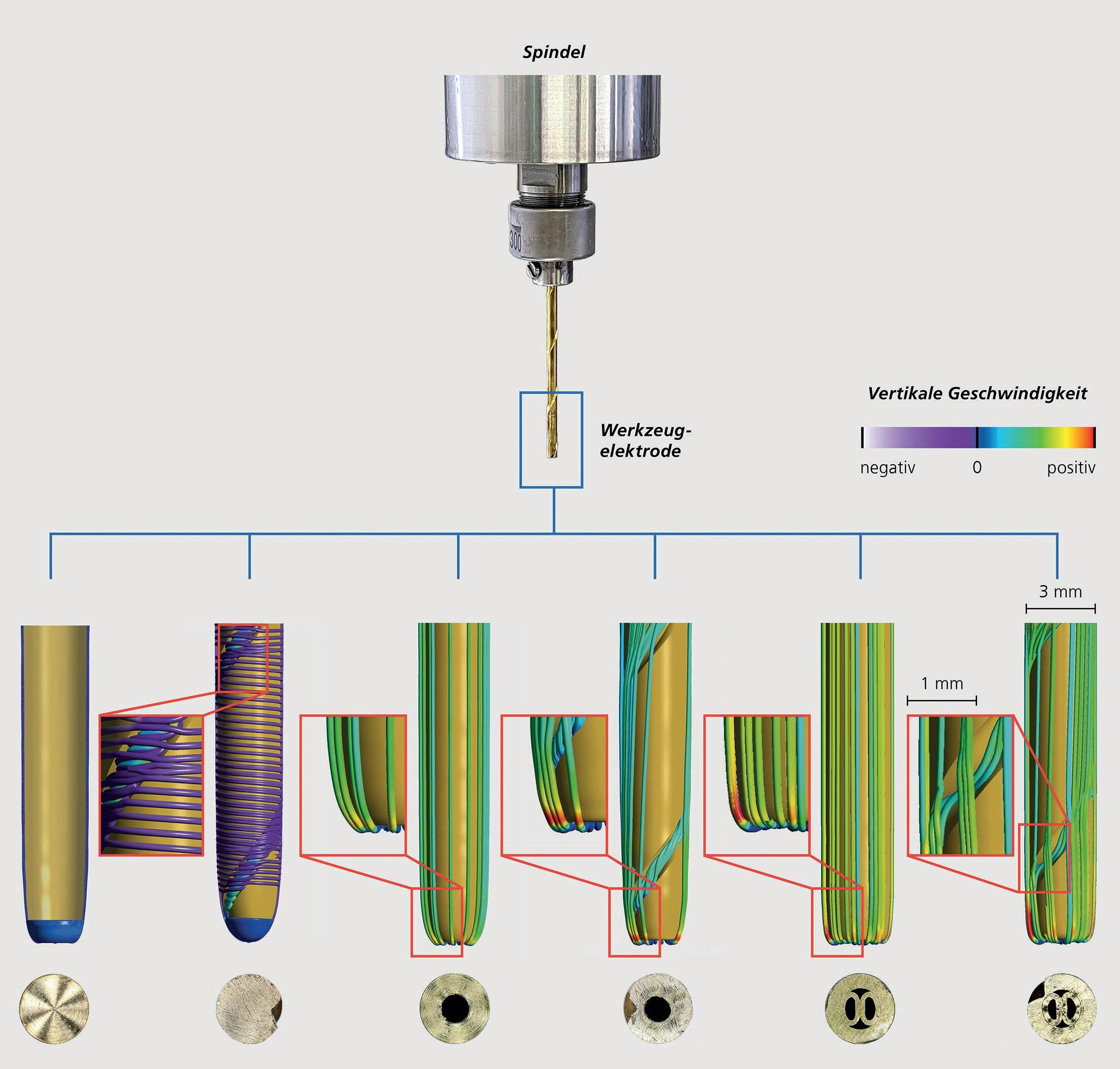
3 minute read
Spark erosion: efficiency through cleanliness
Sparks strike, arcs flash, particles whirl around – spark erosion is probably the most spectacular manufacturing process in production technology. Contactless melting allows extremely fine machining of surface structures of metals.
With the help of a generator, a voltage is applied between two electrodes in a non-conductive liquid, a so-called dielectric. Sparks are generated between two materials. Tool and workpiece do not touch each other – and their separation, the so-called working gap, is just 100 micrometres. This corresponds to the width of a human hair.
Advertisement
Advantages and areas of application
The ablative process, which was discovered by the Soviet couple Lazarenko in 1943, is used in dentistry, among other fields. For example, spark erosion is used to produce precisely fitting abutments that are screwed into the jaw as connecting elements for implants. Spark erosion also allows very hard materials to be precisely machined and individually adapted, which is particularly important in dental technology: if the crowns do not fit, bacteria can accumulate there and cause inflammation.
While machining processes such as drilling and milling are probably familiar to every hobby craftsman, very few are aware of the key role that material removal processes play in the manufacture of high-precision components in many industrial applications. Examples of micro- bores produced by EDM range from cooling air bores in turbine components, fuel injection systems, gas nozzles and control valves in automotive engineering to thre- ad guides and spinning nozzles in the textile industry. In its main areas of application – tool and mould making, aerospace and medical technology – electrical disch- arge machining is usually used as the last work step before cleaning the components.
What impairs the quality?
The process presents some challenges: each spark produces gas bubbles and ablation particles that float around in the dielectric and pose the risk of short circuits and arc discharges. These discharges not only result in additional control steps or retraction movements, but can also cause damage to the final component surfaces due to hole burning. The dirtier the working gap, the more unstable the process becomes and the more productivity drops. Cleanliness is therefore the „be-all and end-all“ – in EDM too.
To remove the ablation products, the gap must therefore be flushed continuously. In the established process of internal flushing, the non-conductive liquid is forced into the working gap at high pressure. In the process, the ablation particles and gas bubbles are flushed out vertically. However, the higher the pressure, the greater the risk of side discharges and instabilities within the micro-bores. This results in shape deviations and crooked bores.
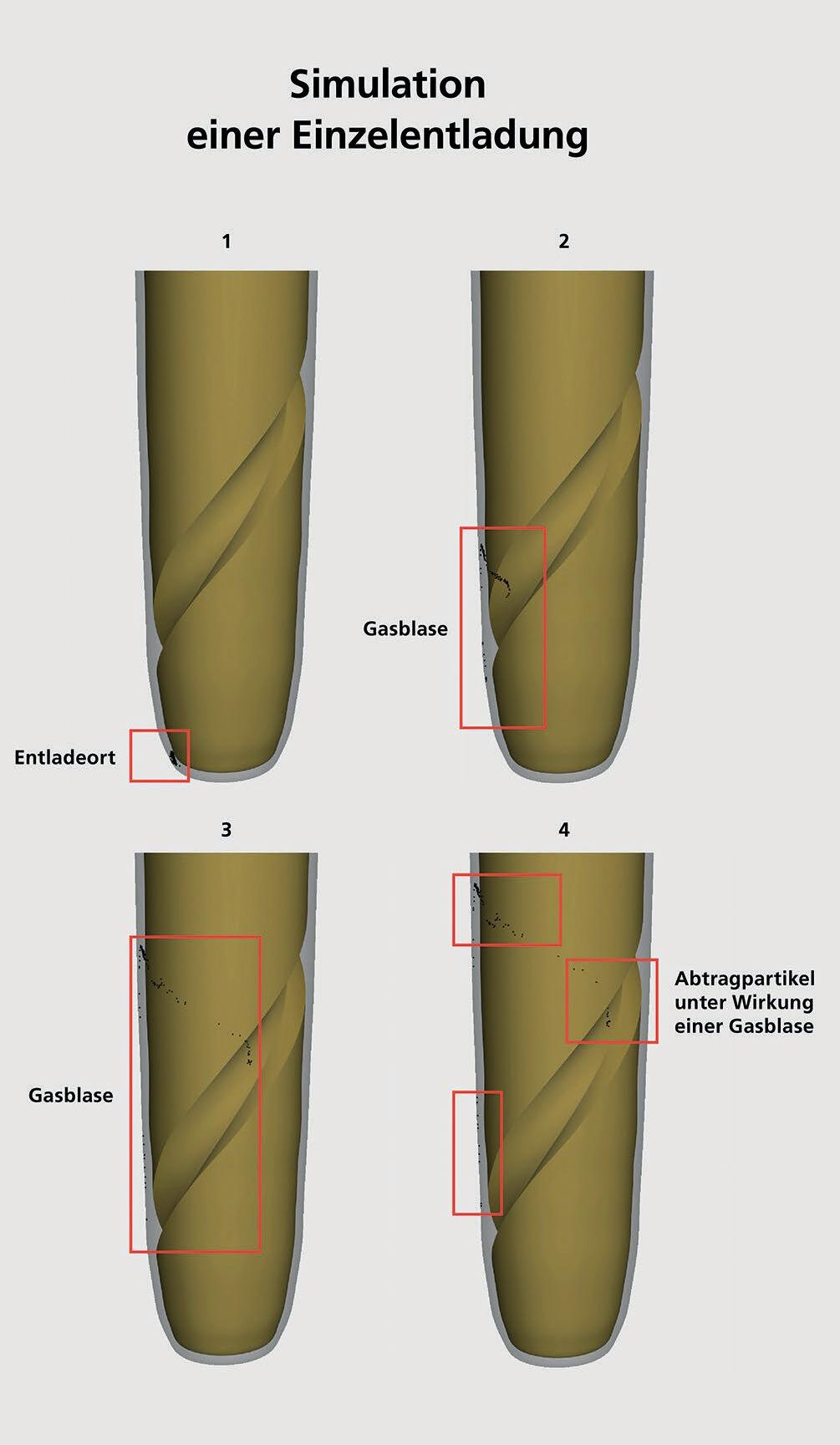
Remedial measures
To meet these highly complex and ever-growing challenges in spark-erosion drilling, additional equipment, tool electrodes and technologies for alternative dielectrics are being developed at the IWF of the TU Berlin. One example is the insertion of external flushing channels in the lateral surfaces of cylindrical tool electrodes. For this purpose, a special sliding headstock lathe was used to mill into the tool electrode a helical groove that winds spirally around the brass shaft. This helical channel creates a kind of escape route for the gas bubbles and ablation particles. If a dielectric is now pressed through the working gap at high pressure, the particles are no longer simply discharged vertically via the shortest path, but can exit via the outer channels. This reduces the risk of lateral discharges and inaccurate drilling.
Research on the fluid dynamics
In a basic research project funded by the German Research Foundation (DFG), a general understanding of the flow dynamic processes in the working gap is to be developed. The practical research problem is that the gap measures less than 0.1 mm, and is thus extremely small and difficult to access. Detailed optical investigations of the purging conditions are therefore hardly possible. However, within the framework of signal analyses, in which process signals of voltage and current are recorded, conclusions can be drawn about the discharges – and thus about how effective the evacuation of the ablation products is.
In contrast, flow simulations offer temporally and spatially unrestricted insights into the highly complex dynamics of electrical discharge machining, Figure 1. By means of a statistical model, it was possible to identify a fluid-mechani- cal operating point that defines the combination of rotational speed and flushing pressure (as necessary for optimum effective behaviour of the helical groove), Figure 2. This prevents the erosion products from simply leaving the bore vertically, despite the helical groove, due to excessively high flushing pressure.
With the appropriate combination of rotational speed and flushing pressure, it can be demonstrated that some of the ablation particles are sucked into the helical groove by local negative pressures, independent of the modelled discharge location, and leave the bore in this way. The extension of the model to include gas bubbles confirms known observations that the rising gas bubbles cause the ablation particles to float on their phase boundary and thus significantly influence the evacuation of the working gap.
Conclusion
By combining traditional experimental drilling tests with classifications of the signal characteristics made using sophisticated software – and not least with the most advanced numerical models – productivity increases in the field of sparkerosive drilling can be achieved with external flushing channels. If you „flush properly“, you end up with clean results.
www.iwf.tu-berlin.de www.ipk.fraunhofer.de
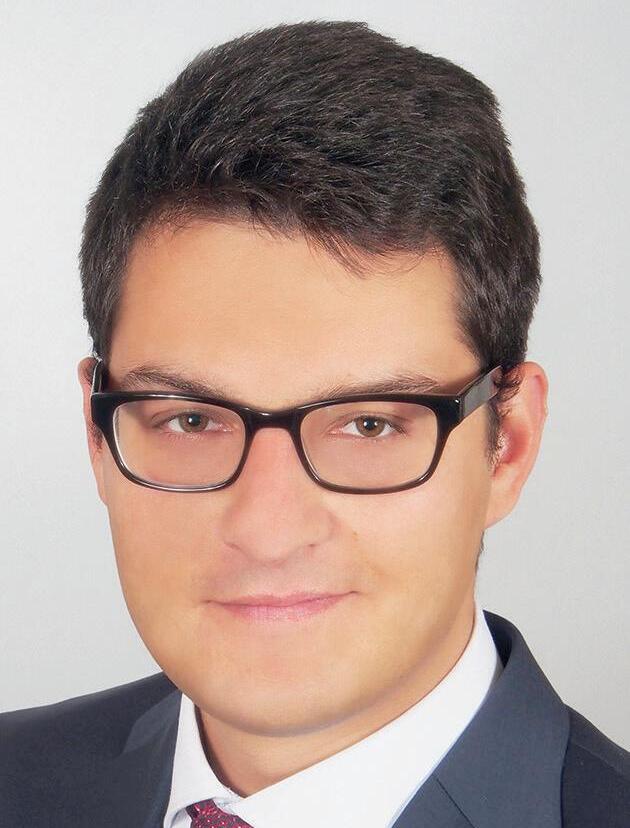