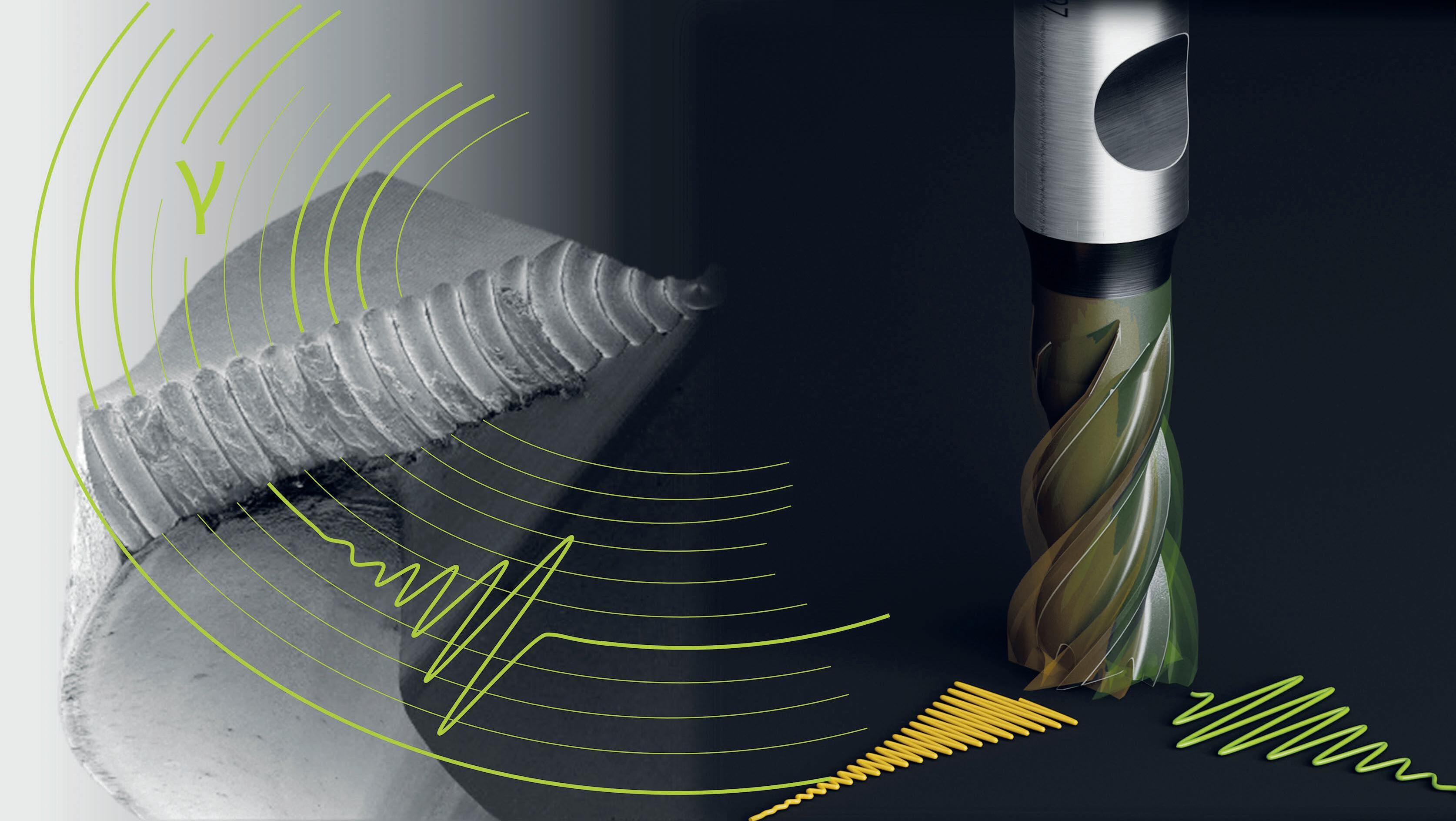
7 minute read
Stable processes through milling tool modification
The machining process is often subject to dynamic disturbances. However, these can be counteracted: Selective modifications on the tool side bring the breakthrough here. Surface structures applieda on the face side or direction-dependent dynamic properties of the tools suppress the development of chatter vibrations.
The aforementioned modifications can increase performance, for example in the machining of high-strength aluminium materials. Especially when the measures are combined, these stabilisation approaches offer great potential for tool and process optimisation.
Advertisement
Initial situation
Since time immemorial, the demand of industry and consumers for the manufacture of technical products has been characterised by increasing requirements. These are subject to dynamic market influences on the one hand and competition-driven trends on the other, to which manufacturing technology must react in the shortest possible time with targeted solutions. Three target variables play a particularly central role in finding solutions: process reliability, productivity and sustainability. Machining plays a particularly important role in the provision of manufacturing capacities.
Today, basic research at the Institute of Machining Technology (ISF) focuses, among other things, on the fundamental interactions in machining technology and their implementation in a geometric-physical simulation environment. The aim is to understand the interactions and properties of tool, workpiece, machine and process configuration in the machining process, but also to be able to determine them predictively [1].
Influential dynamic variables in particular offer great opportunities for process optimisation, as their adjustment has an effect on several target variables at the same time. A dynamically unstable machining process is often accompanied by reduced component surface quality, increased tool wear and dimensional deviations [2]. Various approaches are being pursued to increase dynamic process stability. In addition to structure-oriented approaches, which are particularly relevant in the design of the machine tool, process-oriented approaches are also the subject of current research projects.
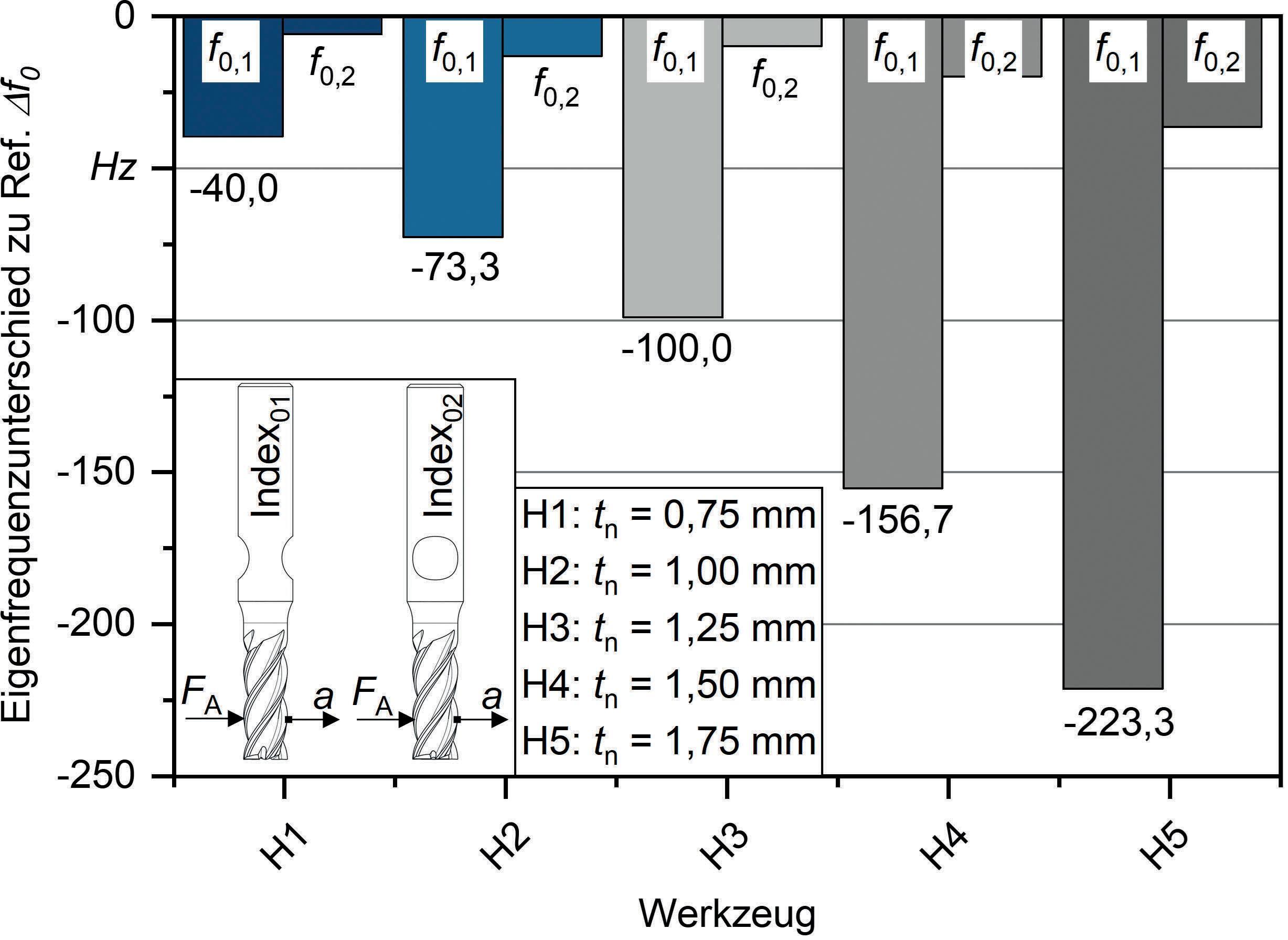
New approaches to process stabilisation
In particular, two (so far independently considered) approaches to process stabilisation deliver promising results, according to initial investigations. Both pursue the strategy of minimising the tool-side vibrations in the milling process through constructive modifications to the milling tool. In the first approach, functional surface structures are applied to the front free surfaces of a milling tool with the aim of dissipating kinetic energy and providing support by exploiting deformation and friction processes between the tool and the workpiece. Initial publications show an increase in the stability limit and thus in productivity of up to 60 % [3].
In the second approach, the changes are not made to the cutting part of the tool, but to the tool shank, Figure 1, which allows easy integration into existing manufacturing processes. Defined, circular arc-shaped notches above the flute run-out result in asymmetric dynamic tool properties, which can permanently inhibit self-excited tool vibrations. In this way, about 70 % greater cutting depths could be achieved [4].
In addition to external periodic disturbances such as concentricity errors, imbalance and externally excited vibrations (e.g. vibrations from a neighbouring press shop), the machining process can also be disturbed by „self-excited“ vibrations. Due to the periodic meshing of the teeth and the associated application of force, the oscillating manufacturing system experiences an excitation to which the components involved react more or less sensitively, depending on the process configuration. The pulse-like excitations lead to tool deflections, whereby the cutting edge leaves its defined path and follows a modified path curve with superimposed vibration.
Figure 1 shows that this path curve with superimposed oscillations also affects the cutting depth h. Since the cutting force depends proportionally on the chip cross-section, e.g. according to Kienzle, the cutting force varies periodically as the tooth meshing angle progresses – it modulates depending on the natural frequency and thus in turn dynamically stimulates the process [3]. A mechanical feedback takes place, referred to in the literature as the regenerative effect.
Combined approach for tool modification
Due to the locally separated constructive interventions of both mentioned approaches, a hybrid tool modification is also possible, which considers both functional free-surface structures and asymmetric dynamic properties. In the basic investigations carried out at the ISF, this „hybrid“ tool approach has now been explored in more detail.
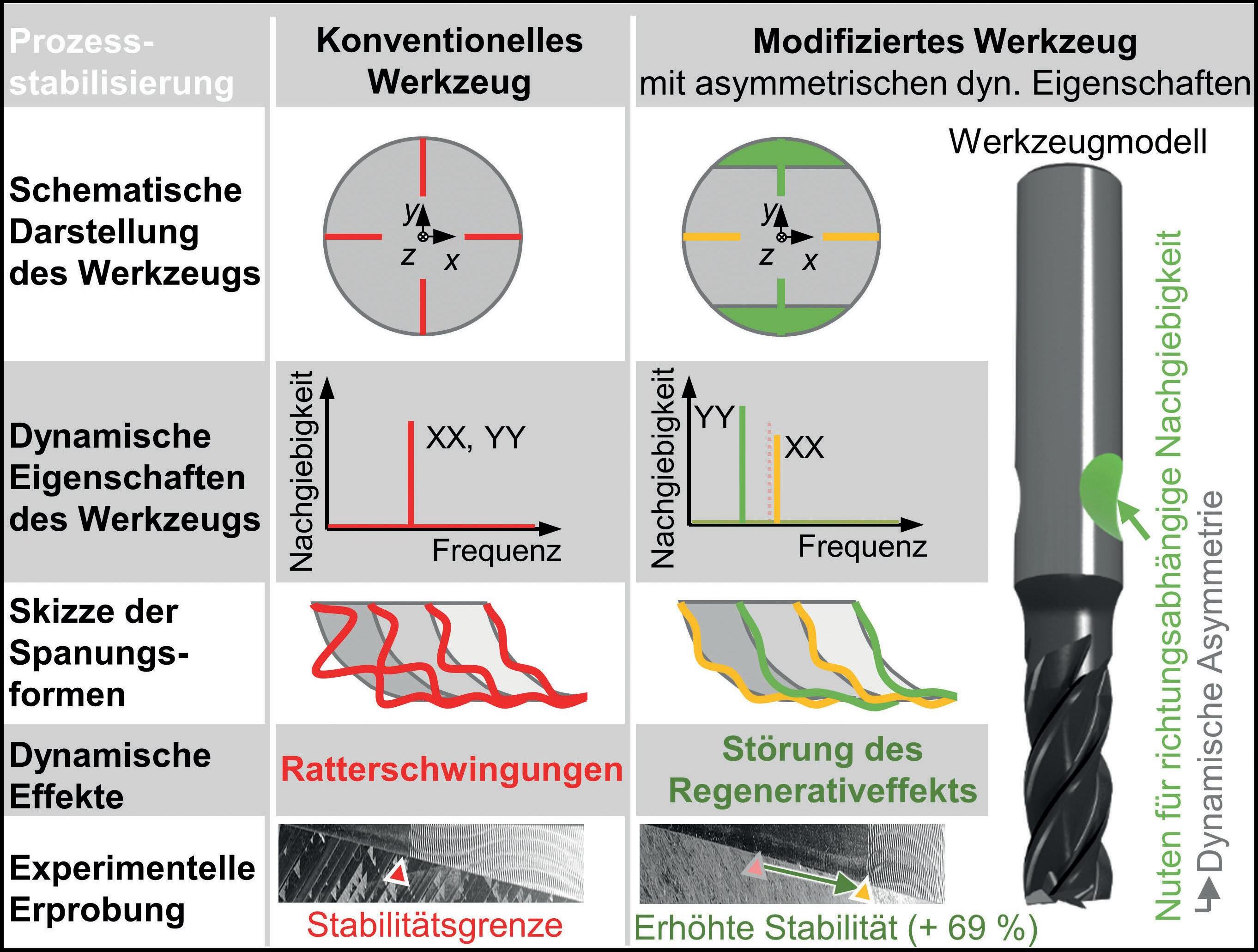
HSS end mills were used so that the desired modifications could be introduced into the test tools by means of milling. Nothing stands in the way of transferring the approach to carbide tools for industrial use. The shape of the structure on the face of the tools was initially not varied, but the depth of the lateral grooves on the tool shank was. The aim was to influence the compliance behaviour of the test tools in a graduated manner, depending on the direction, Figure 2
An experimental set-up served as the test environment, which allowed the stability to be investigated with in-process force, deflection and acoustic emission measurements. The five-axis kinematics of the experimental machine (DMG DMU50) allowed the tool to be set up so that a ramp could be introduced into the workpiece (EN AW-7075) under constant lateral infeed ae by constantly increasing the axial infeed ap. Thanks to this methodology, stability limits due to the continuously increasing depth of cut ap (and the associated process load) can be determined by visually inspecting the workpiece surface for chatter marks.
In addition to the optical evaluation, process forces, tool deflections and acoustic noise emissions were recorded by measurement technology installed in the workspace. High sampling rates of up to 100 kHz allow detailed insights into the physical interactions during the cutting process. Figure 3 shows a comparison of measurements using the reference tool and the hybrid „H3“. With regard to the process force in the X-direction (approximately the feed direction), a reduced vibration superimposition can be seen. The change in the process characteristic at the transition to the unstable range is also less marked. This is presumably mainly due to the dissipative plasticisation processes between the free-surface structure and the workpiece.
The deflection curve of the hybrid tool proves the increased compliance of the tool. While the reference tool only breaks through the – 25µm mark when it enters the unstable area, this can already be seen with tool H3 at a cutting depth of 3 mm. However, the acoustic emission measurements shown in the spectrogram prove that no dominant chatter vibrations occur at a cutting depth of 3 mm and thus a stable condition exists.
Preliminary investigations on tools with direction-dependent compliance properties showed – depending on the groove depth on the tool shank – an uneven influence on the maximum cutting depth [4]. By applying the functional structure, a more even distribution emerges, in which tool H3, with an increase of 85 % compared to the standard tool, benefits particularly from the modifications.
Conclusion and outlook
It has been shown that influencing the dynamic behaviour of milling tools – by introducing initially structurally weakening grooves into the tool shank – can positively influence the machining process by impairing the regenerative effect. In addition, functional structures on the free faces of an end mill help to further stabilise the process. Machining force curves confirm a reduced oscillation superimposition of the milling process. With con- stant process parameters, a considerably reduced tool wear with higher surface quality can be expected.
In the further course of the research project, the coupling of finite element-based models with a geometric-physical process simulation is to be developed for the predictive design of processspecific, but also universally performant, tool modifications. In particular, the optimisation problem of the structural weakening of the tool on the one hand and the productivity-promoting inhibiting of the regenerative effect on the other hand represents a central issue in further research. isf.mb.tu-dortmund.de
The contents were funded by the German Research Foundation (DFG) – project number 495148486 – Basic research on the avoidance of the regenerative effect in milling processes through the targeted design of tools with asymmetric dynamic properties.
Bibliography
[1] Altintas, Y.; Kersting, P.; Biermann, D.; Budak, E.; Denkena, B.; Lazoglu, I.: Virtual process systems for part machining operations. CIRP Annals 63 (2014), Nr. 2, S. 585–605.
[2] Yue, C.; Gao, H.; Liu, X.; Liang, S. Y.; Wang, L.: A review of chatter vibration research in milling. Chinese Journal of Aeronautics 32 (2019), Nr. 2, S. 215–242.
[3] Baumann, J.; Krebs, E.; Biermann, D.: Chatter avoidance in milling by using advanced cutting tools with structured functional surfaces. MM Science Journal 2019 (2019), Nr. 04, S. 3019–3026.
[4] Baumann, J.; Wirtz, A.; Siebrecht, T.; Biermann, D.: Disturbance of the Regenerative Effect by Use of Milling Tools Modified with Asymmetric Dynamic Properties. Journal of Manufacturing and Materials Processing 4 (2020), Nr. 3, S. 67.
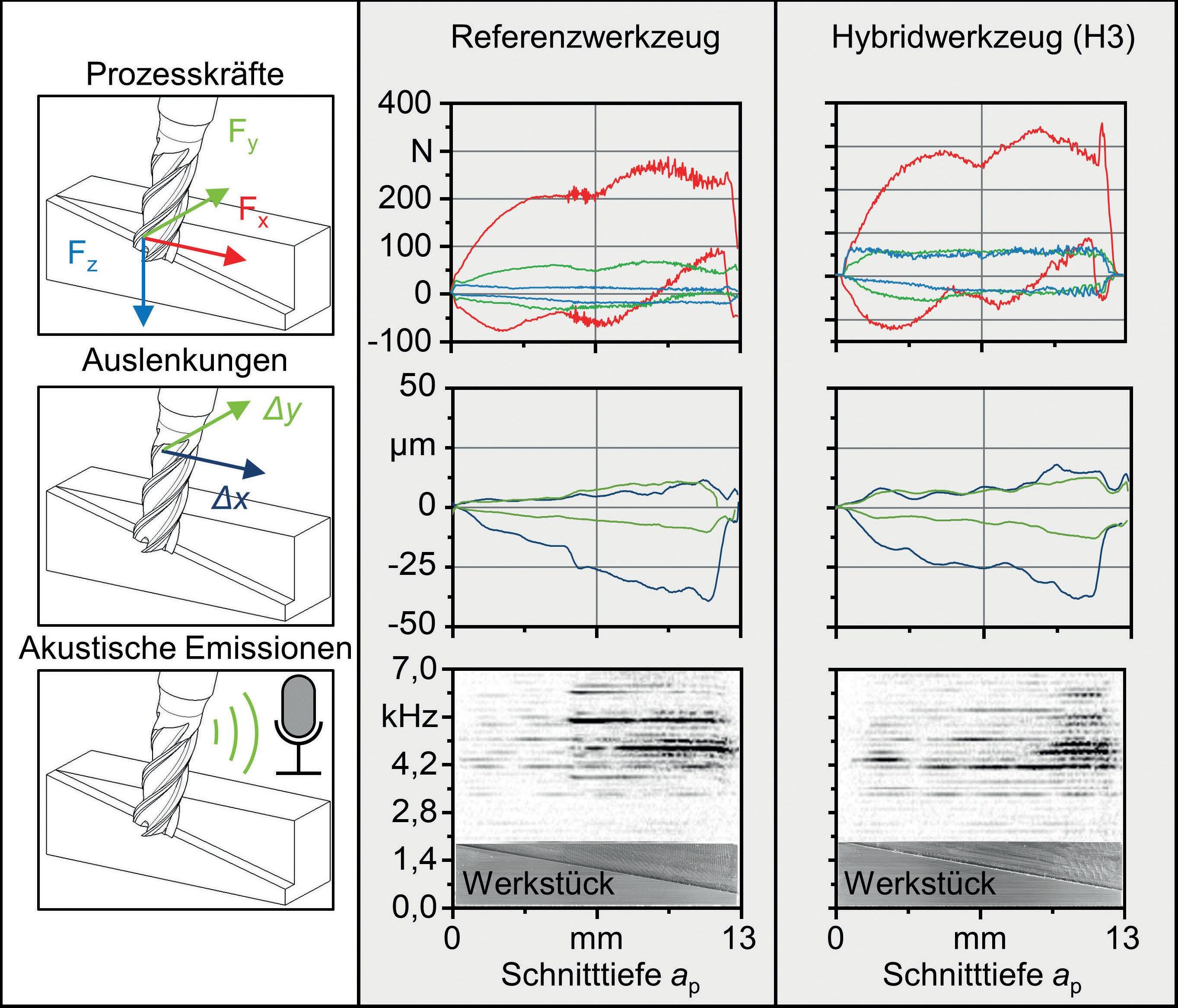
Rafael Garcia Carballo , M. Sc., born in 1992, studied mechanical engineering at the Technical University (TU) Dortmund and is a research assistant at the Institute of Machining Technology (ISF).
Photo: Author
Jonas Baumann , M. Sc., born 1986, studied industrial engineering at the TU Dortmund and is a research associate at the ISF, where he heads the Simulation and Process Development Department.
Prof. Dr.-Ing. Prof. h.c. Dirk Biermann , born in 1963, has headed the ISF since 2007.

The criteria for selecting the optimal cutting tool depend on various factors: the batch size, the type of production, the product range, the materials to be machined, the machines used and the cutting strategy. As a rule, the solution with the highest performance is required, for example with a tool geometry optimised for a specific material or a suitable cutting material grade. However, the chosen combination is material-specific. This means that a tool that can effectively machine cast iron is not automatically the ideal solution for heat-resistant superalloys. After all, if a tool with a long overhang makes the machining of a certain application possible in the first place, in other cases it impairs stability and has a negative effect on the machining performance. Tool manufacturers face a constant challenge in the face of a very wide range of workpieces with different shapes and dimensions.
Factors in economic production
To be able to machine profitably, users must consider and optimise various interdependent factors. For example, effective machine use, expert process planning, available fixtures and tool inventory management are important. It is equally essential to select the appropriate tool.
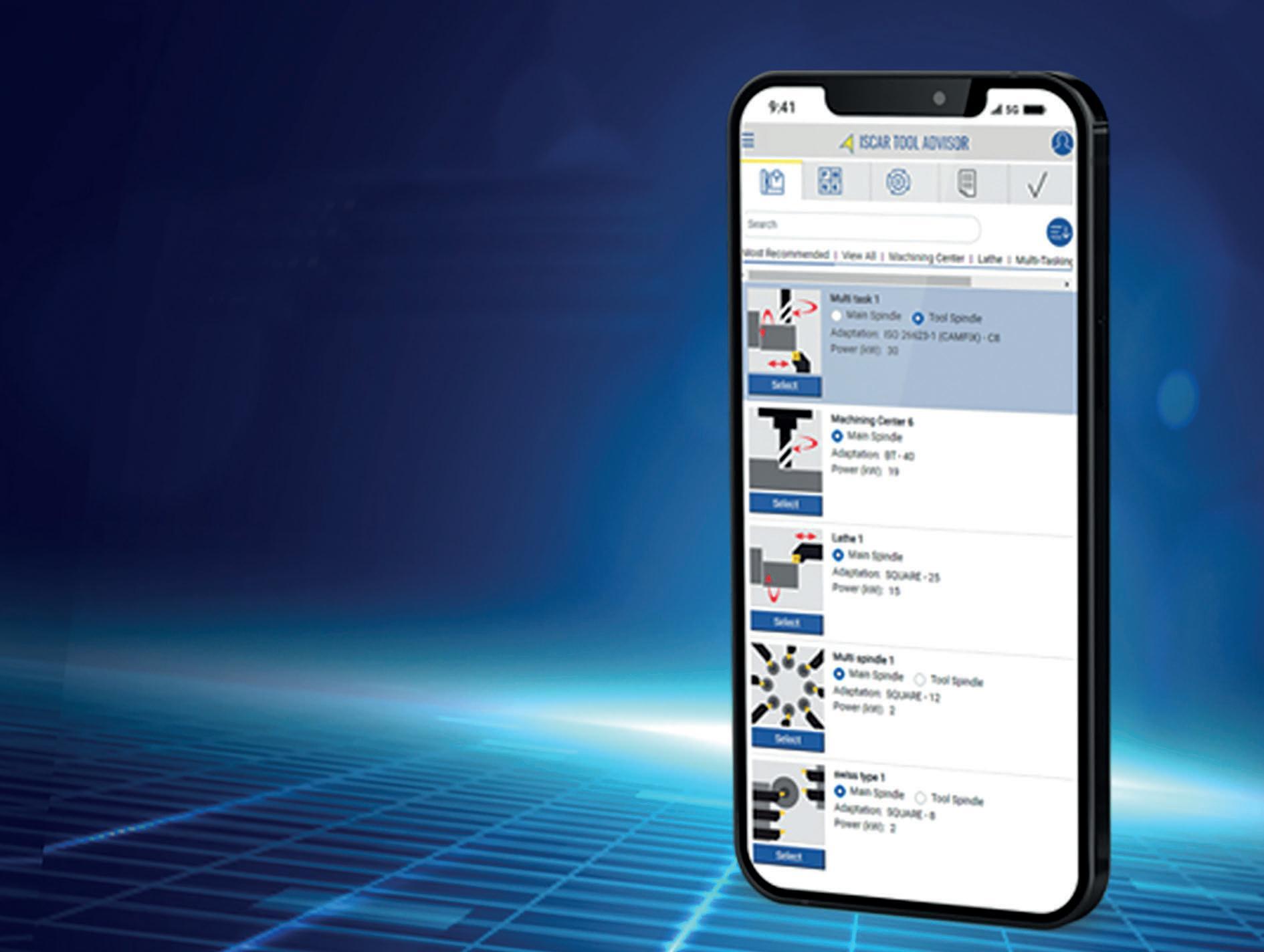
Modern CNC machines are the heart of production. Although they are expensive to purchase, they significantly shorten machining time and thus reduce production costs. The ideal cutting tool for such a machine works reliably, is stable and allows long tool life. For reliable cutting with high metal removal rates at different cutting parameters, manufacturers are constantly developing new cutting edge geometries and cutting material grades that are precisely matched to the different workpiece materials. To reduce production costs, users can also significantly reduce non-productive times with the right tool (Fig.) Short set-up
Systems for turning, grooving, milling and drilling