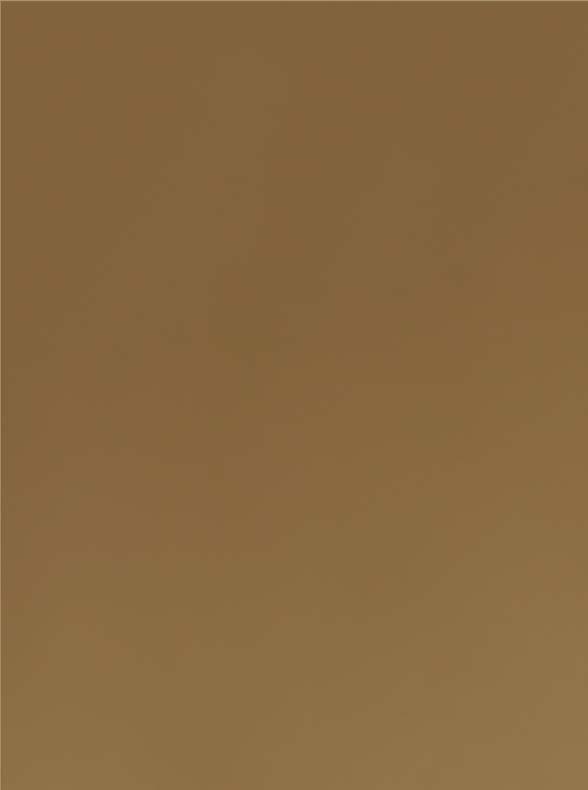
7 minute read
Storage That Lasts
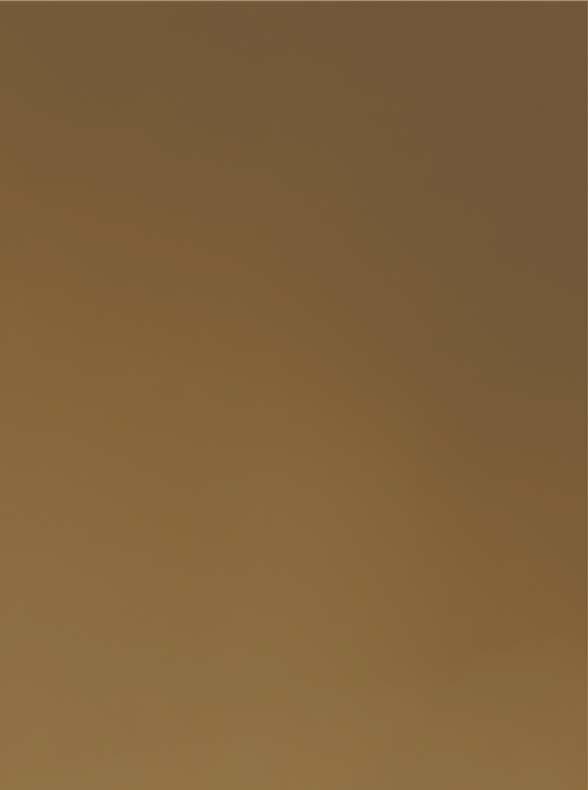
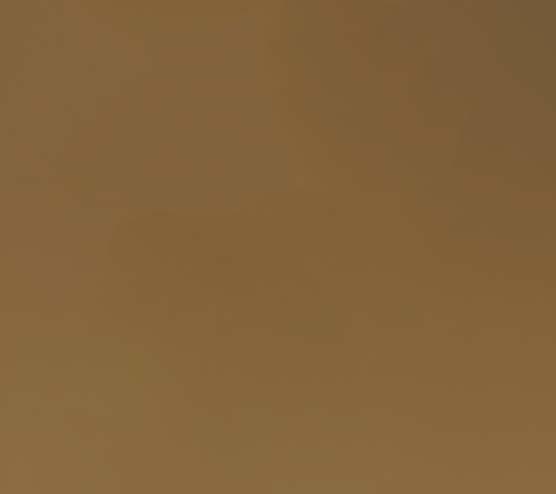
Rebecca Long Pyper, Dome Technology, USA, outlines how domes beat fl at storage in longevity, strength, and capacity.
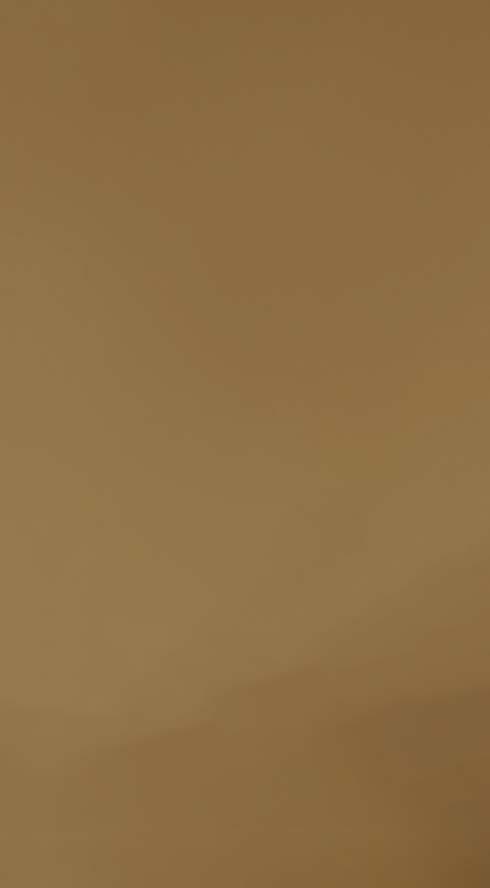
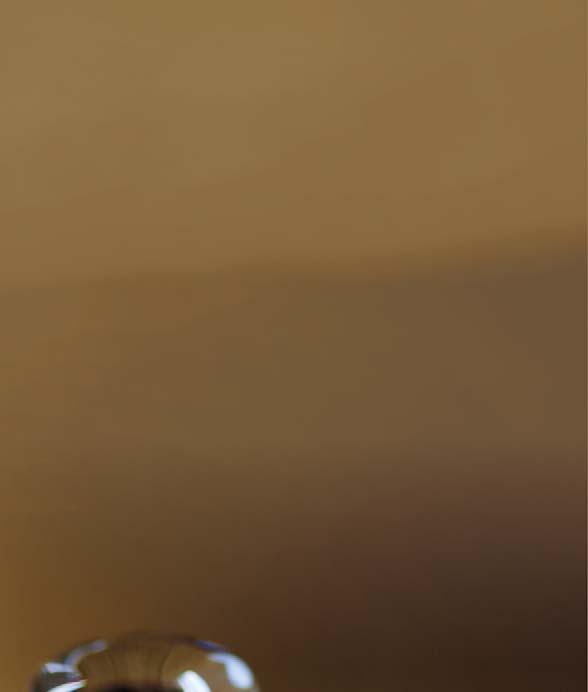
Durability; innovative foundation systems; more storage in a smaller footprint; and simpler product loading and unloading. These benefits have been enticing coal, copper, limestone, molybdenum, potash, bentonite, and other mining companies to choose dome storage for decades. And with systems increasing in sophistication all the time, companies who select a dome invest in longevity too.
Two bulk-storage options dominate the mining industry today: domes and flat storage (warehouses). When choosing a storage facility, companies should consider necessary capacity, site conditions, stored-product requirements, and features built into the two options.
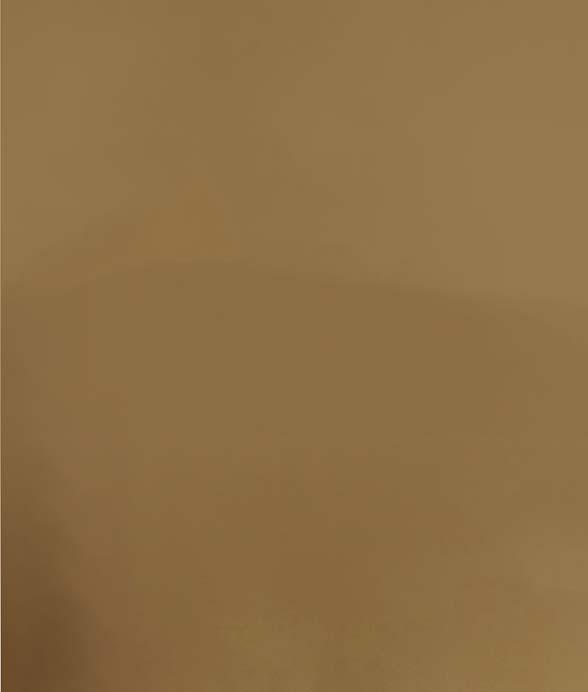
Space requirements and storage ability
The first Dome Technology domes were hemispherical – they required a large footprint, and their diameter was greater than their height. This model is still the go-to option for mining storage, best where capacity is king and land is inexpensive.
Domes store a large volume in a smaller footprint, stacking product deeper and taking up less property at a site. While some customers require three to five warehouses to store product, a single dome will likely accommodate the same amount of material. The double curvature of a dome lends itself to the ability to build up,
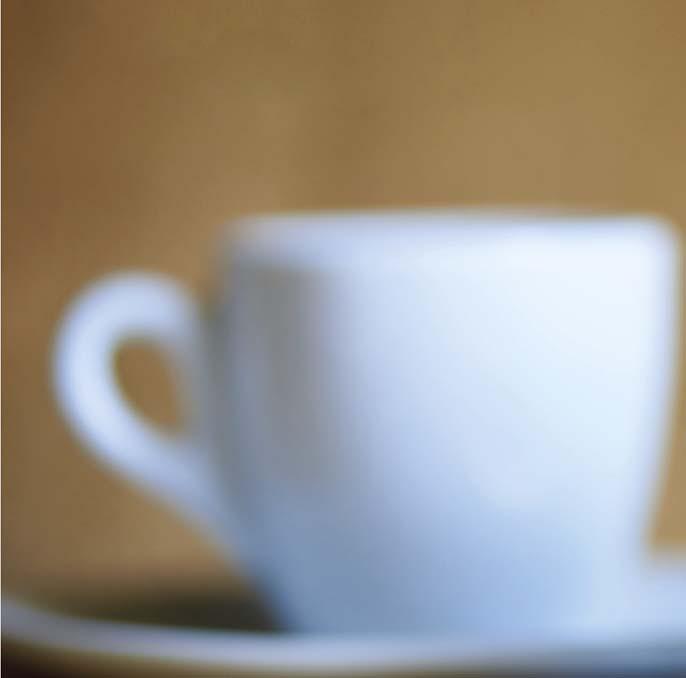
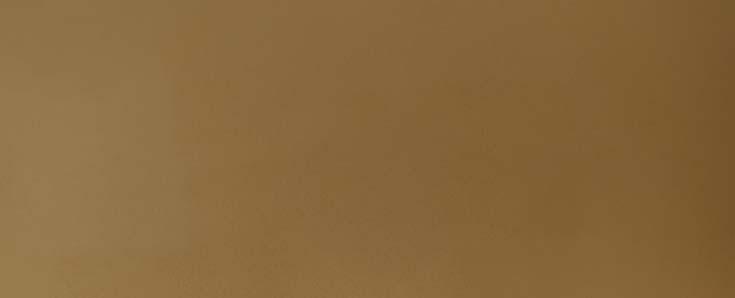
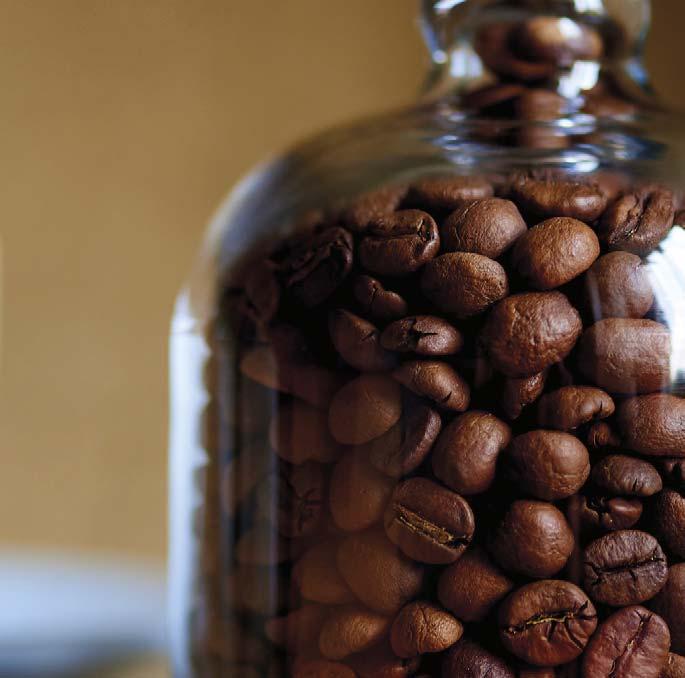

rather than out, and the curve provides strength at all points of the structure. Because domes are monolithic structures, any forces interacting with the dome are distributed evenly throughout the shell, rather than being concentrated to weak areas like corners or joints. This gives the dome a longer life cycle than a steel structure. Also, the dome’s ability to sustain large loads at the apex means ample support for head houses, fill conveyors, and dust-collection systems.
Flat storage in general requires a larger footprint since product is usually stacked a maximum of 20 – 30 m deep. Customers can expect a warehouse to utilise 100 – 150% more area than a dome holding a similar amount of product. Each dome is also planned with the stored product in mind, and thus maximised for optimal capacity and product protection.
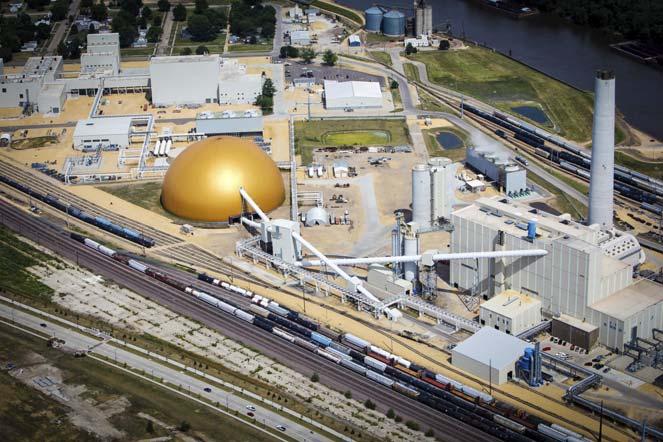
Figure 1. In a dome, product can be stacked deeper than in flat storage. The hemispherical dome like this is still the most popular dome model for mining products.

Figure 2. The Climax Molybdenum dome was designed to interface with existing infrastructure and was built in just four months.

Figure 3. ADM chose a dome for its site in Clinton, Iowa, based on better product protection. Case study: Climax Molybdenum
Climax Molybdenum needed ample storage at its Leadville, Colorado, mine, but there was a catch: in order to make this project economically feasible, the new structure had to utilise an existing conveyor system and be robust enough to hold the weight of the conveyor, headhouse, and expected snowfall.
After seriously considering another type of dome, a monolithic concrete dome from Dome Technology was selected. A dome capable of storing 130 000 t was built to accommodate the existing conveyor system, which was reassembled to feed directly into the apex.
Cost-savings, then, were two-fold: the customer reused an existing conveyor system, and additional costly support systems were not required to share the load. The dome’s strength provided another advantage. With its location in a snowy clime, the structure was engineered to surpass a snow load of 5.27 kN/m2 (110 PSF), while supporting the apex mechanical load. A different type of free-span, column-free storage facility could not support a similar load on its own.
The project came with other challenges too. At an elevation above 3353 m (11 000 ft), weather conditions suitable for building would last just four months of the year. Since a dome’s rapid construction process is ideal for quick construction, project managers and crews maximised workdays to expedite construction and complete the job within the amount of workable time.
Dust control was another concern, but the dome’s seamless storage capabilities easily contained the product, reducing dust throughout the site and the minimising the environmental impact.
Foundations
Flat storage is often built using concrete walls topped with a wood or steel structure. Because flat storage is constructed using different materials, any differential settlement will cause the ‘pieces’ to separate. A deep foundation is often necessary unless the structure is built on firm ground.
As dome engineers have become savvier, foundation options have increased. A dome’s strength and geometry provide a tolerance for differential settlement – an important consideration for heavy materials.
Geotechnical engineering and site analysis ensure proper foundation performance. In contrast to a flat storage, the dome is continuously supported by the ring foundation, as a result some differential settlement does not adversely affect the structure, where some
differential settlement in a flat storage is generally not acceptable.
In a dome, sometimes a ringbeam is the only necessary foundation system, and customers can save millions when a dome’s deep foundation is reduced or eliminated. However, when more stability is required, companies have options: For sites with preferable or acceptable soil conditions, a ringbeam provides a shallow foundation alternative. Where applicable, the frost depth will determine the ringbeam’s depth, but usually the ringbeam is inserted 2 – 4 ft into the ground. For sites where the top 6 – 8 ft of ground is of less-than-ideal material, crews excavate the material, replacing it with controlled structural fill. This model allows for some settlement, but the amount will be within tolerable parameters for a dome. When the top 15 – 50 ft of soil is questionable, stone columns are often an option. First, crews use an auger to remove earth from a hole with a 30 in. dia. until a more stable, soil-bearing layer is reached.
Rock then fills the hole and is compacted, increasing the stiffness of the soil below the dome.
When deeper foundations are required, other systems are available.
Product protection
Higher-maintenance products like coal require special attention. Dust-management systems are always an option with domes, and the truss-free interior means no surfaces for dust to accumulate on. When a coal facility is planned, engineers discuss the best approach for explosion venting.
Case study: ADM
Better product protection was the main reason ADM chose a dome for its coal cogeneration plant in Clinton, Iowa. According to ADM Clinton Cogeneration's Plant Manager, Kevin Duffy, ADM has always stored coal inside some sort of structure to manage dust, but selecting a dome from Dome Technology was an improved means of maintaining coal quality. The dome’s seamless construction protects the coal even during inclement weather events. A dome’s capacity is also advantageous in supplying a way to achieve desired throughput from a single storage structure, rather than requiring multiple silos.
Dome Technology competed for the project against a company providing aluminium or steel domes. In the end, ADM chose a steel-reinforced concrete dome from Dome Technology, as the company could offer a viable solution that was significantly less expensive than the alternative.
ADM liked the dome option because it did not have any beams or trusses for dust to collect on. Not only does this ensure safer operations within the dome, but it will help ADM to be a better neighbour to nearby communities. Domes effectively contain dust and help businesses meet local regulations, while subsequently fostering good relationships with local communities.
The dome was fixed with a circular stacker reclaimer that provides even filling for coal. The advantage with a stacker reclaimer like this is the ability to inventory stored product by age. This helps companies control their inventory and where they stack and reclaim product from the pile.
The project’s success led to Dome Technology securing another ADM project in Columbus, Nebraska, for a dome of similar size storing the same type of coal.
Design-build services
Design-build services address engineering, construction, and all related systems at the design level. The result is greater simplicity, assurance, and value from start to finish. When a single party is chosen to provide the entire project, costs go down. When the plan changes, it is not taxing to spread the word because everyone who needs to know already does.
However, sometimes changes are not necessary at all. When one team oversees every element, it is easier to spot gaps. The result is a turnkey facility with components more likely to run seamlessly because each was planned with the others in mind. Turnkey construction is about more than combining individual parts to create a cohesive whole, it is really about building trust and empowering the customer.
Hexagon PPM transforms your mining operations with intelligent technology, operational excellence and improved productivity.
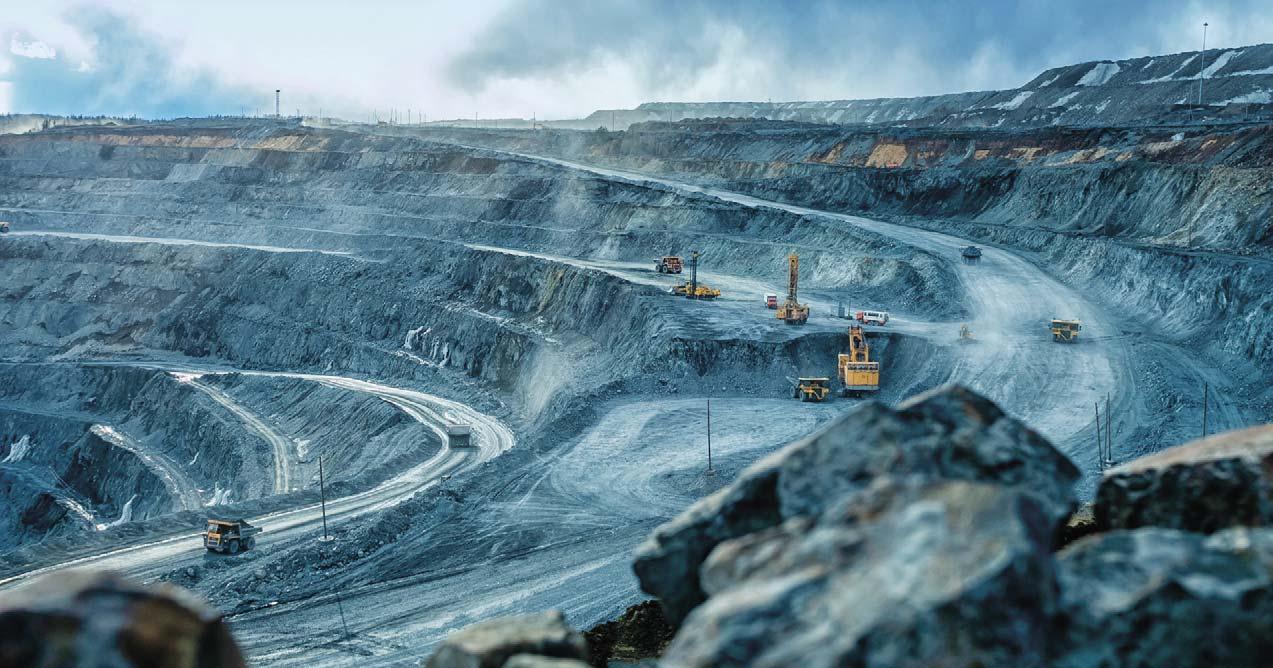
| Visit bit.ly/HexagonOpsExcelMining