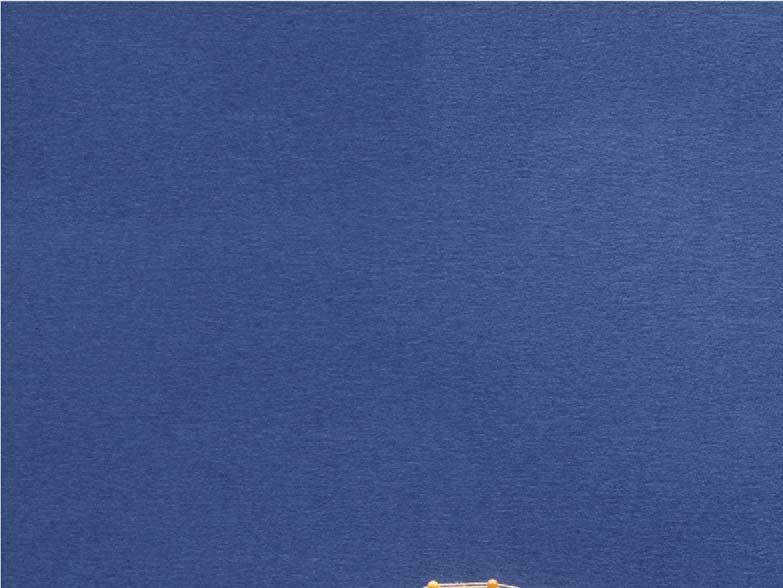
7 minute read
Integrate To Communicate
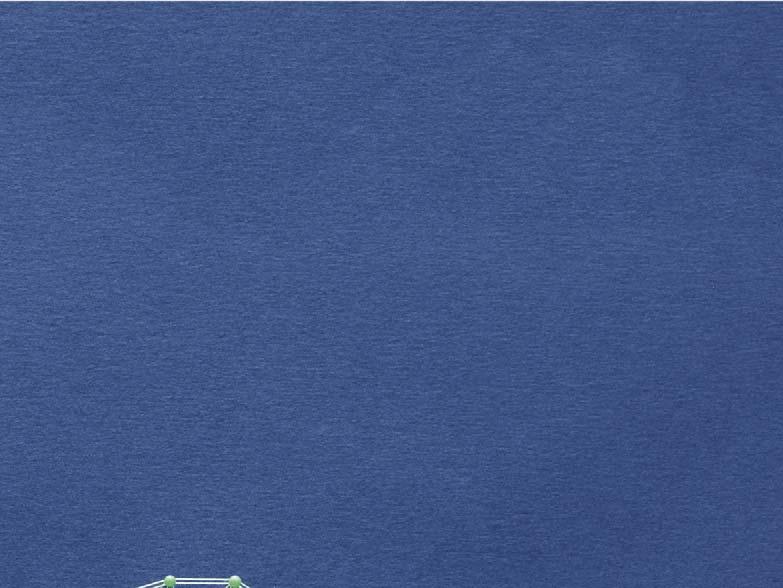

Christian Fimpler and Frank Kathmann, Eaton, explain how recent technological advances are making communicating underground more effi cient and effective.
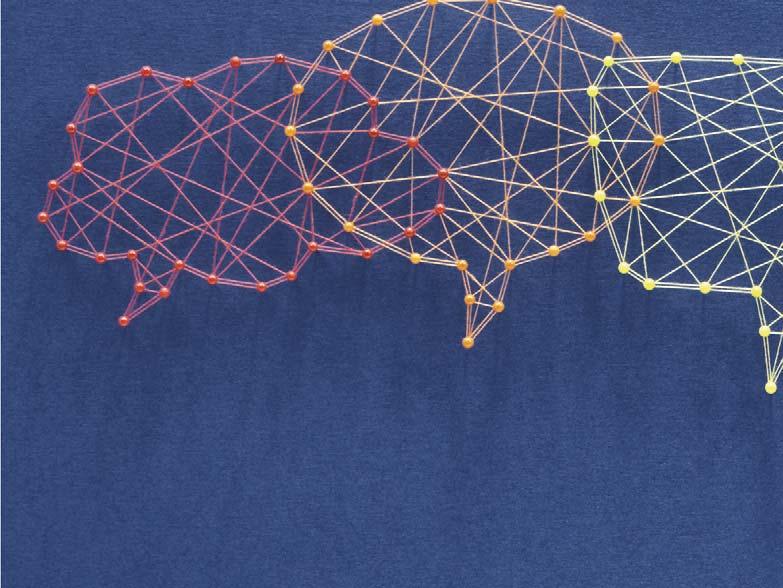
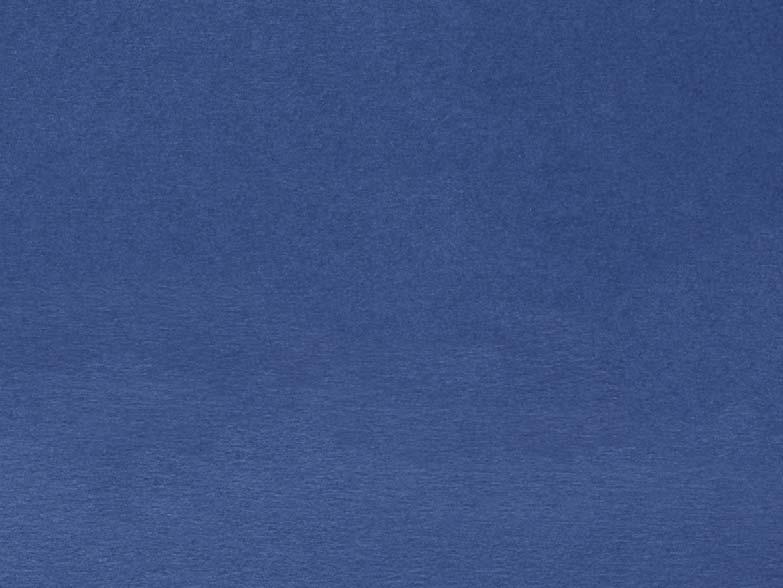
Connectivity and the human-machine interfacing are concepts being embraced across many industries – and with good reason. The ability to share information, analyse data and respond in real time to fault signals or maintenance requirements, is key to optimising production and driving down costs. Indeed, in industries such as mining and tunnelling, the ability to co-ordinate humans and machines, as well as relay essential data about what is happening in real time back to the surface, is not only a matter of optimising production, it can be life-critical.
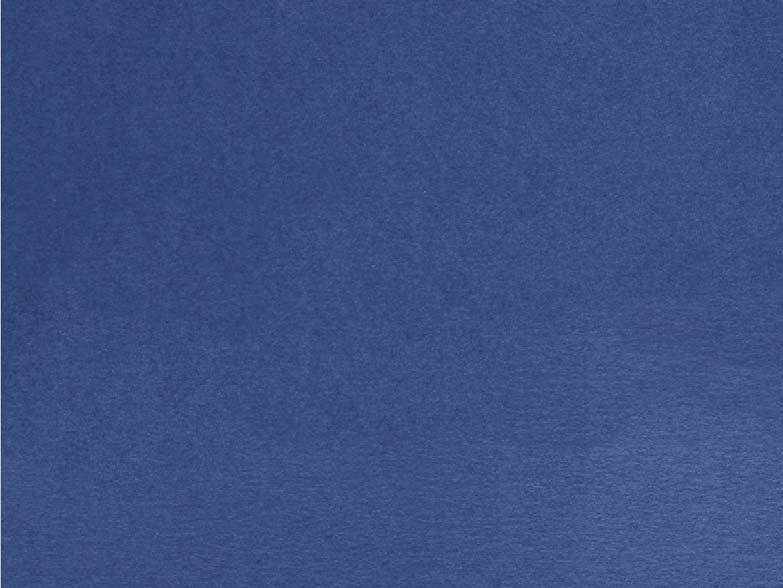
Designing a hazardous area communication system
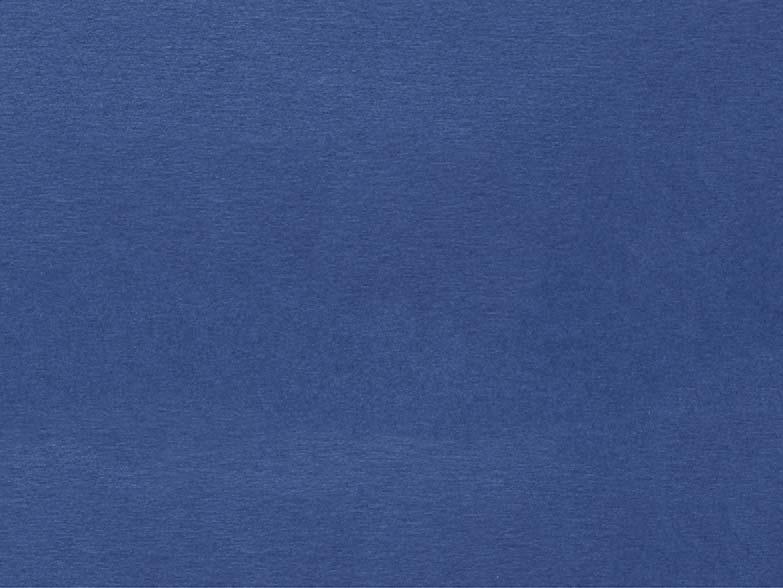
While there is no doubt that communications between the surface and those below ground, between both machines and humans, are essential functions, there are a number of challenges to overcome when designing a hazardous area communication system.
Firstly, there are the natural environmental risks associated with working underground. Damp, dust, and potentially explosive atmospheres are not conducive to the introduction of sophisticated electronic communications networks.
Secondly, the nature of drilling, mining, and tunnelling operations add other environmental phenomena that can be detrimental, such as high levels of vibration and noise. It is therefore important to ensure that essential messages can be relayed without interference, and that they cannot be ‘missed’ by the intended recipient.
A third consideration is the nature of industry. The underground working environment is highly mechanised, and the scale of the equipment involved is colossal. For example, vertical shaft drilling machines – commonly used for sinking sewers, mine, and ventilation shaft s – have a typical diameter of between 4.5 – 9 m. These machines generate a lot of heat and vibration in very confined spaces. Communications devices therefore need to cope with wide variations in temperature and high levels of electronic interference.
Now the environmental conditions have been summarised, the human element needs to be considered. Although far fewer people work below ground now than in previous decades, they are subject to new safety challenges. Proximity to large scale and remotely-controlled machinery is one risk, but also, with fewer personnel underground, workers are now working at more remote distances from both each other and help, should it be needed. It is not unusual for mines and tunnels to stretch for hundreds of kilometres underground, and people are still required to penetrate these vast, manmade caverns to service and repair equipment. The need for reliable and timely communication is growing, rather than diminishing, as operations become more automated than ever.
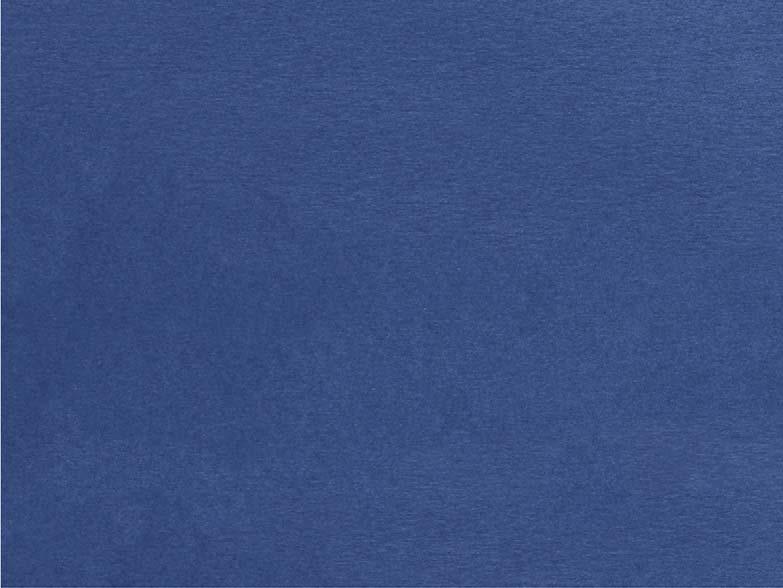
Current communications
The complexities of communicating underground have led to a number of solutions being developed over time. For example, communications systems using public address and voice alarm (PA/VA) technology have evolved to relay voice messages and audible warnings; automation systems exist to enable control and co-ordination of machinery and equipment; and fixed point telephones provide emergency call points for personnel.
Initially, these systems were reliant on analogue technology and hard wiring, limiting the amount of data that could be transferred. However, the fundamental issue with current-state underground communications systems is lack of integration. Each type of communications system has evolved to be separate and distinct from the next, so the benefits of true connectivity are still largely unattainable, despite the advent of digital technology.
Some manufacturers, including Eaton, have sought to close this gap. The MR90 radio system, for example, was introduced in the early years of the 21st century. It serves double duty as a voice transmitter from mining conveyors to the fixed station and back, as well as transmitting data between the fixed station and conveyor station, using omni-directional antennae.
Using the same hardware for communications and production data is progress of sorts, but it still lacks the ability for seamless connectivity between machines and between humans and machines. Nor does it exhibit the agility and flexibility that is possible using the latest technological advances – including mobile phones and tablets – which other industrial sectors already enjoy.
Step change
All this is set to change with the advent of the safety integrated mining automation system – or SIMAS. Developed by Eaton, drawing on its expertise in hazardous area communications, SIMAS is believed to be the world’s first fully integrated IP-based voice, data, WiFi, interlock, and automation system for subsurface industrial applications where rugged and/or explosion proof equipment is required.
The system uses Ethernet to link the automation system components via a SMART connection. This network structure and a high data transfer rate of 100 Mbit means SIMAS meets all requirements for automation processes of equipment, such as: plow and shearer faces, conveyor systems, pump stations, etc. The automation control unit channels all process-specific automation processes and acts as a communication point to the control station. It also allows a data link to third-party systems. The system is equipped with an integrated, safety-oriented PLC with flatscreen display, function keyboard and button-entry mouse, which enables implementation of a control concept in line with IEC 61508.
A system control panel – complete with command/message components, LCD colour backlit display, emergency stop button with interlock, and speaker with audio functions – enables manual control of operating and conveyor equipment. A range of Ex i I/O modules and periphery modules complete the automation functionality.
The emergency stop element of SIMAS comprises a control unit and a choice of emergency stop buttons, rope-pull switches, and coupling devices. The control unit is used as a driver for up to two emergency stop lines. It displays operating and diagnostic data from the system, as well as an overview of the devices connected to the emergency stop lines. The control unit is connected to all devices on the network using a specially developed system line, which routes the emergency stop circuit, the power supply, and the network communication. A factory-set ID allows identification throughout the SIMAS system.
SIMAS WiFi communication options include fixed point radio transmitters (with or without intercom), access points, and emergency rope pull switches with integral intercom and access point. Mobile options include mobile phones and tablets in IS housings.
The overall SIMAS system is designed for ignition protection group ATEX group I M2. In addition, the emergency stop and shutdown facilities use battery backup to meet ATEX group I M1 in the event of a main power supply failure. In combination with a failsafe PLC, SIMAS also meets the requirements of functional safety in line with SIL2.
Potential applications for SIMAS include coal faces, belt conveyor transportation systems, water management and machinery automation, as well as communication along underground roads. Due to its scalability, SIMAS could also be used for shaft signaling, skip loading, or wagon loading.
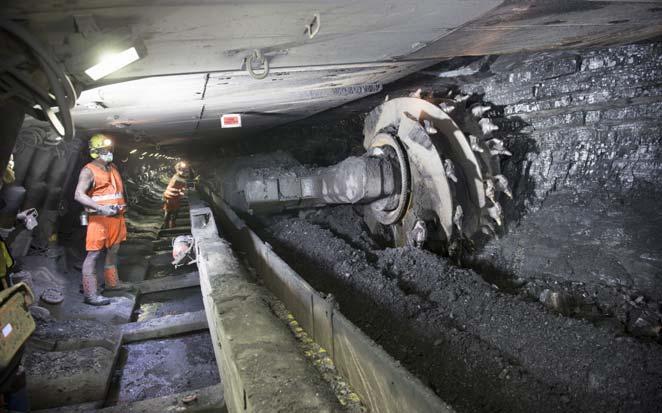
Figure 1. In mining and tunnelling, the ability to co-ordinate humans and machines, as well as relay essential data in real time back to the surface, is not just about production eff iciency, it can be life-critical.
Future developments
A proprietary application, ‘SIMAS Connect’, is currently under development. It will enable voice connections and video conferences between mobile terminals, fixed stations, and computer workstations. Address book functions will allow both private connections and global communications, while authorisations for the mobile devices can be set on the communications server.
In the near future, Eaton also expects to add addressable fire evacuation and the ability to track personnel constantly – with the ability to send tailored, personal messages to further improve eff iciency and safety.
Conclusion
Due to the hazardous nature of mining and tunnelling operations, the sector is understandably cautious about the adoption of new technology. Nonetheless, in the case of a fully integrated communications and automation system, such as SIMAS, it is likely that the significant benefits, in terms of personnel safety and process integration, will overcome any conservatism.
This step-change in connectivity for hazardous underground applications will deliver major improvements in error reduction, maintenance scheduling and uptime, as well as ensuring that personnel receive timely and accurate data at the point it is required.