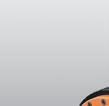
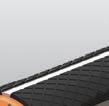
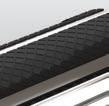
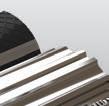


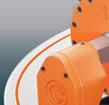
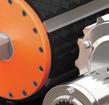

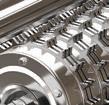
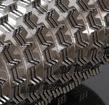
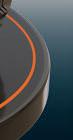
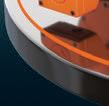
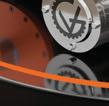
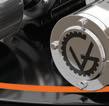
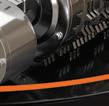
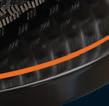





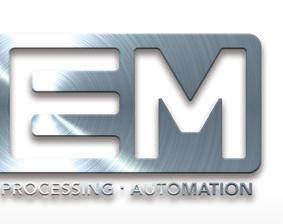
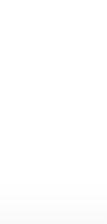
The SSV Series Drum Motor is the most hygienic and efficient conveyor drive for sanitary belt conveyor applications. It has the belt profile machined directly onto the drum and drives modular conveyor belts without using sprockets, reducing time and water used for washdown by 50%.
ELIMINATE Drive Sprockets
ELIMINATE Product Build-Up
ELIMINATE Bacterial Harborage
Engineered for reliability and longevity, VDG Drum Motors are designed for 80,000 hours of continuous operation before maintenance, reducing operational and maintenance costs and increasing throughput.
To suit various belt conveyor applications, a variety of diameter sizes, belt speeds, horsepower, face widths, and industry specific options are available.
patented IronGrip™ Lagging
IMPROVES INCREASES EXTENDS
Learn more: vandergraaf.com/OEM
(888) 326-1476
Belt Tracking
Belt Traction by 40%
Lifespan of the Conveyor Belt
The most notable feature of the EZGUIDE™ system is it does not have any protruding brackets or shafts which could be a major safety hazard. The EZGUIDE™ system does not have any mechanical components which protrude from the sides of the conveyor during adjustment. All the mechanics are done without the need to protrude past the conveyor, keeping everything safe for those walking close by.
Another feature of EZGUIDE™ is it is designed to remain adjustable through curves. That is, the radius of the guides can change as the guide width is increased/decreased in the curve. While there are many traditional guide rail systems which can be made to adjust their width in straight sections, there are very few that can truly be adjustable through a curved portion of conveyor. The reason is because changing the radius of a section is di cult – the guides must bend, and the length of the guide has to increase/ decrease as the radius is changed. The EZGUIDE™ system handles both of those problems with its unique design.
CONNECT WITH US:
OEMmagazine.org
facebook.com/OEMmagazine
@OEMmagazine
BUSINESS INTELLIGENCE
8 Packaging Material Predictions
Rigid plastic, flexible packaging, and metal see biggest gains in 2026.
EMERGING LEADERS
10 Professional Development
PMMI U provides tools, resources for nextgeneration packaging leaders.
INDUSTRY NEWS
12 Design and Sustainability Trends
PMMI and AMERIPEN report on the future of a circular packaging system.
MARKETING INSIGHTS
14 MaX Marketing Share Group
A place for PMMI members to connect and share marketing best practices.
SALES FOCUS
16 A Manager’s Coaching Guide
Tools, training to shi sales culture from reactive to proactive.
SUSTAINABILITY
38 Blister Pack Recyclability Meets Machinability
Amcor, MHI partner on a recycle-ready blister package produced at high speeds.
ASSOCIATION NEWS
40 PMMI’s 2022 Digital Annual Report
PERSPECTIVES
44 Motion Control Components
Real-time collaboration with suppliers shortens lead times.
APPLICATION BRIEF
48 Thompson Duke and Festo
Automating cannabis oil cartridge filling.
WORKFORCE DEVELOPMENT
53 Students at PACK EXPO
Advice to a ract future packaging professionals.
WOMEN’S LEADERSHIP NETWORK
56 PowHER of the Pack
ProMach launches women’s resource group.
NEW PRODUCTS
94 OEM Machine Technology
The latest innovations in control and components.
The official publication of PMMI OEMMAGAZINE.ORG
EDITORIAL
Stephanie Neil Editor-in-Chief sneil@OEMmagazine.org / 781 378 1652
Sean Riley Senior News Director sriley@pmmi.org / 571 266 4419
ART & PRODUCTION
Jonathan Fleming Art Director
David Bacho Creative Director
George Shurtleff Advertising Production Manager
PUBLISHING
Mike Prokopeak Senior Director, Content & Brand Growth
Kim Overstreet Director, Emerging Brands Alliance
Sharon Taylor Director of Marketing
Amber Miller Senior Marketing Manager
Janet Fabiano Financial Services Manager
PMMI Media Group
401 N. Michigan Ave., Suite 1700, Chicago, IL 60611
Phone: 312 222 1010 | Fax: 312 222 1310 www.pmmimediagroup.com
David Newcorn President
Kelly Greeby Sr. Director, Client Success & Media Operations
Elizabeth Kachoris Vice President, Digital
Jen Krepelka Director, Digital Media
PMMI, The Association for Packaging and Processing Technologies
12930 Worldgate Dr., Suite 200, Herndon VA, 20170
Phone: 571 612 3200 | Fax: 703 243 8556 www.pmmi.org
Jim Pi as President and CEO
Joe Angel Executive VP, Industry Outreach
Glen Long Senior VP
Tracy Stout VP, Marketing and Communications
Laura Thompson VP, Trade Shows
Andrew Dougherty Senior Director, Membership
SUBSCRIPTIONS
To subscribe to OEM visit: www.OEMmagazine.org/subscribe
To change or modify a subscription, please contact circulation@OEMmagazine.org
OEM EDITORIAL ADVISORY BOARD
Lisa Hunt CEO, Plexpack
Greg Berguig VP, Sales and Marketing, PAC Machinery
Rick Fox III Director, Engineering Services, Fox IV Technology
Brian Ormanic Senior Applications Engineer, Pearson Packaging Systems
Colin Warnes Director Sales Engineering & Project Management,ADCO Manufacturing
Tom Ivy, President, F.R. Drake
Stacy Johnson, VP Business Development, Hoosier Feeder Company
Supporting high tech OEM’s since 1938
Collaborative Robots.
Automation Solutions.
Custom UL Panels.
Sensors.
Industrial Robots.
Machine Vision.
Safety.
Aluminum Framing.
Inspection Systems.
Linear Motion.
Industrial Wireless.
Contract Manufacturing.
Learn more about our full scope of capabilities
Experience the highest level of service, solutions and innovation from all
In February, I took a trip to Miami, FL to visit Garrido Printing Equipment. I was invited to take a look at their recently built factory training center that includes a skybox conference room overlooking the facility where training and customer FATs take place. It’s truly an impressive space that makes for a first-class experience for visitors, whether they are on the floor with the machinery or meeting in the comfortable conference room.
But what was even more captivating for me was the family history that has a palpable presence. You can see it in pictures on the walls, you can hear it in the Spanish spoken by employees, and you can sense it in the magnanimity of the company executives. The story of this family starts with a brave father, Diego, who left Colombia in the 1980s with his wife and two sons, Juan and Nicolas, to pursue a better life in the U.S. It’s a success story based on perseverance and faith, and one that I am honored to tell—turn to page 20 to learn more.
Also in this issue, contributor Liz Cuneo explores how
the CHIPS and Science Act will impact American manufacturing, with the hope of solving troubling semiconductor shortages that are impacting OEM lead times. More on that on page 28
And Contract Manufacturing & Packaging editor Melissa Griffen reports on a new women’s resource group at ProMach, called PowHER of the Pack, that is making a significant impact on leadership development through networking, mentoring, and empowerment. Learn how the founding council pulled this effort together on page 56.
Speaking of empowering women, PMMI’s Packaging & Processing Women’s Leadership Network (PPWLN) has launched a webinar series, called Learning Circles, that will explore topics and skillsets that can help women navigate a successful career in manufacturing. The first webinar, focused on business acumen, takes place on March 21, 2023 with more scheduled throughout the year. Go to pmmi.org/ ppwln for more information.
U.S. packaging categories are predicted to see big material changes by 2026, including large gains in rigid plastic, flexible packaging, and metal.
Casey Flanagan, Editorial Assistant, PMMI Media GroupThe packaging material landscape may see big shifts in coming years, according to PMMI Business Intelligence’s 2022 report “Future of Packaging and Sustainability.”
In the U.S., rigid plastic, flexible packaging, and metal are expected to see the biggest gains by 2026, but the degree of growth will depend on the category they serve. Overall, the report indicates material usage is expected to increase significantly across all categories, except home care. What this means for initiatives like sustainability is yet to be determined.
The greatest overall projected volume gain from a single material comes through flexible packaging in the food category, with over 10 billion in projected volume gains between 2021 and 2026. Rigid plastic is expected to be the second most popular food packaging material, distantly trailing with projected volume gains of around 3.3 billion
units.
Following closely behind in the food category are paperbased containers, with projected volume gains nearing 3.2 billion units. The report notes an increasing share of sales in folding carton packaging by 2030, driven by the rapid growth of compostable and certified paper-based packaging.
The only material expected to decrease in the food category is metal, with an expected decline of about 467 million units by 2026.
Rigid plastic holds the top spot in the beverage category, with projected absolute volume gains by 2026 exceeding 9.7 billion units. The projected popularity of PET bottles is driven by post-consumer recycled (PCR) content and growth in demand for beverages as a whole, the report says.
Metal takes second place in the beverage category,
trailing behind rigid plastic with a projected growth of about 7.6 billion units in the same time period. Metal beverage cans might hold such a large share due to support from capital investments taken by water, water-like beverages, and seltzers, the report says.
Only liquid cartons are expected to decrease in the beverage category by about 207 million by 2026. Overall, the beverage category is slated to see the greatest increase in material usage by 2026.
Dog and cat food hold a smaller share of packaging volume relative to the food and beverage categories. Despite this, it has seen the largest growth of any category in recent years, with a 5% compound annual growth rate (CAGR) from 2016 to 2021, the report says.
Metal packaging is set to be the most popular in the dog and cat food category, with almost 1.2 billion units in volume growth expected by 2026. Also in the running are rigid plastic and flexible packaging, expected to rise by 753 million and 611 million units, respectively.
Paper-based packaging for pet food is expected to shift slightly but still increase in use by about 25 million units by 2026. Pet food is the only category to see no declines across material types.
Home care holds only a sliver of the packaging volume taken up by the beverage category, but there are a few significant changes taking place within it.
Rigid plastic is expected to see the greatest decline in volume by 2026, down by about 223 million units. Metal packaging is close behind, expected to decline by almost 170 million. Paper-based containers are also expected to decline to the tune of about 146 million by 2026.
Flexible packaging shows the most promise for growth in the home care category, expected to increase by about 56 million units by 2026. Glass packaging is also expected to increase in the same period by about 31 million units.
In an effort to shape the next-generation of packaging and processing leaders, PMMI offers a professional development program designed to outfit individuals with the skills, confidence, and drive necessary to be effective influencers within their own organizations.
Specifically, the PMMI U Leadership Development Program was created by the Emerging Leaders Committee in collaboration with Jim Stryker, president and founder of Leadership Perspectives, Inc., a management consultancy specializing in business transformation. This six-month training course takes place both virtually and in person with the additional benefit of one-on-one coaching sessions. To that end, the program provides a personalized plan for each participant, based on a multi-dimensional assessment measuring behavior, motivation, and leadership attributes. Through a series of impactful exercises,
project-based learning, and professional development opportunities, participants will gain skills to make them more effective managers and leaders.
“In addition to your [personalized] leadership plan, you focus on a project throughout the year,” explains Kate Fiorianti, PMMI’s director of workforce development. “It can look different based on what you are trying to accomplish and is specific to your role.”
The 2023 program is ready to launch on June 1st, and will include:
• Kick-off webinar
• Talent Insights Assessment: A multi-dimensional assessment measuring behavior, motivation, and leadership attributes
• 360-degree feedback evaluation
• In-person leadership training workshop
PMMI’s Leadership Development Program benefits individuals and organizations alike, using established tools and resources that result in true business transformation.
Stephanie Neil, Editor-in-Chief
• Personalized leadership development plan which includes implementation on a current work project
• Monthly one-on-one coaching sessions
• Leadership training workshop in conjunction with PMMI’s Annual Meeting
• Personal coaching report
According to some of the people who have participated this past year, the Leadership Development Program really does make a difference.
“The PMMI Leadership Development Program helped me understand the difference between leading and managing,” says Ryan Beerley, applications engineering manager at Glide-Line. “I’ve gained confidence at the workplace and see my career in a different light since participating in the program.”
Scott Shepard, key account manager at ITW Hartness, agrees that the program has helped define a path forward for him. “First and foremost, the program provided powerful tools and resources to learn a lot about myself, what motivates me, and how I behave as a leader. This, coupled with the exposure the program gives you to a wealth of academia in the field, allowed me to put together a personal improvement plan that has led to real changes in how I behave as a leader both in and outside of the workplace.”
In addition to helping individuals focus on professional
goals and identifying what motivates them as a person, the program is also an introduction to all of the benefits a PMMI membership brings. “For many people, this is their first initial touch point with PMMI, and by attending the PMMI leadership event, they are building a network,” says Fiorianti.
“It does provide great networking opportunities with other industry professionals, some of whom will end up being your own support group through the process,” echoes Kim Overstreet, director of the Emerging Brands Alliance at PMMI Media Group. “Meeting the program participants for an initial two-day kick-off, and then again at PMMI’s Annual Meeting, was also a great way to get to know one another and learn more about what other member companies do.”
The tuition is $6,000 per participant, but the program is eligible for a $1,000 tuition reimbursement from the PMMI Foundation. Or, PMMI members could receive up to $10,000 in matching dollars by using the PMMI U Skills Fund for the current workforce if three or more employees are registered for the Leadership Development Program.
Ultimately, the long-lasting benefit for employers include:
• Better leadership
• Improved company culture
• Better decision making
• Improved productivity
• Increased employee engagement
• Increased retention through effective use of employee talent
• Improved ability to adjust to and manage change
“I’ve had the opportunity to work for some great and some not so great leaders. It’s always easy to differentiate between the two, but challenging to pinpoint the ‘what’ about the great leader that makes them great. I wanted to understand what makes great leaders, and what I needed to do to improve my own leadership ability.”
–Sco Shepard, key account manager, ITW Hartness
“I’d recommend the program for anyone who has a willingness to become a more effective leader. Not only has the experience helped myself and my team in a work se ing, but it’s also helped me improve personal relationships away from the office.”
–Ryan Beerley, applications engineering manager, Glide-Line.
“PMMI’s Leadership Development program enables participants to focus on their professional goals with one-on-one support from a coach, and provides in-depth feedback about how others you work with view your leadership abilities in the workplace, as well as what inspires and motivates you as a person.”
–Kim Overstreet, director of the Emerging Brands Alliance, PMMI Media Group
For questions, please contact: Kate Fiorianti, Director, Workforce Development at 571.266.4406 or kate@pmmi.org . Or register online here: oemgo.to/leadershipdevelopment2023
PMMI and AMERIPEN evaluate trends and implications for the future of a circular packaging system.
Sean Riley, Senior News DirectorOff-shoring dominated the headlines since the early days of the pandemic when the often touted global supply chain was exposed due to lockdowns.
Reshoring became the buzzword as industries clamored to find ways to bring manufacturing closer to home so pandemics and overseas war—like Russia’s invasion of Ukraine—would not cripple economies. Long before COVID-19, the recycling and recovery community had its reckoning with off-shoring when China enacted the National Sword policy restricting plastic waste imports. Overnight, American consumers discovered that most recyclable content was actually just shipped to China and other countries. Some may or may not have been crudely recycled and reused overseas, but most sat in landfills.
Packaging materials waste that once moved internationally must now be recovered and recycled domestically, exposing years of under-investment and the need to ramp up American capacity in recycling and recovery. Seeing this problem and utilizing their combined resources, PMMI and AMERIPEN produced the white paper “PACKAGING COMPASS: Evaluating Trends in U.S. Packaging Design Over the Next Decade and Implications for the Future of a Circular Packaging System.” Later this year, PMMI will release a companion report focused on responses from OEMs and material converters.
What PACKAGING COMPASS determined first and foremost is that packaging design is a multifaceted process that requires balancing various procedures, characteristics, and systems. The data reveals that packaging designers are interested in sustainable packaging and want to support circularity, but they exist in a world that requires balancing these objectives against multiple variables such as price, safety, distribution, material, and environmental impact.
Plastic packaging, particularly flexible plastic pouch formats, will continue to grow and represent an increasing portion of the packaging waste stream based on PMMI and AMERIPEN’s ten-year forecast. Although technically recyclable, flexible packaging is not widely recyclable because very few Americans have access to convenient and consistent recycling due to the challenges in sorting flexibles within
municipal recycling facilities (MRFs). This is where the benefits of designing with flexible packaging need to be balanced with innovation in recovery.
Recycled content, particularly in paper and plastic packaging, can solve some of these issues, but sufficient materials of high enough quality to meet both packaging and, where applicable, food contact requirements are not widely available yet. The promise of compostable packaging also remains enticing, but the size of the compostable packaging market versus other materials remains small. Ideally, the potential for compostable packaging to help divert food and packaging waste from landfill and into composting would be reason enough to conclude that the value of compostable packaging comes both in its use and its end of life. In addition to applying design strategies to simplify packaging for increased recycling, improving the collection, sortation, and reprocessing technologies for these materials could also significantly impact supporting corporate goals and stimulating a domestic recycling community.
These potential design solutions lead us back to the need to invest in recycling and composting infrastructure across the U.S. PACKAGING COMPASS calls for packaging designers and recyclers to share their challenges and opportunities to collectively design systems that incorporate an understanding between all parties in the packaging value chain. Changes in one area of that chain impact others downstream, and collaboration across the value chain will drive successful innovation.
A dialogue on packaging design trends will help packaging stakeholders with the foresight to identify the most effective legislative and investment strategies to support packaging circularity. As extended producer responsibility (EPR) for packaging is adopted in the U.S., and the federal government continues its national dialogue on recycling with programs like the Bipartisan Infrastructure Law: Transforming U.S. Recycling and Waste Management, now is the right time to push the need for discussion on design needs so a circular packaging system can genuinely exist.
A deeper webinar dive into the white paper is available at PMMI.org.
Introducing the cutting-edge HERMA 500 label applicator. Powerful, Flexible and Highly Connected.
The HERMA 500 features a faster, more convenient user interface with touchscreen and intuitive menu guidance. Improved performance correlates to up to 25% faster labeling speeds. The HERMA 500 is also highly flexible and built to accommodate virtually any label size. And you’ll be connected with intelligent controls and browser-based operation. The HERMA 500. No compromises. Absolute performance.
PMMI membership has its privileges. From access to business intelligence to workforce development programs to networking opportunities with customers and peers, PMMI members benefit from access to tools and resources that help drive their business forward.
Building on the success of the OpX Leadership Network, which brings together manufacturers and OEM experts to develop best practices and protocols for free industry adoption, the Industry Relations Committee created the PMMI Manufacturing Excellence (MaX) Forum, which focuses inward with member companies collaborating to drive efficiencies and streamline operations through sharing best practices. It is also developing training under the three pillars of sales and marketing, field service, and engineering and operations.
Under each MaX Member Forum pillar, share groups serve as a collaboration space to network, share best practices, identify challenges, and create solutions. Share groups are open to any member interested in participating. Once the group identifies a challenge to dig deeper into, a smaller team of up to about 20 members convenes to create a solution in the form of a work product accessible to all members. An example work product developed by the field service share group is the best practices guide, “Pandemic Policies for Field Service Personnel.”
➲ See an infographic summarizing the Pandemic Policies for Field Service Personnel guide: h ps://pmmi.docsend.com/view/ vp5xwfwtbrstyp2z
The Marketing Share Group
New for 2023, the marketing share group offers a space for marketers to connect and share industry-relevant best practices, build a peer network, and bring valuable insights
back to their organizations. Led by executive sponsor Mike Stein of Signode, along with me—as the PMMI liaison—we are excited to grow this community throughout 2023 and beyond.
Like all MaX Member Forum share groups, the marketing share group is open to all PMMI members—not just those in a marketing role. So if you have an interest in marketing, we welcome you to join us. Similarly, we welcome participants at all stages of their careers and any level at their companies.
To get started, join us for a discussion in Microsoft Teams. Register at pmmi.media/maxmkt. Once registered, explore the different channels and resources, and start engaging in conversation. Participate as much or as little as you want. And please, invite your colleagues!
Topics covered will evolve based on community interest. A big topic of interest is in discussing lead generation best
“The MaX Member Forum is a great way for PMMI members to interact with colleagues from other PMMI companies, learn about different approaches, and engage with people with similar interests. The tag line ‘by members for members’ nicely summarizes the simple but valuable approach of this program. The newly formed marketing share group provides a Teams site where marketing professionals can share ideas and learn from each other about techniques and best practices to improve their marketing knowledge and expertise. We encourage savvy veterans and those new to field to come together and learn from each other.”
—Mike Stein, VP of sales, marketing & product management, automation & packaging technologies at Signode Industrial Group LLC
practices, marketing team structures, and participation in marketing trends. While there is no shortage of marketing best practices shared through blogs, articles, books, LinkedIn, and more, our goal is to cover marketing through
the lens of the packaging and processing industry to better understand how tactics, tools, and strategies apply to PMMI member organizations. Topics are covered broadly enough to prevent competitive concerns while still providing enough relevant context.
Members are encouraged to post about new topics that interest them, and we’ll be surveying and polling participants along the way. As subject matters rise to the top of member interest, we’ll begin developing work products to distribute best practices to all member organizations.
Beyond connecting through the Microsoft Teams channel, we look forward to hosting virtual and in-person events to help marketers develop their network of industry peers. Look for a marketing share group breakout session at the PMMI Roadshow in July.
I look forward to getting to know many more marketers through the share group. Register at pmmi.media/maxmkt and contact me at staylor@pmmimediagroup.com with any questions.
Easily share this article with your peers: oemgo.to/maxmarketing2023
With 100% more capacity (45 tph) and twice the available tray size/mass than our next largest feeder, Eriez high capacity
76 Series Electromagnetic Vibratory Feeders are designed for packaging applications with high head loads or needing exceptionally long overhang.
•Handles high head loads
•Exceptionally long overhang
•Up to 45 tph
•High speed and high deflection drives
“My reps are winging it on sales calls.”
“Our salespeople are acting in an entirely reactive mode when in front of prospects.”
“When I ride-along with my reps, I am surprised at how unprepared they are for each call.”
Many of us were taught Napoleon Hill’s famous quote at a young age, “plan your work and work your plan.” Many might also be familiar with Ben Franklin’s quote, “if you fail to plan, you are planning to fail.” The challenge for most sales managers is that their people, both seasoned and brand new, are ignoring this wisdom when it comes to their sales calls. Regardless of whether it is an inbound lead, referral, or a follow-up to a cold call, most reps engage without a strategic “pre-game” sales plan.
When asked, the primary reason salespeople will give for the lack of planning is having no time to do so. Although precall planning has always been a challenge, the issue has been amplified in recent times by an increase in demand and the lack of supply. The overabundance of pricing and product inquiries and the perceived need to respond quickly is pushing even the most experienced salespeople into a reactive price-quoting and order-taking mode.
Unfortunately, salespeople who have fallen into this transactional “customer service” approach are vulnerable to heavy price competition, as well as pressure to give additional profitreducing concessions. The problems associated with this mindset are especially evident when salespeople are working on strategic opportunities and transformative equipment purchases. Many of these deals fail to close due to a lack of alignment with the key decision makers that are above the purchasing and lower-level technical contacts. Even when presented with an opportunity to expand existing accounts, things fall apart in the absence of a strategic plan.
Talk with the salespeople, and they’ll say that they are planning every call. From their perspective, a plan should be focused on how best to fulfill the prospect’s request for information and pricing. It is driven by the goal of setting oneself up as a “valued resource” to the prospect. The approach is more of a tactical routine versus a strategic plan and tends to be a one-size fits all that lacks any critical thinking. Typically, this consists of the following steps:
• Prepare all relevant supporting product material, demos, and pricing information.
• Pull together any available technical resources to bring to the sales call.
• Prepare questions to ask regarding technical needs and usage data to create a quote or proposal.
The missing piece in this plan is a route for qualifying the opportunity, gaining clarity on the decision framework, and securing the next steps.
While the basic plan is there—and managers appreciate the effort—it is misguided. Beyond preparing which solutions and pricing to present, most sales managers would like their salespeople to think much more strategically.
The misalignment with their manager’s expectations stems from the fact that most salespeople pride themselves on relationship building, rather than their process and planning skills. Compounding the issue is that most companies are failing to give their salespeople clarity and ongoing guidance
For over 60 years LPS® has earned a reputation for both quality and performance in critical industrial applications. LPS® DETEX® combines that expertise with food safety programs to produce a full line of maintenance solutions specifically formulated for food processing facilities.
LPS® DETEX® lubricants, penetrants, electronic cleaners, and greases save time and money by extending equipment life, reducing repair time, and lowering frequency of preventative maintenance.
Plastic components used to package LPS® DETEX® products are both metal & X-ray detectable, helping to reduce the risk of foreign object contamination within your facility.
To
on a process for creating a strategic pre-call plan.
So how do we create better pre-call planning alignment with our sales team?
It starts with management taking responsibility for the misalignment and providing the planning tools and ongoing coaching. This goes far beyond the occasional tactical sales training on prospecting, listening, and closing skills. A solid pre-call planning tool should promote critical thinking regarding what is known so far and what is yet to be uncovered and should address the following questions:
• What are the prospect’s objectives and desired takeaways for the upcoming meeting?
• What are our objectives, target outcomes, and next-step goals for the meeting?
• What is the impact of the business and operational issues, concerns, and unrealized vision?
• Who will be attending the meeting on the prospect’s side and what are the concerns and questions we need to address with each of them?
• What are the steps the prospect will be taking as part of the decision and budgetary process?
• Are there any other competitive alternatives they are evaluating or other priorities that will interfere?
The above questions are meant to help a salesperson organize their thoughts into a welldocumented strategic plan. A good pre-call plan should help the salespeople consider all that remains to be uncovered about the account, the opportunity, and the stakeholders involved.
Change the organizational mindset, and action will follow. The mistake we see many companies make implementing planning tools is taking the numbers-game approach. Management simply places a number as a goal for building plans, looking for quantity rather than quality. To drive the adoption of a precall planning approach, ongoing coaching and mentoring are required. Rather than simply asking if they created pre-call plans for each meeting, it is critical that sales management prioritize reviewing the actual plans with the salespeople.
If we want our salespeople to think more strategically and plan more effectively, then we need to lead by example. Providing tools, training, and ongoing guidance is paramount in shifting company sales culture from reactive to proactive.
Easily share this article with your peers: oemgo.to/salespregame
On a small side street right off the highway in the heart of Miami sits a sizeable, warehouse-like building. The gray exterior makes this industrial space fairly inconspicuous to the average passerby, except for the large red letter “G” perched above three separate entrances. At first glance, the building on 7258 NW 66th Street is rather unremarkable. But one step inside and a very different—and extraordinary—story unfolds.
This is the home of Garrido Printing Equipment Inc., a former import and export company that first opened its doors in 1986 and has evolved over the years into a supplier of rebuilt printing machinery for the graphics arts industry in 1989 to a manufacturer of paper converting machinery in 1995. In 2007, the company transformed itself yet again by adding shrink wrap and bagging equipment to its portfolio under the Advantage Machinery brand—which is the company’s bread and butter today.
With its growth over the years, Garrido Printing Equipment also expanded its space in this same building that has served as the lifeblood of this family-owned business for almost 40 years. This building, as simple as it may seem, represents the ultimate success story.
The story starts like this: On May 12, 1986, Diego Jose Garrido left Colombia with his wife and two young children, Juan and Nicolas. They were fleeing the country’s socioeconomic strains to pursue a better life living with a relative in the United States.
Diego and his family arrived that day in Miami with just four suitcases and $300.
The next day, May 13, 1986, Diego went to a flower wholesaler, bought a box of flowers, and started selling them on street corners. Driven by family, faith, and
The maker of shrink wrap and bagging equipment built a business from scratch on a foundation of providing the best overall experience for its customers.
Stephanie Neil, Editor-in-Chief
When established: 1986
Leadership (company executives): Diego Jose Garrido, Founder; Nicolas Garrido, VP and General Manager; Juan Garrido, VP and Technical Director
Range of products: Shrink wrap equipment, automated horizontal paper encapsulating machines, stretch wrappers, carton sealers, and case erectors.
Headquarters / manufacturing location(s): Miami, FL and Shenzhen, China
Number of employees: 22
Number of field service personnel: 6
Facility square footage: 20,000
Geographic sales and support areas: North America
kindness, Diego made connections and eventually landed a full-time job at an import/export company that was a tenant in that building on 66th Street. The owner of the import/export business was absent most of the time, so Diego became the point person for customers as well as Norman, the warehouse property owner.
One day, Norman told Diego that he had to evict his boss from the property. It was a devastating moment for him as a Spanish-speaking immigrant who now faced having to find another job. That is, until Norman suggested Diego start his own import/export company in that very same spot. He just needed $500 to create an S Corp., and $1,000 per month to take over the warehouse. Diego felt he could scrape together the money to do that, but he still needed a deposit to purchase the space, which Norman agreed to finance for him.
In that moment, life for the Garrido family changed for the better, but not necessarily in the very beginning. “We had a warehouse, but not enough money to eat,” Diego remembers.
So he put his family to work. “Our summer camps were coming here and getting a broom and sweeping up,” says Nicolas Garrido, who is now a vice president and general manager at Garrido Printing Equipment. “A lot of times, we were making more of a mess than when we started, but for my father, it is always about teaching us how to earn money.”
That strong work ethic catapulted the business forward. Diego persevered in the import/export business until one day he received a request for a Heidelberg printing press. As he researched the machine, he noticed there was a void in the market to supply high-quality, rebuilt printing machinery, and he decided to focus business there. He traveled the world looking for solutions to his clients’ needs, which is when he found another opportunity to deliver paper converting equipment with complementary finishing, sealing, and packaging equipment.
When Juan and Nicolas graduated college and joined the company in the late 1990s and early 2000s respectively, the family team realized the need to move away from printing and paper converting equipment and solidify its place in the packaging industry. So, in 2007, with Diego’s two sons now working alongside him, they introduced the packaging machinery division, known as Advantage Machinery, to focus on the U.S. market through distribution partnerships.
“We came out with the Advantage Machinery brand in 2007, but we really launched it at PACK EXPO Las Vegas in 2009,” says Nicolas.
Advantage Machinery is used in a variety of industries, including food, printing, laundry, carpet, electronics and, most recently, e-commerce. “We have a machine that does the insulation paper for the food kits that are sold through e-commerce,” notes Nicolas.
And, a high-speed, fully automated version of that machine is currently being beta tested at a customer site to replace single-use, non-recyclable plastic with fully curbside recyclable paper packaging that has a coating to make it sealable. “It is very versatile. You can put a pen there and it will wrap a bag around it,” says Juan Garrido, vice president and technical director at Garrido Printing Equipment, describing the proprietary technology they developed.
Today, Juan and Nicolas run the day-to-day operations, including working with distributors and end users and customizing equipment to customers’ needs. Most of the machine manufacturing is done by a partner in Shenzhen, China. They originally moved production to China as a costsaving move, but realized they would have to invest a lot of time and effort to ensure quality control.
“In the beginning, we thought it would be like doing business in Europe,” Nicolas says. “But we found out quickly that the stigma that China held was very true. My brother and I found out the hard way that we’d have to spend a lot of time in China instilling our quality control processes. We did that for a long time, right up until COVID.” Luckily, their hard work paid off. “We had to trust the processes we put in place there, and we found out that we really didn’t have to go back for a lot of the stuff that we used to travel there five or six times a year for. We just had to trust the system we
created, and it worked.”
To that end, they’ve created a strong relationship with their manufacturing partners in China which they’ve been working with now for 14 years. So much so that, when the pandemic hit China, Garrido Printing Equipment was forewarned of the impending impact on the U.S.
“Our partner in China reached out to us and said they were making machines there that make surgical face masks,” Nicolas says. He laughed it off at first, but awoke that same night wondering why they wouldn’t consider making the same equipment. “We sent our technicians that work for us in China to the factory where these machines were made to dissect everything and tell us what parts need to change. We went through every component and sourced it, priced it, tested it, and then promoted them.”
That move got the company through the first part of COVID. Then, as rumblings that competitor lead times were sliding from 12 weeks to 36 weeks, they found yet another opportunity to get into accounts that they could never get a foot in the door before—and that was due to well-stocked inventory shelves.
With the new packaging division formed, Garrido grew its client and distribution base, as well as its stock supply for standard machines. In 2021, the company had the opportunity to purchase yet another warehouse unit in the same building that was two doors down. That unit became storage space for machinery and parts. “Every dollar we had was spent on more inventory,” Nicolas says. “If we sold one part on one machine in the last 15 years, we still have that part in stock.” Whether it’s electrical components, servo motors, PLCs, drives—the OEM stocks one of everything. “We easily have over a million dollars worth of stuff just sitting on a shelf.”
While the inventory doesn’t make any money sitting there, it is extremely valuable because when it’s needed, it’s needed quickly. “When you have a machine down, the solution has to be fast,” says Diego. “If you say it will be four months for a part, forget it.”
In parallel with providing parts and service quickly, the Garrido family also had a vision of providing a first-class training and testing facility onsite. When the warehouse unit that sat between the main facility and the stock room became available, they bought that too. This particular unit was built out as a large FAT center where distributors and clients could send their technicians to get trained on the Garrido line of equipment. The area is also used to perform machinery testing prior to shipment.
And, high above the FAT center is the Garrido “skybox,” a comfortable conference room where customers can work while overlooking the FAT room through a wall of glass. “We wanted people to have a first-class experience,” Nico-
las says. In addition, they wanted to infuse the space with their history. Family photos and antique printing presses are part of the décor, as is a custom-made conference table filled with old printing types that spell out words related to different parts of the company’s heritage. “As we look towards the future, we need to not only remember where we came from, but we want everyone we do business with to know our family’s story as well,” says Nicolas.
And the Garrido story expands to the employees—most of whom speak Spanish as their first language—who have become an extension of the Garrido family. “It does take us a little while to find the right person for the job, but when we do, it is easy to retain them,” says Juan. “We make it a fun place to work, and when we talk to new employee prospects they see that everyone is happy.”
Customers are happy, too, as Juan makes sure that he or his technicians are always available to answer questions. To do that, Garrido supplies distributors and end users with a chat app free of charge. If an issue arises at the client site, they can initiate an encrypted group chat that reaches the distributor representatives and Garrido technicians at the same time.
“Most of the time the issues that arise are because an operator is running a new product or new film, and sometimes they just need someone to push them onto the right
path,” Juan explains. “We try to make ourselves available to solve the problem because it can often be solved within 15 minutes on a chat. They don’t need to pay for onsite service.”
This service-oriented mindset is a strategic mission of the company.
“Our goal in this industry is to have everybody that works with us to be able to say that we offer the best overall experience,” Nicolas says. That comes from the moment a client requests information, to the way Garrido supplies that information, and the way they handle the RFQ process in a timely manner. It also extends to invoicing and purchasing, the skybox experience, the FAT room, and the support provided after installation. “We want the user experience to be the best when they deal with us.”
Treat people the way you want to be treated—that is the bottom line.
It’s a mantra that was born the day the Garrido family arrived in Miami. The company truly was built from the ground up. And as Diego turns the business over to his sons to carve a future path, he can be proud of this legacy he’s created for generations to come.
Easily share this article with your peers: oemgo.to/garridoprintingequipment-
When established: 1953
Headquarters: Canton, Ohio
Range of products: Pneumatic conveying, exhaust and exhaust filtration systems
Headquarters: Canton, Ohio
Number of employees: 45-50
Number of field service personnel: 2
Facility square footage: 68,000
Geographic sales and support areas: Global, but primarily North America
Annual revenues: 10 to 20 million
Executive team: Joe Ovnic, general manager; Andy Grow, engineering manager; Shane Ixos, manufacturing manager; Ray Webb, service manager; Bre Phillabaum, purchasing manager; Chris Rogers, IT manager
For nearly 70 years, Quickdraft, Inc. of Canton, Ohio, has powered its conveying and exhaust systems by deploying Venturi blower technology to efficiently increase air velocity and maintain vacuum pressure with no obstructions in the material conveying or exhaust flow path. OEM magazine spoke with Quickdraft’s Joe Ovnic, general manager, to introduce one of the newest members of PMMI to their fellow members.
Quickdraft was founded as Basic Improvements Co. in 1953 as a provider of Venturi-based equipment that improved the draft for boilers and other equipment that required the exhaust of combustion products. It soon became apparent that this market wasn’t sufficient to support the company as its only product. Through in-house testing and experimentation, Quickdraft could use that same Venturi technology to convey various products pneumatically, most typically waste products generated in manufacturing processes that need to be efficiently and quickly removed, transported, and collected. Quickdraft’s primary market for many years was in the paper industry, removing the trim from slitting equipment. While still an essential part of the business, as the paper industry has declined, Quickdraft has developed other markets, particularly the food industry, where exhaust and exhaust filtration has become more and more significant to Quickdraft. The C.A. Litzler Company has owned Quickdraft since 1979.
Venturi technology is used in the design of most of our dilute phase pneumatic conveying systems and all of our exhausters and exhaust filtration systems. Our design has no moving parts in the conveying or exhaust ducts, as the blower handles ambient air and is outside the conveying or exhaust duct. This design provides our customers with dependable, low-maintenance, and long-lasting solutions. In addition, this allows us to convey continuous trim of various materials in our conveying systems reducing dust and eliminating other potential problems. This design also allows us to handle multiple problem exhaust applications —greasy, particulateladen, extremely hot, acidic, extremely cold, etc.—in a dependable manner.
What’s your approach to new product development?
We direct our research and development projects by listen-
The conveying and exhaust system OEM uses Venturi-powered technology to provide dependable, low-maintenance systems.
Sean Riley, Senior News Director
ing to our customers and addressing issues they are facing in their processes, then improving and expanding our systems’ capabilities.
How has your product line broadened over the years?
We have expanded our line of exhaust filtration systems to handle more challenging and different applications and to make them more user-friendly and efficient in water usage.
Where do you find most of your employees?
A good portion of our shop employees have been early placement students from local vocational high schools, particularly welders, a skill set we prioritize. Often mechanical engineers are found through recruiters. We are fortunate that employee turnover has not been an issue for us. We look for conscientious employees that take our customers’ obligations seriously, and we are a drug-free workplace.
Why do employees love working for your company?
Because we are a relatively small company, each of us has input into different areas of the company’s operations. We take our excellent reputation very seriously as a high-quality equipment provider in the marketplace that takes care of its customers. As a group, we are proud to be associated with a company with that reputation. In addition, all employees participate in an operating income bonus pool, so everyone has a stake in our success.
How do you balance standardized machine configurations with those requiring customization?
A significant portion of our product offerings is standard or pre-engineered. In general, we do not stock most of these components. The remainder of our offerings are engineered to order, typically sold by a sales engineer that visits the customer site to determine the overall specifications of the project. Once sold, an engineer will visit the customer site to laser scan relevant areas of the customer’s plant to generate
general arrangements drawings showing the location of our equipment.
Are you incorporating lean manufacturing?
We embarked on a lean manufacturing program many years ago. As a result, we re-arranged the product flow through our shop and changed certain processes completely. Before this we built most of our components to stock. We continuously look for opportunities to improve our efficiency and quality, including significant investments in production equipment.
What’s your process for handling a customer’s initial inquiry and needs assessment?
For the most part, this is handled by our sales group depending on the geographic location of the inquiry and whether it is a standard (pre-engineered) or an engineered opportunity. We do have some independent sales representatives that generate inquiries. In addition, we have a major distributor that sells our systems to the food processing industry as well as many oven and fryer OEM’s that incorporate our systems in their offerings. We also have outsourced lead generation to an outside company. Once qualified for standard products, a quote would be sent. For engineered opportunities, the sales engineer would typically visit the customer site to determine the customer’s requirements. Then those quotes are generated.
Once a customer issues a purchase order, what happens next?
We send out an acknowledgment of the order, and if it’s standard equipment, it is then released to the shop directly from our configurator, which was used to generate the quote. Engineered orders are assigned to a project engineer, and typically, the engineer visits the customer site to laser scan the portion of their facility where our equipment would be located. From these scans, general arrangement
drawings are generated in Inventor (3D) and issued to the customer for approval. After approval, the system components are released to the shop.
What challenges do you foresee affecting your firm and all companies in this industry?
Finding qualified labor is a continuing problem; we don’t see that changing. We have made investments to mitigate some of that, but we cannot overcome the overall problem. Also, as a niche company in many different markets, we need to continually find new customers and applications for our products to grow; that takes time and money, which will always be a challenge because of our diversified customer base.
Easily share this article with your peers: oemgo.to/quickdraft
Morrison is the expert in container handling, allowing OEMs to focus on and optimize the other critical aspects of their application and machine. With over 25 engineers on the team, we offer a wide range of solutions that pair well with your equipment to make it run more efficiently and give you an edge up on your competition when it comes to positive control of containers.
It’s no secret that supply chain disruptions and the ongoing semiconductor chip shortage have manufacturing across various sectors in a scramble.
We’re three years into the pandemic (or is it over now?), and the economy is certainly not where it was prior to COVID’s grand debut. Within the world of manufacturing, and amidst labor shortages and shipping delays, lies the semiconductor shortage.
A semiconductor is defined as a solid substance that has a conductivity between that of an insulator and that of most metals, either due to the addition of an impurity or because of temperature effects. Devices made of semiconductors, notably silicon, are essential components of most electronic circuits. These circuits are used in automobiles, household appliances, computers, industrial equipment, and even used in defense systems. According to Whitehouse.gov, America invented the semiconductor, but today produces only about 10% of the world’s supply—and none of the most advanced chips. Instead, we rely on East Asia for 75% of global production. The past few years have done much to expose this dependence on chips made abroad and the fragility of those supply chains.
“Part of the lesson in the last three years is that out-
sourced and off-shored activities come with great risk in times of global upheaval,” says Dave Swedes, vice president of engineering at Valco Melton.
To avoid this problem in the future, and in an effort to bring some semiconductor manufacturing back to the States, there is the newly signed (as of August 2022) CHIPS and Science Act. The act aims to boost American semiconductor research, development, and production, all to position the U.S. as a leader in this technology. The CHIPS and Science Act is expected to unlock hundreds of billions more in private-sector semiconductor investment across the entire country, including production essential to critical sectors like manufacturing.
And it’s a good thing as demand for these types of products is only growing. According to McKinsey, it is estimated that worldwide demand will keep growing, with semiconductors poised to become a $1 trillion industry by the end of the decade.
That’s why the act is so important and necessary to meet this new demand and control some of the manufacturing to remedy parts shortages and shipping delays. The overall goal of the act is to strengthen American manufacturing, supply chains, national security, R&D, and workforce. The
act is designed to not only strengthen U.S. semiconductor development but also promote wireless supply chains and investment in new technologies, like artificial intelligence (AI). All of this is designed to up the U.S.’s manufacturing game to ease current supply chain issues—which will help OEMs in the long run as they cope with the ongoing chip shortage and supply chain disruptions.
According to WhiteHouse.gov, the act will work to strengthen manufacturing and keep the United States the leader in the industries of tomorrow, including nanotechnology, clean energy, quantum computing, and AI. It sounds like a tall order, but manufacturers and suppliers fed up with reliance on semiconductors made in China and Taiwan are ready for a solution.
“If there are other sources for semiconductor-based components in the U.S., then I think that will benefit manufacturers all over the world,” says Eric Langen, sales and marketing manager at AFA Systems Ltd, a Canadian-based provider of engineered packaging automation systems. “Last year was an absolute nightmare in trying to procure electronic components [such as] servo drives, IO cards, etc., in a timely manner. It certainly does not make a lot of sense having one dominate supply chain for these components that are critical for any economy.”
While the goal of the act is to promote a better future in manufacturing, let’s look briefly at the past.
According to McKinsey, the ongoing shortages of semiconductors hurt U.S. economic growth by nearly a quartertrillion dollars in 2021, according to the U.S. Department of Commerce. To expand domestic manufacturing of mature and advanced semiconductors, the Department of Commerce will oversee $50 billion in investments over five years, including $11 billion for advanced semiconductor R&D and $39 billion to accelerate and drive domestic chip production.
The Whitehouse.gov breaks it down this way. The CHIPS and Science Act provides $52.7 billion for American semiconductor research, development, manufacturing, and workforce development. This includes:
• $39 billion in manufacturing incentives, including $2 billion for the legacy chips used in automobiles and defense systems
• $13.2 billion in R&D and workforce development
• $500 million to provide for international information communications technology security and semiconductor supply chain activities
It also provides a 25% investment tax credit for capital expenses for manufacturing semiconductors and related equipment. These incentives are said to secure domestic supply and create thousands of high-skilled manufacturing jobs.
But the questions to ask are: “When is relief really expected to be felt? And by whom?”
“Incentivizing investment for chips and other electronic components to be manufactured in the U.S. certainly has merit,” says Swedes. “Market forces have been driving that change anyway, as many manufacturers have realized their vulnerability to global markets that have single points of sourcing. Clearly, building this kind of capacity has a five to 10-year horizon, so the effects, for many, will not be felt immediately or even in the medium term.”
But while relief is said to be on its way, it doesn’t seem to come as a surprise that there is a lag in overall technology investments in the U.S.
“The U.S. has often lagged in creating incentives for small to mid-size companies to make investments in technology, labor-force education, and expansion, as well as improving manufacturing processes,” continues Swedes. “The Europeans do a much better job of that. With that in mind, the spending is welcome news. The downside is that much of this money will be targeting defense industries and consumer technology rather than industrial equipment.”
The CHIPS and Science Act makes some big claims and has lofty goals to get American manufacturing in key sectors back up and running and position them as industry leaders like never before. Given the scale of investment required, building new semiconductor fabrication plants will take more than government funding. Private investment is needed too. And luckily, the industry is responding.
Take, for instance, Micron, an American producer of computer memory and computer data storage. The company has announced a $40 billion investment in memory chip manufacturing, which is critical for computers and electronic devices. This investment will create up to 40,000 new jobs in construction and manufacturing and bring the U.S. market share of memory chip production from less than 2% to up to 10%.
Then there’s Qualcomm, a leading wireless tech innovator, and GlobalFoundries, a multinational semiconductor contract manufacturer and design company. The two companies have announced a new partnership that includes $4.2 billion to manufacture chips in an expansion of GlobalFoundries’ New York facility. Qualcomm, the leading fabless semiconductor company in the world, announced plans to increase semiconductor production in the U.S. by up to 50% over the next five years.
Another unwelcome result of pandemic shutdowns is, of course, labor shortages. Part of the CHIPS and Science Act addresses these challenges to be sure that when semiconductor manufacturing, as well as other technologies, is up and running here in the U.S., we have the workforce to support it.
A well-known issue within manufacturing lies within a missing skilled workforce. Focusing on science, technology,
engineering, and mathematics (STEM) education and workforce development activities is critical to developing skills needed for taking on the highly skilled jobs of emerging industries built on the technologies of the future. That’s why the act will work to provide STEM opportunities to more Americans.
The CHIPS and Science Act authorizes new and expanded investments in STEM education and training from K-12 to community college, undergraduate, and graduate education. Whitehouse.gov states that it does so “to ensure more people from all backgrounds and all regions and communities around the country, especially people from marginalized, under-served, and under-resourced communities, can benefit from and participate in STEM education and training opportunities.”
Based on current manufacturing challenges, including the skilled labor gap, and supply chain delays, the collective hope for the CHIPS and Science Act is that it will provide relief for today’s manufacturers.
“Every manufacturer in America will benefit from the CHIPS and Science Act, whether they make chips, make products that require chips, or are part of a supply chain disrupted by the semiconductor shortage,” said National Association of Manufacturers (NAM) president and CEO Jay Timmons in a statement.
The future of the segment should be bright with the promise of semiconductor manufacturing taking place on U.S. soil and thus not requiring overseas shipping and potential shipping delays. As an OEM, know that help is on the way, and your current struggle with components, parts, chips, and even labor shortages will (hopefully) soon be a thing of the past.
“Our economic future and America’s leadership in the world depend on a competitive manufacturing industry. Congress has acted wisely with the CHIPS and Science Act. Now we need Congress to continue standing with manufacturers and focus on policies that will help us compete with China and other countries, not make it more expensive to make things in America,” Timmons stated.
In summary, the act aims to leverage the latest technology today to create manufacturing plants of the future, with more intelligent systems and processes that require less labor and less dependence on foreign aid. The takeaway for OEMs? Stay tuned to see how soon the benefits of the CHIPS and Science Act will be felt in today’s manufacturing plants. But stay positive that while progress may move slowly, it is moving in the right direction to bring more U.S.-made parts and technology right here to our shores.
Easily share this article with your peers: oemgo.to/chipsandscienceact
Fenner Drives enhanced the performance of its polyurethane O-Rings, relying on Bi-Modulus Technology developed in partnership with Michelin’s High-Tech Materials Division.
Eagle XLD O-Rings last at least six times longer than traditional O-Rings.
Eagle XLD O-Rings provides four times the load capacity than traditional O-Rings.
Eagle XLD O-Rings lose less than 1% of their load transfer from roller to roller.
Eagle XLD O-Rings are easy to use and readily available in 12 standard sizes, supporting the most common center distances.
Connect with the Fenner Drives team to nd out how Eagle XLD O-Rings or any of our standard products can address your application needs: fennerdrives.com/Eagle-XLD
Measurement in progress
Sensor switching
Process malfunction
It’s 2023, and packaging and processing OEMs are still saddled with supply chain problems, which are primarily tied to a shortage of electronic devices, including motors and controllers. To date, the only solution has been to overstock the shelves when components are available.
For machine builders trying to fulfill customer orders, it’s been a frustrating experience that has required resourceful, out-of-the-box actions.
“Our workaround has been brute force—pre-ordering items that are standard and forecasted for use, as well as getting engineering to find alternative suppliers, which is painful and tedious, but we have made substitutions,” says Brian Ormanic, senior applications engineer at Pearson Packaging Systems. “There’s been a lot of communication and time investment from our supply chain department.”
Stacy Johnson, vice president of business development for Hoosier Feeder Company, has had a similar experience. “We are still seeing supply chain issues primarily tied to motors, controls, and sensors. It’s a unique situation because often, in the past, customers would specify items like controls. But now, they’re having to choose between getting the accessories they want with a longer lead time or letting us use the accessories we have available on the shelf to build their product.”
OEMs aren’t the only ones struggling right now. Their CPG customers, too, are trying to balance customer needs with product and material availability.
“Different components are coming from different vendors, and one of the most important components to manage for is lead times,” says Diego Pantoja-Navajas, vice president of AWS Supply Chain at Amazon Web Service, Inc. (AWS). “Incorrect lead times can lead to disastrous manufacturing outcomes.”
But, it’s hard to manage because the manufacturing supply chain is so complex. There are changing demands for product, varying levels of lead times for supplies, the balancing of production capacity, and logistics bottlenecks. Throw a global pandemic on top of that, coupled with a raw
material shortage and even a ship wedged across the Suez Canal—among other things—and it’s a business nightmare.
“It’s a big Rubik’s cube,” says Adrian Wood, director of strategy and marketing for Dassault Systemes’ Delmia brand. “Companies are trying to get the best forecast of supply and demand, and crunch that into a strategic plan. It’s an optimization problem that companies today normally solve through Excel and manual processes.”
But companies are waking up to the fact that they must move off of manual processes and start automating aspects of their supply chain. That doesn’t mean throwing a robot into the mix. Rather, it requires the creation of a virtual replica of what’s going on as a way to predict outcomes that can be preemptively acted upon.
And the simulation software providers are responding.
For example, Dassault Systemes is known for its digital models that virtually simulate products, processes, and factory operations via its 3DExperience platform. It has traditionally been used to test out an airplane or automotive design or to experiment with layout and process flows in a manufacturing facility. With the company’s acquisition of Quintiq in 2014, those simulation capabilities were extended to supply chain planning and optimization.
“The supply chain deserves to have a digital twin of its own,” Wood says. “It’s a model of the capabilities and constraints of an organization that allows you to play with ‘what if’ [scenarios].”
Creating a virtual replica of the physical infrastructure can help OEMs and CPGs overcome logistical obstacles.The AWS Supply Chain map provides visibility into where inventory is in stock or has an out-ofstock risk, providing a mechanism to drill down into the product levels. Source AWS
What if demand suddenly skyrockets? What if demand falls off a cliff? What if the supplier goes out of business? What if we open a new distribution center? “When the pandemic came in, I don’t think there were many dramatically new problems, but they were all exaggerated. And the magnitude of problems has forced [manufacturers] to get off the manual processes and to design a virtual twin model to prepare for future disruption and have the agility to react,” says Wood.
The supply chain is quickly becoming a strategic priority. According to the IDC white paper “A Modern, Connected Cloud Environment Optimizes Supply Chain Collaboration—A North American Perspective,” published in June of 2020, “the supply chain has traditionally been thought of as a support organization that works in the background to ensure that products are planned, made, and fulfilled to customers and consumers. That is changing. The supply chain is now perceived by manufacturers and retailers as a strategic tool for business performance and growth—and is moving from a cost center to an opportunity center.”
But it’s not so easy to re-engineer that monolithic ERP system that has been coordinating supply chain schedules,which is why, according to IDC, cloud and Software-as-a-Service (SaaS) applications that can be layered over the manufacturing and enterprise systems are rapidly becoming the default choice for the supply chain.
Case in point: In November, Amazon Web Services (AWS) rolled out its AWS Supply Chain application, which is based on nearly 30 years of Amazon.com’s own logistics network experience.
“For many years, our customers have told us that they are running complex global networks of suppliers, manufacturers, shippers, and ports, and trying to meet the needs of connecting all of those different entities within the supply chain. That’s not easy to do,” explains PantojaNavajas. “All of these different entities of the supply chain are using different systems and technologies… With all of the data scattered across a vast network of systems, we started to appreciate that data is one of the most important components [needed] to run an effective supply chain. And we want to make sure we can help by bringing it all into one system to harmonize the data and make it available to customers without the need to migrate or move from one system to another.”
AWS Supply Chain is a cloud-based system that uses electronic data interchange (EDI) feeds to pull data from a variety of sources (including ERP and supply chain management systems) into a data lake. It then unifies and contextualizes the data by applying machine learning (ML) and natural language processing (NLP)—based on Amazon’s own proprietary algorithm—to understand and learn from the data. According to AWS, much of the industry spends significant time and third-party consulting resources to get various platforms to work together, but this app removes those big deployment costs without overhauling existing IT.
In addition, there is demand planning and a collaboration tool built-into the platform. The collaborative communication within the app is also a core capability, PantojaNavajas says, because it provides a way to quickly respond to supply chain risks as supply chain leaders have a shared context and reference for determining next steps.
Early customers using AWS Supply Chain, like Amazon’s subsidiary, Whole Foods Market, are experiencing benefits.
Whole Foods has more than 500 stores across the U.S., including some in the U.K. and Canada, with 11 distribution centers serving the stores. The perishable side of the business is complex due in part to the locally sourced products.
“We have a strong and efficient operation, but are always looking for improvement,” says Leandro Balbinot, CTO of Whole Foods Market, who was speaking at the AWS re:Invent 2022 event in November. “Supply chain systems are good for transactions day to day, but are hard to innovate.”
Balbinot noted that AWS Supply Chain’s natural language processing has been instrumental in the company’s ability to easily integrate complex data and, more importantly, comprehend it.
“It’s not about having the data; it is about having the data in a way that makes sense. That is what you can get with the NLP capabilities the platform offers,” Balbinot says, noting that it provides a way to quickly see current and future
inventory situations. “We started a proof of concept and in a few days got the data to provide on-hand inventory positions to the team, as well as future predictions about risks for all the distribution centers.”
This “future aware” aspect of the AWS algorithm provides options to rebalance inventory for the best possible outcome, taking into consideration outside conditions, like weather patterns, for example. “At the end of the day, we are simulating scenarios,” explains Pantoja-Navajas. “The algorithms will provide different outcomes based on the data it has. You can run and re-run scenarios by adding more variables into the system, so we are simulating multiple scenarios for [the customer] to select which one best fits their needs.”
And a graphical component—a map—provides visibility of where inventory is in stock or has an excess or out-of-stock risk, providing a mechanism to drill down into the product levels.
“The map is what supply chain managers love,” says Balbinot. “It’s good to have an easy way to understand what the inventory looks like for every distribution center and drill down to see what actions we have to take to mitigate the risk.”
Pantoja-Navajas adds that the AWS application offers a holistic view of different systems, which is an impactful approach to visibility across the supply chain. “With the unified view of the supply chain data, and using ML to power the insights of data, you are able to see what is important. You can have data visibility, but if [you] don’t have insights into that data to what will happen next, the only thing you are doing is telling me the news that happened yesterday, and you are not predicting how the supply chain will be affected by a natural event like a hurricane or snowstorm or other disruptions.”
SCM Globe offers its own supply chain modeling and map-based simulation tool that has been used for military logistics, humanitarian supply chains, business planning, and even for training students. The company, started in 2012 by Michael Hugos, former CIO for an $8 billion distribution company and author of several books, including Essentials of Supply Chain Management, aims to make the supply chain more understandable through real-world visualization and intelligence.
Hugos explains that the supply chain is made up of four entities: products, facilities, vehicles, and delivery routes. Basically, it is a massive multiplayer situation comprised of people, factories, raw materials, and transportation. With that in mind, he developed an easy-tounderstand game-like interface that keeps all of the complicated math computations under the hood.
Data is imported from ERP and other applications to automatically create supply chain models. The cloudbased app sits on top of Google Maps and leverages a
satellite tool to zoom in and find buildings, ports, and infrastructure, thereby merging real-time mapping and 3D data displays of the landscape.
“If I know that a factory is 150 miles away from a port, and that port will ship products to four other places, and I can see facilities and vehicles and routes that connect the facilities, I can do a lot of calculations automatically,” Hugos says, explaining that those calculations govern how the four entities interact, adjusting to changing circumstances and applying simulation to optimize the data. “We try to create useful models everyone can see and understand, and within that context can talk about specific issues.”
In one business example, SCM Globe worked with a large furniture manufacturer in Europe that wanted to redesign its supply chain to accommodate its biggest business unit in Indonesia. The company put together a supply chain task force composed of people from different geographical areas and responsibilities, including operations, purchasing, sales, and finance. However, different groups within the company were fixated on different parts of the supply chain, emphasizing their own interests without understanding the overall effects of different actions. For example, the finance folks focused on how to increase productivity in factories. Operations argued for improved movement of products between the factory and the port. Purchasing wanted to know if they should line up new suppliers or shippers. And sales just wanted to do whatever it took to increase production to support rising worldwide sales.
To get everyone on the same page, they need to see the big-picture and how changes in one part of the supply chain can affect other parts. And the best way to do that is to show everyone an overview of the supply chain via a global map with the ability to zoom down into it for more detail. For example, the team could identify a particular shipping port on Google Maps and then switch to satellite view to see the actual facility. Then they were able to run a
simulation to answer questions, such as how the existing supply chain would support a 40% sales increase.
“You need to make sure everyone can see the big picture in an understandable format with enough detail to make strategic decisions, but not so much detail that your splitting hairs,” Hugos says.
These supply chain simulation tools—Delmia Quintek, AWS Supply Chain, and SMC Globe—are designed to work more effectively with more data points, enabling better decisions. But the real value is the ability to roll with the punches, regardless of what happens, to deliver products.
“Agility and visibility are the two foundation components that companies need to develop as part of their operational processes,” says Dassault’s Wood. “And that adds a host of potential benefits in terms of getting new products to market sooner at a lower cost with higher quality.”
And the next step, Wood says, is to link manufacturing and the supply chain. The root cause of disruption is not always because a ship got stuck. Often, it’s because there was a problem with the product design or in manufacturing.
As such, the digital twin of the supply chain can be made even better by connecting it to the digital twin of the product. So, if you are adding a new component to a product, you can go to the supply chain model and ask it if you can actually source that component. The simulation may say, “no,” but offer an alternative supplier with a similar component that has a longer lead time. Then, you can start building that into the design of the product.
The point: “Don’t think about the supply chain in isolation,” says Wood. “Think broader of its impact across the organization.”
Easily share this article with your peers: oemgo.to/simulatedsupplychain2023
A ordable and highly integratable automation options. Small lowpro le conveyors, accumulators and surge tables. For packaging, labeling, laser or ink jet printing, vision inspection & checkweighing systems. Made in USA.
t Mini Conveyors
t Extended-Length Conveyors
t Rotary Table Accumulators
t Surge-Option Accumulators
t Uni-Mate® Kit
Top 3 takeaways
2.
As pharmaceutical brand owners look to upgrade packaging to newer, more sustainable options—including lightweight, renewable, and recycle-ready offerings—many are facing questions about whether new materials can run on existing packaging machines.
With so many tried-and-true materials used in life sciences packaging, machines are typically built to work with established offerings that have been on the market for years. This is certainly the case for the popular blister package, an ironclad packaging solution for tablets, capsules, and other oral solid dose (OSD) medicines and nutraceuticals. Blisters consistently outperform bottles in protecting drugs against moisture, which is crucial for moisture-sensitive products while also offering patient adherence benefits and child resistance.
In terms of sustainability, blister packaging has lagged over the past decade, but strides have been made in the R&D-intensive journey of developing high-performance blisters compatible with existing recycling streams.
A couple of companies have brought blisters to market that have recyclability claims—and even then, successfully balancing eco-friendliness with adequate barrier protection remains a challenge. From there, a final hurdle remains the ability to actually produce the packaging in large capacities and at high speeds, also known as machinability. Simply put, a solution that can’t be reliably and rapidly reproduced isn’t really a solution.
With this in mind, Amcorembarked on a journey with Maruho Hatsujyo Innovations, Inc. (MHI), to ensure its novel recycle-ready blister package could be processed on a commercialscale packaging line.
3. For those looking to update materials without purchasing new equipment, determining machinability is a key step.
Amcor is a developer and producer of responsible packaging solutions for a variety of sectors, including pharmaceuticals and nutraceuticals. The company supplies a range of flexible and rigid packaging solutions, cartons, and closures.
Among Amcor’s specialties is blister packaging, and in April of 2021, the company introduced its recyclable AmSky Blister System. AmSky is a blister and lidding combination comprised entirely of high-density polyethylene (HDPE). By contrast, conventional systems typically involve a polyvinyl chloride (PVC) blister and an aluminum lid.
“The PVC/aluminum combination exemplifies blister packaging’s sustainability challenges because, together,
they are proven to protect drugs but suffer an exceedingly poor sustainability reputation,” says Michelle West, pharma product manager for Amcor Flexibles North America. “On the other hand, HDPE is a commonly recycled plastic in many existing streams; in the U.S., for example, HDPE can be placed in the ‘#2’ curbside plastic stream, which includes common items such as milk jugs and laundry detergent bottles. HDPE films also fit the PE film stream, currently, a ‘store drop-off’ option in which consumers take relevant items to store drop-off locations, often at grocery stores, where they are collected and transported to recycling centers for processing.”
A key aspect of AmSky’s sustainability success is that the blister and lidding are both HDPE. If the blister and lid are in different streams (or if one is detrimental to recycling), the entire product ends up in the landfill rather than the recycling center. Based on company estimates, AmSky can offer a carbon footprint reduction exceeding 50% versus traditional PVC/foil blisters, even when it’s not recycled. When it is recycled, that figure approaches 70%.
Of course, sustainability must not sacrifice barrier protection. An ever-increasing share of today’s oral solid dose (OSD) drugs require at least some degree of protection against moisture. The base AmSky blister package has substantially more moisture barrier than a standard PVCaluminum system and delivers package moisture barrier similar to PVC/PVdC + foil lid combinations and PVC/Aclar + foil lid constructions frequently utilized for moisturesensitive products. This exceeds the moisture barrier protection offered by other recycle-ready blisters comprised of polypropylene (PP) or polyethylene terephthalate (PET).
While the initial AmSky featured a white base with clear lidding, some applications require through-the-blister visual inspection. Amcor also has a clear blister with white lidding or can make both either white or clear—all with preprinting options. It also can be upgraded to a thicker push-through lidding for increased child resistance.
Presently, AmSky is the only entirely HDPE-based blister package listed on the Association of Plastic Recyclers’ website as meeting Critical Guidance Recognition and is the only blister packaging system listed on Walmart’s Circular Connector website, which is intended to broaden recognition of preferred sustainable packaging materials. “So AmSky could meet pharma and nutraceutical industry needs for safety, end product stability, and sustainability. However, one question remained, and it meant the difference between a successful prototype and a successful product. Could AmSky be processed on a commercial scale packaging line?”
For trials, Amcor turned to prominent blister machinery supplier MHI, the U.S. subsidiary of Maruho Corp. Ltd., which distributes premium medical packaging equipment whose designs lean upon more than 60 years of manufac-
turing experience.
Modern blister machines like the ones offered by MHI are designed to produce blisters rapidly and reliably for pharma companies requiring protection for millions upon millions of pills. And by far, the most dependable, thermoformable film material is PVC.
An obstacle to the wide adoption of recyclable blister packages, then, is the ability of newer, more sustainable materials to be “machinable”—that is, to be produced on a large scale with a precise level of sealing repetition.
Other materials are comparably fickle, and AmSky was no exception, reports Amcor. The HDPE construct requires different operating parameters and has a narrower operating window on machines accustomed to running standard PVC + foil packaging. So, when Amcor approached MHI, both parties knew that finding the optimal production parameters would require some trials and line time.
“The goal was achieving a one-to-one ratio, meaning a scenario where the AmSky system could be produced with the same sealing and speed efficiencies as PVC blisters,” says Hideo Yonenaga, president, Medical Packaging Machinery Division for Maruho Hatsujyo Innovations, Inc. “In reality, Amcor and MHI knew that even approaching production parity would be a win. Close counts in horseshoes, hand grenades, and sustainability initiatives.”
Several tests were conducted, both at MHI’s facility and the production floor of an Amcor customer. The trials were conducted on MHI’s EAGLE-Rx Blister Machine, a compact, balcony design, servo-driven unit capable of running up to 100 cycles/minute at a format area of 90x130mm.
Obstacles the teams encountered included some difficulty chopping the trim of the HDPE, as well as some card jamming issues. At Amcor’s customer’s plant, the card jamming was efficiently resolved with adjustments to the timing of the suction arm; the trim cutting would require some minor machine modifications. Soon, the team was able to validate material at the customer’s current top-line speed.
Amcor and MHI also conducted trials using MHI’s EAGLE-Omni machine, notable for its deep-draw thermoforming capabilities. “Tests incorporated a flat upper sealing plate to assist with leak detection. At first, they encountered some issues achieving consistent forming and reaching maximum run speeds. MHI determined that the challenge revolved around air flow and was able to rectify the issue. Coupled with more exacting temperature settings, the team was able to achieve top run speeds,” explains Yonenaga.
The successful Amcor-MHI partnership could serve as a roadmap of sorts—one whose destination is the widespread adoption of sustainable blister packaging systems across the pharma and nutraceutical sectors. The pairing of materials science innovation with versatile, easily adjusted thermoforming equipment is a must-have combination to bring such next-generation packaging systems to market expediently and effectively.
Using video, images, and stories to capture the many ways PMMI brought the industry together, Highlights provides a look at the best of 2022 – from our Executive Leadership Conference to the success of PACK EXPO International and everything in between. You will see videos from familiar faces such as Jim Pittas, Dave Newcorn, Tom Egan, Laura Thompson, and Patty Andersen, PMMI’s first female chairperson of the Board.
New initiatives such as PMMI ProSource, PACK Challenge, the PMMI 365 membership campaign, the Emerging Brands Summit, and the Young Professionals Conference are showcased, as well as many of our successful ongoing initiatives such as our PMMI UnPACKed podcast, the latest Business Intelligence reports, the return to international trade shows and much more.
Highlights will allow you to see, hear, and experience 2022 in a new and different way.
The lack of skilled labor continues as one of our industry’s biggest challenges – act now to ensure long-term industry success. Donate to support the PMMI Foundation’s 2023 Silent Auction, taking place April 16-18, during PMMI’s Executive Leadership Conference.
Donations of items to be featured in the auction may include (but are not limited to) travel packages, tickets to events, alcohol (beer, wine, and spirits), unique experiences, entertainment items, food and gourmet items, items for pets, memorabilia, collectibles, golf, sports gear, and artwork.
Proceeds from the Silent Auction go directly to the PMMI Foundation, addressing workforce shortages by promoting careers in the packaging and processing industry, providing educational scholarships and financial assistance, and building partnerships with schools and programs that develop skilled professionals to fill the workforce gap. Visit pmmi.org/ELCAuction2023 to learn more about suggested donation items.
Join PMMI for the three-day learning and networking event infused with fun as PMMI welcomes back some of its most popular speakers and dives into the timely industry topics you’ve been waiting for! Don’t miss this unique opportunity to take your business strategy to the next level. Connect with 150+ C-suite industry executives, participate in over
15 networking events and fun activities, including dinners, golf, kayaking, and bocce ball, and learn new tactics and solutions to address the challenges impacting your business. Meeting highlights include:
• Keynote speakers, including generational researcher Jason Dorsey, president, The Center for Generational Kinetics, on Millennials in Management and Leadership, Daniel Burrus, founder and CEO, Burrus Research, Inc., Alan Beaulieu, speaker, and president, ITR Economics, Richard Bahr, EOS Coach, and special guest, pro football Hall of Famer Howie Long, sharing his experience and thought-provoking insights to questions on the inner workings of professional sports and broadcasting.
• Peer-to-Peer Roundtables
Leadership Development Registration
Organizations with influential leaders outperform competitors. The PMMI U Leadership Development Program was designed to assist PMMI member companies in developing future leaders and managers in their organizations. Through impactful exercises, project-based learning, and professional development opportunities, participants will
gain skills to make them more effective managers and leaders. For more information on the program, see p. 10. To register, visit pmmi.org
Certified Trainer
• June 22 – 23: nVenia – Chicago area, Wood Dale, Illinois
• Sept. 11 – 12: PACK EXPO Las Vegas
• Oct. 5 – 6: Toronto area, Canada
Certified Technical Sales Professional (New)
• March 28 – 29: PMMI Offices, Herndon, Virginia Fundamentals of Field Service
• June 20 – 21: nVenia – Wood Dale, Illinois
• Sept.11 – 12: PACK EXPO Las Vegas
• Oct. 3 – 4: Toronto area, Canada Risk Assessment
• Sept. 9 – 10: PACK EXPO Las Vegas
For more information or to register, contact pmmiu@pmmi.org
As you plan out this new year, make it a goal to understand and anticipate your customers’ needs. PMMI Media Group Custom Research can help. Using our extensive database of engaged end users built from PACK EXPO attendees and PMMI Media Group contacts, we can help you learn more about your customers’ demands and deliver the intelligence you require to grow your business.
Contact Jorge Izquierdo, vice president, market development, at JIzquierdo@pmmi.org to set up a time to walk through your goals and discuss how PMMI Media Group Custom Research can provide the in-depth insight you need to compete in today’s changing market.
PMMI and Euromonitor International partnered on a new report, Future of Packaging and Sustainability. It provides an overview and exploration of the future of sustainable packaging options toward materials, use, consumers, full-circle solutions, and more—all according to consumer and CPG opinion. Members have access to this report for free in the Business Intelligence Library.
Fast Facts: Workforce
Download “Challenges and Opportunities for Packaging and Processing Operations,” the new whitepaper focused on four key industry topics: sustainability, workforce, predictive maintenance, and remote technologies. Here are three fast facts from the white paper:
• Recent research published by The Manufacturing In-
stitute showed that 93% of respondents needed help finding skilled applicants for vacancies within their companies.
• Over 70% of CPGs think that robots could have a moderate or significant impact on addressing labor shortages in their plant.
• Technology could reduce costs and the demand for more workers by automating manual tasks and processes, but it can also assist with retention by automating repetitive tasks, making work more exciting, increasing the span of control of current operators, and accommodating lower-skilled workers.
Whether you are unsure of how to expand internationally or have specific international trade questions, PMMI’s ExportEXPERTS program provides members with free counseling from experienced consultants and PMMI members with experience doing business in global markets. These experts advise on topics such as:
• Working with international agents
• Pricing for international markets
• Tariff intelligence
• Cost of doing business overseas
• International standards
Reserve your booth before it’s gone!
Showcase your latest packaging and processing solutions and connect with key decision-makers in Mexico and Latin America in 2023. With imported machinery supplying nearly 89% of total demand in Mexico, exhibiting at EXPO PACK Guadalajara provides ample opportunity to connect with these key contacts in Latin America.
Take advantage of your PMMI membership and exhibit in the PMMI Pavilion, which provides a central location in the exhibit hall for PMMI members, a discounted space rate, a turnkey booth package option, private meeting space, and more.
One type of cyberattack rising in recent years is the manin-the-middle (MiTM) attack. This attack method is a sort of “eavesdropping” where two computers or devices communicate with each other (for example, your laptop and a website you’re logging into). The attacker intercepts the messages being sent between you and the website, enabling them to see what information you are sending, and possibly even steal your password or personal information.
➲ For more information on MiTM attacks, scan the QR code. Got a more specific question? Email cyberhealth@ pmmi.org. Be sure to sign up for the CyberHealth e-newsletter to get cybersecurity updates straight to your inbox.
cific question? Email cyberhealth@pmmi.org. Be sure to sign up for the CyberHealth e-newsletter to get cybersecurity updates straight to your inbox.
Attending Interpack 2023 in Düsseldorf? Mark your calendar for the PACK EXPO reception at the Hotel Kö59 on Saturday, May 6, beginning at 6:00 p.m. Cocktails and hors d’oeuvres will be served. Questions? Contact Veronika Brumm at vbrumm@pmmi.org
Join the MaX Marketing Share Group
The MaX Marketing Share Group is where PMMI member marketers connect, explore, and create new work product solutions. Whether you’re a seasoned marketing executive or just starting your career, we invite you to join this community. It’s open to all PMMI members—marketers or otherwise. Start networking and engaging with your peers today by registering at https://pmmi.media/maxmkt
Gain
PMMI ProSource is the most complete online directory of packaging and processing technology suppliers in North America and is a FREE benefit to all PMMI members. ProSource harnesses the search engine traffic of customers searching for your product category, drives traffic back to your website, and makes it easier for new customers to find you.
Take full advantage of this updated platform and optimize your company’s listing by updating your machinery and product features regularly to ensure customers easily find you based on your specialties. Join the Link Booster Program for another great way to increase your company’s visibility and capture your customer’s attention. Link any ProSource article to your profile, and we will help drive traffic directly to your door.
Learn more at pmmi.org/prosource
Listen to your favorite packing and processing podcast every Wednesday with industry influencers, executive Q&As, case studies, and more as we dive into your most pressing business challenges in real time. Listen to unPACKed with PMMI on Apple Podcast, Spotify, or wherever you listen to your podcasts.
Supply chain delays result in longer than expected lead times for motion control components, contributing to rising prices and the inability of machine OEMs to promise delivery.
Design engineers are increasingly forced to trade off cost, delivery time, performance, and other variables to ensure they have a functioning component capable of meeting their basic design specs in time. They are also, however, finding that real-time collaboration with vendors can be one of their best weapons for optimizing motion system designs across a volatile supply chain. Today’s well-publicized supply chain bottlenecks are changing technology purchasing processes dramatically. The days when a motion control vendor could stand by a quote for a year or more are gone for now and maybe forever. Nowadays, a design engineer starts a project with an assumed delivery time in mind and plenty of supplier inventory on the shelf, but by the time they are ready to order, the stock may be gone. Whether such delays are caused by issues with other critical path components or by other factors, they can bump delivery schedules from days to weeks and even months. Faced with the prospect of not getting the exact parts they need in time to meet their customer commitments, designers must often accept tradeoffs between delivery, price, performance, and other variables. The challenge is to do so without sacrificing quality.
The motion control industry implemented real-time collaboration well before this current supply chain crisis. Machine designers are increasingly spending more time in a virtual 3D world. They are comfortable engaging in real-time collaboration to optimize their designs, streamline purchasing, keep projects on track, and add expert perspectives. This has become more relevant over the past few years as the pandemic has forced more people to work remotely. Now, in what many believe is a related supply chain crisis, the value of real-time collaboration is even more pronounced.
A collaboration session might begin when a motion system designer visits a linear motion website looking for a part. Most websites now have tools that streamline searching and product development, but some offer an immediate consult with a motion specialist, speeding time to design considerably. If no instant session is available, many sites will have an online scheduling calendar.
During such sessions, customers and vendors can surmise the motion profile and learn other critical details like the duty cycle, application environment, and commercial information such as time preferences and requirements. Likewise, the vendor can share CAD drawings of standard modules that meet the basic needs and then propose modifications.
In an example of a stepper motor linear actuator, the project started with an initial design consultation between a team designing a self-righting crutch under guidance from a linear motion expert from Thomson Industries. The designers wanted to use a single actuator to enable legs to form a supporting tripod whenever designated events, such as letting go of the crutch handle, occurred. On the Thomson
This stepper motor linear actuator assembly enables crutches to automatically stand on their own. A team of designers, interacting in real time online with motion engineers, was able to build a working prototype that included a custom antirotational guidance block in a fraction of the time that more traditional methods would have required. (Image courtesy of Waterloo University, FYDP Group 35)
More and more original equipment manufacturers are specifying Lubriplate Lubricants for their machinery. Why? With 153 years of lubrication experience, they know Lubriplate has the quality products and services to meet their needs, the needs of their equipment and the needs of their customers. Products include...
NSF H1 REGISTERED FOOD GRADE LUBRICANTS
HIGH-PERFORMANCE SYNTHETIC GEAR OILS
SYNTHETIC AIR COMPRESSOR FLUIDS
SYNTHETIC HYDRAULIC FLUIDS
HIGH-PERFORMANCE SYNTHETIC GREASES
ECO-FRIENDLY LUBRICANTS
SPECIALTY LUBRICANTS
Scan QR Code for More Information About Lubriplate’s Products and Services.
site, the designers used online design tools to enter basic motion profile information and further refined the design after scheduling a live engineering consultation. The consultation streamlined the process significantly as the engineer was able to quickly view and address the need for custom anti-rotational guidance functionality that might have taken those without advanced linear motion expertise a long time to figure out on their own.
If the customer needs to bring colleagues into the process, they can use online calendars to schedule group sessions with colleagues. This approach is valuable in pinpointing the impact of tradeoffs on other members of the machine builder’s team. Likewise, it gives the vendor engineer more opportunity to involve colleagues who might have complementary specialties.
Further improving this process’ communications, real-time collaboration enables augmentation of the virtual 3D models with cameras that can show the application that will host the motion products.
Tradeoffs might include price, delivery time, select elements of the motion profile or any aspect of the project that may be contributing to the delay. The benefits of collaborating with a motion control expert in real-time are espe -
cially evident in situations in which multiple elements of the configuration must change for maximum optimization. If the expected project load is heavier than the standard model allows, the vendor engineer can provide various options to boost it. They might suggest, for example, different gearing or screw lead, or altering the mechanical advantages. Or, if the customer wants position feedback, the vendor can help sort through the numerous options and their impact on the schedule. The solution might include opting for an available smart linear actuator. All adjustments could be in real-time,
so customers can instantly visualize each choice’s impact on the overall motion performance.
Many tradeoff discussions involve customized products. Suppose the customization is extending the lead time. In that case, the customer and vendor engineer can work together to compare the features and benefits of a standard product that may have a shorter lead time. The customer may, for example, have specified a product with hightemperature resistance that requires a hightemperature grease but must now evaluate whether the high-temperature capability is more important than having the part sooner. Or, if a particular connector is contributing to the long lead time, they may determine whether the expected benefit is more important than the delivery time.
Sometimes the customer may be looking for customizations specifically to accelerate timeto-market. They may, for example, order an actuator that is longer than their motion profile requires just because it can be installed and mounted quickly without modifying the host system. The vendor expert would help them evaluate and understand its potential impact on cost, performance, and delivery schedules. If the customization does extend the timeline, the vendor may ship standard units the customer can use to validate concepts while the vendor builds out the customized units.
In most cases, the vendor engineer can present a “good-better-best” set of options for the customer. To a customer wanting to increase stiffness on a polymer bushing bearing they were considering, the vendor engineer might suggest a $2,000 profile rail with slightly higher stiffness available in a week, or a $4,000 rail with maximum stiffness for delivery in six weeks.
Just as customers are responsible for providing accurate information on their motion requirements and application environments, vendors must come to the table with precise lead times for each solution based on a realistic assessment of their respective supply chains.
Vendors should also work closely with buyers on release schedules, understanding exactly what the customer may need and when. If they can’t deliver the entire order on time, they may be able to ship enough partials to meet immediate obligations. Suppliers with multiple manufacturing plants might be able to transfer orders from one to another to meet urgent delivery requirements.
It’s not clear how long it will take the supply chain to return to normalcy, but if what we are in now is the “new normal,” design engineers and motion control experts are armed with more capabilities than ever before to manage change together.
Easily share this article with your peers: oemgo.to/thomsonsupplychain
A seemingly simple filling application demonstrates that handling cannabis requires understanding its unique properties.
James McCall, District Sales Manager and Bridger Popish, Sales Engineer, FestoLegal cannabis is now a $13.2 billion industry that is expected to grow to $42.3 billion by 2030. Nineteen states permit recreational use, and a total of 37 states allow the medical use of cannabis products. While some original equipment manufacturers have been hesitant to enter the cannabis industry, others see an expanding market in need of the productivity, quality, and labor savings benefits of industrial automation.
In 2014, before the avalanche of legalization, Portland Engineering, a leading provider of industrial automation and control solutions, was one of the earliest to embrace the opportunities of the cannabis industry. Today, Thompson Duke Industrial, a wholly owned subsidiary of Portland Engineering, is the leader in cannabis oil vaporizer device filling and capping equipment. While Thompson Duke Industrial provides solutions for the cannabis industry specifically, it sees itself as a traditional OEM supplier of innovative filling and capping equipment.
Thompson Duke Industrial’s engineering and manufacturing expertise helps to significantly increase productivity and decrease the labor associated with vaporizer device filling and capping applications. The company’s experience demonstrates that to achieve success in the cannabis industry, OEMs must understand the unique properties of the material and the limited new-to-automation capabilities of many customers.
In 2014, Portland Engineering, with decades of process industry experience in the water/wastewater, manufacturing, and energy sectors, engaged in a project to replace manual controls on an OEM’s cannabis oil extraction machines and replace them with a PLC-controlled automated system. Portland Engineering’s team became so expert at setting up and fine-tuning the control system of the extraction process, they were asked by the OEM to go onsite and set these
machines up for the OEM’s customers.
“The customer would have kilos of cannabis oil coming out of the extractor,” says Mike Hogan, managing director of Thompson Duke Industrial, and vice president and board member of Portland Engineering. “The customer’s personnel were using syringes to laboriously draw the oil out of flasks and dispense a specified volume into a cartridge destined for a vaporizing device. As the oil cooled, it became much harder to draw and accurately dispense. The process was physically and mentally taxing, not to mention slow and wasteful.”
The Portland Engineering team looked at that manual process and immediately began considering how to make a machine perform the task. They started to purpose-design a machine for filling cannabis oil vaporizer devices.
“One thing about designing a cannabis cartridge filling machine that we knew was extremely important was solving the issue of variable viscosity of the oil,” says Chris
Our3Dvis Our 3D vision, soft
JUDVSLQJ D JUDVSLQJDQGDUWL FLDO
LQWHOOLJHQFH LQWHOOLJHQFHVROXWLRQVDUH
VROYLQJWKH VROYLQJWKHPRVWSUHVVLQJ
FKDOOHQJHV FKDOOHQJHVLQWKHIRRG
SURFHVVLQJ SURFHVVLQJLQGXVWU\ȃ
RQHSLFNDW RQHSLFNDWDWLPH
Contact us to see where we can help.
ZZZVRIWURE ZZZVRIWURERWLFVLQFFRP
6ROXWLRQV#V 6ROXWLRQV#VRIWURERWLFVLQFFRP R R 6RO LRQV#
Gardella, Thompson Duke Industrial’s chief technology officer. “Cannabis oil does not behave like any other fluid. Each oil formula will have a different native viscosity. Some formulations may be so thick that the oil will not pour out of the jar at room temperature.”
Gardella said that the material must be heated to facilitate the flow of oil. The temperature must be controlled precisely, however, as too high a temperature may damage key components of the oil, while too cool slows the flow. Another consideration is that some formulations must be dispensed gently, or they can be damaged.
The Portland Engineering team came up with an initial design for the oil path that involved a heated reservoir and a short tube running to a stationary dispense head. In this path, a pneumatically controlled actuator raised a syringe plunger, drawing in a specific volume of oil. A second actuator lowered the syringe to an empty cartridge, and the plunger was depressed by the actuator. The syringe assembly would then be raised for the process to be repeated.
The team needed to have an X-Y table beneath the syringe to index a matrix arrangement of cartridges held in specially designed tooling. The problem was coordinating speed and positioning of two different systems – electric motion and pneumatic motion.
Furthermore, each oil formulation would dispense at a different speed, and as the oil warmed, it could be dispensed faster. Complicating this already complex process was the fact that the vaporizer device industry was moving toward many different cartridge configurations. To future-proof the machine, Thompson Duke would have to provide operators with an easy way of adjusting temperature, dispensing speed, and the ability to adapt to changing cartridge form factors.
Portland Engineering’s team saw the potential of being first to market with a solution that met these criteria, but also realized it would not be an easy machine design challenge. A fortuitous meeting with Festo sales and application engineers showed the way forward.
“Portland Engineering and Festo were co-suppliers on a project,” Gardella explains. “After a meeting with the client on that project, we walked into the parking lot together. I mentioned we saw this need for innovation in the cannabis industry. I asked them whether they might have products and the application bandwidth to help. Basically, I wanted to know how much they had to offer. It turned out to be a lot.”
The Festo team explained that the company produced an X-Y table developed for the laboratory automation industry that would be ideal in terms of footprint, speed, and precision for the table-top filling machine Portland Engineering envisioned. Festo also offered a small touchscreen HMI, pneumatic valves, cylinders, sensors, air preparation, and tubing – the entire basket of critically important components for a one-stop shop. Most importantly for Portland Engineering, there was a small, powerful Festo Codesys-
based PLC integrated with the touchscreen HMI that would be ideal for providing the mechatronics control of both electric and pneumatic components. And, all Festo products were off-the-shelf for ease of replacement and supply, as well as designed to easily integrate.
“Portland Engineering works with all of the controls suppliers but had never been exposed to a Codesys-based PLC,” Gardella says. “We asked about learning curve and about product availability. What we learned on both fronts gave us a lot of confidence that Festo would be a strong partner, and we selected them to be our key components supplier.”
Gardella added that the Festo EXCM X-Y table was, in their opinion, the best available. Festo provided the support needed for Portland Engineering personnel to quickly feel confident when using the Codesys structured programming language. The partners worked diligently for a year on the first machine, the ACF1, which featured 9 x 13 cartridge tooling for the X-Y table.
That machine debuted in 2016 at a cannabis industry trade show and was widely welcomed. The Thompson Duke machine increased output from manual to automated by a factor of 10. Furthermore, it was accurate and low waste–particularly important as cannabis oil is a costly material.
Soon customers were asking for a semi-automatic machine as their output did not justify 1,000 filled cartridges per hour. Others asked for higher output. Over time the MCF1 semi-automatic and the IZR high-capacity machines were introduced. The IZR featured the same basic design as the original ACF1 9 x 13 machine with a larger filling area to support the cartridge factory packaging and offered the potential for 252 cartridges per run and an increased oil capacity of 500 ml, up from 140 ml on the smaller automated filler.
As orders came in, Portland Engineering realized that a separate business needed to be formed, one that would have a sole focus on the machine’s success and on customer satisfaction. Thompson Duke Industrial became a wholly-owned subsidiary in 2016. The move proved to be the correct one as the new company was solely dedicated to serving the market through new innovations, maintaining build quality, and ensuring world-class customer support.
To ensure Thompson Duke has the components for production, Festo stocks all the components for each model under a single part number unique to Thompson Duke. The level of inventory held at Festo’s Mason, Ohio, Regional Service Center, is based on Thompson Duke’s sales forecast.
“Festo stocking has helped with cash flow,” Hogan says. “That was a game changer. Having a relationship like this has greatly contributed to our success.”
One of the things to note about Thompson Duke is that the company is scrupulous about not overstating performance claims, such as throughput, and typically says 1,000 cartridges per hour is the expected throughput. Speeds of some thinner oil viscosities on the high-capacity IZR machine, however, range from 1,500 to 3,000 per hour.
With this level of production, customers noted throughput limited by the time required to take cartridges out of their shipping carton and load them into the tooling for the X-Y table. To ease this bottleneck, Thompson Duke developed a rapid cartridge loader system. Then bottlenecks began to show up in capping operations. Thompson Duke, with the support of Festo, developed a pneumatically powered capping press.
The engineers at Portland Engineering and Thompson Duke applied decades of process automation experience to solve the issues of efficient, high-speed cartridge filling with cannabis oil. They partnered with Festo and subsequently developed both a patented mechatronic solution and a robust supply chain. Thompson Duke also understood the needs of its customers for simplicity of operation and customer support.
As the cannabis industry matures, there is no doubt that higher levels of automation will be applied, increasing productivity and uptime. Certainly, the Thompson Duke pioneering effort can serve as a model as the industry moves toward greater automation.
For more on the Thompson Duke filling application and its use with Loud Labs’ cannabis oil packaged cartridges, go to: oemgo.to/thompsondukeandfesto
“Throughout the year, PMMI stayed focused on connecting the industry in many ways – through our trade shows, meetings, media outlets, programs, services, as well as key resources. Despite many of the issues our industry faced, such as supply chain slowdowns, workforce gaps, and even economic uncertainties, PMMI connected the industry, bringing solutions and resources to create opportunity and advance our industry.”
VICE PRESIDENT OF HUMAN RESOURCES & AFTERMARKET SERVICES, DELKOR SYSTEMS, INC. CHAIRWOMAN OF THE BOARD, PMMI•See how PMMI brought our industry together
•Hear how we kept members up-to-date on critical industry news and trends
•Experience the success of PACK EXPO East, PACK EXPO International and our Member Meetings
•And so much more…
Students offered advice to a ract future professionals like them as they got handson with packaging and processing at PACK EXPO International.
Casey Flanagan, Editorial Assistant, PMMI Media GroupPackaging and processing companies scouting for the next generation of professionals needed to look no further than the floor of PACK EXPO International.
Dozens of students were among the 40,000 attendees at last year’s expo in Chicago. Most participated in competitions to gain hands-on industry education. Many came to the show with their own unique interests in mind, and some offered advice on how companies can attract up-and-coming talent like them.
For the first time at PACK EXPO, high school engineering teams took part in a machine-building competition dubbed the PACK Challenge. Six teams participated from across Chicagoland and surrounding areas, each working with a kit that included all the components needed for a filling machine. Teams were judged on their machine’s filling performance, and also the machine’s design, operator training, safety, ease of changeover, and a sales and marketing presentation.
“We spent a lot of time on this project and this was super important to us,” says Zach Mettille, a junior at the competition winner Waterford Union High School in Waterford, Wis. “We were just happy if we had a working machine, and to see us win something like this is really awesome for us.”
Mettille entered the competition with an interest in roller coasters and mechanical engineering, but the show opened
his eyes to the potential of the packaging industry. “I had no clue how large the filling industry was until we did this,” he says. “I heard about PACK EXPO, and coming here, it really shows you how big of an industry and how important it actually is. And so I think doing more student outreach programs and competitions and stuff to really engage [students] in what they do is a huge opportunity.”
Mike Richmond, a PACK Challenge judge and co-founder of packaging consultancy PTIS, says students might just need to be shown that packaging is an option. Richmond explains that students can learn unique skills in engineering through their own interests, with roller coasters as a prime example. These students can bring that expertise and new thinking to innovate packaging technologies and even learn from packaging to bring new ideas to other fields.
Thinking green could also help companies attract young talent, Richmond says. “It’s important for them to be able to leave their footprint better than they started with. If [companies] don’t have a sustainability program, kids just don’t want to go to it.”
Richmond was tasked with judging each team’s marketing and design plan and says he was impressed with their ingenuity and ability to identify what differentiated them. “I thought the presenters were succinct, they were clear, they had a lot of
novel little things that they added into it,” he says. “I couldn’t have been more proud of what they’re learning and what they put together.”
Perhaps the most noticeable students on the show floor were those participating in the Amazing Packaging Race, marked by their bright-colored competition T-shirts as they rushed through the aisles. These students were engineering majors from universities across the U.S., racing in groups to solve problems and complete tasks at participating booths.
“Each booth had a wide variety of tasks; one was programming a robot to go to certain points, some were answering questions, some were just listening to them talk and taking a picture with them,” says Virginia Tech engineering student Noah Madel, who joined his school’s packaging program last spring after touring the packaging lab, and “it just kind of exploded,” he says. “You can just do so much with it; there are
so many applications for packaging.”
Growth opportunities are a top priority as Madel eyes the industry. He says he would like to see companies “demonstrate what their workplace environment is like, how much freedom you have and how much growth is available once you get there.” Madel says he also looks for engaging and impactful work, hoping to “really put your mind to work and see your projects come to fruition.”
Race participant Jessie Imorde, also from Virginia Tech, picked up an interest in packaging through her school’s majors fair. She says getting attention from young engineers like her might be as simple as “explaining how things work,” as she had been introduced to several unfamiliar products at the show. Imorde stresses the importance of “making the industry more well-known because people don’t really know what packaging is.”
Aidyn Voeltz, a sophomore at Northwood Tech in New Richmond, Wis., first entered engineering to learn about wiring and mechanics but became fascinated by robotics during his time at school. Stepping onto the floor at PACK EXPO, Voeltz says the amount of equipment, people, and information available was overwhelming. “It’s unreal what you can learn just by connecting with companies, talking with people, and even just seeing most of this stuff,” says Voeltz.
Packaging appeals to Voeltz for the variety of technologies and disciplines involved, with a chance to focus on wiring panels, programming, mechanical engineering, and more.
“The room for growth, the different opportunities, obviously all the different directions you can go, it’s really amazing,” he says. “I never thought anything of it until I got into the program, and now it’s bigger and better than I could ever imagine.”
Zachary Weston, a Virginia Tech senior in the race, was drawn to packaging for the opportunity to have an impact on the environment. “I want to be able to make something that contributes to the world,” Weston says. “With packaging, the ability to cut down on these single-use plastics, or at least reduce their lifespan on this earth, is making a tremendous difference. Even if you’re just altering a few SKUs for a company, that’s thousands and thousands of pounds of plastic.”
Packaging design is what drew Virginia Tech student Joy Mendoza to the race. Packaging appeals to her in that it is “so interdisciplinary, from engineering, supply chain, to graphic arts.” While packaging struck Mendoza as a great career option, “I think a lot of people aren’t aware that going into the package industry is possible,” she says.
Sustainability should also be at the forefront for brands, Mendoza says. She sees her generation focusing on environmentally-friendly solutions and more companies following suit with green innovations.
Easily share this article with your peers: oemgo.to/packagingstudents2023
Women’s resource group has exponential success connecting ProMach’s female workforce and training them up to be leaders.
Over the past few years, the world of work has changed dramatically.
This is due in large part to a global pandemic that forced people to work remotely and led to company downsizing in many industries. And, while businesses are seemingly back on track, women are still suffering from the pandemic-related aftermath.
According to a 2021 McKinsey & Company report on COVID-19’s impact on women’s employment, one in four women considered leaving their careers (vs. one in five men). A U.S. Bureau of Labor Statistics report substantiates those findings, showing that from February 2020 to January 2022, 1.1 million women left the labor force, accounting for 63% of all jobs lost. The bigger problem for the future of women in the workforce is that they may not come back at all—especially to male-dominated industries like manufacturing.
And while the national statistics show a troubling trend, the impact is felt at the local level.
At ProMach, a packaging machinery company with numerous product brands under its corporate umbrella, women represent 20% of the global workforce. Employees noticed a shift in the female workforce within their own organization. As a result, a group of women—and one man—joined forces in 2021 to create a plan for a women’s resource group that would improve female employee retention and leadership development across the many business units of the company.
“Around the time of COVID, we looked outside the organization, saw what was happening, and looked inside the organization, and saw the same thing—which is very few women in manufacturing,” says Krista Combs, vice president of human resources at ProMach. “And it was a sobering realization to know that with COVID, a lot more women were leaving manufacturing.”
Armed with that information, Combs, together with Julie Dropik, vice president of finance for ProMach’s primary packaging business unit, and Doug Stambaugh, president of the primary packaging business unit, decided they
needed to start addressing this problem in a more aggressive way.
“It was even surprising to us, a group of women in leadership roles, how unique we were, and the opportunity in front of us. We considered what type of impact we could have in connecting not only the team but also being that conduit, if you will, to sharing our experience,” says Dropik.
Combs and Dropik recruited Lisa Propati, vice president and general manager of Weiler Labeling Systems (WLS), a ProMach product brand, who is also the co-chair of PMMI’s Packaging & Processing Women’s Leadership Network (PPWLN). Together the women outlined the statistics in a
presentation for their senior leadership team, which led to them presenting at the company’s October 2021 General Managers meeting, where they kickstarted the “PowHER of the Pack” women’s resource group.
PowHER of the Pack began with 20 members and has since increased to 90 members—all either customerfacing, in engineering, or in leadership roles within ProMach—which Dropik asserts is still only the tip of the iceberg as the group continues its outreach efforts to the women at ProMach.
“When we had our annual meeting, I was questioning, is this going to work out well? Are they going to love it as much as we hope they will? And we were blown away at the engagement. No one looked at their phone for hours,” remembers Combs. “Being part of building this is amazing. And you can tell we love it by how much we put into it, but then we are getting so much out of it at the same time. This is what this is about, this is amazing.”
To engage ProMach’s female leaders and leverage them to help the organization continue to grow and build future female leaders, Propati, Combs, and Dropik recruited three additional female senior leaders in the organization—Geri Krech, vice president of finance for ProMach’s filling business line, Kate Farley, director of sales at Modern, a ProMach product brand, and Susan Marshall, vice president and general manager of Edson, another ProMach product brand. Together, they created a mission statement and a space where the female employees could feel connected within ProMach’s decentralized structure.
The six women leaders meet as a small group on a regular basis to plan tangible, monthly connection opportunities ranging from a book club, to speakers in both virtual and inperson meetings. On the off-month of a speaker’s presentation, PowHER of
the Pack meets in breakout sessions of five or six to discuss the speaker’s insights.
“We put together a calendar, and we try to make it somewhat different but relatable each month,” explains Propati. “We do have some speakers, like [ProMach president and CEO] Mark Anderson spoke to the group on International Women’s Day, and we’re going to do something similar this year.”
In October 2022, PowHer of the Pack was able to meet as an entire group in Athens, Ga., with an onsite speaker facilitating a discussion about what leadership looks like for each of them. This was followed by personal development and goal setting.
“That in-person event allowed people across a geographic space to get to meet other people, and it’s blossoming—a launching pad of where we could go next,” says Dropik, noting that they will continue to hold an annual in-person event.
Beyond meetings and clubs, the
PowHER of the Pack leadership has a new initiative in store for 2023: the Open Door Mentoring program. In an effort to make the program selfsustainable and easily accessible for early-career females, the concept of a hand-picked mentor-matching process was thrown out the window and replaced with a friendlier setup. Instead, senior female leaders within ProMach were contacted to take on the role of mentor. These women then drafted short bios and provided headshots to be posted on the PowHER of the Pack Microsoft Teams channel. Ownership is then placed on the PowHER of the Pack members to decide—based on skills, interests, and connections they’d like to make—whom they would like to meet with and schedule a meeting based on the office hours that the mentor has set up. Mentors have been asked to commit up to twelve hours a quarter.
“This provides an easy and less scary way of reaching out to a senior leader in the organization,” says
New Buyers: 81% of PACK EXPO East attendees attended no other PACK EXPO event in 2022 - making this the place to be in 2024 to connect with East Coast Buyers.
Ready to Buy: 72% of attendees have purchasing power.
Key Titles: Nearly half of attendees hold management and C-level titles.
One Powerful Region: 72% of exhibitors expect to sell their products or services due to exhibiting at PACK EXPO East.
Have questions? Contact us at 571.612.3200 or sales@pmmi.org
Combs. “We’re going to be conducting some training for the mentors and the mentees on how to make those sessions as effective as possible. That’s going to be starting here in the first quarter of 2023.”
Dropik notes that the Open Door Mentoring program is just one piece of the plans that these women leaders have in store for PowHER of the Pack. Other areas of opportunity include:
• PowHER of the Pack at a local level
• The job fair environment
• Delegation of leadership to PowHER of the Pack members
• Empowering women to lead discussions on diversity, equity, and inclusion (DEI) initiatives and environment, social, and governance (ESG) initiatives at the local level
Stambaugh was a strong supporter from the beginning and encouraged Propati, Combs, and Dropik to connect and see what could come of the collaboration. On top of that support, the ladies’ leadership team—all the way up to ProMach’s CEO—have given PowHER of the Pack their full backing. The resource group has become a marketable internal brand and may become an external brand as well.
“The support and encouragement from our leadership team really changes the trajectory of where we’re going,” says Dropik. “The engagement at that level sets the tone for the company and really sets us up to be successful.”
The support and encouragement of leadership at ProMach are ultimately what has allowed PowHER of the Pack to grow and even extend beyond the women’s resource group. Through the unique lens of the group’s female leaders, methods and tools for connecting, educating, and training are being extrapolated to benefit all of ProMach’s employees, and the Open Door Mentoring program may even be extended to new resource groups in the works.
As Combs points out, it can be daunting to enter a workforce without having someone to talk to who can relate to the issues and problems you are facing. PowHER of the Pack, and the mentoring program in particular, is doing its part to help women navigate a career in a male-dominated industry. The hope is
that the program will serve to let women candidates know that they have a community they can join to support their careers, help them succeed, and train them to move up to senior leadership positions.
Easily share this article with your peers: oemgo.to/powhertopromach
Download whitepaper for free.
Future of coffee roasting is electric.
PMMI forms strong connections between members and customers, and helps to build unbreakable bonds, for example:
• PMMI’s ProSource is where customers go to nd solutions. Offered exclusively— and free—to PMMI members, ProSource is an online directory of technology suppliers designed to elicit lasting partnerships: pmmi.org/prosource
• PMMI’s Packaging & Processing Women’s Leadership Network provides opportunities for members and end-users to collaborate and address common challenges: pmmi.org/ppwln
PMMI is your answer. Learn more pmmi.org/pmmi365
PMMI is your answer, connecting you to customers 365 days a year.
www.oemmagazine.org
The following section, Partner Leaders, features profiles of leading pckaging and processing automation suppliers that stand to deliver value to you, the OEM. These companies specialize in bringing you the innovative products and services that you need, such as controls, components, integration, and more. Plus, you’ll find a companion Partner Leaders box prominently featured on the homepage of OEM (www.oemmagazine. org), with a dropdown menu of the participating companies listed by product category.
Join us on March 21 at 1pm for a 30 minute discussion about how understanding finances can lead to career advancement.
LEARNING CIRCLE WEBINARS WILL HELP YOU:
| Gain insights from subject matter experts.
| Hear from peers and discover answers to common challenges.
| Learn how to strengthen a career in packaging and processing.
The PPWLN Learning Circles are an interactive extension of the digital resource: Connect, Share, Inspire: Voices of Women in Packaging and Processing These Learning Circles will outline five key skill sets: business acumen, networking, negotiation, emotional intelligence, and communication.
All-Pro Fasteners is focused on providing reliable fastener supply solutions to its many manufacturing customers. If that solution involves sourcing, All-Pro is expert at selecting the most reliable and cost-effective supply of quality fasteners, whether domestic or international.
If the right fastener cannot be immediately sourced, All-Pro can also manufacture the fastener you need, with product quality assured based on testing at the company’s A2LA Quality Lab. All-Pro further provides its customers with a broad range of related services, including VMI/JMI and kitting services, along with assisting with inventory control and paperwork-reduction initiatives.
All-Pro’s people, products, and programs go beyond simply providing quality fasteners to delivering a wide range of related products and services…and solutions…to improve customers products, processes, and operations.
Phone: 860/585-1254
www.amci.com
Email: sales@amci.com
AMCI is a globally recognized company and one of the world’s leading suppliers of industrial control solutions. AMCI products not only improve PLC-based automation systems with specialized position sensing and motion control technology but also simplify automation and add reliability to the manufacturing processes.
PLC based products provide a unique approach to engineering and AMCI has been building expertise in this area for 30+ years. The engineering team designs a dependable, quality product that is manufactured in house, enabling superior quality and innovation. With a core team of engineers onsite, the design and production process work hand in hand to deliver you the most efficient and reliable products in a timely and effortless manner.
A breakthrough for industrial controls, PLC Network Products provides an all in one solution. Putting the products on the network increased use, lowered costs, and simplified installation, especially for distributed applications. Today, with AMCI’s E2 technology, PLC Network Products provide access to Ethernet/IP, Modbus TCP, EtherCat, Profinet, and Profibus. This innovative multi-protocol approach for PLC Industrial Ethernet networking, features dual port networking, PLC Programmable, and a web server.
AMCI offers you the best PLC integration available with their complete line of industrial ethernet motion control products. E2 Technology products are simple and intuitive, allowing easy transitions between multiple common industrial Ethernet protocols without the need to physically switch parts. An advanced web server integrated in all AMCI E2 Technology devices facilitates simple device configuration and troubleshooting via web-browser. Furthermore, an impressive array of advanced features for each supported protocol has been incorporated into the devices to meet many unique application requirements.
AMCI’s E2 Technology makes moving from one industrial Ethernet protocol to another simple, offering a seamless transition to industrial Ethernet, whichever industrial Ethernet protocol that may be.
P.O. Box 19560, 2061 E. Glenwood Ave Philadelphia, PA 19124 USA
Phone: (800) 278-8107
www.cssintl.com
Email: sales@cssintl.com
With tool and die shop heritage our highly experienced workforce, great engineering expertise and commitment to quality materials provides the best solution for OEMs.
PROVEN “OUT OF THE BOX” DEPENDABILITY
— Timing screws
— Bottom code and inspection diverters (unique with CSS)
— Quick change parts
— Drive units
— Side grip belt units
— Vacuum reject systems
We are committed to providing the most cost-effective engineered solutions using quality materials to ensure long-term reliability. We customize our equipment and materials to suit line conditions. We test components prior to shipment to assure hassle-free installation as well as follow-up with our customers to guarantee satisfaction.
With over 75 years of experience you can be confident of the long term reliability of our products.
To learn more about our products, visit www.cssintl.com.
To place an order, contact sales@cssintl.com or call (800) 278-8107
At Dorner, our mission is to Transform Conveyor Automation by providing cutting edge solutions with best-in-class support. It’s that commitment and history of proven excellence that has made the Dorner Brand a recognized leader in product handling for over 50 years. With our complete line of customizable stainless steel and aluminum conveyor automation systems, Dorner can provide solutions for almost any conveyor need.
Dorner conveyors are designed to simplify conveyor integration for packaging & processing equipment manufacturers. Purchasing conveyors from Dorner allows you to expand your product offering while continuing to focus design and manufacturing resources on what you do best!
Dorner is ISO 9001-2015 certified, which means that all equipment is built consistently and backed by rigorous quality control processes. Dorner quality ensures that the conveyors you provide will compliment the quality of your brand.
Our conveyors move product to the exact location, at the exact time and in the exact position it needs to be for the next phase of the production line. With benefits such as industry best product transfers and in-house belting capabilities, Dorner is leading the market in precision conveyance. This extremely accurate product control allows Dorner conveyors to easily integrate with robots, workers and equipment.
Using Dorner’s Online Configurator, you can design and engineer simple or complex conveyors to meet your needs in minutes. The industry leading tool delivers a complete 3D CAD assembly model for instant validation of fit.
Dorner’s Engineered Solutions Group is transforming product handling with innovative solutions that easily integrate into your designs. We can provide systems for applications such as accumulation, indexing, positioning, product flow and much more. With a custom-designed conveyor system in place, products are built faster, services are delivered quicker, and profits are increased with the help of highly specialized engineering technology.
Dorner’s new ERT150 Conveyors utilize Edge Roller Technology to provide efficient, non-contact zoning for small and light-load assembly automation applications. They feature a clean, open roller design and are ISO Class 4 approved for cleanrooms.
To keep up to date with what is happening at Dorner and see our next product release, visit our website at www.dornerconveyors.com.
464276 Highway 95, Sagle, ID 83860 USA
Phone: 800-366-5412
www.encoder.com
Email: sales@encoder.com
At Encoder Products Company, we strive to serve you with expert service, quality products, and fast delivery. EPC specializes in encoders for motion feedback in industrial automation applications such as packaging, printing, & labeling, vision systems, food and beverage, motor feedback, and more.
We understand that each industrial automation application is different, and you need encoders that fit the requirements of your applications. That’s why our encoders are highly configurable, offering a wide array of shaft or bore sizes, output types, connector types, mounting options, and resolutions up to as 65,536 CPR. You’ll also get an industry-leading warranty, and fast delivery from Idaho, USA.
EPC offers:
• Tru-Trac linear measurement solutions – an integrated encoder, measuring wheel, and pivot arm in one compact unit
• Draw wire units with wire lengths up to 42.5 meters
• Accu-CoderPro programmable encoders
• Magnetic multi-turn absolute encoders that operate in the absence of power without gear trains or batteries
• Robust mechanical housings for harsh operating environments, with stainless steel and corrosion-resistant options
• Magnetic encoder modules with sealing to IP69K
• Temperature ranges from -40° C to 120° C
• Competitor cross referencing and drop-in ready Direct Replacement encoders
• Engineering services for your custom motion feedback needs
EPC is ISO 9001:2015 certified, and we design, manufacture, and assemble most of our encoders and accessories at our corporate headquarters in Idaho, USA. When you call EPC, you’ll talk to engineers and encoder experts who can help you find the right motion feedback for your application. Contact us today.
Asbury Road, Erie, PA 16506 USA
Eriez’ equipment for the packaging industry includes metal detectors and magnetic separators for metal contaminant removal, as well as a full line of vibratory feeders, conveyors and screeners. Eriez’ compact Vibratory Feeders handle high-speed packaging, difficult products like flour, leafy and gummy products, and high material flow applications. These electromagnetic drives are energy efficient, low maintenance with no moving parts, and can be mated with a range of sanitary and non-sanitary trays.
Eriez Xtreme Metal Detectors offer best-in-class performance to safeguard against both ferrous and nonferrous metal contaminants. This equipment is very effective for identifying and removing stainless steel fragments in conveyed, gravity flow and liquid line sanitary processing applications. Detectors are positioned at different locations throughout the process from bulk and raw material through final package inspection.
There is no better solution to ensure your product is metal-free than using Eriez magnets for steel removal and using Eriez Xtreme® metal detectors to reject nonferrous metals like aluminum, brass, stainless steel and more. Many of Eriez’ most popular magnetic separators, vibratory feeders and controls are available for next day shipment.
Fenner Precision Polymers is a Michelin Group Company. With over 900 employees worldwide, Fenner Precision Polymers is a trusted supplier of engineered solutions. Product lines support clients across a variety of industries including 3D printing, document handling, transportation, mining, agriculture, aerospace, climate control, material handling, food processing, and manufacturing. Product lines include coated fabrics and technical textiles, link belting for power transmission and conveying, precision/timing belts, keyless locking devices, Eagle polyurethane belting, industrial conveyor belting, wire cloth, silicone and organic rubber hoses, customized bearing solutions, and PowerMax composite products.
Fenner Drives, a trusted brand of Fenner Precision Polymers, has enhanced the performance of its roller conveyor O-Rings, relying on Bi-Modulus Technology developed in partnership with Michelin’s High-Tech Materials Division. The Eagle XLD product line combines two separate patents, the result being a drop-in replacement that can transmit up to 4 times the load of an O-ring and last at least 6 times longer. Because of the Bi-Modulus reinforcement in XLD, it resists creep, resulting in longer life and transmission of higher loads over more rollers. XLD belts reduce the total cost of ownership for manufacturing, distribution, and fulfillment centers, and expands design capabilities for conveyor design engineers.
Fenner’s Eagle XLD belts strengthen the weakest point in a roller conveyor system thus reducing maintenance costs and downtime. By strengthening the belt while leaving enough flexibility, no additional components are required to maintain a consistent tension on the drive system resulting in a direct replacement of an O-ring. The reinforcement allows OEM design engineers to use up to 3 times fewer motors when designing a system because the belts can transmit more load at 99% transfer efficiency and notably less downtime than a conventional O-ring driven conveyor.
39
Phone: 973.521.7254
www.herma.us
Email:
HERMA US Inc. is a subsidiary of HERMA GmbH, a Germany-based provider of labeling machinery and self-adhesive labels and materials to the global packaging marketplace. HERMA GmbH’s comprehensive range of products spans the labeling production process to include labeling machinery, a variety of adhesive materials, and finished self-adhesive products.
The HERMA 500 label applicator offers machine builders an ideal solution for integration into automation machinery. Its compact size and absence of external control box, combined with exceptionally high levels of precision and reliability, give the HERMA 500 significant advantages over competing modules.
Capable of achieving labeling speeds up to 200m/min, the HERMA 500 can handle label widths between 80-320mm and roll diameters from 300–600mm. A wide range of interfaces are available, including Ethernet IP for seamless integration into Allen Bradley-based control systems. A 4.3” on-board touchscreen provides localized control, if required.
HERMA also offers a “tamp” version of the HERMA 500, which incorporates a patented moving dispensing beak that allows the unit to achieve placement accuracy of better than +/- 1/64, even with very small labels. This iteration is widely used in assembly machines for medical devices and similar applications.
W134 N5373 Campbell Drive, Menomonee Falls, WI 53051 USA
Phone: 1-800-782-8850
http://www.jax.com
Email: info@jax.com
Are you evaluating machine performance? JAX has been the industry leader in specialty industrial and food-grade lubricants for nearly 70 years.
We offer a wide range of synthetic, semi-synthetic and mineral based lubricants for a wide variety of applications. These include hydraulic, gear, compressor, conveyor, chain, and eco-friendly lubricants, as well as grease and aerosol products. Our NSF H1 and 3H lubricants are manufactured in ISO 9001 and 21469 certified facilities.
Our team of technical service representatives, scientists and chemists provide customers with continuous assistance for optimal machinery performance. Field service representatives are ready to support your business and provide training as needed.
All research and development activities are conducted in-house to identify products and formulas to meet your desired specifications. We also have our RPM lab, which conducts all our in-house used oil analyses to monitor performance and troubleshoot any potential concerns.
Innovation is the core of our business. If you have a unique challenge, let us know. Our team is ready to help you develop a solution.
The expanding John Henry Foster Group of Companies, comprised of Accu-Tech USA, Automation & Robotics Solutions (A&RS), Celco Automation, PTS Products, Sensors Incorporated and Sensors Integration, represents a strategic collection of industry-leading manufacturers, experienced engineers, support teams and automation & robotics distributors. This enables us to provide total turnkey systems, both nationally and internationally.
For decades, John Henry Foster (JHFoster) was known as only a local regional compressed air equipment and parts distributor. As the innovation of technology continued to advance, so did we. Our customers now benefit from our combined efforts of providing a single efficient production solution in automation, motion and robotics across our extended divisions.
The John Henry Foster Group of Companies has expanded service offerings and market reach, enabling us to investigate new technologies and touch more industries. Together we provide an additional range of value-add products that delivers a comprehensive, full-service automation and robotic solution, including electrical and pneumatic products, robotic applications, package inspection systems, industrial sensing capabilities and compressed air systems to name a few.
Our accumulated experience guides us in building successful solutions and integrating systems. We’re committed to delivering results customized to our customer’s specific needs. By partnering with each division, we provide a single source solution for delivering efficiency, cost savings and a smooth and hassle-free journey.
Leister Technologies offers affordable and reliable industrial heating solutions like heaters, blowers and hot air blowers for manufacturers. We cover the majority of industrial process heat and plastic connection applications with affordable and reliable industrial heating solutions like heaters, blowers and hot air blowers for manufacturers.
The company’s products can aid users in increasing cost- effectiveness and efficiency of their process systems. Whether for activating, heating, deflashing, melting, shrinking, sterilizing, drying, or warming, Leister has a solution for your industrial process. Try a MISTRAL or HOTWIND hot air blower with a nozzle to serve as an air knife to blow water off your products during production or to create a simple shrink tunnel when applying tamper-evident seals prior to packaging. Pair one or multiple Leister air heaters with a high-pressure blower to provide additional heat to a larger area within your production line. Is gate vestige, flash, or problematic stringing an issue for you? No problem, place a Leister hot air blower in your process to quickly and easily deflash or remove any remnant plastic.
Quality Management - As an innovator, Leister commits to transparent and consistent quality management. Experienced engineers, product managers and specialists from ISO9001-certified Leister Technologies AG in Switzerland develop products and systems for plastic welding applications and for generating industrial process heat. Based on innovative technologies including hot air, contact heat, extrusion, laser and infrared, and our passion for customized solutions, we’re able to significantly influence our market segment and set high standards worldwide.
Testing and Certification - Our products are designed and developed to comply with nationally and internationally recognized standards. These include both product-specific— ISO, IEC, EN or UL—as well as application-specific standards. For our clients’ protection, tests are carried out by accredited, independent, test institutes.
Application and Laboratory Testing - Leister’s internal applications laboratory allows for comprehensive testing of all manufactured tools and equipment.
“The best machines and production facilities around the world use Lenze.”
Lenze is a leading automation company for the machine-building industry, and a specialist in Motion Centric Automation. As a systems supplier with solutions competence, Lenze works with you to create high-quality mechatronic products and packages, powerful systems consisting of hardware and software for machine automation, as well as digitalization services in areas such as big data management, cloud or mobile solutions, and software for the Internet of Things (IoT). We are a reliable partner with the knowledge and expertise to provide you with the best overall solutions reducing machine development times and enabling faster time-to-market.
If you are looking to implement cutting-edge machines and plant concepts, or modernize existing installations, you can trust Lenze. We help you choose the best solutions, providing energy efficient drive dimensioning, and are with you through the steps of project planning, implementation, and commissioning. We make it easy for precise implementation of your machine tasks.
As a global manufacturer of electrical and mechanical drives, motion control and automation technology, we provide automation solutions to the following industries: consumer goods packaging, automotive, material handling and logistics, robotics, and commercial pumps/fans. With a global network of engineers, sales representatives, and manufacturing facilities, Lenze is well-positioned to meet the motion control needs of customers worldwide. Lenze Americas, a subsidiary of German-based Lenze SE, is headquartered in Uxbridge, Massachusetts.
4647 Hugh Howell Road Tucker GA 30084 USA
Phone: 800/241-8334
www.itwprobrands.com
For over 60 years LPS® has earned a reputation for both quality and performance in critical industrial and aerospace applications. LPS® DETEX® combines that expertise with food safety programs to produce a full line of maintenance solutions specifically formulated for food processing facilities. Including lubricants, penetrants, electronic cleaners, greases, and specialty products, LPS DETEX covers a wide variety of maintenance tasks. These premium-performance chemicals save time and money by extending equipment life, reducing repair time, and lowering frequency of preventative maintenance all while food is in production.
LPS DETEX packaging is also designed with food safety in mind. Utilizing a unique patented formula, the plastic packaging components are both metal & X-ray detectable. Additionally, the slip-resistant can features NSF® ratings clearly marked on top, and highly visible bright blue lithographed labels that won’t tear or smudge.
LPS DETEX helps reduce the risk of foreign object contamination that can result in recalled product, facility downtime, delayed customer deliveries, and compromised brand reputation.
Newark, NJ 07105 / Toledo, OH 43605 USA
Phone: 800-733-4755
www.lubriplate.com
Email: LubeXpert@lubriplate.com
Lubriplate Lubricants Company
Advancing Lubrication For 153 Years.
Back in 1870, Lubriplate’s founders set out to make the highest quality, best performing lubricants available. In doing so, they helped pioneer the use of anti-wear additives that significantly increased lubricant performance through the years. Today, that innovative tradition continues with their complete line of ultra high-performance, 100% Synthetic, NSF H1 Registered, Food Grade Lubricants. Manufactured under strict NSF/ ISO 21469 Certified and ISO 9001 Registered quality control standards, these lubricants are formulated to deliver a number of significant, cost effective advantages, including; extended lube and fluid change intervals, multiple application capability, lubricant inventory consolidation and improved performance. Clean, safe and non-toxic, their use can eliminate lubrication as a critical control point in HACCP programs.
All Lubriplate Lubricants come with Lubriplate’s ESP Extra Services Package at no additional charge. Services include; a complimentary plant lubrication survey by a factory direct representative, color coded lubrication charts and machinery tags, a toll free technical support hotline and email, and follow-up lubricant analysis.
Innovation in the pursuit of greater line efficiencies has kept Morrison Container Handling Solutions the leading manufacturer of automated container handling equipment for over 51 years, all backed with expert design and Support Built In®. Utilizing a variety of our product lines to create custom integrated systems that solve container handling challenges, we approach every line with a unique opportunity to improve throughput and container handling prowess. In addition to being the leading manufacturer of timing screws in North America, we design a variety of automated equipment that address many productivity related items for other OEM equipment.
We offer a wide range of solutions that pair well with your equipment to make it run more efficiently to give you an edge up on the competition when it comes to control of product. Whether it be to increase speed, automate container presentation, or a variety of other things, our products work with yours to present your customer with the best solution possible when it comes to packaging equipment.
With over 25 engineers on staff, OEMs often leverage our team to solve simple to complex challenges. Our standard product lines include timing screws, drive units [metering, feeding, turning, grouping], change parts, combiners, dividers, down bottle rejects, can openers, denesters, collating, stacking, multi-packing, orienting, and inverting systems. And when standard solutions won’t work, we provide some of the most robust, flexible custom equipment in the business.
With PMMI Certified Trainers on staff, we fully back our customers and your customers every step of the way. With every product, you receive expert-backed Support Built In® --- our personal customer service program for any general questions or technical support you need before, during, and after installation. It’s our promise to be there for you when it counts, so you can be there for your customers.
Let’s form a partnership you can count on! Contact us today to learn more about how we can pair our solutions with yours to help advance automation on packaging lines all over the world.
As both a custom conveyor and standard plastic chain and belt system manufacturer, MultiConveyor’s products are multiple and unique. We’ve built some of the most complicated OEM conveyor requests ever imagined, yet provide simplistic conveyor solutions on a regular basis as well. We’re committed to providing a more functional, affordable conveyor designed to maximize productivity, meet or exceed sanitary expectations and save essential floor space in the process.
Multi-Conveyor’s team specializes in creating OEE engineered conveyors or devices to accumulate, rotate, elevate, lift-gate, incline, combine, decline, alpine, grip, flip, split, invert, divert, merge, sort, twist, turn, curve, transfer, push, stack, reject, hand pack or serpentine – to name a few. Our factory-direct team of experts include:
Concept/Design: Multi-Conveyor’s designers and mechanical engineers factor in productivity, functionality, ease of use, reduced overall footprint, safety, sanitation (as required), maintenance, longevity and future growth. We use quality components that meet or exceed your conveyor project scope requirements.
Engineering/Electrical: Our engineers make sure your systems “talk”. We integrate technology driven operator-to-controls communications. HMI interface and servos provide faster, more efficient changeovers. Adaptability to various shapes, weights and sizes allows flexibility to match our solutions to your products for increased throughput and future expansion.
Project Management: Concise approval drawings clarify functionality of equipment prior to fabrication. We facilitate the entire project from start to finish, often time adapting unforeseen equipment changes mid-stream. Ending with OEM or customer approved performance FATs prior to shipment.
Let us quote your next project. Chances are, we’ve already built a system that’s similar to the project you’re working on right now - or made one pretty dang close.
Novanta is trusted technology partner to medical and advanced industrial OEMs, with deep proprietary expertise in photonics, vision and precision motion technologies. We engineer mission-critical core components and sub-systems that deliver extreme precision and performance, enabling our customers to improve productivity, achieve breakthrough performance and enhance people’s lives. Through our globally recognized Novanta brands in advanced photonics, ARGES, Cambridge Technology, Laser Quantum and Synrad, we deliver tailored laser and beam delivery solutions to OEMs in a broad range of industrial and medical markets.
Novanta develops photonics solutions, specializing in cutting-edge components and subsystems for laser-based diagnostic, analytical, micromachining and fine material processing applications. Powerful lasers, coupled with advanced beam steering and intelligent subsystems incorporating software and controls, deliver extreme precision and performance, tailored to our customers’ demanding applications. Unlike other laser or beam delivery providers who are limited to one technology and cannot offer integrated solutions, we deliver optional solutions through collaborative approaches, developing pivotal laser-based components and seamless sub-systems.
Through our photonics technologies, we deliver finely tuned laser sources and beam delivery systems that enable customers to improve their process, increase productivity and achieve breakthrough performance. We bring unprecedented value to our customers through engineer-to-engineer collaboration, a wide range of application expertise, and state-of-the-art application labs.
To learn more about Novanta visit www.NovantaPhotonics.com
www.patlite.com
Since 1947, PATLITE has positioned itself as a global leader in visual and audible signaling with a strong commitment to innovate in the safety, security and industrial problem-solving sectors. Backed by years of industry experience and knowledge, PATLITE offers cuttingedge solutions to the process and automation industries worldwide through products that solve real-world dilemmas in the harshest and busiest of environments. Headquartered in Osaka, Japan, PATLITE has more than 1000 employees in wholly-owned sales subsidiaries in the U.S.A., Mexico, Germany, Singapore, Korea, Thailand, Taiwan and China. With a constant drive to meet and exceed customers’ expectations for reliable, in-stock products, PATLITE continues to deliver peace of mind to facilities worldwide.
IP69K-rated Products from a Global Leader in Signaling
Wash away your harmful bacteria concerns with IP69K-rated products from PATLITE. These long-lasting products are made with durable and suitable materials that can withstand harsh environments and are ideal for use in the food and beverage and pharmaceutical industries, where attention to microscopic details is highly prioritized.
PATLITE’s robust IP69K product line has it all: modular signal towers for a custom touch, durable light bars for maximum visibility and multi-color compact beacons that economizes factory floor space. All products are designed to feature the added benefit of ranking highest on the protection scale to meet strict sanitary and cleanliness guidelines.
https://www.paxtonproducts.com
“Paxton Products manufactures high efficiency centrifugal blowers and custom-engineered air delivery devices used for drying, air rinsing, and blow off, to improve product quality through better cleaning, rinsing, labeling, marking, and coding processes. Air Delivery Devices are custom-engineered to maximize and improve the quality of drying, blow off, and cleaning of products and surfaces. Our team configures the air delivery device specifically for your unique application - sizing air knives, nozzles, and manifolds for peak efficiency.
Available in both aluminum and 304 stainless steel, Paxton’s Air Knives and Knife Systems are designed to give maximum efficiency for high velocity drying and blow off applications. These systems feature a continuous, uninterrupted air slot design that gives uniform air coverage over the targeted area. Because of this, you’re able to significantly reduce the amount of product quality rejects for your business.
Coupled with Paxton’s high efficiency centrifugal blowers and air delivery devices, Paxton’s Ionizing Rinsing Systems remove particulates, dust, and contaminants using powerful ionization. The Ionizing Rinsing System provides static control and static elimination so that dirt and dust don’t adhere to surfaces, and then blasts contaminants away using a Paxton PX-series centrifugal blower.
For drying, Paxton’s patented PowerDry Drying System sets the standard for a complete, power drying and blow off air system that can used for a wide variety of cans, bottles, jars, and pouches. By incorporating Paxton’s PX-series centrifugal blower, the PowerDry System lowers energy costs by as much as 80% through reduced compressed air usage in bottling, canning, and other packaging operations.”
Phone: 800-253-0421
www.reidsupply.com
Email: sales@reidsupply.com
Established in 1948, Reid Supply, also known as Reid Tool Supply back in the day, is a premier provider of industrial parts and supplies to the North American manufacturing market. We maintain strong partnerships with over 300 leading brands, such as Destaco, Kipp, Vlier, Jergens, Northwestern Tool, JW Winco, CD Hardware, Colson, DimcoGray, Elesa, 80/20, ER Wagner, Garr Tool, Little Giant, Mitutoyo, Starrett, and many more. As a preferred distributor, we can source the entire catalog of products from our vast supplier network – not just the products we stock daily in our warehouse.
We carry a broad range of industrial parts that include knobs, handles, handwheels, latches, catches, hinges, workholding, toggle clamps, tooling and positioning, casters, leveling feet and more for any manufacturing application.
Having a hard time finding the right product for your application? We are here to help. We have a team of specialists dedicated to finding the hard-to-find products. Our team of experts are focused on solutions and that includes finding alternative parts that fit your application … all you have to do is ask!
We specialize in unmatched customer service and knowledge, that’s what sets us apart. Our goal is to create solutions for your application by end of the business day. Our team takes pride in servicing our customers and want your experience to be as hassle-free as possible.
Reid Supply not only serves the Packaging and Food Processing industry, we can service virtually any industry such as Medical, Automotive, Machine Builders and MORE.
We offer price quotes in 4-hours or less, same-day shipping on most stock items, eCommerce digital catalogs, and free downloadable CAD drawings on our website.
You may email our team at sales@reidsupply.com 24/7 or call us at (800) 253-0421. Response time is essential for us to be the best customer service team possible.
Check out our company video at: https://www.youtube.com/watch?v=k-Q2-bkycCw
Check out our product catalogs at https://reidsupply.dcatalog.com/r/Reid-SupplyCatalogs/?openarchive=1&page=1
Visit our website for our complete parts offering: https://www.reidsupply.com/en-us
Advertisement SPRING 2023 85
Phone: 864/439-7537
www.seweurodrive.com
Drive and Automation Expertise from SEW-EURODRIVE
In addition to our industry-leading line of gearmotors and other components, our dedicated team of automation engineers provides the expertise, project planning, software, commissioning, and worldwide support for your most challenging motion control projects. Our experts will provide a solution of perfectly matched SEW components that work together seamlessly — because we designed them that way!
Our MOVI-C® modular automation system is a one-software, one-hardware automation platform that combines fully integrated components, control electronics and automation software – like our MOVIKIT® pre-built software modules. These simple to use modules benefit engineers of all experience levels by reducing time in automation programming.
MOVIGEAR® is the mechatronic drive system that combines the gear unit, IE4 motor and electronics in one compact unit. Recent updates include fully integrated Ethernet/ IP communications and digital motor integration. This advanced single-cable technology carries power, feedback information and control signals along a single hybrid cable between decentralized devices.
SEW-EURODRIVE now offers a full complement of drive maintenance and management services with our 24/7 online portal and complete overview of your drive components, the condition of your units, drive usage, and service details. Plus, our new on-site Pick-Up Box service frees up your maintenance team for other tasks. Just place your drives that need repair in the supplied box, and we’ll handle the pick-up and return of your drive units.
Phone: 508/854-0799
www.slideways.com
Slideways was founded in 1994 as a manufacturer of superior quality machined plastic components for the conveying, packaging and processing industries. OEMs appreciate our 2D/2W service standard. Customers receive quotes on custom parts in 1-2 days and finished parts in 2-3 weeks. OEMs rely on this standard to keep them on schedule.
Our core products are used in food and beverage, pharmaceutical, bakery, and conveyor applications.
Solutions that increase productivity and reduce cost.
• Engineering and Design Assistance
• Chain and Belt Guides
• Custom Machined Plastics
• Guide Rails
• Extruded Wear Strips
• Guide Rail Brackets and Accessories
• Levelers (Foot Pads)
• Bearings and Bushings
Advertisement SPRING 2023 86 SPRING 2023 86
Service levels are supported by CNC equipment and ample inventory.
32 Crosby Drive, Suite 101, Bedford, MA 01730 USA
Soft Robotics is an industry-leading technology company that designs and builds automated high-speed picking solutions using proprietary soft robotic grippers, 3D machine vision and artificial intelligence software. The company’s transformational robotic automation solutions enable System Integrators, OEM machine builders and Food Processors to automate complex production processors in the food and consumer packaged goods industries – solving supply chain issues and eliminating the reliance of human labor to maintain operational efficiencies.
Products Offerings: Soft Robotics offers revolutionary food-grade robotic automation solutions that solve the many challenges in the food processing industry.
mGrip™ - The mGrip modular gripping system is a suite of configurable soft grippers and controller products that enables singulated picking for hard-to-grasp items in the food processing industry. mGrip’s proven soft gripper technology allows robots to safely and efficiently pick and pack products while also increasing throughput and efficiency.
mGripAI™ - mGripAI is an easy-to-integrate, high-speed automation solution combining 3D vision, soft grasping, and artificial intelligence (AI) software enabling the deployment of robots in food processing applications previously reliant on human labor. This unprecedented combination of robotic “hands,” “eyes” and “brains” enables, for the first time ever, the automation of bulk picking processes (e.g. bin picking) in the food supply chain.
Span Tech leads the industry as an innovative material handling company. We are known throughout the world for our quality, reliability, and excellent customer service. Today we are recognized as a global leader in developing unique and customizable solutions for conveying applications.
Our customized solutions ensure that your products get where they need to be when they need to be there and with countless number of chain configurations the possibilities are endless. From changing elevation while curving to transferring, our conveyor solutions have been proven effective time and time again.
Need to integrate? No problem. Span Tech conveyors can be designed to integrate with almost any type of machinery, work station, or robotics. We do not shy away from your challenges, we embrace them. If solutions do not exist yet, we create them.
Our Core Industries Include:
• Food & Beverage Production, Pharmaceuticals, Packaging, Manufacturing, Warehousing, Distribution, E-Commerce, Cosmetics
Through product evolution and innovation, we provide our customers with the lowest total cost of ownership, as well as the longest service life available.
Contact us and let us show you how together we can Outlast, Outperform and Outdeliver the competition. We are committed to building the best conveyor systems possible. It’s more than a goal. –It’s how we do business.
13771 Cavaliere Dr, Shelby Township, MI 48315
Phone: (888) 326-1476
www.vandergraaf.com
Email: info@vandergraaf.com
VDG is the leader in the design and manufacturing of drum motors for belt conveyors, with a strong focus on safety, reliability, and longevity. Manufacturing in-house in USA and Canada for 37 years, using cutting-edge production technology and automation, and with continuous improvements through R&D, VDG ensures product quality, fast delivery, and after sales support.
All drive components of the VDG Drum Motor including the electric motor, gear reducer, and bearings are enclosed inside the drum, increasing energy efficiency, operator safety and optimizing space. VDG Drum Motors are designed for 80,000 hours of continuous operation before maintenance, minimizing downtime and reducing maintenance, and operational costs.
The VDG patented IronGrip™ lagging, offered for VDG Drum Motors, enhances the durability and lifespan of the conveyor belt and the lagging. It consists of steel bars welded symmetrically on the drum with hot-bond vulcanized lagging inserts between the bars. IronGrip™ lagging eliminates uneven belt wear, improves belt tracking, increases belt traction by 40%, and has a 4-5 times longer service life compared to standard lagging.
VDG’s stainless steel SSV Series Drum Motor features an IP69K rated sealing system, withstands up to 3,000 psi washdown pressure, and drives modular, wire mesh, and monolithic conveyor belts without using sprockets. The SSV Drum Motor eliminates crevices that trap food by-products and bacterial harborage, reducing washdown time and water usage by 50% and providing the most efficient and hygienic drive solution for food processing and handling belt conveyors.
The IntelliDrive™ Drum Motor features new synchronous permanent magnet motor technology, delivering 40% increased electrical efficiency, a wider range of belt speeds without loss of torque and an increase in electric motor lifespan compared to a traditional conveyor drive. It enables onsite diagnostics, full motor indexing speed control, and communications with other automated plant equipment.
For more than 70 years, VEGA Americas, Inc. has provided industry-leading products for the measurement of level, pressure, and density. VEGA’s full product line of measurement instrumentation and accompanying devices and software allow us to provide one of the most complete ranges of measurement solutions in the industry.
VEGA’s continued innovation in level, point level, and pressure measurement instrumentation ensures packaging and food processing OEMs can optimize their processes and keep up with ever-shifting market demands. The future of instrumentation lies in the ability to produce high-quality products that keep pace with technological advancements and to provide service and value to one’s customers in a competitive environment. VEGA’s goal is to develop innovative measurement technology that is easy to install and operate and that offers maximum safety and reliability.
Through constant innovation, VEGA has become the market leader in radar level measurement instrumentation, pioneering the first two-wire radar in 1997. In 2015, we unveiled the first 80 GHz radar sensor – VEGAPULS 69 – specifically designed for bulk solids level measurements. Two years later, we released the 80 GHz liquids level radar, VEGAPULS 64. Most recently, in 2022, VEGA announced VEGAPULS 6X, one sensor designed for any level measurement application, liquids or bulk solids. VEGAPULS 6X is built according to the needs of the application, ensuring users receive the precise, reliable, and easy-to-use sensor that’s right for them.
Located in Cincinnati, Ohio, VEGA Americas combines manufacturing, distribution, and service for products that represent the most sophisticated process measurement technologies anywhere in the world. VEGA Americas is a wholly-owned subsidiary of VEGA Grieshaber KG in Schiltach, Baden-Württemberg, Germany. A family-owned company, VEGA employs over 2,100 people worldwide, including over 350 in VEGA Americas.
VEGA understands the benefit of investing in community and employees, because it’s people who make the difference in achieving success. This success transfers to the solutions we provide to customers.
WIPOTEC North America – weighing technology at its best: WIPOTEC North America is a subsidiary of the German weighing technology specialist WIPOTEC GmbH based in Kaiserslautern, Germany. WIPOTEC is a technology leader in the production of weighing and inspection systems. The company has a worldwide staff of over 1,000 employees, and subsidiaries in Europe, Asia and USA.
The core business of WIPOTEC is the development, production and integration of ultra-fast precision Weigh Cells and high-tech weighing systems for high-speed applications.
WIPOTEC Weigh Cells are used in a wide range of industrial production processes. Application examples include check weighing, product filling, dosing and price labeling systems, as well as integration into packaging machines. Furthermore, highly specific solutions, tailored to the needs of the customers, are implemented for the pharmaceutical industry to weigh capsules, tablets, syringes and vials, and in dry or wet food processing and packaging.
WIPOTEC Weigh Cells work according to the principle of Electro Magnetic Force Restoration (EMFR). They are based on the monoblock technology which makes them extremely precise and fast and enables them to render accurate weighing results even at highest speeds and under the most adverse conditions. Vibrations can be actively compensated within the weigh cell. The product range includes models which can weigh a mere microgram and others which can deal with loads up to 120 kg.
The heart of all WIPOTEC Weigh Cells is the monoblock, and it is manufactured in our in-house machining center using state-of-the-art CNC milling machines. The in-house development and project engineering departments enable the company to support unique customer requirements. For example, numerous combinations of infeed, outfeed and weighing conveyors are avialble for use with our weigh cells to provie complete weighing kits designed to easily integrate into OEM machines.
Certified to DIN EN ISO 9001.
2121
At Yaskawa, we help you explore what’s possible, and open new doors to opportunity. Rather than accepting the status quo, we invite you to wonder, “What if …?” And then we make it possible. That dedication to engineering and innovation is what makes us different.
Experience is often the difference between solving a problem the right way and settling for “good enough.” Our global expertise is unmatched and unquestioned, with 100+ Years of manufacturing excellence, 30 countries with sales, service, and manufacturing locations, and $4.5 billion in global sales per year.
We provide both standard products and tailor-made solutions, all backed by proven quality and reliability. We continuously work to save you money, time, and energy, because we believe your machine can always run faster, smoother and more productively. It’s about making the correct diagnoses, creating the right automation machinery, and implementing it in the best way possible. From case packing to labeling, filling to palletizing, Yaskawa can increase pack rates, improve throughput, and simplify motion and robotic control to maximize the performance of your machine.
Yaskawa AC Servo Systems come to a precise position with a speed and consistency that is unmatched in the industry. Connect our rotary, linear, and direct drive motors to an advanced Yaskawa machine controller to achieve SINGULAR CONTROL: the ability to manage robots, servos and drives with a single controller and familiar IEC 61131-3 programming.
Over 500,000 Yaskawa Robots are at work worldwide, with 150+ models to choose from and the strength of decades of packaging application expertise. Yaskawa’s Motoman robots are successfully picking, packing and palletizing a wide variety of food, beverage and consumer products for global CPG leaders.
Yaskawa variable frequency drives cover every application in the industrial plant, with power ranges from fractional HP to 16,000 HP and a legendary reputation for reliability and advanced technology. Our latest VFDs provide simple motor setup with flexible network communications, embedded functional safety, no-power programming, and easy-to-use tools featuring mobile device connectivity with our DriveWizard® mobile app.
13200 Sixth Avenue North, Plymouth, MN 55441 USA
Phone: 763/546-4300
www.zero-max.com
Email: bmishuk@zero-max.com
Redefining Innovation & Leadership.
For over 70 years, Zero-Max, Inc. has been a leading provider of motion control and power transmission solutions worldwide. With strategic distribution points located throughout the world, Zero-Max can deliver your motion control component solution. The Zero-Max brand is known throughout the world for its high quality and premium performance. The Zero-Max team is committed to providing best in class service with passion. If the extensive standard product offering doesn’t provide exactly what you need, Zero-Max application specialists can engineer a solution to meet your unique requirements.
With many years of application experience Zero-Max excels in these areas: •Customized Solutions, •Experienced Practical Application Advice, •Responsive to our Customers Needs, •Predictable High Quality, •ISO 9001: 2015 Certified, •Fast Delivery
Zero-Max Primary Product lines are: Flexible Shaft Couplings and Torque Limiters for Servomotors, Linear Actuators, Wind Turbines, Printing Presses, Label Printing, Converting Machines, Machine Tools, Test Equipment, Feedback devices, Packaging Machines, Process Equipment, Dynamometers, and other high-performance applications. Variable Speed Mechanical Drives for Agricultural, Printing, Peristaltic Pumps, Food Processing, Pharmaceutical, Packaging, and many other applications. Overhung Load Adaptors for Timber Processing, Brush Clearing, Road Construction, Marine, and other rugged applications that need overhung load protection for hydraulic pumps and motors. Keyless Locking Bushings for Packaging, Processing, Tooling, Automated Assembly, and applications that would benefit from the unique qualities of a keyless locking bushing. Contact us for more information regarding quality motion control components that can solve your most demanding motion requirements.
Configurable 3D CAD downloads at www.zero-max.com
Carlo Gavazzi, gavazzionline.com
Carlo Gavazzi introduced the SPDE Power Supply series, ultra-compact single-phase DIN-rail power supplies designed for electrical panels.
The SPDE Series consists of three frame sizes, starting from 75 W with 32 mm width, through a 480 W with 48 mm width. Their ultra-compact housing design allows them to save up to 50% panel space, making them ideal for applications where space is limited.
The high quality of the SPDE is certified by a series of industry approvals: CE, UKCA, UL61010, and UL62368. Integrated diagnostic and protection functions such as output short circuit, over current, over voltage, and over temperature provide the user with maximum output protection.
Wago, wago.com
Wago’s new Compact Controller 100 is a small-scale PLC with a wide variety of remote I/O for use in smaller applications. Engineered for OEMs, IIOT digitization projects, and building automation applications, this easy to use device is cost effective for small, but demanding applications.
This PLC can interface with industrial devices using protocols such as Modbus TCP/UDP, EtherNet/IP, or EtherCat with the two on board EtherNet ports. The flexibility of the two Ethernet ports allows for the use of a switch or two unique IP addresses, with one port for field devices and the other for SCADA or cloud services.
The CC100 uses Codesys 3.5, allowing users to program in one or more of the IEC 61131-3 compatible languages and utilize the controller’s built-in Web Server to develop HTML 5 visualizations at no additional charge.
NewTek, newteksensors.com
NewTek Sensor Solutions offers its Hermetically Sealed Position Sensors with a 4 – 20 mA current loop output. Offering rugged operations and high performance with low power consumption, Newtek’s HI Series of Hermetically Sealed 4-20 mA LVDTs ensure highly reliable and consistent data output for factory automation, materials testing, and packaging equipment applications. Requiring less power than similar DC-operated LVDTs and signal conditioners, these 4-20mA sensors also satisfy low power budgets.
Sustaining accuracy with no errors over long distance transmissions, the 4 – 20 mA current does not degrade over long connections and is less sensitive to background electrical noise. Simple to connect and configure, the 4-20 mA output position sensors offer plug and play compatibility with most PLCs and controllers. .
Festo, festo.com
Festo adds a new space-optimized product to its line of pneumatic cylinders--the ultra-compact ADN-S– for performing small movements in tight quarters and, in so doing, helping machine designers keep their projects as space efficient as possible.
Festo took the ISO standard ADN double-acting cylinder and shrank the housing length to create a significantly smaller, lighter weight, and a ractively-priced choice for space-critical applications. ADN-S comes with multiple mounting options and a choice of fixed or no endposition cushioning. A proximity sensor can be added. The piston rod is available with internal or external threading,
The ADN-S joins the Festo DSNU-S round cylinder, a space-optimized version of the ISO DSNU round air actuated cylinder.
OEM Magazine (ISSN# 2377-293X) is a trademark application of PMMI, The Association for Packaging and Processing Technologies. OEM Magazine is published four times annually by PMMI with its publishing office, PMMI Media Group, located at 401 N. Michigan Ave., Suite 1700, Chicago, IL 60611; 312.222.1010; Fax: 312.222.1310. Periodicals postage paid at Chicago, IL, and additional mailing offices. Copyright 2023 by PMMI. All rights reserved. Materials in this publication must not be reproduced in any form without written permission of the publisher. Applications for a free subscription may be made online at www.oemmagazine.org/subscribe. Paid subscription rates per year are $80 in the U.S., $125 Canada and Mexico by surface mail; $200 Europe, $400 Far East and Australia by air mail. Single copy price in U.S. is $20. To subscribe or manage your subscription to OEM Magazine, visit www.oemmagazine.org/subscribe. Free digital edition available to qualified individuals outside the United States. POSTMASTER; Send address changes to OEM Magazine, 401 N. Michigan Ave., Suite 1700, Chicago, IL 60611-3789. PRINTED IN USA by Quad Graphics. The opinions expressed in articles are those of the authors and not necessarily those of PMMI. Comments, questions and letters to the editor are welcome and can be sent to:
Iwas all prepared to kick off another year of OEM columns with the usual: Wishing everyone a Happy New Year and outlining the year ahead for PMMI. It does feel like the first time in a long time that we have a full slate of in-person trade shows (EXPO PACK Guadalajara, June 13 –15 and PACK EXPO Las Vegas, Sept. 11-13), meetings (Executive Leadership Conference, April 15 – 18 and the Young Professionals Conference and PMMI Road Show July 19-20), as well as other PMMI and industry events to look forward to.
But, I was interrupted by a ping notifying me of a LinkedIn post that shifted my focus to another excellent, yet underutilized, PMMI member benefit.
The post was about PMMI member Hoosier Feeder Company taking advantage of the PMMI U Skills Fund to provide Whitewater Career Center of Connersville, Indiana, with funds to improve its Welding Technology Program. Like trade schools, these local career centers offer high school students real-life experiences, skills, and knowledge to succeed in today’s working world. This came across my screen just as we are approaching our March 31st closing date for applications for PMMI Foundation scholarships.
To that end, the PMMI U Skills Fund is a no-brainer for members seeking to form partnerships with regional twoto four-year colleges, technical schools, and high schools. This can lead to ready-made internships and apprenticeships in the short term. Long-term, it’s an investment in the skills and knowledge of students to ensure a highly skilled workforce of the future. The PMMI U Skills Fund will match your company’s contributions of up to $50,000 per year to programs of your choice. It could even be a STEM summer camp that already exists. In the case of Pearson Packaging, they sponsored a school’s robotics team and created a three-week manufacturing academy to promote packaging and processing careers. For its part, JLS Automation supported Penn State York via funds and equipment, and found eight interns and four full-time employees as part of their Skills Fund partnership.
These are just some of the ways members have used the money provided by the PMMI Foundation. The PMMI Foundation works to grow awareness of careers in packaging and processing and aids schools and programs that develop students to excel in the industry. It also provides financial support for packaging and processing education throughout the U.S. and Canada. In the past 25 years, the PMMI Foundation has given almost $3 million to strengthen the workforce within the packaging and processing industry via camps, training, tuition reimbursement for
JIM PITTAS PRESIDENT & CEO, PMMIcurrent employees, and over a dozen scholarship offerings.
The funds are raised at events such as the Foundation golf tournament, PACK Gives Back, the Amazing Packaging Race, the Executive Leadership Conference silent auction, and generous donations from individuals at PMMI member companies.
The workforce issues plaguing all of manufacturing are not going away. Therefore, it is on us to find ways to attract and educate the current and future workforce on the many benefits of a career in packaging and processing. PMMI Foundation scholarships can help.
For a full list of available PMMI Foundation scholarships go to: pmmi.org/foundation/scholarships
PACK EXPO Las Vegas 2023 (Sept. 11-13, 2023) exhibitors will receive frequent exhibitor updates, including important information and deadlines regarding the show starting in March. Add reply@ mailpackexpo.com to your safe sender list to receive all updates.
April 1, 2023: Booth personnel and a endee registration opens. Make sure your online listing is populated before a endees begin registering and searching for your company.
May 2023: Exhibitor Service Manual Launch
PACK EXPO East 2024 in Philadelphia (March 18-20, 2024)
Booth space is available on a first-come, first-served basis. Visit www.packexpoeast.com to submit your application.
PACK EXPO International 2024 in Chicago (Nov. 3-6, 2024)
Currently accepting booth space applications for PACK EXPO International 2024. To participate in priority booth selection starting in late May, an application must be submi ed by Wednesday, May 17, 2023. For more information, visit www.packexpointernational.com. Have Questions? Please reach out to the Show Department at expo@pmmi.org or call 571-612-3200.
Jim Pittas is the President & CEO of PMMI. He may be reached at jpittas@pmmi.org or at linkedin.com/in/jimpittas.
Fully integrated drive components, control electronics and automation software – all from a single source – and all designed to work together perfectly.