TECHNICAL: Foundation systems for scaffolding
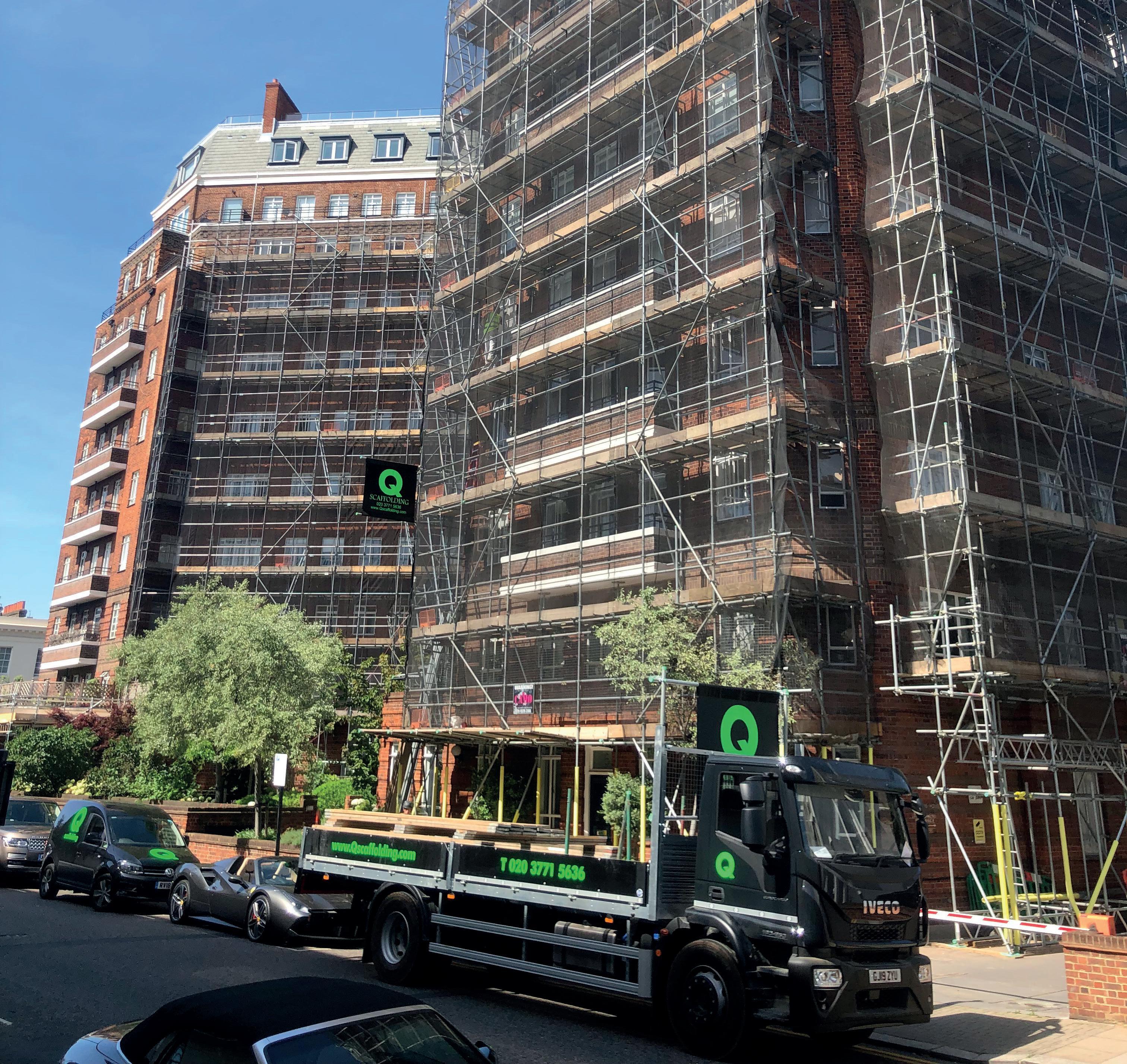
TECHNICAL: Foundation systems for scaffolding
The Federation of Master Builders (FMB) has unveiled plans for the mandatory licensing scheme for all UK construction companies to transform the sector into a high-quality and professional industry.
A new Construction Licensing Task Force, supported by leading industry bodies, is at the centre of the licensing scheme. More than three-quarters of small and medium-sized (SME) construction firms support the introduction of licensing to professionalise the industry, protect consumers and side-line unprofessional and incompetent building firms; and 78 per cent of consumers want a licensing scheme for construction introduced.
The decision to establish a Construction Licensing Task Force follows a recommendation in Licence to build: A pathway to licensing UK construction, an independent research report published in 2018, which detailed the benefits of introducing a licensing scheme for the whole construction industry and put forward a proposal for how it could work.
The Task Force will be chaired by Liz Peace CBE, former chief executive of the British Property Federation.
FIND OUT MORE www.accesspoint.org.uk
EDITORIAL
Editor: Adrian JG Marsh
Assistant Editor: Jenny Gibson Telephone: 01926 420 660
Email: newsdesk@campbellmarsh.com
AccessPoint, Althorpe Enterprise Hub Althorpe Street, Leamington Spa CV31 2GB
Design: Matthew Glover
SUBSCRIPTIONS
AccessPoint is distributed to members of the Scaffolding Association and other selected access and scaffolding businesses. If you wish to receive a copy of AccessPoint or would like to amend or cancel your subscription, please contact either info@scaffolding-association.org or call 0300 124 0470.
ADVERTISING Advertising enquiries: Sally Smith Tel: 0300 124 0470 sally@scaffolding-association.org
Scaffolding Association Tel: 0300 124 0470 www.scaffolding-association.org
Email: info@scaffolding-association.org
ISNN: 2055-2033
New research from Market.biz has revealed that the scaffolding accessories market in the UK was estimated at around £230 million in 2018, growing at a compound average growth rate (CAGR) between 2 and 3 per cent over the forecast period (2020-2029).
The global scaffolding accessories market is expected to reach £33 billion by 2026, expanding at a CAGR of 6.1 per cent from 2018 to 2026.
According to the report, the total market size for China and North America held the highest market share in the scaffolding accessories market in 2017.
Increasing scaffolding demand from the construction industry with high rise commercial buildings and improvement in residential infrastructure along with new constructions is expected to support the growth of the global scaffolding accessories market over the forecast timeline.
Maintenance, which involves cleaning, repairs, painting jobs, electrical installations and other activities, will drive the demand for scaffolding accessories over the forecast period.
FIND OUT MORE www.market.biz
The construction industry united last month in calling for a delay to changes to the way VAT is charged and paid – due to come into effect on 1 October – because it will affect cashflow and could force some companies out of business.
In a letter to the Chancellor from a coalition of the major trade bodies, including the Scaffolding Association, calls were made to push back implementation by at least six months, highlighting issues with timing and the associated pressures on the industry regarding material prices, increased pension contributions and skills shortages.
Robert Candy, chief executive of the Scaffolding Association, said: “The implementation of Reverse VAT Charging will have a significant impact on the cashflow of scaffolding contractors. By delaying its implementation, these businesses will have the opportunity to suitably prepare themselves for the planned changes. But scaffolding contractors should make sure that they are prepared if the government does not delay the changes.”
As of 1 October, HMRC plans to introduce VAT Reverse Charging on the majority of construction-related services. Companies who
are VAT registered and Construction Industry Scheme registered will no longer pay VAT to the majority of their subcontractors.
VAT will only be paid to firms who supply labour only (employment businesses) and to the merchants and businesses that sell building materials only without any fix. The purpose of the change is to combat VAT fraud perpetrated by organised crime gangs.
FIND OUT MORE Turn to page 14 for more information on Reverse VAT Charging
Castle Scaffolding is the latest Scaffolding Association member to successfully complete the independent audit to reach Audited Membership status.
A key part of the Association audit is a thorough on-site assessment of a live project –the project audited for Castle Scaffolding had been up for almost a year. Managing director Ryan Jewell explained why the audit strongly demonstrates to clients a company’s actual on-site quality and continuing standards, not just the quality of a company’s paperwork.
Mr Jewell said: “Audited Membership gives our company so much over and above other accreditations.
“It reinforces that what we do, we do consistently well – all day, all year. Being Audited Members of the Scaffolding Association reassures main contractors that they are employing a professional and established company that understands the importance of delivering consistently high quality standards and high service levels.”
FIND OUT MORE www.scaffolding-association.org/membership-levels
Our experienced customer driven team provides a seamless service from product development, supply chain management, production, quality control, delivery and local engineering support available for fast, effective solutions where required.
The Scaffolding Association has agreed a partnership with Mates in Mind, the national mental health charity, to improve awareness and understanding of mental health across the access and scaffolding sector.
Recent surveys suggest that two-thirds of construction workers want better physical and mental wellbeing support from their employers. There have also been calls for construction to have a greater awareness of mental health and eradicate the stigma associated with it.
Robert Candy, chief executive of the Scaffolding Association, said: “We are very pleased to be partnering with Mates in Mind to highlight this important area of welfare to all our members. Such issues can go unrecognised and have impact on the business directly, so a change in culture must be activated for the benefit of both the worker and the employer.”
Mates in Mind will be engaging the Scaffolding Association’s members. Support will include the development of a tailored action plan, campaign materials, access to a suite of communication and advice, as well as a range of training opportunities and more, to enable organisations to drive long-lasting and meaningful change.
FIND OUT MORE Turn to page 24: The reality of mental health
AT-PAC HAS UNPARALLELED EXPERTISE AND PROFESSIONALISM WHICH ENABLES US TO CONSISTENTLY DELIVER COMPLETE SCAFFOLDING SOLUTIONS.AT-PAC Ringlock is a modular system scaffold which enables users to quickly and efficiently erect, use and dismantle temporary work structures. The AT-PAC Ringlock system conforms to European standards BS EN12810 and BS EN12811 and it is compliant with NASC Code of Practice for System Scaffold. Castle provided scaffolding for the refurbishment of The Minster Building, London.
Suicide kills more construction workers than falls do, and to help scaffolding contractors tackle this sensitive issue, the Scaffolding Association has teamed up with Mates in Mind (see page 3) to encourage the sector to boost awareness of mental health and eradicate the stigma associated with it.
Increasingly, we know how important it is to treat mental health as seriously as physical health. Early action can prevent employees reaching a desperate stage where some sufferers feel there is no other option.
Employers who recognise the challenge and take steps to provide support find that it not only helps their employees but can also improve the productivity of their businesses.
On page 24, read how one scaffolding business has been taking big steps to combat the issue. Pro Scaffolding (South West) should be congratulated for the important work they are doing.
Inside this issue (turn to page 18), we learn more about the importance of adhering to the correct standards when designing and erecting scaffolds. As structures become more sophisticated, contractors need to recognise the importance of selecting the right products to do the right job.
Commercial pressures are often a temptation to purchase look-a-likes or clones that just don’t perform as you would expect. Product test certification was introduced to give buyers confidence that the products they are buying had passed performance tests and meet the criteria stipulated.
Two years on from the Grenfell Tower disaster, clients and insurers want to know more about products being used on sites. Contractors look to manufacturers and distributors for an assurance in the quality of the products being used. But contractors must read test certificates provided with greater care, otherwise they could be putting themselves at risk.
Without a valid test certificate, buyers could use a product that might not be safe (turn to page 16). But how often do contractors inspect a test certificate and, if they do, do they understand what it means?
We exist in a world that increasingly tests the sectors to deliver a wider range of services. People and products are key to safer and more profitable performance.
Adrian JG Marsh EditorIt is difficult to slow down progress and avoid change. Those who avoid change and innovation will ultimately see it take place elsewhere, and so future opportunities could either be missed or lost forever.
The sector’s capacity to respond to the changing access and scaffolding environment is restricted by the availability of well-trained and skilled scaffolders. Increasingly, the sector has focused on ensuring that anyone working on-site can demonstrate that they have achieved a nationally recognised standard of competency.
This is a good thing, but what’s the most appropriate way to both bring new people into the sector and upskill those already working in it?
Earlier this year, the Construction Skills Certification Scheme (CSCS) confirmed the withdrawal of Industry Accreditation cards, also known as Grandfather Rights. These gave workers the opportunity to obtain a CSCS card on employer recommendations rather than with proof of a recognised qualification.
Workers wanting to stay in the sector, from January 2020, will now need to hold an NVQ and those without qualifications will be required to register for the appropriate qualification for their occupation before their cards expire. Once a card expires, it could take two years for an individual without an NVQ to gain or regain the qualification.
My suspicion is that there are potentially a large number of more mature construction workers, supervisors and managers who do not hold an NVQ – probably because, when they started, it was not necessary. Now the goal posts are changing and inadvertently the powers that be may be excluding a number of trade-qualified personnel from being able to work.
The Scaffolding Association has tried to work within the established structures to bring about change in the training of scaffolders – but bringing about meaningful change has been a challenge. This is why plans to increase training and skills delivery capacity for access and scaffolding contractors led to setting up the Access Industry Training Scheme (AITS).
As an employer-led solution, AITS is more receptive to the needs of contractors, with training programmes developed to be flexible and suited to the needs of the type of work a company carries out.
There is no one size fits all. The requirements of a scaffolding contractor working in the nuclear or oil industry are likely to be different to those of a contractor servicing the needs of housebuilders and domestic homeowners.
We need to have a minimum standard of competency that is then flexible enough to allow every individual scaffolder the opportunity to progress as far as they want to progress.
AITS is helping to tackle a shortfall in training capacity and those successfully completing a course become accredited to the Access Industry Competence Scheme (AICS). AICS covers a range of scaffolding and access-related categories and aims to apply common standards for all sector professionals.
We have been working with the Home Builders Federation to develop a flexible and focused way to ensure that scaffolders working on their members’ sites have the appropriate skills to work safely and efficiently. These are early days, but there are now hundreds of AICS skills cards in the sector and more employers are seeing the benefits of this route as an alternative to the established and rigid structures in construction.
We want to ensure that everyone employed in an access- and scaffolding-related trade has achieved an appropriate level of competency. Creating the skilled workforce that the country needs to achieve ambitious housebuilding and infrastructure targets requires change and is absolutely fundamental to the future of our sector.
Robert Candy Chief executive Scaffolding Association www.scaffolding-association.orgIn 2018/19, the HSE reported 40 fatal injuries to workers due to falls from height and the rate of fatal injury within construction at four times higher than the average across all industries. The Construction (Design and Management) Regulations 2015 state that commercial clients must make sure their projects are suitably managed to ensure the health and safety of all who might be affected by the work, including members of the public. Failure to provide a safe environment can lead to unlimited fines and up to two years in prison. The HSE regularly prosecutes contractors and other scaffold clients for a failure to carry out comprehensive inspections by a qualified person.
The weekly scaffold inspection is a vital element of keeping workers safe and preventing the scaffolder or contractor ending up in court, facing hefty fines. The use of specialist scaffold
inspection apps helps to improve the quality and consistency of inspections because they prompt the inspector to report defects from a defined list and also provide the ability to attach photos and other relevant information to the reports.
Another advantage of using a mobile app for scaffold inspections is that the data can be used to analyse and report the most commonly occurring defects. This, combined with the photos attached to the reports, provides clear evidence of where either scaffolders need further training or trades have been repeatedly interfering with scaffolds, such as removing toe-boards, ties and boards.
SMART Inspector has been used on more than 365,000 weekly scaffold inspections across all clients in the past year, providing a valuable insight into the most common defects. Obstructions (50 per cent), debris (14 per cent) and board condition (10 per cent) are the most
common faults reported. Additionally, guardrails and toe-boards were often either missing or incorrectly placed/secured (4 per cent). Other common faults were materials stacked above toe-boards, damaged cladding, missing ties, undermined foundations and missing ladders. The ability to use modern cloud-based reporting techniques allows managers to improve safety on-site for everyone and to address reoccurring issues earlier. The photographic evidence removes any potential argument and the management reports ensure no inspections are missed, no reports are lost and that all legal duties have been met.
Ian Chambers Sales and marketing director SMART ScaffolderWith slips, trips and falls still the number one cause of accidents and injuries on scaffolds, it is imperative that both scaffolders and contractors understand the most common reasons that scaffolds fail the weekly inspection.
Ian Chambers, sales and marketing director at SMART Scaffolder software, looks at how digital technology is the key to understanding on-site risks.
UK System Scaffold Hire has introduced a new security gate system designed to control access to all types of HAKI Stair Towers and Public Access Staircases.
The security gate system is quick to install on HAKI Stair Towers, whether they have staggered or in-line standards or are Mk2 stairs.
Robust and providing a totally enclosed security system, the gate is lockable from both sides and features cladding panels which can accommodate signage and advertising.
The UK System Scaffold Hire gate system provides a good security solution for when site staircases are accessed from pavements or for other areas used by the public. In addition, the solution provides a cost-effective way for event organisers to ensure that Public Access Staircases and Bridges can only be used by visitors during public opening times.
www.ukssh.co.uk
Scaffolding sheeting from Industrial Textiles & Plastics (ITP) has been used to wrap historic Leinster House in Dublin – the Georgian building that is home to the Houses of the Oireachtas – during a major programme of restoration while government business continued as usual.
For temporary containment and weather protection during the project, the client wanted a full PVC building wrap, digitally printed with an image of Leinster House’s facade. The material had to be flame retardant and certified to the highest standards, but they discovered that the cost would be very expensive and the installation would require specialist contractors.
Scaffolding contractors McCrory Access Solutions approached ITP, manufacturers of Powerclad FR Scaffold Sheeting that is certified for both plain and printed sheeting.
ITP’s in-house design and print department took up the challenge of recreating the facade image on 2m-wide scaffold sheeting and then enhanced, tiled and layered the image for digital printing on custom 52m length sheeting to accommodate the building’s full 50m width.
McCrory Access Solutions meticulously installed the precisely aligned and printed sheeting, enabling restoration work to progress safely behind a full-size, flame retardant reproduction of the building’s elegant facade. www.itpltd.com
New SMART Scaffold Designer is a desktop software package that allows for the rapid calculation of leg loads, tie duty and bridge beam checks for tube and fitting independent scaffolding as well as the TG20:13 wind factor for sites in the UK and Ireland.
SMART Scaffold Designer, which can be used by any competent person with an understanding of TG20:13, is for use either on its own or with SMART Estimator Check IT TG20:13 or the NASC TG20:13 eGuide when a client needs calculations or drawings. The software checks scaffold bridges of up to 20m span, including moment and shear capacity, deflection, coupler slip and standard capacity, with an option to double the standards.
Leg loads are calculated precisely, allow for the number of boarded lifts and can be supplied to the client to check the foundations. The tie duties are also calculated exactly and the reduced loads can allow the user to use fewer ties where permitted by TG20. www.smartscaffolder.com
MACDECK Safety Decking from Teesside-based J.Mac Safety Systems is improving contractor safety and productivity on-site for housebuilders including Persimmon, David Wilson Homes and Story Homes.
The MACDECK internal fall protection system is available to buy or hire and has been tested to support J.Mac’s statement that it is the strongest injection moulded system on the market. J.Mac manufactures all of its products in the UK.
In addition to providing a safe working platform on-site, the decking can be manufactured with a client’s branding, making the system unique to that specific client and adding security as a theft deterrent.
New products to promote safety on construction sites include an Extendable Leg, Brickguard, MACHATCH and MACLADDERSAFE.
www.jmacsafetysystems.co.uk
SCP Forgeco is celebrating its one millionth tube weld nine years after introducing a scaffolding tube welding service.
As part of its multi-million-pound move to new premises in 2010, SCP Forgeco installed an automated Fusion Tube Welder commissioned specifically for the welding of recycled scaffolding tube. Initially in partnership with Lyndon SGB, the project was envisaged to re-life their underutilised short tubes by converting them to higher-demand 16ft and 21ft lengths. Traditionally these short lengths would have been ‘scrapped’ and new tubes purchased – welding them offered an environmentally conscious and financially beneficial option.
The same high-quality processes and testing procedures initially introduced are still followed today with full in-house production records and third-party batch testing.
Nine years on and with dozens of customers regularly taking advantage of the process, SCP Forgeco has completed its one millionth weld.
Managing director R Dale commented: “This is another milestone in SCP Forgeco’s history. We were proud to be chosen to partner with Lyndon SGB and it’s great to see where that original idea has led.
“The welding plant has generated and maintained many local jobs. Additionally, re-lifing has recycled more than 18 million feet of scaffold tube, giving a carbon saving of over 55,000 tonnes.”
www.scpgroup.co.uk
The CITB levy imposed on employers within the construction industry is used to support the development of a skilled workforce. Stacey Underhill, head of external affairs at the Scaffolding Association, provides an overview of the skills development opportunity for the access and scaffolding sector.
The levy applied by CITB – the Construction Industry Training Board – is dedicated to ensuring that the construction workforce has the right skills for both the present and the future, with some of the money raised from the levy allocated to supporting training development through grants and funding and through the offer of apprenticeships.
As an employer within the construction industry, there are different ways that you can claim grants and funding from CITB to help develop your workforce. One of these is through the Skills and Training Fund. This fund, which is available every 12 months, supports CITB-registered employers who have up to 99 directly employed staff on their payroll:
• Employers with one to 49 directly employed staff can receive up to £5,000
• Employers with 50 to 74 directly employed staff can receive up to £7,500
• Employers with 75 to 99 directly employed staff can receive up to £10,000
Since its 2015 launch, the Skills and Training Fund has awarded close to £14 million for a number of training projects. However, in 2017/18, only £41,000 was claimed by companies to support the training needs of scaffolders. This low figure demonstrates the current missed opportunity within the access and scaffolding sector to claim funds to boost skills development.
Any company wishing to claim CITB funding must make a formal application which includes:
• Details about your company
• What your current training needs are
• What training you are planning to undertake
• The training provider you are intending to use, and the quality of training that will be delivered
The following are important points to consider when applying for funding:
• The person completing the application must be employed by you
• You must be registered with the CITB and provide your registration number
• Including your bank details will reduce the time it takes to receive the funding, if your application is successful
• Clearly describe the problems or opportunities that your company is facing
• Explain how the training solutions you are proposing will address the problems or opportunities you face, and what difference it will make to your business
• Specify who will receive the training, including their job title and role within your organisation
• The Skills and Training Fund is an enhanced incentive for construction courses that attract CITB grant
• Ensure that you provide the name of the training course or training as it appears on course documentation
• List every course or training initiative you are planning on delivering
• If you are looking to fund a course that is not on the CITB-approved list, then there are options for you to submit requests for consideration
• Include the name of the training provider, the start/end dates of the course, and the number of people who will be attending
• If you are VAT registered, exclude the VAT in the amount you are requesting; if you aren’t VAT registered, ensure that you include it in your request
• Include the amount of CITB grant you can claim for each course or training
• Explain how you selected your current training provider
• If possible, include quotes from other providers
The current window for the Skills and Training Fund runs until the 29 March 2020 – an application can be made at any time. The terms and conditions associated with the CITB’s Skills and Training Fund can be read at: www.citb. co.uk/levy-grants-and-funding/grants-funding
How CITB levy funds are distributed to construction employers of all sizes to support training (Source: CITB data from 2017/18 annual statistics).
Scaffolding on a Grade II-listed apartment complex in the heart of Chelsea is being delivered by Q Scaffolding, where their pre-planning and innovative thinking have been integral components in keeping a tight programme on schedule.
reports.
John Martindale from Q’s design partner, the Scaffold Design Company, explained: “Luckily, for the south elevation, it was easy to identify the structural members support in the car park roof and therefore we could indicate the scaffold support locations over the structural members below. We believed that the structural members would be capable of supporting the proposed loads applied by the temporary scaffolding.
“By working closely with clients and consulting engineers, our design team supplied our client with the proposed load so that they could assess the structural member capacity. This analysis led the project team to devise the back-propping layout for the review and agreement. We designed additional beams at the car park entrance to ensure access was maintained.”
“There were many challenges to overcome with this project and the presence of residents, busy pavements with passing pedestrians and a lot of local traffic meant we had to plan the work in detail and manage the installation carefully,” said Andrew Morgan from London-based Q Scaffolding.
Q Scaffolding was appointed to design and erect scaffolding for Savoy Construction as part of the refurbishment and redecoration of listed windows and balconies at Whitelands House. The 10-storey apartment block stands on London’s fashionable, and very busy, Kings Road, between Cheltenham Terrace and Walpole Street. The 1930s complex was designed by architects Verity and Beverley, who were famous for designing the Lord’s Pavilion, many London theatres and Paramount cinemas across the UK.
As with many older buildings, architectural and structural information can be thin and Whitelands House was no different. There was limited information and drawings available on the existing building.
The apartment block, which has an hour-glass shaped footprint, sits above a public car park – understanding the ground conditions posed a challenge to the scaffolding team. At certain points, the scaffold had to be launched from the roof of the car park. Scaffolding on the 30-metre-long south elevation, above the car park entrance, rose 24 metres and incorporated a complex beam structure to ensure access was maintained.
Q’s on-site team of six is led by a Black Hat supervisor. Working on tight sites, often with restricted access, led Q to adopt a construction strategy using tube and fitting and then use system for either staircase access.
Traffic management has played an important role in ensuring safety and minimal disruption on-site. Each day, an exclusion zone and signage were set up to protect both residents and the public, with a permanent traffic marshal appointed to manage access and egress from the public car park, which was in constant use. Communication among the scaffold team kept them aware of vehicle movements. With vehicles entering the car park and the entrance to Whitelands House, it was paramount these arrangements were discussed during the pre-start meetings and written into the risk assessments and method statements.
The design and installation was completed on time, and a robust inspection regime has also ensured on-site safety is high and the impact on local residents is minimised.
PROJECT TEAM:
Main contractor: Savoy Construction
Scaffolding contractor: Q Scaffolding
Scaffold designer: Scaffold Design Company
Site start: April 2019
BSI has published a new edition of BS 5975:2019, Code of practice for temporary works procedures and the permissible stress design of falsework. The standard has been updated to take account of the Construction (Design and Management) Regulations 2015, particularly in respect of the interface between the design of permanent works and the design of temporary works. Robert Candy, chief executive at the Scaffolding Association, highlights some key points that scaffolding contractors may need to consider.
The long-awaited update to BS 5975 is here. It should be noted that the changes in this revision affect Sections 1 and 2 only, and that Section 3 remains unchanged. That said, with the sections that cover procedures extended from 15 pages to 49 pages, you might expect drastic changes. However, with the exception of a new duty holder and information when dealing with Domestic Clients, little has changed.
The update contains more detail about organisational procedures and the interface on-site with details of roles and responsibilities specific to the duty holder within an organisation. Where the previous version generalised in its outcomes, the new update adds clarification to organisational and duty holder requirements. For example:
6.3.1.1 (from original BS 5975) – Every organisation involved in temporary works should have a designated individual responsible for: a) establishing, implementing and maintaining a procedure for the control of temporary works for that organisation.
5.1.1.3 (from updated BS 5975) – When a project has, or might be anticipated to have, the requirement for any temporary works, all organisations involved in the management of the temporary works, whether implemented by themselves or others, should have and implement a procedure which outlines how they are to discharge their duties in relation to the temporary works.
The update contains more detailed information relating to the duty holders’ responsibilities specific to the type of organisation for which they undertake their role. The additional duty holder identified is the Principal Contractor’s Temporary Works Coordinator (PC’s TWC). The introduction of this role means there can be more than one Temporary Works Coordinator (TWC) on a project. The PC’s TWC is responsible for the implementation of temporary works procedures and checking that other contractors who are directly or indirectly engaged on the project are implementing their procedures.
This creates an opportunity for Scaffold Contracting companies to undertake the role of TWC and manage the temporary works process themselves. Although they would report to the PC’s TWC, it should speed up the design brief, alterations, design checking and drawing approval process, providing that the company has the required qualified temporary works duty holders and organisational procedures in place. Companies will need to check with their insurance broker that they have the required insurance to undertake the role of TWC.
The types of project where this approach may be implemented could be small works packages with multiple locations, and maintenance or refurbishment projects where scaffolding is the only temporary works discipline being undertaken.
Over the last decade, there have been major changes to working practices. The growth of specialist sub-contracting across most construction works means it has become necessary for BS 5975 to reflect all types of working practices. The update provides scope for the interface between the duty holders and organisations to be structured in a way that suits the project.
This allows for the interface on-site to be segregated where required. An example would be on a new-build housing site where an existing building had to be demolished/shored or retained for planning consent. The area could be demarked and a different site/ temporary works management team and Scaffolding Contractor used for each area.
The update provides more detail about the procedures required for organisations. Information for Clients, Principal Designers (PD), Temporary Works Designers (TWD) and Manufacturers/Suppliers is now specific to their organisation. This will clarify the information that is required from all organisations to simplify the procurement of competent companies. Competent companies will provide contractors with the information required – if a contractor has to ask for information, it could imply the company doesn’t know what is required.
The standard now details a list of information that should be included in the temporary works register, which should help organisations involved in the process provide the relevant information to populate the register.
The standard has also been updated to align with the Construction (Design and Management) Regulations 2015 and the procedures now allow other contractors to plan and manage their own temporary works while ensuring that the Principal Contractor retains overall responsibility.
BS 5975:2019 now provides recommendations for education and training. It is good to see that these relate to practical understanding of the works being undertaken and the procedures and process of control required to undertake the work safely.
Expectations for projects involving Domestic Clients are included in the update and take into account that the site would have a trade-based supervisor handling the day-to-day site temporary works. Whoever takes on the duties of the Client and Contractor should have a suitable temporary works management procedure to suit the complexity of the project. This should incorporate their own duties as well as the Clients’ duties relating to temporary works as outlined in this document. The various duty holders should carry out their duties in proportion to the risks involved in the project.
The update has given scope for better management of projects large and small but still reinforces that, irrespective of the complexity of the project, the same basic procedures should be followed. Scaffolding Association members wishing to purchase the latest version of BS 5975 can receive a discount. Email sally@scaffolding-association.org
Robert Candy Chief executive Scaffolding Association www.scaffolding-association.org‘
The example schedule above should be used for each of your contracts. It incorporates legal requirements relating to the payment process and alerts you to the dates when the various notices are to be sent or are to be expected.
It is vital that you familiarise yourself with your contract provisions governing the submission of applications. These usually indicate:
• the form of the application (i.e. some particular format may be required)
• the time for submission
• the content of the application
• how the application is to be submitted (i.e. paper and/or electronically)
• to whom and/or to what address the application is to be sent
• All your applications must show a build-up of the amount you are claiming, that is, the basis of your calculation
• Keep strictly to the contractual requirements governing the submission of your applications
If your application does not conform to the requirements of the contract and show the basis of your calculation, it will be invalid. If the
application is invalid, there is another consequence (other than the risk of not being paid). In the event that your payer fails to issue you with any payment notices, your application then becomes the amount that must be paid. If it is invalid, this will not, of course, happen.
By law, your contract must indicate the due dates on which all your payments become due and the final dates by which your due payments must be discharged. If you cannot ascertain the due and final dates, you should get back to your paying party to seek clarification. Having clarity is essential since because, as we shall see, issuing payment notices is linked to the due and final dates for payment.
If you do not have clarity in this context, the first due date will fall on the expiry of 35 days after first commencing your works; and, thereafter, the next 35 days, and so on. The final date for payment will fall on 17 days following the due date.
The law requires that no later than five days after the due payment dates, your payer must issue you with a payment notice. This must state the amount the payer proposes to pay and the basis of the calculation. In fact, your contract should state who is to issue this notice – you or the payer. If it doesn’t state this, the onus is on the payer to issue the notice.
The payer can also issue a pay less notice. To be valid, this must be issued before the final date for payment and, again, must show how the revised amount has been calculated. In practice, pay less notices are issued a day before the final date for payment. This can make cashflow difficult to manage if, for example, you have 60-day payment terms and, then, out of the blue, you receive a pay less notice on the 59th day.
If you do not receive any payment notices from your payer, a valid payment application from you will become the amount that has to be paid.
The law provides you with a measure of protection in relation to your payment entitlements. Use it to your advantage. If due payments are not made by the final date for payment, you have a statutory right to suspend any or all of your contractual obligations on the giving of seven days’ notice.
Research from Barbour ABI has found that the value of all construction contract awards in July 2019 was £5.1 billion based on a three-month rolling average, which is a slight decrease of 1.8 per cent on June. However, yearly comparisons indicate that contract award values in July 2019 were 11 per cent higher than in July 2018.
In the three-month period ending July 2019, total construction contract awards were valued at £15.3 billion, which is an increase of 14 per cent on the previous quarter and 13.8 per cent higher than for the comparable quarter ending July 2018.
The number of contract awards in July was 1,011, which is an increase of 38.5 per cent on June and is also 3.7 per cent higher than July 2018. Regional analysis shows that London was the leading region for contract awards in June with a 32.1 per cent value share.
London was the largest region in July and was also the location for the three largest contract awards. The largest was in Southwark – the Stoney Street Commercial and Office development which is part of the Borough Yards redevelopment valued at £300 million.
Tom Hall, chief economist at Barbour ABI, said: “The planning pipeline continues to defy recent negative economic news. We have seen significant activity for contract awards across the UK for the past three months, with a 13.8 per cent increase on the comparable quarter ending July 2018. Over the next three months, we will be rolling steadily towards the Brexit deadline which may impact figures as uncertainty once again sets in.”
The access and scaffolding sector is waking up to changes in VAT invoicing and payments that come into force next month. At the time of going to press, a united construction industry was lobbying hard to have the changes delayed for six months, but, whether the new VAT Reverse Charging comes into effect or not, what is certain is the sector will need to implement it. Adrian JG Marsh reports.
Changes to VAT charging are being introduced in order to tackle the growing problem of VAT fraud in the construction industry. HMRC’s new domestic reverse charge for construction services is due to come into force on 1 October 2019 and its introduction seems likely to have a significant impact.
David Redfern from DRS Tax Claims said: “These changes mean that the recipient of the construction services and supplies will now be responsible for charging themselves the VAT and accounting for it, and businesses which provide construction services will need to state clearly on their invoices that the VAT is subject to this reverse charge.”
Robert Candy, chief executive of the Scaffolding Association, said: “The implementation of VAT Reverse Charging will have a significant impact on the cashflow of scaffolding contractors. Right or wrong, businesses have been using VAT receipts as working capital. Scaffolding contractors are no different to many businesses and they should make sure that they are prepared when it begins.
“Contractors affected by the new VAT regulations could lose 20 per cent of the cash going through their business. For a £1 million turnover contractor, that’s £200,000 they won’t see again. The potential impact is huge.”
Mr Redfern stated: “Affected construction services are very similar to those which come under the Construction Industry Scheme (CIS), with professions such as surveying and architecture remaining out of scope for the reverse charge. In terms of charging, the main difference is that, unlike the CIS, materials are also included within the reverse VAT charge.
“However, this reverse charge won’t apply to zero-rated services nor if the customer is not registered for VAT. While the VAT responsibility will shift to the customer, the good news is that this will not impact on the
VAT registration threshold so smaller businesses needn’t worry that these changes will push them within the scope of VAT registration.”
HMRC has said that it intends to take a “light touch” towards errors made within the first six months of the charge being introduced as long as suppliers have made the errors in good faith and have attempted to comply. However, errors
are far easier to rectify if they are spotted and picked up sooner rather than later.
“Before October, construction-based businesses need to check whether they are going to be impacted by the reverse VAT charge. If so, accounting software and systems will need to be updated to ensure that they are compliant,” Mr Redfern said. He continued: “Smaller businesses may find that their cashflow is affected by this change, so precautionary measures need to be taken and staff need to be familiar with what is going to happen.”
Mr Candy reiterated that the key impact of this change is the substantial effect this may have on cashflow. He said: “Access and scaffolding contractors should be planning for this change as soon as possible and we strongly suggest that they read the HMRC website and seek external advice. Different forms of contract may also influence the way the new scheme is applied.”
• The new rules only affect supplies you make to your clients who are NOT the final user of the building or structure and
o If you invoice for labour only, then this will be included in reverse charging VAT
o If you invoice for labour and materials, then the whole of the invoice will still come under the new scheme
o If, however, you invoice for materials only and there is no labour or service element, then you will submit a VAT invoice as normal as this does not come under the scheme
• If you carry out work for end users, such as domestic customers or for customers who are either not VAT registered or not CIS registered, you will continue to invoice them including VAT
• Scaffolding hire (with no labour) is outside the scope of CIS, so VAT will continue to be charged.
On, or after, 1 October, you submit an invoice for £1,000 of construction work:
• You will invoice for £1,000 showing your supply as standard rated but not adding the £200 VAT to the amount due
• Because you have not been paid £200 VAT, you now do not owe HMRC £200 VAT
• If your invoice includes VAT after 1 October 2019, your client will return the invoice to you and this could delay payment
• Invoices dated up to 30 September 2019 will request VAT and can be paid with the VAT
• Invoices dated on or after the 1 October 2019 should not show VAT.
www.gov.uk/guidance/vat-domestic-reverse-charge-for-building-and-construction-services
Stage 3 Scaffolder
Expiry Date 01/12/2023
Card No: 19-A0000
Name Surname
AICS is the industry’s newest card scheme for access and scaffolding professionals, providing a simple and consistent way for them to demonstrate their competence.
“Knowing that what you are buying is fit for purpose is an absolute requirement of the supply chain and no more so than when scaffolding contractors are sourcing tube, fittings and system,” said Matt Shore from SCP Forgeco.
But temptation may soon be a thing of the past because the Hackitt Report into the Grenfell Tower disaster could fundamentally change the construction industry’s attitude towards design and construction, not just from a fire safety perspective but right across the industry – and including access and scaffolding.
Mr Shore explained: “It’s essential that clear measures are taken to ensure that in future any product used in the construction process, including non-mechanical construction equipment, is compliant with appropriate standards and backed by valid test certificates.”
Manufacturers spend many thousands of pounds on auditing and testing to demonstrate that what they are manufacturing meets the standards required. A substandard component, or a poorly fitted one, can lead to catastrophic results.
Demonstrating that suppliers’ products have been manufactured to the correct standard demands rigid quality control procedures and constant checking and verification.
“Every month, we take delivery of thousands of fittings from our production plants in the UK and overseas. It is essential we can prove to our customers that what they are buying meets the appropriate standard,” Mr Shore continued.
“Our quality control procedures mean we can trace every batch from when it was manufactured to who it was sold to. We also inspect and test our products on a random basis at independent testing facilities. This gives us the confidence to know that all our products will perform.”
Being able to rely on independent test data gives contractors confidence that a product can be trusted. In today’s litigious world, such a high level of traceability and testing gives
wholesalers and contractors an assurance in the quality of the tube, fittings and accessories being used.
Marc van der Voort, managing director at Industrial Textiles & Plastics (ITP), is aware of two major suppliers of flame-retardant debris netting and flame-retardant sheeting in the UK who do not provide test reports and whose product data sheets only specify fire-retardant additives. He said: “Without testing to recognised standards, the efficacy and performance of debris netting and sheeting cannot be verified. We’ve also seen a test report that shows that the material of one product had actually failed a test…!”
To help contractors navigate test certificates and product markings, ITP has produced a technical briefing that points out to scaffolders what to look for on flame-retardant certification for scaffold sheeting. Building projects using products that have not been tested and certified by internationally recognised third-party certification boards increase risk and compromise safety of both the site and workers.
Paul Beck at insurance brokers Amicus said: “Post-Grenfell, insurance companies have focused on building facades and will now only cover installations that use non-flammable products. As the use of netting and sheeting has grown, the scaffolding sector needs to look carefully at the products it uses to wrap a scaffold structure, which
could well fall under the definition of ‘facade’. If you use a non-flame-retardant sheeting product, you could invalidate your insurance.”
The same goes for the scaffolding structure, warns Mr Beck, commenting: “You could also be at risk if you use accessories or fittings that you have not verified as fit for purpose. So, check your test certificates carefully and, if in doubt, run it past your insurer for their approval.”
Commercial pressures are a temptation to purchase look-a-likes or clones that just don’t perform as you would expect. Product test certification was introduced to give buyers confidence that the products they are buying had passed performance tests and meet the criteria stipulated. Without a valid test certificate, buyers are putting themselves at risk of using a product that might not be safe. But how often do you inspect a test certificate, and do you understand what it means? Adrian JG Marsh reports.
We all understand that businesses in the construction sector have to spend significant amounts on general insurances, particularly on the essential and compulsory liability covers, and on insuring heavy vehicles and machinery.
However, an area that is by no means compulsory, but is often overlooked, is using insurance to protect the ownership of the business.
When a business owner or partner dies, in addition to the obvious sadness and everyday problems associated with the loss of a driving force, companies often overlook the destabilising effect such a loss can have on the business.
Following the death of an owner/partner, their stake in the business is likely to pass directly to their family. If the owner/partner was a majority shareholder, the remaining owners could lose control of some or all of the business and have to work with the family of a former owner, which can be stressful for both parties.
Whoever inherits a part of the business may choose to be a silent partner, but there is no guarantee. Some will want a more active role and may have different ideas about which direction the firm should be taking. Another possibility is that the beneficiary may want to sell their stake. However, if the remaining owners can’t find the funds to buy this shareholding, the stake could be sold to a competitor or not sold at all.
The ideal solution is often for the remaining owners to buy back the shares, giving the family a cash sum while ensuring they retain control of the business. The question is, do they have, or will they be able to raise, the funds to do this? This is where Share Protection insurance can help, which provides a cash payout to buy back shares.
There are two parts to this insurance. A ‘life insurance’ policy, which will pay out the value of their shareholding on the death of one of the owners, and a ‘legal agreement’, which sets out when and how these shares will be bought back and at what price.
These simple steps provide the business and its owners with certainty at the worst of times, ensuring that the beneficiaries receive the cash value they are entitled to and the ownership of the business is protected.
FIND OUT MORE
martin.ward@amicus-insurance.com
“From little acorns do mighty oaks grow” goes the old English proverb. It implies that, despite the most humble of beginnings, true strength can be nurtured from even the most unpromising starting points.
It is a proverb that can be applied across the construction sector but has particular resonance in the scaffolding sector, where even the most complicated of structures spring from seemingly the most modest of foundations.
And yet even though it is important, the subject of foundation systems for scaffolds is one that despite the design codes and standards is rarely recognised on-site. It is an area that should be more widely understood, according to Scaffolding Association’s chief executive, Robert Candy.
“There are various configurations available to scaffolders that help spread the load of the scaffold and act as health and safety precautions to both site staff and the general public. There are soleboards, baseplates and ‘tredda’ or footplates, but does everyone know enough about where they should be used, how they should be positioned, and on what material they can be used on?” he commented.
Like with much of the access and scaffolding sector, the design and provision of these boards and plates is shrouded in mystique and myth with reference to design guidance and standards with a large spoonful of time-worn experience.
Scaffolding has always had an element of art about it – as much as engineering has – and the type of foundation or bearing plate used is no exception.
For Chris Harrison, director at design specialist Apex Scaffold Design, it is an area that needs to be formalised before any tubes are even unloaded from the lorry.
“We make it quite clear on our designs that it is the responsibility of the principal contractor to ensure the ground and/or the structure will safely support the loads applied from the scaffold.
“We also make it clear that it is down to the principal contractor to design, supply and maintain a suitable, flat, load-bearing base and provide details of these bases and spreaders to suit. It is really important to have those
stipulations made clear,” he explained.
There are standards for baseplates and soleboards: baseplate manufacture is covered by EN74-3:2007 and soleboards are covered in BS 2482:2009, but there is scant mention of under what conditions these components can be used.
Traditionally, soleboards are little more than sawn down scaffold boards. It is their last job on site before they are unceremoniously thrown into the skip or shredder. These are boards that have been deemed too old or damaged for use above ground level but are considered capable of transferring and spreading loads from the scaffold through to the ground itself.
Mr Harrison continued: “They are used where the scaffold is bearing onto grass or the exposed ground of the site. If a scaffold is bearing directly onto a concrete or asphalt surface then a baseplate is considered enough. Contractors might use soleboards or footplates to protect the surface, though.”
Scaffold system design is something that those supplying baseplates shy away from. Tony Mills is sales director at Walsall-based producer Trademagic. It sells more than 1.5 million standard sized 150 x 150mm scaffolding baseplates each year to clients across the UK and beyond, which gives some indication for the industry’s insatiable demand.
“They should go on a soleboard which is a minimum 450mm long – they should sit on one of those for stability as much as anything. We don’t get involved in the specification of baseplates; that’s down to the contractor and its designers. We look at only supplying products that are manufactured to the correct standards,” he said.
For David Eveleigh, director at footplate supplier BLC Construction Supplies, it is a slightly different story. With no inherent load-transfer qualities, he argues that footplates are only there to help protect the existing surface and provide a hi-visibility guard against trips and falls.
“Our footplates are manufactured using high-impact polymers and are really about making the baseplate and the rest of the scaffolding more visible for pedestrians, both on- and off- site. It is a safety product – but it is not safety critical. They are rated to eight tonnes impact resistance but that is not a requirement as such.
Like many things in the scaffolding sector, they probably stem from one person’s bright idea that has now been taken on as the norm,” he said.
There are plenty of variables that should be given careful consideration when inspecting, designing and installing scaffold foundations systems. Size, thickness, length, condition and type of founding strata can all play their role in the final specification – but, thankfully, scaffold failures are rare.
“The correct design and specification for soleboards and baseplates is important. I can’t recall an incident where a scaffold collapse has been due to soleboard or baseplate failure, but that doesn’t mean we should ignore them,” concluded Mr Harrison.
Scaffold contractors, designers and temporary works managers should pay careful consideration to the foundations of scaffold systems – how many do? Paul Thompson reports.
HAKI and CCS Scaffolding were engaged by Wessex Capacity Alliance –a collaboration between Skanska UK, Mott MacDonald, AECOM, Colas Rail – to provide safe, temporary access solutions at Waterloo Station, while around £400m worth of improvements are made.
As part of the ongoing Waterloo Station upgrade, Wessex Capacity Alliance were required to install a new suspended ceiling to infill steelwork. A 24-metre-high working platform was needed for this work to be completed. Various solutions were considered by Wessex Capacity Alliance, including the use of MEWPs. However, a birdcage scaffold design concept was approved by the client. This method offered the quickest programme, provided easy access to materials on deck through a built-in loading bay, and did not require MEWPs.
Both HAKI and CCS Scaffolding were engaged at an early stage of the project to ensure build-ability of the planned birdcage scaffold and that it was Safe by Design.
The temporary works project was an example of Safe by Design best practice from Wessex Capacity Alliance. And by collaborating with HAKI and CCS Scaffolding, the ceiling installation programme was reduced from 16 weeks to 3 weeks.
CCS Scaffolding supervisors were trained on the Universal system by HAKI’s expert technical team to guarantee that the scaffold was erected safely and to design specifications. On-site technical support was also provided while the works were ongoing.
In industries such as construction, where the operative rarely drives for a living, an error in exceeding the allowed driving hours can occur simply because of ‘not being in the know’. Heba Najib from transport management consultancy GVL Management Limited sets out the all-important rules on drivers’ hours.
Construction workers, including scaffolders, are often under the impression that a tachograph is not needed. But this is often a misunderstanding because a tachograph must be used if the vehicle driven comes under EU or AETR (European Agreement Concerning the Work of Crews of Vehicles Engaged in International Road Transport) rules. This inexperience or lack of awareness of the rules has often led scaffolders to either think that they do not require a tachograph or not place importance on downloading or analysing the tachograph’s data.
This is an important aspect of remaining compliant with a company’s operator’s licence and rules on drivers’ hours. While some may deem this a simple error, this infringement could potentially lead to a Public Inquiry or revocation of the licence.
Recent data findings of tachographs revealed that the most common infringements are inadequate breaks in the day, the daily drive limit being surpassed, going above the maximum working hours in the week, and unsatisfactory daily rests.
It is essential for access and scaffolding contractors to be acutely aware of the rules and definitions for drivers’ hours. They are there for safety: safety of the driver, safety of other motorists and safety of pedestrians. Compliance with drivers’ hours rules is important, not only to ensure a company’s operator’s licence is not at risk but also to affirm and establish that a business cares about the safety of its drivers and other road users. When driving a goods vehicle or a passenger-carrying vehicle, the rules regarding drivers’ hours must be adhered to. AETR rules, EU rules and GB domestic rules are the three sets of rules that may pertain to a driver’s journey. Depending on the country a driver is driving in, what a driver is using the vehicle for and the type of vehicle they are operating, these rules will apply.
In most cases, scaffolders will be required to adhere to either the EU rules or the GB domestic rules for drivers’ hours.
The EU rules apply if the maximum permissible weight of the vehicle or vehicle combination is more than 3.5 tonnes. In addition to this, the rules will pertain if driving in the EU (currently including the UK), a European Economic Area country or Switzerland.
EU rules on drivers’ hours:
• You must not drive more than
o nine hours in a day (which can be extended to 10 hours twice a week)
o 56 hours within a week
o 90 hours in any two consecutive weeks
Core EU rules on breaks and rest:
• You must take, at the minimum, 11 hours of rest every day (which may be reduced to nine hours of rest, three times between
any two weekly rest periods)
• There must be a rest period of 45 hours every week, which is undisturbed (this also may be reduced to 24 hours every other week)
• After four hours and 30 minutes, the driver should take one break or a number of breaks equal to 45 minutes at the minimum
• After six consecutive 24-hour periods of working, a weekly rest must be taken, starting from the end of the last weekly rest period taken Scaffolding contractors might be exempt from the EU rules if they operate a vehicle or combinations of vehicles with a maximum permissible weight of 7.5 tonnes or less used for carrying work equipment for the driver where the distance is less than 100km.
The GB domestic drivers’ hours rules apply to most passenger-carrying vehicles and goods vehicles that do not have to follow the EU rules. For goods vehicles, the daily driving limit is that you must not drive for more than 10 hours in a day on a public road or off-road if not during duty time. This covers areas including building work and civil engineering. Companies must also ensure that for the daily duty limit the driver does not exceed 11 hours in any working day. This limit doesn’t apply on any working day when the operative does not drive.
What is most important for drivers in regard to compliance is having the knowledge and awareness needed to be able to comply. More often than not, if a person is not aware of the definitions and rules of drivers’ hours, they will find it difficult to ensure compliance.
Prevention of incompliance is far better than dealing with enforcement from the DVSA (Driver and Vehicle Standards Agency) or, even worse, the outcome of an accident caused by a tired driver who’s driven for longer than the allowable hours.
Amicus
We have been working with the Scaffolding Association since 2015 and are proud to insure many of the UK’s leading Scaffold companies.
We really understand scaffolding insurance and we love it. We have even employed some former scaffolders within our business so you can be 100% confident that we really do talk your language!
All that expertise, enthusiasm and industry knowledge means that you can trust Amicus to not only find the best insurance to protect you, your business and your employees, but that you can also rely upon us to do it at the most competitive price. We even offer additional discounts for Scaffolding Association and NASC members.
www.amicus-insurance.co.uk
At MSA, we focus on two aspects of testing: representative testing and exceeding standards. BS EN 795:2012 is an important fall protection standard that relates to the testing of anchor devices – it is the minimum requirement for people working at height. I strongly urge anyone choosing fall protection systems to do so in accordance with this standard and supportive representative testing. As an industry, we have a responsibility to do our utmost to help ensure people go home safely at the end of each day. Choosing equipment that passes strenuous tests and meets all relevant standards is crucial to doing just that.
Fall protection solutions are generally split into two categories: Personal Protective Equipment (PPE) and engineered systems. PPE covers products such as lanyards, self-retracting lifelines and harnesses, while an engineered system is essentially a product that is permanently attached to a structure or a building. It is what operatives attach themselves to, to stay safe while working at height.
The role performed by an engineered system is to control energy. In doing so, a well-designed system should achieve two things: the protection of people and the integrity of the structures on which they are working. In the unfortunate event of a fall from height, a significant amount of energy is generated with force put on both the person falling and the building. To help mitigate the effect of this force, MSA fall protection systems are designed with smart, integrated energy-absorption technology. This technology means that the system itself absorbs the majority of the force from the fall, rather than the building or, importantly, the operative.
First and foremost, think about the Health and Safety Executive’s (HSE) hierarchy of risk control. One, is it essential to work at height? Two, if it’s unavoidable, can collective protection (guard rails, etc.) be implemented? And three, if an engineered system is required, make sure it has been specified and designed with its specific use in mind and tested against not only the latest standards but also the application in hand. Finally, as with any work at height, prior to work taking place it is crucial that the end-user has received high-quality training from a reputable provider specific to the work required.
The fundamental consideration should be how and where the system will be used. Transmission towers, industrial buildings and wind turbines, for instance, all have very different requirements and typically systems must be designed to be durable enough to last 25-30 years. Care must be taken to implement an appropriate system for each unique application: there is no such thing as a one-size-fits-all approach with height safety systems.
As far as possible, representative testing should be carried out, which means testing a system on the actual substrate it’s going to be attached to. There is little point testing products bolted to concrete floors if they are intended to be installed on aluminium roof sheet, as performance could be completely different. A new standard, BS EN 17235, is being looked at under construction regulation CPR EU 305/2011. It will be an absolute game changer for the industry as it will make this type of testing a requirement. MSA welcomes this move, as we have been conducting representative testing since we first designed the Latchways Constant Force Post (MSA’s engineered system) 20 years ago.
Construction capabilities have grown massively in the past five years, so we’re seeing a lot of different structures. Curved and uniquely shaped buildings, for example, come with differing needs for fall protection. These often-complex structures can put even more of an impetus on the quality of both the height safety system itself and its installation, which is why it’s vital to partner with reputable organisations, including manufacturers, training providers and installers.
There’s also been a growth in the range of systems available, so it’s important to understand the different offerings. The priority must always be to select the proper fit for the unique application, rather than selecting on cost alone. That said, Europe has and continues to drive full protection in terms of standards and regulations. Generally speaking, the rest of the world looks to Europe as a leading example.
Understand clearly what is required of the engineered system so that the right equipment can be chosen, and accurate system designs implemented. Make sure that the system has been tested to and meets the very latest standards. Principal designers, specifiers, contractors, and others in the fall protection chain should, as far as possible, insist that the very best height safety specification is stuck with and not changed for an option that may not perform as well or be as well suited to the application.
Andrew Pass from MSA Safety –a global designer, manufacturer and distributor of safety products – talks about engineered systems and the integral role they play in keeping those that work at height safe.
and consequence of any fall, e.g. fall arrest systems, safety nets and air bags
• Include prominent warning signs at any location where persons may pass near to or work on a fragile surface
Often the risk of falls themselves cannot be avoided entirely. Therefore, it’s important that work equipment and other measures are implemented to reduce the possible distance and consequence of those falls. This primarily means the use of safety nets that must be manufactured to recognised standards and designed to catch both falling people and falling materials. Safety nets should only ever be installed by competent, trained individuals who can ensure that the tension in the net is set correctly to enable the safe catching of the falling objects.
The latest statistics from the HSE on Working at height show a steep rise in fatal injuries over the last year, revealing that 147 workers were fatally injured in 2018/19 – a rise of 4 per cent on the previous year. Forty of those individuals were killed by falling from a height, making falls from height the single biggest cause of death from fatal injuries at work in the UK – when major injuries are also included, this is a big problem that needs to be addressed as a priority.
The most common causes of these incidents occurring involve over-reaching, over-balancing, or the failure of a fragile surface that weight is being applied to without support. However, falls from height also involve unguarded holes in floors, including hatchways, inspection holes and pits, or falls into tanks and machinery. Other hazards include falling objects or platforms overturning or collapsing. This highlights just how varied the risks can be when working from height and how important it is for organisations to have clear procedures in place to mitigate each of these risks – every time their teams carry out work.
A systematic approach should be taken prior to conducting any activity at height. The steps should be considered to ensure the risk is as low as reasonably practicable:
• Consider whether working at height can be avoided – if you don’t need to, don’t do it!
• Complete as much of the work as possible from ground level
• Complete the work using an existing means of access and egress
• Use suitable work equipment to prevent a fall occurring, e.g. edge protection
• Use equipment to reduce the distance and consequences of a fall, e.g. fall arrest systems
• Provide training and clear instructions to those who will carry out the work to ensure the activity is conducted in a safe manner with the appropriate serviceable equipment
Although working at height should be avoided where possible, the reality is that, quite often, it cannot be avoided, particularly in the access and scaffolding sector. Therefore, it is vital that an existing safe place of work is employed. The means of access or egress should:
• Be strong and stable enough to hold the weight of the operatives carrying out the work and rest on an equally strong and stable platform
• Be big enough to facilitate the operatives and any materials and machinery
• Avoid having gaps through which operatives or materials could fall
• Be constructed, used and maintained to prevent the risks of slipping or tripping, or of any person being trapped between the working location and any adjacent structure
• Provide suitable protection, such as platforms, coverings, crawling boards or guardrails, or, where not practicable, measures taken to minimise the distance
Prevention of falling objects is important and often overlooked when considering the risks of working at height. Passers-by and other workers at ground level are just as at risk from falling objects as those operating at height.
In the first instance, steps should be taken to prevent the fall of objects or materials, e.g. tools fitted with lanyards, installation of toe-boards, sheeting and fans on scaffolding. Where this isn’t reasonable, measures should be implemented to ensure that persons are not struck by falling objects, e.g. barrier-off danger areas below and prevent unauthorised access.
Chutes must be used to control the transport of materials and waste from a height to a safe location.
The reality is that the few examples of working at height risks covered in this article just scratch the surface. The potential risk to those at height, as well as those operating below, are many and of varying nature.
In a series of articles for AccessPoint, Marcus Rose, technical manager at SMAS Worksafe, will look at the risks and preventative measures for those working at height and the equipment and procedures which can be implemented to mitigate the risks, or reduce them to as low as reasonably practicable.
“Sadly, my 18-year-old brother took his own life this year. He had worked for our company and within the construction industry since leaving school early,” said Dan Sullivan, owner and managing director at Somerset-based Pro Scaffolding (South West), highlighting how tragedy can strike close to home.
Suicide is the biggest killer of men under the age of 45. However, male site workers are three times more likely to commit suicide than the average male in the UK. Suicide kills more construction workers than falls do.
Construction represents around 7 per cent of the UK workforce and, according to the Office for National Statistics, between 2011 and 2015, of the 13,232 in-work suicides, the construction industry accounted for 13.2 per cent.
Recent surveys suggest that two-thirds of construction workers want better physical and mental wellbeing support from their employers. There have also been calls for construction to have a greater awareness of mental health and eradicate the stigma associated with it.
Dan continued: “With the shock and devastation this caused, and also experiencing mental health issues first-hand three years ago, we decided as a company it was time to see what we could do to help any of our employees who might be struggling with mental health.
“Scaffolding is a very macho industry – but it’s important to treat mental health as seriously as physical health. Early action can prevent employees reaching that desperate stage. That’s why we wanted to encourage any of our lads to reach out and talk – we wanted to break the stigma and silence surrounding mental health in our industry.”
Dan’s wife, Heather, who is Pro Scaffolding’s works co-ordinator, researched courses to attend so that their company could be better prepared to help, and so Heather went on the Mind charity’s mental health in the workplace course.
Dan said: “We gained a much better understanding regarding mental health
and also valuable knowledge on how I, as a manager, and we, as a company, could help anyone struggling. My new moto became ‘it’s ok not to be ok’.
“Our employees now have a port of call. They can come and talk to Heather privately, in total confidence, and have a chat, talk about issues that may be causing them emotional and mental distress. A lot of these issues we can help with. If a work-related issue is contributing to a feeling of anxiety or poor mental health, we can go through options and in most cases just talking for 30 minutes or knowing someone is there to listen can really help.
“I’ve noticed that some of our team have not been performing at their best, but by being more caring about mental health as well as focusing on traditional health and safety, we’ve been able to make changes and improve performance. It’s helping our workers and also helping us to improve productivity.
“We’re planning on building a ‘quiet room’ so we have a better environment for our staff. We’ll also attend more courses to learn more about mental health so as a company we are best prepared to spot the signs and reduce the stigma surrounding mental health in men in construction.”
Today, with work being such a big part of our everyday life, mental health has increasingly become something for managers and business owners to be more in tune with. Many businesses recognise that they need to do something, but are not sure why, how or what this really means to their business – so the issue of poor mental health becomes doubly challenging. The Scaffolding Association has teamed up with Mates in Mind to provide a way for scaffolding contractors to find out more and put in place a better structure to tackle issues of mental health.
Jocelyne Shaw, director of strategy at Mates in Mind, said: “We have quickly become a leading industry charity that supports organisations of any size across the UK to help recognise and improve their workforces’ mental health. With evidence suggesting that three out of every five employees are experiencing mental health issues because of work, at Mates in Mind we believe this needs to change.
Physical health still predominates in construction. Signs remind workers to wear personal protection equipment and there is regular attendance at safety talks and courses. But where is the discussion on mental health and its importance?
Adrian JG Marsh reports.
“Our supportive approach provides employers with the necessary skills, clarity and confidence to raise awareness, improve understanding, and enable positive action to address the barriers that surround mental health at work. Our work with organisations is showing that this can be achieved through existing management, and businesses are often not starting from scratch.
“Regardless of where your organisation is in its mental health journey, Mates in Mind can provide the insight and expertise to help both organisations and individuals to understand how, when and where they can get support.”
A final word from Dan: “Some people laughed at us when we started our campaign, but many now respect us. We’ve seen a positive response; more people are applying to join us because we’ve got a reputation for looking after our employees and our productivity is improving. Our proactive response to mental health is making a real difference.”
FIND OUT MORE www.matesinmind.org support@matesinmind.org
020 3510 5018
www.accesspoint.org.uk
AAA Scaffold Limited 0121 5531611
Advanced Scaffolding UK Limited 01268 728211
Alto Access Products
www.altoaccess.com
A.M.L Scaffolding Limited www.amlscaffolding.co.uk
Archis Scaffolding Solutions Limited www.archisscaffolding.co.uk
B & H Access Scaffolding Limited 01752 767068
Cobra Scaffolding Limited www.cobrascaffolding.co.uk
Concise Scaffolding Solutions 01268 527787
Corinthian Access Limited www.corinthianaccess.co.uk
County Scaffolding Services Limited www.county-scaffolding.co.uk
Embassy Site Services Limited www.embassysiteservices.co.uk
FL Scaffold Limited 01782 715442
Ledger Scaffolding Limited www.ledgerscaffolding.co.uk
Lewdown Scaffolding Limited www.lewdownscaffolding.co.uk
Markon Services Limited 07818 065273
MR Scaffolding UK Limited www.mrscaffoldinguk.com
Newgen Scaffolding Limited 07949 794384
RDL Scaffolding Limited 07437 667546
Red and Black Scaffolding Limited www.redandblackscaffolding.uk
Reliable British Scaffolders Limited www.rbs-scaffolding-devon.co.uk
Safe Access Solutions Limited www.safe-access-solutions.co.uk
SKYE Scaffolding (London) Limited www.skyescaffolding.com
Tilbury Scaffolding Limited www.tilbury-scaffolding.com
Time Scaffolding Solutions Limited www.timescaffolding.co.uk
Tubular Access Scaffolds & Hire Limited 0151 545 1537
Wise Scaffold Services Limited www.wisescaffoldservices.co.uk
PRODUCTS AND SERVICES
ScaffGap Limited www.scaffgap.com
SMAS Worksafe www.smasltd.com
12 September 2019
Scaffolding Association AGM Union Jack Club, London
16 October 2019
Scaffolding Association exhibiting at SMAS Worksafe AJ Bell Stadium, Manchester
17 October 2019
Birketts Contractual Seminar Manchester (venue TBC)
27 and 28 November 2019
London Build Olympia London
Scaffolding design consultancy 48.3 has been acquired by Richter Associates for an undisclosed sum. The company said the acquisition is a strategic development in 48.3’s drive to transform the scaffolding industry with fully integrated service offerings in temporary and permanent works.
To date, the focus of Surrey-based 48.3’s service offering has specifically been on the design, planning and management of scaffolding to provide commercially viable, efficient and risk-reduced scaffolding solutions across the UK.
Ben Beaumont, founder of 48.3, said: “This is a really exciting time for 48.3 – it’s the start of a new chapter in our development and growth. I believe this is the future of scaffold design, bringing it in line with other aspects of temporary works.
“48.3 and Richter Associates share many common views on the development of the industry. Our companies offer complementary temporary works, permanent works and geotechnical services that, when combined, create a unique service offering available nowhere else in the industry.”
FIND OUT MORE www.483.co.uk
On 27 and 28 November, the Scaffolding Association will exhibit at London Build, Olympia, where chief executive Robert Candy will moderate a health and safety panel discussion on the second day.
The free-to-attend event – which is the leading construction and design show in the UK – features 500 speakers, 220 hours of CPD, 350 exhibitors and unrivalled networking events. Attendees to London Build will learn about the latest developments and opportunities in residential, commercial and infrastructure build across Greater London and the UK.
Chelmsford-based contractor WellMax Scaffolding has taken on new projects and introduced new vehicles in recent months. Project awards include the refurbishment of an existing Grade II-listed building in Bloomsbury. Scope of works include scaffold to rear elevation for repairs and clean down of facade and windows along with a temporary roof for roof repairs.
In another project where WellMax is currently on-site in Campden, the client authorised graffiti to the hoardings, resulting in some standout artwork decorating the development.
WellMax has also introduced two new vehicles to its fleet, both being Ultra Low Emission Zone (ULEZ) compliant and crane mounted.
FIND OUT MORE
www.wellmax.co.uk
London Build’s ‘Festival of Construction’ is all about making business in construction fun! Join thousands across the industry for two full days of inspiring content, high-level networking and entertainment, including live music, celebrity guests, street food, beer festivals, prize giveaways and performers!
Connect with more than 25,000 industry professionals and meet senior figures from across all top 100 companies from tier 1 contractors, general contractors, architects, developers, house builders, engineers, government and 33 local councils across greater London.
Networking events and feature areas include the Sustainability Summit (35 speakers from leading architect, developers, contractors and engineers), Women in Construction (the largest meeting of women working in construction in the UK), Constructionline Meet the Buyer, LinkedIn Networking Lounge, Humans of Construction Photography Gallery and Movement with Movember (a first-of-its-kind collaboration moustache-growing record attempt from the construction industry), alongside Hub in the Pub (in partnership with the CIOB), Built Environment Networking Hub, LGBT Feature and the Architects Hub, where you can experience the latest architectural designs and 3D models across the capital).
REGISTER FOR FREE TICKETS
www.londonbuildexpo.com/scaffolding-association2019
The Scaffolding Association attended both the Northern Housing Consortium: Health & Safety in Housing Conference 2019 and the London Work at Height Seminar in June and July.
At the Health & Safety in Housing Conference – organised by the Northern Housing Consortium, which represents the views of housing organisations in the North of England –Scaffolding Association chief executive Robert Candy gave a talk on Temporary Works Procurement and Health and Safety Responsibilities. The well-supported session for delegates covered CDM 2015, BS 5975 alignment along with best practice and early design decisions.
The audience at the London Work at Height Seminar was professionals with an interest in working at height within the City of London and beyond, including local government authorities, procurement professionals, health and safety specialists, and building and facility managers. Exhibiting at this event provided an excellent opportunity for the Association to promote its campaigning to raise standards of safety, technical quality and workforce skills in this area.
Speakers at the seminar included Alison Thewliss MP, who discussed the APPG Working at Height Report issued earlier this year.
STAK Scaffold has been contracted at the historic Drapers’ Hall, in Throgmorton Avenue, London, to provide a protection deck for work to be carried out above the ceiling.
The completely freestanding scaffold is nearly 10m high. The 10-week project encompasses two weeks for scaffold erection, four weeks for works to be carried out and four weeks for dismantling and clearing.
Due to the weight limit on the access road into Drapers’ Hall, all material has to be walked down Throgmorton Avenue and taken through the main door into the courtyard then stacked, ready to be passed up a 5m tower erected by STAK Scaffold to access the first-floor window.
With the make-up of the floor, spreader beams were fixed to the bottom line of standards on the independent scaffolds and secondary standards fixed at every 700mm.
SUPPLIERS TO THE SCAFFOLD AND CONSTRUCTION INDUSTRY
BLC Construction Supplies have grown through your continual support, our product & service innovation and expanding our wide range of scaffolding consumables to meet your needs.
We hold substantial stocks of many key national brands Monarflex, JSP, Makita, Miller, MSA, P&P, Scafftag, etc at our national distribution warehouse. Ready and available for next day delivery where required.
OUR FULLY CERTIFIED NETTING WILL ENSURE YOU MEET YOUR INSURANCE REQUIREMENTS.
TETHERED TOOLS, BELTS & FROGS. AVAILABLE IN STANDARD KIT OPTIONS OR TAILORED TO YOUR REQUIREMENTS.
We have provided a fast, friendly and efficient service for many years. Don’t just take our word for it, give us a try. For more information or to request a brochure please get in contact t. 01179 828180 | e. office@blccs.co.uk | w. www.blccs.co.uk
Annual audit exceeds PAS91 standards
Membership of the Association is an assurance of quality, demonstrating an ability to carry out safe design, installation and commissioning of scaffolding systems.
By using a Scaffolding Association member, employers can be confident that they are pre-qualifying and awarding work to contractors who have undertaken an rigorous assessment of their experience and capabilities. Members must provide client references and commercial insurance details amongst other documentation that is checked by the Association before membership is gained.