
10 minute read
Putting Drones In The Picture

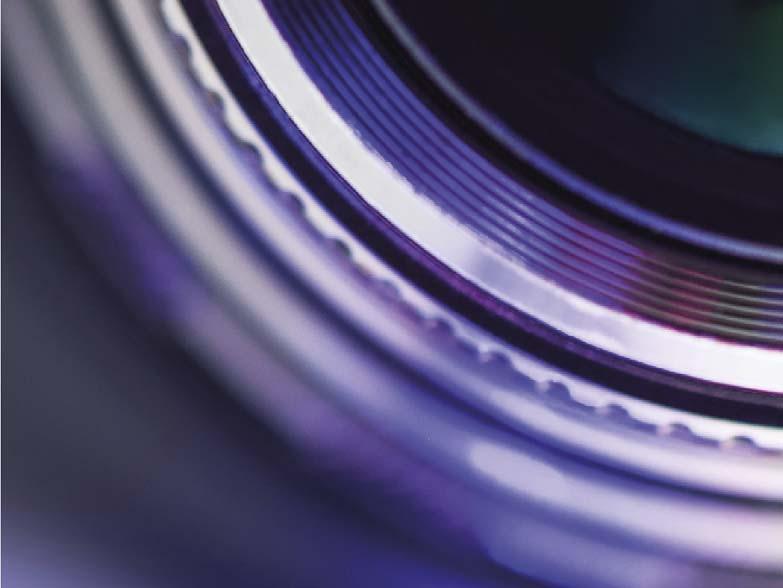
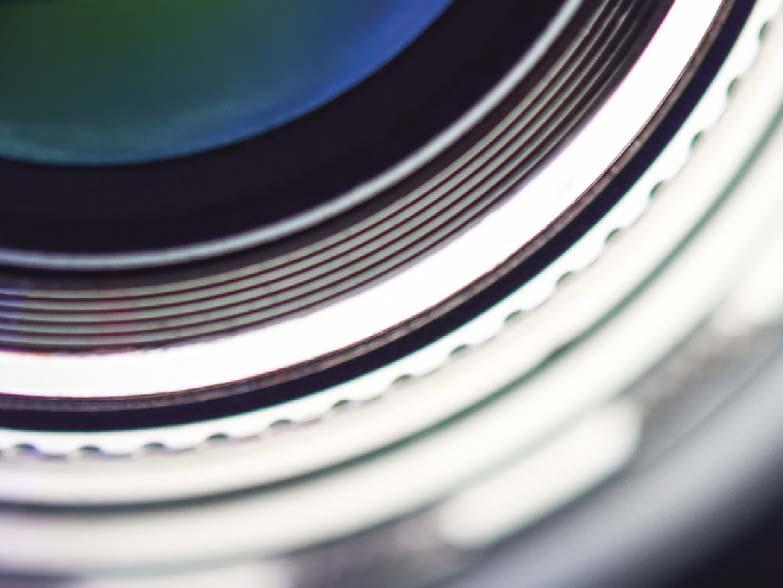
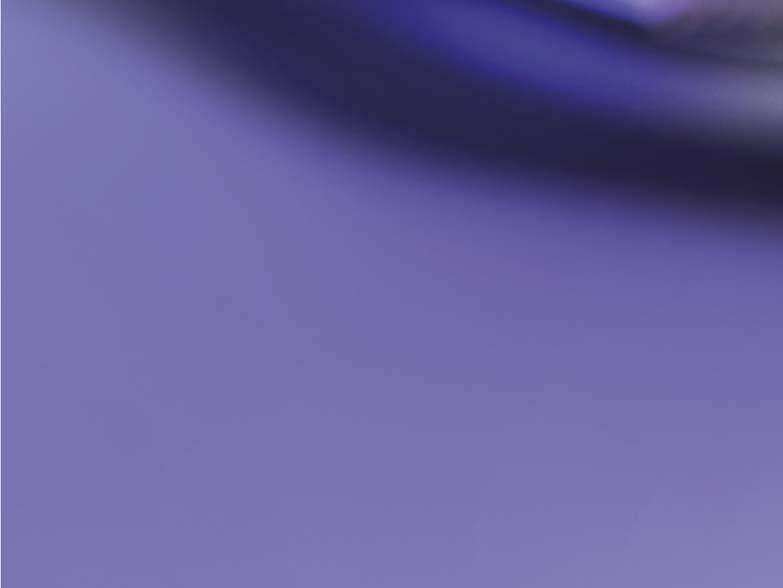

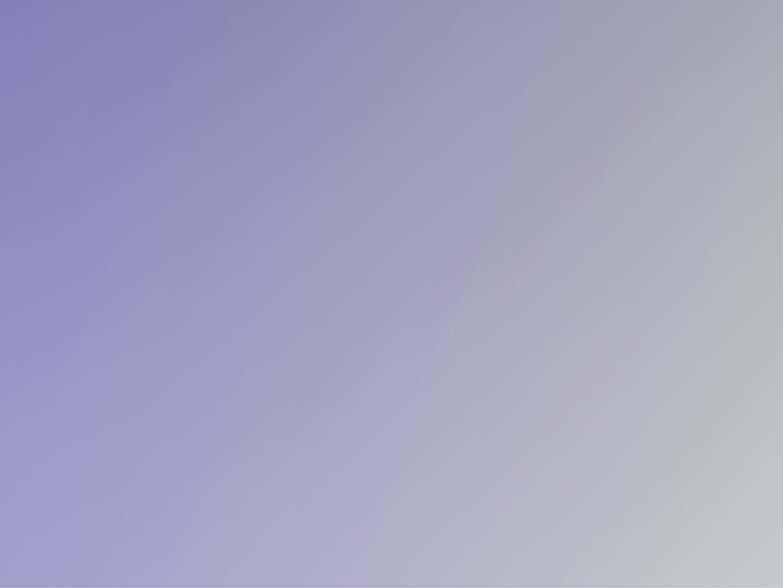
Eloise McMinn Mitchell, Pix4D,
Switzerland, asks the question: what is the point of using a drone?
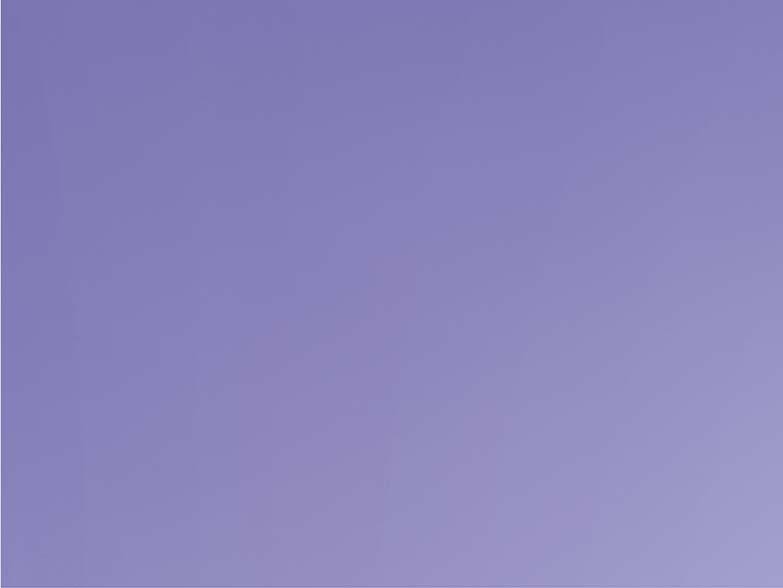
The mining industry has always faced huge challenges as it tries to meet the constant demand for its resources. Streamlined and optimised workflows are critical to keeping material moving from one place to the next, saving money and time. However, in order to stay safe, mining sites need constant monitoring and care. Revolutionary new tools and practices, when proven to work, become hugely influential in the industry. Drones and unmanned aerial vehicles (UAVs) are already doing this. This article explains how, and why.
Introducing drones
Firstly, what is the point in using a drone? Drones are manoeuvrable, adaptable pieces of technology, and as a result of this adaptability, they can be used in all forms of mining, from opencast to placer, or even underground mines. For example, there are specific drones built to move around in enclosed spaces. These are equipped with protective cages so their rotors are not damaged as they fly.
The value of using drones in mining is fairly obvious: they see more. Drones can cover large areas of a site, capturing images faster and in more depth than people on the ground. They can provide a video feed of a site, showing live movement across the mine, but the true value comes in their photos. A typical 4K video can be captured with most standard drones today, but the still images extracted from a video only have a resolution of approximately eight megapixels. Alternatively, most cameras fixed to a UAV nowadays are capable of producing a photo of 20 megapixels and more. That scale-up in resolution provides far more detail and information. There are cases where a video is better than imagery, and some data collection plans rely on video, but this can create a trade-off in terms of image quality, although whether this aff ects a project depends on the outputs that are desired.
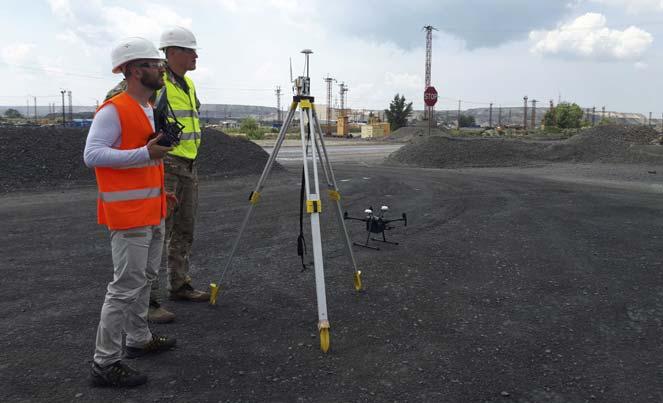
Figure 1. A drone inspection of a mine is quick and eff ective.

Figure 2. Open quarry sites can easily be 3D modelled with photogrammetry soft ware.
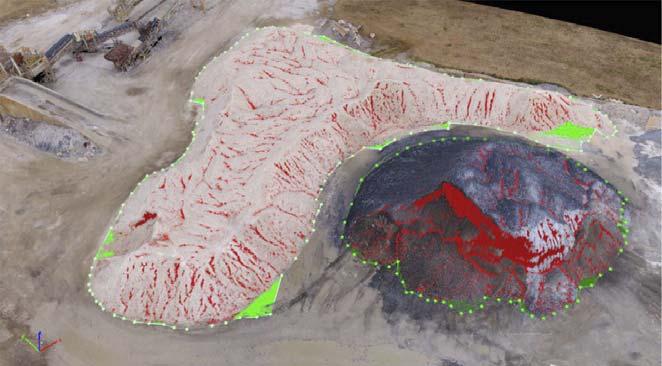
Figure 3. Measuring stockpiles with a drone is a straightforward process.
Drone imagery
What good are photos of a mine? There is a huge range of applications for drone imagery.
Surveying the site
An obvious use for drones is mapping, and using them to capture topographical data. Many drones can now use RTK or PPK technology to provide incredibly precise geolocation data alongside their imagery, which can be used to confirm measurements and calculations of a mine. This can be used to generate a 3D map and/or point cloud with the right photogrammetry soft ware. Other outputs include a Digital Surface Map and Digital Terrain Map. All the information about the site’s dimensions, volume of stockpiles, etc., is available in that model.
Improving site safety and asset management
The information gathered with drones can be used to assess current safety standards – e.g. to measure the width of a track across the site to check for subsidence, or aerially inspect machinery for faults. Assets can be checked for damage or rusting, where specialised soft ware can automatically detect rusting as well as allow inspectors a detailed view of a potential fault.
Measuring details of a mine
Whether it is the volume of a stockpile, the distance travelled by employees while carrying equipment, or the depth of an opencast mine, drone imagery can provide these details faster than manual measurements.
Streamlining operations
Whether it is taking inventory of equipment, or just saving the time spent tracking changes to the site, drones help speed up all of these processes with minimal eff ort, providing a cost-eff ective alternative to repetitive, manual labour.
Long-term records
Maintaining records of historical drone data makes it possible to observe how a mine has changed over time, including measures taken for environmental protection, refilling of opencasts, and any upgrades that may have been made.
These applications culminate in drones being used worldwide by mining companies for site surveying, blast engineering, stockpile inventory and volume calculations, asset management, topography engineering, and environmental monitoring and regeneration.
There are, of course, some potential challenges in working with UAV technology. Firstly, there can be hanging obstacles on a site, such as power lines, that a drone pilot should avoid crashing into. Magnetic interference from large quantities of specific materials can be problematic for hardware, including some drones, as it can disrupt components. Finally, the shift ing landscape of a mine means that records taken with a drone need to be kept up to date, although automated flight plans can mitigate the eff ort required in this.
Interpreting drone imagery
The photos captured by a drone include crucial geolocation data, as well as the physical image of the site. This can all be imported to specialised photogrammetry soft ware that measures from images. This soft ware then uses that information to create actionable, useful outputs for mining teams and corporations.
One of the typical outputs from photogrammetry is the orthomosaic, which is a 2D flat map built from the images that can be exported as a GeoTIFF. Orthomosaics are used to give an overview of site information and are oft en used in presentations for decision-making. Additionally, photogrammetry soft ware generates a point cloud (a collection of points where each one has specific coordinates), a raster surface model (to quantify and visualise terrain), Digital Surface Models and Digital Terrain Models, contour maps, and even thermal maps if needed. These outputs can be consolidated with laser scanning or LiDAR data as well, which can be imported into CAD soft ware for further logistical planning.
Working with drones can be incorporated into existing workflows, as the drones can fly overhead quickly and eff iciently around a site, minimising (if not negating) the need to turn off or move equipment out of the way, and saves inspectors long walks around the space. The soft ware provided by Pix4D is not hardware specific, so surveyors can use hardware of their choosing, the majority of which is supported by Pix4D soft ware. Pix4D has five products that are specifically useful for the mining industry, including: PIX4Dmapper, a comprehensive photogrammetry soft ware capable of a large range of outputs, including thermal imaging; PIX4Dmatic, specialised for large scale and corridor mapping, and thus well-suited for large mining sites; PIX4Dsurvey, which incorporates photogrammetry outputs with LiDAR to bridge the gap between photogrammetry and CAD, allowing outputs to be vectorised and merged; PIX4Dcloud, an online photogrammetry platform, which makes it easy to share results, inspections, and outputs with teams wherever they are in the world; and PIX4Dcatch, a terrestrial photogrammetry application which uses the latest phones and tablets’ incorporation of LiDAR and ToF sensors to gather ground-level data from mobile devices, which can later be processed in PIX4Dmapper, PIX4Dmatic, or PIX4Dcloud to generate precise 3D models.
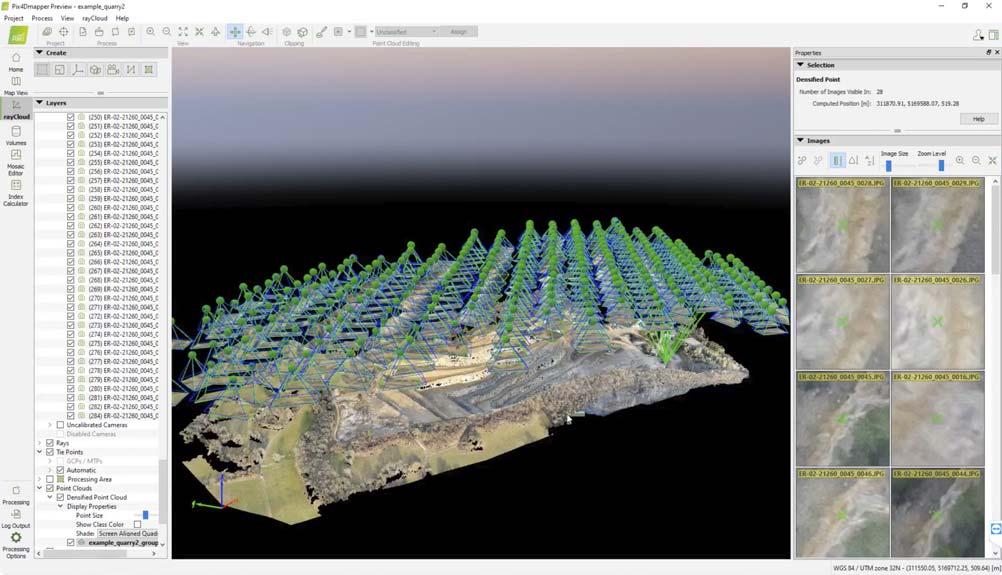
Figure 4. PIX4Dmapper enables users to look at individual images, as well as the 3D model. Figure 5. Drone imagery is eff ective underground, although specialised drones are best for this.

Soft ware such as this off ers three key features that benefit mining companies, besides the obvious ‘bigger picture’ and 3D mapping capabilities: Reduces operational risk: The software removes the need for visits and site inspections without losing track of everything. Fewer people required on site keeps people safe and prevents disruptions to workflows. Supply chain management: The software can track where the material is on-site, where it needs to be, and can spot delays or issues early on. Asset lifecycle management: Equipment can be inspected from the comfort of a computer screen, working with technology that will help automatically identify faults and measure features.
Results of using drone mapping
A precise, accurate 3D map of a site is incredibly valuable, especially for a mine where large objects are being moved around and uninformed decisions can have a big impact on a job site. Project managers can share their findings with colleagues and make the right decisions with the most up-to-date and accurate information. They can equally share identified hazards or issues with their superiors and corporations more easily, exporting pdf reports as well as imagery. This information can then be used to solve problems, as well as plan future expansions and measure or assess the current state of a mine.
Volume measurements are a critical element in mining. Shift ing large volumes of earth or materials is a huge undertaking, and can pose a safety risk if not done correctly. This being the case, risks can be easily mitigated if everyone is informed and site changes are carefully tracked, which is simple to do with regularly updated site surveys. Routine updates mean that everyone can follow site movement and progress, as well as identify logistical challenges early on, saving money and time later down the line.
Drone mapping in action
Case study: Montana, USA
The narrow passageways of an underground mine were once an insurmountable barrier to drone mapping, as the small paths were too diff icult to navigate without the drone crashing.
Barrick Gold, working on Golden Sunlight Mine in Montana, USA, took advantage of a modern drone that solved that problem. The ELIOS 2 is a UAV designed for enclosed spaces, surrounded by a small frame that prevents it from bumping into walls and getting damaged. It also has a mounted lighting system, so that it can gather illuminated images in the darkness of underground mines.
In order to survey for unstable material that could be a threat to people and equipment, Barrick Gold sent a drone into the mine to check that recently blasted areas were safe for miners to enter and pass through. The company repeated the flight several times over a week and processed their data with PIX4Dmapper. The 3D models were then compared to each other to identify material that had moved and flag risks.
The outputs of this were two-fold. Firstly, the team had a model of the mine to use for checking if the mucker was at risk of damage from a rockfall, as well the current status of recently blasted material. Secondly, the mine owners had a perfect replica of the mine that could be used for company records, including planning and tracking expansions across the site, even underground.

Figure 6. Monitoring site access, such as roads, is another use for drones in mining. Case study: Aberthaw, Wales
Before being decommissioned in March 2020, the coal plant at Aberthaw in Wales was a huge site that needed to be inspected and well maintained. PricewaterhouseCoopers (PwC) was brought in to audit stock at Aberthaw, in order to help keep track of resources and material being moved on the site.
The company flew its drone for just over 30 minutes, gathering over 300 images. These were collected with a fixed-wing drone from QuestUAV. Fixed-wing drones have a longer flight time and can be paired with a base station to ensure absolute geolocational accuracy. Rotary drones, in contrast, can have more manoeuvrable flight plans and a direct ascent take-off .
Originally, manual measurements taken on the site would take over four hours, which disrupted work and machinery. The drone took just 30 minutes – an 85% reduction in inspection time. The 3D model generated by PIX4Dmapper with the collected data was used to measure volumes of the stockpile with results having an overall accuracy of 99%. The soft ware also provided a digital twin of the site, which can be used to plan how the stockpile will be moved or added to.
A report filed by PwC following this trial projected that using drones to boost productivity in the UK in similar cases could save around £16 billion (US$20 billion) by 2030.
Conclusion
Drones themselves are a useful tool, but it is how they are used in combination with photogrammetry that is the game-changer for the mining industry. Drones save time, improve safety and cut down on wasted money, whilst the application of photogrammetry introduces new, valuable resources like accurate maps and on-demand inspections to the industry. With the right photogrammetry tools, there is almost unlimited potential for what can drones can achieve at a mine.