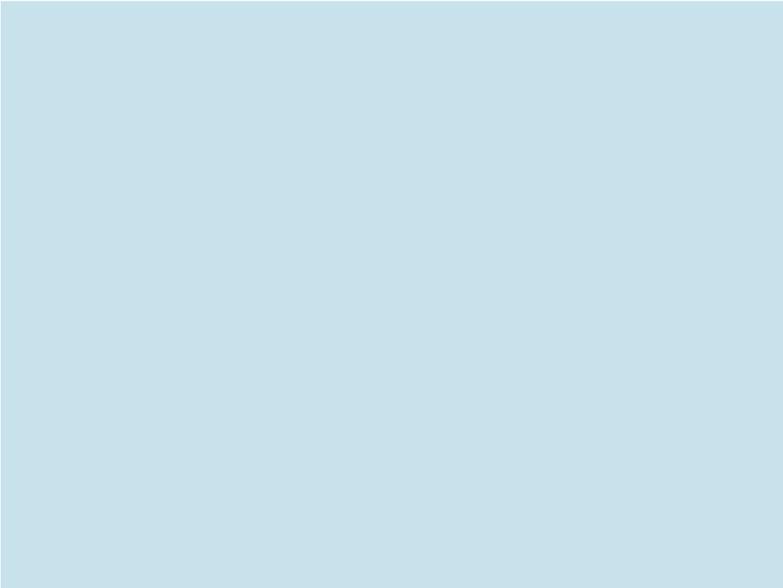
9 minute read
Setting A New Pace
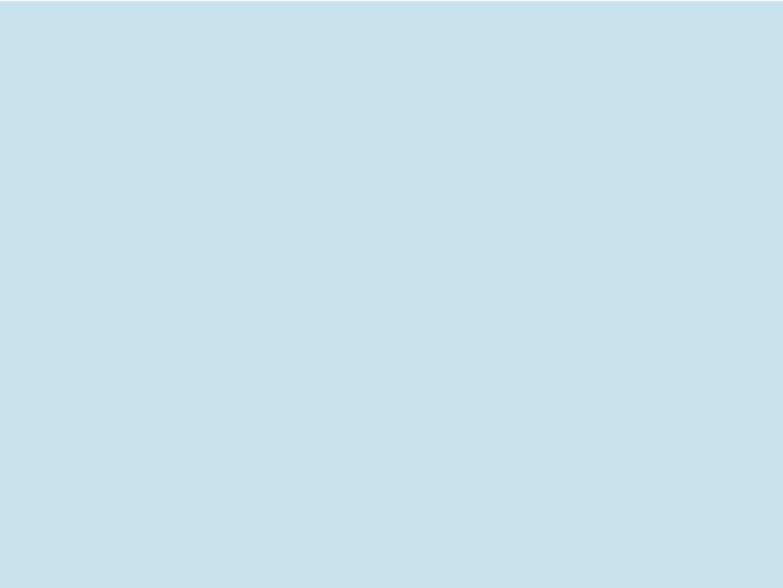

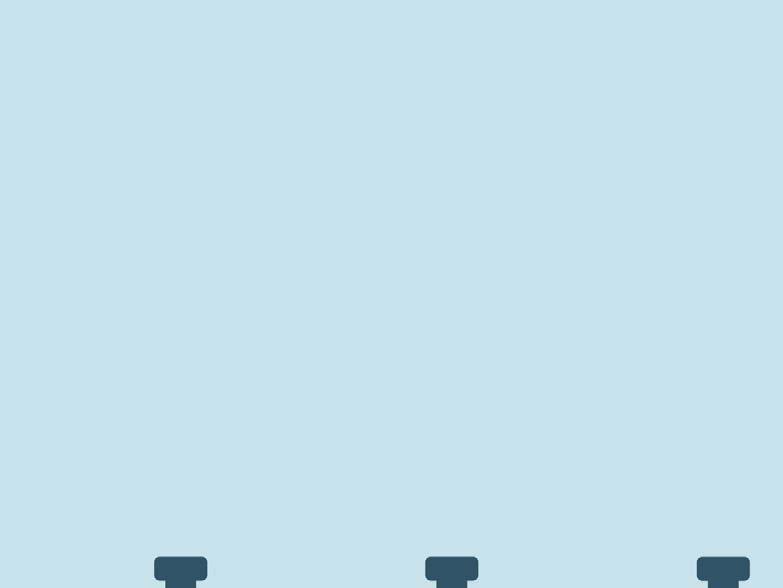
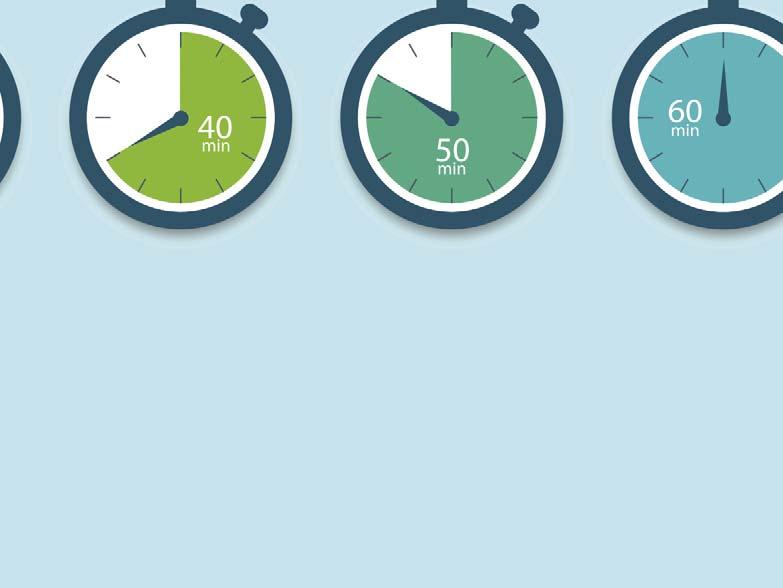
Emily Loosli, Wingtra, Switzerland, identifi es how drone mine surveys are setting a new pace for the industry, using a Canadian coal mine as an example.
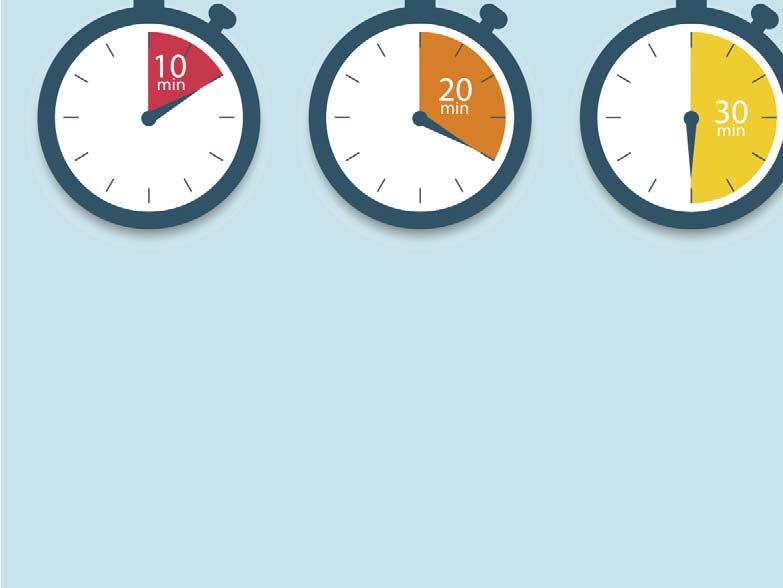
Located in Southeastern Saskatchewan, Canada, between the city of Estevan and the town of Bienfait, is the Estevan Mine site, which is operated by Westmoreland Mining, LLC. The site spans 20 331 ha. (50 240 acres) and the mine comprises four active pits supplying lignite coal to the two power generating stations in Saskatchewan – the Boundary Dam Generating Station and the Shand Generating Station – as well as the activated carbon plant and char plant. It also supplies some domestic sales. The mine’s production is approximately 6 million tpy.
Like all mine sites, Estevan presents a range of challenges, including measuring volumes accurately and generating views of the mining pits and work progress on a regular basis. In addition, there are also increasingly detailed safety regulations that mine sites must adhere to. In order to stay competitive and ensure that working conditions remained as safe as possible, Westmoreland did what it has always done to keep business thriving over the last 150 years: it changed with the times.
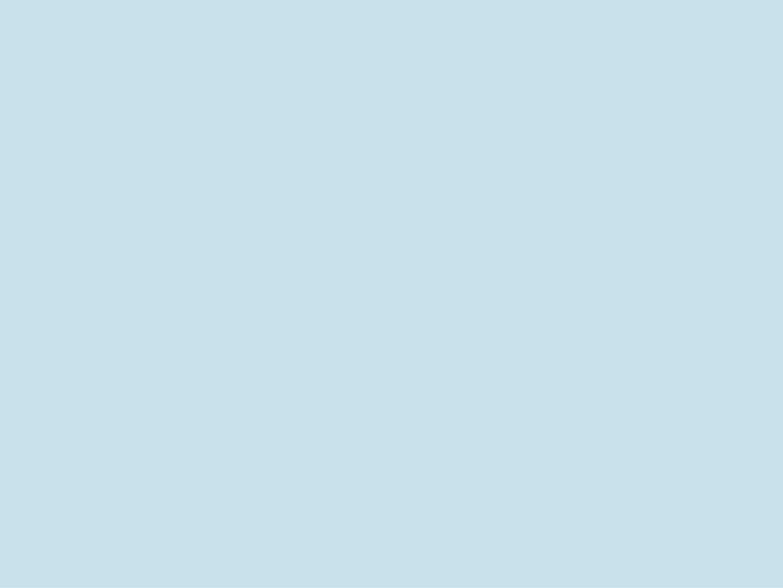
Mining’s next frontier: drones and high-accuracy data
By now, it is no secret that commercial drones have the power to transform how work is done across industries, including mining. Specifically, a drone can fly over a pit and collect visual data that is both clear and geo-referenced for 3D accuracies, facilitating the
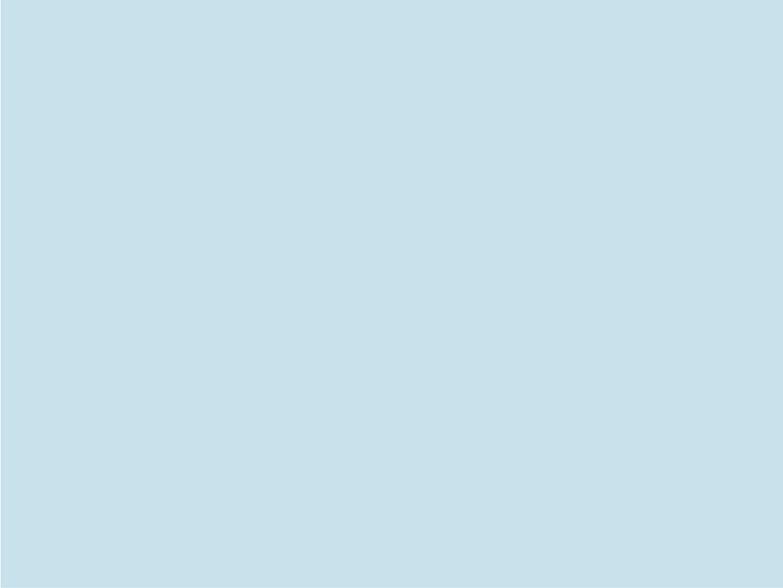
creation of digital twins of the area. Additionally, because it is much faster than covering the area on foot, it can be done more frequently.
Seeing all the ways that drones improve operations, Westmoreland started incorporating drone technology into its workflows in 2014. A co-op engineering student at Westmoreland, working with the WingtraOne drone on the Estevan Mine pits, said that compared to other data collection techniques, drones are the most accurate way to get data on a mine site, by far. How so?
The accuracy of stockpile overall mine pit measurements depends on the data points collected along the site’s surface. Depending on the quality of the sensor on the drone, this can be as much as a data point every square centimetre or so. Data like this greatly reduces the difference between the actual volumes and surfaces and those measured by the drone data.
The WingtraOne drone, in particular, can capture at sub-centimetre ground sample distance (GSD), which means centimetre-level accuracy across the entire mine site.
In the past, surveyors used GPS equipment as they walked around the mine pits. To an extent this worked, however, due to safety concerns, they could not effectively survey the side slopes. In the places where they could reach, they collected several hundred data points. Now, in 15 minutes, a drone can pick up millions of data points across an area that used to take two hours to cover on foot.
This level of accuracy saves time by offering a new level of precision with regards to how much earth or residual is in a given place, at a given time. When working with this much detail, mining operations become more and more predictable and trackable. Furthermore, when high-accuracy drone data is the basis for discussions, potential confusion among stakeholders about stockpile volumes are also minimised, thanks to software that allows team access to datasets in real time.
Mine managers can rest assured about safety as well, because surveyors no longer need to walk amidst moving industrial equipment or climb up onto stockpiles. In fact, drone technology removes most of the major worksite safety risks in an opencast mine.

Figure 1. Drone pilots fly WingtraOne approximately three times a week to gather vital details around the mining pits at Estevan mining complex.
Figure 2. The WingtraOne drone helps track operations at Estevan mine, which occur on a massive scale and quickly. ‘Big Lo’ is a Bucyrus-Erie 2570-W dragline vehicle at the complex and is considered a wonder of the region for its science-fiction-grade size and ability to haul 230 t in one suspended load.

Choosing the right drone
Westmoreland has been incorporating drone technology into operations across its mining sites for the last seven years. In that time, what drones can do has changed, so the mining firm has added to its fleet accordingly. At first, multi-rotors, like the DJI Phantom, were the dominant means of collecting data. These drones instantly became a much better option than covering the same grounds on foot. However, a multi-rotor’s limited flight time and coverage range per battery presented challenges that became obvious when fixed-wing commercial drone technology started to develop.
Fixed-wings broke through a coverage barrier, allowing data capture over areas many times larger than multi-rotors, due to the aerodynamics of their design. Specifically, fixed-wing drones, like commercial aeroplanes, rely on passive lift to stay in flight, so they consume less power and stay airborne longer. Yet, for mine sites, these have presented one key challenge: how they land.
Classical fixed-wing drones must either be launched by hand or catapult, and will belly land. On a rugged mine site, this introduces a lot of risk that the drone and its sensor will be damaged. In fact, the landing of the fixed-wing drones the mine had been using could be described as a ‘crash landing’. This risked not only causing damage to the drone and data, but also collision with nearby equipment or operators, since the drone would land in unexpected places.
For all of the above reasons, when Wingtra came out with its vertical take-off and landing (VTOL) drone, WingtraOne, it presented a step forward in large-area mapping drone technology and attracted the attention of Westmoreland.
VTOL: the optimal solution for drone mining surveys
On rocky work sites that present limited take-off and landing areas, VTOL drones off er the best of both worlds: direct lift -off from the home position, large-area data
collection, and a controlled touch-down landing that both protects the equipment and ensures minimal safety risks.
These features are already a big step forward for mines. Yet VTOL goes further, as it enables the use of higher quality sensors that would not be viable with either a fixed-wing (due to the hard landings) or a multi-rotor (due to the constant lift it requires to fly).
What difference do high-quality sensors make? First, they offer higher resolution, so more data per image. Next, as is the case with WingtraOne, they can carry heavier, full-frame cameras, so the capture area is even larger. This means that the drone can fly higher, fit larger areas into every shot, and cover much more ground in a single flight, at a higher accuracy, and with better resolution.
All of this not only speeds up the survey process, but it also avails an entirely new way to manage mining operations. For example, instead of waiting for a semi-annual mine site survey, site managers can request a map of a pit or some stockpiles on-demand, and then often receive the data within the same day, depending on the size of the survey.
Through minimising disruption of operations with a safe, fast drone survey, site managers can get more frequent looks at their operations and fine-tune schedules accordingly. For example, WingtraOne can map an area that used to take up to five hours on foot in 30 minutes, at a significantly higher accuracy.

Figure 3. A WingtraOne stockpile image from an Estevan Mine pit. This output, based on rich data, is used to generate contours and calculate the volume of the stockpile.
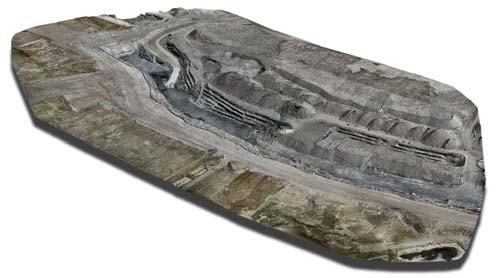
Figure 4. A WingtraOne data output of an Estevan Mine pit. This is used to see if the draglines are working to design and to calculate how much dirt has been moved since the last flight. It is also used to design ramps down to the pits as part of a plan for reclamation of the dirt that has been moved. Most importantly, it is used to see if there are any conditions within the pit that could be dangerous or cause burial of coal (such as high wall failures).
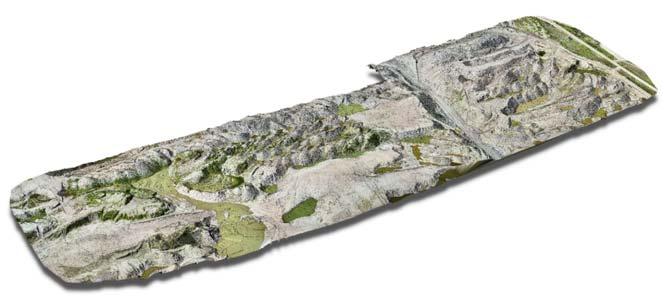
Figure 5. This WingtraOne drone data output off ers rich data on an area of Estevan Mine that Westmoreland plans to reclaim. The output is used to design a reclaim surface that is sent to the dozer operators, in order to accurately restore the area to design.
How much training and knowledge transfer is required to go high-tech?
All of the benefits of drone technology are powerful to consider, but if using the technology presents hassle and setbacks, the return on investment is significantly reduced.
In fact, the ease-of-use and compatibility of the data with other software and pre-existing workflows is vitally important to how much a drone proves to be an asset for a large mining firm with large teams of workers and demanding timelines. In an increasingly competitive marketplace, more and more reliant on new technology, the level of ease and efficiency is not just convenient. It is actually the key to staying ahead.
Additionally, drone data needs to be compatible with a range of software so that the latest data processing and sharing technology is also available to stakeholders. In fact, some mining software can generate specific measurements such as safety berm heights, crests and toes, road boundaries, widths, crests, slope, length, and elevation change. Then artificial intelligence can highlight where a site falls out of sync with safety standards or presents hazards.
Westmoreland’s latest choice in drone technology – emphasising ease-of-use and software compatibility – reflects its consistent spirit of innovation and keeping up with the times in order to stay well on top of safety regulations and calculate dragline operations, as well as the amount of reclamation they have done to meet sustainability goals. In the end, adopting the most advanced commercial drone technology sets a good example for the mining industry, with the added potential for significant cost savings.
Conclusion
As more mining companies incorporate drone technology into their workflows, a new precedent is quietly being set based on faster, higher-accuracy data collection. Different drones present different advantages, and the technology is developing swiftly. Taking the time to research and learn what is available today will improve the likelihood that the technology will fit into and improve current workflows, as well as contribute to achieving business goals over the long term.