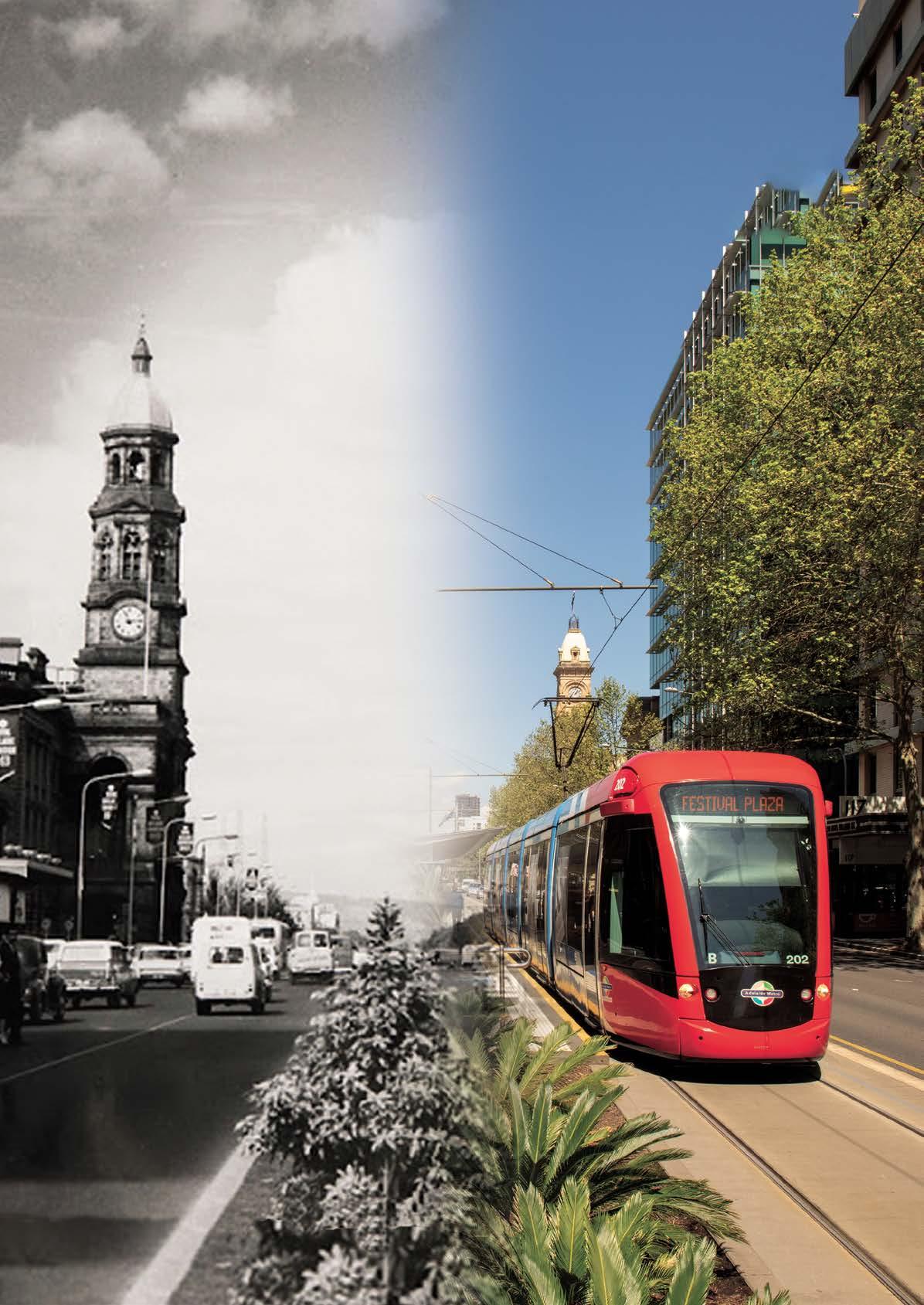
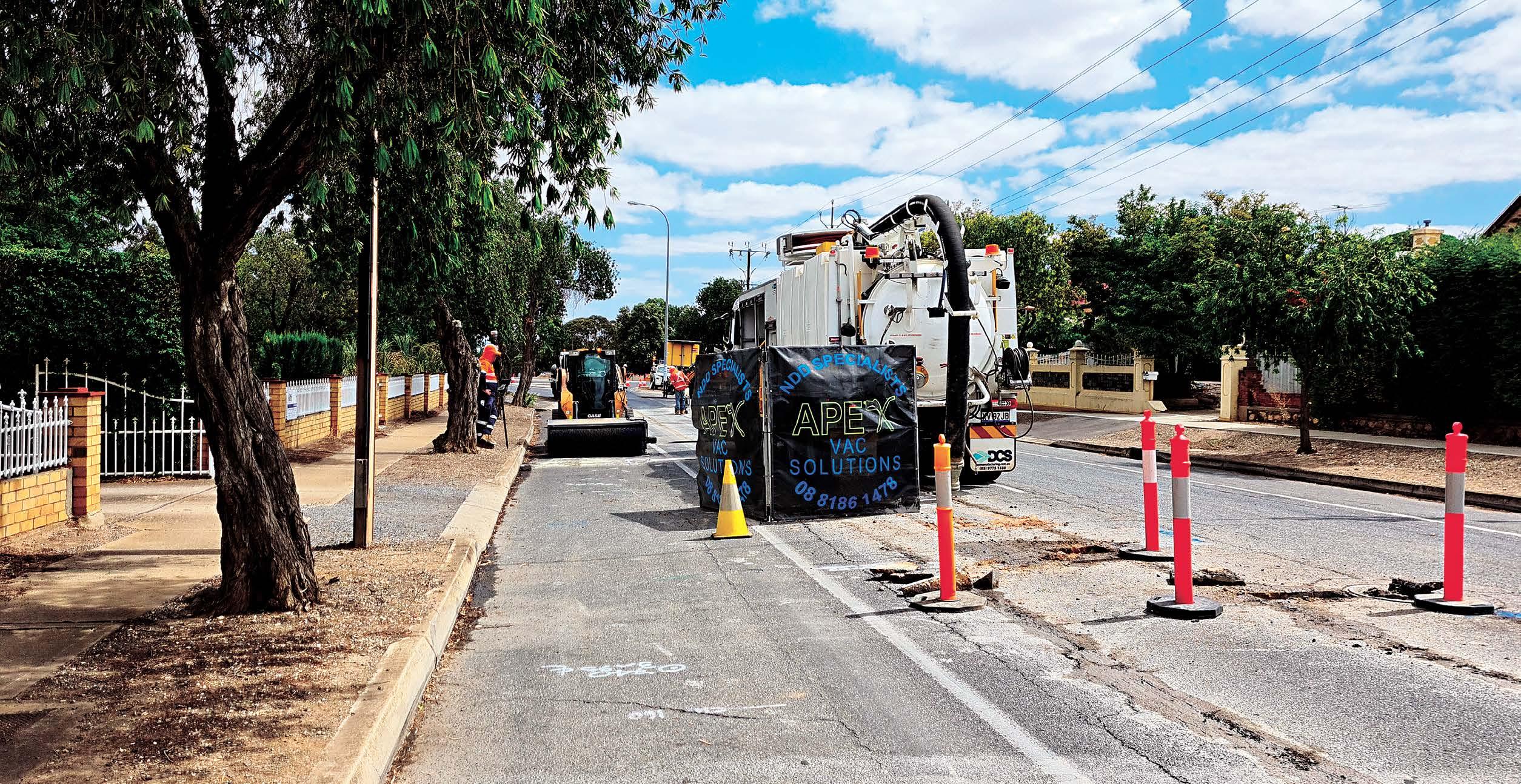




MESSAGE FROM THE CEO
THE DIGITAL REVIEW
CCF SA PRESIDENT'S SUNDOWNER & AGM 2022 + the inside scoop
RELIVING THE GOOD 'OLE DAYS
look how far we have come LIAM MARTIN AT DELTA GROUP 12 meet the boss: BEN TURNER BDT Construction 15 member profile: ACCESS CAPITAL 16 NATIONAL SAFE WORK MONTH 17 look how far we have come CREATING GREENER FUTURES IN ADELAIDE WITH INNOVATIVE LANDSCAPING SOLUTIONS 18 cacl APPRENTICES SEEKING HOSTS 19 meet the team: CIVIL APPRENTICESHIPS AND CAREERS 21 member profile: FLIX PRODUCTIONS AUSTRALIA 22 look how far we have come WORKZONE TRAFFIC CONTROL 23 SAFETY INFLUENCERS - DIT 24 FUTURE INSTITUTE OF AUSTRALIA
Chief Executive Officer & Executive Director Civil Apprenticeships & Careers Ltd p 8111 8028 m 0417 767 688 rpickering@ccfsa.com.au
MING LAU
Director – Finance p 8111 8043 m 0437 660 793 mlau@ccfsa.com.au
MELISSA EKBERG
Director of Industry Engagement p 8111 8022 m 0455 206 528 mekberg@ccfsa.com.au
25 civil train MAKING IT EASIER FOR SCHOOL STUDENTS TO START THEIR CAREER SOONER
28 civil train ROADS2CIVIL ON THE ROAD TO SUCCESS AS FINALISTS FOR THE 2022 SOUTH AUSTRALIAN TRAINING AWARDS! 30 civil train SIGNIFICANT MILESTONES IN CIVIL CONSTRUCTION TRAINING CURRICULUM 32 civil train CONNECTING THE DOTS! 34 CCF SA MEMBERS ONLY EXCLUSIVE OFFERS 36 WELCOME TO OUR NEW MEMBERS
41 member profile: 3D SITEWORX 42 GOLF DAY 43 2022, WOW WHAT A YEAR IT HAS BEEN 44 LOOK HOW FAR WE'VE COME!
50 look how far we have come HELPING AUSTRALIANS BUILD SINCE 1882 52 SA WOMANS PEOPLE'S CHOICE SHINE AWARD WINNER 2022 53 ccf sa women in civil FESTIVE LUNCH
Group Business Development Manager p 8111 8020 m 0405 584 742 btelfordwebb@ccfsa.com.au
ZAC SLADE
GTO Operations Manager p 8111 8011 m 0429 620 965 zslade@ccfsa.com.au
54 past projects
LOOKING BACK AT THE HARBOURS UPGRADE AT CAPE JERVIS AND PENNESHAW
55 past projects RELOCATION OF THE WATER MAIN NEAR SEACOMBE ROAD, STURT FOR THE CONSTRUCTION OF THE SOUTHERN EXPRESSWAYMID - 1990S
56 past projects VINCENT LANDING MARINA
58 past projects WHYALLA'S WASTEWATER RECYCLING SCHEMETHEN AND NOW
60 look how far we have come TRIPODI GROUP IS A FAMILY AFFAIR
62 retired members group UPDATE
62 retired members group RMG'S DAY TRIP ON THE SOUTHERN ENCOUNTER 65 WOMEN IN CIVIL UPDATE 65 WOMEN IN CIVIL 30 YEARS - HOW WE'VE CHANGED 68 EARTH AWARDS 2022
70 ROAD TO 78KM NORTHSOUTH CORRIDOR: PAVED BY INNOVATIVE SOLUTIONS 74 SUPPLIERS AND SERVICE PROVIDERS
MATTHEW BLACKBOROUGH Executive Manager, Trainers, Delivery & Product p 8111 8021 m 0427 003 920 mblackborough@ccfsa.com.au
AMY REID
Business Development Manager p 8111 8040 m 0429 307 346 areid@ccfsa.com.au
MARISA KEMP Project Manager – Training p 8111 8042 m 0436 191 464 mkemp@ccfsa.com.au
KARYN GRANT
Operations Manager – Civil Train WA m 0400 223 470 kgrant@ccfsa.com.au
MARK HOPKINS Regional Manager – Civil Train NT p 8953 3515 m 0427 003 913 mhopkins@ccfsa.com.au
FIND US ONLINE: ccfsa.com.au civiltrain.com.au
The material contained in this magazine is by nature, general comment only. The CCF SA expressly disclaims all and any liability to any person in respect of anything and the consequences of anything done or omitted to be done by any person in whole or partial reliance on all or in part of this magazine.
chief executive officer & executive director civil apprenticeships & careers ltd
As we approach the Festive Season, and hopefully some much-needed downtime, it is timely that we reflect on ‘how far we have come’. This is the theme for this edition of Civil Connect - we seek to pay respect to our past and present. The world is certainly a different place on many fronts, with our industry adapting and flexing to survive, and we are far from done yet. With economic and fiscal pressures bringing about new and different challenges for 2023, our resilience will continue to be tested. We take this opportunity to look back on our history with pride and celebrate what we have achieved to date.
We focus on delivered projects: Whyalla Jetty, Port Vincent Landing Marina, Cape Jervis Penneshaw Harbour works and my personal favourite (a project which I worked on in the late 90s) the Southern Expressway. Be sure to check out the feature photos - a six-page photo collage on SA projects from 1972 – 2022. No other industry has delivered so many iconic projects as our Civil Industry. Meet the Boss shares the story of Ben Turner of BDT Construction, and we also spend some time with the Tripodi Group and ADBRI.
As your CEO, I take this opportunity to reflect on what your membership dollar has allowed CCF SA to achieve through 2021-22 as your Civil industry representative: This list below is by no means exhaustive but is a selection of issues which we understand are/were important to you. These items highlight what we have done to build our civil industry brand across South Australia to support your business and profession:
ф Successful lobbying and the achievement of the ‘essential worker’ classification during the height of COVID-19, which allowed our industry to continue work using close contact exemption rules.
ф Development and implementation of ‘Flexible Industry Pathways’ in South Australian Secondary Schools. A critical industry pathway into civil careers for our young South Australian future civil professionals that was not previously available.
ф Achieved Roads2Civil Program funding – this facilitates the delivery of the civil pre-apprenticeship program in schools
ф With the previous Liberal Government, achievements were as follows:
• Industry roundtable commencement meetings held on various civil industry concerns.
• Establishment of the Industry and Skills Working Group to support the North-South Corridor (Torrens2Darlington – T2D) project. This working group continues today to prepare our industry for this unique and monolithic project.
• Industry Advisory Group (IAG) member. The IAG is an information and advisory body which provides a forum for you to share your industry expertise with the South Australian Government and other IAG members, and provide input on policy development, emergent trends, and opportunities for improvements relating to government procurement activities.
• Designated Area Migration Agreement access for: ○ Civil Supervisor ○ Civil Tradesperson
ф
With the new 2022 State Government, the following has been achieved to date:
• Prior to the 2022 State Government Election, written confirmation from SA Labor Leader, Peter Malinauskas stated that union related ‘no ticket, no start’ was not supported; here is an extract:
○ “As per our response to The Advertiser article, a Malinauskas Labor Government will not introduce a set of labour conditions requiring contractors to support or join union membership. It was never our policy during our previous term in government and will not be part of our policy if we are fortunate enough to be elected on Saturday.”
• Cost escalation mechanisms inclusion in contracts with ongoing work are now underway to consolidate industry feedback to the Department for Infrastructure and Transport. This is to ensure rise and fall works best for our infrastructure industry eco-system.
Consideration of additional costs inclusions (e.g., utilities) are also being prepared for submission.
• Through 2021-22 CCF SA were/ are Members on the following new Government Roundtables: ○ Civil Apprenticeship Inclusion on Federal Funding Lists ○ Small Business and Family Enterprise ○ SA Companies Construction Forum ○ Industry Advisory Group (Procurement) ○ Consumer and Business Services (Licensing)
ф
○
South Eastern Freeway Safety Group
○ Industrial Manslaughter
○ Wage Theft
○ Technical Colleges
○ Industry and Skills Workgroup –North-South Corridor
• Met and presented to Premier Peter Malinauskas, Treasurer Steven Mullighan, and Tom Koutsantonis Infrastructure and Transport Minister, within weeks of Labor winning the 2022 State Election.
• CCF SA invited to, and presented, to the new Labor Government Cabinet in 2022.
Other significant achievements include:
• Women in Civil events continue to lead the way with several, well attended and positive forums held through the period
• Future in Civil committee relaunched and focussed on future leaders by developing a professional development program
• Retired Members Group reconnection and recognition
• Digital communications revamp, including the introduction of the
○ The Dirt – newsletter
○ Civil Connect – magazine
ф New service lines:
• Health Industry and Wellbeing (HIW)
• Konekt Workcare Program –provides industry access to workers, whilst attracting reimbursement
• E-learning platform development – including blended delivery models to assist industry worker’s availability to attend training
ф Achieving and continue to build upon new CCF SA ‘Strategy Priority
1
– Building Industry Profile’
• Community awareness program promoting the civil industry implementation, with 64 Schools and Community programs currently engaged
• Attended 42 schools, several with civil industry leaders
• Invited and presented at several industry events
• Social media enhancements with the highest engagement achieved since commencement
• New and well-attended events – regional, networking, technical and political.
ф CCF SA, its members, and industry continue to work together with Civil Apprenticeships and Careers Ltd (CACL) to support Civil Apprenticeships. Now more than 50 civil apprentices are actively hosted, with an additional 47 apprentices at various stages of employment engagement. There is a wealth of opportunity to address our industry skills shortage needs.
ф Raising industry and community awareness regarding Civil Apprenticeships federal funding shortfalls relating to the Australian Apprentice Incentive System released early 2022.
As I conclude my contribution, I leave you with a familiar call to action:
I hope you enjoy the read and as always keep up the incredible work. We look to taking on 2023 with you, keep us in the loop with what is impacting you and your business. We are here for you. My details are available via the QR Code, please don’t hesitate to reach
I take this opportunity to thank and express my appreciation to the CCF SA members, Team, and Board, in acknowledgement of all the hard work and commitment for our 2022 achievements. Everyone involved in CCF SA understands the gravity of the work undertaken to date. We love this new sense of purpose and opportunity, so we are far from done.
Our success to date is only due to the amazing people we employ, those we have in our membership, the people in our industry, our Board members and those external stakeholders who share our mission and purpose. We will continue to punch well above our weight to achieve great things for our industry.
I look forward to working with you all to make 2023 even bigger, better, and brighter for us all.
From our team to yours, wishing you a fun and safe festive break, and a brilliant year ahead with health and happiness throughout.
INTERACTION OF SOCIAL MEDIA HAS BECOME MORE IMPORTANT THAN EVER. IT’S BEEN GREAT TO SEE OUR MEMBERS ENGAGE WITH US ACROSS THESE SOCIAL PLATFORMS.
With CEO Rebecca Pickering emceeing the event, the AGM was one to remember.
It included a couple of firsts – new President Charles Hatcher delivering his maiden State of the Federation Report as dusk was settling in, right next to Adelaide’s animal kingdom (another first).
“Morning or Evening?”
Which translates loosely to: Hearty breakfast bacon and eggs with a strong wake-up brew, or dainty finger nosh washed down by the top notes of an SA tipple while the sun goes down? What do we want for our next AGM?
Seriously, this question from the CEO required a vote count by a show of hands from the attendees.
Indeed, when people thought it couldn’t get any more interesting than the sort of rhetoric that often surfaces at a typical industry association AGM. But then again, we were sitting practically next to the lions and baboons… before long, their primeval instincts could make us raucous with the fading of the light.
Thankfully, Charles Hatcher put the day’s proceedings in order with The President’s State of the Federation Report by declaring the successful delivery of strategy a significant milestone in his first year as President. On the matter of governance, he graciously thanked his predecessor Paul Davison and paid tribute to his excellent
Among other matters, he spoke about the current state of affairs of the civil industry and the uncertainties associated with training future civil workforces, but assured all present that CCF SA will always be there for its members.
The Hon Tom Koutsantonis MP, Minister of Infrastructure and Transport, and Minister for Energy and Mining delivered the keynote speech. Stressing that the
leadership. As the Board farewelled two members – Michael Jeffery and Emma Ebert, it welcomed Simon Abrahams, Kerry Yeates and Sharon Van Kempen.
Hatcher noticed that people are getting increasingly busy nowadays. With the 500% increase in civil works happening over the next four years, are we optimising the procurement process and engaging with our supply chains efficiently to take on the increased workload? In other words, are we busy fools?
He reminded businesses to genuinely engage with the supply chain, build on strong market tested contracts and adopt smart, and planned procurement to build strong relationships.
There is also the need to ensure probity and transparency in business to boost productivity.
Are there better reasons for better planning? Sure. That could shrink contract management time and procurement resources that cause bottlenecks, and improve productivity in the process. And that could translate into direct carbon emission savings.
The Board is also thinking about its biggest need – Getting Boots on Ground resources. It is something Hatcher thinks should be done to get kids ready for the next project, not just waiting for the next project.
“We want parents to know kids can have a respectable career in civil, and that it’s
DATE: Thursday 29 September 2022
TIME: 4pm – 6pm
VENUE: The Sanctuary – Adelaide Zoo
MAIN EVENT SPONSOR: ResourceCo SUPPORTING PARTNER: AusPress
government is here to fix things deemed not working, make the right decisions, and act to achieve the best outcomes for the economy and community, the doyen of the state government held court like no other.
We sincerely thank our sponsors ResourceCo and AusPress for their generosity and assistance in making this event a resounding success.
not just what they do when all else fails,” said the President.
With CCF SA successfully training and getting more than 97 apprentices on their way to a productive career in the civil sector (with many already employed), Hatcher expressed his sadness that we are now unsure of our training future, and encouraged everyone to fight to keep the funding for our civil apprentices and training.
Does industry succession matter? According to him, right now, the economy is ‘hot’. With no slowing down in sight as ‘The Horse Has Bolted’. What are the implications for the industry in SA?
We want a net migration of workers. We need an industry that can self-deliver, and at the same time also deliver a good legacy.
“Lean on us. We’re here for you,” said Hatcher.
That was followed by the Treasurer’s report from Tim Bishop that went without question, and the appointment of auditors, bringing the AGM to a close.
The guest speaker, the Hon Tom Koutsantonis MP, needed no special introduction. Having sparred in the political arena for 26 years, mostly in opposition (which sucks), the sprightly 51-year-old joked about how good it was to see no tears had been shed so far at the AGM.
He started by sharing how highly respected Rebecca Pickering is in the Adelaide business community, and the good relationship we have with Labor even when it was in opposition, thanks to Paul Davison who he thinks holds his position in industry very well.
Admitting he gets a lot of complaints on the job regularly, processes for improvement are continuously being put in place so “Keep us informed,” said the Minister.
He hopes that contractors and industry can mutually benefit from the infrastructure spend. With the money committed to the duplication of Main South Road, Grand Junction Road, Port Adelaide, the Interchange at O’Halloran Hill etc, the government wants locals to be involved as there is more than $18 billion in the investment kitty.
Especially with the Torrens to Darlington Motorway, the government is working to ensure as much of the work that can be done using local resources, will be.
In addition, it is fixing the design of this project to get it right as it is such an important piece of infrastructure. For example, the exit points must be right and the tunnel usable, to mitigate the incidence of queuing and crashes, and certainly to avoid the development of gridlocks. “Be patient with us so we can get this right,” pleaded Koutsantonis.
“It’s about our economy,” he continued. According to him, the government believes in upgrading regional roads and is delivering a dramatic sum of money for this purpose… more than $50 million.
Social infrastructure is also very important to this government. Like The new Women’s and Children’s Hospital to be built at the heritage listed SAPOL Barracks site. “A right choice. Forget the politics…” He asked people to forget about the protest… the heritage… for experts have worked on getting the best outcome from building where the Barracks are. (We could almost detect the roar of a lion…) In fact, nobody can visit the Barracks anyway as it is a work
building. “And we’re making a decision for the next 100 years.” (Were the heritage conservationists in the room starting to fidget?)
As far as procurement is concerned, the government is working to get more SA people employed and in business so taxpayers can get more value for money, jobs can be created, and trainees skilled. Processes have been put in place to enforce 90% labour hour minimum by SA workers on major infrastructure projects, construction contracts focusing on local suppliers, reporting obligations, and repercussions for those who do not meet them.
To support SA businesses, the government will mandate lead contractors on government projects to pay subcontractors within 15 days, and the government to pay contractors within 15 days.
With so much happening, department staff are being kept up to date with policies and changes, and procurement information will be published three months in advance to give people adequate time to prepare tenders, to bring about a win-win situation for the government and the people. In the long term, he envisages it will get more people employed (local providers, local people on site, local architects on the job etc), more infrastructure projects undertaken, and ultimately, more money into the economy.
Other topics covered included the breaking up of public projects valued at more than $5Million into smaller parts so more people can get involved, and the early use of tenders and contractors to cut back on project delays.
At Question Time, a gentleman asked from where will the bums on seat (for us) come from? Looking at our population, how can we fill the void?
“We’re our own worst enemy,” Koutsantonis conceded, noting that UniSA has struck Surveying from its list of courses. And everywhere, it’s
happening – less bums on seat. We need more migration, more training. Importantly, we need to change our thinking too. Maybe people don’t need to get a Uni degree. Maybe get into a trade. That said, we can’t just flip a switch to change the mindset – it’s an education process for the long term. In the short term, skilled migration will help fix the gap.
In any case, it’s a good problem to have. “Who’s complaining about full employment?” he quipped.
“The pandemic has taught us we’ve been relying on the rest of the world for supply. We’ve got to stop. We need to develop our local industry. There are tough decisions to make.”
Other questions included issues on land tax and payroll tax, and how our resources are often made up of foreign based directors. And also the concerns about the peaks and troughs for work in the industry.
To the latter, the Minister replied that the increase in infrastructure expenditure will help to improve consistency in that area and we’ll get our bang for the buck.
Finally, when asked: “Are you living the dream after being with the new governing team for six months?” he replied: “It’s a great honour to be a minister.” This boy from Cowandilla is very proud man.
With that, the official part of the event concluded as the nocturnal zoo residents came to life.
So, back to “Morning or Evening?”
Well, with the crowd mingling freely without having to rush back to work, it’s not hard to guess how they voted.
See you next year for another Sundowner AGM. We may even let some ‘owls’ in to ask the treasurer a few questions on dollars and numbers. Hoot! Hoot!
In the mid-70s, the Colonnades Shopping Centre was just a sheep paddock back then, and McMahon Services, (now a major mining company), was doing the civil works.
This picture featured here is supposed to show that I used to work once upon a time. I was changing the wheel bearing on a Terex S35E Scraper that was clearing a paddock down south where they were going to build a brand new ‘state-of-theart’ shopping centre.
It is now called Colonnades Shopping Centre.
I guess this is showing my age but check out the size of the Axle Hub Shaft! I didn't have a forklift or a crane to help me take the wheel off, and to put it back on etc, so I had to use an old
backhoe, that only just managed to hold the weight of the wheel that is in the picture behind me.
I didn't do a JSA, I didn't have any SOPS, the slings I used didn't have any SWL Tags on them, it was about 41 degrees, no safety officer on site, because it was a Saturday morning, and I was doing Field Service on my own as a second-year apprentice. I am not sure if you could get away with doing it like that today? Anyway, I had a great time getting heaps of overtime, and kept the machines going after hours.
Note the standard issue Blackwood Hodge Terex Green Overalls! All part
of my life that I still love. Every day is different, and I still do what my mother taught me: "You must learn something new every day of your life."
I always have, and I always will… Enjoy life and keep learning something different every day!
Steve Kennedy International Sales ManagerLiam Martin started with the Delta Group on the 25 March 2020.
At the time, he was an all-rounder operator and a man on the ground. Ambitious, with a head for detail, and a strategic thinker.
Within 12 months, Liam had secured his place, representing Delta Group as a senior figure on both machinery and the ground, and in 2021 he commenced running work elements of our construction projects, which included the demolition and civil works for the Repatriation Hospital.
In 2022, Liam Martin led our Aboriginal partnership – Widi Ngaruwa’s project – Tarrkarri. This project is of huge national significance and will provide a platform for the world to learn about the unique cultures and incredible story of Australia’s Aboriginal and Torres Strait Islander People.
As part of this project, Liam led a multimillion-dollar package including piling, retention works, concreting, detailed and bulk excavation. Notably, throughout the delivery of this project, Liam was at the forefront of providing an inclusive and culturally safe work environment.
Liam’s dedication to both delivery and maintaining a safe working environment whilst representing the Delta Group is nothing short of outstanding. His story is testimony to the strength and tenacity that drives Liam to succeed.
Delta Group is very proud to have Liam as a valued member of our team.
BDT Construction m: 0416 498 886 e: admin@bdtconstructionsa.com.au
For Ben Turner of BDT Construction, a professional building company based in Hallett Cove in Adelaide, the opportunity to open his own business in June 2022 was an opportunity to take charge of his professional life.
On this score, the 35-year-old former plumber is already kicking plenty of goals. After just three short months, the team of one has expanded to a company of four, with three civil construction specialists now employed by BDT Construction.
According to Turner, BDT Constructions is involved wholly in civil construction activities, including earthmoving, and is now getting into subdivisions. “We are gearing up to do that sort of stuff, and we’re doing a big remediation project at the moment,” he said.
The project is on the site of an old school, so his team is digging out all the footings and everything that was there and filling it back to a Level 1 standard. The remediation work will enable the site to be released as a subdivision in two stages, and Turner is pitching to be involved in this project too. If the subdivision work comes off, this will have significant growth ramifications for the budding business. “If I win work on these two subdivisions, I’ll buy some machinery,” said Turner, who is currently leasing excavators through Cat Rental.
But despite his youth, Turner is no overnight sensation and he started cutting his teeth in the industry as an apprentice plumber in 2004. He switched to the civil construction industry full-time when he started with Drasol, a construction firm with extensive experience across light and heavy rail.
Turner recalls, “I was with Drasol for around about four years. There were
five of us when we started, and Drasol ended up with thirty-fiveish employees in the railway division by the time I left.”
Turner then shifted to another civil firm where he was involved in major construction projects, including the Royal Adelaide Hospital project, which required piles up to 1200mm in diameter and 30m to be driven deep into stiff clays and cemented sand. The young civil construction specialist was also involved in the shotcrete retaining walls on the Southern Expressway. Turner returned to plumbing for a few years and was mainly engaged in drainage work for several small community subdivisions.
In his last paid job before starting his own business, Turner worked for another civil construction company on some small bridges and subdivisions. Then at the beginning of 2022, the ambitious Turner decided, “Bugger it, it’s time to start my own thing.”
Turner shies away from the idea that being his own boss was a long-term dream for him. “I just realised that when you’re working for somebody and supervising others, you’re busting your guts out all the time to get the job done for someone else.
“So, I thought I may as well go out on my own and do that for myself. At least I’m, busting my guts for myself.
“I never wanted to own my own company. I always just thought it was just easier to work for somebody. But then, just one day, I just, literally on a whim, decided ‘bugger it’ and started a company. As soon as the ABN was done, I handed my notice in and here I am.”
A straight shooter, Turner also admits that renovating his home also encouraged the timing of his move into his own small business. “I’m renovating and doing an extension to the home as well. The quotes I was getting for that are astronomical. My theory was that if I don’t have much work with BDT, I can fall back onto the house I’m building to tie in the time in between projects.
“That hasn’t happened, and I’ve had no time to spend on the renovation.”
BDT has taken some contract work with several developers in just three short months while Turner set the business up. This regular flow of work includes mainly remediation jobs, including a contract at Davoren Park, where BDT had been on site for five weeks with another ten weeks to go. Not a bad earn for a company that was only two months old at the start of this contract.
There is no question that Ben Turner loves a challenge. Not only has he launched a new business this year, but in May, he also became a dad for the first time with the birth of his son Finn. Don’t forget – the courageous Turner is also renovating his home with his wife, Chloe!
Those life-changing challenges aside, Turner admits that starting a new business has been more involved than anticipated. “There’s a lot more involved in being a boss. Trying to get the safety compliance and that stuff in place took a lot of time and patience.
“I’m trying to balance doing the work, doing the invoices, and paying for everybody while writing my safety policies and getting compliant. I’ve got
my Civil Contractors Federation audit tomorrow,” said the remarkably calm BDT boss.
“Getting all the paperwork and everything in line has been a lot. So, it’s been a bit harder than what I’d anticipated, but I’ve had the work behind me to support me financially.
“I guess the stress of trying to find the work and what to do about money hasn’t been a problem. What has been a lot more stressful has been the setup of the actual business itself. Yeah, it’s very involved.”
The new boss feels he’s better at managing the job than his employees, but that handling people is central to longerterm business success.
“Managing people in the civil industry is something that comes with it. I wouldn’t call it my favourite part,” admits Turner. “However, I’m fair, and as I’m just starting up, I’m trying to take advice and learn from everybody where I can.
“I’m open to listening to how everybody wants to do it or their opinions and collaborating with them and coming up with the best process involving everybody. I feel I’m approachable and hands-on, so I’m not just sitting back and seeing everybody work and fall in line. So, I’m definitely not a ‘Do as I say’ sort of person.
“I’m out there and doing it with them. And so, I get dirtier and wetter than they all do.”
Turner says he doesn’t have a small business mentor as such. “One developer I’m working with is very hands-on with me and supports me a lot.
“So, anything I struggle with, he’s delighted to assist me because I think he likes working with me.”
He adds, “I’ve got a few old supervisors I’m friends with that I bounce ideas off, processes and methodologies. But because I’ve been a supervisor for quite some time, I guess the running of a job is less of an area I need to investigate. It’s more of the business side, but I’m just riding out there and seeing how I go.”
Turner adds that one of his last employers also left a lasting impression on how to manage his employees positively. “They were fair to everybody and took care of the workers.”
Turner admits that as a younger boss, growing BDT is not out of the question. “But growth comes with its challenges.
“I’d like to be big enough to enable me to step back. No one wants to start a business and then slave away forever.
“You want to reach that point where you could step back a little to get it to the point it was running itself. I don’t want the business to get massive and take over the world, but just enough so that
everybody who works for me can work a reasonable 40-hour week without having to do significant hours, and the company can sustain itself.
Finally, while still new to business ownership, Turner already sees plenty of upsides. “While I don’t get more time to myself, the freedom of deciding to do things and everything is very rewarding.
“And then doing a good job becomes more rewarding because it’s all you, and you’ve done it all.
“So, preparing all your documents for a pitch, and when it all comes together and you show them to a client, and they say it’s all very professional, and everybody likes it, that is rewarding.
“You know that it’s something you’ve developed and everything you’ve done. It’s very rewarding in that way. You also see your company growing, especially when you start paying yourself. That is a real buzz.
“When you start seeing some money come in, it’s a good feeling to know that you’ve accomplished something and you’re achieving to get somewhere where you want to be.”
ACCESS CAPITAL was established in 1989 in response to a growing need for specialised, dedicated finance experts to assist with sourcing and managing the equipment finance requirements of their clients.
Access Capital’s core focus has been about building lasting business relationships with clients ensuring a deep understanding of their business is developed and nurtured over time. This has provided the foundation to provide our clients with the best finance solutions to meet their immediate and long-term requirements.
Physically located at Level 1, 69 Fullarton Road Kent Town SA, Access Capital’s team of brokers travel far and wide throughout Australia to service our diverse client base.
Access Capital currently works with clients across all industries in both metropolitan and rural South Australia. We are available to meet our client needs, ensuring a fast, efficient, and highly personalised service to accommodate individual business needs.
We have 13 dedicated staff comprising of 6 Brokers, 3 Credit Managers, 3 Business Support Officers and a General Manager.
Access Capital has been a finance specialist for over 33 years, providing
a full range of finance solutions to its clients. Specialising in Equipment Finance, our offering also includes, commercial loans, finance leases, commercial hire purchase, operating leases, insurance premium funding, registration funding, real estate finance and cashflow finance.
Access Capital’s management and staff have extensive experience (totalling over 200 years) in the finance industry. Added to this, Access Capital has a vast network of specialists which it draws upon as required to ensure it is at the forefront of market, industry and regulatory enhancements and changes.
As the largest equipment finance brokers in South Australia and the Northern Territory we have accreditations with over 35 financiers, enabling us the flexibility to source funds for all our client’s equipment financing needs, without the need to rely on real estate security.
Our wide range of finance options means you don’t have to be tied to any one particular lender, ensuring you receive the very best range of finance products available in the marketplace.
We understand that our client’s time is important, so to support this, we have developed a ‘one stop shop’ service and sales proposition. This allows our clients to get on with their business and pass any of their time constraints associated with arranging equipment finance to us.
Our team of finance brokers share a wealth of experience within the
civil construction industry, currently partnering with several successful civil contractors across the state. We pride ourselves on investing the time required to gain a sound understanding of your business ensuring all finance facilities are tailored to meet your business needs now and into the future. Specialising in Equipment Finance, we understand the urgency that often exists with financing equipment. To compliment this, we have adopted a value service proposition of providing fast, efficient and seamless service for each client interaction.
Continue to build a relationship with Civil Contractors Federation SA and its members.
Partner with CCF members to provide advice and finance solutions to assist them prosper into the future.
We welcome the opportunity to review CCF SA members’ current and future financial needs. To arrange a free, no obligation review of your finances at a time that is convenient to you, contact Todd Howson either by email todd@accesscapital.com.au or phone 0437 769 317 or 08 8334 2100.
At Access Capital we believe that ‘your business is your business’ and pride ourselves that the business and staff are fully compliant with the New Privacy Amendment Act. To find out more, you can review the Access Capital Privacy Policy on our website www.accesscapital.com.au
EMAIL todd@accesscapital.com.au
CCF SA’s commitment to help build a safe and healthy workplace
During the month of October Civil Contractors Federation SA celebrated National Safe Work Month. Each week focused on a different area of WHS to engage businesses, employers, and workers across Australia to commit to building a safe and healthy workplace for all Australians.
This year’s National Safe Work Month theme was ‘Know Safety, Work Safely’, which was designed to spotlight a range of WHS topics including injury and illness at work, as well as psychological health and managing work health and safety, to create a safe and healthy workplace for all.
CCF SA kick-started the month by aligning with Return to Work SA and SafeWork SA to deliver a free workshop for our members. It covered topics such as mental health, managing WHS risk and preventing harm, injuries at work, and a safe and healthy workplace for all.
It also covered Return to Work legislative requirement for employers. For example, businesses with 30 or more employees hired for a period of more than 3 months are required to have a Return to Work Coordinator based in South Australia. This is a service CCF SA can assist you with. For more information on how we can assist you
with your Return to Work requirement, please contact Michelle Taylor at mtaylor@ccfsa.com.au or on 0485 883 545.
The feedback from the attendees was the workshop was informative and interesting.
Left to right: Paul Finlay (SafeWork SA), Mardi Webber, Houda
Sadauskas (ReturntoWork SA), and Michelle Taylor (CCF SA).
Peters and Amanda @bigchiefhireaustralia /bigchiefhire /big-chief Truganina, VICDelivering successful landscapes for major infrastructure projects across Adelaide is all about innovation.
Diverse landscaping projects require innovative methods in response to site constraints, weather conditions, project program changes and available resources. The ecoDynamics team in South Australia prides itself on delivering quality landscapes through its commitment to working smarter and applying innovative solutions to materials, treatments and project delivery.
Landscaping occurs at the end of a project and often deals with constraints. Overcoming them means applying innovative and novel equipment. When we worked on the Adelaide Desalination project, we faced steep batters that conventional plant and equipment couldn’t operate on. Our equipment solution was delivering our Blower trucks from Victoria to install the mulch. Similarly, we brought our Slinger trucks in onto the Northern Connector Project to install mulch and stone products onto steep batters in the project’s closing stages. Slingers use a fast-moving conveyor that slings (or throws) mulch, soil or stone from up to 10m away from the truck placing over 100t of material a day.
That allowed both landscape projects to move finish on time. Our approach is part of the routine operations that supports on time project completion.
A conventional approach to landscaping is installing topsoil which is then seeded with grass or planted with seedlings. Leaning on our market product knowledge, we can offer alternatives using hydraulically applied products.
Hydraulically applied products are a mixture of organic mulch, glues, fertiliser, and seed mixed into a slurry and applied via a hose or monitor. Hydraulic application means mixtures can be applied to steep slopes and across large areas from a distance without the need for workers or smaller equipment traversing the slopes.
We offer a range of competitive solutions to traditional approaches where topsoil, mulch, jute and tube stock would be used for a fraction of the cost. After completing the large hydroseeding areas of salt bush on the Port Wakefield
Highway project, the landscape has flourished in one of the harshest environments in the state. Our approach provides enormous opportunities to improve project delivery outcomes and generate client savings.
Along with our extensive project knowledge and landscaping experience, our South Australian reputation is built on our team’s willingness to review designs and develop alternatives that successfully deliver landscape results.
Over our 10+ year involvement with major projects in South Australia, we have seen delivery standards and landscape outcomes improve from adopting learnings from across the country and applying them locally.
ecoDynamics is regularly engaged by construction teams to review designs and offer delivery advice that will enhance landscape works through design alternatives. Our commitment to creating greener futures across Adelaide is sparked by our innovative landscaping methods that demonstrate our ability to overcome project constraints and deliver quality landscaping solutions for our clients and the wider community.
LOOK HOW FAR WE HAVE COME
CACL has a cohort of apprentices currently available for Host placement.
This cohort of Apprentices will be the last group to attract the BAC funding:
ф
Boosting Apprenticeship Commencements (BAC) wage subsidy initiative – 50% apprentice wage (1st year). The subsidy is available for eligible training contracts between 5 October 2020 to 30 June 2022. Up to $7k
ф
per quarter, per eligible apprentice. Funding completed on 30 June 2022, and the subsidy is no longer available for any apprentice receiving any other form of Australian Government wage subsidy.
Completing Apprenticeship Commencements (CAC) wage subsidy – eligible employers of BAC supported apprentice will transition onto the time-limited CAC wage subsidy for the second and third
year of their apprenticeship. A 10% apprentice wage (2nd year) up to a maximum of $1,500 per quarter, per eligible Apprentice, and 5% apprentice wage (3rd year) to a maximum of $750 per quarter per eligible Apprentice, is reimbursed to the eligible host.
Contact us today for more information on (08) 8111 8099 or email cacl@ccfsa.com.au
A hard question given all the amazing people in the world and all those I have the pleasure of meeting and working with every day.
REBECCAEXECUTIVEPICKERING DIRECTORA ‘normal day’ is a ‘different day’ at CACL and I love it and what it brings to the role I hold. Life at CACL feels like a permanent puzzle: always a challenge, dynamic and never static. A day for me involves advocacy for civil apprenticeships, working with the State Government specifically in Education, Skills and Infrastructure Agencies, and working with allied employment and youth entities, strategy, governance and finance matters. Speaking with amazing apprentices when they are at CCF SA House or at Burton is always a highlight as is speaking with our incredible hosts.
As for love, forging new Vet Reform Flexible Industry Pathways – Roads2Civil – in the Education system for students, school leavers and the Civil Industry is something that I am incredibly proud of. It has taken years of work since to build these groundbreaking and innovative programs. Roads2Civil programs now reach across Career Influencers (teachers, parents, coordinators, councillors), students from Year 7 to Year 12, and includes school leavers. With 64 schools currently engaged and with this same work extended to support career pathways for disadvantaged South Australians, my hope is that this work provides future leaders and professionals into our civil industry for decades to come.
Perhaps the most important part of the job that I love will remain the establishment of Civil Apprenticeships and Careers Ltd. To establish an entire business from an idea, into feasibility modelling and planning and then into an operating entity employing over 100 people, in less than 3 years, is something I have loved the most. I will always reflect on this as a highlight in my life and career.
Receiving Federal funding, recognition and support for civil construction apprentices and maintaining our momentum in the education and skills systems is the largest challenge that I can foresee immediately.
Other challenges continue too; these include lobbying Government to ensure a reliable, consistent, and transparent pipeline of short-term and long-term work exists. This pipeline provides our industry confident and the opportunity to host apprentices. Activating greater understanding of Group Training Organisations across the business community is another challenge over the next 12 months as we seek greater diversity with our Host pool.
I am not sure I can pinpoint one person, but I do know for all my life I have always looked up to, and held the highest respect for, business owners. No matter the size or type of business, I look up to them all – even the young girl who sells lemonade in her driveway.
I love entrepreneurial thinking and I am inspired by anyone who can take a dream, a love, an idea and turn it into a business.
Unlike working for a business, running a business means there is no safety net, it can be lonely, risky, can deliver both amazing and at time heart breaking outcomes.
Whether an individual is running a side hustle or an ‘all-in’ start up employing others, they are all brilliant to me. Having run my first small business at 20, and later a side hustle consultancy company (now 13 years old) to support my new, young family at the time, I know how hard life is for a business owner.
So, to all the past and present business owners, keep on keeping on, you are all inspirational particularly through these tough times. I hope our CACL apprentices look to become our next cohort of business owners in our civil industry.
WHAT DID YOUR 8-YEAR-OLD SELF LOVE DOING?
I always loved being active and outdoors. I have always been naturally curious so as an eight-year-old I would spend any time I could exploring, camping, and enjoying what our amazing outdoors has to offer.
WHAT IS YOUR FAVOURITE THING ABOUT THE FESTIVE SEASON?
The summertime. Summer seems to bring uplift and positivity; it brings everyone together.
On a standard day at work (and the thing I love the most about my job) is overseeing the mental and physical health of our apprentices, providing them with guidance and continuous support to effectively work through the requirements of their apprenticeship both on site and at training. I liaise with our hosts to assist them with any enquiries they may have and work with them to generate the best outcomes for their business and our apprentices.
FINLAY FIELD COORDINATORWHAT DO YOU THINK IS THE BIGGEST CHALLENGE THAT YOU WILL BE FACING IN THE NEXT 12 MONTHS?
Generating apprentice placement opportunities in our industry as new projects commence.
WHO DO YOU LOOK UP TO?
I admire Terry Crews. He demonstrates that you can show strength through compassion and kindness and is an incredible role model for fathers. He is also an advocate for owning your mistakes which provides valuable learning and personal growth opportunities.
WHAT DID YOUR 8-YEAR-OLD SELF LOVE DOING?
I was always an avid video game enthusiast as a youngster with a keen interest in all things sci-fi. Some would say I’m a bit of a nerd and I own that.
WHAT DID YOUR 8-YEAR-OLD SELF LOVE DOING?
Spending time with my daughter and my parents. Christmas is for the kids in my family, and it is always warming to see their faces light up when they see what Santa has sent them. And eggnog!
WHAT DOES A NORMAL DAY AT CACL LOOK LIKE FOR YOU AND WHAT DO YOU LOVE MOST ABOUT YOUR JOB?
WHO DO YOU LOOK UP TO?
My wife, Amy. She is a constant inspiration to me. I have never met someone as hard working, dedicated and driven. The work that she does in the breast cancer research space is incredible and the outcomes of her research will help the millions of people diagnosed with breast cancer each year.
WHAT DID YOUR 8-YEAR-OLD SELF LOVE DOING?
I was a keen Star Wars fan and was forever eating. Luckily for me, I also had a keen interest in playing football to keep me fit!
WHAT IS YOUR FAVOURITE THING ABOUT THE FESTIVE SEASON? Taking a break to recharge my batteries and enjoying the downtime.
WHAT DOES A NORMAL DAY AT CACL LOOK LIKE FOR YOU AND WHAT DO YOU LOVE MOST ABOUT YOUR JOB?
A normal day at CACL involves assisting our apprentices and hosts with their payroll enquiries, providing guidance to apprentices on how to correctly complete their timesheets and overseeing CACL’s finances. I love helping and supporting our industry by alleviating the stress of managing the apprentice’s payroll and other financial processes for our hosts.
SIGN THE "SAVE MY APPRENTICESHIP" PETITION HERE
No two days are the same at CACL! However, a normal day for me involves overseeing the employment, training, and development of our apprentices and business operations, providing leadership and mentoring for CACL’s staff and apprentices, driving strategic business strategies, and building strong relationships with new and current hosts and stakeholders. What I love most about my job is seeing the progression of our apprentices as they work through their apprenticeship to become incredible assets for our industry’s work force.
WHAT DO YOU THINK IS THE BIGGEST CHALLENGE THAT YOU WILL BE FACING IN THE NEXT 12 MONTHS?
I believe that continuing to lobby for funding parity for our apprenticeship will be a challenging road ahead. Our apprentices deserve the recognition and support from Federal Government that other trades receive. By signing the ‘Save My Apprenticeship’ petition, our industry can help us help our apprentices.
WHAT DO YOU THINK IS THE BIGGEST CHALLENGE THAT YOU WILL BE FACING IN THE NEXT 12 MONTHS?
Funding! As a charity and not-for-profit organisation, CACL is partially reliant on government support to provide sustainability for the organisation. Without it, our apprentices and hosts do not have access to financial support as compared to other trades.
WHO DO YOU LOOK UP TO?
Jacinda Ardern is an inspirationto me. A strong female leader who is passionate about helping those around her and support an entire country. Also, she is an incredible working mother who understands the importance of a healthy work-life balance.
WHAT DID YOUR 8-YEAR-OLD SELF LOVE DOING?
As a child, I loved to study and learn different languages. I always found comfort in learning new things and expanding my knowledge.
WHAT IS YOUR FAVOURITE THING ABOUT THE FESTIVE SEASON? Spending time with my family, especially my little one.
Flix Productions Australia is a multiaward-winning, cost-effective production firm with over 15 years of experience assisting businesses across Film, Social Media, TV, Corporate, Sports, Documentaries and News.
We flourish at the crossroads of strategy, creativity, technology, and production, leveraging our integrated methodology, our people's wide experience, and unique creative insights to tell captivating stories, deepen connections, and ultimately grow our clients' businesses.
We work with our clients to, create, develop and produce a quality scripted and/or unscripted video to showcase your business or project.
We became a CCF SA member as we were asked to work on the Earth Awards back in 2017, to put together the works of all the finalists for that year. We have been the chosen partner to continue to work on the production, voice-overs and creation of this event ever since.
We have also worked with CCF SA for projects like: Member Video (scan QR code to view the work), Civil Train Corporate videos, and CCF SA Corporate videos.
We have also worked with CCF SA members: ф Topcoat Asphalt ф Raw SA
Brooks Hire
ITR – Indigenous Training and Recruitment
MEH Hire
Bowhill Engineering
Workzone Traffic Control
While Flix Productions Australia is based in Adelaide, South Australia, we are regularly required to travel both interstate and internationally to assist our clients.
Flix Productions can fulfil all of your video needs… even drone work.
We specialise in Corporate videos, Business stories, Commercials, Sports and TV/News/Features.
Our network of industry experts allows us to create a package for any need, size, or budget.
We can provide one-man services from the beginning to the end, as well as a full crew of the industry's best talents.
Flix Productions has worked on everything from feature-length documentaries and newsgathering on all major networks to corporate
videos for some of Australia’s well-known businesses.
Flix Productions is proud of its ability to see a project through from beginning to end with minimal outsourcing, saving CCF SA members money.
Flix Productions will shoot, edit, convert and deliver your content to endless platforms in multiple formats. We work closely with you to tell your stories or showcase your civil works.
Video is the best way to showcase your project work or product and services to potential future clients. With the use of Time-lapse, Drone work or even realtime capturing, video is one of the best ways to engage, communicate and a great return on investment.
WHAT OTHER COMPANIES AND INDUSTRIES HAVE FLIX PRODUCTIONS WORKED WITH? We have worked with a wide range of industries and companies across Australia and the world.
WEBSITE
Workzone Traffic Control was established by Andrew White in 2004 and is still proudly South Australian owned and operated. Some of the first works were for SA Power Networks and we have enjoyed a successful collaboration since that time.
Workzone Traffic Control has a number of long term employees. There is a strong emphasis at Workzone that there should be a career path within the traffic management industry. Workzone is proud to have 5 of the 7 Planners who have come from traffic control positions. This gives the Planners a
greater insight into the requirements on the road. The 2 Schedulers have come from a traffic control background and several others are now in Sales/Administration positions. This is a win-win with young people seeing a professional pathway in traffic management and Workzone retaining the best staff in the business.
All completed in paper copy including TGS
Assignar software manages our job bookings, project flow, traffic management worker and asset scheduling. Our field staff use these systems on mobile tablet technology, that allows for live, on-site submission of job safety analysis sheets, incident reporting, time sheet submission and back to base communication, allowing for seamless on-site activity.
TGS are prepared using NearMap and MetroMaps.
Stop/Slow Bats
Portable booms
Arrow boards on vehicles On site moveable Traffic Lights with remote access
Arrow Boards including speed radar and VMS display
Variable Message Signs (VMS) including built in speed radar
Truck Mounted Attenuator x 2 (TMA)
Light Truck Mounted Attenuator x 2 including 1 x HYBRID Model
Cone Deployment Vehicle Radar Speed Display
Unit 3, 280 Grand Junction Rd 12 Circuit Drive Hendon Approximately 300 sq metres Approximately 2000 Sq metres
The Department for Infrastructure and Transport (DIT) and its civil construction industry partners are working together and continuing to raise safety performance on their projects.
An industry safety influencer’s group has been established and is meeting regularly to discuss safety improvement opportunities to guide and support the industry to make DIT work sites safer for all.
The group is committed to sharing best practice approaches to safety management and seeking innovative practices which can be applied across projects.
At present the group is looking at ways to improve safety in traffic management and control. A working group has been established which includes representatives from industry, government and the Traffic Management Association of Australia, South Australia Division.
The working group’s aim is to progress initiatives which will enhance safety in traffic management.
ф Support Industry, drive innovation & encourage best practice traffic management.
ф Consult broadly to drive legislative and process change for safer practices.
ф Consult and inform Industry of progress and potential change.
ф Implement best for Industry safety in the traffic management realm.
The remediation works included intermediate waste soils, and low-level and high-level contaminated waste.
We are incredibly proud of you, and all of SA’s 2022's Earth Award entrants and winners. We do amazing things in South Australia!
A massive congratulations to McMahon Services for taking out the Civil Contractors Federation National Earth Award for their project, ‘The Australian Bragg Centre Civil and Environmental Remediation Works’, in the $10M-$30M category!
The Australian Bragg Centre Civil and Environmental Remediation Works project site included demolition of existing structures, bulk earthworks, and remediation of an on-site soil contamination plume.
The biggest issue facing a lot of companies at the moment is skill shortage. Many companies are promoting workers into supervisory positions, but they don’t yet have the relevant leadership skills. Future Institute are offering a 10% discount for CCF SA members during the month of January to up-skill their leaders through either of our leadership intensive programs.
The recent Jobs and Skills Summit 2022 has really brought forward the growing concerns for Australian businesses in relation to attracting and retaining skilled staff, as well as up-skilling existing staff for expected future growth.
As highlighted in the Jobs and Skills Issues paper. “Almost a third of businesses reported having difficulty finding suitable staff in June, and most cited a lack of experience or skills as a major factor.”
The Australian labour market is currently operating at close to full employment, resulting in a lot of businesses having to promote staff from within, who may not yet have the skills and capabilities of their new role.
In such volatile times, finding the time to upskill staff can seem impossible. This is why Future Institute has developed a suite of intensive leadership programs. These programs will assist businesses in upskilling their new and existing leaders and can be delivered in just 1 – 7 days.
Future Institute’s leadership programs enable businesses to leverage their existing workforce to meet the conditions of the current environment; fill in leadership gaps; improve retention; and attract talent for business success in a competitive market.
10% off is a limited time offer, must engage before 31/01/2022 to take advantage of this great offer!
Do you already know the areas in which your leadership team needs to develop? The Leadership Essentials Program is a 'Pick and Mix' leadership course, where you pick the topics to be delivered and is conducted over 1 - 7 days.
Every organisation is different, and so are their needs when it comes to developing their supervisors and managers. As a collective, they may excel in some areas however need development in others. Our ‘Pick and Mix’ program allows you to choose the topics that will meet the needs of your team, all of which will be customised to your industry and organisation’s challenges by our curriculum team prior to delivery.
After many years working with leaders, Future Institute have identified a set of core skills that are essential in building effective leaders.
Conducted over 4 days, this program challenges participants to reflect on their behaviours and how they can positively and negatively impact others. They will understand the need for using different styles of leadership, develop strategies to get ‘buy in’ from their teams, and learn how to better manage performance.
Future institute also offers BSB40520 Certificate IV in Leadership and Management.
SCAN ME TO FIND OUT MORE!
The South Australian Government has reformed the vocational education, industry engagement and career education in schools so that all young people are well prepared for their future careers. These reforms will benefit students and help ensure that they are able to grasp the opportunities available within our growing and transforming South Australian economy.
A new Vocational Education and Training for School Students policy has been created that sets out the government’s strategic direction and plans of how vocational education and training (VET) is delivered to South Australian secondary school students.
The Policy builds on existing good practice across South Australia and sets out the state government’s framework for system-wide reform that improves completions of both VET qualifications and SACE, drives transitions to skilled careers and better meets the needs of industry for underpinning strong economic growth.
In summary, the measures of success are to:
ф increase the proportion of young South Australians participating in post-school education, training or employment
ф increase completion rates of the SACE for students on a vocational pathway
ф increase the number of young people entering apprenticeships and traineeships
ф increase the number of school students completing VET qualifications at school
ф increase the number of school students transitioning to VET post school
ф provide a pipeline of young skilled workers to meet employer needs.
As part of the reform Vocational Education and Training (VET) pathways have also been clearly mapped out that lead to real jobs, right here in South Australia. For the first time, we now have a Civil Construction, Resources and Infrastructure Student pathway featured in the Foundation for Young Australians ‘Artisans’ job cluster. Jobs in Civil Construction has been identified as one of the key areas for young people looking
to obtain a skilled trade in jobs that require skills in manual tasks related to construction, production, maintenance or technical customer service.
In making vocational education more accessible to young people, the South Australian Government’s Department for Education has released The VET for School Students (VSS) List, which is government subsidised courses available to South Australian School Students. As part of the new VET reform and subsidised list we are excited to see the follow opportunities in a Civil Construction, Resources and Infrastructure Student pathway:
Flexible Industry Pathways (FIP)
FIPs include Certificate II and III VET qualifications that lead to further education and/or entry-level employment in key South Australian industries. FIPs enable a student to commence a VET qualification whilst at school completing their SACE and are a great option for students looking for a skilled career.
Qualifications for Institutional Delivery
Year 11 – RII20120 Certificate II in Resources and Infrastructure Work Preparation
Contract of Training (on-the-job)
RII20120 Certificate II in Resources and Infrastructure Work Preparation
RII20720 Certificate II in Civil Construction
RII30120 Certificate III in Surface
Extraction Operations
RII30820 Certificate III in Civil Construction Plant Operations
RII30920 Certificate III in Civil Construction
The Artisans
in Civil Construction are in the Foundation for Young Australians ‘Artisans’ job cluster. These jobs require skill in manual tasks related to construction, production, maintenance or technical customer service.
Source: Foundation for Young Australians (2016), “The New Work Mindset”.
studentpathways.sa.edu.au
CCF SA were honoured to be shortlisted as a Finalist for the Civil Industry Schoolbased Pre-Apprenticeship model at the 2022 South Australian Training Awards. Although the project remained as a finalist, we are proud to be recognised for the success of ROADS2Civil.
In addition, Roads2Civil became proud FINALIST for the Industry Collaboration Award. Why an Industry collaboration award? Well, it is the 8 collaborative partners who support this project to ensure its success.
Roads2Civil is a school based pre apprenticeship program creating opportunities for students to become Civil Apprentices. CCF SA have created a streamline pathway into the Civil industry, with Civil Train SA delivering the accredited training and employability skills to students, and CACL GTO activating Industry support and employment opportunities.
Our extended partners who drive the project, have come together to produce a partnership program that offers practical real-life experience to participants on live work sites that will result in the beautification of the grounds where they work on to acquire their skills – the local councils, community centres and local host schools.
Renewal SA supports live site visits, and CITB supplies PPE to all the students. Local Secondary schools enable the exposure of the project for all Year 10-12 students. These support the $10 billion infrastructure investment from government whose key focus is to create sustainable careers in the sector for a new and younger workforce.
WHY IS THE ROADS2CIVIL MODEL PAVING THE WAY FOR THE FUTURE WORKFORCE IN CIVIL?
Roads2Civil model is an intensive, immersive training project with innovative, alternative delivery pathways that addresses the needs of the SACE system and our Civil industry.
The ability to deliver a cluster of units rather than a whole qualification to meet SACE requirements has allowed us to tailor flexible and appropriate programs that meet our industry’s needs.
Secondary Schools now have a viable alternative trade pathway with genuine employment opportunities at the end of each program for suitable participants, either as a school-based apprenticeship or full-time apprenticeship at the completion of their schooling years.
The future introduction of a new Flexible Industry Pathway, by Department of Education in Civil Construction, will be a key outcome and acknowledgement of the program's success.
Local communities will benefit from the beautification of the community spaces and the positive engagement of young people in their local areas. Many of them are at risk of disengaging from the school environment and missing opportunities to access positive connection relating to local community support, training opportunities, employment, and workplace experiences.
Secondary schools have been able to secure employment outcomes for many of their students using clear, established pathways to create opportunities to those interested in pursuing careers in the Civil industry. Activating an innovative method of SACE completion.
The GTO is able to take time over the course of each program, to carefully screen potential apprentices before offering apprenticeships to the right candidates. Thus, the potential of improving the completion rates of each of those apprenticeships is exponential.
Industry partners have the option to either hire apprentices directly, or they can choose to use the services of CACL (the GTO) to broker the recruitment of their apprentices. They can also meet with prospective apprentices and observe their development over a sustained period, which should result in improving apprenticeship completion and ongoing employment rates.
In review of historical training practices is very easy to reflect on the technological advancements in the physical resources we use today as both industry and training organisations continue to evolve.
The Australian Conciliation and Arbitration Commission introduced a new pay structure that was based on the structural efficiency principle in August 1988. In exchange for higher pay, unions agreed to help rewrite industrial awards to better reflect the shifting demands of contemporary business and to support employee multiskilling. Major changes to skill development and training arrangements were to serve as the foundation for the restructuring. In the paper A Changing Workforce, Dawkins (1988) emphasised the implications for education and training: workers should be ‘multiskilled’, ‘adaptable’ and ‘mobile’, with the entire process known as ‘award restructuring’. The policy's main components included fewer job classifications, a clearer line of demarcation between jobs, and the substitution of 'time served' apprenticeships with a competencybased approach.
To do this, the newly constituted National Board of Employment, Education, and Training mandated that industry develop national standards in vocational education and training that were consistent with a national framework (NBEET). Additionally, individual States and Territories committed to offering vocational education and training that would adhere to the national criteria (Dawkins, 1990). The development of worker competence and skills was the focus.
overhead projector
To ‘streamline the interaction between industrial bodies, training organisations, State and Territory authorities, and ANTA’, the National Training Framework went into effect in January 1998. (DETIR, 1997a:7). The Australian Recognition Framework (ARF) and training packages are the two interconnected parts of the National Training Framework. With the national registration of providers who can create and offer their own training and services, the Australian Recognition Framework (ARF) will replace the previous accreditation of individual courses. Through VETEC, providers are registered in Queensland. Training organisations can offer assessment services and issue nationally regarded credentials once they have registered. Figure 1 presents a list of the new system's features.
interactive smart board (touch screen and internet access)
The Australian Recognition Framework (ARF) was created to:
ф ensure nationally consistent administrative arrangements through reciprocal state and territory recognition
ф simplify the regulation of training; clarify the roles and responsibilities of various organisations within the training system
ф introduce audit arrangements of services and products; and establish a relationship between nationally recognised training packages, nationally recognised certifications, and nationally recognised training institutions
Creation of training packages is the second element of the national training framework. The National Framework Committee of ANTA has approved a set of national training resources called Training Packages that registered training organisations can use as the foundation for their training initiatives in particular industrial sectors. The packages will include endorsed and uniform
figure 1: the australian recognition framework (arf)
competency standards, assessment criteria, and qualification levels that are in conformity with the Australian Qualifications Framework for each industry area (AQF).
The National Training Framework committee and the Commonwealth, State, and Territory Ministers both approved the civil construction training programme in October 1998. (Australian National Training Authority, 2000). It covers important tasks performed by civil construction sector employees who operate both plants and non-plants. In this industry, plant operators frequently use a variety of equipment, such as backhoes, graders, scrapers, frontend loaders, tractors, and excavators. Non-plant operators typically work on building and maintaining roads, tunnels, rail and track systems, bridges, and ships, and laying pipes.
The (VET) in Schools programme and Labour Market Programs were the main inspirations for this particular set of Certificate I skills.
The Civil Construction package has been developed to Australian Qualification Framework level III, with three further levels planned. The organisation of the standards for the industry is shown in
The Level II Civil Construction units of competency are drawn from the 1000 (Level I) and 2000 (Level II) series and are divided into core and elective categories to reflect the fundamental abilities and information needed in the field and to allow for customization to meet the demands of specific occupational groups. In response to the demands of the industry and current working procedures, training pathways leading to general construction, concreting, and steel fixing have been designed at this level. The nine competences that make up this level therefore have a ‘technical’ bent, and most of them are electives.
There are seven groups of competences at certificate level III that have been chosen to mirror trade jobs in this sector. These are, as seen below: ф Civil Construction – Plant Group A ф Road Construction and Maintenance ф Tunnel Construction ф Foundation Work –Anchors and Piling ф Pipe laying ф Railway Construction and Maintenance ф Bridge/Marine Construction and Maintenance
2006
In July 2006, the BCC98 Training package was superseded by the RII06 – Resource and infrastructure industry training package. This was another huge milestone for the civil construction industry as there was a clear divide from the building construction training packages.
Infrastructure Training Packages: RII06 Civil Construction Training Package, MNQ03 Extractive Industries Training Package, MNM05 Metalliferous Mining Training Package, DRT03 Drilling Training Package, MNC04 Coal Training Package and BCC03 Civil Construction Training Package were consolidated into the RII09 – Resources and Infrastructure Industry Training Package.
Nationally recognised training for occupations in the Mining, Drilling and Civil Infrastructure industry was and continues to be delivered under the RII – Resources and Infrastructure Industry Training Package. This includes knowledge and skills specific to Civil Infrastructure, Coal Mining, Drilling, Extractive Industries and Metalliferous Mining sectors.
2021
In 2021, the latest release of the RII qualifications occurred, and it is fair to say we have now seen significant changes in sectors and shear quantity of units available to learners from the beginnings of curriculum set by industry for Civil construction training.
Plant – plant group A became RII30820 – Certificate III in Civil Construction Plant Operations, a total number of 20 units, 15 core units plus 5 elective units is derived from the total 65 units within the training package.
The RII30920 – Certificate III in Civil Construction has a massive 202 units within the training package including core and elective units of competency that cover the skills for the following eight (8) specialist and one (1) general civil construction specialisations:
Table 2 below.
The first level of competency consists of fifteen units, fourteen of which are core or obligatory. They also serve as prerequisites for more advanced competencies. Four of these units might be categorised as ‘generic’, while eleven of them are ‘technical’ in character.
These general competencies are:
ф Carry out interactive workplace communication
ф Carry out occupational health and safety requirements
ф Plan and organise work ф Carry out measurements and calculations
The Resources and Infrastructure Civil Construction Training Package RII06 became the first Training Package to be developed under the Resources and Infrastructure Industry Skills Council (RIISC) and is an addition to the Civil Construction Training Package BCC03. RIISC is in the process of consolidating all Training Packages under its coverage and this involves recoding all Units of Competency and qualifications as Resources and Infrastructure (RII) units and qualifications as each Training Package is reviewed.
2009
In July 2009, as a result of rationalisation all five existing Resources and
participants undertaking a skillset program conducted at kintore (cfat/nt government funded) for the nagurratjuta/pmara ntjarra aboriginal corporation.
While the NT and SA may have parted ways in 1911 in relation to territorial governance, the bonds (especially in Central Australia) still run deep. This strong connection manifests itself in numerous ways ie Family, Education, Health Care, Sport, Social Events etc. Above all, the economic and employment ties have remained firm over time, with SA still representing a major core of Central Australia’s skill-based workforce.
To this end, CCF SA (resource and infrastructure expertise) has played a significant role in the economic expansion of the NT operation, in many cases working alongside the CCF NT to identify and foster the numerous commercial opportunities, with the aim to benefit the sector as a whole.
As mentioned in the previous NT articles, the future civil and mining activity in the centre of Australia is expected to increase significantly which will undoubtedly lead to industry shortages on numerous fronts, bringing with it potential growth prospects for countless companies and organisations. Many SA based businesses have an advantage (numerous logistical reasons) in relation to tapping into this shortage.
Servicing SA based companies and organisations in relation to NT Traffic management, heavy machinery, high risk NT Worksafe accreditation etc is now a common occurrence for CT NT, as we have formed a strong working relationship with numerous CCF SA members and do our best to prioritise their requests and compliance requirements, enabling a smooth transition between boarders. Civil Train NT is always here to assist CCF NT and SA members in any way we can.
ф Increased productivity ф Greater advancement opportunities for employees
ф Stronger regional prospects and benefits for all.
For those who have followed the CT NT journey over the years, which has involved numerous sectors and industries ie, Civil, General Construction, Education, Defence, Corrections, Cattle, Mining, Land Management, Power and Water etc, I think it would be the consensus, our most significant achievement to date has been the relationships we have formed with numerous Indigenous organisations and communities.
training at kintore, 530km west of alice springs (mostly dirt roads) and 40km from the wa border. an example of how civil train nt can cater to the communities’ needs re compliant, practical skillset training, irrelevant of the location.
The ongoing support received By CT NT, not only from our Civil Train SA head office, but CCF SA Board and members, has been instrumental in successfully establishing a viable permanent training service that now has the capacity to facilitate nationally accredited certification in the most remote regions of the country (SA/WA/NT).
The commercial and community flow-on effects from providing relevant, accredited, remote training (to an industry standard), are evident for all to see.
ф Greater employment prospects (opportunities)
ф Safer workforce
ф A stronger (workplace) focus on the environment and cultural awareness
ф Reduction in operational cost (utilising local labour)
While the CCF SA staff and membership take some time to reflect on the accomplishments of the last 50 years (well done by the way!) what should also be celebrated is the positive impact the entire Civil Train team, SA/WA/NT, along with the support of the CCF, has provided to the First Nations People of this country. Not just conducting training related to projects and employment, but engagement, a sense of achievement, community enhancement and beautification, nurturing leadership, and positive influences. This has been life-changing for hundreds of people (throughout Australia) particularly those individuals living in remote locations and in many cases, under extremely difficult circumstances. The Civil Train SA/WA/ NT teams have, and will continue to, make a difference!
Since the last edition (July 2022) the CT NT mob, yet again, have been out and about covering thousands of kilometres, providing our services far and wide, apart from facilitating numerous training programs in Darwin, Katherine, and Alice.
The following is a list of communities where CfAT and CT NT have been
involved in facilitating nationally accredited training programs working with multiple agencies: ф Ti Tree ф Nyirripi ф Kintore ф Atitjere ф Willowra ф Utopia ф Finke ф Yuelamu ф Yuendumu
Without exception, the above communities, and many others, still require some form of (significant) improvements in relation to better living conditions and amenities. I am confident all at the CCF & Civil Train are supportive of this objective and want to be part of this story.
At this point it would be remiss of me to not mention the assistance, guidance and trust we continuously receive from the Centre of Appropriate Technology (CfAT). This relationship is growing stronger by the day with both
organisations now involved in numerous joint initiatives that are mutually beneficial to the parties involved, local Indigenous people and the various industries operating in the region.
With a new Desert Knowledge Precinct (DKP) CEO Jimmy Cocking at the helm, there are exciting times ahead. It is my understanding that Civil Train NT will play a role in relation to the future direction of the precinct.
CT NT would like to acknowledge the outgoing CEO, Dr Dan Tyson for his contribution to the DKP, including, steering the ship through a worldwide pandemic. Good luck with your next chapter.
Finally, a big congratulation to the CCF SA family on the resilience and performance demonstrated over the past 50 years, especially during recent events.
Yet again, as with all forms of emergencies, disasters and even post-war crises, the infrastructure sector just keeps on digging!
To all of our Civil Train SA/WA colleagues, CCF SA staff and members, have an enjoyable festive season. Take care and see you in 2023!
Mark Hopkinsjason bloomfield, kevin abbott, henry bloomfield, aaron healy (new trainer), and jason lerm at ti tree (grader training) mid-2022
An extensive range of Plant & Equipment for Dry Hire.
ANDREW LINSCOTT 0401 147 288
RICK MARTINO 0499 111 598
DYLAN COPE 0411 310 845
ST MARY (08) 8177 0246
POORAKA (08) 7231 5950
We offer a competitive discount hire and rental rate for all CCF SA Members. Mention you are a member at the time of booking.
KATYA SAWYER m 0411 592 338
All CCF SA Members Receive 10% off New Instrument Purchases. See flyer on CCF SA members only section for more information. Contact Katya Sawyer.
Permanent placement and Labour Hire employment services.
PETER MURPHY p (08) 8261 1111
265 NORTH EAST ROAD HAMPSTED GARDENS SA 5086
WWW.FLEXABLEFORCE.COM.AU
Permanent placement fee fix at 10% of anticipated annual income and 3 months guarantee as per our terms and conditions for salary staff. Quote CCF SA discount.
PATRICK BUYING – ACCOUNT MANAGER m 0414 476 148 p 1800 818 233
SALES@BOWDENGROUP.COM.AU
WWW.BOWDENGROUP.COM.AU
Wambeti Legal is a law firm that specialises in construction law, initial contract negotiations, contract management, risk management and commercial advice. We provide smart strategies and creative solutions for businesses involved in the engineering and construction industries. We work with clients in a range of industries including: oil and gas, energy, technology, engineering, and construction. Our services are tailored to protect you before, during and after your projects. We offer expertise, experience and project management services to help you with: 1 legal issues that may arise during your project, including any potential for litigation; 2 contract management in construction law; 3 risk management in construction projects.
FLORA WAMBETI m 0423 825 235
FLORA@WAMBETILEGAL.COM.AU
Free initial 15-minute consultation with the Principal.
CHRISTINA GULLIVER – PARTNER m 0437 719 723 p (08) 8241 8444
255 PORT ROAD HINDMARSH SA
Christina is offering a free initial meeting to discuss your business accounting and tax affairs.
Wombats Heavy Towing are offering $20/ hour off of their standard hourly rate and for longer jobs (12+ hours) $0.20/km off of their standard rate to all CCFSA Members.
m 0438 757 388
For something out of the ordinary, give Andrew a call and he will be able to provide a quote. Please mention that you are CCF SA Members at the time of booking.
CCF SA is pleased to announce a great new initiative for Members requiring legal assistance with construction issues. Construction law specialist, Fenwick Elliott Grace (FEG) has entered into an agreement with the CCF SA to provide no obligation, free legal advice to CCF SA Members. FEG is a law firm that provides legal support to businesses working in the construction and engineering fields. FEG’s lawyers have many years of experience in the construction law field with some holding qualifications in both law and engineering. FEG has advised on many civil construction projects, including roads, bridges, harbours, quarries and mines.
phone ccf sa to request a consultation (08) 8111 8000
FEG.COM.AU
Members wanting legal advice should initially call CCF SA who will then forward the member’s enquiry to a dedicated FEG enquiry line. One of FEG’s specialist construction lawyers will return the member’s call that day and provide the advice. The consultation will generally be limited to a 20-minute duration. FEG also offers discounted rates to CCF SA Members who require more extensive advice or assistance.
KELLIE CHADWICK m 0457 026 905
KELLIE@SITEPODIUM.COM
We are offering CCF SA Members 50% off their first project.
U9/21 BEAFIELD ROAD PARA HILLS WEST SA 5096
MICHAEL SHEPPARD m 0499 993 777
25% discount off the normal price for the SMS Geotechnical educational seminars.
STEPHEN LAIRD m 0417 656 221
SLAIRD@ROYALWOLF.COM.AU
CAVAN SA 5094
National company, specialising in the hire of containerbased units including static storage, site buildings (office and lunchroom), dangerous goods, and refrigerated units.
MICHAEL FIORAVANTI p 08 8168 7200
MF@SADB.COM.AU
NEWTON SA 5074
SADB was established in 1995 and is a civil construction company that specialises in Civil Works, HDD (Horizontal Directional Drilling), Project Management, Civil and Pipeline Design & Construction, and NDE (Non-Destructive Excavation). SADB provides these services for both public and private sectors and remains a local South Australian family owned and operated business.
MITCHELL NOBLE p 08 8333 7300
MNOBLE@THNKADVISORY.COM.AU
ROSE PARK SA 5067
Thnk Advisory provides a comprehensive suite of services to clients including business advisory, tax and compliance, self-managed superannuation administration, bookkeeping, estate and succession planning, and process improvement reviews, to name a few.
STEPHEN PORTELLI m 0401 565 002
STEPHEN.PORTELLI@NCI.COM.AU
ADELAIDE SA 5000
We have established ourselves as the premier trade credit insurance broker in Australia, New Zealand and Singapore. Trade credit insurance is a highly specialised area of insurance, and, with over 35 years of experience, we have developed an unmatched depth of expertise in arranging the right protection at the best price for particular trading needs. On offer is a complete range of trade credit solutions to help you safeguard your business against bad debts in order to enhance your credit management.
JOSH DANNATT m 0407 023 622
SALES@XCMGADELAIDE.COM.AU
GREEN FIELDS SA 5107
Founded in 1943 in China, XCMG is the 3rd largest construction machinery company in the world. XCMG has a product sales network that covers more than 183 countries and regions, with an annual export value exceeding US $1.6 billion. It has maintained its place as the industry leader by export value for 27 consecutive years. Today, XCMG enjoys the leading market share in nine types of machinery and three types of basic components.
STEVE LEWIS p 08 8244 2335
ADELAIDEADMIN@SHAMROCKCIVIL.COM.AU
PORT ADELAIDE SA 5015
Shamrock Civil Engineering is a privately owned civil construction company, delivering services to the gas and mining, transport infrastructure, commercial, defence and government development sectors. Our team of more than 150 staff operates across offices in Brisbane, Townsville, Melbourne, Adelaide and Rockhampton. Our business is driven by a collaborative approach to project delivery and the diversity of our skills and capabilities. Shamrock Civil Engineering has been providing safe, sustainable and smart solutions since 1994. We are committed to our clients and place value and emphasis on creating and maintaining longterm relationships. The breadth of our civil construction expertise combined with our integrated management system, enables us to deliver complex solutions efficiently and effectively. Through our comprehensive service offering, our priorities are maintaining the safety of our people, delivering better value for our clients, and supporting our local communities.
BEN SCHWIDDER m 0427 601 025
BEN.SCHWIDDER@GRAYS.COM.AU
POORAKA SA 5098
Grays is the largest industrial, auto and commercial eCommerce business in Australasia. We offer vendors an efficient sales channel to unlock value from their assets. Our online selling platform and commitment to first-class customer service mean you can trust us to make buying and selling easy, efficient, fair and transparent. We help with all aspects of a sale program from valuations to cataloguing, project management, marketing, WHS compliance and reporting.
Our key civil construction services include:
Roads and bridges
Dams and ponds
Stormwater drainage and fittings
Water pipelines and infrastructure
Sewerage pipelines and infrastructure
Bulk earthworks
Land and soil remediation
In ground services excavation, trenching and conduiting
Hardstand and lay down areas
Building and construction pads
Landfill cells and facilities
Airport runways, aprons and ancillary works
Railway holding and marshalling yards, sidings and station works
SALLY DELUCA m 0401 300 257
SALLYD@UNITEDTRAFFIC.COM.AU
GEPPS CROSS SA 5094
Providing Traffic Management Services across South Australia, United Traffic Management have been operating since 2018, from our Gepps Cross and Old Noarlunga depots. With 33 Traffic Management Vehicles, strong and building, we employ over 6o qualified traffic controllers. United Traffic Management are available to cater to all needs, short or long term, 24/7.
GREG CLOTHIER
GREG.CLOTHIER@IQMS.COM.AU
ADELAIDE SA 5000
IQMS Australasia Pty Ltd has worked in compliance and business management systems for over 20 years in industries including mining, civil, oil and gas, construction, and defence. We help you to develop management systems that are responsive to your needs and provide return on investment.
JOHN VOZZO m 0408 815 220
JVOZZO@HWLE.COM.AU
ADELAIDE SA 5000
Despite what many law firm websites say, it can be very difficult to differentiate one firm from another. The more they claim to be different, the more similar they appear to be. Let us introduce you to a genuinely different firm. A firm offering exceptional quality legal advice to its commercial and government clients from offices located in every Australian State and Territory. A firm delivering unrivalled value for money as a result of running its business in the same way that its clients do. A firm allowing all team members to reach their potential by rewarding and promoting talent solely on the basis of merit. A firm that is not distracted by overseas ambitions. A firm without a tenured sense of entitlement.
CHARLIE
CHARLIE.CONDO@LUTUM.COM.AU
POORAKA SA 5098
Lutum purchased the Boral Masonry business in November 2012. We are manufacturers of Concrete Masonry products servicing the building and construction industry in SA; products and services include pavers, retaining walls, bricks and blocks. We are also one of the largest paving contractors in SA servicing the civil construction industry and local government. Boral Hollostone Masonry have been previous members of CCF SA. Charlie Condo has been involved in the industry for over 40 years.
JAMES
CIVILGRADECO@OUTLOOK.COM
NAIRNE SA 5252
Civil construction, earthworks, grading specialists.
MARK BURLEY m 0419 957 897
MARK.BURLEY@MILWAUKEETOOLS.COM.AU
DANDENONG SOUTH VIC 3175
Milwaukee Tools, founded in 1924, is a global leader in delivering innovative solutions to the professional trades that offer increased productivity and unmatched efficiency. Whether it is through our world-leading M12™, M18™, and MX FUEL™ cordless systems; the groundbreaking performance of our M12 FUEL™ and M18 FUEL™ range; job site lighting, time-saving accessories, or innovative hand tools and storage equipment, Milwaukee Tools is dedicated to providing a steady stream of advanced, trade-specific products.
Standing side-by-side with tradespeople on the job site, we learn first-hand where our products are most needed, and how we can make them even better. We develop solutions that overcome the very real challenges and frustrations that users face on the job site, in ways that have never been done before through disruptive innovation.
At Milwaukee Tools, we look to push the boundaries of what’s possible. Every year, we develop groundbreaking solutions with a single aim in mind: improve the lives of our users.
SCOTT COSSICH m 0428 326 788
SCOTT@OVERLANDSERVICES.COM.AU
MURRAY BRIDGE SA 5253
ANDREW EVERETT m 0455 972 529
BDM.SA@TRAFQUIP.COM
ELIZABETH SOUTH SA 5112
Providing exceptional service to streamline your traffic requirements.
Trafquip began in 2007. Our team has over 30 years’ experience in civil construction and traffic management services. We pride ourselves in offering outstanding customer service to our clients, delivering superior traffic solutions you need to get the job done.
We specialise in traffic control equipment hire including VMS trailers and utes, portable solar traffic lights, eSTOP traffic signals, traffic control utes, traffic mounted attenuators, cone trucks and more.
Together we’ll create a safer, more efficient workplace. Our clients include council, civil construction, traffic control companies, events and businesses who need to hire traffic control equipment or utilise our traffic consultancy services. We strive to provide our clients with a comprehensive solution to traffic planning procedures and safety. We work with our clients to increase worksite productivity while reducing risk and cost.
Our ethos is simple... ф Minimise Risk ф Minimise Cost
Maximise Productivity
Overland Services has been providing specialist plumbing & earthmoving services for over 16 years including excavation, bulk earthworks & trenching. Equipment includes excavators from 4T through to 25T, skid steers, tippers & trailers, vermeer trencher, vibrating rollers & associated attachments for all equipment. HDPE pipeline installations for water & fire systems including HDPE pipe welding up to 630mm diameter. Supply and installation of large water storage tanks suitable for fire, potable, stormwater, bore and desal water, and 25KL to 1 meg capacity tanks. Diesel & Electric drive pump sets for general water transfer and fire systems constructed as pre-packaged containerised systems. Overland Services offers contract services to larger civil, plumbing and mining companies, government agencies and private clients. We also offer a design and construct service for many clients and project types.
MICHAEL KOSTER m 0405 745 427
MICHAEL@FLOWEXCAVATIONS.COM
WINGFIELD SA 5013
Flow Excavations is a small, growing civil construction contracting company providing exceptionally competitive rates while delivering projects with paramount safety, environmental focus and attention to detail in quality to ensure the client is completely satisfied with the end product. Flow Excavations focuses on underground electrical, communications and stormwater installation projects; however we are continuously developing our skilled team to take on all civil and earthworks projects.
HOW LONG HAVE YOU BEEN IN BUSINESS?
Two years.
WHERE ARE YOU LOCATED?
3/32 Simper Crescent, Mt Barker SA 5251.
WHICH AREAS OF ADELAIDE DO YOU SERVICE? State and nationwide.
HOW MANY STAFF DO YOU EMPLOY? Six.
WHAT ARE YOUR CORE BUSINESS SERVICES/ SPECIALISED SERVICES?
At 3D SiteWorx, we help you achieve new levels of speed, efficiency and precision on your next civil project through implementing machine positioning technology and complementary solutions.
3D SiteWorx is a rental company which actively works with contractors of all sizes to provide consultation of accurate guidance solutions to the Geospatial and Civil Construction Industry.
We work with you in the lead up and during your project to make sure things run as smooth as possible for the length of the project.
Our involvement ranges from initial site setup with survey control and Data conversion right through to renting
Survey, and Machine Control components suited to your task.
Increase our dry hire/wet hire machine variety. More focus on a national scale. Look at autonomous digital construction technologies.
3D Siteworx is a family-run business which prides itself on being a one-stop shop for all your rental guidance solutions.
When you ring our business, you will be speaking to someone who understands your urgency and time restrictions, and we are able to implement the best solution to solve or fix a problem.
Our remote support is second to none, and we use this to our advantage to save you time with site visits and costly downtime.
Machine control install/ support
Site setup and verifications
MOBILE 0438 221 502 CONTACT Lloyd Ritchie
Let us do the work for you!
As the lunch partner, all you need to do is select 10-15 companies that you would like to invite and what business unit within that organisation you would like to attend (e.g. Project Management, Human Resources, Procurement, WHSE, etc). Then we do the rest! You can expect a total of 15 guests, which includes 2 people from your business, and 2 from CCF SA.
During lunch, you will be able to present your business to the intimate group. Post event, you will be provided with the contact details of those who attended and also post-print acknowledgement in the CCF SA Magazine.
Lunches are held at Enzo’s Ristorante, Jarmer’s Kitchen, Louca’s Seafood Restaurant, Coccobello. ‘Let’s do lunch’ opportunity is provided once per calendar month and are subject to availability. COVID19 restrictions must be complied with at all times. Contact the Members Services team via ccfsa@ccfsa.com.au or 8111 8000 for more information.
Friday 4th November, we held our Annual CCF SA Golf Day at West Lakes Golf Course.
The event was another sell out, seeing 144 avid golfers (and a few NAGA’s) take the course.
After a concerning week of unprecedented winter blast, we asked Mother Nature to be kind. She delivered, giving us near perfect conditions for a day of golf.
In a first, all teams were given a golf buggy, thanks to our industry partners Loadex. Dan, our resident photographer, was also on course to capture the moments that some will want to remember (Head over to our social media to see all the photos). Some stories that we have been told from the day include a driver was broken, and a buggy got stuck over a crest of a small hill on the course. The hole in one was nearly won too – just a metre short! Keep practising, you never know what will happen next year!
Graham Cornes spoke to the attendees during lunch, giving us an insight to his footy career, and his time served in the armed forces, followed by the presentation of the coveted golf trophy, and bragging rights for 2022!
1st: Loadex Hire
John Szczypiorski, Aaron Browne, Rhys Crampton, Damian Morgan
2nd: RawSA
Adam Latemore, David Hagen, Lincoln Blewitt, Stephen Campbell
3rd: Adelaide Fuels / Orca Civil Products
Daryl Evans, Ian Brook, Clinton Hewett, Adam Medlen
NAGA Winners: Downer
Paul Banwell, Alan Waldron, Matt Taylor, Julianne Standish Longest Drive
Hole 1: Matt Ormsby (*Trafquip)
13th: Josh Dannett – (*Assigner)
14th: Jason from Win Attachments (*Alexander Symonds)
Nearest to Pin
3rd: Matt Shippway (*Adelaide Heavy Machinery)
6th: George D’Agostino (*Loadex)
15th: Rhys Crampton –(*Shamrock)
Nearest to the Pin in 2
10th: Amanda Brumm (*MEH)
17th: Aaron Brown (*Pro Bitumen)
*Prizes donated by
Keep our eye on your emails, we have already begun planning for 2023’s Golf Day, which will be our 20th year of Golf Days – we promise it will be our biggest and best yet!
In line with the theme of this issue of Civil Connect (Look how far we’ve come), I thought it would be a good opportunity to reflect on what we as a committee have achieved.
We started off the year in planning mode, working on developing our inaugural professional development program, with facilitator Peter Karounos. The 8-week program will give participants the knowledge, skills and motivation to grow, improve, perform and change to ultimately achieve success. Delivered in a mixture of online and face to face, the inaugural program has 8 participants, and we can’t wait to share with you their experiences and feedback. We will be running two programs in 2023, so keep your eyes out for those dates early next year.
I would like to thank Stewart Edwards (formally from BMD) for his commitment to working with Peter to pull this program together. Stewart is about to embark on a new adventure, as he is moving to the UK. We wish him the best of luck, and we will miss his energy and commitment for the FIC.
We have held 2 social media workshops, thanks to CCF SA Business Partners, Digital Marketing AOK. Attendees learnt who their celebrity twin is, and how to get the most out of your profiles on LinkedIn. Another successful program which we will look at hosting again in 2023.
Committee members Markus Schuster, from Bennett Plumbing & Civil, worked
with the team at Biancos and arranged a site tour of the precast yards. A great turn out from across industry, along with attendees representing Uni SA and DIT. We have the most exciting news to kick off 2023 – with a big celebration to match. Make sure you get along to our first event in 2023 to find out more!
If you, or anyone you know would like to get involved in the Future in Civil Committee, please send an email to futureincivil@ccfsa.com.au to find out more!
On behalf of the FIC, I would like to wish you, your team, and your families a very happy Christmas and a here’s cheers to a prosperous 2023.
A ‘Bobcat’ Skid Steer Loader demonstrating a new backhoe attachment. Driver Reece Pockock.
F.T. and B.I Thomson and Son Pty Ltd were engaged in constructing up to seven kilometres a day of seismic lines in the Simpson Desert.
A TD25C with a full blade in one of the numerous sandhills in the Simpson Desert.
Constructing haul road in the Simpson Desert.
Newly constructed section of Riddoch Highway, with Graduate Engineer on left, Wayne Buckerfield, now Deputy Chief Executive, and Jeff Darley.
Early Fishing Expedition
1985 Bill Murrell, Executive Officer, Construction Industry Training Council, congratulating a Trainee at Grader plant operating training course.
Finished product
All construction at low tide. Paddock rock used again for core and armour from Ramsay Quarry near Minlaton.
The ponds were constructed to enable dredging to allow large boats to the wharf.
Not many Australian companies can claim 140 years of history. Yet in 1882, one person William Lewis decided to have a go where many would not, starting his own business from scratch and launching Brighton Cement Works and thus began the Adbri (ASX: ABC) story.
Adbri is one of Australia’s most successful and enduring domestic manufacturers, producing cement, lime, concrete, aggregates, industrial minerals, and masonry products across its national footprint. Adbri operates cement manufacturing facilities in South Australia, the Northern Territory, Western Australia, and New South Wales and is the parent of Adelaide Brighton Cement, which traces its history back to William Lewis. Significantly, the launch of William Lewis’ Brighton Cement Works in 1882 also marked the commencement of the Portland cement industry within Australia. It was an extraordinary feat for the time, with the colony of South Australia barely 20 years old.
A lorry fitted with solid rubber tyres which was the first motor vehicle to be used for delivery of cement packed in paper for the Brighton cement company in August 1927.
Adbri has evolved into a company with annual revenues of $1.57 billion in the 2021 calendar year and total assets of $2.3 billioni, while always maintaining its reputation as trusted manufacturer and supplier in the industry.
Today thirteen brands, including Adelaide Brighton Cement, operate under the Adbri umbrella, complemented by seven joint venture companies. With the Adbri group of companies focusing on ‘Building a Better Australia’, they have had a significant hand in creating roads, ports, airports, processing plants and energy facilities across the nation. Adbri supports 11,520 full-time equivalent positions indirectly across Australia, and its gross value add annual is around $3.2 million.
With a strong focus on corporate social responsibility (CSR), Adbri is doing its bit to support local economies and communities and is using new technology, alternate fuels, renewable energy, and lower carbon emitting products to contribute to a sustainable future.
For historical context, Adelaide Brighton Cement launched at roughly the same time as the Adelaide to Port Augusta railway opened in the late 1800s.
Less than a decade laterii in 1891, William Lewis and his business partner William Shearing erected an experimental cement plant in Portland.
“By using limestone and clay, they manufactured a crude
version of Portland cement and after some technical refinement, the first batch of marketable cement was produced,” said Brett Brown, Adbri’s Chief Operating Officer – Cement and Lime.
By the next year, along with several shareholders, the pair founded The South Australian Portland Cement Company Limited. A new manufacturing plant was built, and later opened in December.
Increasing financial debt and a change of government (who at the time reduced existing import tariffs), caused the company to go into liquidation in late 1895. However just a year later, private investors, many of them previous shareholders, purchased the company to form a private company, The South Australian Portland Cement Company.
Over the following decade, The S.A. Portland Cement Company flourished, growing in size and in stature. However, a terrible fire in November 1909 destroyed the Marino Works and an important financial loss was the result, driving the company into voluntary administration in order to gain financial funding.
By 1911, many of the existing shareholders registered a new business, The S.A. Portland Cement Company. Numerous upgrades were made, such as the implementation of the first cement mill powered by electricity. Demand was such that the works could not maintain supply.
Two years later, due to the growing demand, A.W.G. Pitt founded Adelaide Cement Company Limited at Birkenhead, recognised as the rival company to the S.A. Portland Cement Company. The new rival used limestone from Yorke Peninsula that was transported across the gulf by steamship, and black mud (clay) from the Port River. In 1927 the
Board examined a proposal of merging the S.A. Portland Cement Company and its competitor, however, the proposal lapsed due to a lack of enthusiasm from the shareholders.
As a result of direct competition, the S.A. Portland Cement Company took steps to increase production by refitting much of its plant and increasing the number of employees to 104. Over the next 40 years, many advances in technology helped the cement industry to grow substantially.
In 1930, due to the lack of stone reserves, the S.A. Portland Cement Company decided to relocate the works. After extensive testing, it was decided that the new works would be situated at Angaston due to the vast natural stone deposits.
Twenty years later in June 1950, construction of the Angaston Works commenced, with the concrete chimney stack reaching its full height of 204 feet by Christmas 1951. After the new Works at Angaston had been successfully tested, the old raw mill at Marino was switched-off, and the new Angaston Works was officially declared open in December 1952.
In 1957, talks recommenced between The S.A. Portland Cement Company and Adelaide Cement Company Limited, discussing the possibility of a merger, proposing the combination of their resources to increase supply in an attempt to meet the growing market demand.
By November 1959, a sales agreement was signed, which developed into a profitable arrangement for both companies for over a decade.
Until then, the S.A. Portland Cement Company had only made two types of cement, ‘normal’ and ‘high early strength’, the latter having been introduced in 1929. In the 1960’s three more types of cement were introduced to the marketplace, ‘sulphate resisting’, ‘masonry’ and very light-coloured cement that in keeping with the history of the company, was named ‘Brightonlite’.
After almost three weeks of intense movement on the Stock Exchange, ‘Adelaide’ announced that it had secured more than 75 per cent of the ‘Brighton’
shares and in April 1971, the Boards of the two companies announced the forming of what is now known as Adelaide Brighton Cement Limited.
Today, Adelaide Brighton Cement Limited is part of the Adbri Ltd group of companies, with operations in every mainland state, and over 1500 employees nationally.
With its purpose of ‘Building a Better Australia’ in mind, Adelaide Brighton Cement’s parent company Adbri goal is to net zero emissions by 2050, recently launching their Net Zero Emissions Roadmap.
With a plan to ‘decarbonise’ its entire operation, Adbri operates two emissions-intensive and hard -to - abate processes –the integrated manufacture of clinker and cement and lime production.iii
“We have demonstrated a strong performance over the past decade in reducing our operational emissions by 32% since FY10,” said Mr Brett Brown, Adbri’s Chief Operating Officer –Cement and Lime.
“Our net zero emissions pathway is being approached in two stages. From 2020–2030, the priority is to deliver emissions reductions through conventional abatement approaches like process and energy efficiency, increasing the use of alternative fuels and a transition to zero emissions electricity. In parallel, we will also be building our capabilities in breakthrough technologies that will be required post-2030.
“From 2030–2050, we will work to close the technology gap for our hard-toabate clinker and lime manufacturing by supporting the development and
de-risking of breakthrough technologies at scale, via partnerships in research and development (R&D) and potential pilot-scale demonstrations to accelerate commercial deployment.”
Adbri say that one of its product-related strategies is to increase the use of supplementary cementitious materials (SCMs) in their cement and concrete products.
Clinker is the most emissionsintensive product in the clinkercement-concrete process, however SCMs can partly replace clinker in cement (and therefore concrete).
According to Brett, SCMs that are used most in Australia are ground granulated blast furnace slag (GGBFS), fly ash from coal-fired power plants and limestone, all of which have much lower embodied carbon than clinker.
The clinker to cement ratio is an industry metric which reflects the utilisation of SCMs. By decreasing the amount of clinker and increasing the SCM content, the emissions intensity of cement can be reduced, while still producing a durable, resilient product that meets stringent standards. Adbri claim that their clinker to cement ratio in 2020 was 77 per cent better than the Australian average of 84 per cent.
Adbri also plans to collaborate with key partners such as the Heavy Industry Low-carbon Transition Co-operative Research Centre (HILT CRC) and SmartCrete CRC; a member of the Material and Embodied Carbon Leaders Alliance (MECLA), as well as other industry associations to help with
Then... 22 horses taking a 30-ton steel mill to the Brighton cement works.
transforming the heavy industry sector for a low carbon economy. They also share an annual progress report, updating the public on their performance against their targets in an annual Sustainability Report.iv
“As a hard-to-abate industry, the challenges of achieving net zero will require future investment in technology and partnerships,” said Brett.
“In 2021 we increased the use of refuse derived fuel (RDF) as an alternative fuel source at Birkenhead, with the substitution rate increased from 28% to 35%. Our target is up 50% alternative fuel by 2024.”
With so many exciting plans in place and a forward-thinking mentality at the helm, it seems that Adbri, and Adelaide Brighton Cement, are unstoppable when it comes to longevity and innovation in business.
Proudly keeping the tradition of high quality, locally manufactured cement alive and viable, it is not surprising that Adelaide Brighton has notched up 140 years in business. And with sustainability at the forefront of their future ambitions, it could be very reasonably assumed that the company has another 140 years in them.
To find out more about the history of Adelaide Brighton Cement and its current and future projects go to adelaidebrighton.com.au or contact them on (08) 8300 0520.
i https://wcsecure.weblink.com.au/pdf/ ABC/02560806.pdf
ii https://adelaidebrighton.com.au/who-we-are/ about-us/
iii https://www.adbri.com.au/sustainability/netzero/
iv https://www.adbri.com.au/wp-content/ uploads/2022/02/2021-Sustainability-Reportextract-from-2021-Annual-Report.pdf
Today, Adbri supplies bulk and bagged cement from its Birkenhead and Angaston manufacturing facilities
Congratulations
enables her to support local civil contractors across all levels of their business.
Melissa commenced her career in the civil industry over 20 years ago working for civil construction contractors and has been a part of several significant projects in SA. Melissa's understanding of small business and the importance of a pipeline of work for contractors and the supply chain is invaluable, and her experience and knowledge
Melissa's passion for the civil contracting sector is second to none, dedicated to supporting, promoting, and protecting the interests of civil contractors through South Australia. Join us in congratulating Melissa on this welldeserved award!
We all listened intently as our hosts Hayley and Lauren, who are Adelady, welcomed us and introduced our guest speakers and panel. This year’s theme – Look How Far We’ve Come was addressed by Matthew ‘Doc’ Clarke and our panel of inspirational speakers – Claudette Renfrey, Evonne Penrose and ‘Doc’ Clarke.
After a gloomy, wet few weeks prior, the sun came out for the CCF SA Women in Civil Festive Lunch on Friday 25th November. The view over Adelaide was spectacular as guests arrived at the William Magarey Room at the Adelaide Oval.
The room was full of beautiful, happy people from so many different companies and branches of the industry. It was more than likely a combination of the gorgeous weather and view and the fact that it was Friday afternoon.
The day began with the Welcome to Country by Jack Buckskin, who always entertains with his refreshing, insightful stories.
One of the highlights for me and many others would have to be when Melissa Ekberg led a fair swag of the room onto the stage to throw our hands in the air and dance and sing to Dancing Queen, taking her leadership lesson from the Dancing Guy – she made sure to lead the movement in less than three minutes.
One thing’s for certain, I’m glad I’ve pre-purchased my seat for the International Women’s Day Lunch next year, because I definitely don’t want to miss it if the Festive Lunch is a sign of what we’re in for.
Started in 1998, the $2.5 million harbours upgrade at Cape Jervis and Penneshaw involved the deepening of the existing rock floors of the harbours in an exposed and sensitive coastal environment. The Penneshaw breakwater was also constructed with minimal disruption to the ferry services, the local community, and the penguin population.
The contract to undertake the project involving the difficult underwater rock excavation required the use of equipment mounted on barges, and the constant repositioning of cables and anchors. Between May and September, 47,000 tonnes of rock were excavated!
The significant project provided both the opportunities for the application of skills and experience, as well as the exposure to new challenges at the coastal environment. Jobs were created both at Cape Jervis and Penneshaw.
John Chappell (specialist coastal engineering firm) and the Ports Corp of South Australia, together with Sealink, collaborated to adopt the successful methods employed.
For excavation to happen without interruption to the ferry services, stability calculations were undertaken and the Samsung excavator used had to be modified to enable it to operate above tidal levels.
This allowed the turret excavator to position itself on the harbour floor and use its breakout power to excavate the rock floors.
The contractor also created a floating conveyor to transport the rock material directly from the excavator to the adjacent shore where it was then offloaded at stockpile areas. It was something that could not be achieved by conventional means then.
With over 47,000 tonnes of rock excavated and more supplied by the quarry behind Penneshaw, the adjacent 100,000 tonne breakwater for Penneshaw harbour was built using these resources.
To overcome the extra height to cater for the winter tides, the sub frame was split –the result was that 1 metre height and additional stability.
Upgrade work in progress.
The deepening of the harbours, construction of the breakwater and associated works were achieved in a sensitive ecological, social and political environment with community involvement.
All these led to new businesses and jobs, and provided a valuable tourist and commercial link to Kangaroo Island.
Designed and created by South Australians to world standards, it was a job well done!
In October 2020, the Cape Jervis Jetty was to facilitate repair works on the Kangaroo Island berthing facilities. These included the removal of disused fenders, propping and levelling the deck and the bracing of several piles to maintain their integrity, with the work done on the jetty during this closure. The jetty was reopened in April 2021.
Apart from the jetty that is teaming with marine life, the adjacent breakwater yields salmon, whiting, tommies, school sharks and the occasional yellowtail kingfish.
Forming the southern part of the North-South Corridor, and built to relieve heavy traffic from the major arterial, Main South Road (in Adelaide's south), the 18.5 km Southern Expressway runs through the southern suburbs of Adelaide. Originally built as a reversible one-way freeway, it was the world's longest after its completion in 2001. Between 2010 and 2014, it was expanded and is now a regular 2-direction freeway.
The construction of the Southern Expressway was a complex exercise, challenging the stakeholders involved. In the 1990s, a 2100mm diameter mild
Sturt had to be relocated. The new freeway design included the construction of a 7-metre-deep underpass at Seacombe Road. The existing water main intersected the new alignment of the freeway at that location.
United Water secured the job and managed the relocation of the 150-metre section of the major pipeline from the Happy Valley Water Filtration Plant to the metropolitan area.
The pipes, sourced and trucked from Queensland, were each 166mm thick (steel plate), with one that was 9 metres long, priced at $30,000!
Carrying out the installation, the 5-metre-deep excavation was battered before being laid with chases cut out at each joint to allow welders access to the underside of the pipe. The pipes were then laid in the trench using two mobile cranes (50 tonne and 25 tonne capacity).
Subcontractor John Ranger & Associates welded the ball and socket joints. Then each joint was air tested for leaks before its inside was mortared to prevent material corrosion.
The project was then completed on time and within budget.
Port Vincent in Yorke Peninsula was historically an old port and it served as one of the landing spots for ketches sailing up and down the peninsula.
Initially also a home port of fishermen, the introduction of Government regulations in the late 70s lead to the decline of fishing. The shipping of bagged grain also ended around then.
Today, it has reinvented itself as a holiday destination with a magnificent coastline and a sheltered bay. Its establishment as a tourism drawcard was boosted by the building of the $12.2 million Vincent Landing that was completed in 2003.
Below is an account of how the locals got involved in the Vincent Landing Marina project 20 years ago.
Farmers, some as far as 25km away contributed 45,000 tonnes of paddock rocks for Vincent Landing Marina, a highly venturesome project, now nearing completion at Port Vincent on York Peninsula, South Australia.
Locals have stockpiles of limestone rock, created from raking their paddocks over the years. Some weighing up to 3t, from about 20 properties for breakwater construction. “Once we started moving it other farmers kept ringing us,” project manager Peter Lee recalls.
Paradise Developments (Port Vincent) p/l is spending $10m on the marina, which is immediately north of Port Vincent and 33 nautical miles across Gulf St Vincent from Outer Harbor. The 50ha site extends one kilometre along the coast and half a kilometre out to sea. It lies beneath 30m high cliffs that overlook, what was formerly a muddy beach.
The completed development will consist of a new excavated harbor protected by two 500m long breakwaters, and a reclaimed 71-allotment residential land division. Both breakwaters and the reclaimed area will be supported by 150,000t of rock, placed on the soft marine clays forming the seabed in order to provide adequate support for the fills above.
Each of the waterfront allotments can have a floating berth capable of mooring a 10-12m yacht. The other allotments are at the foot of the cliffs. Work started in mid-January this year and is due for completion in December. A peak workforce of 40 is using seven hydraulic excavators in the 30-40t range, six 6-wheel-drive articulated trucks, up to 15 semi-trailers and B-doubles plus swamp dozers, loaders and general equipment.
At the time of publication the breakwaters are in place, the marina has been pumped dry and about 80,000 of the total 240,000cu m of the excavated material has been placed as fill. Graham Kimber describes the project as ‘adventurous’. Unlike many other inland or on-shore marinas, the breakwaters are in 7m of water and temporarily joined at the marina mouth to form a giant D-shaped bund. This bund must hold back the sea while the enclosed area is pumped dry and excavated to provide a minimum of 3m of water depth at the lowest known tide.
The presence of the sea is emphasised by the sight of excavators and trucks operating up to 8m below where peak tides lap the outer edge of the breakwater/bund. Rock used to support the fill and breakwater cones and to provide armoured protection for the breakwaters and allotment revetments varies from 200mm to 5t (2m3).
Four submersible pumps that output 200/sec were used to pump dry, the harbor. They were driven by twin 100 kVA gensets set up on the adjacent bund. The water was pumped into a specially prepared rock basin lined with filter cloth to stop sedimentation entering the sea and the resultant pluming (discolouration). Secci disc readings were
taken daily to monitor clarity of the surrounding water.
The harbour excavation is to RL-5.5 or about 7m below mean sea level. During the excavation phase pumping was at a reduced level to cope with seepage and natural drainage from the sea floor. The excavated material is levelled and compacted to create the allotments that are filled to a depth of 1 to 4m.
On completion of excavation, the harbour entrance will be opened and the marina flooded.
Graham Kimber decided that sourcing of the rock was best served by opening a quarry nearby. A study of Mines Department information maps showed a deposit of Ramsay limestone or dolomite on a farm 20km away. Negotiations with the owners resulted in test drilling to prove the resource. Quarrying began in March this year.
The marina will require about 60,000t of rock on the floor of the filled areas and a further 240,000t in and under the breakwaters and facing the revetments. A fleet of 12 vehicles comprising B-doubles, semi-trailers and side-tippers has delivered up to 5,000t of rock a day. Access to the development site has been via a purpose-built ramp down a gully in the cliff face to avoid damaging local roads.
A significant issue in the construction of the breakwaters was the discovery during excavation of particularly plastic and porous marine clays that are difficult to handle when wet, especially in fresh water. Following extensive studies by local and Melbourne-based geotechnical engineers, and testing by FMG at Kent Town (SA) and the University of Adelaide, the revetment rockwork was increased from 700mm to 2m thick. This required
the importation of an additional 75,000t of rock and an extension of production at the quarry.
As a further precaution, a 2.5m deep cut-off or agricultural drain was installed parallel to the cliff face and just above the filled allotments so that fresh water which continually seeps to the sea from perched inland aquifers is diverted from the marine clays. These clays,
having been formed in slat water, are susceptible to weakening and erosion in a freshwater environment.
On completion of filling, the road system, sewers, water and electrical reticulation will be constructed. A 90-berth floating marina will be built within the harbour and consist of four primary fingers each having about 20 serviced berths of varying sizes. Pacific Pontoon & Pier of Brisbane was the construction contractor. The floating units will be made at the company’s Coolangatta facility and assembled and installed at Port Vincent.
The berths will be supported and stabilised by 42, 400mm-diametre tubular steel piles driven into the seabed and encased in a high-density polyethylene jacket that effectively deprives the steel of oxygen and eliminates corrosion. Also to be constructed are a carpark, boat
ramp and a beach. The beach will be just south of the southern breakwater and formed by excavating and removing existing foreshore clay and importing clean white sand.
About 4t of fish, mainly whiting and mullet, were removed from the enclosed basin. Locals took as many as they could; the local dump got the rest.
As the lunch partner, all you need to do is select 10-15 company executives that you would like to attend. You can expect a total of 15 guests, which includes 2 people from your business, and 3 from CCF SA (including CCF SA CEO).
During lunch, you will be able to present your business to the industry executives. Post event, you will be provided with the contact details of those who attended and also post-print acknowledgement in CCF SA Magazine.
Lunches are held at Chianti, Sean’s Kitchen,
‘Let’s do lunch’ opportunity is provided once per calendar month and are subject to availability. COVID19 restrictions must be complied with at all times. Contact the Members Services team via ccfsa@ccfsa.com.au or 8111 8000 for more information.
In 2005, Whyalla (population 21, 600) was SA’s second largest city. For 40 years then, its treated wastewater had been going into a creek that emptied into the Spencer Gulf. In July that year, a radical change happened when owner/operator SA Water completed a $14.3m water reuse scheme for the city.
Below is an extract from a water reuse scheme report (released that year) outlining what was done during that time to address the issue of wastewater.
The scheme will collect water collected from about 6500 Whyalla properties – or about 75% of the city. A new water reclamation plant and associated infrastructure has been built to intercept the existing sewer and treat the water to Class B quality.
Most of the recycled water will be used to irrigate the local golf course, city parks, gardens and ovals. This will ensure minimal or no discharge of treated wastewater into Spencer Gulf for more than four months each year.
The state government is committed to phasing out discharges into the marine environment wherever economically and environmentally sustainable. The reuse scheme is part of its $300m ongoing program of wastewater treatment plant upgrades.
Parsons Brinkerchoff designed the reuse scheme. The $6m civil works contract had a civil workforce on site that peaked at 30. The equipment included excavators, graders and rollers, and the job required large areas of concrete formwork.
The new reclamation plant occupies a rectangular area bounded by a landscaped (trees) security fence near the Anderson Racecourse on the city’s southern edge. Other aspects included: Three new pipelines (from 450mm down to 350mm diameter) running for 6km. These take raw wastewater to the new plant, treated wastewater to the golf
Finishing of the floor pour of the SBRs seen through 4.5m-high walling reinforcement.
course, and sludge from the treatment process back to the original wastewater treatment plant (WWTP) – a series of open lagoons completed in 1965 and a short distance away downstream.
An upgrade of the WWTP. Modifications involved the recommissioning of lagoons 3, 5, and 6, and new connection pipes. Lagoons 1, 3, 5, and 6 would be online for the summer months.
The new plant out at the racecourse will have a capacity of 3.15ML/day. It incorporates two parallel sequencing batch reactors (SBRs) for biological nitrogen removal and two parallel balancing ponds each capable of holding 1.3ML of recycled water. (An overflow line discharges excess treated effluent to the existing WWTP.) The balancing ponds have a HDPE liner to prevent infiltration loss and soil/groundwater contamination.
Walling of the SBRs basin with inlet pipework inserts.
SA Water’s Whyalla
The SBRs measure 40m x 30m overall and contain 10 individual compartments of varying capacities. A total length of 280m of 4.5m high walling was constructed of 400mm thick concrete and 250t of steel.
The biggest challenge was working to the very exacting standards of SA Water both for concrete manufacture and placement. The concrete is a relatively high strength and low shrinkage product, the design of which although ideal for water retaining structures having durability and resistance to attack in a wastewater environment, is difficult to both pour and finish. The slump is low and setting times are short.
Super plasticisers must be added to achieve the slumps required for both pumping and pouring in high-lift situations. Pouring of concrete was generally commenced at 2am and completed by 10am to avoid the daytime temperatures of up to 48 degrees which are common to this area.
Wingtip view showing the water reclamation plant (centre rectangle), the racing track top right and a spill stockpile left foreground.
Recycled Water Plant (built in 2008), currently supplies around 2.5 million litres of recycled water per day.
In early October, SA Water released new upgrade plans for the plant as part of the utility’s $200,000 investment to enhance sewage treatment and the plant’s overall performance.
More than 1,300 diffusers in both of the plant’s treatment basins would be replaced to improve the efficiency of the biological process that breaks down nutrients in the sewage. These diffusers distribute a constant supply of oxygen to help micro-organisms remove the nutrients, which is an important step in recycling sewage.
The treatment plants are now rich resource recovery centres capable of creating sustainable sources of recycled water. When sewage is treated, the solid organic material is separated from water. The recycled water can be used by the local council to help irrigate and green the city’s ovals and parks, while helping keep the golf courses’ playing surface looking lush.
Measures are already in place to manage any temporary increases in sewer odour from the plant during the upgrade.
Based in Cavan in Adelaide's north, Tripodi Group is a civil construction and earthmoving company that's operated for 50 years and counting.
A member of the Civil Contractors Federation SA for 47 years, the business was founded by Joe Tripodi OAM in 1972 with about 25 employees. He also recruited his brothers Dominic, Steve, Peter, brothers-in-law Brian Coombs, and Reggio Martini.
Some large projects Tripodi Group has supported since launching include the Leigh Creek Retention Dam, the West Lakes Scheme, Devil's Elbow preliminary bulk earthworks and Port Augusta Power Station. The firm was also involved in Golden Grove, Walkley Heights, and Seaford Meadows Bio-Retention Basins. Moreover, in the past five years the Tripodi Group has continued to clock up major project work including an involvement in the Enfield Stages 1-5 redevelopment of former Enfield High School into 170 lot medium density residential development. There was also the Seaford Vista Residential development, which involved converting a greenfield site into 1200 allotments.
Another noteworthy development, The Entrance at Angle Vale, involved a 340-allotment residential subdivision constructed over six stages.
Long term employee Phil Hendy, Project Manager, Tripodi Group, said, "We have created communities in Seaford Meadows and Seaford Heights. In addition, there are developments in Enfield, Almond Grove Munno Para and now The Entrance at Angle Vale."
The thriving company operates on the principle that only construction professionals can deliver peace of mind when dealing with building issues or purchasing construction products. Asked what motivates him to achieve, Joe Tripodi responds: "Honesty and decency. We can do it better – nothing will stop me from achieving."
Tripodi was born in Kalgoorlie, WA, in 1940 but grew up in Campbelltown, where he and five brothers and two sisters helped their father, a market gardener. Told by his father at 15 to get a job, Joe approached the Campbelltown council office and was soon hired as a labourer.
Around this time, Tripodi met a fellow named Rodney, a surveyor who offered him a job as a chainman. Joe recalls, "I didn't know what a bloody chainman was, but I said yes. Rodney taught me a great deal and gave me the confidence and ability to progress within the civil construction earthmoving industry."
As Campbelltown Council grew, an engineer was hired who took on Rodney's role, and Tripodi returned to the field with a gang to manage stormwater projects. He was 17 at the time and was working with a crew ranging in age up to 50.
At 19, Tripodi left the council after winning his first tender to complete the Sturt Road stormwater project. He landed a permanent position with a Dutchmen named Dan Struik. This employment opportunity launched the next chapter of Joe Tripodi's stellar career, taking on work within stormwater, roadworks, and general civil construction.
In 1961, at the spritely age of 21, a concreting company offered the energetic Joe Tripodi a subcontracting role which consisted of sourcing work and submitting tenders. In addition, he surveyed all their projects and learnt about kerbing. Then he caught the eye of Rocla – the leading concrete solutions supplier was impressed by the young Tripodi's gang's speed and efficiency.
He recalls, "They provided me with details of a large project commencing in Whyalla through a company named Beltrame.
The work in Whyalla kept me busy for a year. At 23, I married Patricia and purchased a fruit and veg store at my father's insistence."
HOW FAR WE HAVE COME
After a trip to Kalgoorlie, Joe Tripodi returned to South Australia for another civil construction job offer, this time within the new estate of West Lakes. "What a money pit that was," he said. "A private developer from Sydney was making a hell of a mess. I became the works manager and had 120 people working under me, including several of my brothers.
After a change of developer, Tripodi took over the civil construction side completely. One of the first things he did was to get hold of as many scrapers as possible, and he quickly got the job back on track.
After West Lakes, Tripodi did surveying for McMahon in Alice Springs. However, inexperienced crews landed him managing the entire civil construction side of works. Ten weeks later, McMahon's moved him to Ceduna to complete surveying work there. He was with McMahon for three years in total.
Straightening Devil's Elbow on Mount Barker Road was memorable because it attracted massive publicity. "We got that job because of our innovative approach. We installed a conveyor belt over the road and used large volumes of dynamite to move over 100,000 cubic metres of rock," Joe recalled.
Another significant achievement was completing the construction of the Port Augusta Power Station on time in 1983 by working 24 hours, seven days a week, for 12 months. Asked if he would do things differently if he was starting his career today, Joe said: "Hindsight is a wonderful thing; maybe don't fear the big players."
When Tripodi launched when Gough Whitlam was Prime Minister, and Don Dunstan was Premier of South Australia, the civil construction firm started with levels and string lines. "Now we have GPS-controlled machines," says Phil Hendy.
"Our plant equipment has had huge advancements.
"Also, materials today have far better quality control, and communication can be more direct and reactive. We now have software that can accurately track projects, costings and estimating."
Apart from better project management and a sharp focus on technology, Hendy says the learnings at Tripodi have been manifold over the past 50 years. "We have learnt the importance of good working relationships with our clients, construction partners and utility services (SA Water/SAPN/APA), councils and suppliers."
Employees are treated like part of the family. Possibly Tripodi Groups' proudest accomplishment to date is its ability to retain staff.
Hendy confirms, "More than half our employees have worked for us for over 10 years, and 20% of our staff have worked for Tripodi Group for 20 years."
These long-term staffers include Ian Crosby, who, in two significant stints from 1982 to 1990 and 1991 to now, has clocked up almost 40 years with Tripodi, which is second only to founder Joe Tripodi.
Crosby commenced as a tandem truck driver and labourer. He progressed to an operator, then leading hand. Initially, Crosby supervised 2-3 workers. Then after more progression, he was appointed as a site foreman, managing staff within a single site. Today Crosby is a project/operations manager overseeing all job sites to manage their daily requirements.
Adam Tustin was employed by Tripodi from 1983 to 1994, finishing up due to a slowdown in work. Adam started as a labourer before progressing to a role as an operator. He returned to Tripodi in 1995 and in 1998 was offered and declined a position as a foreman. However, within two years, Tustin ran sites independently and is still with Tripodi today.
Thirty-year veteran Brenton John started with Tripodi in 1993 as a backhoe operator and is now a foreman. Tony Costanzo began in 1996 as an estimator before progressing to contracts manager. Costanzo now runs all facets of the Tripodi business as its construction manager. Another Tripodi veteran is Phil Hendy, with 23 years of employment. Commencing in 1999 as a foreman, Hendy is today the firm's Project Manager.
Simone Jones, HR & Payroll Manager, Tripodi Group, who assisted with this article, said discussing staff accomplishments was the favourite
part of her research. Jones started with Tripodi in 2016.
“Employees spoke about personal situations where Joe, his children and his extended family had gone above and beyond to support them,” said Jones.
“These stories ranged from being provided opportunities they may not have been given otherwise, to reminiscing about kindnesses they would never imagine could come from a workplace.”
One employee who spoke to Jones told of his son's adoption from Thailand. The entire Tripodi family were waiting at the airport for boy’s arrival. “The Tripodi family's excitement over the employee’s new son was incredibly moving for this employee,” Jones outlined.
There was another story where the Tripodi family collectively attended the funeral of a staff member's father. Jones takes it from here. “The Tripodi’s had to take care of their unwell grandmother while attending. So that none of the family missed the service, they took turns caring for their grandmother resting in a car outside. These were just two stories, and I could go on.
“The family is so much more than an employer. Tripodi wants to celebrate your achievements and mourn your losses,” explained Jones.
“We don’t feel like employees to Tripodi Group. We feel like extended parts of their family.”
If you’re looking for an extremely well-established specialist in civil construction and earth moving, call Tripodi Group Construction on (08) 8359 1500.
ADRIAN DONALD
ADRIAN LANGLEY
ALAN (ROSS) LEWIS
ANTONIO (TONY) MUSOLINO
BARRY & GLENDA MURRAY
BRIAN WILLIAMS
CATHERINE TRURAN
CHRIS REED
CHRISTOPHER JOHN MARLES
CHRISTOPHER REYNOLDS
CLAUDETTE RENFREY
DARRYL BEALL
DAVID TRURAN
DENNIS LORENZIN
GLEN BLACKMORE
GRAEME BOSLEY
GREGORY ROSSER
IAN BUTTERWORTH
JOE CAUDO
JOE TRIPODI OAM
JOHN CHAMBERLAIN
JOHN DAVISON
JOHN LEWIS
JOHN WELSBY
KENNETH BULMER
MALCOLM HEALEY
MICHAEL BARNHURST
MICHAEL & RAELENE PRIDHAM
MICHAEL ROWE
MIKE SHERRIFF
PETER JEFFERY - CHAIR
PETER KEANE
PETER TODD
REX HERDE
RICHARD & SUE TOLMER
ROBERT (BOB) FARLEY
ROBERT (BOB) OSBORNE
ROGER ROSE
TED PALUSZEK
TONY BAULDERSTONE
VALERIE STANIFORD
WILLIAM (BILL) LORENZIN
If you know of any retired or semi-retired Members interested in joining the Retired Members Group (RMG) of CCF SA, please contact Peter on 0417 995 035.
continuous member of the organisation from 1964, pro-active on countless deputations worthy of higher recognition, and was also honoured on the CCF SA Hall of Fame Honour Roll.
Both David and his wife remained loyal and proactive members of the organisation, even into retirement, by creating with Bob Osborne the Retired Members Group (social club) and serving as Chair for many years.
The news that David had suddenly passed away on 17 September 2022, just a few weeks after his wife’s death, sent shockwaves through the entire organisation and the local civil sector.
The word ‘legend’ is generally used to recognise a person who is considered a leader, star, or celebrity in the pathway of life that stands them apart from the crowd. David Truran was a legend.
For more than 50 years, David and wife Catherine (Cath) jointly ran a successful medium size family business, located in the western suburb of Osborne. During the same period David became a crusader for his industry. He was one of the founders of the Earthmoving Contractors Association (later known as Civil Contractors Federation South Australia) which he helped create in 1964.
It can be said that along with earthmoving, the CCF SA became a way of life for him and Cath; David put service before self. He was a
As part of the RMG committee’s social calendar for 2022, RMG members were offered an opportunity to venture on the SteamRanger train for a return trip from Mt Barker to Victor Harbor, with a lovely lunch at the Crown Hotel in Victor Harbor included.
Booked for Sunday 18 September, and we had the best acceptance from our RMG members
David’s influence and involvement in the Civil Contractors Federation’s many achievements along with Cath’s support, will be remembered long into the future.
When witnessing the coming of Civil Train’s modern facilities and industry standing as one of the largest training facilities in Australia, David’s stated: “Nothing was impossible if one had the want and patience to succeed”. CCF SA and our industry thanks you, David.
above any previous event! Forty members and partners boarded the train at Mt Barker at 10am and enjoyed the 2.5 hour scenic train ride to Victor Harbor.
With the generous annual donation from CCF SA and RMG members fees, the RMG committee subsidised the train trip by $30 for each member and partner, along with a fully paid for meal each at the Crown Hotel for lunch.
During the lunch in Victor Harbor, we paid our respect with a minute’s silence to David Truran (founder and previous chair of the RMG), who had passed away just the day before. It was a big shock to us all and he will be deeply missed by the RMG committee and the members who had known him as a friend and advocate for so many years.
On the trip back quite a few RMG members and partners indulged in a bit of a nanna nap on the way back to Mount Barker. On disembarking late that afternoon, it was acknowledged by all that the day was a great success and most enjoyable. Even the weather was kind to us. Sadly, it was one of the final SteamRanger trips ever.
If you are a retired or semi-retired CCF SA member and would like to join the RMG, please contact Peter Jeffery on 0417 995 035 | for just $55 (incl gst) per year we have three subsidised social activities a year. It’s a great way to keep in touch and have fun!
Since the Women in Civil committee was created in 2010, we have a long list of achievements. The thing that we are most proud of however, is the increase of female participation in the industry, across all levels.
It is now the ‘norm’ to see women in high vis. We now have sizing in PPE that is made for us. There are even ladies toilets on most construction sites. To think that as little as 5 years ago this was not normal practice, is astounding. But we see this as a benefit for all. Traditional roles such as picking up the kids is now accepted as both a mum and dad task,
along with other domestic tasks. Equality for all is just about there, and we as an industry are leading the way.
That’s why our next big event is a must attend for everyone. We are holding an International Women’s Day luncheon on Wednesday 8th March 2023 at the Adelaide Convention Centre, and you are invited. The global theme for International Women’s Day is ‘Embrace Equity’. Equity isn’t just a nice-to have, it’s a must have, and we challenge every CCF SA member to commit to at least one person from your organisation to attend what is shaping up to be one of the
biggest yet. Let’s demonstrate that our industry is leading the path for us all.
We have Susan Alberti as our guest, who has had and continues to have an extraordinary life. At 75 years young, she has had to prove herself often and has seen so much change in her lifetime. Google her to see just how far she has come, and while you’re there, head to the CCF SA website to book your tickets.
On behalf of the Women in Civil Committee, I would like to wish you and yours a very Happy Christmas, and a safe and prosperous 2023. We are looking forward to seeing you on the 8th of March!
It may only feel like yesterday that I finished my degree and ventured up to Olympic Dam, 560km north of Adelaide to begin my role as a graduate surveyor for Western Mining Corporation, but this month it’s actually been 30 years.
I have seen so many changes over the years (and decades) with how we do what we do and which tools we operate with.
An integral part of being a surveyor is the technology and equipment that we all use and there have been some massive changes through the years.
In October 1992, I got on a plane and headed to a small island in Vanuatu, called Tanna Island, to complete the practical element of my final year project of my degree, on plate tectonic movements using GPS (global positioning system), with three of my lecturers from the University of South Australia. Before leaving, we needed to research our optimum time for using the massive (and expensive) equipment we took away with us. At that time, we only had a 4-hour window where 4 (the minimum required) satellites were available for use in the sky above, at Tanna. We were extremely fortunate that the best time for static observations was between 10am and 2pm, when we could leisurely make our way to survey stations, see the sites while the GPS was recording measurements for the full 4 hours, and return to our accommodation in time for dinner. The next year, the team had to do observations in the middle of the night.
Fast forward 30 years and GPS equipment can get readings from as many as 15 satellites any time of the day.
Olympic Dam utilises long hole open stoping with cement aggregate fill to mine ore. Once ore from stopes is completely extracted and before backfilling, they are surveyed to assess the amount of ore extracted and evaluate the integrity of the design and blasting techniques.
When I first started surveying these in 1992, we used a theodolite (before they were total stations) with a WILD DI 1000, which was one of the first
modern EDM (electronic distance measuring) devices.
A few years later a fancy machine called a CMS (cavity measurement system) was purchased (the first in Australia) to measure the gigantic empty holes left in the ground from stoping. This early prototype was essentially a rotating scanner mounted on the end of a 10-metre pole and fed into the stope to reflectorlessly measure the stope. Points along the pole were surveyed to coordinate the scanner head, while being supported away from the stope opening.
I haven’t worked in mining since the late 1990s but with the development of scanners, drones and LIDAR, I’m sure there are much safer, quicker and easier methods available to obtain better results.
When I surveyed my first tunnel project in Melbourne in 1997, we were using the very best of surveying instruments at the time, but they still weren’t reflectorless or what are known as total stations nowadays. You were still tethered to the theodolite. Once this equipment was capable of being used remotely and read to surfaces without a target, the surveyor’s job was made a whole lot safer. It also enabled surveyors to measure areas previously inaccessible.
Wow, how things have changed regarding safety.
The first time you really saw hi viz clothing was when the Hypercolour t-shirts debuted in the early 90s. We wore brown, green and blue work gear. Reflective strips weren’t even seen on site, even underground. Personal visibility came from the cap lamp that you wore. Back in 1998 on the Adelaide Tunnels project saw a sea of blue on all of us as we broke through our first tunnel. It’s extremely rare now to see anyone in anything but hi viz orange and yellow.
I have attended many, many project inductions but in the 90s, we were
informed that safety glasses should be worn when we felt they were required but were not compulsory. Long pants and long sleeves weren’t mandatory as we weren’t as sun smart as we are today.
On one project, marking out the tunnel face was always done by accessing the tunnel face out of a loader bucket which would never happen today.
Filling out paperwork for JSEAs, SWMS, etc only really started to be a regular part of project life from the early 2000s.
I remember being given a quick lesson on how to manoeuvre a 2-tonne excavator, and from there I was seen as capable of moving or operating all sorts of plant. I wouldn’t even think about doing this now.
I’m sure I wouldn’t recognise this place now if I were to go back.
My first exposure to Olympic Dam was December 1992, after which Western Mining Corporation bought out BP Minerals 49% share. BHP now owns and operates the mine.
In 1992, there were around 50kms of underground roadway, now there are over 700kms.
Thirty years ago, the town of Roxby Downs, built to service the mine, was home to around 2000 people, with 850 of those working on the project. Now there are over 4000 who live in Roxby Downs. Many more fly in or out for work. In 1992, there were around 400 homes built in town; now there are over 1770.
When change is small and happens over a long time, you tend to not realise how significant these advances are.
I was one of only two females who worked underground at Olympic Dam in the 1992. On the project I am on now, women make up nearly a third of the staff in our offices. There are a few working out on site as well. The numbers have increased significantly but still have a way to go.
When I first began in the industry, there were often no facilities allocated to women and I had to share with the men. This is no longer a problem.
BREAKTHROUGH ON THE ADELAIDE HEYSEN TUNNELS, 1998. MICHELLE GROSE PICTURED FAR LEFT
Whenever I needed things like boots or a hard hat or glasses, they either had to be ordered in or I had to be creative with how to make them fit properly.
Size 5 steel capped boots are readily available now but early on, I would have to pre order them at least 4 weeks before I needed them. Gloves were always far too long for my short fingers and hands and the habit of wearing a headband to fill out a hard hat, made too big for my head, is still with me to this day. I would often have to fit 2 or 3 additional sweat bands around a hard hat harness to make sure it fitted correctly. I even used to sew my own Velcro sealed sweat bands to ensure a snug fit.
Fortunately, we can now purchase these basic items of PPE easily.
I consider myself so lucky to have begun my surveying career back when I did where I can see how much it has changed, mostly for the better. It really makes me appreciate what we have readily available to all now.
The CCF SA Earth Awards was held on Friday 12th August at the Adelaide Convention Centre.
This year displayed some incredible projects in South Australia, with this year seeing some new award incentives also. With close to 300 industry representatives in attendance, we were all entertained with the hypnosis antics of Isaac Lomman, and his chosen volunteers, who showed us just how speedy some of us are, and that no one is safe from losing their shoes! We also raised much needed funds for CCF SA’s 2022 Charity Partner, the Sammy D Foundation. All winners then go onto the CCF National Earth Awards which was held in Canberra on 11th November. From the 15 high quality nominations, there could only be 6 winners. Congratulations to all winners of the 2022 CCF SA Earth Awards!
The North-South Corridor is one of the most ambitious, forward-thinking road infrastructure initiatives ever undertaken in South Australia.
The corridor is being progressively completed, piece by piece, by a succession of major infrastructure projects which have each left their own built legacy to the South Australian community.
But as construction has progressed, the various component projects have developed different innovative solutions in response to construction complexities and evolving community expectations.
Plans to build an efficient road transport route connecting the north of Adelaide with the south of Adelaide have been floated since the Metropolitan Adelaide Transport Study, released in 1968, proposed a “North-South Freeway”. However, the current iteration of the North-South Corridor – a 78km, traffic light-free motorway between Gawler and Old Noarlunga – was first identified in the South Australian Planning Strategy and other associated State Government strategic policies in the 2000s.
These documents set out the vision for the North-South Corridor to be the major route for north- and south- bound traffic, including freight vehicles, running between Gawler and Old Noarlunga.
The majority of the North-South Corridor has now been completed, thanks to the delivery of a number of major infrastructure projects focused on constructing individual sections of the corridor. Almost $5 billion of combined investment (in nominal terms) has gone into delivering these completed projects, with the Australian and South Australian governments working together to jointly fund the majority of these and the South Australian Government fully funding others.
Each of the North-South Corridor projects has faced its own engineering and project management challenges and complexities, given the different urban development, land management requirements and existing road and services infrastructure along the corridor.
For example, the Northern Expressway was, at 23km in length, the largest road construction project undertaken in the state since the 1960s at the time of its construction, while the Regency Road to Pym Street (R2P) Project contributed 1.8km of non-stop roadway but in a highly-developed and complex urban environment.
The community and government’s expectations of how major infrastructure projects should be built, in terms of which materials to use or how to support local motorists, residents and businesses, has also continued to evolve over time.
This map shows the major completed sections of the 78km North-South Corridor to date, with
Hindmarsh) currently in the planning phase.
As a result, each project developed different and often innovative solutions to adapt to these challenges.
The Darlington Upgrade Project involved the design and construction of approximately 3.3km of upgrades to Main South Road, including a nonstop motorway between the Southern Expressway and north of Tonsley Boulevard and the construction of eight bridges, resulting in the removal of five sets of traffic lights.
The project was delivered by Gateway South, a joint venture between Laing O’Rourke and Fulton Hogan, with design undertaken by Jacobs Group, Kellogg Brown & Root and SMEC Australia.
Gateway South realised from the outset that adopting a traditional bridge construction method for three of the eight structures would result in significant traffic and community impacts, given the complexity and size of the intersections involved: the Southern Expressway/Main South Road and Ayliffes Road/South Road/Shepherds Hill Road intersections.
To keep disruptions to a minimum for the many tens of thousands of vehicles which travel through Main South Road every day, the project did something that had never been done before
The 15.5km, three-lane Northern Connector is South Australia's first ever major concrete road. in South Australia and, for a civil construction project of its scale, the whole of Australia.
The three-span bridges, weighing between 3,000 and 3,200 tonnes and varying in length between 180 and 197m, were constructed ‘off-site’ and then transported into position and manoeuvred into place using ‘selfpropelled modular transporters’ (SPMTs).
By designing, constructing and installing the bridges in this innovative way, rather than traditional methods, the number of weekend road closures that were required was reduced from at least seven per structure, to one single closure per bridge.
It also provided additional employment opportunities for South Australians, with Bowhill Engineering undertaking the work to fabricate the bridge segments at its workshop.
This type of bridge installation had, prior to the start of the project, commonly been used in Europe and America, however only for single-span bridges between 500 and 1,000 tonnes in weight and two-span structures with an average weight of 2,000 tonnes.
For three-span structures, methodologies trialled at that point in time accounted for steel bridge components only and weights significantly less than 3,000 tonnes.
Further, previous full bridge installations around the world using SPMTs had been on flat ground with the structure moving only a short distance.
The Darlington Upgrade Project structures, in contrast, were constructed with steel girders, concrete deck and parapets already in place, before being transported along the existing road network over a distance of approximately 400m per bridge, with significant differences in gradients along the travel path.
As a result of the unprecedented complexity of the activity, the project team was required to develop innovative methods to pre-wire the structure before transporting it, in order to monitor any changes in stress or strain, in real time, through its movements.
The project generated new knowledge in relation to this method of three-span bridge construction and transportation, and it has since been repeated on other South Australian infrastructure projects, such as the Regency Road to Pym Street (R2P) and Ovingham Level Crossing Removal projects.
The R2P Project involved constructing 1.8km of new non-stop roadway (three lanes in each direction) and a surface road (two lanes in each direction) and grade-separating the intersection of South Road and Regency Road.
The R2P Project also had a key focus on minimisation of materials and the reuse of existing materials on site, resulting in it becoming the first project in Australasia to obtain a certified Infrastructure Sustainability Council of Australia V2.0 Design Rating.
The project sealed the construction office car park with 100 per cent recycled materials, allowing it to save 9.4 tonnes of carbon dioxide.
It also worked to reduce greenhouse gas emissions throughout the project’s construction, through measures such
100 per cent recycled material was used for the R2P Hudson Avenue site office car park.
To do this, the R2P Alliance – a consortium of McConnell Dowell Constructors (Aust) Pty Ltd, Mott MacDonald Australia Pty Ltd and Arup Group Pty Ltd – considered a number of alternative approaches to deliver improved outcomes.
For example, rather than encouraging vehicles to avoid using South Road and seek alternative routes during construction, the R2P Alliance implemented a staged removal of right turn movements at the South Road and Regency Road intersection, and provision of alternative routes, to increase the through-capacity of the busy intersection.
To improve engagement with the various local businesses adjacent the roadway and support ongoing trade and access during construction, the R2P Alliance trialled the use of an Australian-first smartphone app which allowed for quick and easy communication with local businesses and residents for the first time in Australia.
The SitePodium app enabled local businesses and residents to regularly engage with the R2P Alliance on areas of interest.
as installing lower wattage lighting, using GreenPower at its project site compound and using lower emissions materials such as recycled asphalt pavement, reduced Portland cement concrete and recycled materials in kerbing.
Measures such as these are expected to become more commonplace in the future, as the South Australian Government commits to net zero emissions by 2050 and looks to shift the infrastructure sector towards low-carbon materials and construction practices.
Supporting local industry, businesses and creating jobs were key focuses in the delivery of the Northern Connector Project.
The project, delivered by Lendlease, involved constructing a completely new six-lane, 15.5km motorway providing a vital freight and commuter link between the Northern Expressway, South Road Superway and Port River Expressway.
As part of the Industry Participation Strategy, the project was set a challenge to achieve over 90 per cent investment back into the South Australian economy.
To this end, the Northern Connector was designed and constructed to be the first major concrete road in South Australia.
One of the pre-constructed bridge spans for the Darlington Upgrade Project being transported onto site by a self-propelled modular transporter in 2017.
The resultant use of concrete and steel enabled local companies to be engaged to maximise reinvestment back into South Australia.
Adelaide Brighton and Southern Quarries and Direct Mix provided the materials required for the 175,000 cubic metres of concrete that was used for the new pavement of the motorway.
The project set a target to use 6,500 tonnes of Whyalla Steel, through InfraBuild (formerly OneSteel) to maximise local investment in the state. In late 2019, the target was surpassed with a total of 6,750 tonnes of steel used on the project.
The project was also proudly supported by local Industry Partners Catcon and LR&M Constructions, which played a key role in delivering three of the
major interchanges and sections of the motorway including earthworks, drainage and bridge structures.
Additionally, Lendlease established NorthHub, an employment, skills and training centre to help northern jobseekers secure some of the 480 jobs a year on average on the project, particularly displaced automotive workers.
The project reached a total of 91 per cent reinvestment (almost $400 million) back into South Australia, delivering not only value for money, but strong investment and support for the State and local businesses.
The 10.5km Torrens to Darlington (T2D) Project is the final piece of the North-
South Corridor, the most significant infrastructure project ever undertaken in South Australia.
The project is set to bypass 21 sets of traffic lights between the River Torrens and Darlington, and has been modelled to use a combination of twin threelane tunnels, lowered and ground-level motorways, as well as overpasses and underpasses at key intersections.
In continuing the state-of-the-art practices used on the North-South Corridor to date, both the Southern Tunnels and Northern Tunnels are planned to be constructed using tunnelboring machines (TBMs).
TBMs planned to be used will be approximately 100m long and will excavate tunnels 15m in diameter, progressing about 8-10m per day.
Early works are underway, with main construction works proposed to start in 2025. TBM works for the Southern Tunnels are planned to begin in 2026 and project completion is expected in 2031.
Creating a pipeline of skilled workers for the Civil Construction Industry.
CITB will fund eligible employers up to $2,500 per school-based apprentice/trainee:
• $1,250 after completion of probation
• $1,250 after SACE completion
For additional information, visit: citb.org.au/sbats
doorways2construction®
citb.org.au citb.sacitb_sa CITB South Australia
KENNARDS
KOMATSU
LIFTQUIP AUSTRALIA
LOADEX
LOADEX.COM.AU
MANHEIM AUCTIONS
MARSON HIRE
MAUGHAN
MEH
MEHHIRE.COM.AU
MILWAUKEE TOOL
ADELAIDE FUEL DISTRIBUTORS p 8349 5868
ADELAIDEFUEL.NET.AU
ADELAIDE BRIGHTON CEMENT ltd
BORAL CONSTRUCTION MATERIALS GROUP
CLAY & MINERAL SALES pty ltd
DK QUARRIES pty ltd
FITZGERALD QUARRIES
HALLETT RESOURCES
HOLCIM (AUSTRALIA)
PETER
NEISUZU.COM.AU
PICKLES AUCTIONS p (08) 7087 0777
PICKLES.COM.AU
BOWDEN