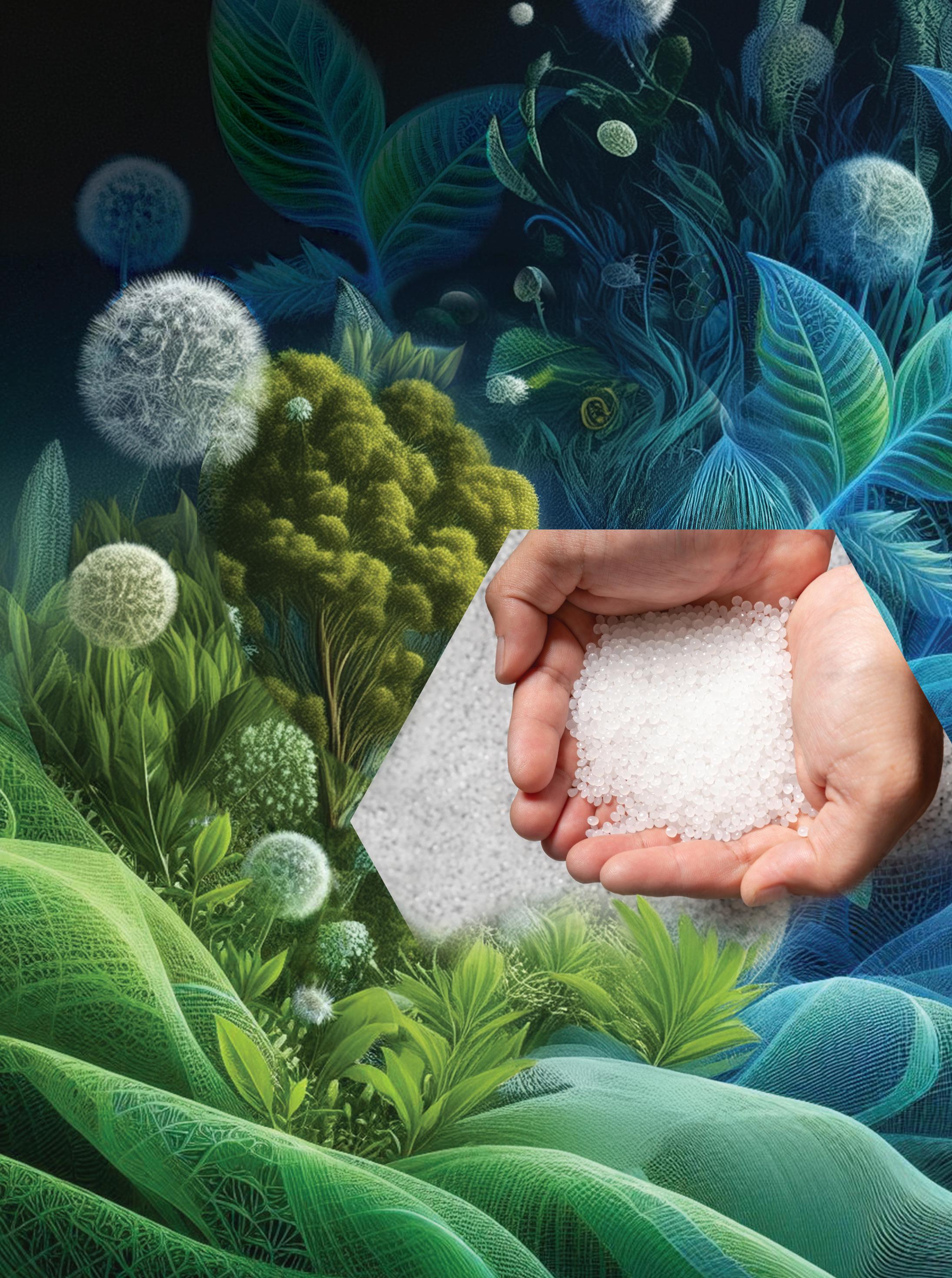

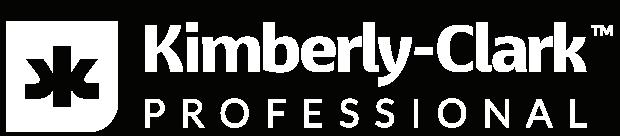
Advance your Nonwoven Skills and Career
Training for those who are new to nonwovens, who come from non-technical backgrounds, or are seasoned nonwovens professionals. From raw materials, to processes, to products.
Elementary Nonwovens Course
INDA Headquarters, Cary, NC
Intermediate Nonwovens Course
INDA Headquarters, Cary, NC & The Nonwovens Institute, Raleigh, NC
Meltblown Technology Course
The Nonwovens Institute, Raleigh, NC
Spunbond Technology Course
The Nonwovens Institute, Raleigh, NC
Nonwoven Fabric
Property Development & Characterization Course
The Nonwovens Institute, Raleigh, NC
Fiber & Filament Extrusion Fundamentals Course
The Nonwovens Institute, Raleigh, NC
Nonwoven Product Development & Innovation Course
The Nonwovens Institute, Raleigh, NC
Nonwoven Bonding Fundamentals Course
The Nonwovens Institute, Raleigh, NC
WIPES Academy
@World of Wipes International Conference
Absorbent Hygiene Course
INDA Headquarters, Cary, NC
INDA’s Pillars of Sustainability Take Center Stage in Nonwovens By Tony
Fragnito
The Crossroads of Environmentally Sustainable Nonwoven Materials By Chris Astley
North American Nonwovens Industry Outlook Report By Mark Snider
The Ultimate Circularity of Single-Use Plastic By Bryan Haynes
CEO Q&A: The Potential and Trends of PCR in Nonwovens By Caryn Smith, Chief Content Officer & Publisher, IFJ
Regulatory Pressures & Significant Threats to Industry By Wes Fisher
Technological Trends for Bio-Based Nonwovens
By Jason Chen, International Correspondent, China, IFJ
Cellulose Fibers and Nonwovens By Monique Buch
Sustainable Advances in PLA Spunbond Nonwovens for Hygiene Applications By Koen Bastiaens
Driving the Future of Lightweight Mobility Design By Geoff Fisher, European Editor, IFJ
Filtration for the Future By Bruce Lorange, Suzana Vidakovic, and Nick Wang
Absorbent Hygiene Products
By Adrian Wilson, International Correspondent, IFJ
Single-Use Wipes – An Industry Never Far From Drama By Adrian Wilson, International Correspondent, IFJ
A Multi-Generational Look at Plastics & Polymers By Matt O’Sickey
Durables and Disposables at the End of the Road By Adrian Wilson, International Correspondent, IFJ
Revolutionizing Recycling in the Hygiene Sector By Christy Sapp and Kim Evans
Sustainable Bonding By Esra Cinar 4 | Viewpoint
Progress By Caryn Smith, Chief Content Officer & Publisher, IFJ
Showcasing Solutions for Success Solution Center: CEREX
Innovations Roundup: Nonwovens Industry Moves Sustainability Forward
New for 2025! The American Filtration & Separations Society (AFS) is partnering with INDA to create a world-class FiltXPO™ conference program.
The two-day FiltXPO conference program will share technical insights in filtration innovations and technologies from industry professionals all over the world. Conference program details will be released in the fall of 2024.
Immerse yourself in the next generation of filtration technologies and innovations. Discover the latest developments from world-class exhibitors. Gain new intelligence on what is driving the filtration market.
Unlock business opportunities, gain exposure to new products, and build connections with key players in the filtration industry. Your next success story starts here.
This is the first time in IFJ history that I know of that we’ve dedicated our pages to a singular theme. Sponsored by INDA, the Association of the Nonwoven Fabrics Industry, this Special 7th Issue of IFJ explores the issue of “Sustainability in Nonwovens.” Sustainability is the 2024-25 theme of the Association, which is reflected in every aspect of their efforts, leading up to the IDEA® 2025 Show in Miami Beach, FL, USA, April 29-May 1, 2025.
INDA is focused on the entire value chain around the nonwoven industry, from polymeric resin and fibers, through nonwovens, and into the final nonwoven containing consumer goods. Members convene and connect, as well as innovate and develop their businesses through INDA’s educational courses, business intelligence and market insights, test methods, consultancy and issue advocacy. The goal is to help members succeed by providing information they need to better plan and execute their business strategies.
IFJ strives to maintain fair and balanced industry coverage, yet it must be told that INDA Media is the business-to-business publishing arm of INDA, which also publishes International Filtration News. While ownership is focused solely on nonwovens, our publications report on the entirety of fiber and filtration, as ultimately it is all interconnected.
In this Special Issue, we explore sustainability through the eyes of the many expert contributors and thought leaders
to provide readers a compass on where the nonwovens industry is on the journey.
Here are highlights: Tony Fragnito, President & CEO of INDA shares on page 12 how the Association is leading discussions on sustainability. On page 15, Mark Snider, INDA Chief Market and Industry Analyst, explains in detail the many ways INDA is keeping members and the industry on task with market intelligence.
On page 16, Bryan Haynes, Technical Director Global Nonwovens, KimberlyClark, addresses issues head-on, detailing the many layers of the plastics issue, and calling for “coopetition” within the industry to lead change.
PLASTICS association leaders Matt Seaholm, President & CEO, and Patrick Krieger, Vice President, Sustainability, dialogued in an exclusive Q&A on page 21 with IFJ, providing their association’s position on the task at hand.
On page 24, Wes Fisher, Director of Government Affairs at INDA, details the current regulatory landscape impacting the nonwovens industry. Ongoing global industry participation on issues around nonwovens and the environment is critical.
Matt O’Sickey, Director of Education & Technical Affairs at INDA, explores nonwovens’ end-of-life challenges and opportunities and addresses “tools” at the disposal to industry on page 45.
IFJ regular correspondents Jason Chen, page 26, Geoff Fisher, page 33, and Adrian Wilson, pages 39, 42, and 48, highlight marketplace advancements to watch. As always, I encourage you to send your thoughts on this issue to csmith@inda.org.
Enjoy! — Caryn Smith, Publisher & CCO
Tracking Fiber Trends & Innovation, Nonwovens Sustainability, Material Science, & Supply Chain Impacts You Need to Know
Get Your Complimentary Subscription at www.fiberjournal.com/subscription
Your business depends on a global network of industry peers and business partners.
Let INDA personally introduce you to materials, technologies, services, and logistics suppliers to improve your products and sustainability strategies.
Make INDA your “go to” resource for accurate intelligence in responsible sourcing, innovations in sustainability, and end-of-life solutions.
• Leverage INDA’s extensive industry relationships to expand your nonwovens network.
• Share your expertise on conference planning committees, such as WOW, RISE®, and Hygienix™.
• Take part in driving policy and regulation at the state, federal, and international levels.
• Shape the conversation around issues, such as wipes labeling, plastics in the environment, trade, and chemicals.
• Be among the first to know about potential legislative and regulatory activities, from the bi-monthly Washington Alert.
• Acquire market intelligence with the monthly Price Trends newsletter, quarterly Market Pulse, and the North American Nonwovens Supply Report.
• Receive substantial discounts on INDA events, training courses, webinars and exclusive industry reports.
Connect with your industry in ways that matter. Join INDA today. All it takes is a few clicks via www.inda.org/join-inda.
Questions? Contact INDA Membership membership@inda.org +1 919 459 3700
A
INDA, the Association of the Nonwoven Fabrics Industry, and The Nonwovens Institute (NWI), announced a collaboration agreement to provide continuing education to the nonwovens industry. This agreement expands upon the ongoing partnership between INDA and NWI, whereby the two organizations have successfully presented training programs, covering the full spectrum of the nonwovens value chain from raw materials to processes to products.
Under terms of the agreement, INDA and NWI will develop and present a full roster of training courses, featuring a combination of classroom learning supported by hands-on activities in NWI’s world-class nonwoven production and testing labs on the Centennial Campus of North Carolina State University. The two organizations will also work together to explore additional educational programming to serve the needs of the nonwovens industry as they evolve over time.
“This collaboration agreement represents a significant next step in the partnership between INDA and NWI, as we build upon our training course offering to ensure it is meeting the needs of the nonwovens industry now and going forward,” said Matt O’Sickey, director of education and technical affairs at INDA. “We are also committed to pursuing new avenues to expand the knowledge base of professionals working in areas related to nonwovens.”
The current roster of INDA/NWI training courses include:
• Elementary Nonwovens
• Intermediate Nonwovens
• Fiber and Filament Extrusion Fundamentals
• Meltblown Technology
• Nonwoven Bonding Fundamentals
• Nonwoven Fabric Property Development and Characterization
• Nonwoven Product Development and Innovation
• Spunbond Technology
Course registration is open to INDA/NWI members and non-members. The INDA/ NWI Short Course Value Pack program enables companies to purchase a block of registrations, which can be used by any combination of employees to register for any combination of training courses, at a discounted rate, and available in bundles of 5, 10, 15, and 20 registrations, with discounts ranging from 10 percent to 25 percent, depending on the Value Pack size. Visit https://thenonwovens institute.com/short-course-value-pack/. www.inda.org/training
Tommi Björnman, President and CEO of Suominen.
Suominen strengthens its capabilities in sustainable products by enhancing and upgrading one of its production lines in Bethune, South Carolina, USA. The investment is made in line with Suominen’s strategy and supports company’s vision to be the frontrunner in nonwovens innovation and sustainability.
“With this investment we strengthen our position as the leader in sustainable nonwovens in America’s market and respond to the increased demand of environmentally friendly products. This investment also enhances our operational performance in terms of safety, quality and productivity,” says Tommi Björnman, President and CEO of Suominen.
The total value of the investment is approximately EUR 10 million and the investment project will be completed in the first half of 2025. www.suominen.fi
Berry Global and nonwovens manufacturer Glatfelter Corporation announced they have signed an agreement that will see Berry spin off and merge the majority of its Health, Hygiene and Specialties business, including its Global Nonwovens and Films (HHNF) business with Glatfelter.
Berry announced late 2023 that it was exploring strategic alternatives for its health and hygiene business, which is a major supplier to a broad range of end markets including healthcare, hygiene, consumer, building and construction, and industrials.
Under the terms, Berry is expected to receive net cash proceeds of approximately $1 billion once the transaction closes. Berry shareholders will own 90% of the combined company’s common shares with Glatfelter shareholders owning the remaining 10% of the combined company.
With unanimous approval from the boards of directors of both companies, the combined company will offer a highly complementary range of nonwovens and films including both polymer-based and fiber-based products, with significant geographic diversification and a presence in all major markets. The remaining health and hygiene businesses, including Berry’s tapes business, will be retained by Berry. www.berryglobal.com
INDA, the Association of the Nonwovens Fabrics Industry, announces the publication of the eleventh edition of the annual North American Nonwovens Supply Report.
Based on extensive research, producer surveys and interviews with industry leaders, this report provides a comprehensive view of the North American supply of nonwoven materials including the key metrics of capacity, production and operating rates, and regional trade through 2023.
“INDA provides valuable data and actionable industry information to enhance decision making in our capital-intensive industry. This report is the most complete and accurate portrayal for both rolled goods and other nonwoven materials produced in North America. These supply and demand balance metrics are essential for strategic planning and business investment decisions,” said Tony Fragnito, INDA President.
The Executive Summary from annual Supply Reports, the quarterly INDA Market Pulse and monthly Price Trends Summary are provided to INDA members on a complimentary basis as part of their membership. The data gathered for this annual report serves as the foundation for both the biennial Global Nonwoven Markets Report to be published in October 2024 with EDANA and the biennial North American Nonwovens Industry Outlook, which was published in October 2023. Findings from this year’s Supply Report include:
• North American capacity continues to increase with investments being made across all processes and for a variety of end-uses. Production output is shifting and has slowed down in 2023 to reflect larger machine installations just now coming on-line.
• In 2023, the capacity of nonwovens in North America reached 5.713 million tonnes, an increase from the previous year of over 230,000 tonnes.
• Many new nonwoven production lines were installed in 2023, but mostly in the long-life sectors which shows a positive move towards sustainable goals across the board.
“Similar to 2023, we had quite an impressive producer response from the industry. The markets are shifting to adjust to competitive pressure within the global supply chain. This report highlights significant metrics describing the changes and the reasons behind them,” said Mark Snider, Chief Market and Industry Analyst. www.inda.org
Freudenberg Performance Materials has unveiled a new 100 percent synthetic wetlaid nonwoven product line made in Germany. The new materials can be manufactured from various types of polymer-based fibers, including ultra-fine micro-fibers.
These unique wetlaid materials from Freudenberg are designed for use in filtration applications as well as other industrial applications. This product line rounds off the wide range of wetlaid nonwoven capabilities from the leading manufacturer of high-performance materials.
Customers in the filtration business can use Freudenberg’s new fully synthetic wetlaid nonwovens in both liquid and air filtration. Applications include reverse osmosis membrane support, support for nanofibers or PTFE membranes as well as oil filtration media. The new materials are suited to use in the building & construction industry or the composites industry. www.freudenberg-pm.com
INDA, the Association of the Nonwoven Fabrics Industry, announced three worthy recipients for the INDA Lifetime Service Award and Lifetime Technical Achievement Awards.
David Powling, Paul Latten and Arnold Wilkie are being recognized for their key contributions to the advancement of the nonwovens industry and INDA.
“It is our pleasure to recognize David, Paul, and Arnold with these well-deserved awards. INDA appreciates their contributions in advancing the nonwovens industry and being advocates for INDA,” said Tony Fragnito, INDA president and CEO. “These awards honor individuals with long-established records of service and technical achievement. All three have given their best both personally and professionally to the nonwovens industry and INDA.” www.inda.org
Danish Femcare company Mewalii has introduced the period pads crafted from Sero™ regenerative hemp fibers without the use of cotton. The January 2024 launch marks a significant milestone for the founders after more than four years of dedicated effort and passion of development.
“We had an amazing launch, and it was so soothing to be able to say that from this day you be able to buy Mewaliis hemp pads – it was unbelievable amazing,” said Frederikke Dahl, Co-Founder of Mewalii.
Mewalii’s journey began in 2019, inspired by a university entrepreneurship program, envisioned developing fully biodegradable sanitary pads. During the founders’ research, they investigated the use of different types of natural fibers and found hemp used less water than other materials and could be grown without the use of pesticides.
Mewalii pads are made from around 75 percent of Sero™ natural hemp fibre – the core is made entirely from hemp, while the topsheet is a blend of hemp and viscose for added softness. www.mewalii.com
Fiberpartner ApS, a leading global supplier of responsible and innovative fiber solutions, is entering a strategic partnership with Stein Fibers, LLC, a renowned distributor of special fibers and materials. This partnership is designed to make new and innovative fiber solutions widely available and accessible, contributing to a more responsible future. The goal is to support the transition towards a non-petroleum-based development of fibers and an environmentally friendly tomorrow.
The collaboration offers several advantages, such as:
• Enhanced Availability: Increased availability for fiber solutions, providing customers with easier access to these responsible materials for seamless integration into their products – this is gained through Stein Fibers’ leading distribution network across the USA, enabling them to meet their sustainability goals and reduce their environmental impact.
• Sustainable collaboration: Fiberpartner ApS and Stein Fibers, LLC share a commitment to driving innovation in sustainability. Their collective efforts will be strengthened, promoting the delivery of environmentally friendly solutions to the market.
• Expertise and Assistance: Customers will gain valuable insights and support from both companies, guaranteeing a seamless transition to these more sustainable fiber alternatives.
“We are excited about our partnership with Stein Fibers, LLC,” said Thomas Wittrup, CEO of Fiberpartner ApS. “Together, we are better equipped to meet the growing demand for better and less harmful fiber solutions. We are committed to making our solutions more readily available to businesses worldwide. Stein Fibers is a market leader in the distribution of textile fibers for the fiberfill, nonwovens, and spinning industries. Together we can provide our global customers world class supply chain solutions.”
“We are pleased about this collaboration with Fiberpartner ApS in promoting our supply chain solutions in conjunction with their innovative fiber solutions,” said Jaren Edwards, President at Stein Fibers, LLC. “This partnership aligns perfectly with our mission to provide cutting-edge fiber materials with a lower footprint to our customers. We believe that these innovative fibers will play a vital role in reducing the environmental impact of the industries we serve.” www.fiberpartner.com
The Nonwovens Institute (NWI) announced its expanded Filtration Testing Lab, featuring services for facemasks and respirators, along with filter media for automotive, HEPA and HVAC applications. Importantly, NWI’s Filtration Testing Lab is A2LA Accredited for ISO 17025*, enabling it to meet NIOSH requirements for testing materials used in respirators, and it is outfitted with equipment to perform ASTM F2299 testing for the measurement of Particle Filtration Efficiency (PFE) at 0.1 microns. In addition to NWI’s Filtration Testing Lab, NWI offers a fully equipped Analytical and Physical Testing Lab with more than 60 tests available for nonwoven materials.
NWI also offers lab- and pilot-scale capabilities for Fiber Spinning, Meltblown, Spunbond and Hydroentangling, Staple/Carded Nonwovens, among others. www.thenonwovensinstitute.com
Global nonwoven fabric manufacturer PFNonwovens, a leading innovator in the nonwovens industry, announced the launch of its newest sustainable nonwoven product portfolio based on 100% renewable resin, leveraging the latest Reicofil 5 technology. The portfolio is highlighted by a number of breakthrough materials made entirely from polylactic acid (PLA) resins. These products are setting new standards for eco-friendly spunmelt nonwovens and reinforce PFNonwovens’ commitment to sustainability and environmental stewardship.
The commercial launch of the new bio-based nonwoven products, produced from 100% PLA and enabled by the Reicofil 5 technology, is the most recent step in the company’s drive to address environmental challenges. These innovative materials set new standards for eco-friendly spunmelt nonwovens, while delivering the performance and quality levels expected in applications such as advanced hygiene products, filtration, medical and many others. These new products composed entirely of PLA (from NatureWorks LLC) are industrially compostable and include both spunbond and SMS structures. Developing products that met the goal was a challenge and was enabled by the state-of-the-art Reicofil 5 technology. www.pfnonwovens.com
KMD Plastifizierungstechnik GmbH officially launched the first benchtop Minitype Spunmelt nonwoven equipment in April of 2023, and it has since attracted extensive attention from the industry. KMD continues to upgrade and improve the configuration scheme, optimize the product series, and systematically launch the latest integrated model configuration, which optimizes the mini design of Spunmelt nonwoven equipment & fiber spinning equipment.
KMD Mini type benchtop equipment includes three main categories: Benchtop Spunbond & Melt-blown machines, Benchtop POY/FDY spinning machines, and benchtop extruders. Based on the function of the conventional equipment, the upgraded configuration complies with following design principles:
• Compact design, small size, easy and fast installation;
• Single hole/fewer holes spinneret designs are optional;
• Mono- and Bi-component are optional;
• Very little raw material consumption;
• Integrated & intelligent control, easy to operate;
• Fast test speed, greatly shorten the complex and lengthy R&D cycle;
• Ultra-low energy consumption, friendly to the environment;
• Components and configuration can be customized;
• Economical price, easy to invest.
To enable more customers to get convenient services and provide a variety of choices, KMD has authorized Triumph Equipment Manufacturing (Yantai) Co., Ltd. to produce benchtop spinning machines & Spunmelt nonwoven lab machines in Asia. www.kmd-industrie.de
Freudenberg Performance Materials is extending its ECO range of sustainable nonwoven carpet backings: Lutradur ECO-R and Colback ECO-R backings contain high percentages of recycled raw materials. With its ECO portfolio Freudenberg supports carpet manufacturers in their transition towards an increasingly sustainable product offering.
Freudenberg’s spunbond nonwoven primary and secondary carpet backings contribute to manufacturers’ easy and efficient production processes as well as to high-performance end products. The company is now extending its ECO range in Europe with Colback ECO-R and Lutradur ECO-R backings that contain a recycled content of between 51 and 90%. Replacing virgin raw materials with recycled polyester saves on natural resources and improves the carbon footprint of end products. The ECO-R backings are specifically suitable for carpet tiles, broadloom, dust control mats and automotive option mats.
The company launched its ECO range for sustainable primary backings in early 2023 with the introduction of the ECO-RE resourceefficient backings that use less raw materials and support end product
recyclability. To achieve this, Freudenberg R&D teams further developed the company’s proprietary yarn production technology allowing for extremely thin filaments.
“With the extended ECO range, Freudenberg now offers a variety of different solutions supporting carpet manufacturers in making sustainable choices to suit their ambitions and processes,” said Albert Hammerschmied, Director for EMEA carpet business with responsibility for New Business Development and Sustainability. “Freudenberg is a long-term supplier to the industry with a strong history of developing tailored solutions for and with our industry partners. The continuous development of backings with recycled content is one result of these efforts.” www.freudenberg-pm.com
The Nonwovens Institute (NWI) announced that Mehmet Dasdemir, Ph.D., has been appointed to the position of Director of Product Development for the Institute, in Dec. 2023, succeeding Pierre Grondin who retired from NWI earlier this year after 30 years of service to the nonwovens industry.
In this new role, Dr. Dasdemir is leading the management of NWI’s sponsored product development projects portfolio. He is focused on working with NWI’s industry partners on the development of new nonwoven products and applications, including scale-up using NWI’s extensive pilot facilities. This is an area where NWI brings high value to the nonwovens industry – i.e., in providing an environment where early-stage product designs can benefit from the Institute’s decades of nonwovens application knowledge, along with in-house fabrication and testing capability, to enable proof-of-concept in an extremely cost-effective manner. He is also serving as an internal and external advocate for products developed at NWI. www.thenonwovensinstitute.com
INDA, the Association of the Nonwoven Fabrics Industry, has released a new report, North American Nonwovens Industry Outlook, 2022-2027. This report is the twelfth edition detailing demand data for 2017 through 2022, with forecasts to 2027.
The report provides analysis across all nonwoven end-use markets, providing a comprehensive and accurate view of the total North American nonwovens industry. INDA redesigned this report to support strategic business planning and decision-making. The projections in the report were made by analyzing current market trends and drivers to highlight the market potential in terms of dollar value, units, and volume in both square meters and tonnage.
Tony Fragnito, INDA’s President, said, “This report provides insights on nonwoven demand in the short-life and long-life market segments. The intelligence included in this report is critical for business leaders who manage the assets or operational planning for their organization.”
This report includes:
• Economic and population drivers contributing to market growth over the next five years for markets in the U.S., Mexico, and Canada.
• Disposable, Filtration, Wipes, Medical and Other applications.
• Long-Life durable sectors for Transportation, Building and Construction, Furnishings, Geo and Agro Textiles, and Apparel.
• Key drivers for the demand models and reasons for market upsets like the COVID pandemic.
• A summary of historical and future trends that will affect the nonwovens market. www.inda.org
Circular Polymers by Ascend, a market-leading recycler of postconsumer carpet, announced the launch of Cerene™, a line of recycled polymers and materials made from the company’s proprietary carpet reclaiming technology. Cerene is available as polyamide 6 and 66, PET, polypropylene and calcium carbonate as a consistent, sustainable feedstock for many applications, including molding and compounding.
Ascend Performance Materials, a fully integrated producer of durable high-performance materials and the majority owner of Circular Polymers by Ascend, is known for its innovations in nylon 6,6. Cerene will continue that legacy with offerings in nylon 6,6 while also bringing to market recycled polymers such as nylon 6, PET and PP.
“Customers around the globe are seeking consistent and reliable post-consumer recycled materials,” said Maria Field, business director of Circular Polymers by Ascend. “Cerene is mechanically recycled using a process that minimizes our carbon footprint and environmental impact.”
Circular Polymers by Ascend converts post-consumer carpet into fiber and pellets. The company uses a proprietary process in its Californiabased facilities to achieve unparalleled efficiency in recycling, successfully providing a new life for virtually every component of the carpet and backing. The company has redirected 85 million pounds of carpet from landfills into new goods since 2018. www.ascendmaterials.com
CEREX Advanced Fabrics, Inc. introduces their newest addition to the NyStat™ static dissipating product family with a 50 gsm high strength fabric to minimize electrostatic discharges (ESDs) in high pressure hydraulic systems. The 50 gsm fabric is three times stronger than the 20 gsm product and has a maximum resistivity value of 20,000 ohms vs. 50,000 ohms for the 20 gsm media.
The 20 gsm and 50 gsm NyStat™ media are based on CEREX® brand nylon 66 spunbond fabrics that are known to offer superior strength, excellent web uniformity, high temperature resistance, and exceptional chemical resistance especially in high-performance hydraulic fluids used today.
NyStat™ media is coated with a proprietary, conductive polymer that is bound to the nylon filaments. There are no carbon particles or metal in NyStat™ media which can be released downstream and damage sensitive system components.
The NyStat™ products are 30% thinner than other spunbond fabrics at the same basis weight, which allows for more pleats per filter and lower pressure drops that can generate ESD.
NyStat™ static dissipative media is ideal for Aviation, Power Generation, Heavy Industrial, Mining, and Transportation enduses that can generate electrostatic discharges (ESD) that can cause fluid degradation and damage to filter media that may allow contaminants downstream.
Both NyStat™ products are available in fabric widths up to 1.15 meters (45 inches).
NyStat™ can easily be co-pleated with cellulose, micro-glass, meltblown and nanofilament materials. It provides the same great filter media protection that CEREX® products are known for, with excellent anti-static capabilities.
CEREX Advanced Fabrics has been serving customers around the world for over 50 years. We offer a variety of highquality specialty nonwoven spunbond products based on nylon 66 polymer technology, including CEREX® flat bond fabrics and PBN-II® thermal bond fabrics.
We offer custom colors in our Vibratex® and Spectralon® product families and have recently introduced NyBan™ products with antimicrobial protection and NyFlame™ with improved flame resistance.
CEREX Advanced Fabrics, Inc. is located in Pensacola, Florida USA and is an ISO 9001 certified manufacturer.
For more information, visit www.cerex.com, or contact us at 800-572-3739.
For our Technical Partner in Europe, visit www.anowo.com or tel: +41 612 82 8220.
www.cerex.com
By Tony Fragnito
Sustainability remains one of the most discussed topics, and biggest challenges, within the nonwovens industry. The topic is a significant component of every conference, committee meeting, leadership event and a driver of much of the industry’s investment and innovation – as it should be. The nonwovens industry, like many others, is attune to the importance of sustainability spurred by consumer sentiment, resource depletion and energy conservation, all of which underscore the urgent need for sustainable practices in all industries and in all parts of the world.
Members of INDA, The Association of the Nonwoven Fabrics Industry, are committed to addressing sustainability while remaining focused on product innovation and performance. For these reasons, INDA chose sustainability as its 2024-25 focus. INDA is committed to representing the industry on this broad and important topic. While sustainability within individual organizations impacts many aspects of their business, INDA is most engaged on the topics which form our three pillars: Sustainable Sourcing; End-of-Life Solutions; and Industry Innovations.
6. Sustainability in Nonwovens Conference at IDEA® 2025: INDA’s preeminent convergence of industry professionals, IDEA® 2025, is the most significant industry global trade event. The upcoming show in Miami Beach, FL, USA on April 29 - May 1, 2025, will be devoted to sustainability, which you will see in the event branding and programming. Additionally, sustainability continues to be a focus topic across all INDA-hosted conferences, ensuring critical discussions and insights into sustainable practices throughout the industry.
Our goal is to raise awareness about the industry’s sustainability activities and innovations to those who have an interest in the actions and accountability of our industry.
7. Engagement on Policy and Technical Issues: INDA devotes its knowledge and resources to address public policy issues, develop position statements, and evaluate technical matters vital to the nonwovens industry. As discussions surrounding sustainability gains momentum, INDA aims to be a critical resource to educate, inform, and promote the position of our industry to achieve managed progress.
As part of our 2024-2025 sustainability focus, INDA is offering new channels to share practices and keep the industry informed and educated about ongoing and emerging initiatives related to sustainability both regionally and internationally. Our goal is to raise awareness about the industry’s sustainability activities and innovations to internal and external stakeholders who have an interest in the actions and accountability of our industry.
Examples of INDA’s initiatives include:
1. International Fiber Journal: This special issue of IFJ highlights both the industry’s sustainability journey and the innovation pathways that will guide our industry to a more sustainable future. We have also created an ongoing “Nonwovens” section in each issue of IFJ to highlight stories and interviews specifically dedicated to the advancement of the category in the fiber and filtration industry.
2. Webinars: An expanded webinar series to educate industry professionals and stakeholders on pressing sustainability issues, innovative solutions, and other pertinent topics crucial for advancing sustainability goals within the industry.
3. Market Intelligence Research Report: A comprehensive research report on sustainability in the nonwovens industry, offering valuable insights and data to inform strategic decision-making and drive sustainable practices.
4. Industry Position Statements: Crafting and disseminating industry position statements on key topics which outline our industry’s stance and recommendations on issues vital to a sustainable future.
5. Partnership with Good360: A leading nonprofit organization dedicated to distributing corporate product donations to vetted charities. Through this partnership, we will explore innovative solutions to repurpose surplus materials, reduce waste, and support communities in need.
8. Collaboration Beyond Borders: INDA will continue its efforts to increase collaboration with EDANA, as well as other international and regional societies, to improve communications and ensure we speak with the collective voice of the industry on sustainability topics.
Of course, INDA’s sustainability efforts will continue beyond IDEA® 2025, as these issues will remain significant for our industry over time. We are engaging our members in new sustainabilityfocused committees to connect thought-leaders and decisionmakers. These events, and others in the industry, will facilitate sharing insights and enhancing dialogue among a wide range of stakeholders relevant to our industry’s long-term success.
Collectively, these initiatives empower INDA and its members to navigate the complexities of sustainability, drive meaningful change, and lead the nonwovens industry toward a more sustainable future.
I urge all industry participants to actively join us in this endeavor. Your feedback and ideas are invaluable as we continue to refine our approach, identify new opportunities for collaboration and highlight the industry’s innovation. Together, we can make significant strides in sustainability, ensuring a resilient and prosperous future for the nonwovens industry.
Please join us in Miami Beach, FL USA for the Sustainability in Nonwovens Conference at IDEA ®2025.
This major industry gathering highlights the future of nonwoven materials, their applications, and how nonwoven materials and practices are evolving to support a broad range of market sectors. It is sure to invigorate new ideas!
These topics and others will be discussed in more depth in the INDA Sustainability Report being released in the fall 2024. www.inda.org | www.ideashow.org
Tony Fragnito, President & CEO of INDA, The Association of the Nonwoven Fabrics Industry. He can be reached at tfragnito@inda.org.
By Chris Astley
he global nonwoven industry is at a crossroads, facing increasing pressure to address environmental concerns and develop sustainable alternatives to traditional materials. As the world shifts toward a more sustainable future, collaboration across the industry will be essential to drive innovation and create environmentally friendly solutions. We must explore the key strategies, challenges, and opportunities of collaboration in developing environmentally sustainable nonwoven materials.
While the nonwovens industry continues to evolve and its use of environmentally friendly materials, including natural cellulose, grows, the industry has long been associated with the use of synthetic fibers derived from non-renewable resources, such as petroleum. While these materials offer versatility and performance, they can also have significant environmental impacts, including resource depletion, pollution, and waste. As awareness of environmental issues grows, there is a growing demand for sustainable alternatives.
Sustainable nonwoven materials are designed to minimize environmental impact throughout their life cycle, from sourcing raw materials to disposal. Key considerations for sustainability include the use of renewable and recycled materials, energy-efficient manufacturing processes, and recyclability or biodegradability of the end product.
Collaboration across the value chain is essential for developing sustainable nonwoven materials. Key stakeholders, including raw material suppliers, manufacturers, converters, and end-users, must work together to drive innovation and promote sustainability. Collaborative efforts can focus on various value chain aspects, like:
• Raw Material Sourcing: Suppliers can collaborate to develop sustainable alternatives to traditional synthetic fibers, such as recycled or bio-based fibers. By working together, they can scale up production and improve the availability of sustainable materials.
• Manufacturing: Manufacturers can collaborate to adopt energyefficient production processes and environmentally-friendly technologies. By sharing best practices and resources, manufacturers can reduce resource consumption and emissions.
• Conversion: Converters can collaborate with manufacturers to ensure that sustainable materials are used in the conversion process. By working together, converters can minimize waste and optimize resource utilization.
• End Use: End-users play a crucial role in driving demand for sustainable products and influencing product design and specifications. By collaborating with manufacturers and converters,
end-users can ensure that sustainable materials meet their needs and expectations.
While sustainable nonwovens have the potential to offer many benefits, successful development and commercialization is not without its challenges, often viewed in the following categories:
• Cost: Sustainable nonwoven materials can be more expensive to produce than traditional materials, due to the use of recycled or bio-based fibers and eco-friendly manufacturing processes. However, as demand continues to grow, economies of scale and technological advancements should help to reduce costs over time.
• Performance: Materials must meet or exceed the performance standards of traditional materials to be viable alternatives. Innovations in material science and manufacturing technologies are helping to improve the performance and mitigate the costs associated with newer and more sustainable materials.
• Consumer Awareness: It will be critical to continue to raise awareness among consumers about the environmental benefits of more sustainable raw materials, the role that sustainable nonwoven materials can play in their end-products, and the importance of choosing eco-friendly products.
• Regulatory Environment: Regulatory frameworks will continue to play a crucial role in shaping the development and adoption of sustainable nonwoven materials. Policies that promote sustainability and encourage the use of sustainable materials can drive industry-wide change.
Despite these challenges, there are significant opportunities supporting the development of sustainable nonwoven materials.
• Market Demand: Increasing consumer awareness and demand for sustainable products are driving companies to invest in sustainable nonwoven materials, creating new market opportunities.
• Innovation: Continued innovation in material science, manufacturing technologies, and recycling processes will lead to the development of new and improved sustainable nonwoven materials.
• Collaboration: Partnership across the value chain is essential for driving innovation and promoting sustainability in the nonwoven industry.
Ultimately, collaboration is pivotal to the sustainable nonwoven materials that meet the needs of today’s society while preserving the environment for future generations. As demand grows, collaboration drives industry towards a thriving green marketplace.
Chris Astley is a Senior Executive with successful full P&L leadership and strong Commercial & Innovation leadership for complex, global, multi-billion dollar B2B and B2C organizations.
By Mark R. Snider
The INDA Market Intelligence department began 2024 with directive to re-envision INDA’s focus as a valuable data-driven resource and expand the market tools that we provide to the INDA membership and industry. I had the honor of leading this ambitious effort, along with Cindy Garcia, Senior Research & Market Analyst.
We began work to produce the Nonwovens Annual Study (Supply Report), Quarterly (member) Market Pulse Report, and the North American Nonwovens Industry Outlook Report – a 319-page volume of statistics, figures, graphs and supporting text that provides critical market business intelligence. The report is the result of a minimum of four months of intense concentrated data analysis.
To add more value, INDA also now offers new reports like Long-life Durables, Sustainability, and regional reports as they become significant in the market.
While some of the data in the North American Nonwovens Industry Outlook Report is historical, most of it covers the latest trends and statistics for the industry by primarily covering the demand or end-use market segments. This report also covers processes and does it with greater precision than ever before, providing intricate details on baseline economic and demographic trends along with consumption figures to support those trends. The Outlook report offers a complete and comprehensive picture of the North American nonwovens industry with key trends which accurately forecasts the future of the nonwovens industry for the next five years.
Gathering all of the information for a report like this is extensive, and requires hours of market study, peer review, and interface with key individuals within the nonwovens industry. Development of mathematical algorithms is an important
part of the data research, which accurately calculates the amount of nonwoven in a specific automobile model, baby diaper, adult incontinence product or a household filter, as an example.
As a part of the overall strategy, INDA’s focused theme for 2024-2025 is “Sustainability,” and is reflected in INDA’s events – World of Wipes™ (WOW), RISE™ and Hygienix™, and culminates at IDEA®2025, April 29-May 1, 2025 in Miami Beach, FL, USA and is co-located with FiltXPO™
INDA has placed a priority on improved training programs, both for on-demand and inperson experiences at beginner, intermediate and advanced levels. We have increased engagement in industry partnerships that provide mutuallybeneficial collaboration, such as in the California Waste Collection Study and co-sponsored educational programs with Nonwovens Institute at North Carolina State University (NWI).
We are also pleased to share about INDA’s inaugural Sustainability in Nonwoven Conference will be April 29-30th, 2025.
Sustainability, often misunderstood, has the current emphasis on ways to reduce the carbon footprint. INDA’s mission is to elevate discussions to include innovation towards planetary health, while still achieving lifestyle benefits that the nonwovens industry provides consumers.
INDA will embrace sustainable initiatives going forward and will continue to think globally. Our sustainability initiatives include webinars, UN plastic pollution reduction initiatives, online sustainability success stories, dedicated conference programs, and provoking thought leadership. INDA communications seeks to effectively report to internal and external stakeholders on the industry’s commitment to progress, as well as offering opportunities to showcase it through the INDA Awards program.
Our membership benefits and improvements to information accessibility have been enhanced and are well-received based on recent member interviews conducted. A more open Association dialogue has offered a unique opportunity to engage with the industry like never before.
INDA’s Government Affairs initiatives are involved at the policy level from United Nations treaties to tariffs to promoting manufacturer-friendly legislation through committees and organized coalitions. Our strong presence in Washington, D.C. keeps watch over important issues like international 301 tariffs, flushability standards, the UN plastics treaty, FTC green guides, PFAS and other chemical issues.
Relationship-building is a key part of INDA’s strategy for the future, utilizing responsible stewardship, technical expertise, and engagement through dialogue to protect industry, promote progress and connect INDA’s nonwovens network to opportunity for greater success. Valuable behind-the-scenes functions at INDA contribute through Marketing, Technical Affairs, Events, Membership, Government Affairs, Publications, and others.
We hope that you will support our efforts by purchasing INDA reports, attending events, participating on committees, reading publications, and attending our training courses and webinars.
Mark R. Snider is the INDA Chief Market and Industry Analyst.
By Bryan Haynes
lastic has been part of our lives for the past 70 years.
For the sake of history, in 1953, high-density polyethylene (HDPE) brought expansion to low-density radical polyethylene (LDPE), used for rigid products such as bottles, automotive, etc. Low-density PE is used for producing flexible items like bags, films, sachets, and flexible tubes. Simultaneously, polycarbonate (PC) made its debut, representing an exceptionally transparent plastic highly resistant material in 1969. The subsequent year marked the invention of polypropylene (PP).
Considered a materials marvel, plastic has since been applied to a wide range of applications including aerospace, construction, fishing, agriculture, medical, and packaging to name a few. The most prevalent usage of plastic in our everyday lives is for the convenience of single-use disposable products. According to recent figures, over 18 trillion pounds have been produced so far with no end in sight. Unfortunately, only 9 percent of plastic has been recycled with most ending up in landfills and waterways including oceans.
Our oceans are under attack with a staggering 33 billion pounds of plastic waste added every year, according to Oceana.org. What is even more concerning is the increase of published reports on the negative effects of microplastics, now defined as nano-plastics, on the environment and wildlife, and including humans. What can we do as a society, governments, and industry to address this global crisis?
The Single Use Plastics Directive1 in Europe was a wakeup call to many, and prompted a high degree of industry response including lofty sustainability goals. There has been a lot of discussion and debate on the definition of plastic and, as a result, we are all closely monitoring the
To accelerate technical innovation pathways, industry needs to partner in a collaborative manner, which I call coopetition!
outcome of the United Nations Plastics Treaty2, where 175 nations agreed to develop a legally binding agreement on plastic pollution by 2024, prompting a major step towards reducing greenhouse gas emissions from plastic production, use and disposal.
How will plastic be defined outside of Europe? One thing is for sure, it will be difficult to regulate industries to an encompassing effective solution. From a technical perspective, no silver bullet or a long-term solution has been identified.
The current ‘best solution’ starts with us, as consumers, utilizing the proper disposal of plastics through recycling. Yet, to accelerate technical innovation pathways, industry needs to partner in a collaborative manner, which I call coopetition!
I constantly inform my family and close friends about the plastics issue. It amazes me how the average person knows so little about the issue. During a recent vacation to St. Lucia, my wife and I snorkeled at the beautiful Marigot Bay on the seaside of the island. I dove down about 15 feet to the sea floor and plastic trash could be found everywhere including bottle caps, candy wrappers, forks, fishing line, PVC pipe, and a lot of visible smaller fragments.
These smaller plastic particles look like food to many small creatures including
turtles and fish; this is how plastic gets into the food chain. Unfortunately, these particles also kill animals including smaller turtles by blocking the digestion system3.
I brought up some of the trash to show the other people on the cruise. I went into some details on the hidden dangers of microplastics and how this trash is impacting wildlife including humans. I could tell a few of them were shocked and unaware of this issue. Perhaps in the future, they will all be more mindful how they dispose of plastic trash.
If the previous images are not disturbing enough, consider the trillions of particles we can’t see. Dr. Branson Ritchie from the University of Georgia coined the term “plasticosis4” for plastics-related health issues caused by these microplastics. The term nanoplastics is now being used, because the particles that are being discovered are getting even smaller.
The negative effects of plastics on wildlife are vast, but making more recent news is the growing concern about the impacts on human health. Unfortunately, there are more studies being published that validate the concerns on the negative impact on human health. A recent study out of Italy reported that micro-plastics were found in human placentas5. More recently, micro-plastics were also found in plaques in heart patients6. Some plastics additives are being connected to certain types of cancers7.
The European Union was first to address the plastics issue with passage of the Single Use Plastics Directive (SUPD). The passing of this legislation serves as a significant wake up call to all industries that utilize plastics in manufacturing. It has prompted numerous academic debates on solution pathways and the definition of plastic, including what is natural and not chemically modified.
Like many companies around the world, Kimberly-Clark has developed a wide-arching sustainability strategy9 for the company and its suppliers, that includes aggressive goals to be met by 2030.
tion is to ensure the Life Cycle Analysis is within acceptable standards, and there are no unintended negative environmental consequences.
“Plastic Free” is a major claim companies would like to use to market their environmentally friendly products. Yet, the SUPD definition of plastic limits “plastic free” to natural fibers, rayon and lyocell. There is hope that when the SUPD is re-examined in 2026 there will be modification to the plastic definition to be more inclusive for potential solution pathways that are based more on end-of-life properties versus how it was made11
Dr. Branson Ritchie from the University of Georgia coined the term “plasticosis4” for plastics-related health issues caused by these microplastics. GRID-Arendal/Studio Atlantis
My concern is the more we look the more we will find, where there is smoke there is fire! The case of evidence is mounting that plastic pollution poses a severe risk to human health – and that of other living creatures – and is also a contributing factor for the issue of global warming8 We can debate on global temperature changes, amounts of ice as melted, ongoing severity of storms, etc., however there is no debate on the images of pollution caused by the disposal of plastic.
Our “Better Care for a Better World” strategy sets a goal that supports our 50% plastic footprint reduction10
There are several innovation pathways to address the plastics issue, including minimizing dependency on petroleumbased resins via plant-based resins like PLA and PHA. Unfortunately, these two potential solutions are still considered plastic due to its current definition. It is this author’s opinion that a more important characteristic of a material is its end-of-life properties, not solely how it is produced. The only caveat on produc-
In March 2022, a historic resolution was adopted by the United Nations Environment Assembly to develop an international binding instrument on plastic pollution including in the marine environment12 . The first session of the Intergovernmental Negotiating Committee (INC-1) was held in Punta del Este, Uruguay.
I attended this meeting and was pleased to see the heightened passion and sense of urgency from most of the counties on addressing the plastics issue. Unfortunately, to my dismay, the political tensions unrelated to plastics dominated the meeting and discussions. It is yet to be seen if governments can unify enough to develop a meaningful treaty that addresses the complexity of the plastics issue. It is critical that any global agreement enables various innovation pathways to address the issue since there is not a silver bullet.
Sustainability in corporate strategy is a major factor in most every industry and company today. These strategies cover a wide range of metrics including recycling, green house gas emissions, plastic footprint reductions, decrease dependency on petroleum, etc. In most cases, these targets are aspirational, and some appear almost impossible.
On one hand, if there are no drastic steps taken on virgin plastic production, the forecast for global plastic use will increase 22% by 2050 and plastic pollution is expected to triple by 206013. The current state of global affairs suggests that the later seems to be more realistic than the former. On the other hand, many companies are forecasting significant reductions in their plastic footprints. Yet, it will take industry working with governments to work together to make significant impacts.
In determining outcomes, we should define the problem we are working to solve. The microplastics waste stream issue isn’t solved by simply putting an end to littering. The complex issue demands a multi-front tactic from a global perspective on waste management, consumer habits, regulations, chemicals of concern, etc. We did not get in the current crisis overnight, and it cannot be solved by in fell swoop – but we must start somewhere.
A“circular economy’ is touted as being the ultimate solution. On a global scale, this is very aspirational due to the required infrastructure and time required. Every year the problem gets worse; but what can we do today? Even with a robust recycling system today, there would still be leakage. Key material solutions that address the issue are shown in Figure 1.
To effectively address the plastic issue, it will take numerous solution pathways. Before we develop and implement alternate material solutions, we can at least minimize plastic in our products.
In fact, over the last couple of decades, nonwoven producers have taken mass out of products through more efficient production of nonwovens. For example, spunbonded fabrics produced today are made of much finer fibers which provides more coverage and tensile strength. This enables producers to provide the required material specifications with lighter weight materials.
The nonwoven industry is tuned for polypropylene. Should we invest in existing technology to reduce mass or new technologies to process biodegradable polymers? To advance quickly, we need biodegradable solutions. The good news is much of the technology that has been developed to process polypropylene more effectively can be used to help with processing alternate resins.
Recycling is an obvious solution, yet is has its own set of issues, such as water management, including collection and contamination. Advanced or chemical recycling has a lot of advantages, like the ability to recycle products comprised of many components without the need for separation. This may be an excellent bridge solution while we are still predominately use petrochemical-based polymers. Yet, it should be mentioned – again – that
over the past 70 years we have only recycled 9% of all plastic produced.
Biobased polymers can reduce our dependency on petroleum; however, if these materials are not biodegradable, we are not really addressing the problem. Figure 2 shows the level of biodegradation for various materials.
Marine degradability is the high bar and only a few synthetic fibers can
achieve this including PHA, viscose and lyocell. Unfortunately, these materials can’t be processed on existing nonwoven machines. PHA and PLA, for instance, can be processed on existing assets. PHA is known for its ability to degrade in a marine environment. More recently a study was published that indicated PLA does not result in persistent microplastics in a marine environment14. It would be very
beneficial for the market if companies could make a plastic-free claim when incorporating these marine degradable resins into their products. In the eventuality these materials did leak into the environment at least they would biodegrade and not result in microplastics. Due to their desirable end-of-life properties, these materials are being considered as alternatives. PHA, for instance, has been around for some time but due to high costs and lack of supply chain it has not been incorporated into high volume applications, like wipes and hygiene products. Fortunately, there are numerous suppliers working on solutions including RWDC, Danimer Scientific, Mango, Newlight, CJ Biomaterials, and Kaneka to name a few. The reality of the situation is there will need to be a significant investment of capital to install capacity to supply the growing markets; this could realistically take decades. In the mean-
At Fiberpartner we provide fiber in many forms and shapes. We support a broad variety of industries, and we are happy to help whether you are looking for traditional polyester, the newest plant-based technology, or something in between.
Fiberpartner is a Danish advisor and supplier of textiles including PrimaLoft®Bio™. We understand the urgent need to transform polyester production and consumption for a more sustainable future.
We recently added PolyPlant® – a new innovative fiber that looks, feels, and acts like polyester, while not sharing its impact on the environment.
See you at IDEA®25 in Miami Beach.
time, there are other materials like PLA that can play a significant part in the solution due to existing supply.
Every minute, more than 300,000 disposable diapers around the world are incinerated, sent to landfill, or pollute the environment15. If we could instantly make diapers out of biodegradable materials today, would we solve the problem or make things worse? It turns out that if we start disposing more biodegradable materials into landfills, we will in fact produce more methane due to biodegradation in an anaerobic environment. Methane is a potent greenhouse gas that has more than 80 times the warming power of carbon dioxide over the first 20 years after it reaches the atmosphere.
Even though CO2 has a longer-lasting effect, methane sets the pace for warming in the near term16. A better way to handle these biodegradable materials is through industrial composting. Composting is simpler than recycling in that more complex products would not need to be broken down like advance recycling. Furthermore, the compost can be used to produce the feedstock for biopolymer production, see the circular carbon cycle for PHA.
I am encouraged by all the industry activity and focus to develop the products solutions and supply chains for alternate polymers like PHA. Many suppliers have plans to install more capacity. The larger issue is the demand for substitute poly-
harmful methane gas emissions, 20 times more harmful than carbon dioxide, according to Euromonitor 2017.
mers is now, not later. For the previous example of the diaper market, we would need 400 25kT plants to supply the nonwovens for only one product category. Realistically, it will take time to develop the solutions and supply chains for these alternate materials. With the criticality of the problems to solve and potential
impacts on humanity, we must fast-track efforts to effectively address the situation.
Based on the dire circumstances presented in images, scientific data, and our collective personal observations, it is clearly apparent that we are in a precarious situation as an industry. There is no immediate solution. I argue that unless our industry works together more effectively, we may be ineffective in developing viable solutions. Furthermore, it will require cooperation between our industry and governments, as well.
Regulation will play a key role on testing standards and evaluating impacts on the environment and health. In an ideal situation of cooperation, companies would seamlessly share data in order to develop solutions faster. The coopetition across the industry is more for the thriving of humanity versus achieving corporate imposed quarterly earnings.
Consider this a call to industry to drop the corporate veil and operate more openly to solve the problem. The question at hand is: Will you join us in this cause?
Reach out today INDA to join the conversation on sustainability.
Bryan Haynes is the Technical Director Global Nonwovens at Kimberly-Clark, driving the development and governance of key strategies including: Open Innovation, Intellectual Property, and Nonwoven Platform Technologies. He is also past-Chairman of the INDA Board of Directors.
1 https://environment.ec.europa.eu/topics/plastics/single-use-plastics_en
2 https://www.un.org/en/climatechange/nations-agree-end-plastic-pollution
3 https://marinedebris.noaa.gov/why-marine-debris-problem/ingestion
4 https://newmaterials.uga.edu/what-is-plasticosis-is-it-a-ticking-time-bomb-for-human-and-animal-health/
5 https://www.sciencedirect.com/science/article/pii/S0160412020322297
6 https://www.sciencenews.org/article/microplastics-nanoplastics-heart-attacks-strokes-health
7 https://www.latimes.com/environment/story/2024-01-18/health-costs-of-plastics-run-250-billion-a-year
8 https://www.genevaenvironmentnetwork.org/resources/updates/plastics-and-climate/
9 https://www.kimberly-clark.com/en-us/company/supplier-link/standards-and-requirements/socialcompliance/sustainability-policies and https://www.kimberly-clark.com/en-us/esg/2030-ambition
10 https://www.kimberly-clark.com/en-us/esg/2030-ambition/esg-article/product-packaging-circular-systems
11 https://environment.ec.europa.eu/topics/plastics/biobased-biodegradable-and-compostable-plastics_en
12 https://www.unep.org/inc-plastic-pollution
13 https://www.oecd.org/en/about/news/press-releases/2022/06/global-plastic-waste-set-to-almost-tripleby-2060.html
14 https://www.nature.com/articles/s41428-020-00396-5
15 https://www.weforum.org/agenda/2023/08/disposable-nappies-landfill-plastic-circular-economy/
16 https://www.edf.org/climate/methane-crucial-opportunity-climate-fight
By Caryn Smith, Chief Content Officer & Publisher, IFJ
The nonwovens industry faces a huge challenge to transition from non-sustainable product applications to responsibly sourced eco-friendly products that contribute to the health of the planet, as well as to the benefit of consumers who depend on these products in their daily life.
International Fiber Journal interviewed with Matt Seaholm, President and CEO of the Plastics Industry Association (PLASTICS), as well as Patrick Krieger, Vice President of Sustainability, on the issue of PCR in Nonwovens – including the research and development, trends, roadblocks, potential, and successes, and the collaborations between industries that increase the circularity factor in nonwovens to produce real change. Here is what they had to say.
International Fiber Journal: Explain how PLASTICS is aligning with other industries to tackle the plastics problem in general? What are some current initiatives that you are spearheading of note?
Matt Seaholm: Plastics are a part of every industry. If we think about how plastic is woven into all the supply chains of every manufacturing sector, it’s important for us to work across a variety of industries to ultimately keep more plastic in the economy and out of the environment.
President & CEO PLASTICS
PATRICK KRIEGER Vice President, Sustainability
One example of how we’re working across the value chain right now is our recently announced Flexible Film Recycling Alliance. This initiative is about working with retailers, environmental NGOs, brands, manufacturers, and that includes parts of supply chain of the plastics industry to make sure that we are increasing recycling rates for all plastics, including flexible plastics.
IFJ: What is your position on plastics and circularity? How do you see the plastics industry in general collaborating with its customers to improve environmental effects of plastics?
Seaholm: Circularity is about the value capture of plastic waste. If waste is more valuable because it’s in demand and because it’s easy to recycle, less of it will go into the environment and more of it will stay in the economy. We can work to improve the recyclability of the product, but we also need to make sure that consumers help us get more of that plastic back, and that sometimes comes in the form of education or deposits. We must make sure that the value is there in the plastic waste so that it stays in the economy and doesn’t end up in the environment or a landfill.
IFJ: How do you imagine or believe that nonwovens producers can partner with the PLASTICS and industry to achieve greater good for the future? How is your organization shepherding those kinds of efforts?
Seaholm: First, there needs to be an echo chamber for the value of plastic. We all have a desire to end plastic pollution, and we all know the value that plastic plays in society, from health to safety to stable supply chains. Across the board, plastic is a wonderful material as long as it stays out of the environment. We need to work together to tout its benefits and work hard to keep more of it out of the environment. In addition, I would stress innovative solutions as a key responsibility of the industry. Any manufacturer of any plastic
product should be innovating new and exciting manufacturing techniques and different materials. For example, those innovations could be about recyclability or bio-based material that can either break down in a compostable setting or perhaps even biodegrade. Manufacturing plastic and plastic products in America is a good thing and we should make sure that it doesn’t stop, and we do everything we can to keep waste out of the environment.
IFJ: How does PLASTICS view petroleumderived vs bio-derived plastics?
Seaholm: We strongly believe and support both. We believe in an ‘all the above’ approach that’s based on performance and sustainability. I think there is some healthy competition there, but that’s a good thing and we would certainly support a free market that encourages that competition and promotes the value and benefits of both bio-based and petroleumbased material.
IFJ: What is the current stance of PLASTICS on mechanical recycling of plastics considering the large amount of recent skeptical to outright negative press it is receiving?
Seaholm: We need mechanical recycling, period. It’s an important part of the present and the future. Mechanical recycling is the right thing to do for a variety of products, so it is absolutely going to be maintained as an important mechanism for circularity, and we strongly support it. With advances in advanced recycling technology, there exists a third source of raw materials for plastics that is “wastederived,” rather than petroleum or bioderived.
IFJ: What is PLASTICS stance on such materials and how advanced recycling derived inputs can be counted for with respect to “recycled content” claims?
Patrick Krieger: Advanced recycling comprises a wide range of recycling technologies that can result in very diverse products. We have a “plastics into materials”
approach, which means that only outputs from plastics recycling that are made into plastics or other products are recycled plastics content.
While we aren’t aware of a cumulative estimate of the amount GHG emissions “saved” by using plastics in lieu of other materials, a recently published study in Environmental Science & Technology showed that non-plastics alternatives were 35% to 700% more impactful in emissions.1
IFJ: Considering the many benefits of plastics, does PLASTICS have an estimate of the total positive impact of plastics on the environment in terms of reduced GHG emissions and/or reduced carbon footprint?
Seaholm: Recent research points to exactly this. An independent report by McKinsey found that plastics have lower total greenhouse gas contribution than alternatives. Another report by Environmental Science and Technology came to the same conclusion. Plastic wins, there’s no doubt about it. Plastic is the best material in the vast majority of the applications that it’s used for, we just have to make sure that we collect, sort and ultimately recycle more of it.
IFJ: How does PLASTICS view the related, but separate, topics of biodegradable and
compostable plastics? For instance, what is your position on potential regulation requiring “biodegradable” plastics to breakdown molecularly rather than breaking down to micro- and nano-plastics? Where do you see compostability of plastics going in the future?
Krieger: Appreciate the recognition of the differences between “biodegradability” and “compostable plastics.” I like to say that biodegradability is like the word “delicious” – pizza and ice cream are both delicious, but in very different ways. Terms like home- or commercially-compostable are much more context-specific and provide consumers with more information on how to dispose of a product at end of use. We encourage the use of the more specific terminology.
I don’t know which specific regulations you are referring to, but I think they may misunderstand the process of biodegradation. Biodegradation by its nature includes fragmentation into smaller and smaller pieces, much like an ice cube melting. At some point, these fragments will be at the micro- and nano-scale and will continue to further break down completely into products like biomass, carbon dioxide, and other elements and molecules found in nature.
Compostable plastics can help consumers divert organics like yard and food waste – the largest component of waste to landfill – into processes that convert them into compost, which is used as a soil amendment and fertilizer. If the US is committed to reducing waste to landfill, composting will need to be a big part of that future. Growth of the industry is contingent on the US building more commercial composters that accept these products, and there are bills currently being debated in Congress, like the COMPOST Act, that will help invest in these important pieces of infrastructure.
IFJ: Considering potential bans on singleuse plastic items and/or requirements for reduction of plastics in packaging, how is PLASTICS advocating for sensible legislation rather than broad sweeping legislation or out-right bans?
Krieger: There needs to be strong end markets for the recyclable material and that’s why we support recycled content requirements. If you guarantee an end market for that recyclable material, you guarantee that there is value in it and the combination of public and private financing will come into place to make sure that it is collected, sorted and ultimately recycled.
Secondarily, we have to modernize and improve our recycling infrastructure and that’s where we now support extended producer responsibility laws that apply a small fee to the different types of packaging in order to make sure that they ultimately get recycled.
Matt Seaholm is the President and CEO of the Plastics Industry Association (PLASTICS) as of April 2022, leading the only association representing the entire plastics supply chain, employing nearly one million Americans in a $468 billion dollar plastics industry, the sixth largest manufacturing sector in the United States. Matt has since reestablished the association’s mission, built the foundation for a newly principled set of strategic priorities, assembled a seasoned, experienced executive team, and authenticated an advanced approach to the message and mission of PLASTICS. Along with the PLASTICS executive officers and board, and on behalf of the industry, Matt has led an enhanced focus in the areas of sustainability, communications and advocacy, prioritizing the protection, promotion and growth of the industry as well as business opportunities and engagement for association members. Prior to becoming President & CEO, Matt served as PLASTICS’ Vice President of Government Affairs. He has been with PLASTICS since 2016.
Patrick Krieger is the Vice President, Sustainability at the Plastics Industry Association (PLASTICS). He leads the association’s efforts in advocating for the growth of the plastics industry in a sustainable way by working with its members and the leadership of the Sustainability Advisory Board. He works to promote the recycling of plastics through demand-side projects in the New End Market Opportunities program as well as advocating for policies that strengthen US mechanical and advanced recycling. He also manages the international plastic resin stewardship program, Operation Clean Sweep. He joined the PLASTICS in March 2015.
v3Half Horizontal Print Advertisement.pdf 1 6/18/24 11:21 AM
We’ve been asleep at the wheel for a couple of decades in many regards when it comes to the collection and sortation of recyclable material, and it’s made the economics of recycling a little bit untenable. We have to improve those economics and we can do it by guaranteeing end markets and by modernizing the infrastructure to make it more efficient.
1 Environmental Science and Technology, “Replacing Plastics with Alternatives Is Worse for Greenhouse Gas Emissions in Most Cases;” Fanran Meng, Miguel Brandão, and Jonathan M Cullen, https://pubs.acs.org/ doi/10.1021/acs.est.3c05191?ref=pdf
By Wes Fisher
Sustainability topics are top of mind for virtually every industry across the globe, and nonwovens are no exception. In fact, the nonwovens industry has been at the forefront of innovation in terms of sustainability with significant investments being made in the areas of natural inputs, biopolymers, and other breakthrough innovations in the areas of composting and degradation.
Despite industry advancements, significant regulatory headwinds across the globe will have an impact on the global nonwovens industry and will provide significant direction for the industry over the next decade.
While many of these global legislative and regulatory activities are aimed at serving noble causes such as alleviating plastic pollution, microplastics, and carbon outputs, many of these policies often intentionally or unintentionally shut off pathways to innovation to the detriment of the consumer, companies, and the environment.
Here in the United States, the question I get the most is, “What is single-use plastics regulation going to look like at the national level?” Unlike, Europe, there has been no significant movement of enacting single-use plastic bans at the federal level, and any action regarding plastics regulation is likely to come from federal agencies as opposed to Congress. Last year, the Environmental Protection Agency released a “Draft National Strategy to Prevent Plastic Pollution,” which aims to eliminate the release of plastic waste from land-based sources into the environment by 2040 by reducing, reusing, composting, collecting and capturing plastic waste in
coordination with existing national recycling programs. This strategy has drawn some criticism from industry groups for focusing on reducing plastic production rather than end-of-life considerations.
In short, the answer to the question of what national plastics policy will look like in the United States is that any significant federal policy will likely take years to implement. With this in mind, many states will not wait for the federal government to act on this issue. States including Connecticut, California, Delaware, Hawaii, Maine, New York, Oregon, and Vermont, have acted on single-use plastics, with plastic bags being the first products to be targeted. Since 2014, all the states mentioned above have enacted bans on plastic bags, with some exemptions, and have begun to move on to items such as straws, plastic bottles, utensils, and carry-out containers. Significantly, many of these bans were first seen at the local level as early as 2007 and many cities, towns, and counties have enacted highly restrictive plastic bans, while seventeen states have some sort of state-level preemption that precludes localities from enacting such policies.
State and federal policy in the United States has yet to significantly target plastic-based nonwoven products however hand wipes have been included in some legislation requiring plastic items to be available only upon request. This is likely to change in the coming years as some states, such as Massachusetts, have seen the introduction of wide-sweeping plastic ban legislation that would prohibit the sale of plastic-containing wipes. While that language is not expected to become law in Massachusetts in 2024, the inclusion of wipes in such legislation should indicate to the nonwovens industry that state-level regulation of plastic contain-
ing nonwovens should not be something to overlook.
This increased focus on state government affairs is a trend we have seen throughout industry groups as many groups have recognized that while Congressional dysfunction continues, resources must be invested to educate state policymakers about the importance of making science-based policy decisions.
Meanwhile, the European Commission’s single-use plastics directive, which stemmed from the commission’s 2018 plastics strategy has become well-known for its breadth and is among the most discussed regulatory developments in the nonwovens industry in recent years. The directive is ostensibly targeted at reducing
marine litter and targets items based on the most commonly found plastic items on beaches. Nonwoven products including absorbent hygiene and wet wipes were addressed in the directive, which includes approaches including bans, reduction targets, and Extended Producer Responsibility (EPR) schemes where producers contribute to clean-up costs and consumer awareness campaigns.
Our friends at EDANA have been engaged with the European Single-Use Plastics Directive since its launch in 2018, signing on to a variety of position statements calling for revisions to the definition of plastic to ensure cellulose fibers would not be included in the scope of the regulation, and in 2020 calling for a withdrawal or revision of the EU’s seven-year budget that included a plastics tax that would an 80 cent levy on each kilogram of non-recycled plastic packaging, which the European Commission calculated would generate €6.6 billion a year.
One criticism of Europe’s single-use plastics policies has been a perceived lack of emphasis on bioplastics as a piece of the puzzle in solving the issue of plastics pollution. A 2022 “EU policy framework on biobased, biodegradable and compostable plastics” laid out the thinking of the EU’s approach to plastics stating that “The EU’s transition to a circular, resource-efficient and climate neutral economy, together with the ambition to reach zero pollution and the need to protect and enhance biodiversity have triggered an overall rethinking of how plastics are produced, used and disposed of.”
In weighing potential subsidies and other options for encouraging the increased production and use of bioplastics, the EU has stated bio-materials will need to be labeled in a manner that would indicate how long it would take to biodegrade and whether, for example, if the material can be home composted or if it would require industrial composting.
European Technical Committee for Standardization for biobased products (CEN/TC411) has shouldered most of the EU’s ongoing work regarding bioplastics definitions and in 2021 released the first EU standards for biobased products,
which included details on terminology, sampling, certification, bio-based content, life cycle analysis, and sustainability criteria for biomass used and for final products.
The EU is expected to prioritize circularity when weighing potential regulations. For example, in a 2022 proposal on packaging legislation, the EU stated that it wanted to prioritize bioplastics made from waste byproducts rather than bioplastics made from crops grown specifically for that purpose in order to avoid using extra land and agricultural resources that, according to the EU, would further “strain” the environment.
treaty should be comprised of voluntary national action plans or a more robust legally binding international agreement. INDA and EDANA are engaged in the UN plastics treaty process as accredited UN stakeholders and will continue to provide feedback to the UN on behalf of the global nonwoven industry.
In conclusion, sustainability trends are rightfully at the top of mind for most in the nonwovens industry. While the United States and Europe are at different points in terms of plastics and sustainability regulation, the overarching themes are very much the same, with some U.S. states looking to legislate more aggres-
Many states will not wait for the federal government to act on this issue. States including Connecticut, California, Delaware, Hawaii, Maine, New York, Oregon, and Vermont, have acted on single-use plastics, with plastic bags being the first products to be targeted.
The EU and national governments aren’t the only bodies discussing bold action on plastics and sustainability. At the United Nations, there is an ongoing treaty negotiation regarding plastic pollution. The ongoing treaty negotiations are formally titled “Intergovernmental Negotiating Committee to develop an international legally binding instrument on plastic pollution, including in the marine environment.” The treaty is slated for a fifth in-person negotiation session in late-November 2024 following a slow start during the first four sessions and delegations are being pressured to meet a self-imposed deadline to finalize a treaty by the end of 2024.
The more ambitious countries and NGOs engaged in treaty negotiations have called for a treaty that phases out the global production of most types of plastics while others have promoted an application-based approach that looks at which plastics applications are most likely to contribute to environmental harm. Furthermore, much of the conversations surrounding the treaty have included conversations about whether the
sively and quickly than the U.S. federal government when it comes to environmental issues.
Outside the United States, from Europe to the United Nations, plastics and sustainability are at the top of mind for policymakers. Over the next decade, it is expected that the focus on these issues will only expand with more products, including many nonwovens, that had not been previously regulated, having the potential to be pulled into scope. Throughout this period of significant regulatory activity, INDA will continue to advocate for regulators to take into account the importance of nonwoven materials and the need for flexibility in regulation to allow for innovation.
Wes Fisher is the Director of Government Affairs at INDA, the Association of the Nonwoven Fabrics Industry, where he leads the association’s global and domestic government and regulatory affairs activities and manages strategic relationships with allied organizations, government officials, industry partners, and stakeholders in support of the nonwovens industry.
By Jason Chen, International Correspondent, China, IFJ
Today, the world’s nonwoven production is dominated by petroleumbased resins, most prominently polypropylene (PP) and polyethylene terephthalate (PET). But bio-based materials have also gained significant momentums in recent years due to their advantages in sustainability and low carbon footprint – the global efforts for carbon reduction, environmental protection, as well as less reliance on oil and petrochemicals have provided key driving forces to the growth of nonwoven fabrics made of bio-based materials such as cotton, viscose, and polylactic acid (PLA).
However, the disadvantages of biobased nonwoven fabrics in performance, cost, and efficiency still inhibit their growth in various product segments and applications. Currently, researchers are working on new solutions to tackle these problems, covering sections from fiber treatment, nonwoven structures, composites, modifications, to customized processing methods and equipment for bio-based nonwoven production.
Bio-based materials for nonwoven production include three major types: biobased natural fibers, regenerated fibers, and bio-based synthetic resins.
Natural fibers include plant fibers, animal fibers, and mineral fibers. Plant fibers (e.g., cotton, hemp, flax, jute) and animal fibers (e.g., wool, silk) are bio-based, while mineral fibers (e.g., asbestos) are not. Regenerated fibers include regenerated cellulose (e.g., viscose, lyocell), protein, and chitosan fibers. They are all biodegradable. Bio-based synthetic resins are produced by chemically or biologically synthesizing renewable organic materials such as corn, sugarcane, and straws. Polyhydroxyalkanoates (PHAs), polybutylene succinate (PBS), and PLA are bio-
Forecasts report that global PLA capacity could be fivefold from 460 thousand metric tons in 2022 to 2.38 million metric tons by 2027.
degradable, while the bio-based editions of polytrimethylene terephthalate (PTT), polyethene (PE), polyamide (PA), PP, and PET are not.
Cotton is the most widely-used plant fiber for making nonwoven fabrics. It played an important role in the early stage of nonwoven industry, and has been in the spotlight again because of recent advancements in green production.
As a natural fiber, cotton has many good characteristics: it is bio-based, biodegradable, comfortable, and processable, and has good absorbency, among many other benefits. However, cotton also has its own problems, even in the environmental field where it claims to be “natural” and “green.” For example, its cultivation requires extensive land use, vast amounts of water consumption, and significant use of pesticides and fertilizers. Another example is that the cleaning and treating process that turns cotton fibers to nonwo ven raw materials also consumes a substantial amount of water, chemicals, and energy.
The cultivation problems can be solved by using organic cotton, although at a premium price, while the cleaning and treating problems require innovated methods such as mechanical cleaning and vision systems. For example, the Greenwood, MS-based WildWood Cotton Technologies (WCT) has a mechanical cleaning process, which cleans cotton fibers without using water, chemicals or process heat, for its unbleached TruCotton grades for nonwoven production. Recent research and development in this section may also incorporate vision systems with deep learning (DL), a branch of machine learning (ML) and artificial
Industrial grade of TruCotton™ is engineered for needlepunch nonwovens. This low-cost grade is also used as a high-quality pre-cleaned, contaminationfree stock for bleaching.
EcoCosy® is Sateri’s flagship brand for its viscose rayon fibres, made from wood cellulose from sustainably-managed plantations. It’s soft, comfortable, breathable, absorbent, and biodegradable
intelligence (AI), into the cotton cleaning and purifying process, aiming to further improve efficiency and purity, according to the technologies under development by China’s Xi’an Polytechnic University and several other universities and companies.
At the same time, conventional cotton nonwoven producers are also working on optimizing their cleaning and treating process to consume less water, chemicals, and energy. Other innovations for cotton nonwoven fabrics include improving their tensile strength, biocompatibility, antibacterial property, softness, and other performances, while turning the whole cotton nonwoven manufacturing process to a greener way by energy saving.
On the other hand, bast fibers (e.g., hemp, flax, jute) are regarded as an alternative to cotton in nonwoven production because they use less arable lands, water, pesticides, and fertilizers. However, the patterns and characteristics of bast fibers often have negative impact on production efficiency and nonwoven fabric properties – they are very coarse and difficult to be processed, and often require extensive treatment before being put into
nonwoven production lines. Therefore, pretreatment technologies become a pivot for bast fibers being used.
The Canada-based Bast Fibre Technologies (BFT) is one of the active developers in this field. The company has a patented technology that treats bast fibers to provide crimps – using a portion of these treated bast fibers in nonwoven production will secure the desired properties and performance of the final nonwoven fabrics.
Recent research and development from other companies and universities mainly focus on customized equipment for bast fiber-based nonwoven fabric production, and formulas or composites for additional or improved characteristics such as flame retardants, abrasion resistance, antibacterial property, and liquid absorbency.
Animal fibers, such as wool and silk, are often too expensive to be used in nonwoven production. Therefore, researchers use two methods to reduce their costs:
The first method is to use reclaimed or discarded animal fibers and cuttings. Reclaimed wools and cuttings have cre-
ated a substantial recycling market in some countries, but discarded wools are also everywhere – for example, the wools of some species of mutton sheep are low-quality and often discarded directly because there is no place to sell. These recycled animal fibers at low costs are suitable for nonwoven production after appropriate treatment.
The second method is making composite nonwoven fabrics of animal fibers with other less-expensive bio-based materials such as cotton and regenerated cellulose. For example, the China-based Suzhou Xianchan has a patented technology for producing spunlace composite nonwoven fabric from silk and less-expensive natural fibers or regenerated fibers. With only a small portion of silk being used, the final nonwoven fabric has a surface, touch, and luster similar to natural silk, while maintaining its bio-based and biodegradable advantages.
Some researchers combines the advantages of above two methods. For example, Xi’an Polytechnic University has developed a composite nonwoven fabric for packaging applications from reclaimed wools, polylactic acid (PLA), and woodpulp cellulose through a wet-laid process. Similar researches from other universities and companies show that composite wool-based nonwoven fabrics can be used in medical, sports, protective, automotive, and other applications.
Chitosan is a chemically cellulose-like biopolymer processed from chitin, the world’s second largest natural polymer after cellulose in terms of annual production volume.
Regenerated cellulose fibers have long taken a considerable market share in nonwoven production. Today regenerated cellulose manufacturers provide many different products and grades for nonwoven production. These grades include the Austria-headquartered Lenzing’s VEOCEL™ Lyocell fibers, a certified net-zero carbon footprint, the China-based Sateri’s EcoCosy® viscose rayon fibers, and other cellulose fibers from Kelheim Fibres GmbH (Germany), Birla Cellulose (India), Shanyou (China), among many others.
But regenerated cellulose fibers have their own environmental problems. The manufacturing process may involve washing and bleaching with chlorine, or other chemicals which exacerbate pollutants.
In addition, the pretreatment process for regenerated cellulose fibers before nonwoven production often causes problems such as surface damage and strength reduction. Current research and development mainly focus on solving these problems. For example, the Chinabased Chenyang, a nonwoven producer, developed an equipment for cleaning while protecting viscose fibers before they are put into nonwoven lines.
Protein materials have also made some progresses in nonwoven production recently. For example, in addition to being used as a natural fiber in nonwoven production, as mentioned above, reclaimed wools are also used to extract keratin, a protein that can be used for making nonwoven fabrics.
According to the patented technologies developed by China’s Wuhan Textile University and several other institutes, protein nonwoven fabrics originated from reclaimed wools could exhibit excellent antistatic property, good abrasion resistance, and several other benefits.
Researchers also use chitosan as a raw material, along with bamboo-pulp fibers or other bio-based fibers, in making multiple-component nonwoven fabrics.
Chitosan is a chemically cellulose-like biopolymer processed from chitin, the world’s second largest natural polymer after cellulose in terms of annual production volume, which indicates its potential of abundant supply globally in the future.
Protein and chitosan nonwoven fabrics are currently not been available in the market at a large scale. But these two types have been used in modifying other commercialized bio-based or petroleum-based nonwoven fabrics to increase the finish products’ biocompatibility, antibacterial performance, and other properties.
Bio-based synthetic resins will be the fastest-growing segment among the three major bio-based nonwoven types, although their current market size is still
far smaller than natural fibers and regenerated fibers. It is where many are placing priority in the race to create a closed loop value chain (Figure 1).
PLA is the most promising one is this segment. European Bioplastics e.V. forecasted that the global PLA capacity could be fivefold from 460 thousand metric tons in 2022 to 2.38 million metric tons by 2027, which will provide substantial amounts of raw materials for bio-based nonwoven production (Figure 2).
Unmodified PLA has disadvantages such as brittleness and low heat distortion temperatures. Therefore, it is often modified through chemical or physical modification methods or blended with other resins to improve their tensile strength, tensile modulus, thermal stability, biodegradability, biocompatibility, and other properties before being used in nonwoven production. For example, the Brazil-headquartered Fitesa produces spunmelt nonwoven from a blend of biobased PE and bio-based PLA. However, as bio-based PE is not biodegradable, the nonwoven’s biodegradability decreases. Other companies and institutes have developed similar solutions that blend PLA with bio-based PTT or other nonbiodegradable resins.
PLA manufacturers also face problems
about nonwoven equipment. Most of the nonwoven equipment available in the market today are for the production of PP, PET, PA, PE, and other conventional petroleum-based nonwoven fabrics.
The China-based Dalian Hualun Nonwoven Equipment Engineering Co. Ltd. (Hualun), a nonwoven equipment developer and manufacturer, concluded that PLA nonwoven equipment should be specifically designed to prevent fiber breakage, improve web softness and uniformity, and increase tensile strength, compared to other conventional nonwoven equipment.
Hualun is the manufacturer of a PLA nonwoven production line operated by the Hong Kong-headquartered U.S. Pacific Nonwovens Industry Ltd. in its Dongguan, China-based facility. This line has an annual capacity of 2,800 metric tons with widths of 2.4 meters and weights ranging from 17 to 150 grams per square meters (gsm).
Polyhydroxyalkanoates (PHAs) are also promising bio-based synthetic resin for nonwoven production, with a potential production of million metric tons per year in the future. The most prominent commercially available PHAs are polyhydroxybutyrate (PHB) and polyhydroxybutyrate hydroxyvalerate (PHBV). However, the capacity and development of PHAs
are still in the early stage. Currently global consumption of PHAs for both woven and nonwoven fabrics stays at only around 1,000 metric tons per year.
Pure PHAs nonwoven fabrics have similar problems as their PLA counterparts: brittleness, low tensile strength, etc. In addition to chemical and physical modification methods, researchers are also trying to use innovated structure to solve these problems.
For example, the China-based Zhuhai Maidefa Biotechnology Co. Ltd. (Maidefa) developed a three-layer structure to enhance the performance of their PHAs nonwoven fabrics. Researchers from the company found that excessive tensile deformation in both weft and warp directions would happen when a PHAs nonwoven is under external force. The excessive deformation at that level would limit the use of PHAs nonwoven fabrics in many applications.
To solve the problem, the researchers develops a three-layer structure, which includes two PHA surface layers and one base layer made of cotton fabric in the middle, with a thin cotton fabric covered the edges of the nonwoven long wise. The base layer, bonded to the surface layers with starch adhesive, and the covered fabric, stitched to the nonwoven with
cotton yarns, provide enhanced strength to the nonwoven fabric. An additional benefit of this structure is that it helps prevent the roughness and unevenness of fabric edges. Maidefa was founded in 2019 as one of the early developers for PHAs nonwoven. It received approximate $10 million of series-A funding in 2022.
Multiple-component nonwoven fabrics made of PLA and PHAs or PBS are also under development. Researchers from Jofo, a major global nonwoven producer, and other companies show that spunmelt nonwoven fabric made of blends of PLA and PHAs or PBS have benefits of less brittleness, larger elongation, and higher softness, compared to those spunmelt nonwoven fabrics solely made of PLA resins.
Alternatively, the bio-based but nonbiodegradable synthetic resins such as PP, PET, PE, and PA may gain more market shares from their petroleum-based counterparts in the near future. Although being non-biodegradable, they still have a significantly reduced carbon footprint.
Their main advantage is that their petroleum-based counterparts have had very mature methods and equipment for nonwoven production readily available in the market, which is relatively easy to be adapted for corresponding bio-based nonwoven production.
As global chemical giants such as Braskem, LG, Borealis, and LyondellBasell have unveiled their ambitious plans on bio-based PP, whose petroleum-based counterpart has grabbed nearly half of the global nonwoven production, this segment may see a significant growth in the following decade.
Jason Chen is an international correspondent for International Fiber Journal . He is a leading journalist covering the fiber industry in Asia and a senior analyst who has published more than 50 books and reports for polymers, composites, and other advanced materials and technologies. He can be reached at jasonchen200501@hotmail.com
By Monique Buch
As a leader in wood-based cellulosic fibers, Lenzing has a particular responsibility and ambition to help raise the bar for sustainability in nonwovens industry.
Wood and dissolving wood pulp are the most important raw materials for Lenzing and there are potential risks associated with their sourcing, such as deforestation, climate changes and biodiversity loss. This is why Lenzing only procures wood from sustainable managed forests. More than 99% of the company’s wood and pulp sourcing is certified by globally recognized standards, such as the Forest Stewardship Council (FSC®) and the Programme for the Endorsement of Forest Certification (PEFC).
Lenzing proudly wears a “dark green shirt” in Canopy’s Hot Button Ranking, signifying its exemplary performance in responsible sourcing. Furthermore, the company has achieved an “A” rating from CDP Forests, reflecting its dedication to forest conservation efforts. Additionally, the Lenzing Group has been awarded EcoVadis Platinum status for the second consecutive time, highlighting its outstanding sustainability practices and leadership in the industry.
Driven by the Single-Use Plastics Directive within the European Union, there’s a noticeable surge in demand for nonwoven materials engineered to be biodegradable and compostable, reflecting a growing preference for sustainable alternatives that mitigate the ecological impact of traditional single-use plastics. Cellulosic fibers such as VEOCEL™ fibers derived from the natural raw material wood, offer a biodegradable alternative to
plastics, helping to reduce the impact of lost materials on ecosystems, water and soil compared to plastics, which have not been disposed correctly. We also see a similar trend of switching from synthetics to cellulosic fibers as there is an increased understanding of ‘leakage,’ wear of synthetic products and as such releasing micro plastics into the environment, e.g. glaciers or even into food and beverages in case of some filtration applications.
When considering sustainable sourcing solutions in their company offerings, organizations should begin by prioritizing transparency and traceability throughout the supply chain. This ensures the verification of sustainability credentials for both raw materials and suppliers. Additionally, it’s crucial to evaluate the environmental impact of sourcing decisions, taking into account factors like carbon footprint, water usage, and waste management. Seeking certifications and standards, such as FSC, OEKO-TEX®, and ISO 14001, further validates the sustain-
ability and ethical practices of suppliers and products. Moreover, investing in research and development enables the exploration of innovative materials and production processes that align closely with sustainable sourcing goals. By integrating these considerations into their sourcing strategies, companies can contribute to a more sustainable and resilient nonwovens industry while meeting the evolving needs of customers and stakeholders.
Monique Buch holds the position of Executive Vice President Nonwovens at Lenzing AG, where she is P&L accountable for the Nonwovens division and leads all commercial activities within the nonwovens sector while also driving the strategic development and growth of the VEOCEL™ brand. With extensive experience in commercial and strategic management across diverse B2B manufacturing environments, she has occupied leadership roles at prominent companies such as Freudenberg Performance Materials and Owens Corning. Monique’s expertise lies in driving profitable growth, fostering the commitment to sustainability and the advancement of responsibly produced cellulosic fibers.
By Koen Bastiaens
s sustainable innovations in biomaterials continue to proliferate, the nonwovens industry faces challenges – but also enormous opportunities.
Recent advances in applications development for polylactic acid (PLA) nonwovens provide new performance benefits that allow for expanded commercial use of PLA at scale in new hygiene applications. These developments accompany an increased focus from brands on the carbon footprint and source of the materials they use as they look at sourcing improvements and carbon reductions for their sustainability reports and ESG disclosures.
Biomaterials like PLA may not be the perfect solution for all nonwoven applications yet, but their performance benefits and sustainability credentials make them an immediately available swap for many petrochemical-based nonwovens. With recent technical advances like achieving low basis weights, improved softness and strength, fluid management that outperforms polypropylene, and increased conversion efficiencies, PLA demonstrates potential for biobased nonwovens to meet both performance and sustainability needs for hygiene products.
Sustainable sourcing of materials is a top priority for hygiene brands that are looking to market products as biobased or plant-based to consumers who are looking for more sustainable hygiene products. Incumbent materials like polypropylene are made from non-renewable fossil feedstocks like natural gas. In contrast, PLA is made by fermenting plant sugars derived from annually-renewable
feedstocks into lactic acid, the building block for polylactic acid.
Transitioning to PLA and simi lar biobased materials enables brands to decouple their products from fossil-based materials and integrate biomaterials with low carbon footprints into their products. In fact, based on peer reviewed data published in third-party journals, Ingeo™ PLA has a car bon footprint 62% smaller than polypro pylene1,2 and 77% smaller than polyester To translate this into a real-life compari son, replacing 1 PET wipe with one made from Ingeo PLA is equivalent to reducing the carbon emissions equivalent to driving a new car 100 feet.
they are unwilling to accept substitutions that sacrifice performance attributes and manufacturing speeds delivered by fossilbased incumbent materials.
Additionally, biobased nonwovens made from PLA can achieve biobased certifications like OK Biobased or USDA Biopreferred as they contain measurable biogenic carbon, or carbon captured by plants. These certifications underpin a brand’s ability to make claims on biobased content to consumers while adhering to the FTC’s Green Guides which regulate the advertising of environ-mental claims.
We’ve observed that while hygiene brands are interested in replacing fossil-based
We believe the future of PLA is direct greenhouse gas conversion, in which biomaterials will be made from greenhouse gasses themselves, rather than biogenic carbon. To achieve such innovations, however, the industry must first continue to grow in applications and commercial availability. This will encourage more partial biobased solutions and enable more products to transition fully to biobased materials. Promising new advances point toward active development in that direction.
Engineers at NatureWorks developed Ingeo grades that could be converted into a bicomponent spunbond nonwoven with a PLA core and a polyethylene sheath. With a basis weight less than 15 gsm and fibers less than 0.5 denier –roughly half of what was previously available – this new combination improved the productivity of the spunbond process by at least 30%. When made into hygiene masks, the new nonwoven achieved Level 2 requirements for both filtration and breathability conforming to the ASTM F3502-21 standard.
Within the diapers market, we understood there was a strong desire for a
material that was not only durably hydrophilic and soft, but still offered conversion efficiency. After years of innovation and reviewing various biomaterials such as PBAT, PBS, PHA, and others, we found a promising result in Ingeo 6500D. The
new Ingeo grade is 50% softer and 80% stronger than generic PLA and meets the needed at low basis weights for products desired for top sheets in diapers.
A more recent request we received was to increase the strength of biobased spunbond nonwovens for hygiene applications such as medical gowns and hygiene textiles. In response, NatureWorks applications engineers developed a biobased Ingeo PLA/PBSa blend using materials from PTT MCC that delivers increased tensile strength and elongation, allowing manufacturers to further optimize their material use with lower basis weight fabrics.
Of course, to continue achieving these sustainable innovations, the industry must grow in more sustainable adaptations and commercial availability. Biobased materials have become a viable solution across many nonwoven applications – wipes, face masks, diapers and
medical gowns are just a few – and can not only achieve performance parity, but outperform petrochemical-based nonwovens in certain applications. We are optimistic that these new and promising advancements indicate a continued and active development toward sustainable and biobased solutions.
To learn more about Ingeo PLA and its applications, visit natureworksllc.com.
1. Life Cycle Inventory and Impact Assessment data for 2014 Ingeo™ Polylactide Production. Industrial Biotechnology, Vol 11, No. 3. Pgs 167-180. June 2015
2. Comparison between the eco-profile data for Ingeo and an average of PP data published by PlasticsEurope and the American Chemistry Council.
3. Comparison between the eco-profile data for Ingeo and an average of PET data published by PlasticsEurope and the American Chemistry Council.
Koen Bastiaens is the Strategic Marketing Manager of NatureWorks.
By Geoff Fisher, European Editor, IFJ
In the new era of mobility, with electrification at the forefront, original equipment manufacturers (OEMs) are looking for lightweight and high-strength materials for environmentally friendly and high-performance vehicles, with the aim of reducing weight and therefore carbon dioxide (CO2) emissions that contribute to global warming.
OEMs are continuing to prioritize mass reduction in vehicles, driving demand for lightweight alternatives, such as highstrength steels, aluminum and composites. Nonwovens, too, can be of value in the transportation sector by helping to make vehicles lighter, quieter and more comfortable as well as saving resources.
With an eye on efforts to reduce fuel emissions, the transportation sector is looking to increase the use of non-metallic components of vehicles, as well as railway carriages, aircraft and maritime vessels, by replacing metal components with nonwovens or fibrous composites that can reduce overall vehicle weight, thereby resulting in increased fuel efficiency.
In volume terms, the amount of textiles/ nonwovens used in the average vehicle is relatively small compared with the overall vehicle weight, although the figure is growing.
As a result of higher demand for increased comfort and improved safety, the use of fiber-based materials has increased from 20 kg in a mid-size car in 2000 to around 40 kg today, according to the latest estimates.
While woven and knitted fabrics continue to dominate this total amount of textiles used within the automotive industry, nonwovens are becoming an increasingly attractive option for designers owing to their low weight and lower cost,
as well as other key properties such as sound insulation.
However, achieving scale in sustainable production will be essential for the widespread adoption of nonwovens, emphasizing the need for support in integrating these lightweight materials into mass-produced vehicles.
At present, nonwovens or composites that include nonwovens are used in around 40 different components in passenger vehicles, including seats, floorcoverings, headliners, trunk liners and hood liners, as well as underbody and wheel arch materials. They are also used in vehicle batteries, belts and tubes and single-use items such as filters.
Further, nonwovens are easy to handle during vehicle assembly: they are tailormade for their function and can be heatformed, embossed, lined, coated and
printed. And owing to their versatility and numerous benefits they are also widely used in the design and construction of other vehicles and transportation modes, such as aircraft, trains, boats, spacecraft and satellites.
The consumption of automotive nonwovens is currently estimated at around 40 m2 per vehicle; visible nonwovens account for only 10% of the entire amount of the total flat textile surfaces in vehicles, or around 4 m2. However, the gradual replacement of traditional textiles and even
Today more than 40 automotive parts are made with nonwovens fabrics, from trunk liners and carpets to air and fuel filters. EDANA
non-traditional materials, particularly certain hard plastic or metal components, with nonwovens is ongoing.
In addition, a number of automakers have made some undertakings to use more recycled materials in their latest models, aiming for acoustic performance, light weight, and recycled and recyclable content. However, the development of these eco-designed products has been hampered by higher costs and potential risks linked with using recycled materials, according to Refashion, the French textile, household linen and footwear industry’s eco-organization.
A major application for lightweight nonwovens in internal combustion engine vehicles is in insulating materials for absorbing engine noise and dampening the vibrations caused by it.
This is obviously unnecessary in electric vehicles (EVs), but noise reduction becomes even more critical for EVs
because external as well as internal noise sources are more audible to drivers and passengers. In addition, without excess heat from the engine, the cabin of an EV can be significantly cooler than that of a conventional vehicle, which requires different insulating solutions.
While needle punched nonwoven layers have been used for several decades as acoustic insulation components for the interior of vehicles, they are now increasingly employed as undershields and outer wheel arch liners, replacing the heavier polyvinyl chloride layers and providing a significant reduction in weight.
Switzerland-based Autoneum, a leading supplier of vehicle acoustic and thermal insulation, is now offering its lightweight Propylat technology to reduce both interior and exterior noise of vehicles.
The technology was originally developed by Germany’s Borgers Automotive, which was acquired by Autoneum in early 2023. It is characterized by a flexible material composition of natural and synthet-
ic fibers with a high recycled content and is said to contribute to significant waste reduction owing to its complete vertical integration.
The company said Propylat-based products not only contribute to reducing pass-by noise and improving driver comfort but are also up to 50% lighter than equivalent plastic alternatives, which results in a lower vehicle weight and, consequently, less fuel and energy consumption as well as lower CO 2 emissions.
Propylat technology consists of a mixture of recycled synthetic and natural fibers, including cotton, jute, flax or hemp, which are consolidated using thermoplastic binding fibers without adding any chemical binders.
Owing to the flexible technology, fiber composition and the variable density and thickness of the porous material, the properties of the respective Propylat variant, for example with regards to acoustic performance, can be tailored to individual customer requirements.
This allows the technology to be applied in a variety of interior and exterior components, such as wheelhouse outer liners, trunk trim, underbody systems and carpets. For instance, Propylat-based wheelhouse outer liners are said to significantly reduce rolling noise, both inside and outside the vehicle, while at the same time offering protection against stone chipping and spray water.
Moreover, the Propylat PET variant, which consists of 100% polyethylene terephthalate, of which up to 70% are recycled fibers, is fully recyclable at the end of product life.
Earlier, Autoneum added an integrated damping function to fiber-based trim components, such as carpets or inner dashes, to improve their acoustic performance. Owing to the use of particle dampers, the company’s Zeta-Light not only insulates and absorbs airborne noise, but also reduces low-frequency vibrations of the vehicle body, independent of temperature.
The technology is designed to improve the acoustic comfort of vehicle occupants
while contributing to significant weight savings. It also simplifies parts logistics and the assembly process as well as recyclability in production and at the end of the vehicle’s life.
The integrated particle dampers developed by Autoneum complement the sound-insulating and absorbing properties of fiber-based, lightweight and sustainable technologies, such as HybridAcoustics Eco+ or Prime-Light, with a new function for damping low-frequency vibrations of the vehicle body.
Compared with conventional damping alternatives, Zeta-Light allows for the reduction of both noise and vibration in a wider frequency range and at lower weight. In addition, the acoustic performance of the particle dampers is not affected by temperature, said Autoneum.
With Zeta-Light, small particles are enclosed in thin nonwoven capsules and integrated into the vehicle body side of noise-insulating components such as carpets or inner dashes. The capsule transfers the vibrations of the vehicle body to the particles and sets them in motion. Damping is achieved through collisions and friction between the individual particles.
Freudenberg Performance Materials showed several sustainable solutions for the automotive sector at this year’s Techtextil exhibition held in Frankfurt am Main, Germany.
A highlight at the trade fair was a novel polyester nonwoven material for car seat padding. Also available as a nonwoven composite with polyurethane foam, the
A number of automakers have made some undertakings to use more recycled materials in their latest models.
material is said to be not only easier for automotive seat manufacturers to handle during the mounting process, but also ensures better dimensional stability as well as providing soft and flexible padding.
Further, the material is single origin and has low volatile organic compounds, ensuring a lower environmental impact. It also has a minimum of 25% recycled content, for example, by reusing nonwoven clippings and waste, and is fully recyclable. The company said full supply chain transparency enables customers to easily trace and verify the content of the nonwoven and thus ensures a responsible production process.
Freudenberg also showed several other nonwoven solutions made of up to 80% recycled materials that can be used in car seat manufacturing. For example, nonwovens based on its Lutraflor technology can be used for automotive carpets, insert mats and interior and trunk linings.
Made from recycled polyester, the material has a high-quality appearance, an environmentally friendly production process and excellent formability, while completely eliminating the use of latex and other chemical binders, the company stated. And compared with conventional automotive carpets, these nonwovens provide weight savings of up to 40%.
UK-based Technical Fibre Products (TFP), part of the James Cropper group, showed its portfolio of lightweight nonwovens at the JEC World trade fair held in March in Paris, France.
Featuring nonwoven veils as light as 2 g/ m2, TFP’s products offer improved finish, enhanced fabrication and superior composites across industries including aerospace and advanced air mobility, wind energy, automotive applications and sporting goods.
Incorporated at the surface of the composite, on top of the structural component, TFP veils are highly porous and feature consistent fiber distribution and weight, ensuring a uniform resin wet-out and zero dry spots, the company stated.
Easy to handle and incorporate, the nonwovens minimize print-through from the underlying reinforcement, reducing the need for further processing of the finished part.
TFP’s lightweight nonwovens are accredited to AS 9100 and are already used extensively in the aerospace industry as an adhesive carrier or support for a fragile material.
Geoff Fisher is the European editor of International Fiber Journal and editorial director of UK-based Textile Media Services, a B2B publisher of news and market reports on transport textiles, medical textiles, smart materials and emerging markets. He has almost 40 years of experience covering fibers and technical textiles. He can be contacted at gfisher@textilemedia.com or +44 7803 718443.
By Bruce Lorange, Suzana Vidakovic and Nick Wang
In the nonwovens and filtration industry, there is a desire to create more sustainable materials that reduce environmental impact, especially given that filtration products are consumables with fixed lifespans. They are also notoriously difficult to recycle. As a result, efforts to support the circular economy remain challenging.
The industry recognizes the changing needs of the planet and the shifting desires of people, as it navigates an increase in environmental awareness, greater demand for sustainable practices and a need for innovative solutions. At Hollingsworth & Vose, we work diligently to lead by example in taking responsibility for developing products with superior performance and reduced impact, innovating for more than 200 years.
While investments are being made in the industry on research and development around the use of more sustainable fibers
and through earth-friendly supply chains, the issue remains that scalable and affordable solutions take time, significant financial resources and require commercial acceptance. Given the urgency of the problems facing the planet, there are ways for manufacturers and suppliers to make an immediate dent in environmental outcomes beyond focusing on greener materials and the supply chains that go into their filtration products.
Consider the matter of energy, for example. According to the Environmental Protection Agency, the energy sector is the largest emitter of greenhouse gases into the atmosphere, contributing to climate change1. Globally, buildings are responsible for around 37% of carbon emissions and 34% of energy use2. In most commercial buildings, the HVAC system is the primary consumer of energy. The pressure drop of air filters can greatly impact how hard HVAC fans must work, which impacts those energy outcomes. Filter media technology that promotes
reduced energy burdens without sacrificing performance – while keeping occupants and downstream assets safe – can lead to real gains in the decarbonization of buildings.
Here are three areas that H&V has demonstrated leadership to innovate filtration for the future. They are an example of developing solutions that consider the demands of the marketplace.
Have you used Google search today? If so, Google estimates that your search required as much energy as illuminating a 60-watt light bulb for 17 seconds and emitted 0.2 grams of CO23. Given the headturning statistic that 90% percent of the world’s data was created in the last two years, and that every two years the volume of data across the world doubles in size4, one can imagine the extraordinary energy and associated greenhouse emissions that come with the data territory.
In fact, data centers have the highest energy usage density among all building types, and they are being built at a staggering rate. Bill Vass, vice president of engineering at Amazon Web Services, was recently quoted as saying the world adds a new data center every three days.5
In the midst of ever-increasing data loads and the growth of technology like artificial intelligence, data centers will continue to have an outsized impact on the amount of energy they consume versus other buildings. They will also continue to require significant energy for cooling, which helps prevent devastating downtime. However, some of that energy use can be offset through decisions made at the HVAC level.
That’s because data centers use a metric called Power Usage Effectiveness
(PUE), which is designed to measure and isolate where and how improvements can be made in the efficiency performance of the electrical and mechanical infrastructure of the building. A major contributor to energy expenditure in data centers is the cooling system. By reducing fan energy, largely impacted by the pressure drop of the filters in the system, a more beneficial PUE ratio can be achieved.
H&V has developed a proprietary synthetic media called NanoWave®, which can achieve extraordinarily low pressure
drop results at superior dust-holding capacity (DHC) compared to traditional synthetic medias and glass mat. This energy-efficient media is increasingly being deployed in data center filters to help improve the PUE ratio. To ensure our NanoWave® solutions are contributing to positive sustainability outcomes, a thirdparty review of our material by Sustainserv concluded that NanoWave® emits 32 times less carbon and generates a savings of -326 kgs CO2e per filter use from cradle-to-gate compared to other standard glass mat media. That equates to less energy for increased performance – a winning combination to support data center decarbonization efforts through reduced energy usage.
In the automotive sector, cabin air filters protect drivers and passengers from harmful pollutants such as dust, debris, bacteria, gases, volatile organic compounds and allergens. Even an hour or two riding in a vehicle can expose people to dangerous levels of air pollution, which can lead to serious diseases. That is why good vehicle interior air quality (VIAQ) is essential in all types of vehicles, from cars and commercial trucks to buses, trains, agricultural vehicles and even airplanes. At the heart of VIAQ and cabin air filtration is the filter media, which largely determines the performance and reliability of the filter.
There are different approaches and perspectives when talking about creating more sustainable filtration solutions for the VIAQ segment. One of the possibilities is exploring the filtration properties of cabin air filters – for example, extending the lifetime of filters by increasing their efficiency and dust-holding capacity. Another way to make a cabin air filter more sustainable is to improve its energy usage by providing filter media with the lowest possible pressure drop. Considering recycled or biobased raw materials, lowering transportation cost, and keeping operational costs minimal are certainly ways to make cabin air filters more sustainable.
This new synthetic air filter media has been developed especially for use during rainy seasons and in humid conditions.
H&V took the extended media approach and has developed a patented high-performance filtration solution, CabinPro™ XT HEPA cabin air filter media. This highly stable HEPA efficiency filter media offers best-in-class protection against particulate contamination for vehicle occupants. Internal tests have shown it provides a much higher DHC than other similar products on the market, meaning filters using CabinPro™ XT HEPA filter media have a much longer lifespan.
If the final application has a dedicated prefilter upstream of the filter made of CabinPro™ XT HEPA filter media, automotive OEMs and AC manufacturers can reverse the orientation of the filter to further reduce pressure drop and maximize energy savings.
Over its lifetime, CabinPro™ XT HEPA filter media shows a lower pressure drop compared to other products on the market, even the ones having a lower initial pressure drop. This is significant for the overall energy consumption over the lifetime of a filter.
In addition, CabinPro™ XT HEPA is made without the use of per- and polyfluoroalkyl substances (PFAS), which are coming under increased regulatory and environmental scrutiny. Therefore, the media not only improves VIAQ but also minimizes the environmental impact of the filters after their service life.
Air filtration systems in heavy-duty vehicles are responsible for the filtration of dust particles in the air, which ensures clean air for the fuel combustion in internal combustion engines (ICE). The filtration performance of the air filtration system, including air resistance, efficiency, and service interval, mainly depends on the filtration media in the element. H&V has designed and produced multiple filtration media with exceptional performance for these kinds of heavy-duty applications.
In recent years, truck manufacturers have begun to highlight the fuel combustion efficiency of their engines. OEMs have also promised to become carbon neutral and to begin cutting CO2 emissions within the next 10 years. Air filtration systems plays a key role combustion efficiency. Researchers have revealed that insufficient air provision can cause incomplete combustion in the engine, which leads to a lack of power, excessive fuel consumption and toxic emissions.
One of H&V’s core product lines has historically been cellulose-based heavyduty air media, used to protect engines in on- and off-road transportation and agricultural equipment. As a continual innovator with a focus on sustainability, researchers developed a next-generation synthetic media, which enables fuel saving in use. This new synthetic air filter
media has been developed especially for use during rainy seasons and in humid conditions. Its nonwoven fiber composition ensures stable air flow from the filtration system, compared to the decreased air flow that comes when using regular cellulose media.
These fuel savings were proven through a set of rigorous field studies in the north and south of China. While the cellulose media had half of the carbon footprint of the synthetic media, the synthetic media enabled emissions reduction (via annual fuel savings) of between 43 and more than 130 times the footprint, with one long haul truck saving more than 5MT CO 2 emission per year –the same impact of planting 300 trees.
One company alone cannot make the outsized difference necessary. H&V is proud to prioritize our sustainable activities and product solutions to ensure we can support our industry for the next 200 years, as we navigate the issues at the forefront of our culture. Yet, it will certainly take a consortium of companies and stakeholders in the nonwovens and filtration sector to make a meaningful and measurable global impact. We invite others to work alongside us in our mission to create a cleaner, healthier, more sustainable world.
Bruce Lorange is the Marketing Director of IAQ, Hollingsworth & Vose.
Suzana Vidakovic is the Marketing Director for Cabin Air, H&V.
Nick Wang is the Marketing Director for Engine Filtration, H&V.
1Climate Change Impacts on Energy | US EPA
22022 Global Status Report for Buildings and Construction | UNEP - UN Environment Programme
3Energy Hogs: Can World’s Huge Data Centers Be Made More Efficient? - Yale E360
4Data Statistics (2024) - How much data is there in the world? (rivery.io)
5Big Tech’s Latest Obsession Is Finding Enough Energy (msn.com)
By Adrian Wilson, International Correspondent, IFJ
s a leading supplier of spunmelt nonwovens to the absorbent hygiene products (AHPs) industry, Fibertex Personal Care, headquartered in Aalborg, Denmark, reports that the market is still being impacted by excess capacity in Asia.
AManufacturers have invested heavily in recent years to ramp up their production capacities in the Asian region to support the continuing growth in the AHPs market, but this is currently resulting in a very competitive environment, with an imbalance between supply and demand and resulting pressure on selling prices.
Fibertex Personal Care expects this situation to continue throughout 2024 and has yet to commence operations on its new production line in Malaysia. It is also strengthening its reliability of supply to customers by establishing local warehouse facilities. The first of these, located in Vietnam, has already been established and more are expected to follow.
The excess production capacity in Asia will remain a challenge for some time, the company believes, but the market is still expected to see underlying growth which will absorb the idle capacity over time.
A bright spot in Europe meanwhile, is the growth of the training pants market – products aimed at assisting toddlers to transition from diapers to regular underwear and, like adult incontinence (AI) products, requiring significantly more nonwovens in their construction than diapers.
According to Nielsen data for the 12-month period ending April 2023, training pants are the only volume-growing segment in Europe, with a notable growth rate of 13%, which is largely being driven by retail brands. Euromonitor further predicts that training pants will continue to grow over the next five years with the acceptance of pants among parents a key factor.
The situation is pretty similar in North America too, where capacities are generally not currently as tight, and new investments for both spunmelt nonwovens and AHPs have recently been announced.
Thanks mainly to capacity investments already made in the North American market, Fibertex Personal Care has been able to expand its print operations for AHPs to include printing on laminated
materials and on both breathable and non-breathables. Print operations have grown into an increasingly important part of overall business for the company in recent years.
New small digital printers now installed in both Germany and the USA will enable new value-creating services for customers, including small volume production for testing and digital approval of print designs. These are now part of the service package offered under the company’s Innowo Print brand.
In a further innovation, during 2023, Fibertex Personal Care launched a nonwoven material weighing just 5gsm, with the lightest nonwoven materials in diapers today typically weighing 8-10gsm. The lower weight product promises to significantly reduce raw material consumption, transport volumes and CO2 emissions in the value chain.
First Quality Enterprises, a long-established producer of AHPs headquartered in Great Neck, New York, has also listed new training pant lines as a priority for its new U.S. manufacturing plant. The plant, at an as-yet unidentified location, will additionally house new baby diaper lines, along with a state-of-the-art automated warehouse facility. It will increase the company’s capacity for both diapers and training pants by 50% and is expected to be completed by June of 2025.
First Quality currently has manufacturing sites in McElhattan, Philadelphia, Macon, Georgia, and Drummondville, Quebec.
PFNonwovens, another nonwovens supplier to the AHPs market formed in 2018 when R2G, of Prague, Czech Republic, purchased First Quality Nonwovens and combined with Pegas Nonwovens, is actively pursuing use of sustainable feedstocks. A recent emphasis for PFN, which like R2G is headquartered in Prague, has been on the development of sustainable resins for spunmelt nonwovens production on the latest Reifenhäuser Reicofil 5 technology. This includes new materials made entirely from NatureWorks Ingeo polylactic acid (PLA) as a more sustainable alternative to polypropylene (PP) or polyethylene (PE).
“Developing 100% PLA spunmelt nonwovens that meet the industry expectations posed substantial challenges,” explains Simon Frisk, global R&D director at PFN. “PLA differs greatly from the usual synthetic resins in both processing and properties. Overcoming these obstacles required intensive in-house and collaborative development work. The Reicofil 5 technology played a pivotal role, ensuring top-notch quality, consistency and performance in the final products.”
Bornewables, developed by Borealis, headquartered in Vienna, Austria, are a second product being incorporated into nonwovens for AHPs by PFN.
Bornewables can be used as direct dropin replacements for comparable fossil-
based polyolefins and in PFN’s nonwoven production require no changes to the existing manufacturing process while delivering the same high quality and performance as non-renewable virgin materials.
The Bornewables PP being used by PFN is made with second-generation raw material feedstock derived entirely from waste and residue vegetable oil streams. The renewable content in all Bornewables products is mass balance accredited under the ISCC (International Sustainability and Carbon Certification) PLUS certification standard, confirming authenticity and fully transparent traceability from the raw materials to the finished products.
Mass balancing makes it possible for customers to meet ambitious sustainability targets and stay on top of changing legislation. For every ton of certified Bornewables PP used in production, a maximum equivalent amount of nonwoven material can be certified as renewable.
“Anticipating the growing demand for more sustainable nonwoven solutions, we have focused our development resources over the past few years on the circular sphere,” says Tonny De Beer, chief product, technology and sustainability officer at PFN. “Using the Borealis Bornewables instead of standard fossil-based resins will significantly reduce our carbon footprint, even enabling products with a carbon footprint below zero.”
Further innovations for training pants, in addition to AI products, have been incorporated into the private label retail products of Aalst, Belgium-headquartered Ontex. The design of training pants, the company observes, has now evolved to provide a true alternative to traditional open diapers rather than for transitional use.
In a latest evolution, Ontex is introducing the Dreamshield back pocket to upgrade leakage protection and enable extended use, including during the night. Dreamshield consists of two layers – a soft-to-the skin outer layer and a robust and secure absorbent containment layer.
The market for AI disposable pants is also growing. “We know that many people have moderate incontinence and lead active lives, so we make sure our pants are affordable, discreet and easy to wear,” says Annick De Poorter, chief innovation and sustainability officer at Ontex. “We estimate that one in four women over the age of forty and one in nine men over sixty have some form of incontinence, so adult incontinence pants can enable many people to live a normal life.”
The new Ontex X-Core is channeled to provide instant absorption in adult pants and keep humidity away from the skin in a discrete pant that is said to feel closer to regular underwear than ever before. The channel’s unique X-Shape allows for extra distribution at the back of the adult pants and further prevents leakage. Product lab testing has shown a substantial improvement in absorption speed and instant dryness.
Another major supplier of private label AHPs also headquartered in Belgium (in the municipality of Zele) is Drylock Technologies, which has just announced the expansion of its baby care product manufacturing capacity with a new plant in Reidsville, North Carolina.
With an incontinence product plant established seven years ago in Eau Claire, Wisconsin, Drylock purchased Presto which had been making incon-
tinence products for possibly decades. Drylock is making a further multimillion dollar investment in the USA to meet the increasing demand for baby care products from North American customers.
“People have often asked me when I would be establishing a baby products plant in the USA and I’m very happy to say that the time is now,” says CEO, Bart Van Malderen. “With a localized manufacturing presence, we can support faster product development for our US customers and empower them with unparalleled speed to market.
“The move is part of our strategy to follow our customers – it is answering the increasing demand for baby care products among our valued North American customers and serves as the perfect addition to our plant in Wisconsin, which has served as the bedrock of our incontinence products business in the USA for seven years.”
Drylock, which achieved record sales of more than €1.2 billion in 2023, reports that the private label sector of the market, and particularly retailer own brands, has seen significant growth in recent years, driven by enhanced product quality and range extensions, optimized positioning and high innovation levels, in addition to bringing more sustainable solutions, all designed to compete directly with the national brands.
The new facility will create significant employment opportunities for the Reidsville region, with some 300 direct positions and a significant number of indirect jobs to be created in the local area.
Adrian Wilson is an international correspondent for International Fiber Journal . He is a leading journalist covering fiber, filtration, nonwovens and technical textiles. He can be reached at adawilson@gmail.com.
By Adrian Wilson, International Correspondent, IFJ
On March 8, 2024, South Carolina’s Charleston Water System (CWS) settled a class action lawsuit against the wipes retailers and manufacturers Costco, CVS, Procter & Gamble, Walgreens, Target and Walmart.
It should go some way to ensuring that all wipes marketed to consumers across the USA will be truly flushable and that packaging for all non-flushable wipes will clearly indicate they should not be flushed.
CWS brought the suit in January 2021 seeking injunctive relief to remedy costly and ongoing damage to sewer systems and treatment facilities due in a significant part to the inability of allegedly flushable wipes to break down, often clogging wastewater infrastructure and causing sewer overflows that damage the environment.
Kimberly-Clark, which manufactures Cottonelle flushable wipes as well as nonflushable wipe products, previously settled with CWS in January 20222 and its products now already comply with the suit’s requirements.
“When we filed this suit, only the wipes of one brand were actually flushable and no product packaging offered disposal instructions that were clearly visible,” said Mark Cline, CEO at CWS. “We’ve won a very significant battle, as wipes have been public enemy number one for the entire wastewater industry since they were invented.
“We knew this litigation would be tough and that the stakes were high for these international corporations, so we’re extremely pleased with the skilled work of our counsel. These settlements bring significant benefits to wastewater utilities nationwide and their customers, while reinforcing the commitments of the companies to being good corporate and environmental stewards. It’s a major step forward for us and the whole country in that respect.”
of this has subsequently been exhibited in the Museum of London.
The UK has now gone a stage further than the USA, with Water UK having just shelved its “Fine to Flush” certification scheme for wipes introduced in 2019. The certification’s label featured a toilet seat and a check mark.
The settlements commit the defendants to meeting an international flushability standard supported by the wastewater industry, with two years of confirmatory performance testing, and significant nonflushable wipes labelling enhancements.
“The final battle in the wastewater industry’s war against wipes is still to come and that involves changing human behavior,” Cline said. “We hope consumers will follow the clear instructions on the packaging. If so, customer sewer costs would go down and the vast majority of sewer overflows nationwide would be eliminated, making our environment the big winner.”
The disposable nonwoven wipes industry has gone through rather a lot over the past decade and the issue of flushability has never been far from top of the agenda, following horror stories of huge ‘fatbergs’ – mountains of oil and grease congealed with wet wipes and other sanitary products blocking sewer systems.
The UK has been particularly impacted by them and in September 2017 the largest to date was discovered in a sewer under Whitechapel, London – at 820 feet long and weighing 130 tons! A portion
In October 2023, the UK Government launched a consultation on potentially banning wet wipes containing plastic nationwide, as part of its wider Plan for Water.
Now, however, in place of “Fine to Flush,” Water UK has introduced a new “Bin the Wipe” campaign aimed at ending consumer confusion and advising that all single-use wipes, whether flushable or not, should no longer be flushed down toilets.
In the United States, INDA, Association of the Nonwoven Fabrics Industry is engaging in flushability as a priority. “We are tracking at least 25 different bills or initiatives at the state, federal, and, in some cases, even the municipal level,” says Matt O’Sickey, INDA Director of Education & Technical Affairs. “
Many U.S. state’s initiatives will be affected the Wastewater Infrastructure Pollution Prevention and Environments Safety (WIPPES) Act (H.R. 2964), recently passing in the U.S. House of Representatives, working its way through Congress. “This bipartisan legislation is intended to address the growing problem of sewer system clogs caused by improper disposal of consumer wipes that are not intended to be disposed of in toilets,” says O’Sickey.
In the fall of 2023, INDA joined forces with CASA, the California Association
of Sanitation Agencies, and RFA, the Responsible Flushing Alliance, along with a contracted engineering firm, to conduct a practical micro-study on wipes flushability, in response to a directive from the 2021 Wet Wipes Labelling Law AB 818. The goal was to see what Californians are flushing to help form consumer education campaigns. The team spent over two weeks at the Inland Empire Utilities Agency in Southern California and Central San in Contra Costa County in Northern California, analyzing material pulled from the waste stream.
“We collected 1,745 samples over four days – two days in northern CA and two days in southern CA. We also collected the items during peak flow time so that it could be a good, indicative sample,” says Lara Wyss, President, Responsible Flushing Alliance. “
The results indicated that flushable wipes are indeed biodegradable, with .9% of what was collected being Nonwoven - Labeled Flushable. The biggest culprit collected were paper products at 52.8%, and second was Nonwoven - Labeled Do Not Flush at 34.1%. Feminine Hygiene and Trash collected was 12.1%.
“Our approach is to educate consumers to look for the ‘Do Not Flush’ symbol on packaging, and explain why that’s important,” says Wyss. “This study really verified that this is the right approach.”
All of these occurrences are definitely a blow for the nonwoven wipes supply chain – from machine builders and fiber suppliers to converters – which has worked diligently to enable the production of fully flushable wipes over the past 20 years.
All of this work did, however, help the supply chain in responding to the European Union’s Single-Use Plastics Directive (SUPD) to some extent.
This legislation, first announced in 2019, was devised to take action against the ten single-use plastic products most commonly found discarded on European beaches, including both wipes and nonwoven-based femcare products.
Since July 2021, any of these products containing plastics have had to carry prominent warning labels and extended producer responsibility (EPR) for the col-
lection of the single-use products from European beaches and their disposal comes into place in December 2024.
No brand, of course, could contend with issuing products carrying both its logo and a prominent warning label on its packaging, but as things turned out, the SUPD couldn’t have come at a worse time, with preparations for it coinciding directly with the COVID-19 pandemic.
In a memorable presentation, Martin Henderson, technical manager for wipes converter Rockline Industries UK, described the multi-faceted challenges the industry faced in 2019 and 2020.
“When the pandemic hit, the demand for products and consumer priorities changed overnight and in many cases it just simply was not possible for the industry to react in time,” he said. “The demand for disinfecting wipes flew off the shelves while skin care wipes dropped off significantly as people stayed at home, and new product formats evolved as manufacturers scrambled to cope with the shift in demand.
“Meanwhile, the emergence of the SUPD really put huge pressure on our industry to make changes to the products we supply and come up with sustainable solutions. Even in normal circumstances this wouldn’t have been easy, but in the midst of a pandemic the challenges were magnified. In the UK at least, the pressure on plastic has been intensified by the media and NGOs, some of whom have directly called out UK retailers, which has accelerated product changes and led brands to transform entire product portfolios to move away from plastic.”
Facial and make-up wipes were among the second highest category recovered in the Nonwovens - Do Not Flush wipe category.
The sorting process was time consuming, and included washing, drying, labeling, data recording and photographing 1,745 samples that were collected over two weeks.
Manufacturing lines were repurposed and production schedules streamlined which all came at a cost, Henderson added, and when adding 100% cellulose products into the mix the challenges became even greater.
“It’s widely known in the industry that 100% cellulosic products cause challenges
throughout the supply chain and when consumer portfolios changed in a matter of months, the impacts were felt by both roll goods manufacturers and converters. Reduced efficiencies and increasing materials costs were unavoidable and the demand for viscose and other cellulosebased fibers began to increase drastically at just the wrong time.”
Nevertheless, Rockline UK fully succeeded in removing 2,400 tons of plastic from its wipes in 2021, compared to the previous year. The successful response to the SUPD is further underlined by a second UK wipes brand, NicePak, which
supplies an annual 500 million packs of wipes to global brands and retailers. In 2018, just 9% of these were plastic free. By 2022 the percentage had jumped to 90%.
In parallel, cellulosic fibers for the flushable wipes market have also advanced rapidly in a very short space of time.
Lenzing, for example, has recently launched upgraded Veocel™ shortcut lyocell fibers which not only have higher dispersibility but also benefit from a new finish which improves processability and enhances efficiency in wetlaid nonwoven
wipes production by providing protection against mechanical stress at commonly used water temperatures (0-40°C). This helps to avoid the creation of fiber lumps during the opening and dilution of the fibers in preparation tanks. The finished product also has enhanced physical quality and appearance because the finish improves web formation during the process.
The latest Veocel fibers are now being employed in products such as Albaad’s Hydrofine – the leading flushable wetlaid wipe sold in Europe.
Whatever’s next for the nonwoven wipes industry, it has certainly come a long way since inventor Arthur Julius first trademarked his original Wet-Nap in 1958 and five years later sold it to Colonel Harland Sanders for use in his Kentucky Fried Chicken restaurants.
The industry exploded in the 1970s and has been growing ever since – in 2024 Smithers puts the value of the global consumer wipes market at $18.8 billion, and that of industrial wipes at $4.3 billion. Annual growth in the coming years is put at a healthy 6.2% and the market is currently consuming around 1.5 million tons of nonwovens per year.
Similar demands to those made by the EU’s SUPD could soon arise in North America, following on from the CWS lawsuit and legislation such as the California Circular Economy and Plastics Pollution Reduction Act.
However, the hygiene and health benefits that wipes provide, along with their convenience, makes any outright ban on them as suggested in the UK highly unlikely, and meanwhile, the supply chain continues to develop ever-better performing and fully biodegradable materials.
Adrian Wilson is an international correspondent for International Fiber Journal . He is a leading journalist covering fiber, filtration, nonwovens and technical textiles. He can be reached at adawilson@gmail.com.
By Matt O’Sickey
We are living in the exciting third generation of plastics and polymers. The first generation was the dawn of the commodity polymers that were highly affordable, exceptionally durable, and able to displace many packaging, single-use, or commodity applications. Examples being polyethylene films and bags, polypropylene and polyester containers and fibers, PVC pipes, and polystyrene packaging. The second generation included the development of polymers for more intense and strenuous applications including use in high heat and/or chemically hazardous environments and high strength and toughness requiring applications.
Examples of these include many from the transportation sectors – both automotive and aircraft, composites, and protective technologies. All of these were produced from petrochemical sources and endured long after their use application’s end-of-life. The third generation of plastics and polymers is one that builds materials from a variety of sources, not only petroleum and/or are designed to NOT endure past the applications end of useful life.
The topic around the sourcing of the building blocks to make these thirdgeneration plastics and polymers has already been discussed. Here, the focus will be upon what happens after the product has exceeded its useful life. Certainly, the most desirable end-of-life (EOL) goal is reuse and recycling, whether mechanical or advanced, to maintain the greatest raw material value. However, when reuse and recycling is not possible or otherwise fails to occur, consideration towards biodegradability and compostability come into play.
Recent polls by IPSOS, the World Wildlife Federation, Data for Progress, and
others are consistent in showing that a large majority of Americans are concerned about plastic pollution in the environment. Regardless of political affiliation, 75% of Americans are concerned or very concerned about the impact of plastic in the environment. A significant percentage of respondents in various surveys believe that government and manufacturers of both plastics and plastics products are best positioned to address the issue of plastics in the environment.
In considering governmental actions, depending upon respondent country, 63-80% of surveyed Europeans were in favor of the European Union Single-Use Plastics Directive. Similarly, a WWF global survey indicated nearly 90% of respondents believed that a global plastics pollution treaty was important or essential. A smaller portion, around one-in-three, have made changes to their buying and use behavior to reduce the amount of single-use plastics that they are directly responsible for.
Studies by McKinsey and NielsenIQ have demonstrated that not only do consumers say they are willing to change pur-
chase habits, but have actually increased purchases of products with sustainability stories. This is occurring even when those purchases are at a higher cost.
Looking at those buying choices, it is seen that consumers are intentionally purchasing products that indicate that the packaging and/or product is made using recycled content, is recyclable, can be composted or is biodegradable. While consumers are reasonably clear and certain as to what the claims relating to recycled content or recyclable mean, there is less certainty around compostability and biodegradability. The Composting Consortium have noted that 49% of respondents have difficulty distinguishing between the terms compostable and biodegradable. Furthermore, about half of consumers interpret the packaging claim “plant-based” to be equivalent with compostable and dispose of plant-based packaging materials with compostable waste. This education gap will become increasingly critical to address as more products (not only packaging materials)
are produced with non-plastic materials, whether due to regulatory drivers or consumer pull, that are potentially biodegradable and/or compostable.
Thankfully, there have been improvements in the claim language that is permitted on products and claims of biodegradability and compostability must be validated against rigorously defined standards. Past claims of biodegradability were made based on the premise that under at least some conditions of water, heat, and light exposure, the product would break down in some manner. The time required to biodegrade and the extent of biodegradation were generally not specified, which meant that a claim of biodegradability was often disingenuous at best.
However, ISO, OECD, EN and ASTM standards have been implemented that have addressed these gaps and now require a minimum degree of product degradation at controlled conditions, including both aerobic and anaerobic environments, defined temperature, humidity, and duration. Similarly, there are standards against which compostability claims may be evaluated.
While this is a significant improvement, it is also fair to say that consumers are generally ill-equipped to understand the differences between products labelled as biodegradable per ASTM D5511 and ASTM 5526 or ISO 14855 or ...! Ultimately, consumers need to understand in accessible terms what “biodegradable per method XYZ” means with respect to the proper disposal of the product. The test method used is merely the proof that when disposed of appropriately, that the product has the potential to biodegrade. Similar comments apply to compostability claims which may be a step ahead of general biodegradability claims. This is due to often legislated requirements to label products as municipal/industrially compostable versus home or backyard compostable.
Before moving to some of the materials and technology, here are a few final words on product claims and labeling requirements. Product claims should abide by the requirements of the European Directive to Combat Greenwashing and
Promote Sustainability and the United States Federal Trade Commission Green Guides. Each of these strives to provide clarity around claim language and in the case of the European directive demands that claims be validated with data. The efforts around both standards development and claim language regulation are significantly reducing consumer frustration and confusion over potential “green-washing.”
For much of the nonwovens industry’s history, the biodegradability and compostability story centered around cotton, wood pulp, and viscose materials. Over the last few decades, significant strides have been made to expand the source of materials that can be used to generate viscose perhaps most notably the rapidly replenishing bamboo. These cellulosic materials were the predominant biodegradable raw materials and were limited by their inability to be thermally extruded in spunmelt processes. Additionally, they could not be thermally bonded or welded without the addition of some synthetic polymer fibers such as polypropylene, polyethylene, or polyester.
There were, of course, some other sources of biodegradable fibers such as wool, hemp, seaweed, silk, other animal fur, poultry feathers, and even chitosan from waste shellfish shells. These were generally niche products and not of appreciable commercial significance. However, in localized regions where alternate fibers are more readily available, such as wool in New Zealand and banana fibers in India, there has been increased commercialization in recent years.
There has also been an increased interest in hemp as a source of biodegradable fibers, particularly in the United States as both stigma and regulatory restrictions have diminished. Each of these fiber sources presents opportunities and challenges to the manufacturers of the nonwovens and products made from them. It should also be noted, that processing of the source raw materials to create fibers can also impact the materials ability to biodegrade, sometimes for the better, sometimes for the worse.
Noted above was the general inability of these materials to be extruded or otherwise thermally processed, which meant that for high output processes like spunbond and meltblown, that only nonbiodegradable thermoplastic polymers such as polypropylene, polyethylene, nylon, and polyester could be used.
Since the 1990s, that reality has been changing as polymers such as polylactic acid (PLA), polyhydroxyalkanoate (PHA), and polyhydroxybutyrate (PHB) amongst others have moved from the lab into commercial production and are being thermally extruded into fibers and nonwovens. These new bioplastics represent a prime example of the third generation of polymers that are either bio-sourced, biodegradable or both.
Significant advances are being made to improve these materials extrudability, physical properties, and biodegradability. Products made with such materials are potentially compostable either industrially or at home and more importantly may biodegrade should they be released into the environment.
Coming back to some of the first-generation polymers, such as polypropylene, there have been available for a couple decades, oxidative additives that could facilitate biodegradation of articles made with such polymers. Unfortunately, this type of biodegradation often resulted in a large plastic article being broken into smaller, potentially micro-plastic, sized pieces of plastic. While this approach had the potential to avoid seabirds strangling in six-pack holders and animals and fish choking on plastic fabrics, it created a different, micro-plastic, problem.
Recently, a next generation of additives has been developed that, rather than simply breaking a large plastic into many smaller plastics, converts the plastic into smaller waxy or grease-like molecules that may be bio-available to microbes for complete digestion. The various developers of these technologies are clear in stating that this is not meant to be the primary disposal pathway for these plastics, but rather as a safety net for those instances
when plastic articles are inadvertently introduced into the environment rather than properly recycled or disposed of.
The advent of biodegradable polymers and/or additives that can allow biodegradation of polymers historically not considered to be biodegradable will assuredly challenge the existing legislative, regulatory, and standards approaches. It will similarly put greater burden on manufacturers and retailers to educate consumers regarding appropriate end-oflife considerations for the products they purchase. As composting infrastructure and product designs advance to facilitate the viability of nonwovens and other products to be made compostable, labeling regulation and consumer education will be critical to ensure that each material is appropriately introduced to the next phase of its existence, whether reuse, recycle, composting, or landfill.
The array of tools in the product designers’ toolbox to address these end-of-life
considerations continues to increase year-after-year. Many of these new tools have been recent finalists and/or winners of innovation awards from INDA, the Association of the Nonwoven Fabrics Industry and EDANA, the Voice of Nonwovens. These topics and others will be covered in more depth in the INDA Sustainability Report being released in the fall 2024 and INDA’s inaugural Sustainability in Nonwovens Conference, April 29-30, 2025,
https://www.ipsos.com/en-us/three-four-americanssupport-national-policies-reduce-single-use-plastic. Accessed 2024 July 8.
https://www.protein-evolution.com/perspective/ americans-views-on-plastics-recycling-andsustainability. Accessed 2024 July 8.
https://www.worldwildlife.org/blogs/sustainabilityworks/posts/what-do-americans-think-about-plasticwaste-in-2024. Accessed 2024 July 8.
https://www.dataforprogress.org/blog/2023/3/27/ voters-express-concern-about-plastic-pollution-stronglysupport-mitigation-proposals. Accessed 2024 July 8.
https://www.pbs.org/newshour/science/1-in-3americans-say-theyve-reduced-how-much-plastictheyre-using. Accessed 2024 July 9.
held at the IDEA® 2025 Expo (April 29May 1). These also run in conjunction with FiltXPO™. We hope to see you there. Register now for www.ideashow.org
Matt O’Sickey, PhD is Director of Education & Technical Affairs at INDA, Association of the Nonwoven Fabrics Industry. He can be reached at mosickey@inda.org or +1 919 459-3748.
https://www.statista.com/statistics/1341670/europesingle-use-plastic-ban-support-by-country. Accessed 2024 July 9.
https://wwfint.awsassets.panda.org/downloads/rising_ tides__ii___1_.pdf. Acccessed 2024 July 9. https://www.mckinsey.com/industries/consumerpackaged-goods/our-insights/consumers-are-in-factbuying-sustainable-goods-highlights-from-new-research. Accessed 2024 July 9.
https://www.mckinsey.com/industries/consumerpackaged-goods/our-insights/consumers-care-aboutsustainability-and-back-it-up-with-their-wallets. Accessed 2024 July 9.
https://www.closedlooppartners.com/wp-content/ uploads/2023/08/Composting-Consortium-Report_ Updated.pdf. Accessed 2024 July 9.
By Adrian Wilson, International Correspondent, IFJ
End-of-life options for nonwoven fabrics are very much dependent on their end-use application, with around 50% of them being employed in durable products such as filter media, construction materials, floor and wall coverings and geotextiles. Once at the end of their useful life, such materials, are theoretically recyclable using established mechanical tearing processes, but the reality is inevitably much more complex.
Many hundreds of heavy-duty needlepunched filter bags, for example, can be used at a single site in industries such as power generation, cement manufacturing and waste incineration. These filter bags can be up to 40 feet long and need to be replaced at regular intervals, suggesting the potential for establishing some kind of circular system.
Manufacturers of new geotextiles, however, are now facing impossible demands from specifiers for products that are both 100% plastic-free and at the same time have a guaranteed performance life of 50, or even 100 years.
Chris Quirk, managing director of Naue Geosynthetics UK, has outlined this dilemma following his company’s introduction of a high performance range of geotextiles called GreenLine, which are available in a weight range of 3001,000gsm and based on PLA.
They are, however, extremely difficult to clean and can contain heavy metals, dioxins and other toxic substances, depending on the application. Cleaning processes would therefore have to be extremely aggressive, consuming a lot of energy and producing a large amount of waste, while at the same time severely damaging and reducing the value of the materials being recovered. When all other costs are factored in, such recycling is a far from practical exercise.
Similar cost obstacles exist for geotextiles, which are buried under structures and intended to remain there for many decades. This means that no thought was given at all to the recyclability of the materials that may now be nearing their end-of-life and recovery is generally in the hands of independent reclamation companies who have no idea of what they’re dealing with.
“The problem we face is that under the current European Union Construction Products Directive, geotextiles based on bioplastics, as well as recycled products, can only receive a durability rating of five years,” Quirk says. “This is as opposed to virgin plastics like polypropylene which can have guaranteed durability of up to 100 years.
“It means that our new PLA products can only be used in temporary works at present, although we know that PLA has far greater durability than the guarantee we are allowed to give.”
Meanwhile there is a rise in the application of bans on the use of plastics in construction works, notably in National Parks in Europe, California and New Zealand.
“It’s a tick-box exercise for contractors who ask for both no plastic and a 100-years guarantee,” Quirk observed. “For some challenging applications, fossilbased plastic will always have to be used and there is good bio-based plastic too, but this is not understood by regulators.”
Potentially valuable materials from end-of-life vehicles rather tragically referred to as ‘automotive shredder residue’ (ASR). Adrian Wilson
Many nonwoven-based automotive interior components are now being both made from recycled materials and marketed as suitable for recycling and in July 2023 the European Commission published its proposal for an End of Life Vehicles Directive. This will mandate the reuse, recycling and recovery targets for plastic and fibers from the more than six million vehicles that are scrapped in the European Union each year. What currently happens to such waste is far from ideal.
In many instances, metals, tires and glass account for 80-90% of the materials from end-of-life vehicles that are recycled through traditional mechanical recycling streams, while the other 10-20% is rather tragically referred to as ‘automotive shredder residue’ (ASR). This consists of mixed plastic and other non-recycled materials that today generally end up in landfills or are recovered through waste-to-energy technologies – including the many nonwovens and technical textiles employed in vehicles such as interior surface fabrics, insulating materials, filters, cords and belts.
Even ASR, however, can potentially be given a second life, and this was the aim of chemicals major Eastman, working in a 2023 project with the United States Automotive Materials Partnership (USAMP),
the automotive scrap recycler Padnos and global automotive interiors supplier Yanfeng. In this project, Padnos, headquartered in Holland, Michigan, supplied a plastic-rich fraction of ASR as a sustainable feedstock for Eastman’s carbon renewal technology (CRT).
Eastman has subsequently demonstrated the conversion of the ASR feedstock into a synthesis gas (syngas) which is then used downstream in the production of its polyester and cellulosic thermoplastics.
Resins from this production process were further formulated and then supplied to Yanfeng and molded into demonstration components meeting the requirements of OEM vehicle manufacturers Ford, GM and Stellantis, demonstrating proof of concept for a truly circular solution.
The study proved the feasibility of Eastman’s CRT, which breaks down the plasticrich ASR into molecular building blocks. By recycling these complex plastics into their monomers, the company can replace fossil-based feedstock and create polymers without compromising performance, for use in new automotive applications.
This is a pragmatic potential solution to an existing industry practice, but the system must adapt to the circular economy.
The other 50% of nonwovens produced globally are meanwhile used in absorbent hygiene products (AHPs) and other singleuse consumer items, where end-of-life options are also exceedingly limited, despite ongoing small-scale industry initiatives.
The considerable post-consumer waste AHPs generate is estimated to be in the region of 30 million tons each year, most of which is either incinerated or sent to landfill. Considering the $65 billion baby diaper market alone, this equates to 1.5 billion diapers that are disposed of globally on a daily basis – 18,000 each second – and this is waste that is not currently in a fit state to be recycled by simple recovery of its constituent parts.
Various projects have been established in recent years, such as the pilot diaper collection bins in Amsterdam by Procter & Gamble and partners, while FaterSMART has operated a diaper recycling plant in Contarina, Italy, for the past decade, with an annual capacity of 10,000 tons.
Ontex and Les Alchimistes in France operate a regional diaper collection scheme with the goal of dealing with 500 million diapers by 2030 and the scheme is currently being expanded to Belgium.
In Australia, Kimberly-Clark has established a collection and recycling scheme in Australia in which around 1.5 billion diapers are being collected annually.
Most recent, Kimberly-Clark’s Huggies brand is partnering with select Bright Horizons childcare centers in Boston to collect used diapers & wipes, and turn the waste into electricity, heat or fuel. Waste-toenergy technology, a process managed by Covanta, offsets the use of fossil fuels and reduces carbon emissions and methane generation from landfills at many facilities around North America, including Boston.
Waste-to-energy takes non-hazardous waste – otherwise destined for landfill – and combusts it, generating steam for electricity production. The resulting ash is also processed to recover metal for recycling while all gases are collected, filtered, and cleaned to minimize environmental impact. The pilot will run at select Bostonarea Bright Horizons centers and pending outcomes, Huggies and Bright Horizons could expand it to other cities.
Dyper, headquartered in Scottsdale, Arizona, is already running diaper collections in 21 U.S. cities through its Redyper system, with the waste having initially been separated by a combination of composting and pyrolysis, with carbon sequestration.
The company has subsequently developed a process for turning used diapers into biochar, which it believes is
a potentially economic and realistic solution to this major consumer waste stream. This is the first time biochar will be used to address disposable diaper waste.
Biochar is a carbon-rich product which allows for waste to be transformed into a reusable commodity that can improve soil, assist in air and water purification and be used as an additive in paints and inks for improved pigmentation.
“While there are no silver bullets to solving the plastic diaper dilemma, we feel it is our obligation to continuously look for solutions,” said Sergio Radovcic, founder and CEO of Dyper. “We’ve started with composting, fully aware of the inherent difficulties of doing it at scale. With this innovation, we will bring modular disposal technology to complement or replace composting closer to the consumer, reducing processing and transfer times.”
Redyper composts diaper waste to create topsoil and Byochar™ reduces the processing time for this from several months to minutes. In addition, an efficient Byochar™ reactor needs less space and electricity than a traditional composting facility. The reactors have the capacity to process two tons of diapers per day – 7,200 diapers every 10 hours, or 12 diapers a minute. Converting Dyper diapers and wipes to biochar yields an 80% reduction in mass –100 pounds of dry diapers yields approximately 20 pounds of biochar. The potential impact – and scale are enormous.
Adrian Wilson is an international correspondent for International Fiber Journal . He is a leading journalist covering fiber, filtration, nonwovens and technical textiles. He can be reached at adawilson@gmail.com.
By Christy Sapp and Kim Evans
The urgent need for sustainable waste management solutions in the hygiene industry is underscored by the staggering annual disposal of over 4.1 million tons of diapers in U.S. landfills alone, comprising a significant percentage of the planet’s municipal waste.
Nexus has extensive experience in recycling various streams of scrap plastic from hygiene product manufacturers. This upstream knowledge provides insights into how recyclers and the hygiene industry can work together to increase the recyclability of plastic waste. It is essential to take steps now to ensure diaper and other hygiene product matrices are inherently recyclable, laying the foundation for future innovations to address postconsumer hygiene waste. By fostering collaboration across the sector, Nexus and other advanced recyclers aim to guide the industry towards a sustainable future, transforming hygiene waste into valuable resources through advanced recycling processes.
Diapers are complex products, typically composed of three main materials: plastics, cellulose, and superabsorbent polymers (SAP). Globally, a few companies, including North America’s Recyc PHP Inc., have the capability to effectively process rejected pre-consumer diapers and separate these components. Daniel Fortin, CEO of the company, states that his company has well-established recycling markets for both cellulose and SAP. However, reclaimed plastic, which comprise 25-40% of a diaper’s total weight, poses significant recycling challenges. These challenges stem from their mixed nature – often a blend of polyethylene (PE) and poly-
propylene (PP) – and from their form as flexibles and films. Traditional mechanical recycling methods struggle with these materials, as they are well-suited for rigid feedstocks composed of mono-materials.
The burgeoning advanced recycling industry presents an alternative pathway for reclaimed and scrap plastic materials from hygiene products. The plastics-toplastics enabling technology developed by Nexus Circular, and similar advanced recycling processes, effectively transform those reclaimed plastic materials into a valuable resource for new plastics.
Founded in 2008, Nexus Circular has developed a pioneering advanced recycling process aimed at addressing the limitations of traditional recycling. The company employs thermal depolymerization – a conversion technology that applies heat in an oxygen-free environment at atmospheric pressure, ensuring no combustion or incineration occurs. The process transforms polyolefins back into their original molecular building blocks at a very high yield. The resulting circular feedstock is revolutionary, serving as direct substitute for fossil-based resources in the production of new, virgin-quality plastics.
Nexus has been operating at commercial scale since 2018 and is one of a handful of commercial advanced recycling companies in North America, including Eastman, Purecycle, and ExxonMobil. Nexus is aligned and partnered with global polyolefin resin producers including Braskem, Chevron-Phillips Chemical Company, LyondellBasell, and Shell, supporting their plastic circularity commitments. Nexus’s circular feedstock allows those companies to produce virgingrade plastics that meet stringent quality standards.
Each tanker or rail car of circular feedstock can directly displace an equivalent volume of fossil-based feedstocks, offering a significant opportunity to reduce reliance on non-renewable resources and decouple plastic manufacturing from extraction.
Advanced recycling technologies are designed to handle a broader range of used plastics and more challenging formats than traditional recycling processes. Examples from the absorbent hygiene product (AHP) value chain include rejected bicomponent nonwoven materials from
converters and product trimmings from diaper and feminine care manufacturers.
Nexus also partners with innovative companies like diaper reclaimer Recyc PHP, Inc. (Montreal, Canada) to ensure that complex diaper materials are recycled. A key study by Nexus and Recyc PHP, presented at Hygienix 2023, showcased the suitability of reclaimed plastics from various rejected diaper brands and products. The results are presented in Table 1
The results were compelling: Four of five samples had acceptable polymer compositions for Nexus’ recycling process, including polypropylene (PP) and polyethylene (PE). However, the presence of airlaid materials in one sample (NR5) illustrated the challenges posed by such materials, which complicate the separation process for diaper reclaimers and reduce the yield of circular feedstock for plastic recyclers. Reclaimed plastics from formulations that contain airlaid material must be controlled and metered in carefully to minimize yield, operational, and financial impacts to the recycler.
Sample NR3 revealed the presence of benzoic acid, a depolymerization product of polyethylene terephthalate (PET), indicating the use of polyester in that specific diaper product. Deeper analysis and characterization revealed that PET was used in the top sheet, whereas the other four diapers utilized a polyolefinbased top sheet.
The study underscores the complexity of diapers and the challenges that mixed polymer systems pose for reclaimers and recyclers. Diapers utilizing single polymers or combinations of PE and PP polyolefins significantly improve the matrix’s recyclability. This highlights the importance for manufacturers to consider recyclability in the design phase, aiming to use plastics from the same polymer family to enable compatibility with recycling technologies.
Designing end products with plastics from discrete plastic families is crucial for recycling due to the inherent chemical differences between these families. This is
particularly true for the major plastic families in hygiene products – polyesters and polyolefins. Polyesters, such as PET, require different processing conditions due to their higher melting points. Additionally, PET tends to degrade into undesirable by-products under conditions suitable for the advanced recycling of polyolefins. This degradation not only diminishes the quality and yield of the recycled material, but also increases maintenance and operational costs due to the by-products that can damage recycling equipment.
This same concept extends to materials that intertwine non-wovens with cotton as well as PLA and other non-polyolefin
bioplastics. When non-polyolefin plastic materials are included in the diaper matrix, the value of the resulting reclaimed plastic is greatly reduced.
While advanced recycling technologies can process polyester (through methanolysis) and polyolefins (through pyrolysis) separately, producing high-quality circular feedstocks, they struggle with efficiently processing mixtures of polyester and polyolefin materials. This critical distinction underlines that mixing these materials can severely restrict recycling options. Therefore, it is vital for manufacturers to consider these recycling implications when designing hygiene products.
Hygiene product manufacturers are continually innovating to meet consumer demands for comfort, performance, convenience, and affordability. Concurrently, there is a growing imperative to address environmental sustainability, driven by stringent government regulations and evolving consumer expectations. Many companies have responded by dedicating entire teams to minimize waste generation, ensure effective landfill diversion, and achieve significant reductions in Scope 1, 2, and 3 emissions.
The aspects of design and sustainability are intertwined, as the selection of materials during the design phase directly impacts the recyclability of the final product. If sustainability considerations are not integrated with cost and consumer expectations during design, formulators may inadvertently select materials from different polymer families, complicating or even precluding recycling opportunities.
This issue was highlighted in the study presented at the 2023 Hygienix conference, demonstrating that plastics reclaimed from diapers containing both polyester and polyolefin components are unsuitable for commercial advanced recycling processes. Although the differences when incorporating polyester are subtle and often indistinguishable to consumers, they result in a plastic matrix that lacks a viable recycling pathway.
Encouragingly, many reclaimed plastic streams from diapers have already proven to be excellent feedstocks for advanced recycling, indicating that many products are already designed with solely polyolefin materials. Despite this progress, polyester-based plastics are still used in diaper components such as the top sheet and acquisition distribution layer (ADL), as indicated on ingredient lists of major brands.
Addressing these challenges requires a paradigm shift towards
designing products using single polymer family systems. This shift is critical not only in the hygiene sector but across all industries reliant on polymer-based products. By standardizing materials, especially in the initial design phase, manufacturers can gain immediate benefits in waste diversion and carbon footprint reduction.
This strategic shift also lays the groundwork for long-term benefits from future recycling innovations. The recycling of post-consumer diapers will require consumer support alongside substantial infrastructural and engineering investments. A robust and dependable recycling market for all reclaimed materials is essential to justify these investments. A collaborative effort between producers and recyclers is crucial to establish a sustainable framework that supports the long-term viability of recycling initiatives for complex post-consumer plastic feedstocks and material circularity.
The EPA defines a circular economy as “an economy that uses a systems-focused approach and involves industrial processes and economic activities that are restorative or regenerative by design, enable resources used in such processes and activities to maintain their highest value for as long as possible, and aim for the elimination of waste through the superior design of materials, products, and systems (including business models).”
A key advantage of advanced recycling is its ability to return plastics to the value chain at their highest value – as virgingrade plastic. Nexus actively works within the hygiene industry to convert waste from the manufacture and distribution of hygiene products into circular feedstocks through its plastic-to-plastic recycling process.
An essential aspect of circular recycling is a transparent and verifiable system that tracks the journey of recyclable materials within the supply chain, enhancing accountability and sustainability. Nexus holds the International Sustainability and Carbon Certification (ISCC+) certification, indicating that its supply chain uses materials that are fully traceable and sustainably sourced. Since its initial certification in 2020, Nexus has been recertified annually, reflecting its ongoing commitment to sustainability.
GHG Emissions for Pyrolysis Oil Prduction, (A) energy-based allocation, (B) market-based allocation. For pyrolysis oil, conversion emissions are the main contributors to total GHG emissions in all facility groups. The energy requirements in pioneer plants are higher than those of the Nth-plants and the highest-capacity facility. This is particularly important because it highlights the impact that economies of scale have in reducing the GHG emissions for the production of pyrolysis oil, where emission reductions of 19% and 45% are achieved for the Nth-plant (50 KTA) and highest-capacity facilities, respectively.
Argonne National Laboratory Life-cycle Analysis of Conversion of Post-Use Plastic via Pyrolysis with the GREET Model
These ISCC+ certified liquid feedstocks from advanced recycling set the foundation for resins that meet strict specifications and purity standards, essential for foodcontact and hygiene products. Such resins represent a transformative development for industries that traditionally struggle to use recycled materials due to stringent purity and regulatory requirements. Advanced recyclers are creating a mechanism for plastic waste to return to the value chain at its highest potential value, making true circularity a tangible reality for the hygiene sector.
Nexus feedstock film bales. Nexus plant floor sorting line. Nexus Circular
In considering the role of the circular economy in enhancing resource efficiency, addressing the environmental impacts of circular systems and materials, especially in terms of reducing greenhouse gas emissions (GHGs), is crucial. Advanced recycling technologies support both recycling and landfill diversion and play a key role in mitigating climate change via their potential to reduce GHG emissions. This aligns with the global initiatives by plastic converters and absorbent hygiene product (AHP) manufacturers to lower their carbon footprints.
The Argonne National Laboratory, part of the U.S. Department of Energy, recently completed a comprehensive Life Cycle Analysis for pyrolysis-based advanced recycling. The Argonne study confirms that, at commercial scale, pyrolysis can reduce GHGs by 35% compared to fossil-based resources.
The analysis accounts only for Scope 1 emissions, which are directly emitted by sources under company control. It does not account for additional potential benefits such as reducing fossil fuel reliance, enhancing landfill diversion, and
avoiding the environmental and energy impacts of incineration.
With its capacity to enable landfill diversion and reduce GHG emissions, advanced recycling technologies like those developed by Nexus are ideally positioned to partner with the hygiene industry in its transition towards circularity.
Nexus Circular and its peers in the advanced recycling industry are pioneering a path forward in the recycling of polyolefin flexible materials, offering a viable solution to help address a global waste challenge. Nexus’s technology is complemented by a suite of other advanced recycling technologies and innovative companies that are scaling rapidly to offer solutions for challenging plastic waste streams across polymer families and industries. These companies offer an opportunity to divert waste from landfills and incineration while simultaneously reducing GHG emissions.
Partnerships between hygiene companies and advanced recyclers are essential to support the transition towards a circular economy and set a new standard for
sustainability in the hygiene industry. It is imperative that manufacturers, consumers, and recyclers collaborate to foster designs that prioritize both functionality and recyclability. By acting now to design recyclable hygiene product matrixes, the industry sets a foundation for future recycling innovations. Our collective commitment to these design principles will ensure that environmental benefits and circularity are realized alongside consumer satisfaction.
Norihiro Itsubo, et al. “Life Cycle Assessment of the Closed-Loop Recycling of Used Disposable Diapers.” Resources 2020 9 (34). DOI: 10.3390/ resources9030034.
U.S. Environmental Protection Agency. “Facts and Figures about Materials, Waste and Recycling: Nondurable Goods: Product-Specific Data.” https:// www.epa.gov/facts-and-figures-about-materialswaste-and-recycling/nondurable-goods-productspecific-data#DisposableDiapers (Accessed April 11, 2024).
Joan Manuel F. Mendoza, et al. “Improving Resource Efficiency and Environmental Impacts through Novel Design and Manufacturing of Disposable Baby Diapers.” Journal of Cleaner Production 2019 (210), 916-928. DOI: 10.1016/j. jclepro.2018.11.046.
Ulises R. Gracida-Alvarez, et al. “Life-cycle analysis of recycling of post-use plastic to plastic via pyrolysis.” Journal of Cleaner Production, Volume 425 (2023). DOI: 10.1016/j.jclepro.2023.138867.
U.S. Environmental Protection Agency. (2021). “National recycling strategy: Part one of a series on building a circular economy for all.” Retrieved from http://www.epa.gov/recyclingstrategy (Accessed April 12, 2024).
Christy Sapp is the Strategic Feedstock Sourcing Director at Nexus Circular. Christy earned a B.S. in Biochemistry before embarking on a career dedicated to sustainability and recycling. She resides on St. Simons Island, Georgia, drawing daily inspiration from her surroundings to advocate for and advance sustainable practices in the plastics industry.
Kim Evans is a chemical engineer and freelance writer who has spent most of her career in the environmental sector. Kim is a prolific technical writer and has published numerous scientific and educational books. Kim joined Nexus Circular in 2019 to support feedstock development and feasibility studies.
By Esra Cinar
Sustainability is increasingly important in today’s world. Manufacturers of absorbent hygiene products face significant challenges. They must combine environmental compatibility with the highest product quality while minimizing the carbon footprint of their products. Advanced technologies and collaboration along the value chain are opening up new ways to increase production efficiency and lay the foundation for a circular economy. But how do you make products more sustainable without compromising quality and performance?
Absorbent hygiene products such as diapers, adult incontinence products and menstrual care are in constant contact
with the skin. This results in a wide range of requirements for product development and manufacturing: consumers demand products that are safe and effective, do not cause irritation, are free from harmful chemicals and allow freedom of movement. Demographics are also driving the need for adult incontinence products as the world’s population ages. Declining birth rates, later childbearing and fewer children are leading to a shift towards premium products over cheaper brands.
In recent years, demand for another product attribute has increased across all age groups: Sustainability. There is a desire for products that are made from natural materials, contain bio-based ingredients, are biodegradable, and have no negative impact on ecosystems.
All these requirements present the absorbent hygiene industry with a decisive turning point. It is faced with the challenge of developing innovative and sustainable materials and processes for all needs. These should include different types of absorbent hygiene products: for example, fully flushable and biodegradable products, reusable solutions such as washable incontinence and period underwear, and disposable hygiene products such as sanitary towels. The design of sustainable hygiene products includes materials such as bamboo, recycled fibers and PLA, which need to be qualified and integrated.
For manufacturers, the goal is to meet these consumer demands as well as fulfill their own sustainability goals. These include reducing the carbon footprint, minimizing energy consumption and reducing production waste – without compromising operational efficiency.
Baby diapers illustrate the potential for sustainable production in the hygiene industry. Every minute around the world over 300,000 disposable nappies enter landfills, incineration or pollute the environment, according to BBIA UK, most of which are made from fossil-based materials. Plastics derived from petroleum and cellulose processed with fossil fuels dominate the material composition and thus contribute significantly to the ecological footprint.
Analysis of the CO2 contribution shows that materials account for about 50 percent, the manufacturing process for 10 to 15 percent and the end of life for about 35 percent of a product’s total CO2 emissions. These figures underscore the urgency
of minimizing dependence on fossilbased materials and pursuing alternative approaches.
Adhesives play a crucial role in this context. They are an essential component of most hygiene products, from diapers to incontinence products to feminine hygiene products. Adhesives are used to bond the different layers of these products, provide elasticity, and ensure product functionality. Their selection and application therefore have a direct impact on product quality, processing efficiency and, ultimately, the environmental impact of the final product.
Given this central role, adhesive technologies play a key role in managing the balancing act between meeting consumer demands and achieving sustainability goals. Innovative adhesive solutions
developed specifically for the absorbent hygiene industry offer the opportunity to optimize production processes, save energy and reduce the use of raw materials.
Bio-based materials are becoming increasingly important in the manufacture of hygiene products to minimize the environmental footprint and at the same time meet consumer demand for sustainable products. These materials, which are derived from renewable resources, offer a sustainable alternative to conventional raw materials based on fossil fuels. Henkel is a pioneer in the development and implementation of bio-based solutions with its Technomelt® DM ECO products. These adhesives consist of more than 60 percent bio-based materials. In addition to the reduction of CO 2 emissions in the
manufacturing process, the compatibility of these adhesives with bio-based substrates is another decisive factor. Technomelt DM ECO adhesives offer optimum adhesion to a wide range of biobased materials, making them a key component in the manufacture of sustainable hygiene products.
Another innovation is Henkel’s Technomelt DM COOL series. These adhesives have been specially developed for use at lower temperatures and are therefore particularly suitable for use with biobased films, which can be sensitive to the higher temperatures of conventional hot melts. The lower application temperatures reduce the risk of damage to the bio-based films, contributing to longer life and higher quality of the end product. At the same time, they enable significant energy savings due to their lower application temperature, which in turn reduces the carbon footprint of production.
As well as having a positive impact on product quality and sustainability, adhesives can also help to optimize production processes in the absorbent hygiene products industry. The focus is on energy consumption and waste generation. Henkel’s Easyflow® system uses micro-chubs in a non-sticky, free-flowing form that are automatically fed into melters. They remain in solid form until needed. This “melt-on-demand” functionality allows the adhesive to be melted precisely as needed. This results in energy savings of about 23 percent compared to manual replenishment. There is no need to keep the adhesive at a high temperature all the time, and employees do not have to constantly open the tank lid, preventing colder ambient air from entering the melting system. This results in lower operating costs and a reduced carbon footprint. In addition, the closed system helps prevent contamination and foreign matter from entering the adhesive. This significantly reduces problems such as clogged nozzles and filters that would otherwise require frequent maintenance. The resulting increase in production efficiency and product quality reduces waste by up to 40 percent, significantly reducing material loss. Another advantage of the Easyflow system over conventional technologies is the increased yield of olefin-based adhesives. This increase in efficiency reduces adhesive consumption by about 15 percent compared to rubber-based products. In addition, the ability to deliver the adhesive in large, recyclable big bags instead of individual cartons results in a significant reduction in packaging waste.
Another important aspect of sustainability in the hygiene industry is the handling of products at the end of their life cycle, known as end-of-life management. The disposal of hygiene products can have a significant impact on the environment, especially if they are not biodegradable or contain harmful chemicals. For example, according to Science of The Total Envi-
To achieve greater sustainability, cross-industry collaboration along the value chain is essential. Manufacturers, raw material suppliers, disposers and recyclers must work together to create closedloop systems that enable the environmentally sound disposal and recycling of hygiene products.
ronment, 12 billion pads and seven billion tampons are discarded each year in the United States.
A key element in this process is compostable adhesives, such as those offered by Henkel with Technomelt DM RE. These products not only meet the high performance and safety requirements for the manufacture and use of hygiene articles, but also the compostability requirements of ASTM 6400, the standard specification for labeling plastic materials that are aerobically composted in municipal and industrial facilities. With a bio-based content of over 64 percent, these adhesives not only help reduce the use of fossil resources, but also allow the end products to be composted after use, returning them to the natural cycle.
To achieve greater sustainability, cross-industry collaboration along the value chain is essential. Manufacturers, raw material suppliers, disposers and recyclers must work together to create closed-loop systems that enable the environmentally sound disposal and recycling of hygiene products. This collaboration is critical to developing effective collection and recycling processes that recover valuable materials and reduce waste. Through continued dialogue and collaboration between all stakeholders, the end-of-life management of hygiene products can be significantly improved, ultimately reducing the environmental footprint and promoting a more sustainable and responsible industry.
The absorbent hygiene industry faces the challenge of reconciling growing con-
sumer demand for sustainable products with the need for sustainable production. Innovative adhesive technologies, especially bio-based and compostable adhesives such as Henkel’s Technomelt DM ECO and DM RE, are leading the way. They not only provide an effective response to environmental and economic demands, but also make a significant contribution to reducing the carbon footprint and conserving natural resources. By integrating these sustainable adhesive solutions, manufacturers can improve the entire lifecycle of their products, from manufacturing to disposal.
Critical to the success of these efforts is industry-wide collaboration along the value chain to ensure sustainable development from product conception to end-of-life management. By embracing advanced adhesive technologies and promoting a circular economy, the industry is moving toward a more sustainable future that both meets the needs of consumers and protects the environment.
Esra Cinar has been a professional in the chemical industry for 14 years, with a background in Research and Development, Product Management, and now serving as the Senior Market Strategy Manager at Henkel, overseeing the Nonwovens and Tissue Towel segments in US, Canada and Mexico. With a Bachelor of Science in Chemistry from William Paterson University and an MBA from NYU Stern, her expertise spans science and business. She is a recognized Sustainability Champion, dedicated to driving positive change.
The quality of air intake is a substantial factor in the overall performance of today’s engines. An efficient air intake filtration supports optimal operation, preventing particulate contaminants from entering the engine while optimizing fuel consumption and reducing engine wear. In this context, a longer filter lifetime is a key benefit as it ensures continuous removal of contaminants while extending service intervals and minimizing environmental impact.
Ahlstrom introduces a new dual-layer filter media technology, available globally, that represents a leap forward in filtration and is a perfect solution to comply with future market needs. The dual-layer design offers up to double dust holding capacity compared to the single-layer design, as each layer serves a distinct purpose to optimize the overall retention of particles in the depth of the material.
In automotive engine air intake applications, the technology has proven to extend by over 50% the filter lifetime in the same configuration. It also offers the possibility to reduce both size and weight of the filter element in vehicles where these parameters are important.
Dual-layer filter materials are designed to comply with current and future engine air intake specifications, including fuel cells. The media can be customized with flame retardancy properties to increase safety in use without compromising performance. The technology is highly adaptable and can be extended to filter air and liquid in many other transportation and industrial applications.
“Leveraging our advanced manufacturing processes and know-how, Ahlstrom’s dual-layer filter media are setting new standards for filtration performance on the market,” says Tamara Quatrano, VP of R&D and Product Development for the Filtration division. “They can be adapted to different environments, and they not only purify and protect but also contribute to a more sustainable future,” she continues.
For more information, please contact Tamara Quatrano, Vice President, R&D and Product Development, Filtration, tamara.quatrano@ahlstrom.com.
Americhem, Inc., a global leader in innovative polymer solutions, is advancing its global sustainability campaign with the launch of nShield ®, a natural antimicrobial and odor control treatment for textiles and other synthetic fibers. nShield® is formulated as an antimicrobial masterbatch containing a plant-based, renewable-sourced solution. Delivered in pellet form, it is specially designed for synthetic fiber applications such as textiles, carpets, and nonwovens. The masterbatch incorporates natural essential oil into a carrier system, ensuring protection
able alternative to the harsh chemicals traditionally used in textiles. This substitution not only enhances ingredient sustainability but also preserves fabric longevity while reducing environmental impact. By unlocking antimicrobial and odor control properties within textiles, Americhem’s peppermint oilbased additive reduces the need for frequent wash cycles, conserving energy and preserving water. nShield® has been proven to inhibit microbial growth and provide longer-lasting odor control for up to 50 washes.
The masterbatch is suitable for synthetic fibers such as PET, nylon, and polypropylene. It has successfully passed antibacterial testing standards, including ISO 20743, JIS L 1902, AATCC 100, and GB/T 20994. Moreover, nShield® complies with EPA and BPR regulatory requirements, and its active ingredient (peppermint extract) is fully traceable.
With high thermal stability, excellent dispersion, and ecological friendliness, nShield ® sets new industry benchmarks for performance and sustainability in antimicrobial masterbatches. Its ability to provide superior antimicrobial protection while maintaining environmental integrity makes it a game-changer in the realm of sustainable polymer solutions. By introducing this plant-based innovation, Americhem helps fiber manufacturers optimize their supply chains for sustainability and regulatory compliance while advancing environmental stewardship.
of the active substance during heat processing. This novel approach aids fiber manufacturers in establishing a sustainable supply chain, enhancing environmental stewardship, meeting regulatory obligations, and cultivating a more adaptable and intelligent supply network.
Peppermint oil, a key ingredient in nShield®, provides a natural, renewable, and sustain-
The addition of nShield ® to Americhem’s product portfolio demonstrates the company’s commitment to driving sustainable innovation in polymer solutions. Their continued efforts aim to establish a more resilient and intelligent supply network, enhancing adaptability to shifting consumer demands and regulatory landscapes.
Please contact Robert Baldy, Business Director Fibers and Packaging at rbaldy@ americhem.com for more information.
When speaking of our environment, climate crisis, environmental pollution and resource scarcity are three of the most urgent challenges of our time. And time is the crucial factor here. To create a better future for our children and grandchildren, we must build a new and greener economy. We at ANDRITZ are doing everything to drive this change: We enable our customers to make the world a greener place with our sustainable products and solutions. To underline this, we have just recently announced our “FOR THE CHANGE” initiative, which combines sustainable technologies and solutions, making them visible to the market.
One great example is the ANDRITZ nonwoven processes for biodegradable wipes. It includes all technologies available on the market, like AirlaceTM, spunlace, WetlaceTM and WetlaceTM CP, with one goal in mind: reduction and elimination of plastic components, while maintaining the highquality of the desired product properties.
Textile recycling in Europe is now evolving with a sense of urgency as it becomes clear that the discarding of garments and apparels of clothing represent a major threat to the environment. Governments are now catching up with the threat; in Europe, the latest regulations mean that the whole fashion and clothing industry has to completely rethink how textiles are managed at end-of-life. ANDRITZ has been aware of the situation for some time and has been working on solutions and innovations to counter the challenge. In its latest move, the company has partnered with textile experts in France to launch a major revolution in automated sorting for further recycling into new products.
It is estimated that around 7.5 million tons of textiles are discarded in Europe every year. Currently only 2.2 tons are collected, with the rest going to landfill or incineration. Due to new regulations, the volume of textiles collected is estimated to rise by 4.5 – 7.2 million tons by 2030.
ANDRITZ complete production processes for this kind of wipes can perfectly handle a blend of fibers, such as cellulose, viscose, lyocell, cotton, hemp, bamboo, or linen.
line.
With the latest acquisition of Dan-Web in Denmark, ANDRITZ completes this range with the airlaid/AirlaceTM technology. Airlaid forming can perfectly process short fibers, like wood pulp, which allows to manufacture products with high content of natural raw material including biodegradable and flushable wipes. By combining this with the hydroentanglement technology, plastic fibers and chemical additives can be avoided.
“The new regulations mean that by 2025, all European countries will no longer be able to dispense of clothing by landfill or burning,” says Alexandre Butte, General Manager, ANDRITZ Laroche. “All of these countries will have to have collection systems in place by that time.”
To address this dramatic upscale of regulations, French startup company, Nouvelles Fibres Textiles, has recently launched a revolutionary new industrial-scale line in Amplepuis (central France). This unique line is designed to speedily and autonomously sort discarded garments by color and composition
Moreover, ANDRITZ also has the expertise to offer the full spectrum of upgrades and retrofits for existing production lines. For instance, spunlace producers can upgrade their lines with a wetlaid or airlaid forming unit to open new business opportunities and achieve greater flexibility in terms of product variants. ANDRITZ advises its customers on the selection of the right technology and the most suitable upgrade according to their process, constraints, and future requirements.
Another market example is the increasing demand for flushable, plastic-free wipes and their technologies. In recent years, the threat of plastic pollution and stricter regulations from governments and industry associations has increased. The ANDRITZ WetlaceTM technology produces a 100% sustainable wipe that precisely meets customer needs and flushability guidelines and supports the strong move away from plastic and synthetic materials.
utilizing the very latest in digital and infrared technology. The entire line has been supplied by ANDRITZ, with infrared technology supplied by French company Pellenc ST, also a partner in the new venture.
Added to the sorting of garments, the line will remove non-textile parts of garments including zippers and buttons and start the first stage of tearing. The remaining sorted garments are then sent on for further processing by textile producers for further tearing and on to either spinning for the production of new products, including nonwovens and composite materials.
The goal of Nouvelles Fibres Textiles is to trigger the circular economy at an industrial scale when it comes to the sorting and recycling of textiles in France. The technology used in the new demonstration plant, supplied by the partners, ANDRITZ and Pellenc ST, represents the missing link to the industrialization of textile recycling.
Although the recycling of textiles is nothing new in the industry, the main challenge has
BASF’s Acrodur ® portfolio offers a range of high-performance products that serve as innovative and low-emission alternatives to conventional formaldehyde-based resins, such as phenol, melamine, and urea resins. Acrodur products have outstanding wet and dry strength, excellent adhesive properties, and the ability to reinforce natural, glass, and synthetic nonwovens, as well as cork and other particles.
Acrodur products are water-based, which eliminates the need for organic solvents, reducing VOC emissions and environmental impact. Unlike traditional formaldehyde-based resins, Acrodur does not release any toxic or hazardous substances during the cross-linking process. The only by-product is water, making it a safe and environmentally friendly choice. These factors contribute to a healthier and safer environment for both workers and end-users.
Furthermore, Acrodur offers high thermomechanical stability after curing, making it suitable for applications that require dura -
been the automating of the sorting process. As can be imagined, this sorting is a demanding task, simply because of the range of composition, colors and sizes involved. Nouvelles Fibres Textiles, decided to take on this mammoth task, but it needed help; and this is where ANDRITZ, with its vast experience in the recycling industry and the building of complete manufacturing lines, joined the challenge, together with specialist provider of infrared sensors for sorting, Pellenc ST. All four companies are now in partnership on the project which will see the line running on 60% commercial operations with 40% of time set aside for R&D.
The plant was launched at the end of 2023 to an audience of guests from all over Europe, and included politicians, industry players,
bility and resistance to high temperatures. It also exhibits excellent compatibility with flame retardants, pigments, and fillers, allowing for versatile customization options. The water-based nature of Acrodur makes it compatible with various application methods, including foulard, curtain-coating, blow-line impregnation, and spray application.
Acrodur utilizes thermosetting resin technology and is B-stage curable, giving producers flexibility with manufacturing timing. Its outstanding binder properties enable the incorporation of a high percentage of natural fibers in components, contributing to the development of sustainable and lightweight products.
BASF’s North American portfolio contains three products that span multiple fiber types and application needs. Acrodur PLUS 2580 is a solution polymer that provides excellent heat resistance and stiffness with very low color. The high solid composition also helps contribute to lower transportation costs. Acrodur
950 L is also a solution polymer that provides excellent heat resistance and stiffness and can be used in a variety of glass fiber applications. Finally, Acrodur DS 3515 is a dispersion polymer that provides excellent thermal stability, flex modulus, and hydrophobicity.
In summary, BASF’s Acrodur products are sustainable solutions for a variety of nonwovens. Its water-based and formaldehyde-free composition, combined with its outstanding strength properties and application versatility, make it a superior alternative to formaldehyde-based resins. Acrodur not only improves the properties of the finished product but also ensures safe working conditions during production. By choosing Acrodur, manufacturers can enhance sustainability claims, reduce emissions, and contribute to healthier indoor environments.
Visit: https://www.basf.com/us/en/products/General-Business-Topics/dispersions/Products/Acrodur-acrylic-resins.html
universities, and textile technical institutions. The event included a demonstration of the line, as well as speeches from the partners of the project and a panel discussion featuring major customers of the textile industry in France, including the French supermarket giant Auchan.
The new automated textile sorting and recycling plant represents the first step in a journey that will see millions of tons discarded textiles collected, sorted and recycled for making new products in the future. As a signal to the opportunities ahead, Nouvelles Fibres Textiles has already laid the foundations for a full-scale recovered textile preparation plant which will have an annual capacity of 25,000 tons of post-consumer textile waste planned for start-up in 2025.
Benoit Rombaut, Technology Director, ANDRITZ Laroche, says, “The line is the first and important milestone of a long journey. In France, due to tightening regulations and the increased collection rate of 60% of all textiles manufactured, there is now around 240,000 tons of textiles for recycling. In three
years’ time this will raise to 300,000 tons. This means that we need at least another 12 high-capacity sorting and recycling lines to cope with the demand.
ANDRITZ One-Stop-Shop for Textile Circularity
ANDRITZ has huge experience in the recycling of textiles, with both mechanical and chemical solutions. Now with its expertise in sorting, complete lines from collected textiles to full recycling is possible, representing a revolution in circularity for the industry.
“At ANDRITZ we are completing our goal with the new line,” says Butte. “We can now provide a one-stop-shop for our customers and provide complete lines for textile recycling from sorting to mechanical or chemical recycling.”
The textile industry faces a critical challenge to reach its climate goals, with raw materials contributing two-thirds of its harmful climate impact, according to Quantis Environmental Sustainability Consultancy. To align with ESG targets and anticipated legislation, companies must transition to lowerimpact raw materials. To address this need, regenerative material systems company BFT produces Sero™ natural performance fibres at an industrial scale at their two wholly owned mills in Europe and North America.
Made from 100% recycled materials, Berry Global’s Chicopee rMicrofibre stands as a groundbreaking solution in the nonwoven wiping industry, being the first and only wipe made entirely from 100% post-industrial recycled (PIR) and post-consumer recycled (PCR) fibers.
The Sero™ materials portfolio encompasses a range of natural, low-impact fibres, including hemp, cotton, and flax. Hemp cultivation plays a vital role in regenerative agriculture as it sequesters large amounts of carbon, improves soil health, and supports ecosystem diversity. Hemp significantly reduces the carbon footprint of Sero™ products and facilitates the creation of nature-positive fabrics. Noel Hall, Executive Chair of BFT, emphasizes, “Sero™ fibres are a Climate+ solution, meaning our partners not only address their decarbonization goals but also their plastics reduction and forest preservation targets.”
While Sero™ regenerative fibres are natural, they are engineered as technical performance fibres that match or exceed the properties of the materials they replace. Their strength and versatility ensure products meet desired standards without compromising softness, absorbency, breathability, or durability.
To drive widespread adoption, regenerative fibres must be designed as a drop-in solution for existing nonwoven and textile platforms. Manufacturers appreciate the cost-effectiveness and ease of production with Sero™ fibres for eco-friendly everyday care and hygiene products, apparel, and home furnishings. The inherent properties of Sero™ fibres makes them an excellent blending partner that adds unique performance benefits.
Collaborating for Positive Impact: Sero™ Partners with Period Care Brands
BFT collaborates closely with fabric industry partners to create circular, nature-positive products. Noel says: “Partners like Hempress Hygienics (US) and Mewalii (DK) are using Sero™ fibres in their products to revolutionize the femcare industry. Together, we make healthy and eco-friendly period choices accessible to the mass market.” Mewalii’s hemp period pads are made with 75% Sero™ regenerative hemp fibres, offering a comfortable, absorbent, and climate-friendly option that is better for both people and the environment.
“With Sero™, let’s collectively shape the textile future with fibres that give back to nature and humanity, and begin to repair the damage done to our planet” Noel closes.
Join us in creating regenerative products and learn more about Sero™ fibres at Serofibre.com.
Reducing the carbon footprint of the wipe and giving new life to recycled materials, rMicrofibre is unlike alternatives available on the market. Often, these products do not contain 100% recycled materials and lack pure microfiber, including blends with viscose that compromise performance. rMicrofibre remains unrivalled, ensuring sustainable and superior cleaning. This innovation aligns perfectly with sustainability goals, supporting the EU Green Deal’s chemical strategy to cut greenhouse gas emissions by at least 55% by 2030 through reduced chemical usage while maximizing cleaning efficacy and sustainable cleaning solutions.
Certified to achieve an astonishing 99.97% bacteria removal using just water, rMicrofibre acts as a powerful bacteria magnet, trapping unseen bacteria and dirt in its fibers. By splitting fibers into microfibers > 80% finer than reusable alternatives, rMicrofibre ensures superior surface contact, magnetically removing bacteria and dirt that may otherwise be missed. This not only guarantees exceptional cleaning results but also minimizes the risk of cross-contamination in high-risk environments.
With touchscreens becoming ubiquitous in modern facilities, the demand for effective cleaning solutions is higher than ever. rMicrofibre wipes excel in delivering streak-free cleaning on glass, stainless steel, mirrors, and touchscreens, effectively removing greasy fingerprints and reducing the risk of bacteria transfer. Their 100% microfibre composition allows for enhanced absorption, enabling the removal of up to 20% more natural oils compared to other wipes, making them ideal for phones, tablets, and monitors.
Designed for short-term use to mitigate the risk of crosscontamination, rMicrofibre wipes ensure maximum hygiene without compromising on practicality. Unlike reusable alternatives, which have been shown to retain dangerous levels of bacteria even after laundering , rMicrofibre offers a costeffective and environmentally friendly solution to maintain cleanliness in high-traffic areas which are prone to crosscontamination. This includes workspaces, healthcare facilities, airports, hotels, and restaurants, targeting surfaces such as door handles, touchscreens, monitors, glass, and stainless steel. By reducing laundry requirements and maximizing cleaning efficacy, these wipes provide a cleaner and safer environment for users in high-traffic and traffic areas.
In today’s rapidly evolving consumer landscape, sustainability has become a paramount concern across industries, including the wipes market. Heightened environmental awareness and a surge in consumer demand for eco-friendly products have posed significant challenges for companies. The pressure to innovate and offer sustainable solutions that meet both performance and environmental criteria has never been greater.
As businesses adapt to these changing consumer preferences, the importance of sustainability in the wipes market cannot be overstated. Companies are proactively embracing sustainable practices to differentiate themselves in a competitive market while also contributing to broader environmental goals.
Our Group is no exception. The Hygiene Division of BW Converting has developed the new VERTIS interfolder for wet wipes, which not only meets consumer expectations but also addresses environmental concerns head-on.
Market analysis reveals several key trends driving the wipes market. The increasing popularity of single-use wet wipes projects significant growth, but it also presents envi-
ronmental and economic challenges. Consumers often flush wipes that are not compatible with municipal sewer systems, leading to poor environmental outcomes. Non-renewable plastics and materials that do not biodegrade under disposal conditions further exacerbate these challenges, prompting the need for tough regulations. Innovative solutions are required to address the main environmental and technical challenges associated with flushable and non-flushable wipes.
Consumers’ quality perception and requirements are enduring and demanding. Disposable single-use wipes present environmental, technical, and social challenges. In response, our company has developed cutting-edge technology to improve the quality and sustainability of wipes.
Our new converting technology VERTIS enhances the final product quality and consumer experience. With features such as
a small footprint, zero-speed auto-splice system, and precise add-on lotion system, the VERTIS sets a new standard for hygienic and efficient wipes production.
The benefits of our technology are manifold. Its unique design results in a superior user dispensing experience, with better pop-up and folding capabilities. Simplified operation, small footprint, and Smart Touch© technology make it easy to use and maintain. Moreover, our VERTIS interfolder stand is compatible with biodegradable materials, reducing environmental impact. With its fully servo system, it ensures durability and flexibility, capable of recording data and settings for future machine learning and repeatability.
For more information about our innovative solution and how it can benefit your business, please contact us at nonwovens@bwconverting. com. We are committed to driving sustainability in the wipes market and invite you to join us in this journey towards a greener future.
Exposome Pvt. Ltd. is a material chemistry provider – enabling various industries achieve their sustainability and Net Zero goals. With our cost-effective and energy-conserving filtration solutions we are enabling industries in re-using and recycling their wastewater effectively and/or meeting stringent discharge norms.
Our air filtration molecular filters enable a safe, healthy and breathable environment for the people working in the heavily polluted industrial areas.
We manufacture regenerable, hence re-usable effluent treatment media for waste water and air. Based on the principle of absorption, adsorption, and redox, our filtration media for waste water efficiently removes COD, recalcitrant COD, BOD, colour, odour, hardness, etc.
We also have specialised filtration media which can selectively
remove aluminium, heavy metals (such as zinc, chromium, iron, cadmium and copper), cyanide, silica and total ammonical nitrogen from waste water. Our molecular filters for air are very efficient in removing commonly seen air pollutants across various industries: SOX, NOX, VOC, H2S, odour, humidity etc.
Why are our filtration solutions more sustainable than the rest?
• Because our molecular filters are regenerable on-site, operating costs are significantly low.
• As it requires a simple flow-through mode, electricity consumption is nil or negligible.
• With 60-90% reduction in COD and other parameters, industries are able to reuse the water in their facilities hence enabling zero liquid discharge plants.
• Our raw materials are natural in origin and biodegradable. Email us at info@exposome.in or visit www.exposome.in.
Kelheim Fibres, a leading manufacturer of specialty viscose fibres, recently unveiled their latest findings at this year’s Cellulose Fibres Conference. Led by Dr. Ingo Bernt, Group Leader of Fibre & Application Development at Kelheim Fibres, and in collaboration with Dr. Thomas Harter from Graz University of Technology, the study provided invaluable insights into the complex relationship between the geometric structure of viscose fibres and their liquid absorption capacity, particularly in the context of tampon applications.
For decades, Kelheim Fibres has been a trusted partner in the tampon industry, supplying specialty fibres pivotal for tampon performance. Modified fibre cross-sections often serve as the cornerstone for the distinctive functionalities of Kelheim’s specialty fibres. A prime illustration is the renowned trilobal Galaxy®, distinguished by its Y-shaped crosssection, boasting up to 30% higher absorption capacity than standard viscose fibres and serving as a flagship product in tampon manufacturing.
The latest research has shed light on the mechanisms governing liquid absorption and
retention in tampons. The study compared the efficacy of two commonly used tampon viscose fibre types: round standard fibres and trilobal fibres. Tampons crafted from trilobal Galaxy® fibres demonstrate markedly superior absorption capacity compared to those made from round fibres, with trilobal fibres also providing higher water retention capacity. This could be attributed to the greater specific surface area of trilobal fibres, allowing liquid accumulation along the three legs of the Y-shaped cross-section, alongside their higher fibre porosity relative to round fibres. However, fibre swelling alone cannot entirely account for the augmented tampon absorption, as it contributes only about 11-13% to the total liquid uptake of tampons.
The research findings underscore the pivotal role of fibre behavior within tampons or
NeenahPure™GESSNER’s Sustainable Solutions for Pocket Filters
Our world without pocket filters would be characterized by a sharp deterioration in air quality within industrial settings and surrounding areas. Without these filters, production facilities and industrial areas would be much more contaminated with harmful particles and pollutants, which would not only endanger the health of employees and residents but would also have a serious environmental impact.
In such a scenario, we could expect more frequent and more severe pollution, which would have a negative impact on ecosys -
tems, soils, water bodies and air quality. This could lead to a rise in disasters affecting nature and health issues, as people and animals would be exposed to more toxic substances.
Pocket filters are not only a technological innovation but also a significant contribution to the preservation of our planet and sustainable practices.
With NeenahPure,™ you can make a positive impact on our environment. Our meltblown media for pleated and pocket filter applications are covering all efficiencies from ePM10 50% to ePM1 80% as per
nonwoven fabrics. Here, the trilobal Galaxy® fosters the formation and sustenance of a more voluminous and expansive network, ensuring a larger volume is accessible for liquid absorption, thereby enhancing the overall performance of the end product.
Dr. Ingo Bernt emphasizes the broader implications of the study results, extending beyond tampon applications. The remarkable absorption capacity of Galaxy ® fibres transcends various absorbent products, offering novel solutions across diverse industries. Particularly amidst the increasing demand sustainable and environmentally friendly alternatives, this aspect this aspect is highly relevant. It underscores the potential of biobased and biodegradable fibres to substitute numerous synthetic solutions without compromising performance.
ISO 16890 standards, and M5-F9 according to EN779:2012. The combination of fine and coarse fibers ensures high separation efficiencies with low pressure drop and a good dust holding capacity.
Let’s continue to invest together in innovative technologies that help make our environment safer, cleaner & more healthier!
For more information visit NeenahPure™ Bag Filter Media - Enhance Indoor Air Quality at https://www.gessner-filtration.com.
The textile industry has been increasingly focused on circular materials as a solution to combat the ongoing increase in waste pollution. In a world where fashion is still mostly looked at through the lens of speed, Eastman creates value from hard-to-recycle waste that would otherwise go into landfills, thus investing in sustainable innovation.
A perfect example of this is Naia™ Renew ES, a game changer for the industry: it’s a solution that blends fashion and environmental responsibility, made from 40% certified recycled waste material, 20% certified recycled cellulose and 40% sustainably sourced wood pulp. It is Eastman’s fiber with the most recycled content yet, first launched for a pilot project in collaboration with Patagonia in September 2022.
Early this year at Première Vision Paris, Naia™ announced the launch of Naia™ Renew ES at scale, as the perfect solution for brands that want to enhance their sustainable story. One valuable example is the renowned American brand Reformation, which has presented three gowns featuring Naia™ Renew ES in its latest bridal collection. This goes to show the versatility that this fiber can have in the fashion world, with applications that range from activewear to formal and bridal clothing. “Like silk but better” is the brand promise, which has chosen this yarn as a silk alternative due to its inherent properties – elegant drape, silky soft hand and luxurious luster – with all the benefits of circularity.
The high percentage of the recycled content in Naia™ Renew ES is possible through Eastman’s molecular recycling technology, which breaks down waste into its molecular building blocks. This process produces a fully traceable and biodegradable cellulosic fiber, proven by a series of
certifications that highlight the fiber’s biodegradable and compostable nature (such as the TÜV Austria one).
Unlike other cellulose-based yarns and fibers, Naia™ Renew ES requires fewer virgin materials to make an eco-friendly alternative to natural or man-made fibers, ensuring elegance, comfort and high performance without compromising on sustainability. In the words of Carolina Sister Cohn, Global Marketing Leader for Eastman’s textiles division “...we’re proud to offer a 60% recycled content fiber at scale for the fashion market. With Naia™ Renew ES, we offer a sustainable and circular solution that meets the demands of both fashion and environmental responsibility, and we’re making significant strides in transforming the fashion industry and inspiring others to embrace sustainability as a design decision.”
Furthermore, Naia™ Renew ES received GRS certification in December 2023. This certifies the fiber’s recycled content, chain of custody, social and environmental practices, and chemical restrictions. Earned after an independent third-party audit, GRS certification provides increased traceability, environmental principles, social requirements, chemical content and labeling. The certification aids in building brand trustworthiness around the world, fostering relationships with more customers and collaborators around the world and strengthening Naia™’s expansion plans.
Eastman’s technologies are driving a revolution in materials – from a linear life cycle that results in waste to a circular life cycle that keeps materials in use, creates sustainable value, and enhances quality of life.
Learn more at www.eastman.com.
According to WWF1, on the current trajectory, by 2040 global plastic production will double, plastic leakage into oceans will triple, and the total volume of plastic pollution in oceans will quadruple. This surge in plastic production is going well beyond what any country can properly deal with, resulting in a plastic pollution crisis affecting the environment, especially the oceans.
Addressing plastic pollution demands systemic change, government regulations, and individual actions that can help the Earth. With consumers becoming more conscious of their choices, industries are adapting to offer more responsible options.
This shift is happening across industries but not fast enough. Using advancements in research and development, fibers are evolving to provide the consumer with alternative choices and address concerns about plastic waste. The balance is to do this without losing important characteristics of the fiber.
VEOCEL™, the flagship specialty nonwo -
vens brand of Lenzing Group, has embraced these changes without compromising on quality or performance. Offering LENZING™ Lyocell Dry fibers to meet the growing need for non-plastic nonwoven products, VEOCEL™ adheres to EU SUPD 2 regulations to deliver high-performance absorbency and comfort. This innovative approach makes it the optimum fiber choice for responsible absorbent personal care and hygiene products.
These fibers feature Lenzing’s unique Dry technology which is high-performing hydrophobicity and has liquid-controlling properties. The fiber retains its softness in both dry and wet environments, as tested by Lenzing.
LENZING™ Lyocell Dry is a cellulosic environment-friendly wood-based alternative to synthetic fibers. Derived from wood, the VEOCEL™ branded lyocell fibers with Dry technology are made using a closed-loop production process with low water consumption, while being biodegradable and compostable3 at end-of-life. The fibers bring the inherent
advantages of cellulose to personal care and hygiene products: natural absorbency, liquid distribution, gentle on the skin, naturally smooth and soft, biodegradability, and versatility. Manufacturers have the opportunity to protect the planet without compromising on performance or comfort.
As an industry, it is our responsibility to provide more responsible options and contribute to a better future for the planet and future generations. Let’s come together to set higher standards for industry sustainability and comfort.
1 https://wwf.panda.org/wwf_news/?8607466/WWFban-on-harmful-single-use-plastics-treaty.
2 Directive (EU) 2019/904 of the European Parliament and of the Council of 5 June 2019 https://eur-lex.europa.eu/ eli/dir/2019/904/oj.
3 LENZING™ Lyocell Dry fiber has been certified as biodegradable in soil and compostable under industrial and home conditions.
With the XHL (Extra High Loft) Technology Reifenhäuser Reicofil enables producers to easily combine superior softness with unseen drapability in nonwovens. The material is especially in demand among premium diaper manufacturers.
Manufacturers of baby diapers are looking for nonwovens that are particularly soft and adapt well to the baby’s body shape. Nonwovens producers, however, have only ever been able to satisfy one of these properties, and thus have not been able to make customers 100 percent happy. With Reicofil XHL technology, they can produce nonwovens that combine exceptional softness and super drapability in one material.
The Reicofil Technology Behind Extra High Loft Nonwovens
All that is needed to produce super-soft, drapable nonwovens is the proven Reicofil Bico spunbond process, which combines two polypropylene raw materials in one fiber. For Extra High Loft (XHL), Reicofil has developed a special recipe which – run as an eccentric
core-sheath fiber – ensures optimum crimp with reduced fiber diameter.
Compared to common spunbond without crimped fibers, Extra High Loft technology enables 30 percent thicker material. At the same time, softness parameters such as drape and haptic are improved compared to
processes that consolidate nonwovens using hot air. The result is a particularly soft feel combined with high abrasion resistance. By using a state-of-the-art Reicofil 5 line the fiber size is reduced to almost one denier in XHL mode, thus lowering raw material consumption. Because bonding does not require hot air, the process also saves energy costs. In addition, XHL enables the processing of polypropylene raw materials only, which are ideally suited for inline recycling processes, thus reducing production costs and conserving resources.
Visit https://reifenhauser.com/en/linescomponents/xhl-extra-high-loft
In March 20204, the Thermore group debuted its most dynamic stretch insulation in its five decades of innovation: Freedom. Made from 50% post-consumer recycled polyester, this unique and compelling insulation offers groundbreaking stretch while providing warmth across a multitude of uses including alpine sports, running, golf, commuter, fishing & hunting, cycling and a host of other active pursuits.
The new Freedom insulation adds a higher level of comfort and functionality than what was previously attainable in the stretch category. It reaffirms Thermore’s place in the textile industry as a true innovator that is deeply rooted in performance and sustainability.
Dynamometer testing shows that the insulation – which comes in four levels of warmth, ranging from 60-150 grams per square meter –has incredible elasticity and recovers to 100% of itspre-stretch size time after time. The ability to provide warmth while also allowing for a dynamic range of motion is what impels performance brands to utilize Thermore.
The Freedom insulation is GRS certified. It’s machine washable, can be dry cleaned and is easy-care for the consumer – and very design friendly for product developers with its high resistance to fiber migration. This represents another step forward in Thermore’s ongoing dedication to commit to a sustainable product line. Thermore pioneered the use of recycled fibers in the 1980’s and has mastered the technology ever since. Visit https://www. thermore.com/en/