

TOWERING ABOVE THE REST
WELCOME
ROLL CALL FOR NEW SCAFFOLDING ASSOCIATION
MEMBERS

Ace Scaffolding Contractors Ltd
www.acescaffolding-uk.com 01273 305030
Bournemouth Scaffolding Limited www.bournemouthscaffolding. co.uk 01202 772659
C S Scaffolding Limited www.candsscaffolding.co.uk 01325 247278
C.O.G Scaffolding Services Ltd www.cogscaffolding.co.uk 01977 361401
Colliers Scaffolding 07939 274739
Davey Scaffolding Services Limited 07307 852033
DMB Scaffolding Ltd www.dmbscaffoldingltd.co.uk 07789 224407
Elco Scaffolding Limited www.elcoscaffoldingltd.co.uk 01268 906230
Everest Scaffolding Ltd www.everest-scaffoldingltd. co.uk 020 3151 7818
Fagan Scaffolding Ltd 07497 426091
Hope Valley Scaffolding Ltd www.hopevalleyscaffolding. co.uk 01298 938070
Jet Scaffolding Ltd www.jetscaffoldingltd.co.uk 01923 518933
LCE Access Ltd 07927 177322
Lester (UK) Limited www.lesteruk.com 01375 893759
Linmar Scaffolding Limited www.scaffoldingcardiff.com 02920 460999
Lita Scaffolding Ltd 07367 901303 https://litascaffolding.co.uk
MAC Access Ltd http://mac-access.co.uk 07586 757540
Main Scaffolding Services Ltd www.mainscaffoldingservices. co.uk 01604 953844
Mark One Scaffolding Ltd https://markonescaffolding. co.uk 07891 422195
Noble Scaffolding Limited www.noblescaffolding.co.uk 01604 968368
Pinnacle Scaffolding Solutions Limited www.pinnaclescaffolding.co.uk 01474 397071
Portway Scaffold (Midlands) Limited
www.portwayscaffolding.com 01789 551563
Portway Scaffold (NW) Limited www.portwayscaffoldnorthwest. com 01527 520670
R&L Scaffolding Ltd www.prscaffoldingliverpool. co.uk 07787 528564
Ross Campbell Scaffolding Limited http:// rosscampbellscaffolding.com 07765 707179
Royale Scaffolding Ltd www.royalescaffolding.com 01795 873437
SAM Scaffolding Limited www.samscaffolding.co.uk 020 3633 5953
Scaffold Management Ltd 07920 015603
Silvercrest Scaffolding Ltd https://silvercrestscaffolding. co.uk 01702 555999
Wilkes & Sons Limited https://wilkesandsons.uk 020 8543 3995
Yorkshire Scaffold Group Ltd 07874 441849
MEMBER CLIENT CONTACT US
Editorial
Enquiries: Alison Hurman
T: 0300 124 0470
E: alison@scaffolding-association.org
Advertising
Enquiries: Trish Meyer
T: 0300 124 0470
E: trish@scaffolding-association.org
Scaffolding Association
T: 0300 124 0470
www.scaffolding-association.org
E: info@scaffolding-association.org
Subscriptions
AccessPoint is distributed to members of the Scaffolding Association and other selected access and scaffolding businesses.
If you wish to receive a copy of AccessPoint or would like to amend or cancel your subscription, please call 0300 124 0470 or email info@scaffolding-association.org
AccessPoint is published on behalf of the Scaffolding Association. The views expressed in this journal are not necessarily those held by the Scaffolding Association. The Scaffolding Association shall not be under any liability in respect of the contents of the contributed articles. The Editor reserves the right to edit, abridge or alter articles for publication.
ISNN: 2055-2033 (Print)
© All editorial contents AccessPoint 2024 Printed by Tewkesbury Printing Company Designed by Gladstone Design
Booker and Best Ltd www.bookerbest.co.uk 01424 434391
Cover and inside front cover images: JTL Group Ltd
NEWS
P3-5 Stories from the sector
COMMENT
P6 Robert Candy, CEO of the Scaffolding Association discusses what is needed from the next Prime Minister
TRANSPORT
P7 Scaffolding Association’s lowdown on changes coming that may impact your fleet
P9 D.tec International discuss the summer drink and drug drivers campaign
LEGAL
P10 Holmes & Hills ask will we ever not talk about extra hire and what can you do?
GUIDANCE
P11 A guide to the HSE’s Fee for Intervention
PROJECTS
P14-15 JTL Group tower above the rest on subsea drill project
P16 SA Scaffolding provide cover for remedial works at St Georges Court EVENTS
P17 Events coming up in 2024 HEALTH & SAFETY
P18 360 Degrees Consultancy discuss audits and inspections
P19 Scafom-rux asks what happens to scaffolding in a fire?
P21 JS Safety Associates considers the topic of dropped objects
COMMERCIAL
P22 Key takeaways from the CITB Business Plan 2024-25
PRODUCT NEWS
P23 SpanSet’s Grabba Bag helping to avoid dropped objects
P23 Afix Group embrace sustainable steel decks
Scaffolding Conference adds dinner dance and moves to The Belfry Hotel and Resort
The Scaffolding Conference, organised by the Scaffolding Association, is open to all and now includes an evening dinner dance with live band and DJ. The event is set to take place on Friday 11th October 2024 at The Belfry Hotel and Resort, a prestigious and world-famous venue, having held the Ryder Cup and numerous PGA Tours.
This year’s keynote speaker is Tim Balcon, Chief Executive of the CITB, who will be discussing current industry issues that affect the sector, as well as the post-election landscape.
Other speakers include Lee Greatorex, HSE Inspector from the Regulatory Support Unit, Construction Sector of the HSE, and Robert Candy, CEO of the Scaffolding Association.
There will be a range of discussion panels, the first one of which is “Demystifying Temporary Works” led by Robin James, Operations Director at the Temporary Works Forum (previously Managing Director of the NASC). The other two panels are “Working at Height Updates” and “Project Management” with live examples. These panels will focus on current scaffolding industry regulations, best practice, skills and training.
A limited number of combined Early Bird tickets are available at the discounted price of £250 per person plus VAT.
For more information contact sally@scaffolding-association.org or scan here to visit the Scaffolding Conference website.
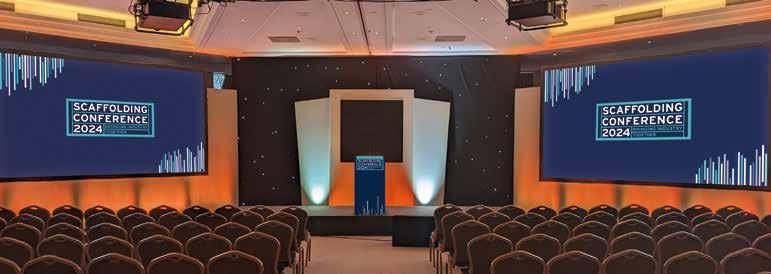
Scaffolding Association makes list of top 100 trade associations
MemberWise, an independent professional network that provides practical help and support to circa 8,000+ membership and association professionals based in the UK and overseas, publish an annual list of the top 100 UK trade associations using the following qualification criteria:
• A headquarters based in the UK
• Membership is optional and charged for directly via an annual membership fee
• The majority of members are organisations or businesses (not individuals) or only the business / organisation member total is considered for this purpose
• Over 50% of membership are based in the UK
There are thousands of membership organisations in the UK that meet this criteria and the Scaffolding Association are delighted to have been included within the latest listing which ranks the association as the 95th largest trade association in the UK by the number of member organisations it represents.
Scan here to view the full listing on the MemberWise website.
Scaffolding Association proudly partners with the HSE’s Working Minds campaign
The Scaffolding Association proudly announced to be partnering with the HSE’s Working Minds campaign.
The Working Minds campaign was created by the Health and Safety Executive (HSE) to bring together a range of tools and support to help businesses and workers understand the best ways to prevent work related stress and encourage good mental health.
Robert Candy, Chief Executive of the Scaffolding Association, commented:
“Celebrating our commitment to mental health and workplace safety, we are proud to support the Health and Safety Executive’s Working Minds campaign. Working in the scaffolding sector can be challenging with a wide
range of pressures that include finding skilled workers, maintaining a pipeline of work, and managing cash flow.
At the Scaffolding Association, we firmly believe in fostering a culture of well-being and proactive support in the workplace. Through our partnership with the Working Minds campaign, we are reaffirming our dedication to promoting mental health awareness and providing support to our members in the scaffolding sector. Our members are undertaking some inspiring and innovative initiatives in this vital area, and we look forward to continuing our collaborative efforts to prioritise mental health.”
Scan here to find out more.
Mabey Hire Ltd. becomes part of the PERI Group
PERI SE (Weissenhorn, Germany) has taken over the Mabey Hire Ltd. headquarters in Dewsbury (UK).
The PERI Group is a family-owned company based in Weissenhorn. With approximately 9.000 employees, more than 160 locations worldwide and a turnover of 1.9 billion EUR, PERI is one of the leading manufacturers of Formwork and Scaffolding Systems worldwide.
Mabey Hire is a market leader in the UK, providing solutions for infrastructure and renovation construction projects. Their portfolio includes groundshoring for excavations, propping and jacking for renovations, temporary bridges for access and sensors for all phases of construction projects. The company has around 400 employees and is represented at 16 different locations in the UK.
Scan here to find out more.
APA Height Access announce partnership with Pilosio
APA Height Access announced their official appointment as an approved UK installer and distributor of Flydeck, Pilosio’s innovative suspended decking platform. This system allows for quick and safe installation of a durable, lightweight deck. It facilitates access to horizontal structures like bridges, jetties, stadiums, commercial and retail environments, while minimising disruption and install times.
Darren Shepherd, Operations Director of APA Height Access commented:
“We’re excited to introduce Flydeck to the UK market. It’s a game-changer for many applications. Pilosio’s innovation, combining Italian design flair with precision engineering makes Flydeck an exciting suspended access solution for the UK market.
The APA Height Access management team recently visited the impressive Pilosio Group of factories in Italy to observe the manufacturing process of the aluminium Flydeck system. A site visit to see Flydeck in use on a large highway bridge, 80m high, was a highlight of the trip. The Flydeck system was installed 50% quicker than traditional methods, providing a stable multi directional access solution for the planned bridge renovations.”
To learn more about Flydeck or to arrange a live demo, visit www.apaheightaccess.uk, email access@apagroup.uk, or call 01422 377741.
CITB state over 250,000 extra construction workers required by 2028 to meet demand
The annual industry forecast from the Construction Industry Training Board (CITB) highlights the continuing persistent gap between what the UK needs to keep up with demand and the workforce available to meet the challenge.
CITB’s Construction Skills Network (CSN) 2024-28 report reveals that:
The UK’s construction output:
· Rose by 2% in 2023, the third consecutive year of growth
· Will grow by an average 2.4% a year between now and 2028
To meet this growth, an equivalent of more than 251,500 extra construction workers are needed over the next five
years, with construction employment rising to 2.75m by 2028.
Despite the industry managing to recruit around 200,000 people every year, in 2023, an average of 38,000 vacancies were advertised per month. For almost a third (31%) of construction employers, finding suitably skilled staff remains their key challenge, particularly with more older workers retiring and not being replaced.
Although the construction industry welcomed 200,000 new workers, it saw the loss of more (210,000 workers). With the ongoing difference between the predicted need for construction work and the available workforce,
CITB’s forecast shows how important it is for the industry to tackle the issues with effective recruitment and training to replace those leaving and better prepare for the future, as well as to take advantage of key opportunities such as productivity improvements and meeting net zero retrofit targets.
In response to the challenges, CITB has invested £267m to help the industry improve diversity, quality and productivity as well as making construction a more attractive career choice for future generations.
Scan here to find out more.
Shaun Hanney raising money for hospital that saved son’s life
Scaffolding Association members Shaun Hanney Ltd are looking for sponsors for a night of boxing to help raise funds for the hospital who saved their son’s life.
Shaun’s 3 year-old son, Tyson, had Meningitis which led to sepsis and resulted in him being in an induced coma, brain injuries and having his leg amputated. Tyson was under 24hour care at Addenbrooke’s Paediatric Intensive Care Unit, and the family are on a fundraising mission to give back to the hospital that saved his son’s life.
They have already raised over £19,000 on their Just Giving page and have a
boxing night coming up. Shaun Hanney commented:
“My good friends have arranged a night of boxing to raise money and we are looking to sponsor the fighters for each bout. We are looking for £200 per fighter for this good cause or anything you could do to help, there’s 34 fights and this helps to set up the event.”
If you would like to get involved email shaun@shaunhanneyltd.co.uk
Scan here to make a donation.
RoSPA release tips to prevent getting distracted whilst driving
RoSPA has released their top tips to help prevent people getting distracted whilst driving.
RoSPA state:
“When we talk about driver distractions, we often think about a motorist being on their mobile phone behind the wheel. But mobile phones are not the only distraction. Many of us are less aware of the other things that can distract us while we are driving, taking our full attention off the driving task and increasing our chances of being involved in a crash.
A driver is distracted when they pay attention to a second activity while
driving. People cannot always safely multi-task in this way, especially if the second activity is time consuming or complex.”
A roundup of RoSPA’s tips are:
• If you need to do something distracting, find a safe place to pull over.
• Recognise what makes you distracted.
• Concentrate on your driving.
• Use technology sensibly.
• Plan your route in advance.
• Take refresher or further driver training.
Scan here to read RoSPA’s advice in full and to download their Driver Distraction Factsheet.
No Falls
Foundation launches first of its kind research into falls from height
Falls from height remain the leading cause of workplace fatalities and injuries in the UK, accounting for an alarming 30% of all deaths in 2022/2023.
In order to gather more comprehensive data on the underlying causes and circumstances of falls from height, the No Falls Foundation, the first and only UK-based charity devoted exclusively to the work at height sector, is embarking on the largest study of its kind in the UK to date.
Hannah Williams, Charity Manager at the No Falls Foundation said:
“Current reporting focuses on the type of incident, as opposed to what caused it in the first place. We want to gain insight into the root cause which will inform future research projects and focus resources to prevent falls from height.
We encourage anyone who has experienced, witnessed, or investigated a fall from height to participate in this important research survey to help us ensure everyone who works at height comes down safely.”
Scan here to take part in the falls from height research study.
PDC Scaffolding successfully completes merger with London’s Kopa Scaffolding
Romford-based PDC Scaffolding Limited, who are Audited Members of the Scaffolding Association, and specialise in reactive works and social housing, has successfully completed its merger with Kopa Scaffolding, in a move which is expected to create 25 new local jobs.
The merger will see the family-run business maintain its Essex base, with the expanded Kopa Group set to operate from a large yard in Romford and a second depot in Horsham.
Kopa’s own scaffolding arm, Kopa Scaffolding is a well-known name in Brighton and London. With a focus on scalability, it provides tailored scaffolding solutions for commercial and residential renovation and new build projects.
Its parent company, Kopa Group, has interests in construction, real estate and finance.
Paul Casey, the managing director of PDC will serve as MD of the combined PDC and Kopa Scaffolding group. He commented:
“PDC’s expertise in reactive works and social housing complements Kopa’s focus on social and new build housing. We’re looking forward to pooling our knowledge and working together – and growing our team with dozens of new roles to boost the local economy. This is the start of a really exciting new chapter and we’re excited about what’s to come.”
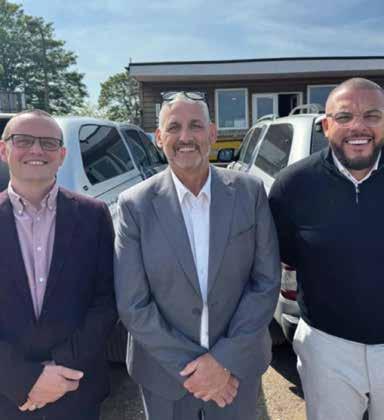
Scan here to find out more.
Comment
As this latest edition of AccessPoint magazine lands on doormats, the General Election campaign will be concluding, and in a few days, the UK will have chosen a Prime Minister, gifting him or her with a new mandate to lead the nation for up to five years.
Whoever lands the top job in UK politics, regardless of their political party, faces an in-tray of burning issues that need urgent attention.
Those most important to voters in this election will not surprise you - cost of living, health and social care, immigration and asylum, the environment, defence and security, education and crime.
Suffice to say, these matters are where you would expect the next Prime Minister and government to focus their immediate attention.
However, regardless of how important these matters are, and they are without doubt all very important, there are plenty of industry and sector specific challenges, also requiring urgent attention – not least the construction industry.
As well as a new Prime Minister, a new government means dozens of new Secretaries of State appointed to lead key government departments and dozens more newly appointed government ministers who will be handed portfolios covering thousands of subjects and issues, across every industry and sub-sector imaginable.
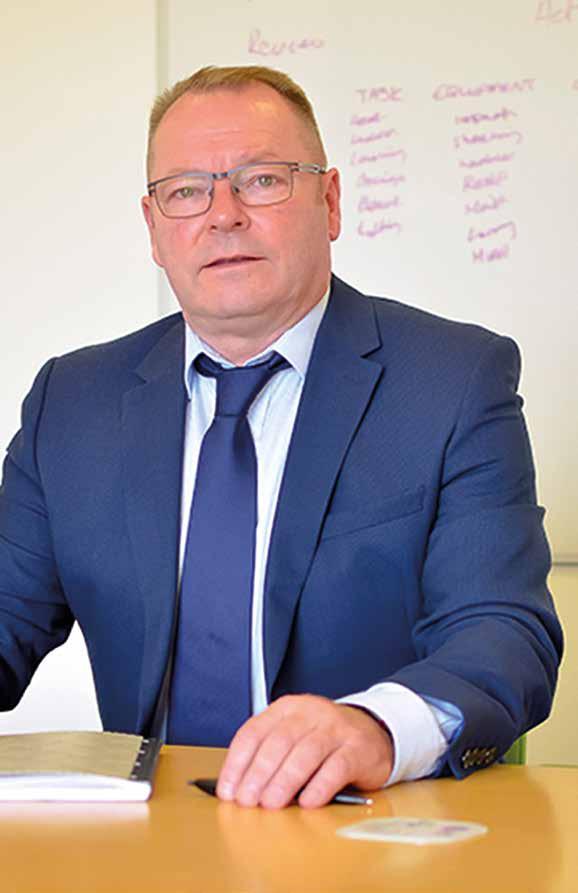
The construction industry is no stranger to new ministers. The current minister for construction, Alan Mak, appointed days before the General Election was announced, is the 22nd to hold the post since 2001 and the 11th postholder in the past five years.
One of my asks of the next government would be to give us a minister that can do the job that needs doing and leave the minister in office for enough time so that they can make a difference. The revolving door at the top of our industry has not been helpful – we need commitment and continuity first and foremost.
We also need a Prime Minister, government and construction minister capable of understanding and addressing the challenges we face.
Labour shortages, cash flow, prompt payment, procurement practices, net zero, rising costs of supplies, technology and digital transformation, material shortages and housing supply are issues and challenges that will resonate with most construction businesses – particularly the 880,000 small and medium sized enterprises (SME’s) which operate within construction – more than any other industry.
The good news is that the Scaffolding Association is in a much stronger position now than it ever has been and we can hit the ground running with the new government and continue the vital work we’re doing on behalf of our members and the scaffolding and access industry.
We know that there is an enormous amount of work to do and that for many businesses within our sector, time isn’t on their side.
However, you can be sure that the Scaffolding Association is leading the way for industry and will continue representing members on the issues that are most important to them, regardless of who gets the keys to number 10 in a few days’ time.
ROBERT CANDY CHIEF EXECUTIVE, SCAFFOLDING ASSOCIATION
The good news is that the Scaffolding Association is in a much stronger position now than it ever has been and we can hit the ground running with the new government and continue the vital work we’re doing on behalf of our members and the scaffolding and access industry.
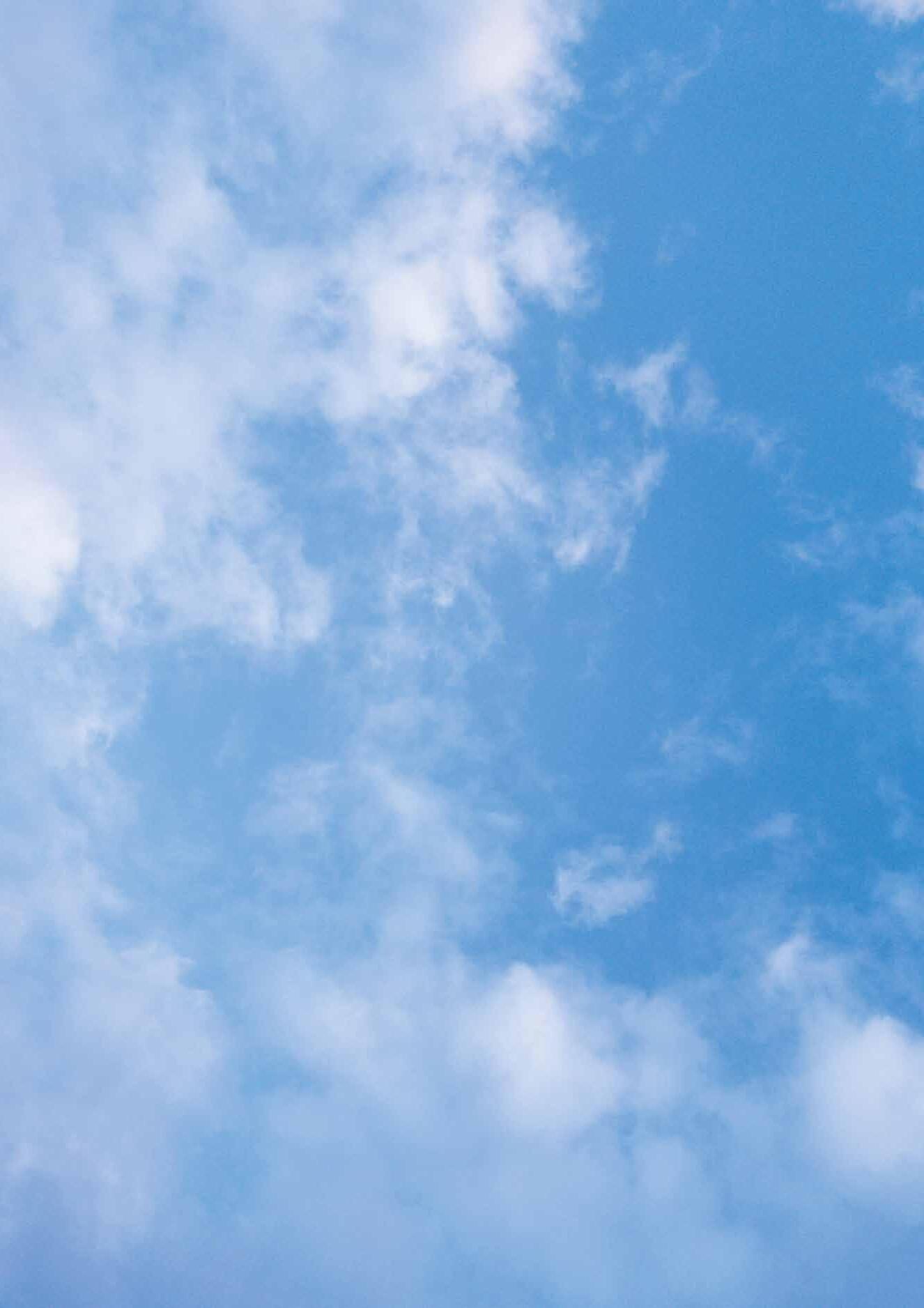
The Scaffolding Association’s lowdown on changes coming in 2024 that may impact your fleet of vehicles
Most scaffolding companies will be operating fleets of vehicles consisting of a mix of HGV’s, vans, pickups and cars. In this article the Scaffolding Association clarifies the changes and deadlines coming in 2024 that you should be aware of that might impact your fleet of vehicles and their operation.
Clean Air Zones
Four Clean Air Zones in Scotland went live on 1st June 2024. Zones in Aberdeen, Dundee, Edinburgh and Glasgow were launched throughout 2022 and 2023 without enforcement. However, from 1st June 2024 enforcement will apply across these areas.
Importantly, these zones differ from those in England and Wales because businesses and individuals cannot pay to enter with non-compliant vehicles – they will instead be automatically fined for doing so.
Typically, the following vehicles will comply:
• Petrol cars and vans generally registered from 2006
• Diesel cars and vans generally registered from 2015
• Buses, coaches and HGVs generally registered from 2013.
You should always check before travelling, which you can do by scanning here.
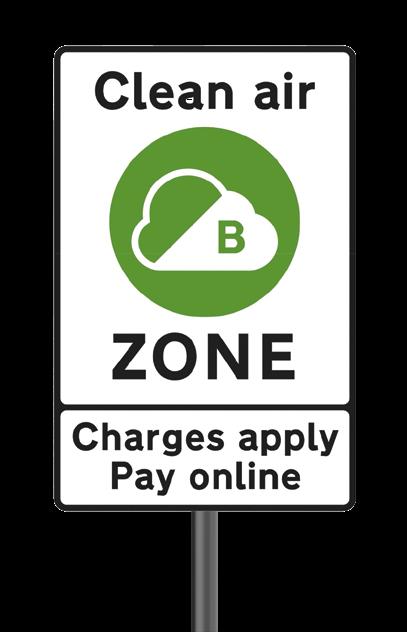
Direct Vision Standard (DVS)
The new Progressive Safe System (PSS) is due to be launched on 28th October 2024. From this date, the minimum star rating requirement will increase from one to three stars, meaning that vehicles that fall short of the star rating will need to be equipped with extra safety equipment to obtain a permit.
A three month grace period for compliance has already been announced by Transport for London (TfL). However, TfL is under increased pressure from commercial vehicle operators and their representative organisations to delay the launch by as much as two years – a position which the Scaffolding Association strongly supports.
Scan here to head over to the TfL website for more information.
Driver Certificate of Professional Competence (CPC)
The deadline for many drivers to complete their Driver CPC training is 9th September 2024. To make sure your drivers can find training in time, the Scaffolding Association would like to remind companies to encourage drivers whose Driver CPC runs out this September to check that they have completed 35 hours well before the 9th September deadline.
Demand for training will be high because September 2024 is the 15-year anniversary of Driver CPC for lorry drivers. When it was first introduced all lorry drivers had to get their driver qualification card by 9th September 2014. This means that many current cards will run out simultaneously. Meaning every 5 years there are many drivers trying to complete their 35 hours of training at the same time.
If drivers miss their training deadline, they cannot drive professionally until they finish their training, and could be fined up to £1,000 for driving professionally without having a Driver CPC.
Scan here to check the number of hours you have completed towards your Driver CPC and to check the deadline.
Scan here to download a free copy of the Scaffolding Association’s Clean Air Zone Tracker Guidance.
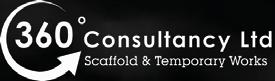

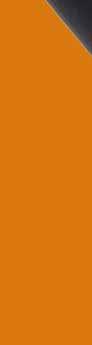

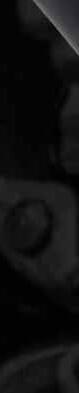
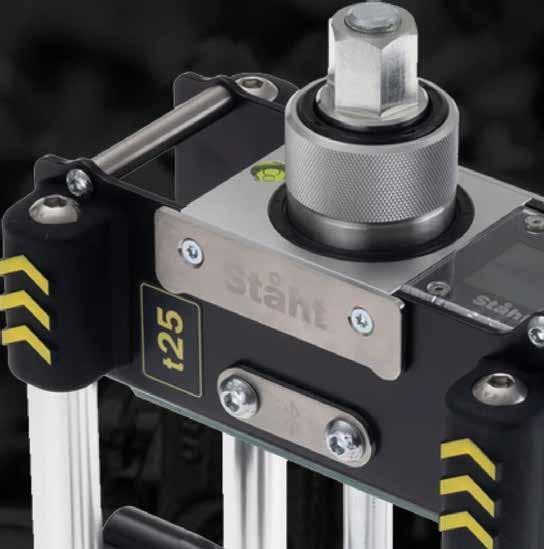
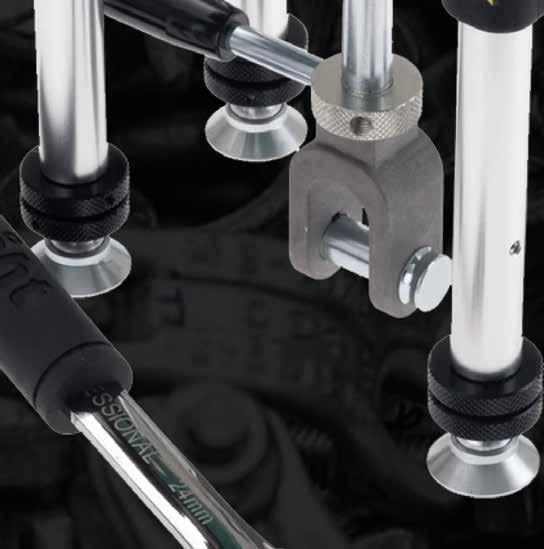
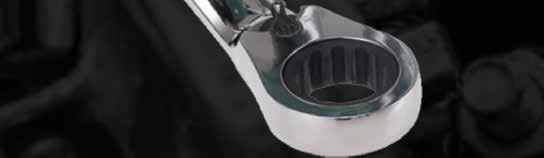


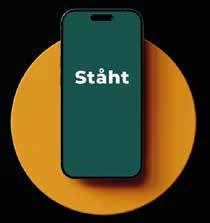
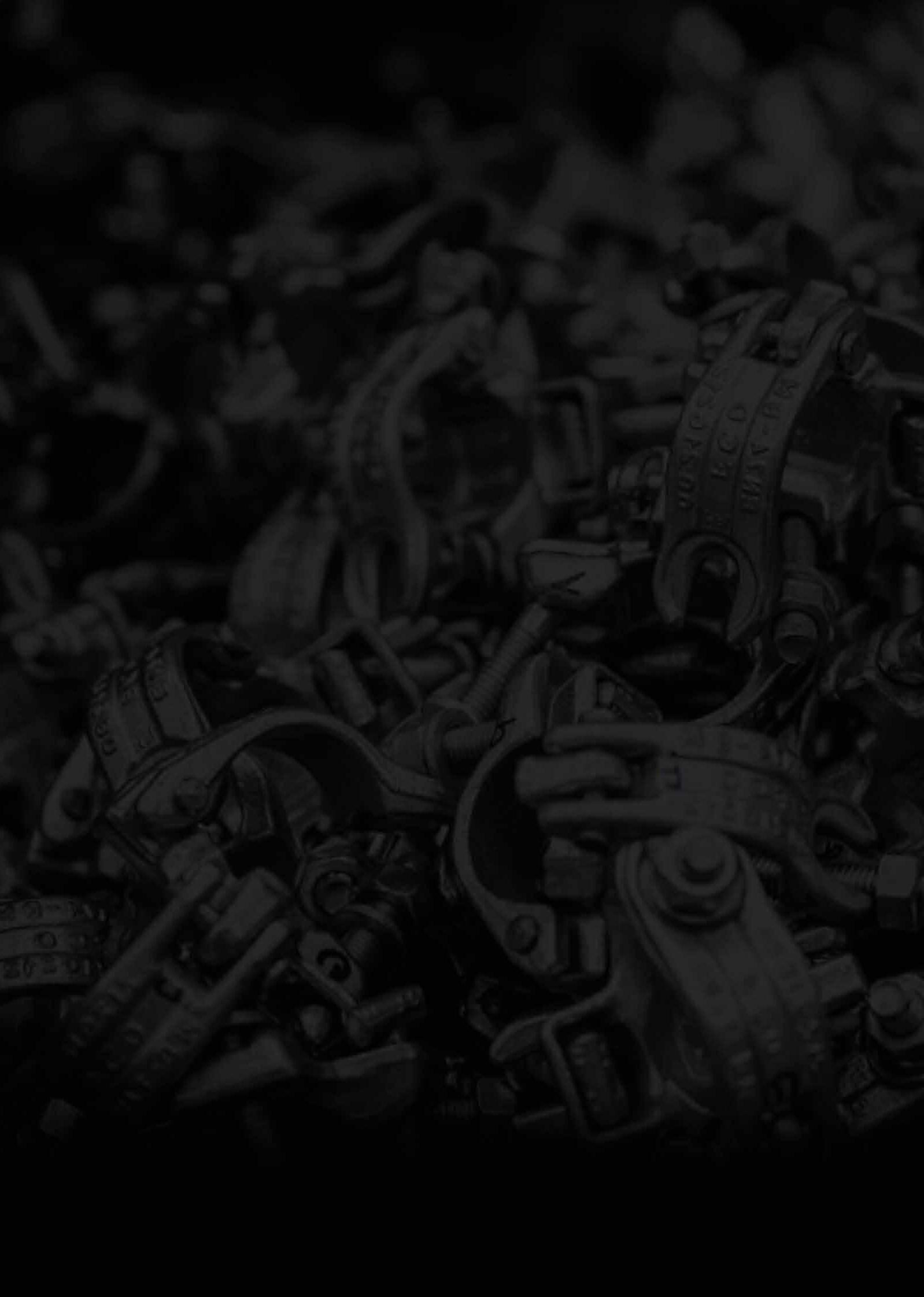
Summer drink and drug drivers campaign
Did you know that more drink and drug drivers are caught during the summer than at Christmas?
In this article D.tec International, who are specialists in the drug and alcohol screening industry, discusses what you can do to safeguard your business and employees.
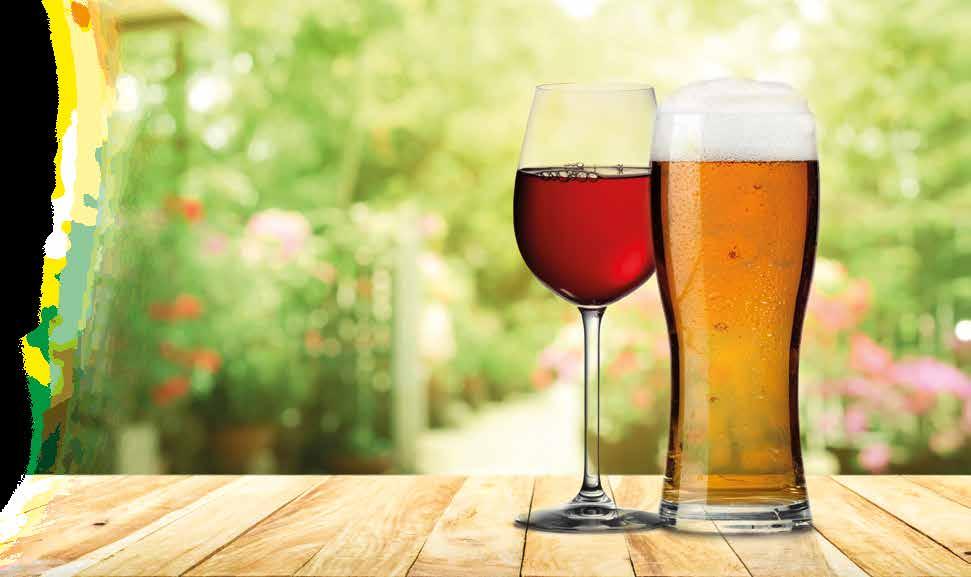
You will perhaps be aware that police forces across the UK focus on drink and drug driving over the Christmas period, this campaign is known as Operation Limit. Operation Limit has been so successful that this summer will see the first nationally coordinated Summer Drink Drug Drive Campaign.
Drink and drugs are very emotive subjects to address, especially for businesses. Scaffolding and access businesses face an even bigger challenge with the majority of employees working remotely on sites that change regularly, as opposed to working within a more easily controlled office environment.
In addition, they are often driving on public roads in large commercial vehicles and when they arrive they are then working at height.
Where these safety critical workers are concerned, making sure that they are fit to undertake their duties is critically important to any business which takes its moral, legal and reputational responsibilities seriously.
The likelihood of someone on your workforce being unfit to work through drugs, whether that is during the summer, Christmas or any other time of year, is higher than you might think.
As we approach the summer, and police forces from across the UK increase their focus on catching drink and drug drivers, it’s the ideal time to consider whether you are doing enough to protect your business and its employees.
In some parts of the UK, over half of those caught drug driving are driving to work or for work.
3 in every 4 (75%) of illegal substance users are in full-time employment.
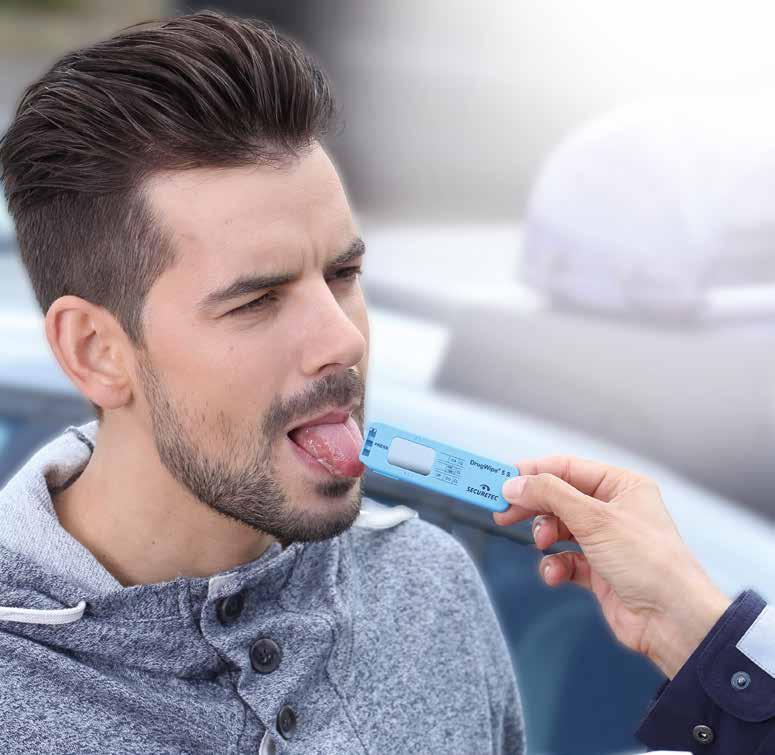
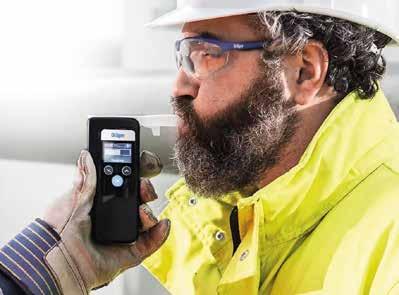
It’s not just about screening either –far from it in fact. It’s as much about having the right policies in place, providing education and creating an effective deterrent as it is about detecting and addressing improper drug and drink use.
D.tec International provides an unrivalled Drug and Alcohol Safety Service supported by experts who understand the challenges in protecting your business from the potential consequences for not addressing this sensitive subject.
Will we ever not talk about extra hire – what can you do?
Back in 2021 the Scaffolding Association’s legal partners, Holmes & Hills, put on a webinar focusing on extra hire and the frustrations that scaffolding contractors were having. In this article, 3 years later, they discuss “has anything really changed” (Quick answer: No!)
Unsurprisingly, we still frequently receive instructions from clients seeking to recover extra hire costs following a main contractor’s refusal to pay for this additional hire. So, let’s dive into where the problems are arising by looking at a typical example of the type of ‘extra hire’ disputes that come our way.
The typical dispute
The classic scenario we encounter is a delay in project completion, leading the scaffolding contractor to believe they’re entitled to extra hire. What follows is the main contractor’s refusal to pay further costs due to an understanding (rightly or wrongly) that they’re not liable for any additional payments if the project overruns.
Typically, we hear phrases like: “I’ve got the contract, but it’s really straightforward We quoted for 24 weeks hire and it’s now been 35 weeks and they won’t pay.” While that might have been in the quote, it doesn’t automatically mean you’re entitled to payment for extra hire. Remember, the contract is king! We routinely see two main wrongful assumptions and oversights tripping scaffolding contractors up.
Assumption 1: “Extra Hire was in my quotation”
The biggest oversight is scaffolding contractors relying on the quotation/ tender document as proof that the contractor was ‘aware’ or ‘agreed’ to pay extra hire. Often, we see emails negotiating project aspects, including an extra hire rate. However, contractors overlook the golden ticket clause in 99% of main contractors’ contracts/terms & conditions, which states something like: “The Subcontract and the documents referred to contain the entire agreement between the
parties concerning the subject matter of the Subcontract, to the exclusion of all other terms. The Subcontractor acknowledges and agrees that, in entering into each Subcontract it does not rely on and shall have no remedy in respect of, any statement or representation which is not expressly set out in the Subcontract.” This ‘entire agreement clause’ means that despite negotiating terms, it’s worth nothing unless expressly amended in the contract or appended to it.
Assumption 2: “Extra hire is part of my quote and is included in the contract”
Consider the scenario where your quote, containing a provision for extra hire, is appended to the contract. This sounds promising, but 99% of main contractors have a clause stating their terms apply ahead of yours if a ‘discrepancy’ arises. This is known as an Order of Precedence clause, which typically states: “Should any discrepancies exist between these terms and the contract documents, the order of precedence shall be read as follows:
1. These Terms and Conditions
2. The Pre-Commencement Meeting Minutes
3. The Purchase Order (if applicable)
4. The Sub-Contractor’s Quote/Tender”
In practice, this means that even if your quote includes extra hire, but the main contract states ‘no extra hire,’ the main contract terms overrule the quote. This may seem unfair, but it’s a common clause throughout the construction industry, so it’s something to be aware of.
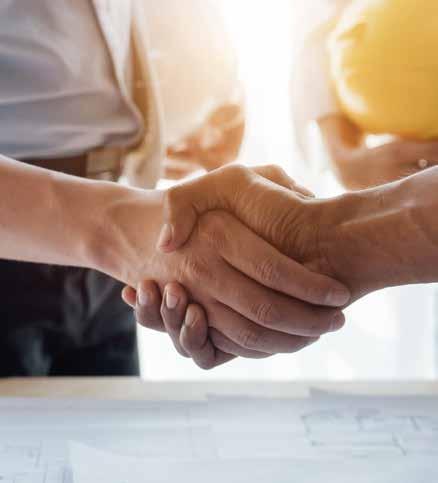
Now you know, what can you do about it?
Scaffolding contractors risk inadvertently agreeing that no extra hire is payable if they don’t thoroughly review the contract. Even a cursory look should flag an entire agreement clause or an Order of Precedence clause.
We understand that amending these types of clauses without jeopardising commercial relationships is tough. However, we can assist by reviewing the terms and conditions and providing you with the tools to position yourself as favourably as possible, similar to how the main contractor positions themselves.
Scan here for more information on the Construction Team at Holmes & Hills LLP.
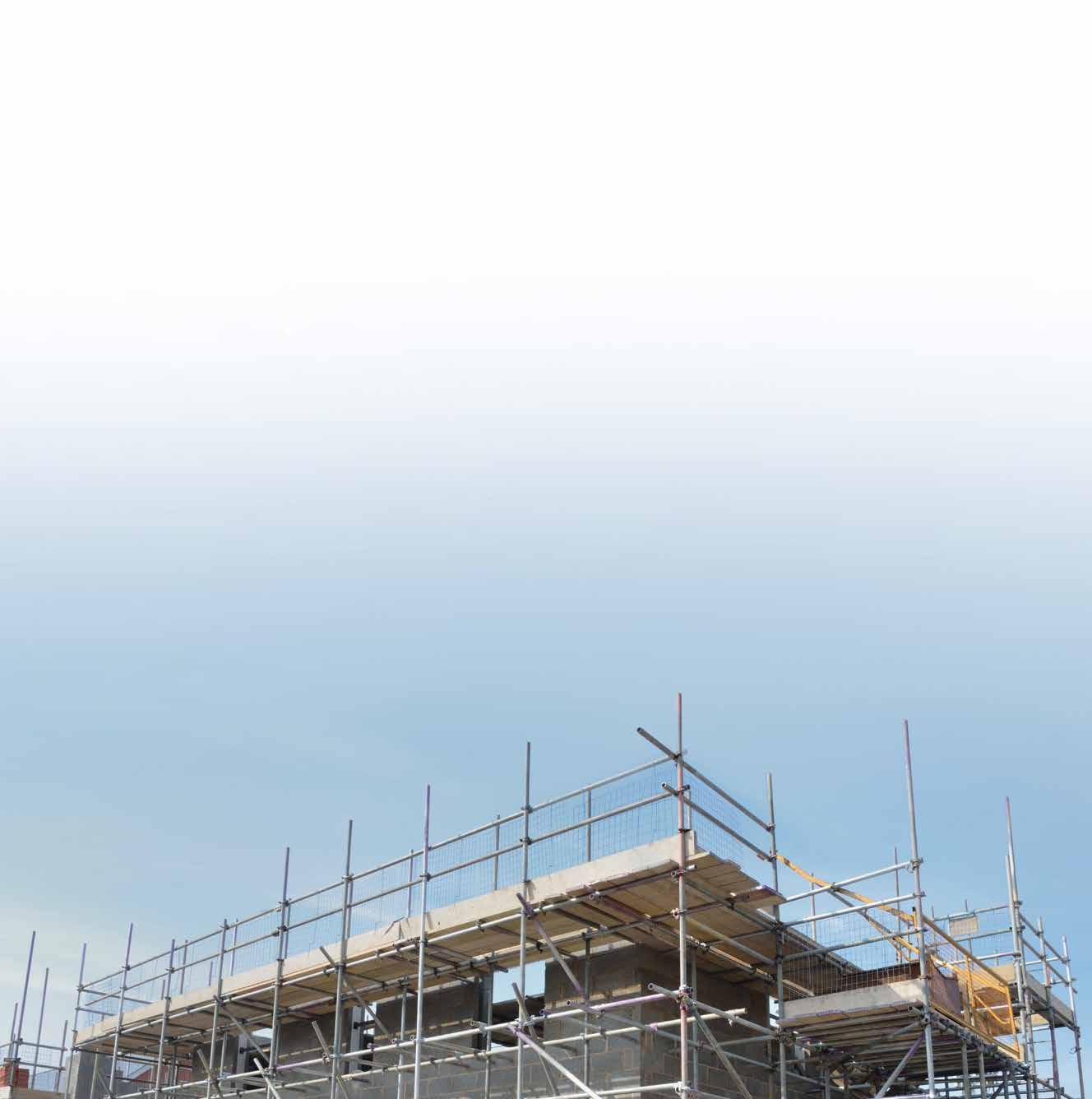
A guide to the HSE’s Fee for Intervention
According to the British Safety Council, the Health and Safety Executive (HSE) imposed a total of £35.8 million in fines for health and safety breaches in 2023. On the 1st of April 2024 the HSE increased their hourly recovery rates of their Fee for Intervention. In this article we have compiled information from the HSE’s website to help you understand how the Fee for Intervention works and the HSE’s approach to enforcement.
What is Fee for Intervention?
If the HSE visits your workplace and finds that you are in material breach of health and safety law, you will have to pay for the time it takes them to identify what is wrong and to help you put things right, this is the Fee for Intervention (FFI).
If the HSE visits your workplace and finds no material breach, you will not be charged FFI for any work that HSE does.
Who does the FFI apply to?
The FFI applies to dutyholders where HSE is the enforcing authority, including:
• employers
• self-employed who put others at risk
• public and limited companies
• general, limited and limited liability partnerships
• Crown and public bodies

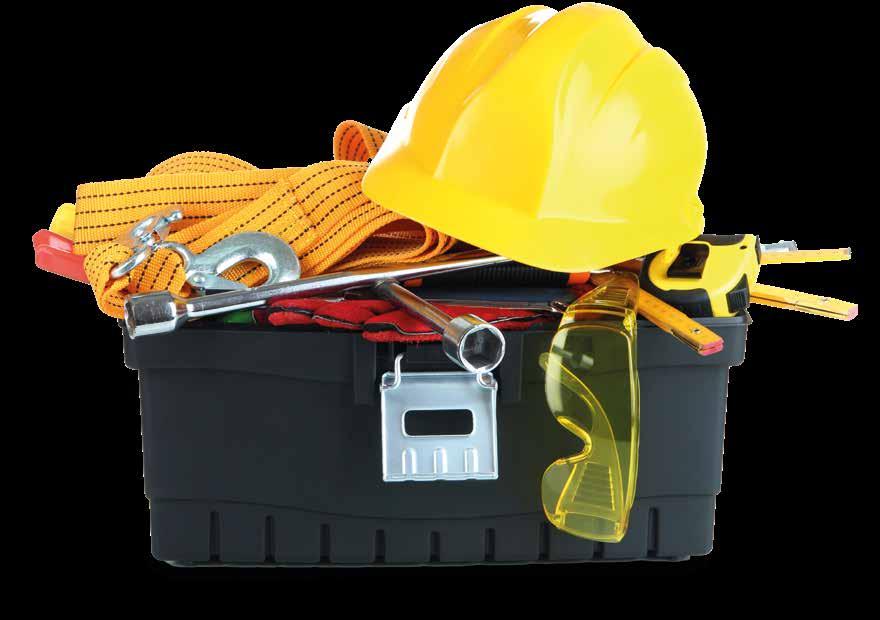
imposed a total of £35.8 million in fines for health and safety breaches.” British Safety Council
How does the FFI work?
HSE’s regulatory work includes inspecting work activities, investigating incidents resulting in death, injury and ill health, following up complaints about poor standards and taking enforcement action. A fee is payable if:
• a person is or has been contravening relevant health and safety at work law;
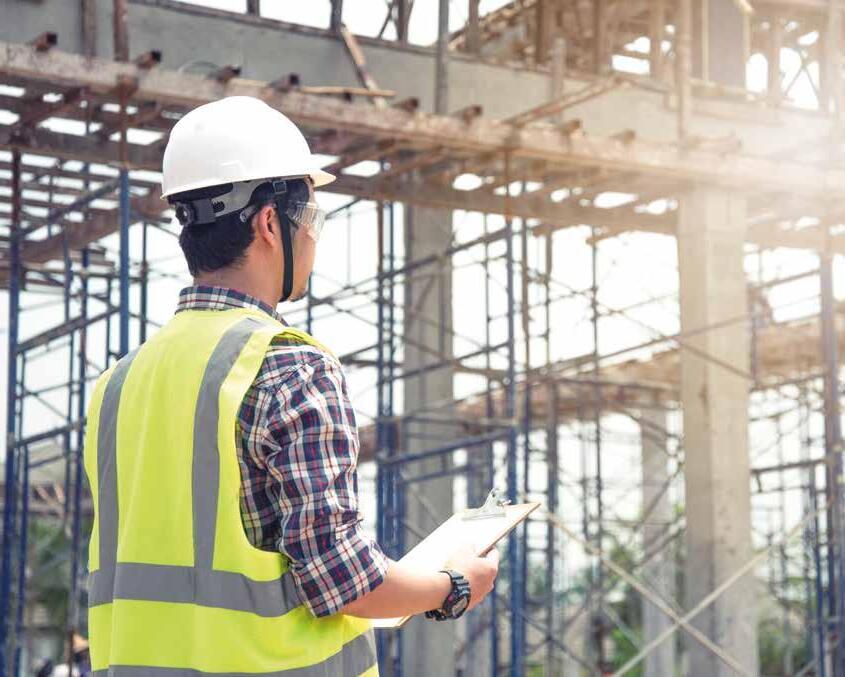
• an inspector is of the opinion that the person is contravening/has contravened the law;
• the inspector notifies the person in writing of that opinion.
A material breach is something which an inspector considers serious enough that they need to formally write to the business requiring action to be taken, this is a Notification of Contravention (NoC). The NoC must include:
• the law that the inspector considers has been broken
• the reason(s) for their opinion
• notification that a fee is payable to HSE
Where an inspector simply gives you advice, either verbal or written, you won’t have to pay anything. How much does it cost?
The HSE has recently increased their hourly recovery rate from £166 to £174.
The fee may include time spent at your business or workplace, preparing reports, getting specialist advice, talking to you after the visit and talking to your workers.
The fee can vary depending on how long the visit was, the time spent helping you put things right, the time it took to investigate your case and any time spent on taking action.
Scan here for more information on Fee for Intervention.
Telephone: 0300 0033 190
Email: feeforintervention@hse.gov.uk
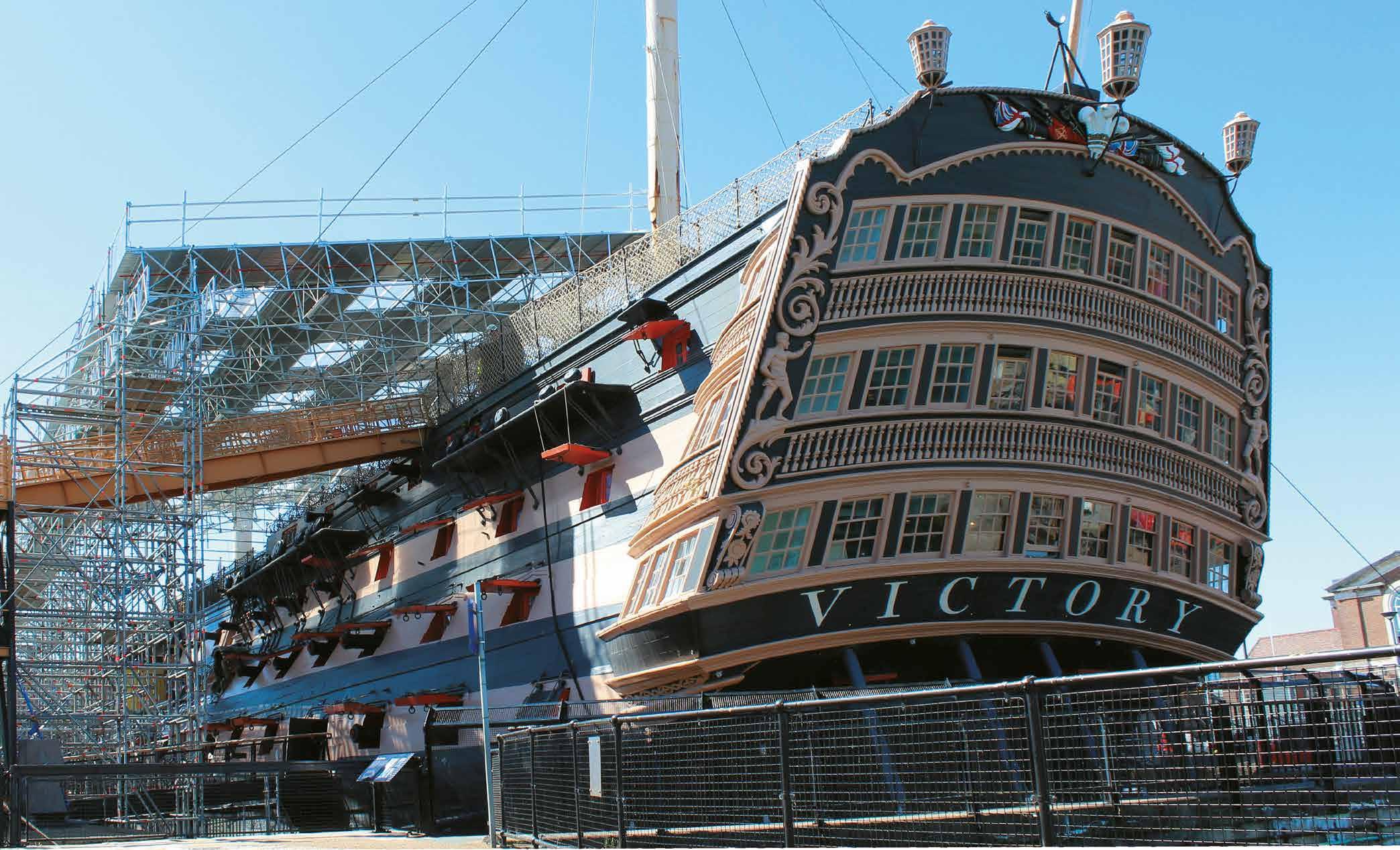
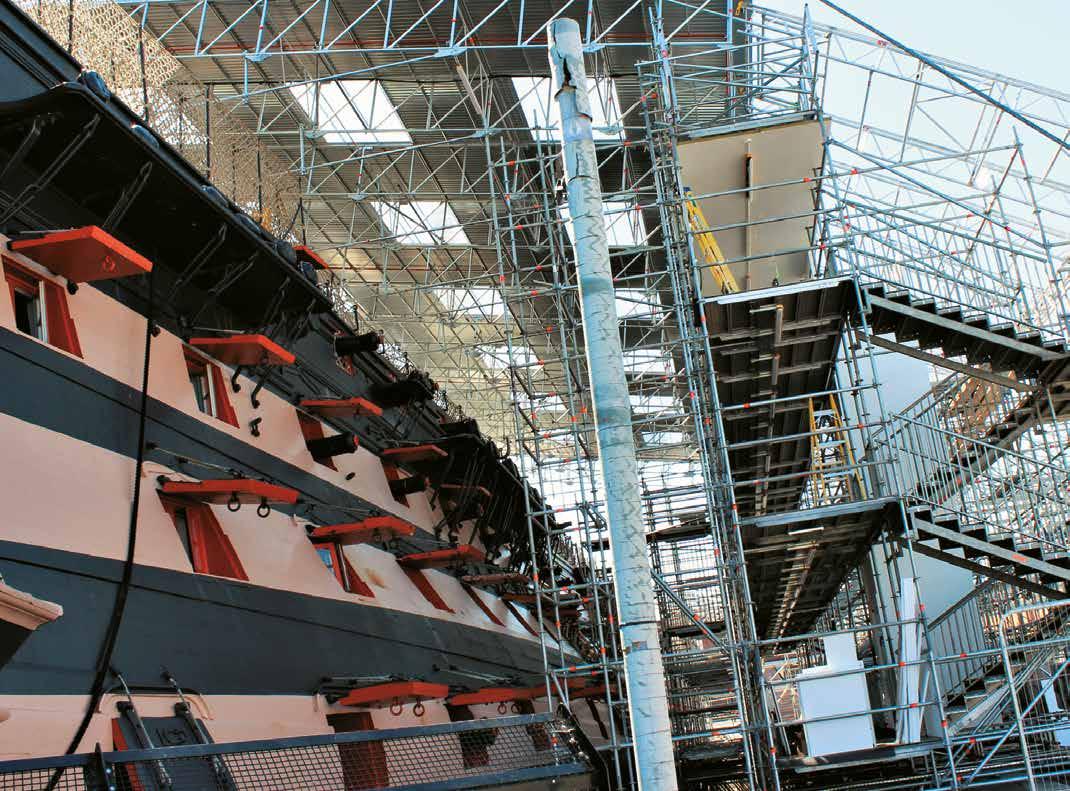
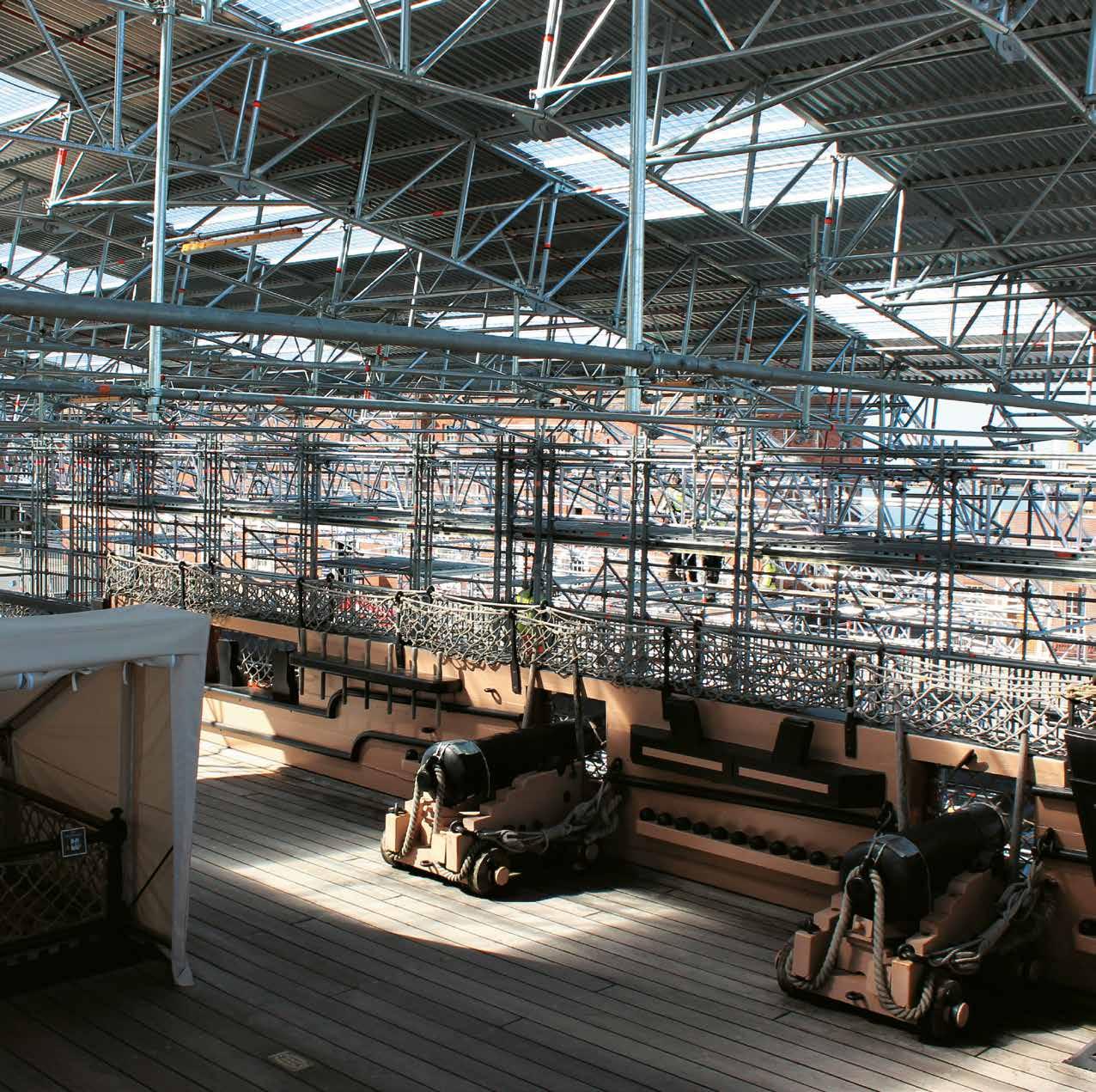
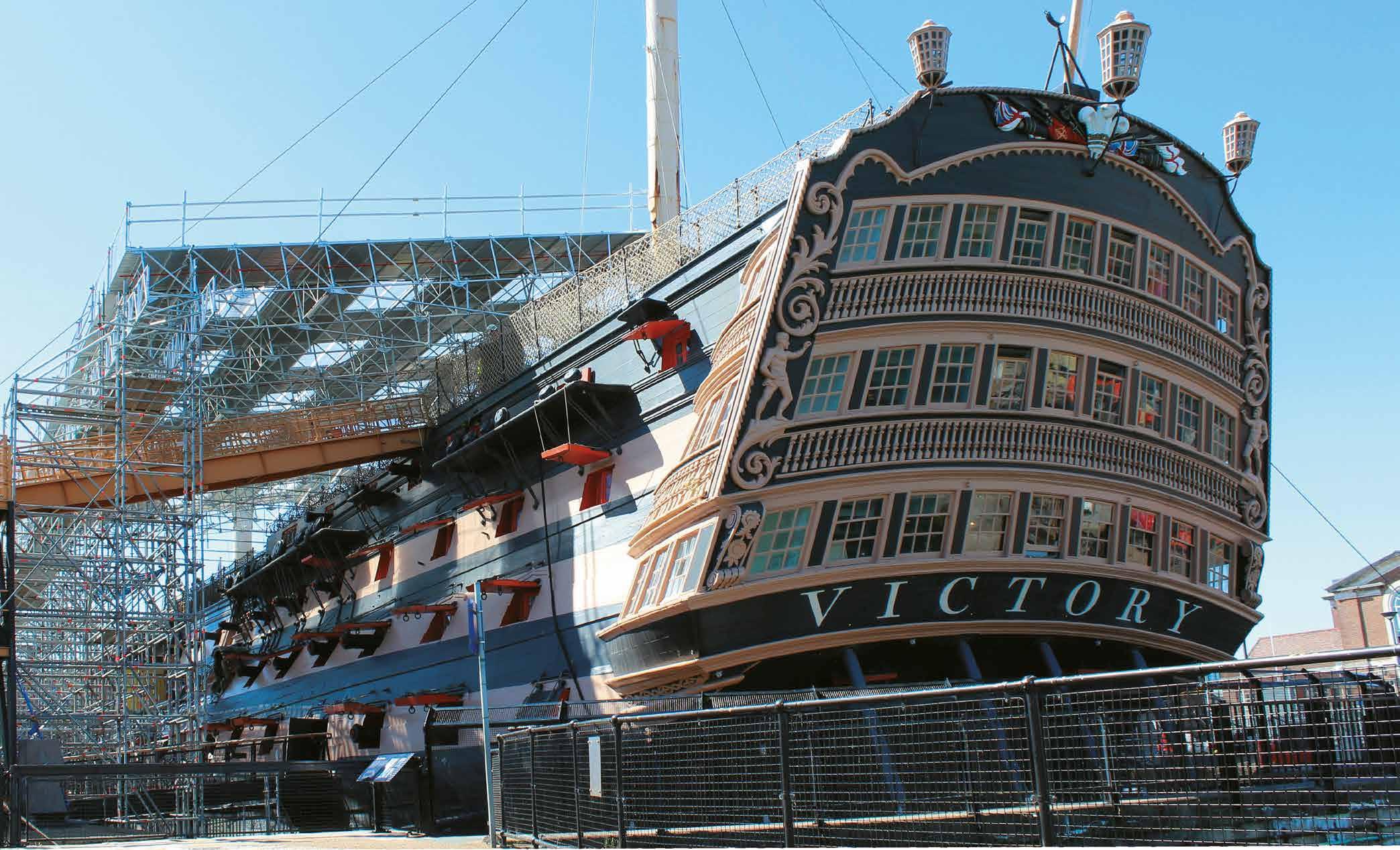
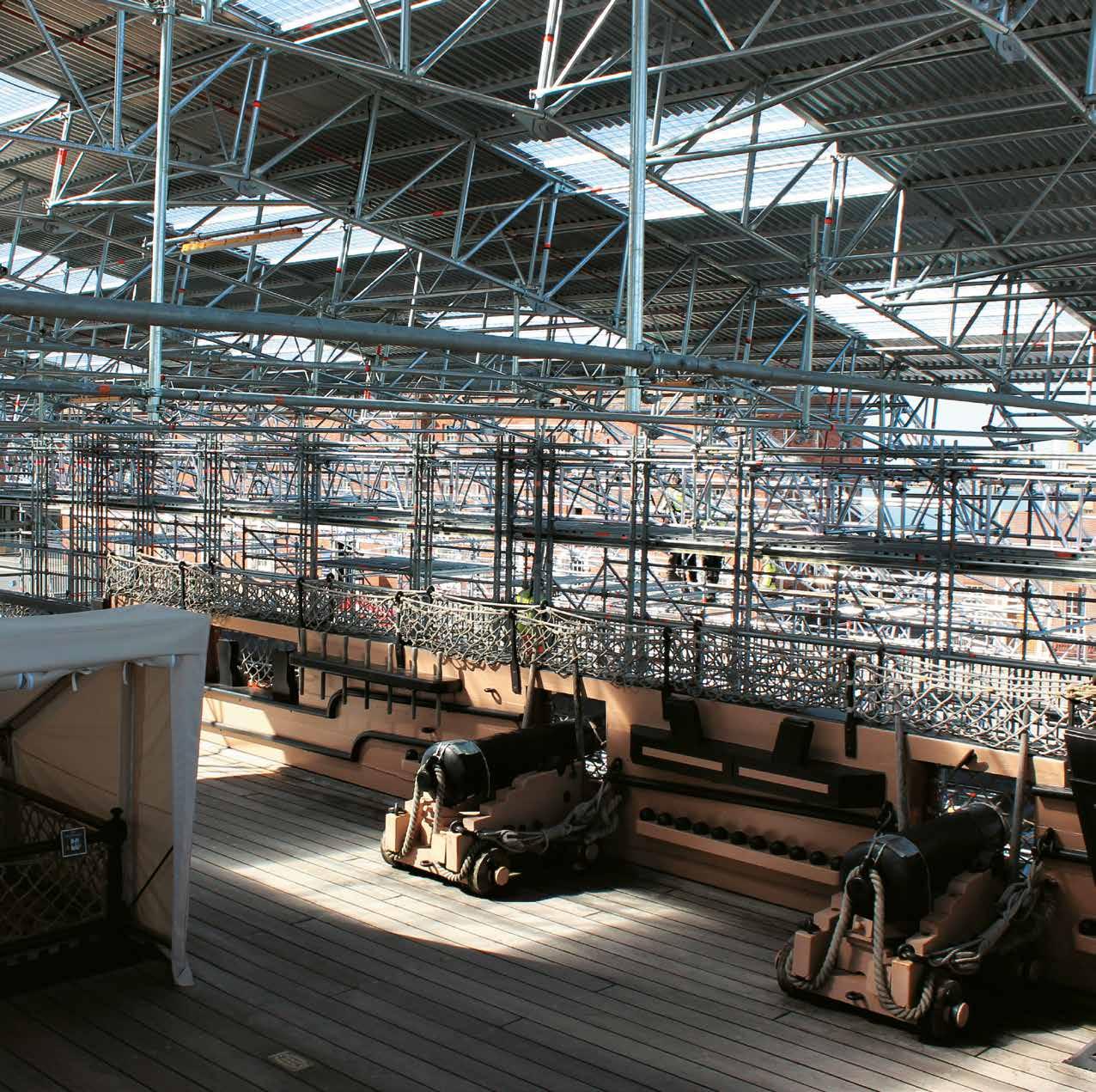
PROTECTING our HERITAGE
INNOVATIVE SOLUTIONS FROM LAYHER
THE WORLD’S
LEADING MANUFACTURER OF MODULAR SCAFFOLDING SYSTEMS
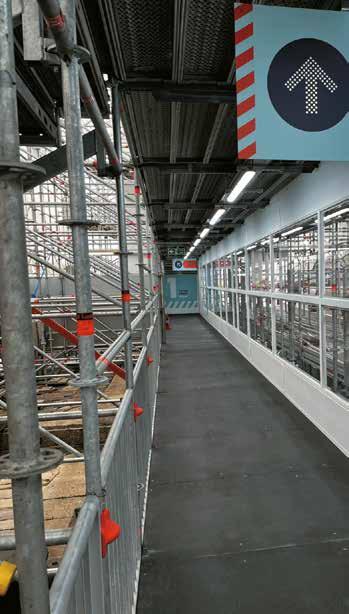
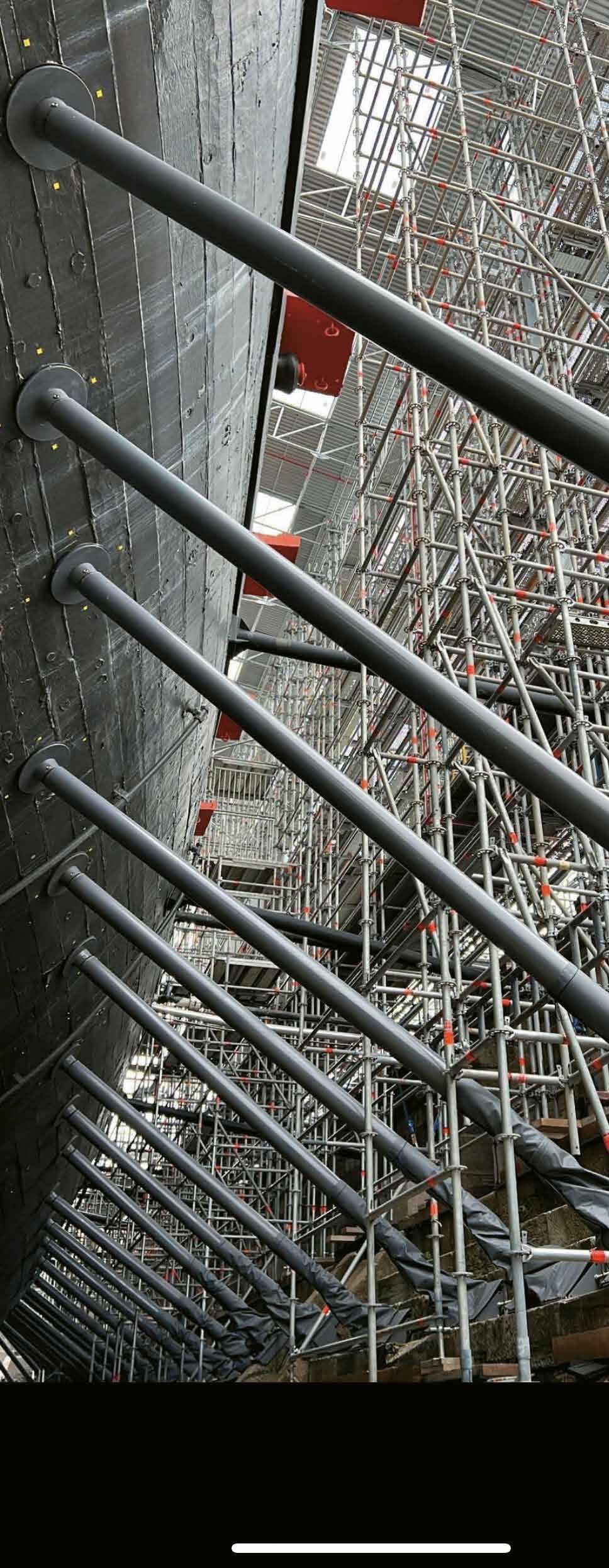
JTL tower above the rest on largest of its kind subsea drill project
JTL Scaffolding and JTL Special Projects have successfully delivered a project on the largest diameter subsea drill that has ever been produced for the purpose of drilling foundations for offshore wind turbines, leading the way for future growth in windfarm installation.
JTL Group, who are fully Audited Members of the Scaffolding Association, were appointed by TEXO to provide a complete scaffolding package for this complex and specialist project that involved multiple stakeholders working together, including Saipem (Principle Contractor for EDF), Large Diameter Drilling Ltd (The Mission Equipment Supplier who are part of the Acteon Group) and TEXO (Project Site Support for the build).
With a diameter of 8.50m, it is currently the largest subsea drill of its kind in the world and was developed to reduce noise pollution in the Courseulles Windfarm Project.
The base of the structure, the Drill Leader Tower (DLT), being manufactured within the port of Blyth, currently stands at 33.5m tall and weighs approximately 980ton. A further structure (The Crown) is to be placed on top of this when in operation and will give a total height of 38m. By the time the 56m long Drill is installed, the combined weight will be approximately 2000ton.

Matthew Johnson, Engineering Manager at JTL Scaffolding, detailed the extent of the works they undertook:
“Whilst the original scope for this project was external access, it quickly changed to become full scaffolding access to both external and internal
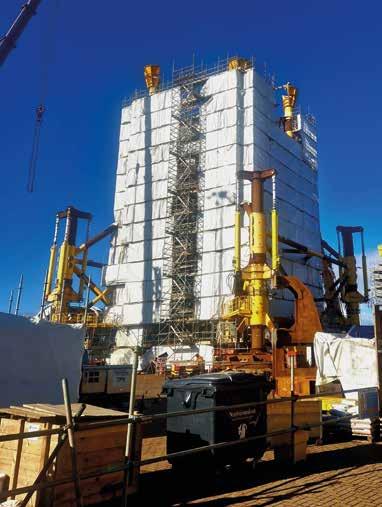
areas, in addition to a vast 36m free standing and sliding temporary roof, which was to be purposed as a temporary paint workshop to allow items to be fabricated and painted on-site. It slid open to allow large items to be loaded with a land-based crane and then closed to create a controlled environment suitable for blasting and painting.”
Project in numbers
• June 2023 to May 2024
• 24/7 site presence
• Over 250ton of Futuro delivered by Generation
• 49865 Man Hours
• Zero incidents
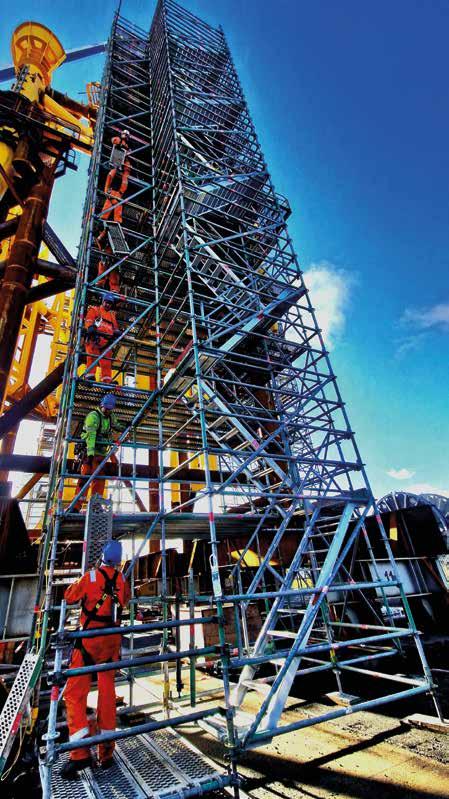
Although the scaffolding required was relatively straight forward, the adaptions and constant change of purpose/ requirements for the scaffold meant that it was constantly evolving to enable different trades to use the same scaffold without issue.
As this had never been done before, the challenges JTL faced were often unforeseen and therefore had to be planned and implemented quickly and efficiently. The tight timescales and limited space also required careful consideration. Matthew gave an example that highlight this:
“4 full height towers were required for The Crown, however we could only start preparation for this once it was announced it had been loaded onto a barge and left Italy, a 3-day voyage with 1-day to unload. This gave us a 4-day turnaround to organise all materials and labour. We already had approximately 100ton of Futuro on-site and The Crown required a further 100ton. This caused laydown issues, meaning we had to plan and schedule deliveries very precisely. Our supplier, Generation, ensured that the load lists were accurate to allow each stage to be carried out with a very high level of efficiency.”
Safety was at the forefront of this unique project receiving positive feedback from both the fire and rescue teams and the Coast Guard during a rescue exercise resulting in comments highlighting that the scaffolding was not only ideal for daily operations but also exceptionally wellsuited for emergency rescues.
JTL overcame everything thrown at them and met all requirements for the works to take place, but JTL faced one more huge mission as Matthew explained:
“The client requested that the whole DLT scaffold was to be stripped over 48 hours to allow for testing to be carried out. This saw 40 operatives, 2 forklift drivers and 3 supervisors arriving at the port of Blyth on a Saturday morning facing a mammoth task and a hard 2 days. All other trades had been stood down for the weekend to allow us to have complete control of the site to ensure the task could be executed safely. Split into two teams, working day and night, we started to strike the scaffold in 2 halves. By 3pm on Sunday all scaffolding was removed and we handed back over to the client.
A Challenge? Nae
bother! A challenge is exactly what this project posed for all vendors, However, JTL powered through even with the toughest of weathers and toughest timescales. Few companies could deliver what we asked of JTL over the last year. Their management, timekeeping and cost control kept it so.”
Chris Hickling, Site/Pre-Com Manager at Large Diameter Drilling Ltd
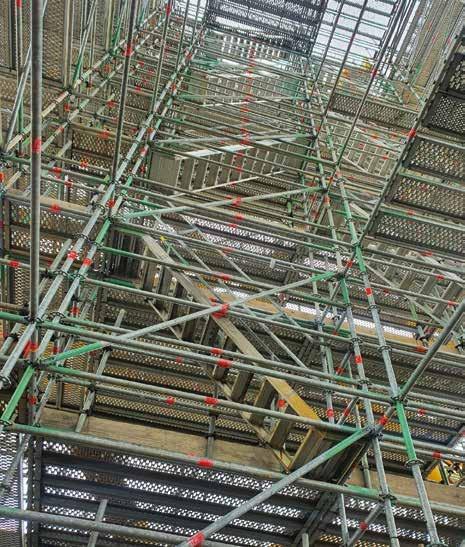
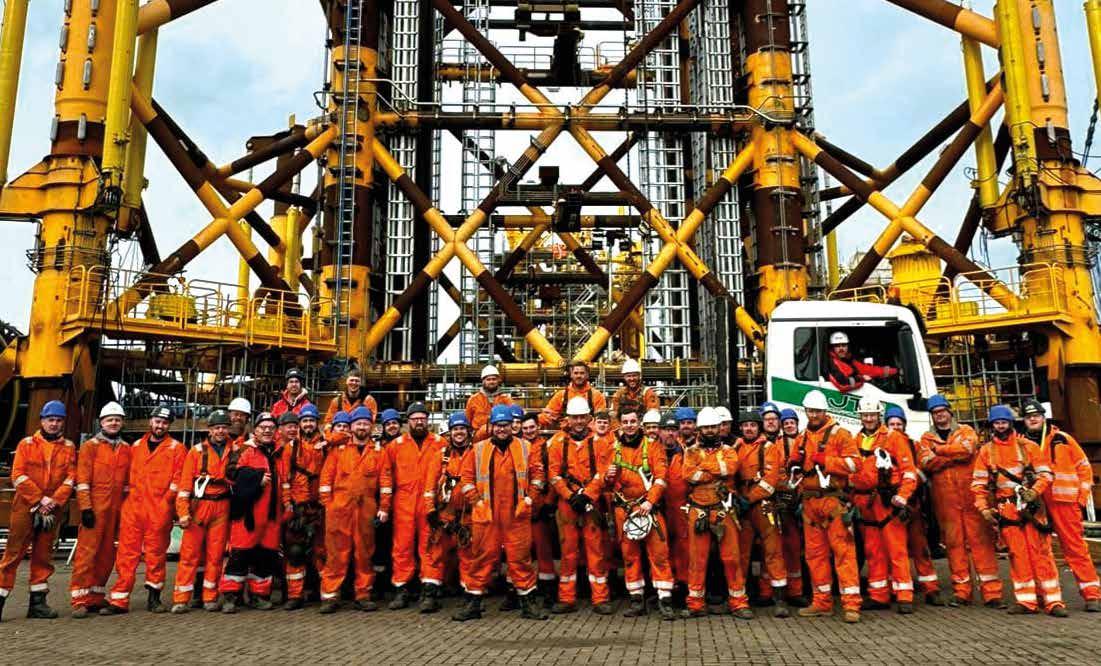
That would be the key part of the project that stands out for me, seeing everyone come together to strip 150ton of scaffold in a single weekend allowed the whole company to come together as a single team to deliver what was said to be impossible.”
As the Engineering Manager, Matthew spent the bulk of his time providing solutions, modifications and adaptions in situ to free up new work scopes and keep the project moving. He concluded:
“It is very rewarding being able to deliver advice on-site for such a large-scale project whilst working alongside such a great team. It has been frustrating at times with timescales being requested on the verge of being impossible to meet, but we spent time talking and finding solutions and meeting agreed expectations. The constant communication, not only with other companies, but with individuals from all over the world, allowed us as a company to grow
and learn in ways most other projects wouldn’t allow.”
TEXO, commenting on their long standing relationship with JTL, had only positive comments to make on JTL’s performance, Brand Executive, Alan Conway said:
“JTL delivered exceptional results on this project. The scaffolding was expertly designed and constructed with comprehensive consideration for ingress and egress, making it extremely user-friendly for contractors manoeuvring tools and equipment throughout the tower. TEXO will undoubtedly partner with JTL for future projects.”
Hugh Skivington, CEO of JTL Group, was equally pleased with the results, concluding:
“This has been a huge project for JTL and even with the challenges presented, the team has pulled together and delivered the project flawlessly and without incident.”
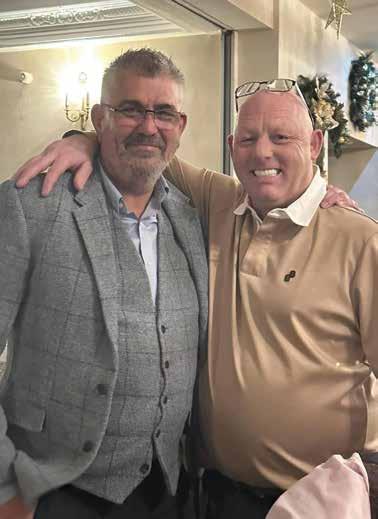
The project was a monumental success, but it was a bittersweet one, it was started and ran by JTL’s Operations Director, Gerry McNally, who helped to deliver everything from day 1. Sadly, in January 2024, Gerry passed away suddenly following a very short illness.
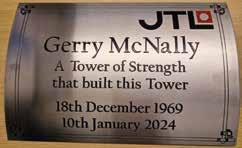
“Gerry was the true success story of this whole project, his death cast a very sober mood over the whole project and affected many people from all trades and companies involved in the project.”
Matthew Johnson, Engineering Manager at JTL Scaffolding
SA Scaffolding provide cover for remedial works at busy St Georges Court
SA Scaffolding Ltd, who are Audited Members of the Scaffolding Association, have been providing access and protection at St Georges Court in Camberley, Surrey.
With water ingress through the roof that was damaging internals of all the properties, SA Scaffolding were tasked with providing a structure that spanned the entire roof to allow remedial work to be undertaken.
From the beginning SA Scaffolding worked closely with Prime Scaffold and Structural Designs Limited (PSD), who are Associate Members of the Scaffolding Association, to come up with solutions to the many challenges they faced in making the project a huge success. Craig Withers, Manager at SA Scaffolding commented:
“PSD were fundamental from the outset finding solutions to cover the vast span, the total size of the roof was 1584m2, and we had to gain 26kn per tie area as there was 12m of freestanding scaffold to the total perimeter. The 36m span was manually fixed without the use of a crane.”
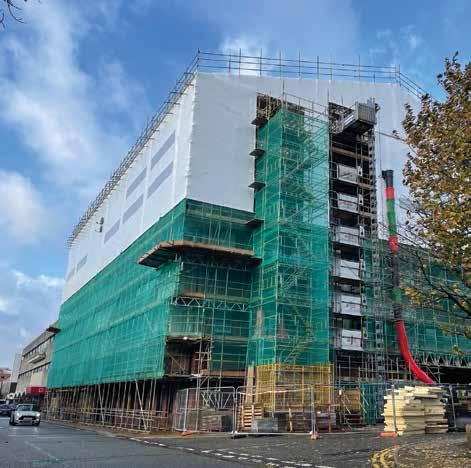
The structure had to span the entire roof to allow works to continue at all times, Craig explained their solutions:
“We decided to go with lighter shrink wrap [provided by Assessed Members of the Scaffolding Association, Coveredinshrinkwrap Ltd], rather than corrugated sheeting.
The ties were tested at low level until we found that 3no singular ties rather than 1no Apollo fixing would be the only way to gain the 26kn required.”
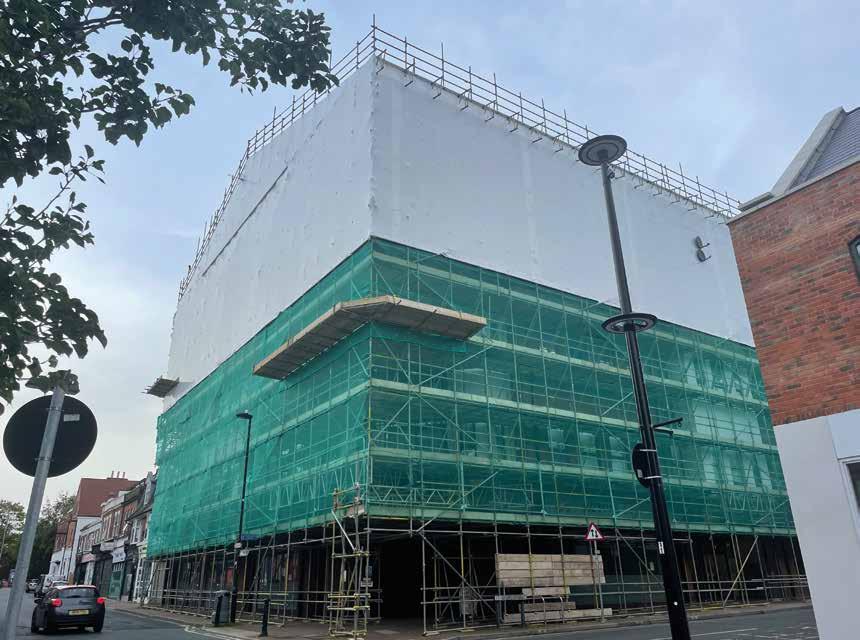
Craig noted the size and scale of the project:
“The total size of the roof was 1584m2 , we had over 4000m of varying beams in this project, with over 900no individual ties.”
St Georges Court is a busy area, which also effected SA Scaffolding’s work schedule, Craig commented:
“Working in close proximity to the residents and general public meant that we had restricted delivery times, in addition to having to work closely with Southern Hoist Services (SHS) to ensure that we hoisted materials to the roof level within strict allotted times.”
When asked about the project Craig mentioned:
“My favourite part was the completion of a fantastic structure, and it was also great working with a client that understood the complexity of the brief. The project was complex and had many problems to overcome but at SA Scaffolding we love the challenge.”
The project was a huge success and has been handed over to the client, Attleys Roofing, who commented:
“To see this fantastic project come together showed a great thought process from the original site visit to completion of the structure, SA Scaffolding were nothing but diligent from start to finish.”
Contact Craig on craig@sascaffoldinglimited.co.uk
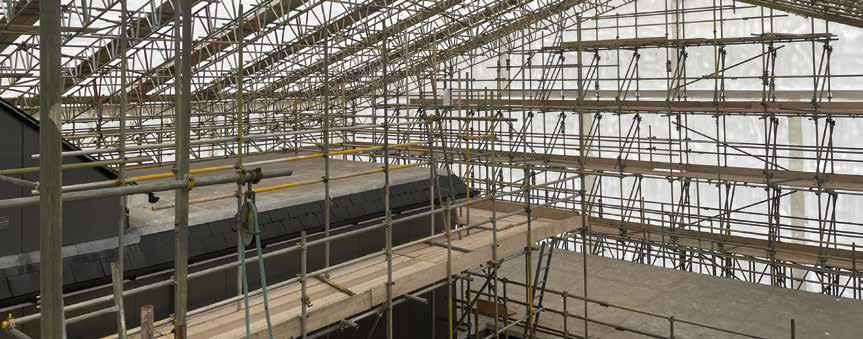
Events coming up in 2024
September
27-29 | Homebuilding & Renovating Show | London www.london.homebuildingshow.co.uk
October
1-3 | UK Construction Week | Birmingham www.ukconstructionweek.com
7-11 | National Scaffolding Week | UK wide www.nationalscaffoldingweek.com
9 | Welsh Construction Show | Swansea www.twcs.wales
11 | Scaffolding Conference & Dinner Dance | Midlands www.scaffoldconference.co.uk
24 | Roofing, Cladding & Insulation Show | Milton Keynes www.rcishow.co.uk
November
20-21 | London Build Expo | London www.londonbuildexpo.com
27-28 | Homes UK | London www.homesevent.co.uk
December
2-4 | Anticipate London (Safety & Health Expo) | London www.anticipate-event.com
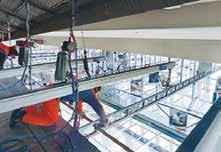
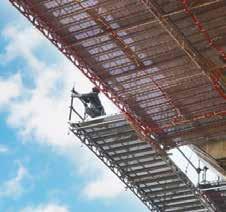
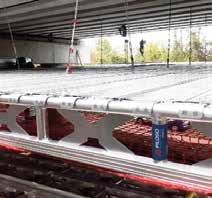
CUT INSTALL TIME BY UP TO 50%
Introducing Flydeck, a ground-breaking suspended access solution from the Italian company Pilosio. Now available in the UK through APA Height Access, the authorised installer and partner of PILOSIO UK, with coverage across the entirety of the country.
Thanks to its aluminium structure and innovative design, Flydeck when coupled with Flyrail reduces install time by 30 to 50% compared to traditional scaffolding solutions.
This system allows for quick and safe installation of a durable, lightweight deck. It facilitates access to horizontal structures like bridges, jetties, stadiums, commercial and retail environments, while minimising disruption and install times.
For more information on Flydeck, scan the QR code or visit apaheightaccess.uk/flydeck to arrange a free live demonstration and see Flydeck in action.
WHERE TRENDS MEET TRADITION


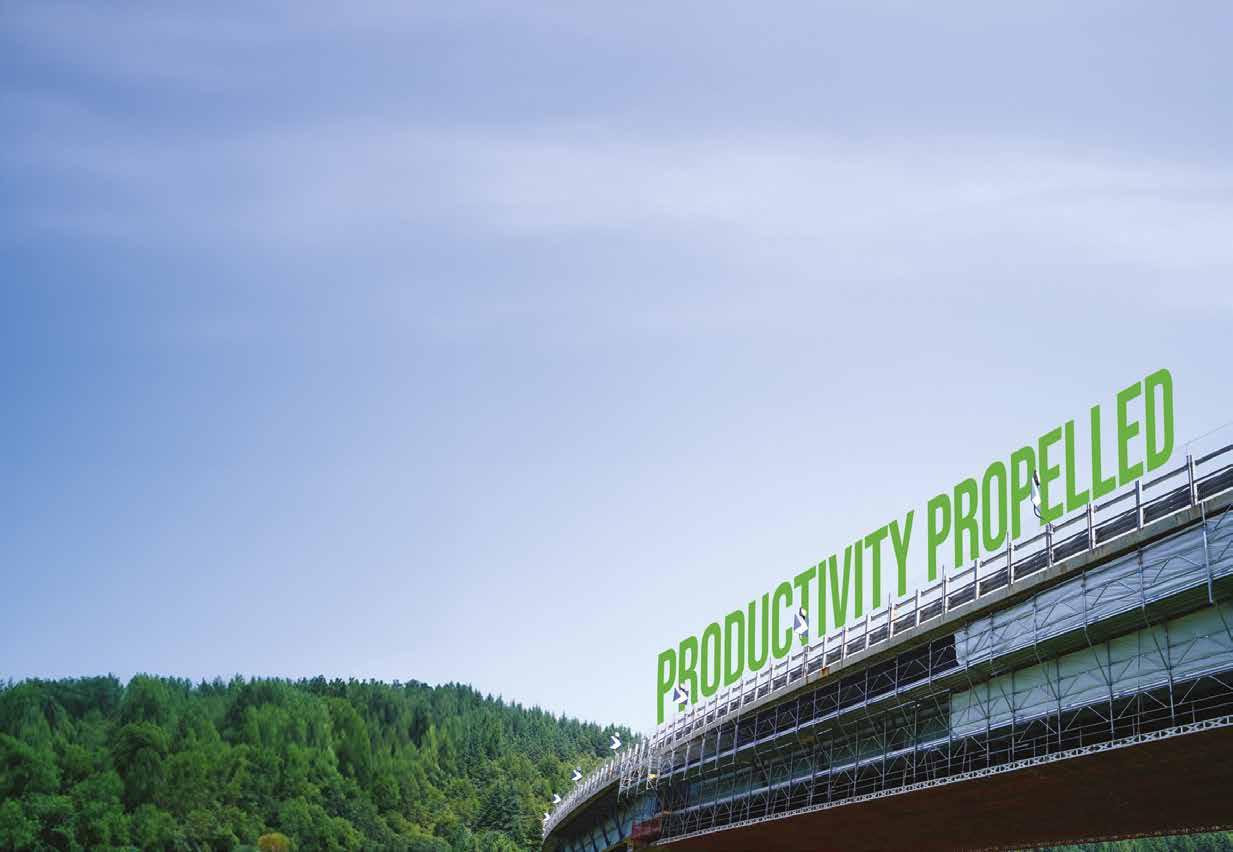
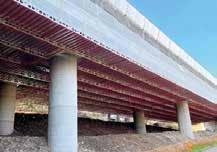
Audits and inspections: the purposes and the differences
In this article Karl DeGroot, Managing Director of 360 Degrees Consultancy, seeks to clarify the purposes of audits and inspections, as well as providing a better understanding of the differences between the two.
Inspections are compliance tasks with a checklist
Inspections are typically the recurring completion of checklists by facilitylevel personnel, such as facility EHS coordinators and managers. Internal or visiting managers with operational roles that encompass inspection regimes, or external third-party providers in many cases now, who have additional levels of subject matter expertise and impartiality.
Inspections can be thought of as compliance tasks with checklists. For example, an inspection can be a targeted verification to see if a specific piece of equipment, or a process, is operating in a safe and environmentally friendly way. Corporate, site-level or OHS managers and coordinators, who need to implement a compliance system within a company or site, seek ways to improve the way inspections are conducted.
For example, an environmental operating permit may require a facility to do a weekly inspection on a piece of equipment to ensure it is operating correctly. A scaffolding might be inspected weekly under the Work at Height Regulations to ensure that no third-party interference has occurred, or environmental impacts such as weather haven’t affected the stability. The corporation may then conduct an annual audit to check compliance with the requirement to do the inspections.
Audits assess compliance
Audits are typically performed less frequently than inspections, potentially just annually. The goal of an audit is usually to assess overall compliance with one or more regulations, such as internal policies, other compliance drivers or trade association certification.
Audits are typically conducted by a thirdparty to the client/member or site being audited, which could include an auditor from an internal corporate department or an auditor completely external to the company. Audits also allow a company, or certification body to “self-check” to make sure everything is fine.
Corporate-level compliance managers and audit program managers are constantly seeking ways to automate and improve the management of audits, through a variety of methods, company platforms, bespoke software and now A.I.
How to tell the difference?
It is helpful to think of the Plan-Do-Check-Act (PDCA) cycle to differentiate between audits and inspections.
Inspection
At high-level, inspections are a “do” Typically required to do by a compliance obligation
Audit
At high-level, audits are a “check”
Process of checking that compliance obligations have been met
Skill levels
Audits take expertise to deliver well, too many people take on the role without having the skills or competence to deliver them.
That competence comes from understanding the processes being audited and understanding the framework which they are delivered against – not just the organisation’s own procedures or controls but the standards themselves.
An auditor should understand the requirements in the standard, then they can evaluate the process controls against those requirements. They can then audit compliance against non-compliant process controls and add value to the business.
If you would like more information or have any questions on audits or inspections, you can email Karl on karl@360degreesconsultancy.co.uk
Scafom-rux: What happens to scaffolding in a fire?
In this article Frederike Berg from the global manufacturer of premium quality scaffolding solutions, Scafom-rux, clarifies what exactly happens to scaffolding in a fire and which influences it can withstand.
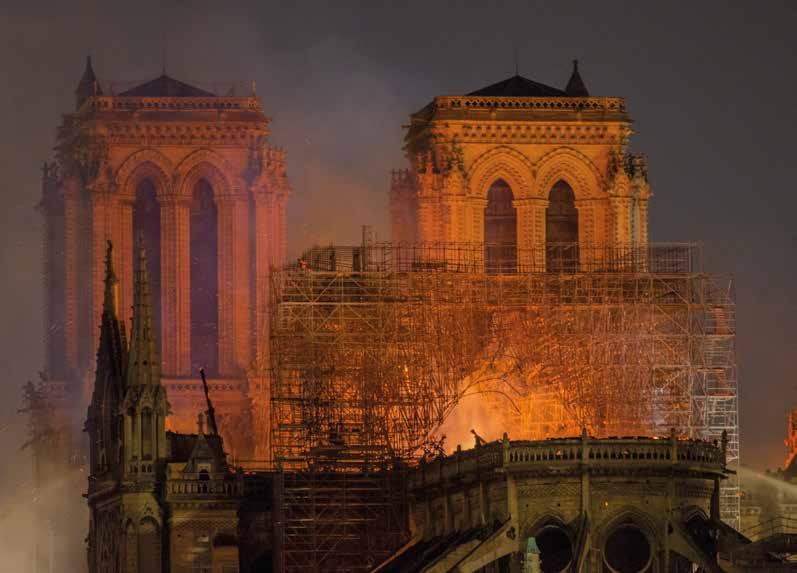
Exactly five years and one day after Notre-Dame Cathedral burned down, Copenhagen’s Old Stock Exchange suffered a devastating fire on 16th April 2024, both landmarks were scaffolded for renovation work at the time of the fire.
Can scaffolding melt in a fire?
When a building is burning, temperatures can typically reach around 1000°C. During the Notre-Dame fire, for example, the scaffolding was exposed to temperatures even exceeding the 1000°C degree mark in some areas. At such temperatures, a metal scaffold does not melt, which would only occur at 1400°C to 1500°C.
However, the heat is sufficient to make the material more malleable and thus severely deform it - especially when the weight of the scaffold itself acts on the material. This resulted in an unstable, nearly 200ton network of 40,000 metal scaffold parts at Notre-Dame, which had to be painstakingly dismantled within 6 months.
Similar dismantling work began just two days after the fire at the Copenhagen Old Stock Exchange. Here too, the scaffolding was deformed by the heat and partially collapsed.
Does scaffolding collapse in a fire?
Whether scaffolding collapses in a fire, as partially occurred at the Old Stock Exchange, depends on factors such as how and where it was anchored. If a wall or roof to which scaffolding was attached and secured collapses, it is very likely that the scaffolding will also come down. Backdraft or other explosions, caused by gas cylinders and propane tanks used for welding or tarring, can also lead to the collapse of scaffolding. Additionally, falling heavy debris, such as roof truss, can damage scaffolding to the point of instability, and ultimately, collapse.
During the Notre-Dame fire, the scaffolding itself withstood the collapse of the spire and roof even though it was heavily damaged by the heat.
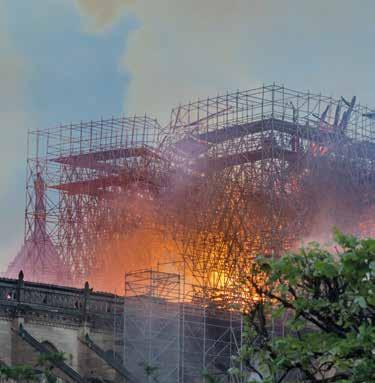
Can scaffolding itself catch fire and become a fire hazard to its surroundings?
It is actually rather unlikely that a burning scaffold will ignite objects in its immediate vicinity. This is because zinc on the scaffold would only begin to burn and detach from the steel at temperatures above 450°C. At this point, it could run down or splatter from the scaffold, potentially igniting flammable objects nearby or underneath. However, considering that at such temperatures, the immediate surroundings of the scaffold are likely already engulfed in flames, a fire directly caused by the scaffold is not very probable.

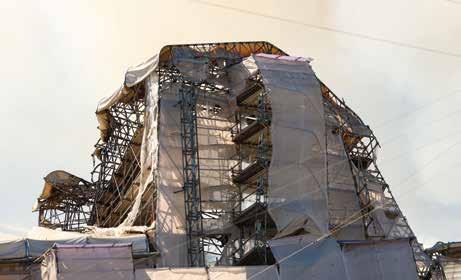
While it’s not very likely that the scaffold itself would contribute to inflaming its surroundings, it’s more plausible that it could delay firefighting efforts. If firefighters cannot get close enough to the fire because the scaffolding is blocking their path, it could make it more difficult for them to extinguish the fire.
In the next edition Scafom-rux will be discussing the best practices to prevent fires on construction sites.
More: www.scafom-rux.com
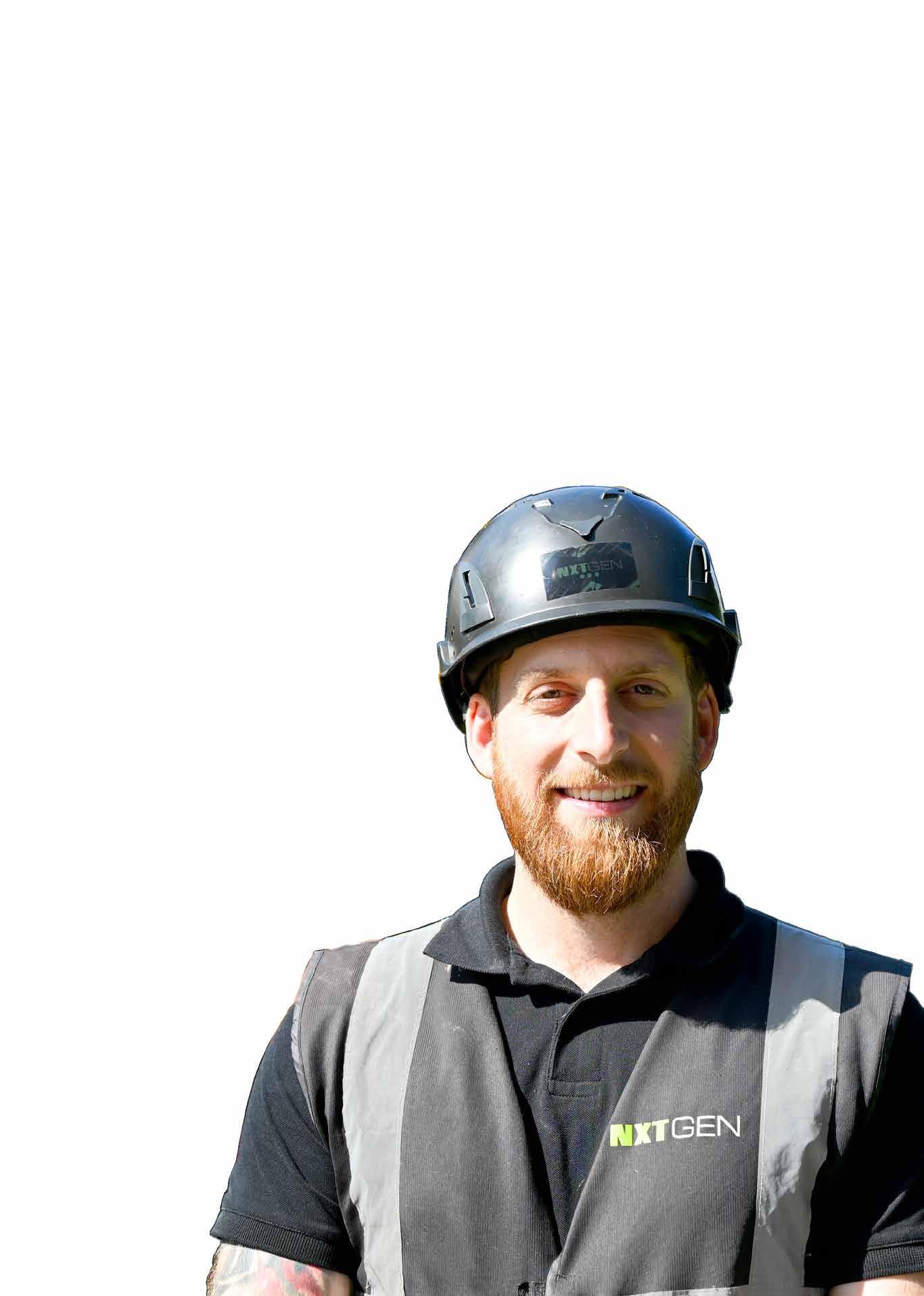
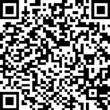
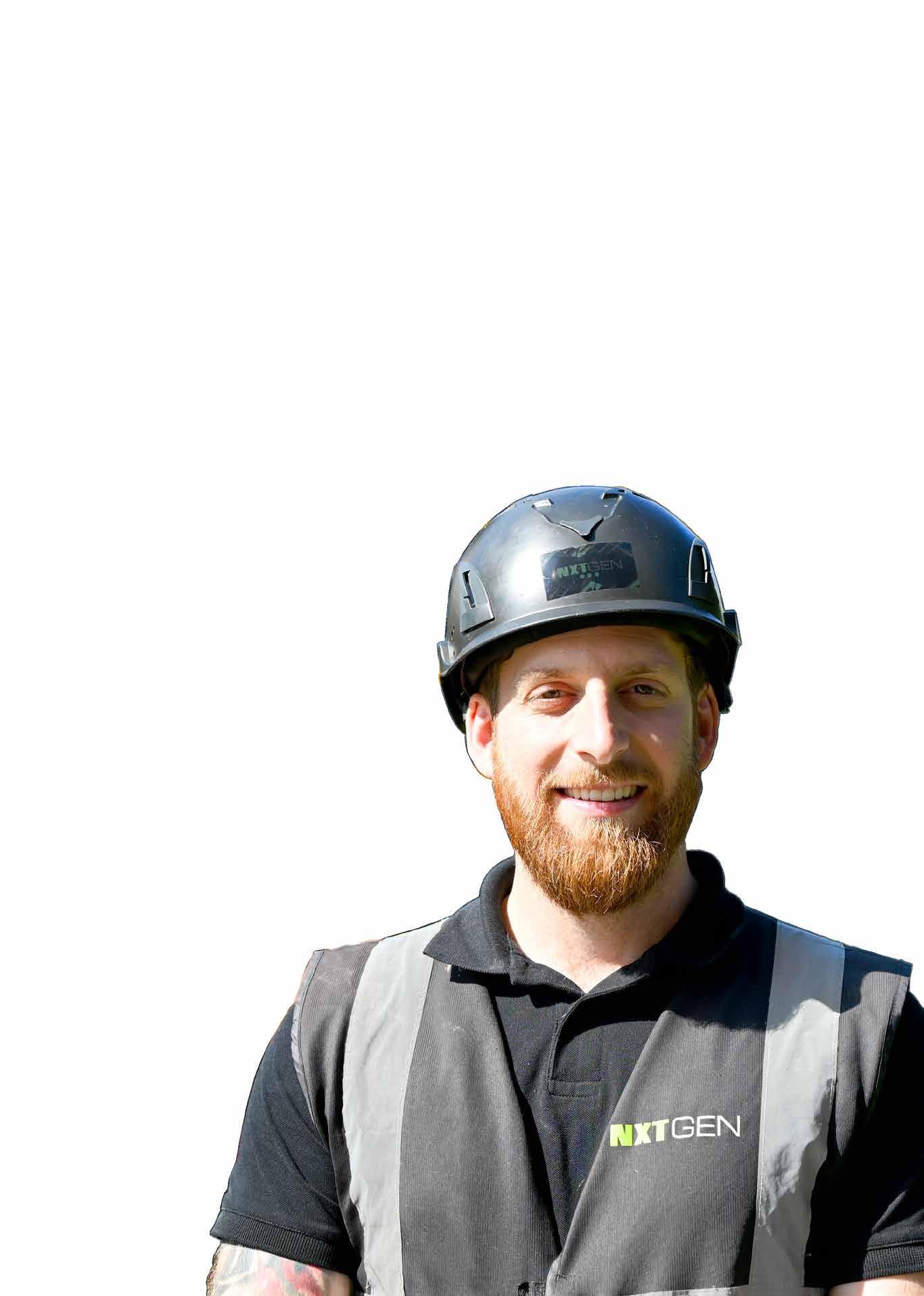
Your guide to
and what you can do to prevent incidents
droppedobjects
In this article John Steven Simons, from Scaffolding Association members, JS Safety Associates, considers the topic of dropped objects, highlighting the many contributing factors and how dropped objects can be eliminated or prevented on-site.
In the first instance, potential dropped objects should be eliminated at source with the following actions:
• Remove any unnecessary equipment and tools
• Mechanise lifting equipment where possible
• Stop work during adverse weather conditions
• Install toe boards
• Use solid barriers and brick guards to close open edges
HSE’s Construction statistics in GB 2023
The HSE statistics for the 2020/21- 2022/23 period have identified that construction’s RIDDOR reportable work- related specified injuries by accident as a result of being struck by dropped or moving objects were:
• 10% of all fatal
A dropped object is any item or object that falls, or has the potential to fall, from its position. Dropped objects fall into two categories: Static Dropped Objects and Dynamic Dropped Objects.
A Static Dropped Object is an object that falls from its position under its own weight, such as an inadequately secured fitting. Whereas a Dynamic Dropped Object is one that falls from its position due to applied force, such as severe weather.
A number of factors can contribute to a dropped object incident. These include:
• Inadequate risk assessment
• Human factors
• Inadequate work processes
• Failed fixtures and fittings
• Poor housekeeping
• Inadequate inspection and maintenance
• Environmental factors Dropped objects are a fundamental hazard of working at height, and there should be a clear system in place to identify, prevent and manage the associated risks. Policies should detail the appropriate inspection and control mechanisms that are implemented to identify, assess, eliminate or manage the risks from dropped objects. Preventative and mitigating controls should be detailed within safe systems of work and method statements.
The risks associated with potential dropped objects should be reduced to the lowest reasonably practicable level in line with the hierarchy of controls. Effective task planning and risk assessment will eliminate, reduce, isolate and control hazards.
• Install board gap fillers
• Close ladder hatches
Where potential dropped objects cannot be completely eliminated, it is important to assess the likelihood of a potential fall and determine the severity of the consequence. From this, the following measures can be devised and put into place to reduce the distance of a fall and prevent personal injury:
• Store required equipment and tools securely
• Stagger ladder hatches
• Install protection fans
• Build a pavement gantry
• Create exclusion zones with barriers and safety signs
• Tether tools and equipment
• Prevent ‘hemping’ of long tube
• Ensure all operatives are competent to work at height
• Regularly undertake dropped objects Toolbox Talks and safety meetings
• 14% of all non-fatal
This data has to be interpreted with care because it is well known that non-fatal injuries are significantly under-reported.
Scan here to read the full report.
Although having a robust management system in place is the primary tool in preventing dropped objects, there is a fundamental requirement for all personnel on-site to remain vigilant of the associated hazards, by:
• Being aware of the hazard and associated risks, and being prepared to stop work if the conditions or actions are unsafe
• Recording and reporting all incidents
• Removing potential dropped object hazards
• Controlling tools and equipment which have the potential to become a dropped object hazard
• Designing the work environment and selecting suitable tools and equipment which mitigate the risk of potential dropped objects
• Undertaking regular worksite inspections This article details just some of the important considerations and solutions when preventing dropped objects. However, it is not exhaustive and should always be supplemented with additional checks and processes specific to the individual location, task and environment.
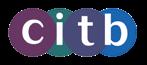
CITB Business Plan 2024-25
The Construction Industry Training Board (CITB) has recently unveiled its Business Plan for 2024-25 which sets out how it will build on previous plans and support and empower employers by investing £267m in the coming year. Here are some of the key takeaways from the Three Pillars of the Plan.
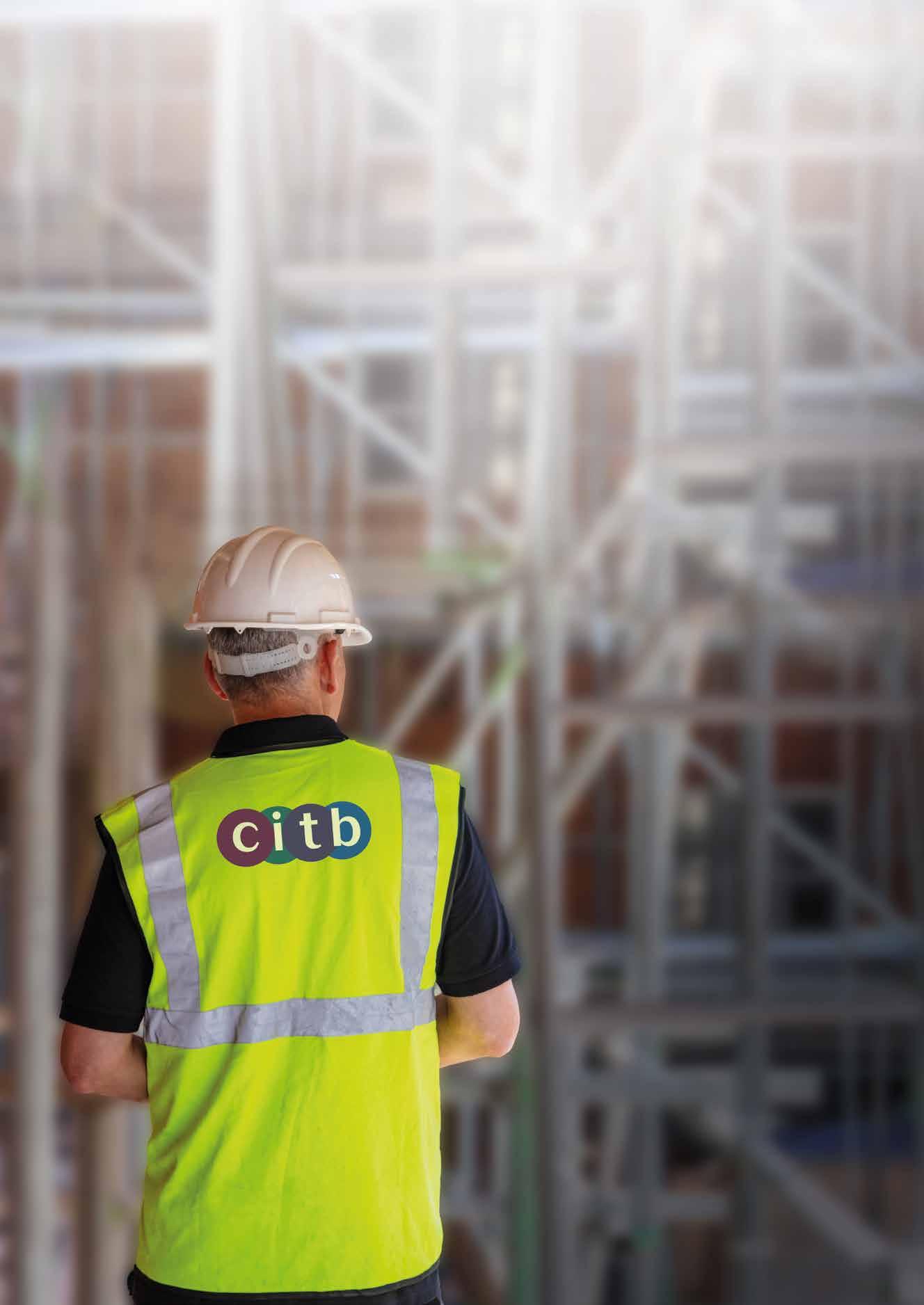
Inform and enable diverse and skilled people into construction
• Expand the Go Construct platform by adding a service that will link people directly to local support and opportunities.
1 2
• Continue to deliver New Entrant Support Team (NEST)
• National Construction College (NCC) to deliver an expanded range of quality Apprenticeships
Develop a training and skills system to meet current and future needs
• Develop new Competence Frameworks to cover more occupations

Develop the CITB Construction Training Register so that it records skills and capabilities aligned with competence
Continue Standards Setting Body role to ensure all are up to date and fit for purpose
Support the industry to train and develop its workforce
• Expand the Employer Network to cover the breadth of Great Britain
3
• Expand the New Industry Impact Fund to support and fund solutions to increase trainer and assessor numbers
• Design, develop, and test a Training Needs Analysis (TNA) service
To empower and enable the construction industry to succeed, both now and in the future, is a challenge both I and my team relish.
The 2024-25 Business Plan represents a pivotal step in our ongoing commitment to transform the skills landscape of the construction industry in Great Britain.
It is one of several detailed documents we will launch this year that will outline our plans to support employers to recruit and train the workforce they need, now and in the future.
Tim Balcon, CITB Chief Executive
SpanSet’s Grabba Bag – avoid dropped objects with the original rated lifting bag!
As highlighted in the guide to preventing dropped objects on the previous page, dropped objects when lifting equipment on scaffolding is a serious hazard and measures should be put in place to avoid the risk of items hitting workers below the lift.
SpanSet observed loads on construction sites, for example scaffold connectors, being lifted using an inspected and certified crane, sling and hook but being put into the equivalent of a ‘rusty bucket’ with no certification, rating or inspection, this led to the design of their popular Grabba bag.
SpanSet’s Grabba bag allows workers to load tools and materials into a safe containments bag and lift them in compliance with Lifting Operations and Lifting Equipment Regulations (LOLER), and is CE marked in compliance with the machinery directive to EN1492.1 for lifting.
The Grabba Lifting Bags are available in 3 sizes:
• Small (400mm dia x 320mm high)

• Medium - 125kg SWL (400mm dia x 500mm high)
• Large - 250kg SWL (800mm dia x 400mm high)

The large Grabba bag allows workers to load tools and materials into a safe containment bag and lift them in compliance with LOLER, whereas the small to medium bags have an integrated master link to allow the worker to attach it to any lifting device with a suitable hook.
Spanset have supplied both safe lifting equipment and training to the scaffolding industry for 50 years.
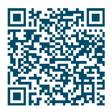
SpanSet have an extensive range of scaffolding lifting equipment supported with a wide range of training courses. Scan here to visit their scaffolding page.
Afix Group’s Staalprofiel embraces sustainable steel decks with ArcelorMittal’s XCarb® Magnelis®
Staalprofiel, the innovative joint venture between Afix Group NV and SP Projecten, is revolutionising the scaffolding industry with its commitment to sustainability.
EU Green Deal – Staalprofiel is leading the charge in offering eco-friendly solutions for system scaffolding steel decks used in construction and renovation scaffolding.
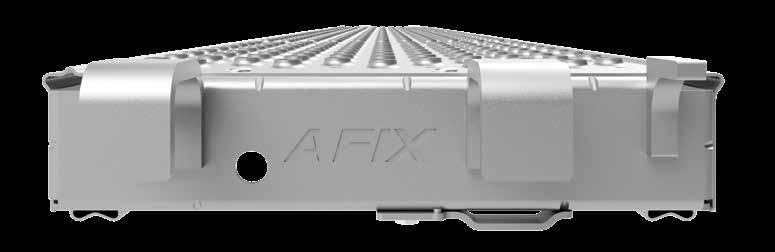
For years, Staalprofiel has trusted ArcelorMittal’s Magnelis® coated steel for its superior performance Now Staalprofiel implements XCarb® recycled and renewably produced Magnelis® for the production of Afix Fast steel decks.

Stephan Hillaert, CEO of Afix Group commented:
“Our sustainability journey demonstrates responsible business practices. By integrating ESG principles into our operations, we are investing together with industry peers, in a sustainable future.”
Scan here for more information.


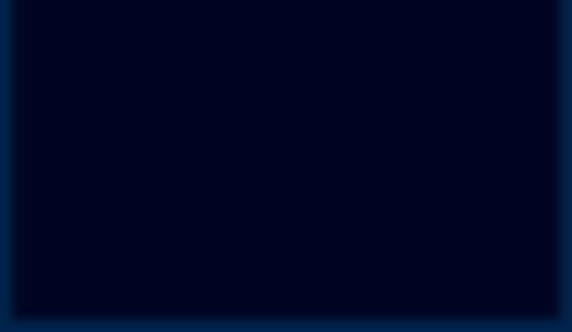
This year’s Conference and Exhibition is open to all, and is now followed by an evening DINNER DANCE with live band and DJ.
The Belfry Hotel & Resort
ScaffCon24 has a range of speakers and panellists such as: TIM BALCON, Chief Executive of the CITB; ROBERT CANDY, CEO of the Scaffolding Association; ROBIN JAMES, Operations Director at the Temporary Works Forum, formerly MD of NASC; and LEE GREATOREX, HSE Inspector, Construction Sector.
The panel’s topics are: Working at Height Updates, Demystifying Temporary Works and Project Management – focusing on current regulations, best practice, skills and training.
www.scaffoldconference.co.uk
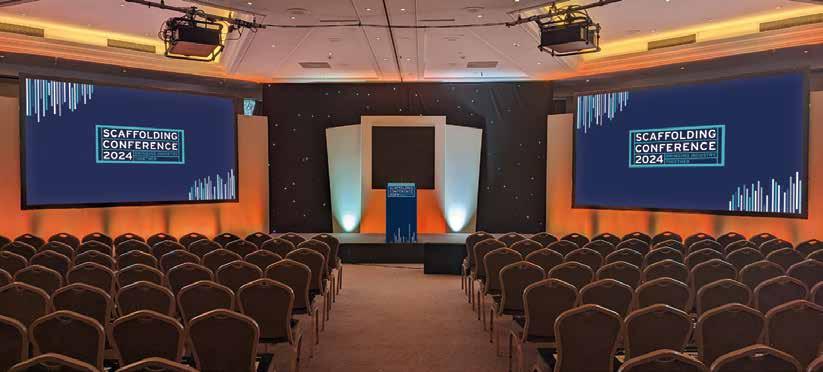
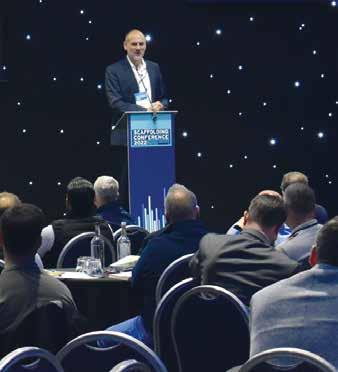
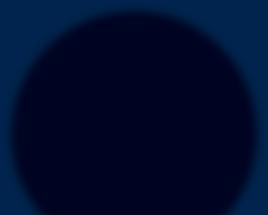

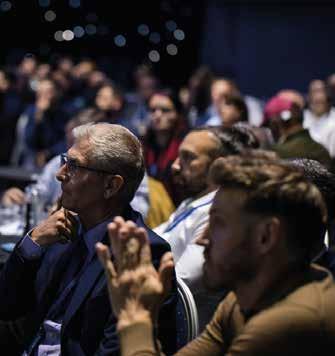

bird tickets are available from the event website: