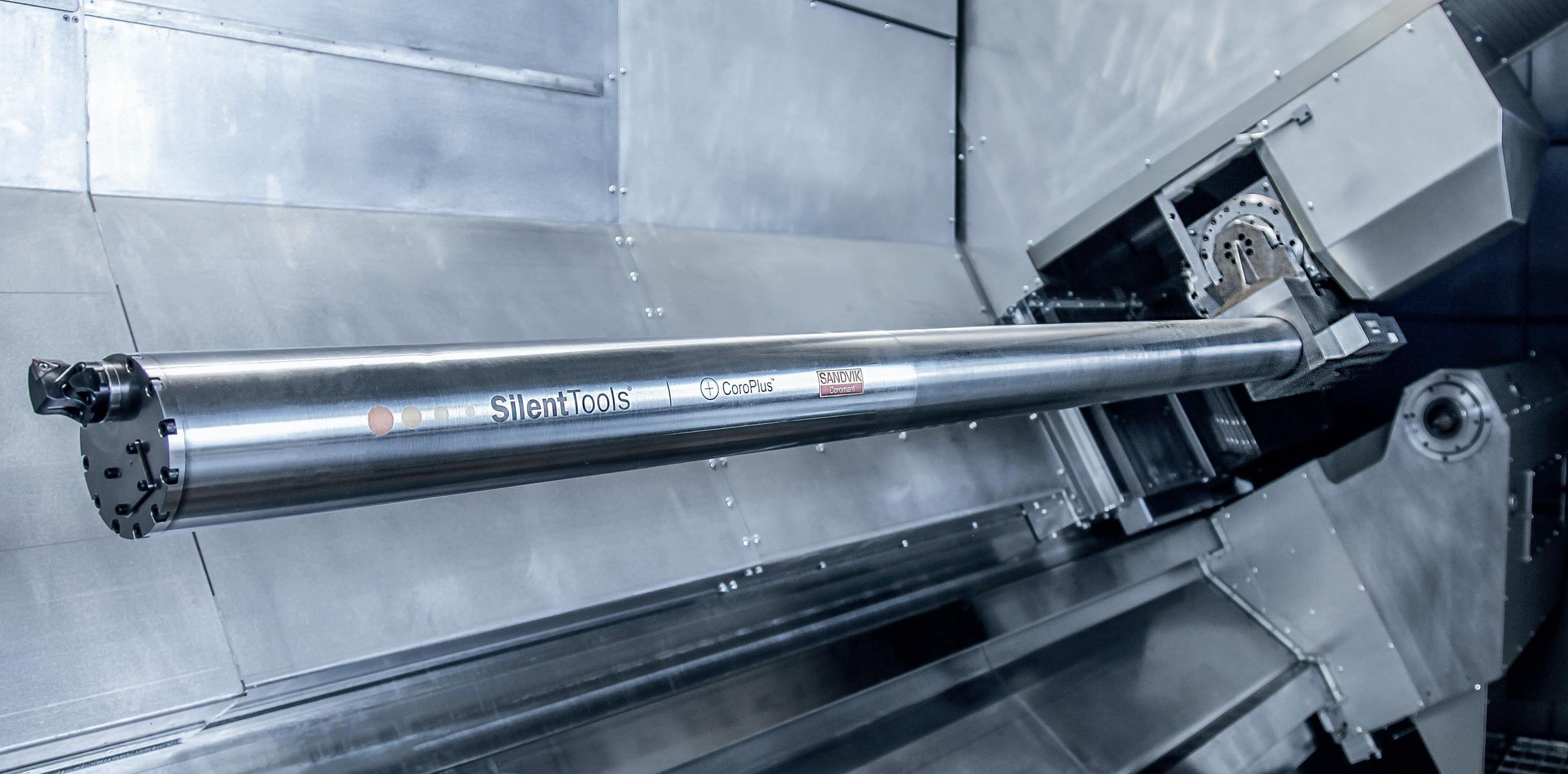
3 minute read
Silent Tools expand turn/drill/ mill centres
The geometry of workpieces and the materials used are becoming increasingly complex. Intelligent solutions are needed to increase transparency in the machining process and to make better use of the performance of machine tools.
In addition to the growing complexity of the machining task, the market also demands a fast response capability and high flexibility. Increased productivity is not just a topic for discussion – it is a demand of the customers. For machine manufacturers, it is a matter of mastering these challenges.
Advertisement
A new solution to cope with this issue is the boring bar „Silent Tools Plus“. It is used with great success on the complete machining centres of an Austrian machine tool specialist. Thanks to the integrated sensors, the solution from Sandvik Coromant provides information about utilisation, temperature, displacement and the surface quality achieved. If the limit para- meters are exceeded, it intervenes adaptively in the machining process. The transparency gained allows the processes to be significantly optimised.
Specialist for complete machining systems
The machines from Linz are known under the brand name „Millturn“ (Figure 1), which is a combination of the two terms „Milling“ and „Turning“. They combine a number of technologies in one machine, so that reclamping processes, which are necessary when producing a component on several special machines, are eliminated. In turning, the tool is used in different angular positions and (by turning the cutting edge of the tool) for lefthand or right-hand machining.
In drilling, machining can be carried out axially, radially and in all angular orientations to the axis of rotation with internal coolant supply. When milling, the machining of surfaces and grooves is also possible in all angular orientations. By interpolating up to five axes, any geometric shape can be produced. Gear hobbing, cam hobbing, crank pin hobbing, circular hobbing and turn hobbing are possible. Other integrated technologies include inprocess measuring, grinding and fine machining, internal machining or slotting. With this variety of possibilities and com- plexity, safe processes are particularly important.
Increased performance included
The installation of intelligent sensors in tools makes it possible to call up detailed tool information or machining states on the machine control, tablet or PC (Figure 2) Different sensors installed in the boring bar pass on numerous data. The signals are transmitted via Bluetooth so that the machine can react interactively to a defined trigger event. For documentation purposes, the process can be visualised and documented and thus becomes completely transparent. The energy supply to the sensors with inductive coupling instead of an accumulator is completely new.
The integrated sensors are located at different points in the boring bar. The cutting head is equipped with a vibration sensor: vibrations can thus be detected at an early stage. The operator or the machine control can react in real time, prevent the associated problems and thus reduce the scrap rate and rework. With the temperature sensor built into the damping unit, the actual temperature is monitored and displayed. This increases process reliability and ensures better maintainability of the boring bar. Sensors are also installed that provide information about the force exerted on the boring bar.
Perfect protection of machine, workpiece and tool
In combination with the „iControl“ process monitoring system, the machine operator receives the ultimate protection for the machine, workpiece and tool to ensure reliable and economical production, especially in spare parts production or small batch sizes. On the one hand, the machine and tools should be used with maximum productivity; on the other hand, the process must run as stably and reliably as possible. The up to 16 process signals to be monitored are configured by WFL at our factory according to the machine equipment and displayed live on the control screen. Important process signals are the forces / torques in the NC axes and spindles, but also the signals derived from the integrated sensors.
Learning mode for process limits
The learning mode in WFL iControl offers an ideal strategy. The process signal of a complete machining sequence with the Silent-Tools-Plus boring bar can be acquired in one learning cut. By assigning upper and lower process limits, the tolerance band is defined in which the process signal must remain during machining. If these limits are exceeded or underrun, the machine stops. When using a new insert, for example, a specific process limit can be set at the beginning of the machining process with the help of the load signal. After a few millimetres, the operator receives information about the cutting force and can set a limit, including oversize. During the entire cutting pro- cess, the machine will automatically detect an overload.
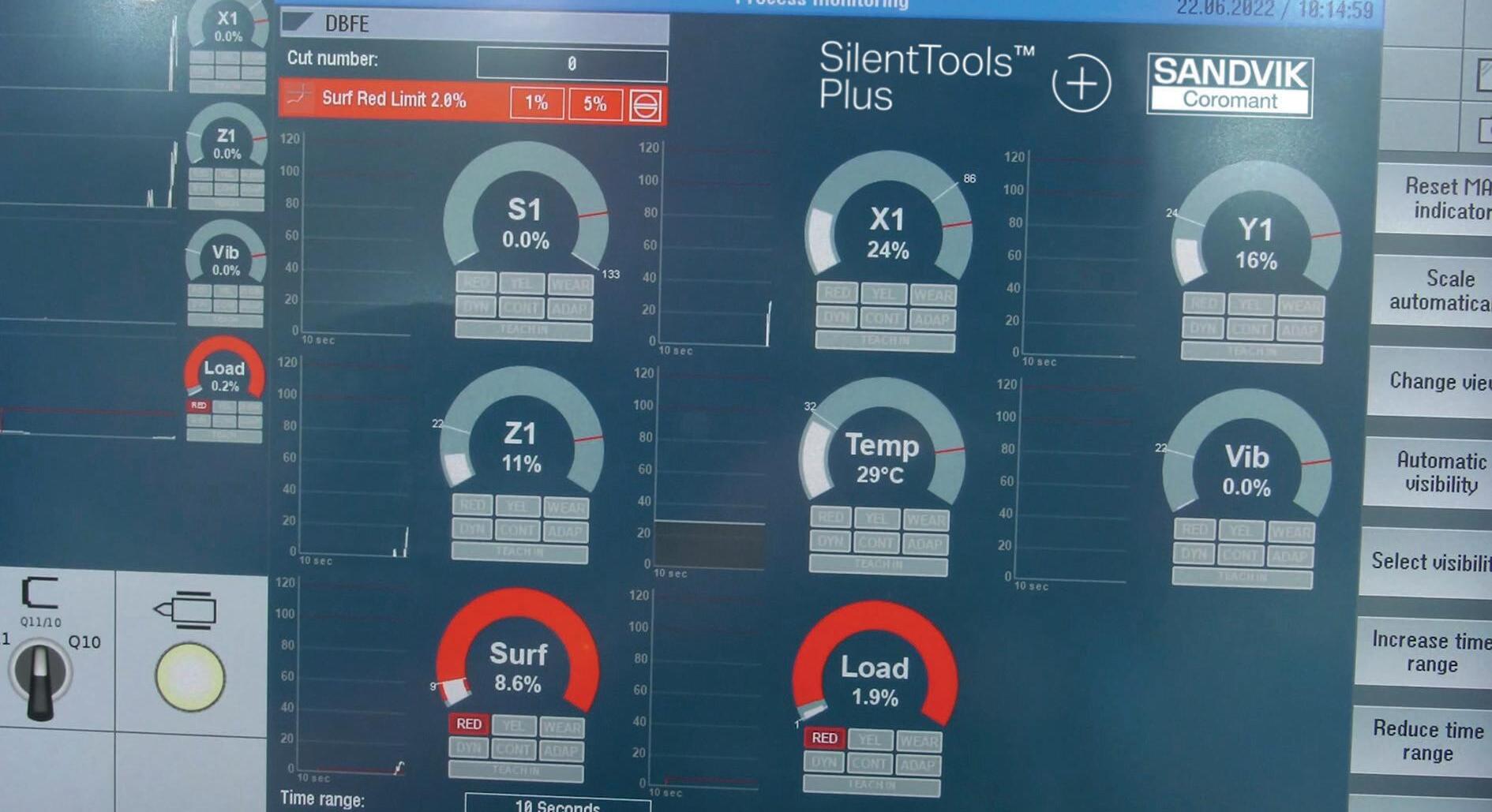
Holistic solutions
The ability to implement holistic solutions is particularly important for complete machining. In the larger machines of the Millturn series, there is an additional cross slide to accommodate a large vibration-damped boring bar. This can be realised with a length-diameter ratio of up to 18 x D. This additional slide enables an automatic tool change at the front of the boring bar, a programmable projection length and „Ultra-High Pressure Coolant“ (UHPC).
www.wfl.at

How to achieve productivity gains with flushing channels