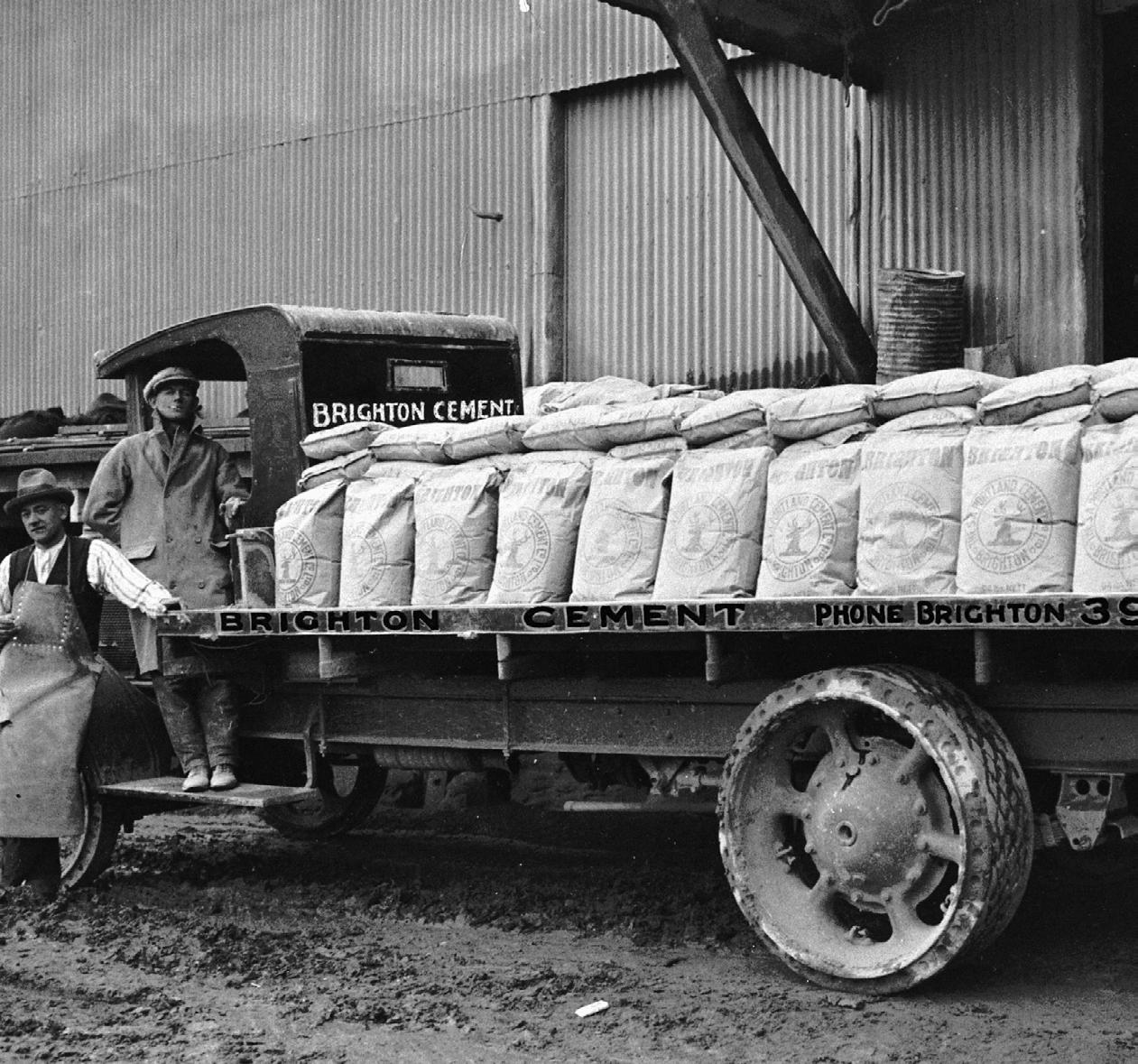
7 minute read
look how far we have come
HELPING AUSTRALIANS BUILD SINCE 1882
By Jess Verrender, Corpwrite Australia
Not many Australian companies can claim 140 years of history. Yet in 1882, one person William Lewis decided to have a go where many would not, starting his own business from scratch and launching Brighton Cement Works and thus began the Adbri (ASX: ABC) story. Adbri is one of Australia’s most successful and enduring domestic manufacturers, producing cement, lime, concrete, aggregates, industrial minerals, and masonry products across its national footprint. Adbri operates cement manufacturing facilities in South Australia, the Northern Territory, Western Australia, and New South Wales and is the parent of Adelaide Brighton Cement, which traces its history back to William Lewis. Significantly, the launch of William Lewis’ Brighton Cement Works in 1882 also marked the commencement of the Portland cement industry within Australia. It was an extraordinary feat for the time, with the colony of South Australia barely 20 years old. Adbri has evolved into a company with annual revenues of $1.57 billion in the 2021 calendar year and total assets of $2.3 billioni, while always maintaining its reputation as trusted manufacturer and supplier in the industry. Today thirteen brands, including Adelaide Brighton Cement, operate under the Adbri umbrella, complemented by seven joint venture companies. With the Adbri group of companies focusing on ‘Building a Better Australia’, they have had a significant hand in creating roads, ports, airports, processing plants and energy facilities across the nation. Adbri supports 11,520 full-time equivalent positions indirectly across Australia, and its gross value add annual is around $3.2 million. With a strong focus on corporate social responsibility (CSR), Adbri is doing its bit to support local economies and communities and is using new technology, alternate fuels, renewable energy, and lower carbon emitting products to contribute to a sustainable future.
A lorry fitted with solid rubber tyres which was the first motor vehicle to be used for delivery of cement packed in paper for the Brighton cement company in August 1927. LAUNCHING INTO HISTORY
For historical context, Adelaide Brighton Cement launched at roughly the same time as the Adelaide to Port Augusta railway opened in the late 1800s. Less than a decade laterii in 1891, William Lewis and his business partner William Shearing erected an experimental cement plant in Portland. “By using limestone and clay, they manufactured a crude version of Portland cement and after some technical refinement, the first batch of marketable cement was produced,” said Brett Brown, Adbri’s Chief Operating Officer – Cement and Lime.
By the next year, along with several shareholders, the pair founded The South Australian Portland Cement Company Limited. A new manufacturing plant was built, and later opened in December. Increasing financial debt and a change of government (who at the time reduced existing import tariffs), caused the company to go into liquidation in late 1895. However just a year later, private investors, many of them previous shareholders, purchased the company to form a private company, The South Australian Portland Cement Company.
DEALING WITH ADVERSITY IN THE NEW CENTURY
Over the following decade, The S.A. Portland Cement Company flourished, growing in size and in stature. However, a terrible fire in November 1909 destroyed the Marino Works and an important financial loss was the result, driving the company into voluntary administration in order to gain financial funding. By 1911, many of the existing shareholders registered a new business, The S.A. Portland Cement Company. Numerous upgrades were made, such as the implementation of the first cement mill powered by electricity. Demand was such that the works could not maintain supply. Two years later, due to the growing demand, A.W.G. Pitt founded Adelaide Cement Company Limited at Birkenhead, recognised as the rival company to the S.A. Portland Cement Company. The new rival used limestone from Yorke Peninsula that was transported across the gulf by steamship, and black mud (clay) from the Port River. In 1927 the
Board examined a proposal of merging the S.A. Portland Cement Company and its competitor, however, the proposal lapsed due to a lack of enthusiasm from the shareholders.
CEMENTING ITS REPUTATION THROUGH TECHNOLOGY ADOPTION
As a result of direct competition, the S.A. Portland Cement Company took steps to increase production by refitting much of its plant and increasing the number of employees to 104. Over the next 40 years, many advances in technology helped the cement industry to grow substantially. In 1930, due to the lack of stone reserves, the S.A. Portland Cement Company decided to relocate the works. After extensive testing, it was decided that the new works would be situated at Angaston due to the vast natural stone deposits. Twenty years later in June 1950, construction of the Angaston Works commenced, with the concrete chimney stack reaching its full height of 204 feet by Christmas 1951. After the new Works at Angaston had been successfully tested, the old raw mill at Marino was switched-off, and the new Angaston Works was officially declared open in December 1952.
MERGER ON THE TABLE
In 1957, talks recommenced between The S.A. Portland Cement Company and Adelaide Cement Company Limited, discussing the possibility of a merger, proposing the combination of their resources to increase supply in an attempt to meet the growing market demand.
By November 1959, a sales agreement was signed, which developed into a profitable arrangement for both companies for over a decade. Until then, the S.A. Portland Cement Company had only made two types of cement, ‘normal’ and ‘high early strength’, the latter having been introduced in 1929. In the 1960’s three more types of cement were introduced to the marketplace, ‘sulphate resisting’, ‘masonry’ and very light-coloured cement that in keeping with the history of the company, was named ‘Brightonlite’. After almost three weeks of intense movement on the Stock Exchange, ‘Adelaide’ announced that it had secured more than 75 per cent of the ‘Brighton’ shares and in April 1971, the Boards of the two companies announced the forming of what is now known as Adelaide Brighton Cement Limited. Today, Adelaide Brighton Cement Limited is part of the Adbri Ltd group of companies, with operations in every mainland state, and over 1500 employees nationally.
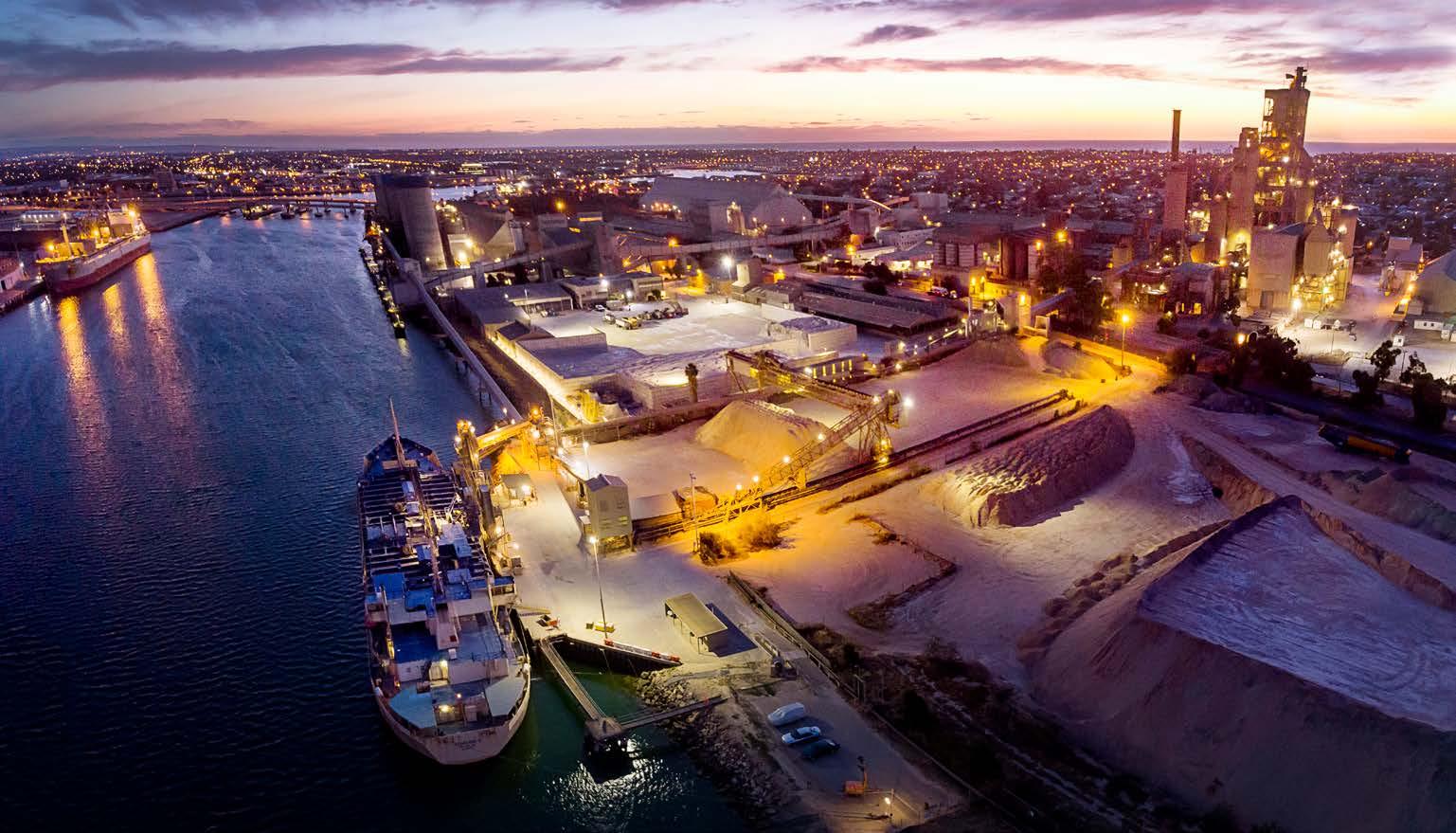
NET ZERO ON THE PATH TO A SUSTAINABLE FUTURE
With its purpose of ‘Building a Better Australia’ in mind, Adelaide Brighton Cement’s parent company Adbri goal is to net zero emissions by 2050, recently launching their Net Zero Emissions Roadmap. With a plan to ‘decarbonise’ its entire operation, Adbri operates two emissions-intensive and hard-to-abate processes – the integrated manufacture of clinker and cement and lime production.iii “We have demonstrated a strong performance over the past decade in reducing our operational emissions by 32% since FY10,” said Mr Brett Brown, Adbri’s Chief Operating Officer – Cement and Lime.
“Our net zero emissions pathway is being approached in two stages. From 2020–2030, the priority is to deliver emissions reductions through conventional abatement approaches like process and energy efficiency, increasing the use of alternative fuels and a transition to zero emissions electricity. In parallel, we will also be building our capabilities in breakthrough technologies that will be required post-2030. “From 2030–2050, we will work to close the technology gap for our hard-toabate clinker and lime manufacturing by supporting the development and de-risking of breakthrough technologies at scale, via partnerships in research and development (R&D) and potential pilot-scale demonstrations to accelerate commercial deployment.”
Adbri's Birkenhead facility is one of only five integrated cement manufacturing plants in Australia
TINKERING WITH CLINKER
Adbri say that one of its product-related strategies is to increase the use of supplementary cementitious materials (SCMs) in their cement and concrete products. Clinker is the most emissionsintensive product in the clinkercement-concrete process, however SCMs can partly replace clinker in cement (and therefore concrete). According to Brett, SCMs that are used most in Australia are ground granulated blast furnace slag (GGBFS), fly ash from coal-fired power plants and limestone, all of which have much lower embodied carbon than clinker.
The clinker to cement ratio is an industry metric which reflects the utilisation of SCMs. By decreasing the amount of clinker and increasing the SCM content, the emissions intensity of cement can be reduced, while still producing a durable, resilient product that meets stringent standards. Adbri claim that their clinker to cement ratio in 2020 was 77 per cent better than the Australian average of 84 per cent. Adbri also plans to collaborate with key partners such as the Heavy Industry Low-carbon Transition Co-operative Research Centre (HILT CRC) and SmartCrete CRC; a member of the Material and Embodied Carbon Leaders Alliance (MECLA), as well as other industry associations to help with