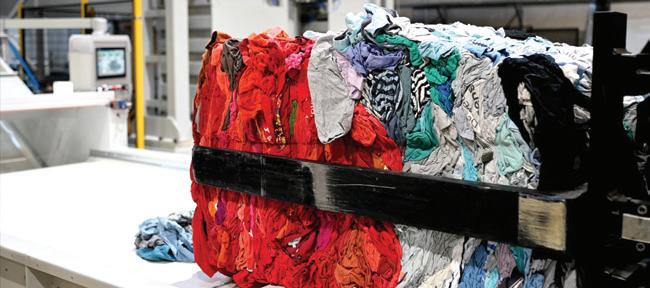
3 minute read
BASF Acrodur® Range of Products for Sustainable Solutions for Nonwovens
BASF’s Acrodur ® portfolio offers a range of high-performance products that serve as innovative and low-emission alternatives to conventional formaldehyde-based resins, such as phenol, melamine, and urea resins. Acrodur products have outstanding wet and dry strength, excellent adhesive properties, and the ability to reinforce natural, glass, and synthetic nonwovens, as well as cork and other particles.
Acrodur products are water-based, which eliminates the need for organic solvents, reducing VOC emissions and environmental impact. Unlike traditional formaldehyde-based resins, Acrodur does not release any toxic or hazardous substances during the cross-linking process. The only by-product is water, making it a safe and environmentally friendly choice. These factors contribute to a healthier and safer environment for both workers and end-users.
Furthermore, Acrodur offers high thermomechanical stability after curing, making it suitable for applications that require dura - been the automating of the sorting process. As can be imagined, this sorting is a demanding task, simply because of the range of composition, colors and sizes involved. Nouvelles Fibres Textiles, decided to take on this mammoth task, but it needed help; and this is where ANDRITZ, with its vast experience in the recycling industry and the building of complete manufacturing lines, joined the challenge, together with specialist provider of infrared sensors for sorting, Pellenc ST. All four companies are now in partnership on the project which will see the line running on 60% commercial operations with 40% of time set aside for R&D.
The plant was launched at the end of 2023 to an audience of guests from all over Europe, and included politicians, industry players, bility and resistance to high temperatures. It also exhibits excellent compatibility with flame retardants, pigments, and fillers, allowing for versatile customization options. The water-based nature of Acrodur makes it compatible with various application methods, including foulard, curtain-coating, blow-line impregnation, and spray application.
Acrodur utilizes thermosetting resin technology and is B-stage curable, giving producers flexibility with manufacturing timing. Its outstanding binder properties enable the incorporation of a high percentage of natural fibers in components, contributing to the development of sustainable and lightweight products.
BASF’s North American portfolio contains three products that span multiple fiber types and application needs. Acrodur PLUS 2580 is a solution polymer that provides excellent heat resistance and stiffness with very low color. The high solid composition also helps contribute to lower transportation costs. Acrodur
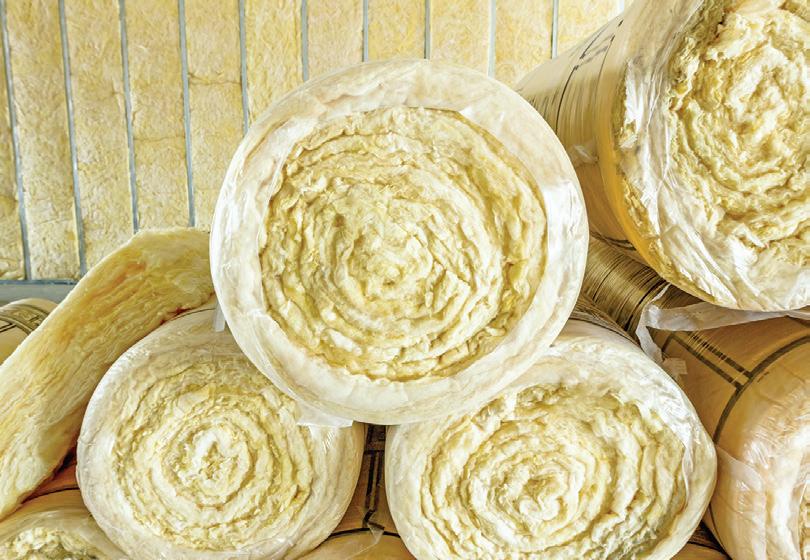
950 L is also a solution polymer that provides excellent heat resistance and stiffness and can be used in a variety of glass fiber applications. Finally, Acrodur DS 3515 is a dispersion polymer that provides excellent thermal stability, flex modulus, and hydrophobicity.
In summary, BASF’s Acrodur products are sustainable solutions for a variety of nonwovens. Its water-based and formaldehyde-free composition, combined with its outstanding strength properties and application versatility, make it a superior alternative to formaldehyde-based resins. Acrodur not only improves the properties of the finished product but also ensures safe working conditions during production. By choosing Acrodur, manufacturers can enhance sustainability claims, reduce emissions, and contribute to healthier indoor environments.
Visit: https://www.basf.com/us/en/products/General-Business-Topics/dispersions/Products/Acrodur-acrylic-resins.html universities, and textile technical institutions. The event included a demonstration of the line, as well as speeches from the partners of the project and a panel discussion featuring major customers of the textile industry in France, including the French supermarket giant Auchan.
The First Step in a Long Journey
The new automated textile sorting and recycling plant represents the first step in a journey that will see millions of tons discarded textiles collected, sorted and recycled for making new products in the future. As a signal to the opportunities ahead, Nouvelles Fibres Textiles has already laid the foundations for a full-scale recovered textile preparation plant which will have an annual capacity of 25,000 tons of post-consumer textile waste planned for start-up in 2025.
Benoit Rombaut, Technology Director, ANDRITZ Laroche, says, “The line is the first and important milestone of a long journey. In France, due to tightening regulations and the increased collection rate of 60% of all textiles manufactured, there is now around 240,000 tons of textiles for recycling. In three years’ time this will raise to 300,000 tons. This means that we need at least another 12 high-capacity sorting and recycling lines to cope with the demand.
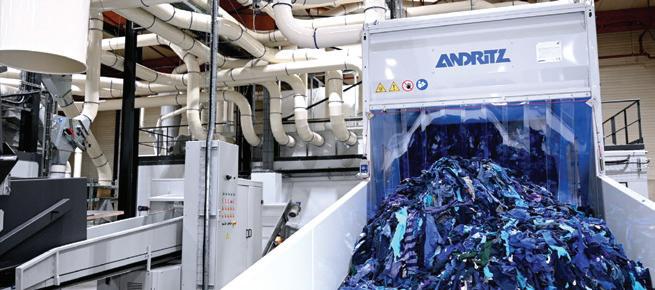
ANDRITZ One-Stop-Shop for Textile Circularity
ANDRITZ has huge experience in the recycling of textiles, with both mechanical and chemical solutions. Now with its expertise in sorting, complete lines from collected textiles to full recycling is possible, representing a revolution in circularity for the industry.
“At ANDRITZ we are completing our goal with the new line,” says Butte. “We can now provide a one-stop-shop for our customers and provide complete lines for textile recycling from sorting to mechanical or chemical recycling.”