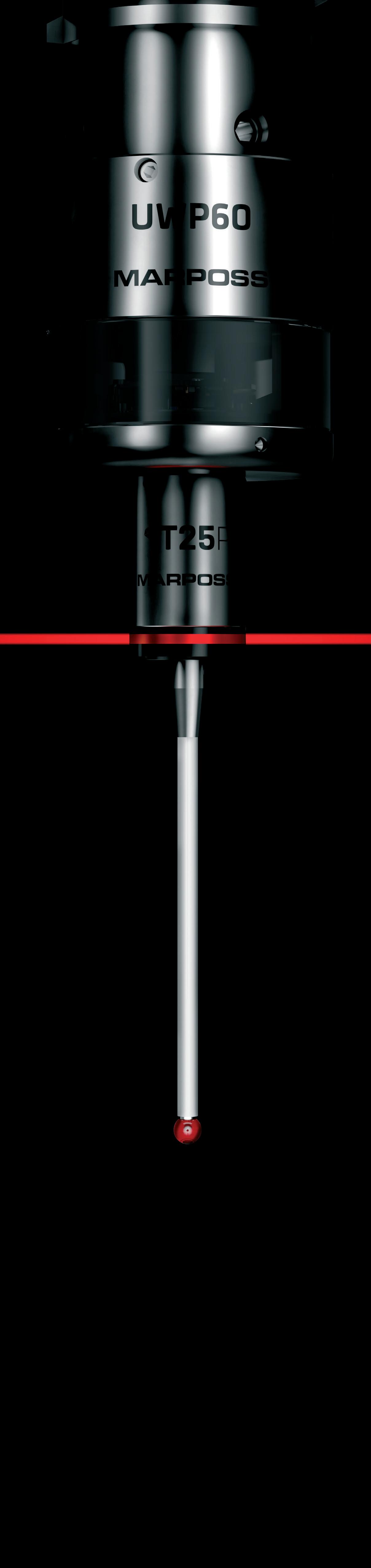
7 minute read
Big Data leads to new business models
The intelligent use of production data, for example, makes machines more efficient and enables completely new data-based business models.Such innovations will be on show at EMO Hannover 2023. Under the new heading „Innovate Manufacturing“, the VDW (German Machine Tool Builders‘ Association) invites experts from all over the world to the world‘s leading trade fair for production technology from 18 to 23 September 2023.
How does one deal with the huge amounts of data? Data is „the new oil“. And such an oil well lies, figuratively speaking, in every factory. Huge amounts of data are generated in all production processes. This treasure trove of data is a valuable raw material that industry can, to stay with the metaphor, refine and exploit profitably. For example, insights gained from „big data“ can be used to make production more efficient, robust and sustainable. In addition, completely new digital business models are possible if production data is systematically collected, professionally processed and intelligently used. For example, it is possible to pay machines based on their use, measured by the performance they deliver in a certain period of time.
Advertisement
In this way, production technology can make the transition to subscription business models: away from the pure purchase of machines and towards time-limited as well as flexible use (Figure 1). Whether it is better for the machine to belong to the operator or the maker is ultimately a sober cost-benefit consideration.
Use instead of own data-based business models can help to stay a decisive step ahead of the competition. „For German production technology manufacturers, business models in the form of Everything-as-a-Service, or XaaS for short, are particularly suitable. These are subscription-based value propositions that combine industrial services with physical and digital elements to create customeroriented solutions,“ explains Prof. Dr.-Ing.
Thomas Bauernhansl, head of the Fraunhofer Institute for Manufacturing Engineering and Automation (IPA) in Stuttgart and the Institute for Industrial Manufacturing and Factory Operation at the University of Stuttgart (Figure 2). „Increasing data transparency increases customer understanding.“
One possibility would be for tailormade solutions to be offered across the entire value-added process, while new payment models (for example „Pay per Part“ or „Pay per Productivity“) as well as the accompanying shift in responsibility transitions strengthen customer loyalty. Through cross-selling and up-selling, Bauernhansl says, this type of business model makes growth possible even in saturated markets. „The new value propositions create differentiation in global competition.“
Machine tool manufacturer DMG Mori from Bielefeld has implemented this insight and supplies equipment as part of its „Payzr“ offer, which the customer can pay for depending on use. The acronym

Payzr stands for „Pay with zero risk“. The core idea of the subscription business model is to give customers exactly what they need, when they need it.
In detail, Equipment-as-a-Service can look like this: The customer orders, configures his machines in the manufacturer‘s online store and then receives the equipment against payment of a monthly basic fee. This can vary depending on the configuration and contract period – for example 12, 24 or 36 months. The flat fee covers maintenance, service and insurance. In addition to the basic fee, there are costs for machine use, which are calculated by the manufacturer on the basis of the hours worked. The advantages for the customer are increased planning security through price and cost transparency as well as the avoidance of long-term capital expenditure, so that innovation cycles can be accelerated.
The machine tool and laser technology manufacturer Trumpf from Ditzingen also relies on data-based innovations. The high-tech company has created a digital business model called „Pay Per Part“. Product Manager Maximilian Rolle explains how this works in detail: „We offer our customers simply the use of the fully automatic laser machines of the ‚TruLaser Center 7030‘ series. In this case, the machine is located in the customer‘s production facility, but the Trumpf Remote Control Center in Neukirch monitors and controls it remotely.“The experts also provide support in programming and setting up the machine: „In the end, the customer pays a pre-guaranteed price for the manufactured parts.“
This business model has the advantage, he says, that the customer can run the machine in three shifts without hiring additional staff. „If there is a malfunction or a standstill, we step in immediately. This increases machine utilisation and boosts productivity,“ Rolle promises. In addition, he says, the experts at Trumpf are able to get the maximum out of the machines. Industrial manufacturing is considered rather conservative and new ideas are slow to catch on. Rolle also admits this: „When it comes to digital business models, many customers are reluctant at first“. However, he observes that services that help customers to increase efficiency and productivity are very well received. „Pay per part is also attracting more and more interest. We expect the number of users to continue to rise.“
Deeper insight into own production processes
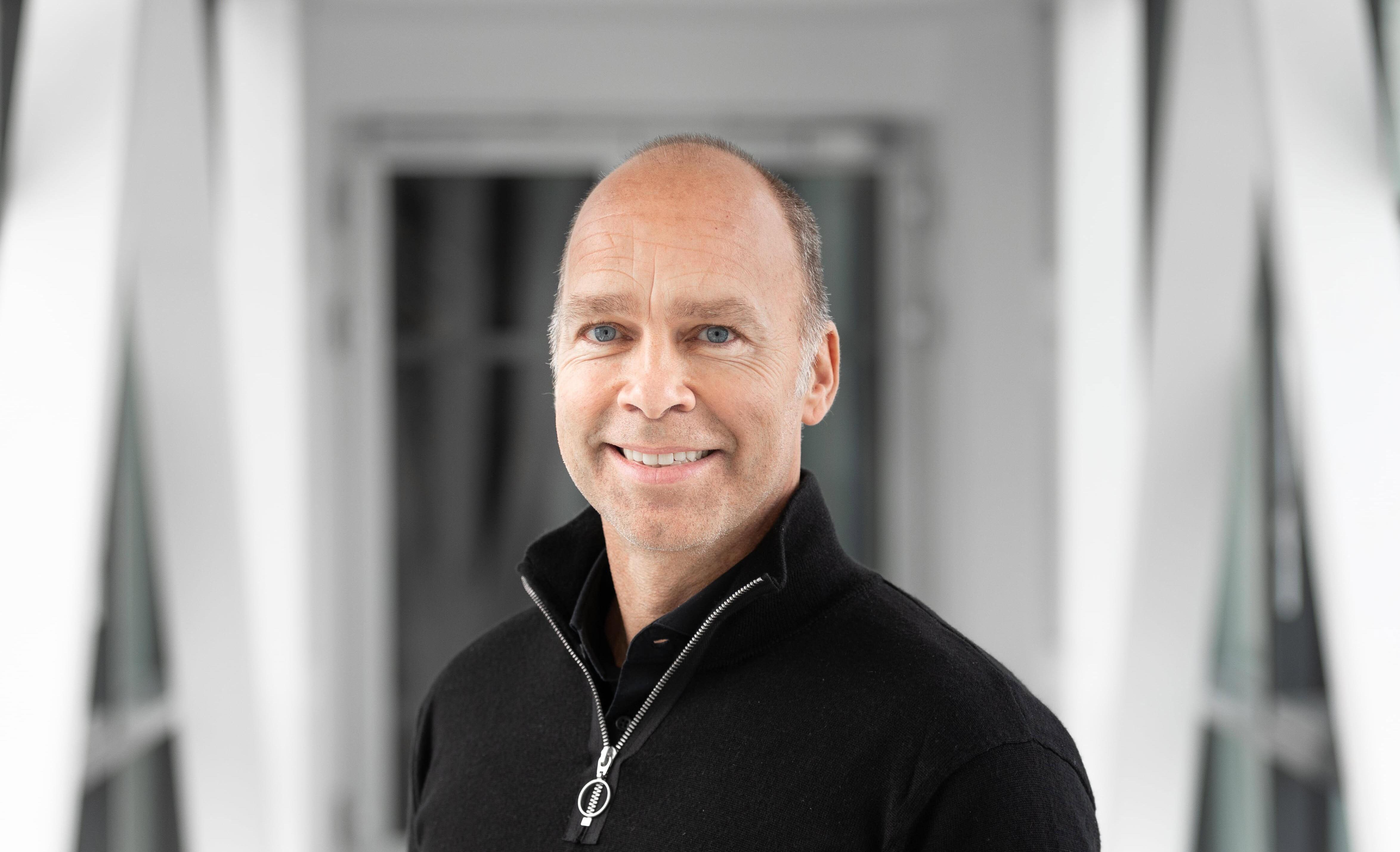
Machine data can also be used to quickly identify errors in production. For this purpose, the company c-Com from Aalen, a subsidiary of the Mapal Group, which specialises in precision tools, operates collaborative data management for tools and other components in the production environment in an open cloud platform. This is intended to give companies deep insight into their processes and solve any occurring problems more quickly.
When production data is monitored in real time, anomalies can be detected in the data streams. And if the data is also viewed in the context of the entire pro- duction process, the analyses can provide precise indications of which production factor – for example, the tool, the machine or the raw material – deviates from the norm.
Predictive maintenance, i.e. repairing a machine before a defect occurs, can be achieved with the help of IoT (Internet of Things) software such as MindSphere from Siemens. The solution stores operating data and makes it accessible via digital applications. Greatly simplified, the software can be thought of as an operating system on a computer or mobile phone. It processes the raw data collected by sensors in the production machines. By analysing patterns in the data, it is possible to see whether a machine is defective, consumes an excessive amount of electricity or will soon need maintenance because the wear of a critical part is already far advanced.
DATA-DRIVEN PRODUCTION AT EMO
Data-driven manufacturing processes are playing an increasingly important role in industrial production – and are therefore firmly anchored at EMO Hannover. On the exhibitor side, numerous companies will be presenting machines, systems and components with which manufacturing can be made more efficient and sustainable through intelligent data analysis and with which innovative data-based business models can be implemented. An excellent platform for this is offered, among other things, by the joint stand „Future of Connectivity Area“, which focuses on the networking of production processes. Further information is available at https://emo-hannover.de/gemeinschafts stand
Data protection in view
Digital business models require trust. Many companies fear losing control over their data if it leaves the premises and is uploaded to the cloud. Therefore, data protection-compliant solutions are in demand.
This is where the „Gaia-X“ project comes in: a European consortium is to create the basis for a European data infrastructure through which companies can merge, share and use data in a trustworthy manner. There is great demand: almost half (46 %) of all companies with 20 or more employees in Germany indicated in a survey by the German Information and Telecommunications Industry Association (Bitkom) that they are interested in using services of the European cloud and data infrastructure. Data sovereignty is also at the heart of the „Manufacturing-X“ project, which aims to provide a protected industrial data space for production technology manufacturers. A consortium of SAP and German mechanical engineering companies is therefore developing a cloud platform for the manufacturing industry to facilitate the exchange of information in a decentralised data space with precisely defined access rights. At its core is the idea of making supply chains more transparent and resilient with end-to-end data networking.
„In supply chains, data-based business models create transparency so that disruptions can be detected and remedied at an early stage – for example through remote service,“ says Fraunhofer scientist Bauernhansl. In production, intelligent algorithms increase resource utilisation and thus reduce waste. „With the goal of reducing the CO2 footprint, for example, intelligent algorithms can be used, among other things, to adapt production planning to the availability of renewable energies,“ Bauernhansl continues.
The topic of data security „is enormously important in digital business models“, says Rolle. In his view, cloud solutions offer today‘s best possible data protection. Trumpf also ensures with a data use agreement that the user only shares the relevant and agreed data. „We create the necessary conditions so that our customers can decide for themselves which data they make available to us when using digital business models,“ says Rolle. Manufacturing-X is one possible initiative to allow this data sovereignty and could lead to a new industry standard in the medium term.
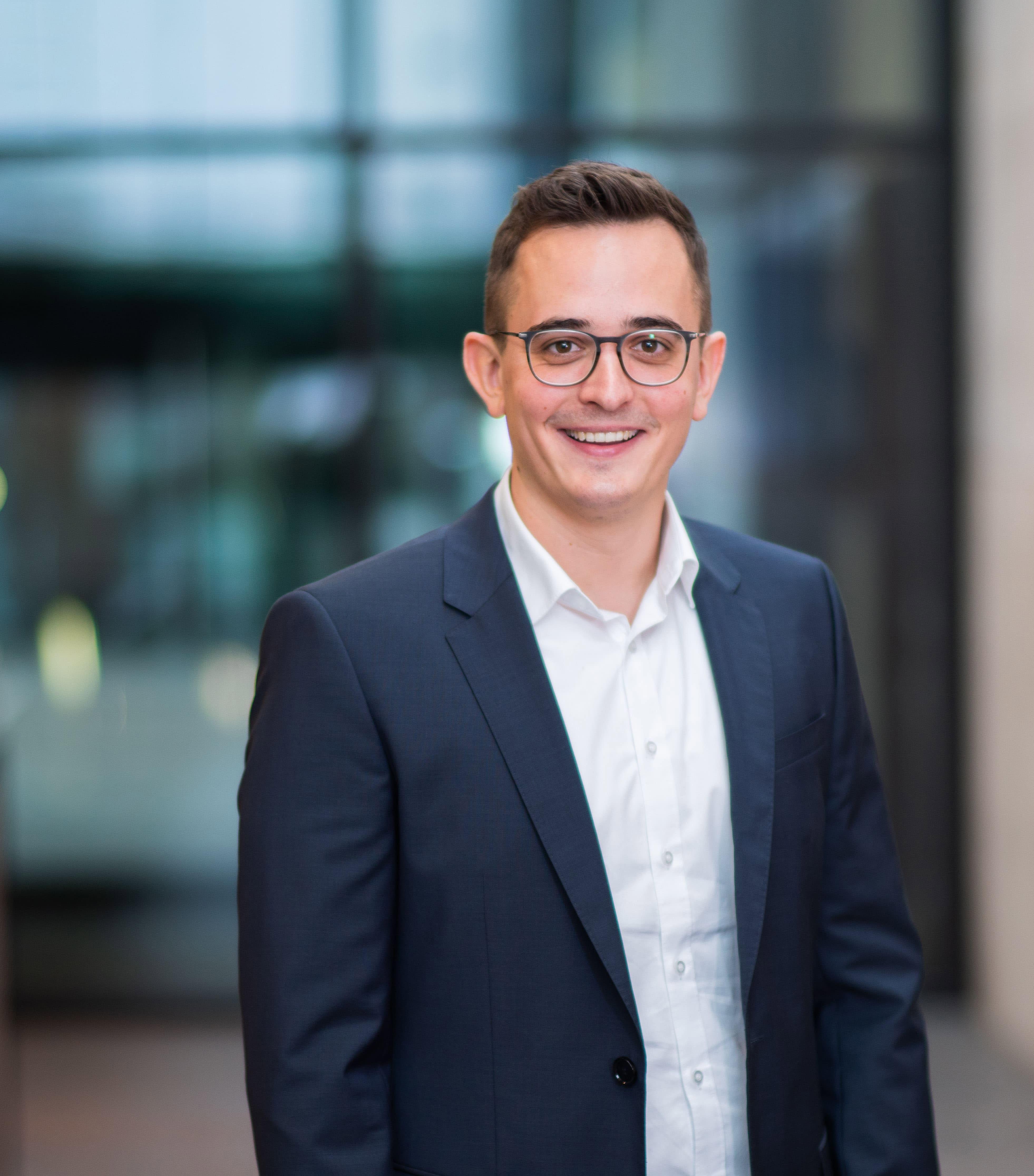
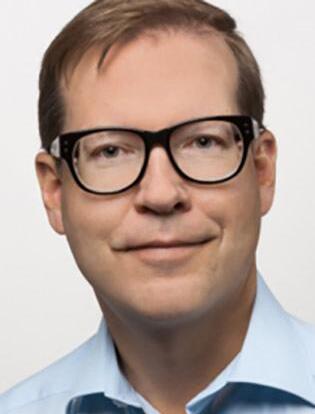
Indispensable for competitiveness
Around 91 % of German industrial companies describe Industry 4.0 as „indispensable“ in order to be able to compete internationally, as the IT industry association Bitkom 2022 has determined. There is potential especially in the reduction of emissions; 81 % expect a contribution to sustainable production.
In this context, German industry is also counting on being able to use its competitive edge in international comparison, especially with regard to the USA and suppliers in the Far East. „With regard to service-oriented business models, we in Germany still have an advantage over the Far East and the USA due to in-depth customer understanding, the high level of engineering competence, creativity and problem-solving skills,“ says Bauernhansl The many hidden champions in Germany with their rapidly growing range of services in novel value propositions are the best proof of this, he says. „Initiatives such as Gaia-X, Catena-X or, more recently, Manufacturing-X are helping to maintain the lead,“ he continues. „Currently we are still ahead, but we can already feel the breath of the international competition on our necks – speed of implementation and courage for new ideas count!“