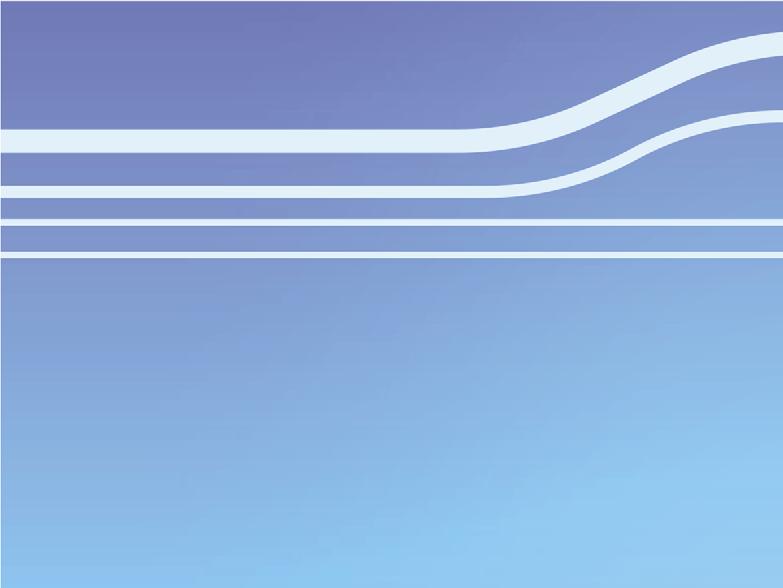
8 minute read
The Connected Mine

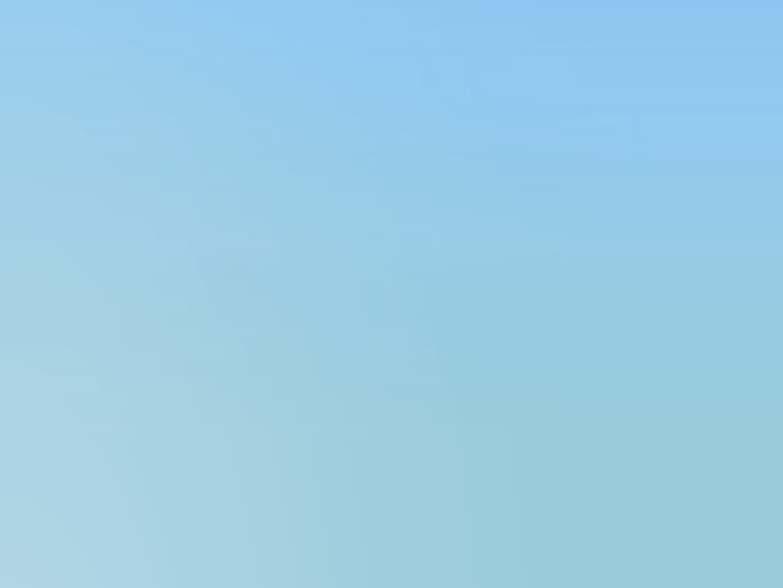
James Trevelyan, Speedcast, UK, provides insight into how the Connected Mine can revolutionise the mining industry.
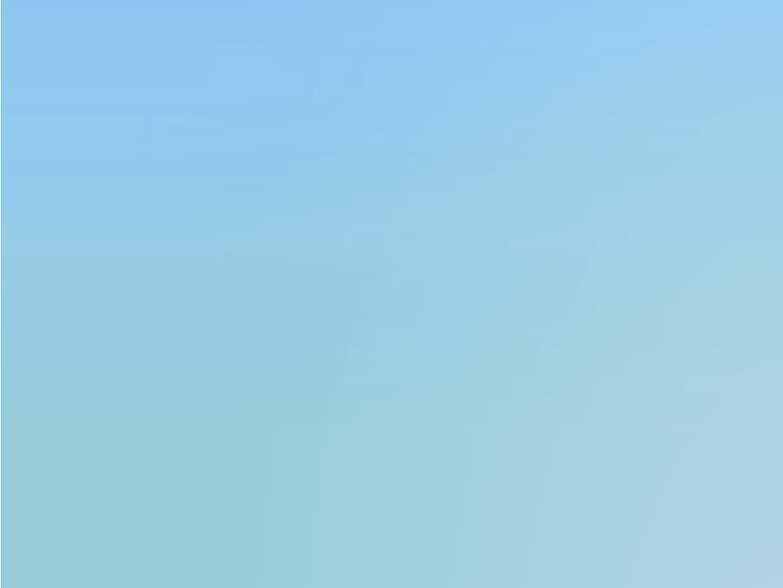
Having already undergone decades of change to improve safety and productivity levels, the mining industry is no stranger to transformation. It has been predicted by McKinsey and Co. that digitalisation will not only put predictability within the grasp of operators, but offer the sector an economic impact worth US$370 billion/yr globally in 2025.1 Technology, when utilised the correct way, has huge potential to make mining big business once again, through the optimisation of operations.
Digitalisation is already paving a way forward, revolutionising the industry in a way that has never been seen before. Some operators are already starting to take notice, with estimates that the worldwide automation market for mining will grow at a rate of 7.3% compound annual growth rate (CAGR) over the
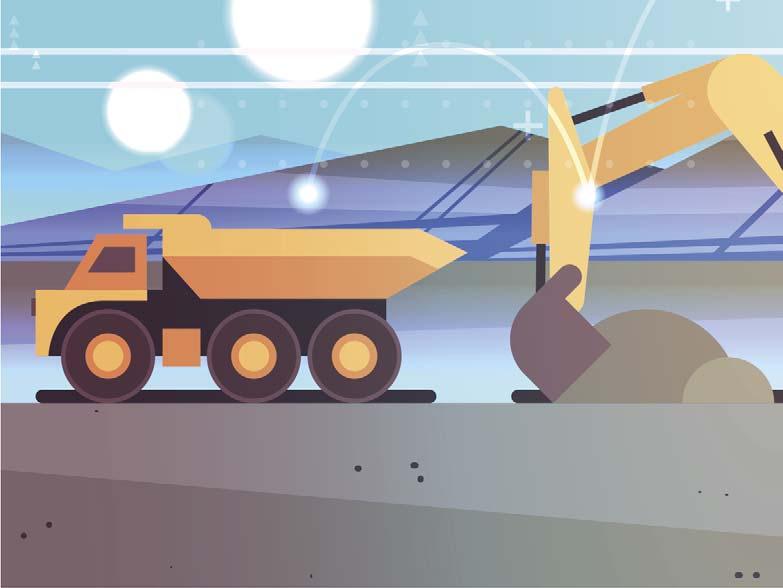
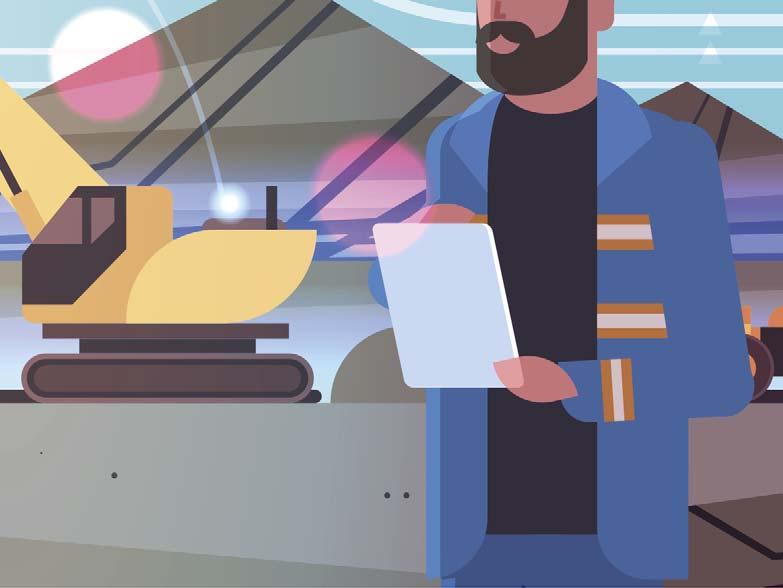

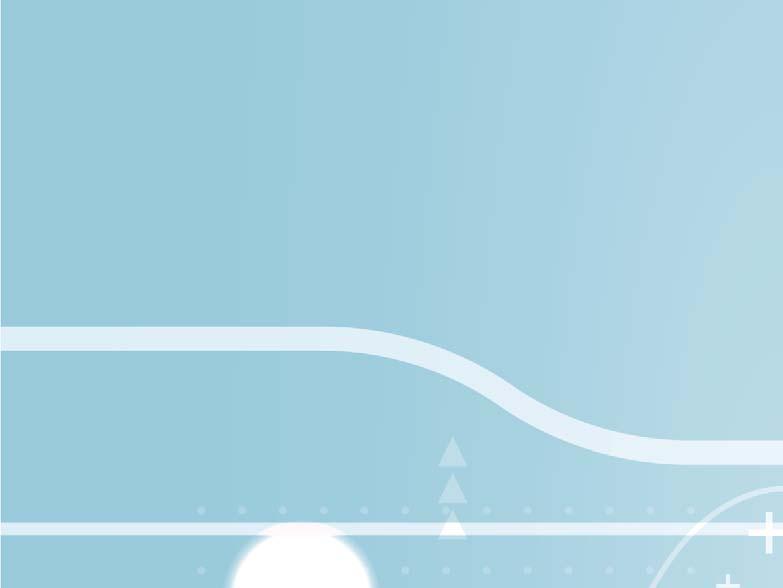
next five years.2 This shows this is a trend that organisations cannot fail to ignore, with technological adoption increasing in popularity. Failure to comply will trap businesses into an ever-declining cycle where prices remain high and efficiencies are not maintained.
A real need for digitalisation
There is a clear need for technology and the benefits it can bring. The business of mining is facing increasing pressure, as companies struggle to boost productivity levels and cut the rising costs of operation. With many mines maturing and ore grades declining, levels of exploration investment have also fallen significantly. According to Ernst and Young, despite some recovery in the last two years, budgets now are half of what they were in 2012.3
On top of this, worldwide mining operations are almost a third less productive today than they were a decade ago, as mines juggle finite levels of resources with a declining workforce.1 Achieving a breakthrough will take more than just money, instead a radical breakthrough is needed, and digitalisation will be the answer.
However, only seven of the top 40 mining operators have a chief technology officer, chief information officer or chief digital officer in their senior management team, highlighting that digitalisation has yet to become a major priority.4 It seems a breakthrough in the thinking of how mining makes use of technology is needed. Miners need to look beyond their backyard to discover the range of benefits that the digital world and Industry 4.0 has to offer.
This being the case, there are already some players in the mining industry that have embraced digitalisation. For example, in 2019, Rio Tinto announced the launch of the industry’s first autonomous railway network to transport iron ore to the company’s ports in Western Australia, saving the organisation time and money.5 Furthermore, at the Syama Complex in Mali, Resolute Mining uses automation within its drill equipment and automated vehicles to extract 300 000 oz/yr of gold, boosting its operational efficiency by 30%.6 Incorporating technology using robotics allowed the company to train native Malians to do the work, rather than relying on experienced miners with training and extensive knowledge of drill operations.
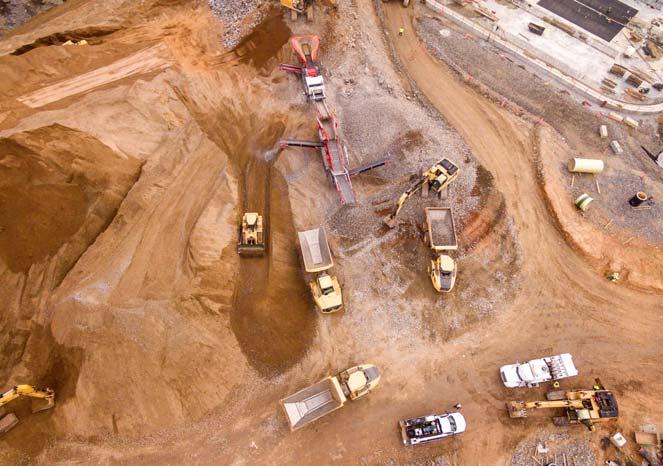
Figure 1. From automated vehicles using GPS and wireless sensors to workers using wearable technology, the Connected Mine drastically improves the process.
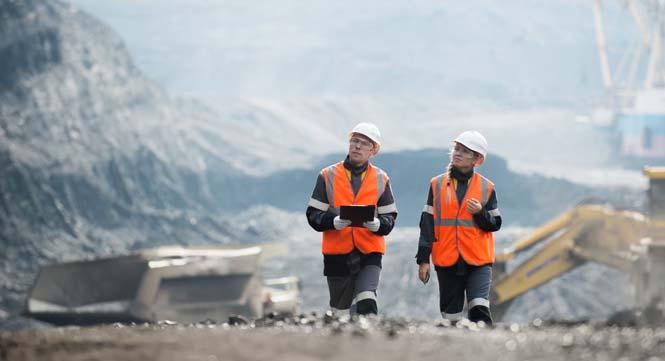
Figure 2. The Connected Mine puts predictability within the grasp of managers, giving them greater control and allowing for better decision making.
The Connected Mine
For operators wanting to take similar advantage of technology, they should look at incorporating elements of the ‘Connected Mine.’ This concept sees a mine harnessing a range of integrated solutions, such as: the Internet of Things (IoT), mining machinery, surveillance systems, ventilators, and autonomous vehicles. Data is drawn from all of these solutions and subsequently used to improve every aspect of operations, by making each mine part of a comprehensive management platform. This ensures that managers have access to all the information and online services they require, in order to make the important decisions needed to support and protect on-site workers and assets.
From automated vehicles hauling ore while navigating rough tracks with the assistance of GPS technology and wireless sensors on the ground, to wearable technologies which monitor where workers are on-site via radio frequency identification, technology can be adopted in many ways. Telematics provides predictive maintenance schedules for vehicles and surveillance systems monitoring for potential hazards. Not only do these drastically improve safety, but they also dramatically improve productivity and operational efficiency, lowering running costs and boosting profits, but also revolutionising the business of mining.
Mission-critical communication
The Connected Mine only works if reliable, affordable, high-capacity communication is made available. For all the benefits to be unlocked, connectivity needs to be reliable, with no interruptions, as managers rely heavily on the system’s ability to draw massive amounts of real-time data. The design of communications infrastructure and the management of networks is essential to the safe, productive running of the mine. With mine sites often being remote, several technologies must be integrated together to provide the high-performing connectivity required.
Connectivity needs to incorporate a few key elements, including:
LTE technology
Wi-Fi is essential for communication between devices and people on-site, in order to keep daily operations running safely and eff iciently. However, this can prove problematic with accessibility being balanced with short range and lower power. To overcome this, the staple of point-to-point microwave has been swapped for long term evolution (LTE) technology. Providing long-range coverage that can penetrate thicker walls and barriers, that is ultra-reliable with high bandwidth, private LTE is now the preferred option for operators. Speedcast works with Nokia to provide the Digital Automation Cloud, which uses LTE to interconnect all aspects of operations, acting as an eff icient management platform for all IoT and automation applications.
Satellite connectivity
Satellites off er the most aff ordable method for hard-to-reach remote mining sites. Some mines are able to install optical fibre with backhaul as a back-up, and some rely on it for their base layer of communications. Providing this connectivity, however, requires a network of teleports, satellites, fibre and high-performance cellular base stations, as well as high bandwidth peering with a variety of networks to guarantee connectivity to the rest of the world.
Backhaul access terminals
Supporting a variety of satellite bands, cellular service, optical fibre, and microwave links these multi-mode terminals are essential for the seamless connectivity for mine communication networks.
Smart network management
With so many methods of connectivity, smart intelligence is critical for identifying the available transmission routes that off er the best price performance ratio. Using technologies, such as soft ware-defined wide area networks (SD-WANs), in order to automatically analyse and manage data among routes, off ers the best possible performance and provides reliable service with better utilisation of bandwidth. A management platform can also provide end-to-end visibility into remote sites and applications, as well as cybersecurity with direct connection to cloud services.
With most mines having a long life cycle, well-designed communications should cover the entire process and adapt to the mine’s changing requirements quickly and eff iciently. During the exploratory stage, a very small aperture terminal (VSAT) in a box off ers local Wi-Fi, cybersecurity, and optimised file synchronisation. Later on in development, LTE, fixed VSAT, and broadband global area network (BGAN) systems support asset tracking, IoT, and video surveillance. During the extraction phase, the priority is focused on communications by Wi-Fi, private LTE and two-way radio, in order to ensure high performance for IoT and autonomous parts of the Connected Mine.
Making an impact
The largest global gold mining operator, Newcrest Mining, has demonstrated the impact technology can have.7 In Australia, over 100 000 sensors have been used to create digital twins and build predictive maintenance models. Newcrest's chief information off icer reports these initiatives saved the company over AUS$50 million during 2018. Moreover, at the Hecla Mining Co. in Canada, an extra hour per day was added to operations through technology being incorporated into machinery and vehicles, reducing downtime and allowing issues to be diagnosed immediately.
Huge advantages have also been seen at Telstra in Papua New Guinea, which has used connected and automated excavators, bulldozers, and excavators to drastically improved levels of safety.8 The deployment of LTE has also delivered significant performance improvements, and is designed to meet the mine’s long-term plan with reliable, fast connectivity with low latency.
Conclusion
As the industry continues to see prices falling and productivity slowing, it is imperative managers have access to technology which puts predictability within their grasp and grants them a degree of control. The Connected Mine, with all its diff erent elements, revolutionises the business of mining, enabling sites to become profitable and more eff icient in their operations. In the future, utilising digital technology will have huge benefits in terms of reducing hazards, improving bottlenecks, as well as combatting other issues. Managers being equipped with deeper insights signals a bright future ahead for the whole of the mining sector, facilitating the best use of assets and employees.
References
1. ‘How digital innovation can improve mining productivity,’
McKinsey & Company, www.mckinsey.com/~/media/McKinsey/
Industries/Chemicals/Our Insights/How digital innovation can improve mining productivity/How_digital_innovation_can_ improve_mining_productivity.pdf 2. ‘Mining Automation Market Size, Share & Trends Analysis
Report By Solution (Software Automation, Services, Equipment
Automation), By Application (Metal, Coal, Mineral), And
Segment Forecasts, 2018 – 2025,’ Grand View Research, www.grandviewresearch.com/industry-analysis/miningautomation-market 3. ‘Top 10 business risks and opportunities – 2020,’ EY, www.ey.com/ en_gl/mining-metals/10-business-risks-facing-mining-and-metals 4. ‘Mine 2019: Resourcing the future,’ PWC, www.pwc.com/gx/en/ energy-utilities-mining/publications/pdf/pwc-mine-report-2019. pdf 5. ‘World-first autonomous trains deployed at Rio Tinto’s iron ore operations,’ Rio Tinto, www.riotinto.com/en/news/releases/
World-first-autonomous-trains-deployed 6. ‘What does the future hold for automation in the mining industry?’, NS Energy, www.nsenergybusiness.com/features/ automation-mining-industry-future/ 7. ‘Leading with Industrial Internet of Things to drive data science initiatives,’ Insight, au.insight.com/en_AU/content-and-resources/ case-studies/newcrest.html 8. ‘Three private LTE deployments in the mining industry,’
Enterprise IoT Insights, https://enterpriseiotinsights. com/20191017/channels/fundamentals/three-private-ltedeployments-in-the-mining-industry