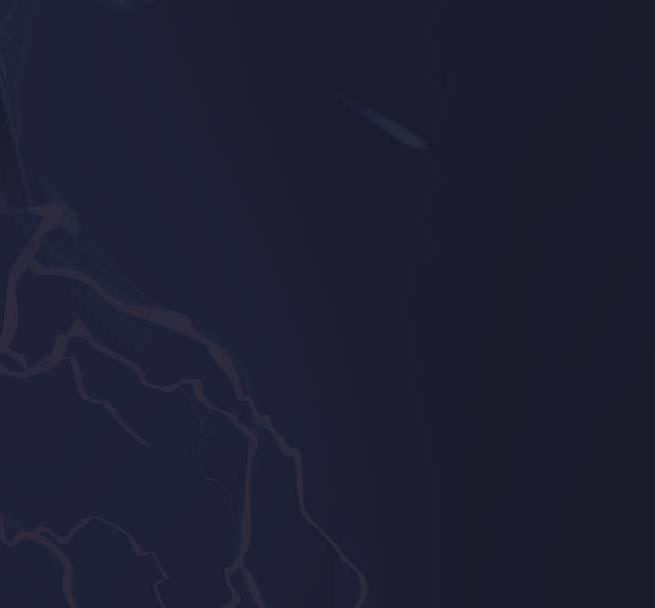
8 minute read
Preparing For The Underground Electric Revolution
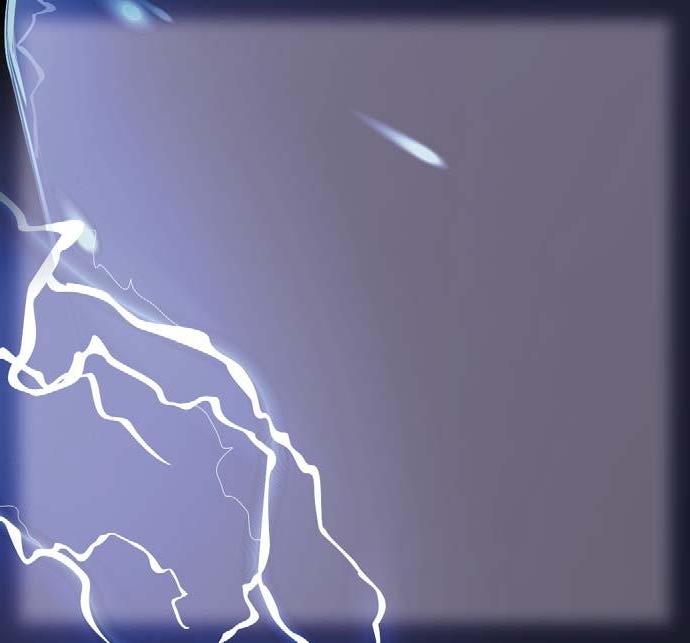
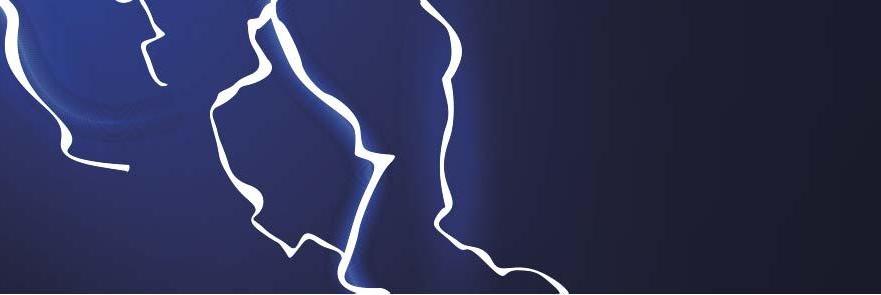
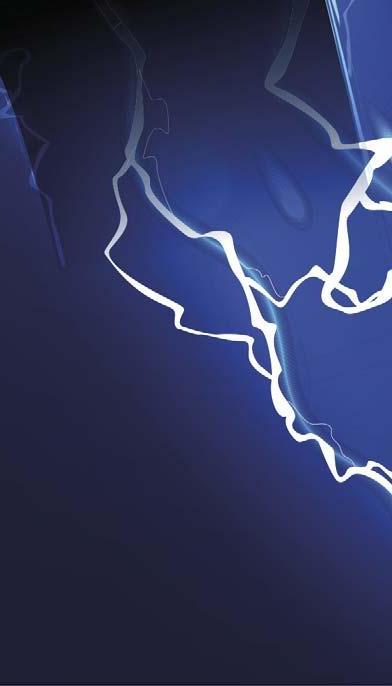
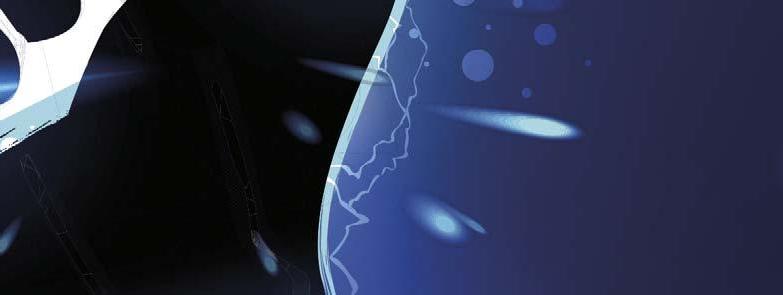

Xavier Iraçabal, Saft, France, explores the growing advantages of battery electric power for underground mining vehicles and summarises key strategic choices in their charge management.
In addition to improving workplace health and safety with their emission-free operation, battery electric vehicles (BEVs) have the potential to control costs for mining companies. In order to maximise their economic and practical benefits, owners must choose the right combination of charging approach and battery chemistry for their specific application.
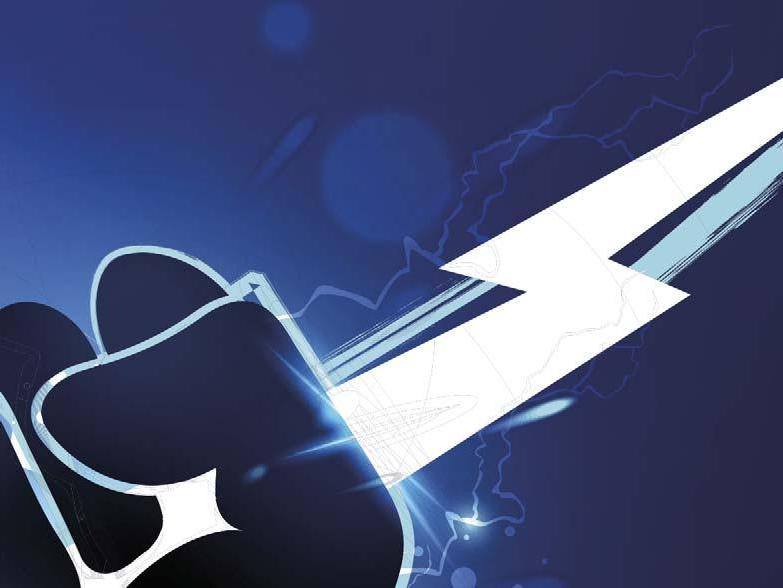
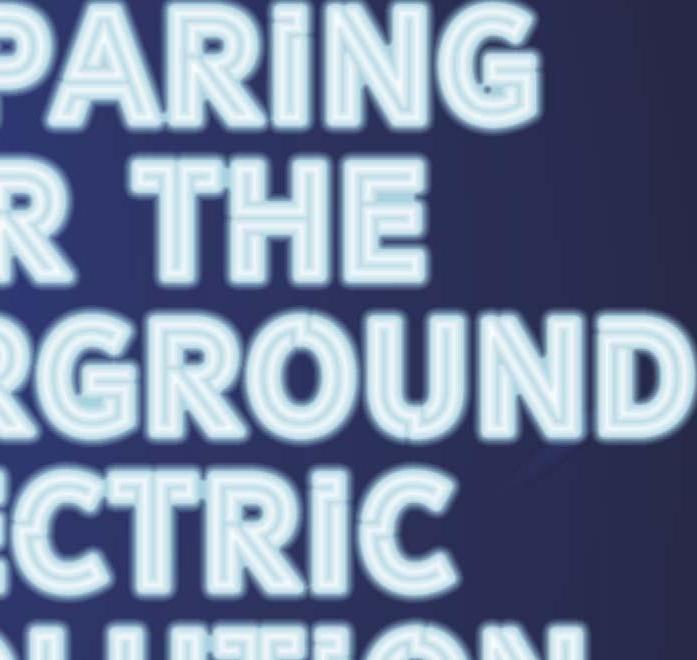





Diesel or battery?
Diesel-powered load, haul, and dump (LHD) machines – and other underground vehicles used for the transport of people, equipment, and materials – emit noxious gases and harmful particulate pollution. They also generate extra heat. The cost of ventilation and cooling to deal with these problems increases almost exponentially as mines become deeper.
Ventilation alone is estimated to account for approximately 40% of the energy used by a typical underground mine, and then there is the cost of installing and maintaining the required infrastructure.
BEVs, producing zero emissions and easily meeting increasingly stringent environmental regulations, are a much healthier option. As well as protecting air quality, they generate less noise, vibration and heat, creating healthier and productive working conditions.
With lower pollution levels in the mine, ventilation systems can be downsized – saving on both capital and operational expenditure. If the electricity needed for battery charging is supplied from renewable sources, such as solar and wind, the reduction in carbon dioxide and cost-saving eff ects of BEVs are even greater.
BEVs are inherently more energy eff icient than diesel vehicles, and use sophisticated electronic control systems that optimise the delivery of power and torque. In simulations, the energy cost per tonne of material handled has been shown to be three times higher for diesel than for battery electric machinery. BEVs also save considerably on maintenance costs, as they have fewer moving parts.
Continuing developments in lithium-ion (Li-ion) battery technology have extended BEV advantages over diesel machines. Ideally suited for underground mine work, Li-ion batteries can provide high levels of performance, energy density, safety, longevity and temperature tolerance (-25˚C – 55˚C).
Battery swapping or fast charging?
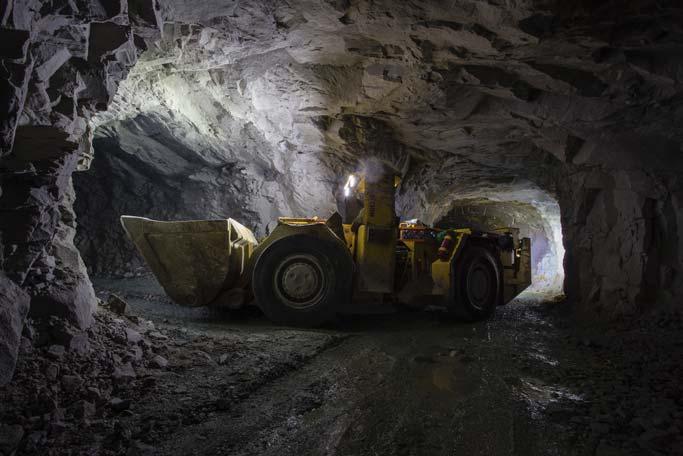
Figure 1. Battery systems need to match the typical five-year life of underground mining vehicles
An underground mining vehicle normally carries out a five-year tour of duty, aft er which it is repaired, refurbished, or scrapped. Its batteries must have the durability and robustness to perform with total reliability over that period, despite heavy use in harsh and oft en hot environments. They must also cope with extreme charge and discharge cycles, supporting 24-hour vehicle operation. The need for frequent charging of BEV batteries was once seen as a limitation to their use in underground mines, but modern Li-ion technology has overcome this. In particular, it has brought about faster and more flexible charging. Users can choose between two charging strategies: battery swapping or fast charging. Battery swapping requires two batteries per vehicle. While one is powering it, the other is being charged in the swap-and-charge station. A heavily worked battery may need charging aft er approximately four hours or more. It is then swapped for a freshly charged one. The swap typically takes approximately 15 minutes, and can be timed to coincide with a planned work break. With this approach, the battery can be charged relatively slowly, putting less pressure on the mine’s existing electrical infrastructure. However, the downside is the need for lift ing equipment, space, and labour to handle the swapping safely. The alternative is to use a fast-charging battery, which stays onboard the vehicle and is rapidly charged during shift breaks. As an example, Saft batteries can be fast-charged in approximately 15 minutes. With conveniently placed electrical points, drivers can also top up the charge level by ‘opportunity charging’ during even shorter breaks. Unlike traditional lead-acid technology, Li-ion gives flexibility for this type of partial and opportunity charging, regardless of the existing state of charge, without adversely aff ecting the battery. The specialised equipment and higher currents needed for fast charging may require investment in upgrading the mine’s electrical infrastructure. This demand increases if large numbers of vehicles are to be charged simultaneously. Both approaches have their place in the mining industry, and the best choice will depend on applications and circumstances. To give some idea of Table 2. Comparison of charging regime outcomes in real-life scenarios how their diff erences play out in real Chemistry Energy density Cycle life Calendar life Fast charge Safety life, Table 1 compares outcomes in two scenarios. Each is based on an LHD NMC/Graphite +++ ++ ++ ++ + weighing 45 t laden and 60 t fully LFP/Graphite ++ ++ ++ ++ ++ loaded, with a load capacity of 6 – 8 m3 NMC/LTO + +++ ++ +++ +++ of material.
Table 1. Comparison of charging regime outcomes in real-life scenarios
Battery swapping Fast charging (single battery) Typical LHD shift 4 – 6 hours operation (+15 minutes swap time) 2 – 3 hours operation Charging time 3 hours (battery off vehicle) 15 minutes (battery of vehicle, with ultra-fast charge) Expected calendar life 3 – 5 years 5 – 7 years Expected cycle life 2500 cycles 20 000 cycles
Charging-related downtime is lower in the case of battery swapping – at 15 minutes/6 hours of operation, as opposed to 15 minutes/3 hours. Either way, the swap or fast charge can be timed to take place when the vehicle would already have been idle anyway. More noticeably, the fast-charging scenario delivers a longer battery lifespan and cycle life.
NMC, LFP, or LTO?
Like traditional batteries, Li-ion cells store and release energy via electrochemical processes. A crucial diff erence with Li-ion is that those processes are controlled by an inbuilt electronic battery management system (BMS).
This monitors cell voltage and temperature, manages charge and discharge for optimum performance, protects the battery, extends its life, and safely shuts it down if a short circuit or thermal runaway is detected. It also monitors state of charge (SOC), indicating how long the vehicle can run before recharging, and state of health (SOH), indicating the battery’s remaining lifespan.
A wide choice of Li-ion chemistries exists. These can be used singly or blended to give the ideal combination of properties for a specific application. Key factors include: Energy density: how much energy the battery can hold in proportion to its weight or volume. Cycle life: the number of charging and recharging cycles possible within its useful life. Calendar life: the number of years it will last. Fast-charging capability. Safety.
Most commonly, the Li-ion cell’s positive electrode (cathode) will be made from lithium nickel-manganese-cobalt oxide (NMC), lithium manganese oxide (LMO), or lithium iron phosphate (LFP). The negative electrode (anode) is usually graphite or some other form of carbon.
NMC and LFP are currently the most popular choices for underground BEVs, especially with battery-swapping regimes. Both off er long runtime and can charge in less than one hour. LFP has a lower energy density, so the battery needs to be larger to achieve the same voltage and energy. However, its materials are less susceptible to price fluctuation and it requires fewer additional safeguards.
LTO batteries are a more recent development, combining an NMC cathode with an lithium titanate oxide (LTO) anode. These can be fully charged in just 15 minutes and deliver a very long cycle life – three to five times that of other Li-ion batteries – even under extreme charge and discharge cycles.
Ideal for fast-charging regimes, they also score well on safety and reduce the need for costly preventative measures. While their lower energy density means they take up more space on the vehicle, there is no need to mount them in an accessible position as they are charged on board.
Table 2 compares the three main electrochemistry choices with regards to five key factors.
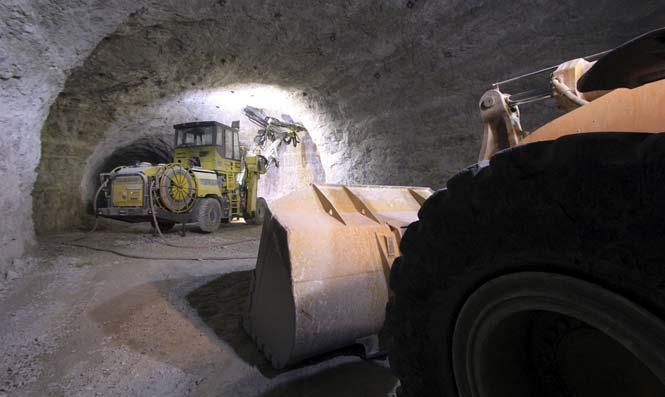
Figure 2. Choice of Li-ion technology gives OEMs flexibility to meet specific requirements for mine operators
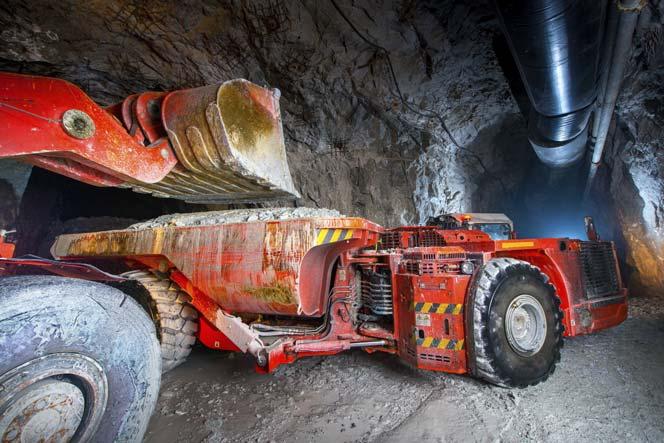
Figure 3. Today’s Li-ion technology has the right performance and reliability for underground mining.
Future fl exibility?
To meet changing needs and variation in requirements between diff erent vehicles and applications, Saft favours a modular and easily implemented approach to battery design, manufacture, and supply. Its plug-and-play systems are based on standardised 48 V building blocks, which can be readily assembled and adapted to each situation.
This echoes the strategy of vehicle manufacturers, who prefer to use a single electrical system as the framework for equipping a variety of BEVs. In doing so, they shorten the development and testing time for each model, bringing new products to market more quickly and cutting costs.
Saft ’s battery system modules off er LFP, NMC and LTO options, incorporating Li-ion cells and all the necessary monitoring functionality. Each will meet high performance needs and can be tailored for specific applications by adding extras such as heavy-duty metal enclosures and thermal management or fire suppression systems.
Conclusion
Zero-emission BEVs for underground mining vehicles are gaining in popularity, thanks largely to their health, environmental, and cost-saving benefits. High productivity can be maintained through battery swapping or fast charging, with an appropriate choice of batteries from the various Li-ion chemistries now available.
Once the mine operator has decided on its preferred mode of charging, it is up to vehicle OEMs to specify the battery to deliver the required properties and capabilities. Through extended choice, modularity and specialist advice, battery companies can provide both mine businesses and vehicle manufacturers with the flexibility they need to meet all of their needs.