

MAINTAINING AN ICON
SCAFFOLDING PROJECT FACILITATING WORKS AT HARRODS
WELCOME
ROLL CALL FOR NEW SCAFFOLDING ASSOCIATION MEMBERS
SCAFFOLD CONTRACTOR
Bury Scaffolding Services (Manchester) Ltd
http://buryscaff.co.uk 0161 763 5033
CJW Scaffolding Limited 07498 036790
Kidd Scaffolding Ltd t/a Abbott Scaffolding
www.abbottscaffolding.com 01279 653345
More Site Services Ltd
www.moresiteservices.co.uk
07828 310850
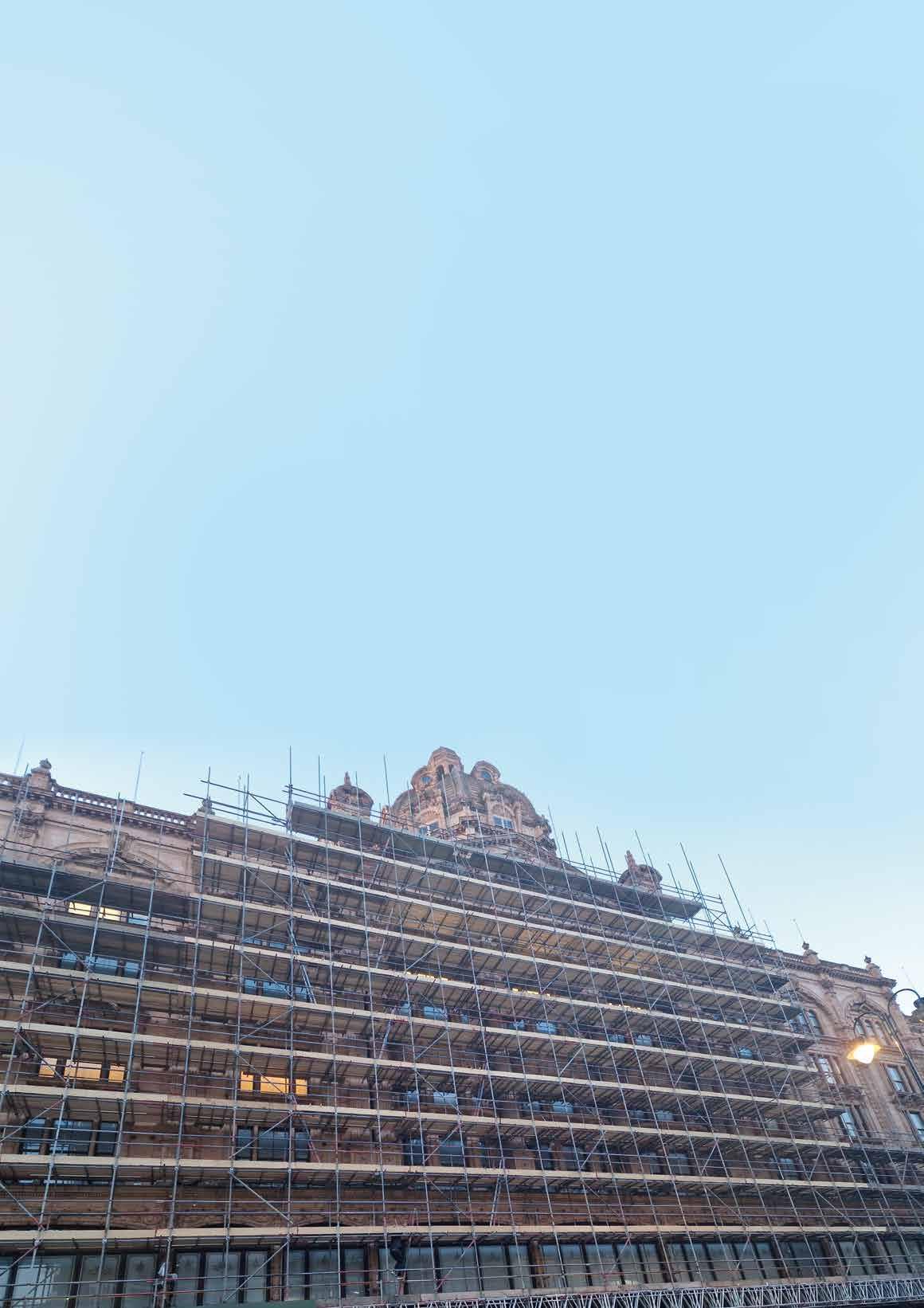
SCAFFOLD CONTRACTOR
No.1 Scaffolding –
Cardiff Ltd
https://no1scaffold.co.uk
07780 578955
Oak Scaffolding Ltd
www.oakscaffolding.co.uk
01903 706055
Oculus Group Ltd
https://oculus-group.co.uk
07467 521692
R & T Scaffolding Limited
http://www.rtscaffolding.co.uk
01474 825052
CONTACT US
Editorial
Enquiries: Alison Hurman
T: 0300 124 0470
E: alison@scaffolding-association.org
Advertising
Enquiries: Trish Meyer
T: 0300 124 0470
E: trish@scaffolding-association.org
Scaffolding Association
T: 0300 124 0470 www.scaffolding-association.org
E: info@scaffolding-association.org
Subscriptions
AccessPoint is distributed to members of the Scaffolding Association and other selected access and scaffolding businesses.
If you wish to receive a copy of
AccessPoint or would like to amend or cancel your subscription, please call 0300 124 0470 or email info@scaffolding-association.org
SCAFFOLD CONTRACTOR
Shuel Construction Limited www.shuelconstruction.co.uk 07715 835038
Southcoast Scaffolding Limited
www.southcoastscaffolding.com 01273 514637
STAK Scaffold Limited
www.stakscaffold.co.uk 01883 330188
Strata Roofing Cambridge Ltd 01223 944041
AccessPoint is published on behalf of the Scaffolding Association. The views expressed in this journal are not necessarily those held by the Scaffolding Association. The Scaffolding Association shall not be under any liability in respect of the contents of the contributed articles. The Editor reserves the right to edit, abridge or alter articles for publication.
ISNN: 2055-2033 (Print)
© All editorial contents AccessPoint 2024
by Tewkesbury Printing Company
Designed by Gladstone Design
SCAFFOLD CONTRACTOR
T J R Scaffolding Ltd
www.tjrscaffoldingltd.co.uk
01840 211503
Tiger Specialist Access Ltd
www.tigerspecialistaccess.co.uk
SERVICE PROVIDER MEMBER DESIGNER
Site-X Security Ltd 07521 010188
Oryx Scaffold Design Ltd 0117 329 0050
Printed CoverNEWS
P3-5 Stories from the sector
COMMENT
P6 Robert Candy, CEO of the Scaffolding Association discusses retention of the WAHR
COMMERCIAL
P7 CITB Levy lowdown
OPINION
P8 Holmes & Hills: The fragility of the construction industry
TECHNOLOGY
P10-11 Scafom-rux: Using drones in scaffolding
PROJECTS
P14-15 GWC Consultants and Stak Scaffolding: Harrods maintenance
P16-17 AMP Scaffolding: Red House Glass Cone restoration works
P18 PERI: Façade access at Treadgold House
TRANSPORT
P19 Road Haulage Association: Changes to operating HGVs in London
HEALTH & SAFETY
P20w-21 HAVSPRO: Guide to HAVS Risk Assessments
PRODUCT NEWS
P22 UKSSH: Public Access Staircases Range
P22 Scafftech Designs Ltd: Mattless Roof Clip
P23 G-DECK: Adjustable Threshold Ramp
NEWS
Product recall: five point full body harness
The Office for Product Safety and Standards (OPSS) has announced a Product recall: five point full body harness sold via Fruugo.
The product has been identified as presenting a serious risk of injuries or falling from a height as it is classed as Personal Protective Equipment (PPE) and was not supplied with the required compliance documentation or markings to demonstrate that it has been adequately conformity assessed.
Mandatory third-party conformity assessment by a body authorised for PPE is required by the relevant regulations for those products which protect against more serious risks.
The absence of such independent assessment for such a product may increase the risk to the consumer that the product may not perform as expected when relied upon across a wide range of uses.
The product does not meet the requirements of Regulation (EU) 2016/425 on Personal Protective Equipment or the Personal Protective Equipment (Enforcement) Regulations 2018.
OPSS is requiring the recall of the product from end users. The listing has been removed by the online marketplace (Fruugo).
Scan to find out more:
National Minimum Wage increase
The National Living and Minimum Wage rates increased on 1 April 2024, the National Living Wage was also extended to workers aged 21 and over (previously only for age 23 and over).
All employers should ensure that their workers are paid correctly, according to the new rates. Businesses can take these simple actions to meet their legal responsibilities and avoid falling foul of the law:
• check the new rates on GOV.UK
• identify which staff are due the new rate
• update payroll and communicate the changes to staff as soon as possible
• call the Acas helpline to get advice and support on paying workers correctly on 0300 123 1100
• visit the calculating the minimum wage guidance page to view practical advice.
Scan to find out more:
Updates to first-aid at work guidance publications
The Health and Safety Executive have issued updates to First aid at work: Guidance on regulations (L74). This publication sets out what you need to do to address first-aid provision in the workplace.
Guidance accompanying the Health and Safety (First-Aid) Regulations 1981 has been updated to:
• Emphasise employers’ responsibilities to take account of employees’ mental health in their first aid needs assessment
• Change the term ‘catastrophic bleeding’ to ‘life-threatening bleeding’ with more guidance on what employers should

do if they identify this as a risk in their workplace
• Simplify guidance on first aid training providers
The Selecting a first aid training provider: A guide for employers (GEIS3), which helps you identify and select a competent training provider to deliver your first aid training needs, has also been updated to simplify guidance on first aid training providers.
Scan for more information and to view the updated guidance
Shocking 79% of PPE from non-registered providers fails BSIF tests
The British Safety Industry Federation (BSIF) has issued a warning to those overseeing personal protective equipment (PPE) and safety product procurement after their latest tests on non-member products highlight the widespread availability of substandard and even dangerous items.
Between December 2022 and December 2023, the BSIF examined 123 nonmember products, assessing advertised performance, marking adequacy and compliance with standards. Shockingly, only 21% – 26 products – proved fully compliant, leaving a staggering 79% – 97 products – falling short of testing criteria. Worryingly, many of these substandard products are still available and in use, posing serious risks to unsuspecting users.
Some examples of products from nonBSIF-registered members that failed testing include:
• A pair of safety boots
• A pair of safety spectacles
• Three pairs of protective gloves
For buyers and end users seeking assurance, the BSIF Shield is a respected mark of credibility. Companies displaying this shield have pledged a binding declaration that their offered PPE and safety equipment meets the correct standards, fully complies with regulations, and bears the necessary UKCA and/ or CE markings. Choosing a Registered Safety Supplier ensures not only genuine products fit for purpose but also authentic information and guidance.
Scan to find out more:
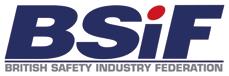
BGB giving apprentices opportunity to learn on an international stage
The North Wales based BGB Scaffolding, who are fully Audited Members of the Scaffolding Association, have opened two international bases following offshore wind farm contract success.
BGB Renewables and BGB New Energy Taiwan, both part of the RGB Scaffolding group, have opened bases in Providence, Rhode Island and Taichung City, Taiwan.
BGB employs up to 100 staff, including 7 apprentices, and are passionate about giving young people opportunities within the industry.
Ben Badham, Managing Director at BGB commented:
“We have got young lads from North Wales now working with us on major offshore energy schemes in Taiwan and the US.
It is important to me to be able to give young people an accessible way into the sector, we are keen to continue working with education providers to develop apprenticeships that allow young men and women in North Wales the opportunity to learn whilst working on an international stage.”
More: www.bgbscaffolding.co.uk
Serious compliance failures and road safety concerns revealed
The recent Public Inquiry into C Evans Scaffolding Ltd, held on January9, 2024, brought to light serious compliance issues and road safety concerns.
The company, operating under a restricted license with five authorised vehicles since August 1, 2022, faced scrutiny for inadequate inspection and maintenance records, deficiencies in driver defect reporting, and lapses in various operational aspects.
A DVSA desk-based assessment on June 5, 2023, reported an unsatisfactory outcome, indicating shortcomings in inspection records, driver defect reporting, inspection facilities, and maintenance arrangements, among other issues. Despite a subsequent DVSA investigation, which revealed a highly unsatisfactory situation, the recent analysis demonstrated little improvement, raising serious road safety concerns.
The sole director, Christopher Evans, attended the inquiry on January 9, 2024, where he faced questioning regarding the company’s compliance history. The inquiry revealed a lack of understanding and a reactive rather than proactive approach to compliance matters.
This case serves as a stark reminder of the critical importance of robust compliance in the transport industry, with regulatory bodies prioritising road safety and operational integrity.
Scan to find out more:
Company fined and director receives suspended prison sentence after scaffolder suffers electric shock
A Kent scaffolding company has been fined and its director given a suspended prison sentence after a scaffolder suffered an 11,000-volt electric shock.
Steven Gilmore, 36, was working for contractor Canterbury City Scaffolding Ltd alongside a small team of scaffolders, to erect a temporary roof scaffold at an open-air drinks depot in Snow Hill, Crawley, West Sussex.
Canterbury City Scaffolding Ltd had been contracted by Drinks Warehouse UK Ltd to erect the temporary roof structure over its open-air depot in order to provide shelter for operations during the winter months.
On 29 November 2021 the father-of-one struck a live 11kV power line running across the site while lifting a six-metre scaffold tube. He then fell over five meters to the ground suffering a badly broken leg.
Mr Gilmore sustained life-changing
electrical burns to both hands, which he will never regain full use of.
An investigation by the Health and Safety Executive (HSE) found that Canterbury City Scaffolding Ltd and its director had failed to ensure the high-risk temporary roof scaffold assembly job near a high voltage line was properly risk assessed.
Scan to find out more:
Changes to Scheme rules regarding COTS and CISRS cards, coming soon
As of 1st March 2024, delegates attending a CISRS Operative Training Scheme (COTS) course will only be eligible to apply for a CISRS Labourer card.
An initial 18-month CISRS Trainee Scaffolders card will only be issued upon successful completion of a CISRS Part 1 course. This will mean that all operatives holding the Trainee card will have received industry recognised training, in basing out, erecting, and dismantling a range of scaffold structures including towers, birdcages, independents plus an introduction to relevant industry guidance and best practice such as SG4, SG6, TG20, Risk Assessment, Method Statements, selection of materials etc. prior to carrying out these jobs on site. This change allows the operative the full 3 years (2 x 18 months cards) to complete their relevant
on-site experience, Part 2 course, S/NVQ2 and skills test.
Under the previous/existing rules if some opted to apply for the Trainee card after the COTS “the clock was already ticking” on their first trainee card, if they did not complete their Part 1 course until the end of this period it meant they needed to complete all other relevant training, experience within the next 18 months life cycle of their 2nd card.
Under the new rules an operative will need to have successfully completed the Part 2 course in order to be eligible to apply for their 2nd 18-month Trainee card.
Scan to find out more:
Afix Group commits to robust ESG strategy
System scaffolding manufacturer
Afix Group is proud to launch its ESG sustainability policy.
As a dynamic player in the scaffolding industry, Afix Group, who have branches in the UK, are aware of the environmental, social and policy (ESG) impact its business activities can have. Responding to new European regulations, Afix Group aims to integrate various ESG criteria into its core activities and corporate culture.
In September 2020, Stephan Hillaert was recruited by Afix Group to strengthen the international structure and achieve expansion. Afix Group have had a nice evolution over the past 3 years with turnover almost tripling from €19 to €55m. Now, stepping into the ESG story, strategy and reporting, he wants to create more transparency in Afix operations both to stakeholders, suppliers and customers. Afix Group’s Sustainability Policy, based on long-term thinking and a holistic approach,revolves around four pillars:
• Climate action
• Quality
• People first
• Social responsibility
Together with, and under the guidance of, Sustacon, expert in sustainability solutions for the construction industry, a plan is drawn up iom measuring and reducing the carbon footprint.
System scaffolding is a sustainable product. Afix Fast scaffolding is manufactured in quality steel that is long-lasting. In addition, these scaffolding products are modular, allowing various applications to be realised with a minimum of components (masonry scaffolding, suspended scaffolding, renovation scaffolding, tank scaffolding, etc.). The scaffolding components are mainly produced from S355 and S235 steel which allows maximum recycling.
Scan to find out more:
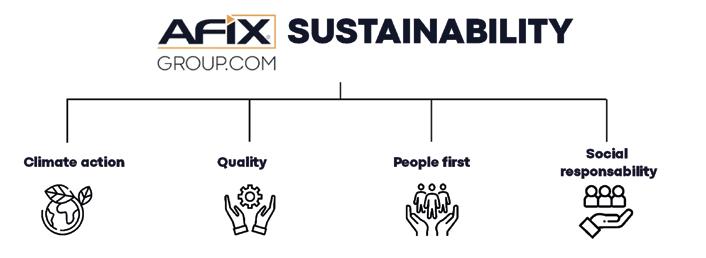
Scaffolding company faces license revocation and director disqualification
Following the revocation of the restricted operator license held by H S Scaffolding Ltd and the disqualification of its director, Karl Yarham, a new application for a restricted license was submitted by Elite Access Scaffolding Ltd, directed by Jake Hull. The two companies appeared unrelated, and the license was granted in October 2022. However, subsequent events raised concerns.
Jake Hull, initially the sole director of Elite Access Scaffolding Ltd, was later appointed a director of H S Scaffolding. Elite Access applied to add an operating centre previously listed in H S Scaffolding’s license. Records showed Karl Yarham held 75% of Elite Access’s shares. A DVSA report in February 2023 highlighted issues such as undownloaded tachograph cards and vehicles registered to H S Scaffolding and a public inquiry was called in response.
The inquiry on December 5, 2023, revealed discrepancies. Hull, previously a scaffolder at H S Scaffolding, became the director of Elite Access with plans to take over H S Scaffolding’s work. The use of H S Scaffolding’s vehicles was deemed informal, with no payments made, contrary to a lease agreement. Hull lacked evidence of payments for fuel, maintenance, or salaries. Compliance with drivers’ hours and maintenance was minimal, attributed to “naivety and lack of experience.”
Despite positive aspects like Hull attending an OLAT course and two MOT passes, the negative factors outweighed. The company’s purpose to deceive and evade regulatory consequences led to poor compliance, and a decision was made:
• Revocation of License: Elite Access Scaffolding’s license is revoked, effective from February 1, 2024, due to unfitness (Sections 13B and 26(1)(h) of the 1995 Act).
• Disqualification: Both Jake Hull and Elite Access Scaffolding Ltd are disqualified from holding or obtaining an operator license until February 2027 (Section 28 of the 1995 Act), reflecting the serious nature of non-compliance.
Government commits to maintaining high regulatory standards and retaining the Working at Height Regulations.
There is no doubt that the introduction of Working at Height Regulations (WAHR) in 2003 has helped to reduce workplace fatalities and injuries.
Latest figures show that there were 135 workers killed in work-related incidents in Great Britain from April 2022 to March 2023. 40 of these deaths were relating to a fall from height compared to 67 the year immediately prior to the introduction of WAHR.
Despite the reduction, falls from height still contribute to more workplace fatalities than any other factor and so more than 20 years on, there are still lessons to learn.
Some of you will recall the cliff edge last year which would have seen thousands of EU-era laws scrapped. It was being dubbed by the media as the post-Brexit bonfire.
Whether you agree with Brexit or not, it is understandable that the Government would want to exercise our freedom as a sovereign nation and create our own laws and regulations, free from the shackles of the EU.
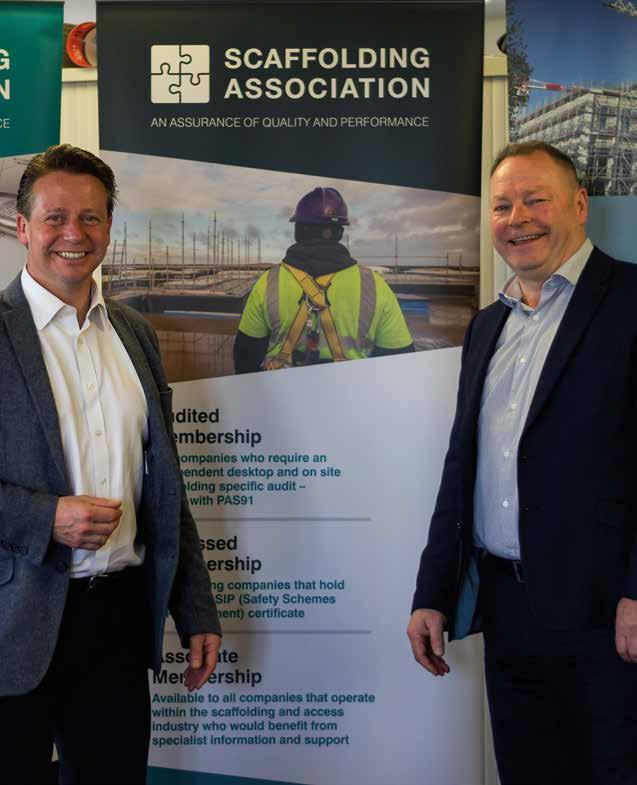
However, I was horrified when I discovered that WAHR were on track to expire at the end 2023 – on course to be in this so-called bonfire.
Such an outcome is unthinkable. Why would the Government allow such important regulations which underpin safety in the workplace to simply disappear?
The association got to work quickly and worked tirelessly over the preceding months, lobbying relevant ministers, ensuring that they fully understood the perhaps unintended consequences.
Common sense prevailed – in May 2023, I was pleased to hear from good friend of the Scaffolding Association, Nigel Huddleston MP, that the Government intended to abandon plans to scrap thousands of EU-era laws.
However, at the time, we were unsure if WAHR was included or not. We therefore had to keep the pressure on.
I am enormously grateful to the trade press and to the scores of members that wrote to their own MP’s. Collectively, we raised the profile of the issue and put pressure on policy makers.
I was delighted to hear back from Nigel Huddleston towards the end of 2023, providing copies of correspondence he had exchanged with the Department for Work and Pensions on our behalf.
Finally, it was clear - the Government was committed to maintaining high regulatory standards, including in the areas of health and safety, and that, accordingly, Working at Height Regulations were assimilated into UK Law on 1st January 2024.
ROBERT CANDY CHIEF EXECUTIVE, SCAFFOLDING ASSOCIATIONLatest figures show that there were 135 workers killed in work-related incidents in Great Britain from April 2022 to March 2023.
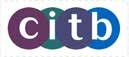
CITB Levy lowdown
CITB is the industry training board for the construction sector in England, Scotland, and Wales. It’s the CITB’s job to help the construction industry attract talent and support skills development to build a better Britain. CITB supports the construction industry to have a skilled, competent and inclusive workforce, now and in the future. In this article the CITB discusses the Levy.
CITB is empowered to impose a Levy on employers in the construction industry. The Levy applies to all employers ‘engaged wholly or mainly in construction industry activities’. In other words, when construction activities take up more than half of your employees’ total time (including subcontractors). Implementing this Levy is important because we use it to:
• Support training development through grants and funding
• Promote the construction industry as a great career choice and offer highquality apprenticeships
• Identify skills needs across the construction industry
• Develop occupational standards and qualifications
How much annual CITB Levy you pay is based on your total wage bill (the amount you pay your workers in a year). Some small businesses do not need to pay the Levy at all, while others pay a reduced rate.
Small, micro and medium CITBregistered employers can apply for funding to deliver training to their team once every 12 months through the Skills and Training Fund.
Large CITB-registered employers can apply for funding through the Leadership and Management Development Fund to help with the costs of delivering leadership and management training for their teams.

The Levy also supports delivery of:
• New Entrant Support Team (NEST): This team will help you to successfully hire apprentices by providing handson, free support, covering areas such as recruitment, paperwork, accessing grants and funding, and ongoing mentoring throughout the apprenticeship.
• Employer Network: The aim is to engage employers with CITB, and get them training, while making it easier to get grants out to smaller employers. They also aim to enable
employers to have a say in how funding is used in their locality.
• Apprenticeship grants: £2,500 is available per apprentice, per year, and £3,500 upon successful completion of their apprenticeship.
• Qualification grants: Employers can also apply for between £300 and £1,500 for
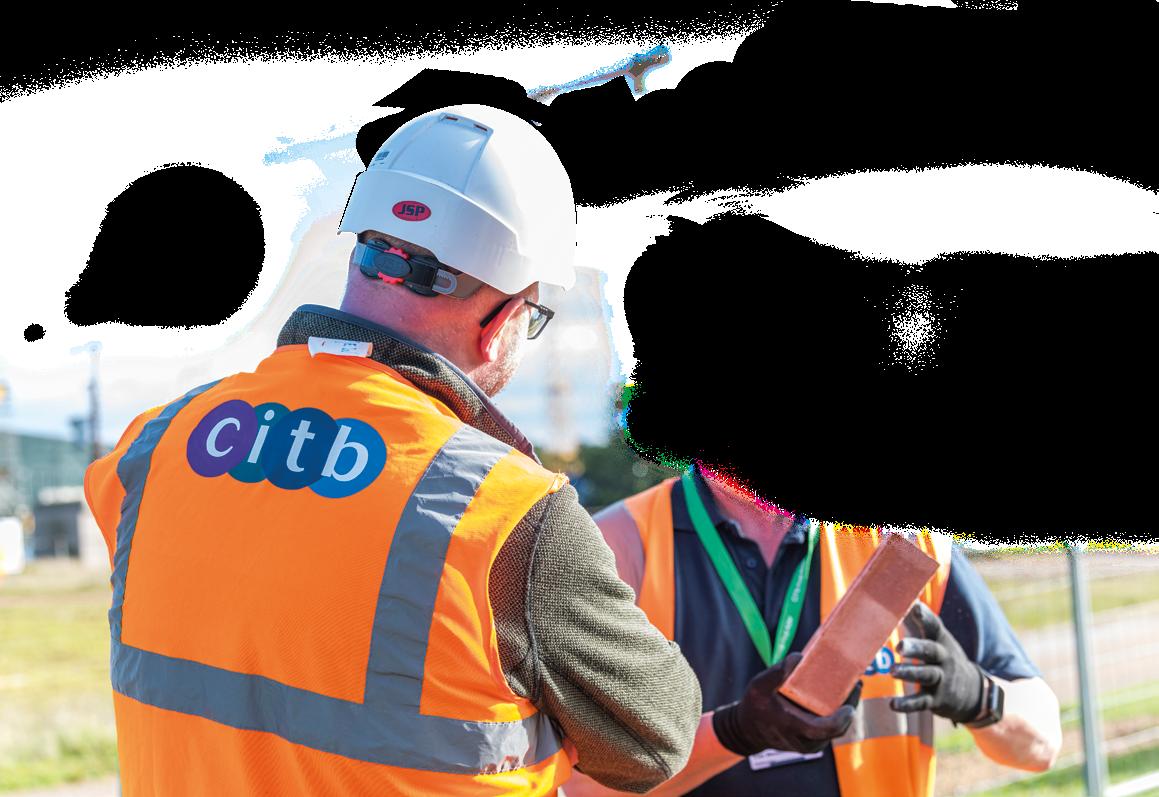

The fragility of the construction industry
In this article the Scaffolding Association’s legal partner, Holmes & Hills, discusses why this is a great time to take stock of your business.
There was much speculation as to how the construction industry would look after the Covid-19 pandemic and it is apparent that, sadly, several companies are now facing administration/ insolvency proceedings, or have already ‘gone under’.
According to the Insolvency Service, the construction sector has, once again, been hard hit with a total of 395 registered company insolvencies as of the end of 2023, compared with the 254 in August 2019, pre-pandemic. In the last three months alone, there has been a 46% increase of construction companies facing insolvency. Long-standing contractors such as James Killelea & Co and M Igoe Ltd are amongst the most recent contractors to fall foul of the industry’s vulnerabilities. Whilst this is attributable to a multitude of reasons, the construction sector’s insolvency status as a whole can be closely linked to poor cash flow management and arduous payment cycles.
However, it is not all doom and gloom; with the end of many companies’ financial year in sight, this is a great time for contractors and subcontractors alike to take stock of their businesses. This includes chasing aged debt and keeping a close eye on when outstanding retention sums (if any) are set to become payable. It is worth remembering that much of these sums of money contribute to the profit of the work undertaken and these additional sums will go a long way to keeping your company afloat.
There’s nothing new as to how many construction contracts are built upon good working commercial relationships. This arrangement is great when business is going well, but in times where finances and cash flow are tight, these relationships may become fraught. Take the common scenario whereby a subcontractor only deals with one point of contact for interim payments as an example. If said individual leaves the contracting company, applications for payment which might have once been processed smoothly between the two
parties may dramatically change upon the new individual taking over from their predecessor. It could cause tension if the new employee oversees the payment process noticeably differently and could suddenly leave one party lacking or without payment.
Going one step further than this, it is vital to be vigilant as to the signs of a company on the brink of insolvency. An all too familiar situation is where a contractor (particularly if out of character) begins missing sums off payments or becomes late in paying. If this starts happening regularly, it could be a sign that the company is suffering with cash flow issues. Similarly, if it all goes a little too quiet, it is worth investigating as to why! Prevention is better than cure, and so getting ahead of the curve by conducting some research could be invaluable to your company in ensuring payment of sums owed to you before they may well become unrecoverable.
A good place to start could involve checking Companies House for a company’s late filing of accounts; checking the Central Registry of Winding Up Petitions (or Companies House) for any proposed winding up petitions; and looking out for a notice for the appointment of administrators. Taking advice early on as to what options are available to your company is always worthwhile, especially when insolvency is involved, as it is vital to act quickly.
Holmes & Hills’ Construction Division recently acted for a large scaffolding subcontractor who was repeatedly receiving non-payment and/or Payless Notices with dubious deductions – to the extent that c.£1,000,000 was outstanding. Having been instructed across several different contracts, by using a combination of initial correspondence and, where necessary, adjudication, the Division successfully recovered the vast majority of the sums owed plus interest, and, in some cases, associated costs.
If you have any concerns then get in touch with the Construction Division at Holmes & Hills who will be able to assist.


Drones in scaffolding
In this article Frederike Berg from the global manufacturer of premium quality scaffolding solutions, Scafom-rux, discusses how Unmanned Aerial Vehicles (UAVs) – better known as drones – can do much more than just be flown by amateur pilots for the fun of it.
Drones, which are small, flexible devices that are flown remotely, hold a lot of potential for the construction and scaffolding industry. With their aerial vantage point and data collection capabilities, drones are opening new possibilities, especially in project planning.
How can drones be used in scaffolding?
The advantages of drones are perfectly clear – they are light, small and, most importantly, they can fly. These characteristics make them extremely flexible and enable a view from completely new angles. Drones can provide us with images, videos and even live broadcasts of areas that would otherwise be difficult or impossible to access. This makes them ideal for a wide range of tasks on construction sites, such as measurements, visual inspections and thermal light scans.

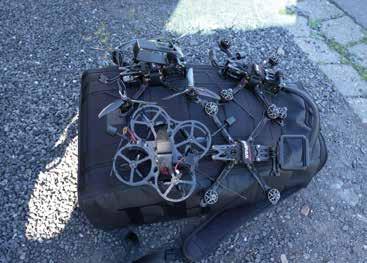
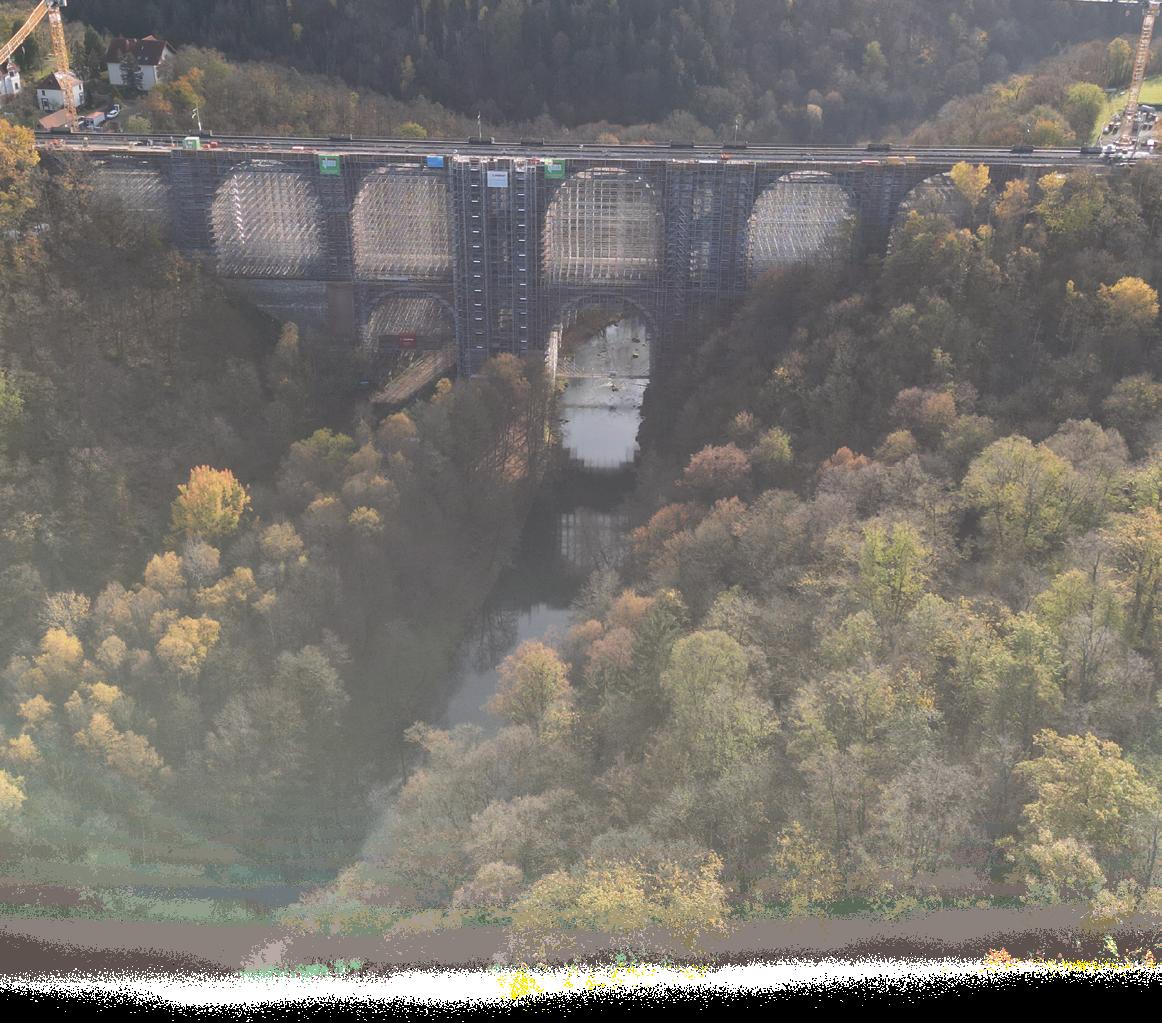
Drones also have decisive advantages for use in scaffolding, especially in project planning: images from drones can be used to create a 3D model of the building that you want to scaffold – accurate down to the millimetre. With this 3D model you can plan your scaffolding quickly and accurately. You can then also easily share it with your client and colleagues.
What are the advantages of using a drone in scaffolding?
Drones offer great potential for digitalisation in scaffolding. Tasks and processes that would normally take several days or weeks can be completed in just a few hours. Drones have many advantages, including:
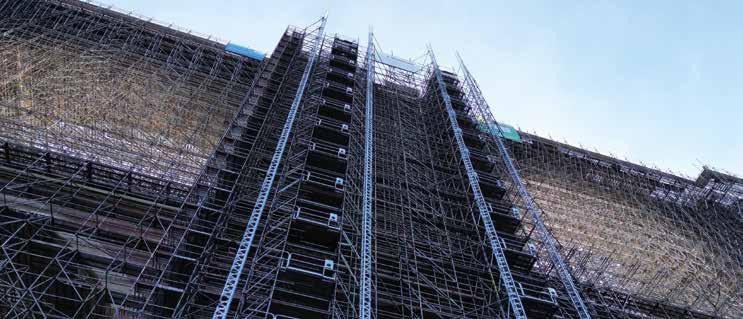
1 2Project planning
Because drones can capture areas down to the centimetre, these can be calculated very quickly. So they take over the surveying process that would otherwise have had to be done by hand. Due to the fast calculation, offers and orders can be created in a time-saving manner. This can significantly reduce the duration of a project. Physical maps that offer full coverage of an area in detail, for example, can also help to reduce errors in your material planning.
Savings in costs
Planning errors are easy to make, especially when the project site has a surprise or two in store. Too much or too little scaffolding material is quickly sent to the site, resulting in unnecessary transport costs and delays to the project. This is where drones come in. By giving you a complete and accurate picture of the project site in advance, with all its details and peculiarities, you can more easily avoid planning errors - and ultimately save money.
Safety on construction sites
Drones can take over simple measurements and inspections that would otherwise have been done by workers e.g. with lift trucks or ladders.
Since the introduction of the use of drones on construction sites, companies reported 55% increased safety standards directly related to them. This makes drones a safe and efficient alternative to controls carried out by humans on construction sites.
What features should a drone have?
Numerous models are available on the market to buy or rent, if you want to use a drone for scaffolding purposes, it should have some important features, including:
• A 4K camera ensures precise and clear images, which are important to support the accuracy of the 3D models.
• Different flight modes ensure control even in strong winds and the drone can take off and land without losing time.
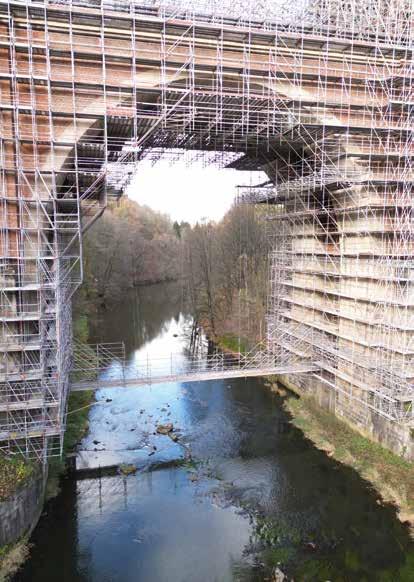
Not only can drones be an efficient work aid, but they can also be used to showcase your project in a spectacular way by capturing footage of a structure from various points of view that are not normally seen.
• A long-lasting battery, preferably a lithium polymer battery. This is important to complete the monitoring process without problems.
• A stabilised camera, so you don’t have to worry about blurry films or photos.
• A good GPS module, because GPS and flight altitude are stored in the metadata of the images so that, for example, the height of the building can be easily assigned.
• If your drone has all these features, it can reach a speed of 60 km/h and stay in the air for a maximum of 25 minutes on one battery charge. In one day, it can cover around 40 hectares – which is more than 40 football fields!
Important things to consider
• You need a pilot’s licence or examination certificate approved by the Federal Aviation Office of your country. The licence is then valid throughout Europe.
• All drones with a take-off weight of more than 250g must have an address plate so that the owner can be quickly identified in case the drone gets damaged.
• Data protection and copyright laws must be observed, otherwise heavy fines may be imposed.
• Inform yourself in advance about no-fly zones like airports, military basis and other protected areas.
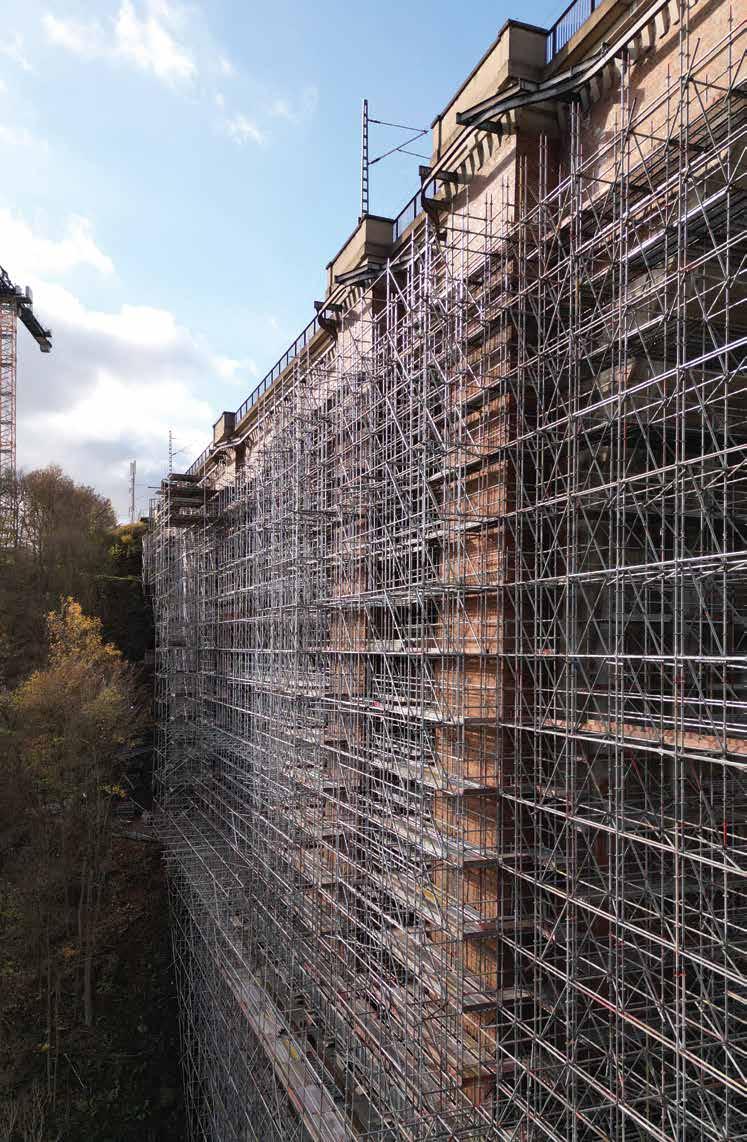
More: www.scafom-rux.com
Scan here to watch some of Scafom-rux’s drone caught footage
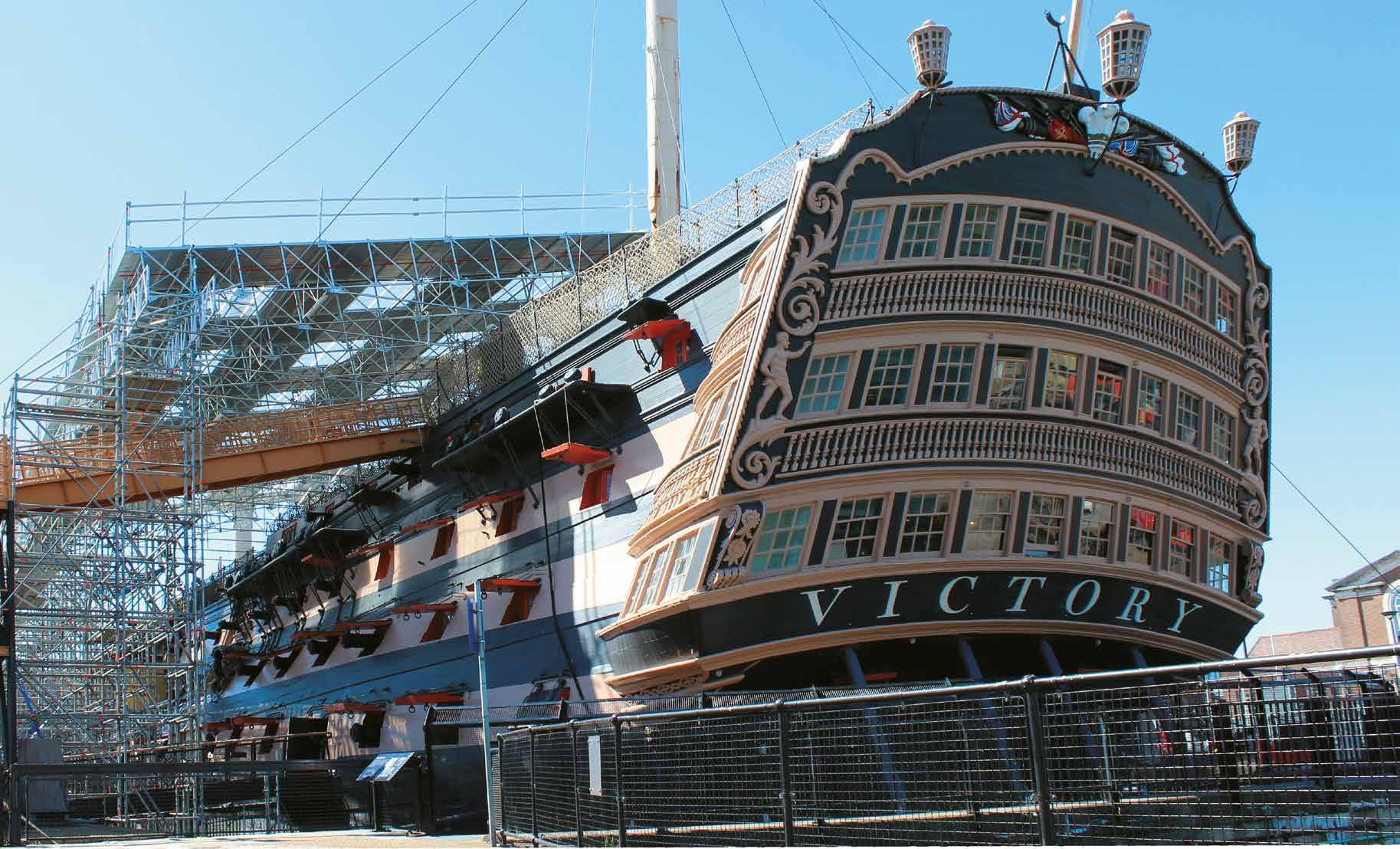

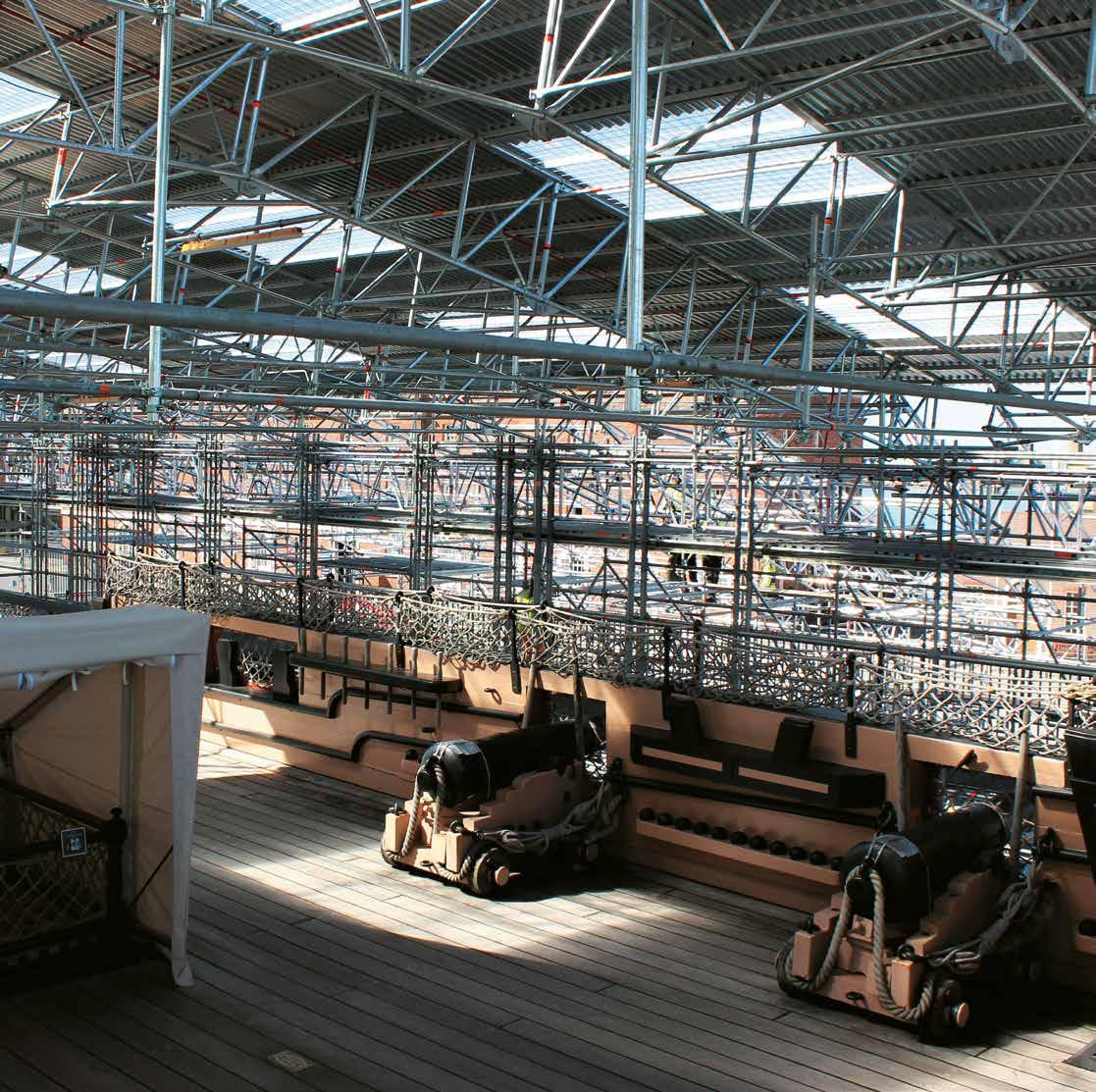
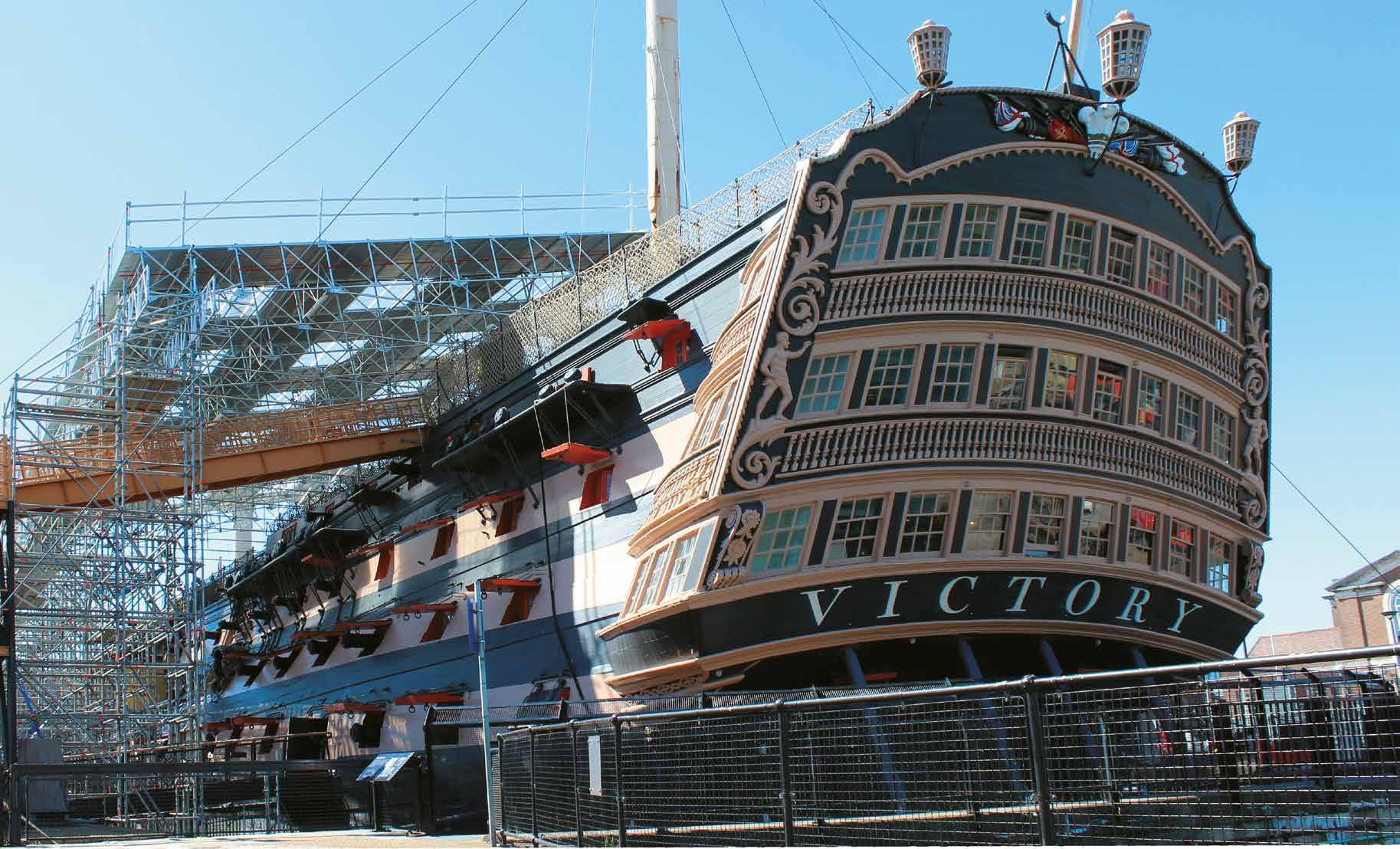
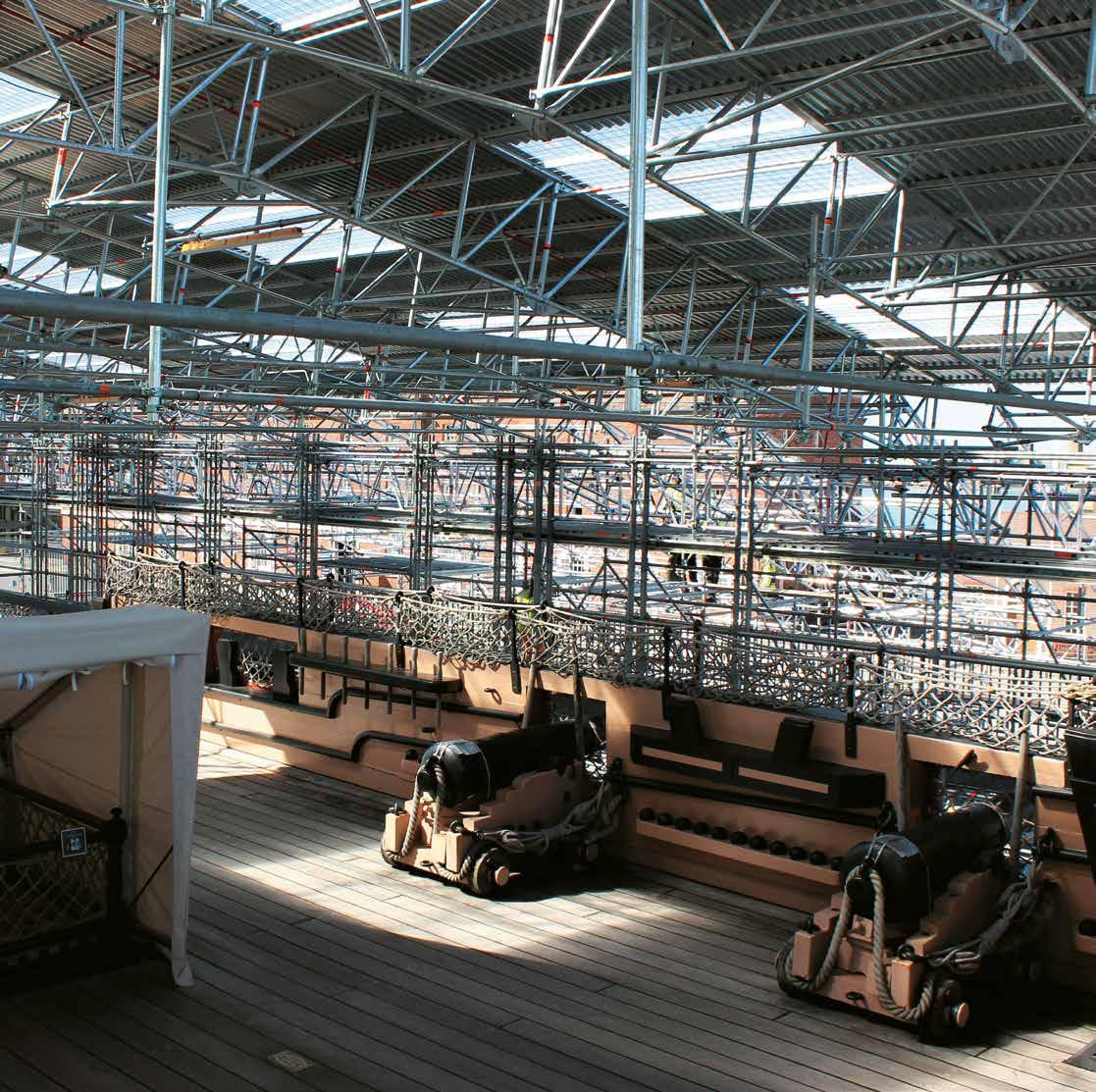
PROTECTING our HERITAGE
INNOVATIVE SOLUTIONS FROM LAYHER
THE WORLD’S LEADING MANUFACTURER OF MODULAR SCAFFOLDING SYSTEMS
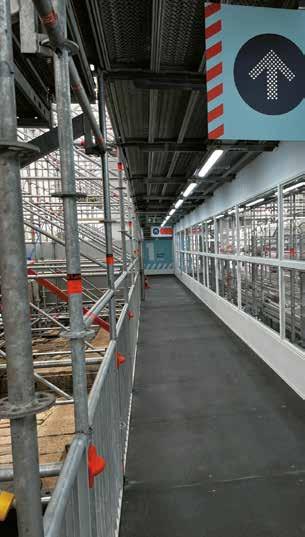
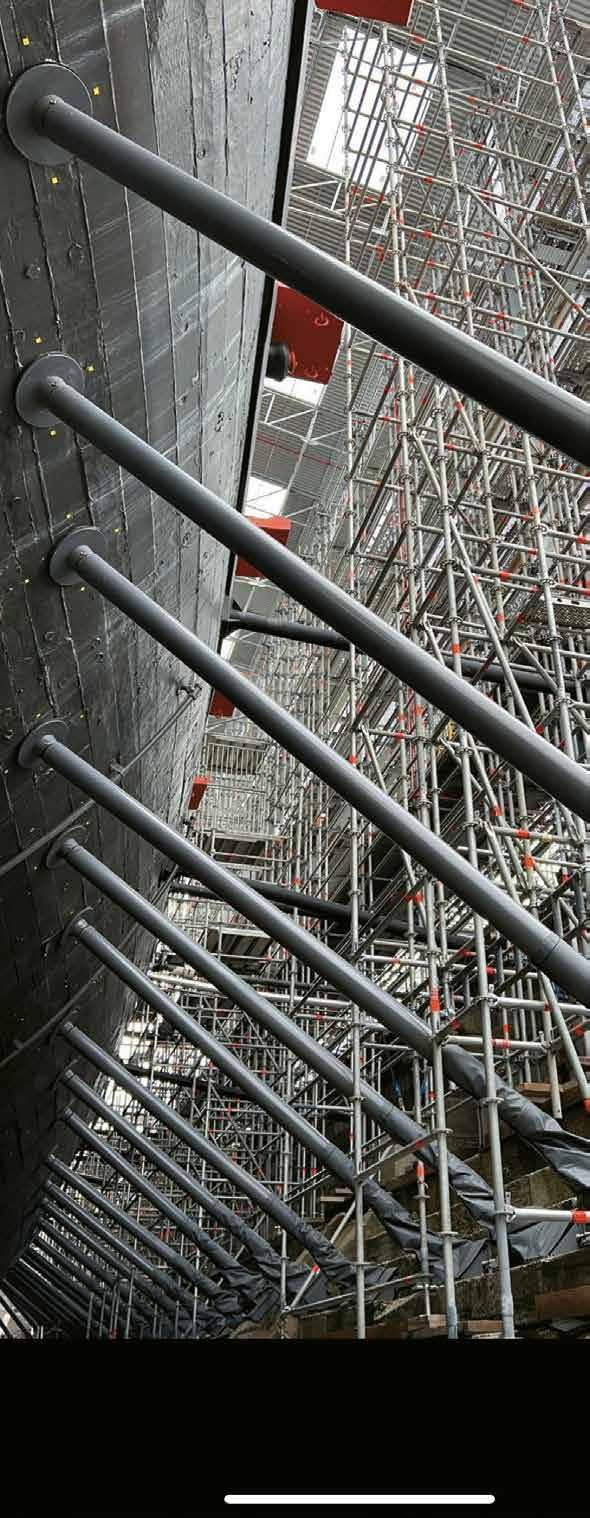
Scaffolding Association members team up for project on iconic Harrods building
GWC Consultants (Associate Members) partnered with Stak Scaffolding (Assessed Members) who were employed by the principal contractor, Restore London Ltd, and awarded the project by Harrods - the world’s most famous department store. The substantial maintenance project started in October 2023 and is due for completion in 2025.
The works were split into several phases that included general repairs, a full clean and lighting upgrades to the front elevation along Brompton Road, side elevations on Hans Crescent and Hans Road, rear elevation along Basil Street, main dome, and corner turrets. A further phase was the construction of a roof-level extension. The scaffolding design also had to support the installation of a full advertising wrap to preserve the aesthetics of the building and generate additional income to fund the extensive works.
One of the main challenges was to maintain uninterrupted and unimpeded public comfort and access, while accommodating obstacles such as street furniture, bus stops, canopies & awnings, phone boxes, pedestrian crossings, narrow pavements & splays, and underground tube entrances.
Due to the extreme level of pedestrian traffic, the scaffold was built during the night and early hours of the morning. This also helped in securing all Kensington and Chelsea Borough
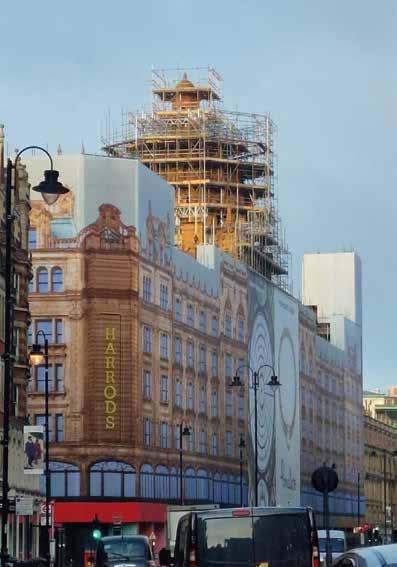
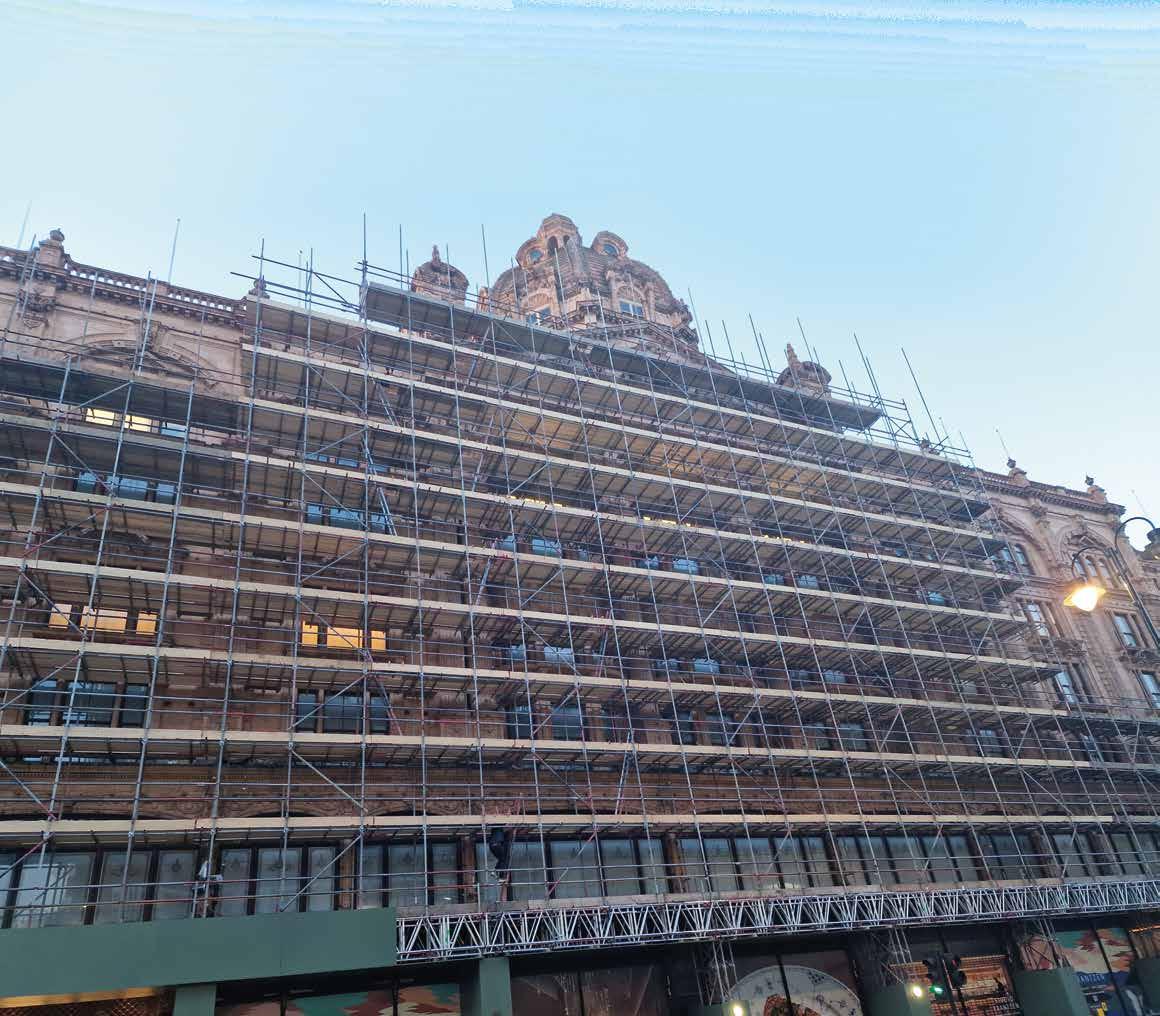
One of the main challenges was to maintain uninterrupted and unimpeded public comfort and access, while accommodating obstacles such as street furniture, bus stops, canopies & awnings, phone boxes, pedestrian crossings, narrow pavements & splays, and underground tube entrances.
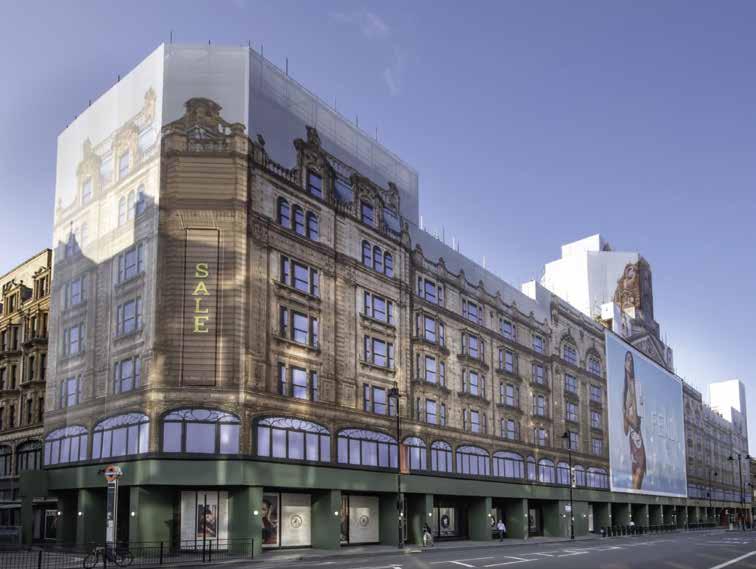
Council’s licences, LUL permissions and TFL’s temporary suspensions of bus lanes and red route permits. Since noise pollution is a big issue in Knightsbridge, Stak Scaffold took the decision not to use standard drills. Despite the restrictions, Stak delivered to the highest standard and on schedule, without compromising safety.
The world-renowned window displays at Harrods had to be kept visible at all times, so the design included support towers erected adjacent to the building columns and beamed above the windows to support the scaffold on top. This proved to be a demanding task because the basement structures and vaults had been modified extensively throughout the building’s 175 years, along with the 7 floors below ground, so finding suitable strongholds for the support towers was not straightforward. After close collaboration with the project’s TWC and Harrods’ structural and geotechnical engineers, the solution comprised a mix of back propping, very large bridge spans, and cantilevers.
Being a Grade II listed building, attention to detail was imperative and required consultations with English Heritage. The main façade is made of thousands of individual terracotta blocks, which are extremely brittle. Any repairs had to be performed with meticulous care, using materials made from the original quarries and supplied by a few very rare hand-pressing manufacturers. Installing the scaffold ties was a complex operation, as there was a need to protect the terracotta, so they had to be installed into mortar joints or into previous tie holes, as no additional drilling was permitted.
The terracotta blocks offer very limited tensile strength for the ties so, in certain areas throughout the building, a bespoke reusable anchor point was designed within the superstructure to withstand 6 tonnes (60kN). This was to ensure that there would be suitable fixing points for all future works and maintenance, also taking into consideration any potential hoist loadings.
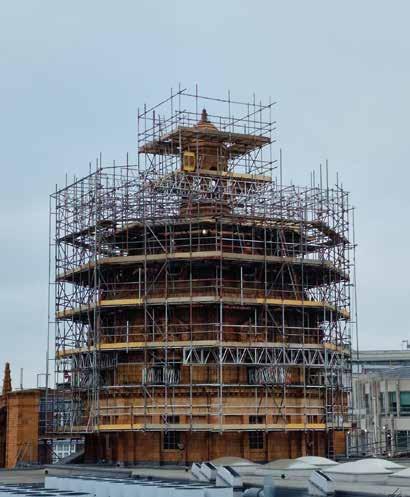
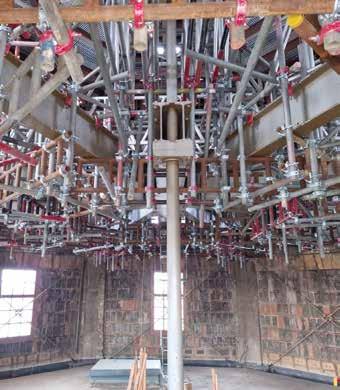
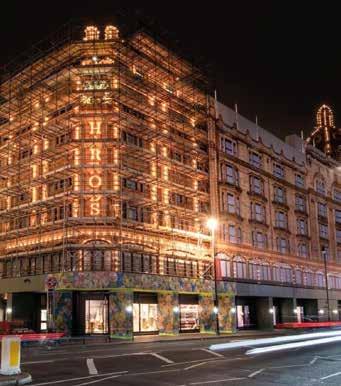
This is the second time that GWC Scaffolding Design has had the privilege of providing scaffold designs for the iconic Harrods building. All those involved are proud to have delivered a quality solution that maintains the authenticity of a listed building, protects the safety of the public, and ensures business as usual during the busiest shopping seasons.
AMP provide access for restoration of distinctive structural monument
Fully Audited Members of the Scaffolding Association, AMP Scaffolding Limited, have provided external and internal access to the remarkable Red House Glass Cone in Stourbridge to enable restoration works.
During the late 17th Century these remarkable conical shaped structures developed across Britain to help boost its glass industry. The buildings acted as chimneys and housed large furnaces in the middle with room for glassmakers to work around them.
The Red House Glass Cone, often referred to as the Stourbridge Glass Cone, is one of only four remaining examples of a glass cone furnace in the UK. It was built in the period 1788-1794 and operated for over 150 years. The Cone’s distinctive shape rises to a height of 100 feet and is now open to the public as a live working museum.
The building requires extensive restoration works that are being carried out by specialist conservation contractors, Phillips and Curry.
Works to be carried out include internal and external repointing of the entire structure from top to bottom with lime mortar, in addition to the removal of the vegetation sprouting from the Cone, which will be carefully removed on a phased basis. Bricks surrounding each growth will be taken out, the vegetation and root growth removed, then the bricks will be replaced and re-mortared. There will also be new drainage around the building and access to the tunnels.
Inside the Cone, the internal gantry and lift will be removed to create a more open, accessible space. A new lift will then be installed by the visitor centre to allow wheelchair access to the upper level, where a viewing platform will allow people to see into the Cone and hot glass studio.
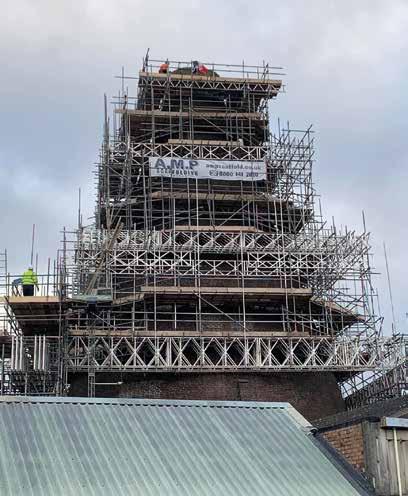
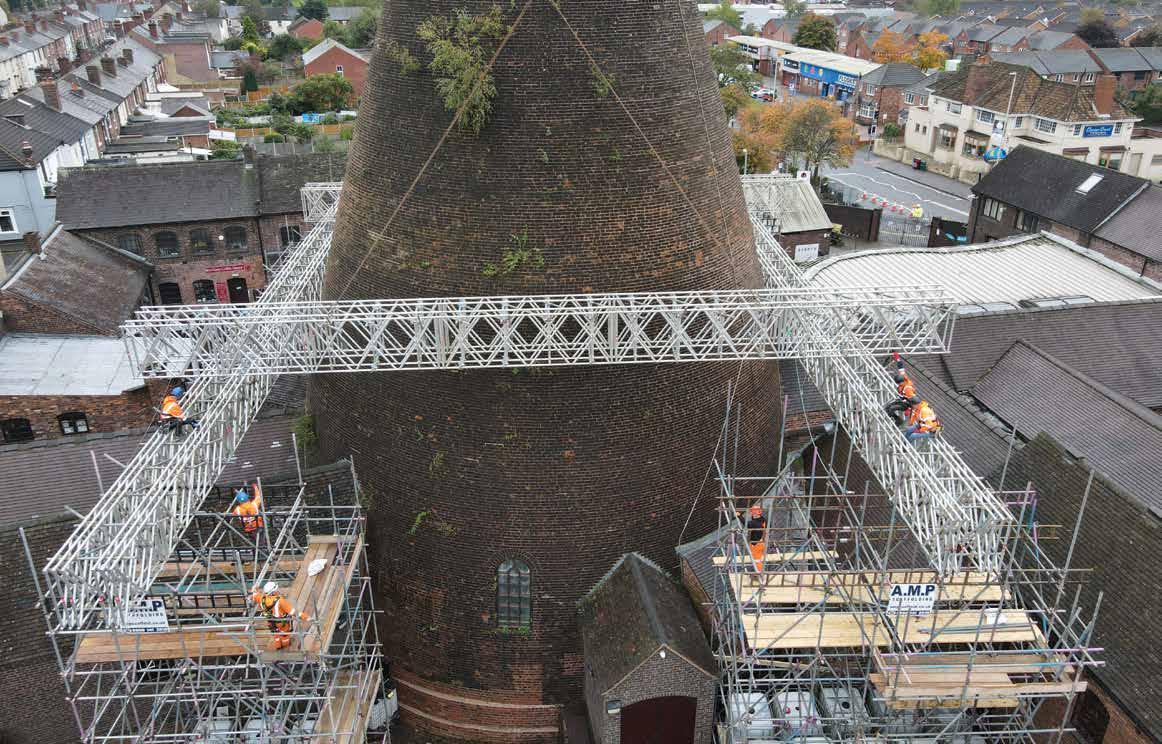
One of the first things we had to take into consideration was that no scaffold could touch the building whatsoever, neither internally nor externally, due to the condition of the building. This led to the creation of a challenging and bespoke design that we did in-house.”
Tony Coleman, Managing Director at AMP ScaffoldingDue to the extensive works to be carried out, the nature and shape of the building itself and its’ Grade II listed status, providing access was always going to require careful consideration, Tony Coleman, Managing Director at AMP Scaffolding explained:
“These jobs are very rarely done as the Cone is one of only four remaining examples of a glass cone furnace in the UK, so we were looking forward to doing our bit to preserve this vital part of British history.
One of the first things we had to take into consideration was that no scaffold could touch the building whatsoever, neither internally nor externally, due to the condition of the building. This led to the creation of a challenging and bespoke design that we did in-house.”
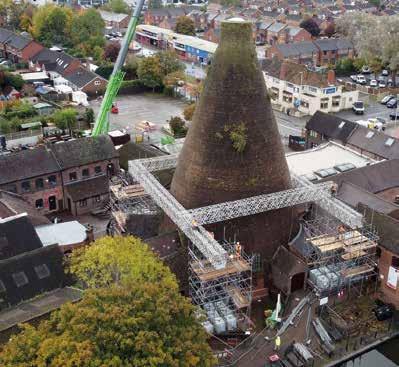
The wealth of knowledge and experience within AMP’s management team, including Managing Director Tony Coleman, who will be celebrating 50 years in the industry in July this year, helped overcome all obstacles for this project, Tony commented:
“Our management and their ‘outside the box’ knowledge of access solutions really helped us come up with excellent solutions to the many challenges we faced with this project.
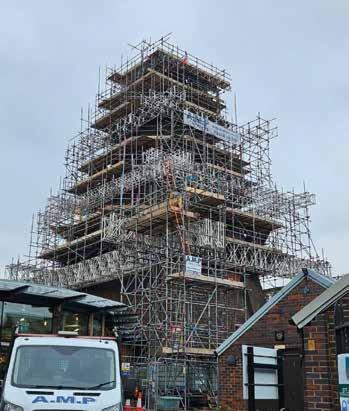
Externally a variety of DESSA beams were used in the complex design including the 750s and 450’s.”
Once a solution to the external scaffolding was decided, AMP turned their attention to the internal scaffolding requirements, Tony commented:
“The internal scaffold was a bespoke independent scaffolding that couldn’t rest against the wall, the height was 26m, same as the outside, and the purpose of the internal scaffold was to complete the internal restoration works.”
It was not just the designs that required careful consideration, with the Cone being a popular tourist attraction that remained open throughout, the erection of the scaffolds also required thorough planning.
Tony explained:
“Inside the Cone itself was closed and fenced off, but the public could go into the shop and surrounding areas. We worked around confined restraints and had a segregated area to store
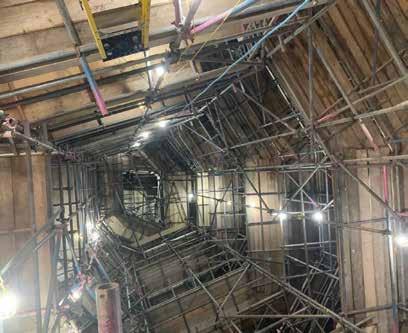
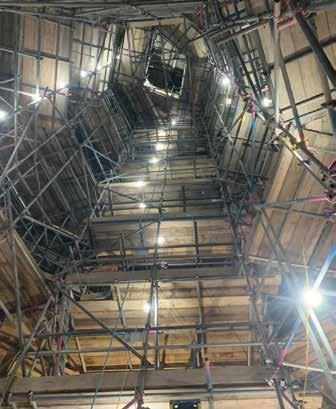
equipment. This meant that the erection of the scaffold took place in normal working hours because we were able to carry the works out without disrupting the public area.
The only day anything was affected was the day of the crane. This required a road closure and the site to be closed, but it only took half a day.”
Overall, the project was a huge success, with the scaffold now handed over to Phillips and Curry to undertake the restoration works, which are expected to take 40 weeks.
Tony concluded:
“All of our operatives, from management and office staff to the onsite supervisors and scaffolders, have thoroughly enjoyed being involved in every stage of this project, from planning to completion.
These jobs are very rare, so it was a privilege to be part of the restoration works on such an historic building in our local area.”
More:
AMP Scaffolding Limited: www.ampscaffold.co.uk
Phillips and Curry: www.phillipsandcurry.co.uk
Red House Glass Cone: www.dudley.gov.uk/things-to-do/museums/red-house-glass-cone
PERI UP façade access facilitates Treadgold House’s journey to carbon-neutral
Scaffolding Association members, PERI, have completed a scaffolding installation on Treadgold House, which will enhance the council-owned estates carbon-neutral credential.
Situated in West London, Treadgold House is a four-storey residential estate which is undergoing refurbishment to provide residents with a more thermally efficient building.
The work involves replacing existing waterproofing coverings, windows and balconies from the building. Two temporary roofs have been installed to provide protection from rain as the current layers are stripped and replaced with energy efficient material.
Although both roofs have been constructed in tube and fitting, scaffolding requirements for façade access have been more stringent. The façade access around both buildings is built entirely out of system scaffolding as per the material specification provided by the local council. Next Generation Scaffolding Ltd was tasked with installing both the temporary access and the roofs. Mitigating the use and risk of combustible materials was a top priority during the refurbishment. This was especially important given the context of widespread remedial façade works on mid to high-rise buildings across the country. To meet this requirement, the PERI UP scaffolding system was specified for the project due to its all-metal design inclusive of its decks and toeboards.
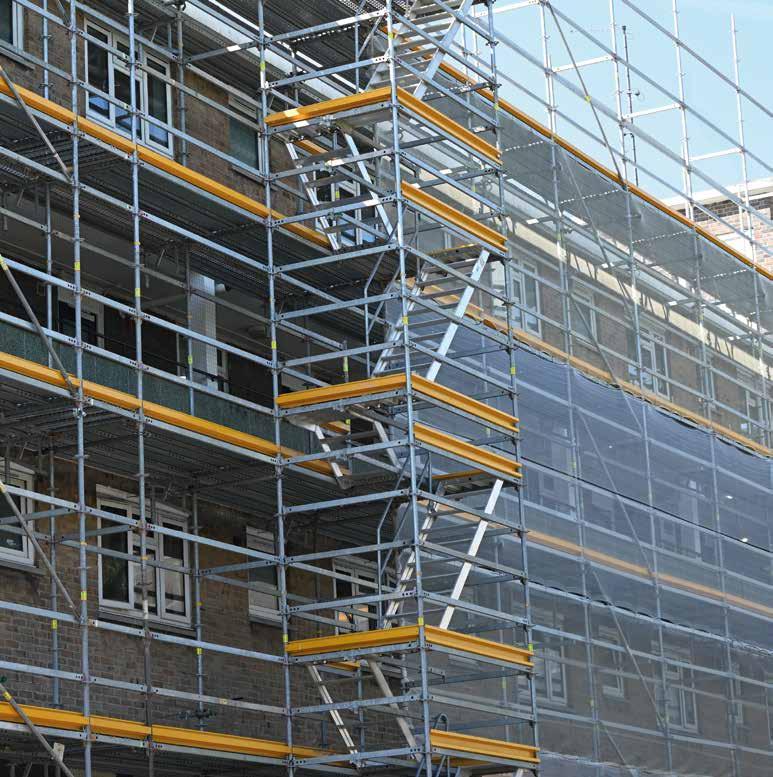
By integrating different systems in the PERI UP range, design consultant Double Scaffold Design were able to catalyse the assembly process and reduce strain on scaffolders during material handling.
PERI UP Easy decks were used for the main scaffolding platforms due to their light weight, while PERI UP Flex was used on the inside brackets to cover any gaps where the façade steps back.
PERI UP was also designed to blend effortlessly with non-system components on this project, such as tube and fitting for the roof structure and the beam work on the building’s east elevation to enable vehicle access.
Using system scaffolding instead of tube and fitting for the façade access

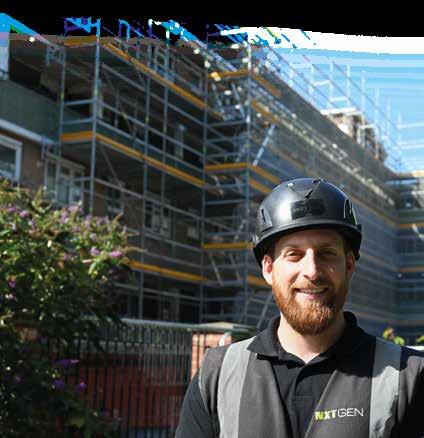
The ledger-to-ledger connections with spigots are handy when working with multiple returns. With these components, we could use multiple deck sizes to cover the area and erect elevations at different points.
requirements provided a clear walkway for Next Generation Scaffolding on each level, as ledger braces did not need to be installed.
The solution was praised by the scaffolding contractor for its flexibility and wide range of components.
The scaffolding structure is expected to be in place until May 2024. In addition to installing new waterproofing and non-combustible insulation, the temporary access will facilitate solar panel installation and an air source heat pump on the roof.

Changes to operating HGVs in London
In this article the Road Haulage Association (RHA) discusses the upcoming changes to London’s Direct Vision Standard (DVS) and whether such schemes could expand to other parts of the UK.
New safety standards for HGVs over 12-tonnes gross vehicle weight operating in the capital are due to come into effect later this year. With Transport for London (TfL) launching its Progressive Safe System (PSS) on 28th October which will replace the current Safe System first introduced in 2019.
Unlike the previous safe permit, which required obstacle detection systems on the nearside, the Progressive Safe System demands technology that can predict collisions based on the trajectories of the vehicle and the vulnerable road user (VRU).
As a leading road transport trade association, the RHA, has been working closely with the Scaffolding Association in recent months to help support scaffolding and access businesses with embracing their fleet related challenges – DVS is just one of those.
RHA represents some 8,500 businesses who between them operate 250,000 HGVs, coaches, and vans - over half of the UK’s heavy commercial fleet.
Whilst a typical logistics or coach business is very much different to that of a typical scaffolding and access business, the one thing that
they do have in common is their heavy commercial vehicles which might look different but are largely regulated in the same way.
This certainly applies to their operation within London and DVS will impact a vehicle carrying scaffolding tubes and boards just as much as it will one carrying palletised goods for an office block or fresh produce for a high street restaurant.
RHA has been a leading voice on the subject, and whilst we want safer roads in London, we have been calling on TfL to implement these new measures in a more considered way.
The RHA have also been asking for affected businesses which are concerned about timescales, affordability, and availability of new kit, to be adequately supported.
These were the common themes from the feedback we received from a recent survey we conducted which resulted in over 700 responses. Over 100 businesses also attended a webinar which RHA hosted on the subject. Feedback on such issues has been crucial in providing RHA the insight it
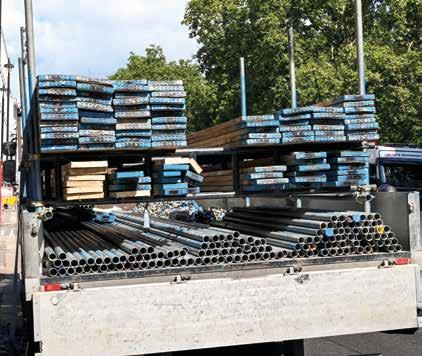
needs to articulate the right solutions to help firms comply with the new criteria and informs our ongoing engagement with TfL.

Collaboration sits at the heart of what RHA does, and continuing to grow and develop relationships with other trade bodies such as the Scaffolding Association is helping to build consensus on common issues.
Whilst DVS will not impact every business within the scaffolding sector, London policy often finds its way to other major towns and cities.
Take Clean Air Zones for example – the Low Emission Zone (LEZ) in London was the first of its kind in the UK. Now, similar initiatives have now been introduced in 15 other locations, with others planned.
The Freight Operator Recognition Scheme (FORS) was first introduced in London and now features prominently in procurement requirements way beyond the capital.
More: www.rha.uk.net
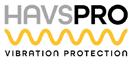
HAVSPRO’s guide to HAVS Risk Assessments
In this article HAVSPRO, an industry-leading vibration monitoring and measuring solution that generates proactive alerts and in-depth reporting, discusses the importance of HAVS Risk Assessments and the consequences of getting them wrong.
Hand Arm Vibration Syndrome (HAVS) is a collective term for the injury to the nerves, muscles, and tendons of the wrist and hand due to the repetitive use of vibrating hand tools. Symptoms often include white fingers or tips (especially when it is cold), painful or red fingers, poor circulation, tingling, or numbness in the fingers, hands or wrist.
HAVS is a serious condition which is irreversible and there is no PPE to protect against it. Prevention and risk management are the only weapons we have to protect workers and organisations against its consequences, so the only way to prevent irreparable damage is to manage the risk to as low as reasonably practicable (ALARP).
Whenever there is an incidence or occurrence of HAVS, or related health conditions, employers are required to report it through RIDDOR (Reporting of Injuries, Diseases and Dangerous Occurrences Regulations), and HAVS is one of the most commonly reported injuries.
Prosecution fines have reached £2.5 million resulting from businesses failing to protect employees in the last 7 years, with almost £1.4 million of these fines coming in the last 4 years alone.
Under the Control of Vibration at Work Regulations 2005, all organisations have a responsibility to reduce vibration exposure to ALARP. Meaning, if there are vibration emitting tools used in your workplace, such as impact wrenches, you are required by law to conduct a risk assessment which will show the risk posed by the specific tool(s) and work undertaken in your workplace or on behalf of your organisation.

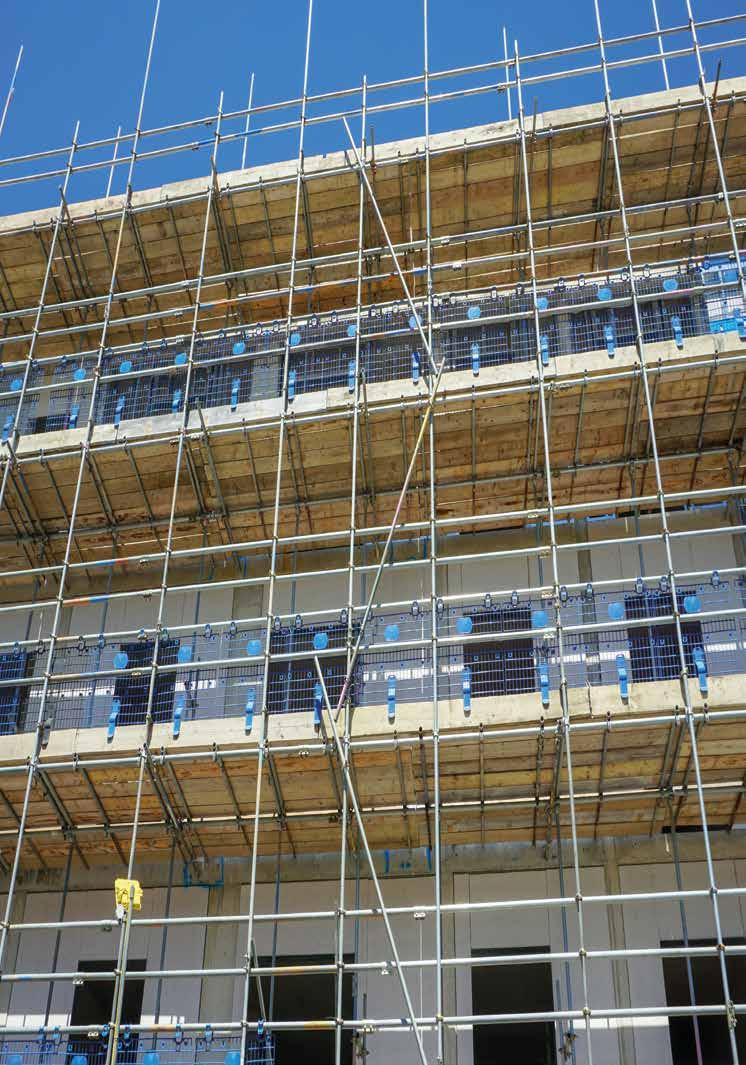
What are some of the likely consequences of HAVS in your workplace?
Reputational costs
There are the intangible, and often immeasurable, costs of a HAVS infringement such as the reputational damage to your organisation.
No one wants to work for the company that neglects its workers - and some of your suppliers and customers may also shy away from any association with a legal case.
Compensation claims
These are made by individuals, through the civil courts, against the employer for whom they were carrying out the work on behalf of when their injuries occurred, and are in addition to fines and legal costs.
Compensation claims can be sizable, depending on the amount and severity of damage the person has received. The severity of a HAVS related health issue is increased due to the irreparable nature of them.
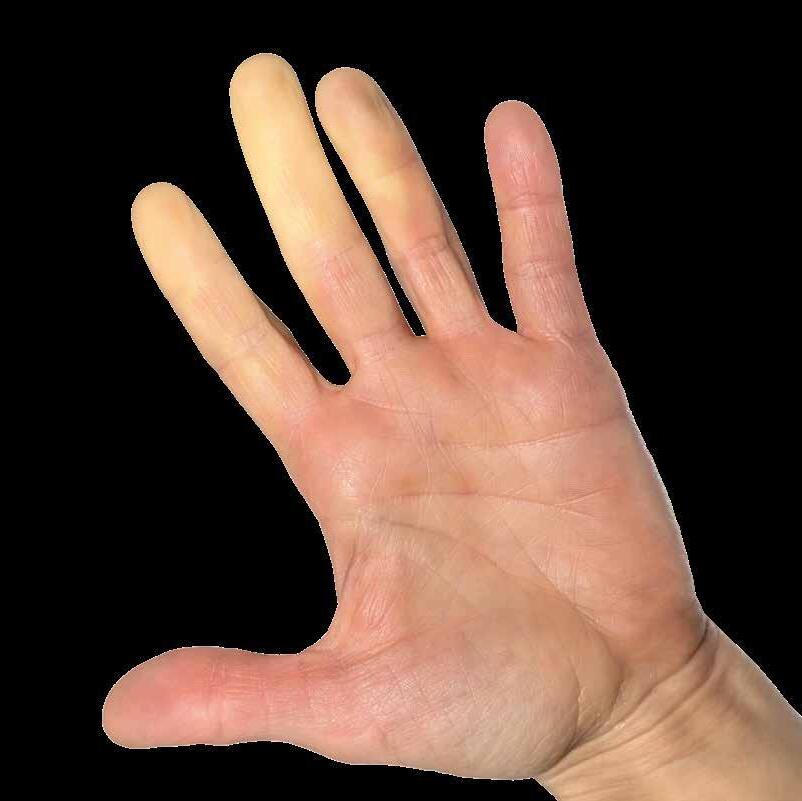
The golden rule is “if an employee, or contractor working on your behalf, is exposed to vibration as part of their work, you will need to carry out a risk assessment.”

As part of your regulatory compliance, you must decide what each worker’s exposure is likely to be, as part of your vibration risk assessment.
So, in order for you to understand the risks, and to help you complete your risk assessment effectively, the HSE recommends a period of monitoring to understand how long workers use particular tools in a typical day or week. Once you know how long a person is spending on a particular tool, you then need to know at what frequency that tool is likely to be emitting vibrations at, commonly referred to as the vibration magnitude level.
The three most common ways of doing this are;
Conclusion
HAVS is not a problem that can be ignored and has very serious consequences to both employers and workers if vibration exposure is mismanaged. The risks associated with vibration exposure should be assessed using a risk assessment which identifies what vibration levels workers are being exposed to, but remember that these risk assessments are only as accurate
A thorough risk assessment will clearly highlight the areas of risk from vibration exposure within your business.
A HAVS risk assessment will show;
• where the risks lie;
• who is most at risk;
• an evidenced estimate of each employee’s exposure using representative tool vibration data, and how it compares to the regulatory limits;
• suitable risk management strategies and controls implemented to reduce risk to ALARP;
• how you plan to maintain and monitor the risks to ensure continued regulatory compliance.
In addition to this initial risk assessment, you need to establish if any of your
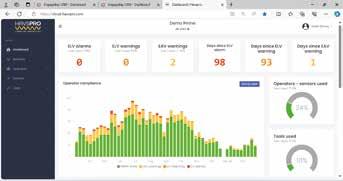
• Manufacturers data
All manufacturers have a legal obligation to supply vibration magnitude data with their tools. However, there are many different variables that will significantly affect the vibration magnitude of a tool and will significantly alter the risk from vibration exposure, therefore making this guesstimated data.
• Sources of vibration magnitude
A similar problem occurs when using the HSEs source of vibration magnitude guide, which features; a lower range (10%), an upper range (90%) and a recommended value (75%). And again, this means the values
as the vibration magnitude data being used in them, they may tick some boxes, but do they protect both the business and the employee?
If you want to fully protect your workers from vibration exposure, you should consider implementing a continuous measuring and monitoring system that is both proactive and accurate and guides you to achieving ALARP.
employees show some, or all, of the following symptoms;
• numbness and tingling in the fingers for up to 20 minutes after tool use;
• reduced grip strength, pain in the hands, and possibly disturbed sleep patterns;
• fingertips turning white, particularly in cold and damp weather, and then turning red and sore on recovery;
• loss of dexterity or feeling in the fingers, hands or wrists.
If any of the above symptoms show, then conducting an additional risk assessment may be necessary to ensure the heightened risk to these employees is managed separately to that of less vulnerable employees.
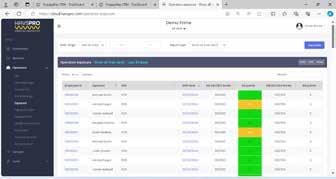
you are entering into the vibration calculator to establish the HSE points a person is likely to be exposed to, are just averages. This means your risk assessment is going to be based on average data
•
Hiring a vibration magnitude measuring device
The third method involves hiring a device or company to measure the vibration produced by your tools, measurements should be made by ‘a competent person’, measuring your tools for three, one-minute periods. It will take an average of the readings it has taken and then provide you with an average of those three readingsthis is called the vector sum.
If you are concerned about any part of your vibration risk management strategy, whether it be your risk assessment, vibration magnitude data or continual measuring and monitoring, HAVSPRO can help.
UKSSH add more features to public access staircases range
UKSSH has been at the forefront of supplying fully compliant public access staircases for over a decade, with a range of step options including solid treads, enclosed backs and GRP (non-slip) treads.
UKSSH stated that:
“Many clients – including those in the rail sector, festival organisers and sporting venues – asked if we could design a temporary public access staircase that goes one step further by delivering maximum privacy for stair users while (just like our existing range of step options) continuing to tick every box on the HSE wish list.
UKSSH’s solutions are fully enclosed treads with integrated non-slip GRP coatings for HAKI public access staircases. Available in addition to all of the existing step options, UKSSH’s latest innovation has already met with widespread approval.”
To find out more scan the QR code

New Mattless Roof Clip set to save time and money
The Mattless Roof Clip, a new product designed by Scafftech Designs Ltd and being sold by Focus Factory, is set to provide a more efficient way to erect temporary roofs.
The current solution to this problem uses additional components and makes the whole process longer and more complicated. Using the Mattless Roof Clip allows the user to clamp the two sheets together without the need for matting to hold it down, therefore saving time, costs & materials.
The fitting has undergone all the relevant safety tests and conforms to European safety standards, it is as strong and reliable as the older style clips or roofing methods.
Simplifying use
It is completely independent and provides comprehensive fixing holding the sheets in place, operatives will no longer have to go back on themselves, once the fitting and sheet have been fixed together, they are complete and fixed without any need for a matting to be laid.
No holes need to be drilled in the corrugated sheets
The sheets can be laid on either side of the clamp and then a screw is used to clamp the sheets together. The curved surface of the corrugated sheets reduces the chance of them rotating, therefore keeping them firmly in place.
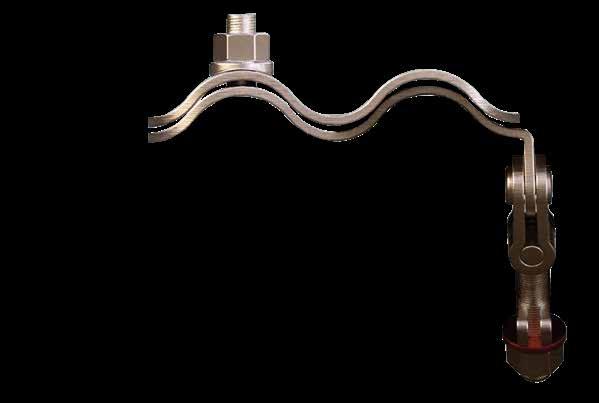
You clamp down on every purlin, saving time getting the tubes up for the mat. You don’t need to bend down three times to make the sheet safe, saving time. You save a row of sheets every 20ft. Also if the weather gets too bad to work in you can stop at any time because the sheets are clamped down safely.”
Jonathan Nolan, Managing Director of Scafftech Designs Ltd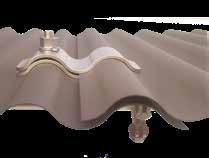

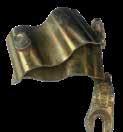
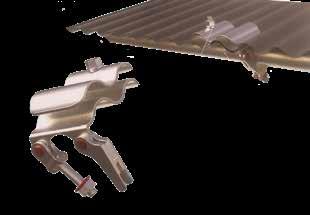
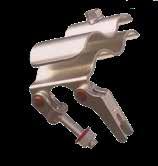
G-DECK launch new Adjustable Threshold Ramps
G-Deck, who are Associate Members of the Scaffolding Association, has released a new threshold safety ramp to add to its growing product portfolio.
Building on the success of their existing Threshold Ramps, these new additions are designed to offer even greater flexibility and convenience in overcoming height differentials.
What sets these new Adjustable Threshold Ramps apart is their unique adaptability, allowing for seamless adjustment from 200mm to 450mm.
Thanks to the inclusion of two heavy-duty jacks on plates, navigating varying threshold heights has never been easier. Whether you’re facing a modest step or a taller obstacle, G-DECK’s ramps provide the solution you need with unparalleled ease.
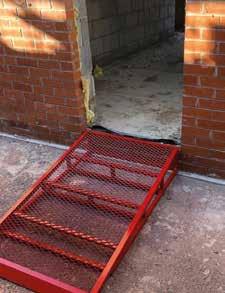
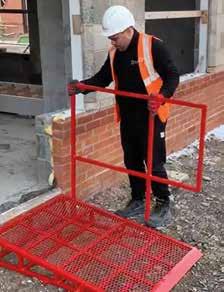
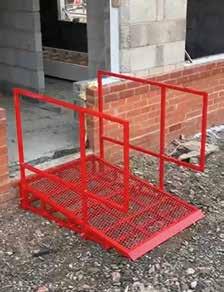
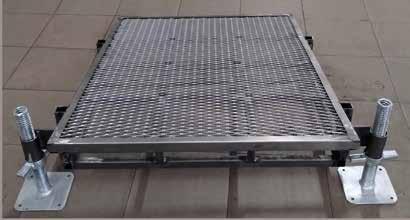
Key features include:
• Adjustable height range from 200mm to 450mm
• Two heavy-duty jacks on plates for sturdy support
• Enhanced flexibility for overcoming varying threshold heights
• Available in ramp-only and ramp-withhandrails options
• Designed for maximum durability and safety
With these new adjustable ramps, G-DECK continues to redefine safety and accessibility standards in the industry. Whether it’s for residential, commercial, or industrial applications, G-DECK’s ramps offer the perfect solution for ensuring smooth transitions across thresholds.
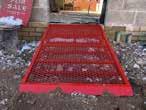
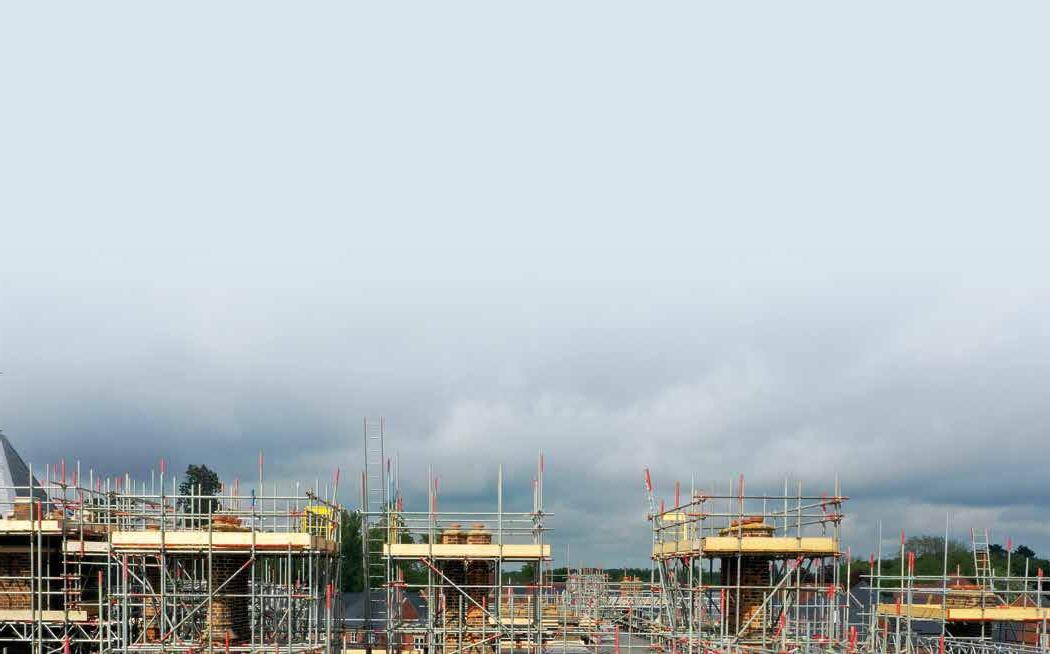
access and scaffolding
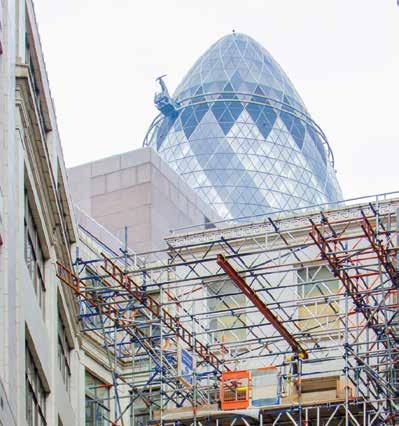
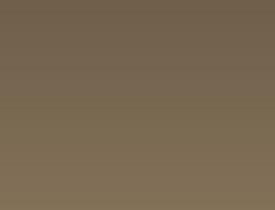
All companies within the scaffolding industry should have access to an organisation which will provide them with specialist information, guidance and support.



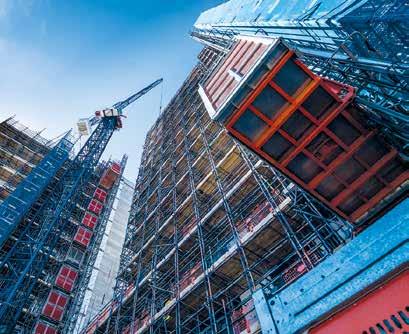
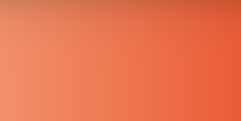
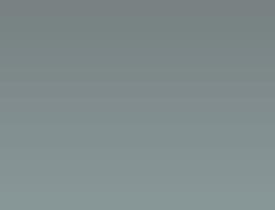
Our Assessed level of membership has been developed specifically to recognise those companies who hold in date certification from a Safety Schemes in Procurement (SSIP) recognised member.
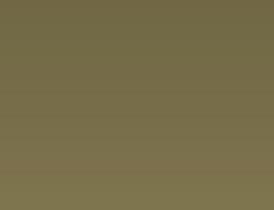
Our third level of membership has been developed in line with PPN 03/23 specifically for scaffolding contractors. It offers an independent third party audit, against a scaffolding specific standard.
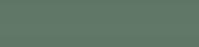
every penny