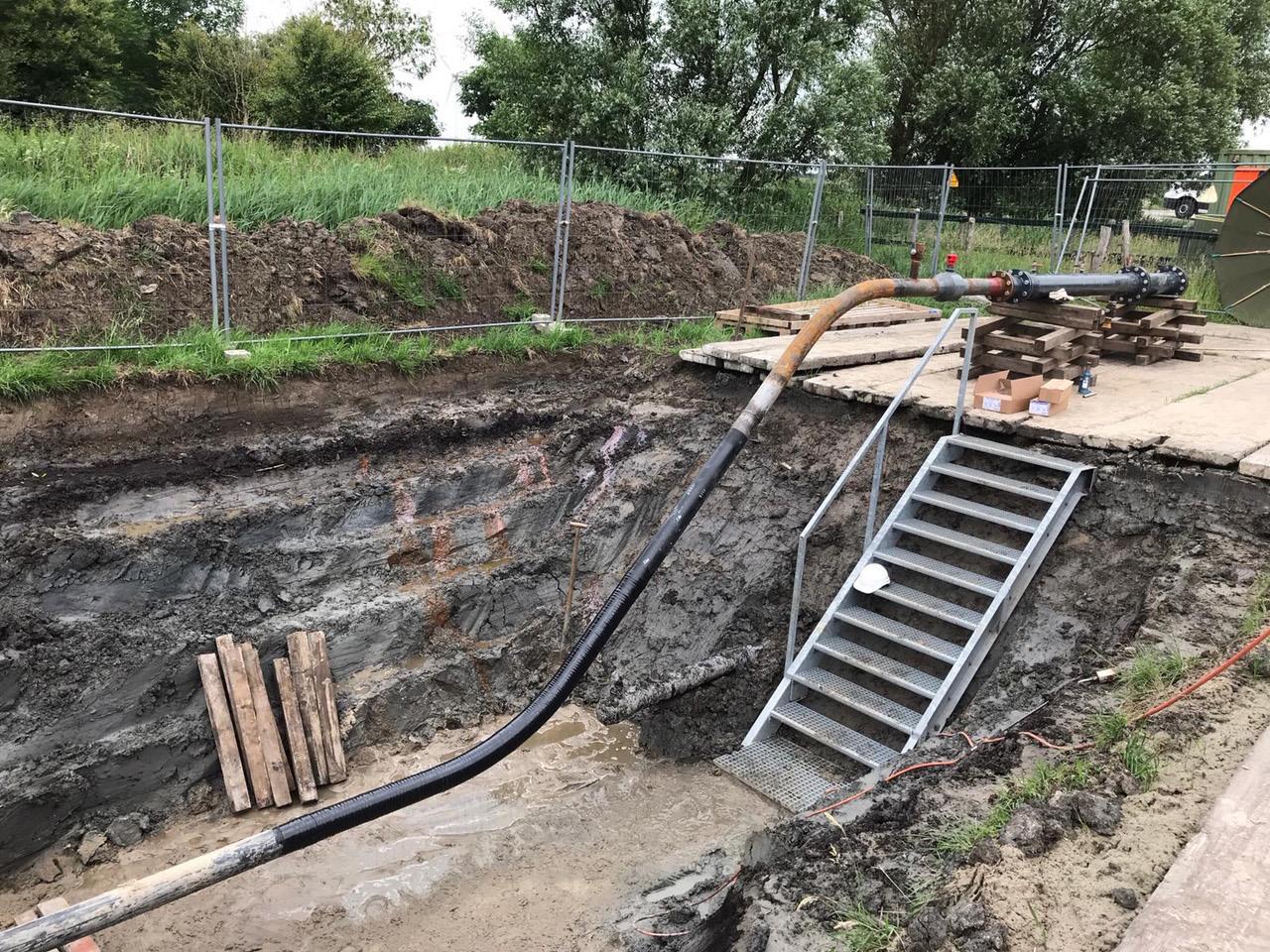
5 minute read
Sweat the small stuff
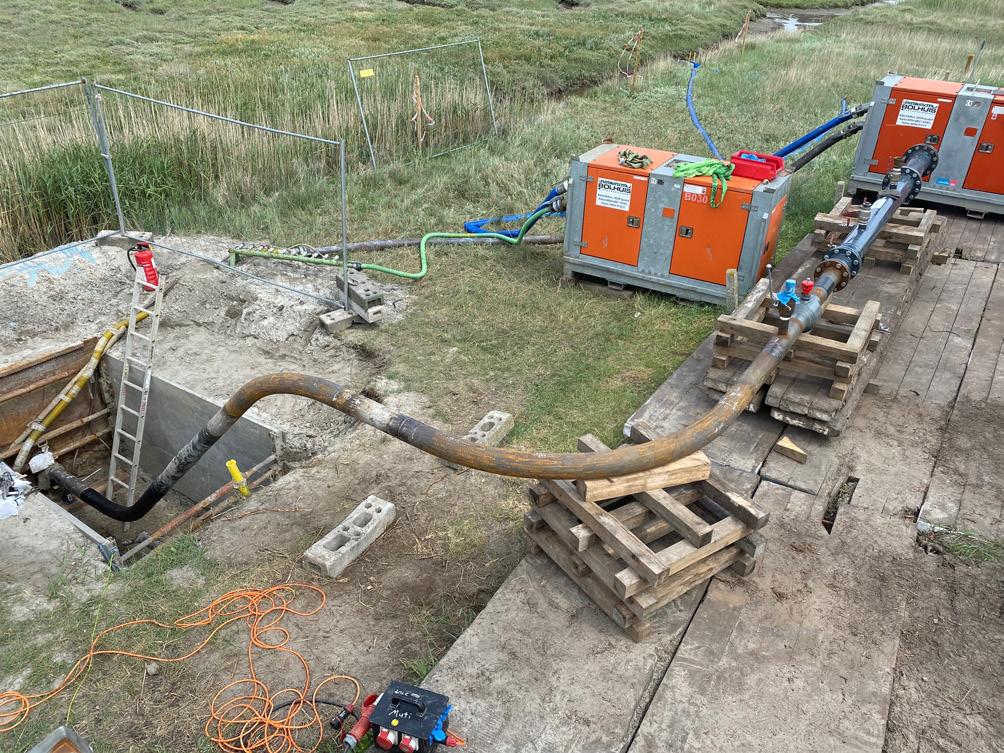
1000 m to increase accuracy of the XYZ survey data. Subsea markers were deployed by a local guide in sections where the line crosses tidal mudflats in the national park. At some locations, this was only possible by foot with the use of a hand cart, and at other positions a ship had to steer to the eventual marker location during high tide, wait for low tide and beach until subsea markers could be deployed. Several low tides were required before all markers were positioned. Each subsea marker position was staked using DGPS. The markers were deployed prior to project execution and collected after the last inspection tool run. The recorded data would then be
downloaded for use in XYZ analysis. Project execution In a first step, the pipeline system was depressurised and excavations where made to facilitate installation of the temporary launcher and receiver. Regulations Figure 4. Water samples from each of the break tanks, prior to laboratory analysis. within the national park required all excavations be done layer by layer to guarantee that after completion of the works, each layer of soil removed is reinstated correctly, minimising the impact on the ecosystem. Additionally, measures to prevent the protected bird population from breeding onsite were taken. After pumping 5 m3 of water, a BiDi tool was launched into the line by pumping a 5 m3 batch of fresh water and cleaning agent. A second BiDi tool was launched thereafter to contain the cleaning batch between the two inline tools. The batch was pumped through the line and received onshore. Flow velocity for this, and every subsequent run, was governed by the capacity of the filtration system at receive. All tools were received in good condition and close to no debris was recovered. After filtration, the water was stored in break tanks located onsite. Samples from the tanks were taken and brought to the laboratory for analysis. The water had to be disposed of separately as the recorded values were above the required threshold values for onsite disposal. All water ran during other tool runs was greenlighted by the laboratory and did not require special disposal. After the line was flooded and cleaned, a profile tool was run. Profile tools are flexible uni-directional tools equipped with a set of aluminium gauge plates arranged to simulate the hard diameter of the inline inspection tools. This tool is run to prove that the internal bore of the pipeline does not represent any restrictions that would prevent the subsequent inline tools from successfully navigating the pipeline. Upon receiving, all aluminium gauge plates were littered with indications believed to originate from excessive weld penetration. In addition, all aluminium plates were deformed on one side, hinting at a possible dent in the line. The propellant was stored onsite in Figure 5. Temporary launcher and receiver locations. break tanks, tested and disposed after being green-lighted by analysis. The next tool in line was the GEO/DMR tool. The GEO sensors map the geometry of the full circumference of the internal pipe wall, and allow for accurate detection and sizing of geometric anomalies such as minimum available diameter, ovalities and dents among other features. The results of the GEO/DMR tool run also proves whether the line can be traversed by the subsequent inspection tool. The tool was received in what appeared to be good condition and recorded a complete GEO data set. However, some secondary sensors were damaged and stopped recording. A number of geometric anomalies, such as dents, were identified as well as several significant excessive weld
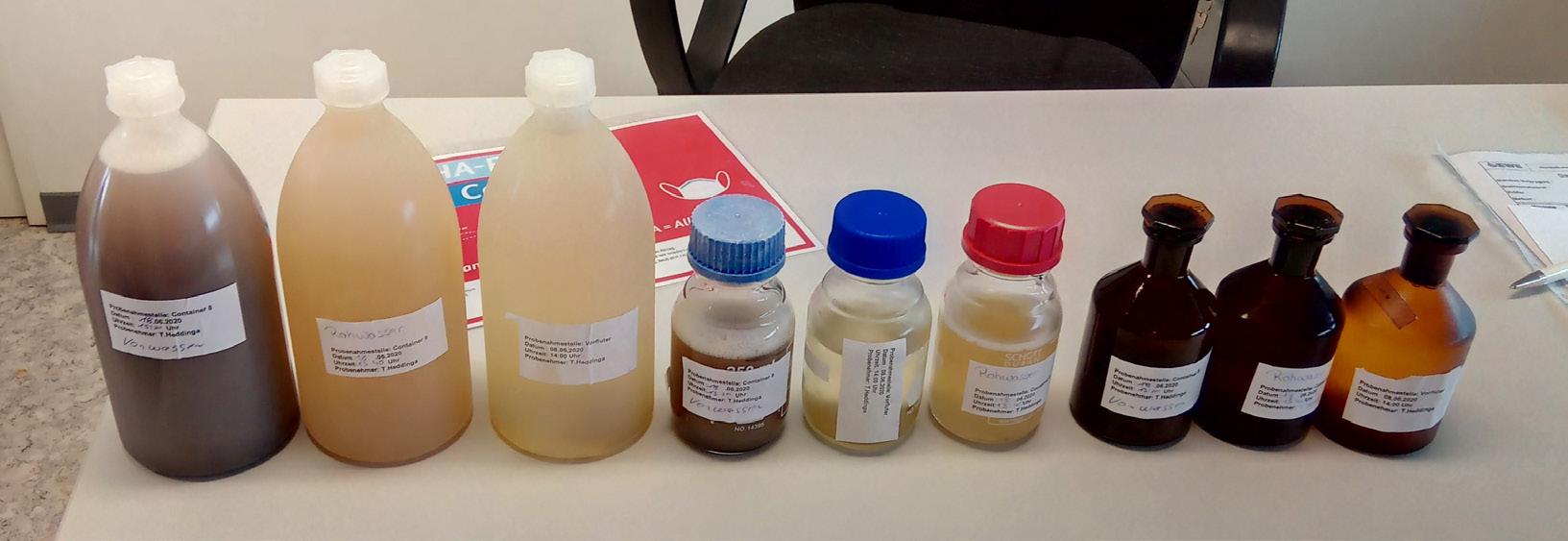
penetrations, which are believed to have caused the damage to the secondary DMR sensor array.
As the recorded internal diameter was above the required diameter for the UT/XYZ tool, the decision was taken to run the tool. The tool was received without any damage and a full set of data.
All locations within the line with reduced internal diameters, as indicated by the recorded GEO data, had been cross checked by use of the additional data gathered by the UT/XYZ tool run. The increased accuracy, as a result of the combined evaluation, revealed that the available internal diameter in several sections of the pipeline was insufficient for the planned final MFL/DMR inspection tool run.
Consideration was given to constructing a new MFL magnetiser module capable of negotiating the restriction. As a certain amount of magnetic power is required to fully magnetise the pipe wall and allow for results in line with the defect detection and sizing performance, the size of the module on the tool with the largest external diameter, the diameter of the magnetiser unit, could not be decreased further. Therefore, the decision was made to not run the MFL/DMR tool.
Dewatering was done with a BiDi tool propelled by compressed air from the island towards shore. Once received onshore, suitable compressors were mobilised and the pipeline was dried by using nitrogen to a dew point of -20°C in the reverse direction.
After completion of all onsite work, both the launcher location on Borkum and the receiver location were reinstated in line with regulations.
Conclusion Site reports were issued after every intelligent inline tool run, confirming the success of each respective run. A preliminary report was issued after 10 days, indicating major geometric anomalies, metal loss indications, and other noteworthy findings. The full final report was issued after 40 days. All reporting was conducted in line with POF regulations.
EWE Netz GmbH decided to conduct an extensive investigation of reported features based on the information provided in the inspection report. Given that some of the features were located in close proximity to tideways, sometimes even underwater, this was no easy task.
Note The authors would like to express their gratitude to EWE Netz GmbH for their trust, the open communication and cooperation throughout the course of this project. This article is based on a paper given at ptc 2022.
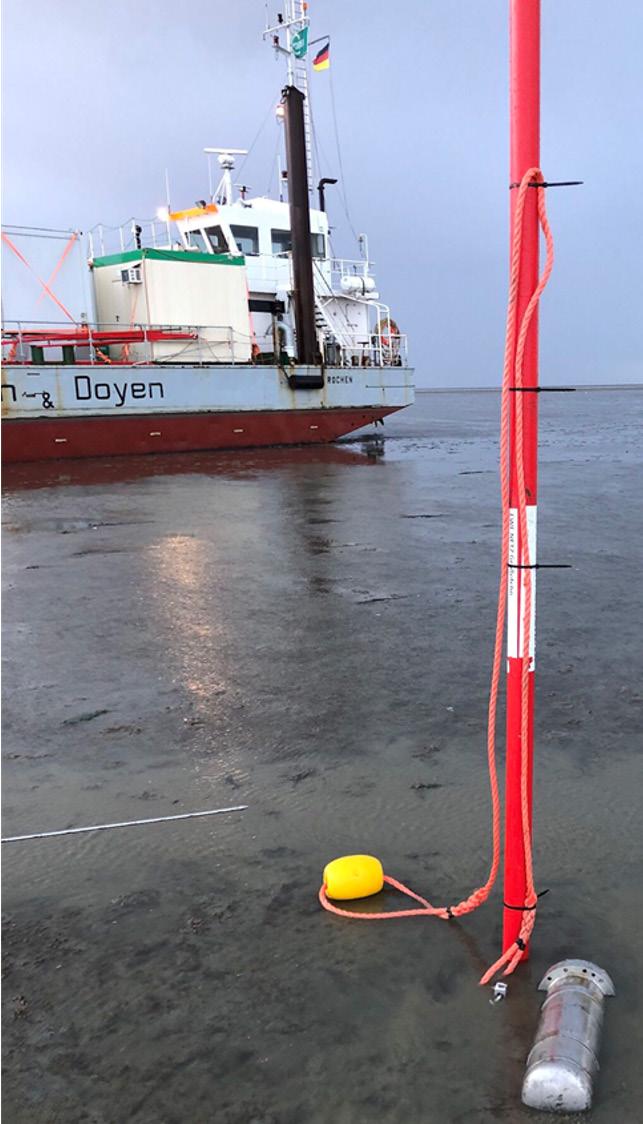
Figure 6. Deployment of subsea markers by boat.
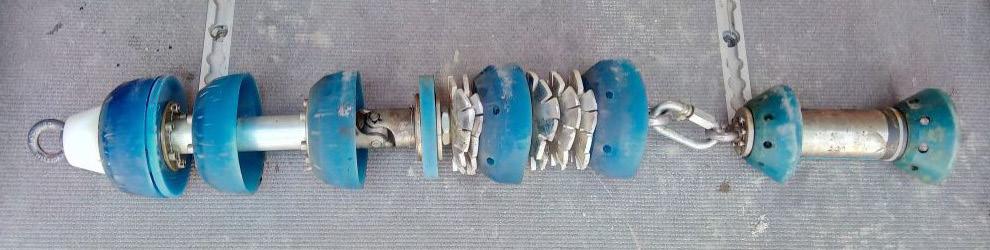
Figure 7. Profile tool after receive.