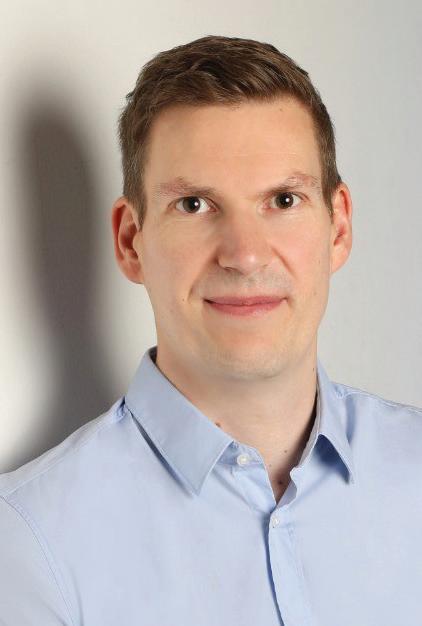
5 minute read
Technical Embroidery Systems
Interview with Sven Böhmer
ZSK is one of the most recognized manufacturers of embroidery machines that combine the highly functional with decorative elements.
Founded in 1984, with a head office based in Krefeld, Germany, the company has a global presence that includes a North American facility in St. Louis, Missouri. They have been leaders in the development of conductive embroidery for e-textiles, a field that is currently expanding technical and market reach for transport, medical and wearable sectors in particular.
I caught up with Sven Böhmer, Sales Technical Embroidery Systems at ZSK, at a recent expo, taking the opportunity to interview him about current and future developments in the sector.
Marie O’Mahony: ZSK has a long history as textile engineers, over one hundred years. Your reputation is well established as a manufacturer of technical embroidery machines. I noticed your business card reads ‘technical embroidery systems.’ Is this a shift in company position?
Sven Böhmer: Technical embroidery systems are because we customise our technical embroidery machines to the needs of the customer so these technical configurations can also be seen as a system.
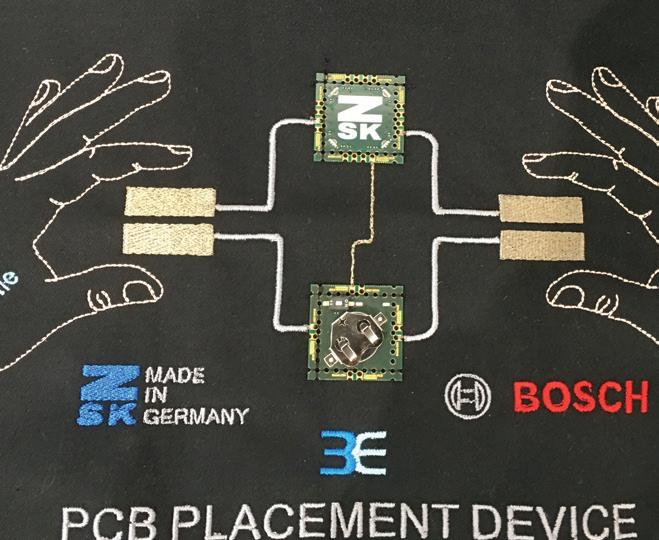
O’Mahony: How do you see Industry 4.0? What does it mean for ZSK?
Böhmer: It is a very challenging industry, so we have set up an in-house engineering office, 3E Smart Solutions, to develop smart and e-textiles for customers, always with a focus on automation and scalability as one of the key drivers for success in the industry.
ZSK’s PCB placement device has been developed in cooperation with BOSCH. Individually designed PCBs are stacked and stored in a magazine in the ZSK embroidery machine for automatic placement on the fabric. Following the placement, conductive paths and electrical connections including sensors are then embroidered so the e-textile including decorative embroidery is produced in a single process. In this example, the control elements are activated in response to pinch, but touch and proximity sensors can also be used.
O’Mahony: ZSK machines work with a number of new fibers (recycled carbon fiber, basalt, volcanic rock fiber etc.). What opportunities and challenges do these present?
Böhmer: New materials can bring new products to the market, which in turn can bring new businesses to the market. Our machines are very adaptable to a wide range of materials, so we are always happy to work with this type of innovation.
O’Mahony: One of your most celebrated innovations for e-textiles has been moss embroidery. Just as everyone is looking to integrate technology more and make it less noticeable, this seems to go against expectation. Can you explain its advantages?
Böhmer: Moss embroidered electrodes can be embroidered in different designs, shapes and sizes depending on the application and needs. They can be produced fully automated and obtain a high conductive surface to generate a clear signal for many types of measurements (e.g., EEG/ECG/EMG). As being a textile, the electrodes are washable and flexible, which are often attributes looked out for in the product development, especially for smart and e-textiles.
O’Mahony: We have connected at two trade shows this year, the first was LOPEC specializing in Printed Electronic and Flexible Hybrid Electronics and the second time a month later at TechTextil focused on advanced and smart textiles. Do you see these two industries coming closer together?
Böhmer: Absolutely, I believe that the two industries do need to come together, otherwise nothing will happen. There needs to be integration. But it is not simple. Product development needs to include IT that is more suited to textile processing. We need to see a greater level of mutual understanding of what each industry is. There are considerations that need to be addressed from a legislative point of view, there needs to be an alignment.
For example, what happens when a power bank fails, where does the responsibility lie between industry partners? This type of issue means that it takes much longer for smart textiles to be commercialized. There is a particularly high risk in areas such as medical applications, so that takes even longer. Do I see a time when the two industries will come closer together? Yes, I think so. It will take some time of course, but we are already seeing some interesting innovations for further development on stitch and print combinations. At ZSK, and with 3E Smart Solutions we are looking at partnerships to combine our expertise to achieve this.
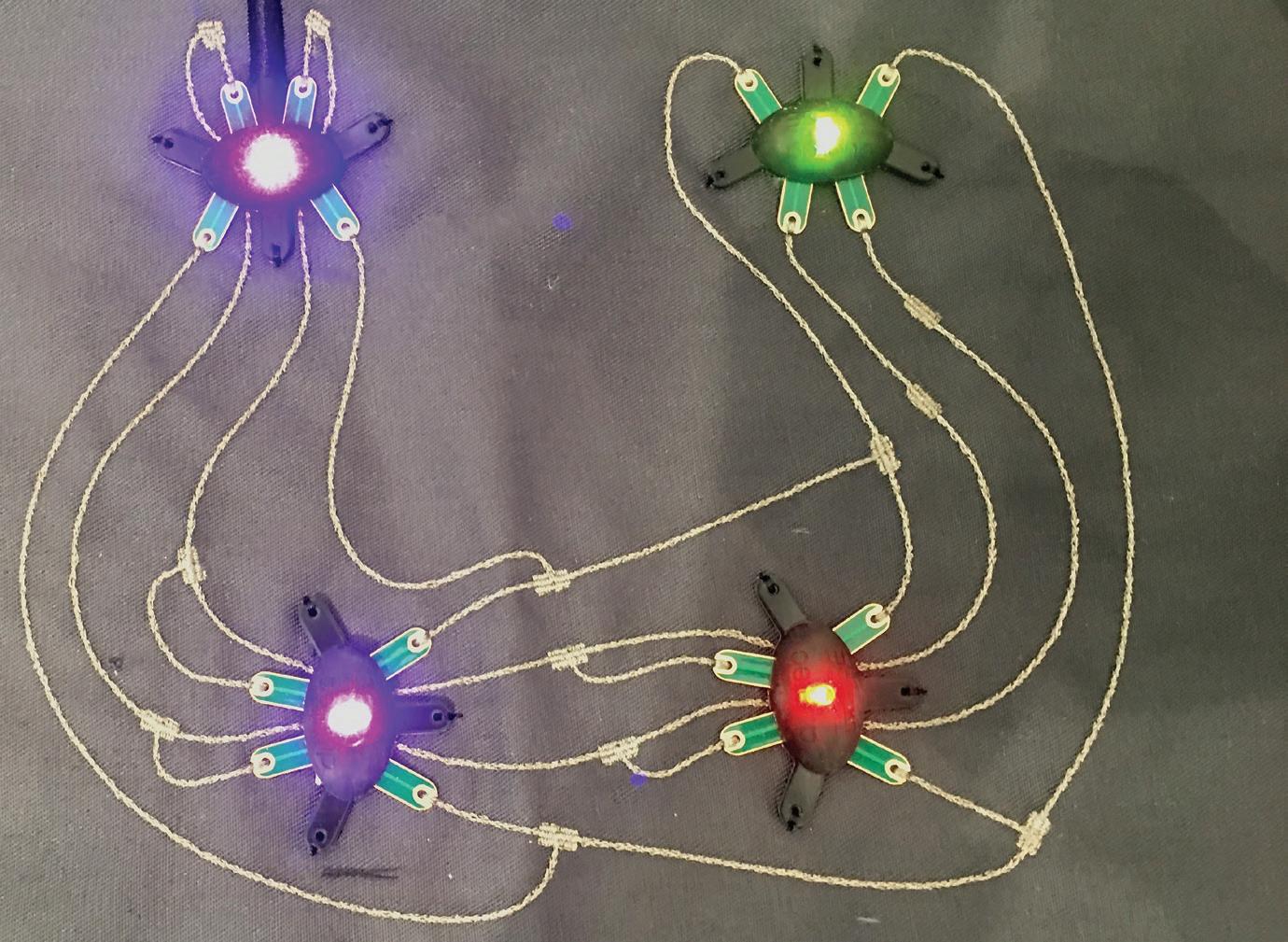
O’Mahony: Where do you see the motivation coming to bring these two related areas together – is it technology or the consumer or something else entirely?
Böhmer: I think the pressure is coming from the market, it is coming because the consumer wants it. Smart and e-textiles are going to play an important role in many aspects of life in the future, I think.
O’Mahony: AI is of course the hot topic now both for manufacturing systems and in the design of wearables. I guess this is a two-part question: First where to you see the opportunity/risk in manufacturing, and second in wearables?
Böhmer: Absolutely, there are specific questions around data and AI when it comes to wearables. Where is the data stored and who is storing it? How secure is it, who owns the data, how long is it stored, etc. There are standards being developed to address some of these issues, and we are involved in the standards committee. But this is a process that takes time. In terms of manufacturing, needs are changing in different parts of the world. In
Asia, for example, there are more handicraft processes involved. We don’t tend to sell as many automatic bobbin changers there as we do in North America or Europe, for example.
O’Mahony: Where do you see the value of the designer in e-textiles?
Böhmer: The value of the designer is that he or she creates new ideas that can lead to innovation and hence to new businesses.
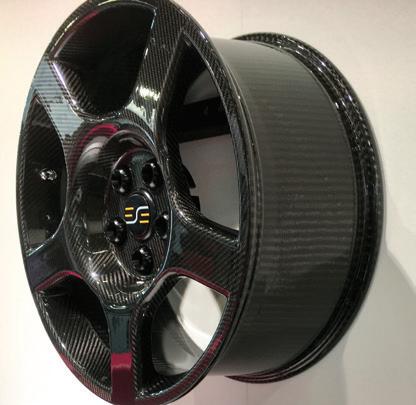
Tailored fiber placement used by ESE Carbon for their carbon fiber wheel produced in a single piece and single cure to achieve a 50% reduction in lay-up times and overall, a better weight to strength ratio in the finished product.

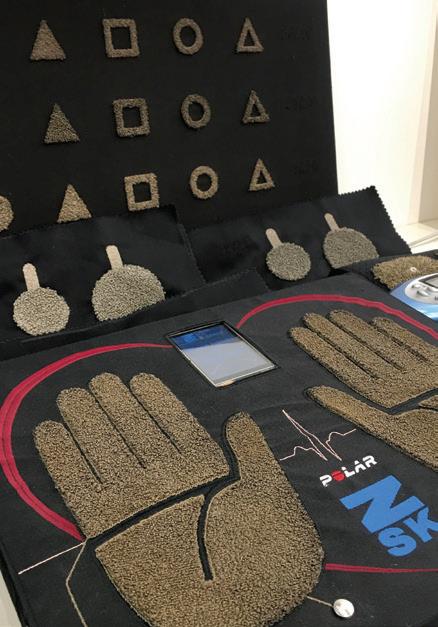
O’Mahony: The nature of textiles and textile processes is constantly changing and expanding to include new capabilities. ZSK have developed fiber-laying capability for composites. Can you discuss the technology that you have developed for this sector and the motivation?
Böhmer: We have developed the capability for fiber-laying primarily for composites at present. These can be used for many different applications in the automotive or aerospace market, for instance, and with our patented technology we are able to integrate functions into composites such as for heating or cooling fully automated.
O’Mahony: How do you see the market for smart composites developing? Do you think that transport will be the market leader in this?
Böhmer: Well, transportation is one of the markets that is driving this technology. But there are other markets, such as aerospace and military, that are also very interested in smart composites.
O’Mahony: What might we expect to see next from ZSK, and when?
Böhmer: We have some exciting developments that we hope to be able to announce soon.
For the present, I’m afraid I can’t tell you any more – but I promise that you will be the first to hear once the information is ready for release!
O’Mahony: Thank you for your time and insights here Sven. It has been invaluable to have your perspective on the sector.