HARVESTING GUIDELINE
This document is intended to be a user friendly operational guide addressed to the hazelnut growers. Special thanks are due to Dr. Nadia Valentini who gave a professional contribution to the development of this Guideline.
Ferrero Group waives any responsibility in respect to the completeness and accuracy of the content of this operational guide which in no case is to be considered as a binding document for the hazelnut growers.
Copyright Reserved - Disclosure of this document is not permitted unless expressly authorized by the Ferrero Group
INTRODUCTION - THE IMPORTANCE OF PRE-HARVEST, HARVEST AND POST-HARVEST ACTIVITIES
3. HARVEST
3.1. Potential harvesting dynamic and importance of collecting crop on time (number of passages etc.)
3.2. Machines for harvest
1.MAIN ISSUES IN PLANNING OF HARVEST
1.1 Planting layout and varietal mix
1.2 Effect of tree shape on the selection of mechanization for harvest
1.3. Pedo-climatic conditions (soil type, terrain configuration, altitude climatic condition)
1.4. Dynamic of yield increasement per year
1.5. Plant protection before and during the harvesting period
2.PREHARVEST ACTIVITIES
2.1. Estimation of production (flowers and fruit counting)
2.2. Planning of pre-harvest and harvest on the basis of estimation of production
2.3 Pre-harvest soil management in different growing conditions
3.2.1. Harvesters
3.2.1.1. Vacuum harvesters
3.2.1.2. Mechanical pick-up harvesters
3.2.2 . Additional equipment
3.2.2.1. Blowers
3.2.2.2. Swipers (windrower)
3.2.2.3. Trailers
3.3. Manual harvest-collecting
3.4. Advantages and disadvantages of different harvesting techniques
3.5. Harvester machine costs
3.6. Safety during harvesting of hazelnuts
3.7. Operations after harvest Reference
INTRODUCTION
THE
IMPORTANCE OF PRE-HARVEST, HARVEST AND POST-HARVEST ACTIVITIES
Harvest is an activity of great importance as it is crucial to maintain the quality of the product obtained in the field. Nuts of the European hazelnut (Corylus avellana L.) fall to the ground when ripe but should remain on the ground as short as possible to avoid the onset of alterations in the seed.
When raising hazelnut plantations, all the factors that can facilitate harvest and make harvesting operations economically sustainable must be taken into consideration. For a quick and effective harvest, soil has to be suitably prepared for the use of harvesting machines.
The fall of the nuts is gradual, and occurs over a short or long period depending on a cultivar and especially on the climate trends throughout the year. Harvesting must be conducted in several steps to preserve the quality of the fruit and to avoid product loss caused by atmospheric factors, particularly in areas with sloping land.
After the harvest, cleaning and drying of the fruit must be carried out quickly; storing must be done under appropriate conditions and will differ in duration depending on the selected type of conservation.
Therefore, a goal of a farmer is to obtain good production in terms of quantity and quality, always keeping in mind that the result achieved in the field can be compromised with a harvest that is not carried out on time or with poor treatment of the hazelnuts in the post-harvest period.
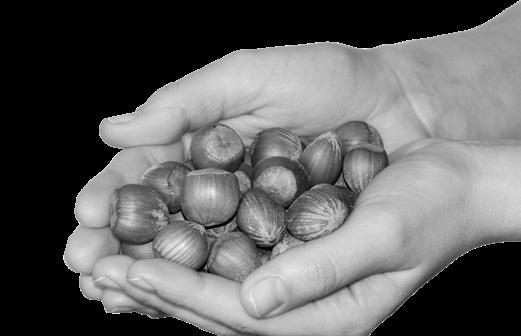
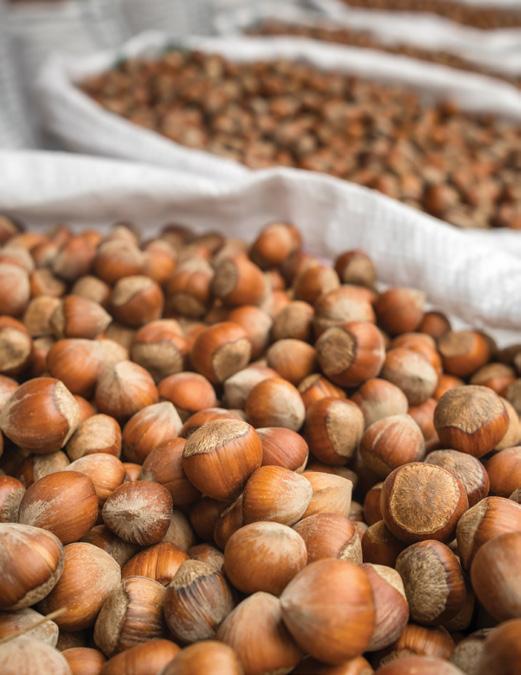
MAIN ISSUES IN PLANNING OF HARVEST
Planting layout and varietal mix 1.1.
Selection of a cultivar is a crucial decision. The choice of a cultivar must be made on the basis of the final destination of the product and its agronomical characteristics (productivity, resistance, or tolerance to main pests). Most of the hazelnuts are intended for industrial processing; therefore, the cultivars that have qualitative (good flavour) and technological characteristics (medium size and round shape, high kernel yield, high peelability) suitable for these purposes are more valued (for example, Tonda Gentile delle Langhe, Tonda di Giffoni, Tonda Gentile Romana, Table 1.1).
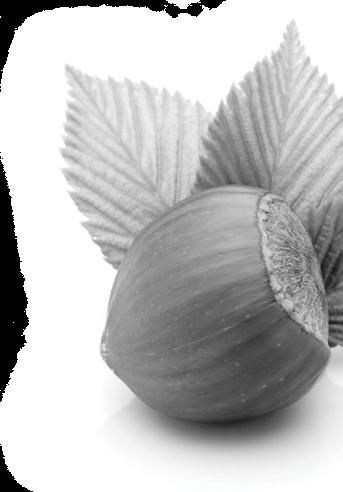
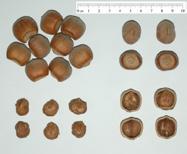
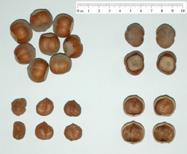
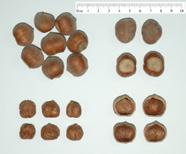
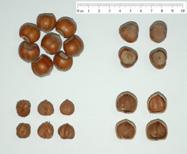
Another important parameter that has to be taken into consideration during selection of the varietal mix is adaptability to climate of a cultivar. The knowledge of phenology of each cultivar (in particular, flowering time of male and female flowers, time of leaf budburst, and time of nut maturity) is essential for the selection of a site for planting the cultivar, for its effective pollination, and selection of the appropriate varietal mix.
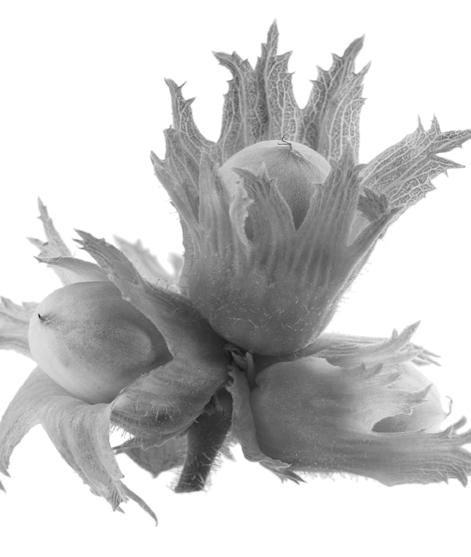
Tonda di Giffoni
Tonda Gentile delle Langhe syn. Tonda Gentile Trilobata
• Originates from southern Italy (Campania)
• Medium-sized nut (2.5-2.8 g) with round shape (IR = 0.90)
• Vigorous tree
• Semi-ver tical growth
• Nut ripening from the middle till the end of the season (September in Italy)
• High productivity
• Easily peelable: 80-90 %
• High kernel yield: 44-47 %
• High adaptability to different environments
• Originates from nor th-western Italy (Piedmont)
• Small to medium-sized nut (2.2-2.4 g) with triangular-round shape (IR = 0.90)
• Vigorous tree
• Semi-ver tical growth
• Early nut maturity (August in Italy)
• Medium-low productivity
• Easily peelable: 80-90 %
• High kernel yield: 44-48 %
• Originates from central Italy (Lazio)
• Medium-sized nut (2.5-2.7 g) with round shape (IR = 0.95)
• Medium-low vigour tree
Tonda Gentile Romana
• Semi-ver tical growth
• Nut ripening from the middle till the end of the season (September in Italy)
• Medium-high productivity
• Fairly peelable: 50-60%
• High kernel yield: 44-48 %
• Originates from Spain. Grown in western Europe and USA (Oregon)
• Large nut (3.8 g) with round shape (IR = 0.91)
• High vigour tree
Barcelona syn. Fertile de Coutard
• Semi-ver tical growth
• Nut ripening from the middle till the end of the season (September in Italy)
• Medium-high productivity
• Fairly peelable: 50%
• Easily becomes rancid
• Medium kernel ratio: 39-42 %
• Originates from central and southern Italy
• Medium to large nut (3.0-3.2 g) with round shape (IR = 0.92)
• Medium-high vigour tree
• Open branching
Nocchione
• Mid-season nut maturity (September in Italy)
• Easily peelable: 80%
• High productivity
• Low kernel ratio: 38-40 %
The time of nut maturity of the main cultivars given in the Fig. 1.2 refers to average time obtained from Italy. There are no reliable data for Serbia since the orchards are not in a full production phase yet. Fruit ripening can be strongly influenced by weather conditions and many other factors (like the plot’s position, presence of irrigation systems, etc.); therefore, the data referring to the beginning of nut drop, and the duration of the ripening period are indicative only.
Hazelnuts are wind pollinated and self-incompatible; therefore, they need cross-pollination. One tree cannot pollinate itself, nor the trees of the same variety. Different varieties may be compatible or incompatible for pollination among themselves, which is based on a complex system of incompatibility.
The aspects to consider when choosing a pollinizer are:
• genetic compatibility between cultivars (Table 1.2)
• simultaneous flowering of male pollinizer flowers and flowering of female flowers of the main cultivar.
Flowering period of female flowers lasts for a long time (more than four weeks), especially in unfavourable climatic conditions. It is advisable to plant two or even three different pollinizers to ensure that compatible pollen is present throughout the entire flowering period of female flowers of the main cultivar. For this reason, the rule is to choose cultivars with subsequent flowering time of male flowers (for example, flowering of male flowers of Tonda Gentile delle Langhe occurs early while in Tonda Gentile Romana flowering of male flowers occurs late).
The position of pollinizers within a plot may affect the nut harvest activities. The right way to locate different cultivars in an orchard is to plant only one variety per row. The reason for using this method of planting is to easily monitor tree development of different varieties and to facilitate selective spraying if needed.
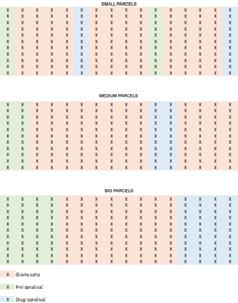
In small plots, one row of pollinizers may be planted for each 4-5 rows of the main cultivar or two rows of pollinizers for every 8-9 rows of the main cultivar. In large plots, trees can be planted in blocks of the same variety using two or, better, three compatible varieties (Fig. 1.3).
The arrangement in rows makes harvesting easier due to different ripening periods and the need to separate nuts of different varieties when it is not possible to market the fruits of two cultivars together. It should be kept in mind that cultivars with late ripening period (for example, Tonda di Giffoni) may show a delay in ripening time of the fruits (even over a month) and harvest may be conditioned by the climatic conditions during autumn months (September-October), which are generally more humid than the summer ones.
A tree to be planted in a plot may be self-rooted or grafted on non-suckering rootstocks. The emission of suckers is a characteristic of most cultivated hazelnuts which requires frequent interventions to eliminate basal shoots that continuously develop from adventitious buds around the root collar. Suckers must be eliminated because they take away water and nutrients from the plant and they are an obstacle to cultivation operations, especially those necessary for maintaining the soil clean and for harvesting the fruits.
The use of low suckering/non-suckering rootstocks, selected from Corylus colurna (also called the Turkish hazel) and its hybrids, may permanently reduce the need for de-suckering (Fig. 1.4). During harvest, the absence of suckers contributes to reduction in loss of products and saves time during soil preparation (collection by means of sweepers and suction, etc.). No less important is the fact that the elimination of suckering increases the environmental sustainability of hazelnut cultivation, because there is no need for chemical interventions for control of suckers (generally 3-4 interventions per year). Seedlings obtained from free pollination of C. colurna have been used as non-suckering rootstocks, but their grafting compatibility and influence on productivity, when used in combination with some main cultivars, are still under research. In addition, the lack of clonal rootstocks limits wider use of grafted plants.

Effect of tree shape on the selection of mechanization for harvest
The tree shaping system used for hazelnut may be divided into a multi-stem form (bush) and a tree form (bush vase and tree shape) depending on the number of main stems in a plant.
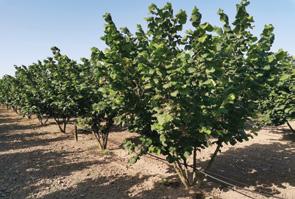
BUSH FORM
Bush is a traditional shape used in many European areas and consists of a plant with a variable number of stems, which is the natural habitus of hazel in nature. Bush form is mainly used in hilly areas characterized by non-irrigated land, sloping position, higher altitude, and in areas subject to wind and abundant snowfalls. In such areas, bush form is preferred because trees can remain productive even if some of the main stems break.
The suggested number of stems is not greater than 4-5 in modern plots (Fig. 1.5); this helps in containing the development of the plant and facilitates the operations of pruning, de-suckering, and harvesting. It is estimated that an average of 25-30 kg per ha is lost when the fruits fall between the main stems which are difficult to reach, especially when de-suckering operations are not done properly. To perform an effective harvest in orchards with bush form plants, pre-harvest activities (such as blowing and sweeping) are essential.
ADVANTAGES
• Easy recovery of plants if damaged by adverse climate conditions
• Growth training pruning for bush is easier than for tree forms
DISADVANTAGES
• Harvesting is more difficult, requires accurate pre-harvest operations
• De-suckering is more complicated and requires more time
1.2. 1.3.
TREE FORMS (bush vase and tree shape)
Tree forms are so called because they have a single main stem (Fig. 1.6). They can be used both for grafted and self-rooted plants, as long as they are properly pruned from the first year of planting. Tree forms allow farmers to reduce the distance between the plants and to completely mechanize working operations on the plantation. Consequently, tree forms are more suitable for flat or slightly sloping land, in fertile soils or where irrigation is possible.
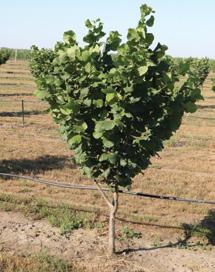
ADVANTAGES
• Harvesting and other activities are easier (de-suckering, weeding, etc.)
• Allow reduction in planting distance
DISADVANTAGES
• Suitable only for vigorous varieties
• Training pruning is more difficult than for bush
• If a plant is seriously damaged, it has to be replaced
• Less productive in the first years
Pedo-climatic conditions (soil type, terrain configuration, altitude, climatic condition)
SOIL
The type of soil and the terrain configuration of a hazelnut grove may have a great influence on harvest. Heavy soils can create harvesting problems due to difficult entry of the machines in case of precipitation, and for this reason it is essential that a hazelnut grove is kept grassed, at least in the space between the rows, to allow greater lift and less soil compaction. Grassing should be also used on sloping land where soil erosion occurs due to the runoff of water following intense rainfall, which can lead to the accumulation of hazelnuts in piles and cracks in the soil. High humidity of the soil leads to rapid deterioration in the quality of the product if it is not dried promptly.
In general, to facilitate harvesting operations, the suggested management of the soil involves the combination of soil processing techniques in the row and controlled grassing in the inter-row, similar to what is done for other fruit species. This type of soil management has to be considered the rule in the first 2-3 years after planting, when competition for water and nutrients between young seedlings and herbaceous cover species must be limited as much as possible. During the following years, it is possible to keep the entire hazelnut grove covered with grass to make the most of the function of the grass cover, using a mulcher with disk to mow grass in the row (Fig. 1.7).
CLIMATE CONDITIONS
The selection of the varietal mix includes an accurate evaluation of climate conditions at the site of planting. In places where the climate is particularly wet in late summer – early autumn, early ripening cultivars (August) are more suitable than the late ones which ripen in late September-early October. Rains during harvesting period delay ripening, since plants vegetate longer and nuts hardly drop to the soil due to the husks that remain green. In addition, the impossibility to enter the orchard causes a delay in mechanical harvesting operations which lead to a deterioration of the quality of the fruit. With the increment of altitude, the ripening period of the fruit can be delayed by 2-3 weeks, especially in cultivars with late maturity. However, some of the main varieties were selected in traditionally hilly areas, characterized by a good ventilation, cool temperatures in summer (hardly above 30 °C) but not particularly cold winters. In such conditions, these cultivars performed well, offering good productivity and products of excellent quality.
Before choosing a cultivar, it is advisable to accurately evaluate climate conditions at the area of cultivation. You can ask for meteorological data from a weather station near your area, especially temperature and precipitation data. During harvest period, you should pay attention to weather forecasts as they help in planning pre-harvest and harvest operations.
Dynamic of yield increasement per year
Grassing can be performed using the spontaneous flora present in the hazelnut grove or by sowing mixtures of different species (Fig. 1.8). The best solution is to use a combination of low vigour grass species (for example, Festuca ovina and Festuca rubra) and self-seeding legumes (such as Trifolium subterraneum). These are particularly suitable because they use a little water for their own development and have a good resistance to shading. Adult hazelnut plants have dense canopies that let little light filter into the ground. For this reason, spontaneously or artificially grown grass can be difficult to keep in good condition once the hazelnut plants enter full production.
The advantages of grassing from the aspect of harvesting operations are:
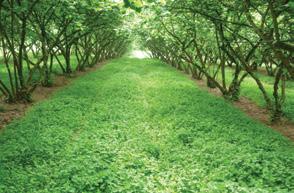

• increasing of bearing capacity of the soil
• lower compaction generated by passing of agricultural machinery
• less production of ‘dust’ during harvesting operations, which is considered one of the main risk factors for the health of farmers (see chapter 3.6)
• keeping the nuts cleaner and more difficult to move in case of heavy rain (especially in sloping terrain).
The precocity of production is strongly influenced by the quality of the plants used for the planting. The best materials are those plants obtained by layering, cutting or micropropagation, which have grown in a nursery for at least one year. They have to display a good root system and a diameter of the stem of 1-2 cm. The plants that come from accredited nurseries, with a certification for genetic identity and absence of pests, ensure greater success in establishing a new orchard in comparison with material with unknown origin. If a hazelnut plant is made with an adequate starting material, the first production is obtained in the third or fourth year of planting and productivity increases till the 8-10th year. The duration of a modern hazelnut grove is estimated at about 30 years; bush plants can have a longer life thanks to the possibility of periodical renewal of the main stems.
The orchard management in first years after planting is crucial for obtaining vigorous and healthy plants. In particular, the competition for water and nutrients has to be minimized keeping the soil clean from weeds. At the same time, the existence of irrigation and the correct fertilization helps to reduce the initial unproductive period and decreases the alternation of production (tendency to alternate years of high productivity with years of low productivity) in the period of full production of the hazelnut grove.
The dynamic of yield growth changes considering different cultivars. In a study conducted in Chilean hazelnut groves, cultivars such as Tonda di Giffoni and Barcelona displayed a very high yield growth rate in the first years after planting and reached their average maximum yield values rapidly (Fig. 1.9). Instead, Tonda Gentile delle Langhe (TGL) has a lower growth rate and its average maximum yield value is reached several years after the previously mentioned cultivars.
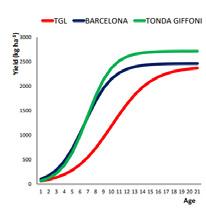
Plant protection before and during the harvesting period 1.5.
A plan for the control of diseases and pests in hazelnut plantations requires good knowledge of the main pathogens of hazelnuts. In general, a hazelnut grove kept in good cultivation conditions displays fewer phytosanitary problems. The correct choice of planting layouts and training system, together with adequate pruning, greatly increases the effectiveness of phytosanitary treatments since they allow easy passage of the sprayers, ensure adequate light penetration into the canopy and good ventilation. A correct control plan includes the phytosanitary treatments during winter and vegetative season, but also a series of agronomic interventions, such as proper pruning and an effective soil management.
At the time of harvest, all phytosanitary treatments for fungi and insect control have to be previously conducted in the hazelnut grove. When the first hazelnuts begin to fall, they must be carefully examined since the fruits that fall early are often not healthy; among the hazelnuts that fall prematurely there are often empty nuts (blanks, that is without seeds), fruits infested by nut weevil and those stung early by bugs, which generally have shrivelled kernels.
Regarding bugs, the most damaging is Brown Marmorated Stink Bug (BMSB, Halyomorpha halys) that attacks hazelnuts in all development stages, from fruit set to harvest (Fig. 1.10). It has a very high reproduction rate, with two generations per year in Europe. The chemical control of BMSB is very difficult since infestations occur very close to harvest, and sometimes the most severe ones are between the first and the second harvesting steps.

Due to its frequent movement between crops (for example, soybean, corn), BMSB is generally more abundant on the edges of the orchard. Bugs move from crops after harvest to shelter in wild untreated areas or on windbreak or other plants on the border. It is necessary to plan spraying of these areas near the hazelnut grove, if the BMSB population is abundant. This strategy of control works well especially for large plots, where the treatments at the edges of the field greatly limit the entry and spread of bugs within the hazelnut grove itself.
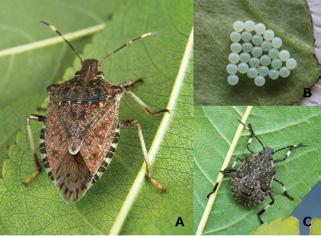
PREHARVEST ACTIVITIES
Estimation of production (flowers and fruit counting) 2.1.
The estimation of production obtainable from a hazelnut orchard can be a difficult task to perform. The main cultivated varieties in Europe can be considered cultivars selected from the wild, that maintain certain inhomogeneity within them. However, planting material coming from accredited nurseries, with a certification on both the varietal identity and the phytosanitary status, should display a better homogeneity.
The aim is to provide an early yield estimation by means of conducting flower and fruit counts at several representative sampling locations within each parcel. Detailed information about the sampling locations, such as age, variety, planting density, yield levels, should always be recorded. Orchard owners or local agronomists can conduct the sampling. At each sampling location, a minimum of six trees has to be randomly selected for sampling. Trees along the orchard perimeter are excluded since they are often affected by external factors and do not fully reflect the growing conditions at the sampling location. With random selection of trees, it will be avoided any bias due to the productivity of a tree.
If a sampling location is large and/or heterogeneous or it is planted with different varieties, it is strongly recommended to subsample the parcel, by selecting points at different cardinal directions.
The purpose of the subsampling is to obtain the most representative estimation of the orchard yield.
In the below examples, a minimum of six subsampling locations has to be defined within the perimeter of a large sampling location, where three cultivars are grown (Example 1) or a minimum of three subsampling for orchard with one main cultivar (Example 2).
Moreover, if multiple varieties are grown in small orchards, minimum one subsampling point per variety may be selected (Example 3).
EXAMPLE 3
• Small orchard (9 ha)
• Three main cultivars
• 3 Sub-sampling locations
At each of these subsampling locations a minimum of six trees will be randomly selected for crop counting. The number of subsampling locations depends on the accuracy that a farmer desires. This strategy ensures that differing yield levels of the selected varieties are considered for the final yield forecast.
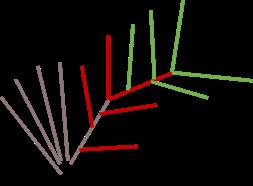
Once the trees for sampling are randomly selected, two different crop counting approaches may be applied depending on the age of the trees:
• Tree is younger than five years: if a tree is still young, the crop counting shall be performed on the entire tree. In the final automated yield forecasting step, the average number of healthy nuts per tree will be calculated and used to estimate yield. Once a tree becomes taller than 1.80 m, the sampling of the entire tree becomes very tedious. In this case, the procedure for trees older than five years (see below) shall be followed.
EXAMPLE 1
• Large orchard (22 ha)
• Three main cultivars
• 6 sub-sampling locations
• 6 plants per location
• Tree is older than five years: if a tree is (or close to be) mature, the crop counting shall be performed on one entire, healthy branch per tree. An entire branch in this context refers to the entirety of second and third level branches diverting from one first level branch (stem) in the diagram (Fig. 2.1).
EXAMPLE 2
• Large orchard (22 ha)
• One main cultivar
• 3 sub-sampling locations
• 6 plants per location
1.level
2.level
3.level
The amount of light and shade (from the adjacent trees) varies in different cardinal directions and heights of the tree, so does the productivity of the selected tree. By means of sampling an entire healthy branch from bottom to top, the height effect is automatically accounted for. To account for the effect of the orientation of a branch, the branches should be sampled in different cardinal directions for each selected tree. For example, on the first selected tree the counting can be conducted on a branch facing south. On the second tree, a branch facing west should be selected, and so on. This strategy is systematically depicted in Figure 2.2.
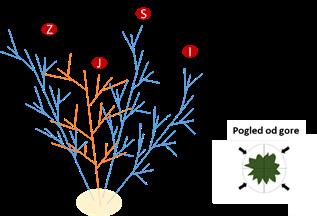
2. Nut clusters counting (May-June). Nut clusters are counted. If flower count was not performed in February-March, the sampled branch/tree is marked, so that it can be counted again during the next counting within the same growing season. The count of the nut clusters is normally more reliable than flower count as it takes place after the period in which yields might be negatively affected by late frost.
The estimation of production potential could be performed in three different period of the fruit development:
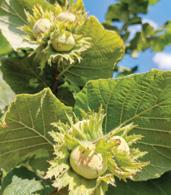
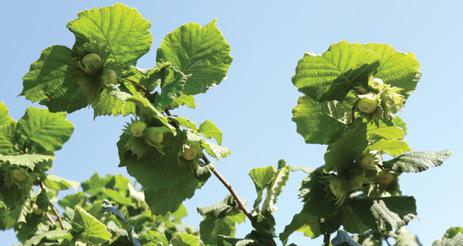

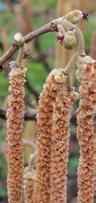
1. Flower count (February-March). Depending on the exact date of the sampling campaign and the visibility of the female flower development, all flowers showing pistils in varying shades from light pink to brownish, as shown in the picture below, will be counted. Upon the completion of the flower count, the sampled branch will be marked, so that it can be counted again during the next counting within the same growing season.
3.Single nuts count (mid-July - early August). All individual nuts are counted. This count provides the most certain estimation because it is performed close to harvest time. Also, trees should have already passed the period in which early dropping of infructescence may occur. This phenomenon is still under investigation, but one of the main causes could be the lack of fertilization due to multiple factors including lack of nutritional elements, adverse climate conditions during late May/early June, when fertilization generally occurs, and the presence of genetic abnormalities in some cultivars. Other causes of early drop can be the attacks by bugs or other insects on young nuts.
Planning of pre-harvest and harvest on the basis of estimation of production 2.2.
Planning correctly pre-harvest and harvest operations is the best way to save time and money, as well as to maintain a high quality of production by collecting the fruits in time thus avoiding its long stay on the ground. The major assumptions for planning are based on yield estimation and on the typical machinery and equipment used in the farm to perform pre-harvest and harvest operations.
Yield estimation (Fig. 2.6). For a hazelnut grove made with good quality plants, the first production is obtained in the fourth year of planting and productivity increases until the10-12th year, then becomes almost steady for the following years.
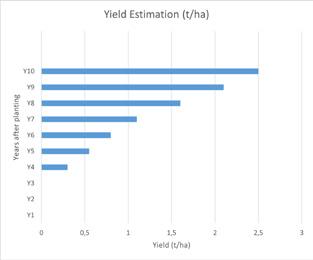
Machinery and equipment. The major assumptions used in developing the plan are:
• Machinery efficiency: average data considering one working shift (8h)
• Harvest period: thir ty harvesting days
• Harvest machine: one harvest machine is needed for every 100 ha of hazelnut grove as well as one mechanical blower and four manual blowers per harvest machine
• Trailers: one for each harvest machine; however, the total number of trailers and their capacity strongly depend on the logistic organization and strategy applied by each farmer. The factor that mostly influence the plan is the size of the farm (Table 2.1).
All the proposed solutions are just indicative and based on average conditions. A farmer has to adjust the procurement plan and select the proper machine based on different parameters such as growth, soil management, average weather conditions at the parcels, strategy process flow of the operations, etc.
Pre-harvest soil management in different growing conditions 2.3.
The floor in the orchard has to be levelled at least one year before the first commercial harvest: the soil pushed into dips and cracks needs time to settle and become firm. If the orchard floor is as smooth and firm as possible before harvest, the harvest operations are more efficient, since operators can adjust the height of the sweeper for maximum efficiency; this helps minimize the quantity of debris that ends up in the tote bins and this makes all post-harvesting operations easier and less expensive.
The pre-harvest operations mainly depend on the adopted type of soil management.
For plots with clean cultivated soil, the final levelling, smoothing, and rolling should be done about 30 days prior to harvest to avoid the presence of holes and cracks in the ground. The fruits that accumulate in dips or on piles keep their humidity high and are more subject to subsequent alterations; they become difficult to collect both manually and by mechanical machines. The fruits get dirty and tend to be dragged in the case of intense rains, especially in hilly terrain with sloping.
For plots managed with grass cover:
•The turfed soil is managed by rotary mowers (3-4 interventions/year are generally necessary) in intervals dictated by the growth speed of the turf. Before harvest, flail mowers should be used to chop vegetation down to ground level; flail-mow also helps mulch leaves and grind up blanks and twigs that have dropped to put the orchard floor in proper condition for harvesting.
• For orchard managed with whole grassing, it is preferable to intervene with cross mulching during summer (if orchard is free from obstacles, such as irrigation with dripping lines on the rows), or with mulcher with disk on the row, to have soil levelled for harvest.
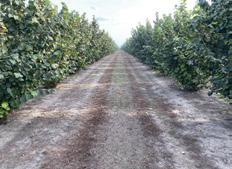
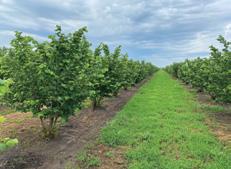
• Close to harvesting, mulching must be particularly accurate and performed according to the characteristics of the machine that will be used for harvesting (see Chapter 3). Plan to leave approximately 2.5 cm.
•If the soil is fertile and grass develops very rapidly, it is preferable to apply herbicide treatment before harvest (Fig. 2.7) The presence of grass can hinder the nut harvesting especially for cultivars with medium and late maturity, since it is impossible to mow grass between the first and the second passage of harvest.

Hazelnut drop-off and weather conditions as main factors
The main hazelnut cultivars have naturally gradual nut drop which can last from 2 to 6 weeks. The quantity of yield (productive load) of the plants and the climate conditions are the factors that most influence the duration of nut drop. The main goal during harvest operation is to leave nuts on the ground as short as possible:
• Harvesting in a single step can compromise the quality of the fruit; for this reason, at least two harvesting passages must be performed.
• The first pickup operation has to be performed when 40-50% of nuts have dropped to the ground, including in the case of low yield.
• In any case, nuts should not be left on the ground for more than 7-10 days, especially if the weather forecast is not favourable.
• Nuts should be cleaned and dried as soon as possible after harvesting, especially if they were collected in wet conditions, to avoid rising humidity which could compromise the quality.
Influence of climate conditions on harvest:
• Very hot and dry summers can cause scaling due to the difficulty of the husks to detach from the ripe nuts, even if they are dried.
• If summer season is cool and rainy, plants vegetate for a long time and husks continue to remain green instead of drying out. For this reason, the ripening period tends to lengthen, especially in late ripening cultivars.
• Harvest plan should be prepared and the soil should be managed in time, according to the weather forecast.
• Farmers should evaluate how to optimize the collection depending on the soil characteristics. In difficult situations such as hazelnut groves with high slopes, the risk of machine roll-over problems has to be considered.
3.1. 3.2.
Machines for harvest
The need to collect nuts quickly and efficiently requires the use of harvesting machines. Different mechanization solutions are available including harvesters connected to the tractor or self-propelled machines. Trailed machines, which are cheaper but still reliable, involve greater use of workforce and longer working times, in comparison to self-propelled machines.
The choice of the machines to be used for harvesting is mainly dictated by:
• the size of the farm
• the availability of workforce
• the location of the hazelnut groves (flat or sloping terrain).
3.2.1. Harvesters
Classification by functioning and displacement
Hazelnut harvesting machines are divided into two main categories, depending on the operating principle:
1)Vacuum harvesting machines
2)Mechanical pick-up harvesting machines
In vacuum machines, air current generated by a suction fan lifts the fruits and conveys them to the subsequent sorting and cleaning apparatuses. In mechanical harvesting machines, the fruit is lifted from the ground by rotating brushes that launch it towards loading conveyors or augers.
A second distinction refers to the type of self-displacement:
• towed (trailed/pulled) machines are coupled to a tractor and activated by the power take-off of the tractor.
• mounted machines are connected to a tractor via the rear three-point hitch or via the front three-point hitch.
• self-propelled machines have their own motor for moving the machine and its operation.
3.2.1.1. Vacuum harvesters
In vacuum harvesters, the collected nuts are conveyed into a depression chamber and then discharged, through a valve, into a conveyor equipped with a side fan. The jet of air generated by this fan hits the raw product transversely as it falls towards the lower part of the conveyor, eliminating the leaves and the lightest impurities mixed with the fruits. The product is then transported by means of an auger to a rotary sieve, consisting of two cylindrical, concentric, and rotating screens, which sort the product. By replacing the double rotary screen with one equipped with holes of suitable size and shape, the machine can be adapted to the collection of different types of nuts. Finally, the product is sent pneumatically in bags or in towed trailers. The air suction used to lift the product passes through one or more cylindrical cyclones for the abatement of dust. The dust-saturated air stream enters the upper part of these funnel-shaped devices, creating a whirling motion; due to the centrifugal effect, the suspended particles crawl on the walls, lose speed and fall downwards; ground dispersion occurs by gravity through valves with rubber blades.
In towed (trailed) machines, harvesting is conducted by means of one or more flexible and light pipes, with diameters between 100 and 140 mm (Fig. 3.1) held by walking operators who guide them over mounds or rows of nuts on the ground. In order to operate with towed vacuum system, it is necessary to have the product piled up in heaps or in rows, in order to minimize the movement times of the operators on foot who carry the pipes.
Potential harvesting dynamic and importance of collecting crop on time (number of passages etc.)
The power required from the tractor varies, depending on the models and their sizes, from a minimum of 20 kW to a maximum of 60 kW. In the most popular models, the internal transmission to the suction and cleaning systems is conducted by means of belts (Fig. 3.2).
For some versions of towed vacuum harvesters, it is also possible to mount an automatic, central or lateral collector (Fig. 3.3), often liftable by means of a hydraulic arm, consisting of a head with brushes, similar to that of the selfpropelled one, through which it is possible to eliminate the manual handling of the pipes, thus limiting the use of work force.
The working capacity of towed vacuum machines is 5-8 h/ha. At least four people are required for the harvest, the tractor driver and three operators who alternate during the tiring work with the pipes. The variability is linked to the orographic and humidity conditions of the soil, the quantity of the product to be harvested, and the training of the staff. In flat plots and with wide headlands access path, the productivity of the harvest benefits from the use of small trailers in which the product is stored. For machines with additional front and side devices, both time and work use are reduced, with the working capacity of about 3-4 hours per hectare.
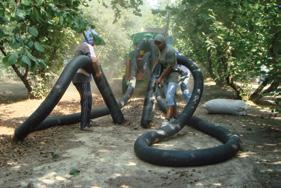
Self-propelled machines are equipped with a three or four-wheel drive propulsion system, hydraulic transmissions, both for propulsion and for the control of the operating parts, and are powered by water-cooled diesel engines, with nominal powers that may vary, depending on a model, from about 30 to 75 kW.
The frame supports a front swathing-collector head with a working front of generally 2.5 m which, in the larger models, can even reach 3.5 m (Fig. 3.4). The collection head consists of a pair of counter-rotating brushes that collect the product towards the suction duct, placed in a central position on a height-adjustable metal slide. In this way, with the same selfpropelled machine it is possible to carry out the swathing and harvesting phases, and collection of the fruit from the ground at the same time. The subsequent cleaning steps of the product are similar to those described for trailed harvesters.
On some self-propelled machines, a side blower is installed whichmoves the fruits that are not reachable by the brushes from under the canopy of the trees towards the centre of the next row, facilitating their collection in the next step and avoiding the use of traditional shoulder blowers. The working capacity of self-propelled machines can even drop below 2 h/ha, if the hazelnut grove is in optimal conditions. The brushing head can also avoid swathing times, collecting the product between the rows with two parallel passes.
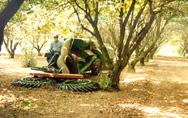
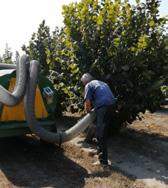
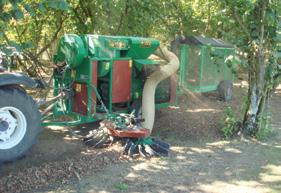
3.2.1.2. Mechanical pick-up harvesters
A common feature of harvesting pick-up machines is that the collection of the product is carried out by means of rotating brushes which physically grip the fruits and throw them on loader belts or transfer screws towards other sorting parts. The fruit is hit by moving parts that have a certain kinetic energy; therefore, these machines are particularly suitable for the collection of nuts with consistent shells, such as hazelnuts. All harvesters need a level ground, since the picking brushes, which rotate transversely to the direction of advancement by acting on a well-defined work surface, lift with difficulty the fruits present in any small depressions or holes. For maximum harvesting performance, it is suggested to prepare the ground, working it for several times by mulcher during a previous year and before the nuts drop to the ground.
Mounted harvesters have reached a high level of functionality and collection capacity, and they are widely used throughout Italy due to their low cost compared to the self-propelled ones; they are particularly suitable for mediumsmall farms, up to a maximum area of about 15 ha. In mounted pick-up harvesters, the worksite generally consists of two people, of which one drives and the other finishes the swath, removes the branches from the collection area, or moves the trailers.
The towed harvesters operate on a collection front with a width of around 150 cm, and generally require preventive swathing of the product. The tractor-harvester-trailer composition, which must necessarily cover the entire surface where the product lies, is particularly long, and therefore difficult to manoeuvre in the case of narrow or sloping orchards without headlands access path (especially when turning, reverse and other manoeuvres).
Mounted harvesters have recently become a success in small and medium-sized farms as they combine productivity (harvesting capacity is 2-4 h/ha), low cost, and ease of use since they are easily applicable to the tractor (Fig. 3.5). The connected harvester can be hooked onto the tractor’s front three-point hitch, both anterior and posterior. The operating principle is generally based on a rotating brush placed frontally and transversely to the direction of advancement. In some versions, the machine is equipped with a side swathing brush, which moves the product to be collected towards the first brush. The collection brush rotates and, licking the ground, lifts and throws the product towards an auger where the product is in contact with defoliator rollers which cause the leaves and soil to crumble and release them onto the surface of the soil. In the internal working chambers the cleaning of the product is completed by mechanical devices.
In self-propelled machines (Fig. 3.6) the differences between the models refer to the power of the engine and the operating width of the machine. The harvest can be done with just one operator, and if necessary, another operator that removes branches from the ground. Having in mind the considerable speed of advancement, harvest can be done making two passes per row, without preliminary swathing. Harvesting capacity for these machines is theoretically below 1 h/ha, but the real capacity is related to yield, dimensions of plots, and soil conditions.
The main technical characteristics of the most used harvest machines are shown in the Table 3.1. Many different models of harvester machines are available on the market, equipped with different accessories to improve harvest efficiency and product cleaning.
Table 3.1 Main characteristics of the most common harvesting machines
3.2.2. Additional equipment
The mechanized harvesting of hazelnuts is preceded by swathing, which consists of gathering the hazelnuts in swaths (or heaps). This operation can be manual or mechanized by means of blowers or windrowing machines (self-propelled or mounted). To facilitate swathing operations, the soil should be compact, well levelled or managed with controlled grassing, suitably mowed before the operation. This last solution allows for reduction of ‘dust’ during swathing and positively affects the performance of self-propelled machines.
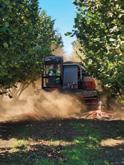
3.2.2.1. Blowers
The blowers are used in orchards which are placed in steep terrain or in plots of irregular shape, such as those in some Italian hazelnut-growing areas which are located in high hilly regions (Piedmont Langhe and Nebrodi Mounts in Sicily), where the use of windrowing machines is complicated. A blower is a small machine carried on a shoulder or driven by a tractor which produces a jet of air that can be directed by an operator thus concentrating the product on the ground in the desired point.
In the so-called “shoulder” blower (Fig. 3.7), the motor and tank are carried on the shoulder of an operator by means of two special straps. A long flexible tube is connected to this part at the base from which a strong jet of air comes out, controlled and directed by the operator through a special handle, which pushes the product on the ground to the desired point. The portable blowers are also equipped with a special start control, lock and accelerator trigger that allows operator to obtain the desired engine speed. It is necessary that the operators who use the blowers wear PPE .
The working capacity of the ‘shoulder’ carried blowers is around 6 h/ha, while the use of blowers connected to the tractor (Figs. 3.8 and 3.9) is a good solution to save time and save operators some strenuous work; however, a shoulder blower is more precise and particularly useful for reaching the nuts that dropped just below the tree trunks.


The self-propelled windrower (Fig. 3.11) is usually equipped with three wheels, two of which are driven at the front and a rear steering wheel. The front of the machine is usually made up of two or more brushes with flexible teeth that rotate in the opposite direction, sliding on the ground. The nuts are all conveyed into the space between the brushes which corresponds to the centre of the row. Alternatively, they can have a work head consisting of a rotor mounted transversely to the line of advancement of the machine and on which the brushes are hinged.
3.2.2.3. Trailers
Trailers are essential equipment for harvesting hazelnuts.They are necessary for emptying of harvesting machines equipped with tanks (or trailers) of limited capacity. Generally, during harvest hazelnuts are conveyed into a trailer positioned on the back of a self-propelled vehicle (Fig. 3.12) or a tractor (for towed and mounted machines). These containers range between 400 to 2000 kg of capacity and once filled they are emptied into a collector trailer (Fig. 3.13).
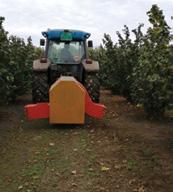
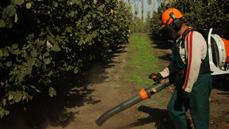
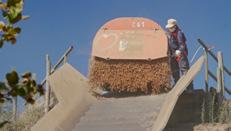
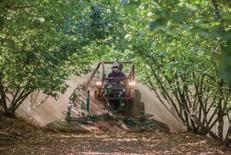
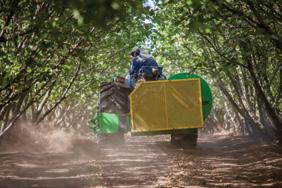
3.2.2.2. Swipers (windrower)
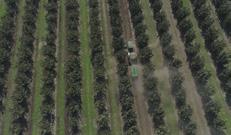
Windrowing (Swipers) machines can be used instead of blowers where the ground is easily accessible; they can be self-propelled or carried by a tractor. Working capacity of these machines is very variable, depending on yield and soil conditions, but they take approximately half the time required by the blowers (for 1.5 t/ha about 2.5 h/ha; 3 t/ha about 5 h/ha).

The mounted windrower machine (Fig. 3.10) consists of a horizontal axis transverse rotor carried by a tractor which is attached to the tractor’s power take-off (which also provides the power source). The combs or rubber strips are inserted into a rotating rotor which scrape the ground and arrange the product in a swath.
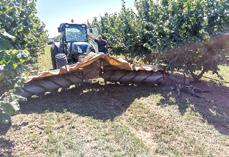
Different types of trailers can be used for nut harvest; the most popular types used in combination with harvester machines are:
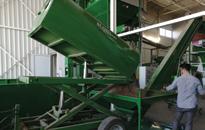
•Hydraulic Lift Trailer used in combination with any type of harvesting machines (capacity of 400-500 kg that is 1.0 -1.2 mc).
•Scissor type lifter (Fig. 3.14) designed for transporting and unloading the product from a height of up to 3.6 meters (capacity of 1400-1600 kg).
• Rear tipping trailer (Fig. 3.15) designed for transport and unloading of products (capacity of 1200-1800 kg).
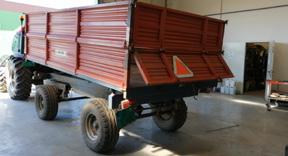
When hazelnuts are conveyed in bins, they can be placed on a trailer pulled by a tractor (which requires adequate turning space) and once filled, the bin is removed by another tractor equipped with forks (such as a forklift). This system involves having enough bins necessary to contain the whole harvest, as they are not emptied, but brought to the company. In small farms the system for collecting hazelnuts in jute bags of 50-70 kg involves longer collection times for unloading the full bag, replacing it, and loading the bags onto the trailer at the end of the collection. Operators are thus exposed to the risk of back diseases due to manual handling of bags.
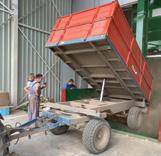
The collector trailers have to be positioned in an easily accessible point and/or in a central point of an orchard to minimize the movement during unloading of the trailer connected to the harvester and for the trailers to be easily moved from the field to the farm for subsequent nut cleaning and drying operations. The collector trailers can be of different sizes, from 5 t up to 20 t of capacity (Fig. 3.16).
Manual collection of hazelnuts still persists in some areas of Italy and in Turkey, where the lack of innovation in the orchards limits the establishment of mechanization. In general, it is not recommended due to high cost and long time required for it which can compromise the nut quality.
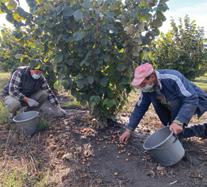
The main reasons for the use of manual harvesting are:
• complex orographic condition of a terrain characterized by excessive steepness of the land,
• high density of trees,
• irregular and limited surfaces of the plots,
• organizational and managerial deficiencies of a farm,
• very low production in the first years after planting.
Manual harvesting is carried out with inexpensive and easily available buckets or bag containers, such as plastic buckets, or other (Fig. 3.17). The efficiency of manual harvesting varies between 5 and 7 kg/h per operator in young hazelnut groves, reaching 15 kg/h in the best conditions or in adult plants distributed evenly and with skilled labour. The cost of manual harvesting can affect up to 50% of the annual crop cost of an orchard.
Manual harvest
ADVANTAGES
• Can be used in particular conditions such as very small plants and very sloping terrain position.
DISADVANTAGES
• It is tiring and expensive because it requires longer time and more workforce (containers should be emptied more frequently) in comparison with mechanical harvest.

• It is unhealthy for the operators who have to move significant weight (for example, jute bags of 60 kg).
• Due to the long time required for the harvest, nut quality can be compromised due to fruits staying on the ground for a long time.
Manual harvestcollecting Advantages and disadvantages of different harvesting techniques
3.3. 3.4.
Vacuum harvester
ADVANTAGES
• Vacuum harvester can be more versatile in comparison to pick-up machines because it can also work in non-optimal situations (sloping terrain, irregular plots).
• Low machine costs especially for the towed models.
• Possibility to add side blowers on the machine to eliminate blowing and swathing before harvest.
DISADVANTAGES
• In simple models of the machines, blowing and swathing operations have to be conducted with precision before harvest, therefore more workforce is needed.
• Harvesting with vacuum machines, especially in case of simple models with pipes, can be very tiring for operators; in addition, this operation produces ‘dust.’
• If blowing and swathing times are considered, it takes a long time to complete harvest.
Mechanical pick-up harvester
ADVANTAGES
• Very fast performance of harvest is an advantage because it is possible to carry out multiple harvests and prevent the fruits from remaining on the ground for a long time, thus preserving the nut quality.
• A few operators are needed during harvest.
• Work with the vacuum pipes is eliminated, and in this way, the physical fatigue of the operators is reduced.
• Less dust’ is formed during harvesting if the soil is properly prepared.
DISADVANTAGES
• Requires optimal soil preparation, which has to be well-levelled and, where orchard is managed with grassing, grass has to be mowed at the suitable height.
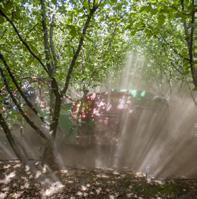
• High machine cost, suitable for medium and large farms.
Harvester machine costs
The presence of different models of harvesters on the market with variable costs together with the shortage of seasonal labour has facilitated spreading of harvesting machines even on small farms (2-3 ha). The cost of harvester machines starts from € 5,000 for the smallest trailed vacuum machine, up to € 50-70,000 for self-propelled machines.
The analysis of harvesting costs (Fig. 3.18) performed by the University of Viterbo (Italy) indicates that the convenience of using different types of nut harvesters mainly depends on the size of a farm:
• for small farms (< 10 ha) the traditional system based on towed vacuum machines is the most affordable,
• for medium size farms (10-20 ha) the mounted pick-up harvester machine is the most preferable,
• for large farms, self-propelled vehicles are suggested despite the high purchase cost, since they can reduce the collection costs even below 500 €/ha thanks to the greater work capacity and the reduction in the number of employees.
3.6.
Safety during harvesting of hazelnuts 3.5.
The collection of hazelnuts involves the risks of diseases due to exposure to dust, noise, and especially in hilly areas, accidents due to the loss of stability of a vehicle (tractor-harvester or self-propelled), with serious consequences (leading cause of death for farmers).
The ‘dust’ production is one of the main health risk factors deriving from mechanized harvesting of hazelnuts (Fig. 3.19). The “respirable” powders (mainly consisting of airborne respirable inorganic particles: PM = particulate matter) are composed of a dimensional fraction of solid particles which are absorbed during the exposure and which are not expelled by means of secretion of the mucosa (particles which are not intercepted at the level of the upper respiratory tract) and which, therefore, reach the bronchial and pulmonary cavities. Unfortunately, the results of some experimental tests performed in Italy indicate that the recommended concentration limits (TLV-TWA of the ACGIH, equal, for PM to 10 mg/m3) are almost always significantly exceeded.
The presence of well dimensioned cyclones for the abatement of dust can significantly reduce the concentration of airborne particles. Among the variables that significantly influence the concentration of respirable dust, the humidity in the soil is particularly important. In this regard, interesting solutions have been developed with self-propelled harvesting machines equipped with a humidification system to reduce dust concentrations by about 50%.
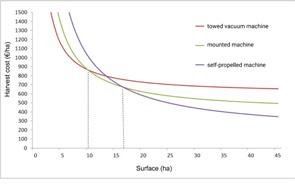
For the safety of the operators during pre-harvest and harvest operations, they must wear personal protective equipment (PPE) for the protection from dust and noise (Fig. 3.20).
Personal Protective Equipment includes:
• KN95 masks or FFP2 masks for dust protection,
• Earmuffs, earplugs, or headphones SRPS EN 352-1-2008 for noise protection,
• Safety helmet for impact protection (optional),
• Safety gloves.
The sound pressure limit value produced by a hazelnut harvesting machine is not such as to limit the daily exposure of workers to the noise.
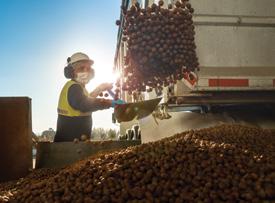
Operations after harvest 3.7.
After harvest, some operations are suggested for managing the orchard which will have beneficial effects on the following vegetation and production season:
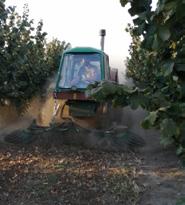
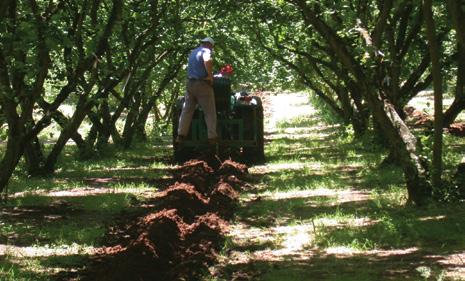
• Flail-mow the orchard floor to pulverize any remaining nuts, twigs, and branches (brush if soil is clear cultivated).
•Pruning the trees when leaves completely fall off;
•Spraying copper to prevent bacterial infections and usage of fungicide, if needed.
• Perform accurate de-suckering thus eliminating any new shoots, together with lignified basal part of suckers that remain after mechanical or chemical treatments applied during summer.
• Subsoiling at about 30-40 cm depth to reduce soil compaction, caused by the passage of vehicles, without destroying surface vegetation. This operation increases soil aeration, improves moisture infiltration, and promotes root penetration, especially in silty and clay loam soil. Subsoiling is also indicated in sloping soils to prevent soil erosion (Fig. 3.22).
• Fertilize with organic fertilizers with low nitrogen content; fertilization has to be made when trees are still in vegetation (generally October) to enable the plant to store nutritive substances for winter.
A radical solution to considerably limit injuries from tractor/machine rollovers and from exposure to dust and noise, is to adopt cabs that are going to be mounted to harvesters or tractors, depending on the type of a harvester. The use of cabs (Fig. 3.21) completely eliminates the problem of dust breathed in by the driver, without counting the benefits in terms of his well-being and comfort.
Before the harvest:
All equipment must be checked and approved in the sense of safety and functionality (accessibility, structure, field of view, start up/shut down the machine, manual equipment, breaks, audible warnings, lights and other signalization, heat and electrical insulation, tires etc.).
REFERENCE LIST
Bessone W. 2013. Prospettive per il rilancio della corilicoltura in zone a rischio di abbandono, attraverso la gestione meccanizzata dei corileti. Tesi di Dottorato in Meccanica Agraria, XXV CICLO. Università degli Studi della Tuscia. Viterbo, Italia Pp: 177.
Botta R., Molnar T.J., Erdogan V., Valentini N., Torello Marinoni D., and Mehlenbacher S.A., 2019. Hazelnut (Corylus spp.)
Breeding: 157-219. Chapter 6 in: Advances in Plant Breeding Strategies, Vol 4: Nut and Beverage Crops. Al-Khayri JM, Jain SM, Johnson DV (eds). Springer Nature, Switzerland. 607 p. DOI: 10.1007/978-3-030-23112-5_6; https://www.springer. com/gp/book/9783030231118
Bregaglio et al., 2020
Cecchini M., Monarca D., Biondi P., Colantoni A., Panaro A., 2005. Il rischio da esposizione a polveri per gli addetti alla raccolta delle nocciole. AIIA 2005: L’ingegneria agraria per lo sviluppo sostenibile dell’area mediterranea, 27-30 giugno.
Corte M., Sonnati C., Peraldo N., Michelatti G., Massobrio V., 2012. Confronto di diverse metodologie chimiche, fisiche e meccaniche per la gestione ed il controllo dei polloni della varietà ‘Tonda Gentile Trilobata’. Ricerca applicata in corilicoltura. Sintesi dei risultati 2012. Supplemento al n. 80 di “Quaderni della Regione Piemonte – Agricoltura”. Pg: 82-96.
Cristofori V., De Gregorio T., 2018. Chapter: Gestione del corileto. In: Il nocciolo. Progettazione e coltivazione del corileto. Edagricole, pg: 77-109.
Franco S., Monarca D., 2001. Technical and economical aspects of hazelnut mechanical harvesting. Acta Horticulturae, 556: 445-451.
Hazelnut Production Manual: Better Management for Higher Yields and Increased Profits. EPI https://prettyedibles.weebly. com/uploads/4/9/1/5/49153815/georgia_epi__hazelnut_production_manual_11.pdf
Hedstrom C., Walton V., Wiman N.G., Shearer P.W., Miller J., Brewer L., 2014 How to Recognize Brown Marmorated Stink Bug Damage in Commercial Hazelnuts. Oregon state University, Extension Service https://catalog.extension.oregonstate. edu/sites/catalog/files/project/pdf/em9102.pdf
Lingero E. 2013. Determinazione e messa a punto di modalità di gestione meccanizzata per la raccolta delle nocciole in aziende corilicole della Provincia di Cuneo”. Tesi di Dottorato, XXV CICLO. Università degli Studi della Tuscia. Viterbo, Italia Pp: 145.
Monarca D., Cecchini M., Guerrieri M., Santi M., Colopardi F., 2009. The evolution of the hazelnut harvesting technique. Acta Horticulturae, 845: 353-358.
Monarca D., Cecchini M., 2018. Chapter: Raccolta delle nocciole. In: Il nocciolo. Progettazione e coltivazione del corileto. Edagricole, pg:111-122.
Monarca D., Cecchini M., Biondi P., Colo-pardi F., Guerrieri M. (2012). Machines for Shell Fruits Harvesting: Technical and Economic Aspects. Acta Horticulture 940: 171-178.
Olsen J., Peachey E., 2013. Growing Hazelnuts in the Pacific Northwest: Orchard Floor Management. Oregon state University, Extension Service Publication.
Pagano M., 2008. Evoluzione della raccolta meccanizzata delle nocciole (Corylus avellana L.) nelle aree vocate della Provincia di Viterbo e messa a punto di un nuovo prototipo di macchina raccattatrice semovente. Tesi di Dottorato in Meccanica Agraria - XIX CICLO. Università della Tuscia di Viterbo, Italia. Pp: 201
Pansa M. G., Asteggiano, L., Costamagna, C., Vittone, G., Tavella, L., 2013. Primo ritrovamento di Halyomorpha halys nei pescheti piemontesi. Informatore Agrario, 69 (37): 60-61.
Valentini N., Botta R. 2018. Chapter: Progettazione del corileto. In: Il nocciolo. Progettazione e coltivazione del corileto. Edagricole, pg:33-62.
Zambon I, Delfanti L, Marucci A, Bedini R, Bessone W, Cecchini M, Monarca D. 2017. Identification of Optimal Mechanization Processes for Harvesting Hazelnuts Based on Geospatial Technologies in Sicily (Southern Italy). Agriculture, 7(7):56. https://doi.org/10.3390/agriculture7070056
Website:
https://www.gf-srl.it/en
https://cerquetani.com/trailers-equipments/?lang=en
https://www.giampimacchineagricole.com/
https://www.facma.it/
https://rivmec.com/en/raccoglitrice-nocciole/
https://www.nocciolare.it/partner/facma-company/gestire-bene-la-raccolta-e-lessicazione-per-avere-nocciole-di-qualitaintervista-ad-un-esperto