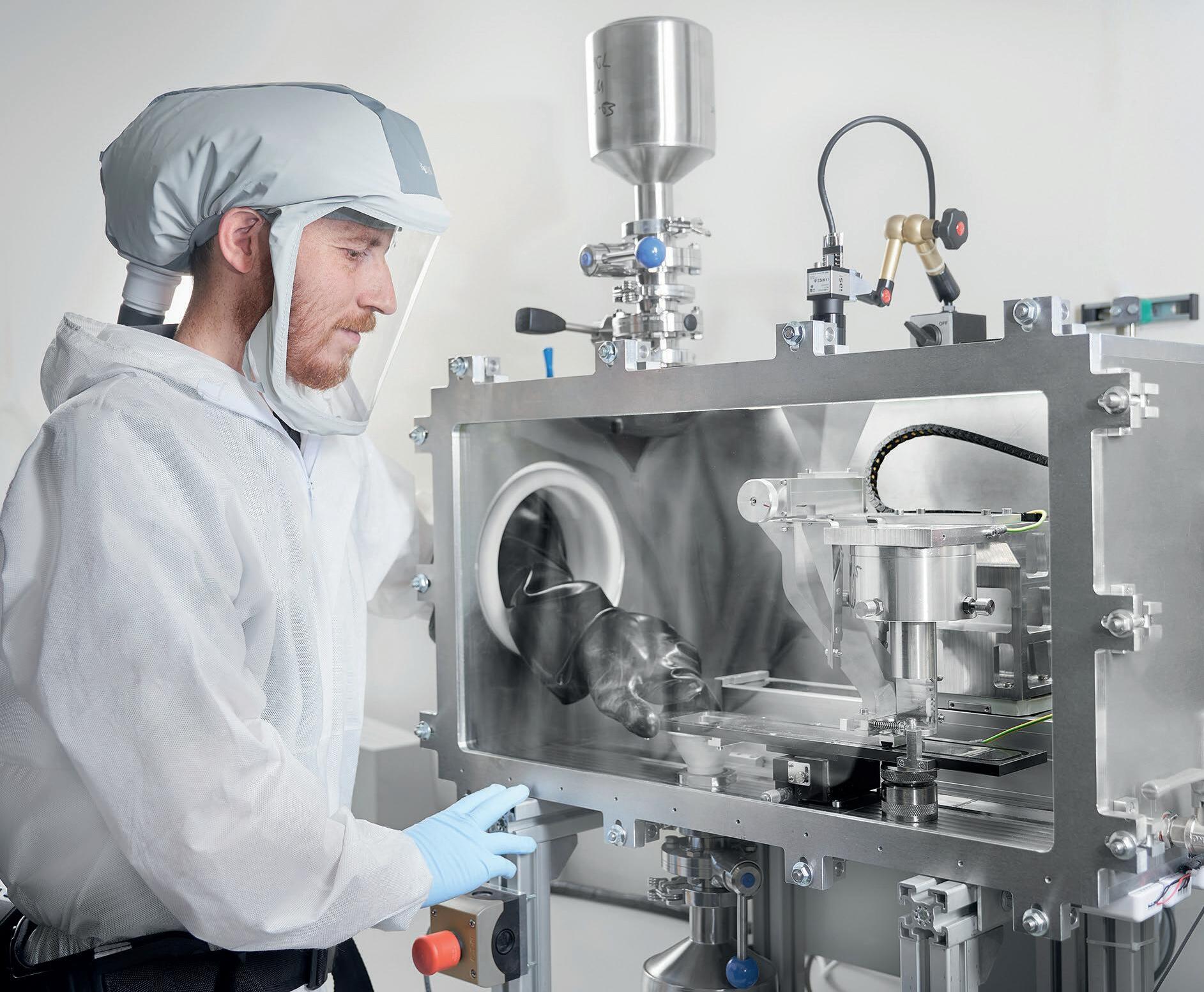
5 minute read
AM: High relevance of feedstock characterisation
Additive manufacturing (AM) processes allow complex component designs. The achievable component quality is not only influenced by the process, but also decisively by the starting material, the so-called feedstock.
The various processes in additive manufacturing have undergone rapid development in recent years. Higher process speeds and a stabilisation of the processes make it possible to increase component quality while at the same time reducing prices. In industrial production, powder bed-based selective laser melting (Powder Bed Fusion – Laser Beam: PBF-LB) for the production of metallic components and bathbased photopolymerisation (Vat Photopolymerization – LED: VPP-LED) for the production of ceramics have become established. These processes allow the production of complex components and offer opportunities for functional integra- tion, for example, through the direct production of internal cooling channels in tools.
Advertisement
Characterisation of PBF-LB powder feedstocks
Mandatory in both processes are starting materials that allow homogeneous and defect-free layer formation. In order to push the process limits further, an optimisation of the feedstocks is necessary. The starting point for this is a reliable and comprehensive characterisation and understanding of their influence and interactions along the entire process chain.
The PBF-LB process is widely used for the production of special tools for machining. Typical applications are specifically guided cooling channels or lightweight special tools that would be too heavy for the tool magazine in conventional production. In order for these to have at least the same tool life as conventionally manufactured tools, it is essential that no defects are introduced by the PBF-LB process. In addition to the process parameters, this is made possible by high-quality powder feedstocks, which can be coated at high density and without defects due to their flowability.
Undesirable: particles that are too fine and too large
One way to ensure flowability is to use feedstocks without fine particles. Depending on the material, particles smaller than 15–20 µm must not be used, as the adhesive forces between small particles are greater than the weight forces acting on them. A feedstock with fine particles can be compared to lumpy flour; without fine particles it behaves more like a liquid. This fine content is often removed by sifting processes.
Depending on the planned coating thickness, larger particles must also be avoided so that all particles can flow under the squeegee during the coating process and do not leave scratches in the coating image. Large particles are classically removed by a screening process. The particle size distribution (PSD) is used to describe the feedstocks. However, the PSD is only a guide value to describe the quality of a powder and to estimate the flowability. Depending on the component properties, an adjustment is worthwhile, for example to achieve a higher build-up rate at the expense of the surface quality or by using a fine feedstock to increase the surface quality. In both cases, however, the flowability of the feedstocks is maintained.
Evaluating flowability
Known quantities for the direct description of flowability are, for example, the Hausner ratio and the flow time, the measurements of which are already described and defined in standards. However, these are only of limited use for describing flowability and reach their limits, especially in the case of feedstocks with low flowability that can nevertheless still be processed. In order to close this characterisation gap, new characteristic values and measurement methods are being investigated in science. One such possibility is the determination of the dynamic angle of repose. For this purpose, the material to be examined is rotated in a transilluminated drum and the feedstock movement is recorded and evaluated as an image sequence.
In order to derive the correlation between measured values and the actual coatability of the feedstock, the wbk Institute for Production Technology has developed a coating test rig. This allows the actual coating process of an additive manufacturing system to be mapped and new coating concepts to be tested in an inert atmosphere. A side window enables highspeed camera recordings of the actual powder movement directly at the squeegee, from which a deeper understanding of the process can be derived (Figure 1).
Adjusting componentspecific powder properties
The logical next step after analysing and understanding the feedstock properties is their targeted adjustment and optimisation. For example, it is possible to adjust the PSD as already mentioned or to add new alloying elements or ceramic hard materials in order to specifically increase the strength, stiffness and hardness of the manufactured materials. Various options are available to make these adjustments. A screening tower can be used to adjust the PSD or to fractionate an existing feedstock. Alternatively or additionally, the feedstocks can then be mixed individually. A mixer, also designed in-house, is available for this purpose, which has two rotary axes aligned perpendicular to each other and independently adjustable in speed (Figure 2). These degrees of freedom allow fast and homogeneous mi- xing of different powder materials with each other in simple storage containers, which are also used for the actual feedstock handling at PBF-LB plants.
Properties and analysis of VPP slurry feedstocks
In slurry-based additive manufacturing processes, suspensions of ceramic or metallic powder and an initially liquid binder are applied and selectively cured by expo- sure to light. This creates other challenges in the design and optimisation of the feedstocks, in this case called slurries. In novel process approaches in particular, in which different materials or slurries are to be combined in a component for local property adaptation, characterisation and precise matching to each other is essential.
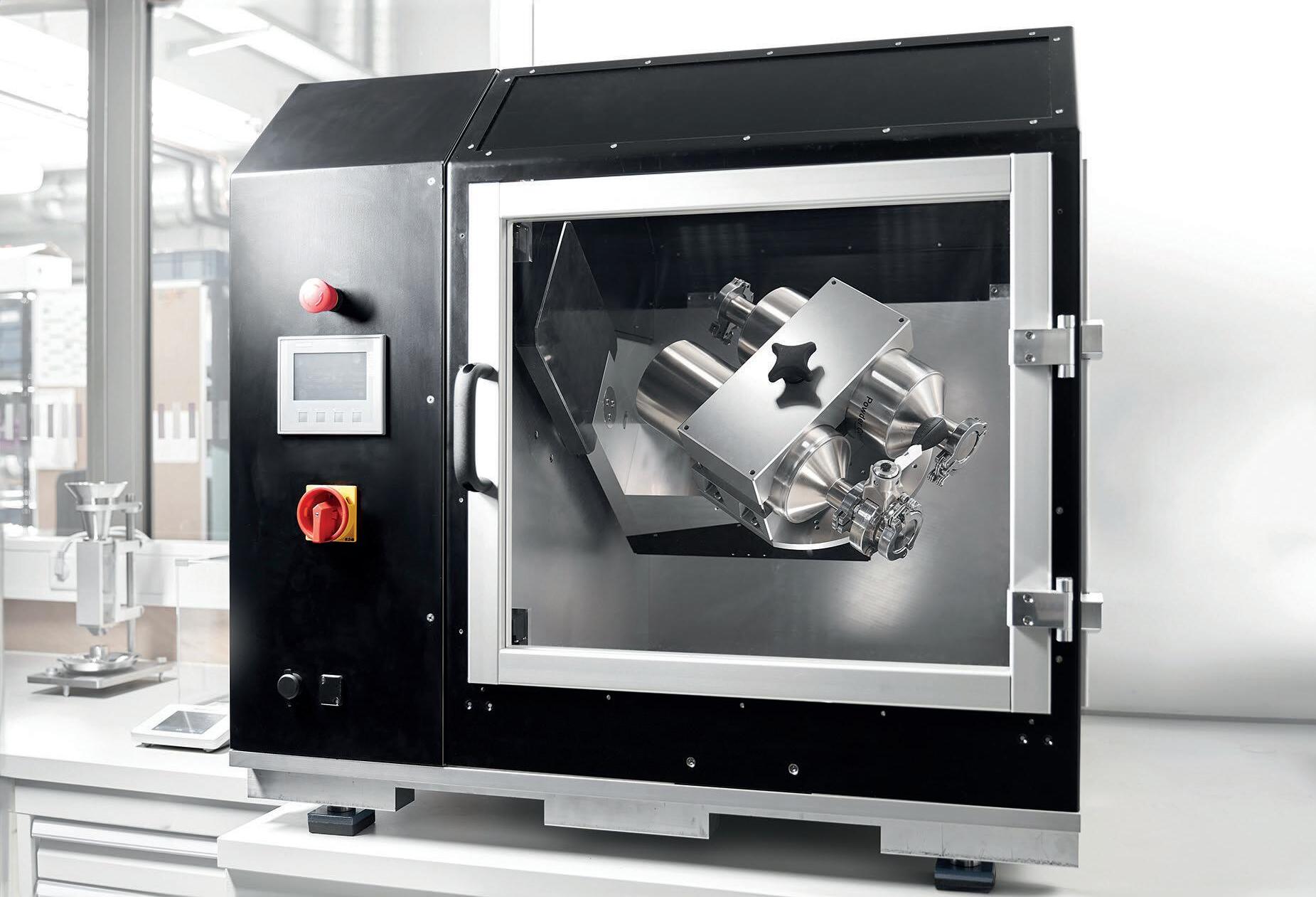
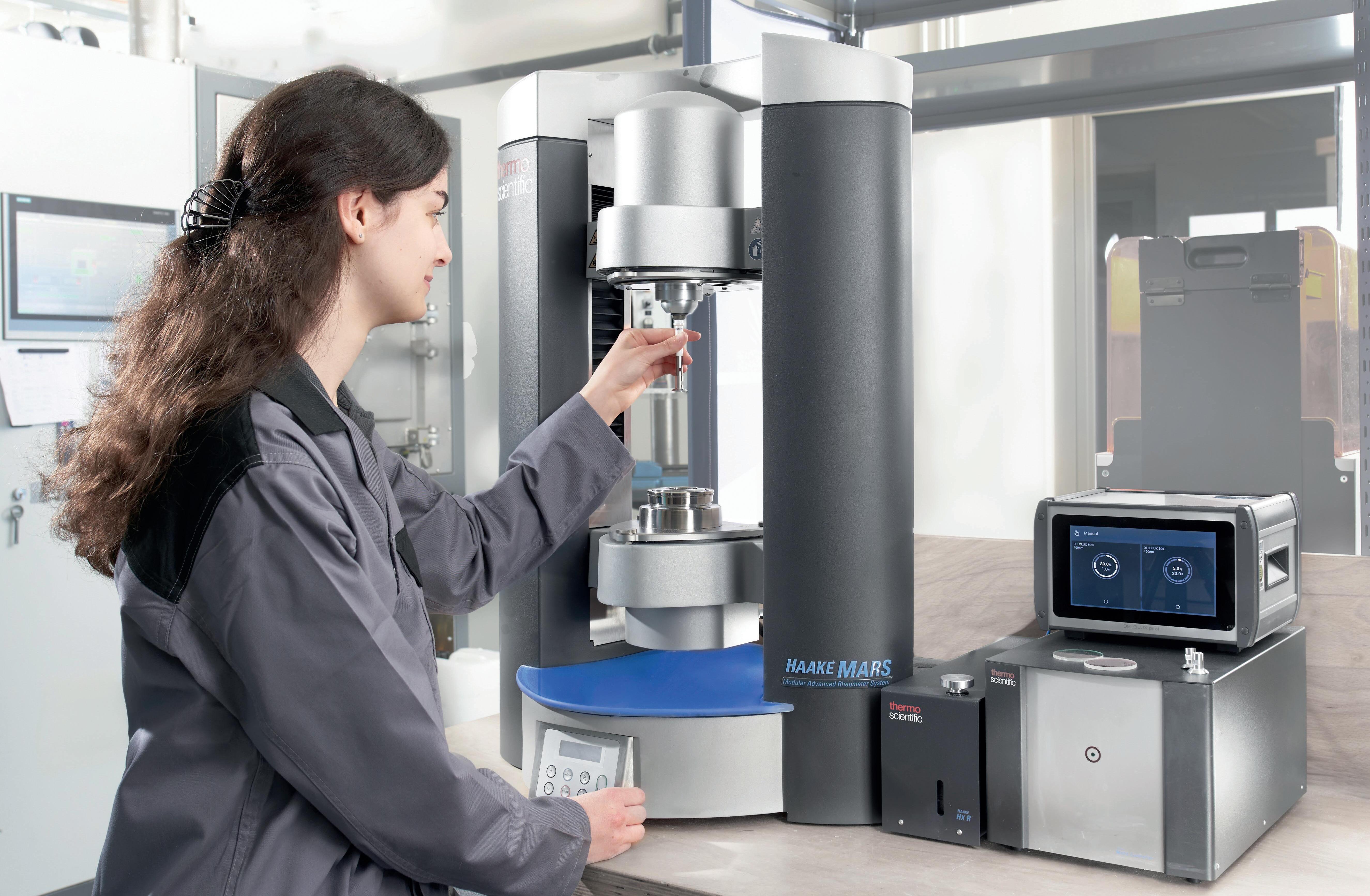
In order for the slurries to be processed in VPP systems, their viscosity must be adjusted within a narrow process window. The viscosity is measured in a rheometer as a function of the shear rate (Figure 3). Optimised slurries have a similar viscosity over a wide shear rate range to ensure a stable process, especially in plants with rotary slurry application. In addition to viscosity, the curing behaviour of the slurry is also of great importance. This can be characterised on the rheometer with connected exposure unit, which imitates the curing process in VPP systems.
The measurements serve to further optimise the slurry composition and to determine suitable parameters for the curing process in the VPP plant on a small scale. Equally relevant for the VPP process is the determination of the granularity of the slurry as well as the curing depth, which influences the minimum realisable layer thicknesses and the resulting print resolution. In this context, characterisation methods actually used in the paint and coating industry, for example by means of a grindometer or wedge section method, can be applied in a target-oriented and reproducible manner.
Conclusion
With the characterisation methods mentioned, an efficient adjustment of the slip constituents and the process parameters is also possible outside the production plant. Through iterative optimisation, it has been possible to reduce the process time so that special gears, for example, can be manufactured economically.
www.wbk.kit.edu
Victor Lubkowitz , M. Eng., born in 1992, studied mechanical engineering at the Universities of Applied Sciences in Stralsund and Coburg. He is a research assistant at the wbk Institute for Production Technology at the Karlsruhe Institute of Technology (KIT).
Johannes Schubert , M. Sc., born in 1997, studied mechanical engineering at KIT and is group leader for additive manufacturing at the wbk Institute for Production Technology at KIT.
Dr.-Ing. Frederik Zanger , born in 1982, has a doctorate in mechanical engineering and works as a KIT Industry Fellow in both research and industry.
Additively manufactured tools
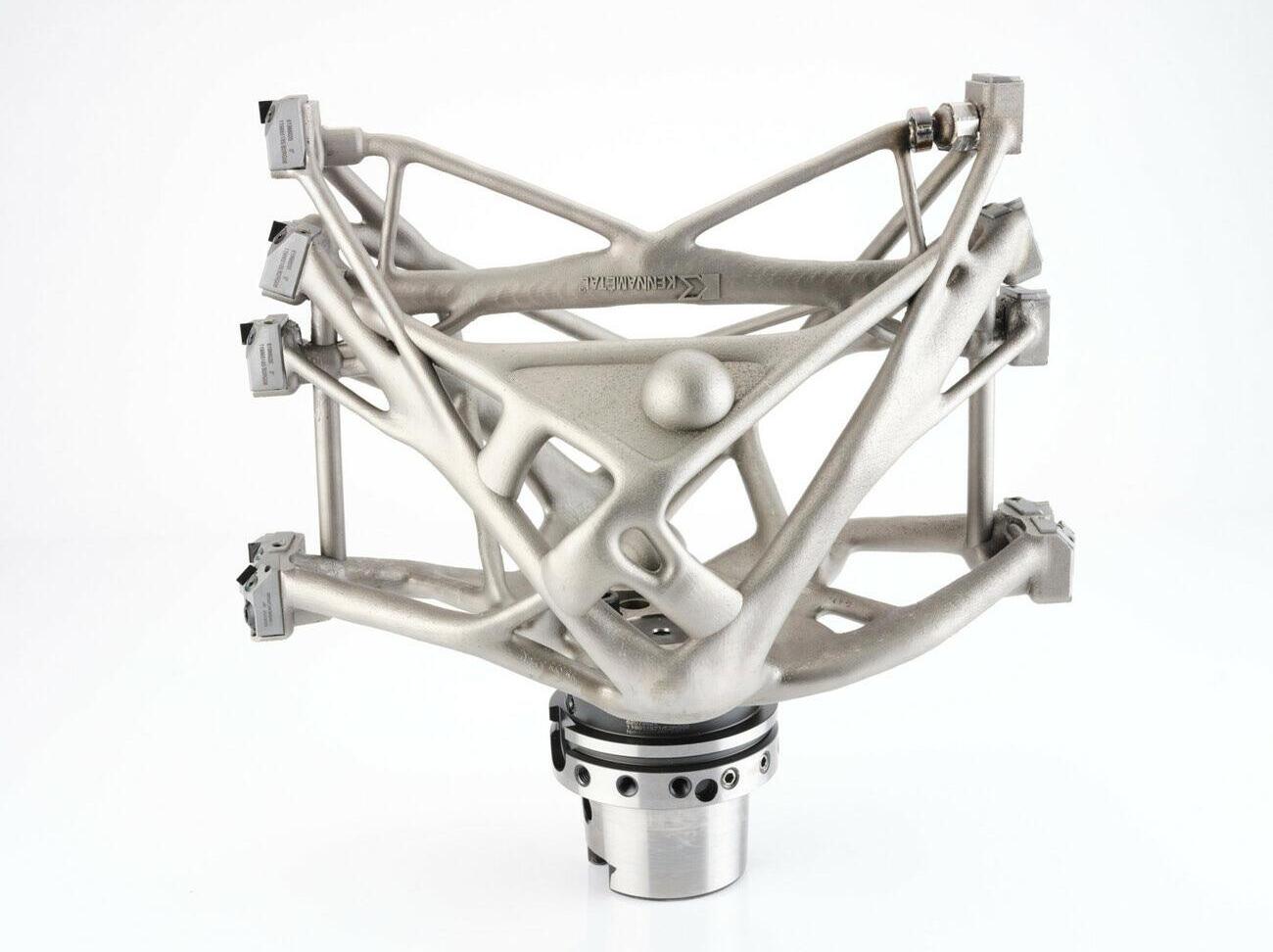