
4 minute read
with indexable inserts
In the 1970s, a tool specialist from Tübingen was the very first manufacturer to present a three-flute tool system with a stationary carbide insert for grooving. A lot has happened since then: radial grooving, parting-off, axial grooving and internal grooving with µm-accurate precision are now part of everyday life in the machining industry.
Standstill is a step backwards
Advertisement
To this day, the 312 plate, which Paul Horn introduced to the public, is popular with users. Building on the company founder‘s incentive at the time to achieve technical perfection in his products, the company continues to set standards in tool technology for this machining pro- cess to this day. Horn has never stopped developing and optimising even successful product families. At the same time, the added value for the entire product range has been 100% integrated into the company‘s own production.
The application possibilities of the tool have grown considerably after the plate was originally used almost exclusively in the automotive industry. The 312 is designed for external machining and is used, among other things, for workpieces in medical technology, in the manufacture of hydraulic components and for everyday objects such as jewellery or ballpoint pens. However, it is not only the CI type 312 that has made the precision tool manufacturer known as a specialist for machining „between the faces“. Numerous other tool systems followed the idea from 1972, which are successfully used in recess turning all over the world.
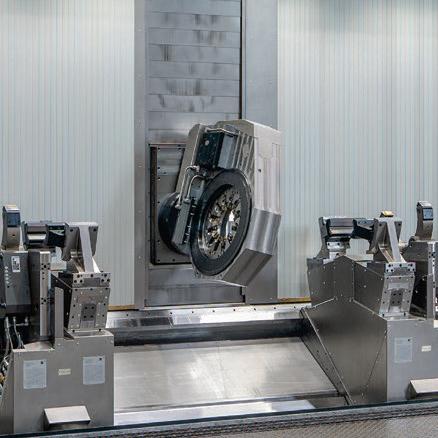
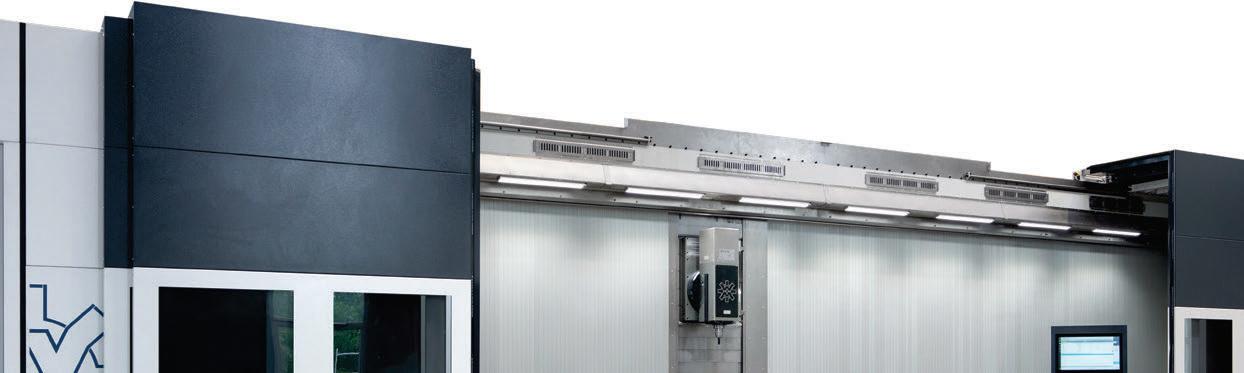

Understanding the process
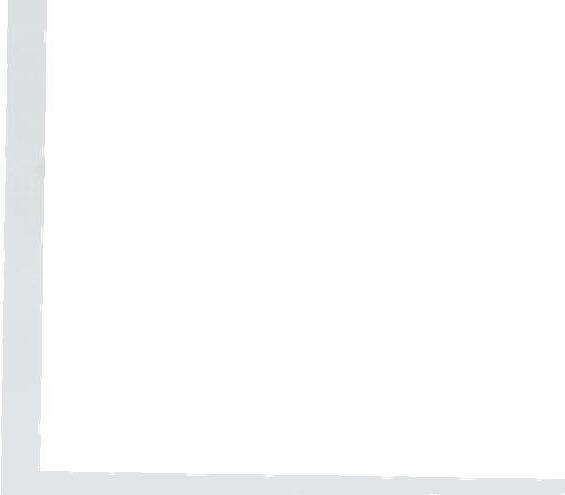
Basically, the grooving process involves a narrow cutting edge that penetrates the workpiece in a radial or axial direction. The art of grooving is, among other things, controlling the chip flow. In practice, it is important to avoid sticking chips, chip jams or long swirling chips, as they have a negative influence on process reliability and can lead to tool breakage or scratched flanks. Depending on the material to be machined and the type of machining, Horn has developed different chip shape geometries that ensure reliable chip taper, chip deflection and chip breakage.
Another important point for an economical grooving process is a sufficient supply of cooling lubricant (KSS). Where cooling used to be carried out with the classic flood cooling system, modern tool carriers are now in use, usually with an internal coolant supply. This ensures effective cooling of the shearing zone between the tool cutting edge and the workpiece. For parting off, Horn also offers a „S100“ type cutting insert, which supplies the contact zone with coolant at high pressure directly through the cutting insert.
Tools are exposed to high loads during parting-off turning. The quality of the carbide used, of the cutting edge and of the coating of the cutting insert also play a decisive role in a reliable and economical grooving process.
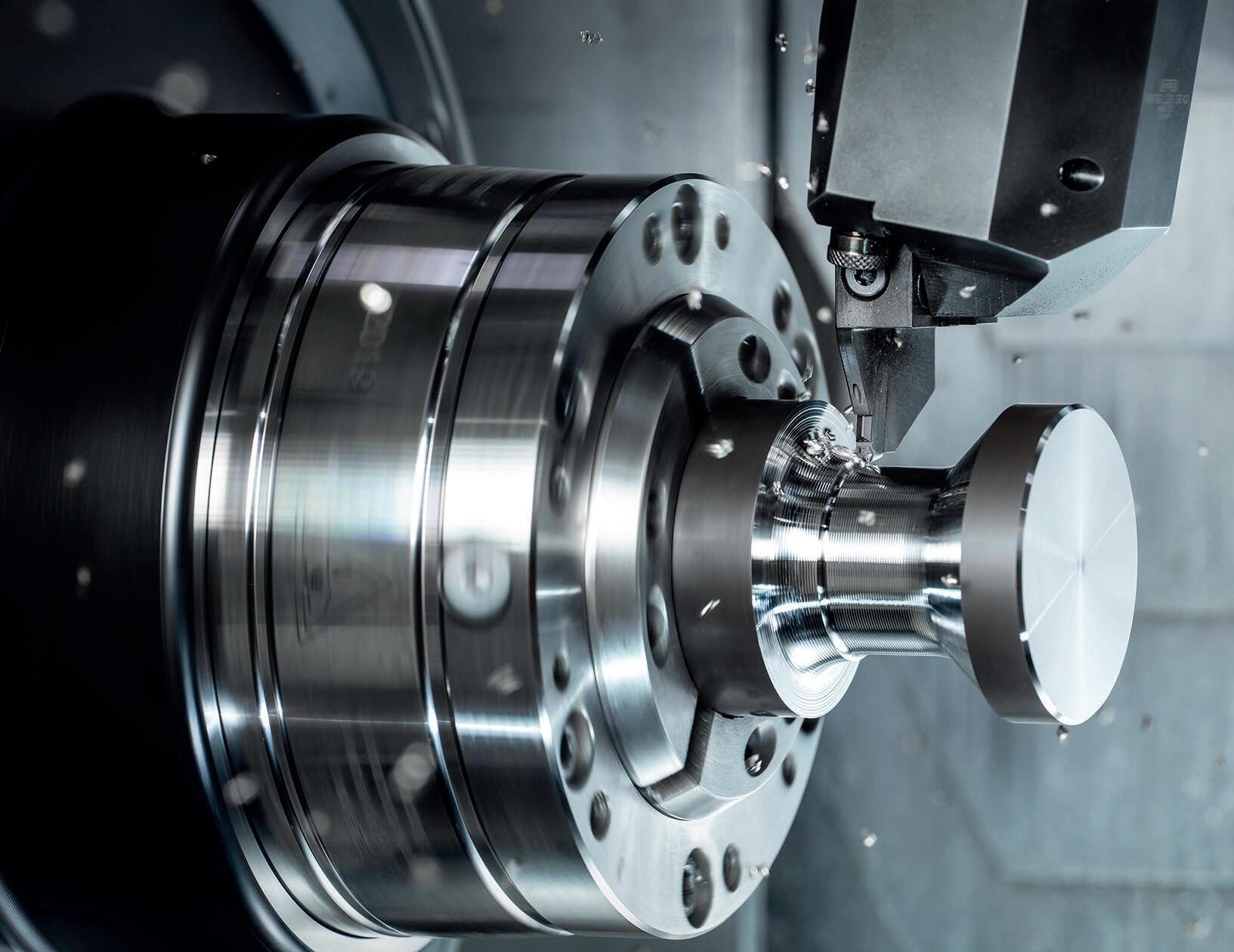
Practical example: trochoidal grooving
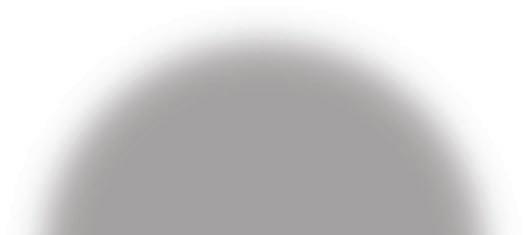
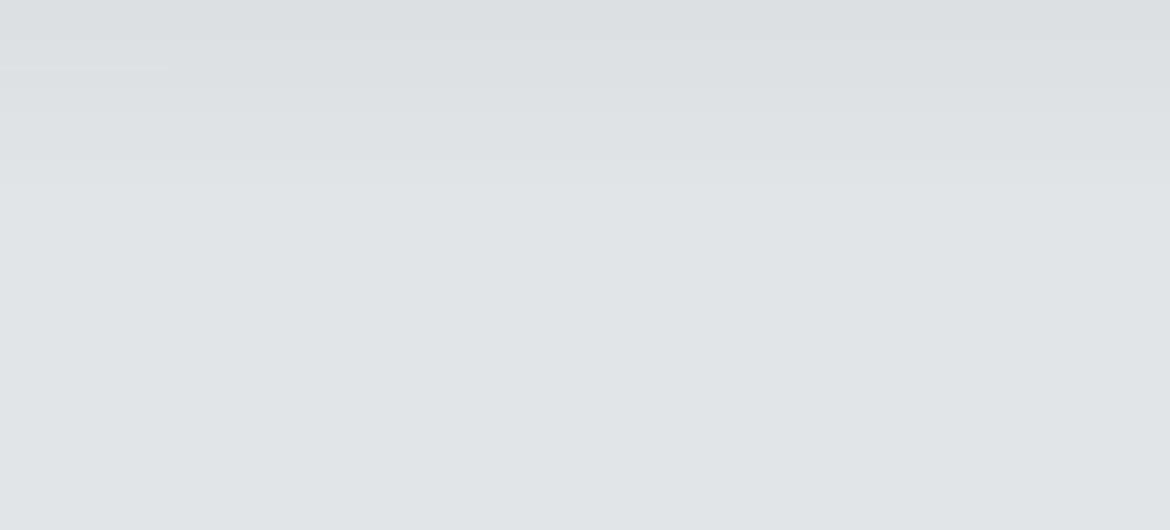
A user produces a wide and deep groove in an aerospace component using the trochoidal grooving process. Trochoidal grooving (Figure 1) is very well suited to the production of deep and wide grooves where a high chip volume has to be generated. The machinists produce the component from 1.4548 (X5CrNiCuNb17-4-4) – a steel with high strength and toughness. A full-radius „S229“ grooving insert with a radius of 2 mm is used for roughing.
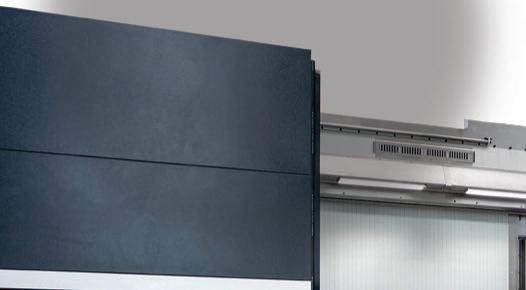
The grooving process is as follows: The 30 mm wide and 15 mm deep (incremental) groove is trochoidally rough cut with the full radius CI at a cutting speed of vc = 140 m/min with a cutting depth of ap = 1 mm. The feed rate is programmed with fn = 0.25 mm-1. The finishing allowance is 0.2 mm. A cutting insert from the S229 system is also used for finishing. Finishing is done from two sides with a 3 mm wide grooving plate. The corner radius is 0.2 mm. The total production time of the groove is less than two minutes.
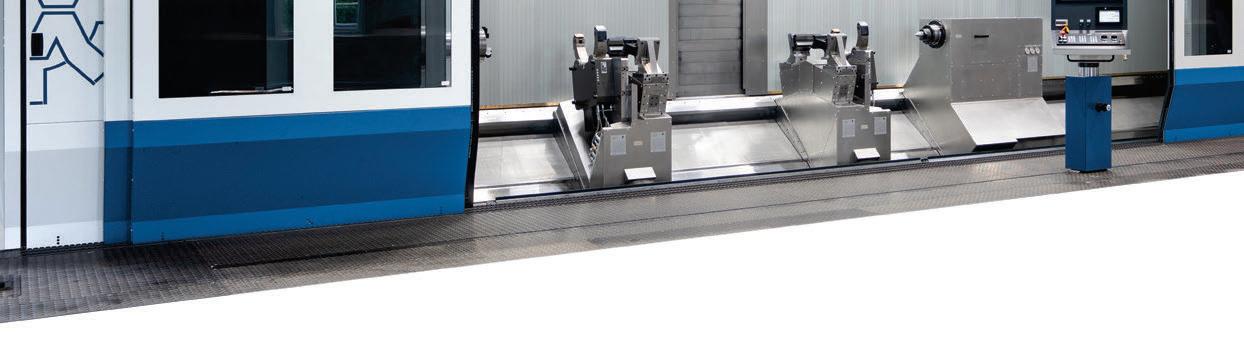
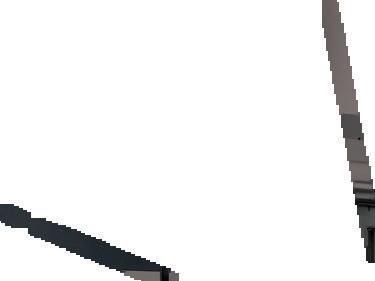
Example 2: Axial grooving in medical technology

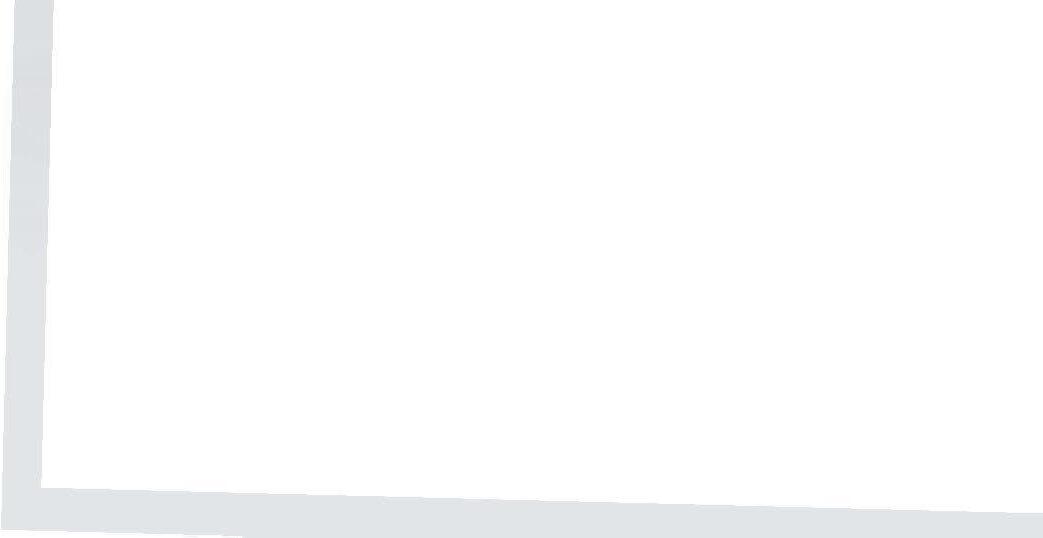
For the production of a thin-walled titanium valve cover for a cerebrospinal fluid shunt system, the Supermini system type „105“ is used (Figure 2). On the one hand, the customer uses a tool for axial grooving and, on the other hand, a special tool for finishing the cover joint. For the close fit on the lid with a length of 0.5 mm, the Supermini tool had to be designed with a corner radius of
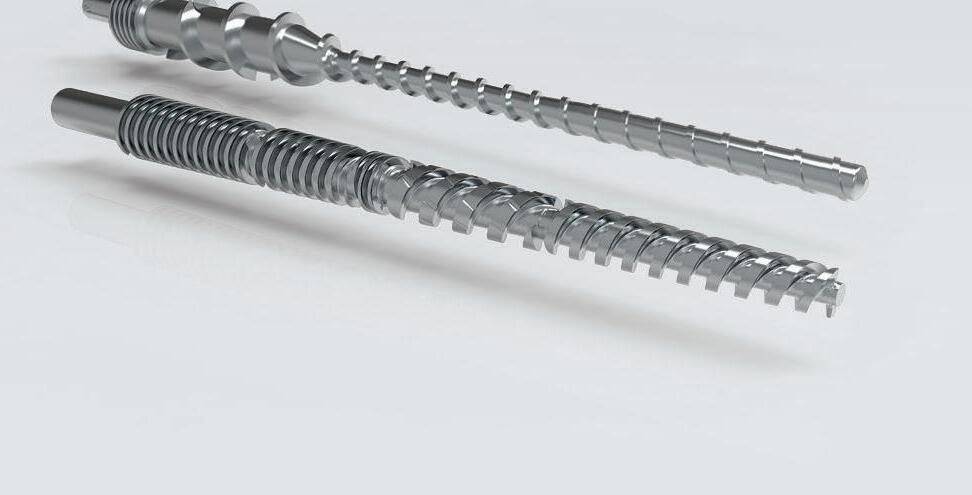
0.05 mm. The difficulty in machining titanium invariably lies in dissipating the heat and controlling the chips. For use as an implant, the user has strict criteria regarding the surface and the absence of burrs on the component. By optimising the traverse paths with a CAM system, the experienced colleagues in the machining department were able to double the tool life from the original 1,000 to now 2,000 components.
Example 3: New grooving strategy
The planet carrier is one of the central components of a built-in screw spindle. This spindle is used in automotive assembly, among other applications. Five screwdriving spindles, assembled as a package, for example, simultaneously fasten all five wheel bolts during wheel assembly. The new tool system for reces- sing with the Y-axis is used for recessing a 50 mm wide recess (Figure 3). Formerly, the user rough-cut the recess with the S229 system – and was satisfied with the performance. This system has always delivered the required performance for this machining, but grooving via the Y-axis „aroused their curiosity“. Together with the responsible technical consultant from Horn, the new grooving method was implemented in the machining process.
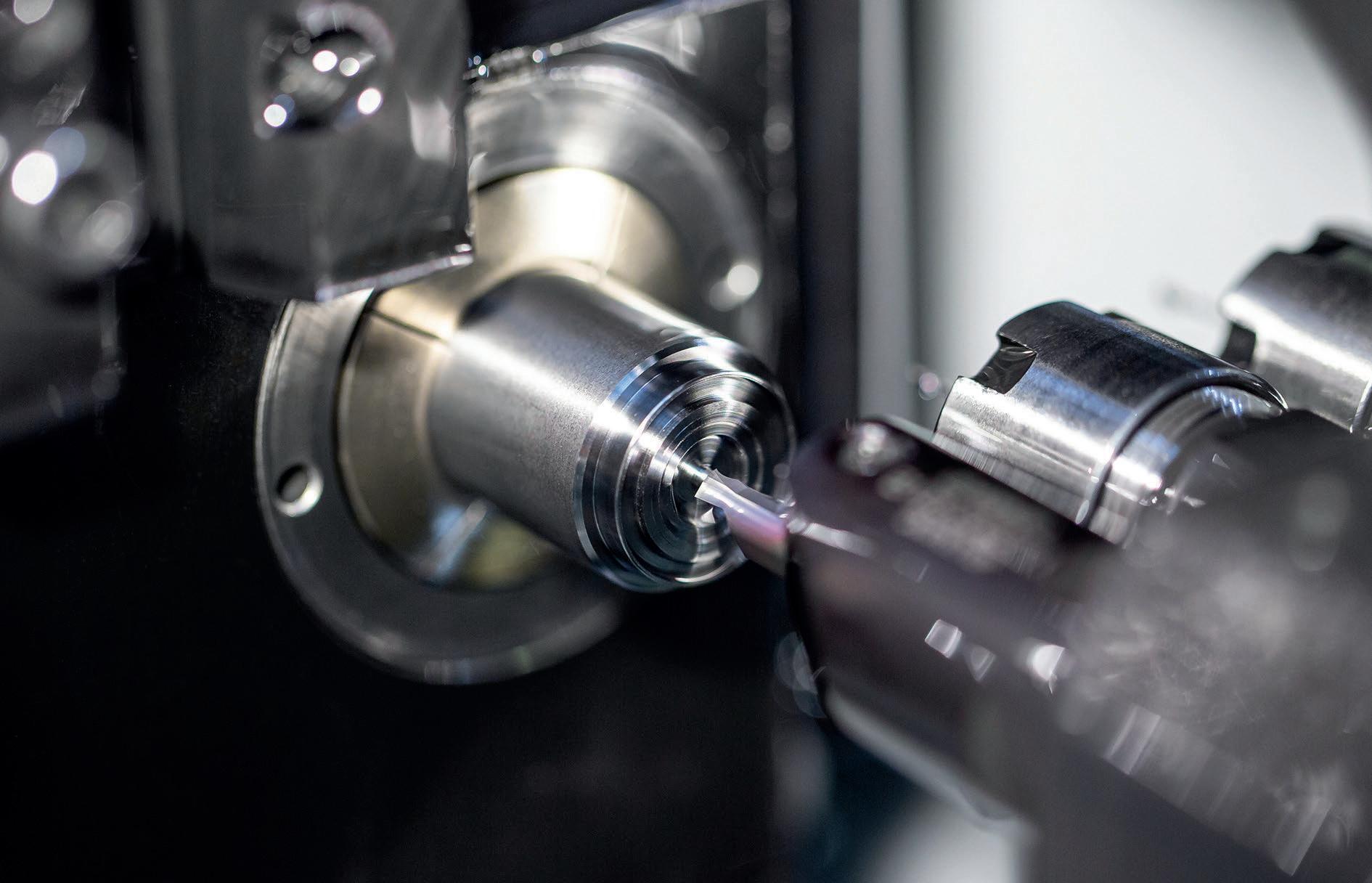
The change of the grooving strategy brought a time advantage of over one minute. This resulted from the possibility of running at double the feed rate with the grooving system. In addition, the tool life and chip control also increased, as the chips are discharged directly downwards.
Parting is now done at a cutting speed of vc = 130 m/min at a feed rate of 0.3 mm/rev. Grooving is a pure roughing operation. The cut-off is made at the diameter of the groove. The groove is finished on the counter spindle with an ISO DCMT cutting insert. Roughing is not done on the counter spindle because of material distortion. Furthermore, the customer works with a smooth collet, which would also make roughing more difficult.
Conclusion
Although Horn‘s tool portfolio has expanded considerably – not only in the area of grooving, but for all applications in the field of demanding machining tasks – grooving and thus machining between two faces is still considered the „supreme discipline“.
www.horn-group.com
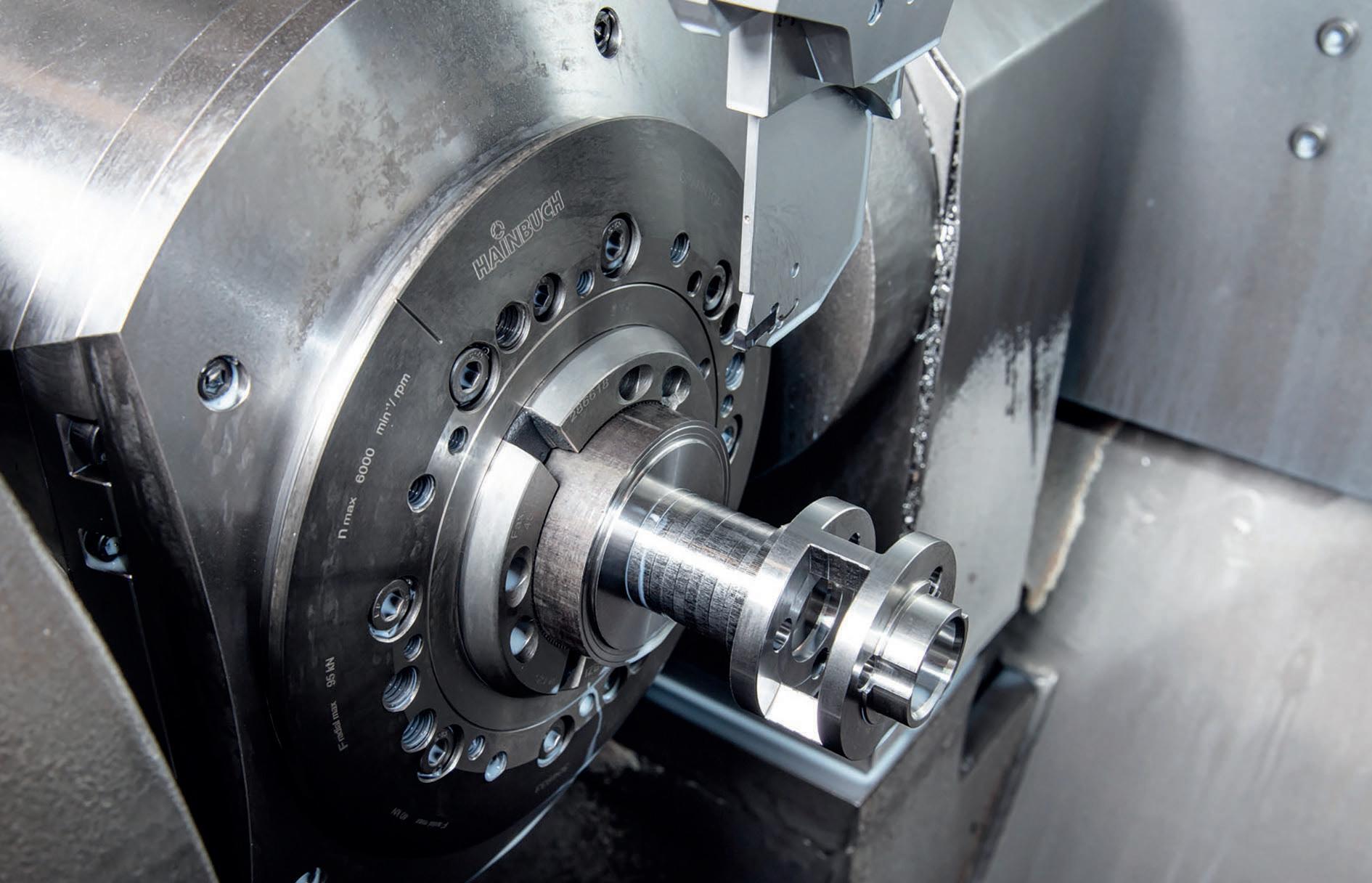