
5 minute read
Smooth data flow
The smart factory relies on connectivity for flexible and efficient production. Standardisation supports the smooth flow of data between measuring systems. For the VDMA‘s Measuring and Testing Technology Association and its working groups, this topic will be in focus at EMO Hannover.
The smart factory is based on connectivity for flexible and efficient production. Machines and components can then be replaced without hindrance. However, production in the sense of Industry 4.0 will only be able to unfold if the flow of data is unhindered and unaltered. Standardised communication channels are a prerequisite for interoperability.
Advertisement
In VDMA working groups, manufacturers of measurement technology are making an important contribution to preparing for the smart factory functioning through connectivity and interoperability.
Standardisation projects are being -addressed in three VDMA working groups. An important step on the way to standar- dising communication has now been taken by the „OPC UA Geometrical Measurement Systems“ working group. The OPC UA Companion Specification for Geometric Measurement Systems (GMS) has been completed and adopted. The companies comprising the VDMA (German Engineering Federation) have completed the development of the interface in record-breaking time. And: The working group „OPC UA Cutting Tools“ has been founded to enable the effective exchange of tool data between CAD/CAM system, tool grinding machine and measuring machine.
The first version of the manufacturerneutral interface „I++ DME“ already has two decades in the field behind it and is now being fundamentally revised in the „I++ DME 2.5“ working group. The release of the current version should take place in the next few weeks.
Geometric measuring systems
Geometric measuring systems are used in mechanical and plant engineering to ensure that parts and components are manufactured within defined tolerances (Figure 1). While manufacturers of geometric measuring devices often used to rely on proprietary systems, also in order to retain customers, this approach contradicts the smart factory, which must efficiently manufacture completely different products with maximum flexibility.
In the OPC UA working group „Geometric Measuring Systems“ at the VDMA, the spectrum of devices ranges from calipers to form and surface measuring devices or coordinate measuring systems. The working group has created five use cases for the application of the systems in the environment of processing machines, reports Dr Karl-Dietrich Imkamp (Figure 2), chairman of the working group and head of Metrological Qualification at Zeiss IQS (Industrial Quality Solutions). The Companion Specification for geometric measuring systems was adopted in record time in the first version just three years after work began. „With this, the self-set task of the working group has been fulfilled. We are waiting for the response to the publication to see if corrections or extensions are necessary,“ adds Imkamp
Goal: Closed Loop
The areas of application include information about the state of the machine. All information about the machine‘s operational capability is relevant. Equally important is the question of which measuring processes are currently running. Parts and order data management can also be used to support the increasingly important automation, but there is currently still a need for development in this area. In the optimal case, the measurement results serve as the basis for the „closed loop“ to control a machining process.
„Unlike other specifications, we don‘t want any process-control equipment on the measuring device,“ says Imkamp. „We inform about which measuring process is currently taking place, but we don‘t give the measuring system commands to move and take measuring points – that‘s not part of the specification.“ What is important for the specification are the results of the measurement. „We need to standardise access to measurement results, but we don‘t want to develop a new format for measurement results.“ The content of the specification includes the information that measurement results exist and where they are stored in the production network.
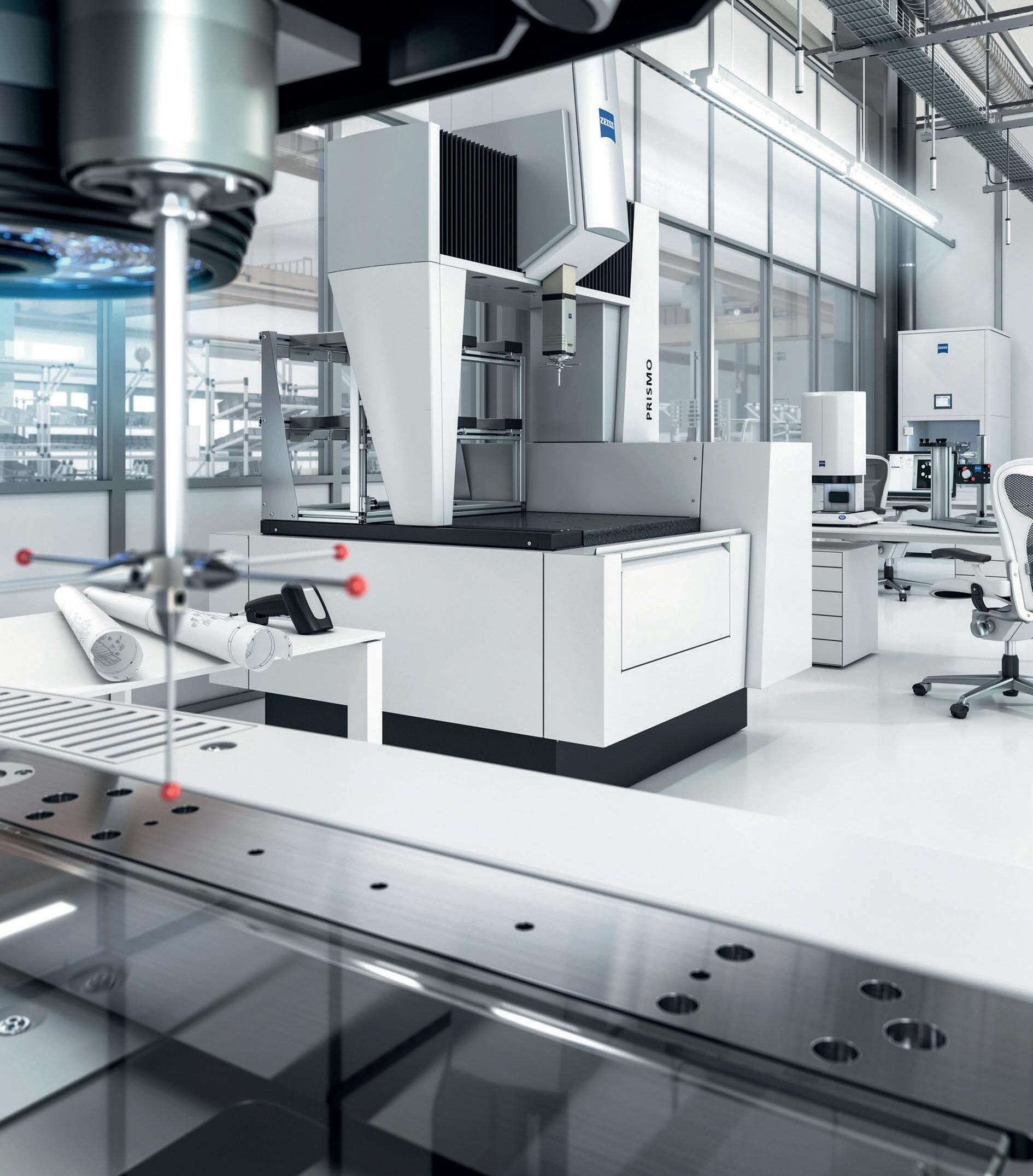
OPC UA becomes the „world language of production“. The device can make its basic information available via this interface. There it reports, for example, what type is involved or what sensor technology it works with. „I suspect that providing information of this kind will become commonplace in the next few years,“ emphasises Imkamp
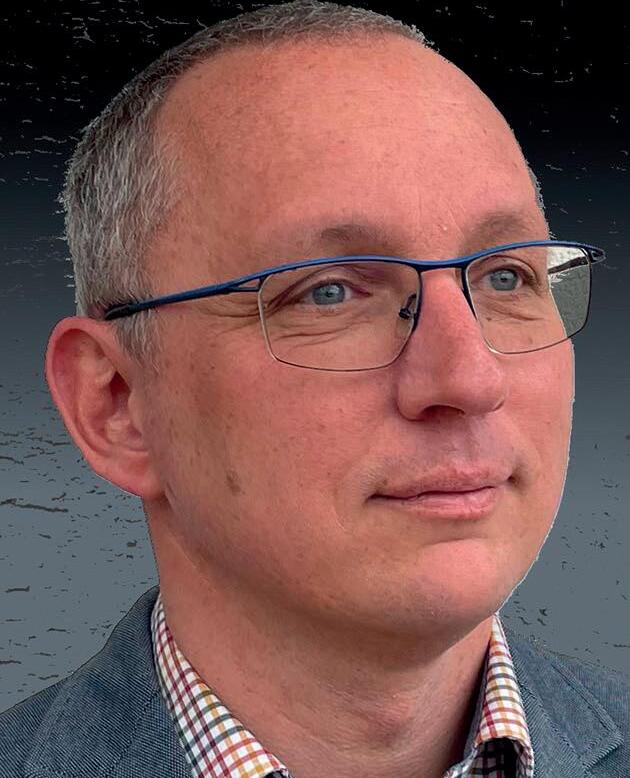
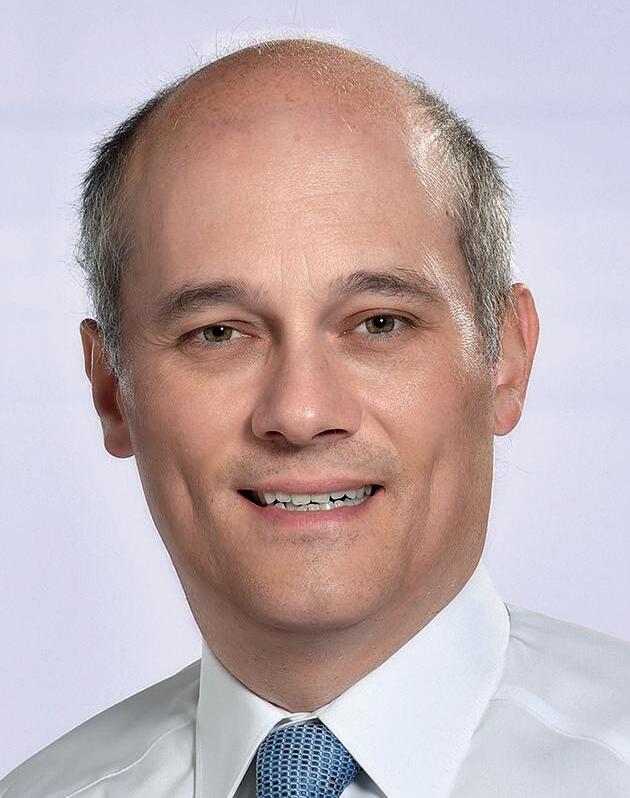
CMM: combination of hardware and software
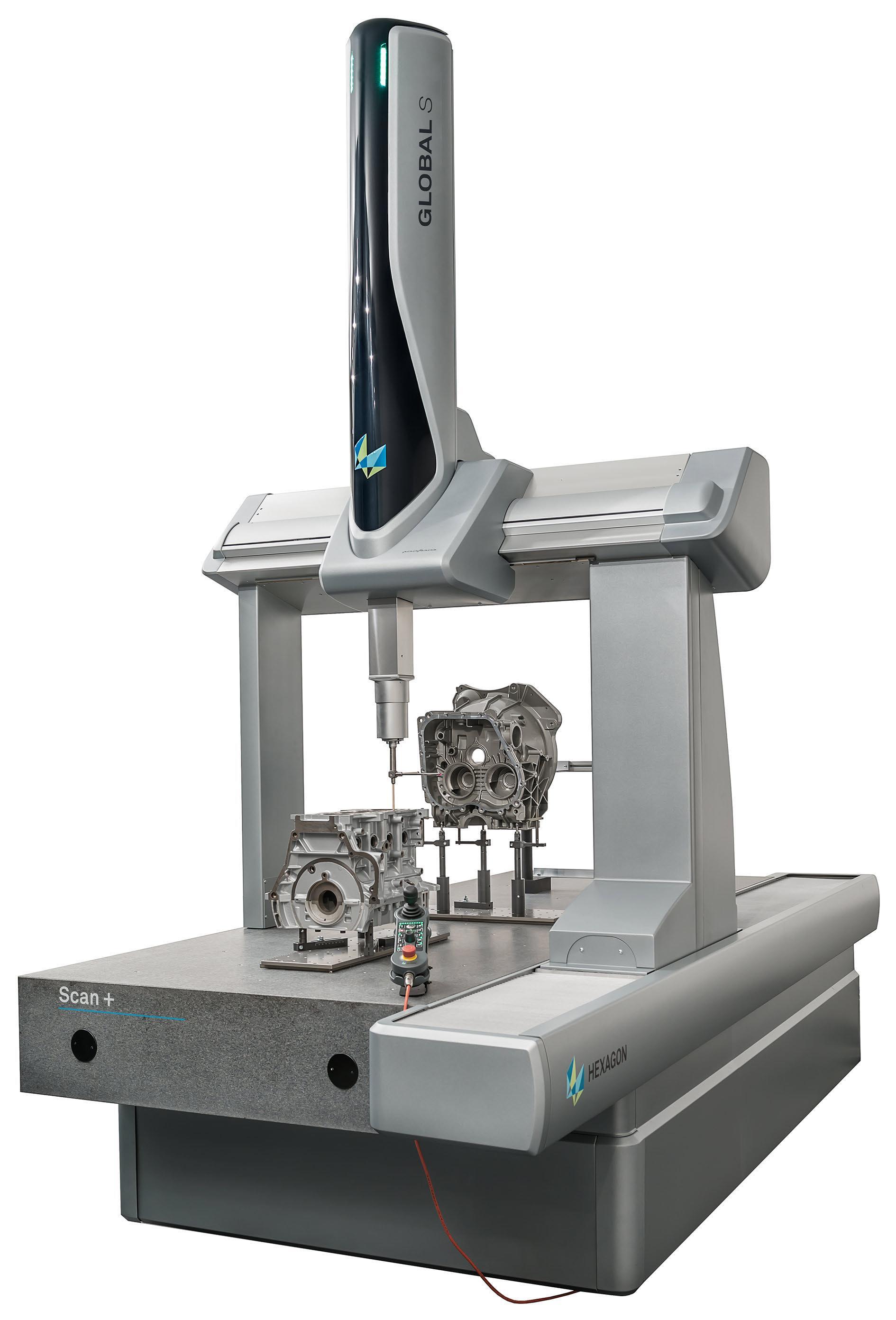
„We have some challenges when we look at the shortcomings of the current specification,“ emphasises Dr Thomas Maresch, Chairman of the VDMA I++ DME Working Group and Senior Product Manager System Components at Hexagon Manufacturing Intelligence. „We are trying to eliminate these in the course of specification 2.5.“ For example, the interface is not optimally designed for large amounts of data, which means that the integration of the laser scanner does not fit compfortably. In addition, options for integrating multi-sensor technology are missing.
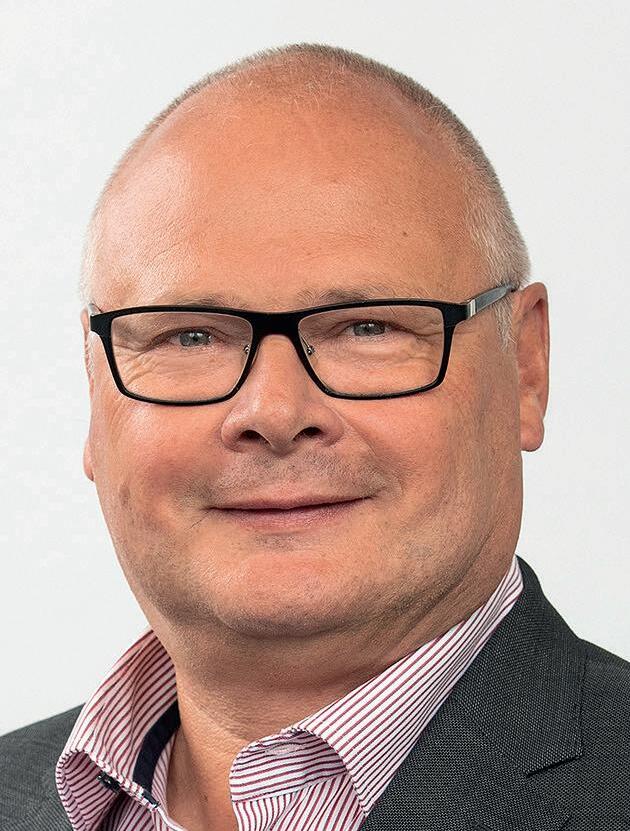
By autumn, version 2.5 should succeed in clearing up the conflicts. „Updating the interface will help to spread and improve the use of measurement technology (Figure 3), Maresch is convinced. He sees further goals: an expansion for open communication protocols such as OPC UA or MQTT is a possibility. Sensor technology and image processing can be integrated on the way to version 3.0.
The VDMA continues to play a significant role in ongoing development. First of all, it is necessary for the different manufacturers to exchange ideas with each other. A lot of diplomatic tact is needed to mediate between the different interests of the manufacturers. Finally, the formalised fixing of the achieved specification as a VDMA standard sheet also plays a major role so that the version can establish itself on the market. A few weeks ago, devices and systems that will use I++ DME were
Networked precision tools
The OPC UA working group „Cutting Tools“, which came into being a few months ago, deals with the exchange of tool data between CAD/CAM system, tool grinding and measurement machines in the production and processing of tools (Figure 4). Here, too, the VDMA plays an important role as a neutral authority and platform for manufacturers from different branches of the mechanical engineering industry. A standard is being created that builds on the specifications for geometric measuring systems and is being further developed for the needs of carbide tool manufacturing. „From my point of view, we have to give up the ‚parochial thinking‘,“ explains Bernd Schwennig, spokesman of the OPC UA working group and Strategic Product –Manager Metrology at Walter Maschinenbau in Tübingen. „Until recently, there were mainly proprietary interfaces, but we need international standards so that everyone uses a uniform language.“

The basis has already been created with the open data interface „GDX“ (Grinding Data Exchange) for the design and manufacture of cutting tools. Generated in the CAD/CAM system, the file can be imported into the tool-grinding machine or measuring machine so that the tool can be manufactured, reground, tested and documented. The closed-loop process is also possible via this data exchange path. This format allows data exchange between different control systems at a very early stage. The standardised interface reduces costs and optimises processes. However, the interface only knows the outdated file transfer system and not, for example, the contemporary OPC-UA communication protocol.
Overcoming the „confusion of languages“
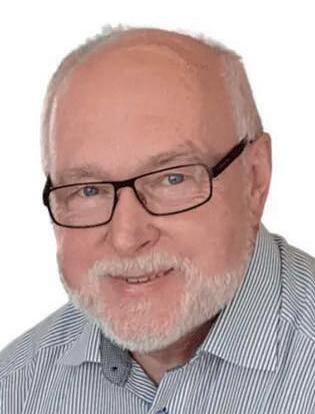
In order to overcome the variety of languages, the VDMA working group has got together with representatives of almost all well-known manufacturers. The documentation is being produced at the Institute for Control Engineering of Machine Tools and Manufacturing Units (ISW) at the University of Stuttgart. The VDMA and OPC Foundation associations are responsible for publication. „At the moment, the concept is being coordinated with all participants,“ says Schwennig, „we want to build up the communication standards in the first step, and then the work with Roundtools should begin before other tool types are tackled.“
If the preliminary work of the GDX working group can be drawn on, then the individual work steps can be mastered very quickly. Schwennig is hopeful: „The preliminary work of over ten years would then pay off. There are already very good elements within GDX that would continue to be used. With OPC UA, we are refining the GDX standard.“
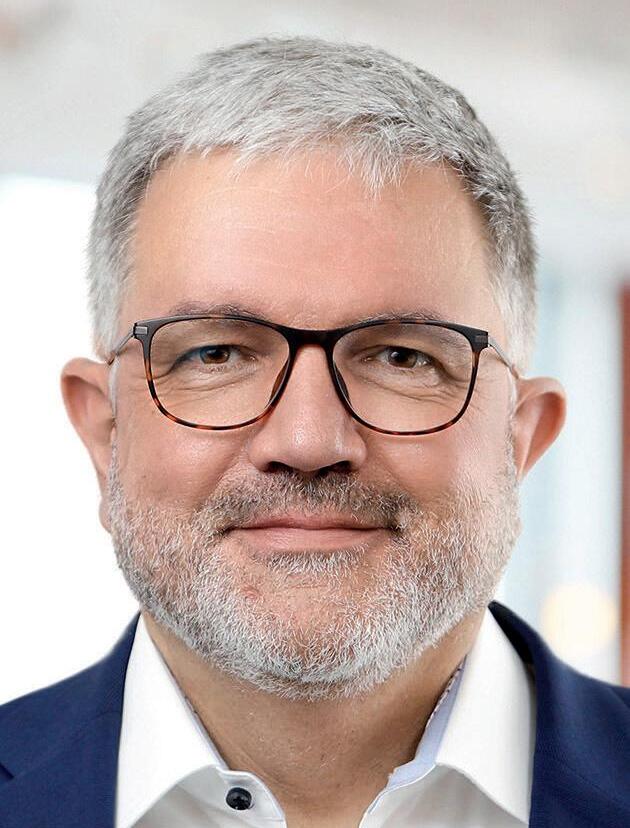
Exhibition booth at EMO
As the conceptual sponsor of EMO Hannover 2023, the VDMA‘s Measuring and Testing Technology Association will be present in Hannover with a booth vdma.org/measurement-technology
(Hall 4, D57) from 18 to 23 September, where it will host a technology forum on three days of the trade fair, from 19 to 21 September. Visitors will learn about current trends first-hand from experts in metrology, precision tools and clamping technology, from institutes and from start-ups.
Better than new with optimised reverse engineering process