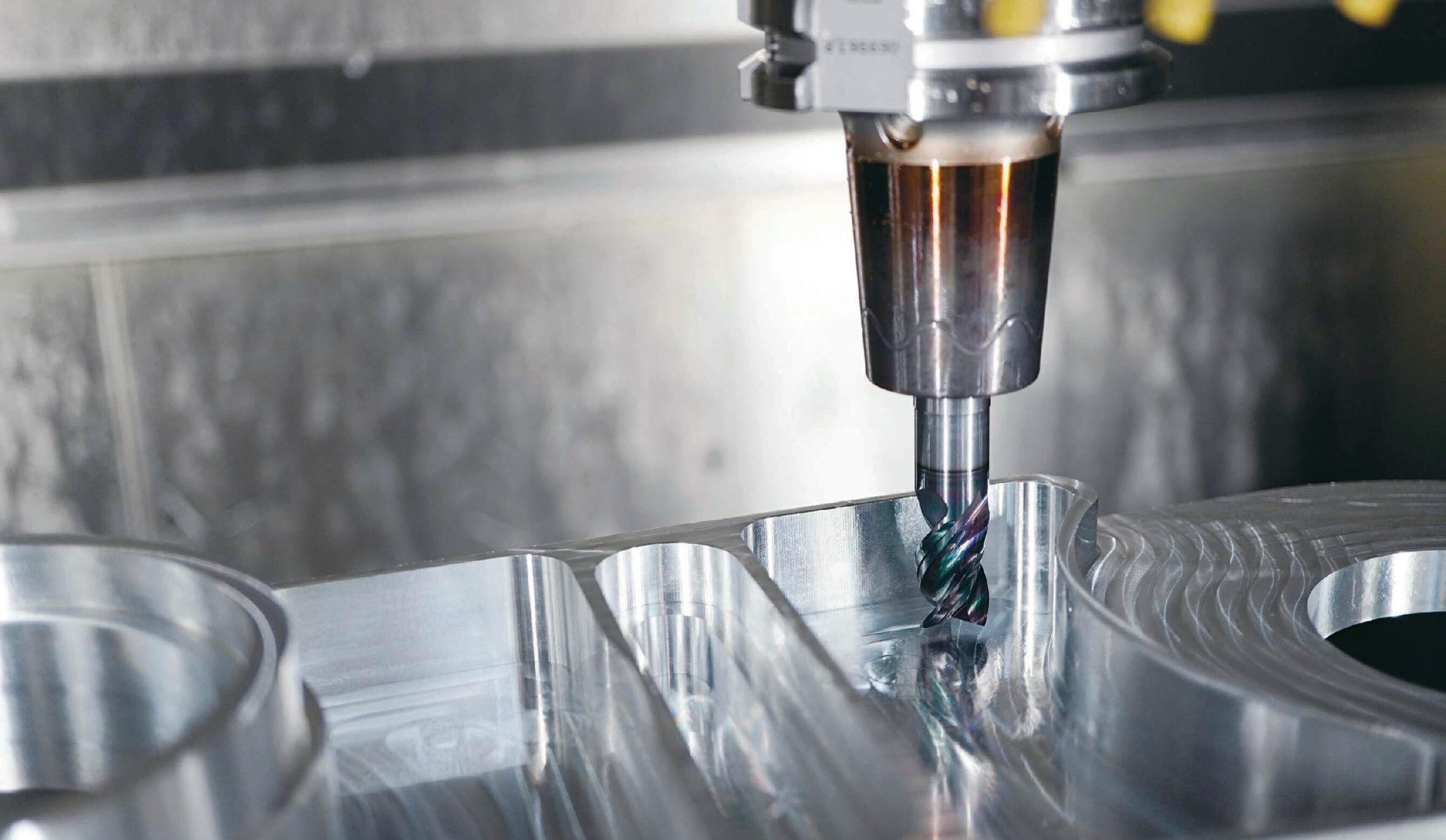
5 minute read
The perfect tool for everyone
Precision tools are constantly pushing the boundaries of what is possible for the benefit of customers – especially when it comes to the topics of sustainability and digitalisation. Experts at EMO Hannover will report on how well this is being achieved by research and industry on the three central days of the trade fair from 19 to 21 September 2023.
Some challenges „can‘t be tackled on your own“: this was also recognised by two leading manufacturers of clamping technology, who entered into a technology partnership in the area of sustainability. The means to this end is hydraulic expansion clamping technology, which they want to establish as the most sustainable clamping method for the machining industry. At the VDMA Technology Forum at EMO, Matthias Brenner
Advertisement
(Schunk GmbH & Co. KG) and Dennis Minder (Mapal Dr. Kress KG) explain how this technology makes „resource savings and significant cost reductions“ possible.
When the clamping jaw measures and communicates
The advantages of direct real-time measurement of the clamping force during machining are mentioned by Thomas
Roth of Röhm GmbH. The focus is on the clamping force measurement by the world innovation „iJaw“, according to the company „the first clamping jaw ever to be equipped with sensor technology and wireless data transmission“.
Simple operation is the hallmark of the shrinking technology which Michael Renz from Helmut Diebold GmbH & Co. Goldring-Werkzeugfabrik presents as „The Smart Concept“. The solution is characterised by the fact that even inexperienced operators can reliably shrink and unshrink tools just by touching an operating button.
Stefan Echle and Stephan Wangler from Haimer GmbH will explain how productivity can be increased enormously and setup costs drastically reduced. They will present shrink collets whose high rigidity and concentricity are said to more than double the service life of tools compared to conventional systems. Also on the agenda is the modular milling system „Duo-Lock“, whose thread design with double cone ensures maximum stability, load capacity and increased process reliability.
Digitised toolholders secure processes
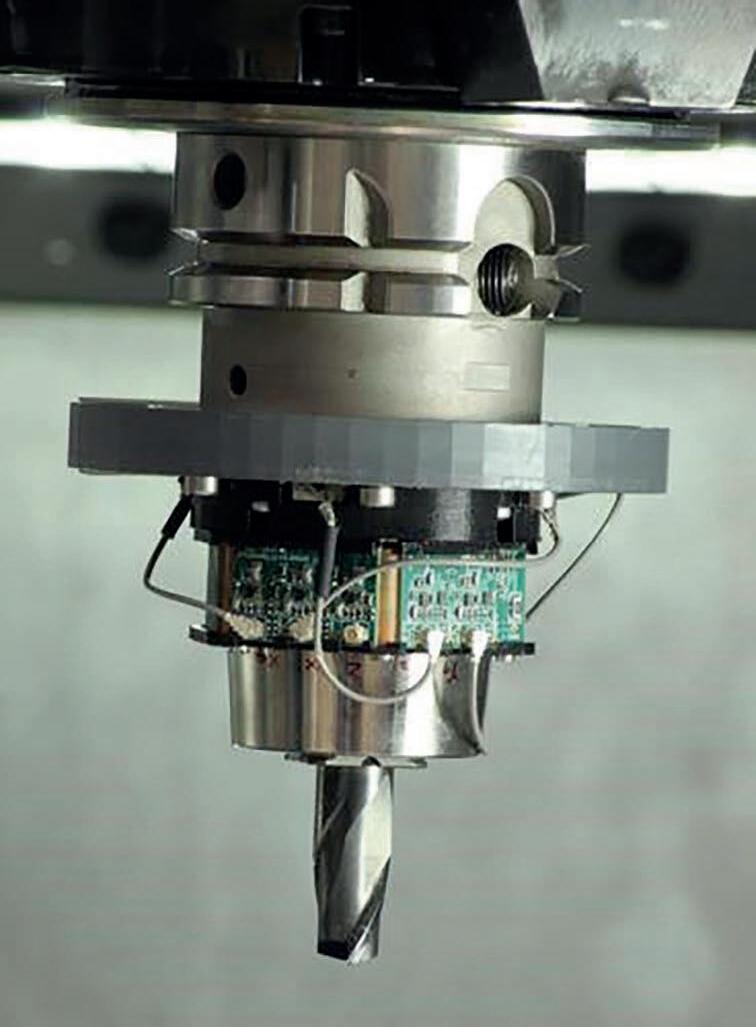
The topic of digitalisation is also in focus for holders. For example, digitalised toolholders for lathes ensure cost-optimised preventive maintenance and process security, as Karl-Heinz Schoppe from mimatic GmbH demonstrates with practical examples (Figure 2). In addition, Horst Leidner from mimatic explains the new international PTI standard for toolholders in lathes and its new mechanical interface, which is intended to make more precise component machining, faster, automatic retooling and digitalisation possible.
The „best toolholder from two worlds“ is how Michael Schinke, Bilz Werkzeugfabrik GmbH & Co. KG, describes the „ThermoGrip TMG“ shrink-fit chuck system. It combines the modularity and damping properties of a collet chuck with the perfect concentricity and operating safety of a shrink-fit chuck, which is said to be particularly suitable for high-performance and high-speed milling with holding forces of over 700 Nm.
Sustainable 3D printing
3D printing is also making its way into tool and clamping technology. For example, the R&D department of Iscar Germany GmbH describes additive manufacturing as a suitable process „for finding the optimal and sustainable solution for special and newly developed products such as indexable inserts“. New options will be presented by Iscar speaker Sebastian Oeking at the Technology Forum, while Dr Ole von Seelen, of trinckle 3D GmbH, will present software tools for creating 3D models of jigs and fixtures quickly and intuitively.
TAKE FIVE: FIVE RESEARCH
Inspirations
Not only industry, but also research is intensively engaged in the topics of machining and clamping. Highlights of the Technology Forum are:
1. Balancing between ecology and economy: „Resource efficiency and high process performance do not have to be a contradiction,“ emphasises Prof. Dr.-Ing. Hans-Christian Möhring from the Institute for Machine Tools (IfW), University of Stuttgart. The scientist proves his thesis with new technologies for machining processes that simultaneously reduce energy and material input and increase productivity.
2. Inspiration (not only) for medical engineers: Modern implants have curved surfaces and non-round cross-sections. This is where the novel machining processes of rotary whirl milling, rotary non-round turning and polygonal turning come into play, as presented by Tassilo Arndt, Karlsruhe Institute of Technology (KIT).
3. 3D-printed steel tool: Supported by VDMA Präzisionswerkzeuge, the AiF project „AddKoSt“ investigated how the 3D printing process „Laser-Powder Bed Fusion“ (LPBF) can be used to produce tool bodies from carbon steels. According to Prof. Dr.Ing. Martin Reuber from the Institute for Tooling and Manufacturing Technology (iWFT) at the RFH Cologne, one of the advantages of LPBF – also known as selective laser melting (SLM) – is that tool bodies can be produced with optimised coolant supply and adapted material and structural properties.

4. Sensors „on board“: The monitoring and control of manufacturing processes is recommended by Martin Ettrichrätz from Fraunhofer IWU and Dr. Joachim Regel and Markus Fuchs from Chemnitz University of Technology (Fig. 1). They present „Tool and clamping device-integrated sensor technology for the in-situ monitoring of cutting manufacturing processes“. The advantage: force and temperature measurement take place in the immediate vicinity of the process without significantly influencing the stiffness of the tool.
5. Hybrid PVD coating for machining extremely hard materials: Dr Florian Welzel and Hannes Joost from GFE Schmalkalden e.V. report on how the best of three worlds can be combined. The scientists from Thuringia present hybrid PVD coatings that are created by simultaneously combining the ARC, sputtering and PECVD processes in a coating system. The presentation describes newly developed coatings and their applications: for example, multicomponent coatings for processing the extremely hard titanium aerospace material Inconel 718.
„Mini all the way – internal machining of bores“ is the topic for Dr Matthias Luik, of Hartmetall Werkzeugfabrik Paul Horn GmbH. This expert will show how their specially designed geometries have a positive effect on internal machining from a bore diameter of 6 mm onwards, using „Mini“-type inserts screwed to the face.
When the lathe hones...
Increasing surface requirements and increasingly tight shape and position tolerances are among the tasks that occupy Dr. Ing. Tobias Knipping of MAS GmbH when honing with a geometrically defined cutting edge. He provides an specialist report on a new method that can be used to reproduce the honing process on a lathe.
A special challenge for machining specialists, however, are also aluminium diecast parts and thin-walled aluminium housings, which are in demand especially in electric cars. Magnus Hoyer from OSG GmbH reports from practice on how these components can be efficiently machined with new tool geometries and technologies.
Intuitive robot „teaching“
Reducing non-productive time is the focus of the presentation „SmartAutoma- tion – the flexible robot loading system“ by
Manuel Nau
,
Andreas
Maier
GmbH & Co.
KG. The speaker will demonstrate how workpieces can be automatically loaded and unloaded on lathes and milling machines (Figure 3). No experts are needed to operate the system; even laymen in robotics should be able to enter orders within a few minutes thanks to intuitive operation.
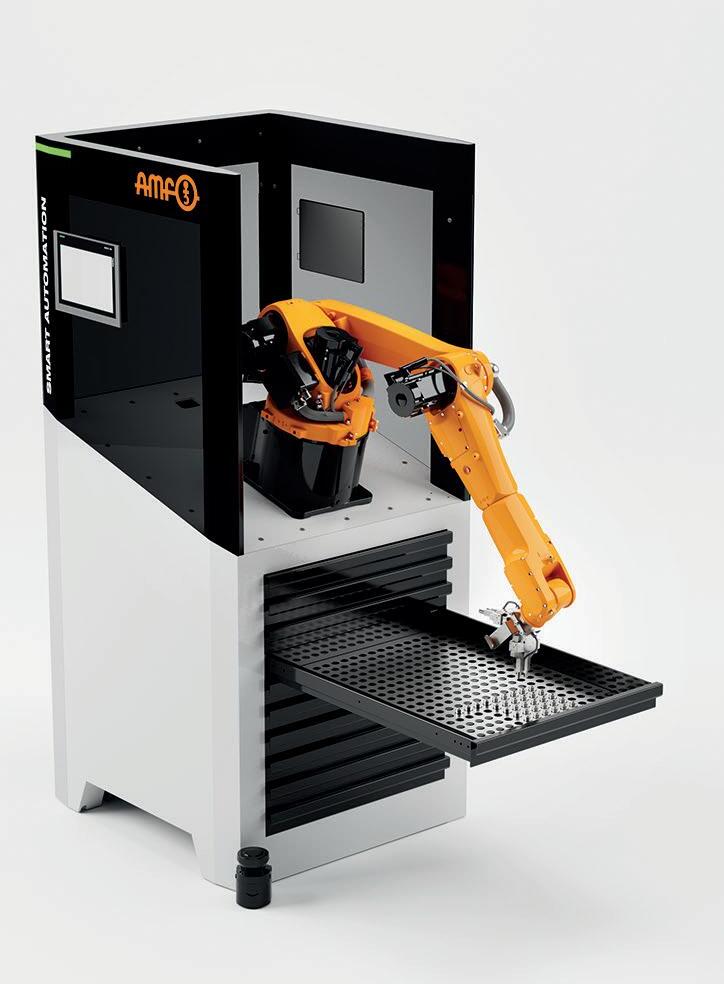
This variety of topics at the VDMA Technology Forum is fascinating and extensive. Stefan Nitsche from Hainbuch GmbH provides the common thread throughout the entire process. The manufacturer of clamping devices sees himself as a companion for the entire production process, who will present exemplary solutions in Hanover that optimise manual and automated production processes. According to Nitsche, the secret of success lies in a meticulous analysis of the process-critical and often time-consuming steps in machining.
Industry well positioned
Following the recovery of the precision tooling industry in 2022, the manufacturers concerned were able to build on the positive development in the first quarter of 2023. Particularly in the subsectors of machining and clamping tools, sales up to March were again 9 % to 10 % higher than in the same period last year. However, the first signs of a slowdown in order intake were evident – even if production is still running at full capacity at many customers, the reluctance to make new investments is making itself felt everywhere. „Here we expect positive impulses from EMO to dispel this reluctance,“ is the opinion of Markus Heseding, Managing Director of VDMA Precision Tools and VDMA Measuring and Testing Technology, Frankfurt/Main. www.vdma.org/praezisionswerkzeuge
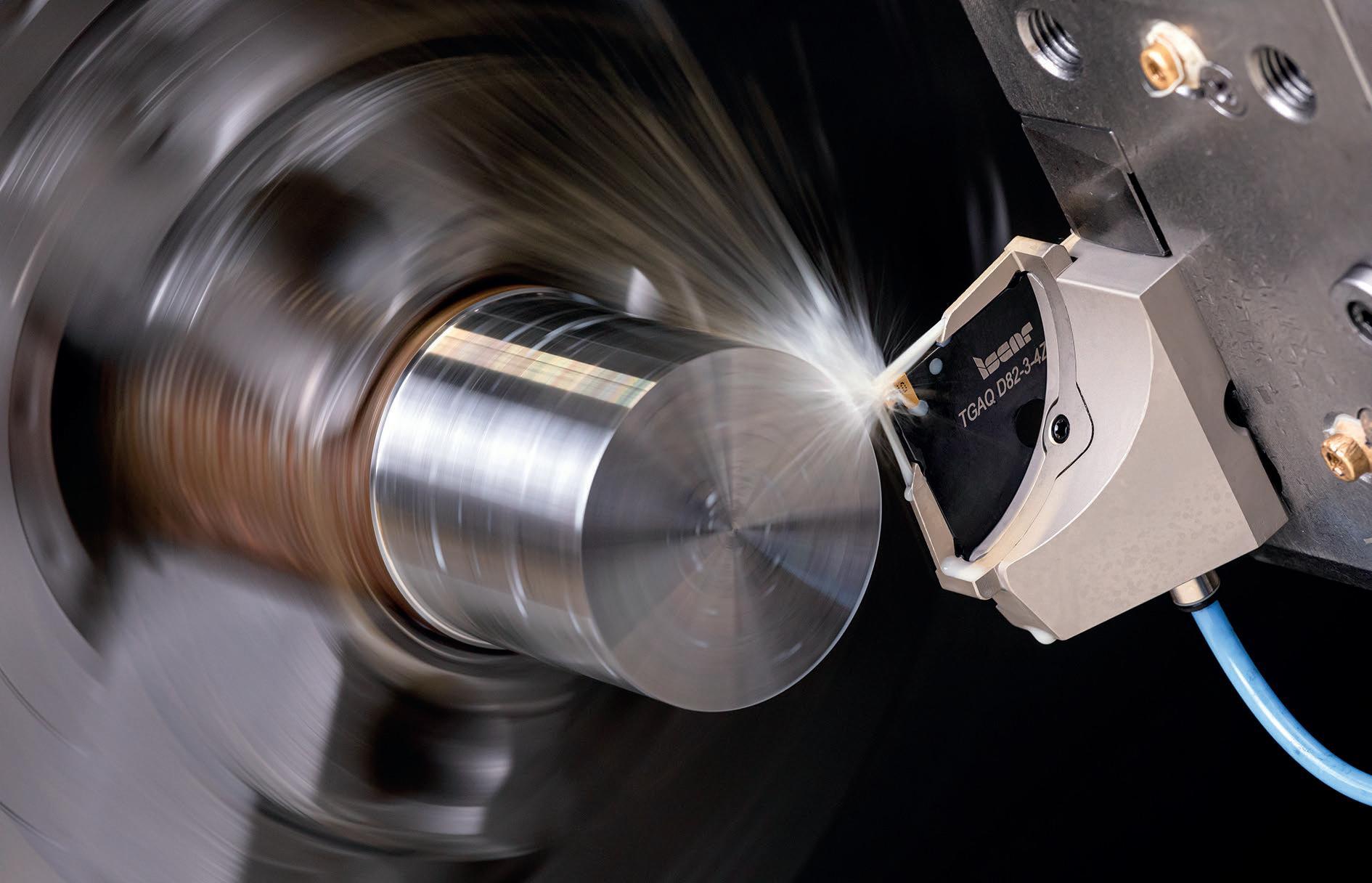
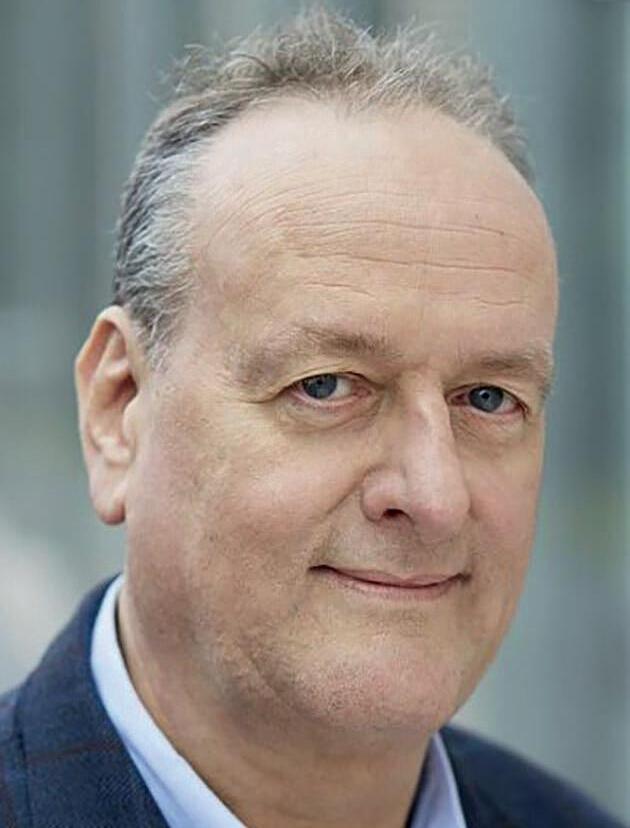
Process monitoring directly at the point of action: towards more efficient machining processes