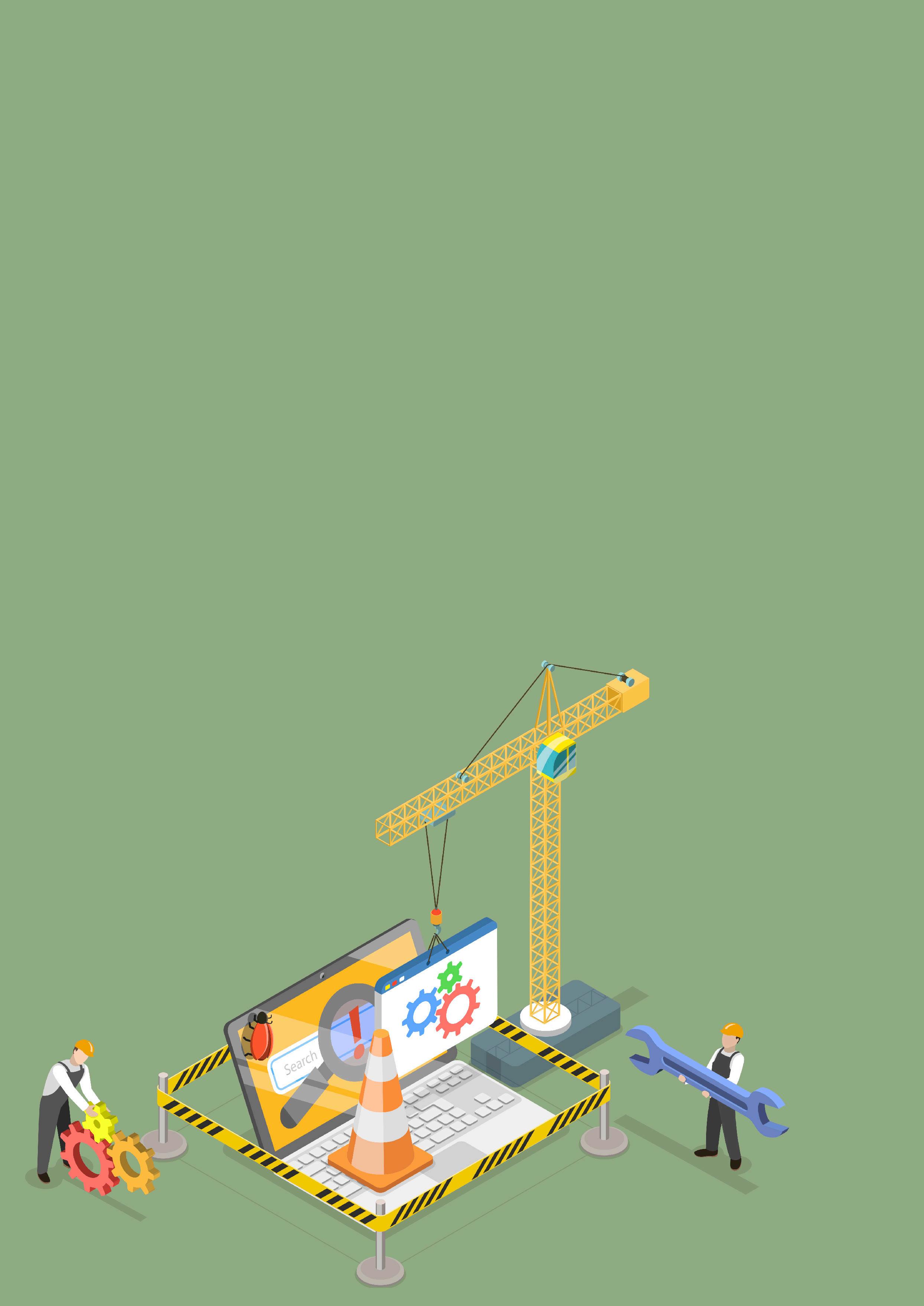
4 minute read
Protecting your workforce
Aaron Moore, CWI, Product Manager, Miller Electric Mfg. LLC, USA, outlines the best practices for improving productivity and reducing downtime in pipeline welding.
Critical pipeline welds demand highly skilled operators capable of meeting strict quality standards and deadline pressures. Failing to be a consistent performer can be a problem, especially in a next-man-up environment. Maximising productivity in pipeline welding – while prioritising quality and avoiding unnecessary downtime – are the main priorities for pipeline welders.
Consider how some best practices and choosing the right welding equipment can help save time and maintain quality on the ROW.
Pipeline welding priorities
Low-carbon, low-alloy steel pipe has traditionally been welded using the shielded metal arc welding (SMAW) process. Cellulosic filler metal electrodes and downhill welding techniques have remained relatively unchanged over the years, but welding codes, testing procedures, and quality standards have become more stringent.
At the same time, contractors face increasing competitive pressures to complete projects more quickly and efficiently. This creates an urgency to ensure projects stay on schedule, meaning high productivity while maintaining weld quality and avoiding repairs is crucial.
For pipeline welders, these changes have meant more pressure to avoid weld defects while keeping up with tight project timelines. Welders often have a quota of the number of weld joints they must complete in a day. They can’t afford to get side-lined by issues with their welding equipment. When that happens, they’re unable to perform their job, or they may need to rely on borrowed equipment.
Following some best practices can help optimise equipment performance and save time. Consider these three tips for pipeline welding:
1. Be flexible to improve versatility The use of harder (X70 and above) variations of pipe has become more common in the field, as engineers design pipelines to maximise service life and reduce maintenance costs. However, factors such as heat input, and the diffusible hydrogen value for the filler metal become more critical. As a result, they may require specialised filler metals and welding processes when being constructed.
The demand for advanced wire welding processes, like pulsed MIG and a modified short-circuit MIG, such as the Regulated Metal Deposition (RMD®) process from Miller, is growing every year. These processes can deliver significant increases in deposition rates and welding speed, while also improving quality and minimising defects. Welders who are proficient with wire welding increase their job opportunities in pipeline welding. Although downhillSMAW welding will be around for the foreseeable future, operators shouldn’t let their welder/generators limit job capabilities, so it’s important to have a welder/generator capable of running different wire processes.
2. Take advantage of new engine-drive technologies When looking to maximise weld quality and machine performance, one place to turn is the welding equipment on the rig. Like some filler metals, much of the welding equipment seen in the field has remained unchanged, leaving significant room for improvement in areas of arc quality and adaptability, machine consistency and ease of use. Newer welding technologies can help improve weld quality while also boosting productivity and reducing rework.
One example is Dynamic DIG™ technology from Miller, which is designed specifically for downhill pipeline welding. It produces a tailorable arc that can be adapted to the welder’s preference and the application. Having an optimised amount of drive in the puddle – combined with a faster adapting arc – means operators can better handle issues like bad fit-up and uneven land thicknesses, ultimately enabling more flexibility to adapt and produce a higher quality of weld. The technology also creates a more manageable, drier puddle, which can maximise drive and penetration and allow the operator to carry a larger puddle at high travel speeds.
Another engine-drive technology to look for is a wireless remote that allows full control of the machine interface in the palm of the operator’s hand. The ability to swap between programmes with the press of a button lets operators adjust settings like amperage, arc control, and dig range for each pass – from the root to the cap pass. This eliminates the time to adjust settings and enables optimal settings for each pass.
A wireless remote also eliminates the need for the heavy control cable, which reduces setup time as well as cable management and maintenance on the right-of-way.
3. Choose reliable and consistent equipment Machine reliability and consistent performance are a basic need for pipeline welders. Look for a welder/generator that won’t require different settings in the hottest time of the day vs when the shift started. Also, keep the welder’s helper busy by looking for equipment that can produce auxiliary power while simultaneously welding – without affecting the weld arc.
New features, like industrial USB ports, have been introduced on some welder/generators. Having access to free software updates from the manufacturer gives operators the ability to quickly troubleshoot their machine while also providing the opportunity to stay up to date with arc development. Software for engine-driven welder/generators is continuously being improved and optimised by the manufacturer.
Pipeline welding best practices For pipeline welders, weld quality and productivity are the two staples that will get them called back for the next job. Following some best practices – and choosing the right welding equipment and technologies – can help operators tackle challenges on the ROW and optimise field welding performance.
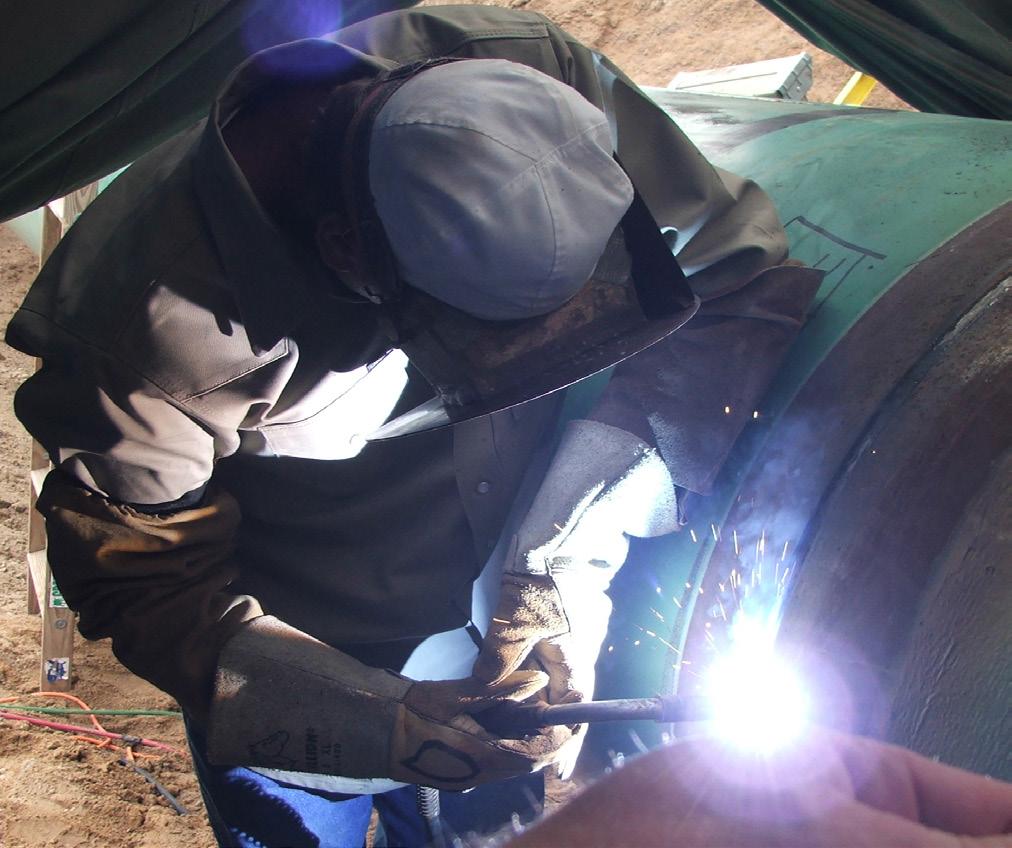
Figure 1. Although downhill-SMAW welding will be around for the foreseeable future, operators shouldn’t let their welder/ generators limit job capabilities. It’s important to have a welder/ generator capable of running different wire processes.
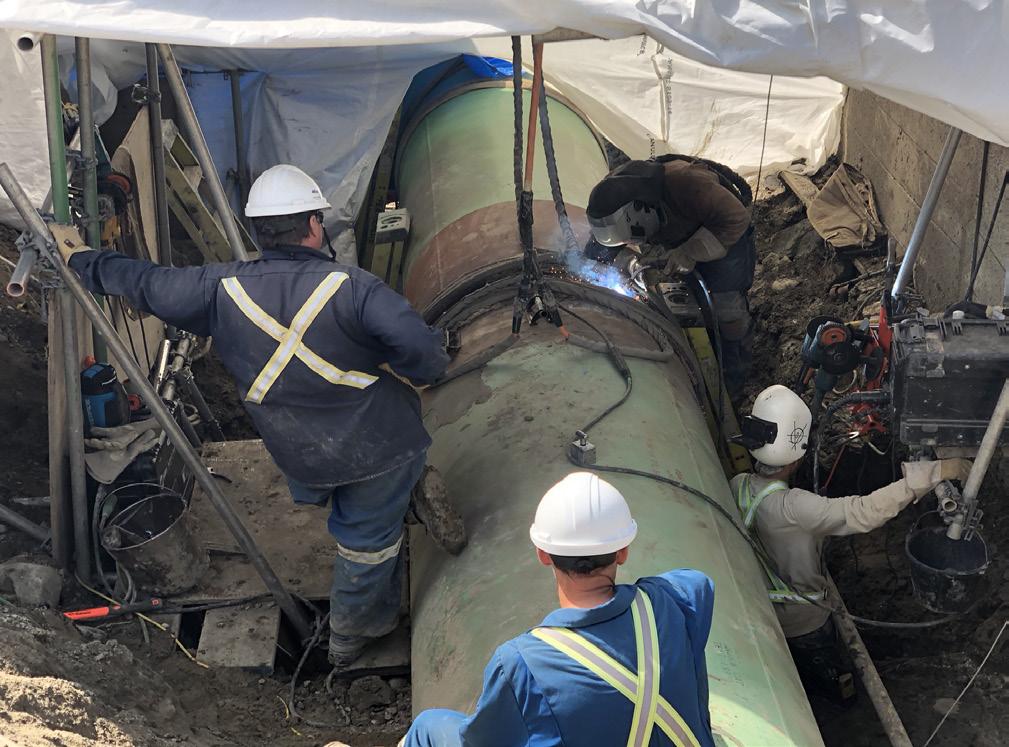
Figure 2. The demand for advanced wire welding processes is growing every year. These processes can deliver significant increases in deposition rates and welding speed, while also improving quality and minimising defects in pipeline welding.
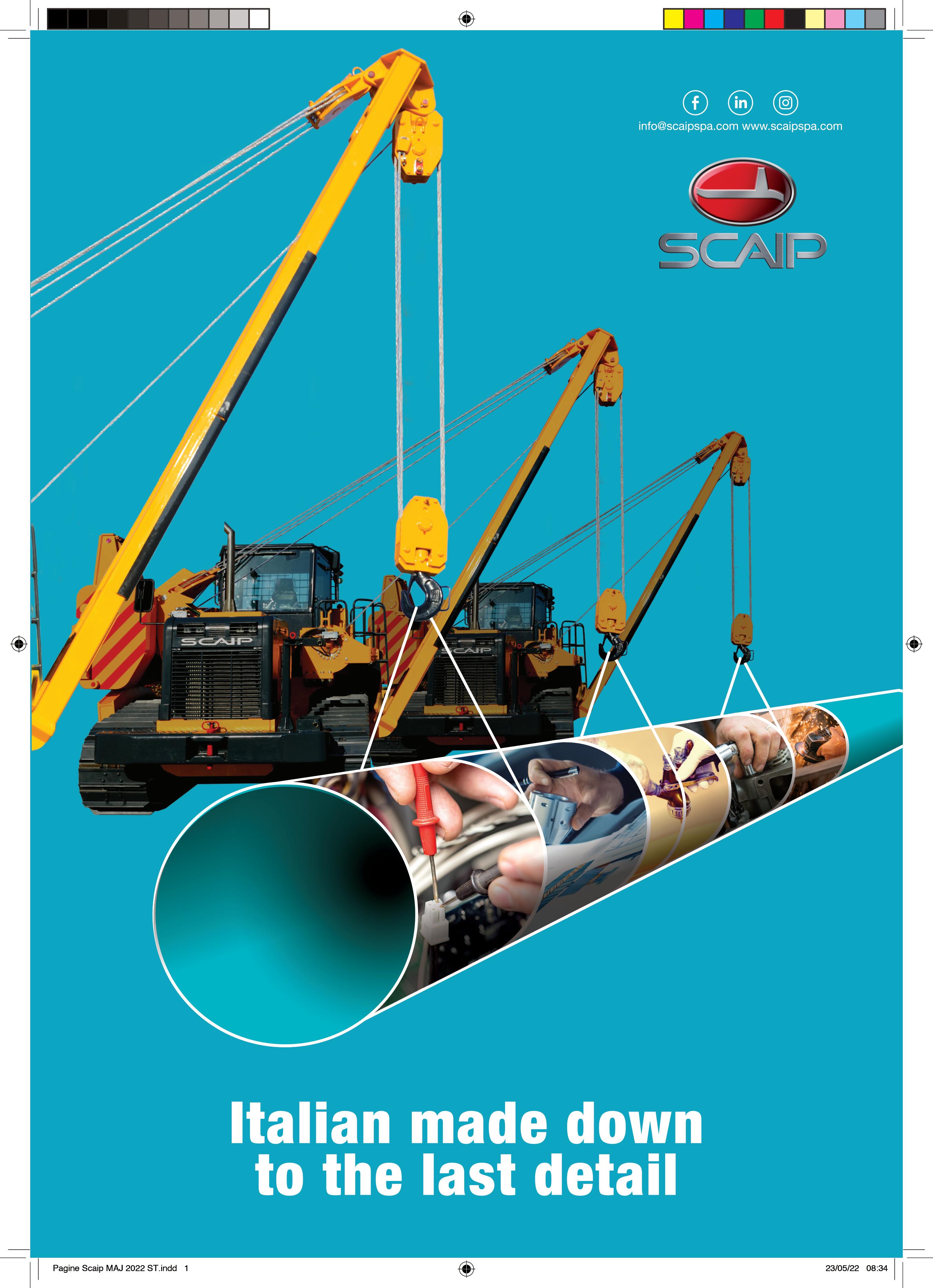
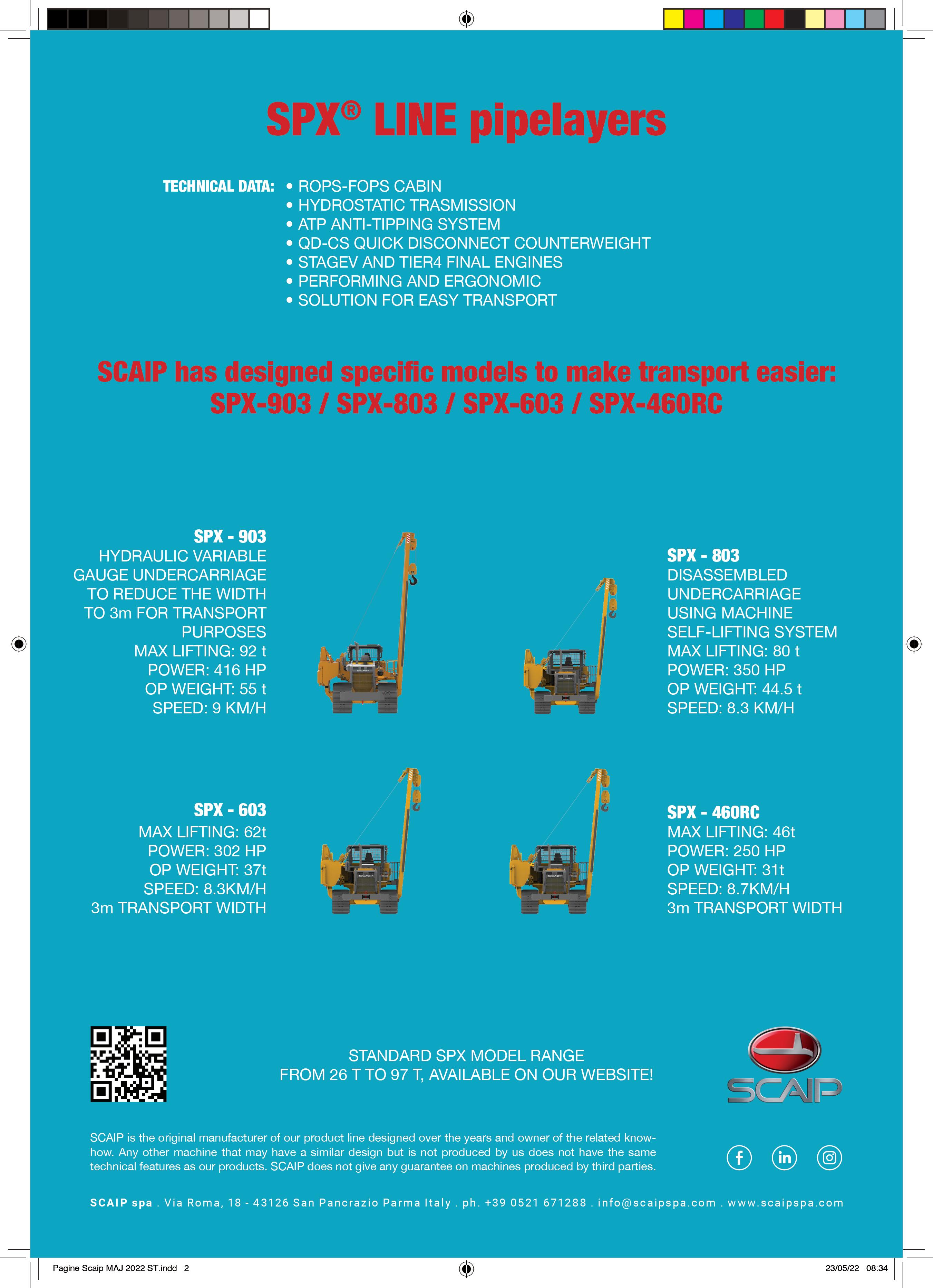