
4 minute read
Smart toolholder as data supplier
Data is the key to continuously improved and adaptively controlled processes. With a narrow database, the potential of modern machine tools can hardly be exploited. But how can data on the machining process and tool condition be collected reliably and effortlessly?
Help is now coming from a Fraunhofer project: the intelligent tool holder „smartTOOL“, developed jointly by Fraunhofer
Advertisement
IWU and Fraunhofer IIS as part of the „Fraunhofer Cluster of Excellence Cognitive Internet Technologies“, CCIT does just that (Figure 1) thanks to highly sensitive in-line measurement directly at the point of action. The „intelligent“ tool holder developed by the two Fraunhofer institutes creates the transparency with meaningful data that is required to increase the productivity, economic efficiency and flexibility of modern manufacturing processes. The tool holder‘s energy supply is completely au- tonomous, and data transmission is likewise wireless.
Extensive measurement directly at the process
The smartTOOL toolholder system is equipped with sensors for measuring vibrations, process forces and temperatu- res. These data are transmitted via a wireless link to an evaluation unit with a graphical user interface. Specific evaluation algorithms then allow conclusions to be drawn about the states of the process and tool as well as the machining result. The measurements must be sensitive enough to reliably register minor, progressive changes, such as „creeping“ tool wear, the occurrence of vibrations or fluctuations in the dimensions and material of the workpiece. Only a digital monitoring system installed in the direct vicinity of the process can meet such stringent requirements for measurement sensitivity. Critical process disturbances, such as collisions, chatter or even tool breakage, are detected with the same reliability.
Radio transmission via Bluetooth Low Energy
Wireless data transmission equips the system for process monitoring in real time as well as for offline diagnosis. The recorded data form the basis for manual intervention for optimisation. In addition, the system can be coupled with a machine control system for the purpose of adaptive process control. For this purpose, meaningful features are extracted from the sensor signals and transferred into action decisions via corresponding evaluation algorithms. The effects of these actions are also identified, enabling independent adjustment of the process parameters.
Autarkic – unrestricted production operation
The electrical energy required for the permanent operation of the smartTOOL is provided by an innovative energy harvesting solution. This completely wireless technology is here used for the first time in the field of process and tool monitoring. A simple component equipped with permanent magnets is mounted on the spindle nose of the machine. Electrical energy is generated by the tool rotation to supply the sensors, signal processing electronics and the radio transmitter. Due to the compact size of the magnetic holder, neither the automatic tool change nor the available working space is restricted. The 3D-printed, easily adaptable moun- ting geometry additionally reduces the retrofitting work to a minimum.
Flexible use on any machine
Almost all electronic components in the toolholder are located on a compact, universal segment between the chuck and the spindle interface. Therefore, the latter two geometries are also largely freely selectable and allow a multitude of application-specific combinations. Since the hardware is fully integrated into this standard segment, smartTOOL has no interfering contours. High static and dynamic rigidity is nevertheless provided, thanks to the optimised geometry. The application is therefore just as versatile as with conventional tool holders.
smartTOOL can be used in many machining processes. For example, the adaptive process control could be used for NC path correction to compensate for elastic tool displacement. Workpieces can thus be machined even more precisely and, in contrast to manual correction, no additional worktime is required for in-process compensation.
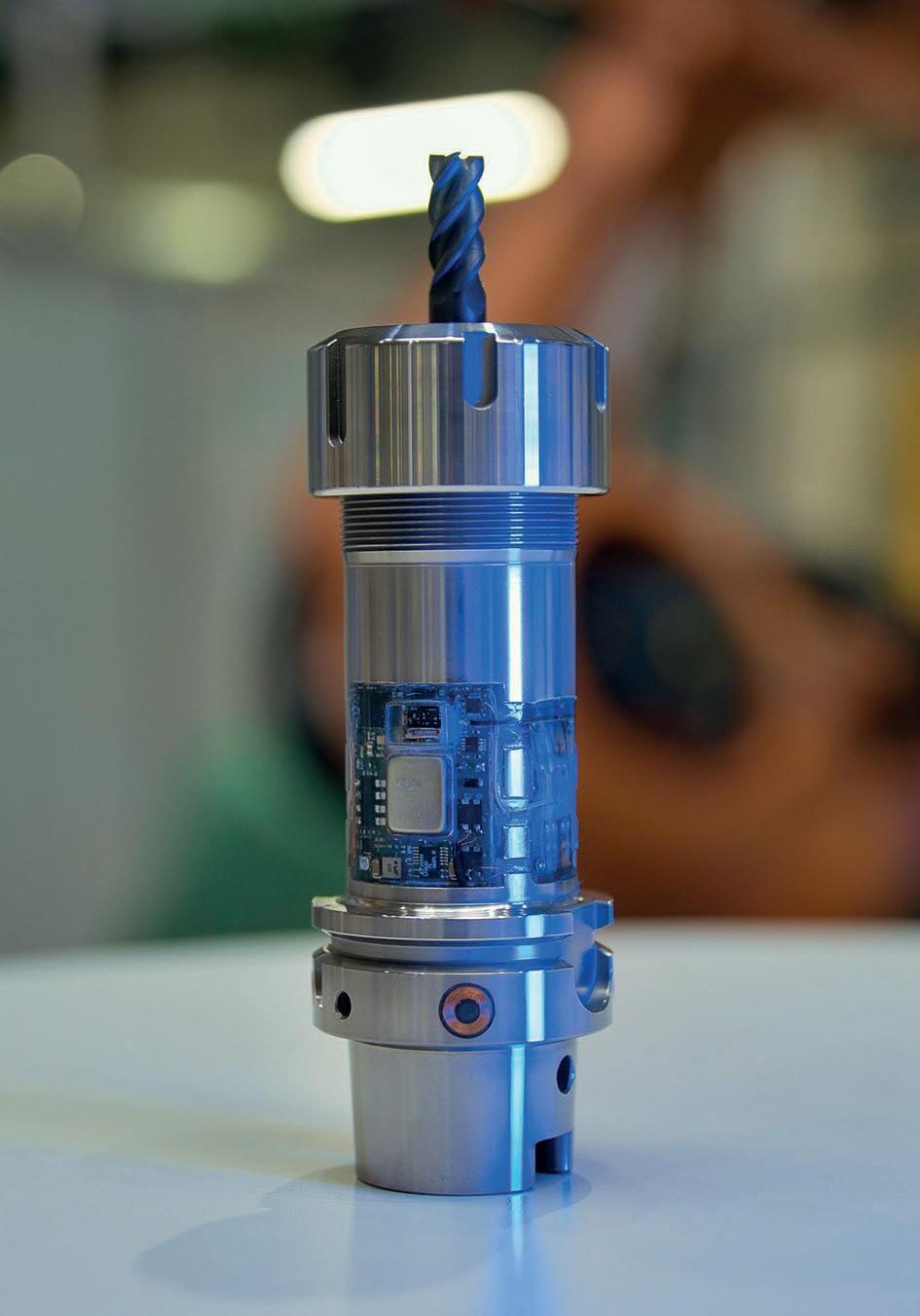
Predictive or even prescriptive maintenance applications are also conceivable: at the end of the tool service life, a pen- ding tool change could be indicated or even initiated automatically. Another option is the adaptive variation of axis feeds to minimise unwanted process vibrations such as chatter. Here, the feed rate is gradually reduced, should any critical vibrations occur, until the vibration level of the process reaches a desirable level. This reduces wear on the tool and machine and ensures the quality of the workpiece surfaces produced.
Already proven in many processes
smartTOOL has already distinguished itself in a large number of milling and drilling processes. But the system is also very useful for the interim analysis of failure-critical processes: it helps to gain a deeper understanding of the causes of failure in order to be able to eliminate them. An application for permanent monitoring – for example of tool wear and tool breakage in series processes – has also been successfully tested.
The high-frequency, sensitive sensor data are also ideally suited as input for modern AI models and digital twins for machine and process monitoring. Through an evaluation methodology based on deep neural networks, for example, a 99.9 % prediction accuracy of the degree of tool wear was achieved. This allows the user to maximise the utilisation of tool life while avoiding the production of scrap. Tool costs decrease, while the main time share increases, as unnecessary tool changes are eliminated.
Help during commissioning
smartTOOL is not only interesting for continuous production processes. It also supports the commissioning and evaluation of new machine tools and tools with the help of short test processes. Tests showed that the sensitive measurement data made these steps more quantifiable and thus easier. In addition to its use in machining, the solution has also proven to be suitable for monitoring customer-specific processes in the areas of forming and joining. The development partners consistently appreciated the absence of interference contours and energy self-sufficiency in combination with the high-quality measurement of process forces and vibrations.
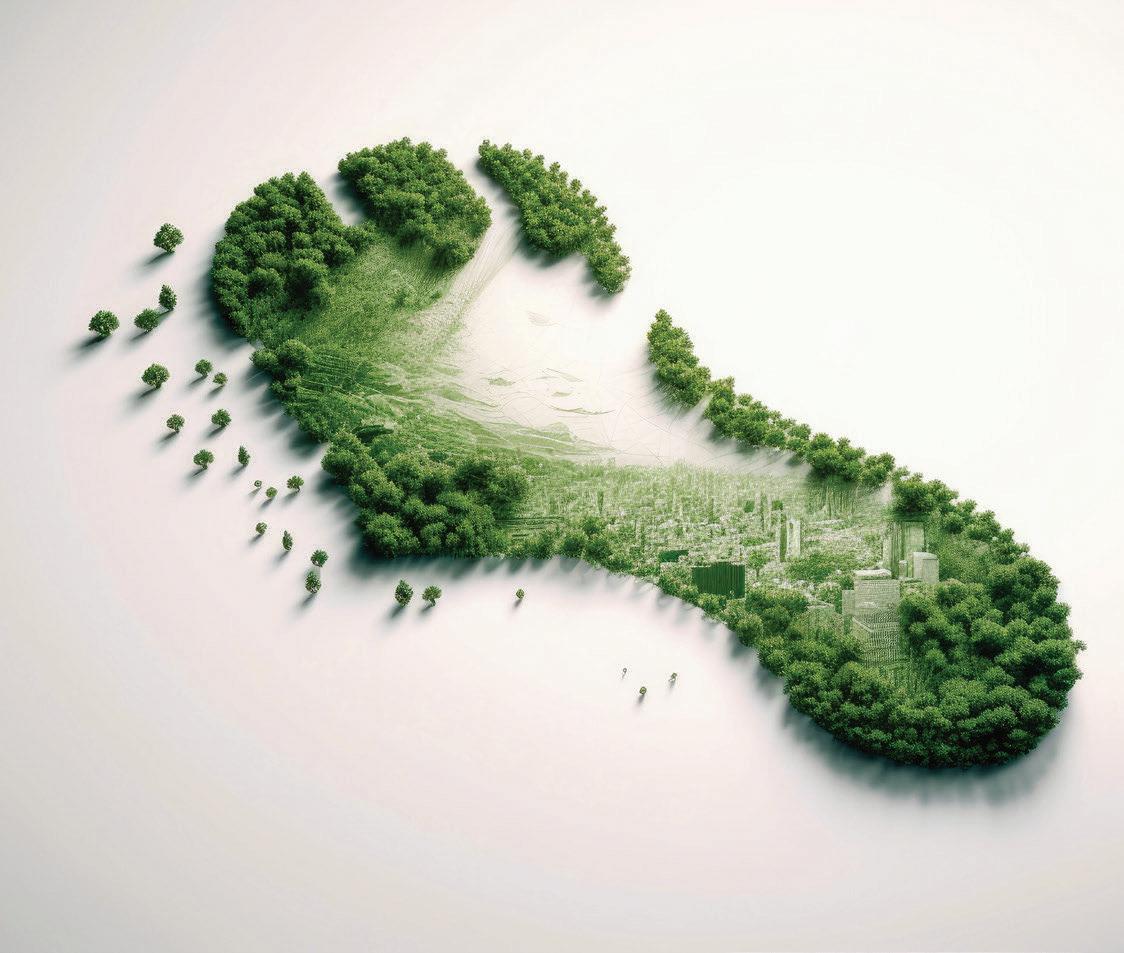
A new generation of the smartTOOL with a reduced electronics segment, a wi- der speed range and additional high-performance sensors and signal processing is currently being developed to make it even easier to use (Figure 2). This will result in even shorter toolholder lengths and further areas of application in the future. www.iwu.fraunhofer.de www.iis.fraunhofer.de is a research associate at the Fraunhofer IWU with a focus on sensory and actuator systems for machine tools and AI-based evaluation models.
Dipl.-Ing.
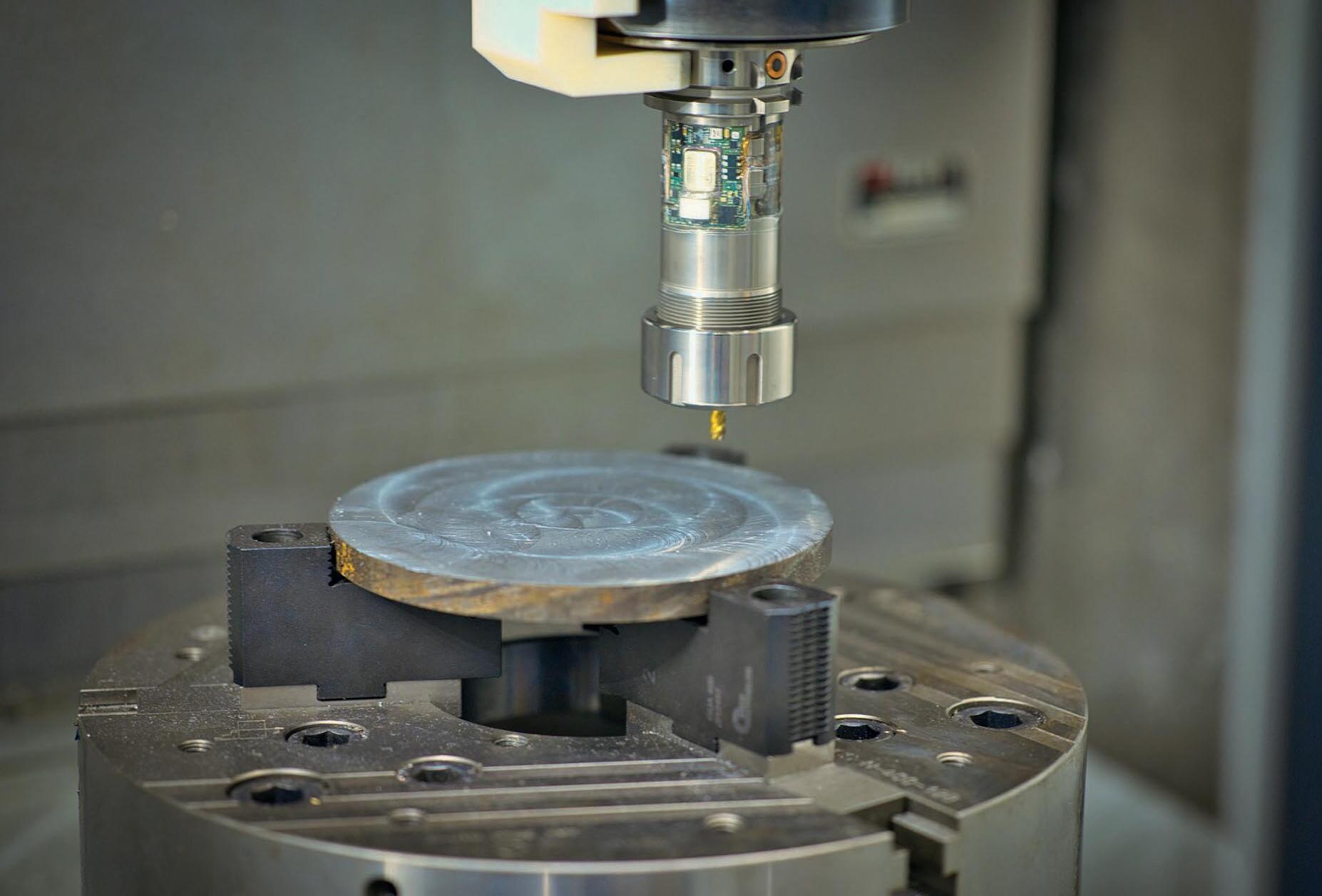
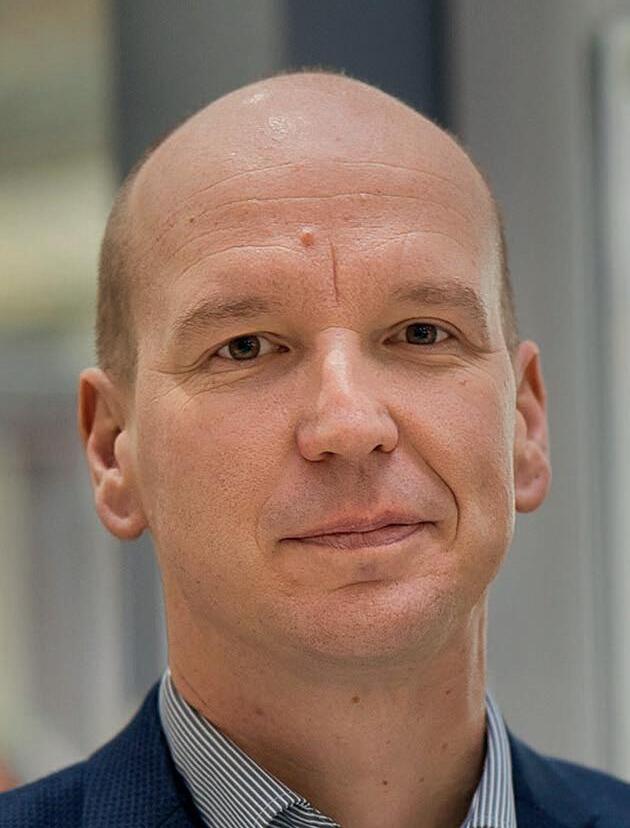
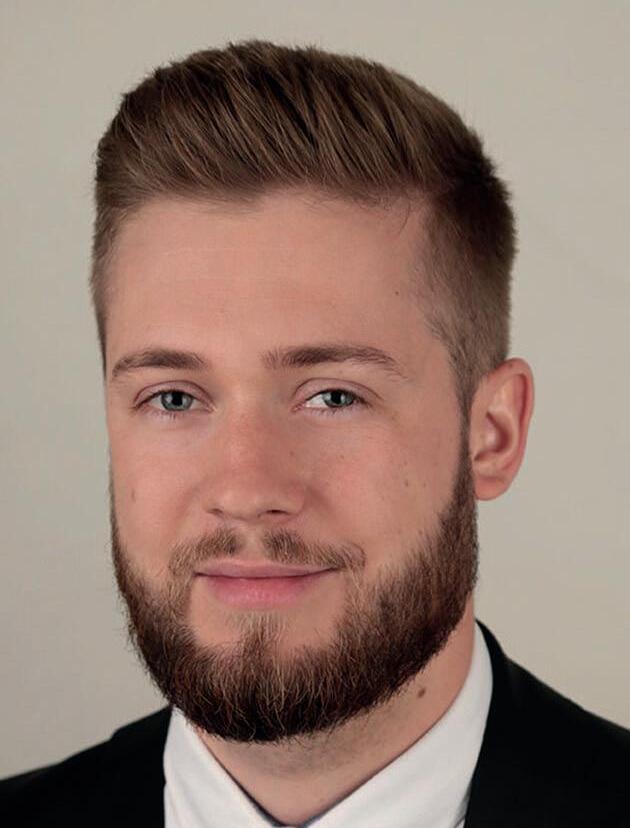