Spring 2025
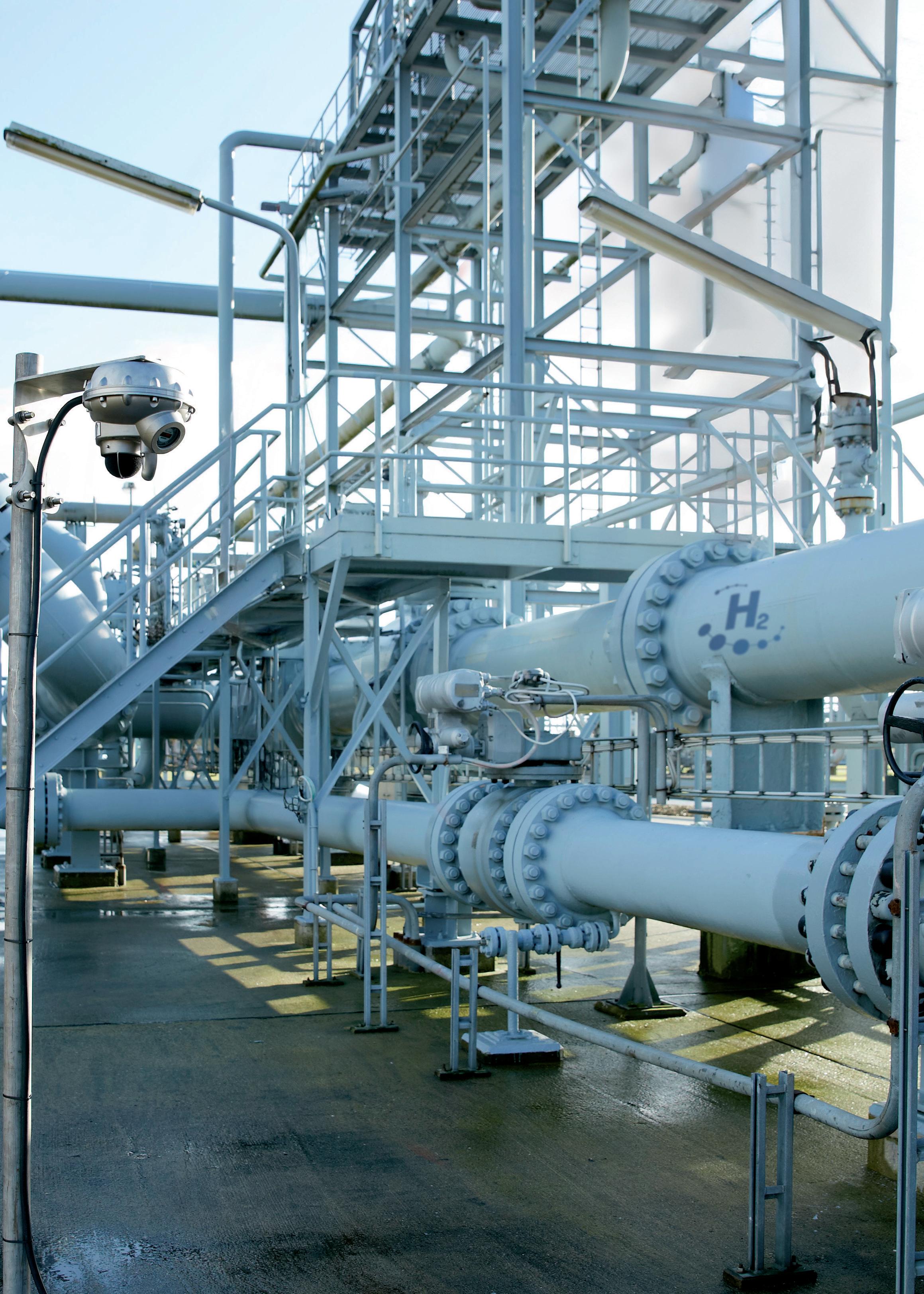
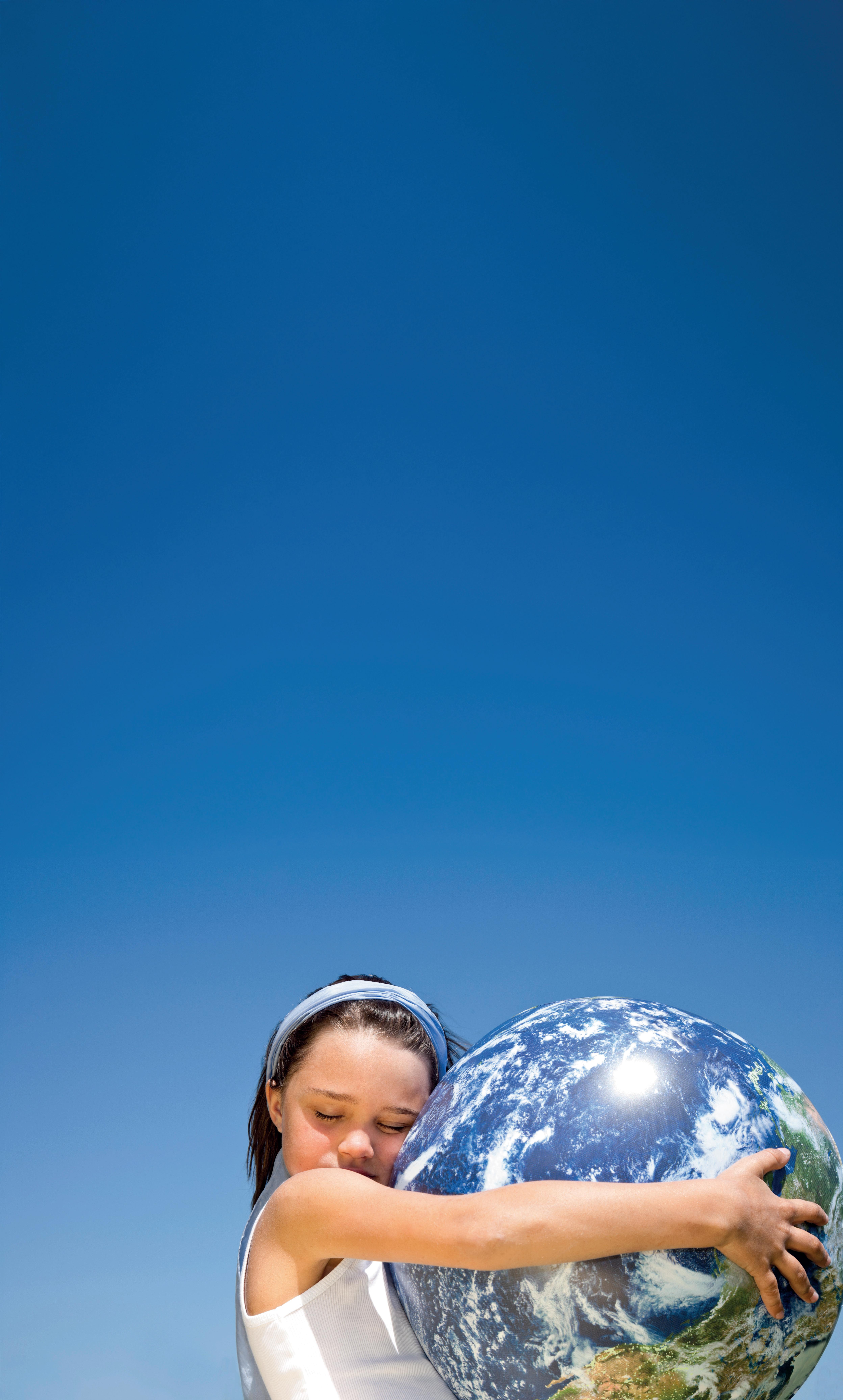
Our goal is to lead the transition towards a net zero economy.
Our FLEXIBLUE® low carbon technologies o er advanced solutions in hydrogen and ammonia, reducing carbon emissions up to 99% while optimizing e ciency.
We are improving sustainable solutions that ensure future generations can meet their needs while respecting the planet, fully believing in research and innovation, integrating technologies, engineering, contracting and construction solutions that reconcile industrial progress with environmental responsibility.
Trust Casale to provide the high-performance, reliable solutions needed to meet your decarbonization goals.
Join us in pioneering a cleaner, more sustainable future.
Comment 04 Asia and the global hydrogen economy
Mark Elliot, Xodus, examines Asia’s role in building and powering the global hydrogen economy.
07 The hydrogen horizon
Dr Phil Ingram, Johnson Matthey, discusses the promise clean hydrogen production holds in the transition towards sustainable energy and the technology supporting the road to a viable, low-carbon hydrogen economy.
12 Hydrogen for industry
Manish Patel, Air Products, explains how renewable hydrogen’s potential to decarbonise an industry presents both opportunities and challenges ahead. 17 Laying the tracks for hydrogen
Afzal Hussain and Corin Taylor, DNV, outline the importance of hydrogen towards perpetuating energy security.
21 Looking beyond the core
Dr Cornelia Neumann, IMI, identifies how Germany’s Hydrogen Core Network is laudable but not the only tool for hydrogen uptake.
25 Fuel cells for data centres
Tim Cortes, Plug Power, analyses how harnessing hydrogen fuel cells can power the future of data centres.
29 Hydrogen on wheels
Patrick Breuer, Hexagon Purus, reveals the role of Type 4 cylinders in fuelling transit buses.
33 Desalination for hydrogen production
Dan Freeman, Kurita Europe GmbH, and Fiona Finlayson, Kurita Water Industries, grant insight into the challenges of offshore seawater desalination for use in hydrogen production.
39 Winning with wastewater
Dr Robert Lutze, Dr Tobias Blach, and Alexander Ghazinuri, EnviroChemie GmbH, explore the use of industrial wastewater as an alternative source for bridging the gap between limited water availability and the potential growth of green hydrogen production.
45 Prioritising detection and protection
Sarah Rajasekera, MSA Safety, explores the best practices to address associated risks in gas leak detection for hydrogen operations.
51 Safe, secure and ready to fuel the future
Gabriele Civati, HIMA Group, Germany, presents functional safety solutions for hydrogen use across various applications.
In a growing hydrogen-powered world, managing gas leak risks is essential. Hydrogen detection systems, such as MSA Safety’s Observer i® Ultrasonic Gas Leak Detector, utilise diverse technologies designed to detect potential leaks. When incorporated into a comprehensive safety strategy, these systems can support efforts to minimise the risk of equipment and property damage, personal injury, and other hazards.
Callum O'Reilly Senior Editor
Managing Editor James Little james.little@palladianpublications.com
Senior Editor Callum O'Reilly callum.oreilly@palladianpublications.com
Assistant Editor Oliver Kleinschmidt oliver.kleinschmidt@palladianpublications.com
Editorial Assistant Emilie Grant emilie.grant@palladianpublications.com
Editorial Assistant Ellie Brosnan ellie.brosnan@palladianpublications.com
Sales Director Rod Hardy rod.hardy@palladianpublications.com
Sales Manager Chris Atkin chris.atkin@palladianpublications.com
Sales Executive Ella Hopwood ella.hopwood@palladianpublications.com
Production Manager Kyla Waller kyla.waller@palladianpublications.com
Head of Events Louise Cameron louise.cameron@palladianpublications.com
Digital Events Coordinator Merili Jurivete merili.jurivete@palladianpublications.com
Digital Content Coordinator Kristian Ilasko kristian.ilasko@palladianpublications.com
Digital Administrator Nicole Harman-Smith nicole.harman-smith@palladianpublications.com
Junior Video Assistant Amélie Meury-Cashman amelie.meury-cashman@palladianpublications.com
Events Coordinator Chloe Lelliott chloe.lelliott@palladianpublications.com
Admin Manager Laura White laura.white@palladianpublications.com
Water, as we all know, is the most precious of resources here on planet Earth. On the most fundamental level, it sustains all life. But it also serves a myriad of crucial purposes that make it indispensable to human civilisation, including cooking, sanitation, cleaning, irrigation of crops, aquaculture, transportation… the list goes on. And, of course, it is an essential resource for the industrial and energy sectors.
This year, World Water Day took place on 22 March, and its key theme was ‘Glacier Preservation’. The theme is timely, with a recent study published in the journal Nature noting that the world’s glaciers are melting faster than ever recorded.1 In the most comprehensive scientific analysis carried out to date, it was discovered that over the past decade or so, glacier losses were more than a third higher than during the period 2000 – 2011.
Glacier preservation is seen as a top priority as the world works to mitigate and adapt to climate change. And the reduction of greenhouse gas emissions is essential to decelerate glacial retreat.
Step forward clean energy technologies. Blue and green hydrogen are widely regarded as having a key role to play in decarbonising our economy and achieving net zero emissions. However, there is, of course, no perfect solution to the challenge of climate change, and it is important to acknowledge that hydrogen does have an indirect influence on atmospheric warming. Research has suggested that the global warming potential (GWP) of hydrogen over a 100-year time horizon is 11 ± 5, which is significantly more than previous estimates.2 According to DNV, the climate benefits of hydrogen are still clear, since co-emitted combustion species (such as carbon monoxide, methane, and VOCs) are also reduced. However, in light of hydrogen’s indirect GWP, efforts should also be made to reduce leakage during production, storage, transportation, and use.3
And this brings us back to the issue of water. While hydrogen has the potential to help reduce the speed of glacial melting by lowering greenhouse gas emissions into the atmosphere, all hydrogen production technologies require significant quantities of water for production and cooling. A 2023 study by the International Renewable Energy Agency (IRENA) and Bluerisk attempted to shed some light on the extent to which water is required.4 Its findings suggest that green hydrogen is the most water efficient of all clean hydrogen types. In terms of water use as a cooling medium, blue hydrogen production is the most intensive, due to the significant water requirements of CCUS systems for heat transfer. Amongst its recommendations, the report suggests that green hydrogen projects should be prioritised for future development, in order to reduce exposure to future water-shortage-related risks. Other recommendations include increased investment and research to reduce the consumption of freshwater for cooling, and incentivising the use of seawater for hydrogen production and cooling in freshwater-stressed coastal areas.
In this issue of Global Hydrogen Review, Kurita considers the challenges of offshore seawater desalination for use in hydrogen production, and explains why it is a clear and viable option for green hydrogen projects wishing to take advantage of readily available wind energy and practically limitless water supply (p. 33). Meanwhile, EnviroChemie GmbH explore the use of industrial wastewater as an alternative source for bridging the gap between limited water availability and potential growth of green hydrogen production (p. 39).
1. ‘Community estimate of global glacier mass changes from 2000 to 2023’, Nature, (19 February 2025).
Editorial/advertisement offices: Palladian Publications 15 South Street, Farnham, Surrey
Tel:
(0) 1252 718 999 www.globalhydrogenreview.com
2. WARWICK, N., GRIFFITHS, P., KEEBLE, J., ARCHIBALD, A., PYLE, J., and SHINE, K., ‘Atmospheric implications of increased hydrogen use’, (April 2022).
3. MAPLE, M., ‘Is hydrogen a greenhouse gas?’, DNV, (5 November 2023).
4. ‘Water for hydrogen production’, IRENA and Bluerisk, (December 2023).
Mark Elliot, Xodus, examines Asia’s role in building and powering the global hydrogen economy.
As the world’s largest producer and consumer of hydrogen, Asia has a pivotal part to play in progressing this crucial pillar of the energy transition. China – the single largest consumer and producer of hydrogen –leads the way in this regard, but a number of other countries in the region have national hydrogen strategies in place, while several others are in the process of formulating theirs.
Much like in Europe, North America, and Australasia, low carbon hydrogen has been charged with shouldering the responsibility for decarbonising Asia’s hard-to-abate sectors, such as aviation, shipping, and heavy industry.
But as with the rest of the world, a very small proportion of the hydrogen currently consumed in Asia is low carbon. The lion’s share of the hydrogen produced and used in the region is still ‘grey’ and produced from fossil fuels, rather than ‘green’.
A major obstacle to this switch is the high cost of green hydrogen, being around three to six times more expensive than grey. Macroeconomic factors in 2024 served to test the economics of
green hydrogen projects further and, as such, only 12% of planned green hydrogen production by 2030 has secured end demand.¹
But as the International Energy Agency (IEA) notes in its ‘Global Hydrogen Review 2023’ paper, “Asia could potentially become one of the biggest importers of low-emissions hydrogen and hydrogen-based fuels”.
Developments in the region, particularly in Japan and South Korea, have been pivotal in advancing the nascent low carbon hydrogen industry, with long-term implications for the future on a global scale.
Both of these countries, united by their heavy reliance on energy imports, have recently introduced substantial commercial assistance programmes for hydrogen production and exports.
These programmes aim to stimulate the production and export of hydrogen, helping these nations to secure a stable and sustainable energy future.
Japan, for instance, has rolled out a funding scheme with incredibly attractive subsidy terms. Current initiatives in other countries and areas tend to have a maximum subsidy term of 10 years, which created financial uncertainty for developers and investors, as it left a substantial risk gap for the remaining 15 years of a typical 25-year project lifecycle.
In contrast, Japan’s new initiative offers 15-year subsidies with an optional five year extension, ensuring better financial coverage and reducing investment risk. This extended coverage is particularly promising for export markets, as it addresses a critical barrier to scaling up hydrogen production.
Interestingly, both Japan and South Korea have taken a more flexible approach to the colour of hydrogen than countries in Europe, which have, by and large, gone all-in on green hydrogen. Both nations are open to blue hydrogen – produced from natural gas with carbon capture – a reflection of their pressing need to decarbonise rapidly while relying on external sources for energy. As such, Japan and South Korea have set a target for
imported hydrogen (including ammonia) of 12 and 5.3 million tpy by 2040, respectively; a substantial target given the short timeframe, one that will undoubtedly pique the interest of hydrogen producing nations around the world.
Looking at the Asia-Pacific region more broadly, Australia has already established itself as one of the world’s major hydrogen players. The Australian government has announced significant funding initiatives, including a production tax credit and the Hydrogen Head Start programme, which have freed up nearly AUS$6.7 billion and AUS$3.5 billion worth of support to hydrogen producers, respectively.
These initiatives aim to position Australia as a major hydrogen exporter, not only to the likes of Japan and South Korea, but also to Europe. There has been a shift in expectations among Australian producers though, with a focus on scaling down overly ambitious projects in favour of smaller, more practical
development for domestic use cases, with a view to getting the industry moving ahead of a broader expansion.
Currently, Australia’s largest operating electrolyser has a capacity of just 1.25 MW, highlighting the gap between existing infrastructure and the scale required for large scale exports. BP is now talking about the first phases of production at project Geri –its large scale integrated renewables and green hydrogen initiative – rather than its endpoint. Companies are recognising the need to walk before they can run.
Domestic use cases include applications in transportation, industrial processes, and blending hydrogen with natural gas for heating. While blending is less commercially attractive due to Australia’s low natural gas prices, it offers a manageable starting point for industry growth and infrastructure development. Projects in South Australia, for example, are leveraging natural gas networks to blend hydrogen and reduce carbon emissions; these initiatives provide valuable learning opportunities and help build the infrastructure and expertise needed for future scaling.
Globally, political uncertainty in the US could create challenges for the industry in North America. This could open the door for other hydrogen-exporting regions, such as South America, the Middle East, and Australia, to step up and fill potential gaps in the global market.
For nations like Australia, which have a small domestic market but aim to become significant exporters of hydrogen, assessing macro-level supply chain readiness at an early stage is vital, and Xodus has undertaken a number of projects focused on fostering domestic capabilities.
If we draw a parallel to the Australian LNG industry, which successfully established a robust export market over the past two decades, it is clear that such an achievement is possible.
However, as green hydrogen in particular is a manufactured molecule, the pool of competition increases to countries with favourable renewable resource but without an established natural resources sector. To capture the first mover advantage, countries like Australia will need to establish domestic capacity to scale up the industry.
This challenge is compounded by global decarbonisation efforts, which are creating competition for resources and infrastructure. For countries like Australia, developing their own domestic capabilities will be critical as they can no longer rely on constrained supply chains in Asia or Europe.
A recent report, commissioned by the British Government and delivered by Xodus, highlighted this very point, emphasising the need for domestic manufacturing and a skilled local workforce to meet the ambitious goals set for Australia’s hydrogen industry. It also identified significant economic opportunities tied to building these supply chains for countries able to export their skills.
Across the APAC region, there are several companies that are driving the hydrogen sector forwards. Small tech start-ups are stepping up to the plate, and while Europe has more well-established players, Asian firms have a unique advantage – they possess the critical minerals essential for hydrogen technology development. This makes the region an attractive
location for companies seeking to establish manufacturing capabilities.
But Asia faces stiff competition in its bid to be the world’s hydrogen superpower. The Middle East is quickly emerging as a leading exporter, particularly of blue hydrogen, the result of its cheap production costs and favourable business environment. Factors such as a low corporate tax rate or even tax exemptions give the region a further advantage. Australia, by contrast, has a relatively high headline tax rate and limited financial concessions, and the government should look to improve these conditions if it wants to attract global investment and remain competitive.
Injecting fresh impetus into the hydrogen industry does not just depend on government subsidies though. Robust carbon policies are a necessity.
Meaningful carbon taxes and stringent emissions reduction targets are vital to incentivise the shift to hydrogen. As it stands, Australia has a weak carbon policy that affects only a small number of emitters, resulting in minimal domestic incentives for change. In contrast, Europe’s policies push emissions reductions across industries, creating stronger drivers for adoption.
Additionally, a liquid carbon trading market would help to reflect the true environmental cost of fossil fuels, making hydrogen more economically viable by comparison.
The path forward requires a balance of measures: government investment to lower the cost of hydrogen and policies that increase the cost of traditional fossil fuels. Accounting for the environmental externalities of fossil fuels through carbon pricing and stricter regulations is as crucial as offering subsidies to the hydrogen sector. This carrot and stick approach is essential for the transition to a sustainable hydrogen-based economy. In Japan’s latest Green Transformation Strategy, a carrot and stick approach has been signalled in several ways but perhaps most notably through the issuance of green government bonds, which the government intends to repay through the revenues received from carbon pricing initiatives.
Asia stands at the forefront of the global hydrogen revolution and while significant challenges remain – particularly around cost and infrastructure – innovative strategies in the likes of Japan, South Korea, and Australia demonstrate that progress is achievable through targeted investment, robust policy frameworks, and a pragmatic approach to hydrogen production methods. And while each country is unique, this also provides a blueprint for others in the region to follow.
Collaboration across industries, governments, and regions will be critical to overcoming these obstacles and scaling the industry. By fostering domestic supply chains, enhancing financial incentives, and integrating meaningful carbon policies, Asia can not only accelerate its decarbonisation journey but also solidify its role as a global hydrogen leader. The region’s ability to adapt and innovate in the face of global competition will determine its success in reshaping the future of clean energy and achieving a more sustainable world.
1. ‘Hydrogen in Asia’, HSBC, (9 September 2024), https://www. business.hsbc.com/en-gb/insights/global-research/hydrogen-inasia#:~:text=Hydrogen’s%20key%20promise%20in%20Asia’s,’%20 %E2%80%93%20produced%20using%20fossil%20fuels.
Dr Phil Ingram, Johnson Matthey, discusses the promise clean hydrogen production holds in the transition towards sustainable energy and the technology supporting the road to a viable, low-carbon hydrogen economy.
Clean hydrogen production holds immense promise as a cornerstone of the global transition towards sustainable energy systems. With its potential to decarbonise various sectors, such as transportation, industry, and power generation, the market for clean hydrogen is experiencing rapid growth and is poised to play a pivotal role in shaping the future energy landscape.
Reducing carbon emissions in syngas production is a critical factor for the energy transition. Although international clean hydrogen standards vary, with the UK being the strictest at ≤ 2.4 kg CO2e/kg H2, there is a clear need to minimise emissions. To reach decarbonisation goals, the International Energy Agency (IEA) estimates that 530 million t of clean hydrogen will be required annually by 2050. The US hydrogen strategy calls for 10 million t of clean hydrogen by 2030, and the EU has doubled its hydrogen production target to 20 million t by 2030. This will require massive investment in hydrogen production – but how can technology help today?
Commercially viable solutions can produce low-carbon hydrogen and achieve up to 99% reduction in carbon dioxide (CO2) emissions. By utilising heat exchange rather than fuel-fired technologies, achieving efficient and sustainable production of hydrogen, ammonia, and methanol is possible and crucial for various industrial applications.
As the primary source of hydrocarbon feedstocks used in steam methane reforming (SMR) processes, the oil and gas industry
plays a crucial role in the transition towards sustainable hydrogen production. By integrating advanced low-carbon technologies into existing hydrogen plants, the industry can not only reduce its environmental impact, but also lead in the creation of a cleaner, hydrogen-powered future. This shift is imperative as the industry seeks to align with global decarbonisation targets and enhance its reputation in the context of environmental sustainability. The transition to blue hydrogen production, supported by carbon capture and sequestration (CCS), offers a pathway for these companies to maintain operational continuity while significantly mitigating their greenhouse gas (GHG) emissions. The US is witnessing a surge in interest and investment in clean hydrogen production technologies. This surge is fuelled by several key factors that converge to create a conducive environment for market expansion. First and foremost, government support and policy initiatives are driving the growth of the clean hydrogen market. The US government has recognised the importance of hydrogen as a clean energy carrier and has taken significant steps to promote its production and adoption. Initiatives such as research and development funding, tax incentives, and regulatory frameworks provide the necessary impetus for companies to invest in hydrogen technologies.
Technological advancements are another critical driver of market growth. Breakthroughs in electrolysis, mainly using renewable energy sources such as wind and solar, have significantly reduced the cost of producing clean hydrogen. Electrolysers are becoming more efficient and cost-effective, enabling scalable hydrogen production from
renewable sources. Furthermore, innovations in hydrogen storage and transportation technologies are enhancing the viability and practicality of hydrogen as an energy carrier.
Industry commitments are also propelling the clean hydrogen market forward. Various sectors, including transportation, manufacturing, and energy, are increasingly recognising hydrogen’s potential as a clean alternative to traditional fossil fuels. Companies invest in hydrogen infrastructure and incorporate hydrogen into their operations to reduce carbon emissions and meet sustainability goals. This growing demand from industry sectors is driving investment in hydrogen production facilities and infrastructure development.
Reforming hydrocarbon feedstocks with CCS represents a primary method for producing low-carbon hydrogen, commonly called blue hydrogen. This approach offers the potential for large scale hydrogen production, thereby significantly reducing GHG emissions.
The US Department of Energy (DOE) has established a target levelised cost of hydrogen (LCOH) of US$2/kg by 2026 and
US$1/kg by 2031 as a benchmark for the widespread adoption of hydrogen as an energy source without significant economic repercussions. Achieving this target necessitates specialised technologies tailored for blue hydrogen production, such as Johnson Matthey’s (JM) LCH™ technology.
The term ‘blue’ encompasses any hydrogen production method involving some degree of decarbonisation. To attain net zero emissions, emphasis must be placed on low-emission production pathways, mainly focusing on maximising CO2 capture rates. Any CO2 emissions associated with hydrogen production must be addressed through alternative technologies, as achieving only partial carbon capture presents challenges in mitigating remaining emissions and exposes facility operators to potential CO2 pricing inflation risks.
LCH technology has been developed based on the specific requirements of blue hydrogen production. The technology uses either an autothermal reformer (ATR) or blends gas heated reformer (GHR) and ATR technologies, offering higher hydrogen yield and superior energy efficiency compared to standard steam methane reforming (SMR). Notably, the LCH technology is more amenable and cost-effective for decarbonisation through CCS than SMR.
The process provides a high CO2 capture rate of up to 99%, delivering enhanced efficiency and cost-effectiveness compared to SMR and alternative ATR technologies. Leveraging established chemical process engineering principles, the approach is designed for scalability, facilitating carbon reduction across various sectors, including industry, power generation, and transportation.
The LCH technology uses a combination of mature unit operations which are already utilised in other JM technologies:
• The JM GHR is used in three LCA (ammonia) plants and one LCM (methanol) plant.
• The JM ATR is used in the above LCA and LCM plants and in over 20 other plants.
• The water gas shift has been used in the three LCA plants.
• The saturator circuit has been used in 18 plants, including the LCA and LCM plants in addition to low pressure methanol (LPM) plants.
The LCA, LCM, and LPM plants are very large, demonstrating that the technology can produce hydrogen at large scale.
chartindustries.com howden.com
Comparative analyses between LCH technology and conventional SMR technologies reveal significant advantages for blue hydrogen production, including lower natural gas consumption, reduced CO2 emissions, and substantially lower capital costs for CO2 capture systems. By minimising the impact of rising feedstock and CO2 transmission costs and potential carbon taxation schemes, LCH technology reduces project risk while enhancing efficiency.
The heart of the LCH technology lies in its GHR-ATR reforming block, which optimises feedstock efficiency through efficient energy transfer. Importantly, when using the technology, all CO2 is contained within the product stream, facilitating easy removal using standard industry technologies. Pre-combustion CO2 removal on high-pressure, high-purity streams further reduces system costs and facilitates system deployment, facilitating the process’s potential to significantly decrease the LCOH and accelerate the adoption of low-carbon hydrogen technologies.
At a basic level, the technology GHR-ATR flowsheet includes the following steps: purified natural gas undergoes initial pre-heating and partial reformation in the GHR. In this stage, approximately 30% of the hydrocarbons react with steam to form syngas. This partially reformed gas then enters the ATR, where oxygen is introduced, causing a portion of the gas to combust and raise the process gas temperature. The resultant high-temperature gas then passes through a bed of reforming catalyst within the same vessel for further reformation. Due to equilibrium limitations, operating the ATR at high temperatures and with high steam flows minimises the methane content in the product gas exiting the reformer. Reducing methane content is crucial, as any remaining methane will contribute to CO2 emissions in the overall process.
The hot gas exiting the ATR flows back to the GHR, providing the necessary heat to drive the reforming reaction in the GHR tubes. This recycling of heat enhances the overall efficiency of the process. Unlike SMR, which relies on burning additional natural gas, the LCH process uses oxygen introduced into the ATR, typically supplied by an air separation unit (ASU). This method allows the ATR to operate at temperatures exceeding 1000°C, significantly enhancing the conversion of hydrocarbons to syngas, achieving levels of efficiency and conversion that SMR processes cannot match. Consequently, using the technology not only improves conversion efficiency, but also enhances CO2 capture capability, effectively reducing methane slip and minimising overall CO2 emissions.
The efficiency of the GHR-ATR reforming block is crucial. The LCH technology flowsheet incorporates a GHR to reduce the combustion required for hydrocarbon conversion and
minimises thermal gradient sizes by redirecting heat into endothermic reforming reactions within the GHR. This strategy maximises the flowsheet’s fundamental energy efficiency. In the ATR process, hydrocarbons undergo partial oxidation and steam reforming reactions, producing heat and syngas. This dual reaction mechanism allows for efficient hydrogen production while generating the heat necessary for the endothermic steam reforming reaction. Integrating a GHR with the LCH technology reduces combustion needs compared to an ATR-only approach, boosting exergy, reducing oxygen requirements, and minimising the size of ASUs. This configuration results in a 10% reduction in natural gas consumption and CO 2 capture duty per unit of hydrogen produced, leading to smaller, intensified unit operations. Enhanced carbon efficiency translates into higher thermal efficiency and economic benefits through decreased natural gas expenditure and lower CO2 disposal costs. Assessing the impact of the LCH technology on overall CAPEX necessitates evaluating both the inside battery limit (ISBL) offering and outside battery limit (OSBL) impacts for the entire complex.
Table 1 shows the carbon intensity of LCH technology. Comparatively, SMR hydrogen production typically produces 8 - 10 kgCO 2/kgH 2. While CCS can be added to the SMR, the upper limit for CO 2 capture is approximately 85 - 90%. Using LCH technology, the ATR can achieve higher capture rates (> 95%) as there is only a single stream of CO 2 from the syngas purification, whereas the SMR also uses a preheater or furnace that generates further CO 2. This relatively dilute CO 2 concentration of natural gas heater emissions results in lower efficiency carbon capture. The ATR also achieves a higher capture potential due to the injection of pure oxygen into the reforming reactor, compared with the SMR, which uses of ambient air, resulting in a lower molar concentration of CO 2 and reduced effectiveness of carbon capture.
Both ATR and ATR-GHR flowsheets support the transition of existing SMR-based hydrogen plants towards low carbon intensity hydrogen production, sustainably aligning with future green hydrogen production goals.
Moreover, the combination of ATR and GHR technologies facilitates the integration of carbon capture and utilisation (CCU) systems, enabling the capture and utilisation of CO 2 emissions generated during the reforming process. This reduces the carbon intensity of hydrogen production and contributes to the circular economy by repurposing captured CO 2 for various industrial applications. Additionally, incorporating renewable energy sources such as wind or solar power into ATR and GHR-based hydrogen plants further enhances sustainability and reduces reliance on fossil fuels. By adopting these advanced technologies, ATR-based hydrogen plants can play a crucial role in the transition towards clean hydrogen production, paving the way for a more sustainable energy future.
Trust Ebara Elliott Energy for comprehensive global turbomachinery service and support.
Ebara Elliott Energy’s renowned global service organization delivers expertise, skills, and capabilities with all types of rotating equipment, including emergency support, spare and replacement parts, repairs, periodic inspections, and equipment drop-in replacements, rerates, upgrades, and modifications. Our strategic service locations around the world enable us to expertly serve customers wherever they are at the time they need us most.
Learn more about our range of service capabilities at elliott-turbo.com.
Trusted Solutions for a Sustainable Future
Manish Patel, Air Products, explains how renewable hydrogen’s potential to decarbonise an industry presents
Governments across the globe are united in their need to tackle the global climate crisis. As part of this, one of the biggest challenges is how to decarbonise hard-to-abate sectors, and hydrogen has quickly emerged as a critical tool in helping to solve this.
The World Economic Forum has highlighted that trucking, shipping, and aviation, combined with aluminium, cement, concrete, and steel production account for around a quarter of global greenhouse gas (GHG) emissions, which could rise to 50% by 2050 if left unchecked. Hydrogen can play a critical role in decarbonising each of these areas. With the production and availability of renewable hydrogen predicted to upscale in the next few years, now is the time for industry to prepare to make a change.
Industries, such as glass, aluminium, and steel manufacturing require substantial energy input to create the high furnace temperature needed for their production process. There are a number of ways to decarbonise this process, including using renewable hydrogen as a fuel to replace carbon-intensive natural gas, where direct electrification is not possible or practical.
Other industries already use hydrogen as a process gas. These include oil refineries – which use hydrogen to make cleanerburning transport fuels to reduce air pollution; semiconductor manufacturing where it is used as a reducing gas; and in chemical processes such as ammonia production. Traditionally, grey hydrogen is used for these applications, but by replacing it with lower carbon
Forterra’s trial with Air Products is a prime example of exploring the transition to cleaner fuels in practice. As a UK manufacturer of essential clay and concrete building products, the company chose to test hydrogen and natural gas blends.
When Forterra published its sustainability strategy in 2022, it set a target to reduce its carbon emissions by 32% by 2030. To do this, it meant tackling the energy mix used to power its brick production kilns –reducing the use of natural gas and increasing the use of hydrogen.
Working with Air Products, Forterra has been able to trial exactly that, while protecting the quality of the bricks the company is known for.
alternatives such as green (renewable) hydrogen, there is a major opportunity to lower CO2 emissions significantly. Indeed, in the long run, to close the gap on net zero targets, replacing natural gas with renewable hydrogen would be needed. However, there are steps which can be taken today to optimise the efficiency of operations and reduce current carbon intensity.
Industrial furnaces function on fuel, combined with air – and it is common for the fuel in these instances to be natural gas, which generates GHGs. Renewable hydrogen represents a viable alternative to natural gas although reliable, large scale hydrogen supply is not immediately available. However, the technology to use hydrogen exists today and Air Products is undertaking trials and exploring options to bridge to cleaner fuels in the future.
Irrespective of hydrogen as a solution, there are steps that manufacturers can take today to reduce their emissions. The first of those steps is to check if the furnace is running at its most optimal level. Applications such as Air Products Smart Technology use diagnostic sensor and wireless technology to collect data to monitor and optimise production. For example, industry traditionally relies on a human estimation to assess when furnaces have reached tapping temperature, which can mean they are being heated for longer or to a higher temperature than needed. Smart Technology can track and monitor data and adjust the approach taken, to further boost efficiency.
Oxy-fuel technology, a proven technology which uses oxygen instead of air, can improve process thermal efficiency and reduce fossil fuel consumption. In fact, it can reduce CO2 emissions by up to 50%. Oxy-fuel technology on its own can, therefore, be an important enabler and, when used with renewable hydrogen as a replacement for fuel, it can achieve zero emissions. For manufacturers investing in Oxy-fuel technology, doing so to make sure that they can operate with hydrogen in the future is an important consideration.
At its Redbank site, where specialist brick products are manufactured, Forterra has trialled a 20% hydrogen blend with 80% natural gas as an alternative to pure natural gas in its kilns. David Manley, Forterra’s Head of Sustainability, said: “Cutting our carbon emissions is central to our mission, but we need to make sure we are not compromising on the quality of the products we are producing.”
When it came to considering how to cut emissions, the company looked at several options including electrification and biomass. Both of these will still have a supporting role in its long-term strategy but it became obvious quite quickly that hydrogen was the most effective option for reaching the company’s long-term decarbonisation targets.
Working closely with Air Products, Forterra has introduced gaseous hydrogen storage, together with a blending skid and control system which has allowed it to produce bricks using a mixture of natural gas and hydrogen. The use of 20% hydrogen is a game changer, given the careful balance the company needs to strike when it comes to temperature and moisture control in brick production.
Air Products, with expertise across multiple hydrogen production pathways, distribution and storage, as well as combustion technologies, guides customers through the full process. Brick production is a balancing act and ensuring that product quality is not compromised by changes in temperature and environment within the kiln is essential. How hydrogen could be introduced to the energy mix to protect that balance was vital to Forterra and Air Products’ testing.
Overseeing trials using a 100% natural gas kiln as a control variable, Forterra used hydrogen at rates between 5% and 20%, increasing the volume of hydrogen use as the project progressed. Approaching the trials in this way worked perfectly. Forterra was aware that it had the potential to be significant for the company and the wider industry, so being careful and testing as it went would allow it to pinpoint to what extent hydrogen could be introduced into the process. Ultimately, at a 20% mix there was no impact on the colour, consistency, and quality of the bricks – which is exactly what it was looking for.
The future is promising. Forterra has expressed excitement at the trial outcome, and it has proved to be a real success for the introduction of hydrogen into the company. As a result, it is now exploring how it can do a similar trial on a slightly smaller kiln but with hydrogen blends up to 100%, as well as how it would fit out larger kilns in the future.
The trial supports what the wider industry is thinking. In its 2024 Decarbonising UK Ceramic Manufacturing Industry Roadmap, Ceramics UK recommended that deeper decarbonisation of UK ceramic manufacturing requires the urgent development and deployment of low-carbon hydrogen – despite its notable absence from the same report only 10 years earlier.
But how much impact can a hydrogen-enabled furnace have on carbon emissions during brick production? It has the potential to be significant. If the company could operate a kiln on 100% hydrogen, it would be able to reduce its carbon output by 40 - 45%. That is significant but there are opportunities with mobile plants too, where the introduction of fuel cells could further reduce carbon emissions by 8 - 10%. That means a business like Forterra could achieve a total reduction of around 55% of its carbon emissions through the introduction of hydrogen.
For both organisations, they are clear that this is just the start, with Forterra looking at expansion plans and uses of hydrogen into the future as they believe it is critical, and Air Products being well-positioned to provide its expertise. As with a lot of businesses working to meet decarbonisation targets, Forterra recognises the need to invest in infrastructure across its UK sites to support a move to hydrogen. But it also wants to see wider investment in hydrogen infrastructure come forwards, as well as greater confidence in the market for the supply of hydrogen.
According to the ‘Industrial Transformation 2050 Report’, an industrial strategy for a climate neutral Europe, the pathways to net zero emissions that require the use of new
low-carbon production routes currently cost 20 - 30% more for steel and 20 - 80% more for cement and chemicals. If economics are not driving the change, then what needs to happen?
Firstly, as fossil fuels are subsidised, hydrogen adoption needs to be encouraged via a series of demand measures as well as cost support. The demand measures are needed in the form of mandates for industry and transport to decarbonise with appropriate measures for non-compliance. At the same time, hydrogen production needs to be supported, at least initially, to enable industry to scale up, which will lead to a reduction of cost in the future.
Currently, there is not enough reliable, cost-efficient hydrogen in the market to give off takers the confidence to fuel switch in order to meet CO2 reduction targets. Domestic production through electrolysis will meet some of the demand but it will not be enough to meet climate reduction targets. Whilst the EU has recognised that there is a need for imported renewable hydrogen, UK policy relies on domestic electrolytic hydrogen production alone and risks being left behind.
Air Products, together with ACWA Power and NEOM, is building a world scale renewable ammonia from hydrogen production facility in Saudi Arabia with plans to transport the ammonia to Northern Europe. Once landed, the ammonia can be converted back to renewable hydrogen. The imports and associated large scale storage would complement domestic production and allow domestic electrolysers to not only right-size their storage but to provide confidence in the renewable energy market. Other companies are following and those countries that take advantage of this pathway are the ones that will gain a competitive advantage for their industries.
The potential for hydrogen to decarbonise an industry is huge. Glass, steel, and ceramics manufacturers are already working with Air Products to trial hydrogen technologies for their furnaces and kilns, while refineries also have the potential to switch to green hydrogen, reducing emissions from petroleum products.
The Hydrogen Council estimates that a switch from fossil fuels to low-carbon hydrogen can propel the industrial sector, along with the heavy-duty transportation sector, to reduce global GHG emissions by 20%, but it is important to move now, and with a real sense of urgency.
This requires a collaborative effort from hydrogen suppliers, governments, and off-takers to work in unison. Without a serious exploration of the potential to introduce hydrogen now, decarbonisation choices will narrow. It is vital that companies consider first steps on the journey to a hydrogen-fuelled future.
Afzal
Hydrogen, like many other clean energy sectors, felt the brute force of various significant macroeconomic forces in 2024. Rising inflation, higher interest rates, disruptions in global energy markets arising from geopolitical crises, supply chain limitations, and unexpectedly high renewable electricity costs, combined to temper enthusiasm around this burgeoning sector.
Renewable and low-carbon hydrogen will invariably play a vital role in reducing emissions in hard-to-electrify,
energy-intensive sectors. Achieving the Paris Agreement’s climate targets requires hydrogen and its derivatives –such as ammonia, e-methanol, and other e-fuels – to supply approximately 15% of global energy demand by 2050. However, projections included in DNV’s latest ‘Energy Transition Outlook’ lay bare a significant gap in adoption. By 2030, hydrogen and its derivatives are anticipated to contribute just 0.25% to the global energy mix, increasing to only 4% by 2050, far short of the required levels.
Even though people believe hydrogen and its derivatives will only account for a modest share of global energy demand by 2050, the improvements in hydrogen technology and infrastructure over the next three decades will be substantial. These developments have the potential to transform various industries.
While there have been several recent and high-profile setbacks, amongst them the failed Danish offshore wind tender – a critical piece of the puzzle in supporting Power-to-X and hydrogen infrastructure – there have also been positive moves. The industry has seen final investment decisions for projects in the Netherlands and Germany, along with significant progress on infrastructure.
A notable example of this progress in the face of adversity is the Delta Rhine Corridor (DRC) project for onshore hydrogen pipelines, which received sign off from the Dutch government at the tail end of 2024. Additionally, initiatives like the European Innovation Fund Project awards and the European Hydrogen Bank’s upcoming auction are providing valuable support. However, much of this progress hinges on subsidies,
making the sector sensitive to government policy and financial stability.
In the north-west of the continent, building a robust pipeline network is essential for connecting low-cost producers in Scandinavia to high-demand regions like Germany. This infrastructure will also enhance resilience, much like natural gas networks, ensuring energy security and continuity in case of disruptions. And just like natural gas, it will enable a genuine hydrogen market to develop, by connecting diverse producers and users.
While the pace of progress is slower than desired, the necessary connecting infrastructure is beginning to take shape; in Germany the ground-breaking country-wide core grid network was approved in 2025 and is getting funded. Clearly the industry is moving forward – even if not as rapidly as some might hope.
Various industry players are actively developing methods to transport hydrogen, either as pure hydrogen or blended with natural gas, to complement or replace natural gas in existing systems. For example, the Germany-wide Hydrogen Core Network (HCN), Europe’s largest hydrogen network, is scheduled for completion by 2032. The total length of the approved core network is 9040 km, consisting mainly of converted natural gas pipelines (approximately 60%), with an investment amounting to €18.9 billion.
However, large scale deployment of hydrogen pipelines necessitates striking an optimal balance between safety and cost-effectiveness. Achieving this balance is critical for designing efficient new pipelines and assessing the feasibility of requalifying existing pipeline infrastructure for hydrogen transport.
Early stakeholder feedback highlighted a lack of guidance, standards, and safety protocols as significant barriers to advancing infrastructure, with no offshore pipeline code covering hydrogen transport or mix of hydrogen. Accelerating the development of the sector hinges on the creation of a comprehensive framework for the pipelines of the future.
DNV is well aware of the critical need to scale hydrogen technology and associated infrastructure, while ensuring safety, cost-efficiency, and sustainability. Expertise in risk management and quality assurance will be vital to quickening the pace of change, and DNV has evaluated more than 400 renewable hydrogen production projects and contributed to numerous joint industry projects (JIPs).
In 2021, DNV initiated H2Pipe JIP together with Equinor and Gassco, a JIP aimed at developing a new code for the design, re-qualification, construction, and operation of offshore pipelines to transport hydrogen – either pure or blended with natural gas. The idea originated from discussions with key customers during 2020, when the hydrogen market began to pick up real momentum after years of promise.
The JIP gathered large interest in the industry and the project quickly expanded. Within a year it featured over 30 participants, including the likes of Equinor, Gassco, BP, Shell, TotalEnergies, Tenaris, Eni, and ExxonMobil.
The first phase of the JIP focused on creating guidelines for the design, construction, and operation of hydrogen pipelines. The scope included pipelines made from carbon manganese steel, covering a range of diameters and materials for transporting hydrogen blends and pure hydrogen gas. Building on DNV’s offshore pipeline standard, DNV-ST-F101, which is used for 70 - 80% of the world’s offshore pipelines, the company applied these principles to hydrogen infrastructure.
With an initial budget of NOK15 million (£1 million or €1.3 million) and participation from a growing number of companies, DNV also initiated a mechanical testing programme. The objective of the programme was to test material susceptibility to hydrogen, to fill gaps in existing knowledge, to explore various test parameters as a preparation, and to narrow down the number of variables for the main test programme in phase two.
Having concluded in 2023, the first phase provided valuable insights into the unique requirements and challenges of hydrogen pipelines and laid the foundation for the next phase.
All the stakeholders were keen to keep momentum going and, as such, phase two of the JIP kicked off before phase one had formally concluded. By this stage, 36 participants had joined, with the budget exceeding NOK50 million (£3.5 million or €4.3 million). Due to run until the end of 2025, the objective of phase two is to further develop the guideline to a level where it can offer direct and detailed support in the design of offshore hydrogen pipelines, and further to issue the first public recommended practice for offshore hydrogen pipelines.
The company’s ongoing work focuses on complementing the experimental testing programme, enhancing safety assessments, and refining design processes for hydrogen pipelines, something that has been extensively discussed with JIP participants. Compared to traditional natural gas pipeline design, defect growth in pipeline welds is more pronounced for hydrogen pipelines and is likely to govern wall thickness design. These insights are critical for creating resilient hydrogen infrastructure in Europe, especially for linking producers in Scandinavia with demand centres in Germany.
In addition to the H2Pipe JIP, DNV is continuing to engage with industry stakeholders, present findings at conferences, and publish related materials, including a white paper on hydrogen qualification and a service specification document.
DNV’s efforts are now expanding to include onshore pipeline considerations, and a task within the JIP recently got underway to identify gaps between onshore and offshore applications and to develop specific guidelines for onshore hydrogen infrastructure.
The benefits of the H2Pipe JIP are significant. First, it will enhance the understanding of how hydrogen gas affects material properties, both when used as 100% hydrogen
and as a blend with natural gas, while also identifying real design limitations. The project will provide a clearer understanding of how pipeline systems can be designed to safely transport hydrogen gas and specify necessary mitigation measures.
It will also contribute to less conservative design and material requirements, allowing for more efficient pipeline designs while maintaining the required safety and reliability. Additionally, the project will offer insights into how third-party interference might affect pipeline integrity, helping to mitigate potential risks. It will enable the possibility of operating pipelines at higher pressures and flow capacities and ensure better utilisation of the pipeline system, optimising its efficiency. Ultimately, the project will lead to improved economic outcomes by making the hydrogen transportation infrastructure more cost-effective.
As with all of DNV’s JIPs, recommended practices, codes and standards, its goal is to address shared challenges in the hydrogen industry through standardisation. Many players in the sector are working independently to solve similar issues. However, by establishing common standards, the company aims to create a foundation that lifts the entire industry, enabling scalable and efficient technology adoption. Standards not only unify practices but also help drive the development and deployment of hydrogen infrastructure.
In Europe, DNV observed some reduction in efforts around hydrogen projects, primarily due to high costs. Hydrogen production, transportation, and end-user adoption remain expensive, raising questions about market readiness and viability. Developing standards can serve as an enabler, particularly by reducing transportation costs and improving efficiency.
At present, there are approximately 4500 km of hydrogen pipelines in operation. These are all onshore and are operated at low utilisation with mostly steady flow. To meet future needs, hydrogen pipelines will have to be operated with a higher utilisation than current practice and will likely experience more frequent pressure variation.
This shift will require adopting more modern pipeline design principles and ensuring pipelines can also function as storage solutions. Importantly, pipeline operations must account for hydrogen’s unique properties. Unlike natural gas, hydrogen cannot endure the same number of pressure cycles without risks of fatigue, cracking, or leakage.
Green hydrogen production, often reliant on solar or wind energy, introduces uneven production cycles. Managing these fluctuations is critical for safe and efficient operations. Achieving this balance requires innovation in pipeline design, materials, and operating strategies.
In the coming years, DNV aims to position the standards delivered by this JIP as key enablers for the hydrogen industry, supporting cost reduction, scalability, and safety. By addressing design and operational challenges collaboratively, it will be possible to pave the way for a robust and reliable hydrogen transport network that meets the needs of a growing market.
Dr Cornelia Neumann, IMI, identifies how Germany’s Hydrogen Core Network is laudable but not the only tool for hydrogen uptake.
While the European Commission’s signoff of €3 billion in German Federal state aid for the construction of the Hydrogen Core Network (HCN) is undoubtedly welcome, it should not be considered a silver bullet for the challenge of decarbonising hardto-electrify industries in Germany. It offers significant long-term promise, but the short-to-medium-term decarbonisation benefits it can deliver are questionable at best. Indeed, there are several other plausible modes of delivery that can offer faster decarbonisation than a pipeline can, most notably the decentralised production of hydrogen.
The HCN is intended to operationalise a network of hydrogen pipelines running the length and breadth of Germany, connecting centres of hydrogen production with difficult to electrify industries. The project is the centrepiece of Germany’s National Hydrogen
Strategy, intended to increase hydrogen’s share of the energy mix as part of efforts to decarbonise Germany’s industrial base.
Despite around 60% of the 9040 km project involving the conversion of existing natural gas pipelines, it still requires the construction of thousands of kilometres of new pipeline infrastructure.¹ Nor is the process of converting natural gas pipelines for hydrogen straightforward. Unlike natural gas, hydrogen causes embrittlement in metals, requiring materials that can withstand these effects to be used. It is expected to take until 2032 for the entire network to become operational. Moreover, as with all major infrastructure projects around the world, the complexity of the undertaking substantially increases the risk of cost overruns, delays, and project failures.²
Given that Germany aims to have reduced greenhouse gas emissions by 65% against 1990 levels by 2030, there is a need
for faster action to decarbonise the country’s hard to electrify industries, such as steel, chemicals, and refining.³
Yet, despite the limitations of the HCN in the near-term, Germany is not mistaken in its backing for hydrogen as a central part of its efforts to decarbonise its industrial base. Rather, it needs to be able to shift key industries to hydrogen much faster than is currently planned.
The key limitation of the HCN is the time and level of complexity involved in delivering the project. As a result, a simpler method for supplying hydrogen has the potential to deliver much faster progress across hard to decarbonise industries. For many energy managers, the logical assumption will be that tanker deliveries of hydrogen are required.
However, the emissions involved in the tanker delivery of hydrogen undermine the fuel’s green credentials. Moreover, the capacity to deliver sufficient quantities of hydrogen by road to allow key industries to shift from fossil fuels is questionable at best. What is more, a tanker delivery-based hydrogen distribution system would require sizeable on-site hydrogen storage capabilities, with a significant demand for space and/or an expensive pressurised set-up. Both the feasibility and decarbonisation credentials of this approach are therefore doubtful.
In contrast, decentralised electrolysis carries with it only minimal storage demands, without requirements for pressurisation. That is where a decentralised approach to hydrogen generation has the potential to pay dividends.
The focus of the HCN is very much on the highest energy users. That makes sense as, once connected, it will enable substantial reductions in carbon emissions. However, this comes at the cost of not connecting large numbers of lower energy users that are not major contributors to emissions on their own, but, when taken together, do contribute substantial levels of emissions.
Away from Germany’s industrial heartlands, the HCN’s coverage is much sparser, with many high energy users potentially being hundreds of miles from the nearest connection. Again, while there is unquestionably value in a focus on areas with a concentrated base of high energy users, the challenge will quickly shift to decarbonising a wider base of high energy users.
The HCN’s blind spots are not only geographic, however. They also largely neglect transport – a major source of emissions.
In fact, road transport is now the second-largest CO2 emissions source in Germany.⁴ While battery-electric technologies are widely seen as being key to the decarbonisation of road transport, there are significant limitations that must be taken into account. Indeed, these limitations may, at least in part, explain the slower progress on decarbonisation made in the sector in recent years compared to the rapid progress made in German industry. Notably, the performance of battery-electric vehicles can be sub-optimal in areas where there is undulating terrain, or where very high levels of vehicle uptime are required owing to their weight and charging time respectively. Likewise, limits to battery capacities can make them unviable for long-distance passenger bus or haulage applications.
Whereas high energy use in industry is typically spread over only a relatively small number of locations, that is not the case for transport, where hauliers and bus operators are dotted across the country, often with relatively small scale operations. The feasibility of a centralised network reaching potentially hundreds of hydrogen refuelling stations across Germany is doubtful. If it ever were achievable, it would likely take many years to implement. In short, it is not a feasible solution for the rapid reduction of road transport emissions.
The next alternative for the distribution of hydrogen in the road transport sector is tanker delivery of hydrogen fuel. Yet this collides with many of the same challenges seen in relation to tanker delivery of hydrogen to industry. The power required to drive tankers, even if sustainable and without tailpipe emissions nevertheless reduces efficiency, requiring more fuel to be produced to achieve the same end result.
Hydrogen storage also represents a hinderance to tanker-deliveries, with constrained urban sites often lacking the necessary space for substantial tanks.
We can see, then, that there are considerable drawbacks to relying on centralised modes of hydrogen production for the rapid decarbonisation of German industry, whether delivered by the HCN or by tankers. Indeed, the more stakeholders involved in a major project such as the HCN, and the longer it takes to move from inception to completion, the greater the opportunity for problems and ensuing delays to occur. By contrast, on-site hydrogen generation will generally involve a much shorter timeframe from the inception of a project to its completion and will involve fewer stakeholders. As a result, such projects can deliver decarbonisation much more quickly than can a major pipeline project.
One of the primary methods for producing hydrogen on-site is polymer electrolyte membrane (PEM) electrolysis, which involves the use of a solid polymer electrolyte to conduct protons, separate product gases, and insulate the electrodes.⁵
PEM electrolysis offers several important advantages. These include high efficiency, purity, and fast dynamic response times. Notably, PEM electrolysers can be delivered as turnkey solutions and in scalable configurations, making their deployment both quick and highly customisable to the applications in question.
The IMI VIVO electrolyser is a case in point, offering a turn-key solution within the footprint of a standard shipping container.
Furthermore, highly scalable on-site generation substantially reduces storage needs compared to delivery by tanker. On site generation means hydrogen can be produced on a last-minute basis, with production ramped up or down according to operational needs.
The independent nature of decentralised electrolysis offers further benefits. Highly interconnected systems, such as a network of pipelines, carry the risk of failures cascading through the system. In the case of the HCN, that would risk an outage across a large swathe of German industry at a significant cost to the economy. Consequently, we can see that there are important security of supply benefits to decentralisation. A failure at one location cannot spread to others.
This same principle applies to the implementation of green hydrogen across Germany. A long-term project carries a greater risk of low probability/high consequence events – black swans. Where these occur, they risk delaying completion across an interconnected network.
Arguably, decentralised hydrogen production has even greater potential for the road transport sector in Germany. On-site production minimises the need for new national infrastructure to be constructed with significant time and cost requirements.
Hydrogen has significant promise in decarbonising large swathes of Germany’s economy. However, the precise methods used to deliver hydrogen to end users will have a considerable impact on how effective it ultimately is in delivering the substantial emissions reduction the country is targeting.
While the HCN has considerable potential to decarbonise hard to electrify applications in Germany’s industrial heartlands it, nevertheless, has limitations. Most significantly, it will take a number of years to come online fully and will only reach those high energy users in close proximity to the pipelines.
Meanwhile, tanker deliveries will have their place in the mix, especially where hydrogen is required in the short-term or at very short notice.
However, it is on-site production that has the promise to bring forward the swift decarbonisation of German industry, with offerings such as the IMI VIVO electrolyser offering scalable turnkey solutions that can help deliver rapid decarbonisation.
1. ‘Hydrogen Core Network’, Bundesnetzagentur,https://www. bundesnetzagentur.de/EN/Areas/Energy/HydrogenCoreNetwork/start. html
2. BAHRA, A., ‘What causes delays and cost overruns on major infrastructure projects?’, ConstructionProductsAssociation, (24 May 2019), https://www.constructionproducts.org.uk/news-mediaevents/blog/2019/may/what-causes-delays-and-cost-overruns-onmajor-infrastructure-projects/
3. APPUNN, K., ERIKSEN, F., and WETTENGEL, J., ‘Germany’s greenhouse gas emissions and energy transition targets’, CleanEnergyWire, (11 September 2024), https://www.cleanenergywire.org/factsheets/ germanys-greenhouse-gas-emissions-and-climate-targets
4. TISEO, I., ‘Greenhouse gas emissions from road transportation in Germany 1990-2023’, Statista, (10 July 2024), https://www.statista. com/statistics/1478776/annual-greenhouse-gas-emissions-by-roadtransport-germany/
5. CARMO, M., FRITZ, D.L., MERGEL, J., and STOLTEN, D., ‘A comprehensive review on PEM water electrolysis’, InternationalJournal ofHydrogenEnergy, vol. 38, no. 12, (22 April 2013), pp. 4901 - 4934.
• RENTALS • SITE SERVICES
High-risk environments demand structures capable of protecting crews and critical systems, while also fostering efficient, sustainable operations. Hunter’s custom modular protective structures offer next-level safety and durability, and are tailored to serve your site-specific needs on every front.
• Blast-Resistant Design Options Available
• Single & Multi-Module Capabilities
• Rapid Deployment & Scalability
• Enhanced Safety & Security
SCAN TO REQUEST A QUOTE TODAY BUILD YOUR FACILITY WITH HUNTER
Tim Cortes, Plug Power, analyses how harnessing hydrogen fuel cells can power the future of data centres.
The rapid growth of digital services and technologies has fundamentally changed how we live and work. Data centres, the backbone of the modern economy, are at the heart of this transformation; supporting everything from cloud computing to artificial intelligence (AI) applications. However, as demand for digital services continues to surge, these data centres face an increasing challenge: how to meet energy needs without exacerbating the environmental crisis. Traditionally, many data centres rely on non-renewable energy sources, contributing significantly to greenhouse gas emissions. As the pressure to adopt cleaner energy solutions grows, hydrogen fuel cells have emerged as a potential game changer, offering a clean, efficient alternative that could revolutionise data centre power.
Hydrogen fuel cells work by converting hydrogen gas and oxygen into electricity through an electrochemical reaction, producing only water and heat as by-products. This makes them a highly attractive energy source for data centres, where reliability, uptime, and sustainability are critical. With their potential to reduce carbon footprints while ensuring a stable power supply, hydrogen fuel cells are poised to play an important role in the future of data centre energy strategies.
At their core, hydrogen fuel cells generate electricity by splitting hydrogen gas into protons and electrons. The protons pass through an electrolyte membrane, while the electrons travel through an external circuit, generating electrical energy.
At the cathode, the protons and electrons combine with oxygen to form water. This electrochemical process produces no carbon emissions, making it a clean energy solution. Hydrogen fuel cells come in different forms, with proton exchange membrane fuel cells (PEMFCs) and solid oxide fuel cells (SOFCs) being two of the most commonly used types for data centre applications.
PEMFCs are well-suited for environments where power demand fluctuates quickly. They are typically used for backup power in data centres, offering rapid response times during grid outages or periods of peak demand. On the other hand, SOFCs operate at higher temperatures and can provide steady, high-efficiency power, making them ideal for large scale data centres that require continuous, reliable energy.
Data centres are essential to the functioning of the digital world. They support a range of activities, from hosting massive amounts of cloud data to running AI algorithms and machine learning (ML) models. As the demand for digital services grows, so too does the energy consumption of data centres. Unfortunately, much of this energy still comes from fossil fuels, contributing to harmful emissions and climate change. To address these concerns, the data centre industry must shift toward cleaner, more sustainable energy sources.
Hydrogen fuel cells offer a promising solution. These cells provide a stable and efficient energy source that can support both primary and backup power needs while aligning with the growing demand for sustainability. As companies face increasing pressure to meet environmental regulations and reduce their carbon footprints, hydrogen power could become a key component of data centre energy strategies.
One of the most compelling reasons to adopt hydrogen fuel cells is their environmental impact. Unlike fossil fuels, which release harmful pollutants into the atmosphere, hydrogen fuel cells produce only water vapour and heat as by-products, making them a zero-emission energy source. This is particularly significant for data centres, which are under growing pressure to reduce their environmental impact.
Additionally, when hydrogen is produced through renewable methods – such as water electrolysis powered by wind or solar energy – the entire process becomes carbon-free. This allows data centres to operate with minimal impact on the environment, aligning with broader sustainability goals. By replacing traditional diesel or natural gas backup generators with hydrogen fuel cells, data centres can reduce their reliance on fossil fuels, decrease emissions, and mitigate the environmental damage caused by conventional power infrastructure.
Beyond their environmental benefits, hydrogen fuel cells offer several operational advantages for data centres. One of the most notable is their reliability. Hydrogen fuel cells can serve as either a primary energy source or as a backup during grid failures. For large scale data centres, SOFCs are ideal for continuous power supply, offering high efficiency and stable output. For backup power, PEMFCs excel due to their quick response times and ability to handle sudden fluctuations in power demand.
Hydrogen fuel cells also provide data centres with greater energy security and independence. By generating hydrogen on-site, through renewable methods like electrolysis, data centres can reduce their dependence on the external grid and power suppliers. This not only ensures a more reliable power supply but also lowers the cost and environmental impact associated with energy transportation.
Additionally, hydrogen offers flexibility in terms of production. It can be generated through various methods, including water electrolysis, natural gas reforming, and biomass conversion. This flexibility provides a range of options for fuel sourcing, which could help reduce costs and enhance energy security.
Despite their clear advantages, the adoption of hydrogen fuel cells in data centres faces several challenges. The most significant of these is the high initial investment required for hydrogen infrastructure. Building the necessary infrastructure, including hydrogen storage tanks, fuel cells, and electrolysis equipment, can be expensive. However, as technology improves and economies of scale are realised, costs are expected to decrease. In addition, government incentives and subsidies
for renewable energy projects may help offset some of these initial costs.
Another challenge is the storage and transportation of hydrogen. As a highly volatile gas, hydrogen requires specialised infrastructure for safe storage and distribution. While advancements in compression techniques and cryogenic storage are addressing these issues, the logistics of hydrogen distribution are still developing.
Safety is also a critical concern. Hydrogen is flammable and can be hazardous if not handled properly. However, modern hydrogen systems come with advanced safety measures, and industry standards and guidelines are continually evolving to ensure that hydrogen can be used safely in data centres.
Several leading companies have already begun experimenting with hydrogen fuel cells in their data centres. Microsoft, for example, has tested hydrogen as a backup power source, powering server racks for 48 hours using fuel cells. Google, similarly, is researching hydrogen fuel cells as part of its broader goal of achieving carbon-free energy for its data centres by 2030. Both companies are working to integrate hydrogen into their existing renewable energy strategies, demonstrating the potential of this technology in the data centre industry.
The future of hydrogen fuel cells in data centres looks promising. Technological advancements in hydrogen production and
fuel cell efficiency will likely continue to lower costs, improve energy output, and increase the longevity of fuel cells, making them an even more viable option for large scale applications. Governments around the world are increasingly recognising the importance of hydrogen in the transition to a low-carbon economy, and policies supporting clean energy are expected to accelerate the adoption of hydrogen-powered data centres. Moreover, hydrogen fuel cells can be integrated with renewable energy sources to create hybrid systems. In such systems, excess renewable energy can be used to produce hydrogen, which can then be stored and converted back to electricity when needed. This approach enhances energy storage and helps balance the intermittency of renewable power sources.
Hydrogen fuel cells represent a promising solution for powering the data centres that support our digital world. With their ability to reduce carbon emissions, improve energy efficiency, and provide reliable power, hydrogen fuel cells are poised to play a crucial role in the transition to a more sustainable digital infrastructure. While there are still hurdles to overcome – such as high initial costs and infrastructure challenges –the combination of ongoing technological advancements, supportive policy frameworks, and private sector investment suggests a bright future for hydrogen-powered data centres. As the world moves toward a cleaner, more resilient energy future, hydrogen fuel cells could help data centres meet the energy demands of tomorrow while minimising their environmental impact.
In cities around the world, buses serve as the lifeblood of public transportation, moving millions of people every day.
The diesel bus, long a staple of public transportation systems worldwide, is gradually being phased out as cities race to meet ambitious climate goals.
Enter hydrogen-powered fuel cell buses – an innovative solution poised to revolutionise urban mobility. As governments push for zero-emission fleets and transit authorities seek alternatives to battery-electric buses, hydrogen fuel cell buses offer a unique blend of power, efficiency, and
operational flexibility. With advances in hydrogen storage technology, particularly the development of lightweight Type 4 cylinders, hydrogen fuel cell buses are becoming a critical piece of the puzzle in cities dealing with challenging climates, long routes, or high-utilisation needs.
The push for hydrogen buses varies significantly across regions. In Europe, hydrogen fuel cell buses are gaining momentum thanks to strong policy support and collaborative
initiatives like the Clean Hydrogen Partnership. Leading European manufacturers, including Solaris and CaetanoBus, are spearheading adoption. Solaris, for example, has already delivered 370 hydrogen-powered buses to 31 cities across 10 European countries, with nearly 500 additional buses on order, while CaetanoBus has advanced its hydrogen offerings with support from Toyota.
In North America, adoption remains more localised. There are almost 100 hydrogen buses in operation in the US today,
most of those located in California. Leading US manufacturer New Flyer already has hydrogen powered buses on the road, while Gillig is actively integrating hydrogen solutions into its vehicle offering, supported by Hexagon Purus’s Type 4 cylinder technology.
China stands out as the global leader in hydrogen bus deployment, with over 10 000 fuel cell buses in operation. This rapid expansion is fuelled by significant government investment in hydrogen infrastructure and technology, as well as high-profile demonstrations such as those seen during the 2022 Winter Olympics. The scale of adoption in China highlights the potential role that hydrogen buses can play in driving large scale decarbonisation efforts.
While battery-electric buses have gained significant market share in recent years, they are not a one-size-fits-all solution. Hydrogen-powered buses are a complementary solution, offering distinct advantages in several key areas:
• Extended range: hydrogen buses can exceed 400 km on a single refuelling, significantly more than most battery-electric buses, making them ideal for inter-city and rural routes.
• Rapid refuelling: refuelling a hydrogen bus takes less than 15 minutes, compared to hours for battery-electric buses, minimising downtime and maximising fleet availability.
• Energy resilience: hydrogen buses maintain consistent performance in extreme weather conditions. For instance, during cold winters or hot summers, the energy demands of heating and cooling systems significantly reduce the range of battery electric vehicles (BEVs). Hydrogen fuel cells, however, are mostly unaffected by these conditions.
• Operational flexibility: hydrogen buses are better suited than battery electric buses in high-frequency operations, where it would not be practical to charge, and in routes requiring significant energy consumption, such as those with steep inclines or high passenger loads.
At the heart of hydrogen-powered buses is their advanced storage system. Type 4 composite cylinders – originally developed six decades ago by the legacy companies that Hexagon Purus emerged from – have become the gold standard for hydrogen storage in transit vehicles. These lightweight, high-performance pressure cylinders enable safe and efficient storage of compressed hydrogen gas at standard working pressures of 350 bar.
Type 4 cylinders are fully wrapped composite pressure cylinders featuring a polymer liner and a carbon fibre composite structural layer. This combination provides several key benefits:
• Lightweight design: the use of polymer liners and carbon fibre significantly reduces weight, which directly enhances the range and efficiency of hydrogen buses.
• Corrosion resistance: unlike metal cylinders, Type 4 cylinders are resistant to hydrogen embrittlement and corrosion, ensuring durability over time.
• High storage capacity: Type 4 cylinders are designed to handle the highest pressures among hydrogen cylinder types – up to 700 bar or more – with the highest efficiency.
Reaching a sustainable future is like kayaking. With a skilled partner, you can make the right decisions.
Reaching a sustainable future is demanding in many ways. Obstacles and change must be well anticipated to make the right decisions. We are ready to tackle these challenges with you! We will help you to improve your processes to meet your ESG goals, operational optimization and sustainable manufacturing efforts. Let’s team up to improve!
Hydrogen storage systems for transit buses must adhere to stringent regulations to ensure safety, reliability, and performance. The key regulation for the EU market is R134, which sets the benchmarks for the type-approval and safety requirements of hydrogen-powered vehicles and their components.
Hexagon Purus’s systems are specifically designed for intra-city and inter-city operations and can address the unique needs of various bus configurations, from 12 m single-deck buses to large articulated models.
Hexagon Purus is among the select few manufacturers globally capable of delivering hydrogen storage solutions for transit buses compliant with R134 standards. Key advancements include:
• Higher capacity with fewer cylinders: transit buses often require 30 - 50 kg of hydrogen to achieve ranges comparable to diesel buses. Hexagon Purus’s modular cylinder designs allow for scalable configurations, ensuring optimal storage capacity without compromising vehicle design. The new R134 compliant bus system can store up to 50 kg of hydrogen with just five cylinders, reducing weight, material costs, and complexity.
• Safety standards: Type 4 cylinders must meet stringent safety requirements. Hexagon Purus incorporates advanced features like additional thermal protective coatings to ensure safe behaviour under extreme conditions.
• Enhanced durability: advanced composite materials and sealing technologies reduce hydrogen permeation, ensuring long-term reliability.
• Modular integration: transit bus manufacturers require flexible storage solutions that can be integrated seamlessly into vehicle designs. Hexagon Purus works closely with OEMs to develop custom configurations, whether for rooftop arrays or underfloor compartments.
Hexagon Purus’s new R134 systems are manufactured at the company’s expanded facility in Kassel, Germany.
Despite the advantages of hydrogen fuel cell technology, three hurdles in particular stand out which are hindering faster adoption of hydrogen fuelled buses:
Even though hydrogen can be produced using renewable energy, the availability of green hydrogen, produced using clean electricity from sources like wind and solar, is limited. Most hydrogen currently used for buses is produced from natural gas, which is not carbon neutral. This delay in scaling up hydrogen production can slow the expansion of hydrogen bus fleets.
Hydrogen buses are significantly more expensive than diesel or battery-electric buses and running them is also more expensive due to the current cost of green hydrogen. To achieve a competitive and sustainable total cost of ownership (TCO) and broader market acceptance, the price needs to drop significantly. The cost of hydrogen fuel will decrease significantly as production scale increases, renewable energy costs decrease, and supply chain efficiency improves. Vehicle cost will also come down as volume grows and manufacturing reaches industrial scale.
Although buses can refuel at centralised depots, making them less dependent on a national network of hydrogen refuelling stations like heavy-duty trucks, setting up hydrogen refuelling stations and on-site production facilities is capital-intensive, which can deter transit agencies with limited budgets. These systems must be scaled up as fleets grow.
Hexagon Purus’s Type 4 cylinders have been deployed in hydrogen-powered buses across Europe and North America, including those manufactured by Solaris, CaetanoBus, and New Flyer. Recent projects have demonstrated ranges exceeding 400 km on a single refuelling, highlighting the potential for hydrogen buses to replace diesel fleets and complement battery-electric fleets in high-demand environments.
Looking ahead, the continued evolution of hydrogen storage technology, combined with investments in hydrogen production and policy support, will drive wider adoption of hydrogen transit buses. Already, Hexagon Purus sees the market maturing, with more clients having confidence that intra-city transit buses are working well and an increasing readiness among coach manufacturers to discuss adopting hydrogen powered coaches into their portfolio for inter-city routes. Hexagon Purus is listening to customers’ needs and requirements for next-gen models which will need to have even higher storage capacity for extended ranges.
As cities worldwide strive to meet ambitious decarbonisation goals, hydrogen fuel cell technology will play an increasingly important role in shaping the future of sustainable mobility.
Dan Freeman, Kurita Europe GmbH, and Fiona Finlayson, Kurita Water Industries, grant insight into the challenges of offshore seawater desalination for use in hydrogen production.
In recent years, offshore wind has gained much attention as a potential energy source for green hydrogen production. The prospective advantages are clear: the ready availability of renewable wind energy in locations distant from the human population and a practically limitless source of water. Offshore wind farms have been shown to provide significantly more power output than similar-sized onshore units on average, and several offshore hydrogen schemes and projects have already been proposed for the North Sea (see Figure 1).
There are several possible schemes in which offshore energy can be utilised for hydrogen production as outlined in
Figure 2. One of the principal questions is whether the production process itself takes place offshore or whether it is more efficient to transport electrical energy to an onshore facility. Ultimately, the viability of any scheme will depend on the available wind resource, the distance from shore, electrical losses in transmission, pipeline integrity and maintenance, storage capacity, and distribution.
For those schemes with offshore processing, the environment will provide significant challenges in terms of set-up, logistics, operation, and maintenance. Fortunately, much experience in this regard has already been gained in these areas in the oil and gas industry. This article will focus
on one element where significant operating history has been accumulated: the desalination process. Large scale desalination systems, specifically membrane systems, have been in operation on North Sea platforms for more than 20 years, and the challenge of maintaining them is well understood (Figure 3).
Generally, the requirements of offshore operators are the same as those onshore; the desire is to maintain the production of good quality water from their membrane system with minimum cost and effort. For the most part, this comes down to keeping the membrane surface in good condition. Seawater provides plenty of challenges in this regard, mostly as a result of the tendency for organic matter, usually of biological origin, to accumulate at the membrane surface, causing reductions in permeate flow rate and quality.
The marine environment provides the conditions for significant algal growth during the spring and summer months. It can accelerate very rapidly, often overloading the pre-treatment processes. Algae can provide both an organic foulant challenge and an inorganic component in the form of diatom and coccolithophore shells. Additionally, the warmer waters associated with the summer months, coupled with the sudden increase in the availability of
organic nutrients, means that microbial growth in situ can also provide a challenge, further increasing the complexity of the foulant matrix. In short, the summer months are always more interesting for plant operators in the North Sea than those in the winter.
In practice, this means that there needs to be an allowance for regular cleaning and maintenance between May and October in particular, to maintain desalination operations. The membrane manufacturers provide clear guidance on the trigger points at which cleaning should be conducted in order to maintain their membrane elements in good condition. Failure to comply with these guidelines usually means reduced membrane life. Certainly, experience has shown that the temptation to delay cleaning when it is required, often as a result of the desire to maintain oil production, has meant much inconvenience and significant costs down the line.
For the offshore oil platform, this trade-off between stopping to clean and maintaining production is often critical; the requirements of the energy market are complex and subject to abrupt change, so short-term commercial considerations will always be a primary factor. One potential advantage for hydrogen production, however, is that wind availability itself is intermittent, allowing for maintenance breaks within the natural cycle of operation without production losses.
While there has certainly been some effort in recent years to find chemical-free solutions, for the time being, operators of seawater desalination plants need to allow for the handling, application and discharge of antiscalants, biocides, and cleaning chemical solutions.
Since in an offshore environment everything is discharged into the sea, it is necessary that the environmental impact associated with these chemicals are minimal. These concerns are addressed by the OSPAR Commission, the mechanism by which the 15 countries with North Sea coastlines cooperate to protect the marine environment. OSPAR was instrumental in creating the Offshore Chemical Notification Scheme (OCNS), enforced by governmental regulatory bodies in each country to control chemical discharge in the North Sea.
2. Potential outline schemes for offshore wind hydrogen facilities. (a) Offshore wind turbines providing power for an onshore facility. (b) Offshore wind turbines powering an offshore production facility and a pipeline for hydrogen transport. (c) Individual wind turbines each with their own production and pipeline transport to shore.
OCNS seeks to ensure that any chemicals used in the North Sea are selected by operators to ensure minimum impact. There are minimum requirements for bioaccumulation, aquatic toxicity, and biodegradation in the marine environment and whenever there is another, environmentally more acceptable option, this must be taken. Most conventional membrane cleaning chemicals are not acceptable within these confines and there has been a requirement for specialist products to be formulated for the North Sea.
Oil Free design compressors, with 0% to 100%
Modular and scalable design that can include one or two compressors
24/7 Aftersales service for installation and start-up, supply and manteinance
Seawater reverse osmosis (RO) systems present a surprisingly minor challenge from a scale point of view compared to fresh and brackish water sources because of the high sodium chloride content. Nonetheless the risk of scale formation remains, and continuous antiscalant dosing is recommended in order to avoid the accumulation of sparingly soluble salts on the membrane surface. Most commonly used antiscalants, basic phosphonates or polyacrylates, do not demonstrate a sufficient tendency for biodegradation in the marine
3. Oil platforms in the North Sea that operate, or have operated, large scale desalination systems.
4. A membrane surface with accumulated slime, a combination of algal detritus and biofilm.
Figure 5. A CEI image at 1500x magnification showing diatom-based debris accumulated at a membrane surface. Diatoms are a kind of microalgae with silicate based ‘shells’. The mix of inorganic and organic material makes for a challenging foulant.
environment to comply with the regulations, so product selection in the offshore environment requires care.
Biocide dosing has shown itself to be extremely effective at extending run times on offshore seawater systems, particularly during the summer months. Of course, the issue with biocides is that they are toxic, making their use somewhat onerous. It is interesting to note, however, that it is not always the case that the most aggressive biocide is the most effective.
Chlorine is the most commonly used form of bio-control in offshore membrane systems usually generated in situ by electrolysis of seawater. Chlorine, however, is not compatible with polyamide RO membranes themselves, and is really only used to treat the upstream pipework and processes. It must be removed by the use of a chlorine scavenger. In fact, continuous dosing of aggressive biocides like chlorine into the feed of an RO can be highly detrimental from the point of view of membrane fouling for the following reasons:
• Chlorine is strongly oxidising, breaking organic materials and biomaterials down into more easily digestible nutrients encouraging microbial activity downstream.
• Chlorine tends to stimulate microbes to produce organic materials (extra-cellular polymeric substances) in order to protect themselves. These polymers can contribute to membrane fouling and, in fact, are far more problematic than the microbes themselves.
• Failure of the chlorine scavenger dosing can lead to irreversible membrane damage resulting in much poorer quality permeate product.
• Although it degrades reasonably quickly in the environment, chlorine, of course, is highly toxic to aquatic organisms.
While other membrane-compatible biocides are available and commonly used, aquatic toxicity remains an issue. New options are on the way. However, Kuriverter® biofilm control agents are membrane-compatible, less aggressive, and function more by inhibiting microbial activity rather than outright kill.
There are two considerations regarding cleaning operations:
1. The design of the clean-in-place (CIP) system.
2. The selection of the chemical cleaning treatment.
There are very significant and specific challenges to both in the offshore environment.
The design of a CIP system is critical to the effectiveness of cleaning. The system needs to provide the correct type of cleaning chemicals, the correct cleaning solution volume, the availability of hot water and the correct hydrodynamic conditions during the cleaning process. From an offshore perspective, one thing that is invariably in short supply is space; the size of the tank and its location become important considerations. There is a tendency, even with onshore systems, for the CIP system
to be too small for the size of the membrane plant, often as a result of the desire to minimise capital costs. Too small a tank is a false economy and mis-sizing the pumps even more, so some care is required here.
Temperature is a big factor in the success of cleaning, so the requirement for heating should not be overlooked and heat losses as a result of circulation through extended sections of pipework can be a consideration in the harsh offshore weather conditions.
With liquid cleaners, the cleaning process can be automated, but easy access for delivery vessels is necessary, meaning that often, the chemical is stored remotely from the CIP system. Exposed conditions and low temperatures can be an issue if the chemical is prone to freezing or precipitation at low temperatures, making lagged storage and pipework a necessity. There will be the requirement for suitable bunding and the risk of incompatible chemicals coming into contact, either by accidental mixing or in the bund and drainage system.
Another consideration is the construction materials; a seawater environment can be unforgiving for most grades of stainless steel, and there may also be limitations on the use of plastics as a result of the risk of electrostatic charges, which will almost certainly apply to hydrogen production as much as oil. Electrical sparks in an environment where extremely flammable gases are present are not desirable, to say the least.
One final consideration regarding membrane cleaning is that there is a significant requirement for high-quality, softened water for both preparing cleaning solutions and subsequent system flushing. In an onshore situation this is relatively easy to provide, usually requiring only a storage tank for water produced by the system itself. In the offshore environment, where space is limited, the size of the tank should not be underestimated.
As previously mentioned, for cleaning, the sizing of the CIP system is critical. The consequence of a small CIP system is that cleaning is ineffective or that a greater amount of time needs to be dedicated to cleaning, and, given the value of lost production this can present, this situation can be highly undesirable. The option of having an externally operated maintenance programme where the membrane elements are removed, tested, and cleaned onshore can therefore be attractive.
Kurita has purpose-built rigs for testing, cleaning, and servicing RO, ultrafiltration (UF), and microfiltration (MF) membrane modules. In this case, the operator usually carries two sets of membrane elements and changes these out on a cycle as the requirement for cleaning arises.
The change-out itself takes up to a day, but this system has several advantages:
• The membrane elements can be tested for physical integrity and performance.
• Individual testing means tailored cleaning regimes can be adopted for each element according to their respective condition.
Whatever your hydrogen colour category, there is a FCI flow meter solution. FCI provides industry’s broadest offering of thermal mass flow meters specifically calibrated in and for hydrogen, and at your application conditions to deliver unmatched installed accuracy, repeatability, and longest service life with no routine maintenance.
For Pipe Size 6 mm to 2500 mm (1/2 in to 99 in)
Flow Rate + Temperature + Totalized Flow
No Moving Parts, Virtually No Pressure Drop
Global Approvals for Zone 1/Div.1 Locations
Wide Measuring Range, 100:1 Turndown
Direct Mass Flow Measurement
Visit FCI’s website today to find a flow meter optimized for your hydrogen application(s) www.FluidComponents.com/hydrogen
• There are fewer restrictions on cleaning chemistry, allowing for better outcomes.
• Chemical availability is not limited in the way that it must be offshore from the point of view of supply and storage. All options are available at the time they are required or at least at short notice.
• Cleaning can be as intensive as required; time is less critical.
• Access to good quality water is not an issue and does not limit production.
• Clean conditions can be further optimised since the cleaning environment is not limited to its location in the pressure vessels on site.
• Experienced technicians can ensure the best results.
• Chemical handling, stock control, storage, and logistics are no longer critical for the platform.
• Membrane elements get the very best maintenance, maintaining their performance and extending their life.
• The condition of the system on start-up is predictable since each element can be tested prior to return.
Offshore desalination provides some unique challenges for system operators but there are numerous precedents that show they can be successful and well-operated. Most of the issues have already been addressed in the context of energy production, making it a viable option for green hydrogen projects wishing to take advantage of sources of readily available wind energy and practically limitless water supply.
Dr Robert Lutze, Dr Tobias Blach, and Alexander Ghazinuri, EnviroChemie GmbH, explore the use of industrial wastewater as an alternative source for bridging the gap between limited water availability and the potential growth of green hydrogen production.
According to estimates, around 40% of the world’s population will live in water-scarce regions by 2050. At the same time, the demand for water will increase by up to 30% due to climate change and population growth. Even formerly water-rich regions in Europe are now struggling with periods of drought and falling groundwater levels. A sufficient and secure supply of water is closely linked to food and energy supplies which is why different utilisation interests can lead to distribution conflicts.
The conversion of the energy and chemical industry to green hydrogen could further exacerbate this situation due to high water consumption for production. The electrolysis process
requires roughly 10 l of water per kg of hydrogen (l/kg H2) for feedstock, and a total of 30 - 70 l/kg H2 for feedstock and cooling depending on electrolyser technology and local climate conditions.1 The potential water demand based on the estimated growth in green hydrogen production in the coming years is provided in Table 1. By 2050, clean hydrogen demand could increase up to 585 tpy which corresponds to a water demand for feedstock up to 5850 million m2/y.2 This potential water demand equals the drinking water consumption of approximately 134 million people. If the water requirement for cooling is included, the amount shown increases tenfold and corresponds to the water use of 1 billion people.
Alternative water sources and innovative water treatment technologies must now be found in order to avoid distribution disputes and increase local water scarcity (Figure 1). The following options are available as alternative water sources to the drinking water network:
• Seawater.
• Surface water (lake or river).
Table 1. Potential water demand for green hydrogen production in the upcoming years
1 According to McKinsey Energy Solutions Global Energy Perspective (2023)
2 Calculated with 10 l/kg H2
3 Calculated within drinking water consumption of 120 l/(person*d)
• Wastewater reuse from municipal wastewater treatment plants (WWTPs).
• Wastewater reuse from Industrial WWTPs.
When selecting suitable processes, the aim is to keep costs, labour efforts, energy consumption, and environmental impacts low. Seawater treatment and surface treatment are state-of-the-art but will not solve the challenges on their own. Seawater treatment leads to high energy consumption (2.6 - 8.5 kWh/m3) and environmental effects of brine discharge back into the sea.3 Surface water treatment is low in energy demand, but problematic in terms of year-round availability of water in sufficient quantities to minimise downstream effects. Using effluent of municipal wastewater treatment plants, the energy consumption is reported between 1.2 and 1.96 kWh/m3 , depending on the process technology used.4 But, the centralised nature of municipal wastewater treatment plants may be difficult to distribute large quantities of water to remote locations.
To provide sufficient feedstock water for hydrogen production, decentralised sources, especially industrial wastewaters, are moving into focus. This article will introduce alternative water supply solutions based on using industrial wastewaters, including solutions for both slightly contaminated wastewater and heavily contaminated wastewater, which could be used as feedstock water for an electrolyser or for relieving pressure on the drinking water network.
For treating inorganically and organically low-polluted mine wastewater, a process chain combining pre-filtration, ozone dosing, ceramic ultrafiltration, activated carbon filter, and reverse osmosis (RO) is suggested (see Figure 2). The centrepiece is a ceramic membrane filtration, which is supported by upstream ozone treatment. The ozone
Mokveld supplied the first valves for hydrogen applications over 30 years ago. At present our axial control valves, on-off valves and check valves are operating in various H2 applications. This includes pure H2 and mixes, like syngas.
Mokveld axial flow valves are lower in weight and in many cases smaller valves can be used than with other valve types. This results in low energy consumption to produce Mokveld valves and therefore lower GHG Scope 3 emissions for our clients.
The one piece body casting of our axial valves reduces the number of leak paths to atmosphere versus many other body-designs. Our Zero Emission Valve even eliminates the dynamic seal to atmosphere thus assuring a lifetime zero emission to atmosphere. Less leak paths not only reduces emissions, but also increases safety.
Historically Mokveld axial valves are found in syngas applications in the Steam Methane Reforming (SMR) process, the hydrogen flow in refineries and fertiliser plants and in the ammonia flow in chemical plants. The minimum pressure loss, perfect tight-shut-off and excellent controllability is highly appreciated by our clients.
Recently new applications are seen. At the outlet of the electrolyser a high integrity safety valve is required to avoid pressure and flow to return from the compressor into the electrolyser. In the production, transport and storage of hydrogen Mokveld over-pressure protection systems, often with mechanical initiators are installed to protect equipment and personnel.
Hydrogen appears as H2, H alone is the smallest molecule. Although H2 is slightly bigger than for example Helium it is still very small. Therefore attention shall be paid to leakage to atmosphere. Also while H2 could be considered a GreenHouse Gas, the 20 year Global Warming Potential is over 30 times that of CO2
Testing for leakage could be performed with Helium. While Helium is finite in the world we prefer to use forming gas (5% H2 + 95% N2) as a safe and sustainable alternate. API 6D Annex M covers forming gas as well.
Hydrogen may cause material degradation, such as embrittlement, but also may degrade surface treatments. Therefore the correct material selection is highly important and dependent of the specific application. (Partial) pressure, temperature, presence of water etc. has an impact on the proper selection. Mokveld can supply the proper material for your application
Mokveld is involved in European (EN), American (API, ASME) and international (IEC) standardization committees to closely follow the developments and advise the best solution for you.
The plant is designed for a permeate volume flow of 4800 m3/d, which, greatly simplified, could be converted to 480 t H2/d. This combination of technologies is also suitable for the energy-efficient treatment of surface water.
destroys both organic pollutants and significantly reduces fouling potential on the membrane. This solution is labelled CembrOzone and minimises membrane fouling with maximum membrane performance and membrane service life. An activated carbon filter to remove residual ozone is followed by reverse osmosis to provide the required water quality.
For a mine in Sweden, the inorganically and organically low-polluted mining wastewater (TOC < 5 mg/l and 16 nephelometric turbidity unit (NTU)) is treated in oversea containers, which allowed a modular design of the plant (see Figure 3). The net flux of the plant is 200 l/(m2h) and the operation pressure is very low at -0.1 to -0.25 bar due to the special silicon carbide (SiC) membrane. The system requires 3 - 5 g O3/m3, which results in a total energy consumption of 0.15 - 0.25 kWh/m3 including peripherals. Added to this is the energy required to treat the water to the quality required by the electrolyser.
One of the largest dairies in Germany produces a wide range of products at the site, including skimmed milk concentrate, condensed milk, and milk powder, the production of which generates vapour condensate.5 Together with the dairy, EnviroChemie GmbH has developed a treatment strategy to facilitate the reuse of this vapour condensate in the production area.
The vapour condensate is low in organic (TOC < 50 mg/l) and inorganic pollution (el. Conductivity < 15 µS/cm). Treatment starts with an aerobic biological process in which dissolved organic compounds are biodegraded by microorganisms that grow in biofilm compounds. Downstream of the aerobic bioreactor is the second stage, a fixed-bed reactor, in which the solids are reduced, and the organic load and nitrogen compounds are further degraded at the same time. The purified water from the fixed-bed reactor is of high quality, but subsequent treatment steps can polish the water. The combination of a multi-stage membrane process with the option of hot water sanitisation are essential features to produce treated water that meets drinking water quality standards. Biological pre-treatment has the advantage of breaking down small organic compounds that might otherwise pass through a reverse osmosis membrane and makes the water storable with a lower risk of microbial regrowth/contamination (Figure 4).
At the dairy in Germany, 188 000 m3/y of process water are provided with this solution (Figure 5). Required energy input for treatment is around 1.2 kWh/m3 of process water. By relieving the drinking water network, an electrolyser producing 20 000 tpy of hydrogen could be installed in this case.
Wastewater with a high organic load often requires complex treatment and multiple process steps for wastewater recycling. As an example, an existing wastewater treatment plant at a potato
processing company in Germany with just a biological aerobic treatment step was expanded and modernised with a flotation, an anaerobic digestion, ultrafiltration, and reverse osmosis (see Figure 6). By expanding the plant and returning the permeate from reverse osmosis to the production, water consumption was reduced by 30 - 40%.
The treatment plant processes 1800 m3/d with a 4170 mg/l COD, 1540 mg/l TOC, and 310 mg/l chloride. In
Table 2. Feedstock water source and energy consumption
the reuse water, the quality criteria of TOC < 4 mg/l, chloride < 50 mg/l, and coliform bacteria of 0 CFU/100 ml were met. Figure 7 shows the specific energy consumption during the modernisation phases. Expanding the existing plant by a flotation and anaerobic biological treatment (2015, 2017) reduced the specific energy consumption to approximately 35% of the reference (2013, 2014). This was realised by generating energy from the methane produced during the anaerobic digestion of organic substances. By modernising the plant for water reuse in 2018, the specific energy consumption increased to approximately 60% of the reference (2013, 2014). The subsequent optimisation phase showed the potential and importance for operational improvements to reduce the energy consumption. By optimising, among other things, the chemical cleaning to extend the filtration cycles of the ultrafiltration, the specific energy consumption could be reduced by 50% to 3.5 - 3.7 kWh/m3 compared to the old plant in 2013/2014. Due to the high effluent quality, the treated wastewater is a good basis for further processing to hydrogen.
In this example, after deducting 40% for water reuse, 1080 m3/d of process water would be available for further use. Assuming a recovery rate of 75% at the reverse osmosis, around 80 t H2/d could be produced from the 800 m3/d of water.
The case studies presented show that industrial wastewater can take a key role in the development of alternative water sources for providing feedstock water required for green hydrogen production. They emphasise the importance of a holistic, systemic approach to local and integrated hydrogen production. In addition, the case studies demonstrate that the suitable combination and optimisation of different technologies can not only provide sufficient water in a required quality, but also provide energetically advantageous and thus economical solutions. The solutions presented offer promising approaches for companies to respond to the challenges of hydrogen production.
Energy consumption during the modernisation of a wastewater treatment plant for potato processing industry.
1. ‘Global Hydrogen Review’, International Energy Agency (IEA), 2024. www.iea. org.
2. ‘Global Energy Perspective 2023: Hydrogen Outlook’, McKinsey & Co., (10 January 2024), https://www. mckinsey.com/industries/oil-and-gas/ our-insights/global-energy-perspective2023-hydrogen-outlook
3. NASSRULLAH, H., ANIS, S., HASHAIKEH, R., and HILAL, N., ‘Energy for desalination: A state-of-the-art review’, Centre for Water Advanced Technologies and Environmental Research (CWATER), (2020).
4. SCHAUM, C., LENSCH, D., and CORNEL, P., ‘Water reuse and reclamation: a contribution to energy efficiency in the water cycle’, Journal of Water Reuse and Desalination, 05.2, p. 83 - 94, (2015).
5. LUTZE, R., WEISSER, T., POERTNER, N.,and KIEFERLE, J., ‘Sustainable Processing: Water Reuse in Dairy Processing’, in: McSweeney, P.L.H., McNamara, J.P. (Eds.), Encyclopedia of Dairy Sciences, Vol. 4. Elsevier, Academic Press, p. 855 - 873, (2022).
Hydrogen, the simplest and most abundant element in the universe, is gaining significant attention as a clean energy carrier. Its applications span industries such as energy, manufacturing, and transportation. However, while hydrogen is celebrated for its sustainability benefits, it also presents unique safety challenges due to its physical and chemical properties. Ensuring safe handling, storage, and use of hydrogen requires robust detection and mitigation strategies. This article explores hydrogen gas detection and safety, emphasising technologies, protocols, and best practices to address the associated risks.
Understanding hydrogen’s key properties is essential to developing safety measures and detection systems. These properties drive the need for specialised technologies and designs:
• Flammability: hydrogen’s wide flammability range (4 - 77% by volume in air) necessitates precise detection to monitor even minute concentrations.
• Low ignition energy: with ignition requiring as little as 0.02 mJ, systems must address risks from static electricity, electrical sparks, or mechanical friction.
• High diffusivity: hydrogen’s rapid diffusion in the air can disperse leaks but also complicates containment and localisation efforts.
• Colourless and odourless: detection depends entirely on sensitive instruments, as hydrogen lacks visual or olfactory indicators.
• Lighter than air: hydrogen rises quickly, accumulating near ceilings or confined spaces, making ventilation and strategic sensor placement important.
Detecting hydrogen hazards promptly helps in mitigating risks. Modern technologies offer a range of solutions tailored for specific applications:
Electrochemical sensors
Electrochemical sensors measure hydrogen concentrations by detecting chemical reactions with the sensor’s electrolyte. They are highly sensitive, capable of detecting hydrogen at parts-per-million (ppm) levels, making them ideal for low-level leak detection. However, regular calibration is required to maintain their accuracy and reliability over time.
Catalytic bead sensors detect flammable hydrogen concentrations by measuring resistance changes caused by a reaction between hydrogen and oxygen on a heated bead. These sensors are particularly effective for detecting hydrogen levels near or above the lower explosive limit (%LEL), making them reliable for high-concentration detection.
When pressurised hydrogen leaks, it produces an ultrasonic sound at the exit point. Ultrasonic detectors
sense this sound, helping to provide rapid detection of leaks, often within milliseconds, regardless of hydrogen concentration, wind, or plume direction. Ideal for monitoring pressurised pipes and vessels in well-ventilated areas, these detectors can identify even small leaks from a distance.
Flame detectors use ultraviolet (UV) and/or infrared (IR) sensing technologies to detect the unique radiation emitted by hydrogen flames. Their rapid response capabilities are desirable for mitigating risks in hydrogen storage, processing, and fuelling environments. Properly installed flame detectors enhance safety by enabling immediate alarms and system shutdowns, helping to prevent the escalation of hazardous situations. Selecting the right detection technology depends on the specific application, required sensitivity, and environmental conditions.
Hydrogen’s unique properties introduce several safety challenges that should be addressed for industrial and commercial applications:
Hydrogen’s small molecular size allows it to escape through tiny cracks or imperfections in storage tanks, pipelines, and fittings. Regular inspections and maintenance are important in preventing leaks.
In confined spaces, leaked hydrogen can accumulate and create an explosive atmosphere. Proper ventilation helps disperse any leaked hydrogen.
Hydrogen’s low ignition energy makes it prone to ignition from static electricity, electrical equipment, or mechanical sparks. Grounding and bonding systems, as well as spark-resistant equipment, are critical in hydrogen facilities.
Hydrogen can cause embrittlement in certain metals, leading to cracks or failures. Using materials specifically designed for hydrogen service mitigates this risk.
Fire and explosion are the main safety considerations associated with handling hydrogen, especially considering wide flammability range of 4 - 77% of volume in air. Explosion protection is currently governed internationally by the IEC/EN/ISA 60079 and ISO/IEC 80079 standards, with many regions adopting almost identical standards locally. Additionally, specific international
Hydrogen leaks and flames can be difficult to detect without the right technology. MSA’s advanced fire and gas detection systems can help mitigate risks and support a safer workplace. Explore Hydrogen Detection Solutions at msasafety.com/hydrogen-detection-solutions
standards for hydrogen facilities are also available, for example:
• ISO 22734 – Hydrogen generators using water electrolysis – Industrial, commercial, and residential applications: manufacturers of electrolysers are required to perform a risk assessment. However, depending on the final placement location of the equipment, plant owners/operators may need to perform their own additional assessment on the hydrogen generator, applying zone classification using IEC 60079-10-1 or an appropriate national standard.
• ISO 19880 – Gaseous hydrogen – Fuelling stations: sites must be inspected in accordance with the IEC 60079-10-1 standard or sufficient national regulations. This includes zone classification and ignition protection methods to IEC 60079 and IEC 80079.
Both standards also specify requirements for risk mitigation with gas detection systems as one of the methods to prevent accumulation of ignitable gas mixtures. However, these standards do not give detailed guidance about selection or installation of gas detectors. Therefore, by following IEC/EN/ISA 60079 series of
standards, organisations can help to ensure that their fixed hydrogen gas detection systems are properly specified, installed, and maintained to enhance safety in hazardous environments.
Additionally, NFPA 2 is a US standard developed by the National Fire Protection Association (NFPA), a non-profit organisation based in the US:
• NFPA 2 – Hydrogen Technologies Code, developed by the NFPA, provides guidance on the safe design, installation, and operation of hydrogen systems. It outlines safety practices for hydrogen storage, production, handling, and use across various applications, including fuelling stations and fuel cell technologies. The code addresses fire prevention and mitigation measures to reduce risks associated with hydrogen. Compliance with NFPA 2 supports organisations in implementing best practices for safety in hydrogen-related operations.
While this standard is primarily intended for use within the US, it is also referenced and adopted internationally in regions where hydrogen technologies are being implemented, given its comprehensive approach to hydrogen safety. It serves as a valuable resource for local jurisdictions, industries, and facilities working with hydrogen to align with US fire and safety codes. Compliance with these standards helps ensure the safe implementation of hydrogen technologies across industries.
An effective hydrogen safety system encompasses detection, ventilation, suppression, and emergency response capabilities. Key considerations should include the following.
Deploy a combination of hydrogen gas sensors at critical points, such as storage areas, pipelines, and confined spaces. Sensors should be strategically placed near potential leak sources and high-risk zones.
Proper ventilation is necessary to prevent hydrogen accumulation. Natural or mechanical ventilation systems should provide continuous air exchange to disperse leaked hydrogen.
Install flame arrestors to help prevent flame propagation in pipelines. Fire suppression systems, such as water spray or foam systems, should be readily available.
Incorporate automatic shut-off valves that activate during a leak to isolate hydrogen flow and minimise risks.
Link detection systems to audible and visual alarms to alert personnel of leaks promptly. Integration with facility control systems enhances response coordination.
HEAR FROM OVER 400 LEADING HYDROGEN EXPERTS AND GOVERNMENT OFFICIALS
NETWORK WITH OVER 15,000 GLOBAL ATTENDEES ACROSS 3 EVENT DAYS
EXPLORE A WORLD CLASS EXHIBITION AND OVER 700 EXHIBITORS
THE INDUSTRY’S MOST INFLUENTIAL EVENT, WORLD HYDROGEN 2025 SUMMIT & EXHIBITION RETURNS TO ROTTERDAM FOR THE LARGEST EVENT YET.
JOIN THE LARGEST AND MOST GLOBAL HYDROGEN-FOCUSED EXHIBITION IN THE WORLD, VISIT THE H2 TECH SERIES, EXPLORE THE SITE VISITS TO THE PORT OF ROTTERDAM AND HEAR FROM TOP HYDROGEN EXPERTS ACROSS 3 FULL DAYS OF CONTENT!
Implementing best practices enhances the safety of hydrogen operations:
• Training and awareness: regularly train employees on hydrogen safety protocols, emergency response procedures, and the proper use of detection equipment.
• Periodic inspections: conduct routine inspections of storage tanks, pipelines, and detection systems to identify and rectify potential issues.
• Use of personal protective equipment (PPE): ensure workers have access to appropriate PPE, such as portable gas detectors, flame-resistant clothing, and face shields.
• Risk assessment: conduct comprehensive risk assessments to identify hazards and implement mitigation measures tailored to specific applications.
• Incident documentation and review: record all incidents involving hydrogen and analyse them to identify root causes and improve safety protocols.
The growing use of hydrogen in green energy applications, such as hydrogen production, storage, and distribution,
introduces new safety considerations, including the following.
Green hydrogen generation often requires co-locating hydrogen production with renewable energy production sites, like wind turbines, solar panel farms, or hydropower systems. This may cause additional issues for the whole local production infrastructure in the event of a hydrogen gas leakage, ignition, or explosion. Therefore, mitigation systems should be installed to ensure safe operation.
For most applications, hydrogen is stored as a gas and is often compressed in high-pressure tanks. When under pressure, hydrogen gas leaks are likely to be in the form of gas jets. The shape of these jets is typically long but narrow, and the momentum of release can maintain this shape for a considerable time. This increases the likelihood of the gas jet bypassing conventional gas detectors for a lengthy period, requiring diversified sensing technologies.
For hydrogen distribution, pipelines are seen as the primary method for mass transport of hydrogen gas. However, existing infrastructure, such as the natural gas network, would need to be adapted before it could distribute hydrogen from production centres to places of use. This is because hydrogen can degrade certain materials, such as commonly used metals, and make them brittle and more prone to leaking.
Hydrogen is mainly used for industrial needs, such as refining, ammonia, and methanol production. However, with green hydrogen cost optimisation, usage for mobility, electricity production, decarbonised steel production, and energy storage will grow. Critical challenges for any site handling hydrogen include detecting leaks outside, where the gas cannot accumulate, and installing detectors in appropriate quantities and locations is difficult to plan.
Hydrogen presents significant potential as a clean energy carrier, but its adoption requires addressing associated safety considerations. By gaining a thorough understanding of hydrogen’s properties, utilising advanced detection technologies, adhering to established safety standards, and following recommended best practices, industries can work toward safely utilising hydrogen.
A safe transition to a hydrogen-powered future depends on maintaining safety as a priority throughout its lifecycle. Implementing robust safety measures at every stage – from production and storage to transportation and application – supports the sustainable and secure use of hydrogen.
Gabriele
Hydrogen holds immense promise as a sustainable energy source that can drive the world towards a zero-carbon emission future. By using renewable resources for production, green hydrogen eliminates CO2 emissions at the source, setting a new standard for clean energy. However, hydrogen is highly flammable and explosive, and special safety measures need to be in place when handling and storing it. Leak detection and control is crucial to prevent accidents. Looking at the value chain of hydrogen, some typical and well-established safety solutions used for the process industries, such as those supplied by HIMA Group, can be used for hydrogen service, but some have to be adapted due to the higher risks that hydrogen presents.
What is now called ‘grey’ hydrogen is used as a fuel when combined with natural gas in boilers. ‘Green’ or decarbonised hydrogen is a very small percentage of the hydrogen used in industrial processes, such as steam reforming, hydrocracking, and hydrotreating, but it is expected to increase in percentage dramatically in the near-term. The petroleum refining sector accounts for most hydrogen usage now, but there are other sectors where hydrogen is used extensively. Producing ammonia for fertilizers using the Haber-Bosch Process uses a considerable amount of hydrogen. Hydrogen is also used in making many important industrial chemicals, and it is used significantly in the food and pharmaceuticals industries for making vitamins and hydrogenated oils. In the metals industries, hydrogen is mixed with inert gases to produce a reducing atmosphere for applications like direct reduction of iron ore, as well as heat-treating and welding. The most common method of producing hydrogen currently is the steam methane reformer process. Sometimes hydrogen is manufactured from coal gasification.
Some significant markets are emerging for decarbonised hydrogen. Making hydrogen in a carbon-neutral way will be extremely important. Unfortunately, the cost of making decarbonised hydrogen by electrolysis is currently about four times the cost of a steam reformer process. As the cost is reduced, hydrogen is expected to replace natural gas as a fuel in power plants and generation facilities. It is also likely to be used for applications
like fuel cells for transportation with no carbon emissions. It is expected that hydrogen will be used to manufacture sustainable synthetic fuels along with capturing CO2
Safety instrumented systems have been used in many applications in plants and pipelines for decades. Oil and gas industries are making use of hydrogen at various applications. HIMA Group, a global provider of safety-related automation solutions for the process and rail industries, offers safety solutions for the industrial usage of hydrogen. These functional safety solutions can be used at hydrogen services discussed here without special modifications. The new challenges are the issues of the physical behaviour of hydrogen, including aspects like the pressure rating of pipes, which in conjunction with the embrittlement of steel pipes and structures, can cause additional risks. As a consequence of such risks, special attention needs to be paid to leakages.
Wind farms are being installed for producing carbon-free energy. Along with solar power, these clean energy sources are used for
the electrolysis of water to produce green hydrogen. For wind farm management – especially for offshore installations – SCADA+ is available to collect and process all relevant data required to safely operate such wind farms. This product is providing comprehensive, user-friendly functionalities supporting effective wind farm management. SCADA+ is a digital platform of HIMA, developed by Origo Solutions – A HIMA company, and is powering control rooms for offshore wind farms.
Several safety requirements must be considered for electrolysers. Emergency shut down systems are designed to control and monitor the safety functions such as pressure, temperature, and fill level. Electrolysers produce decarbonised hydrogen from water which is called green hydrogen. These safety functions today are typically SIL 2 rated. If larger electrolysers are considered, they will become SIL 3 systems as the production of green hydrogen scales up, leading to a higher embedded operational risk.
The biggest issue in transportation and storage of hydrogen is that the hydrogen molecule is extremely small in comparison to other, heavier molecules like methane (CH4), and it can infiltrate the lattices of metals and permeate into the metal. Hydrogen absorption by metals such as alloy steel used in piping and valves and wet ends of pumps and compressors lowers the mechanical stress allowable before failures occur. This is called embrittlement and produces fractures and damage to pipes and vessels used to move or contain hydrogen. Since hydrogen is so intensely flammable, one of the things users and manufacturers of hydrogen must do is to ensure that hydrogen in its gaseous form is not leaking from unsuspected cracks in the piping or tankage.
Hydrogen occurs in the gaseous state at standard temperature and pressure (STP), and liquifies at a very low temperature, requiring a lot of energy to be removed from the hydrogen. Safety functions are required in machine controls for these applications. To transport hydrogen easily, it should be transported in its liquid state, in vessels and vehicles designed for transport of very cold materials, requiring supervision. For delivering hydrogen to users, energy needs to be injected, triggering regasification.
There are common applications such as turbomachinery control (TMC) for compressors, emergency shut down (ESD) for supervisory, and burner management systems (BMS) for regasification. In addition, fire and gas safety systems are required to create mitigation functionalities supporting an adequate operational risk reduction, if large scale hydrogen processing plants are installed in industrial or urban areas. In each of these cases, the use of safety controllers, exactly as in other process applications, enables traditional methodology to be applied for safety instrumented systems as an appropriate means of risk reduction. Special attention is required when looking
Hydrogen is the most plentiful element in the known universe. It is the lightest element, formed early after the big bang, and constitutes approximately 75% of all the matter in the universe. It is commonly found on earth as a two-element molecule, called dihydrogen, and at standard temperature and pressure it is a gas. Liquified hydrogen at atmospheric pressure is produced by reducing the temperature of the gas to -252.87 °C.
Hydrogen is extremely flammable and has a relatively low autoignition temperature (500˚C). Because of the ubiquity of hydrogen, and the fact that it can be produced by electrolysing water, it has been touted for a long time as the fuel for a decarbonised future. The ‘hydrogen economy’ is a term for using hydrogen alongside low-carbon electricity to help reduce the greenhouse gas emissions.
Hydrogen is transported within plants by pipelines and stored in tanks for future use. These pipelines, and the valves, meters, and other components of the pipelines themselves, as well as the storage tanks, are subject to hydrogen embrittlement. Because hydrogen is flammable, the areas where tanks stand, and where pipelines go, are classified as hazardous areas. The use of safety instrumented systems in these areas is required.
Outside the plant, hydrogen is transported by truck, train, and ships. The vessels and piping on each of these modalities must be designed and built specifically for hydrogen service. In nearly all cases, the hydrogen is transported in its liquified form to reduce the bulk and increase the quantity that can be carried. This means that the vessels must be cryogenic and maintained at a very cold temperature internally. This temperature must be maintained to a very close tolerance, or the liquified hydrogen will gas off, producing flow problems in the pipelines, cavitation in flowmeters, valves, and compressors, and make transporting hydrogen very difficult.
at the reliability of emergency shut down valves, as these components are crucial for the safe operation of hydrogen plants and are also exposed to high levels of mechanical stress. For such kind of applications, the HIMA technology for implementing high pressure protection systems (HIPPS) across the oil and gas industries helps operators to safely run and monitor such valves. For transportation by train, HIMA offers the Automated Power Changeover solution, developed by Sella Controls – A HIMA Company.
When looking at hydrogen as a source of energy supporting public transportation, the mix of different fuels, depending on the existing infrastructure, is an important topic. For areas where electrical overhead lines exist, the most effective source of energy is electricity. Areas with no overhead lines can be covered using hydrogen as an alternative source of energy.
One of the technical challenges when doing this, is to decide when and where to lift the pantograph of the electrical supply system. As part of the SIL 2 certified TrackLink® 3 application suite, HIMA offers an application that allows the pantographs to be automatically lifted and lowered in a safe fashion. This allows the most effective source of energy to be utilised depending on the infrastructure along the track sites while fully supporting operational safety.
Because of the known tendency for hydrogen embrittlement of pipes, valves, and storage vessels, it is necessary to have automatic, continuous leak detection systems. These systems are designed to increase the safety of the hydrogen transport. In pipeline applications, one of the most important safety systems is the leak detection system (LDS). The market for hydrogen pipelines is growing rapidly, with over 90% of demand in Europe and North America. Hydrogen pipelines pose significantly increased dangers and risks compared to conventional natural gas pipelines. Accurate, reliable, and fast leak detection is crucial to the safe operation and control of hydrogen pipelines.
Group.
An example of pipeline management is HIMA’s FLOWorX® leak detection solution, commonly used for water, oil, and gas pipelines and now also ready for hydrogen. This leak detection solution uses a combination of different measurements (pressure, flow, and temperature) combined with a mathematical model of the individual pipeline for calculating the thermodynamic properties of the hydrogen transported. The combination of this approach with multiple, traditional pipeline-monitoring computational methods (e.g. enhanced pressure wave, the pressure drop method, compensated volume balance) to monitor and protect the pipeline under all operating conditions, covers steady operations, start-up and shut down, as well as stand still. The accuracy of the determination of hydrogen’s thermodynamic properties is critical, especially for the accuracy of the leak detection and leak allocation functions.
This special supplement focuses on decarbonisation pathways for the downstream sector, highlighting innovative technology and solutions that will help you thrive within the energy transition.
Scan the QR code to download your free copy of EnviroTech 2024.
Computation of accurate mathematical results requires high-accuracy flow, pressure, and temperature measurements tailored to hydrogen service along the entire pipeline. In case the leak detection is added to an existing automation solution, the accuracy, repeatability, and scan time of the instrumentation, as well as the data processing times at the existing programmable logic controller (PLCs) or connected distributed control system (DCS), need to be reviewed. A processing time of 0.5 seconds will cause an inaccuracy at the leak allocation of approximately 1.2 km. It is important to detect small leakages to minimise the ignition risk at the location of the leak. It is also important to prevent noise from the pressure transmitters. A potential noise of just 0.1 bar will jeopardise such important functionality.
With the increase in computer- and network-based controls and systems, one of the most significant potential risks of the modern day is a cyberattack, targeting security vulnerabilities. Without a sufficient level of security, there can neither be reliable automation nor functional safety at all. In simple words: there is no safety without security. Even though functional safety and OT security are strongly linked, both are still different things, requiring different strategies for implementation. While functional safety and automation reliability are focusing on technical malfunctions following static fault models, OT security is focusing on vulnerabilities which, in combination with an attack, may lead to a loss of either functionality or data, or both. In order to cope with the security challenges in a safe way, HIMA is following the concept of establishing a security environment for functional safety.
This in practice means that all components of a solution are encapsulated in a virtual space where all devices are protected on a certain level and the gates open to exchange data with the outer world are limited and protected in a way limiting the usage to what is required to run the desired functionalities. Based on specific device hardening concepts, in combination with long-term service agreements, it allows customers to maintain secure operation for long periods of time.
When safety and security are prioritised, hydrogen can fulfil its potential as a clean energy source, ready to fuel the future.
A podcast series for professionals in the downstream refining, petrochemical and gas processing industries
Sponsored by
Alan Gelder, Senior Vice President of Refining, Chemicals and Oil Markets at Wood Mackenzie, provides a review of downstream markets in 2024 and looks ahead to what 2025 may hold for the sector.
Dr Klaus Brun, Global Director of Research & Development, Ebara Elliott Energy, joins us to discuss the progress that is being made towards adapting centrifugal compressors for high-speed hydrogen compression.
Peter Davidson, CEO of the Tank Storage Association (TSA), joins us to discuss the essential role that the tank storage sector has to play in ensuring supply security and resilience, as well as in facilitating the energy transition.