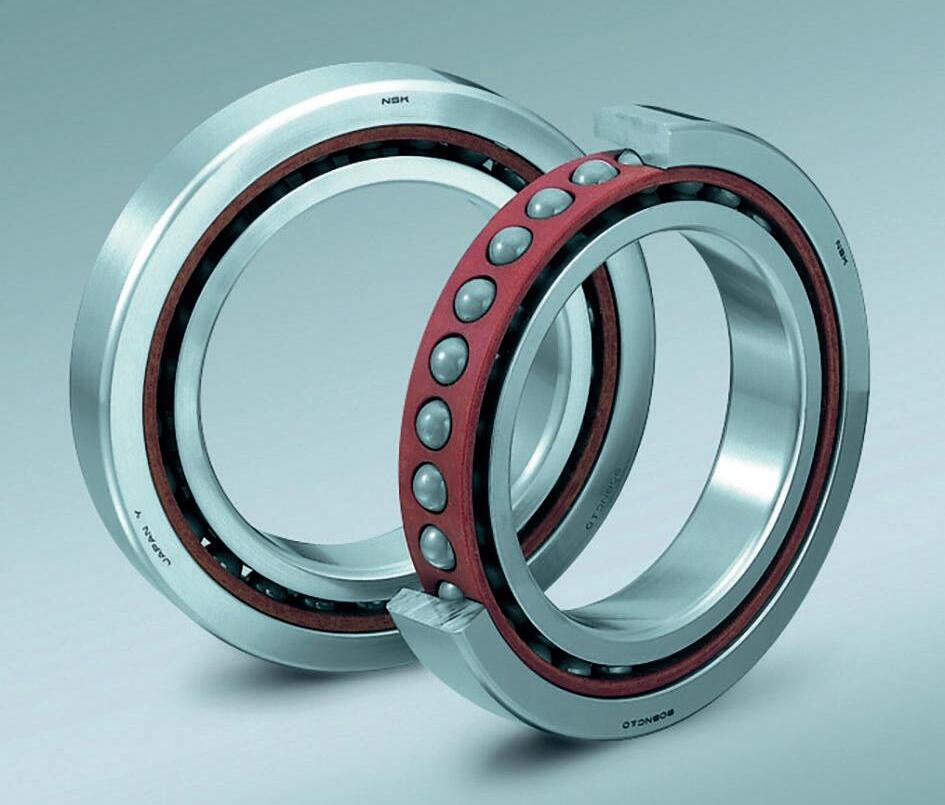
3 minute read
Spindle bearings for machine tools
Production of high-quality components with tight tolerances with minimum machining time and, if possible, without post-processing: this is the ideal vision of machine tool users and, at the same time, the industry trend that will be in the foreground for many exhibitors at EMO 2023. A rolling bearing series specifically developed for this application contributes to this because of its suitability for extremely high speeds combined with high loads.
Rolling bearings used in the main spindles of machine tools have to meet very high requirements
Advertisement
(Figure 1) – for example with regard to the speed setting. In high-speed machining, a speed parameter n × dm of two to three million and above is not unusual.
Very high forces occur on lathes because the material removal can be particularly large when the tool plunges into the workpiece and is inevitably introduced into the bearing as a high load. Depending on the shape of the milled parts and the milling speed, very high forces also arise during milling. In this case, high demands are made on therunning accuracy – also in turning. Any inaccuracies in the running of the spindle, no matter how small, would lead to defects or faults in the machining – and that means in the machined products.
Tight specifications for typical characteristic values
Typical parameters, such as bearing frictional torque and non-repeatable radial runout (NRRO), must therefore remain within narrow limits (Figure 2). This requires extremely precise manufacturing and assembly of the bearing components, and it also requires a bearing design that is adapted to the operating conditions and requirements.
To meet these requirements, NSK has developed various series of angular contact ball and cylindrical roller bearings of the „Robust“ series, which are characterised, among other things, by increased limiting speeds and very high running accuracy.
The entire range of spindle bearings will be on display at EMO, and the focus will be on a European premiere: the Robustdyna series of angular contact ball bearings (Figure 3). It is suitable for extremely high speeds in combination with high loads and thus, for example, for excellent results in combined roughing and finishing operations. Design features such as the use of larger balls and the NSK-developed SHX steel provide the prerequisite for increasing the dynamic load rating by 15 %, while the speed characteristic value of around three million n × dm is at a very high level.
With these values, Robustdyna is suitable for ultra-high-speed machining with short cycle numbers and high loads as well as for machining demanding materials, such as titanium and composites.
Risk of bearing damage is reduced
But not only the dynamic load capacity, but also the static load capacity of the high-performance spindle bearings has been increased by around 15 % through design optimisation. This reduces the risk of bearing damage for the user of Robustdyna angular contact ball bearings in the event of unexpected collisions between spindle, cutting tool, workpiece carrier or component. This feature contributes to long-term reliable and failure-free operation of the spindle.
Another important new introduction at the show is NSK‘s Robustgrd grease for high-speed spindle bearing applications. Compared to conventional NSK grease, it improves seizure resistance considerably – by up to five times – depending on the application. It thus contributes to higher productivity and the long-term stable operation of machine tools. Another advantage: pure grease lubrication enables energy savings compared to oil-air lubrication methods.
Also on the stand is NSK‘s Sursave (TSR) bearing cage for main spindle angular contact ball bearings (Figure 4). This outer-ring-guided cage made of PPS has already been presented to the trade public, but is only now going into series production. Users benefit from energy savings, low temperatures, low vibrations, a low noise level and very low non-repeatable runout (NRRO). A 20 % reduction in friction compared to conventional bearings results in energy savings and higher accuracy by reducing thermal expansion of the shaft. This reduction in friction is due to the optimisation of clearance, guide width and surface structure.
The latter has a major impact on the lubricating film, while grease life is also longer due to better sliding performance and lower temperature.
At EMO, NSK will be showing sectional models of various rolling bearings, especially spindle bearings. These include ten angular contact ball bearings alone with the same bore diameter of 70 mm and different specifications. This highlights different property profiles made possible by the respective design features.
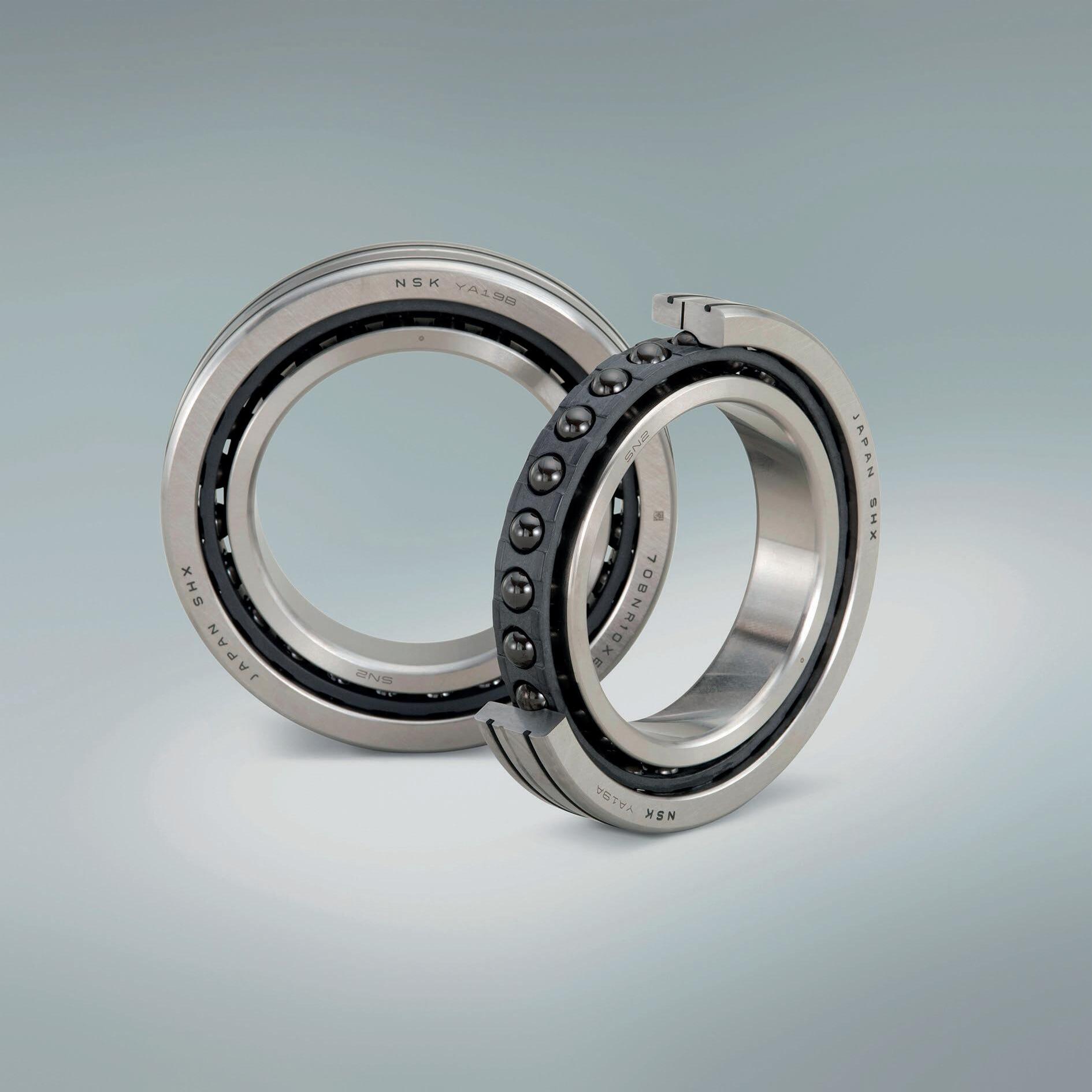
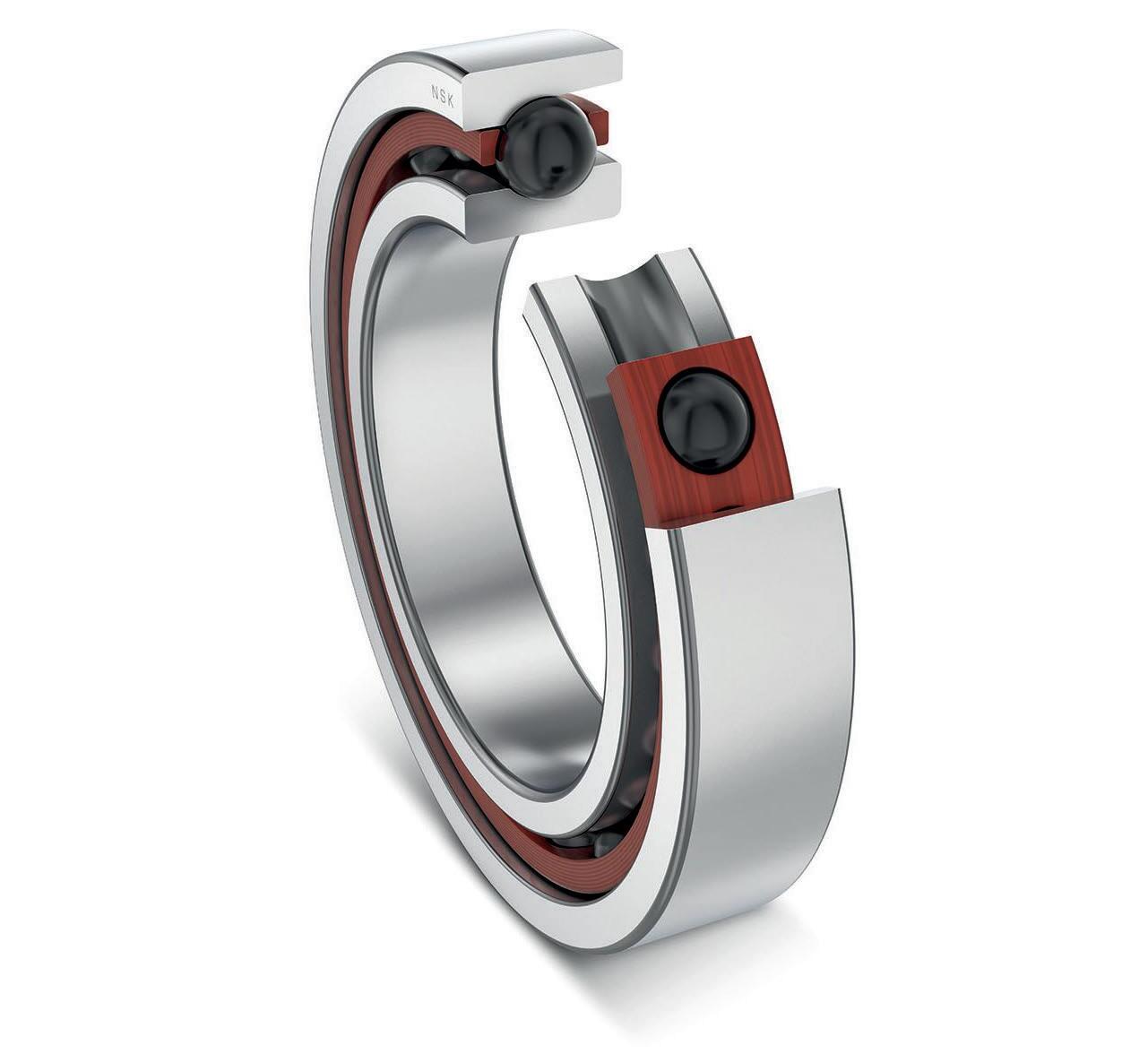
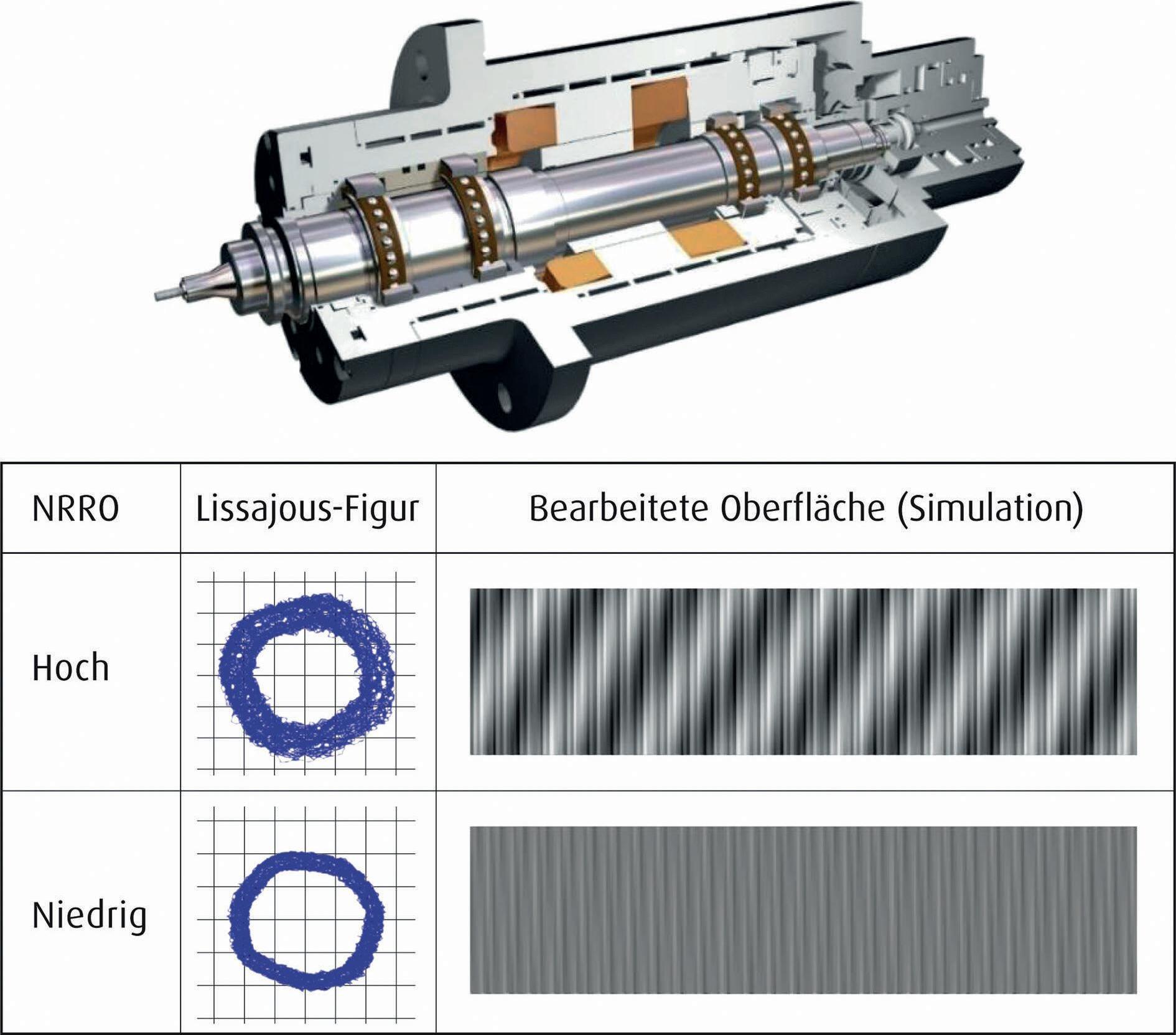
Ensuring powder quality for producing high-performance components in additive manufacturing
