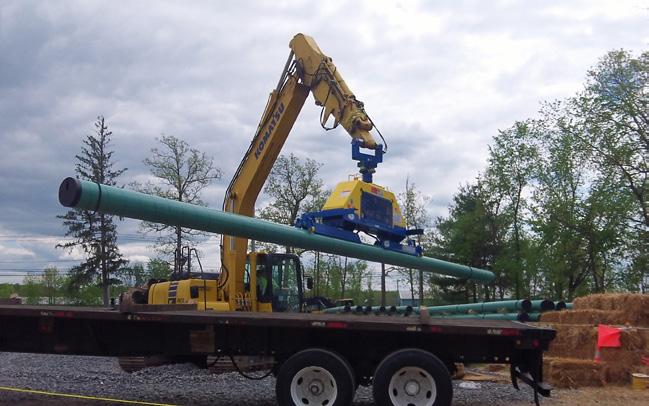
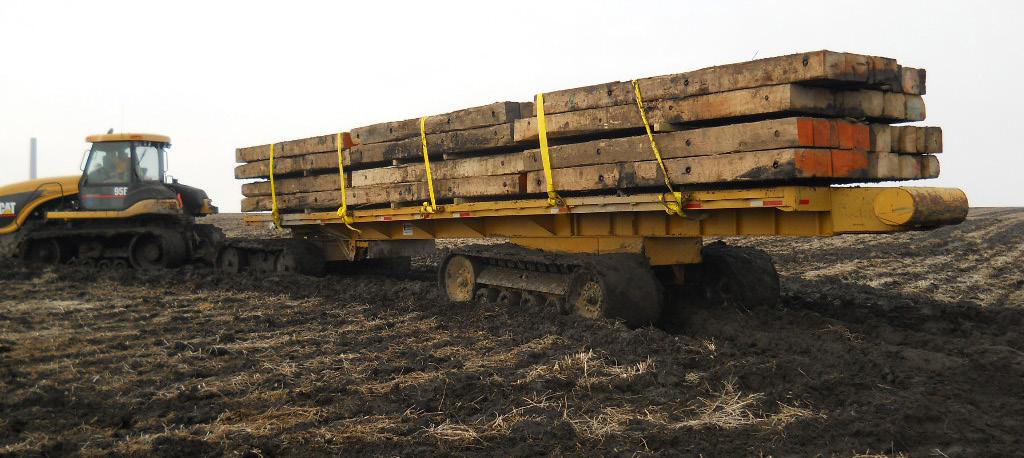
37
With Novarc’s SWR, pipe fabrication shops and offshore platform construction projects that involve welding stainless steel and carbon steel pipes also experience significant gains
Novarc’s collaborative SWR helps to minimise the manufacturing bottleneck caused by the dwindling supply of qualified labour being experienced in a number of traditional industries, by enabling welders working with the cobot to be significantly more productive and efficient.
W
Mahyar Asadi, VP Innovations, Novarc Technologies, Canada, highlights the importance of automated welding technology in manufacturing operations, particularly when used in conjunction with human operators.
elding automation is being adopted rapidly throughout a variety of industries such as energy, oil and gas, and offshore construction, and it is increasingly becoming standard welding practice. Not only does automation mitigate the dangers of high-risk welding jobs, but it also significantly increases productivity and weld quality, allowing customers to become more competitive when bidding on jobs, and increasing margins on contracts they’ve already won.Novarc has been at the forefront of automation, as the company was one of the first to introduce advanced welding technology in 2016 with its Spool Welding Robot (SWR), essentially the world’s first collaborative pipe welding robot, or in short, cobot.
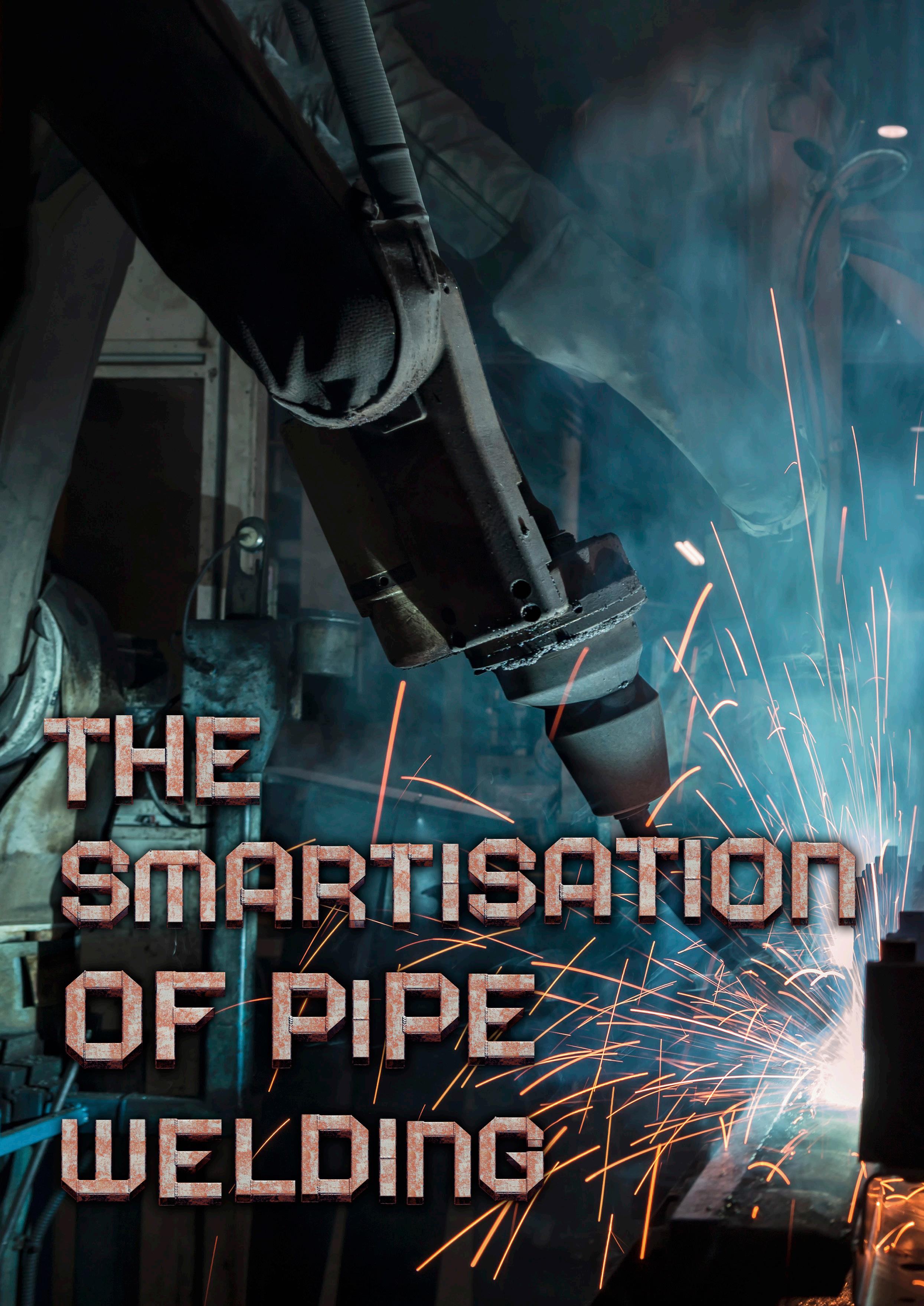
Currently, there are many market demands for smart welding systems, including:
) Adaptive seam tracking and control of misalignments in the welding preparations.
Existing Industry 4.0 platforms spread out the learning domain to incorporate information from other welding machines. These platforms enrich the Figure 2. Novarc’s welding automation technology does not abandon the human operator, but works alongside the welder.
NovEye increases the autonomy of the cobot, and allows the operator to work on more sophisticated tasks. NovEye monitors and makes real-time corrections to the welding operation, based on years of data collection and machine learning.Being able to produce an AI system that can control a weld pool with the required latency and weld quality performance that’s required is a significant task, and a challenge that is not immediately realised. AI systems are no longer explicitly programmed to deliver a perfect task; instead, these smart systems are designed to learn and improve over time. In other words, they can start with the current state of your welding process and self-direct through the machine learning to a better state.
) Maintaining the stability of the welding process through noises, fluctuations, and external instablers to retain a uniform quality along the weld.
NovEye™ is a vision-based weld monitoring and control software that can analyse the weld pool and make adjustments in real-time, just as a human operator would use their eyes and biological neural nets to move their hands.
Welding technology has continued to evolve and the mechatronic-based advancement is now maturing. Today, innovation is trending to integrating artificial intelligence (AI) tools such as machine learning and smart vision systems.
Using AI to fully automate the pipe welding process
NovEye is now operating as a sophisticated piece of software that ties into the control system of the robot, and in that way, the robots – the actuators – can control the weld puddle in the same way a human welder would. This is revolutionary for many industries, as they need to evolve their capabilities to remain competitive.
) Auto-learning from good and bad weld practice over time to avoid repetitive mistakes, constantly exploring opportunities for a better weld.
in weld quality, payback and support while typically seeing a 300 - 500% increase in productivity.
Figure 1. NovEyeTM is a vision-based weld monitoring and control software that can analyse the weld pool and make adjustments in realtime, just like a human operator.
Novarc’s SWR works with an operator, who is not required to learn a special programming language, nor have multiple years of robotic experience. The cobot can also be positioned anywhere in the shop, requiring only a 4 x 4 ft footprint, as the built-in safety system effectively eliminates the need for fencing. The cobot can integrate with two to five positioners for maximum arc-on time, and is fast and easy to set up. A number of additional features allow the SWR to pivot and address the everyday variability associated with pipe welding and fabrication.
38 World Pipelines / AUGUST 2022
For example, initially NovEye had to be implemented in a low-level code so it could run efficiently on the robot. It took a number of years to develop as it required a considerable amount of effort to examine the weld data, and create high-quality and reliable code at low levels.Today, the technology can record certain features in the weld dimension in exactly the same way welders would be looking at the weld pool (how it’s wetting on the sides, the position of the torch, etc.) and decide the next move, whether it’s increasing or decreasing weld parameters, wire feed speed or travel speed. Neural networks and AI allow the cobot to follow the same procedures as the human operator, assessing those features as it’s been trained to command the control system to make the necessary corrections – in real-time – during the weld.
However, Novarc’s welding automation technology does not abandon the human operator, but works alongside the welder, helping junior welders complete challenging welds which previously could only be performed by senior welders.
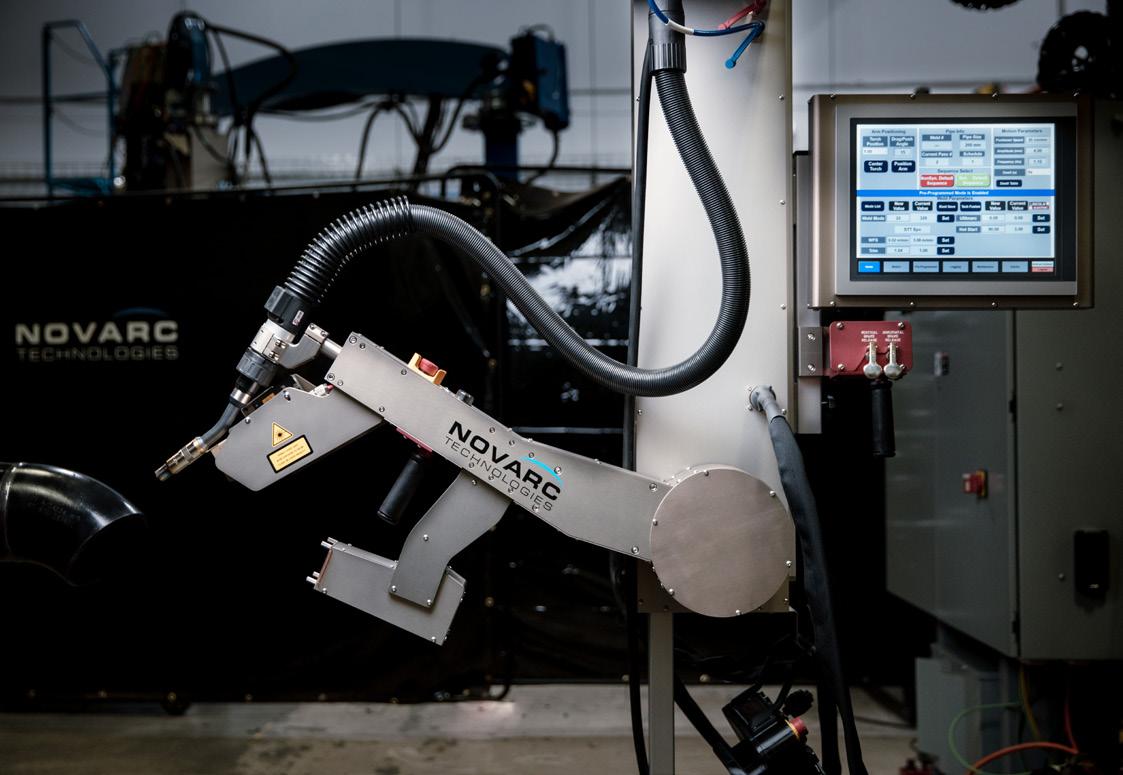
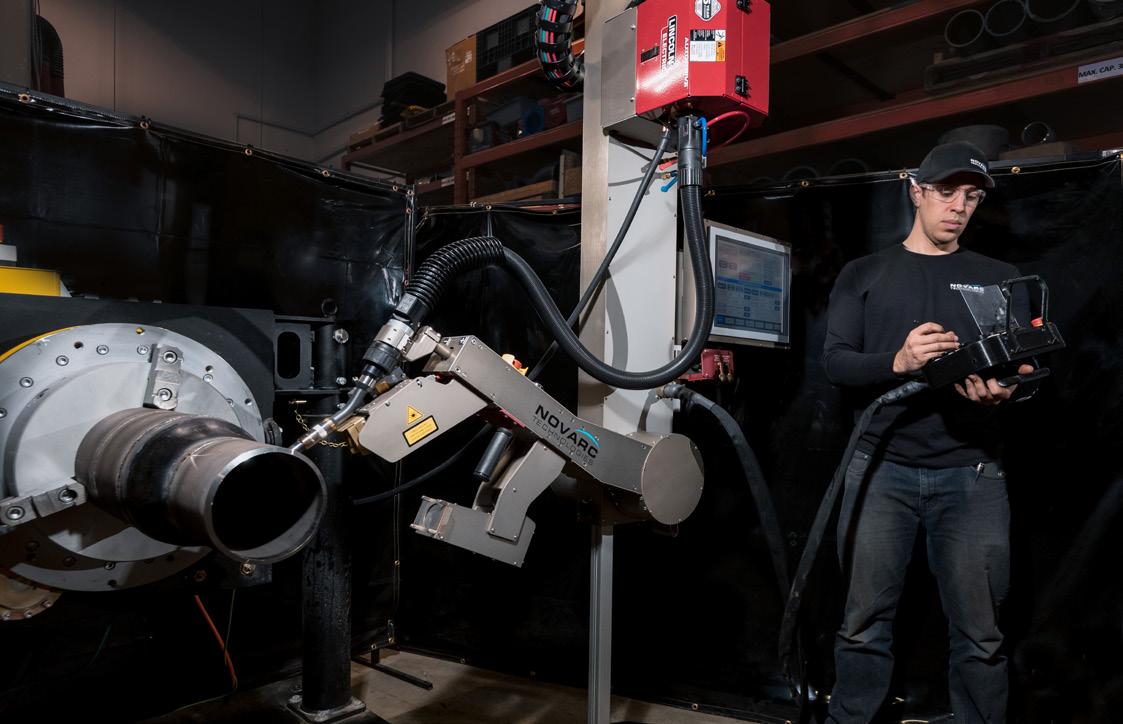
Pipelines DefenceFacilities PowerRenewablesCSG Gathering TURNKEY ENERGY INFRASTRUCTURE SOLUTION PROVIDER ◊ Transmission Pipelines ◊ CSG Gathering and Wellhead Connections ◊ Above Ground and Buried Facilities ◊ Refinery Facilities including Brownfield Sites CAPABILITIES nacap.com.au +61 3 8848 1888 (Melbourne, Head Office) +61 7 3328 8800 (Brisbane) +61 7 3029 1111 (Brisbane, PNG Office) +61 2 6884 7878 (Dubbo) +61 418 441 827 (Darwin) +61 8 6229 6500 (Perth) +675 321 1001 (Port Moresby) INTEGRITY - TEAMWORK - STRIVE TO BE BETTER Angore Project - Papua New Guinea WE BRING ENERGY TO ITS DESTINATION
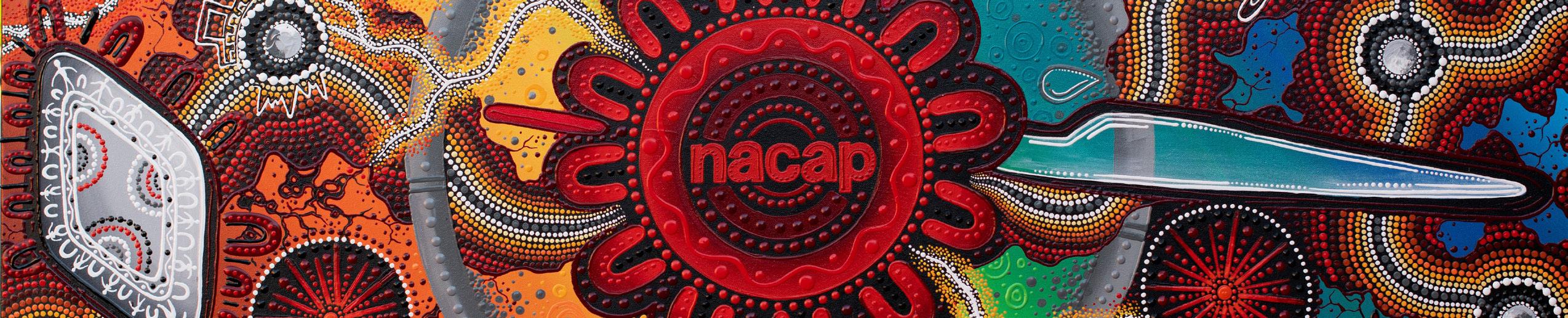
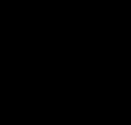
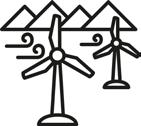
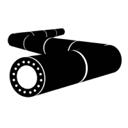
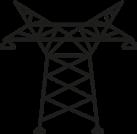
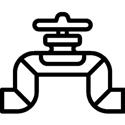
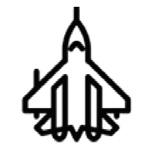
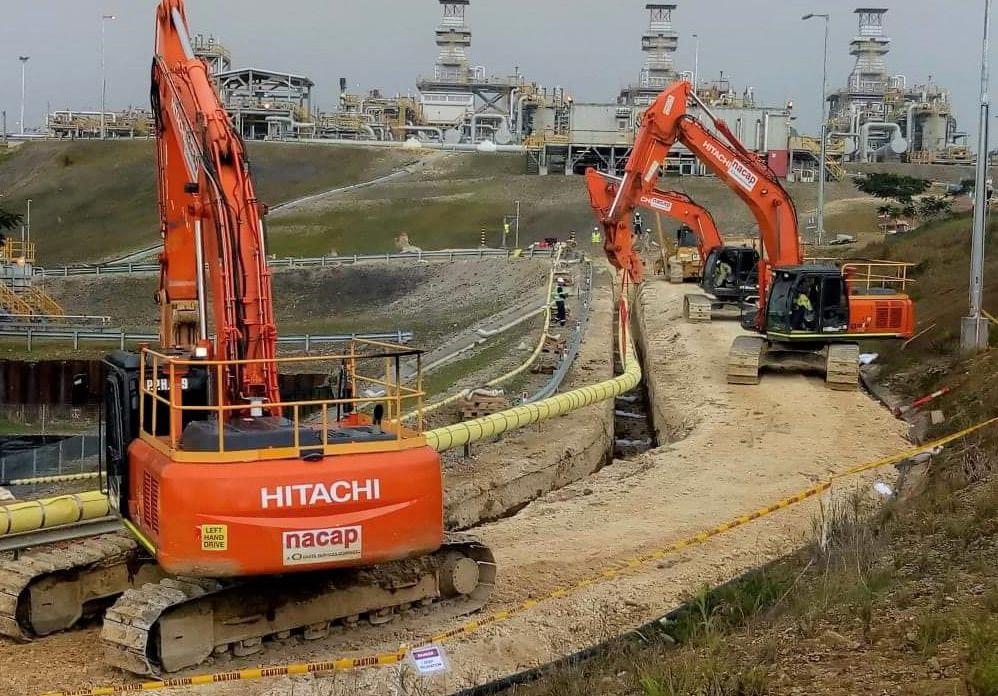
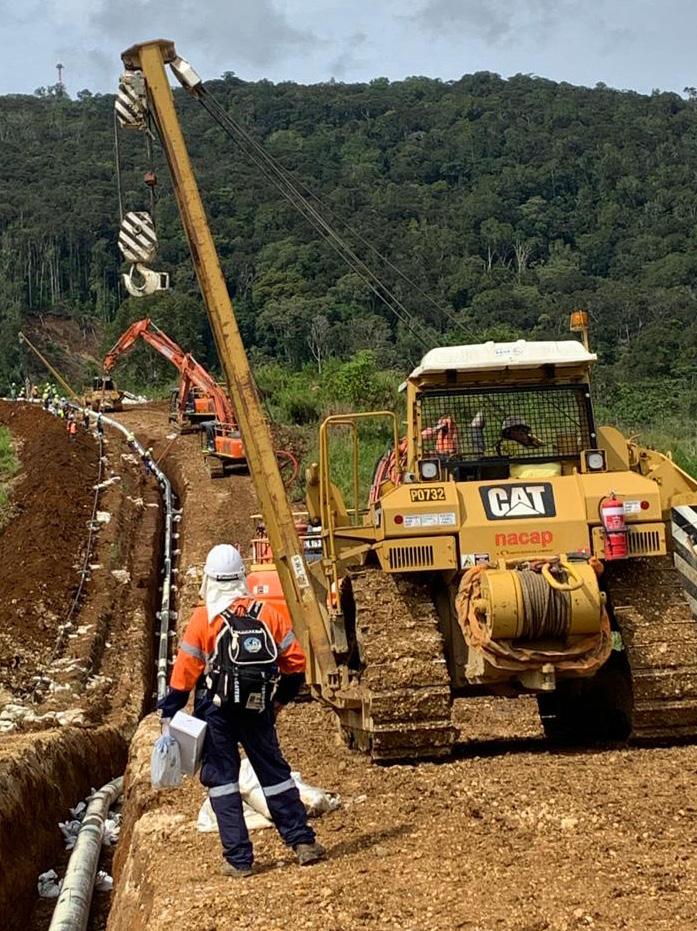
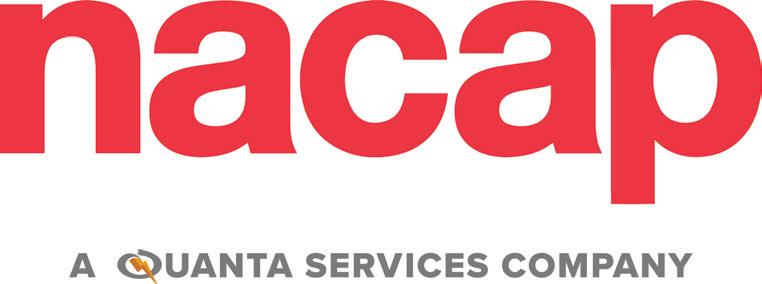
Moving to a dynamic process of innovation and improvement However, pipe welding is more than a technical or commercial debate for automation. Pipe welding ‘smartisation’ is a dynamic process of innovation and continuous improvement in response to the market’s technical, commercial, environmental, cultural, and socialNovarc’sdemands.commitment to welding automation – through AI and tech developments – is meeting the increasing demand for greater productivity and efficiency. However, these developments have the larger impact of attracting more individuals into the welding industry. With the implementation of sophisticated machine learning systems, the job of welding will become cleaner and less dangerous than ever before. The high-tech component will be of more interest to younger generations that might not be inclined to do the dangerous and tiring work that welding jobs traditionally required. Welding automation is also creating opportunities for technicians, developers and engineers to join the industry and continue to improve the way AI is utilised in manufacturing operations around the world. On a critical trend, welding is a core process in most GHG-intensive industries including oil and gas, and mining. Many countries have committed billions of dollars to reduce GHG emissions as part of Paris agreement targets. However, there are a number of sustainability hurdles that need to be overcome within the welding industry:
40 World Pipelines / AUGUST 2022
The R&D team of Novarc is working diligently to extend the on-welding intelligence of NoveEye to mitigate the requirement for post-weld NDT by tracking the defects at the Onsource.acultural level, the next wave of Industry 4.0 will move AI and cobots beyond human capabilities and make a tremendous difference across the spectrum of commercial industries. Advancements in machine learning algorithms, real-time computational power, and big data are currently enabling technologies that are literally transforming industries and cultural norms across the globe.
Figure 3. NovEye ties into the control system of the robot, and can control the weld puddle in the same way a human welder would. This is key for many industries as they have imminent market demands for smart welding systems.
) Welding releases metal pollutants into the air, such as vapourised heavy metals and oxides from the molten puddle.
) Welding fumes emit CO 2, CO, and ozone, the main driver of global warming and climate change.
Welding metal waste control is critical for minimising overexploitation of natural resources.
Using an at-source fume extraction torch with Novarc’s AI-driven welding control technology delivers the lowest airborne, energy consumption, and metal waste for the fabrication phase. Manual welding has no control over arc time and is significantly slower. Other mechanised welding machines do not have the flexibility of Novarc’s robotic system for lowering the arc-time needed for completing the joining.
Real-time reporting to improve welding operations Novarc recently introduced a product called NovSync™ to provide visibility of the welds of the collaborative robot, specifically usage and production statistics and metrics, that can be customised and scheduled. In this way, production efficiency can be increased as users analyse the welds. These advanced analytics can be employed to track production and machine trends over time. NovSync provides centralised and secure access to weld videos, daily reports and data logs. Fabrication shops using NovSync can easily receive information, in real-time, to improve welding operations and become more competitive.
NovEye is a leading product in the market for intelligent vision control of weld arc and puddle, and no other technology is capable of delivering better precision. These smart eyes enable precise control of the final weld shape to avoid wasting metal during welding, and eliminate the requirement of extra work for grinding the excessive weld bead.Novarc’s automation system also reduces human exposure to all welding hazards: dangerous welding fumes such as manganese, hexavalent and chromium. This is achieved by an at-source fume extraction on the torch, and having the welding operator work several meters away from the welding arc. Novarc’s welding technology allows the operators to work remotely from the arc, and with the use of proper ventilation, most fumes can be eliminated.
intellectual level of our local system to dive deep into massive data collected from around the globe and develop actionable insights.
) Welding processes take a large amount of energy during every weld, imposing a significant burden on our energy system.
)
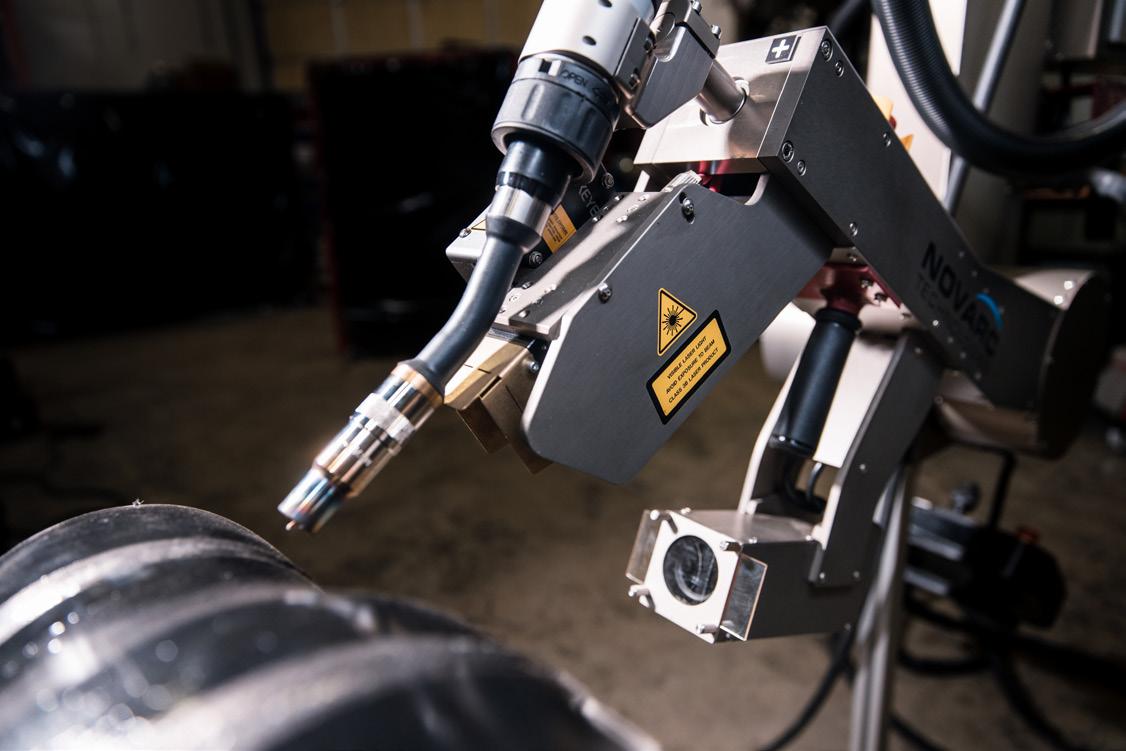
DrillTec GUT GmbH Großbohr- und Umwelttechnik Josef-Wallner-Str. 10 · 94469 Deggendorf · Germany T +49 991 37212-400 · E info@drilltec.de · www drilltec.de System provider for pipeline, plant and network construction STREICHER OFFERS COMPLETE SOLUTIONS IN PIPELINE AND PLANT CONSTRUCTION MAX STREICHER GmbH & Co. KG aA Schwaigerbreite 17 · 94469 Deggendorf · Germany T +49 991 330-0 · E info@streicher.de · www streicher.de STREICHER Group: Comprehensive technical know-how and many years of experience within the business sectors of Pipelines & Plants, Mechanical Engineering, Electrical Engineering, Civil & Structural Engineering and Raw & Construction Material. Modern machine technology as well as highly qualified specialists guarantee a timely and high quality execution of complex projects. Feasibility studies, planning, procurement, commissioning, execution, technical services and innovative working methods for pipeline and plant construction Drilling rigs for hydrocarbon and geothermal exploration HDD rigs for trenchless pipe laying Integrated execution for drilling services
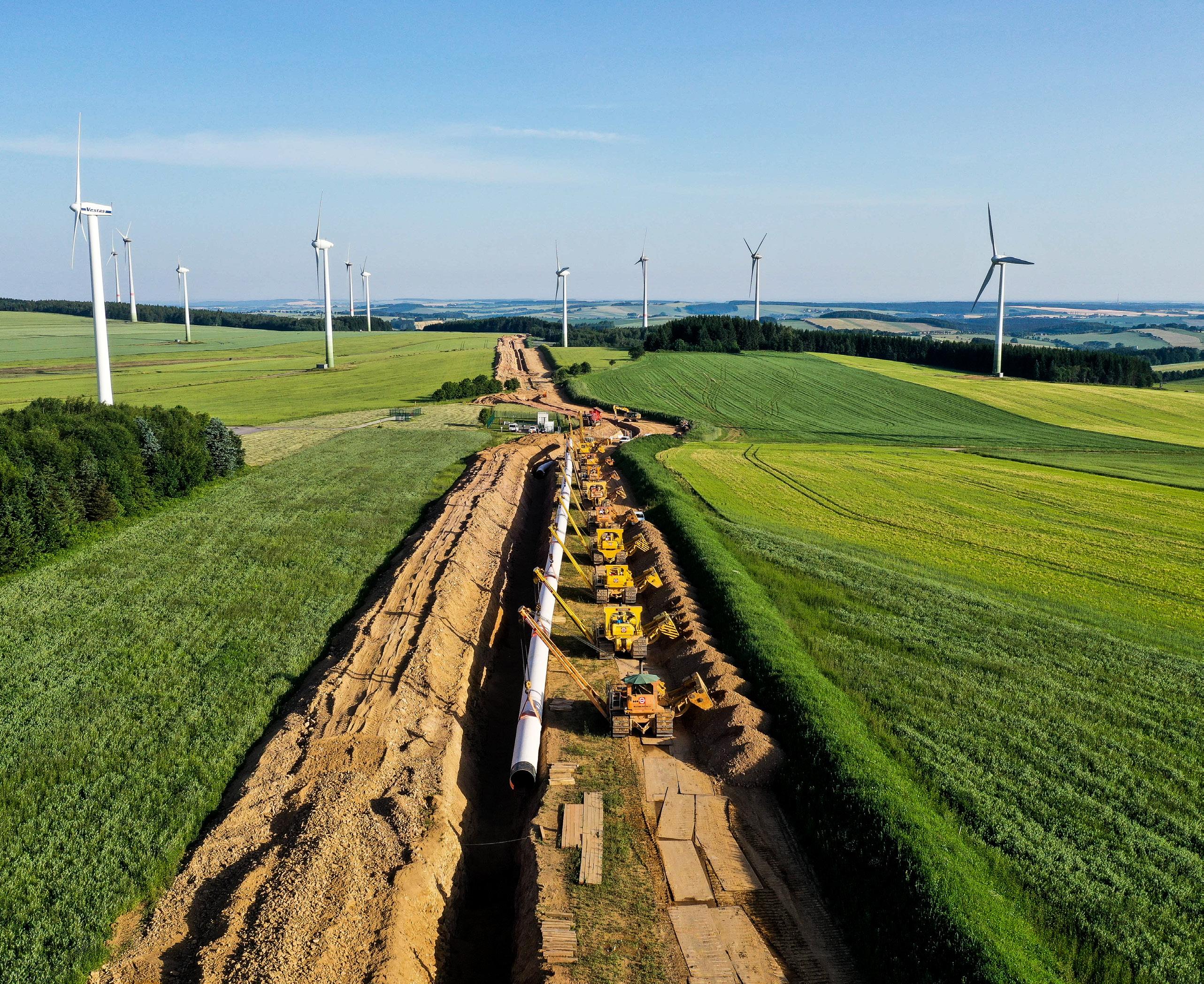
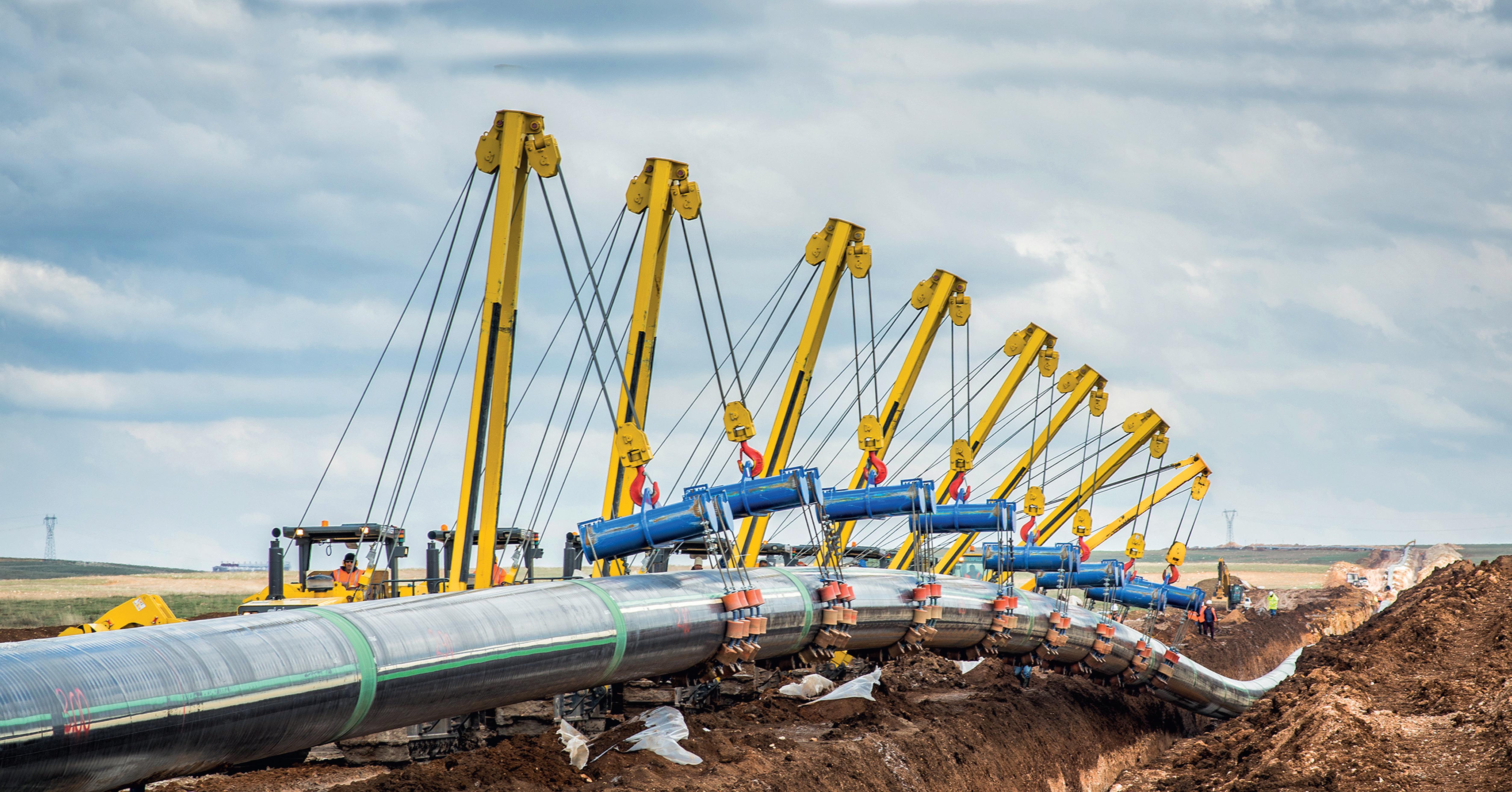
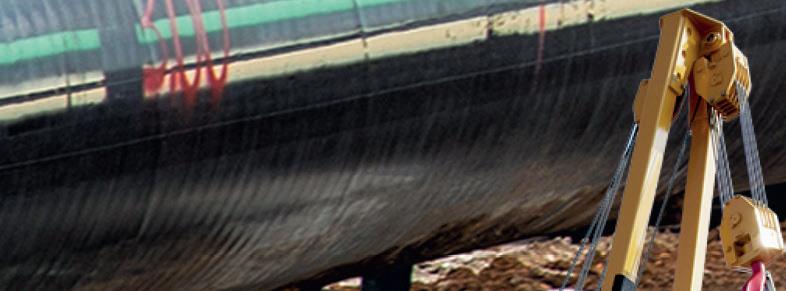
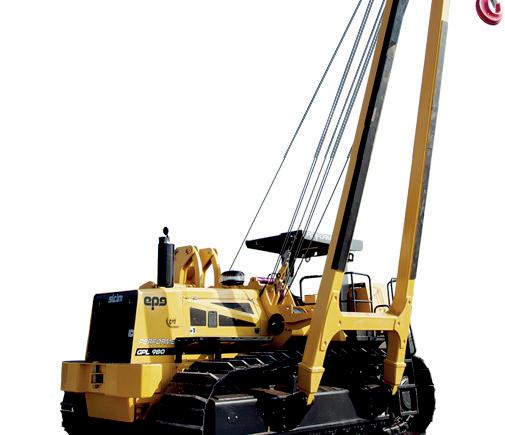
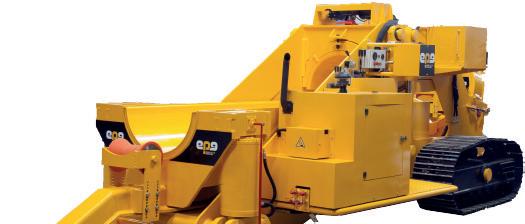
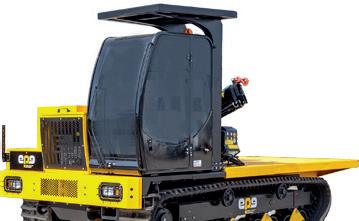

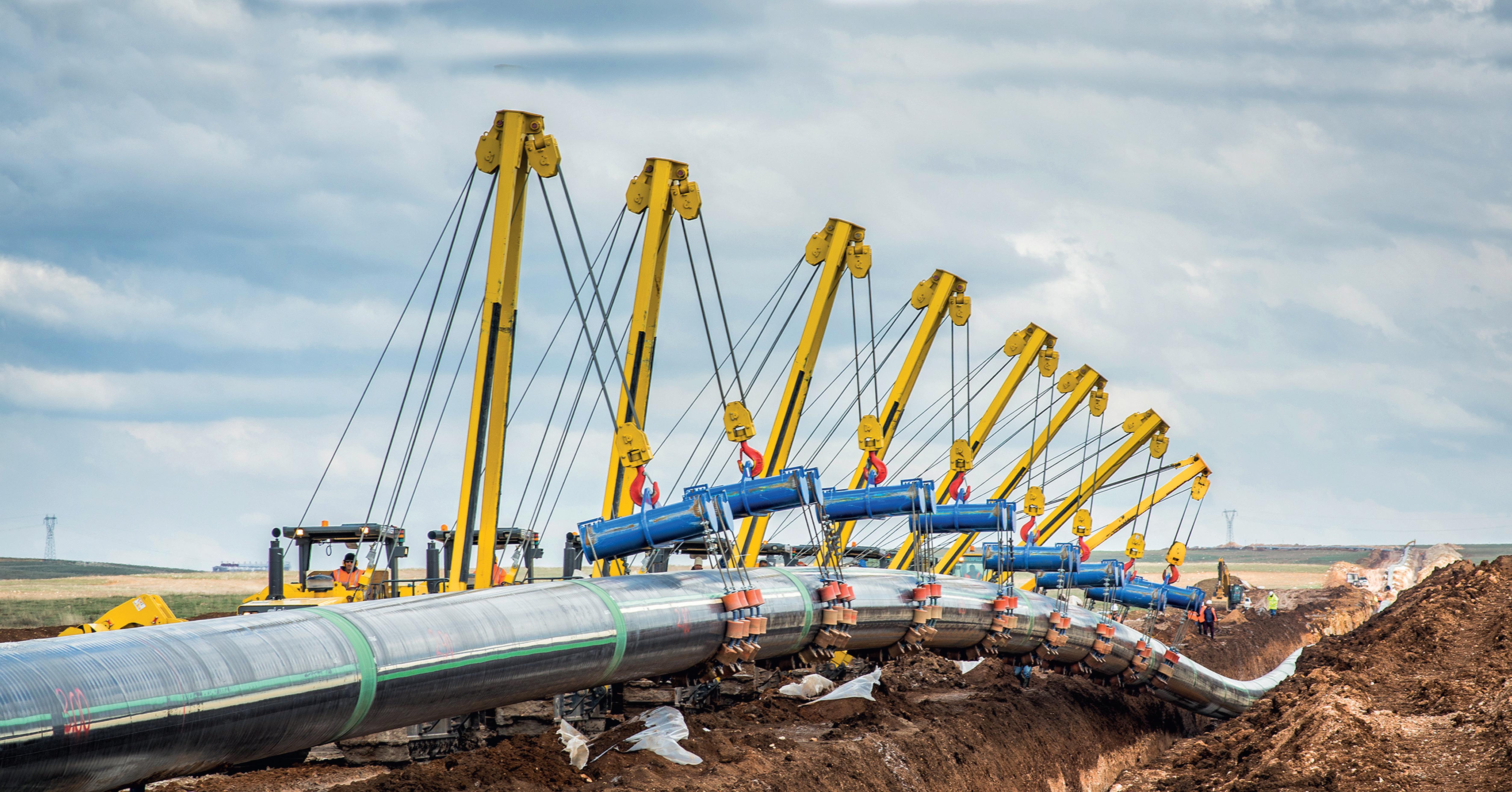
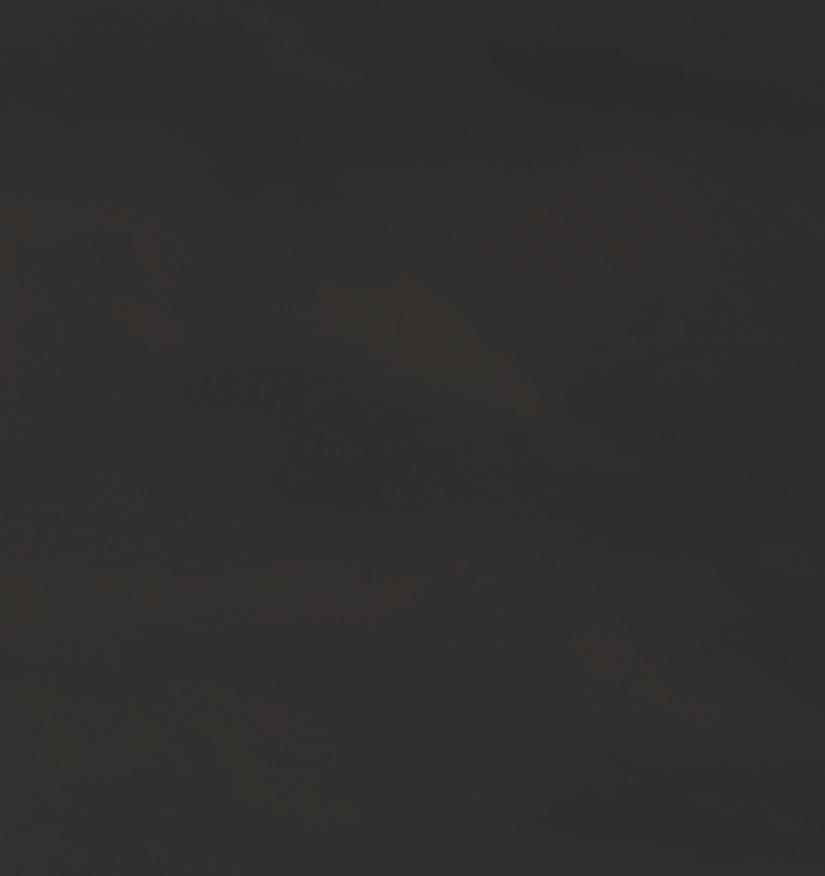
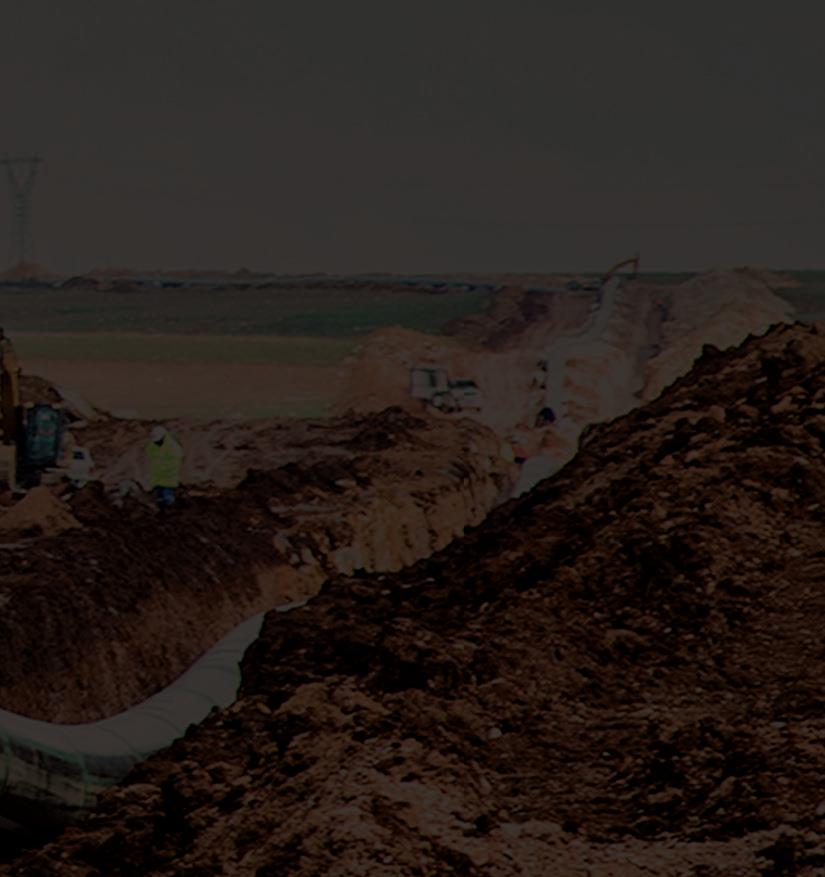
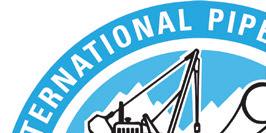
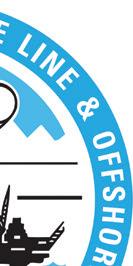
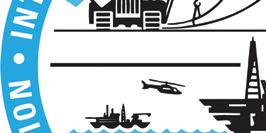
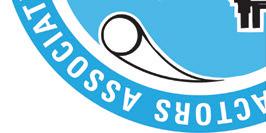
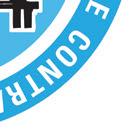
Francesco Ciccomascolo, Full Welding Solutions Manager, voestalpine Böhler Welding, Austria, introduces a new solution for orbital pipeline welding with flux cored wires. I n the pipeline industry, perfect pipeline girth welds with consistent mechanical properties, paired with high productivity, and low repair rates are key priorities.
The new solution minimise repair rates, thanks to the fine-tuning of the high quality diamondspark flux cored wires, the movements and wire feeding precision offered by Böhler Welding’s pipeRunner orbital welding system, and the stable electric arc performance of the TERRA 400 PRM welding power source.
Böhler Welding’s full welding solution is, for example, ideal for pipeline contractors that want to introduce mechanisation in their welding process within a limited budget, avoiding sophisticated operations such as narrow gap preparations and fully automated root pass, for which specific expertise and equipment, such as site bevelling machines and internal pipe clamping systems, are necessary.
Additionally, each weld seam is executed using a single set of parameters from 6:00 o’clock to 12:00 o’clock, thanks to the performance of the system in combination with the Böhler Welding flux cored wires. Hence, key benefits of the solution include easy installation and user friendly operation.
Böhler Welding’s latest GMAW/FCAW orbital welding solutions, which guarantee repeatable high quality welds with reduced downtime, can bring these benefits to costsensitive pipeline contractors.
Time comparison with a fully SMAW procedure At the start of the solution is the use of the TERRA 400 PRM power source for manually welding the root and hot pass. This can be done with SMAW electrodes, or by 44
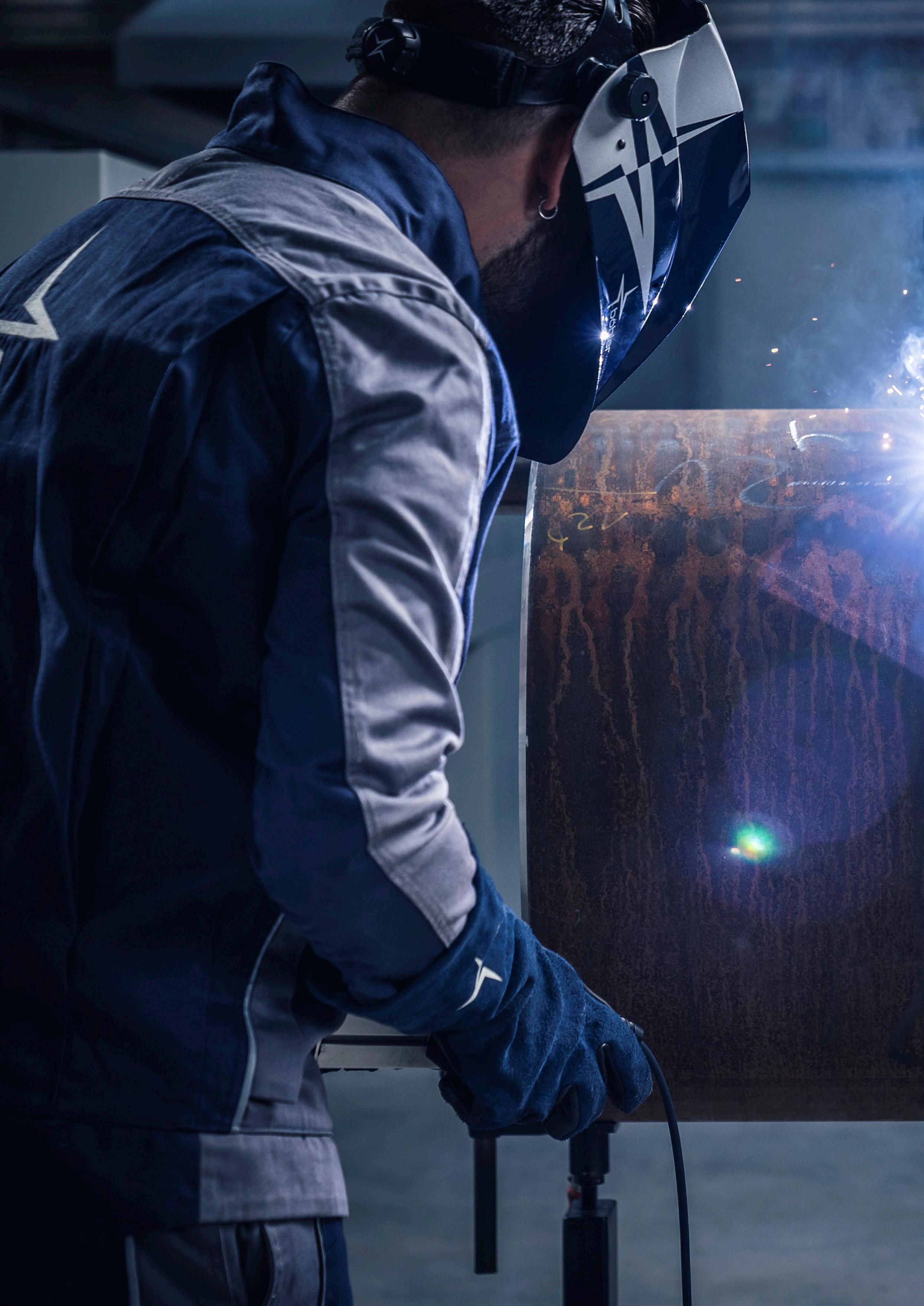
For the mechanised fill and capping passes, the diamonspark X70 RC-Pipe (E91T1-K2M-JH4) consumable was used with the weld metal being deposited using a pipeRunner moving vertically up from the 6:00 o’clock to 12:00 o’clock positions. A seamless rutile nickel-manganese alloyed flux-cored wire, the X70 RC-Pipe, is the perfect match for this pipe material and ideal for multilayer 45
The hot pass was completed using SMAW, using the FOX CEL 80-P (E8010-P1). This cellulosic electrode meets the strength requirement of the API 5L X70 pipe, and was designed for vertical-down welding of high strength pipeline materials. Both welding consumables are HIC/ SSIC proven and meeting the NACE requirements.
Figure 1. In-house welding trials with the new pipeRunner, a state-of-the-art programmable mechanised GMAW/FCAW orbital system designed for girth welding of pipelines and process piping. completing a manual GTAW root (this latter, e.g. for piping applications or for high alloys and clad pipes). Once these two passes are completed, however, the flux-cored process is used for the fill and cap weld passes, which are laid down using Böhler Welding’s pipeRunner orbital bug and the diamondspark range of flux-cored wires for pipeline welding.
In order to evaluate the gain in terms of productivity, trial welds on Grade API 5L X 70 pipe with a diameter of 910 mm and a wall thickness of 15.0 mm have been performed using the above mentioned method for the fully manual SMAW process on another weld joint. For both, the root consumable used was the FOX CEL (E6010), Böhler Welding’s cellulose electrode designed for verticaldown welding of pipelines. This electrode is especially recommended for root run pass welding and offers good deposition efficiency and speed economy, particularly when compared to vertical-up welding. It also offers excellent gap bridging characteristics, and outstanding impact and strength values.
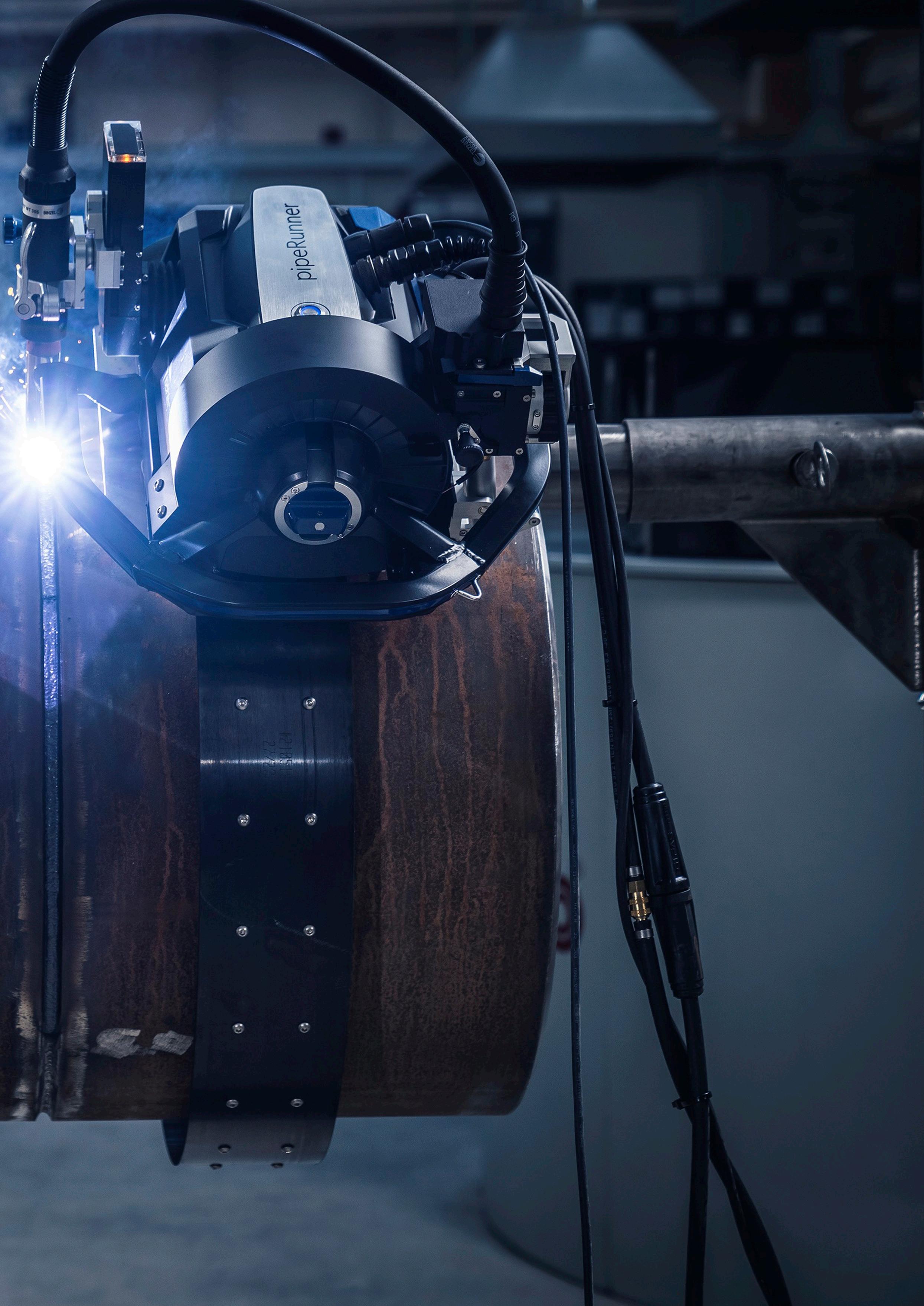
Obviously greater additional saving might be achieved by implementing more welding stations.
The compact and robust design of Böhler Welding’s TERRA welding machines makes it possible to use them in a variety of working environments, even in confined spaces. Suitable for MMA, dc TIG and GMAW/flux-cored processes, the machines deliver power in the 150 - 500 A range. The machines are built to cope with heavy loading and harsh environments while guaranteeing accurate and consistent welding parameters.
Programmable mechanised GMAW/FCAW orbital system
This procedure enabled a defect-free, high quality joint with an excellent bead appearance to be completed in five layers with outstanding productivity results. For the manual fill and cap passes FOX CEL 80-P was used, depositing two layersComparedmore. to the joint completed using the full cellulosic SMAW procedure, the use of pipeRunner with the diamonspark flux-cored wire reduced arc time by 51% and total welding time, including fit-up, by 66%, while net savings in terms of the mass of the consumables deposited amounted to 46%.
welding of carbon-manganese steels and high strength steels with Ar-CO 2 shielding gas, typically M21.
Featuring excellent weldability in all positions and giving an excellent bead appearance with very low spatter losses, the slag produced is also fast freezing, supporting the welding pool and easy to remove. The exceptional mechanical properties of this wire, particularly the low temperatures toughness values, and the low diffusible hydrogen content produced in the weld metal, make this consumable especially suitable for pipeline applications.
Multi-process inverter
46 World Pipelines / AUGUST 2022
The TERRA 400 PRM pipeline welding power source is a robust and reliable three-phase, new-generation, multiprocess inverter designed to suit the needs of orbital pipeline welding while also capable of root and hot pass runs in manual or semi-automatic welding mode. The 400 PRM is equipped with a special display to manage all the welding processes involved, and an RC 100 MP remote control specifically designed for pipeline use.
Figure 2. A
Böhler Welding’s new pipeRunner is a programmable mechanised GMAW/FCAW orbital system designed for girth welding of pipelines and process piping. This is a state-of-the-art in-house Böhler Welding system that is designed from premium components, mostly manufactured in Germany and chosen to optimise system performance andAnreliability.intelligent intuitive and logical arrangement of all operating elements such as the welding torch, positioner, spool-holder, release lever, circumferential band, etc, makes setting up this system easy and quick. With all the electronics incorporated, the system still weighs only 14 kg, making pipeRunner one of the lightest welding bugs on the market. Modern DC brushless electric motors are used to ensure accurate and remotecomprehensiveuser-friendlytheweldingclockwise(CW)betweeneasilysameisweldingbutweldingverticalwastoapproachthehightravelconsistentspeedsandreliability,andmodulardesignlendsitselfpossibleupgrades.ThesystemdesignedwithupFCAWinmind,verticaldownusingGMAWalsopossible.Thedevicecanbeswitchedclockwiseandcounter(CCW)aroundpipe,andtheandcontrolgivesview of the clean weaved capping layer of a pipe weld completed using pipeRunner.
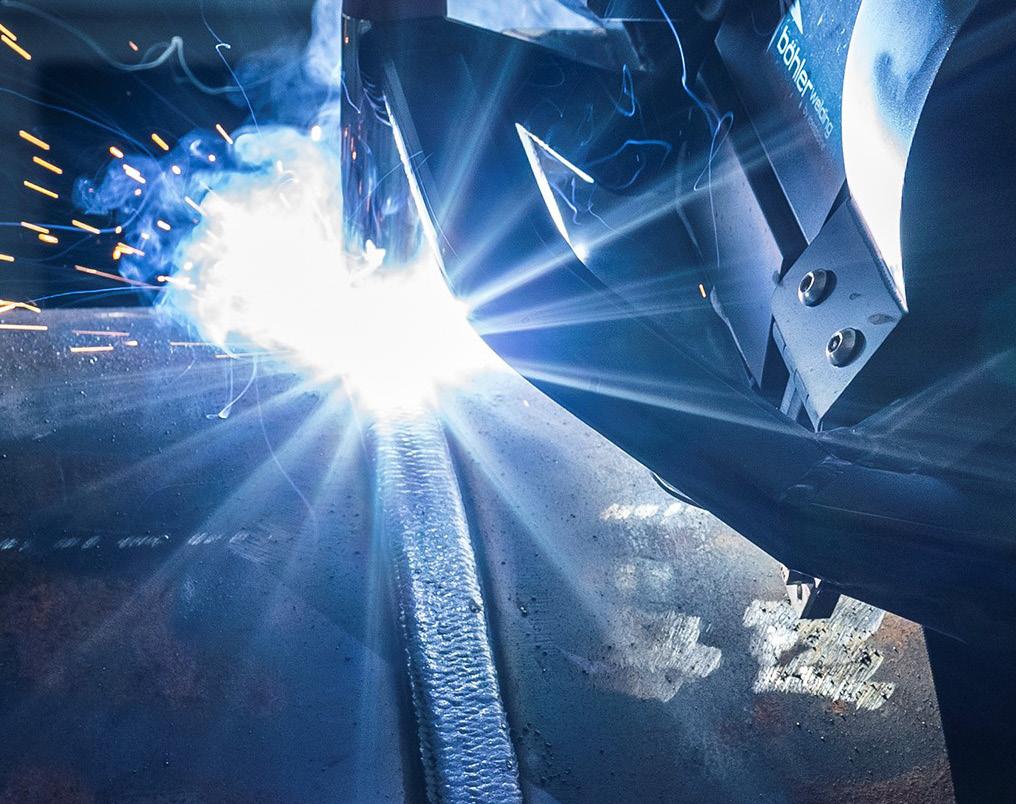
The answer to the most extreme conditions: DEKOTEC® shrink sleeves Reliable corrosion protection - even for largest pipe diameters and extreme temperatures. Meets ISO 21809-3 and EN 12068. denso-group.com DEKOTEC® Made for Extremes DEKOTEC® Shrink Sleeves Ready for the greatest challenges. North Africa, 128 Inches (DN 3200) NEW: SecureDEKOTEC®-HTS100protectionupto 100°C/212°F.
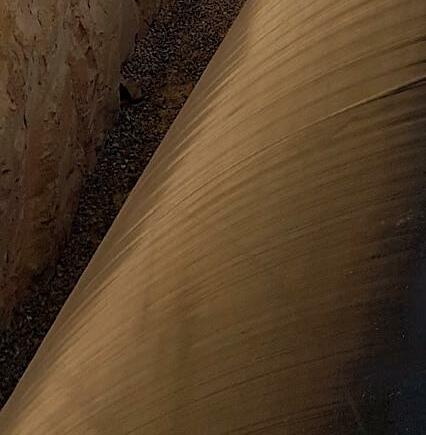
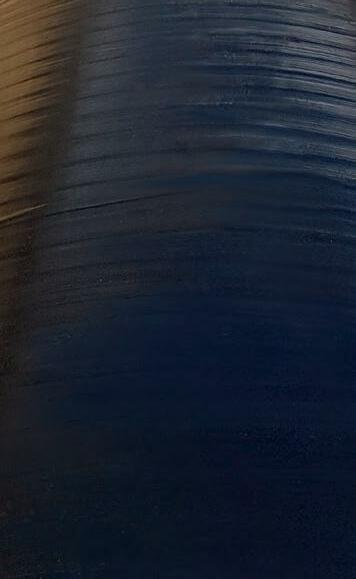
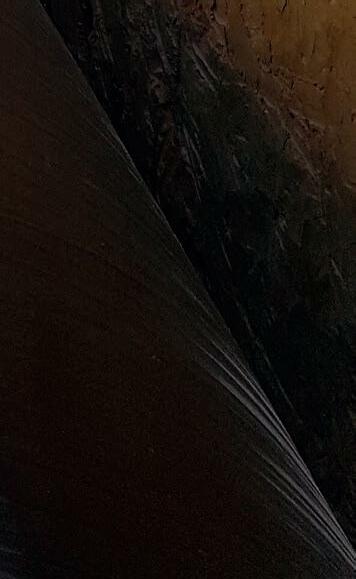
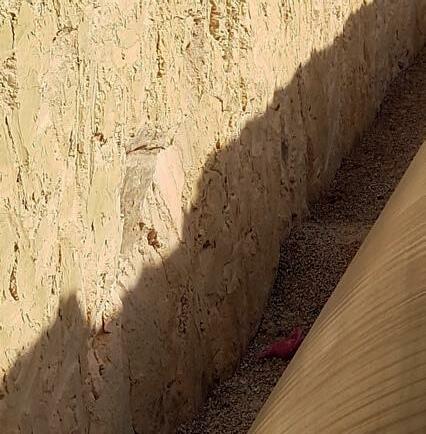
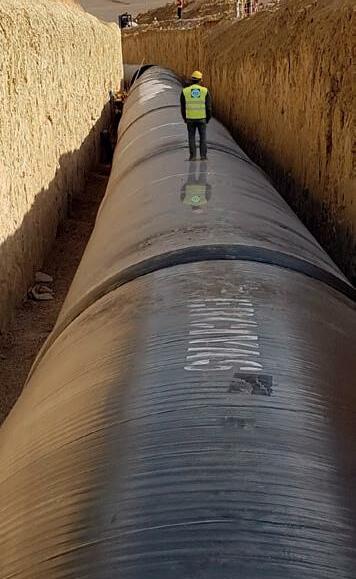
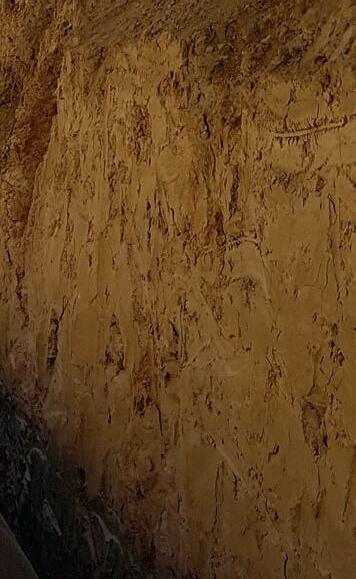
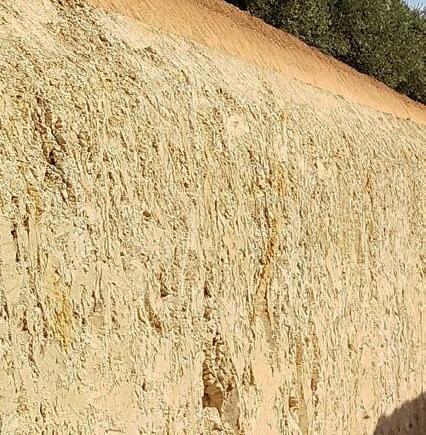
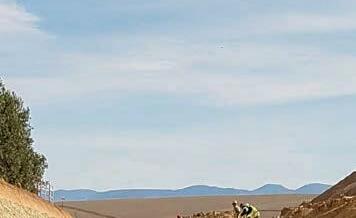
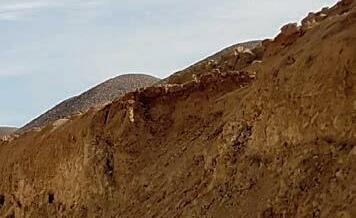

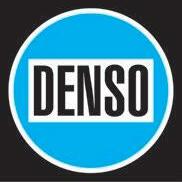
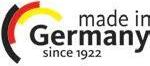
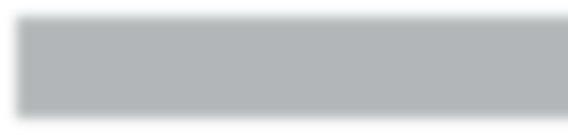

High alloys and clad pipeline
Further procedures have been developed and successfully applied using high alloys Böhler Welding flux cored wires, such as the all positional FOXCore 308L-T1 (on 304L stainless steel pipels) and FOXCores 625-T1 (on alloy 625 clad pipes). Excellent results both in terms of quality and productivity, therefore the solution is definitely optimal for high-alloys pipeworks and clad pipeline. Application engineering services
For voestalpine Böhler Welding, being a full welding solutions provider means acting as a partner for pipeline contractors through the weldTECH Application Services, which include a team of welding engineers experienced in pipeline construction. The team developed a number of complete procedures on various pipe grades and dimensions, and it is available to fine tune weldingparameters on demand according to the customers need.
the operator access to all movements functions using one hand.With respect to programming, proprietary software is already included, which is compatible with all standard PCs, and an optional heavy duty tablet is also available. Welding parameters and sequences for up to 11 different passes can be programmed.Intermsofergonomics, optimised weight distribution makes the unit particularly easy to handle compared to conventional bugs. A 4-handle aluminium spaceframe makes for easy lifting, comfortable transportation and handling in any position. The adjustable welding torch is mounted on the upper part of the frame, and the wire feed unit also works as an integrated pedestal on the opposite part of the frame, assuring a comfortable, stable operating position. The system comes with a high quality box and suitcase to make it easy to transport to and from the site.
48 World Pipelines / AUGUST 2022 Table 1. Böhler Welding pipeRunner technical data. Horizontal torch movement 65 mm Vertical torch movement 30 mm Oscillating width 0 - 60 mm Torch head inclination ±25° Oscillation speed 0 - 350 cm/min. Travel speed 0 - 1.6 m/min. Wire diameter 1.0 - 1.6 mm Oscillation dwell time I ndividually adjustable Weight 14 kg (excl spool) Dimensions 480 × 400 × 260 mm Maximum wire feed speed 19 m/min Maximum welding current 300 A 100% (CO2)
free feeding, which further increases arc time. The pipeline-optimised flux recipe guarantees a thick slag to support the molten weld pool when travelling up, but the slag is easily Pipeline-dedicateddetached.wireformulas further improve the weld metal mechanical properties, keeping high toughness while delivering high productivity. diamondspark X RC-Pipes are suitable for sour service and, using the diamondspark X70 RC-Pipe (N), are NACE compliant up to the X70 Grades, which means they can be used for pipe materials exposed to H 2 S in oil and gas production environments.
aretipandexcellentcoated,productdiamondsparkanddelayedtheandpickcontentlowcoreddiamondsparkWelding’sflux-wiresensuresdiffusiblehydrogenwithnomoistureupduringstoragehandling,reducingriskofhydrogencrackingwormholes.TheXRC-Piperangeiscopperwhichgivescurrenttransferreducedcontactwear.Thesewiresknownfortrouble-
The seamless design of Böhler
wirePipeline-dedicatedformulas
Figure 3. Together with the TERRA 400 PRM pipeline welding power source, the pipeRunner enables high productivity pipe welding, particularly when using Böhler’s diamondspark flux-cored welding wires for mechanised fill and cap runs.
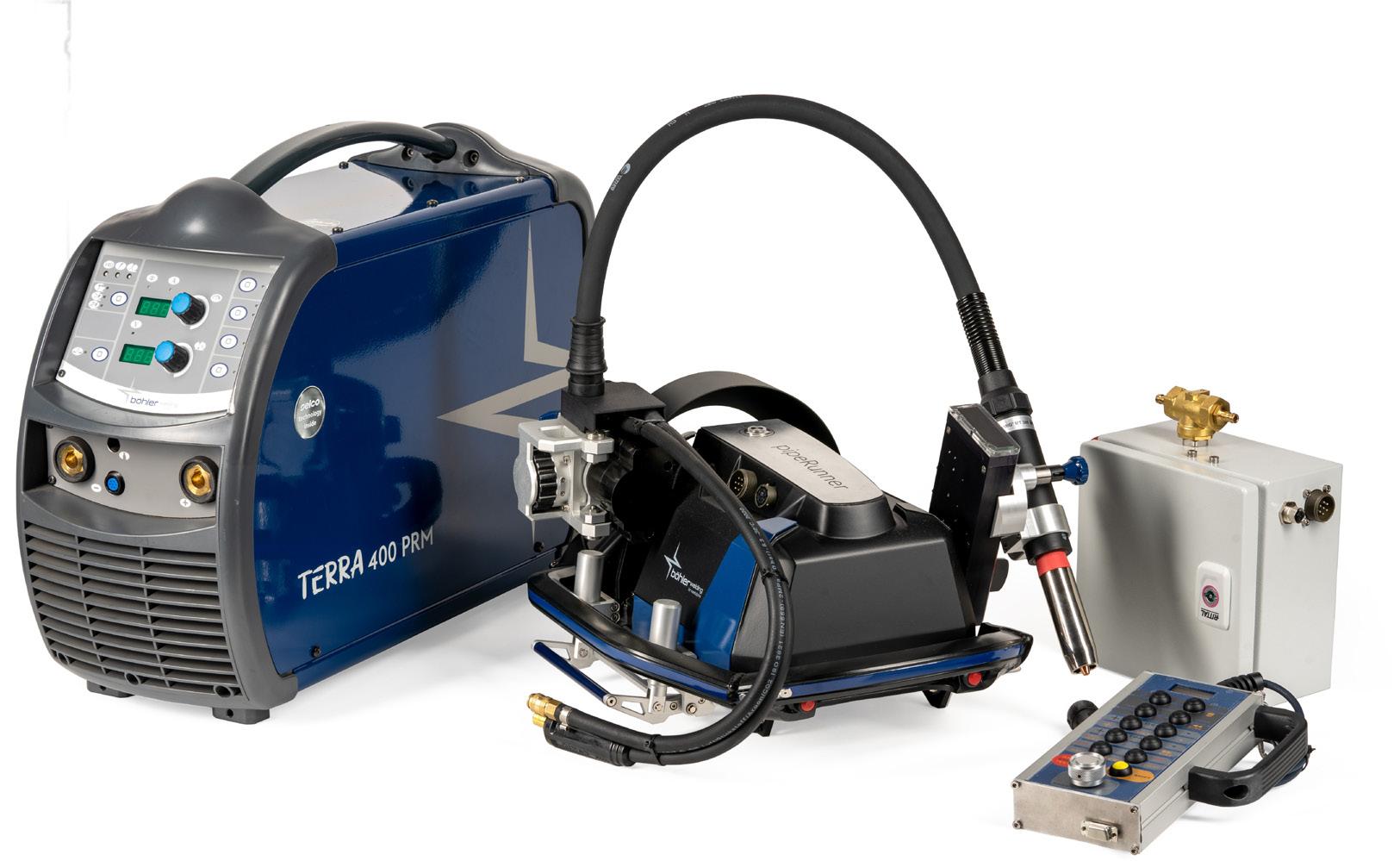
An organisation’s digital attack surface is defined as the totality of connection points available to a malicious hacker seeking unauthorised access. Vulnerabilities in these connection points are how hackers gain entry to software and systems to do theirThesedamage.hackers are persistent and patient. They know that just as technology evolves, so do security vulnerabilities. If your security posture means you have comprehensively protected your pipeline IT infrastructure against all known threats, it unfortunately does not mean that you will be protected against unknown and evolving threats in the near Tomorrowfuture.is another day, as they say. And tomorrow, there is always the potential of new vulnerabilities being discovered in your systems. Robust cyber defences must therefore continuously test for cybersecurity threats, and be able to pre-empt the creativity of these hackers.
While major industries like pipeline providers, airlines, port authorities, etc. can face serious real-world consequences if their cybersecurity is compromised, the financial costs of a successful attack can also be staggering. In 2021, the annual ‘IBM Cost of a Data Breach Report’ found that the global average cost of a successful data breach on individual businesses was US$4.24 million (up from US$3.86 million in 2020).1 The trend looks set to continue, and some security experts are estimating that global cybercrime will hit US$10+ trillion by 2025.2 In 2021, the cost had already topped US$6 trillion. If that were GDP, it would make cybercrime the third-largest economy in the world, after China and the USA. Beyond bearing the financial brunt of these attacks, organisations often also suffer damage to their reputations, and see major disruptions to the work they do. For gas and oil pipelines providers, the crippling of operating systems has the potential to cause not only major financial losses, but also disruption of critical energy supplies that can impact people far and wide. In short, the stakes are high, and with the number of malicious attacks trending upwards, the need for effective and continuous security monitoring of digital attack surfaces has become a high priority.
Problems with common cybersecurity approaches Until recently, automated scanning and pen testing were considered among the most viable ways to protect an organisation against cyberattack. But such security methods, while useful, are far from providing a symmetrical response to the creativity of the world’s malicious hackers. First, they test primarily for known vulnerabilities and have no ability to creatively
Evolving threats on the digital attack surface
Today’s pipelines are monitored and controlled by advanced software and hardware systems, and these are open to attack from that decidedly modern type of saboteur: the malicious hacker.Why would a hacker spend hours trying to bypass the cybersecurity a pipeline operator has put in place? Put simply: to steal or compromise digital assets. System functionality is a common area of attack through ransomware and denialof-service attacks (DoS), but these hackers may also be after customer and financial information, intellectual property, and other sensitive data.
Inti De Ceukelaire, Head of Hackers, Intigriti, Belgium, emphasises the need for continuous cybersecurity testing in the oil and gas pipeline sector.
The cost of cybercrime
49
Mention oil and gas pipeline security, and most people think of large physical assets, sometimes spanning continents, needing protection from saboteurs. But protecting the digital attack surface has become just as critical for the safety and functioning of this vital infrastructure.
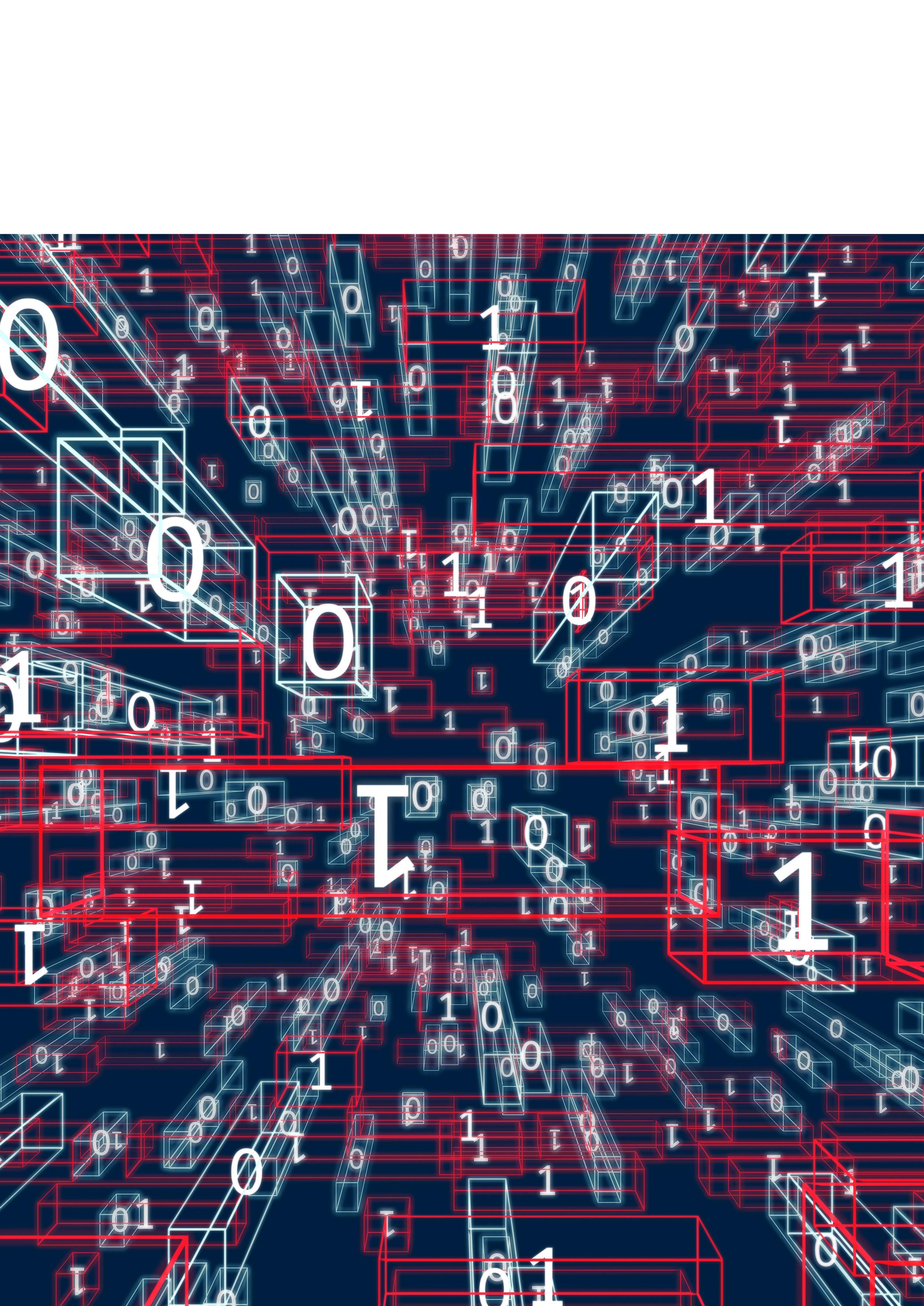
The growth of crowdsourced bug bounty programs
While that might sound overwhelming, it is a lot less to deal with than a successful attack. Moreover, Intigriti offers a unique, time-saving triage service as part of every program where secure researcher submissions are checked for uniqueness and validity before they are delivered to the customer.
References 1. www.ibm.com/security/data-breach 2. cybersecurityventures.com/hackerpocalypse-cybercrime-report-2016/ 3. www.intigriti.com/landing/the-ethical-hacker-insights-report-2022
A bug bounty program uses the crowdsourcing of independent security researchers – often called ‘ethical hackers’ – to test an organisation’s security. If bugs (vulnerabilities) are found, they are reported in a legally compliant matter. Bug bounty programs have been around in various guises since the 1980s, but have seen accelerated adoption among enterprise, government and other large organisations in the past ten years. The reason? More and more security experts have come to recognise them as the best way to provide continuous security testing that functions at the same level of ingenuity as malicious hackers.Major companies like Intel, Meta, Google, Microsoft, and many more now run bug bounty programs. Governments too have been fast to adopt this method of cybersecurity. In Europe, the EU runs an ongoing program, and the US government has been running programs since March 2016 when its first bug bounty program, known as the ‘Hack the Pentagon’ program, saw 138 unique, valid reports from over 1400 security experts.
In its 2022 ‘Ethical Hacker Insights Report’, Intigriti interviewed over 1700 security experts on this very subject.3 Of the respondents, 90% agreed that “pen tests cannot provide continuous assurance that an organisation is secure year-round.”
User experience is maximised, and set-up, budgeting and launch of a program are so streamlined that even a non-technical user can run a program – though ample documentation and human support is always available. Programs can also be private or public. With a private program, you select only the researchers you want to work with and no one else knows about the program. Alternatively, launching a public program will make it open to our full, global ethical hacker community. In both cases, all the ethical hackers working with Intigriti are contractually bound to respect high standards of privacy and Customerssafety.launching a bug bounty program regularly see multiple vulnerabilities reported within a couple of days of launch.
Each platform provider will have a different offering, and while we can’t speak for others, Intigriti has developed some very effective services that make running bug bounty programs particularly suited to the business world.
As a cloud platform, getting up-and-running is greatly simplified compared to building an internal bug bounty program.
The evolution of bug bounty platforms
explore for evolving attack vectors – and these undiscovered weaknesses are precisely what the most sophisticated hackers are looking for. Secondly, and perhaps most importantly, pen tests –once the gold standard for cybersecurity testing – assess attack surface vulnerabilities only at a single moment in time, and are not performed day-in day-out. To put it bluntly, that is not frequently enough to secure your pipeline systems.
So how do you get started with running a bug bounty program? While some organisations still set up their own bug bounty programs, today, increasingly sophisticated bug bounty platforms are becoming the norm for businesses and institutions because of the many benefits they provide.
50 World Pipelines / AUGUST 2022
A bug bounty ‘platform’ is usually a cloud-based offering from an independent company that allows for the set-up and administration of bug bounty programs.
These are just some of the reasons why organisations like PortXchange, European Commission, Brussels Airlines, and Europe’s second-largest port – Port of Antwerp – choose Intigriti as their bug bounty platform.
Businesses deploying bug bounty programs can also scale their security testing at any time by running additional programs or increasing the scope of existing ones. This will frequently turn up new vulnerabilities of different severity levels, enabling security teams to gain awareness of vulnerabilities faster, and, in turn, introduce fixes faster.
Throughout the lifecycle of each program, the platform also provides a 100% transparent status overview, comprehensive budget reports, and real-time updates that can include centralised communication with the ethical hackers working for you.
Penetration tests focus on one snapshot in time, whereas bug bounty programs are continuous; as attackers shift tactics, cyber defences must too. The only way to test their effectiveness is to apply continuous pressure against them. Considering that an organisation’s security posture will change with each new feature release or update, it’s not only a logical step to implement more security testing, but also critical.
The popularity of bug bounty programs can be explained by the distinct advantages they deliver over traditional cybersecurity approaches. For a start, they enable organisations to leverage the skills, experience, and creativity of thousands of security experts from across the globe. These ethical hackers will be working around the clock to test for vulnerabilities in a customer’s systems, with a hope of gaining a ‘bug bounty’ – often a financial reward.
Crowdsourced bug bounty programs are also seen as providing guaranteed ROI. Unlike a pen test, where you pay a fee irrespective of whether vulnerabilities are discovered or not, bug bounty hunters are only paid when they report a unique and valid vulnerability. This increases the motivation of ethical hackers and ensures businesses only pay when something useful is uncovered.
In a world of fast-evolving tech, the key to effective cybersecurity for the oil and gas pipeline industry is to deliver continuous security testing that can anticipate the actions of malicious hackers. In the best of both worlds, this type of cybersecurity would also be affordable and would deliver critical results rapidly. This is precisely what a bug bounty platform like Intigriti provides to businesses across the globe.
Advantages of crowdsourced cybersecurity
Effective cybersecurity for oil and gas pipelines
JOIN! THE FULL WELDING SOLUTIONS! for High Productivity Pipeline Orbital Welding Get the perfect girth welds for your pipeline job site with outstanding material properties with the pipeRunner ® from Böhler Welding. It is one of the lightest systems on the market, easy to handle and programmable, with first-class components designed in Germany. pipeRunner ® delivers the perfect results welding fill and cap layers uphill with our diamondspark cored wire range specifically designed for pipelines, featuring ultra low hydrogen content and offers a great productivity improvement with a total saving of time (incl. line up) of 66 % compared to full cellulosic SMAW welding procedures.* *test executed on API 5L X70 pipe O.D. 36" W.T. 15 mm Scan for more infos voestalpine Böhler Welding www.voestalpine.com/welding
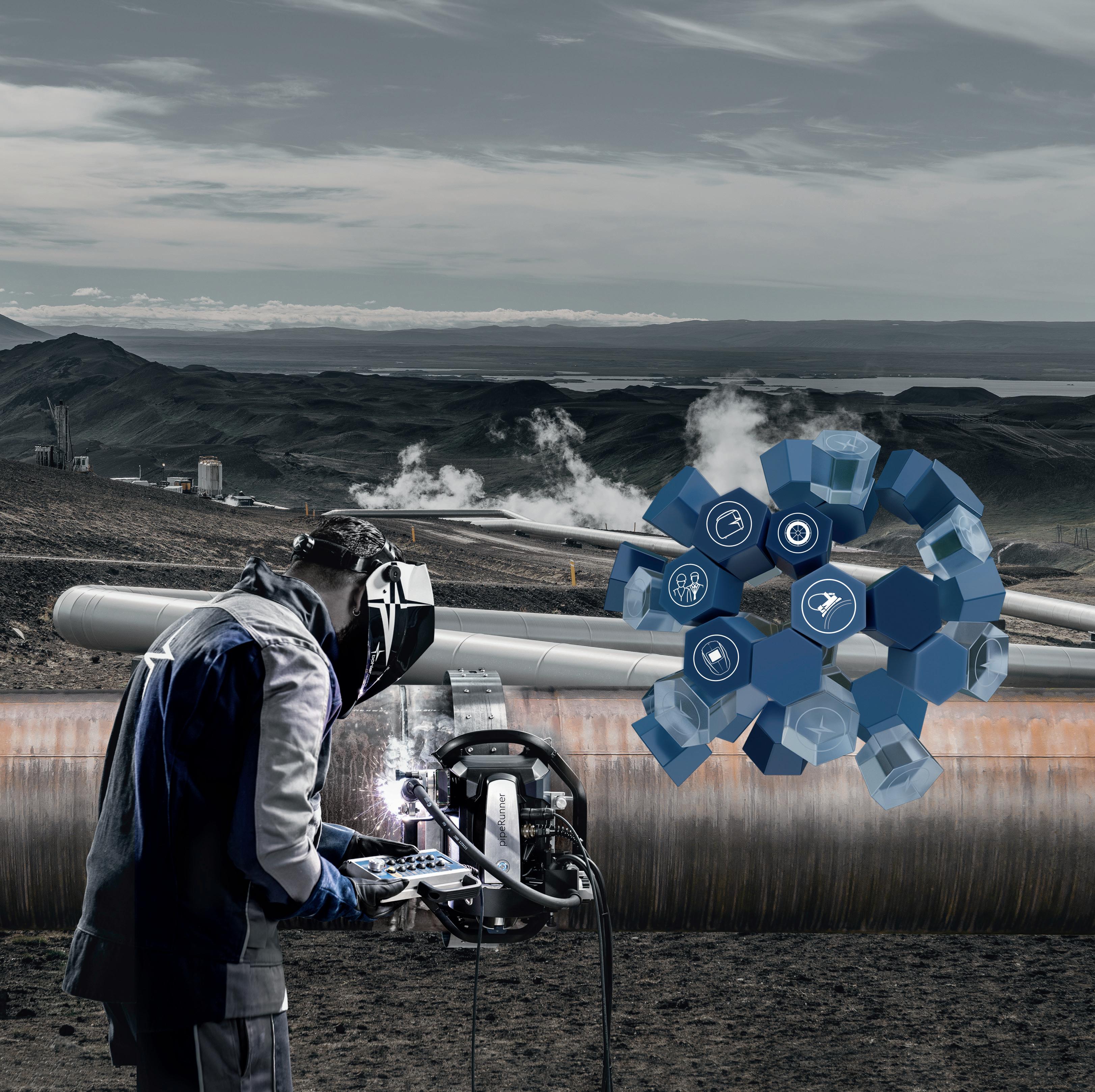
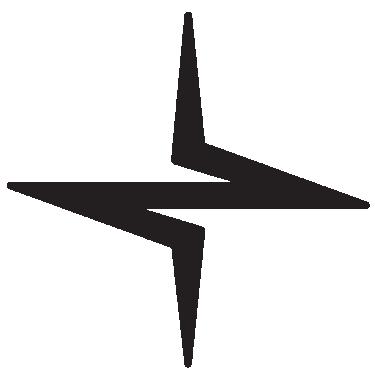
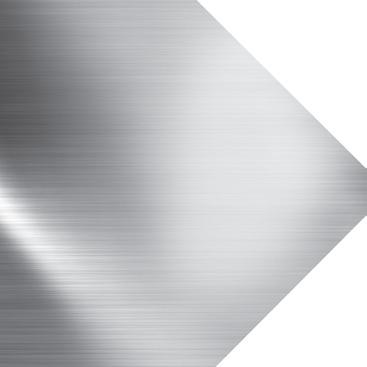
Expect A Higher Standard
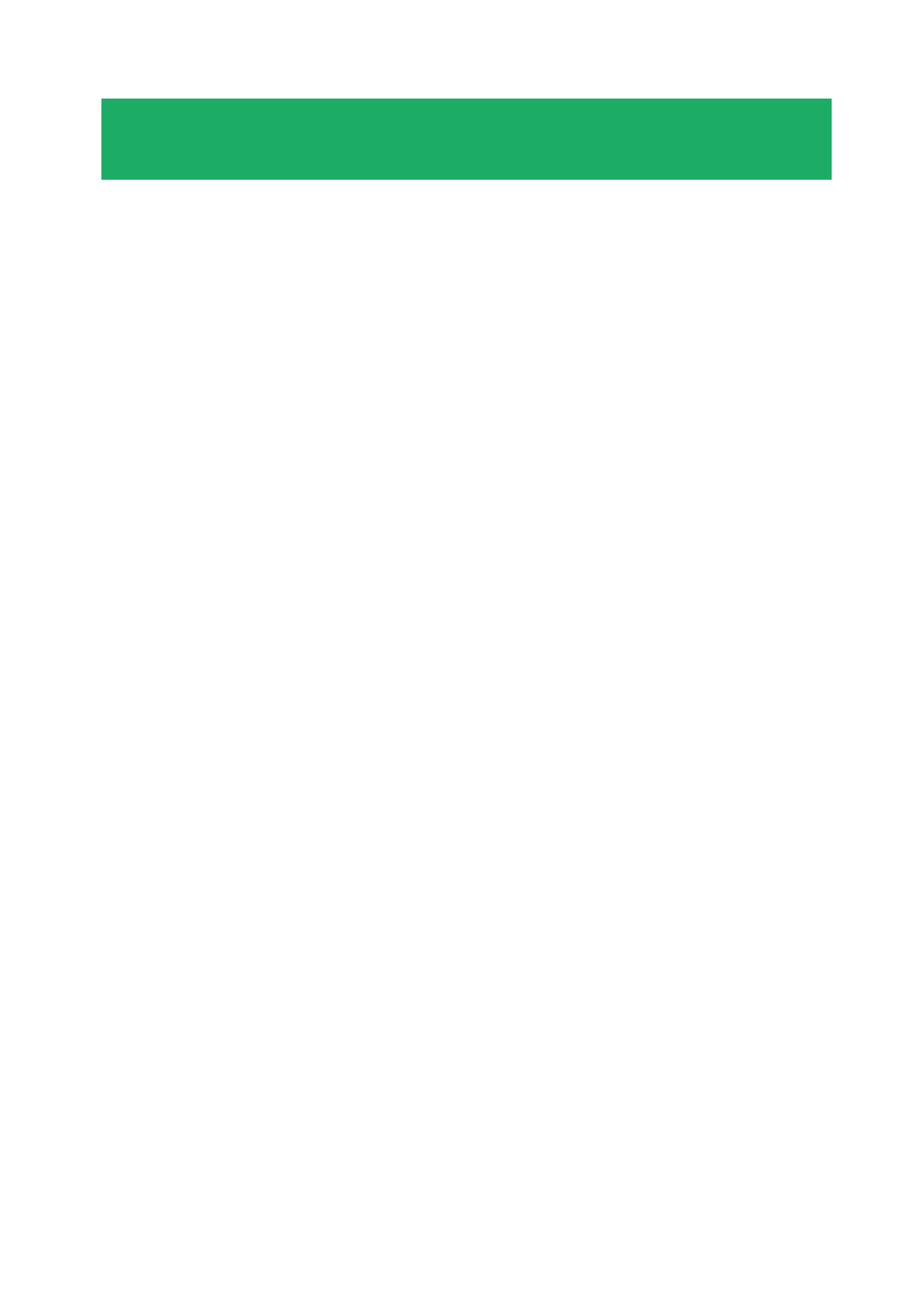
The oil and gas industry as a whole is increasingly waking up to the potential applications of AR and VR technology, suggests Francesca Gregory, GlobalData, UK.
ugmented reality (AR) allows users to see the real world overlaid with a layer of digital content. This digital content layer can include sensor-based data, location-based data, sound, video, graphics, or other datasets. The use of AR can involve headsets that overlay information onto the viewer’s field of view or the use of AR software, which can overlay the data onto a live video feed. While the application of AR to the oil and gas sector is still in its early stages, this technology has the potential to significantly disrupt the industry within the next few years. AR provides a means of addressing key challenges Adoption of AR within the sector will accelerate as oil and gas companies increasingly realise the potential for AR to improve the efficiency of their operations. AR will be used to streamline workflows in two key ways. Firstly, AR’s ability to facilitate remote assistance saves machine downtime and lengthy maintenance visits to sites. Remote experts can support field technicians by overlaying annotations and instructions onto their field of view. As a result, AR can improve the efficiency of planning, maintenance, and repair tasks. Furthermore, AR devices will help workers utilise large volumes of data as the oil and gas industry integrates Internet of Things (IoT) technology into its operations. AR devices that are safe, secure, and handsfree will be the missing link between data and the meaningful application of this information.
AR’s second primary use case relates to the oil and gas industry’s shifting workforce. AR is a technology that can be used to tackle the industry’s ageing workforce and the need to train a new generation of workers. The next few years will be crucial for oil and gas companies as they seek to expedite the training of younger workers and pursue more flexible ways of working to maximise knowledge capture from those that are 53
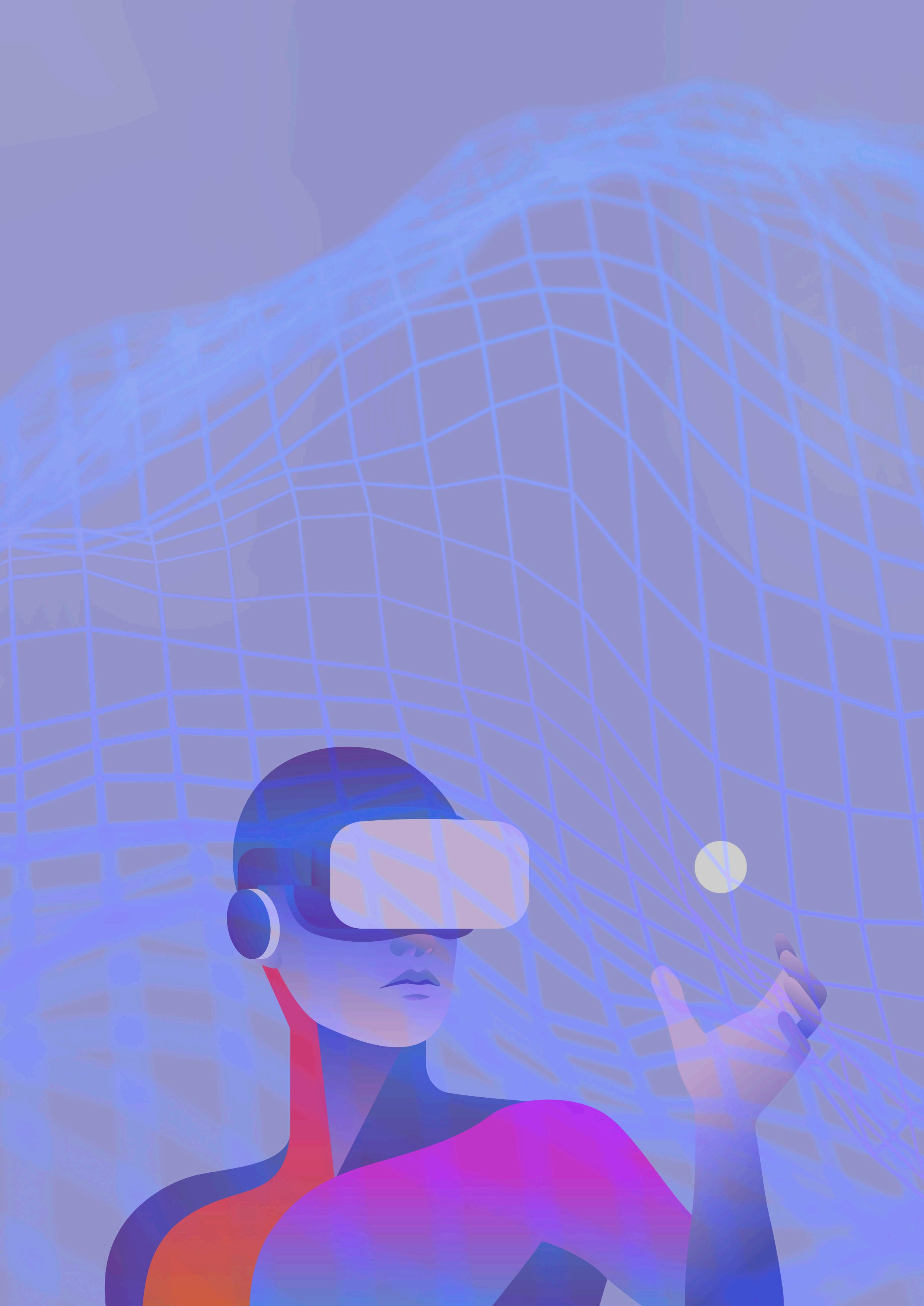
Source: GlobalData. 54 World Pipelines / AUGUST 2022
retiring. Emerging technologies such as AR will be a vital piece of the puzzle for knowledge capture and transfer, and will help prevent a skills gap from emerging. Companies that are realistic about the use cases of AR, and apply the technology appropriately, stand to benefit significantly. The integration of technologies such as AR into workflows as part of the industry’s wider digitalisation will yield both time and cost savings, rewarding innovative companies with an edge over their competitors and a workforce resilient to disruption.
The oil and gas industry as a whole is increasingly waking up to the potential applications of AR and Virtual Reality (VR) technology. GlobalData’s company filing analytics database (Figure 2) reveals that in 2021, these two technologies were mentioned on 302 occasions in oil and gas companies’ filings. The number of companies mentioning the technology within their filings also increased, rising from 59 in 2017 to 106 in 2020. The significant increase in companies mentioning AR and VR can be attributed to the release of industrial AR headsets. In particular, the release of rugged and intrinsically safe headsets, such as the Trimble XR10 and HoloLens 2 combination and the RealWear HMT1Z1, increased the potential for AR to provide a hands-free solution to many technical challenges in the oil and gas industry, boosting the number of companies talking about this technology within their filings. AR active jobs are also on the rise within the oil and gas industry (Figure 2). GlobalData’s jobs analytics database shows a 61% increase in active jobs related to AR and VR within oil and gas companies between March 2021 and March 2022. The growth trend across this year is particularly interesting given the COVID-19 context. Despite the pandemic disrupting demand and causing oil prices to decline, the increase in hiring activity around Global AR revenue by end user, 2020 - 2030. The global AR market will reach US$37 billion by 2025 and US$152 billion by 2030.
The global AR market will grow rapidly AR revenue is expected to increase as the rate of adoption rises. GlobalData forecasts that the market will increase from US$7 billion in 2020 to US$37 billion by 2025. In this early phase of AR’s growth, the market size of consumer and enterprise AR are similar, each contributing just under US$20 billion. In this stage, the price point will restrict the uptake of AR wearable devices. In February 2022, a consumer Microsoft HoloLens 2 is priced at US$3500. Similarly, with additional certifications, the industrial edition will cost companies US$4950 per headset. This price point for industrial devices has historically limited AR adoption to the oil and gas industry’s biggest players, such as Chevron, Baker Hughes, BP, and Shell. The AR market will enjoy strong growth beyond 2025 (Figure 1). AR revenue will reach US$150 billion by 2030, with a CAGR of 33% between 2025 and 2030, according to GlobalData forecasts. This can be attributed to the cost of AR devices decreasing as the technology becomes increasingly ubiquitous and the improved user experience. The growth will largely be facilitated by enterprise applications, which will contribute US$100 billion to the size of the overall market in 2030, compared to US$50 billion for the consumer segment. The increasing proportion of enterprise AR revenue also reflects a growing awareness of the number of potential use cases for the technology.MoreAR wearables being certified as intrinsically safe will catalyse adoption in the oil and gas industry. As a result, the oil and gas industry will become a key market for both AR
hardware and software. Technology vendors are also positioning themselves to address oil and gas companies’ requirements. This was confirmed in an interview conducted by GlobalData with industrial technology company Trimble, where the Director of Product Strategy and Innovation revealed how the company had tailored its products for oil and gas use cases. Examples of modifications include achieving a Class 1 Division 2 safety rating on the ruggedised AR headset, the Trimble XR10. Trimble also added bone conduction to the original audio device of the HoloLens 2 for ease of hearing. In addition, the clip-on Trimble HoloTint provides a sunshade for outdoor use in hot environments. While still an emerging technology in the oil and gas sector, the specialisation of AR devices to the industry’s requirements is already taking place and will facilitate future adoption. AR mentions are on the rise
Figure 1.
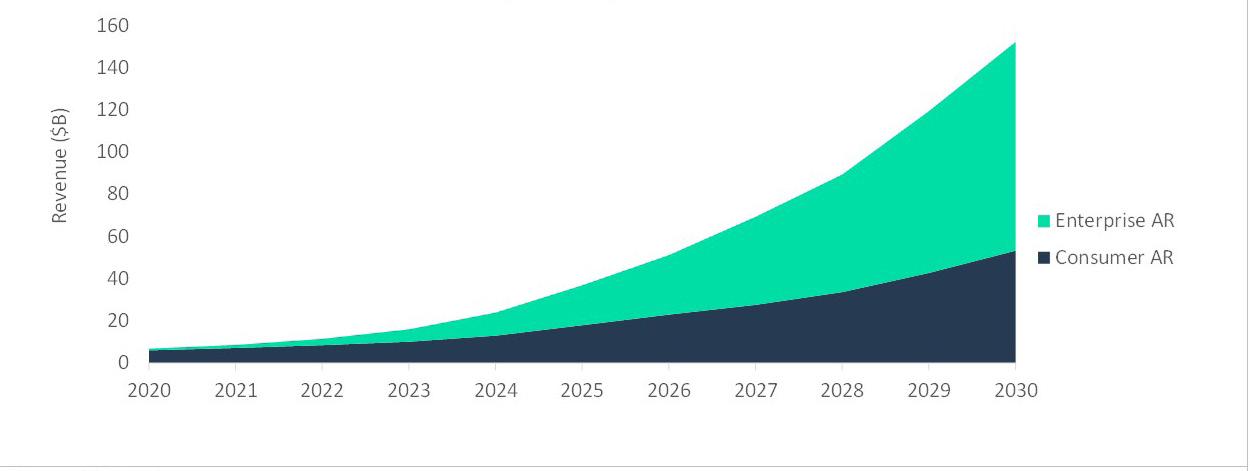
Several oil and gas companies have used this tool within their operations. For example, in 2018, Shell used the QuickVision tool to save 10 days on its drilling operations in the North Sea. This is a significant reduction and would have resulted in large cost savings for Shell. Fugro continues to assist oil and gas companies with their subsea installations and, in January 2022, was awarded a contract to support the installation of an anchorage system for the Sepetiba vessel in Petrobras’ deepwater Mero 2 project off the coast of Brazil.
AR and VR suggests that oil and gas companies continued to invest in emerging technologies despite the financial hardship. The pandemic disrupted the travel of experts to different field sites. Consequently, demand for remote assistance was very high, contributing to the increased AR and VR hiring activity. However, realising cost and time savings will mean that elevated hiring activity within AR and VR is likely to be a mainstay as the industry undergoes digitalisation.
In January 2021, Fugro also agreed to deploy RealWear HMT-1 voice-enabled AR headsets throughout its fleet. Where next for AR in oil and gas? Ultimately, AR is an emerging technology capable of delivering a significant return on investment to companies. This technology can streamline maintenance and repair activities by providing a remote collaboration tool between onsite technicians and disparately located experts, reducing lengthy site visits and machine downtime. As seen in the case of Fugro, AR can also be used for remote planning and surveying activities, which, in potentially hazardous environments, saves time while mitigating risk. As AR technology becomes more affordable and use cases within the industry broaden, we can expect adoption to increase within oil and gas. AR technology can also be used to bridge the growing skills gap within the oil and gas industry, as it continues to suffer from an ageing workforce. Remote collaboration tools that use AR can provide hands-on collaboration between retiring workers seeking more flexible working arrangements and younger workers requiring training. This arrangement is also pandemicproof to some extent, which presents an advantage as COVID-19 continues to cause disruption in parts of the world. As a result, AR will become a mainstay within the training programmes of all major companies operating in the sector. Overall, companies that invest in this technology stand to gain against competitors that fail to realise its potential.
Figure 3. Fugro’s QuickVision AR protractor tool. Source: Fugro. Figure 2. While AR is still an emerging technology, a growing number of companies list it in their filings. Source: GlobalData.
56 World Pipelines / AUGUST 2022
Fugro has developed a tool called QuickVision (Figure 3), which harnesses the power of AR to reduce the time required for subsea installations. The solution uses a subsea camera capable of mixing video with VR measurement tools and Fugro’s Starfix navigation suite. This software-hardware combination provides numerous tools and capabilities, such as a bounding box, which helps measure the position and orientation of a structure. Other tools, such as the virtual protractor, allow incline measurement, while virtual marker buoys indicate the proposed location of a structure. These virtual measuring tools overlaid onto livestream footage eliminate the need for other pieces of physical equipment, and provide a touchless survey solution. This greatly reduces the risk associated with the installation project.
AR in oil and gas: case study Although GlobalData’s alternative datasets reveal that AR is becoming more prevalent as a technology within the wider oil and gas industry, certain companies are leading the way in terms of innovation. For example, Fugro is a geo-data company that helps oil and gas companies with the subsea asset positioning process.
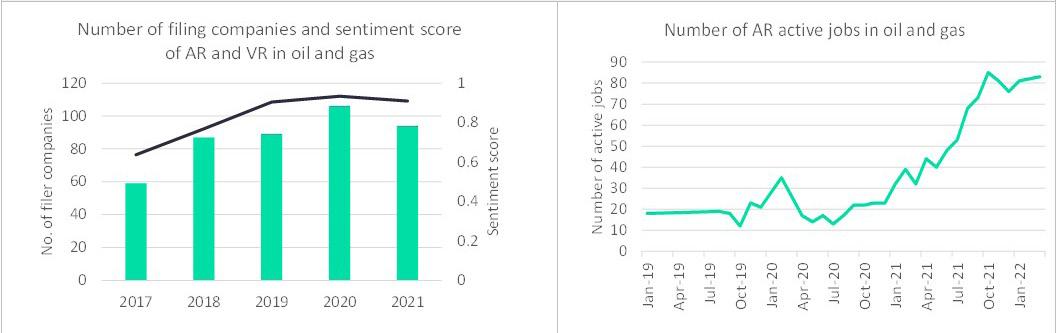
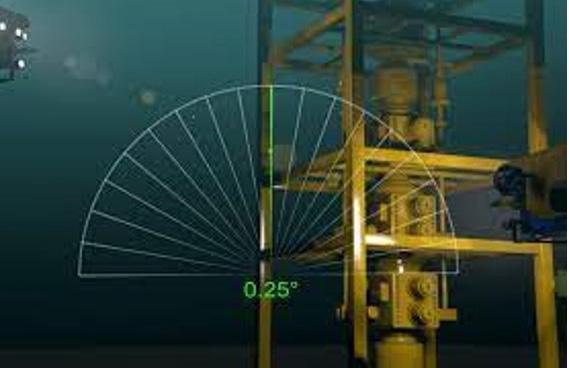
The In-Line Figure 800 Quick Actuating Closure puts safety first. Our patented Clamp Ring Retainer works in conjunction with the Toggle Actuator and the Pressure Alert Fitting to provide an extra level of safety, locking the Clamp Rings in position while the Closure is in the closed position. To ensure lasting value, the Closure incorporates industry-standard O-rings that do not require special order. Go with the In-Line advantage. Safety first. Value that lasts. EaseSafety.of Operation. Lower Operating Costs. 9426-39 Ave, Edmonton, AB, Canada T6E 5T9 1-866-416-9003 info@in-line.ca www.in-line.ca
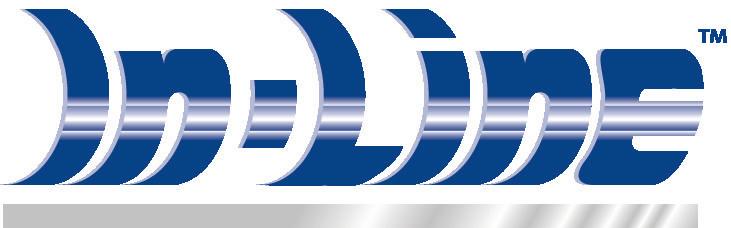
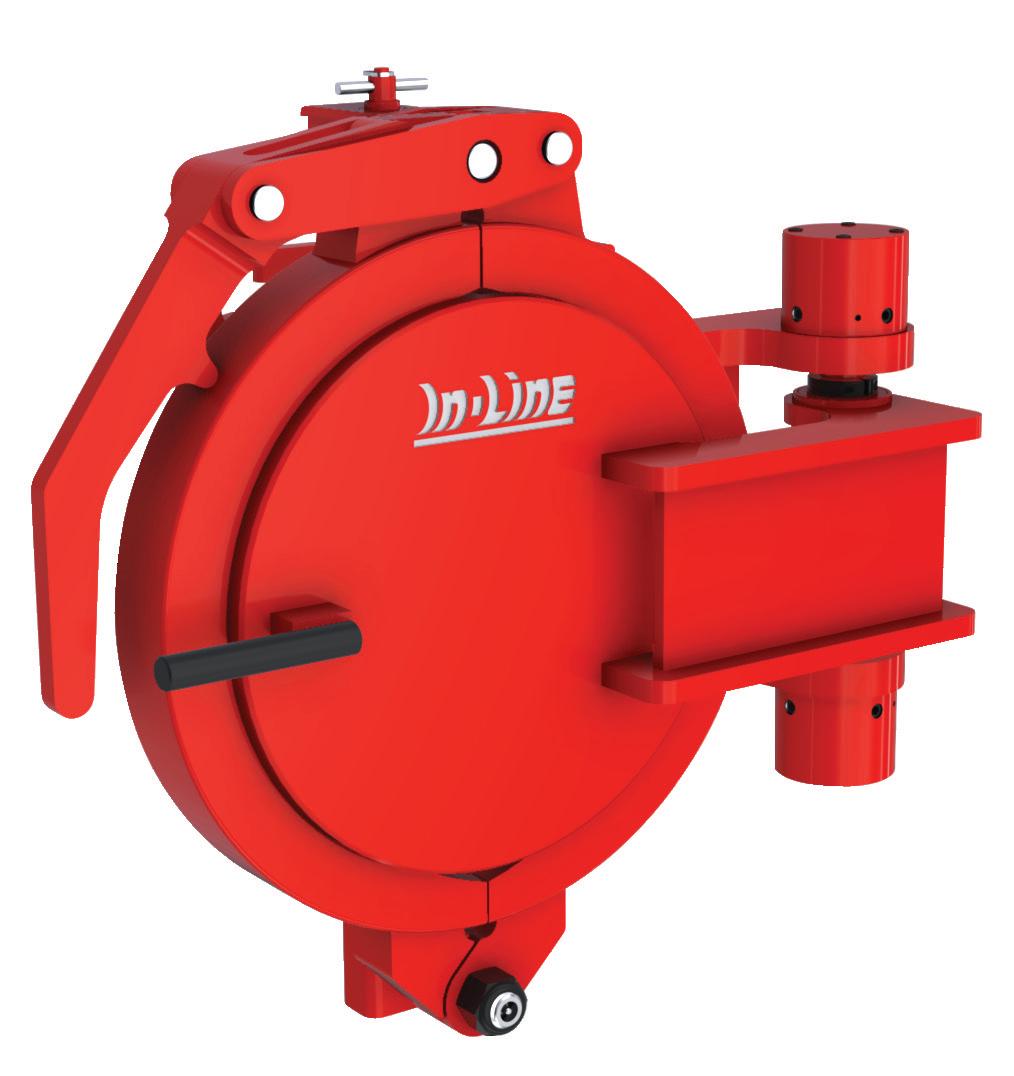
+1 800 383 2666 + sales@wwmach.com + worldwidemachinery.com/SUPERIOR SUPERIOR Manufacturing is a trademark of Worldwide Machinery SUPERIOR INNOVATION Dump Bed Welding Deck Personnel CarrierFlat Bed Water Tank Sand-blasting Deck, and more! • Swappable decks to tackle different tasks • Interchangeable u/c (rubber or steel) • One or two crew cabin • Three sizes – up to 13,600 kg capacity Rotating Unit
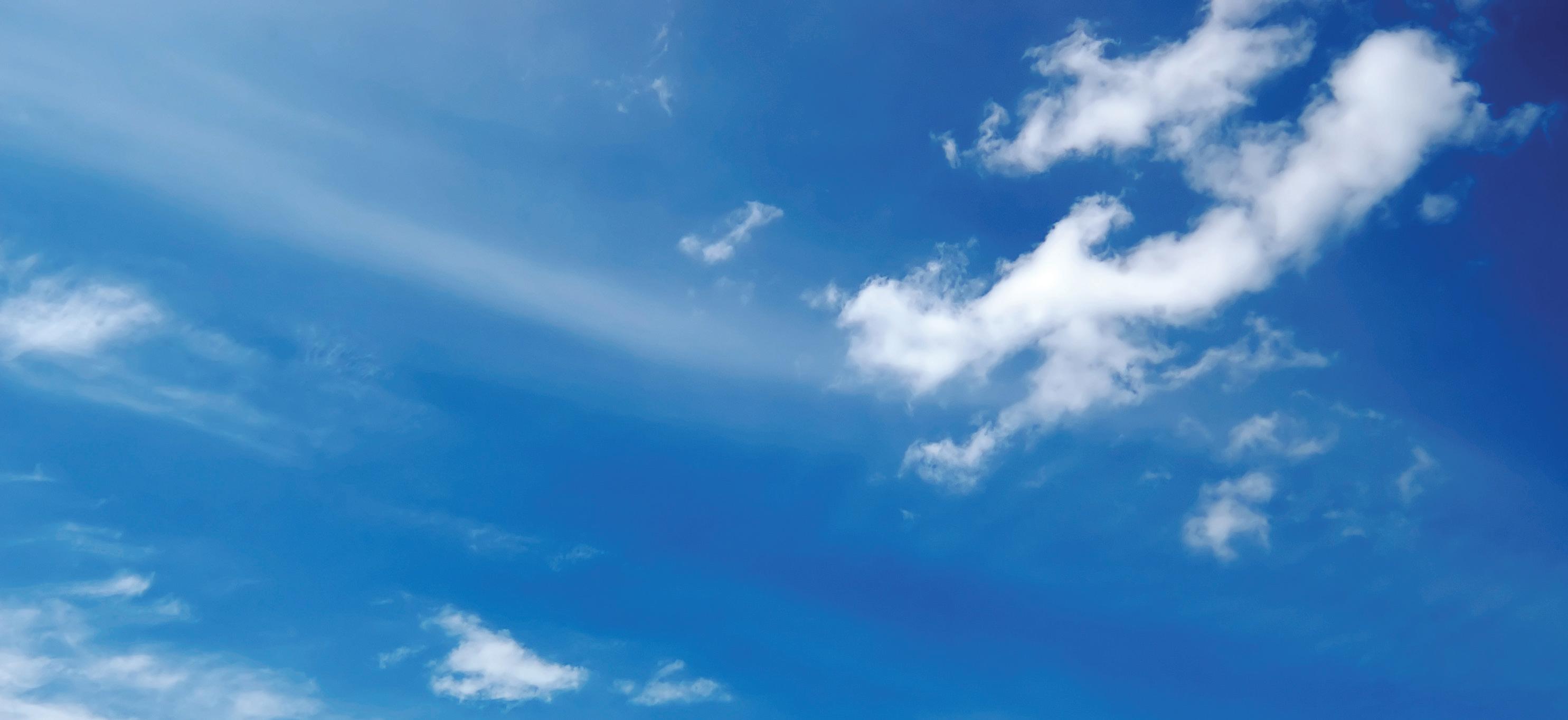
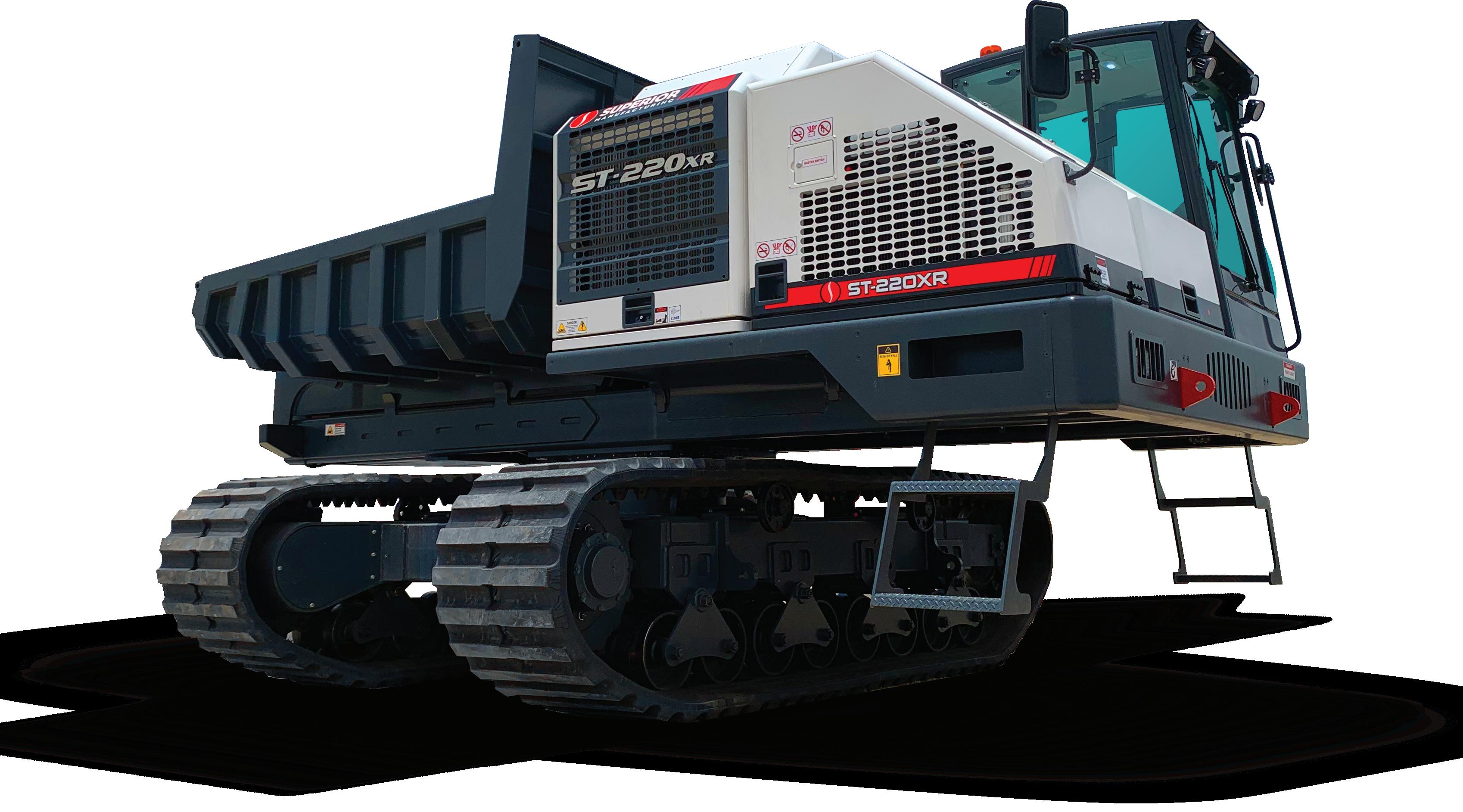
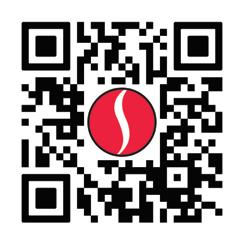
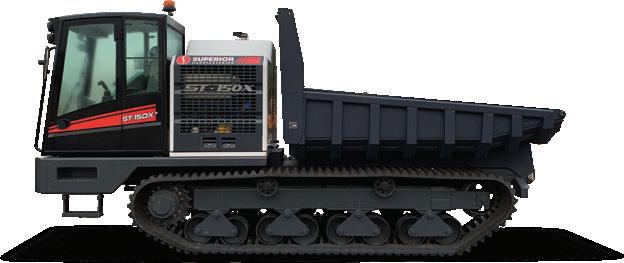
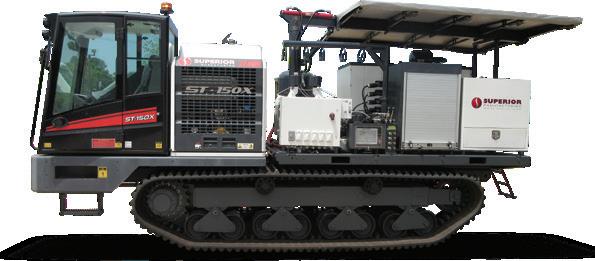
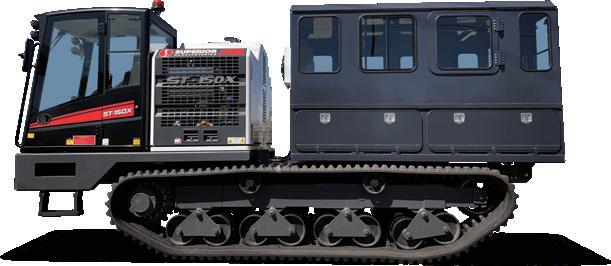
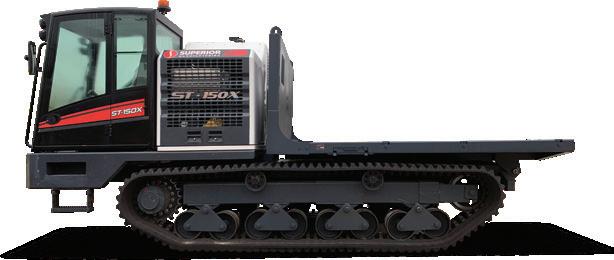
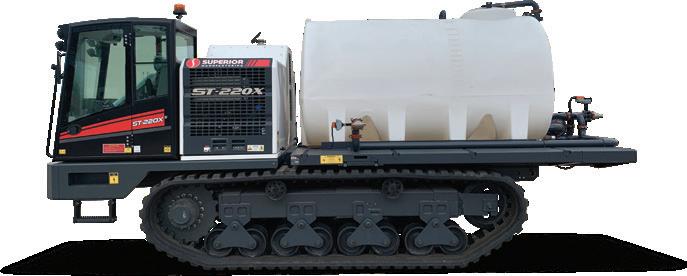
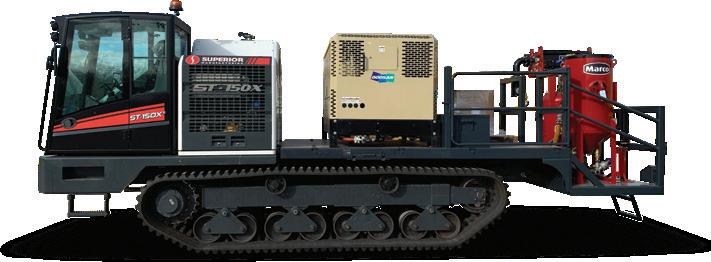
With oil and gas in mind, how do you approach risk management in an evolving risk landscape? The best way for an organisation to approach risk management in the oil and gas sector is through 59
Why is important?managementcontractorso
Leveraging contractor management practices can assist businesses in the oil and gas sector in a multitude of ways. Contractor management platforms act as a centralised location for organisations to access relevant information and resources that may affect their businesses, including written safety policies, security and compliance requirements, virtual training courses, and metrics related to environmental, social, and governance (ESG). Best practices contractor management also enables businesses to participate in client roundtables and other networking discussions to help drive improvement across the industry, and help companies implement best practices derived from data analysis and industry benchmarking. Operator qualifications (OQ) change frequently in the pipeline industry, and effective contractor management monitors these changes in regulations, and ensures that all affected businesses update their policies and procedures to adapt to the changes. By leveraging contractor management software, oil and gas businesses can ensure they are adhering to regulatory requirements and offering the most up-to-date trainings through partnerships with education foundations, such as NCCER®, NACE®, or OQSG®.
Bonney Hodges, Energy Operations Director, ISN, USA, answers some questions about risk management for contractors in the oil and gas sector.
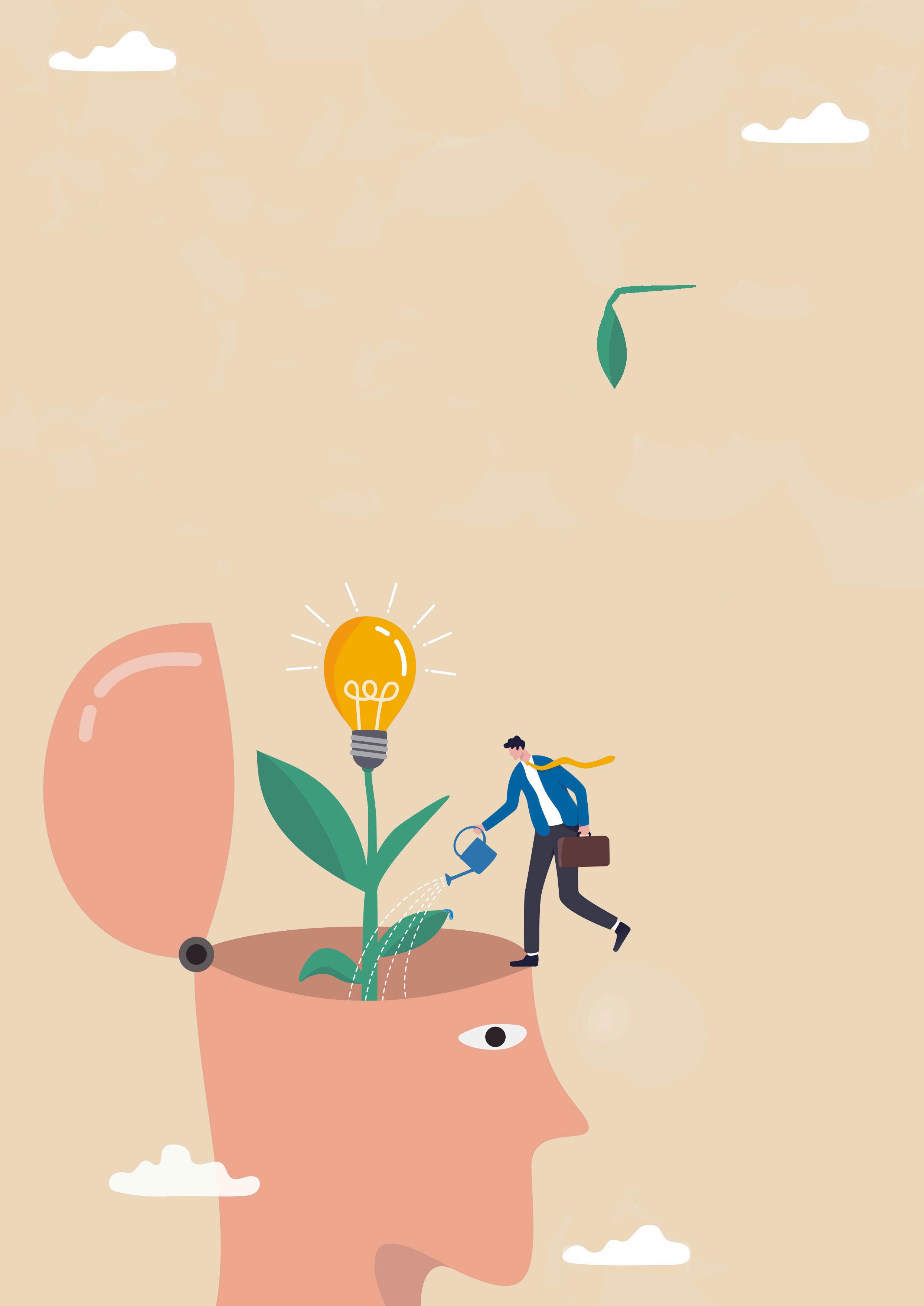
effectively. Through the analysis of data, organisations can identify trends and unveil underlying risks from incident assessments, and as a result, can better understand potential causes of SIFs in the workplace.
What is the significance of company culture? How can contractors work to improve safety culture? A company culture that prioritises safety in the workplace is critical to reducing injuries in every industry. The development of an effective safety culture is founded on awareness, commitment, and empowerment of organisations and individuals. Organisations must ensure that all personnel have appropriate training and support to identify safety risks and express any concerns they may have. This can significantly reduce the amount of employee risk in the Organisationsworkplace.can work to improve their safety culture by receiving feedback directly from the workforce through comprehensive perception surveys. While productivity is essential in the oil and gas industry, organisations must prioritise safety. Online surveys can help organisations assess their safety culture values and implement actions to improve their safety culture.
Organisations are continuing to use data analytics to assist them from a risk management perspective in implementing preventative measures. The leading indicator insights from the data analysis help organisations pinpoint specific activities or equipment that are putting their employees at risk, and attempt to mitigate the problem through a datadriven approach. With more data available, risk management professionals can leverage predictive analytics models to prevent future incidents. Ultimately, data analysis enables organisations to improve their performance by adjusting workplace practices and procedures to protect themselves with a stronger safety culture.
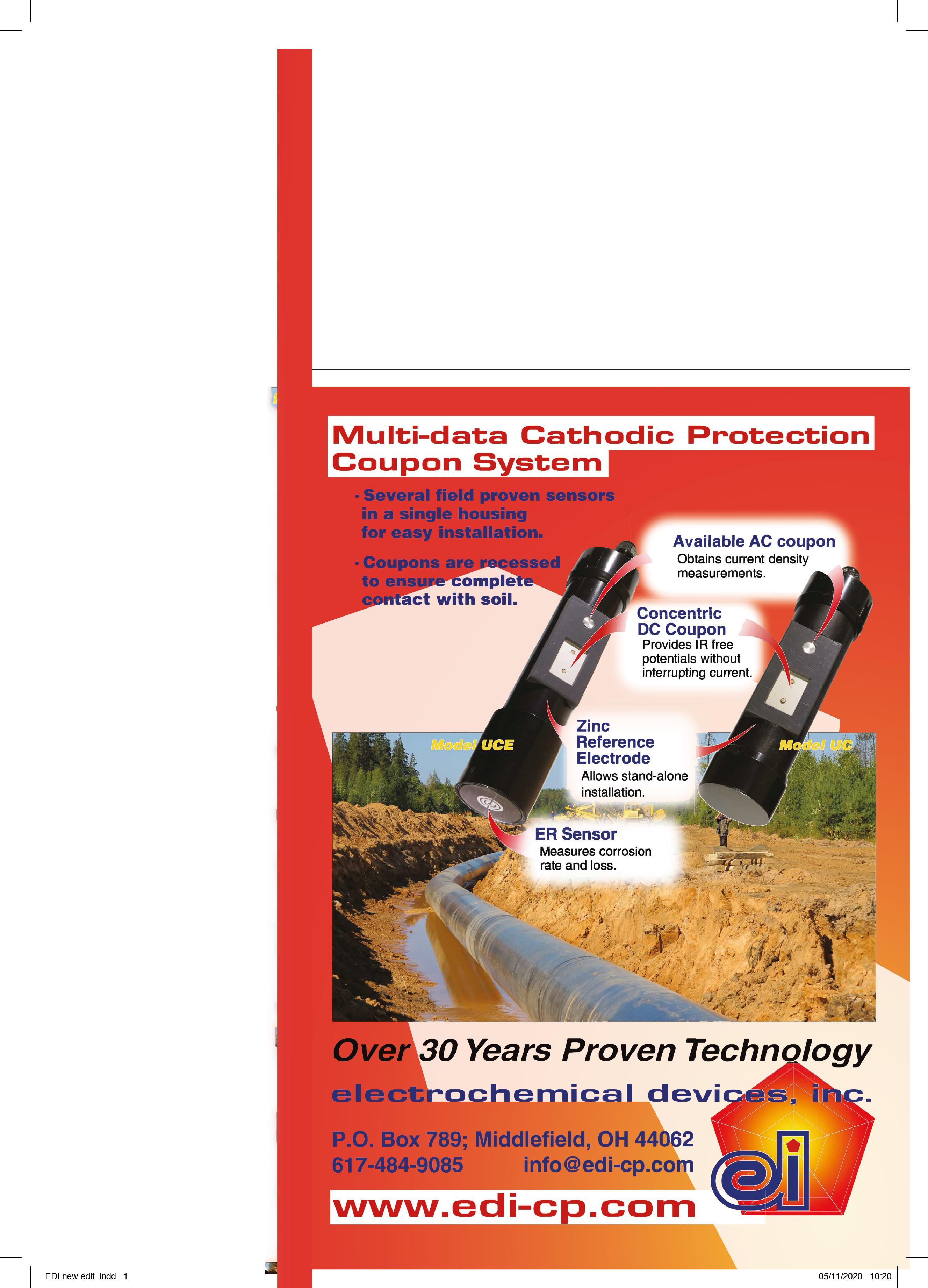
61
Of the existing 2.6 million miles of pipelines that quietly carry trillions of cubic feet of natural gas and hundreds of billions of tons/miles of liquid petroleum products and hazardous materials throughout the US, more than half are at least 50 years old. While ageing infrastructure is an issue, it is not a sole indicator of potential risk. Materials, installation techniques, seam type, corrosion prevention measures, and pipeline maintenance are all factors that impact the likelihood of an accident, as are underground disturbances, freeze-thaw cycles, soil erosion, and nearby excavation.
The future of pipeline integrity and security depends on the industry’s ability to embrace new technologies, argues Jason Chadee, SparkCognition, USA.
ipelines are considered the safest and most efficient way to transport energy products, moving two-thirds of the petroleum volume in the US or more than 600 billion gal./yr. The pipelines represent a more efficient and economic alternative to tanker trucks, freight trains, or air freight for oil and natural gas. However, they are not without fault. When they are compromised by physical failures or digital attacks, the consequences can be catastrophic.
In 2020, the US Department of Homeland Security (DHS) and Infrastructure Security Agency (CISA) reported a ransomware attack on a US natural gas facility that shut down a pipeline for twoIndays.2021, Colonial Pipeline was hacked due to a single compromised password on the dark web. The breach took down the largest fuel pipeline in the US, led to shortages across the east coast, and cost Colonial Pipeline US$4.4 million in ransom. This followed a massive 2020 gasoline spill that was discovered on a Colonial Pipeline in Huntersville, North Carolina, the largest gasoline spill on land in the US. Over a year later, officials are still researching the extent of the spill and assessing clean-up efforts. Also in 2021, an underwater gas pipe leak sparked a swirling fire in the Gulf of Mexico that raged for hours. The leak occurred in an underwater pipeline 150 m from a platform at Ku-Maloob-Zaap, an offshore oilfield in the Bay of Campeche.
P
The pressing problem
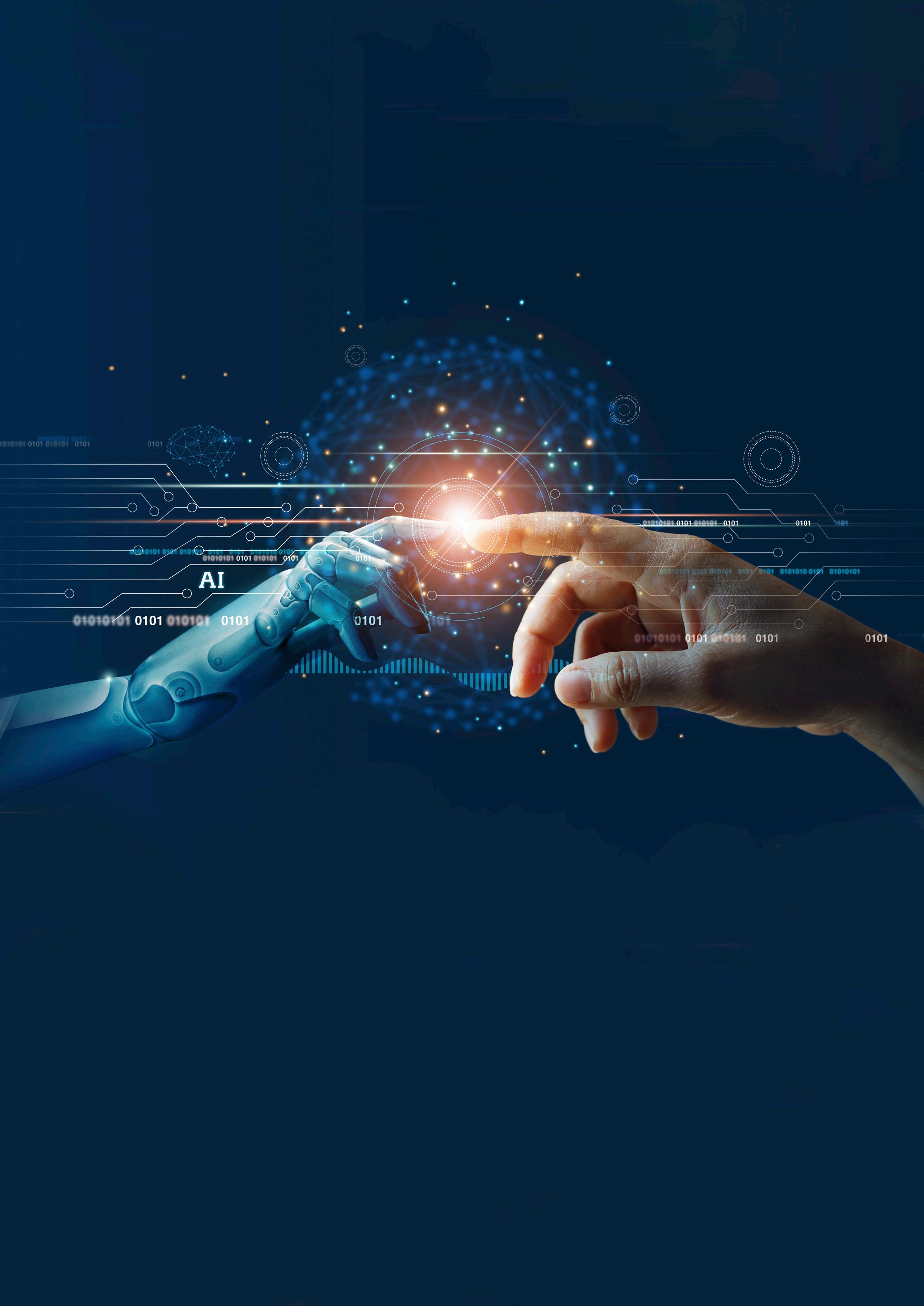
Pipeline and Hazardous Materials Safety Administration (PHMSA), a US agency housed within the Department of Transportation, is responsible for much of the monitoring and enforcement of pipeline safety in the US. Their mandate is honourable, but inspection criteria were initially quite irregular.
Propelled by flowing oil, they probe the pipe from within with magnetic fields, ultrasonic waves, and calipers to record data for analysis. However, ‘smart’ pigs often fail to identify all flaws, and the data collected can take months or a year to analyse.
Figure 1. DeepArmor is an AI-powered endpoint protection product that continuously trains on millions of malicious and benign files, providing next-generation endpoint protection against a broad spectrum of threats.
An airspace management system built on AI and blockchain provides owners and operators with a next-generation approach to inspecting pipelines autonomously with drones. The technology platform includes automatic inspection planning, autonomous fleet execution, and intelligent issue recognition. The operating system (OS) leverages AI and blockchain technologies to intelligently define, synchronise, and execute independent drone inspections in complex airspace. Using a unique algorithm initially developed for rapid intelligence, surveillance, and reconnaissance (ISR) missions, sensor-equipped drones are trained to identify pipeline leaks, spills, and damage. Drone operators can either define the area they wish to survey and the size of their fleet to determine the time necessary to survey an area; or define the area and time required for a survey to determine the optimal search pattern and the number of drones needed to complete an inspection. It is suitable for a variety of tasks, from remote monitoring and methane management, to asset maintenance and emergency response operations.
The Industrial Internet of Things (IIoT) helps monitor aspects of the pipelines with sensors that measure a broad range of parameters, such as pressure, flow, soil movement, and corrosion, streaming terabytes of data daily. However, it also opens the doors for malicious actors to exploit vulnerabilities. A compromised pipeline system could result in explosions, equipment destruction, unanticipated shutdowns or sabotage, theft of intellectual property, and downstream impacts to National Critical Functions (NCF) and, therefore, impact national safety and business success.
The Transportation and Security Administration (TSA) has advocated for voluntary pipeline cybersecurity standards for two decades. In the wake of the Colonial Pipeline attack, TSA issued mandatory cybersecurity rules on owners and operators of pipelines to protect against ransomware attacks and other known threats to IT and OT systems. Owners and operators are now required to develop and implement cybersecurity contingency and recovery plans, and conduct a cybersecurity architecture design review.
Monitoring and maintenance approaches are costly and inefficient because pipelines are often installed on large-scale and in inaccessible and hazardous environments. Physical inspections have typically involved smart pigs, but they are not without issues.
Figure 2. With millions of new malware variants showing up each month, DeepArmor uses AI models to detect and prevent cyberattacks, including zero-days, ransomware, trojans, malware, crypto-miners, etc.
Originally, the agency only required 7% of natural gas lines and 44% of all hazardous liquid lines to be subject to their rigorous inspection criteria and inspected regularly. The rest of the regulated pipelines were still checked, but less often. Later reforms mandated more testing for oil pipelines. Nearly a decade ago, PHMSA began considering human factors as a significant influence on compliance, so it began requiring owners and operators to test pipelines in ‘high consequence’ areas, which included population centres or areas near drinking water. Only recently have gathering lines, the connection from wells to processing facilities or larger transmission lines, come under PHMSA regulation, wherein regulatory requirements were added to over 400 000 miles of gas pipelines previously deemed unregulated.
62 World Pipelines / AUGUST 2022
AI as the solution Pipeline owners and operators are turning to artificial intelligence (AI) as the first-in-line technology to solve their daunting physical and cyber challenges. AI can monitor various operating parameters of pipelines simultaneously in real-time, 24/7, and combine the information to assess the state of the pipeline system, growing smarter with each new piece of information. The data that AI proactively collects can be analysed to generate immediate responses.
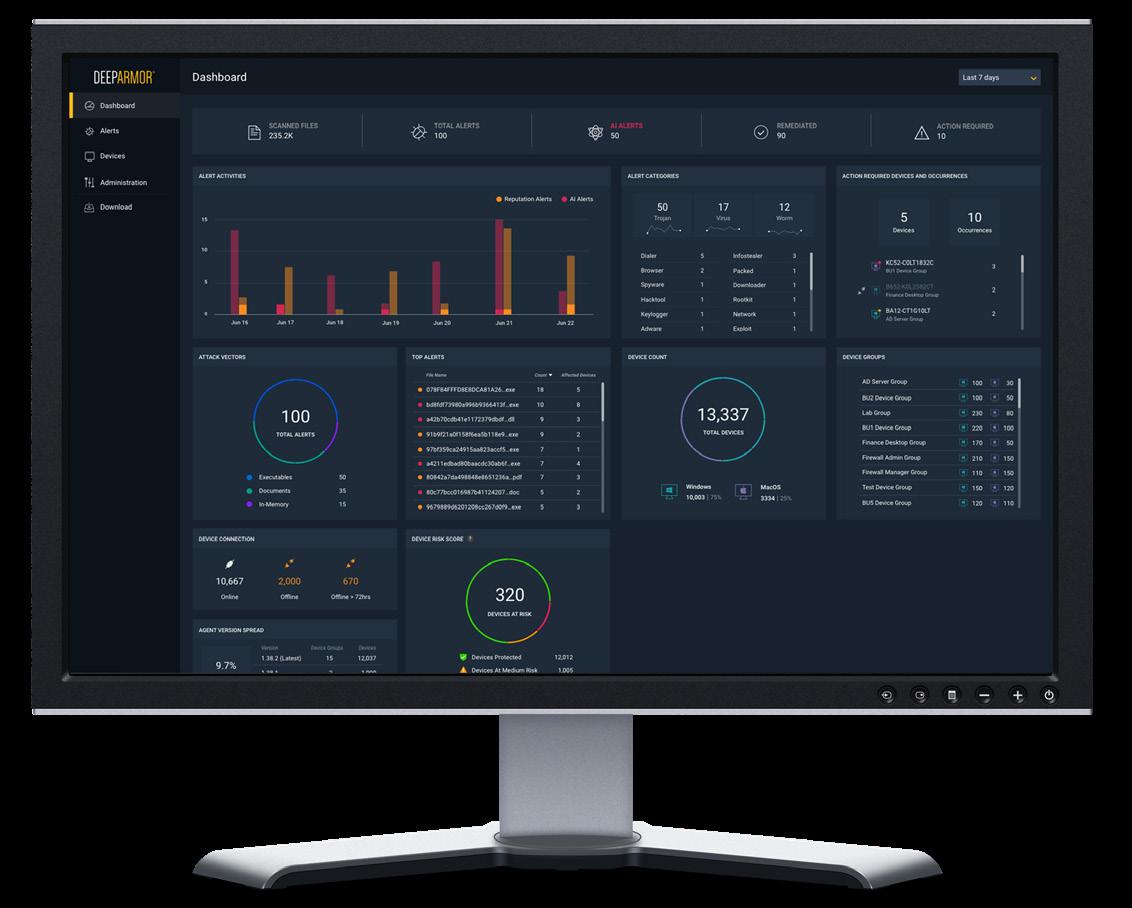
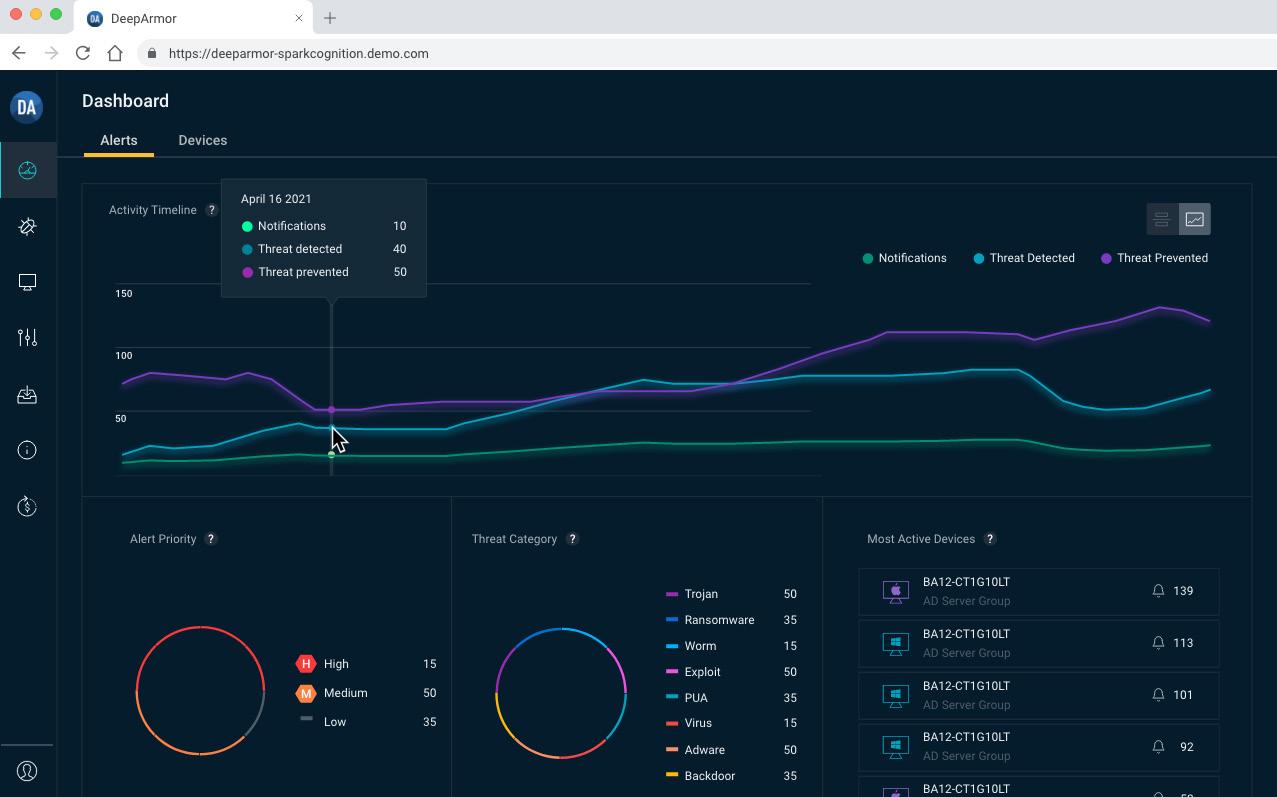
You’re looking for a partner that provides the best service in sales & rental in pipeline equipment. One that deals in all the big brands and offers worldwide delivery. A company you can rely on, one that keeps its promises, thinks ahead and always delivers... You can build on BAUMA! BAUMA-PIPELINE.COM Only one call away... Vermiet- und Handels GmbH
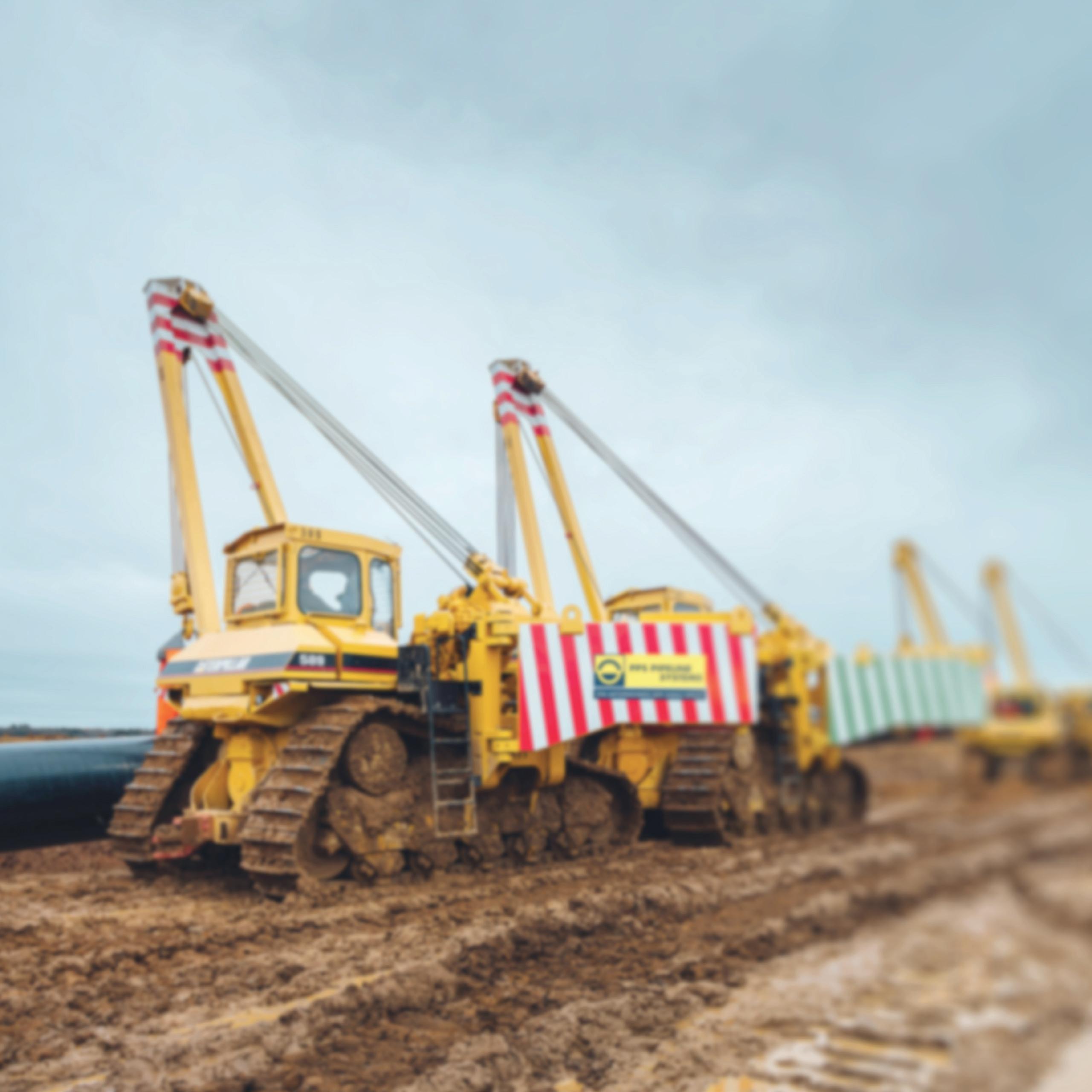
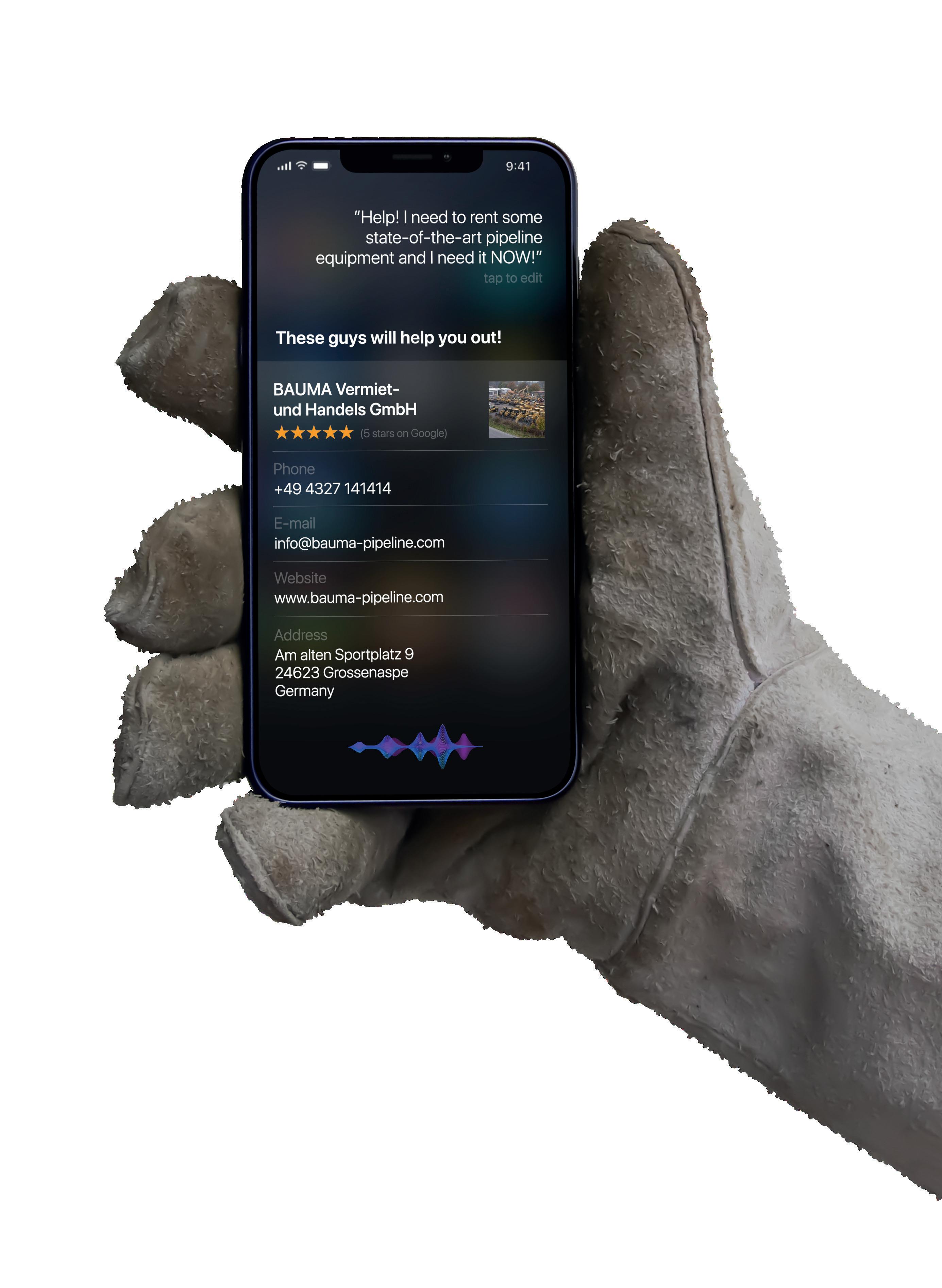
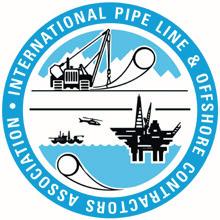
Using the technology platform, the area of the pipeline that is needed to survey is defined. The system automatically provisions airspace where possible and then determines the number of vehicles required and optimal routes for drone fleet inspections. When launched, the drones autonomously execute their individually coordinated missions.
Detects holidays, pinholes, and other discontinuities using pulse DC High voltage Holiday Detector +1-315-393-4450 www.defelsko.com Choose from a wide range of rolling spring electrodes and wire brushes — custom sizes available DeFelsko Corporation l Ogdensburg, New York USA Tel: +1 315 393 4450 l Email: techsale@defelsko com n Lightweight, ergonomic design provides comfortable all day use, reducing operator fatigue n Regulated pulse DC voltage output that won't change under load ±5% voltage accuracy n Voltage calculator feature choose one of 11 international standards, and input the coating thickness to automatically calculate the required test voltage n Long Form Certificate of Calibration included with each instrument
Over the years, cyberthreats have increased in direct correlation with more weak points in pipeline infrastructure. As owners and operators embrace big data, edge computing, and automated solutions to reduce costs and improve efficiencies, they are naturally adopting risk-based approaches to securing the technologies and processes that serve as the foundation for their hyperconnected IIoT AImodel.isthe transformative technology that is prepared to tackle sophisticated cyberattacks on pipelines and critical infrastructures.
The future of AI for midstream Over the past two decades, experts have been at war with ageing infrastructure using inadequate tools, technologies, and resources. Physical failures and cyberattacks have been met with a reactive response, instead of a proactive prioritisation of AI’s role in securing and optimising energy, monitoring integrity, and reducing safety risk and environmental impact. The future of pipeline integrity and security will depend on the industry’s ability to embrace new technologies, including AI and machine learning.
SparkCognition, working with Siemens Energy, developed DeepArmor®, an AI-based cybersecurity solution that provides zero-day protection against the most advanced ransomware, viruses, malware, and more. It uses machine learning to flag never-before-seen cyber threats, protecting critical assets, and using advanced algorithms to determine when a nefarious action or event might turn into malware and then defend against it. The AI-driven solution provides a defence layer independent of threat intelligence while eliminating the need for threat signature updates or specialised analysts to secure individual operational technology systems. The platform uses behavioural analysis to continuously monitor and detect new threats and provide the first line of defence and immediate protection against both previously identified and zero-day attacks on endpoint devices. As a result, the solution can prevent or mitigate attacks from new sources that are still unknown to the industry or security professionals while lowering the security spend for asset owners.
Drones can be equipped with specialised thermal, infrared, and LiDAR sensors to identify equipment failures, methane leaks, or spills. Using additional AI algorithms can automatically distinguish inventory or substances from their surroundings. Owners and operators have access to real-time video feed as drone fleets execute their missions.
AI-powered cybersecurity Pipeline anomalies and threats do not wait, and neither should threat analysis and management.
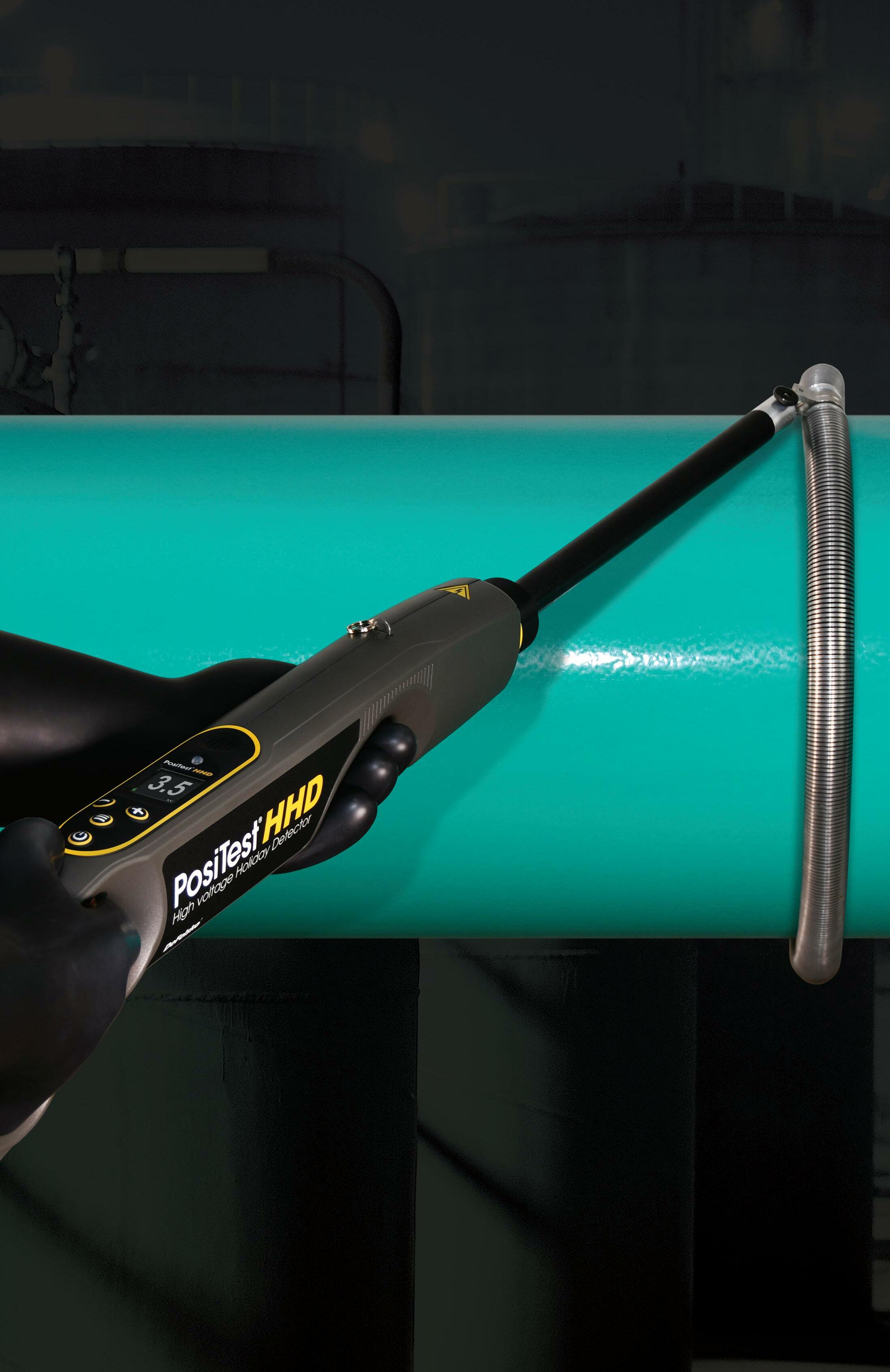
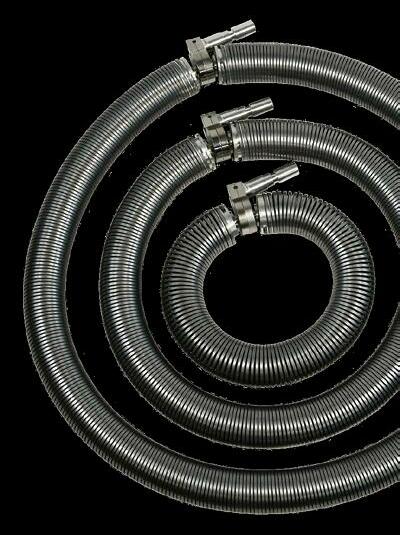
Autonomous shipping is still in a nascent state, but the elements required for progress – regulation, operational issues and technology – continue to evolve, writes Gareth Burton, VP Technology, ABS, USA. uch progress has been made in the development of maritime autonomous technology in the last three years. Ongoing projects being held across the world trailing autonomous technology have progressed and new collaborations between stakeholders have been formed. In a step forward, the International Maritime Organisation (IMO) has concluded the Maritime Autonomous Surface Ships (MASS) Regulatory Scoping Exercise. The discourse on maritime autonomy has tended to view vessels in a uniform manner. However, this may not be suitable when addressing the unique characteristics of autonomous ships. The technological and regulatory challenges vary depending on vessel type and size.
The Regulatory Scoping Exercise was scheduled to be completed by the MSC 102 meeting in November 2020. However, due to the COVID-19 pandemic, conclusion of this scoping exercise was deferred, and the Regulatory Scoping Exercise was completed and finalised at the MSC 103 meeting in May 2021.
IMO’s Legal (LEG) and Facilitation (FAL) Committees are conducting separate Regulatory Scoping Exercises on the instruments under their purview. The LEG Committee has 65
Regulation A key activity in the development of regulations for autonomous operations was concluded in May 2021. However, this is by no means the end of this journey. Rather, the conclusion of the IMO MASS Regulatory Scoping Exercise marks a step towards the drafting of requirements governing autonomous operations by the IMO.
The Regulatory Scoping Exercise was carried out in two steps. At the first step, IMO instruments were reviewed to identify the instruments which are applicable to MASS, and determine if the instrument needs to be amended or to be adapted to MASS operations.Thesecond step was conducted to analyse and determine the most appropriate way of addressing MASS operations. At this step, detailed discussions were held to determine if the existing instruments were required to be amended or new instruments need to be developed to address MASS operations.
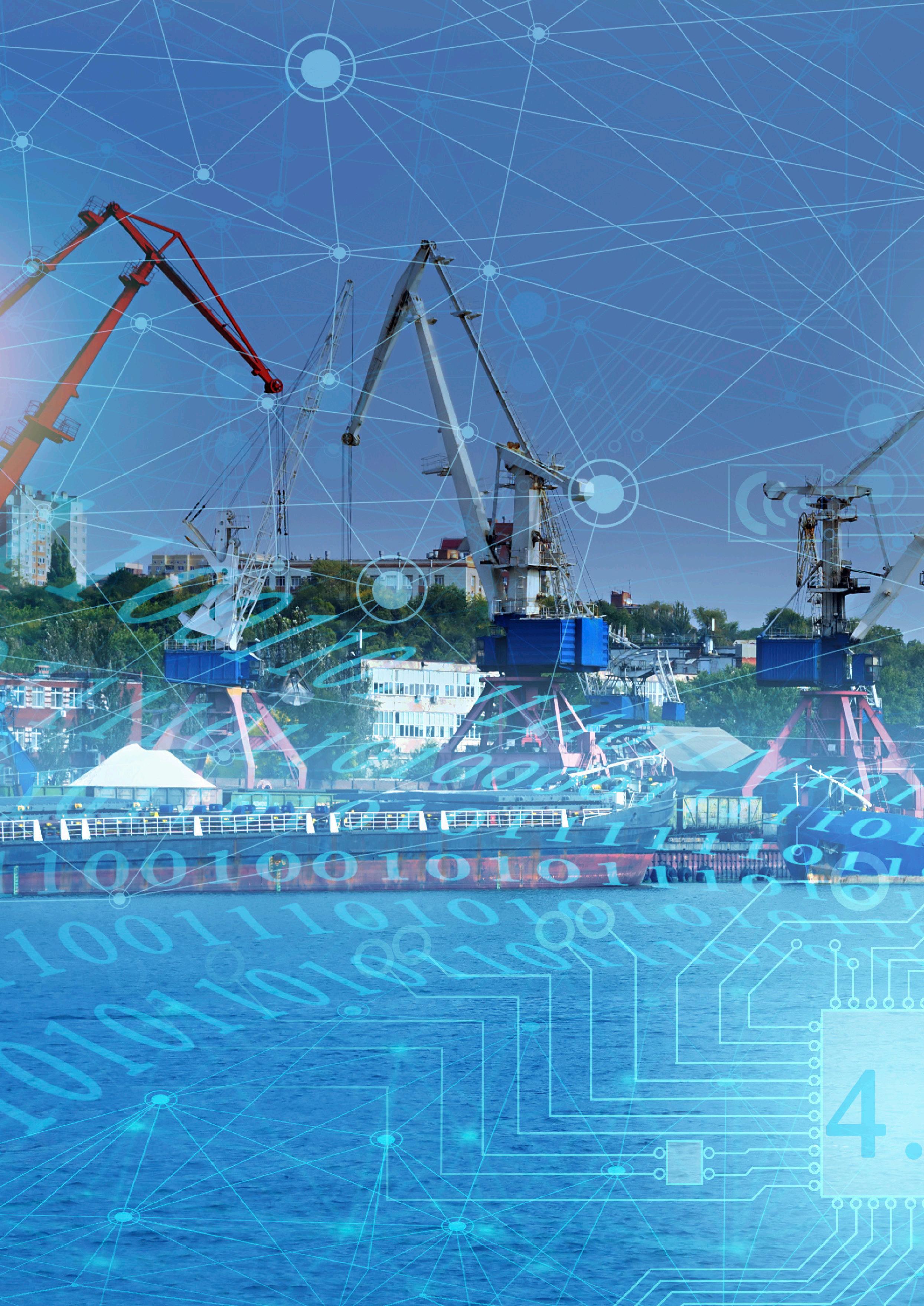
The failure of autonomous and remote-control functions can have a serious impact on their mission, performance, or safety. Thus, they should be thoroughly tested and verified to prevent potential failures, covering comprehensive, diverse and critical situations for both normal and abnormal operational conditions.
66 World Pipelines / AUGUST 2022
completed their scoping exercise, whereas the scoping exercise for the FAL Committee is still underway and is expected to be completed in 2022. From the review of the various instruments under the purview of the Maritime Safety Committee (MSC), the scoping exercise identified a list of 11 common potential gaps and/or themes which need to be addressed to advance the development of regulations for autonomous operations. From this list, the IMO has identified four potential gaps and/or themes as high-priority issues that cut through critical IMO instruments and may require a policy decision or determination to progress further.
Software underpins the delivery of autonomous and remotecontrol functions. To deliver these functions as intended and safely, software quality and reliability are crucial. In addition, the underlying algorithms may not be understandable and directly verifiable.There are many questions about the validation of software and algorithms used in advanced automation, autonomous and remotecontrol functions, such as: How do we define reliability? How do we track and evaluate decisions taken by software? How do we supervise correct behaviour to achieve trust and control learning? How do we define liability in the event of software failure?
Operational considerations
The operational issues surrounding autonomous shipping are numerous – including connectivity, the use of augmented reality, human factors and cybersecurity. Continuous and reliable communication and connectivity between the autonomous vessel and the remote operator station is a key enabler. The communication will need to be bidirectional, accurate, scalable, and supported by multiple systems – creating redundancy and minimising risk. Reliability of the communication channel between the vessel and remote-control or operator station is crucial to safe operations. The connectivity between the vessel and the remote station that performs monitoring and control is essential to autonomous and remote-control functions, and there are various factors to be considered, such as the bandwidth, data integrity, reliability, and latency. Data integrity should be verified and corrupted or invalid data should have timely recovery. Data connection to the vessel should be robust and fault resilient. For autonomous or remote-control functions of higher risk, the functions are not to be compromised even with degradation of network or complete loss of connection. Network latency should satisfy the functional and performance needs of the specific autonomous or remote-control function. With operators potentially away from the vessel, the situational awareness of the operator could be reduced. A key concern from stakeholders and regulators is: will a reduced situational awareness have any adverse impact on safety of operations? What is the minimum required level of situational awareness a remote operator should be provided in order to attain an equivalent level of safety and operational efficiency? Against this backdrop, AR technology will be useful in assisting to bridge the gap between perception and reality. AR is a technology that allows the superimposition of digital contents (images, sounds, text) over a real-world environment. AR has started to be utilised in this field. For example, AR combined with cellular network connectivity allowed operators at a remote-control centre to monitor and guide the operations of a tug remotely.Theremote operator will be at the core of remote-control/ operator station operations. Their skills and competence will be an important factor in supporting safe autonomous and/or remotecontrolled operations. Currently, the International Convention on Standards of Training, Certification and Watchkeeping for Seafarers (STCW) Convention sets precise requirements for education, training and experience (sea service) for personnel working on board vessels. For shore personnel and management of vessels, the International Safety Management (ISM) Code provides requirements for the safe management and operation of ships. The availability and necessity for autonomous and remotecontrol operations to be in constant communication via satellite or cellular communications greatly increases the cyber vulnerability of the ship or offshore unit. Cybersecurity can no longer be considered on the periphery of autonomous discussions: it has to sit at the core of Dueit.to the repercussions of a cyber incident, cybersecurity is now front and centre of maritime stakeholders’ concerns. A holistic view on cybersecurity covering the entire ecosystem enabling autonomous and remote-control operations is required, i.e. from a vessel’s onboard systems, communication systems, remote-control/ operator station systems, human operators and other interfacing systems such as a Port Vessel Traffic Systems (VTS) and other service provider.
Figure 1. A new ABS Guide for Autonomous and RemoteControl Functions sets out a goal-based framework for the implementation of these technologies on vessels and offshore units, and introduces two new notations.
Upon the conclusion of the Regulatory Scoping Exercise, the IMO has agreed that they should embark on plans to develop requirements for autonomous operations with the target of publishing these requirements by 2025.
Applying advanced techniques
Traditional validation methods are typically costly, timeconsuming, limited in the reproducible scenarios, and risky in case of non-acceptable behaviours.
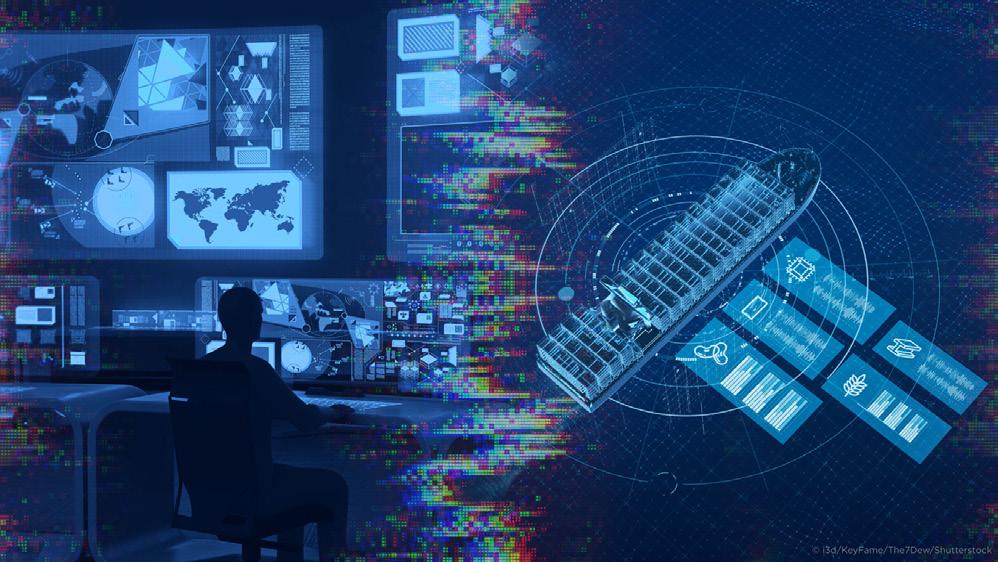
QUALITY RELIABILITY FLEXIBILITY RENSALES TAL L AYING BENDING WELDING STRENGTH, PERFORMANCE & RELIABILITY UNDER ALL CIRCUMSTANCES . MAATS PIPELINE PROFESSIONALS P.O. Box 165 | 7470 AD Goor the Netherlands T + 31 547 260 000 F + 31 547 261 000 E info@maats.com CO2 neutral rental STAAMmoc. MAATS.com your equipment partner since 1981
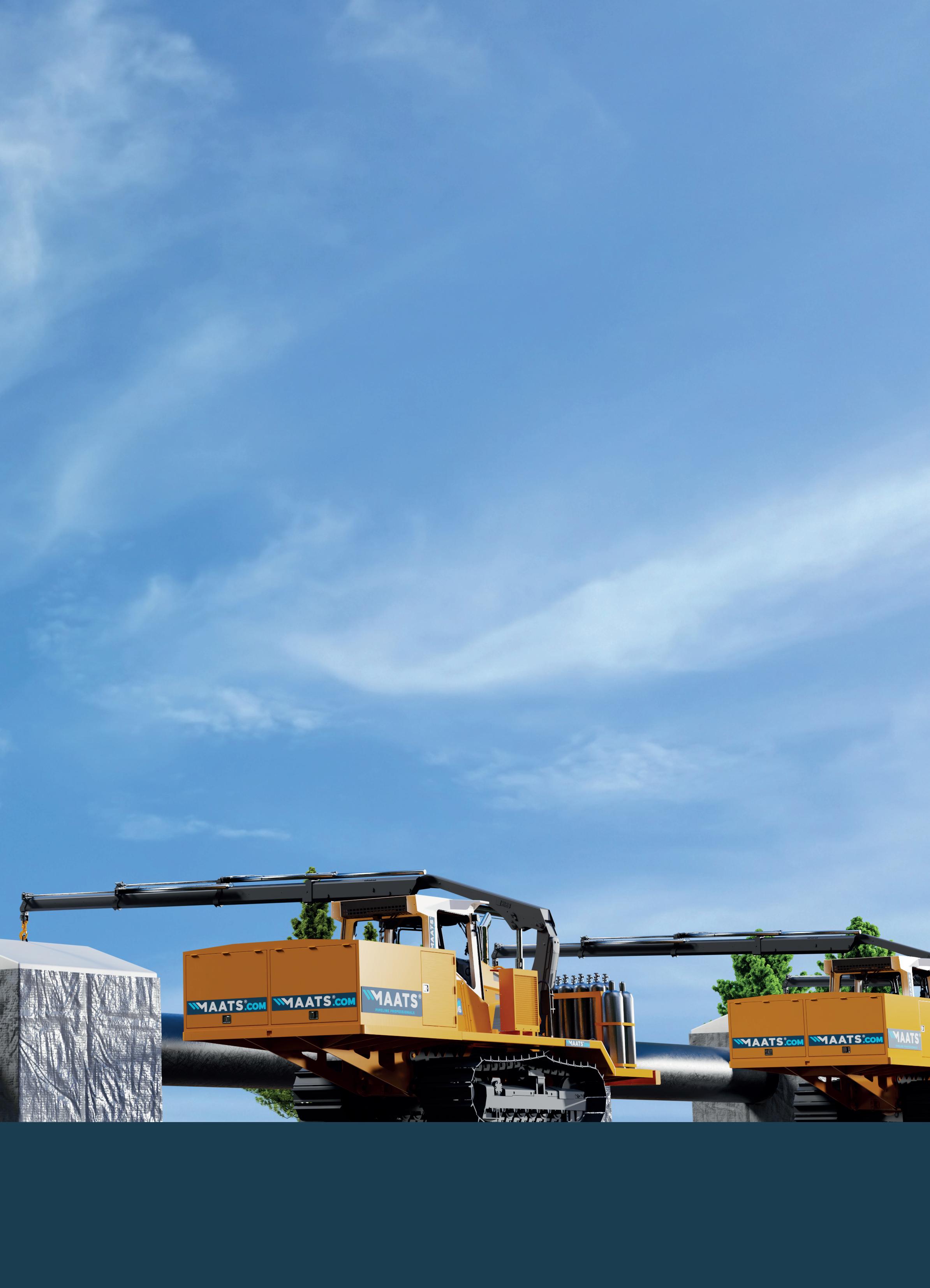
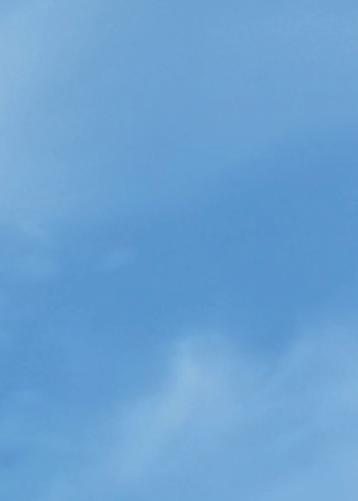
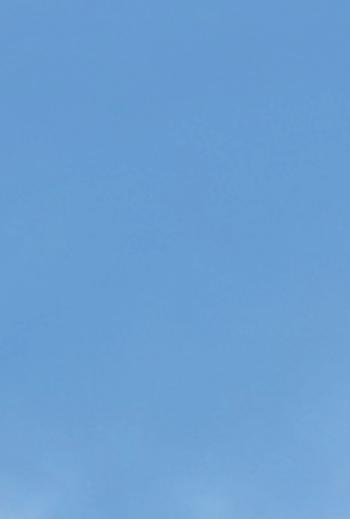
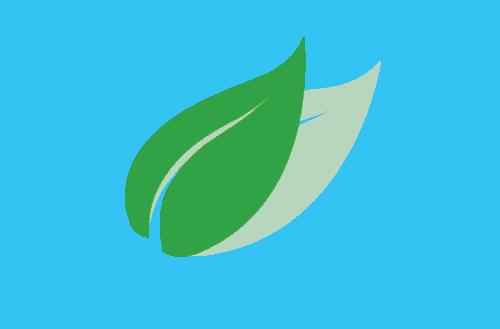
Machine learning (ML) is a subfield of AI, which enables machines to learn from past historical data without being explicitly programmed. AI and ML techniques are increasingly being used in smart and autonomous functions.
CONTACT US FOR DETAILSCONTACT US FOR DETAILS Real Estate Available as TURNKEY OPPORTUNITY PRIVATE TREATY SALEPRIVATE TREATY SALE Stupp Corporation Baton Rouge Campus 60” SMS (PWS) 2 Step API Spiral Pipe Mill 24 Torrance/SMS API ERW Tube Mill Selmers ID/OD Coating Facility & Mill Joining Facility Served by 2 Class 1 Railroads KCS and CN 12 5 Miles from Greater Baton Rouge Port Close Proximity to Major Interstates I 10, I 55, I 49 Total Site 170 Acres SMS 2-Step Submerged-Arc Welded Helical Spiral Pipe Mill 24" Torrance/SMS ERW API Tube Mill Selmers ID/OD Coating Facility Brian NationalMachy.combrian@nationalmachy.com917-327-3724Epstein Nick TheBranfordGroup.comnromaine@thebranfordgroup.com508-846-1034Romaine Entire Plant Installed in Baton Rouge, Louisiana
Model-in-the-Loopdeployment.(MIL),Software-in-the-Loop (SIL) and Hardware-in-the-loop (HIL) simulation techniques, which are approaches that have been widely used in model-based design (MBD) in the aerospace, military and automotive industries, can be leveraged for autonomous and remote-control functions.
Conclusions Discussions surrounding autonomous developments are starting to take on a practical shape. Various projects to understand and propose solutions to enable practical use and implementation of autonomous technology have been completed, and some are still ongoing. Nonetheless, the industry is facing up to the intricate challenges and obstacles which have to be overcome.
The pre-processing of the data set that will be imported to the ML algorithms is a crucial step for ML. ML requires highquality data. Thus, a suitable data and Internet-of-Things (IoT) architecture which defines and facilitates clear processes for collecting data from different sources, filtering, standardising, pre-processing, and merging data in a common platform and checking its quality is often necessary.
The conclusion of the MASS Regulatory Scoping Exercise at the IMO and subsequent efforts to map out the way forward to drafting international regulations is a good progress. While there are significant challenges ahead, this is a good sign that the industry sees value in autonomous technology and that it has the potential to bring improvement to maritime operations and Assafety.the industry endeavours to develop regulations and requirements for autonomous vessel design and operations, this article has proposed a goal-based framework based on the intent of the requirements contained in current conventional regulations. This leverages on the wealth of experience which formed the basis of these regulations.
From ongoing autonomous technology trials and projects, some key issues have surfaced. Some of these issues pertain to the difficulty for autonomous vessels to meet current requirements, whereas some issues are new to the maritime industry. To allow the adoption of autonomous technology and operations, regulations being planned for autonomous vessel design and operations will have to address these issues.
For example, different regression algorithms have been used for the prediction of a ship’s operational parameters, such as the required main engine power, deep learning has been used for ship recognition and tracking, reinforcement learning (RL) and neural networks (NN) have been used for ship’s path planning and optimisation.
To improve reliability and to avoid catastrophic failures, software can be tested using system-level pre-validation that is done in virtual worlds through simulation, to discover faults and fix them before
Artificial intelligence (AI) is a technology for creating intelligent systems that can simulate human intelligence.
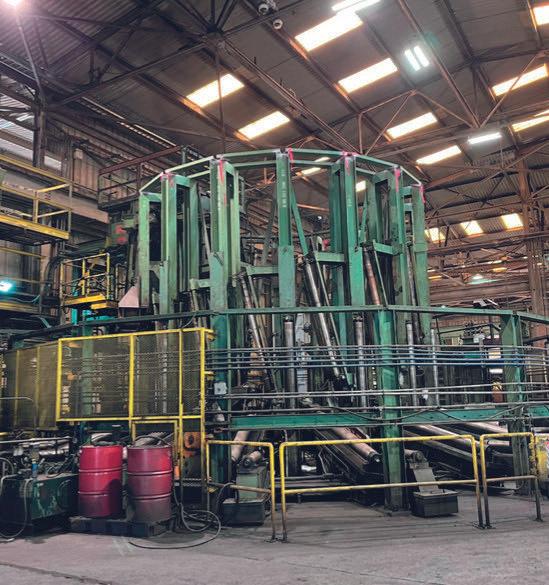

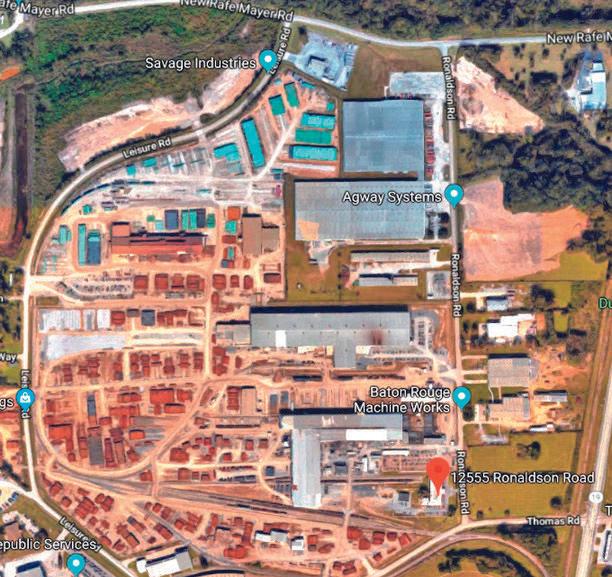
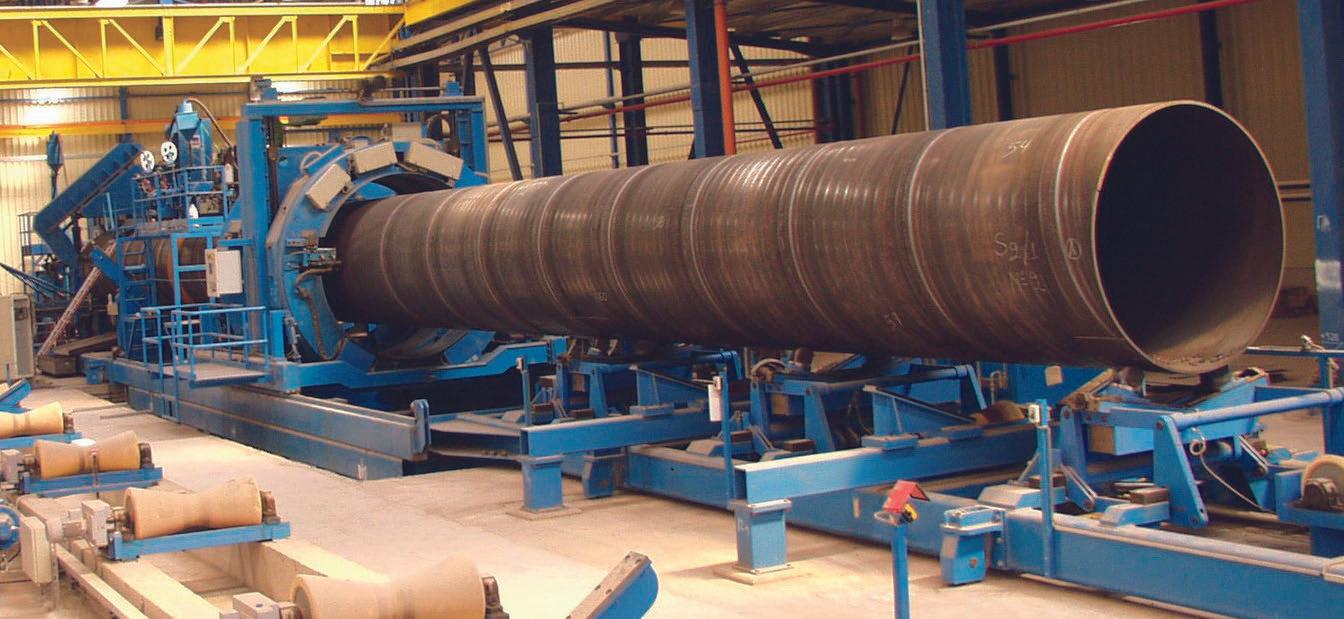
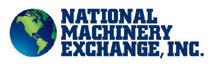
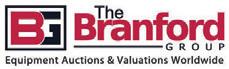
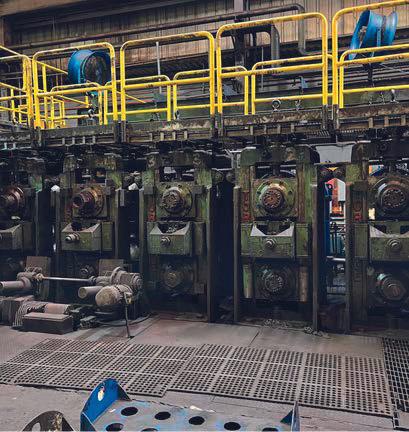
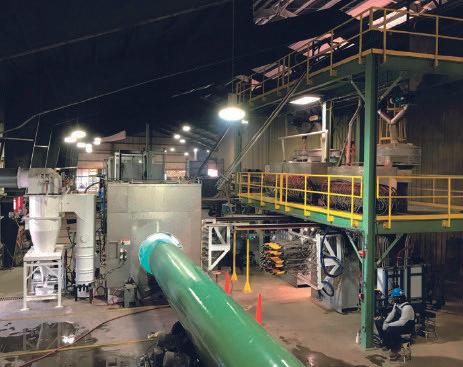
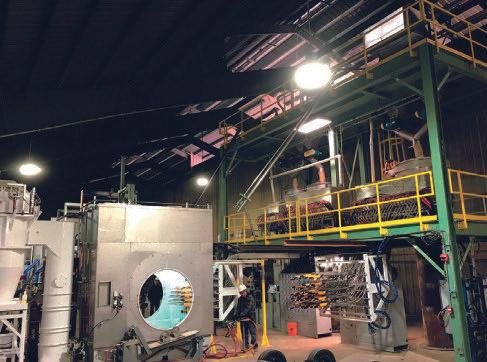
The pipeline industry can be divided into three major segments: upstream, midstream and downstream. Much of the critical pipeline infrastructure consists of transmission pipelines, which are a part of the midstream sector. According to a variety of references and studies, approximately 40% of those lines are ‘unpiggable’. Considering the large number of pipelines operating in the upstream sector – for instance in-field (onshore and offshore), storage and loading lines, as well as pipelines used downstream, including high-pressure distribution pipes – the total length of lines requiring inspection globally is considerably higher than 2 000 000 km, so the number of pipelines that are challenging to inspect is even higher. Business is a balance of risk and economic efficiency. Inspecting all 2 000 000 km in one year is simply impossible; therefore, we need to know where specifically to focus our people, resources and budgets. Essentially, we cannot readily inspect them all, so which pipelines are the highest priority?
ROSEN, consider approaching ‘unpiggable’ pipelines from all angles to find the best integrity management solution.
Corey (Canada)ChristopherRichards,HollidayandSimonIrvine (UK),
69
ipelines, like all energy assets, are a critical part of our societal infrastructure. They provide us with the ability to heat our homes, supply our drinking water, drive our cars, fly our planes, and even to transport critical hydrocarbons required for the development of plastics. With such crucial functions, ensuring these assets are protected and safeguarded is the main priority of pipeline operators. Stringent integrity programmes help operators with this task through regular inspections, followed by integrity assessments and, when required, repair and rehabilitation measures. While these methods are straightforward for more standard pipelines that are setup for inline inspections (ILI), a large gap remains for assets outside of the norm, such as, in particular, challenging to inspect or ‘unpiggable’ pipelines.
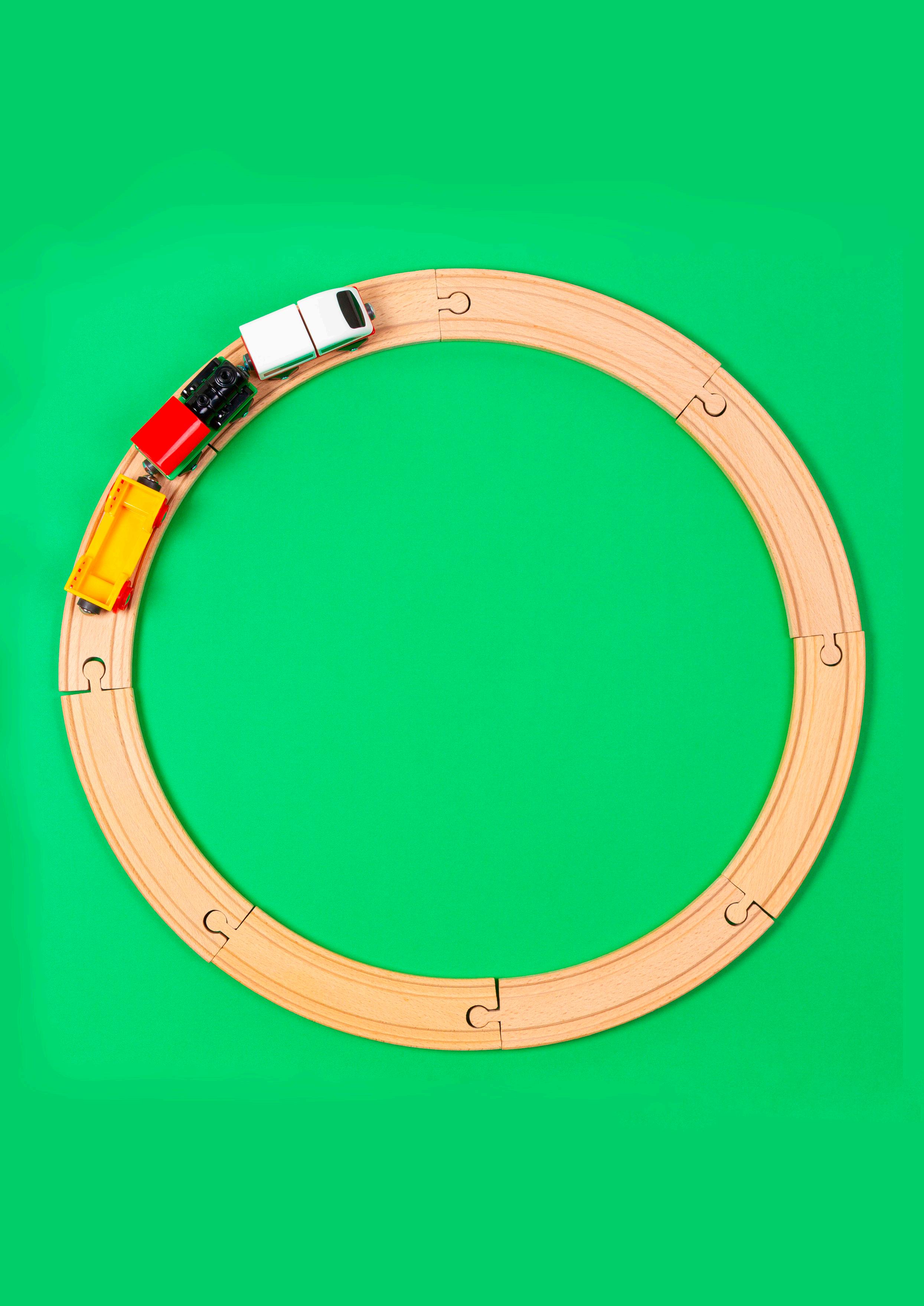
For the greater part of 40 years, ILI technologies have been collecting data on pipelines from all over the world. Now, the accumulated data lake has matured to a point where it can begin to power modern artificial intelligence (AI) solutions for inspection, integrity and risk analysis.
As a result of these risk assessments, a pipeline will be segmented into risk categories such as low, medium and high risk. A risk category will be determined for a variety of pipeline integrity threats, such as corrosion, fatigue, geohazards, third-party damage, stress corrosion cracking etc. Those pipelines that are considered higher risk will be the priority for inspection, and the inspection technology will be selected based on which threats are considered most likely or of the highest consequence. These risk assessments can be quite coarse and could benefit from a more granular approach, such as a risk assessment conducted on a jointby-joint basis, rather than a pipeline-by-pipeline basis. This more-detailed assessment would consider local variations in conditions such as soil pH, localised coating types, ground conditions and slopes. This is where predictive analytics can come in to support. Predictive analytics and applying the digital warehouse
Figure 2. Pipelines, unpiggable or not, are a critical part of our societal infrastructure.
As part of the Integrity Analytics project, ROSEN has developed, and continues to expand, a large repository of historical ILI results (feature listings) and corresponding pipeline information called the Integrity Data Warehouse (IDW). To date, the IDW contains detailed information for over 12 000 pipelines from around the world. The IDW is growing rapidly and will soon include information from the majority of inspections since 2000, as well as information from all newly completed inspections. This data – paired with relevant geo-enriched, socioeconomic or operational metadata – provides a clear foundation for scalable AI solutions.Historically, unpiggable pipelines have been managed with direct assessment techniques, which involve traditional modelling or susceptibility analyses, followed by direct examination. Although this can be effective, it is a costly process that may not scale well across a network, especially if accurate and timely data is not available.
70 World Pipelines / AUGUST 2022
Figure 1. Predictive analytics can be used as a tool by operators who want to make more-informed decisions.
When looking at ensuring the safety of an entire network, operators need to apply a full 360° approach: starting with an outline of the assets that are the highest risk, followed by the selection of solutions available to inspect the pipeline, evaluation of the data, remediation and the feeding of all the information gained back into a controlled system used to evaluate other assets in the network. When looking at a small or large network of assets deemed ‘unpiggable’, determining where to begin is a daunting task in itself. Typically, this task is complemented by system-wide risk assessments in which the likelihood of a certain event – e.g. loss of containment – is calculated, as is the consequence of such an event happening – e.g. environmental damage. This is usually done at a pipeline level rather than at a joint level, so we are metaphorically looking at our pipelines with the naked eye, rather than with a microscope.
But where and what is the information exactly? How can it be used to support integrity and risk analyses?
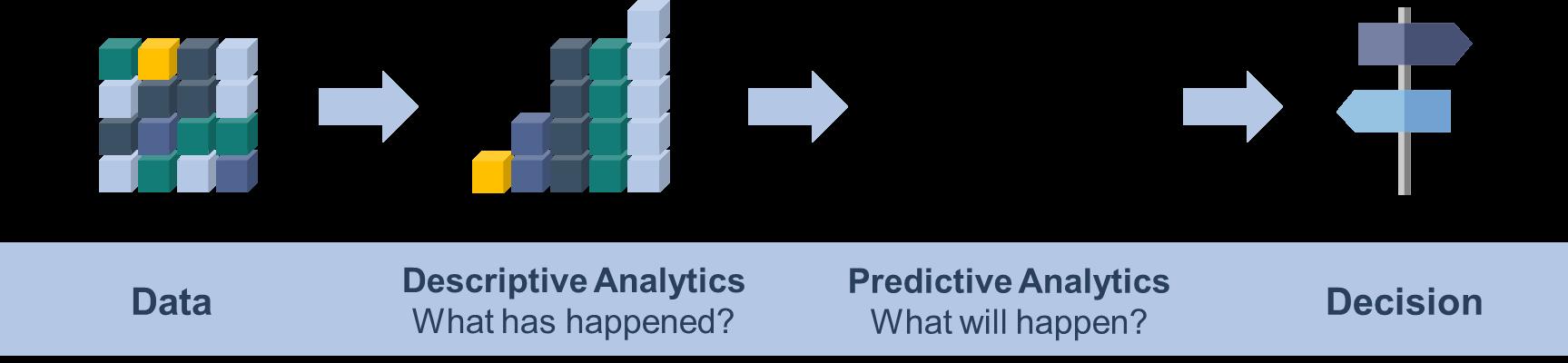
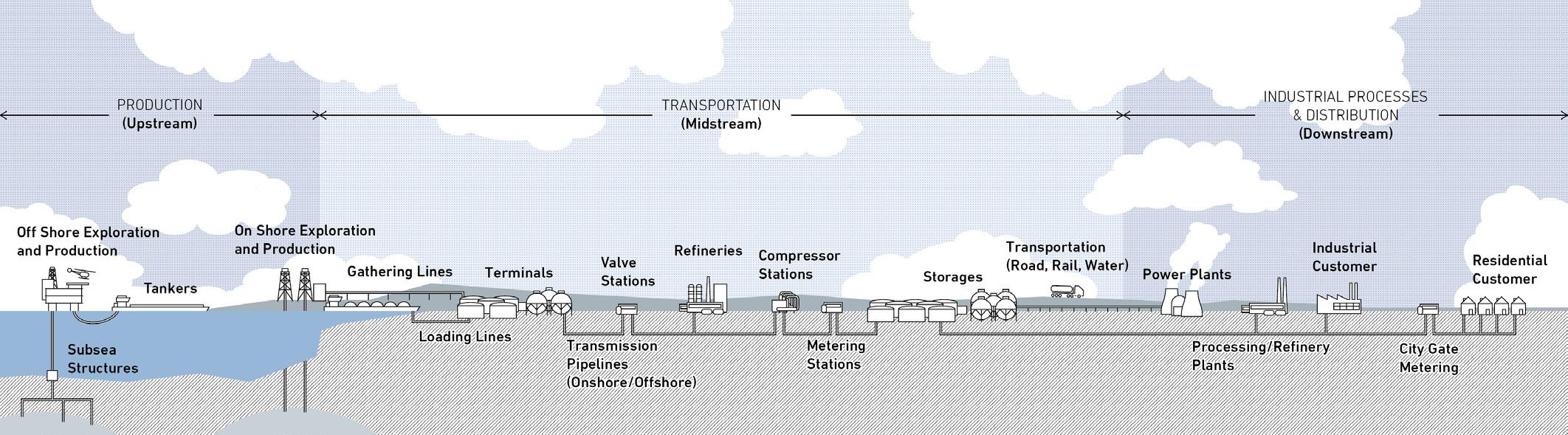
Together, we create the most distinctive and integrated welding solutions for the construction of reliable and sustainable pipelines.
As a family business, we think long term. Dedicated and continuously improving, we always challenge ourselves to go the extra mile. Joining solutions.
• Increase productivity • Increase quality • Lower repair rates • High level of support Oilserv - Nigeria
Qapqa.
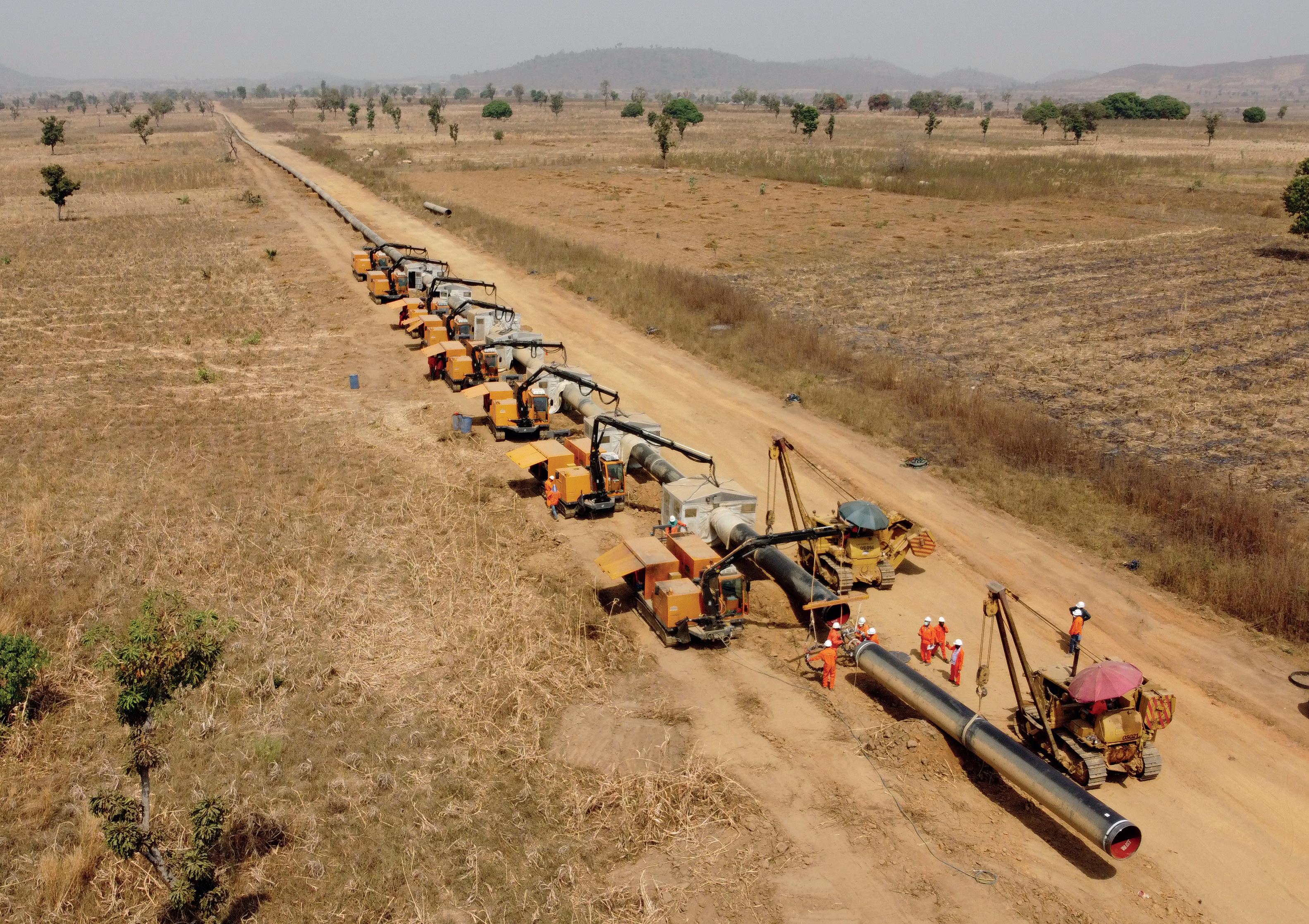
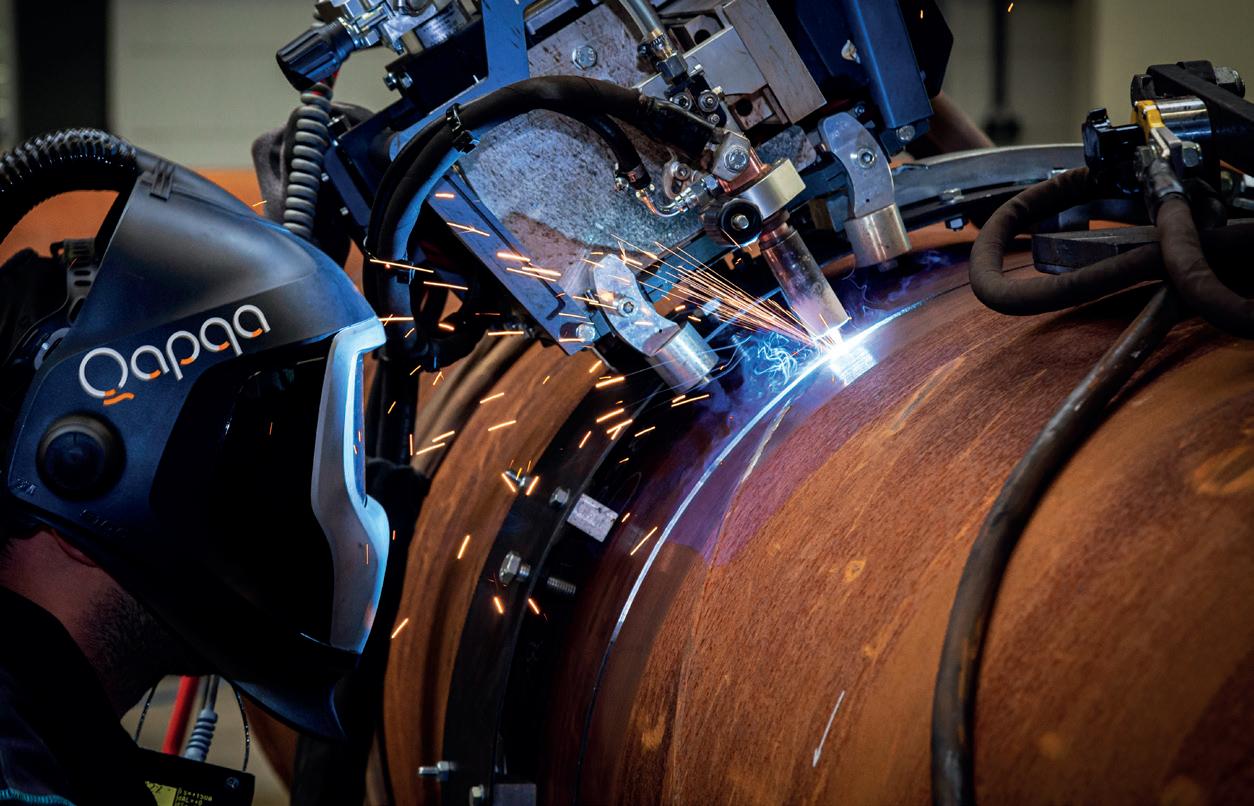
Figuresources.3.
72 World Pipelines / AUGUST 2022
We therefore tend to know relatively little about the true condition of uninspected pipelines, particularly when they are at the bottom of the ocean or buried underground. This is an example of how data science can bring real value: by learning from the condition of similar pipelines that have been inspected in the past, we can begin to understand the different variables that predict pipeline threats and develop models to predict the condition of uninspected pipelines.Wecan observe trends in inspected pipelines and apply what we have learned to uninspected pipelines. This technique can be applied to a number of different pipeline threats, but initial work has focused heavily on the endemic and ever-present threat of external corrosion. These models serve as ‘ECDA-lite’, because they do not require the same volume of target pipeline data, and because they can be very useful when comparing pipelines within a network. They can provide an operator with a clear ranking of ‘problem pipelines’ in their network (whether unpiggable or not) and focus resources on more-targeted ECDA desk studies. Greater insights also allow operators to adjust inspection intervals or, in the case of some larger companies, the ability to foresee where they need to perform in-field work to optimise logistics and resource planning.
Figure
Condition prediction can be conducted on a pipelineby-pipeline basis. However, the benefits multiply when it can be done on a joint-by-joint basis; an approach that produces a far more refined approach to identifying joints in poor condition than other, more-traditional approaches such as direct assessment (ECDA, ICDA, SCCDA, etc.), which are costly and time-consuming because they require excavation and possibly even a temporary reduction of the operating pressure. While direct assessment, unlike ‘virtual ILI’, does provide a real view of the pipeline condition, it is highly dependent on ensuring the correct joints have been excavated. Each joint is typically mutually exclusive; for example, just because one joint is free of a given anomaly type – e.g. corrosion, SCC, etc. – that does not mean a joint a few 100 m away also is not affected by the same anomaly type. Conversely, we cannot assume the entire pipeline is damaged just because one joint is in really bad condition.
ROSEN has been advancing this initiative, and partnering with operators, to explore many applications of the IDW, such as: corrosion prediction, external interference hit rate, crack prediction, condition metrics benchmarking and ranking, and corrosion growth rate prediction for uninspected pipelines. Future areas of interest include condition of offshore assets, pipeline movement, bending strain and enhancing ILI anomaly classification. 4 The IDW features metadata from ILI listings and relevant
T he Integrity Data Warehouse (IDW) contains over 200 000 000 metal loss anomalies.
Generalisable ML models are useful for predicting condition (from severity to density) at the network, pipeline or joint level, but real value can only be delivered by combining subject-matter expertise from the operator and consultants with high-quality data inputs to improve the models and inform robust validation methods (i.e. ILI). Studies leveraging data science not only provide pipeline owners with useful insights to support their integrity management decisionmaking, they also foster a culture of purposeful data collection and governance. Once data-science principles are adopted and practices aligned with business needs, these capabilities, datasets and insights can be applied to other threat types and other business problems beyond the purely technical.
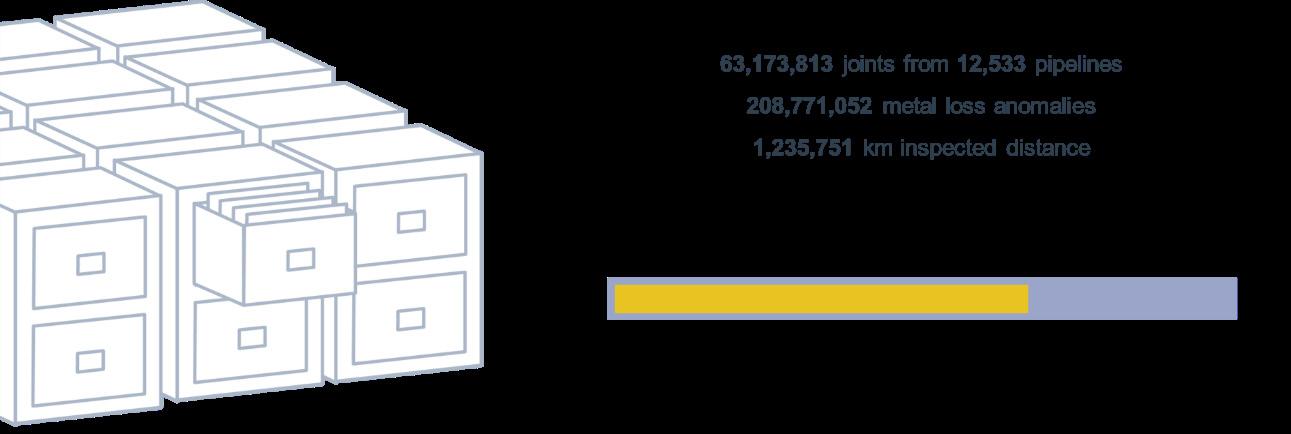
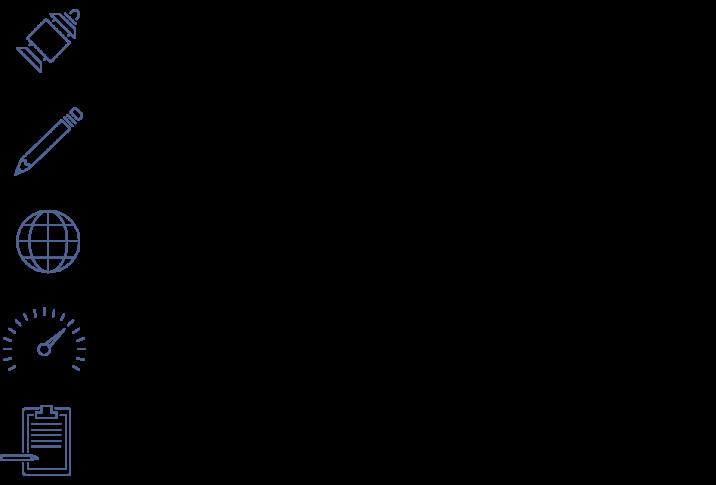
Over the last six years Xrok Granite 400 pipe padding machines worked on many major and some of the most challenging pipeline projects around the world. Having gained invaluable working experience in the eld plus listening to valuable customer feedback our design team have made cutting edge improvements and upgrades to the current model with some innovative advances to further improve production, versatility and reliability. Some of the major advancements are to the screen box which is the heart of a padding machine, our new improved stepped double deck technology greatly improves both e ciency and performance putting the Granite 400 into a class of its own. Whether deployed to the driest of deserts or to the wettest and harshest environ ments in the World, the new improved Xrok Granite 400's superior performance will outperform and pad more pipe per day than any other machine currently on the market which equals a huge cost saving to the customer. xrok.com
Delta Machinery is the sole distributor for Xrok Voltstraat 19, 5753 RL Deurne, the Netherlands • T: +31 (0) 888 966 966 • sales@deltamachinery.nl deltamachinery.nl WORLD LEADERS IN PADDING TECHNOLOGY
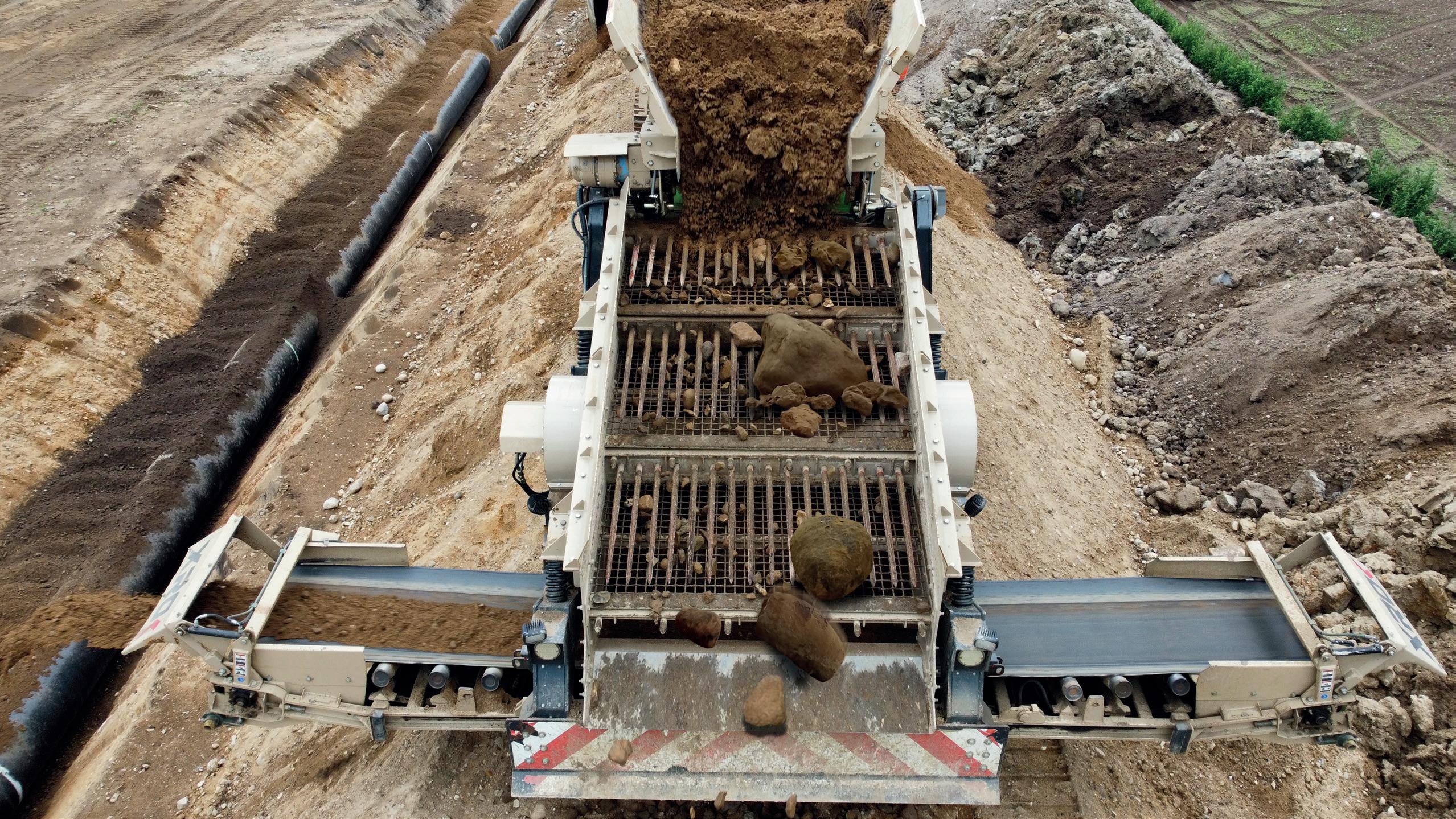
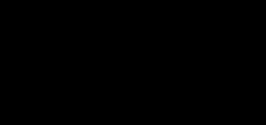


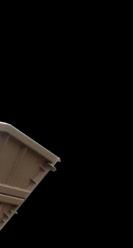
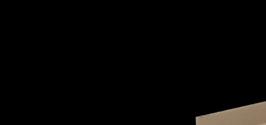
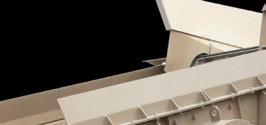
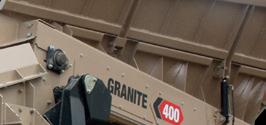
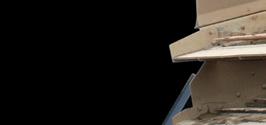
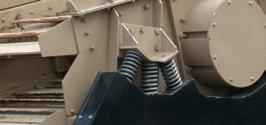
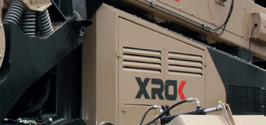
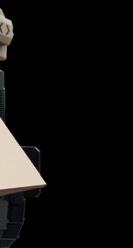
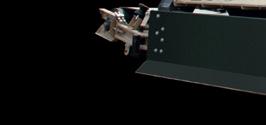
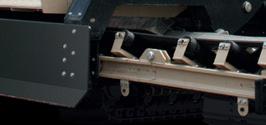
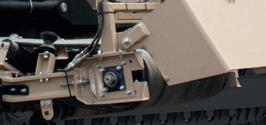
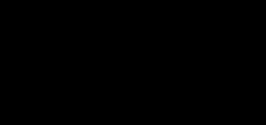
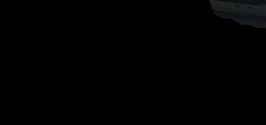
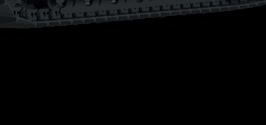
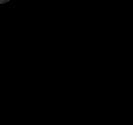
When you do have to inspect Of course, there will be a few cases where the AI engine and algorithms will not be able to give us all the answers, or will predict such a high-risk pipeline that an inspection is prudent or even necessary. So, when direct or indirect measurement data of an unpiggable pipeline is really needed, an ILI may become unavoidable. How should we approach an ‘unpiggable’ pipeline? This is where a ‘toolbox’ of solutions, approaches, technologies and experiences comes into play. A variety of challenges can be present, but most commonly, multiple challenges exist to make a pipeline truly ‘unpiggable’. When it comes to assessing a pipeline to determine piggability, three main factors must always be considered: accessibility, negotiability and propulsion. Accessibility • How do I get the tool into the line? • Launchers and receivers? • Single access only? • Subsea launch? Negotiability • Any obstacles getting through the line? • Bends? • Diameter variations? • Difficult valves or other installations? Propulsion • Can the tool be pumped? • Can the tool be pumped, but with constraints and under difficult operational conditions (pressure, temperature, etc.)? • Can the tool be pulled? • Does the tool require its own drive? As with any ILI, access to the pipeline is critical to provide an insertion/extraction point for the ILI tool. In standard pipelines, this is easily remedied with launchers and receivers, but with challenging lines, small modifications to both the tool and the pipeline itself may be required. In some lines, simply adding rental barrels may be a straightforward fix; others may require a cut into the line – possibly supported by hot tapping to reroute the product – to allow for temporary access. With standardised ILI technology, more conventional methods are needed, but using specialised tools, insertion and extraction can often be performed with just a spool piece tied in with a flange. In order to reduce the need for additional modifications to access points, tool technologies play a significant role. Where unidirectional technologies were once the main technology available, bidirectional tools across various measurement platforms, including magnetic flux leakage (MFL) and ultrasonic wall measurement (UTWM), are readily available on the market. Bidirectional tools allow for the reduction of separate tool insertion and extraction points into a single insertion/extraction point, greatly reducing operational expenditures.
Once one or more access points have been defined, the general pipeline layout needs to be understood in terms of installations such as bends, offtakes, diameter changes and wall thickness transitions. Also critical are geometric features that could impede the passage of an ILI tool. While most such features as 1.5D bends do not typically pose a risk for ILI tools, they may cause fluctuations in tool run behaviour, resulting in degraded data. More significant features, such as external damage or diameter changes, will require more specialised tool technologies. While most installations can be overcome with nonstandard tools, it is critical that close collaboration occurs between the vendor and operator to ensure all the details of the line are understood. This critical step ensures that all risks are fully aligned with all parties, resulting in proper tools being selected along with the corresponding work procedures.
Figure 5. Supervised machine learning for condition prediction. 74 World Pipelines / AUGUST 2022
While most standard systems operate at flow speeds within this threshold, many operate at lower flow and low pressures. In these instances, without proper usages of low-friction tool technologies, speed excursions, stop-starts, and accelerations and decelerations may occur, causing missing or degraded data in potentially critical areas. Similarly to low-flow pipelines, the tool may experience intermittent speed fluctuations due to excessive tool drag and product bypass across the sealing cups/elements.
Or, in the case of a line without product flow, self-propelled
Vendors who specialise in challenging assets tend to follow a toolbox technology-development approach where, in lieu of designing tools with a specific need to meet a vast market requirement, separate elements are built in order to customdesign a tool for each challenging application. In the case of a low-pressure line, a compact low-friction MFL tool may be built. Or, with a low-flow line, a high-sealing UT tool can be utilised.
ILI technologies are primarily designed to run with the flow of the product, with each tool having minimum pressure and/ or flow requirements to ensure it will not only pass the line but pass the line with a stable velocity. Industry-wide, most highresolution MFL, caliper and UT technologies can capture data that meets their specifications at velocities of up to ~5 m/sec.
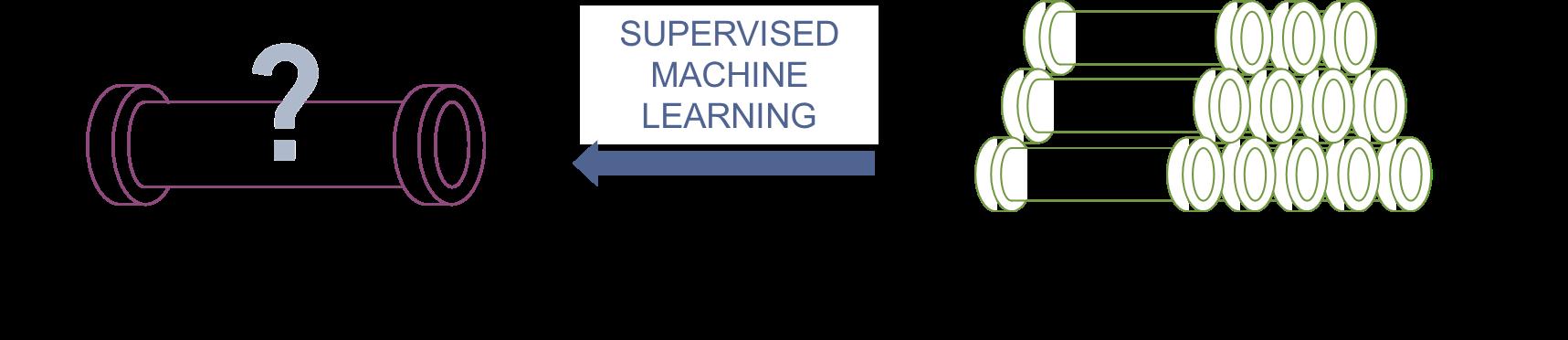
In these instances, without proper usages of low-friction tool technologies, speed excursions, stop-starts, and accelerations and decelerations may occur, causing missing or degraded data in potentially critical areas. Similarly to low-flow pipelines, the tool may experience intermittent speed fluctuations due to excessive tool drag and product bypass across the sealing cups/elements.
References 1. Global Data 2015. 2. BELLER, M. and SABIDO PONCE, C., 2021. Options for Internal Inspection of Difficult-to-Check Pipelines. Pipeline & Gas Journal, [online] 248(6). Available at: internal-inspection-of-difficult-to-check-pipelinespgjonline.com/magazine/2021/june-2021-vol-248-no-6/features/options-for-[Accessed1June2022].
As with any ILI, access to the pipeline is critical to provide an insertion/extraction point for the ILI tool. In standard pipelines, this is easily remedied with launchers and receivers, but with challenging lines, small modifications to both the tool and the pipeline itself may be required. In some lines, simply adding rental barrels may be a straightforward fix; others may require a cut into the line – possibly supported by hot tapping to reroute the product – to allow for temporary access. With standardised ILI technology, more conventional methods are needed, but using specialised tools, insertion and extraction can often be performed with just a spool piece tied in with a flange. In order to reduce the need for additional modifications to access points, tool technologies play a significant role. Where unidirectional technologies were once the main technology available, bidirectional tools across various measurement platforms, including magnetic flux leakage (MFL) and ultrasonic wall measurement (UTWM), are readily available on the market. Bidirectional tools allow for the reduction of separate tool insertion and extraction points into a single insertion/extraction point, greatly reducing operational expenditures.
3. BELLER, M., STEINVOORTE, T. and VAGES, S., 2015. Mastering Inspection of Challenging Pipelines. Pipeline and Gas Journal, [online] 242(10). Available at: mastering-inspection-of-challenging-pipelinespgjonline.com/magazine/2015/october-2015-vol-242-no-10/features/[Accessed1June2022].
Figure 6. Predictive analytics can help operators to identify low to high-risk joints within a pipeline and prioritise those joints for investigation and mitigation.
AUGUST 2022 / World Pipelines 75
Vendors who specialise in challenging assets tend to follow a toolbox technology-development approach where, in lieu of designing tools with a specific need to meet a vast market requirement, separate elements are built in order to customdesign a tool for each challenging application. In the case of a low-pressure line, a compact low-friction MFL tool may be built.
ILI technologies are primarily designed to run with the flow of the product, with each tool having minimum pressure and/ or flow requirements to ensure it will not only pass the line but pass the line with a stable velocity. Industry-wide, most highresolution MFL, caliper and UT technologies can capture data that meets their specifications at velocities of up to ~5 m/sec.
Or, with a low-flow line, a high-sealing UT tool can be utilised. Or, in the case of a line without product flow, self-propelled drive units can be equipped for use on a variety of measurement technologies.
drive units can be equipped for use on a variety of measurement technologies.Whileindeed not all challenging pipelines have an ‘off-theshelf’ solution, most can be solved with a toolbox approach.
Once one or more access points have been defined, the general pipeline layout needs to be understood in terms of installations such as bends, offtakes, diameter changes and wall thickness transitions. Also critical are geometric features that could impede the passage of an ILI tool. While most such features as 1.5D bends do not typically pose a risk for ILI tools, they may cause fluctuations in tool run behaviour, resulting in degraded data. More significant features, such as external damage or diameter changes, will require more specialised tool technologies. While most installations can be overcome with nonstandard tools, it is critical that close collaboration occurs between the vendor and operator to ensure all the details of the line are understood. This critical step ensures that all risks are fully aligned with all parties, resulting in proper tools being selected along with the corresponding work procedures.
While most standard systems operate at flow speeds within this threshold, many operate at lower flow and low pressures.
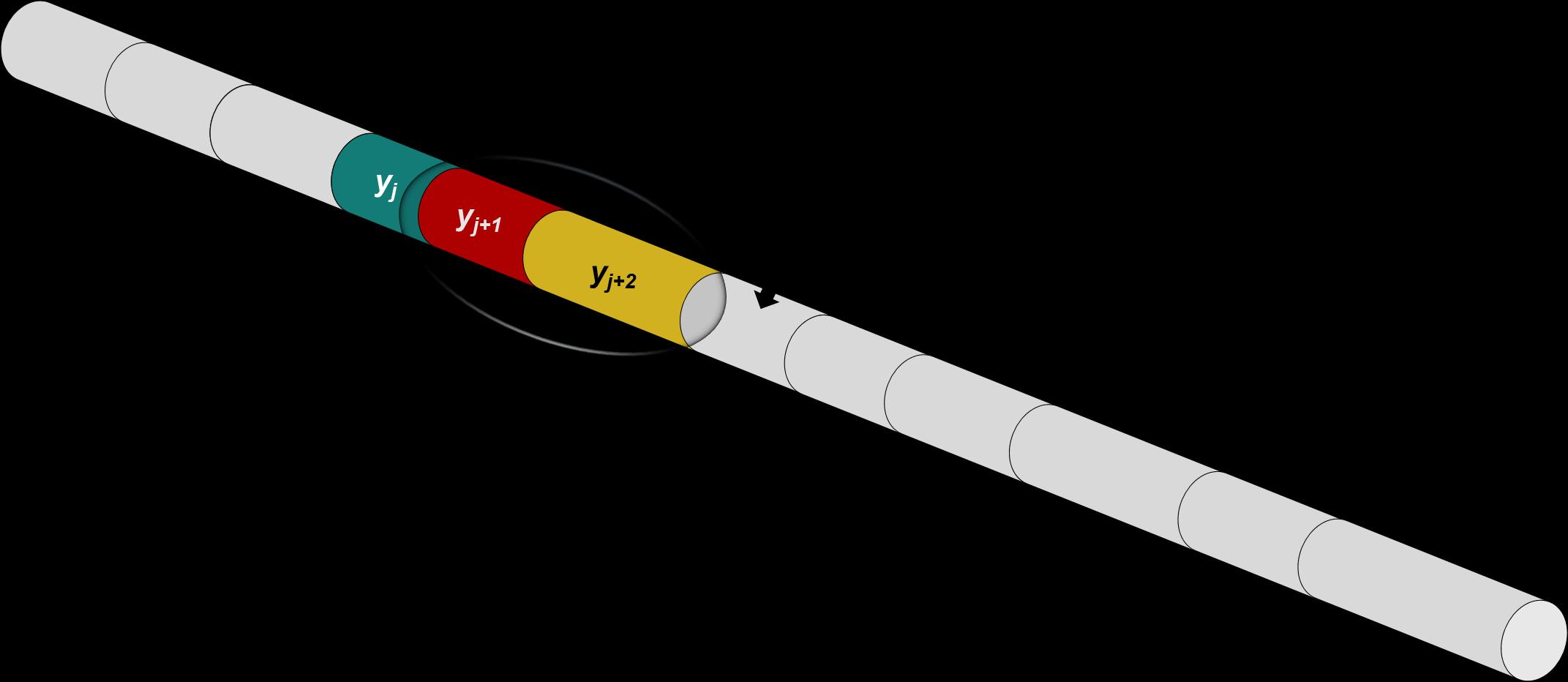
Maik Bäcker, EWE Netz GmbH, Hendrik Friemann and Basil Hostage, 3P Services GmbH & Co. KG, Germany, explore the inline inspection of ageing assets in sensitive environments. 76
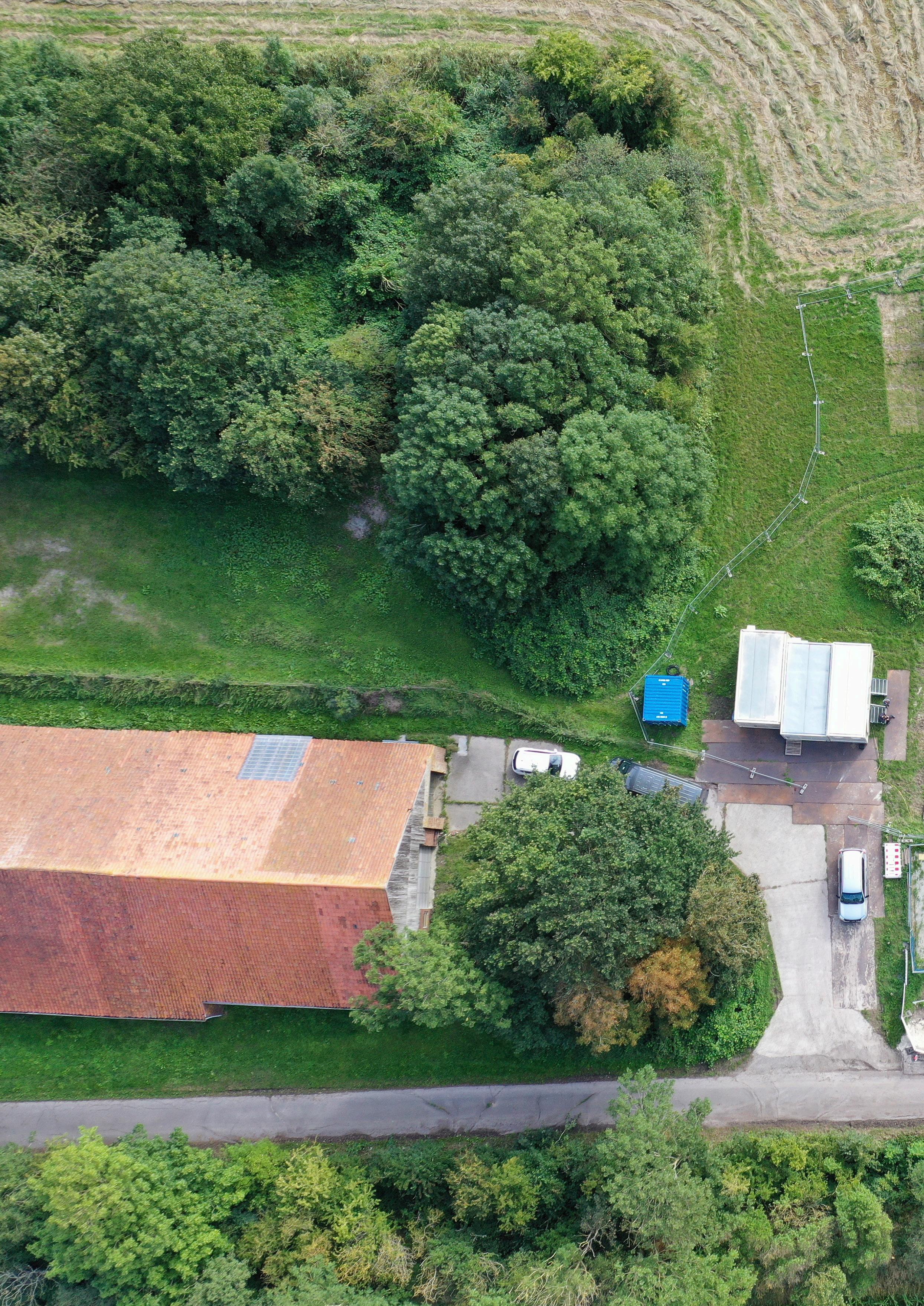
Introduction EWE Netz GmbH awarded 3P Services the inspection of a 5 in. gas pipeline connecting Borkum with the German onshore grid. The natural gas transported through the pipeline is fed into the local grid on the island and is used mainly for domestic heating. The pipeline in question was built in 1981 and had never before been inspected by use of inline tools. No pipeline launcher or receiver installations exist. For operational reasons, the gas flow could not be regulated to accommodate velocities suitable for inline inspections, and the decision was Figure 1. Onshore receiving site with filtration system and break tanks.
A mong others, the East Frisian island of Borkum is supplied with gas by EWE Netz GmbH. This project was very sensitive since major parts of the pipeline route, as well as the launch location, are located in a national park and UNESCO World Heritage Site.
Scheduling the field works was governed by both breeding periods of protected bird populations and requirements of downstream consumers. Specialised filtration equipment to clean the water used to propel the inline tools was included.
Field works were scheduled during mid to late summer after preparation of the ‘low impact’ launch and receive positions were complete. All onsite personnel received specialised training from a third-party nature conservation consultant. The island of Borkum is separated from the mainland by tidal mudflats and subsea, which serve as reference positions for the XYZ unit when deployed along the pipeline during low tide. The line was flooded, cleaned by use of a chemical batch, cleaning tools and inspected by means of GEO/XYZ and ultrasonic inline inspection tools. In a last step, the line was dewatered and dried with nitrogen. All propellant used during this operation was run through the filtration skid, and then tested before either being drained or disposed of separately. The inspection operations were completed within a tight schedule, and the final report delivered on time. Using this information and in conjunction with the regulator, the client is performing an extensive campaign of investigating features that were reported.
77
Planning and preparation included liaison with relevant local and environmental authorities from the start to ensure that the project would have the minimum possible footprint.
3P Services’ work included provision of pumping spread to propel the inline tools. Inspection technologies to be deployed included GEO (geometric), MFL, UT and XYZ mapping in the 5 in. diameter line.
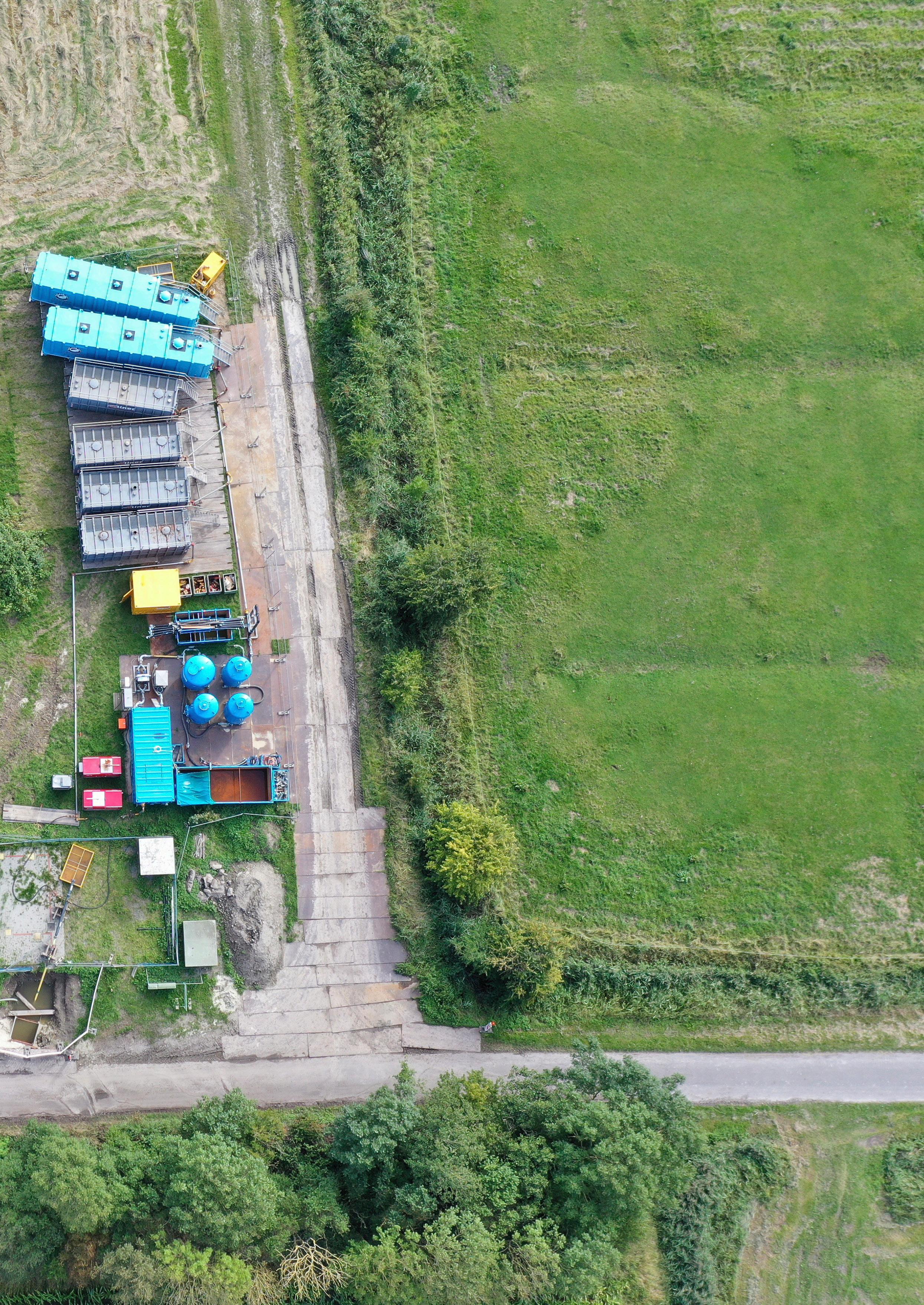
The inspection schedule was influenced by a number of factors, one of which was the requirement to affect the inhabitants of the island as little as possible. The inspection was therefore only possible during the warm summer months.
For the purpose of water management and environmental regulations, it was decided that all inline inspection tools were to be launched on the island of Borkum and received on land. As the water pumped through the pipeline could not be discharged in either a national park or nature conservation area, specialised water handling was required. All pumped water was run through a filtration system, stored in break tanks and tested for contamination by laboratory analysis. Only if green-lighted by the results of the laboratory tests, the water could be disposed into a ditch. Since laboratory analysis was scheduled to take place at least once day, and would have to be conducted after every run, even if the water pumped in the proceeding run was deemed okay, break tank capacity equal to more than the line fill was required at the eventual receiving site. Regulations in the national park demand the footprint at this location be as small as possible, and break tanks and filtration system are positioned in the nature reserve onshore. All temporary equipment was placed on mats to distribute the weight and limit the amount of compaction of the soil. A maximum of 40 m3/hr of fresh water as propellant was supplied by local public utilities via a hydrant close to the launch site.Prior to mobilisation, factory acceptance tests of all inline inspection tools were conducted.
Given the sensitive environment and the nature of the Wadden Sea, a full set of inspection tools was prepared including cleaning tools, a geometric calliper inspection tool (GEO), ultrasonic wall thickness (UT) and magnetic flux leakage inspection (MFL/DMR) tools in conjunction with pipeline mapping (XYZ). The progressive pre-ILI tool sequence considered various potential types of geometric deformation caused by dropped anchors, misalignment due to tidal currents, as well as general corrosion caused by coating damage.
EWE Netz provided a test spool with artificial defects, hidden underneath a layer of external wrapping. The artificial defects ranged from general corrosion to pitting defects. All defects were scanned in 3D before the spool was wrapped, and the spool was then incorporated into the pump test layout at 3P Services’ testing grounds. Both the MFL and the UT tools were pumped through the spool and the recorded data sets were analysed and presented to EWE Netz GmbH.Position referencing markers were placed along the pipeline route everyFigure 3. Factory acceptance test of ILI tools incorporating blind test spool. Figure 2. Equipment spread on launch and receive site.
All relevant authorities and governmental bodies were informed of the intended inline inspection operation at a very early stage. Throughout all phases of the project, communication between the relevant parties were open, constructive and allowed for a seamless project execution.
therefore made to conduct all operations in fresh water with a temporary pumping spread.
Project preparation
Operational timing was also impacted by breeding periods of the resident bird population, and the rest periods for migratory birds. Since the island of Borkum is also a popular destination for tourists, the inspection was scheduled between Easter and summer holidays, as all equipment and machinery had to be brought onto the island on ferries that were fully booked during the holiday seasons.
78 World Pipelines / AUGUST 2022
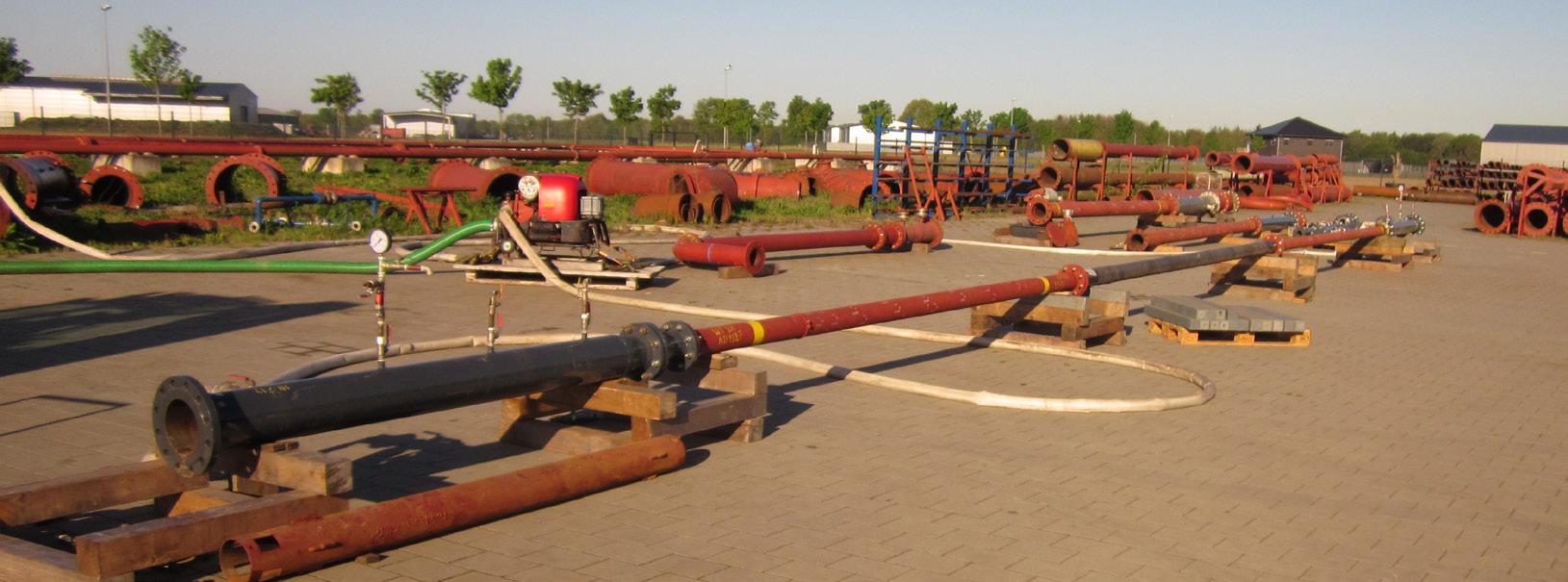
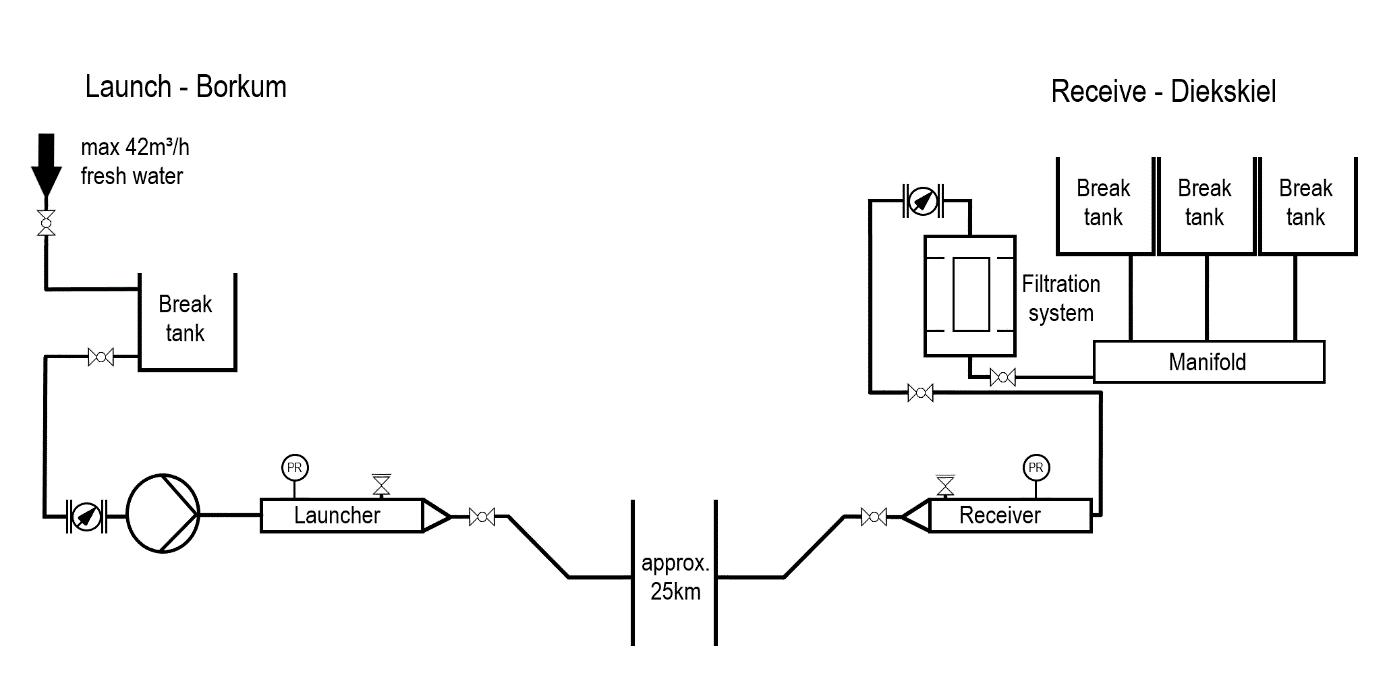
sidebooms.com I 918-858-4201 Modernize your 583R pipelayer with a state-of-the-art MIDWESTERN hydraulic conversion kit. Our new 583R-MMC kit replaces the old, unconventional OEM draw works and linkage controls with a high-efficiency, electro-hydraulic winch package that puts all the boom controls back in your right hand! This is a cost effective way to get your 583R back on the right-of-way, while improving safety and increasing productivity. Let MIDWESTERN put you back to work!
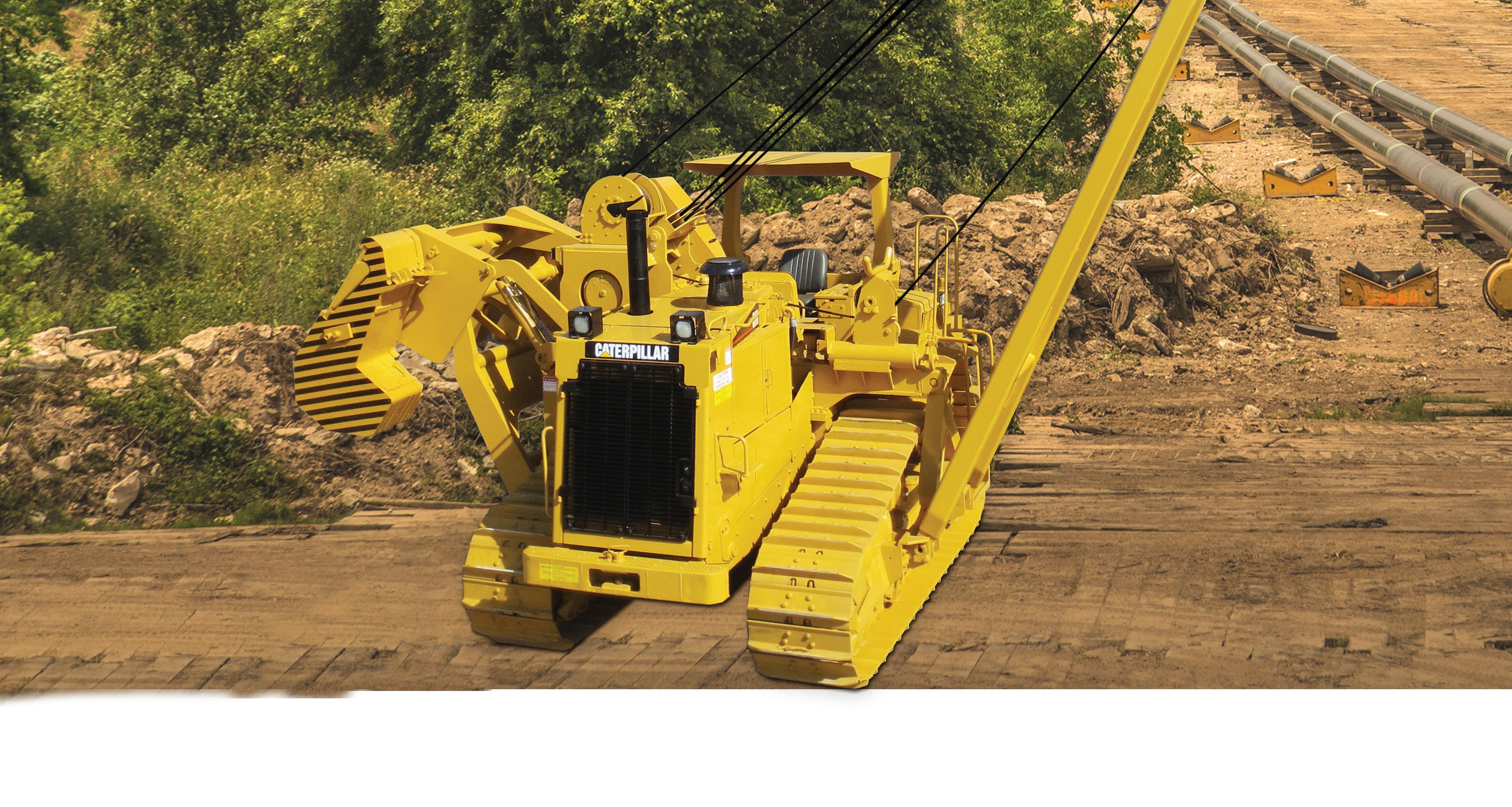
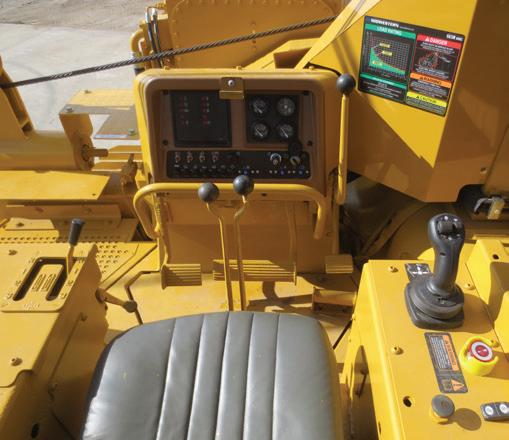
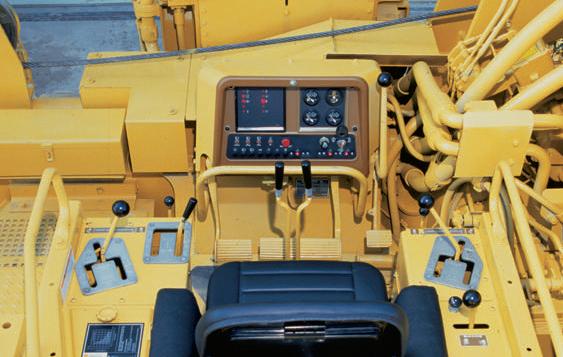
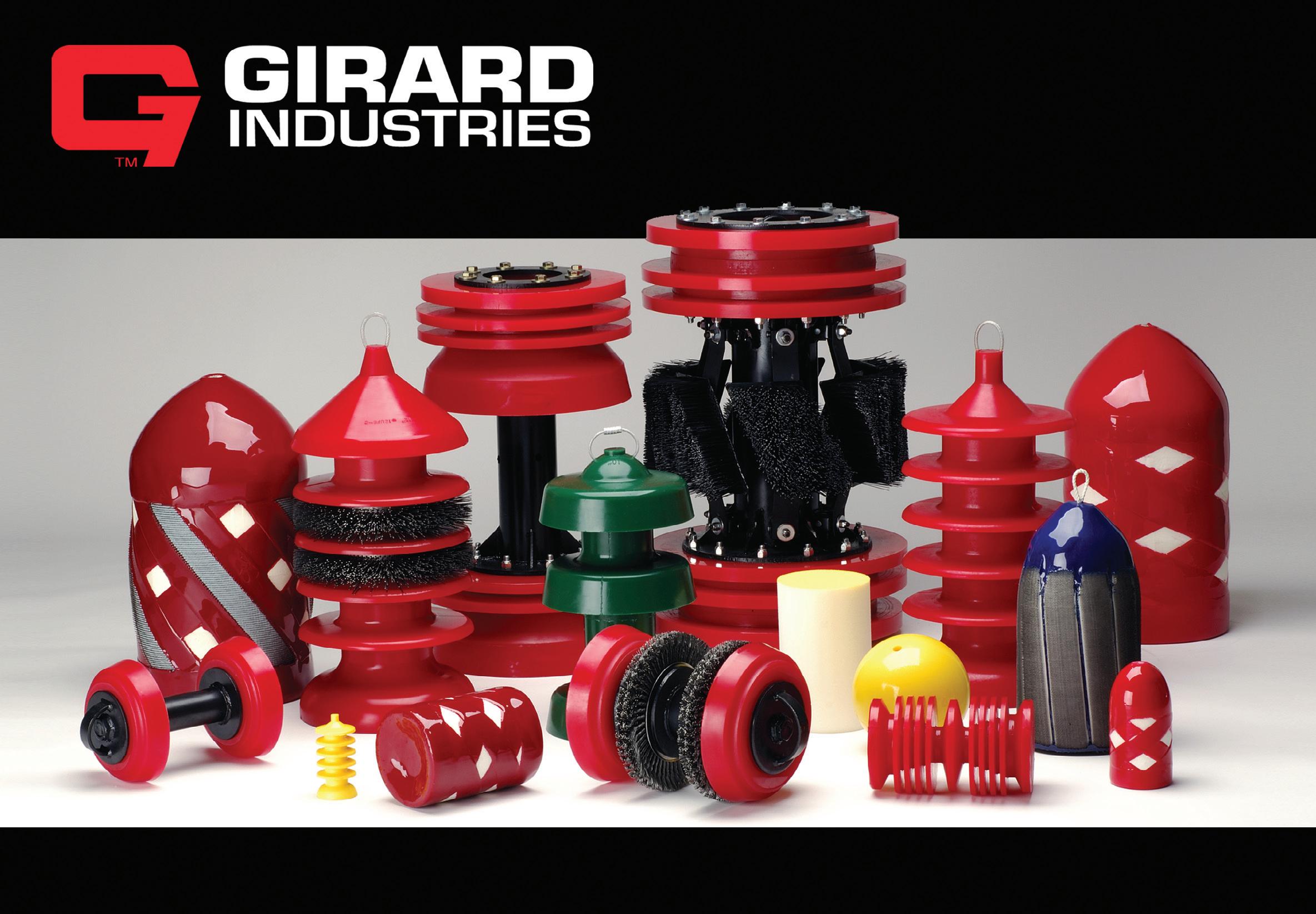
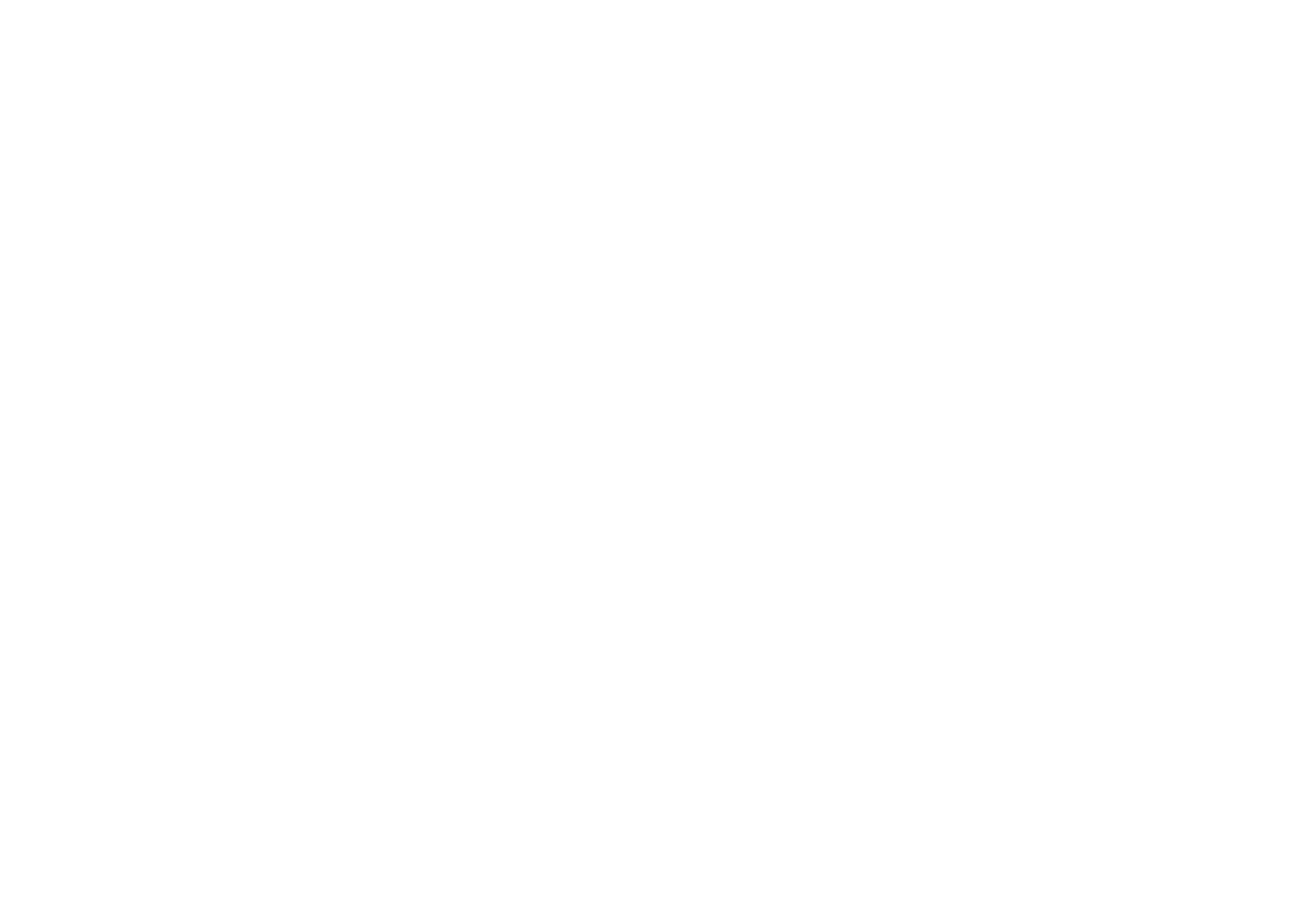
1000 m to increase accuracy of the XYZ survey data. Subsea markers were deployed by a local guide in sections where the line crosses tidal mudflats in the national park. At some locations, this was only possible by foot with the use of a hand cart, and at other positions a ship had to steer to the eventual marker location during high tide, wait for low tide and beach until subsea markers could be deployed. Several low tides were required before all markers were positioned. Each subsea marker position was staked using DGPS. The markers were deployed prior to project execution and collected after the last inspection tool run. The recorded data would then be downloaded for use in XYZ analysis. Project execution In a first step, the pipeline system was depressurised and excavations where made to facilitate installation of the temporary launcher and receiver. Regulations within the national park required all excavations be done layer by layer to guarantee that after completion of the works, each layer of soil removed is reinstated correctly, minimising the impact on the ecosystem. Additionally, measures to prevent the protected bird population from breeding onsite were taken. After pumping 5 m3 of water, a BiDi tool was launched into the line by pumping a 5 m3 batch of fresh water and cleaning agent. A second BiDi tool was launched thereafter to contain the cleaning batch between the two inline tools. The batch was pumped through the line and received onshore. Flow velocity for this, and every subsequent run, was governed by the capacity of the filtration system at receive. All tools were received in good condition and close to no debris was recovered. After filtration, the water was stored in break tanks located onsite. Samples from the tanks were taken and brought to the laboratory for analysis. The water had to be disposed of separately as the recorded values were above the required threshold values for onsite disposal. All water ran during other tool runs was greenlighted by the laboratory and did not require special disposal. After the line was flooded and cleaned, a profile tool was run. Profile tools are flexible uni-directional tools equipped with a set of aluminium gauge plates arranged to simulate the hard diameter of the inline inspection tools. This tool is run to prove that the internal bore of the pipeline does not represent any restrictions that would prevent the subsequent inline tools from successfully navigating the pipeline. Upon receiving, all aluminium gauge plates were littered with indications believed to originate from excessive weld penetration. In addition, all aluminium plates were deformed on one side, hinting at a possible dent in the line. The propellant was stored onsite in break tanks, tested and disposed after being green-lighted by analysis.The next tool in line was the GEO/DMR tool. The GEO sensors map the geometry of the full circumference of the internal pipe wall, and allow for accurate detection and sizing of geometric anomalies such as minimum available diameter, ovalities and dents among other features. The results of the GEO/DMR tool run also proves whether the line can be traversed by the subsequent inspection tool. The tool was received in what appeared to be good condition and recorded a complete GEO data set. However, some secondary sensors were damaged and stopped recording. A number of geometric anomalies, such as dents, were identified as well as several significant excessive weld
80 World Pipelines / AUGUST 2022
Figure 4. Water samples from each of the break tanks, prior to laboratory analysis.
Figure 5. Temporary launcher and receiver locations.
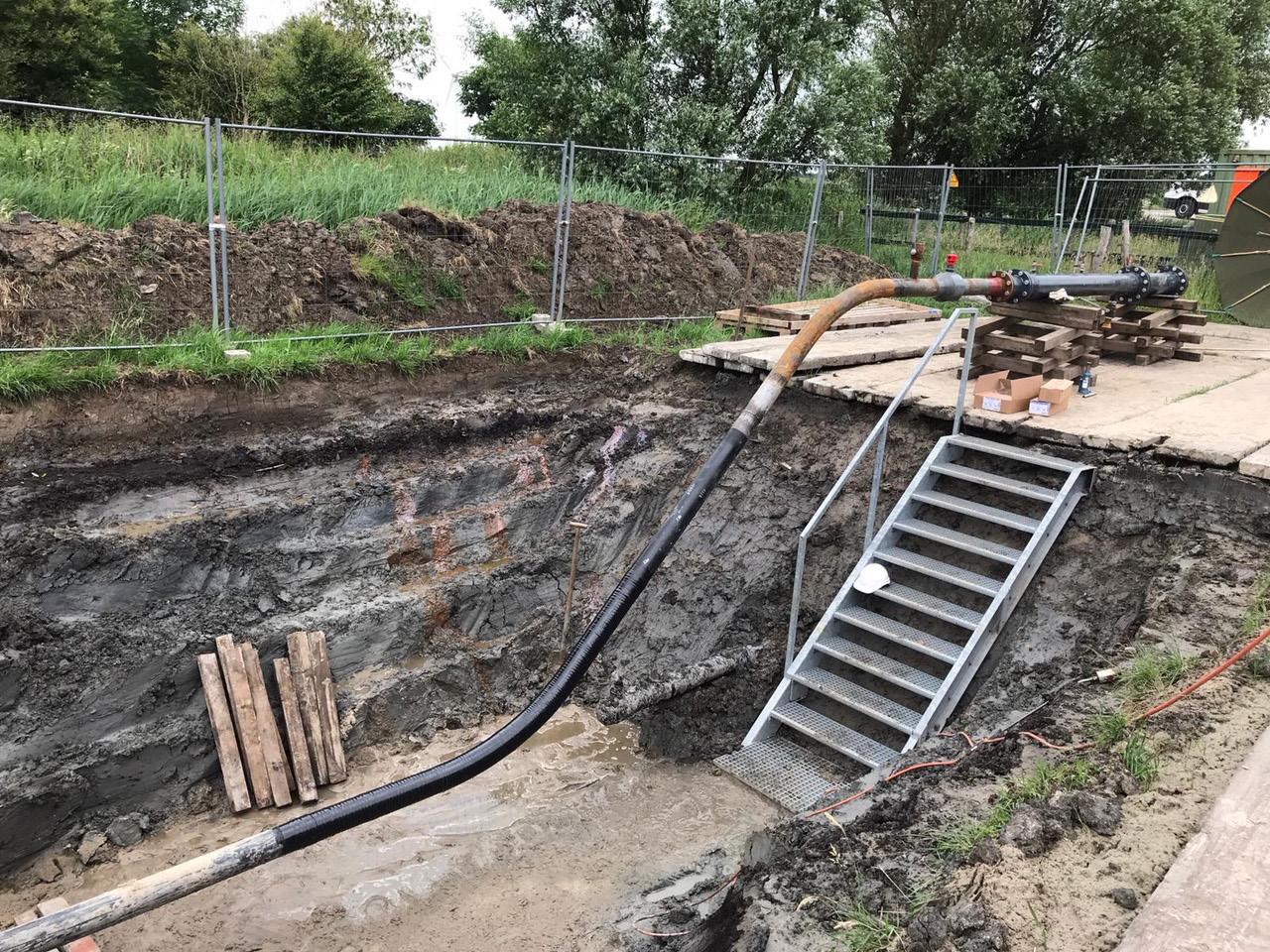
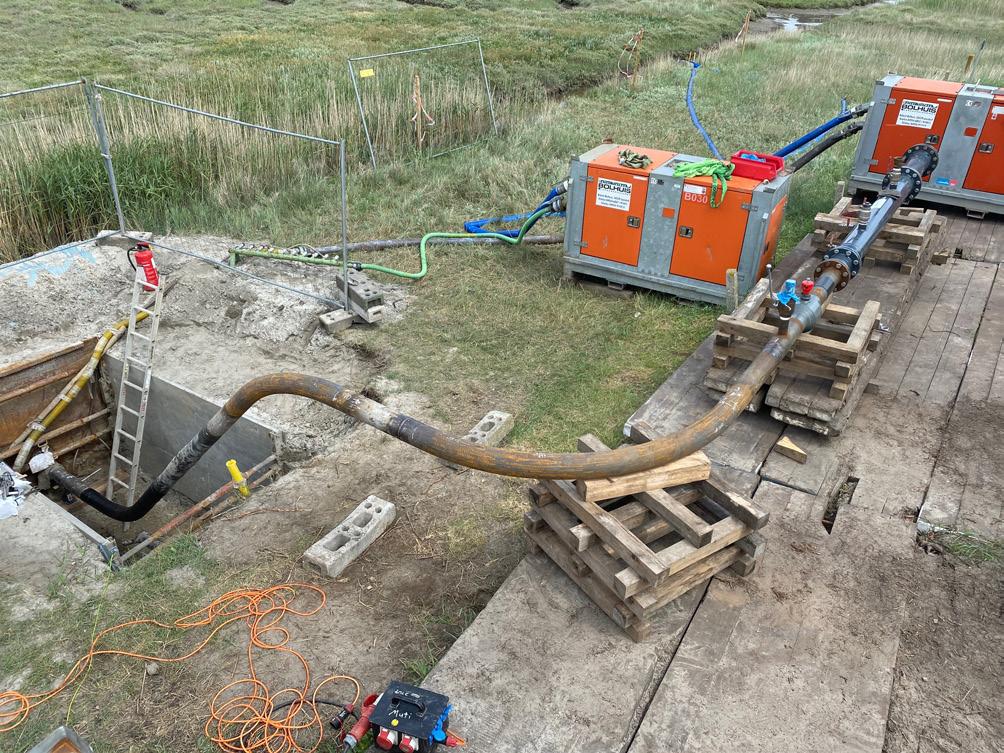
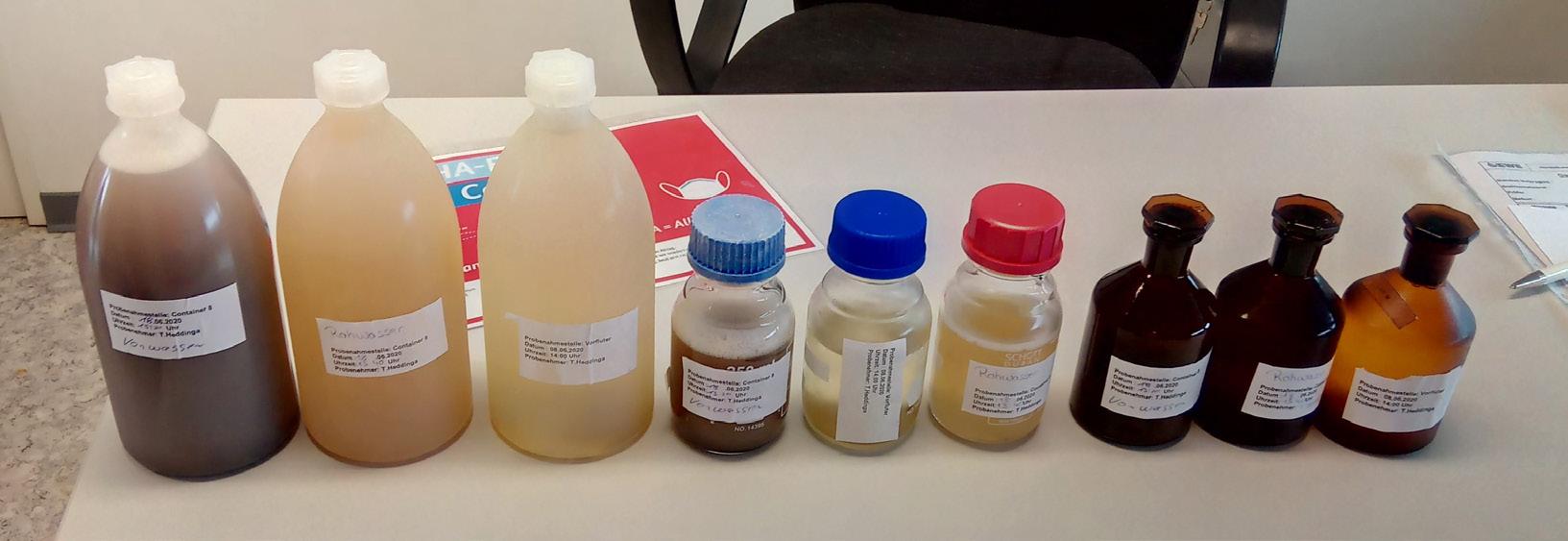
Driven from legacy. Engineered for the future. The do-it-all pipeline welder built for the right-of-way. FRONTIER® 400X PIPE promotions.lincolnelectric.com/frontier AR22-04 | ©2022 Lincoln Global, Inc. All Rights Reserved.
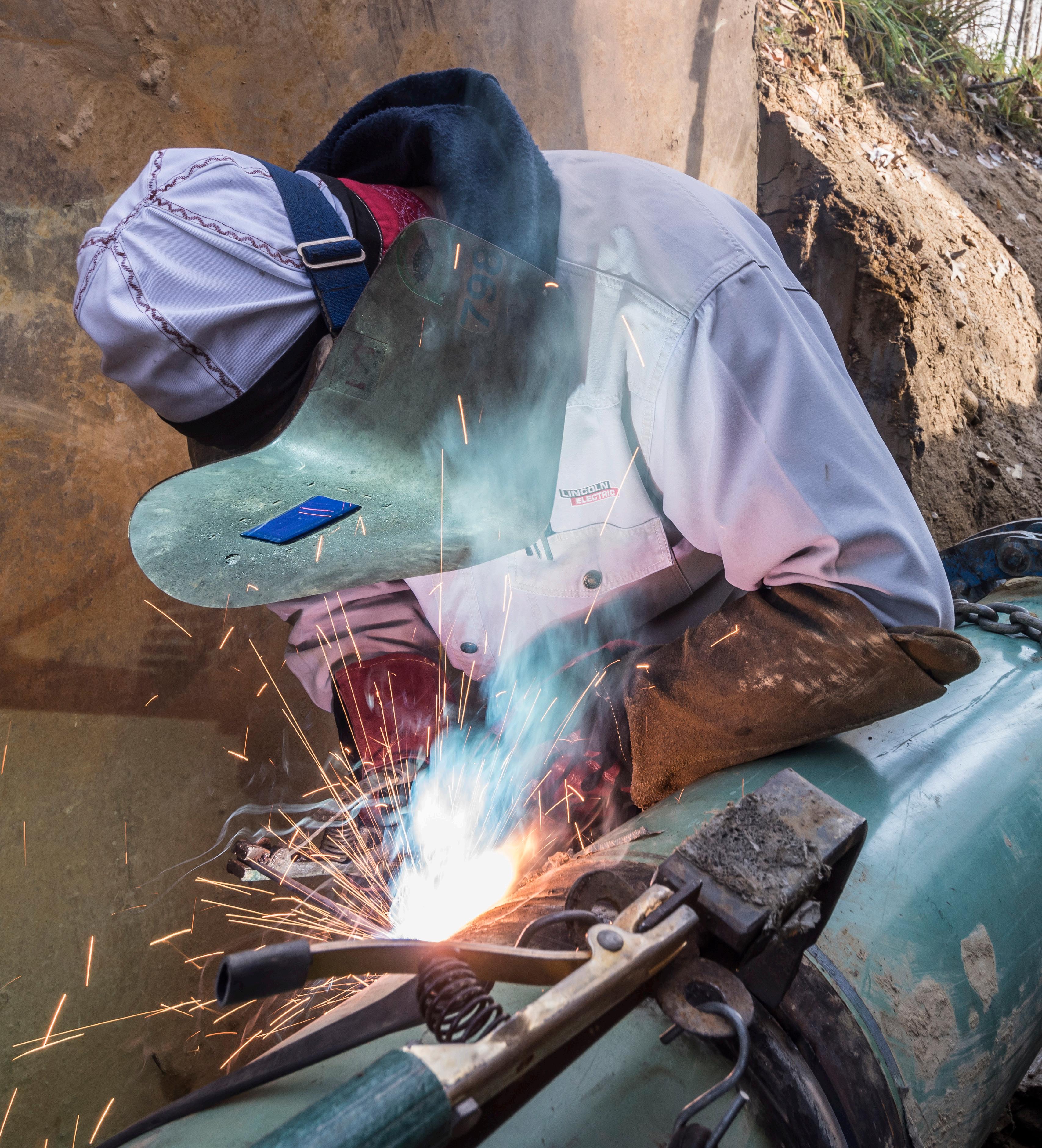
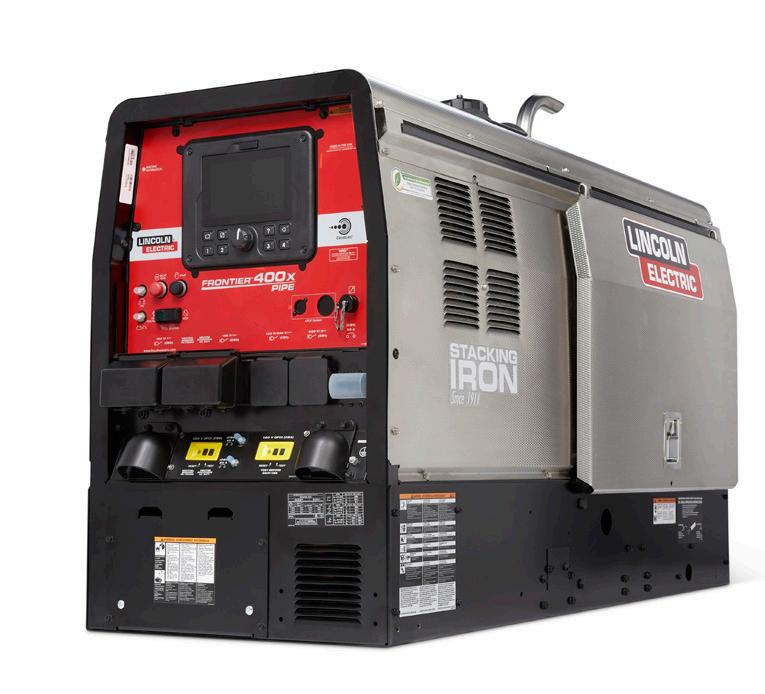
Note The authors would like to express their gratitude to EWE Netz GmbH for their trust, the open communication and cooperation throughout the course of this project. This article is based on a paper given at ptc 2022.
A preliminary report was issued after 10 days, indicating major geometric anomalies, metal loss indications, and other noteworthy findings. The full final report was issued after 40 days. All reporting was conducted in line with POF regulations.EWENetz GmbH decided to conduct an extensive investigation of reported features based on the information provided in the inspection report. Given that some of the features were located in close proximity to tideways, sometimes even underwater, this was no easy task.
Conclusion Site reports were issued after every intelligent inline tool run, confirming the success of each respective run.
Figure 6. Deployment of subsea markers by boat. Figure 7. Profile tool after receive. 82 World Pipelines / AUGUST 2022
penetrations, which are believed to have caused the damage to the secondary DMR sensor array. As the recorded internal diameter was above the required diameter for the UT/XYZ tool, the decision was taken to run the tool. The tool was received without any damage and a full set of data. All locations within the line with reduced internal diameters, as indicated by the recorded GEO data, had been cross checked by use of the additional data gathered by the UT/XYZ tool run. The increased accuracy, as a result of the combined evaluation, revealed that the available internal diameter in several sections of the pipeline was insufficient for the planned final MFL/DMR inspection tool run.
Consideration was given to constructing a new MFL magnetiser module capable of negotiating the restriction. As a certain amount of magnetic power is required to fully magnetise the pipe wall and allow for results in line with the defect detection and sizing performance, the size of the module on the tool with the largest external diameter, the diameter of the magnetiser unit, could not be decreased further. Therefore, the decision was made to not run the MFL/DMRDewateringtool. was done with a BiDi tool propelled by compressed air from the island towards shore. Once received onshore, suitable compressors were mobilised and the pipeline was dried by using nitrogen to a dew point of -20°C in the reverse direction.
After completion of all onsite work, both the launcher location on Borkum and the receiver location were reinstated in line with regulations.
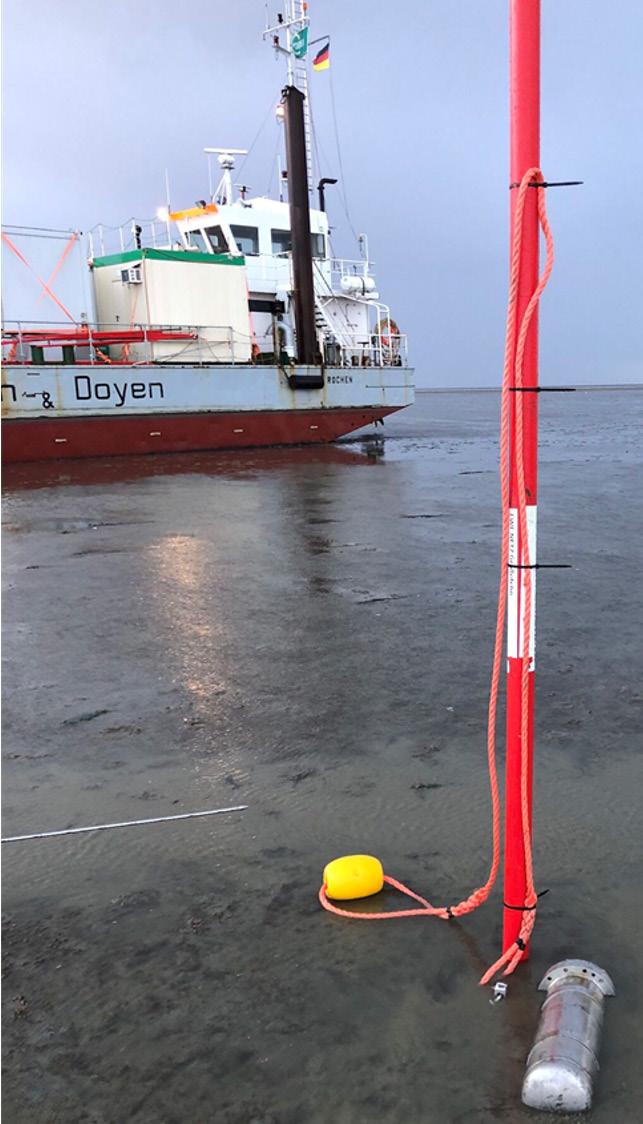
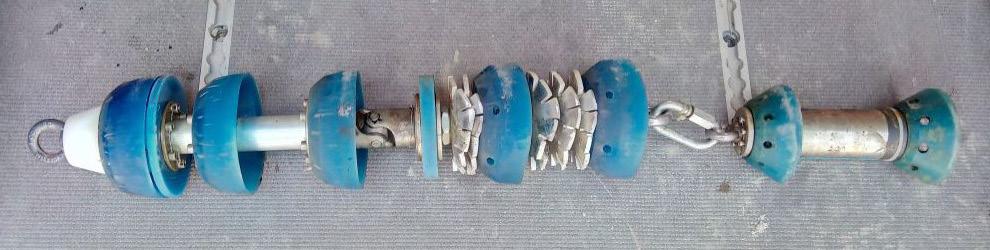
Today’s advancements in microprocessor computational power, memory density, sensor technology, engineering design and modelling software, as well as rare earth magnetics, have allowed the evolution of an MFL inline inspection (ILI) system that can detect and locate far more than just metal
ntelligent pigs have come a long way since their introduction more than half a century ago. The first commercial ‘smart pig’ – utilising MFL technology – had few sensors, no odometer wheel, only collected data on the bottom quadrant of the pipe, and recorded information on reel-to-reel tape.
) Mitred bends. Heavy wall tees. Bore restrictions. Back-to-back bends.
) Thick or thin pipe wall.
Ken Maxfield (USA) and Mark Briell (Canada), KMAX Inspection LLC, unravel the many challenges of inspecting ‘unpiggable’ small diameter pipelines.
) Vertical pipe.
)
)
)
Traditionally,loss.these ILI tool advancements have not been applied to small diameter tools due to space constraints and pipeline geometry. As such, many small diameter pipelines have been labeled as ‘unpiggable’ and have never had an ILI. Moreover, most small diameter pipelines were designed and built without consideration for ILI tool passage. Even so, those that were built for ILI tool passage may have fittings installed, or have operational conditions that do not allow for an ILI tool to inspect the pipeline.
Here is a partial list of pipeline features that have caused these small diameter pipelines to be classified as ‘unpiggable’:
) Short radius elbows.
) Lack of launcher/receiver facilities. Accessibility. 83
) Unbarred tees, Y connections, offtakes, laterals and deadlegs.
)
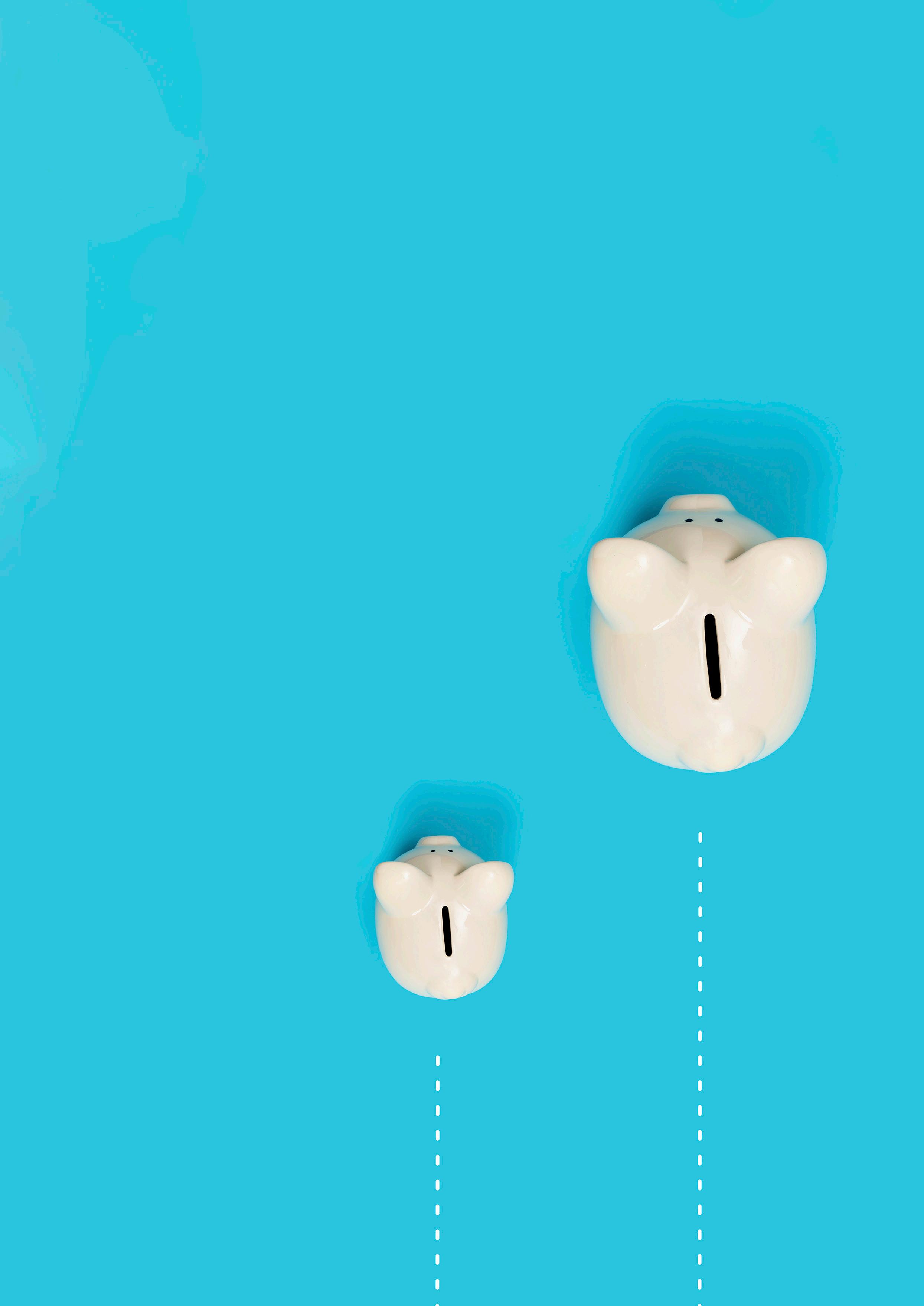
Elbows If a pipeline contains forged elbows, the bend radius and wall-thickness of the elbow fitting needs to be determined. Bear in mind, small diameter forged elbows have a radius that is calculated on the nominal OD of the pipe size, and not the actual OD of the pipe. For example, a 3 in. pipe has an OD of 3.5 in., but the elbow radius is calculated using the nominal OD of 3 in. This pattern holds for all pipe sizes below 14 in. If we applied the same formula for 3 in. elbows as we did for 14 in. elbows, a 3 in. 1.5D elbow is really a 1.29D elbow! If the pipeline contains forged elbows, determine if any of the elbows are considered back-to-back, or an elbow welded to another elbow. If so, are the back-to-back elbows on the same axis, or different axes? Some new MFL ILI tools can pass back-to-back 1.5D bends in 4 in. and some 1.5D back-to-back bends in 3 in. pipelines. Any backto-back elbows need to be evaluated to make sure an MFL ILI tool can pass the elbow configuration.
Table 1.
is
Another issue we see with elbows in small diameter pipelines is heavy weld penetration between the elbow and straight pipe which can cause a major restriction in the pipeline bore. Tees Tees are very problematic in 3 in. and 4 in. pipelines as they are not inspected for bore diameter before being installed, and in our experience many heavy wall tees are used in small-bore pipelines. If you are designing small diameter pipelines, do not select fittings that are a higher schedule of wall thickness than the nominal wall thickness of the pipeline, and remember, there is no minimum bore requirements for fittings. ASME B16.9 states “Bore diameters away from the ends are not specified. If special flow path requirements are needed, the bore dimensions shall be specified by the purchaser”.
We recently inspected a 3 in. pipeline for which a new receiver was fabricated for the upcoming inspection. A tee was installed in the new trap that had a wall thickness of 22.3 mm (0.878 in.). This represented a bore restriction of more than 40% when compared to the outer diameter of the pipe. Consequently, the tee had to be replaced prior to conducting the MFL ILI inspection of the pipeline. Elbow radius calculated the nominal diameter of the pipe instead of the actual diameter pipe nominal diameter
of the pipe instead of the actual diameter for all pipe diameters below 14 in. 84 World Pipelines / AUGUST 2022
for all
Arguably, one could modify a pipeline to be made ‘piggable’, but this would require an interruption of service to modify and/or remove any ‘unpiggable’ features; a task which would invariably prove to be expensive, time consuming, and in some cases impossible due to high costs, technical feasibility, risk factors and a host of other
using
considerations.KMAXInspection has made significant advancements that has allowed many of these lines classified as ‘unpiggable’ to be inspected with MFL ILI technology without modification to the pipeline, with over 59% of the MFL ILI inspections performed by KMAX having been first time ILI inspections. And yet, the biggest challenge remains that most wall thickness changes happen on the inside of the pipeline, creating significant bore restrictions when measured as a percentage of pipe diameter. Thus, the risk of an ILI tool becoming lodged in a small diameter pipeline is considerably higher than an ILI tool becoming lodged in a larger-diameter pipeline.Before undertaking an inspection of a small diameter pipeline, some upfront work is necessary to determine if an ILI tool can successfully navigate the pipeline. Here are some pipeline features that need to be evaluated: Pipe wall thickness The maximum wallthickness needs to be determined. Small diameter pipe is remarkably strong.
diameters below 14 in. ‘D’Dimension Dimension ‘A’ (for a 1.5 dia. elbow) 3.5 in. 4.5 in. (3 in. x 1.5) 4.5 in. 6 in. (4 in. x 1.5) 6.625 in. 9 in. (6 in. x 1.5) 12.75 in. 18 in. (12 in. x 1.5) 14 in. 21 in. (14 in. x 1.5) Figure 1. Elbow radius is calculated using the
For example, a 3 in., schedule 40 wall, X42 grade pipe has a burst pressure of 357.42 bar (5184 psi). Even so, some 3 in. and 4 in. pipelines have schedule 80 or thicker pipe wall installed. MFL technology in 3 in. and 4 in. sizes can magnetise schedule 40 pipe, but because of the physical restrictions on tool size are not able to magnetically saturate thicker wall pipe. Older pipelines rarely have accurate and complete as-built records and repair documentation. Thus, the easiest way to obtain a sample of WT’s is to take measurements of all above-ground piping using a handheld ultrasonic wall-thickness measuring device. If feasible, the best and most complete way to obtain wall-thickness information is to run a geometry tool.
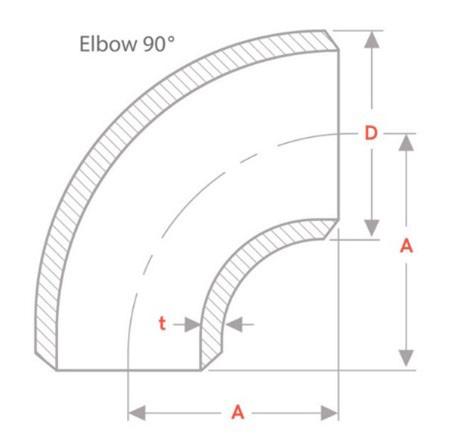
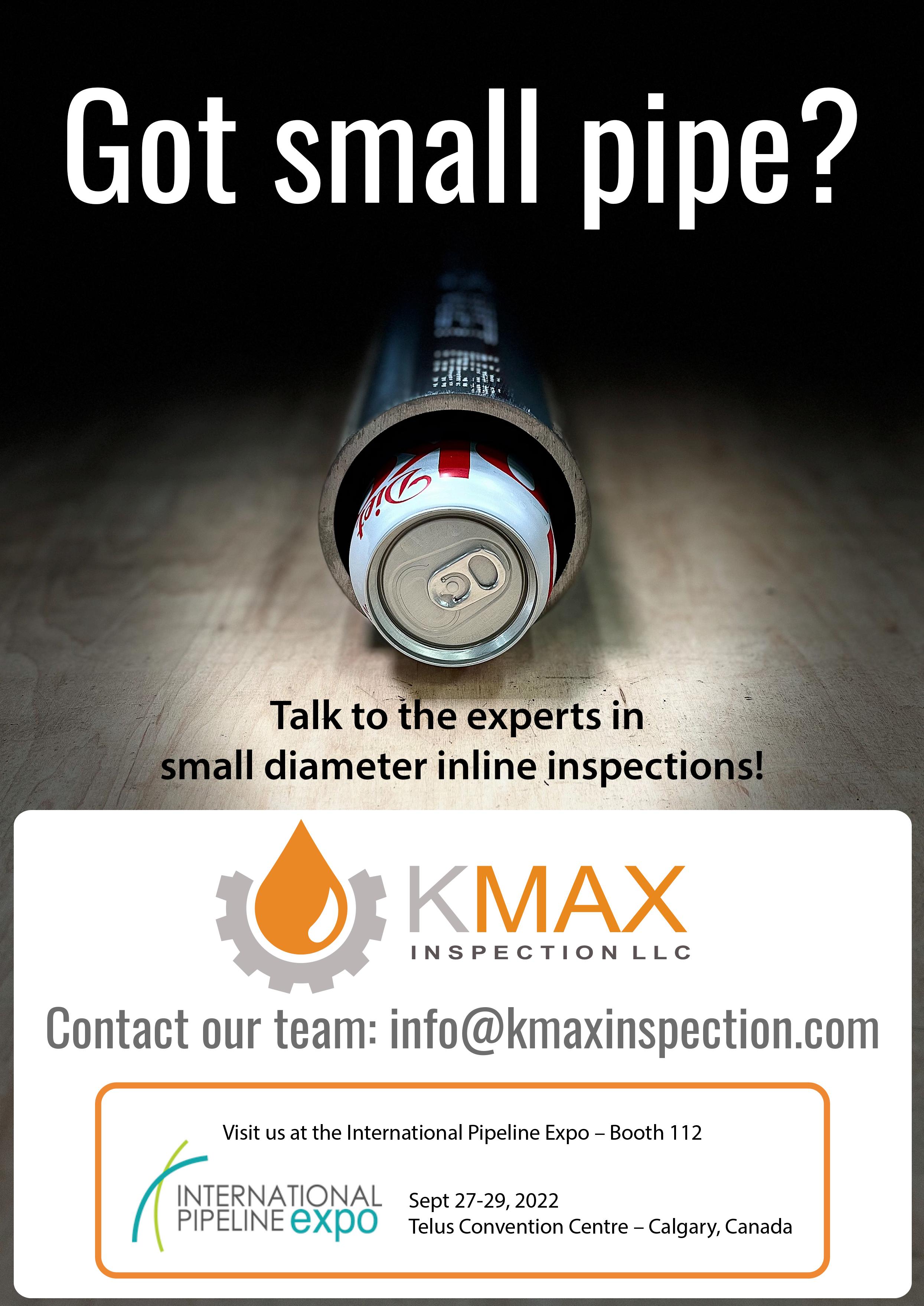
Pipeline product and speed during the ILI inspection The pipeline must be evaluated to determine if the product and flow rate are compatible with the chosen ILI tool. If not, the pipeline might have to be evacuated and another product used to propel the ILI tool. For example, a low-pressure gas line that does not have enough pressure or flow to run an MFL tool, might have to have nitrogen or liquid introduced into the pipeline to create enough pressure and flow to run the MFL tool. Surging can present significant challenges when running small diameter tools in gas pipelines. Surging occurs due to internal bore restrictions caused by wall thickness changes and fittings. Surging when running an ILI tool in a compressible medium such as gas occurs when the differential pressure needed to propel the ILI tool increases due to a bore restriction or bend. Pressure builds behind the ILI tool until the required differential pressure has been built to propel the ILI tool past the bore restriction. Once past the bore restriction, the tool now experiences a higher differential pressure than was present or necessary before the bore restriction. The tool will now accelerate to a high speed due to the higher differential pressure. The tool speed will accelerate rapidly and then deaccelerate as the differential pressure is reduced.
Internal debris
Figure 2. Elbow with heavy weld penetration.
The pipeline should be free and clear of internal debris, ferrous material and paraffin. If the pipeline has never had a magnetic cleaning pig run through the pipeline, plan on running this type of cleaning tool to remove ferrous material that could be in the pipeline from construction or internal corrosion. MFL ILI tools contain strong magnets that will attract ferrous debris that will have a negative impact on the sensor readings. Any pigging programme for a small diameter pipeline should be very conservative if the pipeline has never been pigged. Start by running foam pigs through the pipeline. Once a foam pig can be run through the pipeline without damage, run a polyurethane cast pig through the pipeline. If all goes well, run a gauge plate pig through the pipeline. Once a gauge plate pig is run through the pipeline, you might consider running a geometry tool through the line to determine wall thickness ranges if they are not known. With all this information, you should be able to determine if you can now run an MFL ILI tool through your line.
86 World Pipelines / AUGUST 2022
Summary Small diameter pipelines are difficult to inspect with ILI tools, and as such many have never been pigged. With the advancement of magnet strength, magnet design, and electronics, it is now possible to inspect some of these previously ‘unpiggable’ pipelines with MFL ILI technology.
Determining the wall thickness of pipe and fittings in a small diameter pipeline are critical to determine if the pipeline segment is a candidate for an MFL ILI inspection. Lastly, cleaning is vital to a successful ILI, especially if the line has never had a magnetic cleaning pig or MFL inspection. Ferrous debris can remain inside a pipe even after running a foam or cup pig through the pipeline segment, thus compromising data quality.
Dents in the pipeline are often caused during the construction of the pipeline, by equipment operating near the pipeline (third-party damage), or by ground movement. A large dent may cause an ILI tool to become stuck in the pipeline. The existence of dents in the pipeline should be identified by running a gauge plate pig, or an ILI geometry tool.
Dents
Traps If the pipeline has a launcher and receiver, it might require modification for the ILI tool. At the launcher, the most important dimension is the length of the oversized pipe. The oversized section of the launcher must be longer than the ILI tool, unless there is a way to pull the ILI tool into the nominal pipe of the launcher. At the receiver, the most important dimension is the length of nominal size pipe after the receiver valve. Most modern ILI tools drive from the front, so the length of nominal pipe must be longer than the ILI tool to be able to pull the tool past the receiver valve.
Minimum bore For safe passage of an inspection tool, the minimum bore of the pipeline must be determined. This can be accomplished by running a gauge plate pig or a geometry tool through the pipeline. Minimum bore in the pipeline is usually the result of heavy wall fittings, elbows, dents and/ or heavy weld penetration. Magnet design and strength along with other technical advances have allowed new MFL ILI tools to be built that will pass through significant bore restrictions.
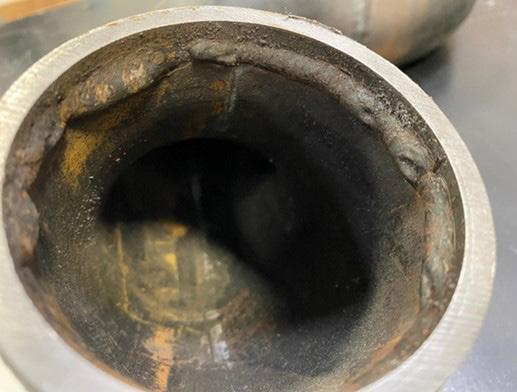
‘Our subsea space is changing’ From our polymer heritage, we pride ourselves as material pioneers, striving to introduce the latest and greatest into our industry; always seeking to evolve and improve our products and the engineering methods we utilise to assure them, but our subsea space is changing. From the moment our highly engineered; technologically advanced; polymer solutions started being referred to as ‘dumb’ it wasn’t the panic of commoditisation we felt, but vindication that our journey toward digitisation was well placed, and as the statement was quickly followed by ‘your smart products’ we knew the past six years of development was the correct course. Back in 2014/2015, prompted by our then parent company, an internal initiative sought to improve products across their broad portfolio, by digitising them. This desire to diversify products and to better engage digitally, whether through improved customer apps or inherent digital features, started our journey into the digital monitoring space.
Initially reviewing our portfolio of deep sea buoyancy, pipeline and cable protection ancillaries, we focused inward. Our path began with production, improving real-time tracking 87
From our vantage point of affixing products to pipelines (be they buoyancy, strake, or clamp) we historically focused our engineering analysis on the delivery system, the clamp or receptacle that holds a payload, since ease of deployment, retention and, in this case, how the response is passed through to the sensor is critical to its success. But when it comes to the introduction of our pipeline monitoring range, our journey wasn’t so clear cut.
Austin Harbison, Smart Technology Manager, CRP Subsea, UK, considers the future of how monitoring systems can support pipelines globally.
N o longer should pipelines and risers exist isolated from monitored structures in the dark abyssal plains of the ocean. We have a duty to illuminate them with insight that can inform the latest engineers and scientists joining our industry. Engineers who live in a world where everything from their quality of sleep, to blood oxygen levels, and every Watt expended, is captured, displayed and visualised with a few simple swipes of their finger. We just can’t continue with high-cost mobilisations, leading to single datapoint visual inspections. We need an array of low cost, always on, always tracking, easy to deploy, trouble free devices – reminiscent of a Silicon Valley visionary – and why shouldn’t we have it. With the advent of ultra-low power electronics, perpetuating miniaturisation in line with Moore’s law, and sensors that can far outperform the technology of even five years ago, captive in eye strainingly miniscule form, coupled with the strides being made in batteries and fledging energy harvesting opportunities; it feels like now is the time to take hold of our pipelines, to know every movement, strain, degree and Monitoringdecibel.pipelines for the purpose of life extension, or to quantify actual response to conditions, has been implemented to varying degrees over the years, but the approach has always seemingly focused on the monitoring device itself, whether it be tethered for real-time delivery or standalone.
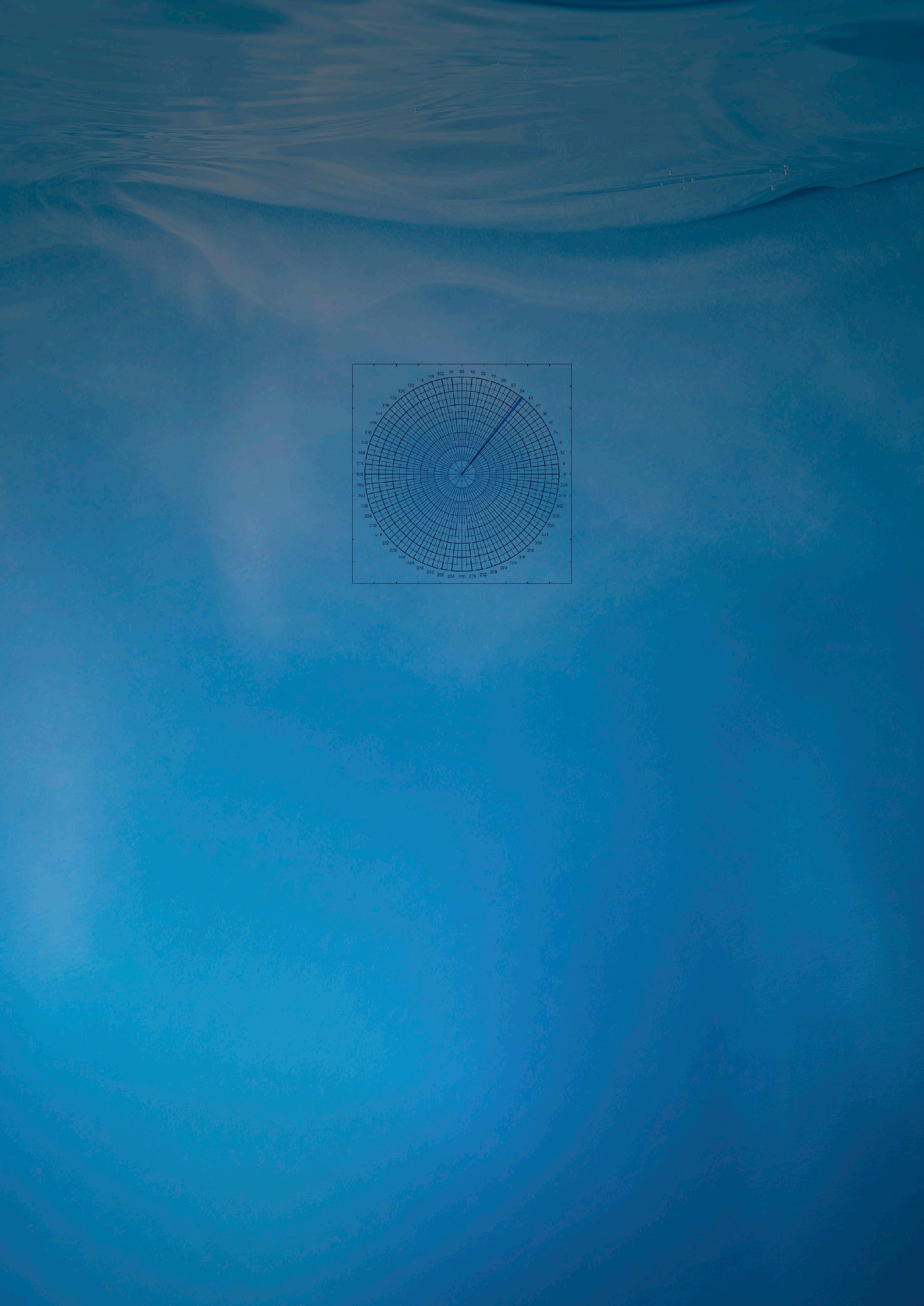
of assets through our factories, via QR codes or inset RFID. Whilst this seemed for us to be a natural path to fulfil our parent companies’ aspirations, our manufacturing excellence teams were way ahead of us, already having implemented QR codes with full ERP integration; so, what could we digitise? By chance, we were in the midst of qualifying a new type of drill riser buoyancy module, which offered reduced vibration risk by the inclusion of inverted strakes on its outer surface and, all of a sudden, the need to validate our product, and to that end pipelines themselves, became clear.
Figure 2. Monitoring systems: closing the loop on design insight. Figure 3. Monitoring systems awaiting shipment. 88 World Pipelines / AUGUST 2022
When we look at the subsea space, the inclusion of monitoring onto buoyancy, affixed to pipelines traversing some complex bathymetry, or integrated into vibration suppression devices suddenly opened our eyes to the simplicity of integration within our products. But what about existing infrastructure? Attaching monitoring to pipelines before they are laid is not without its challenges, especially if some torsional loading may cause a system initially located atop the pipeline to be laid in a very different orientation. So again, we looked to our heritage of clamping, more specifically the design expertise accrued from retaining large buoyancy modules onto pipelines, and so a new standalone clamping range was born.Over the years we have monitored slug induced vibrations, riser and pipeline movements and will soon add a new type of bending strain measurement clamp to replace strain gauges, capable of up to a decade of continuous monitoring. Whilst this product line continues to grow with countless design options for diver and ROV installation, we consider the future of how our monitoring systems can support pipelines globally. Given the challenges faced with subsea installation, it seems only fitting that the robustness, assurance and longevity sought in the subsea space, migrates topside, to support the digitisation of surface pipelines, with the added benefit of in-air communication. We have also seen the need for digitisation of pipelines starting to support being assembled.
Figure 1 . Monitoring clamps
Being at the forefront of offshore polymer solutions for 44 years, our knowledge of pipeline ancillaries is arguably second to none, with market leading bend protection, drilling and production riser buoyancy, and more recently buckling mitigation rotating buoyancy, our breadth of pipeline protection products and depth of knowledge therein puts us in a unique position to provide retrofittable, or indeed integrated monitoring. From the engineering complexity of affixing and assuring these products over decades; providing a means of quantifying pipeline condition felt like a natural progression. As a pipeline ancillary specialist, we are including monitoring to the products we know intimately, not seeking to discover the product by adding monitoring, with no view on just how they may be seated and what pitfalls they may contain. For us, the seed of monitoring design was how we could attach or integrate an electronic unit, what form of full-scale testing would be needed to demonstrate its applicability, and just how well both would interact.
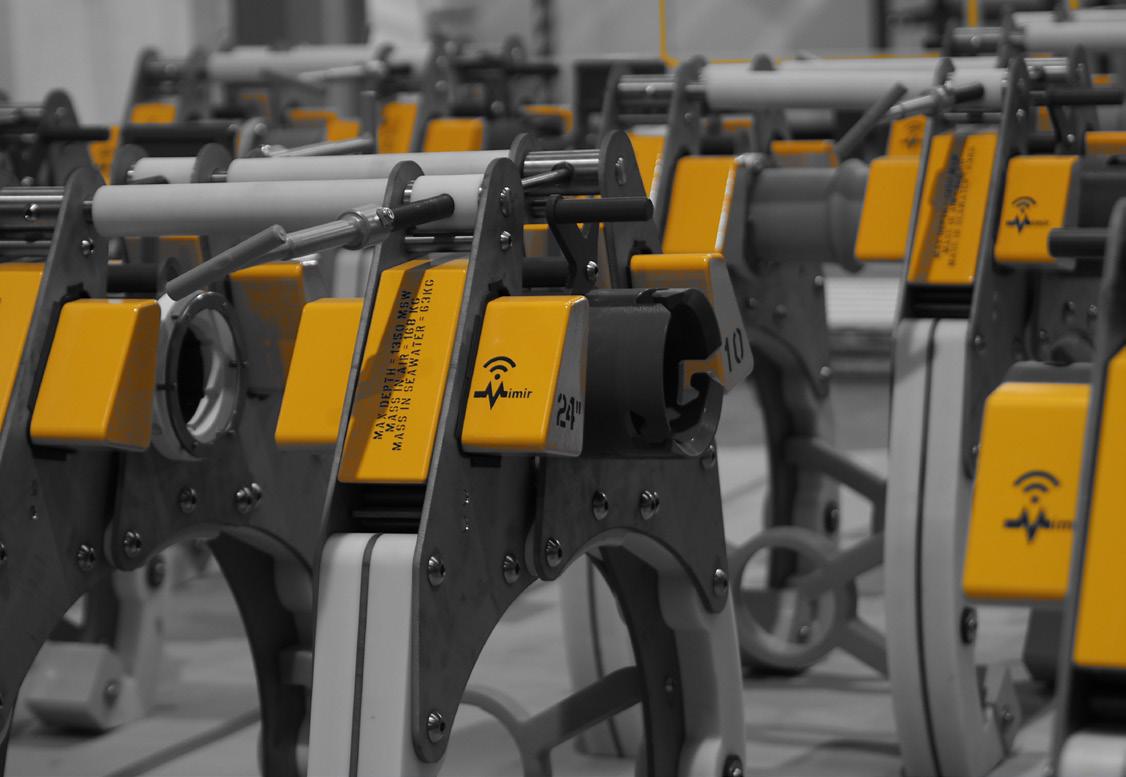
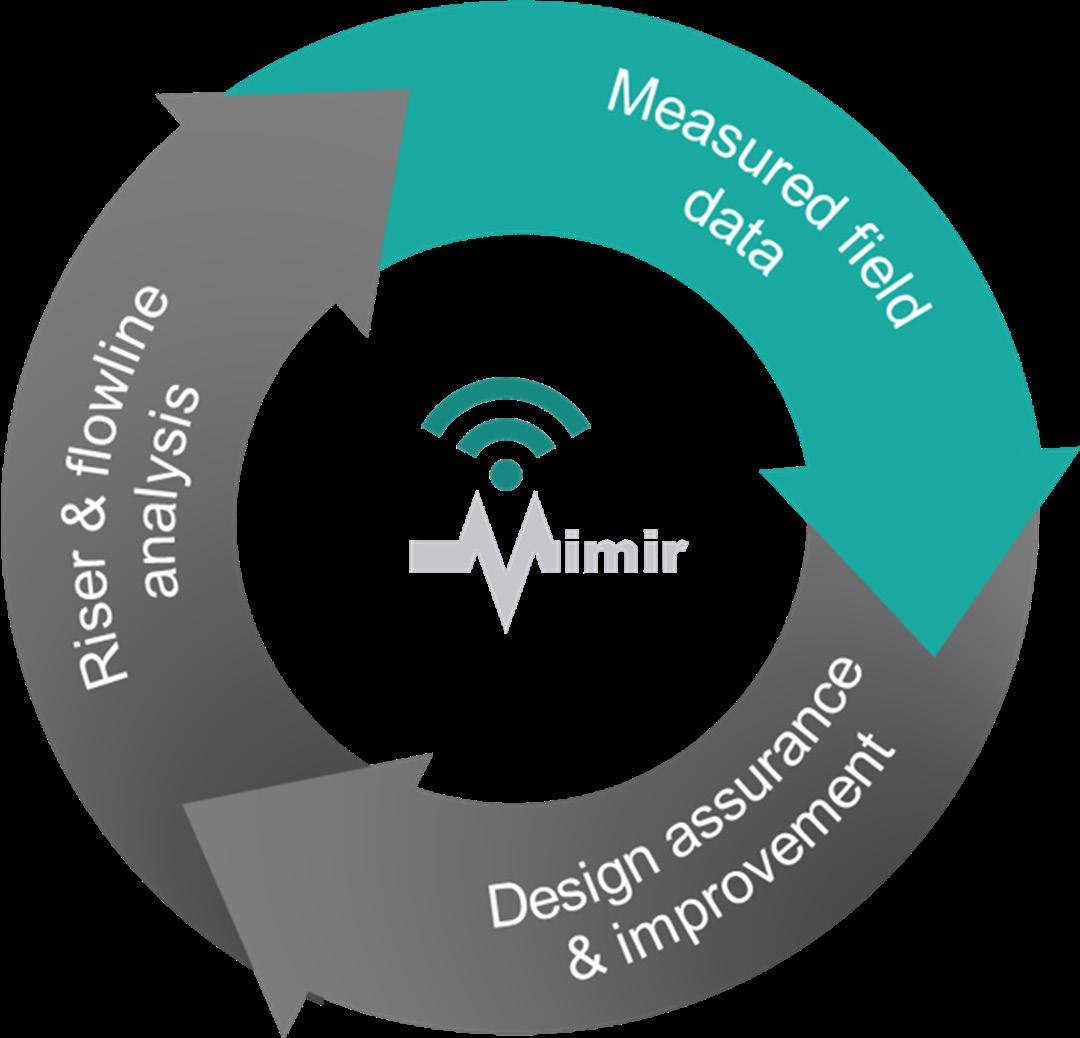
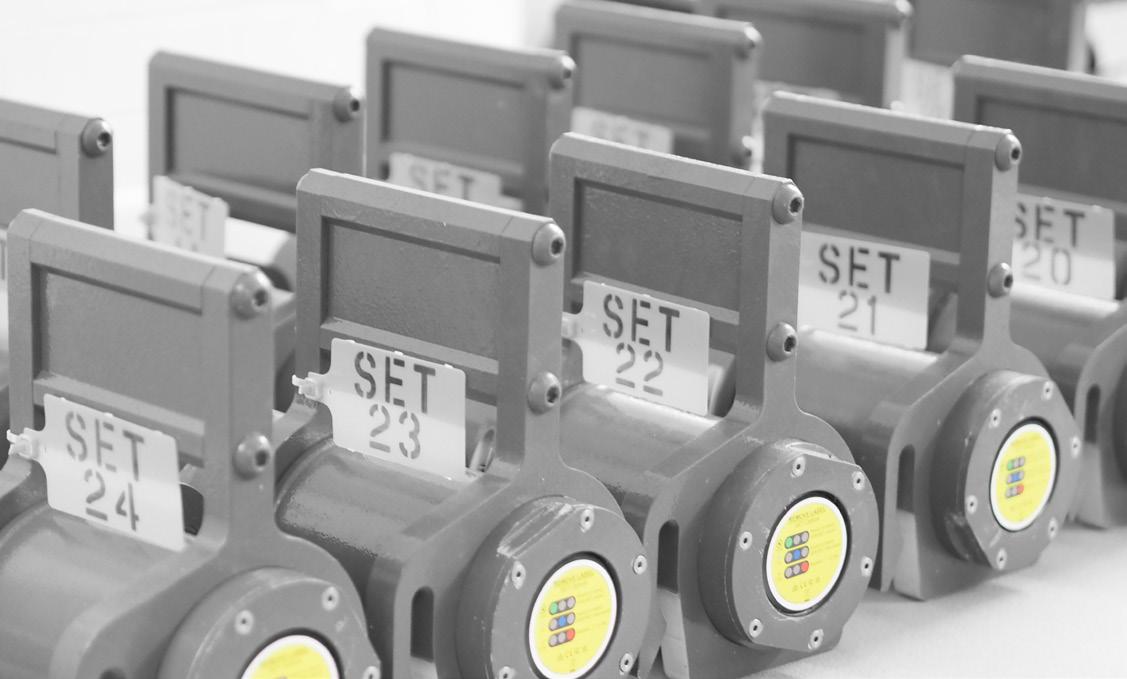
ALLU Transformer, Saving you time and money and increasing your sustainability. ALLU Transformer are designed for excavators, wheel loaders, skid steers, tractors, backhoe loaders, and telehandlers to screen, crush, pulverize, aerate, blend, mix, separate, feed, and load materials all in a one-step process for pipeline padding needs. Benefits that you’ll get by utilizing ALLU; • No additional equipment at the job site • Reduce transport costs since excavated material can be re-used on job site • Screen all unwanted hard impurities away from the padding material • End-product always according to wanted and required fragment size and quality • No need for electricity at site • Plug-and-play feature ALLU Screener Crusher is a trustworthy partner for all your pipeline jobsites. Come and meet ALLU at IPLOCA conference in Prague. www.piggingsmarter.com TRIDENT APEX-500 The ONLY combined pig tracker and pig signaller in one unique multi-functional device Used for: • Pig Location • Pig Launch / Receipt Confirmation • Pig Passage Signalling • Confirm EM Transmitter Operation • Simultaneous Multiple Pig Tracking • Magnetic Pig Detection EM Receiver / Magnetic Pig Signaller / Bluetooth Capable / IP Rated / Android Device c/w PigView Software / Portable Carry Handle / Audible Alarm TRIDENT - The Future of Pig Tracking
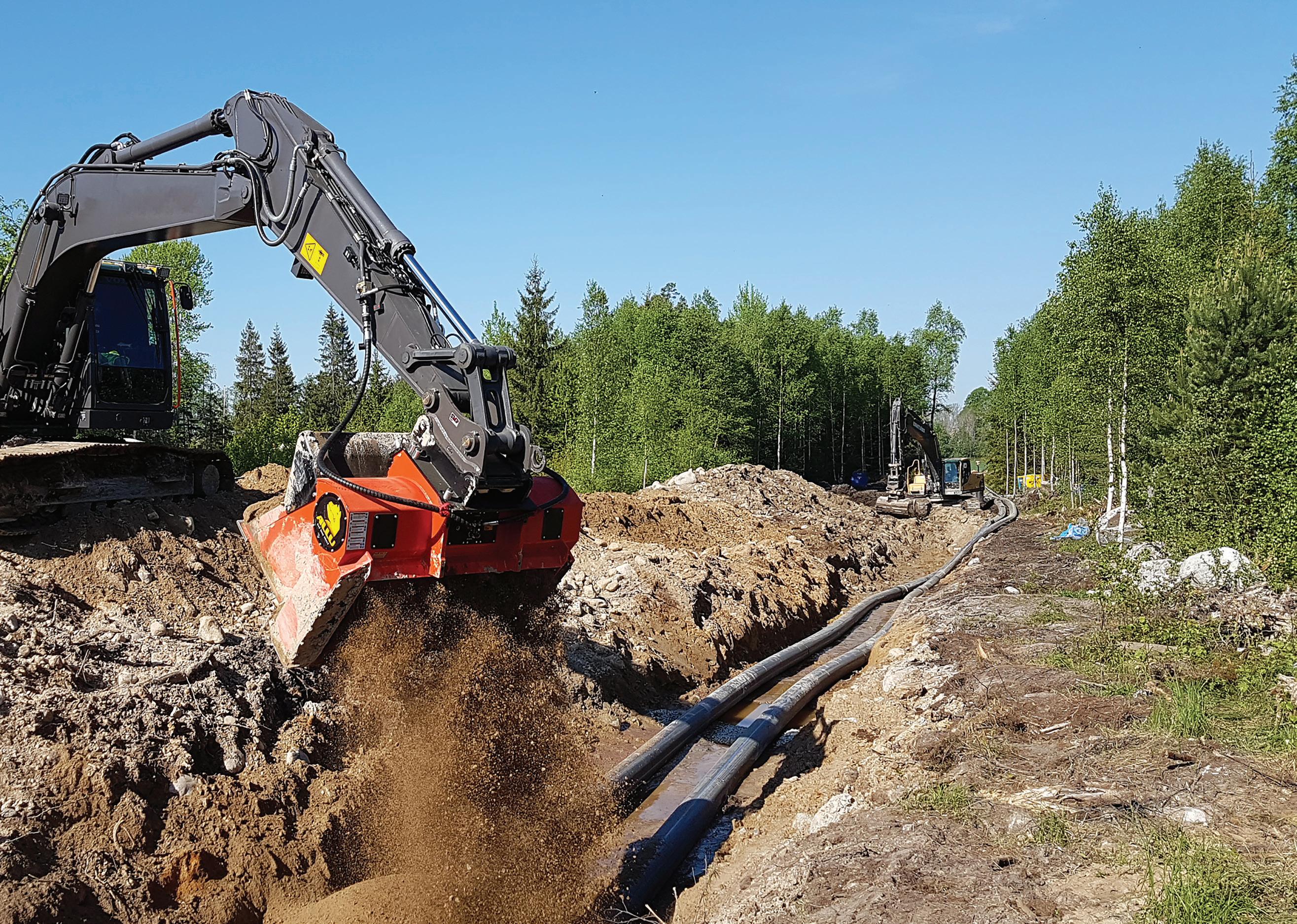
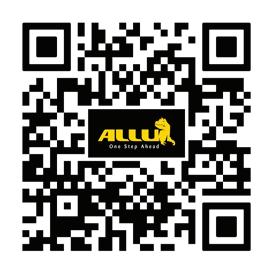
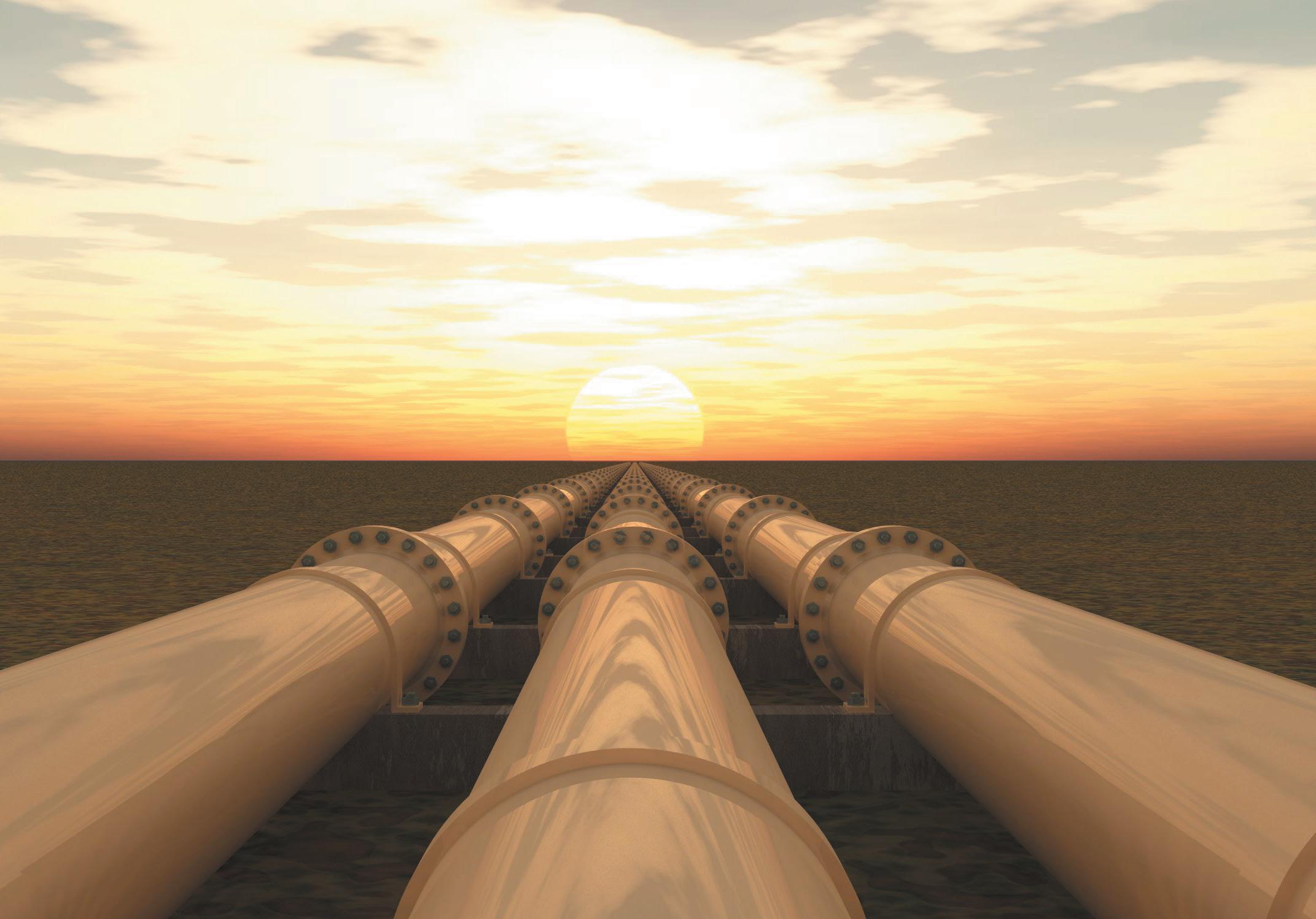
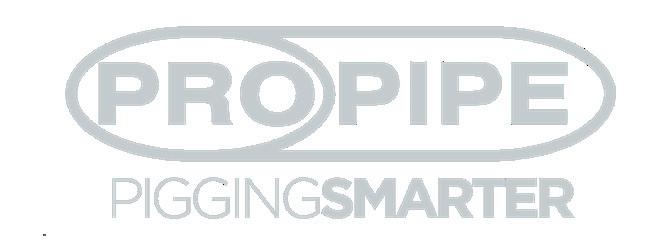
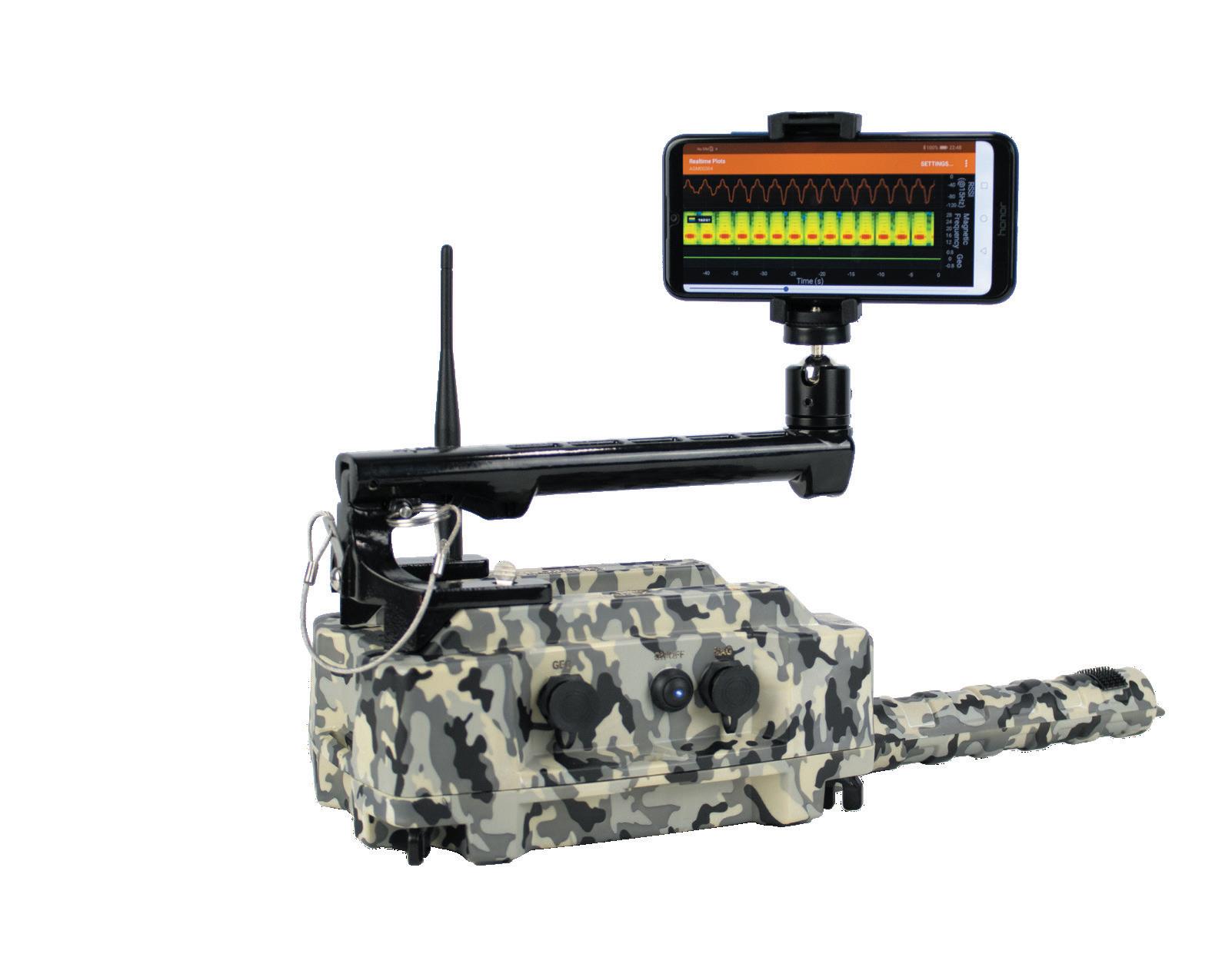
• OUTSTANDING LIFE SPAN • FAST AND EASY INSTALLATION • FOR HIGH-VOLUME FLOWS • HIGH-QUALITY MATERIALS • EXPERTISE IN PLASTICS PROCESSING AGRULINE XXL PIPES HDPE piping systems for horizontal directional drilling agru Kunststofftechnik Gesellschaft m.b.H. | Ing.-Pesendorfer-Strasse 31 | 4540 Bad Hall, Austria T. +43 7258 7900 | office@agru.at | www.agru.at | @agruworld |
Figure 4. Subsea monitoring clamps, with optical health response.
the ever-growing wind industry, where near surface cables connecting wind turbines are seeing far more movement than predicted, unfortunately resulting in failures. Again, in this industry, single-point snapshots of cable state are taken on clear days, at high tides, but when the winter storms roll in, the actual environmental response remains elusive, only the deleterious evidence of excessive movement can be witnessed upon return.
Monitoring, whether it be subsea, topside, on umbilical, pipeline or riser, is no longer an inaccessible thought. Bending strains for fatigue assessments, vibration from external or internal fluid flow, overbending, temperature, noise, abrasion, and wall loss are all available for full integration into digitalCRPtwins.Subsea has moved from a single circuit board, captive within a moulded pressure vessel, retained by a basic piggyback clamp; to over 10 circuit boards talking amongst themselves and across the water boundary, determining how a pipeline is moving in hot-swappable canisters, all retained within clamps which act in one state during installation and another in operation, fabricated from the lightest weight buoyancy titanium, and engineering polymers. These are qualified over several years, with thousands of tests from the smallest electronics to factory filling test jigs, packaged with intuitive apps to ensure data custody, system health and tracking, loaded with videos, documents and learning for users. The evolution of our digital journey to support life extension and asset integrity management of pipelines may have started from a tenure of perceived ‘dumb’ products, but it is this building block that continues to allow us to advance our offering, as the pipeline monitoring company of choice, well into the future.
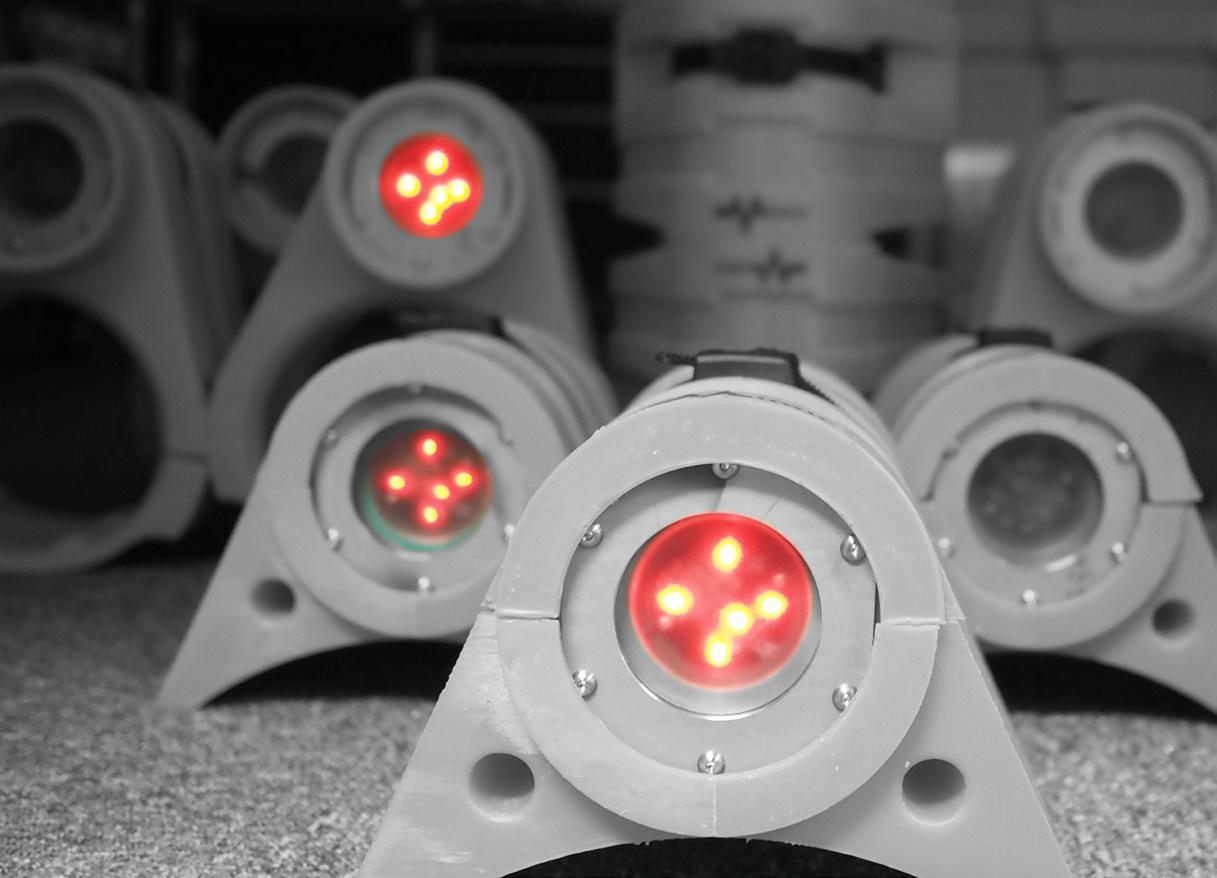
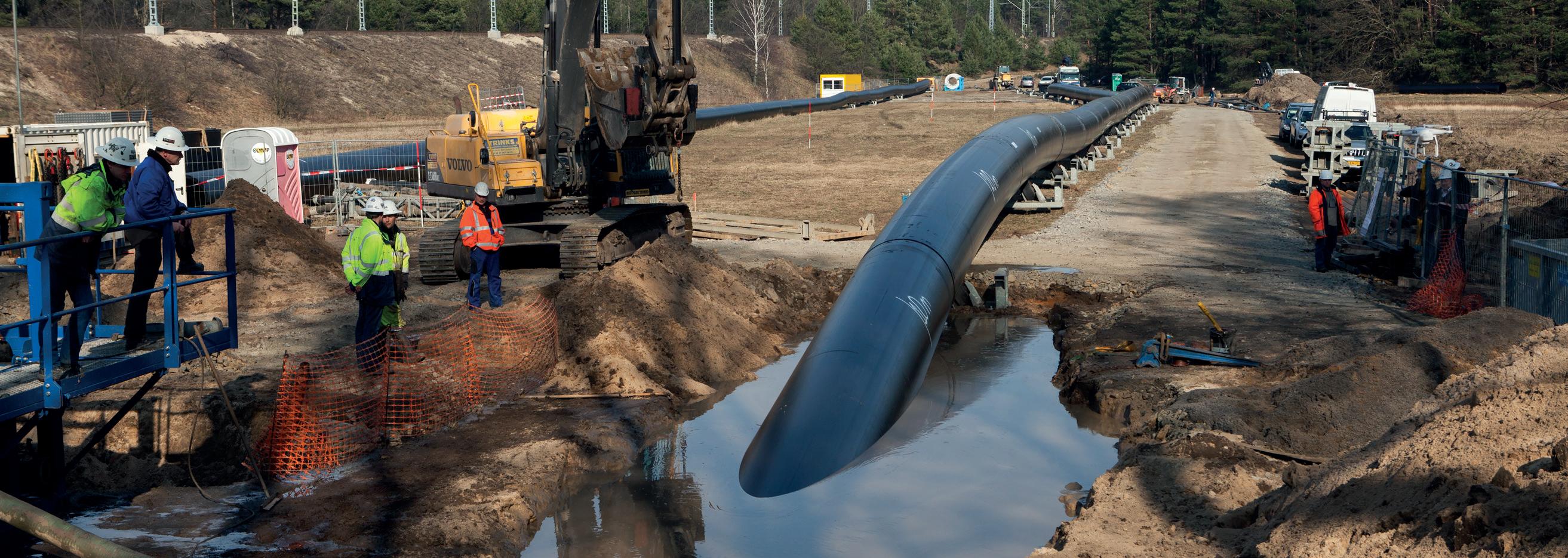
he Australian oil and gas sector is seeing an increasing focus on the decommissioning of offshore assets as they reach the end of their productive life. With volumes of work anticipated to grow significantly, CODA (Centre of Decommissioning Australia) has released a series of three studies to help the sector learn from experiences in other regions, and accelerate its preparation for this coming work.1
Individually, each study fills a separate knowledge gap and will allow the sector to move up the knowledge and technology curve faster. Collectively, the suite of studies and associated materials help to build a picture of the potential future of Australian decommissioning. This picture is one where best in class, most appropriate technologies are deployed using globally benchmarked planning and execution practices, with the safely removed equipment then managed through cost effective and comprehensive dismantling, recycling and disposal pathways. This future would see much of the work undertaken locally, and as 91
These studies build on CODA’s 2021 offshore decommissioning liability study, which found that there is up to AUS$40 billion of activity to be undertaken in the coming 50 years.2 The new studies comprise; a global review of decommissioning planning and execution learnings, research to provide an understanding of the opportunity for local disposal and recycling pathways, and the development of a decommissioning innovation and technology roadmap.3,4,5
Dr Francis Norman, CODA, Australia, discusses preparing for Australia’s upcoming decommissioning workload.
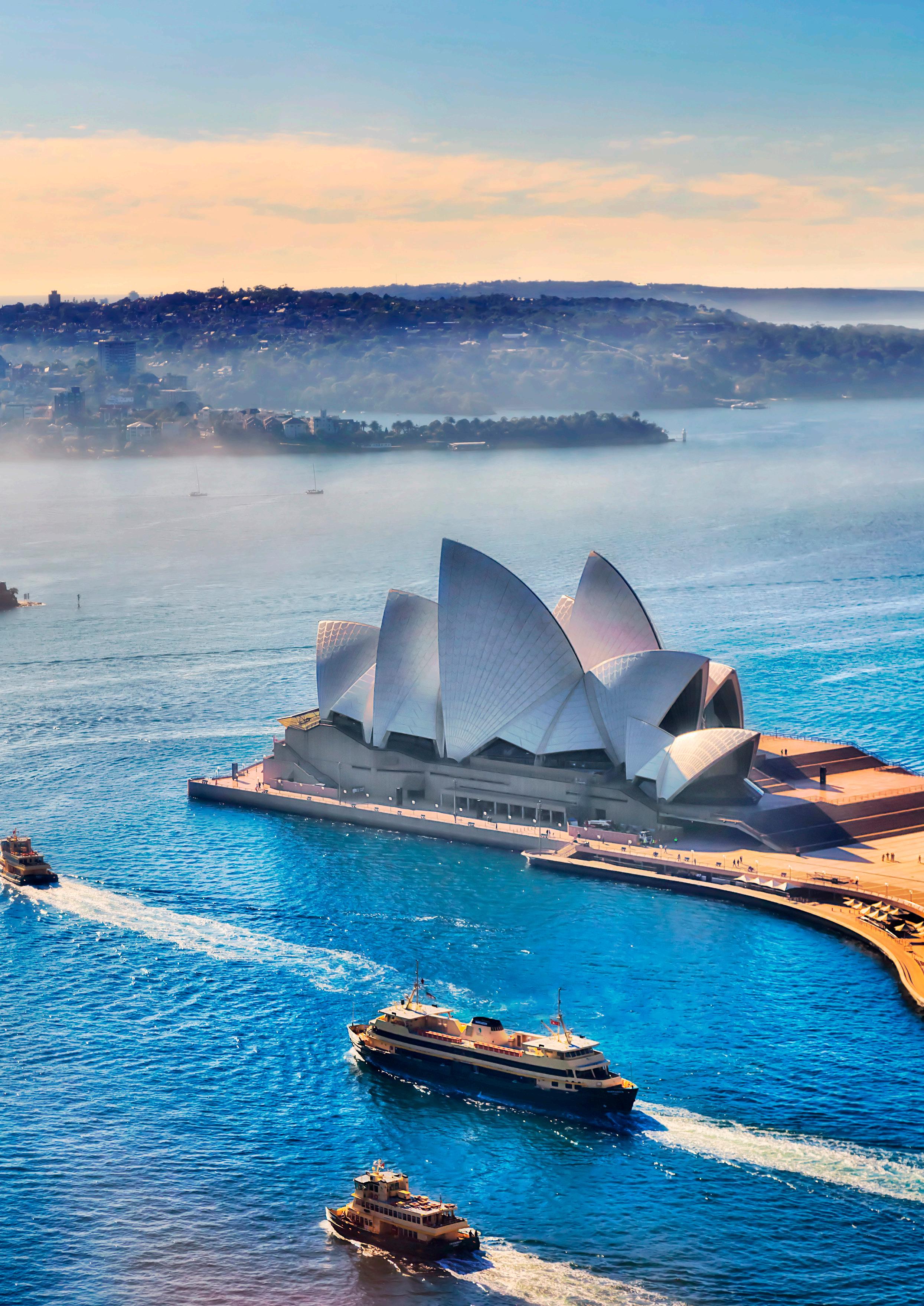
such, growing local employment opportunities and the smallest volumes of materials possible ending in landfill.
valueaddwhichprioritisedandimpactbeenstructure,workdecommissioningbreakdownwhichhavecategorisedforandapplicability,thenprovidedalistingofareaswereseentothemostimmediate(Table1). Table 1. High priority lessons learned and best practices Strategic theme Subtopic Register entries transformationCommercial Enabling decommissioning at scale (e.g. campaigns) 7 Planning decommissioningfor Clearly defined strategy and contingency planning before CoP 23 Process and guidance Regulatory process(es) that support decommissioningefficient 4 Fit for purpose guidance and expectations 6 Enhanced governance of the decommissioning option frameworkdecision 5 Safety risk reduction Promotion of safer and more efficient methods 8 Instilling decommissioninga mindset and strong safety culture 2 Circular economy Development of a competitive and sustainable local disposal market 2 Figure 1. Relative decommissioning jurisdiction maturity. 92 World Pipelines / AUGUST 2022
Similar opportunities are also being explored in Western Australia, which already has the Gorgon CO2 sequestration facility operating, with the state government looking to introduce legislation to allow such facilities to be established in the state, and operators such as Woodside exploring large-scale sequestration projects associated with the Karratha operations.8
Pipeline repurposing opportunities to support CCS
The most progressed of these is in the Northern Territory, where a consortium comprising the Northern Territory government, CSIRO, Santos, INPEX, Woodside, Eni, Origin Energy and Xodus undertook an extensive study, with Santos recently announcing the commencement of FEED for the project, which could annually store up to 10 million t of CO2 6 ESSO Australia have also recently announced the initiation of a study into the viability of a similar project associated with the Bream field in the Gippsland basin.7
As part of the planning for decommissioning in Australia, a number of companies and regions are exploring the potential to repurpose depleted fields and associated wells and pipelines for the sequestration of carbon dioxide (CO2). There is significant opportunity at a number of operations to repurpose existing trunk lines and wells to transport captured CO2 via these pipelines for storage. Where feasible, this would enable the operators of these facilities to extract additional use and value from their network of pipelines and potentially use the sequestration facilities to underpin the production of blue hydrogen, as well as reducing their own CO2 emissions.
Decommissioning planning and execution learnings Australia is a very mature oil and gas production jurisdiction but has, so far undertaken only relatively small volumes of decommissioning work. As the volumes increase, Australia can learn significant lessons from more mature centres, such as the Gulf of Mexico and the North Sea (Figure 1), allowing the nation to bring these best practices to bear on its work more quickly. This accelerated learning will help to reduce costs, improve safety, efficiency and deliver the best possible outcomes for all stakeholders.Theplanning and execution learnings study captured some 140 best practices and lessons learned across the
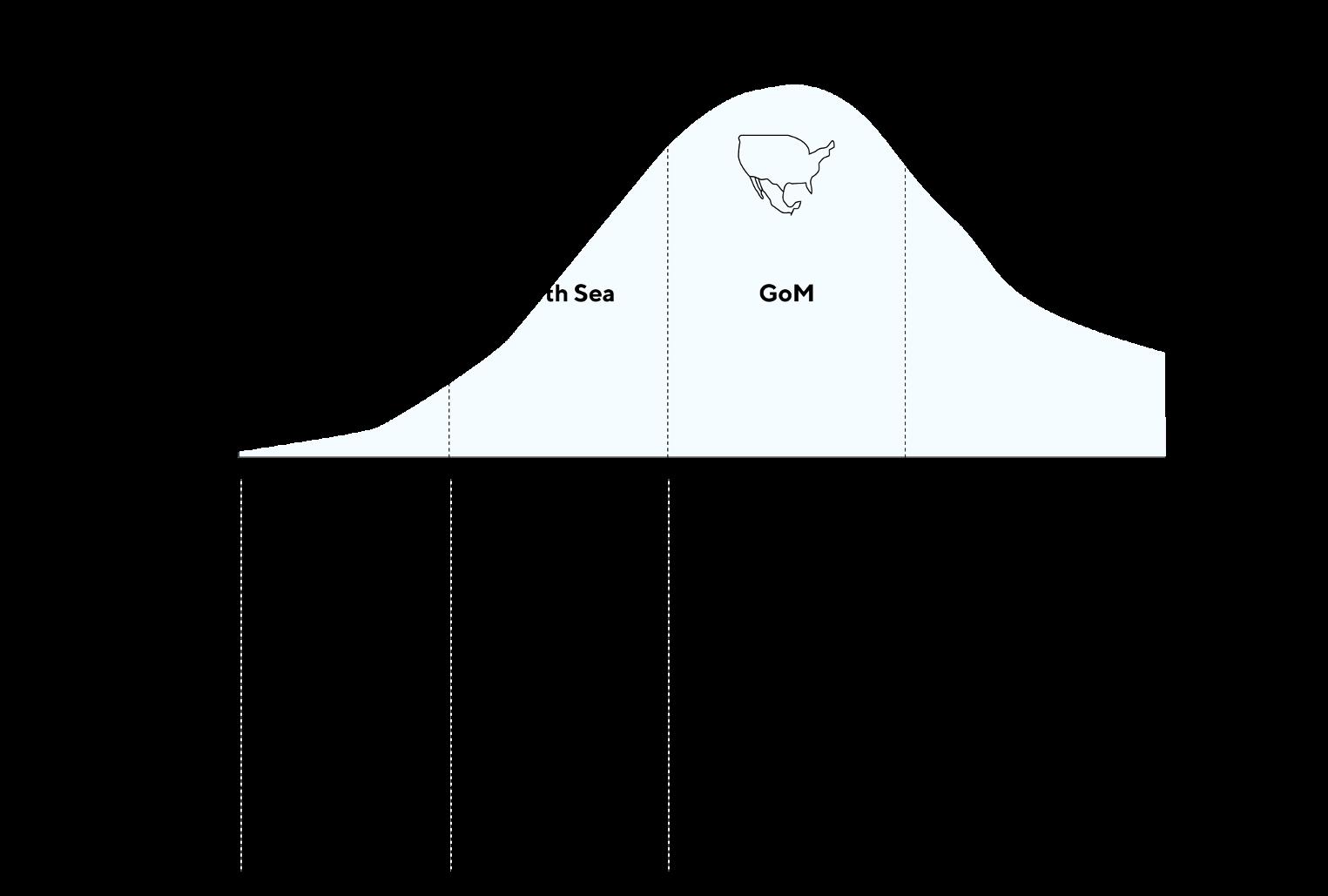
info@gdi.com.mx +52 (55) 4040 2100 | (55) 5662 8690 We provide high-quality, adequate, adaptable and timely solutions, backed by international certifications, always taking care of the environmental impact and the safety of our collaborators. - Pipeline Construction - Trenching and open cut - Horizontal Directional Drilling - Microtunneling, Direct Pipe and Trenchless EPC - Mining civil works - EPC Midstream facilities Contact us
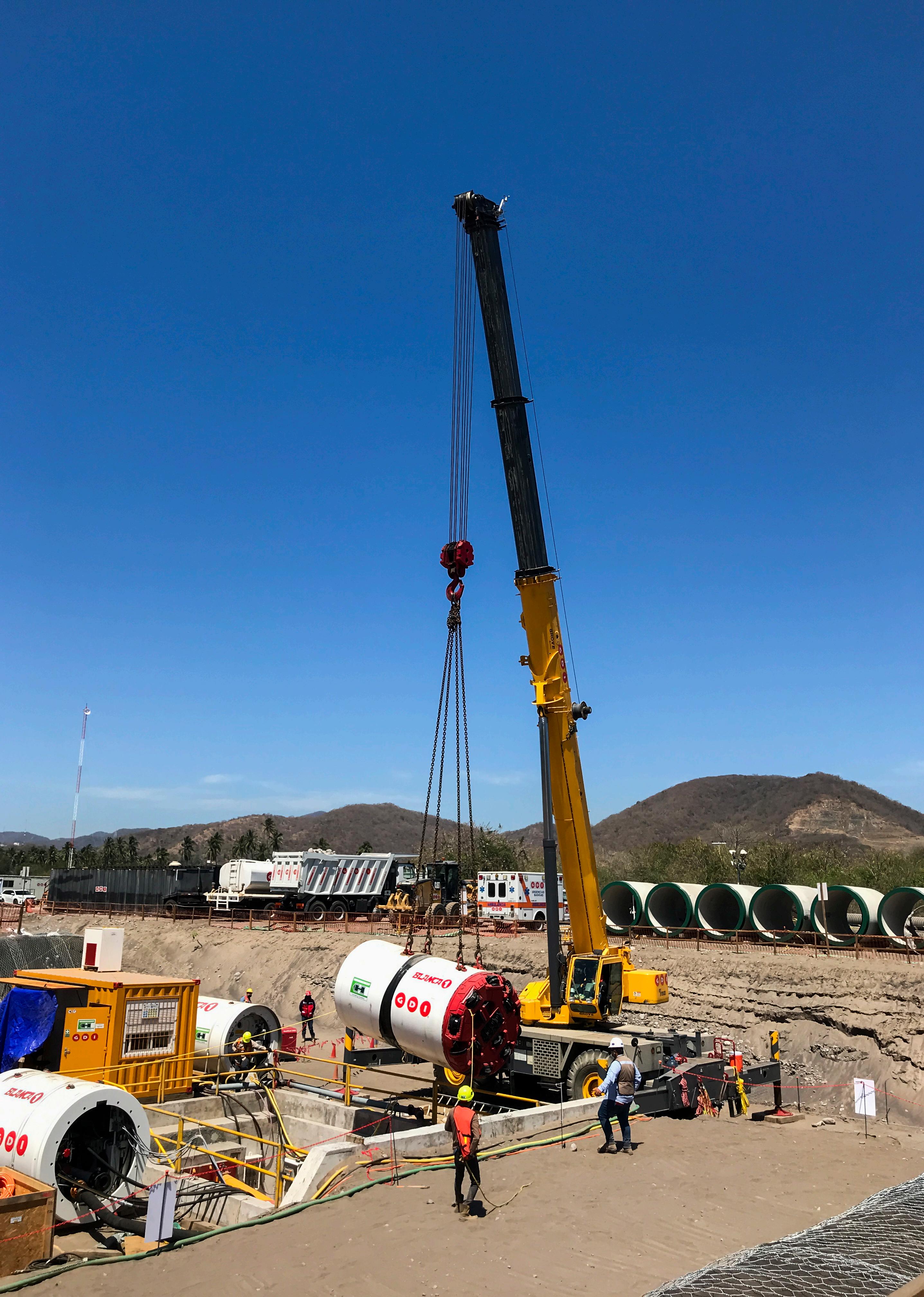
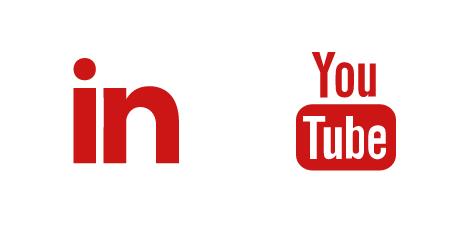
4. Encourage operators and the supply chain to integrate decommissioning into ‘business as usual’, driving safer outcomes through project and workforce continuity.
Understanding of the opportunity for local disposal and recycling pathways
5. Raise awareness of global trends and challenges, emphasising the decommissioning market, and provide clearer forecasts expedited through data tools that are accessible to the supply chain.
2. Facilitate a structured engagement framework using knowledge transfer, benchmarking and continuous improvement to promote timely planning of decommissioning activities.
1. To build a collaborative culture, improve data transparency and align activities to enable decommissioning at scale.
3. Work across the stakeholder suite to ensure that the Australian regulatory process supports the delivery of efficient decommissioning.
To grow a world class decommissioning industry, Australia needs to understand and, in some cases, expand its dismantling, processing and recycling/disposal capacities. Only through being able to receive removed equipment and infrastructure onshore in a cost competitive and safe manner, then undertake the associated dismantling, will Australia be able to undertake the full decommissioning scope and operate at the scale future decommissioning workloads are indicating.
This study looked at capability from both the perspective of full service providers and those who offer services in only one phase of the dismantling, processing and recycling/disposal continuum (Figure 2).
The local disposal and recycling pathways report is therefore critical in showing where Australia’s capacity lies and, equally importantly, where gaps exist. Using potential quantities of removed materials derived from CODA’s 2020 liability study, the recycling and disposal study identified that there is forecast annual average of up to 120 000 t of materials that could be removed for disposal (this figure is based on a base case of full removal of inventory and may well decrease dependent on approvals to leave some equipment in situ). These volumes are dominated by steel, followed by concrete from pipeline casing and gravity-based structures, then plastics, polymers and non-ferrous metals. However, while the study found that there is capacity across the Australian dismantling and disposal industry to receive and process most of this volume, there are also disconnects in terms of locations of facilities relative to the potential landing points of removed materials. Some states were found to have significant dismantling capability, and it is noted that much of this is also mobile so can be deployed across the country as needed; capacity to undertake much of the recycling, however, still remains low in many parts of the country.Inlooking to the future, the study identified a number of activities to undertake as priorities:
Figure 2. Decommissioning capability continuity map.
94 World Pipelines / AUGUST 2022
These are further consolidated into five recommendations for adoption by the Australian decommissioning industry:
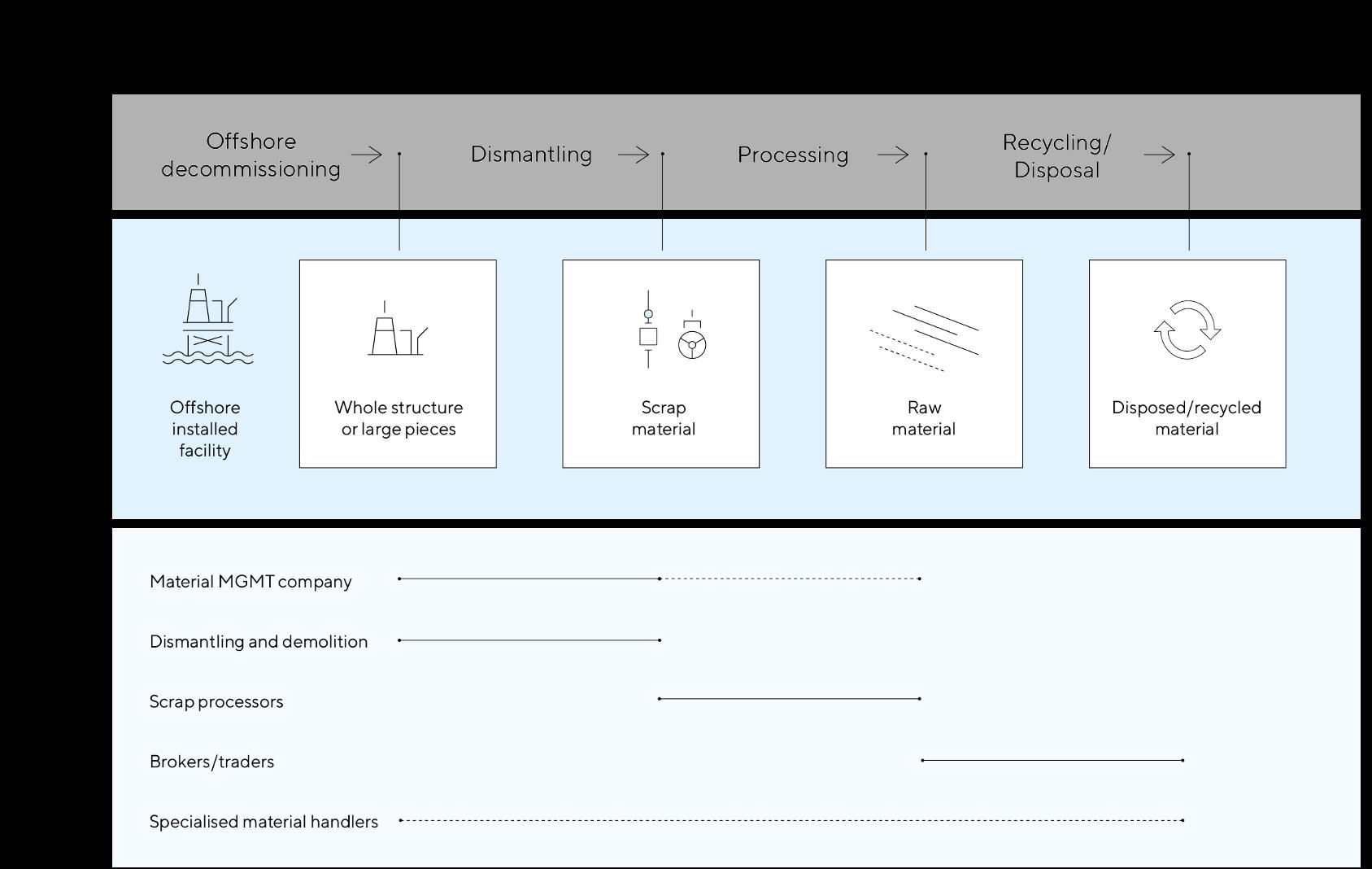
) Advocate research and development on disposal solutions for specific materials, e.g. plastics or NORMs.
) Establish a disposal contractor forum to facilitate systematic industry engagement.
Decommissioning innovation and technology roadmap
Figure 3.
) Undertake a deep dive analysis of the port import facilities to understand current constraints, as well as potential upgrade or expansion opportunities.
) Develop and maintain a decommissioning project timeline with industry support to identify future project critical mass.
The study also identified a number of blockers and enablers to the adoption of technologies into the Australian industry. Some of these include that much decommissioning activity is seen as one of regulatory compliance and not economic stimulus, yet a mature domestic decommissioning industry could provide employment and economic opportunities for large numbers of personnel and businesses; much of Australian industry operates as a consumer of technology and not as a developer; new ideas are often conceived in Australia but cultural barriers in the users of the technology mean that they will often look elsewhere for solutions rather than develop or adopt local ideas.
The decommissioning innovation and technology roadmap provides a comprehensive review of technologies that are either available or used in other jurisdictions and which, if adopted locally, could provide benefits to the Australian decommissioning industry through improved efficiency, safety or technical outcomes.
) Develop decommissioning project case studies based on Australia’s offshore infrastructure, to assess disposal solutions in detail through engagement with selected service providers.
) Evaluate the disposal cost base across the value chain (dismantling, processing and recycling) for competitiveness, considering the transport saving benefits against an overseas solution.
) Market analysis of specialist recycling and disposal facilities, e.g. NORMs, hazardous materials and plastics.
Collaboration is not a common activity in Australian industry, many companies at all levels prefer to go it alone rather than work with others. Some hold the often-mistaken belief that this control gives them advantages in outcomes; there is a prevailing mindset that technology development is the domain of new developments and that decommissioning is about risk avoidance and therefore not an appropriate environment for newManytechnologies.ofthese blockers and enablers then translate into recommended activities that, if embraced, could accelerate the growth of the Australian sector. These recommendations include reviewing the identified list of blockers and enablers to reduce impediments to deploying best practice technologies into the Australian market, and operationalising the outputs Path toward full domestic decommissioning recycling capability.
AUGUST 2022 / World Pipelines 95
The study identified a number of technologies and solutions from around the world, categorised them against different phases in the decommissioning work breakdown structure, then ranked them against a number of innovation value drivers that were developed in consultation with the industry. These drivers were improved safety, net environmental benefit, societal benefit, their probability of success, strategic/tactical merit, such as whether developing new solutions to local problems could result in an export product, and the economics of the solution.
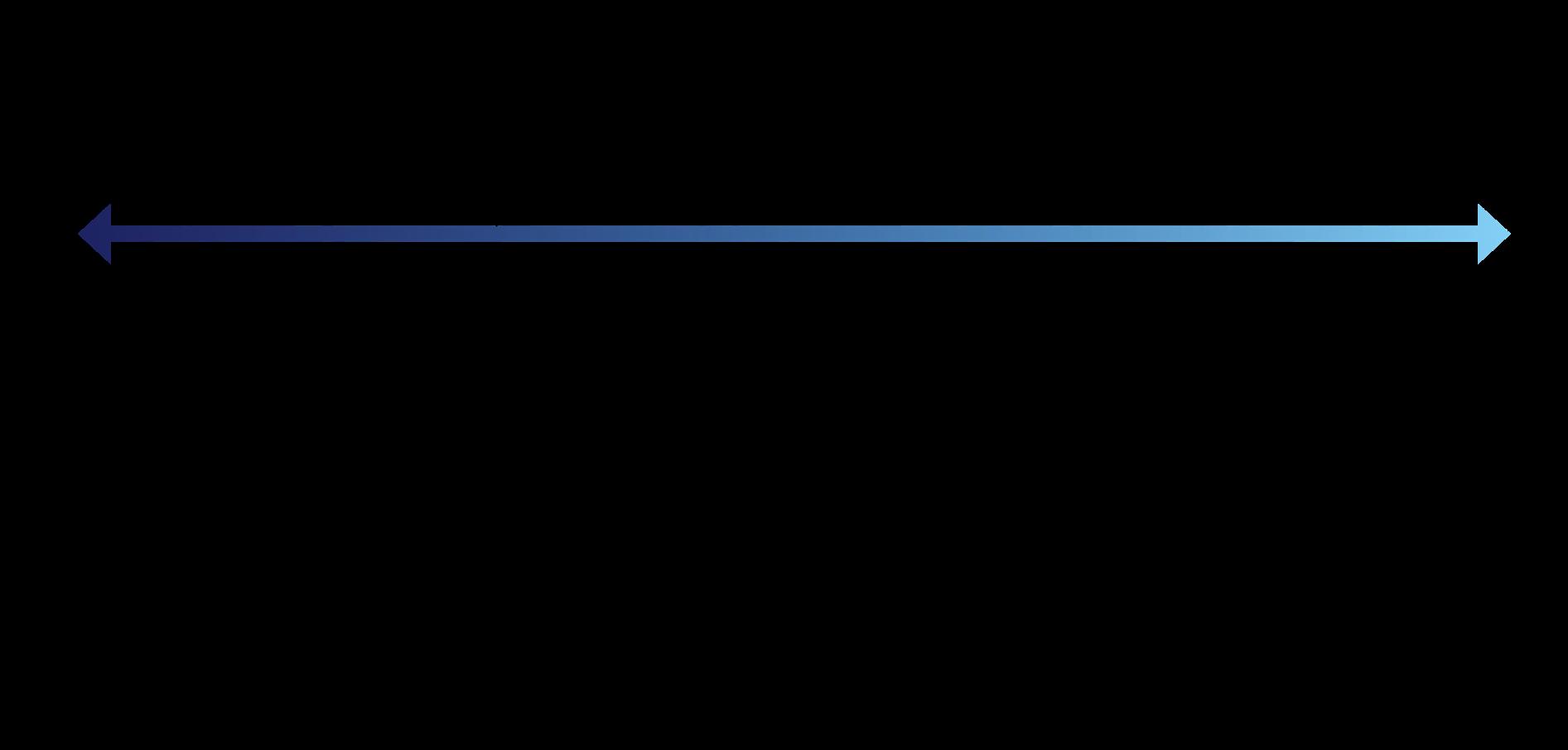
Next steps Against a backdrop of growing volumes of known decommissioning activity, now is the time for the Australian decommissioning sector to come together and prepare to address the future workload collectively. Through the suite of studies discussed above and its deep, independent and trusted engagement across the whole of the value chain, including operators, the service sector, research institutions, government and the regulators, CODA is now beginning to operationalise many of theCODArecommendations.hasestablished a partnership model to bring together like-minded and committed organisations to work collaboratively on solutions, CODA will undertake community building and interaction activities to build trust between partners, identify challenges that can be addressed collaboratively and share emerging best practices. The best practice and lessons learned database is being made available to partners to interrogate, add to and maintain as a go-to place for ideas and solutions for the Australian industry. A publicly accessible capability directory is also being developed that will be a one-stop shop to discover partners, suppliers and customers in the decommissioning landscape, streamlining the otherwise protracted and difficult methods currently in operation, where individuals must spend considerable periods of time online searching for potential companies with which to doWhile,business.assuggested in Figure 1, Australia may be an emerging player in decommissioning, with the right focus and application it can quickly accelerate its capability, capacity, skills, knowledge and technology solutions to emerge as a significant participant in the global decommissioning community. The studies discussed above and their associated materials, along with an industry-wide focus on early sharing of upcoming opportunities and challenges in an open and collaborative environment, such as CODA, is creating a lot to support this acceleration.
of the roadmap into an ongoing programme. This is done to identify future technology needs, screen for available solutions, understand the barriers to the adoption of technologies available elsewhere into Australia or establish programmes to develop new solutions locally through collaboration between users and developers.
6.
8.
4.
3.
ADVERTISERS’DIRECTORY Advertiser Page AGRU Kunststofftechnik 90 ALLU Finland OY 89 API 21 BAUMA 63 C.A.T. Group 4 Challenger Services 36 CRC-Evans 6 Darby 52 DeFelsko 64 Delta Machinery 73 DENSO GmbH 47 EDI 60 Euro Pipeline Equipment 42 - 43 Gastech 2022 IBC Grupo Desarrollo Infraestructura S.A. de C.V. 93 Girard Industries 79 Herrenknecht AG 27 In-Line Flow Products 57 KMAX 85 Laurini 29 Lincoln Electric 81 Maats b.v. 67 MAX STREICHER 41 Midwestern 79 NACAP Pty Ltd 39 National Machinery Exchange 68 Pigs Unlimited International LLC 23 Pipeline & Gas Expo 2024 2 Pipeline Inspection Company 35 PipeLine Machinery International 19 Propipe 89 Qapqa 71 ROSEN IFC Scaip SpA bound insert Sicim S.p.A. 24 Spiecapag 30 Stark Solutions 15 Stats Group 13 Vacuworx OBC Vietz GmbH 55 voestalpine Böhler Welding 51 Winn & Coales International OFC, 9 Worldwide Machinery 58
References 1. for-local-disposal-and-recycling-pathways/www.decommissioning.org.au/our-studies/understanding-the-opportunity2. decommissioning-innovation-and-technology-roadmap/www.decommissioning.org.au/our-studies/development-ofdecommissioning-liability-australia/www.decommissioning.org.au/our-studies/offshore-oil-and-gaswww.decommissioning.org.au/ 5. planning-and-execution-learnings/www.decommissioning.org.au/our-studies/global-review-decommissioningproject-a-step-closer/www.santos.com/news/globally-significant-carbon-capture-and-storageHub#CarbonCaptureandStorageUpstream-operations/The-South-East-Australia-Carbon-Capture-www.exxonmobil.com.au/Energy-and-environment/Energy-resources/ carbon-capture-and-storage-to-clean-up-lng-industry/2-1-1181417www.upstreamonline.com/energy-transition/western-australia-looks-to-
7.
Host Region Host City Host Venue Organised byUnder the patronage of Supported by Co-Hosts Visitor registration is now open In a time of unprecedented change, join us at Gastech Milan 2022! As the global energy landscape undertakes a rapid transformation, being present at Gastech 2022 will be critical in securing the position of your business in our new energy future. Access the latest industry knowledge, technical expertise, products, solutions, and services. Register for your complimentary visitor pass register.gastechevent.com Scan the QR code

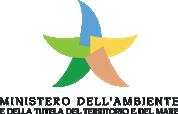
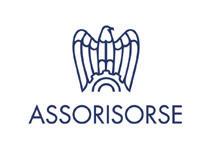
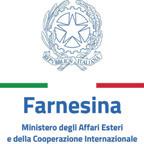
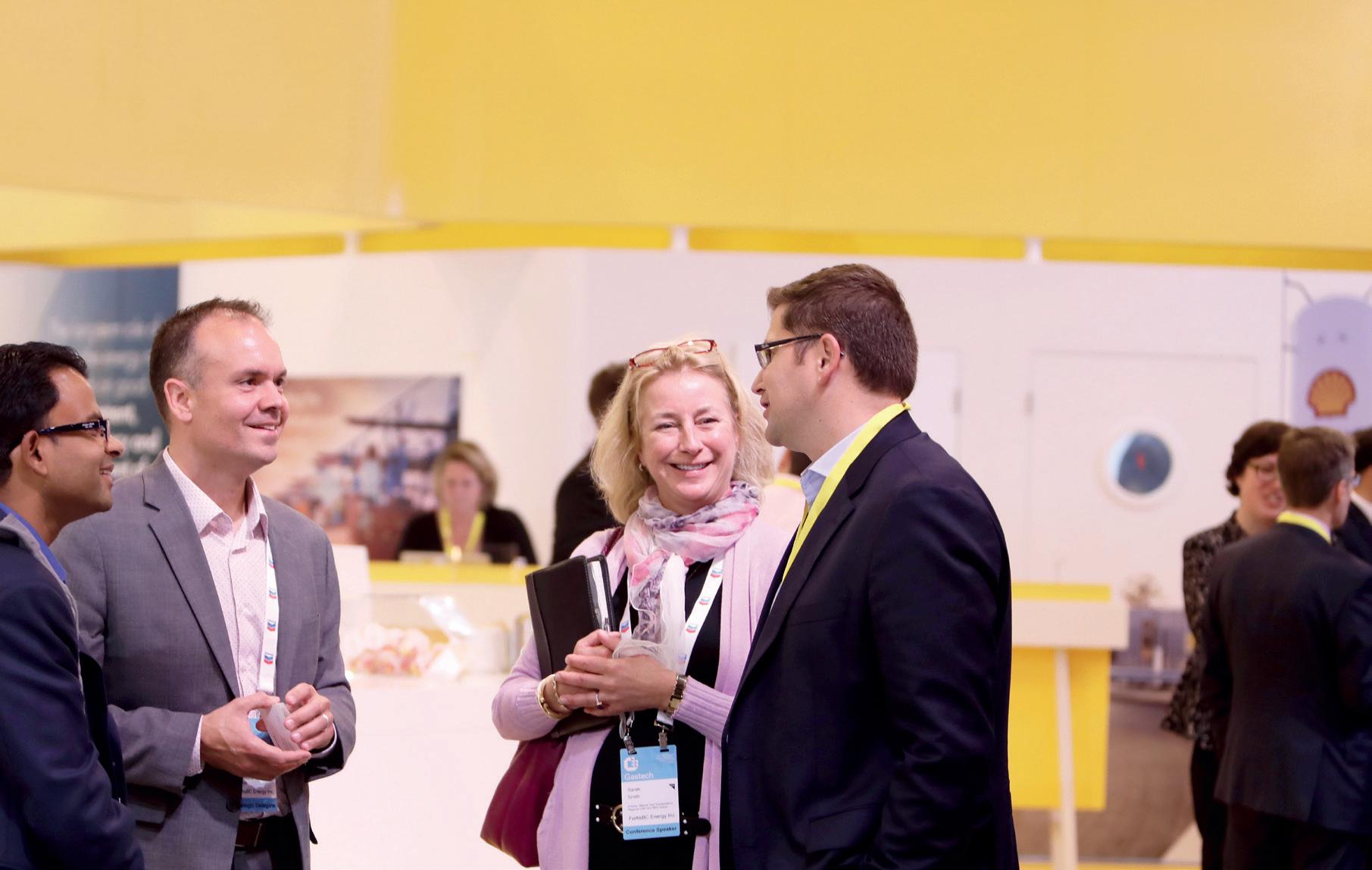
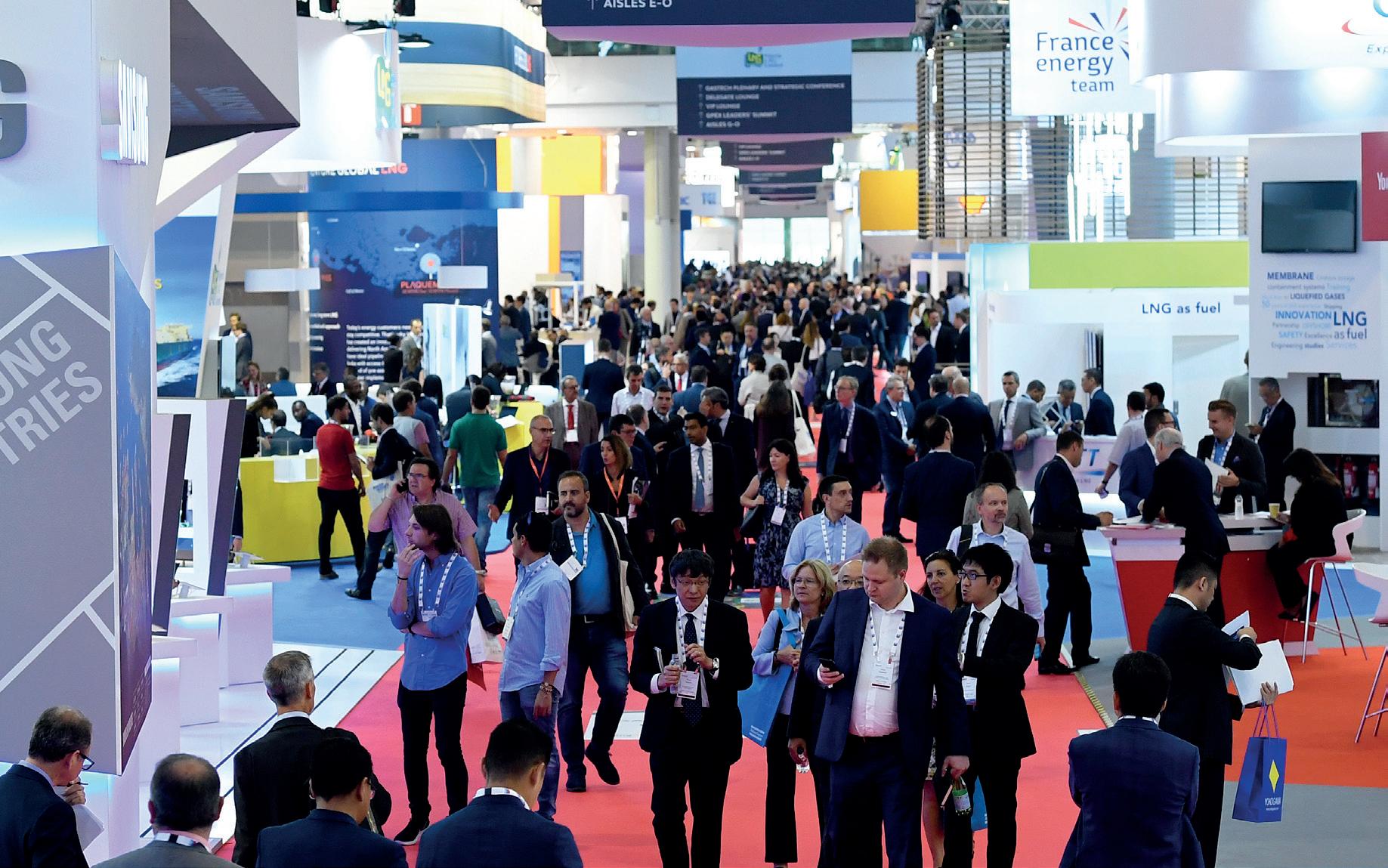
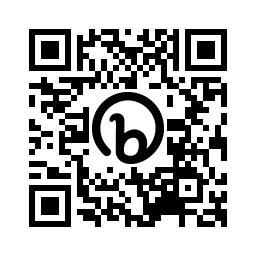
offering the best vacuum lifting systems
For over 20 years, has set the for in the In addition to on the also backed by experience no one else can
Vacuworx
copy.
market, Vacuworx
Creating safer, more efficient material handling solutions www.vacuworx.comworldwide.
standard
vacuum lifting
delivers unparalleled service and technical support,
field.
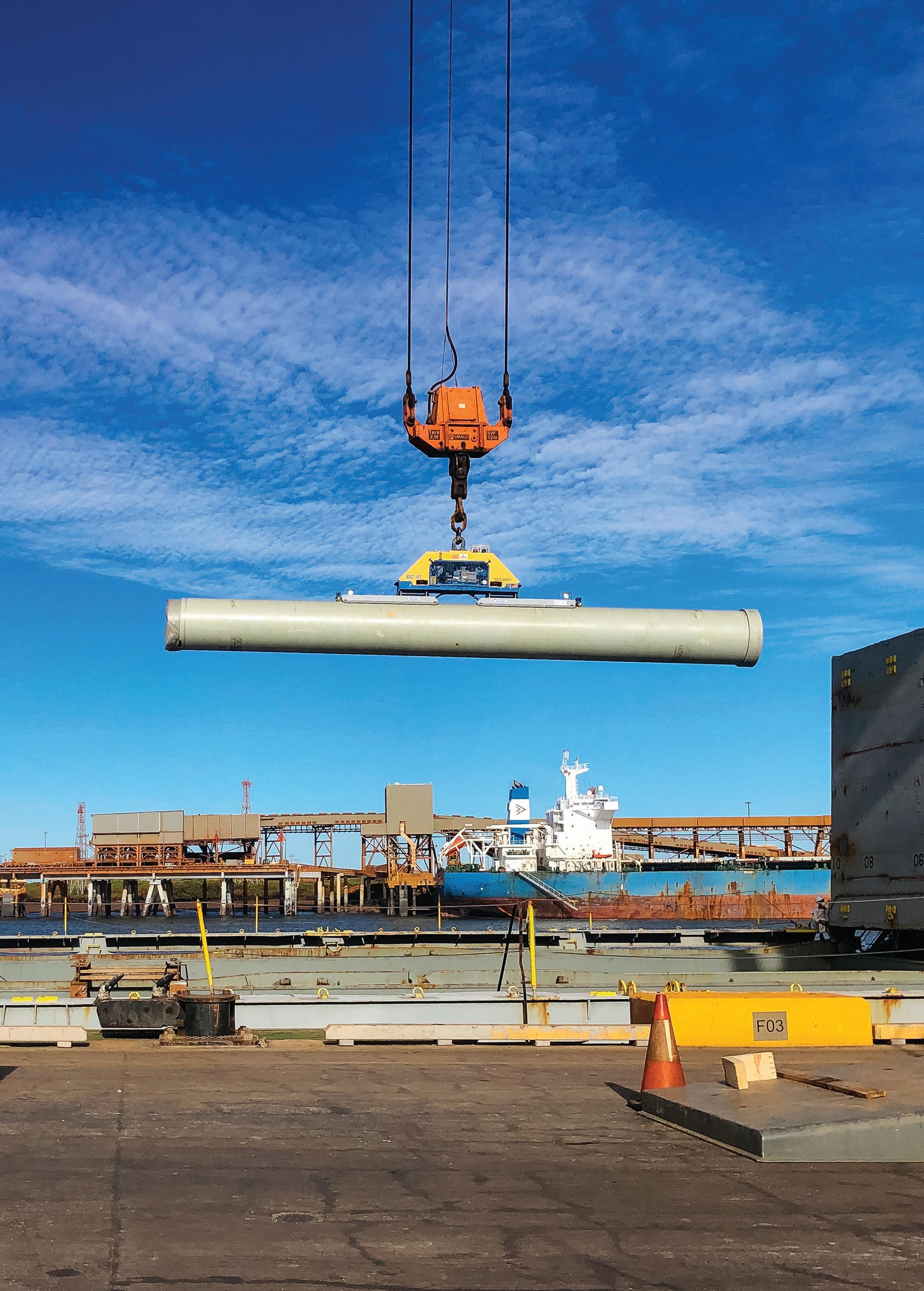