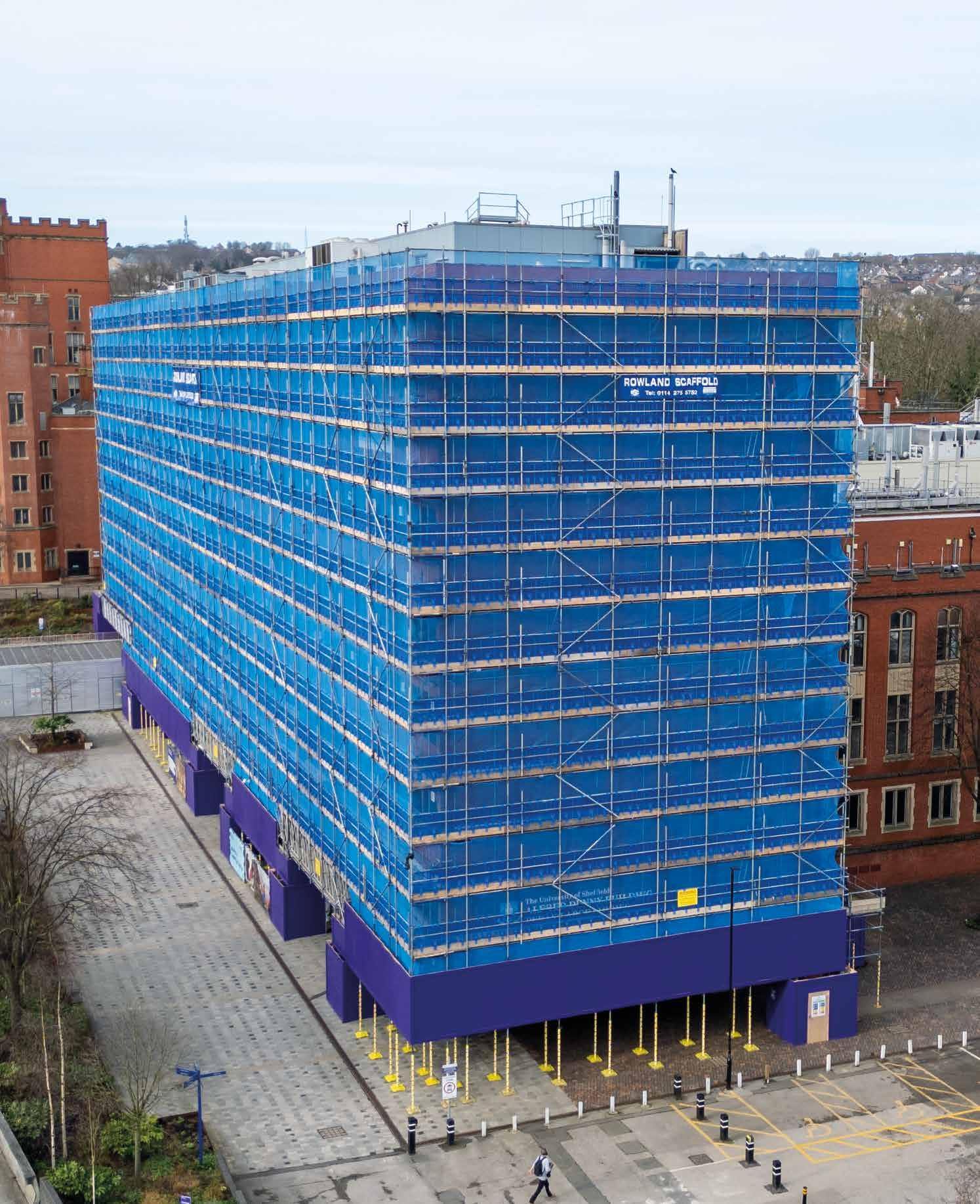
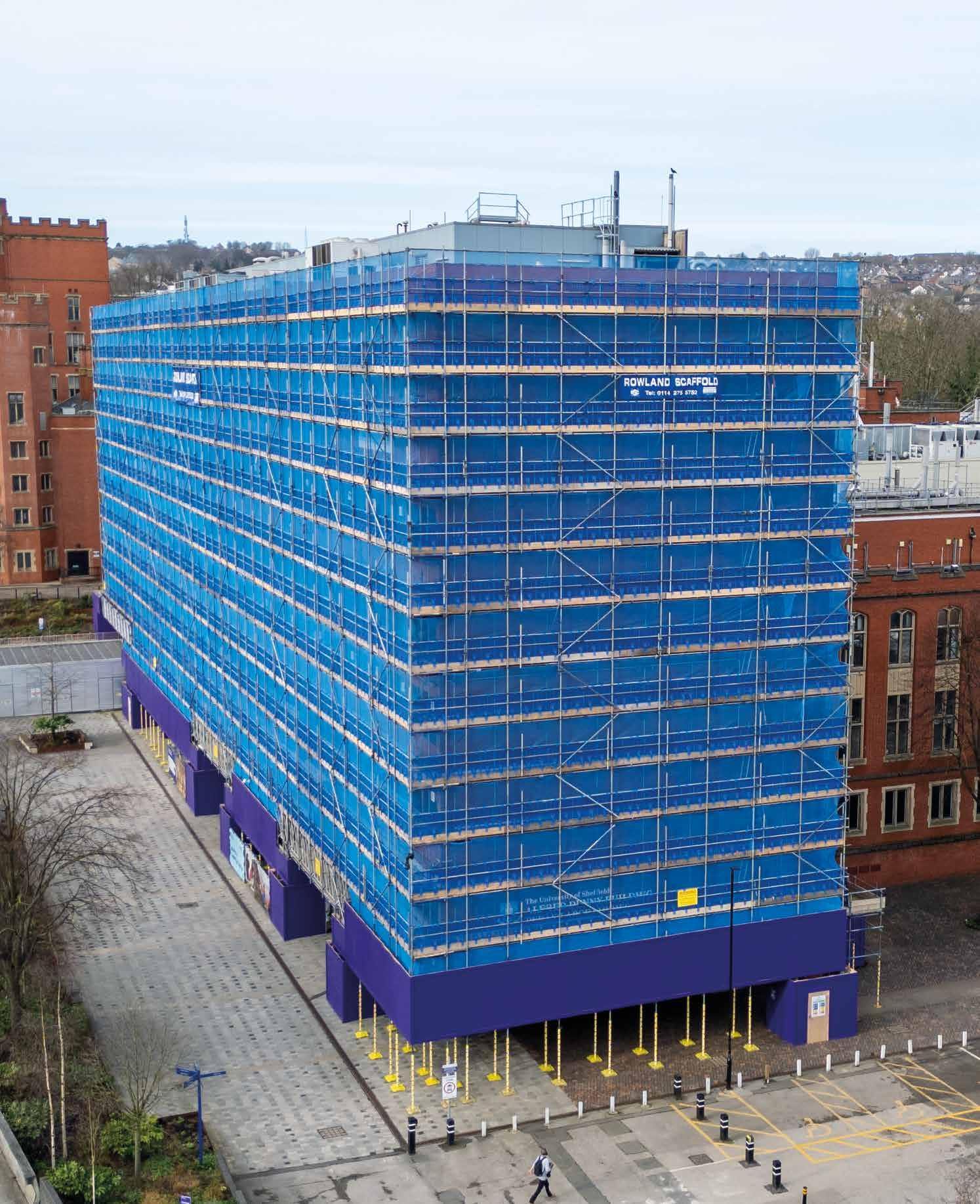
GOOD VIBRATIONS
WELCOME
ROLL CALL FOR NEW SCAFFOLDING ASSOCIATION MEMBERS
SCAFFOLD CONTRACTOR
Access Group Industrial Services Limited
www.agis-ltd.co.uk 01656 656800
Armstrong Scaffolding Ltd www.armstrongscaffolding. co.uk 07745 203385
ASM Scaffold Solutions Limited www.asmscaffoldsolutions.co.uk 01206 211900
Assure Scaffolding Limited www.assurescaffolding.co.uk 07734 903383
Bury Scaffolding Services (Manchester) Ltd www.buryscaff.co.uk 0161 763 5033
C and V Scaffolding Ltd www.cvscaffolding.com 01639 766602
Castle Scaffolding Hire Ltd www.castle-scaffolding.uk 0115 772 0055
Churchill Contractors (UK) Ltd www.churchillcontractors.co.uk 01483 234566
CJW Scaffolding Limited 07498 036790
Colossus Scaffolding UK Limited www.colossus-scaffolding.co.uk 01424 466661
CONTACT US
Editorial
Enquiries: Alison Hurman
T: 0300 124 0470
E: alison@scaffolding-association.org
Advertising
T: 0300 124 0470
E: admin@accesspoint.org.uk
Scaffolding Association
T: 0300 124 0470
www.scaffolding-association.org
E: info@scaffolding-association.org
SCAFFOLD CONTRACTOR
Concell Scaffolding Limited 07733 655274
Direct Scaffold Services Limited
www.directscaffoldservices. co.uk 01302 876056
DJB Scaffolding (Leeds) Limited 07870 597438
High Class Scaffolding Limited www.highclassscaffolding.com 07903 962776
High-Tek Scaffolding Limited www.hightekscaffolding.co.uk 01202 423723
Ibuild Scaffolding Services Limited 07522 785613
J J Scaffolding (Leicester) Limited www.jjscaffoldinglimited.co.uk 07525 027633
Laker Scaffolding and Building Ltd www.lakerscaffolding.co.uk 020 8670 2688
Magdon Scaffolding (Uk) Ltd 01202 841133
More Site Services Ltd www.moresiteservices.co.uk 07828 310850
No.1 Scaffolding - Cardiff Ltd www.no1scaffold.co.uk 07780 578955
Subscriptions
AccessPoint is distributed to members of the Scaffolding Association and other selected access and scaffolding businesses.
If you wish to receive a copy of AccessPoint or would like to amend or cancel your subscription, please call 0300 124 0470 or email info@scaffolding-association.org
Oak Scaffolding Ltd www.oakscaffolding.co.uk 01903 706055
Oculus Group Ltd www.oculus-group.co.uk 07467 521692
Patos Construction Ltd 020 8804 2057
Premier Scaffolding (Harrogate) Limited www.premier-scaffolding.com 01423 502070
Redz Scaffolding Limited www.redzscaffolding.co.uk 07769 700666
Rickie Hadfield Access Solutions Ltd www.rhas.co.uk 07454 201149
Scaffold Services (Chesterfield) Ltd 07967 097562
Secure Scaffolding Services Limited www.securescaffoldingservices. co.uk 07414 886236
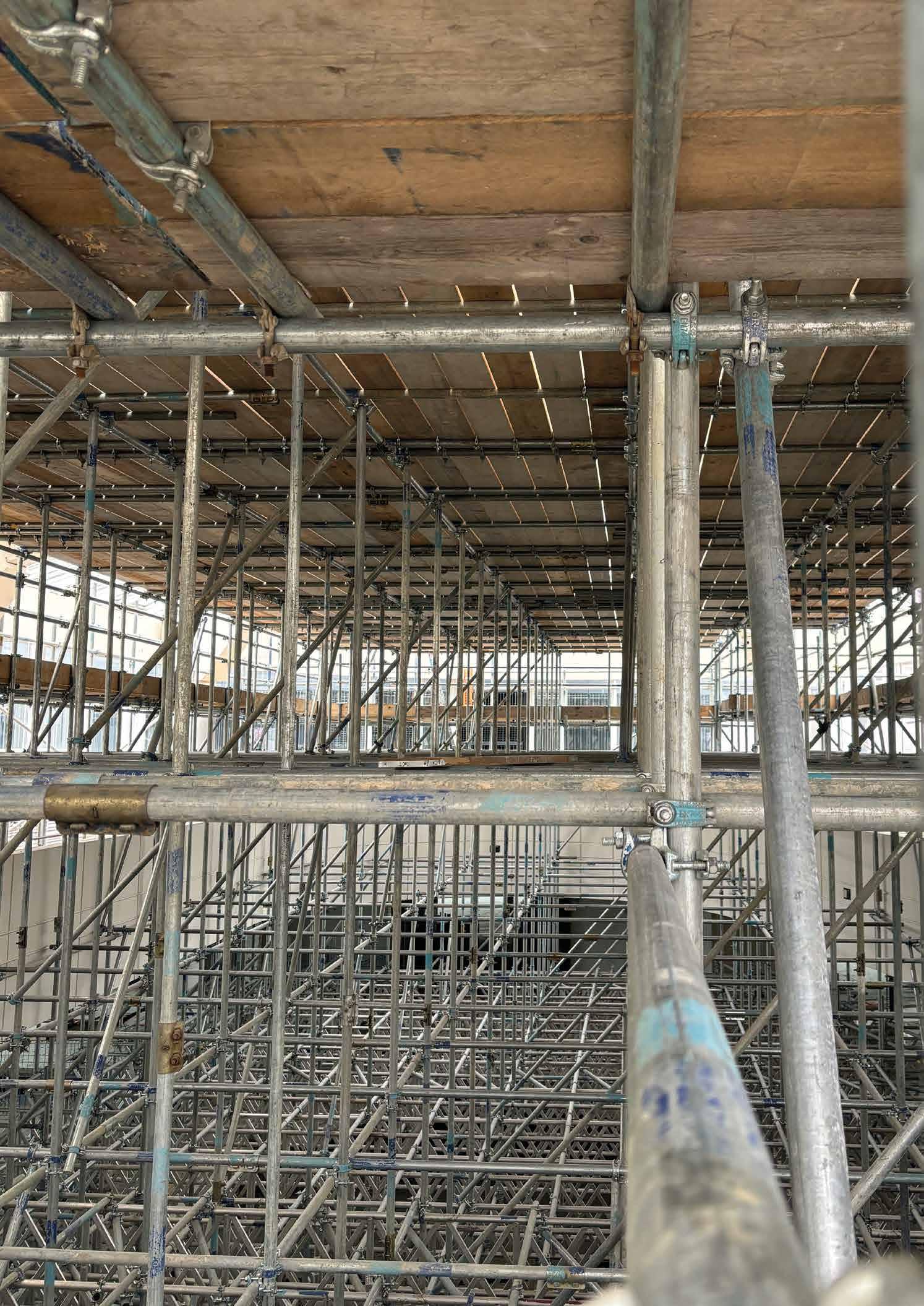
SCAFFOLD CONTRACTOR SCAFFOLD CONTRACTOR MEMBER SERVICE PR0VIDER MEMBER DESIGNER
Select Scaffolds Ltd www.selectscaffoldsltd.co.uk 0151 523 9003
Shuel Construction Limited www.shuelconstruction.co.uk 07715 835038
Southcoast Scaffolding Limited www.southcoastscaffolding. com 01273 514637
STAK Scaffold Limited www.stakscaffold.co.uk 01883 330188
Strata Roofing Cambridge Ltd ww.strataroofing.co.uk 01223 944041
T J R Scaffolding Ltd www.tjrscaffoldingltd.co.uk 01840 211503
TG4 Scaffolding Ltd 07479 910382
Tiger Specialist Access Ltd www.tigerspecialistaccess.co.uk 07543 221009
TR Scaffold Limited www.trscaffoldltd.co.uk 07521 598757
Site-X Security Ltd 07521 010188
AccessPoint is published on behalf of the Scaffolding Association. The views expressed in this journal are not necessarily those held by the Scaffolding Association. The Scaffolding Association shall not be under any liability in respect of the contents of the contributed articles. The Editor reserves the right to edit, abridge or alter articles for publication.
ISNN: 2055-2033 (Print)
© All editorial contents AccessPoint 2025
Printed by Tewkesbury Printing Company
Designed by Gladstone Design
Oryx Scaffold Design Ltd 0117 329 0050
NEWS
P3-5 Stories from the sector
COMMENT
P6 Robert Candy, CEO of the Scaffolding Association, discusses how he has been championing the interests of the scaffolding and access sector
EVENTS
P7 UK Construction Week announces partnership with Scaffolding Association
INTERVIEW
P8-9 An interview with Richard Smith, Road Haulage Association, Managing Director
EMPLOYMENT
P11 Citation explores the Employment Rights Bill and its impact on scaffolding businesses
PROJECTS
P12-13 Scaftec and Sean Doyle Scaffolding | Fleet Street
P14-15 Creator and Rowland Scaffold | Alfred Denny Building
P16 CS Scaffolding | Newgate Shopping Centre
INSURANCE
P18 Clegg Gifford breaks down the key types of insurance for UK scaffolding businesses
TRANSPORT
P19 Safe Loading and Vehicle Checks for Scaffolders: The essential new training module launched by the Scaffolding Association and the Road Haulage Association
LEGAL
P20-21 Holmes & Hills Solicitors discuss The Procurement Act 2023
PRODUCT
P23 D.tec International examine why drug and alcohol screening should be a priority
Mark Parkin appointed as Strategic Director of the Scaffolding Association
The Scaffolding Association has announced the appointment of Mark Parkin as its new Strategic Director, reinforcing its commitment to raising standards, improving safety, and advocating for the industry’s recognition as a highly skilled and essential industry.
With 37 years of experience in scaffolding—including 31 years in roles such as advanced scaffolder, supervisor, managing director, CEO, and operations director—Mark has developed a profound understanding of the industry. His expertise spans operations, health and safety, and business management, making him a valuable addition to the Scaffolding Association’s team.
Through his role at the Scaffolding Association, Mark will work closely with the team to support its members, enhance industry-wide collaboration, and contribute to the ongoing development of best practices. His focus will be on
strengthening the Association’s initiatives, helping to drive positive change, and ensuring the industry continues to evolve to meet future challenges. By working together, the Association and its members can build a stronger, more resilient scaffolding industry for generations to come.
Scan here to read more:
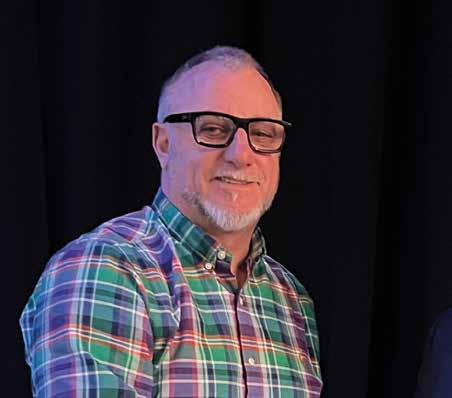
Scaffolding Association achieves ISO 9001 Certification
The Scaffolding Association is proud to announce its achievement of ISO 9001 certification, a significant step in reinforcing its commitment to quality, efficiency, and continuous improvement within the scaffolding industry.
ISO 9001 is the world’s most recognised standard for quality management systems, focusing on strong leadership, risk management, and operational effectiveness. This certification demonstrates that the Scaffolding Association operates to the highest industry standards and ensures that its processes are transparent, efficient, and continually improved.
This milestone further strengthens the Scaffolding Association’s Audited Membership scheme. ISO 9001 certification enhances the auditing process, ensuring that assessments
are consistent, structured, and aligned with global best practices. It assures members and clients that the Association is committed to delivering excellence and maintaining the highest levels of professionalism.
The benefits of this certification include:
• Improved Processes – Standardised audits that are consistent, fair, and transparent.
• Ongoing Improvement – Regular reviews to refine the audit process and ensure it remains effective.
• Alignment with International Standards – Bringing global best practices to the Association’s operations.
Scan here to read more:
CITB Consensus dates moved
New dates for the Construction Industry Training Board (CITB) Consensus process is 17 March 2025 until 9 May 2025.
The five-week move allows greater opportunity for CITB to align its upcoming 2025-29 Strategic Plan with the outcomes of the CITB Review.
Usually undertaken every three years, Consensus is the process through which CITB seeks Levy-paying employers’ views and agreement on its plans for generating the Levy and the skills and training this will deliver to the industry. CITB’s core focus for the 2026-29 draft Levy Proposals being consulted on is
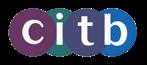
to ensure that the Levy exemption and reduction thresholds remain current and appropriate.
During Consensus, CITB consults at least 11,000 Levy paying employers. In March 2019, nearly 30,000 employers were liable to pay a Levy.
The Levy plays a vital role in investing in the British construction industry, ensuring the development of a skilled workforce to meet the sector’s current and future demands.
Scan here to read more:
Scaffolding Association applauds UK Government’s apprenticeship reforms to strengthen industry workforce
The Scaffolding Association welcomes the UK Government’s recent announcement of apprenticeship reforms aimed at reducing bureaucracy and enhancing flexibility within the apprenticeship system. These changes are anticipated to create up to 10,000 additional apprenticeship opportunities annually, significantly benefiting sectors like construction and scaffolding.
Key reforms include:
Revised English and Maths Requirements: Employers now have the discretion to determine whether apprentices aged over 19 need to achieve Level 2 English and
Maths qualifications to complete their apprenticeship. This change allows apprentices to focus more on developing occupation-specific skills, thereby accelerating their readiness for the workforce.
Shortened Minimum Apprenticeship
Duration: The minimum length of an apprenticeship will be reduced from 12 months to 8 months, enabling a more rapid transition of qualified individuals into industries with pressing demands, such as scaffolding.
Scan here to read more:
Roofer given suspended sentence after man falls from scaffold
A self-employed roofer has received a suspended prison sentence after a man suffered serious injuries after falling from scaffold in Devon.
Daniel Hooper was given a 16-week custodial sentence, which will be suspended for a period of 12 months, following Iain Smith, 36, falling from a height of more than 25 feet while working for him, on 13 June 2023.
Father of three Mr Smith had been manually carrying old roof slates down a ladder attached to the scaffold platform at a domestic property in Honiton when he fell, suffering serious injury, including five broken vertebrae, as well as skull and rib fractures. Devon Air Ambulance took Mr Smith to Derriford Hospital where he was put into an induced coma for five days. He has since made a remarkable recovery but does still suffer from the effects of his injuries.
An investigation by the Health and Safety Executive (HSE) found that Daniel Hooper, 28, trading as Hooper Roofing, failed to ensure the health, safety and welfare of his employee as he did not undertake any planning or appropriately supervise the work at height or supply suitable equipment to do the task safely.
Scan here to read more:
ITP appoints new Managing Director to support next phase of growth
Yorkshire-based manufacturer of protective textiles for construction, Industrial Textiles and Plastics (ITP) Ltd, is supporting its global expansion with the appointment of Carl Morse as Managing Director.
With 30 years of senior leadership experience in the manufacturing industry, including successful tenures with international companies supplying cutting-edge technologies, Carl brings a wealth of expertise to the position. He will oversee ITP’s strategy to develop worldwide markets across a diverse product portfolio, which includes sheeting for scaffolding and temporary fencing,
acoustic barriers, debris netting, defence products, keder sheeting, protective building membranes for roof and wall applications, and ground gas barriers.
Based in Easingwold, North Yorkshire, ITP’s factory provides in-house manufacturing of materials, including surface coating, finishing, and large-format flexographic or digital printing. The company’s product range has continually expanded to offer hundreds of materials in various sizes, specifications, and applications.
Scan here to read more:
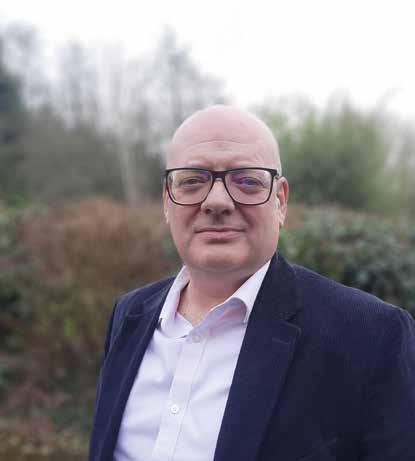
Scaffolding Association announces partnership with Rightlease
The Scaffolding Association, the UK’s largest trade body for scaffolding contractors with over 650 member companies, is pleased to announce its partnership with Rightlease, a leading car and commercial vehicle leasing brokerage. Rightlease is able to source any make and model of car, van and pick-up on a lease or purchase agreement for corporate or personal contracts. They have a wealth of experience within the vehicle leasing market, with the ability to tailor the needs of each contract, finding the right vehicle at an affordable price.
Robert Candy, Chief Executive, Scaffolding Association said:
“We are delighted to partner with Rightlease who will support our members with an experienced and personal approach from many years in the vehicle leasing industry. As a trade association, we understand that getting the right partner in this ever-changing vehicle market place is increasingly important.”
Gary Hodder, Managing Director, Rightlease said:
“I am excited to launch this strategic partnership with the Scaffolding Association, bringing this outstanding offering to their members. We will leverage our strong relationships with manufacturers and our wide panel of lenders who provide us with exceptional
buying power, enabling us to pass on significant savings, add real value and deliver exceptional service.”
Testimonial from Sean Phillips, Director, Inner City Scaffolding:
“I have worked with Gary and his team for several years, and they have consistently provided exceptional service at highly competitive rates. Their professionalism, reliability and commitment to delivering on their promises set them apart. My experience has been nothing short of outstanding and I confidently endorse their services.”
For further information about Rightlease and how their team can find the best deal for you, please use code TSA and visit www.rightlease.co.uk, email info@rightlease.co.uk or call 01708 988132.
For further details about the Scaffolding Association and becoming a member, visit www.scaffolding-association.org, email info@scaffolding-association.org or call 0300 124 0470
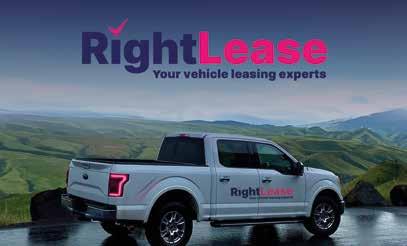
Health and Safety Executive turns 50
The national regulator for health and safety in Great Britain has celebrated its 50th Anniversary. Created by the Health and Safety at Work etc Act 1974, the Health and Safety Executive (HSE) was officially launched on 1st January 1975.
For the last 50 years it has played a central role in reducing workplace death and
injury, helping Great Britain become one of the safest places in the world to work. In 1974, 651 employees were killed at work; HSE’s latest annual statistics for 2023/24 show that number had reduced to 138.
Scan here to read more:
CIOB
shares insights on attracting more young people to construction
New insights into how positively young people and parents view careers in the construction industry have been released by the Chartered Institute of Building (CIOB).
Surveys of 2,000 16-24-year-olds* and 2,000 parents** of young people in that age range were carried out for CIOB in February 2025, which explored perceptions of the industry as well as what influences careers choices.
Two thirds (65%) of young people surveyed hold a positive view of construction careers while more than three quarters (79%) of parents are supportive of their child pursuing a career in the sector. Just under half (42%) said they would recommend a career in construction to their child.
Young people survey key findings:
• Almost half of young people surveyed selected working on a building site in their top three options for describing construction careers. It was the most chosen option.
• 36% say construction is not a respected career path.
• 35% say the industry has a poor workplace culture.
• 53% say the industry is not welcoming to women.
• 28% feel careers in construction are not accessible to young people.
• 25% say they think their parents would be embarrassed if they pursue a career in construction. Only 8% of parents said they’d be embarrassed if their child worked in construction.
• 47% say construction was not covered in careers advice they received while in education.
Scan here to read more:
CSCS celebrates 30 years of raising standards and improving safety in UK construction
The Construction Skills Certification Scheme (CSCS) marks its 30th anniversary in 2025 – a significant milestone in the improvement of standards and safety across UK construction. Since being established in 1995, CSCS has been at the forefront of verifying qualification and training
records and embedding a culture of consistent standards across the sector.
To commemorate this 30th anniversary, CSCS will host a year-long programme of engagement with stakeholders through a series of special events, campaigns, and initiatives. These activities will not only reflect on the
progress made but also reinforce the scheme’s current role in industry and outline what the coming years look set to bring, particularly in light of the Building Safety Act
Scan here to read more:
Comment
The Scaffolding Association is undergoing a period of significant growth and transformation, reinforcing our commitment to providing outstanding value to our members.
As the scaffolding and access industry evolves, we are strengthening our support to ensure businesses of all sizes have the resources, guidance, and advocacy needed to thrive.
A major milestone in our journey has been achieving ISO 9001 certification, a globally recognised standard demonstrating our commitment to quality management and continuous improvement. This accreditation strengthens the integrity of our processes, ensuring we operate with transparency, efficiency, and accountability in everything we do. It also enhances our Audited Membership scheme, providing members with greater assurance that our assessments are rigorous and aligned with international best practices.
To further support our members, we are pleased to welcome Mark Parkin as Strategic Director. With 37 years of hands-on experience in scaffolding, Mark has worked across the industry in roles ranging from advanced scaffolder to CEO and operations director. His in-depth knowledge of business operations, health and safety, and workforce development means he understands the challenges businesses face and how to navigate them. Mark’s role will focus on providing practical guidance, sharing industry insights, and working closely with members to help them strengthen their businesses. His appointment reflects our commitment to offering the best possible support, ensuring scaffolding companies of all sizes have access to the resources and advice they need to succeed.

Beyond membership numbers, our focus is on deepening the impact of our support. From technical advice and training to policy advocacy and industry representation, we are dedicated to ensuring that your interests are heard and acted upon at every level. Our work spans engagement with government bodies, regulatory authorities, and key stakeholders to ensure that the scaffolding and access industry has a voice where it matters most.
We understand the challenges facing our sector, including skills shortages, evolving regulations, economic pressures, and the increasing emphasis on sustainability. The Scaffolding Association is here to help navigate these complexities, providing practical solutions, insights, and opportunities to ensure businesses remain competitive and resilient. We are also committed to supporting skills development, attracting new talent to the industry, and ensuring that the workforce of the future is equipped with the necessary expertise to meet industry demands.
As part of our commitment to raising industry standards, we are pleased to highlight an important new training initiative: the Safe Loading and Vehicle Checks for Scaffolders training course, developed in partnership with the Road Haulage Association (RHA). This course ensures that scaffolding transport meets essential safety and compliance standards, reducing risks and safeguarding businesses. Load security and vehicle compliance are critical issues, and enforcement agencies are increasingly focusing on non-compliant vehicles. This course supports HGV drivers required to complete periodic Driver CPC (DCPC) training and is also relevant to anyone responsible for safe loading and vehicle checks, including drivers who do not require DCPC accreditation. Looking ahead, we remain committed to championing the interests of the scaffolding and access sector. We will continue to work on key issues such as improving access to training, enhancing safety standards, and ensuring that businesses have the support they need to adapt and grow in an evolving landscape.
Thank you for your continued support and for being part of our expanding community. Together, we will drive positive change and secure a prosperous future for the scaffolding and access industry.
ROBERT CANDY CHIEF EXECUTIVE, SCAFFOLDING ASSOCIATION
To further support our members, we are pleased to welcome Mark Parkin as Strategic Director. With 37 years of hands on experience in scaffolding, Mark has worked across the industry in roles ranging from advanced scaffolder to CEO and operations director.
Left: Mark Parkin
Right: Robert Candy
•
•
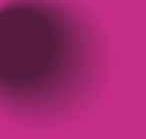
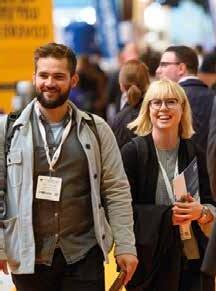
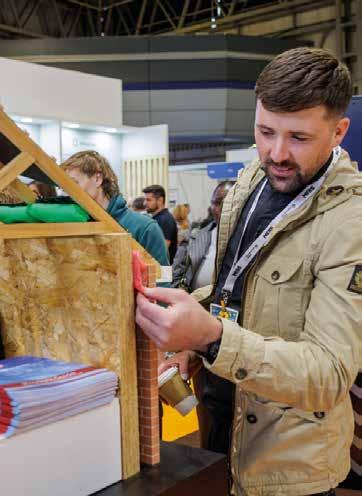
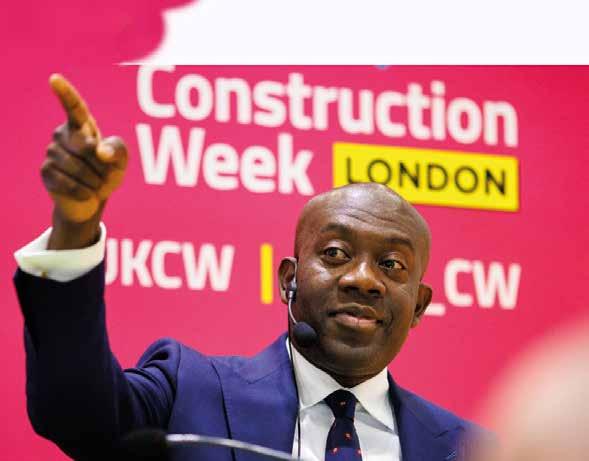
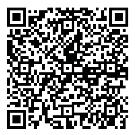
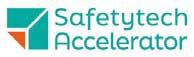


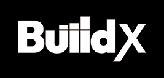
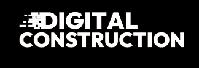
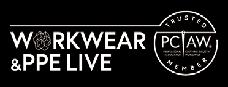


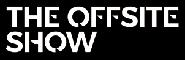
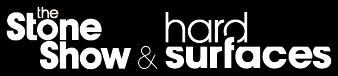
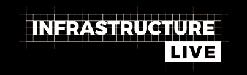

UK Construction Week announces new partnership with the Scaffolding Association
UK Construction Week (UKCW) is proud to announce a new partnership with the Scaffolding Association, one of the UK’s leading scaffolding trade bodies. The partnership will kick off at UK Construction Week London, taking place at ExCeL London between 7–9 May, followed by UK Construction Week Birmingham at NEC Birmingham on 30 Sept–2 Oct.
The partnership aims to elevate the conversation around scaffolding, ensuring that safety, standards, and new technological developments remain at the forefront of the UK construction industry. By joining forces, UK Construction Week and the Scaffolding Association will provide an invaluable platform for industry professionals to collaborate, share knowledge, and explore new solutions within the scaffolding sector.
For UK Construction Week, this partnership represents a significant step in its mission to bring together all corners of the construction industry. With the Scaffolding Association’s expertise and commitment to raising industry standards, UKCW will benefit from enhanced programming that highlights
the importance of scaffolding in the broader construction process.
For the Scaffolding Association, partnering with UK Construction Week presents a unique opportunity to further strengthen its visibility, engage with key stakeholders, and continue its work in improving safety and efficiency across the sector. The association’s presence at the event will bring added focus to the critical role scaffolding plays in ensuring safe and successful construction projects.

This collaboration is a natural fit for us as we continue to drive the conversation around innovation and safety within construction. We look forward to working together to elevate the importance of scaffolding, promote best practices, and create valuable opportunities for the entire construction industry to come together and push boundaries.
For more information on UK Construction Week and to register, visit: www.ukconstructionweek.com
For further details about the Scaffolding Association visit: www.scaffolding-association.org
Neil Gaisford, Divisional Director of Construction at UK Construction Week.
An interview with
Richard Smith Managing Director Road Haulage Association (RHA)
Q. Can you give us an overview of the RHA and its role in the road transport industry?
A The Road Haulage Association (RHA) has represented the road transport sector for over 80 years. We advocate for HGV, coach and van operators, provide training and compliance support, and engage with policy makers to ensure the sector’s voice is heard on critical issues like infrastructure investment, skills, and sustainability.
Q. Why is compliance crucial for fleet operators, and what is the RHA doing to support members in this area?
A Compliance is fundamental for safety, efficiency, and protecting operator licences. The RHA offers guidance, audits, and training to help operators meet and exceed their legal obligations, from vehicle maintenance to drivers’ hours. Ensuring compliance reduces risk and protects the reputation of operators across all sectors.
Q. Non-traditional hauliers, such as those in scaffolding and access, are increasingly operating fleets.
What advice do you have for these operators to safeguard their businesses?
A Non-traditional hauliers must familiarise themselves with the responsibilities that come with operating an HGV fleet. This includes ensuring vehicles are wellmaintained, drivers are trained, and operations comply with legislation.
Q. The RHA recently collaborated with the Scaffolding Association to develop a Driver CPC module. How did this come about?
A This collaboration was driven by a shared goal of addressing the unique challenges faced by the scaffolding and access sector, particularly in areas such as safe loading and securing of equipment. Proper loading is critical not only for road safety but also for ensuring compliance with regulations. By combining expertise, we created a bespoke Driver CPC module that provides drivers with the practical skills and knowledge needed to handle scaffolding loads securely and efficiently. It’s an excellent example of how trade associations can work together to deliver tailored solutions that address specific industry needs.
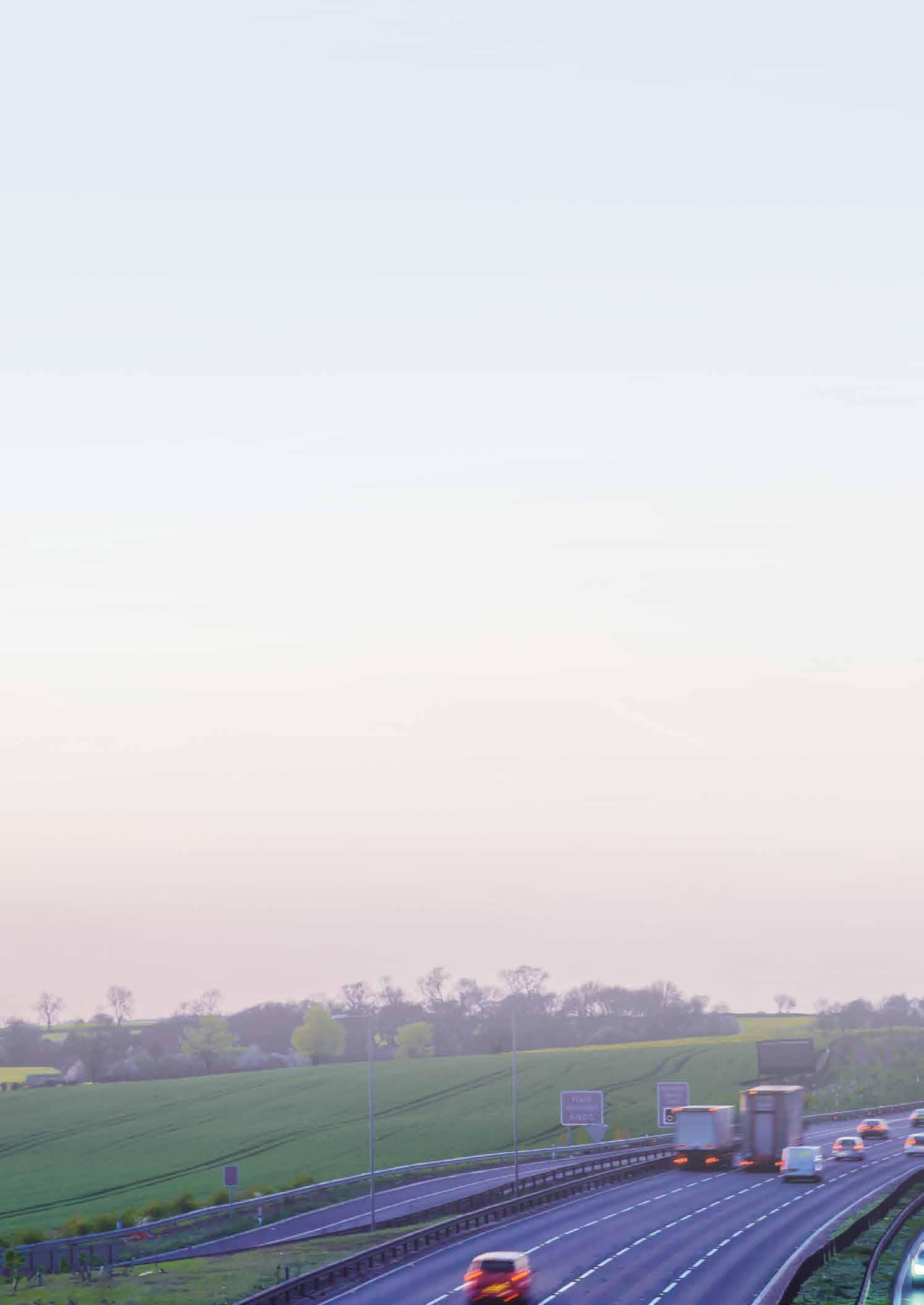
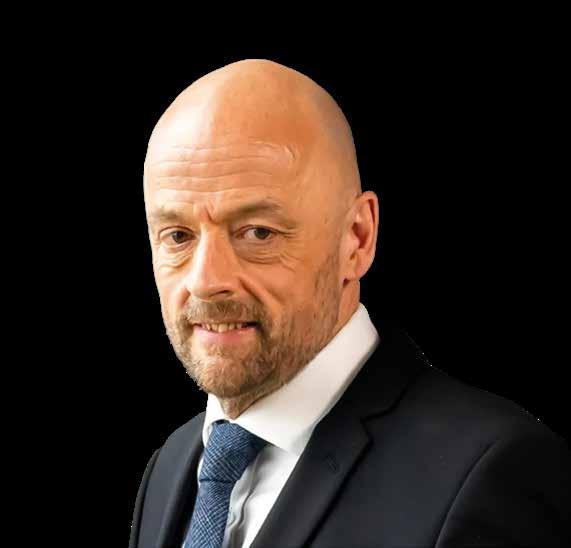
Q. Scaffolding trucks are often seen by authorities as less compliant with fleet regulations. What is the RHA doing to address this perception?
A The RHA recognises this issue and is working with the Scaffolding Association to change the narrative by promoting practices within the industry. Through our collaboration with the Scaffolding Association, we’ve developed targeted training programs, such as the bespoke Driver CPC module, to address specific challenges like safe loading, securing equipment, and adhering to operator licence requirements. By equipping operators and drivers with the knowledge and tools to meet and exceed regulatory standards, we aim to build trust with authorities and demonstrate that scaffolding operators are committed to running safe, compliant fleets
Q. Drink and drug driving remains a significant concern for fleet operators. What is the RHA doing to tackle this issue?
A The RHA is committed to promoting a zero-tolerance culture toward drink and drug driving. Like the Scaffolding Association, we collaborate with
organisations like D.tec International to supply tools like DrugWipe screening kits to help businesses identify risks early. Education, awareness campaigns, and access to these tools are key aspects of our approach
Q. How are commercial vehicle operators addressing the safety of vulnerable road users, and what role does the RHA play?
A Protecting vulnerable road users, such as cyclists and pedestrians, is a top priority for our industry. Many operators are investing in advanced vehicle technology like 360-degree cameras, proximity sensors, and automatic braking systems to reduce risks. The RHA actively promotes safety training and awareness for drivers, emphasising the importance of understanding blind spots and sharing the road responsibly. Additionally, we’re working with policymakers to ensure that new safety regulations are practical and effective without imposing undue costs on operators.
Q. Richard, you are the Chair of the Trade Association Forum (TAF), and Robert Candy from the Scaffolding Association also serves on its board. How does this collaboration benefit the wider trade association community?
A TAF is a vital platform for bringing trade associations together to share knowledge, advocate for common interests, and strengthen their impact. With Robert and I both on the TAF board, we’re able to align our efforts to represent our respective industries while fostering collaboration across sectors. This partnership exemplifies how associations can work together for mutual benefit.
Q. The RHA has been heavily involved in the truck cartel legal action. Can you update us on its progress?
A The truck cartel legal action has been advancing, and we actively encouraged affected businesses to opt into the claim. The deadline to participate was 28th February 2025. We are now working with operators who have opted in to collect the necessary information to support their claims and help secure compensation for overpayments caused by price fixing
Q. What are the biggest challenges facing commercial vehicle operators regarding clean air zones (CAZs) and environmental regulations?
A Clean air zones are becoming increasingly prevalent as cities look to reduce emissions, and while the RHA supports efforts to improve air quality, these measures can place a significant financial burden on operators. Upgrading fleets to meet CAZ requirements is costly, and many businesses, particularly SMEs, struggle to absorb these expenses. The RHA is advocating for more support, including financial incentives for fleet upgrades and a clearer, more consistent approach to CAZ implementation across the UK. We’re also working with members to explore practical solutions, such as alternative fuels and vehicle retrofitting
Q. What challenges do commercial vehicle operators face in transitioning to zero-emission vehicles (ZEVs), and how is the RHA supporting them?
A The transition to zero-emission vehicles (ZEVs) is one of the most significant challenges facing our industry. While we fully support

the move toward greener fleets, the high upfront costs of ZEVs, limited charging or refuelling infrastructure, and concerns over vehicle range create significant barriers for operators. The RHA is actively advocating for government support, including grants, subsidies, and accelerated investment in infrastructure, to make the transition more viable. We’re also working with manufacturers and technology providers to ensure operators have access to practical information and solutions for integrating ZEVs into their fleets. Our goal is to ensure this transition is manageable and sustainable for businesses of all sizes.
Q. What is your top message to the government as the voice of the road transport industry?
A My top message to the government is simple: listen to the industry and work with us to build a sustainable, efficient, and fair future for road transport. Whether it’s investing in infrastructure, supporting the transition to zero-emission vehicles, addressing driver shortages, or providing clarity on environmental regulations, we need practical policies that reflect the realities faced by operators.
For specialist fleet operators like scaffolders, whose vehicles face unique operational challenges alongside those experienced by traditional heavy goods fleets such as hauliers and coach operators, certainty and investment are just as critical. These businesses play a vital role in supporting the UK economy, ensuring safe and efficient transport of materials and equipment. To thrive and continue delivering for the country, they need a government that is willing to collaborate to help overcome shared and sector-specific challenges.
More information on:
Page 19: Safe Loading and Vehicle Checks for Scaffolders Driver CPC module
Page 23: D.tec International
“The site engineer wanted to make adjustments to the leg loads on the pavement after the scaffolding was installed. Thanks to the flexibility of the PERI UP system, we were able to modify the structure with ease.”
Charlie Wheeler | Managing Director – IE Access
PERI UP Flex for versatility
EXPLORE
PERI UP FLEX
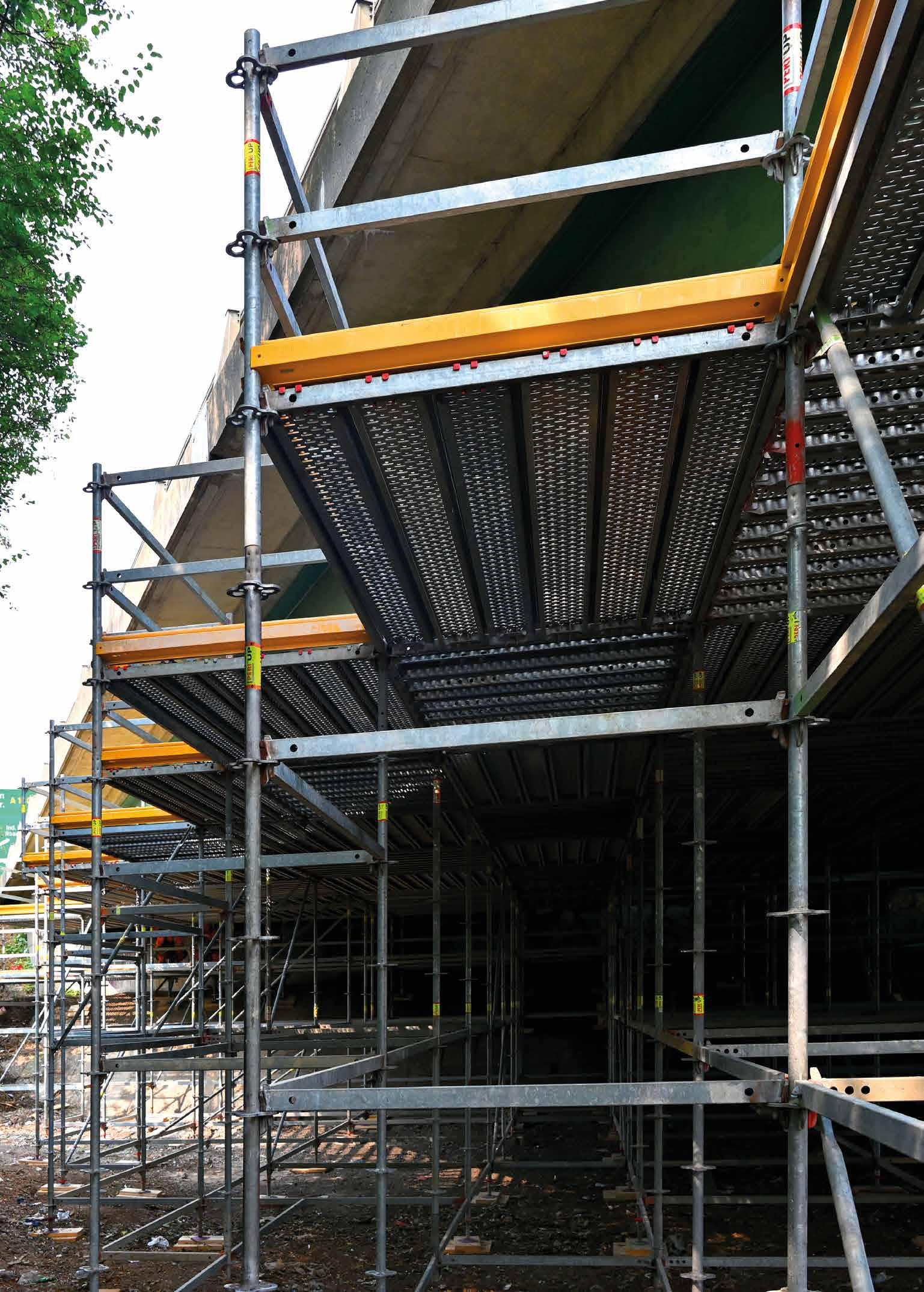
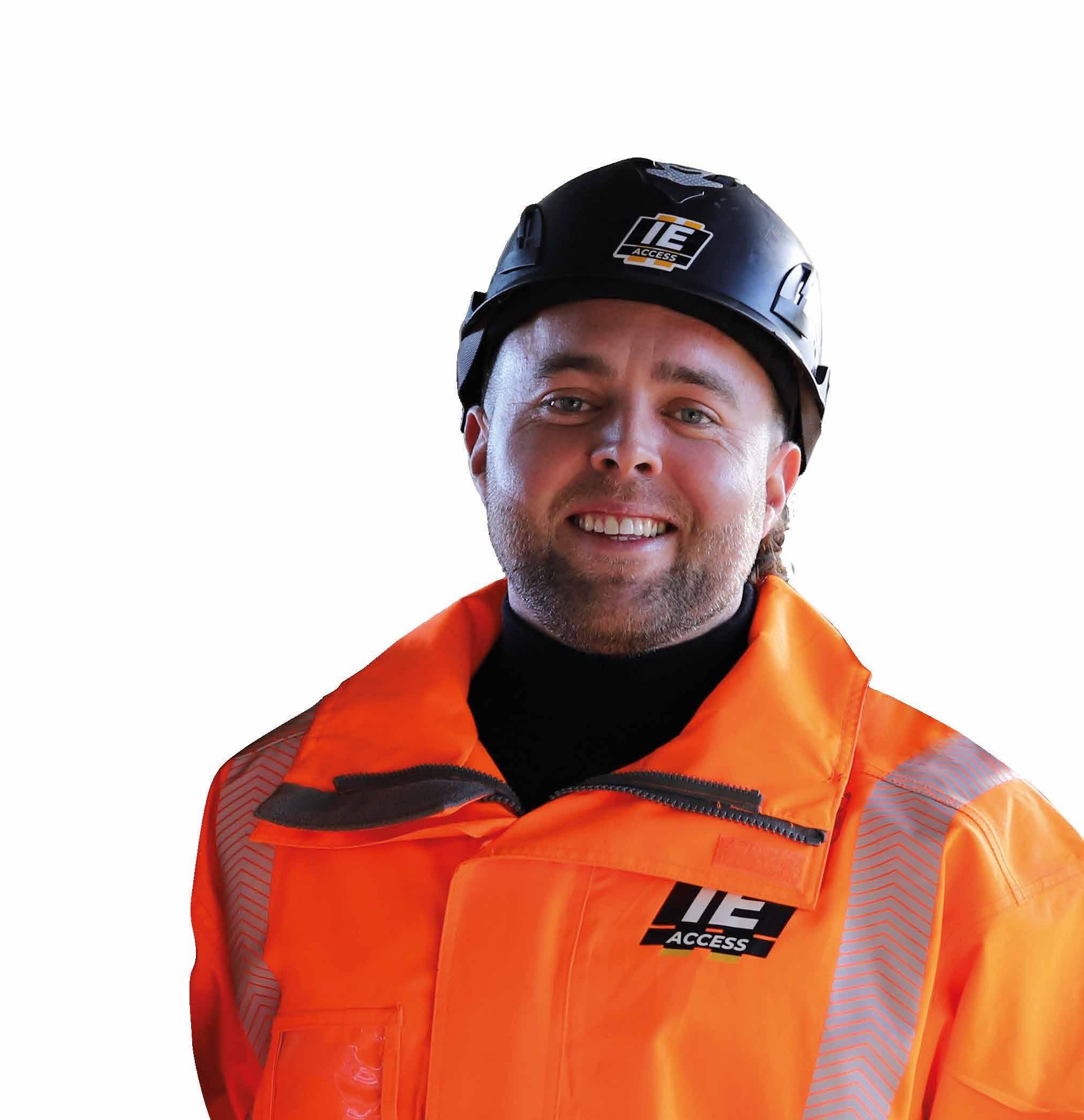
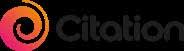
Employment Rights Bill and your scaffolding business
Like all industries, the scaffolding sector is gearing up for one of the most significant overhauls to employment law in decades. With the impending introduction of the Employment Rights Bill, scaffolding businesses need to start preparing for change. In this article Citation, HR and Employment Law experts, take you through a few of the biggest changes facing your business in the next couple of years.
1
2
3
4

Day-one employment rights
One of the most dramatic changes is the removal of the two-year qualifying period for unfair dismissal claims. Under the new rules, employees will get the right to claim unfair dismissal and access parental leave from day one of their employment. For scaffolding businesses, this means probationary periods will need clear documentation and fair processes to avoid disputes. Updating your contracts and dismissal procedures now will be critical to staying compliant.
Statutory Sick Pay (SSP) reforms
The reforms to SSP mean sickness benefits will now be accessible from the first day of absence, with no lower earnings threshold required for eligibility. While this could increase costs for you as a business owner, it does come with benefits – workers who are unwell are more likely to stay home, which reduces the risk of accidents onsite and improving your overall Health & Safety standards.
Default to flexible working
Construction businesses might find it challenging to adapt to flexible working being promoted as the default arrangement, especially in roles needing onsite presence. But, under the new legislation, any rejections of flexibleworking requests will need to be justified properly. Start by thinking about which roles could accommodate flexibility to retain talent and improve workforce satisfaction.
Banning exploitative zero-hours contracts
The Bill aims to tackle “one-sided flexibility” by banning exploitative zero-hours contracts. Employees will gain the right to a contract that reflects their regular average hours, and you will have to give reasonable notice of shift changes. You might need to revisit contract arrangements to make sure everything stays fair and compliant.
Preparing for change
With significant reforms on the horizon, you will need to adapt over the next year or so by reviewing your employment contracts, adjusting policies and investing in training to make sure everyone is compliant. These changes could mean a fundamental shift in the way you run your business, and their overall aim is to improve fairness and worker welfare, which align with building a sustainable and resilient business.
Citation – how we can help
There is a lot of change in store – so now is the right time to make sure you are keeping up with it. As a Scaffolding Association Associate Member, we have got in-depth knowledge and understanding of the industry – so you can have faith that we know how to help you manage the challenges unique to your business. For more support on all things HR and Employment Law, call Citation on 0345 844 1111. If you are a Scaffolding Association Member, make sure to have your Membership Number ready and ask to access preferential rates off a new client contract with Citation.
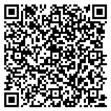
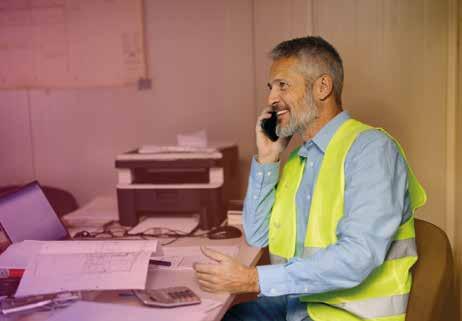
Scaffolding Association members deliver sky-high success on atrium roof demolition
Scaffolding Association members team up to successfully provide a complex heavy-duty loading and working platform 20m above ground level to facilitate the removal of an existing atrium roof light and supporting steel, to allow a tower crane to be installed inside a prestigious building on Fleet Street, London.
Specialist design & build contractors, McAleer & Rushe, were appointed as main contractors for this complicated and ambitious project. They instructed Sean Doyle Scaffolding Ltd (Audited Members of the Scaffolding Association), and Scaftec Limited (Member Designers) to come up with a
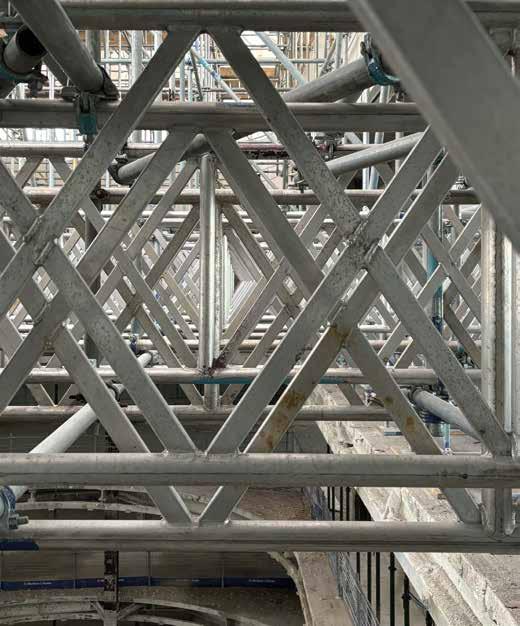

workable scaffolding solution to enable Ground Construction demolition (GCL) to undertake the demolition of the atrium roof and the installation of the internal tower crane.
The brief was a complex one that required a crane to be set up outside on a busy London street to assist with the strike and demolition of the atrium’s heavy steel frame, which was cut down to more manageable pieces before being craned out of the building. To enable this a scaffold structure was needed to support multiple small alloy towers, and operatives with their tools, to allow GCL to carry out the works.
Shawn Richardson, Contracts Director at Sean Doyle Scaffolding explained:
“The solution was a bridged birdcage spanning an open atrium of 12m first coming across level 6 approx. With 3x2m lifts punched up off the beams to reach the underside of the dome roof.”
The structure required a Safe Working Load (SWL) of 300kg per m2, Grant Keys, Technical Director at Scaftec commented:
“The imposed loadings onto the support slab had to be carefully
coordinated with permanent structure engineers to ensure the slab edge was not overloaded.”
However, it was not just the technical aspects that the designers had to take into consideration for this complicated project, Grant continued:
“The most unique challenge was being aware of the build process. The floor opening was 12m in some locations and we had to ensure our design was buildable, some 20m above the ground level.”
With careful consideration and excellent communication between Scaftec and Sean Doyle Scaffolding, a safe and successful solution was devised, Shawn explained:
“The main challenge was spanning the beams over from one side to another to connect them to the support towers, without having to push the beams out within the atrium where the weight of the beams being suspended over the void would have become heavy and unable to man handle.
We overcame this by attaching a rope and wheel to the opposite side to where the beam was being installed. The 750mm deep beams were then
connected on the level 6 floor slab within our safe zone. The ropes were then attached to the beams, one which was taking the weight of the cantilevered beam while it was being pushed out from the safe zone into the open atrium, and the other rope was put in place as a secondary safety precautions acting as a tether.”
Once the workable design and method were confirmed and agreed by all stakeholders, one of the final challenges for the Sean Doyle team to overcome was the logistics of getting all the required scaffold materials up to where it was needed. Shawn described how they managed this:
“We had a challenge of getting the materials up to level 6, as the only mechanical means we had was a small 500kg hoist, which was located within a lift shaft. We overcame this by strategic planning, reducing the size of the material we used, and ensuring we had a sufficient number of operatives to achieve this.
We also set up a Big Ben rope and wheel for the longer materials like the beams that were secured to the building structure.”
The most unique challenge was being aware of the build process. The floor opening was 12m in some locations and we had to ensure our design was buildable, some 20m above the ground level.
Grant
Keys,
Scaftec Ltd, Technical Director

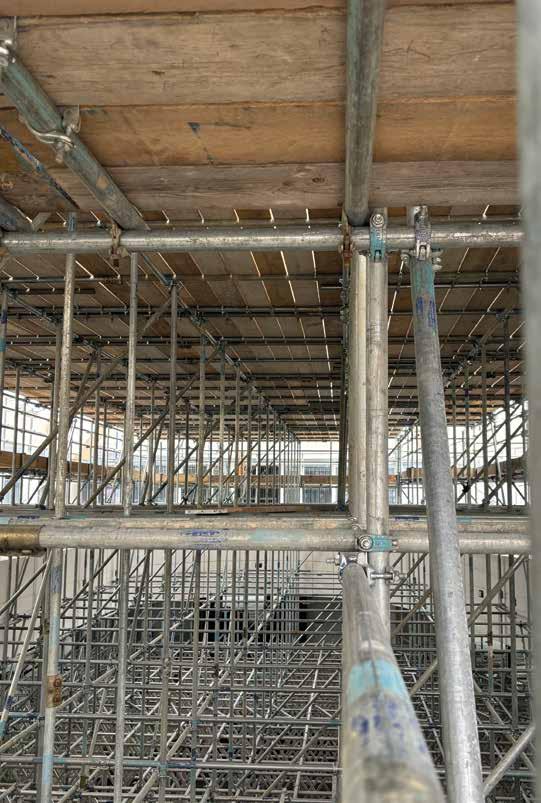
The teams collaborated effectively and worked tirelessly to deliver this project successfully.
Grant concluded:
“We are thrilled to have been a part of this project. At Scaftec, we thrive on tackling complex challenges and delivering effective solutions. This project was another successful collaboration with multiple parties, all working together to achieve a safe and efficient structure. We look forward to continuing our successful partnership with Sean Doyle Scaffolding on future endeavours.”
Shawn concluded:
“Our favourite part of this job was how it was such a complex designed scaffold, it was not your usual everyday scaffold, and I am very proud of how well the teams collaborated to make such a unique scaffold a big success.”
Scaffolding Association members’ close collaboration ensures smooth solutions
Two members of the Scaffolding Association, Rowland Scaffold Co Limited and Creator Scaffold Design and Temporary Works Consultants Limited, combined their expertise to ensure smooth running of a complex project on a building containing machines that are sensitive to vibration.
Rowland Scaffold were tasked with providing access for brickwork repair works to the Alfred Denny Building, a 7-storey structure that is part of the University of Sheffield, and is home to the University’s Biological Sciences courses. The University uses machines that are sensitive to vibrations throughout the building and run 24 hours a day, 7 days a week.
Zac Rowland, Contracts Director at Rowland Scaffold explained the consequences of this:
“Due to the sensitivity of the machines throughout the building, and the need for the building to remain open and operational, we carried out extensive vibration
and acoustic testing prior to any works commencing, it was these vibrational and noise restrictions that changed the way we had to construct the scaffolding. We were unable to tie the scaffolding over three consecutive floors, therefore the challenge was to build a scaffold that was untied for 12m.”
A project of this complexity required close cooperation between scaffold designer and contractor to ensure its success. Rowland Scaffold and Creator, both well-respected experts in the scaffolding industry, have worked together on numerous projects over many years. They drew on their excellent working
relationship to overcome the many challenges this project threw at them. Ahmeth Al Hanan M Ameen, Graduate Design Engineer at Creator, explained:
“We designed a tied, debris netted access scaffold with multiple bridge spans, to provide access to the full façade. We worked closely with Rowland Scaffold to design a scaffold that fulfilled all their client’s needs. A key technical challenge was the limitation of ties in the midsection of the structure, particularly at five intermediate scaffold levels (3 floor levels) due to the client’s requirement to keep these levels clear of obstructions and to limit the noise and vibrations induced from installing ties.”
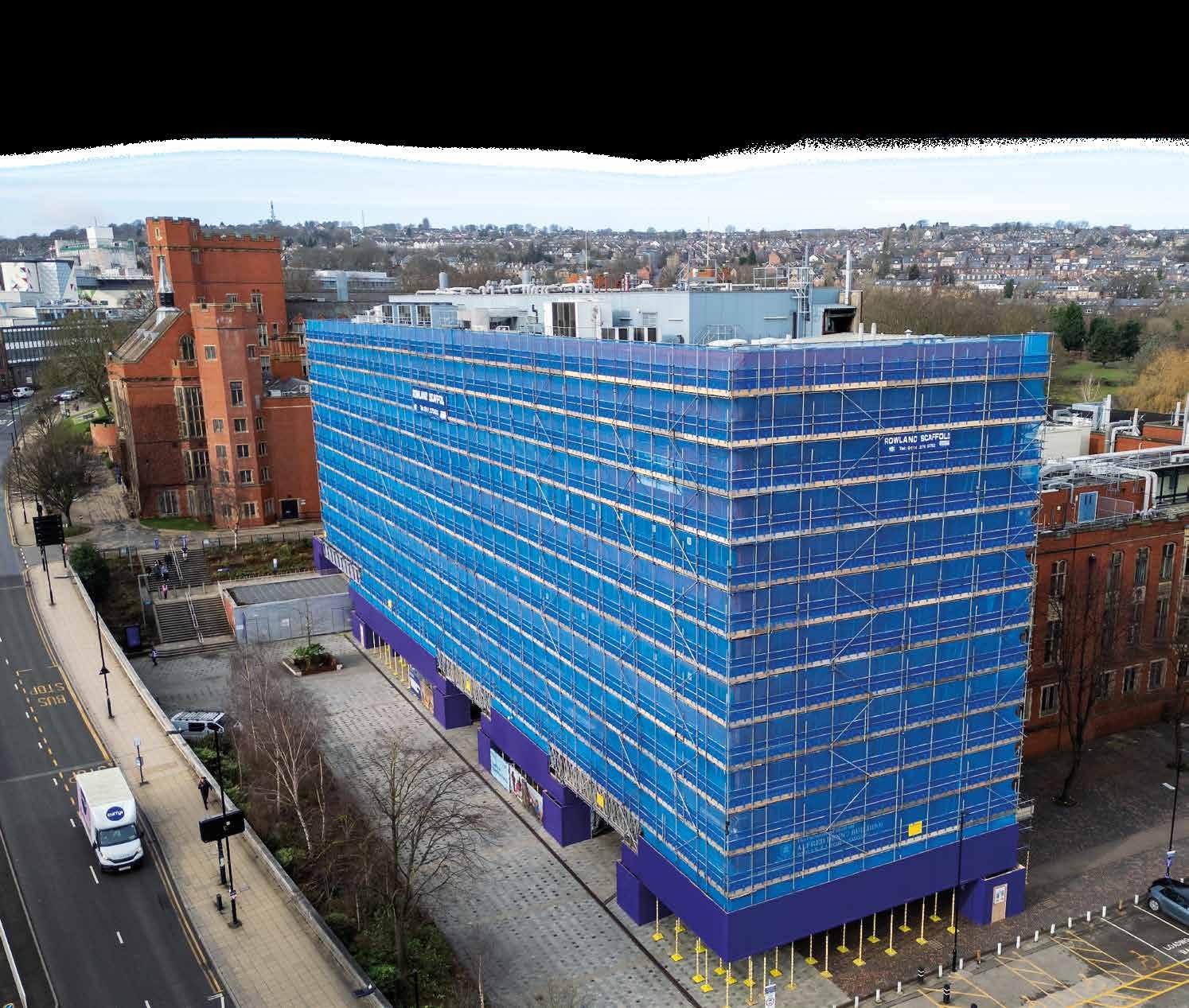
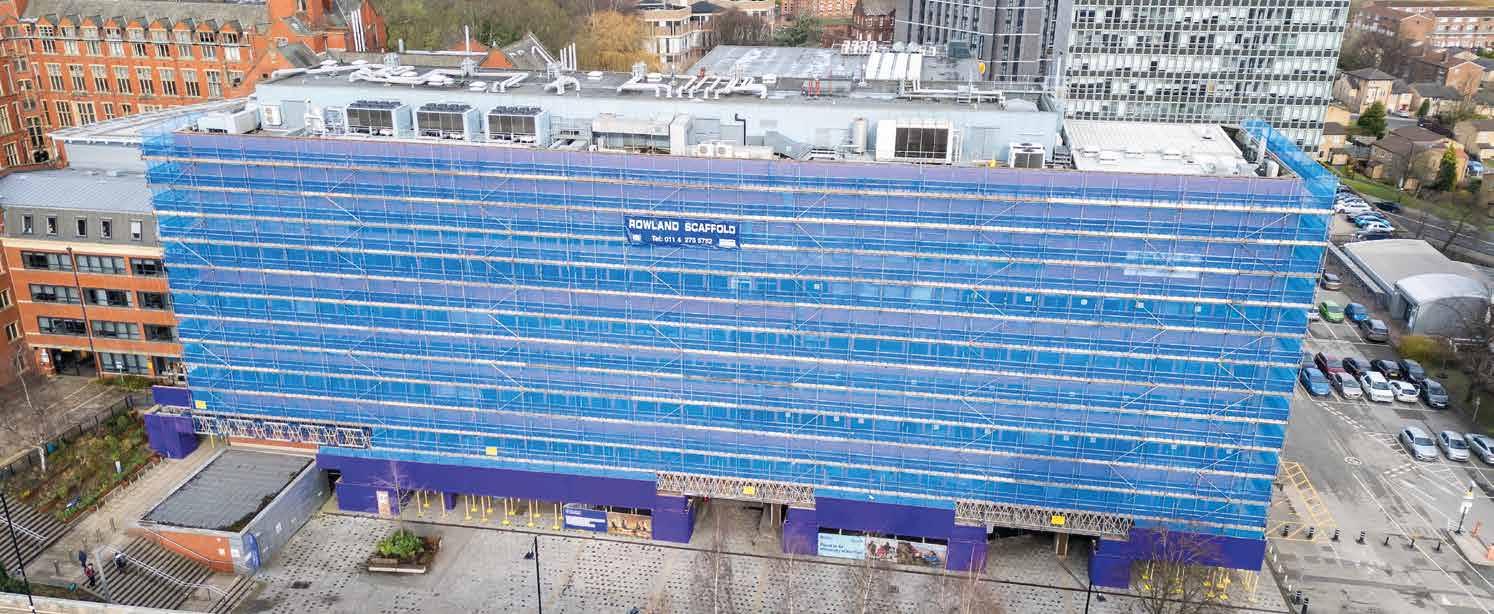
The unique tie pattern, the length and height of the existing structure, and the various obstacles at the base that had to be overcome to maintain access for vehicles and pedestrians at the main entrance, all added to the complexity of the design, Hanan continued:
“The tie pattern gave us a challenge in stabilising the scaffold both temporarily during erection and dismantling, and in a finished state. In a temporary state the scaffold was approximately 10.0m free-standing above the last tie. In a finished state we had to ensure the internal bracing could sufficiently distribute loads into the ties. Additionally, certain areas at base had to remain clear for pedestrian access. Due to the height of the scaffold and restrictions on tie positions we had to utilise specialist 1.5m deep X-beams, specifically designed to handle exceptionally high loads, to include bridge spans at required locations. This design feature was critical given the substantial vertical loads and the importance of maintaining the openings.”
This project was complex and technical throughout the entire process, Hanan explained:
“The restriction on tie locations in the mid-section of the scaffold heavily affected both the design process and how the design was communicated to all parties due to the requirements for the installation methodology and the internal load distribution in the scaffold frame. It became imperative to develop an effective load distribution methodology. The team devised
a solution to transfer wind forces across the structure using safe load patterns, ensuring lateral stability without compromising the design intent or functional use of the scaffold structure. This innovative approach significantly reduced the dependency on physical tension ties while maintaining structural integrity.”
It was not just the technical details that had to be carefully considered, Zac commented:
“Due to the location of the building, which is in the centre of the campus, we set out to produce the neatest and aesthetically pleasing scaffolding possible, which I believe that we did. We took on the challenge of hoarding the scaffolding with 18mm ply board, which turned out to be some of the best hoarding I have seen.”
Over the years Rowland Scaffold and Creator have built a solid working relationship, Hanan mentioned:
“Our favourite part of the project was the detailing and structural analysis of the 1.5m deep beams, Rowland Scaffold were extremely helpful by providing practical sitebased guidance on exactly how they needed to be installed.”
The multi-faceted project demonstrated close collaboration of highly skilled expertise, Hanan concluded:
“The design and erection of the Alfred Denny Building scaffold demonstrates an integration of high-level structural engineering principles with practical construction
challenges. The ability to effectively address the high shear and bending capacities, reduce tie dependency, and ensure practical usability of the structure under extreme environmental conditions highlights the project’s engineering value. We thoroughly enjoyed working with Rowland Scaffold throughout the project and respect their level of precision and skill.”
The project was a huge success all round, Zac concluded:
“We have been working with the University of Sheffield for over 30 years, and this project is one of the highest profile projects to date. This project took months of planning and weekly check-up meetings, given the sensitivity with the machinery and building users, along with location of the building, it was our time to showcase what Rowland Scaffold is about. It was great to work with Creator on this, there are many reasons that we have worked with them for many years, namely we trust, and appreciate, their level of expertise and professionalism.
Finally, I would like to thank all our lads who worked on this, it was at the height of winter which slowed the installation process down, but they worked hard, in difficult conditions to get the job done.”
More:
Creator Scaffold Design and Temporary Works Consultants Limited www.creator-scaffolddesigns.co.uk Rowland Scaffold Co Limited www.rowlandscaffold.co.uk
Public safety key on multi-storey project
CS Scaffolding Limited, who are Assessed Members of the Scaffolding Association, have provided safe access solutions for necessary repair works on the flat roofs of Newgate Shopping Centre, Bishop Auckland.
The project brief outlined several essential requirements to ensure both operational efficiency and public safety. One of the key specifications was to maintain uninterrupted access to the multi-storey car park throughout the duration of the works. CS Scaffolding achieved this with a gantry system.
Chris Wright, Director at CS Scaffolding Limited, explained:
“The gantry design had to accommodate both pedestrian and vehicular access while maintaining structural integrity. What made this particularly special was its sheer size and the bespoke load calculations. The structure height was 55 feet and required precise engineering calculations, particularly for the working platforms.”
The safety of both shoppers below and personnel carrying out the works overhead were of the utmost importance. The project also coincided with an adjacent £11.8 million bus station redevelopment, all of this
required careful consideration, Chris commented:
“Operating over a busy shopping centre meant strict adherence to time windows for erection work. We needed to obtain specific pavement permits and coordinate with local authorities to ensure public safety.
The proximity to the bus station redevelopment project also required careful planning of site access and material storage.”
The location and logistics of the project made precise planning necessary, Chris continued:
“The most challenging aspect was coordinating the complex installation in such a busy location, though with our well-established project management processes and experienced team, we were able to handle this efficiently. Our methodical approach to planning and execution meant we could tackle these logistical challenges without disrupting the shopping centre’s operations.”
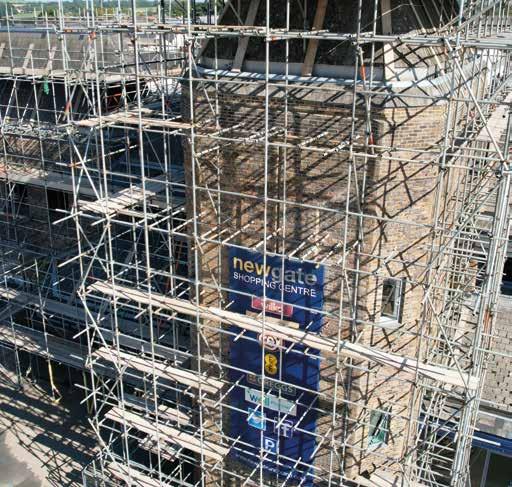
When asked what the most rewarding aspect of the job was Chris commented:
“Stepping back after the completion and seeing what our team had accomplished. When you’re working day-to-day on a project of this scale, you’re focused on each specific task, but once it’s finished, you can truly appreciate the impressive structure created.”
The project was a huge success, when reflecting on it Chris concluded:
“As one of the most reputable scaffolding companies in the North East, this project exemplifies what CS Scaffolding do best — first class scaffolding projects. The Newgate Centre presented unique challenges, but our experienced team delivered. As a company, we’re particularly proud to be part of Bishop Auckland’s ongoing transformation — projects like this showcase not just our technical capabilities, but also our commitment to supporting local development.”
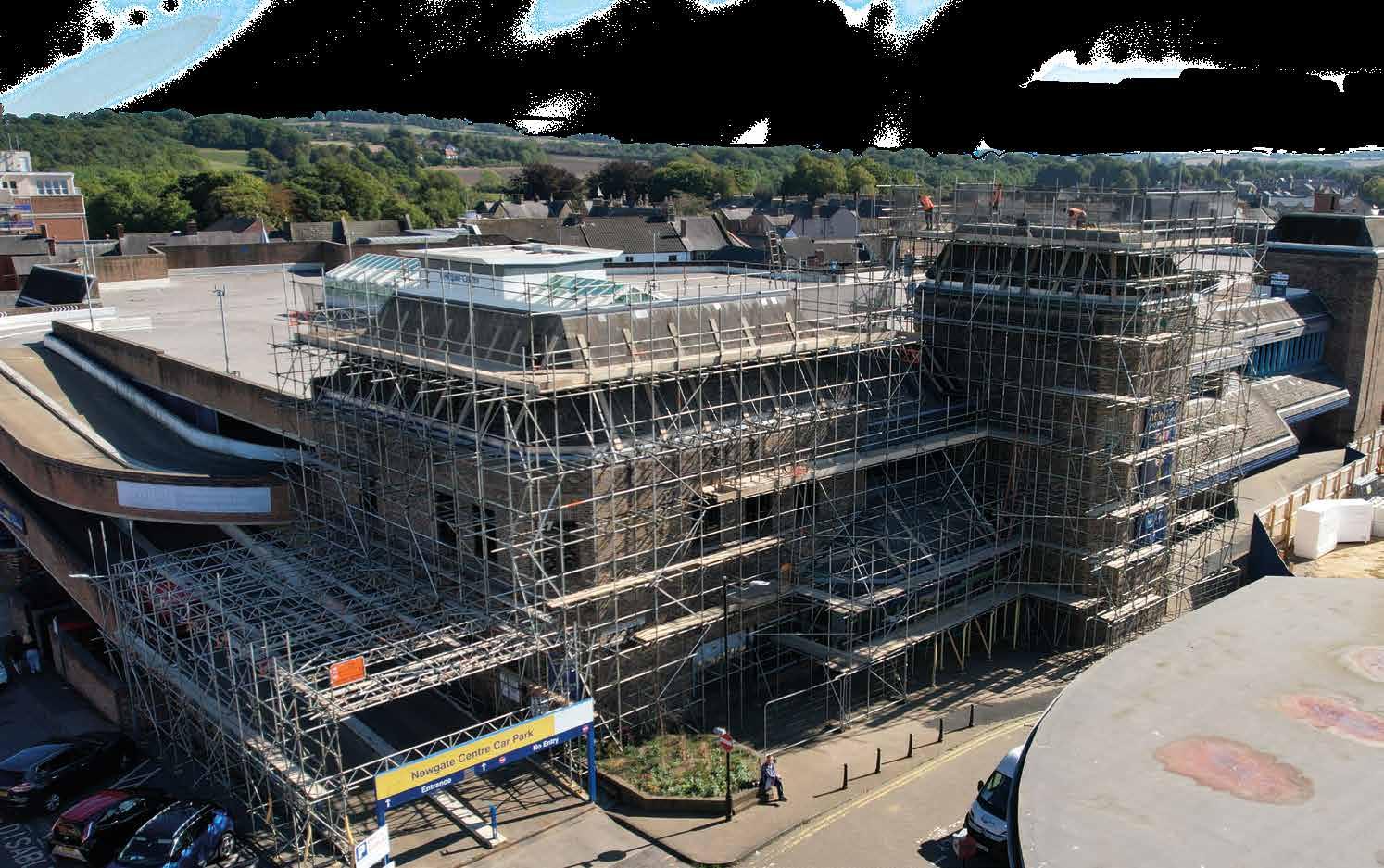
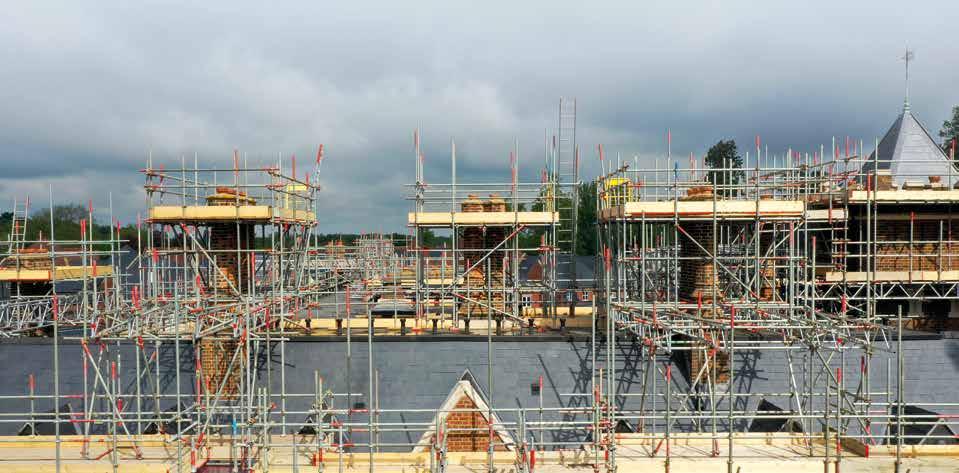
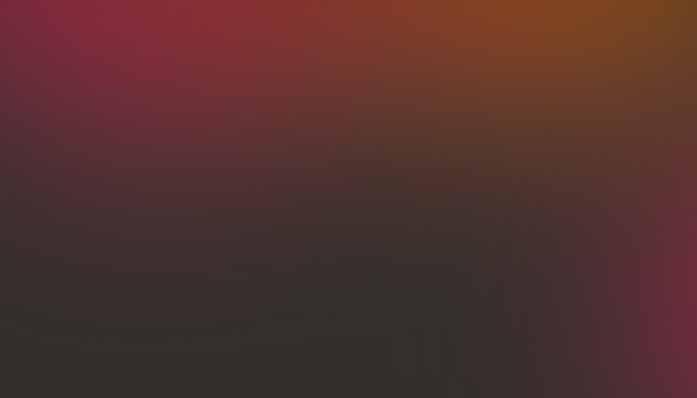

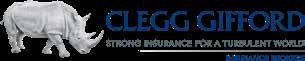
Not just another expense: Why insurance is essential for UK scaffolders
In this article Toby Clegg, CEO at Clegg Gifford, breaks down the key types of insurance every UK scaffolding firm should consider, and highlights how the Scaffolding Association and its partners, like Clegg Gifford, are helping you manage risks.
Insurance might not set your pulse racing like winning a big scaffolding contract, but it’s as essential to your business as a strong foundation is to a building. In the high-risk world of scaffolding, accidents can and do happen – and having the right insurance means your business is protected when the unexpected occurs.
Essential insurance cover
Operating in the scaffolding trade means working at height, handling heavy materials, and being responsible for public and employee safety. To protect your employees, the public, and your company’s livelihood, you need a few essential insurance covers in place.

Disclaimer;
Here are the big three every scaffolder should consider:
Public liability insurance
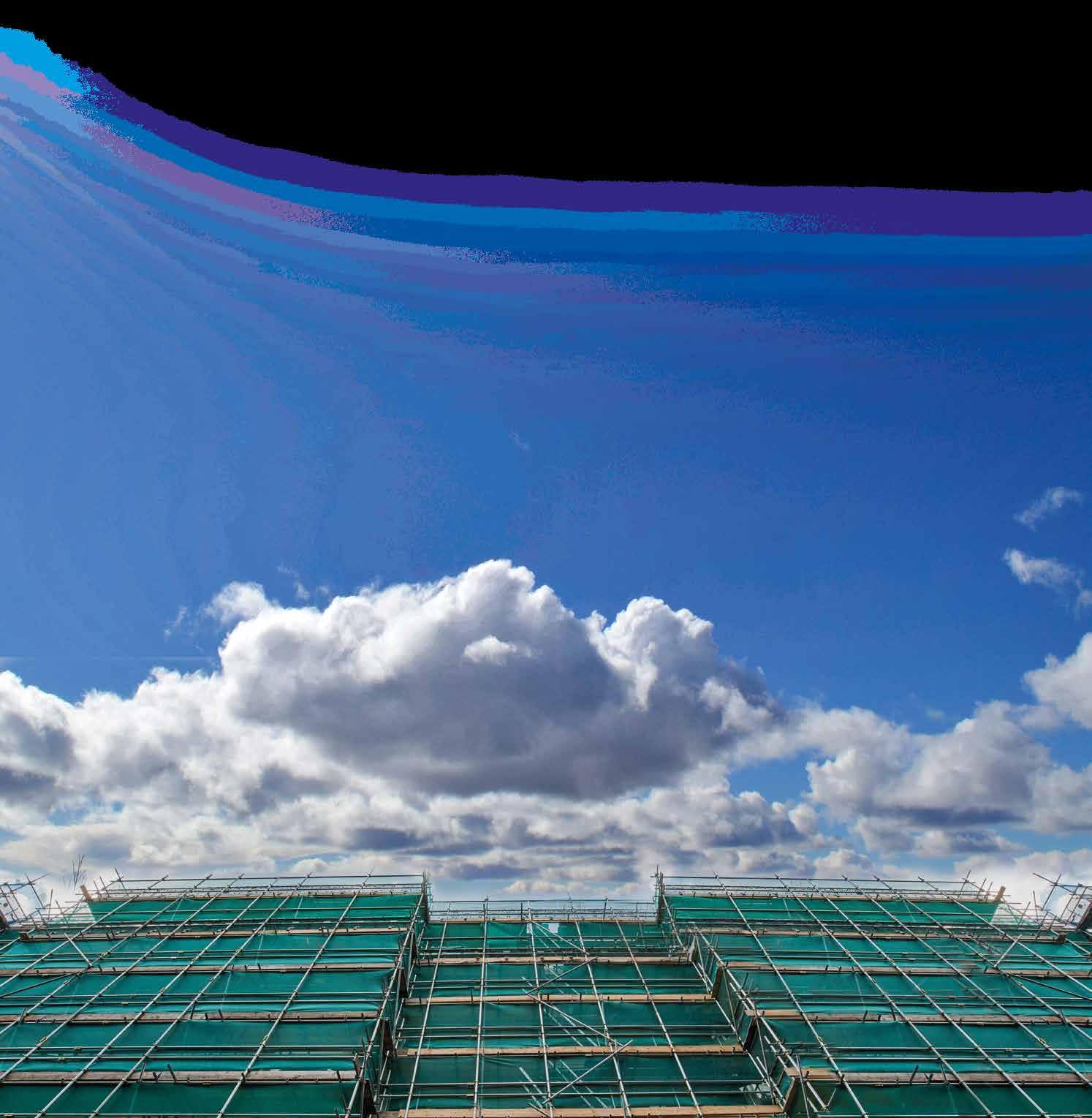
Public liability insurance covers the cost of legal fees and pay-outs if your business is held liable for injury or property damage to a third party.
For example, if a passer-by trips over your equipment or a falling tool damages a client’s property, this policy would cover the compensation and legal costs. Scaffolders often work in public and client sites where accidents can impact others, so this cover is critical. Policies typically offer cover limits from £1 million upwards, depending on the size of your projects.
Importantly, many clients or main contractors will insist on proof of public liability cover before you are allowed on site – it’s truly a cornerstone of doing business safely.
Employers’ liability insurance
If you employ staff (even labour-only subcontractors in some cases), employers’ liability insurance is not optional – it’s required by UK law. This insurance protects your business if an employee is injured or falls ill due to their work. Given the elevated risk in scaffolding, having this cover is absolutely vital.
Scaffolding and roofing are high-risk trades where injuries tend to be more severe, so robust employer’s liability cover is a must. The law requires this cover in place and fines or worse can be imposed for not carrying it.
Contractors’ All-Risks insurance (Contract Works)
Contractors’ All-Risks (CAR) insurance, sometimes called Contract Works insurance, provides cover for loss or damage to the building works, materials, and equipment on site. For scaffolders, this means if your scaffold structure or materials are damaged by, say, a storm, fire, theft or even a collapse, the policy can cover the cost of repairs or replacement. While not mandated by law, CAR insurance is often a contractual requirement on construction projects.
It protects both the contractor and the client in case of accidents or damage during the project.
Scaffolding is a high-risk trade, and your insurance needs to work just as hard as you do.
Scan here to find out more about how Clegg Gifford can help with all your insurance needs.
Safe Loading and Vehicle Checks for Scaffolders:
The essential new training module launched by the Scaffolding Association and the Road Haulage Association
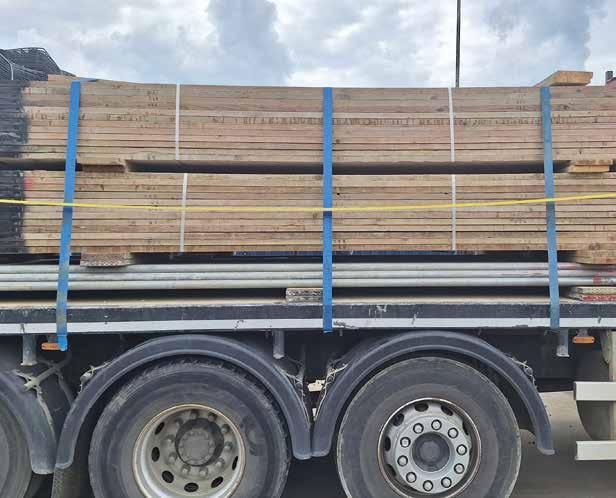
Scaffolding transport carries inherent risks, and getting it wrong can have severe consequences, from legal penalties to serious accidents.
Poorly secured scaffolding loads pose a significant hazard to road users, leading to prohibitions, fines, operator license revocations, and, in the worst cases, injury or loss of life. Recognising these challenges, the Scaffolding Association and the Road Haulage Association (RHA) have launched a critical new training module: Safe Loading and Vehicle Checks for Scaffolders.
This specialised course is designed to address the unique transport needs of the scaffolding industry, ensuring that professional HGV drivers meet their mandatory 35 hours of periodic Driver CPC (DCPC) training while significantly improving safety and compliance. However, it is also highly relevant to anyone responsible for the safe loading of vehicles, including drivers who do not require DCPC accreditation. Safe and secure loading is a shared responsibility across the industry, and understanding best practice can prevent costly enforcement actions and enhance workplace safety.
Key benefits of the course
The Safe Loading and Vehicle Checks for Scaffolders training module ensures that drivers and operators fully understand and adhere to load security legislation. It educates them on the proper methods to transport scaffolding materials safely, reducing the risk of enforcement actions and costly legal penalties. The course also reinforces the importance of maintaining vehicle roadworthiness, crucial for retaining an operator’s license.
Delegates will gain critical insights into:
• Load security and responsibilities
• Best practices for loading and securing scaffolding materials
• The legal and financial consequences of non-compliance
• Daily vehicle checks, including defect reporting and documentation
• The role of enforcement agencies and how to navigate compliance checks.
Who should attend?
This course is essential for:
• Professional HGV drivers transporting scaffolding materials
• Anyone responsible for the safe loading of vehicles, including operators, supervisors and drivers who do not require DCPC accreditation
• Business owners aiming to protect their operator’s license and avoid enforcement actions.
By investing in this training, scaffolding and access businesses can ensure compliance, enhance safety standards, and mitigate risks associated with unsecured loads. The benefits extend beyond legal compliance; they contribute to the overall professionalism and reputation of the scaffolding and access sector, reinforcing a commitment to best practice.
Booking and further information
The Safe Loading and Vehicle Checks for Scaffolders training module is now available, with scheduled courses accessible via the RHA website.
Scan here for full details, including dates and locations:
As the UK’s largest trade body for scaffolding contractors, the Scaffolding Association continues to advocate for higher safety standards across the industry. This collaboration with the RHA marks a significant step forward in ensuring scaffolding transport is carried out safely, efficiently, and legally, benefiting businesses, drivers, and the public alike.
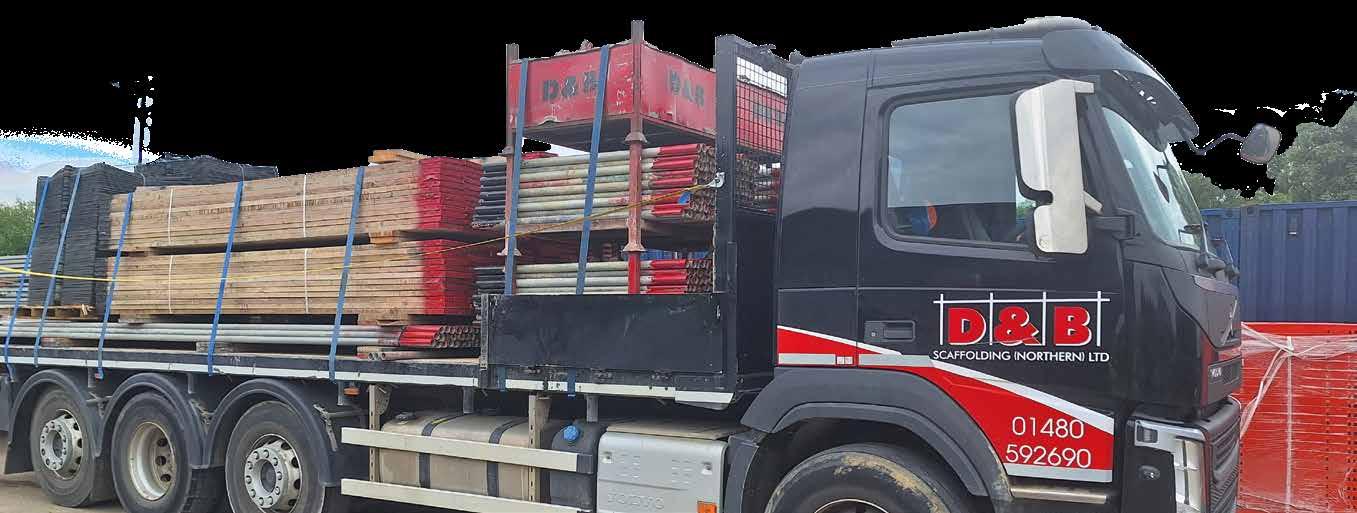
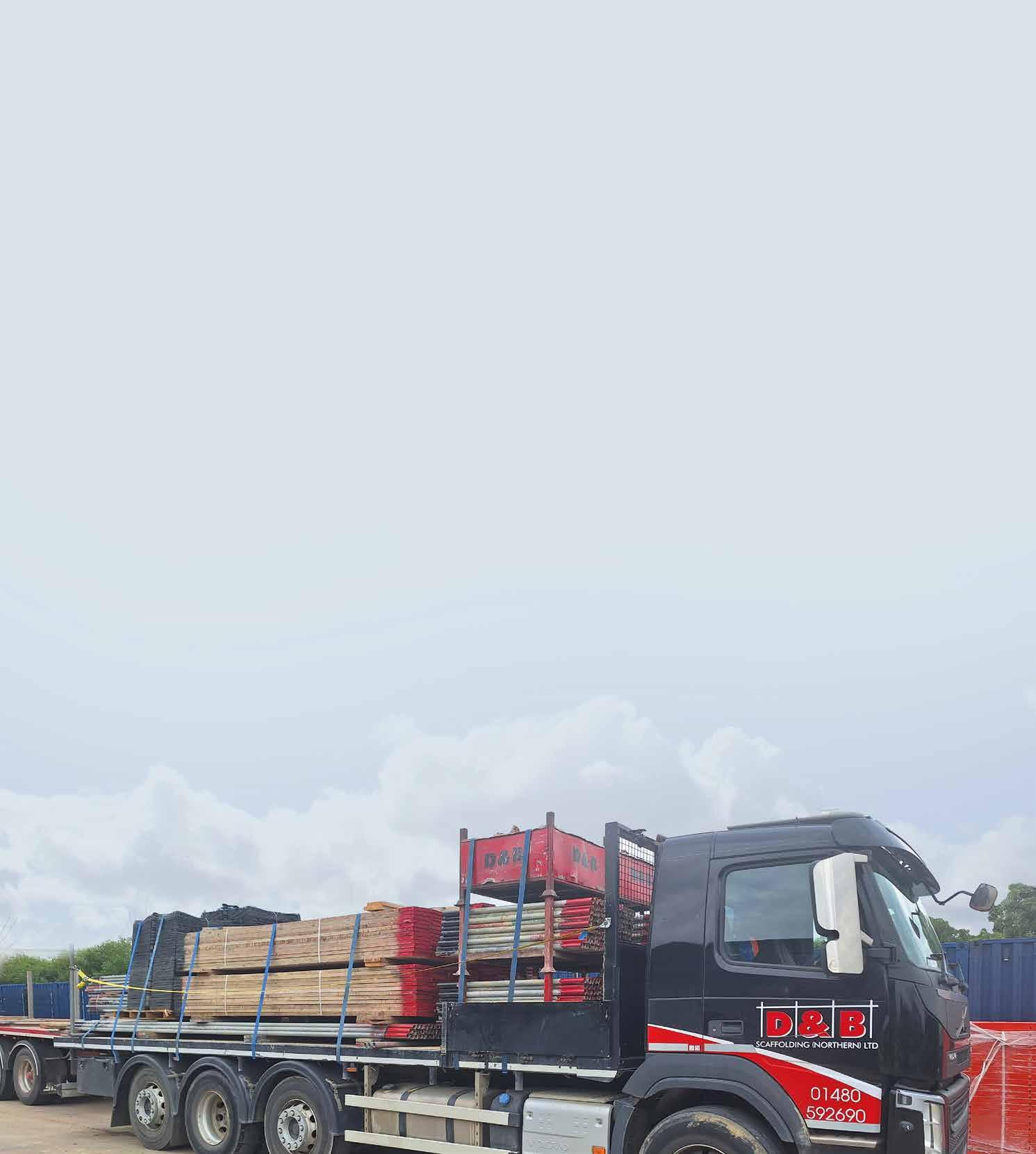
Holmes & Hills: The Procurement Act 2023
In this article, the Scaffolding Association’s legal partners, Holmes & Hills Solicitors, discuss the Procurement Act 2023 which came into effect on 24 February 2025.
The Act aims to create a streamlined, more versatile, and effective procurement. This means that Procurements (and the following contracts) started on or after 24 February 2025 have to comply with the new Act, except for payment and contract performance provisions which will come into force at a later date.
Although not an exhaustive list, the Key Changes to know about for your contracts are as follows:
1
4 Provisions made into 1 Key Act
The new Act brings together multiple pieces of legislation and compiles them into one central Act. The Public Contracts Regulations 2015, Utilities Contracts Regulations 2016, Defence and Security Public Contracts Regulations 2011 and Concession Contracts Regulations 2016 have been revoked as of 24 February and will be brought together within the new 2023 Procurement Act.
The aim of this is to make it easier for procurers to know which parts of the legislation will apply to them in their relevant sectors. Some areas are now outside the scope of the Act and will have separate pieces of legislation that govern them. For example, the delivery of healthcare services.
2 Payment
The Act makes prompt payment a key focus point to ensure contractors throughout the whole supply chain are paid swiftly. In order to do this, the Act will imply a term that any sum due from the authority must be paid within whichever is later; 30 days from the day that the authority receives an invoice or the day on which the payment falls due.
In order to benefit contractors will need to ensure that the date on the invoice does not contradict the implied term. This is implied into every public subcontract.
3
Notices
The Act also requires more transparency from procurers. Authorities will need to publish various types of notices. This means the decisions they make in procurement, as well as how effectively contracts are managed and performed will all be made public. There will be 14 new forms of notice. Some regarding performance in line with KPIS and even regarding termination.
Eventually (although not coming into force on 24 February 2025) this will include notices regarding payment and how promptly authorities pay their contractors.
4
Remedies
Under new legislation, there will be a new test to determine whether claims being brought are justified. Suppliers will still follow the same process i.e bringing a high court claim for breach of an authority’s statutory duty.
Various pre-contractual remedies include damages, an order suspending procurement, automatic suspension of the authority’s award decision (if made during a standstill period), an order suspending entry into a contract or an order suspending a decision or action taken in procurement. Authorities can still apply to lift any automatic suspensions granted. Post-contractual remedies include damages and/or setaside of the contract.
The time limit for procurement claims (other than set-aside) is 30 days starting on the day which the supplier first knew, or ought to have known, about the circumstances giving rise to the claim.
5 6
Barred contractors
The Act introduces a public debarment list. Essentially this will be a list of contractors who are unable to apply for public contracts.
Reasons contractors might end up on the list are as follows:
- If an investigation determines that a contractor meets one of the Acts new exclusion grounds.
- If a contractor fails to comply with the above investigation. Which will also place it within the exclusion grounds.
Contractors will be given notice ahead of being placed on the list and can appeal the decision. Following a notice being given, there is provision for an 8 working day standstill period. If necessary, contractors can apply for ‘interim relief’ until matters are resolved. Such interim relief would be that the Court will suspend the minister’s decision to place the contractor on the list.
As and when necessary, the list will be reviewed, and contractors can either appeal decisions or apply to be removed from the list if there is a change to their circumstances.
Implied terms –Termination
The Act implies certain terms aimed at ensuring compliance with the new legislation.
One of these implied terms is a right to terminate, of which there will be 3 grounds implied into all public contracts. They are:
- If the contract was awarded unlawfully.
- A supplier has become an excluded supplier during the contract.
- A supplier is an excluded supplier.
7 Variations
One new implementation of the Act is that it aims to provide clarity on when variations can be instructed without the need for new procurement. There are now 10 situations where this can be done.
Authorities will be required to publish a change notice. There will also then be an 8 working day standstill in case contractors wish to challenge the decision.
Some examples of when variations will not require a new procurement include:
- If there is an ambiguous clause already in the contract that allows the variation.
- Unforeseeable circumstances (with same 50% increase limit).
- Economic or technical reasons require additional work to take place (50% limit on contract sum increase).
Conclusion
It appears as though the new Procurement Act 2023 will allow for contractors and authorities to have greater certainty when taking on public contracts. Contractors can benefit from the implied 30-day payment terms (so long as invoices do not specify otherwise) and the 8 working day standstill periods. The introduction of the barred list will highlight those contractors who should not be awarded contracts (so that authorities can avoid them) and will lessen competition for those who do follow the rules and ensure they do a good job on all projects.
This is not a list of all the changes brought in by the legislation but is an outline of some of the key features.
Holmes & Hills’ Construction Division are industry experts. It is always best to get in touch if you have any further questions.
Scan here to contact the team if you would like some more information
EASIER. SAFER. SMARTER.
As an industry-leading provider for scaffolding and construction safety products, TRAD UK has always championed innovation. Our comprehensive range sets new standards for access equipment and safety systems.
Our efficiency and safety are matched by the highest levels of service delivered by our experienced team and nationwide support network of depots. So, it’s easier than ever to find the right solution for your project.
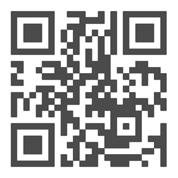
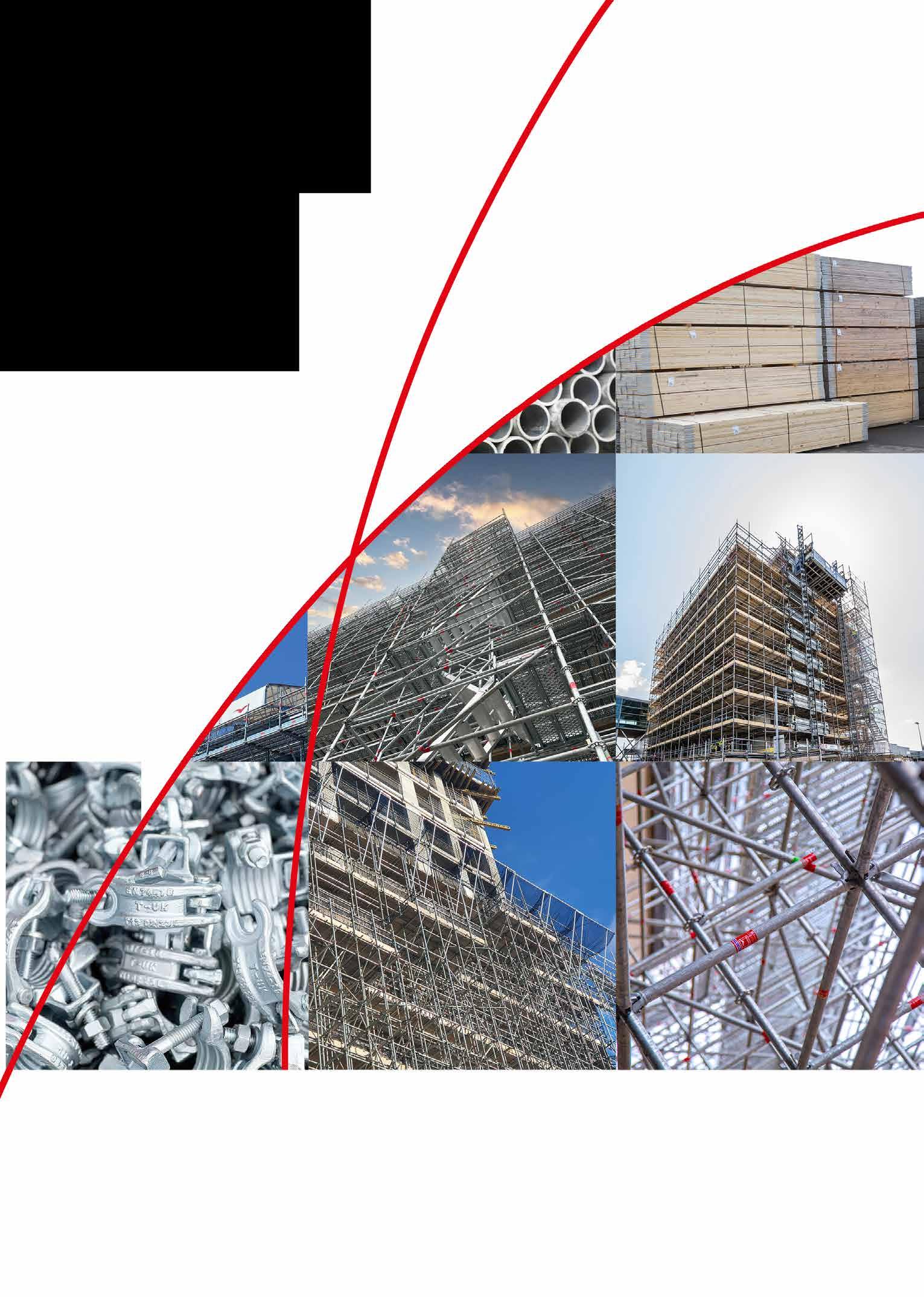
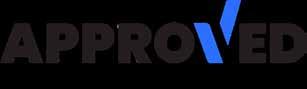
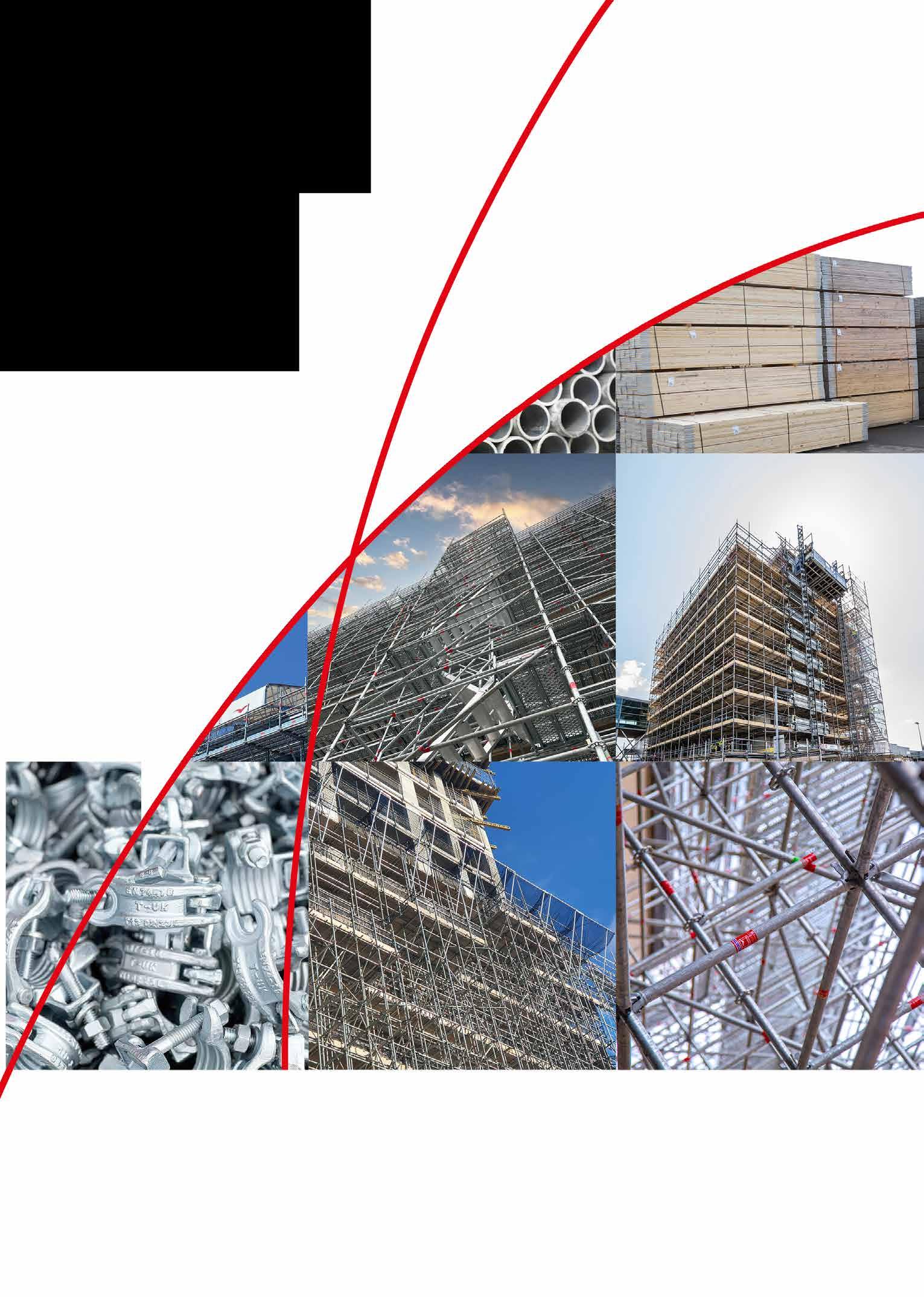
D.tec: Why drug and alcohol screening should be a priority
Scaffolding Association partners, D.tec International, who are drug and alcohol screening industry specialists, examine the reasons why drug and alcohol screening should be a priority for every scaffolding company.
When businesses in the scaffolding and access sector review their budgets and set priorities, one area that must not be overlooked is workplace safety – including the growing need for robust drug and alcohol screening measures.
The growing risk of substance misuse in construction
The construction industry faces significant safety challenges, with workers often operating at height, handling heavy equipment, and working in potentially hazardous environments. The impact of drug and alcohol misuse in such settings can be devastating, leading to serious accidents, injuries, and even fatalities.
Data from the Health and Safety Executive (HSE) consistently highlights that a significant number of workplace accidents in the UK involve individuals under the influence of drugs or alcohol and with around 75% of substance abusers in full-time employment, the risk to businesses - particularly in highrisk sectors like scaffolding and access - is substantial.
Why drug and alcohol testing is essential in the scaffolding and access industry
For scaffolding and access businesses, ensuring a safe working environment is not just about compliance - it’s about protecting lives. Drug and alcohol misuse can impair judgment, slow reaction times, and increase the likelihood of errors, all of which pose a heightened risk when working at height.
It’s not just about being onsite either - getting to and from work safely is just as critical. With convictions for driving under the influence on the rise and drug-driving outpacing drink-driving offences across much of the country, the risks extend far beyond site.
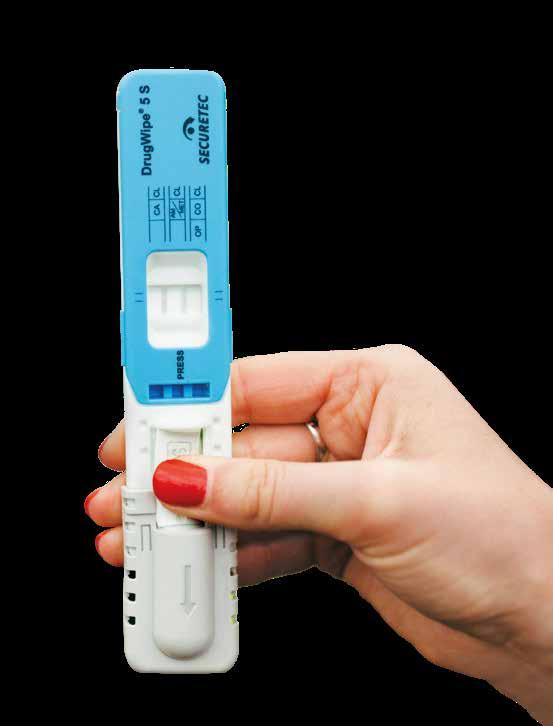

Making drug and alcohol screening a budget priority
Allocating funds towards drug and alcohol screening is a strategic investment in workplace safety and business continuity. The cost of implementing a structured testing programme is negligible compared to the potential financial and human costs of workplace accidents caused by impairment. Proactive screening helps businesses safeguard their workforce, maintain contractual compliance, and protect their reputation. Investing in such measures can also lead to long-term cost savings by reducing absenteeism, increasing productivity, and minimising the risk of insurance claims and legal disputes.
Take action today
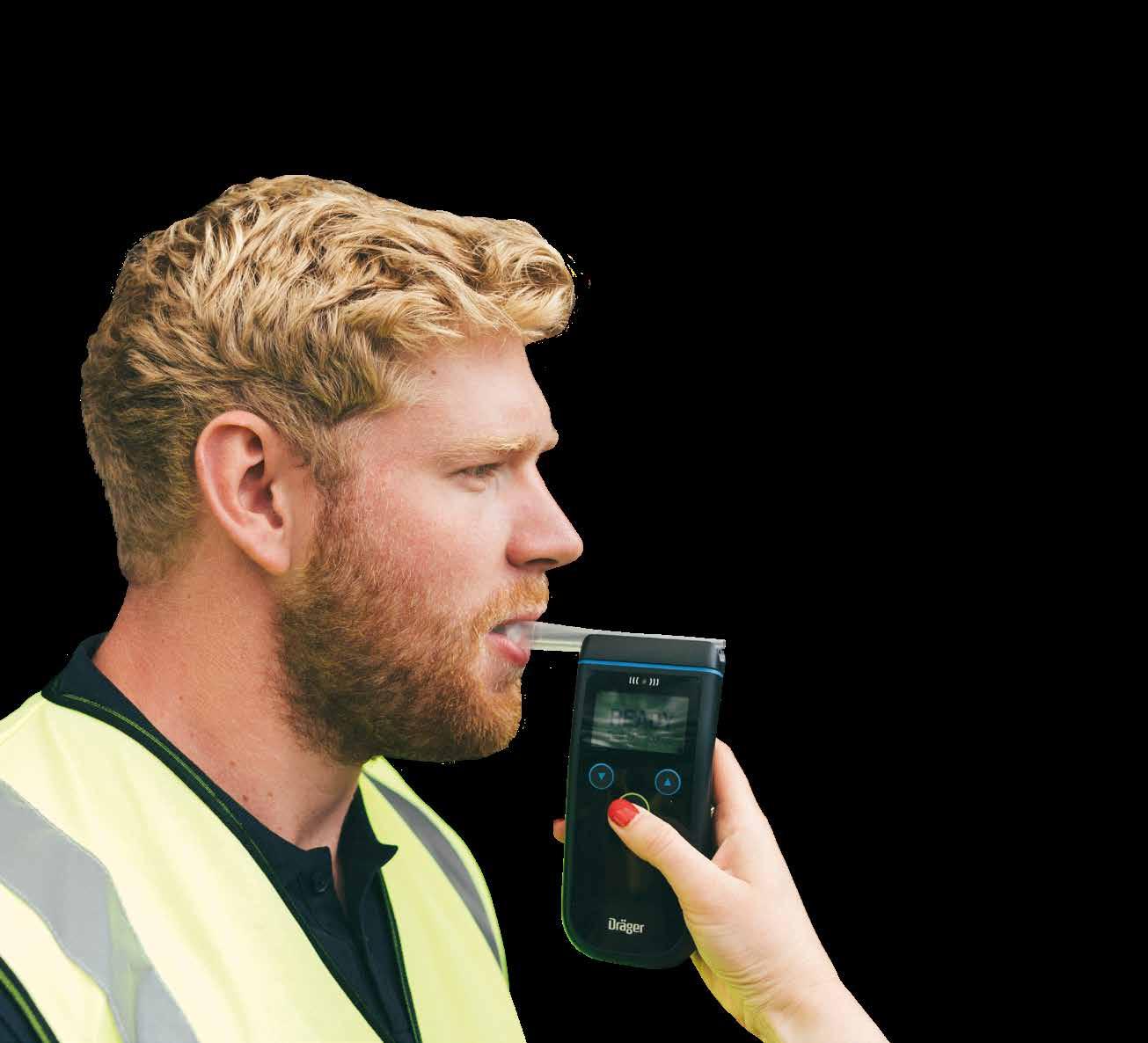
Contact Scaffolding Association partner D.tec International today on 0800 371898 or visit www.dtecinternational.com to safeguard your business and workforce.
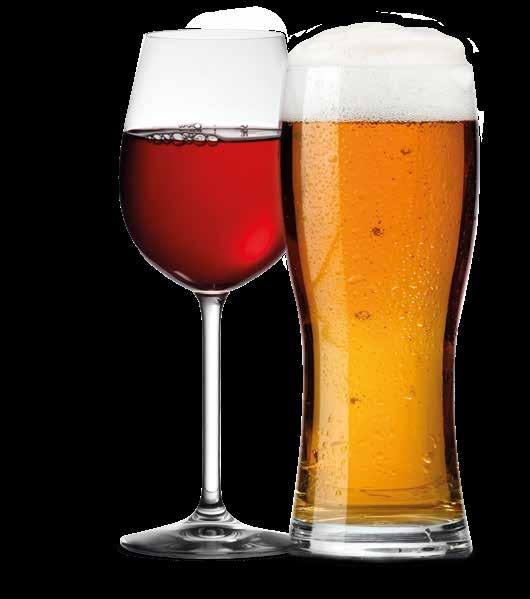
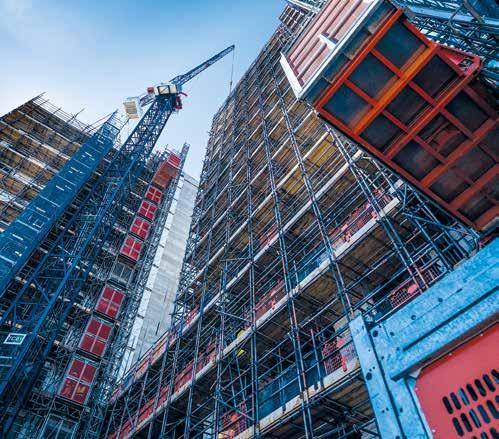
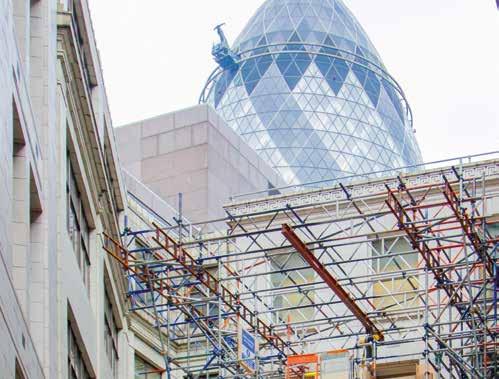
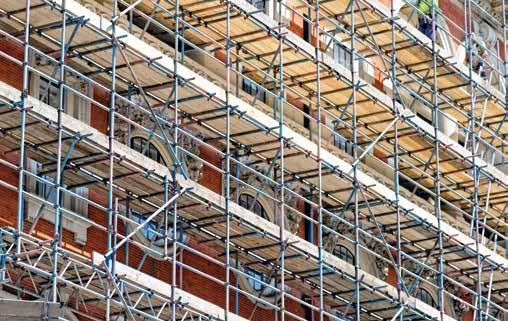
Without Question

Being a member of the Scaffolding Association is a mark of competence, professionalism, and quality that is recognised across the construction industry. It demonstrates a company’s ability to perform scaffolding projects to the highest standards.
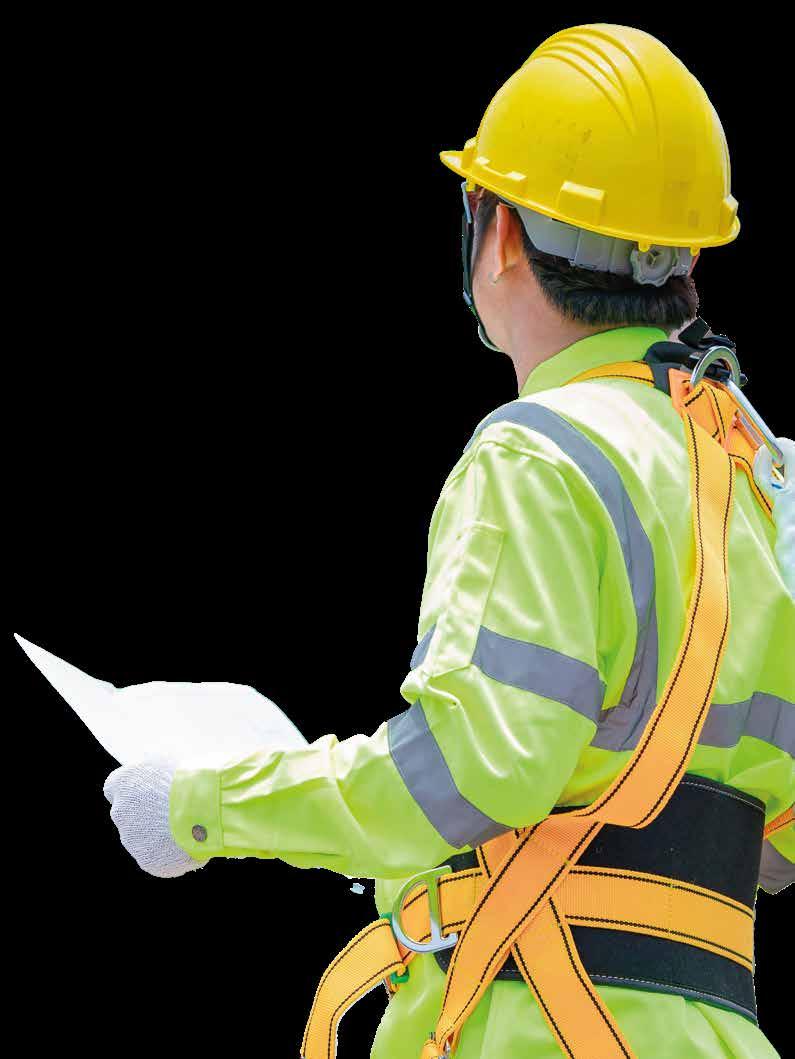
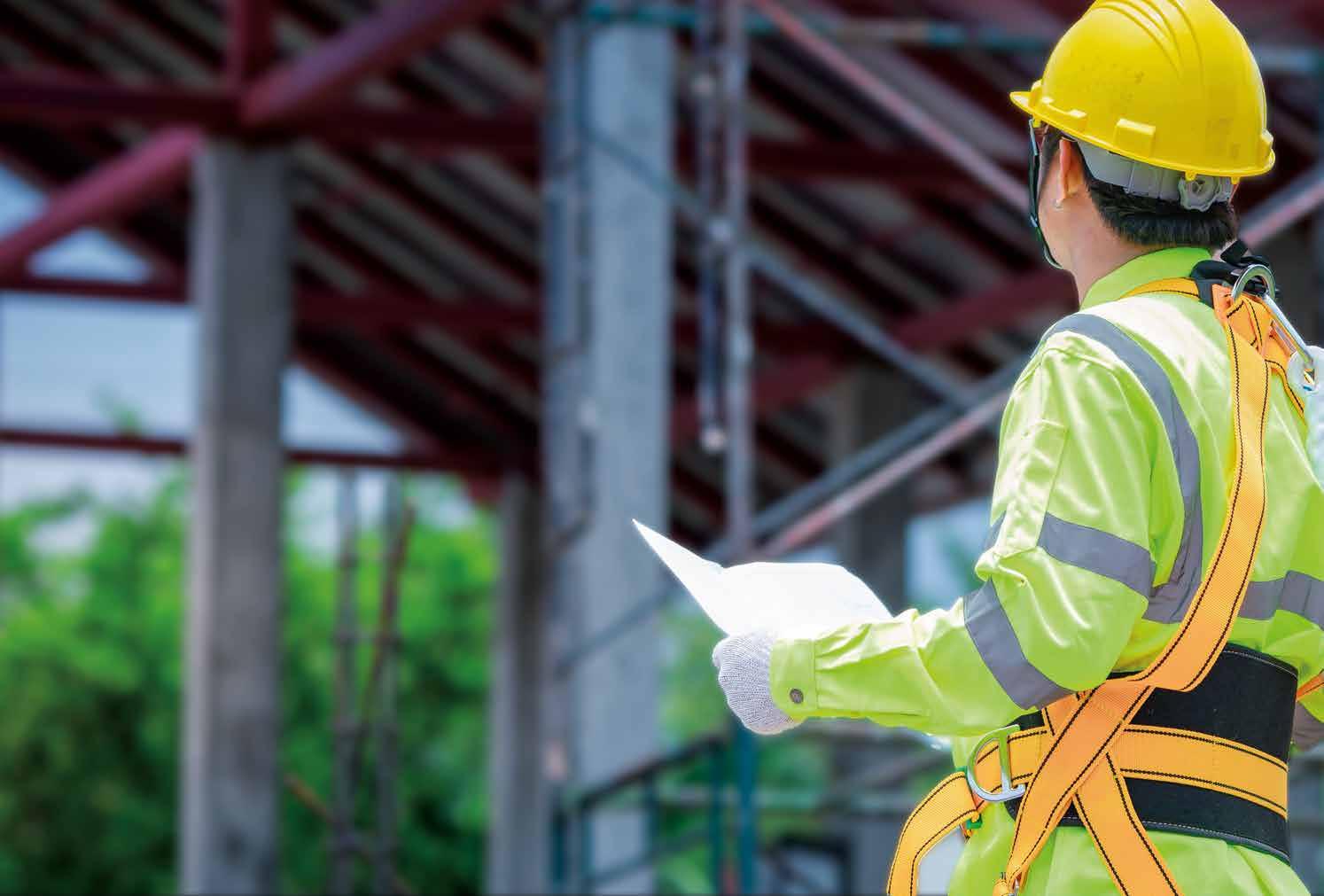
Members undergo an industry recognised audit process, ensuring they meet industry Standards. This gives clients confidence, ensuring recognition & compliance to regulations.
Scaffolding Association members employ CISRS-trained and qualified scaffolders, ensuring all work is carried out by skilled professionals.
Member companies vary in size, with a range of specialisms and capabilities –there is a Scaffolding Association member for every project.