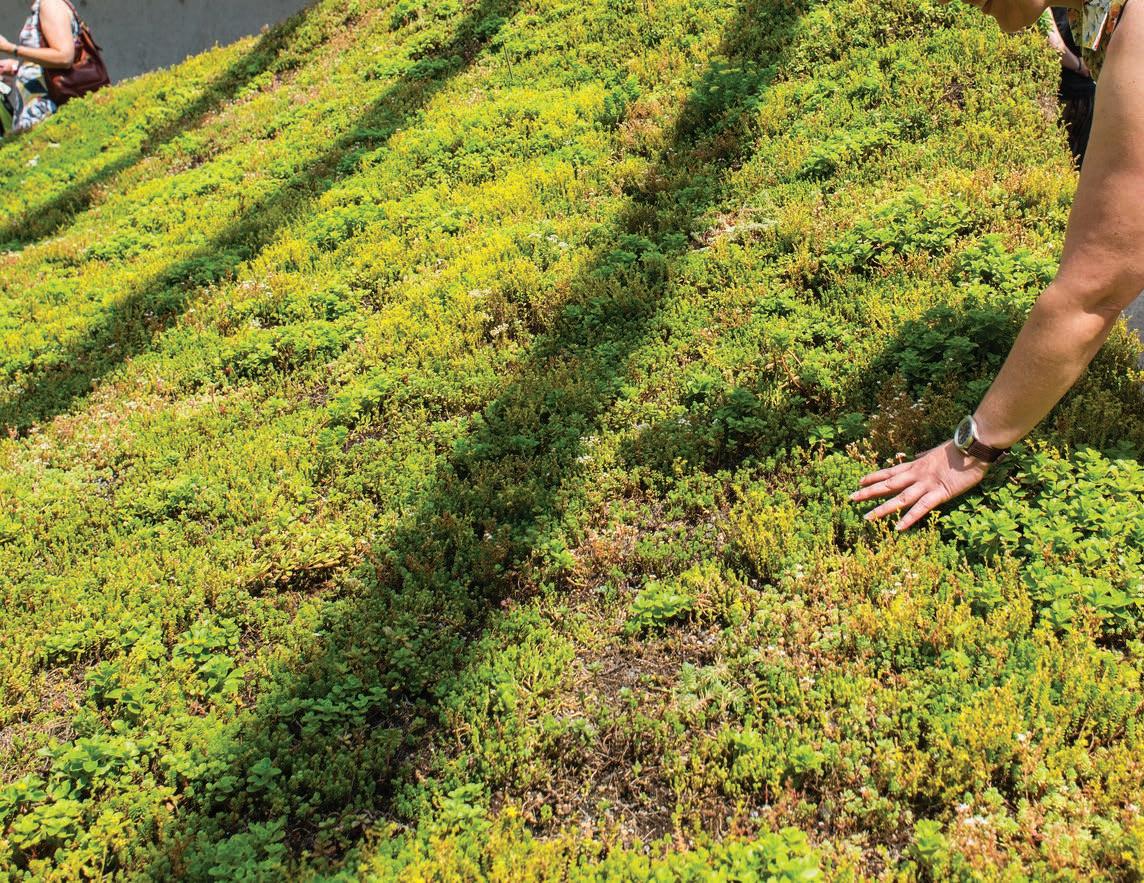
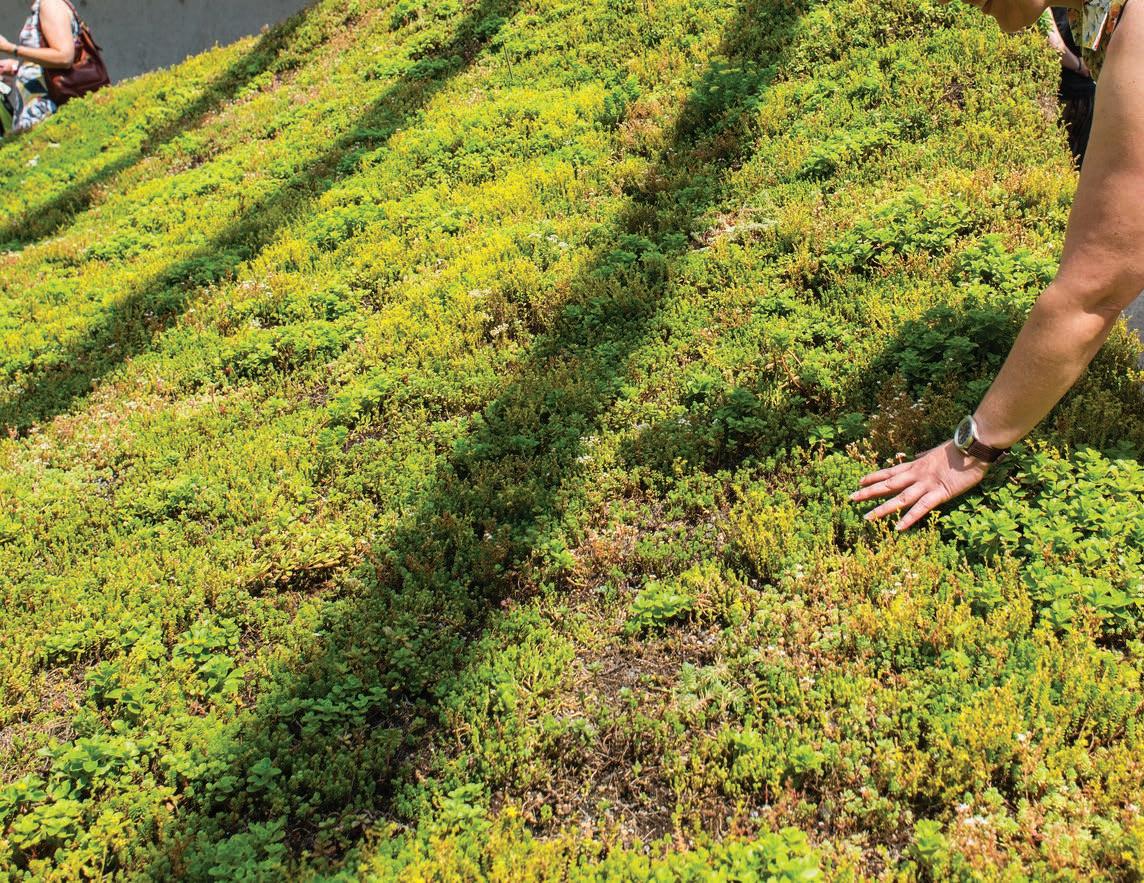
SPECIES
Sedum Sideways
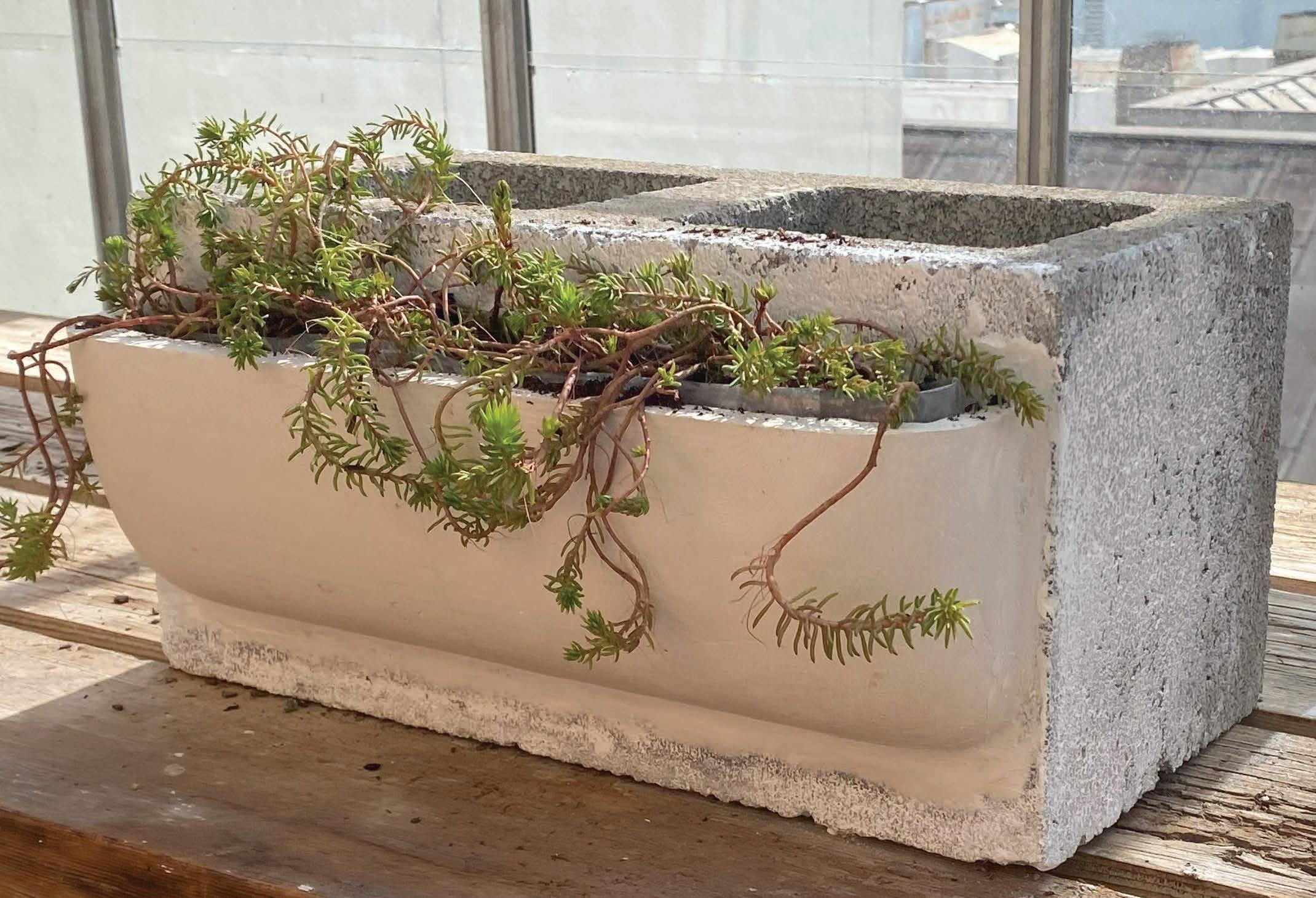
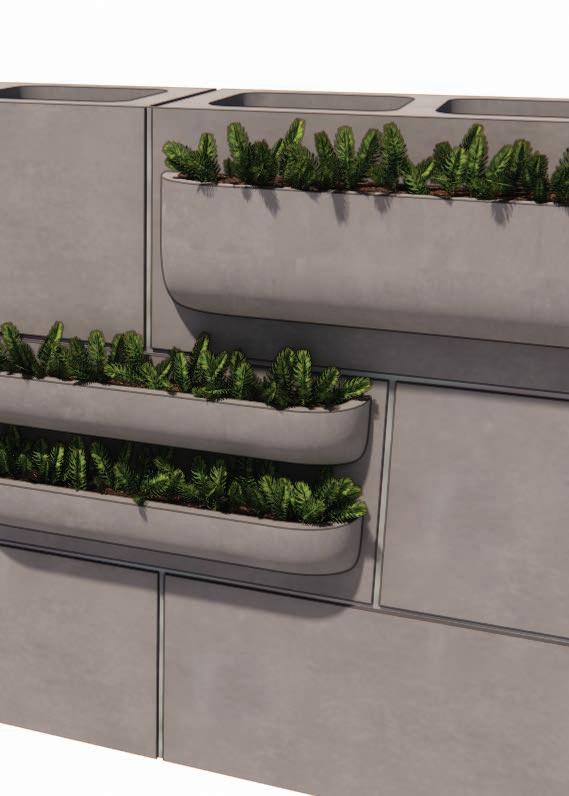
Sedum has been a favorite green roof species across the globe because of its resilient nature and its wide range of subspecies. But this species has not been implemented in a living wall, because of their weight and the low volume creeping varieties. To address these challenges, I propose a system which adapts concrete masonry units (aka. CMU or cinder blocks) by the addition of a cast concrete
planter. Concrete is porous which aids in draining soil. And angled planters would allow for soil depth without overlapping the vegetation. Before creating the final prototype, to investigate the minimum soil depth required test models will be planted with Fenugreek seeds, an alternative fast-growing species. The outcome of the soil depth testing was that the 2” control and the 4” and 3” test models were
the most successful, producing the highest number of sprouts. Therefore, the final prototype was designed and successfully fabricated with an overall depth of 4 ½” and a width of 2 ½”. This investigation could expand the use cases for Sedum, a versatile and accessible species, bringing air purifying and sound dampening benefits to the interior. The use of CMU as the base structure for this system
means it will be easily replicable and offers an opportunity for the adaptation of existing structures or for the reuse of existing materials because of the additive construction methods. Additionally, the use of 3D printed molds for casting is a more accessible alternative to the popular innovation of 3D concrete and ceramics extrusions.
ABSTRACT
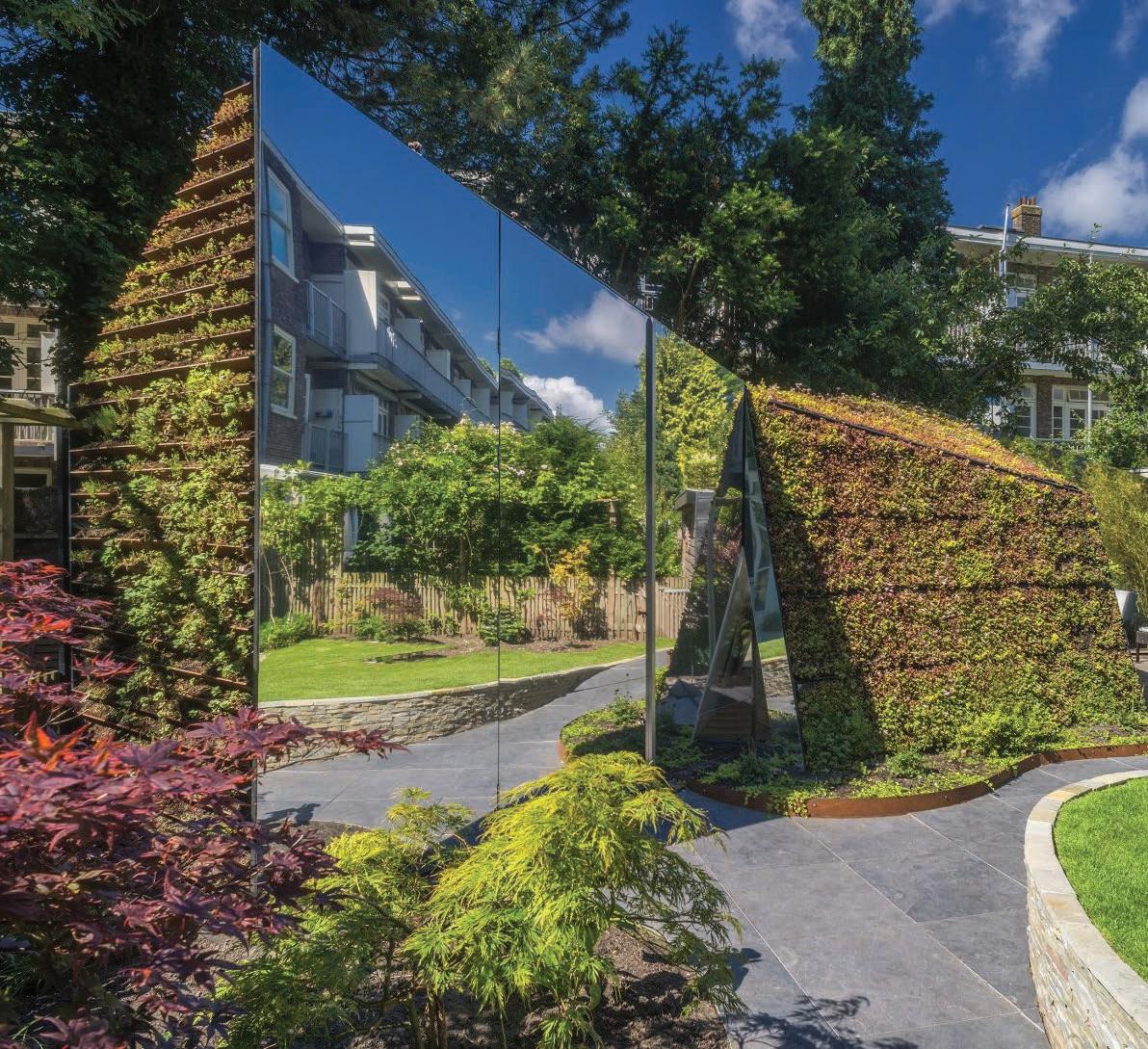
GARDEN STUDIO
The exterior features two living systems, on the moderate incline there appears to be a tray system in place and on the steeper incline the sedum is supported by ‘faceted angular surfaces.’ Tray systems are a common green roof construction type in which plastic modular trays of sedum are joined with brackets to create a uniform surface. The second support structure seems
to be constructed from thin metal formed into tiered triangular rails upon which the sedum grows in a small amount of soil. The sedum facade is intended to regulate temperature by obstructing windows from sunlight and improve air quality with a vapor permeable cellulose installation that allows air to pass through the envelope of the studio.
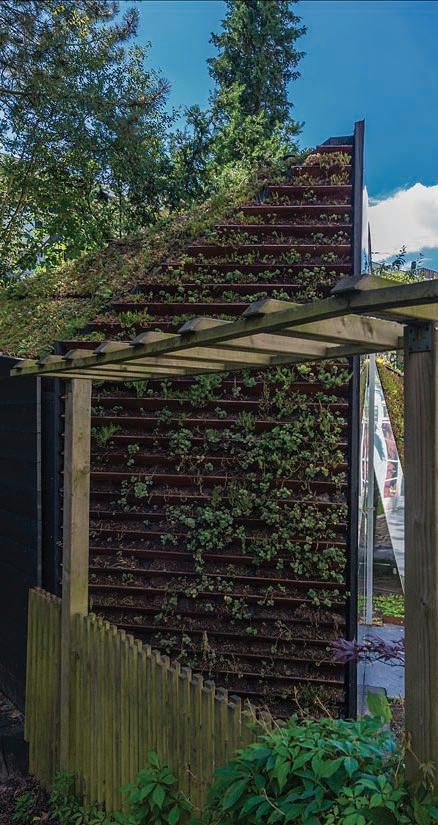
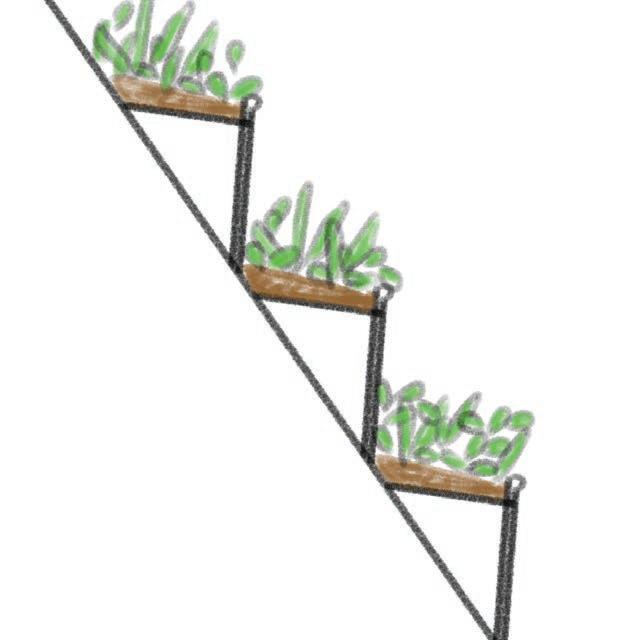
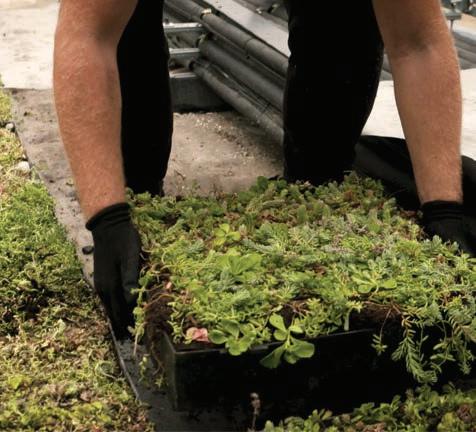
1_ Alarcón, Jonathan. “Garden Studio in Amsterdam Watergraafsmeer / CC-Studio.” ArchDaily, ArchDaily, 8 Oct. 2012, www.archdaily.com/279735/garden-studio-in-amsterdam-watergraafsmeer-cc-studio?ad_source=search&ad_medium=bookmark-open.
CC-STUDIO
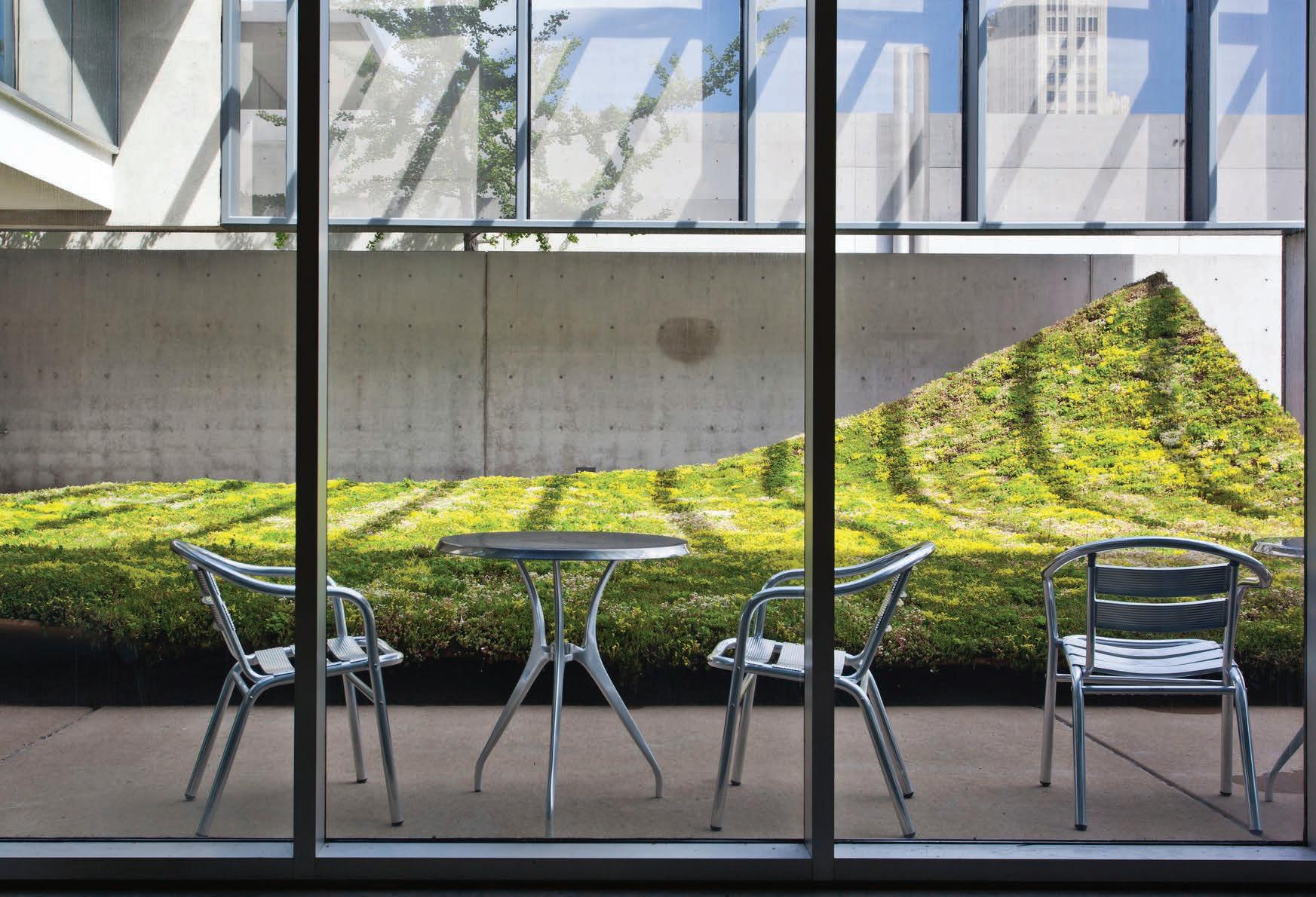
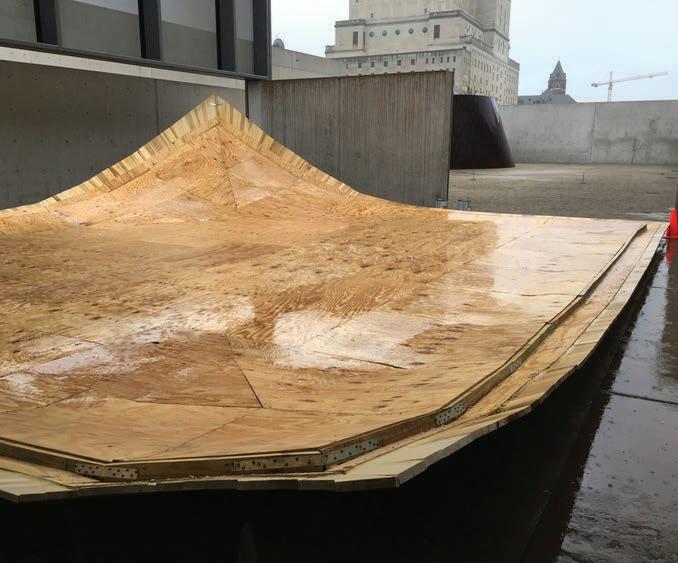
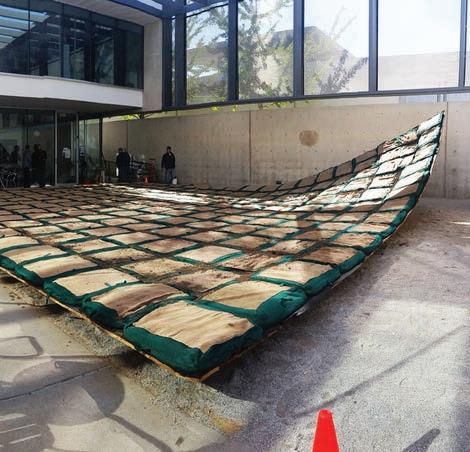
Installed in a courtyard in the Contemporary Art Museum of Saint Louis in 2015, Green Varnish is a sculptural landscape installation. Landscape design studio Nomad Studio intended this to be a conversational piece about greenwashing strategies. The green blanket is supported by a wooden frame covered in plywood and a moisture barrier. On top of the
substructure, they laid fabric bags of soil as the growth medium for the installation and finally mats of mixed sixteen varieties sedum are installed on top. It seems they have chosen a mix of creeping sedum, which have small blooms which appear during the installation. To finish the piece, they panel the outer edges of the floating corners with wood planks, adding a rustic element. This
example represents a very similar system to what is commonly used in sedum green roofs; There is virtually no lateral structure within the growth medium or vegetation.
1_ Fracalossi, Igor. “Green Varnish / Nomad Studio.” ArchDaily, ArchDaily, 1 Oct. 2015, www.archdaily.com/774340/green-varnish-nomad-studio?ad_medium=widget&ad_ name=more-from-office-article-show.
2_ “Green Varnish.” Nomad.Studio : Landscape Architecture : Design + Art, www.thenomadstudio.net/greenvarnish/. Accessed 25 Jan. 2024.
NOMAD STUDIO
GREEN VARNISH
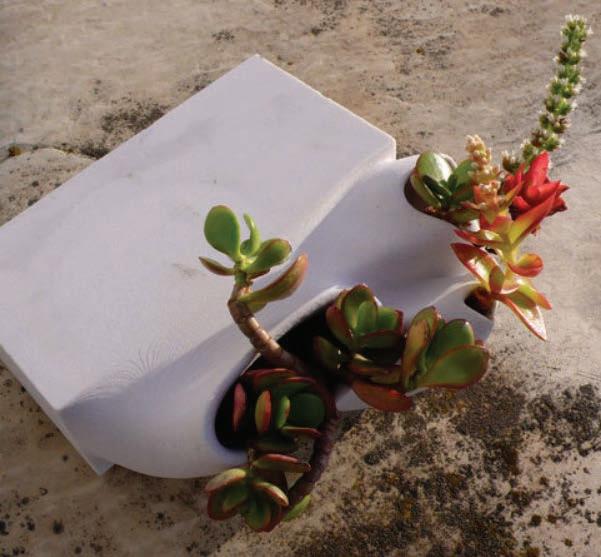
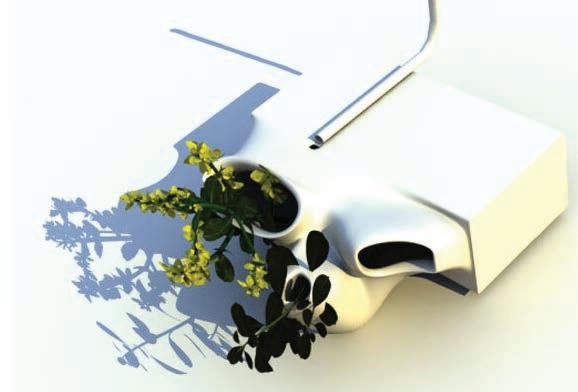
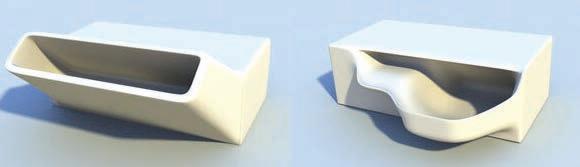
Planter bricks are innovative 3D printed ceramic and concrete bricks which can be adapted to accommodate virtually any species. Bricks are digitally modeled, and 3D printed which streamlines customizations and prototyping, cavities can vary in form, size and number. The bricks are dimensioned to match standard masonry bricks so that they can be used
in conjunction. Although, due to their size they are best suited for shallow rooted species; Sedum was an example of one of their successfully implemented species. The vegetation is watered with integrated drip irrigation system which also provides liquid nutrients; and the ceramic can be glazed for waterproofing. This system is intended as a solution to the heat
island effect, and subsequently as a sound barrier and air purification system.
1_ Rael San Fratello Architects. “Planter Bricks.” Emerging Objects, emergingobjects.com/project/planter-bricks/. Accessed 23 Jan. 2024.
2_ Rael, Ronald, et al. “Emerging Objects.” RAEL SAN FRATELLO, 2009, www.rael-sanfratello. com/made/digital-cement.
EMERGING OBJECTS
PLANTER BRICKS
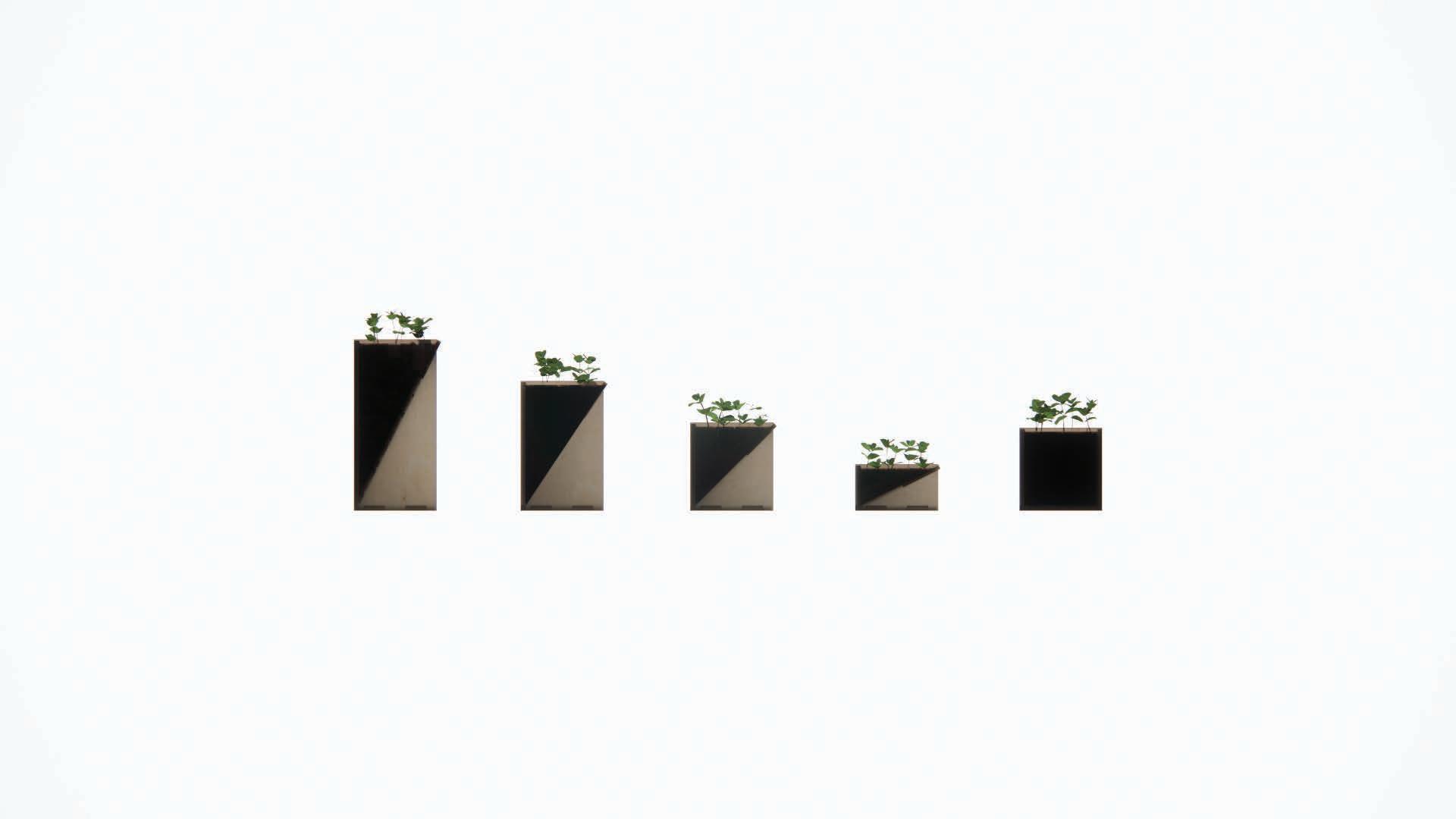
The first phase of model testing is dedicated to the investigation of the minimum soil depth necessary for sedum to grow. This will be tested by creating custom pots of different depths in which Fenugreek seeds will be planted and their growth will be recorded and analyzed. Fenugreek seeds will act as a fastgrowing alternative for sedum, with shallow, fibrous roots and
requiring well drained soil. This final prototype’s form is mainly inspired by the angular support structure used for the Garden Studio. The 3D printed mold for casting is an attempt at an alternative to the innovative 3D printing of ceramics used in the construction of the Planter Bricks. Lastly, the use of concrete masonry units as the prototype’s structure is a feature
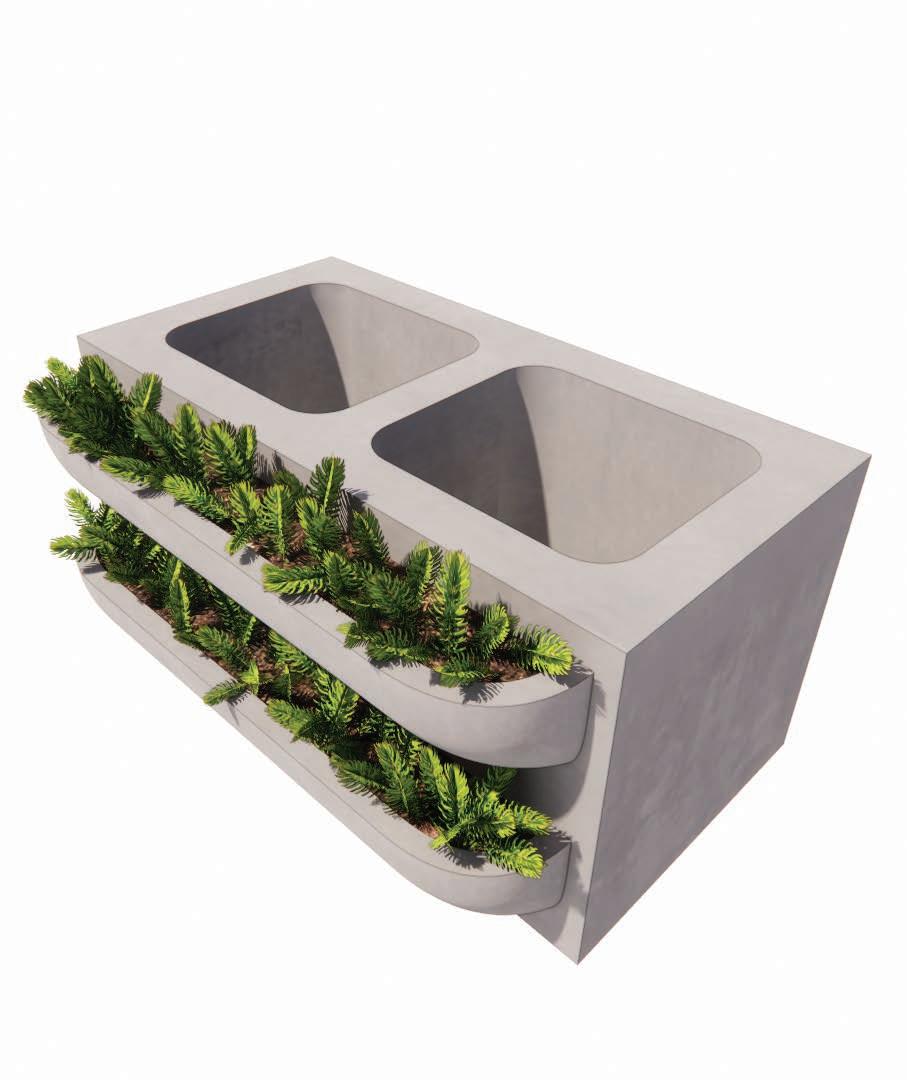
to expand the applications of this prototype, as the cast planters could be added to existing walls or could utilize recycled units to construct a new wall.
SOIL DEPTH TEST MODELS
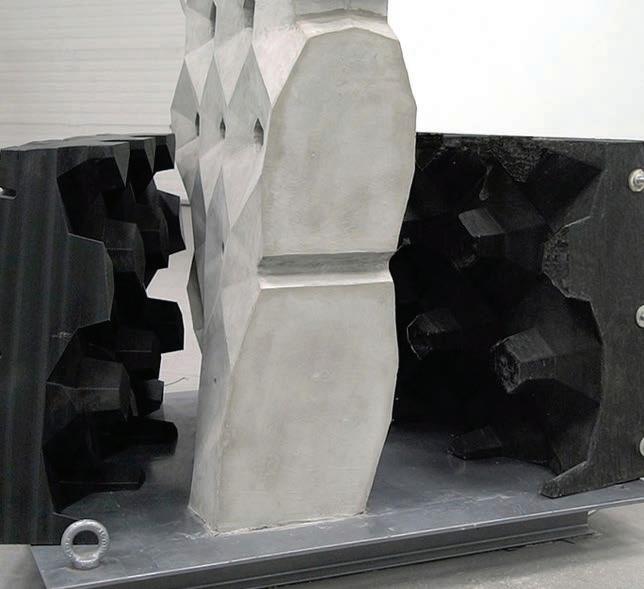
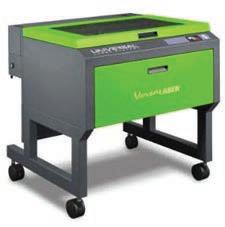
Test models will be laser cut out of balsa wood, for accurate dimensions and efficiency. Once assembled they will be planted with Fenugreek seeds and monitored for 2 weeks. Although my concept would feature a concrete planter, this will not be possible for my prototype which will be constructed using plaster. Additionally, the final prototype will not feature a drip
irrigation system. The assembly of the final prototype will start with the creation of 3D models of the mold for the final plaster prototype, which will be 3D printed. Once the mold is finished and assembled it will be cast in plaster to produce the planter, which will be attached to the concrete masonry unit using plaster paste. Finally, the sedum can be planted once the prototype is fully dry.
1_ Fabrication, Further, and Instructables. “Create Concrete Products with 3D Printed Molds.” Instructables, Instructables, 25 Sept. 2018, www.instructables.com/Create-ConcreteProducts-With-3D-Printed-Molds/.
2_ Bagchi, Anirban. “Immensa and CCC’s Make Breakthrough for Concrete Formwork Using Large Format 3D Printing.” Middle East Construction News, 5 Aug. 2018, meconstructionnews.com/30748/immensa-and-cccsmake-breakthrough-for-concrete-formworkusing-large-format-3d-printing.
FABRICATION PROCESS
METHODOLOGY
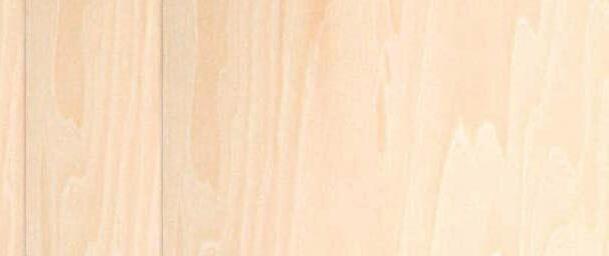
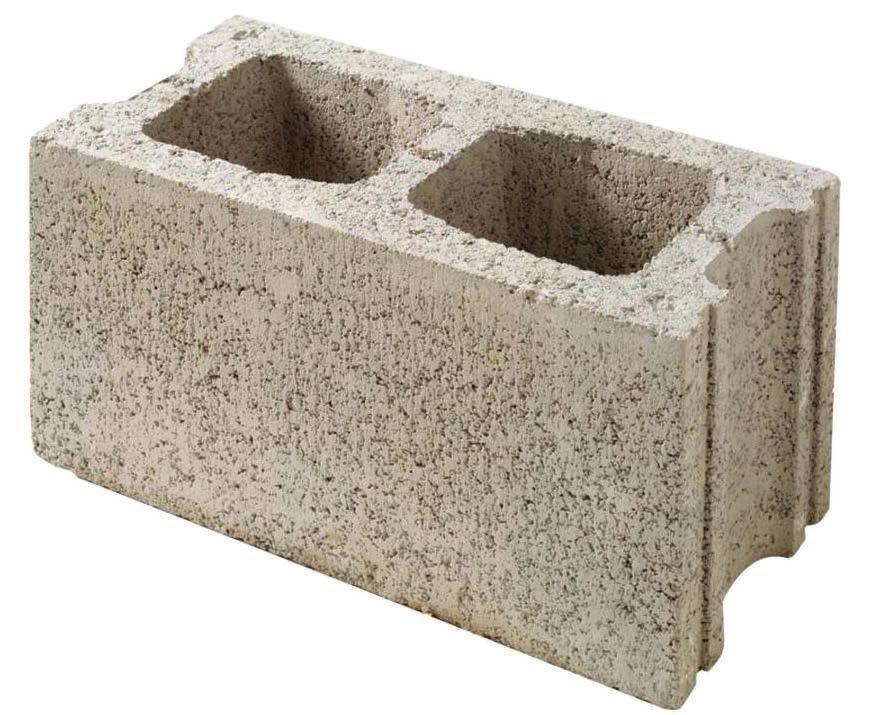
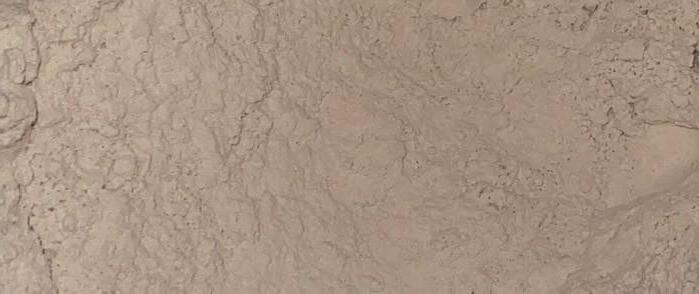
MATERIALS
METHODOLOGY
Additional materials required for the casting process include water, Vaseline, rubber bands, plastic cups, stirring stick, sandpaper (50 and 120 grit), superglue, plastic tray, plastic bags, and tape.
BALSA PLYWOOD SHEETS
TEST MODELS
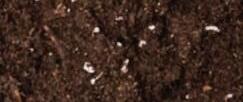
CONCRETE MASONRY UNIT
PROTOTYPE
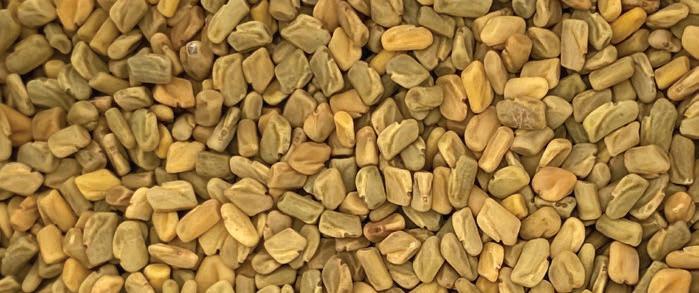
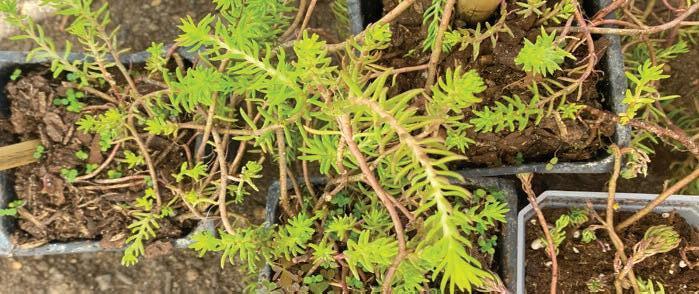
PLASTER
PROTOTYPE
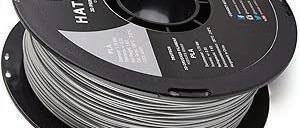
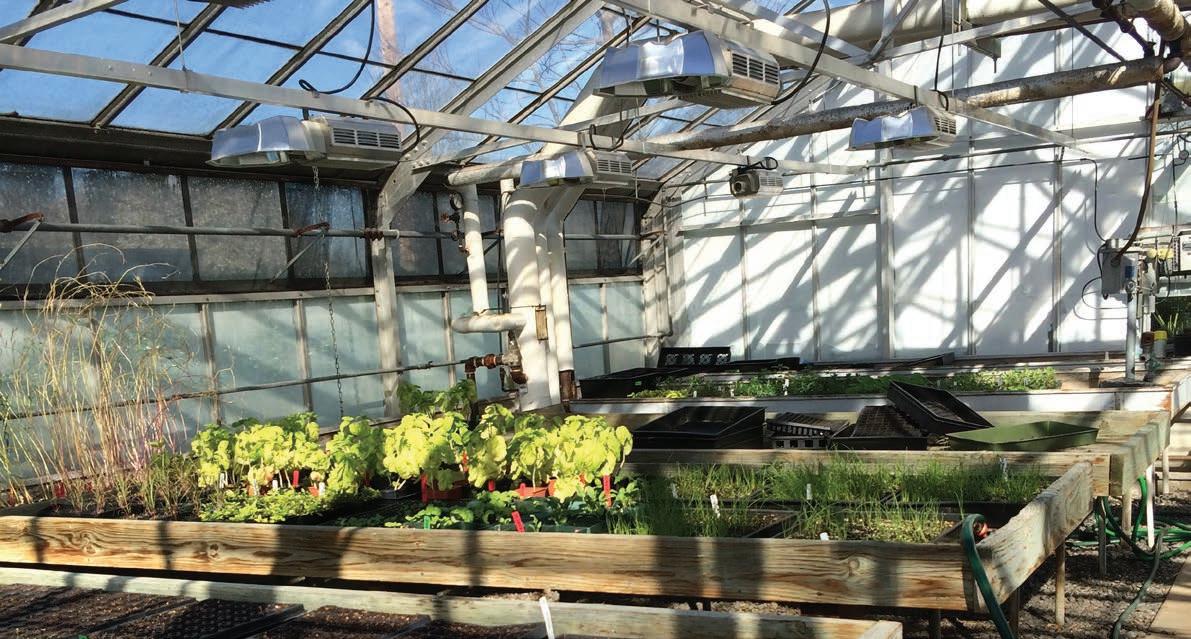
WELL-DRAINING
SOIL
TEST MODELS AND PROTOTYPE
FENUGREEK SEEDS
TEST MODELS
SEDUM PLANTS
PROTOTYPE
3D PRINTING FILAMENT
PROTOTYPE
GREENHOUSE
GROWTH FACTORS SUCH AS SUNLIGHT LEVELS AND WATERING WILL BE MONITORED AND RECORDED
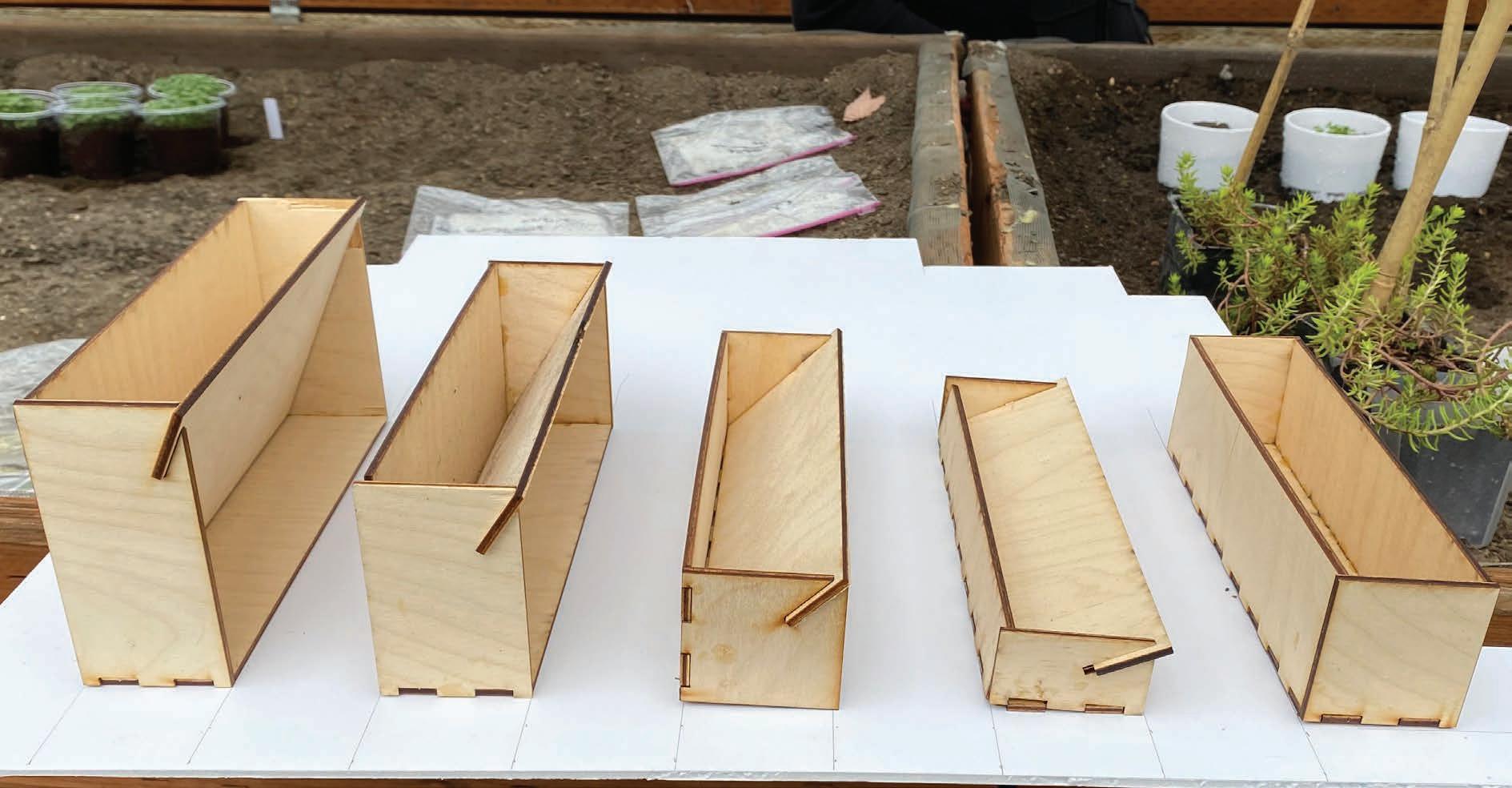
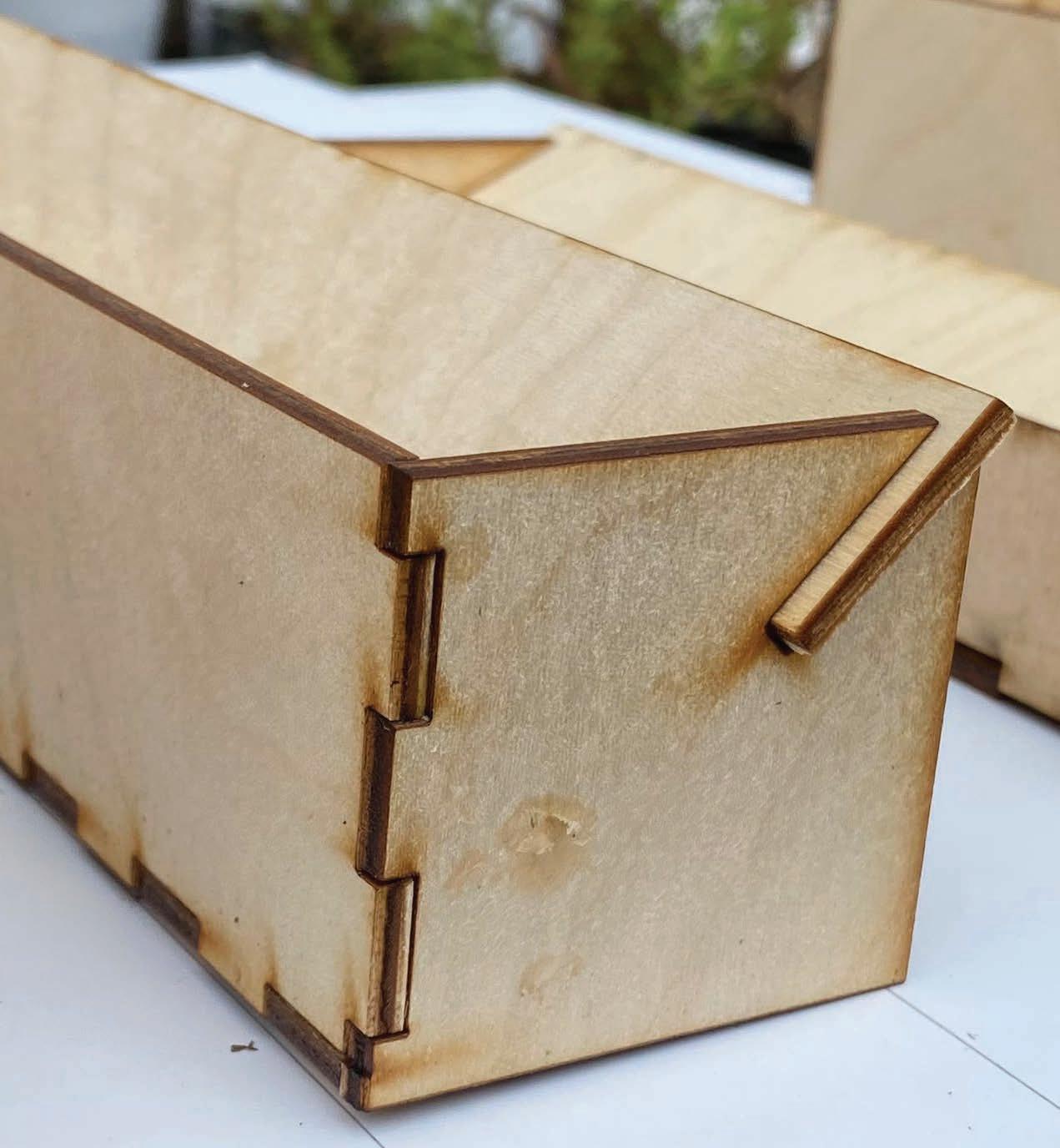
TEST MODELS
TEST MODELS
PARTS AND ASSEMBLY
Test models will be designed with CAD programs. The test models will be laser cut from balsa wood. They will vary in depth from 1”-4”. With one non-angled control model with a depth of 2”. They will be planted with soil and seeds and observed.
LASER CUTTING TEMPLATES
PROGRESS
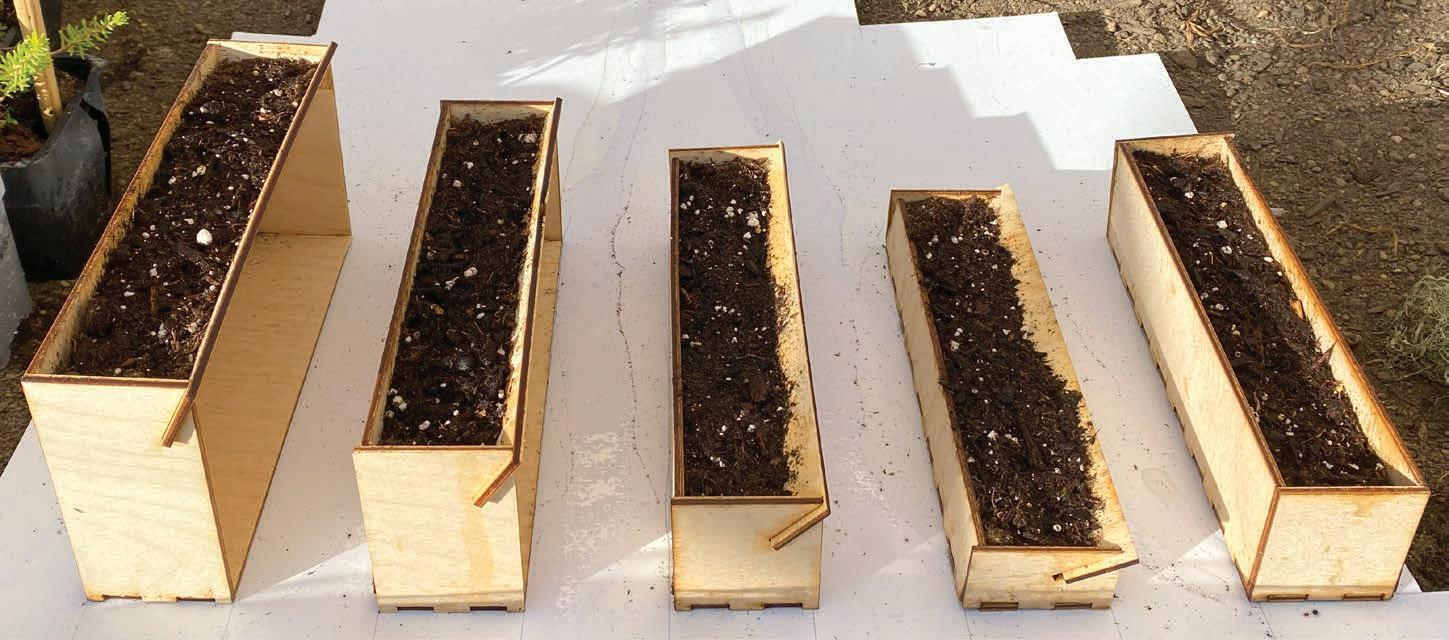
DAY 3 - 2/23
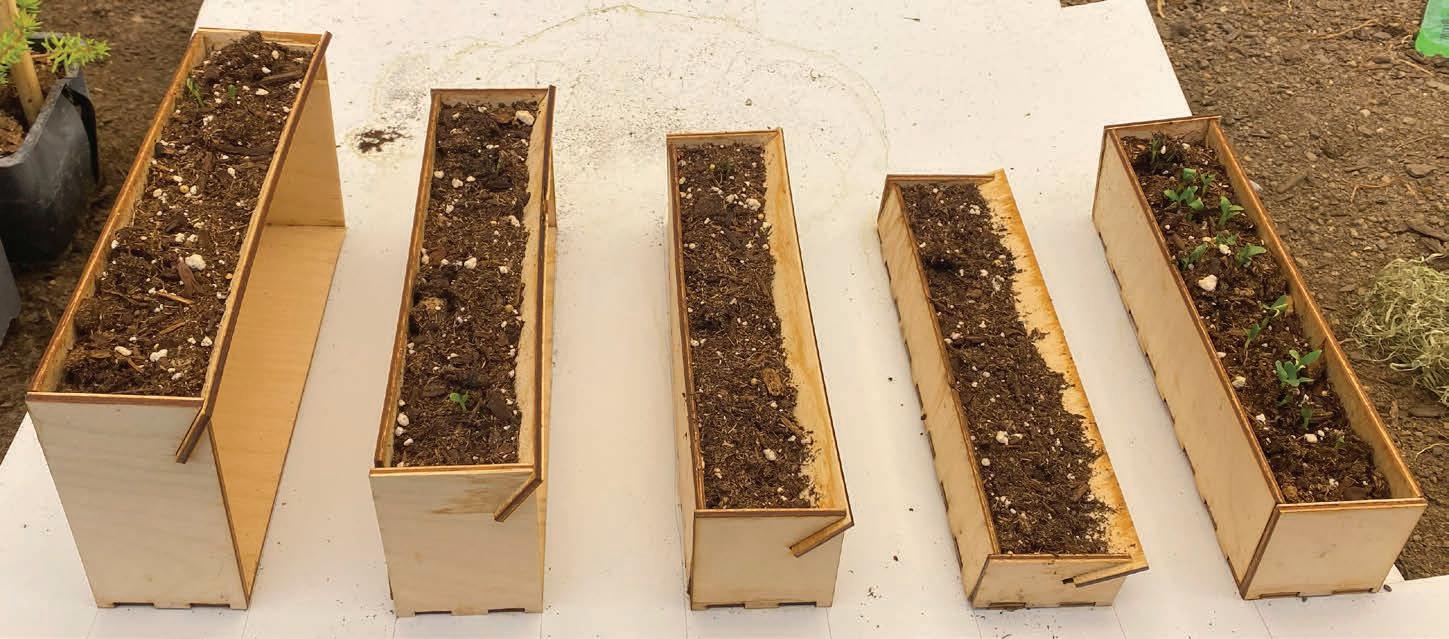
DAY 8 - 2/28
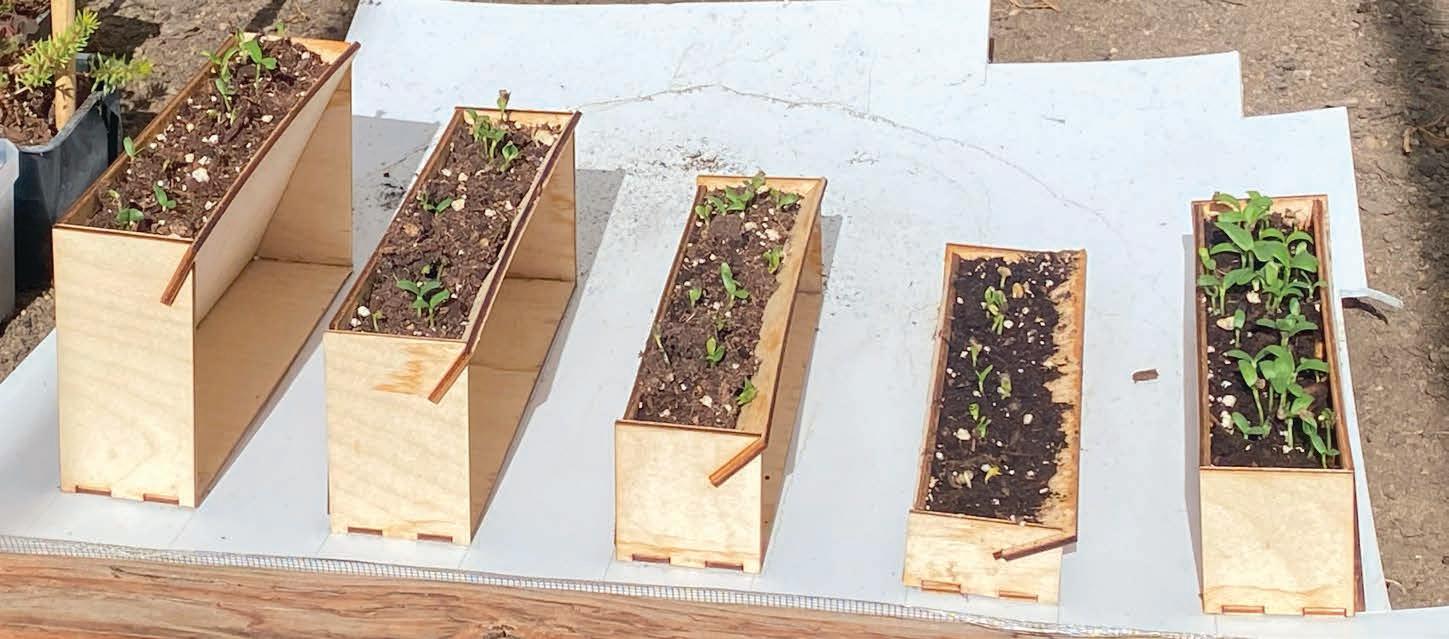
DAY 10 - 3/1 TEST MODEL
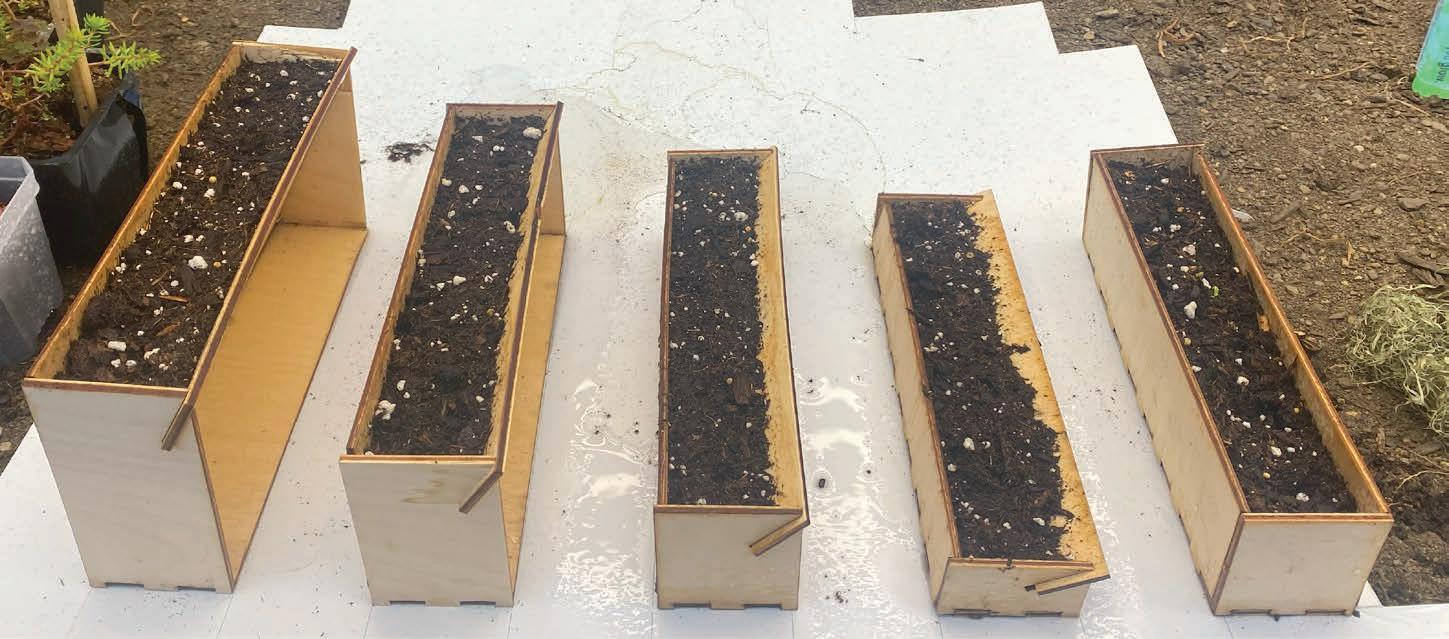
DAY 5 - 2/25
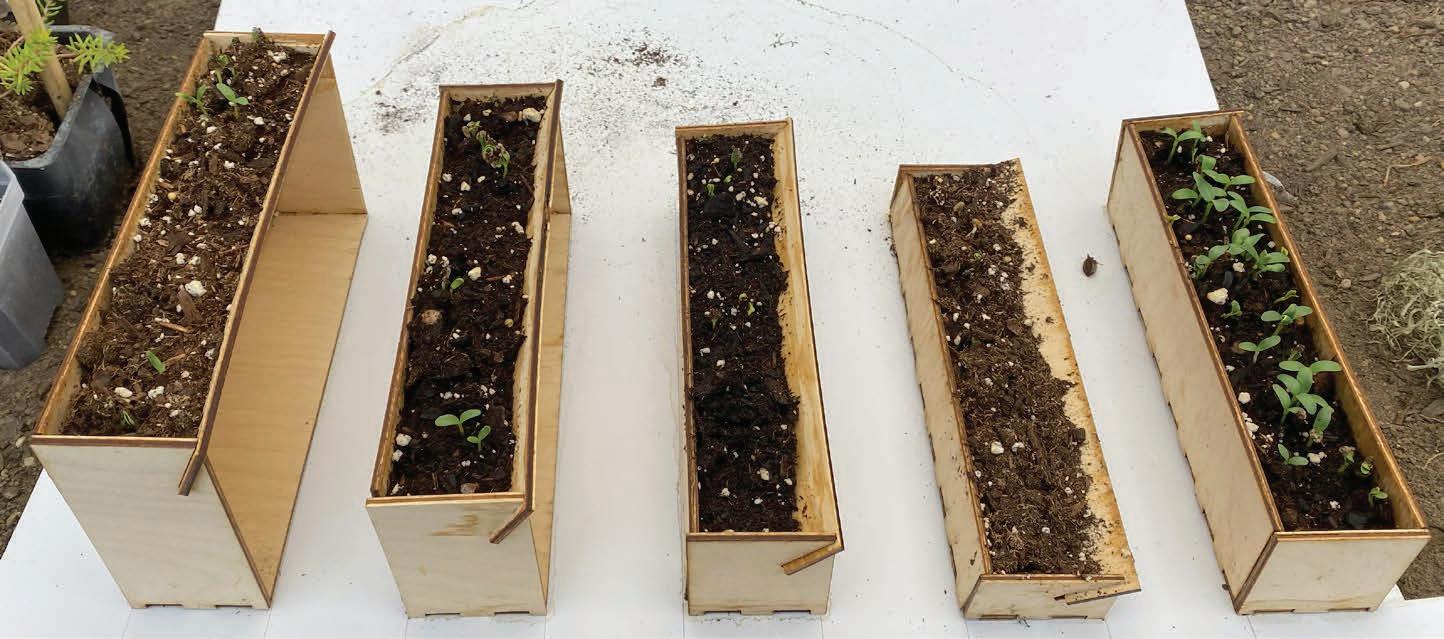
DAY 9 - 2/29
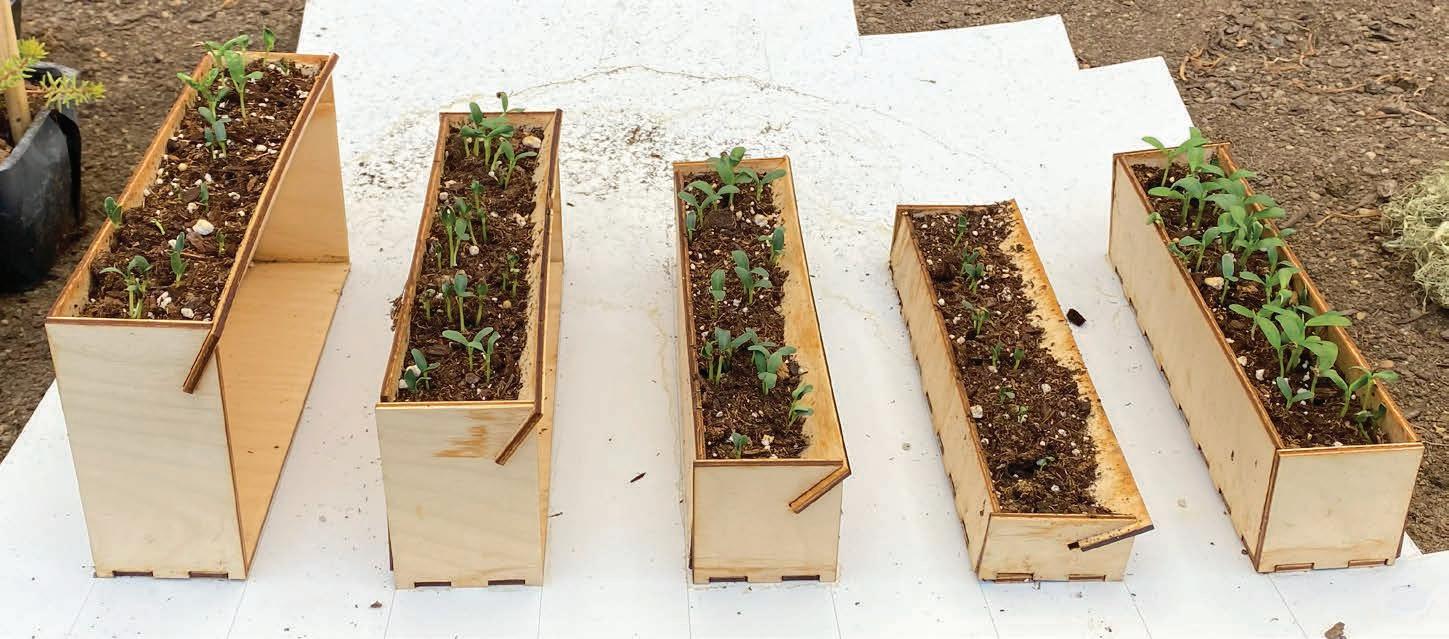
DAY 13 - 3/4
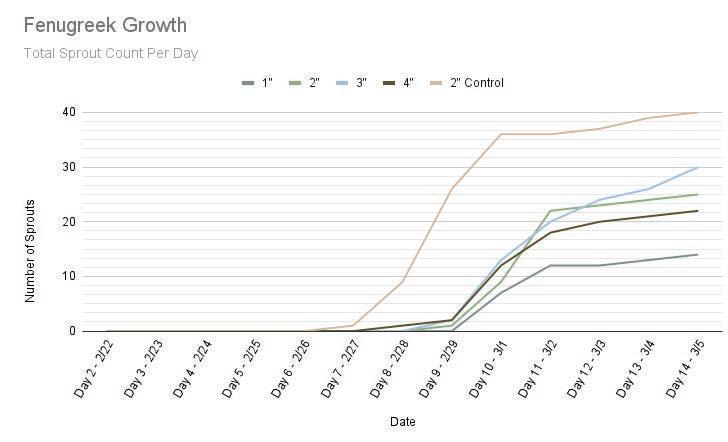
TEST RESULTS
DESIGN DEVELOPMENT
As illustrated by the graph above, the 2” control test model had the earliest sprout on day 6 and the greatest number of sprouts over the test period, with 41 sprouts on day 14. The 2” control test model’s Fenugreek sprouts matured enough to start developing a second set of leaves, a point which none of the other tests reached during the test period. Although delayed, there
was also success in germinating Fenugreek seeds in the lesser soil depths, producing their first sprouts on day 8. Overall, the test models with greater soil depth and volume, the 2” control and 3” and 4”, produced a greater number of sprouts. I predict these results are due to the volume of the soil holding moisture between watering, the test models with greater volumes of soil
were more successful at producing sprouts because of the greater amount of water available to seeds and sprouts.
DESIGN ADJUSTMENTS
ELEVATION (NTS)
FINAL PROTOTYPE
DESIGN DEVELOPMENT
The initial prototype has been developed into a final prototype design for fabrication. The success of both the 2” control test model and the 4” test model inform the dimensions of the final prototype; With an overall depth of 4 ½” and a width of 2 ½”.
1_ Diagram, workflow process
2_ Photography, physical model
3_ Mosaic, material properties
4_ Photography sequence
5_ Masterplan strategies
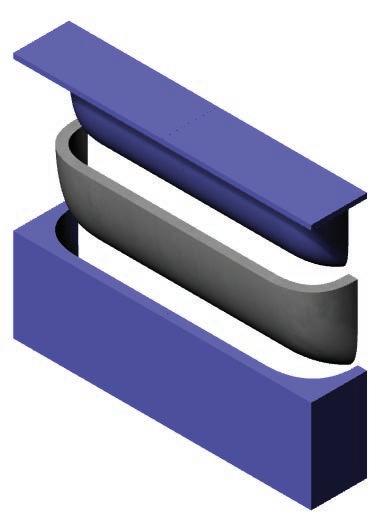
PARTS AND ASSEMBLY
The 3D printed mold consists of two sides which will each be constructed by two parts, since the overall dimension of the mold is more the double the size of the print bed of the Replicator +. Once printed the molds will be sanded to remove any imperfections and the halves will be attached with superglue.
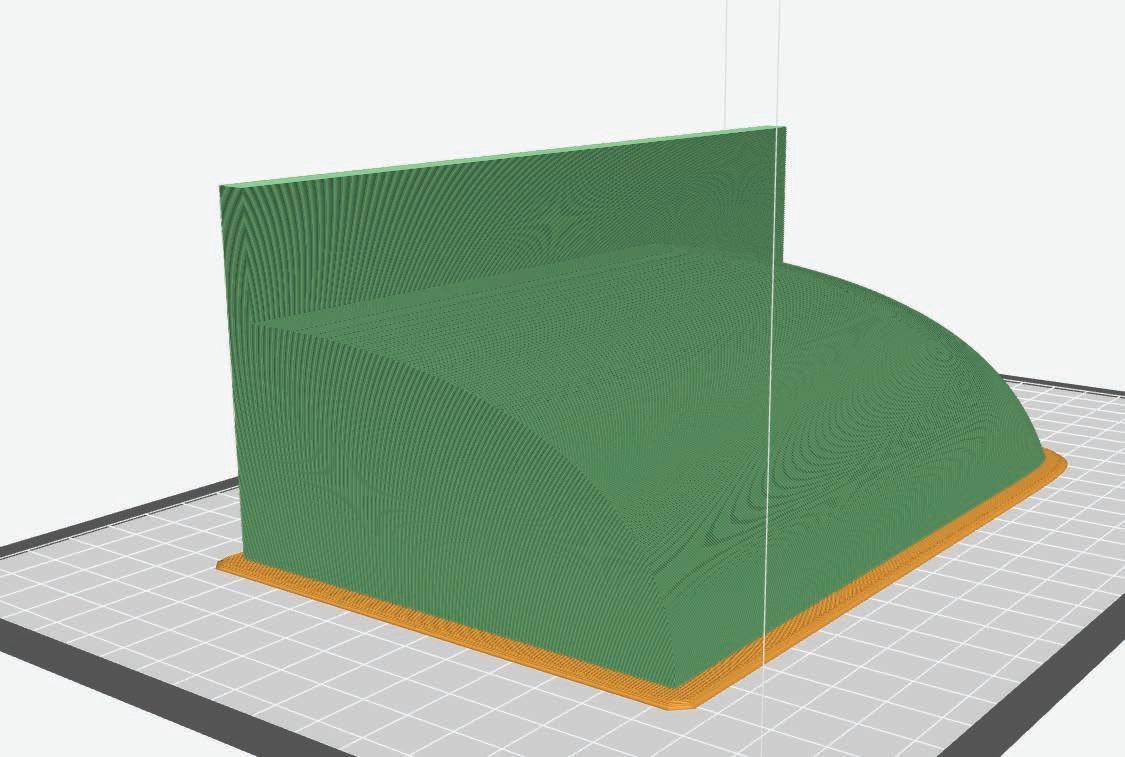
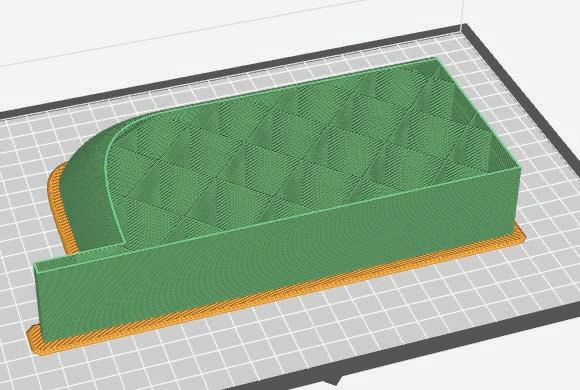
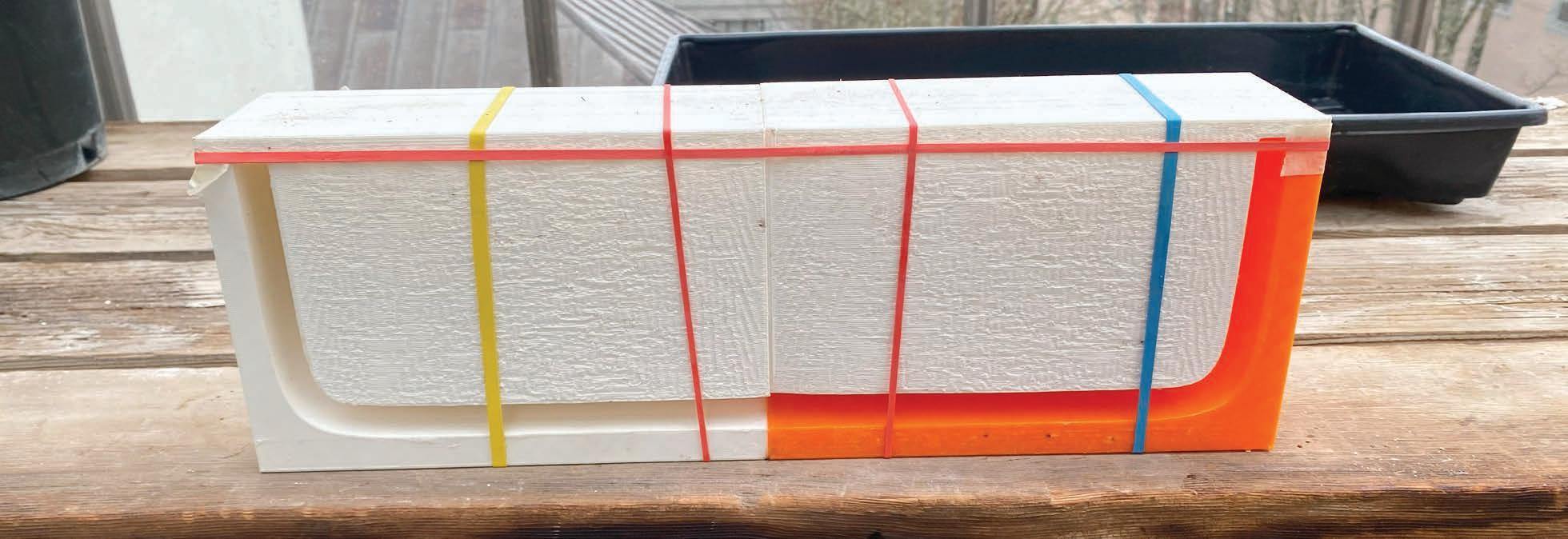
1_ 3D Concept Imagery
2_ MakerBot 3D Print Preview
3_ MakerBot 3D Print Fill Preview
4_ Final Assembled Mold
FINAL PROTOTYPE
PARTS AND ASSEMBLY
Once the mold is finished, it will be lubricated using a layer of Vaseline and then assembled and held in place using rubber bands, and taped around the seam where the molds meet to reduce the chance of leakage. After the mold has been assembled, mixed plaster can be poured into the mold until it is full to the edge, gently tapping the mold to ensure it fills the mold entirely. After
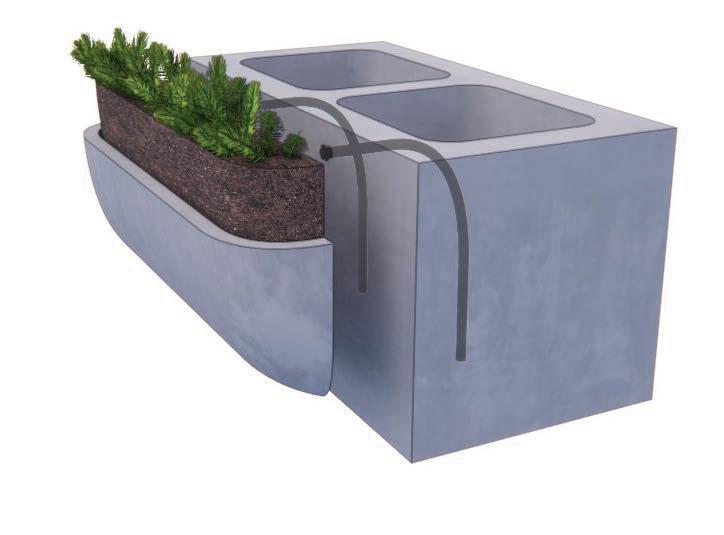
the excess plaster has been cleaned off the mold and the plaster has fully set, the piece can be removed from the mold. Finally, the planter is adhered to the concrete masonry unit (CMU) using a thicker mix of plaster paste. Once the prototype is fully dry the sedum can be planted, with a plastic liner to protect the plaster from the mositure of the soil.
3_
4_
1_ Sedum Angelica
2_ Well Draining Soil Mix
Casted Concrete
Drip Irrigation
5_ Concrete Masonry Unit
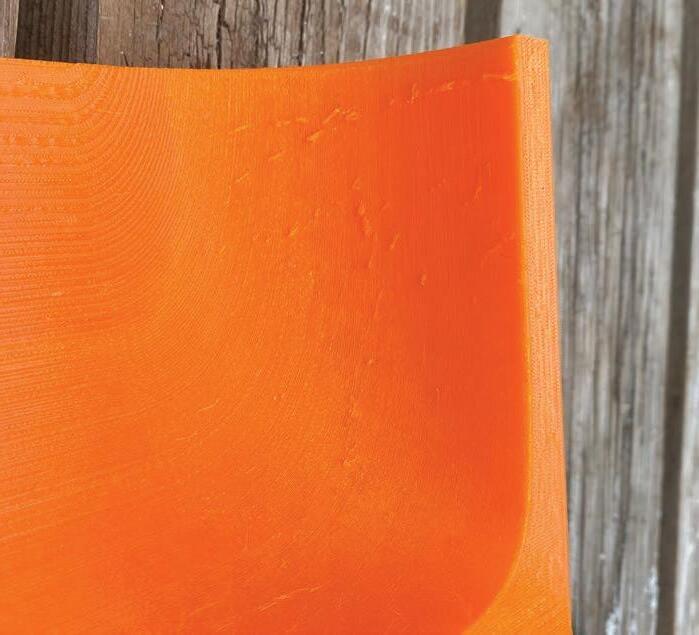
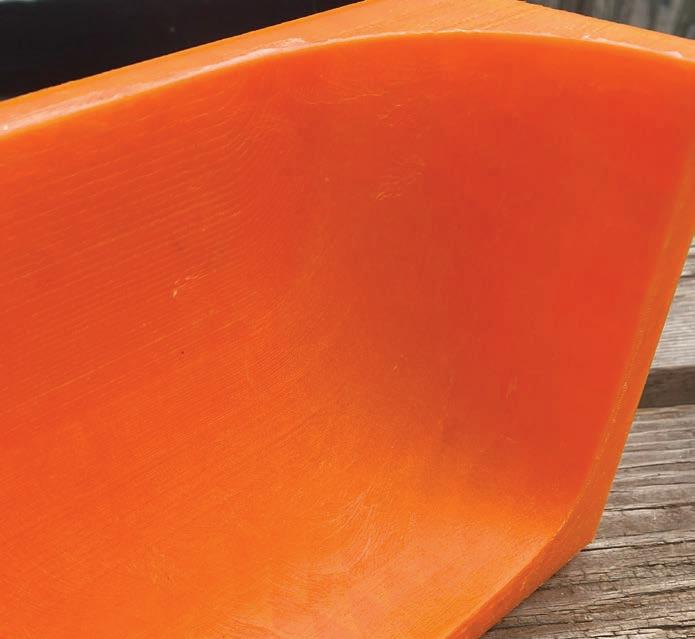
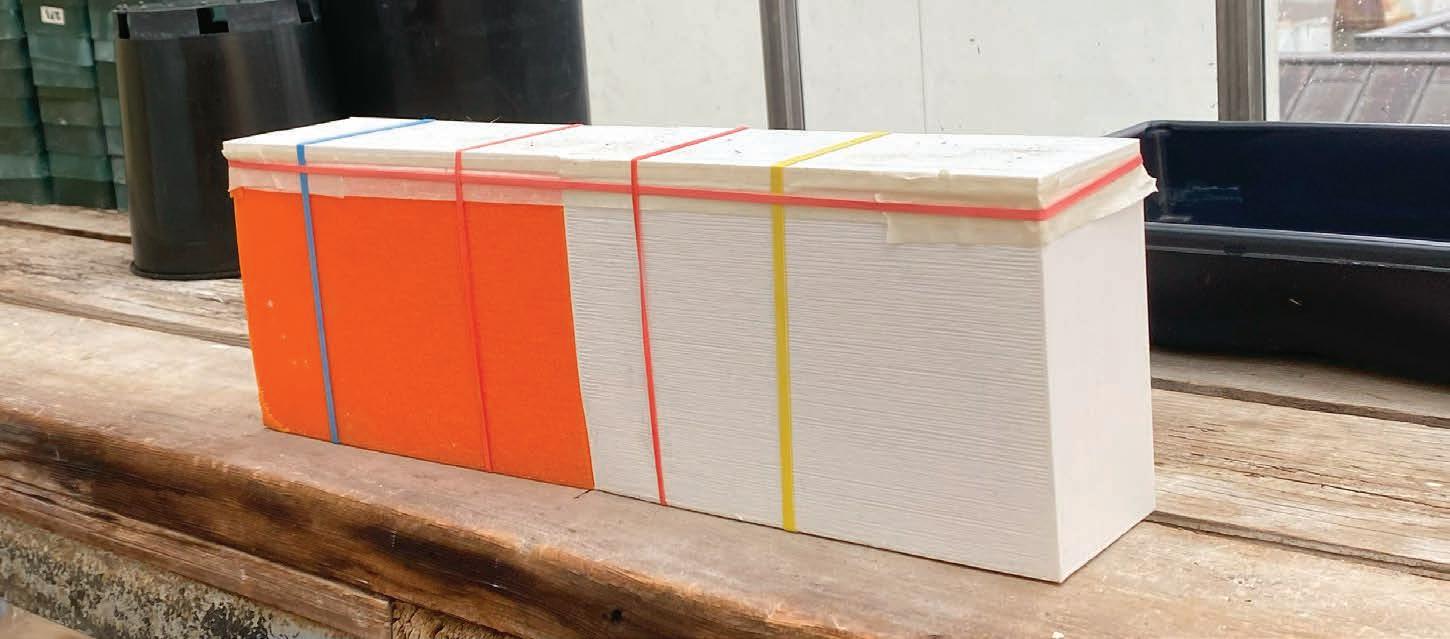
ASSEMBLE MOLD AND SECURE WITH RUBBER BANDS
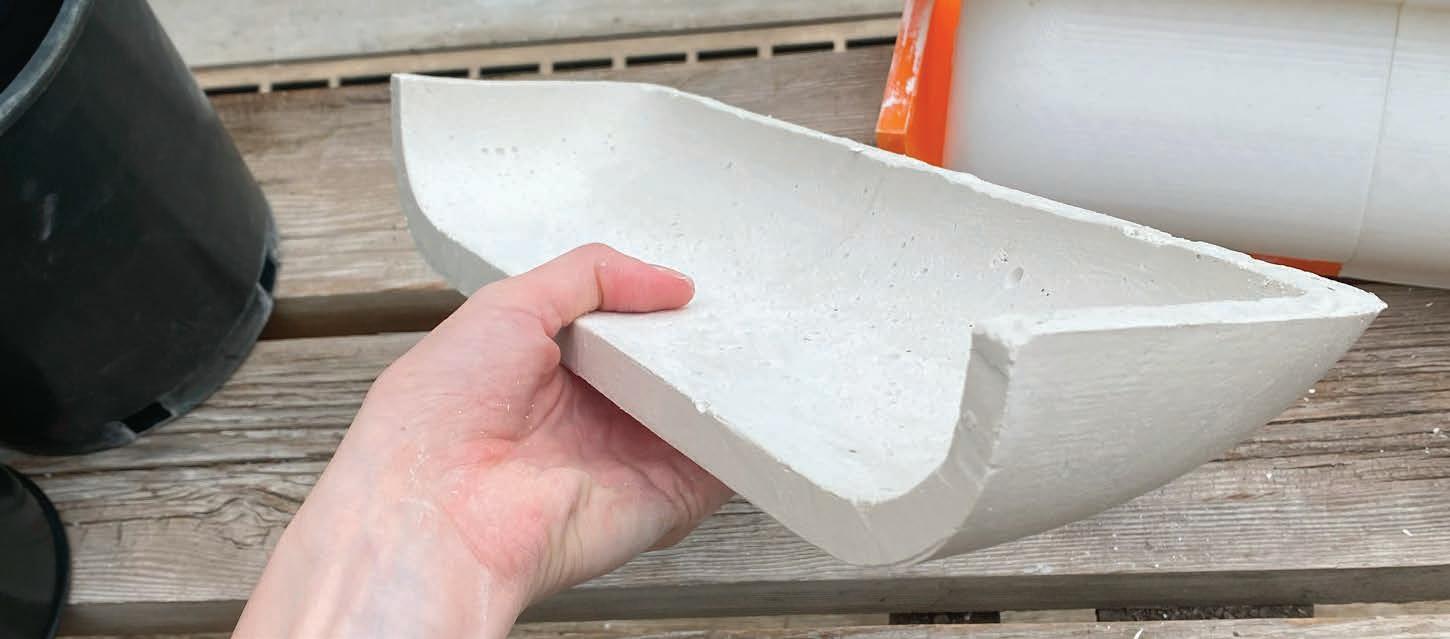
REMOVE FROM MOLD
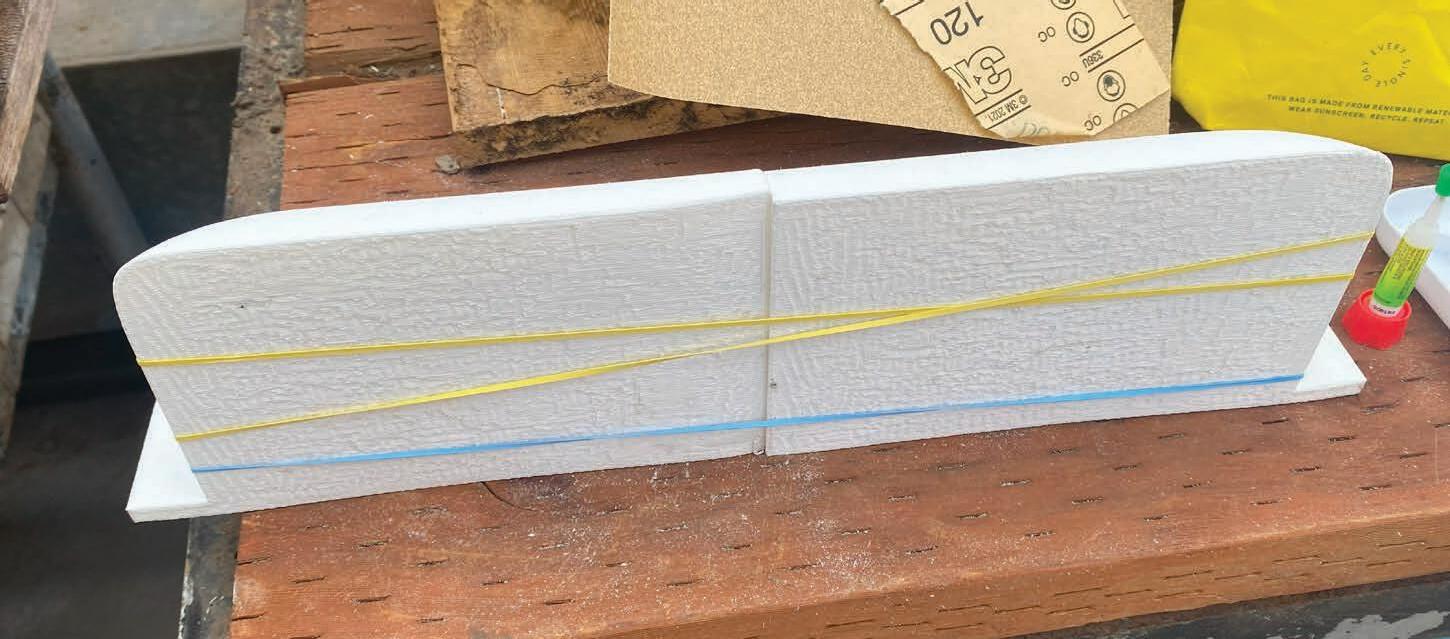
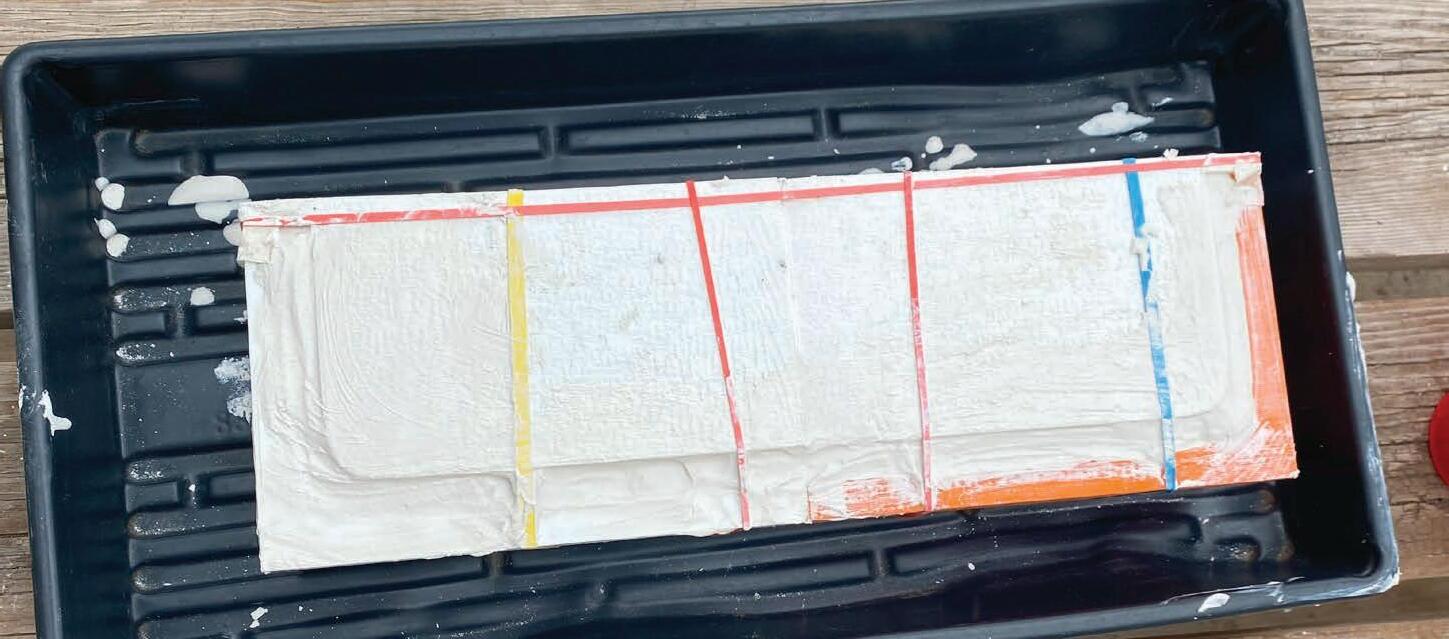

GLUE HALVES TOGETHER
SAND MOLDS - BEFORE
POUR PLASTER INTO MOLD ATTACH
SAND MOLDS - AFTER
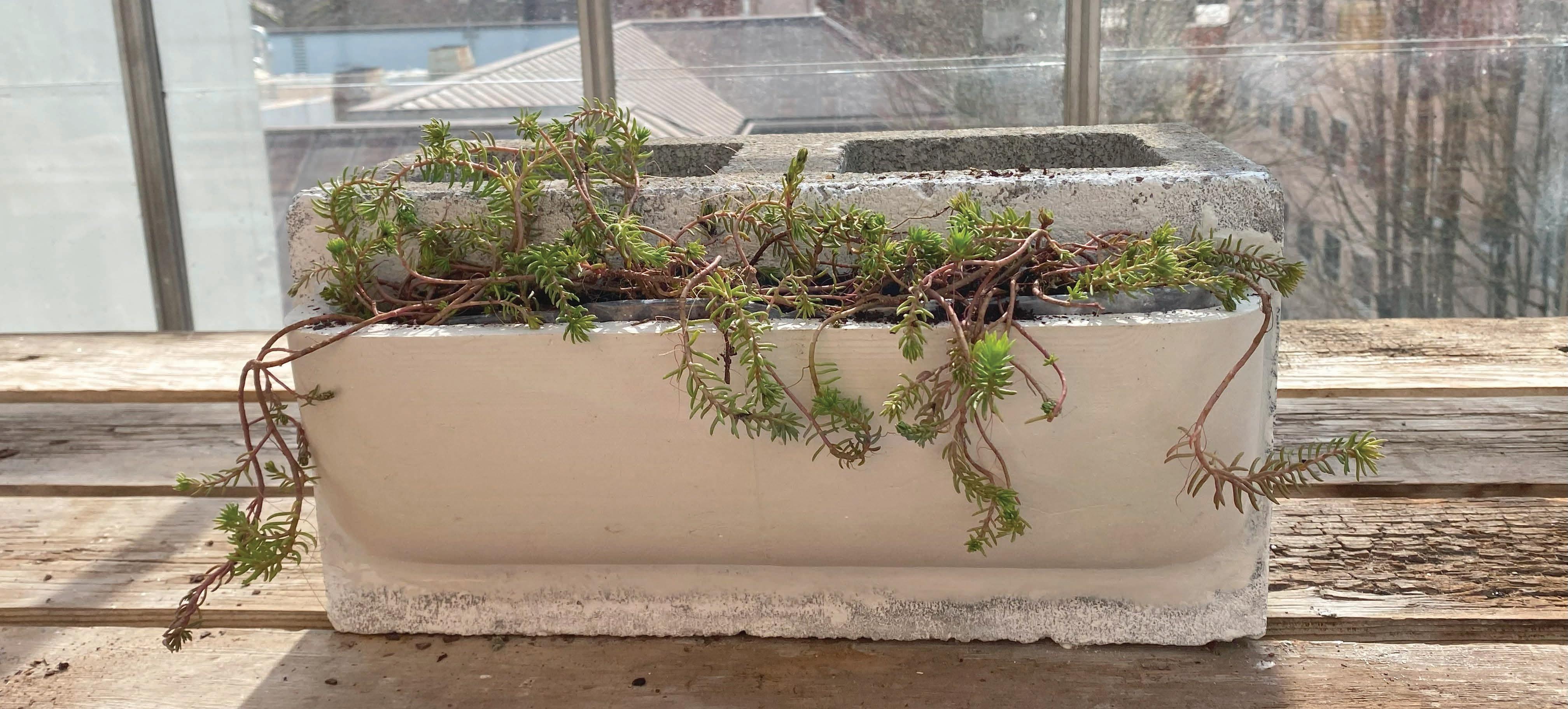
CONCLUSION
Ultimately, although the soil depth testing did not produce results indicating the possibility of using a soil depth of less than 3”, this project was successful in investigating new methods of construction for possible green walls. I believe the results of the soil depth testing are not entirely conclusive, given all soil depths successfully produced sprouts and most of the testing period was taken
by the germination of the Fenugreek seeds. Although the germination and early development is an indication of the plant’s survival, I believe that a trial with a longer observation period of plants with a developed root system might reveal different results as they would require less watering. Overall, the success of plaster casting using a 3D printed mold shows promise for the
ability to also cast concrete using the same methods. This technique could be used in numerous applications, making use of common fabrication tools and design techniques to achieve equivalent results to 3D printing ceramic or concrete extrusions.
FINAL PROTOTYPE
REFERENCES
Alarcón, Jonathan. “Garden Studio in Amsterdam Watergraafsmeer / CC-Studio.” ArchDaily, ArchDaily, 8 Oct. 2012, www.archdaily. com/279735/garden-studio-in-amsterdam-watergraafsmeer-cc-studio?ad_source=search&ad_medium=bookmark-open.
Bagchi, Anirban. “Immensa and CCC’s Make Breakthrough for Concrete Formwork Using Large Format 3D Printing.” Middle East Construction News, 5 Aug. 2018, meconstructionnews.com/30748/immensa-and-cccs-make-breakthrough-for-concrete-formwork-using-large-format-3d-printing.
“Design.” Habitat Horticulture | Process, habitathorticulture.com/process. Accessed 25 Jan. 2024.
Fabrication, Further, and Instructables. “Create Concrete Products with 3D Printed Molds.” Instructables, Instructables, 25 Sept. 2018, www. instructables.com/Create-Concrete-Products-With-3D-Printed-Molds/.
Fracalossi, Igor. “Green Varnish / Nomad Studio.” ArchDaily, ArchDaily, 1 Oct. 2015, www.archdaily.com/774340/green-varnish-nomad-studio?ad_ medium=widget&ad_name=more-from-office-article-show.
“Gallery of KCEV / Petr Hajek Architekti - 1.” ArchDaily, www.archdaily.com/516085/kcev-petr-hajek-architekti/539a74a8c07a80569e000807-kcevpetr-hajek-architekti-photo. Accessed 25 Jan. 2024.
“Green Varnish.” Nomad.Studio : Landscape Architecture : Design + Art, www.thenomadstudio.net/greenvarnish/. Accessed 25 Jan. 2024.
“The Living Wall.” SFMOMA, 29 Dec. 2022, www.sfmoma.org/watch/the-living-wall/.
Marcus, Adam, and Jessica Rossi-Mastracci. “Earthen Tectonics .” Variable Projects, 2022, https://www.variableprojects.com/earthen-tectonics. Accessed 23 Jan. 2024.
Peter , Brian. “Building Bytes .” Architizer, 13 Dec. 2020, architizer.com/projects/building-bytes/.
Pintos, Paula. “Garden of Communities Pavilion / Hello Wood.” Arch Daily, Arch Daily, 8 June 2023, www.archdaily.com/1002164/garden-ofcommunities-pavilion-hello-wood.
Rael San Fratello Architects. “Planter Bricks.” Emerging Objects, emergingobjects.com/project/planter-bricks/. Accessed 23 Jan. 2024. Rael, Ronald, et al. “Emerging Objects.” RAEL SAN FRATELLO, 2009, www.rael-sanfratello.com/made/digital-cement.
Rosenfield, Karissa. “Neri Oxman and SOM Among Fast Company’s Innovation by Design Award Winners.” Arch Daily, 18 Sept. 2015, www.archdaily. com/773938/neri-oxman-and-som-among-fast-companys-innovation-by-design-award-winners.
“San Francisco Museum of Modern Art.” Habitat Horticulture | SFMOMA Living Wall, www.habitathorticulture.com/projects/sfmoma. Accessed 25 Jan. 2024.
Valenzuela, Karen. “KCEV / Petr Hajek Architekti.” ArchDaily, ArchDaily, 19 June 2014, www.archdaily.com/516085/kcev-petr-hajek-architekti.
APPENDIX
MODULE 1 GANTT CHART
Prototype Timeline
Investigation
Research Presentation
Model Module
Construct testing components
Record data
Analyze data
Full-Scale Model Module
Full-scale prototype design
Finalize prototype
Cast construction
Concrete casting
Prototype testing
Fabricate Module
Presentation Preparation
Final Presentation
Exhibition
TESTING DATA