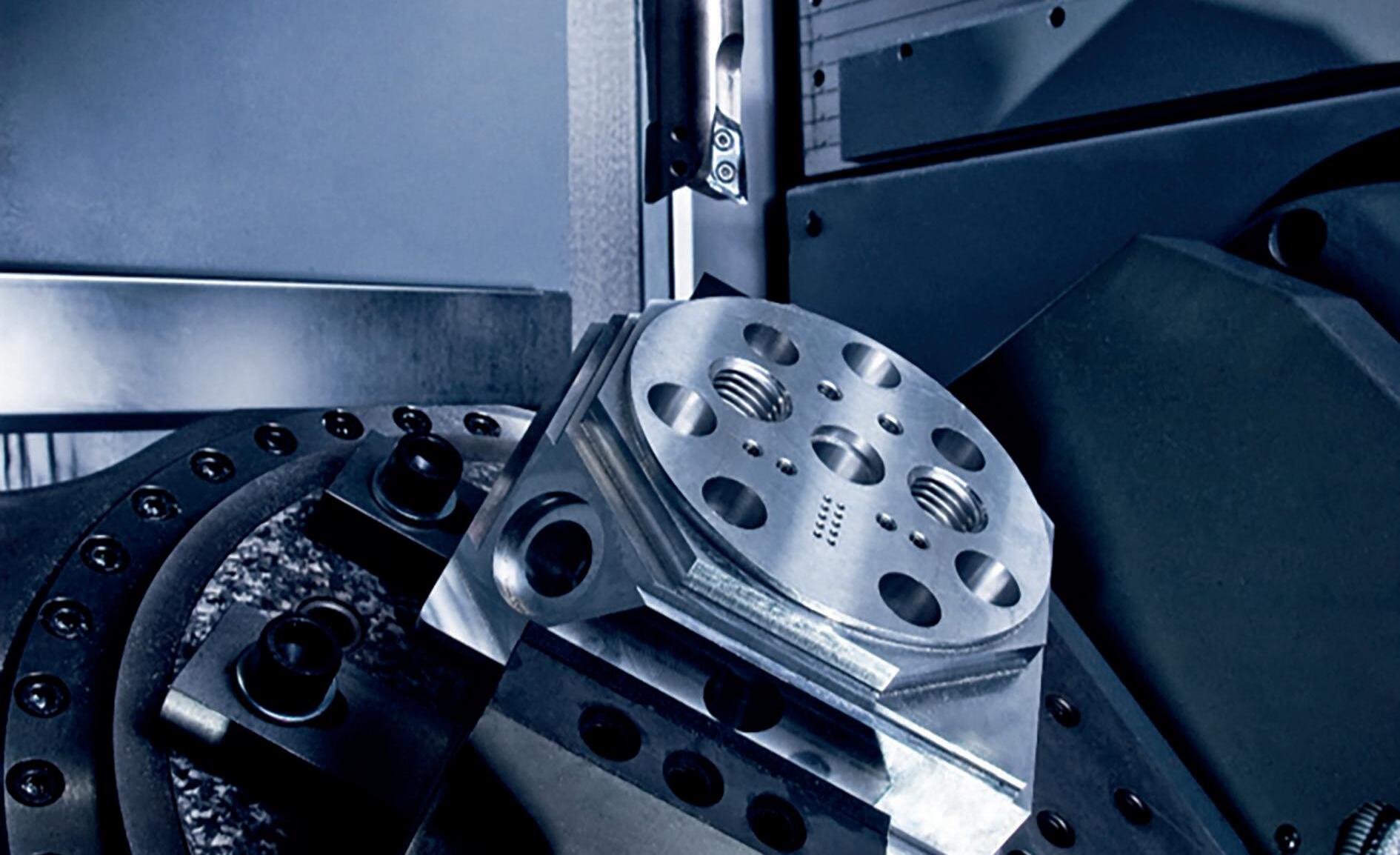
5 minute read
Online-capable chatter early warning system
When designing machining processes, a central conflict of goals between productivity and component quality often leads to conservative process planning. One essential limiting factor for productivity is the occurrence of regenerative chatter. An early warning system for chatter on the machine can optimise the process design and reduce the reject rate.
Acentral goal for increasing the sustainability contribution of production plants is the more efficient use of machine tools. If the productivity of the machine tool is increased, for example through a reduced reject rate or optimised process design, the number of machines required to meet product demand can be reduced.
Advertisement
In particular, the occurrence of self-excited and regeneratively self-amplifying vibrations (chatter) limits productivity. The process instabilities associated with chatter have a variety of negative effects on the machining process. These include reduced surface quality, increased tool wear, impaired dimensional accuracy and high noise generation. In order to exploit the full potential of a machine tool, a chatter prevention system is needed that ensures high productivity while maintaining part quality.
Process design with stability maps
One approach to a solution lies in the targeted avoidance of process instabilities through a suitable choice of machining parameters for the process. So-called stability maps, which show stability limits as a function of cutting depth and speed, are an important tool for the optimal selection of process parameters (Figure 1). Although the procedure for experimentally determining stability maps has been optimised in recent years [1], it is still too time-consuming and uneconomical for use in small-batch production, since a new stability map must be determined in preliminary tests for each combination of tool, workpiece and machine. This is not compatible with the trend towards sustainable and resource-efficient production.
Model-based stability calculation
In order to avoid the high costs of test series, stability limits can be determined using models. This is done on the basis of an analytical model that describes the interaction between machine and process. The main disadvantage of the model-based approach is an uncertain data basis, which is based on preliminary tests and tabulated values.
In this paper, a new concept for model-based online identification and early warning of process instabilities for a milling process is presented. The disadvantage of an uncertain data basis is eliminated by using machine data recorded parallel to the process. The early warning system provides a tool for solving the existing conflict of objectives between productivity and component quality. The processparallel checking of the stability limit supports in particular „first-part-right“ approaches to the production of complex and expensive individual parts in a resource-saving approach. The methodology of the chatter early warning system is shown in Figure 2 and comprises five central components.
1. Identification of the machine dynamics
For model-based simulation, the central problem is to efficiently map the va- riable dynamics of the machine-tool-material system. This is solved by new findings in the field of substructure coupling [2]. A uniquely measured model of the machine tool is coupled with analytical tool models in order to reduce the experimental measurement efforts to a minimum.
2. Determination of the cutting parameters
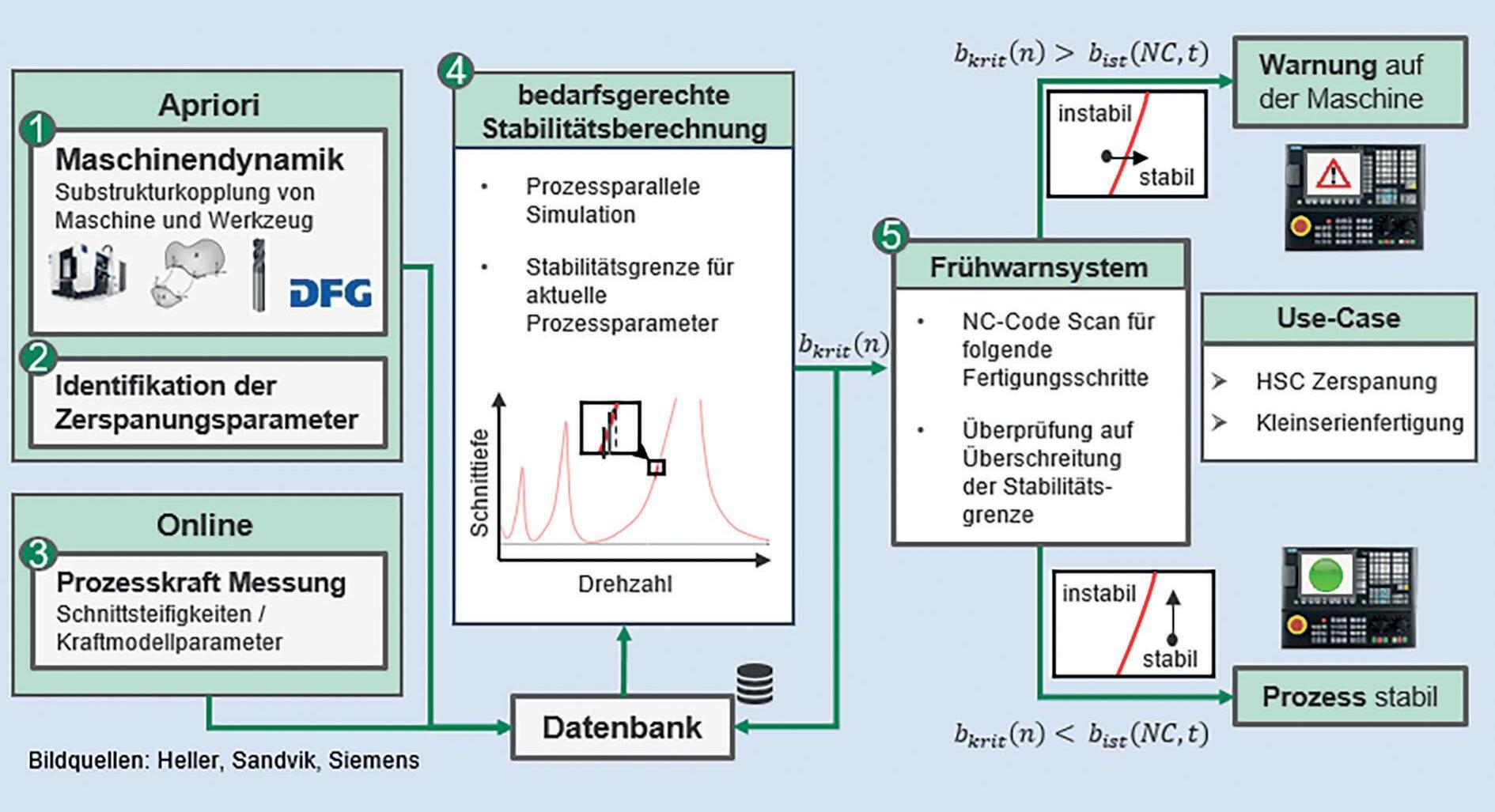
With a penetration simulation based on a 3D model of the blank and the NC code, the machining parameters can be identified a priori. From this, the process variables required for the stability simulation, such as the depth of cut (ap) and the radial depth of cut ratio (ae), can be extracted in relation to the different machining steps. This is followed by a segmentation of the machining process based on different tools and programmed process parameters. Based on this data, the most critical machining parameters for different segments of the process can be identified.
3. Online force model parameterisation.
In addition to the machine dynamics, knowledge of the cutting stiffnesses is required. Due to the great progress in the field of real-time recording of process forces, e.g. through spindle-integrated sensor technology [3], the cutting stiffnesses can be parameterised parallel to the process. This is done on the basis of a comparison of measured and simulated process force with an „ensemble Kalman filter“ which has already been established for the application of a continuous parameter identification of analytical force models in the milling process [4].
Through a process-parallel identification of the section stiffnesses, the input variables required for the stability simulation can be determined on the basis of the real boundary conditions of the running process. This offers an advantage over conventional model-based approaches that simulate the stability boundary a priori and whose data basis relies on preliminary tests or tabulated values.

4. Demand-based stability calculation
The stability limits are determined in parallel with the process within a demand-based simulation. Demand-based means that only the currently relevant speeds and cutting depths of the current machining step are evaluated for the stability simulation. Unlike conventional model-based approaches to stability simulation, therefore, it is not the entire stability map that is calculated, but only a range around the currently relevant working point. The required input variables for the stability calculation are shown in Figure 3. With this approach, the fast calculation times required for the processparallel approach can be guaranteed.
5 Early warning system
Based on the calculated stability limit, future processing steps can be checked in a kind of „look-ahead function“ for possible exceeding of this limit. The early warning system provides an online functionality that warns of potential process insta-
Bibliography
[1] Brecher, C.; Chavan, P.; Epple, A.: Effiziente Ermittlung von Stabilitätskarten beim Fräsen. In: Fräsen und Bohren, 2018b, Nr. 5, pp. 56–57.
[2] Brecher, C.; Chavan, P.; Fey, M.: Efficient joint identification and fluted segment modelling of shrink-fit tool assemblies by updating extended tool models. In: Production Engineering, 15. Jg., 2021, Nr. 1, pp. 21–33.
[3] Brecher, C.; Eckel, H.-M.; Fey, M.; Butz, F.: Prozesskraftmessung mit spindelintegrierter Sensorik. In: ZWF Zeitschrift für wirtschaftlichen Fabrikbetrieb, 113. Jg., 2018a, Nr. 10, pp. 660–663.
[4] Schwenzer, M.; Stemmler, S.; Ay, M.; Bergs, T.; Abel, D.: Continuous identification for mechanistic force models in milling. In: IFAC-PapersOnLine, 52. Jg., 2019, Nr. 13, pp. 1791–1796.
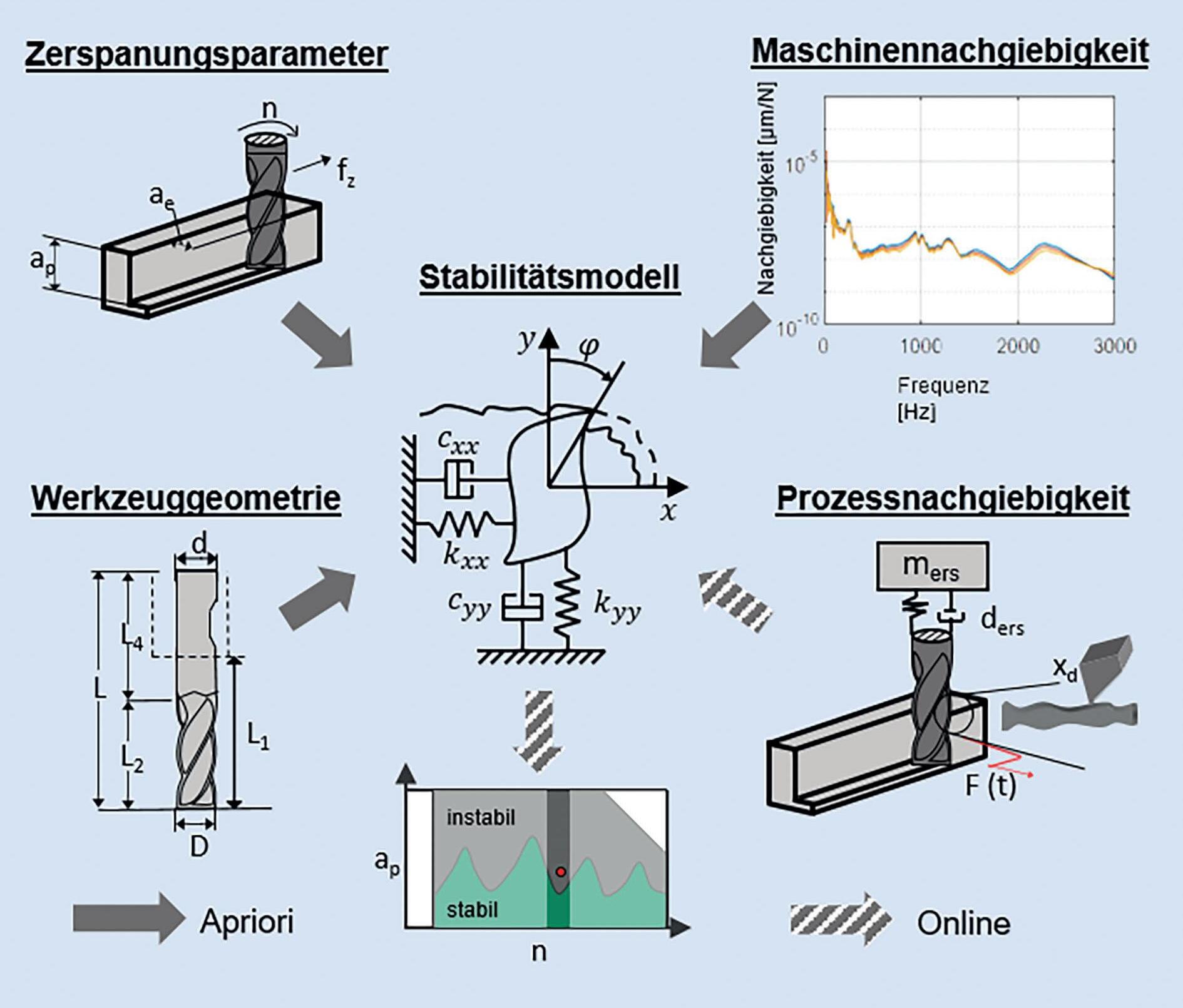
bilities in the further course of processing. The statement of the early warning system can be provided within five seconds. Based on the warning, the occurrence of process instabilities can be prevented by operator intervention.
Conclusion and outlook
The paper has presented a new methodology for an online chatter early warning system. The combination of efficient determination of the machine dynamics and the process-parallel data basis offers advantages over conventional approaches for model-based determination of stability limits. The evaluation of the stability around the current operating point enables fast computing times, which are neces- sary for the online approach. A warning from the system statement can already take place after a few seconds.
In a next step, the accuracy of the early warning system is investigated by means of machining tests. The tests cover both different tools and materials. www.wzl.rwth-aachen.de
Funding Acknowledgements: Supported by the German Research Foundation (DFG) – Project Number 467600151.
Prof. Dr.-Ing. Christian Brecher holds the Chair of Machine Tools at the Laboratory for Machine Tools and Production Engineering (WZL) at RWTH Aachen University.
Photo: WZL
Dr.-Ing. Marcel Fey is a senior engineer and head of the Machine Data Analysis & NC Technology Department at the WZL of RWTH Aachen University.


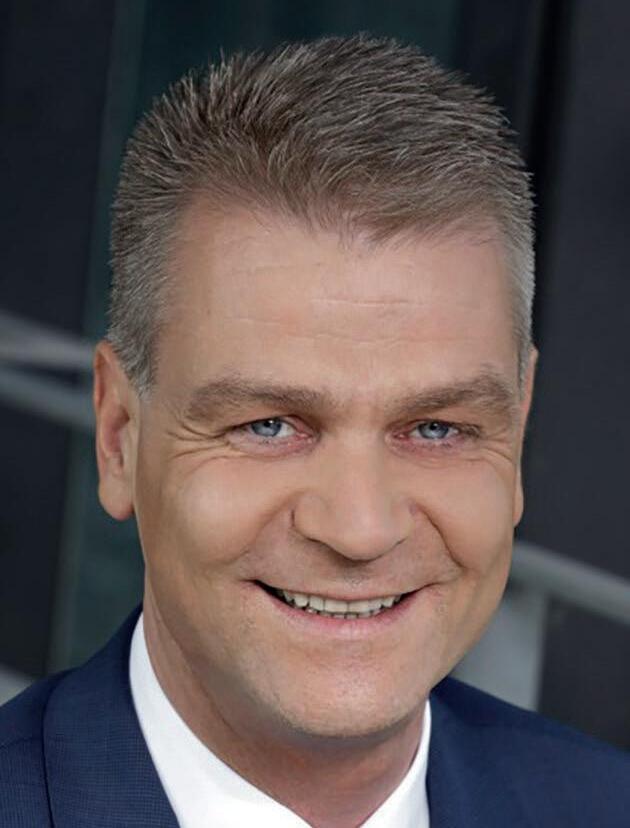
Photo: WZL
Marcel Wittmann , M. Sc. RWTH, is a research assistant at the Institute for Machine Tools at the WZL of RWTH Aachen in the department Machine Data Analysis & NC Technology. Photo: WZL