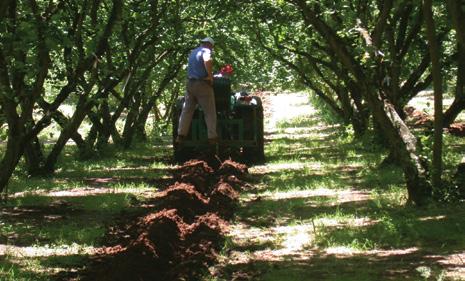
18 minute read
Pre-harvest soil management in different growing conditions 2.3.
The floor in the orchard has to be levelled at least one year before the first commercial harvest: the soil pushed into dips and cracks needs time to settle and become firm. If the orchard floor is as smooth and firm as possible before harvest, the harvest operations are more efficient, since operators can adjust the height of the sweeper for maximum efficiency; this helps minimize the quantity of debris that ends up in the tote bins and this makes all post-harvesting operations easier and less expensive.
The pre-harvest operations mainly depend on the adopted type of soil management.
Advertisement
For plots with clean cultivated soil, the final levelling, smoothing, and rolling should be done about 30 days prior to harvest to avoid the presence of holes and cracks in the ground. The fruits that accumulate in dips or on piles keep their humidity high and are more subject to subsequent alterations; they become difficult to collect both manually and by mechanical machines. The fruits get dirty and tend to be dragged in the case of intense rains, especially in hilly terrain with sloping.
For plots managed with grass cover:
•The turfed soil is managed by rotary mowers (3-4 interventions/year are generally necessary) in intervals dictated by the growth speed of the turf. Before harvest, flail mowers should be used to chop vegetation down to ground level; flail-mow also helps mulch leaves and grind up blanks and twigs that have dropped to put the orchard floor in proper condition for harvesting.
• For orchard managed with whole grassing, it is preferable to intervene with cross mulching during summer (if orchard is free from obstacles, such as irrigation with dripping lines on the rows), or with mulcher with disk on the row, to have soil levelled for harvest.
• Close to harvesting, mulching must be particularly accurate and performed according to the characteristics of the machine that will be used for harvesting (see Chapter 3). Plan to leave approximately 2.5 cm.
•If the soil is fertile and grass develops very rapidly, it is preferable to apply herbicide treatment before harvest (Fig. 2.7) The presence of grass can hinder the nut harvesting especially for cultivars with medium and late maturity, since it is impossible to mow grass between the first and the second passage of harvest.
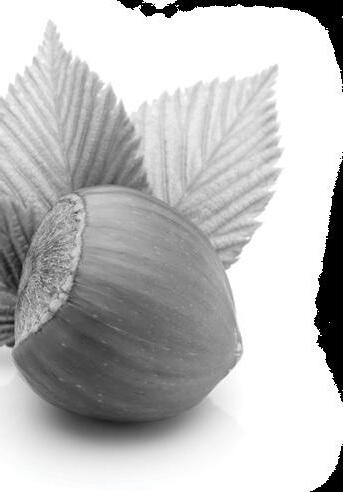
Hazelnut drop-off and weather conditions as main factors
The main hazelnut cultivars have naturally gradual nut drop which can last from 2 to 6 weeks. The quantity of yield (productive load) of the plants and the climate conditions are the factors that most influence the duration of nut drop. The main goal during harvest operation is to leave nuts on the ground as short as possible:
• Harvesting in a single step can compromise the quality of the fruit; for this reason, at least two harvesting passages must be performed.
• The first pickup operation has to be performed when 40-50% of nuts have dropped to the ground, including in the case of low yield.
• In any case, nuts should not be left on the ground for more than 7-10 days, especially if the weather forecast is not favourable.
• Nuts should be cleaned and dried as soon as possible after harvesting, especially if they were collected in wet conditions, to avoid rising humidity which could compromise the quality.
Influence of climate conditions on harvest:
• Very hot and dry summers can cause scaling due to the difficulty of the husks to detach from the ripe nuts, even if they are dried.
• If summer season is cool and rainy, plants vegetate for a long time and husks continue to remain green instead of drying out. For this reason, the ripening period tends to lengthen, especially in late ripening cultivars.
• Harvest plan should be prepared and the soil should be managed in time, according to the weather forecast.
• Farmers should evaluate how to optimize the collection depending on the soil characteristics. In difficult situations such as hazelnut groves with high slopes, the risk of machine roll-over problems has to be considered.
3.1. 3.2.
Machines for harvest
The need to collect nuts quickly and efficiently requires the use of harvesting machines. Different mechanization solutions are available including harvesters connected to the tractor or self-propelled machines. Trailed machines, which are cheaper but still reliable, involve greater use of workforce and longer working times, in comparison to self-propelled machines.
The choice of the machines to be used for harvesting is mainly dictated by:
• the size of the farm
• the availability of workforce
• the location of the hazelnut groves (flat or sloping terrain).
3.2.1. Harvesters
Classification by functioning and displacement
Hazelnut harvesting machines are divided into two main categories, depending on the operating principle:
1)Vacuum harvesting machines
2)Mechanical pick-up harvesting machines
In vacuum machines, air current generated by a suction fan lifts the fruits and conveys them to the subsequent sorting and cleaning apparatuses. In mechanical harvesting machines, the fruit is lifted from the ground by rotating brushes that launch it towards loading conveyors or augers.
A second distinction refers to the type of self-displacement:
• towed (trailed/pulled) machines are coupled to a tractor and activated by the power take-off of the tractor.
• mounted machines are connected to a tractor via the rear three-point hitch or via the front three-point hitch.
• self-propelled machines have their own motor for moving the machine and its operation.
3.2.1.1. Vacuum harvesters
In vacuum harvesters, the collected nuts are conveyed into a depression chamber and then discharged, through a valve, into a conveyor equipped with a side fan. The jet of air generated by this fan hits the raw product transversely as it falls towards the lower part of the conveyor, eliminating the leaves and the lightest impurities mixed with the fruits. The product is then transported by means of an auger to a rotary sieve, consisting of two cylindrical, concentric, and rotating screens, which sort the product. By replacing the double rotary screen with one equipped with holes of suitable size and shape, the machine can be adapted to the collection of different types of nuts. Finally, the product is sent pneumatically in bags or in towed trailers. The air suction used to lift the product passes through one or more cylindrical cyclones for the abatement of dust. The dust-saturated air stream enters the upper part of these funnel-shaped devices, creating a whirling motion; due to the centrifugal effect, the suspended particles crawl on the walls, lose speed and fall downwards; ground dispersion occurs by gravity through valves with rubber blades.
In towed (trailed) machines, harvesting is conducted by means of one or more flexible and light pipes, with diameters between 100 and 140 mm (Fig. 3.1) held by walking operators who guide them over mounds or rows of nuts on the ground. In order to operate with towed vacuum system, it is necessary to have the product piled up in heaps or in rows, in order to minimize the movement times of the operators on foot who carry the pipes.
The power required from the tractor varies, depending on the models and their sizes, from a minimum of 20 kW to a maximum of 60 kW. In the most popular models, the internal transmission to the suction and cleaning systems is conducted by means of belts (Fig. 3.2).
For some versions of towed vacuum harvesters, it is also possible to mount an automatic, central or lateral collector (Fig. 3.3), often liftable by means of a hydraulic arm, consisting of a head with brushes, similar to that of the selfpropelled one, through which it is possible to eliminate the manual handling of the pipes, thus limiting the use of work force.
The working capacity of towed vacuum machines is 5-8 h/ha. At least four people are required for the harvest, the tractor driver and three operators who alternate during the tiring work with the pipes. The variability is linked to the orographic and humidity conditions of the soil, the quantity of the product to be harvested, and the training of the staff. In flat plots and with wide headlands access path, the productivity of the harvest benefits from the use of small trailers in which the product is stored. For machines with additional front and side devices, both time and work use are reduced, with the working capacity of about 3-4 hours per hectare.
Self-propelled machines are equipped with a three or four-wheel drive propulsion system, hydraulic transmissions, both for propulsion and for the control of the operating parts, and are powered by water-cooled diesel engines, with nominal powers that may vary, depending on a model, from about 30 to 75 kW.
The frame supports a front swathing-collector head with a working front of generally 2.5 m which, in the larger models, can even reach 3.5 m (Fig. 3.4). The collection head consists of a pair of counter-rotating brushes that collect the product towards the suction duct, placed in a central position on a height-adjustable metal slide. In this way, with the same selfpropelled machine it is possible to carry out the swathing and harvesting phases, and collection of the fruit from the ground at the same time. The subsequent cleaning steps of the product are similar to those described for trailed harvesters.
On some self-propelled machines, a side blower is installed whichmoves the fruits that are not reachable by the brushes from under the canopy of the trees towards the centre of the next row, facilitating their collection in the next step and avoiding the use of traditional shoulder blowers. The working capacity of self-propelled machines can even drop below 2 h/ha, if the hazelnut grove is in optimal conditions. The brushing head can also avoid swathing times, collecting the product between the rows with two parallel passes.
3.2.1.2. Mechanical pick-up harvesters
A common feature of harvesting pick-up machines is that the collection of the product is carried out by means of rotating brushes which physically grip the fruits and throw them on loader belts or transfer screws towards other sorting parts. The fruit is hit by moving parts that have a certain kinetic energy; therefore, these machines are particularly suitable for the collection of nuts with consistent shells, such as hazelnuts. All harvesters need a level ground, since the picking brushes, which rotate transversely to the direction of advancement by acting on a well-defined work surface, lift with difficulty the fruits present in any small depressions or holes. For maximum harvesting performance, it is suggested to prepare the ground, working it for several times by mulcher during a previous year and before the nuts drop to the ground.
Mounted harvesters have reached a high level of functionality and collection capacity, and they are widely used throughout Italy due to their low cost compared to the self-propelled ones; they are particularly suitable for mediumsmall farms, up to a maximum area of about 15 ha. In mounted pick-up harvesters, the worksite generally consists of two people, of which one drives and the other finishes the swath, removes the branches from the collection area, or moves the trailers.
The towed harvesters operate on a collection front with a width of around 150 cm, and generally require preventive swathing of the product. The tractor-harvester-trailer composition, which must necessarily cover the entire surface where the product lies, is particularly long, and therefore difficult to manoeuvre in the case of narrow or sloping orchards without headlands access path (especially when turning, reverse and other manoeuvres).
Mounted harvesters have recently become a success in small and medium-sized farms as they combine productivity (harvesting capacity is 2-4 h/ha), low cost, and ease of use since they are easily applicable to the tractor (Fig. 3.5). The connected harvester can be hooked onto the tractor’s front three-point hitch, both anterior and posterior. The operating principle is generally based on a rotating brush placed frontally and transversely to the direction of advancement. In some versions, the machine is equipped with a side swathing brush, which moves the product to be collected towards the first brush. The collection brush rotates and, licking the ground, lifts and throws the product towards an auger where the product is in contact with defoliator rollers which cause the leaves and soil to crumble and release them onto the surface of the soil. In the internal working chambers the cleaning of the product is completed by mechanical devices.
In self-propelled machines (Fig. 3.6) the differences between the models refer to the power of the engine and the operating width of the machine. The harvest can be done with just one operator, and if necessary, another operator that removes branches from the ground. Having in mind the considerable speed of advancement, harvest can be done making two passes per row, without preliminary swathing. Harvesting capacity for these machines is theoretically below 1 h/ha, but the real capacity is related to yield, dimensions of plots, and soil conditions.
The main technical characteristics of the most used harvest machines are shown in the Table 3.1. Many different models of harvester machines are available on the market, equipped with different accessories to improve harvest efficiency and product cleaning.
Table 3.1 Main characteristics of the most common harvesting machines
3.2.2. Additional equipment
The mechanized harvesting of hazelnuts is preceded by swathing, which consists of gathering the hazelnuts in swaths (or heaps). This operation can be manual or mechanized by means of blowers or windrowing machines (self-propelled or mounted). To facilitate swathing operations, the soil should be compact, well levelled or managed with controlled grassing, suitably mowed before the operation. This last solution allows for reduction of ‘dust’ during swathing and positively affects the performance of self-propelled machines.
3.2.2.1. Blowers
The blowers are used in orchards which are placed in steep terrain or in plots of irregular shape, such as those in some Italian hazelnut-growing areas which are located in high hilly regions (Piedmont Langhe and Nebrodi Mounts in Sicily), where the use of windrowing machines is complicated. A blower is a small machine carried on a shoulder or driven by a tractor which produces a jet of air that can be directed by an operator thus concentrating the product on the ground in the desired point.
In the so-called “shoulder” blower (Fig. 3.7), the motor and tank are carried on the shoulder of an operator by means of two special straps. A long flexible tube is connected to this part at the base from which a strong jet of air comes out, controlled and directed by the operator through a special handle, which pushes the product on the ground to the desired point. The portable blowers are also equipped with a special start control, lock and accelerator trigger that allows operator to obtain the desired engine speed. It is necessary that the operators who use the blowers wear PPE .
The working capacity of the ‘shoulder’ carried blowers is around 6 h/ha, while the use of blowers connected to the tractor (Figs. 3.8 and 3.9) is a good solution to save time and save operators some strenuous work; however, a shoulder blower is more precise and particularly useful for reaching the nuts that dropped just below the tree trunks.
The self-propelled windrower (Fig. 3.11) is usually equipped with three wheels, two of which are driven at the front and a rear steering wheel. The front of the machine is usually made up of two or more brushes with flexible teeth that rotate in the opposite direction, sliding on the ground. The nuts are all conveyed into the space between the brushes which corresponds to the centre of the row. Alternatively, they can have a work head consisting of a rotor mounted transversely to the line of advancement of the machine and on which the brushes are hinged.
3.2.2.3. Trailers
Trailers are essential equipment for harvesting hazelnuts.They are necessary for emptying of harvesting machines equipped with tanks (or trailers) of limited capacity. Generally, during harvest hazelnuts are conveyed into a trailer positioned on the back of a self-propelled vehicle (Fig. 3.12) or a tractor (for towed and mounted machines). These containers range between 400 to 2000 kg of capacity and once filled they are emptied into a collector trailer (Fig. 3.13).
3.2.2.2. Swipers (windrower)
Windrowing (Swipers) machines can be used instead of blowers where the ground is easily accessible; they can be self-propelled or carried by a tractor. Working capacity of these machines is very variable, depending on yield and soil conditions, but they take approximately half the time required by the blowers (for 1.5 t/ha about 2.5 h/ha; 3 t/ha about 5 h/ha).
The mounted windrower machine (Fig. 3.10) consists of a horizontal axis transverse rotor carried by a tractor which is attached to the tractor’s power take-off (which also provides the power source). The combs or rubber strips are inserted into a rotating rotor which scrape the ground and arrange the product in a swath.
Different types of trailers can be used for nut harvest; the most popular types used in combination with harvester machines are:
•Hydraulic Lift Trailer used in combination with any type of harvesting machines (capacity of 400-500 kg that is 1.0 -1.2 mc).
•Scissor type lifter (Fig. 3.14) designed for transporting and unloading the product from a height of up to 3.6 meters (capacity of 1400-1600 kg).
• Rear tipping trailer (Fig. 3.15) designed for transport and unloading of products (capacity of 1200-1800 kg).
When hazelnuts are conveyed in bins, they can be placed on a trailer pulled by a tractor (which requires adequate turning space) and once filled, the bin is removed by another tractor equipped with forks (such as a forklift). This system involves having enough bins necessary to contain the whole harvest, as they are not emptied, but brought to the company. In small farms the system for collecting hazelnuts in jute bags of 50-70 kg involves longer collection times for unloading the full bag, replacing it, and loading the bags onto the trailer at the end of the collection. Operators are thus exposed to the risk of back diseases due to manual handling of bags.
The collector trailers have to be positioned in an easily accessible point and/or in a central point of an orchard to minimize the movement during unloading of the trailer connected to the harvester and for the trailers to be easily moved from the field to the farm for subsequent nut cleaning and drying operations. The collector trailers can be of different sizes, from 5 t up to 20 t of capacity (Fig. 3.16).
Manual collection of hazelnuts still persists in some areas of Italy and in Turkey, where the lack of innovation in the orchards limits the establishment of mechanization. In general, it is not recommended due to high cost and long time required for it which can compromise the nut quality.
The main reasons for the use of manual harvesting are:
• complex orographic condition of a terrain characterized by excessive steepness of the land,
• high density of trees,
• irregular and limited surfaces of the plots,
• organizational and managerial deficiencies of a farm,
• very low production in the first years after planting.
Manual harvesting is carried out with inexpensive and easily available buckets or bag containers, such as plastic buckets, or other (Fig. 3.17). The efficiency of manual harvesting varies between 5 and 7 kg/h per operator in young hazelnut groves, reaching 15 kg/h in the best conditions or in adult plants distributed evenly and with skilled labour. The cost of manual harvesting can affect up to 50% of the annual crop cost of an orchard.
Manual harvest
ADVANTAGES
• Can be used in particular conditions such as very small plants and very sloping terrain position.
DISADVANTAGES
• It is tiring and expensive because it requires longer time and more workforce (containers should be emptied more frequently) in comparison with mechanical harvest.
• It is unhealthy for the operators who have to move significant weight (for example, jute bags of 60 kg).
• Due to the long time required for the harvest, nut quality can be compromised due to fruits staying on the ground for a long time.
Vacuum harvester
ADVANTAGES
• Vacuum harvester can be more versatile in comparison to pick-up machines because it can also work in non-optimal situations (sloping terrain, irregular plots).
• Low machine costs especially for the towed models.
• Possibility to add side blowers on the machine to eliminate blowing and swathing before harvest.
DISADVANTAGES
• In simple models of the machines, blowing and swathing operations have to be conducted with precision before harvest, therefore more workforce is needed.
• Harvesting with vacuum machines, especially in case of simple models with pipes, can be very tiring for operators; in addition, this operation produces ‘dust.’
• If blowing and swathing times are considered, it takes a long time to complete harvest.
Mechanical pick-up harvester
ADVANTAGES
• Very fast performance of harvest is an advantage because it is possible to carry out multiple harvests and prevent the fruits from remaining on the ground for a long time, thus preserving the nut quality.
• A few operators are needed during harvest.
• Work with the vacuum pipes is eliminated, and in this way, the physical fatigue of the operators is reduced.
• Less dust’ is formed during harvesting if the soil is properly prepared.
DISADVANTAGES
• Requires optimal soil preparation, which has to be well-levelled and, where orchard is managed with grassing, grass has to be mowed at the suitable height.
• High machine cost, suitable for medium and large farms.
Harvester machine costs
The presence of different models of harvesters on the market with variable costs together with the shortage of seasonal labour has facilitated spreading of harvesting machines even on small farms (2-3 ha). The cost of harvester machines starts from € 5,000 for the smallest trailed vacuum machine, up to € 50-70,000 for self-propelled machines.
The analysis of harvesting costs (Fig. 3.18) performed by the University of Viterbo (Italy) indicates that the convenience of using different types of nut harvesters mainly depends on the size of a farm:
• for small farms (< 10 ha) the traditional system based on towed vacuum machines is the most affordable,
• for medium size farms (10-20 ha) the mounted pick-up harvester machine is the most preferable,
• for large farms, self-propelled vehicles are suggested despite the high purchase cost, since they can reduce the collection costs even below 500 €/ha thanks to the greater work capacity and the reduction in the number of employees.
3.6.
Safety during harvesting of hazelnuts 3.5.
The collection of hazelnuts involves the risks of diseases due to exposure to dust, noise, and especially in hilly areas, accidents due to the loss of stability of a vehicle (tractor-harvester or self-propelled), with serious consequences (leading cause of death for farmers).
The ‘dust’ production is one of the main health risk factors deriving from mechanized harvesting of hazelnuts (Fig. 3.19). The “respirable” powders (mainly consisting of airborne respirable inorganic particles: PM = particulate matter) are composed of a dimensional fraction of solid particles which are absorbed during the exposure and which are not expelled by means of secretion of the mucosa (particles which are not intercepted at the level of the upper respiratory tract) and which, therefore, reach the bronchial and pulmonary cavities. Unfortunately, the results of some experimental tests performed in Italy indicate that the recommended concentration limits (TLV-TWA of the ACGIH, equal, for PM to 10 mg/m3) are almost always significantly exceeded.
The presence of well dimensioned cyclones for the abatement of dust can significantly reduce the concentration of airborne particles. Among the variables that significantly influence the concentration of respirable dust, the humidity in the soil is particularly important. In this regard, interesting solutions have been developed with self-propelled harvesting machines equipped with a humidification system to reduce dust concentrations by about 50%.
For the safety of the operators during pre-harvest and harvest operations, they must wear personal protective equipment (PPE) for the protection from dust and noise (Fig. 3.20).
Personal Protective Equipment includes:
• KN95 masks or FFP2 masks for dust protection,
• Earmuffs, earplugs, or headphones SRPS EN 352-1-2008 for noise protection,
• Safety helmet for impact protection (optional),
• Safety gloves.
The sound pressure limit value produced by a hazelnut harvesting machine is not such as to limit the daily exposure of workers to the noise.
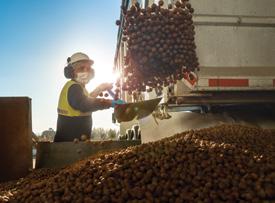
Operations after harvest 3.7.
After harvest, some operations are suggested for managing the orchard which will have beneficial effects on the following vegetation and production season:
• Flail-mow the orchard floor to pulverize any remaining nuts, twigs, and branches (brush if soil is clear cultivated).
•Pruning the trees when leaves completely fall off;
•Spraying copper to prevent bacterial infections and usage of fungicide, if needed.
• Perform accurate de-suckering thus eliminating any new shoots, together with lignified basal part of suckers that remain after mechanical or chemical treatments applied during summer.
• Subsoiling at about 30-40 cm depth to reduce soil compaction, caused by the passage of vehicles, without destroying surface vegetation. This operation increases soil aeration, improves moisture infiltration, and promotes root penetration, especially in silty and clay loam soil. Subsoiling is also indicated in sloping soils to prevent soil erosion (Fig. 3.22).
• Fertilize with organic fertilizers with low nitrogen content; fertilization has to be made when trees are still in vegetation (generally October) to enable the plant to store nutritive substances for winter.
A radical solution to considerably limit injuries from tractor/machine rollovers and from exposure to dust and noise, is to adopt cabs that are going to be mounted to harvesters or tractors, depending on the type of a harvester. The use of cabs (Fig. 3.21) completely eliminates the problem of dust breathed in by the driver, without counting the benefits in terms of his well-being and comfort.
Before the harvest:
All equipment must be checked and approved in the sense of safety and functionality (accessibility, structure, field of view, start up/shut down the machine, manual equipment, breaks, audible warnings, lights and other signalization, heat and electrical insulation, tires etc.).