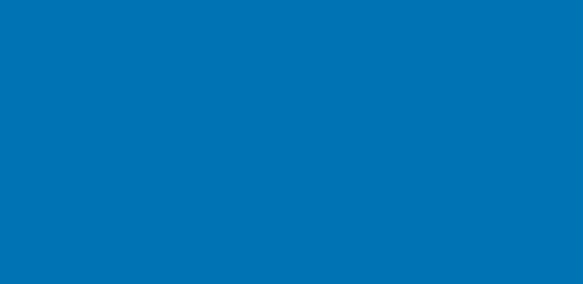
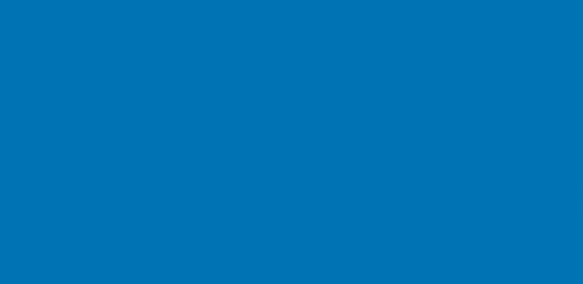


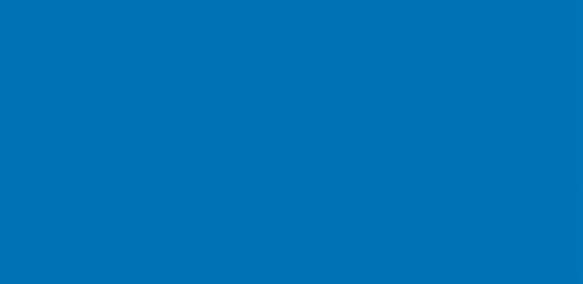

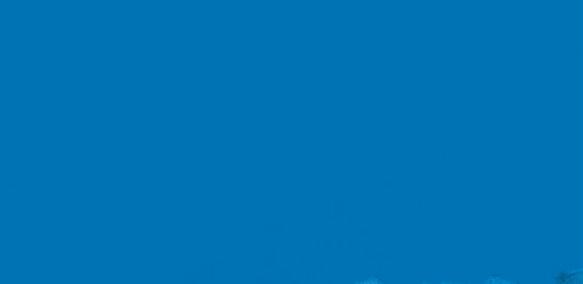
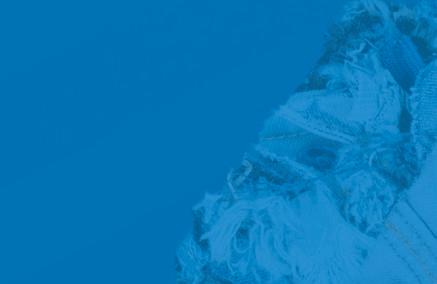
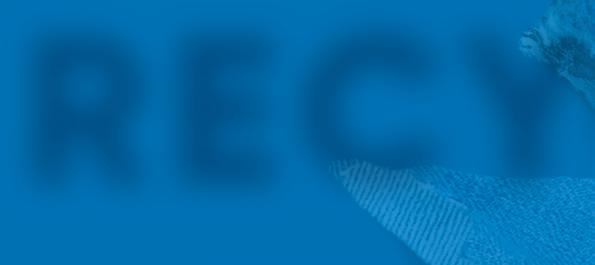
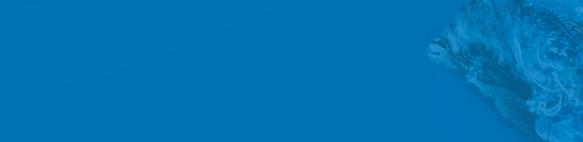
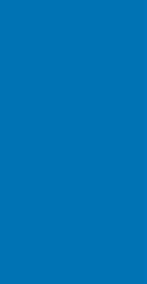

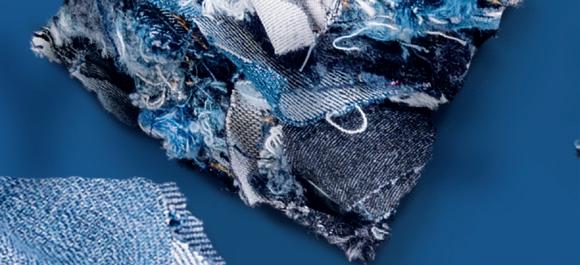

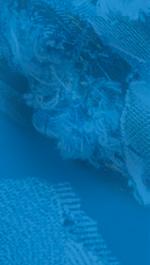
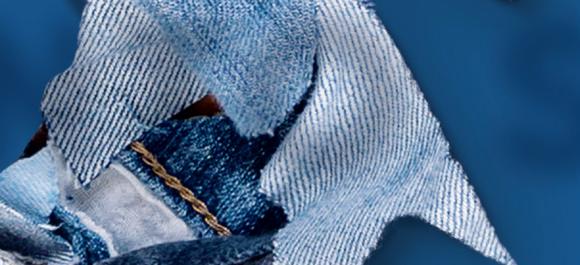
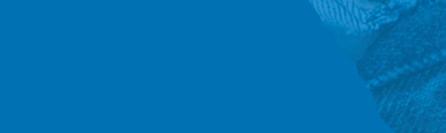
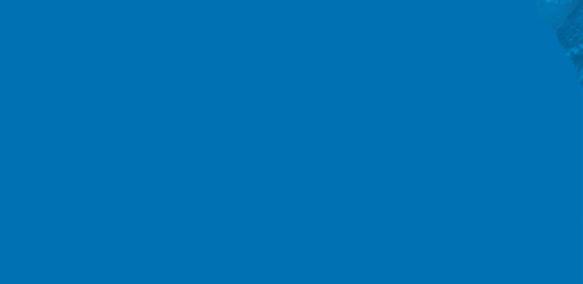
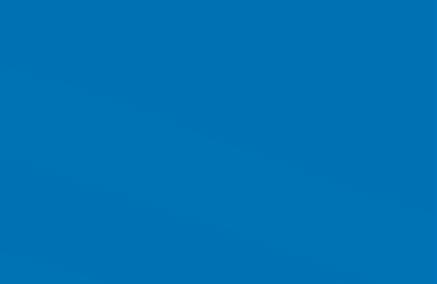
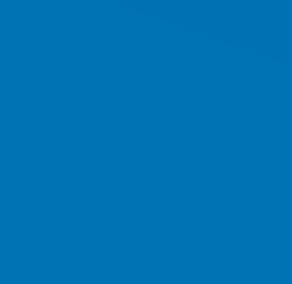
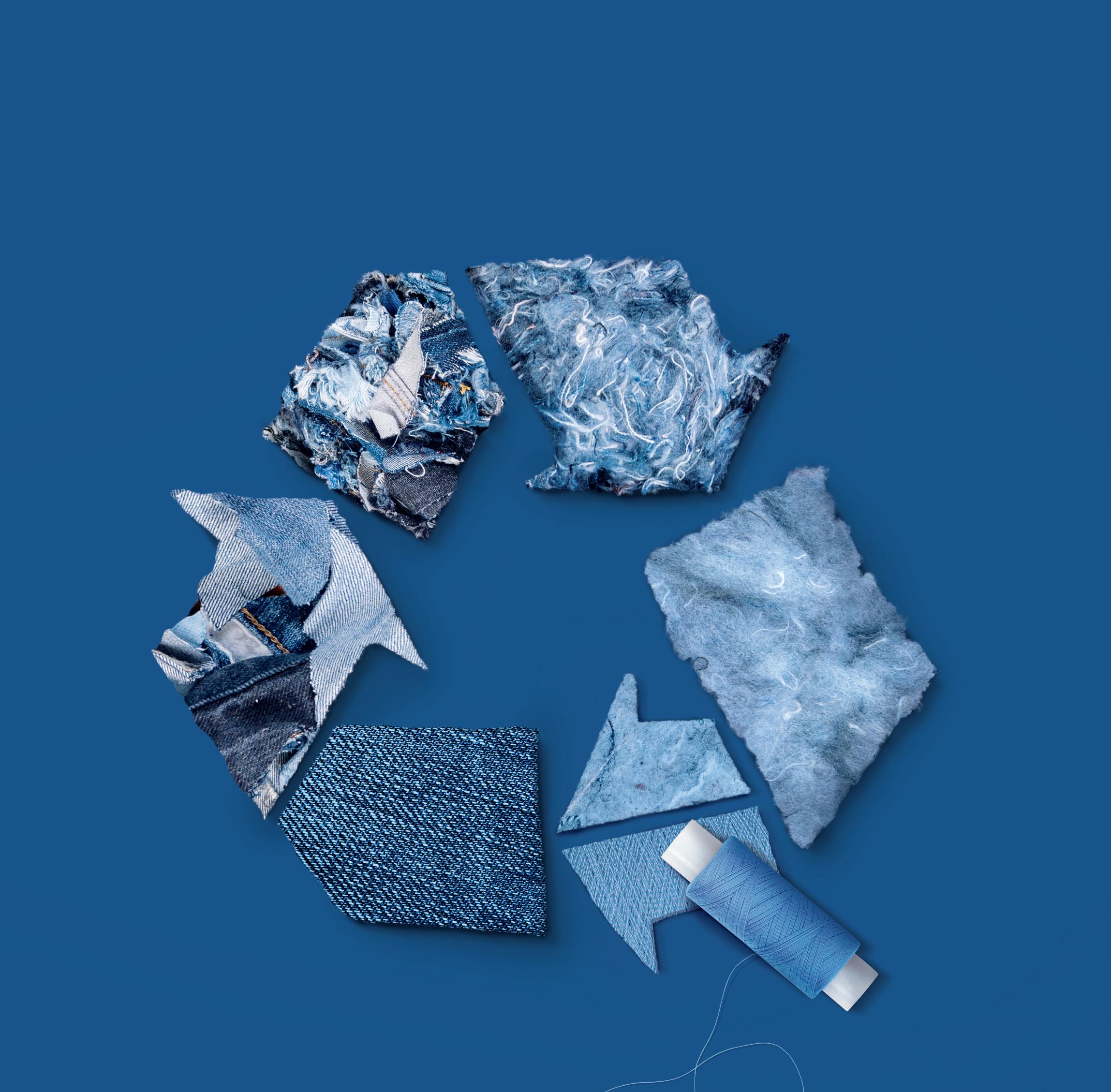
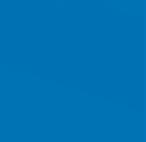
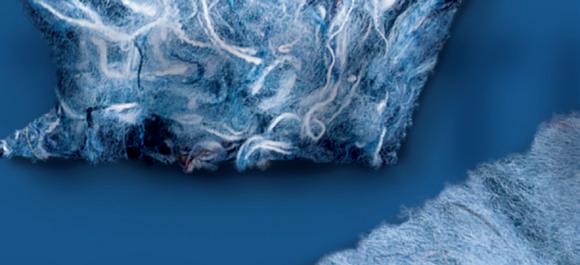
ANDRITZ is the right partner when it comes to automated sorting, textile fiber preparation, mechanical and chemical recycling or combined recycling solutions for pre- and post-consumer or industrial textile waste. We accompany you throughout the product life cycle and beyond.
For more information, visit our website.
For years to come
Take advantage of our profound experience and skills to leverage your production, create new products, and make the right investment decisions, so that you can recycle your textiles into success.
Along and beyond your entire Production
Compact spinning line for PET (virgin, recyclate, bottle flakes), PA6, PA6.6, PP, BiCo, mother yarn and others on request
Air-texturizing line for processing POY and FDY made from PET, PA6, PA6.6 or PP
PET recycling line for textile and fiber waste to filament recycling
Liquid state polycondensation for IV increase and homogenization
Caryn Smith
Chief Content Officer & Publisher, INDA Media csmith@inda.org +1 239.225.6137
Geoff Fisher European Editor gfisher@textilemedia.com +44 1603.308158
Marie O’Mahony Smart & Advanced Textiles Correspondent marie.consultant@gmail.com
Raymond Chimhandamba Handas Consulting ray@raychimhandamba.com
International Fiber Journal reaches a vast network of qualified professionals who employ fibers, nonwovens, technologies, equipment and more to optimize operations. With readers in markets that have strong crossover, IFJ offers print and digital opportunities to maximize marketing investments with a range of solutions based on true thought-leadership platforms. IFJ subscribers are in 67 countries. There are 17 countries with significant readership (print and digital) that include USA, Hong Kong, Germany, China, India, Italy, United Kingdom, France, Spain, Belgium, Japan, Canada, Australia, Mexico, Switzerland, Brazil, and Taiwan.
Don’t Leave Your SUCCESS to Chance. Get a Media Kit: Advertising@inda.media today!
Increase Your Company Exposure to Fiber & Filtration Professionals! GET 3X EXPOSURE – PRINT GUIDE, DIGITAL GUIDE + SOCIAL MEDIA! Take advantage of this incredible way to be found among the best of the industry!
w For $495, Standard Company Listings receive:
• Up to 5 categories for a searchable listing + logo for 1 year in online guide
• Print listing + logo with categories listed in IFJ publication
w For $995, Premiere Vendor Category Listings receive all the Standard Company Listings (listed left), with the additional value of:
• Up to 12 categories for a searchable listing + logo for 1 year in online guide
• NEW: Buyer’s Guide link accessible from INDA.ORG website, increasing SEO
• NEW: Promotion of Buyer’s Guide on IFJ Social Media & in the Monthly E-Newsletter
• NEW: New “Premiere Vendors” Buyer’s Guide landing webpage* – only for this category – with clickable company logo
• NEW: Digital Flipbook with clickable links on Home Page of IFJ websites
• NEW: Two “Buyer’s Guide e-Promotions” with the logos of all “Premiere Vendors” (clickable) sent to IFJ promo lists
s the demand for sustainable materials continues to rise, bio-based fibers are gaining importance in the textile and hygiene industries. Cellulose-based fibers are widely preferred due to their natural origin and processability. However, alternative biomaterials vary in terms of their mechanical performance and compatibility with existing production processes.
Cellulose-based materials are environmentally friendly and biodegradable, but they are sensitive to water and chemicals. On the other hand, Thermoplastics are more durable, formable and cost-effective, but their environmental impact is more negative. Cellulose should be preferred for sustainability and thermoplastics for durability.
In this context, cellulose plays a crucial role in hygiene-focused applications such as spunlace nonwovens, while new bio-based materials are also expanding their market presence. Among these, PLA (Polylactic Acid) is emerging as the most viable competitor to cellulose.
PLA is a bio-based and biodegradable material developed to replace conventional plastics. While it is not the only bio-based fiber suitable for spunlace processes, it distinguishes itself with superior processability and mechanical strength among biodegradable alternatives. Meanwhile, alternative biomaterials such as PHA (Polyhydroxyalkanoates), PHB (Polyhydroxybutyrate), and PBAT (Polybutylene Adipate Terephthalate) are also striving to secure their place in the market.
Although PHA and PHB offer biodegradability, their lower processability and mechanical strength present challenges in industrial applications. PBAT, while having a better environmental profile than conventional plastics, does not provide as sustainable a solution as PLA.
In addition to existing PLA fibers in the market, Fiberpartner’s brand PolyPlant ® PLA-based fiber offers enhanced mechanical strength and superior processability than standard PLA fibers. There are several impact modifiers that were used to increase the toughness of PLA and PLA composites. However, the majority of them are not bio-based, they are mainly ethylene and acrylic copolymers. The fiber owned by Fiberpartner is a fiber technology made entirely with bio-based/biodegradable modifiers. With a specialized additive technology, PolyPlant ® provides a much more efficient alternative in terms of processability. With its potential to push the boundaries in many nonwoven technologies both forming and bonding different applications, it is also set to accelerate transformation in the market.
One of the known limitations of PLA is its reduced durability over time, particularly after processing. However, Fiberpartner’s internal data on nonwovens made from PolyPlant ® fibers indicates that strength loss remains minimal during the first six to seven months:
After Ageing
fibers on the market offer a sustainable and eco-friendly alternative to conventional synthetic fibers, making them a promising material for future applications.
PolyPlant ® fiber is an environmentally friendly product developed by Fiberpartner and has chosen with the right subsidiaries of the materials and designed to have:
• Superior durability and mechanical strength
• Versatile compatibility with existing nonwoven processes
• Enhanced thermal stability compared to conventional biopolymers
Our formulation combines shorter molecular chains with longer, more complex chains and is configured for specific use cases to match the basic specifications. The resulting biopolymer fibers demonstrate high thermoplastic performance, making them suitable for efficient spinning and stable textile surface formation.
Since PolyPlant® fibers are entirely derived from sugar cane, their carbon footprint is significantly lower compared to petroleumbased plastics. Considering that CO 2 is captured from the atmosphere by plants during photosynthesis, at the end of the life cycle this carbon is removed from the inventory analysis. Biobased PLA production has a 75% smaller carbon footprint, including biogenic carbon, compared to fossil-based plastics.1
PolyPlant® fiber is a biodegradable and renewable polymer that has gained significant attention in recent years due to its environmentally friendly properties. It has been extensively studied for various applications in sectors such as textiles, packaging, and biomedical engineering.
Potential applications of PolyPlant® fibers include textiles, nonwovens, composites, and medical implants. In general, biopolymer
Bio-based and biodegradable fibers are expected to play an increasingly vital role in sustainable manufacturing. While cellulose-based fibers remain the dominant material, PLA and next-generation fibers offer significant advantages in terms of processability and durability.
Innovative solutions like PolyPlant ® are poised to accelerate this transition, reinforcing the role of biomaterials in the nonwoven industry.
www.fiberpartner.com
1Peer reviewed LCA analyses reference: Life Cycle Impact Assessment of Polylactic Acid (PLA) Produced from Sugarcane in Thailand | Journal of Polymers and the Environment.
Ontex Group NV, a leading international developer and producer of personal care solutions, announced the commercial launch of its Dreamshields ® technology for baby diapers. Offering superior performance, all-round leakage protection, and enhanced comfort, Dreamshields® ensures optimal dryness while prioritizing sustainability. The Dreamshields® technology is now available on shelf in several European markets in Europe and is being rolled out to more customers soon.
Laurent Nielly, President Europe at Ontex, says, “Dreamshields® is a key technology in our portfolio, offering a perfect balance of quality, affordability, and sustainability. By combining effective protection with a design that reduces CO 2 emissions and plastic use, Dreamshields ® meets the demands of today’s families while supporting our commitment to environmental responsibility. At Ontex, we focus on delivering relevant innovation that make everyday life easier for parents and families.”
Dreamshields ® technology integrates a range of advanced features that benefit both parents and babies, enhancing comfort, protection, and ease of use. Panel scores show Dreamshields® performs great, especially when it comes to leakage protection. These innovations address both the needs of babies for comfort and the expectations of parents for reliability and sustainability:
• Unique channel design with gender-specific zones: enhances fast liquid flow across the entire core for superior absorption, ensuring babies stay dry and comfortable.
• SeconDRY ® system provides instant dryness by rapidly drawing moisture away from the skin, minimizing the risk of irritation
• Double-layer core with dual SAP (Super Absorbent Polymer) features two types of SAP, optimizing fast liquid attraction and solid retention for a lighter, more flexible diaper.
• 360° protection combines front and back barriers with anti-leak cuffs, effectively preventing leaks and blow-outs in all directions.
• Heat release feature promotes air circulation, maintaining fresh and healthy skin conditions to prevent discomfort and rashes.
• High waist fit offers a snug and stretchy fit that adapts to baby’s movements, ensuring comfort at all times. www.ontex.com
TUBICOAT PET-H is used for the stiffening of polyester fabrics and nonwovens in many technical applications. Since TUBICOAT PET-H itself consists of polyester, the treated goods can be declared as single-variety, recycled and returned to the material cycle.
Together for a sustainable future
NDRITZ Nonwoven & Textile is one of the world’s leading suppliers of technologies for the nonwoven and textile industry. The company stands for high-quality performance for all technology areas they operate, top-class service, and prompt, smooth project execution.
ANDRITZ is a global player in the wipes market with a comprehensive range of production solutions, from conventional wipes to flushable and sustainable wipes. ANDRITZ is at the forefront of developing spot-on technologies to leverage the market. The company’s expertise spans across airlaid, spunlace, WetlaceTM, and AirlaceTM processes. By combining these technologies in various ways, ANDRITZ can cater to different segments of the wipes market. ANDRITZ is highly committed to adapting, optimizing, and combining its technologies to provide the perfect solution for customer and market needs.
Pulp, which is sourced from natural cellulosic fibers, is a versatile and biodegradable raw material that is often used to produce wet wipes. It offers excellent absorbency, softness and strength, making it ideal for various types of wipes, especially biodegradable and flushable wipes. ANDRITZ plays a crucial role in this sector by providing advanced pulp production plants, fiber processing technologies and solutions for integrating pulp into nonwoven fabrics.
For instance, the innovative Wetlace CP (carded pulp) as well as the Airlace process combines wet/air forming with pulp and hydroentanglement, enabling the production of high-quality, sustainable wipes from 100% natural and renewable raw materials. This approach not only enhances product performance but also supports the industry’s shift towards eco-friendly and biodegradable products.
ANDRITZ continuously adapts, optimizes, and integrates its technologies to meet evolving customer and market demands. Recent trends, such as retrofitting conventional spunlace lines with airlaid or wetlaid web-forming capabilities, underscore the
drive for innovation. These upgrades open up new market opportunities, such as bio-wipes and flushable wipes, and provide greater flexibility for diversified applications.
A cornerstone of ANDRITZ’s success is its state-of-the-art technical centers, which act as hubs for innovation and development. These centers offer customers the opportunity to test and further enhance their processes with the latest equipment and technologies. For wipes processes, ANDRITZ hosts three technical centers with different competences and test opportunities.
The Montbonnot, France, facility hosts a complete spunlace and a Wetlace CP line. It is the world’s first nonwoven test center for wipes, featuring integrated cellulose formation and the neXecodry energy recovery system. In Krefeld, Germany, the wetlaid/Wetlace pilot line allows for the development and testing of all types of wetlaid processes, including wipes. In addition, the Graz, Austria, center specializes in stock preparation, offering expertise in fiber processing to enhance nonwoven material quality. Together, these facilities help customers achieve high efficiency, sustainability, and premium product performance in the wipes industry. www.andritz.com/nonwoven
or more than 50 years, FiTech has connected the synthetic fiber, nonwoven and technical textile industries to the leading suppliers of production machinery and technical components. Since our founding in 1972, Fi-Tech consistently brings to the market the most advanced suppliers with unique and technologically superior solutions
FOur principals include:
giving our customers the competitive advantages they need to be successful today and well into the future.
From our home bases in Richmond, VA and San Luis Potosi, Mexico, the Fi-Tech Team is with you every step of the way from technical specification, to order placement, to delivery and after startup spare parts support. The Fi-Tech Team is dedicated to providing the best
products and customer service and to your success.
www.fi-tech.com
ntroducing the Highly Flexible Packer (HFP) Twin at the IDEA®25 – the ultimate flexible packaging solution designed to revolutionize packaging operations. The HFP Twin is designed to streamline the packaging process, reduce downtime, and enhance overall output. Its user-friendly features and advanced technology make it an indispensable asset for any business looking to stay ahead in the competitive nonwovens packaging industry.
The HFP Twin combines gentle product handling with high flexibility in case packing. This innovative system allows for multiple packing configurations that normally cannot be achieved with a typical case packer, by integrating both side load and top load capabilities on one single platform.
The use of robot arms ensures the same level of flexibility as manual packaging and its unique approach of moving the case instead of the product ensures gentle handling, thereby minimizing the risk of damage and offering a crease-free product. The HFP Twin offers an automated fast and tool-less size change feature reducing downtime and maximizing productivity. Optional separated safety circuits ensure enhanced safety by allowing for two independent robot cells to minimize downtime risks and maximize efficiency in the automated packaging process. Reliable technology, completed by various, modular layout applications for highest efficiency, the HFP Twin is the proven partner for EOL automation.
Equipped with FOCKE VISU 3000 HMI, Focke’s HFP Twin is future proven.
The modular design of the HMI allows simple extension with added functions and requirements. The on-screen help, as well as integrated machine documentation, support the operator in tasks and enable quick solutions to any issues.
FOCKE & CO is a leading manufacturer of packaging solutions worldwide. Among others FOCKE & CO offers various case packer applications for packing products such as bags filled with pads or diapers. In addition to the headquarter and divisions in Germany, the familyowned enterprise operates sales and service branches on all continents. Since the foundation in 1955, FOCKE & CO has delivered over 22,000 machines to more than 70 countries.
• Integration of both, side and top load, capabilities on one platform
• Flexible pack patterns – even different orientations mixed in on case
• Proven partner for End-of-line automation for nonwovens packaging
• Serving the nonwovens industry with stand-alone or turnkey packaging lines
www.nonwovens.focke.com
IFJ goes behind the scenes as legacy brand Stein Fibers announces its corporate rebranding as Everra, sealing the company’s lasting commitment on “delivering sustainable solutions to an ever-evolving world.”
By Caryn Smith, Chief Content Officer, IFJ
ndustry demands for new and improved solutions to textile industry challenges are on the rise. With the focus squarely on sustainability and circularity, supply chain brands are stepping up to supply top-quality options to help their partners achieve high-impact results at an industrial scale.
With a legacy of 50 years of service to the textile industry, Stein Fibers is achieving remarkable results from its ever-growing portfolio in synthetic fibers, so much so that they have outgrown the word ‘fiber’ in its brand name. The company has grown through research and development of its core products and through acquisitions to grow its potential in new niches. In a bold move, the company executives launched a repositioning exercise and created a new brand name to take them into the future.
JAREN EDWARDS, CO-CEO
ROBERT TAYLOR, CO-CEO
Everra is cleverly derived from the words “Ever,” “Evolving,” and “Terra” – symbolizing enduring partnership, constant evolution, and a deep commitment to sustainability. The company’s logo reinforces these values, featuring a knot for union and collaboration, a link to fill supply chain gaps, and clasped hands to represent reliability and working together toward a sustainable future.
As Everra, the company remains steadfast in its core mission to help the world turn recycled plastic bottles into new products. This reinforces its position as a leader in sustainable solutions, and its staple products serve the entire fiber supply chain.
Stein Fibers just unveiled its rebranded name change to Everra, effective immediately. The company’s tagline shares its vision: “Forever committed to delivering sustainable solutions to an everevolving world.”
This new name represents a bold evolution for the company and reflects its ongoing commitment to sustainability, innovation, and leadership in the global PET market. Their company focus remains the same: a sustainability-focused, marketleading distribution partner in the PET industry, helping transform recycled plastic bottles into new products. Everra’s
expanded focus includes adjacent PET markets like polymers and filament as the company continues to adapt and innovate in response to the growing demand for sustainable solutions.
Jaren Edwards is co-CEO with Robert Taylor of the Charlotte, NC-based company. With nearly 30 years of experience in the PET industry, Edwards has a keen eye on the global marketplace and the demands placed on fiber producers. He did not enter the rebranding endeavor lightly, having spent most of his career with Stein Fibers after graduating from NC State University in 1996 with a degree in Textile Engineering. He moved through the ranks as a sales representative, gaining extensive experience across various markets, and then as Vice President of Sales, leading domestic and international teams and moving from traditional fiber approaches to sustainable business development. Robert Taylor joined Stein Fibers in 2015 as the co-CEO and COO and has over 30 years of experience in the PET
One of Everra’s greatest competitive advantages is the expertise gained from operating our own recycled PET facility. This firsthand knowledge allows us to assess the raw material stream before manufacturing even begins, ensuring we select the right materials and processes to achieve the desired fiber characteristics.
Companies that thrive today are those with deep supply chain knowledge, a global network of partners, and the ability to move materials efficiently despite these obstacles.
For manufacturers in North America, we believe that their focus should be on producing high-quality products and expanding sales channels, not on navigating the complexities of fragmented global supply chains. That’s where we thrive and excel. We bridge the gap between global suppliers in Africa, India, Southeast Asia, and Korea, offering seamless, cost-effective logistics across the fiber and polymer markets.
Instead of managing twelve different supply chains for twelve different products, U.S. customers can rely on Everra’s expertise in distribution models and supply chain integration. We bring partners together, creating synergistic value and ensuring that businesses can focus on what they do best – while we handle the rest.
IFJ: How has acquisitions positioned your company for future growth?
Edwards: Quite simply, Everra’s most significant acquisitions have strengthened our legacy polyester staple fiber business and expanded our market reach. We were strategic in our efforts, and found brands with depth to grow Everra’s potential.
In 2021, we acquired Consolidated Fibers, a 60-year leader in synthetic fiber solutions for the nonwovens industry. Shortly after, we brought Fibertex into our portfolio – a 30-year industry leader specializing in nonwovens and fiberfill fiber products. These two acquisitions provided significant synergies, broadening our product offerings and reinforcing our position in the fiber industry.
Most recently, we acquired Banyan Plastics, a leading distributor of recycled materials. This strategic move accelerated our growth in the polymer sector, enhancing our ability to serve the world’s most strategic PET manufacturers while reinforcing our commitment to sustainability.
You could say this latest acquisition set the stage for our recent brand exploration, which ultimately led us to Everra.
IFJ: Let’s discuss the rebranding effort. Are you repositioning or extending your brand for the future growth you plan?
Edwards: Our rebrand is a natural extension of the work we do every day. The primary goal? Clarity. As we expanded significantly into the polymer sector, the word “Fiber” in our company name no longer fully represented our business. We saw firsthand how it led to confusion through misguided inquiries, signaling the need for a change.
Partnering with a marketing firm, we embraced an open-minded approach throughout the discovery process. Ultimately, we recognized that our name should not only reflect who we are today but also position us for the future. Everra embodies our evolution – staying true to our legacy while embracing the opportunities ahead.
IFJ: You mention partnerships as an Everra core business value. One recent and significant relationship for your company is Fiberpartner™. How are you working together?
Edwards: We look for strong partnerships that are built on shared core values and a commitment to excellence. With Europe often serving as a sustainability forecast
for North America, our collaboration with Fiberpartner was a natural fit.
Based in Denmark, Fiberpartner has a long history in the global textile marketplace and faces similar supply chain challenges when entering Western markets. As they expand their polyester portfolio – including biodegradable and bio-based materials – they look to Everra to help navigate these obstacles, particularly in the U.S. market.
Together, we are bridging supply chain gaps and driving sustainable solutions forward.
Taylor: We are also helping in Europe with packaging applications. Our partnerships are a two-way street. We will continue to try to leverage expertise to benefit both of us.
Edwards: We are sharing a booth at INDA’s IDEA ® 25 Show in Miami Beach, FL [April 29-May 1]. We are there independently, but we have the same booth number and the booth design illustrates this collaboration theme well.
IFJ: In today’s vast marketplace, what would you say is Everra’s dominant sector?
Taylor: This is a great question, because we want everyone to know that our mission for the company hasn’t changed – we rebranded to best convey our future-forward mindset. Everra continues to operate across the entire fiber marketplace, with primary end markets in furniture, bedding, automotive, and nonwovens. Additionally, we remain deeply involved in spinning and disposable nonwovens, supplying major brands and their downstream partners.
Beyond fibers, we play a key role in the packaging industry, supporting beverage and food packaging – like sheet and film manufacturers – through our expertise
in PET, polyethylene, and polypropylene, with a strong focus on recycled materials.
Our global reach extends beyond North America, helping bridge Asian and international customers to the U.S. marketplace. Whether in nonwovens, fiberfill for bedding and furniture, spunlace, spinning, or packaging, the common denominator is the polyester molecule – and our ability to connect supply with demand.
We are a strong partner in that the diversity of our market segments provides Everra with leverage and stability. When disruptions impact one industry, our broad portfolio allows us to adapt and remain flexible, ensuring continuity and growth for all of our partners.
Edwards: The team at Everra has set an ambitious yet attainable growth goal for 2030, driven by a strong organic growth strategy and accelerated by strategic acquisitions.
Today, 65% of our business consists of recycled materials, reinforcing our commitment to sustainability. In the coming years, we expect this number to grow to 80% of our portfolio, further solidifying our role as a leader in sustainable solutions. By staying focused on innovation and responsible growth, Everra is shaping a more sustainable future for the industry.
Sustainability and circularity continue to be at the forefront of trends, and our goal is to be an industry leader in this effort, as well as a quality provider
Everra products are designed to meet the diverse needs of industries ranging from hygiene and medical to automotive and filtration, providing the performance, durability, and versatility required for a wide array of applications. Everra
of solutions for others focused on environmentally-friendly options. In our rebranding effort, we incorporated the work “terra” that signifies earth, land, solid ground and sustainability.
IFJ: What is hindering the adoption of more sustainable options, especially in the nonwoven sector?
Edwards: I believe that success starts with understanding the obstacles – whether processing or end-use applications.
There are also many ways to achieve sustainability goals, from choice of raw materials, manufacturing for durability, to end-of-life variables.
One of Everra’s greatest competitive advantages is the expertise gained from operating our own recycled PET facility. This firsthand knowledge allows us to assess the raw material stream before manufacturing even begins, ensuring we select the right materials and processes to achieve the desired fiber characteristics.
We take a different approach – solving the problem first to then drive both performance and value. By identifying challenges upfront, we believe forward-thinking companies can eliminate inefficiencies and produce the highest-quality products.
Taylor: Also, the Everra team is one of our core assets to help customers solve these kinds of problems in a complex marketplace. Our sales and technical teams are composed primarily of professionals with textile backgrounds or textile engineering expertise. This deep industry knowledge allows us to do more than just supply materials – we help solve supply chain challenges and provide technical support to ensure our customers have the best product solutions available.
With our team’s hands-on expertise, we bridge the gap between innovation and application, ensuring that every solution we offer is practical, efficient, and tailored to our partners’ needs.
IFJ: What is the appeal of polyester? Why is it misunderstood?
Taylor: Polyester is a unique molecule with endless recycling potential. From a technical standpoint, it can be recycled over and over again, making it one of the most sustainable plastics available. Unfortunately, the general public do not trust recycling systems in place, and mishandle plastic waste. Despite its bad publicity due to litter and low bottle recycling rates, polyester remains the most recyclable plastic in the world.
Through mechanical recycling, polyester can be transformed into new products with minimal impact on performance.
While some physical characteristics –such as color – may shift after multiple recycling cycles, polyester can continue to be reused indefinitely if properly returned to the recycling stream. This gives it a clear advantage over alternatives like polycarbonate, polyethylene, and polypropylene.
Emerging chemical recycling technologies offer additional promise, particularly for contaminated material streams. These advancements could allow for more efficient separation of synthetic and natural fibers, such as cotton-polyester blends, further enhancing polyester’s role in sustainable material solutions.
Edwards: In sustainability and recycling, the conversation isn’t just about the cost of recycled polyester – it’s about how it compares to other materials. Companies must consider the trade-offs: polyester fiber vs. viscose rayon, nonwoven vs. polyurethane foam, or the price difference between recycled and virgin polyester. These factors shape short-term decisions, but long-term momentum is being driven by a more fundamental shift – consumers simply do not want to see waste in landfills when viable recycling solutions exist.
Major global brands are already leading the way with 100% recycled products, and as adoption rates grow, more will follow. Recent developments in packaging have also shown how quickly market perspectives can shift – plastic, once vilified, is now gaining favor over aluminum in certain applications. These unpredictable shifts reinforce the need for adaptability and transparency in sustainability efforts.
At Everra, we provide confidence and security to our customers in the
sustainability space. Through thirdparty documentation, full traceability, and an on-the-ground presence in Asia, we offer unmatched transparency and accountability. When working with large brands and programs, the ability to ensure supply chain integrity – backed by inperson engagement and verification – is a powerful advantage.
IFJ: Circling back to your rebrand launch, what excites you most about the effort and how will you educate customers on the change?
Edwards: As we unveil our new brand Everra, we will prominently display “formerly Stein Fibers” alongside it for a significant period. Our goal is to provide clarity and ensure that our long-standing partners and customers are not confused during this transition.
We want to create excitement in our adjacent growth markets while generating buzz around our new identity. With this major rebranding effort underway, we’re particularly enthusiastic about 2026, when we will celebrate our 50th anniversary. This milestone will reinforce that, while our name may be new, we have a rich legacy built over decades.
Throughout this project, we’ve engaged in deep introspection, and now we’re ready to focus our energy on enhancing customer responsiveness. We look forward to building on our foundation and strengthening our commitment to our clients as Everra moves into its next chapter.
Taylor: This rebrand is an incredible opportunity to reinvigorate our existing customer base by showcasing our 50-year commitment to excellence. It also allows us to highlight the expanded product offerings that better align with our evolving services.
By reinforcing our legacy while embracing innovation, we ensure that our current and future business partners have the solutions they need to grow and succeed in a rapidly changing market.
www.everraglobal.com
As the leading suppliers in the international nonwoven industry, YINGYANG has extensive experience in the field of nonwoven machinery with Multiple Solutions Under One Roof Across Industrial End-use Segments. YINGYANG has achieved a high level of reputation for accurate design, precise manufacturing, rigid assembly and attentive service.
For 33 years, YINGYANG has provided thousands of complete set of customized high quality nonwoven technology solutions in 78 countries globally.
International technology YINGYANG NONWOVEN MACHINERY will be presenting its innovative nonwovens production solutions at
APRIL 29 - MAY 1
BOOTH NO. 424
The idea and prospect of YINGYANG development is to supply machinery based on the request of lower production costs, higher throughputs and speeds, improved product quality as well as sustainable and intelligent production. We would like to cooperate with the international nonwoven industry to provide:
determine the fiber content of individual items destined for recycling.
Currently, less than 1% of textiles are recycled in a closed-loop back into new items, according to the Ellen MacArthur Foundation – the vast majority ends up as waste sent for landfill or incineration.
And with the global textile industry responsible for an estimated 6% – and rising – of landfill volume, recycling offers a circular material solution that can shrink this figure, as well as reducing water- and energy-intensive virgin manufacturing, and the pollution caused from dyeing and finishing new textiles.
Perhaps the easiest and most energyefficient recycling process is mechanical recycling, where waste fibers are shredded and ground into similar lengths before being reused as a low-quality recyclate with limited end uses.
ANDRITZ, a leading European textile machine builder, offers a range of component machinery for textile recycling, including shredding/tearing, cleaning, cutting, blending and baling.
These machines and processes have been combined with automated sorting equipment from Pellenc ST and are now operating as an industrial-scale production line in France for Nouvelles Fibres Textiles, founded by Les Tissages de Charlieu and Synergies TLC.
Meanwhile, Germany’s Trützschler Group and Balkan Textile Machinery of Türkiye have collaborated in the development of the Truecycled range of recycling machinery, from mechanical recycling to the spinning preparation of torn secondary fibers.
Trützschler now offers a complete system covering the whole process, from cutting and tearing textile waste through to carding and drawing secondary fibers. The new range was launched at the ITMA 2023 textile machinery event in Milan, Italy.
However, mechanical recycling is only part of the solution – on the downside it results in significant material loss and a shortening of the fibers,
Spain’s Zara has collaborated with U.S.-based fashion technology company Circ to develop a capsule women’s collection produced using Circ lyocell made from 50% recycled textile waste. Zara-Circ
blending with virgin fibers is required to achieve high-quality yarns, and it cannot efficiently discriminate between synthetic fibers such as polyester and polyamide, for example.
In addition, post-consumer feedstocks are not available from mechanical recyclers in the required purity, leading to downcycled products such as materials for making insulation, industrial clothing or other lower-value uses.
Also launched at the last ITMA show was PureLoop’s ISEC evo FibrePro:IV machine for the recycling of polyethylene terephthalate (PET) continuous fibers and fabrics. The unit is fed with unshredded fiber waste from production processes. Beyond the shredder it passes in a controlled flow into the extruder and is filtered.
After extrusion, the melt is fine-tuned in the intrinsic viscosity optimizer to meet the requirements of the fiber industry. A fineness of 2 dtex is possible with 100% recycled pellet content, said PureLoop.
The company is a subsidiary of Austria-based Erema Group, which itself offers a range of plastics recycling solutions including systems for polymerbased fibers, nonwovens, tapes and textile fabrics.
Switzerland’s LIST Technology, specializes in high-viscosity processes for the fiber industry as well as other sectors, developing and manufacturing kneaderreactors. Part of Jakob Müller Holding, the company is developing recycling pathways for textiles, including cotton recycling with the lyocell process, PA6 recycling through depolymerization and the separation of textile blends such as polyester/cotton and mixed synthetics.
Meanwhile, the Omni recycling system from Germany’s Gneuss, for processing of industrial and post-consumer waste from all kinds of polymers, provides a high-quality output with excellent decontamination and a low carbon dioxide (CO2) footprint in a compact and smart design.
Currently, less than 1% of textiles are recycled in a closed-loop back into new items, according to the Ellen MacArthur Foundation – the vast majority ends up as waste sent for landfill or incineration.
Valvan offers the Fibersort automatic textile sorting machine based on NIR technology and optimized with artificial intelligence technology to improve sorting based on such parameters as fiber composition, color composition, fabric structure and RFID tag information. Valvan’s Trimclean solution can then be used to remove trims such as labels, zippers, buttons and metals to prepare the textile stream for recycling processes.
Chemical recycling, such as solvent dissolution, depolymerization, gasification and pulping, perhaps offers the only practical long-term solution, in conjunction with mechanical recycling
methods, according to Parker Bovee, an associate in waste and recycling with Cleantech Group.
Solvent dissolution, as the name implies, involves the use of solvents to dissolve polymer fibers out of mixedtextile waste, particularly polyester/ cotton blends, resulting in pure cotton and polyester fibers.
Depolymerization breaks down synthetic fibers such as polyester and polyamide into monomers that can be repolymerized into textile fibers. (PET bottles are frequently depolymerized and converted into polyester fibers for textile applications.) However, this method is less suitable than solvent dissolution for blended polyester/cotton textiles.
Gasification involves heating textile waste at high temperatures with CO2 as a gasifying agent to manufacture synthetic gas. This process is mainly used to convert highly contaminated or difficult-tosort textile waste into fuel, energy and chemical products.
In the pulping process cellulosic fiberbased textiles are broken down into a pulp, similar to paper recycling. This technology is already at scale and is especially used for the production of viscose.
Elastane in particular can be difficult to separate out from other fabric materials. Now, researchers from Denmark have created a technology that can remove elastane from polyamide, a common fabric blend for figure-hugging clothing such as leggings and other activewear, shapewear and swimwear.
The links in the elastane chain are bound together by diamine molecules.
By Jason Chen, China Correspondent, IFJ
Our world generates approximate 200 billion pounds of textile waste every year, but only 13% of which are recycled. In addition, of the recycled textiles, more than 90% are downcycled, wherein the recycled textiles are of lower quality or value than the original products. Only less than 10% go to high value products with similar or higher quality as the virgin ones.
These numbers depict an image that highlights two fundamental problems in the textile recycling industry: First, textile waste recycling remains at a low level. Most of the textile waste will end up in landfills or incineration, which not only result in a huge waste of resources, but
also emit greenhouse gas and leach toxic chemicals into groundwater and soil, causing excess pollution on the top of what the textile industry has already produced. Second, recycled textiles are mostly low quality products that partially lose their values in the recycling process. This further decreases the values and competitiveness of the textile recycling industry.
This article will discuss the reasons that lie behind this dilemma, as well the potential solutions for these problems.
The low recycling rate is partially a result of the difficult sorting process. Textile recycling usually involves several steps: collection, sorting, and recycling. In the
sorting step, workers sort the collected textiles according to their fiber types and colors, remove unwanted materials, and then send the sorted textiles to the next step. The value of recycled textiles depends a great deal on the quality of sorting, as improperly sorted materials could damage the machinery or result in failed products.
Waste textiles are usually collected from three major sources: cut waste from factories, pre-consumer textiles from brands, and post-consumer textiles. Sorting pre- and post-consumer textile is often a challenge, as this process could be very time-consuming and labor-intensive.
For example, for sorting pre- and post-consumer jeans, workers should
first separate them by denim constituent (cotton or blends such as cotton/spandex and cotton/polyester) and color, and then remove metal and leather parts, such as rivets, zippers, buttons and patches, manually before sending the textiles for shredding.
Even with all these efforts, mistakes and interruption still always happen: sometimes the denim constituents are difficult to identify as the labels on the jeans are worn out; sometimes the metal or leather parts are not totally removed, which could cause problems to the machinery and following process, leading to damaged recycled batch or malfunction of production lines. Therefore, additional testing or separation devices are often needed to be deployed, which further increase the cost and complexity of the process.
On the other hand, cut waste from the factories are much easier to be divided into individual waste streams based on fabric type and color as the separation can be controlled at the source. As a result, reclamation mills often turn away from pre- and post-consumer textiles to cut waste.
This issue leads to the overall failure of recycling pre- and post-consumer textiles in many countries. According to several news reports from Chinese media, many Chinese fiber reclamation mills admitted that more than 90% of their recycled fibers were from cut waste from factories, and they had given up most of the preand post-consumer garment because sorting them were too laborious and even economically impracticable.
As cut waste usually account for only 10%-15% of the fabric a textile mill uses, we can easily see why the global textile waste recovery rate stays at only 13%, and understand how little the pre- and post-consumer textiles are recycled. This has been prevailing worldwide for a long time, keeping the global recycling rate at a low level. For example, China’s textile recycling rate stays at around 15% in recent years, according to Prof. Wang Huaping of Donghua University, after a rapid growth from 5% to 15% from 2000 to 2015. In the U.S., textile recycling rates also stay at around 15% after a fast-growing period between 1970
Even in India and Bangladesh where labor cost is relatively low and sorting pre- and post-consumer textiles were considered possible and profitable, the economic incentive has been declining rapidly in recent years as the workers’ salaries and working conditions continue to improve.
and 2005, according to the United States Environmental Protection Agency (EPA) – the U.S. recycled only 3% of its two million tons of generated textile waste in 1970; but the rate rose to 15% in 2005 and the recycled volume grew by a whopping 30 times to 1.8 million U.S. tons between 1970 and 2005. However, the recycling rate stagnated in the following years, and EPA’s latest number updated was 14.7% in 2018.
Even in India and Bangladesh where the labor cost is relatively low and sorting preand post-consumer textiles were considered possible and profitable, the economic incentive has been declining rapidly in recent years as the workers’ salaries and working conditions continue to improve.
This situation is also true for recycling denim and jeans. Each year, the world generates about seven billion pounds of waste denim, mostly pre-consumer and post-consumer jeans, and the U.S. and China contribute to, respectively, 700 million and 200 million pounds of waste denim. Although the governments, brands, and communities have put a lot of efforts to reuse or recycle denim and jeans, most of them still end up in landfills or incineration.
Governments, brands, and communities have been working toward reusing and recycling pre- and post-consumer textile products for decades. However, these efforts often bring new problems and the effects are discounted. For example, good quality collected clothing are sorted out to be donated to less developed countries or sold in the second-hand markets. However, a substantial amount of them would be discarded even before wearing because of improper sizes, styles,
color, and other issues. In addition, these countries often suffer from a lack of recycling facilities – being reused or not, the clothing would inevitably end up without being recycled.
Another example is that brands, communities, and consumers often sort recyclables prior to collection to reduce the difficulty of further recycling. However, these sorting efforts are often proved to be inefficient, because additional sorting still needs to be done as there might be contamination from improperly sorted materials.
The fundamental solution to the laborintensive problem is automation. There are several automated identification and sorting systems that separate textile waste by color or fiber type available in the market. Devices that identify fiber types by physical or chemical properties usually use some spectroscopic techniques. These optical sorting technologies have been rapidly improving since the early 2010s, and developers often update technologies and machines every few years. IFJ’s recent articles introduce the recent development of automated systems from ANDRITZ, Tomra, Pellenc ST, Picvisa, and Valvan, among others.
As their accuracy and efficiency improve, automated systems gradually grabbed more market shares in the last 15 years. The market drivers include global efforts to push waste recycling, the rising labor cost, and the growing demand for diversified raw materials supply; on the other hand, the inhibitors to their growth include the initial investment and maintenance cost on machinery, and the supply of alternative materials, e.g., cut waste from factories that may not have an urgent need for the automated sorting systems.
While the evolution of automated sorting solutions has increased the possibility of recycling more pre- and post-consumer textile waste, the question remains if the value they create can offset the increased cost of machinery.
Recycled fibers seek to take market shares from virgin fibers. They must compete, in terms of price and quality, with the materials it will replace. Applications in which recycled materials are less expensive and of suitable quality have traditionally been successful markets.
As mentioned prior, more than 90% of the world’s recycled textiles are downcycled into low-value nonwovens or filling materials rather than re-spun into yarns to be used for new apparel or other high-value textile products. Downcycled fibers have competitive price against virgin fibers, while maintaining suitable quality, in these applications; therefore, they have grabbed a big market share from virgin fibers.
There are three main recycling methods for textiles: mechanical, chemical, and feedstock recycling. Today, most of the textile waste are recycled through mechanical method, which is usually less expensive but often shortens the fiber length and lowers fiber quality, resulting in downcycling.
These low-value products may not have enough profits to support the high sorting cost for pre- and post-consumer textile waste, no matter through automated sorting systems or intensive manual works. In this case, the industry is seeking to create new values to make the whole process more economically practicable.
One simple solution is mixing the downcycled fibers with virgin fibers. A fabric can include up to 20%-30% mechanically recycled materials while maintaining its quality not being significantly reduced – several patents published in the last two years worked on designing and making high-value textiles from a mix of recycled and virgin fibers.
At the same times, designers and artists are also trying to upcycle used jeans and other textile waste into blankets, wall hangers, and other textile products with
aesthetic advantages; these efforts can be sporadically found in news reports or social media, but still are in a small scale, compared to the billion pounds denim waste and more other textile waste the world produce every year.
Currently, industry-scale solutions for making high-value and high-quality recycled textiles mainly lie on chemical recycling solutions, especially those for recycling polyester textile waste, which account for more than 50% of the world’s total textile waste produced every year. Examples include the Textile to Textile (T2T) projects from Ambercycle and Jiaren.
The Los Angeles-headquartered Ambercycle provides cycora®, a recycled polyester fiber that offers the same strength and performance as virgin polyester fiber, at less than half the CO2 emissions associated with petroleum-based fibers.
The Zhejiang, China-based Jiaren has launched its first T2T factory, with capacity of treating 40,000 metric tons of polyester textile waste and producing 30,000 metric tons of recycled polyester fibers per year; unlike most of other recycling lines, which produce recycled polyester through downcycling bottlegrade polyester waste, Jiaren’s factory turns used polyester garment and home textiles into high-quality polyester fibers, which are re-spun into yarns to be used for new apparel or other high-value textile products.
A recent notable development came from China’s Amino. The company has developed a biomimetic enzyme targeted catalysis technology, which can accurately detect polyester and disaggregate it to monomers at a temperature below 90°C.
Amino has successfully developed a series of systems to reclaim polyester/spandex, polyester/cotton, polyester/wools, and polyester/spandex/cotton blends based on this technology. The reclamation rate of each fiber has all exceeded 99%, at less than 60% the greenhouse gas emission by virgin fibers. Last September, Amino has launched its first pilot factory for recycling polyester/spandex blends.
These solutions are still expensive. Recycled fibers made through these methods may not be able to compete with virgin fibers in terms of price and quality. However, recycled materials could earn a substantial share from the market even if they are, initially, more expensive than the material they seek to replace. They offer some performance or lifecycle advantage which can be turned to real economic incentive through governmental regulations and public awareness. For example, the Chinese government provides a tax break for fiber reclamation mills, and the European Union has set its 2030 Strategy for Textiles to encourage textile products to be durable, recyclable, and made of recycled fibers, among other goals.
Another example is that reclamation companies partner with brands to promote their recycled fibers as premium products so as to secure a profit to support their long-term operations. Currently, Jiaren has partnered with Decathlon, H&M, Zara and Puma for its T2T project; Ambercycle has signed agreements with Inditex, the owner of Zara, and Ganni, a Danish womenswear brand, to supply cycora® for making high-value garment; and Amino had also announced that they have begun to build an alliance with brands to bring their technologies and products to the public.
Jason Chen is an international correspondent for International Fiber Journal . He is a leading journalist covering the fiber industry in Asia and a senior analyst who has published more than 50 books and reports for polymers, composites, and other advanced materials and technologies. He can be reached at jasonchen200501@hotmail.com
PUMA and RE&UP Announce a Multi-Year Collaboration to Scale Circular Textile Solution
ports company PUMA and RE&UP Recycling Technologies have signed a Letter of Intent (LoI) to scale a fully circular textile solution, transforming textile waste into RE&UP’s Next-Gen Recycled Cotton Fibers and Recycled Polyester Chips, materials that maintain the same performance as virgin fibers.
For more than 75 years, PUMA has pushed sport and culture forward by creating fast products for the world’s fastest athletes. The company distributes its products in more than 120 countries, employs about 20,000 people worldwide.
Circularity is one of the focus areas of PUMA’s Vision 2030 sustainability goals and the company has already scaled up its RE:FIBRE textile-to-textile recycling program, producing millions of football jerseys made out of an increasing share of recycled textiles. RE&UP has become a key Next-Gen raw material partner in the RE:FIBRE program supporting PUMA’s ambition to reduce reliance on bottlerecycled polyester, enhancing true circularity while minimizing textile waste. Due to its previous success, this collaboration has now evolved into a broader global commitment to fully enabling circularity.
“As part of our Vision 2030 goals, we want to have 30% of our polyester fabric in apparel fiber-to-fiber recycled by 2030 and our collaboration with RE&UP opens exciting possibilities for integrating virgin-equivalent recycled materials into our products,” said Howard Williams, Director Global Innovation Apparel & Accessories at PUMA. “These materials offer the performance we need while helping us achieve our circularity goals.”
As part of the expansion, PUMA will introduce RE:FIBRE to the Americas, leveraging RE&UP’s recycled raw materials
within its local supply chain. Both companies have a long-term commitment to scaling sustainable solutions in the textile industry.
RE&UP’s revolutionary recycling technology is a key enabler of the circular transition of the industry, especially due to its unique capability to process diverse textile feedstocks, including postconsumer and post-industrial waste, as well as complex blended textiles like polycotton and polyester-elastane –materials, traditionally difficult to recycle. Powered with 100% renewable energy and leveraging advanced technologies such as decolorization processes, RE&UP sets a new benchmark for sustainable, low-impact recycled textile fibers.
RE&UP creates a seamless circular ecosystem that transforms end-of-life textile waste into high-quality raw materials at scale: a commitment to opening up a more responsible and technologically evolved future for textiles and fashion.
“We are proud to elevate our collaboration with PUMA to the next level, building on our existing work through PUMA’s RE:FIBRE program,” said Özgür Atsan, Chief Commercial Officer at RE&UP.
“PUMA, as one of the most forwardthinking brands in the industry, shares our vision for closing the recycled material gap. The proven quality of our products, our ability to process diverse textile compositions, our annual capacity of 80,000 tons, and our commitment to renewable energy reinforces our mission to produce Next-Gen materials and establish circularity as the standard for the textile industry,” Atsan continues. “We proudly define our products as Next-Gen materials, as they are designed to meet the needs of the next generation in the textile industry.” www.reandup.com
By Jean-Francois
The global textile industry is facing an unprecedented challenge: the rapid increase in textile waste. With fashion consumption at an all-time high and fast fashion accelerating production cycles, the volume of discarded textiles has surged dramatically. The Ellen MacArthur Foundation estimates that over 92 million tons of textile waste are generated annually, with less than 1% being recycled into new garments. One of the major hurdles in textile recycling is contamination from trims such as buttons, zippers, labels, and metallic components. These small but disruptive elements make it difficult to process textile waste efficiently and limit the quality of recycled materials.
Historically, the removal of trims from textile waste was a labor-intensive process, requiring manual sorting or rudimentary mechanical systems that lacked precision. Many recycling facilities resorted to shredding entire garments, leading to mixed fiber outputs that were unsuitable for high-quality reuse. Inconsistent sorting also resulted in impurities that reduced the viability of recycled fibers for new textile production, leading to downcycling into low-value products such as insulation materials or rags rather than true circular reuse.
Additionally, traditional methods often struggled with efficiency and scale. Manual sorting was slow and costly, while simple magnetic separation could
only remove metallic components, leaving behind plastic labels, synthetic patches, or colored trims that still compromised the purity of the material.
To overcome these challenges, the textile recycling industry has turned to automated solutions that incorporate advanced detection technologies, such as nearinfrared (NIR) spectroscopy. These technologies enable more accurate identification of unwanted trims and contaminants, ensuring the production of higher-quality recycled fibers.
A standout solution in this field is the Trimclean® system, developed by Valvan. Trimclean integrates multiple detection
techniques to efficiently remove trims from textile clippings, with artificial intelligence (AI) playing a crucial role. This combination increases the proportion of material that can be reused in high-value recycling applications.
Trimclean utilizes four advanced detection methods to accurately sort textiles:
1. Color Camera Technology – Detects color discrepancies in textile clippings, helping to identify trims that differ from the main fabric.
2. Metal Detection – Identifies and removes metallic components such as buttons, rivets, and zippers to prevent contamination in the recycling process.
3. Artificial Intelligence (AI) – Uses machine learning algorithms to recognize patterns, shapes, and textures of trims for highly precise sorting.
4. Near-Infrared (NIR) Spectroscopy –Differentiates textile materials based on fiber composition, improving the sorting process for blended textiles. A key feature that sets Trimclean apart is its dual-sided inspection, which ensures that trims on both sides of a fabric clipping are detected and removed. Traditional sorting systems often inspect only one side, leading to overlooked contaminants and lower material recovery rates. By increasing accuracy and efficiency, Trimclean helps recycling facilities process textiles faster while ensuring a higher purity of recovered fibers.
With automated trim removal, recyclers can significantly increase the percentage of textiles that remain viable for reuse in high-quality applications. Instead of resorting to downcycling, more materials can be repurposed into new garments, reducing textile waste and supporting a circular economy.
As regulations tighten on textile disposal and consumer demand for sustainable fashion grows, the need for scalable, efficient recycling solutions becomes more urgent. Innovations like Trimclean demonstrate how technological advancements are shaping the future
of textile recycling by improving material recovery rates and reducing dependency on virgin
Jean-Francois is the Sales and Business Development Manager at Valvan, market leader and pioneer of sorting and baling systems for the textile and recycling sectors. With extensive experience in sales and engineering, he specialises in machinery automated solutions and is dedicated to sustainability. Jean-Francois has led the development of sorting and preprocessing equipment for post-consumer textiles, facilitating their reuse or recycling.
By Raymond Chimhandamba
Nonwoven materials are becoming more popular across multiple industries due to their lightness and ability to protect against microorganisms. However, concerns regarding their sustainability are beginning to emerge owing to their disposable nature and potential for environmental pollution. The 2020 pandemic gave a huge stimulus for the nonwoven industry, with a surge global demand for steril-
ized consumer goods in hygiene, medical, and personal care. At the same time, the pandemic demand also exacerbated and highlighted the problems of waste and environmental pollution associated with this multipurpose material.
The world generated trillions of discarded masks and gloves with virtually no recycling solution. We now continue to repair personal protection equipment (PPE) and disposable mask challenges years after the
pandemic. According to Cornell News, one hospital with 300 medical personnel could generate more than a ton of medical garb waste daily. That translates to more than 400 tons of annual medical PPE waste in a single COVID-handling facility, which is about six times the pre-COVID levels.
According to Science Direct, an astounding 129 billion face masks and 65 billion plastic gloves were manufactured and disposed globally every month during the
COVID-19 outbreak. Although nonwovens’ disposable nature is essential to preventing infections, many now want to see the mounting problem of waste replaced with biodegradable alternatives. A small but growing sub-segment of woven goods are made from renewable, organic fibres, creating a great scope for a biodegradable nonwoven industry.
The World Economic Forum suggests that recycling and the circular economy is a billion-dollar opportunity for Africa, pointing out that the circular economy offers a promising opportunity for economic development, value creation, and skills development for the region. Indeed, in some countries in the region, there is already evidence that plastic waste recycling and recycled garments already exist, as well as vibrant circular economy business opportunities on the African continent.
In the plastic recycling sector in South Africa, there are PROs (Producer Responsibility Organizations) focused on dealing with everything plastic and its recycling. They coordinate the industry efforts on behalf of plastic manufacturers, packaging companies, the relevant government departments, municipalities, retailers, waste pickers and recycling companies. They collect, manage, and invest in the Extended Producer Responsibility (EPR) proceeds and funding.
EPR is a global legislation policy approach that makes producers responsible for their products throughout their entire lifecycle, including at the post-consumer stage. In a nutshell, a brand owner must demonstrate to the responsible local authority how to minimize the environmental damage caused by their brand. Therefore the brand owner must show their plan to collect their brand packaging long after the consumer has used the product. Adding recycled content to the packaging is one of the ways of minimizing damage to the environment.
In South Africa there are several PROs. PETCO is one of them, trusted by its members and the collection and recycling
industry to drive change across the packaging value chain. While initially PETCO was focused on PET (Polyethylene terephthalate) plastics, the most common thermoplastic polymer resin of the polyester family and is used in fibres for clothing, containers for liquids and foods, and thermoforming for manufacturing, now PETCO’s responsibility also includes caps (the majority of which are made from polypropylene), labels and Liquid Board Packaging (Tetrapak). PETCO also manages EPR schemes and is opening its presence in countries like Kenya and other key African countries.
In South Africa, some of the key players in the plastics manufacturing and packaging sector are Darunfa, Alpla and Extrupet. Darunfa Chemical Fibre is a leading regenerated polyester fiber manufacturer established in 2012. The company assists with PET recycling across South Africa and converts this recycled waste into a high-quality polyester fiber for three deniers and larger fills.
Alpla is an Austrian packaging company that has bought an existing South African packaging company that had businesses in 20 African countries including the Indian Ocean Islands in 2017. It was the most significant investment in
the company’s history. In 2020 they built one mega factory in Johannesburg that replaced the 9 factories scattered across South Africa. In 2024, Alpla commissioned their 35,000T p.a. PET bottle-to-bottle plastic recycling plant in Durban for 60 million euros.
Extrupet has a 60,000 tons p.a. recycling capacity and is a world-class plastic recycling company whose rPET is certified by global bodies. Established in 2000, Extrupet has become one of the largest and most advanced recyclers of PET bottle materials on the African continent, specializing in reclaiming and converting waste PET bottles into various grades of PET flakes and chips.
Further afield on the continent, Mr. Green Africa is one of the most prominent recyclers in Kenya. It is primarily focused on three types of plastics, ensuring highquality sorting and processing. Mr. Green integrates informal waste pickers into its supply chain, contributing to social equity and economic development. Mr. Green has recently upgraded its recycling capacity to 70,000T p.a.
Another very active PRO in South Africa is Polyco whose key role aims to grow the collection and recycling of all plastic packaging in South Africa and to promote the responsible use and reuse of this plastic packaging. South African Plastics Recycling Organisation (SAPRO) represents the plastics re-processors in South Africa. Members procure sorted, baled end-of-life plastics and re-process it into new plastic products.
South Africa is amongst the top recycling countries in the world. Ahead of Europe at 46% versus 31%, according to Plastic SA. The Southern African Vinyls Association (SAVA) is the voluntary industry association representing the entire PVC industry value chain. SAVA strives to grow the industry and protect its stature by communicating the latest, scientifically based, and researched information in the sub-Saharan region.
What could be interesting is to compare bodies that manage EPR programs and funding in South Africa to the United States of America. In the U.S., the National Caucus of Environmental Legislators
(NCEL) is one such organization. According to their website, the goal of the NCEL is to empower a nonpartisan network of state legislative champions. Created by and for state legislators, NCEL is a resource for lawmakers working to protect, conserve, and improve the natural and human environment. State lawmakers are advancing bills to make plastic producers more responsible for the waste they create through EPR programs. EPR has been gaining traction as a promising waste management and reduction approach, with California, Colorado, Maine, and Oregon enacting EPR programs for plastic waste in recent years. Building on legislation from these states, at least 11 other states have introduced 24 policies in 2024 to help improve their waste systems by establishing their own EPR for packaging programs.
At least 11 states in the U.S. have introduced legislation in 2024 to advance EPR for packaging programs. Minnesota, New York, Tennessee have established new EPR programs. Other states considering legislation establishing new EPR programs in 2024 include Illinois, North Carolina, Rhode Island, and New Hampshire. Hawaii and Massachusetts are planning and studying EPR approaches.
Over the years, Africa has actually built an interesting nonwovens recycling capability. Interesting examples are a company called Brits Nonwovens which prides itself in turning trash into treasure by transforming 100-150T of discarded textile products into valuable materials such as Isotherm, which is a thermal insulation product made from 100% thermally bonded polyester derived from recycled PET bottles. Applications of Isotherm include its use in roofs, walls, and geysers, providing effective insulation that helps
reduce energy costs. Other applications include automotive, construction, apparel and textiles. In terms of upcycling and sustainability, Brits Nonwovens emphasizes a commitment to sustainability by ensuring that all its finished nonwoven products are 100% recyclable. They also implement an environmental management policy that includes measures for waste minimization and pollution prevention
Other examples of companies that recycle nonwovens in South Africa are Tufflex Plastic Products and Koogan Plastics. Tufflex specializes in recycling both post-consumer and post-industrial polyolefin waste and operates one of the most sophisticated plastic wash-plants on the African continent.
pellets. Tufflex also processes flexible PP from the manufacturing of diapers and sanitary pads. Koogan Plastics, which has existed for more than 30 years, and other recycling capabilities, also recycles flexible PP from the diaper manufacturing process.
The nonwovens industry in Africa presents a significant recycling opportunity for flexible PP from AHP convertors in Africa. There are more than 120 AHP lines convertors in SSA alone, and even more in North Africa. Using flexible polypropylene in the diaper manufacturing process provides significant technical advantages such as low MFI (melt flow index), enhanced flexibility, impact resistance, chemical stability, lightweight properties and customization potential, and improved processability.
Most of Africa’s recycling sector is informal. In places, they are making strides toward formalizing the sector. The African Reclaimers Organisation (ARO) has taken this task very seriously in South Africa. Over the last decade, they have started working with and protecting the rights of informal waste pickers, or ‘reclaimers,’ who play a central role in South Africa’s waste economy. According to Future Earth, reclaimers in South Africa collect 80-90 percent of recycled used packaging and paper, which are key in achieving South Africa’s 57 percent overall recycling rate.
The Company has also developed a unique drying and processing line to convert hard to recycle waste polyolefin powders back into usable
Made from recycled PET bottles, Isotherm’s thermally-bonded polyester insulation is eco-friendly and non-toxic and is the insulation of choice in South Africa. Isotherm’s insulation is used in roofs, walls, geysers, hot water pipes and more.
Brits Nonwoven
According to Socio-economic Rights Institute of South Africa, reclaimers save municipalities an estimated R780 million to R750 million ($45M) annually in landfill airspace costs alone. ARO is a membership-based democratic organization of reclaimers working in residential areas and landfills. With a membership of over 5,500 reclaimers in and around the City of Johannesburg, they sort, collect and sell recyclable materials. Each reclaimer diverts approximately 16 to 24 tonnes of recyclable materials annually from landfills.
Africa also has interesting garment and textile waste management initiatives. According to Fibre to Fashion, an organization with a presence in Nigeria and Kenya called Africa Collect Textiles
has collected 197,981 kilograms of textile waste and saved 1,200 tons of carbon dioxide from the environment. Municipalities and legislators are also doing their part. In 2024, Nigeria’s Lagos Waste Management Authority (LAWMA) announced plans to ban textile waste from all landfills in the state within three months.
A few champions are beginning to emerge in the textile waste management space. According to an article in Holistic Approach to the Environment, the industry estimates the textile recycling industry has the capacity to divert about two million tons of post-consumer textile waste each year. The phenomenon of fast fashion leads to high volume of textile and garment waste. Textile waste presents opportunities for establishing large-scale regeneration and recycling facilities, offering the potential for employment generation and skill development in Africa. Introducing second-hand clothing as an alternative to mitigate textile waste is advantageous for providing affordable clothing. Textile recycling also includes reprocessing pre-consumer or postconsumer textile waste to produce new or non-textile goods. Some fabrics,
Recycling is a significant employer in South Africa, Africa’s second-biggest economy. According to Plastic SA, another PRO in South Africa, 8,319 people are employed in recycling factories and 95,889 in the supply chain, translating to 51.9 tons per employee in 2023.
such as T-shirts, are redesigned into polishing and cleaning materials. Highquality textiles, are repurposed into second-hand clothing.
Sofrip Textile Recycling company, with over 25 years of experience, is a Tunisian North African company and a leader in the textile recycling industry specializing in used clothing, shoes, wiping. Rewoven is a Cape Town-based company that diverts textile waste from landfill and ensures it gets recycled. They also sell materials and products made from recycled textile waste. FabricAid, with its head office in Lebanon and operations in Africa, is shaping a future where fashion empowers people, protects the planet, and transforms lives. Its circular model gives a new purpose to unwanted products and limits fashion’s socio-economic and environmental damage, predominantly by offering decent clothing at extremely affordable prices to marginalized communities through a dignified shopping experience.
Recycling Sector as a Significant Employer and the Success Story
South Africa’s recycling rates are impressive, ranking 46.3% according to the RoundUp organization, second only
to India. One of the key drivers of South Africa’s recycling rate is unemployment. Very little of the waste is separated at source (i.e., in the household), therefore the bulk of it is retrieved from the landfills, which is inefficient. “(Global) recycling rates vary by location, plastic type and application. Scientists estimate that only 9% of all plastic waste globally is recycled. Most plastic waste – a whopping 79% –ends up in landfills or in nature. Some 12% is incinerated,” according to a UNDP report in 2023.
Recycling is a significant employer in South Africa, Africa’s second-biggest economy. According to Plastic SA, another PRO in South Africa, 8,319 people are employed in recycling factories and 95,889 in the supply chain, translating to 51.9 tons per employee in 2023.
The Glass Company in South Africa represents one of South Africa’s recycling successes. TGRC is registered with the Department of Forestry, Fisheries, and the Environment (DFFE) as a PRO in the Extended Producer Responsibility Regulations. Since May 2021, TGRC’s membership grew from 18 to 90 producers needing an EPR scheme to facilitate their EPR obligations for glass packaging.
By Seshadri Ramkumar, Professor, Texas Tech University, USA
On March 19, 2025, Jerome Powell, Chair of the United States’ Federal Reserve indicated tariffs have partly played its role with the elevated inflation situation. Given the headline inflation is at 2.8%, federal interest rate remains at 4.25-4.5%, which will influence consumer spending. Surveys indicate consumer confidence is down, which in turn will affect the buying of non-essential items as these depend on discretionary spending. Speaking about tariffs, Powell stated “they tend to bring growth down, they tend to bring inflation up.”
On March 20, 2025, Bank of England also chose to maintain the current interest rate at 4.5% while its domestic economy is weak. Again, the global economic uncertainty due to tariff situations has weighed heavily to maintain the current interest rate.
United States, China, India are countries with sizeable middle-class population have interests in textiles as they engage in exporting and importing fibers and textiles. United States is the largest market for consumer goods and its economy matters for global trade. While the United States’ economy is on a strong footing, the growth this year will be slightly less than expected at 1.7 percent. According to Chair Powell, the growth in the next two years will be slightly less than 2 percent.
The tariff situation, consumers’ spending power and more importantly confidence will determine the amount of trade in textiles and apparels. As textile manufacturing is labor intensive with less margins, the tariffs are not at a level to shift the manufacturing of commodity textiles to the United States. Developed economies like United States and EU are poised to grow its advanced textiles sector. More importantly, with EU countries committing to spending more on their defense budget, opportunities in defense, healthcare, and
Bangladesh, Vietnam, and Indonesia being an importer of cotton will have constraints in exponentially increasing its manufacturing, but their appetite for cotton will grow.
industrial textiles will grow and may support new investments.
What will be the textiles sector’s landscape in the tariff scenario?
Trade between China and United States will see some change. China’s export to the United States will take a hit. Other countries like Bangladesh, Vietnam, India, and Indonesia may see a bump up in exports of apparels. However, industries with Chinese investments in Vietnam and low wage countries would see export enhancements. China’s importing of United States’ cotton will show a decreasing trend, which is already happening due to its weak domestic consumption. But this can be offset by exporting to other major textiles and apparel manufacturing nations. How much the shift will be is difficult to predict at this uncertain time.
India is currently in the fourth position as an exporter of apparels to the United States. It is unlikely to see a sudden shift in its ranking, but its share of exports will increase. According to United States’ Office of Textiles and Apparels, in 2024, India exported about US$4.69 billion worth of apparels, while Bangladesh exported about US$7.34 billion.
Bangladesh, Vietnam, and Indonesia being an importer of cotton will have constraints in exponentially increasing its manufacturing, but their appetite for cotton will grow. India is poised to enhance its apparels exports to the United States. India needs to increase its cotton availability with improving its productivity. This crop year (October 2024 - September 2025), the production will be about 30 million bales (170 kgs each) which is less
than last year’s production. This scenario opens opportunity for cotton exporting countries to trade with India while India maintains a 11% tariff of imported upland cottons. At the present times, mills are showing interest in procuring cotton from Brazil which comes out to be competitive in terms of prize. United States’ cotton sector needs to promote its cotton for its quality, timely delivery and after sales support although it is relatively highly priced against Brazilian cotton.
I had an opportunity to discuss cotton trade dynamics with Velmurugan Shanmugam, general manager of India-based Jayalakshmi Textiles which has recently bought Brazilian cotton for using it as a blend with Indian cotton. According to Shanmugam, balancing the cost and quality of imported cotton is a critical activity while making decisions on purchasing imported cotton. While Brazilian cotton comes out to be economical, United States cotton is still better in terms of nep counts stated Velmurugan Shanmugam.
Given the reciprocity tariff policy taking effect on April 2nd, textile trade with India will not be affected much as India’s basic custom duty on knitted products is 20% and normally apparels’ tariff differential is about 7%. India will be competitive against China as United States has imposed 20% additional tariff over the existing ones making its expensive from this point of view.
Indian industry should utilize the opportunity to enhance its productivity and strengthen its cotton and synthetic base. Importantly, the apparel and garment sectors should increase the size of their product basket.
While it is difficult to predict what would be loss in export share of China to the United States, given the amount of export it has been doing in recent years, certainly other South Asian countries will benefit. This in turn provides opportunities for cotton exporting countries like the United States to realign its market space.
In cotton trade, Brazil remains a competitor for the United States to penetrate India, but it is possible with coordinated marketing efforts. Global textile landscape will see a shift.
ig ideas come from many sources, but great big ideas come to life when strategic partners leverage collaboration in its highest form, including face-to-face networking, sharing of business intelligence, and mutually beneficial strategic planning. This opportunity mindset is what INDA, the Association of the Nonwoven Fabrics Industry, hopes to inspire as it hosts the most significant event in its portfolio – the IDEA®25 Show to be held April 29-May 1 in Miami Beach, Florida, USA.
Adjacent to the IDEA®25 Show is INDA’s FiltXPO® Show, with 110 exhibitors and its own programming track, and shares the IDEA expo floor. This show allows the filtration and separations industry to connect with peers and visit new and existing nonwovens suppliers, making this one event INDA’s finest and largest collection of collaborative attendees and exhibitors in North America.
IDEA®25 Show is tracking to be the largest in their history with over 500 exhibitors and an expected 6,500 visitors. Companies such as Aplix, BASF, Cotton, Everra, ExxonMobil, H.B. Fuller, KimberlyClark, Magnera, PFG, and Welspun have much to share on their sustainability efforts to support the industry. A complete list of exhibitors with booth location is found at https://inda.expocad. com/events/ifx25/index.html. FiltXPO exhibitors are also listed.
INDA has compiled a robust program anchored in sustainability and circularity for attendees to be inspired and educated by top experts from the industry. The full schedule of events is at https://idea show.org/wp-content/uploads/2025/03/ IDEA25-Conference-Schedule-Mar-13. pdf. The following are highlights.
the evolving regulatory landscape in the European Union and its impact on disposable products, with a focus on nonwovens. As recent EU regulations transform the nonwoven sector, van den Hul forecasts the future landscape of nonwoven products in Europe and the opportunities and challenges that lie ahead, including the implementation of Digital Product Passports by 2027
In the “Leveraging Data & Technology for Sustainable Material Decisions,” speaker Madyson Partenheimer, Global Business Sustainability Manager at Magnera, delves into the critical factors that shape a robust sustainability strategy. She will demonstrate how to build a compelling sustainability story that resonates with customers and consumers and accelerates progress toward a more sustainable future.
Attendees are welcomed on April 29 by Matt O’Sickey, Ph.D., Director of Technology & Education, INDA, who sets the stage for two full days of programming, introducing an overview on “Navigating the Shifting Winds of Sustainability Regulations: U.S. and EU Perspectives on Compliance & Innovation.” Wes Fisher, Director of Government Affairs, INDA, speaks on the “U.S. Sustainability Policy – Near and Long Term,” focused on how policies around single-use plastics, chemicals, recycling, and dozens of other sustainability topics are being rolled out globally, as well as a five-year forecast for potential regulatory action in the U.S. Bringing the EU perspective, Heidi van den Hul, Principal, FabriCreation, discusses “ESPR & Nonwoven Products: Regulatory Impact on Product Design, Manufacturing & Disposal,” exploring
David Brabham, senior director of customer Engagement, Sustainability, and Stewardship at GP Cellulose, shares how forest and biodiversity loss are major concerns and issues that should be considered when evaluating raw materials. GP Cellulose utilizes the ForestLogic™ technology platform as an example of how technology solutions are rapidly emerging to meet the demand for increased transparency, enhanced reporting, and protection of the planet’s most special places.
“Innovative & Sustainable Materials: Greener Products Start with Greener Nonwovens” and sessions on integrating “Hemp Fibers in Nonwovens” round out the first day before the networking commences at the Welcome Reception in the Miami Beach Convention Center, Lincoln Road Ballroom.
Day two sessions offer more detail on innovative ideas launched into the marketplace in sessions on “Cradle
to Grave Bioplastics – Starting and Ending Green.” In Creating Sustainable Nonwovens with Thermally Processable Polyvinyl Alcohol and a Water-soluble, Environmentally Friendly, and Highperformance Polymer, Jack Eaton, Product Manager – Nonwovens, AquaPak Polymers Ltd, reveals how Aquapak technology now allows for the production of staple fibers and spun melt nonwovens via melt extrusion, using existing machinery, achieved without polymer modification, maintaining full product functionality and end-of-life biodegradation.
In a segment on “Design for Sustainability – Don’t Overlook the Impacts of Equipment and Process,” presenter Akhlak Mahmood, Ph.D., Product Innovation Manager, Matmerize, discusses AI-Driven Polymer Informatics for Sustainable Innovation. Artificial intelligence (AI) is transforming the polymer and nonwoven industries by enabling the development of sustainable materials. This presentation explores AI’s pivotal role in creating polymers with tailored properties to meet diverse industrial needs.
New Generation Innovative Compact Filter for Nonwovens & Soft Disposables presenter Saravanan Palani, General Manager & Director of Sales, Luwa America, Inc., shares that with increased machine speeds, meaning higher dust levels, stringent government regulations in the nonwovens & hygiene process,
compactness, etc., Luwa’s Swiss R&D team working over the years with the industry giants, came up with an innovative, high-performance filter that would replace the Traditional RDF – it’s the latest Multicell Filter (MCV). It has multiple linear V-shaped filters with specialized media elements for the best cleaning efficiency.
A series of case studies and discussions on the “Cradle to Next Life –Shifting Away from the ‘To the Grave’ Mentality” focus attendees on circular solutions and closes out the educational portion of the IDEA®25 Show.
INDA does not miss an opportunity to reward innovation with industry recognition voted on by its peers. Read about 2025 IDEA innovators at https:// ideashow.org/2025-awards-finalists/. The from each category winners will be announced at the show.
All in all, attendees will want to plan their time ahead of arriving in Miami to maximize time spent on site in order get the most from the robust line-up of sustainability sessions and the vibrant exposition that will surely inspire industry change.
www.ideashow.org
Take advantage of INDA’s pre-show opportunity for newcomers to learn the key elements of manufacturing nonwovens, and seasoned professionals to get the knowledge they need in technical design and performance, within baby and adult care absorbent systems, wet wipes, and period products.
This is a bootcamp for those relatively new to the industry and those attending IDEA®25 and FiltXPO™ for the first time. Attendees will leave with an understanding of the many different types of nonwovens including the raw materials used to make the nonwovens, how the nonwovens are manufactured, key characteristics and properties of nonwovens, and new options to make these nonwovens more sustainable. Instructor: Matt O’Sickey, Ph.D. Director of Education and Technical Affairs, INDA
Review the various absorbent system technologies used in disposable hygiene products to learn the pros and cons of different superabsorbents (SAPs) and absorbent systems and why they are used, including representative example products in which the systems are used. The course includes a review of the state-of-the-art sustainable absorbent systems – often viewed as the final piece of making entirely sustainable absorbent hygiene products. Instructor: James Robinson Principal, Absorbent Hygiene Insights
Period Products Innovation Workshop
Review the diverse approaches to period care, the materials and systems used, product innovation directions, and options for producing sustainable products. Attendees will gain an understanding of the whys and why nots of different approaches, changes in the market, and what’s happening in different regions of the world. Instructor: Heidi Beatty, Chief Executive Officer, Crown Abbey
This is condensed version of INDA’s highly-rated Wipes Academy focuses solely on wet wipes in the postpandemic world. State-of-the-art materials, lotion formulations, and manufacturing processes will be reviewed, including a focus on the challenges and opportunities of producing plastic-free wet wipes for diverse applications. Instructor: Heidi Beatty, Chief Executive Officer, Crown Abbey
The EDANA Innovation Forum is designed to be an immersive experience including inspirational activities focusing on innovation across all nonwovens’ applications.
The intriguing Forum gathers an interdisciplinary group of thought leaders and experts, including academics, start-ups, researchers, scientists, and nonwovens professionals across all sectors. The conference aims to explore the significance of innovation for nonwovens and what it entails. The goal is to transcend the ‘confidentiality’ aspect of innovation to enable and facilitate strategic partnerships which are the key to moving innovation from idea to implementation.
The EDANA Innovation Forum will be held on June 11-12, 2025, at Station F in Paris, France. Housed in a former railway depot, Station F serves as a hub of creativity and pioneering ideas that cultivates bold thinking and innovative solutions. Among the community at the campus are 1,000 startups and 30+ incubators programs that engage in innovation daily. The space offers work and event spaces, and numerous programs to support early-stage businesses that foster the future of business.
This year’s Forum program is a mix of presentations and insights, drawing from the nonwovens industry and other forward-thinking industries, as well as attendee participation in the workshops. Cross-pollination of ideas will spark new perspectives, and fresh solutions to the complex challenges companies face. At this time, themes include:
• Advancing Nonwovens: Circularity, Fortitude & Smart Tech
• Biobased Breakthroughs: Advancing Sustainable Nonwoven Fibers
• Advancing Knowledge: Strategic Priorities & (Global) Partnerships in Research
• Redefining Nonwovens: Sustainable Materials & Smart Solutions
Last year, the event drew over 110 participants from 78 companies and 22 countries, making it a truly global gathering. “Our aim was to create a platform for the nonwovens community to explore the latest technical innovations and gain insights from external speakers and startups,” expressed Murat Dogru, EDANA’s General Manager. “I’m excited about the future possibilities these discussions and innovations will bring to our industry.”
It featured over 20 speakers over three days addressing topics such as the increased use of cellulosic fibers in hygiene products, particularly wipes, cellulose-based thermoformable durables, and the use of nano fibrillated cellulose to improve the performance and footprint of nonwovens in composites. There were also papers on improving polyolefins’ carbon footprint, additives’ developments, and processing PP/PLA bico fibers. Following their introductions, the presenters moderated roundtable discussions, inviting participants to share their experiences, also planned for 2025.
“What I really like is that people are coming from all over Europe and beyond to share their expertise, research, insights,
and best practices for the nonwovens market. They share this valuable information with each other, so you can really see open innovation in action happening right here at the event,” said Joachim De Vos, Co-chair & Managing Partner, Living Tomorrow, TomorrowLab and one of the keynote speakers at the forum.
“The event focused on nonwovens innovation, where we heard impressive talks from industry experts about new directions and technology. The gathering was an invaluable opportunity for networking, learning and envisioning the future of nonwovens. As we continue to push the boundaries of what’s possible, events like these are crucial for sparking the ideas that will shape our industry’s products and solutions. Exciting times are ahead of us!” shared Lancelot Woolley, Global R&D Director, Fibertex Nonwovens.
To ensure an immersive and highly engaging atmosphere to connect, exchange and collaborate, EDANA is limiting registration, so a timely registration is suggested.
Register and learn more at www.edana.org/ events/edana-innovation-forum.
By Marie O'Mahony, Smart & Advanced Textiles Correspondent, IFJ
eld in late 2024, E-Textiles: International Conference on the Challenges, Opportunities, Innovations, and Applications in Electronic Textiles, was hosted by the E-Textiles Network, and brought together many of the discussion points that have come to the forefront, from commercializing innovation to environmental impact, the role of design and embedding testing within the development process. Founded in 2018, the Network aims to accelerate the development and adoption of e-textile technology.
The annual conference facilitates and highlights research activities from academia, research institutes, and industry, attracting delegates from these sectors. The event rotates around a series of European cities; Fraunhofer Forum in Berlin, Germany, was the location for E-Textiles 2024 held in November, where the Fraunhofer IZM hosted it with sponsorship from IEEE and the IEEE Electronics Packaging Society EPS.
The conference provided a packed program of six sessions over three days, with the themes of Research and Technology, Design and Fashion, Sustainability and Circularity, Reliability and Testing, and Manufacturing and Applications. While the Network is thus far primarily European, the perspective is global, attracting speakers and delegates such as AFFOA, Nautilus Defense, North Carolina State
University, and Meta from North America. The addition of an exhibit area and the poster pitch sessions were well received and showcased early-stage research and more established start-ups and SMEs.
So, how has e-Textiles 2024 expanded the field? What key discussions dominated the event? How might these be seen as harbingers of near-future trends?
‘Time to market’ has been a big topic for industry and researchers in academia. In the opening address, Rolf Aschenbrenner, Deputy Head of Fraunhofer IZM, emphasized its importance. While it is not as headline-grabbing as artificial intelligence (AI), it is more of a defined entity that can be addressed within and by
industry and academia. The bottom line is that research and innovation will decline without the very real possibility of achieving scale and commercialization. Cooperation enables the scaling of ideas, as illustrated by a joint paper from Tuomas Happonen, VTT Technical Research Center of Finland, and Mikko Paakkolanvaara, Screentec. Their paper, “Stretching reliability of SMD electronics integrated on elastic fabric,” discusses the manufacturing flow of integrating surface-mounted devices (SMDs) into the stretch fabric. This process is based on printing, converting, and assembly to integrate rigid SMD electronics exploiting novel material solutions such as stretchable inks and adhesive bonding technology needed to achieve the required electromechanical performance at low processing temperatures. SMD thermistors, printed wiring, multiple materials, and design configurations were integrated on both thermoplastic polyurethane (TPU) and a stretch fabric using a TPU lamination process. Tests and electromechanical characterization revealed the importance of material stack strengths and the layout design. The overall results were positive, and in maximum stretch tests, 100% stretchability without catastrophic failure was achievable.
The interconnection process needed to integrate electronic modules into textiles is one of the most vexing challenges in bringing e-textiles and wearables to scale
The poster sessions precipitated discussions around new developments, such as a sensing glove for patients with Parkinson’s disease submitted by Vignesh Ravindrachan and colleagues from the University of Rhode Island, Nautilus Defense, Rock Steady Boxing, and the Indian Institute of Information Technology. Fraunhofer IZM/Pauline Stockmann
Textile Band with Direct Inkjet Printed Electronic Island,” inkjet printing was brought together with e-embroidery as part of the FFG-funded TEXhype project. The aim is to integrate multiple sensor islands into a stretchable textile-based belt seamlessly. This is done using a combination of direct-to-garment inkjet printing of multi-material electronic islands along with conductive yarn embroidery. The researchers believe that the versatility offered by bringing these two processes together will pave the way for a scalable process and commercialization that addresses the need for the optical heart rate sensor to directly contact the skin. This will detect changes in the reflection of emitted light that varies with blood volume fluctuations occurring beneath surface of the skin. To do this, the electronic island for heart rate detection is located on the inner side of the belt ensuring
a consistent contact with the wearer’s skin during use. The work is currently at proof-of-concept stage with the next step to conduct a clinical validation study.
Gillian Lake-Thompson presented “Design and development of a knitted e-textile sensing environment for fetal heart monitoring”, work undertaken by the speaker and colleagues at WSA, University of Southampton and the Beijing Institute of Fashion Technology. The intention here is to offer an alternative to rigid devices such as cardiotocography (CTG) in the form of a flexible, wearable garment that is visually discreet and can be
Sofia Guridi is speaking at E-Textiles Conference 2024, and the opening slide shows the final prototype of her biodegradable e-textile capacitive sensor. The sensor uses wool yarn and CMC films to create a textile pocket, where the sensor’s core is introduced.
Marie O’Mahony
Sara Robertson, Lucie Hernandez, and Emma Wright presenting the E-Stitches Collective representing a dynamic international community of creators, makers, hackers, designers, and researchers in the field that also saw the launch of their E-Stitches Zine. A number of members address environmental concerns. Melissa Coleman and Rachel Freire’s E-textiles Crystallography, explores luxurious futuristic garments with salt crystals on a washable and reusable electronic base garment. The base consists of e-textile taffeta traces, customized LED, and resistors. When the fabric needs to be cleaned or has shed too many crystals, it can be returned to the crystallographer to be regrown into a new shape. Marie O’Mahony
used for long-term monitoring in clinical environments as well as in the patient’s home. Researchers at ETH Zurich and Donghua University, Shanghai, addressed the need to make sensing during motion monitoring visible to the eye for applications in personal healthcare, disease detection and diagnosis. Their paper titled “Mechanoluminescent Fibers for Visualizing Motion Sensing” proposed a novel luminous fiber based on the mechanoluminescent (ML) effect. A core layer of (ZnS:Cu2+) was surrounded by a rubber elastomer sleeve with the fiber shown to emit a visible green light at 520 nm within a tensile strain range of 30%, with the light positively correlated to tensile acceleration. This is achieved without needing to be plugged in or relying on additional electronic components such as batteries or chips making it well-suited for integration to clothing.
E-Textiles 2025 will be held November 12-14, 2025 at ENSAIT, University of Lille, Roubaix, France.
Dr. Marie O’Mahony is an industry consultant, author and academic, the author of several books on advanced and smart textiles published by Thames and Hudson. She is Programme Leader for MSc E-Textiles and Wearable Technologies (launching 2026) at WSA, University of Southampton and can be contacted at marie.consultant@gmail.com or found on LinkedIn at https://www.linkedin. com/in/dr-marie-o-mahony-94776836/.
Converters Expo 2025 in Wisconsin is a one-day event set to take place on May 20-21, 2025, at the iconic Lambeau Field in Green Bay, home of the Green Bay Packers. Now in its 18th year, this expo is a key gathering for professionals in the converting industry, bringing together converters of paper, film, plastics, and nonwovens with industry buyers, specialists, and suppliers.
The expo is designed to cater to a wide range of industries, attracting material converters and manufacturers eager to discover cutting-edge technology and solutions. With over 150 vendors and service providers spread across two floors of booths, attendees can expect a dynamic show floor buzzing with activity. From state-of-the-art testing and prototyping equipment to innovative printing and packaging technologies, Converters Expo 2025 promises to showcase the tools and techniques driving the industry forward, making it a must-visit for those looking to stay competitive.
Networking at Converters Expo offers attendees opportunities to connect with other professionals, allowing participants to build relationships, exchange ideas, and potentially forge new manufacturing partnerships that could shape the future of their businesses.
Education is a key focus of the expo, with a robust lineup of vendor-led sessions and editorial presentations. These sessions cover the latest developments in the converting industry, of-
Sessions cover the latest developments in the converting industry, offering insights into topics such as environmental sustainability, advanced printing techniques, and equipment efficiency.
fering insights into topics such as environmental sustainability, advanced printing techniques, and equipment efficiency. Sessions include:
• State of the Industry: Converting Trends – Douglas J. Peckenpaugh, publisher, The Packaging Group, BNP Media, looks at the changing nature of the converting supply chain; current and pending extended producer responsibility (EPR) legislation; and global economic factors impacting material converting, including packaging
• New Technologies for Web Guiding and Inspection
• Advanced Static Control for Converting
• Identifying Web Handling Problems Before They Happen: How Simulation Can Help
Converters Expo 2025 is organized by BNP Media’s Packaging Group and is expected to draw hundreds of participants, continuing its tradition of growth and influence.
The event starts with a reception at the Green Bay Packers Hall of Fame in the evening of May 20th, and the exhibit the following day. Registration is open now, and with its blend of innovation, education, and networking, Converters Expo 2025 in Wisconsin is poised to be a pivotal event for the industry. www.packagingstrategies.com/converters-expo
Representing a comprehensive range of product categories, find the latest in functional apparel textiles, including wearable smart textiles, new performance technologies, and much more!
Hundreds of leading exhibitors and knowledgesharing opportunities await. Don’t miss out on insights essential for thriving in today’s competitive textile landscape.
Register today for the 2025 edition of Techtextil North America!
Co-located with Incorporated with
MAY 6 – 8, 2025
ATLANTA, GEORGIA
Scan the QR code for more attendee information!
Navis TubeTex and Fibroline officially launched the Fibroline USA Innovation Lab in February to operate as part of the Navis Sustainable Coating Development Center, located in Lexington, North Carolina.
This new facility represents a gateway for American companies to access Fibroline’s eco-friendly patented technologies. A French engineering company based out of Lyon, Fibroline has developed a portfolio of dry powder impregnation solutions for textile functionalization. These innovative technologies are based on the use of alternating electric fields to impregnate materials in powder form throughout all types of media. Fibroline has a strategic partnership with Navis TubeTex, a USbased leader in finishing machinery for the global textile industry. It designs and manufactures machinery for the global knit, woven, nonwoven, technical and geotextile sectors.
Over the course of the three days of that inauguration event, delegations from several companies as well as media met with the innovation teams of
IFibroline and Navis TubeTex. All these potential partners make applications in various sectors such as military, automotive, filtration and healthcare. The event gave the attendees the opportunity to discover Fibroline’s unique dry impregnation solutions through live demonstrations and a full platform visit, followed with series of brainstorming sessions, opening discussions for future collaborations.
Fibroline has experienced significant growth in recent years, with more than 15 technology transfers carried out or in progress, mostly with European partners. Based on these achievements and confident in its unique impregnation solutions, Fibroline wanted to expand its capacities to the north American market and set up shop in this part of North Carolina, a true hub for textile innovators. “The North American market for advanced textile manufacturing is a key sector, and we aimed to introduce our eco-friendly tech-
Registration Now Open for the World of Wipes® International Conference NDA, the Association of the Nonwoven Fabrics Industry, announced registration has opened for the World of Wipes® (WOW) International Conference, July 2124,2025, at the Hilton Columbus Downtown in Ohio.
This year’s theme, Wipe to Win: Innovating for a Sustainable and Profitable Future, will feature industry leaders discussing pivotal challenges and opportunities, including business profitability, sustainability, and flushability.
Attendees at WOW 2025 will gain vital insights into formulation and fragrance innovations, specialty wipes, retailer perspectives, tariffs and regulations, recycling advancements, new technologies, and market trends and statistics.
WOW 2025 offers a unique opportunity for end-use wipe manufacturers, converters, and suppliers across the supply chain to connect, collaborate on new products and applications, and explore the latest trends, challenges, and breakthroughs shaping the wipes industry. Highlights include:
Pre-Conference Webinars – Gain essential insights into traderelated issues leading to WOW 2025. Program updates will be posted on the INDA website.
WIPES Academy, July 21-22 – Attend 12 expert-led sessions by Heidi Beatty, Chief Executive Officer, Crown Abbey, covering all aspects from wipes product concept to commercialization.
nologies to this region,” Jerome Ville, CEO of Fibroline, said. “This partnership marks a significant step forward in the global expansion of our company”.
As for Navis TubeTex, this strategic partnership represents an opportunity to position itself as the prime manufacturer for this technology. Will Motchar, President and CEO of Navis TubeTex is confident this will open a wide range of possibilities for both companies. “By combining Fibroline’s expertise in dry powder impregnation with our deep understanding of textile processing and the American market, we’re creating something truly unique,” Motchar said. “We’re not just offering a new technology –we’re opening doors to possibilities that weren’t feasible before.” www.fibroline.com
Tabletop Exhibits and Lightning Talks, July 22-23 – Experience a dynamic showcase of the latest innovations. Tabletop exhibitors will present five-minute product overviews, followed by networking during the evening reception.
World of Wipes Innovation Award®, July 22 and 24 – Celebrate excellence by recognizing innovations that leverage nonwoven fabric/technology to enhance wipe product functionality and expand applications. Nominations are open until May 19. Finalists will present their products on July 22, and the winner will be unveiled on July 24.
WOW Conference details will be released at a later date. www.worldofwipes.org
With 40% of participants coming from outside of Europe, this is truly a global event. Don’t miss your chance to be part of the world’s most diverse and influential gathering in the nonwovens industry.
From machinery, raw material suppliers, producers to converters, this event gathers every key player in the value chain. Expand your network, foster partnerships, and explore new opportunities with professionals across the entire industry spectrum.
Access up to 13,000 business professionals from over 100 countries, representing a large range of applications in automotive, construction, filtration, food & beverage, geotextiles, hygiene, medical, packaging, and wipes. These decision-makers are on the lookout for creative and pioneering suppliers – make sure you’re one of them !
For more information, come and visit us on our EDANA/INDEX booth #2342 at IDEA®25.
At this year’s JEC Composites Innovation Awards ceremony, the award in the “Construction & Civil Engineering” category went to the “DACCUSS” project, coordinated by the DITF. TechnoCarbon Technologies GbR, the inventor of Carbon Fiber Stone (CFS), received the JEC Award together with its development partners. The award is for the development of house walls made of Carbon Fiber Stone (CFS), a CO2 negative composite material.
Each year, the JEC Composites Innovation Awards recognize innovative and creative projects that demonstrate the full potential of composite materials. With the help of a development team from 12 companies and research institutions, TechnoCarbon Technologies GbR successfully submitted its innovative
FDACCUSS building element for house walls made of Carbon Fiber Stone.
Carbon Fiber Stone is a building material made of natural rocks and bio-based carbon fibers. It serves as an environmentally friendly replacement for CO2-intensive concrete in the construction industry. While conventional concrete walls release large amounts of CO2 during production, the DACCUS building element binds 59 kg of CO2 per square meter and therefore has a negative carbon footprint. In addition, the panels weigh only one-third of equivalent reinforced concrete house walls.
i-Tech announced the addition of Joe Bernard to the sales team as Sales and Market Development Manager. Inthisrole,Joewillberesponsibleformarketdevelopment and customer management in the Northeast, Mid-West and Western USA in addition to other duties on our sales team. Joe brings 15 years of manufacturing and sales experience in the textile and technical textile industries and holds a bachelor’s degree in Textile Technology from NC State University.
“We are thrilled to welcome Joe to our team,” said Managing Director, Jeffrey G. Bassett. “His vast experience and expertise in textile manufacturing and more recent sales and market development experience will enhance Fi-Tech’s service to our customers and European principals. Joe has a tremendous work ethic, an established reputation, and strong communication skills, allowing him to connect with and to serve our growing customer base.”
Joe Bernard also expressed excitement about joining Fi-Tech, saying, “I first worked with Fi-Tech on a project in 2014. The company and its staff have always been recognized as a provider of market leading products and services with the utmost professionalism. I experienced this firsthand in manufacturing and now I am excited to join their team.”
As Fi-Tech continues to expand, the addition of Joe reinforces the commitment to providing excellent service to our global customers. www.fi-tech.com
NDA, the Association of the Nonwoven Fabrics Industry, in partnership with Nonwovens Industry magazine, announced the finalists for the 2025 IDEA® Achievement Awards. These awards recognize the most innovative new product introductions in the nonwoven and engineered materials industry since the last IDEA® event in 2022.
The IDEA® Achievement Awards celebrate excellence in product innovation across multiple categories, with nominees evaluated on creativity, novelty of approach, uniqueness, and technical sophistication. The awards will be presented during IDEA®25, the global event for nonwovens and engineered fabrics, taking place April 29-May 1, 2025, in Miami Beach, FL.
See all the finalists at https://ideashow.org/2025-awards-finalists/.
Jeanologia recently celebrated the 25th anniversary of its pioneering laser technology with a unique capsule collection that blends the nostalgia of traditional denim with technological advances that have revolutionized the industry. This celebration took place at Kingpins Amsterdam late last year, and the global impact of laser technology through a visual installation that traces a quarter century of innovation, with a focus on the future was highlighted.
The launch of Jeanologia’s first laser in 1999 marked the beginning of a new era for the textile industry, improving sustainability, quality, and efficiency. By eliminating hazardous practices like sandblasting, this disruptive technology enhanced processes and redefined the concepts of innovation and sustainability in an industry rooted in craftsmanship. Today, this technology is used in 50% of global jean production, solidifying its position as an essential tool for top manufacturers and fashion brands.
“Laser has enabled more sustainable production and opened up creative possibilities that were once unimaginable,” says Fernando Cardona, Head of Jeanologia’s Brainbox. www.jeanologia.com
he British Textile Machinery Association (BTMA) is hitting the ground running in 2025, having expanded membership to its highest level in many decades, reflecting a continuing push into many other fields beyond commodity textiles.
TBringing BTMA membership up to a total of 49 companies this year are Lancashire firms B&M Longworth and E+R Group.
With a long history in the manufacture and supply of specialized cleaning and waste-reduction technologies for the polymer and coating industries, Longworth is the developer of the DEECOM system for the recycling of both fibers and polymers. DEECOM technology exploits pressurized steam in a process called pressolysis to successfully separate and reclaim fibers and polymers
ADVERTISING | SALES
PUBLISHER Driven By Design LLC
General Inquiries: advertising@inda.media
Vickie Smead
SALES REPRESENTATIVE, NONWOVENS BUYER’S GUIDE
INDA, the Association of the Nonwoven Fabrics Industry vsmead@inda.org | +1 919.549.3715
Jay Mason
SALES REPRESENTATIVE, NEW BUSINESS sales@drivenbydesign.net | +1 239.225.6137
Sabine Dussey GERMANY, FRANCE, AUSTRIA, SWITZERLAND, SCANDANAVIA, BENELUX sabine.dussey@dussey.de | +49 2129.348390
Filippo Silvera ITALY & SPAIN info@silvera.it | +39 02.284.6716
Zhang Xiaohua CHINA ifj_china@126.com | +86 13522898423
Dan Noonan DIRECTOR OF BUSINESS DEVELOPMENT + EXHIBIT SALES
INDA, the Association of the Nonwoven Fabrics Industry dnoonan@inda.org | +1 919.459.3754
E+R’s latest Genesis Air coater is used for development in sectors such as battery technologies, fuel cells and medical products.
B&M Longworth DEECOM fibre reclamation unit. BTMA
from composite parts for reuse, enabling true circularity for materials without the needs for solvents, chemicals, burning or mechanical grinding.
E+R Group is a leading manufacturer of roll-to-roll production machinery including advanced printing, coating, forming and vacuum deposition systems for end-use applications as diverse as carbon fiber prepregs, medical textiles, hydrophobic protective apparel and PEM fuel cells.
The group is also active in groundbreaking projects such as the Faraday Battery Challenge involving a consortium working to develop solid-state battery technology for automotive applications. These contrast with lithiumion and other batteries which contain liquid or polymer gel electrolytes and could prove crucial in the UK’s quest to reach net-zero carbon emissions by 2050, through electrifying transport and devices.
The group’s low carbon machines are characterized by their robust design and ability to offer numerous substrate options, and their design is aided by scientists at its in-house technology center, who often work on game-changing projects with outside companies or universities. www.btma.org.uk
ASF India Limited has broken ground on a new plant to increase the production capacity of its Cellasto® microcellular polyurethane (MCU) in Dahej, India. Under BASF’s new “Winning Ways” strategy, the plant will be constructed with state-of-the-art technologies and automation systems to ensure that BASF’s high standards of safety and quality are upheld. The plant, expected to be operational in the second half of 2026, features a new mold line in its first stage and empowers Cellasto® to meet the high demands of the rapidly growing local market. www.performance-materials.basf.com