Stronger and smaller than polyester or nylon, Spectra® UF BIO fiber is designed to deliver a lifetime of durability for even the smallest cardiovascular devices.
Scan the code to learn more.
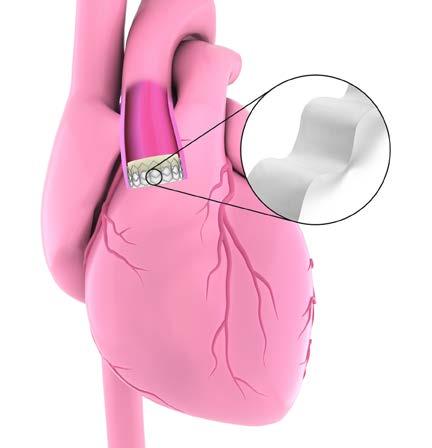
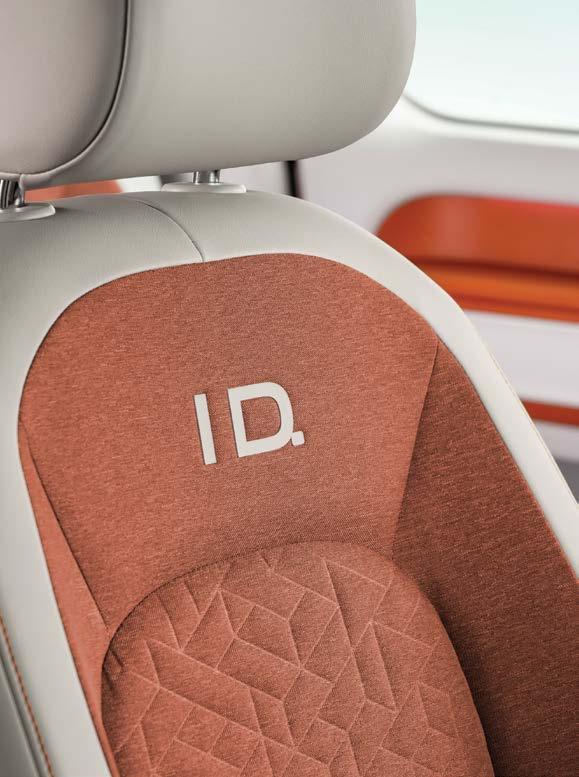
Stronger and smaller than polyester or nylon, Spectra® UF BIO fiber is designed to deliver a lifetime of durability for even the smallest cardiovascular devices.
Scan the code to learn more.
SYMPOSIUM
Experience thought-provoking discussions, where where industry experts delve into trends and innovations shaping the future of nonwovens and technical textiles.
TECH TALKS
Participate in strategic, solution-focused sessions covering the latest advancements and new technologies.
THE EVENT
In addition to an unparalleled educational program, join thousands of industry professionals in networking and business development opportunities.
Scan the QR code for registration information.
AUGUST 20 – 22, 2024
RALEIGH, NORTH CAROLINA
Showcasing solutions for success Showfloor Showcase: Honeywell, Zund
CEO Q&A:
Quality Is Not Visible at First Glance By Caryn Smith, Chief Content Officer & Publisher, IFJ
Fiber in the Driver’s Seat By Geoff Fisher, European Editor, IFJ
Driving Solutions By Marie O’Mahony
DOMEination in Geotextiles By Adrian Wilson
Overcoming Challenges of Industrial Bio-Composites By Caryn Smith, Chief Content Officer & Publisher, IFJ
Biocarbon Fiber Takes Flight By Adrian Wilson
FOCUS ON NONWOVENS
Q&A: Hey DUDE, Wipes Are In By Caryn Smith, Chief Content Officer & Publisher, IFJ
Show Review: Advancing Wipes at WOW 2024
Show Previews
Expo / 45
/ 46
Asia / 50
Tech Spotlight
BioFibreLoop Project Explores Circularity & Sustainability in Outdoor and Work Clothing
Tech Notes
Technology Briefs
Tech
& Shakers
Caryn Smith
Chief Content Officer & Publisher, INDA Media csmith@inda.org +1 239.225.6137
Marie O’Mahony
Feature Writer, IFJ
Visiting Professor, RCA, London marie.consultant@gmail.com
Geoff Fisher
European Editor, IFJ gfisher@textilemedia.com +44 1603.308158
Adrian Wilson
International Correspondent, IFJ adawilson@gmail.com +44 7897.913134
This is a unique opportunity to help inform, educate and inspire the global textile fiber industry.
Do you have an interest to be more involved in International Fiber Journal as an IFJ Editorial Advisory Board Member? We are accepting applications! Email Caryn Smith at CSmith@inda.org to receive the Guidelines.
This is a two-year renewable service term. Active participation is expected. Commitment to meet basic participation requirements annually are:
1. Write and/or obtain one exclusive technical article for publication in International Fiber Journal per year.
2. Participate in minimum of two, and no more than four, conference calls per year to collaborte with the Editor and provide feedback on the IFJ editorial direction.
3. Contribute to the development of focus topics that follow fiber and nonwovens current trends is expected in early fall timeframe for our Editorial Calendar Media Kit.
3. Review and comment on technical articles submitted for publication in IFJ as needed (in your area of expertise).
4. Provide contacts for potential contributors on specific topics as needed.
International Fiber Journal is actively seeking contributed technical, educational, and thought leadership articles from qualified industry professionals and those allied to the fiber industry. If you would like to pitch an article for publication in IFJ, please contact Caryn Smith at CSmith@inda.org or +1 239.225.6137. Inquire to receive an Editorial Calendar of each issue topics.
We are looking for individuals with their pulse on the marketplace. We are especially seeking viewpoints on technology, artifical intelligence, robotics, materials sourcing, innovation, institutional research, biomaterials from all regions across the globe. Represent your marketplace in our pages!
International Fiber Journal reaches a vast network of qualified professionals who employ fibers, nonwovens, technologies, equipment and more to optimiz se operations. With unique readers in markets that have strong crossover, IFJ offers print and digital opportunities to maximize marketing investments with a range of solutions based on true thought-leadership platforms. IFJ subscribers are in 67 countries. There are 17 countries with signficant readership (print and digital) that include USA, Hong Kong, Germany, China, India, Italy, United Kingdom, France, Spain, Belgium, Japan, Canada, Australia, Mexico, Switzerland, Brazil, and Taiwan. Don’t Leave Your Fate to Chance. Get a Media Kit: Email Advertising@inda.media today! Your Point of View Could
“Never confuse movement with progress. Because you can run in place and not get anywhere.”
– Denzel
Washington
any think that the move to all electric vehicles check the box on automotive circularity.
Yet these vehicles only address the emissions challenge of the world’s complex environmental concerns. Remember, there is still the rest of the vehicle to consider, beyond the battery. Most vehicles are 75-80% percent recycled by the automotive recycling industry, which is quite savvy at the three R’s – Reuse, Reduce, Recycle. To these businesses, recycling is the last option, because they make good money on the reuse of auto parts that ultimately reduce emissions which is generated when new parts are made. Reused auto parts are essential to the mechanical and collision repair industry, worldwide. It’s a booming, albeit misunderstood, industry for the last 80 years.
What needs to be considered is that 75-80% of a vehicle that is recycled is the ferrous and nonferrous metals. “The remaining 20-25 percent – the ‘fluff’ – includes everything else from the car, such as plastics, polyurethane foam, residual metals, fabric, rubber, glass, and dirt,” reports the Recycled Materials Association (formerly ISRI). “This fluff has long been considered a waste and has thus been discarded, burned in incinerators, or – if it’s lucky – beneficially ‘reused’ as daily cover in landfills.”
My question to consider: once in a landfill, how long does fluff take to breakdown? Does it ever break down?
That is where the textile industry comes in. Autos, airplanes, trains and boats, and other things that move people, all need environments that accommodate passengers. We know that every vehicle will reach an end of life, eventually, and will be dealt with in some way – either by auto recyclers, scrap yards or waste management.
How is the textile and nonwovens industry addressing this? Are we moving
people in well-designed environments, but not addressing the material waste stream?
The good news: The answer to that question is we do see progress being made, large and small. And it is imperative that this industry continue to investigate materials that meet customer expectations for comfort, utility and safety, yet also can help the environmental mission at hand.
On page 16, Geoff Fisher highlights initiatives in various transportation sectors. In automotive, he notes, “Many producers are now designing automotive interior materials that meet the 2030 end-of-life vehicle requirements and the ambitions of original equipment manufacturers (OEMs) with regard to circular economy targets. ... For example, by constructing mono-polymer carpets and flooring that are 100% recyclable at end of life.”
Marie O’Mahony, on page 21, reports on sensory aspects of transportation textiles, and also collaboration between corporations. “Ford has launched a wide range of biomaterial products that include wheat straw for storage bins and cup holders, kenaf plant door bolsters, rice hulls for electrical harnesses, tomato skins for wiring brackets and storage bins. In a collaboration with McDonald’s, the dried skin of the coffee bean, the coffee chaff, is used in a composite for car headlight housing. ... The resulting components Ford estimates to be 20% lighter and needing around 25% less energy during the moulding process.”
It seems that transportation manufacturers are making end of life and sustainability a goal, and this is movement towards real progress. Enjoy the read!
Caryn Smith Chief Content Officer & Publisher, INDA Media, IFJ
Partners at the BioFibreLoop’s
The German Institute of Textile and Fiber Research Denkendorf (DITF) is coordinating a research project, funded as part of the European Union’s Horizon Europe research and innovation program, that aims to develop recyclable outdoor and work clothing made from renewable bio-based materials. The project has been named BioFibreLoop, and the kick-off event took place in Denkendorf, Germany at the end of June.
The textile industry is facing two particular challenges: on the one hand, production must become more sustainable and environmentally friendly, and, on the other hand, consumers are expecting more and more smart functions from clothing.
In addition, the production of functional textiles often involves the use of chemicals that are harmful to the environment and health and make subsequent recycling more difficult.
Intelligent innovations must therefore ensure that harmful chemicals are replaced, water is saved, and more durable, recyclable bio-based materials are used, thereby reducing the usually considerable carbon footprint of textile products. Digitalized processes are intended to ensure greater efficiency and a closed cycle.
For example, the BioFibreLoop project uses laser technology to imitate natural structures
in order to produce garments with water and oil-repellent, self-cleaning and antibacterial properties. At the end of the research project, the result work will be affordable, resource and environmentally friendly, yet high-performance and durable fibers and textiles made from renewable sources such as lignin, cellulose and polylactic acid. All processes are aimed at a circular economy with comprehensive recycling and virtually waste-free functionalization based on nature’s example. In this way, greenhouse gas emissions could be reduced by 20 percent by 2035.
The technology for the functionalization and recycling of bio-based materials is being developed in three industrial demonstration projects in Austria, the Czech Republic and Germany. At the end of the project, a patented circular, sustainable and reliable process for the production of recyclable functional textiles will be established.
The BioFibreLoop project has a duration of 42 months and a total budget of almost 7 million euros, with 1.5 million going to the coordinator DITF.
The consortium consists of 13 partners from nine countries who contribute expertise and resources from science and industry:
• German Institutes of Textile and Fiber Research Denkendorf (DITF), Coordinator, Germany
• Next Technology
Tecnotessile
Società nazionale
di ricerca R. L., Italy
• Centre Technologique ALPhANOV, France
• G. Knopf’s Sohn GmbH & Co. KG, Germany
• FreyZein Urban Outdoor GmbH, Austria
• BEES - BE Engineers for Society, Italy
• BAT Graphics Vernitech, France
• Interuniversitair Micro-Electronica Centrum, Belgium
• Idener Research & Development Agrupacion de Interes Economico, Spain
• Teknologian tutkimuskeskus VTT Oy, Finland
• Det Nationale Forskningscenter for Arbejdsmiljø, Denmark
• Steinbeis Innovation gGmbH, Germany
• NIL Textile SRO, Czech Republic
The DITF form the largest textile research center in Europe with more than 250 scientific and technical staff. As the world’s only textile research facility and covering an area of more than 25,000 m², the DITF work right across the textile production and value chains. Since 1921, it has been researching across all the major fields within textiles and is considered among the leading research institutions worldwide.
For more information contact: Dr.-Ing. Thomas Fischer, Deputy Head of Center of Management Research
T +49 (0)711 93 40-419
E thomas.fischer@ditf.de
For details on how to submit your company’s technology for consideration as a “Technology Spotlight” in IFJ, contact Ken Norberg at ken@ifj.com or +1 202.682.2022.
Freudenberg Performance Materials Apparel recently announced the global launch of the complete RCY 99xx series recycled polyester (rPET) shirt interlinings. This innovative product line serves as a sustainable counterpart to Freudenberg’s renowned 95xx series, which has been a staple in the industry for over twenty years.
The 95xx series, celebrated for its unique bi-elastic properties, has earned its place as one of Freudenberg’s most sought-after shirt interlining ranges worldwide. Cherished by customers across the globe, the 95xx series has consistently delivered on quality and performance.
Now, taking a leap towards sustainability, Freudenberg introduces the complete RCY 99xx series. Crafted from rPET, these bi-elastic interlinings are designed to complement an array of contemporary fabrics, including pure cotton, T/C, flannel, oxford, cotton & linen blends, seersucker, jersey and all types of stretch knits. The RCY 99xx series not only preserves the natural hand feel, texture, and shape of these fabrics but also infuses a fresh creative dimension into shirt design.
The RCY 99xx series boasts an impressive weight range of 30-150 g/m2, offering versatility for a diverse spectrum of shirt styles, from men’s casual shirts and women’s blouses to polo shirts, sports shirts, and even denim shirts. This adaptability ensures that designers and manufacturers have the flexibility to meet the evolving demands of the market while upholding sustainability principles. www.freudenberg-pm.com
ZymoChem, a leading biotech company dedicated to creating sustainable materials for everyday products, announced the launch of BAYSE™, the world’s first scalable, 100% bio-based, and biodegradable Super Absorbent Polymer (SAP). This groundbreaking innovation is set to revolutionize the $145 billion global hygiene industry and pave the way for a more sustainable future.
BAYSE™ is a drop-in replacement for traditional, fossil fuel-based SAPs, which are a key component in disposable, absorbent hygiene products such as infant diapers. Unlike petroleum-derived, polyacrylate counterparts, BAYSE™ is made from renewable resources, maintains a lower carbon footprint, and is readily biodegradable, addressing the environmental concerns associated with the 300,000 diapers that enter landfills or are incinerated every minute.
ZymoChem’s proprietary technology platform enables the production of BAYSE™ at a cost which is competitive with traditional SAPs, ensuring that sustainability can be achieved without a premium. Intent on creating a positive environmental impact and inspiring change across sectors, ZymoChem’s BAYSE™ boasts additional applications in industries such as agriculture, cosmetics, and water treatment. The creation of microplastics from fossil-based petroleum SAP has been a concern for those industries, which BAYSE™ addresses as a high-performance, microplastic-free alternative.
ZymoChem recently raised $21 million in Series A funding to accelerate the commercialization of BAYSE™. For more information about ZymoChem and BAYSE™. www.zymochem.com
Fig.1 has introduced dissolvable Micellar Oil Wipes. The wipes are derm-developed to melt away makeup and sunscreen, revealing clean, soft, radiant skin and individually wrapped for easy travel. Fig.1 partnered with skincare innovator Conserving Beauty to unite sustainability with beauty so consumers can enjoy a zero-trace cleanse. Each wipe dissolves within seconds in water, leaving zero waste and skin glowingly clean.
Fig. 1 recommends dissolving the wipe in the shower or sink. Wipes that go into the garbage instead will biodegrade within 14 days. fig-1.co
Mann+Hummel has launched Mann-Filter FreciousPlus featuring nanofibers for cabin air filtration. The new filter is designed to effectively filter ultra-fine particles, along with pollutants from both outside and inside the vehicle, and it also offers proven protection against allergens, bacteria, and mold.
In recent years, international studies have proven the impact of the smallest particles on our health: The smaller the particles, the more dangerous they are, as they can penetrate deeper into the human respiratory system and cause serious health problems, including death. With the evolved FreciousPlus featuring nanofibers, MANN-FILTER sets new standards in cabin air filtration. The new filter not only impresses with its filtration of ultra-fine particles, but also with the filtration of pollutants both from outside and inside the vehicle. The new filter continues to offer proven protection against allergens, bacteria, and mold.
Mann+Hummel has been successfully using nanofiber technology to filter out the finest particles for a number of years, and it is this technology that is now available on the automotive aftermarket for premium brand Mann-Filter cabin air filters. Since January 2024, these have been available in the form of the Mann-Filter FreciousPlus FP 38 004 for the BMW 5 Series and 7 Series saloons, and now feature in the 5 Series Touring wagon, too.
“Our Mann-Filter FreciousPlus FP 38 004 has the finest nanofibers, which are about 100 times thinner than the fibers of conventional filter linings,” said Thomas Heininger, director Engineering Cabin Air Filters at Mann+Hummel. “These fibers form a spider’s web-like structure over the other filtration layers with coarser fibers, enabling them to capture ultra-fine particles. This means that, in addition to the PM10 and PM2.5 particles, the FreciousPlus featuring nanofibers can remove 90% of the even finer PM1 class i.e. particulates with an aerodynamic diameter of less than 1 micrometer (0.0001 cm). The nanofibers in the FreciousPlus filter up to 80% of ultra-fine particles (UFP) smaller than 0.1 micrometers, thus achieving maximum values. For context, these extremely small particles are about 700 times smaller than a human hair.”
The extremely thin nanofiber ensures that the FP 38 004 is resistant to humidity and temperature fluctuations and provides consistently high filtration throughout the entire service interval. To ensure that the FreciousPlus cabin air filter with nanofibers can work reliably, it must be replaced once a year or every 15,000 kilometers. “We recommend that local experts regularly inform vehicle owners of the importance and benefits of the cabin air filter. Most car drivers are unfortunately unaware of this,” says Heininger. www.mann-hummel.com
For more than 50 years, Fi-Tech has successfully worked with manufacturers of machines and key techical components used in the production of:
traditional single use plastic-based disinfectant wipes, which currently dominate the North American market and take hundreds of years to degrade once discarded.
On the sustainability side, the Disinfectant 1 Wipe boasts exciting degradation capabilities, reaching 94.3% relative biodegradation in a 15-day accelerated test, demonstrating full decomposition into non-hazardous byproducts. www.ecolab.com
Our customers trust us to provide the best quality and rely on our commitment to their needs when exploring new opportunities to grow and to improve their manufacturing businesses.
Equally, our suppliers highly value the service, dedication, and access to the markets we provide.
Lenzing Group, a leading global producer of wood-based specialty fibers, announced the launch of its latest Black Towel Collection made with LENZING™ ECOVERO™ branded black viscose fibers and TENCEL™ branded black modal fibers. The collection features six essential everyday washable and reusable face and body care items, from makeup removal pads, makeup removal towels, gym towels, bath towels, hand towels, hair bonnets, to beach towels, designed to cater to the ever-changing consumers’ needs for quality, responsible personal care items for every aspect of daily life. Made with ingredients that are responsibly produced, the Black Towel Collection presents an alternative choice for a societal norm where conventional makeup removal products are mostly single-use disposable items, and reusable towels often get stained or discoloration due to repeated usage. The collection will bring about a refined experience to consumers through its exceptional durability, softness and color vibrancy.
The Black Towel Collection is woven with a blend of cotton and TENCEL™ Modal black fibers or LENZING™ ECOVERO™ Viscose black fibers with a unique fabric composition to enhance durability. Even after multiple washes, these products retain their softness and gentle feel on the skin, making them ideal for repeated use. Derived from controlled or certified wood sources, these specialty fibers are made from resource-saving processes, using at least 50% less carbon emissions and water consumption. Additionally, the LENZING™ ECOVERO™ Viscose black fibers are certified biodegradable and compostable at the end of their lifecycle. Both reusable and responsibly produced, this towel collection is an excellent solution for individuals looking to minimize the carbon footprint of their everyday care practices. www.lenzing.com
Autoliv, a global leader in automotive safety solutions, continues its journey to a sustainable future by introducing airbag cushions made of 100% recycled polyester which significantly reduce the greenhouse gas (GHG) footprint of airbags.
In collaboration with key supply chain partners, Autoliv has developed yarns, fabrics, and cushions made from 100% recycled polyester for use in airbag production. The completed testing of the new material demonstrates that the airbag cushion provides equal safety functionality to a standard polyester airbag while reducing GHG emissions by approximately 50% at the polymer level.
Using this new recycled material is a crucial step toward Autoliv’s commitment to reduce emissions across its product range and will contribute to Autoliv’s ambition to achieve net-zero GHG emissions across the supply chain by 2040.
Autoliv’s Chief Technology Officer, Jordi Lombarte, states, “We are walking the talk on our climate ambitions at Autoliv, by bringing the first technology to create airbags using 100% recycled polyester fabric. We have successfully proven the technology and are ready to offer it to our customers worldwide.”
Autoliv continuously develops processes and products in a resource-efficient manner while minimizing environmental impact. As part of Autoliv’s product portfolio, the new material is now available for global customers. www.autoliv.com
DuPont Performance Building Solutions, a leading innovator in material science, has announced the launch of its latest generation breather membrane, Tyvek® Trifecta™. The innovative product offers exceptional fire safety and moisture protection, making it an ideal solution for external walls of high-rise buildings in a convenient and light-weight roll size of 1.5m x 25m. Tyvek® Trifecta™ is a non-combustible breather membrane designed to provide all the benefits of a standard Tyvek® breather membrane, but with A2-s1, d0 Class Fire Performance to the current European Fire Classification Standard EN 13501-1. It surpasses current UK Building Regulations, which require membranes to meet Class B. www.dupont.com
The rise in heart valve disease and other cardiovascular conditions has led to a growing demand for minimally invasive devices and technologies. In addition, medical devices need to meet specific tissue response and durability criteria for the biomedical structures to elicit proper biologic responses. This means that medical devices need to be small and flexible to enable minimally invasive surgeries while also being strong and durable so they can last for the full life of the patient. The use of ultra-high molecular weight polyethylene fibers like Honeywell Spectra® UF BIO can play a significant and useful role in the development of biocompatible medical devices, particularly in the field of cardiovascular applications such as heart valves.
Spectra® UF BIO Fiber is a product portfolio that falls under the Honeywell medical grade fibers offering that is known as Spectra® MG BIO Fibers. All of the products within the Spectra MG fiber portfolio are 100% ultra-high molecular weight polyethylene (UHMWPE) fibers. These fibers are manufactured through a unique gel spinning process — the first of its kind. It’s one of the world’s strongest and lightest fibers, enabling the design of medical devices that have higher surgical accuracy rates, faster recoveries, and better patient outcomes.
Ultra-fine UHMWPE fiber like Spectra MG is 15 times stronger than steel by weight, 40% stronger than aramids on a weight-byweight basis and three times stronger than polyester on a volume basis. It also offers high pliability, low elongation and a low coefficient of friction that allow the development of stronger, lowerprofile devices.
Strong, thin fiber ideal for lower profile devices
Smaller-profile medical devices are important especially for cardiovascular patients. They help facilitate less invasive procedures that reduce patient discomfort and recovery time. Honeywell’s Spectra UF BIO offers a stronger, thinner solution as compared to traditional materials such as nylon and polyester making it ideal for even the smallest cardiovascular devices. Available from 100 denier down to the 10 dtex, this UHMWPE fiber allows for smaller devices that can access smaller anatomical structures other devices can’t reach.
Spectra UF BIO can be shaped into a variety of textile constructions, including braids, woven shapes and knits to enhance the design of implantable cardiovascular devices. Spectra UF BIO is biocompatible, chemically inert and offers superior resistance to fatigue and abrasion compared to polyester – extending the life of in-body devices compared to those using a polyester fiber. This creates the potential for improved patient quality of life by reducing the need for revision surgeries in the future. Spectra UF BIO also has a lower coefficient of friction than polyester, resulting in easier transfer through tissue and enabling lower levels of patient inflammation after surgery.
Use of Spectra UF BIO in cardiovascular is just one of the many key areas that benefit from the use of this small, yet strong fiber. Spectra UF BIO can also be used in orthopedics, surgical robotics, and more.
Interested in learning more?
Customers have trusted Honeywell to solve their greatest challenges for more than a century, and we’re committed to helping innovate with you. Our lineup of medicalgrade fibers is produced at our world-class U.S. manufacturing sites and is backed by our strong technical support and expertise in UHMWPE.
Zund America with headquarters in Oak Creek, Wisconsin, is the sister company of Zünd Systemtechnik AG, the family-owned Swiss manufacturer of multifunctional digital cutting systems. Zünd has been developing and manufacturing digital cutters for four decades — in fact, 2024 marks the 40th anniversary of Zünd Switzerland, while Zund America is proud to be celebrating its 20th!
Zünd has gained a worldwide reputation for being the leading manufacturer of high-quality cutting solutions uniquely geared towards meeting the needs of each customer and industry. While Zünd systems are widely used in textile/ technical textile, and composites, they can also be found in countless leather, graphics, packaging, and many other industrial applications. Built for 24/7 operation and powered by applicationspecific control software, Zünd cutters offer an extensive selection of modular, specialized tool options and workflow automation. Zünd makes digital cutting of textiles — and many other types of flexible or rigid materials — simple, productive, and profitable.
Zünd has created production workflows for state-of-the-art, digital textile cutting that begin well before any actual cutting takes place and don’t end as soon as cutting is over. Innovative solutions are available for every phase of the process, including the latest version of the powerful MindCUT Studio Production software with a range of exciting new features.
Among these is Feature Recognition, a digital workflow that enables the software to detect motifs and different parts of a garment using AI. In the blink of an eye, it selects the model, aligns the motif and reference points, and attributes individual parts for perfectly precise subsequent cutting. This automates a previously very time-consuming, manual process.
MindCUT now also offers a Printed Cut function that automatically captures printed designs in addition to Pattern
Matching, which recognizes repeating patterns, compensates for material distortions, and automatically matches the markers to the pattern.
The new Roll Handling System – RHS is the latest Zünd material-handling solution for textile applications. The system can hold up to ten rolls of fabric, which can be identical or of different types.
The large, fully automated RHS enables extended, uninterrupted production cutting by autonomously feeding material onto the cutter. The only remaining operator intervention consists of scanning barcodes of individual rolls while loading them onto the RHS. The material assignment and the RHS itself are controlled directly through the MindCUT software.
• Zünd modular, multifunctional digital cutting systems can be tailored to individual production needs with a wide range of specialized tool options for maximum versatility, cut quality, and efficiency.
• All Zünd cutters can be expanded and upgraded any time with addi-
tional tooling and workflow automation to meet increases or changes in demand.
• Zünd’s open architecture makes these cutting systems easy to integrate in existing production environments.
• Modularity, versatility, productivity, and low cost of ownership: Your First choice in digital cutting—for 40 years.
www.zund.com
Also exhibiting at CAMX 2024, Booth LL25, San Diego, CA; IBEX 2024, Booth 3-1437, Tampa, FL.
By Caryn Smith, Chief Content Officer & Publisher, IFJ
nternational Fiber Journal spoke with Simon Papo, President of the Board, and Ceki Papo, COO, of Ş afak Technical Textile, a leading technical textile manufacturer located in Tuzla, Istanbul Province, Türkiye. We discussed the company’s long history and exciting new developments – including a groundbreaking sustainable advanced textile. Since its founding in 1958 by Mr. Jak Papo, this three-generation family business has been dedicated to solving complex textile problems.
Şafak operates with 30,000 square meters of factory floor space, producing over two million meters of textiles per month, and exporting to around 30 countries across five continents. The primary sectors served include automotive, aviation, marine, railways, outdoor upholstery, shoes and bags, sportswear, wall coverings, and more. The company is diligently working on digitalization, implementing a sustainable manufacturing system, traceability, carbon footprint calculations, and life cycle assessment analyses. Here is their story.
International Fiber Journal: Give us a history of your family business, and its legacy.
Simon Papo: Şafak Technical Textile was established in 1958 by my father, Jak, before I was born, as one of the first circular knitting production facilities in Türkiye. In 1972, we became the first company in Türkiye to produce synthetic leather
backing for a large German company, for whom we were the sole supplier. This milestone paved the way for what we do today. In the early 1990s, the Turkish synthetic leather market began booming, and we have remained the main technical backing supplier ever since.
I joined the company in 1987 after completing my studies in mechanical engineering with a focus on robotics and automation at the Technion, Israel Institute of Technology. The company was focused on technical textiles, though we didn't refer to them as such back then. I always urged my father to pursue the technical direction to gain a stronger competitive advantage. Our company’s hallmark is innovation; we don’t copy and paste – we create unique materials, a key focus for our research and development unit.
IFJ: Being a family business, how has the company evolved with the generations?
Simon: We have always prioritized R&D and innovation. Our history is filled with milestones that demonstrate success in various projects. For instance, in 2004-05, Trenitalia (Italian railways) needed a synthetic leather product for their seats that had challenging mechanical strength requirements. Achieving this required an unconventional approach. Inspired by Da Vinci’s dome, which carries itself, we developed a solution that had a similar selfsupporting knit structure.
Looking ahead, I am proud that my son, Ceki, who studied at the Johns Hopkins University, chose to join the family business, seeing the bright future we have. My other son, Erel, will join us next year after completing his studies in computer science and applied mathematics at the University of Southern California. We consistently produce solutions to our clients' complex challenges, adding value to their needs. We are very excited about the future.
We created a waterbased impregnation-like process to replace the DMF, eliminating harmful chemicals. Corium™ was born from this innovation, requiring significantly less water in production and avoiding chemicals under regulatory scrutiny.
IFJ: What is the process working with Şafak clients – your ‘competitive edge.’
Ceki Papo: We pride ourselves on our customer service. While we produce tangible technical textiles, we understand that high-quality service must accompany our products. Our R&D service is our competitive edge. We rarely say no to challenges; instead, we strive to find solutions, defining ourselves as solution providers. This approach often entails developing new equipment and optimizing production flows to provide our clients with a competitive edge.
IFJ: Tell us about Şafak’s product innovation, Corium™ – why is it a never-seenbefore textile?
Simon: Over the years, we have delved deeper into the synthetic leather business, which involves coating or coagulating processes. Polyurethane resin coagulation, typically done with DMF, faces potential bans in Europe. Seeking alternatives, we were inspired by the 1970s Italian automotive interior applications to develop a similar end-product but through a completely different manufacturing process.
We created a water-based impregnation-like process to replace the DMF, eliminating harmful chemicals. Corium™ was born from this innovation, requiring significantly less water in production and avoiding chemicals under regulatory scrutiny. Additionally, our state-of-the-art production line uses recycled energy re-
covered from our exhaust gasses. Hence, Corium™ products are environmentally responsible, made from recycled fibers combined with water-based PU.
Today, Corium™ has numerous applications across various markets, becoming one of Şafak’s flagship products.
IFJ: You also created your own machinery to produce it, correct?
Simon: Yes, we built our own machine because the process we came up with is unique. No existing machine could produce Corium™ as we needed, so we developed our own.
IFJ: What are your plans for Corium™?
Ceki: The potential of Corium™ is larger than we initially imagined. While we are meeting current contracted demands, its applications span wall coverings, upholstery, automotive, footwear, and more. We are in the early stages of this journey, building the right team to address technical, sales, and marketing challenges to supply various industries simultaneously with one product family.
IFJ: Share more about your sustainability efforts.
Simon: In 2012, we were the first to produce fully recycled textiles for a global leading sports shoes brand for the London Summer Olympics, using recycled polyester. That was a pioneering project in Türkiye's recycled textiles industry.
Ceki: Our sustainability efforts gained momentum in recent years. We have advanced our digitalization journey with an in-house developed ERP system and are expanding our IT team with new software engineers. Traceability is at the core of our new system, allowing us to track production parameters and ensure target parameters match the realized ones. Our goal is to complete life cycle assessments and carbon footprint calculations using
our system, sharing this data with clients to support their sustainability tracking.
IFJ: What is the structure of your team?
Ceki: Our unique team structure distinguishes us, placing R&D and engineering at the core of our business operations. As we continue to develop innovative digital solutions, our organizational framework is evolving to better manage daily tasks and workflows. This evolution is leading us to expand our team with an increasing number of computer scientists and engineers, strengthening our capabilities and driving our progress forward.
IFJ: How does your company work with universities and students?
Ceki: For several years, we’ve collaborated with Istanbul Technical University, known for its renowned textile engineering department. We benefit from their guidance and mentorship on R&D projects and use their accredited textile laboratories for physical and chemical tests. Additionally, we are collaborating with Shenkar College of Engineering and Design in Tel Aviv to create a hub that combines academia and industry, assisting students in realizing their dreams in textile design and manufacturing.
IFJ: Your tagline is, “Quality is not visible at first glance.” What does that mean?
Simon: At first glance, one cannot fully appreciate the innovation and customization that define our approach. This motto signifies that the depth of our commitment to quality and the advanced technological processes we employ are not immediately evident. It requires a deeper look to truly understand the precision, innovation, and customization embedded in every product.
Note: Şafak Technical Textile will be exhibiting in the U.S. at the Advanced Textiles Expo on September 24-26, in Anaheim, CA. www.safaktekstil.com.tr
Elementary Nonwovens Course
INDA Headquarters, Cary, NC
Intermediate Nonwovens Course
INDA Headquarters, Cary, NC & The Nonwovens Institute, Raleigh, NC
Meltblown Technology Course
The Nonwovens Institute, Raleigh, NC
Spunbond Technology Course
The Nonwovens Institute, Raleigh, NC
Nonwoven Fabric
Property Development & Characterization Course
The Nonwovens Institute, Raleigh, NC
Fiber & Filament Extrusion Fundamentals Course
The Nonwovens Institute, Raleigh, NC
Nonwoven Product Development & Innovation Course
The Nonwovens Institute, Raleigh, NC
Nonwoven FundamentalsBondingCourse
The Nonwovens Institute, Raleigh, NC
WIPES Academy
@World of Wipes International Conference
Absorbent Hygiene Course
INDA Headquarters, Cary, NC
For more information, visit: inda.org/training
Questions? Contact the Registrar registrar@inda.org +1 919 459 3724
By Geoff Fisher, European Editor, IFJ
Transportation, which includes the automotive, aerospace, railways and marine sectors, represents one of the largest markets for technical textiles, with fibers used in significant volumes for a wide range of end uses.
Fabrics for transport are subjected to a range of environmental conditions, including abrasion and fluctuating temperatures, while developments have been geared towards improving durability, weather resistance and safety.
In the automotive industry, textiles are used in such applications as seat upholstery, headliners, floorcoverings, seatbelts, airbags, tire cord, headliners, insulation and filtration. Modern passenger vehicles currently use an average of 30-35 kg of yarn in various applications that are especially focused on comfort and safety.
Most forecasters estimate the global automotive textiles market to be worth in excess of US$40 billion by 2030 with a compound annual growth rate of 4%.
Many producers are now designing automotive interior materials that meet the 2030 end-of-life vehicle requirements and the ambitions of original equipment manufacturers (OEMs) with regard to circular economy targets.
Most carmakers are now emphasizing the integration of “eco-friendly” materials in their latest models, where recycled fabrics and sustainably treated leather are increasingly featuring in seat upholstery, interior trim, and door panels.
At the same time, consumer demand for customized and personalized vehicle interiors continues to grow, driven by preferences for individualization and self-expression. Fabric manufacturers are beginning to offer customizable fabric options in a range of colors, textures, patterns and finishes, catering to diverse consumer tastes and preferences.
According to a recent report from market research company The Brainy Insights, integrating smart technologies into vehicle interiors presents an opportunity for automotive fabric manufacturers, where fabrics embedded with sensors, heating elements, lighting systems and interactive displays can offer enhanced functionality, comfort, and convenience for passengers.
In addition, the incorporation of temperature regulation, moisture management and antimicrobial properties into automotive fabrics can be used to enhance passenger comfort and well-being during travel.
At the same time, momentum is growing amongst automotive OEMs and Tier 1 suppliers for the development of products that, from the initial design phase, consider eco-design, for example, by constructing mono-polymer carpets and flooring that are 100% recyclable at end of life.
For example, Autoneum has introduced an automotive tufted carpet made of 100% polyester that is fully recyclable. The floorcovering also has a high content of recycled polyethylene terephthalate (PET), according to the Switzerland-based producer of acoustic and thermal insulation systems. The company’s zero-waste and latex-free manufacturing process is claimed to significantly reduce carbon dioxide (CO2) emissions as well as water and energy consumption.
Belgium-based BIG Yarns, part of Beaulieu International Group, expects the automotive carpet market to grow strongly in the coming decade with the increased demand for vehicle customization and personalization driven by owners looking to upgrade and enhance interiors, including the flooring area.
The company notes that a growing
UK-based Footfalls & Heartbeats has developed simple, non-intrusive sensing technology in a knitted car seat cover to enhance comfort, safety and occupational health. Footfalls & Heartbeats
awareness around hygiene is also boosting the market as consumers become more conscious of maintaining cleanliness in their vehicles, including the floors.
“Automotive carpets provide an effective solution by trapping dirt and preventing it from spreading to other areas,” said BIG Yarns.
Polestar’s second all-electric model, the Polestar 4, features interior materials that focus on sustainability through a mono-material approach for effective recycling. These include a tailored knitted textile made of 100% recycled PET; bioattributed MicroTech vinyl, which was introduced in the Polestar 3 and replaces crude oil with pine oil and features a
recycled textile backing; and traced leather sourced from Bridge of Weir Leather.
The new Polestar vehicle also features inlay carpets in the interior made from recycled PET, floor carpets made from Econyl that incorporate polyamide fiber from reclaimed fishing nets, and door trim panels made from a natural fiber/ polypropylene composite that results in up to 50% less virgin plastic and a weight saving of up to 40%, says the Swedish automotive manufacturer, owned by Volvo.
Yarns used in airbags are mainly made of polyamide, although polyester is increasing in usage. In an effort to reduce the greenhouse (CHG) gas footprint of airbags, Sweden-based automotive safety systems provider Autoliv recently introduced airbag cushions made of 100% recycled polyester.
Tests show that the new material used in these airbag cushions provides equal safety functionality to a standard polyester airbag while reducing GHG emissions by approximately 50% at the polymer level.
In the aviation industry, textile furnishings for aircraft include seat covers, seatbelts, lifejackets, curtain fabrics, carpets and floorcoverings, wallcoverings, blankets and headrest covers – elements of an aircraft interior that enable an airline to develop and reinforce its corporate identity and offer much greater scope
for customization than most other interior products.
According to interior designers, passengers register an airline’s identity within the cabin environment through the stimuli of a number of factors in which textiles have the greatest part to play.
Importantly, all textiles used in aircraft cabins must be flame retardant in air with a normal concentration of oxygen. They should also be wear-resistant, stain-resistant, non-toxic, and as light as possible – the lighter the aircraft, the lower the airline’s fuel consumption and therefore its CO2 emissions.
Seat upholstery must also be comfortable against the skin. Seat covers for aircraft can be made of a wide range of materials, from blended fabrics containing wool, viscose, and synthetic fibers, as well as leather.
A blend of wool and polyamide is an industry standard for seat covers, with wool fibers often accounting for 90-95% of the fabric, which also helps to make the fabric flame retardant. The use of polyester in seat upholstery, meanwhile, is dependent on being combined with fire-blocking materials.
Real leather has a high-quality look, and with ultrathin coatings it is still a popular material for aircraft seat covers. However, recent developments have focused on vegan, fully recyclable leather substitutes made from a wide range of plant-based materials, as well as products such as Alcantara, a luxury microfiber fabric that offers light weight, durability, softness and high-performance properties.
UK-based Generation Phoenix, in partnership with Sabeti Wain Aerospace and Doy Design, has launched what is claimed to be the aviation industry’s first fully recyclable aircraft dress cover.
This is said to represent a closed-loop solution that allows airlines to recycle 100% of their end-of-life seat covers into new seat cover material with the same quality, durability, and certification requirements.
This fully circular cover is upholstered in Helios, a new material developed by Gen Phoenix, made using recycled endof-life waste in a closed-loop process, which can be recycled continuously.
According to Gen Phoenix (formerly ELeather), which uses leather offcuts destined for landfill and regenerates them into a premium recycled leather material, current seat covers are traditionally made from a mix of non-recyclable materials that are hard to separate and end up in landfill or incinerated after their typical service life.
For aircraft carpets, European airlines almost always favor products with a high wool content, while U.S. airlines are just as adamant about using polyamide. Meanwhile, seatbelts in aircraft must, of course, have high tensile strength, but must also be resistant to light and acids, have flame-retardant properties and keep their shape.
Outside the Earth’s atmosphere, aerospace textiles include fiber-containing articles for specific functional requirements
to work in space suits, space shuttles and spacecraft, such as for future lunar and Mars missions.
Thomas Stegmaier, sustainability officer and research director for technical textiles at the German Institutes of Textile and Fiber Research (DITF) Denkendorf, Germany, expects further development of textiles for aircraft applications.
“What is going to be really interesting are smart textiles with additional functions,” he said, citing the work currently being done on self-illuminating textiles, which incorporate metal fibers that emit light when electrified. “Upholstering the aircraft cabin ceiling with this kind of fabric would mark a significant reduction in weight. Ultimately, that is what all developments in textile technology are trying to achieve.”
Interior textiles for the railways include tufted carpets, entrance mats and fabrics for seat covers, curtains, wallcoverings, and headrests, while textiles for buses include woven and tufted carpets, entrance mats and fabrics for seat covers, curtains and headrests. Many public transport operators still use durable wool-rich moquette for seat upholstery, including cushions, headrests and armrests, particularly in long-distance vehicles where seat comfort is a key requirement.
However, in the mass transit sector there are an increasing number of metro and subway systems, as well as buses, which are replacing fabric upholstered
seats with alternative materials, principally to provide a cleaner and more comfortable environment for passengers.
Recent examples include the Seoul Metro in the South Korean capital, which is replacing its all-fabric upholstered seats with reinforced plastic chairs, and the Dallas Area Rapid Transit (DART) in Dallas, Texas, USA, which is replacing 34,000 fabric seat cushions with new vinyl ones across its bus fleet.
In the marine sector, textiles are used as fabric for inflatable boats and lifejackets, as well as carpets and fabrics for the complete interior furnishing of cruise liners and yachts, including woven and tufted carpets, hand-tufted and hand-woven carpets as well as stitched carpets.
In this market, the demands placed on textiles are not only high in terms of fire protection, but also with regards to
light resistance and durability. This is particularly true for textiles used in outdoor marine applications, which must be extremely robust as they are exposed to moisture and sunlight.
While most textiles and nonwovens used in the transportation sector are made from synthetics such as polyester, poly-
• Advanced digital cutting technology
• Reliable cutting & kitting automation
• Superior workflow integration, productivity
• Maximum material yield
• Modular, versatile, adaptable
www.zund.com
amide and polypropylene, sustainability and climate change issues have promoted the use of, and interest in, biodegradable and compostable materials.
Biodegradable bast fibers, particularly flax and hemp, are now being used as the reinforcement material to produce sustainable, lightweight biocomposites that help make vehicles, such as cars, trucks and buses, more durable and
safer as they will not splinter in a collision. They are increasingly being used in place of petrochemical-based carbon fibers and glass fibers in both structural and non-structural applications such as car bumpers, door linings, package trays, dashboards and trunk parts, where different materials are combined to enhance mechanical strength and durability as well as other important properties, such as impact resistance and scratch resistance, to produce natural fiber composites that are lightweight, renewable and low cost.
These properties are especially important in aviation where, for example, the Boeing 787-9 Dreamliner aircraft – the world’s first major commercial airliner to use composite materials as the prima ry material in its airframe – uses around 80% carbon fiber reinforced composites
and other composites by volume (50% by weight). Owing to their light weight and strength attributes, the use of composites in the primary structure, including the fuselage and wing, has helped to make the Dreamliner 20% more fuel efficient than the comparable aircraft it has replaced. The newer Airbus equivalent aircraft, the A350, also uses carbon fiber composites extensively.
In the automotive industry, the intrinsic properties of flax fibers allow carmakers to combine excellent performance with more sustainable production methods, according to the Paris, France based Alliance for European Flax-Linen & Hemp.
Its excellent shock absorption capacities and resistance to breakage make this natural fiber composite a promising element in automotive safety. On the other hand, as flax has a low density it can be used to make lightweight composites, which is crucial in reducing the weight of vehicle batteries.
In the marine industry, the adoption of composite parts based on flax fibers in particular continues to grow, with major OEMs as well as smaller shipyards now aiming to take advantage of the reduced carbon impact and mechanical properties they can provide.
However, the main disadvantage for using natural fibers is that they are hydrophilic materials, which when exposed to humidity and moisture over a number of years could lead to swelling and loss of its shape and can also lead to a loss of strength. Current research is looking to develop treatments that make natural materials more compatible with plastics in terms of safety by maintaining the mechanical strength required while minimizing the risk of moisture absorption.
Another issue is the consistency and reliability of natural fibers compared with that of, say, carbon fibers in terms of such attributes as diameter, strength and density.
Overall, textiles are transitioning to carbon-reducing materials however they make the most sense for their value. More and more, transportation segments will be under scrutiny for their sustainability efforts as fallout from regulators expands beyond the focus of EVs. Most are working towards solutions before that happens.
Geoff Fisher is the European editor of International Fiber Journal and editorial director of UKbased Textile Media Services, a B2B publisher of news and market reports on transport textiles, medical textiles, smart materials and emerging markets. He has more than 35 years of experience covering fibers and technical textiles. He can be contacted at gfisher@textilemedia.com or +44 7803 718443.
By Marie O’Mahony, Smart & Advanced Textiles Correspondent, IFJ
In the transport sector, three key trends of development for automotive textiles are taking the lead – materials with characteristics that provide smartness, lighter weights, and reductions in environmental impact. Real market needs are driving the research and development (R&D) yielding innovation across smart textiles, such as Flexible Hybrid Electron ics (FHE), used to achieve lightness and re duce fuel consumption, and natural fibers that bring about more sustainable com posites. In examining these three areas, we will highlight some of the new develop ments that are emerging.
In the transport sector, three key trends of development for automotive textiles are taking the lead – materials with char acteristics that provide smartness, lighter weights, and reductions in environmental impact. Real market needs are driving the research and development (R&D) yield ing innovation across smart textiles, such as Flexible Hybrid Electronics (FHE), used to achieve lightness and reduce fuel consumption, and natural fibers that bring about more sustainable composites. In examining these three areas, we will highlight some of the new developments that are emerging.
Smart textiles for the transport market is estimated to be worth $1.04 billion in 2024 globally, and this is expected to rise to $3.92 billion by 2029, growing at a CAGR of 25.51% during that time according to a report by Mordor Intelligence. Caus-
miniaturization of electronics and other components, and the crucial growth of electric vehicles (EVs) – themselves seeing tremendous growth projected to be around $623.3 billion in 2024, growing to $906.7 billion by 2028 at a CAGR of 9.82%.
Mayer TechConcepts specializes in coating and printing including smart textiles for applications that includes the automotive sector. Exhibiting earlier this year at TechTextil Frankfurt, the company showcased examples of their innovations in the market. In one development, a car seat uses Alcantara (also referred to as synthetic leather) that has been printed with a lily pattern and red quilting edges. The headrest uses an artificial leather with a larger lily motif, with the colour enhanced by backlighting. Backlighting is also employed in the side bolsters that house the touch-activated switch func-
A further development shown was the inside panel for a car door. Here the textile has been printed with a 3D heating paste that uses carbon nanotubes coupled with printed touch sensors. The development uses CERAPUR, a patented 3D hard ceramic coating that provides surface protection for sensitive materials as well as providing a technical aesthetic. It has the capability to be electrically conductive providing heating or lighting.
Lighting is achieved using a base layer printed with the desired visualization points, this is glued to a second layer that sits on top and contains the corresponding perforations. In a recent development directed at sustainability, a bio-polyurethane using rice and coconut oil is used.
FORVIA is a relatively young automotive technology company launched in 2022, bringing together Faurecia and HELLA. Future mobility lies at the core, with smart systems and sustainability providing the primary direction. FORVIA’s VIBE® technology offers occupants an immersive driving experience that promises enhanced safety, comfort as well as entertainment integrated into the smart seating. This looks to the EV market in particular as it senses and analyses occupants seated position to actively detect
and offer guidance or take action against stress or poor back posture for example. The integration of intelligent actuators is an important aspect of the system and a primary focus of the company’s 40 filed patents. VIBE® is set to make its debut in a next-generation premium SUV end of 2025. Vibe can be set up with an Advanced Driver Assistance System (ADAS) that includes haptic alerts for driver blind spots, lane changing, speed limit and drowsiness. Alongside the safety and wellness features is the entertainment in the form of 4D sound technology. This uses an algorithm that automatically gener-
ates a tactile vibration that synchronizes with the music being played to deliver an immersive haptic experience – hence the term 4D. There is also a wellness package aimed at reducing stress and drowsiness. This has been developed in partnership with Aurasen, curated with leading haptic artists to provide relaxation, recovery, and energy-enhancing programs.
“We are on the brink of mass-producing composites that can be decomposed and recycled,” announced Ed van Hinte in his book written with Adriaan Beukers titled Designing Lightness – structures for saving energy (2020). The development of composites for the automotive sector in particular is focused on offering weight reduction that reduces energy and environmental impacts. The global automotive lightweight materials market size was given a value of $72.16 billion in 2022 and is expected to reach $137.8 billion by 2032, growing at a CAGR of 6.7% during that period with North America the fastest growing region according to a report by Spherical Insights.
Replacing synthetic fibers with natural fibers in nonwovens for the automotive sector is extending from its use in mats, seating and acoustic lining to structural elements most notably composites. Natural fiber reinforced polymer composites (NFRPCs) can provide environmental benefit through the inherent lightness, renewabaility and biodegradability of the fibers. Hemp, kenaf, jute and flax are some of the primary fibers,
with potential also seen in pineapple, sisal and agave leaf fibers.
Located in France, EcoTechnilin has been developing NFRPCs for automotive interiors of many of the leading car manufacturers primarily in Europe, but also is looking to the North American market. In Normandy region, 60% of the world’s flax is grown therefore this is a primary fiber used in their composites for interior trim parts, engine, passenger glove and trunk compartments as well as rocker panels. These conform to reinforcement needs while bringing a weight and carbon footprint reduction to the vehicle. The company’s next ambition is to see the NFRPC embraced as an aesthetic to be seen, encouraging even more widespread use and reducing the number of materials and processes needed in the automotive interior.
Topp Textil showcased a viable hemp solution that is still in development for automotive interiors at recent expos. Their laminated hemp fabrics produce sustainable and high-quality interior surfaces. The company sees clear potential for hemp in the composites sector and presented hemp developments for composite components, most recently at JEC World. Hemp can easily achieve the mechanical strength of glass fibres and would be an ideal basis for bio-based or recycling-optimized composites. “We are confident it’s the right way for innovations,” as an alternative to cotton, says Elvan Sentürk, Head of Application Projects, at Techtextil Frankfurt.
Hyosung Advanced Materials have developed a number of advances for tire reinforcement, a market area that they have been supplying since 1968 with the claim that 50% of all passenger cars now use their PET tirecords. They offer a number of fiber options such as aramid, nylon, steel cord, bead wire, PET and Lyocell. Typically, the outer tread making contact with the road is made from rubber. This is followed by the ‘carcass,’ an inner layer that is load and shock absorbing usually using a polyester. The belt is located between the tread and the carcass, and its function is to resist puncture and improve safety using nylon tirecords and steel cords. A cap ply helps the tire to maintain its shape while the bead wire comes in contact with the rim, providing reinforcement and preventing air leakage from within the tyre.
A key driver of R&D is lowering the environmental impact of the tire and contributing to a more sustainable automotive sector. The company produce an ultra-tensile (UT) steel cord for use in lightweight tires for the EV market, for example. New developments include a bio-PET yarn that is manufactured from ethylene glycol extracted from sugar cane or corn, contributing a 16% reduction in greenhouse gas emissions compared with
existing polyester tirecords by company estimates. Lyocell tirecords have also been developed as a replacement for nylon in applications where high speed and durability are key factors. The raw material is extracted from wood and does not emit carbon bisulfide or sulfureted hydrogen during production. This reduces water contamination during the processing. This development using Lyocell has the potential for a 30% reduction in greenhouse gas emissions.
The automotive sector has long been interested in the potential for biomaterials in reducing environmental impact and vehicle weight with some of the biggest names in the sector already involved. Recently retired from the Ford Motor Company where she served as Technical Fellow of Sustainability, Dr. Deborah Mielewski initiated the biomaterials program at Ford research in 2001. While there, she showed that soy-based foam could meet all of the requirements for automotive seating, resulting in the launch of the foam in the 2008 Mustang.
Since then, Ford has launched a wide range of biomaterial products that include wheat straw for storage bins and cup holders, kenaf plant door bolsters, rice hulls for electrical harnesses, tomato
skins for wiring brackets and storage bins. In a collaboration with McDonald’s, the dried skin of the coffee bean, the coffee chaff, is used in a composite for car headlight housing. The coffee chaff comes away naturally during the roasting, this is taken and heated to a higher temperature under low oxygen missing it with polymers and other additives to make pellets that are then used in the composite. The resulting components Ford estimates to be 20% lighter and needing around 25% less energy during the moulding process.
The development of biomaterials received an impetus in Europe in 2022 when the EU adopted the Sustainable Products Initiative (SPI) – otherwise known as the
using a pure aliphatic polyester
‘Green Deal.’ The conservation of resources and product lifecycle have risen as important considerations in new material development. In the development of synthetic leathers, a textile substrate is commonly used as a base material with a polymer layer then applied. The polymer layer usually consists of an adhesive layer and a top layer that is usually embossed. Woven, knitted, or nonwoven fabrics made of PET, PET/cotton, or polyamide are often used as the textile substrate, while PVC and various polyurethanes are generally used for coatings.
This is not ideal as they are not biodegradable and recycling by type can be very costly, or even impossible. The German Institutes of Textile and Fiber Research Denkendorf, together with the Freiberg Institute GmbH (FILK) in a German Federation of Industrial Research Associations (AiF) project to develop a synthetic leather in which both the fiber material and the coating polymer are identical. The base layer consists of an aliphatic polyester polybutylene succinate (PBS) that can be produced from biogenic sources and is now available to scale in several grades. Both the fiber material and the coating can be processed thermoplastically, and subsequent product recycling is facilitated by the thermoplastic properties.
In order to realize a successful primary spinning process and to obtain PBS filaments with good textile mechanical properties, process adjustments had to be made in the cooling shaft at the DITF. In the end, it was possible to spin POY yarns
Ford has launched a wide range of biomaterial products that include wheat straw for storage bins and cup holders, kenaf plant door bolsters, rice hulls for electrical harnesses, tomato skins for wiring brackets and storage bins.
at relatively high speeds of up to 3,000 m/ min, which had a tenacity of just under 30 cN/tex when stretched. The yarns could be easily processed into pure PBS fabrics. These in turn were used at FILK as a textile base substrate for the subsequent extrusion coating, where PBS was also used as a thermoplastic. With optimized production steps, PBS composite materials with the typical structure of artificial leather can be produced. Purity and biodegradability have yielded positive results, fulfilling the requirements for a closed loop recycling process.
Mycellium continues to attract interest and development with Antolin developing mycelium-based materials derived from fungi for use in automotive components. The mycelium binds with vegetable residues in order to produce a material that is structural. The company are enthusiastic that this form of production is carbon neutral because the material development occurs organically directly in the mould, as opposed to the conventional injection moulding process needed for plastics. Antolin see this as contributing to decarbonization and leveraging natural
resources, giving a second life to waste of natural origin that can be used in an industrial setting and to scale.
Smartness, lightness and sustainability have been discussed here as three different trends on the rise. There are already developments bringing these three together for a positive for consumer and environment, as well as the design potential for exciting new innovations. More are on the horizon, as they make their way out of research and development and into new vehicles of productions lines in various countries.
Dr. Marie O’Mahony is Smart & Advanced Textiles Correspondent for the International Fiber Journal. She is an industry consultant for a global portfolio of clients, and the author of several books on advanced and smart textiles published by Thames and Hudson. Reach her at marie.consultant@gmail.com.
and nascent technologies in nonwovens. Thought leaders spanning the entire supply chain will converge to discuss cutting-edge advancements and research. Participants will gain invaluable insights in advanced recycling methods, nextgen materials, bio-based adhesives, packaging transitions, and machinery efficiency.
At RISE®, innovation merges with tangible realworld applications, transforming possibilities into nonwoven reality.
more information, visit: riseconf.net
By Adrian Wilson, International Correspondent, IFJ
When it rains in Tamil Nadu, the southernmost state of India, it certainly rains. In this monsoonal region, 90% of annual precipitation can occur in just two months, making water storage a huge challenge.
Rising to this challenge is a project currently being undertaken in the unique township of Auroville.
Auroville – the City of Dawn –was founded in the optimistic hippy years of the late 1960s, following the vision of FrenchIndian spiritual guru, occultist and yoga teacher Mirra Alfassa to establish “a place on earth that no nation could claim as its sole property, for all humanity with no distinction.”
At the township’s opening in 1968, over 5,000 people from 124 countries gathered to listen to Alfassa – known to her followers as the Mother – outline her beliefs from The Auroville Charter.
Today, Auroville is home to over 2,600 people from over 61 countries and cash free, with residents provided with person-
al accounts and debit cards for transactions managed by the Auroville Foundation. All assets in the township are owned by this foundation, which, in turn, is owned by the Government of India.
Residents enjoy free electricity, healthcare, and schooling (without exams), while providing manpower and making contributions to the foundation on a monthly basis for maintenance, supplemented by income from daily visitors and longer-term guests, alongside various businesses.
Such an idealist commitment to doing things differently has not been without challenges and some controversy over the years, and the ownership of Auroville is the subject of ongoing court disputes. The venture could be open to mockery were it not for the fact that the forward-thinking residents of Auroville have also established many pioneering practices in sustainable development over the years.
In addition to producing crops consumed by the township, farmlands owned by Auroville serve as research centers for sustainable agriculture and water conservation. Buddha Garden, for example, is a farm employing a sensor-based precision irrigation system that has reduced water consumption by around 80%.
Auroville Consulting now provides advice and training to many other organizations in Tamil Nadu, especially in the areas of wind and solar energy generation. Following decades of meticulous silviculture, Auroville’s extensive forests are also among India’s most successful and have set a blueprint for further afforestation projects.
At the heart of Auroville is the Matrimandir temple, an elaborate gold-plated structure that took 37 years to complete. It is called the Soul of the City and is situated in a large open space called Peace. It comprises 1,415 large gold discs and is suspended above 12 ‘petals’ – themed meditation rooms – each of which is flanked by a themed garden.
This entire area is currently being surrounded by a new artificial lake in order to further develop a water management system that will benefit the entire surrounding region. With a surface area of 170,000 square meters and a depth of ten meters, the lake is being built to store one billion liters of rainwater over ten months, ensuring water availability throughout the year.
Its construction relies on Carbofol HDPE (high-density polyethylene) geo-
regional commitment to developing an area-wide innovative water management system. In the monsoonal months of rainfall in Tamil Nadu, 90% annual precipitation occurs in just two months and water storage is a crucial challenge. The geomembrane’s installation is a critical process, immediately following the fine grading of the slopes to prevent damage from rain. The lake’s shores will store one billion liters of rainwater over ten months and are carefully designed with a 1:3 slope, reinforced with large concrete blocks. The slopes are meticulously smoothed and compacted before the HDPE waterproofing layer is installed, to ensure zero water loss.
membranes which are being supplied by Naue, based in Espelkamp, Germany. HDPE provides exceptional durability and effectiveness in preventing water seepage and the membranes have a projected lifespan of 100 years.
The lake’s shores have been carefully designed with a 1:3 slope and reinforced with large concrete blocks. The slopes are being meticulously smoothed and compacted before the HDPE waterproofing layer is installed. Once installed, the geomembrane ensures zero water loss.
In addition, the lake will contain a series of underwater fluid storage cushions made from Naue’s Carbofol, designed to store up to one million liters of drinking water, which can be filled or emptied as needed. These cushions, separated from the lake’s main water body, demonstrate
flexibility and efficiency in water storage. They also offer potential applications beyond Auroville, such as freshwater storage for desalination plants.
The geomembrane’s installation is a critical process, immediately following the fine grading of the slopes to prevent damage from rain. The process involves layering a nonwoven geotextile under and over the HDPE geomembrane, topped by a 30-centimeter layer of granite chips for added protection. The meticulous engineering of the lakebed has been based on extensive soil stability and friction tests and the rainwater harvesting channel feeding the lake is also waterproofed with HDPE and connects to the lake via two pipes.
Overall, the Matrimandir Lake project is a significant leap forward in urban water management for India. Its scale, technical sophistication, and the use of
Carbofol geomembranes set a new standard for sustainable water management, tailored to meet local environmental needs while integrating the latest global engineering practices.
In a second recent project closer to home and involving protection from water as opposed to its provision, Naue’s Secutex H sand mats are being installed around the pier of the harbor at the Baltic seaside resort of Prerow in the Western Pomerania Lagoon Area National Park in northern Germany.
These multi-layered needlepunched staple fiber nonwovens are filled with quartz sand and employed as a filter and separation layer for underwater installation in hydraulic engineering applications.
In the Prerow harbor project, they have been installed at depths of up to five meters to provide the filter layer between the seabed and breakwaters.
The positioning of the sand mats was meticulously carried out according to a
Multi-layered needlepunched staple fiber nonwovens are filled with quartz sand as a filter and separation layer for underwater installation in hydraulic engineering.
detailed installation plan and the mats were delivered to the site pre-fabricated and numbered to further streamline the installation process.
No additional ballast layer was required during installation, saving time and costs compared to conventional constructions.
In a notable development for the construction industry, Naue has introduced the Geosynthetics GPT bot which is now available on the ChatGPT Store.
The tool connects expertise in geotechnical engineering with the artificial intelligence capabilities of ChatGPT and aims to assist users in simplifying complex decisions related to the use of geosynthetic materials.
The AI-based platform efficiently and comprehensively answers questions on various topics such as erosion protection, material savings in road construction and environmental considerations in nature conservation areas.
Another important feature of the bot is its ability to evaluate different construction methods in terms of their CO2 emissions and economic costs. This will help users in the environmentally conscious and cost-effective planning of their projects.
With the introduction of Geosynthetics, Naue is demonstrating how AI technology can be effectively utilized in the planning and execution of construction projects. The company is committed to continuously improving and expanding it to meet the evolving needs of the construction industry.
Geosynthetics is available for use with ChatGPT 4.0 in the ChatGPT Store or directly from the company.
Adrian Wilson is an international correspondent for International Fiber Journal . He is a leading journalist covering fiber, filtration, nonwovens and technical textiles. He can be reached at adawilson@gmail.com.
By Caryn Smith, Chief Content Officer & Publisher, IFJ
The utilization of biological materials as reinforcement in the development of industrial composites emerges as a potential, more economical and sustainable alternative to replace synthetic components like carbon fiber or glass fiber. However, the use of biocomposites also presents technical challenges in the case of structural applications due to their less regular and solid properties.
The Spanish technology centre IDEKO has been participating since this year in the European BioStruct project to solve the technical problems associated with the use of bio-based composites in industrial structures for sectors such as the wind energy or maritime.
The main objective of the initiative, funded by the EU’s Horizon 2020 programme, is to develop and validate new manufacturing processes to boost the use of biocomposites.
The solution proposed by the project will be validated through two use cases: the manufacturing of a hull for a six-metre electric boat and the production of rotor blades for wind turbines. In both cases, natural fibers and bio-based resins will be used as construction materials, paving the way towards a greener and more sustainable industry.
International Fiber Journal spoke with Roberto Alonso, researcher from IDEKO and a spokesman for the project, to shed light on the ongoing project that concludes in 2026.
International Fiber Journal: Please provide a general description of the project.
Roberto Alonso: The BioStruct project aims at the development of advanced technologies for the manufacturing of composite parts made from biomaterials. This will enhance the use of such materials in parts with structural requirements and thus reduce the need for conventional carbon and glass fibre composites.
IFJ: Explain the process to incorporate hemp and flax into these 3D construction materials. What led to their use?
Alonso: There are persistent economical and technical problems with the recycling of conventional fibre-reinforced composites made from glass or carbon fibre. The use of biomaterials for such composites would provide a solution, but there are
issues with the use of such materials in parts that have structural requirements.
The BioStruct project aims to bring biocomposites one step closer to structural applications by addressing technological topics that relate to the manufacturing of such parts. The following key technical topics have been identified:
• Natural products such as bio-based fibres have a higher variability in term of dimensions, weight and appearance. Nevertheless, high precision is required when handling fabric made of natural fibres.
• The mechanical properties of natural fibres and resins need to be better understood to enable the accurate design of structural parts and thus make such material usable also for structural applications.
IFJ: What confirmed the use of hemp and flax for biomaterials in 3D structures?
Alonso: The process of handling a piece of fabric (typically glass or carbon fibre) and placing it in a mold is called draping. The main challenge is to ensure that the piece of fabric (ply) is placed in the correct location (typical tolerance: 1mm and below) and to control how the fibres re-orient themselves during the draping process (typical tolerance: ±3-5°). This re-orientation happens, when the flat fabric adapts to the complex 3D free-form shape of the mold. Controlling this process is important, because fibre orientation has substantial impact on the mechanical performance of the part. The
draping strategy often includes so called seed points or seed lines from where the draping starts and propagates through the fabric.
The main challenge when handling fabric made from natural material is the higher variability of the material. Compared to carbon and glass fibre, the material properties vary much stronger within a batch of material, but also between different batches as the properties depend on the climate and weather conditions during which the plants have grown. In order to ensure that the handling is done with high precision, the BioStruct project needs to advance the state of the art in the following aspects:
• The weight of the fabric might be higher than this is the case for glass or carbon fibre. In contrast to the distortions of glass and carbon fibres with needle grippers, it is not expected that natural fibres are distorted or even damaged by this method which might be able to hold heavier fabrics more accurately.
• The friction between the surface of the suction heads and the fabric has impact on the draping process. To account for the higher variability of the material, control methods will be developed.
• The well-defined appearance of carbon and glass fibre makes it easy to perform accurate measurements.
• Measurement of fibre orientation will require a new approach that does not rely on the particular reflectance properties.
All of the measurement systems mentioned above will be equipped with real-time capabilities to ensure that inprocess measurements can be done, and inline process control will be feasible.
IFJ: How does sourcing from Europe add to the benefits of BioStruct and its circularity and sustainability goals?
Alonso: These developments will advance the use of bio-composites in domains, where these are not yet considered at a larger scale, e.g., in boatbuilding and sports equipment. This will replace glass or carbon fibre and thermoplastic or thermoset resins that are difficult to recycle. Based on the current use of composite materials in different domains, a share of 25%-45% of the total market could possibly be addressed through biocomposites with a potential market value of 100M€ for BioStruct technologies by 2030. It is understood that currently biocomposites are not suitable for high-end structural applications in aerospace. This domain (structural parts I aerospace) is thus not the main focus of the project.
IFJ: Explain the manufacturing processes being explored in this process.
Alonso: The overall concept of the BioStruct project is to enable the accurate manufacturing of parts made from biocomposites, with a particular focus on quality so that they fulfil requirements in terms of mechanical properties. The main developments are summarized per objective O1-O3 below and are further detailed in the following subsections.
• Handling of natural fabric: handling and draping of the fabric will have to deal with and compensate the higher variability of the material to ensure constant quality as required for structural parts.
• Material models of bio-composites: to enable the use of bio-composites in structural applications, accurate material models are needed for finite element simulations and to obtain high-performance part designs that have minimal weight.
• Integrated load sensors: to enhance the applicability of bio-composites, a manufacturing technology for integrated load sensors will be developed to monitor of loads and deformations.
IFJ: What is the role of 3D scanning in the research process?
Alonso: 3D Measurements will be used to assist with the development of the material models. The main technology is 3D scanning that use the laser triangulation principle to obtain a dense cloud of points. The second technology is 3D scanning by photogrammetry. This technique allows the fast measurement of all the details of the shape, along with inner and difficult-to-access surfaces. The first development in this objective will be a correct fusion of these techniques.
IFJ: How is BioStruct expected to increase productivity and quality in high-precision manufacturing to meet the EU objectives?
Alonso: Reductions in the use of materials, waste, defects and energy consumption, also lead indirectly to reductions in GHG emissions. Through the manufacturing technologies resulting from the BioStruct project, a substantial reduction of green hour gases can be achieved. Due to the focus on structural applications of biocomposites, the market potential is up to 45% of the total market, assuming that there are no applications in aerospace. This is somewhat of a worst-case estimate because there is certainly a potential for the use of biomaterials in aerospace interior parts.
The rough balance in terms of CO2 emissions is shown in the table below on the example of hemp fibre (flax will have similar numbers) in comparison to glass and carbon fibre. The main factors are the reduction of CO2 through the replacement of carbon and glass, the sequestration of CO2 during the growth of hemp and the CO2 generated during the processing of hemp fibres. The BioStruct project thus has a potential of saving between 2.5 and 4.3 Mt of CO2 per year, assuming that
a significant market share in non-aerospace applications can be achieved.
IFJ: What industries were chosen as the project's first focus?
Alonso: The current competitive position of Europe in carbon and glass fibre manufacturing is not very strong. 80% of all such fibres are manufactured outside of Europe and of the remaining 20% about half of it is manufactured under foreign licenses. This creates a dependence on other countries. Biocomposites will be one possibility to reduce such dependence, especially if it is possible to take the step from single prototype and ‘decorative’ parts to a wider range of applications in series production of structural parts. The BioStruct project aims at achieving this step.
Aside from the aerospace and defense market, where very tight restrictions exist in terms of materials and processes (and for good reasons), the whole remaining composite market is relevant for biocomposites. The total market share (by weight) is about 50% with sports equipment, wind turbines, automotive, construction and maritime applications being the most relevant ones. The BioStruct project directly addresses 25% of the market, through the use cases in the field of boat building and wind energy.
However, there is also big potential for applications in sports equipment (contacts with Decathlon already established) and automotive, which will increase the share to 45% of the market. Through the introduction of biomaterials, the project has the potential to reduce the dependence on foreign raw materials. Hemp is grown all across Europe, with France (62%) being the largest producer.
Currently about 32.000 hectares are used for hemp cultivation, producing more than 150.000t per year. Similar numbers apply to flax, where 80% of the flax needed in Europe is also grown here. Consequently, by using natural fibres, the dependence on imported goods will substantially reduce, thus enhancing the autonomy of the European composites industry.
IFJ: How does the partner consortium work together on this project?
Alonso: The consortium has been selected to cover all key components to demonstrate high-precision manufacturing of biocomposite parts. The project was cofunded by Horizon Europe, the European Union’s research and innovation program, and this public-private European partnership involves 10 organizations European organizations, both public and private: Profactor, Abele, Amura, Bladeworks, CIDETEC, Enginsoft, IDEKO, Lumoscribe, NOMA, Techtera.
Amura and Bladeworks will provide the manufacturing lines for manufacturing of a boat and a rotor blade. This manufacturing line will be equipped with additional systems for process control for draping (Profactor, Abele), for cure monitoring and 3D dimensional measurement (IDEKO) to enable high-quality products in the presence of higher variability of the materials. A process for manufacturing and integrating bio-based load sensors (Profactor, lumoscribe) will be developed. The bonding process will be provided by CIDETEC. Enginsoft will provide the simulation support for part design, including new material models, and for process monitoring (draping, curing).
All processes mentioned above will be integrated into the manufacturing processes for the final demonstration.
Bio-resins will be provided by NOMA, bio-adhesives will be provided jointly by CIDETEC and NOMA. Natural fabric and the cure monitoring systems are available on the market and will be used for the purposes of the project but are not in the focus of the developments. Techtera will support the consortium with dissemination activities and perform a mapping of suppliers of biomaterials in Europe.
IFJ: What is the next step in BioStruct?
Alonso: Currently, the first test coupons of these materials are being developed while the technical specifications are being defined to begin the initial measurements.
IFJ: We will be following your progress.
By Adrian Wilson, International Correspondent, IFJ
Despite its currently unmatchable benefits in enabling the production of lightweight parts that are exceptionally strong and have been critical to reducing emissions in numerous end-use applications – most significantly the aerospace industry – carbon fiber remains based on oil-based raw materials and is extremely energy intensive to produce, as well as very expensive to buy.
As a result, much research is being undertaken to develop lower-cost alternative monomers to polyacrylonitrile (PAN), the usual precursor material for carbon fibers, including biobased materials.
Airbus, for example, has recently been flight testing an experimental and non-structural composite nose panel on its PioneerLab helicopter which is based on biobased
carbon fibers made from acrylonitrile derived from the capture of atmospheric carbon dioxide. The new panel is said to be as stiff and strong as a conventional part and the chemically identical acrylonitrile is used to produce the fibers with the same performance level. It is obtained from sustainable ISCC-certified non-fossil feedstocks such as wood and food waste, recycled cooking oils and
algae, along with renewable sources of ammonia and propylene.
A full life cycle analysis undertaken by Airbus suggests that producing sustainable acrylonitrile and other biobased chemicals and intermediates generates significantly less CO2 than the crude oil alternative. The industrialization of these products, however, is in its infancy and scaling up to the extent where corresponding CO 2 reductions move the dial will require regulatory commitment and massive capital investment.
For now, the PioneerLab nose panel remains a proof of concept. The challenge for Airbus and others is to work with supply chains to make bio-fiber production economically viable, and to ensure it can be ramped up cost effectively to meet accelerating aircraft production.
The production of composite parts can also be very wasteful, with scrap rates averaging 30-40%, and both this waste, as well as finished parts at end-of-life, have to date largely being disposed of by landfilling or incineration. Globally, it has been estimated that around 62,000 tons of waste is generated simply from manufacturing operations each year.
As a result, there has also been an intensive supply chain-wide campaign to develop recycling routes for carbon fiber. A fast-rising star in this field is Parisheadquartered Fairmat.
Having only been founded in 2020, Fairmat has successfully secured the funding – around $45.5 million to date – to enable it to open its first ‘virtuous recycling’ plant in Bouguenais, close to Nantes in
France, at the end of 2022, and this year, to bring its technology to the USA, with a plant in Salt Lake City, Utah, currently ramping up operations.
“Fairmat is here to enable a wave of sustainable progress, putting advanced recycled materials at the heart of forward-thinking industrials worldwide, to make product manufacturing more circular,” says founder Benjamin Saada. “The idea is not only to substitute with recycled materials, but to produce differently while at the same time creating a new ecosystem with our customers and partners.”
Traditional waste-management techniques involving pyrolysis or solvolysis use significant amounts of energy, mitigating the environmental benefits of the recycling of carbon fiber. Mechanical re-
cycling to date has meanwhile involved chopping and milling which significantly compromise fiber strength.
By contrast, Fairmat’s process uses proprietary cutting technologies and robotic tools equipped with machine learning to disassemble the carbon fiber components and convert the pieces into the building blocks for new parts and products.
Using AI tools such as digital twins to model different 3D arrangements during the design phase, the company can assemble its recycled carbon chips into a variety of layouts and structures. These simulations enable it to customize the mechanical properties of the resulting product, such as, for example, extremely low weight for transportation components and localized, unidirectional strength for impact surfaces. Big data combined with AI algorithms meanwhile
ensure absolute traceability and generate better understanding of the materials to continuously improve the process.
It is planned that the Bouguenais plant in France, which has an initial annual capacity of 3,500 tons, will eventually deploy over a hundred robotic arms to allow the company to upscale the operation and treatment capacity.
The company has budgeted for an annual R&D spend of between €7-8 million for continuous improvement through machine learning, and the current team of 80 people will eventually swell to 400. Fairmat is seeking to recruit the best talent in robotics and data science and further intends its plants to become selfsufficient in energy.
In Europe, Fairmat has rapidly secured the supply of around 35% of all available carbon fiber scrap across the continent, via partnerships with leading manufacturers including Dassault Aviation, Exel Composites, Hexcel, MerConcept, Siemens Gamesa and Tarmac Aerosave.
Exel Composites, headquartered in Mäntyharju, Finland, is now transferring the carbon fiber scrap from its plants in Europe to Fairmat, for the production of second-generation carbon fiber chips, as well as high-performance composite parts.
“Fairmat’s recycling methodology enables its products to retain the high strength and stiffness of the original
Fairmat’s materials are said to be ten times less expensive than new composites as well as being significantly more resistant and twice as light as aluminum.
embedded fibers,” explains Kim Sjödahl, senior VP of technology and sustainability at Exel. “Combined with its minimal energy input, Fairmat’s process is genuinely game-changing for sustainability in the composites industry. What’s more, the successful recycling of process waste also opens possibilities to recycle the end-of-life waste from our customers.”
Fairmat’s materials are said to be ten times less expensive than new composites as well as being significantly more resistant and twice as light as aluminum. They represent a potential replacement for many materials, from wood to steel, in addition to new composite parts.
In addition, with a lifespan of about 20 years, the materials are said to be capable of being recycled up to five times without loss of performance. Current markets being served include sports equipment, automotive and medical components
The new plant in Utah has very quickly followed on from a study trip carried out by Saada and Fairmat director Antoine de Turckheim in 2023, which confirmed very robust carbon fiber and composite activities in the region, with reference companies such as, for example, Albany
Composites, Northrop Grumman and TCR Composites, but also the absence of a structured recycling sector.
“The Salt Lake City site has several advantages, and the local authorities in Utah rapidly facilitated the negotiations,” said de Turckheim. “Additionally, in May this year we concluded a long-term agreement with Hexcel, which operates a major prepreg plant in Salt Lake City. The strengthening of our ties with Hexcel obviously represented a valuable foundation for the new plant. Our industrial model is also easily replicable as it relies on the cloud and uses AI.”
“Recycling advanced materials like carbon fiber composites is one of the strongest actions we can take to accelerate the decarbonization of the manufacturing sector,” added Saada. “We are thrilled to see our vision of a next generation of materials come to life as we are accelerating our production and expanding our international development.”
Adrian Wilson is an international correspondent for International Fiber Journal. He is a leading journalist covering fiber, filtration, nonwovens and technical textiles. He can be reached at adawilson@gmail.com.
By Caryn Smith, Chief Content Officer & Publisher IFJ
ounders of DUDE Wipes® proudly proclaim, “Best Clean, Pants Down” and “Wetter is Better,” using toilet humor to grab the attention of manly men who want fresh results in private places. And there seem to be at least 150 million dollars’ worth of them frequenting the brand, according to the company.
The flushable wipes business is booming in general. In 2018, flushable wipes account for $2.1 billion in sales, and consumed 1.9 billion square metres or 98,900
DUDE Wipes has been named to Bain & Company’s 2024 Insurgent Brands list, which identifies companies disrupting their fast-moving consumer goods (FMCG) categories in the US. DUDE Wipes® is one of 97 brands to make this year’s list.
It is a long haul to overnight success, so let’s have Jeff tell the behind-thescenes story.
International Fiber Journal: Let’s start with a bit of history.
Jeffrey Klimkowski, Co-Founder/CFO: Absolutely. So, my lifelong friends Sean Riley/ CEO, Ryan Meegan/CMO and I – the three co-founders within the business today – grew up together in Chicago. Sean and I met in second grade and rode the bus to school together. Ryan and I met later
tonnes of nonwovens. By the end of 2023, flushable wipes were said to grow at almost twice the rate of all other nonwovens. Users are growing and breaking demographic molds. What used to be known as a women’s category now includes men who want fresh options, too! In fact, even Mark Cuban is among them.
International Fiber Journal got real with Jeffrey Klimkowski, Co-Founder/ CFO of DUDE Wipes®, talking about the experience of creating and growing successful wipes business in the shadow of giant global brand whom we all know. For the last ten years, Klimkowski and his co-founders have dedicated their sweat equity in building a brand now getting its own notoriety.
in life in travel baseball. So, we’ve known each other for some quite some time. We all went our separate ways for college to different schools. When we came back, we lived a typical post-college lifestyle, if you will, just down the street from Wrigley Field in a bro-cave.
Just starting out in our careers, I was an investment banker working in an office building. Sean was in construction management selling HVAC units for high rises for buildings downtown. Ryan worked in sales and marketing with his father’s company which rented high-end port-a-johns at events. We were doing our own thing during the week.
We’d go out on the weekends – and you can read this on the back of our packets –and after a weekend of beers and burritos, when Monday rolls around, you have a cup of coffee, you go to the bathroom, and then you sit in an office chair or you’re on a jobsite, and you don’t feel fresh.
Sean, being the innovator of the group, started doing what you should absolutely never do – he bought baby wipes from Sam’s Club in bulk. I was putting them in little sandwich baggies tucked in my coat pocket because I was at an investment bank and didn’t want to walk around with baby wipes. We quickly adopted the habit. All of our friends started using them when they hung out at our place.
We wondered why there isn’t a product like this for men? We did some research and discovered the flushable wipes category. Remember, this is 2010, so no one is talking to men about it. And in our opinion, men stink the most, especially guys in their early 20s.
So, when we discovered flushable wipes, we immediately stopped flushing baby wipes, because we realized that we were causing larger problems. We started the company and we got to work on our men’s wipes solution, and found a manufacturer for the first product, Wipes On-the-Go, which we still sell today. It is not our bestselling product, but it was our first product. In the design process, we sought to solve our own problem, wanting extralarge wipes. All other flushable wipes on the market were too small; they didn’t cover our hands. We all wanted maxi-
mum coverage. We created what we called “DUDE size” wipes, but for some reason, people didn’t get it so now we just say extra-large. But that is how we got the name DUDE Wipes®.
Our first order with the manufacturer was placed in 2011. In 2012, our first order arrived – it took us that long. We were amateurs, we knew nothing about the world of wipes or even getting a delivery! The truck driver pulled up to my apartment complex and he says, “There is no loading dock.” A few unsavory words later, he parked down the street, and the three of us unloaded his truck case by case to my city of Chicago third-floor apartment spare bedroom. The load filled up the bedroom all the way up to the ceiling and into the stairway.
We feel like we’re just getting started. We are only 1% of the bath tissue category market. Our goal is to be 8% over the next 10 years, which equals a billion-dollar brand.
After the Cuban investment, we tried to raise venture capital, and no one thought we had a chance to be successful.
They basically all said, ‘This might be a good idea and we understand it, but once you get to scale, you’re just going to get clobbered by Procter and Gamble, Georgia Pacific, and Kimberly Clark. It’s an oligopoly that you’re entering.’
So, our next strategy was to get profitable – and we did. We’ve been profitable ever since 2016 and we’ve been growing. Now our sales are north of $150 million for 2023. It’s been a wild ride. We’ve learned a ton along the way. We feel like we’re just getting started. We are only 1% of the bath tissue category market. Our goal is to be 8% over the next 10 years, which equals a billion-dollar brand.
IFJ: Who is your demographic and how are you attracting consumers?
Klimkowski: It’s competitive. Up until now, we really haven’t been where we can afford promotional marketing, like within Cuban’s esports team. We have done a little bit. But this year is the first year that we are at scale with our growth profile.
We slowly started by fulfilling orders from Amazon. A week at a time, we would all take took turns to leave work early to get packages to the UPS store before 7p.m. We started selling to some small brick-and-mortar retailers, and the business started to accelerate. Essentially, we doubled the business every single year for over 10 years. That gets us to larger numbers.
IFJ: How did you get to $150 million in sales?
Klimkowski: In 2015, we did the deal with Mark Cuban on Shark Tank. It was a big tailwind for us. At that time, we had just one distribution channel – our first brick and mortar distribution deal with Kroger.
We say our target demographic is 18to 55-year-old men. One thing that is very interesting is that purchasers of our product are 70% women and 30% men. Women are typically the purchasers for the household. Our users are 50/50 men to women; once DUDE Wipes® get into the household, they’re not just for dudes; women use them, too. Even my wife and six-year-old daughter use them.
We target men and try to get them to adopt good cleaning habits; we think they need it the most. Yet, we see the whole household adopting their use, and it is really growing. It has been something that really surprised us.
IFJ: Tell us about your clever marketing campaigns in the media and the internet.
Klimkowski: So, our claim is, you know, ‘Wetter is Better,’ and ‘Wet Beats Dry.’ You’ll also see our tagline is essentially, DUDE Wipes® – ‘Best Clean Pants Down.’ We are saying that we deliver a solution
that’s better than just dry toilet paper. I mean, if you were to get your hands dirty or anything like that, you wouldn’t just take a dry piece of paper and wipe it. So why are we using only dry toilet paper, it’s just something that’s archaic.
We have scientific studies that we will be sharing that exposes how much people are leaving behind when they just use dry toilet paper. So, everything is about providing a better clean than a consumer has with their current habits. We are running our first ever national media campaign, which kicked off in March, that includes television, radio, billboards and more. In our commercial, you will see side by side wiping of television-safe blue goo. Everybody makes fun of us for using blue goo, but you have to use it, otherwise you can’t illustrate this properly on TV.
IFJ: What have been the biggest challenges getting this brand to where you are today?
Klimkowski: I would say there are two things. Number one is the simple cash thing. Just because you’re growing real fast doesn’t mean you have a lot of money. I think people don’t understand that or forget about that. Now, we’re in a good position, scaled, and we’re profitable and doing well. But I would say the first 10 years – say 2011 through 2019 – that’s the part nobody talks about, really. You are working tirelessly to grow a company, but you don’t have enough money for anything at that point.
Those are growing pains for every business – finding working capital, balancing that with marketing, balancing that with having enough product – all these kinds of things are growing pains that you must get through. There’s nothing you can do unless you raise a ton of money, which we weren’t able to do.
Now, I look back at it. I’m thankful that we didn’t raise a lot of money, because it allowed us to grow in a smart way. Instead of just going as fast as we possibly could, we built this business to last, you know, through systems, infrastructure, and people; making sure every piece was perfect before we moved to the next one because we didn’t have time to get tripped up later.
We didn’t have the money to solve our problems later. So that’s the first one. I would say the second one is just the lack of focus. This is one where we walked into the wall, and it hurt. We grew up during the Dollar Shave Club era, you know. When the Dollar Shave Club was coming out, it offered all these different products – razors, body wash, etc. We saw that, and wow, we wanted to do that, too. So, we started coming out with deodorant, body wash, all of this stuff. We just lost all focus.
In 2019, we noticed DUDE Wipes® is the only thing growing consistently every year. All these other products are barely growing. We asked ourselves why are we wasting our time and struggling for money over these products that impact our working capital and marketing dollars? It was a lack of focus, and we learned that the hard way. We are now firm believers that consumers hire you to do one thing. That one thing, for us, is to wipe people’s butts. Anything that does not revolve around that, we are not going to do, and we’ve been cutting product line down ever since.
In fact, we just discontinued face wipes; now we’re going to work them through the system, but we will be done with that. At the end of the day, we will
just be footing two products, which is DUDE Wipes® that makes up 99% of our sales and DUDE Shower Wipes, which are a full body wipe. Now, we are a very focused company. We had shiny object syndrome and thought we could be everything to everybody, but when you’re competing with large CPG companies, it’s just super important to be 100% focused on what you do best. Your competitors have more money, so you must be more focused and be quicker than them.
IFJ: What is your goal for the future? Where are you positioning your company for the long haul?
Klimkowski: So that’s a great question. With this focus, today we stand only just over 1% of the bath tissue category. Our
goal is in the next five years to be 4% of the total bath tissue category. In 10 years, it’s to be 8% of category. Creating this message and letting consumers know about the advantages of wet cleaning being better than dry, that’s really the big AHA moment for us.
We’ve noticed with this new national media campaign; it is resonating with consumers – they don’t realize that they need this until they use it.
We also did a consumer study where we asked folks that have never used flushable wipes to use a leading brand best-in-class dry toilet paper for seven days, and journal how they felt; they did it and they said that they felt great. They scored it 8-9s out of 10, mostly.
Then, we said, ‘Here’s your toilet paper, the same toilet paper you just used, but use DUDE Wipes®, which were unbranded in a white package, in conjunction. The rankings were fantastic, again 8-9s out of 10. We then took away the flushable wipes and said just use that same quality dry toilet paper again for another week. At the end, all the rankings dropped down, ranging from 5-7 out of 10. They didn’t realize what they were missing until they tried this new habit.
It’s funny. You can change people’s habits through humorously pointing out what they are missing and understand what we’re trying to do. Everybody likes our new marketing. We have a long way to go. Our survey data shows that seven out of 10 people that try flushable wipes stick with the category. We have decades of growth ahead of us. We’re so excited about just doubling down on this category and growing it.
IFJ: What makes you the “go to” brand?
Klimkowski: We are extra-large, flushable and the first ones ever to do that. We continue to improve it, in fact, we are transitioning to be the thickest, most premium flushable wipes on the market. That’ll be fully rolled out by July 1 into the marketplace. With size and scale at this point, we have a competitive advantage.
You know, being the only native brand (cruelty free and never
Just launched is the first ever DUDE Wipes Odor Destroyer Flushable Wipes available at Walmart.
tested on animals) to this category, our goal is to be the Kleenex of the category. When you think of flushable wipes, we want consumers to think of DUDE Wipes.
tion will create a uniform label for products that have and/or require a “Do Not Flush” label, creating a national standard.
IFJ: What advice would you give to those seeking to enter the hygiene category?
Klimkowski: The advice I’d give to those trying to disrupt and create a category is lean into the power of staying FOCUSED. The one strategic advantage you have as a small, insurgent brand is the ability to move quickly, much quicker than large competitors with lots of cash, so take advantage of that strategic advantage by staying laser focused on the category you are trying to disrupt. Innovate within the confines of that category and do not let “shinny objects” take you off the path of continuing to push forward to design and grow your category. Everyone in the startup world likes to talk about new products, new products, but innovating within the confines of our category allows insurgent brands to concentrate resources in a specific category and efficiently drive future growth.
IFJ: You were part of INDA, Association of the Nonwovens Fabrics Industry’s U.S. Capitol Hill Fly-In event. Tell us about the experience.
Klimkowski: I think the Fly-In was fantastic. There’s nothing cooler or more American than being a constituent, going on the Hill, and talking to elected officials about issues that are important to you as a citizen. It gives you more confidence in the system, given all the media headlines about the dysfunction. Maybe things are more functional than you think.
We represented support for the WIPPES Act 9H.R. 2964, Wastewater Infrastructure Pollution Prevention and Environmental Safety, which passed the U.S. House of Representativeson June 11]. This legisla-
Right now, only six states have adopted legislation that is similar to the WIPPES Act. With different regulations in different states, it becomes cost-prohibitive for manufacturers to follow. The Responsible Flushing Alliance, CASA and INDA conducted a joint study, proving that less than 1% of the items pulled out of wastewater are flushable wipes. It’s baby wipes, paper towels, FEM care products that are really causing the issues with our water systems.
We believe that establishing the WIPPES Act as law will enable standardized labeling and consumer education on what’s flushable and not flushable.
IFJ: Do you have any other news to share?
Klimkowski: We continue to push innovation within the category. We’re excited about our first ever DUDE Wipes Odor Destroyer Flushable Wipes that launched at Walmart. It will deliver up to 24 hours of odor control. Pushing the envelope on odor control is part of that cleaning sensation that’s important to us to continue to disrupt.
IFJ: Why do you think odor is such a big deal for people?
Klimkowski: It’s a big deal. You know, it has to do with confidence. That’s one of the things that we say in our community, ‘pretty confidently clean.’ People don’t want to worry over a nagging sensation that there’s some sort of odor issue, or anything that hinders the perception that you are ready to perform. I think that is an important personal preference for consumers, and especially our customers who are purchasing DUDE Wipes®.
Rome / Italy
Rome Cavalieri, A Waldorf Astoria Hotel 24 > 26 September 2024
• 30+ inspirational speakers, including 3 keynotes .
• 2 networking events + programme adapted to allow more time for networking without missing presentations.
• Possibility to book meeting rooms for side meetings.
• New for 2024 an exhibition space providing a unique opportunity limited to 20 companies only. 70% SOLD!
Draft programme available online:
• Day 1: Markets & Trends; Innovation & Ecodesign
• Day 2: EU Legal Framework; Future of AHPs
Gathering 500+ nonwovens experts, OUTLOOK™ is the world’s premier conference for nonwovens hygiene, personal care, and wipes products. SCAN FOR INFORMATION OR TO REGISTER
• Day 3: Wet Wipes: Re conciling Consumer Needs with Sustainability & Legislative Pressures
outlook@edana.org
John Iarocci, Vice President of Research and Development, Nice-Pak, addresses WOW attendees.
In a special recognition, INDA, the Association of the Nonwoven Fabrics Industry, presented the 2024 Lifetime Service Award to David Powling, Technical Leader, Kimberly-Clark Corporation (retired), and the 2024 Lifetime Technical Achievement Award to Paul Latten, Director of Research & Development & New Business, Southeast Nonwovens, Inc. INDA is pleased to honor both Powling and Latten for their decades of contributions to the nonwovens industry as well as being strong advocates for INDA.
They were honored at the as wipes leaders across the supply chain convened for new connections, intelligence, sustainability strategies, and business at the World of Wipes® (WOW) International Conference, June 17-20 in Minneapolis, Minnesota.
“I met many first timers at the event which is great to see,” says Steve Gallo, Chief Executive Officer, Diamond Wipes International. “I found the content on innovation to be particularly useful this
year. The lunch around was a very nice touch. That provided a business intimacy that is difficult to achieve in any other format. And the coffee area with the high tables was perfect. We literally got to meet with every company that we needed to,
due to the ease of just texting people to connect in that area!”
“There is no better conference than WOW to hear nonwoven industry thought leaders views on such a wide range of important topics impacting the nonwovens industry such as innovation, legal/ legislative and sustainability trends,” notes Jeff Klimkowski, DUDE Wipes®. “It would take our team months to learn and/or get access to everyone I spoke to over a busy four days.”
The winner of the World of Wipes Innovation Award® was Rockline Industries
David Powling, Technical Leader, Kimberly-Clark (retired), center, is the recipient of the 2024 INDA Lifetime Service Award for his contributions and advocacy for the nonwovens industry and INDA. Tony Fragnito, CEO, left, and Matt O'Sickey, Director of Education and Technical Affairs, right, bestowed the honors. INDA
Paul Latten, Director of Research & Development & New Business, Southeastern Nonwovens receives the 2024 INDA Lifetime Technical Achievement Award, for his service to the industry and INDA. INDA
for their Facial Care Wipe with Glycine Amino Acid Complex. This new skin care wipe contains a unique multifunctional complex of two medium chain glycine, a phospholipid and a blend of special glycol ingredients that provides for a multitude of skin care benefits as well as providing a unique preservation system for nonwovens. The skin care wipe provides substantiated improved skin smoothness, elasticity, and hydration alongside an antiageing claim. This innovation is amongst the first to use these unique glycine ingredients in a skin care wipe formulation.
As in past years, the 1.5-day WIPES Academy, led by Heidi Beatty, Chief Executive Officer, Crown Abbey, LLC, and Paul Davies, Ph.D., Consultant, Crown Abbey, LLC, preceded the WOW Conference June 17-18. This course focused on the essentials of wet wipes construction and ingredients. Participants learned how to bring nonwovens, lotions, and packaging together to launch a successful product. The next WIPES Academy will be held July 21-22, 2025 at the Hilton Columbus Downtown, Columbus, Ohio in conjunction with WOW 2025.
The WOW conference program featured experts discussing these key topics:
• Sparkle & Shine: How Wipes Became WOW
• Wiping Smart: The Rise of Sustainable Practices in the Institutional and Industrial Wipe Markets
• Transformative Trends in Wet Wipe
Formulations: A Dual Focus on Skin Health and Sustainability
• Leading Alternatives to Traditional Plastics Used in Wipes
• Panel Discussion: Leading Alternatives to Traditional Plastics Used in Wipes
• Eclectic Perspectives: Unraveling the Threads of I&I Wipes and Scaling Strategies
• Putting $$ in Your Pocket
• Recycling & Regulations
In addition to the premium content in the conference program, WOW featured four pre-conference webinars (with recordings available for full conference attendees), tabletop exhibits, Lightning Talks, a Skin Care Formulation Workshop 101, and a mentorship program for participants who are new to the wipes industry.
"World of Wipes 2024 in Minneapolis materialized to be a landmark event for our organization this year,” says Sam
Nebel, Co-founder, Goodwipes. “We connected with industry peers, revisited with mentors, and engaged with partners to share insights and forge long-lasting, and meaningful partnerships. As an emerging brand, we felt right at home as industry veterans warmly extended their hand to us in an effort to ingratiate us further in the industry. This gathering not only fuels innovation and growth but also showcases the exceptional work of INDA in leading our industry forward."
For more information, visit www.worldofwipes.org.
Mark your calendars for WOW 2025 to be held July 21-25 at the Hilton Columbus Downtown, Columbus, OH!
The Intersection of Nonwoven Materials & Sustainability. Emerging Trends. Empowering Innovation. Enhancing Knowledge. Global Reach.
IDEA®25 is a gathering of the international nonwovens industry to discuss the future of nonwoven materials, their applications, and how they will shape both form and function in various market sectors.
Attend – Experiencing IDEA®25 provides a unique opportunity to see, touch and feel innovations in person. Meet and create new business with the professionals and companies behind these developments.
Exhibit – Showcasing your company at IDEA®25 inspires brand owners and brand marketers as they interact with your materials, technologies and processes. Partner with industry leaders to create new products with the intent of recycling, reusing and repurposing…for a healthier planet.
By Marie O’Mahony Smart & Advanced Textiles Correspondent & Feature Writer, IFJ
Dr. Marie O’Mahony is Smart & Advanced Textiles Correspondent for the International Fiber Journal. She is an industry consultant for a global portfolio of clients, and the author of several books on advanced and smart textiles published by Thames and Hudson. She can be reached at marie.consultant@gmail.com.
ZSK is one of the most recognized manufacturers of embroidery machines that combine the highly functional with decorative elements.
Founded in 1984, with a head office based in Krefeld, Germany, the company has a global presence that includes a North American facility in St. Louis, Missouri. They have been leaders in the development of conductive embroidery for e-textiles, a field that is currently expanding technical and market reach for transport, medical and wearable sectors in particular.
I caught up with Sven Böhmer, Sales Technical Embroidery Systems at ZSK, at a recent expo, taking the opportunity to interview him about current and future developments in the sector.
Marie O’Mahony: ZSK has a long history as textile engineers, over one hundred years. Your reputation is well established as a manufacturer of technical embroidery machines. I noticed your business card reads ‘technical embroidery systems.’ Is this a shift in company position?
Sven Böhmer: Technical embroidery systems are because we customise our technical embroidery machines to the needs of the customer so these technical configurations can also be seen as a system.
O’Mahony: How do you see Industry 4.0? What does it mean for ZSK?
Böhmer: It is a very challenging industry, so we have set up an in-house engineering office, 3E Smart Solutions, to develop smart and e-textiles for customers, always with a focus on automation and scalability as one of the key drivers for success in the industry.
ZSK’s PCB placement device has been developed in cooperation with BOSCH. Individually designed PCBs are stacked and stored in a magazine in the ZSK embroidery machine for automatic placement on the fabric. Following the placement, conductive paths and electrical connections including sensors are then embroidered so the e-textile including decorative embroidery is produced in a single process. In this example, the control elements are activated in response to pinch, but touch and proximity sensors can also be used.
O’Mahony: ZSK machines work with a number of new fibers (recycled carbon fiber, basalt, volcanic rock fiber etc.). What opportunities and challenges do these present?
Böhmer: New materials can bring new products to the market, which in turn can bring new businesses to the market. Our machines are very adaptable to a wide range of materials, so we are always happy to work with this type of innovation.
O’Mahony: One of your most celebrated innovations for e-textiles has been moss embroidery. Just as everyone is looking to integrate technology more and make it less noticeable, this seems to go against expectation. Can you explain its advantages?
Böhmer: Moss embroidered electrodes can be embroidered in different designs, shapes and sizes depending on the application and needs. They can be produced fully automated and obtain a high conductive surface to generate a clear signal for many types of measurements (e.g., EEG/ECG/EMG). As being a textile, the electrodes are washable and flexible, which are often attributes looked out for in the product development, especially for smart and e-textiles.
O’Mahony: We have connected at two trade shows this year, the first was LOPEC specializing in Printed Electronic and Flexible Hybrid Electronics and the second time a month later at TechTextil focused on advanced and smart textiles. Do you see these two industries coming closer together?
Böhmer: Absolutely, I believe that the two industries do need to come together, otherwise nothing will happen. There needs to be integration. But it is not simple. Product development needs to include IT that is more suited to textile processing. We need to see a greater level of mutual understanding of what each industry is. There are considerations that need to be addressed from a legislative point of view, there needs to be an alignment.
For example, what happens when a power bank fails, where does the responsibility lie between industry partners? This type of issue means that it takes much longer for smart textiles to be
commercialized. There is a particularly high risk in areas such as medical applications, so that takes even longer. Do I see a time when the two industries will come closer together? Yes, I think so. It will take some time of course, but we are already seeing some interesting innovations for further development on stitch and print combinations. At ZSK, and with 3E Smart Solutions we are looking at partnerships to combine our expertise to achieve this.
O’Mahony: Where do you see the motivation coming to bring these two related areas together – is it technology or the consumer or something else entirely?
Böhmer: I think the pressure is coming from the market, it is coming because the consumer wants it. Smart and e-textiles are going to play an important role in many aspects of life in the future, I think.
O’Mahony: AI is of course the hot topic now both for manufacturing systems and in the design of wearables. I guess this is a two-part question: First where to you see the opportunity/risk in manufacturing, and second in wearables?
Böhmer: Absolutely, there are specific questions around data and AI when it comes to wearables. Where is the data stored and who is storing it? How secure is it, who owns the data, how long is it stored, etc. There are standards being developed to address some of these issues, and we are involved in the standards committee. But this is a process that takes time. In terms of manufacturing, needs are changing in different parts of the world. In
Asia, for example, there are more handicraft processes involved. We don’t tend to sell as many automatic bobbin changers there as we do in North America or Europe, for example.
O’Mahony: Where do you see the value of the designer in e-textiles?
Böhmer: The value of the designer is that he or she creates new ideas that can lead to innovation and hence to new businesses.
Tailored fiber placement used by ESE Carbon for their carbon fiber wheel produced in a single piece and single cure to achieve a 50% reduction in lay-up times and overall, a better weight to strength ratio in the finished product.
O’Mahony: The nature of textiles and textile processes is constantly changing and expanding to include new capabilities. ZSK have developed fiber-laying capability for composites. Can you discuss the technology that you have developed for this sector and the motivation?
Böhmer: We have developed the capability for fiber-laying primarily for composites at present. These can be used for many different applications in the automotive or aerospace market, for instance, and with our patented technology we are able to integrate functions into composites such as for heating or cooling fully automated.
O’Mahony: How do you see the market for smart composites developing? Do you think that transport will be the market leader in this?
Böhmer: Well, transportation is one of the markets that is driving this technology. But there are other markets, such as aerospace and military, that are also very interested in smart composites.
O’Mahony: What might we expect to see next from ZSK, and when?
Böhmer: We have some exciting developments that we hope to be able to announce soon.
For the present, I’m afraid I can’t tell you any more – but I promise that you will be the first to hear once the information is ready for release!
O’Mahony: Thank you for your time and insights here Sven. It has been invaluable to have your perspective on the sector.
By Marie O’Mahony, Smart & Advanced Textiles Correspondent, IFJ
The AT EXPO is held in different cities across North America each year and AT EXPO 2024 is being held in Anaheim, California, September 24-26. The education programme highlight will be the AT Emerging Technologies Conference starting on September 23, and running for an extended day and a half. Programming has now been finalised, covering a wide range of topics from sustainability in healthcare to addressing PFAS regulations to textiles in the new Space economy.
“Our attendees told us they wanted to see more education on the show floor, so we now have more opportunities than ever before to learn during the show,” says Jonathan Sweet, Director of Content and Member Programs. “We’re very excited about our new approach to education at this year’s Advanced Textiles Expo, along with an expanded Emerging Technologies Conference and more content aimed at the next generation and women leaders.”
Many of the speakers are new to EXPO, including Holly Morris a Consultant Hand Surgeon, Medical Textiles Expert and a coauthor of the UK Green Surgery Report. She will be bringing her unique perspective to bear in a presentation titled,”‘A clinical perspective on improving sustainability within healthcare textiles.” Morris makes a compelling argument for the importance of addressing this issue that has such a large environmental, social and monetary cost: “By generating almost 5% of the world’s carbon emissions, healthcare, if it
were a country, would be the world’s fifth biggest polluter.” The presentation will be solution focused, looking at obstacles to implementation and strategies to address these across the value chain.
A regular speaker at AT EXPO, Frank Keohan, Senior Technology Manager, Bolger & O’Hearn Inc, is well-placed to address one of the hottest issues of the textile industry, PFAS – sometimes referred to as “forever chemicals” because of their persistence in the environmental. Perfluoroalkyl substances (PFAS) are under intense scrutiny in North America and globally. The EPA is unequivocal in the risks posed by the chemicals stating in their PFAS Strategic Roadmap: Second Annual Progress Report published at the end of 2023: “The science is clear: exposure to certain PFAS poses significant risks to human health, including cancer, even at very low levels.” They have been used throughout the textile industry since the 1950s, particularly as liquid repellents for applications such as water repellency. Finding an alternative that is fluorine-free with a comparable performance is challenging. Keohan will look at the critical choices around repellent and application conditions while providing the basics around PFAS, how to detect it, regulatory issues and the evolving technology set to increase repellency performance.
Axiom Space took part in the AT EXPO
2024 space and sportswear panel, one of the most exciting discussions of the conference last year. This year there will be a presentation from Salman Chaundry who is a Senior Technical Advisor for KBR Inc, partnering with Axiom Space to support the NASA Artemis III Mission. An expert in fibers and material science, his presentation is titled, “Weaving the future: how textiles ensure astronaut survival in space.”
Driven by the demanding requirements of the Artemis III Mission Chaundry will highlight the very harsh environment faced by astronauts in the Low Earth Orbit and the Lunar Surface. The list of challenges include flammability, extreme temperature fluctuations, UV radiations, atomic oxygen influx, micro-meteoroid orbital debris risks and how it correlates to textile material performance for the space environment qualification. Any one of these would be a challenge. Looking to the next generation of space exploration, these are the conditions that astronauts, and the textile designers and manufacturers must find solutions for.
There will be an additional education program available to all EXPO 2024 exhibitors and attendees on the show floor throughout the exhibition at no additional charge. Highlighted events include a Next Gen Takeover Day, with networking and education aimed at young leaders and employees to be held on Wednesday and a Women’s Leadership Session to be held on Thursday.
Further information on the Education program and speakers at AT EXPO 2024 can be found at: https://advancedtextilesexpo. com/education/
An education programme will run throughout AT EXPO 2024, with the AT Emerging Technologies Conference starting the day before the trade show opens on 23rd September 2024. ATA
Organizers at EDANA – Europe’s voice of the nonwoven sector – expect 600 international industry professionals to converge at OUTLOOK™2024 in Rome this fall. Delegates will gather at the Cavalieri, Waldorf Astoria Hotel from September 24-26 to discuss the ever-changing marketplace of nonwovens personal care and hygiene and wipes products.
Discussions around market growth and opportunities, sustainability, innovations, technological developments and regulatory activities for the diapers, wet wipes, menstrual health, and incontinence product categories will take place over two-and-a-half days of. The event also comprises networking opportunities – including two evening events – and new for 2024, for the first time OUTLOOK will feature 20 tabletop displays in the exposition hall. This event attracts middleto senior management in the hygiene products supply chain.
“The marketplace is really challenging at the moment, says Johan Berlin, Managing Director, Investkonsult Sweden, who is a key sponsor of the event. “I think that the OUTLOOK conference in general provides great opportunity for the attendees, whether they are leaders in their segment, multinationals, private label, or national companies, to get valuable insight and learn about the trends and innovations in the market, which is crucial at this point.
There’s always something new to learn, be it new materials that can be used in a converted product, or even new materials to be used in the nonwoven product that comes before the converted product. New production techniques that use less energy or gives a higher output, or what is being done in terms of sustainability in certain areas, and what is being done in terms of legislation in certain other areas.”
Each day of the conference will start with a keynote presentation, and then the agenda is split across five sessions. Like in 2023, the agenda structure and timings have been slightly adapted to allow more time for networking, without missing out on the presentations.
Day one opens with a presentation from Joachim De Vos (prof, MSc. ing. MBA), co-founder at Living Tomorrow since 1995, the leading international innovation platform connecting with 5M+ visitors about what the future could look like. He founded TomorrowLab in 2007 as an innovation consulting company working with
over 600 companies on innovation, future strategy, technology and innovation. He is also a professor at the University of Ghent, and author of the book, Why Innovation Fails, bringing the real story of Kodak together with the inventor of the digital camera, Steven Sasson. The “Why Innovation Fails & 7 Keys to Success” keynote explores organizational innovation to stay relevant in challenging times.
His keynote is followed by session one which looks at the driving forces, trends, and market data for both absorbent hygiene products and wet wipes. Moderated by Jacques Prigneaux, Market Analysis and Economic Affairs Director at EDANA, with two confirmed speakers so far including Professor Sarah Harper CBE, Director and Clore Professor of Gerontology, University of Oxford and Per Brandberg, Consultant, Euromonitor International (UK).
Session Two addresses “Innovation & Ecodesign in Absorbent Hygiene Products.” Stakeholders will present their experience with new materials use in absorbent hygiene products to improve the sustainability profile of the end products.
Presenters will be selected from across the entire value chain (from raw material producer to converter) to provide a holistic overview of the topic, after which speakers will debate the merits of using new materials in an interactive panel discussion. The first confirmed participant is Dr. Asta Partanen, Senior Expert – Nova Institute, who will address sustainable options, green claims directive, and balancing demands for sustainable hygiene products with other industry demands.
“We live in a changing world where innovation is no longer limited to market concerns and having the best possible product, but also needs to factor in consumer demand for sustainability and increasing pressure from regulators,” explained Murat Dogru. “At EDANA we work hard to stay ahead of the curve and to ensure that our events address these evolutions.”
That is why this year the policy and regulations session on the second day at OUTLOOK will focus on navigating the EU’s legal framework, sharing strategic approaches to help the hygiene industry understand the latest expectations and how these changes will affect products and operators across the supply chain.
Dogru further elaborated that this session is essential for companies looking to stay ahead in a rapidly evolving regulatory environment, while enhancing their strategic approach to compliance and sustainability. Day two will also feature a session on the future of the AHPs category.
Day three will conclude the conference with a spotlight on wet wipes and how to reconcile consumer needs with sustainability and legislative pressures? This product segment has grown rapidly over the last 20 years as many consumers can’t live without them, yet environmental and sustainability concerns are resulting in stricter regulations. Experts will discuss how to reconcile wipes’ popularity among consumers, public services, and businesses with increasingly critical views from environmentally conscious consumers, NGOs, and some water companies.
“We support the event because almost everyone in the industry is there,” continues Berlin. “It saves us a lot of time and travelling being able to meet so many high-level decision makers in one venue. Yet, its size also manages productive, especially during the networking, to be able to connect with industry peers.”
Visit www.edana.org/events/outlook/ outlook-2024 to register.
RISE is the sustainability platform for emerging and nascent technologies in nonwovens. Held at the James B. Hunt. Jr. Library, North Carolina State’s award-winning library, in Raleigh, North Carolina on October 1-2, 2024, thought leaders spanning the entire supply chain will converge to discuss cutting-edge advancements and research. At RISE®, innovation merges with tangible real-world applications, transforming possibilities into nonwoven reality.
Attendeed gain invaluable insights in:
• Advancements in Natural & Bio-Based Fibers
• Sustainability in Chemistry
• Energy Efficiencies in Machinery
• Advanced Recycling Techniques & Methods
• Current Events in Legislation & Regulation
Noteworthy Sessions:
Using Artificial Intelligence
Rishi Gurani, Ph.D., Director of Software & Algorithms, Matmerize
The steam engine, the light bulb, and the Internet; these are among the handful of technologies that have shaped every in-
dustry, including nonwovens. With each passing day, it appears increasingly likely that artificial intelligence (AI) will leave a commensurate mark.
AI has already improved the development of novel materials and chemical formulations in academia and industry. To fully harness AI’s potential, strategic investments and planning are needed in a few key areas, including digitalization, data capture and management, as well as AI algorithms and their limitations. This presentation provides a comprehensive overview of those areas, culminating in impactful and value-added use cases in the nonwovens and polymeric materials domain.
Don Walter, Director of R&D, Darling Fibers Polyester has been an integral material in society for many years. Its properties can be engineered as tire cord for its strength and stability, designed for safe packaging for food and drink, and formed into various denier textiles for use in a myriad of end uses. Additionally, the low-cost and flexibility of polyester has made it a popular choice in many single-use products. Its durability is an asset in many cases but
also creates a concern as products reach end-of-life. Untreated polyester does not degrade effectively in landfills which creates long-term environmental issues. Sustainable technologies for PET are expanding quickly, and it is unlikely that any one method will optimally handle the variety of ecological challenges. This presentation will focus on recycling, and discuss the practical challenges and benefits of the leading options. It will also layout some of the key hurdles in rPET production and usage in the near term.
Carmen Covelli, Technical Laurate, Celanese Neolast™ fiber is designed to offer elevated stretch performance while helping address sustainability challenges (including recyclability) associated with elastane, which is commonly referred to as spandex. Apparel designers can now create more sustainable power-stretch clothing that also delivers elite performance. Deolast(TM) fiber is melt spun using thermoplastic copolyester elastomer which is classified under the generic category of elastoester. The thermoplastic nature of the polymer enables melt processing, allowing fiber formation without the need for solvents. Celanese expertise in thermoplastic copolyester elastomer chemistry and formulation has led to innovation of two new grades of Neolast™ polymer created for fiber spinning.
Katrina Knauer, Ph.D., Senior Researcher & CTO of BOTTLE, NREL
The plastic pollution crisis is intrinsically tied to an energy crisis, with projections indicating that roughly 20% of fossil fuel consumption will be allocated to plastic production by 2050, accounting for nearly
15% of global greenhouse gas emissions (twice that of the aviation sector). Existing polymerization processes offer limited potential for efficiency enhancements and reducing energy demand. Moreover, reliance on mechanical recycling, the predominant method at scale, is hampered by its finite life cycles due to polymer degradation and contamination. In light of these challenges, the most promising avenues for decarbonizing the U.S. plastic industry necessitate comprehensive systemic transformations.
This involves integrating bio- and wastebased supply chains and establishing a circular economy loop for plastics through innovative recycling techniques aimed at reclaiming plastic waste. At the forefront of these efforts is the Bio-Optimized Technologies to keep Thermoplastics out of Landfills and the Environment (BOTTLE™) Consortium, a multi-organization initiative led by the U.S. Department of Energy. This presentation will showcase the flagship technologies developed by the BOTTLE Consortium, including lowenergy plastic deconstruction methods, innovative upcycling approaches for waste intermediates, and the development of recyclable-by-design (RBD) polymers poised to revolutionize the plastic industry landscape.
Tony De la Hoz, Director – R&D, Hills, Inc.
We are witnessing a significant surge in developmental efforts within the nonwovens sector aimed at crafting the next generation of materials. This momentum spans various segments of the industry, including hygiene, medical, filtration, apparel, furniture, acoustics, insulation, and more. Amidst this fervor for innovation, it is crucial to recognize that sustainability has emerged as the primary driving force propelling technology and materials forward.
In light of this paradigm shift, let us contemplate the implications of integrating bicomponent extrusion capabilities. This advancement not only facilitates the introduction of sustainable solutions or materials to the market but also enhances value proposition. By leveraging
bicomponent extrusion, we can elevate innovation to unprecedented levels, augmenting product performance, durability, and efficiency. Furthermore, this technology holds the promise of reducing carbon footprints, conserving energy, and boosting production rates, thereby reshaping the landscape of the industry – a true game changer.
It is imperative to acknowledge that with the incorporation of bicomponent extrusion, the conventional approach to polymer utilization undergoes a fundamental transformation. Rather than viewing polymers in isolation, it becomes imperative to comprehend the synergistic potential inherent in combining distinct materials through bicomponent extrusion.
Ross Ward, Ph.D., CCO, NIRI
The need for PFAS replacement is disrupting the nonwoven industry. Revised EU and U.S. regulations are on the horizon, and there is growing evidence that exposure contributes to organ disease, cancer, and reduced fertility. Companies are now challenged to explore options to reduce or eliminate their dependency on PFAS while maintaining product performance. This is no small undertaking, as no single route to PFAS replacement exists. Potential solutions will likely incorporate PFASfree additives or coatings, intelligent fibre designs, and textile constructions.
This presentation will focus on strategies for intelligent fibre and nonwoven design, which can serve as a reference for
manufacturers wishing to exploit application development approaches for PFAS replacement.
Plus:
How Adhesives Help You Exceed Performance & Sustainability Goals
Christophe Morel-Fourrier, Ph.D., Global Sustainability Leader, Bostik, Inc.
Opportunities for Large Scale Water Blocking with Super Absorbent Fibre (SAF) Technology
John Rose, Ph.D., Development Director, Technical Absorbents (UK)
Olaf Isele, Strategic Director of Product Development, Trace Femcare, Inc.
Wes Fisher, Director of Government Relations, INDA
The INDA Lifetime Technical Achievement Award will recognize an individual whose technical achievements, over a career of 20 years or more, have meaningfully contributed to the growth of the nonwovens industry. This technical professional will have a long history of innovation, INDA involvement, and/or commercial success.
The Asia Nonwovens Technology Expo (ANTEX Asia) is taking place in Bangkok, Thailand at the Bangkok International Trade & Exhibition Centre, November 13-15, 2024. The show fosters networking, knowledge exchange, and an exploration of the everevolving realm nonwoven materials and technology in that region of the world. Organizers expect over 200 exhibitors in more than five pavilions, with 4,000+ attendees from at least 20 countries.
The nonwovens market is thriving globally, with Southeast Asia serving as a key driver of growth. The increasing demand for nonwoven fabrics can be attributed to their growing applications in the healthcare and personal care industries, as well as automotive, especially electric vehicles (EV). Multiple research studies1 indicate that:
• The global nonwoven fabrics market size is projected to reach US$68.1 billion by 2030, growing at a CAGR of 6.0% from 2021 to 2030.
• By 2030, the region will also be home to 60% of the world’s population aged 65 years or older. The total healthcare expenditure in Asia is estimated to exceed US$4 trillion by 2024.
• EV market in Southeast Asia is expected to grow rapidly, with an annual growth rate (CAGR 2023-2028) of 5.5%, resulting in a market volume of US$1,871.0m (US$1,871 million) by 2028. The unit sales of EV market in Thailand are expected to reach 27,000 vehicles in 2028.
• The textile industry in China is booming with increasing investments and government support. Textile production reached 3.18 billion meters of clothing fabric in October 2022. ANTEX Asia 2024 aims to boost the industry’s growth by constructing a knowledge graph to explore emerging ap-
plications, anticipate future trends, and comprehend the groundbreaking technologies that will further drive the Asian nonwovens development, particularly in automotive, filtration, wipes, medical and personal care sectors. It goes beyond the current state of the industry with a prominent emphasis on sustainability, showcasing manufacturers who are actively integrating recycled or biodegradable materials and adopting eco-friendly production processes. Additionally, advancements in technology and automation play a pivotal role in enhancing product quality, performance, and manufacturing efficiency.
The Expo is organized by a team of industry professionals with extensive experience in managing trade shows.
Mr. Nao Kozuka, Tradelink Co. Ltd., is a pioneer who launched the first nonwoven trade show in Asia 35 years ago and has been actively involved in various nonwoven events since. “We are thrilled to launch ANTEX Asia, marking a new era of collaboration and innovation across the nonwoven field,” he said. “An active dialogue with key stakeholders including local government officials has been established and positive responses were received.”
“Bangkok is the perfect location for the Expo as this country is talented with nonwovens manufacturing. It provides a platform for global leaders to share in-
sights and business strategies customized for the Southern Asian market,” said Culsin Li, Managing Director at Baobab Tree Event Management Co., Ltd., exhibition and event specialist.
“ANTEX Asia will act as a central hub for industry experts, fostering the exchange of knowledge, technology, and innovation across various sectors.” stated Grace Mak, Managing Director at MGT Expo Planning and Management Ltd. Mak is successful executing successful exhibition strategies in Asia, and is well connected with many professional trade associations globally.
In May 2024, ANTEX Asia announced that the Thailand Textile Institute (THTI) and the Thai Nonwoven Fabrics Industry Association (TNFA) will also co-host the event. Mak welcomed their support, “Together, we aim to host a market-driven event in Thailand, showcasing the immense potential of the nonwovens industry in the ASEAN region. With Thailand’s rich textile heritage, strategic location, and strong manufacturing capabilities, it is the perfect place to host this prestigious trade show.”
Esteemed leaders and experts will unveil the latest industry insights and technologies at the concurrent Summit, presenting new fabric materials that enable responsible production and enhance sustainability within the nonwovens industry, to help attendees stay ahead of the curve, and become part of the transformative journey in this unique opportunity provided by ANTEX Asia.
www.antexasia.com
1 https://www.antexasia.com/antex-asia-2024-thelargest-dedicated-nonwovens-show-in-southeast-asiaoffering-the-best-marketing-opportunities/
Global engineered polymer group Trelleborg has announced a greenfield development for its engineered coated fabrics operations in Gateway West Commerce Park in Rutherford County, North Carolina.
The site, part of Rutherford County’s development vision for advanced manufacturing, will be Trelleborg’s second major facility in the area and is expected to cement Trelleborg’s position both as an industry leader and as a major local employer.
In addition to investments in state-ofthe-art production capabilities Trelleborg will further invest in ensuring that the building and its operations are at the forefront of sustainability. The initial investment exceeds $30 million.
nternational technology Group
IANDRITZ has received an order from C&S Paper to supply two PrimeLineCOMPACT tissue machines for its mill in Suqian City, Jiangsu Province, China. The machines will produce tissue for household paper, napkins, handkerchiefs, facial tissues, and toilet paper at a maximum capacity of 94 t/d each. They have a design speed of 1,650 m/min and a width of 3.5 m.
Both machines will be equipped with suction pressure rolls with innovative roll covers and PrimeDry Steel Yankees for energy-efficient, high-quality production. The scope of supply also includes undermachine pulpers and flow and consistency transmitters for both lines, as well as PrimeControl automation systems for efficient control and monitoring of the entire production process.
C&S Paper Co., Ltd., is one of China’s largest household paper producers, with C&S and Sun as its two main brands.
This order once confirms ANDRITZ’s strong market position as one of the leading suppliers of machines and systems for the Chinese tissue industry, and ANDRITZ’s expertise specifically in highquality and resource-saving components. www.andritz.com
“By investing in sustainability as well as capacity, we will be better positioned to meet our customers’ needs and have a positive impact on our local community,” said Steve Brockman, President of Trelleborg Engineered Coated Fabrics. “Our new facility will be built to achieve LEED certification, and our operations will be carbon neutral and emit zero emissions. This investment helps us expand our use of bio-based polymers and recycled raw materials, aiding Trelle-
borg and our customers in meeting their product circularity targets.”
Trelleborg expects to break ground on the new facility in Q4 2024 and start production in Q1 2026.
www.trelleborg.com
To meet rising demand for its fully automated and digitized fabric and part handling solutions, Eton Systems has just moved into modernized new premises in Borås.
The company was founded in 1967 in Borås – widely known as Sweden’s textile city and home to worldwide brands and companies, as well as the prestigious Swedish School of Textiles – as a result of future-looking research and development at shirt maker Eton Shirts.
Eton Shirts, founded in 1928 and still also headquartered in Borås, was very early to realize the benefits of streamlining its production processes, minimizing downtime and better utilizing factory space. Its internal R&D led to the world’s first overhead unit production system (UPS).
Today, Eton Systems UPS technologies have a positive impact on the productivity of thousands of production lines for a range of industries. Designed to increase value-added time in production by eliminating manual transportation and minimizing handling, the individually addressable product carriers are now fully managed and controlled by the company’s advanced software.
“We’re very happy that we have been able to realize our plans and site our new premises with advanced technologies here in Borås, staying true to our roots and heritage,” says Eton Systems CEO Jerker Krabbe. “Digitalization and the push for more sustainable, shorter and less expensive supply chains are currently making manufacturing in high-cost countries within Europe more attractive and our technologies are very much a part of making reshoring a feasible option for our customers.”
“Sustainable interior design is as much about the present as the future,” says Kinnarps Global Range Director Jenny Hörberg. “When choosing interior design and furniture, it is important to take the entire life cycle into account. It’s also about choosing furniture with carefully selected materials that are designed and prepared for renewal, to maximize the life span and create conditions for sustainable circularity.” www.etonsystems.com
oft N Dry Diapers Corp. recently announced the launch of their innovative Tree Free disposable baby diapers in Europe, with sales and distribution capabilities in France, Germany, and the UK on a white label basis for retailers. Soft N Dry is marketready at scale for its customers in the EU and complies with the EU Deforestation-Free Regulation (EUDR) era, which ensures disposable baby diapers sold in the EU do not cause deforestation and degrade the climate. Under the EUDR, diaper manufacturers using tree fiber must comply by January 1, 2025. As part of this strategic growth, the company has also appointed Alexander Valle Burkert as the new Chief Technology Officer (CTO), effective July 11, 2024. www.softndrycorp.com
ADVERTISING | SALES
PUBLISHER Driven By Design LLC advertising@inda.media • +1 239.225.6137
Frank Strazzulla UNITED STATES franks@tmsmedia.net • +1 949.459.1767
Sabine Dussey GERMANY, FRANCE, AUSTRIA, SWITZERLAND, SCANDANAVIA, BENELUX sabine.dussey@dussey.de • +49 2129.348390
Joan Oakley BUYER’S GUIDE & CLASSIFIED ADS joakley@inda.media • +1 248.347.3486
Ferruccio Silvera & Filippo Silvera ITALY & SPAIN info@silvera.it • +39 02.284.6716
Zhang Xiaohua CHINA ifj_china@126.com • +86 13522898423
ADVERTISING COORDINATOR VICKIE SMEAD vsmead@inda.org • +1 919 459 3700 x 3720
NDA, the Association of the Nonwoven Fabrics Industry, and The Nonwovens Institute (NWI), announced a collaboration agreement to provide continuing education to the nonwovens industry. This agreement expands upon the ongoing partnership between INDA and NWI, whereby the two organizations have successfully presented training programs, covering the full spectrum of the nonwovens value chain from raw materials to processes to products.
Under terms of the agreement, INDA and NWI will develop and present a full roster of training courses, featuring a combination of classroom learning supported by hands-on activities in NWI’s world-class nonwoven production and testing labs on the Centennial Campus of North Carolina State University. The two organizations will also work together to explore additional educational programming to serve the needs of the nonwovens industry as they evolve over time.
“This collaboration agreement represents a significant next step in the partnership between INDA and NWI, as we build upon our training course offering to ensure it is meeting the needs of the nonwovens industry now and going forward,” said Matt O’Sickey, director of education and technical affairs at INDA. “We are also committed to pursuing new avenues to expand the knowledge base of professionals working in areas related to nonwovens.”
The current roster of INDA/NWI training courses include:
• Elementary Nonwovens
• Intermediate Nonwovens
• Fiber and Filament Extrusion Fundamentals
• Meltblown Technology
• Nonwoven Bonding Fundamentals
• Nonwoven Fabric Property Development and Characterization
• Nonwoven Product Development and Innovation
• Spunbond Technology
Course registration is open to INDA/NWI members and non-members. The INDA/ NWI Short Course Value Pack program enables companies to purchase a block of registrations, which can be used by any combination of employees to register for any combination of training courses, at a discounted rate. Value Packs are available in bundles of 5, 10, 15, and 20 registrations, with discounts ranging from 10 percent to 25 percent, depending on the size of the Value Pack. For more information about the Value Pack program, visit https://thenonwovensinstitute.com/short-course-value-pack/. www.inda.org/training
PET/PBT/PBAT/PBS/PTT/PLA/PETG/PC/PA6/PA66..
POLYMER: Physics / Chemistry
BDO/EG/MeOH/Heat recovery and comprehensive u�liza�on
HP
Hydrogen Peroxide, H2O2
R&D
Own R&D Center and pilot plant
Project EPC Contrac�ng (Turn-key)
Manufacturing of Cri�cal Equipment
POLYTEX is a professional chemical engineering company and technology supplier integra�ng R&D, engineering, equipment manufacturing, procurement and EPC management services. From technology licensing, project planning, equipment manufacturing and engineering design, procurement and construc�on management, as well as start-up and opera�on services, Polytex provides diversified services and one-stop solu�ons to customers all over the world.
POLYTEX ENGINEERING GROUP
Corp: 5th Floor, No.20 Wenchang Mid Rd. Yangzhou, Jiangsu, PRC.
Head: No.1, Private Industrial Park, Yuetang, Yizheng, Jiangsu, PRC.
Tel: +86-514-85553618; +86-514-87859276
Mail: market@polytex.cc; polytex@vip.sohu.com
Website: www.polytex.cc
24/7
Technical Support & Service
EPLASTMER NEW MATERIAL CO., LTD
Bo�le grade, Tex�le grade, Film grade PET chips will be launched soon. Our own factory capacity in phase-1st will reach up to 1260 tons per day.
China Sales:
Mr Sun Mob: +86-133 1990 0139; Email: sg_sun@e-plastmer.com
Mr Cao Mob: +86-181 5290 1436; Email: cao@e-plastmer.com
Ms Pu Mob: +86-185 0992 5214; Email: pu@e-plastmer.com
Russia and Central Asia Sales:
Mr Li Mob: +86-189 5105 3772; Email: �ger@e-plastmer.com
Mr Gao Mob: +86-138 5159 0251; Email: gaocx@e-plastmer.com
Mr Dos Mob: +86-135 1991 0418; Email: dos@e-plastmer.com
Other markets:
Ms Emma Mob: +86-158 9939 1075; Email: emma@e-plastmer.com