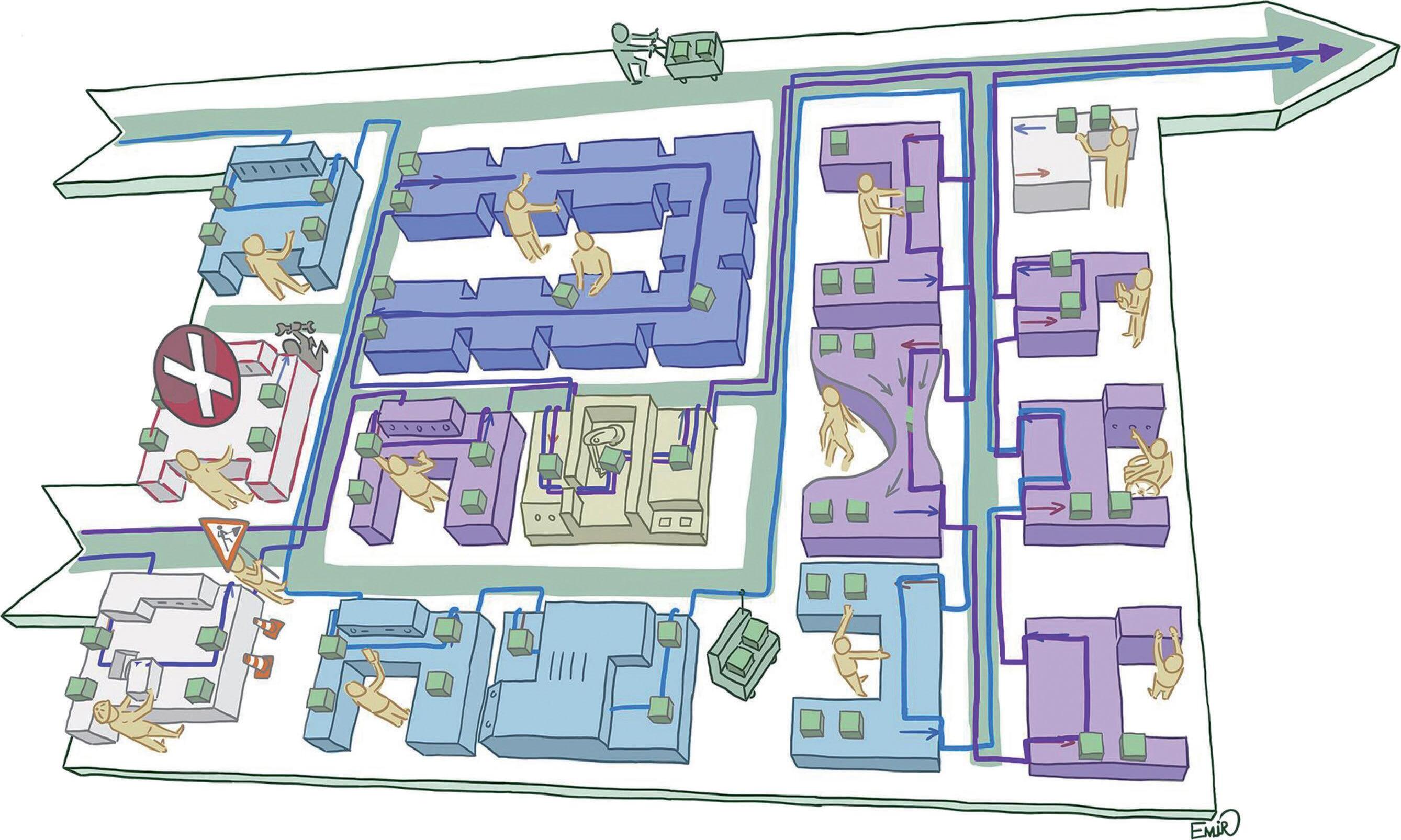
4 minute read
Matrix production systems flexible and productive
How can manufacturing companies react faster to global crises, cope with supply bottlenecks and at the same time respond to individual customer demands?
Cyber-physical matrix production systems are seen as the key to flexible and at the same time productive production, which helps companies to increase their resilience and thus to survive even in turbulent times.
Advertisement
Crisis and war-related interruptions in supply chains, cancellations or changes in orders at short notice, a trend towards ever smaller order batches and increasing individualisation of products are part of everyday life in many manufacturing companies today. At the same time, companies need to increase their productivity in order to survive in global competition. Cyber-physical matrix production systems offer an answer to market changes such as decreasing quantities, increasing diversity of variants and low predictability of customer requirements. This is what the
Fraunhofer Institutes IPA (Institute for Manufacturing Engineering and Automation) in Stuttgart and IWU (Institute for Machine Tools and Forming Technology) in Chemnitz have jointly found out in a report on the implementation of cyberphysical matrix production systems commissioned by the German Academy of Science and Engineering acatech. It can be downloaded free of charge (Figure).
What are matrix production systems?
The term matrix originally comes from mathematics and describes a rectangular arrangement of objects in rows and columns. Production engineers understand a matrix to be a chessboardshaped arrangement of so-called process modules. A process module can be an automated station, a manual station, a hybrid station or a line segment. The process modules can be freely accessed, individually planned logistically and connected via a flexible material flow. In contrast to classic line production, the matrix production system also allows for return flows. However, the process modules are still basically arranged in a flow. Certain processes can be carried out at each process module. Often, these process modules are also planned redundantly.
A decisive special feature of the matrix production system is the flexibility of the sequence of operations. This means that it is not defined in advance how an order will run through the production system or at which process modules the necessary process steps for a product will be carried out. The sequence of operations is therefore determined ad hoc. For example, if individual process modules are down, other process modules can be started or processes can be executed later. In a matrix production system, the products can be transported manually or automatically.
Flexible and productive
Classical production lines usually reach their limits when changes are made, for example the integration of a new product variant or changes in the number of pieces. They lack flexibility. For example, cycle time spreads can no longer be accommodated and the integration of a new product variant is difficult. Single workstations, on the other hand, are very flexible, but not very productive.
Matrix production systems allow flexible production with high productivity. Different product variants are manufactured or assembled in one production system without incurring a high level of waste. In the event of fluctuations in the number of units, a balance can be struck between different product variants. By adding or removing production modules, adjustments can also be made to the output quantity as part of a reconfiguration. New product variants and new technologies can be integrated with little effort. The utilisation of production staff is optimised in the matrix production system. Shared production resources can also increase plant utilisation – so automation pays off more often.
Cyberphysical networking
A cyber-physical networking of the modules supports the matrix production system. In virtual space, there is a digital twin that maps the production processes and manufacturing modules. It can be used, for example, to optimise material flows, employee utilisation and machine utilisation. The simulation results are then used to control the real – physical – modules.
Matrix production systems have been researched at the Fraunhofer IPA for many years. In recent years, they successfully made the leap into industrial practice.
Success stories prove the opportunities
Successful examples of implemented matrix production, for example in the semiconductor industry, electronics production or the automotive industry – they are explained in the report – show that improvements to the existing production system can be achieved when switching to a matrix production system. In many of the companies that use matrix production systems, the solutions already have a high degree of maturity. This is measured, for example, by the modular structure of the production units, the implementation level of a digital twin, the use of automated transport systems and the reconfigurability of the process, which allows production to be quickly adapted to changing market requirements. One conclusion of the report is that matrix production systems enable economic production in the face of difficult market requirements and that companies with different production processes from different sectors are already implementing them partially or even completely.
Complete solutions for SMEs are missing
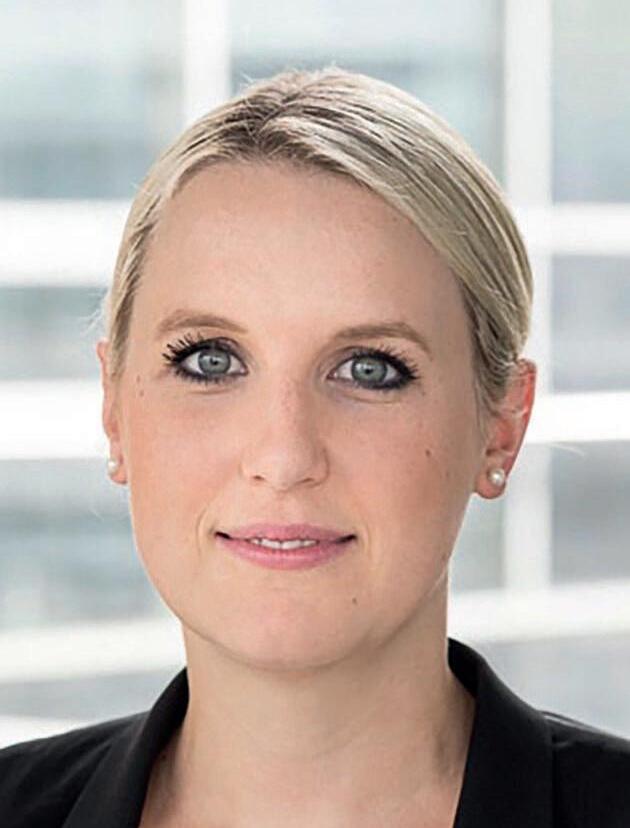
What is missing so far are complete solutions which are ready for the market. Individual solutions for matrix production systems are available commercially, but no complete packages including integration. The companies that work with the new modular systems have often developed them themselves. Small and medium-sized enterprises (SMEs) that cannot afford their own technology development are left behind. Individual solutions have to be integrated into an overall system at great expense. The Fraunhofer IPA has tackled this problem.
Matrix production systems offer great opportunities. Basically, they have potential wherever high flexibility and high productivity are required at the same time. With a matrix production system, the demands of the market – such as increasing variant diversity, frequent changes and hardly predictable customer requirements – can be successfully met.
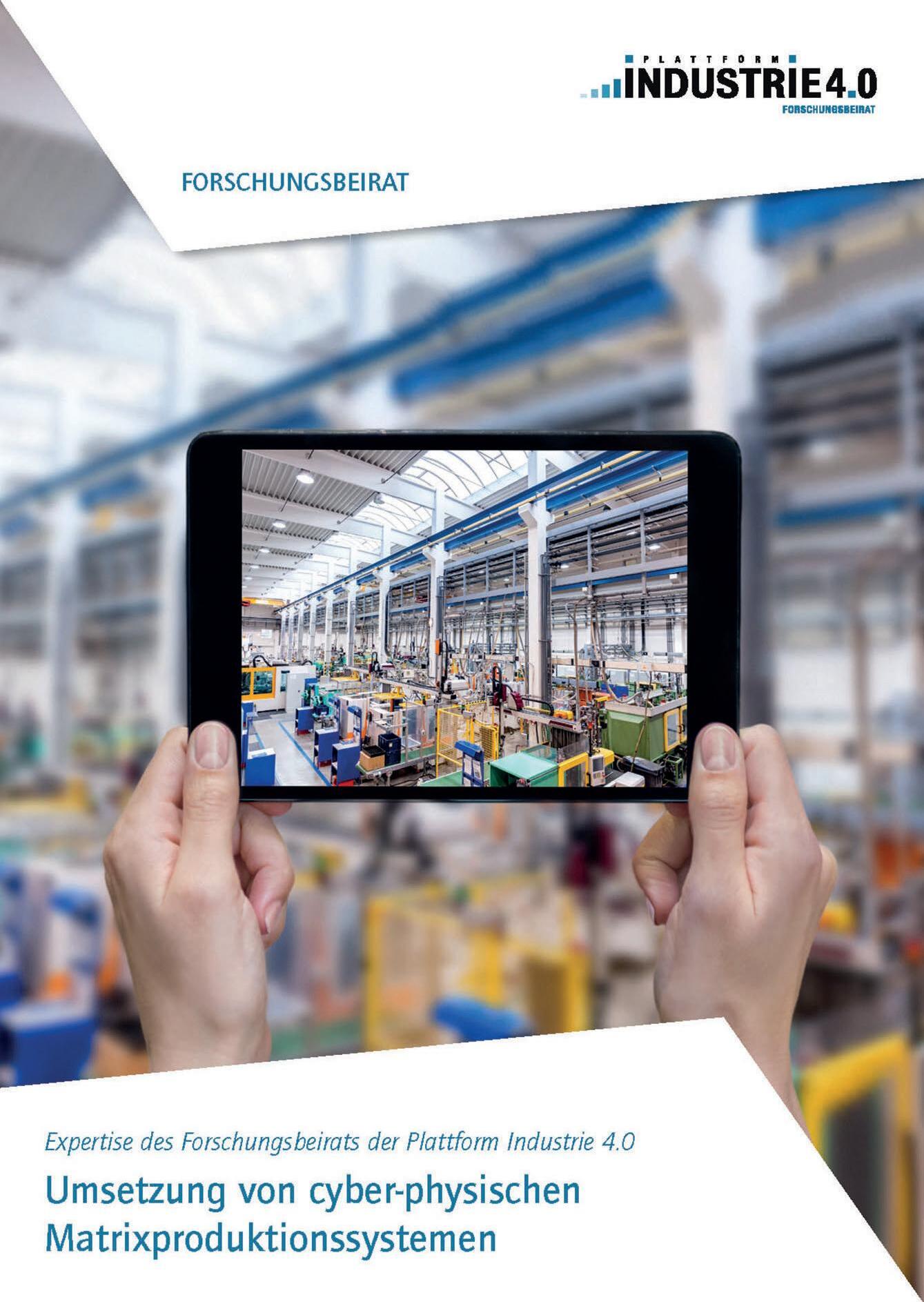
The matrix opens up new degrees of freedom for the design, planning and control of the assembly system. Common planning methods in „lean line design“ cannot be transferred 1-to-1 to matrix production. Simply pulling apart previously linked stations and outsourcing special equipment to secondary stations falls far short of exploiting the potential. The Fraunhofer IPA has therefore developed process-oriented methods for planning matrix production systems.
Further information is available at: https:// www.ipa.fraunhofer.de/de/Kompe tenzen/fabrikplanung-und-produktionsmanagement/montageplanung/modulare-matrixmontage.html
Equipment-as-a-Service increases competitiveness
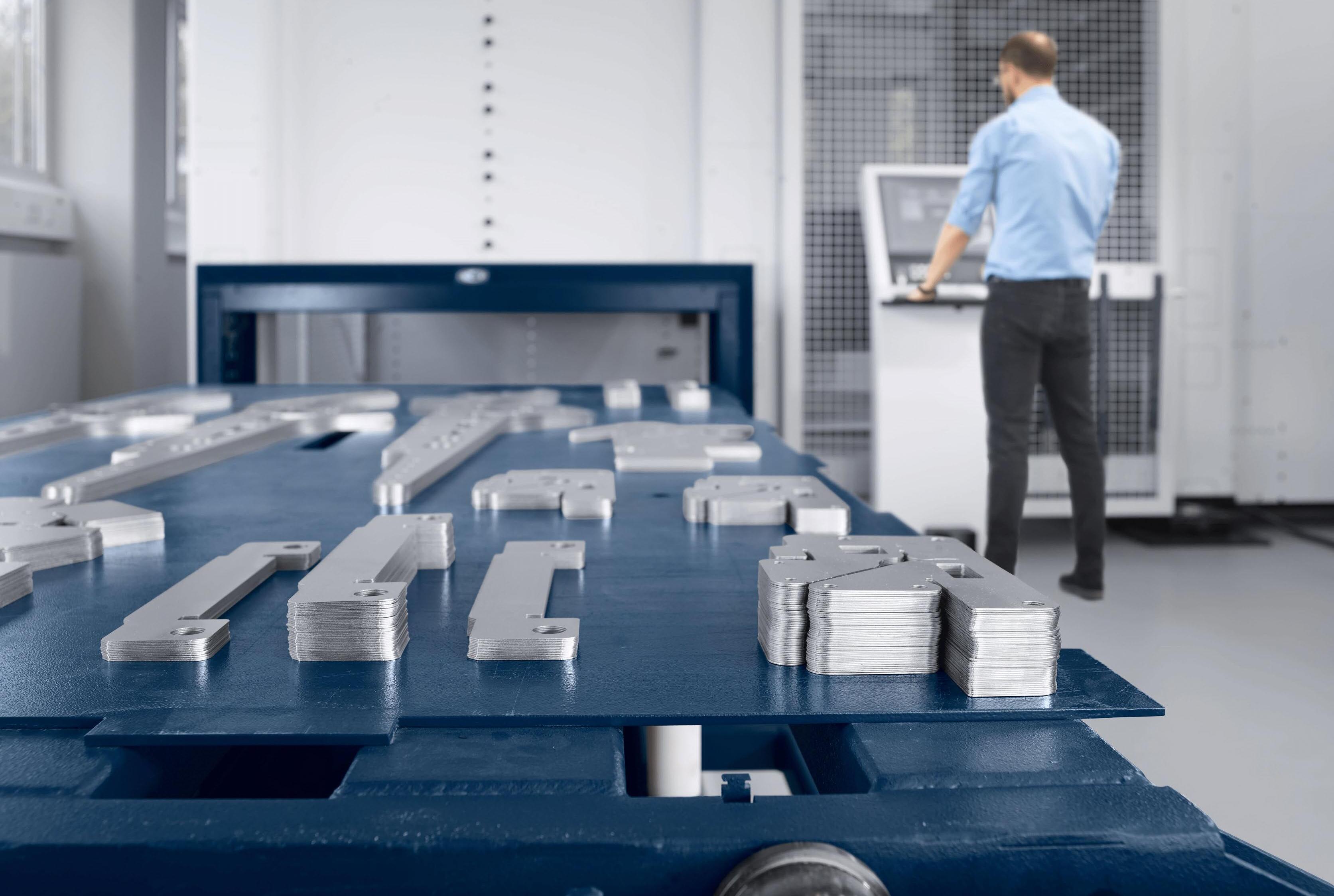