Styx headlines PACK gives BACK
Stretcher smoothes seals
A pneumatic bag stretcher mechanism on medical-grade heat sealers from Packworld USA (Booth N-5913) helps prevent seal imperfections. At the start of the heat-sealing cycle, the stretcher grips the bag and produces just enough tension to remove any wrinkles or creases before making a perfect seal. Improved ergonomics reduce repetitive actions. SD
Partners supply liquid filling systems
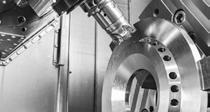
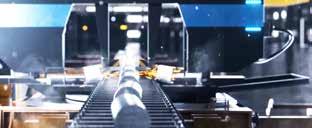
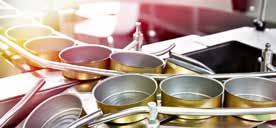

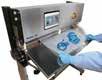
Oden Machinery, E-PAK Machinery and Change Parts (Booth S-3914) join forces to offer cost-effective liquid filling systems, which combine simplicity and efficiency with high productivity. Firms offer more than 70 years, experience in ma chine design, engineering and assembly. SD


eBook shares shrinksleeve case studies
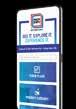

PDC International (Booth N-4921) highlights unique and ef fective uses for shrink-sleeve labeling in a new eBook, Innova tions in Shrink Sleeve Packaging. Case studies involve packages used in the beverage, dairy, wine and spirits and personal care industries. Learn more at https://resources.pdc-corp.com/ innovations-in-shrink-sleeve-packaging. SD
Ticket sales raise funds for the PMMI Foundation.
The PACK gives BACK performance by Styx, sponsored by Rockwell Automation (Booth S-1660, drew a huge crowd and raised thou sands of dollars for the PMMI Foundation and its scholarship program.

During the pre-concert reception, the PMMI Foundation awarded 2022 PACK EXPO Scholarships to six students from PMMI Education Partner schools:
• Morgan Bartholomew - Pennsylvania College of Technology
• Katelynn Chavez - Rutgers
• Brandon Coleman - Michigan State
• Caroline Joseph - Clemson
• Sarvesh Kinariwala - Rochester Institute of Technology
• Maribel Morales - California Polytechnic State - San Luis Obispo
“Fundraising events, such as PACK gives BACK™, provide critical resources to help our in dustry advance. We are thankful for the generosity of

Vote by noon for TEAs
Don’t delay. Vote before noon today for your favorite finalists in the 2022 Technology Excellence Awards (TEAs) competition (see story, p. 54), which recognizes technology being exhibited for the first time at a PACK EXPO.

HMI connects many devices
Pro-face by Schneider Electric (Booth LU-7243) supplies Pro-face brand human/machine interface (HMI) software and hardware and both panel- and box-style industrial PCs with broad connectivity to PLCs and industrial devices. Programma ble HMIs offer easy-to-read displays and multiple screen size options. State-of-the-art facility in Greensboro, NC, assembles, customizes and repairs products. SD
There are three finalists in four categories: Food/ Beverage, General Packaging & Processing, Person al Care/Pharma and Sustainability. Winners will be announced this afternoon (Oct. 25).
Vote onsite at the Attendee Solutions Center (Booth N-4552) in the North Hall Concourse or Lakeside Upper Hall Lobby (Booth LU-7000); via the PACK EXPO International mobile App, sponsored by ProMach (Booth N-5534, N-5540); or online.
For more info, visit www.PACKEXPOinternational.com. SD
our sponsors, partners and attendees who help drive our industry forward,” says Jim Pittas, president and CEO, PMMI.
To qualify for the $5,000 scholarship, students must attend a PMMI Education Partner, have a minimum 3.0 grade point average, major in engineering, pack aging, processing, mechatronics or a related field and demonstrate a commitment to the industry. SD
Hall
Graffin, Oesterle, Pienaar, Rhodehamel form Class of ’22.
The Packaging & Processing Hall of Fame inducted the late Jean-Jacques Graffin, Rebecca Oesterle, Pierre Pienaar and E. Jeffrey Rhodehamel, Ph.D., in a ceremony yes terday at the Industry Speaks Stage (Booth N-4565)
Graffin dedicated his life to improving manufac turing and packaging for the food industry. A tireless inventor, he revolutionized dairy manufacturing and packaging; his weight filler and the rotary machine
.
This system WILL dramatically reduce operator touch-time, WILL speed up changeovers beyond your wildest dreams, and WILL eliminate costly downtime on your labeler. Our simple fix to your complex problems.
Nita is the original 100% Servo Labeler that WILL change your production universe forever.
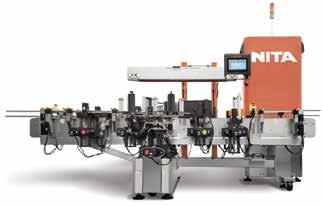
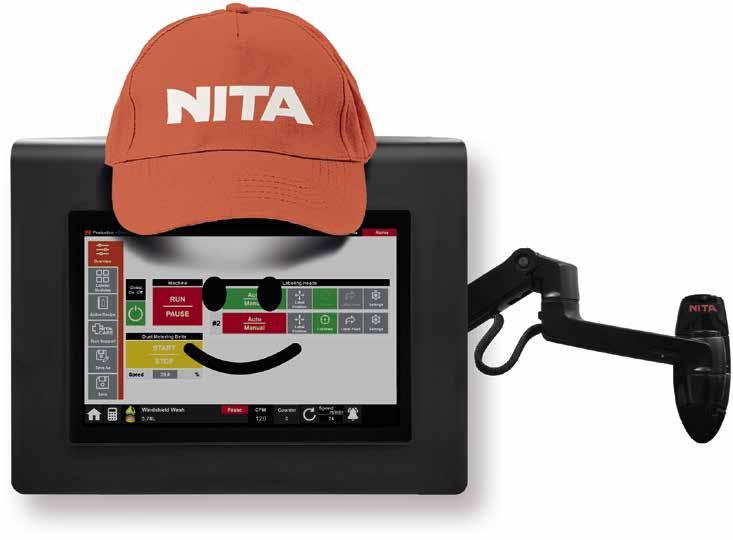
SOMETIMES “LESS IS MORE” IS JUST LESS.















Monobloc machine counts, fills and caps
Marchesini Group USA (Booth W-17005) marks its 30th anniversary with the Compact 24 monobloc machine, which counts tablets, capsules or pills, fills and caps bottles in a sin gle unit. A magnet-based transport system allows independent handling of each bottle. SD
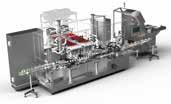
Need project advice?
Industry veterans at the “Ask the Experts” Station in the At tendee Solutions Center (Booth N-4552, LU-7000) stand ready to answer packaging and processing questions. Attendees can stop by for guidance to narrow their search for suppliers and navigate the show. SD

Vertical conveying benefits warehouses
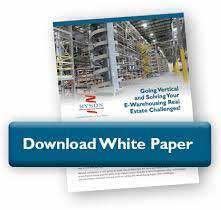
Vertical Conveying in the Growing Warehousing Market white paper, published by Ryson Inter national (Booth N-5945), describes how warehousing and or der fulfillment can benefit by taking advantage of vertical space with spiral conveyors. Download the paper at www.ryson.com/ ryson-spotlights/Ryson-warehousing.pdf. SD
Scales integrate with baggers
Combination scales from Yamato (Booth S-3783) seamlessly integrate with bagging equipment elsewhere on the show floor, including Matrix Packaging Machinery (Booth N-5334), Syntegon Packaging Technology (Booth S-3514) and Ma mata Enterprises (Booth S-2536). SD
Spiral offers notouch handling
AccuVeyor AVh line from AmbaFlex (Booth N-4941) combines notouch handling with first-in/first-out movement, a small footprint and one-belt configuration. An S-shaped belt transfer connects the up and down moving spiral segments on both sides. A high-capacity design integrates two towers to double the standard capacity. SD
Ronchi marks 25th
Ronchi America (Booth N-6228), subsidiary of Italy-based Ronchi Mario, was founded in 1997. Now located just outside Atlanta, GA, the company builds fillers and supports the U.S. and Canadian markets with sales and after-sales activities, in cluding the installation of machines, onsite support and train ing and spare parts inventory. SD
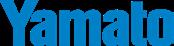
W&H presents sustainable products
Options include recycle-ready and recycled-content structures.
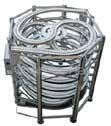
Windmoeller & Hoelscher (Booth LU7919), specialist for machinery in the flexible packaging market, is presenting developments in three areas: efficient production, Circular Economy and digitization.

FILMS FOR A CIRCULAR ECONOMY
W&H is highlighting new flexible packaging ma terials ready for the Circular Economy: Six examples are designed to be recyclable; four options contain high percentages of recycled content. All films have been extruded and printed on W&H equipment and tested on W&H sack-making lines and with con verting partners to confirm runnability.
Recycle-ready products include:
• Pet Food Bags: Options include one blown film with a coextruded barrier layer of eth ylene vinyl alcohol (EVOH) and one made with a functional barrier coating during the printing process. Printing can be gravure or flexographic.
• Coffee Pouch: A stretched machine-direc tion-oriented polyethylene (PE) film with an EVOH barrier layer combined with PE sealing film. With a total amount of only 2% EVOH, this material exceeds the current recy cling regulations, while at the same time pro viding the barrier properties for oxygen and water vapor required for this type of product.
Recycled-content films include:
• 50% PCR Collation Shrink: All-new col lation shrink film with 50% post-consumer recycled (PCR) material offers the same shrink values and mechanical properties as conventional, non-PCR recipes.
• PE Valve Sack: All-new film recipe with 30% post-industrial material displays mechanical properties similar to virgin resin structures.
PRODUCTIVITY AND DIGITIZATION
The new EASY2 Change assistance system, an autopilot for changeover, supports the operator at each step, saving time, waste and resources. De signed for use on VAREX blown film lines, the sys tem cuts product change time by more than 50% and eliminates the potential for errors. This is especially important for difficult products, for example, those containing recycled materials, which can be variable in quality. The system also monitors 200 parameters and provides a dashboard that tells the operator set tings are correct or need adjustment. “It’s like having 10 sets of eyes,” says Javeed Buch, senior vice presi dent, Windmoeller & Hoelscher.
Another new product, RUBY Gain software, col lects machine data and can provide optimized settings for first-time or repeat products. This prevents operator error, production of out-of-tolerance product and waste. For more info, visit www.whcorp.com. SD

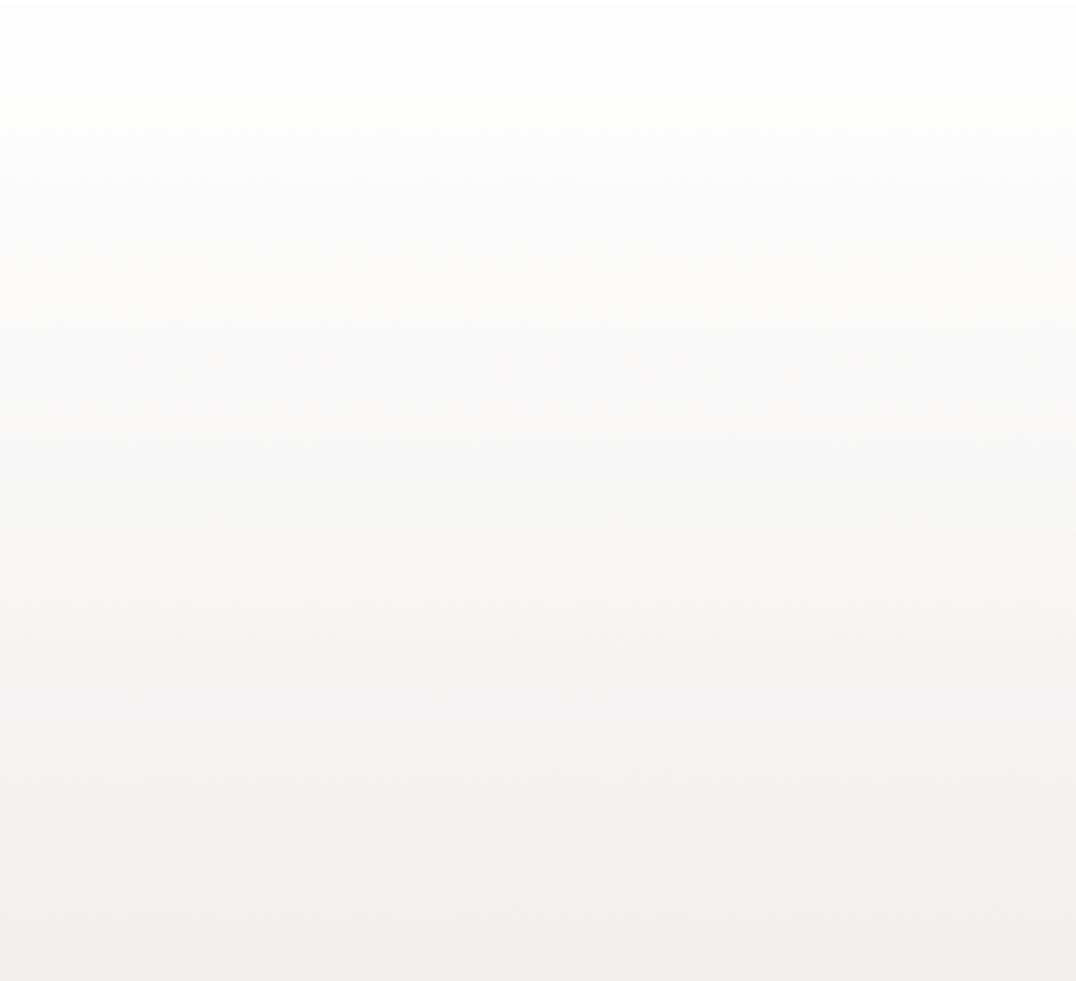
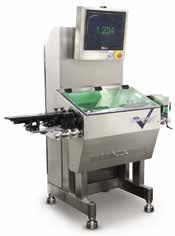
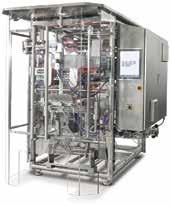
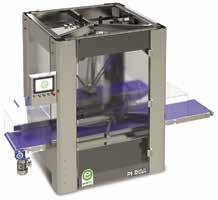
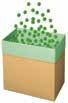

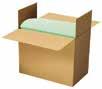
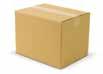


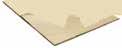
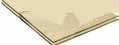

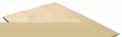
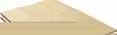
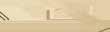
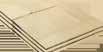
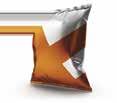

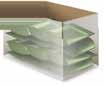

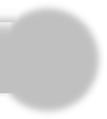
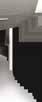





















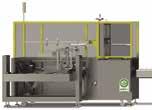
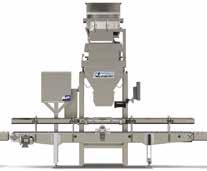
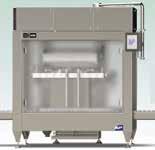
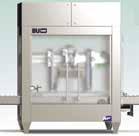

groninger expands
To address expanding de mand, groninger (Booth W-18001) has added a new storage and logistics center, including a fully automated small parts and high-bay warehouse at its headquarters in Crailsheim, Germany. The new facilities represent an investment of more than €20 million, the largest single investment in the more than 40-year history of the company. The expansion at the Crailsheim site continues in fiscal 2022 with preparatory work for a new assembly hall. SD
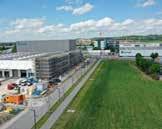
All-Fill sponsors robotics team Team plans to compete in local, regional competitions.
All-Fill (Booth S-1706) sponsors the Robot ics Team at Malvern Preparatory School, a boys’ school in Malvern, PA, with funding to cover travel expenses to competitions and source parts and components they need for their robots.
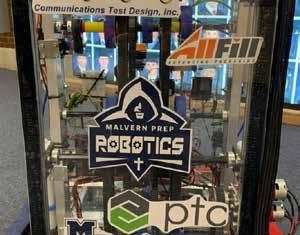
Sustainability revives interest in paper bags
Windmoeller & Hoelscher (W&H) (Booth LU-7919) devel oped the first cone bag machine in 1898. Now, with sustain ability concerns reviving interest in renewable paper packaging, Garant, a member of W&H Group, has developed the compact, servo-controlled Rotadia edition of this traditional machine. Carefully designed perforation yields precisely formed and powder-dense cone bags. Options include an inline printer. SD
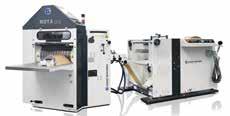
Pressure check
Force Sensor from Teledyne TapTone (Booth S-4126) detects leaks and low pressure in containers dosed with liquid nitrogen, carbonated beverage containers and aerosol containers. Parallel belts transport the container at speeds up to 2.67 m/sec. (525 ft./min.). As containers move past, a sensor measures the ten sion on the sidewall. The system can check pressures up to 11 bar or 160 psi. SD
Renewable films recycle
Renewable, monomaterial films advance efforts to establish a Circular Economy, reduce carbon footprint and maximize re cyclability while delivering functional features. The films, un der development by ITP, parent company of ITP USA (Booth W-21027), offer gloss, transparency and shrink properties for
The Robotics Club at Malvern Prep engages stu dents who want to develop higher skills in designing and building a robot to take to competitions such as the FIRST (For Inspiration and Recognition of Science and Technology) Robotics Competition in hopes of qualifying for the Regional Championship. Members of the club dedicate time after hours and on Saturdays to design and build a robot to compete.
Dr. Kevin Quinn, team mentor, notes the club is “one of the best educational opportunities that we provide at the school, and it simply wouldn’t exist and wouldn’t be as accessible without support and sponsorship.”
Cade Heppelmann (Class of 2024) oversees fi nance/sponsorship of Malvern’s Robotics Team. In a conversation with All-Fill President/CEO Ryan Edginton, Heppelmann mentioned that the team is growing significantly and focused on raising funds to
pay expenses to compete in its first district event in more than a decade.
So, All-Fill decided to become a sponsor. Edgin ton concludes, “It is really encouraging to see young minds developing an affinity for robotics. This group of young students are the future engineers and pro grammers that All-Fill will seek in the near future.”
For more info, visit www.all-fill.com. SD
Linear slides eliminate extra sensors
AZ Series linear slides from Oriental Motor USA (Booth N-4605) reduce heat generated by the motor and boast abso lute-type positioning via an Absolute Sensor. The sensor oper ates without battery backup or external sensors. SD
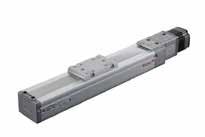
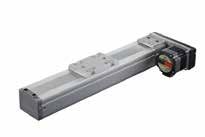
PACK EXPO International 2022
Publisher
PMMI Media Group
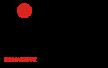
Editorial Director

Hallie Forcinio
Associate Editors
Kari Moosmann and Barbara Rook
Production Manager
Mary Thorne
Art Director
Debi Friedmann
IT/Production Support Manny Dominguez
Photographers
Miles Boone, George Burns and Martina Magnusson Advertising Sales Management
Dave Newcorn President, PMMI Media Group Wendy Sawtell, Vice President, Sales, PMMI Media Group
rapping












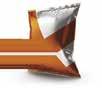

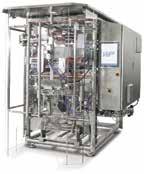

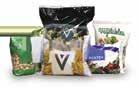
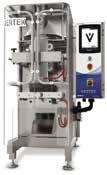


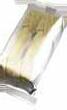


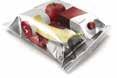


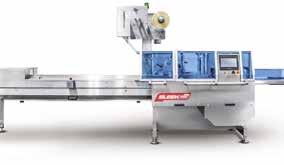




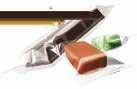
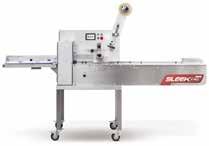


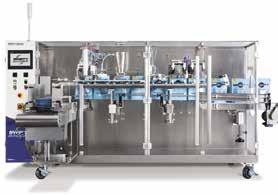















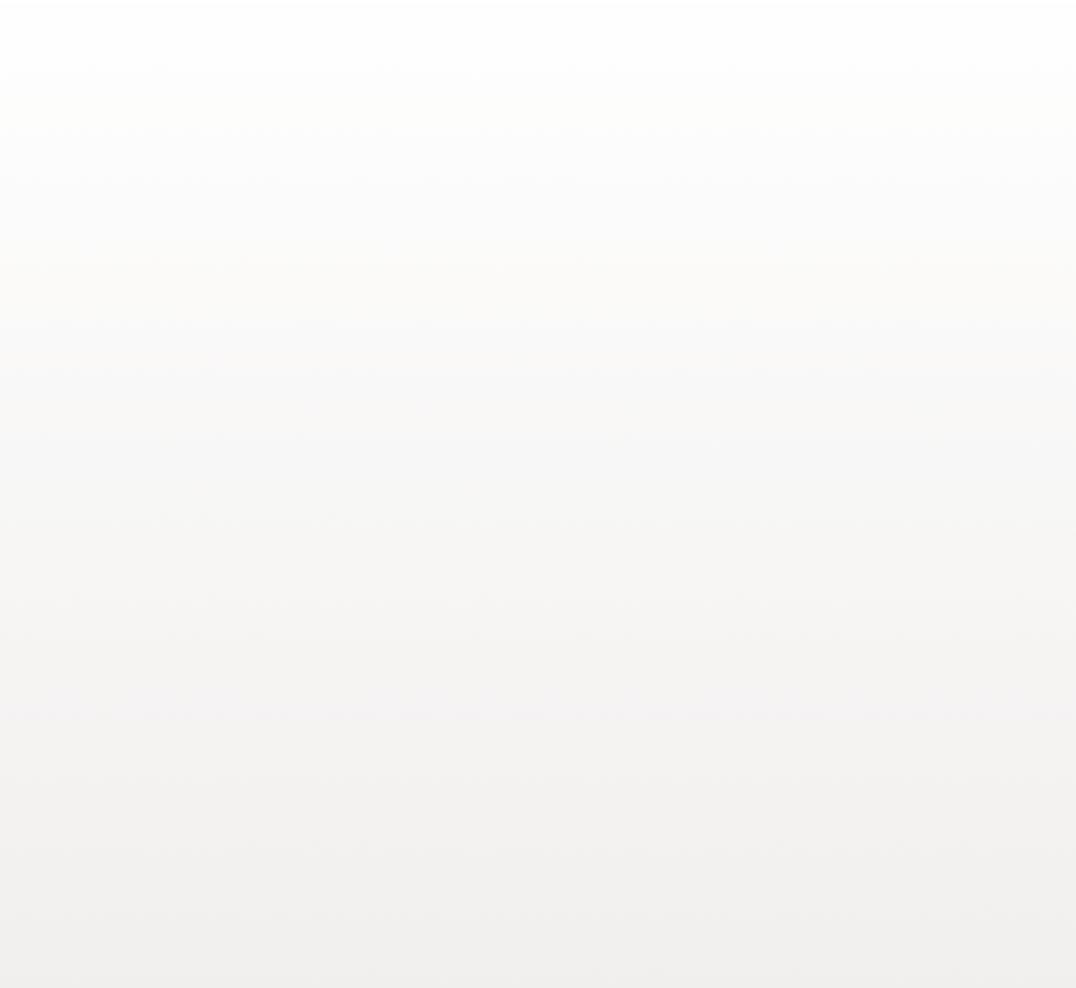
Sunday – Tuesday: 11:00 am – 3:00 pm Happy hour: 3:00 pm – 5:00 pm Wednesday: 11:00 am – 3:00 pm
Automation takes center stage Report indicates labor shortages drive push toward automation.
Labor shortages are driving consumer packaged goods (CPG) companies to adopt automated solutions, according to The Future of Automation in Packaging and Processing report, released yesterday at PACK EXPO International.
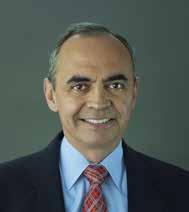
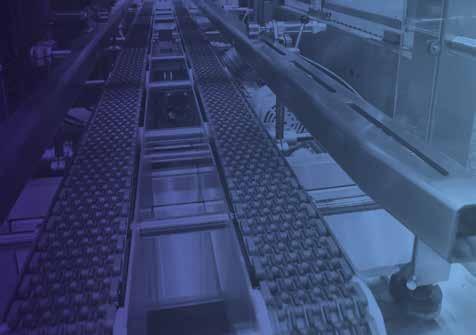
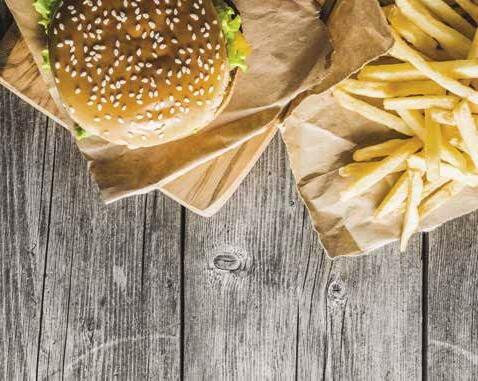
The report, produced by show organizer PMMI, The Association for Packag ing and Processing Technologies (Booth N-4550), highlights how CPG com panies are looking to enhance and optimize their production, storage and distri bution processes using automated solutions including automated guided vehicles, industrial robots, collaborative robots and mobile robots, with some of these tech nologies being supported by artificial intelligence (AI) and advanced vision tools.
According to the report, eCommerce is fuel ing the automation trend, moving companies to ward more responsive modes of distribution such as Direct-to-Customer, disrupting traditionally highly manual warehousing formats, and in some cases eliminating the need for warehousing.
LOGISTICS PAVILION
With this boom in eCommerce, coupled with the challenges arising from widespread sup ply chain issues, the Logistics Pavilion (North Building) is particularly relevant. Attendees can find targeted solutions related to the supply chain, including warehousing, fulfillment, distribution logistics services and transportation providers.
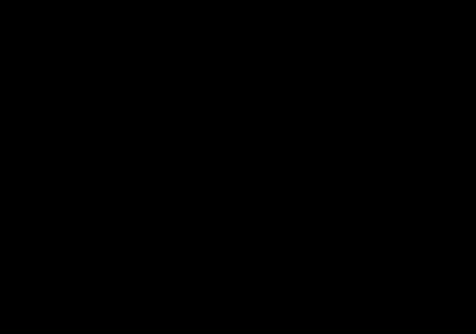
WORKFORCE FOR THE FUTURE
Additionally, 60% of companies report that labor shortages are extremely impactful on their packaging and processing operations, pushing CPG compa nies toward automation, and increasing the importance of developing a skilled workforce. With more than 1,500 high school and college students expected at PACK EXPO International, upskilling the future workforce is front and center at the show. PACK EXPO International offers many activities aimed at getting students excited about careers in packaging and processing and connecting them with professional mentors in the industry.
Further supporting these findings, in a separate PMMI survey of PACK EXPO International attendees asking for thoughts on what they were planning to look for at the show, it is clear automation is top of mind. Once again, the potential for automation and robotics to reduce the reliance on personnel and accommodate lower-skilled workers was cited, as was the possibility of reducing the amount of monotonous and less rewarding work that must be done manually. One partici pant said they would be “looking at technologies to drive out drudgery type work,” while another planned to seek “automation for some of our simpler tasks so we can move the employees we have around to more complex jobs.”
Training and productivity aids and new user interface technologies were of keen interest to some, while several participants highlighted the potential of PACK EXPO International to provide a forum for sharing ideas and innova tions, learning from experts and networking, with one CPG attendee stating their aim is “gathering insights from counterparts.”
It seems clear that automation technologies play an increasing role in the fu ture of the packaging and processing industry and are a key focus of companies looking to cut costs, improve productivity and reduce dependency on personnel as skills and retention problems continue to affect them.
For more info, visit www.PMMI.org. SD
Spiral Conveyors & Bucket Elevators Ryson Vertical Conveying Solutions
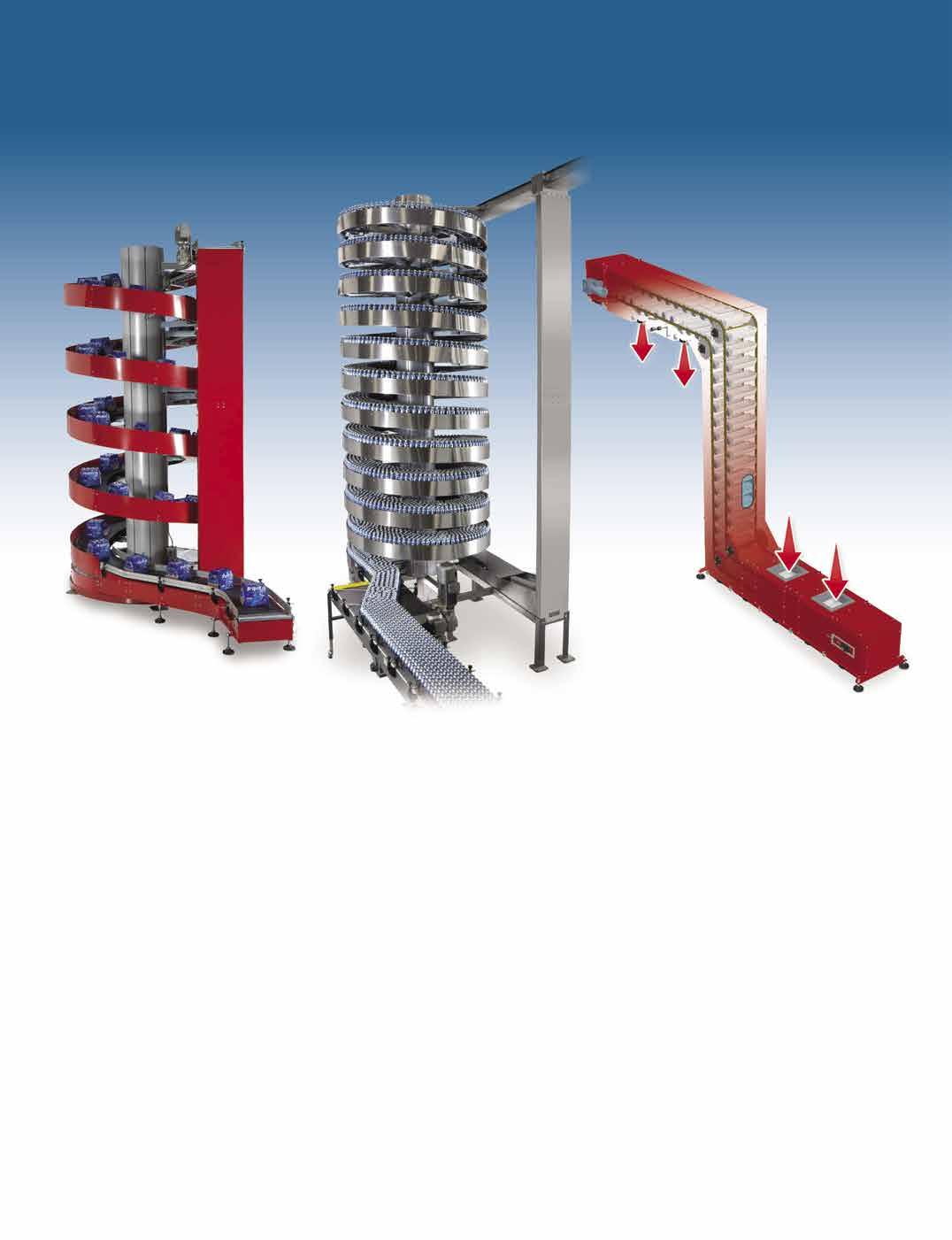
Ryson Spiral Conveyors need less floor space than conventional conveyors and are faster and more reliable than any elevator or lift.
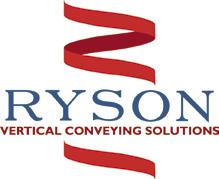
Unit Load Spirals convey cases, totes and packaged goods smoothly on our slat style belts and come in 9 standard slat widths ranging from 6” to 30”. Available in powder coated carbon steel, stainless steel, wet environment and freezer versions.
Mass Flow Spirals handle full and empty bottles, cans and jars in mass up to 2000 units per minute. Available in 4 different slat widths ranging from 6” to 20”.
Narrow Trak Spirals are super compact and designed to handle your smaller loads. Our 6” and 9” wide nesting slats can end-transfer small cartons and packages or side-transfer small bottles and containers in a single file or in mass at speeds in excess of 200 FPM.
Ryson’s Bucket Elevators combine vertical and horizontal transportation of bulk materials in one integral unit.
Ryson Bucket Elevators are designed for gentle handling and well-suited to transport a broad range of bulk products. Our signature feature is that they are completely enclosed with overlapping pivoting buckets, that prevent spillage and helps mitigate foreign debris.
Their modular design enables us to customize with ease. They can be configured with multiple inlets or outlets that can be controlled individually. The design makes them easy to install and modify. Available in three standard bucket sizes, yielding capacities up to 300, 700 or 1,800 cubic feet per hour. They can also be delivered in powder-coated carbon-steel, stainless-steel or wet environment versions.
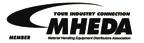


www.ryson.com

Wednesday, Oct.
THE PARTI IPANT
from across the country.
THE M N
GOAL
for filling milk remain in use to this day. The founder of Serac (Booth S-2847), Graffin received more than 100 patents, as well as multiple awards, including the Nobel Prize for Entrepreneurs by French Academy.
During her decades-long career, Oesterle led the charge at Energizer on sev eral package development and project management innovations; she deployed those same skills during her time at Just Born Quality Confections. Currently, she brings more than 40 years of packaging and project management experience as chair of the Board of Directors at the Institute of Packaging Professionals (IoPP) (Booth N-4523)
Pienaar has become one of the most prolific and recognizable packaging educa tors in the world. President of the World Packaging Organisation (WPO) (Booth N-4902), his passion is educating the world about packaging, the science of pack aging, and the need to properly recycle. In addition to running a packaging consul tancy in Australia, Pienaar lectures on food innovation and packaging at universities around the world.
Rhodehamel earns his spot in the 47th class in the Hall of Fame as a true food-safety renaissance man. Between his work protecting public health in the U.S. Food and Drug Administration, innovating package design at Sealed Air (Booth S-2939) and passing the torch to the next generation of food scientists at Clemson University (Booth W-20001, W-20035), Rhodehamel has been a leader throughout his career.
“We look forward to wel coming these four profession als to the Hall of Fame,” adds Jim Pittas, president and CEO, PMMI, The Association for Packaging and Processing Technologies (Booth N-4550), organizer of the Hall of Fame. “It’s with gratitude and appreci ation that we acknowledge their contributions, which have en riched the packaging and pro cessing industry worldwide.”
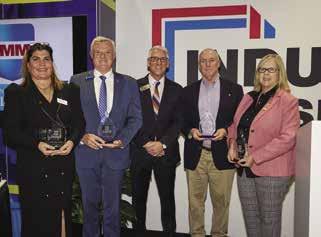
The Hall of Fame welcomes new members every other year. Inductees are chosen by the Hall of Fame Commission, which selects class members from a pool of nominees. Commission member Joe Angel, new executive vice president, Industry Outreach at PMMI and former president, PMMI Media Group (N-4550, W-20052) and publisher, Packaging World, shares his thoughts: “This year’s inductees are an ex ceptional group. Their knowledge, vision and lifelong dedication are an inspiration to our entire industry.”
The 14-member Packaging & Processing Hall of Fame Commission consists of Angel plus:
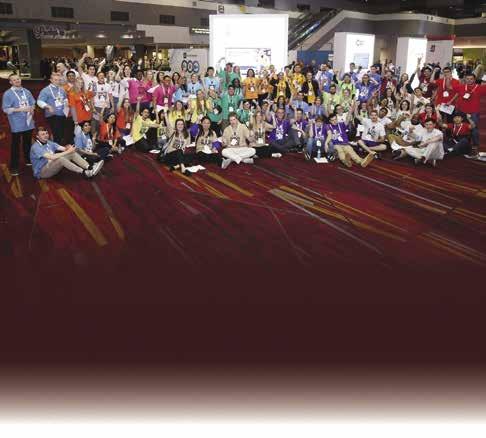
• Kim Carswell, consultant, formerly with Target
• Kay Cooksey, Ph.D., professor and Cryovac Endowed Chair, Department of Food, Nutrition and Packaging Sciences, Clemson University
• James Downham, president & CEO, PAC Global
• Suzanne Fisher, CPP, Fisher Packaging
• Mary Gregg, president, Springboard Packaging Solutions
• Glen Long, senior vice president, PMMI
• James Perry, director, Package Innovation + Sustainability, Abbott Nutrition
• Bill Rice, principal, Packaging Technology, SC Johnson & Son
• Michael Richmond, Ph.D., PTIS, Global Management & Packaging Consultants
• Mark Shaye, vice president of Engineering, Ken’s Foods
• Thomas L. Schneider, CPP, past chairman, IoPP, past president, WPO
• David S. Smith, Ph.D., R&D executive, consultant, David S. Smith Associates
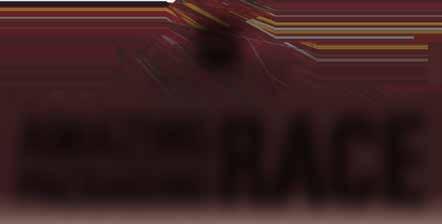
• Nancy Wilson, CEO, Morrison Container Handling Solutions (Booth N-4906)
For more info, visit www.PACKEXPOinternational.com. SD






































































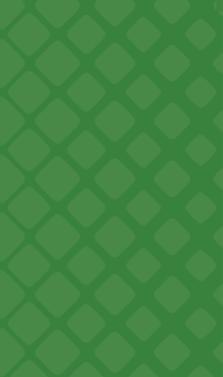



















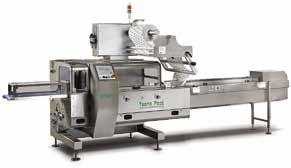
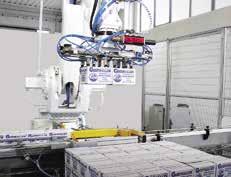

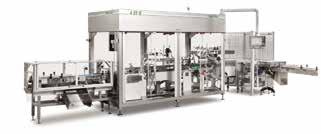
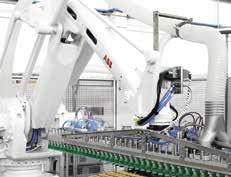
Sealstrip wins People’s Choice Award
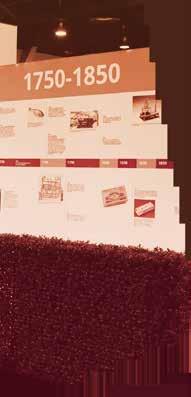
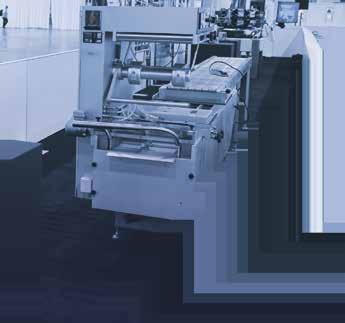
IoPP recognizes winners in 2022 AmeriStar competition.
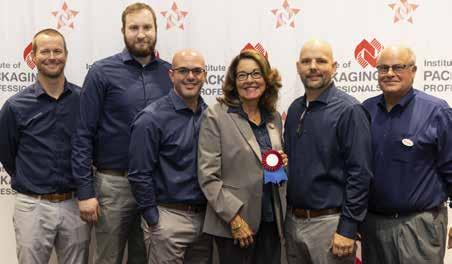
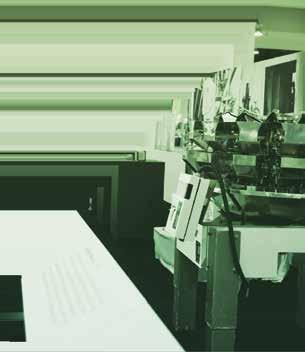
Sealstrip (Booth N-5224) won the People’s Choice Award in the annual AmeriStar competition, sponsored by the Institute of Packaging Pro fessionals (IoPP) (Booth N-4523, W-20052). The winner of a vote by attendees at PACK EXPO International, the Sealstrip’s Peel&Seal® reseal tape addresses complaints of stale products with freezer burn. The Peel&Seal ma terial was reduced by 25% without compromising seal effectiveness, consumer experience or production efficiency, providing end-of-life waste reduction. Ret rofitting Peel&Seal applicators maximizes production efficiency.
The 2022 AmeriStar awards presentation recognized professional and student winners. A roster of 21 judges from various packaging industry segments eval uated this year’s entries, considering product protection, packaging innovation and performance, economics, marketing and environmental impact. Additional evaluations for 2022 coincided with the introduction of Design Excellence and Sustainability categories.
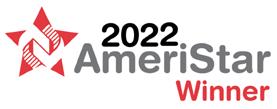
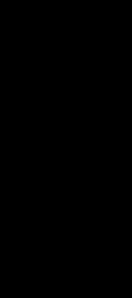
Judges reviewed entries across 19 categories for professional and student awards and the program’s prestigious Best in Show. Winning packages may be viewed in the Showcase of Packaging Innovations® (Booth W-20052), spon sored by WestRock (Booth S-2130) (see story, p. 26). Some of the award winners are described below.
BEST IN SHOW
Blue Buffalo Tastefuls Spoonless Singles from General Mills are designed to provide a perfectly portioned, split cup offering with a built-in chopper. The re cyclable polypropylene (PP) cup easily breaks in half, allowing for flexible feed ing options and reducing the need to refrigerate leftovers. According to General Mills, significant work went into the formula to ensure the matrix would hold together with enough firmness, and the packaging was fine-tuned for better evacuation. The judges also recognized this package for Design Excellence.
DESIGN EXCELLENCE
Hard Hat Packaging from Klein Tools is a package system consisting of two product-conforming, interlocking thermoforms paired with a die-cut corrugat ed carton. Compared to a non-nesting design, this nesting package fits 207% more product inside a shipping container.
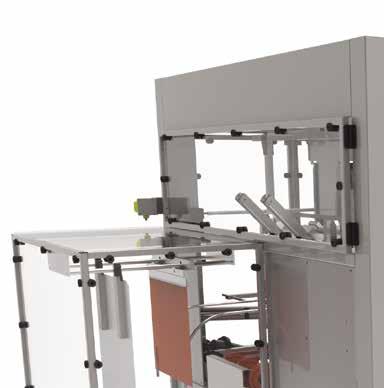
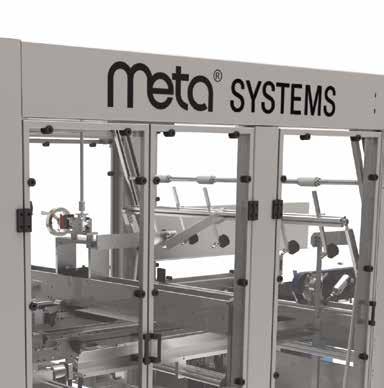
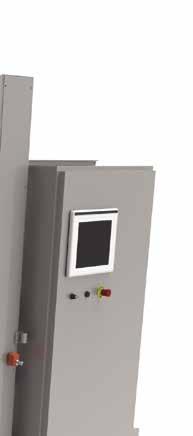
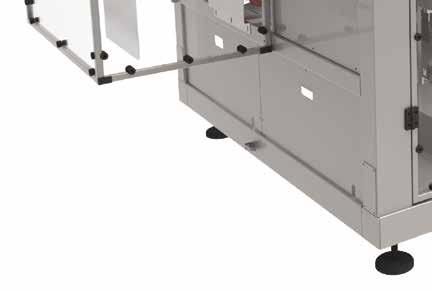

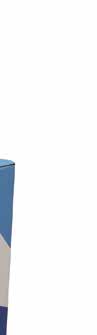
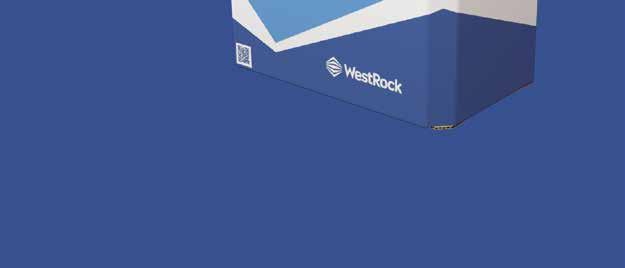
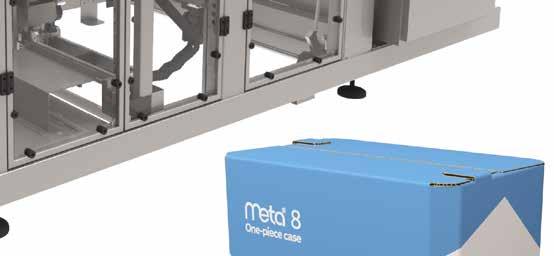

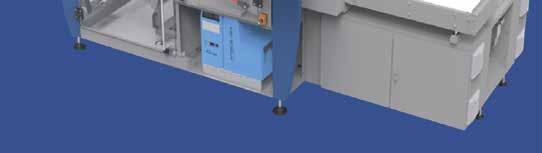

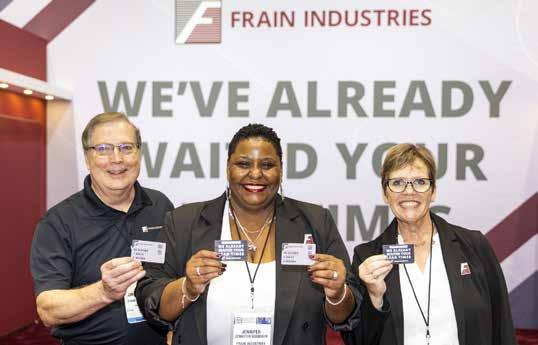












































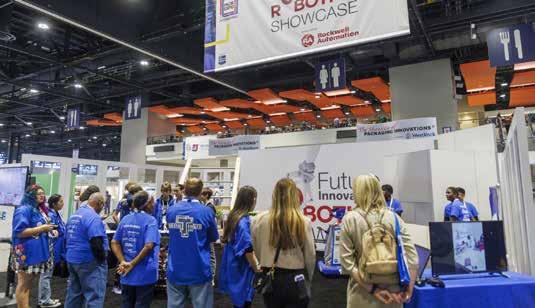
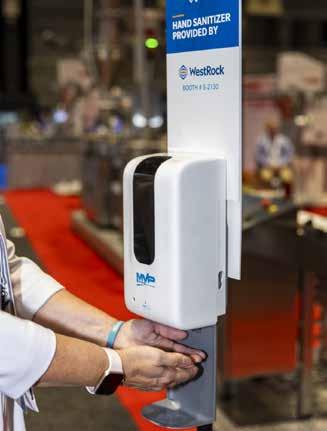
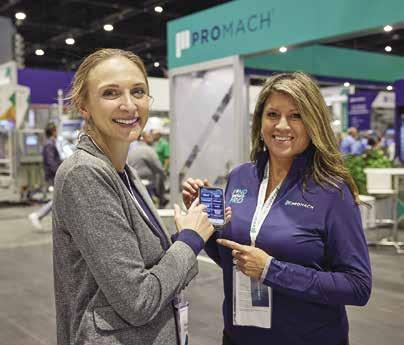

OxyStar barrier material utilizes a multilayer PET with an oxygen scavenging agent. PET has a naturally low oxygen transmission rate (OTR) and this construction slows down the flow of oxygen molecules through the package from the outside. Once the scavenger agent finds an oxygen molecule, it attaches to it and binds the oxygen within the sidewall of the package to keep your product fresh and lasting longer.
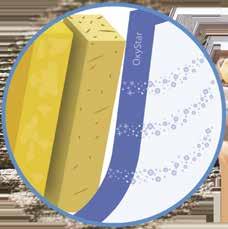
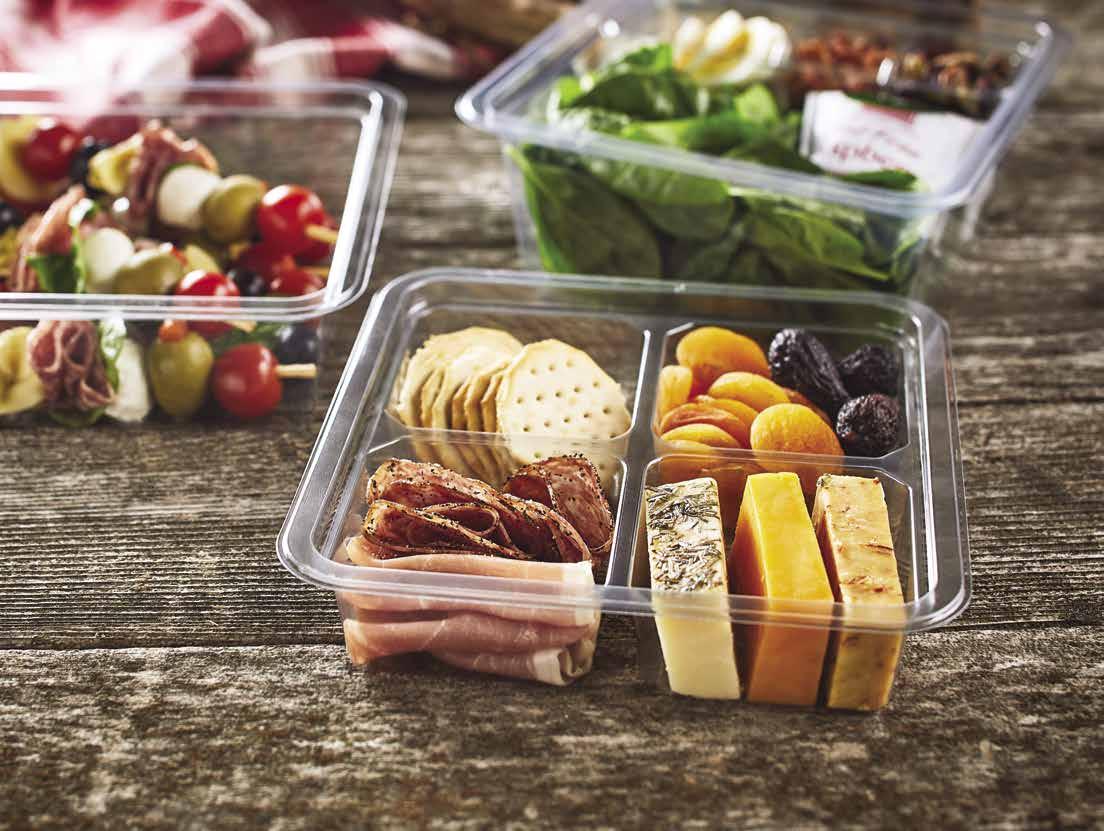

DRUG AND PHARMACEUTICAL


Vital Proteins’ Collagen Peptides Powder container from Selig Group (Booth N-4961) has an interrupted thread closure that allows for material re duction and less thread distortion when the closure is stripped from the mold. A tamper band and heat-induction liner provide two levels of protection.
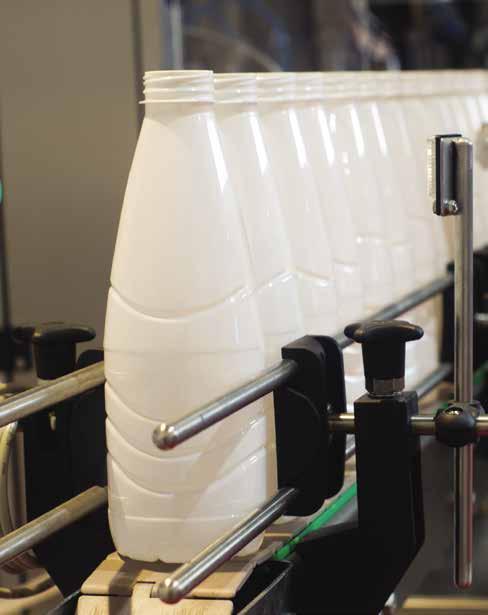
FOOD (REFRIGERATED)
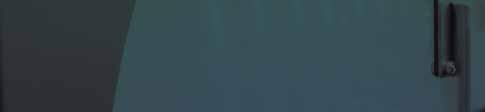

PaperSeal® tray from Graphic Packaging International (Booth S-1730) for New Seasons fresh pasta uses an inventive design to create a one-piece, contin uous-sealing flange around the edge of the tray.
FOOD (SHELF STABLE)
Four packages won in this category: two from McCormick, an Adjustable Grind with a removable grinder head for recycling, and a package renovation for McCor mick food coloring; and two from TricorBraun, a renewable, compostable zipper bag for Brandywine Coffee Roasters, and a compartmented container for Ferrara Candy Nerds Twist & Mix.
INDUSTRIAL/COMMERCIAL
In the Industrial/Commercial group, winners included the RP System® from Mitsubishi Gas Chemical, which provides 24/7 protection from moisture and oxygen damage during shipping and long-term storage; the TerpLoc® automat ed curing and long-term storage cannabis pouch from Kinzie Advanced Poly mers, dba Grove Bags; and the Master Builders Solutions Tray Pals from Placon (Booth W-24033)


SUSTAINABLE PACKAGING
AmSky™ thermoform blister system from Amcor Flexibles Healthcare North America (Booth S-3705, S-3814, W-16031) takes a unique approach to recycle-ready blister packaging by using high-density polyethylene in a propri etary formulation to create both the formed blister and lidding.
Colgate Keep Toothbrush from Colgate-Palmolive has a handle that is the first of its kind, made with aluminum instead of plastic—eliminating 80% of the plastic waste from a typical toothbrush. It also has a 100% paper-based package.




Recyclable Mono-Material Pump – Future from Aptar Beauty + Home and Dermalogica features a plastic spring that makes it possible to recycle the bottle and pump as one unit.
SimpliCycle valve from AptarGroup (Booth N-4740) is a 100%-recyclable valve for food, beverage and foodservice products. It is comprised of proprietary low-density material that floats, allowing easy separation during recycling.
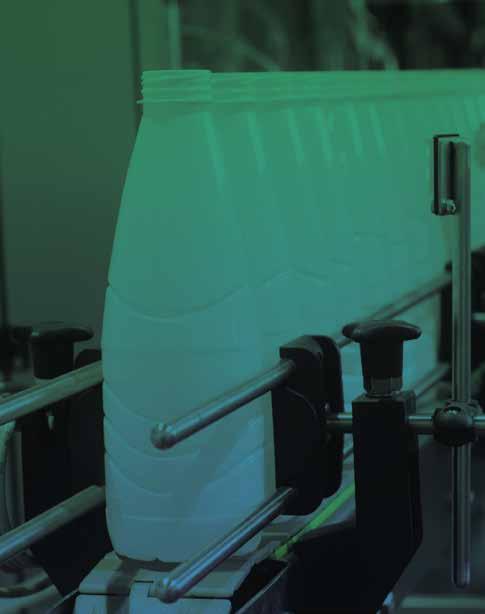
The Slide liner-free polypropylene closure from AptarGroup does not require a foil liner. Eliminating the liner improves the consumer opening convenience, eliminates nonrecyclable waste and reduces greenhouse gas emissions by 16%.

STUDENT WINNERS
AstroKnot from Ryerson University is a pretzel bites package that can hold a product and two flavored dips in the same container.
Ensemble - Australian Oat Packaging from Ryerson University was created to solve the many obstacles of traditional bagged oat packaging. Compared to plastic, paperboard is a more cost-effective material, and the carton design al lows for easy stacking.
Frankencell Battery Packaging from Ryerson University dispenses and dis poses batteries from a compact cube shape, designed to address critical issues such as inaccessibility when opening and retrieving batteries from the package and a lack of storage once consumers open the product.

Omnichannel Corrugate Board Cactus Package from Ryerson University is designed to minimize transportation damage of fragile, live products like plants. A door-like closure helps contain and protect the product.

OUCH! First Aid Kit from the University of Cincinnati opens like a book to organize the contents and provide more structure and protection.
Rinse from the University of Cincinnati is a collection of all-gender, sustain able personal care products geared toward bridging the gap between products specified for a single gender, which will reduce the amount of both manufactur ing and purchasing needs and result in a more inclusive and sustainable system.


See images of all the 2022 AmeriStar Award winners at IoPP’s website.












For more info, visit www.iopp.org. SD

Wherever you are and whatever your industry, there’s a PACK EXPO event to provide solutions you need today and the inspiration for tomorrow.
June 13-15, 2023 Guadalajara, Mex.
Sept. 11-13, 2023 Las Vegas, USA
March 18-20, 2024 Philadelphia, USA
June 11-14, 2024 Mexico City, Mex.
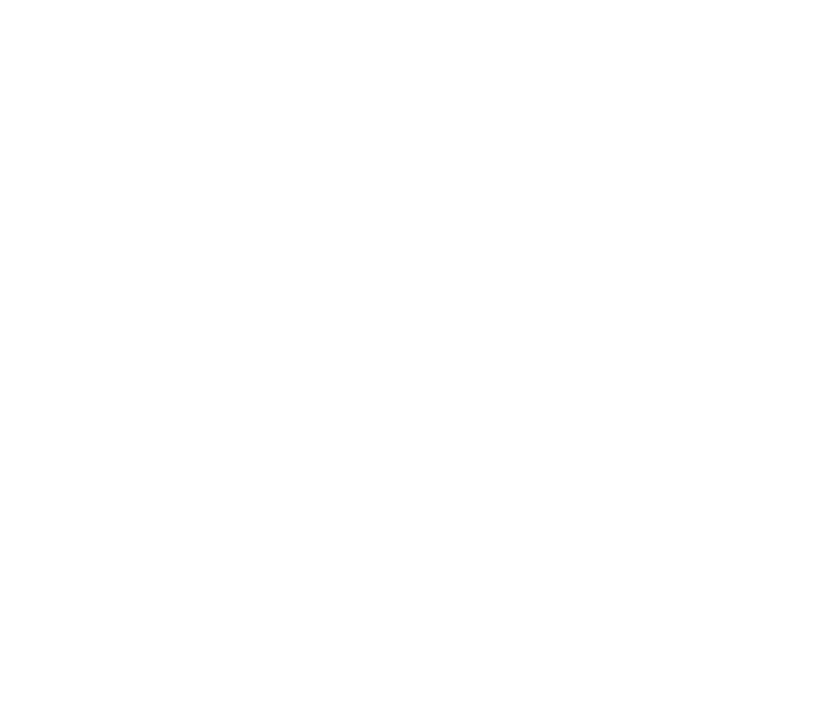
Nov. 3-6, 2024 Chicago, USA
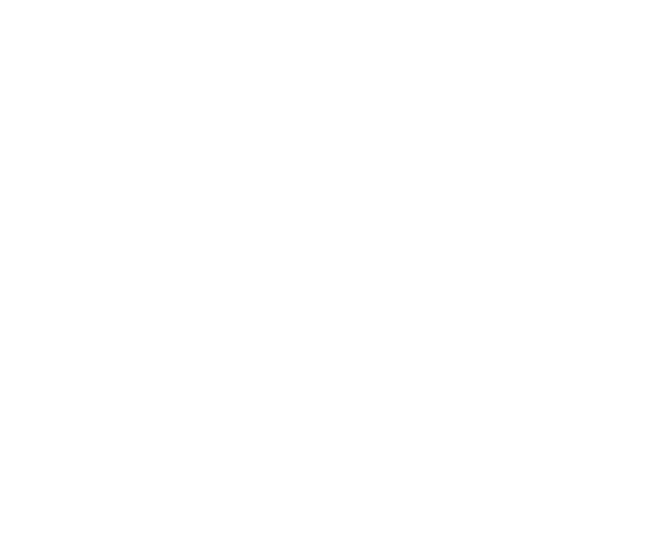
PACK to the Future arrives
Historical exhibit serves as foundation for advancements.
The interactive PACK to the Future Exhib it (Booth W-20001) celebrates the role of packaging and processing throughout histo ry and the impact it is poised to have on the future. The exhibit follows the evolution of modern pack aging and processing over 250 years to the present and shifts to explore key trends shaping the future in daily live sessions on the PACK to the Future Stage (Booth W-20025)
Launched in 2021 at PACK EXPO Las Vegas, the curated, interactive PACK to the Future exhibit tells the story of packaging and people who saw a better way, solved challenges and provided the foun dation for today’s—and tomorrow’s—innovations.
The exhibit includes:
• 30 historial packaging machines and replicas dating back to the 1800s
• Timeline walls displaying 250 years of history
• An area dedicated to women in packaging and processing
• An interactive display of past, present and future sustainability efforts, including a Corrugated Car of the Future Virtual Reality (VR) Experience. Sponsored by The Paper and Packaging Board, the experience allows attendees to sit in a replica of a futuristic car and use a VR headset to learn about sus tainable packaging and the industry’s Box to Nature program, an initiative to educate consumers about the importance of recycling corrugated materials and boxes
• An interactive audio tour revealing interesting facts and historical details
• Fun quizzes that test attendees’ knowledge of the industry.
Each day on the PACK to the Future Stage, in
TUESDAY, OCTOBER 25, 2022
dustry experts provide 30-minute presentations on cutting-edge advancements in sustainability, circu larity, net-zero goals, returnables and manufacturing trends.
The session schedule is outlined below. PACK EXPO International offers many other free educa tional opportunities, including the long-running In novation Stage (Booth N-4560, N-4580, N-4585) plus the new Processing Innovation Stage (Booth LU-7130) (see schedule, p. 28), The Forum at PACK EXPO (Booth N-4543) (see schedule, p. 40) the new Industry Speaks (Booth N-4565) (see schedule p. 24). The Reusable Packaging Learning Center (Booth LU-6737) also will present educational sessions.
Updated schedules may be found on the PACK EXPO International App or the show website.
For more info, visit www.PACKEXPOinternational.com. SD
LIVING CARBONSMART
9:30-10:00 AM
To achieve climate goals, we need a systems-level view and solutions that can draw on multiple sources of waste carbon. Advances in technology and a global momentum to avert the deepening climate crisis have brought us to the cusp of a new industrial era. Recy cled CO₂ will be the feedstock, and clean electricity the energy source, to produce the climate-safe materi als and fuels that are today made from oil. Hear about examples of carbon recycling and the opportunities to establish a new carbon economy and create materials for consumer goods, from packaging to textiles.
Dr. Sean Simpson
Chief Science Officer & Founder LanzaTechPACKAGING – FRIEND OR FOE. CHALLENGES AND DEMANDS OF A GLOBAL FOOTPRINT
10:30-11:00 AM
There are many parameters to be taken into consider ation when choosing the right packaging for the job, including product needs and legislative, investment and consumer considerations. This session will touch on some of the elements that make this such a topical, challenging and interesting field, including where fo cus could be spent in the future.
Graeme Smith
Global Sustainable Packaging Dir Mars Petcare
BEYOND PEAK PLASTIC: ENGINEERING AN AFFORDABLE HIGH-PERFORMANCE FUTURE
11:30-12:00 PM
According to McKinsey, more than 75% of millenni-
als say they think about sustainability when making purchases. The packaging industry has long accepted ubiquitous plastic use; however, changing consumer preferences no longer make unsustainable materials a viable option for long-term business strat egy. Zume CEO Alex Garden discusses how plastic alternatives like molded fiber can be an economically viable solution to help brands and packaging manu facturers reach their sustainability commitments.
Alex Garden Chairman & CEO Zume
THE RETURNITY PACKAGE DEAL: LESS WASTE, LOWER COSTS
12:30-1:00 PM
With 100 billion global parcel deliveries a year, and over 200 billion by 2026, the environmental impact is undeniable. U.S. packaging alone can pave a milewide cardboard road from New York City to Los An geles and back—three times over. Returnity replaces single-use shipping and delivery packaging by design ing, manufacturing and implementing cost-effective reusable packaging and circular logistics systems for companies like Walmart, Estée Lauder, New Bal ance and Rent the Runway. Its packaging is now used for more than 2 million shipments and deliveries a month. Returnity identifies high-return rate oppor tunities for clients and is especially passionate about educating businesses and consumers on the value of the package return rate. Rates below 75% are actually worse for the planet. The average Returnity bag or box can be used for 20 customer shipment cycles (40 total) with a 95.5% return rate.
Mike Newman CEO
Returnity
INNOVATING PACKAGE PORTFOLIOS THROUGH A POSTPANDEMIC DEMAND
1:30-2:00 PM
Learn about innovating package portfolios through a post-pandemic demand via holistic packaging design and engineering approach.
Kory Nook VP, Packaging R&I DANONE
PET PACKAGING TRENDS AND COMPARATIVE LCA RESULTS
2:30-3:00 PM
Polyethylene terephthalate (PET) is the perfect mate rial for numerous applications and achieves legislative and brand commitments. This session on all things PET covers trends, debunks myths and describes a new comparative life cycle analysis (LCA) that eval uates environmental impacts for several widely used types and sizes of containers.
Laura Stewart Dir, Operations National Assn for PET Container Resources LOOP’S ROLE IN THE FUTURE OF REUSABLE PACKAGING
3:30-4:00 PM
Learn about the evolution of the Loop platform and how it works with brands, retailers and quick-serve restaurants to build a network of reusability. Discuss approaches to reusable packaging including design, material type, labeling and dispensers/closures; Loop as a “pre-fill” platform; and its growth since mid-2019.
Tony Rossi
EVP, Business Development TerraCycle

WEDNESDAY, OCTOBER 26, 2022
DEVELOPING PRODUCTS AND SOLUTIONS TO SUPPORT A CIRCULAR ECONOMY
9:30-10:00 AM
Urgent focus is being directed at climate change, greener transportation, fresh food, personal care, clean water, Circular Economy, plastic waste and renewable feedstocks. This presentation addresses these challeng es, relays them through the UN Sustainability Devel opment Goals and outlines a portfolio of solutions to support downstream customers as they set their sus tainability and Circular Economy goals.
Matthew Marks Leader, Circular Economy, Americas SABIC
HEADWINDS, TAILWINDS AND REALISTIC EXPECTATIONS FOR PET RECYCLING IN 2025
10:30-11:00 AM
PET recycling is at a crossroads as the industry drives toward 2025 goals. Brands, consumers, regulatory agencies and NGOs support systemic improvements, while known limitations restrain success. We will consider what is reasonably possible for increased PET recycling, what changes are needed, and what the rPET industry might look like in 2025.
Steve Lyons Dir of Strategic Environmental Analysis SBAcci Consulting Group
THE EVOLUTION OF PHARMACEUTICAL PACKAGING
11:30-12:00 PM
An examination of the future of pharmaceutical packaging as it becomes more sustainable and meets the needs for greater convenience, self-administered drugs, reduced hospital stays and serving patients at home. We also will look at how past and present innovations focused on meeting patient and product needs offer a path for the future.
Ron Yakubison Exec Dir, Global Technology Packaging Merck
IMPROVING RESIDENTIAL RECYCLING WITH BOX TO NATURE!
12:30-1:00 PM
The paper industry, partnering with the Paper and Packaging Board, is introducing a residential recy cling shipping box messaging initiative called Box to Nature. The partnership is working with customers and large brands to educate consumers about the box with easy instructions on recycling right, every time. Learn how to become part of this initiative.
Mary Anne Hansan President Paper and Packaging Board SD
Packaging’s invisible technology Hot-melt adhesive application evolves to meet industry needs.
The packaging industry’s main challenge is striking a balance between sustainability and client demands, as well as between circulari ty and product protection. All of the strategies of the sector’s stakeholders are pointing in this direction, and Meler, parent company of Meler USA (Booth N-5376), a specialist in hot-melt applications, has spent years addressing this challenge as well.
Adhesive and sealant application is one of those “invisible” technologies behind many of our society’s innovations, and we are surrounded by examples of them on a daily basis: corrugated boxes, bottle label ling, food packaging, etc. Hot-melt application sys tems are designed to be integrated into all types of machinery—they fit the production line like a glove. Production processes can require one or various glu ing stations in order to manufacture the end product.
The Show Daily talked to Javier Suescun, Focke Meler’s product manager for the packaging sector, to learn more about the keys to this close collaboration.
SD: Gluing systems are an essential part of the packaging manufacturing process. What real im pact do they have on the production process?
Suescun: Packaging production lines are very complex. They’re the result of hours and hours of en gineering work, and each element plays an essential role. However, we could say that those of us suppli ers working in this industry need to adapt to new demands that are becoming commonplace, like the automation of processes, increased productivity and reducing line stoppages.
SD: How has Meler needed to change to meet this production demand?
Suescun: Since the beginning, Meler’s main ob jective has been to find solutions for its clients’ needs. This joint effort is what has allowed us, little by lit tle, to roll out a large portfolio of products for many sectors, not just the packaging sector. If our client needed the adhesive to be dispensed with more pre cision, for example, we developed a new applicator, thus, increasing the production line’s profitability.
SD: There’s nothing like taking an inside look to get it right, is there?
Suescun: It’s not a matter of luck. Meler’s knowhow is what helps us detect the problems beforehand and resolve them. Thanks to this relationship, we also can offer the most innovative solutions for improving hot-melt installations. Our clients are experts at man ufacturing their own products. Their objective is to achieve a quality end product and, to do so, Meler has to guarantee that our systems are efficient. This ensures that everything runs smoothly and works as it should.
SD: And what are the most important points in an adhesive application installation?
Suescun: Proper maintenance is obviously a ba sic, but, in reality, everything comes down to the
design phase: Gluing systems might be found at various points of the production line and each appli cation has its own technology. Everything depends on the end product in question and it’s important to understand the client from the beginning.
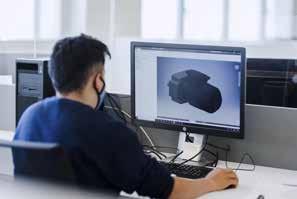
Once the scope of the project has been outlined, Meler designs a complete solution consisting of the key elements for adhesive application: a melter, heat ed hoses, a shot programmer and an applicator. Its installation and integration is another critical phase. We configure our systems together with the client, but our equipment is user-friendly, and workers are able to make changes by themselves. That’s another one of the industry’s demands.
SD: What trends are you detecting?
Suescun: Production methods are currently being reassessed, due to issues such as sustainability and companies that are reducing their carbon footprint. Manufacturers are exploring new technologies and looking for strategies to achieve profitability, such as using new adhesives, updating equipment or having more control of consumption.
At Meler we’re committed to developing tools that meet these needs, by providing equipment with instant monitoring of adhesive consumption, greater energy efficiency and 100% electric applicators.
SD: To wrap up, as a specialist in the packaging sector, what “proven tips” could you give us for us ing gluing systems on the packaging line?
Suescun: We always remind everyone that pre ventative maintenance is the best way to avoid ad hesive carbonization and problems with the system that result from this.
As manufacturers of machinery, we have an ob ligation to help workers carry out this task. Meler equipment automates this process with notifications to change the filters, for example, or by activating “Stand-by” mode when the system detects that it isn’t being used.
In my opinion, automating the parameters relat ed to installation guarantees the production process will operate smoothly in the packaging sector or any other industry.
For more info, visit www.melerusa.com. SD
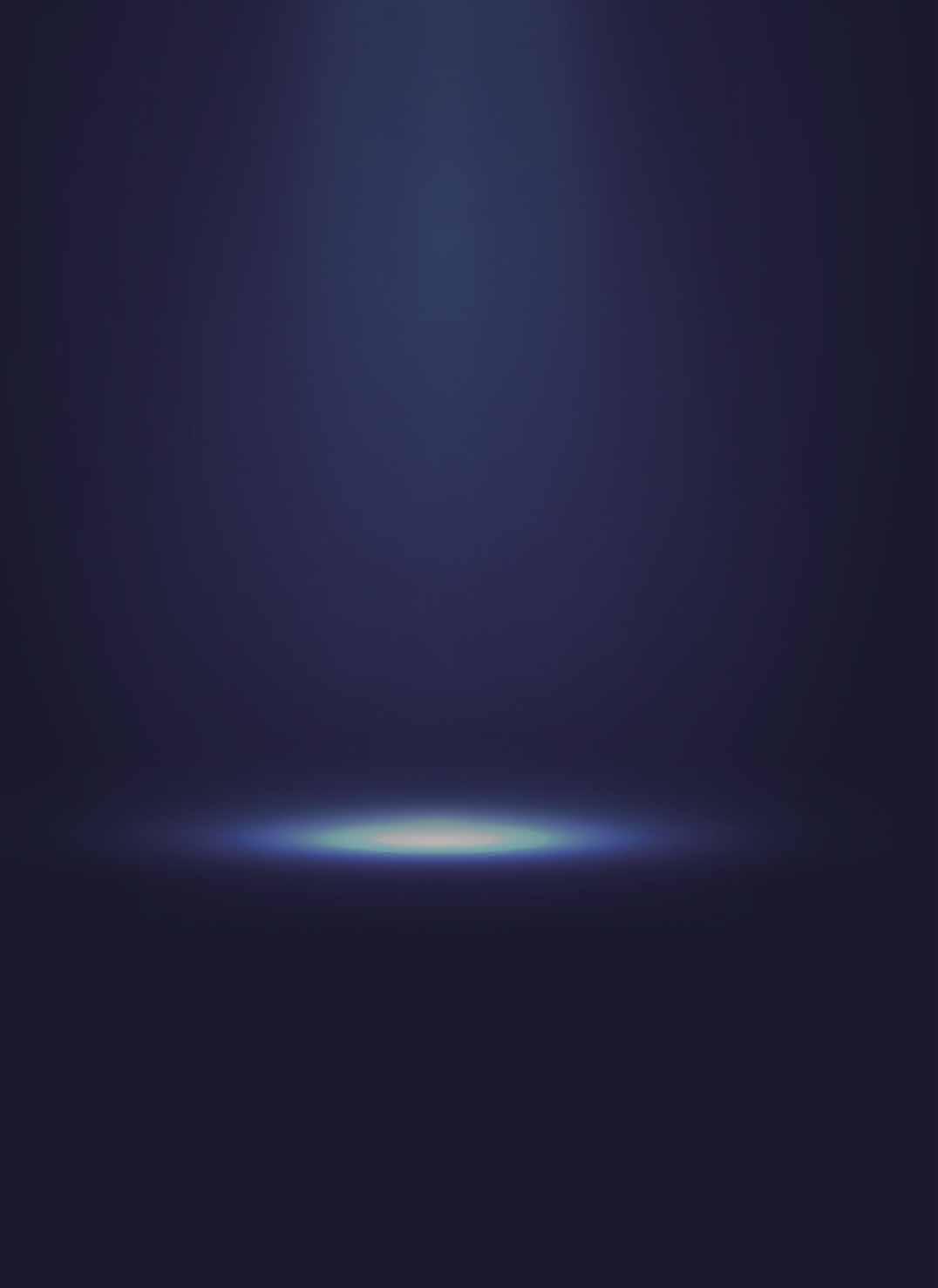

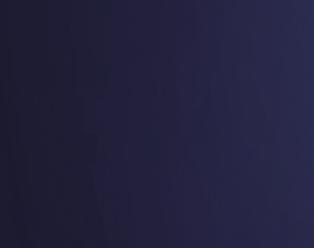
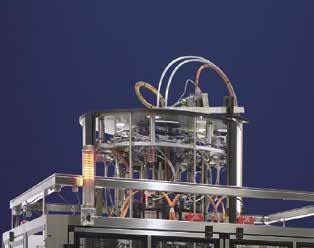
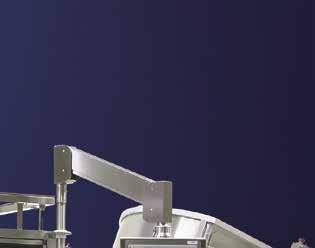
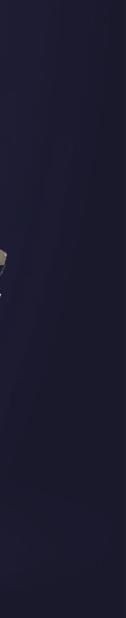

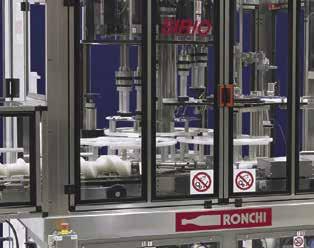
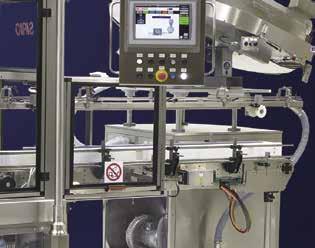
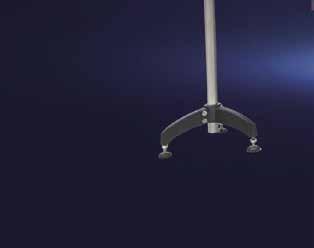
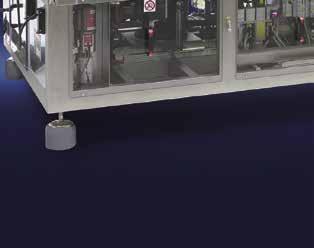
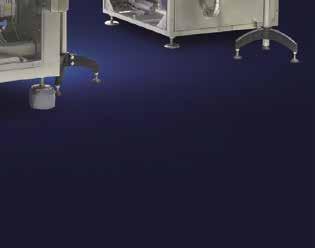
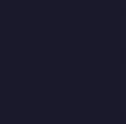
Association Partner Program grows
Learn, network at Industry Meets and Industry Speaks.
The PACK EXPO Association Partner Pro gram connects attendees to leading associ ations from all segments of packaging and processing. This year’s program, the largest in PACK EXPO history, offers an unparalleled breadth and depth of industry knowledge to attendees.
The Association Partner Pavilion, in the North Hall, provides a central location for attendees to ac cess these resources. Participants in the 2022 PACK EXPO International Association Partner Program are listed at the bottom of this page.
New this year is the Association Partner Plus des ignation and Industry Meets schedule of ancillary events and meetings hosted by groups listed in the far right column. Events include a hygienic equip ment design seminar, design for recycling training, a fluid power forum and Fundamentals of Medical Device Packaging course. Check the PACK EXPO International App or show website for the latest schedule and pre-registration requirements.
“We are thrilled with the positive response to the Association Partner Program and newly launched Industry Meets Program at PACK EXPO Inter national,” says Laura Thompson, vice president of Trade Shows at show producer PMMI, The Associ ation for Packaging and Processing Technologies (Booth N-4550). “PACK EXPO International is making a triumphant return to Chicago after four years away, and it is only possible with the strong support of these prestigious associations.”
Another new feature, the Industry Speaks Stage (Booth N-4565), offers educational sessions led by experts from PACK EXPO Partner Associations on
hot-button topics and trends across multiple indus try verticals. A schedule may be found on p. 24, the PACK EXPO International App or show website.
In addition to the Association Partner Program, PMMI has partnered with industry associations from
PAVILION HOSTS
CCPIT - China Council for the Promotion of International Trade
CFPMA - China Food and Packaging Machinery Industry Association
Confederation of the Danish Industry (LU-7560)
Fundacion Argentina para la Promocion de Inversiones y Comercio Internacional (Booth LU-8755)
INP – Brazilian Plastic Institute/Think Plastic Brazil (Booth W-25011)
Italian Trade Agency (Booth LU-8541)
Korean Packaging Machinery Association
Mouvement Des Enterprises De France International (Booth N-5564)
Switzerland Global Enterprise
UCIMA – Italian Packaging Machinery Manufacturers Association (Booth N-6002)
VDMA – Food Processing and Packaging Machinery Association
across the globe to host pavilions on the show floor. International Pavilion Organizer Partners include the 11 organizations listed under Pavilion Hosts. For more info, visit www.PACKEXPOinternational.com. SD
INDUSTRY MEETS
3-A Sanitary Standards (Booth N-5901)
Active & Intelligent Packaging Industry Association (Booth N-5802)
Cold Pressure Council (Booth N-4525)
Contract Packaging Association (Booth N-4518)
Flexible Packaging Association (Booth N-4533)
Institute of Packaging Professionals (Booth N-4523)
International Bottled Water Association
MHI Automation Industry Groups (Booth N-5701)
National Fluid Power Association
OMAC – The Organization for Machine Automation and Control (Booth N-5100)
The Association of Plastic Recyclers (Booth N-5902)
INTERNATIONAL PARTNER PROGRAM
AIM (Booth N-5000)
AIMCAL - The Association of International Metallizers, Coaters and Laminators (Booth N-4527)
Asociacion Mexicana de Envase y Embalaje
ASD Turkish Packaging Manufacturers Association (Booth N-4900)
Australian Institute of Packaging
ABRE – Brazilian Packaging Association (Booth N-6003)
CANAINCA
Chicagoland Food & Beverage Network (N-4511)
Composite Can and Tube Institute (Booth N-4512)
Digital Twin Consortium (Booth N-6102)
Foil & Specialty Effects Association (Booth N-4536)
F4SS – Foundation for Supply Solutions
Flexographic Technical Association (Booth N-4510)
In-Mold Decorating Association (Booth N-4534)
IAE - Instituto Argentino del Envase (Booth N-6101)
International Society of Beverage Technologists (Booth N-5702)
ISTA - International Safe Transit Association (Booth N-4537)
Midwest Food Products Association
National Confectioner’s Association (Candy Bar Lounge, Booth S-2583)
OPC Foundation (Booth N-5001)
PLCopen (Booth N-5002)
Reusable Packaging Association (Booth LU-6737)
SNAC International (Booth N-5801)
The Anuga FoodTec Family
The Australian Packaging and Processing Machinery Association
The Paper and Packaging Board
The Tube Council of North America (Booth W-20052)
UCIMA – Italian Packaging Machinery Manufacturers Association (Booth N-6002)
U.S. Department of Commerce (Booth N-4901)
World Packaging Organisation (Booth N-4902)
BLISTER MACHINE
From the leader in blister packaging across the pharmaceutical, nutraceutical, animal health, medical device and consumer goods industries comes a new blister packaging solution. The new TF1 is a cost-effective, pharma-grade solution that requires minimal training and maintenance.
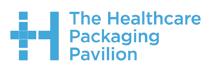

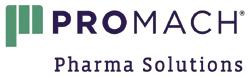

ERSATILE

PACKAGING
Quality and performance you expect from

Simple to operate and maintain
Perfect for entry-level
smaller
Excellent for solid dose, liquid filled and consumer product blister
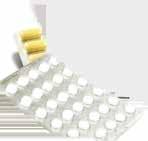
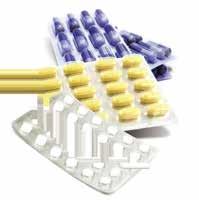
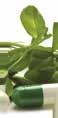


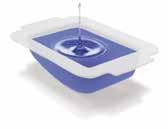
TUESDAY, OCTOBER 25, 2022
10:30-11:00 AM
DIGITAL TWIN CONSORTIUM APPLICATIONS OF DIGITAL TWIN FOR THE PACKAGING SECTOR
The Digital Twin Consortium presents its activities for the development of Digital Twin technologies and specific pilot projects in the packaging sector. Learn how the use of Digital Twin technologies, both real time and offline, improve the efficiency and effective ness of the traditional process, in terms of costs, qual ity, time, OEE and improving ESG factors (environ mental, social and governance).
Dan Isaacs
Chief Technology Officer Giuseppe Padula Regional Branch Organizer Digital Twin Consortium
11:30-12:00 PM
INTERNATIONAL SOCIETY OF BEVERAGE TECHNOLOGISTS
WHAT IS THE PROCESS TO CREATE A NEW PRODUCT
New Product Innovation (NPI) is creating, produc ing, selling and delivering a new product to the con sumer. The definition of an NPI process is to define, establish and provide standardized processes to ensure cross-functional alignment through a product’s devel opment life cycle, delivering on-time and on-budget. The NPI process completes three phases: ideation (con cept or creation), design (development) and execution (commercialization). Each phase will have a series of gates to complete before moving to the next phase. Learn the total NPI process and the roles of differ ent departmental functions, and where they enter the process. Understand where your function fits into the process and what is needed to ensure a success
ful product launch. A good NPI process is needed for projects large or small to ensure success.
Brian Stegman Exec Dir
International Society of Beverage Technologists
2:30-3:00 PM
AMERIPEN
PACKAGING POLICY FOR NOW AND THE FUTURE
We are standing at a critical precipice on packaging and environment policy proposals and implementa tion here in the United States. New laws on packag ing producer responsibility, labeling and recycled con tent mandates are coming at us fast and furious. Join AMERIPEN Executive Director Dan Felton for a lively discussion about how this will impact the entire packaging value chain now and in the future.
Dan Felton Exec Dir
AMERIPEN - American Institute for Packaging and the Environment
3:30-4:15 PM
CHICAGOLAND FOOD & BEVERAGE NETWORK
WHAT IS THE FOOD MANUFACTURING FACILITY OF THE FUTURE?
The last two years have transformed our lives and businesses. How has it changed what is needed in a food manufacturing facility? How are supply chain disruptions, labor challenges (including the Great Resignation), and evolving customer and consum er expectations changing how we manufacture food and beverage? How have food and beverage industry expectations changed? How will we adjust our man ufacturing processes, strategies, tactics and teams to best meet these evolving expectations? Join our panel
HMI/PLC withstands washdown
The programmable TX700FB series of hu man/machine interface (HMI)/program mable logic controller (PLC) combinations from Turck (Booth N-4923) offer IP69K front-side protection against high-pressure cleaning regimens required on food, beverage and pharmaceutical lines.
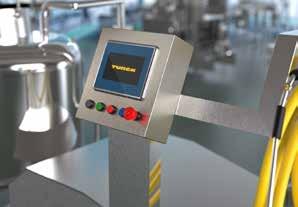
The FB devices comply with hygienic design re quirements (DIN EN1672-2, EHEDG/FDA 21 CFR 177.2006). The stainless-steel front has been designed with protection to IP69K so the devices are waterproof at high pressure up to 80 C.
The TX700 series opens the door to new appli cations by providing a flexible range of HMI de-
vices for visualization, as well as HMIs with Codesys PLCs and a Cloud connection. A gateway function for data exchange with PLCs and end devices works with multiple protocols (up to eight simultaneously).
Alarm and system visualization is easy, and overall system complexity is reduced because a single device functions as both the HMI interface and logic con troller. Available in 15- or 7-in. variants, the all-glass capacitive touch display with a polyester coating pro vides intuitive operation with gesture control similar to that used in Smartphones. Display brightness of 800 candela/sq. m enables use in direct sunlight.
For more info, visit www.turck.us. SD
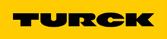
of experts to learn how they are adjusting their ap proaches and playbooks to deal with the new realities of business today and what they see as the implica tions for imagining and creating the Food Manufac turing Facility of the Future. Don’t miss this import ant discussion.
Alan Reed - Moderator Exec Dir
Chicagoland Food & Beverage Network
WEDNESDAY, OCTOBER 26, 2002
10:30-11:00 AM
CONTRACT PACKAGING ASSOCIATION
WHAT IS DRIVING THE INTEREST IN THE CONTRACT PACKAGING AND MANUFACTURING INDUSTRY?
Using data from our State of the Industry Report, member feedback and our RFQ platform, we will take a dive into the changing demands of this dynamically growing industry. Often a confusing and frustrating segment, these essential providers of capabilities and services are addressing the needs of emerging brands as well as legacy brands seeking to launch new food and CPG retail products. We will explore how Co Mans and CoPacks are adding value as consumer- and market-driven needs are moving the packaged goods supply chain. Learn how the newest and innovative products have become key opportunities for CoMans. Understand how brands are adapting to meet new challenges with strategic CoMan and CoPack part nerships and accelerate time to market.
Carl Melville President
Melville group on behalf of Contract Packaging Ron Puvak Exec Dir
Contract Packaging Association SD
Sullair celebrates 5th anniversary
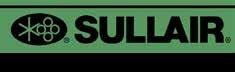
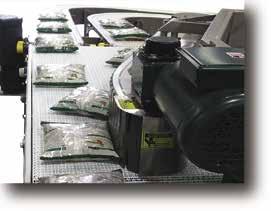
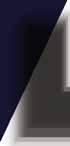



















































































Company welcomes executives from Hitachi headquarters.

Sullair (Booth S-3752), a leader in innovative compressed air technology since 1965, commemorated its fifth anniversary as part of Hitachi Group with a company picnic and tree planting.
Sullair, headquartered in Michigan City, IN, observed the anniversary on Au gust 8, 2022, with an all-employee event. In attendance were Hitachi executives from the company’s headquarters in Tokyo; Consul-General of Japan in Chica go Hiroshi Tajima; Michigan City Mayor Duane Parry; and Executive Direc tor Clarence Hulse of the Economic Development Center of Michigan City. During a brief presentation, Mayor Parry presented Sullair with a Proclamation declaring August 8 Sullair Appreciation Day in Michigan City.

Following the presentation, Sullair and Hitachi executives planted a cherry blossom tree to commemorate the joining of the two companies. Hitachi execu tives then presented Sullair with a Kabuto, or warrior’s helmet, to display in the lobby. The Kabuto symbolizes courage and good health in Japanese culture.
Due to the threat of severe weather, the celebration was capped by an indoor picnic where employees in green anniversary T-shirts and guests were treated to barbecue and sweets.
Hitachi acquired Sullair in July 2017 to complement its existing compressed air capabilities and gain a larger footprint in North and South America. Since the acquisition, Hitachi has invested more than $45 million in Sullair, mostly in the Michigan City facility. Investments include a large manufacturing process expansion that created more than two dozen full-time jobs and other localized investments that helped propel growth.
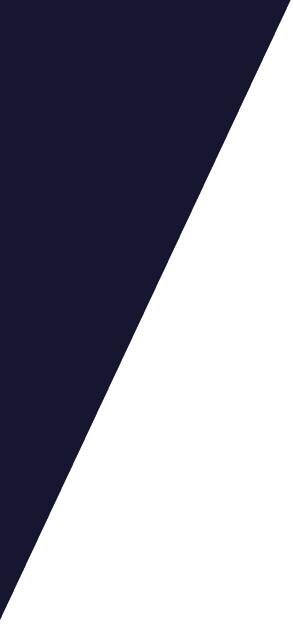







“Hitachi is a world-class, innovative and values-driven organization,” says John Randall, president and CEO, Sullair. He explains, “Joining a company of this caliber and capability has been extremely positive for Sullair, not only be cause of the direct investments Hitachi has made in our business, but the compa ny’s promotion of Social Innovation Business—a strategy that seeks to improve the lives of people in our community and around the world. Operating under this forward-looking cause makes now an exciting time to be at Sullair and an exciting time to be a Hitachi Group Company.”





“Since becoming a Hitachi Group Company we have realized a lot of oppor tunities,” adds Kyle Sanders, director IT Services. “Sullair has always been a great place to work, but with the backing of Hitachi we are growing and changing in new and exciting ways.”
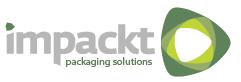
For more info, visit www.sullair.com. SD
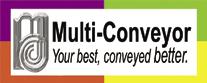
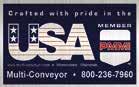


WestRock sponsors Showcase
Exhibit displays award-winning packages from around globe.
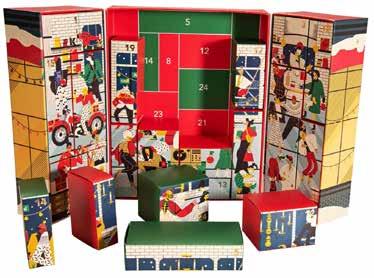
WestRock (Booth S-2130) presents win ning entries from worldwide packaging competitions as the exclusive sponsor of this year’s Showcase of Packaging Innovations® (Booth W-20052).
“At WestRock, we are focused on delivering bold innovation to solve our customers’ biggest challeng es,” says Margaret Herndon, the company’s chief marketing officer. “The Showcase displays the best the industry has to offer in packaging innovation, and we are excited to be part of a program that en gages customers and generates new thinking and new solutions.”
Show producer, PMMI, The Association for Packaging and Processing Technologies (Booth N-4550), is pleased to partner with WestRock on this initiative.
“The Showcase of Packaging Innovations has come to be a show floor favorite at PACK EXPO,” says Jim Pittas, president and CEO, PMMI. “We are thankful for companies like WestRock who seek to inspire the future of our industry and motivate package designers by showcasing packaging that is functional, innovative and sustainable.”
This year’s Showcase participants include 13 or ganizations from around the world. A sampling of the award winners on display is pictured here.
For more info, visit www.PACKEXPOinternational.com, www.westrock. com, www.abre.org.br, www.aimcal.org, www.dow.com, www.flexpack.org, www.fsea.com, www.imdassociation. com, www.packaging.com.ar, iopp.org, www.profood world.com, https://paperbox.org/, www.reusables.org, www.tube.org, www.worldpackaging.org. SD
The Best in Show package in IoPP’s AmeriStar competi tion, Blue Buffalo Tastefuls Spoonless Singles from General Mills and Product Ventures, provides a perfectly portioned split cup with a built-in chopper. The recyclable polypropyl ene split cup separates easily, reducing the need to store opened containers in the refrigerator.
PARTICIPANTS
ABRE - Brazilian Packaging Association (Booth N-6003)
AIMCAL - Association of International Metallizers, Coaters and Laminators (Booth N-4527)
Dow (Booth W-22017) Dow Packaging Innovation Awards
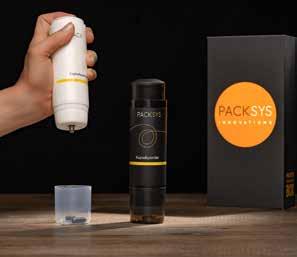
Flexible Packaging Association (Booth N-4533)

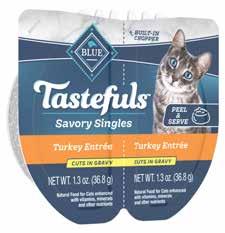
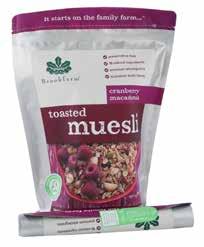
Foil & Specialty Effects Association (Booth N-4536)
In-Mold Decorating Association (Booth N-4534)
IAE - Instituto Argentino del Envase (Booth N-6101)
Institute of Packaging Professionals (IoPP) (Booth N-4523)
PMMI Media Group (Booth N-4550)
ProFood World’s 2021 Sustainability Excellence in Manufacturing Awards
Paperboard Packaging Council (Booth W-20052)
Reusable Packaging Association (Booth LU-6737)
Tube Council of North America (Booth W-20052)
World Packaging Organisation (WPO) (Booth N-4902)
Last year,
of the
O MO ASO O U D S O S O .
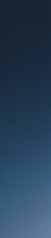

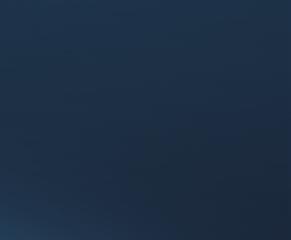
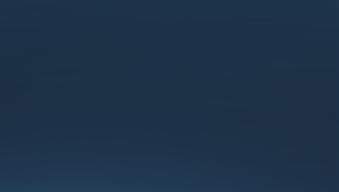
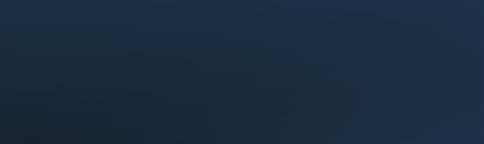
The lightline machines from Schubert can be delivered quickly and are extremely attractive in terms of price . With the preconfi gured machines, customers can adapt more fl exibly to market trends and signifi cantly shorten their time-to-market.
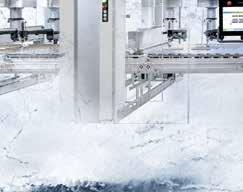
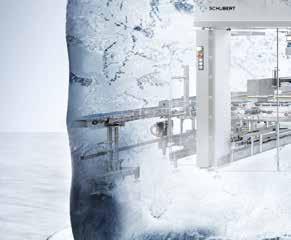
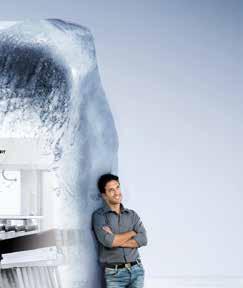

The consists of pick & place robots as well as one or more several tray inserters, and packs products into trays made of plastic or cardboard. It offers an affordable and highly flexible possibility to automate packaging processes with the most effi cient technology on the market while ensuring the highest availability and packaging quality.
The world’s leading FMCG and private label manufacturers rely on Schubert. www.schubert.group
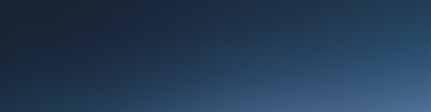
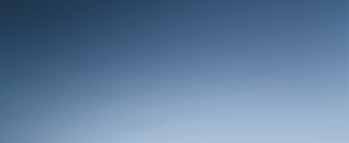
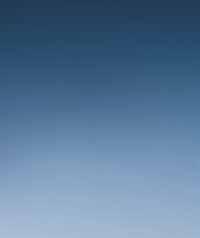
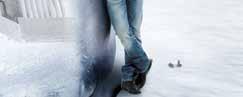
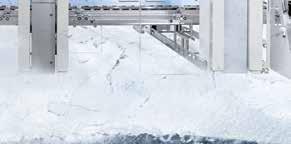


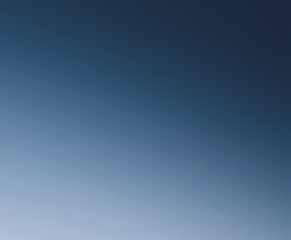

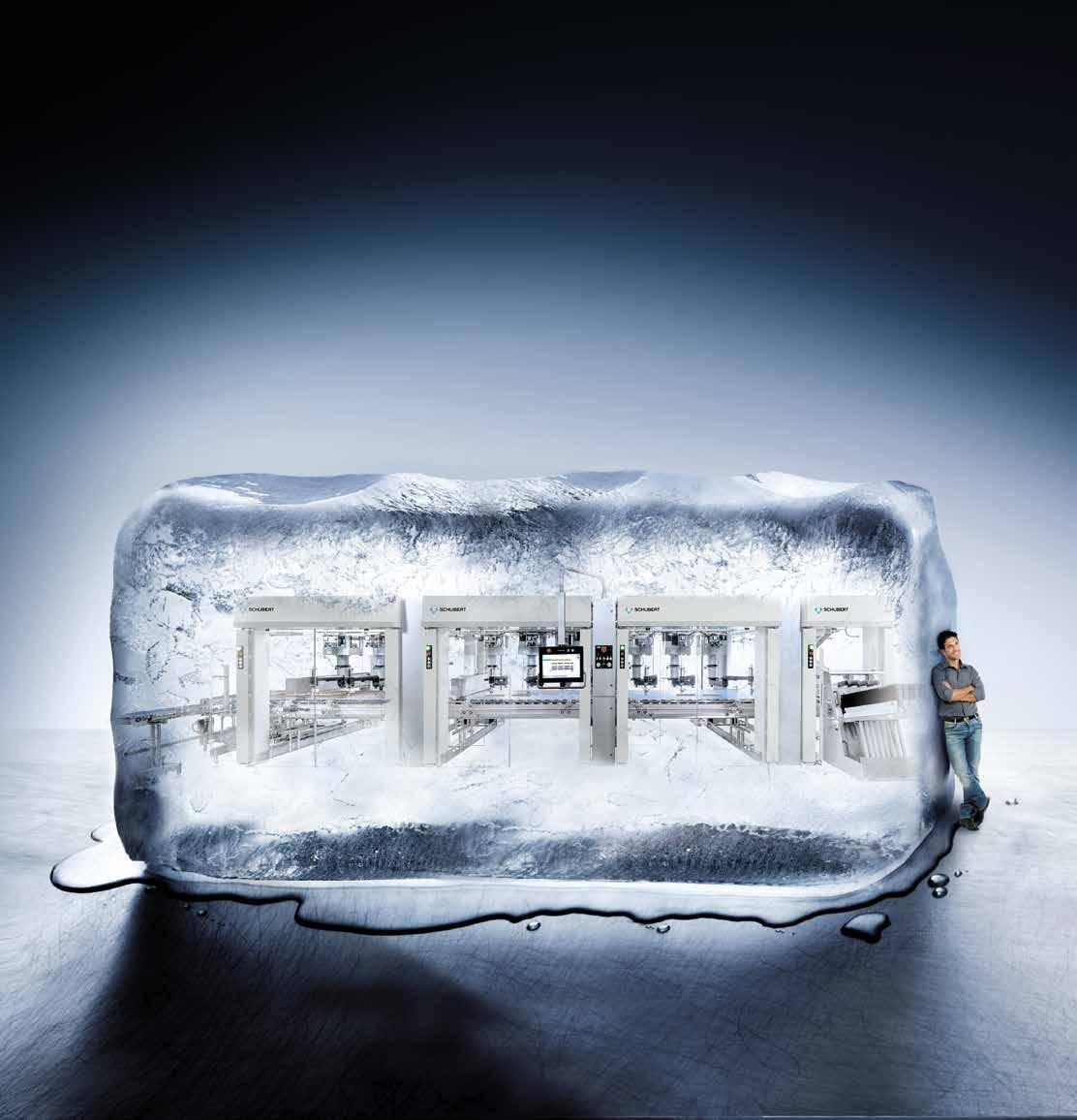
U A D A ODU S O AYS.
Innovation Stage hosts 60+ sessions
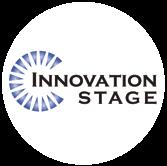
Processing Innovation Stage makes Chicago debut.
Anattendee favorite, the Innovation Stage, returns to PACK EXPO In ternational with more than 50 informative sessions. The free, 30-minute presentations occur throughout each day on three stages (Booth N-4560, N-4580 and N-4585) in the concourse of the North Building near Starbucks.
Topics include sustainability and eCommerce, building a resilient supply chain, automating minimal material operations, cyber resilience, robotics, upgrading from heat sealing to ultrasonic sealing, brand protection and smart sensors.
New this year, after a successful launch at PACK EXPO Las Vegas, the Pro cessing Innovation Stage (Booth LU-7130) in the Lakeside Center concourse will feature sessions focused on high-pressure pasteurization, product handling, batching and blending, clean-out-of-place parts washers and sanitary drainage system design.
Innovation Stage presenters rank as subject matter experts and represent a cross-section of exhibitors, including Syntegon Packaging Technology (Booth
S-3514), Amcor Rigid Packaging (Booth S-3705, S-3814), Placon (Booth W-24033), SMAC Moving Coil Actuators (Booth N-5774), Michigan State University (Booth W-20044), Siemens Digital Industries (Booth N-5148), WestRock (Booth S-2130), Amcor Flexibles North America (Booth S-3705, S-3814), Brenton, a ProMach product brand (Booth N-5546), Emerson (Booth N-4736), Soft Robotics (Booth N-5230) and JBT-Avure (Booth LU7118)
PACK EXPO International offers many other educational opportunities, in cluding PACK to the Future (Booth W-20025) (see program, p. 18), The Forum at PACK EXPO (Booth N-4543) (see program on p. 40) and the new Industry Speaks (Booth N-4565) (see program on p. 24). The Reusable Packaging Learn ing Center (Booth (LU-6737) also is hosting daily educational sessions. Check the PACK EXPO International App or the show website for the latest updates.
For more info, visit www.PACKEXPOinternational.com. SD
TUESDAY, OCTOBER 25, 2022
MECHATRONIC CASE PACKING TRANSFORMS FROZEN FOOD PRODUCTION
10:00-10:30 AM
Innovation Stage 1|N-4560
Explore how food, food service and personal care manufacturers can increase flexibility and through put while reducing machine and plant footprint with mechatronics-enabled case packing machinery. A case study with best practices and lessons learned demon strates how to capitalize on intelligent linear transport technology in case packing.
Rick Forsgren
Packaging Industry Business Development Mgr Beckhoff Automation


Mike Grinager VP, Technology
Brenton, a ProMach product brand HOW TO AUTOMATE PAPERBASED PACKAGING SOLUTIONS
10:00-10:30 AM
Innovation Stage 2|N-4580
The word sustainability has never been as important as it is now. Globally, consumers increasingly demand that brands “walk the talk” when it comes to support ing sustainable practices, with packaging at the fore front of that conversation. While standing out at the shelf remains a big priority for brands, how they do so will affect consumers’ perception and loyalty. Learn how our scalable and flexible packaging automation technology can support your brand’s plastic replace ment journey.
Douglas Hicks
VP, Machinery, Beverage Design
Graphic Packaging International BUZZWORD HANGOVER
10:00-10:30 AM
Innovation Stage 3|N-4585
Demystifying common manufacturing technologies.
Jason Petri Solutions Consultant Mgr - Private Markets Brightly Software
ENTERAL FEEDING –DIRECT CONNECT NUTRITION DELIVERY
10:00-10:30 AM
Processing Innovation Stage|LU-7130
EnteraLoc Flow is a complete enteral feeding system fea turing a spouted pouch and ENFit connector that direct ly fits into a feeding tube. This provides enteral patients with an optimal feeding experience that promotes supe rior nutritional intake and improved patient outcomes.
Keith Smith Pres
Vonco
CLOSING THE LOOP
11:00-11:30 AM
Innovation Stage 1|N-4560
Learn about recycling plastics into innovative reus able pallets, plus large container solutions enhancing sustainability.
Jean-Marc Van Maren
Chief Product Officer
Cabka North America
RECYCLE-READY PACKAGING INNOVATIONS IN HEALTHCARE AND THEIR IMPACT BEYOND END OF LIFE
11:00-11:30 AM
Innovation Stage 2|N-4580
Recycle-Ready packaging innovations are hitting the Healthcare market at an increasing pace. Is the endof-life the only story? Join Amcor as we explore the full impact of recycle-ready innovations using Amcor’s certified life cycle assessment tool, ASSET™, and demonstrate recycle-ready innovations are the right technologies to drive sustainable packaging solutions.
Brian Ingraham
Sr R&D Dir, Healthcare Amcor
3D VISION, SOFT GRIPPER AND AI AUTOMATION SOLUTION
11:00-11:30 AM
Innovation Stage 3|N-4585
mGripAI™ is a one-of-a-kind automation solution combining 3D vision, soft grasping and artificial in telligence, offering a single automation solution for food and consumer packaged goods at high speeds.
Harley Green Dir, Business Development Soft Robotics
INNOVATIVE SOLUTIONS CREATE R&D PARTNERSHIPS
11:00-11:30 AM
Processing Innovation Stage|LU-7130
The past two years have forced companies to provide solutions to the market in record time. This session will focus on the need for integral testing partnerships between food manufacturers and equipment manu facturers. Such partnerships have led to quick changes and new manufacturing innovations.
Paul Krechel Dir, Sales Deville Technologies
REDUCE WASTE & INCREASE EFFICIENCY IN CLEAN-IN-PLACE PROCESS
12:00-12:30 PM
Innovation Stage 1|N-4560
Food and beverage and life science manufacturers must maintain strict hygienic standards to ensure compli ance with local/national regulations and product qual ity. To do this, tanks and piping systems go through a clean-in-place (CIP) process between batches. CIP processes are vital to hygienic practices but can be a
SHOW DAILY
source of inefficiencies, leading to high utility costs and wasted product. The correct instrumentation can help optimize the CIP process and reduce overall op erating costs. This sesssion addresses seven common CIP efficiency challenges, along with seven solutions using proper measurement instrumentation.
Vince Massey Mgr, Business Development Emerson
THINKING ABOUT THE BOX
12:00-12:30 PM
Innovation Stage 2|N-4580
Learn about cutting-edge packaging industry innova tions to help improve your logistics capability, reduce labor needs and accelerate your ability to deliver.
Hanko Kiessner
Founder, Executive Chairman Packsize
BATCHING AND BLENDING OPTIMIZATION IN THE BEVERAGE INDUSTRY
12:00-12:30 PM
Processing Innovation Stage|LU-7130
The beverage industry is highly complex, but new, in novative solutions can simplify complicated processes without sacrificing quality. This session explores how a new horizontal injector and radial jet mixer can trans form your process and bottom line.
Richard Chapman Business Development Mgr, USA & CanadaLiquid Food Solutions Beverage Tetra Pak
BUILDING YOUR CYBER RESILIENCE PROGRAM
1:00-1:30 PM
Innovation Stage 1|N-4560
The importance of cyber resilience continues to grow as manufacturers face mounting challenges, including unplanned downtime, supply chain shortages and ran somware attacks. This session discusses best practices for building a cyber-resilience program, from physical infrastructure to network management to industrial security, using a holistic strategy to improve overall cyber posture.
Brian Deken
Connected Services Business Development Mgr

Rockwell Automation
IS THE WORLD READY FOR SUSTAINABLE PACKAGING?
1:00-1:30 PM
Innovation Stage 2|N-4580
Session discusses international research findings that identify challenges faced by manufacturers looking to transition to more sustainable packaging materials.
Sean Kohl Dir, Global Product Line
Industrial Physics ∆
Go reliability.
Emerson advanced analytics, machine health monitoring, smart pneumatics and self-diagnosing instrumentation deliver real time insights so food & beverage and packaging manufacturers can run more reliably.
Learn more at Emerson.com/FoodBeverageReliability
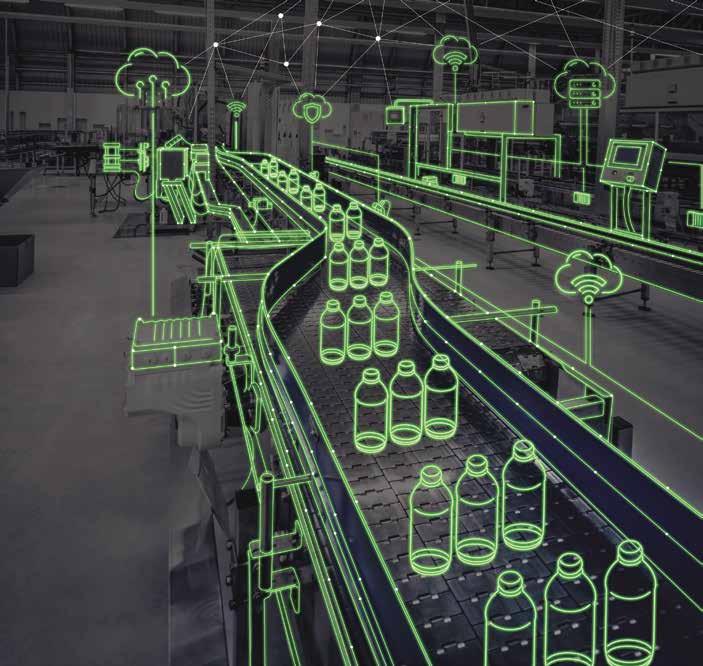
TUESDAY, OCT. 25, 2022 (CONT’D)
COMBAT LABOR ISSUES WITH FLEXIBLE ROBOTIC AUTOMATION
1:00-1:30 PM
Innovation Stage 3|N-4585
Labor challenges in today’s manufacturing and pack aging environments require real solutions for reduc ing the need for engineering staff without giving up production flexibility. Contract manufacturers need to support multiple customers with fast changeovers to keep productivity and performance high. Learn about real-world success leveraging durable, high-speed ro bots in an interactive environment, leveraging simple robot programming through gestures and voice com mands. Gain insights into how to increase speed to market and throughput without increasing labor costs.
Patrick Varley
Product Marketing Mgr, Mechatronics




Mitsubishi Electric Automation
BUYING A SEPARATOR MACHINE? AVOID THESE FIVE COSTLY MISTAKES
1:00-1:30 PM
Processing Innovation Stage|LU-7130
Buyers of new vibratory separator machines learn what to look for when selecting one for a new product or application to help avoid costly mistakes.
Larry Koehn
Technical Application Mgr – Separation Products
Gerard Daniel Worldwide ∆
SHELF-READY LABELING THAT MARKETING/OPERATIONS CAN AGREE ON
2:00-2:30 PM
Innovation Stage 1|N-4560
How food items are packaged has a significant impact on their attractiveness to consumers. Finding a solu tion that looks good on the retail shelf and minimiz es labor during processing/packaging has never been more critical. This session reviews the pros and cons of various packaging technologies from the perspective of on-the-shelf appearance and labor requirements.
Lisa Barrieau
Banding Sales Mgr, Food Felins
REINVENT SUPPLY CHAIN INSPECTION WITH 3D MMWAVE IMAGING
2:00-2:30 PM
Innovation Stage 2|N-4580
Learn how to automatically inspect inside sealed box es and totes moving on conveyors to automate your quality control and improve operational efficiencies, using human-safe 3D mmWave imaging.
Andreas Pedross-Engel
Founder, VP, Technology & Engineering ThruWave
USING SUPPLY CHAIN TRACEABILITY TO COMBAT COUNTERFEITING
2:00-2:30 PM
Innovation Stage 3|N-4585
Counterfeit products cost the cosmetics industry more than $5 billion annually. Learn how supply chain traceability can protect manufacturers, brand owners and consumers using unique digital identities that trace the product from raw materials to end users, protecting reputations and lives.
Monica Coffano Development Mgr
Antares Vision Group - Cosmetics
STICK THE LANDING: FIVE PRODUCT HANDLING IDEAS TO WIN PROCESSING GOLD
2:00-2:30 PM
Processing Innovation Stage|LU-7130
Squeezing more capacity out of your existing plant can be a real challenge. From crowded spaces to awk ward rooms, it can take real gymnastics to get your product from receiving to final packaging. This session explores five creative solutions to help flip, twist and spin your goods from point A to point B.
Jim Stahlman Sr Packaging Mgr POWER Engineer ∆
SIMPLIFYING THE COMPLEXITIES OF LABELING AND ARTWORK IN THE PHARMA INDUSTRY
3:00-3:30 PM
Innovation Stage 1|N-4560
Streamline artwork and labeling content processes with digital tools that enable collation, reuse and quality in packaging.
Jackie Leslie Category Specialist - Life Sciences
Esko Brand Solutions
ADDRESSING CONVENIENCE TREND WITH RETORT POUCHES
3:00-3:30 PM
Innovation Stage 2|N-4580
The pandemic has greatly affected consumers’ eating habits. As day-to-day life continues to be increasingl ly fast-paced, consumers seek to prepare food quick er and eat on-the-go, without sacrificing quality and freshness. As a result, global demand is increasing for ready-to-eat and shelf-stable food items. For safety, convenience, freshness and a long shelf life, many of these products rely on retort packaging. Retort pouch es owe their growing popularity to excellent thermal processing during the sterilization process, room tem perature storage conditions and no need for refrigera tion unless opened. Flextra™ SBA5250/XA2250 sol vent-based flexible packaging adhesive cures at room temperature in seven days or less. It is PAA-, cyclic ester-, epoxy silane- and organotin-free.
Chip Reisman Sr Scientist
H.B. Fuller
SUCCESS FOR VISION SYSTEMS DEEP LEARNING IMPLEMENTATION
3:00-3:30 PM
Innovation Stage 3|N-4585

This overview of best practices for determining when to use deep learning vision systems describes practical applications. It covers rules-based and deep learning vision tools integration, considerations for regulated vertical markets and validation, configuration options, stakeholder roles and impact of engineering biases.
Chris Gilmet
Equipment Engineering Mgr Verista
GREAT ENERGY EFFICIENCY IN PROCESSING; EVAPORATION AND OHMIC
3:00-3:30 PM
Processing Innovation Stage|LU-7130
MVR concentration and ohmic heating technologies are revolutionizing food processing by significant ly reducing energy consumption and CO₂ emissions with remarkable advantages on product quality too.
Mario Gozzi
Regional Sales Mgr CFT Group
MANUFACTURING INNOVATION AWARDS
4:15-5:00 PM
Processing Innovation Stage|LU-7130
Speakers from Sugarlands Distilling and United Air lines Catering Kitchen Operations present technol ogy innovations from their recent greenfield facility projects and discuss how increased automation im proves product quality and yield.
Joyce Fassl - Moderator Editor at Large ProFood World
WEDNESDAY, OCTOBER 26, 2022
THE RISE OF SOFTWARE AS A SERVICE
10:00-10:30 AM
Innovation Stage 1|N-4560
Explore what software as a service means for manu facturing or machine-building businesses of any size. Sesssion addresses the “IT won’t let us” challenge and breaks down six real-world ways to can incorporate the cloud for productivity improvement, cost contain ment and workforce support.
Jim Taylor
CPG Industry Consultant Rockwell Automation
CYBERSECURITY BEST PRACTICES IN A CONNECTED IIOT WORLD
10:00-10:30 AM
Innovation Stage 2|N-4580
Being and staying cyber secure in an increasingly digital, connected industrial world requires an ag gressive, proactive approach. The risks to your opera tions and brand reputation are palpable. This session provides best practices to establish a strong cyber security foundation and address your organization’s most burning questions: What should you do to pro actively defend your operation and ensure ongoing vigilance? What standards and best practices apply to your business? Who is responsible for ensuring cybersecurity at your organization?
Grant Geyer
Chief Product Officer
Claroty Paula Mott
Cybersecurity Business Consultant Schneider Electric
PESTS TO WATCH OUT FOR AS MOISTURE LEVELS FLUCTUATE
10:00-10:30 AM
Innovation Stage 3|N-4585
Fungus feeders are extremely common pests in ware houses and can become problematic when moisture levels rise, allowing molds and fungus to grow. These conditions offer pests such as psocids and a few types of beetles the food they need to survive in storage environments. Managing moisture, humidity and air movement is critical to keeping these pests out. Fungus feeders can be found in pallets, on and inside packaging, in supplies and many other places. Learn what fungus feeders are, the risks they pose, proactive measures you can take to avoid them and how an In tegrated Pest Management plan can help proactively manage them in your facility.
Benjamin Hottel Ph.D., B.C.E, Mgr, Technical Services Orkin
LEAK TESTING FOR MICROORGANISMS IN MEDICAL/ PHARMA PACKAGING

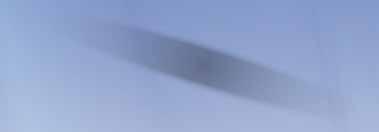

11:00-11:30 AM
Innovation Stage 1|N-4560
Innovative sensor technologies facilitate non-destruc tive container closure integrity and package leak tests to below the scale that allows microbial ingress to your packages. In this workshop, learn how helium leak testing aids in simple, fast, repeatable, quantitative and non-destructive leak test cycles, providing potential escape from the archaic dye-penetration tests.
Bill Burnard

General Industrial & Package Integrity Sales & Business Development Mgr - NA INFICON
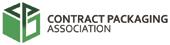


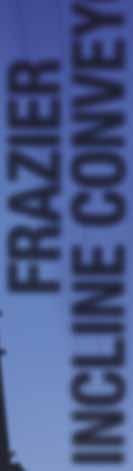
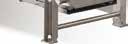
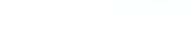
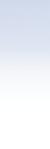
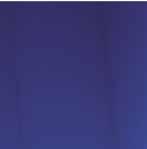
RECYCLABLE AND RECYCLEREADY PACKAGING FOR THE DAIRY MARKET
11:00-11:30 AM
Innovation Stage 2|N-4580
A void exists in the dairy alternatives, nutritional drinks and ready-to-drink coffee markets for packaging made from recycled material and recyclable in most markets. ClearCor technology offers significant sustainability benefits compared to aseptic carton packaging, which experiences high damage rates and poses a challenge for convenience stores, where traditional refrigerated shelf space is designed for round, rigid, plastic bottles. The ClearCor bottle contains post-consumer recycled (PCR) resin and provides a recyclable packaging solu tion, as well as easy access to eCommerce and conve nience store distribution channels. It also delivers a positive drinking experience. A recyclable PET bottle, utilizing the ClearCor technology, offers the same taste and feel as other packaging, delivers a positive drinking experience and extends shelf life.
Terry Patcheak
VP, R&D, Sustainability & PM Excellence

Amcor Rigid Packaging
OXYSTAR—THE FIRST RECYCLABLE BARRIER MATERIAL
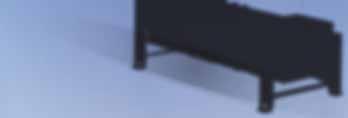
11:00-11:30 AM
Innovation Stage 3|N-4585

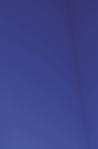
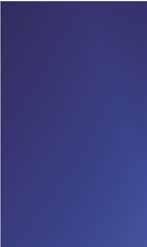
This session explores more sustainable alternatives to barrier materials that achieve the same barrier protec tion. In an economy with limited resources, longer shelf life is a desirable objective for food processors. How do we further promote a Circular Economy where reusing materials reduces reliance on new materials?
Ron Haub VP, Sales Placon
FRESH FOOD TO-GO AND THE CIRCULAR ECONOMY
12:00-12:30 PM
Innovation Stage 1|N-4560
This session, including a short case study, takes at tendees through existing fresh food to-go packaging in the market, including how flexible packaging and material changes can better support sustainability goals and the Circular Economy.
Nathan Klettinger Dir, Global Marketing ProAmpac
SMART SENSORS: THE BACKBONE OF DIGITAL TRANSFORMATION
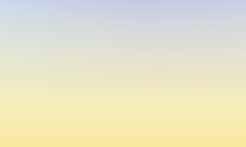
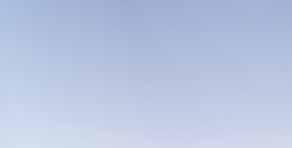
12:00-12:30 PM
Innovation Stage 2|N-4580
Discuss Industry 4.0 as it relates to smart sensing technol ogy. Modern manufacturing is saturated with data, even from the most basic sensors. Learn how this data “over load” can be leveraged to make manufacturing smarter and can continue driving the current digital transforma tion. Learn about trends in using this data and clear, ac tionable steps to join this new industrial revolution.
Divya Prakash
Dir, Business Consulting SICK SD
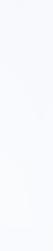
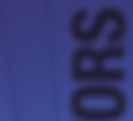
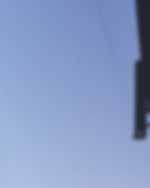

LAKESIDE UPPER HALL
The Processing Zone
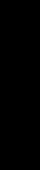
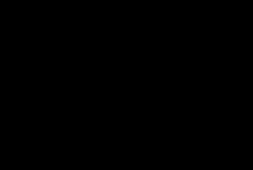
Find front-of-the-line solutions for food and beverage processing and discover ways to increase safety, improve efficiency and achieve total system integration.
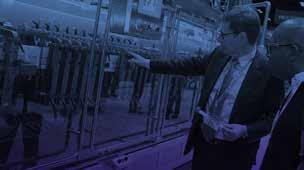
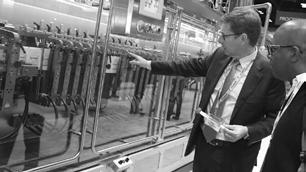
The Reusable Packaging Pavilion
Learn how to increase sustainability in your supply chain through reus able packaging assets and services.
Sponsored by:
NORTH HALL
The Logistics Pavilion
See supply chain solutions, including warehousing, fulfillments, distribution logistics services and transportation providers.
SOUTH HALL
The Confectionery Pavilion
Uncover specialized equipment and integrated systems for your candy, confectionery and gum production lines.
Sponsored by:
PACKage Printing Pavilion
Explore technology that makes customization, promotions, small runs, on-demand production and smart packaging cost effective.
WEST HALL
The Containers and Materials Pavilion
Find new recyclables, bio-based materials, flexible packaging printable films and much more –and see creative packaging and trends at:
Healthcare Packaging Pavilion
A one-stop shop for solutions targeted to pharmaceuticals, biologics, nutraceuticals, medical devices and more.

Out with the old, in with the color Epson distribution center upgrades to color labeling.
Adistribution facility in the Indianapolis suburb of Plainfield, IN, houses warehous ing and distribution operations for Epson America (Booth N-5265, N-5363), plus a repair de pot and sales of parts and accessories.
The 750,000-sq.-ft. facility with 200 dock doors sees a tremendous amount of movement, day in and day out. More than 25 million pieces and nearly 2 million orders are shipped out every year, each re quiring a label to be printed for outbound shipping.
“Our goal is to provide Epson customers and re tailers with the best service possible and deliver or ders that perfectly meet the specific requirements, on-time,” says Mauricio Villaveces, director, Dis tribution Operations at Epson America. He adds, “Making sure that customer requirements are met is paramount. We never want to say ‘no’ to a customer when they introduce a new requirement.”
For decades, the Epson facility relied on ther mal-transfer printers for labeling operations, which Villaveces notes had plenty of opportunities for im provement due to the lack of color capability and frequent jams, resulting in downtime. Often, pack ages needed to be visually marked for sorting or pro cessing, and because the thermal printers could not print color, it required secondary steps to apply color or manually mark the package. The operations team also found it difficult to change thermal ribbons because it required getting the ribbon complete ly smooth across the roller. Plus, they complained about the rising prices of thermal labels and ribbons.
“Epson trusts and relies on its own technology,” says Rand Rozar, vice president, Service and Logis tics, Epson America. He explains, “The most recent testament includes modernizing our headquarters in California with business inkjet MFP [models] and projection solutions. When we looked at upgrading our labeling operations in Plainfield, the Color Works C6000 Series made sense as it was engineered for this exact application and environment. With ColorWorks, Epson is able to compete and lead in this type of logistics environment, printing labels with much higher resolution and image quality than the previous thermal labels.”
DEMANDING REQUIREMENTS AND HARSH ENVIRONMENTS
Most distribution centers are not climate-con trolled, and labels created with legacy label-print ing systems can be severely affected by moisture, heat and freezing temperatures, with the tendency to fade over time when a product is stored. Tough,
heavy-duty technology is essential since environ ments like these are naturally rough on technology.
The industrial-strength ColorWorks C6000 Se ries inkjet label printers are engineered for challeng ing applications and environments.
“We work with a number of big-box retailers that have demanding labeling requirements,” says Villa veces. “So much is at stake every day when Epson ships to these customers. Labels that are not compli ant or do not meet customer requirements can result in shipping delays, penalties and fines, and this can negatively affect customer relationships in terms of credibility and dependability, too.”
Villaveces explains that entire pallets or truck loads can be rejected for seemingly minor discrepan cies. And nothing is trivial. Even the exact placement of an individual label is important especially with mixed products in a pallet.
Per compliance requirements, each label print ed must be readable and scannable for 24 months, meaning it must not smudge, bleed or fade. Case and pallet labels must incorporate the purchase order number, SKU number, vendor model number and master carton quantity, and these labels cannot be even slightly misaligned when printed. In some cas es, even “mixed product” and “do not break down” labels are required. These examples represent a min iscule fraction of the total labeling requirements out lined by retailers.
“With thermal-transfer labels, on one too many occasions, a label on a pallet that has been stored will not scan because the barcode or QR code has faded, or because the image quality of the print was sub-par,” recalls Villaveces. “When this happens,” he says, “we
“With ColorWorks, Epson is able to compete and lead in this type of logistics environment, printing labels with much higher resolution and image quality than the previous ther mal labels.”
—Rand Roza Epson America
have to manually enter the information. In a fast-mov ing environment with a tremendous amount of activity, we cannot afford to take the time for this extra step. Plus, if retailers are not able to successfully scan a label on their end, fines will result.”
HARDWARE, SOFTWARE SOLVE WOES
Though thermal-transfer label printers are com monly found in distribution centers, a one-sizefits-all solution is antiquated for such demanding environments.
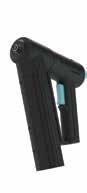

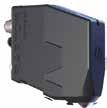
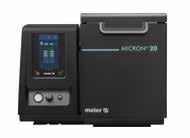
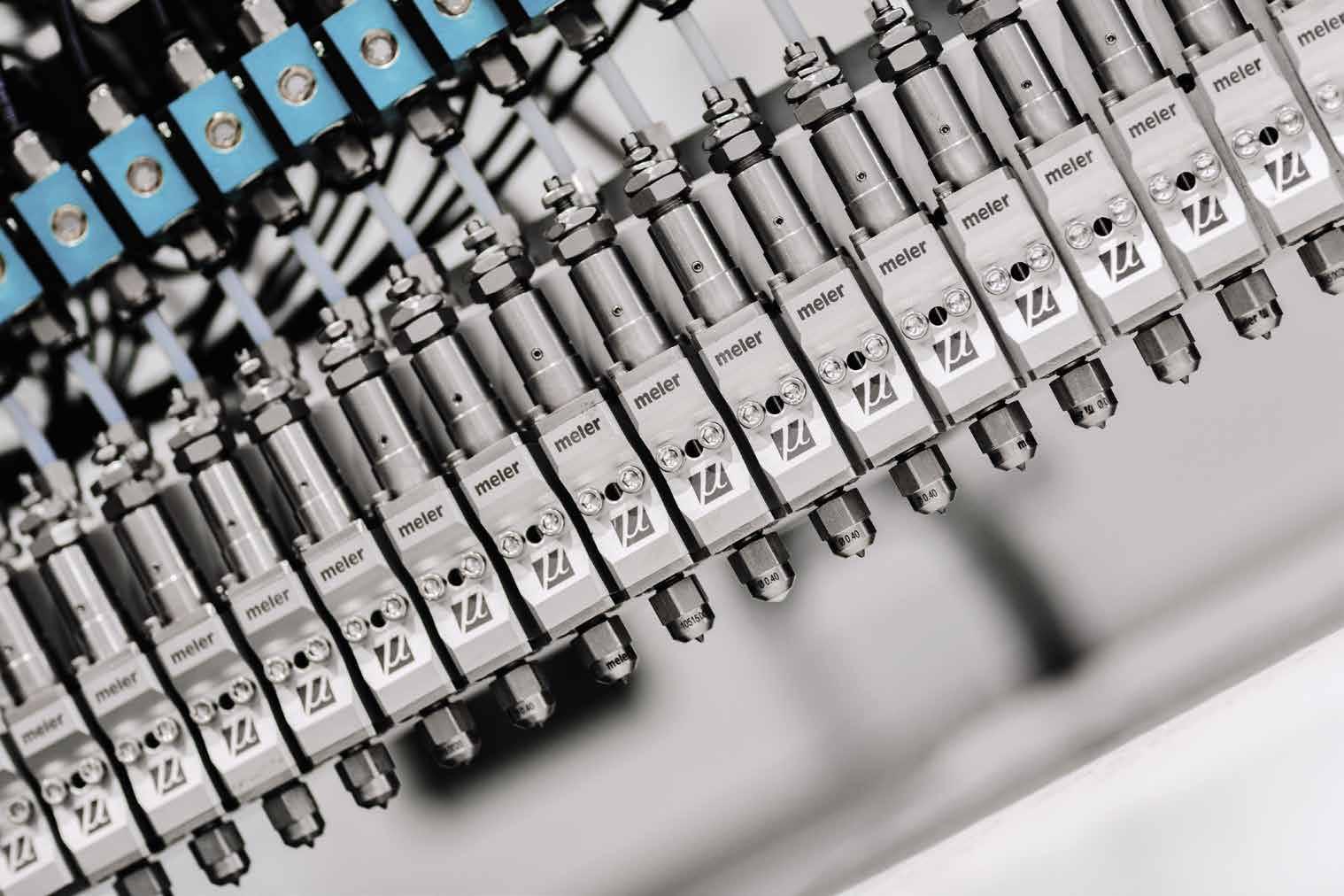
The facility has a variety of labeling stations— from UCC-128 labeling to small pack billing, eCom merce, system devices, microdevices and more—and each has unique labeling requirements. Each re quirement varies by customer and labeling area, and in some cases, can change on a weekly basis, thereby
requiring some level of custom configuration. For more than 20 years, the Epson facility has leveraged Loftware to design labels for its enterprise resource planning applications. The facility also leverages software from partners, TEKLYNX and BarTender from Seagull Scientific. “Loftware has been integral in developing label configurations to meet any customer requirement. Starting the process to overhaul the previous labeling operations has been simple because of the synergies with hardware and software,” saysVillaveces.
Converting each of the major labeling stations to ColorWorks area-by-area, Villa veces and his team are replacing all thermal printers with more than 70 ColorWorks C6000 color inkjet label printers.
“The ColorWorks C6000P models have a peel-and-present feature, which elimi nates the manual step of peeling the label from the liner. While it might seem trivial, it actually makes a significant impact on streamlin ing and speeding up labeling when you’re printing and applying millions of labels every month,” says Villaveces.
OPENING NEW DOORS WITH COLOR
“Frequently, we hear customers speaking about incorporating color label requirements,” says Villa veces. “Now, we’re prepared for color requirements that retailers might ask of us.”
When complete, the transition to CW-C6000P printers and integration of color capabilities will help augment operational efficiency, reduce the chance of fines due to unscannable labels and simplify labeling processes in the distribution center.
“We, like any distribution center, focus on cost per piece, piece per hour and speed for service,” says Villaveces. “We have to pay close attention to certain aspects of operations, such as the precise placement of labels and requirements of the like, so it’s import ant that we don’t have to worry about labeling need ing our intervention. The label creation and printing process can take care of itself so we can focus on getting the product correctly shipped out and make sure it arrives to customers just as they require.”
“With ColorWorks, Epson is able to compete and lead in this type of logistics environment, printing labels with much higher resolution and image quality than the previous thermal labels,” concludes Rozar.

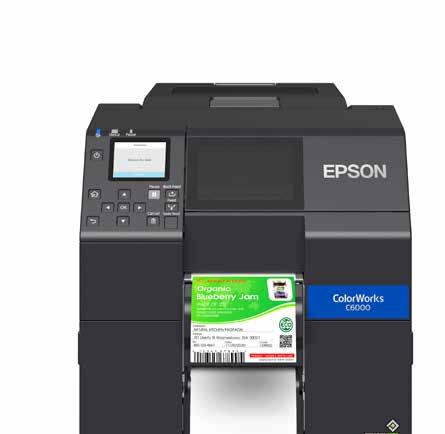
For more info, visit www.epson.com. SD
partner
melerusa.com
We provide you with the widest range of hot melt adhesive application products, with the best specialist team who will find the solution to boost your business.
“Frequently, we hear customers speaking about incorporating color label requirements. Now we’re prepared.”
—Mauricio Villaveces Epson America
Gas Analysis Solutions Center opens
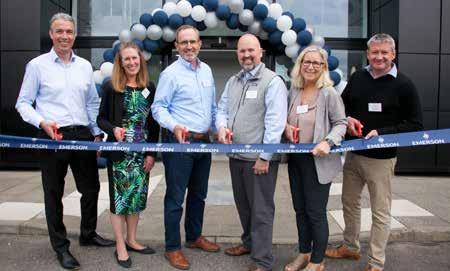


Emerson facility helps processors meet sustainability goals.
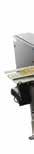
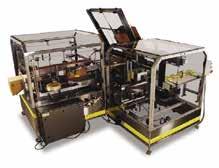
Anew Gas Analysis Solutions Center in Cumbernauld, Scotland, pro duces more than 10 sensing technologies that can measure more than 60 gas components, delivering on the commitment Emerson (Booth N-4736) has made to support end users’ decarbonization efforts.

As a global hub for the production and distribution of gas-sensing technol ogies, the 62,000-sq.-ft. facility engineers and manufactures Emerson’s Rose mount™ continuous gas analyzers and gas chromatographs, which are used to improve emissions monitoring, plant safety, quality control and operational
efficiency. These tools are critical to helping process plants meet increasingly stringent environmental regulations and to ensuring process control in food and beverage, pharmaceutical and aerosol manufacturing.

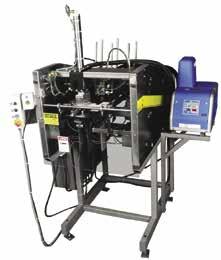

“The mission of our new Gas Analysis Solutions Center is to support in dustrial manufacturers in achieving their decarbonization and environmental sustainability goals, including the deployment of low-carbon fuels and power sources, reducing emissions and decreasing waste,” says Jon Stokes, group presi dent of Emerson’s Measurement Solutions Business.
The center includes a training space and offers classroom, onsite and web-based training options, giving Emerson greater ability to demonstrate how the latest gas analysis technologies can help run operations reliably, safely and efficiently. It is certified by the International Organization for Standardization (ISO) and comple ments Emerson’s global network of facilities certified by ISO standards for quality, occupational health and safety and environmental management systems.
The facility also is equipped with a gas-extraction system, an environmental chamber and external gas storage to facilitate gas analyzer testing and applica tion research and development. Combined with calibration capabilities, a dedi cated area for performing factory acceptance testing and a customer collabora tion space, these capabilities help assure product performance and integrity and streamline the customer experience.
For more info, visit www.emerson.com/en-us/automation/measurement-instrumen tation/gas-analysis. SD
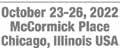
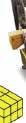

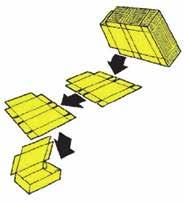
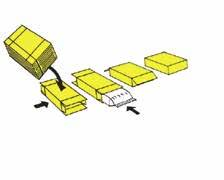


players, one team.
No matter if it is stand-alone machines, complete systems or services: Syntegon’s innovative process and packaging technology is backed by over 80 years of trusted solutions focused on a sustainable future. For our customers, this means tailor-made and reliable production processes for perfect results. From a spare part to complete production systems – with us you get everything from one source. That’s what we’re doing, how about you? Please visit us in the South Hall.
Line delivers top performance
Packaging redesign saves material, transport costs.
Hosta’s chocolate-coated Nippon puffed rice snacks are as popular as ever. To further expand its output, the long-established southern German company turned to packaging machine manufacturer Schubert, parent compa ny of Schubert North America (Booth W-19008, LU-8730). With a combination of three Schubert packaging machines—a pick-and-place machine, a Flowpacker flow-wrapping machine and a case packer—Hosta now benefits from a reliable pack aging process with top performance. A redesign of the trays and cases also opens up considerable cost savings for the confectionery manufacturer in terms of materials and transport.
When it comes to the “hidden champions” in the food sector, Hosta is perhaps the best example: The tradition-rich company still produces its full range of snacks at its headquarters in Stimpfach in Franconia (Germany). Hosta is a perfect example of the fact that it doesn’t take a major international corporation to make a product famous. In 70 years of compa ny history, the down-to-earth family business has developed into a professional confectionery manu facturer whose top product, Nippon, enjoys a brand awareness level of close to 90% in Germany. Such growth demands change—in production as well as in packaging. Nippon, the chocolate-coated puffed rice snacks, were introduced to the market as early as 1956. Since then, they have enjoyed ever-increasing popularity. In their search for a reliable partner who could meet the requirements for a new packaging solution for the rectangular treats, Hosta relied on an old connection in the region, just eight kilometers from Stimpfach—packaging expert Schubert.
FACTS & FIGURES
PRECISE SPECS, HIGH EXPECTATIONS
Medium-size companies in particular often have less tolerance for errors than large corporations. Therefore, the specifications that Hosta Plant Man ager Max Schäuble placed on the new packaging plant were demanding: The entire process could not be stopped for longer than 5 min.—any longer and
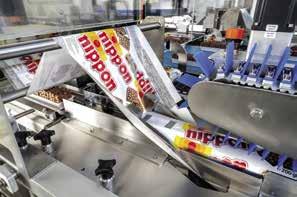
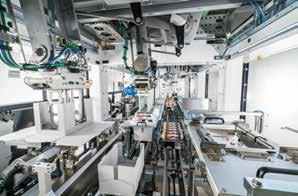
product handling
optimized by Schubert
in
the quality of the puffed rice snacks, which are meltin-the-mouth on the outside and crispy on the in side, would be compromised.
Even the production staff’s shift changes are geared to this tight schedule. Products had to be re liably packed directly from production to stacking in shipping cases at a rate of 2,500/min. To keep the process running reliably, the line had to offer a high level of redundancy. Therefore, fallback levels were required for each section. Additionally, it would have to be possible to switch off various stations individu ally in the event of maintenance.
“Fortunately, Schäuble’s team contacted us at an early project stage,” recalls Jonas Müller, sales account manager at Schubert, reflecting on the beginning of the collaboration with Hosta. “This enabled us to plan the entire packaging process in partnership with each other right from the start and to jointly opti mize the packaging materials, among other things.”
EFFICIENT TRIO
It was clear from the outset that the complex packaging processes could only be mastered at the required speed with the aid of highly efficient ro bot technology. The expertise of the Schubert spe cialists was literally in demand right down the line, as the new system consists of three interconnected Schubert packaging machines: a pick-and-place ma chine, a Flowpacker flow-wrapping machine and a case packer. To ensure the system provides the re quired redundancy, the engineers decided to use two flowpack aggregates in the Flowpacker that operate in parallel.
The integrated line consists of a total of 18 ma chine frames and packs 2,500 products/min. as re quired. The Nippon squares are fed directly from the production line through a cooling tunnel and are first fed to the picker line on a 1.8m-wide product belt. There, 28 pick-and-place robots work in a dou ble-pick process. They group 16 individual products into a plastic tray, standing one behind the other, to form a 200-g formation. The tolerances of the puffed rice wafers and the sensitive chocolate coating led to the decision to use suction tools instead of gripper tools for the robots.

After filling the trays, the line moves on to the next station, a two-in-one Flowpacker where four F4 robots pick up 157 trays/min. These are then inserted directly into two parallel Flowmodul chains using the counter flow principle. Thanks to complex forming shoulders, the two flow-wrapping units then pack the trays with the puffed rice bites reliably and safely into the tightly dimensioned film. A safety level has been integrated in case a flow-wrapping unit fails. “Then the total output of the pre-machine is simply reduced to 70% and one of the two Flowmoduls (flow-wrapping units) contin ues to pack the corresponding quantity of 110 trays/ min.,” Müller explains.
Once the trays have been packed into the pro tective flowpacks, the last step is the Schubert case packer. There, 24 of the trays, each with a product weight of 200 g, are packed into a shipping case, which is then sealed with a separate lid. The integrat ed Transmodul transport robot connects the individ ual process steps and ensures high efficiency in the last packaging step. As a fall-back, if the casepacker stops, loading the outer cases can be done manually for a short time.
SAVING IN THE RIGHT PLACES
As Schubert was brought in as a partner early in the project, the packaging experts from Crailsheim were able to supply plant technology that exactly matched the requirements and also provided neigh borly help with regard to the packaging design. Thanks to the pick-and-place robots, which work precisely even with the large tolerances of the puffed
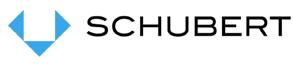
machines connected in series
rice snacks, the developers were able to shorten the plastic trays by 10mm. This optimization made it possible to reduce the film repeat of the flowpacks by another 6mm. This saves packaging material and costs in the long run.
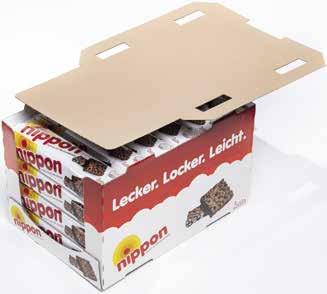
The case was reworked too. It now consists of a single flat blank with a lid, rather than three sepa rate pieces. Taken together, the improved packaging yields so much savings that there is now room for nine cases instead of eight per layer on the ship ping pallet. “The bottom line is that this represents an enormous cost saving for us,” confirms Schäuble. “Thanks to Schubert, we now not only save on pack aging material, but also on many truck journeys. From our point of view, the investment in the system has therefore been worthwhile overall.”
Schubert also benefits from the close collaboration with Hosta and its physical proximity, as Müller reports: “We are currently working on a joint service project to better understand cus tomer needs and further improve our services.” The Schubert develop ment team has already been onsite, as the complex production with the various ma chines is well-suited for tests. “Even our international customers are allowed to visit the plant at Hosta,” Müller reports. “As
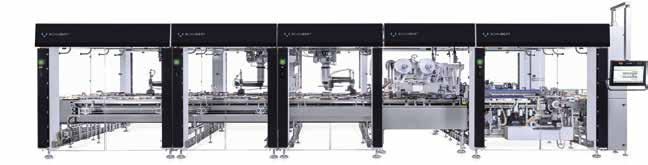
know which
leaking?
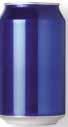
a sales account manager, I’m naturally de lighted, because the project and this part nership are very special for us.”
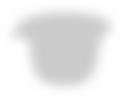
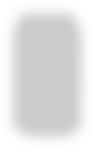
TRADITIONAL FRANCONIAN
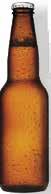

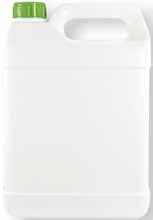
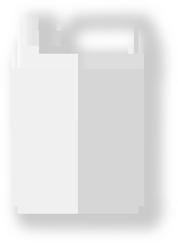
Nippon snacks, the Mr. Tom peanut bar, the Romy coconut chocolate—Hosta products have played a part in the childhoods of millions of peo ple. And Hosta’s continued success speaks for the fact that the traditional snacks are still winning new fans. The family-owned company impressively proves that medium-size German businesses are also at the cutting edge in terms of innovation and customer proximity. In the third generation, Laura Opferkuch, granddaughter of company founder Hermann Op ferkuch, Sr., has been successfully leading Hosta into the future since 2019.
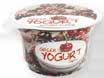
For more info, visit www.schubert.group. SD
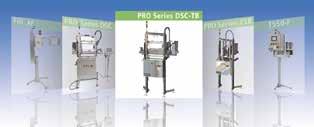
Pregis joins 1% for the Planet
Pledges portion of Inspyre product sales to provide clean water.
As a member of 1% for the Planet, Pregis (Booth S-3834), a global manufacturer of protective packaging, pledges to donate 1% of its Inspyre™ brand product sales to support non profit organizations. 1% for the Planet is a global
organization with a mission to create high-impact partnerships between businesses and nonprofits, ac celerate smart environmental giving and amplify the impact of donations.
Pregis introduced its Inspyre brand in 2018 with

Smart Packaging Solutions by Lenze
Are you looking for the highest degree of regulation from the wrapping application in your machine utilizing the very thinnest films?
Rely on the highest torque regulation performance in the market to increase your Flow-wrapper’s uptime, while reducing engineering time with our Smar t Servo Axis solution.
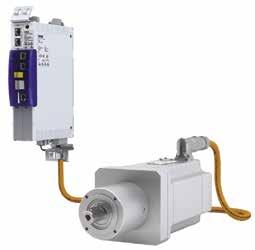
the mission of providing packaging that does good for the world. Since the introduction, Pregis has donated a portion of the proceeds of these products, including Inspyre hybrid cushioning with water blue color tint and tissue paper packaging, to Uzima Clean Water Mission and helped bring clean water to more than 170,000 people in communities around the world.
“We’re committed to making a real impact not only through efforts to run our business in the most sustainable manner possible and to offer sustainable packaging solutions, but also by making significant contributions that help people and our planet,” says Daché Davidson, chief marketing officer, Pregis. “Our partnership with 1% for the Planet and support of Uzima are testaments to our commitment as en vironmental stewards to give back to nonprofits that are driving real change.”
Pregis plans to expand the Inspyre product offer ing to increase its global impact and recently added a mailer to the Inspyre lineup, which includes HC™ Inspyre performance inflatable cushioning and Inspyre Paper, a decorative void fill.
THE INSPYRE MAILER
The Inspyre mailer offers a packaging option that supports global charity and builds brand loyalty.
The mailer offers an efficient, lightweight and sustainable way to ship non-fragile items and soft goods, such as apparel and linens, in direct-to-con sumer eCommerce applications. Made with a mini mum of 30% recycled content, the new Inspyre poly mailer offers customers packaging that contributes to sustainability goals and positive change.
Available in fanfold and rollstock formats, the mailer runs through Pregis Sharp automated bag ging systems, which can increase throughput by four times compared to manual packing, helping fulfill ment centers maximize efficiency and minimize la bor constraints.
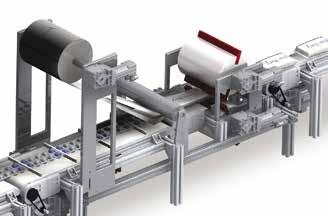
The Inspyre mailer is available in a stock print or custom designs to further connect brands to the Inspyre program. All Inspyre mailers have a stock footer with messaging to consumers communicating the val ue of this cause marketing initiative with a 1% for the Planet logo, How2Recycle® label, consumer-friendly recyclability instructions and a QR code to learn more about the corporate social responsibility program.
By packaging with Inspyre mailers, brands help fund a vital charity while reaping other benefits. “We are thrilled to expand the Inspyre product portfolio and offer brand owners another way to join Pregis in making a positive impact in the world,” says David son. She adds, “Through our support of Uzima and brand membership with 1% for the Planet, we can do this on a larger scale. The Inspyre mailer clearly com municates the environmental attributes of recycled materials, store drop-off recyclability, and informs
consumers that the brand is socially responsible. This message helps brand owners build awareness and loyalty through a meaningful consumer experience.”
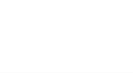
As an added value, Pregis provides end users with a marketing collateral toolkit to help promote their participation and commitment to social and environ mental change. For companies with a growing ESG (environmental, social and governance) commit ment, the Inspyre line of protective packaging cre ates an opportunity to build strong connections with consumers and make progress toward their goals.
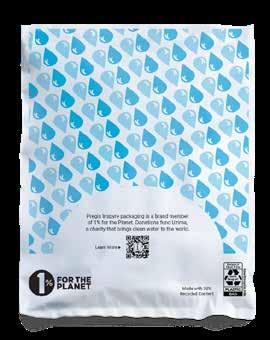
1% FOR THE PLANET


1% for the Planet is a global organization that exists to ensure our planet and future generations thrive. Its goal is to inspire businesses and individuals to support environmental nonprofits through membership and everyday actions. It makes environmental giving easy and effective through partnership advising, impact sto rytelling and third-party certification.
Kate Williams, CEO of 1% for the Planet, notes, “Currently, only 3% of total philanthropy goes to the environment, and only 5% of that comes from busi nesses. The planet needs bigger support than this, and our growing network of business members is doing its valuable part to increase giving and support on-the-ground outcomes. We’re excited to welcome Pregis to our global movement.”
Since its founding in 2002 by Yvon Chouinard, founder of Patagonia, and Craig Mathews, founder of Blue Ribbon Flies, business and individual mem bers have raised more than $300 million to support thousands of approved environmental nonprofits around the globe. Nonprofits are approved based on referrals, track record and environmental focus. Today, 1% for the Planet’s global network consists of thousands of businesses, individuals and environ mental nonprofits working toward a better future.
UZIMA




Atlanta-based Uzima Clean Water Mission, a whol ly owned subsidiary of Start With One Interna tional, was borne in 2015 out of a desire to remedy one of the greatest challenges facing the poor in





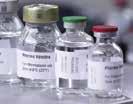
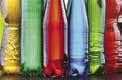
rural Kenya. Uzima has since transformed into a global organization with a variety of filtration solutions to make clean water affordable, measur able and attainable.
For more info, visit www.pregis.com. SD
Partner With the Product Inspection Experts

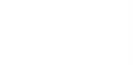
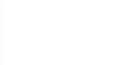




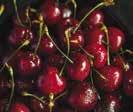
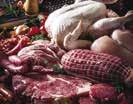
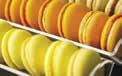
METTLER TOLEDO offers a wide range of solutions for all types of bulk and packaged products for environments ranging from dry to heavy washdown.

Our systems are supported by the most comprehensive engineering solutions, product testing, customer service and training in the industry.

The Forum program returns Learn best practices for automation, cybersecurity and sustainability.
Another attendee favorite, The Forum at PACK EXPO (Booth N-4543), presents a daily schedule of sessions about the latest industry trends. Each 45-minute session includes small group dicussions and a ques tion-and-answer period.

Topics include cybersecurity, digital transformation, sustainability, deploy ment of robots/cobots, collaborating with copackers, automation, improving packaging line performance and post-COVID packaging design trends.
Speakers include a range of experts from various organizations, including: PMMI, The Association for Packaging and Processing Technologies (Booth N-4550); OMAC - The Organization for Machine Automation and Con trol (Booth N-5100); the World Packaging Organisation (Booth N-4902,
TUESDAY, OCTOBER 25, 2022
HOW ARE EMERGING BRANDS ENGAGING WITH COMANS/ COPACKS TO MAXIMIZE PROFITS AND SHRINK TIME TO MARKET?
10:30-11:15 AM
Using data from our State of the Industry Report and our RFQ platform, we will look at the changing de mands of emerging brands as well as legacy brands seeking to launch new food and CPG retail products. We will explore how CoMan and CoPacks are add ing value as consumer and market-driven needs are moving the packaged goods supply chain. Learn how the newest innovative products have become the key opportunites for CoMans. Data presented will iden tify these new products, explain how are they being packaged and the challenges these fledging brands are facing getting product to market. See how these emerging brands are adapting to meet new challenges with strategic CoMan and CoPack partnerships.
Ron Puvak Exec Dir Contract Packaging AssociationTHE CHALLENGES FACING GLOBAL SUSTAINABLE PACKAGING
11:30-12:15 PM
The packaging sector is growing at an astonishing rate, making it all the more important that materials used are suitably sustainable. Packaging materials are very visible to the consumer. There are growing pressures from consumers, retailers, packaging suppliers, regu lators and environmental groups to develop environ mentally friendly packaging. In addition, end-of-life processes need to improve packaging sustainability by reducing its societal and environmental impacts. The hugely significant and growing trend toward sus tainability is an important influence on the packaging industry. Consumers are demanding more sustainable systems, which are formalised and publicised in the media. The result is that sustainability has become a necessity for attracting consumers and protecting market share. It is now an expectation, not simply an identifier. Packaging, and more so plastic packaging, is receiving intense focus and scrutiny, resulting in sig-
W-20052); and the Contract Packaging Association (Booth N-4518)
The Forum schedule is listed below. Updates may be found on the PACK EXPO Internationl App or the show website.
Attendees also may participate in several other free educational offerings, in cluding: the Innovation Stage (Booth N-4560, N-4580, N-4585) with the new Processing Innovation Stage (Booth LU-7130) (see schedule, p. 28); the PACK to the Future Stage (Booth W-20025) (see schedule, p. 18); and the new Industry Speaks (Booth N-4565) (see schedule, p. 24). The Reusable Packaging Learning Center (Booth LU-6737) also will present educational sessions.
For more info, visit www.PACKEXPOinternational.com. SD
nificant advances in sustainability. However, this has been a challenging process. Pierre Pienaar will share his thoughts on what can solve the global packaging issue and make our planet more sustainable.
Prof Pierre Pienaar
President World Packaging Organisation (WPO)
THE EVOLUTION OF AUTOMATION
1:30-2:15 PM
Analysts present latest foresight into future of au tomation in packaging, processing and distribution. This recently published insight covers the challenges currently facing CPGs and the innovative automated solutions being explored by the industry.
Adrian Lloyd Research Dir Jonathan Pipe Sr Consulting Analyst Interact AnalysisCYBER ATTACKS: RESPONDING TO A BREACH
2:30-3:15 PM
Do you know what to do once you’ve discovered you’ve been hit by ransomware? What if your industrial con trol system has been taken over by hackers and your machinery is shut down? In this session, we’ll talk about what happens once a cybersecurity breach has occurred and cover a variety of incident response sce narios to empower you to be prepared.
Andy Lomasky Dir of IT PMMI
THE SIX TRAITS OF HIGHLY SUCCESSFUL EMERGENT BRAND/ COMAN RELATIONSHIPS
3:30-4:15 PM
Why do some emergent brands successfully partner with external manufacturing and packaging firms while others struggle or completely fail? Why have some re lationships flourished post-COVID, while others have struggled or flopped? Delve into the six traits of highly successful emergent brand/coMan relationships. With a nod to Stephen Covey, take a look at the specifics and the fundamentals of successful relationships, as well as
a few flameouts. We can’t name names but will dig deep into the best practices of emergent brands and their contract manufacturing partners and look at what can be done to increase the value of these vital and evolving supply chain relationships.
Carl Melville PresidentMelville Group on behalf of the Contract Packaging Association
WEDNESDAY, OCTOBER 26, 2022
DRIVING PACKAGING LINE PERFORMANCE
10:30-11:15 AM
Today’s packaging lines are increasingly more com plex and expensive, so ensuring performance is more critical than ever. This hands-on session will give par ticipants insight into getting the most out of their existing packaging lines by applying straightforward line-balancing techniques, in combination with the information already available from the machines. Learn how to keep your bottleneck machine running, recognize starved and blocked conditions and how to manage your machine speeds to ensure optimum performance. Learn how the PackML standard makes this performance information readily available to use.
Ron MacDonald Chairman
OMAC - Organization for Machine Automation and Control & Sr Principal Engineer Nestlé Purina Research
CYBERSECURITY AND THE IT/OT GAP
11:30-12:15 PM
Cybersecurity is becoming increasingly important in day-to-day manufacturing. IT and OT have the same end goal—to keep our plants safe. However, their differing priorities sometimes clash. Learn the differ ences and see how you fit to help make a safer, more secure plant floor.
Daniel Maeyaert VP, Manufacturing Operations Fallas Automation SD
THAT DELIVERS MORE, H SE








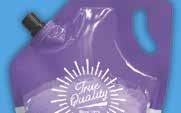



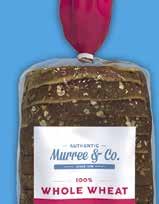
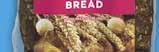

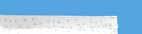
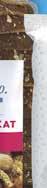
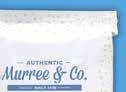





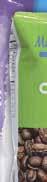
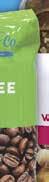




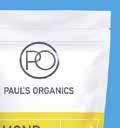





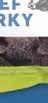








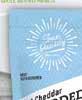





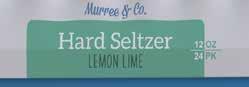









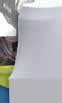





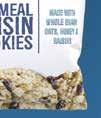


























Pouch-to-pouch recycling
Project shows pouches can be part of Circular Economy.
Dow Packaging and Specialty Plastics, a business unit of Dow (Booth W-22017, W-20052), together with HP Indigo, Reif enhäuser Group, Cadel Deinking and Karlville
Development (Booth LU-8037), have developed a pouch-to-pouch mechanical recycling concept. The approach uses a multi-stage process to contrib ute to a circular economy for digitally printed pouch
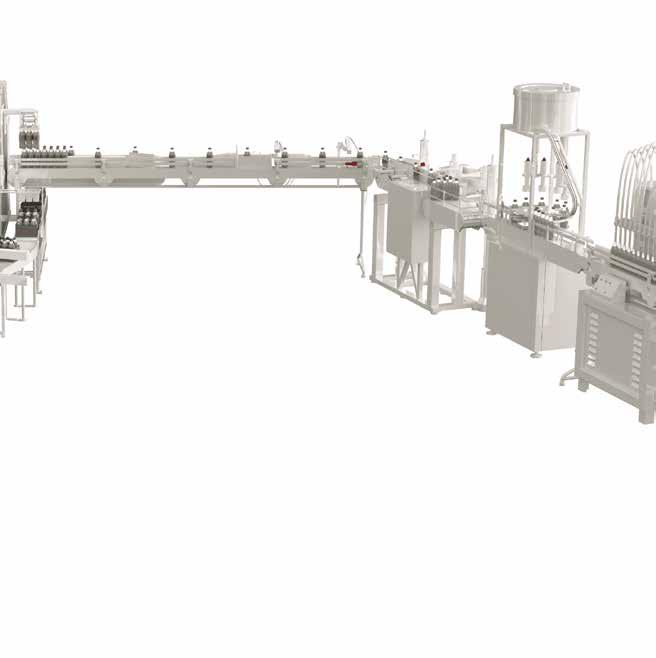
es. Starting with a polyethylene (PE)-based barrier food pouch designed for recyclability, the project team used mechanical recycling and de-inking to create a high-quality, recycling-compatible dishwasher pod pouch from machine direction-oriented polyethylene (MDO-PE) containing 30% recycled content.
In a next step, the team is working on a digital product passport pilot to allow for recycling-relevant packaging properties to be recorded and to make the pouch identifiable for high-quality recycling within post-consumer waste management.
OPTIMAL RECYCLING OUTPUT DESIGNED FROM THE OUTSET

Delivering the high-quality PE-pouch requires several steps in a coordinated, collaborative process.

“The requirements for plastic packaging products have never been more complex than today,” com ments Ralf Wiechmann, head of Film Innovation at Reifenhäuser. He continues, “...we have modified and enhanced our Reifenhäuser production lines to enable films and packages not just to be economical and functional, but to meet the vast demand for recy clable packaging based on monomaterial structures.
Model 15T/H
M o d e l 1 5 T / H

Thru or
“For this project, we’ve broadened our machinery expertise to coextrude the new resins on our highly flexible EVO nine-layer blown film line and produce PE-based packaging films at fast line speeds. This project shows that we can successfully both produce recyclable packaging, according to Recyclass and CEFLEX guidelines, and use recycled materials in high-value applications if we collaborate effectively along the value chain.”
“To create the new pouch, HP reverse-printed the recyclable MDO-PE film on the HP Indigo 25K digital press with the dishwasher [pod] pouch artwork to have it ready for lamination to the film using recycled resins at Dow’s Pack Studios,” adds Itai Shifriss, head of Indigo Business Supplies at HP.
“Thanks to Dow’s Pack Studios and a team of world-class scientists, we could apply our full exper tise and testing capabilities to make our resins work in this proof of concept,” explains Laura Evangelio, senior technical service and development specialist at Dow Packaging and Specialty Plastics. “The first PE-rich pouch was designed for recyclability with up to 5% ethylene vinyl alcohol in the total structure for barrier functionality, and Dow’s innovative resins provided a remarkable stiffness-toughness balance, low-temperature sealability, adhesion to extruded barrier layers and excellent bubble stability. For the second PE-based pouch, we used a high-performing solventless adhesive to enable the lamination of the MDO-PE film to the PE-film containing recycled resins from the first pouch. The project is not only a triumph in our industry’s sustainability efforts, but a
true example of focused scientific teamwork.”

“To produce the recycled PE resins for the second pouch, we used our de-inking technology to achieve the best outcome,” says Pablo Cartagena, business de velopment manager at Cadel Deinking. “The de-inking process is key because it effectively removes ink from the plastic surface to obtain a plastic with similar char acteristics to the raw virgin material, which helps to provide high-quality pouch-to-pouch recycling.”
“The Karlville pouch machine is one with the most compact footprint on the market, designed for ex tremely low setup waste and quick changeover, perfect ly suitable for recyclable materials,” says Gustavo Guzzi, EMEA sales manager from Karlville. “We are proud to be part of this project to manufacture a high-quality PE-based pouch which is itself already challenging. But to allow for recyclability is amazing, and with the right project partners it is now within reach.”
CLOSING THE LOOP FOR TRACEABILITY











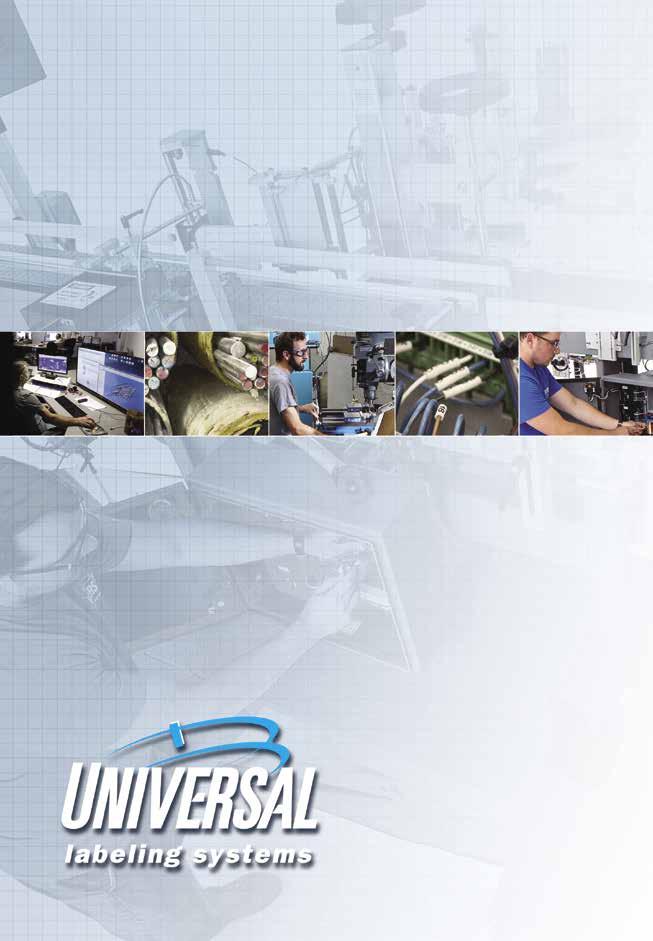
As a further evolution of the project, the companies are working to add digital traceability to the pouches in line with the R-Cycle initiative, a cross-company effort to develop an open and globally applicable traceability standard for sustainable plastic packaging. The aim of this initiative is to automatically record recycling-rel evant packaging properties during production by pro viding a digital product passport and to pass the infor mation through the value chain.
Using special markings, usable packaging can then be identified in the recycling process and sort ed into single-type fractions. This is the key to ob taining high-quality recyclates to continue efforts to close the loop.
“Dow is engaged to drive the adoption of PEbased packaging designed for recyclability, which works in recycling and recovers the value of the ini tial use as shown in this project,” concludes Jaroslaw Jelinek, global marketing manager for oriented PE technologies, Dow Packaging and Specialty Plastics. “Through Pack Studios, Dow is contributing to in dustry-scale testing and production capabilities to

accelerate the development of such projects glob ally. This announcement represents the latest in our efforts to address both climate change and plastic waste with our extended sustainability targets to pro
WHEN IT COMES
tect the climate, stop the waste and close the loop.”
For more info, visit www.dow.com, www.hp.com, www.reifenhauser.com, www.cadeldeinking.com, www. karlville.com. SD
OUR NAME.
FOR SPONSORING THE HOTEL KEYCARDS AT PACK EXPO
Sensitive x-ray systems debut
Systems detect hard-to-find contaminants.
Advanced x-ray inspection technology from Mettler-Toledo Product Inspection (Booth S-1714) offers advanced technol ogy that improves the ability to detect low-density contaminants in packaged food products. The new technology helps food manufacturers avoid prod uct recalls, reduces unnecessary product waste and associated costs and enhances product integrity and brand protection.
The new Mettler-Toledo DXD and DXD+ du al-energy detector technology is optimized for identifying foreign bodies such as calcified bone, low-mineral glass, rubber and some plastics. These types of contaminants are traditionally hard to detect within the “cluttered” or “noisy” x-ray images gen erated by overlapping and multi-textured products such as packs of pasta, chicken breasts, sausages and frozen potato-based goods.
Such applications are a perfect match for DXD and DXD+ high-quality detector technology, in conjunc tion with new Mettler-Toledo Advanced Material Dis crimination software tools. The software helps separate and remove the prominent material of the food product within the x-ray image, revealing the presence of any lower density contaminants. As a result of the accura cy and reliability of DXD and DXD+ detection, food manufacturers can be more confident that products are safe for consumers, and that they will benefit from re duced false-reject rates and product waste, helping to deliver a fast return on investment.
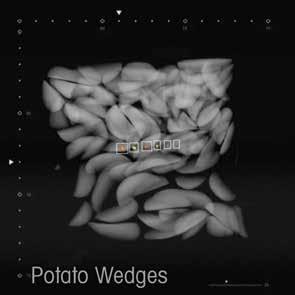
The reliable performance of this technology has
been shown in tests conducted by Mettler-Toledo, in which a range of different foreign bodies were hid den in 650g packs of chicken breasts. Table I illus trates these results.
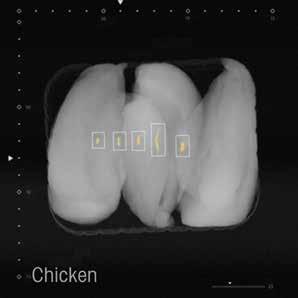
Detection of low-density contaminants was even more graphically illustrated in tests using a 500g bag of pasta as shown in Table II.
It must be noted that the test results are de pendent on individual applications. The test results shown are for guidance purposes only.
The new detector technology is available in two versions, giving customers two levels of dual-energy
x-ray performance:
• DXD: high-quality x-ray performance at an af fordable price; can operate in the same environ ments as single-energy solutions and can be used with line speeds typically up to 100m/min.
• DXD+: reliable detector technology for the most challenging applications; collects more data about the product being inspected; improved image analysis software provides clearer images with higher resolution; and DXD+ can be used with line speeds typically up to 45m/min.
“This new technology meets a real demand in the market for x-ray inspection; it is capable of de tecting low-density contaminants in a wide range of packaged food products,” says Gareth Jones, head of Engineering for Mettler-Toledo Product Inspection. He explains, “DXD and DXD+ provide high levels of detection in the most challenging applications our customers face. The benefits are both economic and reputational: They can better protect the integrity of their products and their brand, while also reducing cost and waste through improved false reject rates and less product throwaway.”
DXD and DXD+ dual-energy detectors now can be specified with new purchases of Mettler-Toledo X36 x-ray inspection systems. Only a small amount of extra operator training is required due to auto matic job setup and the similarities between the Advanced Material Discrimination software and the ContamPlus™ software that is familiar to existing Mettler-Toledo x-ray users.
Mettler-Toledo is offering personalized consulta tions to prospective users of this latest technology ei ther virtually or on a one-on-one basis at its Lutz fa cility. The consultations include live testing with brand owners’ actual products, as well as the opportunity to engage with experts in the x-ray inspection field.
For more info, visit www.mt.com/pi. SD
Almond producer improves quality
Metal separators and electromagnetic feeders meet goals.
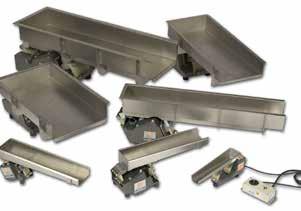
Almost 80% of the world’s almonds are pro duced in California, so it’s not too surpris ing that California Gold Almonds (CGA) is using state-of-the-art operational procedures and technologically innovative equipment to harvest and handle this increasingly popular cash crop.

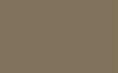
Like all food manufacturers, CGA needs to meet rigid food-safety guidelines, especially with the USDA, FDA and the British Retail Consortium (BRC), since the company exports almost half of its total volume to a European customer base, where al monds have always been a food mainstay.
Helping CGA maintain product purity are a se ries of Eriez® 66C and 46C electromagnetic feed ers, Model FF metal separators and a variety of Rare Earth (RE) plate and tube magnets from Eriez (Booth N-5214). The Eriez equipment is installed at the company’s Tenaya and El Roya processing plants in Modesto, CA, part of the lush San Joaquin Valley.
“Eriez helps us stay in compliance with the USDA and FDA, and it is a key for our BRC certification,” says Mick Tobin, GM at CGA. “The equipment gives us a cut above in the almond industry, and it gives us a competitive ad vantage from a technological standpoint. It allows us to build more efficient processing lines, while reducing hu man touching and handling of the almonds.”
some well pumps are powered via solar panels.
Along with the Eriez products, the company’s top-of-the-line, food-grade facilities contain cut ting-edge equipment to shell, sort, pasteurize, roast, dice, slice, mill and pack almonds. This enables CGA to have high-standard, confectionery-grade almonds. Technology on the shop floor includes optical and infrared sorting, low-moisture pasteurization and constant-vibration roasting.
ERIEZ EQUIPMENT ENSURES QUALITY
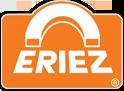
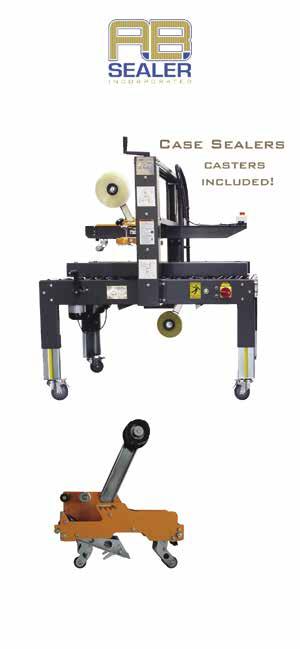
The Tenaya and El Roya processing facilities are a quarter mile from each other but serve different customer bases. Built about three years ago, the 35,000-sq.-ft. Tenaya facility processes almonds for domestic customers, while the larger, 84,000-sq.ft. El Roya facility, built two years ago, satisfies the company’s export business. By processing millions of pounds of almonds annually between the two fa cilities, CGA satisfies the demands of a vast array of customers, including yogurt and ice cream shops, chocolatiers, bakeries, gluten-free baking mix makers and industrial giants.
The Tenaya facility is designed for confection ery-grade almond processing at the retail level. Here, the incoming raw almonds fall freely through a se ries of Eriez Model FF metal separators, which are designed to detect all magnetic and non-magnetic metal contamination, even when embedded in the product. Metal contaminants are rejected through the “Quick Flap” reject unit.
equipment is installed on a main processing line conveying almonds at 20,000 lb./hr. and a secondary line conveying 15,000 lb./hr.
Plate magnets installed in chutes, spouts, ducts and pipes or suspended over conveyors remove tramp iron to help prevent costly shutdowns associated with machinery damage. Individual tube magnets are used as a quality-control check of dry bulk materials and in many other ways where a powerful, portable magnetic power source is needed.
“I like the consistency of the feed rates on our main conveyor lines at both facilities,” says Tobin. “The metal detectors are a key component of our Critical Control Point, especially when we are audit ed by the FDA for food-quality standards.”
“I’ve been in the food processing business for more than 20 years, and I’ve had a chance to see many different operations. I’ve been able to take my experience and Eriez technology to help maintain a highly efficient processing operation here at CGA,” Tobin concludes.
For more info, visit www.eriez.com. SD
Almonds are California’s top agricultural export and the largest tree nut crop in total dollar value and acreage. They also rank as the largest U.S. spe cialty crop export, according to the Almond Board of California. Those figures correspond with CGA shipments as the company ships 70% of its crop in ternationally, according to Tobin.
CGA produces premium almond ingredients by managing control from tree to package. The almonds are grown primarily on farms that the company owns and operates in the heart of almond country. The 35-employee company also collaborates with neighboring farmers, whose almonds meet CGA’s standards for quality and freshness.
Almonds grow from tree varieties developed using natural breeding, meaning the almonds are not ge netically modified (non-GMO). CGA pumps water from its wells supplied by the Sierra Mountains and rents honeybees to pollinate the almond orchards;
Next, the Eriez 66C and 46C Hi-Vi electromag netic feeders properly convey the precise amount of raw almonds—approximately 12,000 lb./hr.—that eventually pass through an optical sorting line and into the packaging process.
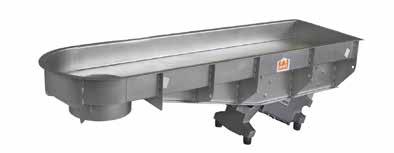
Eriez feeders feature a totally-enclosed patent ed magnetic drive and can feed practically any bulk material from micron size to bulky chunks. Standard systems operate at temperatures up to 130 F, while high-temperature units handle up to 300 F.
“We have the Eriez feeders and metal separators in strategic locations to help us monitor contamina tion and maintain accurate feed rates,” says Tobin. “The Eriez equipment gives me a lot of confidence for precise operation, especially when we also have our optical sorting, hand sorting and dicing, slicing and packing going on.”
Meanwhile, at the El Roya plant, two Model FF metal separators and several RE plate and tube mag nets help detect and remove contamination from almonds destined for export to Europe. The Eriez
Future Innovators
SHOWCASE
ATS machines fill, seal, overcap
With today’s growing global demand and market for packaged foods, ATS Engineering (Booth S-3274) is recognized as a manufacturer of precision packaging equipment for the food industry.



The company combines years of experience, technological expertise and in tense understanding of end-users’ expectations to provide customized systems. Over the years, it has earned a worldwide reputation as a single-source, highly specialized supplier of high-speed filling, sealing and overcapping machines for a wide range of applications.
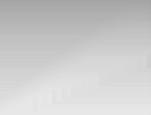




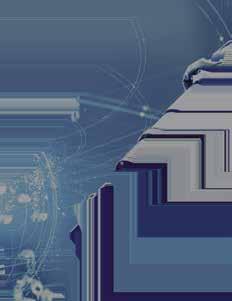
As a custom designer and manufacturer of high-quality precision equipment, ATS offers durable rotary and straight-line machines that package a variety of liquid and viscous products, including cottage cheese, sour cream, yogurt, ricotta, ice cream, dips, margarine, cocktail sauce, honey, pesto, dough, batter, garlic and horseradish.

Come see Chicago-area high school students showcase their “bot skills”.
Interact with the bright minds of the future and ask questions about their innovative robot designs. Located in the West Hall in Booth W-21028
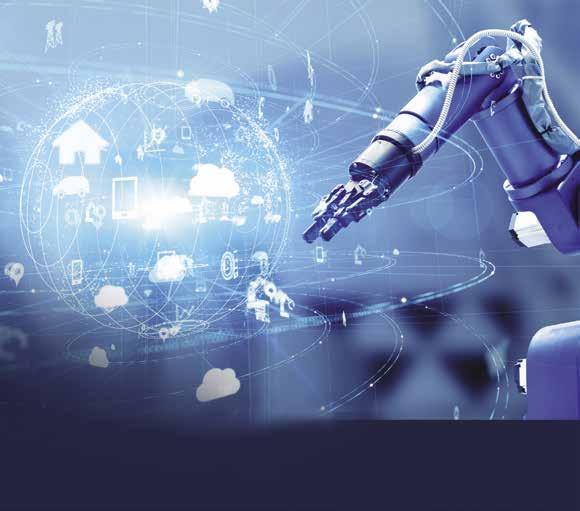
Sunday - Tuesday | 9:00 am - 5:00 pm Wednesday | 9:00 am - 3:00 pm
Adaptable for either single or multiple filling operations, the affordable ma chines meet and/or exceed USDA, FDA and 3-A standards. Since long-term performance is paramount, all equipment is rigorously tested prior to being shipped so systems provide years of trouble-free operation.
Beyond simply building equipment, the company serves as a packaging engi neering consultant for design, build, installation, startup, training and follow-up needs. A long history of applications experience enables it to ensure end users receive optimum results through every stage of production.
For more info, visit www.atseng.ca. SD
For more information about supporting student programs, visit the PMMI U booth at W-20042.

by:




HITACHI (BOOTH S-3752) AND SULLAIR (BOOTH S-3752) FOR SPONSORING THE ATTENDEE BAGS AT PACK EXPO INTERNATIONAL.
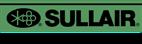
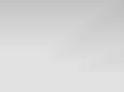
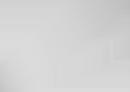
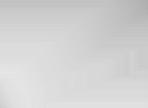



















Pavilions help narrow the search
Dedicated floor space groups interests.
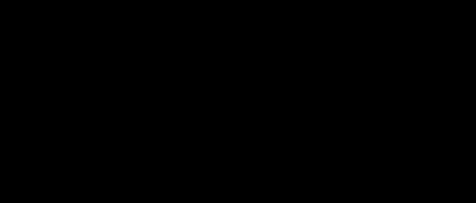
Dedicating certain areas of the show floor to pavilions devoted to specific technologies, verticals or business concerns helps attendees quickly lo cate, compare and contrast what their organization needs.
This year’s show features several pavilions. The Processing Zone, joined for the first time at PACK EXPO International by the Processing Innovation Stage (Booth LU-7130) (see schedule, p. 28), returns to present the latest break throughs in processing. It’s on the upper level of Lakeside Center.
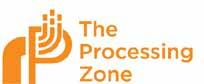
New this year, The Healthcare Packaging Pavilion in the West Hall is devoted to innovations for pharmaceuticals, biopharmaceuticals, nutraceuticals and medi cal devices. With 70,000 sq. ft. of exhibits, it’s a life sciences show within the show.
Another newcomer is The Logistics Pavilion in the North Building. With the boom in eCommerce, it is the place to find targeted solutions related to the supply chain, including warehousing, fulfillment, distribution logistics services and transportation providers.

Returning favorites include the Containers and Materials Pavilion, a prime destination for attendees looking for innovative containers and materials to meet sustainability goals, refresh a brand or launch new products. This pavil ion in the West Building also houses award-nominated packaging solutions in The Showcase of Packaging Innovations® (Booth W-20052), sponsored by WestRock (Booth S-2130)
The Confectionery Pavilion at the back of the South Hall highlights candy trends and tech. Visit the Candy Bar Lounge (Booth S-2583) for some casual networking and idea sharing. It’s hosted by the National Confectioners Asso ciation and sponsored by Syntegon Packaging Technology (Booth S-3514)
The PACKage Printing Pavilion features digital printing and converting, labeling, coding and marking technologies. It’s located in the South Building.
The Reusable Packaging Pavilion, sponsored by the Reusable Packaging Association (Booth LU-6737), showcases reusable packaging solutions to help reduce waste, cut costs and gain supply chain efficiency. The pavilion houses nearly 50 exhibitors, as well as the Reusable Packaging Learning Center and its roster of educational sessions.
The Education and Workforce Development Pavilion (Booth N-4550) in the North Building is PACK EXPO International’s one-stop-shop for resources to strengthen and grow the workforce.
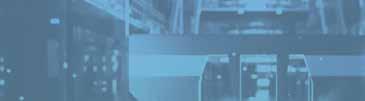
The nearby Association Partner Pavilion (see story, p. 22) houses leading as sociations dedicated to advancing packaging and processing and offering signif icant resources, insights and expertise in a central location.
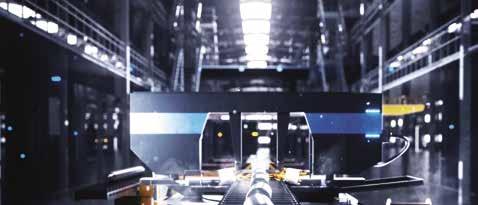
For more info, visit www.PACKEXPOinternational.com. SD
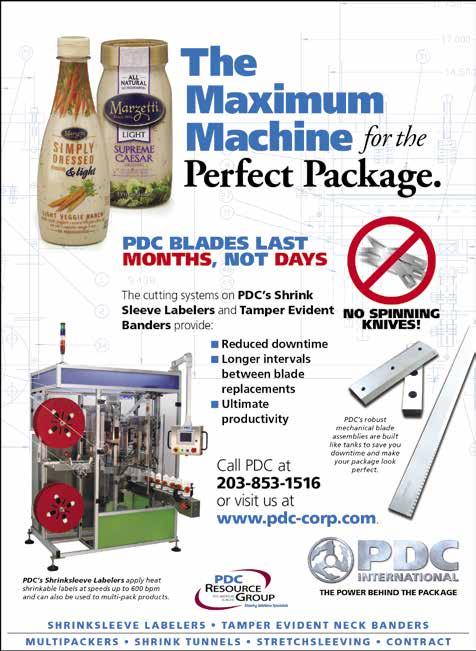
Download the Mobile App to:
Search exhibitors, products and educational sessions
Access Your My Show Planner and add to your personal agenda
Navigate from booth-to-booth using interactive floor plans
Get news and notifications about show happenings, giveaways and more
Vote in the 2022 Technology Excellence Awards
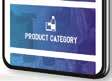
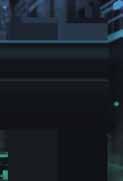
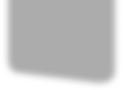
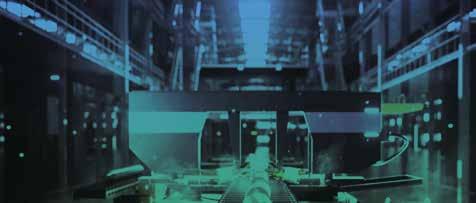

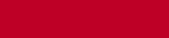
Search “PACK EXPO” in the App Store or Google Play, or scan the QR code here:

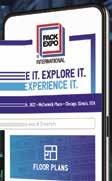
System handles cookies, crackers
Linear motors provide gentle handling.
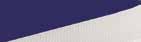
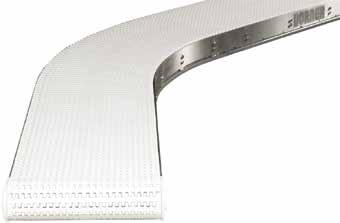
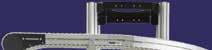
The IDH (Intelligent Direct Handling) pickand-place system from Syntegon, parent company of Syntegon Packaging Technol ogy (Booth S-3514) handles and portions cookies and crackers. On display for the first time in com bination with a Pack 202 flow-wrapping machine, the equipment is based on newly developed picker technology using linear motors. This not only en sures especially gentle product handling but also of fers a compact design along with high output and the option of loading different products both flat and on-edge—making it a highly efficient and flexible addition to Syntegon’s pick-and-place portfolio.
The IDH system picks the cookies directly from the process belt to keep the transport distances be tween the oven and the packaged product as short as possible, thereby reducing abrasion. This results in less product waste and reduces cleaning require ments because less product residue accumulates.
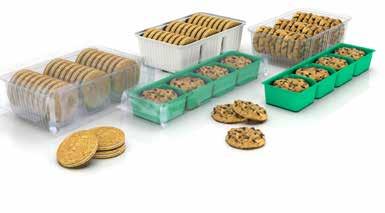
An integrated camera-based vision system detects the position and shape of the cookies and crackers on the infeed belt and transmits this information to the picker control system. It identifies and reliably pro cesses different product patterns or random arrange ments. Each picker can be aligned individually to ensure all products are placed into trays or the infeed chain correctly. Moreover, an integrated mini buffer automatically fills incomplete product rows, thus increasing system efficiency.
FLEXIBLE AND FUTURE-PROOF
either on-edge or flat. This allowed us to omit long belts with chicanes [curves] and make the system de sign even more flexible.”
COMPACT DESIGN, HIGH OUTPUT
With its sophisticated overall concept, the Syn tegon IDH system makes the packaging process less complex: its space-saving design not only minimizes conveying distances, but also allows for new system layouts traditionally used in bar production. Despite its compact dimensions, the IDH unit achieves a maximum output rate of up to 800 products/min. Combined with its low reject rate and short down times, this ensures high overall equipment effective ness (OEE).
GENTLE HANDLING
The linear motor bar forms the heart of the new machine, as Philipp Kathan, lead engineer IDH at Syntegon, explains: “With a nominal 30 cycles/min., the bar’s up to 40 pickers pick the products from the process belt and place them into a flow-wrapper in feed or into trays. Thanks to the slow and smooth movements of the linear motor movers, the cookies and crackers are handled with minimal mechanical stress and vacuum application—preventing breakage or damage to the product surface and ensuring opti mal production efficiency.”
In addition to gentle handling, the IDH system impresses with its product and pack style flexibility: The number of vacuum pickers can be adjusted depending on the product and the production volume. For example, manufacturers can increase the number of vacuum pickers to as many as 40 as process output increases. When integrated into horizontal packaging lines, the Syntegon IDH system provides a high degree of flexi bility to handle different pack styles.
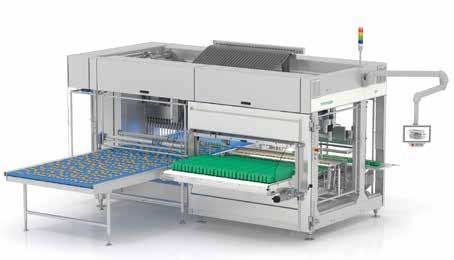
Daniel Bossel, product manager at Syntegon, explains, “With the IDH, we are launching a compact and flexible solution that offers manufacturers a variety of options for packaging different product shapes and siz es. Cookies and crackers are picked directly from the process belt and placed into trays or the infeed of the downstream flow-wrapping machine
“The Syntegon IDH complements the Syntegon RPP pick-and-place platform launched in 2021 per fectly,” says Bossel. “While the RPP’s delta robots pick up to 120 products/min. from a narrow belt, the IDH is ideal for higher volumes and particularly wide process belts. With our comprehensive portfo lio for the cookie and cracker industry, we are able to offer our customers tailored system solutions with a low total cost of ownership from a single source.”
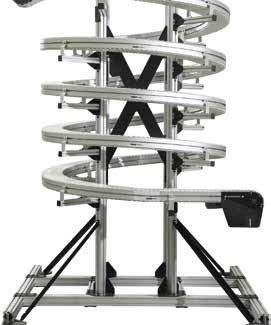
For more info, visit www.syntegon.com. SD

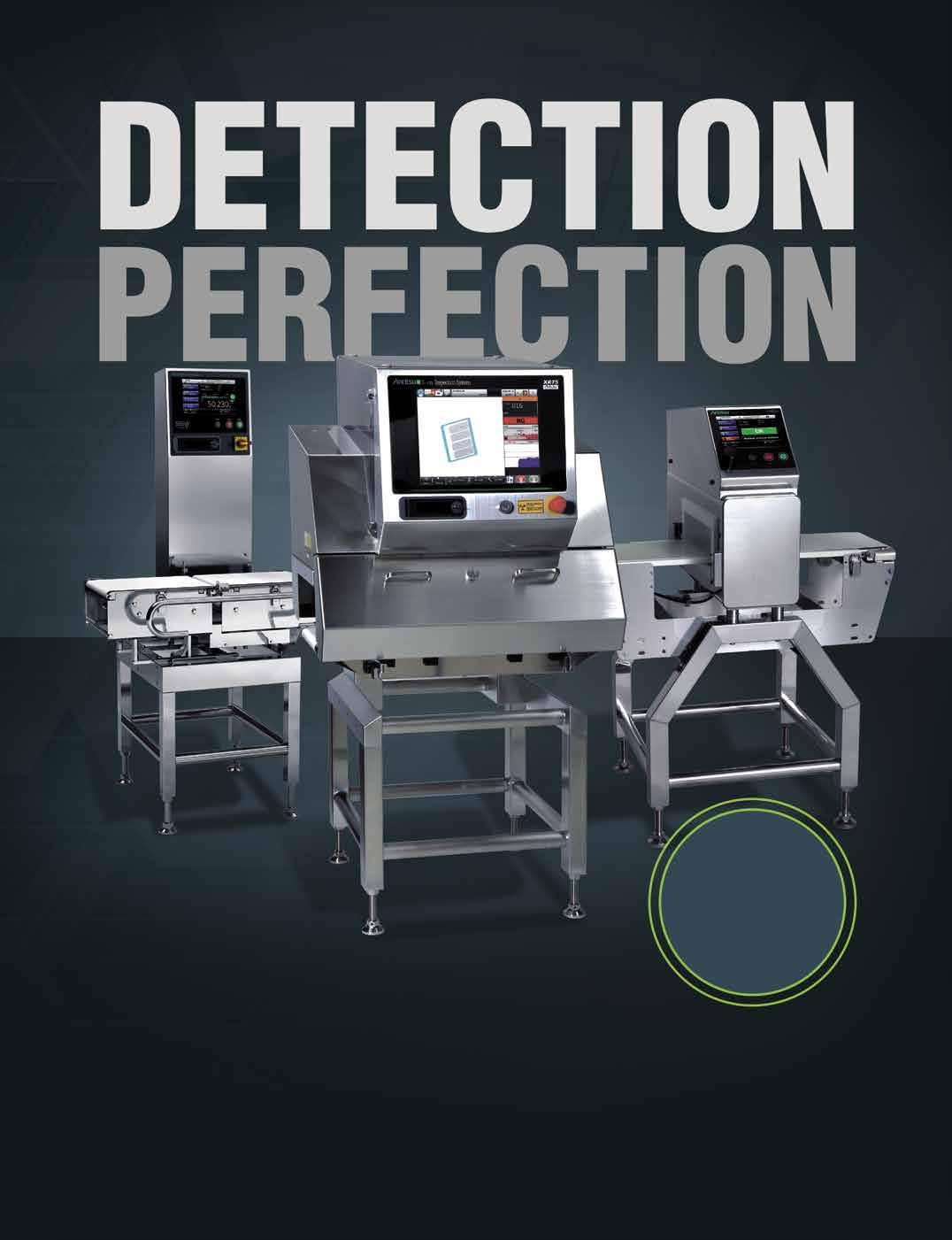
Mt. Olive streamlines production
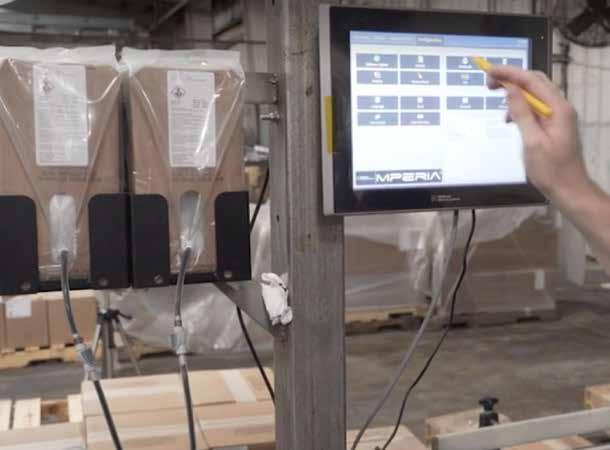
Upgrading marking and coding cuts downtime, expenses.
Mt. Olive Pickle produces millions of cases of pickles, peppers and relish annually in a 300,000-sq.-ft. facility located, appro priately enough, in Mt. Olive, NC. The over 95-yearold company’s 10 production lines support both sixpack cases and 12-pack cases of Mt. Olive-branded products as well as third-party products.
Like all manufacturers of packaged goods, Mt. Olive Pickle has long placed human- and ma chine-readable marks such as date codes and bar codes on packaging as part of the manufacturing process. As marking and coding requirements have evolved over the years, the company found that its dated marking equipment required substantial main tenance and did not provide the flexibility needed for the variety of tray packs the company produces. Additionally, the printed barcodes were inconsistent and not always readable, causing quality holds and potential rejection at distribution centers.
support. This ultimately led Mt. Olive to Matthews Marking Systems (Booth S-2142)

Beckman recalls, “We looked at three or four other companies and other marking systems, but we chose Matthews for a variety of reasons. Number 1, we liked their technology, and the setup and custom ization we were able to do. Matthews worked with us throughout the whole project, including a long testing timeline, and we were able to do customiza tions that we needed. The customer service was just excellent.”
The marking solution Mt. Olive Pickle selected is centered around MPERIA L-Series thermal inkjet printers (TIJs) used on 10 of Mt. Olive’s manufac turing lines. The L-Series TIJ printers are used to place high-resolution marks on both sides of tray packs and cases.
For maximum flexibility, the compact L-Series printheads can be stitched together in an array to print messages ranging from ½-in. (12mm) to 2-in. (50mm) in vertical height with up to 600-dot-per-in. resolution. This configuration flexibility has allowed Mt. Olive to eliminate the redundant sets of printers it had previously and consolidate everything into one print area on each line.
CENTRALIZED CONTROL
Beyond the challenge presented by unreliable high-maintenance equipment, another ongoing challenge for manufacturers is figuring out how to
efficiently update and manage the messages being placed on products and cases without introducing errors. At Mt. Olive, this entire process has been streamlined and centralized using networked, easyto-use MPERIA controllers.
The MPERIA platform gives manufacturers con solidated control over marking and coding across primary, secondary and tertiary packaging lines and integrates with virtually any coding equipment (both from Matthews and other providers), data files or enterprise system. As a result, Mt. Olive did not need to re-engineer its data systems or modify workflows to adopt modern print technology.
Further adding efficiency, MPERIA netFolder, a shared folder technology, synchronizes variable data between MPERIA and existing enterprise systems. This provides an automated way to push updated messaging to the printers on a packaging line with no need for specialized server software or hardware. And since MPERIA netFolder doesn’t require an internet connection or access to enterprise systems, there’s no cybersecurity risk.
REDUCED SCRAP AND REWORK
With this solution in place, Mt. Olive found that the crisp, legible barcodes produced by the TIJ print ers resulted in a notable boost in overall equipment effectiveness. Cases and tray packs of pickles did not have to be reworked because of poor print quality, which has helped to keep lines running at full speed
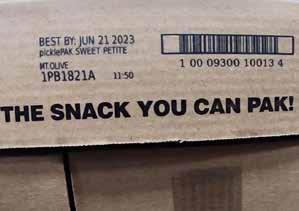
Among the challenges were older dot-matrixstyle printers that were prone to clogged ports. This would leave lines in barcodes that made them un readable. Moreover, the legacy system was inflexible and forced Mt. Olive to deploy two sets of printers to accommodate the variety of cases and tray packs. And customers wanted higher-quality marks that would enable barcodes to be scanned from a greater distance.
Making things worse from a cost standpoint, keeping the older printers at some level of service ability was a full-time job, literally. “With the pre vious printing system, we had one technician who spent probably 90% of his time doing nothing but maintaining the print systems,” says Larry Beckman, vice president of manufacturing.
EXTENSIVE SEARCH
Clearly it was time to modernize. But with many marking technologies and vendors to choose from, what option and supplier would be the best fit? High on the list of requirements were modern, low er-maintenance technology and top-tier customer
while reducing costly and disruptive quality holds at distribution centers.

“We saw a reduction of 70–75% downtime related just to printer technology. And then we reduced our quality holds related to printing issues around 80% just by going to the new technology,” says Beckman.
And, unlike the legacy marking system that required regular monitoring and maintenance, the TIJ printers proved to be easy to maintain. Instead of having to shut down lines to clean printheads, Mt. Olive operators simply swap print cartridges, which include a new printhead, when ink runs low.
FULL ROI
For operations printing at high volumes across a large facility, the cost of ink can add up quickly. To help manufacturers manage ink costs, MPERIA includes a built-in cost calculator that allows users to optimize each mark by fine-tuning variables such as message height, length, font and resolution—all from a Smart phone-like touch screen.
And, as it turns out, this can lead to impressive savings and return on invest ment. For Mt. Olive, the MPERIA platform has led to a 30% reduction in the cost per mark on cases and tray packs.
Add it up, as David Martin, a project manager for Mt. Olive explains, “Through ink savings alone, we will have the entire cost as a capital project paid off in two-and-a-half years.”
Martin adds that the time to ROI calculation would be much faster when maintenance and labor hours savings are factored in, which he says have been “immense.”
ROLLING WITH CHANGE
Across the manufacturing, packaging and distribution landscape, automation is playing an increasingly important role as organizations struggle with staff shortages and high costs. Legible, machine-readable marks, including 2D bar codes, that can be applied consistently and cost-effectively are vital to success in this changing world.
This is where reliable print technology with responsive support can be a sig nificant asset.
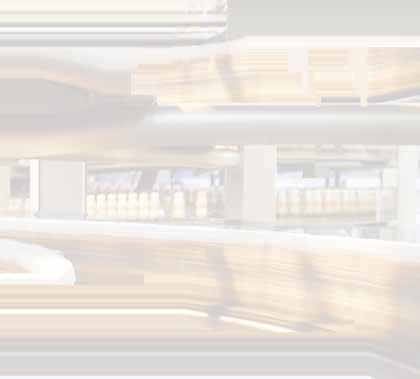
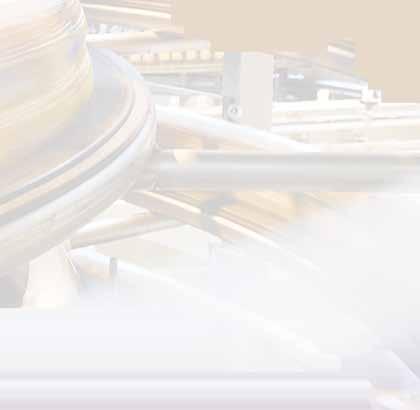
Says Beckman: “Matthews has been very responsive to our needs, very prompt in providing assistance and help when we need it. I’ve been very pleased with the whole Matthews system including the customer service, reliability of the equipment and the quality of the print that we get out of the system.”
For more info, visit www.matthewsmarking.com. SD
Spiral conveying. Straight up!
As the market leader in spiral conveyors in the bottling and canning industry we think of solutions for elevating and accumulating cans and bottles. It’s what we do. At AmbaFlex it’s not just about building the right equipment, it’s about developing a special solution for you. Here’s to spiral conveying.
Spiral Elevators & Accumulators for pack, single file and mass flow handling.

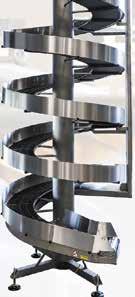
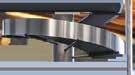

Robotics help boost production
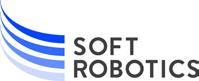
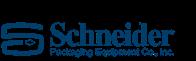
Small potato producer contains costs, addresses growing sales.
Using robotics to fuel growth while staying competitive, a leading North American grower, shipper and packer of bite-sized po tatoes is keeping costs down and employment and production up.
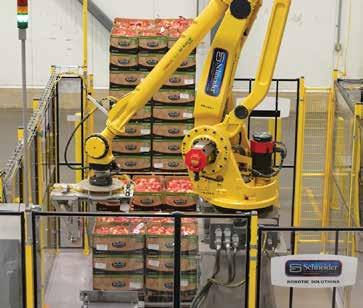
The multi-generational potato farmers of Tasteful Selections began in Nebraska, relocating to Arvin, CA, to take advantage of the rich farmland and yearround growing season. The journey since has been not only geographical but one of innovation as well. Always searching for business growth opportunities, the company pioneered the category of bite-sized potatoes to offer consumers a simpler and more con venient source of nutritious potatoes.
Tasteful Selections also employs state-of-the-art production technology. To maintain high standards of quality, flavor, freshness, size uniformity and best prac tices for sustainability, the company owns the entire planting, growing, harvesting and packaging process. And when it wanted to expand and optimize its potato production, robotic automation was seen as the key.
ing to our employees to bring consistency to the line and bring consistency to our costs.”
Tasteful Selections got its start in robotics with the help of Schneider Packaging Equipment (Booth S-3500), a FANUC Authorized Systems Integrator. The potato company liked Schneider’s OptiStak, which creates recipes for the layers of boxes to be stacked on the pallets. Based on FANUC software, OptiStak quickly optimizes pallet configurations and enables op erators to change patterns on the fly.
“They have been turnkey, out of the box, mini mal programming that we needed to do on our end, and super, super successful on creating consistencies throughout our plant,” Waldo says.
In just a few years, Tasteful Selections has grown from 100 workers to close to 900. The robotic pallet izers have also made a difference in employee acci dents and injuries. Previously, workers stacked 50-lb. boxes onto pallets up to 92 in. high, but now the ro botic palletizers perform that task. “We were able to come up with a very modular, unique design for our palletizers,” says Justin McHenry, vice president of plant operations for Tasteful Selections. “It’s capable of picking up any one of our boxes in this facility, stacking a pallet as high as will fit in the back of any refrigerated truck, and does all that without requir ing any tooling change.”
FINDING THE RIGHT ROBOTIC GRIPPER
As the company increased the speed of the pro cessing lines, manually packing the bags of potatoes in boxes became an issue. The packing space did not allow for additional line staff. Plus, the company

wanted to minimize the human touch points to en sure the best food safety and quality practices.
“We want to make sure our potatoes are the safest they can be from farm to fork,” says Lindsey Mebane, food safety manager for Tasteful Selections. “Before we had the robotics, everything was done by hand. For food safety, that is a little bit of a concern because there are more hands touching the product. Granted, they are wearing gloves, but there’s still human contact.”
Robots handling the potatoes, however, were cause for concern as well, since they could potential ly cause more bumps and bruises than human han dling. Having not only a food-safe but gentle robotic solution was of utmost importance.
“We are constantly planting, harvesting and picking the freshest product for our customers,” says Nathan Bender, COO for Tasteful Selections. “We’re growing so fast that without automation, we can’t keep up.”
Robots from FANUC America (Booth N-6116) have been a big part of Tasteful Selections’ journey, including 11 FANUC M-410iB palletizing robots and five FANUC M-3iA delta robots for case pack ing. “What we’re trying to do is flatten our curve of our costs, so we can provide a great service to our customers and keep our pricing down,” says Ernie Waldo, plant manager for Tasteful Selections. “As we’ve rolled out automation, it has been a real bless
Tasteful Selections approached Soft Robotics (Booth N-5230), a supplier of advanced technolo gies that enable automation of a wide variety of products, to find a robotic gripper that could reliably grab a shifting bag of potatoes while easing the posi tioning tolerance requirements of the robot and the machine vision imaging system guiding it. The solu tion was Soft Robotics’ mGrip soft gripper.
“The end-of-arm tooling for this application needed to be able to handle a lot of variability,” ex plains Ben Gibson, applications engineering manag er of packaging solutions for Soft Robotics. “These are mesh bags of baby potatoes. Depending on how
“If we don’t innovate, we’re not going to be competitive. Our prices will go up. We haven’t taken a price increase in 10 years on our product. We’re able to maintain that through automation.”
—Justin McHenry Tasteful Selections
the product settles on the belt, it can end up in lots of different shapes or sizes. We were able to handle
all of this with a single end-of-arm tool.”
Plus, the unique gripper material allows the bags to be grabbed without any concern of damaging the product by applying too much force or using a rigid gripping tool. “We chose Soft Robotics because of the softness of the plastic and its integration with the FANUC robot,” says Emilio Lemus, automation manager for Tasteful Selections. “It speeds up the process a lot, and at the same time, takes care of our product the way we want it.”
The pneumatic-actuated tool allows the operators to control the air pressure to either tighten or loosen the grip on the bags of potatoes. It also knows exact ly the correct number of bags to fill a box as well as where to place them in the box.
“It helps with the quality—hands aren’t being harsh on them—and it helps with the overall effi ciency because we are sending what we are supposed to be sending out, so it eliminates a lot of human error,” Mebane says.
INNOVATION GETS RESULTS
As a result of the mGrip-enabled robotic work cell, Tasteful Selections was able to exceed 45 bags/min. and increase its packing line’s overall equipment effective
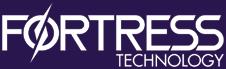
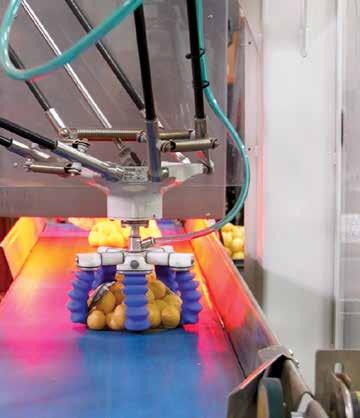
ness by 15%, achieving 100% ROI within nine months.

Adding robotics also enabled the company to achieve another advantage in 2020—a way to easi ly social distance employees on the production line. “Because of the robotics, we had fewer people on the line, so that really helped with the social distancing,” Mebane says. “It allows the people to be farther apart because the person putting the bags in boxes isn’t standing right next to the person putting boxes on the pallet.”
With the investment in automation, Tasteful Selections has been able to grow very quickly as well as maintain the quality of its small potatoes for customers. And it’s all been done at an attrac tive price point.
“If we don’t innovate, we’re not going to be competi tive. Our prices will go up,” McHenry says. “We haven’t taken a price increase in 10 years on our product. We’re able to maintain that through automation.”
For more info, visit www.fanucamerica.com, www.schneiderequip.com, www.softroboticsinc.com. SD
Editor’s Note: The original version of this article appeared in August 2022 in ProFood World
INSPECTION SYSTEMS

The Raptor is a highly accurate, fully integrated checkweighing system, specifically designed for high care food production environments.
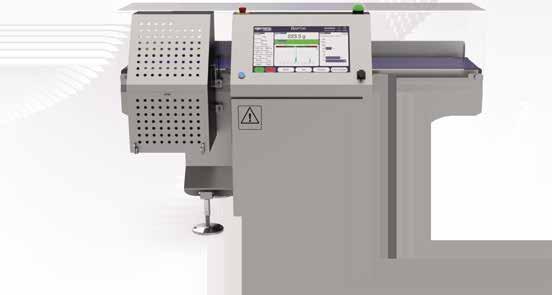
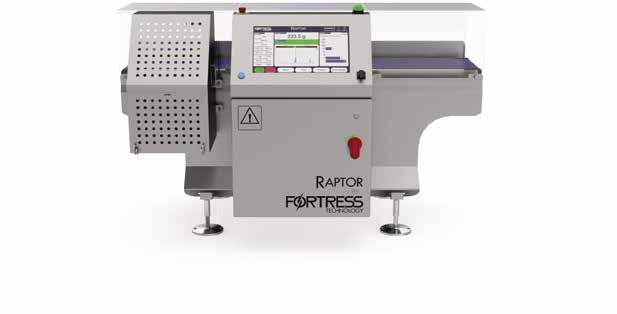
The Raptor is employed to verify the weight of each product and reject non-conforming packs. The system has been designed, engineered, and constructed to the highest care/food grade engineering standards. It is capable of processing packaged products up to 8 kg.
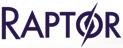
Checkweighing System

Vote now to pick best TEA finalists
Winners in each category will be announced this afternoon.
Exhibitors nominated many candidates for the 2022 Technology Excellence Awards (TEAs). This group was narrowed down to three finalists in each category, and attendees at PACK EXPO International will select the winners.
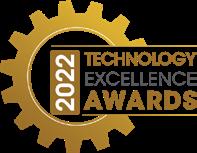

Voting continues through noon today (Tuesday, Oct. 25), after which winners will be announced. There are three ways to vote: onsite at the Attendee Solutions Center in the North Hall Concourse and Lakeside Upper Hall Lobby; on the PACK EXPO International mobile App, sponsored by ProMach (Booth N-5534, N-5540); and online.
Finalists, described below, were chosen by the TEA Panel:
• Aaron Hand, editor-in-chief, ProFood World (Booth N-4550)
• Jane Chase, executive director, Institute of Packaging Professionals (Booth N-4523, W-20052)
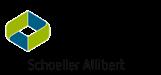
• Keren Sookne, director of Editorial Content, Healthcare Packaging (Booth N-4550)
• Matt Reynolds, editor, Packaging World (Booth N-4550)
• Ron Puvak, executive director, Contract Packaging Association (Booth N-4518)
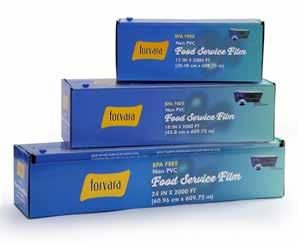
FOOD/BEVERAGE FINALISTS
Maxpack 2023 MFT 7 Ultimate Range vertical form/fill/seal machine from Maxpack Machinery (Booth S-2396)
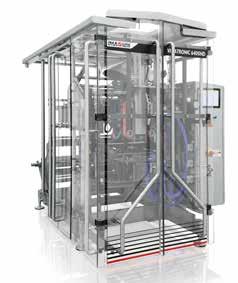
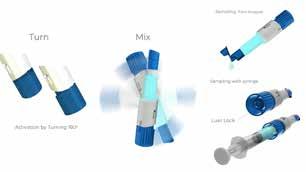

The Maxpack MFT 7 Ultimate Range machine is both rugged and versatile. Engineered on Maxpack’s signature 360-degree open-frame design and built using a multi-format technology to work in dry, hu mid and frozen environments, the machine can form rollstock into a wide array of bag formats includ ing pillow, side gusset, flat-bottom, INNO-LOCK® and EZ-Stand®.
rience for cold-fill and aseptic beverages, including still water and functional drinks. When opened for drinking or pouring, the closure is placed adjacent to the neck at a wide angle, ensuring consumer con venience and easy reclosing. Because the closure re mains with the bottle, caps are less likely to become litter or plastic waste.
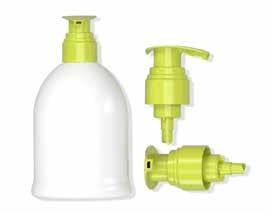
Proxima tethered closure from Berry Global (Booth N-4727)

The tethered closure stays attached after the tamper-evident band has been broken. The design enhances the recyclability of the closure while of fering a convenient and comfortable drinking expe
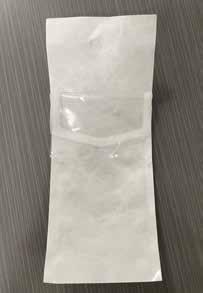
Corona 20-pocket beer crate from Schoeller Allibert (Booth LU-6820)
In 2021, Anheuser-Busch InBev set the goal of developing a highly sustainable beer crate for one brand. Since this brand has a strong focus on pro tecting the natural world, especially the oceans, high-density polyethylene (HDPE) regrind with recycled plastic from the maritime industry, which includes fishing lines, nets and ropes, was recom mended. The Corona 20-pocket beer crate consists of at least 91% recycled plastic with a minimum of 20% maritime waste. AB InBev’s most sustainable packaging to date, the beer crate is the first on the market to use maritime industry waste plastic.
GENERAL PACKAGING & PROCESSING

Amcor Clear Anti-Grease Jerky Pouch from Amcor Flexibles North America (Booth S-3705, S-3814)
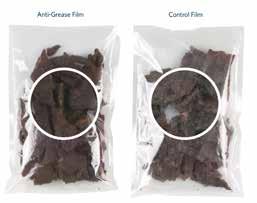

With clear, anti-grease film, beef jerky and oth er meat snacks can power up shelf appeal and gain a competitive advantage. The breakthrough formula prevents grease droplets and smears from appearing on the package surface and eliminates “scratched” windows caused by fatty buildups in the jerky. As a result, brands can significantly enlarge clear product windows, unleashing design possibilities. Because the grease is managed, jerky snacks look leaner, healthier and more delicious.
through a specially engineered combination of select food-grade polymers and process innovation, the film is free from any taste or odor transfer and offers exceptional strength, tackiness and see-through clar ity. The film reliably overwraps a variety of food con tainers without any film entanglement and assures zero spillage.
PERSONAL CARE/PHARMA
Forvara® foodservice films from Special ty Polyfilms (India) (Booth W-27008)
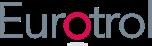
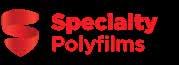
A recyclable PE-based foodservice film provides an alternative to polyvinyl chloride while emulating its characteristics and functionality. Manufactured

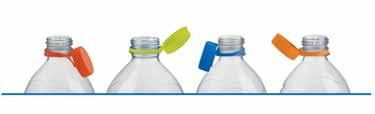
IMA Ilapak Vegatronic 6400 vertical bag ging machine from IMA (Booth S-2514)

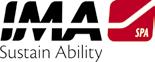
The continuous-motion vertical bagger delivers sanitary design, accessibility, fast changeover and overall equipment effectiveness with full open-frame design; IP66- through IP69K-rated electrical com ponents; AISI 304 stainless steel film reel carriage, rollers and bearings; sloped cabinet tops and splicing table; inclined forming tube support; and European Hygienic Engineering & Design Group-compliant electric panel. Efficiency has been enhanced via a more user-friendly human/machine interface, vacuum-as sisted splicing table, swivel-arm-mounted forming tube and pneumatically activated film reel shaft.
CueSee Mix dual-chamber device from Eurotrol (Booth W-13027)
The patented unit for storing liquids/powdered/ lyophilized components eliminates the need to man ually combine or dilute product components for in vitro diagnostic, pharmaceutical and cosmetic prod ucts. The dual-chamber device separates fractions, preventing premature reactions between components and enhancing ease of use and safety. A simple twist ing motion allows the previously separated compo nents to combine. After mixing via a “static stirrer,” the product is ready to use via the integrated dropper bottle or aspiration into a syringe.

tures include compatibility with high-quality graph ics for excellent product recognition. The material also offers a high degree of flexibility, optimum han dling and high throughput on packaging equipment.
Amcor High-Barrier PCR Pouchstock from Amcor Healthcare Packaging (Booth W-16031)
Amcor’s High-Barrier PCR Pouchstock contains up to 30% post-consumer recycled (PCR) content, which is restricted to the exterior layer of the lami nate. There is no PCR in the product-contact sealant

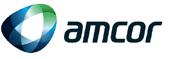
Compact capsule weight checker from WORK Microwave (Booth W-20038)
A microwave-based approach to capsule check weighing ensures correct dosing. Typically located
aging, conventional capsule checkweighers are large, require multiple, parallel mechanical weighing cells to achieve desired throughput, are sensitive to vibra tions and require the capsule to be stationary for the measurement. The microwave-based unit overcomes these drawbacks with a high-speed 50,000 capsule/ hr. channel. The vibration-tolerant, compact, stack able form factor can be integrated on filling or pack aging machines.
SUSTAINABILITY
ClipCombo™ from Graphic Packaging International (Booth S-1730)
The high-speed ClipCombo machine quickly changes over between two paper-based multipack styles. The machine range includes:
• KeelClip™ and EnviroClip™ paper-based clips for can multipacks
• GripClip™ and EnviroClip™ paper-based clips for can multipacks
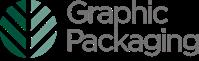
• Cap-It™ and EnviroClip™ paper-based clips for polyethylene terephthalate (PET) bottle multi packs
Recycle-Ready Chevron Pouches from Amcor Healthcare Packaging (Booth W-16031)
The recycle-ready medical device pouch con sists of a PE-based laminate paired with uncoated Tyvek®. The laminate material combines two propri etary technologies: oriented PE film and EZ peel® sealant film. The all-PE structure is recycle-ready in the PE film stream. The pouch’s physical properties are comparable to the common polyester/PE lami nates currently used in healthcare applications.
Wave 2cc dispenser from Berry Global (Booth N-4727)

The recyclable Wave lock-up atmospheric dis penser represents a more sustainable pump for per sonal-care products. Made from 100% polyolefin, with no metal parts, the RecyClass-A-rated dispens er is recyclable when paired with a PET bottle and where appropriate facilities exist. It will be available with up to 70% PCR content that will be inde pendently evaluated by the FDA. The design consists of only eight components instead of 12 to 14. Robust construction earned it ISTA 6 certification. Com patible with highly viscous formulations, it can be adapted to different actuator styles and closure sizes.
For more info, visit www. PACKEXPOinternational.com. SD
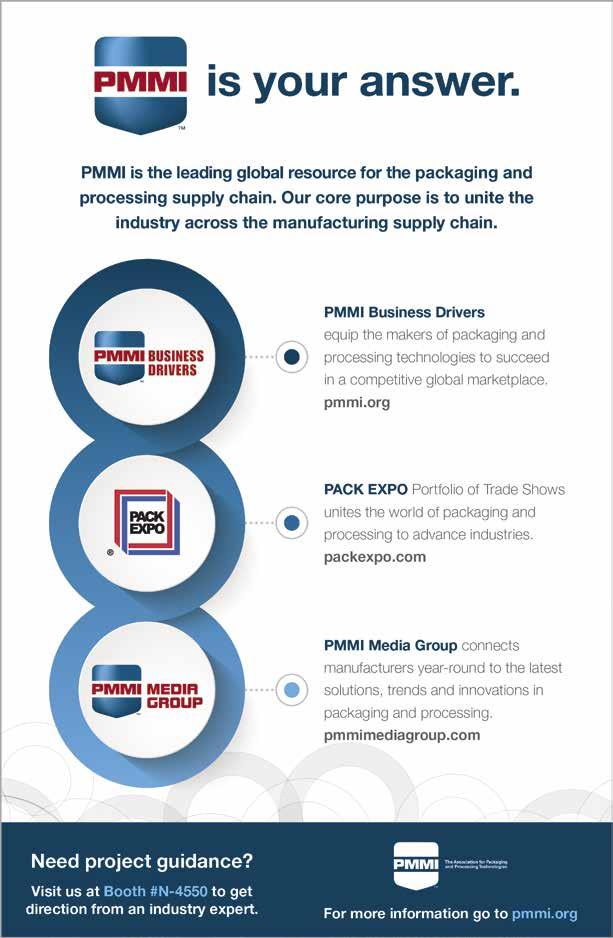
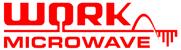
Helping you bring
best products to market since

Delivering Results. With

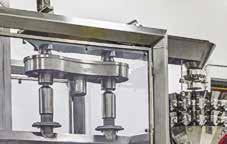

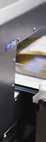
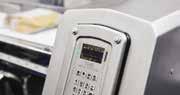
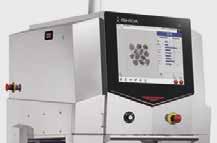

with the
have a
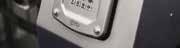
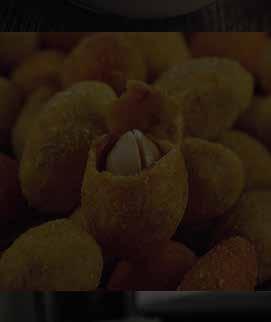
to support
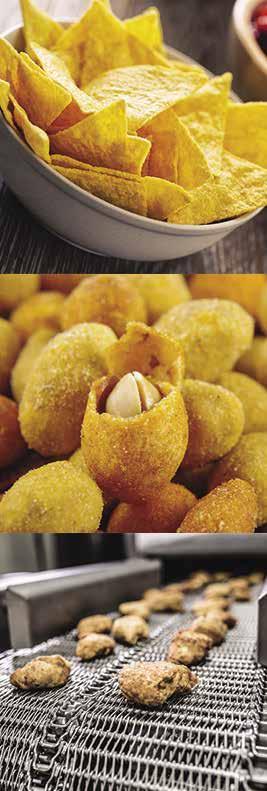
What defines reliability?
Not all equipment is equal when it comes to TCO, profitability. All pouch equipment is not created equal.
Reliability is the number one desired machine attribute for pouch converters, but this de ceptively simple statement can sometimes be misunderstood.
Reliability isn’t only about the sturdiness of the machine. It means that production will be reliable; that pouches will be of consistent quality; that down time, especially unexpected stoppages, is minimized.
It’s about product going out the door on time, at the expected cost.
Similar to how we expect our automobiles to be reliable; to consistently run and give us as little grief as possible—converters expect reliability in their equipment. What are some gauges for reliability?
WELL-MADE EQUIPMENT
The machine should be well-made—designed to provide process stability for many years—and do so without frequent operator intervention.
Obviously, to achieve optimal payback the equip ment should last for years, even decades. But in that time, the stability of the process should not degrade. Some of this comes from overall build quality, raw materials and workmanship. However, the design of the machine also plays a role.
Some converters have the good fortune of having in-house experts that keep lesser quality machinery running. They fix and tinker, adjusting springs and set tings, sometimes even rebuild sections so machines op erate to the converter’s needs and expectations.
This is a vanishing skill set, and more often than not, converters are faced with a shrinking labor pool of skilled workers. Entry-level operators and fre quent turnover require a reliable machine that runs efficiently and effectively, day-in/day-out, without the need for frequent maintenance or monitoring.
“The long-term stability and sustained operation of the machine need to be considered at the design stage, says Scott Fuller, pouch equipment product line manager for CMD (Booth LU-8118). “Our machine includes a simplified mechanical design, with fewer moving parts resulting in fewer opportunities for wear.”
•
Fewer maintenance touchpoints mean less time spent on preventive maintenance tasks.
• Maintenance touchpoints that do remain should be designed to be completed quickly and easily.
In the CMD machine, for example, guillotine knife blade replacements can be done in 20 min., nip-roll changes are simplified, access is easy, and there are fewer lubrication points.
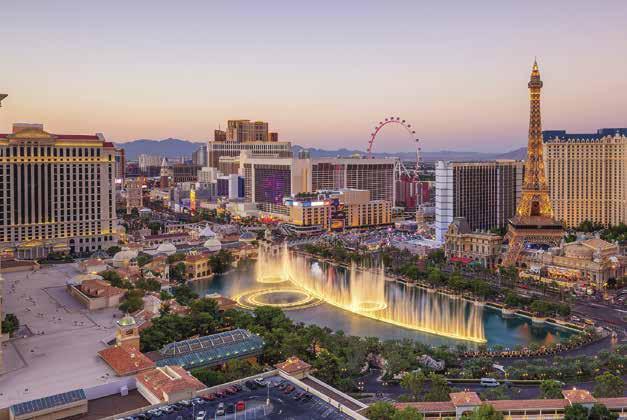
“Our machine includes a simplified mechanical design, with fewer moving parts resulting in fewer opportunities for wear.”
—Scott Fuller, CMD
reliable operation. Converters look for low cost and accessibility for common wear parts. The OEM that provides reliable, consultative service, including pro viding the tools for preventive maintenance to avoid unscheduled downtime, is a valuable partner.
CMD converting equipment includes high-per

engineering, process validation and machine opti mization services are offered from its 126,000-sq.-ft. campus in Appleton, WI.
For more info, visit www.cmd-corp.com. SD
Editor’s Note: This article was written by Scott
LET’SFILLOURWORLD WITHBEAUTY
Reliability, the most-desired machine attribute, means more than sturdiness and consistent production. Reliability also ensures pouches will be of consistent qual ity; that downtime, especially unexpected stops, is minimized; and product ships on time, at the expected cost.
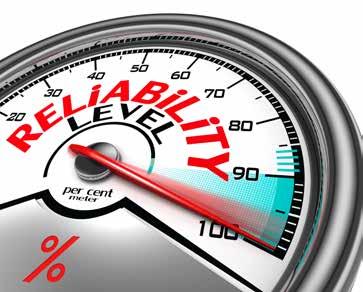
LOW TCO
The machine should offer low total cost of owner ship (TCO). A reliable pouch machine benefits the bottom line by offering truly shorter changeovers and a meaningful reduction in downtime associated with both preventive maintenance tasks, as well as unplanned stops. The end result is the machine pro duces sellable product for more of the time, resulting in a quicker payback and lower cost of ownership.
PERFORMANCE EXPECTATIONS
The machine performs to expectations, which in cludes keeping scrap rates to a specified threshold, and it must consistently produce high-quality pouches.
Speed is important if quality is assured, and waste is minimized (efficiency.) The machine is expected to make a quality pouch and is relied upon to play its part in getting orders out the door on-time.
Pouch machines need to be designed with one goal in mind; to provide the most stable process available, requiring fewer operator interventions during a production run. This results in less scrap.
SIMPLE TO OPERATE, MAINTAIN
Keeping operation and maintenance simple is a sure way to cut costs and save money.
Challenges with recruiting and retaining operators make simple setup and operation imperative. Machin ery that is straightforward to operate, with recipes and adjustments that are easily repeated, mitigate the chal lenges converters face with operator turnover.
Easy-to-operate touchscreen controls and ma chine adjustments contribute to product quality, minimize downtime and support a reliable process control. Pouch equipment has come a long way, and quick-change features significantly reduce startup and changeover time.
Affordable/accessible spare parts and reliable, responsive service are also important to simplified,
We produce machines and lines for the processing and packaging of cosmetic products.
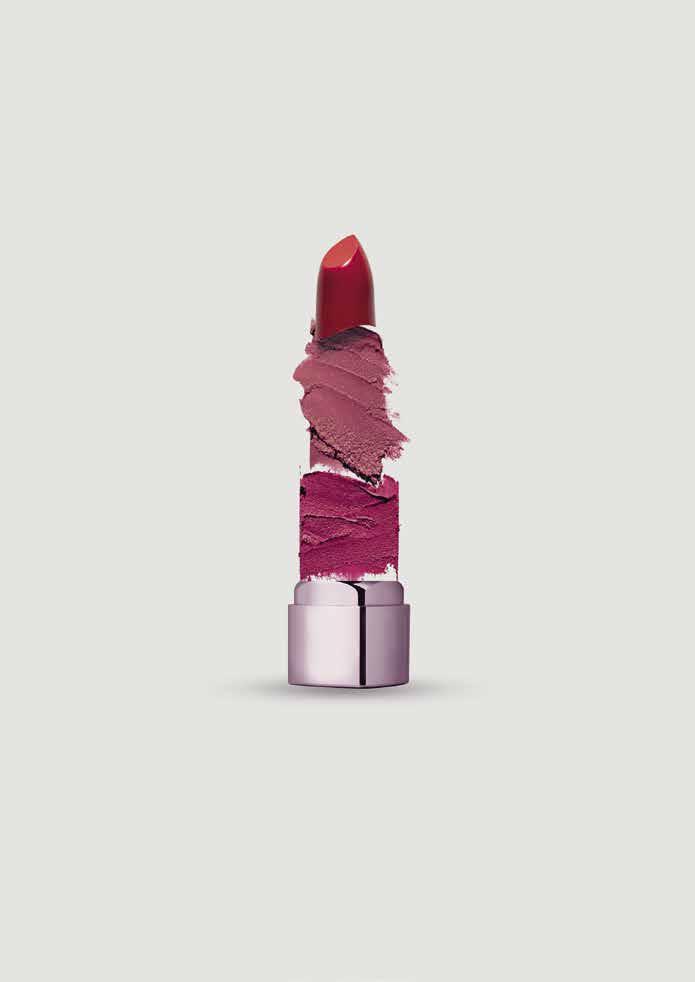
Wearecommittedtorespondingpromptlytoevery type ofrequest-fromlaboratoriesandsmall businessesto extensivecompanies-inordertofulfill ourcommon purpose: filling the world with beauty.
Visit us at: STAND W-17005
OpX updates FAT guidance
The revised “One Voice Factory Acceptance Tests – Protocols for Capital Equipment in the CPG Industry” work product improves the factory acceptance test (FAT) process.
Developed by the OpX Leadership Network (Booth N-4550), the Factory Acceptance Tests work
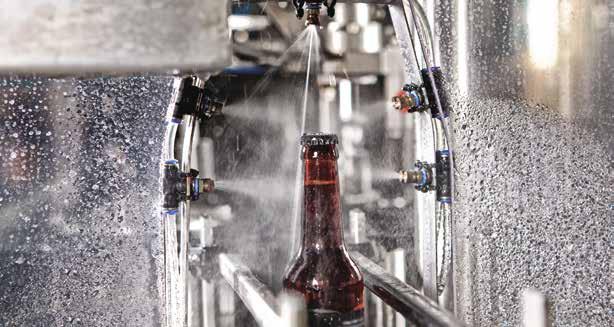
product is designed to resolve FAT criteria, expec tations and miscommunications that often result in unbudgeted travel and material costs, increased timelines and overall confusion for consumer pack aged goods (CPG) companies and original equip ment manufacturers (OEMs).
This update includes new leadership guidance, additional review of responsibilities for OEMs and end users, and the integration of the Virtual FAT work product as an appendix rather than a stand alone product.
“When conducting an effective FAT, clear com munication between all parties is critical,” says Bryan Griffen, senior director, industry services at PMMI, The Association for Packaging and Processing Technologies (Booth N-4550), convener of the OpX Leadership Network. “This latest update helps streamline that communication and facilitate a more productive FAT, regardless of whether it is virtual or in-person.”
The OpX Leadership Network was founded in 2011 by PMMI to ensure CPG companies and OEMs are connected and well-prepared to solve common operational challenges, make smarter deci sions and achieve operational excellence.
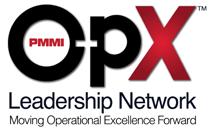
The revised FAT work product and other opera tional resources are available for free by downloading at opxleadershipnetwork.org/projects/download.
For more info, visit www.opxleadershipnetwork.org. SD
Lenze sponsors 6 lounges
Turck tackle whatever packaging automation challenges you are facing. Our wide range of reliable automation solutions – including sensors, industrial cordsets, distributed I/O products, and RFID stand up to the toughest packaging and processing environments. From improving highspeed cap and can detection to cost-effective machine control with a combined HMI/PLC, or more rugged washdown-rated cables, Turck has a solution. Can’t find what you are looking for? Choose from our wide range of custom options.
Lenze Americas (Booth N-5239) is sponsor ing lounges for exhibitors and members of PMMI, The Association for Packaging and Processing Technologies (Booth N-4550), the pro ducer of PACK EXPO International.
The lounges provide meeting space, seating, refresh ments and a chance to take a break away from the busy show floor. “Lenze recognizes how important it is for members and exhibitors to have a space to recharge, and we are proud that we are able to sponsor these lounges again this year,” says Susan Duval, senior mar keting communications manager, Lenze Americas.
“With so much . . . change in the industry and the multitude of new features in Chicago, this year ensures a very busy show floor,” says Jim Pittas, pres ident and CEO, PMMI. “We are grateful to Lenze for supporting this resource again this year.”
Lenze is sponsoring four Exhibitor Lounges (Room E-251, N-229, S-405a and W-470a) and two PMMI Member Lounges (Room N-227b and S-402ab). Lounges are open from 8 a.m. to 5 p.m. today and from 8 a.m. to 3 p.m. tomorrow.
For more info, visit www.PACKEXPOinternational.com. SD
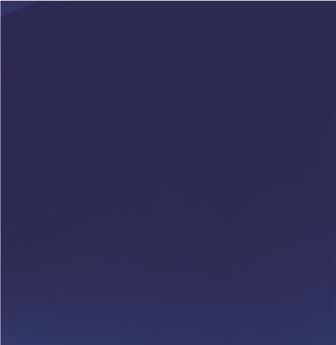

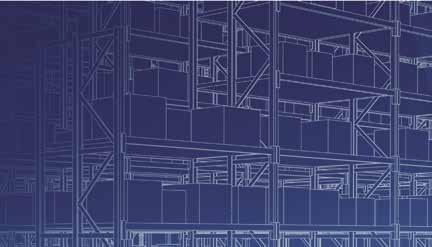
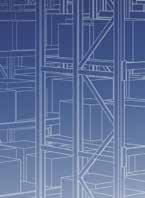

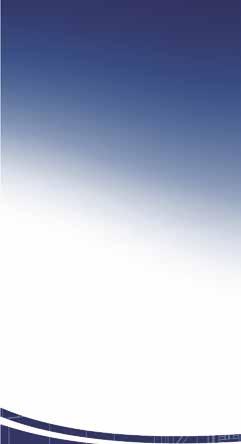
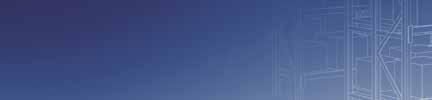

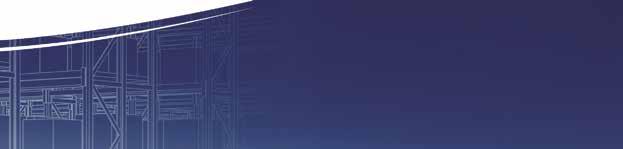
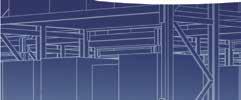

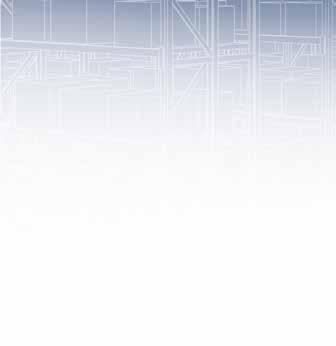

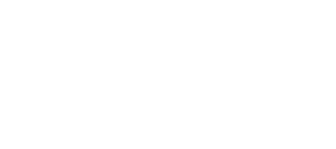







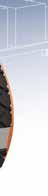














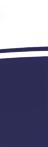
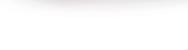
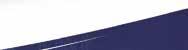
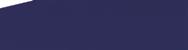































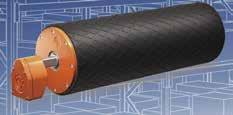
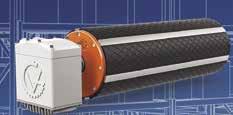







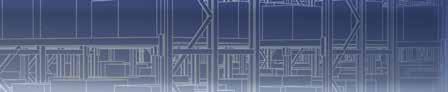
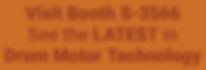
Renting machines shortens lead time
Onsite inventory speeds customization, line integration.
When it comes to sourcing controllers, components and other parts for packag ing and processing equipment, the prob lems for OEMs just keep piling up.
“The supply chain as we know it is stretched be yond belief,” says Edward Young, CEO of PFM Packaging Machinery (Booth S-2554). “It has been a challenge for the last year, and it’s not showing signs of improvement. Anything we thought was an obstacle two months ago may now be under control, but there are always other obstacles that surface.”
As a result, PFM, like just about every OEM out there, is quoting equipment with longer than normal delivery times. These long lead times are not good news for consumer packaged goods (CPG) companies need ing to deliver new products to consumers quickly. And awful news for OEMs that could lose a sale.
PFM makes a range of horizontal flow wrappers, vertical form/fill/seal (F/F/S) machines, multihead weighers and state-of-the art standup pouch equip ment. Regardless of the type of machine, if PFM can’t meet the timeframe, Young knows he’ll lose the deal. “If they’re not buying a machine from us, they’ll go to another OEM and buy from them.”
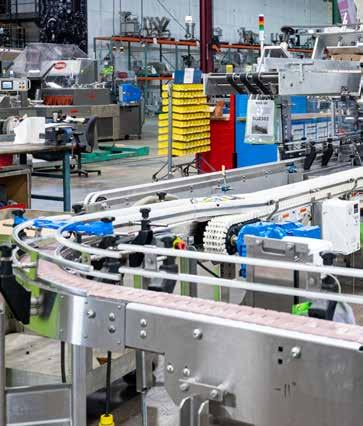
In that situation, Young recommends the end user get a machine from Frain Industries (Booth S-1639), a packaging line integration company that offers a wide range of packaging and process ing equipment including cappers and conveyors, fillers, wrappers and weighers. According to Frain, the company specializes in integrated solutions, not just single machines, so Frain will get any equipment needed for the project.
MACHINE RENTALS
In the past, Frain would buy used equipment to resell into the market. This would make it hard for an OEM selling their new equipment to compete from a cost standpoint. It made for a contentious situation, Young admits. But about six years ago, Frain started buying new equipment from OEMs, like PFM, and renting—not selling—to end users.
This creates a business model that completely changes the industry dynamic.
First, Frain is now a customer, not a competitor, to the OEMs. What started with buying checkweighers and metal detectors from Loma Systens, An ITW Company (Booth N-5220), now spans more than 40 partnerships, giving Frain an enormous inventory of integrated equipment solutions onsite and ready to go.
That means when an end user urgently needs an F/F/S machine from PFM, like, yesterday, for exam ple, rather than waiting for the OEM to build the equipment, PFM can send them to Frain, which al ready has a standard spec version of the machine on its floor that it can customize and have ready in a few weeks (not months).
“It’s a gap solution,” says Matt Wheatley, Frain Industries’ purchasing manager. “We are not selling this equipment, we are renting it, so we are not com peting with the OEM.”
In fact, this business model sometimes provides the OEMs with a new sales channel.
buy the PFM machine directly from us, Frain will turn around and re-order a machine because once they send a machine out, they need to restock. So, it’s a win/win from my perspective.”
nVenia, A Duravant Company (Booth S-3560), a manufacturer of primary, secondary and end-of-line packaging equipment, also has benefitted from the Frain relationship. “What they do affects us in a pos itive way,” says Paul Ferrandino, nVenia’s senior vice president of Sales. “They are the only customer we have that buys our entire product line across industry seg ments including CPG, food and beverage and agricul ture. And when they rent something out, they immedi ately replace it by buying something from us.”
MIND THE GAP
While Frain has been renting new equipment from other OEMs to manufacturers for the past six years, the pandemic and problems with the supply chain has made the model even more appealing to OEMs and end users alike.

“Deploying equipment rapidly is the biggest edge we have to help get projects started and moving cases out the door quicker,” Wheatley says, explaining that large CPG firms with millions of stock keeping units may come out with a new product that only lasts a year and every month they are late getting products on the retail shelves, they lose 10% market share. “That spoke volumes to us. If we helped them get cases out the door and on the shelf in three months, that’s a game changer.”
While it may sound strange to point a potential customer to what seems to be a competitor, in this case, it’s a brilliant move. That’s because Frain Indus tries buys PFM equipment and rents it out to CPG companies. “Frain has historically been viewed as a competitor, but now they’re a partner,” Young says, noting a recent change in the Frain business model that turns the firms from foes to friends.
“If I can’t deliver equipment to a customer with an urgent need, it is to my advantage to suggest to them that they get one of our machines from Frain,” Young explains. The end user can rent it for a few months while waiting for another PFM machine to be built, or they can rent it indefinitely—and even buy it out right from Frain. “But even if the customer doesn’t

And because Frain integrates entire packaging lines, the company is a one-stop shop for building a turnkey line, including training and maintenance. “They provide a really unique service that many equipment OEMs don’t want to get caught up man aging the logistics of,” says nVenia’s Ferrandino. As a result, what nVenia and Frain have is “a true partner ship that will continue to grow.”
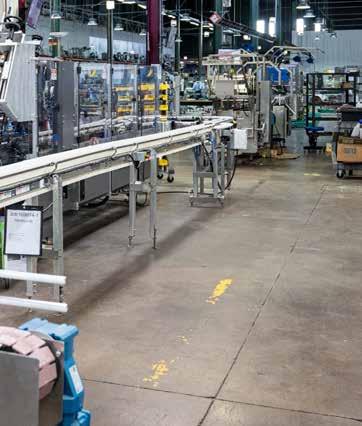
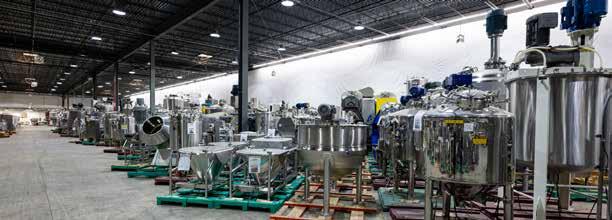
STARTUP SOLUTION
In addition, the rental model appeals to emerg ing brands that may not be able to buy a six-figure machine. Wheatley explains, “A lot of startups don’t have the capital. This offers them the opportunity to get up and running and utilize the equipment as an operational expense vs. a capital expense.”
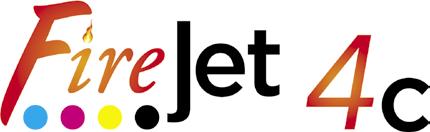
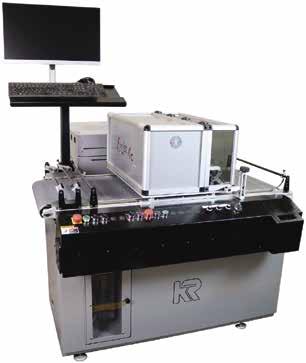

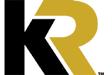
Renting also gives manufacturers the ability to keep production in-house vs. outsourcing to co-man ufacturers and co-packers. So, when retailer Kroger tells the manufacturer they are putting products in 20 more stores next month, they must find a way to ramp up production. Renting from Frain gives the CPG company the ability to ramp up quickly and keep the equipment in-house. “We help bridge the gap of growth,” concludes Wheatley.
For more info, visit www.pfmnorthamerica.com, www.frain.com, www.loma.com, www.nVenia.com. SD
Production jumps 40% by automating inversion
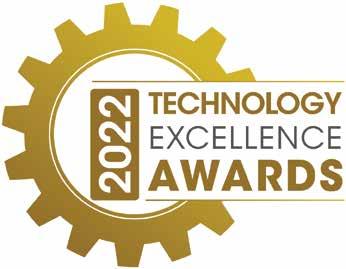
Hot-fill inversion conveyor features missing cap reject, adjustable rails.
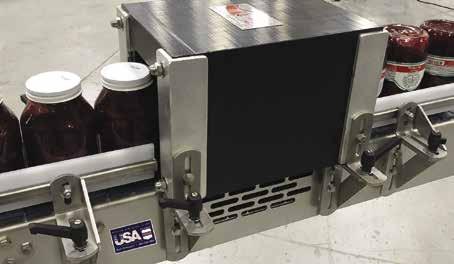
Multi-Conveyor (Booth S-3401) recently built a system to replace a manual hot-fill-jar-inversion process while providing optimum cool ing time after the capper. The line at Seaquist Orchards, a renowned family-owned produce manufacturer in Door County, WI, produces jams, salsas, pie fillings and other products in a variety of container sizes.
Filled glass jars exit an existing capper in a single lane and upright orienta tion, then side transfer at the Multi-Conveyor infeed onto the new inversion conveyor. The jars travel on the conveyor to a non-powered inverter until the jars are in a downturn position. They proceed to travel approximately 30 sec., allowing for proper cooling time in the inverted position, prior to entering a second non-powered jar inverter, which turns product back to the original up right position.
Cole and Lisa Seaquist, co-owners and canning operations managers, Sea quist Orchards, describe the process, needs and benefits of the system—includ ing employee health and safety.
Cole explains, “Prior to this equipment (conveyor line), we were manually flipping jars over on baking sheets and then flipping them over again after our jars finished their inversion (cooling) time in our products. This equipment com pletes the inversion time immediately after the capper and before the labeler, so once the jars exit the labeler they are ready to be cooled and then boxed.”
The conveyor length was critical for cooling the product (up to 200 F), both before and after the 90-degree side-flexing curve, and prior to the final inver sion. Jars then proceed to an existing labeler and staging system where product is manually removed and ultimately case packed.
Multi-Conveyor also added dual-belt drive assemblies prior to the first in verter to ensure accurate inversion of larger, heavier jars.
A missing and cocked-cap reject prior to the first inverter, equipped with sensors, logic and reject, completed the system. Easy-to-use, adjustable guide rails added an unanticipated benefit by simplifying changeover between jar sizes.
The new system has boosted output considerably. Cole reports, “On average we can produce 20-40% more per day. The new equipment with additional line space also gives the flexibility to allow the filling line to continue running a bit longer than before.” Lisa adds, “Last year, we handled about 350 cases/day (4,200 jars) and now are averaging about 500 cases (6,000 jars).”
for
superior innovations in
categories below.
Easy Palletizing with the RC10 Collaborative Robot
The standardized RC10 palletizing cell from FlexLink is compact, quick to install and easy to configure. The use of a collaborative robot significantly reduces the footprint, by over 50% compared to cells with industrial robots.
A fence system or cage is not needed and operators can safely work side-by-side with the robot. The solution permits continuous operations, the operator can easily remove one complete pallet without stopping the collaborative robot.

Read more at Flexlink.com or contact us at info.us@flexlink.com
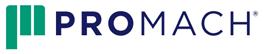
There were several critical decision points in the purchasing process. On a hot-fill line, equipment must be sized to ensure the correct line speed to maintain the proper inversion time between inverters. Cole recalls, “Jerry and everyone at Multi-Conveyor helped with that [specification] process. Development and testing of the equipment was very smooth. Any required changes were implemented quickly, and everyone at Multi-Conveyor was great to deal with.”
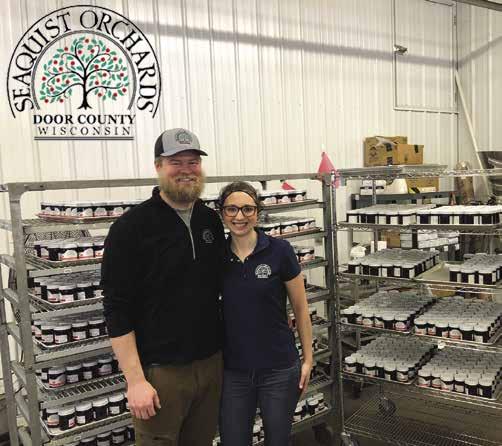
Seaquist currently runs one line at its Sister Bay, WI, canning facility and two lines at its Egg Harbor, WI, cherry plant. Regarding future expansion, Cole re sponds, “It is very likely as we continue to grow, Multi-Conveyor will definitely be our first choice for conveyor needs at either plant.” Watch the Seaquists demonstrate system benefits at https://youtu.be/hQa PHkPAbCM.
For more info, visit www.multi-conveyor.com. SD
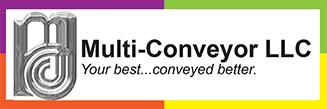
PROMACH (BOOTH N-5534, N-5540) FOR SPONSORING THE PACK EXPO INTERNATIONAL MOBILE APP.
Paxiom oversees multiple brands













Provides primary, secondary, end-of-line packaging machines.
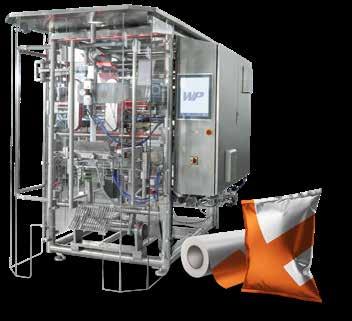
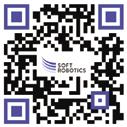




























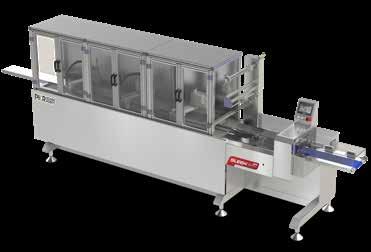
State-of-the-art packaging systems from Paxi om (Booth S-2153) are engineered to fit a va riety of production requirements and budgets. Designed and manufactured through WeighPack Systems, EndFlex and ValTara brands, and supported by Paxiom Service, technologies include net-weigh filling, multi-head weighing, auger filling, optical counting, vertical/horizontal form/fill/seal (F/F/S) bagging, premade pouch bagging, flow-wrapping, container unscrambling, capping, labeling, cartoning, case erecting, tray forming, case packing, sealing and robotic palletizing. During the past 30 years, the group has delivered more than 6,000 packaging
machines and fully automated systems throughout the world.




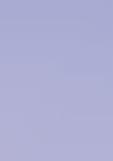
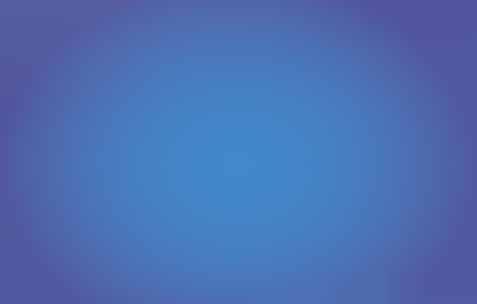
ROBOTIC SYSTEMS


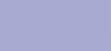
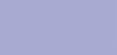
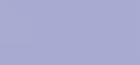
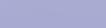


Robotics has become an important element in Pax iom’s portfolio with systems for robotic loading, bottle packaging and pick-and-place cells. EndFlex recent ly completed a highly customized end-of-line bottle packaging system. Engineered for a personal hygiene application, the fully automated system conveys bottled product into the Traypacker modular pick-and-place cell where it is packed into a tray that is fully formed and sealed by dual Poplok tray formers. In the final stages, the Boxxer all-in-one system forms, packs and seals the loaded trays into cases before conveying them to the Z.Zag robotic palletizer where the cases are pre cisely stacked for shipping.
ValTara customizes robotic loading systems for flow-wrapping lines. The pick-and-place system eliminates the need for manual loading stations and associated repetitive motion. Other benefits include reduced overhead, improved ergonomics and increased efficiency and throughput.
In another robotic system, the PKR modular pickand-place cell from EndFlex, a delta robot loads bags and packages into cases and trays. The modular pickand-place cells can be customized to fit into any ex isting production line. Cells also can be integrated with automatic case erecting, tray forming, sealing and robotic palletizing.
ValTara also offers robotic loading systems, cus tomized for flow-wrapping lines. The robot picks the
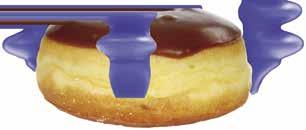
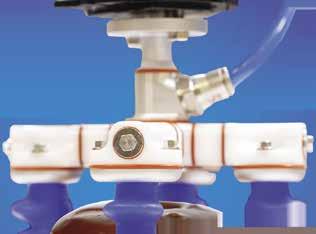
The VF 1200 continuous-motion, vertical form/fill/seal (F/F/S) machine handles multiple package formats and produces a wide range of package sizes providing flexibility for both retail and club-store packaging. In additon, CM machines run faster then intermittent-motion alternatives.
product and precisely places it on the infeed convey or, eliminating the need for manual loading stations and associated repetitive motion. Other benefits in clude reduced overhead, improved ergonomics and increased efficiency and throughput.
High-Speed, Bulk-Picking Automation Solutions




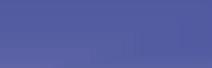

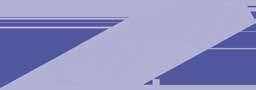
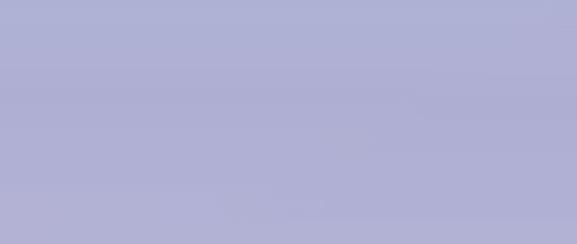
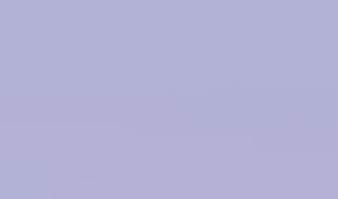
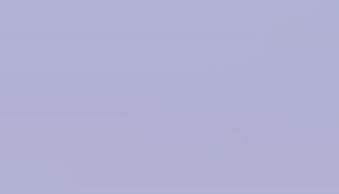
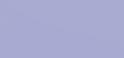
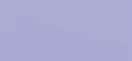


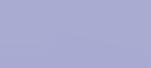
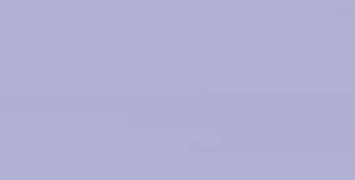



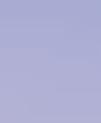



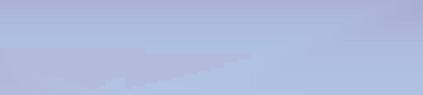



Fast. Reliable Proven. See for yourself. Visit us at Pack Expo International in Booth 5230 North.























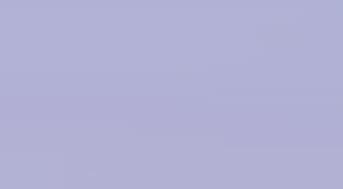



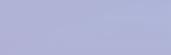
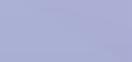













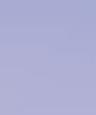
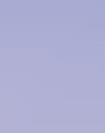
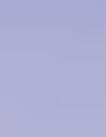
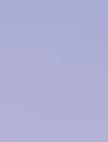
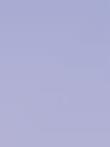
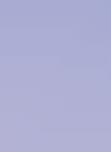
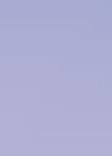
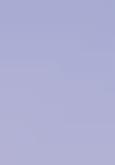
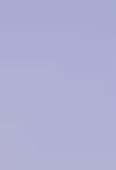
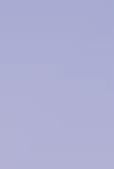



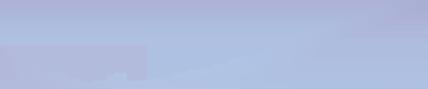
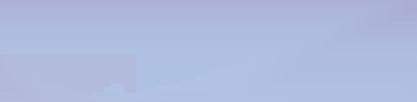
Our groundbreaking robotic solutions with 3D vision, soft grasping and artificial intelligence software are changing how food processors operate—one pick at a time.
FLEXIBLE PACKAGING




Paxiom also serves the flexible packaging segment. Its VF 1200 continuous-motion, vertical F/F/S ma chine handles multiple package formats and produces a wide range of package sizes providing flexibility for both retail and club-store packaging.
In the company’s flow-wrapper lineup, the Val Tara SleekWrapper i65 machine is designed for hard-to-handle products such as soft baked goods, tortillas, fresh produce, meats and multipack trays. The Sleek i65 machine feeds film from below so delicate and hard-towrap products are securely carried on top of the pack aging, maintain ing product integrity and esthetics. Built with reliability and serviceability in mind, this af
fordable flow-wrapper features integrated infeed and exit conveyors, a stainless-steel frame and discharge chute, an easily accessible film carriage and a large color touchscreen.
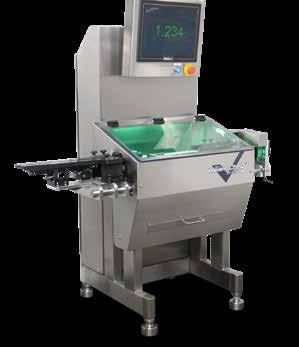
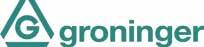













The F/F/S and flow-wrapping machines integrate with the company’s weigh fillers and labelers as well as its case erectors, tray formers and case packers.



BAG INSERTER/UNCUFFER
WeighPack’s new automatic bag inserter fills a com mon need when packaging items for bulk sale such as frozen foods, baked goods, ingredients and chemicals. Starting with tubular film on a roll in either pillow or



gusseted formats, the heavy-duty BI 600 machine au tomatically dispenses the film, then cuts, impulse seals and inserts the formed bags into a case, tote, tray or bin.

A companion unit, the BU 600 automatic bag un cuffer from Paxiom, is designed for bulk packaging of products ranging from fruit and vegetables to candy and snacks. It uncuffs a filled bag from a corrugated case and folds it in over the top of the product. This machine integrates seamlessly into a turnkey bulk-bag filling system with bag inserter, bulk-weigh filler and box-indexing conveyor. Features include 304 stain less-steel frame construction and storage for 20 recipes. Optional sealing and vacuum assemblies are available.
QUALITY CONTROL








The WeightCheQ 0-250 checkweigher from WeighPack weighs super-light products with an ac curacy of +/- 0.01g to reduce waste and increase mar gins. Powered by electromagnetic force restoration weight-cell technology, the system is engineered for applications requiring high precision and high con sistency. Built with a heavy-duty 304 stainless-steel frame, the checkweigher features at-a-glance light ing to detect out-of-tolerance products and does not need compressed air or changeover parts to operate.
For more info, visit www.paxiom.com. SD
No two scales are the same
Product characteristics must govern choice of model, features.
If I had a nickel for every time a customer asked for a ballpark price on a 14-head combination scale from Yamato (Booth S-3783) or wanted to know if a used 6-L scale will work instead of the 6-L scale I quoted them, I wouldn’t be drafting this article.
It is true, if you have a few key pieces of infor mation about a scale, you can get a decent idea of its capability and cost. However, it doesn’t tell you the whole story about how that scale will perform in the application, or if it is even the best configuration to provide you with optimum speed and accuracy.
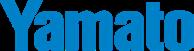
The truth is: No two scales are the same. Let’s investigate this a bit further.
A customer may call and say they have an existing 5- to 6-L scale with 14 weigh heads. They ask me for a budgetary price on a new combination scale. To answer the question, I need some basic information:
• What products are you running?
• What are your target weights?
• What speeds do you need to run?
The Yamato Alpha Series scale is an excellent option to run dry, free-flowing products with target weights under 1,000g at 50-60 weighments/min. Your product is IQF (individually quick frozen)? The Alpha scale is wipe-down-rated, but you need a washdown-rated scale. We will have to look at a different series now.
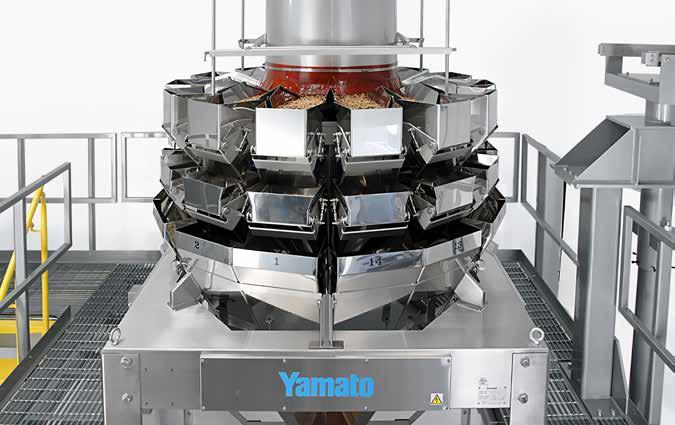
DIFFERENT PRODUCTS REQUIRE DIFFERENT SCALES
Using an IQF application as our example, I would recommend the Yamato Epsilon or Omega Series. The Epsilon scale is washdown-rated and will be a smart choice to run IQF products. What do you think?
But then you inform me you are running IQF chicken pieces and need a high-sanitation scale.
In that case, your multihead weigher will require continuous welding and no flat surfaces that allow standing water. I would recommend a scale from our Omega Series with all the high-sanitation features for this application.
FOUND A USED COMBINATION SCALE? PROCEED WITH CAUTION
If you tell me you found a used Yamato Omega 6-L scale with 14 heads that is available immedi ately, I’d be happy to look up the configuration for you. Let’s say I do that, and I tell you this scale was configured to run salad and leafy greens. It has a steep-angled top cone and tilted linear feed pans to help the large leafy greens move on the top of the scale.
If you were to run IQF chicken on this scale, the product would move so fast down the cone and feed pans, it would fly off the top of the scale and never drop into the scale’s buckets. It would be exceedingly difficult to control the feed into the buckets, making this scale essentially useless for you. Also, our sal ad scale uses dimpled sharkskin product surfaces to prevent the leafy greens from sticking. This surface could damage IQF chicken. I would recommend an embossed product-contact surface for IQF chicken.
SO WHAT?
This story highlights how differently a scale can be configured depending on the application and the information provided. The high-sanitation scale the IQF chicken needed would be triple the price of the original scale discussed, even though all three options were 6-L combination scales with 14 weigh heads.
I can go into even more detail on scale options and configurations. So far, we have discussed three scale series offered by Yamato: the Alpha Series for
dry, free-flowing applications; the Epsilon Series for higher volumes and washdown or IQF products; and the Omega Series for high-speed, multiple output, or high sanitation applications.
Now, let’s see how we can configure these scales.
CHOICES ARE COMPLEX
• Top Cone (also referred to as center disper sion cone): The product is loaded onto the scale by dropping it onto its top cone. There are many different top-cone options. The angle of the top cone can be increased to help sticky products move onto the linear feed pans. If product is free-flowing, the angle can be reduced to slow the movement of product onto the scale’s linear feed pans. Yamato offers horned top cones for small granular products. There are also two-stage top cones with dif ferent angles to help reduce buildup of sticky product on the center of the scale. There are even different infeed funnels and feed rings that can be used in conjunction with the top cone to ensure even dispersion of product onto the top of the scale. The correct top cone will properly move the product onto the linear feed pans of the scale.
• Linear Feed Pans (also known as vibratory feed pans): The linear feed pans use vibratory coils to move the product from the top cone into the feed buckets. In addition to moving the product, the linear feed pans need to be able to accurately control the flow of product into the feed buckets. Overfeeding or under feeding the feed buckets can negatively affect the performance of the scale. Yamato offers more than 25 unique styles of linear feed pans to provide the best flow of your product into the feed buckets.
• Feed Buckets and Weigh Buckets (also known as feed hoppers and weigh hoppers): The feed buckets are a staging area for product to be introduced into the weigh buckets. The weigh buckets are where the product weight is measured. There are not a lot of options on the feed buckets or the weigh buckets. A single door or double door could be preferred, depending on the stickiness of the product.
Different product surfaces could be recom mended as well: flat for free-flowing products; embossed or sharkskin for sticky products.
• Collating Chute: Once the product is re leased from the scale’s weigh bucket, it drops into a collating chute. The collating chute can be segmented (the most common option).
Baffles can be included to help reduce swirling
Specifying a scale that will provide optimum performance depends on many fac tors, including target weight, speed, regulatory requirements and, most critically, product characteristics.
THE BOTTOM LINE? NO TWO SCALES ARE THE SAME
Hopefully, this information and insight shows some of the complexities and variables that go into selecting the correct combination scale. Yamato of fers more than 100 different models and 1,000+ con
figurations to customize the best scale for your needs. For more info, visit www.yamatoamericas.com. SD
Editor’s Note: The original version of this article appeared as a blog post by Jason Quade, OEM ac counts manager at Yamato.
of product and increase speeds. Yamato also has individual collating chutes available to help increase speeds. There are different chute angles, too. Steeper, 65-degree angles will in crease the speed of the product as it leaves the scale. On the other hand, a 50-degree angle could be used to slow the product and reduce impact as it exits the chutes. These chutes guide the product charge down into the collat ing funnel as it prepares to leave the scale.
• Collating Funnel: The collating funnel of the scale accepts the charges from all the buckets used in a combination and combines them as all the product leaves the scale. The collating funnel can be optioned with baffles to help reduce swirling. The angles of the collating funnels also can be modified like the collat ing chutes. Yamato also offers a proprietary Frontier system that utilizes a double-acting weigh bucket and an inside and outside chute to simultaneously collect and drop charges to increase speeds.
WE’RE NOT DONE YET!
Once the product leaves the funnel, there are more options!

• Forming Tube: Some applications drop right into a forming tube on a vertical form/fill/seal bagger.
• Collection Bucket (also known as a timing hopper): Some applications may benefit from using a collection bucket to collect the charge, which can help create charge separation and increase speed. Some collection buckets can be used to reject as well.
IN SUMMARY. . .
As you can see, quite a few variables and config urations are available to ensure the best-performing combination scale for the application. It is important to provide as much information about the applica tion as possible so we can select the correct scale. Simply asking for a duplicate scale with the same configuration and specs as an existing scale may be okay. However, it’s important to consider a few things before doing so:
• Have any of your products changed since you last purchased a scale?
• Do you still need to accommodate that high target weight product?
• Has your packaging changed at all?
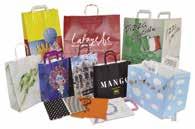

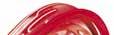
Efficient Production | Circular Economy | Digitization
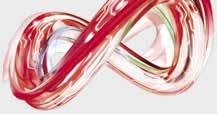
Paper or Plastic? We do both. Let’s talk.
Building machinery to produce flexible packaging is our gig. In fact, we’ve been doing it for over 150 years. That’s a lot of experience with both paper and plastic.
•Live demos on GARANT’s ROTADIA paper cone bag machine
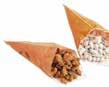
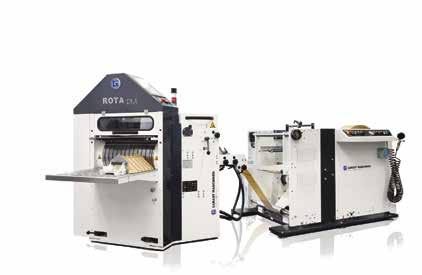
•Daily videos direct from W&H at K 2022 – automation breakthroughs, PCR films, and more.
IN THE L P
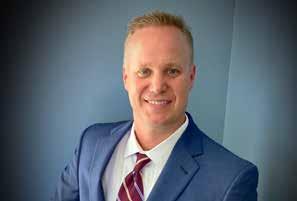
Recycle-ready film for flow-wrappers
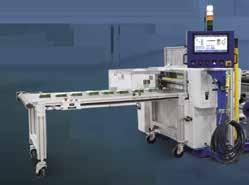

PE-based film combines barrier, sealability, machinability.
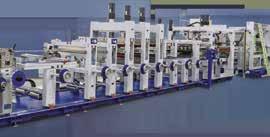

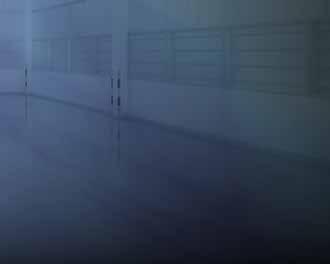
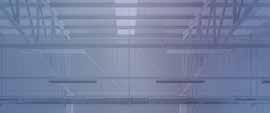
Typically, wet-wipe packs include oriented polyethylene terephthalate (OPET) or ori ented polypropylene layers that render the substrates unrecyclable. This presents a problem for brand owners who want to improve the sustainabil ity of their packaging and meet the expectations of retailers and consumers.
With a growing commitment to move to packag ing formats that meet recyclability standards, brand owners in the cleaning and convenience product space are looking for options to differentiate prod ucts in market segments such as:

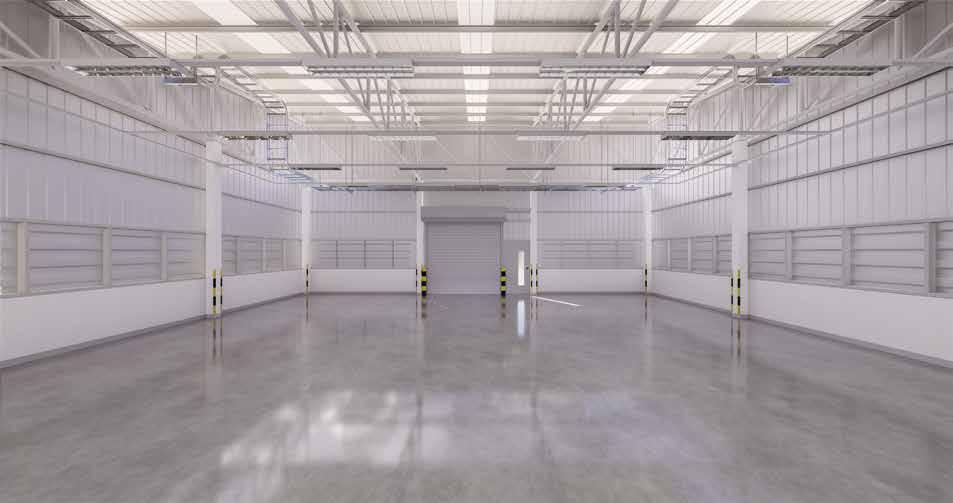
• Baby care
along the pack edges and around any opening fitments.
To meet the need for recyclability, Amcor Flex ibles North America (Booth S-3705, S-3814) has developed the AmPrima™ polyethylene (PE)-based, recycle-ready film family. One of the AmPrima™ PE Plus offerings, a flow-wrap structure for wet wipe packaging, provides heat resistance, clarity and stiff ness comparable to the unrecyclable, multi-material laminations currently in use.
A custom-engineered sealant layer allows for improved hermeticity, preventing leakage and mi cro-contamination, even on the tallest jumbo packs.
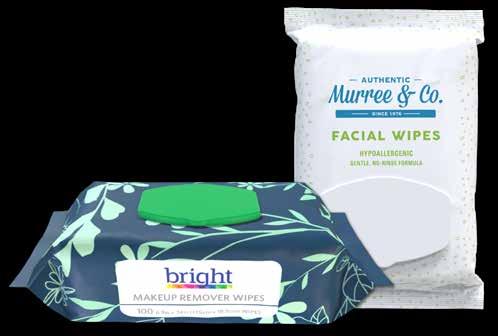

Improved heat resistance in the outer web permits faster processing speeds than conventional recycle-ready solutions to match line out puts of non-recyclable OPET laminates. In one recent produc tion run, throughput increased by 100% compared to conven tional PE-based solutions. This massively reduces total cost of ownership.
Packs have passed elevated shelf-life tests and have achieved water vapor transmission rates of 0.15 g/sq. m/day in lab-controlled barrier tests. This will deliver lon ger than the minimum two-year shelf life required.
Post-consumer recycled content can be included at loading levels up to 30% of the film structure, further reducing the overall environmental impact.

Using reverse-printing for graphics protec tion, the film can be printed with high-quality graphics for enhanced shelf appeal. Film can be finished with gloss, registered- or flood-coated matte finishes.
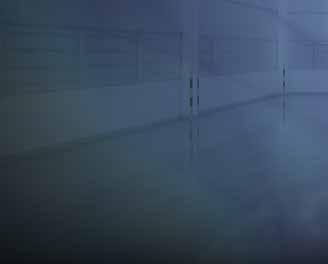
An Amcor ASSET™ life-cycle assessment of the production and manufacture of an AmPrima PE Plus film vs. the incumbent PET/PE struc ture shows the AmPrima film, when recycled, delivers:
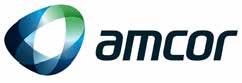
• 68% reduction in non-renewable energy use
• 50% reduction in carbon footprint

• 40% reduction in water consumption.
AmPrima PE Plus Heat Resistant film is listed as an enabling technology for recyclable flexible pack aging in APR Design® Guide published by the As sociation of Plastic Recyclers (Booth N-5902) and the Design For Recycled Content Guide, published by the Sustainable Packaging Coalition.
AMPRIMA PORTFOLIO
The AmPrima portfolio results in a package that is designed to be recycled, if clean and dry, through existing store drop-offs or curbside (where available) . It is the result of many years of research into how to replace OPET or other outer layers in mixed-ma terial films with a structure that is compatible with the flexible PE recycling stream. The challenge was to ensure that the replacement delivered all the re quired performance criteria, such as stiffness and strength, clarity, line speeds, fitment requirements, graphics and print finishes.
For more info, visit www.amcor.com/amprima. SD
THANK YOU TO OUR PARTNERS!



These organizations are an integral part of PACK EXPO International 2022 and played a pivotal role in bringing the entire packaging and processing industry together for this event.

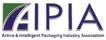


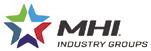

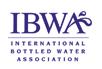

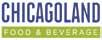



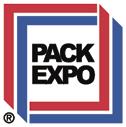
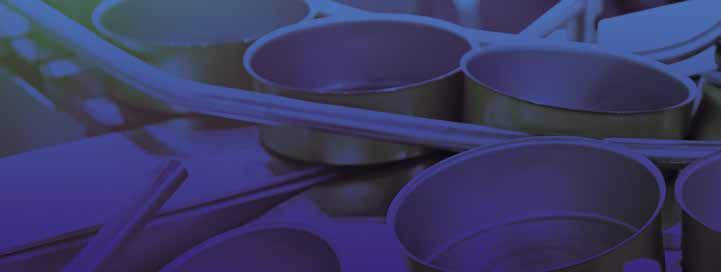
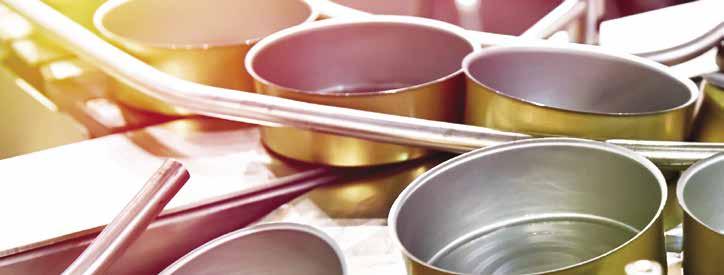
PRODUCTS - PROCESSING ZONE
The Processing Zone in the Lakeside Center building houses 180 exhibits, essentially presenting a processing show within the show. On display are innovations in homogenizing, mixing, forming, sizing and other front-of-the-line technologies such as coating/enrobing, cooling and heat treating. This area also is home to the Processing Innovation
Stage (Booth LU-7130) (see schedule, p. 28). A sampling of the products on display in The Processing Zone may be viewed on the following pages. For more information, visit www.PACKEXPOinternational.com. SD Editor’s Note: Product information and photos were provided by ProFood World
PROTEIN DICER
MONITORING INSPECTION
Utilizing web-based architecture, the Contact 4.0 digital reporting feature captures valuable produc tion data across an entire suite of networked inspec tion machines. It can remotely monitor equipment, track events and document all potential product risks, turning massive data streams into tightly mon itored operational insight. With Contact 4.0, food processors can tether multiple front-end inspection machines to back-end reporting software in real time—live, streamlined and centralized. Contact 4.0 can be installed on all digital Stealth, Interceptor and Interceptor DF metal detectors, as well as the Raptor checkweigher series.
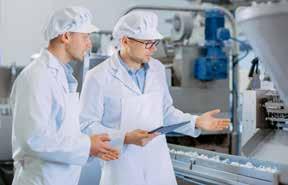
Fortress Technology Booth S-1752 www.fortresstechnology.com
FOUR-PHASE DESIGN-BUILD
Engage early using a progressive design-build contracting approach. Minimal capital investments provide initial scope development, drawings and schedules necessary for preliminary project approvals. Content experts provide customized Development and Execution Plans to optimize business needs and requirements. Strategic information generated through this proven methodology allows owners to evaluate risk and the funding commitments required to deliver a successful project.
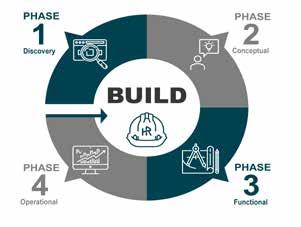
Hansen-Rice Booth LU-7727 www.hansen-rice.com
DRUM MOTOR
An exchangeable profiled sleeve on the hygienic SSV-XP drum motor makes it possible to use differ ent styles of modular belts on the same drum motor. The profiled sleeve is easily removed and replaced simply by exchanging it to match the desired belt profile without having to change the entire drum motor. Constructed of 316 stainless steel, the SSVXP drum motor is USDA-approved. It comes in a range of diameter sizes, belt speeds and horsepower, and is available with industry-specific options and features to suit various food processing and packag ing belt conveyor applications.
VDG (Van der Graaf) Booth S-3566 www.vandergraaf.com
BALANCE WEAVE BELTING
Patented side-shaped wire design of Lums den Sidewinder balance weave belting revitalizes 100-year-old technology to extend belt life up to eight times versus comparable belts. I-beam design also triples structural support for products and pro vides a greater open area for breading, coating, cool ing or drying applications.
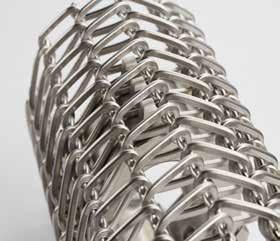
Fenner Precision Polymers Booth LU-7020 www.fennerppd.com
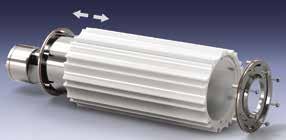
The M VersaPro 2D dicer excels in the process ing of meat, poultry and alternative proteins. It of fers 33% increased feeding capacity vs. the standard M6 model due to wider belts, optimized cutting and increased horsepower. The IP69K-certified electri cal enclosure features a double-sealed door for ex tra protection during washdowns. The mechanical zone is isolated from the product zone to promote sanitation. The dicer has stainless-steel construction throughout, including the solid, round bar frame; motors; and hinged panels. The new fluted crosscut option provides gentler cutting action. The dicer is available with an intuitive optional touchscreen hu man/machine interface.
Urschel Laboratories Booth LU-7112 www.urschel.com
PNEUMATIC VACUUM CONVEYING

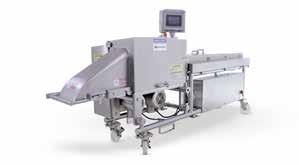
The VS Series pneumatic vacuum conveying sys tem transfers powders, granules, pellets, small com ponents and other bulk materials safely, gently and automatically. The conveyor can be operated in dense phase or lean phase and can be disassembled quickly without tools for easy cleaning to support frequent product changeovers. The VS Series pneumatic vac uum conveying system often is used with the RNT180 bag-discharge station, which automatically captures fine particles as material is loaded into the hopper to prevent nuisance dust from entering the workplace. The conveyor and bag dump station are ATEX-certified as explosion-proof.
Volkmann USA Booth S-2991 www.volkmannusa.com
PRODUCTS - PROCESSING ZONE

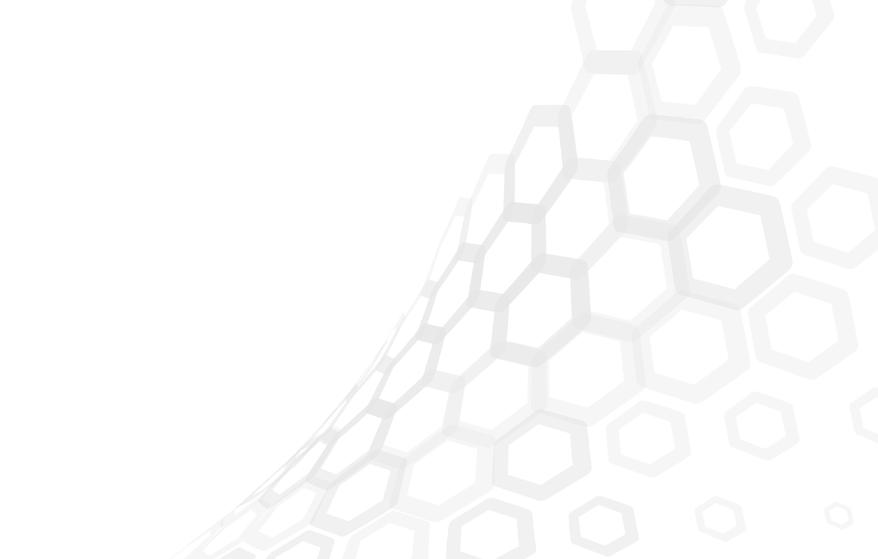
QUALITY-CONTROL MACHINES
Extremely adaptable, TQS-MD quality-control machines incorporate the company’s new Trace able Quality System Modular Design, which uses a “building block” concept for compatibility with a broad array of products. Depending on a product’s size, shape, weight and desired throughput speed, modules can be combined and tailored to specific needs. Regardless of the number of functionalities a model entails—including weighing, marking and verifying, labeling, metal detection and serializa tion/aggregation integration, among others—the unit employs one user interface, making product changes, article setup and layout modifications less error-prone and more user-friendly.
Wipotec-OCS Booth S-4172 www.wipotec-ocs.com
ROBOTIC HPP ARM
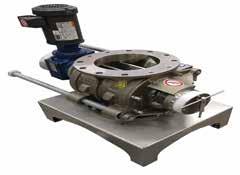
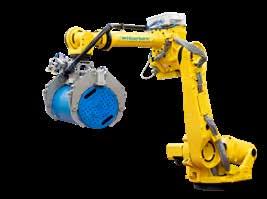
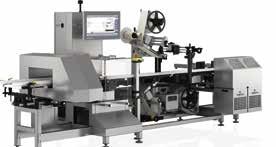
The robotic high-pressure processing (HPP) arm picks up an HPP basket containing food or bever ages after processing in the HPP chamber, empties the basket contents onto a conveyor and returns the basket to be reloaded. The robotic arm can be used with any Hiperbaric machine (55 to 525 L) for any HPP application, from juices to meats. It reduces manual labor and heavy lifting—sometimes more than 16,000 lb. of lifting per day—reducing work place injuries and labor costs.
Hiperbaric Booth LU-7341 www.hiperbaric.com
HYGIENIC AIRLOCK
The Global hygienic airlock (GHA) is a USDA dairy-accepted dismountable airlock that is suited to applications where dry raw or finished products are being handled in the process and where inspec tion or system cleanout is required. A key feature of the product is a rail system that simplifies removal and provides access to the internal valve, cavity, rotor pockets and all other product-contact areas for quick and easy cleaning. A valve interference detection sys tem protects the airlock from damage and prevents product contamination due to interference between the valve rotor and housing.
Schenck Process Booth LU-7247 www.schenckprocess.com
Feeders, Conveyors
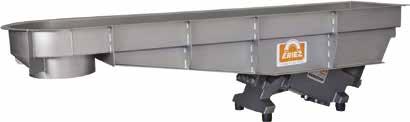
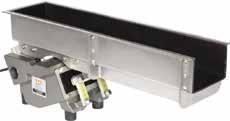
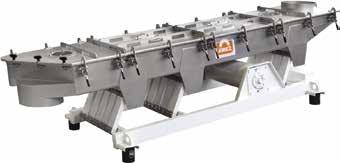
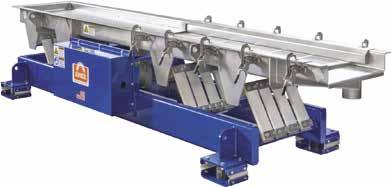

Screeners
PRODUCTS - PROCESSING ZONE
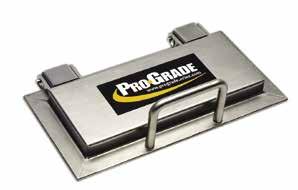
SORTING MACHINE
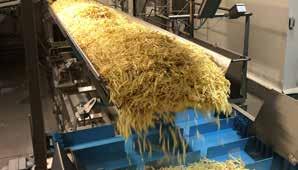
Biometric signature identification technology is now available to frozen vegetable and fruit processors on the Tomra 5C premium sorting machine. By locating the unit between the IQF (individually quick frozen) tun nel and the packing station, final checks for food safety and product quality can be made with accuracy. As the frozen product reaches the end of the line, the sorter recognizes and removes any remaining foreign material, extraneous vegetable matter and hard-to-detect product defects. These detection capabilities greatly reduce the risks of consumer complaints or product recalls.
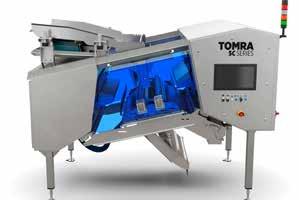
Tomra Booth LU-7135 www.tomra.com
DOUBLE DIAPHRAGM PUMPS
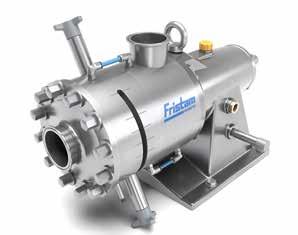
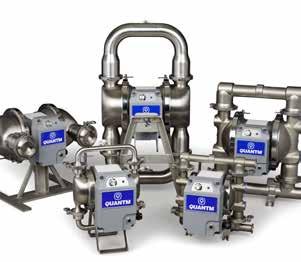
Quantm electric diaphragm pumps leverage a transverse flux motor that is suited for a range of hy gienic applications. A standard air motor is replaced with an electric drive that can produce high torque at low speeds. This allows Quantm pumps to operate without gearboxes, reducing footprints, weights and price points, while increasing efficiencies and gener ating an ROI on energy use reduction. The pumps can be used in the production of candies, fondants, bakery products, sauces and dressings, as well as in meat and poultry plants.
Graco Booth LU-8303 www.graco.com
REVERSIBLE HORIZONTALMOTION CONVEYOR
The Zephyr conveyor moves product with min imal bounce to protect quality and reduce noise. Equipped to flow in either direction, the revers ible system maximizes production line versatility. Its unique motion profile gently slides and conveys product with no segregation or stratification and reduces product damage and the loss of coatings, such as seasoning, batter and certain types of oil. The Zephyr accommodates varying flow rates, maximiz ing the flexibility of the system and is suitable for handling frozen bulk foods, including potato prod ucts, fruits, vegetables, meat and poultry, as well as dry products such as potato chips, nuts and cereals.
Key Technology Booth S-3553 www.key.net
COLLOID MILL
The patent-pending FCM colloid mill is designed for hands-off clean-in-place (CIP) applications; nothing needs to be removed for CIP, saving main tenance time and effort. The FCM mill’s timesaving, external variable gap adjustment lever provides onthe-fly internal gap adjustment to produce more or less shear, without moving the front or top ports, or even pausing operation. The mill’s variable internal gap allows users to dial in the particle size they need for shelf-stable emulsions and provides consistent particle sizes with a tight distribution.
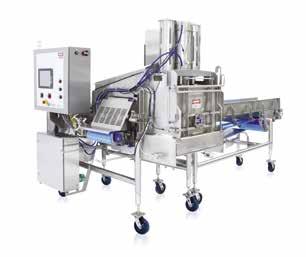
Fristam Pumps USA Booth LU-7303 www.fristam.com/usa
SANITARY CUBER
The pneumatic two-way cuber reduces cheese blocks to optimize downstream dicer/shredders. The larger belt width and cheese chamber are optimal for processing non-standard cheese sizes. Not only does the guillotine feature (executed via the local human/ machine interface) optimize working with off-cuts and soft cheese, it eliminates the cumbersome task of manually spacing out batches of off-cuts during production, thereby allowing an operator to fill the belt and let the machine cycle without further inter vention. The cuber is robust, hygienic and easy to use.
Deville Technologies Booth LU-7332 www.devilletechnologies.com
RARE EARTH PLATE MAGNETS
Xtreme Rare Earth+ plate magnets are now avail able in all of the company’s deep-reach, round-pipe, and hump-style magnetic separators. Separators with these new, stronger magnets demonstrate a sig nificant increase in both surface gauss value and pull test strength, compared with competitive units and the company’s separators with the previous genera tion of rare earth plates. Gauss and pull testing, the standard methods for testing a magnet’s strength, in dicate a magnetic separator’s ability to deliver a pure, contaminant-free product.
Eriez Booth N-5214 www.eriez.com
PRODUCTS - PROCESSING ZONE
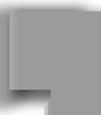





PASTEURIZE PLANT-BASED MILK
DSI Series pasteurizer uses direct steam injection to reduce pasteurization timie. The faster the product is heated and cooled, the less impact the heat has on the product. In the case of plant-based drinks, the impact can include discoloration, caramelization and the introduction of off-tastes.

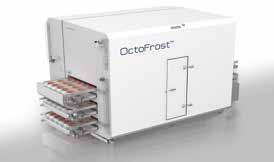
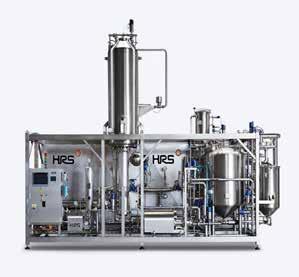
HRS Heat Exchangers

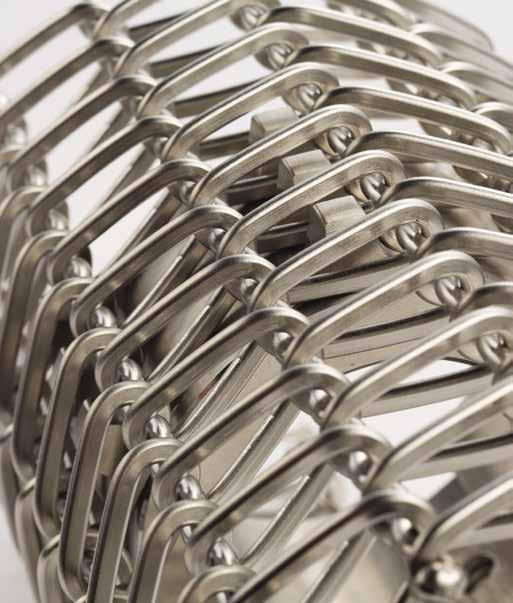
Booth LU-7535 www.hrs-heatexchangers.com
IMPINGEMENT FREEZER
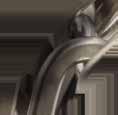
In a multi-level impingement freezer, a highspeed airstream from above and below the product achieves quick freezing in a few minutes. Suitable for various thin food products, such as hamburgers, fish or chicken fillets, shrimp and dumplings, the freezer also can be used for crust freezing prior to slicing larger products, guaranteeing minimum product de hydration and premium product quality. The use of multiple straight belts in a single freezer preserves the product’s appearance, doubles production capac ity per square meter of factory space compared to traditional impingement technology, and allows dif ferent products to be run on each level.
OctoFrost
Booth LU-7048 www.octofrost.com
Where Food Processing Takes Shape
MIXING SYSTEMS
Thomas L. Green, Reading Pretzel, Exact Mixing and Reading Thermal brands offer production lines that produce a range of snack products, innovative continuous mixing solutions and oven profiling and consulting services. Exact continuous mixing sys tems reduce labor requirements, cut costs, improve consistency and simplify mixing processes. Flexible snack systems produce a range of products including pretzels, bread snacks, crackers, baked crisps, cookies, biscuits and pet treats.
Reading Bakery Systems Booth LU-7906 www.readingbakery.com
Coat, cool, and dry with less down time
Sidewinder by Lumsden
of this
Learn more at
PRODUCTS
iDRIVE2 MAG-DRIVE MAGNET
MOTOR
The gearless iDrive 2 permanent magnet motor, a new option on the AquaPruf conveyor, runs at higher speeds while using less energy. The motor’s direct-drive system uses fewer rotating parts and specially engineered magnetic arrays to cut down on energy loss through gear motion transfer. The oil-free motorized roller eliminates product contamination from leaking oil. The conveyor can be disassembled in less than 3 min. for cleaning.
Dorner Booth N-5725 www.dorner.com
STACKING FOR SLEEVING
System accepts five lanes of chewing tobacco cans from a vertical, gravity-fed twist chute. The containers are fed into the mini-stacked feed screws via plastic guides and travel in a horizontal direction with the synchronized screws maintaining control of the containers. After being pitched to match the platform conveyor, a dead plate terminates, and the containers transition to a lug conveyor. A multi-lev el starwheel accepts the stack on the first lug and squares up the containers, creating a perfect stack for the sleeving process. Servo drives control each independent operation, and a pneumatic container stop at the beginning of the system ensures enough backlog is present
Morrison Container Handling Solutions Booth N-4906 www.morrison-chs.com
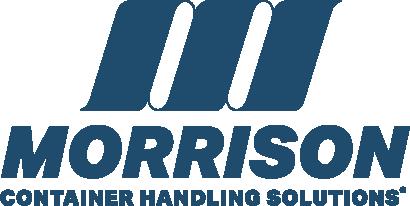
M3000 CASE PACKER
The M3000 case packer can pack up to 50 wrap around or tray-style cases/min., filling a need for mid-range packaged personal care and food manu facturers. The linear transport system allows cases to dwell in some stations longer than others, resulting in a smaller footprint with a higher case output rate. Servo-driven changeover assist and easy mainte nance decrease downtime.

Brenton, a ProMach product brand Booth N-5546 www.brentonengineering.com
VERTICAL ROTARY CARTONER
The VRC-60 vertical rotary cartoner combines loading, printing, leaflet inserting, coding, inspecting and more into one 3 x 3-ft., 12-station machine. In tegrated suction cups hold cartons in place through out the entire arc path, preventing scuffing and scratching of delicate carton surfaces. The cartoner can run up to 60 packs/min., with loading options from single to double to bulk.
Nuspark Booth S-3634 www.nuspark.com
AUTOMATION SOFTWARE
Movicon.NexT™ HMI/SCADA is a modular, highly scalable platform that goes beyond SCADA to solve automation problems for both end users and OEMs, from the single machine level to a complete plantwide IIoT project implementation. Among Movicon.NExT modules, Movicon Pro.Lean™ provides performance data and analytics for eval uations of OEE. Movicon Pro.Energy™ measures and tracks consumption, while the advanced Mov icon NExT.AR solves operational problems through visualization tools that allow personnel to evaluate previously unreachable equipment. For maximum flexibility, Movicon WebHMI, an HTML5-based visualization tool, can be used as a standalone HMI product running on Windows or Linux operator panels, or as a web client for Movicon.NExT SCA DA applications, as well as Connext™, an industrial protocol gateway.
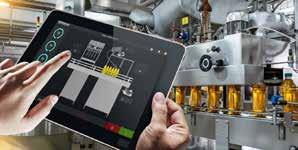
Emerson Booth N-4736 www.emerson.com/en-us/industries/automation/ food-beverage
DIRECT-TO-BOX INKJET PRINTER
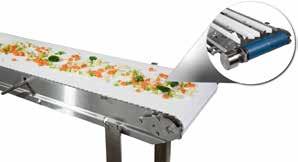
A direct-to-box inkjet printer imprints high-qual ity, low-cost, GS1-compliant, machine-readable codes, and batch and product information onto cas es, trays and other types of secondary packaging. The Cx350i offers a lower-cost alternative to printand-apply labeling, which can add large ink volume enables longer print runs; a large internal reservoir allows ink to be changed without interrupting pro duction. complexity, cost and waste.
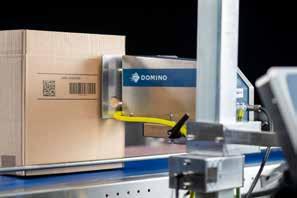
Domino Printing Service Booth S-3506 www.domino-na.com/

THE CENTER OF YOUR SMART FACTORY

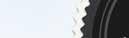
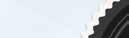

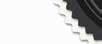

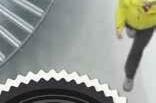
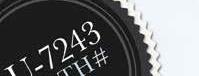

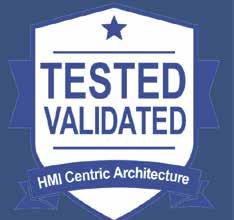
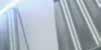
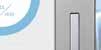
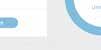

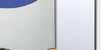
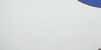
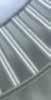

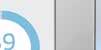

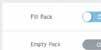

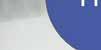
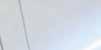
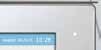

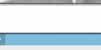
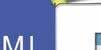
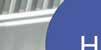
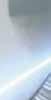
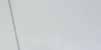
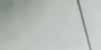
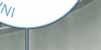
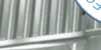
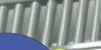
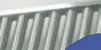

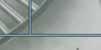
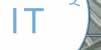
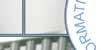

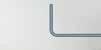
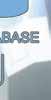
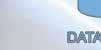

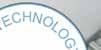
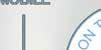


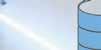
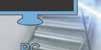
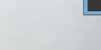
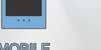
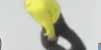
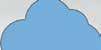
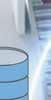
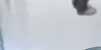
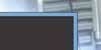
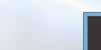
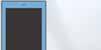
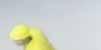


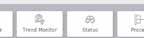
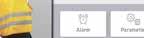
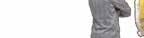
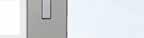
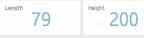
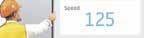
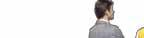


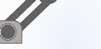
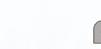
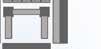
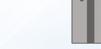

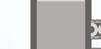
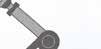
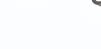
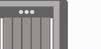

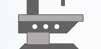

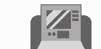
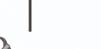
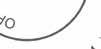
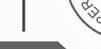
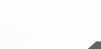
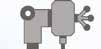

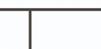
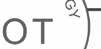
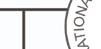
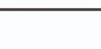


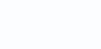
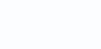



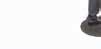
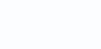

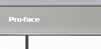
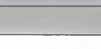
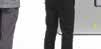
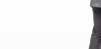
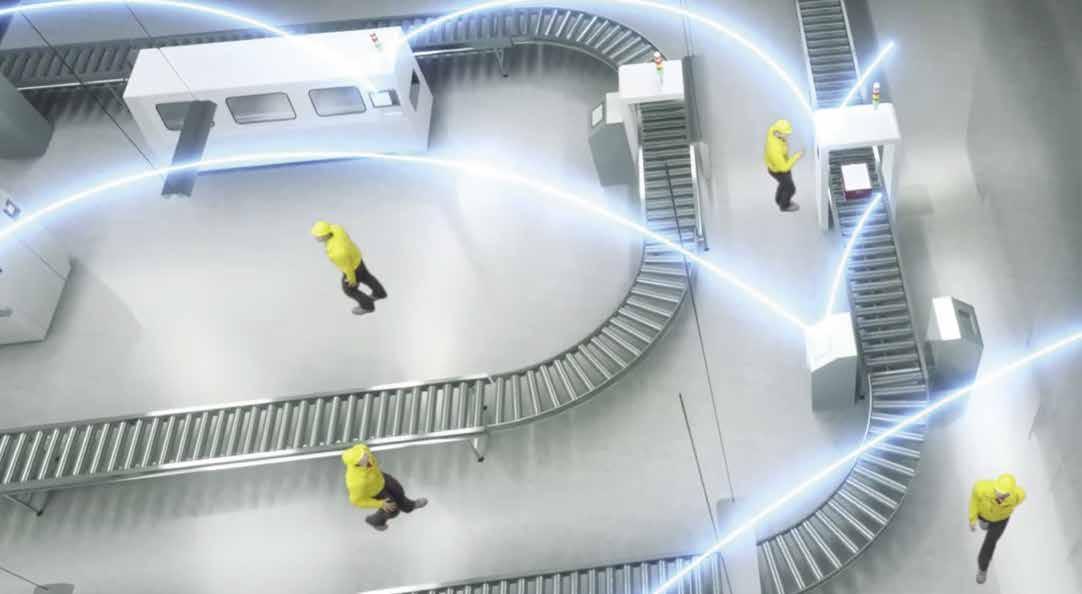
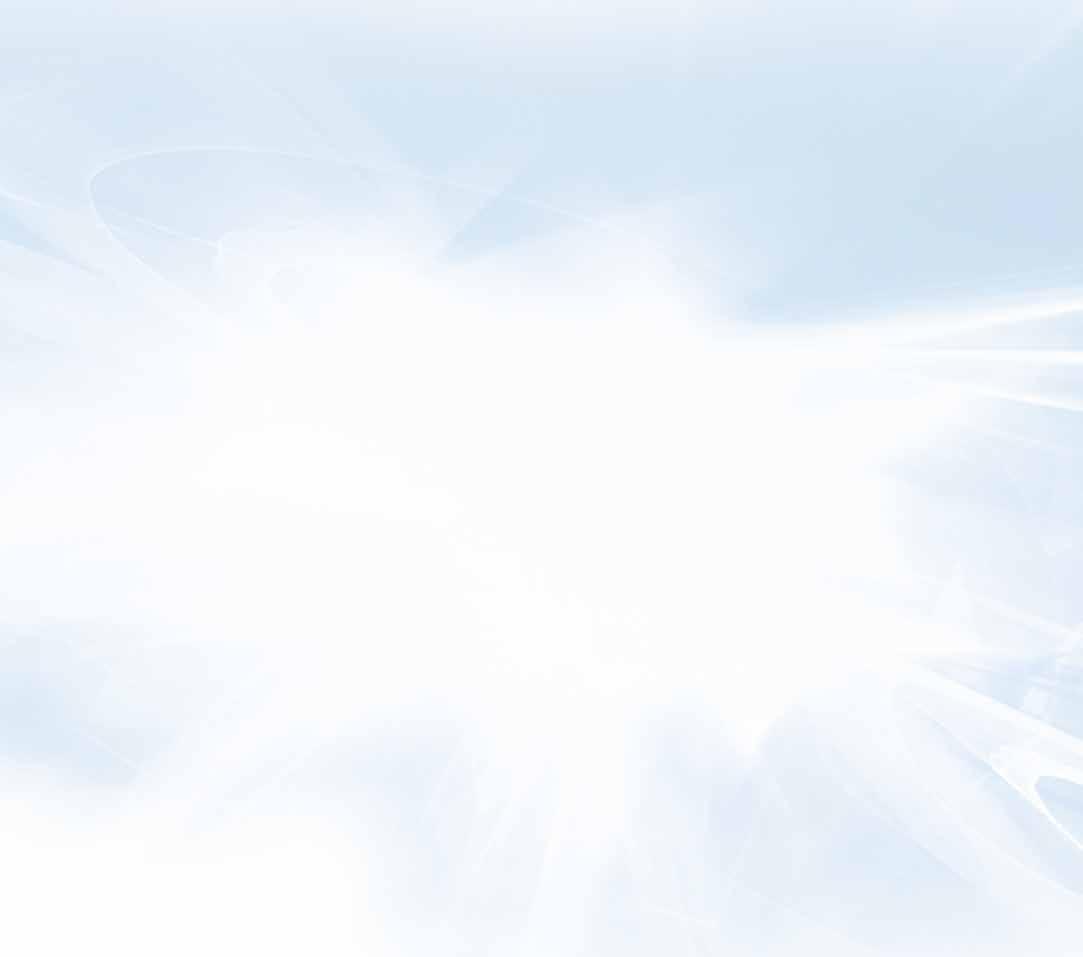
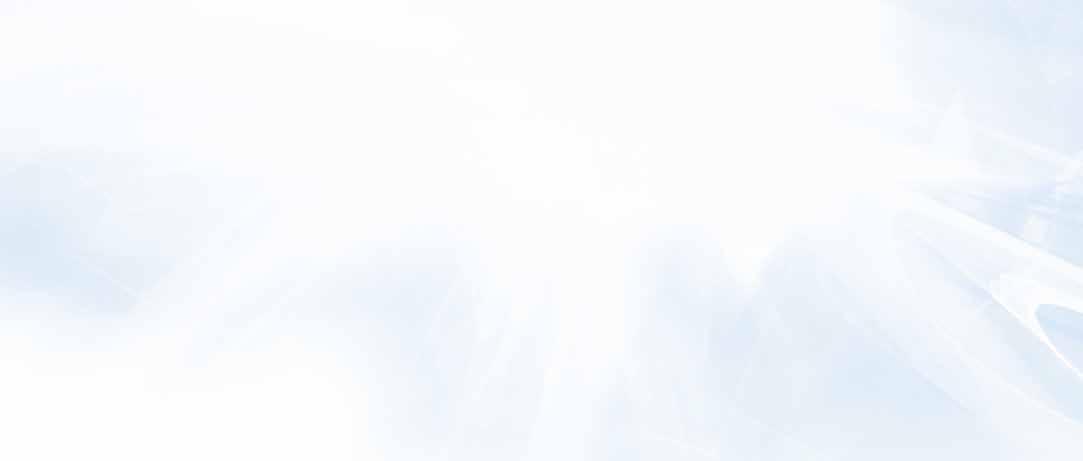
INSPECTION, WEIGHING AND METAL DETECTION SOLUTIONS
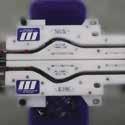

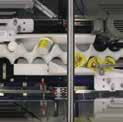
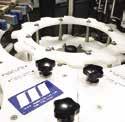
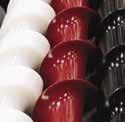
Inspection, weighing and metal detection team up to ensure product integrity. The IX-series x-ray inspec tion systems apply sophisticated image processing to reliably detect foreign objects including stainless metal, glass, plastic, bone and rubber. Checkweighers accu rately verify package weight or count and detect miss ing components. THS-Series metal detectors feature superior sensitivity to detect magnetic, non-magnetic and stainless-steel metal contaminants.
Heat and Control Booth N-4704, N-4706 www.heatandcontrol.com
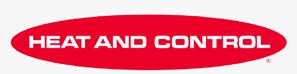
info@morrison-chs.com www.morrison-chs.com 335 W. 184th Street Glenwood, Illinois 60440
DRAG CHAIN CONVEYOR/ STRETCH WRAPPER


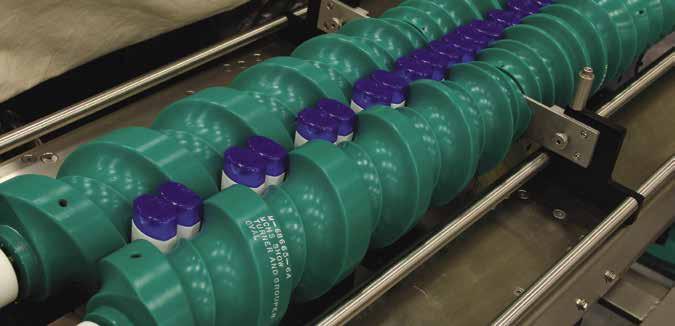
Developed for the beverage industry, the MA-DX LoPro drag chain conveyor system and automatic RTC rotary tower stretch wrapper handle tall pal lets of beer and other beverages. The system auto matically receives, wraps and discharges up to three, 2,500-lb. pallets at a time and can be run by a single operator. Loads automatically sequence through in feed, wrap zone and exit conveyors.

Orion Packaging Systems, a ProMach product brand Booth N-5646 www.OrionPackaging.com
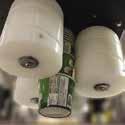


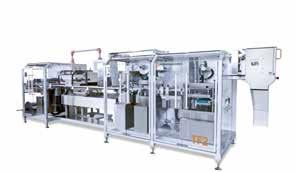
BLISTER MACHINE


The TF2 blister machine accommodates me dium- to high-output needs. A format range of 170mm x 300mm suits a wide range of applica tions, including standard hospital unit dose and Bingo-card-style blister packs. A 40mm forming depth makes the unit ideal for medical device and tray packaging applications. Features include ser vo-driven stations, no-tool changeover, sealing overload detection and seal force monitoring. The machine also supports cold-forming applications.
Pharmaworks, a ProMach Pharma brand Booth N-5650, W-17002 www.pharmaworks.com
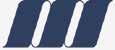

KEEP UP WITH INDUSTRY NEWS AND TRENDS
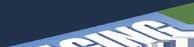
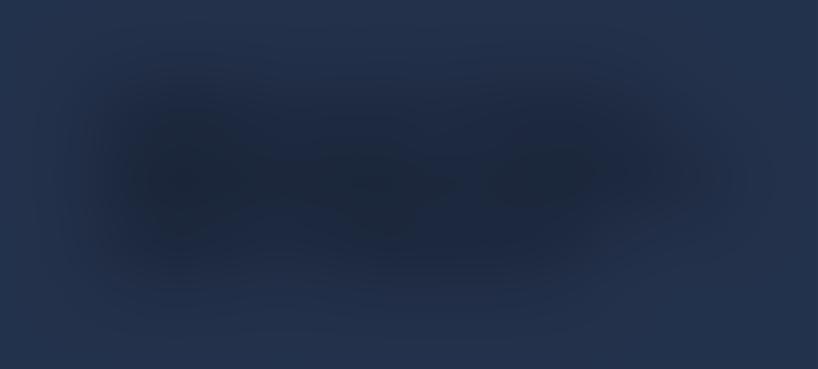
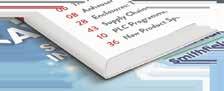
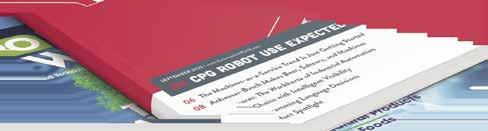
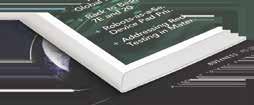

PMMI Media Group is the premier media resource for the global packaging, processing, and automation marketplaces.
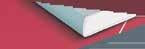
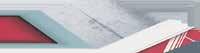
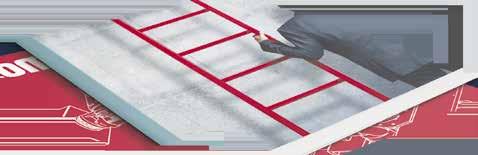
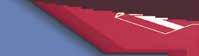
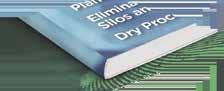

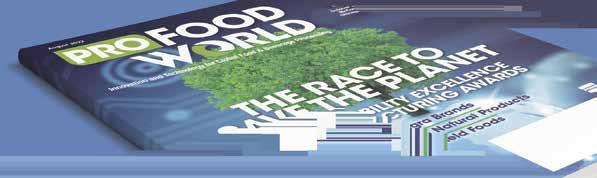
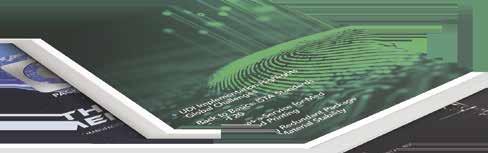
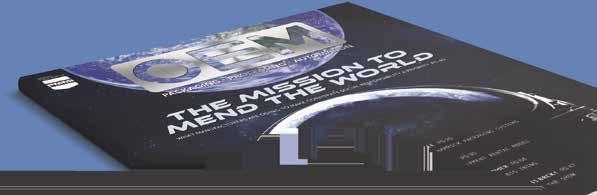
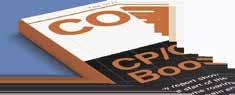
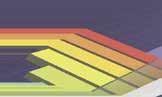
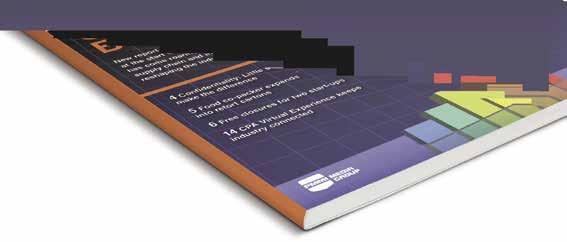
Read our latest editorial coverage online or through our print magazines.
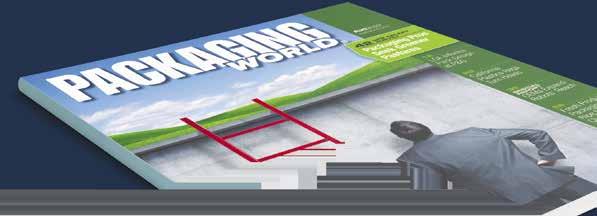
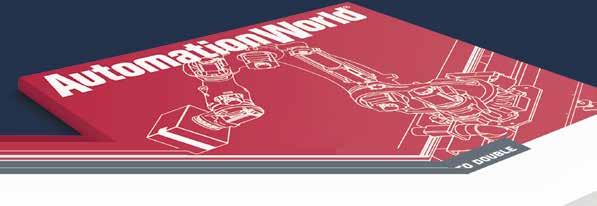

PMMIMediaGroup.com
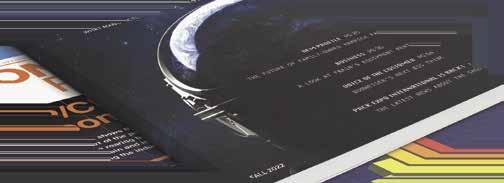
PIERCEABLE FOIL LIDDING PRODUCT




Suitable for sensitive testing environments, the AccuPierce pierceable foil lidding seals to a wide variety










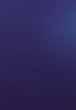

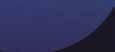

of materials, including polypropylene, polyethylene and cyclic olefiin copolymer, and enables a clean, quick, lowforce puncture. The composite material is made from a high-controlled aluminum foil paired with a chemical ly resistant, high-barrier sealant, making it compatible with compounds including dimethyl sulfoxide reagents, organic solvents, ethanol and isopropanol.
Paxxus Booth N-6161 www. paxxus.com
by










RECYCLABLE AIR CUSHIONING FILM


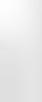


Made from 50% post-consumer recycled content and 50% renewable, sustainable plant waste, the new Renew Zero air cushioning film is recyclable in the PE waste stream. The carbon-neutral film achieves its goal without using an offset method such as planting trees.
Pregis Booth S-3834 www.pregis.com
HORIZONTAL FLOW-WRAPPER






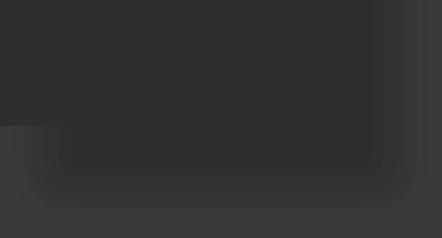




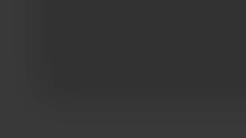






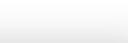


















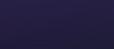

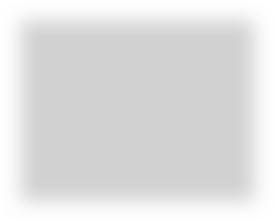
The Pack 520 horizontal flow-wrapper handles sin gle-dose and multiple food and non-food packages at speeds up to 200 packs/min. The machine flow wraps bakery products, snacks, confectionery, meat and frozen products packaged in heat- or cold-sealable films.

Plan IT Packaging Systems Booth S-2422 www.planitpackaging.com
TIGHT RADIUS CORNERS

Tight radius corners ensure superior container control for any 90- and 180-degree corner, S-bend, zig-zag or space-constrained line configuration. In side or outside curves can be adjusted in seconds without change parts or fine tuning. Adjustments are repeatable and accurate to +/- 1 mm.
Septimatech Group Booth N-5934 www.septimatech.com
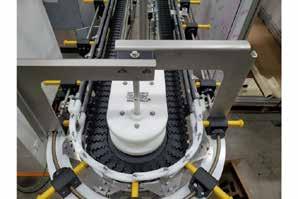
impulse heat sealing
Impulse Temperature Controllers
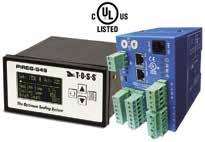
The PIREG ® heatseal temperature controllers are designed specifically for controlling the heat sealing operations performed in a wide range of applications including: vertical and horizontal form, fill, and seal; pouch filling and sealing; film wrapping, and pouch making. The PIREG ® impulse temperature controllers are cUL Listed and universally adaptable to almost any application, and do not require the use of thermocouples or RTD’s. PIREG ® temperature controllers are designed for “in cabinet” and “panel mount” uses and also available with EtherNet/IP® communication capabilities. TOSS Technology— delivering perfect impulse heat seals every time. www.tossheatseal.com
Here’s WALDO! Booth N-5913
Waldo Packaging Machinery is a manufacturer of fully automated vertical form-fill-seal packaging machines for packaging liquids, slurries and high viscosity products. Servicing businesses of all sizes in a range of markets that include food/beverage, cosmetics, and cleaning fluids, their complete line of machines are compact, user friendly and cost efficient. www.waldo.com.mx

PackworldUSA Medical Sealers




What sets PackworldUSA apart from all the rest is its use of the high response, state of-art, TOSS Technology All PackworldUSA machines come equipped with the advanced PIREG ® temperature controller. Only TOSS uses Variable Resistance Controlled (VRC) heat sealing technology to monitor and adjust temperature precisely over the full length and width of the heat sealing element, accurate up to 500°C. www.packworldusa.com
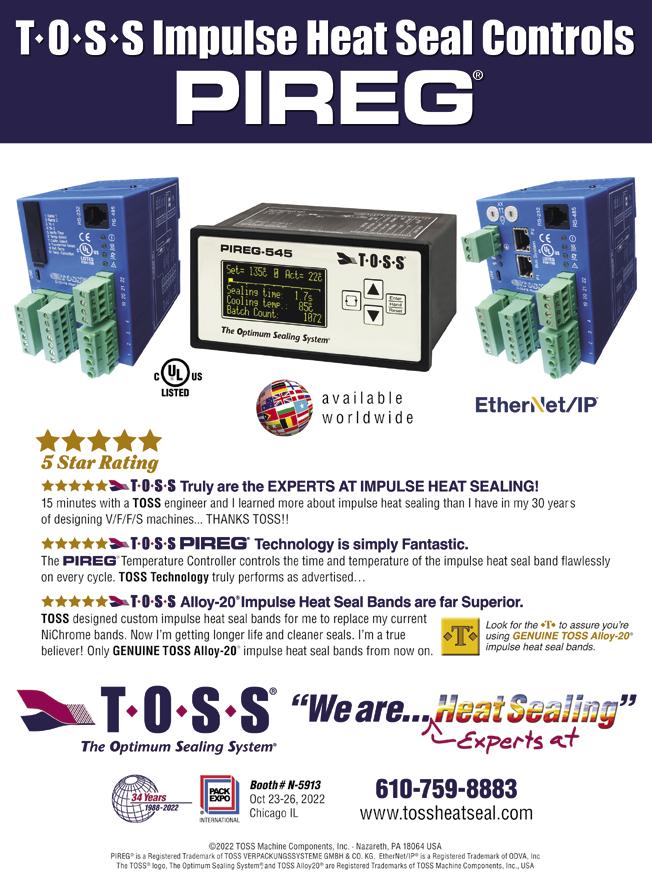
HeTOSS Alloy-20 ® and Norex ® Heat Seal Bands
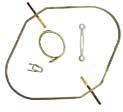


TOSS Alloy-20 ® and Norex® Heatseal Bands are available in over 350 styles, shapes and sizes. Custom designed for any application, new or existing, TOSS Alloy-20 ® Heatseal Band are longer lasting and provide for effective sealing at optimum speeds. When used in conjunction with the PIREG ® Temperature Controllers, the TOSS Alloy-20 ® heatseal bands provide instant thermostatic feedback eliminating the need for thermocouples. This instant feedback assures precise, repeatable results on each and every seal. www.tossheatseal.com

TOSS Heat Seal Cover Materials
In the optimum sealing set up, the heatseal band must be electrically and thermally insulated from the jaw bar. TOSS offers a wide selection of PTFE cover cloths and tapes that are available in standard and custom sizes. Other insulating materials available from TOSS include Silicone Rubber, Durit ® and Siglaha ® www.tossheatseal.com
PRODUCTS
INCLINE CONVEYORS

Featuring robust stain less steel, sanitary construc tion with an innovative quick release fold-out side board and belt lifter system for fast, toolless washdown, these incline conveyors are designed for high-end ap plications with heavy duty sanitary construction. They feature the elimination of tubing, hollows and harbor age points, continuously welded standoffs and seams, and minimal use of fasteners. The unit’s continuous carry-way support maintains control of the belt and the positive drive belting and dynamic guides ensure reli able tracking. These incline conveyors offer a number of innovative design features to speed cleaning, washdown and belt changes.
Frazier & Son Booth N-4913 www.frazierandson.com
CARRIER INSERTER
Automating loading of fourand six-pack carriers into mas ter cases saves time and labor. The CES25 machine erects and inserts beverage carriers into the master carton. The compact machine handles 25 carriers/min. and quickly changes over between four- and six-packs.
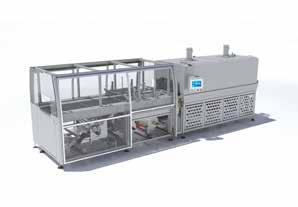

A.B. Sealer Booth N-5154 www.absealer.com

COMPACT SHRINK LABELER
The versatile R-150 shrink labeler accommodates oval, square and other non-round packages, includ ing twin packs, whether empty or full. Labels made from PVC, PETG, OPS and labels in gauges as thin as 30 microns can be applied at speeds exceeding 150 containers per minute, thanks to the manufacturer’s patented Mandrel technology.
PDC International Booth N-4921 www.pdc-corp.com
PROGRAMMABLE TEMPERATURE SENSORS

Programmable, probe-style tempera ture sensors measure industrial process temperature of a media, which helps identify potential issues. Monitoring temperatures and providing early warn ings and realtime measurements of crit ical fluids can reduce costly downtime. A rotating, multi-color display can be oriented for optimum viewing after in stallation. The stainless-steel housing is sealed against dust and high-pressure jet washing for a longer service life.
Turck Booth N-4923 www.turck.us/en/
PICK-AND-PLACE FEEDER
Boasting a new vibratory feed track, the enhanced FA1 pick-and-place feeder for small- and medium-for mat blister machines can feed even difficult-to-handle, solid-dose pharmaceuticals and nutraceuticals at speeds up to 80 cycles per minute. Through gentle handling, the FA1 feeder virtually eliminates particulates from reaching the blister web and accurately positions prod ucts within the blister cavities.
Pharmaworks, a ProMach Product brand Booth N-5650, W-17002 www.ProMachBuilt.com
KAYAT SRX SERIES SINGLE-ROLL BUNDLING SYSTEMS
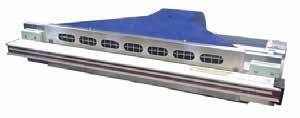

The SRX Series single-roll bundling systems in clude an option to add graphics with print-registered shrink film. The system’s resulting overlap seal offers a strong seal and better product presentation. Tool less adjustable wrap bar assembly allows adjustments without change parts.
Texwrap, a ProMach product brand Booth N-5346 www.Texwrap.com
DIGITAL COLOR PRINTING
The FireJet 4C full-color inkjet printing system, powered by Memjet, delivers high-speed digital color printing at near offset quality. The FireJet 4C printer handles A3+ and A4 cut sheets and reproduces 1,600 x 1,600 dot/in. resolution at speeds to 150 ft./min. The newly designed printhead has been engineered to provide longer life. An integrated wiper system automates servicing of the printhead. Kirk-Rudy Booth S-3278 www.kirkrudy.com
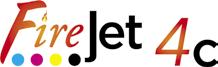
MULTIPLE AUGER FILLERS
Multiple spindle auger systems dispense prod uct across three to 12+ lanes on fill/seal, form/fill/ seal and strip/pouch machines. Individual servo drives enable independent adjustment of each au ger. Mounting options include baseplate, cantilever or overhead gantry configurations. Options include 360-degree agitation.
All-Fill Booth S-1706 www.all-fill.com
STATIC NEUTRALIZING BLOWER
IQ Power Fantom™ wide-format blower adds a lower fan speed to the adjustable knob and redesigns optional tilt bracket. Ionization delivery is improved from moving webs to injection molded plastic parts. It can be mounted at a close range and blow across unsupported thin film, thin-cut sheets of film or light, small plastic parts without interference. The tilt bracket enables a variety of mounting positions and angles to target an object.
Simco-Ion Booth N-5020 ww.simco-ion.com/industrial
Are you looking for packaging or processing solutions and you don’t know where to start?
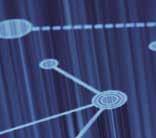


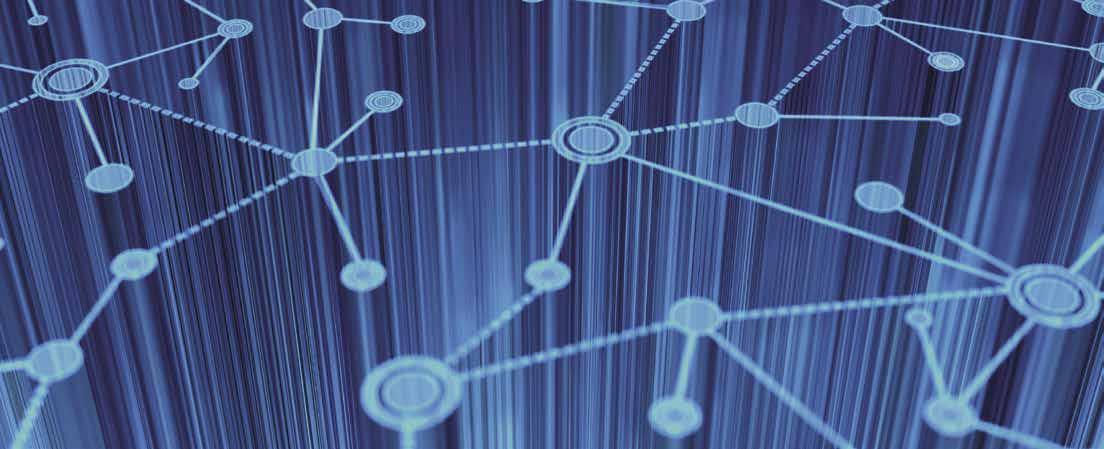
The most reliable and complete online directory of packaging and processing technology suppliers in North America –designed from the buyer’s perspective.
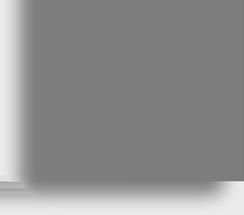
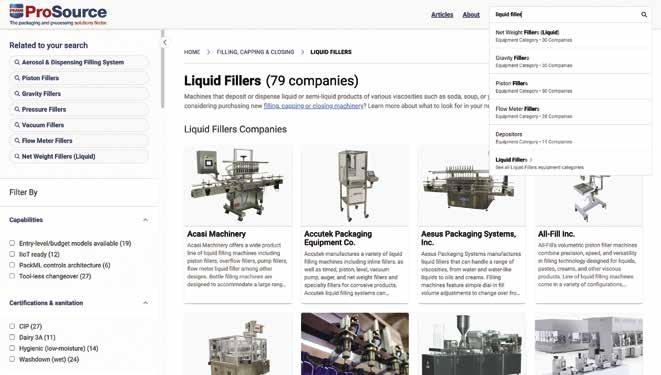
Features include:
• Plain-language filters so it’s easy to find what you need.

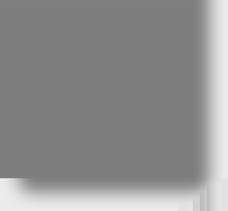





• Type-ahead keyword search.
• Visual navigation by machine or desired package type.

• Packaging-specific filters that are tailored to each product category.
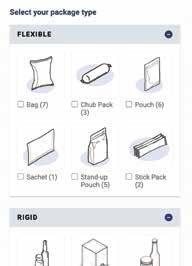
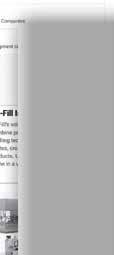
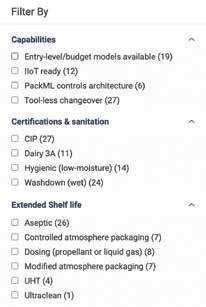
We want your feedback!
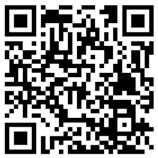
Complete a 15-minute survey about PMMI ProSource at the PMMI Booth (N-4550) for a complimentary $25 gift card. Survey slots are first come, first served!
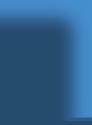

today at

PRODUCTS
X36 X-RAY INSPECTION SYSTEM
The configurable X36 x-ray inspection system for small, medium and large packaged products boasts superior contamination detection, product integrity checks and presentation verification across multiple lanes at fast throughputs.
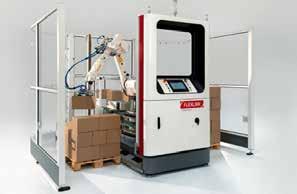
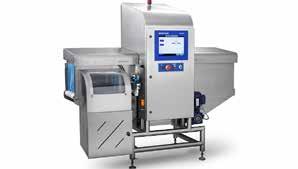
Mettler Toledo Product Inspection Booth S-1714 www.mt.com/pi
racking. Distinct design features, including permanent, molded-in frictional elements, reduce load shifting and prevent slippage. The easy-clean plastic construction eliminates potential damage from nails or loose boards associated with wood pallets.
ORBIS Booth LU-6800 www.orbiscorporation.com
speeds up to 3,000 in./min.
Universal Labeling Systems Booth N-5512 www.universal1.com
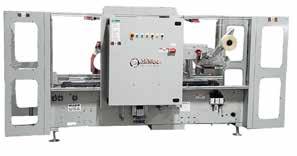
SEVERE-DUTY AC MOTOR
SIMOTICS SD200 severe-duty motor in frame size 440 powers pumps, fans, compressors, hoists, winders and similar equipment in harsh environments. SD200 motors offer 75-800hp output and feature 4445013 cast-iron frames for operation in 460V and 575V ranges. They meet or exceed NEMA Premium® MG1 Table 12-12 efficiencies. Options include IP56 ingress protection, encoders, brakes and blowers, plus others to suit the applications presented.
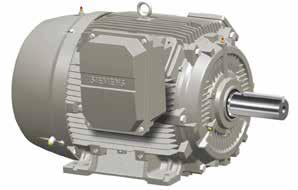
Siemens Booth N-5148 www.usa.siemens.com/packaging
PRODUCT SETTLING
Manufacturers can reduce corrugated costs by pre-settling product before shipping. Product settlers utilize controlled vibration technology to reduce over-pack and allow case flaps to be closed without product interference. Sealing and non-sealing ver sions are available. A variety of industries use this company’s product settlers to minimize in-transit settling of products. Some applications include veg etables, frozen foods, nuts and bolts, powdered prod ucts, small plastic parts, almonds and much more.
MARQ Packaging Systems Booth N-5721 www.marq.net
PALLETIZING CELL
The semi-open palletizing cell with an industrial robot arm simplifies complex processes. The RI20 pal letizer is suitable for palletizing closed boxes within fast-moving consumer goods industries. The unit in cludes enhanced safety features that allow a safe coexis tence between the robot and operators on the produc tion floor. The presence of operators in the safety area dynamically adjusts the speed of the robot instead of stopping it, reducing unnecessary downtime.
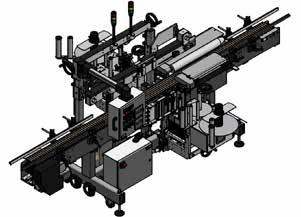
FlexLink Systems Booth S-2501 www.flexlink.com
HEAVY-DUTY PLASTIC PALLET
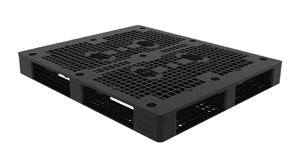
In durability testing, the Odyssey ® rackable plastic pallet demonstrated 36 times the life span of a 40x48inch whitewood stringer pallet. The pallet supports heavy loads up to 2,800 pounds, even in unsupported
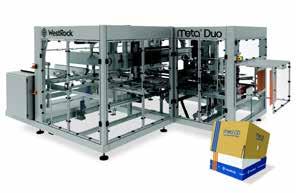
ENHANCED LABELING SYSTEM
An expansive touchscreen control package on the Contract Packager Series labelers features step per- and servo-driven technologies along with AC drive motors. CP2000 and CP1000 front-and-back multipurpose labeling systems offer four-axis label applicator adjustments, built-in Z-axis adjustments and password protection. Other attributes include a multi-level menu system; synchronous electronic controls; a wide, servo-driven, synchronous, overhead hold-down belt; servo-driven synchronous product positioning without change parts; extra heavy-duty welded framework; and variable label dispense
MANDREL-FORMING TECHNOLOGY
Precision mandrel-forming technology of the Meta® Duo machine transitions among four-sid ed, eight-sided and half-slotted cases and one- and two-piece shelf-ready designs with minimal change over. With Meta Systems technology for gluing and forming shelf- and retail-ready packaging, one small-footprint machine can streamline operations while meeting multiple channel requirements. This automation technology eliminates the need for co-packers or third-party logistics providers and the associated packaging and freight redundancy.
WestRock Booth S-2130 www.westrock.com/ap
AUTOMATIC CAPSULE FILLER
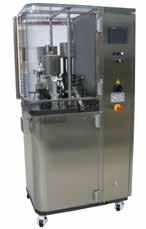
Ideal for R&D labs and clinical trials, the Flex aLAB capsule filler can fill the same capsule with different products, thanks to the machine’s modular design. At either continuous or intermittent motion, the unit can fill up to 3,000 capsules/hr with a wide product range, including powder, pellets, tablets, Micro-tablets, capsule-in-capsule, liquids and more. Optional MultiNETT or 100% weight inspector en sures accurate weights.
MG America Booth W-15003 www.mgamerica.com
DRAW WIRE SENSORS
LCX Series draw wire sensors work with encoders to measure position and provide motion feedback in motion-control applications. Available in wire lengths from 1-42.5m, draw wires install quickly and easily. Coupled with an encoder, the draw wire sensors are good for motion control in robotics, extrusion presses, control gate position ing, gantries, forklift booms and motion-control applications. LCX Series draw wire units work with encoders with a 36mm-diameter clamping flange and 10 x 20mm shaft.
Encoder Products Booth S-4026 www.encoder.com
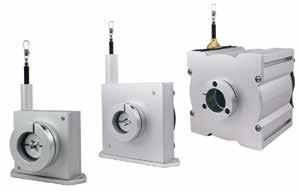
CONTINUOUS INKJET PRINTER
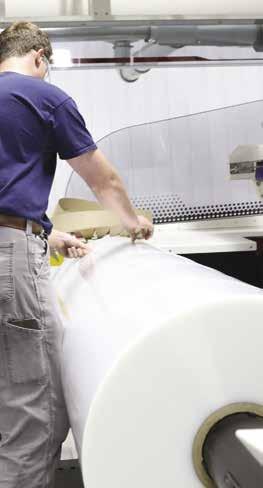
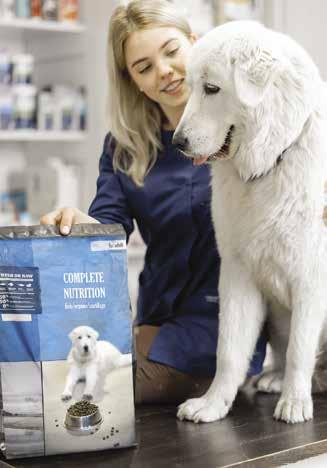

The UX2 continuous inkjet printer brings the next generation of coding to your production lines. It provides added convenience with onboard safe clean printhead station, a newly designed printhead, en hanced code quality at high speed and easy-to access troubleshooting videos. The UX Series improves on the existing continuous inkjet products and is versa tile enough to provide industry-leading marking on food, beverage and dairy products, health and beauty products, and a variety of containers from lip balm tubes to bag printing and oversized PVC piping.
Hitachi Industrial Equipment & Solutions America
Booth S-3752 www.hitachi-iesa.com
PRODUCTS
CIP UTILITIES & AUTOMATED REPORTING
This package delivers utilities monitoring and automated reporting for clean-in-place (CIP) and steam-in-place (SIP) applications. The package can be delivered via PACEdge™ or Movicon™, de signed for the food and beverage industries. The software aids in digitally transforming manual and semi-automated systems by optimizing utilities con sumption, benchmarking against a known cycle and generating automated reports. Equipped with the right data and analytics, plant managers, operators and maintenance personnel can view the informa tion on a dashboard and share the insights with sustainability officers and other stakeholders to op timize their CIP cycles. This information can reduce energy consumption and improve productivity in a single system or throughout a facility.
Emerson Booth N-4736 www.emerson.com/en-us/industries/automation/ food-beverage
DELTA PICK & PLACE CELL
A partner company’s Sniper Cell easily integrates with this company’s delta and R series robots. The ultra-high speed delta robot can perform a pick and place application using vision sensors and conveyors. Delta robots operate at ultra-high speeds that max imize product line efficiency. The Sniper Cell is de signed for high-speed, vision-guided pick and place, case packing, carton loading, kitting and assembling applications. Its pre-engineered, modular design provides flexibility with a minimized footprint to easily fit into existing or new production lines. The Sniper Cell is known for enhancing packaging as sembly lines, making them more standardized, scal able and user friendly.
Kawasaki Robotics (USA) Booth N-5946 www.kawasakirobotics.com
LABEL PRINTER APPLICATOR
The 265 Label Printer Applicator with Carbon Flex™ servo-controlled applicator module is engi neered to apply one or two labels to shipping cases, shrinkwrapped trays or pallets. With CarbonFlex™ technology, the 265 decouples the print speed from the applicator speed and ultimately, prints slower and applies faster. This prints the best possible bar code quality separate from the label’s application rate requirements. Several key features ensure safe inter action with an operator and live operations. The 265 high-speed case, tray and pallet labeling automation system is engineered to maximize productivity.
ID Technology, a ProMach product brand Booth N-5544 www.idtechnology.com
SANITARY DESIGN X-RAY
Built on the XR75 platform, the new IP69k san itary x-ray offers the XR75’s reliability, ease of use, and low cost of ownership in a rugged, compact footprint. The system is ideal for plants with harsh washdown practices and stringent hygiene standards. Washdown protection features include gasketed joints, a robust HMI screen guard, etched labels and heavy-duty stacklight cage. Sanitary features include solid frame and rollers, full seal welds, stand-offs, an gled surfaces, drainage slots and toolless disassembly for cleaning ease.
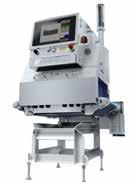
Anritsu - Product Detection & Inspection Booth N-4730 www.anritsu.com/infivis
BOTTLE PACKAGING SYSTEM
This company recently completed a highly cus tomized end-of-line bottle packaging system in just 20 weeks. Engineered for its client in the personal hygiene market, the fully automated system conveys bottled product into the Traypacker modular pickand-place cell where it is packed into a tray that is fully formed and sealed by dual Poplok tray formers. In the final stages, the Boxxer all-in-one system forms, packs and seals the loaded trays into cases be fore conveying them to the Z.Zag robotic palletizer, where the cases are precisely stacked for shipping. Customized end-of-line solutions can be made to meet any production need.
EndFlex/Paxiom Booth S-2153 www.endflex.com
V/F/F/S PACKAGING SYSTEM

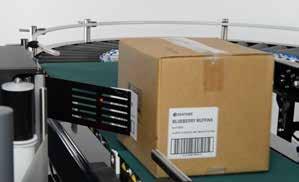
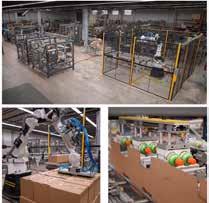
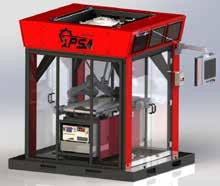

Featuring EtherCAT® real-time protocol and an integrated display controller system, robag® vf/f/s packaging system reduces cabling infrastructure by 20%, enabling easier servicing and lower total installed costs. The system shares common core components with roflo® distribution conveyors and the intelli-flav® seasoning system reducing the need for additional spare parts stocking, and features integrated LED lighting in the packaging jaw area to make maintenance safer and easier to perform. Equipped with smart diagnostics and remote connectivity, the robag® 3e also offers real-time communication and status updates, enabling faster global servicing support.
tna North America Booth N-5312 www.tnasolutions.com SD
A Sweet Spot for Networking
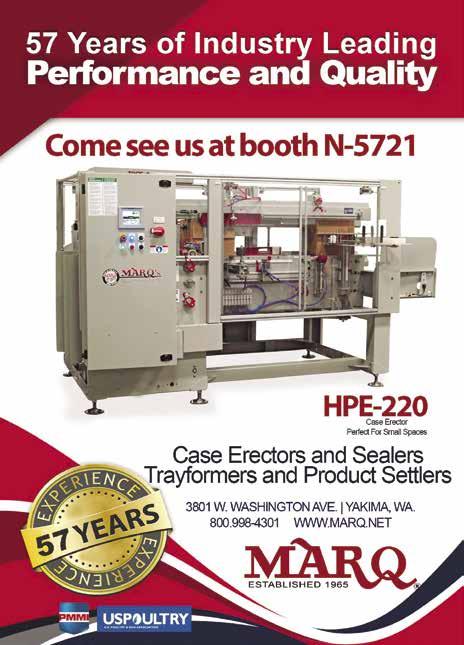
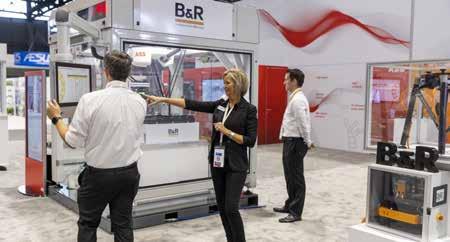
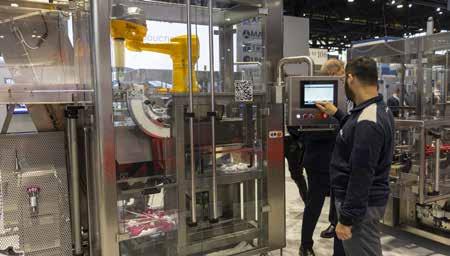
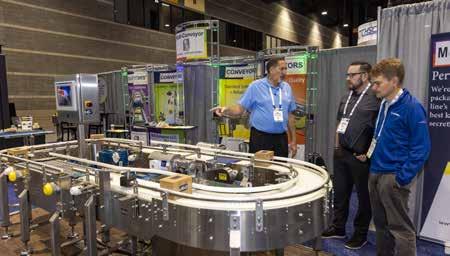
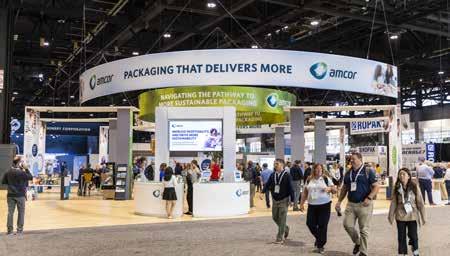
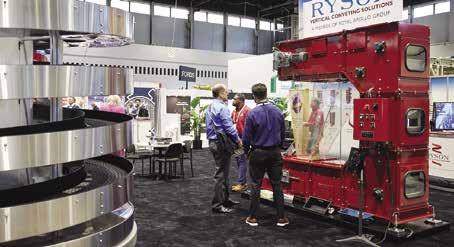
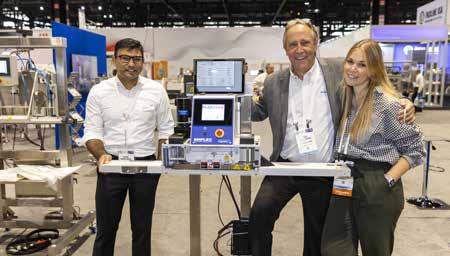
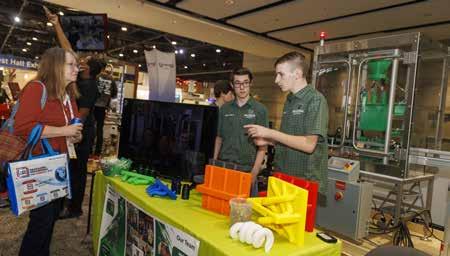
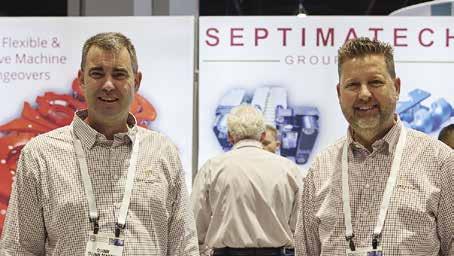
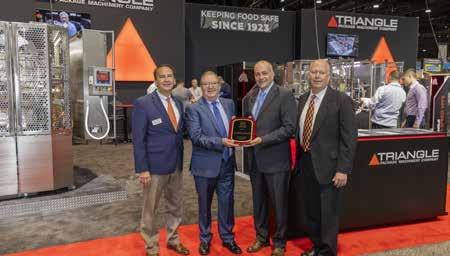
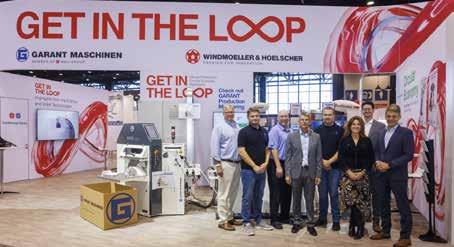
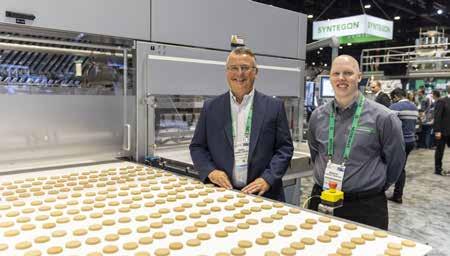
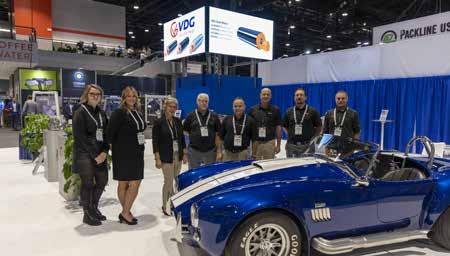
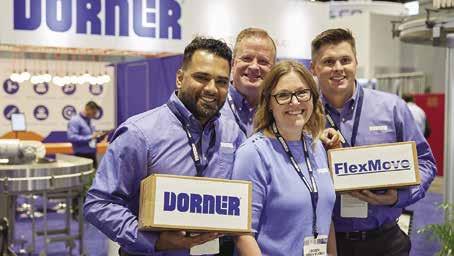
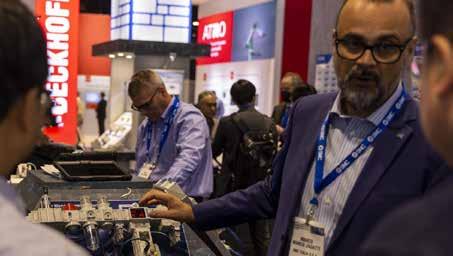
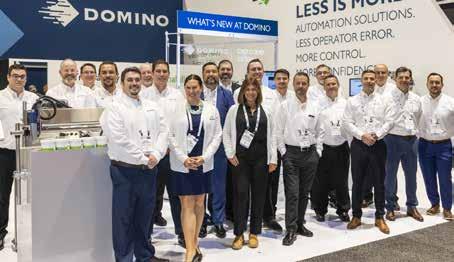
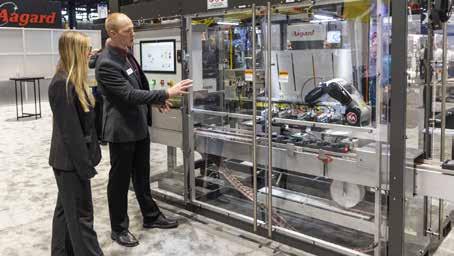
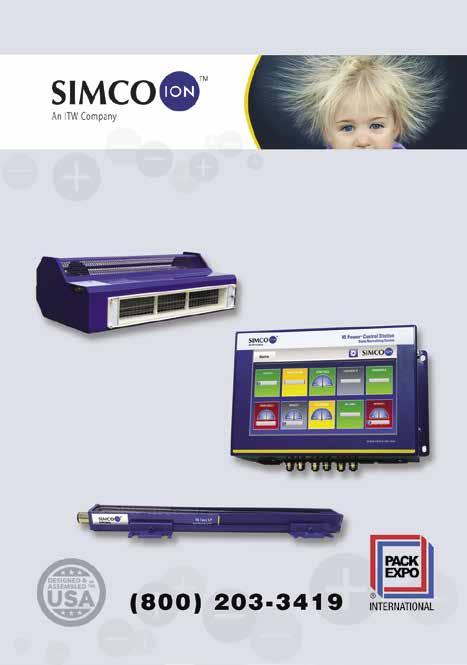

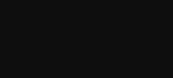
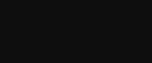
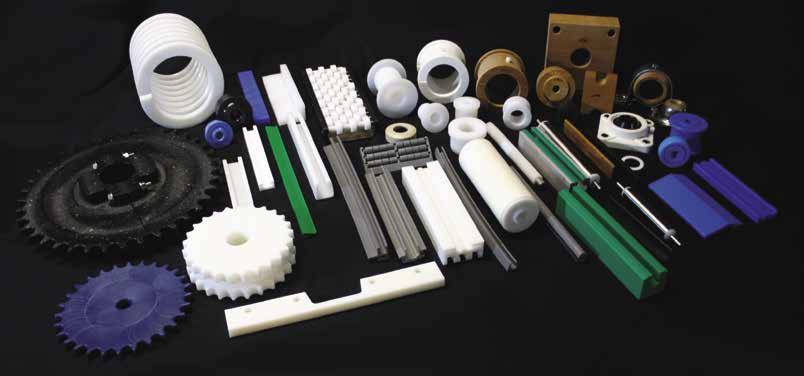
Industry
Certified Trainer Workshops
Develop
skills.
Fundamentals of Field Service (for PMMI members only)


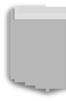
the
skills they need to provide great
Mechatronic Certifications
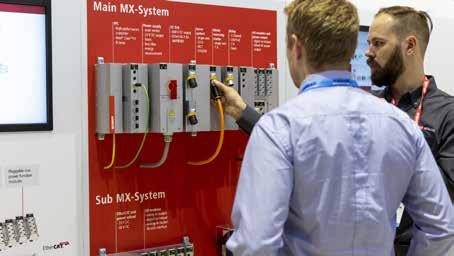
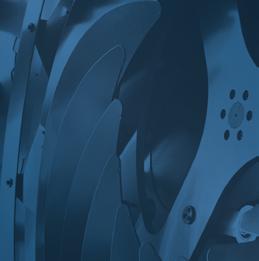

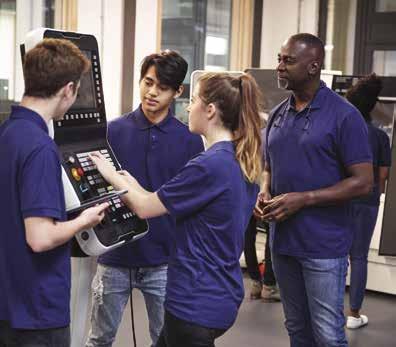
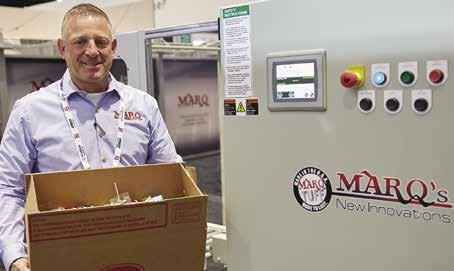
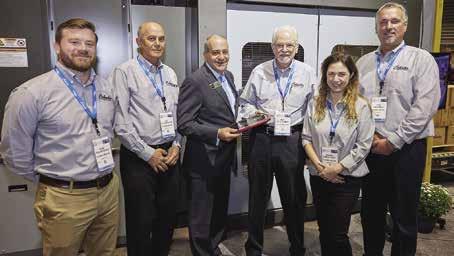
Risk Assessment Workshops
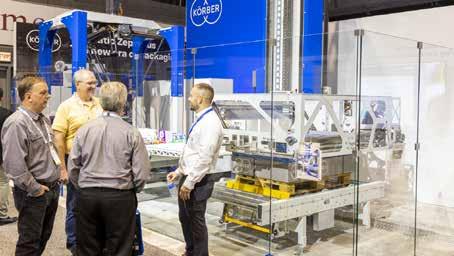

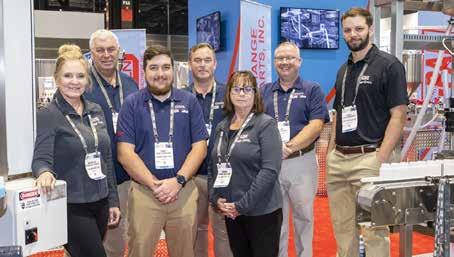

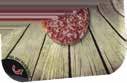
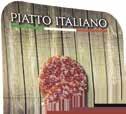
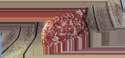
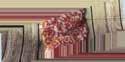
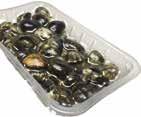

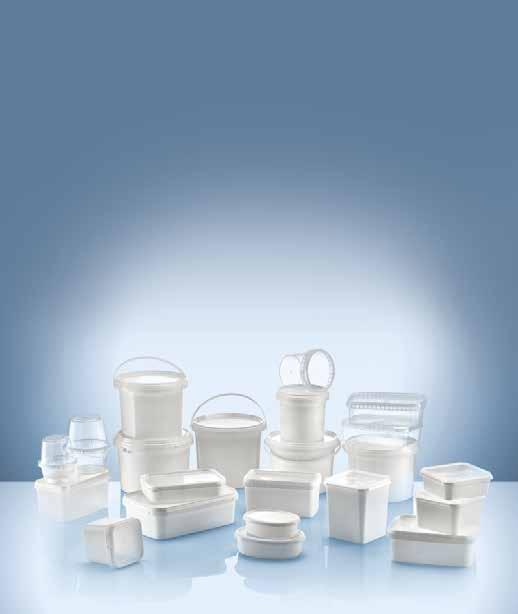



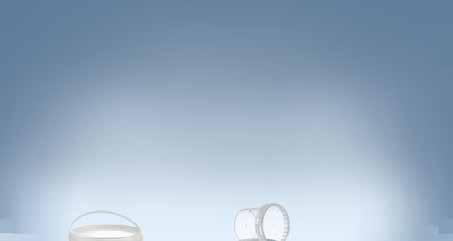
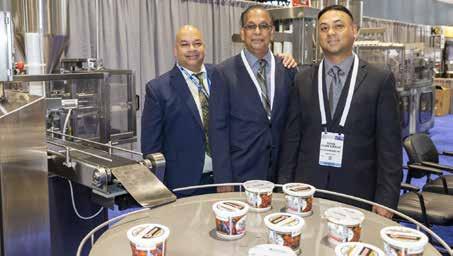
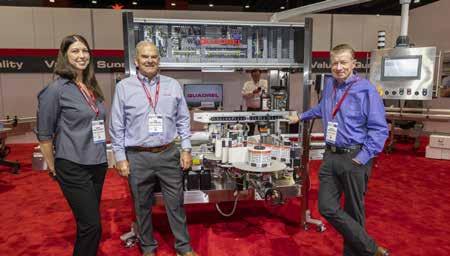
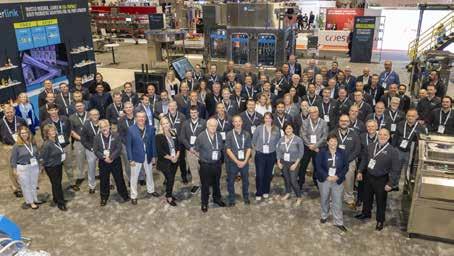

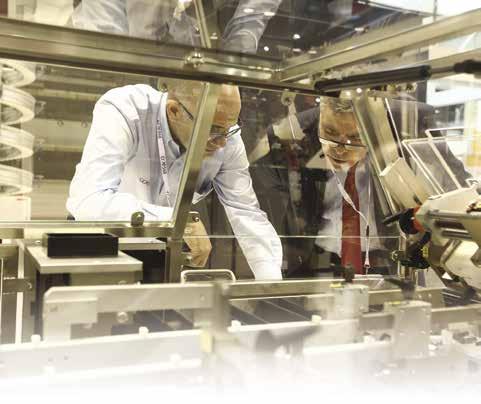
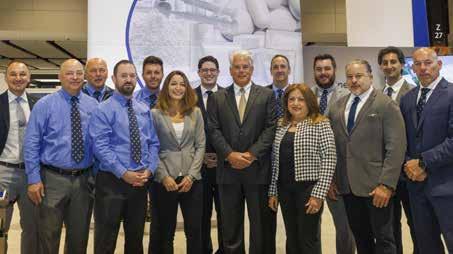
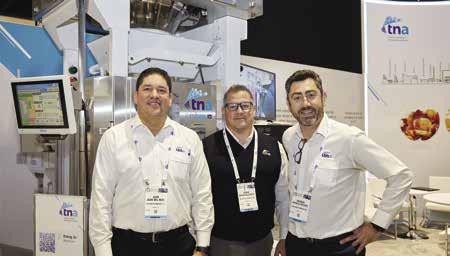
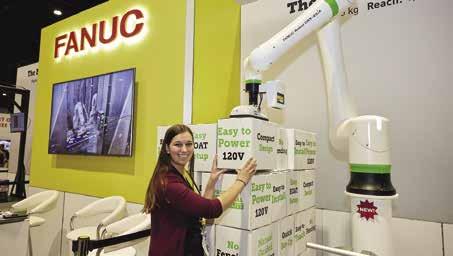

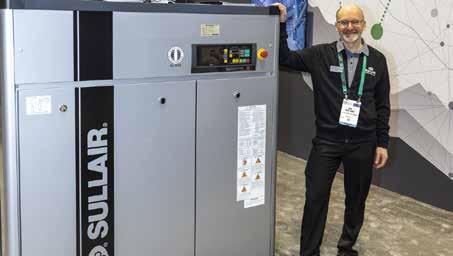
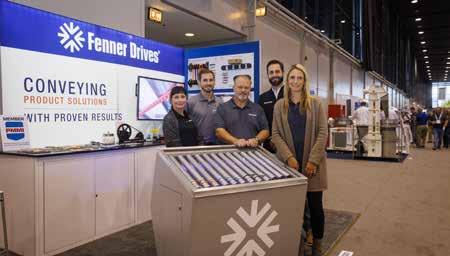


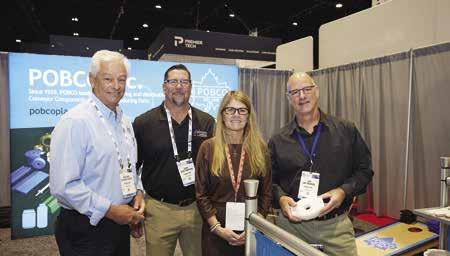
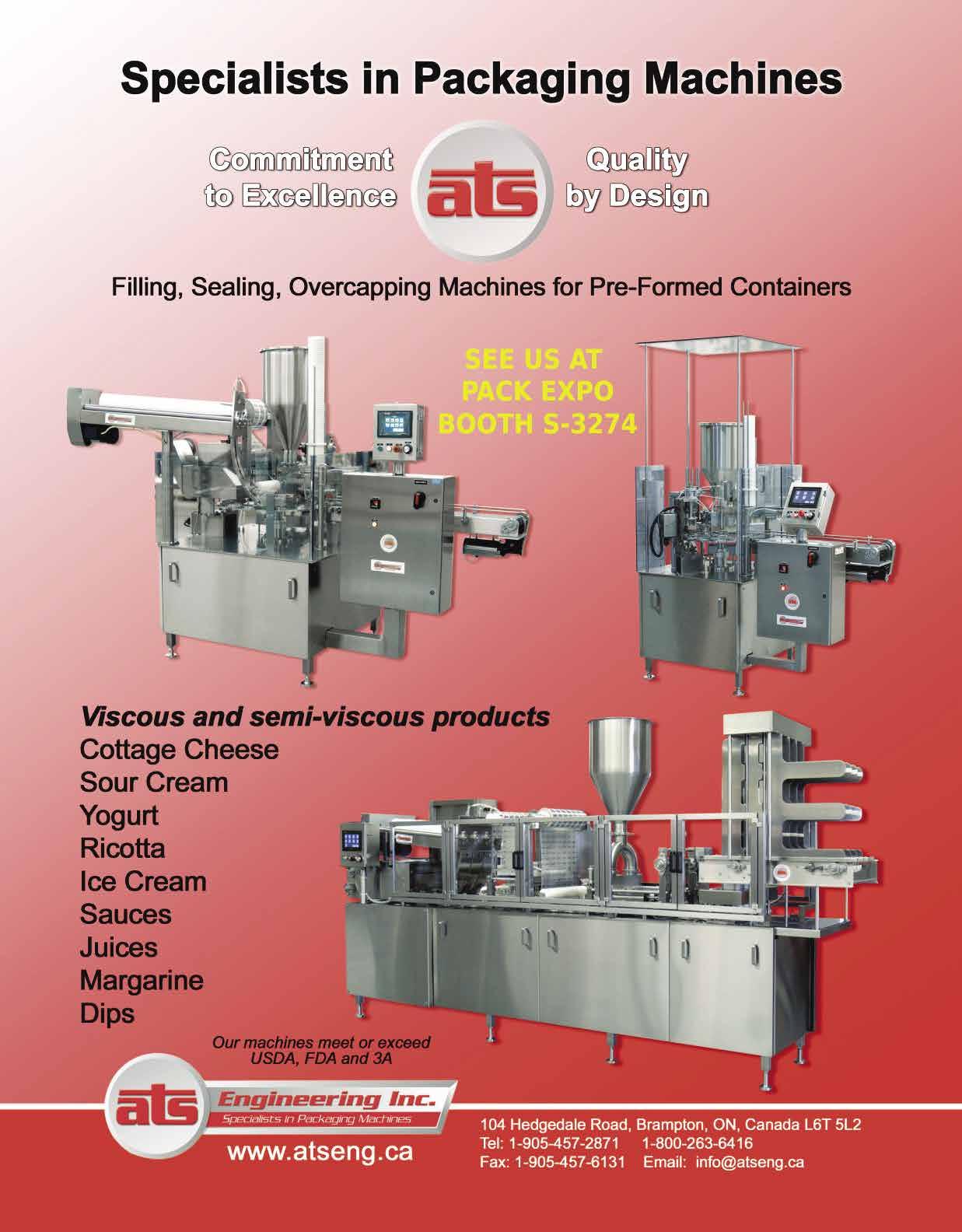
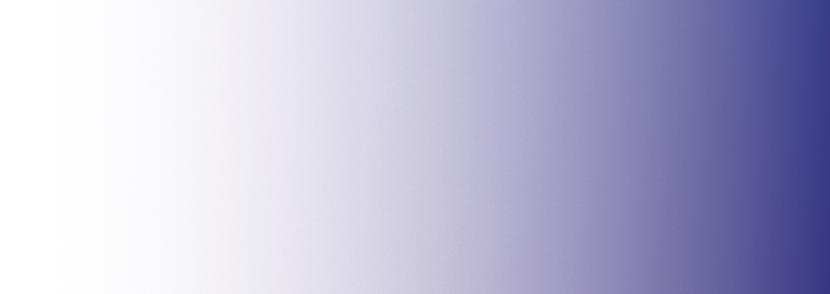
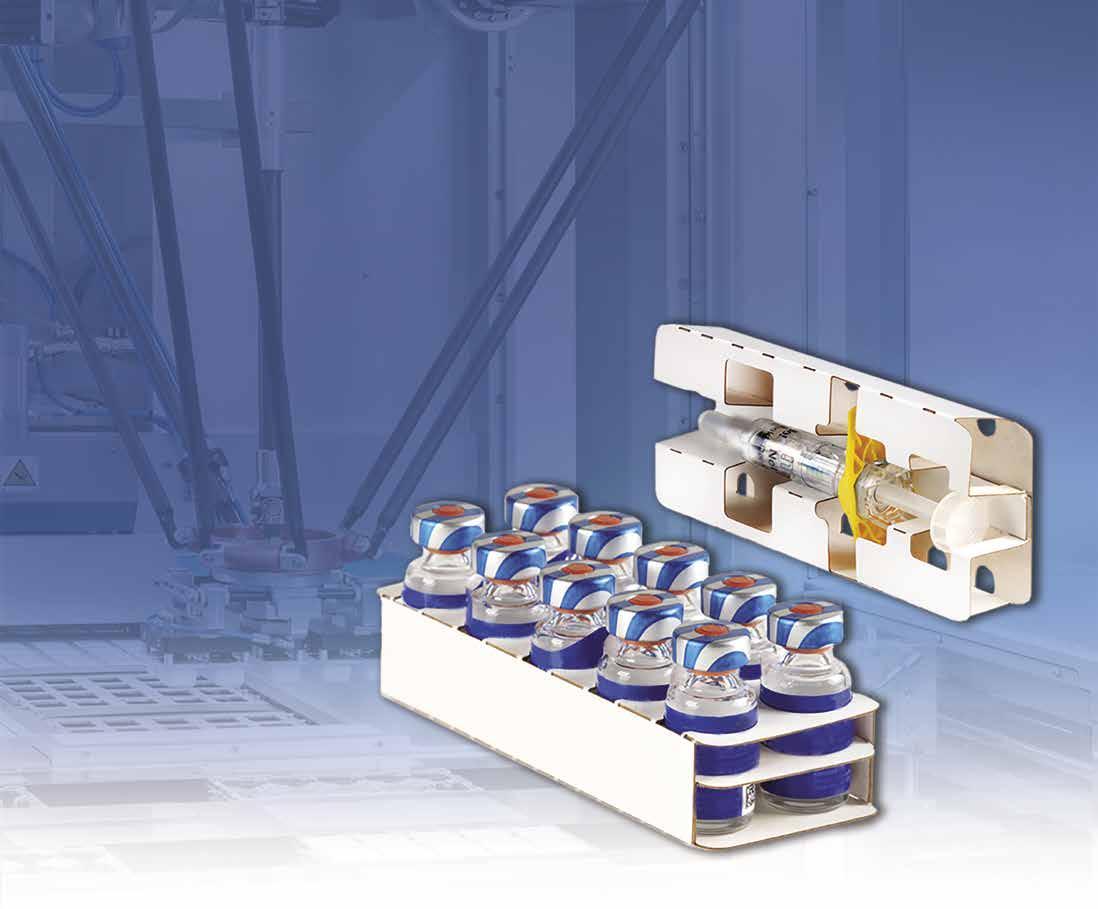
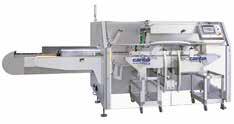

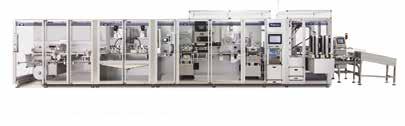