
8 minute read
PRODUCT SHOWCASE - parts2clean
© ipcm
The two tanks containing the chemical product used in the tunnel. Le due cisterne contenenti il prodotto chimico del tunnel di lavaggio.
industry, such as carbon bumpers, crankcases, spoilers, roofs, bonnets, and underbodies with many different shapes and sizes. Inside it, the components undergo a cleaning stage with a detergent product dispensed through blade nozzles in a chamber with a 1,500-litre tank, followed by a rinse with demineralised water in a second chamber with an 800-litre tank. A third chamber for compressed air blow-off and an oven with five turbines and 230-m3/hour blowers that reaches a temperature of 150 °C ensure that all components are drained and dried. “The tunnel’s bottom is inclined to facilitate the return of liquids into the tank,” explains Marcello Maffei, Area Manager at Teknox. “Moreover, in order to simplify the personnel’s work in handling very large, complex-shaped components, this tunnel model includes a transport system with a one-rail overhead conveyor, which has a maximum load capacity of 4,000 kilograms and a part support system featuring load bars that accommodate several parts at the same time in order to better support C.P.C.’s production volumes. This allows producing over 3,500 parts per day in two shifts. Finally, staff safety is guaranteed by the presence of several switches to stop the system immediately; the loading and unloading areas – located in the sanding per esempio i paraurti, i carter, gli spoiler, i tetti, i cofani e le sottoscocche in carbonio di molteplici forme e dimensioni che l’azienda produce. All’interno, i componenti subiscono un lavaggio con detergente erogato tramite ugelli a lama in una camera con vasca da 1.500 litri e un risciacquo con acqua demineralizzata in una seconda camera con vasca da 800 litri. Successivamente, una terza camera per il soffiaggio ad aria compressa e un forno con cinque turbine e soffianti da 230 metri3/ora che raggiunge i 150° C, assicurando così il drenaggio e l’asciugatura di tutti i componenti. “Abbiamo progettato il fondo del tunnel in modo che fosse inclinato, per facilitare il ritorno in vasca dei liquidi”, chiarisce Marcello Maffei, Area Manager di Teknox. “Inoltre, per semplificare le attività del personale – che deve movimentare componenti molto grandi e con geometrie complesse – questo modello di tunnel prevedere un sistema di trasporto con un convogliatore aereo monorotaia che ha una portata massima di 4.000 chilogrammi e un sistema di sostegno dei pezzi tramite bilancelle attrezzate per sostenere più componenti, in modo da supportare meglio il volume produttivo di C.P.C. – che realizza oltre 3.500 pezzi al giorno su due turni lavorativi. Infine, per garantire la sicurezza del personale, sono presenti numerosi interruttori per fermare immediatamente l’impianto, e le zone di
and coating departments respectively and physically separated by a wall – are equipped with weight-sensitive platforms that stop the conveyor’s advance in both areas when they are stepped on.” In addition, the tunnel is equipped with several accessories that improve the sustainability of the cleaning operation, the healthiness of the working environment, and the cost-effectiveness of the entire process: a 50 µm and a 5 µm insulated bag filter in the cleaning bath, two emptying pumps, two detergent dispensers, two pumps recirculating the liquid from the rinsing to the cleaning station, four centrifugal steam condensers, and a kit for abrasive contaminants.
Future prospects
“This investment was made with a view to the future. In fact, we intend to integrate the cleaning tunnel within our sanding and coating plants, thus joining two separate departments and speeding up the entire production cycle. This will improve the speed of our operations because, thanks to Teknox technicians’ helpfulness and professionalism, the high cleanliness degree we achieve is consistent, so much so that additional manual cleaning is no longer necessary,” summarises Torelli. carico e scarico – posizionate rispettivamente nel reparto di carteggiatura e verniciatura e separate fisicamente da un muro – sono equipaggiate con delle pedane sensibili al peso che interrompono l’avanzamento del trasportatore in entrambe le aree in caso siano calpestate”. Il tunnel è inoltre equipaggiato con molteplici accessori che migliorano l’ecosostenibilità del lavaggio, la salubrità dell’ambiente di lavoro e l’economicità dell’intero processo: due filtri a sacco coibentato nel bagno di lavaggio da 50 e 5 µm, due pompe di svuotamento, due dosatori di detergenti, due pompe di rilancio dal risciacquo al lavaggio, quattro condensatori di vapore centrifugo e un kit per contaminanti abrasivi.
Prospettive future
“Questo investimento è stato effettuato in ottica futura: l’obiettivo è infatti quello di integrare il tunnel di lavaggio all’interno dell’impianto di carteggiatura e di quello di verniciatura, unendo così due reparti separati e velocizzare l’intero ciclo produttivo. Potrà migliorare la rapidità delle operazioni, perché, grazie alla disponibilità e alla professionalità dimostrata dai tecnici di Teknox, l’elevato grado di pulizia raggiunto è costante, dunque non sono più necessarie delle ulteriori fasi di pulizia manuale”, conclude Torelli.
The storage area for parts to be pre-approved. L’area di stoccaggio dei componenti in pre-delibera.
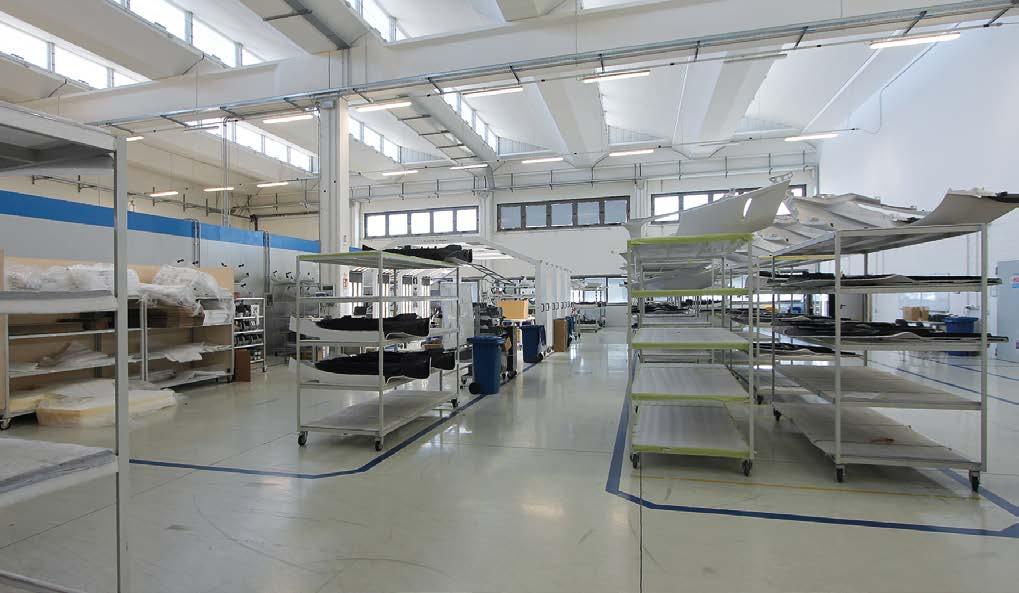
© ipcm
Cleaning more energy-efficiently
In the wake of rising electricity, oil and gas prices, energy efficiency in parts cleaning has become increasingly important. Opportunities to reduce energy consumption can be implemented in both existing cleaning systems and in those yet to be procured.
Reducing energy consumption and the associated carbon footprint has been an issue for quite some time now. Not least because when banks evaluate companies, the aspect of how well they are positioned to achieve climate protection targets is playing an increasingly important role. However, due to the enormous increase in energy prices in recent months and the uncertain fossil fuel supply situation, saving energy has become an economic necessity. As a result, companies are looking for potential savings in all areas, and parts cleaning as a quality-assuring manufacturing step is no exception.
Sulla scia dell’aumento dei prezzi di elettricità, petrolio e gas, l’efficienza energetica nel lavaggio industriale sta diventando sempre più importante. Le opportunità per ridurre il consumo energetico possono essere implementate sia nei sistemi di lavaggio esistenti sia in quelli in via di acquisizione.
La riduzione del consumo energetico e dell’associata impronta di carbonio è un problema ormai da tempo. Anche perché nella valutazione aziendale da parte delle banche, il posizionamento della società rispetto al raggiungimento degli obiettivi di protezione ambientale ha un ruolo sempre più importante. Tuttavia, a causa dell’enorme aumento dei prezzi dell’energia negli ultimi mesi e dell’incertezza nell’approvvigionamento di combustibili fossili, risparmiare energia è diventata una necessità economica. Di conseguenza, le aziende stanno cercando potenziali risparmi in tutti gli ambiti e il lavaggio industriale, come fase produttiva che garantisce la qualità, non è da meno.
Drying is the most energy-intensive step of the cleaning process. Savings here are made possible, among other things, by combining such drying technologies as infrared and vacuum drying.
L’asciugatura è la fase più energivora del processo di lavaggio. È possibile ottenere dei risparmi combinando tra loro alcune tecnologie come l’asciugatura a infrarossi e quella sottovuoto.
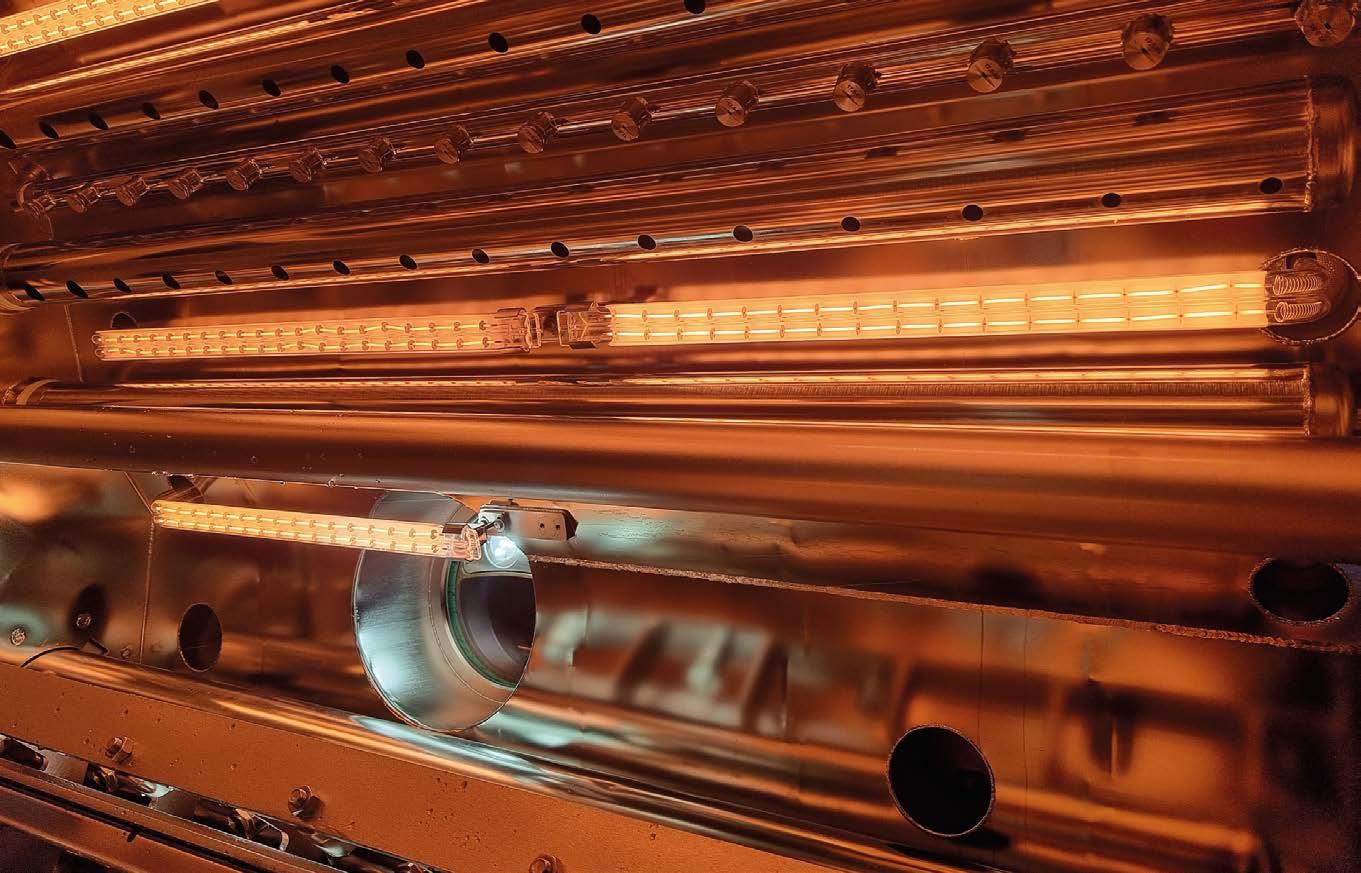
© BvL Oberflächentechnik
Intelligent control and monitoring of the system with exhaust air management, drying and automatic bath control helps to reduce energy consumption and costs. Il monitoraggio intelligente del sistema con gestione dell’aria di scarico, controllo dell’asciugatura e controllo automatico del bagno aiuta a ridurre consumi e costi energetici.
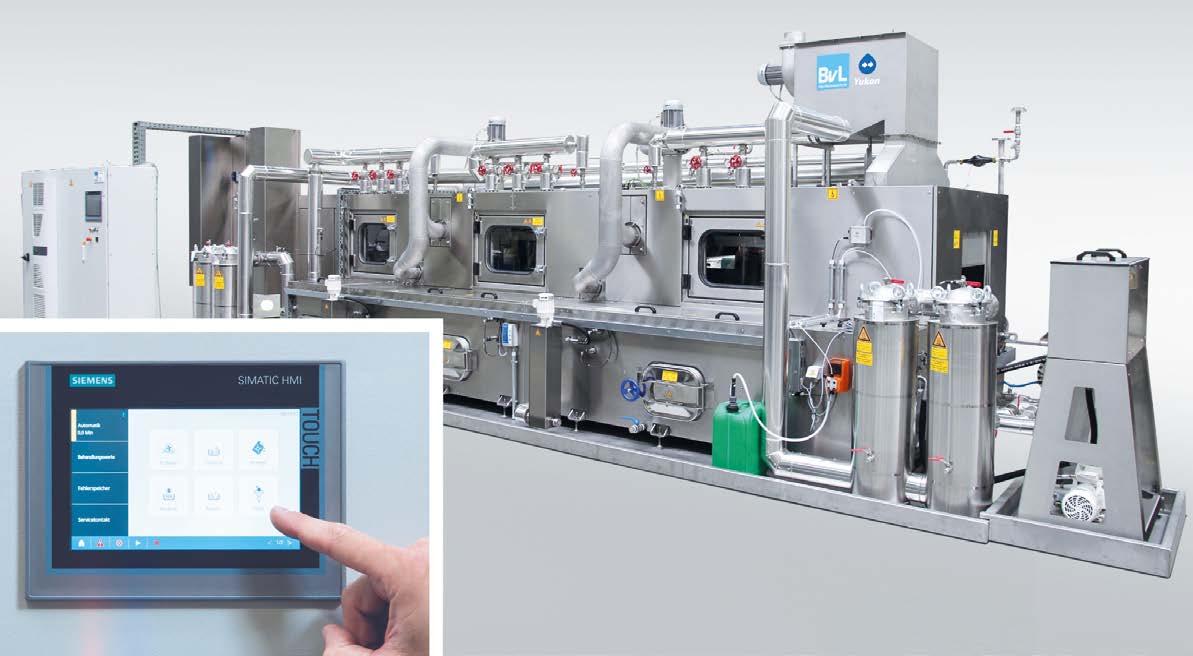
Parts cleaning not to be seen in isolation
The most energy-saving and cost-effective cleaning is the cleaning that does not need to be done. Conversely, the less cleaning required to achieve the specified technical cleanliness, the lower the energy demands and costs. In addition to the choice of the right cleaning method and process, this is why the amount of contamination introduced influences the energy and time required. In many cases, savings potentials can be exploited cost-effectively without any technical changes to the plant, including checking the partspecific process parameters once they have been defined. They are usually defined on the basis of a worst-case part, resulting in treatment times of ten to 15 minutes or even longer for cleaning, rinsing and drying. However, since the vast majority of workpieces to be cleaned are much less dirty, energy and time are wasted – these parts are cleaned for longer than necessary. If it is possible to avoid worst-case parts and to transport workpieces into the plant with as little contamination as possible, treatment times can be significantly shortened and energy consumption reduced accordingly.
Il lavaggio non deve essere valutato in modo isolato
Il lavaggio più efficiente dal punto di vista energetico ed economico è quello che non necessita di essere fatto. Per contro, minore è il lavaggio necessario a soddisfare le specifiche tecniche, minori saranno la richiesta energetica e i relativi costi. Oltre alla scelta del giusto processo di lavaggio, la quantità di contaminanti presenti influenza il tempo e l’energia richiesti. In molti casi i potenziali di risparmio possono essere sfruttati in modo economicamente vantaggioso senza modifiche tecniche all’impianto, compreso il controllo dei parametri di processo dopo la loro definizione. Questi sono solitamente definiti basandosi sull’ipotesi di contaminazione peggiore, con tempi di trattamento da 10 a 15 minuti - o anche di più - per lavaggio, risciacquo e asciugatura. Tuttavia, poiché la maggior parte dei manufatti è solitamente molto meno sporca, vi è uno spreco di tempo ed energia – i componenti sono lavati più a lungo del necessario. Se fosse possibile evitare questo metodo e trasportare i componenti all’impianto con la minor contaminazione possibile, si potrebbero accorciare in modo significativo i tempi di lavaggio e quindi il consumo di energia.