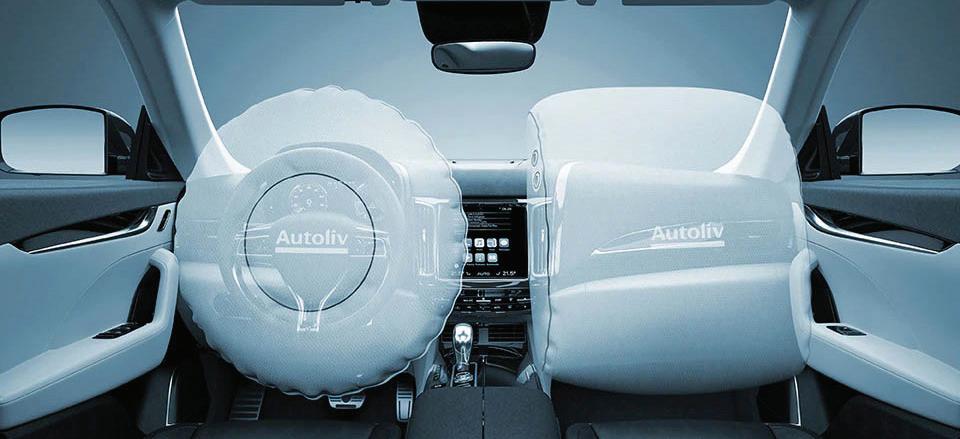
2 minute read
Lenzing Introduces New Black Towel Collection
Autoliv Introduces Airbags Made with 100% Recycled Polyester
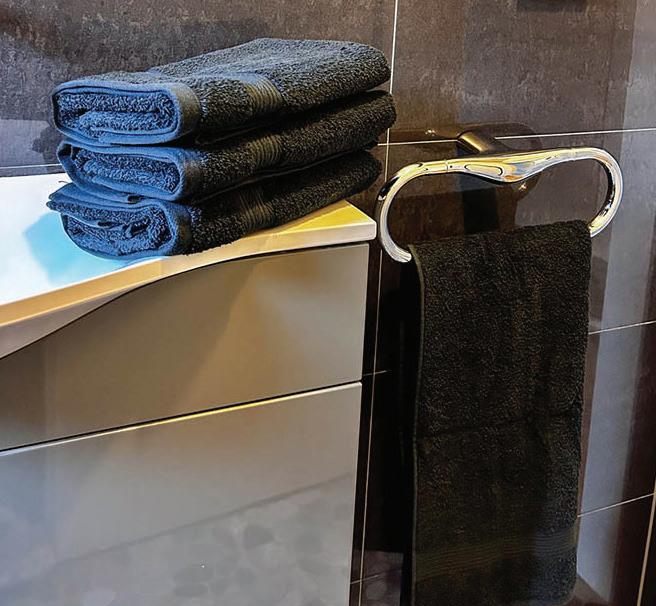
Lenzing Group, a leading global producer of wood-based specialty fibers, announced the launch of its latest Black Towel Collection made with LENZING™ ECOVERO™ branded black viscose fibers and TENCEL™ branded black modal fibers. The collection features six essential everyday washable and reusable face and body care items, from makeup removal pads, makeup removal towels, gym towels, bath towels, hand towels, hair bonnets, to beach towels, designed to cater to the ever-changing consumers’ needs for quality, responsible personal care items for every aspect of daily life. Made with ingredients that are responsibly produced, the Black Towel Collection presents an alternative choice for a societal norm where conventional makeup removal products are mostly single-use disposable items, and reusable towels often get stained or discoloration due to repeated usage. The collection will bring about a refined experience to consumers through its exceptional durability, softness and color vibrancy.
The Black Towel Collection is woven with a blend of cotton and TENCEL™ Modal black fibers or LENZING™ ECOVERO™ Viscose black fibers with a unique fabric composition to enhance durability. Even after multiple washes, these products retain their softness and gentle feel on the skin, making them ideal for repeated use. Derived from controlled or certified wood sources, these specialty fibers are made from resource-saving processes, using at least 50% less carbon emissions and water consumption. Additionally, the LENZING™ ECOVERO™ Viscose black fibers are certified biodegradable and compostable at the end of their lifecycle. Both reusable and responsibly produced, this towel collection is an excellent solution for individuals looking to minimize the carbon footprint of their everyday care practices. www.lenzing.com
Autoliv, a global leader in automotive safety solutions, continues its journey to a sustainable future by introducing airbag cushions made of 100% recycled polyester which significantly reduce the greenhouse gas (GHG) footprint of airbags.
In collaboration with key supply chain partners, Autoliv has developed yarns, fabrics, and cushions made from 100% recycled polyester for use in airbag production. The completed testing of the new material demonstrates that the airbag cushion provides equal safety functionality to a standard polyester airbag while reducing GHG emissions by approximately 50% at the polymer level.
Using this new recycled material is a crucial step toward Autoliv’s commitment to reduce emissions across its product range and will contribute to Autoliv’s ambition to achieve net-zero GHG emissions across the supply chain by 2040.
Autoliv’s Chief Technology Officer, Jordi Lombarte, states, “We are walking the talk on our climate ambitions at Autoliv, by bringing the first technology to create airbags using 100% recycled polyester fabric. We have successfully proven the technology and are ready to offer it to our customers worldwide.”
Autoliv continuously develops processes and products in a resource-efficient manner while minimizing environmental impact. As part of Autoliv’s product portfolio, the new material is now available for global customers. www.autoliv.com
DuPont Unveils Latest Generation Breather Membrane, DuPont™ Tyvek® Trifecta™
DuPont Performance Building Solutions, a leading innovator in material science, has announced the launch of its latest generation breather membrane, Tyvek® Trifecta™. The innovative product offers exceptional fire safety and moisture protection, making it an ideal solution for external walls of high-rise buildings in a convenient and light-weight roll size of 1.5m x 25m. Tyvek® Trifecta™ is a non-combustible breather membrane designed to provide all the benefits of a standard Tyvek® breather membrane, but with A2-s1, d0 Class Fire Performance to the current European Fire Classification Standard EN 13501-1. It surpasses current UK Building Regulations, which require membranes to meet Class B. www.dupont.com
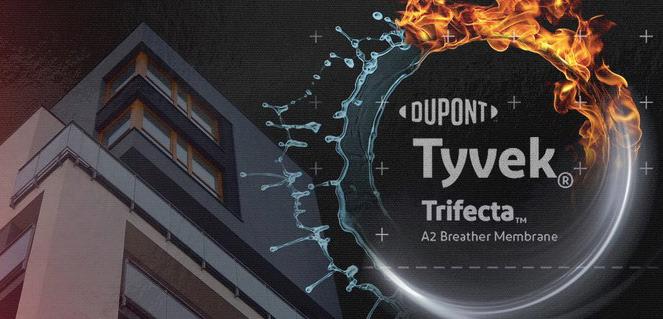