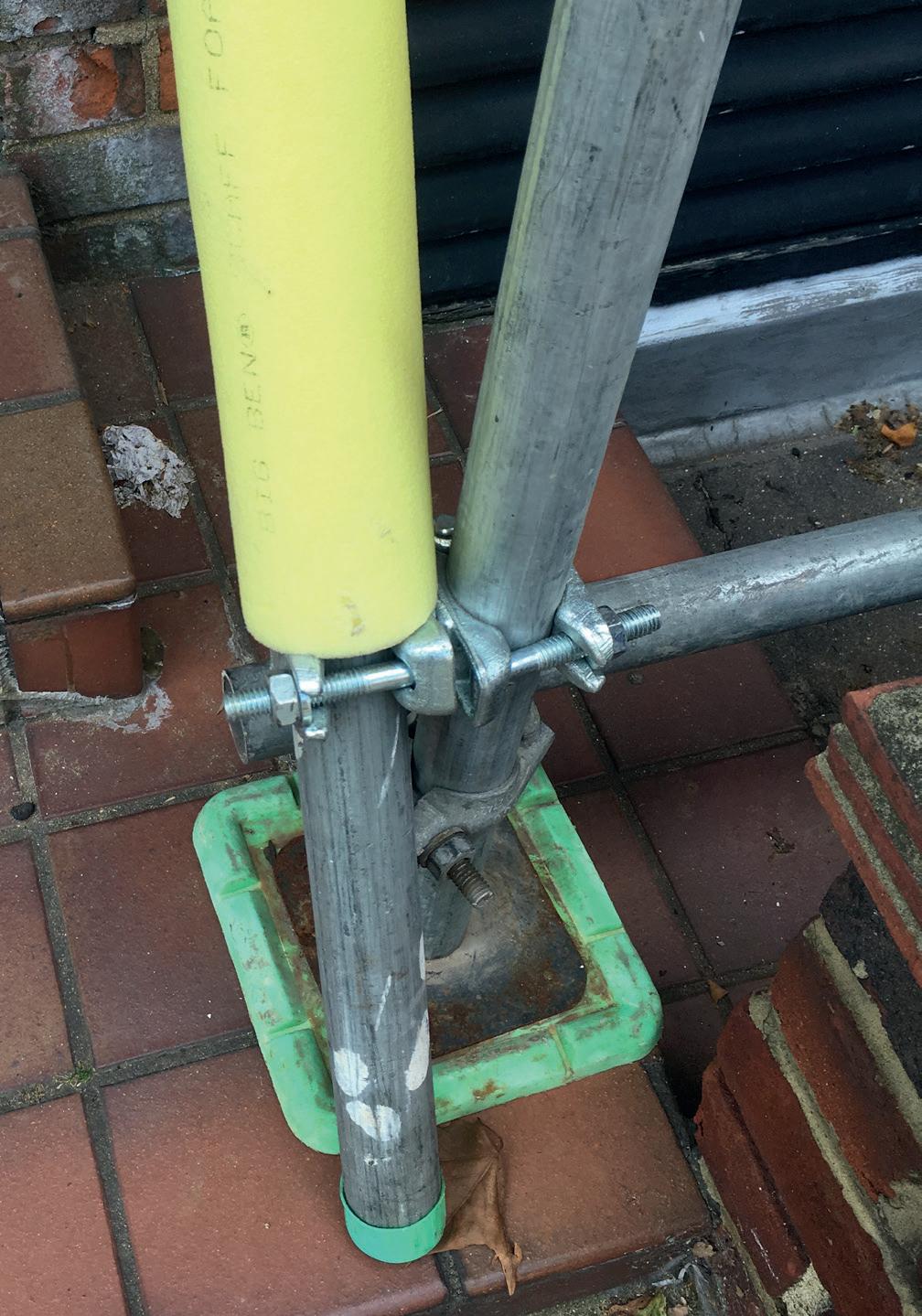
3 minute read
Foundation systems for scaffolding
from AccessPoint Issue 10
by AccessPoint
“From little acorns do mighty oaks grow” goes the old English proverb. It implies that, despite the most humble of beginnings, true strength can be nurtured from even the most unpromising starting points.
It is a proverb that can be applied across the construction sector but has particular resonance in the scaffolding sector, where even the most complicated of structures spring from seemingly the most modest of foundations.
And yet even though it is important, the subject of foundation systems for scaffolds is one that despite the design codes and standards is rarely recognised on-site. It is an area that should be more widely understood, according to Scaffolding Association’s chief executive, Robert Candy.
“There are various configurations available to scaffolders that help spread the load of the scaffold and act as health and safety precautions to both site staff and the general public. There are soleboards, baseplates and ‘tredda’ or footplates, but does everyone know enough about where they should be used, how they should be positioned, and on what material they can be used on?” he commented.
Like with much of the access and scaffolding sector, the design and provision of these boards and plates is shrouded in mystique and myth with reference to design guidance and standards with a large spoonful of time-worn experience.
Scaffolding has always had an element of art about it – as much as engineering has – and the type of foundation or bearing plate used is no exception.
For Chris Harrison, director at design specialist Apex Scaffold Design, it is an area that needs to be formalised before any tubes are even unloaded from the lorry.
“We make it quite clear on our designs that it is the responsibility of the principal contractor to ensure the ground and/or the structure will safely support the loads applied from the scaffold.
“We also make it clear that it is down to the principal contractor to design, supply and maintain a suitable, flat, load-bearing base and provide details of these bases and spreaders to suit. It is really important to have those stipulations made clear,” he explained.
There are standards for baseplates and soleboards: baseplate manufacture is covered by EN74-3:2007 and soleboards are covered in BS 2482:2009, but there is scant mention of under what conditions these components can be used.
Traditionally, soleboards are little more than sawn down scaffold boards. It is their last job on site before they are unceremoniously thrown into the skip or shredder. These are boards that have been deemed too old or damaged for use above ground level but are considered capable of transferring and spreading loads from the scaffold through to the ground itself.
Mr Harrison continued: “They are used where the scaffold is bearing onto grass or the exposed ground of the site. If a scaffold is bearing directly onto a concrete or asphalt surface then a baseplate is considered enough. Contractors might use soleboards or footplates to protect the surface, though.”
Scaffold system design is something that those supplying baseplates shy away from. Tony Mills is sales director at Walsall-based producer Trademagic. It sells more than 1.5 million standard sized 150 x 150mm scaffolding baseplates each year to clients across the UK and beyond, which gives some indication for the industry’s insatiable demand.
“They should go on a soleboard which is a minimum 450mm long – they should sit on one of those for stability as much as anything. We don’t get involved in the specification of baseplates; that’s down to the contractor and its designers. We look at only supplying products that are manufactured to the correct standards,” he said.
For David Eveleigh, director at footplate supplier BLC Construction Supplies, it is a slightly different story. With no inherent load-transfer qualities, he argues that footplates are only there to help protect the existing surface and provide a hi-visibility guard against trips and falls.
“Our footplates are manufactured using high-impact polymers and are really about making the baseplate and the rest of the scaffolding more visible for pedestrians, both on- and off- site. It is a safety product – but it is not safety critical. They are rated to eight tonnes impact resistance but that is not a requirement as such.
Like many things in the scaffolding sector, they probably stem from one person’s bright idea that has now been taken on as the norm,” he said.
There are plenty of variables that should be given careful consideration when inspecting, designing and installing scaffold foundations systems. Size, thickness, length, condition and type of founding strata can all play their role in the final specification – but, thankfully, scaffold failures are rare.
“The correct design and specification for soleboards and baseplates is important. I can’t recall an incident where a scaffold collapse has been due to soleboard or baseplate failure, but that doesn’t mean we should ignore them,” concluded Mr Harrison.