
4 minute read
How does manufacturing technology advance e-mobility?
The vehicle industry is consistently pushing ahead with electromobility. This also has implications for manufacturing technology. For example, it is increasingly necessary to machine lightweight and filigree parts.
What is the most economical way to machine battery components? What challenges have to be overcome in the production of gears and gearboxes? These and other questions will be top issues at EMO Hannover 2023. Insights will be provided by machine tool and tool manufacturers as well as experts from research.
Advertisement
„Quiet“ gearing
Gear noise is an essential quality criterion in gearboxes for electrically driven vehicles. With the elimination of the rather noisy combustion engine, the noise development of the other drive components comes into focus. Klingelnberg from Hückeswagen has adapted its production system to this. The focus at EMO Hannover is on gear grinding as well as quality assurance. „In gear grinding, ‚Quiet Surface Shifting‘ (QSS) provides the user with an intelligent dressing and grinding strategy to break up the regular grinding surface structures on the gears and thus achieve improved noise behaviour,“ explains Dr Christof Gorgels, Vice President Technology and Innovation at Klingelnberg. „The single flank rolling test with all its characteristics allows a close-up noise test of the gears synchronised with the grinding process.“
The deviation analysis also offers the evaluation of waviness as a regular part of the form error. This makes noise-critical deviations on the tooth flank visible and corrective measures can be laid down. The connection of all three systems to form a closed loop (Figure 1) allows close-meshed monitoring and correction of the production process. The singleflank rolling inspection gives 100 % monitoring of the grinding process. „Noisy components are detected directly, rejected and fed to the precision measurement.
The measurement then makes the deviations visible and, ideally, the processing machine can be corrected directly and automatically. This results in a short, fast control loop for quiet gears.“
Crossover range for e-mobility components
The company Grob-Werke from Mindelheim is known for its broad and differentiated machine portfolio. The range is increasingly aimed at manufacturers from the e-mobility sector. „The development continues, the market not only demands equipment for the production of stators, rotors and batteries. Battery trays, subframes, frame structure components and much more also have to be manufactured in lightweight construction“ (Figure 2), explains Christian Müller, CSO and Member of the Board. A current machine range has been developed to produce components for the e-drive in lightweight construction. The single- and two-spindle machines are also being further developed accordingly. New sizes are on the agenda for 2023 in order to mill even larger components for e-drives in a single casting. In the meantime, this range comprises five machine types: „Component-optimised workspaces, dynamic and stable – the machines have to combine all of this,“ Müller specifies.
A strategy for the battery frame
The battery frame is a central component in every electrically powered vehicle. The experts for electromobility at Mapal Fabrik für Präzisionswerkzeuge Dr. Kress KG in Aalen have developed a sample process from various customer components. It reproduces the main machining operations on the battery frame on a „generic component“.
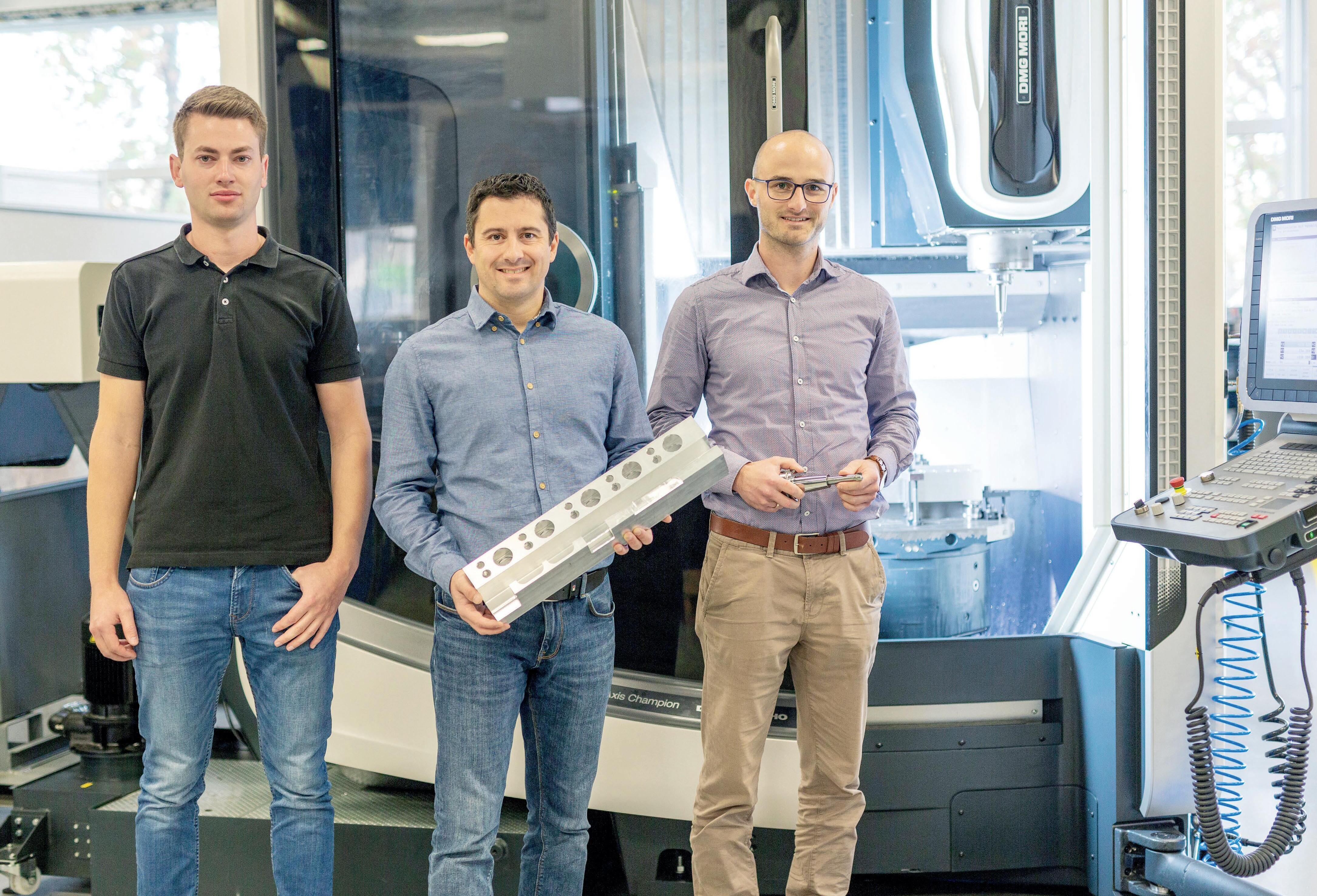
Challenges in the machining process include stepped bores, bores with different diameters through several layers, milled pockets with different dimensions, shoulders and, above all, the susceptibility to vibration due to thin rib structures and the control of chip breakage. „Mapal masters these challenges above all with milling cutters optimally designed for this purpose. Even most of the holes on the frame component are milled“ (Figure 3), reports Matthias Winter, Global Head of Segment Management Automotive.
„Although the cycle time is somewhat longer when milling bores, the process offers clear advantages in this specific case – short milling chips that can be easily removed, less burring, saved tool changes and process reliability.“
To rough the shoulders, pockets and grooves and to finish the pockets, the Aalen-based company recommends a special solid carbide (SC) milling cutter. This achieves the best possible surfaces and works stably even in the corners with large wrap-around and high loads. Special feature: Users can finish large depths in one pass. This saves time and is therefore particularly economical. In finishing the battery frame, a surface of up to Rz = 1 µm (average roughness depth) is achieved. A total of seven tools – including six milling cutters – are used for the entire reference process. A complete package of polycrystalline diamond (PCD) and solid carbide tools, chucks and the corresponding process is offered for the task. The specialists adapt the sample process individually to the respective conditions.
Digitalisation as an enabler of new gearbox architectures
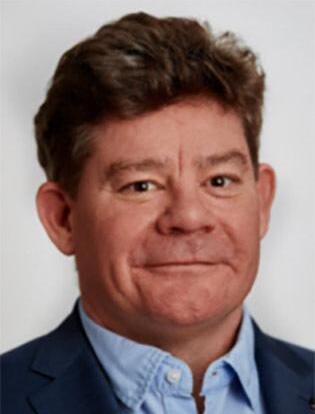
High-speed motors open up the possibility of producing an electric motor with low volume and high power. „However, this drive concept requires a high gear ratio to get to the relatively low wheel speed. At the same time, the gearboxes must achieve higher efficiencies than before in order not to negatively affect the range of the vehicle and the continuous power of the drive,“ explains Prof. Dr.-Ing. Jürgen Fleischer, Institute Director for Machines, Plants and Process Automation at the wbk Institute for Production Technology in Karlsruhe.
Gear concepts based on planetary trains meet these requirements. However, the economic production of the required thin-walled internal gears and stepped planets with close interference contours is limited due to a possible collision between the workpiece and the tool. The hob peeling process developed to series-production maturity at the wbk permits the highly productive and flexible manufacture of such gears (Figure 4).
In large-scale industrial production, however, the quality of the gears fluctuates considerably due to tool wear and changing material batches. Due to the lack of in-process data acquisition, a wide range of options for correcting the gear geometry remain largely unused to this day. „The synergy of simulation-based soft sensor technology and machine-integrated edge computing makes it possible to detect profile and flank deviations,“ adds the Institute director. Here, machining forces and tool centre point displacements are calculated on the basis of the machine‘s own data. The effect of the machining forces on the manufactured gear quality can be predicted and corrected by means of a real-time gear profile prognosis (Figure 5).
Conclusion
E-mobility is without question one of the current megatrends. Lightweight and sometimes filigree components as well as demanding materials have to be machined economically. The processing machines, precision tools and testing methods used must, as far as possible, be considered as part of an overall process. Which manufacturing processes do leading suppliers use here? – EMO 2023 in Hannover offers an excellent platform for information on these and many other manufacturing topics. www.klingelnberg.com www.grobgroup.com www.mapal.com www.wbk.kit.edu
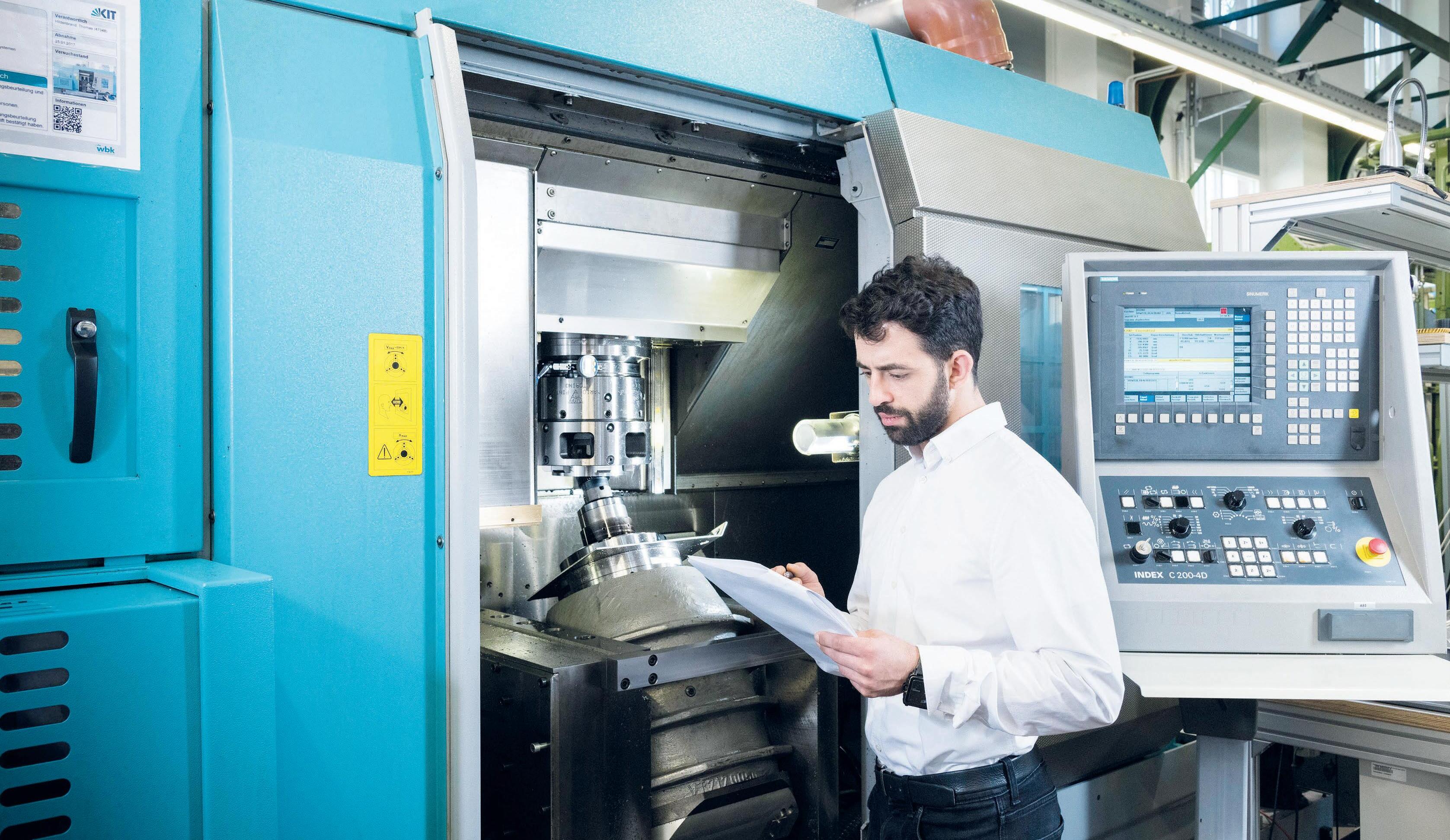

New angular contact ball bearings for high-speed machining under heavy load