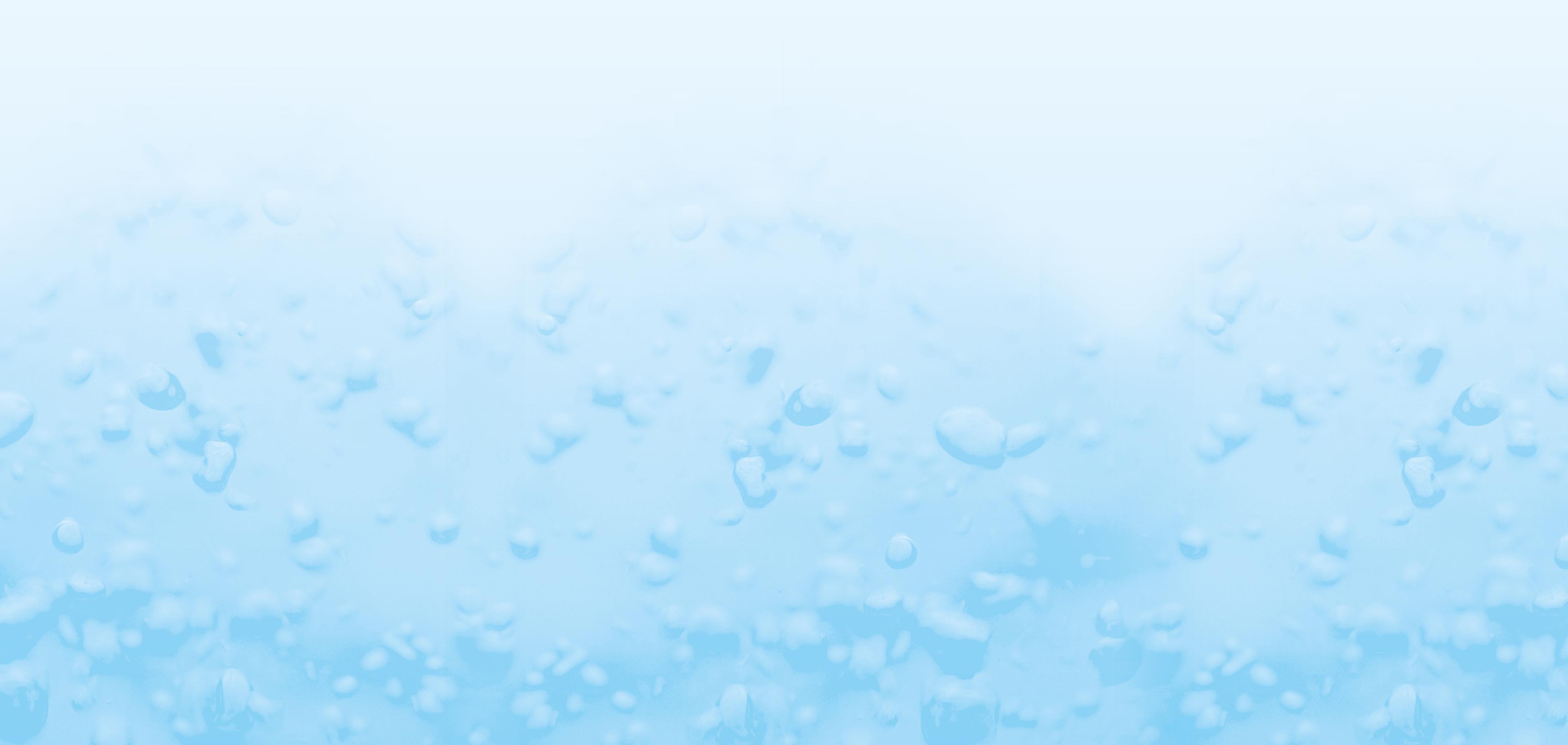
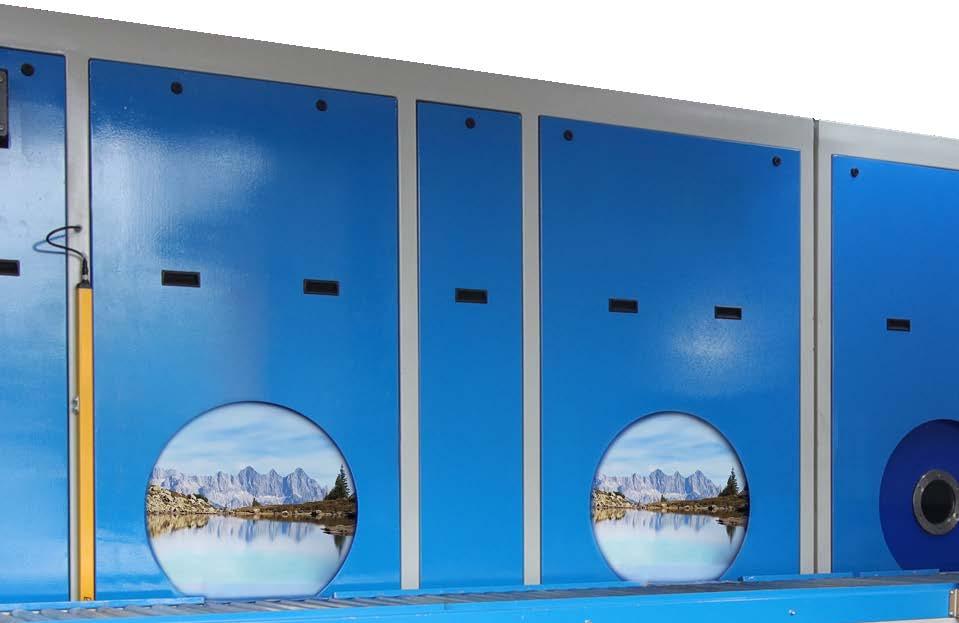

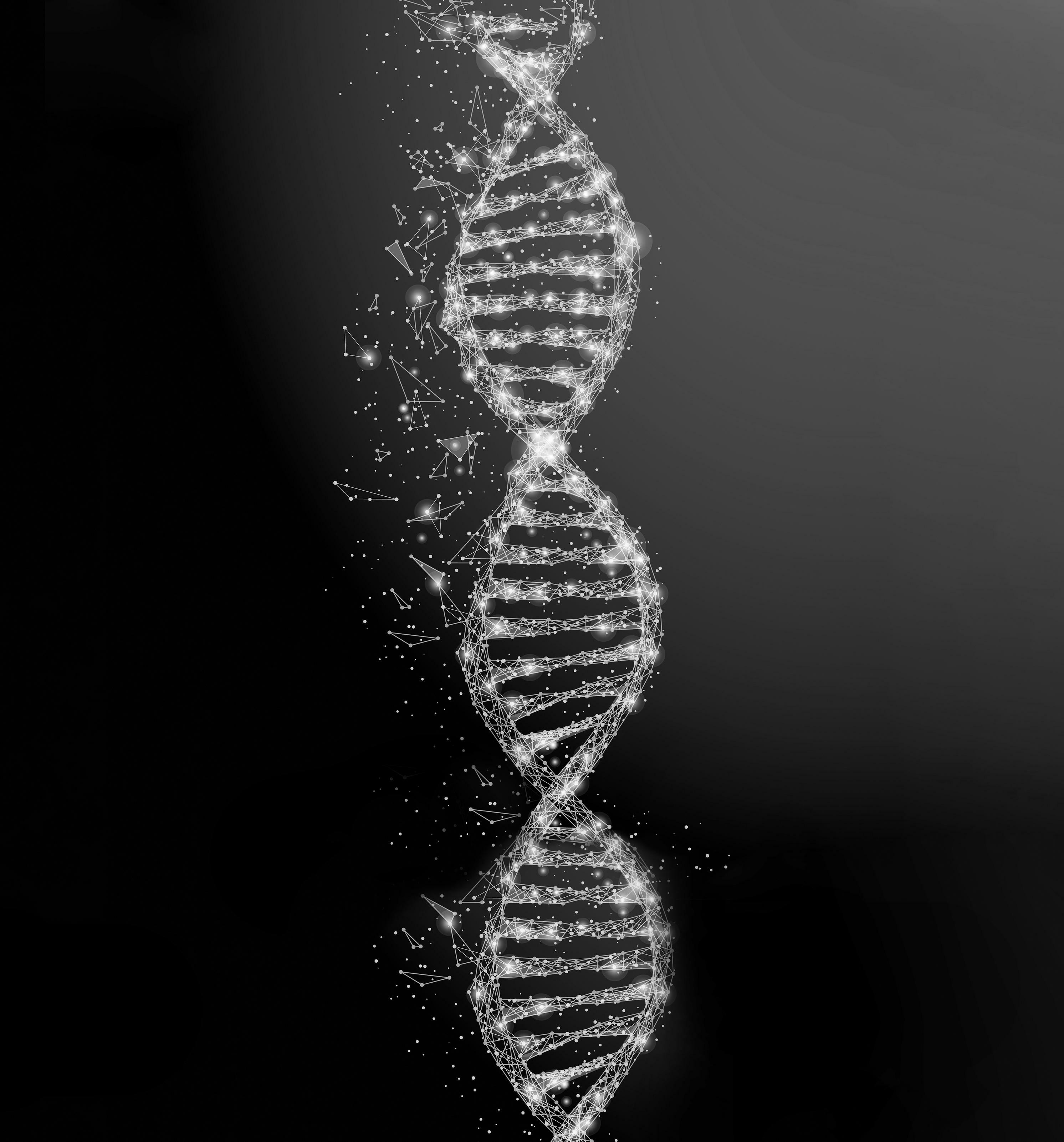
Pretrattamento metalli alla verniciatura
Galvanica Decorativa
Processi di conversione esenti Cromo e Fosfati Fosfatanti a bassa temperatura Passivanti per acciaio zincato a caldo Passivazione conduttiva su Alluminio TCP Rame, Nichel e Cromo Deposizione su plastica (POP) Stagno e leghe di Stagno Pretrattamento
Precision cleaning - consistently meeting the highest requirements for cleanliness
Lavaggio di precisione – soddisfare in modo costante i più elevati requisiti di pulizia
Reliable cleaning of stainless steel sheets for surgical baskets
Lavaggio affidabile di lamiere in acciaio inossidabile per ceste chirurgiche
Walther Trowal: Perfect surface finishes for products made with additive manufacturing
Walther Trowal: perfetta finitura superficiale per prodotti realizzati con manifattura additiva
Digitalisation, circularity, and flexibility in the choice of the cleaning agent: the parameters of T&T’s future-proof investment
Digitalizzazione, economia circolare e flessibilità nell’agente di lavaggio: i parametri per un investimento a prova di futuro in T&T
Producing quality instead of testing it: SITA Messtechnik GmbH celebrates two anniversaries at parts2clean 2022 Produrre qualità invece di testarla: SITA Messtechnik GmbH festeggia due anniversari al parts2clean 2022
October/Ottobre
A cleaning tunnel suitable for components with various geometries: C.P.C. Group’s challenge Un tunnel di lavaggio adatto a componenti con differenti geometrie: la sfida di C.P.C. Group
Cleaning more energy-efficiently Lavaggio più efficiente dal punto di vista energetico
Future-oriented parts cleaning
Lavaggio di componenti orientato al futuro
TCN Vehicles Division’s effective cleaning solution arose from careful co-design with the media and system supplier
In TCN Vehicles Division la soluzione di lavaggio efficace nasce dall’attento co-design con il fornitore di prodotto e impianto
D.B.M. Tecnologie triples its cleaning solutions
D.B.M. Tecnologie triplica le soluzioni per il lavaggio
Machinesforprecisioncleaningwithultrasonics
Cleaning,rinsinganddryingin10minutes
Useoflastgenerationsolvents:non-flammable, non-ozone-depleting,low-boiling
Strongreductionofenergyconsumptionand environmentalpollution
Applications:mechanicsandprecisionmechanics, electronics,medicalandmanymore.
Maximumflexibilitywithdifferentin-linepositionsas cleaningtanks,rinsingandhotairdryers
Solutionsforanycleaningneed,eventhemost complicated
Applications:mechanics,automotive,optical,jewellery, watchmakingandmanymore.Possibilityofadditional treatmentsaspicklingandpassivation
meg.it info@meg.it
In September, ICT was among the 1,816 exhibitors at IMTS - International Manufacturing Technology Show in Chicago, the western hemisphere’s largest and longest-running trade fair on manufacturing and mechanical engineering.
ICT was the only European magazine to be present, representing an industry, that of systems and processes for washing, cleaning, and surface preparation of parts, with a far more comprehensive and sophisticated technological offering than its American equivalent.
It is also more exclusive: vacuum cleaning concepts with modified hydrocarbons or alcohols are the prerogative of European companies alone, many of which have long been collaborating with ICT.
American manufacturers only offer water-based cleaning systems, which are far less sophisticated than the multi-stage, robotised waterwashing/solvent-drying, cleaning+deburring, or cleaning+impregnation combined lines and spray units integrated in machining centres that we are used to seeing here in Europe, with Italian and German firms dominating the scene (as well as the trade fair’s surface treatment hall). The European industry, therefore, confirmed to be at the forefront of technology and of customer demands, with plenty of sales and business growth opportunities available to be seized in the North American market.
The investment required to explore this market is certainly burdensome for companies, now even more so, given the escalating prices of air travel and, in general, of everything revolving around business travel. In addition, it is essential to have a person, a network, or a small structure closely follow the market: it is not feasible to manage this from Europe. Nevertheless, we believe that looking west, and not east, can offer more opportunities for our companies.
In the meantime, in this issue of ICT we have collected the most interesting case studies from the past months to present to all visitors of the parts2clean trade fair in Stuttgart, which is going to open its doors to visitors and exhibitors from all over the world on 12 October and once again confirm itself as the world’s most important exhibition for industrial parts cleaning. We are going to be there – in the media lounge reserved for trade magazines – with a magazine issue full of application examples, innovations, and analyses of the parts cleaning market’s needs.
Lo scorso settembre ICT era fra i 1816 espositori di IMTS - International Manufacturing Technology Show di Chicago, la fiera più grande e più duratura dell’emisfero occidentale sull’industria manifatturiera e meccanica. ICT era l’unica rivista europea presente, a rappresentare un’industria - quella dei sistemi e dei processi di lavaggio, pulizia e preparazione superficiale dei pezzi – che ha un’offerta tecnologica di gran lunga più completa e sofisticata della corrispettiva industria americana. E anche più esclusiva: i concept di lavaggio sottovuoto a idrocarburi o alcoli modificati sono appannaggio di sole aziende europee, molte delle quali collaborano da tempo con ICT. I produttori americani offrono unicamente sistemi di lavaggio a base acqua, ma di gran lunga meno sofisticati delle linee multistadio, robotizzate, con combinazione lavaggio ad acqua/asciugatura a solvente o, ancora, dei sistemi di lavaggio+sbavatura, lavaggio+impregnazione e delle macchine a spruzzo integrate nei centri di lavorazione meccanica che siamo abituati a vedere qui in Europa, con aziende soprattutto italiane e tedesche a dominare la scena (nonché il padiglione dei trattamenti di superficie).
L’industria europea, dunque, si riconferma ai vertici della tecnologia e all’avanguardia rispetto alle richieste di mercato, e ci sono molte opportunità di vendita e di crescita commerciale disponibili da cogliere sul mercato nordamericano.
Certo, gli investimenti per esplorare questo mercato sono gravosi per le aziende, oggi ancora di più vista l’escalation dei prezzi del trasporto aereo e, in generale, di tutto quanto ruota attorno alle trasferte di lavoro. Inoltre, è fondamentale prevedere una persona, un network o una piccola struttura che segua da vicino il mercato. Non è fattibile gestirlo dall’Europa. Tuttavia riteniamo che guardare a ovest, e non ad est, possa offrire maggiori opportunità alle nostre aziende.
Nel frattempo, in questo numero di ICT abbiamo raccolto i casi di studio più interessanti degli ultimi mesi da presentare a tutti i visitatori della fiera parts2clean di Stoccarda, che aprirà le porte a visitatori ed espositori da tutto il mondo il prossimo 12 ottobre e che si riconferma la più importante fiera al mondo specializzata nel lavaggio industriale dei pezzi.
Noi ci saremo, nella media lounge riservata alle riviste di settore, con un numero ricco di applicazioni, innovazioni e analisi delle esigenze del mercato in materia di pulizia dei pezzi.
Francesco Stucchi EditorParticulate cleanliness specifications in the single-digit micrometre range and below, as well as extremely high specifications with regard to residual film chemical contamination, are the order of the day in many industrial sectors today. These values can only be reliably met in series production when optimally matched cleaning solutions are used.
This involves such industries as the semiconductor supply industry, optics, medical and pharmaceutical technology, metrology, electronics, sensor and microtechnology, and aerospace that require ultra-clean surfaces and components. Sometimes extremely high specifications for the particulate and filmic-chemical cleanliness of the components is the result.
Le specifiche di pulizia dai residui particellari nella gamma del micrometro a singola cifra e inferiore, nonché le specifiche estremamente elevate relative ai residui di contaminazione pellicolare chimica, sono all’ordine del giorno in molti settori industriali. Nella produzione in serie questi valori si possono ottenere in modo affidabile solo utilizzando soluzioni di lavaggio adattate in modo ottimale ad essi.
La tematica coinvolge settori quali l’industria dei semiconduttori, l’ottica, la tecnologia medica e farmaceutica, la metrologia, l’elettronica, la microtecnologia e la tecnologia dei sensori e l’industria aerospaziale, che richiedono componenti e superfici ultrapuliti e che forniscono specifiche di pulizia dai residui particellari e pellicolari-chimici estremamente elevate.
I sistemi di riscaldamento sottovuoto per il lavaggio finale dei componenti di precisione utilizzano le alte temperature per rimuovere dalla superfice i residui di contaminanti atmosferici.
Vacuum-based bake-out systems for the final cleaning step in precision components use high temperatures to remove residual contamination of atmospheric components from the surface.To ensure that the required cleanliness is achieved with high reliability, the plant and process technology, in this case a special spray rinsing system developed for ultra-fine cleaning, is tailored to the specific application.
Per garantire che il livello di pulizia richiesto sia ottenuto in modo affidabile, impianto e processo – in questo caso uno speciale sistema di risciacquo a spruzzo sviluppato per il lavaggio ultra-fine - devono essere adattati al tipo di applicazione.
Depending on the industrial sector and component, cleanliness criteria such as outgassing rates for organic substances and residual moisture and, in the case of surface analyses for residues of inorganic substances, it is also necessary to comply with limit values down to the atomic percentage range. These requirements result in very demanding tasks for component cleaning that can affect the entire production chain.
During production, precision parts go through such manufacturing steps as machining, forming, and grinding, which are associated with the introduction of dirt. Very high cleanliness requirements can only be met if the components consistently meet a defined initial condition. Important aspects are, among others, the clean execution and quality of upstream processing steps, the avoidance of re- and crosscontamination by upstream or downstream processes as well as by the part handling, the quality of a deburring and/or the surface finish. The design of adequate part take-ups as well as adapted handling and environmental conditions are further issues that should be taken into consideration.
Wet chemical processes are widely used in ultra-fine cleaning and are considered as state of the art. The cleaning process is carried out using ultrasonic inline immersion systems, which, depending on the cleaning
A seconda del settore industriale e del componente, per alcuni criteri di pulizia come il tasso di degasaggio delle sostanze organiche e l’umidità residua e, nel caso di analisi superficiali, i residui di sostanze inorganiche, è necessario conformarsi a valori limite che arrivano fino alla gamma atomica percentuale. Questi requisiti si traducono in attività di lavaggio molto impegnative, che si possono ripercuotere sull’intera catena produttiva.
Durante la produzione i componenti di precisione sono sottoposti a fasi quali lavorazione, formatura e rettifica, associate all’introduzione di sporco. Requisiti di pulizia molto elevati si possono soddisfare solo se i manufatti mantengono una condizione iniziale definita. Aspetti importanti sono la pulizia e la qualità delle fasi produttive a monte, l’elusione della ricontaminazione e contaminazione incrociata tra processi a monte e a valle, nonché la movimentazione dei manufatti e la qualità della sbavatura e della finitura superficiale. La progettazione di adeguati sistemi di movimentazione dei componenti e l’adattamento delle condizioni ambientali sono ulteriori aspetti da prendere in considerazione.
Sistemi a camera e a immersione in linea per lavaggio ultra-fine
I processi chimici a umido sono ampiamente usati nel lavaggio ultrafine e sono considerati lo stato dell’arte. Il lavaggio avviene utilizzando sistemi in linea ad immersione con ultrasuoni che, a seconda del processo
task, are equipped with an appropriate number of treatment stations for cleaning, rinsing and drying. Alternatively, chamber systems with one or more work chambers are available. These systems can be operated using both aqueous media and solvents. Both system concepts can be connected directly to cleanrooms or integrated into them. Regardless of whether an inline immersion or chamber system is used, it must be ensured that the materials and manufacturing processes used to construct the cleaning system do not cause re- or cross-contamination. Using solutions for continuous control and recording of plant and process parameters is often already a standard in wet chemical plants for ultra-fine cleaning. Measuring systems for permanent inline monitoring and control of the cleaning baths not only enable the exact documentation of the conditions during cleaning, but also the automatic replenishment of the cleaning media as required. When providing and preparing the media, it must be ensured that it is of the appropriate quality for the purity requirement, through the use of an ultrapure water supply, for example.
The starting point for the task-specific design of the system and cleaning processes are the materials and geometry of the parts to be cleaned, the degree and type of contamination, and the selection of the appropriate cleaning medium.
previsto, sono dotati di un adeguato numero di stazioni di lavaggio, risciacquo e asciugatura. In alternativa, sono disponibili sistemi a una o più camere. Questi sistemi funzionano sia con prodotti a base acqua sia con solventi. Entrambi i concept di sistema possono essere collegati direttamente alle camere bianche o integrati in esse. Indipendentemente dal tipo di sistema, immersione in linea o camera, è necessario assicurarsi che i materiali e i processi utilizzati per costruire il sistema di lavaggio non causino ricontaminazione o contaminazione incrociata. L’utilizzo di sistemi di controllo continuo e di registrazione dei parametri di processo è già spesso uno standard negli impianti chimici a umido per il lavaggio ultrafine. I sistemi di misurazione per il monitoraggio in linea permanente dei bagni di lavaggio permettono non solo l’esatta documentazione delle condizioni durante il lavaggio, ma anche il reintegro automatico del prodotto di lavaggio quando necessario. Quando si fornisce e si prepara il prodotto di lavaggio è necessario assicurarsi che questo abbia una qualità adeguata ai requisiti di purezza, per esempio utilizzando una fornitura di acqua ultra pura.
Il punto di partenza per la progettazione dell’impianto e del processo di lavaggio sono sempre il materiale e la geometria dei manufatti da lavare, il grado e il tipo di contaminazione e la selezione del prodotto di lavaggio appropriato.
©
Thanks to its wide range of features, including the CNp process, the chamber cleaning system is designed for cleaning precision components and is integrated into a clean room.
Grazie alle sue numerose caratteristiche, incluso il processo CNp, il sistema di lavaggio a camera è progettato per il lavaggio di componenti di precisione e integrato in una camera bianca.
For ultra-fine degreasing, prior to bonding and coating processes for example, chamber systems operated with aqueous media or solvents can be equipped with low-pressure plasma.
Per lo sgrassaggio ultra-fine, che precede incollaggio e verniciatura, i sistemi a camera ad acqua o a solvente possono essere dotati di plasma a bassa pressione.
When determining the process technology, ultrasound or megasonic, spraying, dipping, high pressure and plasma, for example, it must be taken into account that undercuts, blind holes, capillary, lumen or pore structures of components influence the cleaning effect. This is because cleaning media and process technology can sometimes only reach certain areas with difficulty or not at all. This can be remedied, for example, by ultrasonic cleaning solutions that work in combination with vacuum. Alternatives include new process technologies such as cyclic nucleation (CNp), Vacuum Activated Purification (VAP) and Pulse Pressure Cleaning (PPC).
Various dry processes, such as vacuum baking, plasma and CO2 snow jet cleaning, are also available for ultra-fine cleaning tasks. The components are baked under vacuum in specially developed vacuum furnaces. In this process, residues of filmic contaminants are removed from material surfaces at high temperatures (e.g. 180 °C). The adhering molecules then pass into the gas phase due to the vacuum environment and are pumped off. It is also possible to simultaneously determine the molecular components of the outgassing by means of mass spectrometry-based residual gas analysis (RGA) during the heating process, so that the cleanliness of the components can be generated, tested and confirmed in-situ.
Nel determinare la tecnologia di processo, a ultrasuoni o megasonica, a spruzzo, a immersione, ad alta pressione o al plasma, si deve tener conto che i sottosquadra, i fori ciechi, la struttura capillare, i pori e le cavità dei manufatti influenzano il risultato di lavaggio. Questo perché il prodotto e la tecnologia di lavaggio a volte raggiungono con difficoltà certe aree, o non le raggiungono affatto. A questo si può rimediare, per esempio, con soluzioni a ultrasuoni che funzionano in combinazione con il vuoto. Tra le alternative troviamo nuove tecnologie come la nucleazione ciclica, la purificazione attivata sottovuoto e il lavaggio a pressione pulsata.
Per il lavaggio ultrafine sono disponibili anche diversi processi a secco, come il riscaldamento sottovuoto e il lavaggio al plasma o con getto di neve di CO2. I manufatti sono cotti sottovuoto in forni appositamente sviluppati. In questo processo i residui di contaminanti pellicolari vengono rimossi dalle superfici ad alte temperature (180°C). Le molecole che aderiscono alla superficie passano così alla fase gassosa grazie all’ambiente sottovuoto e sono pompate via. È anche possibile determinare simultaneamente i componenti molecolari del degassamento mediante analisi dei gas residui basata sulla spettrometria di massa durante il processo di riscaldamento, di modo che il livello di pulizia possa essere generato, testato e confermato in situ.
Defined ambient and handling conditions, as in this case a clean room, are indispensable for ultra-fine cleaning applications in order to meet high cleanliness specifications.
Nel lavaggio ultra-fine condizioni ambientali e di movimentazione ben definite, come in questo caso una camera bianca, sono indispensabili per poter soddisfare le elevate specifiche di pulizia.
EFFICIENT CLEANING AND DEBURRING SYSTEMS FOR VARIOUS INDUSTRIAL PARTS AND COMPONENTS.
A modular configuration in terms of hardware and software enables solutions that are designed for the respective application and components. Plasma cleaning can also be used to remove thin residual organic contaminants, whereby the surface is cleaned and activated at the same time.
This dual function is based on a physical and chemical reaction of the process, through which an increase in surface energy is achieved. The use of so-called “cold” plasma sources makes it possible to treat even temperature-sensitive materials.
The removal of filmic and particulate contaminants down to the submicrometre range is made possible by CO2 snow jet cleaning, which uses liquid, climate-neutral carbon dioxide as a medium. It is passed through a wear-free two-substance ring nozzle, relaxes as it emerges to form fine CO2 crystals, which are bundled by an annular compressed air jacket jet and accelerated to supersonic speed. When the jet of compressed snow air hits the surface to be cleaned, it causes a combination of thermal, mechanical, sublimation and solvent effects. Systems are available in cleanroom-compatible design with integrated process monitoring as standard for use in ultra-fine cleaning.
Regardless of which process is used to clean precision components, it is also necessary to take a look at packaging and logistics. Is it possible to transport the parts to the next step in a high state of cleanliness?
More information and innovative solutions on precision cleaning will be provided at parts2clean
Una configurazione modulare in termini di hardware e software permette di creare soluzioni adatte alle diverse applicazioni e ai diversi tipi di manufatto. Il lavaggio al plasma può essere utilizzato anche per rimuovere sottili contaminanti organici, in questo modo la superficie è lavata e attivata contemporaneamente.
Questa doppia funzione si basa su una reazione fisica e chimica, con cui si ottiene un aumento dell’energia superficiale. L’utilizzo del cosiddetto plasma “freddo” dà la possibilità di trattare anche materiali termosensibili. La rimozione di contaminanti particellari e pellicolari nella gamma del sub-micrometro è possibile con il lavaggio a getto di neve di CO2, che utilizza l’anidride carbonica liquida e neutra per l’ambiente. Questa passa in un ugello circolare antiusura sottoforma di sottili cristalli, che sono poi aggregati da un getto anulare di aria compressa e accelerati a velocità supersonica. Quando il getto colpisce la superficie da lavare si crea una combinazione tra effetto termico, meccanico, di sublimazione e solvente. Questo tipo di sistema è disponibile in un design compatibile con la camera bianca e con monitoraggio integrato, come standard per il lavaggio ultra-fine. Indipendentemente dal processo utilizzato per lavare i componenti di precisione è necessario prendere in considerazione anche l’imballaggio e la logistica. È possibile trasportare i componenti mantenendo l’elevato livello di pulizia?
Maggiori informazioni e innovative soluzioni per il lavaggio di precisione saranno offerte a parts2clean
In the JetCell-HP, which is designed to meet cleanroom requirements, CO2 snow jet fine cleaning processes can be automated and integrated into production lines.
Nel JetCell-HP, progettato per soddisfare i requisiti della camera bianca, i processi di lavaggio fine con neve di CO2 possono essere automatizzati e integrati nelle linee produttive.
Cleanliness requirements in medical technology are particularly high and certainly not limited to accessory equipment. Mechanical engineering and metal processing company MBengineering (Tuttlingen, Germany) meets such stringent specifications with a MAFAC PALMA 100 spray-flood cleaning machine, equipped with a specially designed basket container and a three-bath system to produce residue-free and dry surfaces.
MBengineering GmbH (Dürbheim, near Tuttlingen, in Germany) has been producing machines, sheet metal parts, and individual components for the medical engineering, mechanical engineering, ventilation engineering, and plastics processing industries since 1995. It employs 40 staff members and, thanks to its high-level in-house production and wide-ranging catalogue, it is one of the leading manufacturing companies in South West Germany.
“We were specifically looking for a parts cleaning machine that used validated processes and could treat a high variety of workpieces. We also wanted to be able to optimise it from time to time depending on requirements, both for our current cleaning needs and with a view to increasingly complex requirements and workpiece geometries,” explains project engineer Martin Zepf.
Crucial for deciding to purchase the machine was a new order placed by a renowned manufacturer in the medical engineering field, for which MBengineering manufactures punched filigree sheets in stainless steel with a size of 730 x 450 x 1 mm (L/W/H), which are later formed into surgical baskets. Along their path from blanks to punched sheets, the material undergoes a manufacturing process that includes laser punching, straightening, grinding, and deburring.
“Before the punched sheets leave our premises, they must be thoroughly cleaned of any processing residues such as oil, swarf, and abrasives and perfectly dried. This guarantees that the subsequent forming process can take place without the machines being contaminated. Also, no faulty connections must occur during spot welding, as the baskets must be very resistant to withstand sterilisation,” says team member Gianni Leocata while illustrating the cleaning task performed by the new plant. The cleaned sheets must also pass a cytotoxicity test in compliance with ISO 10993-1. “Since the resulting baskets are used to store and transport surgical instruments, their surfaces must not have any adverse effect on human tissues.”
With its high-grade machinery, MBengineering manufactures a wide range of sheet metal parts and individual components for different industrial sectors, from medical engineering and mechanical engineering to ventilation engineering and plastics processing. An important product segment is that of punched sheets for surgical baskets, manufactured with a laser punching and cutting process.
MAFAC – E. Schwarz GmbH Co. KG AlpirsbachI requisiti di pulizia nella tecnologia medica sono elevati e non si limitano alle apparecchiature accessorie. L’azienda di ingegneria meccanica e lavorazione dei metalli MBengineering di Tuttlingen (Germania), soddisfa queste rigorose specifiche con una MAFAC PALMA 100, una macchina di lavaggio a spruzzo-immersione con contenitore delle ceste di formato speciale e un sistema a triplo bagno che garantiscono superfici prive di residui e perfettamente asciutte.
Dal 1995 MBengineering GmbH di Dürbheim, vicino Tuttlingen, produce macchinari, componenti in lamiera e componenti per ingegneria medica e meccanica, per la ventilazione e per l’industria della lavorazione della plastica. L’azienda ha 40 dipendenti e, grazie al suo elevato livello di produzione interna e all’ampia gamma di prodotti, rientra tra le aziende manifatturiere leader del sudest della Germania. “Stavamo cercando nello specifico una macchina di lavaggio che utilizzasse processi certificati e che consentisse un’ampia varietà di applicazioni in termini di tipologia dei componenti, nonché che permettesse un’ottimizzazione del processo a seconda delle richieste, per poter gestire i requisiti sempre più elevati e le geometrie più complesse”, spiega il Project Engineer Martin Zepf. Cruciale nell’acquisto della macchina è stato un ordine effettuato da un rinomato produttore nel campo dell’ingegneria medica, per il quale MBengineering produce lamiere in acciaio inox fustellate filigranate delle dimensioni di 730 x 450 x 1 mm (L/P/A), che sono successivamente formate per produrre ceste chirurgiche. Nel suo percorso dal grezzo alla lamiera fustellata, l’acciaio inox è sottoposto a punzonatura laser, raddrizzatura, rettifica e sbavatura. “Prima che le lastre punzonate lascino il nostro stabilimento devono essere lavate in modo affidabile dai residui di oli di lavorazione, trucioli e abrasivi nonché perfettamente asciutte. Garantiamo in questo modo che il successivo processo di lavorazione possa avere luogo senza contaminazione dei macchinari. Inoltre, durante la saldatura a punti non devono verificarsi connessioni errate, poiché le ceste devono essere molto robuste per sopportare la sterilizzazione”, afferma il collega Gianni Leocata spiegando il processo di lavaggio del nuovo impianto. Le lamiere lavate devono superare anche il test di citotossicità secondo ISO 10993-1. “Poiché gli strumenti chirurgici sono stoccati e trasportati nelle ceste, le loro superfici non devono avere alcun effetto avverso sui tessuti umani”.
Con i suoi macchinari di alta qualità, MBengineering produce un’ampia gamma di lamiere e componenti per diversi settori industriali: ingegneria medica, ingegneria meccanica, ventilazione e industria della lavorazione della plastica. Un importante segmento di prodotto sono i punzonati per ceste chirurgiche, prodotti con punzonatura laser.
MBengineering can meet the highest medical engineering standards with its specially sized spray-flood cleaning machine MAFAC PALMA 100. The stainless steel sheets are stacked on top of each other in densely packed batches, which is particularly challenging when it comes to cleaning and drying them.
Mbengineering soddisfa gli elevati requisiti dell’ingegneria medica con la macchina di lavaggio a spruzzo-immersione MAFAC PALMA 100, di dimensioni speciali. Le lamiere in accio inox sono impilate a formare piccoli lotti, una configurazione impegnativa per quanto riguarda il lavaggio e l’asciugatura.
According to Martin Zepf and Gianni Leocata, the MAFAC PALMA 100 machine meets all these requirements. This spray-flood cleaning machine features a rotating, multi-sided spray system and a counter-rotating basket container with the special dimensions of 1000 x 480 x 338 mm (L/W/H). The spraying and flooding processes can be combined in different ways to ensure maximum process flexibility, as the cycle can be adjusted to any cleaning task in a highly customised manner. Another convincing advantage of MAFAC PALMA 100 was the possibility to add a third tank for rinsing. The cascade layout and the additional rinse guarantee a long bath service life despite the high oil volumes generated by the laser punching and cutting operations: “Currently, we only change the cleaning baths every three to four months, despite the high workload,” explains Gianni Leocata.
The blanks are subjected to both an intermediate and a final cleaning stage in order to be carefully cleaned of any residues and particles and subsequently dried. The cleaning process starts with a ten-minute intermediate treatment during which the oil residues are removed through cleaning, rinsing, and pulse blowing. A mild cleaning agent is added to the first tank to be applied during the spray-flooding
Fiore all’occhiello del sistema: un terza vasca di risciacquo Secondo Martin Zepf e Gianni Leocata MAFAC PALMA 100 soddisfa tutti questi requisiti. La macchina è dotata di un sistema di spruzzatura rotante e multi-lato e un contenitore controrotante di dimensioni speciali pari a 1000 x 480 x 338 mm. Entrambi i processi, spruzzo e immersione, possono essere combinati in diversi modi per garantire massima flessibilità di processo, poichè il ciclo può essere regolato in base al lavaggio richiesto in modo molto personalizzato. Un altro convincente vantaggio di MAFAC PALMA 100 è stata la possibilità di aggiungere una terza vasca per il risciacquo. Il layout a cascata e il risciacquo aggiuntivo garantiscono una lunga vita utile del bagno, nonostante l’elevata presenza di olio generata da punzonatura e taglio: “Al momento sostituiamo i bagni di lavaggio solo ogni tre o quattro mesi, nonostante l’elevato carico di lavoro”, ha spiegato Gianni Leocata.
Lavaggio e asciugatura multistadio I fustellati sono sottoposti a lavaggio intemedio e finale, per eliminare accuratamente qualsiasi residuo, e successivamente asciugati. Il processo inizia con un lavaggio intermedio di 10 minuti, durante il quale i residui di olio vengono eliminati con la sequenza lavaggio –risciacquo – soffiatura a impulsi. Per la fase di lavaggio è stato aggiunto un prodotto delicato nella prima vasca, applicato durante la fase a
© MAFAC © MAFACChemical-physical plants
Sludge treatment and compactor systems
Ion exchange demineralization systems and reverse osmosis systems
Oil separators
Filtering systems
Batch type systems
Flotation units
Chemicals and spare parts for water treatment
Technical service, support and maintenance of wastewater treatment plants
Processing residues such as oil or swarf have been carefully removed and surfaces are absolutely dry.
I residui di lavorazione come oli o trucioli sono stati accuratamente rimossi e le superfici sono completamente asciutte.
process. The parts are then rinsed in the second tank. Afterwards, they are dried and sent to the straightening and grinding stations. A 30-minute final cleaning process follows to remove the new processing residues through a similar sequence. However, compared with the intermediate cleaning phase, a further rinsing stage is added to this process, taking place in the third tank. This is followed by a twostage drying operation with pulse blowing and hot air, as well as a double vacuum drying stage. The sheets pass through the drying and cleaning stations in densely packed batches. “Due to this, drying takes about as long as cleaning. Nevertheless, we continue to prefer this type of loading arrangement because we can have about 800 punched sheets per shift ready for delivery, thus meeting all our customers’ requests. The results are impeccable: the surfaces leaving our new system are free of any residues, absolutely dry, and free of corrosion,” states Martin Zepf with pride.
spruzzo-immersione. Successivamente i componenti vengono risciacquati nella seconda vasca e indirizzati al processo di raddrizzatura e rettifica. A queste segue un lavaggio finale di 30 minuti, che rimuove i nuovi residui di lavorazione con una sequenza simile alla precedente.
Tuttavia, rispetto al lavaggio intermedio, il lavaggio finale ha un’ulteriore fase di risciacquo nella terza vasca. A questa segue un’asciugatura a due stadi con soffiaggio a impulsi e aria calda, nonché con doppia asciugatura sottovuoto.
Le lamiere passano nelle stazioni di lavaggio e asciugatura impilate in modo molto compatto.
“In questo modo l’asciugatura richiede circa lo stesso tempo del lavaggio. Tuttavia manteniamo questa configurazione perché possiamo così avere circa 800 lamiere punzonate per turno pronte per la spedizione, soddisfando così tutte le richieste dei nostri clienti.
I risultati sono impeccabili: le superfici sono prive di residui, perfettamente asciutte e senza segni di corrosione”, si rallegra Martin Zepf.
Beware of imitations, buy the original!
info@waterenergy.it www.waterenergy.it
f.siegel@walther-trowal.de
Walther Trowal will display its mass finishing and coating technologies for 3D printed components at the next Formnext exhibition.
At the Formnext 2022 exhibition (Frankfurt am Main – Germany, 15-18 November), Walther Trowal presents two surface treatment technologies: mass finishing and coating of small components in rotary drums. In the AM post processing machine the surface of 3D printed components is refined by deburring, smoothing or polishing; in the Rotamat coater the component surface is coated with lacquer materials.
Durante la prossima edizione di Formnext, Walther Trowal esporrà le sue tecnologie di verniciatura e finitura in massa per componenti stampati in 3D.
Alla fiera Formnext 2022 (Francoforte – Germania, 15-18 Novembre), Walther Trowal presenterà due tecnologie di trattamento superficiale: finitura in massa e verniciatura di piccoli componenti in tamburi rotanti. Nella post-produzione della manifattura additiva i componenti stampati in 3D sono rifiniti con sbavatura, levigatura o lucidatura; nella macchina Rotamat la superficie del componente è verniciata con smalti.
In one single operation the AM post processing machine AM 2 eliminates the surface roughness typical for components produced by additive manufacturing.
Con un’unica operazione la macchina di post-lavorazione additiva AM 2 elimina la rugosità superficiale tipica dei componenti realizzati con manifattura additiva.
The Rotamat R 60 applies a homogeneous lacquer coating on the surface of 3D printed components. This machine was specifically developed for small work piece batches, which are typical for additive manufacturing.
In one single operation the AM post processing machine, model A2, eliminates the high surface roughness that is typical for 3D printed components. Usually, such rough surfaces are caused by the so-called “staircasing” effect, markings from removed support structures and residual powder sintered onto the component surface.
Walther Trowal developed the A2 machine specifically for treating complex metal components. Topology-optimized work pieces with intricate – frequently bionic – shapes cannot be finished manually with consistent results. Mass finishing has proven to be the ideal technology for dealing with such challenging finishing applications. The constant “rubbing” of the grinding/polishing media against the work pieces is not only gentle but also produces a homogeneous surface finish. Moreover,
Rotamat R 60 applica uno strato di vernice omogeneo sulla superficie dei componenti stampati in 3D. Questa macchina è stata appositamente sviluppata per lotti piccoli, tipici della manifattura additiva.
La macchina di post produzione, modello A2, elimina con una sola operazione l’elevata rugosità superficiale tipica dei componenti stampati in 3D. Solitamente le superfici così rugose sono causate dal cosiddetto “effetto scalettatura”, ovvero i segni delle strutture di supporto e della polvere residua sinterizzata sulla superficie del manufatto.
Walther Trowal ha sviluppato la macchina A2 appositamente per il trattamento di componenti metallici complessi. Infatti, i manufatti ottimizzati per la topologia con forme intricate – spesso bioniche- non possono essere finiti manualmente con risultati omogenei. La finitura in massa ha dimostrato di essere la tecnologia ideale per queste impegnative applicazioni. Lo “sfregamento” continuo del prodotto di smerigliatura/lucidatura sui componenti è delicato e garantisce una
the media also reaches difficult-to reach internal surface areas and undercuts.
The design of the new finishing machine is based on the rotary vibrator concept. These machines have proven themselves in numerous industrial finishing applications around the world.
AM post processing systems are running fully automatically and produce excellent and consistent surface finishes. In contrast to electro-chemical finishing systems the high lustre polishing effect is achieved in one single operation. Because of their compact design and small foot-print the A2 machines can be easily integrated into interlinked manufacturing operations.
With the Rotamat R 60 3D printed components can be quickly and evenly coated with a variety of different lacquer materials.
Like the A2 finishing machine the R 60 coater was specifically adapted to the requirements of additive manufacturing: Even the most complex and intricate components can be evenly coated with absolutely repeatable results.
finitura superficiale omogenea. Inoltre, il prodotto riesce a raggiungere anche le superfici interne di difficile accesso e i sottosquadra.
Il design della nuova macchina è basato sul concetto di vibratore rotante. Queste macchine si sono affermate in numerose applicazioni industriali di finitura in tutto il mondo.
I sistemi di post-produzione additiva sono completamente automatici e producono finiture superficiali eccellenti e omogenee. Rispetto ai sistemi di finitura elettrochimici, l’elevata lucentezza si ottiene con un’unica operazione. Grazie al loro design compatto e all’ingombro ridotto le macchine A2 si possono facilmente integrare nei processi produttivi interconnessi.
Con Rotamat R 60 i componenti stampati in 3D possono essere verniciati rapidamente e uniformemente con una varietà di diversi prodotti di verniciatura. Come la macchina A2 anche la R 60 è stata appositamente adattata ai requisiti della manifattura additiva: anche i più complessi e intricati componenti possono essere verniciati in modo omogeneo con risultati assolutamente ripetibili.
© Walther Trowal After treatment in the AM post processing machine the 3D printed components have a perfect surface finish. Dopo il trattamento nella macchina di post-lavorazione additiva i componenti stampati hanno una perfetta finitura superficiale.Since additive manufacturing is usually utilized for relatively small production volumes, the Rotamat offers a capacity (expressed in volume) from 2 to 15 litres per batch. Such a capacity is more than sufficient for the small production runs typical for 3D printing operations. Why should the customer invest in larger and significantly more expensive machines, if they are not required? Frank Siegel, the sales manager “coating technology” at Walther Trowal, wants to ensure that his customers are well taken care of: “The lacquer producers are currently working very hard to develop new coating systems for the base materials used in 3D printed components. By closely working with them we make sure that our customers achieve excellent coating results on their 3D printed components with the new lacquer materials in their existing Rotamat machines”.
Walther Trowal will showcase its technologies at Formnext exhibition (Frankfurt am Main – Germany, November 15 to 18, 2022) in Hall 11, Booth 11.0C29.
Poiché la manifattura additiva si utilizza solitamente per volumi produttivi piccoli, Rotamat offre una capacità da 2 a 15 litri per lotto. Questa capacità è più che sufficiente per le tirature piccole tipiche dello stampaggio 3D. Perché il cliente dovrebbe investire in macchinari più grandi e molto più costosi se non sono necessari? Frank Siegel, direttore commerciale del ramo Tecnologia di Verniciatura di Walther Trowal, vuole assicurarsi che i suoi clienti siano ben seguiti: “Al momento i produttori di vernici stanno lavorando duramente per sviluppare nuovi sistemi vernicianti adatti ai materiali utilizzati nella stampa 3D. Lavorando a stretto contatto con loro ci assicuramo che i nostri clienti ottengano eccellenti risultati di verniciatura con le nuove vernici e nelle loro macchine Rotamat”.
Walther Trowal esporrà le sue tecnologie alla fiera Formnext (Francoforte – Germania, 15-18 novembre 2022) nel Padiglione 1, Stand 11.0C29.
Digitalisation is now an established quality in the manufacturing industry: any new system acquired must have a platform for integration with the other machines in the same factory. The circular economy, i.e. not only using environmentally friendly products but also recovering them and putting them back into the production cycle, is also a growing requirement for companies. Flexibility, finally, is what enables firms to respond quickly and readily to any change in the demands and needs of their customers. Let us see how T&T Srl (Villa d’Adda, Italy) achieved all three of these goals in relation to its parts final cleaning process, by investing in a hydrocarbon vacuum cleaning machine supplied by ILSA-MC (Bologna, Italy).
Founded in 1998 by Stefano Ronzoni and managed since 2018 by his daughter Sara and husband Tommaso Locatelli, T&T specialises in turning metals – brass, stainless steel, and free cutting steel – to produce small metal parts to customer drawings, mainly for the automotive, pneumatic, and hydraulic sectors. With its 19 machines, including 15 multi-spindle cam-controlled lathes and 4 sliding-head lathes, this company based in Villa d’Adda (Bergamo, Italy) produces between 15 and 20 million components per year. “We receive the raw material in the form of 3-metre bars that are processed on different plants according to the type of end component. After machining, all parts undergo a cleaning process, regardless of whether they are to be shipped or stored in our warehouse or whether they require galvanic treatment, which we entrust to a few contractors, or not,” explains Tommaso Locatelli, T&T’s plant manager. “Although the workpieces to be galvanised are subjected to additional pre-treatment before the actual electroplating operation, the requirement placed on us is that they be perfectly clean of machining oil so as not to pollute the treatment baths. When required, the parts undergo also a 100% selection phase with an optical machine after the cleaning or the galvanising phase. At this point, they are ready for packing and shipping or storage”.
Parts manufactured by T&T and the machinery for mechanical processing carried out by them.
Digitalisation, circularity, and flexibility in the choice of the cleaning agent: the parameters of T&T’s future-proof investment
La digitalizzazione è ormai una qualità acquisita nell’industria manifatturiera, dunque qualsiasi nuovo investimento non può prescindere dall’avere una piattaforma di integrazione con le altre macchine della fabbrica. Anche l’economia circolare, quindi non solo usare prodotti ecocompatibili ma anche recuperarli e reimmetterli nel ciclo produttivo, è un’esigenza sempre più spinta delle aziende. La flessibilità, infine, è ciò che consente a un’azienda di rispondere in modo rapido e pronto a qualsiasi cambiamento nelle richieste e nei requisiti dei propri clienti. Vediamo come T&T Srl di Villa d’Adda ha centrato tutti e tre questi obiettivi nella fase di lavaggio finale dei pezzi, investendo in una macchina di lavaggio sottovuoto ad idrocarburi di ILSA-MC di Bologna.
Fondata nel 1998 da Stefano Ronzoni e gestita dal 2018 dalla figlia Sara e dal marito Tommaso Locatelli, T&T si occupa di tornitura di metalli – ottoni, acciai inossidabili e acciai automatici – per produrre minuteria metallica su disegno del cliente e destinata principalmente ai settori dell’automotive, pneumatico e idraulico. Con un parco macchine di 19 unità, di cui 15 torni pluri-mandrino a camme e 4 fantine mobili, l’azienda di Villa d’Adda (BG), produce tra i 15 e i 20 milioni di pezzi l’anno. “Riceviamo la materia prima sottoforma di barre da 3 metri che sono lavorate sulle diverse macchine a seconda del tipo di pezzo. Alla fine della lavorazione meccanica tutti i pezzi prodotti sono sottoposti a un lavaggio, sia che i pezzi vadano spediti oppure stoccati in magazzino, sia che questi pezzi debbano ricevere un trattamento galvanico – che affidiamo a terzisti” spiega Tommaso Locatelli, direttore di stabilimento di T&T. “Nonostante i pezzi da galvanizzare ricevano un ulteriore pretrattamento prima della deposizione galvanica vera e propria, la richiesta è che questi siano perfettamente puliti dagli oli di lavorazione per non inquinare i bagni di trattamento. Su richiesta, dopo il lavaggio o al rientro dalla galvanica i pezzi sono sottoposti ad una fase di selezione al 100% con macchina ottica. A questo punto sono pronti per l’imballaggio e la spedizione oppure lo stoccaggio”.
From left to right:
The EVO series IK 25 hydrocarbon plant supplied by ILSA-MC.
The buffer zone for the baskets.
The touch-screen control panel of the machine.
Da sinistra a destra:
La macchina di lavaggio modello IK 25 serie EVO ad idrocarburi di ILSA-MC.
Il polmone di accumulo dei cestelli.
Il pannello di controllo touch-screen della macchina di lavaggio.
“Our workpieces are contaminated with swarf and neat oil used in machining. Their cleaning specifications are not particularly stringent: for the time being, we are not required to carry out any superfine technical cleaning process,” notes Locatelli. “However, we must ensure that the workpieces are clean, dry, and free of swarf. Until a few months ago, we used a one-chamber perchloroethylene cleaning machine that, however, had insufficient productivity and could no longer easily guarantee the cleanliness degree imposed by ever-evolving specifications. In addition, always attentive to both process sustainability and digitalisation issues, we wanted to eliminate that environmentally unfriendly cleaning product, which also had to be disposed of, while at the same time interfacing our cleaning machine with our factory management system, as we had already done with all other production machines. ILSA-MC offered us the best solution for these (and other) production needs.”
The machine purchased by T&T is an EVO series IK 25 hydrocarbon plant supplied by ILSA-MC (Bologna, Italy). “After analysing T&T’s requirements together with them, we recommended this highproductivity machine that is going to give them ample room for growth in future,” explains Alessandro Pancaldi, the CEO and sales manager of ILSA-MC. “Their current needs are met by half a day’s use of the plant. This largely future-proofs their investment and, at the same time, optimises the system’s utilisation thus reducing energy consumption, as they can treat their daily number of parts to be processed in fewer working hours.”
“Il contaminante dei nostri pezzi è composto da truciolo e olio intero usato per la lavorazione meccanica. Le specifiche di lavaggio non sono particolarmente stringenti, per il momento non ci viene richiesta una pulizia tecnica superfine” specifica Locatelli, “ma dobbiamo garantire che il pezzo sia lavato, asciutto e privo di truciolo. Fino a qualche mese fa utilizzavamo una macchina di lavaggio monocamera a percloroetilene che aveva una produttività insufficiente e non garantiva più facilmente il livello di pulizia necessario per le specifiche in continua evoluzione. Inoltre T&T, da sempre attenta sia alla sostenibilità dei processi sia alla digitalizzazione, voleva eliminare un prodotto di lavaggio poco ecocompatibile e destinato all’eliminazione, nonché interfacciare con il gestionale aziendale anche la macchina di lavaggio, come già lo sono tutte le altre macchine di produzione. ILSA-MC ci ha offerto la soluzione migliore per queste, ed altre, esigenze produttive”.
Lavaggio sottovuoto con idrocarburi La macchina acquistata da T&T è il modello IK 25 serie EVO a idrocarburi di ILSA-MC (Bologna). “Analizzando con T&T il fabbisogno, abbiamo proposto questo modello di macchina ad alta produttività che consente all’azienda di avere un ampio margine di crescita per il futuro” spiega Alessandro Pancaldi, CEO e direttore commerciale di ILSA-MC. “Il loro fabbisogno attuale è soddisfatto da mezza giornata di utilizzo della macchina, dunque un investimento che garantisce loro ampia visibilità sul futuro ma anche di ottimizzare l’uso della macchina e quindi aver un consumo energetico inferiore, perché in meno ore di lavoro riescono a smaltire il quantitativo quotidiano di pezzi da trattare”.
“Within the plant, individual baskets are subjected to dipping, ultrasound treatment (from Weber Ultrasonic GmbH), steam degreasing, and drying, whereas further pre-cleaning and rinsing phases are available, if needed. The entire cycle occurs in a vacuum, with drying in a high vacuum. The cycle time ranges from 8 to 10 minutes. If necessary, the machine can also apply a protective product by spraying at the end of the cycle. We equipped it with automatic loading and unloading systems and a small 3-basket buffer that gives the unmanned machine an autonomy of about 40 minutes. This is very important, given that we reduced the cycle time from 20 minutes to less than 10: the loading and unloading labour commitment would have been too burdensome. Thanks to automation, on the other hand, the machine is less dependent on operators, logistics is simpler, and the machine’s productivity is fully exploited.”
“Another technical choice aimed at ensuring productivity was the integration of double filters to carry out cleaning operations without any downtime and a double distiller to remove solvent from the processing oil again with no downtime,” indicates Pancaldi. “Such stripping process uses different levels of vacuum and mechanical agitation to reduce the presence of solvent in the oil to an infinitesimal amount without stopping the machine, thus allowing the unit to take as much time as necessary to perform its task optimally. In this way, the purified oil can be recovered and recirculated into T&T’s machine tools with two clear advantages: avoiding disposal and reducing the supply of fresh oil and cleaning solvent.”
“The installed cleaning machine has a library of 31 different programmes
“La macchina lavora a cestello singolo con ciclo di immersione, ultrasuoni (della tedesca Weber Ultrasonic GmbH), sgrassaggio a vapori e asciugatura, mentre ulteriori fasi di prelavaggio e risciacquo sono liberamente utilizzabili in caso di necessità. Tutto il ciclo è in vuoto, con asciugatura in vuoto spinto. Il tempo ciclo varia da 8 a 10 minuti. La macchina è anche predisposta per l’applicazione, se necessario, del prodotto protettivo in modalità spray a fine ciclo. L’abbiamo dotata di carico e scarico automatico, con un piccolo polmone di accumulo da 3 cestelli che garantisce alla macchina un’autonomia - non presidiata – di circa 40 minuti. Ciò è molto importante alla luce del fatto che abbiamo ridotto il tempo ciclo da 20 minuti a meno di 10, dunque l’impegno della manodopera di carico e scarico sarebbe stato gravoso. Con l’automazione, invece, la macchina è meno dipendente dagli operatori, la logistica è più semplice e l’utilizzo della produttività garantita dalla macchina è reale”.
“Un’altra scelta tecnica volta a garantire una produttività reale della macchina di lavaggio, è stata quella di inserire doppi filtri per effettuare le operazioni di pulizia senza fermo macchina e un doppio distillatore, per effettuare lo strippaggio del solvente dall’olio di lavorazione in tempo mascherato” aggiunge Pancaldi. “Questo strippaggio spinto sfrutta diversi livelli di vuoto e l’agitazione meccanica per ridurre la presenza di solvente nell’olio a una quantità infinitesimale senza fermare la macchina, quindi prendendosi tutto il tempo necessario per farlo in maniera ottimale. In questo modo l’olio così depurato può essere recuperato e ricircolato nelle macchine utensili, con due vantaggi evidenti: evitarne lo smaltimento e diminuire l’approvvigionamento di olio e di solvente di lavaggio nuovi”.
that can be customised,” adds Pancaldi from ILSA-MC.
“Specifically, since the plant is interfaced with the factory’s management system, the recipe can be chosen through a “dialogue” between the two based on the incoming product’s code. This is part of our Industry 4.0-oriented integration efforts, obtained with a standard platform developed for all ILSA-MC systems that also collects statistical and process data to enable batch tracking and operating conditions monitoring.”
The choice of the right cleaning agent between hydrocarbons and modified alcohols was made after careful consultation with ILSA-MC which verified not only T&T customers’ specifications but also the destination of the parts immediately after cleaning, i.e. shipment or storage.
“We knew for sure that we had to eliminate perchloroethylene,” states Locatelli. “In the end, we opted for hydrocarbon because our production involves the processing of different materials and because a part of our manufactured components is stocked in our warehouse, which, for some customers, translates into the Kanban management of both finished and unprocessed parts. Indeed, hydrocarbon guarantees short to medium-term anti-oxidative protection without calling for a further protective product.”
“As it is isoparaffin, hydrocarbon has a slightly lower degreasing power than modified alcohol (2-4 points less), but it leaves the workpieces naturally protected by an imperceptible patina that does not affect their cleanliness degree while at the same time avoiding the application of
“La macchina di lavaggio installata possiede una libreria di 31 programmi diversi che possono essere personalizzati” riprende Pancaldi di ILSA-MC. “Nello specifico, grazie all’interfaccia con il sistema gestionale della fabbrica, la ricetta può essere scelta attraverso un dialogo tra quest’ultimo e la macchina in base al codice del prodotto in ingresso. Ciò fa parte dell’integrazione 4.0, una piattaforma standard per tutte le macchine ILSA-MC, che raccoglie anche tutti i dati statistici e di processo per consentire tracciabilità dei lotti nel tempo e monitoraggio delle condizioni operative”.
La scelta dell’idrocarburo come agente di lavaggio La scelta dell’agente di lavaggio tra idrocarburi e alcoli modificati, è avvenuta dopo un’attenta consulenza di ILSA-MC, che ha verificato non solo le specifiche di lavaggio dei clienti T&T ma anche la destinazione dei pezzi immediatamente dopo questo lavaggio, ossia spedizione o stoccaggio.
“Ciò di cui eravamo certi era la necessità di eliminare il percloroetilene” ribadisce Locatelli, dopodiché abbiamo optato per l’idrocarburo perché la nostra produzione contempla la lavorazione di vari materiali e una parte di questa produzione è stoccata da T&T la quale, per alcuni clienti, gestisce kanban, scorte e magazzino di pezzi non trattati. L’idrocarburo garantisce una protezione antiossidativa di breve-medio termine senza aggiunta di un ulteriore prodotto di protezione”.
“Trattandosi di isoparaffina, l’idrocarburo ha un potere di sgrassaggio leggermente inferiore all’alcol modificato (2-4 punti di differenza, in meno) ma lascia il pezzo naturalmente protetto da una patina impalpabile che non inficia il grado di pulizia ma evita l’applicazione di un protettivo a fine ciclo, che è invece necessaria qualora si usi un agente di lavaggio
©
Da sinistra: Alessandro Pancaldi di ILSAMC, Tommaso Locatelli di T&T e Veronica Pancaldi di ILSA-MC.
From the left: Alessandro Pancaldi from ILSA-MC, Tommaso Locatelli from T&T and Veronica Pancaldi from ILSA-MC.a protective coating at the end of the cycle, as is necessary if a more aggressive cleaning agent is used. In essence, hydrocarbon guarantees a perfect degree of cleanliness for several applications, also in case of welded and electroplated parts and assemblies whose surfaces operate better if they are slightly smooth, avoiding blockages or interference, especially in the case of automatic assembly operations. Indeed, a growing number of companies is making the same choice as T&T.” “I can confirm that, sometimes, customers ask us to leave parts “slightly oily”. Therefore, rather than perfectly degreasing them with modified alcohol and then protecting them with oil, we chose to use hydrocarbon to objectively clean but also protect them,” states Locatelli. “The machine we purchased, however, is also highly flexible: it would enable us to switch from hydrocarbon to modified alcohol in one working day, should any specifications require it, and it is even prearranged to spray a protective product against oxidation at the end of the cycle.”
“We are very satisfied with our investment choice,” states Tommaso Locatelli. “We had two important goals, a platform 4.0 and a more environmentally friendly process, and we have achieved both. With a view to process optimisation, we have also decided to purchase a machine that is oversized compared to our current requirements, in order to halve our cleaning times and thus reduce consumption.”
“This third factor corresponds to the increasing number of customers, especially in the automotive sector, who buy systems with redundant capacity to maximise plant availability,” concludes Pancaldi. “In other words, the machine has such a high capacity that it is almost always available, and this reduces throughput times by limiting the waiting time between cycles.”
più aggressivo. In sostanza l’idrocarburo restituisce un grado di lavaggio perfetto per molteplici applicazioni, anche in caso di saldature, galvaniche, e per tutte quelle aziende che fanno montaggi e che beneficiano del fatto che le superfici risultino leggermente più scorrevoli, evitando di creare dei bloccaggi o delle interferenze, soprattutto in caso di montaggi automatici. La scelta fatta da T&T in merito al prodotto di lavaggio li accomuna a un numero crescente di aziende”.
“Esatto, a volte la richiesta del cliente è di lasciare pezzi “leggermente oleosi”, quindi piuttosto di sgrassare perfettamente con alcol modificato per poi proteggere con olio, abbiamo scelto di usare l’idrocarburo con cui il pezzo è oggettivamente pulito ma anche protetto” conclude Locatelli.
“La macchina che abbiamo acquistato tuttavia ha una grossa flessibilità perché consente di cambiare da idrocarburo ad alcol modificato in un giorno di lavoro qualora la specifica lo richiedesse, ed è già predisposta per la spruzzatura a fine ciclo di un prodotto protettivo contro l’ossidazione”.
Produttività, flessibilità ed economia circolare “Siamo molto soddisfatti della nostra scelta di investimento” dichiara Tommaso Locatelli. “Per noi gli obiettivi importanti erano due: piattaforma 4.0 e maggiore ecocompatibilità dei processi ed entrambi sono stati raggiunti. In ottica di ottimizzazione abbiamo scelto anche di acquistare una macchina sovradimensionata rispetto all’attuale fabbisogno per dimezzare il tempo di lavaggio e quindi abbattere i consumi”. “Questo terzo fattore coincide con la scelta da parte di un numero sempre maggiore di clienti, soprattutto nel settore auto, di acquistare impianti con una capacità ridondante per avere la macchina sempre disponibile” conclude Pancaldi. “Ciò significa che la macchina ha talmente tanta capacità da essere quasi sempre scarica e riduce così i tempi di attraversamento perché riduce i tempi di attesa fra un ciclo e l’altro”.
SITA Messtechnik GmbH - Dresden (Germany)
juliane.schulze@sita-messtechnik.de
SITA Messtechnik GmbH will be celebrating its 25th anniversary and 15 years of fluorescence measurement technology at this year’s parts2clean (Stuttgart -Germany, 11-13 October).
Founded in 1996 in Dresden by Prof. Dr. Lothar Schulze, SITA Messtechnik GmbH is the market leader not only for measuring and testing technology but also for quality assurance in component cleaning. It has pioneered new technologies for measuring the dynamic surface tension of liquids as well as has developed innovative solutions for quality-assuring process control in industrial parts cleaning.
SITA Messtechnik GmbH will be presenting measuring equipment and customized process solutions for monitoring and controlling the quality-influencing process parameters of parts cleanliness, wettability, bath contamination and cleaner concentration at this year’s parts2clean.
For more than 15 years, it has been researching, developing and working in fluorescence measurement technology for the cleanliness control of components and has consolidated its position as an innovative pioneer of quality assurance in component cleaning. As
SITA Messtechnik GmbH festeggerà il 25° anniversario e i 15 anni della sua tecnologia di misurazione a fluorescenza al parts2clean di quest’anno (Stoccarda – Germania, 11-13 ottobre).
Fondata nel 1996 a Dresda dal Prof. Dr. Lothar Schulze, SITA Messtechnik GmbH è leader di mercato non solo per la tecnologia di misurazione e controllo ma anche per la garanzia di qualità nel lavaggio dei componenti. Ha aperto la strada a nuove tecnologie per la misurazione della tensione superficiale dinamica dei liquidi e ha sviluppato soluzioni innovative per il controllo di processo della garanzia di qualità del lavaggio industriale dei pezzi. Al parts2clean di quest’anno SITA Messtechnik GmbH presenterà i suoi dispositivi di misurazione e le soluzioni personalizzate per il monitoraggio e il controllo dei parametri di processo che influenzano la qualità del lavaggio dei pezzi, la bagnabilità, la contaminazione del bagno e la concentrazione dell’agente di lavaggio. Da oltre 15 anni SITA ricerca, sviluppa e lavora sulla tecnologia di misurazione a fluorescenza per il controllo della pulizia dei componenti e ha consolidato la sua posizione di precursore innovativo della garanzia di qualità nel lavaggio dei componenti. Dal momento che i requisiti di
JULIANE SCHULZEProducing quality instead of testing it - SITA Messtechnik GmbH celebrates two anniversaries at parts2clean 2022The SITA clean line CI inline measuring device. Il dispositivo di misurazione in linea SITA clean line CI.
cleanliness requirements in industrial parts manufacturing have risen sharply in recent years, the demand for practicable solutions for qualityassuring process control has also increased. This is reflected in more than 1,600 fluorescence measuring devices SITA has sold in 64 countries worldwide since 2007.
Depending on the application and requirements, SITA Messtechnik GmbH’s wide product portfolio varies from the SITA CleanoSpector, the mobile and robust handheld measuring device, the SITA clean line CI inline measuring devices, to the SITA FluoScan 3D, the highly automated inspection system accompanying production.
The above-mentioned fluorescence measuring devices are supplemented by the SITA SurfaSpector, a mobile contact angle measuring device that checks the wettability of surfaces.
Clean surfaces are the necessary prerequisite for high and stable quality in coatings, adhesive and welded joints. If components such as gears, steel shafts, valves, contacts or bond pads are not or insufficiently inspected for film residues, residual dirt can cause cost-intensive reworking, product complaints and even order losses.
To prevent this, users from the automotive industry, medical technology, battery production, mechanical engineering, aerospace, the metalworking industry or semiconductor production, rely on quality control with the aid of fluorescence measuring devices.
Fluorescence measuring devices measure the fluorescence that occurs after the absorption of short-wave light in the ultraviolet range and offer
pulizia nella produzione industriale dei componenti sono aumentati notevolmente negli ultimi anni, è aumentata anche la domanda di soluzioni praticabili per il controllo di processo che ne garantisca la qualità. Ciò si riflette negli oltre 1600 strumenti di misurazione a fluorescenza che SITA ha venduto in 64 paesi in tutto il mondo dal 2007.
In base all’applicazione e ai requisiti, l’ampio portfolio prodotti di SITA Messtechnik GmbH varia da SITA CleanoSpector, il dispositivo di misurazione portatile mobile e robusto, ai dispositivi di misurazione in linea SITA clean line CI, al SITA FluoScan 3D, il sistema di ispezione altamente automatizzato che segue la produzione.
Gli strumenti di misura sopra citati sono completati dal SITA SurfaSpector, un dispositivo di misurazione mobile dell’angolo di contatto che verifica la bagnabilità delle superfici.
Le superfici pulite rappresentano il presupposto necessario per una qualità stabile ed elevata dei rivestimenti, degli adesivi e dei giunti saldati. Se componenti come ingranaggi, alberi in acciaio, valvole, cuscinetti di contatto o fissaggio non sono controllati in termini di residui da film sottile o non lo sono sufficientemente, lo sporco residuo può comportare rilavorazioni costose, reclami e persino perdite di ordinativi. Per evitarlo, gli operatori dei settori automotive, tecnologia medica, produzione di batterie, ingegneria meccanica, aerospaziale, metalmeccanico e produzione di semiconduttori, si affidano al controllo qualità con l’aiuto di strumenti di misura a fluorescenza. Questi strumenti misurano la fluorescenza che si determina dopo l’assorbimento della
The evolution of SITA CleanoSpector devices: on the left the 2007 device, on the right the 2009 one. L’evoluzione del CleanoSpector di SITA: a sinistra la versione del 2007, a destra quella del 2009.a precise measuring technique for the non-contact, non-destructive and layer-thickness-sensitive detection of numerous organic substances found on components. Substances such as greases, oils, release agents or lubricants can be detected in terms of quantity and position via fluorescence measurement.
In 2007 SITA rolled out their first fluorescence measuring device for detecting residual contamination on parts. It gave the possibility to test the cleanliness of parts surfaces for the first time within a few seconds and in an objective and repeatable manner without the influence of ambient light.
The second generation of the handheld measuring device introduced the measured variable fluorescence intensity in relation to specifically developed fluorescence standards in 2009. The measuring range was enlarged significantly, fluorescence standards were defined and a device storage was added.
A further extensive product update was realised in 2019 and included hardware modifications for a faster measurement and for a more
luce a onde corte nella gamma degli ultravioletti e offrono una precisa tecnica di misurazione per il rilevamento senza contatto, non distruttivo e sensibile allo spessore degli strati delle numerose sostanze organiche presenti sui componenti. Sostanze come grassi, olii, distaccanti o lubrificanti possono essere rilevate in termini di quantità e posizione tramite la misurazione a fluorescenza.
Dal primo dispositivo di misurazione mobile alle soluzioni automatizzate
Nel 2007 SITA ha presentato il suo primo dispositivo di misurazione a fluorescenza per il rilevamento della contaminazione dei residui sui pezzi, dando per la prima volta la possibilità di testare la pulizia superficiale dei pezzi in pochi secondi e in modo obiettivo e ripetibile senza che sia influenzata dalla luminosità ambientale. La seconda generazione degli strumenti di misura portatili ha introdotto nel 2009 l’intensità misurata di fluorescenza variabile in relazione a standard di fluorescenza appositamente sviluppati. Il range di misurazione è stato notevolmente ampliato, sono stati definiti gli standard di fluorescenza ed è stata aggiunta memoria al dispositivo. Un ulteriore ampio aggiornamento di prodotto è stato realizzato nel 2019 ed ha incluso modifiche hardware per una misurazione più rapida e un
The latest SITA CleanoSpector’s 2019 development. L’ultima evoluzione 2019 del CleanoSpector di SITA.comfortable operability as well as helpful accessories for numerous applications.
2010 saw the market launch of the SITA clean line CI for inline inspection of parts contamination in the manufacturing process. Based on the same measuring principle as the hand-held measuring device it ensured one hundred percent inspection of components. The modularity of the inline measurement technology based on real-time capable industrial PCs offered easy adaptation to customer-specific requirements, for example in combination with robotics.
Equipped with one or multiple sensors and suitable for line or surface scans, the device is used to check the cleanliness of complex, threedimensional surfaces.
To close the gap between mobile and inline measuring systems, SITA developed the SITA FluoScan 3D in 2015 as a highly automated production-accompanying inspection system. It is used for the automatic inspection of geometrically diverse, three-dimensional components and is based on an inline fluorescence sensor that is positioned quickly and precisely via a three-axis positioning unit. The measuring system is able to inspect large surfaces with high spatial resolution in short
funzionamento più confortevole, oltre che accessori utili per numerose applicazioni. Il 2010 ha visto il lancio sul mercato di SITA clean line CI per l’ispezione in linea della contaminazione dei pezzi nel processo produttivo. Basato sullo stesso principio di misurazione del dispositivo portatile, garantiva l’ispezione al 100% dei componenti. La modularità della tecnologia di misurazione in linea basata su PC industriali in tempo reale ha offerto un facile adattamento alle esigenze specifiche del cliente, per esempio in combinazione con la robotica. Dotato di uno o più sensori e adatto per scansioni in linea o di superficie, il dispositivo è utilizzato per controllare la pulizia di superfici tridimensionali complesse. Per colmare il divario tra i sistemi di misura mobili e in linea, nel 2015 SITA ha sviluppato SITA FluoScan 3D come sistema di ispezione ad elevata automazione che segue la produzione. Viene utilizzato per l’ispezione automatica di componenti tridimensionali geometricamente diversi e si basa su un sensore a fluorescenza in linea che viene posizionato in modo rapido e preciso tramite un’unità di posizionamento a tre assi. Il sistema di misura è in grado di ispezionare grandi superfici con un’elevata risoluzione spaziale in tempi brevi. Utilizzando la scansione di più pezzi, diversi componenti possono essere ispezionati automaticamente in una
The SITA FluoScan 3D inspection system. Il sistema di ispezione SITA FluoScan 3D.
As family business with more than 50 years of experience, we are specialists in the field of aqueous parts cleaning. Our claim unites tradition and innovation, our machines are ecological and energy-efficient. We develop process solutions to customer specifications and serve our customers worldwide through a reliable network of sales partners.
MAFAC – E. Schwarz GmbH & Co. KG · Max-Eyth-Str. 2 · 72275 Alpirsbach · www.mafac.de
SITAtime. Using multi-part scanning, several components can be inspected automatically in just one measuring run. Other features include the configuration of individual measurement sequences, autonomous part recognition through an integrated barcode scanner, the visualisation of large amounts of data and a toolbox for creating report templates for automatic reporting. With the use of digital sensors, the measuring variable fluorescence intensity was introduced in relation to specially developed fluorescence standards.
The fluorescence intensity is measured in RFU (Relative Fluorescence Unit). The SITA fluorescence standards ensure worldwide comparability of sensors calibration across devices and easy handling for fast device check on site. The definition of process-specific limit values for sufficient parts cleanliness and continuous cleanliness inspection enable quality control in parts cleaning and ensure high and stable quality in the process chain.
Since the first device delivery, products have been continuously developed, also thanks to close cooperation with customers. Depending on the field of application and requirements, SITA offers a product range that includes mobile handheld measuring devices and automated production solutions. Configurable as well as specially developed software and comprehensive user support, allow SITA’s devices to be used as customized solutions for quality-assuring and economical process control in industrial production.
sola serie di misurazione. Altre caratteristiche includono la configurazione di singole sequenze di misura, il riconoscimento autonomo dei pezzi attraverso uno scanner di barcode integrato, la visualizzazione di grandi quantità di dati e un toolbox per la creazione di modelli di report per la reportistica automatica. Con l’uso dei sensori digitali, è stata introdotta la misurazione dell’intensità di fluorescenza variabile in relazione con standard di fluorescenza appositamente sviluppati.
L’intensità della fluorescenza è misurata in RFU (Unità di fluorescenza relativa). Gli standard di fluorescenza SITA garantiscono la comparabilità mondiale della calibrazione dei sensori tra i dispositivi e una facile gestione per un rapido controllo del dispositivo in loco. La definizione di valori limite specifici del processo per una sufficiente pulizia dei pezzi e un’ispezione continua della pulizia consentono il controllo della qualità nel lavaggio dei pezzi e garantiscono una qualità elevata e stabile nella catena di processo.
Guidare l’innovazione nelle tecnologie di misurazione a fluorescenza da 15 anni Dalla consegna del primo dispositivo, i prodotti sono stati continuamente sviluppati, anche grazie alla stretta collaborazione con i clienti. A seconda dei campi di applicazione e dei requisiti, SITA offre una gamma di prodotti che include dispositivi di misurazione portatili e soluzioni automatizzate. Il software configurabile e appositamente sviluppato e il supporto utente completo, consentono di utilizzare i dispositivi SITA come soluzioni personalizzate per il controllo di processo di qualità ed economico nella produzione industriale.
The SITA’s team and management: Juliane Schulze and Prof. Dr. Lothar Schulze. Il team e la direzione di SITA: Juliane Schulze e il Prof. Dr. Lothar Schulze. © SITA SITASITA Messtechnik GmbH will provide advice on individual solutions for stable component cleanliness in Hall 4, Booth C18. Visitors to the booth can bring their parts and bath samples, and SITA experts will provide information on suitable measurement methods and will recommend appropriate equipment.
In the field of process liquid monitoring, the SITA DynoTester+ and SITA ConSpector handheld instruments will be on display. The former measures both surface tension and surfactant concentration and sends alerts when set limits are exceeded or not achieved.
The latter monitors the degree of contamination of cleaning and rinsing baths.SITA experts André Lohse, Stefan Büttner and Wolfgang Schmitt will give practical insights on individual process solutions and their applicable measuring technologies at the parts2clean technical forum:
• “Quality Assuring Process Control in Component Cleaning” (André Lohse);
• “Established measurement technology in industrial use - monitoring filmic contamination on component surfaces” (Stefan Büttner);
• “Measuring water contact angle instead of determining “surface tension” - the sense and nonsense of water breakage tests, test ink, contact angle and surface energy” (Wolfgang Schmitt).
SITA Messtechnik GmbH develops, produces and sells devices for measuring the dynamic surface tension of liquids for controlling the surfactant concentration, fully automated foam tester for analysing the foaming behaviour of liquids, fluorescence measuring technique for controlling the cleanliness of parts and for monitoring the contamination level in process liquids as well as devices for testing the wettability by measuring the contact angle. The measuring devices are robust and very easy to operate with. They are used in research, development and manufacturing laboratories of the chemical industry for analysis and quality assurance tasks and in the field of surface technology/parts cleaning for monitoring and controlling processes.
SITA Messtechnik GmbH fornirà la propria consulenza su soluzioni individuali per il lavaggio stabile dei componenti nel pad. 4, stand C18. I visitatori potranno portare i loro componenti e campioni del bagno, gli esperti SITA forniranno informazioni sui metodi di misurazione adatti e consiglieranno il dispositivo appropriato. Nel campo del monitoraggio dei liquidi di processo saranno presentati gli strumenti portatili SITA DynoTester+ e SITA ConSpector. Il primo misura sia la tensione superficiale che la concentrazione di tensioattivi e invia allarmi quando i limiti impostati sono superati o non raggiunti. L’altro monitora il grado di contaminazione dei bagni di lavaggio e risciacquo. Al forum tecnico di parts2clean gli esperti SITA André Lohse, Stefan Büttner e Wolfgang Schmitt forniranno approfondimenti pratici sulle singole soluzioni di processo e sulle relative tecnologie di misura applicabili:
• “Controllo del processo di garanzia della qualità nel lavaggio” (André Lohse);
• “Tecnologia di misurazione consolidata nell’uso industriale - monitoraggio della contaminazione pellicolare sulle superfici dei componenti” (Stefan Büttner);
• “Misurare l’angolo di contatto con l’acqua invece di determinare la “tensione superficiale” - senso e nonsenso dei test di rottura dell’acqua, inchiostro di prova, angolo di contatto ed energia superficiale” (Wolfgang Schmitt).
SITA Messtechnik GmbH sviluppa, produce e vende dispositivi per la misurazione della tensione superficiale dinamica dei liquidi per il controllo della concentrazione di tensioattivi, analizzatori di schiuma completamente automatizzati per l’analisi del comportamento della formazione di schiuma dei liquidi, tecnologie di misurazione a fluorescenza per il controllo della pulizia dei pezzi e per il monitoraggio del livello di contaminazione nei liquidi di processo nonché dispositivi per testare la bagnabilità misurando l’angolo di contatto. I dispositivi di misurazione sono robusti e molto facili da usare. Sono utilizzati nei laboratori di ricerca, sviluppo e produzione dell’industria chimica, per le attività di analisi e garanzia della qualità e nel campo delle tecnologie superficiali e del lavaggio dei pezzi per i processi di monitoraggio e controllo.
C.P.C. Group is a manufacturer of customised automotive and racing components in composite materials. Continuously investing in innovative technologies to optimise its processes, it chose to turn to Teknox for an ambitious project: a cleaning tunnel that would be suitable for all the part shapes it handles and that would integrate perfectly into its workflow.
C.P.C. Group è un’azienda specializzata nella produzione customizzata di componenti per il settore automotive e racing in materiale composito. Caratterizzata da continui investimenti in tecnologie innovative per ottimizzare i propri processi, ha scelto di rivolgersi a Teknox per un ambizioso progetto: un tunnel di lavaggio che fosse adatto a tutte le geometrie di pezzi lavorati dall’azienda e che si integrasse perfettamente all’interno del processo produttivo.
The automotive sector has several souls. High-end and racing cars, in particular, are characterised by a customisation degree that calls for constant and total collaboration among all parties involved in their design and manufacture, in order to adapt production processes to the needs of individual components.
Il settore automotive include diverse anime al proprio interno. Le vetture di alta fascia e da corsa sono caratterizzate da livelli di personalizzazione che necessitano del costante confronto e della totale collaborazione di tutte le aziende coinvolte nella loro progettazione e fabbricazione, al fine di adeguare i processi produttivi alle necessità dei singoli componenti.
A component produced by C.P.C. Group. Un componente prodotto da C.P.C. Group.Some equipment manufactured in-house by C.P.C. Group and one of the coating plants available to the company. Alcune delle attrezzature costruite internamente da C.P.C. Group e uno degli impianti di verniciatura a disposizione dell’azienda.
Leveraging its two strengths, namely innovation and continuous research into technologies aimed at optimising its operations, C.P.C. Group (Modena, Italy) has positioned itself in the automotive and racing market as a trusted partner capable of responding quickly to all industry requirements.
C.P.C. Group is indeed an innovative company that for over sixty years has distinguished itself in the field of prototyping and machining of composite materials for numerous interior and exterior components of high-end vehicles, such as doors, front and rear wings, bonnets, tailgates, OPT carbon look parts, and complete chassis for various sectors, including automotive, racing, industrial, and aeronautics, thanks to the quality and flexibility of its production. “With its R&D expertise in composite materials and structural design, C.P.C. contributes to the success of its customers in various markets. For us, the art of perfection is the ability to think creatively about new technologically advanced solutions as a response to the increasingly complex and specific requirements of ever-changing production sectors:” this is how C.P.C Group describes itself on its website. It has about 850 employees working in four plants and a production capacity of 150,000 finished parts per year.
In order to meet the quality standards imposed by its customers, up
Sfruttando i suoi due punti di forza, ovvero l’innovazione e la continua ricerca di tecnologie per ottimizzare i propri processi produttivi, C.P.C. Group (Modena) si è posizionata nel mercato automotive e racing come un partner di fiducia e capace di rispondere rapidamente a tutte le esigenze del settore.
C.P.C. Group è un’innovativa azienda che da oltre sessanta anni si distingue nel settore delle prototipazioni e delle lavorazioni di materiali compositi di parti interne ed esterne per autoveicoli di alta gamma come portiere, parafanghi anteriori e posteriori, cofani, portelloni, parti OPT in carbon look e telai completi per vari settori quali automotive, racing, mercato industriale e aeronautico grazie alla qualità e alla flessibilità della propria produzione. “Grazie alla propria esperienza nella ricerca e nello sviluppo in materiali compositi e nel design strutturale, C.P.C. contribuisce al successo dei propri clienti in svariati settori di mercato. L’arte della perfezione è per noi la capacità di pensare in modo creativo a nuove soluzioni tecnologicamente avanzate come risposta alle esigenze sempre più complesse e specifiche di settori produttivi in continua evoluzione”, si descrive così sul proprio sito web C.P.C Group – azienda con circa 850 dipendenti suddivisi su quattro stabilimenti e che è in grado di raggiungere una capacità produttiva di 150.000 pezzi finiti all’anno.
until recently it implemented manual cleaning operations to remove sanding dust residues from its components. However, this slowed down production. This is why it relied on Texnox (Prunaro di Budrio, Bologna, Italy) to install a spray cleaning tunnel suitable for its workflow and capable of efficiently cleaning all the parts it manufactures completely in-house, characterised by several different geometries.
Established in 1958 as Modelleria C.P.C., a small artisan company specialising in the creation of wooden foundry patterns processed and planed by hand by thirty operators, it has gradually differentiated and expanded its activity. In the 1990s, it was one of the first Italian companies to specialise in the use of 3D design software, also equipping itself with 5-axis CNC milling machines and implementing stereolithography and sintering for use in wind tunnels. The company therefore changed its name to C.P.C. S.r.l., in order to reflect the radical
Al fine di rispettare gli standard qualitativi imposti dai propri clienti, l’azienda attuava delle operazioni di pulizia manuali per eliminare i residui di polvere di carteggiatura dai propri manufatti, che però rallentavano la produzione. Affidandosi a Texnox, azienda di Prunaro di Budrio (BO), ha perciò voluto installare un tunnel di lavaggio a spruzzo adatto alla propria produzione e in grado di pulire efficientemente tutti i pezzi dalle molteplici geometrie realizzati interamente dall’azienda.
La crescita di C.P.C. attraverso innovazione e lungimiranza Fondata nel 1958 come Modelleria C.P.C., una piccola ditta artigianale specializzata nella creazione di modelli per fonderia in legno lavorati e piallati manualmente da trenta operatori, ha successivamente differenziato e ampliato la propria attività.
Negli anni Novanta fu una delle prime aziende italiane a specializzarsi nell’utilizzo di programmi di progettazione 3D, dotandosi inoltre di fresatrici a controllo numerico a 5 assi e introducendo la stereolitografia e la sinterizzazione per l’utilizzo in galleria del vento. L’azienda
Il convogliatore aereo monorotaia. The one-rail overhead conveyor. ipcmtransformation brought about by its new management and its more innovative and dynamic production flow, focused on prototyping and machining of metals and composite materials for the automotive sector, especially Formula 1.
The far-sighted decision to invest from the outset in state-of-theart machinery such as Stratasys and 3D System plants, in advanced personnel training, and in new, young, and qualified human resources, has enabled C.P.C. to grow steadily and in a structured manner, thus becoming globally recognised for its technical-professional and economic competitiveness. With the aim of further differentiating its target markets and specialising in additional sectors, the company then opened the C.P.C. Engineering division in 1998, the C.P.C. Protoservice division in 2003, and C.P.C. Compositi in 2007.
“We are one of the few European companies capable of carrying out a complete manufacturing cycle of parts in composite materials with any geometry, working alongside our customers from design to delivery and part’s installation on vehicles. Our investments in cutting-edge technology and training have enabled us to become a world leader in the manufacture of products in which laminated or pressed composite
cambiò dunque nome in C.P.C. S.r.l., in modo da riflettere la radicale trasformazione apportata dai nuovi dirigenti e la realtà produttiva più innovativa e dinamica incentrata sulla prototipazione e lavorazione di metalli e compositi per il settore automotive, specialmente Formula 1.
La scelta lungimirante di investire fin da subito in macchinari di ultima generazione quali Stratasys e 3D System, in formazione avanzata del personale e in nuove risorse umane giovani e qualificate, ha permesso a C.P.C. di crescere in modo costante e strutturato – affermandosi a livello globale per la propria competitività tecnico-professionale ed economica.
Con lo scopo di differenziare ulteriormente i propri mercati di riferimento e specializzarsi in ulteriori settori, l’azienda aprì poi la divisione C.P.C. Engineering nel 1998, la divisione C.P.C. Protoservice nel 2003 e C.P.C. Compositi nel 2007.
“Siamo una delle poche realtà europee in grado di eseguire un ciclo completo di fabbricazione su materiale composito per pezzi di qualsiasi geometria, affiancando il cliente dal progetto fino alla consegna del particolare finito e all’installazione sul veicolo. I nostri investimenti in tecnologie all’avanguardia e in formazione avanzata ci hanno permesso di diventare un’azienda leader a livello mondiale nella realizzazione di
material parts are combined with mechanical elements,” says Fabio Torelli, the Painting Division Manager of C.P.C. Group. “Using the most advanced technologies and materials available on the market, C.P.C. creates solutions with excellent performance, capable of meeting customer needs in newer and newer and increasingly precise ways.”
Flexible, diversified, and customisable production C.P.C. Group now produces components with different dimensions and geometries for major Italian automotive brands including Ferrari, Lamborghini, and Maserati.
produzioni in cui particolari in materiale composito laminati o fabbricati attraverso la pressa sono abbinati a parti meccaniche”, esordisce Fabio Torelli, Direttore Painting Division di C.P.C. Group. “Utilizzando le tecnologie e i materiali più all’avanguardia disponibili sul mercato, C.P.C. ha saputo creare soluzioni dalle prestazioni eccellenti, capaci di rispondere in modo nuovo e sempre più preciso ai bisogni dei clienti”.
Una produzione flessibile, diversificata e personalizzabile C.P.C. Group produce oggi componenti dalle dimensioni e geometrie differenti per i principali brand del settore automobilistico italiano, tra cui Ferrari, Lamborghini e Maserati.
ipcm The entrance to the cleaning tunnel designed and built by Teknox. L’ingresso del tunnel di lavaggio progettato e costruito da Teknox. Automotive parts inside the cleaning tunnel. Particolari per il settore automotive all’interno del tunnel di lavaggio.“Carbon moulding takes place in our headquarters in Modena, which also deals with machining processes: we have an ever-evolving pressing department, five clean rooms for lamination, a large bonding area, and a wide area devoted to trimming. We listen to requests, we have our technical department design the parts based on the 3D models received from customers, and then we manufacture them, building finished components ready to be assembled with the other car parts,” explains Torelli.
In addition, in order to provide a complete service, the company has created a Painting Division with more than 200 operators, performing both manual and robotised processes1
“All of our parts must meet high quality standards. This means we must carry out multiple cleaning operations, in order to eliminate any defects that might compromise their high performance and aesthetic levels. As major players in the industry, our customers demand imperfection-free components,” Torelli states.
In the past, the company used articulated robots to clean its components prior to coating, in order to remove carbon dust generated by grinding and abrasion as well as sanding dust. However, due to the variety of dimensions and shapes of the parts handled, additional manual cleaning operations were sometimes required, such as rubbing and brushing with damp cloths to ensure that contaminants were also removed from deep cavities or other difficult-to-reach areas.
“Robots are extremely efficient, but we are required to supply customised products: therefore, in some specific cases, automated cleaning had to be followed by further manual operations. However, we wanted to speed up this production stage and achieve process repeatability and quality consistency. When we acquired a new building for our coating department, therefore, we decided to work with Teknox to design and build a spray tunnel meeting all our cleaning needs and able to subsequently send the dried components to our paint booths in an automatic way”, indicates Torelli.
Featuring an inlet opening with a size of 2,000 millimetres in height by 800 millimetres in width, this 16-metre-long tunnel has been specifically upgraded to handle plastic and carbon parts for any
1 Our article on painting automation at C.P.C. will be published in the ipcm® International Paint&Coating Magazine issue no. 78, due out in November 2022.
“Lo stampaggio del carbonio avviene nella storica sede di Modena, dove hanno luogo anche le lavorazioni meccaniche: abbiamo un reparto in evoluzione per la pressatura, cinque clean-room per la laminazione, una vasta area di incollaggio e un’ampia area dedicata alla rifilatura dei componenti. Ascoltiamo le richieste del cliente, progettiamo insieme al nostro ufficio tecnico i componenti secondo il 3D ricevuto dal cliente e poi li fabbrichiamo, costruendo il particolare finito e pronto per essere assemblato con gli altri componenti del veicolo”, spiega Torelli. Inoltre, al fine di fornire un servizio completo, l’azienda ha creato una Painting Division con circa duecento operatori utilizzando sia processi manuali sia robotizzati1
La necessità di un ciclo di lavaggio riproducibile anche con manufatti customizzati
“Tutti i nostri pezzi devono soddisfare elevati standard qualitativi, che ci impongono di effettuare molteplici operazioni di pulizia al fine di eliminare eventuali difetti che potrebbero incidere negativamente sulle prestazioni dei manufatti e comprometterne l’alto valore estetico. I nostri clienti, essendo i maggiori protagonisti dell’industria, richiedono componenti senza imperfezioni”, commenta Torelli. L’azienda utilizzava robot antropomorfi per le operazioni di pulizia dei propri componenti, al fine di rimuovere la polvere di carbonio generata da molatura ed abrasione e la polvere di carteggiatura, preparandoli così alla successiva fase di verniciatura. Tuttavia, a causa delle differenti dimensioni e geometrie dei pezzi, era necessario a volte effettuare delle ulteriori operazioni di pulizia manuali, strofinando la superficie e spazzolandola con dei panni umidi per assicurarsi di aver eliminato le contaminazioni anche da cavità profonde o altre aree difficilmente raggiungibili dai robot. “I robot sono estremamente efficienti, ma i clienti richiedono manufatti personalizzati, pertanto in alcuni casi specifici le operazioni di pulizia automatizzate devono essere seguite da ulteriori interventi manuali. Volevamo però velocizzare questa fase della nostra produzione e ottenere una riproducibilità delle operazioni di pulizia e una qualità costante. Quindi, quando abbiamo acquisito un nuovo stabilimento per il reparto di verniciatura, abbiamo deciso di collaborare con Teknox per la progettazione e realizzazione di un tunnel di lavaggio a spruzzo predisposto per un ciclo di pulizia che fosse adatto a tutte le nostre esigenze e che potesse traslare automaticamente i componenti asciugati verso le cabine di verniciatura”, aggiunge Torelli.
Il tunnel, lungo 16 metri e con una bocca di ingresso di 2.000 millimetri in altezza per 800 millimetri in larghezza, è stato specificamente aggiornato per trattare particolari in plastica e carbonio per qualsiasi settore, come
1 L’articolo sull’automazione della verniciatura in C.P.C. sarà pubblicato sulla rivista ipcm®_International Paint&Coating Magazine n. 78, in uscita a novembre 2022.
industry, such as carbon bumpers, crankcases, spoilers, roofs, bonnets, and underbodies with many different shapes and sizes. Inside it, the components undergo a cleaning stage with a detergent product dispensed through blade nozzles in a chamber with a 1,500-litre tank, followed by a rinse with demineralised water in a second chamber with an 800-litre tank. A third chamber for compressed air blow-off and an oven with five turbines and 230-m3/hour blowers that reaches a temperature of 150 °C ensure that all components are drained and dried. “The tunnel’s bottom is inclined to facilitate the return of liquids into the tank,” explains Marcello Maffei, Area Manager at Teknox. “Moreover, in order to simplify the personnel’s work in handling very large, complex-shaped components, this tunnel model includes a transport system with a one-rail overhead conveyor, which has a maximum load capacity of 4,000 kilograms and a part support system featuring load bars that accommodate several parts at the same time in order to better support C.P.C.’s production volumes. This allows producing over 3,500 parts per day in two shifts. Finally, staff safety is guaranteed by the presence of several switches to stop the system immediately; the loading and unloading areas – located in the sanding
per esempio i paraurti, i carter, gli spoiler, i tetti, i cofani e le sottoscocche in carbonio di molteplici forme e dimensioni che l’azienda produce. All’interno, i componenti subiscono un lavaggio con detergente erogato tramite ugelli a lama in una camera con vasca da 1.500 litri e un risciacquo con acqua demineralizzata in una seconda camera con vasca da 800 litri. Successivamente, una terza camera per il soffiaggio ad aria compressa e un forno con cinque turbine e soffianti da 230 metri3/ora che raggiunge i 150° C, assicurando così il drenaggio e l’asciugatura di tutti i componenti. “Abbiamo progettato il fondo del tunnel in modo che fosse inclinato, per facilitare il ritorno in vasca dei liquidi”, chiarisce Marcello Maffei, Area Manager di Teknox. “Inoltre, per semplificare le attività del personale – che deve movimentare componenti molto grandi e con geometrie complesse – questo modello di tunnel prevedere un sistema di trasporto con un convogliatore aereo monorotaia che ha una portata massima di 4.000 chilogrammi e un sistema di sostegno dei pezzi tramite bilancelle attrezzate per sostenere più componenti, in modo da supportare meglio il volume produttivo di C.P.C. – che realizza oltre 3.500 pezzi al giorno su due turni lavorativi. Infine, per garantire la sicurezza del personale, sono presenti numerosi interruttori per fermare immediatamente l’impianto, e le zone di
and coating departments respectively and physically separated by a wall – are equipped with weight-sensitive platforms that stop the conveyor’s advance in both areas when they are stepped on.” In addition, the tunnel is equipped with several accessories that improve the sustainability of the cleaning operation, the healthiness of the working environment, and the cost-effectiveness of the entire process: a 50 µm and a 5 µm insulated bag filter in the cleaning bath, two emptying pumps, two detergent dispensers, two pumps recirculating the liquid from the rinsing to the cleaning station, four centrifugal steam condensers, and a kit for abrasive contaminants.
“This investment was made with a view to the future. In fact, we intend to integrate the cleaning tunnel within our sanding and coating plants, thus joining two separate departments and speeding up the entire production cycle. This will improve the speed of our operations because, thanks to Teknox technicians’ helpfulness and professionalism, the high cleanliness degree we achieve is consistent, so much so that additional manual cleaning is no longer necessary,” summarises Torelli.
carico e scarico – posizionate rispettivamente nel reparto di carteggiatura e verniciatura e separate fisicamente da un muro – sono equipaggiate con delle pedane sensibili al peso che interrompono l’avanzamento del trasportatore in entrambe le aree in caso siano calpestate”. Il tunnel è inoltre equipaggiato con molteplici accessori che migliorano l’ecosostenibilità del lavaggio, la salubrità dell’ambiente di lavoro e l’economicità dell’intero processo: due filtri a sacco coibentato nel bagno di lavaggio da 50 e 5 µm, due pompe di svuotamento, due dosatori di detergenti, due pompe di rilancio dal risciacquo al lavaggio, quattro condensatori di vapore centrifugo e un kit per contaminanti abrasivi.
“Questo investimento è stato effettuato in ottica futura: l’obiettivo è infatti quello di integrare il tunnel di lavaggio all’interno dell’impianto di carteggiatura e di quello di verniciatura, unendo così due reparti separati e velocizzare l’intero ciclo produttivo. Potrà migliorare la rapidità delle operazioni, perché, grazie alla disponibilità e alla professionalità dimostrata dai tecnici di Teknox, l’elevato grado di pulizia raggiunto è costante, dunque non sono più necessarie delle ulteriori fasi di pulizia manuale”, conclude Torelli.
The storage area for parts to be pre-approved.
L’area di stoccaggio dei componenti in pre-delibera.
In the wake of rising electricity, oil and gas prices, energy efficiency in parts cleaning has become increasingly important. Opportunities to reduce energy consumption can be implemented in both existing cleaning systems and in those yet to be procured.
Reducing energy consumption and the associated carbon footprint has been an issue for quite some time now. Not least because when banks evaluate companies, the aspect of how well they are positioned to achieve climate protection targets is playing an increasingly important role. However, due to the enormous increase in energy prices in recent months and the uncertain fossil fuel supply situation, saving energy has become an economic necessity.
As a result, companies are looking for potential savings in all areas, and parts cleaning as a quality-assuring manufacturing step is no exception.
Drying is the most energy-intensive step of the cleaning process. Savings here are made possible, among other things, by combining such drying technologies as infrared and vacuum drying.
L’asciugatura è la fase più energivora del processo di lavaggio. È possibile ottenere dei risparmi combinando tra loro alcune tecnologie come l’asciugatura a infrarossi e quella sottovuoto.
Sulla scia dell’aumento dei prezzi di elettricità, petrolio e gas, l’efficienza energetica nel lavaggio industriale sta diventando sempre più importante. Le opportunità per ridurre il consumo energetico possono essere implementate sia nei sistemi di lavaggio esistenti sia in quelli in via di acquisizione.
La riduzione del consumo energetico e dell’associata impronta di carbonio è un problema ormai da tempo. Anche perché nella valutazione aziendale da parte delle banche, il posizionamento della società rispetto al raggiungimento degli obiettivi di protezione ambientale ha un ruolo sempre più importante. Tuttavia, a causa dell’enorme aumento dei prezzi dell’energia negli ultimi mesi e dell’incertezza nell’approvvigionamento di combustibili fossili, risparmiare energia è diventata una necessità economica. Di conseguenza, le aziende stanno cercando potenziali risparmi in tutti gli ambiti e il lavaggio industriale, come fase produttiva che garantisce la qualità, non è da meno.
The most energy-saving and cost-effective cleaning is the cleaning that does not need to be done. Conversely, the less cleaning required to achieve the specified technical cleanliness, the lower the energy demands and costs. In addition to the choice of the right cleaning method and process, this is why the amount of contamination introduced influences the energy and time required. In many cases, savings potentials can be exploited cost-effectively without any technical changes to the plant, including checking the partspecific process parameters once they have been defined. They are usually defined on the basis of a worst-case part, resulting in treatment times of ten to 15 minutes or even longer for cleaning, rinsing and drying. However, since the vast majority of workpieces to be cleaned are much less dirty, energy and time are wasted – these parts are cleaned for longer than necessary. If it is possible to avoid worst-case parts and to transport workpieces into the plant with as little contamination as possible, treatment times can be significantly shortened and energy consumption reduced accordingly.
Il lavaggio non deve essere valutato in modo isolato Il lavaggio più efficiente dal punto di vista energetico ed economico è quello che non necessita di essere fatto. Per contro, minore è il lavaggio necessario a soddisfare le specifiche tecniche, minori saranno la richiesta energetica e i relativi costi. Oltre alla scelta del giusto processo di lavaggio, la quantità di contaminanti presenti influenza il tempo e l’energia richiesti. In molti casi i potenziali di risparmio possono essere sfruttati in modo economicamente vantaggioso senza modifiche tecniche all’impianto, compreso il controllo dei parametri di processo dopo la loro definizione. Questi sono solitamente definiti basandosi sull’ipotesi di contaminazione peggiore, con tempi di trattamento da 10 a 15 minuti - o anche di più - per lavaggio, risciacquo e asciugatura. Tuttavia, poiché la maggior parte dei manufatti è solitamente molto meno sporca, vi è uno spreco di tempo ed energia – i componenti sono lavati più a lungo del necessario. Se fosse possibile evitare questo metodo e trasportare i componenti all’impianto con la minor contaminazione possibile, si potrebbero accorciare in modo significativo i tempi di lavaggio e quindi il consumo di energia.
Condensation drying with heat exchangers makes it possible to significantly reduce energy consumption as well as CO2 emissions. Drying is carried out at temperatures between 20 and 90 °C, depending on the part and the application.
L’asciugatura a condensazione con scambiatori di calore permette di ridurre notevolmente il consumo di energia e le emissioni di CO2 Avviene a temperature comprese tra 20 e 90 °C, a seconda del componente e del tipo di applicazione.
This directs attention to the optimization of pre-processes, whereby each production step must be examined from the point of view of technical cleanliness. The goal is to minimize and keep the net contamination before cleaning constant. One measure here can be, for example, a simple intermediate cleaning step in production by blowing off or counter-rinsing with a clean machining medium that is already available. In addition to improved energy efficiency, this approach makes it possible to maintain and secure a certain level of quality. At the same time, the reduced dirt load reduces the energy required for media preparation.
As far as plant and process engineering are concerned, there are a wide variety of measures that help to reduce energy consumption. To prevent or minimize heat loss, for example, piping and relevant system components should be well insulated. Optimized mechanical processes that enable more effective and faster cleaning of particulate and filmic contaminants also offer promising approaches. For example, kinematic cleaning and drying, in which the basket and nozzle systems rotate in the same direction or in opposite directions, can, compared with static
Questo sposta l’attenzione all’ottimizzazione dei pre-processi, dove ogni fase produttiva deve essere esaminata dal punto di vista del livello di pulizia tecnica. L’obiettivo è minimizzare e mantenere costante la contaminazione netta prima del lavaggio. Un’opzione potrebbe essere una semplice pulizia intermedia mediante soffiaggio o contro-risciacquo con un prodotto di lavorazione pulito e già disponibile. Oltre a una migliore efficienza energetica, questo approccio dà la possibilità di garantire e mantenere un certo livello di qualità. Allo stesso tempo, la riduzione dello sporco riduce l’energia richiesta per la preparazione del prodotto di lavaggio.
Opzioni di ottimizzazione dell’impianto Per quanto riguarda l’impiantistica esiste un’ampia varietà di misure che possono aiutare a ridurre il consumo di energia. Per prevenire o minimizzare la dispersione di calore, per esempio, le tubazioni e i componenti rilevanti del sistema dovrebbero essere ben isolati. Anche i processi meccanici ottimizzati, che consentono una più efficiente e più rapida eliminazione dei contaminanti particellari e pellicolari, offrono degli approcci promettenti. Lavaggio e asciugatura cinematici ad esempio, nei quali il cesto e gli ugelli ruotano nella stessa direzione
nozzle systems, save up to 20 percent in terms of the process-specific energy requirements of the machine. The positioning of the parts in the working chamber also influences the energy consumption. They should be easily accessible from all sides for the medium and the process mechanics. This can be achieved by designing the bogie as open as possible in the working chamber. In the case of such units as pumps, frequency control ensures that they do not constantly run at maximum power and thus waste energy. Speaking of continuous operation: Software solutions for efficient energy management, which, for example, shut down the plant to a “real” standby mode during breaks in operation or times when no goods are available, can save a lot of electricity and money. Depending on the design, their use requires effective production planning so that the system is ready for operation when needed. Especially in new plants, the required pump capacity can be noticeably reduced if the piping is routed with fewer bends, angles and kinks. This does, however, require a little more floor space. When it comes to heating the cleaning and rinsing baths, heat recovery solutions, heat pumps and heat exchangers ensure that the energy used is kept in circulation and does not have to be constantly replenished.
o in direzioni opposte, possono, rispetto ai sistemi con ugelli statici, far risparmiare fino al 20% in termini di richiesta energetica della macchina. Anche il posizionamento dei manufatti nella camera di lavaggio influenza il dispendio energetico. Questi dovrebbero essere accessibili da tutti i lati da parte del prodotto di lavaggio e delle meccaniche del processo. Questo si può ottenere progettando il carrello in modo che sia il più aperto possibile all’interno della camera. Nel caso di unità come le pompe, il controllo della frequenza garantisce che queste non funzionino sempre alla massima potenza sprecando energia. A proposito di operazioni in continuo: i software di gestione dell’efficienza energetica che, per esempio, mettono l’impianto in standby durante i fermi operativi o quando non sono presenti prodotti, possono far risparmiare molta elettricità e molto denaro. A seconda del design, il loro utilizzo richiede un’efficace pianificazione della produzione, di modo che il sistema sia pronto a funzionare quando necessario. Soprattutto nei nuovi impianti, la capacità richiesta della pompa può essere notevolmente ridotta se le tubazioni vengono posate con meno curve, angoli e attorcigliamenti. Questo tuttavia richiede uno spazio più ampio sul pavimento. Quando si tratta di riscaldare i bagni di lavaggio e risciacquo, le soluzioni di recupero del calore, le pompe e gli scambiatori di calore garantiscono che l’energia utilizzata rimanga in circolazione e che non debba essere costantemente reintegrata.
Developments such as the Heat X heat exchange module make it possible to couple in heat from external sources, including solar thermal and process heat. The costs for these solutions are still comparatively high in some cases, but due to the rise in energy prices, the payback period is shortening noticeably.
Component drying is the largest energy consumer, especially when cleaning with water-based media. This is why more effective drying technologies offer a comparatively large potential for energy savings. Approaches include the combination of infrared and vacuum drying as well as steam drying. Depending on the parts and the application, condensation drying with a heat pump takes place in a temperature range between 20 and 90 °C. With these solutions, savings of 75 percent and more can be achieved compared to conventional hot air drying. These options can be implemented as a stand-alone drying system or integrated into the working chamber of the cleaning system.
Sviluppi come il modulo di scambio calore Heat X consentono di accoppiare il calore da fonti esterne, incluso il calore solare e quello di processo. Il costo di queste soluzioni è ancora relativamente elevato, ma considerato il forte aumento dei prezzi dell’energia il periodo di ammortamento si è ridotto notevolmente.
Asciugatura – la fase più energivora L’asciugatura è la fase più energivora in assoluto, soprattutto nel lavaggio con prodotti a base acqua. Motivo per cui tecnologie di asciugatura più efficienti offrono un vasto potenziale di risparmio energetico. Tra gli approcci possibili la combinazione tra asciugatura a infrarossi e sottovuoto, nonché l’asciugatura a vapore. A seconda dei componenti e del tipo di applicazione, l’asciugatura a condensazione con pompa di calore avviene a temperature tra i 20 e i 90 °C. Queste opzioni si possono implementare sottoforma di sistemi di asciugatura a sé stanti oppure integrati nella camera di lavaggio.
The cleaning container plays an important role in terms of both energy and quality. In this case, boxes made of galvanized perforated sheeting are counterproductive. They prevent the process mechanics from reaching the parts without restriction, which prolongs the cleaning time. The dripping behaviour is also worse, which makes significantly longer and thus more energy-intensive drying processes necessary. Cleaning baskets made of round wire, which ensure good accessibility from all sides, are optimal.
Depending on the parts, the technical cleanliness required and the possibilities to reduce the input contamination by optimizing the pre-processes, the question arises in many cases as to whether wet chemical cleaning is necessary or whether the requirements can be fulfilled using alternative, dry cleaning processes, including plasma, laser, CO2 snow jet or steam cleaning. In applications that require only partial cleaning, e.g. a bonding, sealing, coating or assembly process, these solutions, which can be easily integrated into the production process, offer more than just energy advantages over conventional all-over cleaning. Plant manufacturers provide support in the optimum design of cleaning processes and parameters and in the optimization of preprocesses, e.g. by offering process analyses and other services.
The development of innovative solutions for the digitalization of cleaning processes and the use of artificial intelligence for the demand-oriented adjustment of cleaning are further steps taken by the manufacturers for energy-efficient and CO2-reduced operation. The intelligent networking of building, supply and production technology also contributes to this.
The exhibitors at parts2clean will inform about solutions to reduce energy consumption and the carbon footprint
Un contenitore adatto rIduce il dispendio energetico
Il contenitore gioca un ruolo importante in termini energetici e qualitativi. In questo caso i contenitori in lamiera forata zincata sono controproducenti. Impediscono alla meccanica di processo di raggiungere i componenti senza restrizioni, allungando i tempi di lavaggio.
Anche il gocciolamento risulta peggiore, aumentando i tempi di asciugatura e l’associato dispendio energetico. I cestelli a filo tondo, che garantiscono una buona accessibilità da tutti i lati, sono la soluzione ottimale.
Lavaggio a secco – un’alternativa a risparmio energetico
A seconda dei componenti, dei requisiti di pulizia e della possibilità di ridurre i contaminanti ottimizzando i pre-processi, in molti casi ci si chiede se sia necessario il lavaggio a umido o se si possa utilizzare in alternativa un processo a secco quale lavaggio con plasma, laser, neve di CO2 o vapore. Nelle applicazioni che richiedono solo un lavaggio parziale (incollaggio, sigillatura, verniciatura o assemblaggio) queste soluzioni, che si possono facilmente integrare nel processo produttivo, offrono anche più del semplice vantaggio energetico rispetto al tradizionale lavaggio completo.
Gli impiantisti offrono supporto nella preparazione ottimale di processi e parametri di lavaggio e nell’ottimizzazione dei pre-processi, offrendo analisi e altri servizi.
Lo sviluppo di soluzioni innovative per la digitalizzazione dei processi di lavaggio e l’utilizzo della IA per l’adattamento orientato alla domanda del processo di lavaggio sono ulteriori step intrapresi dai produttori per un funzionamento efficiente dal punto di vista del consumo energetico e dell’emissione di CO2. A questo contribuisce anche il networking tra tecnologia di costruzione, di fornitura e di produzione.
Gli espositori di parts2clean forniranno informazioni sulle soluzioni per ridurre il consumo energetico e l’impronta di carbonio
Stuttgart Exhibition Centre Stuttgart (Germany) 11 - 13 October 2022
parts2clean showcases a complete range of needs-based configurations and systems for optimized cleaning processes that is unmatched worldwide.
Snow for maximum cleanliness in high-purity components
Whether stricter cleanliness specifications for high-tech parts or pre-assembled components, for example with electronic attachments, in many high-purity applications in cleanrooms increased cleanliness requirements can no longer be met with previously used cleaning processes. In these cases, the efficient quattroClean snow jet technology enables the dry and reliable cleaning using climate-neutral carbon dioxide. Thanks to the interaction of the four active mechanisms (thermal, mechanical, solvent and sublimation effect) of the process, particulate contamination down to the sub-micrometer range as well as filmic contamination are removed in a dependable and reproducible manner. Complete process monitoring and control ensures that each part is cleaned with the validated process parameters. The design of the cleaning systems is adapted to the respective cleanroom class.
acp systems AG 71254 Ditzingen, Germany, Phone +49 7156 480140, www.acp-systems.com Hall 4, Stand B04
Ecoclean is responding to the changing requirements in industrial parts cleaning with greater diversification of its product and service portfolio. Thus, in addition to cleaning equipment and systems for classic tasks in various industries, optimally adapted solutions for high-purity applications, for example components for DUV and EUV technology, for vacuum technology systems (UHV, XHV, UCV), and precision optics are the focus of the company’s trade fair presentation at this year’s parts2clean (hall 4, booth C26). Furthermore, turnkey solutions for cleaning and sterile packaging of medical devices in compliance with MDR and FDA requirements will be featured. Among other things, the Customer Service Station will provide information on future-oriented services, the service app, and ways to make cleaning more energy efficient.
Process transparency through online monitoring of bath and cleaning media concentration
With LiquidSens, SensAction, a brand of Endress+Hauser Flow Deutschland AG, presents an efficient measuring system for precise and reliable online monitoring of the concentration of cleaning media, hardening polymers and corrosion protection products in liquids – even in integrated or Industry 4.0 manufacturing. Even the smallest changes are measured and recorded. An app concept allows the system to be easily and quickly adapted to different applications. In addition, the LiquidSens Mobile is a mobile device for the random monitoring of cleaning systems. The user interface and the memory management have been specially designed for monitoring multiple cleaning systems. Adaptation to the respective application is also simple via media apps.
Nozzles for optimum cleaning performance and efficiency
Eurospray provides a wide range of cleaning solutions for food, beverage, automotive, chemical, pharma, and industrial fields; worldwide. Washing applications depend on many factors such as the cleaning application type, the residue to be removed, and the temperature and sprayed product type. The flat spray nozzle is the most common nozzle for these applications. It delivers a medium force impact spray making it perfect for rinsing and cleaning applications with light to moderate residue. On the other hand, a high-impact nozzle, designed to maximize impact force, is excellent for applications with embedded residue. For applications that require wide cleanings, such as tank cleaning, the ideal solution is rotating washing heads that provide full coverage up to 360° and effective cleaning.
Ecoclean GmbH 70794 Filderstadt, Germany, Phone +49 711 70060, www.ecoclean-group.net Hall 4, Stand C26
Endress+Hauser Flow Deutschland AG 96450 Coburg, Germany, Phone +49 9561 976230, www.sensaction.de Hall 4, Stand C43
Eurospray Spray and Filter Technology S.L. 08970 Sant Joan Despi, Spain, Phone +34 934 773846, www.euspray.com Hall 4, Stand D32
Expert know-how, knowledge transfer and an award for parts cleaning
The Fachverband industrielle Teilereinigung (FiT) e. V. will be coming up with an attractive program at this year’s parts2clean. In addition to support in the form of basic knowledge and recommendations for action, as well as cross-technology initial advice for versatile tasks in industrial parts cleaning, there will be plenty on offer in the action area of the FiT booth. This includes presentations on the latest trends and developments as well as an exciting program of lectures on trend-setting topics. One of the highlights will be the first-ever presentation of the FiT2clean Award on October 13. The award, worth 10,000 euros, recognizes outstanding achievements and solutions to a current challenge in industrial parts cleaning. The FiT2clean Award will be presented annually in the future.
High electricity costs make cleaning parts economically more difficult. Energy efficiency is therefore high on the agenda at Höckh Metall-Reinigungsanlagen GmbH. “With energy efficient and frequency controlled components, intelligent heating adjustment as well as standby mode our Multiclean systems are the first choice to continually ensure technical cleanliness in an economical way”, David Bartels, Head of Laboratory / Process Engineering / Sales at Höckh Metall-Reinigungsanlagen explains. Trade fair visitors can also find out how their parts cleaning machines can communicate with the ERP system via OPC-UA and which advantages this offers. News about Artificial Intelligence in parts cleaning round off the company’s presentation at parts2clean.
New cleaning system with focus on ergonomics and efficiency
At parts2clean, Noyen will present the Compact 100, a new cleaning system designed with ergonomics and efficiency in mind. It makes installation and technical checks of the machine quick and easy. The working chamber is equipped for spray, immersion and ultrasonic cleaning processes. A precise filter system ensures a long service life of the cleaning medium and in addition thermal insulation saves energy. The touchscreen control panel with simple user interface makes working with the machine intuitive. The new cleaning system reliably meets ISO 16232 and VDA 19.1 cleaning standards. The machine’s automation monitors every parameter. To increase productivity and reduce costs, the cleaning system can be further optimized at any time.
Fachverband industrielle Teilereinigung (FiT) e. V. Geschäftsstelle 72639 Neuffen, Germany, Phone +49 7025 8434-100, www.fit-online.org
Hall 4, Stand B01 + C01
HÖCKH Metall-Reinigungsanlagen GmbH 75305 Neuenbürg, Germany, Phone +49 7082 41093110
www.hoeckh.com
Hall 4, Stand C42
NOYEN Sp. Z. o. o. 20-270 Lublin, Poland Phone +48 81 7450598
www.noyen.com Hall 4, Booth D49
Effective, gentle and reliable ultrasonic cleaning of sensitive components
With the Sonopower 3S Megasonic Boost system with frequencies of 500 and 1,000 kHz, Weber Ultrasonics has developed an efficient solution for the demanding cleaning of sensitive components. It ensures particularly gentle and at the same time effective treatment of components with high degrees of cleanliness. The system consists of the intelligent Sonopower 3S Megasonic Boost generator and the tuned Sonoplate HF high-frequency transducers. In operation, the generator, which is available in 250 and 500 watt power classes, uses various innovative features to ensure that cleaning is gentle on the surface but reliably removes contaminants. The combined frequency and amplitude modulation ensures homogeneous sound fields and prevents so-called standing waves. The Sonoscan automatically determines the optimum working frequency, adjusts system settings accordingly and during the process the frequency can be continuously monitored and automatically adjusted. Integration into higher-level plant control systems is achieved via optional fieldbus interfaces, such as Profinet, Ethercat and ModBus TCP.
With the VRX 46 V, Wigol W. Stache GmbH introduces a new, acidic cleaner that has been designed especially for applications on aluminum surfaces. The non-foaming cleaner can be used in spray and pressure liquid circulation cleaning systems. It offers good demulsifying properties. Emulsions, metal soaps, processing oils and dried emulsion residues are reliably removed. A specially adjusted acid mixture also ensures a slight and attractive brightening of aluminum surfaces. AF 03, a water-soluble, temporary anticorrosive, is suitable as a protective measure for corrosion-sensitive steel materials and cast iron. It can be used at high injection pressure and if higher demands are placed on corrosion prevention. The demulsifier VRX P1 is an efficient additive for breaking oil-in-water emulsions. It supports removal of oils and grease if gravity separators are connected to the cleaning system.
Weber Ultrasonics AG 76307 Karlsbad, Germany
Phone +49 7248 92070 www.weber-ultrasonics.com Hall 4, Stand D42
WIGOL W. Stache GmbH 67547 Worm, Germany
Phone +49 6241 41410, www.wigol.de Hall 4, Stand D52
High requirements have to be met for both the production and the cleaning of complex machined precision parts.
Sia la produzione che il lavaggio di complessi componenti di precisione devono soddisfare requisiti molto elevati.
The production of high-precision parts with complex interior geometries requires top quality along the entire production chain. In order to be optimally prepared for future cleanliness requirements, a Swedish manufacturer replaced one of its existing solvent cleaning systems. They chose an Ecoclean EcoCcompact fitted with Ultrasonics PLUS, to mention only one of the system’s features.
When company founder Willy Loeffel came from Switzerland to Växjö in Sweden in 1956, he brought entrepreneurial spirit, extensive technical know-how in the operation of sliding spindle lathes and high quality awareness with him. He combined these qualities with the Swedish business culture to create a company which has been setting standards in the industry to this day. The business which is family-run in the second generation specializes in machining of small complex precision products for partly critical applications in the fields of medical and power engineering, valve technology and general industry.
La produzione di componenti di alta precisione con complesse geometrie interne richiede il massimo della qualità lungo l’intera catena produttiva. Al fine di poter soddisfare in modo ottimale le specifiche di lavaggio future, un produttore svedese ha sostituito uno dei suoi sistemi di lavaggio a solvente scegliendo EcoCcompact di Ecoclean, dotato di Ultrasonic PLUS, per citare solo una delle tante caratteristiche del sistema.
Quando Willy Loeffel, il fondatore dell’azienda, si spostò dalla Svizzera a Växjö (Svezia) nel 1956 portò con sé spirito imprenditoriale, un vasto know-how tecnico sul funzionamento dei torni a mandrino scorrevole e la consapevolezza dell’alta qualità. Combinò queste qualità con la cultura imprenditoriale svedese, per creare un’azienda che ha finora fissato gli standard di settore. L’azienda, alla seconda generazione di conduzione familiare, è specializzata nella lavorazione di piccoli e complessi componenti di precisione per importanti applicazioni nell’ingegneria medica ed energetica, nella tecnologia delle valvole e nella general industry.
DORIS KorntalThe system concept as well as numerous features available as standard options such as the three flood tanks for the Wash, Rinse/Rinse or Preserve process steps were major decision criteria in favour of the EcoCcompact.
La scelta di EcoCcompact è stata dettata principalmente dal concept di sistema e dalle sue numerose caratteristiche opzionali, come le tre vasche per lavaggio, risciacquo/risciacquo o conservazione.
Since the beginning Willo has been experiencing in average two digit growth rates in these business fields. This is why its production area will be extended by approx. 1,500 square meters within the next two years with the construction of a new building. State-of-the-art machinery including innovative measuring technology for constant production monitoring of precision parts made of different steel alloys, aluminium, titan, copper, brass and plastics among others ensures that even tightest tolerances are observed. ‘This also concerns parts cleaning where particles and residues of machining oil have to be removed from exterior and interior part contours. On the one hand, the quality of downstream processes such as heat treatment or coating depends on this cleanliness. On the other hand, the observance of defined cleanliness specifications in final cleaning is a must for both potential further processing in validated processes at our customers’ and for the function of the parts in the final product’, explains Peter Hultkvist, technical manager at Willo.
For parts cleaning the company has been using Ecoclean solvent
Sin dall’inizio Willo ha registrato in questi settori tassi di crescita media a due cifre, motivo per cui amplierà la sua superficie produttiva di circa 1.500 m2 entro i prossimi due anni, con la costruzione di un nuovo edificio.
Dei macchinari all’avanguardia, tra cui un’innovativa tecnologia di misurazione per il monitoraggio continuo dei componenti di precisione realizzati in diverse leghe di acciaio, alluminio, titanio, rame, ottone e plastica, garantiscono il rispetto delle più rigide tolleranze. “Questo aspetto riguarda anche il lavaggio dei manufatti, dalle cui aree esterne e interne è necessario rimuovere i residui particellari e degli oli di lavorazione. Da un lato, la qualità dei processi a valle quali trattamento termico e verniciatura dipende dal livello di pulizia. Dall’altro lato, il rispetto di determinate specifiche di pulizia nel lavaggio finale è un must, sia per le potenziali lavorazioni future validate presso i nostri clienti, sia per il funzionamento dei componenti nel prodotto finale”, spiega Peter Hultkvist, Direttore Tecnico di Willo.
Requisiti di qualità e stabilità di processo più elevati Per il lavaggio dei componenti l’azienda si affida da più di vent’anni ai sistemi a solvente di Ecoclean.
Due to the future-oriented scanner system with integrated software, the cleaning system can be interfaced with the MES at any time. Grazie al suo sistema di scansione orientato al futuro con software integrato, il sistema di lavaggio si può interfacciare con il MES in qualsiasi momento.
cleaning systems for more than two decades. When the almost 25 years old system was to be replaced, it was clear that the new cleaning system had to meet not only present, but also future cleanliness requirements flexibly and reproducibly. ‘It was important for us that we would be optimally prepared for our customers’ future higher demands regarding particle and film-type cleanliness specifications, process consistency and productivity. Maximum process stability as well as being prepared for automatic data transfer to our MRP were further requirements’, explains Peter Hultkvist. Another criterion was the best possible use of the available production time by optimally selecting the cleaning steps used in the system. They talked about these issues with several cleaning system manufacturers.
The fact that they opted for Ecoclean’s EcoCcompact was due both to the system concept and its optional features and their good experience with the manufacturer’s systems and service as well as advice and support based on their cleaning know-how.
The compact solvent cleaning system which only needs 3,200 x 1,600 x 2,450 mm (L x B x H) of space, operates under full vacuum. At Willo’s it is used with the hydrocarbons they have been using so far, however it
Quando è giunto il momento di sostituire il sistema vecchio di quasi 25 anni, è stato chiaro che il nuovo sistema avrebbe dovuto soddisfare i requisiti di lavaggio attuali ma anche futuri, in modo flessibile e riproducibile. “Per noi era importante essere preparati in modo ottimale alle future e più rigide domande dei nostri clienti in merito alle specifiche di pulizia da contaminanti particellari e pellicolari, all’omogeneità e alla produttività. Ulteriori esigenze erano la massima stabilità del processo e il poter trasmettere in automatico i dati al nostro MRP”, spiega Peter Hultkvist. Un altro criterio era il miglior utilizzo possibile del tempo produttivo disponibile tramite la selezione ottimale delle fasi di lavaggio da utilizzare. L’azienda ha discusso di questi argomenti con numerosi impiantisti.
La scelta è ricaduta su EcoCcompact di Ecloclean per il concept del sistema e le sue caratteristiche opzionali, per la positiva esperienza già avuta con i prodotti e servizi di Ecoclean, nonché per il supporto fornito grazie al suo know-how.
Investimento a prova di futuro grazie all’elevata flessibilità
La compatta macchina di lavaggio a solvente, che necessità di soli 3.200 x 1.600 x 2.450 mm di spazio, funziona in pieno vuoto. Willo utilizza gli idrocarburi che ha sempre usato, ma il sistema può funzionare anche
ABcan also easily be operated with modified alcohols (semi-polar solvents) subject to minor modifications. The company opted for a standard machine configuration with three fully integrated flood tanks for the process steps wash, rinse/rinse or preserve.
Depending on type, parts are supplied in bulk or arranged in part carriers and treated in accordance with one of the ten programs stored in the machine control system and which are currently still selected manually. For interfacing with the company’s MRP, the machine is equipped with a future-oriented scanner system with integrated software.
In accordance with the selected cleaning program, the parts can be degreased with vapour before the actual cleaning process. With this technology, the spent solvent is not piped into the flood tank, contrary to common practice, but directly into the distillation unit integrated as a standard feature. This is done to counteract oil accumulation in the solvent. What is more, vapour-degreasing with wash fluid as final cleaning step is feasible.
con alcoli modificati (solventi semi-polari) sottoposti a lievi modifiche.
L’azienda ha optato per una configurazione standard della macchina, con tre vasche completamente integrate per lavaggio, risciacquo/ risciacquo o conservazione.
A seconda della tipologia, i componenti sono sfusi o disposti in cestelli portapezzi e trattati in base a una delle dieci ricette di lavaggio memorizzate nel sistema di controllo della macchina e, al momento, ancora selezionate manualmente. Per l’interfaccia con l’MRP dell’azienda la macchina è dotata di un sistema di scansione con software integrato.
A seconda della ricetta selezionata i componenti possono essere sottoposti a sgrassaggio a vapore prima del lavaggio vero e proprio.
Con questa tecnologia il solvente esausto non viene convogliato nella vasca come accade di solito, bensì nell’unità di distillazione integrata.
Questo per contrastare l’accumulo di olio nel solvente.
Inoltre, è possibile lo sgrassaggio a vapore come fase di lavaggio finale.
from complex interior part geometries.
Ultrasonic PLUS – complementare al classico processo a ultrasuoni – assicura un’affidabile rimozione dei contaminanti anche da manufatti con geometrie interne complesse.
The Ultrasonics PLUS feature - complementing the classical ultrasonic process - ensuresTo ensure reproducible cleanliness results in line with user requirements and increasing demands, the system features the Ultrasonics PLUS option in addition to the standard injection flood wash and ultrasonic processes. In contrast to classical ultrasonic cleaning which takes place under consistent work chamber system pressure, the pressure of the Ultrasonics PLUS process varies and adapts to the part geometry and degree of soiling. Due to these pressure changes, the formation of cavitation bubbles is adapted to the parts requirements so that they also get to interior areas that are not reached with conventional ultrasonic processes. Therefore Ultrasonics PLUS effectively complements classical ultrasonics especially when it comes to parts with complex interior part geometries. Vacuum drying ensures that the parts leaving the machine are completely dry.
The media reconditioning features of the EcoCcompact also contribute to high cleaning quality and process stability. Each tank has a full-flow filtration in the supply and return lines as well as an additional bypass filtration. The combined systems design enables the user to choose filter bags or cartridge filters without having to change the housing. To remove as many chips as possible from the wash fluid after cleaning, bag filters with integrated magnetic separation are mounted in the filtration system of flood tank 1. The other two filtration circuits have cartridge filters which can remove even ultrafine particles from the fluid.
‘We have been using the new EcoCcompact since February 2022 and are achieving cleaning results that will surely be meeting our customers’ future demands’, concludes Peter Hultkvist.
From left to right: Linda Ohlin (Project Manager), Håkan Svensson (Operator) and Peter Hultkvist (Technical Manager).
Da sinistra a destra: Linda Ohlin (Project Manager), Håkan Svensson (Operatore) e Peter Hultkvist (Technical Manager).
Per garantire risultati di lavaggio riproducibili in linea con le crescenti richieste dei clienti, il sistema è dotato dell’opzione Ultrasonic PLUS, che si aggiunge ai processi standard di lavaggio a iniezione e a ultrasuoni. Rispetto al classico lavaggio a ultrasuoni, che avviene con pressione costante della camera, la pressione del processo Ultrasonic PLUS varia e si adatta alla geometria del manufatto e al grado di sporco. Grazie a queste variazioni di pressione la formazione delle bolle di cavitazione si adatta al componente in modo che le bolle raggiungano aree non accessibili con i processi a ultrasuoni tradizionali. Ultrasonic PLUS è quindi complementare agli ultrasuoni classici nel caso di manufatti con geometrie interne complesse. L’asciugatura sottovuoto garantisce che i componenti escano dalla macchina completamente asciutti.
Ricondizionamento del prodotto di lavaggio adattato a requisiti elevati Anche le caratteristiche di ricondizionamento di EcoCcompact contribuiscono all’elevata qualità e stabilità del processo. Ogni vasca ha una filtrazione a pieno flusso nelle linee di alimentazione e recupero, nonché una filtrazione bypass aggiuntiva. Il design del sistema permette all’utilizzatore di scegliere tra filtri a maniche o a cartuccia senza doverne cambiare l’alloggiamento. Per rimuovere il maggior numero di trucioli dal fluido di lavaggio, nel sistema di filtrazione della vasca 1 sono montati filtri a maniche con separazione magnetica integrata. Gli altri due circuiti di filtrazione hanno filtri a cartuccia in grado di rimuovere dal fluido anche le particelle ultrafini. “Utilizziamo il nuovo EcoCcompact dal febbraio 2022 e stiamo ottenendo risultati di lavaggio che sicuramente soddisferanno le richieste future dei nostri clienti”, conclude Peter Hultkvist.
A cleaning plant supplier with in-depth know-how in the formulation of effective detergents for treating car and motorbike components was the ideal partner that TCN Vehicles Division (Alba, Cuneo, Italy) was looking for in order to achieve the high cleanliness levels required by its customers. Thanks to a careful initial co-design phase, STS Srl was able to fully meet its needs.
Un impiantista di lavaggio con un profondo know-how nella formulazione di detergenti efficaci per il lavaggio di componenti automotive e motociclo era il partner che TCN Vehicles Division di Alba (Cuneo) cercava per ottenere gli elevati livelli di pulizia richiesti dai propri clienti: grazie ad un’attenta fase iniziale di co-progettazione, STS srl ha soddisfatto appieno questa ricerca.
f we trace back the history of industrial cleaning and the development of its applications, we realise that only fifteen years ago the motorbike and automotive industry was hardly interested in it,” says Claudio Capello, the technical department manager of TCN Vehicles Division, producing aluminium structural components exactly for this market. “Then, the sector gradually begun to implement cleaning operations to remove machining residues. And today, most car shock absorber components have cleaning requirements that can only be achieved with specific technologies, making cleaning a strategic and indispensable process.”
e ripercorriamo la storia del lavaggio industriale e lo sviluppo delle sue applicazioni ci rendiamo conto che solo 15 anni fa il settore moto e automotive non ne era praticamente interessato” – esordisce così Claudio Capello, responsabile dell’ufficio tecnico di TCN Vehicles Division, che produce componenti strutturali in alluminio per questo mercato. “Il nostro settore ha iniziato gradualmente a introdurre le operazioni di lavaggio per la rimozione dei residui derivanti dalle lavorazioni meccaniche e oggi la maggior parte della componentistica dei sistemi di ammortizzazione delle auto presenta requisiti di pulizia raggiungibili solo con alcune tecnologie di lavaggio, che si è trasformato in un processo strategico e imprescindibile”.
The metal parts produced by TCN Vehicles Division. I particolari metallici prodotti da TCN Vehicles Division.
TCN Vehicles Division’s effective cleaning solution arose from careful co-design with the media and system supplier
The machining process with anthropomorphic robots and the technical office for quality control.
Il reparto di lavorazione meccanica con robot antropomorfi e l’ufficio tecnico per il controllo della qualità.
TCN Vehicles Division belongs to one of the most advanced industrial clusters in the Piedmont region and beyond, the TCN Group (Alba, Cuneo, Italy), which includes numerous companies operating in the most diverse areas – production of machinery for the textile, packaging, and industrial automation sectors, precision machining of aluminium for the motorbikes and cars (the industry in which TCN Vehicles Division has been active since 2001), food sector, and production of electric quadricycles for sustainable mobility (the speciality of the group’s latest addition, Alba Mobility).
“The latest innovations in our industry,” notes Capello, “have led to the development of increasingly complex components with sensors and solenoid valves which require stricter and stricter cleaning requirements, that we were not able to satisfy with the cleaning process we used to carry out until recently. That is why we turned to STS Srl (Ravenna, Italy), a company with twenty-five years’ international experience and sector-specific expertise in surface treatment and cleaning processes, to upgrade our system and the products needed to treat our components. Their proposal convinced us because of their technical team’s know-how: STS started out producing detergents and subsequently I began to design cleaning plants that would provide the best performance with the products they formulated. Their integrated offer system immediately struck us as a virtuous way of approaching the market”.
TCN Vehicles Division specialises in the machining and assembly of forged and billet aluminium components with high mechanical and sealing properties for OEMs. “For the automotive sector, we produce
TCN Vehicles Division fa parte di uno dei poli industriali più avanzati del territorio piemontese e non solo: TCN Group con sede ad Alba (Cuneo) raggruppa numerose aziende le cui attività rientrano negli ambiti più diversi, dalla produzione di macchine per il settore tessile, packaging e per l’automazione industriale, alle lavorazioni meccaniche di precisione e dell’alluminio per il settore moto e automotive, in cui opera dal 2001 TCN Vehicles Division, al settore alimentare fino all’ultima nata del gruppo, Alba Mobility, specializzata nella produzione di quadricicli elettrici per la mobilità sostenibile.
“Le ultime evoluzioni del nostro settore – prosegue Capello - hanno portato allo sviluppo di una componentistica sempre più complessa, dotata di sensori ed elettrovalvole per la quale sono necessari requisiti di pulizia sempre più rigidi che non era possibile ottenere con il processo di lavaggio che effettuavamo fino a poco tempo fa. Ci siamo quindi rivolti a STS srl di Ravenna, che vanta venticinque anni di esperienza internazionale ed una competenza settoriale specifica nelle problematiche di lavaggio e trattamento superfici, per aggiornare la nostra soluzione impiantistica e i prodotti utilizzati per la pulizia dei nostri componenti. La sua proposta ci ha convinto per il know-how del team tecnico: STS è nata per la produzione di detergenti e successivamente ha iniziato a progettare impianti di lavaggio che fornissero le migliori performance con i prodotti da loro formulati. Il loro sistema di offerta integrato ci è sembrato da subito un modo virtuoso per approcciarsi al mercato”.
Il servizio customer-oriented di TCN VD TCN Vehicless Division è specializzata nella lavorazione meccanica e nell’assemblaggio di componenti in alluminio forgiato o ricavati dal pieno con elevate proprietà meccaniche e di tenuta per il primo impianto.
TCN Vehicles Division © TCN Vehicles Divisionchassis and suspension structural components that, in many cases, also incorporate hydraulic circuits, valves, and actuators, mainly for active and semi-active suspensions. We also manufacture engine mounts, tank flanges, anti-vibration systems, and arms for overlapping double trapezoid and multi-link technologies. As for the motorcycle components field, on the other hand, we specialise in the manufacture of steering plates, fork mounts, fork legs with radial brake calliper mounts, rider and passenger mounts, anodised and assembled frame and suspension plates, suspension bases with separate accumulators, and shock absorber bodies. The latter are subjected to anodising, performed by our contractors, and to machining to a very low degree of surface roughness, as required by new the technologies for suspensions.” Aluminium accounts for 95% of the material processed by TCN VD. “Our company’s market approach has always been customer-oriented. Together with our customers, we develop and design the product they require and, thanks to our many years’ experience in the production of suspensions, we work on their mathematical models by already having a clearly in mind the characteristics of the end product that they are going to manufacture. Thanks to this know-how, we handle the
“Per quanto riguarda l’automotive, la nostra realtà produce componenti strutturali dello chassis e delle sospensioni che, in molti casi, incorporano circuiti idraulici, valvole e attuatori elettronici principalmente impiegati per sospensioni attive e semi-attive. Realizziamo anche supporti motore, flange serbatoio, sistemi antivibranti e bracci per tecnologie a doppio trapezio sovrapposto e multilink. Nella componentistica moto siamo invece specializzati nella fabbricazione di piastre di sterzo, portapedana, piedini forcella con attacchi pinze freno radiali, portapedana pilota e passeggero, piastre telaio e sospensioni anodizzati e assemblati, basette per sospensioni con accumulatore separato e corpi ammortizzatore. Questi ultimi sono sottoposti al trattamento di anodizzazione affidato a ditte esterne e a lavorazioni con grado di rugosità superficiale molto basso, che risulta necessario per le nuove tecnologie delle sospensioni”. Il 95% del materiale lavorato da TCN VD è alluminio. “L’approccio al mercato della nostra azienda è da sempre customeroriented: sviluppiamo e progettiamo insieme ai nostri clienti il prodotto da loro richiesto e, grazie alla nostra esperienza pluriennale nella produzione delle sospensioni, agiamo direttamente sui modelli matematici proposti dall’interlocutore avendo già subito chiare le caratteristiche del prodotto
necessary production processes and guide our customers, through advice and proposed changes, towards the design of a product that is 100% industrialisable, functional, and of high quality right from its development. This approach has led us to quickly become Tier 1 suppliers to Ferrari, Maserati, Ducati, KTM, and Triumph, as well as suppliers to all the major suspension OEMs, such as ZF, Tenneco, WP, BWI, Ohlins, and Multimatic, to name but a few.”
The production cycle begins with the receipt of forged aluminium parts produced by external companies based on the instructions of TCN VD’s technical department. It continues with precision machining by chip removal using 4- or 5-axis machines, anodising by some contractors (if this treatment is required, especially in the case of motorbike components), assembly, marking, cleaning, testing, packaging, and shipping.
“Our production,” indicates Capello, “is very varied in terms of both shapes and sizes: it ranges from the 20 -mm length of motorbike
finito che il nostro cliente andrà a realizzare. Grazie a questo knowhow riusciamo a gestire i processi produttivi necessari e indirizziamo il cliente, attraverso consigli e modifiche, verso il design di un manufatto che risulti industrializzabile al 100%, garantendone la funzionalità e la qualità finale sin dal suo sviluppo. Questo approccio ci ha condotto a diventare in poco tempo fornitori Tier 1 di Ferrari, Maserati, Ducati, KTM e Triumph, oltre che fornitori di tutti i principali OEM del settore sospensioni, come ZF, Tenneco, WP, BWI, Ohlins e Multimatic, solo per citarne alcuni”.
Evitare la contaminazione dalla fase di co-design Il ciclo produttivo prende avvio dalla ricezione del manufatto in alluminio forgiato da aziende esterne sulla base delle indicazioni dell’ufficio tecnico di TCN VD e prosegue con le lavorazioni meccaniche di precisione per asportazione di truciolo realizzate con macchine a 4 o 5 assi, con i trattamenti di anodizzazione – se richiesti, in particolare per i componenti motociclo – affidati in esterno, assemblaggio, marcatura, lavaggio, collaudo, imballaggio e spedizione finale.
“La nostra produzione – precisa Capello - è molto variegata sia per geometrie sia per dimensioni: i componenti da noi realizzati variano dai 20 mm di lunghezza degli occhielli degli ammortizzatori dello sterzo delle moto, fino ai 700 mm di un braccetto di sospensione
and suitable for the toughest
steering damper eyelets to the 700-mm length of suspension arms Moreover, most of our products are intended for active and semi-active electronic suspensions: therefore, they require the utmost attention to be paid to surface contamination. Already during the co-design phase, we analyse the possible contamination risks and solve them through the combined action of our 5-axis machines, which minimise the presence of burrs and swarf residues, and of our low or highpressure cleaning system to remove emulsions, lubricants, and any external contaminants that may be deposited on the surfaces during the final operations and transport phases. In fact, the task of preventing contamination does not end with cleaning, but it continues with seal packaging operations aimed at meeting our customers’ precise contamination requirements, which are very often lower than 0.2 mm2 in size for metallic particles, and 0.3 mm2 for non-metallic particles, to be further differentiated among those with fibrous and non-fibrous characteristics and with different dimensions and quantities.”
Fifteen years ago, TCN VD installed a cleaning system to remove the oil residues remaining on the surfaces of a niche product, accounting for a small percentage of its total volumes.
“It is a pressure regulator made in die-cast aluminium, which is assembled with a brass component by gluing. Before doing so, however, it is necessary to clean its surfaces so that they are completely dry and free of any residues.
“Subsequently, the market demanded the development of suspensions with highly complex hydraulic circuits equipped with sensors and solenoid valves, resulting in increasingly stringent cleanliness requirements. At that point, the cleaning cycle we were carrying out was outdated. When we started looking for a new supplier a year ago, however, the experience gained with that first system gave us such a knowledge and awareness level that we could draw up an internal technical specification to be met by the offers received from the different providers. We finally opted for STS because of its environmentally friendly solution, its know-how in plant design combined with in-depth knowledge in product formulation, and its customer-oriented service, which fully reflects our approach. Finding a partner that can perfectly match the characteristics of a system with those of a product is not to be taken for granted in today’s market.”
“One of the most important phases in the implementation of a cleaning plant is certainly the co-design one,” states Pier Damiano D’Ignazio, the marketing and sales director of STS, “and with TCN VD’s team we developed a solution that met all requirements. During numerous online meetings, we defined its features down to the smallest details, such as the machine’s colour. The system, which was installed at the beginning of July, is a 7-stage AQUAROLL MR7 model with some functions specifically adapted to TCN’s needs. This series
auto. La maggior parte dei pezzi da noi lavorati andranno a costituire sospensioni elettroniche attive e semi-attive e necessitano, quindi, di un’attenzione al rischio di contaminazione superficiale molto accurato e meticoloso. Già a partire dalla fase di co-design studiamo quali possono essere i rischi di contaminazione del pezzo e interveniamo con l’azione combinata delle macchine a 5 assi, che riducono al minimo i residui di bave pendule o di truciolo, e dell’impianto di lavaggio a bassa o ad alta pressione per la rimozione di emulsioni e di lubro-refrigeranti, o di contaminanti esterni che potrebbero depositarsi sulla superficie del pezzo durante la fase finale o il trasporto. Infatti, il lavoro per contenere la contaminazione non finisce con il lavaggio, ma procede con un imballaggio sigillato in modo da garantire al cliente finale i precisi requisiti di contaminazione richiesti, che molto spesso si aggirano intorno a valori non superiori a 0,2 mm2 di dimensione per le particelle metalliche, e a 0,3 mm2 per quelle non metalliche, distinte poi tra quelle con caratteristiche fibrose e non con dimensioni e quantità differenti”.
Una nuova esigenza di lavaggio 15 anni fa TCN VD aveva introdotto un impianto di lavaggio per la rimozione dei residui d’olio rimasti sulla superficie di un prodotto di nicchia, che rappresenta una piccola percentuale della produzione. “Si tratta di un riduttore di pressione ricavato da alluminio pressofuso che è assemblato con un componente in ottone tramite incollaggio. Prima di questo intervento è però necessario lavare le superfici in modo che risultino completamente asciutte e prive di residui. Successivamente, il mercato ha richiesto lo sviluppo di sospensioni con circuiti idraulici molto complessi dotati di sensori ed elettrovalvole e requisiti di pulizia sempre più rigidi. Il ciclo di lavaggio che effettuavamo era ormai superato, ma, grazie all’esperienza acquisita con l’impianto in uso, un anno fa abbiamo iniziato a cercare un nuovo fornitore con una conoscenza e consapevolezza che ci ha permesso di redigere un capitolato tecnico interno, a cui i fornitori avrebbero dovuto adeguare l’offerta. Abbiamo infine optato per STS, per la soluzione ecocompatibile proposta, il suo know-how nella progettazione dell’impianto abbinato con un’approfondita conoscenza nella formulazione del prodotto, e il suo servizio customer-oriented, in cui ci rispecchiamo pienamente. Trovare un partner in grado di coniugare perfettamente le caratteristiche dell’impianto con quelle del prodotto non è scontato nel mercato attuale”. “Una delle fasi più importanti nella realizzazione di un impianto di lavaggio è sicuramente quella di co-progettazione” – interviene Pier Damiano D’Ignazio, Marketing & Sales Director di STS – “e con il team di TCN VD abbiamo sviluppato una soluzione in grado di soddisfare tutti i requisiti richiesti. Abbiamo studiato i dettagli in numerose riunioni online definendone le caratteristiche fin nei dettagli più piccoli, incluso ad esempio il colore della macchina. L’impianto, che è stato installato a inizio luglio, è un modello AQUAROLL MR7 a 7 stadi con alcune funzioni adeguate alle esigenze di TCN. Questa serie di macchine è
of machines is designed for cleaning, rinsing, and drying metal parts with a horizontally rotating carousel. The plant consists of a cleaning, rinsing, and drying module that ensures excellent quality results thanks to specially positioned nozzles. The cleaning product used is a flagship of STS: an aqueous solution based on sodium bicarbonate nanotechnology that is non-toxic and not dangerous to humans or the environment.”
In this new system, TCN VD cleans mainly non-anodised engine components, valve housings, and hydraulic components with small dimensions and simple geometries, i.e. featuring few cavities and undercuts. Capello describes the operation performed: “The workpieces are loaded in the plant individually and unloaded at the same point from plates with a control interface capable of handling pallets of different sizes, manufactured in-house by 3D printing or in billet aluminium cut to measure. The first stage is that of spray cleaning with demineralised
stata progettata per il lavaggio, il risciacquo e l’asciugatura di particolari metallici, con movimentazione a giostra rotante orizzontale. L’impianto di lavaggio è composto da un modulo di lavaggio, risciacquo ed asciugatura che permette di ottenere un’eccellente qualità di lavaggio grazie ad ugelli posizionati in modo mirato. Il prodotto detergente utilizzato è una caratteristica distintiva di STS: si tratta di una soluzione acquosa basata sulla nanotecnologia del bicarbonato di sodio atossica e non pericolosa né per l’uomo né per l’ambiente”.
Il ciclo di lavaggio per componenti specifici Nel nuovo impianto TCN VD lava principalmente componenti motociclo non anodizzati, valve housing e componenti idraulici di piccole dimensioni e con geometrie semplici, ossia cavità e sottosquadra limitati. “I componenti – descrive l’operazione Capello - vengono introdotti singolarmente nella macchina e scaricati nello stesso punto da piastre con interfaccia di controllo in grado di gestire pallet di diverse dimensioni, da noi realizzati internamente tramite stampaggio 3D o ricavati dal pieno su misura. Il primo stadio prevede il lavaggio a spruzzo con acqua demi
Effective and reliable process solutions. For a zero liquid discharge production.
Leading companies rely on vacuum distillation systems for the sustainable treatment of industrial wastewater.
Do you want to benefit from a zero liquid production with VACUDEST, too?
We will be delighted to advise you!
Visit our presentation on better cleaning quality with VACUDEST at parts2clean in Stuttgart from 11-13 October!
The entrance stage of the system. La camera di ingresso della macchina. TCN Vehicles Divisionwater and detergent, followed by blow-off and draining to remove water, detergent, and residues and then by rinsing in a separate tank equipped with independent filters. The fourth station performs cleaning with demineralised water, another blow-off phase, and hot air drying before unloading.” The cleaning cycle has a duration of 120 seconds. “It is also possible to load two or three parts at a time. We anticipate that this plant will be able to process almost 300,000 components/year in three shifts for five days a week.”
“Thanks to the demineralisation system combined with the bicarbonate product,” explains Capello, “we obtain clean and residue-free surfaces. At the same time, the extreme purity of water, which is free of impurities and limescale, reduces the frequency of maintenance interventions related to fouling or wear. Another advantage is the reduction of energy consumption. The STS detergent works at lower temperatures and the tanks are insulated to keep the heat without dissipating it. The machine is also equipped with an auto ignition system. All these contribute to reducing consumption. The detergent also has a low environmental impact and increased durability. Further
e detergente, segue la fase di soffiatura e drenaggio per la rimozione dell’acqua, del detergente e dei residui e quindi il risciacquo in una vasca separata dalla prima e dotata di filtri indipendenti. La quarta stazione prevede il lavaggio con acqua demi, un’altra fase di soffiatura e, infine, l’asciugatura ad aria calda prima dello scarico”. Il ciclo di lavaggio ha una durata di 120 secondi. “E’ possibile caricare 2 o 3 pezzi per volta e prevediamo che questo impianto sarà in grado di trattare c.a. 300 mila pezzi/anno in 3 turni lavorativi per 5 gg alla settimana”.
I vantaggi del nuovo impianto “Grazie al sistema di demineralizzazione unito al prodotto a base di bicarbonato – spiega Capello - abbiamo riscontrato una superficie pulita e senza residui. Inoltre, l’estrema purezza dell’acqua priva di impurità e calcare riduce la frequenza degli interventi di manutenzione a causa di sporco o usura. Un ulteriore vantaggio è la riduzione dei consumi energetici. Il detergente STS lavora a temperature più basse e le vasche sono coibentate per mantenere il calore senza disperderlo. La macchina è anche dotata di un sistema di auto accensione. Il detergente inoltre ha un basso impatto ambientale e una maggiore durata nel tempo. Un’ulteriore testimonianza dell’attenzione posta da TCN a questo particolare
evidence of TCN’s focus on this particular production operation is the annual process validation carried out through contamination tests performed by external laboratories. Overall, the plant is flexible and perfectly suited to our needs. STS has an expert, young and strongly customer-oriented team. In an industry like that of machining technologies, making a difference is complicated: a professional and reliable service right from the design phase is certainly a surplus value that adds to a company’s technical expertise and experience.”
intervento produttivo è la validazione annuale del processo tramite test di contaminazione effettuati da laboratori esterni. Nel complesso, l’impianto risulta flessibile e ben adeguato alle nostre esigenze. In STS abbiamo trovato un team esperto, giovane e fortemente orientato al cliente. In un settore come quello delle lavorazioni meccaniche fare la differenza è complesso: un servizio professionale e puntuale che parte dalla progettazione è sicuramente un plusvalore che va ad aggiungersi alla competenza tecnica e all’esperienza”.
From left to right: Small components loaded on the machine and the beginning of the washing cycle with a horizontally rotating carousel movement.
Da sinistra a destra: componenti di piccole dimensioni caricati sulla macchina di lavaggio e inizio del ciclo di lavaggio con movimentazione a giostra rotante orizzontale.
“In a market where suppliers often promise one-size-fits-all solutions, there is an increasing need for a partner with a range of high quality technologies that can help customers choose the best one for their specific requirements. In fact, customers do not just choose a plant: they choose the company that produces it.”
Customer satisfaction and the creation of all-round solutions have always been the main objectives of D.B.M. Tecnologie (Treviso, Italy), a company specialising in the manufacture of customised surface treatment systems and providing design, production, and active aftersales assistance services involving both plant engineering and process development.
In line with these principles, D.B.M. has recently expanded its portfolio with its NYX line of one-chamber vacuum cleaning systems, operating with modified alcohols and class AIII hydrocarbons.
The NYX line complements the company’s already well-known water based cleaning systems (multi-chamber and one-chamber plants with vacuum ultrasound operation, tunnels and turntables for targeted spray cleaning, and high-pressure systems) and low-boiling fluorinated HFE/ HFO solvent-based cleaning system (manual and automatic). There is no revolution entailed here: with this range expansion, D.B.M. precisely aims at helping its customers choose the most suitable system for their specific needs.
Made in AISI 304 stainless steel, the NYX series plants are available in different sizes and they guarantee excellent cleaning results through the use of last generation solvents.
Vacuum operation allows degreasing and drying components with
commerciale@dbmtecnologie.com
“In un mercato dove spesso emergono promesse di soluzioni uniche valide per tutto, c’è sempre più bisogno di un partner che presenti un portfolio di soluzioni di alta qualità e possa indicare la scelta migliore al proprio committente. Perché non si sceglie solo l’impianto. Si sceglie l’azienda che lo produce.”
Da sempre la soddisfazione del cliente e la proposta di soluzioni a 360 gradi è l’obiettivo principale del lavoro di D.B.M. Tecnologie, azienda di Treviso specializzata nella produzione di impianti personalizzati per il trattamento delle superfici, che mette a disposizione un servizio sinergico di progettazione, produzione e assistenza post-vendita attiva sia dal punto di vista impiantistico che di processo. In linea con questi principi, D.B.M. estende la proposta tecnologica, presentando la linea di impianti di lavaggio monocamera sottovuoto NYX, funzionante ad alcoli modificati e idrocarburi classe AIII.
La nuova linea di impianti di lavaggio monocamera sottovuoto NYX
La linea NYX si affianca alle già note produzioni di impianti di lavaggio a base acquosa (multivasca e monocamera con ultrasuoni sottovuoto, tunnel e tavole rotanti per il lavaggio a spruzzo mirato e impianti di lavaggio ad alta pressione) e a base di solventi fluorurati bassobollenti HFE/HFO (sistemi sia manuali che automatici). Nessuna rivoluzione: la mossa di D.B.M. va letta proprio nell’ottica di voler accompagnare i propri clienti nella scelta dell’impianto più adatto alle proprie esigenze di lavaggio. Realizzati in acciaio inox AISI 304, gli impianti della serie NYX si caratterizzano per la varietà di dimensioni disponibili e garantiscono un lavaggio di ottimo livello tramite l’utilizzo di solventi di ultima generazione. Il funzionamento in vuoto permette lo sgrassaggio e l’asciugatura di componenti dalle geometrie complesse anche in presenza di fori ciechi e
D.B.M. Tecnologie, Casale sul Sile (Treviso) – Italy The D.B.M. Tecnologie headquarters in Casale sul Sile (Treviso). La sede di D.B.M. Tecnologie a Casale sul Sile (Treviso).complex shapes, even in the presence of blind holes and capillarity, while guaranteeing reduced consumption and high cycle repeatability, without any loss of efficiency and quality thanks to continuous distillation.
NYX plants are ready to be put to the test: their user-friendly interface, the complete integration with already existing company systems, and their great ease of use and maintenance make them suitable for treating various types of turned parts, fittings, and precision mechanical components in sectors ranging from automotive and aerospace to medical and luxury. Standardisation and customisation coexist in these machines. Indeed, all systems in the NYX series are characterised by:
• Treatment chamber with a frame rotation/tilting system;
• Two tanks for the cleaning fluid;
A machine from the new NYX line of one-chamber vacuum cleaning systems.
Un modello della nuova linea di impianti di lavaggio monocamera sottovuoto NYX.
• Continuous distillation and sludge stripping;
• Continuous filtration of the cleaning fluid;
• Vacuum system;
• Management PLC with a touch screen panel;
• Full integration with Industry 4.0-oriented data collection and traceability systems.
At the same time, they can be integrated with:
• In-cabin ultrasound devices;
• Additional filtration systems;
• Additional tank for the cleaning fluid;
• Protective application system;
• Basket loading/unloading automation with a storage buffer.
Such a variety of automation solutions applicable to its systems is another trademark of D.B.M. Tecnologie. Automatic insertion/ extraction systems, buffer conveyors, pick’n’place loading/unloading conveyors, elevators, basket return conveyors, pass boxes, and rotation/tilting systems are just some of the devices available, all fully designed and manufactured by D.B.M. according to every customer’s logistics requirements.
capillarità, garantendo al contempo consumi ridotti e la riproducibilità nel tempo del ciclo di lavaggio, senza perdita di efficacia e qualità, grazie alla distillazione in continuo del liquido.
Un impianto NYX chiede solo di essere messo alla prova: l’interfaccia user-friendly, la completa integrazione con i sistemi aziendali e la grande facilità di utilizzo e di manutenzione ne fanno un impianto adatto all’uso su svariate tipologie di componenti di minuteria tornita, raccorderia o meccanica di precisione in settori che vanno dall’automotive all’aerospace passando per il medicale e il luxury. La standardizzazione e la customizzazione convivono nel progetto. Infatti, tutti gli impianti della serie NYX sono dotati di:
• Camera di trattamento con sistema di rotazione/basculamento del telaio;
• Due serbatoi per il liquido di lavaggio;
• Distillazione in continuo e strippaggio morchie;
• Filtrazione in continuo del liquido di lavaggio;
• Sistema sottovuoto;
• PLC di gestione con pannello touch screen;
• Completa integrabilità con sistemi di raccolta dati e di tracciabilità in ottica Industry 4.0.
E possono essere integrati con:
• Dispositivi a ultrasuoni in cabina;
• Sistemi di filtrazione supplementari;
• Serbatoio supplementare per il liquido di lavaggio;
• Sistema di applicazione protettivo;
• Automazioni di carico/scarico dei cesti con buffer di accumulo.
Proprio la varietà di automazioni applicabili all’impianto è un altro marchio di fabbrica di D.B.M. Tecnologie: sistemi di inserimento/disinserimento automatico, trasportatori di accumulo, pick’n place di carico/scarico, elevatori, trasportatori di ritorno cesti, pass-box di trasferimento, sistemi di rotazione/ribaltamento sono solo alcuni dei dispositivi applicabili, totalmente progettati e realizzati in D.B.M. seguendo le esigenze di logistica del cliente.
The 19th edition of parts2clean will take place from 11 to 13 October 2022 at the Stuttgart Exhibition Centre in Stuttgart (Germany).
Whether it involves higher cleanliness requirements, new cleaning applications that need to be mastered, or stricter energy efficiency and climate protection standards – the challenges facing manufacturing companies are numerous and varied. The exhibitors at parts2clean will be showcasing ways to master these tasks, while the latest approaches for ideal efficiency will also be covered by an attractive supporting program of side events at the leading international trade fair for parts and surface cleaning. Electromobility and the energy transition, changes in manufacturing and coating technologies, new materials and material combinations and the digitization of manufacturing are just a few of the trends requiring new and adapted processes in parts and surface cleaning. Apart from particulate contaminants, an increasingly important aspect involves filmic organic, inorganic and, in some cases, biological contaminants in the fight to meet cleanliness specifications.
“The exhibitor showcases at this year’s parts2clean will offer solutions in all areas of industrial cleaning technology to meet these new requirements in a leading-edge context,” reports Hendrik Engelking, Global Director at Deutsche Messe. “For example, developments for the removal of fine-particle and filmic-chemical contaminants will be presented, as well as solutions for improved energy and resource efficiency, greater costeffectiveness and flexibility.” The leading international trade fair for parts and surface cleaning runs from 11–13 October 2022 at the Stuttgart (Germany) Exhibition Centre.
Attractive supporting program adds value to the event But it’s not only the cross-industry, cross-technology and cross-materials exhibition portfolio which make a visit to parts2clean 2022 a must for cleaning technology users from all industries. The supporting program’s side events offer knowledge and expertise as well as solution approaches for process adaptation and optimization in a condensed form which cannot be found anywhere else.
Pre-defined cleanliness requirements can be met stably and efficiently by taking a holistic view of the process chain. This includes – as a result of increasingly stiff requirements for component cleanliness – environmental conditions as well. The special show titled “Component Cleanliness – a Holistic View of the Process Chain,” organized jointly with the Cleaning Excellence Centre (CEC), provides visitors with a better grasp of the road to clean components.
With traditional attendance of more than 1,300 participants on-site and many more users worldwide via live streaming, the three-day parts2clean specialist forum is one of the key attractions at the show. “The high quality of information and presentations here have made this forum one of the most sought-after sources of knowledge in the field of parts and surface cleaning for domestic and international visitors,” reports Engelking. Well-known experts from science and research as well as from industry associations and industry itself will offer their knowledge and expertise as well as benchmark solutions in simultaneously translated (German <> English) lectures.
The presentation clusters focusing on challenges in electromobility and the energy industries as well as precision cleaning for extreme requirements will spotlight a number of hot topics. If it is a question of proving the technical cleanliness achieved, the papers in the Analytics, Technical Cleanliness, Rules and Regulations section will provide detailed information, while the “Environmental Relevance and Circular Economy” session will focus on solutions for media preparation, substitution of critical or banned substances, and energy and resource savings, among other topics.
Participation in the parts2clean technical forum is free of charge for tradeshow attendees. In addition, the presentations will be broadcast live on the parts2clean event website.
For further information: www.parts2clean.de/en
La 19a edizione di parts2clean si svolgerà dall’11 al 13 ottobre 2022 presso lo Stuttgart Exhibition Centre a Stoccarda (Germania).
Che si tratti di requisiti di pulizia più elevati, nuove applicazioni che devono essere padroneggiate o standard di efficienza energetica e protezione del clima più rigorosi, le sfide che le aziende manifatturiere devono affrontare sono numerose e varie. Gli espositori di parts2clean mostreranno modi per padroneggiare queste attività, mentre gli approcci più recenti per un’efficienza ideale saranno coperti anche da un interessante programma di supporto di eventi collaterali presso la principale fiera internazionale per la pulizia di parti e superfici. L’elettromobilità e la transizione energetica, i cambiamenti nelle tecnologie di produzione e rivestimento, nuovi materiali e combinazioni e la digitalizzazione sono solo alcune delle tendenze che richiedono processi nuovi e adattati per la pulizia di pezzi e superfici. Oltre alla contaminazione particellare, un aspetto sempre più importante riguarda i contaminanti pellicolari organici, inorganici e, in alcuni casi, biologici nella lotta per soddisfare le specifiche di pulizia. “Gli espositori del parts2clean di quest’anno offriranno soluzioni per tutti i settori e le tecnologie di lavaggio industriale, in modo da soddisfare queste nuove esigenze in un contesto all’avanguardia”, afferma Hendrik Engelking, direttore globale di Deutsche Messe. “Ad esempio, saranno presentati gli sviluppi per la rimozione di particelle fini e contaminanti filmico-chimici, nonché soluzioni per una migliore efficienza energetica, delle risorse e in termini di costi e flessibilità”. La principale fiera internazionale per la pulizia di pezzi e superfici si svolge dall’11 al 13 ottobre 2022 presso lo Stuttgart Exhibition Centre (Germania). Un interessante programma di supporto aggiunge valore all’evento Ma non è solo il portfolio espositivo intersettoriale, intertecnologico
e intermateriale a rendere la partecipazione a parts2clean 2022 un must per gli utilizzatori di tecnologie di pulizia da tutti i settori. Gli eventi collaterali del programma di supporto forniscono conoscenze e competenze, nonché approcci risolutivi per l’adattamento e l’ottimizzazione dei processi in una forma condensata, che non si trova da nessun’altra parte.
Visione olistica della pulizia dei componenti lungo la catena di processo
I requisiti di pulizia predefiniti possono essere soddisfatti in modo stabile ed efficiente adottando una visione olistica della catena di processo.
Ciò include, a causa dei requisiti sempre più rigidi per la pulizia dei componenti, anche le condizioni ambientali. La sezione speciale intitolata “Pulizia dei componenti: una visione olistica della catena di processo”, organizzata insieme al Cleaning Excellence Center (CEC), offre ai visitatori una migliore comprensione della pulizia dei componenti.
Il forum specialistico mette in evidenza il trasferimento di conoscenze, dalle basi alle tendenze generali
Con oltre 1.300 partecipanti in loco e molti più utenti da tutto il mondo connessi in streaming, il forum specialistico di tre giorni è una delle principali attrazioni della fiera. “L’elevata qualità delle presentazioni e delle sessioni hanno reso il forum una delle fonti d’informazione più ricercate dai visitatori nazionali e internazionali operanti nel campo della pulizia di pezzi e superfici”, riferisce Engelking.
Rinomati esperti proveniente da organizzazioni scientifiche e di ricerca, nonché da associazioni di categoria e dall’industria stessa presenteranno le proprie conoscenze e competenze, nonché soluzioni di riferimento in sessioni tradotte in simultanea (tedesco <> inglese). I panel incentrati sulle sfide dell’elettromobilità e delle industrie energetiche, nonché sulla pulizia di precisione per requisiti elevati, metteranno in luce molti argomenti attuali. Gli elaborati della sezione Analisi, Pulizia tecnica, Norme e Regolamenti forniranno informazioni dettagliate su come dimostrare il grado pulizia tecnica raggiunta, mentre la sessione “Rilevanza ambientale ed economia circolare” sarà incentrata sulle soluzioni per la preparazione degli agenti, la sostituzione di sostanze critiche o vietate e il risparmio di energia e risorse.
La partecipazione al forum è gratuita per i partecipanti alla fiera. Inoltre, le presentazioni saranno trasmesse in diretta sul sito web dell’evento.
Per maggiori informazioni: www.parts2clean.de/en
The next edition of the leading trade fair for deburring technology and precision surface finishing will take place from 10th to 12th October 2023 in Karlsruhe (Germany).
The organisers of DeburringEXPO 2023 have announced that the preparations for the 5th edition of the leading trade fair for deburring technology and precision surface finishing are well underway. The international exhibition, which will be held from 10th to 12th October 2023 at the Trade Fair Center in Karlsruhe (Germany), will cover the processing of components manufactured by means of all technologies and from all industry sectors.
The trade fairs of the last few months have shown how much these events have been missed by industry professionals and with what passion exhibitors and visitors are looking to meet face to face again. The need for information on technology, processes and quality assurance for deburring, rounding and the production of precision surfaces is still very high.
With its clear concept, the DeburringEXPO aims to provide an indispensable marketplace for new technologies and solutions.
As a matter of fact, the trade fair will provide a platform to discuss in direct dialogue – with also the use of sample components and drawings – the increasingly complex requirements of the industry in a target-oriented and concrete manner. In addition, it will also offer the opportunity to establish and expand networks and detect upcoming technologies at an early stage.
The 5th edition of DeburringEXPO will welcome prominent companies from the industry sector, including numerous market and technology leaders and a high proportion decision-makers, who have already made firm bookings for their trade fair booths more than a year before. Registrations for the exhibitors will close in May 2023.
For further information: www.deburring-expo.de/en
La prossima edizione della fiera leader sulle tecnologie di sbavatura e sulla finitura superficiale di precisione si svolgerà dal 10 al 12 ottobre 2023 a Karlsruhe (Germania).
Gli organizzatori di DeburringEXPO 2023 hanno annunciato che i preparativi per la 5a edizione della fiera leader sulle tecnologie di sbavatura e sulla finitura superficiale di precisione sono a buon punto. La fiera internazionale, che si terrà dal 10 al 12 ottobre 2023 presso il Centro Fieristico di Karlsruhe (Germania), tratterà i processi relativi a componenti realizzati con tutte le tecnologie e appartenenti a tutti i settori industriali.
Le fiere svoltesi negli ultimi mesi hanno dimostrato quanto questi eventi siano mancati ai professionisti dell’industria e con quale passione espositori e visitatori stiano cercando di trovarsi di nuovo faccia a faccia. Il bisogno di informazioni su tecnologie, processi e qualità nella sbavatura, nell’arrotondamento e nella produzione di superfici di precisione è ancora molto alto.
Con il suo concept molto chiaro, DeburringEXPO mira ad offrire un punto di incontro fondamentale per le nuove tecnologie.
La fiera sarà infatti una piattaforma per discutere con un dialogo diretto – anche con l’utilizzo di componenti campione e disegni – i sempre più elevati requisiti del settore, in modo concreto e mirato. Offrirà inoltre l’opportunità di instaurare ed espandere i network e di individuare in fase iniziale le tecnologie emergenti.
La 5a edizione di DeburringEXPO accoglierà aziende di spicco del settore industriale, inclusi numerosi leader di settore e tecnologici e un elevato numero di decision-maker, che hanno già prenotato il proprio spazio espositivo con più di un anno di anticipo.
L’iscrizione per gli espositori chiuderà a maggio 2023.
Per ulteriori informazioni: www.deburring-expo.de/en
www.eosmarketing.it - info@eosmarketing.it www.myipcm.com - info@ipcm.it
Redazione - Sede Legale: Via Pietro Mascagni, 8 - 20811 - Cesano Maderno (MB) - Italy Tel. +39.0362.503215 - Fax. +39.0362.1794768
Prof. Massimiliano Bestetti: Department of Chemistry, Material and Chemical Engineering, Politecnico of Milan –Section of Applied Chemistry and Physics
Dr. Franco Busato: European environmental legislation and new technologies
Prof. Paolo Gronchi: Department of Chemistry, Material and Chemical Engineering, Politecnico of Milan –Chemical Engineering Section
Kevin Biller: The Powder Coating Research Group
Prof. Stefano Rossi: Material Engineering and Industrial Technologies, University of Trento - Product Design
Dr. Fulvio Zocco: Environment and quality
EDITOR IN CHIEF / DIRETTORE RESPONSABILE
ALESSIA VENTURI venturi@ipcm.it
EDITORIAL DIRECTOR / DIRETTORE EDITORIALE
FRANCESCO STUCCHI stucchi@ipcm.it
EDITORIAL OFFICE / REDAZIONE
PAOLA GIRALDO giraldo@ipcm.it
MONICA FUMAGALLI fumagalli@ipcm.it
NICOLE KRAUS kraus@ipcm.it
MATTEO SOTTI sotti@ipcm.it
BARBARA PENNATI pennati@ipcm.it
ILARIA PAOLOMELO paolomelo@ipcm.it
GABRIELE LAZZARI redazione@ipcm.it
EDITORIAL OFFICE AND GRAPHICS
ELISABETTA VENTURI grafico@ipcm.it
MEDIA SALES
FRANCESCO STUCCHI stucchi@ipcm.it
BARBARA PENNATI pennati@ipcm.it
NICOLE KRAUS kraus@ipcm.it
SVEN KRAUS sven.kraus@ipcm.it
CLAUS GÖRLICH goerlich@ipcm.it
SUBSCRIPTION SERVICE - SERVIZIO ABBONAMENTI: Sale only on subscription - Vendita solo su abbonamento E.mail info@ipcm.it
Subscription Rates 2023 - Tariffe Abbonamento 2023:
Annual subscription print + digital:
EMEA 100,00 € (postage included)
Rest of world 300,00 € (fast airmail shipping included)
Abbonamento annuale cartaceo + digitale: EMEA 100,00 € (spese postali incluse)
Resto del mondo 300,00 € (spedizione via aerea inclusa)
Single copy: 15,00 € EMEA (postage included) - Rest of world (postage excluded)
Back issues: 30,00 € EMEA (postage included) - Rest of world (postage excluded)
Fascicolo singolo: 15,00 € EMEA (spese postali incluse) - resto del mondo (spese postali escluse) Arretrati: 30,00 € EMEA (spese postali incluse) - resto del mondo (spese postali escluse)
grafico@ipcm.it
PRINT/ STAMPA ROTOLITO SPA info@rotolito.com
Subscriptions can be made by bank transfer to the following account: Eos Mktg&Communication Srl IBAN IT97F0844033270000000084801 - SWIFT CODE CRCBIT22 or via payment online at: www.myipcm.com
Gli abbonamenti possono essere sottoscritti versando il relativo importo a mezzo b/b IBAN IT97F0844033270000000084801 intestato a eos Mktg&Communication Srl oppure con carta di credito direttamente dal sito www.myipcm.com L’Iva sugli abbonamenti, nonchè sulla vendita di singole copie è assolta ai sensi dell’art.74 comma 1 lett. C DPR 633/72, DM 29/12/1989.
Registrazione al Tribunale di Monza N° 1970 del 10 Dicembre 2009Eos Mktg&Communication srl è iscritta nel Registro degli Operatori di Comunicazione con il numero 19244 POSTE ITALIANE S.P.A. – SPEDIZIONE IN ABBONAMENTO POSTALE –D.L. 353/2003 (CONV. IN L. 27/02/2004 N.46) ART. 1, COMMA 1 LOM/MI/4351
It is forbidden to reproduce articles and illustrations of “ipcm®” without authorization and without mentioning the source. The ideas expressed by the authors do not commit nor magazine nor eos Mktg&Communication S.r.l and responsibility for what is published is the authors themselves.
È vietata la riproduzione di articoli e illustrazioni di “ipcm®” senza autorizzazione e senza citarne la fonte. Le idee espresse dagli autori non impegnano nè la rivista nè eos Mktg&Communication S.r.l e la responsabilità di quanto viene pubblicato rimane degli autori stessi.
Research, innovation, development.
In 70 years, our vision towards the future has never stopped. Today, Tecnofirma provides quality to the electric market which is the most evolving technology in the automotive industry. Our impregnation, cleaning and painting plants are the result of the constant commitment to offer cutting-edge solutions and products anytime, anywhere.