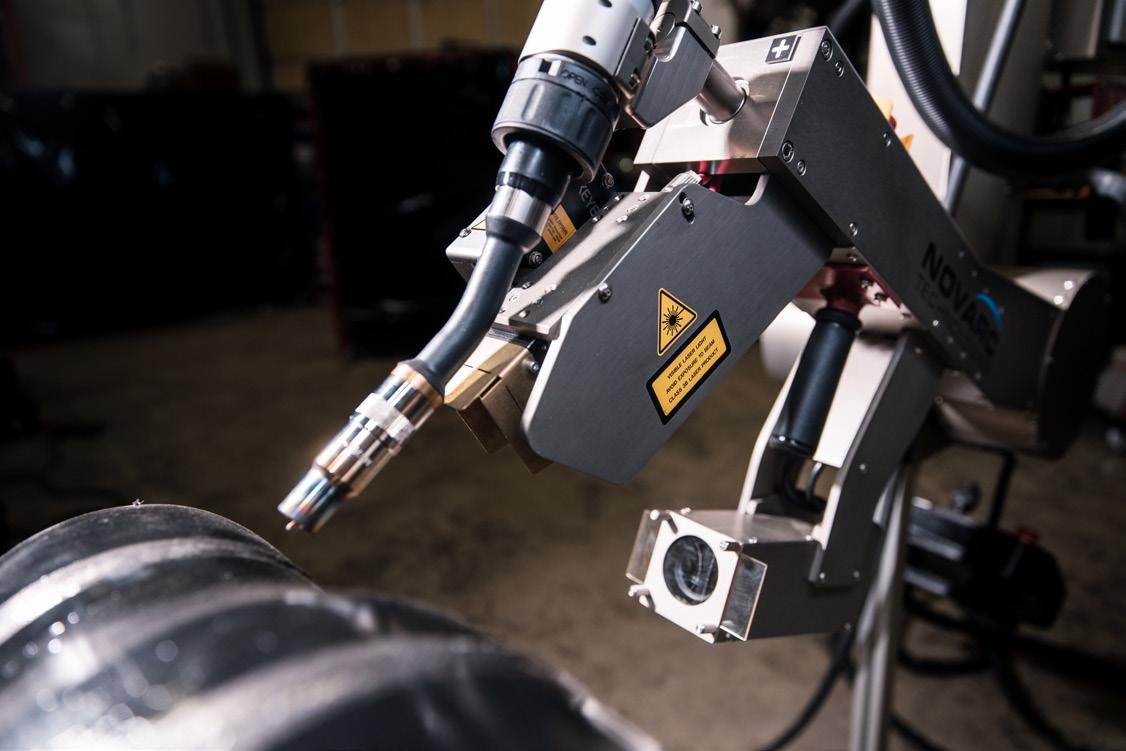
5 minute read
Delivering high productivity
Figure 3. NovEye ties into the control system of the robot, and can control the weld puddle in the same way a human welder would. This is key for many industries as they have imminent market demands for smart welding systems.
intellectual level of our local system to dive deep into massive data collected from around the globe and develop actionable insights.
Real-time reporting to improve welding operations Novarc recently introduced a product called NovSync™ to provide visibility of the welds of the collaborative robot, specifically usage and production statistics and metrics, that can be customised and scheduled. In this way, production efficiency can be increased as users analyse the welds. These advanced analytics can be employed to track production and machine trends over time. NovSync provides centralised and secure access to weld videos, daily reports and data logs. Fabrication shops using NovSync can easily receive information, in real-time, to improve welding operations and become more competitive.
Moving to a dynamic process of innovation and improvement However, pipe welding is more than a technical or commercial debate for automation.
Pipe welding ‘smartisation’ is a dynamic process of innovation and continuous improvement in response to the market’s technical, commercial, environmental, cultural, and social demands.
Novarc’s commitment to welding automation – through AI and tech developments – is meeting the increasing demand for greater productivity and efficiency. However, these developments have the larger impact of attracting more individuals into the welding industry. With the implementation of sophisticated machine learning systems, the job of welding will become cleaner and less dangerous than ever before. The high-tech component will be of more interest to younger generations that might not be inclined to do the dangerous and tiring work that welding jobs traditionally required. Welding automation is also creating opportunities for technicians, developers and engineers to join the industry and continue to improve the way AI is utilised in manufacturing operations around the world.
On a critical trend, welding is a core process in most GHG-intensive industries including oil and gas, and mining. Many countries have committed billions of dollars to reduce GHG emissions as part of Paris agreement targets. However, there are a number of sustainability hurdles that need to be overcome within the welding industry: ) Welding fumes emit CO2, CO, and ozone, the main driver of global warming and climate change.
) Welding releases metal pollutants into the air, such as vapourised heavy metals and oxides from the molten puddle.
) Welding processes take a large amount of energy during every weld, imposing a significant burden on our energy system.
) Welding metal waste control is critical for minimising overexploitation of natural resources.
Using an at-source fume extraction torch with Novarc’s AI-driven welding control technology delivers the lowest airborne, energy consumption, and metal waste for the fabrication phase.
Manual welding has no control over arc time and is significantly slower. Other mechanised welding machines do not have the flexibility of Novarc’s robotic system for lowering the arc-time needed for completing the joining. NovEye is a leading product in the market for intelligent vision control of weld arc and puddle, and no other technology is capable of delivering better precision. These smart eyes enable precise control of the final weld shape to avoid wasting metal during welding, and eliminate the requirement of extra work for grinding the excessive weld bead.
Novarc’s automation system also reduces human exposure to all welding hazards: dangerous welding fumes such as manganese, hexavalent and chromium. This is achieved by an at-source fume extraction on the torch, and having the welding operator work several meters away from the welding arc. Novarc’s welding technology allows the operators to work remotely from the arc, and with the use of proper ventilation, most fumes can be eliminated. The R&D team of Novarc is working diligently to extend the on-welding intelligence of NoveEye to mitigate the requirement for post-weld NDT by tracking the defects at the source.
On a cultural level, the next wave of Industry 4.0 will move AI and cobots beyond human capabilities and make a tremendous difference across the spectrum of commercial industries. Advancements in machine learning algorithms, real-time computational power, and big data are currently enabling technologies that are literally transforming industries and cultural norms across the globe.
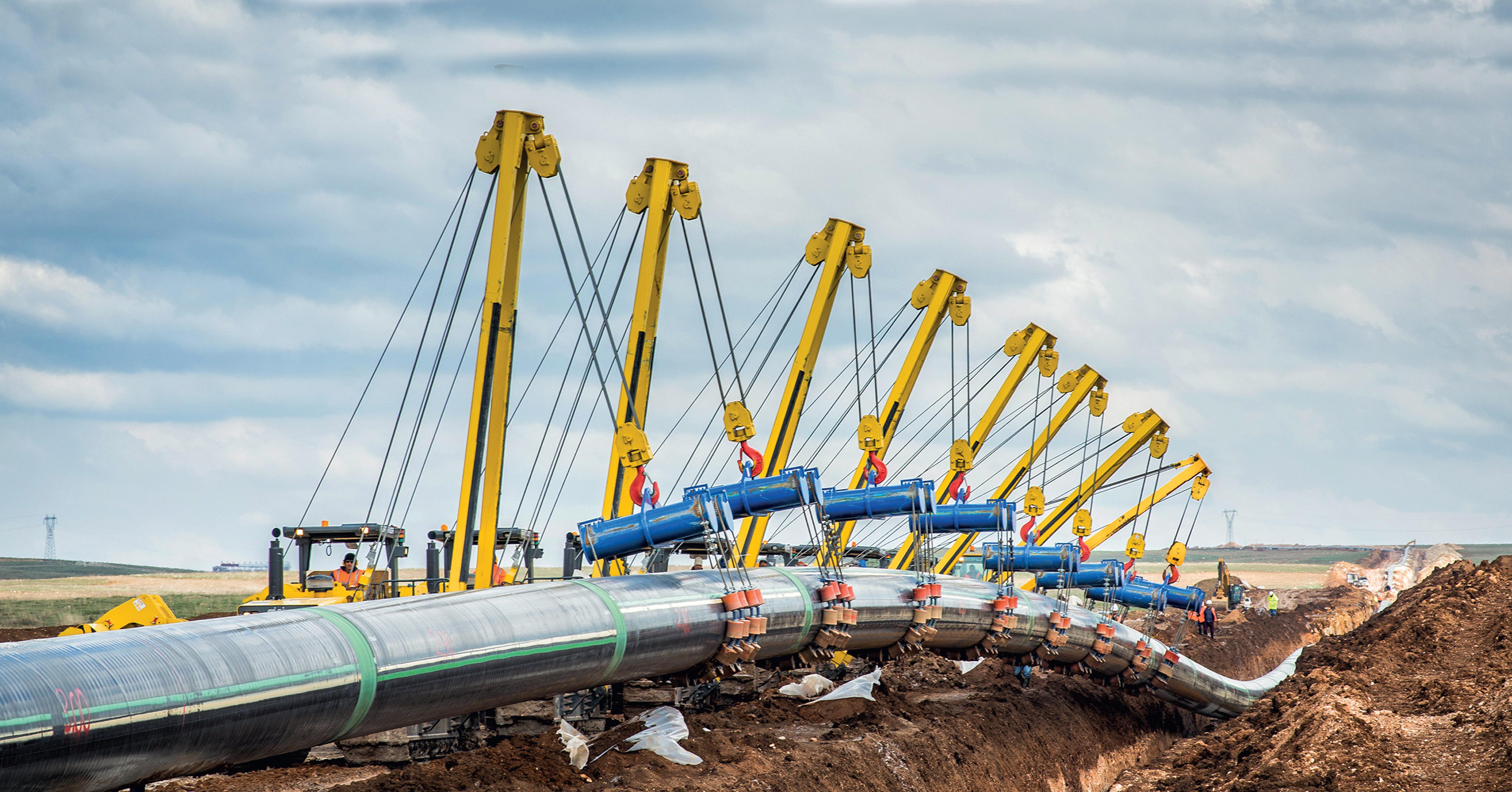
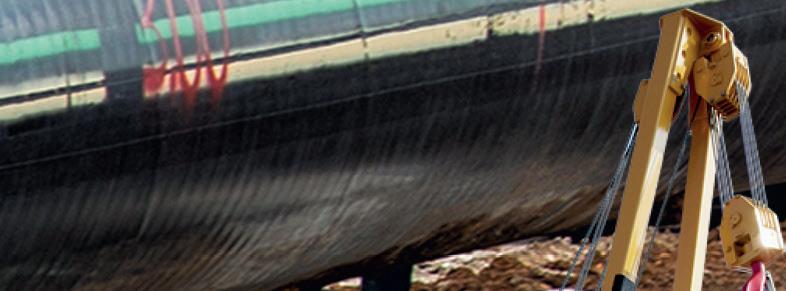
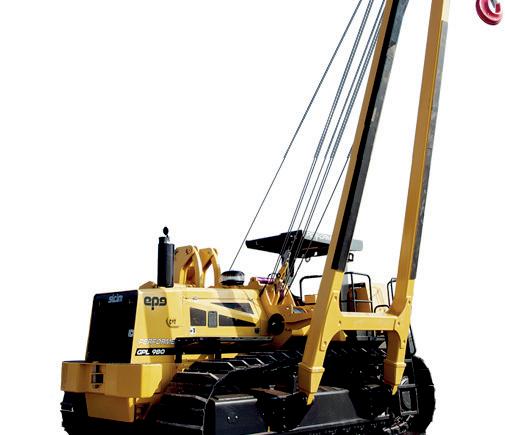
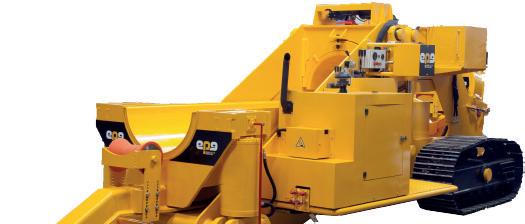
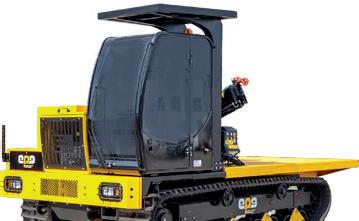
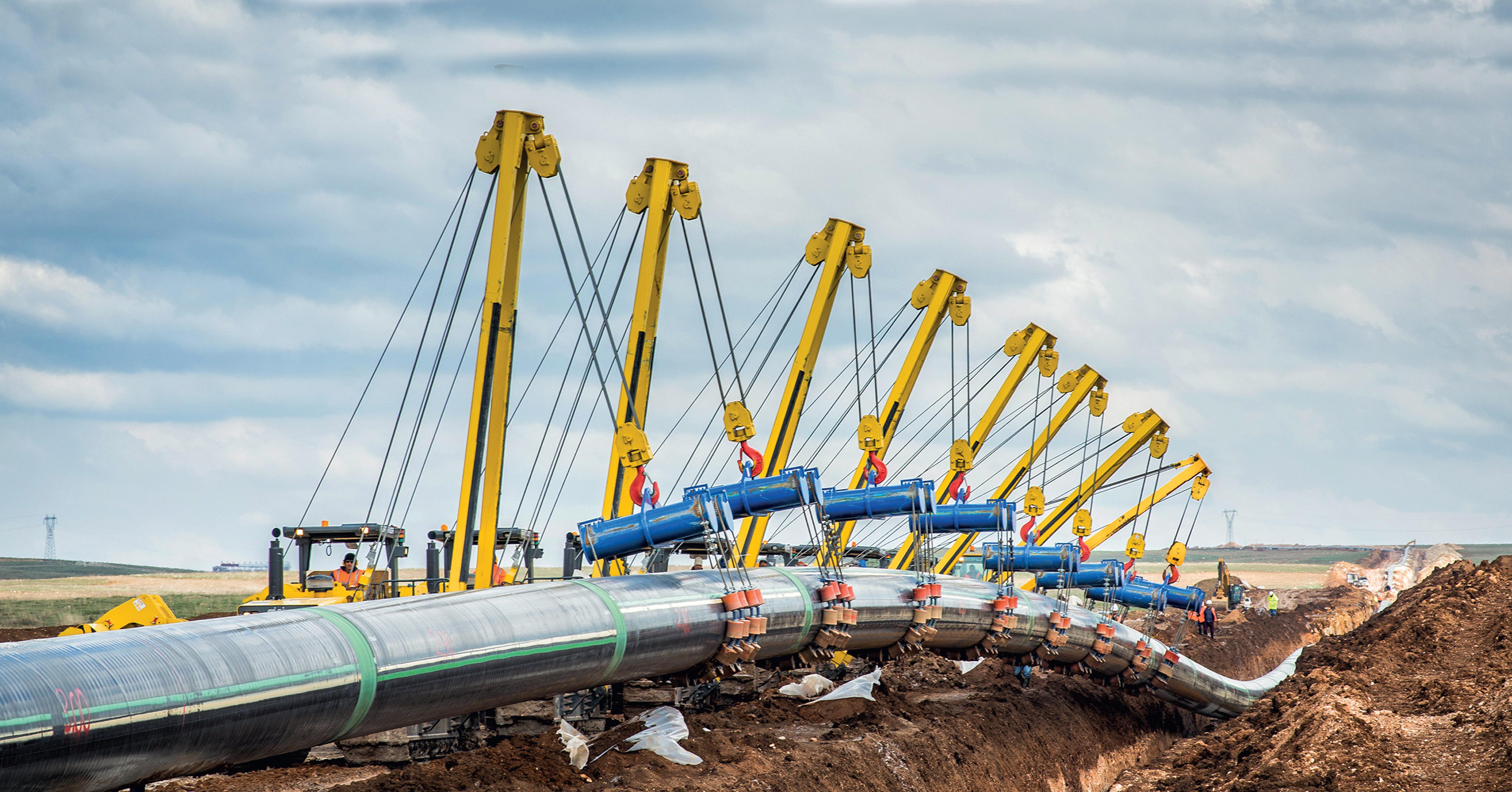
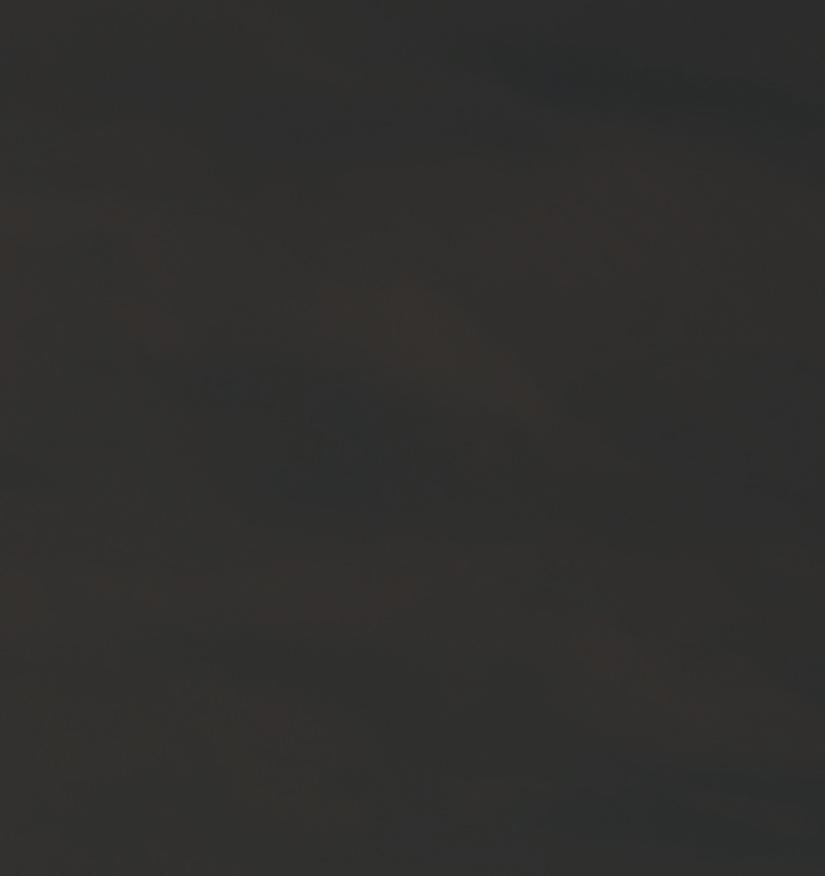
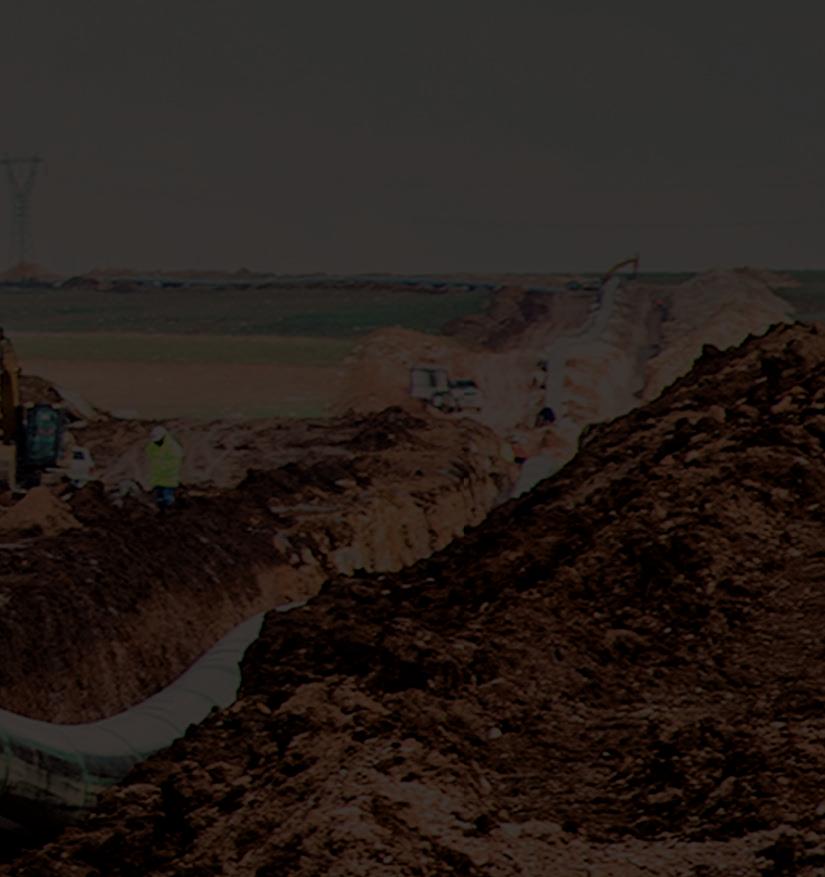
Francesco Ciccomascolo, Full Welding Solutions Manager, voestalpine Böhler Welding, Austria, introduces a new solution for orbital pipeline welding with flux cored wires.
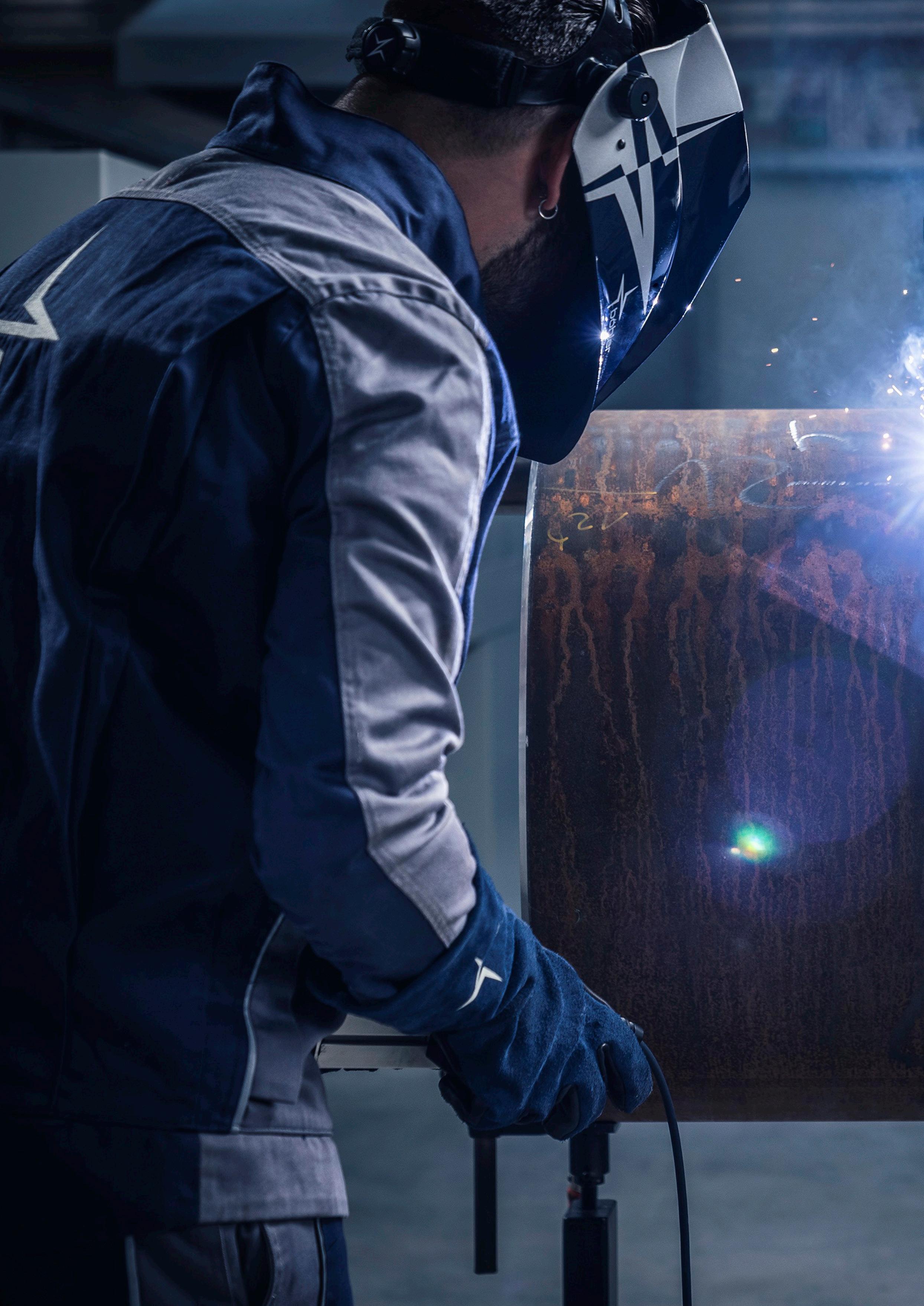
In the pipeline industry, perfect pipeline girth welds with consistent mechanical properties, paired with high productivity, and low repair rates are key priorities. Böhler Welding’s latest GMAW/FCAW orbital welding solutions, which guarantee repeatable high quality welds with reduced downtime, can bring these benefits to costsensitive pipeline contractors. The new solution minimise repair rates, thanks to the fine-tuning of the high quality diamondspark flux cored wires, the movements and wire feeding precision offered by Böhler Welding’s pipeRunner orbital welding system, and the stable electric arc performance of the TERRA 400 PRM welding power source. Böhler Welding’s full welding solution is, for example, ideal for pipeline contractors that want to introduce mechanisation in their welding process within a limited budget, avoiding sophisticated operations such as narrow gap preparations and fully automated root pass, for which specific expertise and equipment, such as site bevelling machines and internal pipe clamping systems, are necessary. Additionally, each weld seam is executed using a single set of parameters from 6:00 o’clock to 12:00 o’clock, thanks to the performance of the system in combination with the Böhler Welding flux cored wires. Hence, key benefits of the solution include easy installation and user friendly operation.
Time comparison with a fully SMAW procedure At the start of the solution is the use of the TERRA 400 PRM power source for manually welding the root and hot pass. This can be done with SMAW electrodes, or by