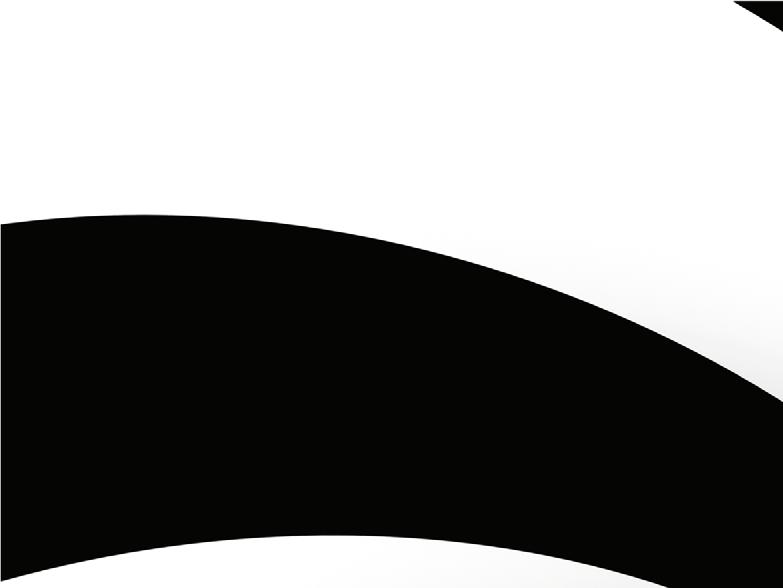
8 minute read
It’s All In The Drilling
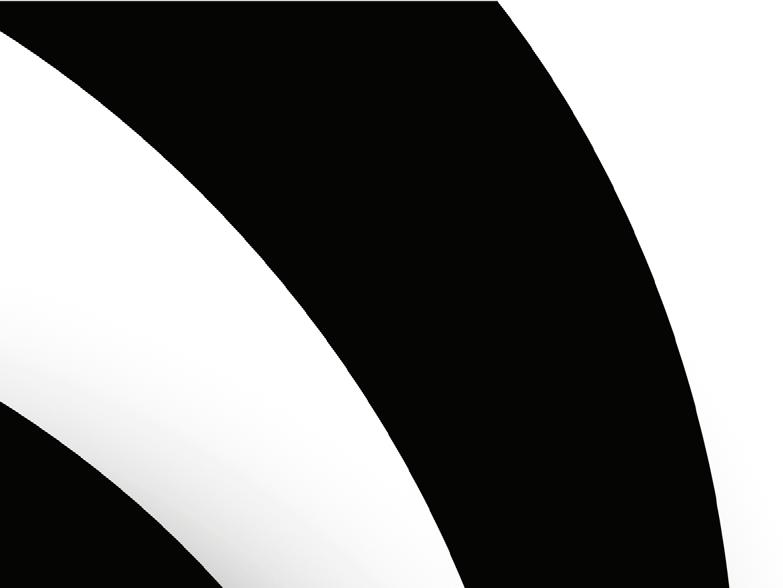
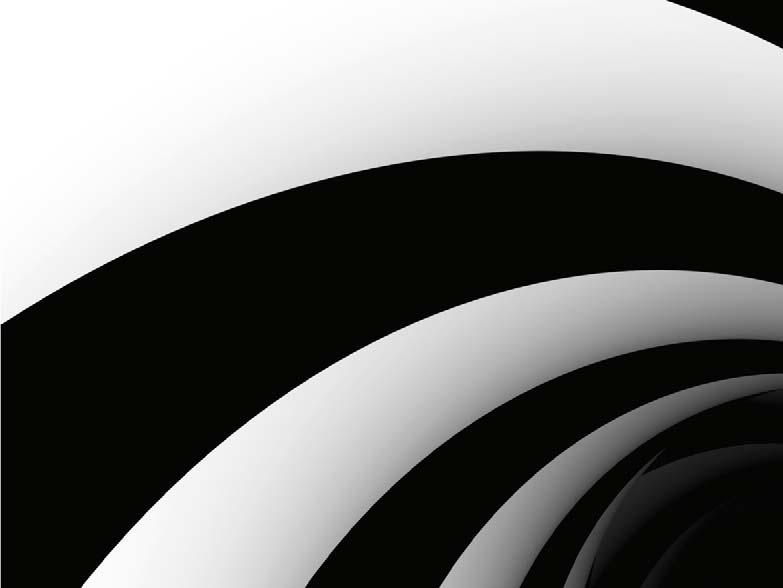
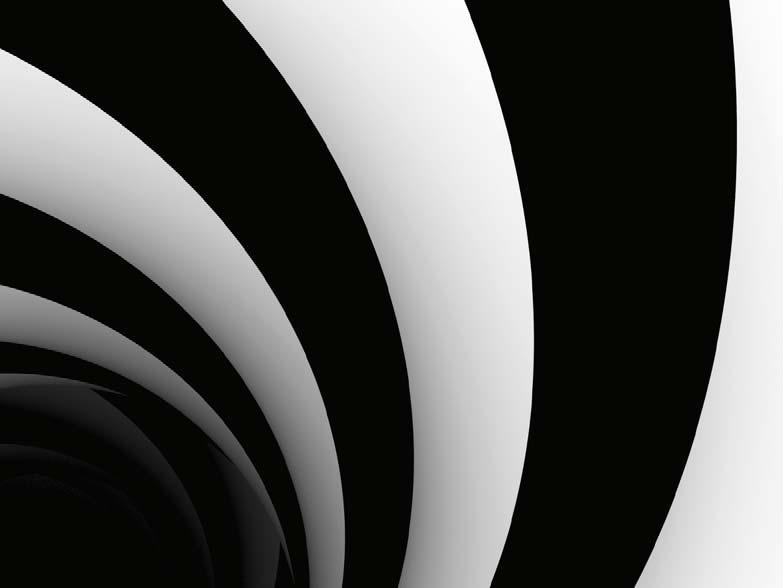
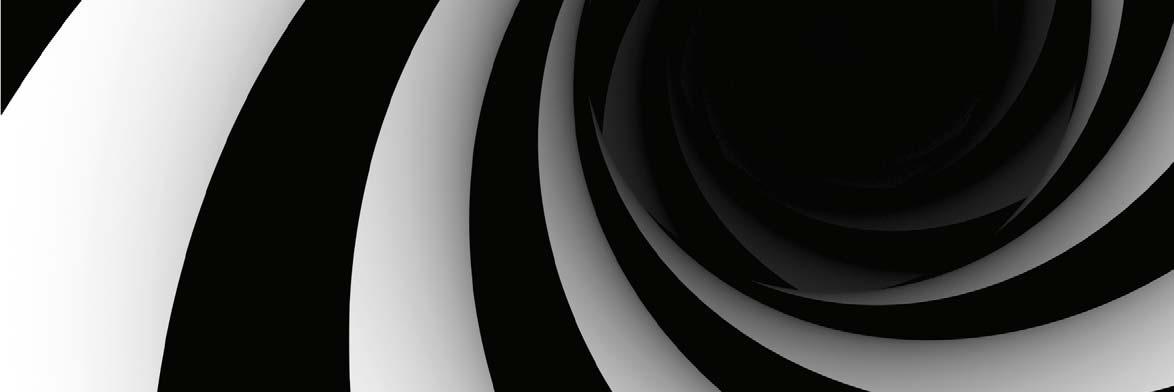
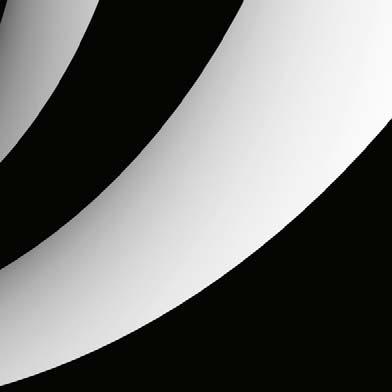
Ceren Şatırlar Balcı, Barkom Group Drilling Rigs and Equipment, Turkey, outlines the importance of the feasibility stage and fi eld investigations of the drilling sector to mining geoscience.
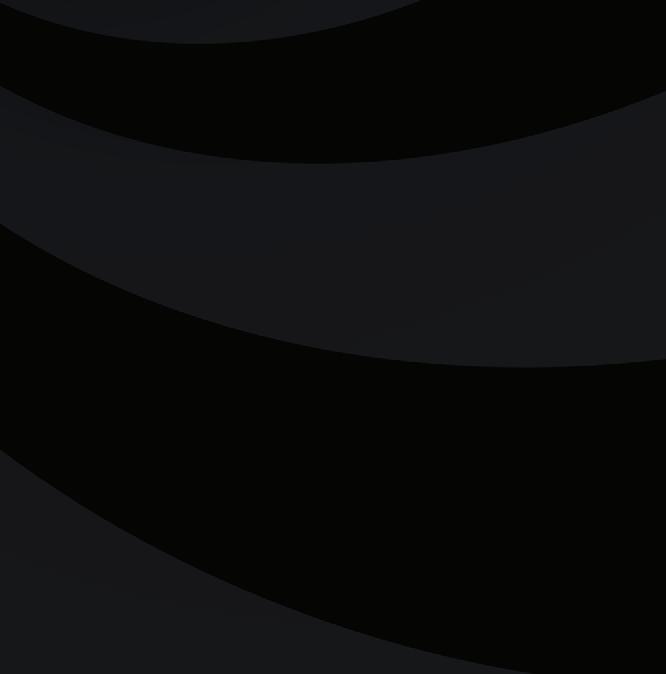

Drilling has become a technique that requires constant improvements, following the increase of raw material needed as a result of the industrial revolution. Deep and shallow drilling has been implemented in petroleum, groundwater exploration, geotechnical investigations and the mining industry, in particular, since the second half of the 19th century. Every drill rig manufacturer should play its role in a drilling industry that is actually a primary supplier to every single industry in the whole world.
In this article, feasibility stage and field investigations of the drilling sector are discussed as one of the most important segments of engineering and mining geoscience. Preliminary stage of field examinations and feasibility investigations are oft en fulfilled with heuristic engineering approaches.
There are several parameters and variables that aff ect the performance and the eff iciency of drilling operations. These include: The experience of the driller. The technical specifications and durability of the drill rig. The quality of the drilling equipment used, and its suitability to the ground conditions. The use of the right drilling additives with the right mixtures.

When drilling takes place in challenging formations, for example where there is a risk of collapse, it constitutes great operational risk and might conclude with the loss of a complete borehole and equipment. When evaluating the drilling performance at the preliminary examination stage, it is of great importance to decide on the right rig and equipment to be used for the drilling, in terms of engineering approaches and determining the profitability of the drilling process.
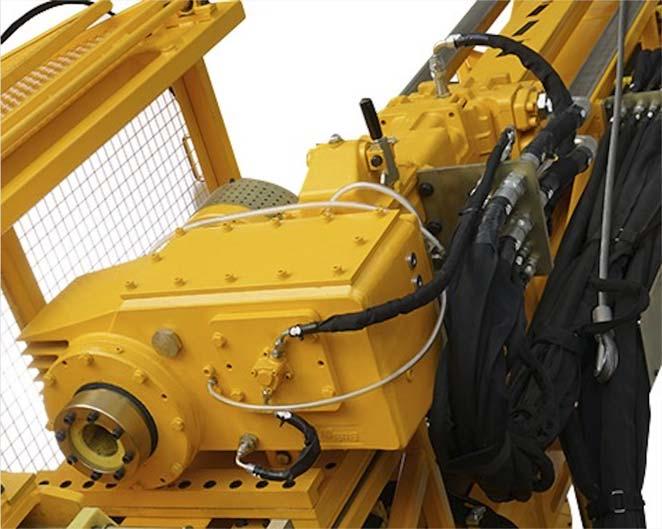
Figure 1. Maximum high performance and eff iciency is provided with the strong four-speed transmission integrated gear box with 9500 Nm torque.
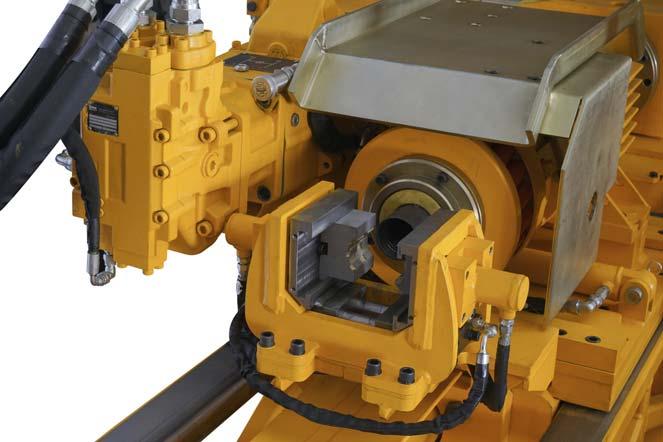
Figure 2. A secondary rod holder system during break out can achieve more thrills with the help of special jaws performance, enabling easy performance and fast rod running out.
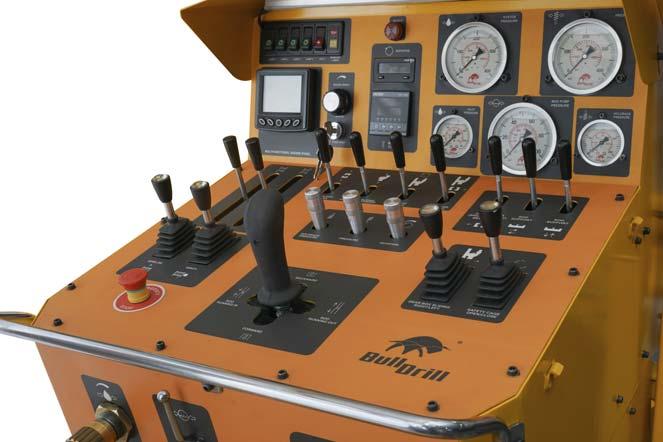
Figure 3. High safety and easy operation is off ered by a pilot monitor control panel.
Preparing for the future
Barkom Group closely follows the latest developments in this rapidly changing world, in-line with its vision. The company puts great eff ort into employing elements such as innovation, sustainability and cooperation, by implementing new generations of products and processes. Based on these factors, it then develops its own technologies to achieve more success in the world.
The company’s research and development (R&D) centre, which is approved by competent government bodies, helps contribute to future solutions by developing reliable products and technologies. Within this context, the company collates its drill rig product range under three main categories, which are: underground, surface, and exproof Atex certified drill rigs. Each drill rig is named according to its specific drilling capacities and diff erent functions.
Barkom's latest rig models is the BULLDRILL® BD1200S surface drilling rig, produced as a result of long and detailed research and design surveys by the company’s R&D team. The rig was made ready for use using the data verified by tests with the following features aft er the design verification phase.
The BD1200S diamond core drill rig meets demanding surface drilling applications. It is designed for shallow and deep hole core drilling, with the functionality to drill rotary for shallow casing. Developed using the latest technologies, it is the most flexible and eff icient drilling rig in its series. It is capable of drilling over 1200 m in depth with NWL, and is equipped with a powerful slide system with which to handle deep drilling. In order to increase its mobility, a compact chassis has been designed by choosing robust crawlers with high carrying capacity. The drill rig has many standard features – such as a second rod holder (adapted to the upper part of the chuck jaw), rod supporting system, and remote control mobility – which are oft en optional on other equivalent rigs. The rotating head, which becomes much stronger with the four-speed gearbox integrated into the drilling unit, has been given the ability to drill with the highest eff iciency, in all conditions, anywhere. All drilling and motion functions can be performed with Rexroth, Parker, or Kawasaki brand powerful hydro motors and pumps, driven by a 300 hp Cummins or Volvo brand diesel engine with proven reliability and eff iciency.
The powerful rotation unit delivers high-levels of torque for greater productivity, and features a simple, open design for ease of maintenance and accessibility. Drillers also benefit from the increased flexibility and mobility provided by the long feed stroke. When changing from 3 m drill rods to 6 m drill rods, almost no eff ort is required because of the additional telescopic piston.
The BD1200S surface drill rig delivers a high-level of eff iciency, thanks to its rigid pole structure, that can be used with a 6 m core barrel, and its telescopically extendable mast. The ergonomic mast, which closes during transportation and provides ease of loading,

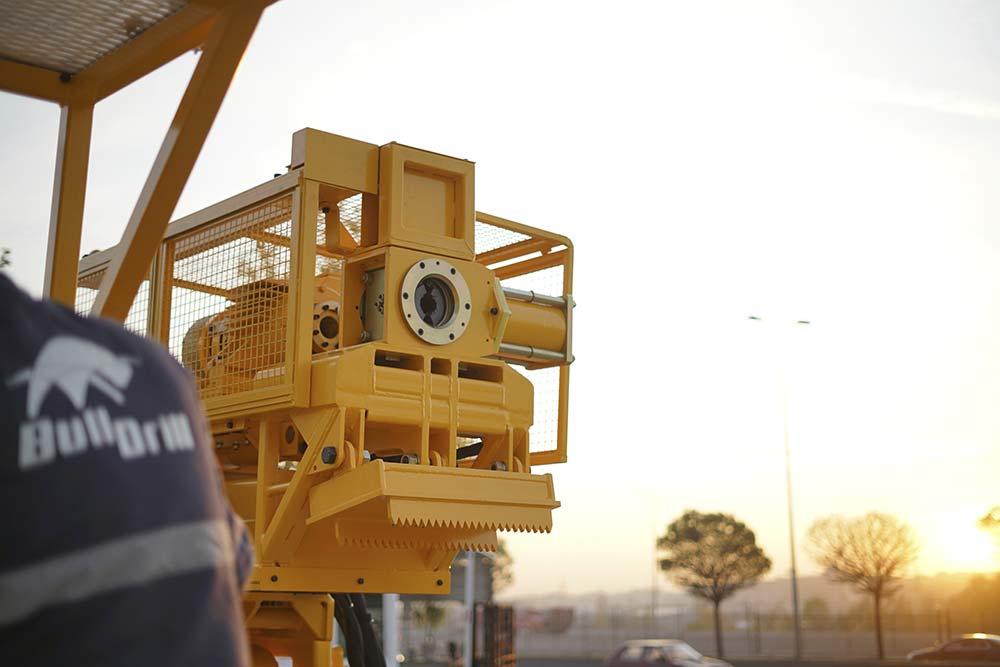
Figure 4. Opened using hydraulics and closed with gas springs, the rod holder system has a rod holding capability of 18.5 t. The jaw system has the feature of holding up to P dia. (114 mm). When the jaws are removed, the inner diameter can be expanded up to 210 mm.
Figure 5. Rod support units, in particularly, ensure that the rods are placed at the same line with the drilling unit and centred when working with a rod of 6 m. It also has a support system to fix the threads during pull up.
Figure 6. The BD1200S off ers eff icient results even at high depths in diamond core drilling with B, N, H and P sizes. creates practical transportation and working opportunity. The poles of the construction that make up the mast are durable; their capacity is more than enough to carry the whole weight of the drill string, and there is a BRADEN brand winch with a carrying capacity of 18 t. The gas-filled rod holder system, which is also strong enough to verify the winch capacity, off ers a robust deep well drilling solution. Control and warning system indicators, that facilitate the monitoring of all drilling equipment and functions, are located on the control panel. In addition, a multifunctional screen (murphy), showing diesel engine functions and engine malfunctions, is located on the control/operator panel.
BD1200S includes mast handling and assembly characteristics. All drilling operations are centrally controlled from the control panel, located at the rear of the rig. The drill rig is easy to operate and maintain, featuring an open design for clear access when servicing.
High safety and easy production is off ered with a pilot monitor control panel. On the panel, there is a red lion speed indication and burkert mud pump flow indicator. With the multifuctional screen, the monitoring of data – such as the diesel engine’s excursion level, oil pressure, engine revolution, and battery voltage value – can be easily monitored from the digital murphy panel. Rod running in and rod running out processes are more practical with joystick use.
It can be adjusted, drilling functions can be followed from the desired point with the moving control panel, and the operator height can be moved to the desired level. The control panel has the capability to rotate axially, while moving up and down with special pistons.

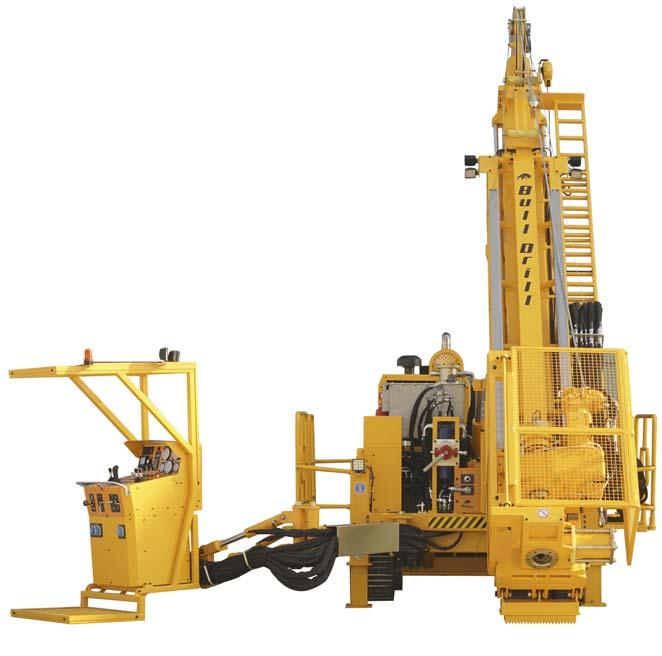
The next steps
The next model from Barkom Group is due to be a multi-functional drill rig capable of performing both diamond core drilling and reverse circulation (RC) drilling. Diamond core drilling and RC drilling are drilling techniques that contain completely diff erent systems. Multi-functional drill rigs allow two methods to be conducted with one single drill rig.
For the BD1200S and the future multi-purpose drill rig, the company worked and is working closely with Drillex International, which has 30 years of knowledge and experience in the sector.
Conclusion
As technology develops day by day in the field of mining and drilling, Barkom Group Drilling Rigs and Equipment recommends to always look for more in less, as it is all in the drilling. Considering that developing technology will bring diff erent engineering solutions with it, the suitability of a certain drill rig for the field and drilling depends on its eff iciency, quality, and multi-functional capability – the crucial factors to success. Each improved piece of equipment, and the development of new systems on the drill rig, will increase productivity by aff ecting the expected drilling performance, as it will provide: safety, durability, mobility, low maintenance requirements, adaptability, a reduced labour requirement, and faster operations.
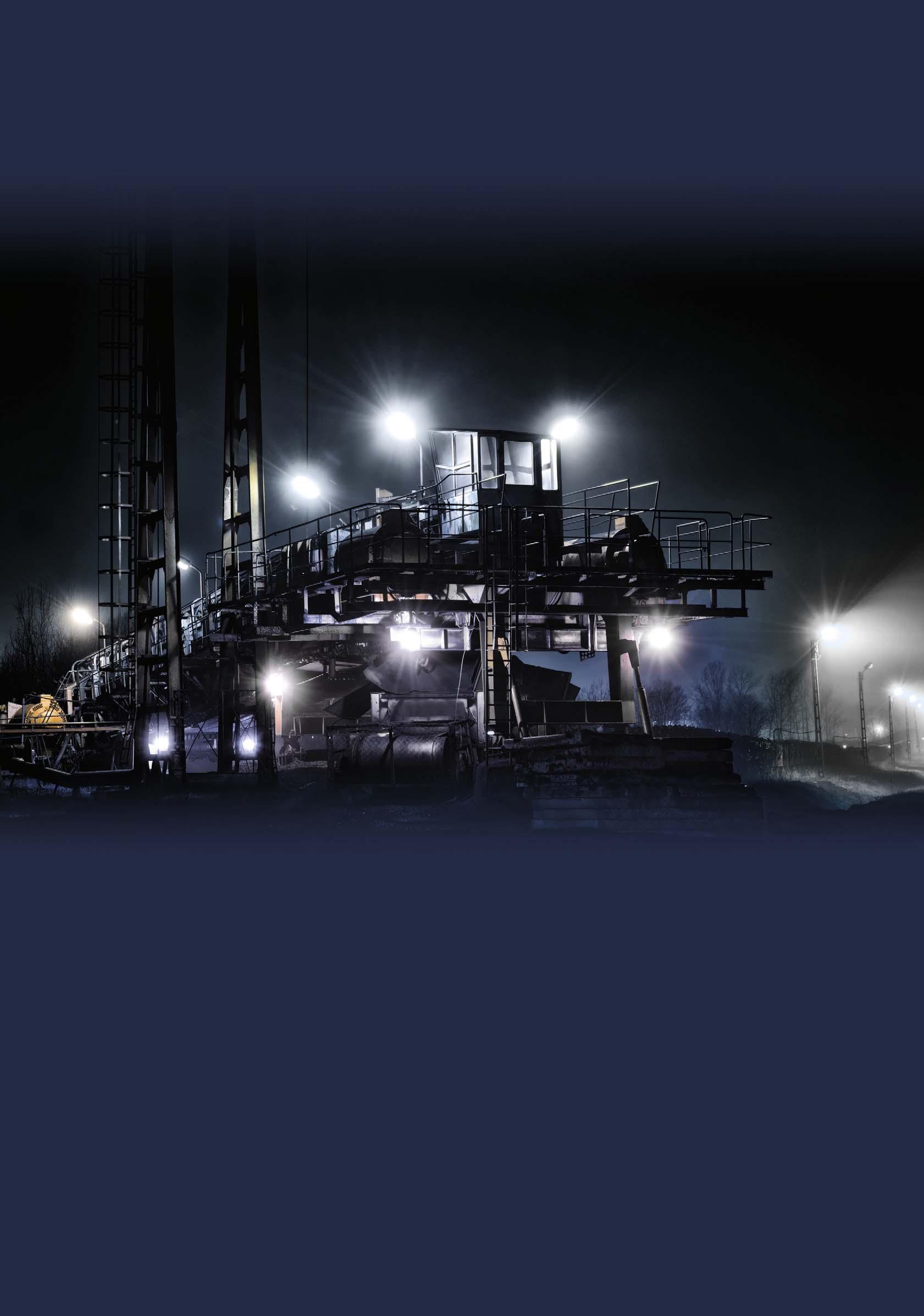

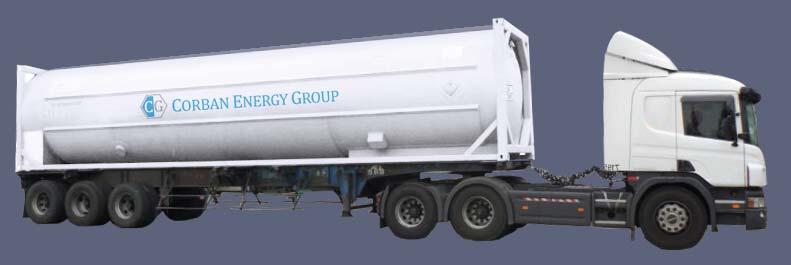