
11 minute read
A Digital Two-Way Street
Mark Roberts and Rahul Suhane, Maptek, outline how digitalisation is the key to unlocking the value of drill and blast, and how all sources of data can be tracked upstream and downstream and integrated into a single source of truth.


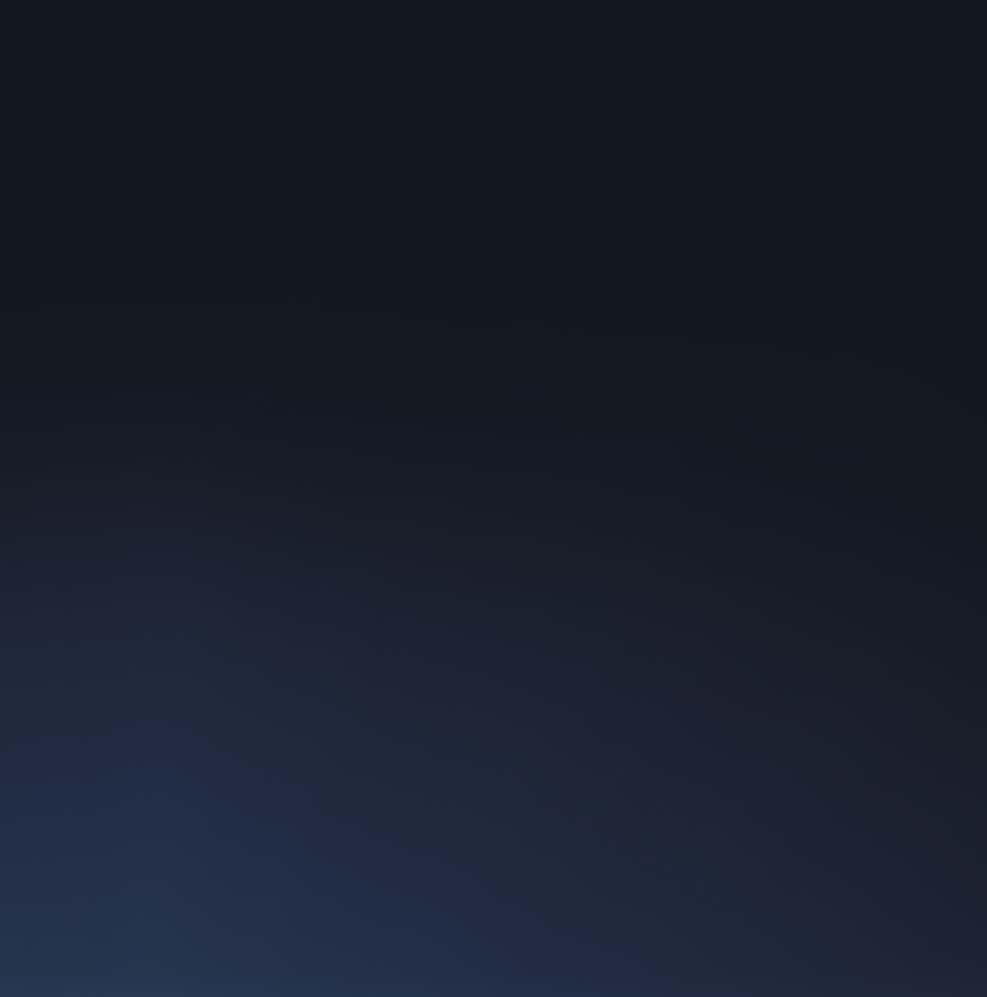
Mines operate around productivity, performance, and profit. Safety and certainty are key drivers for continuous improvement. The need to accurately track and reconcile operational performance across the mining value chain is driving a revolution within the industry, as awareness grows that success hinges on an understanding of the impact of various factors at specific stages of resource recovery.
Drill and blast is an important value driver for mining operations, representing approximately 20% of the cost per tonne, but it is not an exact science. Rather, it is mostly an empirical exercise, where operations learn from previous experience and each site develops its own understanding of how its geology behaves and reacts to explosives.
Digital systems are important in providing the necessary feedback loop for continuous improvement – helping operations to carry out drill and blast activities smarter and safer. Maptek has found that, on top of refining day-to-day drill and blast, digital systems such as Maptek BlastLogic are improving associated processes and opening doors for innovation in the field.
Why digital?
Many existing methods are a one-way street. Digital systems make them two-way, providing the feedback loop needed to improve outcomes. This improvement can come about manually, where engineers look into past data and make adjustments, or it can arise from applying predictive analysis with new machine learning paradigms, which look into past data and outline what is likely to happen in the future.
Digitalisation also provides near-live information on the bench to drive compliance to plan. Without the data feedback loop there is nothing to learn. An operation can still run but there is unlikely to be ongoing improvement, and latent value that could have been unlocked gets lost in the dirt. Losing as little as US$1/t makes a huge impact when considering mines that ship millions of tonnes per year – US$1/t saved, or extracted, obviously means millions of dollars on the bottom line.
Digitalisation facilitates better integration between drill and blast and upstream information, such as resource models and mine plans, and boosts reconciliation of downstream processes, such as: dig rates, crusher throughputs, and vibration events.
Recording information on sheets of paper, which get filed never to see the light of day again, is rightly becoming a thing of the past, as digitalisation brings greater insight, transparency, and accountability.
Taking into account all of these considerations, it makes sense to acknowledge that data is king, with connected digital systems providing a single source of truth to work from.
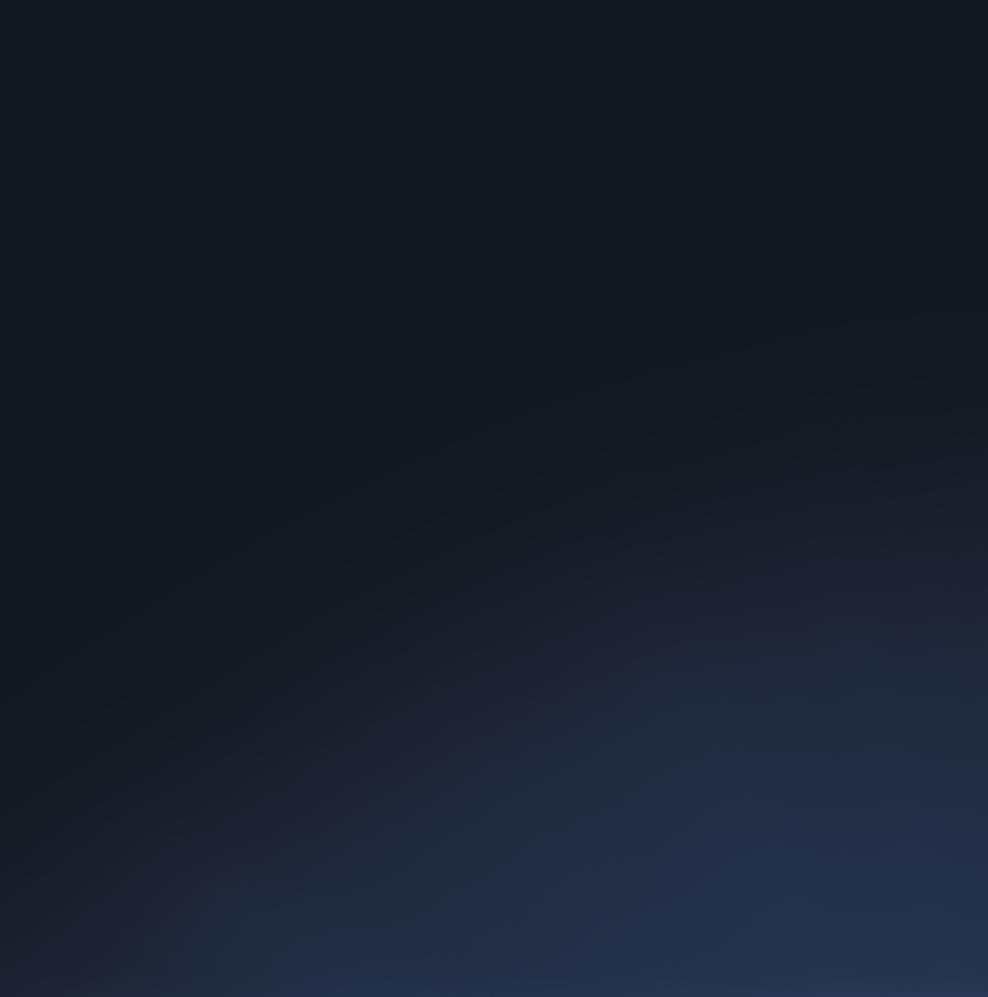
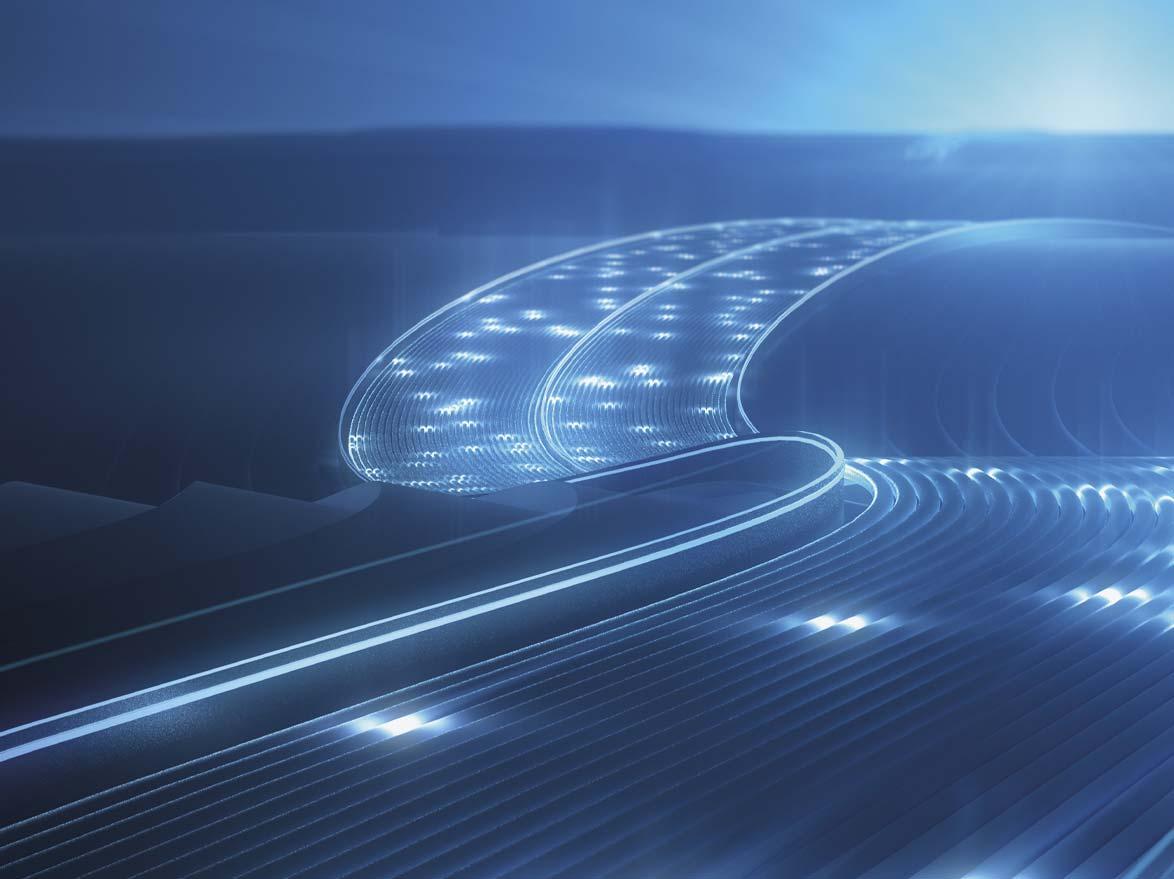

Unlocking value
Not every operation uses digital methods in the same way, but the one thing the operations using BlastLogic have in common is that they are unlocking more value by doing so.
Within the industry, there are many diff erent value drivers. Many operations find they can get quick wins on the board through going digital. For example, in the first week of deployment, a mine was able to simply spatially identify and rectify the fact they were overloading holes by 20%.
Some mines have an obvious problem, with diff iculty around accurate charging and an inability to track performance against design. Getting a handle on their drill data is a primary reason they choose the drill and blast design and reconciliation system.
At mines where the drill and blast processes are poorly defined, the design and the execution are not aligned. When planning teams and operational crews are not on the same page, it can result in poor blast outcomes, compliance, and quality control.
These outcomes dictate the need to do things better, and the industry is now alert to systems that allow them to do so. However, operations must consider how well the new applications will integrate with their existing processes or systems, and how to properly implement change management.
It is rarely a case of ‘one size fits all’. When it comes to BlastLogic, operations have similarities and diff erences in how they deploy and support the system. Many use the system itself as the single source of truth. For others, it is a tool in coordination with other systems to feed into a data warehouse, which forms the single source of truth. For example, customers employing autonomous drill rigs achieve a very low as-drilled error rate, and therefore do not use BlastLogic for automatic validation of drill accuracy.
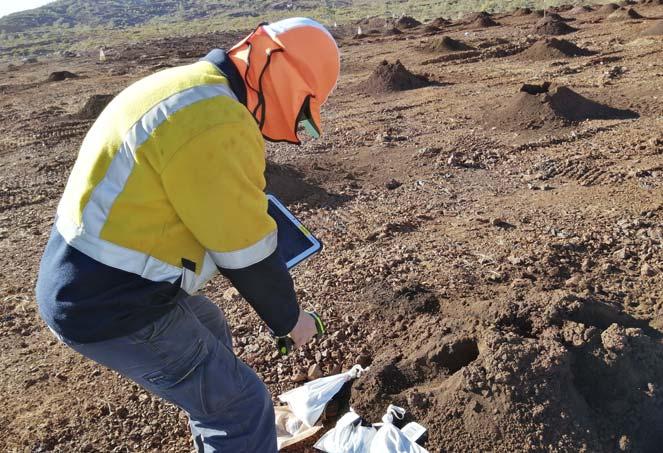
Beyond the average
Figure 1. Sampling crews can conduct blasthole sampling with the BlastLogic Tablet linked to a portable barcode scanner, with sampling records synchronised with BlastLogic Server for analysis and reporting.
Looking solely at the aggregation of performance across an operation can potentially mask issues, especially with drill and blast. On average, the data may indicate that performance is within specification, so it looks like everything is running fine. At a more granular level, such as the explosives deck, a blast may contain overloaded and underloaded sections. Left unchecked, this undermines the productivity, cost, and safety drivers of a mine. Digital systems make it easier to identify trends and watch for anomalies. This is where the adage of a picture conveying a thousand words holds true. For example, a digital heatmap generated in BlastLogic allows simple correlation and visualisation of where the issues lie. Highlighting the data that is out of specification and finding the root cause can help eliminate blame-shift ing across teams. It also brings the issue to light in-shift , where updating charge rules or plans, for example, can actually make a diff erence, rather than waiting for end-of-period reporting. Technology is the enabler to tighten this coordination and, while it does not always happen immediately, systems such as BlastLogic help align teams in a manner that is mutually beneficial. Personnel can move away from demarcation of roles and into a true teamwork model, with hard data trumping Figure 2. Digital data flow supports decisions in drill and blast in response to dynamic real-world opinions and guiding conditions. best practice.
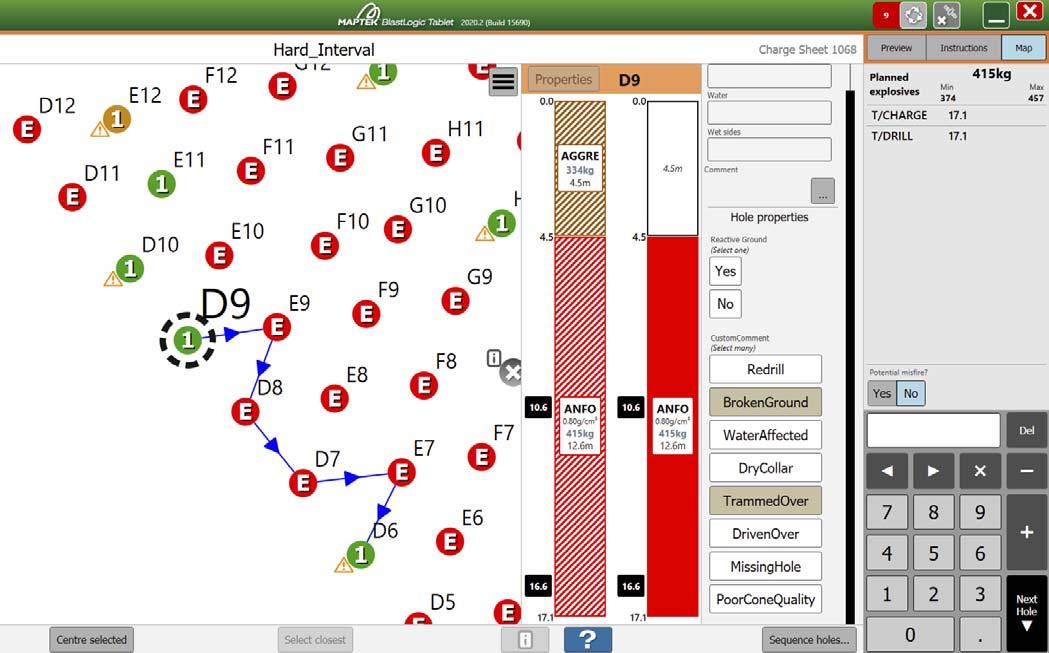
Change management
One common factor which can create resistance to adopting a new digital system is the perception that personnel performance is being audited.
It is therefore important that the system off ers benefits for the day-to-day field operators. Going digital means operators have the maths done for them on the fly. Systems, such as BlastLogic, recalculate a charge plan based on diff erent hole geometry, calculate a top-up deck, or work out how much explosive to use when a hole requires diff erent product to design, based on site rules. Making these jobs easier helps achieve buy-in from individuals and teams, driving better overall results.
This pull-factor for operators to use the system to record data closes the feedback loop with engineers, who can then start to really understand the eff ectiveness of their designs. Engineers can also see first-hand how accurately their designs were executed along with the blast outcomes.
For example, when measuring vibration rates around heritage areas, they can pose questions such as: Was it exceeded? Did operators honour it? In protecting the heritage area, was a good enough fragmentation achieved in order to avoid secondary blasting? Answering these questions informs the learning through experience that epitomises the empirical science of drill and blast.
BlastLogic fits into the complexity of mining operations. Users see the benefits on the ground and how it helps them make better decisions in a streamlined way. ‘If this, then that’ scenarios are simply captured and communicated, removing the clunkiness of paperwork.
Seeing the bigger picture
Many customers are now pushing the envelope in terms of how digital visualisation can drive safety and eff iciency.
Data analytics and reporting teams are able to create a web interface showing a map overview of working mine areas and overlay it with information based on the status of drillholes and data, such as 3D exclusion zones. This contextual schematic informs other functional teams of the drill and blast activities near infrastructure, such as railway lines. Coordinated planning of blasting times with train schedules ensures correct timing to minimise disruption to product movement and the impact of blasting on critical infrastructure.
Such planning is complex, time consuming and near impossible to display clearly using non-digital methods.
Beyond drill and blast
A digital approach proves valuable for processes complementary to drill and blast. For example, BlastLogic can now be used for geological sampling of drillholes. While not a drill and blast function as such, there is a synergy with drill and blast because it is a form of short-interval control to identify holes available for sampling. Samples are recorded using BlastLogic and then

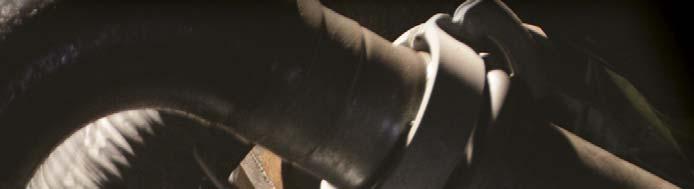
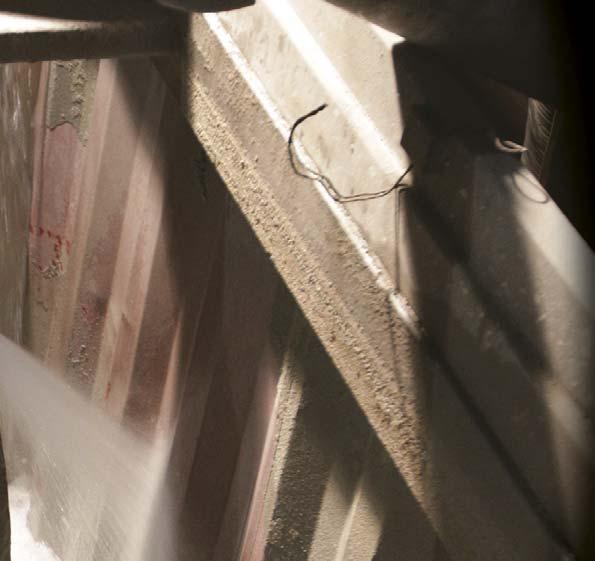

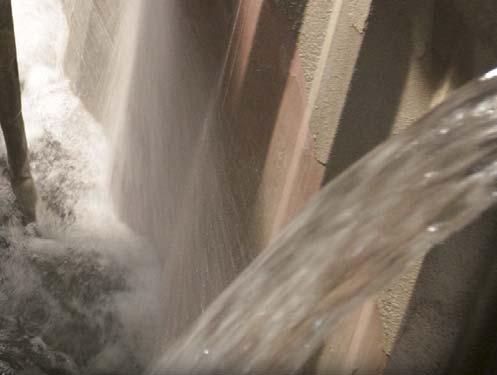


flagged as being ready to be passed back to the drill and blast crews to continue the quality assurance/quality control (QA/QC) or loading of holes. BlastLogic's ability to be customised for such augmented cases allows mine sites to be eff icient, with use of a single system and a data collection point rather than maintaining parallel systems acting on the same data.
Another example is managing geothermal risk, where a specialist team responsible for measuring and tracking hole temperatures may collate and interrogate the data using the BlastLogic Tablet and analysis tools.
On bench integration
Integrated drill and blast management systems and mobile processing units (MPUs) are now available to streamline processes and increase the integrity of data collection. The BlastLogic Tablet communicates directly with MPU or truck control systems.
This serves as an important first step in holistic digitalisation from the mine off ice to the bench. The explosive deck to be loaded is selected and sent to the MPU control system, which loads the hole. Operators no longer have to manually enter the amount of product that goes into the hole into the truck control system. Removing the manual data entry step means higher data integrity and minimises the risk that the data is not recorded at all, due to the operator being distracted or too busy.
While this automation is important for some customers, Maptek is now exploring advancing MPU integration functionality to include additional MPU data that is of value to be digitalised for analysis and reconciliation. For example, open cup density samples – a fundamental QA/QC check for every MPU load of explosives. This is an even more granular level of data, and is important because if an MPU is out of calibration it may be loading the wrong mix of product, heightening the risk of fume, fly rock, and vibration issues.
There is unlimited potential for improving processes through data-driven decision making, facilitated by digitalisation.
Changing the game
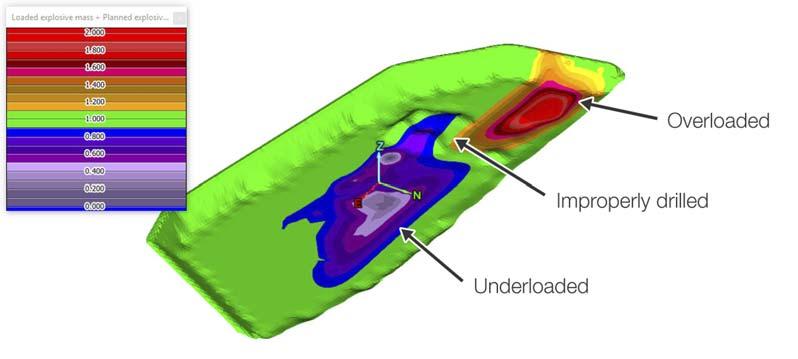
Site practice for generating a charge design has traditionally been based on rule-of-thumb and gut-feeling, followed by time consuming checks to manage confinement. Adopting a digital system lays the foundation for mines to simplify and optimise the process through custom scripting. An example of digitalisation solving complex problems can be seen in Maptek’s work using scaled depth of burial calculations (SDOB) for coal customers. The company designed an algorithm whereby desired SDOB values are input to determine the correct explosive position to achieve the user-specified confinement. The algorithm-based process performs complex iterative calculations for the engineers, so that they can make high value and eff icient decisions. Figure 3. On screen visualisation clearly indicates where blast holes are not The biggest benefit is in saving time and drilled or loaded according to plan. removing variability around blast confinement and coal seam protection. Rather than calculating the SDOB values as a manual ‘check’ for charge confinement, the drill and blast engineer now simply specifies the desired confinement values, and BlastLogic calculates the charge plan that will achieve the required result. In complex scenarios, one day’s work can now be accomplished in minutes. Therefore, through digitalisation, decision makers can analyse historical performance, react in a timely manner to unplanned events, and plan Figure 4. 3D flyrock modelling can be applied on both planned and actual charging data, enabling for continuous operations to create safe exclusion zones. improvement.
