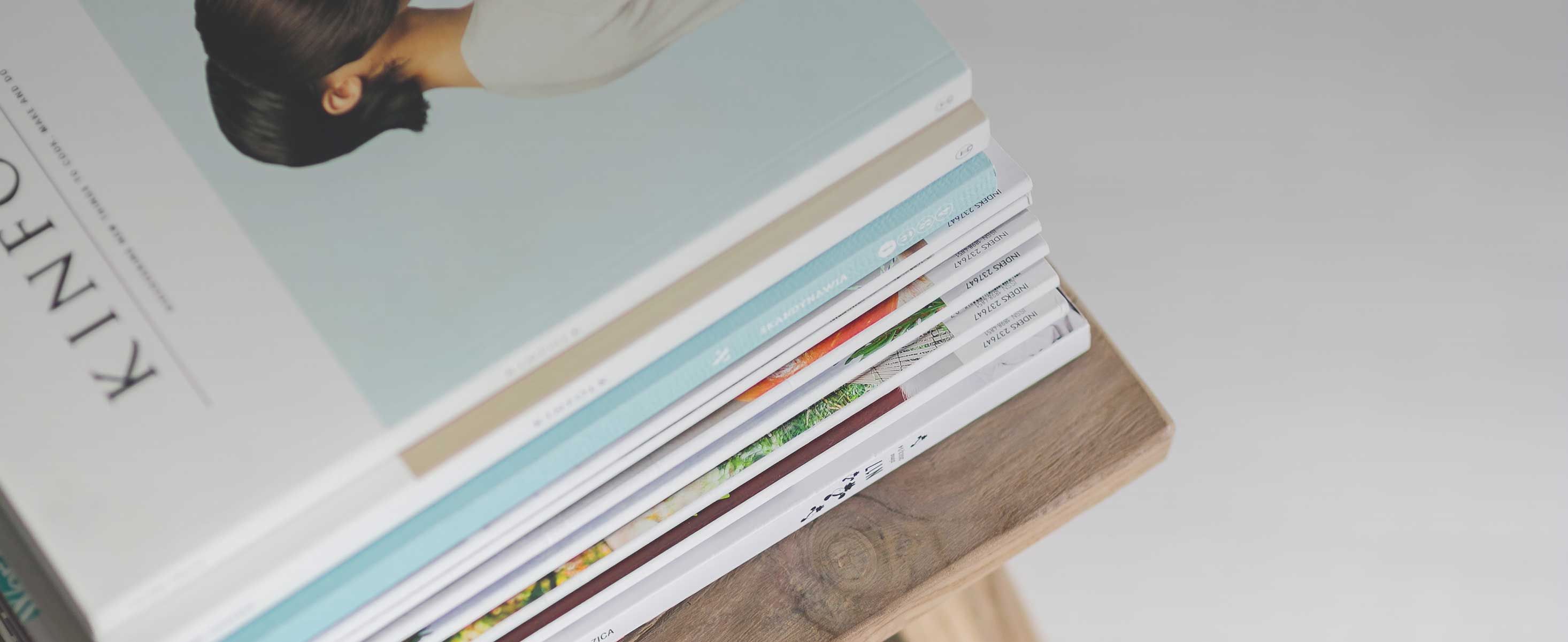
1 minute read
3D-printed tools: „on a par with the steam engine“.
Drills, milling cutters and clamping devices become lighter and easier to cool thanks to a layered structure. Machine tools can thus work more economically.
It is impossible to imagine industry without machine tools. They turn, mill, drill and grind components. Fully automated and at up to several tens of thousands of revolutions per minute. And in the micrometre range. A precision that places great demands on the construction of the tools. Usually several time-consuming processes are involved – from forging, grinding and turning to sharpening. Tool manufacturers are all the more relieved that there is now an alternative to classic subtractive processes: additive manufacturing. One of the most popular 3D printing technologies is Selective Laser Melting (SLM). In this process, the printer spreads a waferthin layer of metal powder on its build platform. A laser then melts the material layer by layer wherever the component is to be created.
Advertisement
The biggest advantage of this tool-free production: design freedom. Tool developers can thus realise highly complex drill geometries that are impossible with subtractive methods. One example of this is integrated cooling channels. In conventional manufacturing, they can usually only be made in a straight line at the core of the drill. Thanks to 3D printing, on the other hand, they can also run in a spiral inside, for example parallel to the secondary cutting edge. This makes it possible to cool heat hotspots that were previously difficult to reach.
The new design flexibility improves the efficiency of the milling machine. Since the component and tool cool down faster, the cycle time is reduced.
Honeycomb structure dampens and reduces weight
Mapal Präzisionswerkzeuge Dr. Kress AG is one of the users of 3D printing in toolmaking. The company from Aalen near Stuttgart has realised a new type of bell tool for milling hose connections. As part of a hybrid production process, the new tool geometry was printed on a base body with an HSK-63 interface. The special feature: the inside of the tool contains a specially designed honeycomb structure – no solid material. This makes the tool 30 % lighter. And due to the damping effect of the structure, the tool life increases by about 40 %, according to Mapal. Machinists can use the tool with higher cutting data without compromising machining quality. In this way, the machining time could be reduced by 50 % compared to the classic tool.
Sandvik Machining Solutions also shows how effective tool printing can be. The tool manufacturer from Sweden offers the „Coromill 390“ product family.