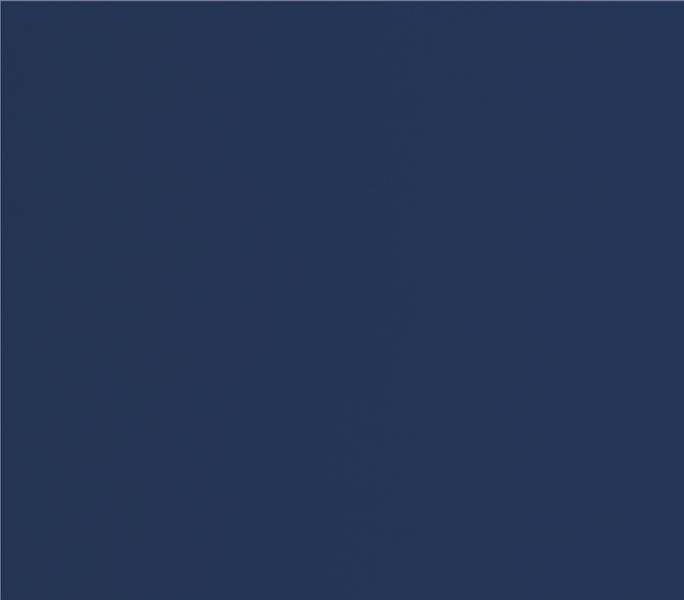
7 minute read
Making The Right Choice
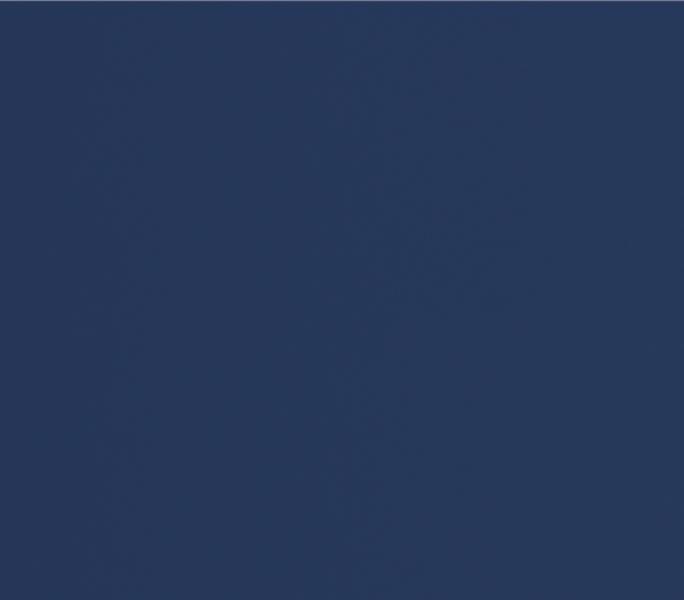
Daniil Victorian, Doofor Inc., Finland, addresses how smart investment plans and the implementation of LEAN principles can help mining companies acquire the right mining equipment for them.
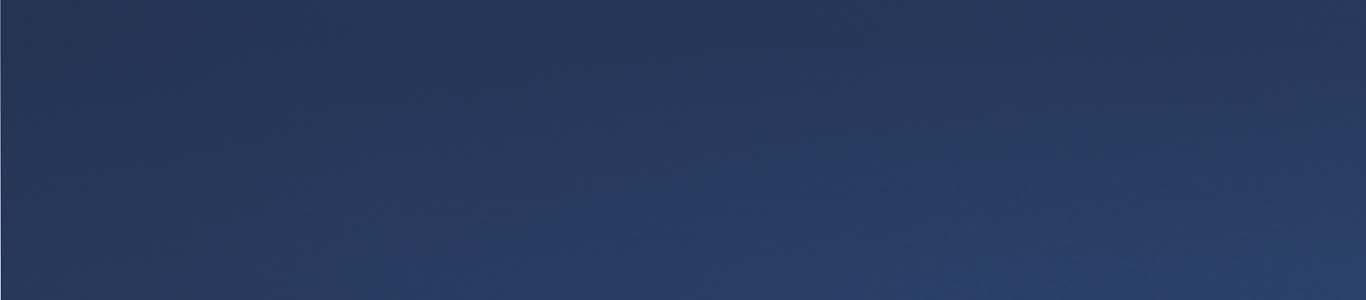
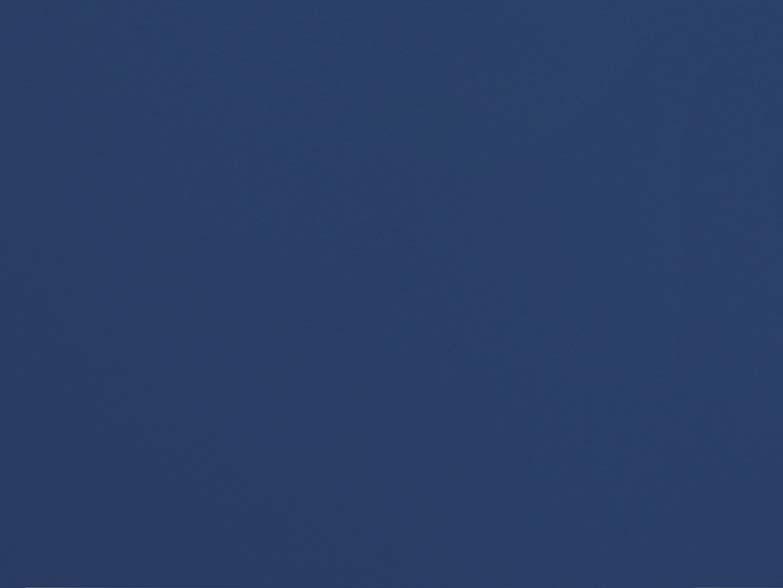
Quarrying is comparatively a simple process; however, it is open to several issues pertaining to logistics, technology, sustainability, and financial performance.
Financial performance
The latter is on the mind of every investor, owner, shareholder, and stakeholder that associates themselves with the mining industry. Cost-eff iciency is the key ingredient which drives the decision-making process for many end-users worldwide. When it comes to acquiring new mining technology, feasibility of use and operator comfort is oft en discarded, in order to preserve a greater return on investment (ROI). Purchasing mining machinery is a long-term investment, in which capital and operating costs are both taken into consideration. Capital expenditure typically includes machinery costs, as well as the cost of transport and deterioration (residual value). Operating expenditure is comprised of fuel costs, maintenance costs,
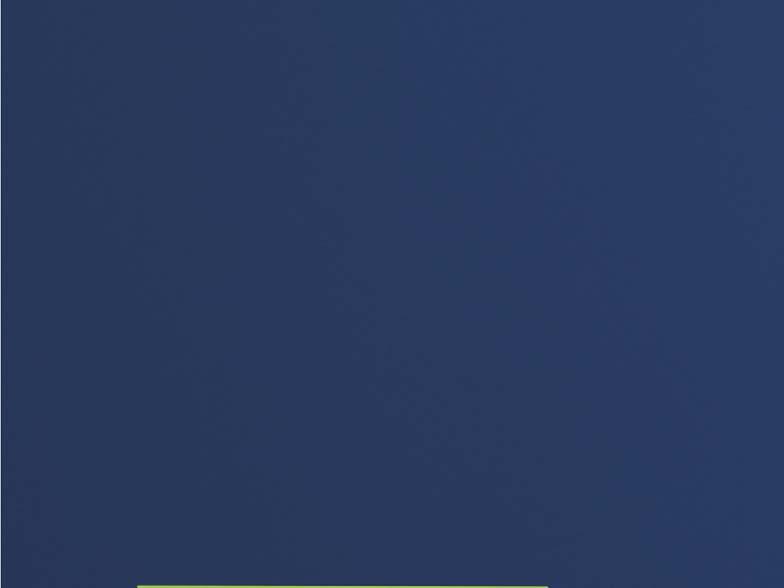

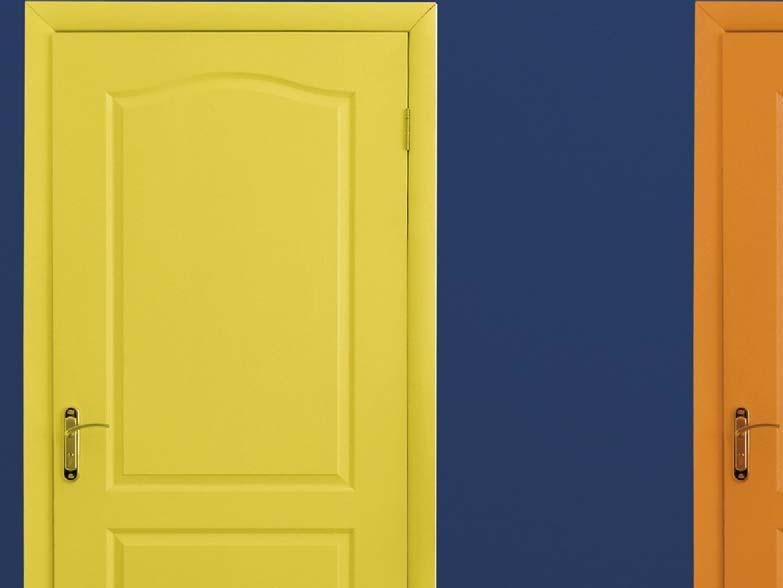

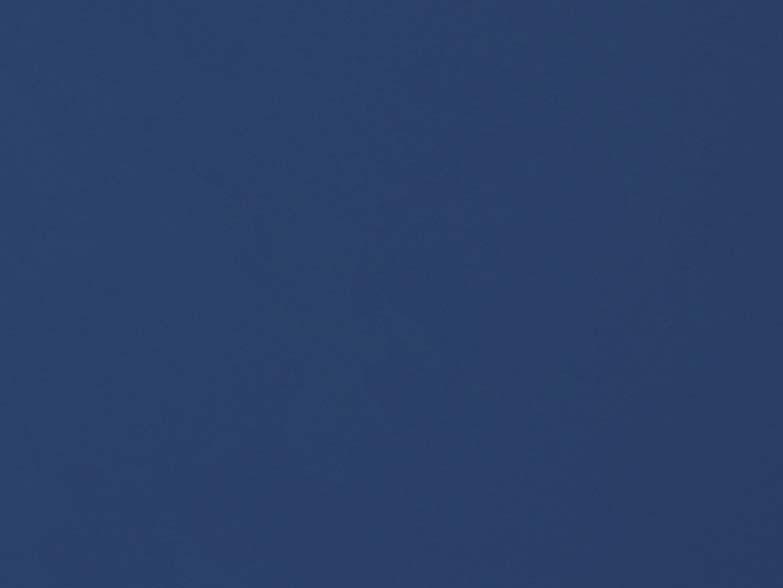
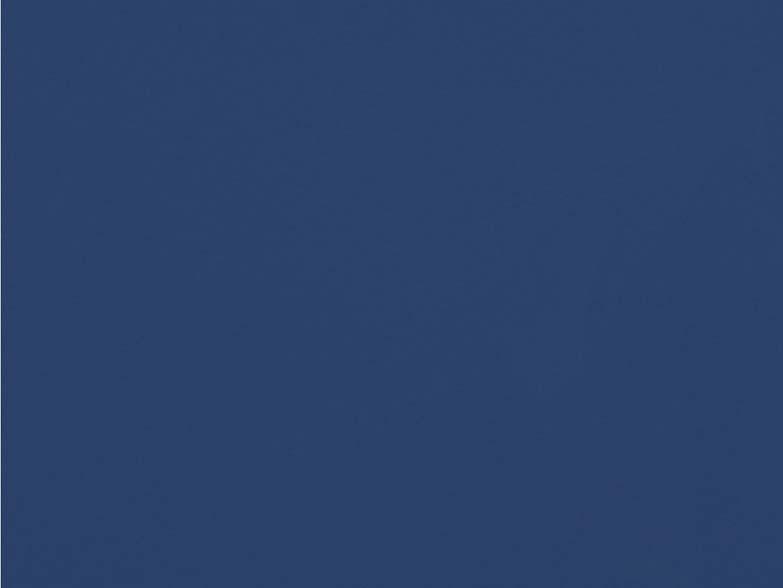
and operator costs. What oft en happens is an attempt to reduce initial capital expenditures in the hope of low operational costs, but this is rarely the case. By saving money in the short-term, companies are inadvertently accepting an economic pitfall, or ‘stepping into monetary quicksand’. There is a reason why newer technologies cost more than their older counterparts.
Although buying the newest, most advanced technology on the market is guaranteed to reap positive results, it is first crucially important to determine exactly what is required. By taking into consideration the size of the quarry and scope of machinery, operators set themselves up to make the right choice and achieve optimum performance. This process is comparable to a well-known car manufacturer with LEAN practices rooted at the core of their production. By operating at optimum capacity and utilising just the right amount of resources, the best possible results can be achieved.
Business suitability
The next step is business suitability. Aft er determining what type of machinery is required, it is important to consider the following elements: Spare parts availability. Mechanical suitability of equipment. After sales service.
If the stars align, i.e., the right product has been chosen from a suitable supplier, a sound financial decision has been made.
To facilitate this choice, WORD Rock Drills have developed an easy-to-use hydraulic quarry drill system that off ers maximum productivity and cost-eff iciency. The ‘RAPTOR’ has been designed with the operator’s comfort in mind and is quickly becoming the drilling solution of choice for many end-users across the US, as well as other countries.
The marginal income of a quarrying business is relatively small, therefore it is vital that the acquired equipment has good ROI potential and is financially sustainable in the long-term. The size of the quarry and the scope of machinery are economically interdependent. WORD Rock Drill’s RAPTOR is a universal solution for quarries of all sizes. In terms of payback, the RAPTOR off ers significant savings.
In addition to being economically eff icient, the RAPTOR provides a comfortable, temperature-controlled cabin for the operator; removes over 35% more airborne dust with a powerful dust collector system; allows the operator to set up drilling parameters from inside the cab; and operates as a self-contained, mobile unit, which does not require any external power source.
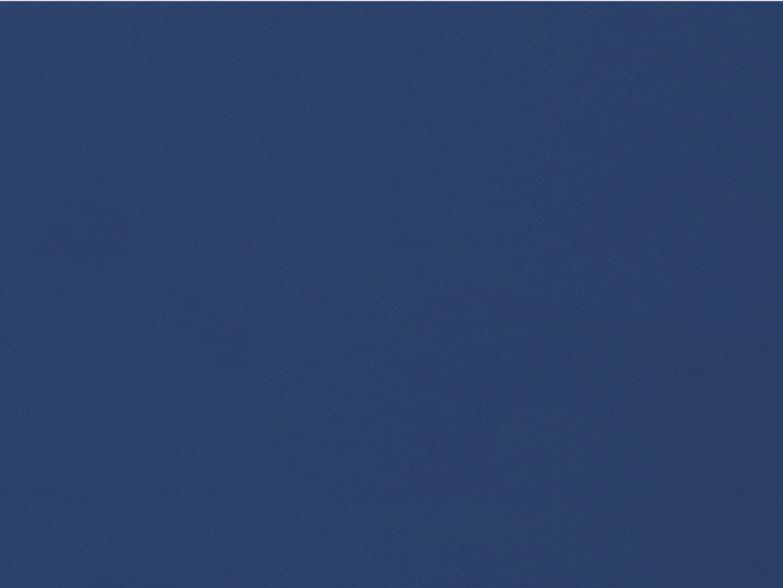

Operational expenditure
A big chunk of operational expenditure for mining machinery comes from labour costs. Machinery that involves a complex control system will be more labour intensive to run and, in turn, will require personnel with unique skill sets that are diff icult to come by. With a system that is user friendly and easy-to-operate, one does not have to worry about the challenges faced from having limited knowledge or expertise. With features such as the ‘SMART shield’ – which detects drill bit and rod breakages, loss in air pressure and blow-outs of the stone – human error can be dramatically reduced.
The SMART shield contains a variety of intelligent sensors, wired by CAN bus technology, to ensure eff ective communication between electrical components, such as: relays, sensors, and encoders. In combination with a camera
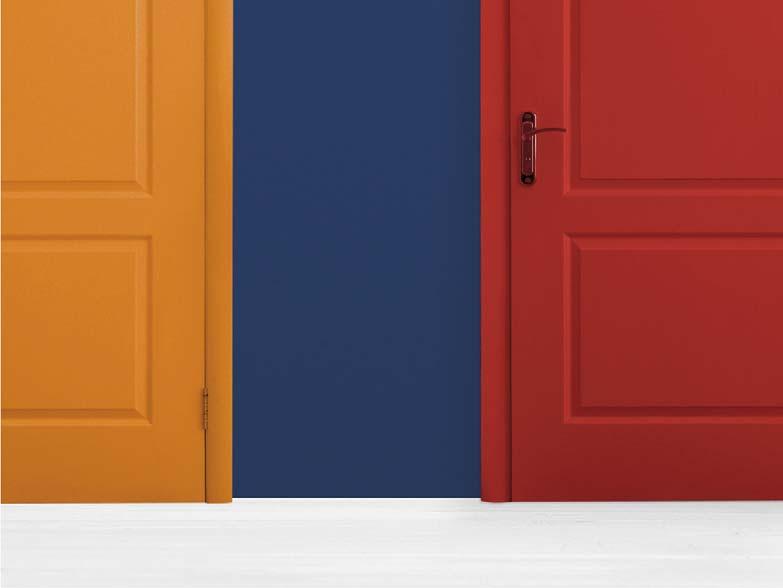
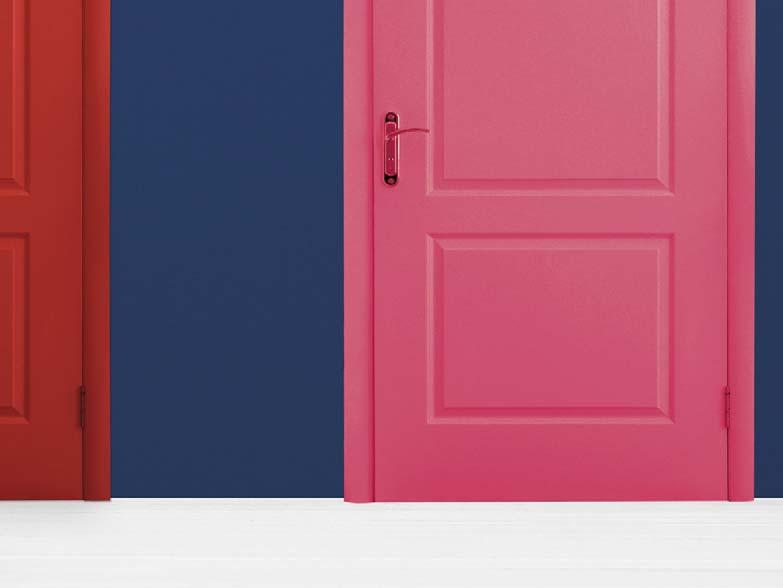
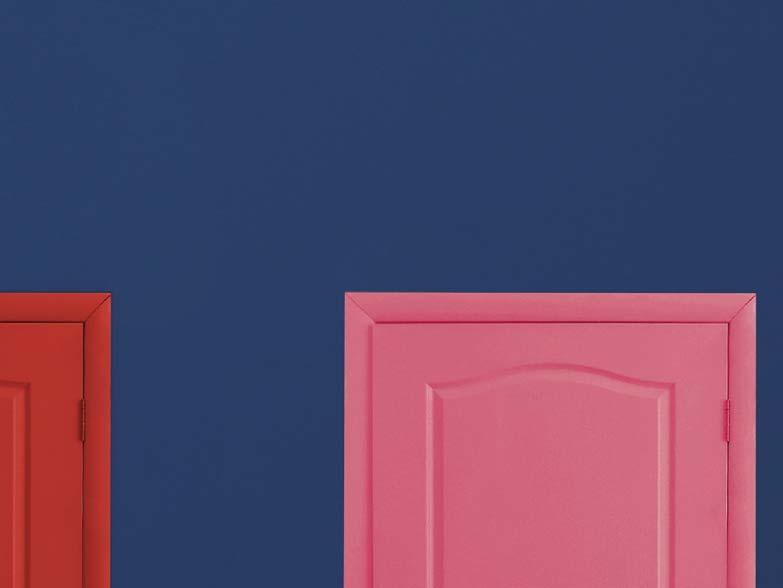
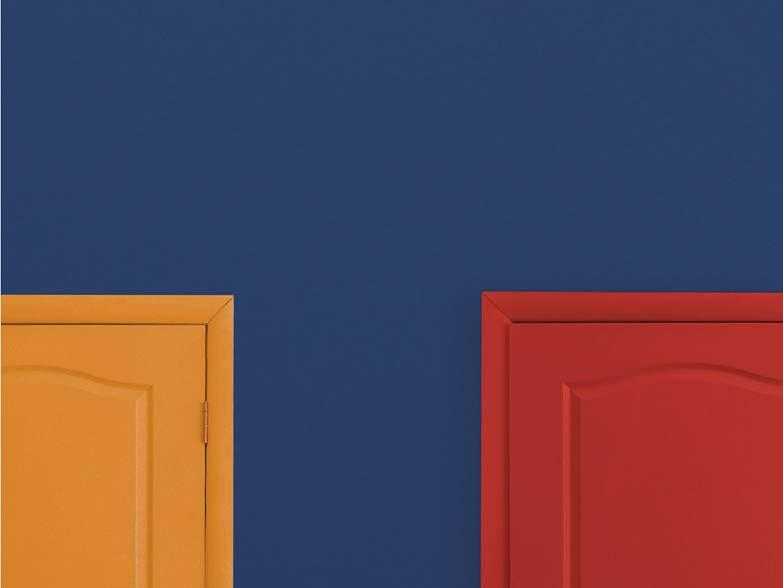
alignment system, which utilises a 20˚ surface level, the operator can drill safely and uninterruptedly, without ever needing to leave the comfort of the cab.
Another key feature of the RAPTOR is flexibility. With a quick coupler system, the front loader attachment can be changed as and when needed. All RAPTORs are equipped with 7/8 in. x 4 ¼ in. steel tapered drills and have 118 in. vertical and 110 in. horizontal hammer travel. Drill hole spacing is programmable to the stone type with three, quick-pick options on the remote: 4 in., 6 in., and 12 in. One can also cycle between diff erent depth configurations, depending on the type of stone being drilled, off ering the option to make on-the-go adjustments.
The high-performance dust collection system is another unique selling point of the product. The dust collector system consists of four major components: vacuum, air compressor, rock box with trap door, and a hydraulic fluid reservoir. The reasons why it is so special are two-fold: All pins and bushings utilise high-quality PTFE bearings, which eliminate the need to use grease, along with hydraulic hose assemblies designed to meet ISO 4406 cleanliness standards. Eliminating the need for grease significantly reduces incidents of stone dust sticking to wear surfaces, resulting in longer component life. Additionally, the operator does not need to spend time greasing the pins, making it, once again, a cost-efficient and time-efficient solution. The on-board compressor is a ‘VMAC Predatair’, which is lightweight, compact, and capable of delivering 100% duty cycle. The use of advanced, digital technology allows for reduced fuel consumption and heat generation with the use of ‘stand-by mode’. When there is no demand for air, the compressor will enter ‘rest mode’ and wake immediately when air is required. An LCD control unit allows operators to monitor compressor oil temperature, air pressure and system hours, making it possible for on the spot analysis to be conducted. Over-temp safety sensors protect against extreme weather conditions and ensure that hydraulic oil is at safe operating temperatures.
The drilling is performed using highly durable and eff icient Doofor DF530X hydraulic rock drills. The DF530X rock drill is designed to maintain optimal percussion pressure at high penetration speed. It is suitable for demanding dimensional stone and quarrying projects, as well as general excavations. Inside the rock drill, a patented trapezoid piston shape enables the piston to generate higher frequency rates and minimise frictions between steel parts. The results of this are good drill tool life and an overall smoother drilling process.
Doofor’s DF530X continues the RAPTOR’s dedication to flexibility by having a compact and modular design, providing the user with plenty of customisation options and ‘problem free’ maintenance. This rock drill can be equipped with a variety of rotation motors – i.e. 8 cc, 12.5 cc, 20 cc, 32 cc, 40 cc, and 50 cc. This, in turn, gives the user more control over the desired rotation speed and torque.
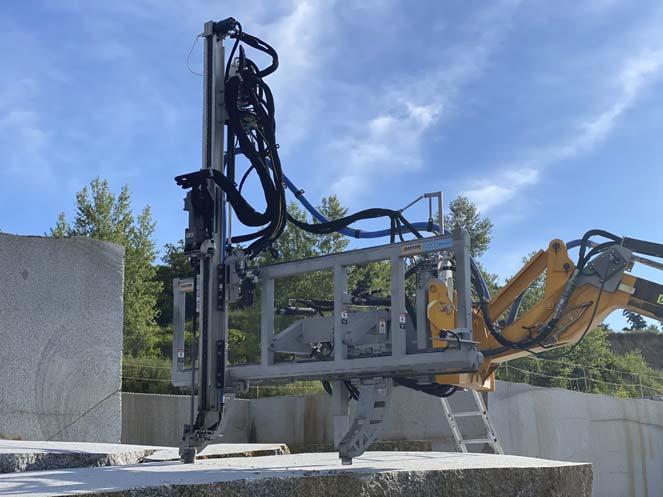
Figure 1. Front loader attachment with SMART shield and Doofor DF530X rock drill.
Figure 2. A side view of the RAPTOR with dust collector system visible.
Figure 3. Operator view inside the RAPTOR cabin.
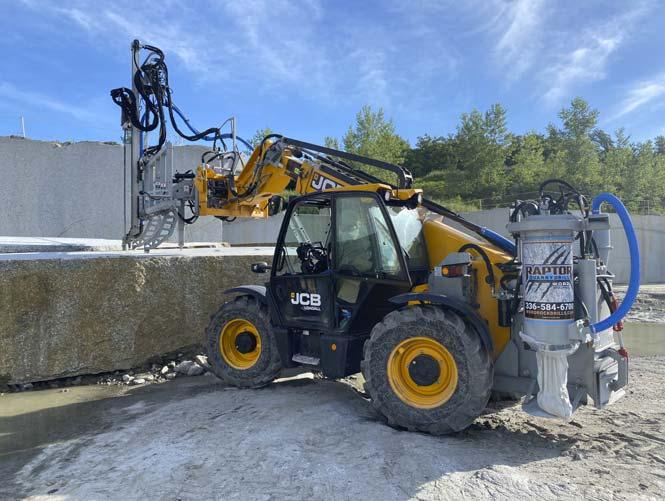
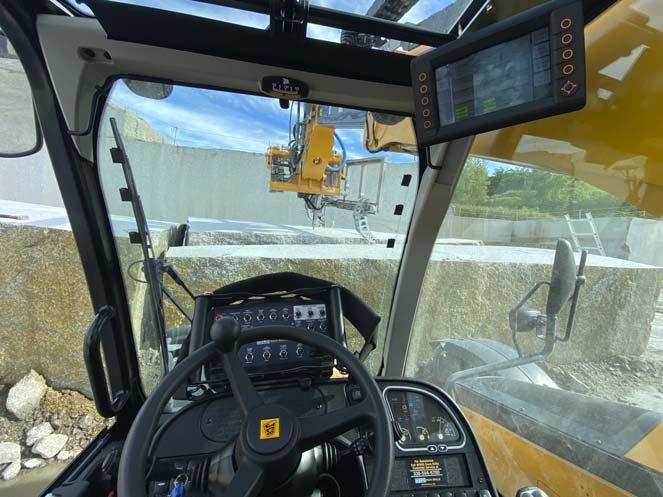
Conclusion
Currently, many mining businesses are seeing a spike in turnover and profitability, due to a rise in fiscal stimulus programmes adopted by governments to support local economies in response to the COVID-19 pandemic. Such businesses should be encouraged to make smart investment plans and implement LEAN principles into their purchasing behaviour. Choosing the right supplier and the right product can be an arduous task, but, once done, it will save time and money in the long run.