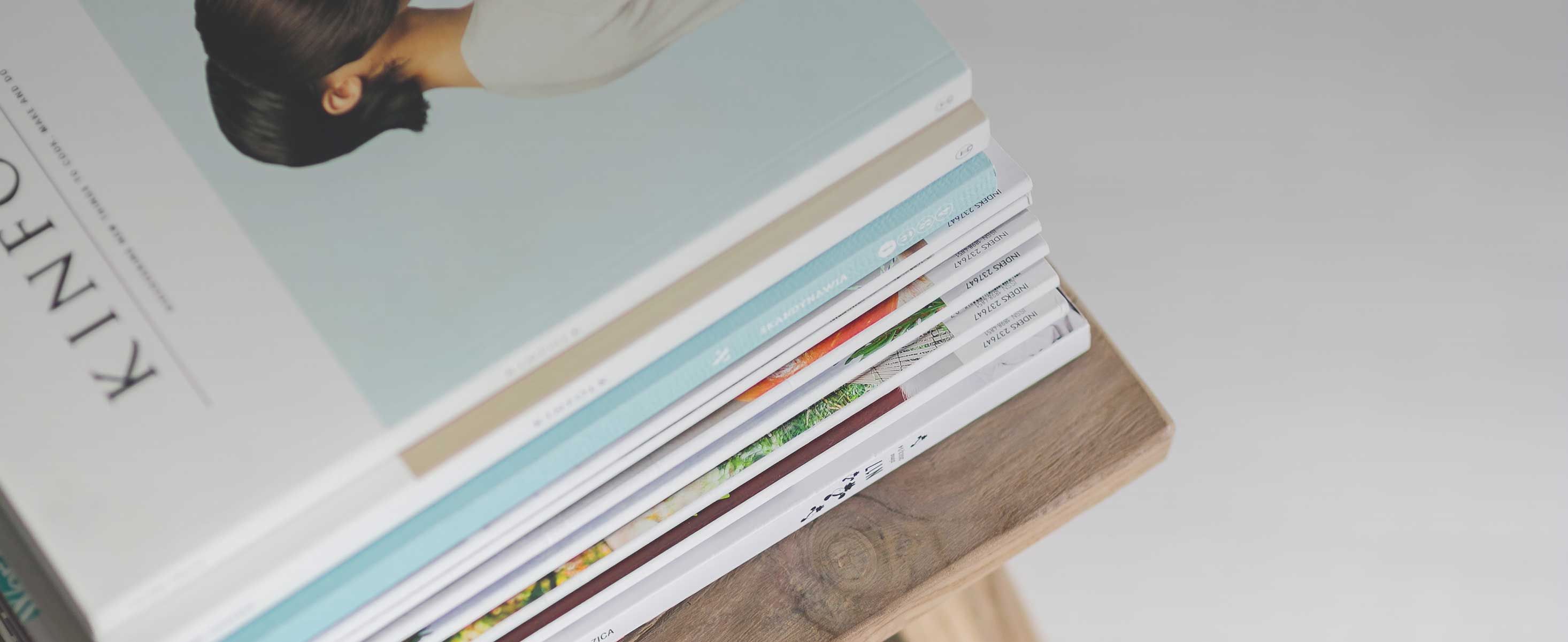
2 minute read
VIEWPOINT Fibers In Motion
“Never confuse movement with progress. Because you can run in place and not get anywhere.”
– Denzel
Washington any think that the move to all electric vehicles check the box on automotive circularity.
Yet these vehicles only address the emissions challenge of the world’s complex environmental concerns. Remember, there is still the rest of the vehicle to consider, beyond the battery. Most vehicles are 75-80% percent recycled by the automotive recycling industry, which is quite savvy at the three R’s – Reuse, Reduce, Recycle. To these businesses, recycling is the last option, because they make good money on the reuse of auto parts that ultimately reduce emissions which is generated when new parts are made. Reused auto parts are essential to the mechanical and collision repair industry, worldwide. It’s a booming, albeit misunderstood, industry for the last 80 years.
What needs to be considered is that 75-80% of a vehicle that is recycled is the ferrous and nonferrous metals. “The remaining 20-25 percent – the ‘fluff’ – includes everything else from the car, such as plastics, polyurethane foam, residual metals, fabric, rubber, glass, and dirt,” reports the Recycled Materials Association (formerly ISRI). “This fluff has long been considered a waste and has thus been discarded, burned in incinerators, or – if it’s lucky – beneficially ‘reused’ as daily cover in landfills.”
My question to consider: once in a landfill, how long does fluff take to breakdown? Does it ever break down?
That is where the textile industry comes in. Autos, airplanes, trains and boats, and other things that move people, all need environments that accommodate passengers. We know that every vehicle will reach an end of life, eventually, and will be dealt with in some way – either by auto recyclers, scrap yards or waste management.
How is the textile and nonwovens industry addressing this? Are we moving people in well-designed environments, but not addressing the material waste stream?
The good news: The answer to that question is we do see progress being made, large and small. And it is imperative that this industry continue to investigate materials that meet customer expectations for comfort, utility and safety, yet also can help the environmental mission at hand.
On page 16, Geoff Fisher highlights initiatives in various transportation sectors. In automotive, he notes, “Many producers are now designing automotive interior materials that meet the 2030 end-of-life vehicle requirements and the ambitions of original equipment manufacturers (OEMs) with regard to circular economy targets. ... For example, by constructing mono-polymer carpets and flooring that are 100% recyclable at end of life.”
Marie O’Mahony, on page 21, reports on sensory aspects of transportation textiles, and also collaboration between corporations. “Ford has launched a wide range of biomaterial products that include wheat straw for storage bins and cup holders, kenaf plant door bolsters, rice hulls for electrical harnesses, tomato skins for wiring brackets and storage bins. In a collaboration with McDonald’s, the dried skin of the coffee bean, the coffee chaff, is used in a composite for car headlight housing. ... The resulting components Ford estimates to be 20% lighter and needing around 25% less energy during the moulding process.”
It seems that transportation manufacturers are making end of life and sustainability a goal, and this is movement towards real progress. Enjoy the read!
Caryn Smith Chief Content Officer & Publisher, INDA Media, IFJ
Partners at the BioFibreLoop’s